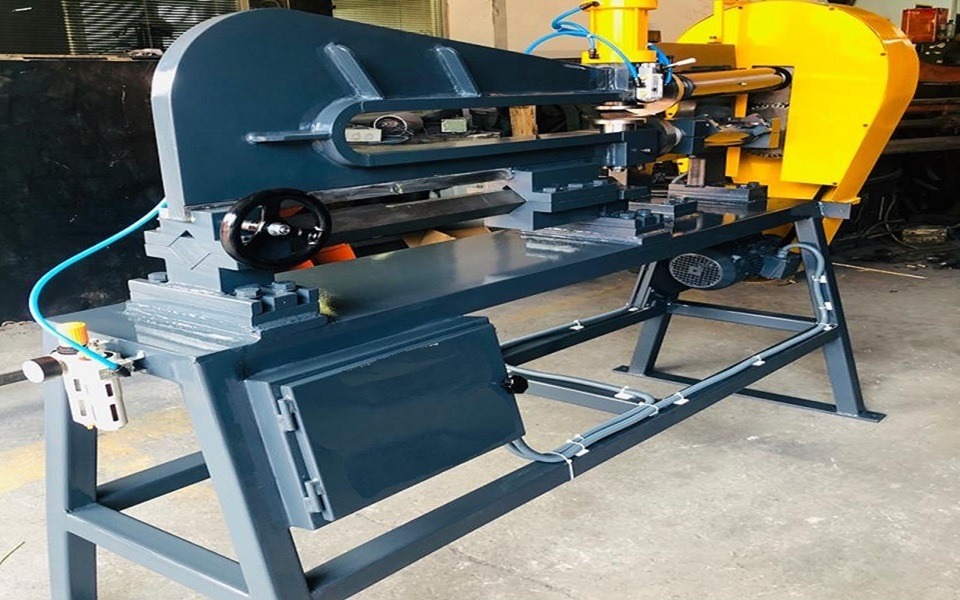
Bleche Schneiden Maschine: Eine Blechschneidemaschine ist ein Werkzeug oder eine Maschine, die speziell dafür entwickelt wurde, Blechmaterialien präzise und effizient zu schneiden. Solche Maschinen werden in verschiedenen Industrien eingesetzt, darunter Automobilbau, Bauwesen, Luft- und Raumfahrt sowie in Handwerks- und Hobbybereichen. Je nach Anforderung und Materialstärke gibt es unterschiedliche Typen von Blechschneidemaschinen. Hier ein Überblick über die wichtigsten Typen:
1. Schlagscheren
- Funktionsweise: Schneiden das Blech mithilfe einer mechanischen oder hydraulischen Klinge, die sich in einem Scherenmechanismus bewegt.
- Einsatzgebiet: Besonders geeignet für das Schneiden von flachen Blechplatten.
- Vorteile: Hohe Präzision und schnelle Schnittgeschwindigkeit. Sie können auch dickere Bleche schneiden und sind oft wirtschaftlicher im Vergleich zu anderen Schneidetechniken.
2. Laser-Schneidemaschinen
- Funktionsweise: Ein hochkonzentrierter Laserstrahl erhitzt und schmilzt das Material entlang der Schnittlinie.
- Einsatzgebiet: Ideal für das Schneiden komplexer Konturen und feiner Details, häufig bei dünneren Metallen.
- Vorteile: Sehr präzise und flexibel. Ermöglicht die Bearbeitung verschiedenster Blechstärken und -formen ohne Werkzeugwechsel.
3. Plasmaschneider
- Funktionsweise: Nutzt einen elektrisch erzeugten Plasmastrahl, der Temperaturen von über 20.000 °C erreichen kann, um das Blech zu schneiden.
- Einsatzgebiet: Vor allem für dickere Materialien und raue Schnitte geeignet.
- Vorteile: Schneller Schnitt auch bei dicken Blechen, eignet sich für leitfähige Materialien wie Stahl, Aluminium und Kupfer.
4. Wasserstrahlschneidemaschinen
- Funktionsweise: Schneidet das Material durch einen Hochdruck-Wasserstrahl, dem oft ein abrasives Material (z. B. Sand) beigemischt wird.
- Einsatzgebiet: Besonders geeignet für hitzeempfindliche Materialien, da der Prozess keine Wärme erzeugt.
- Vorteile: Sehr präzise und sauber, keine Wärmeverformung, geeignet für verschiedenste Materialien, auch nicht-metallische.
5. CNC-Stanzmaschinen
- Funktionsweise: Diese Maschinen verwenden computergesteuerte Werkzeuge, um präzise Löcher und Konturen zu stanzen.
- Einsatzgebiet: Vor allem bei industriellen Anwendungen, die eine hohe Präzision und Wiederholbarkeit erfordern.
- Vorteile: Hohe Geschwindigkeit und Wiederholgenauigkeit, besonders gut für Serienproduktionen geeignet.
Wichtige Faktoren bei der Auswahl einer Blechschneidemaschine
- Materialstärke: Dickere Materialien erfordern stärkere Maschinen, wie z. B. Schlagscheren oder Plasmaschneider.
- Schnittgenauigkeit: Für präzise Arbeiten sind Laser- und Wasserstrahlschneider die beste Wahl.
- Produktionsvolumen: Bei hohen Stückzahlen lohnen sich CNC-gesteuerte Maschinen.
- Budget: Maschinen wie Plasmaschneider sind oft günstiger, während Laser- und Wasserstrahlschneider eine höhere Anfangsinvestition erfordern.
Jede dieser Maschinen hat spezifische Vor- und Nachteile, abhängig von der Anwendung und dem zu verarbeitenden Material. Für industrielle Anwendungen wird oft eine Kombination verschiedener Maschinen genutzt, um maximale Effizienz und Flexibilität zu erreichen.
Schlagscheren: Funktion, Einsatz und Vorteile
Schlagscheren sind essenzielle Werkzeuge in der Metallbearbeitung, die durch ihre robuste Bauweise und einfache Funktionsweise überzeugen. Sie schneiden Bleche und andere Metallmaterialien präzise und effizient. In den folgenden Abschnitten werden wir die Funktionsweise, die verschiedenen Bauarten, Einsatzgebiete, die Vorteile und die wichtigsten Auswahlkriterien für Schlagscheren ausführlich besprechen.
1. Was sind Schlagscheren?
Schlagscheren sind mechanische oder hydraulische Maschinen, die für das Schneiden von Blech und Metall konzipiert sind. Sie bestehen aus zwei Klingen, die übereinander angeordnet sind. Während der Schneidprozess abläuft, bewegt sich eine Klinge gegen eine andere feststehende Klinge und trennt das Material. Diese einfache, aber effektive Technik ermöglicht saubere und präzise Schnitte in verschiedenen Materialstärken und -größen.
2. Funktionsweise von Schlagscheren
Schlagscheren basieren auf einem mechanischen Prinzip, das wie folgt abläuft:
- Schneidklingen: Zwei Klingen, eine bewegliche und eine feste, werden verwendet. Die feste Klinge bleibt stationär, während die bewegliche Klinge mit Kraft auf das Material einwirkt.
- Schneiden durch Schubkraft: Die bewegliche Klinge schiebt das Material gegen die feststehende Klinge und schneidet es durch. Dieser Vorgang wird oft als „Schlag“ beschrieben, da er mit einem schnellen, schlagartigen Druck abläuft.
- Schrägstellung der Klinge: Die Klinge ist oft leicht geneigt, was den Schnitt erleichtert, indem der Druckpunkt verkleinert wird. Dadurch wird die benötigte Kraft reduziert, und der Schnitt verläuft gleichmäßiger.
- Antrieb: Schlagscheren können manuell, mechanisch oder hydraulisch angetrieben sein. Bei hydraulischen Modellen sorgt ein Hydrauliksystem für die notwendige Kraft, während mechanische Schlagscheren eine Schwungscheibe oder einen elektrischen Motor verwenden.
Diese präzise Schnittführung erlaubt eine hohe Schnittqualität und ist geeignet für unterschiedlichste Materialien und Anwendungen.
3. Bauarten von Schlagscheren
Je nach Anwendungsbereich und Materialanforderungen gibt es verschiedene Arten von Schlagscheren. Hier sind die gängigsten Typen:
3.1 Manuelle Schlagscheren
- Merkmale: Manuell betriebene Schlagscheren werden von Hand bedient und eignen sich für dünne Materialien.
- Vorteile: Einfach zu bedienen, wartungsarm und kostengünstig.
- Anwendung: Oft in kleinen Werkstätten, im Modellbau und für einfache Blechbearbeitungen verwendet.
3.2 Mechanische Schlagscheren
- Merkmale: Mechanische Schlagscheren werden elektrisch angetrieben und besitzen eine Schwungscheibe, die Energie speichert und während des Schnitts abgibt.
- Vorteile: Schnelle Schnitte, geeignet für Massenproduktion und mittlere Materialstärken.
- Anwendung: In mittleren bis großen Werkstätten und der industriellen Metallverarbeitung eingesetzt.
3.3 Hydraulische Schlagscheren
- Merkmale: Diese Schlagscheren verwenden hydraulischen Druck, um die Schneidklinge zu bewegen. Sie bieten eine größere Schneidkraft und höhere Präzision.
- Vorteile: Vielseitig, hohe Schneidkraft und präziser Schnitt. Weniger Verschleiß und Geräuschentwicklung.
- Anwendung: Für dickere Materialien und hohe Schnittqualität in der Industrie verwendet.
3.4 CNC-Schlagscheren
- Merkmale: Mit CNC (Computer Numerical Control) ausgestattet, was eine computergesteuerte Bewegung der Klingen ermöglicht.
- Vorteile: Präzise Schnitte, hohe Wiederholgenauigkeit und automatisierte Steuerung.
- Anwendung: Ideal für Serienfertigung und komplexe Zuschnitte.
4. Vorteile von Schlagscheren
Die Schlagschere hat sich als Werkzeug in der Metallverarbeitung aufgrund mehrerer Vorteile durchgesetzt:
4.1 Hohe Effizienz und Geschwindigkeit
Schlagscheren bieten eine hohe Schneidgeschwindigkeit, die insbesondere in der Serienproduktion nützlich ist. Mit mechanischen oder hydraulischen Antrieben können zahlreiche Bleche in kurzer Zeit geschnitten werden.
4.2 Präzision und Qualität der Schnitte
Die exakte Führung der Schneidklinge und die robuste Bauweise führen zu präzisen Schnitten ohne Verformung des Materials. Die Klingen sind oft schräggestellt, was die Schnittqualität zusätzlich verbessert und den Krafteinsatz reduziert.
4.3 Vielseitigkeit
Schlagscheren können für verschiedene Materialien verwendet werden, darunter Stahl, Aluminium, Kupfer und andere Metalle. Auch unterschiedliche Materialstärken lassen sich durch Anpassungen an der Maschine problemlos schneiden.
4.4 Langlebigkeit und geringe Wartung
Durch die robuste Bauweise und hochwertigen Materialien sind Schlagscheren langlebig. Insbesondere hydraulische Schlagscheren haben eine lange Lebensdauer und benötigen weniger Wartung.
4.5 Kostenersparnis
Im Vergleich zu anderen Schneidtechniken wie Laser- oder Wasserstrahlschneiden sind Schlagscheren kostengünstiger in der Anschaffung und im Betrieb. Gerade für Anwendungen, die keine extreme Präzision erfordern, ist die Schlagschere eine wirtschaftliche Lösung.
5. Typische Einsatzgebiete von Schlagscheren
Schlagscheren finden in vielen Bereichen der Industrie Anwendung. Hier einige der häufigsten Einsatzgebiete:
5.1 Metallverarbeitende Industrie
In der metallverarbeitenden Industrie sind Schlagscheren essenziell, um Rohmaterialien schnell und präzise zuzuschneiden. Sie werden in der Produktion von Blechen für Maschinen, Fahrzeuge, Baustellenmaterialien und zahlreiche andere Anwendungen genutzt.
5.2 Automobilindustrie
Die Automobilindustrie setzt Schlagscheren für den Zuschnitt von Karosserieteilen und anderen Bauteilen ein. Aufgrund der hohen Anforderungen an die Produktionsgeschwindigkeit und Genauigkeit sind besonders CNC-gesteuerte Schlagscheren beliebt.
5.3 Bauwesen und Architektur
Im Bauwesen werden Schlagscheren für die Bearbeitung von Metallplatten, Dämmstoffen und Fassadenmaterialien verwendet. Diese Maschinen sind ideal, um große Bleche für Dächer, Wände und andere Bauelemente zuzuschneiden.
5.4 Elektronik- und Geräteindustrie
Auch die Elektronik- und Geräteindustrie profitiert von den präzisen Schneidfähigkeiten der Schlagscheren. Gehäuse und Platinen für elektronische Geräte werden oft mit Schlagscheren bearbeitet.
5.5 Kunsthandwerk und Modellbau
Schlagscheren sind ebenfalls in kleineren Werkstätten und im Kunsthandwerk beliebt, wo sie für Modellbauprojekte, kreative Metallkunst und kleinere Handwerksarbeiten verwendet werden.
6. Auswahlkriterien für Schlagscheren
Beim Kauf einer Schlagschere gibt es mehrere wichtige Faktoren zu beachten:
6.1 Materialstärke und -art
Je nach Materialstärke und -art wird eine bestimmte Leistung und Schneidkraft benötigt. Hydraulische Modelle eignen sich besser für dicke Materialien, während manuelle oder mechanische Scheren für dünnere Bleche ausreichen.
6.2 Schnittlänge
Die Schnittlänge der Schlagschere sollte zur Größe der Werkstücke passen. Größere Maschinen sind für großflächige Bleche ausgelegt, während kleinere Maschinen handlicher und platzsparender sind.
6.3 Präzision und Toleranzanforderungen
Je nach Anwendungsbereich können unterschiedlich hohe Präzisionsanforderungen bestehen. CNC-Schlagscheren bieten die höchste Genauigkeit und Wiederholbarkeit, während einfache manuelle Scheren für weniger präzise Arbeiten ausreichen.
6.4 Bedienkomfort und Sicherheit
Bedienkomfort und Sicherheit sind wichtige Faktoren, insbesondere bei Maschinen, die häufig verwendet werden. Hydraulische Schlagscheren bieten oft einen leisen Betrieb und geringere Vibrationen, während CNC-gesteuerte Modelle die Bedienung durch automatische Programme vereinfachen.
6.5 Budget und Wirtschaftlichkeit
Die Anschaffungskosten sowie die Wartungs- und Betriebskosten sollten berücksichtigt werden. Mechanische Scheren sind meist kostengünstiger, während hydraulische und CNC-Modelle höhere Investitionen erfordern, aber oft langfristig kosteneffizienter sind.
7. Wartung und Pflege von Schlagscheren
Eine regelmäßige Wartung verlängert die Lebensdauer der Schlagscheren und sorgt für eine gleichbleibende Schnittqualität.
- Reinigung: Entfernen Sie regelmäßig Metallspäne und Staub, um die Funktionalität und Präzision der Maschine zu erhalten.
- Klingenwartung: Die Klingen sollten regelmäßig geschärft und ausgerichtet werden, um saubere Schnitte zu gewährleisten.
- Schmierstoffe: Mechanische Teile und bewegliche Komponenten sollten regelmäßig geschmiert werden, um Verschleiß zu vermeiden.
- Hydrauliksystem (bei hydraulischen Modellen): Überprüfen Sie den Hydraulikölstand und die Dichtungen regelmäßig, um eine gleichbleibende Leistung zu gewährleisten.
8. Sicherheitshinweise im Umgang mit Schlagscheren
Schlagscheren können gefährlich sein, insbesondere aufgrund der scharfen Klingen und der hohen Druckkräfte. Die wichtigsten Sicherheitsvorkehrungen umfassen:
- Schutzausrüstung: Tragen Sie stets Schutzbrille, Handschuhe und gegebenenfalls Gehörschutz.
- Not-Aus-Schalter: Stellen Sie sicher, dass die Maschine über einen gut erreichbaren Not-Aus-Schalter verfügt.
- Abstand halten: Halten Sie Hände und Kleidung von der Schneidzone fern, um Verletzungen zu vermeiden.
- Schulung: Nur geschulte Personen sollten die Maschine bedienen, da unsachgemäße Handhabung zu Unfällen führen kann.
Fazit
Schlagscheren sind unverzichtbare Maschinen in der Metallbearbeitung und bieten eine robuste, kostengünstige und präzise Möglichkeit zum Schneiden von Blech und anderen Materialien. Die verschiedenen Bauarten – von manuellen über hydraulische bis hin zu CNC-gesteuerten Modellen – bieten Lösungen für zahlreiche Anforderungen und Einsatzgebiete. Ihre Effizienz und Vielseitigkeit machen sie zur ersten Wahl für zahlreiche Anwendungen in der Industrie, im Bauwesen und im Handwerk.
Schlagscheren sind Maschinen und Werkzeuge, die vor allem in der Metallbearbeitung eingesetzt werden, um Blech und andere flache Materialien präzise zu schneiden. Sie bestehen aus einem robusten, einfachen Aufbau mit zwei Klingen – einer festen und einer beweglichen Klinge. Die Schlagschere übt durch ihre schlagartige Bewegung Kraft auf das Material aus und ermöglicht so schnelle, präzise und saubere Schnitte. Diese Technik hat sich besonders bewährt, um verschiedene Materialien wie Stahl, Aluminium oder Kupferplatten zu verarbeiten.
Übersicht: Die wichtigsten Merkmale und Funktionen von Schlagscheren
- Mechanisches Schneiden: Schlagscheren nutzen ein mechanisches Schneidprinzip, bei dem eine bewegliche Klinge gegen eine feststehende Klinge gedrückt wird. Das Material wird dadurch in zwei Teile getrennt.
- Hohe Präzision und Schnittqualität: Schlagscheren zeichnen sich durch präzise und saubere Schnitte ohne Materialverformung aus, was sie für viele Anwendungen unverzichtbar macht.
- Vielseitiger Einsatz: Sie werden in unterschiedlichen Industrien verwendet – vom Maschinenbau über die Automobilproduktion bis hin zur Metallverarbeitung.
- Kosteneffizienz: Im Vergleich zu anderen Schneidverfahren, wie dem Laser- oder Wasserstrahlschneiden, sind Schlagscheren oft kostengünstiger und für viele Anwendungen ausreichend.
1. Aufbau und Funktionsweise von Schlagscheren
Die grundlegende Funktionsweise einer Schlagschere basiert auf einem einfachen Mechanismus:
- Schneidklingen: Schlagscheren bestehen aus zwei Hauptklingen – einer festen und einer beweglichen. Die feste Klinge bleibt in ihrer Position, während die bewegliche Klinge gegen sie drückt, um das Material zu schneiden.
- Schrägstellung der Klinge: Häufig sind die Klingen schräg gestellt, was die nötige Kraft reduziert und den Schnitt vereinfacht. Diese Schräge ermöglicht einen „rollenden“ Schnitt, der sauber und kontrolliert ist.
- Antriebssystem: Schlagscheren gibt es in verschiedenen Antriebsarten – manuell, mechanisch oder hydraulisch. Der Antrieb entscheidet über die Geschwindigkeit und Kraft, mit der die Maschine schneidet.
Bei hydraulischen und mechanischen Schlagscheren sorgt der Antrieb dafür, dass die bewegliche Klinge schnell und präzise auf das Material trifft und es trennt. Manuelle Schlagscheren erfordern dagegen Muskelkraft, sind jedoch einfacher aufgebaut und wartungsärmer.
2. Verschiedene Arten von Schlagscheren
Es gibt unterschiedliche Typen von Schlagscheren, die jeweils für verschiedene Anforderungen konzipiert sind:
2.1 Manuelle Schlagscheren
Manuelle Schlagscheren werden mit Muskelkraft betrieben und eignen sich eher für dünnere Materialien und kleine Werkstücke. Sie sind in Werkstätten und im Modellbau beliebt, wo kleinere Metallteile zugeschnitten werden müssen.
- Einsatzbereich: Werkstätten, Kunsthandwerk, Modellbau
- Vorteile: Kostengünstig, einfach zu bedienen und wartungsarm
- Nachteile: Begrenzte Schnittkraft, nicht für dicke Materialien geeignet
2.2 Mechanische Schlagscheren
Mechanische Schlagscheren werden von einem elektrischen Motor angetrieben und verwenden oft eine Schwungscheibe, die Energie speichert und beim Schneidprozess freisetzt. Diese Art ist in der industriellen Fertigung weit verbreitet und eignet sich für mittlere Materialstärken.
- Einsatzbereich: Kleine bis mittelgroße Werkstätten, industrielle Produktion
- Vorteile: Schnell, präzise und für häufige Schnitte geeignet
- Nachteile: Mechanische Teile können verschleißen, und regelmäßige Wartung ist erforderlich
2.3 Hydraulische Schlagscheren
Hydraulische Schlagscheren verwenden einen Hydraulikzylinder, um die nötige Kraft für das Schneiden aufzubringen. Sie sind leistungsstärker und ermöglichen das Schneiden dickerer Materialien.
- Einsatzbereich: Metallverarbeitung, schwere Industrie, Automotive
- Vorteile: Hohe Kraft und Präzision, leiser und langlebiger im Betrieb
- Nachteile: Höhere Kosten und komplexere Wartung
2.4 CNC-Schlagscheren
Diese Schlagscheren sind mit einer CNC-Steuerung (Computer Numerical Control) ausgestattet, die automatisierte und präzise Bewegungen ermöglicht. CNC-Schlagscheren sind ideal für Serienproduktionen und wiederholbare Schneidaufgaben, da sie die Materialposition und Schnittführung exakt programmieren.
- Einsatzbereich: Hochpräzise Serienproduktionen in der Industrie
- Vorteile: Automatisierung, hohe Präzision und Wiederholgenauigkeit
- Nachteile: Hohe Anschaffungskosten und Schulungsbedarf
3. Einsatzgebiete und Anwendungen von Schlagscheren
Schlagscheren sind aufgrund ihrer Effizienz, Vielseitigkeit und Präzision in vielen Bereichen unverzichtbar:
3.1 Metallverarbeitung und Maschinenbau
In diesen Industrien werden Schlagscheren genutzt, um Metallplatten zuzuschneiden, die später zu Bauteilen oder Maschinenkomponenten verarbeitet werden. Die Schnelligkeit und Präzision der Schlagscheren sind hier besonders wichtig.
3.2 Automobilindustrie
In der Automobilindustrie werden Schlagscheren für die Bearbeitung von Karosserieteilen und anderen Metallteilen verwendet. Hier sind schnelle, wiederholbare und präzise Schnitte notwendig, was den Einsatz von CNC-Schlagscheren besonders attraktiv macht.
3.3 Bauwesen und Architektur
Schlagscheren sind auch im Bauwesen im Einsatz, um große Metallplatten oder -paneele für Fassaden, Dächer und andere Baukomponenten zuzuschneiden. Sie ermöglichen die präzise und effiziente Verarbeitung großer Mengen an Baumaterialien.
3.4 Kunsthandwerk und Modellbau
Kleinere Schlagscherenmodelle finden auch im Kunsthandwerk und Modellbau Verwendung. Hier geht es oft um die Bearbeitung dünner Bleche für kreative Arbeiten und Modellbauprojekte.
4. Vorteile von Schlagscheren gegenüber anderen Schneidmethoden
Schlagscheren haben gegenüber alternativen Schneidverfahren wie dem Laser- oder Plasmaschneiden verschiedene Vorteile:
4.1 Wirtschaftlichkeit
Schlagscheren sind im Vergleich zu Laser- oder Wasserstrahlschneidern günstiger in der Anschaffung und im Betrieb. Sie benötigen weniger Energie und sind in der Wartung weniger aufwendig.
4.2 Geschwindigkeit und Effizienz
Durch die schlagartige Bewegung der Klinge sind Schlagscheren sehr schnell und ermöglichen das Schneiden großer Materialmengen in kurzer Zeit. Das ist besonders in der Serienproduktion von Vorteil.
4.3 Vielseitigkeit
Schlagscheren sind in der Lage, verschiedene Materialien in unterschiedlichen Stärken zu schneiden. Dabei können sie flexibel an die Anforderungen der jeweiligen Aufgabe angepasst werden.
4.4 Präzision und Schnittqualität
Durch die stabile Führung der Klinge erzielen Schlagscheren saubere Schnitte mit hoher Genauigkeit. Das Material wird nicht thermisch belastet und bleibt formstabil.
5. Sicherheit und Bedienung von Schlagscheren
Da Schlagscheren hohe Kräfte ausüben und scharfe Klingen haben, sind bei der Bedienung strenge Sicherheitsvorkehrungen notwendig.
5.1 Schutzausrüstung und Sicherheitsvorkehrungen
- Schutzausrüstung: Das Tragen von Schutzbrillen, Handschuhen und Gehörschutz ist erforderlich, um Verletzungen zu vermeiden.
- Not-Aus-Schalter: Jede Schlagschere sollte einen gut erreichbaren Not-Aus-Schalter haben, um die Maschine bei Gefahr schnell stoppen zu können.
- Schulungen: Nur geschultes Personal sollte die Maschine bedienen, da unsachgemäße Handhabung zu schweren Unfällen führen kann.
5.2 Richtiges Positionieren des Materials
Das Werkstück sollte sicher auf der Maschine liegen, bevor der Schneidvorgang gestartet wird. Das Material muss genau ausgerichtet sein, um präzise Schnitte zu gewährleisten.
6. Wartung und Pflege von Schlagscheren
Eine regelmäßige Wartung ist entscheidend, um die Leistung und Langlebigkeit einer Schlagschere zu gewährleisten.
6.1 Reinigung und Pflege der Klingen
Die Schneidklingen sollten regelmäßig gereinigt und gegebenenfalls geschärft werden. Saubere Klingen reduzieren den Verschleiß und verbessern die Schnittqualität.
6.2 Schmieren der beweglichen Teile
Durch die ständige Bewegung der Scherklingen und Mechanik ist es wichtig, die beweglichen Teile regelmäßig zu schmieren. Das verringert Reibung und verhindert Abnutzung.
6.3 Überprüfen des Hydrauliksystems (bei hydraulischen Modellen)
Bei hydraulischen Schlagscheren sollte das Hydrauliksystem auf Dichtungen und den Ölstand kontrolliert werden. Ein gut gewartetes Hydrauliksystem sorgt für gleichbleibende Leistung und verhindert Schäden.
7. Auswahlkriterien für die passende Schlagschere
Die Auswahl der richtigen Schlagschere hängt von verschiedenen Faktoren ab:
- Materialart und -stärke: Je dicker das Material, desto mehr Kraft wird benötigt. Hydraulische Schlagscheren eignen sich besser für dickere Materialien.
- Schnittlänge: Die maximale Schnittlänge sollte zum Werkstück passen.
- Produktionsvolumen: Für Serienproduktion sind CNC-Schlagscheren die beste Wahl, da sie Präzision und Wiederholgenauigkeit bieten.
- Budget: Manuelle und mechanische Schlagscheren sind kostengünstiger als hydraulische und CNC-gesteuerte Modelle.
8. Fazit
Schlagscheren sind vielseitige und wirtschaftliche Maschinen, die eine hohe Präzision und Effizienz beim Schneiden von Metall bieten. Sie sind unverzichtbar in der Metallverarbeitung und werden in zahlreichen Industrien und Werkstätten eingesetzt. Ob für die Bearbeitung dicker oder dünner Bleche, für große oder kleine Werkstücke – die verschiedenen Bauarten der Schlagscheren bieten für nahezu jede Anforderung eine passende Lösung. Ihre einfache Bedienung, geringe Betriebskosten und lange Lebensdauer machen sie zu einer wichtigen Investition für alle, die regelmäßig Metall schneiden.
Die Funktionsweise von Schlagscheren
Die Funktionsweise von Schlagscheren basiert auf einem relativ einfachen, aber effizienten mechanischen Prinzip, bei dem ein Werkstück (meist Metall) zwischen zwei Klingen geschnitten wird. Dabei trifft eine bewegliche Klinge mit hoher Kraft auf eine feststehende Klinge, und der Druck schneidet das Material durch. Obwohl das Grundprinzip einfach erscheint, gibt es in der Funktionsweise und den Feinheiten des Schneidprozesses viele technische Aspekte, die Schlagscheren zu leistungsfähigen und vielseitigen Maschinen machen.
In diesem umfassenden Überblick gehen wir detailliert auf die Funktionsweise, Mechanik, verschiedene Antriebsarten und technologische Feinheiten ein, die Schlagscheren zu einem unverzichtbaren Werkzeug in der Metallbearbeitung machen.
1. Grundlagen der Funktionsweise von Schlagscheren
Die Funktionsweise der Schlagschere basiert auf der Verwendung zweier Klingen – einer festen und einer beweglichen Klinge. Das Werkstück, beispielsweise ein Blech, wird zwischen diese Klingen gelegt. Die bewegliche Klinge bewegt sich dann mit hoher Geschwindigkeit und Kraft gegen das Werkstück, welches auf der festen Klinge ruht. Die Klingenführung ist hierbei so konstruiert, dass sie das Material effizient trennt.
Wichtige Grundelemente der Funktionsweise:
- Schneidklingen: Die Klingen bestehen aus extrem widerstandsfähigem Material (z. B. Werkzeugstahl), das hohen Drücken und Verschleiß widersteht. Eine Klinge bleibt fest, während die andere sich bewegt.
- Schrägstellung der Klinge: Die bewegliche Klinge ist meist leicht schräg gestellt, was den Schnitt erleichtert und den benötigten Kraftaufwand reduziert.
- Druckkraft: Die Kraft, die auf die bewegliche Klinge ausgeübt wird, ist entscheidend für die Schnittleistung und Materialdicke, die bearbeitet werden kann.
- Spaltbreite: Der Abstand zwischen den beiden Klingen ist ein wichtiger Faktor, der präzise eingestellt werden muss. Dieser Abstand wird abhängig von der Materialstärke und -art definiert, um eine saubere Trennung ohne Materialverformung zu ermöglichen.
2. Ablauf des Schneidvorgangs
Der Schneidvorgang einer Schlagschere lässt sich in folgende Schritte gliedern:
- Einspannen des Materials: Das Werkstück wird in die Schlagschere gelegt und so positioniert, dass der gewünschte Schnitt exakt durchgeführt werden kann.
- Auslösen des Schneidvorgangs: Je nach Antriebsart wird die bewegliche Klinge entweder mechanisch, hydraulisch oder manuell aktiviert.
- Bewegung der Klinge: Die bewegliche Klinge bewegt sich gegen das Material und übt dabei großen Druck aus, wodurch das Material entlang der Schneidlinie getrennt wird.
- Abschluss des Schnitts: Die Klinge kehrt in ihre Ausgangsposition zurück, das geschnittene Material kann entnommen werden, und die Schlagschere ist bereit für den nächsten Schnitt.
Dieser Ablauf dauert bei einer hydraulischen oder mechanischen Schlagschere nur wenige Sekunden und ermöglicht eine schnelle Verarbeitung von Material in hoher Stückzahl.
3. Mechanische Details und Feinheiten des Schneidprozesses
Schlagscheren sind so konstruiert, dass der Schneidprozess besonders effizient und mit hoher Präzision durchgeführt wird. Im Folgenden betrachten wir die wichtigsten technischen Details.
3.1 Schneidkanten und Schneidspalt
- Schneidkanten: Die Kanten der Klingen sind speziell geschliffen, um saubere und präzise Schnitte zu ermöglichen. Das Material der Klingen ist gehärtet, um Verschleiß zu minimieren.
- Schneidspalt: Der Spalt zwischen der festen und der beweglichen Klinge beeinflusst die Schnittqualität erheblich. Ein zu kleiner Spalt kann zu einer Kantenverformung führen, während ein zu großer Spalt unsaubere Schnittkanten verursacht. Der Schneidspalt wird daher häufig individuell auf das Material und die Materialstärke angepasst.
3.2 Neigungswinkel der Klingen
Durch den leichten Winkel der beweglichen Klinge wird der Schnitt vereinfacht und der Druck auf das Material reduziert. Der Neigungswinkel sorgt dafür, dass der Schnitt an einer Stelle beginnt und sich schnell über das Material ausbreitet, wodurch der nötige Kraftaufwand minimiert wird.
4. Unterschiedliche Antriebsarten und deren Funktionsweise
Die Antriebsart einer Schlagschere hat einen wesentlichen Einfluss auf die Funktionsweise und die Einsatzmöglichkeiten. Es gibt manuelle, mechanische und hydraulische Schlagscheren, die jeweils spezifische Eigenschaften besitzen.
4.1 Manuelle Schlagscheren
Manuelle Schlagscheren werden durch Muskelkraft angetrieben und sind für dünnere Materialien geeignet. Hierbei handelt es sich um kleinere Maschinen, die besonders in Werkstätten, im Handwerk und im Modellbau Anwendung finden.
- Funktionsweise: Die bewegliche Klinge wird über einen Hebel manuell betätigt, wodurch die Kraft direkt auf das Material wirkt.
- Vor- und Nachteile: Manuelle Schlagscheren sind kostengünstig und benötigen keine externe Energiequelle. Allerdings ist der Einsatz auf dünne Bleche und kleine Werkstücke beschränkt.
4.2 Mechanische Schlagscheren
Mechanische Schlagscheren verwenden meist einen Elektromotor, der eine Schwungscheibe oder einen Exzenter bewegt. Diese gespeicherte Energie wird dann auf die bewegliche Klinge übertragen, wodurch ein schneller und präziser Schnitt ermöglicht wird.
- Funktionsweise: Der Elektromotor treibt eine Schwungscheibe an, die sich dreht und Energie speichert. Beim Schneiden wird diese Energie freigesetzt und auf die Klinge übertragen.
- Vor- und Nachteile: Mechanische Schlagscheren sind effizient, schnell und für mittlere Materialstärken geeignet. Da sie jedoch mechanische Komponenten verwenden, kann es zu Verschleiß kommen, was regelmäßige Wartung erforderlich macht.
4.3 Hydraulische Schlagscheren
Hydraulische Schlagscheren nutzen Hydraulikdruck, um die Kraft auf die bewegliche Klinge zu übertragen. Diese Maschinen sind leistungsstark und ermöglichen das Schneiden dickerer Materialien.
- Funktionsweise: In einem hydraulischen System wird die Kraft über einen Hydraulikzylinder auf die Klinge übertragen. Ein hydraulischer Druckaufbau sorgt für eine gleichmäßige und kontrollierte Bewegung der Klinge.
- Vor- und Nachteile: Hydraulische Schlagscheren bieten eine hohe Kraft und Präzision, was sie für dickere Bleche und anspruchsvolle Anwendungen prädestiniert. Sie sind jedoch teurer und wartungsintensiver als mechanische Modelle.
5. Der Einfluss der Schnittparameter auf die Funktionsweise
Die Funktion und Qualität einer Schlagschere hängen stark von den eingestellten Schnittparametern ab. Zu den wichtigsten Parametern gehören:
5.1 Schneidkraft und Materialstärke
Die Schneidkraft muss an die Materialstärke angepasst werden. Für dickere Materialien ist eine höhere Schneidkraft erforderlich, um das Werkstück sauber zu trennen. Hydraulische Schlagscheren bieten hier die größte Flexibilität, da sie eine hohe Druckkraft erzeugen können.
5.2 Schnittgeschwindigkeit
Die Schnittgeschwindigkeit ist entscheidend, um Effizienz und Produktivität zu optimieren. In Serienproduktionen ist eine hohe Geschwindigkeit vorteilhaft, während bei besonders präzisen Arbeiten eine langsamere Geschwindigkeit gewählt werden kann.
5.3 Klingenwinkel und Spaltbreite
Der Klingenwinkel und die Spaltbreite müssen auf das Material abgestimmt sein. Ein zu kleiner Spalt kann zu Materialverformungen führen, während ein zu großer Spalt die Schnittqualität beeinträchtigt.
6. Besondere Technologien und Automatisierung
Mit dem technischen Fortschritt haben sich Schlagscheren weiterentwickelt und sind heute oft mit speziellen Technologien und Automatisierungen ausgestattet, die ihre Funktionsweise optimieren.
6.1 CNC-Steuerung
CNC-gesteuerte Schlagscheren sind mit einer Computersteuerung ausgestattet, die den Schneidprozess automatisiert und die Schnittgenauigkeit erhöht. Die CNC-Technologie ermöglicht es, Schneidprogramme für wiederholte Schnitte zu erstellen und komplexe Schneidprofile zu realisieren.
- Funktionsweise: Der Bediener programmiert die CNC-Steuerung, die dann die Klinge präzise entlang der vorgegebenen Schnittlinien bewegt.
- Vorteile: Erhöhte Präzision, Automatisierung und Eignung für Serienproduktionen.
6.2 Lasersensoren und Sicherheitsvorrichtungen
Moderne Schlagscheren sind oft mit Lasersensoren ausgestattet, die die Position des Werkstücks und der Klinge erfassen. Diese Sensoren erhöhen die Sicherheit und gewährleisten, dass der Schneidvorgang nur ausgeführt wird, wenn das Material korrekt positioniert ist.
- Funktionsweise: Sensoren überwachen den Abstand zwischen Werkstück und Klinge und verhindern das Einschalten der Maschine, wenn das Werkstück falsch positioniert ist.
- Vorteile: Sicherheit, Präzision und Schutz vor Beschädigungen.
6.3 Anpassung der Schneidkraft und Drucksensoren
Einige Schlagscheren verfügen über Drucksensoren, die den benötigten Schneiddruck automatisch an die Materialstärke anpassen. Das sorgt für eine gleichbleibend hohe Schnittqualität und reduziert den Verschleiß.
7. Wartung und Pflege als Teil der Funktionsweise
Um die Funktionsweise und Effizienz der Schlagschere langfristig zu gewährleisten, sind regelmäßige Wartung und Pflege erforderlich. Zu den wichtigsten Maßnahmen gehören:
- Schärfen der Klingen: Abgenutzte oder stumpfe Klingen sollten regelmäßig geschärft werden, um eine gleichbleibend hohe Schnittqualität zu erzielen.
- Reinigung und Schmierung: Bewegliche Teile und Scharniere sollten regelmäßig geschmiert und gereinigt werden, um Reibung und Verschleiß zu minimieren.
- Überprüfung der Spaltbreite: Die Spaltbreite zwischen den Klingen sollte regelmäßig überprüft und nach Bedarf eingestellt werden.
- Hydraulikölwechsel (bei hydraulischen Modellen): Das Hydrauliköl sollte in regelmäßigen Abständen gewechselt und auf Verunreinigungen überprüft werden, um eine konstante Leistung sicherzustellen.
Fazit
Die Funktionsweise von Schlagscheren basiert auf einem effizienten, schlagartigen Schneidprinzip, das durch die Bewegung einer Klinge gegen eine feststehende Klinge umgesetzt wird. Diese Technik ermöglicht präzise, schnelle und saubere Schnitte und ist sowohl in der handwerklichen als auch in der industriellen Metallverarbeitung unverzichtbar. Unterschiedliche Antriebsarten – von manuell über mechanisch bis hydraulisch – bieten für jede Anforderung eine passende Lösung, und moderne Schlagscheren verfügen oft über fortschrittliche Automatisierungstechnologien wie CNC-Steuerungen und Lasersensoren, die den Schneidprozess weiter optimieren.
Mit der richtigen Einstellung der Schnittparameter und regelmäßiger Wartung kann die Funktionsweise einer Schlagschere optimal erhalten und die Langlebigkeit der Maschine gewährleistet werden. Diese Faktoren machen die Schlagschere zu einem unverzichtbaren Werkzeug, das die Anforderungen der modernen Metallbearbeitung auf kosteneffiziente und präzise Weise erfüllt.
Schlagscheren
Schlagscheren sind wesentliche Maschinen in der Metallverarbeitung und werden zum präzisen Schneiden von Blech und anderen Materialien eingesetzt. Je nach Einsatzgebiet, Materialbeschaffenheit und Produktionsanforderungen gibt es verschiedene Bauarten von Schlagscheren, die jeweils spezifische Vorteile und Einsatzmöglichkeiten bieten. In diesem umfassenden Überblick besprechen wir die wichtigsten Bauarten von Schlagscheren, einschließlich ihrer Funktionsweise, Eigenschaften, Vor- und Nachteile sowie typischer Anwendungen.
1. Überblick über die Bauarten von Schlagscheren
Die Wahl der passenden Schlagschere richtet sich nach dem geplanten Anwendungsgebiet, den Materialien, der Produktionsmenge und den Präzisionsanforderungen. Die vier wichtigsten Bauarten von Schlagscheren sind:
- Manuelle Schlagscheren
- Mechanische Schlagscheren
- Hydraulische Schlagscheren
- CNC-Schlagscheren
Jede dieser Bauarten zeichnet sich durch ihre eigenen Merkmale, Vorzüge und optimalen Einsatzbereiche aus.
2. Manuelle Schlagscheren
Manuelle Schlagscheren werden vor allem für kleinere Werkstücke und dünnere Materialien verwendet. Sie sind einfach im Aufbau und benötigen keine elektrische oder hydraulische Energie, da sie ausschließlich mit Muskelkraft betrieben werden.
Funktionsweise und Eigenschaften
- Handbetrieb: Der Schnitt erfolgt durch Muskelkraft, wobei der Bediener einen Hebel betätigt, der die bewegliche Klinge gegen die feststehende Klinge drückt.
- Einfache Bauweise: Da sie ohne Motor oder Hydrauliksystem auskommen, sind manuelle Schlagscheren besonders leicht und kompakt. Sie bestehen hauptsächlich aus einem stabilen Schneidrahmen, einem Schneidhebel und den Klingen.
- Begrenzte Schneidkapazität: Aufgrund der geringen Schneidkraft sind manuelle Schlagscheren für dünne Materialien wie Aluminium- und Kupferbleche sowie für kleine Werkstücke ausgelegt.
Typische Einsatzgebiete
- Werkstätten und Handwerksbetriebe: Manuelle Schlagscheren eignen sich besonders gut für Werkstätten und handwerkliche Betriebe, in denen kleinere Blechbearbeitungen durchgeführt werden.
- Kunsthandwerk und Modellbau: Sie werden häufig für den Zuschnitt von Blech in Kunstprojekten und im Modellbau verwendet, wo präzise, aber nicht hochvolumige Schnitte erforderlich sind.
Vor- und Nachteile
Vorteile | Nachteile |
---|---|
Kostengünstig und wartungsarm | Begrenzte Schneidkraft |
Kein Strom- oder Hydraulikbedarf | Nicht für dicke Materialien geeignet |
Einfache Bedienung und Mobilität | Geringe Produktivität bei großvolumigen Schnitten |
Manuelle Schlagscheren sind ideal für kleine Werkstätten und Anwendungen, bei denen Präzision und Flexibilität erforderlich sind, aber keine hohe Schneidkraft notwendig ist.
3. Mechanische Schlagscheren
Mechanische Schlagscheren sind eine leistungsstärkere Variante und werden elektrisch betrieben. Diese Schlagscheren eignen sich für mittlere Materialstärken und sind oft in der industriellen Produktion zu finden.
Funktionsweise und Eigenschaften
- Antrieb durch Elektromotor: Ein Elektromotor treibt eine Schwungscheibe oder einen Exzenter an. Diese Schwungscheibe speichert die Energie und gibt sie beim Schneiden an die bewegliche Klinge ab, die sich dann gegen das Material bewegt.
- Schnelligkeit und Effizienz: Mechanische Schlagscheren zeichnen sich durch eine hohe Schnittgeschwindigkeit aus und sind damit für die Verarbeitung größerer Mengen an Material in kurzer Zeit geeignet.
- Präzise Schnittführung: Sie ermöglichen präzise Schnitte und sind relativ einfach zu bedienen, was sie für wiederholbare Schnitte und Serienproduktionen prädestiniert.
Typische Einsatzgebiete
- Metallverarbeitung und Maschinenbau: Mechanische Schlagscheren sind in der Fertigung und Montage von Maschinenbauteilen und in der allgemeinen Metallbearbeitung weit verbreitet.
- Automobilindustrie: Auch in der Automobilproduktion werden mechanische Schlagscheren verwendet, um Karosserie- und Strukturteile aus Metall zu schneiden.
Vor- und Nachteile
Vorteile | Nachteile |
---|---|
Hohe Geschwindigkeit und Effizienz | Verschleißanfällig durch mechanische Teile |
Geeignet für mittlere Materialstärken | Wartungsaufwand für Antriebsmechanik |
Ideal für Serienproduktion und wiederholbare Schnitte | Höhere Anschaffungskosten als manuelle Schlagscheren |
Mechanische Schlagscheren sind leistungsstark und effizient und stellen eine kostengünstige Lösung für industrielle Anwendungen dar, in denen mittlere Materialstärken bearbeitet werden.
4. Hydraulische Schlagscheren
Hydraulische Schlagscheren verwenden ein Hydrauliksystem, um die bewegliche Klinge mit hohem Druck gegen die feststehende Klinge zu bewegen. Diese Maschinen bieten die größte Schneidkraft und sind in der Lage, auch dickere und härtere Materialien zu schneiden.
Funktionsweise und Eigenschaften
- Antrieb durch Hydraulikdruck: Das Hydrauliksystem erzeugt den nötigen Druck, um die Klinge mit hoher Kraft zu bewegen. Der Hydraulikzylinder sorgt dafür, dass die Bewegung der Klinge gleichmäßig und kontrolliert erfolgt.
- Hohe Schneidkraft: Hydraulische Schlagscheren sind ideal für dicke Materialien wie Stahlplatten und andere robuste Werkstoffe. Sie bieten eine präzise Schneidführung und sind für anspruchsvolle Anwendungen geeignet.
- Geringe Lärmentwicklung: Im Vergleich zu mechanischen Schlagscheren sind hydraulische Modelle leiser, was in lauten Produktionsumgebungen vorteilhaft ist.
Typische Einsatzgebiete
- Schwere Industrie und Stahlverarbeitung: Hydraulische Schlagscheren sind ideal für schwere Industrieanwendungen, insbesondere wenn dicke und harte Materialien bearbeitet werden müssen.
- Bauindustrie: Auch in der Bauindustrie werden hydraulische Schlagscheren zur Herstellung von Bauteilen aus Metall verwendet, die präzise und saubere Schnitte erfordern.
Vor- und Nachteile
Vorteile | Nachteile |
---|---|
Hohe Kraft und Schneidpräzision | Hohe Anschaffungskosten |
Ideal für dicke Materialien | Wartungsintensives Hydrauliksystem |
Leiser Betrieb und hohe Langlebigkeit | Benötigt Hydrauliköl und spezielle Wartung |
Hydraulische Schlagscheren bieten die größte Flexibilität und Leistung für anspruchsvolle Schneidaufgaben und sind unverzichtbar in Bereichen, in denen dicke und robuste Materialien präzise bearbeitet werden müssen.
5. CNC-Schlagscheren
CNC-Schlagscheren (Computerized Numerical Control) sind computergesteuerte Schlagscheren, die höchste Präzision und Automatisierung bieten. Sie eignen sich besonders für die Serienproduktion und ermöglichen das präzise Zuschneiden von Werkstücken nach vordefinierten Programmen.
Funktionsweise und Eigenschaften
- CNC-Steuerung: Die Maschine wird über ein computergesteuertes System programmiert, das alle Bewegungen der Klinge sowie die Positionierung des Materials exakt steuert.
- Hohe Präzision und Wiederholgenauigkeit: Die CNC-Steuerung ermöglicht äußerst präzise Schnitte und ist ideal für komplexe Konturen und Muster, die in der Serienproduktion in hoher Stückzahl benötigt werden.
- Automatisierte Arbeitsprozesse: CNC-Schlagscheren können rund um die Uhr betrieben werden, was eine hohe Produktivität und Effizienz in der Produktion ermöglicht.
Typische Einsatzgebiete
- Automobil- und Luftfahrtindustrie: Hier werden CNC-Schlagscheren zur Bearbeitung präziser Bauteile eingesetzt, die hohe Anforderungen an Maßgenauigkeit und Wiederholbarkeit stellen.
- Metallverarbeitung und Massenproduktion: Für die industrielle Serienproduktion, wo große Mengen identischer Teile in kurzer Zeit und mit gleichbleibender Präzision produziert werden müssen.
Vor- und Nachteile
Vorteile | Nachteile |
---|---|
Höchste Präzision und Wiederholgenauigkeit | Sehr hohe Anschaffungskosten |
Effizient in der Serienproduktion | Erfordert Schulung und Fachkenntnisse |
Automatisierter Betrieb für rund um die Uhr-Einsatz | Komplexe Wartung und Instandhaltung |
CNC-Schlagscheren sind die ideale Wahl für moderne, automatisierte Produktionslinien, die eine hohe Genauigkeit und Effizienz erfordern.
6. Vergleich der Schlagscheren-Bauarten
Um die verschiedenen Schlagscheren besser vergleichen zu können, fassen wir ihre wichtigsten Merkmale und Anwendungsvorteile in einer Tabelle zusammen:
Bauart | Antrieb | Ideal für | Vorteile | Nachteile |
---|---|---|---|---|
Manuelle Schlagscheren | Muskelkraft | Dünne Materialien, kleine Werkstücke | Kostengünstig, mobil, wartungsarm | Begrenzte Kraft, geringe Produktivität |
Mechanische Schlagscheren | Elektromotor | Mittlere Materialstärken | Hohe Geschwindigkeit, ideal für Serienfertigung | Mechanischer Verschleiß, Wartung notwendig |
Hydraulische Schlagscheren | Hydraulik | Dicke Materialien, anspruchsvolle Schnitte | Hohe Kraft, leiser Betrieb, langlebig | Teurer, Wartungsaufwand für Hydraulik |
CNC-Schlagscheren | CNC (Computersteuerung) | Präzisionsarbeit, Serienproduktion | Höchste Präzision und Automatisierung | Sehr hohe Kosten, Schulung erforderlich |
7. Auswahlkriterien für die richtige Bauart
Die Wahl der geeigneten Schlagschere hängt von verschiedenen Faktoren ab:
- Material und Stärke: Dicke Materialien erfordern hohe Schneidkraft, was für hydraulische oder CNC-gesteuerte Schlagscheren spricht.
- Produktionsvolumen: Für Serienproduktion und wiederholbare Schnitte sind mechanische oder CNC-Schlagscheren ideal.
- Budget: Manuelle und mechanische Schlagscheren sind kostengünstiger, während hydraulische und CNC-Modelle höhere Investitionen erfordern.
- Automatisierungsgrad: CNC-Schlagscheren bieten höchste Automatisierung und Präzision und sind ideal für Anwendungen, die komplexe oder wiederholbare Muster benötigen.
Fazit
Schlagscheren sind unverzichtbare Maschinen in der Metallbearbeitung und bieten eine breite Palette an Bauarten, die für unterschiedlichste Anwendungen optimiert sind. Von der handgeführten, manuellen Schlagschere bis zur hochpräzisen CNC-Schlagschere – jede Bauart hat spezifische Vorteile und Einsatzmöglichkeiten. Die Wahl der richtigen Schlagschere richtet sich nach dem Produktionsbedarf, der Materialbeschaffenheit und den Präzisionsanforderungen und ist ein entscheidender Faktor für eine wirtschaftliche und effiziente Produktion.
Schlagscheren sind vielseitige Maschinen, die vor allem in der Metallbearbeitung zum Einsatz kommen. Sie schneiden Blech und andere Materialien effizient und präzise, was sie in vielen Industrien unverzichtbar macht. Der Einsatz von Schlagscheren bietet eine Vielzahl von Vorteilen, die sowohl die Produktionsprozesse als auch die Qualität der Endprodukte optimieren. In diesem umfassenden Überblick behandeln wir die verschiedenen Vorteile von Schlagscheren, um zu verstehen, warum sie eine zentrale Rolle in der Fertigung spielen.
1. Effizienz und Produktivität
Einer der größten Vorteile von Schlagscheren liegt in ihrer hohen Effizienz. Im Vergleich zu anderen Schneidverfahren, wie etwa dem Laser- oder Wasserstrahlschneiden, bietet die Schlagschere eine einfache und schnelle Möglichkeit, große Materialmengen in kurzer Zeit zu verarbeiten.
- Hohe Schneidgeschwindigkeit: Schlagscheren sind in der Lage, Bleche mit hoher Geschwindigkeit zu schneiden. Dies ist besonders wertvoll in der Serienproduktion, wo eine schnelle Verarbeitung von Materialien zu einer höheren Produktivität führt.
- Serienproduktion: Durch die Möglichkeit, schnell und präzise zu schneiden, eignen sich Schlagscheren ideal für Serienproduktionen und die Herstellung von Bauteilen in großen Stückzahlen.
- Geringer Zeitaufwand: Da die Schlagschere den Schnitt in einem schlagartigen Prozess durchführt, ist die Bearbeitungszeit minimal, was die Effizienz weiter erhöht.
Die Effizienz und Produktivität der Schlagschere führt dazu, dass sie besonders in der Massenproduktion und in Bereichen mit hohem Durchsatz eingesetzt wird.
2. Präzision und Qualität der Schnitte
Schlagscheren bieten eine hohe Präzision und exakte Schnittqualität, was für die Herstellung hochwertiger Produkte essentiell ist.
- Exakte Schnittführung: Die feststehende und die bewegliche Klinge sorgen für eine kontrollierte und gleichmäßige Schnittführung. Dadurch wird das Material präzise und sauber getrennt.
- Hohe Wiederholgenauigkeit: Schlagscheren, insbesondere CNC-gesteuerte Modelle, bieten eine hohe Wiederholgenauigkeit, was bedeutet, dass bei jedem Schnitt das gleiche exakte Ergebnis erzielt wird. Dies ist für die Herstellung identischer Bauteile unverzichtbar.
- Kein Wärmeeinfluss auf das Material: Im Gegensatz zu thermischen Schneidverfahren, wie etwa dem Laserschneiden, kommt es bei der Schlagschere nicht zu einer Erhitzung des Materials. Das bedeutet, dass keine thermischen Verformungen oder Materialveränderungen auftreten, wodurch die ursprünglichen Materialeigenschaften erhalten bleiben.
Die hohe Präzision und Schnittqualität der Schlagschere tragen dazu bei, dass die Endprodukte den gewünschten Maßen und Standards entsprechen, was gerade in anspruchsvollen Industrien wie der Luft- und Raumfahrt oder der Automobilproduktion unerlässlich ist.
3. Vielseitigkeit und Flexibilität
Ein weiterer Vorteil der Schlagschere ist ihre Vielseitigkeit. Schlagscheren können in unterschiedlichen Industrien eingesetzt und für verschiedene Materialien angepasst werden.
- Breites Spektrum an Materialien: Schlagscheren sind in der Lage, verschiedene Materialien wie Stahl, Aluminium, Kupfer und andere Metalle zu schneiden. Dies macht sie zu einem vielseitigen Werkzeug in der Metallbearbeitung.
- Verarbeitung unterschiedlicher Materialstärken: Je nach Bauart (z. B. hydraulische Schlagscheren) können Schlagscheren auch dickere Materialien bearbeiten. Die Anpassung der Klingen und des Schneiddrucks ermöglicht die Bearbeitung verschiedener Materialdicken.
- Vielfältige Einsatzgebiete: Aufgrund ihrer Flexibilität und Vielseitigkeit finden Schlagscheren Anwendung in zahlreichen Industriezweigen wie dem Maschinenbau, der Automobilindustrie, der Bauindustrie und der Elektroindustrie.
Die Fähigkeit der Schlagschere, unterschiedliche Materialien und Materialstärken zu verarbeiten, macht sie zu einem zentralen Bestandteil moderner Fertigungslinien.
4. Wirtschaftlichkeit und Kostenersparnis
Die Wirtschaftlichkeit der Schlagschere ist ein wesentlicher Vorteil, der sie zu einer attraktiven Wahl für viele Betriebe macht.
- Geringe Betriebskosten: Im Vergleich zu anderen Schneidtechniken wie dem Laser- oder Wasserstrahlschneiden sind Schlagscheren oft kostengünstiger in der Anschaffung und im Betrieb.
- Niedriger Energieverbrauch: Schlagscheren benötigen weniger Energie als thermische Schneidverfahren, was die Betriebskosten senkt und zur Energieeffizienz beiträgt.
- Wartungsarm und langlebig: Da Schlagscheren eine relativ einfache Mechanik verwenden, sind sie im Allgemeinen weniger wartungsintensiv als komplexere Schneidmaschinen. Mit regelmäßiger Wartung und Pflege können sie über viele Jahre hinweg zuverlässig betrieben werden.
- Kosteneffizienz in der Serienfertigung: Schlagscheren bieten in der Serienproduktion eine hohe Kosteneffizienz, da sie schnell und in hoher Stückzahl schneiden können. Dies senkt die Stückkosten der gefertigten Teile.
Die Kombination aus niedrigen Betriebskosten, geringen Wartungsanforderungen und Energieeffizienz macht Schlagscheren besonders wirtschaftlich und ideal für Betriebe, die ihre Kosten optimieren möchten.
5. Einfache Bedienung und Benutzerfreundlichkeit
Schlagscheren sind vergleichsweise einfach zu bedienen und bieten eine benutzerfreundliche Arbeitsweise, die Zeit spart und das Risiko von Bedienfehlern minimiert.
- Einfache Bedienung: Im Vergleich zu komplexeren Maschinen wie Laserschneidern erfordern Schlagscheren weniger Fachwissen, was die Schulungsanforderungen reduziert.
- Intuitive Steuerung bei CNC-Modellen: CNC-Schlagscheren sind mit einer leicht verständlichen Benutzeroberfläche ausgestattet, die die Programmierung und Bedienung vereinfacht. Dadurch lassen sich Schnittprogramme erstellen und wiederholbare Schnitte automatisieren.
- Schnelle Einrichtung und Umrüstung: Schlagscheren lassen sich einfach einrichten und an unterschiedliche Materialanforderungen anpassen. Die Umstellung auf neue Materialdicken oder Werkstücke ist in der Regel schnell und problemlos möglich.
Durch die benutzerfreundliche Bedienung eignen sich Schlagscheren sowohl für erfahrene Facharbeiter als auch für weniger spezialisierte Bediener, was die Arbeitskosten senkt und die Produktivität steigert.
6. Sicherheit im Betrieb
Ein weiterer wichtiger Vorteil von Schlagscheren ist die Betriebssicherheit. Im Vergleich zu einigen anderen Schneidverfahren bergen Schlagscheren ein geringeres Verletzungsrisiko.
- Geringes Risiko thermischer Verletzungen: Da die Schlagschere keinen Wärmeeintrag ins Material erzeugt, besteht auch kein Risiko für Verbrennungen durch heiße Oberflächen.
- Not-Aus-Funktionen und Schutzvorrichtungen: Moderne Schlagscheren sind mit Not-Aus-Schaltern und Sicherheitsvorrichtungen ausgestattet, die den Bediener schützen und den Betrieb sicherer machen.
- Lasersensoren und Positionierungshilfen: Einige Schlagscheren verfügen über Lasersensoren und Sicherheitslichtvorhänge, die sicherstellen, dass die Maschine nur in Betrieb geht, wenn das Werkstück korrekt positioniert ist.
Die hohe Sicherheit der Schlagscheren sorgt für eine risikofreie Arbeitsumgebung, was die Arbeitssicherheit erhöht und gleichzeitig die Produktionskosten durch geringere Unfall- und Verletzungsraten reduziert.
7. Geringe Umweltbelastung
Da Schlagscheren ohne Wärme- oder chemische Prozesse arbeiten, ist ihre Umweltbelastung im Vergleich zu anderen Schneidtechniken geringer.
- Kein Emissionsausstoß: Schlagscheren erzeugen keine Emissionen wie bei thermischen Schneidverfahren, die bei der Bearbeitung Abgase oder Rauch freisetzen.
- Geringerer Energieverbrauch: Der Energiebedarf einer Schlagschere ist deutlich geringer als bei energieintensiven Schneidverfahren, wie dem Laser- oder Plasmaschneiden, was zur Energieeinsparung beiträgt.
- Langlebigkeit und Wiederverwendbarkeit: Da Schlagscheren sehr langlebig sind, muss die Maschine seltener ersetzt werden, was Ressourcen spart und die Umweltbelastung durch Produktion und Entsorgung neuer Maschinen reduziert.
Die geringe Umweltbelastung von Schlagscheren macht sie zu einer nachhaltigen Wahl, besonders für Unternehmen, die Wert auf umweltschonende Produktionsmethoden legen.
8. Anpassungsfähigkeit durch unterschiedliche Bauarten
Die verschiedenen Bauarten der Schlagscheren bieten für jeden Anwendungsbereich die passende Lösung.
- Manuelle Schlagscheren: Für kleinere Werkstätten und einfache Arbeiten mit dünnen Blechen sind manuelle Schlagscheren eine kostengünstige und praktische Lösung.
- Mechanische Schlagscheren: Sie bieten eine höhere Geschwindigkeit und sind in der Serienproduktion von mittleren Materialstärken optimal einsetzbar.
- Hydraulische Schlagscheren: Diese Maschinen sind ideal für dicke Materialien und industrielle Anwendungen, die eine hohe Schneidkraft erfordern.
- CNC-Schlagscheren: Mit CNC-Steuerung ausgestattet, bieten diese Modelle die höchste Präzision und Wiederholbarkeit für automatisierte Schneidprozesse.
Dank der verschiedenen Bauarten bieten Schlagscheren eine flexible Lösung, die je nach Material und Produktionsanforderung die optimale Leistung und Effizienz ermöglicht.
9. Minimaler Materialverlust und Effizienz in der Materialnutzung
Schlagscheren ermöglichen präzises Arbeiten mit minimalem Materialverlust.
- Genauer Schnittverlauf: Die präzisen Schnitte der Schlagschere ermöglichen eine exakte Materialnutzung, sodass weniger Abfall entsteht.
- Effiziente Ausnutzung des Rohmaterials: Durch die hohe Präzision lassen sich Werkstücke eng aneinander positionieren, um den Materialverbrauch zu minimieren.
- Reduzierter Verschnitt: Der geringe Verschnitt bedeutet auch niedrigere Materialkosten und eine gesteigerte Effizienz im Produktionsprozess.
Die effiziente Materialnutzung der Schlagschere ist besonders vorteilhaft in Industrien, die kostenintensive Materialien wie spezielle Metalllegierungen verwenden.
10. Zuverlässigkeit und Langlebigkeit
Die robuste Bauweise und die einfache Mechanik der Schlagschere machen sie zu einer zuverlässigen und langlebigen Maschine.
- Langlebige Komponenten: Schlagscheren sind auf eine lange Lebensdauer ausgelegt und können mit regelmäßiger Wartung viele Jahre im Einsatz bleiben.
- Hohe Betriebssicherheit: Die einfache Bauweise reduziert die Anfälligkeit für Fehler und Ausfälle, was die Betriebssicherheit erhöht.
- Minimaler Verschleiß bei richtiger Wartung: Bei regelmäßiger Klingenpflege und Wartung zeigt die Schlagschere einen minimalen Verschleiß, was Ausfallzeiten und Kosten für Reparaturen reduziert.
Durch ihre Zuverlässigkeit und Langlebigkeit bietet die Schlagschere eine nachhaltige Investition, die sich über Jahre hinweg auszahlt und die Gesamtbetriebskosten senkt.
Fazit
Die Vorteile von Schlagscheren reichen von hoher Effizienz und Präzision über vielseitige Einsatzmöglichkeiten bis hin zu Wirtschaftlichkeit und Sicherheit. Ob in kleinen Werkstätten oder großen Industrieanlagen – die Schlagschere ist eine flexible, kosteneffiziente und langlebige Maschine, die in zahlreichen Industrien und Produktionsprozessen unverzichtbar ist. Ihre Fähigkeit, präzise, schnelle und materialschonende Schnitte zu liefern, kombiniert mit einer einfachen Bedienung und geringer Umweltbelastung, macht sie zu einer bevorzugten Wahl für viele Anwendungen in der Metallbearbeitung.
Schlagscheren sind aufgrund ihrer Präzision, Effizienz und Vielseitigkeit in einer Vielzahl von Industrien und Anwendungsbereichen zu finden. Sie ermöglichen das schnelle und exakte Schneiden von Blechen und anderen Materialien, was sie zu einem unverzichtbaren Werkzeug in vielen Produktions- und Bearbeitungsprozessen macht. In diesem umfassenden Überblick gehen wir auf die typischen Einsatzgebiete von Schlagscheren ein und beleuchten, wie sie in verschiedenen Branchen und Anwendungen genutzt werden.
1. Metallverarbeitende Industrie
Die metallverarbeitende Industrie ist eines der wichtigsten Einsatzgebiete von Schlagscheren. Hier werden sie zur Bearbeitung von Rohmetallen und Halbfertigprodukten eingesetzt.
- Blechverarbeitung: Schlagscheren sind optimal geeignet, um große Blechtafeln schnell und präzise in kleinere Abschnitte zu schneiden. Diese Bleche werden anschließend in der weiteren Produktion zu Bauteilen verarbeitet.
- Bearbeitung von Stahl, Aluminium und Kupfer: Verschiedene Metalle wie Stahl, Aluminium und Kupfer können mit Schlagscheren geschnitten werden. Die Vielseitigkeit der Schlagschere macht sie ideal für die Bearbeitung unterschiedlicher Materialstärken und -typen.
- Serienfertigung und Herstellung von Standardkomponenten: In der Serienfertigung werden häufig gleiche Teile in großen Stückzahlen benötigt. Schlagscheren bieten hier eine hohe Effizienz und Wiederholgenauigkeit, was sie ideal für die Herstellung von Standardkomponenten macht.
In der Metallverarbeitung ermöglichen Schlagscheren die schnelle und kosteneffiziente Bearbeitung von Blechmaterialien und reduzieren den Aufwand für weitere Produktionsschritte.
2. Automobilindustrie
Die Automobilindustrie ist ein weiteres typisches Einsatzgebiet von Schlagscheren. Die Herstellung von Fahrzeugkomponenten erfordert oft präzise und schnelle Schnitte in einer Vielzahl von Metallteilen.
- Herstellung von Karosserieteilen: Schlagscheren werden häufig verwendet, um Karosserieteile zuzuschneiden. Diese Teile müssen passgenau und robust sein, da sie zur äußeren Struktur des Fahrzeugs gehören.
- Produktion von Rahmen- und Strukturbauteilen: Rahmen und strukturelle Komponenten eines Fahrzeugs bestehen meist aus Stahl oder Aluminium und müssen exakte Abmessungen haben, um den strengen Sicherheitsanforderungen zu entsprechen.
- Anpassung an unterschiedliche Materialstärken: Fahrzeuge bestehen aus Teilen verschiedener Materialstärken. Schlagscheren sind in der Lage, sowohl dünne Bleche für Karosserieanwendungen als auch dickere Materialien für strukturelle Komponenten zu schneiden.
Die Automobilindustrie profitiert von der Effizienz und Vielseitigkeit der Schlagscheren, die die Massenproduktion und Herstellung präziser und haltbarer Komponenten ermöglicht.
3. Bauwesen und Architektur
Im Bauwesen und in der Architektur werden Schlagscheren zur Bearbeitung und Herstellung von Metallteilen verwendet, die in Gebäude- und Infrastrukturprojekten eingesetzt werden.
- Herstellung von Bau- und Fassadenelementen: Für Gebäude und Fassaden werden oft Bleche benötigt, die Schlagscheren effizient zuschneiden können. Diese Bleche werden für Verkleidungen, Dächer, Fassadenelemente und Verzierungen verwendet.
- Anfertigung von Metallstrukturen und Trägerelementen: Stütz- und Trägerelemente aus Metall, die häufig in der Bauindustrie verwendet werden, müssen exakte Abmessungen haben. Schlagscheren bieten die nötige Präzision für diese Art von Bauteilen.
- Verarbeitung von rostfreiem Stahl und Aluminium: Rostfreier Stahl und Aluminium sind in der Bauindustrie aufgrund ihrer Korrosionsbeständigkeit weit verbreitet. Schlagscheren ermöglichen den Zuschnitt dieser Materialien für Anwendungen in der Außenarchitektur und im Fassadenbau.
Schlagscheren sind im Bauwesen unverzichtbar, um große Metallbleche und Trägerelemente schnell und exakt zu bearbeiten, was den Bauprozess beschleunigt und die Materialkosten senkt.
4. Luft- und Raumfahrtindustrie
In der Luft- und Raumfahrtindustrie sind extrem hohe Präzisionsstandards erforderlich, und Schlagscheren spielen hier eine zentrale Rolle bei der Herstellung hochwertiger Bauteile.
- Herstellung von Rumpf- und Flügelteilen: Rumpf- und Flügelteile müssen exakt geschnitten und frei von Materialverformungen sein, um die aerodynamischen Eigenschaften des Flugzeugs zu gewährleisten. Schlagscheren bieten hier die nötige Präzision und Schnittqualität.
- Bearbeitung von leichten, aber robusten Materialien: Materialien wie Aluminium, Titan und spezielle Metalllegierungen, die für ihre Leichtigkeit und Festigkeit bekannt sind, kommen in der Luftfahrt häufig vor. Schlagscheren können diese Materialien ohne thermische Belastung schneiden und so ihre strukturellen Eigenschaften erhalten.
- Anforderungen an hohe Wiederholgenauigkeit: Viele Komponenten müssen in großer Stückzahl und identischer Qualität gefertigt werden. CNC-Schlagscheren bieten die Wiederholgenauigkeit, die in der Serienproduktion erforderlich ist.
In der Luft- und Raumfahrt bietet die Schlagschere die erforderliche Genauigkeit und Schnittqualität, um Bauteile zu fertigen, die extremen Belastungen standhalten müssen und gleichzeitig leicht genug für den Flug sind.
5. Elektro- und Elektronikindustrie
In der Elektro- und Elektronikindustrie werden Schlagscheren für die Bearbeitung von Metallteilen und Gehäusen eingesetzt, die für elektrische Geräte und elektronische Anwendungen benötigt werden.
- Herstellung von Gehäusen und Abdeckungen: Schlagscheren schneiden Metallgehäuse und Abdeckungen, die für den Schutz von elektronischen Bauteilen verwendet werden. Die präzisen Schnitte der Schlagscheren sorgen für passgenaue Gehäuseteile.
- Bearbeitung von Kupfer und Aluminium für Leiterplatten und Anschlüsse: Kupfer und Aluminium werden oft für Leiterplatten und elektrische Anschlüsse verwendet, da sie eine hohe Leitfähigkeit besitzen. Schlagscheren ermöglichen den exakten Zuschnitt dieser Materialien, um sie für die weitere Verarbeitung vorzubereiten.
- Fertigung von Befestigungs- und Montagematerialien: In der Produktion von Elektro- und Elektronikgeräten werden viele kleine Befestigungs- und Montagematerialien benötigt. Schlagscheren können kleine Teile schnell und präzise zuschneiden.
Dank der Präzision und Flexibilität der Schlagscheren sind sie in der Elektro- und Elektronikindustrie ein unverzichtbares Werkzeug für die Herstellung von Gehäusen, Komponenten und Leitermaterialien.
6. Haushaltsgeräteindustrie
Die Herstellung von Haushaltsgeräten erfordert oft präzise geschnittene Metallteile, die sich passgenau in die Konstruktion der Geräte einfügen. Schlagscheren sind in dieser Branche ein bewährtes Werkzeug.
- Fertigung von Gehäusen und Verkleidungsteilen: Haushaltsgeräte wie Waschmaschinen, Kühlschränke und Öfen bestehen aus Blechgehäusen und Verkleidungen, die durch Schlagscheren in die richtige Form gebracht werden.
- Produktion von Innenteilen und Baugruppen: Innenteile wie Befestigungsplatten, Halterungen und Aufnahmen bestehen oft aus Metall und werden passgenau zugeschnitten.
- Materialvielfalt: In der Haushaltsgeräteindustrie werden verschiedene Metallarten und -stärken verwendet. Schlagscheren bieten die Flexibilität, diese verschiedenen Materialien zu verarbeiten und den Herstellungsprozess effizient zu gestalten.
Schlagscheren unterstützen die Herstellung von Haushaltsgeräten, indem sie hochwertige und präzise Metallteile produzieren, die in die endgültige Montage der Geräte integriert werden.
7. Kunsthandwerk und Modellbau
Im Kunsthandwerk und Modellbau sind Schlagscheren eine wertvolle Hilfe, da sie kleine Metallstücke präzise und schnell zuschneiden können.
- Herstellung von Modellen und Miniaturbauteilen: Schlagscheren sind im Modellbau und Kunsthandwerk ideal, um kleine Metallstücke für detaillierte Projekte zu schneiden. Sie ermöglichen exakte Schnitte, die bei kleinen Teilen notwendig sind.
- Bearbeitung von feinen Metallen und Blech: Im Kunsthandwerk und Modellbau werden oft dünne Bleche und feine Metalle verwendet. Manuelle Schlagscheren eignen sich gut für die präzise Bearbeitung solcher Materialien.
- Künstlerische und kreative Projekte: Schlagscheren sind ideal für kreative Arbeiten, bei denen Blech oder Metallformen mit Präzision geschnitten werden müssen, um verschiedene Designs und Projekte zu realisieren.
Die vielseitige Anwendung von Schlagscheren im Modellbau und Kunsthandwerk ermöglicht die exakte und kreative Bearbeitung von Metall, die für kunsthandwerkliche Projekte und Modellbauprojekte unverzichtbar ist.
8. Möbelindustrie und Innenausbau
In der Möbelindustrie und im Innenausbau werden zunehmend Metallteile eingesetzt, was die Schlagschere auch in dieser Branche zu einem wichtigen Werkzeug macht.
- Fertigung von Metallrahmen und Strukturelementen: Moderne Möbel und Innenausbauten enthalten oft Metallrahmen, die präzise zugeschnitten werden müssen, um die Stabilität und das Design zu gewährleisten.
- Produktion von dekorativen Metallplatten und Oberflächen: Dekorative Elemente aus Metall sind in Möbeln und Innenausstattungen beliebt. Schlagscheren ermöglichen den exakten Zuschnitt dieser Platten und Oberflächen.
- Bearbeitung von rostfreiem Stahl und Aluminium: Materialien wie rostfreier Stahl und Aluminium werden in der Möbelindustrie verwendet, da sie sowohl langlebig als auch ästhetisch ansprechend sind.
Die Schlagschere bietet der Möbelindustrie und dem Innenausbau eine effiziente Lösung für die Produktion von präzisen Metallteilen, die zur Stabilität und Ästhetik von Möbeln und Innenräumen beitragen.
Fazit
Die typischen Einsatzgebiete von Schlagscheren reichen von der Automobilindustrie über das Bauwesen bis hin zur Möbelindustrie und dem Kunsthandwerk. Ihre Vielseitigkeit, Effizienz und Präzision machen Schlagscheren zu einer wertvollen Maschine für eine breite Palette an Anwendungen. Die Fähigkeit, verschiedene Materialtypen und -stärken zu bearbeiten, sowie die Möglichkeit, sowohl großvolumige Serienfertigung als auch kreative Einzelstücke zu realisieren, zeigt die Anpassungsfähigkeit der Schlagscheren an unterschiedliche industrielle und handwerkliche Bedürfnisse.
Indem sie eine kosteneffiziente und produktive Lösung bieten, haben sich Schlagscheren in den genannten Industrien als unverzichtbare Werkzeuge etabliert, die den Herstellungsprozess beschleunigen und die Qualität der Endprodukte sichern.
Die Auswahl einer Schlagschere für industrielle oder handwerkliche Zwecke hängt von mehreren Faktoren ab, die auf die spezifischen Anforderungen des Anwenders abgestimmt sein müssen. Von der Materialart über die Schnittqualität bis hin zu den Betriebskosten – die Auswahlkriterien für Schlagscheren sind vielfältig und spielen eine wichtige Rolle, um Effizienz, Produktivität und Qualität in der Produktion sicherzustellen. In diesem umfassenden Überblick erläutern wir die wichtigsten Auswahlkriterien für Schlagscheren, damit Unternehmen und Werkstätten fundierte Entscheidungen treffen können.
1. Materialart und -stärke
Ein entscheidender Faktor bei der Auswahl einer Schlagschere ist das Material, das bearbeitet werden soll, sowie dessen Stärke.
- Materialart: Die Schlagschere muss für das Material geeignet sein, das hauptsächlich bearbeitet wird. Materialien wie Stahl, Edelstahl, Aluminium und Kupfer haben unterschiedliche Festigkeiten und Anforderungen an die Schnittkraft. Für härtere Materialien wie Edelstahl benötigt man eine Schlagschere mit hoher Schneidkraft, während weichere Materialien wie Aluminium weniger Kraft erfordern.
- Materialstärke: Die Stärke des Materials bestimmt maßgeblich die benötigte Schneidkraft der Schlagschere. Schlagscheren sind in verschiedenen Leistungsklassen erhältlich, die je nach Modell für dünne Bleche oder auch dickere Metallplatten ausgelegt sind. Mechanische Schlagscheren eignen sich oft für mittlere Stärken, während hydraulische Schlagscheren besser für dickere Materialien geeignet sind.
Ein genauer Abgleich zwischen Materialeigenschaften und Maschinenkapazität verhindert Überbeanspruchung und sorgt für eine lange Lebensdauer der Schlagschere.
2. Schnittlänge und Größe des Werkstücks
Die Schnittlänge der Schlagschere muss zu den Abmessungen der zu bearbeitenden Werkstücke passen.
- Maximale Schnittlänge: Die Schnittlänge gibt an, welche maximale Breite eines Werkstücks die Schlagschere schneiden kann. Bei der Verarbeitung großer Blechtafeln, wie sie in der Bauindustrie oder der Metallbearbeitung verwendet werden, ist eine lange Schnittkapazität erforderlich. Kleinere Maschinen mit kürzeren Schnittlängen eignen sich für Werkstätten und den Modellbau.
- Platzbedarf: Die Größe der Schlagschere sollte an die räumlichen Gegebenheiten angepasst sein. Eine große Schlagschere benötigt mehr Platz und kann aufgrund ihres Gewichts schwer zu bewegen sein, was bei der Aufstellung im Betrieb berücksichtigt werden muss.
Je größer das Werkstück, desto leistungsfähiger und größer sollte die Schlagschere dimensioniert sein, um die Materialien effizient bearbeiten zu können.
3. Präzision und Toleranzanforderungen
In Branchen, die hohe Präzisionsanforderungen haben, ist es wichtig, eine Schlagschere zu wählen, die eine exakte Schnittführung ermöglicht.
- Präzision: Für Anwendungen, die eine hohe Genauigkeit erfordern, wie etwa in der Luftfahrt- oder Automobilindustrie, sind CNC-gesteuerte Schlagscheren ideal. CNC-Modelle bieten die Möglichkeit, die Klingenbewegung und das Werkstück präzise zu steuern, was die Wiederholgenauigkeit erhöht.
- Toleranzen: Unterschiedliche Anwendungen erfordern unterschiedliche Toleranzbereiche. Je enger die Toleranzen, desto exakter muss die Schlagschere eingestellt werden können. Präzisionsschlagscheren sind daher mit feinjustierbaren Einstellungen ausgestattet, um die erforderlichen Toleranzgrenzen einzuhalten.
Durch eine präzise Schnittleistung können die Anforderungen der Endkunden erfüllt und Nachbearbeitungen minimiert werden, was den Produktionsprozess effizienter gestaltet.
4. Antriebsart der Schlagschere
Es gibt verschiedene Antriebsarten für Schlagscheren – manuell, mechanisch und hydraulisch –, die jeweils Vor- und Nachteile bieten.
- Manuelle Schlagscheren: Diese werden von Hand betrieben und sind kostengünstig, jedoch für dünnere Materialien und kleinere Arbeiten ausgelegt. Sie eignen sich ideal für Werkstätten oder den Modellbau, wo keine hohen Schnittkräfte erforderlich sind.
- Mechanische Schlagscheren: Diese verwenden einen elektrischen Motor, um die Klinge anzutreiben. Sie sind schnell und für mittlere Materialstärken geeignet, was sie ideal für Serienproduktionen macht. Allerdings sind sie verschleißanfälliger und benötigen regelmäßige Wartung.
- Hydraulische Schlagscheren: Hydraulische Modelle bieten die höchste Schneidkraft und sind für dickere Materialien geeignet. Sie arbeiten leiser als mechanische Schlagscheren und haben einen gleichmäßigen Klingenhub, was die Präzision verbessert. Der Nachteil liegt in den höheren Anschaffungskosten und der Wartungsintensität.
Die Wahl der Antriebsart sollte nach der Materialstärke, der erforderlichen Schneidkraft und den Produktionsanforderungen erfolgen, um den optimalen Einsatz der Schlagschere zu gewährleisten.
5. Automatisierungsgrad
Die Entscheidung für eine einfache oder eine CNC-gesteuerte Schlagschere hängt vom Automatisierungsbedarf und den Anforderungen an die Effizienz in der Produktion ab.
- Konventionelle Schlagscheren: Sie sind einfach zu bedienen und erfordern manuelle Justierungen, was bei Einzelstückfertigungen ausreichend ist. Sie eignen sich besonders für kleine Unternehmen oder Werkstätten.
- CNC-Schlagscheren: Diese bieten eine computergesteuerte Steuerung und sind in der Lage, komplexe Schnitte und Serienfertigungen mit hoher Präzision durchzuführen. Sie sind besonders effizient in der Serienproduktion, da die Programme wiederholbar sind und die Produktionszeit verkürzt wird.
Ein höherer Automatisierungsgrad ermöglicht mehr Effizienz und Präzision, was sich positiv auf die Produktionskosten und -qualität auswirkt. CNC-Schlagscheren erfordern jedoch eine höhere Investition und eine Schulung des Bedienpersonals.
6. Geschwindigkeit und Produktionsvolumen
Die Geschwindigkeit und das Produktionsvolumen sind wichtige Kriterien für die Auswahl einer Schlagschere, insbesondere in Branchen mit hohen Durchsatzanforderungen.
- Schnittgeschwindigkeit: Eine höhere Schnittgeschwindigkeit ist vorteilhaft, wenn große Stückzahlen produziert werden sollen. Mechanische Schlagscheren bieten schnelle Schnitte und sind daher für Massenproduktionen geeignet, während hydraulische Modelle etwas langsamer, dafür aber präziser sind.
- Produktionsvolumen: Bei hohem Produktionsvolumen ist es wichtig, eine Schlagschere zu wählen, die für den Dauerbetrieb ausgelegt ist. Hydraulische und mechanische Modelle sind für hohe Stückzahlen geeignet, während manuelle Schlagscheren eher für kleinere Produktionsserien und den gelegentlichen Gebrauch gedacht sind.
Je nach Produktionsanforderungen sollte eine Schlagschere gewählt werden, die eine hohe Effizienz und Ausdauer in der Verarbeitung bietet.
7. Wartungsanforderungen und Lebensdauer
Die Wartungsanforderungen und die Lebensdauer der Schlagschere beeinflussen die Betriebskosten und die Zuverlässigkeit im täglichen Einsatz.
- Wartungsaufwand: Hydraulische Schlagscheren erfordern regelmäßige Wartung des Hydrauliksystems, während mechanische Modelle hauptsächlich im Antriebsbereich gewartet werden müssen. Manuelle Schlagscheren haben den geringsten Wartungsbedarf und sind daher besonders langlebig.
- Verschleiß und Ersatzteilverfügbarkeit: Schlagscheren unterliegen natürlichem Verschleiß, insbesondere an den Klingen und beweglichen Teilen. Maschinen, bei denen Ersatzteile leicht verfügbar sind, haben einen Vorteil, da sie bei Defekten schnell wieder einsatzfähig gemacht werden können.
- Langlebigkeit: Hochwertige Modelle mit robuster Bauweise und langlebigen Materialien wie gehärtetem Werkzeugstahl bei den Klingen erhöhen die Lebensdauer der Maschine und reduzieren langfristig die Betriebskosten.
Durch die Auswahl einer langlebigen Schlagschere mit minimalem Wartungsbedarf können Unternehmen Kosten einsparen und die Maschinenverfügbarkeit erhöhen.
8. Betriebskosten und Budget
Die Betriebskosten und das Budget spielen bei der Anschaffung einer Schlagschere eine entscheidende Rolle, insbesondere für kleine und mittlere Unternehmen.
- Anschaffungskosten: Manuelle Schlagscheren sind günstiger in der Anschaffung als mechanische oder hydraulische Modelle. CNC-Schlagscheren sind die teuersten, bieten aber die höchste Automatisierung und Präzision.
- Betriebskosten: Der Energieverbrauch und die Wartungskosten variieren je nach Modell und Bauart. Hydraulische Modelle haben tendenziell höhere Betriebskosten aufgrund des Hydrauliksystems, während mechanische Modelle weniger Energie verbrauchen.
- Langfristige Kosten: Neben den Anschaffungskosten sollten auch die langfristigen Kosten in die Kalkulation einfließen, wie etwa die Kosten für Ersatzteile, Reparaturen und Stromverbrauch.
Ein klar definiertes Budget hilft dabei, das optimale Modell auszuwählen, das die gewünschten Leistungen erbringt und dennoch wirtschaftlich ist.
9. Sicherheit und Schutzvorrichtungen
Sicherheitsvorkehrungen sind besonders wichtig, da Schlagscheren mit hoher Kraft arbeiten und scharfe Klingen besitzen.
- Sicherheitsvorrichtungen: Moderne Schlagscheren sind mit Sicherheitsvorrichtungen ausgestattet, wie z. B. Schutzabdeckungen, Lichtschranken oder Sicherheitslichtvorhängen, die den Bediener schützen und die Maschine bei Gefahren automatisch abschalten.
- Not-Aus-Schalter: Ein gut erreichbarer Not-Aus-Schalter ist ein Muss für jede Schlagschere, um bei Bedarf den Schneidprozess sofort zu unterbrechen.
- Bedienerschulung: Für den sicheren Betrieb einer Schlagschere ist eine angemessene Schulung des Personals erforderlich, insbesondere bei CNC-Modellen, die komplexe Programmierungen erfordern.
Die Berücksichtigung von Sicherheitsstandards schützt das Bedienpersonal und verringert das Unfallrisiko im Betrieb.
10. Verfügbarkeit von Zubehör und Erweiterungen
Je nach Anwendung können Zubehör und Erweiterungen die Einsatzmöglichkeiten und Flexibilität der Schlagschere verbessern.
- Klingen: Verschiedene Klingen für unterschiedliche Materialien erhöhen die Vielseitigkeit der Schlagschere. Wechselbare Klingen sind besonders praktisch, wenn häufig zwischen verschiedenen Materialien gewechselt wird.
- Automatische Materialzuführung: Eine automatische Materialzuführung kann den Arbeitsprozess beschleunigen und ist besonders für Serienproduktionen sinnvoll.
- Positionierhilfen und Messtische: Diese Zubehörteile erleichtern die präzise Ausrichtung des Materials und verbessern die Schnittgenauigkeit.
Durch passendes Zubehör und Erweiterungen kann die Effizienz der Schlagschere erhöht und der Arbeitsprozess optimiert werden.
Fazit
Die Wahl der richtigen Schlagschere ist ein komplexer Entscheidungsprozess, der von verschiedenen Faktoren abhängt – vom Material über die Antriebsart und die gewünschte Schnittqualität bis hin zu Betriebskosten und Sicherheit. Schlagscheren bieten eine Vielzahl an Einsatzmöglichkeiten, doch nur mit einer auf die spezifischen Anforderungen zugeschnittenen Maschine können Unternehmen die optimale Leistung und Effizienz erzielen. Eine gründliche Analyse der Einsatzbedingungen, kombiniert mit einer genauen Kostenkalkulation, hilft dabei, die beste Schlagschere für die jeweilige Anwendung zu finden und langfristig eine kosteneffiziente Produktion sicherzustellen.
Metallbearbeitungsmaschinen
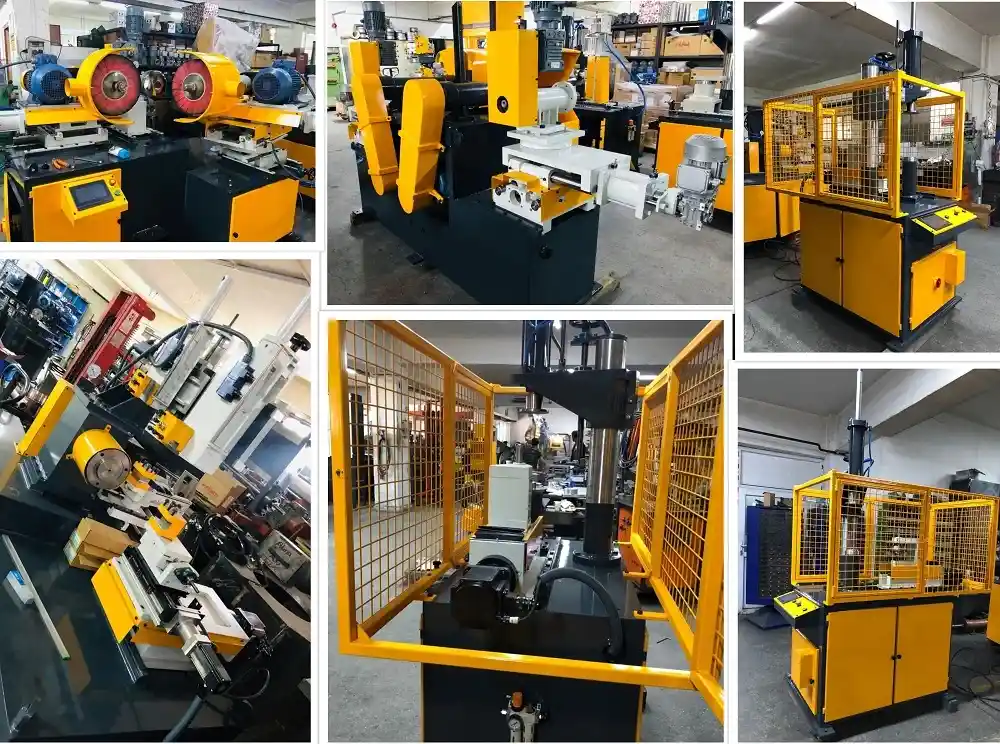
Metallbearbeitungsmaschinen wie Bördel und Beschneide Maschinen, Flanschmaschinen, Beschneide und Bördelmaschinen, Umformtechnik, Rohrbiegemaschinen, Bandsäge für Metall, Hydraulische Horizontalpresse, Kantenschneide-Bördelmaschine, Kantenbördelmaschine, Entgratungsmaschine, Innen- und Außenpoliermaschine für Edelstahltöpfe, Kreisschneidemaschine, Profilbiegemaschine und Rundschweißmaschine
Maßgeschneiderte Skalierung für spezifische Anwendungen
Die automatisierte Herstellung von Behältern, Fässern und Kesseln wird durch unsere Lösungen exakt auf das jeweilige Einsatzgebiet und die gewünschte Ausbringung angepasst. Dabei bieten wir sowohl lineare Lösungen als auch Inselkonzepte an, die eine bedarfsorientierte Automation ermöglichen. Spezielle Kantenvorbereitung für das Laserschweißen sowie wirtschaftliche Rüstkonzepte bis hin zur Fertigung „Just-in-Sequence“ sind Teil unseres Leistungsspektrums. Wir kombinieren Standard- und Sondermaschinen und bieten Ferndiagnose über LAN, WLAN oder GSM an, ergänzt durch umfassende Dokumentation gemäß CE-Richtlinien für die Gesamtanlage.
Unser Konzept
EMS entwickelt und fertigt Maschinen und Anlagen für die automatisierte Herstellung von Behältern in großem Maßstab. Alle Arbeitsschritte, von der Vorbereitung bis zur Fertigung, werden dabei aus einer Hand angeboten. Unsere erprobten Standardkomponenten sind perfekt aufeinander abgestimmt und können nahtlos mit Robotern kombiniert werden, um leistungsfähige Fertigungseinrichtungen zu schaffen.
Flexible Präzisionsfertigung
Unsere Fertigungslinien ermöglichen eine einfache Umstellung auf verschiedene Längen, Durchmesser, Formen und Bearbeitungen durch Programmwechsel. Dabei werden zahlreiche Einzelschritte wie Beschneiden, Formen, Stanzen, Fügen, Montieren, Schweißen und Prüfen automatisch und mit höchster Präzision an die jeweilige Aufgabe angepasst. Besonderes Augenmerk legen wir auf die Kantenvorbereitung für den Schweißprozess, um eine herausragende Prozesssicherheit und minimale Ausschussquoten zu gewährleisten.
Maschinenprogramm für die Metallbearbeitung
Unsere Metallbearbeitungsmaschinen sind:
- Rohrbiegemaschine
- Horizontale Presse
- Bandsäge für Metall
- Profilbiegemaschine
- Tiefziehpresse
- Rundschweißmaschine
- Kantenschneide-Bördelmaschine
- Topf- und Pfannenpoliermaschine
- Poliermaschine für flache Oberflächen
Besteck-Produktionslinie: Eine Besteck-Produktionslinie ist eine Art Maschine, die Besteck in einem kontinuierlichen Prozess herstellt. Es umfasst verschiedene Arten von Maschinen wie den Messerschleifer, den Messerschärfer und den Klingenpolierer.
Kochgeschirr-Herstellungsmaschine: Eine Kochgeschirr-Herstellungsmaschine ist eine Art Maschine, die Kochgeschirr in einem kontinuierlichen Prozess herstellt. Es umfasst verschiedene Arten von Maschinen wie den Topfmacher, den Pfannenmacher und den Wokmacher.
Küchengeschirr-Produktionsmaschine: Eine Küchengeschirr-Produktionsmaschine ist eine Art Maschine, die Küchengeschirr in einem kontinuierlichen Prozess herstellt. Es umfasst verschiedene Arten von Maschinen wie Maschinen zur Herstellung von Teekesseln, Produktionslinien für Besteck, Produktionslinien für Töpfe und Pfannen
Wir entwerfen, fertigen und montieren komplette Produktionslinien für Kochgeschirr, Küchengeschirr, Hotelgeschirr und Besteck sowie einzelne Maschinen für einen bestimmten Zweck