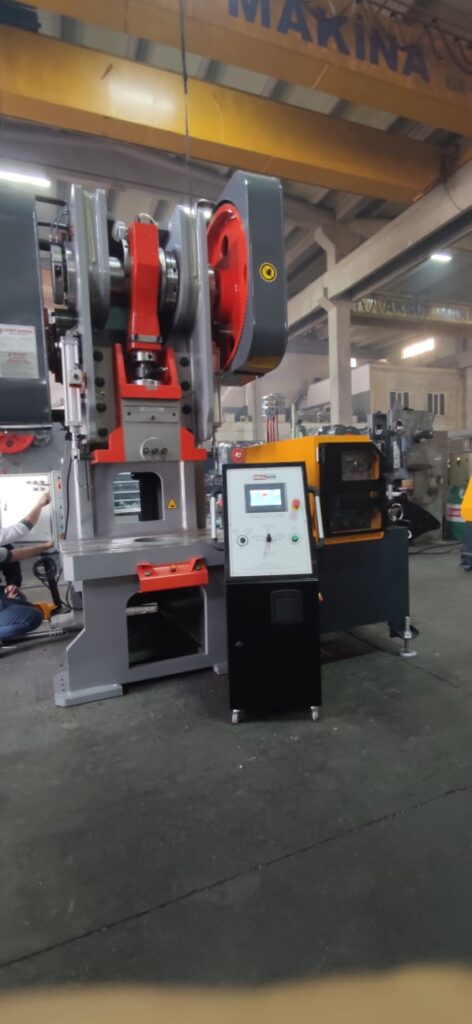
Automatisiertes Formpressen: Das Formpressen ist eines der zentralen Verfahren in der Fertigungstechnik, das zur Herstellung von Bauteilen für verschiedenste Anwendungen eingesetzt wird. Es ist ein Verfahren, bei dem Rohmaterialien unter Einsatz von Druck und Wärme in eine Form gepresst werden, um daraus Teile mit bestimmten geometrischen Eigenschaften herzustellen. Ursprünglich als rein manueller Prozess entwickelt, hat sich das Formpressen in den letzten Jahrzehnten erheblich weiterentwickelt und wird heute durch moderne Technologien und Automatisierungstechnik unterstützt.
Mit der Automatisierung von Formpressverfahren ergeben sich zahlreiche Vorteile. Der Einsatz automatisierter Systeme ermöglicht eine höhere Präzision und gleichbleibende Qualität bei jedem hergestellten Teil. Automatisierte Maschinen können zudem 24/7 in Betrieb sein, was die Effizienz steigert und die Produktionskosten senkt. Durch den Einsatz von Robotern, Sensorik, und intelligenter Steuerungstechnik lassen sich die Prozesse weiter verbessern und die Qualitätssicherung optimieren.
Ausarbeitung des nächsten Abschnitts
Falls diese Gliederung für Sie passend ist, gehe ich gern zur detaillierten Ausarbeitung der ersten Abschnitte über. Geben Sie mir Bescheid, falls Sie Anpassungen an der Struktur wünschen oder wenn bestimmte Punkte tiefergehend behandelt werden sollen.
Hier ist eine detaillierte Einleitung in das Thema „Automatisiertes Formpressen“, die als Grundlage für die gesamte Ausarbeitung dienen kann. In dieser Einführung werden die Grundlagen des Formpressens, die Ziele der Automatisierung und der technologische Fortschritt in diesem Bereich umfassend behandelt, um eine fundierte Basis für eine tiefere Untersuchung der Technologie und ihrer Anwendungsmöglichkeiten zu schaffen.
Formpressen: Definition und Überblick
Das Formpressen ist ein weit verbreitetes Fertigungsverfahren, das in vielen Industriezweigen zur Herstellung von Bauteilen und Komponenten eingesetzt wird. Es ist insbesondere bekannt und geschätzt in Branchen wie der Automobilindustrie, der Luft- und Raumfahrt, der Bauindustrie und der Konsumgüterproduktion. Das Verfahren selbst umfasst das Pressen eines Materials in eine Form unter Einsatz von Druck und oft auch Wärme, um die gewünschte Form und die gewünschten Materialeigenschaften zu erzielen.
Beim Formpressen unterscheidet man grundsätzlich zwischen Heiß- und Kaltpressen:
- Heißpressen wird verwendet, um Werkstoffe zu verformen, die nur bei höheren Temperaturen bearbeitet werden können. Dies ist oft bei Kunststoffen und bestimmten Metallen der Fall.
- Kaltpressen hingegen wird häufig für Materialien verwendet, die bei Raumtemperatur verarbeitet werden können, und findet oft Anwendung bei Metallen und Verbundwerkstoffen.
Abhängig vom Material und dem gewünschten Ergebnis gibt es auch spezielle Verfahren des Formpressens, wie zum Beispiel das Pulverpressen, bei dem Pulvermaterialien in eine Form gepresst und anschließend gesintert werden.
2. Zielsetzung und Nutzen der Automatisierung im Formpressen
Mit der zunehmenden Komplexität moderner Fertigungsprozesse und dem wachsenden Bedarf an hochpräzisen Bauteilen steigt der Bedarf an Automatisierung im Formpressen. Die Automatisierung von Fertigungsverfahren wie dem Formpressen bietet zahlreiche Vorteile und ist heute ein entscheidender Faktor für den Erfolg vieler Unternehmen, die auf maximale Effizienz und Qualität setzen.
Zu den wichtigsten Vorteilen der Automatisierung im Formpressen gehören:
- Erhöhte Präzision und Qualität: Automatisierte Maschinen ermöglichen eine hohe Präzision bei der Herstellung und können die Konsistenz der Qualität gewährleisten. Dies ist besonders wichtig für sicherheitskritische Bauteile, wie sie in der Luft- und Raumfahrt oder im Automobilbau benötigt werden.
- Zeit- und Kosteneffizienz: Automatisierte Prozesse reduzieren die Durchlaufzeit erheblich, da Maschinen kontinuierlich und rund um die Uhr arbeiten können. Dadurch sinken die Produktionskosten pro Bauteil, und die Produktionskapazität kann gesteigert werden.
- Reduzierung von Fehlern und Ausschuss: Durch den Einsatz von Sensoren und Überwachungssystemen können automatisierte Maschinen Fehler frühzeitig erkennen und Anpassungen vornehmen. Dies reduziert den Materialverlust und den Ausschuss, was die Effizienz des gesamten Prozesses steigert.
- Erhöhte Arbeitssicherheit: Automatisierte Systeme verringern die Notwendigkeit menschlicher Eingriffe in gefährlichen Bereichen. Mitarbeiter müssen weniger Zeit in der Nähe heißer Maschinen oder unter hohem Druck arbeitender Systeme verbringen, was das Risiko von Verletzungen senkt.
3. Technologischer Fortschritt und Digitalisierung im Formpressen
Der technologische Fortschritt hat das Formpressen entscheidend verändert. Die Entwicklungen im Bereich der Robotik, der Sensorik und der intelligenten Steuerungssysteme haben den Weg für automatisierte Formpressverfahren geebnet, die in der Lage sind, komplexe und wiederholbare Prozesse mit hoher Präzision und Geschwindigkeit auszuführen. Diese Technologien bieten eine Vielzahl von Möglichkeiten zur Optimierung des gesamten Prozesses und zur Verbesserung der Produktqualität.
Zu den wichtigsten Technologien, die in der Automatisierung des Formpressens zum Einsatz kommen, gehören:
- Robotergestützte Systeme: Industrieroboter können Materialien präzise in die Form einlegen und das fertige Produkt entnehmen. Sie können flexibel auf unterschiedliche Formate und Materialien eingestellt werden und arbeiten schnell und zuverlässig.
- Sensoren und Überwachungssysteme: Moderne Maschinen sind mit Sensoren ausgestattet, die Daten zu Druck, Temperatur und anderen relevanten Prozessparametern sammeln. Diese Daten können in Echtzeit ausgewertet und zur Prozesssteuerung verwendet werden, was eine hohe Kontrolle und Anpassungsfähigkeit ermöglicht.
- Steuerungssysteme und Softwareintegration: Automatisierte Maschinen sind oft mit speziellen Steuerungssystemen ausgestattet, die eine präzise Steuerung des Pressvorgangs erlauben. Moderne Steuerungssysteme können mit der Produktionssoftware eines Unternehmens vernetzt werden und ermöglichen eine umfassende Überwachung und Optimierung des gesamten Produktionsprozesses.
- Maschinelles Lernen und Künstliche Intelligenz (KI): Durch den Einsatz von KI und maschinellem Lernen können Produktionsprozesse kontinuierlich analysiert und optimiert werden. Maschinen können aus vergangenen Prozessen lernen, um Abläufe zu verbessern und die Effizienz weiter zu steigern. Diese Technologien bieten die Grundlage für vorausschauende Wartung und ermöglichen es, frühzeitig auf potenzielle Probleme zu reagieren, bevor diese die Produktion beeinträchtigen.
4. Formpressen im Kontext von Industrie 4.0 und Smart Manufacturing
Das Konzept der Industrie 4.0, das sich auf die Vernetzung und Digitalisierung der Produktion bezieht, hat das Potenzial des Formpressens durch Automatisierung weiter vorangetrieben. Die Integration von Maschinen und Anlagen in ein Netzwerk ermöglicht es, Daten in Echtzeit zu sammeln und Produktionsabläufe flexibel anzupassen.
Smart Manufacturing bedeutet in diesem Zusammenhang, dass die Maschinen in der Lage sind, eigenständig zu kommunizieren und Entscheidungen auf Basis von Datenanalysen zu treffen. Im Bereich des Formpressens bedeutet das beispielsweise, dass Maschinen automatisch erkennen, wenn sich die Eigenschaften des eingesetzten Materials ändern, und die Parameter des Pressvorgangs entsprechend anpassen können.
5. Herausforderungen und Lösungsansätze bei der Automatisierung des Formpressens
Trotz der vielen Vorteile gibt es auch Herausforderungen bei der Implementierung von Automatisierungslösungen im Formpressen. Zu den größten Hürden zählen die hohen Anschaffungskosten für moderne Maschinen und die komplexe Wartung und Instandhaltung. Besonders für kleinere und mittelständische Unternehmen ist die Integration solcher Systeme oft eine bedeutende Investition.
Zusätzlich erfordert die Automatisierung hochspezialisierte Kenntnisse und Fachpersonal, sowohl für die Bedienung als auch für die Instandhaltung der Maschinen. Unternehmen, die in die Automatisierung ihrer Produktionsprozesse investieren, stehen daher oft vor der Herausforderung, entsprechend qualifiziertes Personal zu finden oder auszubilden.
Lösungsansätze beinhalten:
- Schulung und Weiterbildung: Unternehmen investieren zunehmend in die Ausbildung ihrer Mitarbeiter im Umgang mit automatisierten Systemen und in spezifisches Fachwissen zur Wartung und Optimierung der Maschinen.
- Entwicklung skalierbarer Automatisierungslösungen: Anbieter von Automatisierungstechnologien entwickeln Lösungen, die auf die Bedürfnisse kleinerer Betriebe zugeschnitten sind und eine schrittweise Integration ermöglichen.
- Partnerschaften und Kooperationen: Zusammenarbeit zwischen Unternehmen, Maschinenherstellern und Forschungseinrichtungen kann dabei helfen, Kosten zu teilen und Innovationen voranzutreiben, die das Formpressen durch Automatisierung effizienter und erschwinglicher machen.
6. Zukunftsperspektiven des automatisierten Formpressens
Die Entwicklung des automatisierten Formpressens wird weiterhin stark von technologischen Innovationen und der Nachfrage nach effizienten, nachhaltigen Produktionslösungen geprägt sein. Einige der wichtigsten Trends und Zukunftsperspektiven umfassen:
- Nachhaltigkeit und Energieeffizienz: Immer mehr Unternehmen setzen auf energieeffiziente Maschinen und nachhaltige Materialien. Automatisierte Prozesse ermöglichen es, den Energieverbrauch pro hergestelltem Bauteil zu reduzieren und so die Umweltbelastung zu verringern.
- Erweiterung der Anwendungsmöglichkeiten: Durch die Automatisierung werden immer mehr Materialien für das Formpressen zugänglich, und die Anwendungsmöglichkeiten in verschiedenen Industrien erweitern sich. Materialien wie recycelte Kunststoffe oder spezielle Verbundstoffe könnten in Zukunft vermehrt in automatisierten Prozessen eingesetzt werden.
- Integration neuer Technologien: Technologien wie das Internet der Dinge (IoT) und fortschrittliche KI-Systeme werden zunehmend in automatisierte Fertigungssysteme integriert, wodurch die Prozesse flexibler und anpassungsfähiger werden.
Zusammenfassung der Einleitung
Die Automatisierung des Formpressens hat das Potenzial, die industrielle Fertigung auf ein neues Niveau zu heben. Durch den Einsatz modernster Technologien wie Robotik, Sensorik und künstlicher Intelligenz können Prozesse effizienter, sicherer und umweltfreundlicher gestaltet werden. Obwohl die Implementierung solcher Systeme mit Herausforderungen verbunden ist, überwiegen die Vorteile. Mit fortschreitender Technologie und wachsendem Bewusstsein für Nachhaltigkeit wird das automatisierte Formpressen in der Industrie 4.0 zunehmend an Bedeutung gewinnen und die Produktionslandschaft nachhaltig verändern.
Grundlagen und Verfahren des Formpressens
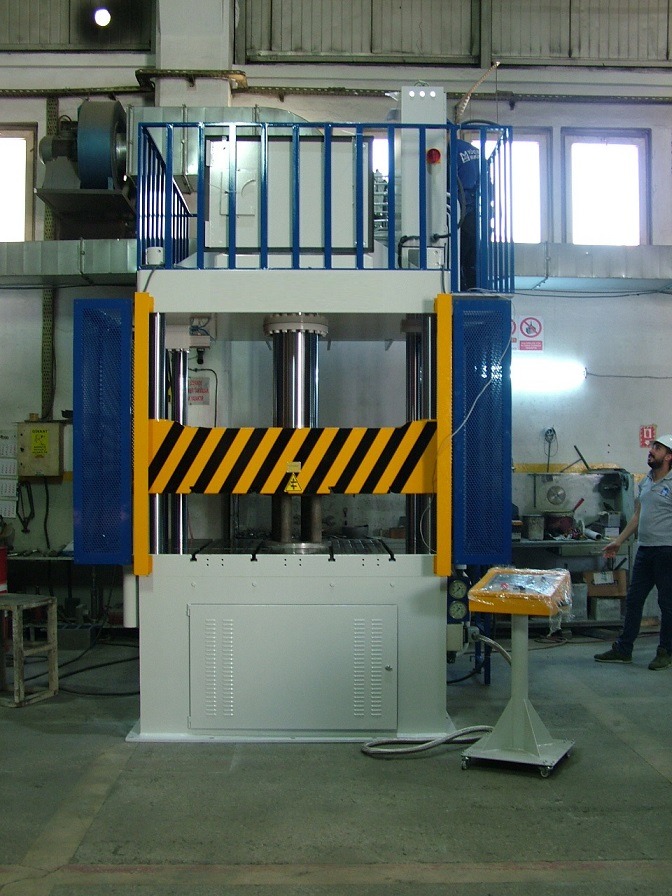
1. Einführung in die Grundlagen des Formpressens
Das Formpressen ist ein weit verbreitetes Umformverfahren, das auf die Herstellung von Bauteilen aus verschiedenen Materialien spezialisiert ist. Dabei wird ein Rohmaterial – oft in Pulver- oder Granulatform, aber auch als flüssiges oder viskoelastisches Material – unter Druck und häufig auch unter Einwirkung von Wärme in eine vorgegebene Form gepresst. Das Ziel ist es, eine dauerhafte Form und spezifische Materialeigenschaften zu erzeugen, die sich für den geplanten Einsatzzweck des Bauteils eignen.
Formpressen wird in unterschiedlichen Branchen angewandt, darunter:
- Automobilindustrie: Fertigung von Struktur- und Karosserieteilen.
- Luft- und Raumfahrt: Herstellung von leichten und gleichzeitig stabilen Komponenten.
- Bauindustrie und Haushaltsgeräte: Produktion von widerstandsfähigen und kostengünstigen Bauteilen.
2. Überblick über die Verfahren des Formpressens
Es gibt verschiedene Formpressverfahren, die auf die unterschiedlichen Anforderungen von Materialien und Endprodukten zugeschnitten sind. Zu den wichtigsten Verfahren gehören:
2.1 Heißpressen
Heißpressen ist ein Formpressverfahren, bei dem das Rohmaterial auf eine hohe Temperatur erhitzt wird, um die Formbarkeit zu erhöhen und die Verarbeitbarkeit zu erleichtern. Beim Heißpressen kommen hauptsächlich thermoplastische und duroplastische Kunststoffe sowie bestimmte Metalle zum Einsatz. Durch die Hitzeeinwirkung lassen sich diese Materialien leicht formen und härten anschließend in der gewünschten Form aus.
- Anwendungsbereiche: Automobilteile, elektronische Komponenten, und medizinische Geräte.
- Vorteile: Reduzierter Formgebungsdruck, schnellere Aushärtung, und gute Oberflächenqualität.
- Nachteile: Hoher Energieverbrauch, größere Abhängigkeit von präzisen Temperatursteuerungen.
2.2 Kaltpressen
Beim Kaltpressen wird das Material ohne zusätzliche Wärmezufuhr geformt. Dieses Verfahren kommt vor allem bei metallischen Werkstoffen zum Einsatz und ist besonders geeignet für Materialien, die auch bei Raumtemperatur eine ausreichende Verformbarkeit aufweisen.
- Anwendungsbereiche: Herstellung von Teilen für die Bau- und Maschinenbauindustrie sowie für den Automobilsektor.
- Vorteile: Energieeffizienz durch Verzicht auf externe Heizungen, geringerer Verschleiß an Werkzeugen.
- Nachteile: Höherer Druckaufwand, Einschränkungen bei bestimmten Materialien (z.B. Kunststoffe).
2.3 Pulverpressen
Pulverpressen wird zur Formgebung von Materialien in Pulverform verwendet. Hierbei wird das Pulver in eine Form gepresst und unter Druck verdichtet. Anschließend durchläuft es meist einen Sinterprozess, bei dem das Material durch hohe Temperaturen verfestigt wird.
- Anwendungsbereiche: Herstellung von Zahnrädern, Lagerteilen und hochpräzisen Metallteilen.
- Vorteile: Hohe Maßgenauigkeit, geringe Materialverluste, Herstellung komplexer Geometrien möglich.
- Nachteile: Begrenzte Materialauswahl, zusätzliche Sinterprozesse notwendig.
2.4 Spritzgießpressen
Das Spritzgießpressen kombiniert Elemente des Spritzgießens und des Formpressens, um Kunststoffteile mit hoher Maßhaltigkeit und guter Oberflächenqualität herzustellen. Beim Spritzgießpressen wird das Material zuerst eingespritzt und anschließend durch Pressen in die endgültige Form gebracht.
- Anwendungsbereiche: Herstellung präziser Kunststoffteile, z.B. für Elektronikgehäuse und Medizintechnik.
- Vorteile: Hohe Präzision, weniger Materialeinsatz, kosteneffizient bei großen Produktionsmengen.
- Nachteile: Teure Werkzeuge, aufwendige Maschinenwartung.
2.5 Verbundpressen
Beim Verbundpressen werden Materialien aus verschiedenen Komponenten (z.B. Fasern und Kunststoffe) in eine Form gepresst. Dieses Verfahren eignet sich besonders gut für Verbundwerkstoffe, die eine hohe Festigkeit und Steifigkeit bei geringem Gewicht bieten.
- Anwendungsbereiche: Automobil- und Luftfahrtindustrie (z.B. für leichte Karosserieteile).
- Vorteile: Herstellung von leichten, belastbaren Materialien, Anpassung der Materialeigenschaften.
- Nachteile: Komplexer Produktionsprozess, teures Ausgangsmaterial.
3. Prozessparameter im Formpressen
Die Effizienz und Qualität eines Formpressprozesses hängen stark von den Prozessparametern ab. Zu den wichtigsten Parametern gehören:
- Druck: Der beim Formpressen angewandte Druck bestimmt, wie gut sich das Material in die Form einfügt und welche Festigkeit das Endprodukt erreicht. Unterschiedliche Materialien erfordern spezifische Druckwerte, um optimale Ergebnisse zu erzielen.
- Temperatur: Besonders beim Heißpressen spielt die Temperatur eine zentrale Rolle. Eine exakte Temperatursteuerung ist erforderlich, um die Fließfähigkeit des Materials zu regulieren und die Aushärtung zu gewährleisten.
- Zykluszeit: Die Zykluszeit beschreibt die Dauer, die für das Pressen, Aushärten und Abkühlen eines Teils benötigt wird. Eine optimierte Zykluszeit ist entscheidend für die Effizienz des gesamten Prozesses.
- Formqualität und Materialzusammensetzung: Die Qualität der verwendeten Form beeinflusst die Präzision des Endprodukts erheblich. Auch die Materialzusammensetzung spielt eine Rolle, da sie die Fließeigenschaften und Festigkeit des Werkstücks beeinflusst.
4. Materialien im Formpressen
Formpressverfahren werden für eine Vielzahl von Materialien verwendet. Jedes Material weist spezifische Eigenschaften auf, die den Pressprozess beeinflussen. Zu den am häufigsten verwendeten Materialien gehören:
4.1 Kunststoffe
- Thermoplaste: Sie werden unter Wärmezufuhr formbar und eignen sich für Prozesse, die auf das Heißpressen setzen. Thermoplaste sind recycelbar und bieten eine hohe Flexibilität in der Gestaltung.
- Duroplaste: Diese Kunststoffe sind nach dem Aushärten nicht mehr formbar und werden häufig für Teile verwendet, die eine hohe thermische und chemische Beständigkeit erfordern.
4.2 Metalle
Metallische Werkstoffe wie Stahl, Aluminium und Titan sind im Formpressen weit verbreitet. Metalle weisen hohe Festigkeit und Beständigkeit auf, sind jedoch oft schwieriger zu formen und erfordern speziell ausgelegte Maschinen.
4.3 Verbundwerkstoffe
Verbundwerkstoffe wie kohlenstofffaserverstärkter Kunststoff (CFK) und glasfaserverstärkter Kunststoff (GFK) vereinen die Vorteile von Kunststoffen und Fasern. Sie sind leicht und extrem fest und werden vor allem im Automobil- und Flugzeugbau eingesetzt.
5. Maschinen und Werkzeuge im Formpressen
Im Formpressen kommen spezielle Maschinen und Werkzeuge zum Einsatz, um das Material in die gewünschte Form zu bringen. Die wichtigsten Maschinen und ihre Funktionen sind:
5.1 Pressen
- Hydraulikpressen: Die häufigste Art von Pressen, die für Formpressprozesse verwendet werden. Sie bieten eine gleichmäßige Druckverteilung und können präzise gesteuert werden.
- Mechanische Pressen: Diese Pressen eignen sich für Hochgeschwindigkeitsanwendungen und sind besonders in der Massenproduktion verbreitet.
5.2 Formen und Werkzeuge
- Gussformen: Diese werden speziell angefertigt, um das gewünschte Produkt präzise zu formen. Sie müssen extrem haltbar und temperaturbeständig sein, besonders bei Heißpressverfahren.
- Werkzeugmaterialien: Formen werden oft aus Stahl oder speziellen hochfesten Legierungen hergestellt, um dem hohen Druck und der Hitze zu widerstehen.
5.3 Heizsysteme und Kühlsysteme
- Heizsysteme: Besonders beim Heißpressen unerlässlich, da die richtige Temperatur für die Materialverformung notwendig ist.
- Kühlsysteme: Sie sorgen dafür, dass das geformte Bauteil kontrolliert abkühlt und sich nicht verzieht.
6. Anwendungsspezifische Beispiele für das Formpressen
Um die Vielfalt der Einsatzmöglichkeiten des Formpressens besser zu verstehen, werden im Folgenden einige konkrete Anwendungsbeispiele aufgeführt:
6.1 Automobilindustrie
In der Automobilindustrie wird das Formpressen verwendet, um leichte und stabile Bauteile für Karosserien, Motoren und Innenraumteile herzustellen. Häufig verwendete Materialien sind CFK und GFK, die eine hohe Festigkeit und ein geringes Gewicht bieten.
6.2 Luft- und Raumfahrt
Die Luft- und Raumfahrtindustrie stellt hohe Anforderungen an die Materialien und Fertigungsverfahren, um Gewicht zu sparen und gleichzeitig Stabilität und Sicherheit zu gewährleisten. Hier werden häufig Verbundwerkstoffe wie CFK und Titan verwendet.
6.3 Bauindustrie
In der Bauindustrie werden Formpressteile für Gebäudefassaden, Fensterrahmen und Innenausstattungen eingesetzt. Materialien wie Aluminium und Stahl sind hier aufgrund ihrer Beständigkeit gegenüber Witterungseinflüssen besonders gefragt.
7. Qualitätssicherung und Optimierung im Formpressen
Um die Qualität der Formpressteile sicherzustellen, ist eine strikte Qualitätssicherung erforderlich. Dies wird erreicht durch:
- Prozessüberwachung: Überwachung von Druck, Temperatur und Zykluszeit während des Pressvorgangs.
- Materialprüfung: Regelmäßige Tests zur Überprüfung der Materialeigenschaften, um sicherzustellen, dass das Material den Anforderungen entspricht.
- Optimierung durch Datenanalyse: Die Analyse von Produktionsdaten ermöglicht es, den Prozess kontinuierlich zu optimieren und die Effizienz zu steigern.
8. Zukunft des Formpressens: Trends und Entwicklungen
Die Zukunft des Formpressens wird durch technische Innovationen geprägt sein, die das Verfahren effizienter und umweltfreundlicher machen sollen. Einige der wichtigsten Trends umfassen:
- Industrie 4.0 und Digitalisierung: Mit der zunehmenden Vernetzung von Maschinen und der Integration intelligenter Steuerungssysteme wird die Produktion flexibler und effizienter.
- Nachhaltigkeit: Die Entwicklung energieeffizienter Maschinen und die Nutzung umweltfreundlicher Materialien gewinnen an Bedeutung.
- Künstliche Intelligenz und maschinelles Lernen: Diese Technologien bieten Möglichkeiten zur Optimierung und Automatisierung der Prozesssteuerung und tragen zur Fehlerreduktion bei.
Zusammenfassung
Das Formpressen ist ein vielseitiges und leistungsstarkes Verfahren, das in vielen Industrien unverzichtbar ist. Die Wahl des richtigen Verfahrens, die Berücksichtigung der Prozessparameter und die Verwendung geeigneter Materialien und Maschinen sind entscheidend für den Erfolg. Moderne Entwicklungen wie die Digitalisierung und Automatisierung tragen dazu bei, das Formpressen noch effizienter und nachhaltiger zu gestalten, sodass die Verfahren in der Industrie auch in Zukunft eine zentrale Rolle spielen werden.
Automatisierungstechnologien im Formpressen
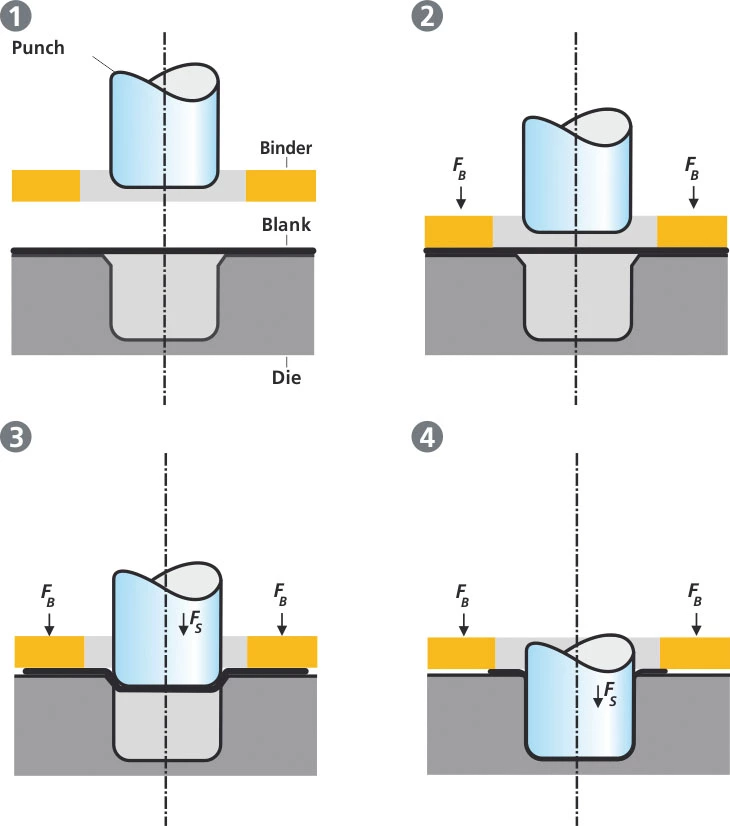
Der Formpressprozess ist ein zentraler Bestandteil der modernen Fertigungstechnik, insbesondere in Industriezweigen wie Automobilbau, Luftfahrt, Bauwesen und Elektronik. Die Automatisierung des Formpressens hat es ermöglicht, die Effizienz und Präzision des Verfahrens erheblich zu steigern und dabei gleichzeitig Kosten und Ausschuss zu reduzieren. Indem automatisierte Technologien in den Produktionsprozess integriert werden, können Unternehmen gleichbleibende Qualität bei gleichzeitig niedrigen Produktionskosten erreichen. Dieser Abschnitt untersucht die verschiedenen Technologien und Methoden, die den Formpressprozess automatisieren und optimieren.
2. Robotik im Formpressen
Die Integration von Industrierobotern hat das Formpressen revolutioniert. Roboter übernehmen viele repetitive und oft gefährliche Aufgaben, die zuvor manuell ausgeführt wurden, und steigern dadurch die Effizienz und Sicherheit.
2.1 Materialhandling und -zuführung
Industrieroboter können das Rohmaterial präzise in die Form einlegen, was eine hohe Wiederholgenauigkeit und eine gleichbleibende Qualität sicherstellt. Hierbei kommen Roboterarme zum Einsatz, die speziell auf das Handling der jeweiligen Materialien abgestimmt sind.
- Automatische Materialzuführung: Roboter können Rohmaterialien direkt aus Speichersystemen entnehmen und präzise positionieren. Dies reduziert den Zeitaufwand und das Risiko von Fehlern.
- Entnahme des fertigen Bauteils: Nach dem Pressen kann der Roboter das Bauteil aus der Form entnehmen und für die Weiterverarbeitung bereitstellen, z.B. durch Abkühlen oder Qualitätssicherung.
2.2 Koordination mit anderen Maschinen
Durch den Einsatz von Robotern kann das Formpressen als Teil eines integrierten, vollständig automatisierten Prozesses betrachtet werden. Roboter interagieren mit Förderbändern, Mess- und Inspektionsgeräten sowie mit anderen Maschinen, um eine nahtlose Produktionskette zu gewährleisten.
- Beispielhafte Integration: In modernen Fertigungsanlagen können Roboter mit CNC-Maschinen oder 3D-Druckern koordiniert arbeiten, um Materialien vor- oder nachzubearbeiten.
2.3 Einsatz von kollaborativen Robotern (Cobots)
Kollaborative Roboter, auch Cobots genannt, sind speziell entwickelte Roboter, die direkt mit Menschen zusammenarbeiten können. Im Formpressen helfen Cobots dabei, Arbeitskräfte in manuellen Aufgaben zu entlasten, und bieten dennoch eine hohe Flexibilität.
3. Sensorik und Prozessüberwachung
Sensoren spielen eine zentrale Rolle bei der Automatisierung des Formpressprozesses, da sie eine Echtzeitüberwachung und -steuerung der wichtigsten Prozessparameter ermöglichen.
3.1 Druck- und Temperatursensoren
- Drucksensoren: Sie überwachen den Anpressdruck während des Formpressens und stellen sicher, dass das Material optimal verdichtet wird.
- Temperatursensoren: Im Heißpressen ist eine präzise Temperatursteuerung entscheidend, und Temperatursensoren liefern die Daten, die für die Steuerung der Heizsysteme benötigt werden.
3.2 Infrarot- und Lasersensoren für die Qualitätskontrolle
Infrarot- und Lasersensoren können zur Überwachung der Oberflächenqualität und zur Erkennung von Fehlstellen im Bauteil eingesetzt werden. Diese Technologien ermöglichen eine schnelle Qualitätskontrolle, ohne den Produktionsfluss zu unterbrechen.
3.3 Kraft- und Wegsensoren
Die Kraftsensoren messen die Belastung, die während des Pressvorgangs auf das Material wirkt, und können Anpassungen vornehmen, um Überlastungen oder ungleichmäßigen Druck zu vermeiden. Wegsensoren überwachen den Bewegungsspielraum der Maschinenkomponenten und helfen dabei, den Prozess auf Mikrometer genau zu steuern.
4. Steuerungssysteme und Software
Moderne Steuerungssysteme sind entscheidend für die präzise Ausführung automatisierter Formpressprozesse. Die Steuerungstechnik im Formpressen umfasst sowohl Hardware- als auch Softwarelösungen.
4.1 Programmierbare Logiksteuerung (PLC) und Echtzeitsteuerung
Programmierbare Logiksteuerungen (PLC) sind die klassischen Steuereinheiten in automatisierten Systemen. Sie bieten eine schnelle und zuverlässige Steuerung und können zur Regelung des gesamten Formpressprozesses verwendet werden.
- Vorteile der PLC-Steuerung: Hohe Zuverlässigkeit, Flexibilität und Anpassungsfähigkeit für verschiedene Prozessanforderungen.
- Echtzeitsteuerung: Durch die Implementierung von Echtzeitsteuerungssystemen können Maschinensteuerungen direkt auf Veränderungen der Prozessparameter reagieren, was die Reaktionszeit minimiert und die Qualität sicherstellt.
4.2 Supervisory Control and Data Acquisition (SCADA)
SCADA-Systeme sind speziell für die Erfassung und Überwachung von Produktionsdaten entwickelt. Diese Daten umfassen Prozessparameter wie Druck, Temperatur und Zykluszeit. Durch die Analyse dieser Daten können Unternehmen Trends erkennen, die Effizienz steigern und den Produktionsprozess weiter optimieren.
- Datenvisualisierung: SCADA-Systeme ermöglichen es Bedienern, Prozessparameter auf einem Dashboard zu überwachen und visuelle Warnungen bei Abweichungen zu erhalten.
- Remote Control: SCADA ermöglicht die Fernüberwachung und -steuerung des Produktionsprozesses, was eine hohe Flexibilität bietet.
4.3 Prozessautomatisierungssoftware
Spezielle Softwarelösungen werden zur Programmierung und Steuerung automatisierter Formpressmaschinen eingesetzt. Moderne Automatisierungssoftware kann leicht in bestehende ERP- und MES-Systeme (Manufacturing Execution Systems) integriert werden und verbessert dadurch die Effizienz der gesamten Produktionskette.
5. Datenintegration und maschinelles Lernen
Mit der Zunahme der Automatisierung und Digitalisierung steigt auch der Bedarf an fortschrittlicher Datenverarbeitung und Analyse. Maschinelles Lernen und Big-Data-Analyse bieten eine Vielzahl an Möglichkeiten zur Optimierung und Fehlerreduktion.
5.1 Echtzeitdatenanalyse und Prozessoptimierung
Durch die Integration von Sensoren und Steuerungssystemen in Netzwerke können die Daten in Echtzeit gesammelt und analysiert werden. Mithilfe maschinellen Lernens können Produktionsmuster erkannt und Prozesse optimiert werden.
5.2 Vorausschauende Wartung (Predictive Maintenance)
Die vorausschauende Wartung ist eine der innovativsten Anwendungen des maschinellen Lernens in der Produktion. Hierbei wird die Wartung auf Grundlage der Echtzeit-Daten durchgeführt, bevor es zu einem Maschinenausfall kommt.
- Reduzierung von Ausfallzeiten: Durch die Analyse von Sensordaten und Maschinenaktivitäten können Anomalien erkannt werden, die auf potenzielle Defekte hinweisen.
- Kostensenkung: Vorausschauende Wartung minimiert unvorhergesehene Ausfallzeiten und senkt die Instandhaltungskosten, da nur dann eingegriffen wird, wenn es nötig ist.
5.3 Qualitätskontrolle und Anomalieerkennung
Maschinelles Lernen kann genutzt werden, um die Qualität der hergestellten Teile kontinuierlich zu überwachen und mögliche Mängel automatisch zu erkennen. Durch die Analyse von Produktionsdaten können Anomalien frühzeitig identifiziert und die Ursachen analysiert werden.
6. Beispiele und führende Technologien in der Automatisierung des Formpressens
6.1 Automobilindustrie
In der Automobilindustrie kommen automatisierte Formpressverfahren häufig zur Herstellung von Karosserieteilen und Innenraumkomponenten zum Einsatz. Beispielhafte Technologien umfassen:
- Vollautomatisierte Produktionsstraßen: Automobilhersteller verwenden komplette Produktionsstraßen mit integrierten Robotern und SCADA-Systemen, um ein hohes Produktionsvolumen bei gleichbleibender Qualität zu gewährleisten.
- Einsatz von KI zur Fehlererkennung: Künstliche Intelligenz wird zur Erkennung von Materialfehlern und Oberflächenmängeln eingesetzt, was den Ausschuss reduziert und die Produktionskosten senkt.
6.2 Luft- und Raumfahrt
Die Luftfahrtindustrie profitiert von der Präzision und Wiederholgenauigkeit, die durch Automatisierungstechnologien ermöglicht wird. Besonders Verbundwerkstoffe werden unter automatisierten Bedingungen in die gewünschte Form gepresst, um hochfeste und leichte Bauteile zu produzieren.
6.3 Bau- und Maschinenbauindustrie
In der Bau- und Maschinenbauindustrie werden automatisierte Formpressverfahren für Komponenten verwendet, die hohe Belastbarkeit erfordern. Hier werden Roboter und Sensoren eingesetzt, um hohe Präzision bei gleichbleibender Produktqualität sicherzustellen.
7. Vorteile und Herausforderungen der Automatisierung im Formpressen
7.1 Vorteile
- Steigerung der Effizienz: Automatisierungstechnologien ermöglichen eine schnellere und kostengünstigere Produktion.
- Reduzierung von Fehlern und Ausschuss: Durch Echtzeitüberwachung und präzise Steuerung können Produktionsfehler minimiert und Ausschuss reduziert werden.
- Flexibilität und Skalierbarkeit: Automatisierte Systeme lassen sich leicht auf verschiedene Produktionsvolumen und Materialtypen anpassen.
7.2 Herausforderungen
- Hohe Investitionskosten: Der Aufbau einer vollautomatisierten Produktionslinie kann teuer sein, insbesondere für kleine und mittelständische Unternehmen.
- Wartung und Instandhaltung: Automatisierte Systeme erfordern regelmäßige Wartung und spezialisierte Techniker, um eine hohe Betriebszeit sicherzustellen.
- Datenschutz und Sicherheit: Mit der zunehmenden Vernetzung steigen auch die Anforderungen an Datenschutz und IT-Sicherheit, um sensible Produktionsdaten zu schützen.
8. Zukunftsperspektiven und Trends
8.1 Industrie 4.0 und Smart Manufacturing
Die Vernetzung von Maschinen, Sensoren und Steuerungssystemen ermöglicht eine intelligente und flexible Produktion, die sich an Echtzeitdaten orientiert und kontinuierlich verbessert.
8.2 Nachhaltigkeit und Energieeffizienz
Automatisierungstechnologien bieten Potenzial zur Energieeinsparung und zur Reduktion von Materialverschwendung, wodurch Unternehmen ihre Produktionskosten und ihren ökologischen Fußabdruck verringern können.
8.3 Entwicklung neuer Materialien und Technologien
Durch den Einsatz neuer Materialien und fortschrittlicher Technologien wie der Additiven Fertigung wird das Formpressen weiter revolutioniert und bietet neue Anwendungsmöglichkeiten.
Zusammenfassung
Die Automatisierung im Formpressen hat die Fertigungsindustrie maßgeblich verändert. Durch den Einsatz von Robotern, Sensorik, Echtzeitsteuerungen und maschinellem Lernen kann die Effizienz gesteigert, die Qualität verbessert und die Produktionskosten gesenkt werden. Die zunehmende Vernetzung und der technologische Fortschritt bieten eine Vielzahl neuer Möglichkeiten und stellen gleichzeitig Unternehmen vor Herausforderungen, insbesondere in Bezug auf IT-Sicherheit und Investitionen. Mit dem Blick in die Zukunft zeigen sich zahlreiche spannende Perspektiven, die die Bedeutung der Automatisierung im Formpressen weiter stärken werden.
Prozessoptimierung und Qualitätsmanagement durch Automatisierung im Formpressen
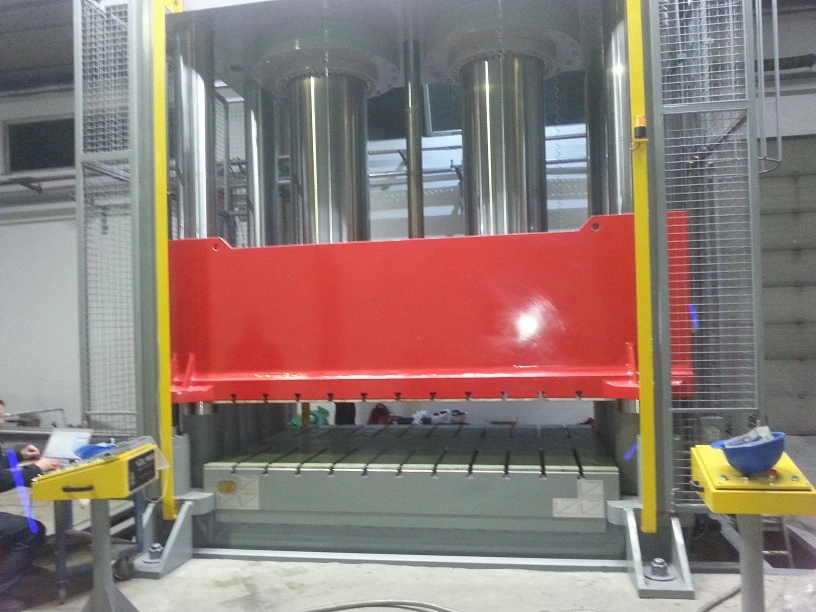
Der steigende Wettbewerb und die Anforderungen an Präzision, Kostenreduktion und Ressourcenschonung zwingen Unternehmen in der Fertigung zur Implementierung von Automatisierungstechnologien zur Prozessoptimierung und Qualitätssicherung. Automatisierte Systeme können Prozessparameter effizient steuern, Fehlerquellen eliminieren und eine gleichbleibend hohe Produktqualität gewährleisten. In dieser Abhandlung werden die verschiedenen Möglichkeiten zur Prozessoptimierung und Qualitätssteigerung durch Automatisierung beleuchtet.
2. Prozessoptimierung im Formpressen
Prozessoptimierung bedeutet im Formpressen, die Produktionseffizienz zu steigern, Materialverschwendung zu reduzieren und die Durchlaufzeiten zu verkürzen. Verschiedene Techniken und Technologien unterstützen die Optimierung des Prozesses:
2.1 Zykluszeitoptimierung
Durch den Einsatz automatisierter Steuerungssysteme und roboterunterstützter Prozesse lassen sich die Zykluszeiten im Formpressen drastisch reduzieren. Dies wird erreicht durch:
- Automatische Steuerung der Pressparameter: Mit automatisierten Systemen kann die Geschwindigkeit und Präzision des Pressvorgangs angepasst werden, um die optimalen Bedingungen zu gewährleisten.
- Minimierung von Rüstzeiten: Durch vordefinierte Einstellungen und flexible Roboterarme können Maschinen in kürzester Zeit auf unterschiedliche Produktvarianten umgestellt werden.
2.2 Reduzierung des Materialverbrauchs und Ausschusses
Automatisierte Überwachungs- und Steuerungssysteme ermöglichen eine präzise Kontrolle der Materialmenge und des Anpressdrucks, was die Materialeffizienz erhöht und Ausschuss reduziert.
- Druck- und Temperaturanpassung in Echtzeit: Sensoren messen kontinuierlich die Druck- und Temperaturbedingungen, sodass der Materialfluss in Echtzeit reguliert und angepasst werden kann.
- Bessere Materialausnutzung durch präzise Positionierung: Roboterarme und Sensoren ermöglichen eine punktgenaue Platzierung des Rohmaterials in der Form, was Materialverluste minimiert.
2.3 Prozessintegration und Produktionsflexibilität
Automatisierte Systeme bieten die Möglichkeit, verschiedene Formpressprozesse zu integrieren und flexibel anzupassen. Dies beinhaltet:
- Kombinierte Formpress- und Nachbearbeitungsprozesse: Maschinen können den Formpressprozess automatisch mit nachgelagerten Schritten wie Kühlung und Inspektion verknüpfen.
- Flexibilität bei Material- und Produktwechseln: Mit modernen Steuerungssystemen kann der Formpressprozess schnell an unterschiedliche Materialien oder Formen angepasst werden, was die Produktivität steigert.
2.4 Effiziente Energieverwendung
Automatisierte Systeme können auch zur Optimierung des Energieverbrauchs beitragen, was die Nachhaltigkeit erhöht und Kosten senkt.
- Einsatz von energieeffizienten Maschinenkomponenten: Steuerungen können Maschinenkomponenten bedarfsgerecht ansteuern und so Energieverschwendung vermeiden.
- Energieoptimierte Zyklussteuerung: Durch präzise Kontrolle der Zykluszeiten und -temperaturen lässt sich der Energiebedarf für jeden Prozessschritt minimieren.
3. Automatisierte Qualitätskontrolle im Formpressen
Die Einführung automatisierter Qualitätskontrollsysteme hat das Qualitätsmanagement im Formpressen revolutioniert. Diese Systeme nutzen Sensorik und moderne Bildverarbeitung zur schnellen und präzisen Überprüfung der produzierten Bauteile.
3.1 Inline-Qualitätskontrolle
Bei der Inline-Qualitätskontrolle erfolgt die Inspektion während des Produktionsprozesses, sodass fehlerhafte Produkte sofort identifiziert und entfernt werden können.
- Einsatz von Lasersensoren und Kamerasystemen: Diese Technologien erkennen Abweichungen in Form und Oberfläche in Echtzeit.
- Automatische Anpassung der Prozessparameter: Bei Abweichungen werden die Prozessparameter wie Druck und Temperatur automatisch angepasst, um die Fehlerquote zu minimieren.
3.2 Prüfung der Materialqualität
Automatisierte Systeme ermöglichen eine durchgängige Kontrolle der Materialqualität, um sicherzustellen, dass das eingesetzte Material den Anforderungen entspricht.
- Spektroskopie und andere Messverfahren: Diese Technologien prüfen das Material auf chemische Zusammensetzung und physikalische Eigenschaften.
- Materialtracing: Durch den Einsatz von RFID- und Barcode-Technologien können Materialien über den gesamten Produktionsprozess hinweg verfolgt werden, was Transparenz und Rückverfolgbarkeit bietet.
3.3 Fehlererkennung und Bauteilvermessung
- 3D-Bildverarbeitung: Mithilfe von 3D-Kameras können Form und Geometrie der Bauteile vermessen und mögliche Formabweichungen identifiziert werden.
- Oberflächenanalyse: Sensoren und Kamerasysteme erfassen Oberflächeneigenschaften und erkennen Fehler wie Risse oder ungleichmäßige Strukturen, die den Produktionsstandard beeinträchtigen könnten.
3.4 Datengestützte Qualitätsanalyse
Automatisierte Qualitätskontrollsysteme erfassen und analysieren kontinuierlich Qualitätsdaten, die in die Prozessoptimierung einfließen. Hierzu zählen:
- Trendanalysen: Qualitätstrends und Abweichungen werden kontinuierlich überwacht, um potenzielle Fehlerquellen zu identifizieren.
- Automatisierte Fehlerdiagnose: Mithilfe von Datenanalyse und KI können Ursachen von Qualitätsabweichungen erkannt und entsprechende Gegenmaßnahmen eingeleitet werden.
4. Rolle der Datenerfassung und -analyse
Die Erfassung und Analyse von Produktionsdaten ist das Fundament jeder Prozessoptimierung und des Qualitätsmanagements im Formpressen. Diese Daten werden von Sensoren und Kontrollsystemen bereitgestellt und in Echtzeit verarbeitet.
4.1 Sensorische Datenerfassung und Echtzeitüberwachung
Sensoren überwachen wesentliche Parameter wie Temperatur, Druck und Zykluszeit während des Formpressens. Diese Daten werden in Echtzeit analysiert, um eine genaue Steuerung und schnelle Anpassung der Maschinenparameter zu ermöglichen.
4.2 Nutzung von Big Data für die Prozessoptimierung
Die Sammlung großer Datenmengen (Big Data) ermöglicht die Anwendung statistischer Modelle und maschinellen Lernens zur Prozessverbesserung.
- Prozessanalyse und Optimierung: Big-Data-Analysen liefern wertvolle Erkenntnisse über ineffiziente Prozessschritte und mögliche Einsparungspotenziale.
- Erkennung von Produktionsmustern: Durch die Analyse historischer Daten können Muster und Zusammenhänge im Produktionsprozess identifiziert werden, die Optimierungsmaßnahmen ermöglichen.
4.3 Prozessdokumentation und Rückverfolgbarkeit
Automatisierte Systeme bieten eine vollständige Dokumentation aller Prozessschritte, wodurch die Rückverfolgbarkeit der Produktion sichergestellt wird. Dies ist besonders wichtig für:
- Qualitätsaudits: Dokumentierte Daten ermöglichen eine lückenlose Rückverfolgbarkeit für interne und externe Audits.
- Kundenspezifische Anforderungen: Unternehmen können ihre Produktionsprozesse individuell auf Kundenanforderungen anpassen und entsprechende Nachweise bereitstellen.
4.4 Datensicherheit und Datenschutz
Da Produktionsdaten sensible Informationen über den Fertigungsprozess enthalten, ist der Schutz dieser Daten von entscheidender Bedeutung.
- Implementierung sicherer Netzwerke: Der Einsatz von verschlüsselten Netzwerken und Sicherheitsprotokollen schützt die Daten vor unbefugtem Zugriff.
- Datenspeicherung und -zugriff: Durch den Einsatz von Cloud-Technologien können Daten sicher gespeichert und weltweit abgerufen werden.
5. Implementierung von KI und maschinellem Lernen
Künstliche Intelligenz und maschinelles Lernen sind wesentliche Bausteine für eine kontinuierliche Verbesserung im automatisierten Formpressen. Diese Technologien helfen bei der Erkennung von Anomalien, Optimierung der Prozesse und Vorhersage von Wartungsbedarf.
5.1 Prozessanalyse und Anomalieerkennung
Maschinelles Lernen wird eingesetzt, um die Prozessparameter zu analysieren und potenzielle Probleme frühzeitig zu identifizieren.
- Erkennung von Anomalien: Algorithmen analysieren große Datenmengen und erkennen Abweichungen, die auf Störungen im Prozess hinweisen könnten.
- Automatische Anpassungen: Bei festgestellten Anomalien passen KI-gestützte Systeme die Prozessparameter automatisch an, um eine gleichbleibende Qualität zu gewährleisten.
5.2 Vorausschauende Wartung (Predictive Maintenance)
Predictive Maintenance ist eine Schlüsseltechnologie im automatisierten Formpressen und reduziert die Ausfallzeiten durch geplante Wartungsmaßnahmen.
- Einsatz von maschinellem Lernen: Algorithmen lernen aus historischen Wartungsdaten und entwickeln Modelle zur Vorhersage von Maschinenproblemen.
- Wartungsplanung in Echtzeit: Daten aus dem Produktionsprozess werden kontinuierlich ausgewertet, um Wartungsbedarf zu erkennen und den Betrieb störungsfrei zu halten.
5.3 Optimierung der Prozessparameter durch KI
KI-gesteuerte Systeme können Prozessparameter in Echtzeit optimieren und den gesamten Produktionsprozess verbessern.
- Selbstlernende Algorithmen: Diese Algorithmen passen die Produktionsparameter an, basierend auf vorangegangenen Prozessen und erzielten Qualitätsdaten.
- Steigerung der Effizienz: KI-gestützte Optimierungen helfen dabei, Produktionsabläufe zu beschleunigen und den Materialverbrauch zu reduzieren.
6. Fallbeispiele und Anwendungen automatisierter Qualitätssysteme
Einige Fallbeispiele demonstrieren die Vorteile automatisierter Systeme im Formpressen und deren Anwendung in verschiedenen Branchen:
6.1 Automobilindustrie
- Produktionsstraßen mit automatisierter Qualitätskontrolle: Automobilhersteller setzen umfassend auf automatisierte Qualitätskontrollen, um sicherheitsrelevante Bauteile fehlerfrei zu produzieren.
- Vorausschauende Wartung für Formpressanlagen: Predictive Maintenance wird verwendet, um die Verfügbarkeit der Maschinen zu maximieren und Produktionsausfälle zu minimieren.
6.2 Luft- und Raumfahrtindustrie
- Hochpräzise Komponenten: Die strengen Qualitätsanforderungen der Luftfahrt erfordern präzise Formpressverfahren, die durch KI und Sensorik unterstützt werden, um höchste Standards zu gewährleisten.
6.3 Medizinische Industrie
- Sterilität und Genauigkeit: In der Medizintechnik wird eine lückenlose Überwachung und Rückverfolgbarkeit gefordert, die durch automatisierte Qualitätsmanagementsysteme gewährleistet wird.
7. Vorteile und Herausforderungen der Automatisierung im Qualitätsmanagement
7.1 Vorteile
- Erhöhte Präzision und Konsistenz: Automatisierte Systeme liefern eine gleichbleibend hohe Qualität durch präzise Steuerung.
- Reduzierung von Ausschuss und Materialverlust: Durch Echtzeitüberwachung und Fehlererkennung wird Ausschuss vermieden und Materialverbrauch minimiert.
7.2 Herausforderungen
- Hohe Kosten für Implementierung: Die Anschaffung und Integration automatisierter Systeme kann kostenintensiv sein, insbesondere für KMUs.
- Anpassungsbedarf bei Änderungen: Automatisierte Systeme müssen regelmäßig an neue Produktanforderungen und Technologien angepasst werden.
8. Zukunftsperspektiven
8.1 Industrie 4.0 und Vernetzung
Industrie 4.0 und das Internet der Dinge ermöglichen eine noch stärkere Vernetzung und Optimierung der automatisierten Systeme.
8.2 Nachhaltigkeit und Ressourcenschonung
Zukunftstrends umfassen auch die ressourcenschonende Produktion und Reduktion des ökologischen Fußabdrucks durch automatisierte Systeme.
8.3 Weiterentwicklung von KI und maschinellem Lernen
Die Weiterentwicklung dieser Technologien wird den Automatisierungsgrad und die Qualität im Formpressen weiter steigern.
Zusammenfassung
Die Automatisierung bietet enorme Potenziale für die Prozessoptimierung und das Qualitätsmanagement im Formpressen. Durch den Einsatz von Sensorik, KI und maschinellem Lernen können Unternehmen ihre Produktion optimieren, Qualitätsstandards erhöhen und Kosten senken. Die Zukunft der automatisierten Prozessoptimierung und des Qualitätsmanagements wird durch technologische Fortschritte und den Fokus auf Nachhaltigkeit weiter geprägt werden.
Einleitung: Bedeutung von Fallstudien für das Verständnis des automatisierten Formpressens
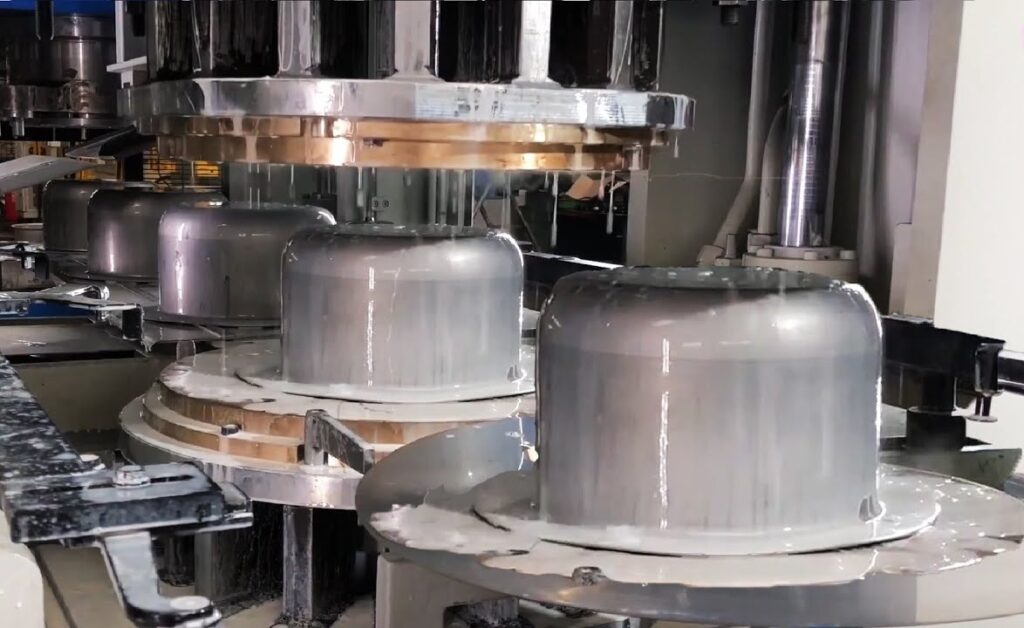
Die industrielle Automatisierung hat das Formpressen in vielen Bereichen revolutioniert und ermöglicht eine effizientere, präzisere und nachhaltigere Produktion. Durch Fallstudien wird die praktische Anwendung des automatisierten Formpressens in unterschiedlichen Branchen verdeutlicht, und die Herausforderungen sowie die positiven Effekte werden klar herausgearbeitet. In den folgenden Abschnitten werden drei zentrale Branchen analysiert: die Automobilindustrie, die Luft- und Raumfahrt sowie die Bau- und Elektronikindustrie.
2. Fallstudie 1: Automobilindustrie
Die Automobilindustrie nutzt das Formpressen seit langem zur Herstellung von leichten und robusten Bauteilen. Besonders durch die Entwicklung von kohlefaserverstärktem Kunststoff (CFK) und glasfaserverstärktem Kunststoff (GFK) hat sich das automatisierte Formpressen in dieser Branche etabliert.
2.1 Anwendungsbereiche und Anforderungen in der Automobilindustrie
- Bauteile: Karosserieteile, Innenverkleidungen, Strukturkomponenten.
- Anforderungen: Hohe Präzision, Leichtbauweise, kurze Zykluszeiten, und starke Belastbarkeit.
2.2 Eingesetzte Automatisierungstechnologien
- Roboter für Materialhandling und -positionierung: Industrieroboter legen das Rohmaterial in die Pressform und entnehmen das fertige Bauteil für die Weiterverarbeitung.
- Automatisierte Qualitätskontrolle: Kamerasysteme und Sensoren überprüfen in Echtzeit die Qualität der Bauteile und melden Abweichungen.
- Temperatur- und Drucküberwachung: Präzise Steuerungssysteme überwachen Temperatur und Druck, um eine gleichbleibende Materialdichte und Festigkeit zu gewährleisten.
2.3 Ergebnisse und Vorteile
- Reduktion der Produktionszeit: Automatisierte Prozesse haben die Zykluszeiten um bis zu 30 % gesenkt.
- Kosteneinsparungen: Materialeinsparung durch präzise Dosierung des CFK und GFK und weniger Ausschuss.
- Verbesserte Sicherheit und Reduktion von Arbeitsaufwand: Reduzierte manuelle Handhabung senkt das Risiko für Arbeitsunfälle und minimiert ergonomische Belastungen.
2.4 Herausforderungen und Lösungsansätze
- Hohe Investitionskosten: Die Kosten für Automatisierung sind hoch, weshalb viele Automobilhersteller Kooperationen mit Maschinenbauern eingehen.
- Anpassung an unterschiedliche Modelle: Modularisierte Systeme helfen, die Anpassung der Maschinen an verschiedene Modelle und Materialien zu erleichtern.
3. Fallstudie 2: Luft- und Raumfahrtindustrie
Die Luft- und Raumfahrt stellt hohe Anforderungen an Materialfestigkeit, Gewichtseinsparung und Präzision. In dieser Branche wird das automatisierte Formpressen verwendet, um leichtere Bauteile herzustellen, die trotzdem starken mechanischen Belastungen standhalten.
3.1 Anwendungsbereiche und Anforderungen in der Luftfahrt
- Bauteile: Tragflächen, Strukturkomponenten, Sitzschalen, Verkleidungselemente.
- Anforderungen: Geringes Gewicht, hohe Materialfestigkeit, genaue Maßhaltigkeit, geringe Toleranzen.
3.2 Eingesetzte Automatisierungstechnologien
- Verbundmaterial-Formpressen: CFK wird automatisiert verarbeitet und in Form gepresst. Präzisionspressen gewährleisten eine gleichmäßige Dichte und hohe Materialqualität.
- Temperaturgesteuerte Pressprozesse: Heizsysteme stellen sicher, dass das Material exakt auf die gewünschte Temperatur gebracht wird, bevor es in die Form gepresst wird.
- Integrierte Sensorik und Qualitätsprüfung: Lasersensoren überprüfen die Materialstärke und -dichte, um sicherzustellen, dass die Bauteile den strengen Qualitätsstandards entsprechen.
3.3 Ergebnisse und Vorteile
- Gewichtsreduktion: Durch den Einsatz leichter Verbundwerkstoffe können Flugzeuge deutlich effizienter und sparsamer konstruiert werden.
- Erhöhung der Lebensdauer: Automatisierte Systeme reduzieren die Schwankungen in Materialstärke und Qualität, was die Haltbarkeit der Bauteile verlängert.
- Qualitätssicherung: Echtzeitüberwachung und Rückverfolgbarkeit aller Produktionsschritte sichern eine gleichbleibende Qualität und erfüllen die hohen Sicherheitsstandards.
3.4 Herausforderungen und Lösungsansätze
- Materialkosten und Komplexität der Verbundmaterialien: Leichte und zugleich stabile Materialien sind teuer. Durch präzises Materialhandling und Optimierung der Prozesse können jedoch Materialverluste minimiert werden.
- Anpassung an hohe Qualitätsstandards: Die Automatisierung muss regelmäßig überprüft und angepasst werden, um die strengen Luftfahrtnormen zu erfüllen.
4. Fallstudie 3: Bauindustrie und Elektronik
Die Bauindustrie und die Elektronikbranche nutzen automatisiertes Formpressen zur Herstellung von robusten und wetterbeständigen Materialien sowie zur Produktion von Kleinbauteilen für elektronische Geräte.
4.1 Anwendungsbereiche und Anforderungen in der Bau- und Elektronikindustrie
- Bauteile in der Bauindustrie: Fensterrahmen, Fassaden, Dachziegel, Bodenplatten.
- Bauteile in der Elektronikindustrie: Gehäuse von Geräten, Leiterplatten.
- Anforderungen: Hohe Witterungsbeständigkeit, hohe mechanische Festigkeit, präzise Formen für kleine Bauteile.
4.2 Eingesetzte Automatisierungstechnologien
- Formpressen mit Polymer- und Kunststoffverbindungen: Diese Materialien sind ideal für elektronische Gehäuse und widerstandsfähige Bauteile in der Bauindustrie.
- Automatisierte Formkontrolle: Sensoren überprüfen die Materialverteilung in der Form und melden sofort, wenn Materialfehler auftreten.
- Integration in Fertigungsstraßen: Automatisierte Formpressprozesse sind in größere Produktionslinien integriert, was eine durchgehende Produktion ohne Unterbrechung ermöglicht.
4.3 Ergebnisse und Vorteile
- Erhöhte Produktionsrate: Automatisierte Produktionsstraßen ermöglichen eine hohe Stückzahl und reduzieren Produktionskosten.
- Erhöhte Präzision: Sensorik und Kamerasysteme sorgen für genaue Bauteilformen und minimieren Abweichungen, was für die Elektronikbranche essenziell ist.
- Reduzierter Arbeitsaufwand: Weniger manuelle Arbeit erforderlich, was den Produktionsprozess sicherer und weniger fehleranfällig macht.
4.4 Herausforderungen und Lösungsansätze
- Verarbeitung spezifischer Materialien: Neue, speziell für die Bauindustrie entwickelte Kunststoffe erfordern präzise Temperatursteuerungen, die durch moderne Steuerungssysteme gewährleistet werden.
- Hoher Materialbedarf und Nachhaltigkeitsansprüche: Durch optimierte Dosierung und Verwendung umweltfreundlicherer Materialien wird der ökologische Fußabdruck reduziert.
5. Vergleichende Analyse: Auswirkungen der Automatisierung in den Branchen
Eine vergleichende Analyse der oben beschriebenen Fallstudien zeigt die branchenübergreifenden Vorteile der Automatisierung im Formpressen:
5.1 Steigerung der Effizienz und Senkung der Produktionskosten
- Automobilindustrie: Effizienzgewinne durch reduzierten Materialverbrauch und schnellere Zykluszeiten.
- Luft- und Raumfahrt: Kostenersparnis durch weniger Materialverluste und geringeren manuellen Aufwand.
- Bau- und Elektronikindustrie: Reduzierte Arbeitskosten und höhere Produktionsvolumen durch integrierte Produktionsstraßen.
5.2 Verbesserung der Produktqualität und Reduzierung von Ausschuss
- Automobil- und Luftfahrtindustrie: Präzise Materialverarbeitung und automatisierte Qualitätskontrolle reduzieren Fehler und erhöhen die Lebensdauer der Bauteile.
- Elektronik: Automatisierte Formpressverfahren ermöglichen präzise, maßhaltige Bauteile, die den Anforderungen der Miniaturisierung in der Elektronik gerecht werden.
5.3 Umweltaspekte und Ressourceneffizienz
In allen Branchen gibt es durch Automatisierung deutliche Fortschritte bei der Ressourcenschonung und Reduzierung des ökologischen Fußabdrucks:
- Reduzierter Materialverbrauch: Durch präzise Dosierung und weniger Ausschuss wird der Materialverbrauch gesenkt.
- Niedrigerer Energieverbrauch: Automatisierte Systeme ermöglichen eine gezielte Steuerung der Energiezufuhr, insbesondere durch Temperatur- und Druckoptimierung.
6. Zukunftsperspektiven und Entwicklungen im automatisierten Formpressen
6.1 Weiterentwicklung von Automatisierungstechnologien
Zukünftige Entwicklungen im automatisierten Formpressen konzentrieren sich auf den Einsatz fortschrittlicher Technologien wie Künstliche Intelligenz (KI) und Machine Learning zur weiteren Prozessoptimierung. Diese Technologien werden in der Lage sein, die Steuerung und Überwachung in Echtzeit zu verbessern und eine noch höhere Präzision zu erreichen.
6.2 Nachhaltigkeit und Recycling
Die Fertigungsindustrie setzt verstärkt auf umweltfreundliche Materialien und Recyclingtechniken. Der Einsatz automatisierter Systeme im Formpressen kann helfen, Abfälle zu minimieren und die Effizienz von Recyclingprozessen zu steigern, was zu einer Reduzierung des CO₂-Ausstoßes beiträgt.
6.3 Integration in Smart-Factory-Umgebungen
Durch die Verknüpfung automatisierter Systeme mit IoT und Industrie-4.0-Technologien wird das Formpressen in Smart-Factory-Umgebungen zunehmend flexibler und anpassungsfähiger.
- Vernetzte Produktionsstraßen: Systeme können miteinander kommunizieren und den Materialfluss sowie die Produktion optimieren.
- Selbstlernende Maschinen: Durch die Analyse von Produktionsdaten und die Anwendung von Machine-Learning-Algorithmen können sich Maschinen an Produktionsänderungen anpassen und eigenständig Verbesserungen vornehmen.
7. Fazit und Zusammenfassung
Die Fallstudien zeigen, wie das automatisierte Formpressen in verschiedenen Branchen zur Effizienzsteigerung, Kostensenkung und Qualitätsverbesserung beigetragen hat. Die Automatisierung des Formpressens ermöglicht nicht nur eine ressourcenschonende Produktion, sondern trägt auch dazu bei, die Wettbewerbsfähigkeit von Unternehmen zu steigern. Die kontinuierliche Weiterentwicklung und Integration von Technologien wie KI und IoT wird in den kommenden Jahren neue Möglichkeiten zur Optimierung und Anpassung des automatisierten Formpressens eröffnen.
Formpressen: Definition und Überblick
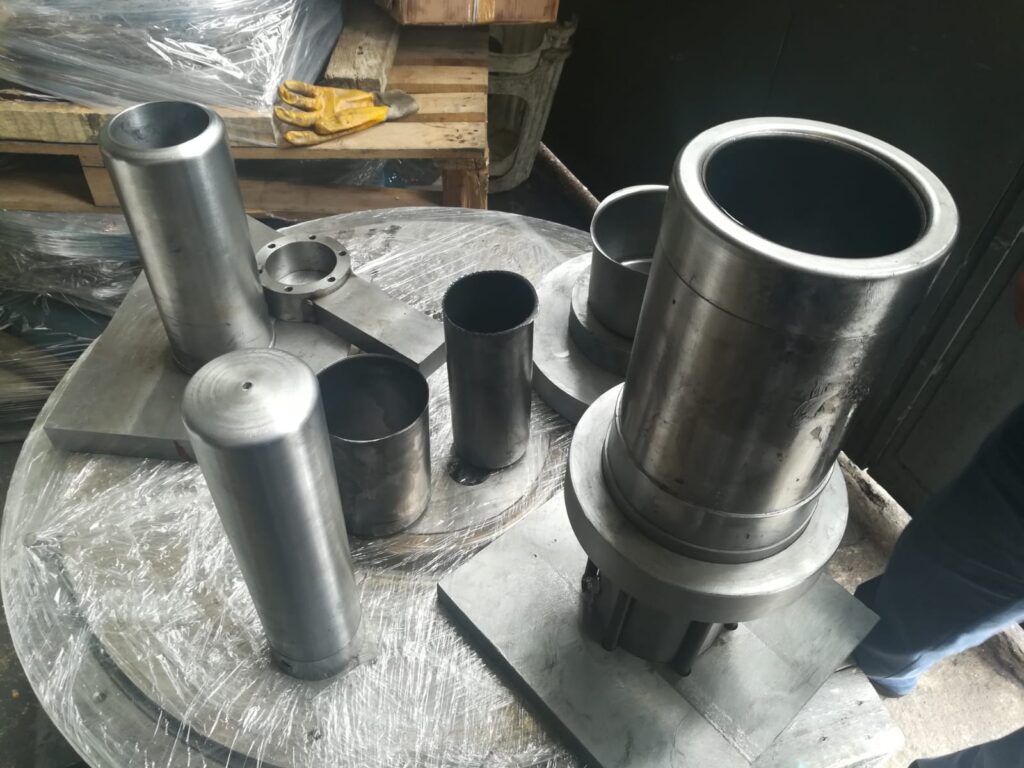
1. Einführung in das Formpressen
Das Formpressen ist ein Fertigungsverfahren, bei dem Materialien unter Druck – und oft auch unter Einwirkung von Wärme – in eine feste Form gebracht werden. Dieser Prozess ermöglicht die Herstellung von Bauteilen mit präzisen Abmessungen und Eigenschaften und wird in vielen Industriebereichen eingesetzt, darunter die Automobilindustrie, Luft- und Raumfahrt sowie die Bau- und Elektroindustrie. Das Verfahren zeichnet sich durch seine Fähigkeit aus, Materialien mit hoher Dichte und Festigkeit herzustellen, was für sicherheitskritische und anspruchsvolle Anwendungen von großer Bedeutung ist.
2. Definition des Formpressens
Formpressen ist ein umformendes Fertigungsverfahren, bei dem Rohmaterialien durch das Einpressen in eine Form ihre endgültige Form und spezifische physikalische Eigenschaften erhalten. Typischerweise werden die Materialien dabei in eine Pressform gegeben und durch Druck und Temperatur so bearbeitet, dass sie dauerhaft ihre Form behalten. Je nach Material und Anforderungen unterscheidet sich der Prozess hinsichtlich Temperatur, Druck, Verarbeitungsdauer und Nachbehandlungsmaßnahmen.
Es gibt zwei Hauptkategorien des Formpressens:
- Heißpressen: Das Material wird erwärmt, um seine Fließfähigkeit zu erhöhen, bevor es in die Form gepresst wird.
- Kaltpressen: Das Material wird ohne zusätzliche Wärmezufuhr unter hohem Druck verformt.
3. Geschichte und Entwicklung des Formpressens
Die Ursprünge des Formpressens reichen bis in die Mitte des 19. Jahrhunderts zurück, als mit der industriellen Revolution und der Entwicklung neuer Materialien erste Formen des Heißpressens in der Metallverarbeitung entstanden. Die Verfügbarkeit neuer Werkstoffe, wie Kunststoffe und Verbundwerkstoffe im 20. Jahrhundert, brachte weitere Fortschritte, und das Formpressen wurde zunehmend zur Herstellung von Massenprodukten genutzt. Mit der Automatisierung und der Digitalisierung in der Industrie 4.0 hat das Formpressen heute ein neues technologisches Niveau erreicht und wird in vielen Bereichen durch Roboter und intelligente Maschinen unterstützt.
4. Grundlegender Prozess des Formpressens
Beim Formpressen wird das Rohmaterial (z.B. Pulver, Granulat, Fasern oder Metall) in eine Form gegeben und durch Druck und oft auch durch Wärme in die gewünschte Form gebracht. Die dabei auftretenden Vorgänge hängen von der Art des Materials ab und können sowohl plastische Verformung als auch chemische Umwandlungen umfassen. Ein typischer Formpressprozess umfasst die folgenden Schritte:
- Materialvorbereitung: Rohmaterial wird aufbereitet und ggf. auf eine bestimmte Temperatur vorgeheizt.
- Positionierung in der Form: Das Material wird in die vorbereitete Form gegeben, die in der Presse fixiert ist.
- Pressvorgang: Die Presse übt den erforderlichen Druck aus, um das Material in die Form zu drücken.
- Aushärtung oder Abkühlung: Je nach Verfahren härtet das Material aus oder wird abgekühlt, um die endgültige Festigkeit und Form zu erreichen.
- Entnahme des Bauteils: Nach dem Pressvorgang wird das Bauteil aus der Form genommen und ggf. nachbearbeitet.
5. Typen des Formpressens
5.1 Heißpressen
Beim Heißpressen wird das Material erwärmt, um seine Fließfähigkeit zu erhöhen und den Formgebungsprozess zu erleichtern. Dieses Verfahren wird vor allem bei Kunststoffen und Metallen angewendet, die bei Raumtemperatur schwer zu verformen sind. Das Heißpressen ermöglicht die Herstellung komplexer Formen und kann eine gute Oberflächenqualität erzeugen.
- Verwendung: In der Automobil-, Luftfahrt- und Elektronikindustrie.
- Vorteile: Gleichmäßige Materialdichte, hohe Präzision, gute Oberflächenqualität.
- Nachteile: Hoher Energieverbrauch, aufwendigere Steuerung des Temperaturprofils.
5.2 Kaltpressen
Das Kaltpressen wird ohne Wärme durchgeführt und findet vor allem bei Materialien Anwendung, die auch bei Raumtemperatur eine gute Verformbarkeit aufweisen, wie z.B. bestimmte Metalle. Beim Kaltpressen wird das Material unter extrem hohem Druck in die Form gepresst, wodurch Bauteile mit hoher Festigkeit und Materialdichte entstehen.
- Verwendung: Herstellung von mechanischen Bauteilen und Strukturelementen.
- Vorteile: Energieeinsparung, geringere Werkzeugbelastung.
- Nachteile: Begrenzte Materialvielfalt, höhere Anforderungen an den Pressdruck.
5.3 Pulverpressen
Das Pulverpressen ist ein Verfahren, bei dem Materialien in Pulverform verwendet werden, um sehr präzise und dichte Bauteile herzustellen. Nachdem das Pulver in die Form gepresst wurde, erfolgt eine Sinterung, bei der das Bauteil erhitzt und so verfestigt wird.
- Verwendung: In der Herstellung von Zahnrädern, Lagern und kleinen präzisen Bauteilen.
- Vorteile: Hohe Maßgenauigkeit, komplexe Formen möglich, geringere Materialkosten.
- Nachteile: Zusätzliche Sinterprozesse erforderlich, begrenzte Werkstoffauswahl.
5.4 Spritzgießpressen
Das Spritzgießpressen kombiniert das Spritzgießen und Pressen und wird hauptsächlich zur Herstellung von Kunststoffteilen verwendet. Beim Spritzgießpressen wird das Material eingespritzt und dann durch Druck in die endgültige Form gebracht.
- Verwendung: Herstellung von Gehäusen, elektrischen Komponenten und medizinischen Produkten.
- Vorteile: Hohe Präzision, schnelle Zykluszeiten, komplexe Formen möglich.
- Nachteile: Höhere Maschinenkosten und Wartungsaufwand.
5.5 Verbundpressen
Das Verbundpressen wird verwendet, um Materialien wie glasfaserverstärkten Kunststoff (GFK) oder kohlenstofffaserverstärkten Kunststoff (CFK) zu verarbeiten. Dabei werden verschiedene Schichten oder Komponenten in eine Form gepresst, um ein leichtes, aber starkes Material herzustellen.
- Verwendung: Herstellung von Strukturbauteilen für die Automobil- und Luftfahrtindustrie.
- Vorteile: Leichtbau, hohe Festigkeit, hohe Formstabilität.
- Nachteile: Teure Materialien, anspruchsvolle Verarbeitung.
6. Materialien im Formpressen
Formpressverfahren werden für eine Vielzahl von Materialien eingesetzt. Die Auswahl des Materials hängt von den spezifischen Anforderungen des Endprodukts und den Eigenschaften des Materials ab.
6.1 Metalle
Metallische Werkstoffe, wie Aluminium, Stahl und Titan, sind weit verbreitet in Formpressverfahren. Metalle bieten hohe Festigkeit und Beständigkeit, erfordern jedoch spezielle Maschinen und hohe Presskräfte, um die gewünschte Form und Qualität zu erzielen.
- Anwendungen: Mechanische Bauteile, Karosserieelemente, Flugzeugstrukturen.
6.2 Kunststoffe
Kunststoffe sind leicht, flexibel und weisen eine gute Formbarkeit auf. Sie werden in der Regel im Heißpressen verarbeitet und sind in vielen verschiedenen Typen verfügbar:
- Thermoplaste: Diese Kunststoffe können mehrfach erwärmt und verformt werden und eignen sich für Produkte, die eine hohe Flexibilität erfordern.
- Duroplaste: Nach dem Aushärten sind Duroplaste fest und beständig, aber nicht erneut verformbar. Sie werden für Bauteile verwendet, die hohen Belastungen und Temperaturen standhalten müssen.
- Anwendungen: Gehäuse, Kabelkanäle, Innenverkleidungen und Bauteile für Elektronik und Medizin.
6.3 Verbundwerkstoffe
Verbundwerkstoffe wie CFK und GFK kombinieren die Eigenschaften von Fasern und Kunststoffen und bieten eine hohe Festigkeit bei geringem Gewicht.
- Anwendungen: Karosserieteile, Flugzeugstrukturen und Leichtbaukonstruktionen.
7. Maschinen und Werkzeuge im Formpressen
Die Maschinen und Werkzeuge im Formpressen müssen speziell ausgelegt sein, um den hohen Kräften und Temperaturen standzuhalten und gleichzeitig eine hohe Präzision zu gewährleisten.
7.1 Pressenarten
Die Haupttypen der Pressen im Formpressen sind:
- Hydraulikpressen: Sie ermöglichen eine gleichmäßige Druckverteilung und eine präzise Steuerung. Hydraulikpressen sind flexibel und können für unterschiedliche Materialien eingesetzt werden.
- Mechanische Pressen: Sie eignen sich für Anwendungen, die schnelle und wiederholbare Bewegungen erfordern, und werden oft in der Massenproduktion eingesetzt.
7.2 Formen und Werkzeuge
Die Form, die das Material in die gewünschte Geometrie bringt, ist oft aus Materialien wie gehärtetem Stahl oder speziellen hochfesten Legierungen gefertigt, um dem hohen Druck und der Temperatur standzuhalten. Die Form muss präzise gefertigt sein, um Maßhaltigkeit und Wiederholgenauigkeit zu gewährleisten.
7.3 Heiz- und Kühlsysteme
Im Heißpressen sind Heizsysteme notwendig, um das Material auf die richtige Temperatur zu bringen. Kühlsysteme helfen, das Bauteil nach der Formgebung kontrolliert abzukühlen und so die Formstabilität sicherzustellen.
8. Anwendungsfelder des Formpressens
Formpressen wird in zahlreichen Industrien verwendet, in denen robuste, langlebige und präzise Bauteile benötigt werden.
8.1 Automobilindustrie
In der Automobilindustrie wird das Formpressen zur Herstellung von Karosserie- und Strukturbauteilen, Innenverkleidungen und Motorabdeckungen verwendet. Leichtbau-Materialien wie CFK und GFK ermöglichen die Produktion von Komponenten, die gleichzeitig stabil und leicht sind.
8.2 Luft- und Raumfahrt
Die Luftfahrtindustrie verwendet das Formpressen zur Herstellung von tragenden Strukturbauteilen und Oberflächenelementen. Hier ist die Gewichtseinsparung besonders wichtig, weshalb häufig Verbundwerkstoffe und spezielle Aluminiumlegierungen eingesetzt werden.
8.3 Bauindustrie
In der Bauindustrie werden formgepresste Bauteile für Fassadenelemente, Fensterrahmen und strukturelle Bauteile verwendet. Hier sind die Witterungsbeständigkeit und die mechanische Belastbarkeit entscheidende Faktoren.
8.4 Medizintechnik und Elektronik
Die Herstellung von präzisen und sterilen Bauteilen, wie Implantaten und Gehäusen für medizinische Geräte, erfolgt ebenfalls durch Formpressen. Auch in der Elektronikindustrie werden formgepresste Gehäuse und Komponenten eingesetzt.
9. Zukunft des Formpressens: Trends und Innovationen
Die Zukunft des Formpressens wird durch technologische Innovationen und die Nachfrage nach effizienteren, nachhaltigeren Produktionsmethoden geprägt sein:
- Industrie 4.0 und Smart Manufacturing: Die Digitalisierung und Vernetzung von Maschinen ermöglicht eine Echtzeitsteuerung und Flexibilität der Produktionsprozesse.
- Materialforschung und Recycling: Neue Materialien und Recyclingmethoden verbessern die Nachhaltigkeit und Effizienz des Formpressens.
- Automatisierung und Robotik: Der Einsatz von Robotern und automatisierten Systemen zur Materialzuführung, -entnahme und Qualitätsprüfung reduziert Arbeitsaufwand und erhöht die Sicherheit.
Zusammenfassung
Das Formpressen ist ein vielseitiges und leistungsstarkes Fertigungsverfahren, das in vielen Industrien weltweit zur Anwendung kommt. Durch die verschiedenen Verfahren des Formpressens lassen sich Materialien präzise und effizient in komplexe Formen bringen, was die Herstellung robuster, leichter und langlebiger Bauteile ermöglicht. Die Kombination von Automation, digitaler Steuerung und neuen Materialien wird das Formpressen in der Zukunft weiter vorantreiben und seine Bedeutung als wichtiges Produktionsverfahren festigen.
Zielsetzung und Nutzen der Automatisierung im Formpressen
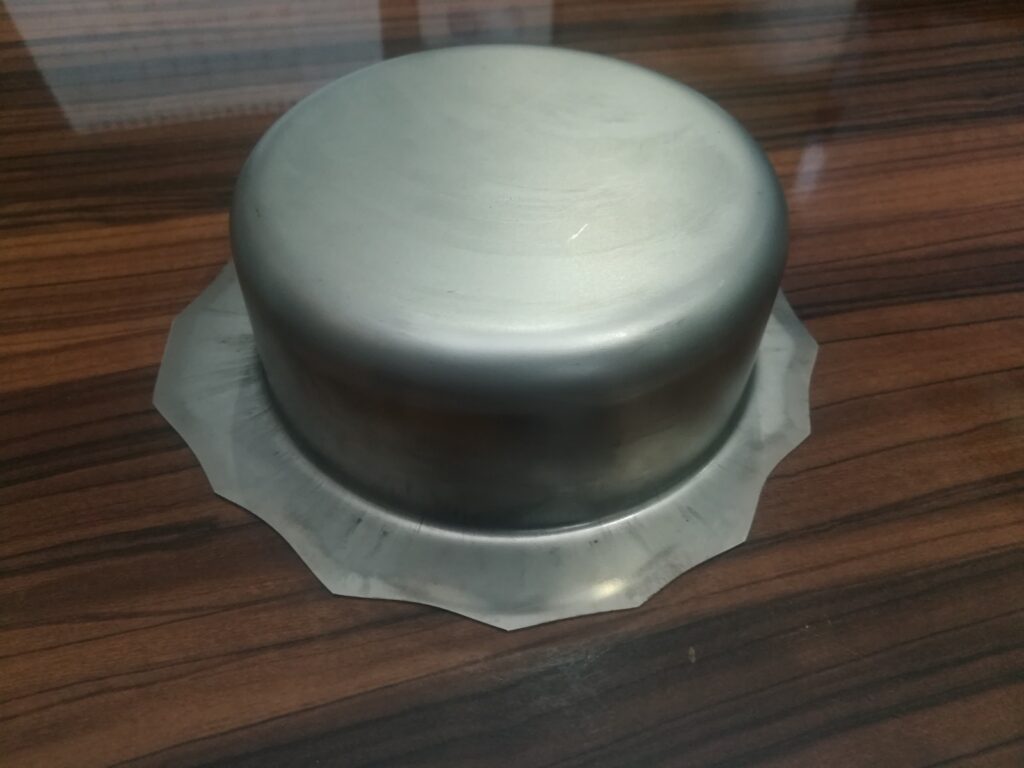
1. Einleitung
In der heutigen industriellen Produktion spielt die Automatisierung des Formpressens eine entscheidende Rolle. Formpressen ist ein verbreitetes Fertigungsverfahren, das zur Herstellung einer Vielzahl von Bauteilen für Branchen wie Automobil, Luftfahrt, Bau und Elektronik genutzt wird. Automatisierung bietet eine Reihe von Vorteilen, die weit über die bloße Effizienzsteigerung hinausgehen. In diesem Abschnitt wird erläutert, welche Ziele Unternehmen mit der Automatisierung verfolgen und welche konkreten Vorteile sich daraus für den Formpressprozess und die gesamte Produktion ergeben.
2. Zielsetzungen der Automatisierung im Formpressen
Die Automatisierung von Formpressverfahren verfolgt mehrere zentrale Ziele, die alle darauf abzielen, die Wettbewerbsfähigkeit der Unternehmen zu verbessern und den Anforderungen einer modernen Industrieproduktion gerecht zu werden.
2.1 Erhöhung der Produktionseffizienz
Ein Hauptziel der Automatisierung ist die Steigerung der Produktionseffizienz. Automatisierte Systeme ermöglichen eine kontinuierliche Produktion, die unabhängig von Schichtwechseln oder Pausen ist. Dadurch wird die Durchlaufzeit verkürzt und der Produktionsausstoß erhöht. Die Zykluszeit eines Pressvorgangs kann so optimiert werden, dass Maschinen effizient und ohne Wartezeiten arbeiten.
- Kontinuierliche Produktion: Automatisierte Formpressanlagen können rund um die Uhr betrieben werden und ermöglichen eine Steigerung des Produktionsvolumens.
- Optimierung der Zykluszeit: Durch automatisierte Steuerung kann die Zykluszeit für jeden Formpressvorgang auf das notwendige Minimum reduziert werden.
2.2 Verbesserung der Produktqualität und Präzision
Die Automatisierung im Formpressen zielt darauf ab, eine hohe Präzision und gleichbleibende Produktqualität zu gewährleisten. Automatisierte Systeme ermöglichen eine genaue Kontrolle der Prozessparameter wie Druck, Temperatur und Zykluszeit. Dadurch lassen sich Bauteile mit hoher Wiederholgenauigkeit und exakten Abmessungen herstellen, was besonders für sicherheitskritische Anwendungen in der Luft- und Raumfahrt oder im Automobilbau wichtig ist.
- Reproduzierbarkeit: Automatisierte Systeme garantieren eine gleichbleibende Qualität bei jeder produzierten Einheit.
- Echtzeitüberwachung der Parameter: Sensoren erfassen die Prozessbedingungen in Echtzeit und melden Abweichungen sofort, wodurch Fehler im Produktionsprozess schnell behoben werden können.
2.3 Reduktion von Fehlern und Ausschuss
Ein weiteres Ziel der Automatisierung im Formpressen ist die Reduktion von Materialausschuss und Produktionsfehlern. Durch die präzise Kontrolle des Pressvorgangs und die Integration von Qualitätskontrollsystemen wird Ausschuss minimiert. Dies führt zu einer höheren Materialausnutzung und einer Verringerung der Produktionskosten.
- Fehlervermeidung durch Sensorik und Echtzeitdaten: Automatisierte Systeme erkennen Fehler im Prozess und passen die Parameter an, um Abweichungen frühzeitig zu beheben.
- Automatische Qualitätskontrolle: Kamerasysteme und Lasersensoren überprüfen die produzierten Bauteile auf Defekte und gewährleisten, dass nur einwandfreie Teile die Produktion verlassen.
2.4 Kostensenkung
Ein weiterer bedeutender Anreiz für die Automatisierung ist die Kosteneffizienz. Durch die Reduzierung des Materialverbrauchs, die Verringerung von Fehlern und die höhere Effizienz sinken die Produktionskosten. Auch die Arbeitskosten können gesenkt werden, da weniger manuelle Eingriffe erforderlich sind und der Maschinenbetrieb durch automatisierte Steuerungen weitgehend selbstständig erfolgt.
- Materialkosten reduzieren: Durch präzises Materialhandling und weniger Ausschuss können die Materialkosten gesenkt werden.
- Einsparungen durch geringeren Personalbedarf: Automatisierte Systeme übernehmen Aufgaben, die zuvor von Fachpersonal durchgeführt wurden, und entlasten so die Belegschaft.
2.5 Verbesserung der Arbeitssicherheit
Automatisierung trägt entscheidend zur Erhöhung der Arbeitssicherheit bei. Formpressverfahren, insbesondere bei hohen Temperaturen und Drücken, bergen Risiken für die Bediener. Durch die Automatisierung können Mitarbeiter von gefährlichen Arbeiten entlastet werden, da Roboter und automatisierte Maschinen die Materialhandhabung, das Formen und die Qualitätsprüfung übernehmen.
- Minimierung der Unfallrisiken: Der Einsatz von Robotern und Automatisierungssystemen reduziert die Notwendigkeit von menschlichen Eingriffen in riskante Prozesse.
- Ergonomische Entlastung: Automatisierte Systeme übernehmen schwere und monotone Arbeiten, was die körperliche Belastung der Mitarbeiter verringert.
2.6 Flexibilität und Anpassungsfähigkeit der Produktion
Ein weiteres Ziel der Automatisierung im Formpressen ist die Steigerung der Flexibilität. In einer dynamischen Produktionsumgebung, in der sich die Anforderungen schnell ändern können, ermöglichen automatisierte Systeme eine schnelle Anpassung an neue Produktvarianten oder Materialien.
- Schnelle Umrüstung: Automatisierte Systeme können durch vordefinierte Einstellungen schnell auf andere Produktparameter oder Materialien umgestellt werden.
- Flexibilität bei Kleinserien und Prototypen: Automatisierte Prozesse lassen sich leicht anpassen, was die Fertigung kleiner Stückzahlen und von Prototypen kosteneffizienter macht.
3. Nutzen der Automatisierung im Formpressen
Die Automatisierung des Formpressens bietet zahlreiche Vorteile, die in verschiedenen Bereichen zu spürbaren Verbesserungen führen.
3.1 Effizienzsteigerung und Durchsatzmaximierung
Automatisierte Formpresssysteme können kontinuierlich und ohne Unterbrechung betrieben werden, was den Durchsatz maximiert und die Effizienz steigert. Die Maschinen können präzise aufeinander abgestimmt werden, was eine optimale Auslastung der Anlagen ermöglicht.
- Höherer Produktionsausstoß: Automatisierte Anlagen können mehr Bauteile in kürzerer Zeit produzieren, was die Kapazität der Produktionslinie erhöht.
- Verringerung von Rüstzeiten: Durch den Einsatz von Robotern und automatisierten Steuerungssystemen können Produktionslinien schneller umgerüstet und ohne Verzögerungen wieder in Betrieb genommen werden.
3.2 Verbesserte Produktqualität und Konsistenz
Ein automatisiertes System überwacht und steuert alle Prozessparameter konstant, wodurch gleichbleibende Qualität gewährleistet wird. Dies ist entscheidend für Branchen, die auf ein hohes Maß an Präzision angewiesen sind, wie die Automobil- und Luftfahrtindustrie.
- Reduzierung von Qualitätsmängeln: Durch die kontinuierliche Überwachung und Anpassung der Prozessparameter werden Fehler minimiert und die Ausschussrate gesenkt.
- Erfüllung strenger Qualitätsstandards: Die hohe Präzision und Reproduzierbarkeit ermöglichen es Unternehmen, den hohen Anforderungen der Kunden gerecht zu werden und Zertifizierungen leichter zu erhalten.
3.3 Kosteneffizienz und Materialeinsparung
Automatisierungstechnologien optimieren den Materialeinsatz und reduzieren Abfälle, was zu einer deutlichen Kostensenkung führt. Die verbesserte Kontrolle des Materialflusses und der Prozessparameter reduziert den Verbrauch von Rohmaterialien und minimiert Abfall.
- Effiziente Materialnutzung: Automatisierte Systeme stellen sicher, dass nur die notwendige Menge an Material verwendet wird, was Materialkosten spart.
- Weniger Ausschuss: Die Reduzierung von Ausschuss senkt die Produktionskosten und trägt zu einer nachhaltigeren Produktion bei.
3.4 Reduzierung von Arbeitskosten und Optimierung der Ressourcennutzung
Die Automatisierung ermöglicht eine effizientere Ressourcennutzung und senkt die Kosten für Arbeitskräfte. Routineaufgaben und einfache Montagearbeiten können durch Maschinen übernommen werden, wodurch das Unternehmen seine Personalressourcen besser einsetzen kann.
- Weniger Personalbedarf für repetitive Aufgaben: Die Automatisierung ersetzt viele manuelle Arbeiten, was die Personalaufwendungen senkt und die vorhandenen Mitarbeiter für anspruchsvollere Aufgaben freistellt.
- Einsparungen bei Schulung und Sicherheit: Durch die Automatisierung gefährlicher Arbeiten sinken die Anforderungen an Schulungen für Arbeitssicherheit und den Umgang mit Maschinen.
3.5 Verbesserung der Arbeitssicherheit und Ergonomie
Die Automatisierung trägt zur Verbesserung der Sicherheit und Arbeitsbedingungen bei. Da Maschinen gefährliche oder anstrengende Arbeiten übernehmen, sinkt das Verletzungsrisiko, und die Mitarbeiter werden entlastet.
- Erhöhung der Arbeitssicherheit: Durch den automatisierten Betrieb in gefährlichen Bereichen wird das Unfallrisiko minimiert.
- Ergonomische Entlastung: Roboter und Maschinen übernehmen schwere und monotone Arbeiten, wodurch das Wohlbefinden der Mitarbeiter gefördert wird.
3.6 Nachhaltigkeit und Energieeffizienz
Die Automatisierung des Formpressens trägt zur Nachhaltigkeit und Energieeffizienz der Produktion bei. Durch die Reduktion von Materialverlusten und die Steuerung des Energieverbrauchs wird der ökologische Fußabdruck der Produktion verringert.
- Reduzierung von Abfall und Energieverbrauch: Präzise Steuerung und weniger Ausschuss führen zu einer ressourcenschonenden Produktion.
- Energieoptimierte Prozesse: Automatisierte Systeme passen die Energiezufuhr bedarfsgerecht an, was den Energieverbrauch senkt und die Produktionskosten reduziert.
3.7 Flexibilität und Zukunftsfähigkeit durch Digitalisierung und Industrie 4.0
Automatisierung im Formpressen ermöglicht die Integration in digitale Netzwerke und unterstützt die Prinzipien der Industrie 4.0. Durch die Verbindung der Maschinen mit digitalen Systemen können Unternehmen schneller auf Veränderungen am Markt reagieren und ihre Produktion flexibel anpassen.
- Verkürzte Reaktionszeiten: Unternehmen können ihre Produktionslinien flexibel auf neue Anforderungen einstellen.
- Echtzeitdaten und Entscheidungsfindung: Vernetzte Maschinen bieten Echtzeitinformationen zur Optimierung und Fehlerbehebung.
4. Herausforderungen und Lösungsansätze bei der Automatisierung
Die Automatisierung bietet zahlreiche Vorteile, bringt jedoch auch einige Herausforderungen mit sich:
- Hohe Investitionskosten: Die Implementierung automatisierter Systeme ist mit hohen Anschaffungskosten verbunden. Unternehmen können jedoch durch schrittweise Automatisierung und Förderprogramme die Kosten kontrollieren.
- Wartung und Instandhaltung: Automatisierte Systeme erfordern regelmäßige Wartung, um ihre Leistung zu gewährleisten. Der Einsatz von vorausschauender Wartung (Predictive Maintenance) kann hier die Zuverlässigkeit der Systeme steigern.
- Notwendigkeit von qualifiziertem Personal: Für die Einrichtung und Wartung automatisierter Systeme sind Fachkenntnisse erforderlich. Unternehmen investieren zunehmend in die Schulung und Weiterbildung ihrer Mitarbeiter, um die Kompetenzen im Umgang mit Automatisierungssystemen zu stärken.
5. Zusammenfassung
Die Automatisierung des Formpressens ist ein wichtiger Schritt in Richtung einer effizienten, sicheren und flexiblen Produktion. Durch die Zielsetzung, die Effizienz zu steigern, Kosten zu senken und die Arbeitssicherheit zu erhöhen, wird das Formpressen durch Automatisierung auf ein neues Niveau gehoben. Mit den Vorteilen wie verbesserter Produktqualität, höherer Materialeffizienz und gesteigerter Flexibilität sowie der Möglichkeit zur Integration in Industrie-4.0-Umgebungen zeigt sich, dass die Automatisierung eine zukunftsweisende Entwicklung darstellt. Die Herausforderung der hohen Anfangskosten kann durch langfristige Einsparungen und Effizienzgewinne ausgeglichen werden, wodurch die Automatisierung zu einer lohnenden Investition wird.
Technologischer Fortschritt und Digitalisierung im Formpressen
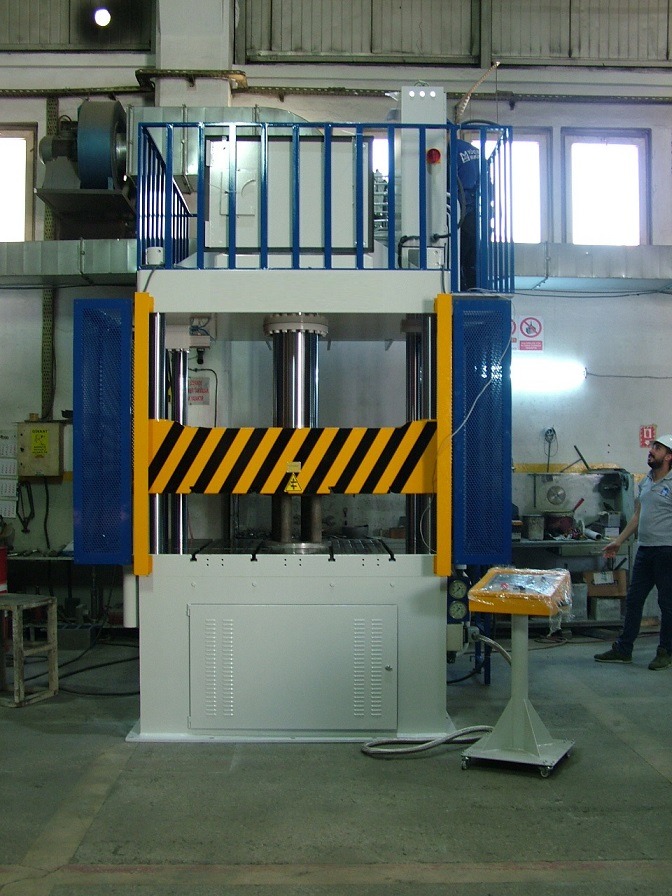
1. Einleitung
Die Digitalisierung und technologische Innovationen haben das Formpressen in den letzten Jahren revolutioniert. Durch Fortschritte in der Robotik, Sensorik, Datenanalyse und intelligente Steuerungssysteme können Formpressprozesse effizienter, flexibler und genauer gestaltet werden. Insbesondere die Prinzipien von Industrie 4.0 und das Internet der Dinge (IoT) haben das Potenzial des Formpressens in eine neue Ära geführt, in der Maschinen miteinander kommunizieren, Prozesse automatisiert ablaufen und Entscheidungen datenbasiert getroffen werden. Dieser Abschnitt beleuchtet, wie technologische Fortschritte und Digitalisierung den Formpressprozess beeinflussen und welche Vorteile dadurch entstehen.
2. Fortschritte in der Robotik und Automatisierung
2.1 Roboterintegration und Automatisiertes Materialhandling
Moderne Robotertechnologie ermöglicht eine umfassende Automatisierung von Formpressprozessen. Roboter übernehmen Aufgaben wie das Einlegen des Materials in die Form, die Positionierung und das Herausnehmen des fertigen Bauteils. Durch die Integration von Robotern können Aufgaben mit hoher Präzision ausgeführt werden, was zu einer Reduzierung von Ausschuss und einer höheren Produktionsgeschwindigkeit führt.
- Vorteile der Roboterintegration: Roboter bieten eine hohe Genauigkeit und Reproduzierbarkeit, die sich besonders bei komplexen Bauteilen auszahlt.
- Flexibilität durch Robotik: Roboter können für verschiedene Formen und Materialien programmiert werden und passen sich somit dynamisch an wechselnde Produktionsanforderungen an.
2.2 Einsatz von Cobots (kollaborative Roboter)
Kollaborative Roboter, auch Cobots genannt, sind Roboter, die mit menschlichen Bedienern zusammenarbeiten und insbesondere in kleinen und mittelständischen Unternehmen Vorteile bringen. Sie unterstützen bei Aufgaben, die Flexibilität und menschliches Know-how erfordern, wie z. B. beim Rüsten der Maschinen und der Feinjustierung der Formparameter.
- Anpassungsfähigkeit: Cobots können flexibel eingesetzt werden und lassen sich in bestehende Fertigungslinien integrieren, ohne die gesamte Anlage zu verändern.
- Erhöhung der Arbeitssicherheit: Cobots reduzieren die körperliche Belastung der Mitarbeiter, da sie monotone oder gefährliche Aufgaben übernehmen.
3. Fortschritte in der Sensorik und Prozessüberwachung
Sensoren spielen eine zentrale Rolle in der Digitalisierung des Formpressens, da sie Echtzeitdaten liefern, die zur Steuerung und Überwachung des Prozesses genutzt werden können. Die Integration von Sensorik ermöglicht die präzise Kontrolle aller wichtigen Parameter und erhöht die Transparenz über den gesamten Produktionsprozess.
3.1 Druck-, Temperatur- und Wegsensoren
- Drucksensoren: Sie messen den Pressdruck während des Formvorgangs und helfen dabei, Abweichungen in der Verdichtung des Materials zu vermeiden.
- Temperatursensoren: Besonders beim Heißpressen ist die exakte Temperaturkontrolle entscheidend, und Temperatursensoren liefern die Informationen, die für eine stabile und gleichmäßige Erwärmung notwendig sind.
- Wegsensoren: Diese Sensoren messen die Position der Maschinenkomponenten und stellen sicher, dass der Pressvorgang präzise und wiederholbar abläuft.
3.2 Infrarot- und Lasersensoren zur Qualitätsüberwachung
- Lasersensoren: Diese kommen zur Oberflächenmessung und zur Erkennung von Fehlstellen auf dem Bauteil zum Einsatz. Sie ermöglichen eine zerstörungsfreie Prüfung und erhöhen die Qualitätssicherung.
- Infrarotsensoren: Diese messen die Temperatur an verschiedenen Punkten des Bauteils, um sicherzustellen, dass die Materialeigenschaften den Anforderungen entsprechen.
4. Digitale Steuerungssysteme und Softwareintegration
4.1 Programmierbare Logiksteuerung (PLC) und Echtzeitsteuerung
Programmierbare Logiksteuerungen (PLC) sind zentrale Komponenten moderner Fertigungslinien. Sie ermöglichen eine präzise Steuerung und Kontrolle der Maschinenparameter und können auf Veränderungen im Prozess sofort reagieren.
- Vorteile der Echtzeitsteuerung: Echtzeitsteuerungssysteme passen sich laufend an Veränderungen an und gewährleisten so eine gleichbleibende Produktqualität. Bei Abweichungen im Prozess greift das System automatisch ein und korrigiert den Ablauf.
- Flexibilität: Moderne PLCs sind einfach programmierbar und können so an unterschiedliche Anforderungen und Produktvariationen angepasst werden.
4.2 SCADA-Systeme zur Datenerfassung und -überwachung
SCADA (Supervisory Control and Data Acquisition)-Systeme werden zur Erfassung, Überwachung und Steuerung von Produktionsprozessen eingesetzt. Sie liefern Informationen über den Status der Maschinen und ermöglichen die Fernüberwachung und -steuerung von Produktionsanlagen.
- Echtzeit-Datenanalyse und Entscheidungsfindung: SCADA-Systeme erfassen und analysieren Daten in Echtzeit und visualisieren diese, sodass die Prozessverantwortlichen sofort auf Probleme reagieren können.
- Effizienzsteigerung: Durch die Überwachung der Prozessdaten lassen sich Ineffizienzen im Formpressprozess frühzeitig erkennen und beheben.
4.3 Prozessautomatisierungssoftware
Automatisierungssoftware spielt eine zentrale Rolle in der Koordination und Optimierung der Produktionsabläufe. Moderne Softwarelösungen lassen sich in ERP- und MES-Systeme (Manufacturing Execution Systems) integrieren, was eine vollständige Digitalisierung und Steuerung der Produktionskette ermöglicht.
- Vernetzte Steuerung und Prozessoptimierung: Die Software analysiert Prozessparameter und optimiert den Produktionsablauf, was zu einer Reduktion der Zykluszeiten und einer Erhöhung der Effizienz führt.
- Flexible Produktionsplanung: Mit Automatisierungssoftware können Produktionslinien auf neue Anforderungen umgestellt werden, was die Flexibilität im Betrieb erhöht.
5. Big Data und Datenanalyse zur Prozessoptimierung
In der digitalisierten Produktion fallen große Mengen an Daten an, die für die Optimierung des Formpressprozesses genutzt werden können. Die Analyse dieser Daten ermöglicht eine bessere Prozesssteuerung und eine vorausschauende Wartung.
5.1 Sammlung und Verarbeitung großer Datenmengen
Durch die Erfassung großer Datenmengen (Big Data) lassen sich Informationen über alle Schritte im Formpressprozess gewinnen. Diese Daten können mithilfe moderner Analysetools verarbeitet und in wertvolle Informationen umgewandelt werden.
- Prozessanalyse: Die Datenanalyse zeigt Schwachstellen im Produktionsablauf auf und ermöglicht die gezielte Optimierung dieser Bereiche.
- Ermittlung von Trends und Mustern: Durch die Analyse historischer Daten können Muster und Trends erkannt werden, die für die langfristige Optimierung genutzt werden.
5.2 Predictive Analytics und vorausschauende Wartung
Predictive Analytics nutzt Datenanalysen und maschinelles Lernen, um Wartungsbedarfe vorherzusagen und so ungeplante Ausfälle zu vermeiden. Durch die Analyse der Sensordaten kann das System Hinweise auf potenzielle Probleme geben, bevor diese den Produktionsprozess beeinträchtigen.
- Reduzierung von Maschinenstillstandzeiten: Vorausschauende Wartung erkennt Verschleiß und Schäden frühzeitig und plant Wartungsmaßnahmen so, dass sie keine Produktionsunterbrechungen verursachen.
- Kosteneffizienz: Predictive Maintenance verlängert die Lebensdauer der Maschinen und reduziert die Wartungskosten durch gezielte Eingriffe.
6. Künstliche Intelligenz und Maschinelles Lernen zur Prozessoptimierung
Die Integration von Künstlicher Intelligenz (KI) und Maschinellem Lernen in den Formpressprozess eröffnet neue Möglichkeiten zur Prozessoptimierung und Fehlervermeidung. Diese Technologien analysieren Prozessparameter, erkennen Abweichungen und passen den Produktionsprozess an, um die Effizienz zu maximieren.
6.1 KI zur Anomalieerkennung und Qualitätskontrolle
KI-Systeme sind in der Lage, Fehler im Produktionsprozess frühzeitig zu erkennen. Maschinelles Lernen ermöglicht es den Systemen, aus historischen Daten zu lernen und Muster zu erkennen, die auf Anomalien hindeuten.
- Früherkennung von Abweichungen: KI erkennt Unregelmäßigkeiten und kann durch automatische Anpassungen den Produktionsfluss optimieren.
- Automatisierte Qualitätskontrolle: KI-Systeme analysieren Qualitätsdaten und sorgen dafür, dass der gesamte Produktionsprozess an die Qualitätsanforderungen angepasst wird.
6.2 Selbstoptimierende Systeme
Maschinelles Lernen ermöglicht es Produktionssystemen, selbständig Entscheidungen zu treffen und Prozessparameter basierend auf bisherigen Erfahrungen zu optimieren.
- Effizienzsteigerung: Selbstoptimierende Systeme verbessern die Produktqualität und senken die Kosten durch die kontinuierliche Anpassung der Prozessparameter.
- Anpassungsfähigkeit: Die KI-basierte Analyse der Produktionsdaten unterstützt die Optimierung des Formpressprozesses und macht den Betrieb flexibel und anpassungsfähig.
7. Industrie 4.0 und IoT im Formpressen
Industrie 4.0 und das Internet der Dinge (IoT) ermöglichen die Vernetzung von Maschinen und Anlagen und fördern die Entwicklung einer flexiblen, intelligenten Produktion. Durch die Implementierung von IoT-Geräten im Formpressen können Maschinen miteinander kommunizieren, was die Flexibilität und Effizienz der Produktion erhöht.
7.1 Vernetzte Maschinen und Smart Manufacturing
Smart Manufacturing ist das Konzept, Maschinen und Anlagen zu vernetzen und so eine durchgehende Datenverfügbarkeit zu schaffen. Im Formpressen ermöglicht diese Vernetzung eine vollständige Transparenz über den gesamten Produktionsprozess.
- Transparenz und Kontrolle: Vernetzte Maschinen liefern Echtzeitdaten über den Prozessstatus und ermöglichen eine umfassende Kontrolle.
- Flexibilität: Die Produktionslinien können an unterschiedliche Anforderungen angepasst werden, was Unternehmen eine höhere Flexibilität bei wechselnden Anforderungen bietet.
7.2 Intelligente Steuerung und dezentrale Entscheidungen
IoT-Geräte ermöglichen dezentrale Entscheidungen und eine intelligente Steuerung der Produktion. Maschinen und Sensoren kommunizieren miteinander und können den Produktionsprozess auf Basis der verfügbaren Informationen steuern.
- Echtzeit-Entscheidungen: Systeme können Prozesse in Echtzeit anpassen und auf Änderungen im Produktionsablauf reagieren.
- Autonome Fertigung: IoT und vernetzte Systeme bieten die Basis für eine autonome Produktion, in der Maschinen selbstständig Entscheidungen treffen.
8. Vorteile des technologischen Fortschritts und der Digitalisierung
Die Fortschritte in der Technologie und Digitalisierung bringen eine Vielzahl an Vorteilen für das Formpressen, darunter:
- Erhöhung der Effizienz: Die automatisierte Steuerung und Überwachung ermöglichen eine schnellere und präzisere Produktion.
- Verbesserte Produktqualität: KI und Sensorik verbessern die Qualitätskontrolle und reduzieren Fehler.
- Kostensenkung: Durch optimierte Prozesse, weniger Ausschuss und Predictive Maintenance sinken die Produktionskosten.
- Flexibilität und Anpassungsfähigkeit: Digitale Systeme ermöglichen eine schnelle Anpassung an neue Anforderungen und Produktionsbedingungen.
- Nachhaltigkeit und Ressourcenschonung: Energieeinsparungen und die Reduktion von Materialverlusten tragen zu einer umweltfreundlicheren Produktion bei.
9. Herausforderungen und Lösungsansätze
Die Implementierung neuer Technologien im Formpressen bringt Herausforderungen mit sich, insbesondere:
- Hohe Implementierungskosten: Die Anschaffung und Integration digitaler Systeme ist kostspielig, doch Förderprogramme und schrittweise Automatisierung können Abhilfe schaffen.
- Schulung und Qualifikation: Der Einsatz neuer Technologien erfordert geschultes Personal. Unternehmen investieren zunehmend in die Weiterbildung ihrer Mitarbeiter.
- Datensicherheit: Mit der zunehmenden Vernetzung steigt das Risiko für Cyberangriffe, weshalb Sicherheitsstrategien wie Firewalls und Verschlüsselungssysteme unabdingbar sind.
10. Fazit
Technologischer Fortschritt und Digitalisierung haben das Formpressen entscheidend verändert und bieten enorme Potenziale für die Zukunft. Die Kombination von Robotik, Sensorik, KI und IoT ermöglicht eine effiziente, flexible und nachhaltige Produktion, die den Anforderungen der modernen Industrie gerecht wird. Trotz der hohen Anfangsinvestitionen und der Notwendigkeit geschulter Fachkräfte sind die langfristigen Vorteile der Digitalisierung und technologischen Innovationen im Formpressen unschätzbar wertvoll und eröffnen neue Wege zur Optimierung und Effizienzsteigerung.
Mit der fortschreitenden Entwicklung wird die Digitalisierung im Formpressen eine Schlüsselrolle spielen, um sich den Anforderungen der Industrie 4.0 anzupassen und das Potenzial der Smart Factory voll auszuschöpfen.
Formpressen im Kontext von Industrie 4.0 und Smart Manufacturing
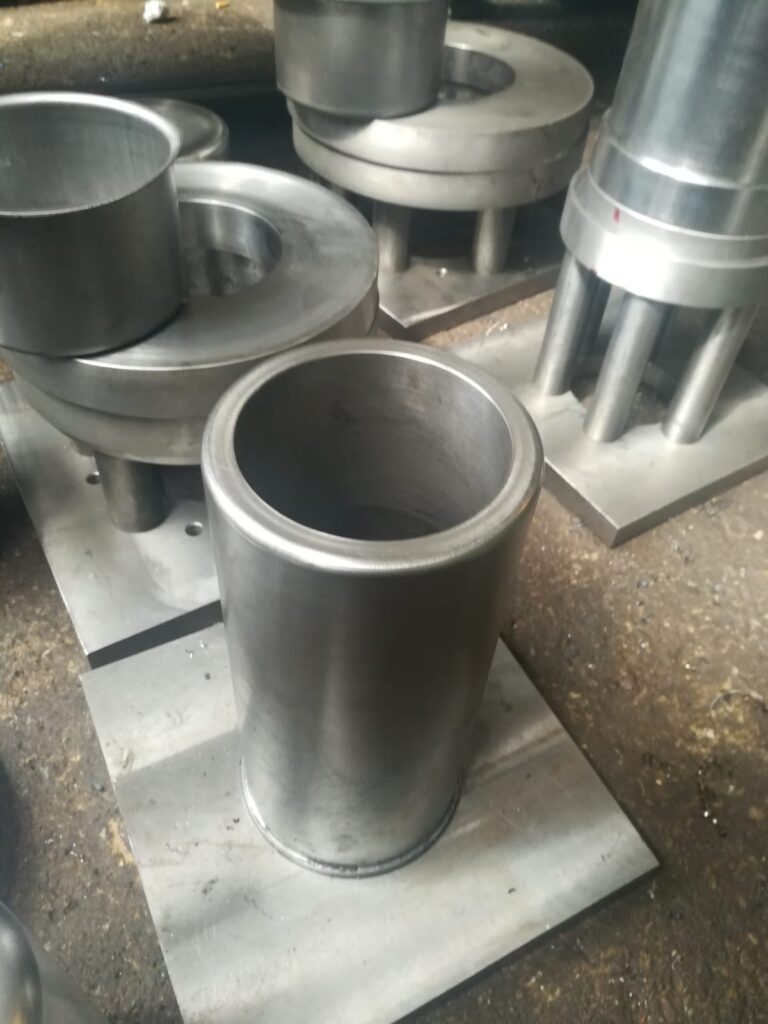
1. Einleitung
Industrie 4.0 steht für die vierte industrielle Revolution und beschreibt die digitale Transformation der Fertigungsprozesse durch Vernetzung, Datenanalyse und Automatisierung. Im Formpressen führt der Einsatz von Smart Manufacturing und Industrie-4.0-Technologien zu einer flexiblen, effizienten und datengetriebenen Produktionsumgebung, die auf Echtzeitdaten basiert. Diese Entwicklung ermöglicht nicht nur eine Verbesserung der Produktionsgeschwindigkeit und Qualität, sondern auch eine gezielte Anpassung an dynamische Marktanforderungen. Im folgenden Abschnitt werden die grundlegenden Konzepte von Industrie 4.0 und deren Anwendung auf das Formpressen untersucht.
2. Industrie 4.0 und die Prinzipien des Smart Manufacturing
Industrie 4.0 basiert auf der Einführung digitaler und vernetzter Systeme in die Produktion. Die zentralen Prinzipien, die die Basis für Industrie 4.0 und Smart Manufacturing bilden, sind:
- Vernetzung: Maschinen, Werkzeuge und Sensoren sind über das Internet der Dinge (IoT) miteinander verbunden und kommunizieren in Echtzeit.
- Datenanalyse und Big Data: Durch die kontinuierliche Erfassung und Auswertung von Prozess- und Produktionsdaten entstehen wertvolle Informationen für die Prozesssteuerung.
- Automatisierung und intelligente Steuerung: Autonome Systeme und künstliche Intelligenz optimieren die Produktionsprozesse und passen sich flexibel an Veränderungen an.
- Dezentrale Entscheidungsfindung: Maschinen und Systeme können Entscheidungen selbstständig treffen, was den Produktionsprozess dynamischer und effizienter gestaltet.
Im Formpressen bieten diese Prinzipien die Möglichkeit, Prozesse effizienter und flexibler zu gestalten, Fehler frühzeitig zu erkennen und gezielt zu optimieren.
3. Das Internet der Dinge (IoT) im Formpressen
Das Internet der Dinge (IoT) ist ein zentraler Bestandteil von Industrie 4.0 und ermöglicht eine Vernetzung von Maschinen und Sensoren, die in Echtzeit Daten erfassen und miteinander kommunizieren. Im Formpressen führt das IoT zur Entwicklung intelligenter Produktionslinien, in denen Maschinen Informationen austauschen und den Prozess autonom steuern.
3.1 Vernetzte Maschinen und Produktionsanlagen
Vernetzte Maschinen können Informationen wie Druck, Temperatur, Position und Zykluszeit erfassen und analysieren. Durch die Verbindung der Maschinen über das IoT entsteht eine durchgängige Transparenz im Formpressprozess.
- Transparenz und Kontrolle: Durch die Echtzeitüberwachung und Datenverarbeitung entsteht eine detaillierte Übersicht über den Produktionsstatus.
- Prozessoptimierung: Vernetzte Maschinen können sich gegenseitig „informieren“, wenn es zu Abweichungen kommt, und so den Produktionsprozess anpassen.
3.2 Datenerfassung und Echtzeit-Analyse
IoT-gestützte Formpresssysteme ermöglichen die Erfassung und Auswertung großer Mengen an Produktionsdaten, was für die Optimierung des Produktionsprozesses unerlässlich ist. Echtzeit-Analysen helfen, Ineffizienzen zu erkennen und den Betrieb kontinuierlich anzupassen.
- Datenbasierte Entscheidungsfindung: Echtzeitdaten liefern Informationen zur Optimierung der Produktionsparameter.
- Reduzierung von Stillstandszeiten: Durch die Überwachung des Maschinenzustands können Anomalien erkannt und proaktiv behoben werden.
4. Big Data und datengetriebene Prozessoptimierung im Formpressen
Durch die Digitalisierung im Formpressen entstehen große Datenmengen, die als Big Data bezeichnet werden. Diese Daten liefern detaillierte Einblicke in den gesamten Produktionsprozess und sind die Grundlage für datengetriebene Entscheidungen.
4.1 Sammlung und Analyse von Produktionsdaten
Big Data ermöglicht eine tiefgehende Analyse der Produktionsprozesse. Im Formpressen können Daten über Druck, Temperatur, Zykluszeiten und andere Parameter gesammelt werden, um ineffiziente Prozesse zu erkennen und Optimierungen vorzunehmen.
- Trendanalysen: Historische Daten können zur Vorhersage von Produktionsmustern verwendet werden, was zu einer besseren Planbarkeit und Effizienz führt.
- Qualitätsmanagement: Durch die Auswertung von Qualitätsdaten lassen sich Ursachen von Abweichungen identifizieren und beheben.
4.2 Predictive Analytics und vorausschauende Wartung
Predictive Analytics nutzt historische Daten und maschinelles Lernen, um künftige Ereignisse vorherzusagen. Die vorausschauende Wartung ist ein herausragendes Beispiel für Predictive Analytics, das die Wartungsintervalle an den tatsächlichen Zustand der Maschinen anpasst.
- Wartungsplanung: Predictive Maintenance reduziert ungeplante Stillstände und verbessert die Maschinenverfügbarkeit.
- Kosteneinsparung: Durch die Verlängerung der Lebensdauer von Maschinen und weniger Ausfällen können Wartungskosten reduziert werden.
5. Künstliche Intelligenz und Maschinelles Lernen zur Prozessoptimierung
Künstliche Intelligenz (KI) und Maschinelles Lernen sind Schlüsseltechnologien in der Industrie 4.0, die es ermöglichen, Prozesse datenbasiert zu steuern und kontinuierlich zu verbessern. Im Formpressen helfen KI-Systeme, die Produktionsparameter in Echtzeit anzupassen und die Qualitätssicherung zu optimieren.
5.1 Anomalieerkennung und Qualitätskontrolle durch KI
KI-gestützte Systeme analysieren die Produktionsparameter und können Abweichungen, die auf Probleme hinweisen, in Echtzeit erkennen. Die Anomalieerkennung verbessert die Effizienz und reduziert Fehlerquoten.
- Früherkennung von Abweichungen: KI identifiziert Muster, die auf Probleme im Formpressprozess hindeuten, und gibt frühzeitig Warnungen.
- Automatisierte Qualitätskontrolle: KI-Systeme analysieren in Echtzeit Qualitätsdaten und ermöglichen die sofortige Anpassung der Parameter bei Abweichungen.
5.2 Selbstlernende und selbstoptimierende Systeme
Selbstlernende Systeme sind in der Lage, den Formpressprozess basierend auf Produktionsdaten eigenständig zu optimieren. Maschinelles Lernen nutzt die Datenanalyse, um die Maschinenparameter zu verbessern und die Effizienz des Prozesses zu steigern.
- Optimierung der Produktionsparameter: KI-basierte Systeme lernen kontinuierlich und passen die Produktionsparameter an, um die Effizienz zu maximieren.
- Anpassungsfähigkeit: Selbstoptimierende Systeme ermöglichen eine flexible Anpassung an Veränderungen im Produktionsablauf.
6. Simulation und digitale Zwillinge im Formpressen
Digitale Zwillinge und Simulationstechnologien sind wichtige Werkzeuge im Rahmen von Industrie 4.0. Ein Digitaler Zwilling ist ein virtuelles Abbild der realen Maschine, das alle Parameter und Prozesse in Echtzeit nachbildet und die Möglichkeit zur Simulation von Prozessänderungen bietet.
6.1 Prozesssimulation und Optimierung
Mit digitalen Zwillingen lassen sich Änderungen im Formpressprozess simulieren und deren Auswirkungen auf die Produktion testen, bevor sie in der Realität umgesetzt werden. Dies minimiert das Risiko und ermöglicht eine schnelle Optimierung.
- Simulation von Szenarien: Digitale Zwillinge ermöglichen die Modellierung verschiedener Produktionsszenarien und die Bewertung ihrer Auswirkungen.
- Optimierung ohne Unterbrechung: Änderungen können zunächst virtuell getestet werden, bevor sie in der realen Produktionslinie umgesetzt werden.
6.2 Monitoring und Fehlererkennung in Echtzeit
Durch die Synchronisation des digitalen Zwillings mit der realen Maschine können Fehler in Echtzeit identifiziert werden. Abweichungen zwischen dem virtuellen Modell und der realen Maschine deuten auf potenzielle Probleme hin und ermöglichen eine proaktive Fehlerbehebung.
- Früherkennung von Problemen: Der digitale Zwilling erkennt Abweichungen im Betrieb und meldet Probleme, bevor sie zu Ausfällen führen.
- Rückverfolgbarkeit: Alle Produktionsschritte sind dokumentiert und können bei Bedarf genau nachvollzogen werden.
7. Vorteile von Industrie 4.0 und Smart Manufacturing im Formpressen
Die Implementierung von Industrie-4.0-Prinzipien und Smart Manufacturing bietet zahlreiche Vorteile für das Formpressen:
7.1 Effizienzsteigerung und Flexibilität
Vernetzte Systeme und Automatisierungstechnologien ermöglichen eine höhere Produktivität und Flexibilität in der Produktion. Unternehmen können schneller auf Veränderungen im Markt reagieren und ihre Produktionskapazitäten flexibel anpassen.
- Flexible Produktion: Maschinen und Anlagen lassen sich schnell auf neue Produkte oder Materialien einstellen.
- Effizientere Abläufe: Automatisierte Prozesse und Echtzeitdatenoptimierung erhöhen die Produktionsgeschwindigkeit.
7.2 Verbesserte Produktqualität und Fehlerreduktion
Durch die kontinuierliche Überwachung und Anpassung der Produktionsparameter lässt sich die Produktqualität erhöhen und die Fehlerquote minimieren. Industrie 4.0 schafft somit eine Grundlage für eine konstant hohe Qualität in der Fertigung.
- Echtzeit-Qualitätsüberwachung: Sensoren und KI erkennen Abweichungen frühzeitig und passen die Prozesse automatisch an.
- Reduktion von Ausschuss: Die präzise Steuerung reduziert den Materialverlust und senkt die Kosten.
7.3 Kosteneinsparung und Ressourcenschonung
Smart Manufacturing trägt zu einer nachhaltigen Produktion bei, da weniger Material verschwendet wird und die Maschinen effizienter genutzt werden. Predictive Maintenance reduziert außerdem die Wartungskosten.
- Kosteneffizienz durch weniger Ausschuss: Geringere Ausschussquoten und weniger Nacharbeit führen zu einer Reduktion der Produktionskosten.
- Ressourcenschonung: Der optimierte Materialverbrauch und die Reduzierung von Energieverschwendung tragen zu einer nachhaltigeren Produktion bei.
7.4 Erhöhung der Arbeitssicherheit
Automatisierte Systeme und smarte Technologien übernehmen Aufgaben, die für den Menschen potenziell gefährlich oder gesundheitsschädlich sein könnten, und verbessern so die Arbeitsbedingungen.
- Reduzierung von Gefährdungen: Roboter und automatisierte Systeme übernehmen schwere und gefährliche Arbeiten.
- Ergonomische Entlastung: Mitarbeitende werden von körperlich belastenden Aufgaben entlastet und können sich auf anspruchsvollere Tätigkeiten konzentrieren.
8. Herausforderungen bei der Implementierung von Industrie 4.0 im Formpressen
Obwohl die Vorteile von Industrie 4.0 und Smart Manufacturing vielversprechend sind, gibt es auch Herausforderungen:
- Hohe Implementierungskosten: Die Einführung von digitalen Systemen und Sensoren ist teuer und erfordert oft große Anfangsinvestitionen.
- Datenschutz und Sicherheit: Die zunehmende Vernetzung erhöht die Gefahr von Cyberangriffen, sodass Maßnahmen zur Datensicherung unabdingbar sind.
- Schulung und Fachkräftemangel: Die Bedienung und Wartung komplexer digitaler Systeme erfordert Fachwissen und regelmäßige Schulungen des Personals.
9. Zukunftsaussichten und Fazit
Die Zukunft des Formpressens im Kontext von Industrie 4.0 verspricht erhebliche Effizienzgewinne, eine gesteigerte Flexibilität und eine verbesserte Produktqualität. Die Kombination aus IoT, Big Data, KI und digitalen Zwillingen schafft eine innovative Produktionsumgebung, die für die Anforderungen der modernen Industrie ideal geeignet ist. Unternehmen, die diese Technologien erfolgreich implementieren, werden langfristig von niedrigeren Produktionskosten, besserer Produktqualität und höherer Anpassungsfähigkeit profitieren.
Industrie 4.0 und Smart Manufacturing werden die Wettbewerbsfähigkeit von Unternehmen in einer globalisierten Wirtschaft stärken und das Formpressen zu einer nachhaltigen und zukunftsfähigen Fertigungstechnologie entwickeln.
Herausforderungen und Lösungsansätze bei der Automatisierung des Formpressens
1. Einleitung
Die Automatisierung des Formpressens bietet zahlreiche Vorteile, wie Effizienzsteigerung, Qualitätsverbesserung und Kosteneinsparungen. Doch der Weg zur vollautomatisierten Produktion ist komplex und bringt einige Herausforderungen mit sich. Zu den wichtigsten Schwierigkeiten gehören hohe Implementierungskosten, die Integration moderner Technologien, der Bedarf an qualifizierten Fachkräften und die Sicherstellung von Datenschutz und Datensicherheit. In diesem Abschnitt werden die zentralen Herausforderungen bei der Automatisierung des Formpressens beleuchtet und geeignete Lösungsansätze vorgestellt, die Unternehmen dabei unterstützen, die Vorteile der Automatisierung zu nutzen.
2. Herausforderung 1: Hohe Implementierungskosten
Die Automatisierung im Formpressen erfordert erhebliche Investitionen in Maschinen, Roboter, Sensorik, Software und Infrastruktur. Insbesondere für kleine und mittlere Unternehmen (KMUs) können diese hohen Implementierungskosten eine große Hürde darstellen. Auch die laufenden Wartungs- und Modernisierungskosten sind nicht zu vernachlässigen.
Lösungsansätze
- Schrittweise Automatisierung: Unternehmen können die Automatisierung schrittweise einführen, anstatt gleich eine vollständig automatisierte Produktionslinie zu installieren. Dies senkt die Investitionskosten und ermöglicht es, Erfahrungen mit der neuen Technologie zu sammeln.
- Nutzung von Förderprogrammen und Finanzierungsmöglichkeiten: Viele Länder bieten Förderprogramme und Finanzierungshilfen für die Einführung von Industrie-4.0-Technologien an. Durch die Nutzung solcher Programme können Unternehmen die finanziellen Belastungen senken und schneller auf neue Technologien zugreifen.
- Leasing-Modelle und Mietlösungen: Hersteller von Automatisierungstechnik bieten zunehmend Leasing-Modelle an, die es Unternehmen ermöglichen, die Kosten auf mehrere Jahre zu verteilen. Diese Flexibilität senkt die finanzielle Hürde für die Implementierung von Automatisierungslösungen.
3. Herausforderung 2: Technische Komplexität und Integration in bestehende Systeme
Die Integration von Automatisierungstechnologien in bestehende Produktionssysteme ist oft schwierig, insbesondere in älteren Anlagen, die nicht für eine nahtlose Kommunikation mit modernen Steuerungssystemen ausgelegt sind. Die Kompatibilität zwischen neuen und alten Technologien und die Anpassung an spezifische Produktionsanforderungen erfordern fundiertes Fachwissen.
Lösungsansätze
- Modularisierte Systeme: Modulare Automatisierungssysteme sind flexibler und lassen sich leichter in bestehende Anlagen integrieren. Unternehmen können spezifische Module nach Bedarf austauschen oder hinzufügen, ohne das gesamte System umzubauen.
- Interoperabilität durch offene Standards: Die Einführung von offenen Kommunikationsstandards wie OPC UA (Open Platform Communications Unified Architecture) erleichtert die Integration unterschiedlicher Systeme und ermöglicht eine reibungslose Datenübertragung.
- Digitale Zwillinge zur Testphase: Mithilfe digitaler Zwillinge können Unternehmen die Integration neuer Komponenten zunächst virtuell testen. So lassen sich Probleme bereits vor der Implementierung identifizieren und beheben.
4. Herausforderung 3: Wartungs- und Instandhaltungsaufwand
Automatisierte Systeme benötigen regelmäßige Wartung und Instandhaltung, um ihre Leistungsfähigkeit und Präzision sicherzustellen. Dies erfordert zusätzliche Ressourcen und führt bei Ausfällen zu hohen Kosten durch Stillstandzeiten. Bei vernetzten Systemen, wie sie in der Industrie 4.0 üblich sind, ist die Wartung noch komplexer, da viele Systeme miteinander interagieren.
Lösungsansätze
- Predictive Maintenance (Vorausschauende Wartung): Predictive Maintenance nutzt Sensorik und Datenanalyse, um den Zustand der Maschinen in Echtzeit zu überwachen. Wartungen können so vorausschauend geplant werden, bevor es zu einem Ausfall kommt, was Stillstandzeiten reduziert und die Lebensdauer der Maschinen verlängert.
- Automatisierte Instandhaltungssysteme: Systeme mit integrierter Selbstüberwachung und automatischer Kalibrierung können Probleme selbstständig erkennen und die Maschinenparameter anpassen, um Abweichungen zu korrigieren.
- Externe Wartungsverträge und Support: Viele Unternehmen schließen Wartungsverträge mit Anbietern ab, die den regelmäßigen Support und die technische Betreuung übernehmen. Dies spart interne Ressourcen und gewährleistet eine professionelle Wartung.
5. Herausforderung 4: Bedarf an qualifiziertem Fachpersonal
Die Bedienung und Wartung automatisierter Systeme im Formpressen erfordert spezifisches Wissen und Fachkenntnisse. Der Fachkräftemangel, insbesondere im Bereich der Automatisierungstechnik und der IT, erschwert jedoch die Einstellung von qualifiziertem Personal. Die Digitalisierung und der Einsatz von Künstlicher Intelligenz erhöhen die Anforderungen an die Qualifikationen der Mitarbeiter weiter.
Lösungsansätze
- Schulungs- und Weiterbildungsprogramme: Unternehmen können eigene Weiterbildungsprogramme für ihre Mitarbeiter entwickeln oder Schulungsangebote nutzen, um die Mitarbeiter mit den neuen Technologien und Systemen vertraut zu machen.
- Zusammenarbeit mit Bildungseinrichtungen: Durch Kooperationen mit Universitäten, technischen Hochschulen und Ausbildungsstätten können Unternehmen Zugang zu qualifiziertem Nachwuchs gewinnen und die Ausbildung praxisnah gestalten.
- Einsatz benutzerfreundlicher Technologien: Die Entwicklung von benutzerfreundlichen Interfaces und intuitiver Steuerungssoftware erleichtert die Bedienung und reduziert die Abhängigkeit von hochqualifizierten Fachkräften.
6. Herausforderung 5: Datensicherheit und Datenschutz
Die zunehmende Vernetzung von Maschinen und die Erfassung großer Mengen an Produktionsdaten machen den Schutz vor Cyberangriffen und den Umgang mit sensiblen Daten zu einer der größten Herausforderungen in der automatisierten Fertigung. Datenlecks und Hackerangriffe können schwere Schäden verursachen, sowohl finanziell als auch für das Firmenimage.
Lösungsansätze
- Mehrstufige Sicherheitsstrategien: Die Implementierung einer mehrstufigen Sicherheitsarchitektur mit Firewalls, Verschlüsselung und Zugriffskontrollen erhöht die Sicherheit der Systeme.
- Sicherheits-Updates und kontinuierliche Überwachung: Regelmäßige Sicherheits-Updates und die Überwachung des Netzwerkverkehrs helfen, Schwachstellen frühzeitig zu erkennen und zu beheben.
- Schulung der Mitarbeiter im Bereich IT-Sicherheit: Durch die Sensibilisierung der Mitarbeiter für IT-Sicherheitsrichtlinien und Cyberrisiken lassen sich potenzielle Bedrohungen minimieren.
7. Herausforderung 6: Qualitätskontrolle und Fehlererkennung in Echtzeit
Die automatisierte Qualitätskontrolle stellt im Formpressen eine besondere Herausforderung dar, da viele Fehler (z. B. Materialfehler oder Oberflächenunregelmäßigkeiten) nur schwer zu erkennen sind. Die Integration von Echtzeit-Qualitätskontrollen erfordert fortschrittliche Sensorik und Bildverarbeitung, die zuverlässig und genau arbeiten.
Lösungsansätze
- Einsatz von KI für die Fehlererkennung: Künstliche Intelligenz (KI) und maschinelles Lernen können zur Erkennung von Fehlern eingesetzt werden, indem sie Produktionsdaten analysieren und Unregelmäßigkeiten selbstständig erkennen.
- Visuelle Inspektionssysteme: Kamerasysteme und optische Sensoren, die mit Algorithmen zur Bildverarbeitung ausgestattet sind, ermöglichen eine kontinuierliche Überwachung und Erkennung von Oberflächenfehlern.
- Echtzeit-Datenanalyse: Die Daten aus den Qualitätskontrollsystemen werden in Echtzeit analysiert und zur Prozessanpassung genutzt, um sicherzustellen, dass die Qualitätsstandards eingehalten werden.
8. Herausforderung 7: Anpassungsfähigkeit und Flexibilität der Produktion
In der modernen Fertigung ist Flexibilität ein entscheidender Faktor, da Unternehmen schnell auf Änderungen in der Nachfrage reagieren müssen. Die Implementierung automatisierter Systeme kann die Anpassungsfähigkeit einschränken, da viele Anlagen speziell für bestimmte Produktionsprozesse ausgelegt sind.
Lösungsansätze
- Modulare Produktionssysteme: Durch den Einsatz modularer Produktionssysteme lassen sich einzelne Module je nach Bedarf austauschen oder erweitern. Dies ermöglicht eine flexible Anpassung an wechselnde Anforderungen.
- Digitale Zwillinge zur Simulation von Änderungen: Mithilfe digitaler Zwillinge können Unternehmen verschiedene Szenarien simulieren und so die Auswirkungen von Änderungen auf den Produktionsprozess im Voraus testen.
- Flexible Robotertechnologie und Cobots: Kollaborative Roboter (Cobots) können schnell auf neue Aufgaben programmiert werden und unterstützen die Produktion bei wechselnden Anforderungen, ohne dass umfassende Umbaumaßnahmen notwendig sind.
9. Herausforderung 8: Nachhaltigkeit und Ressourceneffizienz
Die Herstellung von Bauteilen im Formpressen kann ressourcenintensiv sein. Steigende Materialkosten und der Druck zur Reduzierung des ökologischen Fußabdrucks machen die effiziente Nutzung von Materialien und Energie zu einer wichtigen Herausforderung in der automatisierten Produktion.
Lösungsansätze
- Optimierung der Materialnutzung durch Präzisionssteuerung: Durch die präzise Steuerung des Materialeinsatzes und der Prozessparameter lassen sich Abfälle reduzieren und Materialien effizienter nutzen.
- Energieeffiziente Maschinen und Steuerungssysteme: Der Einsatz energieeffizienter Maschinen und intelligenter Steuerungssysteme senkt den Energieverbrauch und trägt zu einer nachhaltigen Produktion bei.
- Recycling und Wiederverwendung von Materialien: Die Integration von Recyclingprozessen für Abfallprodukte und die Wiederverwendung von Materialien verbessern die Ressourceneffizienz und senken die Produktionskosten.
10. Herausforderungen bei der Skalierung und zukünftige Entwicklungen
Die Skalierung automatisierter Prozesse und deren Anpassung an wachsende Anforderungen sind zentrale Herausforderungen für Unternehmen, die im Bereich Formpressen tätig sind. Industrie 4.0 bietet die Grundlage für die Weiterentwicklung der Automatisierung, jedoch bleiben hohe Anforderungen bestehen.
Lösungsansätze
- Schrittweise Skalierung mit Fokus auf Prozessoptimierung: Unternehmen können zunächst die Produktionsprozesse optimieren, bevor sie zur Skalierung übergehen. Dies sorgt für eine stabilere Basis, auf der die Produktion erweitert werden kann.
- Nutzung von Cloud-basierten Plattformen: Cloud-basierte Plattformen erleichtern die Speicherung und Analyse großer Datenmengen und unterstützen die Skalierung der Produktionskapazitäten.
- Förderung von F&E und Innovationsprogrammen: Forschung und Entwicklung (F&E) sowie Innovationsprogramme unterstützen Unternehmen dabei, neue Technologien und Lösungen zu entwickeln, die die Herausforderungen der Automatisierung überwinden.
Fazit
Die Automatisierung des Formpressens bietet enorme Potenziale für Effizienzsteigerungen, Qualitätsverbesserungen und Kostenersparnisse, bringt jedoch auch zahlreiche Herausforderungen mit sich. Durch gezielte Lösungen wie schrittweise Automatisierung, Predictive Maintenance, den Einsatz von modularen Systemen und die Implementierung modernster Sicherheitstechnologien können Unternehmen diese Herausforderungen erfolgreich meistern.
Die Zukunft der Automatisierung im Formpressen wird stark von der weiteren Entwicklung der Industrie 4.0 und dem Einsatz von Künstlicher Intelligenz und Big Data geprägt sein. Unternehmen, die die Chancen der Digitalisierung nutzen und sich frühzeitig auf diese neuen Technologien einstellen, werden langfristig von einer flexibleren, effizienteren und nachhaltigeren Produktion profitieren.
Metallbearbeitungsmaschinen
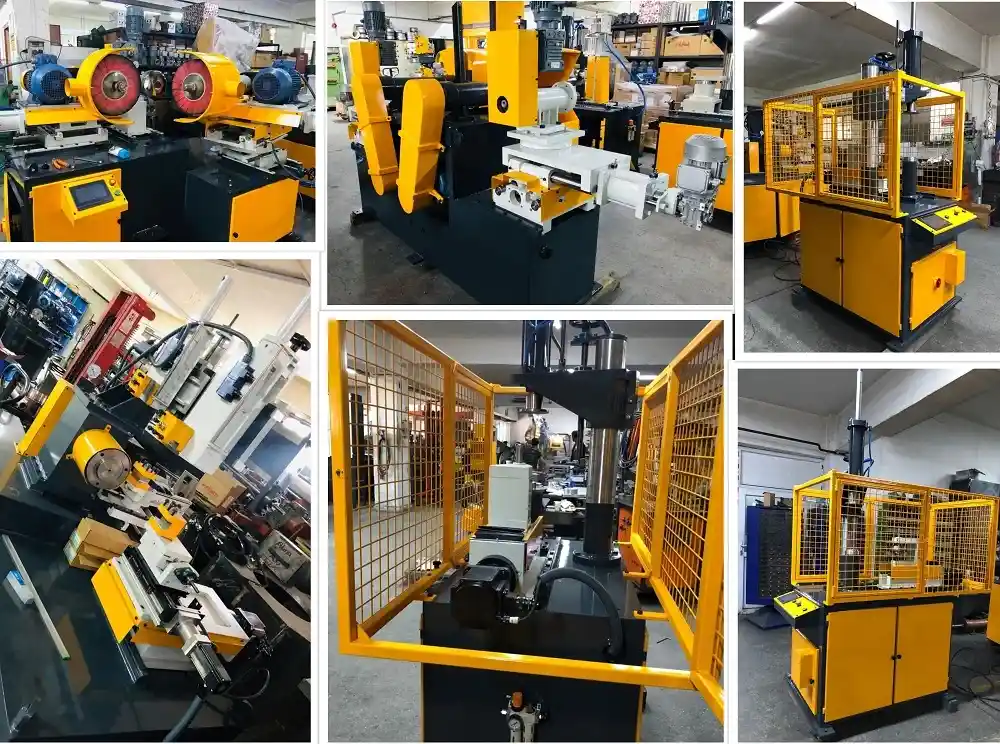
Metallbearbeitungsmaschinen wie Bördel und Beschneide Maschinen, Flanschmaschinen, Beschneide und Bördelmaschinen, Umformtechnik, Rohrbiegemaschinen, Bandsäge für Metall, Hydraulische Horizontalpresse, Kantenschneide-Bördelmaschine, Kantenbördelmaschine, Entgratungsmaschine, Innen- und Außenpoliermaschine für Edelstahltöpfe, Kreisschneidemaschine, Profilbiegemaschine und Rundschweißmaschine
Maßgeschneiderte Skalierung für spezifische Anwendungen
Die automatisierte Herstellung von Behältern, Fässern und Kesseln wird durch unsere Lösungen exakt auf das jeweilige Einsatzgebiet und die gewünschte Ausbringung angepasst. Dabei bieten wir sowohl lineare Lösungen als auch Inselkonzepte an, die eine bedarfsorientierte Automation ermöglichen. Spezielle Kantenvorbereitung für das Laserschweißen sowie wirtschaftliche Rüstkonzepte bis hin zur Fertigung „Just-in-Sequence“ sind Teil unseres Leistungsspektrums. Wir kombinieren Standard- und Sondermaschinen und bieten Ferndiagnose über LAN, WLAN oder GSM an, ergänzt durch umfassende Dokumentation gemäß CE-Richtlinien für die Gesamtanlage.
Unser Konzept
EMS entwickelt und fertigt Maschinen und Anlagen für die automatisierte Herstellung von Behältern in großem Maßstab. Alle Arbeitsschritte, von der Vorbereitung bis zur Fertigung, werden dabei aus einer Hand angeboten. Unsere erprobten Standardkomponenten sind perfekt aufeinander abgestimmt und können nahtlos mit Robotern kombiniert werden, um leistungsfähige Fertigungseinrichtungen zu schaffen.
Flexible Präzisionsfertigung
Unsere Fertigungslinien ermöglichen eine einfache Umstellung auf verschiedene Längen, Durchmesser, Formen und Bearbeitungen durch Programmwechsel. Dabei werden zahlreiche Einzelschritte wie Beschneiden, Formen, Stanzen, Fügen, Montieren, Schweißen und Prüfen automatisch und mit höchster Präzision an die jeweilige Aufgabe angepasst. Besonderes Augenmerk legen wir auf die Kantenvorbereitung für den Schweißprozess, um eine herausragende Prozesssicherheit und minimale Ausschussquoten zu gewährleisten.
Maschinenprogramm für die Metallbearbeitung
Unsere Metallbearbeitungsmaschinen sind:
- Rohrbiegemaschine
- Horizontale Presse
- Bandsäge für Metall
- Profilbiegemaschine
- Tiefziehpresse
- Rundschweißmaschine
- Kantenschneide-Bördelmaschine
- Topf- und Pfannenpoliermaschine
- Poliermaschine für flache Oberflächen
Besteck-Produktionslinie: Eine Besteck-Produktionslinie ist eine Art Maschine, die Besteck in einem kontinuierlichen Prozess herstellt. Es umfasst verschiedene Arten von Maschinen wie den Messerschleifer, den Messerschärfer und den Klingenpolierer.
Kochgeschirr-Herstellungsmaschine: Eine Kochgeschirr-Herstellungsmaschine ist eine Art Maschine, die Kochgeschirr in einem kontinuierlichen Prozess herstellt. Es umfasst verschiedene Arten von Maschinen wie den Topfmacher, den Pfannenmacher und den Wokmacher.
Küchengeschirr-Produktionsmaschine: Eine Küchengeschirr-Produktionsmaschine ist eine Art Maschine, die Küchengeschirr in einem kontinuierlichen Prozess herstellt. Es umfasst verschiedene Arten von Maschinen wie Maschinen zur Herstellung von Teekesseln, Produktionslinien für Besteck, Produktionslinien für Töpfe und Pfannen
Wir entwerfen, fertigen und montieren komplette Produktionslinien für Kochgeschirr, Küchengeschirr, Hotelgeschirr und Besteck sowie einzelne Maschinen für einen bestimmten Zweck