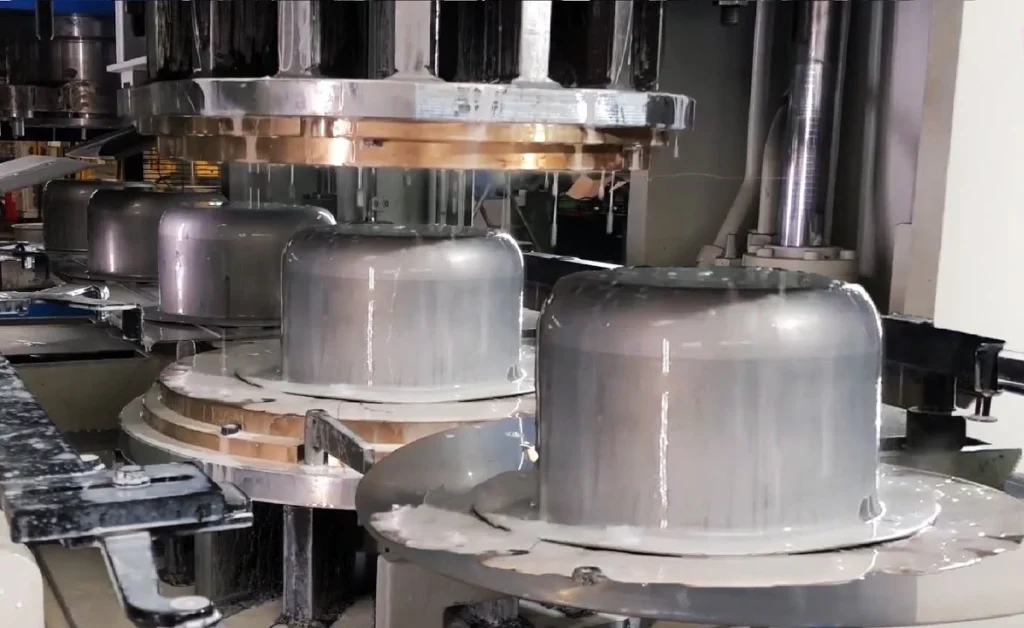
Tiefziehtechnik, Tiefziehen, Tiefziehverfahren, Tiefziehmaschinen, Tiefziehprozess in Metallbearbeitung und Fertigung “Tiefziehen” ist ein Begriff aus dem Bereich der Umformtechnik und bezeichnet ein spezielles Verfahren zum Umformen von Blechen oder Metallfolien. Dabei wird ein flaches Blech durch ein Werkzeug in eine tiefere, meist zylindrische oder komplexe Form gezogen, ohne dass das Material reißt oder bricht.
Was ist Tiefziehen?
- Definition: Tiefziehen ist ein Kaltumformverfahren, bei dem ein Blech durch eine Matrize und einen Stempel so verformt wird, dass eine tiefere Form (z.B. Becher, Dosen, Gehäuse) entsteht.
- Ziel: Die Herstellung von Hohlkörpern oder tiefen Formteilen aus flachen Blechen.
- Werkstoffe: Meist werden dünne Metallbleche aus Aluminium, Stahl, Edelstahl oder Kupfer verwendet.
Ablauf des Tiefziehprozesses
- Blechvorbereitung: Das flache Blech wird passend zugeschnitten.
- Einlegen: Das Blech wird in die Matrize gelegt.
- Stempelbewegung: Der Stempel drückt das Blech in die Matrize hinein.
- Verformung: Das Blech wird tiefgezogen, also plastisch verformt, um die gewünschte Form anzunehmen.
- Auswerfen: Das fertige Teil wird aus der Form entfernt.
Anwendungen
- Herstellung von Getränkedosen
- Auto-Karosserieteilen
- Haushaltsgegenständen (z.B. Waschbecken)
- Elektronische Gehäuse
Tiefziehen ist ein Kaltumformverfahren, bei dem ein flaches Metallblech durch den Einfluss eines Stempels in eine tiefere, dreidimensionale Form gebracht wird, ohne dass das Material reißt. Dabei wird das Blech in eine Matrize gedrückt und passt sich der Kontur der Form an. Das Verfahren ist besonders geeignet für die Herstellung von Hohlkörpern wie Dosen, Bechern oder Gehäusen aus dünnem Blech.
Während des Tiefziehens erfährt das Material eine plastische Verformung, bei der die Länge des Blechs zunimmt und die Wandstärke an manchen Stellen abnehmen kann. Dabei muss die Materialdehnung kontrolliert werden, um das Risiko von Rissen oder Falten zu minimieren. Die Eigenschaften des Materials, die Schmierung sowie die Werkzeuggeometrie spielen eine wichtige Rolle für die Qualität des Endprodukts.
Die Prozessparameter wie Ziehtiefe, Ziehgeschwindigkeit und die Kraft, die auf das Blech wirkt, müssen genau abgestimmt werden, um eine gleichmäßige Verformung zu gewährleisten. Zu den Herausforderungen zählen das Vermeiden von Faltenbildung, besonders an den Flanschen, sowie das Sicherstellen einer homogenen Wandstärke. Spezielle Maschinen und Werkzeuge sorgen dafür, dass das Blech während des Ziehens gespannt und geführt wird.
Tiefziehen ist wirtschaftlich besonders für Serienfertigungen, da die Werkzeugkosten durch hohe Stückzahlen amortisiert werden können. Das Verfahren findet breite Anwendung in der Automobilindustrie, im Haushalt sowie in der Verpackungsindustrie, etwa bei Getränkedosen oder Konservendosen. Varianten des Tiefziehens, wie das Tiefziehen mit Rückstreckung oder das Tiefziehen mit mehreren Ziehschritten, ermöglichen komplexere Formen und höhere Ziehtiefen.
Insgesamt ist Tiefziehen ein äußerst vielseitiges Umformverfahren, das es erlaubt, dünnwandige Hohlkörper mit hoher Maßgenauigkeit und guter Oberflächenqualität effizient herzustellen.
Beim Tiefziehen wird das Blech durch plastische Verformung in die Form der Matrize gedrückt, wobei das Material hauptsächlich in Richtung der Ziehrichtung fließt. Dabei entstehen Zug- und Druckspannungen, die das Verhalten des Materials stark beeinflussen. Die Wandstärke des Blechs kann sich während des Prozesses verändern: In den Zugzonen wird das Material dünner, während es an anderen Stellen, wie z.B. am Boden der Form, dicker bleiben kann. Eine gleichmäßige Wanddicke ist deshalb eine wichtige Qualitätsanforderung.
Um Faltenbildung zu verhindern, wird häufig eine Spannvorrichtung eingesetzt, die das Blech vor dem Stempel unterstützt und kontrolliert spannt. Die Schmierung zwischen Stempel, Blech und Matrize ist ebenfalls entscheidend, da sie die Reibung reduziert und somit das Materialschneiden und Einreißen minimiert.
Beim Tiefziehen mit mehreren Schritten wird das Werkstück in mehreren aufeinanderfolgenden Zügen immer tiefer in die Form gebracht. Das erlaubt die Herstellung von sehr tiefen oder komplexen Formen, die mit einem einzigen Zug nicht möglich wären.
Ein weiteres wichtiges Thema ist das Rückfedern des Materials nach dem Ziehen, das heißt, dass das Blech sich nach Entlastung der Werkzeuge teilweise wieder in seine ursprüngliche Form zurückbewegt. Das wird bei der Werkzeugauslegung berücksichtigt, indem die Matrize entsprechend geformt wird, um die endgültige gewünschte Form zu erhalten.
Moderne Verfahren nutzen numerische Simulationen, um den Tiefziehprozess virtuell zu optimieren und Probleme wie Risse oder Falten frühzeitig zu erkennen. So können Werkzeuggeometrie, Materialeigenschaften und Prozessparameter effizient angepasst werden, um Ausschuss zu minimieren.
Insgesamt ist das Tiefziehen eine bewährte Technik zur Herstellung dünnwandiger, präziser und komplexer Metallteile, die in vielen Industrien unverzichtbar ist.
Ein wichtiger Aspekt beim Tiefziehen ist die Auswahl des richtigen Materials. Typischerweise kommen duktil ausgelegte Metalle zum Einsatz, die sich gut plastisch verformen lassen, wie tiefziehgeeigneter Stahl, Aluminium oder Kupfer. Die Materialeigenschaften wie Dehngrenze, Streckverhalten und Kaltverfestigung beeinflussen maßgeblich, wie tief ein Blech gezogen werden kann, ohne zu reißen. Für besonders anspruchsvolle Anwendungen werden auch Verbundwerkstoffe oder beschichtete Bleche verwendet, die zusätzliche Anforderungen erfüllen, etwa Korrosionsbeständigkeit oder elektrische Leitfähigkeit.
Der Prozess wird durch verschiedene Werkzeuge gesteuert: Der Stempel drückt das Blech in die Matrize, welche die Außenkontur vorgibt. Ein sogenannter Ziehring oder Halteband übt kontrollierten Gegendruck aus und verhindert, dass das Blech an den Flanschen übermäßig faltet oder rutscht. Die richtige Abstimmung dieser Werkzeuge ist entscheidend, um eine gleichmäßige Materialverteilung zu erzielen und Fehler zu vermeiden.
Neben dem klassischen Tiefziehen existieren auch spezialisierte Verfahren wie das Hydro-Tiefziehen, bei dem statt eines Stempels eine Flüssigkeit den Umformdruck auf das Blech überträgt. Dieses Verfahren erlaubt besonders komplexe Formen und schonendere Umformbedingungen, was das Risiko von Rissen weiter verringert.
Im Bereich der Qualitätskontrolle werden heute häufig optische Messsysteme und 3D-Scans eingesetzt, um Maßhaltigkeit und Oberflächenqualität der tiefgezogenen Bauteile zu überprüfen. Auch zerstörungsfreie Prüfverfahren helfen, innere Spannungen oder Materialfehler zu erkennen, die die Lebensdauer des Bauteils beeinflussen könnten.
Durch die Kombination aus optimierter Werkzeugtechnik, sorgfältiger Materialauswahl und digitaler Prozessüberwachung hat sich das Tiefziehen zu einem hochentwickelten und zuverlässigen Verfahren für die industrielle Serienfertigung entwickelt. Die stetige Weiterentwicklung der Verfahrenstechnik, insbesondere durch Simulation und Automatisierung, ermöglicht es, immer komplexere und dünnwandigere Bauteile mit hoher Präzision und Effizienz herzustellen.
Effiziente Tiefziehverfahren für die industrielle Produktion
Effiziente Tiefziehverfahren für die industrielle Produktion zeichnen sich durch eine optimale Kombination aus Prozessgeschwindigkeit, Materialausnutzung, Werkzeugstandzeit und Qualitätskontrolle aus. Um hohe Stückzahlen wirtschaftlich zu fertigen, werden mehrere Aspekte berücksichtigt:
Zum einen spielt die Werkzeuggestaltung eine zentrale Rolle. Werkzeuge mit optimaler Geometrie minimieren Reibung und Materialspannung, wodurch Ausschuss und Werkzeugverschleiß reduziert werden. Moderne CNC- und EDM-Fertigung ermöglichen präzise und komplexe Werkzeuggeometrien, die den Umformprozess stabilisieren.
Automatisierung ist ein weiterer Schlüssel zur Effizienzsteigerung. Robotergestützte Be- und Entladung der Pressen, automatische Werkzeugwechsel und inline Qualitätsprüfungen verkürzen Rüstzeiten und sorgen für gleichbleibende Prozessbedingungen. Dies ist besonders wichtig bei Großserienfertigungen, um Taktzeiten zu senken und Stillstandszeiten zu vermeiden.
Die Verwendung von hochentwickelten Schmierstoffen verbessert die Fließeigenschaften des Materials und verringert Verschleiß an Werkzeugen. Zudem helfen computergestützte Simulationen (Finite-Elemente-Analyse) dabei, die Prozessparameter wie Ziehgeschwindigkeit, Haltekraft und Schmiermittelart optimal einzustellen, was Ausschuss weiter reduziert und Nacharbeit minimiert.
Mehrstufige Tiefziehprozesse erlauben die Herstellung von sehr komplexen und tiefen Bauteilen durch sukzessive Umformschritte, wodurch das Risiko von Rissen und Faltenbildung sinkt. Dabei kommen auch Zwischenoperationen wie Rückstrecken oder Glätten zum Einsatz, um die Werkstückqualität zu verbessern.
Zusätzlich wird zunehmend das Hydro-Tiefziehen eingesetzt, das durch den Einsatz von Flüssigkeitsdruck eine gleichmäßigere Umformung ermöglicht und somit dünnere Wandstärken und komplexere Formen zulässt. Dies führt zu Materialeinsparungen und besserer Produktqualität.
Insgesamt entsteht durch die Kombination von optimierten Werkzeugen, digitaler Prozesssteuerung, Automatisierung und innovativen Verfahren ein effizientes Produktionssystem, das hohen Output bei geringer Ausschussrate gewährleistet und somit die Wirtschaftlichkeit des Tiefziehprozesses in der industriellen Fertigung maßgeblich verbessert.
Effiziente Tiefziehverfahren in der industriellen Produktion setzen auf eine enge Verzahnung von Prozessoptimierung und moderner Fertigungstechnologie. Dabei ist die Integration von Simulationstools ein wesentlicher Faktor, um vorab mögliche Probleme wie Faltenbildung, Risse oder Materialüberschüsse zu identifizieren und auszuschließen. Durch diese Vorhersage können Werkzeuge und Prozessparameter so ausgelegt werden, dass der Umformprozess von Anfang an stabil und reproduzierbar abläuft.
Die Auswahl des Materials und dessen Vorbereitung spielen ebenfalls eine wichtige Rolle. Hochwertige Bleche mit guter Kaltumformbarkeit ermöglichen größere Ziehtiefen und geringeren Ausschuss. Die Oberfläche der Bleche wird oft speziell behandelt oder beschichtet, um die Reibung im Ziehspalt zu reduzieren und eine bessere Fließfähigkeit zu gewährleisten.
Im Bereich der Automatisierung sorgt die Vernetzung von Maschinen und Sensoren für eine kontinuierliche Überwachung und Anpassung der Prozessgrößen. Sensoren messen Kräfte, Temperaturen und Materialverhalten in Echtzeit, sodass bei Abweichungen sofort Gegenmaßnahmen eingeleitet werden können. Dies erhöht nicht nur die Produktqualität, sondern auch die Maschinenverfügbarkeit.
Die Einführung von Mehrstufen-Tiefziehlinien, bei denen mehrere Umformschritte nahtlos aneinandergereiht sind, erlaubt eine hohe Produktivität bei gleichzeitig präzisen Ergebnissen. Zwischen den einzelnen Umformschritten können automatische Zwischenkontrollen und gegebenenfalls Korrekturmaßnahmen integriert werden. Das reduziert Nacharbeit und Ausschuss erheblich.
Durch den Einsatz von innovativen Schmierstoffen und Beschichtungen wird zudem der Verschleiß an Stempel und Matrize minimiert, was die Werkzeugstandzeit verlängert und Stillstandszeiten für Wartungen verringert. Ebenso werden umweltfreundliche und biologisch abbaubare Schmierstoffe zunehmend eingesetzt, um die Nachhaltigkeit der Fertigung zu erhöhen.
Insgesamt führt die Kombination aus modernem Werkzeugbau, digitaler Prozesskontrolle, Automatisierung und Materialinnovation zu effizienten Tiefziehverfahren, die sich durch hohe Stückzahlen, kurze Taktzeiten und hervorragende Produktqualität auszeichnen. Dies macht das Tiefziehen zu einem wirtschaftlichen und zugleich flexiblen Verfahren für die Massenproduktion komplexer Blechbauteile.
Darüber hinaus gewinnen datengetriebene Ansätze und Künstliche Intelligenz zunehmend an Bedeutung, um Tiefziehprozesse weiter zu optimieren. Durch das Sammeln und Analysieren großer Datenmengen aus Produktionslinien können Muster erkannt und Vorhersagen getroffen werden, etwa wann ein Werkzeug verschleißt oder welche Prozessparameter zu einer höheren Qualität führen. So lassen sich Wartungsintervalle besser planen und Ausschussquoten weiter senken.
Auch die Flexibilisierung der Produktion spielt eine wichtige Rolle, insbesondere bei steigenden Anforderungen an Variantenvielfalt und kleinere Losgrößen. Modulare Werkzeugsysteme, schnelle Werkzeugwechsel und adaptive Prozesssteuerungen ermöglichen es, effizient auf wechselnde Produktionsanforderungen zu reagieren, ohne dass die Produktivität stark leidet.
In der Forschung werden zudem neue Materialien und Verbundwerkstoffe getestet, die bessere Umformeigenschaften bei gleichzeitig reduziertem Gewicht bieten. Solche Entwicklungen sind besonders in Branchen wie der Automobil- oder Luftfahrtindustrie gefragt, wo Leichtbau eine Schlüsselrolle spielt.
Zusätzlich wird das Thema Nachhaltigkeit immer relevanter. Energieeffiziente Pressen, optimierte Prozessführung und Recyclingstrategien für Blechreste und Werkzeugmaterialien tragen dazu bei, den ökologischen Fußabdruck der Tiefziehfertigung zu verringern.
Die Zukunft effizienter Tiefziehverfahren liegt somit in der Kombination aus technologischer Innovation, digitaler Vernetzung und nachhaltigem Wirtschaften. Nur so lassen sich steigende Anforderungen an Qualität, Flexibilität und Umweltverträglichkeit in der industriellen Produktion erfolgreich erfüllen.
Ein weiterer Aspekt, der die Effizienz beim Tiefziehen steigert, ist die Integration von Echtzeit-Überwachungssystemen, die mit maschinellem Lernen arbeiten. Diese Systeme analysieren kontinuierlich Prozessdaten, erkennen Abweichungen frühzeitig und ermöglichen eine automatische Anpassung der Umformparameter. Dadurch werden Produktionsfehler minimiert und die Ausschussrate weiter reduziert.
Auch die Entwicklung neuer Werkzeugmaterialien und Beschichtungen trägt zur Effizienzsteigerung bei. Werkzeuge mit hoher Verschleißfestigkeit und guter Gleiteigenschaft verlängern die Standzeiten und senken die Wartungskosten. Dies führt zu weniger Stillstandzeiten und höherer Auslastung der Fertigungslinien.
Parallel dazu wird der Einsatz von additiven Fertigungsverfahren als Ergänzung zum Tiefziehen erforscht. So können komplexe Werkzeugkomponenten schneller und kostengünstiger hergestellt oder individualisierte Werkzeuge produziert werden, was insbesondere bei Kleinserien oder Prototypen Vorteile bringt.
Die Kombination aus präziser Prozesssteuerung, fortschrittlichen Materialien und digitaler Vernetzung ermöglicht es der Industrie, Tiefziehprozesse nicht nur effizienter, sondern auch flexibler und nachhaltiger zu gestalten. Das macht das Verfahren zukunftssicher und eröffnet neue Möglichkeiten für die Herstellung komplexer, hochwertiger Blechbauteile in großen Stückzahlen.
Darüber hinaus gewinnt die Kombination von Tiefziehen mit anderen Umform- oder Fertigungsverfahren an Bedeutung, um Funktionalitäten und Designfreiheiten zu erweitern. Beispielsweise werden Tiefziehteile zunehmend mit Schweiß-, Klebe- oder Fügeverfahren kombiniert, um komplexe Baugruppen in einem wirtschaftlichen Produktionsprozess zu realisieren. Auch das Integrieren von Funktionselementen durch Einlegen von Einsätzen vor dem Tiefziehen wird genutzt, um Montage- und Nachbearbeitungsschritte zu reduzieren.
Die Digitalisierung ermöglicht es, Prozesswissen systematisch zu erfassen und für kontinuierliche Verbesserungen zu nutzen. Digitale Zwillinge, also virtuelle Abbilder der realen Fertigungslinie, erlauben es, Umformprozesse in Echtzeit zu simulieren und zu optimieren. So können Produktionsänderungen schnell bewertet und umgesetzt werden, ohne die reale Fertigung zu unterbrechen.
Darüber hinaus wird das Thema Energieeffizienz in der industriellen Produktion immer wichtiger. Moderne Pressen verfügen über Energiesparfunktionen wie bedarfsgerechte Leistungssteuerung, Rekuperation oder intelligente Stillstandsmodi, die den Energieverbrauch erheblich senken. Gerade bei Großserienfertigungen summieren sich diese Einsparungen zu bedeutenden Kostenvorteilen.
Schließlich ist auch die Ausbildung und Qualifikation der Mitarbeiter ein entscheidender Faktor für die Effizienz. Gut geschulte Fachkräfte können Prozessparameter besser beurteilen, Fehler schneller erkennen und beheben sowie die Maschinen optimal bedienen. Die Kombination aus menschlichem Know-how und technologischer Unterstützung schafft so eine Produktionsumgebung, die höchste Qualität mit maximaler Produktivität verbindet.
Insgesamt bildet die Verzahnung von Technologie, Digitalisierung, Nachhaltigkeit und qualifiziertem Personal das Fundament für effiziente Tiefziehverfahren in der industriellen Produktion – heute und in der Zukunft.
Die Grundlagen des Tiefziehens in der Metallbearbeitung
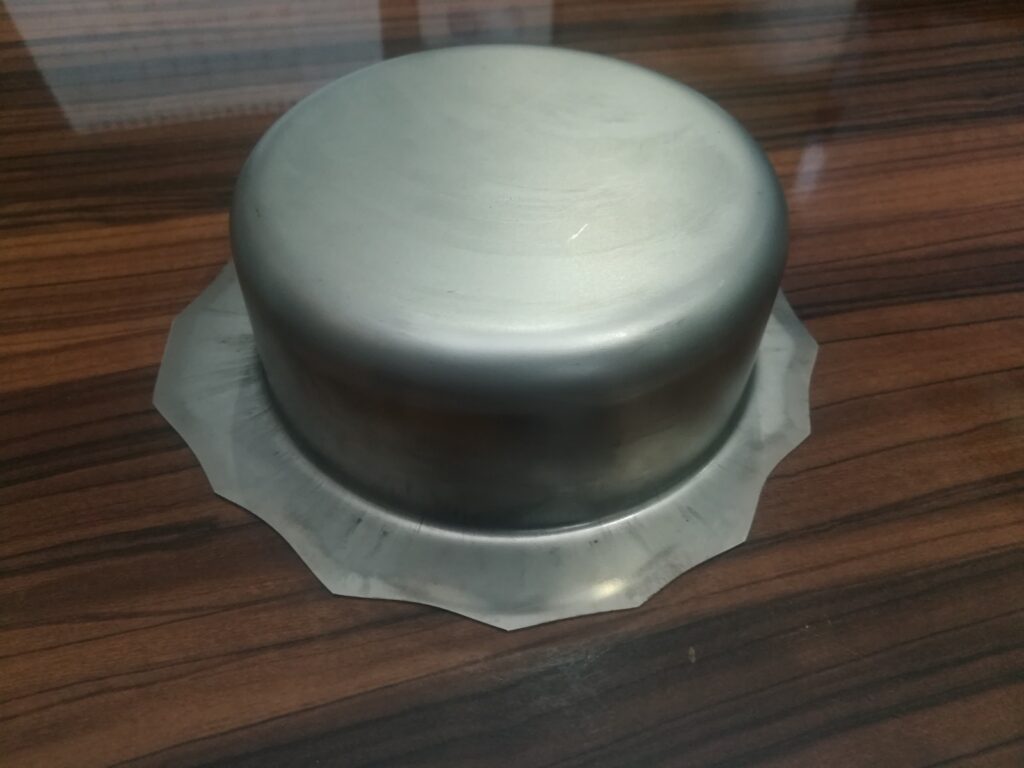
Das Tiefziehen ist ein zentrales Umformverfahren in der Metallbearbeitung, bei dem ein flaches Blech in eine dreidimensionale, meist hohlförmige Form gebracht wird. Dabei wird das Blech durch einen Stempel in eine Matrize gedrückt und dabei plastisch verformt, ohne dass das Material reißt oder bricht. Das Verfahren ermöglicht die Herstellung von komplexen Bauteilen mit dünnen Wänden und hoher Maßgenauigkeit.
Die Grundlagen des Tiefziehens beruhen auf der plastischen Verformung von Metallblechen unter Einwirkung von Zug- und Druckkräften. Während des Ziehvorgangs wird das Blech gedehnt und in die Tiefe gezogen, wobei sich die Wandstärke teilweise verringert. Damit der Prozess gelingt, müssen Materialeigenschaften wie Duktilität, Festigkeit und Kaltumformbarkeit optimal sein. Häufig eingesetzte Materialien sind tiefziehfähiger Stahl, Aluminium und Kupfer.
Wichtig für den Prozess sind die Werkzeuge: Der Stempel, der das Blech in die Matrize drückt, die Matrize selbst, welche die Außenkontur vorgibt, und der Ziehring, der das Blech vor dem Stempel festhält und ein Falten verhindert. Die richtige Abstimmung dieser Werkzeuge ist entscheidend, um eine gleichmäßige Umformung und Wanddickenverteilung zu erzielen.
Die Prozessparameter wie Ziehgeschwindigkeit, Haltekraft und Schmierung beeinflussen den Materialfluss und somit die Qualität des Bauteils. Schmiermittel reduzieren die Reibung und verhindern das Einreißen des Materials. Die Kontrolle von Spannung und Dehnung im Blech ist notwendig, um Fehler wie Faltenbildung oder Risse zu vermeiden.
Das Tiefziehen kann in einem oder mehreren Schritten erfolgen, wobei mehrstufige Verfahren besonders bei tiefen oder komplexen Formen eingesetzt werden. Nach dem Ziehen können weitere Bearbeitungsschritte wie Rückstrecken, Glätten oder Beschneiden folgen, um die gewünschte Form und Oberflächenqualität zu erreichen.
Insgesamt bietet das Tiefziehen eine wirtschaftliche Methode zur Herstellung von Hohlkörpern und komplexen Blechbauteilen mit hoher Präzision, die in vielen Branchen wie Automobilbau, Verpackung und Haushaltswaren unverzichtbar ist.
Das Tiefziehen basiert auf der plastischen Verformung des Metallblechs, bei der das Material über seine Elastizitätsgrenze hinaus gedehnt wird, ohne zu reißen. Dabei ist es wichtig, dass das Material eine ausreichende Duktilität besitzt, also eine hohe Verformungsfähigkeit ohne Bruch. Die Blechdicke spielt ebenfalls eine Rolle: Dünnere Bleche lassen sich leichter tiefziehen, sind aber anfälliger für Faltenbildung und Risse, weshalb der Prozess sorgfältig gesteuert werden muss.
Während des Ziehvorgangs wird das Blech durch den Stempel in die Matrize gedrückt, wobei sich das Material an der Wand der Matrize entlangzieht und in die Tiefe gedrückt wird. Der Ziehring oder Halteband übt dabei eine kontrollierte Haltekraft aus, um das Blech an den Rändern zu fixieren und ein Überschießen oder Falten des Materials zu verhindern. Die richtige Balance zwischen Zieh- und Haltekraft ist entscheidend, damit das Material gleichmäßig fließt und keine Defekte entstehen.
Die Schmierung zwischen Werkzeug und Blech ist ein weiterer wichtiger Faktor. Sie reduziert die Reibung, sorgt für einen gleichmäßigen Materialfluss und verhindert das Einreißen des Materials an scharfen Kanten. Je nach Werkstoff und Anwendung kommen unterschiedliche Schmierstoffe zum Einsatz, von öl- bis zu feststoffbasierten Varianten.
Tiefziehprozesse können ein- oder mehrstufig ausgeführt werden. Beim Mehrstufen-Tiefziehen wird das Blech in mehreren aufeinanderfolgenden Zügen schrittweise in die endgültige Form gebracht. Das ermöglicht größere Ziehtiefen und komplexere Geometrien, da die Belastung auf das Material besser verteilt wird. Nach dem Ziehen folgen oft Nachbearbeitungsschritte wie das Rückstrecken, um durch den Umformprozess entstandene Spannungen abzubauen und die Maßhaltigkeit zu verbessern.
Die genaue Steuerung der Prozessparameter ist essentiell, um eine hohe Qualität des Endprodukts zu gewährleisten. Moderne Fertigungen setzen deshalb auf computergestützte Simulationen und automatisierte Prozessüberwachung, die helfen, optimale Bedingungen zu ermitteln und Fehler frühzeitig zu erkennen.
Durch diese Grundlagen ermöglicht das Tiefziehen die Herstellung vielfältiger Bauteile mit hoher Präzision und Wirtschaftlichkeit, die in zahlreichen Industriezweigen von großer Bedeutung sind.
Neben den mechanischen Grundlagen des Tiefziehens spielt auch das Verständnis der Werkstoffeigenschaften eine zentrale Rolle. Materialien müssen nicht nur eine ausreichende Duktilität besitzen, sondern auch eine geeignete Fließkurve, die beschreibt, wie sie sich unter Belastung plastisch verformen. Dabei ist die sogenannte Kaltverfestigung zu berücksichtigen: Während des Ziehens verhärtet sich das Material lokal, was die weitere Verformung erschweren kann und zu Rissbildung führt, wenn die Belastung zu hoch wird.
Die Kontrolle der Materialdicke ist ebenfalls essentiell, denn zu starke Dickenreduktionen an bestimmten Stellen können die Stabilität des Bauteils beeinträchtigen. Um dies zu vermeiden, wird die Geometrie von Stempel und Matrize oft so gestaltet, dass das Material möglichst gleichmäßig verteilt wird.
Das Verhalten des Werkzeugs ist ein weiterer wichtiger Faktor: Werkzeugverschleiß, vor allem durch Abrieb und Mikro-Risse, beeinflusst die Oberflächenqualität der Bauteile und die Prozessstabilität. Deshalb werden Werkzeuge häufig aus verschleißfesten Materialien gefertigt und mit speziellen Beschichtungen versehen, die Reibung reduzieren und die Standzeit erhöhen.
Im industriellen Umfeld werden außerdem automatisierte Prüfverfahren eingesetzt, um Bauteile direkt nach dem Ziehen auf Maßhaltigkeit, Oberflächenfehler oder Materialunregelmäßigkeiten zu kontrollieren. Optische Systeme oder taktile Messgeräte erfassen präzise Daten, die für eine Qualitätskontrolle und Prozessoptimierung genutzt werden.
Weiterhin werden durch computergestützte Simulationen, beispielsweise mittels Finite-Elemente-Methoden, Tiefziehprozesse vorab digital abgebildet. Dies erlaubt es, verschiedene Werkstoff- und Werkzeugkonfigurationen zu testen, die optimalen Prozessparameter zu finden und Fehler wie Faltenbildung oder Rissbildung bereits vor der Produktion zu vermeiden.
Durch das Zusammenspiel all dieser Faktoren – Materialeigenschaften, Werkzeugtechnik, Prozesssteuerung und Qualitätssicherung – lässt sich das Tiefziehen als zuverlässiges und wirtschaftliches Verfahren in der Metallbearbeitung etablieren, das eine Vielzahl von Produkten mit komplexen Formen und hoher Präzision ermöglicht.
Ein weiterer wesentlicher Punkt bei den Grundlagen des Tiefziehens ist die Bedeutung der Prozessparameter für den Erfolg des Umformvorgangs. Die Ziehgeschwindigkeit beeinflusst sowohl die Materialflussgeschwindigkeit als auch die Temperaturentwicklung im Werkstück. Eine zu hohe Geschwindigkeit kann zu Rissbildung führen, während zu niedrige Geschwindigkeiten die Effizienz senken und Falten begünstigen können. Deshalb wird die Geschwindigkeit genau an das Material und die Werkzeugkonfiguration angepasst.
Die Haltekraft, die der Ziehring oder das Halteband auf das Blech ausübt, muss so eingestellt sein, dass sie das Material an den Flanschen stabilisiert, ohne es zu stark zu quetschen. Zu geringe Haltekraft führt zu Falten, zu hohe Haltekraft kann den Materialfluss blockieren und Risse verursachen.
Ein oft unterschätzter Faktor ist die Werkzeugtemperatur. Besonders bei thermisch sensiblen Materialien oder bei tiefen Ziehprozessen kann eine kontrollierte Werkzeugtemperierung helfen, die Umformbarkeit zu verbessern und Spannungen im Werkstück zu reduzieren.
Die Qualität des eingesetzten Schmiermittels trägt erheblich zur Vermeidung von Materialschäden bei. Neben der Verringerung der Reibung schützt die Schmierung auch das Werkzeug vor Verschleiß und sorgt für eine gleichmäßige Oberflächenqualität des Bauteils.
Zusammenfassend sind die Grundlagen des Tiefziehens eine komplexe Mischung aus Werkstoffkunde, mechanischen Abläufen, Werkzeugtechnik und Prozesssteuerung. Nur wenn alle Faktoren optimal aufeinander abgestimmt sind, lässt sich ein wirtschaftlicher, stabiler und qualitativ hochwertiger Umformprozess realisieren, der den Anforderungen der modernen Industrie gerecht wird.
Darüber hinaus spielt die Werkstückgeometrie eine wichtige Rolle bei den Grundlagen des Tiefziehens. Bestimmte Formen lassen sich leichter herstellen als andere; beispielsweise sind zylindrische oder konische Bauteile mit glatten Übergängen meist einfacher zu ziehen als geometrisch komplexe Teile mit scharfen Kanten oder Tiefenstufen. Solche komplexen Geometrien erfordern oft spezielle Werkzeuge oder mehrstufige Umformprozesse, um die Belastungen auf das Material zu minimieren und Falten oder Risse zu vermeiden.
Der Umformgrad, also das Verhältnis von Anfangsdicke zu Endform, gibt an, wie stark das Material verformt wird. Je höher der Umformgrad, desto anspruchsvoller ist der Prozess, da das Material stärker beansprucht wird. Um größere Umformgrade zu erzielen, werden häufig Zwischenoperationen wie das Rückstrecken eingesetzt, um Spannungen abzubauen und die Umformbarkeit zu erhöhen.
Zusätzlich ist das Thema Rückfederung (Elastizitätsrückstellung) nach dem Ziehen von Bedeutung. Nach dem Entlasten der Werkzeuge zieht sich das Material teilweise wieder zusammen, was die endgültige Form leicht verändert. Dies wird bei der Auslegung der Werkzeuge durch gezielte Übermaßgestaltung berücksichtigt, um die gewünschte Maßhaltigkeit zu gewährleisten.
Nicht zuletzt ist die Umformung auch von äußeren Bedingungen abhängig, wie der Umgebungstemperatur oder der Luftfeuchtigkeit, die die Schmierwirkung und das Verhalten des Materials beeinflussen können. Deshalb werden Produktionsbedingungen in der industriellen Fertigung genau überwacht und kontrolliert.
All diese Grundlagen sind die Basis dafür, dass das Tiefziehen als bewährtes und vielseitiges Verfahren in der Metallverarbeitung für eine Vielzahl von Anwendungen weltweit eingesetzt wird.
Zusätzlich zu den genannten Faktoren gewinnt die Bedeutung der Prozessüberwachung und -regelung im Tiefziehen zunehmend an Gewicht. Moderne Fertigungslinien sind mit Sensoren ausgestattet, die kontinuierlich Kräfte, Positionen, Temperaturen und andere relevante Parameter erfassen. Diese Daten werden in Echtzeit analysiert, um Abweichungen frühzeitig zu erkennen und den Prozess automatisch anzupassen. Dadurch wird eine konstante Produktqualität sichergestellt und der Ausschuss minimiert.
Ein weiterer wichtiger Aspekt ist die Schulung und Qualifikation der Mitarbeiter, die den Tiefziehprozess betreuen. Nur durch fundiertes Wissen über Werkstoffeigenschaften, Werkzeugtechnik und Prozessparameter können Bediener schnell auf Prozessstörungen reagieren und den Produktionsablauf optimieren.
Die Entwicklung neuer Materialien mit verbesserten Tiefzieheigenschaften, etwa hochfeste Stähle mit guter Verformbarkeit, eröffnet zusätzliche Möglichkeiten für die Konstruktion leichter und dennoch stabiler Bauteile, insbesondere in der Automobil- und Luftfahrtindustrie.
Nicht zuletzt spielt die Nachhaltigkeit eine immer größere Rolle. Neben der effizienten Nutzung von Materialien und Energie fließen auch Recyclingfähigkeit der Produkte und Umweltauswirkungen der eingesetzten Schmierstoffe in die Bewertung von Tiefziehverfahren ein.
Insgesamt bilden diese vielfältigen Grundlagen die Basis für ein leistungsfähiges und flexibles Tiefziehverfahren, das den Anforderungen moderner Industrieproduktion gerecht wird und auch in Zukunft ein zentrales Verfahren der Metallumformung bleiben wird.
Tiefziehtechnik: Alles über das Umformen von Blechen

Tiefziehtechnik bezeichnet ein wichtiges Umformverfahren zur Herstellung von Hohlkörpern und komplex geformten Bauteilen aus Metallblechen. Beim Tiefziehen wird ein flaches Blech mit Hilfe eines Stempels in eine Matrize gedrückt, sodass es plastisch verformt wird und die gewünschte dreidimensionale Form annimmt. Dieses Verfahren ist besonders geeignet für die Serienfertigung von dünnwandigen, präzisen Bauteilen mit hoher Oberflächenqualität.
Der Prozess beginnt mit einem Zuschnitt des Rohblechs, das in der Regel aus Werkstoffen mit guter Umformbarkeit wie tiefziehfähigem Stahl, Aluminium oder Kupfer besteht. Anschließend wird das Blech auf das Werkzeug gelegt, wobei der Ziehring das Blech festhält und ein Falten oder Verrutschen verhindert. Durch die Bewegung des Stempels wird das Blech in die Matrize gezogen, wo es die Kontur des Werkzeugs annimmt.
Wichtige Parameter in der Tiefziehtechnik sind die Ziehgeschwindigkeit, die Haltekraft des Ziehrings und die Schmierung. Eine optimale Abstimmung dieser Faktoren ist entscheidend, um Risse, Falten oder andere Defekte zu vermeiden und die Materialausnutzung zu maximieren. Die Schmierung reduziert Reibung und schützt das Werkzeug vor Verschleiß.
Es gibt verschiedene Varianten des Tiefziehens, darunter das Ein-Stufen-Tiefziehen, bei dem die Form in einem Zug erzeugt wird, und das Mehrstufen-Tiefziehen, bei dem das Werkstück in mehreren Schritten schrittweise umgeformt wird. Mehrstufige Verfahren ermöglichen tiefere und komplexere Formen und verbessern die Materialverteilung.
Moderne Tiefziehtechnik nutzt computergestützte Simulationen, um den Umformprozess zu optimieren, sowie automatisierte Fertigungssysteme, die eine hohe Produktivität und gleichbleibende Qualität sicherstellen. Zudem kommen innovative Verfahren wie das Hydro-Tiefziehen zum Einsatz, bei dem flüssiger Druck das Blech formt und so neue Gestaltungsmöglichkeiten eröffnet.
Die Tiefziehtechnik findet breite Anwendung in zahlreichen Industrien, etwa im Automobilbau für Karosserieteile, in der Verpackungsindustrie für Getränkedosen oder in der Haushaltswarenfertigung für Kochgeschirr. Durch die Kombination aus Wirtschaftlichkeit, Flexibilität und hoher Qualität bleibt das Tiefziehen eines der wichtigsten Verfahren in der Metallumformung.
Ein weiterer wichtiger Aspekt der Tiefziehtechnik ist die Materialauswahl, da die Eigenschaften des Blechs maßgeblich den Erfolg des Umformprozesses beeinflussen. Materialien wie kaltgewalzter Stahl, Aluminiumlegierungen und Edelstahl sind aufgrund ihrer guten Verformbarkeit und Festigkeit besonders geeignet. Die Bleche müssen dabei sorgfältig auf ihre Oberflächenqualität und Maßhaltigkeit geprüft werden, da Fehler wie Kratzer oder Materialunregelmäßigkeiten die Umformbarkeit negativ beeinflussen können.
Die Gestaltung der Werkzeuge spielt ebenfalls eine entscheidende Rolle. Der Stempel und die Matrize müssen präzise aufeinander abgestimmt sein, um eine gleichmäßige Umformung sicherzustellen. Die Werkzeuggeometrie beeinflusst die Materialflussrichtung und verhindert Defekte wie Falten oder Risse. Auch der Einsatz von Ziehringen mit variabler Haltekraft ermöglicht eine bessere Kontrolle des Materialflusses.
Fortschritte in der Schmiertechnik tragen dazu bei, die Reibung zwischen Werkzeug und Blech zu reduzieren, wodurch der Verschleiß der Werkzeuge minimiert und die Oberflächenqualität der Bauteile verbessert wird. Umweltfreundliche Schmierstoffe gewinnen dabei zunehmend an Bedeutung, um den ökologischen Fußabdruck der Fertigung zu reduzieren.
Innovative Ansätze wie das Hydroforming oder das Warmumformen erweitern die Möglichkeiten der Tiefziehtechnik, indem sie Materialien ermöglichen, die bei herkömmlichen Verfahren schwer zu verarbeiten wären, oder komplexere Geometrien realisieren lassen. So können neue Designfreiheiten erschlossen werden, die insbesondere in der Automobil- und Luftfahrtindustrie gefragt sind.
Die Kombination aus traditioneller Technik, modernen Werkzeugen, digitaler Prozesskontrolle und innovativen Materialien macht die Tiefziehtechnik zu einem hochentwickelten und vielseitigen Verfahren, das auch zukünftig eine zentrale Rolle in der industriellen Metallumformung spielen wird.
Darüber hinaus gewinnt die Digitalisierung in der Tiefziehtechnik immer mehr an Bedeutung. Durch den Einsatz von Sensorik und Echtzeit-Datenanalyse können Prozessparameter kontinuierlich überwacht und angepasst werden, um eine optimale Materialausnutzung und höchste Bauteilqualität sicherzustellen. Digitale Zwillinge – virtuelle Abbilder des Umformprozesses – ermöglichen es, potenzielle Fehlerquellen frühzeitig zu identifizieren und Prozessoptimierungen bereits im Vorfeld zu testen.
Die Integration von Künstlicher Intelligenz und Machine Learning erlaubt es, aus umfangreichen Produktionsdaten Muster zu erkennen und Vorhersagen zu treffen, etwa zur Werkzeugstandzeit oder optimalen Schmierstoffdosierung. So wird der Tiefziehprozess zunehmend autonomer und effizienter.
Auch im Bereich der Nachhaltigkeit zeigt die Tiefziehtechnik Fortschritte. Durch den Einsatz energieeffizienter Maschinen, optimierter Prozessführung und umweltfreundlicher Schmiermittel wird der ökologische Fußabdruck der Fertigung reduziert. Zudem werden Recyclingstrategien für Restbleche und Werkzeugmaterialien verstärkt umgesetzt.
Neben der technischen Weiterentwicklung sind qualifizierte Fachkräfte ein Schlüssel zum Erfolg. Die Bediener müssen sowohl die komplexen Maschinen sicher steuern als auch Prozessparameter verstehen und anpassen können. Aus- und Weiterbildung spielen daher eine wichtige Rolle, um den hohen Qualitätsstandard und die Effizienz der Tiefziehfertigung zu gewährleisten.
Insgesamt zeigt sich, dass die Tiefziehtechnik durch die Kombination aus bewährten Verfahren, digitalen Innovationen und nachhaltigen Ansätzen zukunftsfähig aufgestellt ist und weiterhin eine wichtige Rolle in der modernen Metallverarbeitung spielen wird.
Zudem wird die Entwicklung neuer Werkstoffe mit verbesserten Tiefzieheigenschaften immer wichtiger. Hochfeste Stähle, Leichtmetalllegierungen und Verbundwerkstoffe bieten die Möglichkeit, Bauteile leichter und gleichzeitig stabiler zu gestalten, was vor allem in der Automobil- und Luftfahrtindustrie zu erheblichen Effizienz- und Umwelteffekten führt. Diese Materialien stellen allerdings auch höhere Anforderungen an das Werkzeugdesign und die Prozesssteuerung, da ihre Umformbarkeit oft eingeschränkt ist.
Die Kombination von Tiefziehen mit anderen Fertigungsverfahren, wie beispielsweise dem Laserschweißen oder dem Einlegen von Funktionselementen vor dem Umformen, erweitert die Möglichkeiten der Bauteilgestaltung und -funktionalität. So können komplexe Baugruppen in einem einzigen Fertigungsprozess hergestellt werden, was Zeit und Kosten spart.
Darüber hinaus gewinnen hybride Verfahren an Bedeutung, bei denen das Tiefziehen mit additiven Fertigungstechniken kombiniert wird. So lassen sich individuelle Werkzeuge schneller und kostengünstiger produzieren, was die Flexibilität in der Produktion erhöht und insbesondere bei Kleinserien oder Prototypen Vorteile bietet.
Nicht zuletzt wird die Automatisierung in der Tiefziehfertigung weiter vorangetrieben. Roboter übernehmen zunehmend Aufgaben wie das Be- und Entladen der Pressen, das Handling der Werkstücke und die Qualitätskontrolle, was die Effizienz steigert und menschliche Fehler reduziert.
Diese Entwicklungen zeigen, dass die Tiefziehtechnik nicht nur ein klassisches Umformverfahren ist, sondern sich kontinuierlich weiterentwickelt, um den steigenden Anforderungen der modernen Industrie gerecht zu werden.
Tiefziehen: Einführung in das Verfahren der Metallumformung
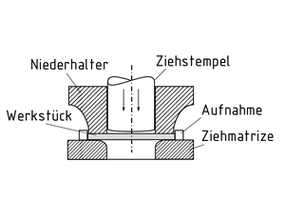
Das Tiefziehen ist ein grundlegendes Verfahren der Metallumformung, bei dem flache Metallbleche in komplexe, dreidimensionale Formen umgewandelt werden. Dabei wird das Blech durch einen Stempel in eine Matrize gedrückt, wodurch es plastisch verformt wird, ohne zu reißen oder zu falten. Dieses Verfahren eignet sich besonders zur Herstellung von Hohlkörpern wie Dosen, Karosserieteilen oder Gehäusen.
Der Prozess beginnt mit einem zugeschnittenen Blech, das auf die Matrize gelegt wird. Ein Ziehring hält das Blech am Rand fest, um ein Verrutschen oder Falten während des Ziehens zu verhindern. Der Stempel bewegt sich dann nach unten und drückt das Blech in die Matrize, wodurch das Material in die gewünschte Form fließt. Entscheidend ist dabei das Zusammenspiel von Ziehkraft, Haltekraft und Schmierung, um eine gleichmäßige Verformung sicherzustellen.
Tiefziehen kann in einem einzigen Schritt erfolgen oder in mehreren aufeinanderfolgenden Zügen, um tiefere oder komplexere Formen zu realisieren. Dabei beeinflussen Werkstoff, Werkzeuggeometrie und Prozessparameter wie Geschwindigkeit und Schmierung das Ergebnis maßgeblich.
Das Verfahren ist wirtschaftlich und vielseitig und findet breite Anwendung in der Automobilindustrie, Verpackungsherstellung, Haushaltswarenproduktion und vielen weiteren Bereichen. Durch Fortschritte in der Werkzeugtechnik, computergestützte Prozesssimulation und automatisierte Fertigungssysteme wird das Tiefziehen heute noch präziser und effizienter ausgeführt.
Insgesamt bietet das Tiefziehen eine effektive Methode zur Herstellung qualitativ hochwertiger, dünnwandiger Metallbauteile mit komplexen Geometrien, die in zahlreichen Industriezweigen unverzichtbar sind.
Ein wichtiger Aspekt beim Tiefziehen ist die Materialauswahl. Das Ausgangsmaterial muss ausreichend duktil sein, um die plastische Verformung ohne Bruch zu ermöglichen. Typische Werkstoffe sind kaltgewalzter Stahl, Aluminiumlegierungen und Kupfer, die sich durch gute Kaltumformbarkeit auszeichnen. Auch die Blechdicke spielt eine Rolle: Dünnere Bleche lassen sich leichter tiefziehen, erfordern jedoch eine präzise Prozesssteuerung, um Faltenbildung zu vermeiden.
Die Werkzeuge beim Tiefziehen – Stempel, Matrize und Ziehring – sind so ausgelegt, dass sie den Materialfluss steuern und eine gleichmäßige Umformung gewährleisten. Der Ziehring übt eine Haltekraft aus, die das Blech am Rand fixiert und so das Entstehen von Falten verhindert. Gleichzeitig muss die Haltekraft so abgestimmt sein, dass das Material nicht einreißt.
Eine optimale Schmierung zwischen Werkzeug und Blech reduziert Reibung, verhindert Materialschäden und verlängert die Lebensdauer der Werkzeuge. Je nach Werkstoff und Anwendung kommen verschiedene Schmiermittel zum Einsatz, darunter Öle, Wachse oder Festschmierstoffe.
Moderne Tiefziehverfahren nutzen computergestützte Simulationen, um den Umformprozess vorab zu optimieren. Dadurch können Fehler wie Risse oder Faltenbildung vermieden und Werkzeugauslegungen verbessert werden. Zudem erlauben automatisierte Fertigungslinien eine präzise Steuerung der Prozessparameter und eine hohe Produktqualität bei großen Stückzahlen.
Durch diese Kombination aus geeigneten Materialien, präzisen Werkzeugen und innovativer Prozesssteuerung bleibt das Tiefziehen eines der wichtigsten und vielseitigsten Umformverfahren in der modernen Metallverarbeitung.
Zusätzlich zu den grundlegenden Parametern spielt die Kontrolle der Umformgeschwindigkeit eine wichtige Rolle beim Tiefziehen. Eine zu hohe Ziehgeschwindigkeit kann zu Materialversprödung und Rissbildung führen, während zu langsames Ziehen den Prozess ineffizient macht und das Risiko von Falten erhöht. Die optimale Geschwindigkeit hängt vom Werkstoff, der Blechdicke und der Komplexität der Form ab.
Ein weiterer kritischer Faktor ist die Temperatur während des Umformprozesses. Obwohl Tiefziehen in der Regel kalt erfolgt, kann bei besonders schwer umformbaren Materialien oder tiefen Ziehprozessen eine Erwärmung des Werkzeugs oder Materials den Umformwiderstand senken und die Verformbarkeit verbessern. Das sogenannte Warm- oder Halbwarmziehen erweitert die Anwendungsmöglichkeiten des Verfahrens auf anspruchsvollere Werkstoffe.
Die Nachbearbeitung von tiefgezogenen Bauteilen umfasst häufig Maßnahmen wie das Rückstrecken, um durch das Ziehen entstandene Eigenspannungen abzubauen und Maßhaltigkeit zu verbessern. Auch das Zuschneiden, Bördeln oder Umformen weiterer Details sind oft notwendig, um das Bauteil fertigzustellen.
Die kontinuierliche Weiterentwicklung der Tiefziehtechnik, insbesondere durch den Einsatz neuer Werkstoffe, moderner Werkzeuge und digitaler Steuerungssysteme, sorgt dafür, dass das Verfahren auch bei steigenden Anforderungen an Präzision, Leichtbau und Nachhaltigkeit eine zentrale Rolle in der industriellen Fertigung einnimmt.
Tiefziehmaschinen und deren Anpassung an Produktionsbedürfnisse
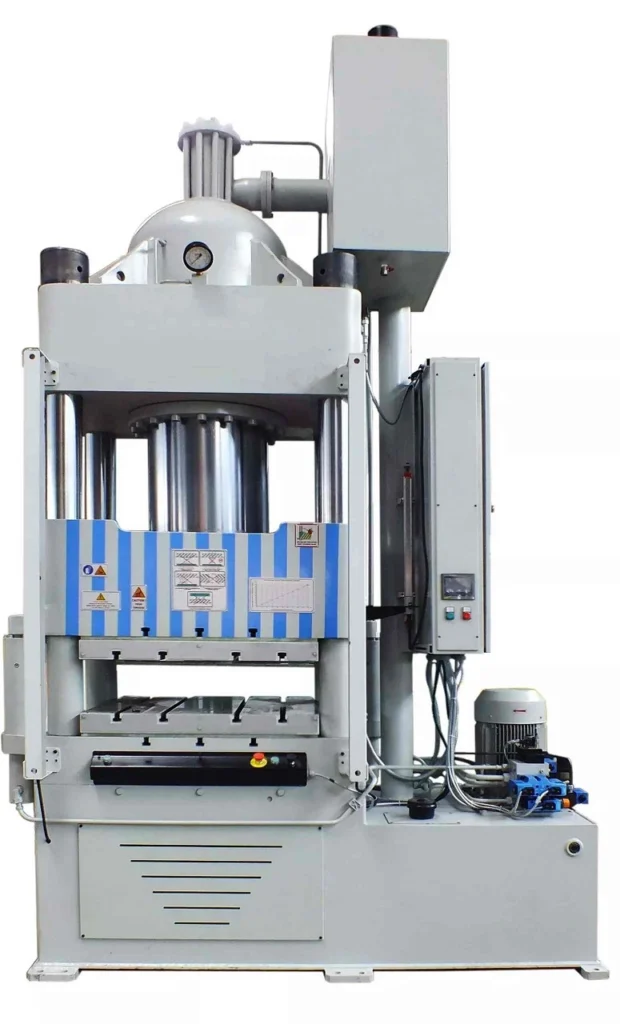
Tiefziehmaschinen sind zentrale Anlagen in der Metallumformung, die speziell dafür ausgelegt sind, Bleche präzise und effizient in die gewünschte Form zu bringen. Sie unterscheiden sich je nach Größe, Leistung, Antriebstechnik und Automatisierungsgrad, um den vielfältigen Anforderungen unterschiedlicher Produktionsumfänge und -arten gerecht zu werden.
Grundsätzlich lassen sich Tiefziehmaschinen in mechanische, hydraulische und servoelektrische Maschinen unterteilen. Mechanische Maschinen arbeiten mit Schwungradantrieb und sind besonders geeignet für hohe Taktzahlen bei gleichbleibender Belastung. Hydraulische Maschinen bieten hingegen eine flexible Kraft- und Geschwindigkeitssteuerung, was sie ideal für komplexe Umformprozesse mit variierenden Anforderungen macht. Servoelektrische Maschinen vereinen Präzision und Energieeffizienz und ermöglichen eine sehr genaue Steuerung von Bewegung und Kraft, was vor allem bei sensiblen Werkstoffen oder filigranen Formen von Vorteil ist.
Je nach Produktionsbedarf können Tiefziehmaschinen mit verschiedenen Werkzeugwechsel- und Automatisierungssystemen ausgestattet werden. In der Serienfertigung ermöglichen automatische Werkzeugwechsler schnelle Umrüstzeiten und reduzieren Stillstandzeiten. Robotergestützte Zuführ- und Entnahmesysteme sorgen für kontinuierlichen Materialfluss und hohe Produktivität.
Für Kleinserien oder Prototypen werden häufig flexible Anlagen mit modularen Werkzeugen genutzt, die sich schnell an wechselnde Anforderungen anpassen lassen. Dabei spielt auch die Integration von Mess- und Überwachungssystemen eine wichtige Rolle, um Qualitätskontrollen direkt in den Fertigungsprozess einzubinden und Ausschuss frühzeitig zu erkennen.
Darüber hinaus wird zunehmend auf energieeffiziente Maschinenkonzepte und umweltfreundliche Schmier- und Kühlsysteme gesetzt, um die Nachhaltigkeit der Fertigung zu verbessern.
Insgesamt ist die Anpassung von Tiefziehmaschinen an die spezifischen Produktionsbedürfnisse entscheidend, um optimale Prozesssicherheit, Produktqualität und Wirtschaftlichkeit zu gewährleisten. Moderne Tiefziehmaschinen bieten deshalb eine hohe Flexibilität, Präzision und Automatisierung, die den Anforderungen der heutigen industriellen Fertigung gerecht werden.
Neben der Wahl des Maschinentyps spielt auch die Größe und Presskraft der Tiefziehmaschine eine wichtige Rolle bei der Anpassung an Produktionsanforderungen. Große Bauteile oder stark beanspruchte Werkstoffe benötigen Maschinen mit hoher Presskraft und entsprechend robustem Maschinenaufbau. Für kleinere Teile oder dünne Bleche können kompaktere und weniger leistungsstarke Maschinen ausreichend sein, was Investitions- und Betriebskosten reduziert.
Ein weiterer Aspekt ist die Integration von Prozessüberwachungssystemen, die in modernen Tiefziehmaschinen zunehmend Standard sind. Sensoren messen während des Umformvorgangs Kräfte, Positionen und Temperaturen, wodurch Abweichungen sofort erkannt werden. Über intelligente Steuerungssysteme können Parameter in Echtzeit angepasst werden, was die Ausschussquote minimiert und die Maschinenlaufzeit maximiert.
Flexible Steuerungskonzepte ermöglichen zudem die einfache Umstellung auf verschiedene Werkstücke oder Fertigungsläufe, was besonders in Branchen mit häufig wechselnden Produktionen von Vorteil ist. Durch programmierbare Steuerungen und benutzerfreundliche Bedienoberflächen wird die Maschine schnell und effizient auf neue Aufgaben eingestellt.
Automatisierungslösungen, wie robotergestützte Materialzuführung, Werkstückentnahme und Nachbearbeitung, erhöhen die Produktivität und reduzieren den manuellen Aufwand. Insbesondere in hochvolumigen Produktionen sorgt dies für eine konstante Qualität und senkt die Personalkosten.
Zukünftig werden auch vernetzte Tiefziehmaschinen, die in Industrie-4.0-Umgebungen integriert sind, eine größere Rolle spielen. Über IoT-Technologien lassen sich Maschinenzustand und Produktionsdaten zentral überwachen, was vorbeugende Wartung und eine durchgängige Prozessoptimierung ermöglicht.
Somit sind Tiefziehmaschinen heute nicht nur reine Umformwerkzeuge, sondern hochentwickelte, flexible Systeme, die sich durch modulare Ausstattung und smarte Technologien optimal an verschiedenste Produktionsbedürfnisse anpassen lassen.
Darüber hinaus spielt die Werkzeugintegration in Tiefziehmaschinen eine zentrale Rolle für die Produktionsflexibilität. Schnellwechsel-Systeme ermöglichen einen zügigen Austausch von Stempeln und Matrizen, wodurch Rüstzeiten deutlich reduziert werden. Dies ist besonders wichtig bei variantenreichen Produktionen oder bei der Fertigung kleinerer Losgrößen.
Moderne Maschinen sind oft mit adaptiven Steuerungen ausgestattet, die den Umformprozess automatisch an unterschiedliche Werkstoffe oder Blechdicken anpassen können. So wird eine gleichbleibende Bauteilqualität auch bei schwankenden Materialeigenschaften sichergestellt.
Im Bereich der Energieeffizienz setzen Hersteller verstärkt auf servoelektrische Antriebe, die den Energieverbrauch im Vergleich zu klassischen Hydrauliksystemen erheblich reduzieren. Diese Antriebe ermöglichen zudem eine präzisere Bewegungskontrolle und damit eine höhere Prozessgenauigkeit.
Ein weiterer Trend ist die zunehmende Vernetzung von Tiefziehmaschinen mit übergeordneten Produktionssystemen. Durch die Einbindung in Manufacturing Execution Systems (MES) und Enterprise Resource Planning (ERP) können Produktionsabläufe besser koordiniert und Ressourcen effizienter eingesetzt werden.
Nicht zuletzt fördern Simulationssoftware und digitale Zwillinge die vorausschauende Planung und Optimierung der Tiefziehprozesse. Bereits vor dem physischen Start der Produktion lassen sich so mögliche Fehlerquellen erkennen und Prozessparameter ideal einstellen.
Diese Kombination aus technischer Innovation, Automatisierung und digitaler Vernetzung macht Tiefziehmaschinen zu Schlüsselkomponenten moderner Fertigungslinien, die flexibel, effizient und qualitativ hochwertig produzieren.
Ein weiterer wichtiger Aspekt bei der Anpassung von Tiefziehmaschinen an Produktionsbedürfnisse ist die ergonomische Gestaltung der Bedienplätze. Durch benutzerfreundliche Schnittstellen, intuitive Bedienpanels und verbesserte Zugänglichkeit der Maschinenkomponenten wird die Arbeit der Maschinenbediener erleichtert, wodurch die Fehlerquote sinkt und die Effizienz steigt.
Zudem ermöglichen integrierte Sicherheitskonzepte, wie Lichtschranken, Schutzverkleidungen und Not-Aus-Systeme, einen sicheren Betrieb auch bei hohem Automatisierungsgrad. Dies ist besonders relevant, wenn Roboter oder andere automatische Handhabungssysteme im Einsatz sind.
Für Spezialanwendungen können Tiefziehmaschinen mit zusätzlichen Modulen ausgestattet werden, beispielsweise für das Einbringen von Prägungen, Stanzen oder das Verpressen von Bauteilen während des Tiefziehprozesses. Dadurch lassen sich mehrere Arbeitsschritte in einem Maschinendurchlauf kombinieren, was die Gesamtproduktionszeit reduziert.
Auch die Wartung und Instandhaltung der Maschinen wird durch modulare Bauweise und Fernwartungssysteme vereinfacht. Sensoren überwachen den Zustand von Verschleißteilen und melden frühzeitig erforderliche Wartungsarbeiten, was ungeplante Stillstände minimiert.
Zusammenfassend lässt sich sagen, dass die Anpassung von Tiefziehmaschinen an die jeweiligen Produktionsbedürfnisse weit über die reine Umformfunktion hinausgeht. Sie umfasst eine Vielzahl von technischen, ergonomischen und digitalen Lösungen, die gemeinsam dazu beitragen, dass die Fertigung effizient, flexibel und sicher abläuft.
Tiefziehverfahren für Präzisionsteile: Ein Überblick
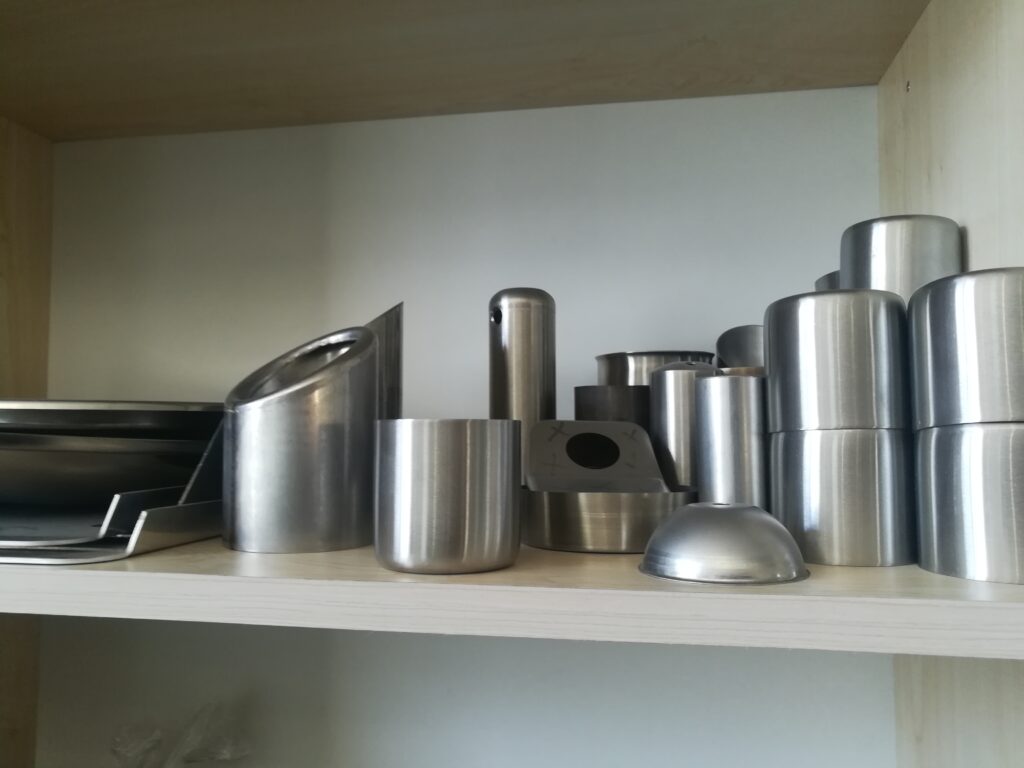
Tiefziehverfahren für Präzisionsteile zeichnen sich durch besonders hohe Anforderungen an Maßhaltigkeit, Oberflächenqualität und Materialverformung aus. Diese Bauteile finden sich häufig in Branchen wie der Medizintechnik, Elektronik, Luft- und Raumfahrt sowie im Automobilbau, wo kleinste Toleranzen und komplexe Geometrien entscheidend sind.
Um Präzisionsteile mittels Tiefziehen herzustellen, kommen häufig spezielle Verfahren und Techniken zum Einsatz:
- Feintiefziehen: Hierbei handelt es sich um ein Tiefziehverfahren mit besonders präziser Werkzeugführung und fein abgestimmten Prozessparametern. Das Ziel ist es, eine sehr hohe Maßgenauigkeit und eine glatte Oberfläche zu erzielen. Feintiefziehen wird oft in Mehrstufenprozessen durchgeführt, um das Werkstück schrittweise und kontrolliert zu formen.
- Hydroform- oder Flüssigdruck-Tiefziehen: Bei diesem Verfahren wird das Blech durch hydraulischen Druck in die Werkzeugform gepresst, was eine sehr gleichmäßige Materialverteilung ermöglicht. Dadurch lassen sich komplexe Formen mit dünnen Wandstärken herstellen, die bei konventionellen Verfahren schwierig zu realisieren wären.
- Warmziehen: Durch die Erwärmung des Materials vor oder während des Ziehvorgangs wird die Verformbarkeit verbessert, was insbesondere bei hochfesten Werkstoffen oder dickeren Blechen von Vorteil ist. Die höhere Duktilität reduziert Riss- und Bruchrisiken und ermöglicht engere Toleranzen.
- Multistufen-Tiefziehen mit Rückstrecken: Um innere Spannungen abzubauen und Maßhaltigkeit zu erhöhen, werden die Bauteile nach mehreren Ziehschritten häufig zurückgespannt und erneut gezogen. Dies verbessert die Formgenauigkeit und verhindert Verformungen im späteren Einsatz.
- Kombination mit Nachbearbeitungsverfahren: Präzisionsteile erfordern oft ergänzende Prozesse wie Feinbearbeitung, Ultraschallreinigung oder Oberflächenbehandlung, um die geforderten Qualitätsstandards zu erfüllen.
Die Werkzeugtechnik bei Präzisionstiefziehen ist besonders aufwendig und erfordert höchste Genauigkeit bei Fertigung und Wartung. Die Werkzeuge sind häufig mit verschleißarmen Beschichtungen versehen und verfügen über integrierte Kühlsysteme, um thermische Verformungen zu minimieren.
Moderne Prozessüberwachung mittels Sensorik und computergestützter Simulation spielt eine zentrale Rolle, um Fehler frühzeitig zu erkennen und den Prozess kontinuierlich zu optimieren. So wird sichergestellt, dass auch bei großen Serien die hohen Qualitätsanforderungen erfüllt werden.
Insgesamt ermöglichen diese spezialisierten Tiefziehverfahren die wirtschaftliche Herstellung hochpräziser, komplexer Metallteile, die in vielen Hightech-Anwendungen unverzichtbar sind.
Darüber hinaus gewinnt die Automatisierung im Präzisionstiefziehen zunehmend an Bedeutung. Roboter und automatisierte Handhabungssysteme sorgen für eine gleichbleibend hohe Prozesssicherheit und Qualität, indem sie Werkstücke präzise positionieren, Be- und Entladevorgänge übernehmen und Kontrollmessungen durchführen. Dies reduziert menschliche Fehler und erhöht die Produktionsgeschwindigkeit, was besonders bei kleinen, aber komplexen Teilen von Vorteil ist.
Ein weiterer Trend ist die verstärkte Nutzung von digitaler Prozesssimulation und digitalen Zwillingen. Diese Technologien erlauben es, den Tiefziehprozess virtuell durchzuspielen und mögliche Problemstellen wie Materialüberdehnung oder Faltenbildung schon im Vorfeld zu identifizieren. So können Werkzeuge und Prozessparameter optimal ausgelegt und die Anzahl der Prototypen deutlich reduziert werden.
Im Bereich der Werkstoffe werden zunehmend hochfeste und leichte Legierungen verwendet, um die Leistungsfähigkeit der Präzisionsteile zu erhöhen, insbesondere in der Luft- und Raumfahrt sowie im Automobilbau. Diese Materialien stellen jedoch höhere Anforderungen an das Tiefziehverfahren, weshalb spezielle Prozessanpassungen und häufig auch das Warmziehen notwendig sind.
Schließlich spielen Qualitätskontrolle und Rückverfolgbarkeit eine entscheidende Rolle. Durch den Einsatz von Inline-Messsystemen, optischer Inspektion und Datenmanagement lassen sich Abweichungen sofort erkennen und dokumentieren. Dies ist besonders in sicherheitskritischen Anwendungen essenziell, um die Einhaltung aller Spezifikationen zu garantieren.
In Summe ermöglichen diese fortschrittlichen Tiefziehverfahren und unterstützenden Technologien die effiziente Produktion von Präzisionsteilen mit höchster Qualität und Wiederholgenauigkeit, die den Anforderungen moderner Hightech-Industrien gerecht werden.
Ein nicht zu unterschätzender Faktor beim Tiefziehen von Präzisionsteilen ist die Werkzeugwartung und -pflege. Da selbst kleinste Abweichungen in der Werkzeuggeometrie oder Oberflächenrauheit die Qualität der Bauteile beeinträchtigen können, werden Werkzeuge regelmäßig gereinigt, nachgeschliffen und bei Bedarf beschichtet. Moderne Maschinen sind zunehmend in der Lage, Werkzeugverschleiß selbstständig zu erkennen und warnen frühzeitig, bevor es zu qualitativen Abweichungen kommt.
Mikrotiefziehen stellt eine besonders spezialisierte Variante dar, bei der winzige, oft nur wenige Millimeter große Präzisionsbauteile hergestellt werden – beispielsweise für medizinische Implantate, Miniatursensoren oder Mikrogehäuse in der Elektronik. Hier bewegen sich Toleranzen im Bereich weniger Mikrometer. Die Werkzeugfertigung erfordert extrem hohe Präzision und häufig den Einsatz von Spezialwerkstoffen sowie feinfühliger Antriebstechnik mit minimalem Spiel.
Zusätzlich zur technischen Optimierung gewinnen nachhaltige Fertigungsaspekte zunehmend an Gewicht. Dazu zählen die Reduktion von Schmiermitteln, die Wiederverwertung von Verschnittmaterial sowie energieeffiziente Maschinenkonzepte. Auch die Minimierung von Ausschuss durch vorausschauende Qualitätssicherung und digitale Überwachung trägt zur Ressourcen- und Kosteneffizienz bei.
In der Praxis werden oft Hybridverfahren eingesetzt, bei denen Tiefziehen mit anderen Prozessen kombiniert wird – z. B. mit Prägeoperationen, Stanzen oder Laserschneiden –, um mehrere Fertigungsschritte in einem einzigen Arbeitszyklus zu vereinen. Das senkt nicht nur die Stückkosten, sondern reduziert auch die Handhabung und erhöht die Prozessstabilität.
Abschließend lässt sich sagen, dass das Tiefziehen von Präzisionsteilen heute ein hochspezialisierter, interdisziplinärer Fertigungsbereich ist. Durch das Zusammenspiel modernster Maschinen, intelligenter Prozesskontrolle, leistungsfähiger Werkstoffe und durchdachter Automatisierung lassen sich selbst anspruchsvollste Geometrien in höchster Qualität reproduzierbar und wirtschaftlich herstellen. Diese Verfahren sichern die Wettbewerbsfähigkeit in jenen Industriezweigen, in denen technologische Präzision, Miniaturisierung und Zuverlässigkeit entscheidend sind.
Tiefziehen in der Luftfahrtindustrie: Anforderungen und Lösungen
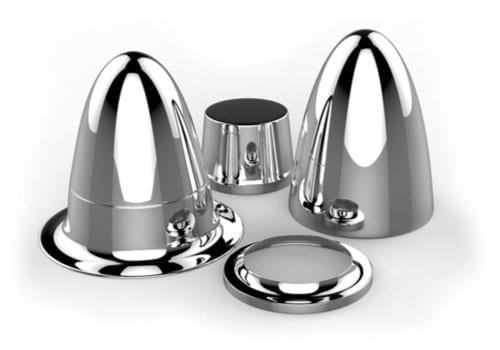
Das Tiefziehen spielt in der Luftfahrtindustrie eine bedeutende Rolle, insbesondere bei der Herstellung von leichten, hochpräzisen und gleichzeitig belastbaren Bauteilen. Die Anforderungen an Werkstoffe, Bauteilgeometrien und Fertigungsprozesse sind in dieser Branche besonders hoch – geprägt durch Sicherheitsvorgaben, Gewichtsoptimierung und extreme Betriebsbedingungen wie Druck- und Temperaturschwankungen.
Anforderungen:
In der Luftfahrt gelten enge Toleranzen, höchste Maßgenauigkeit und perfekte Oberflächen als Standard. Bauteile müssen nicht nur leicht, sondern auch äußerst stabil sein, um den Belastungen während des Fluges standzuhalten. Werkstoffe wie Aluminium- und Titanlegierungen oder spezielle rostfreie Stähle kommen daher häufig zum Einsatz. Diese Materialien stellen besondere Herausforderungen beim Tiefziehen dar, da sie eine hohe Rückfederung oder Festigkeit aufweisen und daher schwer umzuformen sind.
Darüber hinaus ist die Rückverfolgbarkeit jedes einzelnen Bauteils essenziell. Fertigungsprozesse müssen dokumentiert und nachvollziehbar gestaltet sein, um im Schadensfall die Ursache exakt bestimmen zu können. Auch die Werkstoffprüfung und -freigabe unterliegt strengen Luftfahrtstandards (z. B. NADCAP, EN 9100).
Lösungen und Ansätze:
Um diesen hohen Anforderungen gerecht zu werden, werden in der Luftfahrtindustrie spezialisierte Tiefziehverfahren eingesetzt:
– Warmziehen und Halbwarmziehen: Durch gezielte Erwärmung der Werkstoffe wird die Umformbarkeit verbessert, insbesondere bei Titan- oder Nickellegierungen, die bei Raumtemperatur nur schwer umzuformen sind.
– Hydroformen: Dieses Verfahren nutzt flüssigkeitsbasierten Druck zur gleichmäßigen Umformung. Es eignet sich hervorragend für dünnwandige, komplexe Bauteile, wie sie in der Luftfahrt häufig vorkommen – z. B. Luftkanäle, Abdeckungen oder Strukturkomponenten.
– Mehrstufige Tiefziehprozesse: Diese Technik erlaubt die schonende Umformung von hochfesten Werkstoffen durch sequentielle Formänderung. Dabei werden Spannungen reduziert und die Gefahr von Rissen minimiert.
– Präzisionswerkzeuge mit Verschleißschutz: Die Verwendung hochfester Werkzeugstähle mit speziellen Beschichtungen (z. B. TiN oder DLC) gewährleistet nicht nur eine lange Standzeit, sondern auch eine konstant hohe Bauteilqualität über große Serien hinweg.
– Automatisierte Qualitätskontrollen: Berührungslose Messtechniken wie optische 3D-Vermessung oder Laserprofilierung werden eingesetzt, um komplexe Geometrien exakt zu überprüfen und zu dokumentieren.
Zusätzlich profitieren Luftfahrtunternehmen von der Simulationsgestützten Prozessplanung, mit der das Verhalten des Werkstoffs bereits vor der Fertigung digital nachgebildet wird. Dies spart Entwicklungszeit, reduziert Ausschuss und ermöglicht eine gezielte Optimierung von Werkzeugen und Prozessparametern.
Insgesamt ermöglicht das Tiefziehen – angepasst an die speziellen Anforderungen der Luftfahrt – die wirtschaftliche Produktion sicherheitsrelevanter Komponenten mit geringem Gewicht, hoher Funktionalität und absoluter Reproduzierbarkeit. Damit leistet dieses Verfahren einen wichtigen Beitrag zur Effizienz, Sicherheit und Wettbewerbsfähigkeit moderner Luftfahrttechnologien.
In der Praxis zeigt sich, dass das Tiefziehen in der Luftfahrtindustrie nicht nur durch die Auswahl geeigneter Verfahren und Werkstoffe bestimmt wird, sondern auch stark von der Prozesskontrolle und Dokumentation abhängt. Jeder Produktionsschritt muss rückverfolgbar sein, jedes Bauteil einer lückenlosen Qualitätssicherung unterliegen. Um diesem Anspruch gerecht zu werden, werden moderne Tiefziehmaschinen häufig mit umfangreicher Sensorik ausgestattet, die Parameter wie Ziehkraft, Temperatur, Schmiermittelfluss und Materialverhalten in Echtzeit überwacht. Diese Daten fließen in digitale Systeme ein, die eine kontinuierliche Prozessoptimierung ermöglichen und gleichzeitig als Nachweis für die Einhaltung luftfahrtspezifischer Normen dienen.
Die Automatisierung spielt auch hier eine wichtige Rolle, denn durch robotergestützte Materialhandhabung, automatisierte Werkzeugwechsel und In-Line-Messsysteme lässt sich die Reproduzierbarkeit auf ein hohes Niveau heben. Auch die Anforderungen an Oberflächen sind besonders hoch – nicht nur aus funktionalen Gründen, etwa zur Reduktion von Strömungswiderstand oder zur Gewährleistung von Dichtheit, sondern auch im Hinblick auf die Vorbereitung für spätere Beschichtungen, Klebungen oder Nietverbindungen.
Deshalb kommen häufig polierte Ziehwerkzeuge, kontrollierte Schmiermittelverwendung und schonende Nachbearbeitungsschritte wie Gleitschleifen oder chemisches Entgraten zum Einsatz. Darüber hinaus stellt das Verhältnis von Gewicht zu Festigkeit einen zentralen Aspekt dar. Gerade im Tiefziehprozess können durch gezielte Materialverteilung, zum Beispiel durch Wanddickensteuerung oder das Einziehen von Verstärkungsrillen, Bauteile gefertigt werden, die bei minimalem Materialeinsatz maximale Festigkeit bieten.
Diese Formoptimierung wird oft durch numerische Simulationen unterstützt, bevor die Serienfertigung beginnt. Ein weiterer Aspekt ist die zunehmende Einbindung des Tiefziehens in hybride Fertigungslinien, in denen Umformen, Schneiden, Biegen, Nieten und Prüfen als integrierter Prozessablauf realisiert sind. Dadurch werden Durchlaufzeiten verkürzt und mögliche Fehlerquellen reduziert. Letztlich ist das Tiefziehen in der Luftfahrt kein isolierter Fertigungsschritt, sondern Teil einer hochintegrierten Prozesskette, die auf maximale Effizienz, Sicherheit und Materialausnutzung ausgelegt ist. Nur durch diese ganzheitliche Betrachtung lassen sich die strengen Normen und wirtschaftlichen Vorgaben der Branche dauerhaft erfüllen.
In zunehmendem Maße spielt auch die Digitalisierung eine Schlüsselrolle bei der Weiterentwicklung des Tiefziehens für luftfahrttechnische Anwendungen. Die Einbindung von Maschinen in digitale Fertigungsnetzwerke erlaubt nicht nur die zentrale Überwachung und Steuerung mehrerer Produktionsanlagen, sondern auch die Nutzung historischer Prozessdaten für vorausschauende Wartung, Qualitätstrendanalyse und langfristige Optimierung. So lassen sich etwa durch Mustererkennung frühzeitig Unregelmäßigkeiten erkennen, die später zu Ausschuss führen könnten. Diese vorausschauenden Systeme tragen erheblich dazu bei, die ohnehin schon hohen Qualitätsstandards in der Luftfahrt noch weiter zu stabilisieren.
Parallel dazu ermöglichen moderne CAE-Programme eine realitätsnahe Abbildung des Umformverhaltens verschiedenster Werkstoffe unter Berücksichtigung von Anisotropie, Rückfederung und Temperaturverläufen. Durch den Abgleich zwischen Simulation und realen Messergebnissen lassen sich Modelle laufend verfeinern, was die Planbarkeit neuer Tiefziehprozesse deutlich verbessert. Auch das Thema Nachhaltigkeit gewinnt an Bedeutung. Da Material- und Energieeinsparungen in der Luftfahrtindustrie besonders hoch bewertet werden, bietet das präzise gesteuerte Tiefziehverfahren Potenziale für Ressourcenoptimierung.
Durch Reduktion von Materialverschnitt, minimierte Umformkräfte und effizientere Schmierstoffverwendung wird nicht nur die Umwelt entlastet, sondern auch die Wirtschaftlichkeit gesteigert. Besonders bei teuren Werkstoffen wie Titan oder hochfesten Aluminiumlegierungen ist es entscheidend, möglichst materialschonend zu arbeiten und Ausschuss auf ein Minimum zu reduzieren. Schließlich profitieren auch die Konstruktionsabteilungen von der Weiterentwicklung des Tiefziehens, denn die gestiegene Präzision erlaubt neue geometrische Freiheiten. Während früher bestimmte Bauteilgeometrien aus Stabilitätsgründen aus mehreren Teilen zusammengesetzt werden mussten, können sie heute zunehmend monolithisch tiefgezogen werden.
Dies spart Gewicht, reduziert die Anzahl von Fügepunkten und erhöht die strukturelle Integrität. Der Trend geht also klar in Richtung integrierter, automatisierter und digital überwachter Tiefziehprozesse, die auf die spezifischen Anforderungen der Luftfahrt abgestimmt sind. Durch die Verbindung aus bewährter Umformtechnik und modernster Technologie erfüllt das Tiefziehen nicht nur die extremen Anforderungen dieser Branche, sondern schafft auch neue Spielräume für innovative Leichtbaulösungen und effiziente Serienproduktion sicherheitskritischer Komponenten.
Ein weiterer zukunftsweisender Aspekt ist die zunehmende Integration von adaptiven Steuerungssystemen in Tiefziehprozesse für die Luftfahrt. Diese Systeme reagieren in Echtzeit auf kleinste Prozessabweichungen – etwa Veränderungen in der Materialcharge, Temperatur oder Schmierstoffverteilung – und passen Ziehgeschwindigkeit, Presskraft oder Werkzeugposition dynamisch an. Diese Intelligenz im Prozess verhindert Fehler noch bevor sie entstehen und erhöht damit die Reproduzierbarkeit und Ausbeute in der Fertigung. Gleichzeitig reduziert sie den Bedarf an nachträglichen Korrekturen oder Ausschuss, was gerade bei kostenintensiven Materialien ein entscheidender Vorteil ist.
Auch die Zusammenarbeit zwischen Materialwissenschaft und Fertigungstechnologie wird immer enger. Neue, speziell für Umformprozesse entwickelte Werkstoffe mit optimierten Mikrostrukturen bieten deutlich verbesserte Umformeigenschaften bei gleichbleibender Festigkeit. Solche Entwicklungen entstehen häufig in enger Kooperation zwischen Werkstoffherstellern, Forschungsinstituten und Luftfahrtunternehmen und führen zu Bauteilen, die nicht nur leichter und stabiler sind, sondern sich auch besser verarbeiten lassen.
Darüber hinaus eröffnet die Kombination von Tiefziehen mit additiven Fertigungsverfahren zusätzliche Möglichkeiten. So lassen sich beispielsweise Grundstrukturen tiefziehen und anschließend durch 3D-Druck gezielt funktionale Elemente ergänzen – etwa Halterungen, Verstärkungen oder Dämpfungselemente. Diese Hybridansätze erweitern das Spektrum an Bauteildesigns und erlauben eine effizientere Fertigung hochkomplexer Strukturen, die bisher nur durch teure Schweiß- oder Montageprozesse realisierbar waren.
Auch in der Wartung und Ersatzteilversorgung könnte das Tiefziehen eine zunehmend relevante Rolle spielen, insbesondere in Kombination mit modularen Fertigungskonzepten. Durch flexible Werkzeuge und adaptierbare Prozesse können spezifische Komponenten für ältere Flugzeugtypen schnell und bedarfsgerecht nachgefertigt werden – ein klarer Vorteil gegenüber konventionellen Lager- und Beschaffungsstrategien.
Insgesamt zeigt sich, dass das Tiefziehen in der Luftfahrt weit mehr ist als ein klassisches Umformverfahren. Es entwickelt sich kontinuierlich weiter – durch Integration intelligenter Steuerung, durch Kombination mit neuen Fertigungstechnologien, durch materialseitige Innovationen und durch Digitalisierung auf allen Ebenen. Diese Entwicklung macht das Tiefziehen zu einem unverzichtbaren Bestandteil der modernen Luftfahrtproduktion, der nicht nur den hohen technischen Anforderungen gerecht wird, sondern auch langfristig zur Effizienz, Sicherheit und Innovationskraft der gesamten Branche beiträgt.
Die Bedeutung von Schmierstoffen beim Tiefziehen
Schmierstoffe spielen beim Tiefziehen eine entscheidende Rolle, da sie maßgeblich den Erfolg und die Qualität des Umformprozesses beeinflussen. Ihre Hauptaufgaben bestehen darin, Reibung zwischen Blech und Werkzeug zu reduzieren, Verschleiß an den Werkzeugoberflächen zu minimieren und die Materialfließfähigkeit zu verbessern. Dadurch ermöglichen sie eine gleichmäßige Umformung des Werkstoffs, verhindern Risse, Faltenbildung und Beschädigungen am Bauteil.
Ohne geeignete Schmierung kann es zu erhöhtem Werkzeugverschleiß kommen, was nicht nur die Werkzeugstandzeit verkürzt, sondern auch zu schlechteren Bauteilqualitäten führt. Hohe Reibung verursacht zudem höhere Umformkräfte, was den Energieverbrauch steigert und die Belastung der Maschine erhöht.
Die Auswahl des richtigen Schmierstoffs hängt von verschiedenen Faktoren ab, darunter die Art des Werkstoffs (z. B. Aluminium, Stahl, Titan), die Oberflächenbeschaffenheit, die Umformtemperatur und die Komplexität des Bauteils. So werden für Aluminiumbleche oft wasserbasierte Schmierstoffe oder Pasten eingesetzt, die eine ausreichende Schmierwirkung bei gleichzeitiger guter Reinigbarkeit gewährleisten. Für hochfeste Stähle oder titanbasierte Legierungen kommen häufig synthetische oder mineralölbasierte Schmierstoffe mit speziellen Additiven zum Einsatz, die hohen Drücken und Temperaturen standhalten.
Neben der Schmierwirkung ist auch die einfache Entfern- und Reinigbarkeit wichtig, besonders bei Bauteilen, die später lackiert, beschichtet oder weiterverarbeitet werden. Rückstände von Schmierstoffen können sonst zu Haftungsproblemen oder Korrosion führen.
Im industriellen Einsatz werden oft auch Mehrphasen-Schmierstoffe verwendet, die beispielsweise einen festen Schmierstoffanteil (wie Graphit oder Molybdändisulfid) mit flüssigen Trägerstoffen kombinieren. Diese gewährleisten auch bei extremen Bedingungen eine dauerhafte Schmierfilmbildung.
Darüber hinaus gewinnt die ökologische Verträglichkeit von Schmierstoffen zunehmend an Bedeutung. Umweltfreundliche, biologisch abbaubare oder leicht entfernbarere Schmierstoffe sind gefragt, um den Umweltschutzanforderungen gerecht zu werden und die Entsorgungskosten zu senken.
Zusammenfassend sind Schmierstoffe beim Tiefziehen unverzichtbar, um die Prozesssicherheit zu erhöhen, Werkzeug und Werkstück zu schonen und eine gleichbleibend hohe Bauteilqualität sicherzustellen. Die sorgfältige Auswahl und Anwendung des passenden Schmierstoffsystems trägt entscheidend zur Wirtschaftlichkeit und Nachhaltigkeit des Tiefziehprozesses bei.
Neben der Auswahl des richtigen Schmierstoffs ist auch die korrekte Applikation entscheidend für den Erfolg beim Tiefziehen. Schmierstoffe können je nach Prozessanforderung in Form von Sprays, Pasten, Flüssigkeiten oder Folien aufgetragen werden. Die Dosierung muss so gewählt werden, dass genügend Schmierfilm entsteht, um Reibung zu reduzieren, ohne jedoch übermäßige Rückstände zu hinterlassen, die das Nachbearbeiten erschweren. Moderne Applikationssysteme ermöglichen eine präzise und gleichmäßige Verteilung, oft auch automatisiert, um Schwankungen im Prozess zu minimieren.
Darüber hinaus beeinflussen auch Umgebungsbedingungen wie Temperatur, Luftfeuchtigkeit oder die Dauer des Umformprozesses die Schmierwirkung. Insbesondere bei Warm- oder Halbwarmziehen müssen Schmierstoffe hohen Temperaturen standhalten, ohne ihre Eigenschaften zu verlieren oder Rückstände zu verkohlen, die das Werkzeug beschädigen könnten.
Ein weiterer wichtiger Aspekt ist die Wechselwirkung zwischen Schmierstoff und Werkzeugoberfläche. Durch spezielle Oberflächenbehandlungen oder Beschichtungen der Werkzeuge kann die Haftung des Schmierfilms verbessert und der Verschleiß weiter reduziert werden. Beispielsweise führen Beschichtungen mit Diamant-ähnlichen Kohlenstoffschichten (DLC) oder Titannitrid (TiN) zu einer niedrigeren Reibung und längeren Standzeiten, was in Kombination mit passenden Schmierstoffen optimale Ergebnisse erzielt.
Die Überwachung des Schmierstoffverbrauchs und der Schmierfilmdicke während des Prozesses wird zunehmend durch sensorbasierte Systeme unterstützt. So können Fertigungsanlagen in Echtzeit erkennen, ob die Schmierung ausreichend ist, und bei Bedarf nachregeln. Dies vermeidet Prozessunterbrechungen und sichert eine konstante Produktqualität.
Zusätzlich spielt die Umwelt- und Arbeitssicherheit eine wichtige Rolle. Da Schmierstoffe oft ölbasierend sind, ist die Handhabung, Lagerung und Entsorgung unter Berücksichtigung ökologischer und gesundheitlicher Vorschriften zu organisieren. Biologisch abbaubare Schmierstoffe und solche mit geringem Geruchs- oder Dampfaufkommen gewinnen deshalb an Bedeutung.
Insgesamt sind Schmierstoffe beim Tiefziehen weit mehr als nur Hilfsmittel. Sie sind integraler Bestandteil des Fertigungsprozesses, der durch sorgfältige Auswahl, präzise Anwendung und kontinuierliche Überwachung maßgeblich zur Effizienz, Qualität und Nachhaltigkeit beiträgt.
Darüber hinaus entwickeln Hersteller zunehmend spezialisierte Schmierstoffformulierungen, die genau auf bestimmte Tiefziehprozesse und Werkstoffkombinationen abgestimmt sind. Solche maßgeschneiderten Schmierstoffe berücksichtigen etwa die unterschiedlichen Reibungscharakteristika von Aluminium- oder Stahlblechen, die thermischen Belastungen bei Warmumformung oder die spezifischen Anforderungen an die Oberflächenqualität der Bauteile. Durch gezielte Additive können beispielsweise Verschleißschutz, Korrosionshemmung oder auch die Reinigungsfähigkeit verbessert werden, ohne dass dabei die Umweltverträglichkeit leiden muss.
Ein weiterer Trend ist die Integration von Schmierstoffmanagement in digitale Fertigungskonzepte. So werden Verbrauchsdaten und Prozessparameter in Echtzeit erfasst und analysiert, um Schmierstoffeinsatz, Wartungsintervalle und Werkzeugstandzeiten optimal aufeinander abzustimmen. Das führt zu einer ressourcenschonenderen Produktion mit weniger Ausschuss und geringerem Energieverbrauch.
In speziellen Fällen, wie bei der Fertigung von Hochpräzisionsteilen oder bei der Verarbeitung besonders empfindlicher Werkstoffe, können auch trockene Schmierverfahren zum Einsatz kommen. Hier ersetzen beispielsweise Pulverbeschichtungen oder feststoffbasierte Schmierstoffe die klassischen flüssigen Medien und minimieren das Risiko von Schmierstoffrückständen, die die Funktion oder das Aussehen der Bauteile beeinträchtigen könnten.
Zusammenfassend lässt sich sagen, dass Schmierstoffe beim Tiefziehen eine komplexe und dynamische Rolle spielen. Sie sind nicht nur technische Hilfsmittel, sondern zunehmend auch strategische Komponenten eines ganzheitlichen Fertigungskonzepts. Durch innovative Formulierungen, intelligente Applikation und Integration in digitale Systeme tragen sie entscheidend dazu bei, dass Tiefziehprozesse heute effizienter, umweltfreundlicher und qualitativ hochwertiger ablaufen als je zuvor.
Tiefziehen von dünnen Blechen: Techniken und Herausforderungen
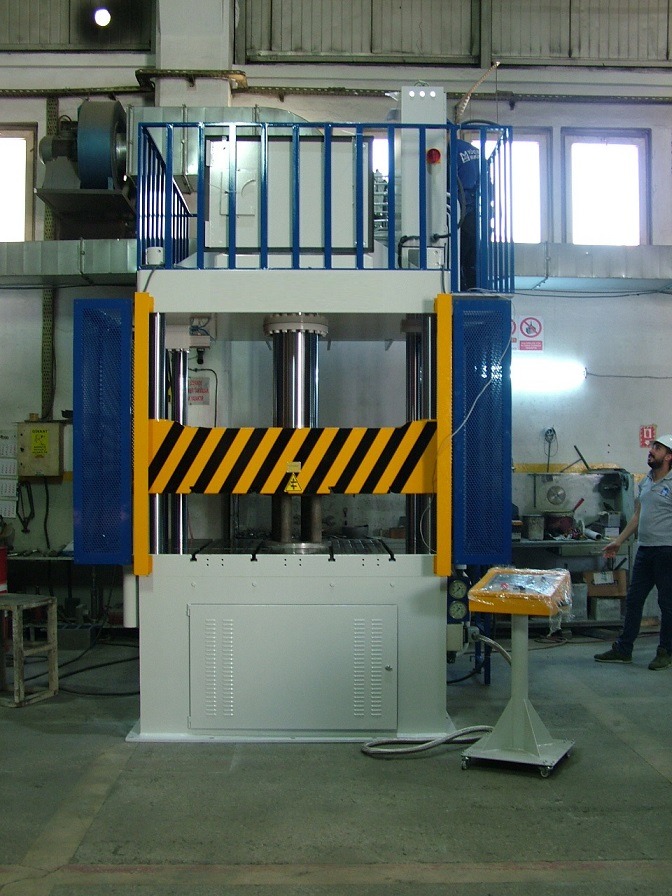
Das Tiefziehen von dünnen Blechen stellt besondere Anforderungen an den Umformprozess, da dünne Werkstoffe empfindlicher gegenüber Rissen, Faltenbildung und Materialverformungen sind. Dünnbleche finden in vielen Branchen Anwendung, etwa in der Automobilindustrie, Elektronik oder im Gerätebau, wo geringe Wandstärken zur Gewichtsreduzierung und Materialersparnis beitragen.
Eine der zentralen Herausforderungen beim Tiefziehen dünner Bleche ist die Kontrolle der Materialfließung. Aufgrund der geringen Dicke besteht eine erhöhte Gefahr, dass sich das Material ungleichmäßig verteilt, was zu Falten oder Einziehungen führt. Um dem entgegenzuwirken, werden spezielle Techniken eingesetzt, wie etwa die gezielte Einstellung der Ziehgeschwindigkeit und der Ziehkraft sowie die Verwendung von angepasstem Werkzeugdesign, das die Blechspannung optimal steuert.
Die Verwendung von Schmierstoffen ist beim Tiefziehen dünner Bleche besonders wichtig, da sie die Reibung minimieren und so Materialschäden verhindern. Gleichzeitig muss die Schmierung jedoch sehr präzise dosiert werden, um ein Verrutschen des Blechs zu vermeiden, das Faltenbildung begünstigen könnte.
Ein weiteres Problem sind Risse am Werkstoffrand, die durch zu hohe Zugspannungen entstehen können. Hier hilft der Einsatz von sogenannten Randbeschickungs- oder Flanschwerkzeugen, die den Materialfluss an den kritischen Stellen verbessern und somit die Gefahr von Rissen reduzieren.
Um das Umformverhalten dünner Bleche besser zu kontrollieren, kommen häufig Simulationssoftware und prozessintegrierte Sensoren zum Einsatz. Sie erlauben es, den Tiefziehprozess im Voraus zu optimieren und während der Produktion Echtzeitdaten zu erfassen, um eventuelle Prozessabweichungen frühzeitig zu erkennen und zu korrigieren.
Bei besonders dünnen oder empfindlichen Materialien wird oft das Hydroforming als Variante des Tiefziehens genutzt. Hierbei unterstützt ein Flüssigkeitsdruck den Umformvorgang und sorgt für eine gleichmäßige Materialverteilung, was die Gefahr von Beschädigungen reduziert.
Insgesamt erfordert das Tiefziehen von dünnen Blechen eine Kombination aus präziser Prozesssteuerung, geeigneten Werkzeugen und optimaler Materialauswahl. Nur so lassen sich hochwertige Bauteile mit minimaler Wandstärke, hoher Maßhaltigkeit und guter Oberflächenqualität fertigen, die den Anforderungen moderner Anwendungen gerecht werden.
Beim Tiefziehen dünner Bleche spielt auch die Werkstoffauswahl eine entscheidende Rolle. Da dünne Bleche besonders anfällig für Versprödung oder Mikrorisse sind, werden häufig spezielle hochfeste und zähe Legierungen eingesetzt, die eine bessere Umformbarkeit bei gleichzeitig hoher Festigkeit bieten. Ebenso wichtig ist die homogene Materialqualität ohne Einschlussfehler oder ungleichmäßige Dickeverteilung, da solche Defekte bei dünnen Blechen sofort zu Formproblemen oder Ausfällen führen können.
Ein weiterer technischer Ansatz, um die Herausforderungen beim Tiefziehen dünner Bleche zu meistern, ist die Optimierung des Werkzeugdesigns. Durch präzise angepasste Radien, flexible Werkzeugelemente oder sogar aktive Werkzeuge mit einstellbaren Parametern lässt sich die Materialspannung gezielt steuern. Dadurch werden Spannungsspitzen vermieden, die häufig Ausgangspunkt für Risse oder Falten sind. Zudem können Werkzeuge mit verbesserten Oberflächenbeschichtungen die Reibung weiter senken und somit eine sanftere Umformung gewährleisten.
Die Prozessparameter wie Ziehgeschwindigkeit, Schmierstoffauftrag und Ziehkraft müssen bei dünnen Blechen besonders fein abgestimmt werden. Zu hohe Geschwindigkeiten können zu Instabilitäten im Materialfluss führen, während zu geringe Kräfte eventuell unzureichende Formgebung bewirken. Daher ist eine präzise Regelung der Maschinensteuerung notwendig, um das Gleichgewicht zwischen Umformgeschwindigkeit und Materialbeanspruchung optimal zu halten.
In der industriellen Praxis kommen oft Mehrstufen-Tiefziehprozesse zum Einsatz, bei denen das Bauteil schrittweise geformt wird. Diese Methode minimiert das Risiko von Fehlern, da das Material in mehreren kontrollierten Schritten umgeformt und entspannt wird, bevor die finale Geometrie erreicht ist. Besonders bei dünnen Blechen trägt dies zur Reduktion von Spannungen und zur Verbesserung der Bauteilqualität bei.
Nicht zuletzt gewinnt auch die Nachbearbeitung an Bedeutung, um die Qualität der tiefgezogenen dünnen Bauteile sicherzustellen. Verfahren wie Gleitschleifen, Polieren oder chemisches Entgraten werden eingesetzt, um Oberflächenfehler zu beseitigen, Gratbildung zu vermeiden und die Bauteilfunktionalität zu gewährleisten.
Zusammenfassend ist das Tiefziehen dünner Bleche ein komplexer Prozess, der fundiertes Know-how, moderne Technologien und präzise Prozesssteuerung erfordert. Nur durch das Zusammenspiel all dieser Faktoren lassen sich dünnwandige Bauteile fertigen, die den hohen Anforderungen an Leichtbau, Stabilität und Oberflächenqualität in modernen Industriezweigen gerecht werden.
Darüber hinaus gewinnen im Tiefziehen dünner Bleche zunehmend intelligente Überwachungssysteme an Bedeutung. Diese erfassen während des Umformprozesses kontinuierlich Daten wie Kraftverlauf, Werkzeugposition oder Materialdehnung. Mithilfe von Algorithmen zur Prozessanalyse können Abweichungen frühzeitig erkannt und Gegenmaßnahmen eingeleitet werden. So lassen sich Ausschussraten minimieren und die Prozessstabilität deutlich erhöhen.
Ein weiterer Trend ist die Kombination des Tiefziehens mit hybriden Fertigungstechnologien. Beispielsweise können vorgefertigte Strukturen durch Laserstrahlschweißen oder Klebetechniken ergänzt werden, um die Funktionalität oder Stabilität der dünnen Bleche gezielt zu verbessern. Diese hybride Vorgehensweise ermöglicht komplexe Bauteildesigns, die mit reinem Tiefziehen allein nur schwer realisierbar wären.
Im Bereich der Materialentwicklung werden zunehmend funktionalisierte Oberflächen erforscht, die die Umformbarkeit dünner Bleche verbessern. Dazu gehören etwa spezielle Beschichtungen, die Reibung reduzieren oder die Haftung von Schmierstoffen verbessern. Solche Oberflächen tragen dazu bei, die Prozessfenster zu erweitern und die Herstellung empfindlicher Bauteile zu erleichtern.
Nicht zuletzt spielt auch die Nachhaltigkeit eine immer größere Rolle. Die Reduzierung von Materialverschnitt und der Einsatz umweltfreundlicher Schmierstoffe sowie energiesparender Maschinenkonzepte sind wichtige Faktoren, um die ökologische Bilanz beim Tiefziehen dünner Bleche zu verbessern.
Insgesamt zeigt sich, dass das Tiefziehen dünner Bleche ein dynamisches Feld ist, das ständig durch technologische Innovationen und interdisziplinäre Ansätze weiterentwickelt wird. Diese Fortschritte tragen dazu bei, den steigenden Anforderungen an Leichtbau, Präzision und Wirtschaftlichkeit in zahlreichen Industriezweigen gerecht zu werden.
Formen und Fertigen: Tiefziehen von komplexen Bauteilen
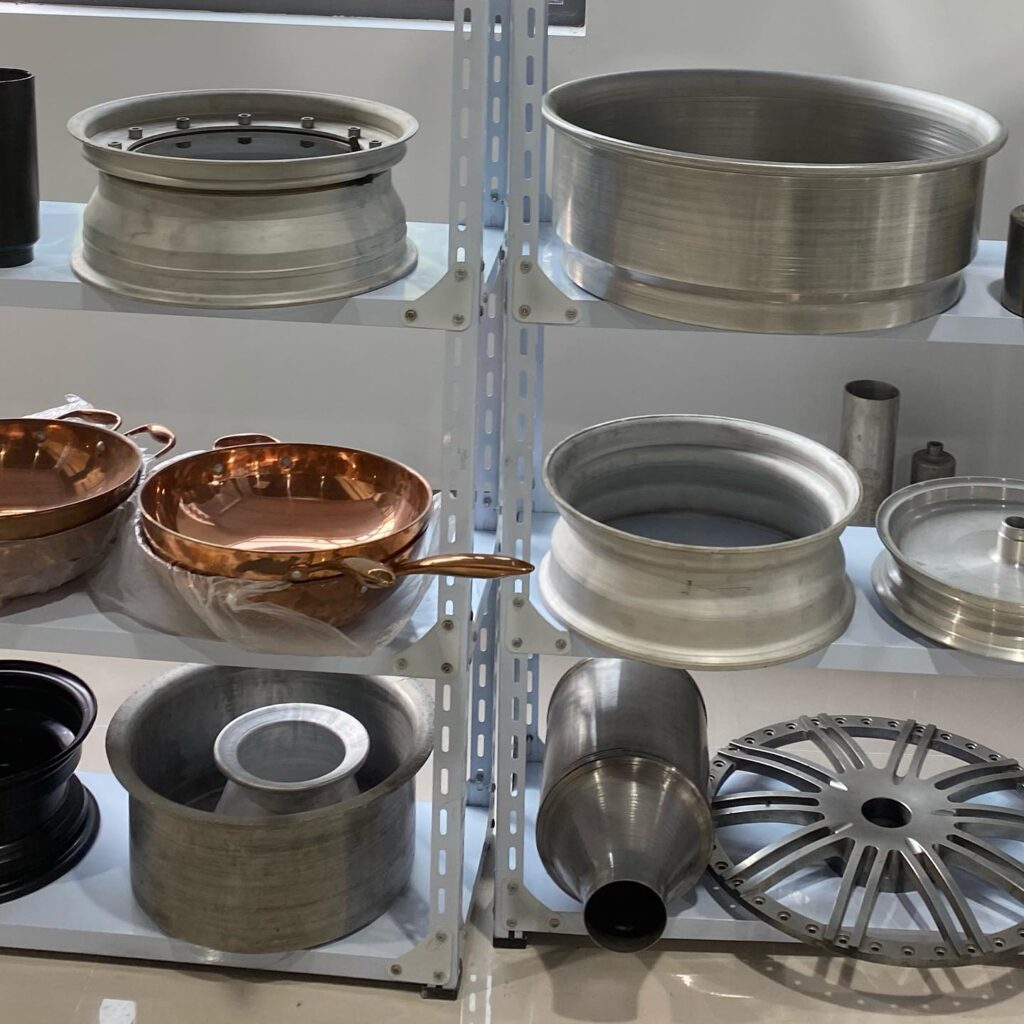
Das Tiefziehen komplexer Bauteile stellt besondere Anforderungen an Werkzeugkonstruktion, Prozesssteuerung und Materialauswahl. Komplexe Geometrien mit mehreren Radien, Hinterschneidungen oder variierenden Wandstärken erfordern präzise abgestimmte Tiefziehprozesse, um Verformungsfehler wie Faltenbildung, Risse oder ungleichmäßige Wanddicken zu vermeiden.
Ein wesentlicher Aspekt ist das Werkzeugdesign. Hier kommen häufig Mehrkomponenten-Werkzeuge zum Einsatz, die beispielsweise flexible Stempel oder modulare Matrizen enthalten, um unterschiedlich geformte Bereiche optimal umzuformen. Moderne Werkzeuge werden oft mithilfe von CAD/CAM-Systemen entworfen und können durch CNC-Bearbeitung oder additive Fertigungsverfahren besonders komplex und passgenau hergestellt werden. Außerdem ermöglichen einstellbare Werkzeugparameter eine dynamische Anpassung des Prozesses, etwa durch variable Anpressdrücke oder wechselbare Ziehringe.
Die Prozesssteuerung komplexer Tiefziehvorgänge wird durch den Einsatz von Simulationen unterstützt. Finite-Elemente-Analysen (FEA) erlauben es, potenzielle Schwachstellen im Umformprozess schon vor der Fertigung zu identifizieren und Prozessparameter entsprechend anzupassen. So lassen sich beispielsweise kritische Stellen mit hohem Spannungsaufkommen oder potenzieller Faltenbildung gezielt optimieren. Diese virtuelle Prozessplanung spart Kosten und verkürzt Entwicklungszeiten.
Materialtechnisch kommen für komplexe Bauteile oft hochfeste oder schwer umformbare Legierungen zum Einsatz, deren Umformverhalten genau berücksichtigt werden muss. Hier helfen spezialisierte Schmierstoffe und Mehrstufenprozesse, um die Umformkräfte zu reduzieren und die Werkstoffstruktur bestmöglich zu erhalten.
Zur Fertigung komplexer Bauteile ist häufig ein Mehrstufiger Tiefziehprozess notwendig. Dabei wird das Werkstück in mehreren aufeinanderfolgenden Zieh- und Rückformschritten schrittweise geformt. Dieses Verfahren verringert die Gefahr von Materialversagen und ermöglicht eine bessere Kontrolle der Wanddickenverteilung.
Darüber hinaus kann die Kombination mit weiteren Umformverfahren wie dem Hydroforming oder dem Stretchforming helfen, besonders anspruchsvolle Geometrien herzustellen. Beim Hydroforming unterstützt ein Flüssigkeitsdruck das Umformen, was insbesondere bei tiefen oder sehr feinen Strukturen von Vorteil ist. Stretchforming ermöglicht eine gezielte Zugbelastung des Blechs und verbessert so die Maßhaltigkeit und Oberflächenqualität.
Die Nachbearbeitung komplexer Bauteile umfasst oft Entgraten, Oberflächenbehandlung und Qualitätskontrolle, um Funktionalität und Ästhetik sicherzustellen. Insbesondere bei sicherheitsrelevanten Bauteilen ist eine zerstörungsfreie Prüfung (z. B. Ultraschall- oder Röntgenprüfung) üblich, um Materialfehler auszuschließen.
Zusammenfassend ist das Tiefziehen komplexer Bauteile ein hochentwickelter Fertigungsprozess, der präzise Planung, innovative Werkzeugtechnologien und fundiertes Materialwissen erfordert. Durch die Kombination moderner Simulation, adaptiver Steuerung und Mehrstufenverfahren lassen sich auch anspruchsvolle Bauteilgeometrien wirtschaftlich und in hoher Qualität herstellen.
Um die Herausforderungen beim Tiefziehen komplexer Bauteile weiter zu meistern, gewinnt die Automatisierung in der Fertigung zunehmend an Bedeutung. Roboter und automatisierte Handling-Systeme sorgen für präzise Positionierung der Bleche, zuverlässiges Zuführen und Entnehmen der Bauteile sowie für die Integration von Zwischenschritten wie Schmierstoffauftrag oder Qualitätsprüfung. Durch die Verkettung mehrerer Prozessschritte in einer automatisierten Fertigungslinie lassen sich Durchlaufzeiten reduzieren und Prozessstabilität erhöhen.
Ein weiterer wichtiger Faktor ist die Prozessüberwachung in Echtzeit. Sensoren messen Kräfte, Verformungen und Temperaturen während des Tiefziehens, während fortschrittliche Algorithmen Abweichungen vom Sollzustand erkennen und automatisch Gegensteuerungen einleiten können. So werden Ausschuss und Maschinenstillstände minimiert.
Im Bereich der Werkstoffe werden zunehmend hochfeste und formbare Legierungen sowie Mehrschichtverbunde eingesetzt, um komplexe Bauteile mit hoher Festigkeit und gleichzeitig niedrigem Gewicht herzustellen. Diese Werkstoffe erfordern eine besonders sorgfältige Prozessauslegung, da ihre Umformbarkeit oft begrenzt ist.
Die Verbindung von Tiefziehen mit nachgelagerten Fertigungsverfahren, wie Schweißen, Kleben oder Beschichten, ermöglicht es, Funktionsintegration und Designfreiheit weiter zu steigern. So lassen sich beispielsweise Bauteile mit integrierten Dichtungen oder Verstärkungen fertigen, die früher aus mehreren Einzelteilen zusammengesetzt wurden.
Nicht zuletzt trägt die fortschreitende Digitalisierung und Vernetzung der Fertigungssysteme – oft im Kontext von Industrie 4.0 – dazu bei, dass Tiefziehprozesse von komplexen Bauteilen immer flexibler, effizienter und transparenter werden. Datenanalyse und Machine Learning unterstützen die Prozessoptimierung, während digitale Zwillinge die Entwicklung und Produktion virtuell abbilden.
Insgesamt führt die Kombination aus innovativen Werkzeugtechnologien, intelligenter Prozesssteuerung, modernen Werkstoffen und digitaler Vernetzung dazu, dass das Tiefziehen komplexer Bauteile heute eine Schlüsselrolle in der modernen industriellen Fertigung einnimmt – mit stetig wachsendem Potenzial für Qualität, Effizienz und Designfreiheit.
Zusätzlich eröffnen neue Fertigungstechnologien wie das additive Fertigen von Werkzeugkomponenten völlig neue Möglichkeiten im Tiefziehprozess komplexer Bauteile. Durch 3D-Druck lassen sich Werkzeuge mit integrierten Kühlkanälen, variablen Wandstärken oder sogar flexiblen Segmenten herstellen, die eine noch präzisere Steuerung der Umformkräfte und -temperaturen erlauben. Solche innovativen Werkzeuge erhöhen die Prozessstabilität und verlängern die Standzeiten.
Auch die Entwicklung intelligenter Werkstoffbeschichtungen trägt zur Verbesserung des Tiefziehprozesses bei. Beschichtungen, die selbstheilende oder reibungsmindernde Eigenschaften besitzen, können den Verschleiß an kritischen Werkzeugstellen deutlich reduzieren. Zudem helfen Beschichtungen dabei, die Schmierstoffaufnahme und -verteilung zu optimieren, was besonders bei komplexen Geometrien von Vorteil ist.
Die Integration von künstlicher Intelligenz (KI) und Machine-Learning-Verfahren gewinnt zunehmend an Bedeutung. Diese Technologien ermöglichen es, große Mengen an Prozessdaten auszuwerten, Muster zu erkennen und Vorhersagen zur Prozessstabilität oder Werkzeugstandzeit zu treffen. Dadurch kann der Tiefziehprozess in Echtzeit optimiert und auf wechselnde Bedingungen flexibel reagiert werden.
Auch im Bereich der Nachhaltigkeit werden innovative Ansätze verfolgt: Der Materialverbrauch wird durch präzisere Simulationen und optimierte Werkzeuge minimiert, Recyclingfähige Schmierstoffe und Werkstoffe reduzieren Umweltbelastungen, und energiesparende Maschinenkonzepte senken den CO₂-Fußabdruck der Fertigung.
Schließlich sind Schulung und Weiterbildung der Fachkräfte entscheidend, um die vielfältigen technologischen Möglichkeiten im Tiefziehen komplexer Bauteile voll auszuschöpfen. Nur durch fundiertes Prozessverständnis und interdisziplinäres Know-how können moderne Fertigungskonzepte erfolgreich umgesetzt werden.
Insgesamt zeigt sich, dass das Tiefziehen komplexer Bauteile ein hochdynamisches Feld ist, das kontinuierlich durch technologische Innovationen, digitale Vernetzung und nachhaltige Ansätze vorangetrieben wird. Diese Entwicklungen eröffnen neue Perspektiven für die industrielle Produktion von Bauteilen mit hoher Präzision, Funktionalität und Wirtschaftlichkeit.
Darüber hinaus gewinnt die Zusammenarbeit zwischen Materialwissenschaftlern, Konstrukteuren und Fertigungstechnikern immer mehr an Bedeutung. Nur durch ein interdisziplinäres Zusammenspiel lassen sich maßgeschneiderte Lösungen für komplexe Tiefziehaufgaben entwickeln. Frühzeitige Abstimmung bei der Bauteilgestaltung und Materialauswahl kann potenzielle Probleme bereits in der Planungsphase minimieren und die spätere Produktion deutlich effizienter gestalten.
Ein weiterer Aspekt ist die zunehmende Integration von virtuellen Prototypen und digitalen Zwillingen in die Entwicklung und Fertigung. Digitale Zwillinge bilden das reale Tiefziehwerkzeug und den Umformprozess virtuell ab, sodass verschiedene Szenarien simuliert und optimiert werden können, bevor physische Prototypen gefertigt werden. Dies spart Zeit und Kosten und erhöht gleichzeitig die Prozesssicherheit.
Auch die flexible Fertigung rückt stärker in den Fokus, um auf wechselnde Marktanforderungen reagieren zu können. Modular aufgebaute Werkzeugsysteme und anpassbare Prozessparameter ermöglichen eine schnelle Umstellung auf unterschiedliche Bauteilgeometrien oder Materialtypen, was besonders in kleinen und mittleren Losgrößen von Vorteil ist.
Nicht zuletzt spielen ergonomische und sicherheitstechnische Gesichtspunkte bei der Gestaltung der Tiefziehmaschinen und Fertigungszellen eine wichtige Rolle. Moderne Anlagen sind darauf ausgelegt, die Bediener zu entlasten und Risiken zu minimieren, was zu einer höheren Produktivität und Mitarbeiterzufriedenheit führt.
Insgesamt macht die Kombination aus technologischem Fortschritt, interdisziplinärer Zusammenarbeit und flexibler Produktion das Tiefziehen komplexer Bauteile zu einem zukunftsweisenden Fertigungsverfahren, das den Anforderungen moderner Industrie 4.0-Umgebungen gerecht wird und gleichzeitig höchste Qualitätsstandards erfüllt.
Tiefziehen in der Automobilindustrie: Anwendungen und Trends
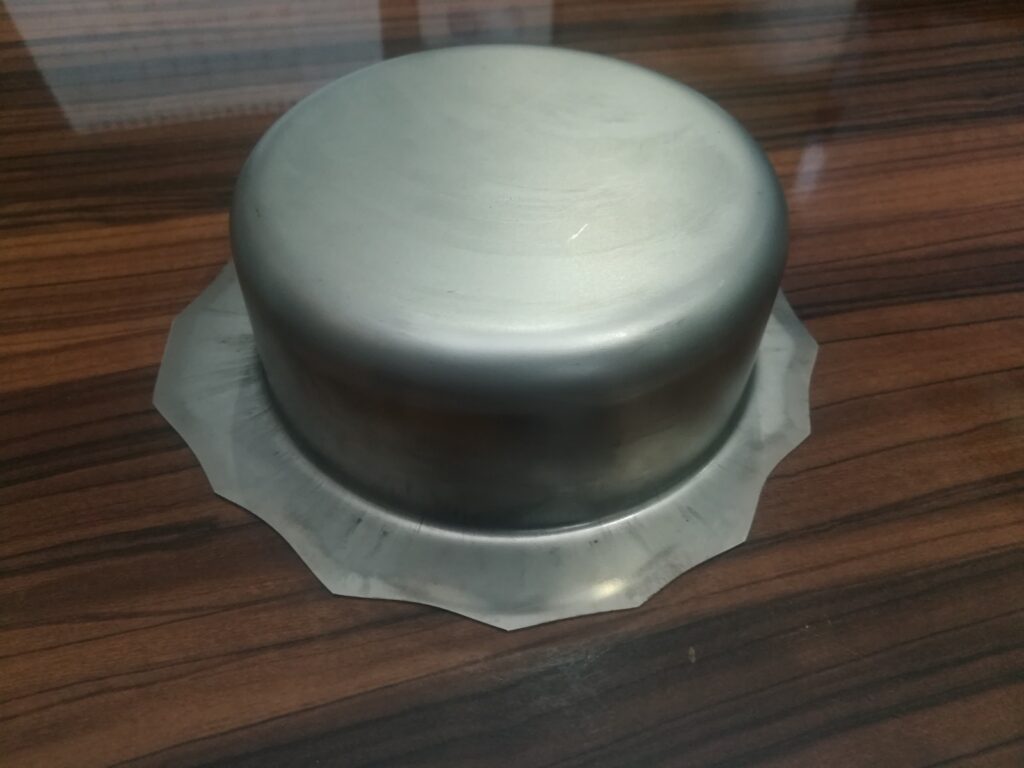
Das Tiefziehen spielt in der Automobilindustrie eine zentrale Rolle bei der Herstellung von Karosseriebauteilen, Strukturkomponenten und Innenraumelementen. Aufgrund der hohen Anforderungen an Leichtbau, Sicherheit und Design ist das Tiefziehen ideal, um komplexe, maßhaltige Bauteile mit dünnen Wandstärken herzustellen, die gleichzeitig stabil und formschön sind.
Typische Anwendungen umfassen äußere Karosseriebleche wie Türen, Kotflügel, Motorhauben und Dachpaneele, aber auch strukturelle Bauteile wie Verstärkungen, Säulen oder Rahmenkomponenten. Darüber hinaus werden innenliegende Bauteile wie Instrumententafeln, Sitzrahmen oder Abdeckungen im Tiefziehverfahren gefertigt.
Ein wichtiger Trend in der Automobilindustrie ist die Verwendung von hochfesten und ultrahochfesten Stählen (HSS und UHSS) sowie Leichtbaumaterialien wie Aluminium und Magnesiumlegierungen. Diese Materialien ermöglichen eine Gewichtsreduktion bei gleichzeitiger Erhöhung der Fahrzeugsicherheit und Energieeffizienz, stellen aber auch besondere Herausforderungen an das Tiefziehverfahren aufgrund ihrer eingeschränkten Umformbarkeit.
Zur Bewältigung dieser Herausforderungen kommen Mehrstufen-Tiefziehprozesse, Hydroforming und Kombinationen mit anderen Umformverfahren zum Einsatz, die eine präzise Steuerung der Materialfließung und Spannungen erlauben. Ebenso gewinnen innovative Schmierstoffe und Werkzeugbeschichtungen an Bedeutung, um Verschleiß zu reduzieren und die Prozesssicherheit zu erhöhen.
Die zunehmende Digitalisierung der Fertigung – oft im Rahmen von Industrie 4.0 – führt zu einer besseren Prozessüberwachung und -optimierung. Sensorik, KI-gestützte Analysen und digitale Zwillinge helfen, Ausschuss zu minimieren, Werkzeugstandzeiten zu verlängern und die Produktionskosten zu senken.
Nicht zuletzt treiben Nachhaltigkeitsaspekte die Entwicklung voran: Der Einsatz recyclingfähiger Materialien, energieeffizienter Maschinen und umweltfreundlicher Schmierstoffe wird immer wichtiger, um den ökologischen Fußabdruck der Automobilfertigung zu reduzieren.
Zusammengefasst ist das Tiefziehen in der Automobilindustrie ein hochdynamischer Bereich, der durch technische Innovationen, Materialentwicklung und digitale Vernetzung kontinuierlich weiterentwickelt wird, um den Anforderungen moderner Fahrzeuge gerecht zu werden.
Ein weiterer bedeutender Trend im Tiefziehen der Automobilindustrie ist die zunehmende Integration von Leichtbaukonzepten. Die Automobilhersteller setzen verstärkt auf dünnere und hochfeste Materialien, um das Fahrzeuggewicht zu reduzieren und damit Kraftstoffverbrauch und CO₂-Emissionen zu senken. Das Tiefziehen ermöglicht dabei die Herstellung von Bauteilen mit komplexen Formen und gleichzeitig minimaler Wandstärke, was für eine optimale Gewichtsreduktion sorgt.
Die Entwicklung von multifunktionalen Bauteilen gewinnt ebenfalls an Bedeutung. Hierbei werden durch gezielte Umform- und Fügeverfahren mehrere Funktionen in einem Bauteil kombiniert – zum Beispiel strukturelle Verstärkung und Integration von Befestigungspunkten oder Dichtungen. Dies führt zu einer Vereinfachung der Baugruppen, weniger Montageaufwand und höherer Zuverlässigkeit.
Ein weiterer Fokus liegt auf der Flexibilisierung der Fertigung. Die Nachfrage nach individualisierten Fahrzeugen erfordert flexible Produktionsanlagen, die schnell auf unterschiedliche Bauteilvarianten und Losgrößen reagieren können. Modulare Werkzeugkonzepte, adaptive Steuerungssysteme und automatisierte Handlinglösungen ermöglichen eine effiziente Fertigung auch kleinerer Serien ohne hohe Rüstzeiten.
Die Integration von sensorbasierten Qualitätskontrollen direkt im Tiefziehprozess stellt sicher, dass Form- und Oberflächenfehler frühzeitig erkannt werden. So lassen sich Ausschuss und Nacharbeit minimieren, was die Wirtschaftlichkeit der Produktion verbessert.
Schließlich wird das Thema Nachhaltigkeit durch den Einsatz von umweltfreundlichen Schmierstoffen, energiesparenden Maschinen und der Wiederverwertung von Restmaterialien immer wichtiger. Auch die Optimierung der Prozessketten unter ökologischen Gesichtspunkten wird in der Automobilindustrie intensiv verfolgt.
Insgesamt zeigt sich, dass das Tiefziehen in der Automobilindustrie nicht nur ein bewährtes Fertigungsverfahren ist, sondern durch ständige Innovationen und Anpassungen an neue Marktanforderungen eine Schlüsselrolle bei der Entwicklung moderner, leichter und sicherer Fahrzeuge einnimmt.
Ein weiterer wesentlicher Aspekt im Tiefziehprozess der Automobilindustrie ist die zunehmende Nutzung von digitalen Planungs- und Simulationswerkzeugen. Mithilfe von Finite-Elemente-Analysen (FEA) können Bauteil- und Prozessparameter bereits in der Entwicklungsphase optimiert werden, um potenzielle Schwachstellen wie Rissbildung oder Faltenwurf zu vermeiden. Dies führt zu kürzeren Entwicklungszeiten, geringeren Prototypkosten und einer höheren Prozesssicherheit.
Zusätzlich werden immer häufiger intelligente Fertigungssysteme eingesetzt, die mit Hilfe von Sensoren und Echtzeitdaten die Prozessparameter automatisch anpassen. Beispielsweise kann die Ziehgeschwindigkeit, der Anpressdruck oder der Schmierstoffeinsatz je nach Materialverhalten dynamisch geregelt werden. Dies ermöglicht eine bessere Kontrolle und höhere Qualität bei variierenden Materialchargen oder Umgebungsbedingungen.
Die Automobilindustrie experimentiert auch mit neuen Werkstoffen und Materialkombinationen, wie etwa hybriden Verbundmaterialien oder umformbaren Hochleistungs-Kunststoffen, die mittels Tiefziehen verarbeitet werden können. Diese Materialien bieten Potenziale zur weiteren Gewichtsreduktion und Funktionsintegration, erfordern aber eine enge Abstimmung zwischen Materialwissenschaft und Fertigungstechnik.
Ein weiterer Trend ist die verstärkte Zusammenarbeit zwischen Automobilherstellern und Zulieferern im Rahmen von integrierten Wertschöpfungsketten. Durch eine enge Verzahnung von Konstruktion, Entwicklung und Produktion können Prozesse besser aufeinander abgestimmt und Innovationen schneller umgesetzt werden.
Abschließend lässt sich sagen, dass das Tiefziehen in der Automobilindustrie ein hochkomplexer und dynamischer Prozess ist, der durch technische Innovationen, Digitalisierung und enge Kooperationen geprägt wird. Diese Entwicklungen sichern die Wettbewerbsfähigkeit und ermöglichen die Produktion moderner Fahrzeuge, die den hohen Ansprüchen an Sicherheit, Effizienz und Design gerecht werden.
Darüber hinaus spielt die Automatisierung der Tiefziehprozesse eine immer größere Rolle in der Automobilproduktion. Roboter übernehmen das Be- und Entladen der Werkzeuge, die Handhabung der Bleche und das Ausrichten der Bauteile, was zu einer höheren Prozessstabilität und Produktivität führt. Durch die Vernetzung dieser automatisierten Systeme mit übergeordneten Produktionssteuerungen lassen sich Fertigungslinien flexibel an unterschiedliche Produktvarianten anpassen.
Ein weiterer wichtiger Trend ist der Einsatz von nachhaltigen Produktionsmethoden. Automobilhersteller setzen vermehrt auf energieeffiziente Maschinen, um den CO₂-Ausstoß der Fertigung zu reduzieren. Gleichzeitig werden umweltfreundliche Schmierstoffe verwendet, die biologisch abbaubar sind und die Entsorgung vereinfachen. Zudem wird der Materialeinsatz durch optimierte Werkzeuggeometrien und Simulationen reduziert, um Abfall zu minimieren.
Auch die Qualitätskontrolle hat sich durch neue Technologien weiterentwickelt. Inline-Messsysteme und optische Inspektionsverfahren erfassen in Echtzeit die Maßhaltigkeit, Oberflächenbeschaffenheit und eventuelle Fehler im Tiefziehprozess. Diese Daten fließen direkt in die Prozesssteuerung ein und ermöglichen eine sofortige Korrektur, was Ausschusskosten senkt und die Gesamteffizienz erhöht.
Nicht zuletzt fördert die zunehmende Modularisierung der Fahrzeugarchitektur die Entwicklung standardisierter Tiefziehprozesse, die für verschiedene Bauteile adaptiert werden können. Dadurch lassen sich Kosten senken und die Produktion von unterschiedlichen Modellen mit ähnlichen Bauteilen wirtschaftlicher gestalten.
Insgesamt zeigt sich, dass das Tiefziehen in der Automobilindustrie ein komplexes Zusammenspiel aus Materialtechnik, Prozessinnovation, Digitalisierung und Nachhaltigkeit ist. Diese Faktoren sind entscheidend, um den ständig steigenden Anforderungen an moderne Fahrzeuge gerecht zu werden und gleichzeitig effizient und umweltbewusst zu produzieren.
Werkstofftechnik beim Tiefziehen: Einfluss auf die Fertigung
Die Werkstofftechnik spielt beim Tiefziehen eine entscheidende Rolle, da die Eigenschaften des verwendeten Materials maßgeblich den Erfolg und die Qualität des Umformprozesses beeinflussen. Verschiedene Werkstoffe zeigen unterschiedliche Verformungs- und Fließeigenschaften, die sich direkt auf die Prozessparameter und das Endprodukt auswirken.
Ein zentraler Einflussfaktor ist die Duktilität des Materials. Werkstoffe mit hoher Duktilität lassen sich leichter und tiefer umformen, ohne dass es zu Rissen oder Brüchen kommt. Materialien mit geringer Duktilität erfordern dagegen oft angepasste Prozessbedingungen oder den Einsatz mehrstufiger Umformverfahren, um Schäden zu vermeiden.
Die Festigkeit des Werkstoffs bestimmt, welche Kräfte beim Tiefziehen aufgebracht werden müssen. Hochfeste Stähle oder Leichtmetalllegierungen bieten Vorteile hinsichtlich Leichtbau und Stabilität, benötigen jedoch stärkere Pressen und eine sorgfältige Prozesssteuerung, um eine gleichmäßige Verteilung der Umformspannung sicherzustellen.
Auch die Wanddickenverteilung während des Tiefziehens wird stark durch die Werkstoffeigenschaften beeinflusst. Elastizität, Kaltverfestigung und anisotrope Fließeigenschaften führen dazu, dass sich das Material unterschiedlich verformt, was gezielte Anpassungen bei Werkzeuggeometrie und Prozessparametern erfordert.
Die Oberflächenbeschaffenheit des Ausgangsmaterials ist ebenfalls wichtig. Glatte, gleichmäßige Oberflächen erleichtern das Umformen und verringern die Gefahr von Kratzern oder Faltenbildung. Beschichtungen oder Verzahnungen können die Reibung zwischen Werkstoff und Werkzeug beeinflussen und somit den Schmierstoffbedarf verändern.
Darüber hinaus spielen spezielle Werkstoffbehandlungen wie Wärmebehandlung, Kaltverformung oder Glühen vor oder nach dem Tiefziehen eine große Rolle, um die mechanischen Eigenschaften zu optimieren oder Eigenspannungen abzubauen.
Für spezielle Anwendungen kommen zunehmend hochfeste und komplexe Legierungen zum Einsatz, die besondere Anforderungen an die Fertigung stellen, aber gleichzeitig durch geringes Gewicht und hohe Belastbarkeit punkten. Ebenso gewinnen Kunststoffe und Verbundwerkstoffe als alternative Werkstoffe an Bedeutung, insbesondere wenn es um Gewichtsersparnis und Korrosionsbeständigkeit geht.
Insgesamt ist die Auswahl und Behandlung des Werkstoffs beim Tiefziehen entscheidend für die Prozesssicherheit, Produktqualität und Wirtschaftlichkeit der Fertigung. Ein tiefes Verständnis der Werkstofftechnik ermöglicht es, das Tiefziehverfahren optimal auf die jeweiligen Materialeigenschaften abzustimmen und so innovative, leistungsfähige Bauteile herzustellen.
Zusätzlich zur Werkstoffauswahl spielt die Materialhomogenität eine wichtige Rolle beim Tiefziehen. Uneinheitliche Materialeigenschaften innerhalb eines Blechs, beispielsweise durch unterschiedliche Kornstrukturen oder Einschlüsse, können zu ungleichmäßiger Verformung, lokalen Schwachstellen oder sogar vorzeitigem Versagen führen. Daher ist eine sorgfältige Qualitätskontrolle des Ausgangsmaterials unerlässlich.
Ein weiterer Einflussfaktor ist die Anisotropie des Materials, also die richtungsabhängigen mechanischen Eigenschaften, die durch Herstellprozesse wie Walzen entstehen. Diese Anisotropie beeinflusst maßgeblich die Fließrichtung und das Verformungsverhalten beim Tiefziehen, weshalb die Orientierung des Blechs im Werkzeug präzise geplant werden muss, um Faltenbildung oder Risse zu vermeiden.
Die Entwicklung spezieller Beschichtungen auf dem Werkstoff, wie zum Beispiel Zink- oder Aluminiumüberzüge, verbessert die Korrosionsbeständigkeit und kann gleichzeitig die Umformbarkeit beeinflussen. Beschichtungen wirken sich oft auch auf die Reibungsverhältnisse zwischen Blech und Werkzeug aus, was wiederum die Schmierstoffwahl und Prozessparameter bestimmt.
Darüber hinaus werden Werkstoffe zunehmend hinsichtlich ihrer Recyclingfähigkeit und Umweltverträglichkeit ausgewählt. Die Forderung nach nachhaltiger Produktion führt zu einer verstärkten Nutzung von recycelbaren Stählen und Leichtmetallen sowie zu einer Reduktion umweltschädlicher Zusatzstoffe.
In der Praxis werden Werkstoffparameter oft in Kombination mit prozessnahen Mess- und Überwachungstechniken analysiert. Durch Rückkopplungsschleifen kann die Fertigung in Echtzeit an Schwankungen im Materialverhalten angepasst werden, was die Prozessstabilität erhöht und Ausschuss reduziert.
Abschließend lässt sich festhalten, dass die Werkstofftechnik beim Tiefziehen nicht nur die Basis für ein erfolgreiches Umformen bildet, sondern auch eine Schlüsselrolle für die Weiterentwicklung effizienter, nachhaltiger und innovativer Fertigungsprozesse spielt. Eine enge Verzahnung von Materialkunde, Prozessgestaltung und Qualitätssicherung ist dabei unerlässlich, um den steigenden Anforderungen moderner Industrien gerecht zu werden.
Darüber hinaus gewinnt die Erforschung und Entwicklung neuartiger Werkstoffe für das Tiefziehen zunehmend an Bedeutung. So werden beispielsweise ultrahochfeste Stähle (UHSS) und metallische Glaslegierungen entwickelt, die durch ihre außergewöhnlichen mechanischen Eigenschaften neue Designmöglichkeiten eröffnen. Diese Werkstoffe ermöglichen dünnere und gleichzeitig stabilere Bauteile, stellen jedoch auch erhöhte Anforderungen an die Werkzeugtechnik und Prozesssteuerung.
Ein weiterer Fokus liegt auf der Optimierung von Materialverbunden, etwa bei Mehrschichtblechen oder Hybridbauteilen aus Metall-Kunststoff-Verbundstoffen. Solche Verbunde vereinen die Vorteile unterschiedlicher Werkstoffe, wie Korrosionsbeständigkeit, Gewichtseinsparung und Festigkeit, und sind zunehmend in der Automobil- und Luftfahrtindustrie im Einsatz. Das Tiefziehen dieser Werkstoffkombinationen erfordert spezielle Verfahren, um Delaminationen und andere Defekte zu vermeiden.
Die Weiterentwicklung von Simulationstechniken erlaubt es, das Verhalten neuer Werkstoffe unter Umformbedingungen detailliert vorherzusagen. So können Prozessparameter gezielt angepasst und Werkzeuggeometrien optimal ausgelegt werden, bevor teure Prototypen gefertigt werden. Dies beschleunigt die Entwicklung und senkt die Kosten.
Schließlich wird auch die Nachbearbeitung von tiefgezogenen Bauteilen durch Werkstofftechnik beeinflusst. Wärmebehandlungen, Oberflächenbehandlungen oder das Aufbringen von Funktionsschichten tragen dazu bei, die Eigenschaften der Bauteile gezielt zu verbessern, etwa durch Erhöhung der Korrosionsbeständigkeit, Verbesserung der Verschleißfestigkeit oder Anpassung der Oberflächenhärte.
Insgesamt ist die Werkstofftechnik ein dynamisches Feld, das maßgeblich zur Weiterentwicklung und Leistungsfähigkeit des Tiefziehverfahrens beiträgt. Durch die Kombination innovativer Materialien, fortschrittlicher Prozesssteuerung und moderner Simulationen entstehen Lösungen, die den hohen Anforderungen der Industrie von heute und morgen gerecht werden.
Tiefziehen von Aluminium: Leichtmetallumformung im Detail
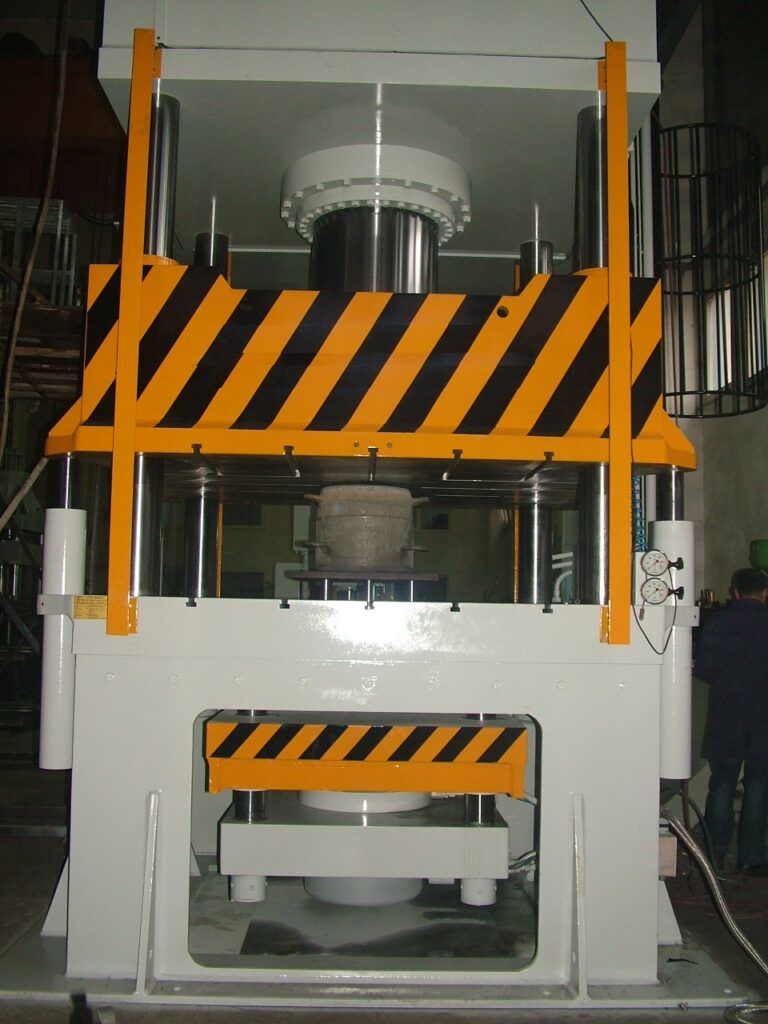
Das Tiefziehen von Aluminium spielt eine zentrale Rolle in vielen Industriezweigen, insbesondere in der Automobil-, Luftfahrt- und Verpackungsindustrie, da Aluminium aufgrund seines geringen Gewichts und seiner guten Korrosionsbeständigkeit ideale Eigenschaften für Leichtbaulösungen bietet. Allerdings bringt das Umformen von Aluminium spezifische Herausforderungen mit sich, die eine angepasste Prozessgestaltung erfordern.
Aluminium weist im Vergleich zu Stahl eine geringere Fließspannung und eine höhere Dehnbarkeit auf, was das Tiefziehen grundsätzlich erleichtert. Gleichzeitig ist das Material aber empfindlicher gegenüber Kaltverfestigung und Rissbildung, besonders bei dünnen Blechen und komplexen Geometrien. Dies erfordert eine sorgfältige Auswahl der Prozessparameter wie Ziehgeschwindigkeit, Schmierstoff und Werkzeuggeometrie.
Ein entscheidender Faktor beim Tiefziehen von Aluminium ist die Anisotropie des Materials, die durch das Walzen entsteht. Unterschiedliche Fließeigenschaften in Längs-, Quer- und Dickenrichtung können zu ungleichmäßiger Verformung, Faltenbildung oder Rissentwicklung führen. Durch gezielte Orientierung des Werkstücks im Werkzeug und Anpassung der Prozessführung lassen sich diese Effekte minimieren.
Ein weiterer wichtiger Aspekt ist die Schmierstofftechnik: Da Aluminium im Umformprozess schnell an der Werkzeugoberfläche haftet, sind spezielle Schmierstoffe notwendig, die sowohl Haftreibung verhindern als auch den Verschleiß der Werkzeuge reduzieren. Hier kommen häufig ölfreie oder teilsynthetische Schmierstoffe mit speziellen Additiven zum Einsatz.
Werkzeuge für das Aluminium-Tiefziehen sind oft aus besonders verschleißfesten Materialien gefertigt und verfügen über präzise Oberflächenbeschichtungen, um die Reibung zu optimieren und eine lange Standzeit zu gewährleisten. Zudem sind Kühl- und Temperiersysteme im Werkzeug wichtig, um thermische Verformungen und Materialveränderungen zu kontrollieren.
Prozessoptimierungen wie der Einsatz von Warmumformung (Warm-Tiefziehen) erweitern die Möglichkeiten, komplexere Bauteile aus Aluminium herzustellen. Durch Erwärmen des Materials auf moderate Temperaturen wird die Duktilität erhöht und das Risiko von Rissen reduziert, während gleichzeitig die Werkzeugbelastung verringert wird.
Insgesamt ermöglicht das Tiefziehen von Aluminium die Herstellung leichter, stabiler und korrosionsbeständiger Bauteile mit vielfältigen Anwendungen. Die Kombination aus angepasster Werkstofftechnik, optimierten Prozessparametern und innovativen Werkzeuglösungen ist dabei entscheidend, um die Potenziale dieses Leichtmetalls voll auszuschöpfen und qualitativ hochwertige Produkte zu fertigen.
Neben den bereits genannten Aspekten spielt auch die Legierungszusammensetzung von Aluminium eine entscheidende Rolle beim Tiefziehen. Unterschiedliche Aluminiumlegierungen weisen stark variierende Umformeigenschaften auf: Während weichere Legierungen wie die Serien 1xxx oder 3xxx besonders gut umformbar sind, bieten Legierungen der 5xxx- oder 7xxx-Serie eine höhere Festigkeit, sind aber gleichzeitig schwieriger zu verarbeiten. Die Wahl der Legierung hängt somit stark von den Anforderungen an das Bauteil ab, wie Belastbarkeit, Korrosionsbeständigkeit und Gewicht.
Die Materialvorbehandlung vor dem Tiefziehen, wie Glühen oder Anlassen, kann die Umformbarkeit deutlich verbessern, indem Eigenspannungen abgebaut und die Duktilität erhöht werden. Besonders bei hochfesten Aluminiumlegierungen ist diese Vorbehandlung oft notwendig, um Rissbildungen während des Umformens zu verhindern.
Ein weiterer Trend ist der Einsatz von hybriden Fertigungsverfahren, bei denen das Tiefziehen mit anderen Umform- oder Fügeverfahren kombiniert wird. So können beispielsweise gezielt verstärkte Bereiche durch Umformen und anschließendes Laserschweißen erzeugt werden, um die Bauteilfunktionalität zu erweitern.
Auch die Nachbearbeitung von tiefgezogenen Aluminiumbauteilen ist wichtig, da das Umformen oft zu Oberflächenveränderungen führt, die für bestimmte Anwendungen unzulässig sind. Verfahren wie Anodisieren, Lackieren oder Pulverbeschichten verbessern die Korrosionsbeständigkeit und das ästhetische Erscheinungsbild der Bauteile.
Schließlich gewinnt die Recyclingfähigkeit von Aluminium in der Fertigung zunehmend an Bedeutung. Aluminium lässt sich nahezu ohne Qualitätsverlust recyceln, was es zu einem nachhaltigen Werkstoff macht. Durch optimierte Fertigungsprozesse und Rückgewinnung von Restmaterialien wird die Umweltbilanz der Aluminium-Tiefziehtechnik kontinuierlich verbessert.
Zusammenfassend bietet das Tiefziehen von Aluminium vielfältige Möglichkeiten, Leichtbauteile effizient und präzise herzustellen. Die Berücksichtigung der spezifischen Werkstoff- und Prozessanforderungen ist dabei entscheidend, um die Vorteile von Aluminium voll auszuschöpfen und qualitativ hochwertige sowie nachhaltige Produkte zu fertigen.
Darüber hinaus gewinnt die Digitalisierung und Automatisierung auch beim Tiefziehen von Aluminium zunehmend an Bedeutung. Moderne Fertigungslinien sind mit Sensoren und Monitoring-Systemen ausgestattet, die Prozessparameter wie Kraft, Temperatur und Blechdicke in Echtzeit erfassen. Diese Daten werden genutzt, um den Tiefziehprozess präzise zu steuern, Abweichungen frühzeitig zu erkennen und die Produktqualität zu sichern.
Mit Hilfe von Simulationstechnologien, wie der Finite-Elemente-Methode (FEM), lassen sich komplexe Umformvorgänge virtuell abbilden. Dadurch können Werkzeuggeometrien und Prozessabläufe optimiert werden, ohne teure und zeitaufwendige Prototypen herstellen zu müssen. Besonders bei anspruchsvollen Aluminiumbauteilen trägt dies zur Reduzierung von Ausschuss und zur Verkürzung der Entwicklungszeiten bei.
Die Kombination von Tiefziehen mit additiven Fertigungstechnologien eröffnet neue Möglichkeiten für die Gestaltung komplexer Aluminiumbauteile mit integrierten Funktionen. So können beispielsweise Werkzeuge oder Vorformen individuell angepasst werden, um den Umformprozess effizienter zu gestalten.
Zudem spielt die Energieeffizienz in der Aluminium-Tiefziehproduktion eine wichtige Rolle. Durch den Einsatz energiesparender Pressen, optimierter Prozessführung und intelligenter Steuerungssysteme wird der Energieverbrauch reduziert, was die Nachhaltigkeit der Fertigung verbessert.
Nicht zuletzt wird die Zusammenarbeit zwischen Materialwissenschaftlern, Fertigungstechnikern und Konstrukteuren immer enger, um Aluminiumbauteile für spezifische Anwendungen maßgeschneidert zu entwickeln. Diese interdisziplinäre Herangehensweise fördert Innovationen und ermöglicht es, die Vorteile von Aluminium als Leichtmetall in immer anspruchsvolleren Einsatzgebieten optimal zu nutzen.
Insgesamt stellt das Tiefziehen von Aluminium eine hochentwickelte Kombination aus Werkstofftechnik, Prozessinnovation und Digitalisierung dar, die entscheidend zur Herstellung leichter, leistungsfähiger und nachhaltiger Bauteile beiträgt.
Ein weiterer Aspekt, der beim Tiefziehen von Aluminium zunehmend an Bedeutung gewinnt, ist die Entwicklung von intelligenten Werkzeugen und adaptiven Steuerungssystemen. Werkzeuge, die mit integrierten Sensoren ausgestattet sind, erfassen während des Umformprozesses wichtige Parameter wie Temperatur, Druck und Reibung. Diese Echtzeitdaten ermöglichen eine dynamische Anpassung der Prozessbedingungen, wodurch die Qualität der Bauteile verbessert und Werkzeugverschleiß minimiert werden kann.
Die Verwendung von modularen Werkzeugkonzepten erleichtert zudem die schnelle Umrüstung auf verschiedene Bauteiltypen und ermöglicht flexible Fertigungslinien. So können Hersteller schneller auf sich ändernde Marktanforderungen reagieren und kleinere Losgrößen wirtschaftlich produzieren.
Auch die Integration von künstlicher Intelligenz (KI) und Maschinellem Lernen (ML) in die Prozesssteuerung gewinnt zunehmend an Bedeutung. Durch die Analyse großer Datenmengen aus den Fertigungsprozessen können Muster erkannt und Vorhersagen getroffen werden, um Prozessabweichungen frühzeitig zu erkennen und zu vermeiden. Dies erhöht die Prozessstabilität und senkt gleichzeitig die Produktionskosten.
Ein besonderes Augenmerk liegt weiterhin auf der Oberflächenqualität der tiefgezogenen Aluminiumbauteile. Fortschrittliche Oberflächenbehandlungen und Beschichtungsverfahren sorgen nicht nur für ästhetische Verbesserungen, sondern erhöhen auch die Widerstandsfähigkeit gegenüber Korrosion und Verschleiß. Dabei spielen umweltfreundliche und nachhaltige Verfahren eine immer größere Rolle.
Zusammengefasst zeigt sich, dass das Tiefziehen von Aluminium heute weit mehr ist als nur ein Umformprozess. Es ist ein hochkomplexer, digital unterstützter Fertigungsprozess, der durch innovative Werkzeuge, intelligente Steuerungssysteme und moderne Materialtechnologien kontinuierlich weiterentwickelt wird. Diese Entwicklungen sind entscheidend, um den wachsenden Anforderungen an Leichtbau, Qualität und Effizienz in der modernen Industrie gerecht zu werden.
Die Rolle der Wärmebehandlung im Tiefziehprozess
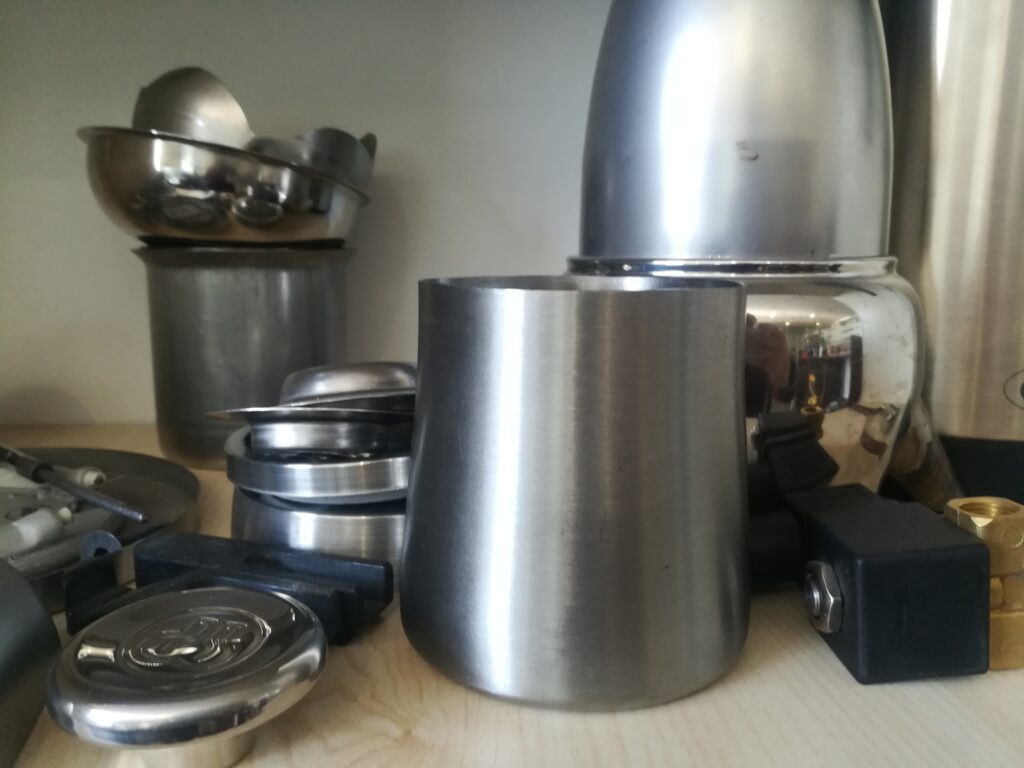
Die Wärmebehandlung spielt im Tiefziehprozess eine zentrale Rolle, da sie die mechanischen Eigenschaften des Werkstoffs gezielt beeinflusst und somit die Umformbarkeit sowie die Qualität der Bauteile verbessert. Gerade bei Werkstoffen wie Stahl, Aluminium oder hochfesten Legierungen sind die richtige Temperaturführung und das passende Wärmebehandlungsverfahren entscheidend für einen erfolgreichen Tiefziehprozess.
Vor dem Tiefziehen kann durch Wärmebehandlung, etwa Glühen, die Duktilität des Materials erhöht und Eigenspannungen aus vorherigen Bearbeitungsschritten abgebaut werden. Dies reduziert die Gefahr von Rissen und Brüchen während des Umformens, insbesondere bei komplexen oder tiefen Umformungen. Das Werkstück wird dadurch geschmeidiger und lässt sich leichter in die gewünschte Form ziehen.
Während oder nach dem Tiefziehen wird häufig eine Zwischenwärmebehandlung oder Rekristallisationsglühen eingesetzt, um die durch das Umformen entstandene Kaltverfestigung zu verringern. Dies ist besonders wichtig, wenn das Bauteil in mehreren Stufen geformt wird oder wenn eine hohe Verformungsreserve für nachfolgende Bearbeitungsschritte benötigt wird.
Nach dem Tiefziehen kann eine Endwärmebehandlung die endgültigen mechanischen Eigenschaften des Bauteils einstellen, wie Härte, Festigkeit und Zähigkeit. So werden beispielsweise durch Abschreck- und Anlasstechniken bei Stahlwerkstoffen die gewünschten Eigenschaften für den späteren Einsatz erzielt. Bei Aluminiumlegierungen dient das Ausscheidungshärten dazu, die Festigkeit nach dem Umformen zu erhöhen.
Ein weiterer Vorteil der Wärmebehandlung ist die Verbesserung der Maßhaltigkeit und Oberflächenqualität. Durch kontrolliertes Tempern lassen sich Verzug und Eigenspannungen reduzieren, die während des Tiefziehens entstehen können, was die Nachbearbeitung vereinfacht und Kosten senkt.
Moderne Fertigungskonzepte integrieren Wärmebehandlungsprozesse zunehmend nahtlos in die Produktionslinien, zum Beispiel durch induktives Erwärmen oder laserbasierte Verfahren, die präzise und energiesparend arbeiten. Dies ermöglicht eine flexible Anpassung an unterschiedliche Werkstoffe und Bauteilgeometrien.
Zusammenfassend ist die Wärmebehandlung ein unverzichtbarer Bestandteil des Tiefziehprozesses, der die Umformbarkeit verbessert, die Qualität der Bauteile sichert und gleichzeitig die Wirtschaftlichkeit der Fertigung steigert. Ein fundiertes Verständnis der thermischen Werkstoffbehandlung ist daher für die Entwicklung und Optimierung von Tiefziehprozessen essenziell.
Die Bedeutung der Wärmebehandlung im Tiefziehprozess erstreckt sich auch auf die Steuerung von Gefügestrukturen im Material. Durch gezielte Temperaturführung können Kornwachstum und Phasenumwandlungen beeinflusst werden, was direkte Auswirkungen auf die mechanischen Eigenschaften hat. Ein feinkörniges Gefüge beispielsweise verbessert die Zähigkeit und verhindert spröde Brüche, was gerade bei hochfesten Stählen und Aluminiumlegierungen von großer Bedeutung ist.
In der Praxis werden verschiedene Wärmebehandlungsverfahren eingesetzt, die sich in Art und Temperatur unterscheiden:
- Weichglühen: Senkung der Härte und Spannungen, Verbesserung der Umformbarkeit, häufig vor dem Tiefziehen angewandt.
- Rekristallisationsglühen: Erzeugung eines neuen, spannungsfreien Korngefüges nach Kaltumformung, wichtig bei mehrstufigen Tiefziehprozessen.
- Aushärtung (Ausscheidungshärten): Speziell bei Aluminiumlegierungen zur Erhöhung der Festigkeit nach dem Umformen.
- Anlassen: Kombination aus Härten und Anlassen zur Optimierung von Festigkeit und Zähigkeit, besonders bei Stahlbauteilen.
Darüber hinaus spielt die Kontrolle der Abkühlgeschwindigkeit nach dem Glühen eine wichtige Rolle, da sie das Entstehen von Eigenspannungen und Verzugserscheinungen beeinflusst. Ungleichmäßiges Abkühlen kann zu inneren Spannungen führen, die später zu Verformungen oder Rissen führen können.
Neuere Entwicklungen in der Wärmebehandlung nutzen lokalisierte und kurzzeitige Erwärmungstechniken, wie das induktive Erwärmen oder Laserwärmebehandlung, um gezielt bestimmte Bereiche eines Bauteils zu bearbeiten. Dies ermöglicht eine punktgenaue Beeinflussung der Werkstoffeigenschaften und minimiert gleichzeitig thermische Belastungen des gesamten Bauteils.
Insgesamt ist die Wärmebehandlung ein flexibles und wirkungsvolles Mittel, um die Herausforderungen beim Tiefziehen unterschiedlicher Werkstoffe zu meistern. Sie sorgt für eine optimale Balance zwischen Umformbarkeit, Festigkeit und Maßhaltigkeit und ist somit ein Schlüsselprozess zur Herstellung hochwertiger, langlebiger Bauteile.
Neben den klassischen Wärmebehandlungsverfahren gewinnt auch die prozessintegrierte Wärmebehandlung zunehmend an Bedeutung. Dabei werden Wärmebehandlungen direkt in den Fertigungsprozess eingebunden, um Zeit und Kosten zu sparen sowie die Effizienz zu steigern. Beispiele hierfür sind das Erwärmen des Werkstücks unmittelbar vor oder während des Tiefziehens, um die Umformbarkeit zu verbessern, sowie die sofortige Nachbehandlung zur Spannungsreduktion.
Ein spezielles Verfahren ist das Warm-Tiefziehen, bei dem das Blech auf moderate Temperaturen (typischerweise zwischen 150 und 350 °C) erhitzt wird. Dies erhöht die Duktilität des Materials deutlich und erlaubt komplexere Formen und tiefere Ziehungen ohne Rissbildung. Besonders bei hochfesten Aluminium- und Stahllegierungen ermöglicht das Warm-Tiefziehen die Herstellung von Bauteilen, die mit konventionellem Kalt-Tiefziehen nur schwer oder gar nicht realisierbar wären.
Darüber hinaus werden zunehmend thermomechanische Prozesse eingesetzt, bei denen mechanische Verformung und Wärmebehandlung kombiniert werden. Diese Prozesse können die Kornfeinung fördern und somit zu verbesserten Werkstoffeigenschaften führen, wie höherer Festigkeit und besserer Zähigkeit.
Die Optimierung der Wärmebehandlungsparameter ist dabei eng mit der Werkstoffauswahl und der angestrebten Bauteilfunktion verbunden. In der Praxis erfolgt häufig eine enge Abstimmung zwischen Materialwissenschaftlern, Fertigungstechnikern und Konstrukteuren, um die bestmögliche Kombination aus Umformbarkeit und Endfestigkeit zu erzielen.
Abschließend lässt sich festhalten, dass die Wärmebehandlung im Tiefziehprozess weit mehr als nur eine unterstützende Maßnahme ist. Sie ist ein integraler Bestandteil moderner Fertigungstechnologien, der maßgeblich zur Prozesssicherheit, Produktqualität und Wirtschaftlichkeit beiträgt. Durch innovative Verfahren und eine enge Verzahnung mit anderen Fertigungsschritten wird die Wärmebehandlung auch in Zukunft eine Schlüsselrolle in der Tiefziehtechnik spielen.
Darüber hinaus eröffnet die zunehmende Integration von digitalen Technologien im Bereich der Wärmebehandlung neue Möglichkeiten, den Tiefziehprozess weiter zu optimieren. Intelligente Steuerungssysteme, basierend auf Echtzeitdaten und Prozesssimulationen, ermöglichen eine präzise Regelung der Temperaturprofile während der Wärmebehandlung. So lassen sich optimale Ergebnisse bei minimalem Energieeinsatz erzielen, was die Nachhaltigkeit und Wirtschaftlichkeit des Prozesses verbessert.
Ein weiterer innovativer Ansatz ist die Verwendung von in-situ Messverfahren, die während der Wärmebehandlung das Gefüge und die mechanischen Eigenschaften des Werkstoffs überwachen. Mittels zerstörungsfreier Prüfverfahren wie Ultraschall oder Laser-Doppler-Vibrometrie können Veränderungen im Materialverhalten erkannt und direkt auf die Prozessführung zurückgeführt werden.
Auch im Bereich der Werkstoffentwicklung werden Wärmebehandlungsprozesse gezielt mit der Materialgestaltung verknüpft. So entstehen speziell legierte Werkstoffe, deren Mikrostruktur sich durch Wärmebehandlung besonders günstig beeinflussen lässt, um optimale Umformeigenschaften und Endfestigkeiten zu erreichen.
Nicht zuletzt spielt die Umweltverträglichkeit der Wärmebehandlungsprozesse eine immer größere Rolle. Moderne Anlagen setzen verstärkt auf energieeffiziente Verfahren, Abwärmenutzung und emissionsarme Technologien, um den ökologischen Fußabdruck der Fertigung zu reduzieren.
Zusammenfassend lässt sich sagen, dass die Rolle der Wärmebehandlung im Tiefziehprozess kontinuierlich wächst und sich durch technische Innovationen ständig weiterentwickelt. Sie bildet das Bindeglied zwischen Werkstoff, Fertigung und Endanwendung und ist damit ein wesentlicher Faktor für die erfolgreiche Produktion moderner, leistungsfähiger Bauteile.
Tiefziehen von Edelstahl: Herausforderungen und Lösungen
Das Tiefziehen von Edelstahl stellt aufgrund der besonderen Materialeigenschaften spezifische Herausforderungen dar, die eine angepasste Prozessführung und Werkstoffbehandlung erfordern. Edelstahl ist bekannt für seine hohe Korrosionsbeständigkeit, Festigkeit und Härte, die aber zugleich die Umformbarkeit erschweren können.
Eine der Hauptschwierigkeiten beim Tiefziehen von Edelstahl liegt in seiner geringen Duktilität und der Neigung zur Kaltverfestigung. Bereits bei geringfügiger Verformung erhöht sich die Härte des Materials stark, was zu Rissbildung und Werkzeugverschleiß führen kann. Deshalb sind präzise abgestimmte Ziehgeschwindigkeiten, geringe Umformgrade pro Schritt und eine optimale Schmierung unerlässlich, um die Oberflächenqualität zu erhalten und Schäden zu vermeiden.
Die Werkstoffauswahl ist entscheidend: Verschiedene Edelstahltypen, etwa ferritische, austenitische oder martensitische Edelstähle, besitzen unterschiedliche Umformeigenschaften. Austenitische Edelstähle (z. B. 1.4301) sind vergleichsweise gut umformbar und werden häufig im Tiefziehen eingesetzt, während martensitische Edelstähle härter und weniger duktil sind und spezielle Umformstrategien erfordern.
Ein wichtiger Lösungsansatz ist die Zwischenwärmebehandlung, um die Kaltverfestigung zu reduzieren. Durch kontrolliertes Glühen kann das Gefüge entspannt und die Umformbarkeit wiederhergestellt werden. Ebenso sind Werkzeuge aus hochverschleißfesten Materialien mit speziell beschichteten Oberflächen notwendig, um die Reibung zu minimieren und den Werkzeugverschleiß bei der Verarbeitung von Edelstahl gering zu halten.
Auch die Schmierung spielt eine zentrale Rolle. Aufgrund der hohen Haftneigung von Edelstahl sind spezielle Schmierstoffe erforderlich, die eine dauerhafte Schmierfilmstabilität sicherstellen und gleichzeitig umweltfreundlich sein sollten. Typischerweise kommen hier Hochdruck- oder Festschmierstoffe zum Einsatz.
Zur Verbesserung der Prozesssicherheit und zur Vermeidung von Fehlern wie Faltenbildung oder Rissen werden häufig Simulationstechniken eingesetzt. Finite-Elemente-Analysen helfen, kritische Stellen zu identifizieren und Werkzeug- sowie Prozessparameter gezielt anzupassen.
Insgesamt erfordert das Tiefziehen von Edelstahl eine Kombination aus sorgfältiger Werkstoffauswahl, optimierter Wärme- und Schmierstoffbehandlung sowie moderner Werkzeugtechnik. Durch diese Maßnahmen lassen sich hochwertige Bauteile mit der typischen Edelstahlqualität herstellen, die in vielen Bereichen wie Medizintechnik, Lebensmittelindustrie oder Automobilbau unverzichtbar sind.
Ein weiterer wichtiger Aspekt beim Tiefziehen von Edelstahl ist die Kühlung und Temperaturkontrolle während des Umformprozesses. Aufgrund der hohen Festigkeit und der damit verbundenen Reibung entstehen erhöhte Temperaturen an den Werkzeugoberflächen, die das Materialverhalten und die Schmierwirkung beeinflussen können. Eine gezielte Kühlung der Werkzeuge hilft, thermische Belastungen zu reduzieren, Verzug zu minimieren und die Standzeiten der Werkzeuge zu erhöhen.
Darüber hinaus werden zunehmend hochmoderne Beschichtungen auf Werkzeugen eingesetzt, wie etwa DLC-Beschichtungen (Diamond-Like Carbon) oder TiN- und TiCN-Schichten, die eine hohe Verschleißfestigkeit und geringe Reibung gewährleisten. Diese Beschichtungen verbessern die Lebensdauer der Werkzeuge und die Oberflächenqualität der Edelstahlbauteile erheblich.
Ein wachsender Trend ist die Anwendung von Warm- oder Heißumformung bei Edelstahl, um die Duktilität des Materials zu erhöhen. Dabei wird das Blech vor oder während des Tiefziehens auf höhere Temperaturen erwärmt, was das Material weicher und formbarer macht. Diese Verfahren sind besonders bei schwer umformbaren Edelstählen sinnvoll, erfordern jedoch eine präzise Temperaturkontrolle, um Oxidation und Materialveränderungen zu vermeiden.
Nicht zuletzt sind qualitätskontrollierende Maßnahmen wie zerstörungsfreie Prüfverfahren (Ultraschall, Magnetpulverprüfung) und Prozessmonitoring wesentliche Bestandteile einer stabilen Produktion. Sie ermöglichen das frühzeitige Erkennen von Fehlern wie Rissen, Falten oder Oberflächendefekten und tragen so zur Reduktion von Ausschuss und Nacharbeit bei.
Durch die Kombination all dieser Technologien und Maßnahmen wird das Tiefziehen von Edelstahl zunehmend effizienter und zuverlässiger, sodass komplexe Bauteile mit hohen Anforderungen an Korrosionsbeständigkeit, Stabilität und Oberflächenqualität gefertigt werden können. Dies macht Edelstahl zu einem wichtigen Werkstoff für vielfältige Anwendungen in der Industrie, vom anspruchsvollen Maschinenbau bis hin zur Medizintechnik.
Neben den technischen Maßnahmen gewinnt auch die Prozessoptimierung durch Digitalisierung zunehmend an Bedeutung beim Tiefziehen von Edelstahl. Mit Hilfe von datenbasierten Analysen und vernetzten Fertigungssystemen lassen sich Prozessparameter in Echtzeit überwachen und anpassen. Sensoren erfassen Kräfte, Temperaturen und Materialverhalten während des Umformens, sodass Abweichungen sofort erkannt und Gegenmaßnahmen eingeleitet werden können. Dies erhöht nicht nur die Prozesssicherheit, sondern ermöglicht auch die Produktion kleiner Losgrößen bei gleichbleibender Qualität.
Zusätzlich kommt der Mitarbeiterschulung eine wichtige Rolle zu. Da Edelstahl wegen seiner besonderen Eigenschaften anspruchsvoll zu verarbeiten ist, sind fundierte Kenntnisse über Werkstoffverhalten, Werkzeugtechnik und Prozesssteuerung essenziell. Schulungen und kontinuierliche Weiterbildung tragen dazu bei, Fehler zu minimieren und die Effizienz zu steigern.
Auch die Nachhaltigkeit im Tiefziehprozess von Edelstahl gewinnt an Bedeutung. Die optimierte Nutzung von Materialressourcen, der Einsatz umweltfreundlicher Schmierstoffe und die Reduktion von Ausschuss tragen zu einer ökologisch verantwortungsvollen Fertigung bei. Gleichzeitig erhöhen energiesparende Anlagen und intelligente Steuerungen die Energieeffizienz der Produktion.
Insgesamt zeigt sich, dass das Tiefziehen von Edelstahl eine hochkomplexe Aufgabe ist, die fundiertes technisches Know-how, modernste Technologien und eine ganzheitliche Betrachtung von Prozess, Material und Umwelt erfordert. Nur durch die Kombination dieser Faktoren lassen sich die hohen Anforderungen moderner Industriezweige an Edelstahlbauteile erfüllen.
Zusätzlich zur Prozess- und Materialoptimierung gewinnt die Entwicklung von neuen Edelstahllegierungen mit verbesserter Umformbarkeit zunehmend an Bedeutung. Forschungsarbeiten konzentrieren sich darauf, Legierungen zu entwickeln, die trotz hoher Festigkeit eine bessere Duktilität aufweisen und somit das Tiefziehen erleichtern. Diese sogenannten „formbaren“ Edelstähle ermöglichen komplexere Geometrien und reduzieren die Anzahl der notwendigen Umformstufen.
Parallel dazu werden hybride Fertigungsverfahren erforscht und eingesetzt, die Tiefziehen mit anderen Umform- oder Fügeverfahren kombinieren. Beispielsweise kann das Tiefziehen mit Laserstrahlschweißen oder Klebetechniken verbunden werden, um Bauteile mit verbesserten funktionalen Eigenschaften oder erhöhten Festigkeiten zu fertigen. Solche Verfahren eröffnen neue Möglichkeiten für Leichtbau und komplexe Baugruppen, insbesondere im Fahrzeug- und Flugzeugbau.
Nicht zu vernachlässigen ist auch der Einfluss der Bauteilgestaltung auf den Tiefziehprozess. Durch gezielte Konstruktion mit optimierten Radien, Wandstärken und Faltvermeidung können die Umformbedingungen verbessert und die Prozesssicherheit erhöht werden. Enge Zusammenarbeit zwischen Konstrukteuren und Fertigungstechnikern ist daher entscheidend, um das volle Potenzial des Werkstoffs Edelstahl auszuschöpfen.
Abschließend lässt sich sagen, dass das Tiefziehen von Edelstahl durch kontinuierliche Innovationen auf Material-, Prozess- und Konstruktionsseite geprägt ist. Diese Entwicklungen tragen dazu bei, die Leistungsfähigkeit und Qualität der Bauteile stetig zu verbessern und gleichzeitig die Fertigung wirtschaftlicher und nachhaltiger zu gestalten. Damit bleibt Edelstahl ein unverzichtbarer Werkstoff in anspruchsvollen Industriebereichen weltweit.
Prozessoptimierung im Tiefziehen: Tipps und Best Practices
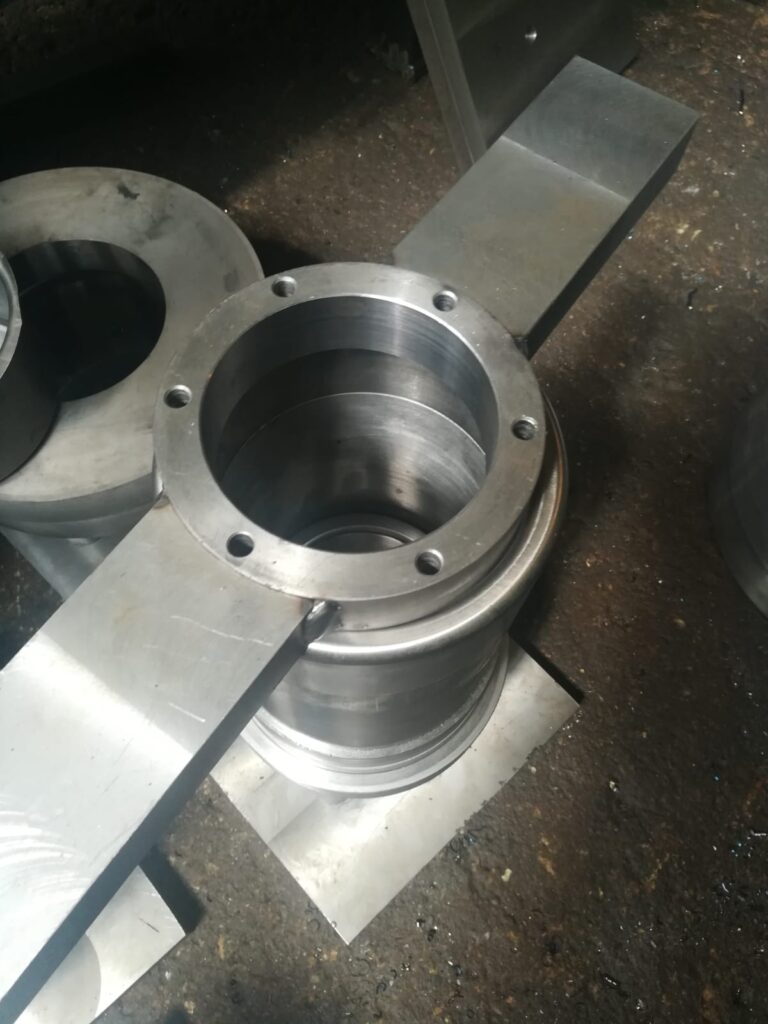
Prozessoptimierung im Tiefziehen ist entscheidend, um Qualität, Effizienz und Wirtschaftlichkeit der Fertigung zu steigern. Hier sind bewährte Tipps und Best Practices, die in der Praxis häufig angewendet werden:
- Werkstoffauswahl und Vorbereitung:
- Wählen Sie den geeigneten Werkstoff mit optimaler Kombination aus Festigkeit und Duktilität.
- Vorbehandlungen wie Glühen zur Spannungsreduzierung und Optimierung der Umformbarkeit sind oft sinnvoll.
- Sorgen Sie für eine gleichmäßige Blechdicke und saubere Oberflächen, um Fehler zu vermeiden.
- Werkzeugauslegung:
- Gestalten Sie Werkzeuge mit optimalen Radien und präzisen Maßen, um Faltenbildung und Risse zu minimieren.
- Verwenden Sie hochwertige und verschleißfeste Materialien sowie geeignete Beschichtungen, um Standzeiten zu erhöhen.
- Integrieren Sie Sensorik für Prozessüberwachung und Steuerung.
- Schmierung:
- Setzen Sie speziell abgestimmte Schmierstoffe ein, die Reibung reduzieren und Oberflächenschäden vermeiden.
- Kontrollieren Sie regelmäßig den Schmierstoffauftrag und passen Sie ihn bei Bedarf an.
- Prozessparameter:
- Optimieren Sie Ziehgeschwindigkeit, Ziehkraft und Stempelhub für den jeweiligen Werkstoff und Bauteil.
- Nutzen Sie Simulationen (z. B. FEM), um kritische Stellen frühzeitig zu erkennen und Parameter anzupassen.
- Verwenden Sie Zwischenwärmebehandlungen bei mehrstufigen Prozessen, um Kaltverfestigung zu reduzieren.
- Maschineneinstellungen:
- Justieren Sie die Presskraft und führen Sie regelmäßige Wartungen durch, um gleichbleibende Qualität sicherzustellen.
- Setzen Sie moderne Steuerungssysteme ein, die adaptive Prozessregelung ermöglichen.
- Qualitätskontrolle:
- Implementieren Sie Inline-Prüfverfahren zur frühzeitigen Fehlererkennung.
- Führen Sie regelmäßige Werkzeuginspektionen und Wartungen durch.
- Nutzen Sie statistische Prozesskontrolle (SPC), um Prozessabweichungen zu minimieren.
- Mitarbeiterschulung:
- Schulen Sie Bedienpersonal regelmäßig in Prozessverständnis und Fehlererkennung.
- Fördern Sie ein Qualitätsbewusstsein und kontinuierliche Verbesserung.
- Datenanalyse und Digitalisierung:
- Erfassen und analysieren Sie Prozessdaten, um Muster zu erkennen und gezielt Optimierungen vorzunehmen.
- Integrieren Sie vernetzte Systeme und KI-gestützte Prozessoptimierung für mehr Effizienz.
Durch die konsequente Anwendung dieser Best Practices lässt sich der Tiefziehprozess stabilisieren, Ausschuss reduzieren und die Produktqualität nachhaltig verbessern. Gleichzeitig wird die Fertigung flexibler und wirtschaftlicher – wichtige Voraussetzungen für den Erfolg in modernen Produktionsumgebungen.
Darüber hinaus kann die Einführung von kontinuierlichen Verbesserungsprozessen (KVP) und Lean-Management-Prinzipien erheblich zur Prozessoptimierung im Tiefziehen beitragen. Das bedeutet, dass Produktionsabläufe regelmäßig analysiert und systematisch verbessert werden, um Verschwendung zu minimieren und Durchlaufzeiten zu verkürzen. Hierzu gehören:
- Standardisierung von Arbeitsabläufen: Einheitliche Verfahren und Checklisten helfen, Fehlerquellen zu reduzieren und Prozesssicherheit zu erhöhen.
- 5S-Methode: Ordnung und Sauberkeit am Arbeitsplatz verbessern die Effizienz und reduzieren Stillstandszeiten.
- Fehlersammelstellen und Root-Cause-Analysen: Ursachen für Qualitätsprobleme werden systematisch ermittelt und beseitigt, statt nur Symptome zu behandeln.
Auch die Modularisierung von Werkzeugen und Anlagen bietet Vorteile, indem Umrüstzeiten verkürzt und Flexibilität erhöht werden. Schnellwechselvorrichtungen und modulare Baukastensysteme ermöglichen eine schnelle Anpassung an unterschiedliche Bauteile und Losgrößen.
Eine weitere wichtige Maßnahme ist die Optimierung der Logistik und Materialversorgung. Just-in-time-Lieferungen und eine durchgängige Materialverfolgung stellen sicher, dass stets die richtigen Werkstoffe in der richtigen Qualität und Menge zur Verfügung stehen, was Produktionsunterbrechungen vermeidet.
Nicht zu vergessen ist der Einsatz von Simulation und virtueller Fertigung, um neue Bauteile und Prozesse vor der Realisierung virtuell zu testen. Dies spart Zeit, Kosten und reduziert das Risiko von Produktionsproblemen.
Schließlich ist eine enge Zusammenarbeit zwischen Konstruktion, Fertigung und Qualitätssicherung entscheidend. Durch frühzeitigen Informationsaustausch können konstruktive Schwachstellen erkannt und behoben werden, was den Tiefziehprozess insgesamt effizienter macht.
Diese Maßnahmen zeigen, dass Prozessoptimierung im Tiefziehen ein ganzheitlicher Ansatz ist, der technische, organisatorische und menschliche Faktoren berücksichtigt. Nur so können langfristig stabile, qualitativ hochwertige und wirtschaftliche Fertigungsprozesse sichergestellt werden.
Ein weiterer entscheidender Faktor für eine erfolgreiche Prozessoptimierung im Tiefziehen ist die Einsatzplanung und Überwachung von Maschinenkapazitäten. Durch eine präzise Planung der Produktionskapazitäten können Engpässe vermieden und die Auslastung der Anlagen maximiert werden. Moderne MES-Systeme (Manufacturing Execution Systems) unterstützen dabei, den Produktionsfluss zu steuern und Produktionskennzahlen in Echtzeit zu erfassen.
Zudem trägt die Etablierung eines robusten Wartungsmanagements erheblich zur Prozessstabilität bei. Präventive Wartung und Zustandserfassung mittels Predictive Maintenance verhindern ungeplante Stillstände und verlängern die Lebensdauer der Maschinen und Werkzeuge. So bleiben Produktionsprozesse zuverlässig und die Qualität der Tiefziehteile konstant hoch.
Ein wichtiger Trend ist auch die zunehmende Nutzung von KI-gestützten Analysen und Machine Learning in der Fertigung. Diese Technologien helfen dabei, aus großen Datenmengen Muster zu erkennen, Prozessabweichungen vorherzusagen und Empfehlungen für Anpassungen zu geben. Dadurch können Fehler frühzeitig vermieden und die Prozessparameter optimal eingestellt werden.
Nicht zuletzt sollte die Nachhaltigkeit bei der Prozessoptimierung berücksichtigt werden. Maßnahmen wie Energieeffizienz, Materialeinsparung und Recycling spielen eine immer größere Rolle. Der Einsatz umweltfreundlicher Schmierstoffe, die Reduktion von Ausschuss und der sparsame Umgang mit Ressourcen schonen nicht nur die Umwelt, sondern senken auch die Produktionskosten langfristig.
Insgesamt zeigt sich, dass Prozessoptimierung im Tiefziehen eine kontinuierliche Aufgabe ist, die technische Innovationen, organisatorische Maßnahmen und qualifizierte Mitarbeiter erfordert. Nur durch ein ganzheitliches Vorgehen können die hohen Anforderungen an Qualität, Effizienz und Nachhaltigkeit heute und in Zukunft erfüllt werden.
Blechumformung durch Tiefziehen: Effiziente Fertigungslösungen
Die Blechumformung durch Tiefziehen ist eine zentrale Fertigungsmethode zur Herstellung komplexer, dünnwandiger Bauteile aus Metall. Effiziente Fertigungslösungen in diesem Bereich setzen auf eine Kombination aus modernster Technologie, optimierten Prozessen und intelligentem Werkstoffmanagement, um Qualität, Produktivität und Wirtschaftlichkeit zu maximieren.
Ein Schlüsselelement ist die Automatisierung der Tiefziehprozesse. Durch den Einsatz von Robotik und automatischen Zuführsystemen können Bauteile präzise und wiederholgenau geformt werden. Automatisierte Systeme reduzieren menschliche Fehler, erhöhen die Taktzeiten und ermöglichen eine flexible Produktion auch bei kleinen Losgrößen.
Zur Steigerung der Effizienz gehört auch der Einsatz von modularen Werkzeugkonzepten. Diese ermöglichen eine schnelle Anpassung an unterschiedliche Bauteilgeometrien und verkürzen Umrüstzeiten erheblich. Werkzeuge können so individuell auf die Anforderungen der Fertigung abgestimmt und bei Bedarf schnell ausgetauscht werden.
Die Nutzung von Simulationssoftware zur Prozess- und Werkzeugauslegung ist ein weiterer entscheidender Faktor. Durch virtuelle Versuche lassen sich kritische Bereiche frühzeitig identifizieren, die Werkzeuggeometrie optimieren und Fehler im Serienprozess vermeiden. Dies reduziert Entwicklungszeiten und Ausschuss.
Ebenso wichtig ist das Materialmanagement, das auf eine optimale Kombination von Werkstoff, Blechstärke und Oberflächenqualität setzt. Die Auswahl geeigneter Werkstoffe, z.B. hochfester Stähle, Aluminium oder Edelstahl, bestimmt maßgeblich die Umformbarkeit und das Endprodukt.
Ein weiterer Fokus liegt auf der Qualitätssicherung durch integrierte Prüf- und Monitoring-Systeme. Inline-Kontrollen mit Kameras oder taktilen Sensoren ermöglichen die sofortige Erkennung von Form- oder Oberflächenfehlern und sichern eine konstante Produktqualität.
Schließlich spielen auch Aspekte der Nachhaltigkeit eine wachsende Rolle. Ressourcenschonende Prozesse, energieeffiziente Maschinen und umweltfreundliche Schmierstoffe tragen dazu bei, die ökologische Bilanz der Fertigung zu verbessern.
Zusammenfassend ermöglichen diese effizienten Fertigungslösungen im Tiefziehen eine wirtschaftliche und flexible Produktion anspruchsvoller Blechbauteile mit hoher Präzision – eine Voraussetzung für moderne Industriebranchen wie Automobil-, Luftfahrt- oder Elektroindustrie.
Neben den bereits genannten Faktoren trägt auch die Integration von flexiblen Fertigungssystemen wesentlich zur Effizienzsteigerung beim Tiefziehen bei. Flexible Anlagen können schnell auf wechselnde Produktvarianten und Losgrößen reagieren, was insbesondere in Zeiten steigender Individualisierung und kürzerer Produktlebenszyklen entscheidend ist. Durch modulare Steuerungstechnik und automatisierte Werkzeugwechsel wird die Umrüstzeit minimiert und die Maschinenverfügbarkeit maximiert.
Ein weiterer wichtiger Aspekt ist die Prozessüberwachung mittels digitaler Zwillinge. Dabei wird der Tiefziehprozess in Echtzeit virtuell abgebildet, sodass Abweichungen sofort erkannt und korrigiert werden können. Dies ermöglicht nicht nur eine höhere Prozessstabilität, sondern auch eine datengetriebene Optimierung der Fertigung.
Die Anwendung von fortschrittlichen Schmierstoffsystemen spielt ebenfalls eine große Rolle. Moderne Schmierstoffe sind nicht nur leistungsfähiger, sondern auch umweltfreundlicher und besser auf spezifische Werkstoffe abgestimmt. Sie reduzieren den Werkzeugverschleiß und verbessern die Oberflächenqualität der Bauteile.
Darüber hinaus führt die verstärkte Nutzung von additiven Fertigungsverfahren in Kombination mit Tiefziehen zu innovativen Lösungen. So können komplexe Werkzeuge oder Vorrichtungen schnell und kostengünstig hergestellt werden, was Entwicklungszeiten verkürzt und individuelle Anpassungen erleichtert.
Nicht zuletzt ist die Mitarbeiterschulung und -qualifikation ein entscheidender Erfolgsfaktor. Gut ausgebildete Fachkräfte können Prozesse besser überwachen, Störungen schneller beheben und zur kontinuierlichen Verbesserung beitragen.
Insgesamt führen diese fortschrittlichen Ansätze in Kombination zu einer signifikanten Steigerung der Effizienz, Flexibilität und Qualität in der Blechumformung durch Tiefziehen – Voraussetzungen, um den steigenden Anforderungen der Industrie gerecht zu werden.
Ein weiterer zentraler Aspekt zur Steigerung der Effizienz in der Blechumformung durch Tiefziehen ist die Optimierung der Materialnutzung. Durch präzise Zuschnittverfahren und intelligente Nesting-Software kann der Materialeinsatz maximiert und Verschnitt minimiert werden. Dies senkt nicht nur die Materialkosten, sondern trägt auch zur Ressourcenschonung bei.
Darüber hinaus gewinnen Nachbearbeitungsverfahren wie das Entgraten oder die Oberflächenbehandlung zunehmend an Bedeutung. Moderne automatisierte Systeme ermöglichen eine schonende und gleichzeitig wirtschaftliche Nachbearbeitung, die die Bauteilqualität verbessert und die Funktionalität sichert.
Die Integration von Industrie-4.0-Technologien erlaubt eine durchgängige Vernetzung aller Prozessschritte – vom Rohblech über die Umformung bis zur Qualitätskontrolle und Logistik. Echtzeitdaten ermöglichen eine präzise Steuerung und schnelle Reaktion auf Prozessabweichungen, was die Ausbeute erhöht und Ausschuss reduziert.
Ein weiteres Effizienzpotenzial liegt in der Entwicklung von Mehrstufen-Tiefziehverfahren, die komplexe Geometrien in mehreren aufeinanderfolgenden Umformschritten herstellen. Durch optimierte Ablaufplanung und Zwischenerwärmungen kann der Prozess robust und wirtschaftlich gestaltet werden.
Nicht zuletzt spielt die enge Zusammenarbeit zwischen Entwicklungs-, Fertigungs- und Qualitätsabteilungen eine entscheidende Rolle. Gemeinsame Optimierungsansätze und Feedback-Schleifen führen zu praxisnahen Lösungen und einer schnellen Anpassung an sich ändernde Anforderungen.
Diese umfassenden Maßnahmen sorgen dafür, dass das Tiefziehen als Verfahren der Blechumformung auch zukünftig eine effiziente, flexible und nachhaltige Fertigungslösung für anspruchsvolle Bauteile bleibt.
Zusätzlich zur Prozess- und Materialoptimierung wird die Bedeutung von digitaler Dokumentation und Rückverfolgbarkeit im Tiefziehprozess immer größer. Durch lückenlose Erfassung aller Fertigungsschritte lassen sich Fehlerquellen besser identifizieren und Prozessabweichungen schneller beheben. Dies verbessert nicht nur die Produktqualität, sondern erleichtert auch die Einhaltung von Zertifizierungs- und Compliance-Anforderungen, die in vielen Branchen zunehmend strenger werden.
Ein weiterer wichtiger Trend ist die Integration von künstlicher Intelligenz (KI) und Machine Learning zur prädiktiven Wartung und Prozessoptimierung. KI-Modelle analysieren kontinuierlich Prozessdaten, erkennen frühzeitig Muster, die auf Werkzeugverschleiß oder Materialfehler hindeuten, und geben Empfehlungen zur Anpassung von Prozessparametern. So können Stillstände minimiert und Ausschussquoten weiter reduziert werden.
Auch die Weiterentwicklung von multifunktionalen Werkzeugen bietet großes Potenzial. Werkzeuge, die mehrere Umformschritte in einem Arbeitsgang ermöglichen, verkürzen die Durchlaufzeiten und reduzieren den Platzbedarf in der Produktion. Solche Werkzeuge erfordern allerdings eine hohe Präzision in der Konstruktion und Fertigung.
Nicht zuletzt gewinnen nachhaltige Fertigungskonzepte an Bedeutung, die den gesamten Lebenszyklus der Bauteile berücksichtigen – von der Rohstoffbeschaffung über die Produktion bis hin zur Recyclingfähigkeit. Hierzu zählen unter anderem der Einsatz recycelter Materialien, energieeffiziente Maschinen und die Minimierung von Abfällen.
Diese Entwicklungen zeigen, dass die Blechumformung durch Tiefziehen ein dynamisches Feld ist, in dem technische Innovationen und ganzheitliche Ansätze Hand in Hand gehen, um effizientere, flexiblere und nachhaltigere Fertigungslösungen zu schaffen.
Materialwahl beim Tiefziehen: Einfluss auf Qualität und Kosten
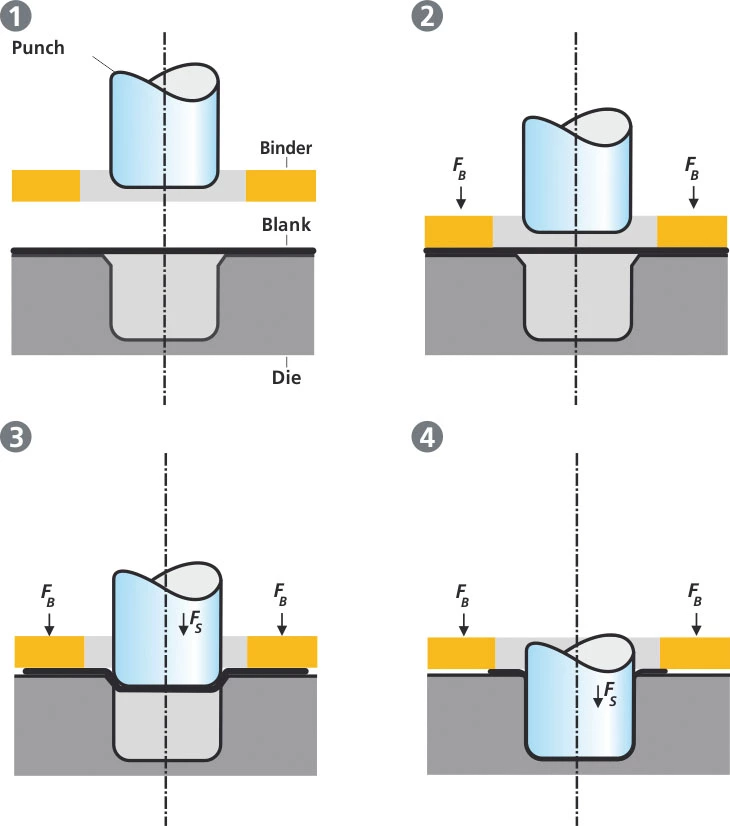
Die Wahl des richtigen Materials beim Tiefziehen ist ein entscheidender Faktor für die Qualität des Endprodukts und die Wirtschaftlichkeit des gesamten Fertigungsprozesses. Werkstoffe unterscheiden sich hinsichtlich ihrer Umformbarkeit, Festigkeit, Oberflächenbeschaffenheit, Kosten und Verfügbarkeit – all das wirkt sich direkt auf die Prozessstabilität, die Werkzeugbeanspruchung und den Ausschuss aus.
Weichere Materialien wie Tiefziehqualitätsstähle (z. B. DC01) eignen sich besonders gut für einfachere Umformungen. Sie lassen sich mit geringem Kraftaufwand verarbeiten und weisen ein gutes Fließverhalten auf. Dadurch wird das Risiko von Rissbildung oder Faltenbildung reduziert, was wiederum geringere Anforderungen an das Werkzeug stellt und die Werkzeugstandzeiten verlängert. Gleichzeitig sind diese Werkstoffe vergleichsweise günstig, was sie für großvolumige Serienproduktionen attraktiv macht.
Hochfeste und höherfeste Stähle (wie z. B. Dualphasenstähle oder mikrolegierte Varianten) bieten Vorteile bei der Gewichtsreduktion von Bauteilen, da sie dünner verarbeitet werden können, ohne an Stabilität zu verlieren. Allerdings steigen mit der Festigkeit auch die Umformkräfte und die Anforderungen an die Werkzeugauslegung. Die Gefahr von Rissen oder Rückfederung nimmt zu, was eine präzisere Prozessführung und ggf. Zwischenwärmebehandlungen nötig macht. Diese Faktoren erhöhen die Produktionskosten, bieten jedoch Vorteile bei sicherheitsrelevanten Bauteilen – z. B. in der Automobilindustrie.
Aluminium und Aluminiumlegierungen sind wegen ihres geringen Gewichts und der guten Korrosionsbeständigkeit in der Luftfahrt- und Automobilindustrie besonders gefragt. Sie erfordern jedoch eine sorgfältige Prozesssteuerung, da Aluminium eine geringere Umformbarkeit als viele Stähle besitzt und zum „Kleben“ auf Werkzeugen neigt. Hier sind speziell angepasste Schmierstoffe und hochpräzise Werkzeuge notwendig, was die Kosten steigert, aber bei richtiger Auslegung ein qualitativ hochwertiges, leichtes Endprodukt liefert.
Edelstähle wie ferritische oder austenitische Legierungen stellen hohe Anforderungen an das Tiefziehverfahren. Sie sind korrosionsbeständig und für Anwendungen in der Lebensmittelindustrie, Medizintechnik oder Architektur geeignet. Die hohe Festigkeit führt zu größerem Werkzeugverschleiß und erfordert oftmals den Einsatz von Ziehöl oder speziell beschichteten Werkzeugen. Die höheren Material- und Bearbeitungskosten müssen gegen die Langlebigkeit und die Funktionalität der Endprodukte abgewogen werden.
Auch Kupfer und Messing lassen sich gut tiefziehen, vor allem wenn es auf elektrische Leitfähigkeit oder dekorative Oberflächen ankommt. Sie bieten sehr gute Umformeigenschaften, sind aber materialseitig teurer und können bei zu hohen Ziehgeschwindigkeiten beschädigt werden.
Zusammenfassend beeinflusst die Materialwahl beim Tiefziehen:
- Umformbarkeit und Ziehvermögen
- Notwendige Schmierung und Werkzeugauslegung
- Ausschussquote und Nacharbeit
- Produktionsgeschwindigkeit
- Bauteilfunktion und Lebensdauer
- Gesamtkosten des Prozesses
Daher ist es entscheidend, Werkstoff, Geometrie, Losgröße und Endanwendung in einem ganzheitlichen Ansatz aufeinander abzustimmen, um die bestmögliche Balance zwischen Qualität und Wirtschaftlichkeit zu erreichen.
Neben den mechanischen Eigenschaften des Materials spielen auch die Oberflächenbeschaffenheit und die Toleranzgenauigkeit eine zentrale Rolle im Tiefziehprozess. Ein gleichmäßiges, sauberes Blech mit definierter Oberflächenrauheit verringert die Reibung während der Umformung und minimiert das Risiko von Oberflächenfehlern wie Kratzern oder Einrissen. Insbesondere bei sichtbaren Bauteilen – etwa in der Automobilkarosserie oder bei Haushaltsgeräten – ist die optische Qualität entscheidend, sodass das Vormaterial entsprechend ausgewählt und vorbereitet werden muss. Auch die Blechdicke beeinflusst das Ziehverhalten stark: Je dünner das Blech, desto anfälliger ist es für Faltenbildung, aber gleichzeitig werden geringere Kräfte benötigt. Bei dickeren Blechen steigt der Energiebedarf, die Werkzeuge werden stärker belastet, und es entstehen höhere Rückstellkräfte im Material, was wiederum die Maßhaltigkeit beeinflussen kann. Ein weiterer Faktor ist die Homogenität des Materials. Schwankungen in der Blechdicke, Streckgrenze oder Härte führen zu ungleichmäßiger Umformung, was besonders in hochautomatisierten Prozessen problematisch ist. Aus diesem Grund greifen viele Hersteller auf chargenüberwachte Werkstoffe mit engeren Toleranzen zurück, um Prozesssicherheit und Wiederholbarkeit zu gewährleisten. Auch der Preis des Materials muss immer im Verhältnis zum gewünschten Qualitätsniveau betrachtet werden. Ein günstiger Werkstoff mit schlechter Umformbarkeit kann durch hohen Ausschuss, Werkzeugverschleiß und Nacharbeit letztlich teurer werden als ein zunächst teureres, aber besser geeignetes Material. Die Entscheidung über den optimalen Werkstoff sollte daher immer in enger Abstimmung zwischen Konstruktion, Fertigung und Einkauf erfolgen – unter Berücksichtigung der Geometrie, Funktion, Stückzahl und des geforderten Qualitätsstandards. Fortschritte in der Werkstoffentwicklung, etwa bei hochumformbaren Aluminiumlegierungen oder niedriglegierten Spezialstählen, bieten heute zusätzliche Optionen, die sowohl qualitativ als auch wirtschaftlich Vorteile bringen können. Letztlich ist die sorgfältige Auswahl und Prüfung des Materials einer der effektivsten Hebel, um Qualität und Kosten im Tiefziehprozess in Einklang zu bringen.
Ein oft unterschätzter Aspekt in Bezug auf die Materialwahl ist das Verhalten des Werkstoffs während der Umformung über mehrere Prozessschritte hinweg. Viele Tiefziehbauteile durchlaufen mehrere Ziehstufen, und nicht jeder Werkstoff reagiert darauf gleich stabil. Materialien mit hoher Kaltverfestigung neigen dazu, nach der ersten Umformung eine deutlich höhere Festigkeit aufzuweisen, was spätere Schritte erschwert oder sogar zusätzliche Zwischenglühen erfordert. Diese zusätzlichen Wärmebehandlungen verursachen nicht nur Kosten, sondern verlängern auch die Produktionszeit. Andererseits können Werkstoffe mit geringer Kaltverfestigung zwar leichter umgeformt werden, verlieren jedoch möglicherweise an Maßstabilität oder neigen zu Rückfederung, was vor allem bei engen Toleranzen problematisch ist.
Die chemische Zusammensetzung des Materials wirkt sich zudem auf das Verhalten während der Umformung aus. Bestimmte Legierungselemente wie Mangan, Silizium oder Chrom verändern die Fließeigenschaften, die Zähigkeit oder die Korrosionsbeständigkeit des Werkstoffs. Das kann Vorteile für die spätere Anwendung bringen, stellt jedoch zusätzliche Anforderungen an den Tiefziehprozess. Zum Beispiel müssen Werkzeuge speziell beschichtet werden, wenn mit abrasiven oder klebenden Werkstoffen gearbeitet wird, um Verschleiß und Anhaftungen zu vermeiden.
In vielen Fällen lohnt sich auch der Blick auf das Recyclingpotenzial des gewählten Materials. Aluminium etwa lässt sich sehr gut recyceln, ohne dass die Werkstoffeigenschaften wesentlich leiden. Das ist ein bedeutender Vorteil in Hinblick auf Ressourceneffizienz und Nachhaltigkeit, der bei der Werkstoffentscheidung zunehmend in den Vordergrund rückt. Für Unternehmen, die auf Umweltzertifizierungen oder CO₂-Bilanzen achten müssen, kann das entscheidend sein.
Nicht zuletzt beeinflusst die Verfügbarkeit eines Werkstoffs die Planungssicherheit und die Liefertreue. In Zeiten angespannter Lieferketten kann es sinnvoll sein, auf Werkstoffe zu setzen, die regional produziert werden oder für die es mehrere Bezugsquellen gibt, um Produktionsausfälle zu vermeiden. Die Wahl eines Materials sollte also nicht nur auf Basis technischer Umformbarkeit und reiner Kostenbetrachtung erfolgen, sondern stets im Kontext eines stabilen, reproduzierbaren und zukunftssicheren Fertigungsprozesses stehen.
Ein weiterer Aspekt, der bei der Materialwahl für das Tiefziehen nicht vernachlässigt werden darf, ist die Wechselwirkung zwischen Werkstoff und Schmierstoffsystem. Unterschiedliche Materialien erfordern spezifische Schmiermittel, um Reibung, Verschleiß und Aufschweißungen an den Werkzeugoberflächen zu vermeiden. Aluminium beispielsweise benötigt andere Schmierstoffe als unlegierter Stahl, da es stärker zur Kaltverschweißung neigt. Wird hier nicht das geeignete Mittel verwendet, steigt der Werkzeugverschleiß rapide, und es kommt zu Defekten an der Bauteiloberfläche. Auch Umweltauflagen oder der Wunsch nach trockenen, leicht entfernbaren Schmierstoffen beeinflussen die Auswahl. Das bedeutet: Schon bei der Entscheidung für einen Werkstoff müssen auch die passenden Hilfsstoffe, Reinigungsverfahren und Entsorgungskonzepte mitgedacht werden.
Die zunehmende Vielfalt an verfügbaren Werkstoffen eröffnet auf der einen Seite neue Möglichkeiten für leichtere, stabilere oder korrosionsbeständigere Produkte, erhöht auf der anderen Seite aber auch die Komplexität im Produktionsalltag. Besonders in der Serienfertigung ist es entscheidend, dass der gewählte Werkstoff konstant in gleicher Qualität verfügbar ist. Schwankungen in der Festigkeit, Härte oder Oberflächenbeschaffenheit – selbst innerhalb derselben Werkstoffsorte – können zu unvorhersehbaren Prozessschwankungen führen. Aus diesem Grund sind viele Hersteller dazu übergegangen, mit klar definierten Werkstoffspezifikationen und Langzeitverträgen zu arbeiten, um Konsistenz und Verfügbarkeit zu sichern.
Zukunftsgerichtet betrachtet, wird der Einsatz hybrider Werkstoffe, etwa durch Beschichtungen oder Verbundwerkstoffe, weiter an Bedeutung gewinnen. Materialien mit funktionellen Schichten – zum Beispiel zur Geräuschdämpfung, Verschleißminimierung oder thermischen Isolation – eröffnen zusätzliche Einsatzfelder, stellen aber auch besondere Anforderungen an die Umformung. Diese Entwicklungen erfordern ein noch tieferes Verständnis der Materialverhalten im gesamten Fertigungsprozess und eine enge Abstimmung zwischen Materialherstellern, Werkzeugbau und Fertigungstechnik.
Letztlich entscheidet die Materialwahl nicht nur über die Qualität des Tiefziehteils, sondern beeinflusst beinahe jede Dimension der Fertigung – von der Umformbarkeit über die Werkzeuglebensdauer und Wartungsintervalle bis hin zur Umweltbilanz und Wirtschaftlichkeit der Gesamtproduktion. Wer hier sorgfältig auswählt und auf abgestimmte Prozesse setzt, schafft die Basis für einen stabilen, kosteneffizienten und zukunftssicheren Tiefziehprozess.
Automatisierung im Tiefziehprozess: Technologien und Lösungen
Die Automatisierung im Tiefziehprozess hat in den letzten Jahren enorme Fortschritte gemacht und ist heute ein entscheidender Faktor für Effizienz, Qualität und Wettbewerbsfähigkeit in der Blechumformung. Moderne Technologien ermöglichen eine durchgängige Automatisierung von der Zuführung der Platinen bis zur Entnahme der fertigen Bauteile. Dabei kommen Roboter, Sensorik, intelligente Steuerungen und adaptive Fertigungssysteme zum Einsatz, um den gesamten Ablauf präzise und störungsfrei zu gestalten.
Ein zentraler Baustein ist die automatisierte Platinenzuführung, bei der Blechzuschnitte mithilfe von Förderbändern, Vakuumgreifern oder Roboterarmen exakt in die Tiefziehpresse eingelegt werden. Kamerasysteme und Positionssensoren überwachen dabei die Lage und Ausrichtung der Bleche in Echtzeit, um Fehlpositionierungen zu vermeiden. Moderne Systeme erkennen sogar automatisch das Material und passen die Prozessparameter entsprechend an.
Während des Ziehvorgangs selbst kommt prozessintegrierte Sensorik zum Einsatz, die Kräfte, Wege, Temperaturen und Schmierstoffverteilungen misst. Diese Daten werden von der Maschinensteuerung kontinuierlich analysiert und bei Bedarf innerhalb von Millisekunden korrigierend eingegriffen. So lässt sich der Prozess stabil halten, auch bei variierenden Materialchargen oder komplexen Bauteilgeometrien.
Nach dem Umformen übernehmen Pick-and-Place-Roboter oder Portalmanipulatoren die Entnahme der Teile. Je nach Anforderung werden die Werkstücke direkt zu Folgeoperationen wie Beschneiden, Kalibrieren, Reinigen oder Qualitätsprüfung weitertransportiert. Durchgängige Fördertechnik und Greifsysteme sorgen dafür, dass keine manuelle Handhabung erforderlich ist, was die Taktzeit verkürzt und die Arbeitssicherheit verbessert.
Ein besonders zukunftsweisender Trend ist der Einsatz von digitalen Zwillingen und vernetzten Steuerungen. Hier wird der gesamte Tiefziehprozess virtuell abgebildet und mit Echtzeitdaten gespeist. Das ermöglicht nicht nur die vorausschauende Wartung von Anlagenkomponenten, sondern auch die automatische Optimierung von Ziehparametern, Werkzeugkühlung und Schmierstoffauftrag. Produktionsanlagen können sich so selbstständig an wechselnde Bedingungen anpassen und stabil produzieren.
Auch die Qualitätssicherung profitiert von der Automatisierung: Inline-Messsysteme mit 3D-Kameras oder Lasertriangulation prüfen während der Produktion Geometrien, Oberflächen oder Wandstärken der Bauteile. Abweichungen werden unmittelbar erkannt und sortiert, bevor fehlerhafte Teile in die nächste Fertigungsstufe gelangen.
Die vollständige Integration dieser Technologien in ein intelligentes Fertigungsleitsystem – oft unter dem Begriff Industrie 4.0 zusammengefasst – schafft ein hohes Maß an Transparenz und Kontrolle. Produktionsdaten werden lückenlos erfasst, analysiert und archiviert, was die Rückverfolgbarkeit erleichtert und eine kontinuierliche Verbesserung auf Basis realer Prozessdaten ermöglicht.
Insgesamt führt die Automatisierung im Tiefziehen zu kürzeren Taktzeiten, weniger Ausschuss, geringeren Personalkosten und einer deutlich höheren Reproduzierbarkeit. Gleichzeitig erlaubt sie eine flexible Anpassung an sich ändernde Stückzahlen, Varianten oder Werkstoffe – ein entscheidender Vorteil in zunehmend individualisierten Märkten.
Ein weiterer wichtiger Vorteil der Automatisierung im Tiefziehprozess liegt in der konstanten Prozessqualität über lange Produktionszeiträume hinweg. Während manuelle Abläufe häufig von menschlicher Erfahrung und Konzentration abhängen, ermöglichen automatisierte Systeme eine präzise Reproduzierbarkeit selbst bei anspruchsvollen Ziehgeometrien und empfindlichen Materialien. Dies ist besonders relevant für Branchen wie die Automobil-, Luftfahrt- oder Medizintechnikindustrie, in denen enge Toleranzen und lückenlose Dokumentation gefordert werden. Die Automatisierung reduziert außerdem die Anfälligkeit für Bedienfehler. Durch fest hinterlegte Parameter, automatisch kontrollierte Abläufe und Selbstüberwachung der Maschinen wird das Risiko von Ausschuss signifikant gesenkt. Auch Umrüstprozesse werden beschleunigt, indem Werkzeuge und Programme über digitale Schnittstellen automatisiert gewechselt und initialisiert werden. Dies erhöht die Anlagenverfügbarkeit und senkt Stillstandzeiten, was wiederum zur Produktivitätssteigerung beiträgt. In Verbindung mit lernfähigen Algorithmen lassen sich zudem langfristige Prozessdaten auswerten, die auf Zusammenhänge zwischen Materialverhalten, Werkzeugverschleiß und Umgebungsbedingungen hinweisen. Daraus können präventive Wartungsmaßnahmen abgeleitet oder Ziehparameter vorausschauend angepasst werden, bevor ein Qualitätsverlust eintritt. Zudem ermöglicht die Automatisierung eine flexiblere Auslegung der Fertigung: Serien mit unterschiedlichen Bauteilvarianten können im sogenannten Losgrößen-1-Modus wirtschaftlich produziert werden, da Roboter und Pressensteuerungen variabel programmiert werden können und nicht mehr auf starre Vorrichtungen angewiesen sind. Dies unterstützt Unternehmen dabei, auch kleine und mittelgroße Serien profitabel herzustellen. Schließlich wirkt sich die Automatisierung positiv auf die Ergonomie und Sicherheit am Arbeitsplatz aus. Schwere körperliche Tätigkeiten wie das Einlegen großer Bleche oder das Handling scharfkantiger Bauteile entfallen, wodurch die Mitarbeiter entlastet und Arbeitsunfälle vermieden werden. Fachkräfte können sich auf die Überwachung, Optimierung und Wartung der automatisierten Systeme konzentrieren, was nicht nur die Produktionsqualität verbessert, sondern auch die Attraktivität der Arbeitsplätze in der Blechumformung steigert. Automatisierung im Tiefziehen ist daher nicht nur ein Mittel zur Effizienzsteigerung, sondern ein strategisches Instrument zur Zukunftssicherung der gesamten Fertigung.
Die Integration von Künstlicher Intelligenz (KI) und maschinellem Lernen in die Automatisierung des Tiefziehprozesses eröffnet weitere Potenziale. Durch die Auswertung großer Datenmengen aus Sensoren und Fertigungssystemen können KI-gestützte Systeme Muster erkennen, die für den Menschen schwer oder gar nicht sichtbar sind. So lassen sich Abweichungen im Prozess frühzeitig prognostizieren und automatisierte Anpassungen in Echtzeit vornehmen. Diese selbstlernenden Systeme erhöhen die Prozessstabilität und reduzieren Stillstandzeiten, da Fehlerquellen schneller identifiziert und beseitigt werden. Zudem können KI-Modelle dabei helfen, die Werkzeugstandzeiten genauer vorherzusagen, indem sie Verschleißerscheinungen erkennen, bevor diese kritisch werden. Dies ermöglicht eine optimierte Wartungsplanung und senkt die Instandhaltungskosten.
Ein weiterer wichtiger Aspekt ist die Vernetzung von Fertigungsanlagen im Rahmen von Industrie 4.0. Tiefziehpressen und Roboter kommunizieren hierbei nicht nur untereinander, sondern tauschen auch Daten mit übergeordneten Produktionsplanungssystemen, Lagerverwaltung und Qualitätsmanagement aus. Diese durchgängige Digitalisierung erlaubt eine flexible Anpassung an Kundenanforderungen und Marktbedingungen, wie kurzfristige Änderungen in der Stückzahl oder Bauteilvariante. Gleichzeitig ermöglicht die lückenlose Dokumentation der Prozessparameter eine umfassende Rückverfolgbarkeit der gefertigten Teile, was besonders bei sicherheitsrelevanten Komponenten von großer Bedeutung ist.
Auch in der Simulation und virtuellen Inbetriebnahme wird die Automatisierung im Tiefziehen unterstützt. Vor Produktionsstart können komplexe Ziehprozesse digital nachgebildet und optimiert werden, wodurch teure Versuche und Werkzeugänderungen reduziert werden. Die Kombination aus Simulation, Echtzeit-Daten und automatischer Prozessanpassung sorgt für eine deutlich schnellere und sicherere Serienanlaufphase.
Nicht zuletzt gewinnen flexible Automatisierungslösungen, wie modulare Robotersysteme oder mobile Handlingeinheiten, zunehmend an Bedeutung. Diese können relativ schnell für unterschiedliche Produkte oder Produktionslinien umgerüstet werden und ermöglichen so eine agile Fertigung, die sich schnell an veränderte Marktbedürfnisse anpasst.
Insgesamt führt die Automatisierung im Tiefziehprozess nicht nur zu Kosteneinsparungen und Qualitätsverbesserungen, sondern auch zu einer höheren Flexibilität, Nachhaltigkeit und Wettbewerbsfähigkeit in einer zunehmend dynamischen Industrieumgebung.
Darüber hinaus spielt die Zusammenarbeit von Mensch und Maschine, das sogenannte Human-Robot-Collaboration (HRC), eine immer größere Rolle in der Automatisierung des Tiefziehprozesses. Statt den Menschen komplett aus der Fertigung zu verdrängen, werden kollaborative Roboter (Cobots) eingesetzt, die sicher und flexibel mit den Bedienern zusammenarbeiten. Diese Cobots können repetitive, ergonomisch belastende oder präzise Handhabungsaufgaben übernehmen, während der Mensch weiterhin Entscheidungen trifft, Eingriffe vornimmt und komplexe Probleme löst. Dadurch wird die Produktivität erhöht, ohne die Flexibilität oder die Qualität zu beeinträchtigen.
Ein weiterer Vorteil von HRC-Systemen liegt in der schnellen Adaptierbarkeit. Im Gegensatz zu starren Automatisierungsanlagen lassen sich Cobots oft mit geringem Aufwand auf neue Produkte oder Prozessschritte umstellen. Gerade in der Klein- und Mittelserienfertigung mit häufig wechselnden Bauteilen ist das ein entscheidender Vorteil.
Die Einbindung von Bedienern in den automatisierten Prozess fördert zudem die Akzeptanz neuer Technologien und erleichtert die kontinuierliche Verbesserung der Fertigung. Mitarbeiter können ihr Wissen direkt in die Prozessoptimierung einbringen und durch die Entlastung von monotone Tätigkeiten motivierter und kreativer arbeiten.
Neben Cobots gewinnen auch autonome Transportfahrzeuge (AGVs) und fahrerlose Transportsysteme (FTS) an Bedeutung, die Material und Werkstücke innerhalb der Fertigung automatisch bewegen. Diese Systeme sind eng mit der Produktionssteuerung vernetzt und sorgen für einen reibungslosen Materialfluss zwischen den Tiefziehpressen, den Nachbearbeitungsstationen und der Lagerlogistik. Dadurch werden Engpässe reduziert und die Durchlaufzeiten verkürzt.
Insgesamt führt die Kombination aus intelligenter Automatisierung, kollaborativen Robotern und digital vernetzten Systemen zu einer flexiblen, effizienten und nachhaltigen Fertigung im Tiefziehprozess. Unternehmen, die diese Technologien frühzeitig adaptieren, sichern sich einen Wettbewerbsvorteil durch höhere Produktqualität, kürzere Lieferzeiten und niedrigere Kosten bei gleichzeitig verbesserter Arbeitssicherheit und Mitarbeiterzufriedenheit.
Tiefziehen vs. andere Umformverfahren: Ein Vergleich
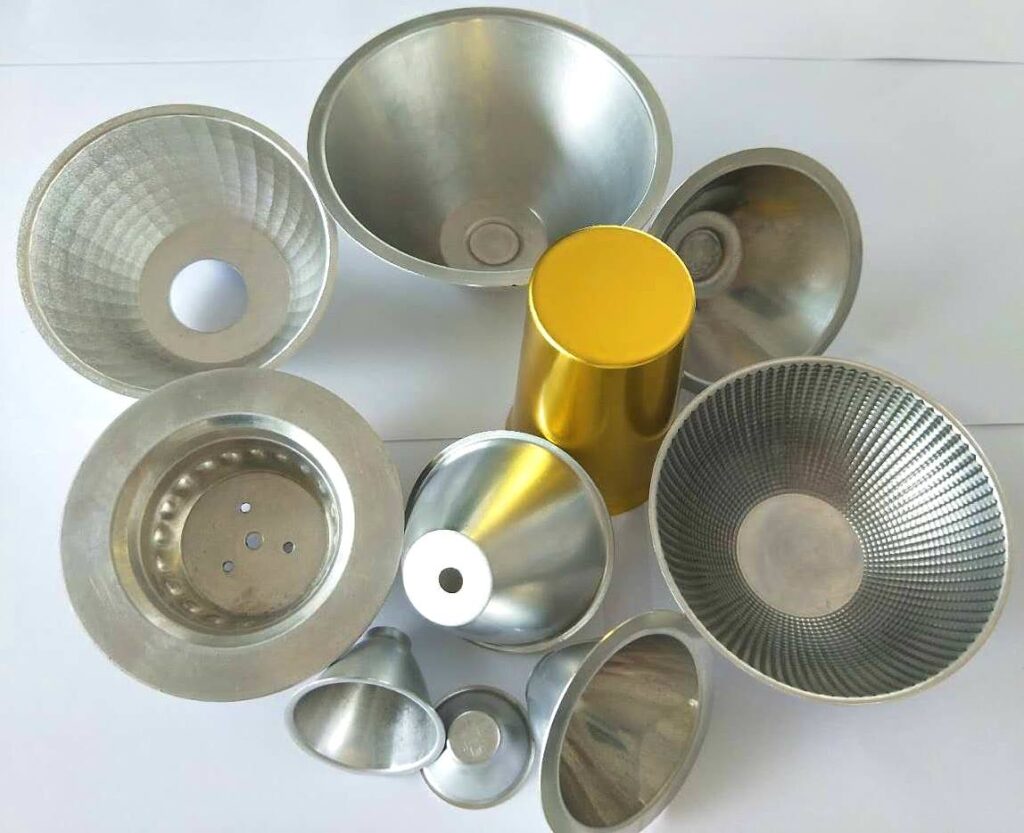
Das Tiefziehen ist ein Umformverfahren, bei dem ein flaches Blech durch einen Stempel in eine Hohlform gezogen wird, um daraus komplexe, oft zylindrische oder rechteckige Bauteile mit vertieften Konturen herzustellen. Im Vergleich zu anderen Umformverfahren zeichnet sich das Tiefziehen durch bestimmte Vorteile und Einschränkungen aus, die je nach Anwendungsfall abgewogen werden müssen.
Im Gegensatz zum Biegen, bei dem das Blech an definierten Linien umgeformt wird, ermöglicht das Tiefziehen eine dreidimensionale Formgebung mit glatten Übergängen und ohne scharfe Knicke. Während Biegen oft einfacher und kostengünstiger ist, bietet Tiefziehen eine größere Gestaltungsfreiheit und ermöglicht die Fertigung komplexer Formen mit tiefen Vertiefungen.
Im Vergleich zum Stauchen oder Schmieden, bei denen Werkstücke meist massiv verformt werden, ist das Tiefziehen ein Flächenumformverfahren, das speziell für Bleche konzipiert ist. Schmieden erzeugt oft höhere Festigkeiten und bessere Werkstoffeigenschaften durch Umstrukturierung des Gefüges, ist aber für dünnwandige, großflächige Bauteile ungeeignet. Das Tiefziehen ermöglicht hingegen dünnwandige, leichte Bauteile mit hoher Formgenauigkeit, was besonders in der Automobil- oder Haushaltsgeräteindustrie geschätzt wird.
Im Gegensatz zum Walzen, das primär zur Dickenreduzierung und Formgebung von Bändern oder Blechen dient, erzeugt das Tiefziehen geometrisch definierte Vertiefungen oder Hohlkörper. Walzen ist eher für die Massenfertigung von Blechmaterialien geeignet, während Tiefziehen direkt zur Endformung von Bauteilen eingesetzt wird.
Das Stanzen ist ein trennendes Verfahren, das oft vor oder nach dem Tiefziehen zum Zuschneiden von Blechen genutzt wird. Tiefziehen hingegen verändert die Form ohne Materialverlust. Die Kombination beider Verfahren ist häufig in der industriellen Fertigung anzutreffen.
Ein entscheidender Vorteil des Tiefziehens gegenüber vielen anderen Umformverfahren ist die Möglichkeit, komplexe, nahtlose Bauteile mit hoher Oberflächenqualität und Materialeffizienz herzustellen. Es entstehen keine Schweißnähte oder Fügeverbindungen, was die Festigkeit und das Aussehen verbessert. Die Verfahrensflexibilität ermöglicht zudem die Serienfertigung von kleinen bis großen Stückzahlen mit relativ kurzen Taktzeiten.
Allerdings sind die Werkzeuge für das Tiefziehen oft kostenintensiver als für einfachere Umformverfahren. Zudem erfordert das Verfahren präzise Steuerung der Umformkräfte, Reibung und Materialeigenschaften, um Defekte wie Faltenbildung, Einreißen oder Rückfederung zu vermeiden. Daher ist eine sorgfältige Prozessplanung und Materialauswahl unerlässlich.
Zusammenfassend bietet das Tiefziehen gegenüber anderen Umformverfahren eine optimale Kombination aus Komplexität der Formgebung, Oberflächenqualität und Materialausnutzung, ist aber mit höheren Werkzeugkosten und Prozessanforderungen verbunden. Die Wahl des geeigneten Verfahrens hängt letztlich von der Geometrie, Stückzahl, Materialart und den Qualitätsanforderungen des Bauteils ab.
Ein weiterer wichtiger Aspekt im Vergleich zwischen Tiefziehen und anderen Umformverfahren ist die Flexibilität bei der Fertigung von Bauteilvarianten. Tiefziehen ermöglicht durch den Einsatz modularer Werkzeugsysteme und variabler Prozessparameter eine relativ einfache Anpassung an unterschiedliche Formen und Größen. Dies ist besonders vorteilhaft bei der Herstellung von Kleinserien oder individualisierten Produkten. Im Gegensatz dazu sind Verfahren wie das Stanzen oder Prägen häufig auf starre Werkzeuggeometrien angewiesen, was Umrüstzeiten und -kosten erhöht. Gleichzeitig erlaubt das Tiefziehen eine hohe Maßhaltigkeit und Reproduzierbarkeit, was in der Serienproduktion von großer Bedeutung ist.
Die Materialausnutzung beim Tiefziehen ist ebenfalls hervorzuheben. Da das Verfahren auf das Umformen des Ausgangsblechs ohne wesentlichen Materialverlust ausgelegt ist, entstehen im Gegensatz zum Trennen oder Fräsen kaum Abfälle. Dies führt zu Kosteneinsparungen und ist auch aus ökologischer Sicht ein Vorteil. Dennoch müssen beim Tiefziehen die Eigenschaften des Werkstoffs wie Dehnbarkeit und Rückfederungsverhalten sorgfältig berücksichtigt werden, um Ausschuss zu minimieren. Andere Umformverfahren, wie das Walzen oder Schmieden, beeinflussen dagegen stärker die Mikrostruktur und mechanischen Eigenschaften des Materials, was für bestimmte Anwendungen wünschenswert sein kann.
Darüber hinaus sind die Anforderungen an Maschinen und Werkzeuge beim Tiefziehen hoch. Die Pressen müssen große Kräfte präzise übertragen können, und die Werkzeuge müssen den hohen Belastungen standhalten, ohne sich zu verformen oder zu verschleißen. Dies führt zu höheren Investitionskosten im Vergleich zu einfacheren Umformverfahren wie Biegen oder Schneiden. Allerdings amortisieren sich diese Kosten durch die hohe Produktionsgeschwindigkeit und die Möglichkeit, komplexe Formen in einem Arbeitsgang herzustellen.
In Bezug auf die Nachbearbeitung sind Tiefziehteile häufig nahezu fertig bearbeitet und benötigen nur geringe zusätzliche Schritte wie Entgraten oder Beschichten. Andere Verfahren, wie das Schmieden oder Gießen, erfordern oft umfangreiche mechanische Nachbearbeitungen, um die gewünschte Oberflächenqualität und Maßhaltigkeit zu erreichen.
Zusammenfassend lässt sich sagen, dass das Tiefziehen vor allem dort seine Stärken ausspielt, wo komplexe, dünnwandige Bauteile mit hoher Präzision, guter Oberflächenqualität und wirtschaftlich in mittleren bis großen Serien hergestellt werden sollen. Die Wahl zwischen Tiefziehen und alternativen Umformverfahren ist letztlich eine Frage der Anforderungen an Bauteilgeometrie, Materialeigenschaften, Stückzahlen, Kosten und Qualität. Ein umfassendes Verständnis der jeweiligen Vor- und Nachteile ist daher für eine optimale Fertigungsentscheidung unerlässlich.
Neben den genannten Aspekten gewinnt im Vergleich der Umformverfahren auch die Integration von Mehrstufenprozessen an Bedeutung. Tiefziehen wird häufig in Kombination mit anderen Umformverfahren eingesetzt, um komplexe Bauteile in mehreren Schritten herzustellen. So können durch mehrstufiges Tiefziehen mit Zwischenstreckung oder -glühung die Umformgrade erhöht und Bauteile mit besonders tiefen oder komplizierten Geometrien gefertigt werden. Dabei werden im Gegensatz zu einfachen Umformverfahren wie Biegen oder Stanzen mehrere Zieh- und Rückformschritte aufeinander abgestimmt, um optimale Materialverteilung und Formgenauigkeit zu erreichen.
Ein weiterer Punkt ist die Oberflächenbehandlung und Veredelung der Bauteile nach dem Umformprozess. Tiefgezogene Teile weisen durch den schonenden Umformprozess meist eine hohe Oberflächengüte auf, wodurch aufwendige Nachbearbeitungen wie Schleifen oder Polieren häufig entfallen können. Dies unterscheidet das Tiefziehen von Verfahren wie dem Schmieden, bei dem oft grobe Oberflächenstrukturen entstehen, die weiter bearbeitet werden müssen. Die hohe Oberflächenqualität ist gerade in Bereichen wie der Lebensmittelverpackung, Medizintechnik oder Automobilindustrie entscheidend.
Die Umweltverträglichkeit und Nachhaltigkeit spielen ebenfalls eine immer größere Rolle. Das Tiefziehen zeichnet sich durch einen geringen Materialverlust und Energieverbrauch im Vergleich zu Verfahren wie Gießen oder Fräsen aus. Zudem ermöglicht die Verwendung von Leichtmetallen wie Aluminium oder Edelstahl im Tiefziehprozess die Herstellung leichter, aber gleichzeitig stabiler Bauteile, was wiederum die Energieeffizienz in späteren Anwendungen, etwa im Fahrzeugbau, verbessert.
Schließlich ist auch die Automatisierung und Digitalisierung der Prozesse ein Unterscheidungsmerkmal. Während Tiefziehprozesse durch moderne Steuerungs- und Sensoriksysteme gut automatisierbar sind, sind manche Umformverfahren mit hoher manuellem Aufwand verbunden oder schwieriger in bestehende Fertigungslinien integrierbar. Dies macht das Tiefziehen besonders attraktiv für die moderne, flexible und vernetzte Fertigung.
Insgesamt ist das Tiefziehen ein vielseitiges und wirtschaftliches Umformverfahren, das sich durch seine Fähigkeit auszeichnet, komplexe Bauteile mit hoher Präzision und Qualität effizient herzustellen. Die Entscheidung für das Tiefziehen oder alternative Verfahren sollte stets auf einer fundierten Analyse der spezifischen Anforderungen basieren, um die beste Kombination aus Kosten, Qualität und Produktivität zu erzielen.
Neben den technischen und wirtschaftlichen Aspekten ist auch die Qualifikation der Fachkräfte ein wichtiger Faktor beim Einsatz von Tiefziehverfahren im Vergleich zu anderen Umformverfahren. Das Tiefziehen erfordert ein hohes Maß an Prozessverständnis, insbesondere in Bezug auf Materialverhalten, Werkzeugauslegung und Prozessparameter wie Ziehgeschwindigkeit, Schmierung und Umformkraft. Facharbeiter und Ingenieure müssen in der Lage sein, diese Faktoren gezielt zu steuern und bei Abweichungen schnell gegenzusteuern, um Ausschuss zu vermeiden. Im Gegensatz dazu sind manche einfachere Verfahren, wie das Biegen oder Stanzen, weniger komplex in der Prozesssteuerung und daher leichter zu erlernen.
Die Entwicklung moderner Simulationssoftware hat jedoch die Lernkurve für das Tiefziehen deutlich reduziert. Virtuelle Prozesssimulationen ermöglichen es, potenzielle Probleme bereits in der Planungsphase zu erkennen und Werkzeuge sowie Prozessparameter zu optimieren, bevor die Produktion startet. Dies reduziert teure Versuche und Nacharbeit erheblich und macht das Tiefziehen auch für Unternehmen mit weniger Erfahrung zugänglicher.
Ein weiterer Vorteil im Vergleich zu anderen Verfahren ist die Möglichkeit, durch den Einsatz spezieller Werkstoffe, wie hochfester Stähle oder Aluminiumlegierungen, Bauteile mit sehr guten mechanischen Eigenschaften bei geringem Gewicht herzustellen. Dies ist besonders in der Automobil- und Luftfahrtindustrie wichtig, wo Gewichtseinsparungen direkt zu Kraftstoff- und Emissionseinsparungen führen. Während andere Umformverfahren wie Schmieden oder Gießen oft mehr Materialverlust oder höhere Nachbearbeitungsaufwände mit sich bringen, bietet das Tiefziehen hier eine effiziente Alternative.
Nicht zuletzt ermöglicht die Kombination von Tiefziehen mit nachgelagerten Prozessen wie Fügeverfahren, Oberflächenbeschichtungen oder Wärmebehandlungen eine flexible und wirtschaftliche Fertigungskette. Durch die nahtlose Integration dieser Prozesse kann die Gesamtproduktivität gesteigert und die Qualität der Endprodukte weiter verbessert werden.
Insgesamt zeigt sich, dass das Tiefziehen trotz seiner Komplexität eine Reihe von Vorteilen gegenüber anderen Umformverfahren bietet, insbesondere wenn es um die Herstellung leichter, präziser und qualitativ hochwertiger Bauteile geht. Die Investition in Technologie, Fachwissen und Prozessoptimierung zahlt sich durch erhöhte Effizienz, bessere Produktqualität und größere Fertigungsspielräume aus.
Tiefziehmaschinen: Die richtige Auswahl für Ihr Unternehmen
Bei der Auswahl der passenden Tiefziehmaschine für ein Unternehmen spielen verschiedene Faktoren eine entscheidende Rolle, um eine effiziente und wirtschaftliche Produktion sicherzustellen. Zunächst ist die Art des zu verarbeitenden Materials maßgeblich: Unterschiedliche Materialien wie Stahl, Aluminium oder Edelstahl haben unterschiedliche Umformeigenschaften, die eine entsprechende Maschinenkraft und Werkzeugauslegung erfordern. Hochfeste Materialien benötigen beispielsweise stärkere Pressen mit präziser Steuerung, während weichere Werkstoffe oft geringere Kräfte erfordern.
Die Bauteilgröße und -komplexität beeinflussen ebenfalls die Maschinenwahl. Für kleine, einfache Teile reichen oft kleinere Pressen mit geringerer Schlagkraft aus, während große oder komplex geformte Bauteile größere Pressen mit höherem Hub und entsprechend dimensionierten Werkzeugen benötigen. Auch die maximale Blechdicke, die verarbeitet werden soll, bestimmt die notwendige Presskraft.
Ein weiterer wesentlicher Punkt ist die Produktionsmenge und Seriengröße. Für hohe Stückzahlen bieten sich vollautomatisierte Tiefziehmaschinen mit integrierten Zuführ- und Entnahmesystemen an, die eine hohe Taktzeit und gleichbleibende Qualität ermöglichen. Kleinserien oder variantenreiche Produktionen profitieren dagegen von flexiblen Maschinen mit schneller Umrüstbarkeit und einfacher Bedienung, beispielsweise durch modulare Werkzeugsysteme oder programmierbare Steuerungen.
Die Technologie der Maschine ist ebenfalls entscheidend. Hydraulische Pressen punkten durch hohe Kraft bei kontrollierbarer Geschwindigkeit und Sanftanlauf, sind aber oft langsamer. Mechanische Pressen bieten höhere Taktzeiten, eignen sich jedoch besser für weniger komplexe Umformungen mit konstanten Kräften. Servohydraulische Maschinen kombinieren Vorteile beider Systeme und ermöglichen präzise, energieeffiziente Prozesse mit variabler Geschwindigkeit.
Auch die Automatisierungsoptionen und Schnittstellen zur Fertigungssteuerung sollten berücksichtigt werden. Maschinen mit integrierter Sensorik, Prozessüberwachung und Anbindung an Industrie-4.0-Systeme ermöglichen eine lückenlose Dokumentation, Qualitätskontrolle und schnelle Reaktion auf Prozessabweichungen.
Darüber hinaus spielen Aspekte wie der Platzbedarf, die Energieeffizienz und die Wartungsfreundlichkeit eine Rolle, um Betriebskosten und Ausfallzeiten gering zu halten. Die Verfügbarkeit von Service und Ersatzteilen sowie Schulungsangebote für das Bedienpersonal runden die Entscheidungsgrundlage ab.
Schließlich ist es empfehlenswert, die Auswahl gemeinsam mit erfahrenen Maschinenherstellern und Prozessingenieuren zu treffen, um die Maschine optimal auf die spezifischen Anforderungen des Unternehmens abzustimmen. So wird sichergestellt, dass die Tiefziehmaschine nicht nur kurzfristig, sondern auch langfristig zur Steigerung von Produktivität und Qualität beiträgt.
Wichtig bei der Auswahl einer Tiefziehmaschine ist auch die Berücksichtigung der zukünftigen Produktionsanforderungen. Unternehmen sollten Maschinen bevorzugen, die eine gewisse Flexibilität für zukünftige Produktänderungen oder Erweiterungen bieten. Dies kann durch modulare Maschinenkonzepte oder durch die Möglichkeit zur Nachrüstung von Automatisierungskomponenten gewährleistet werden. So wird vermieden, dass bereits nach kurzer Zeit eine neue Investition notwendig wird, weil die Maschine den steigenden oder sich ändernden Anforderungen nicht mehr gerecht wird.
Ein weiterer Aspekt betrifft die Ergonomie und Bedienerfreundlichkeit der Maschine. Moderne Tiefziehmaschinen verfügen über intuitive Benutzeroberflächen, Touchscreens und umfangreiche Assistenzsysteme, die den Bedienern helfen, Prozesse schnell einzurichten und Fehler zu vermeiden. Eine einfache Handhabung trägt dazu bei, Schulungszeiten zu verkürzen und die Produktivität zu steigern. Gleichzeitig sinkt durch die bessere Prozesskontrolle die Ausschussquote, was Kosten senkt.
Im Hinblick auf die Umweltauswirkungen spielt die Energieeffizienz eine immer größere Rolle. Servoantriebe und optimierte Hydrauliksysteme reduzieren den Energieverbrauch erheblich im Vergleich zu älteren Maschinen. Dies senkt nicht nur die Betriebskosten, sondern unterstützt auch unternehmerische Nachhaltigkeitsziele. Einige Maschinenhersteller bieten darüber hinaus Konzepte zur Rückgewinnung von Energie oder den Einsatz von umweltfreundlichen Schmierstoffen an, was den ökologischen Fußabdruck weiter verringert.
Nicht zuletzt ist die Integration der Tiefziehmaschine in das bestehende Fertigungssystem entscheidend. Die Maschine sollte kompatibel sein mit vorhandenen ERP- und MES-Systemen, um eine durchgängige Produktionsplanung und -steuerung zu ermöglichen. Vernetzte Maschinen erlauben Echtzeitüberwachung, vorausschauende Wartung und eine bessere Auslastung der Produktionskapazitäten. Dies erhöht die Gesamtanlageneffektivität (OEE) und trägt zur Wettbewerbsfähigkeit des Unternehmens bei.
Abschließend lässt sich sagen, dass die richtige Auswahl einer Tiefziehmaschine weit über die reine Maschinenleistung hinausgeht. Sie umfasst auch Aspekte wie Flexibilität, Bedienkomfort, Energieeffizienz und Vernetzbarkeit. Eine ganzheitliche Betrachtung hilft Unternehmen, eine langfristig sinnvolle Investition zu tätigen, die zu höherer Produktivität, besserer Produktqualität und geringeren Betriebskosten führt.
Neben den bereits genannten Faktoren ist bei der Auswahl einer Tiefziehmaschine auch die Berücksichtigung von Sicherheitsaspekten unerlässlich. Moderne Maschinen sind mit umfassenden Sicherheitsvorrichtungen ausgestattet, die nicht nur den Bediener schützen, sondern auch die Einhaltung gesetzlicher Vorschriften gewährleisten. Dazu gehören Schutzabdeckungen, Lichtschranken, Not-Aus-Systeme und Überwachungseinrichtungen, die Unfälle verhindern und gleichzeitig die Produktivität durch sichere Arbeitsbedingungen fördern.
Die Investitions- und Betriebskosten spielen ebenfalls eine wesentliche Rolle bei der Entscheidungsfindung. Während hochmoderne, vollautomatisierte Tiefziehmaschinen mit komplexer Steuerung und Automatisierung hohe Anschaffungskosten verursachen, amortisieren sich diese durch reduzierte Produktionszeiten, geringeren Materialausschuss und niedrigere Personalkosten. Ein Kosten-Nutzen-Vergleich sollte daher immer auch die langfristigen Einsparungen und Produktivitätsgewinne berücksichtigen.
Ein weiterer wichtiger Punkt ist die Verfügbarkeit von Schulungen und technischem Support seitens des Herstellers. Eine gute Betreuung nach dem Kauf sichert einen reibungslosen Produktionsstart und unterstützt bei der Optimierung der Prozesse. Unternehmen profitieren zudem von regelmäßigen Updates der Maschinensteuerung und Wartungsangeboten, die Ausfallzeiten minimieren.
Nicht zu vergessen ist die Möglichkeit, die Tiefziehmaschine mit weiteren Fertigungstechnologien zu kombinieren. Beispielsweise kann die Maschine in Fertigungslinien mit automatischer Materialzuführung, Entgratungs- oder Lackierstationen integriert werden. Dies erhöht die Prozessintegration und ermöglicht eine schlanke, effiziente Produktion.
Insgesamt ist die Auswahl der richtigen Tiefziehmaschine ein komplexer Prozess, der technische, wirtschaftliche und organisatorische Aspekte gleichermaßen berücksichtigt. Ein fundiertes Verständnis der eigenen Fertigungsanforderungen, verbunden mit einer engen Zusammenarbeit mit Maschinenherstellern und Prozessexperten, ist der Schlüssel zu einer Investition, die langfristig den Unternehmenserfolg sichert.
Darüber hinaus gewinnt die Digitalisierung in der Tiefziehtechnik zunehmend an Bedeutung. Intelligente Steuerungssysteme ermöglichen eine präzise Überwachung und Steuerung des Tiefziehprozesses in Echtzeit. Sensoren erfassen dabei wichtige Parameter wie Kraft, Geschwindigkeit, Position und Temperatur, die über digitale Schnittstellen an zentrale Leitsysteme oder Cloud-Plattformen übertragen werden. So können Abweichungen sofort erkannt und korrigiert werden, was die Qualität der Bauteile erhöht und Ausschuss reduziert.
Diese Vernetzung ermöglicht zudem die Implementierung von Predictive Maintenance, also der vorausschauenden Wartung. Durch die kontinuierliche Analyse von Maschinendaten lassen sich Verschleißerscheinungen frühzeitig erkennen und Wartungsarbeiten gezielt planen, bevor es zu ungeplanten Stillständen kommt. Dies steigert die Verfügbarkeit der Tiefziehmaschinen und reduziert die Betriebskosten.
Ein weiterer Vorteil digital vernetzter Tiefziehmaschinen ist die einfache Integration in Industrie-4.0-Fertigungsumgebungen. Hierbei kommunizieren Maschinen, Werkzeuge und Materialflüsse miteinander, um die Produktion flexibel und effizient zu gestalten. Änderungen im Produktionsplan können schnell umgesetzt werden, und die gesamte Fertigungskette passt sich dynamisch an neue Anforderungen an.
Neben der Prozessoptimierung bietet die Digitalisierung auch verbesserte Möglichkeiten zur Dokumentation und Rückverfolgbarkeit. Fertigungsdaten können lückenlos protokolliert werden, was besonders in Branchen mit hohen Qualitätsanforderungen wie der Automobil- oder Luftfahrtindustrie entscheidend ist. So lassen sich Produktionschargen genau nachvollziehen, und eventuelle Fehlerquellen können schneller identifiziert werden.
Abschließend lässt sich festhalten, dass die Auswahl einer Tiefziehmaschine heute nicht nur auf mechanischen Kriterien beruhen sollte, sondern auch auf deren Fähigkeit, digitale Technologien zu integrieren und damit die Fertigung zukunftssicher zu gestalten. Unternehmen, die frühzeitig auf solche vernetzten Systeme setzen, profitieren von höherer Effizienz, besserer Qualität und größerer Flexibilität im Wettbewerb.
Tiefziehen von Metall: Prozessoptimierung und Techniken
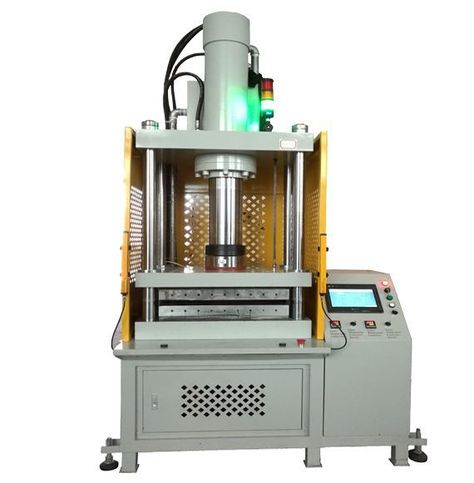
Das Tiefziehen von Metall ist ein komplexer Umformprozess, bei dem flache Bleche in dreidimensionale Hohlkörper oder komplexe Formen umgewandelt werden. Eine gezielte Prozessoptimierung ist entscheidend, um Ausschuss zu minimieren, die Materialausnutzung zu verbessern und die Qualität der Bauteile sicherzustellen. Dabei spielen sowohl technologische als auch organisatorische Faktoren eine Rolle.
Ein zentraler Ansatz zur Optimierung besteht in der präzisen Steuerung der Umformparameter. Dies umfasst die Anpassung von Ziehgeschwindigkeit, Druckkräften und Schmierbedingungen. Eine zu hohe Ziehgeschwindigkeit kann beispielsweise zu Rissen im Material führen, während zu geringe Geschwindigkeiten den Produktionsdurchsatz verringern. Ebenso beeinflusst die richtige Wahl und Dosierung von Schmierstoffen die Reibung zwischen Werkzeug und Blech, was maßgeblich die Materialfließgrenzen und damit die Umformbarkeit bestimmt.
Die Auslegung und Wartung der Werkzeuge ist ein weiterer wesentlicher Faktor. Werkzeuge müssen passgenau gefertigt und regelmäßig überprüft werden, um Maßhaltigkeit und Oberflächenqualität zu gewährleisten. Verschleißteile sollten rechtzeitig ersetzt werden, um Prozessstörungen zu vermeiden. Moderne Werkzeuge verfügen oft über integrierte Sensorik, die während des Ziehvorgangs Daten zur Werkzeugbelastung liefert und so eine vorausschauende Instandhaltung ermöglicht.
Darüber hinaus kann der Einsatz von Mehrstufenverfahren, bei denen das Werkstück in mehreren Ziehschritten geformt wird, die Umformbarkeit verbessern und die Entstehung von Fehlern wie Falten oder Rissen reduzieren. Zwischenstufen wie das Strecken oder Zwischenglühen helfen, Spannungen im Material abzubauen und dessen Dehnbarkeit zu erhöhen.
Simulationen spielen bei der Prozessoptimierung eine immer größere Rolle. Mithilfe von computergestützten Modellen können komplexe Umformvorgänge bereits in der Planungsphase virtuell getestet werden. Dies reduziert teure Versuchsläufe und ermöglicht eine gezielte Anpassung von Werkzeuggeometrie und Prozessparametern.
Nicht zuletzt trägt auch die Schulung der Mitarbeiter zur Optimierung bei. Qualifizierte Fachkräfte sind in der Lage, Prozessabweichungen frühzeitig zu erkennen und gegenzusteuern. Die Kombination aus technologischem Know-how, moderner Ausrüstung und systematischem Monitoring bildet die Grundlage für einen effizienten und qualitativ hochwertigen Tiefziehprozess.
Durch diese ganzheitliche Betrachtung von Technik, Material, Werkzeug und Mensch lässt sich das Tiefziehen von Metall nachhaltig verbessern, was zu höherer Produktivität, besserer Bauteilqualität und geringeren Kosten führt.
Eine wesentliche Rolle bei der Prozessoptimierung im Tiefziehen spielt die Auswahl und Anpassung der Schmierstoffe. Schmierstoffe reduzieren die Reibung zwischen Werkzeug und Blech, verhindern das Anhaften von Material und minimieren den Verschleiß der Werkzeuge. Die richtige Schmierstoffwahl hängt von verschiedenen Faktoren ab, darunter das Werkstoffpaar, die Umformgeschwindigkeit und die geplante Oberflächenqualität des Bauteils. Organische Schmierstoffe sind oft umweltfreundlicher, während synthetische oder mineralische Schmierstoffe höhere Belastungen und Temperaturen besser verkraften können. Auch die Applikationsmethode, ob als Öl, Paste oder Trockenschmierstoff, beeinflusst die Prozessstabilität und sollte an den spezifischen Anwendungsfall angepasst werden.
Weiterhin ist die Kontrolle der Umformkräfte entscheidend. Moderne Tiefziehpressen sind mit Sensoren ausgestattet, die die Kraftverläufe während des Ziehens überwachen. Abweichungen von den Sollwerten können frühzeitig auf Werkzeugverschleiß, falsche Blechparameter oder unzureichende Schmierung hinweisen. So lassen sich Stillstände reduzieren und Ausschuss vermeiden. Darüber hinaus ermöglichen adaptive Steuerungssysteme eine dynamische Anpassung der Umformkräfte in Echtzeit, was insbesondere bei variierenden Materialchargen oder komplexen Bauteilgeometrien von Vorteil ist.
Das Material selbst spielt ebenfalls eine zentrale Rolle für die Prozessqualität. Die Auswahl eines geeigneten Werkstoffs mit passenden mechanischen Eigenschaften und einer homogenen Struktur sorgt für eine gleichmäßige Verformung. Unregelmäßigkeiten wie Einschlüsse, Gefügeheterogenitäten oder Oberflächenfehler können zu Schwachstellen führen, die Risse oder Falten verursachen. Eine enge Zusammenarbeit mit Materiallieferanten und die Durchführung von Qualitätskontrollen vor dem Umformprozess sind daher unerlässlich.
Zudem ist die Temperaturführung im Tiefziehprozess ein bedeutender Faktor. Während kaltumgeformte Prozesse die Festigkeit erhöhen, kann eine gezielte Erwärmung des Materials dessen Umformbarkeit verbessern und die Gefahr von Rissbildungen reduzieren. Thermisches Tiefziehen, bei dem das Werkstück vor dem Umformen erwärmt wird, wird zunehmend bei schwer umformbaren Materialien oder komplexen Geometrien eingesetzt.
Schließlich ermöglicht die Integration von digitaler Messtechnik und optischer Inspektion eine sofortige Qualitätskontrolle der gefertigten Bauteile. Messsysteme erfassen Maße, Oberflächenbeschaffenheit und eventuelle Defekte direkt nach dem Ziehen, sodass fehlerhafte Teile sofort aussortiert oder nachbearbeitet werden können. Dies trägt dazu bei, Nacharbeit zu minimieren und die Prozesssicherheit zu erhöhen.
Insgesamt führt die Kombination aus präziser Prozesssteuerung, geeigneten Materialien, optimaler Schmierung, moderner Sensorik und digitaler Kontrolle zu einer signifikanten Steigerung der Effizienz und Qualität beim Tiefziehen. Unternehmen, die diese Faktoren konsequent berücksichtigen, können Wettbewerbsvorteile durch reduzierte Kosten, kürzere Durchlaufzeiten und bessere Produktqualität erzielen.
Ein weiterer wichtiger Aspekt der Prozessoptimierung beim Tiefziehen ist die Berücksichtigung der Werkstückgeometrie und deren Einfluss auf die Umformbarkeit. Komplexe Formen mit scharfen Kanten, tiefen Vertiefungen oder variierenden Wandstärken stellen besondere Herausforderungen dar. Durch gezielte Anpassungen der Werkzeuggeometrie, wie beispielsweise abgerundete Kanten und optimierte Ziehringe, lassen sich Spannungsspitzen im Material reduzieren und die Gefahr von Rissen oder Falten minimieren. Auch der Einsatz von sogenannten Mehrstufen-Tiefziehverfahren, bei denen das Bauteil in mehreren Schritten geformt wird, kann die Umformbarkeit komplexer Teile verbessern und die Qualität steigern.
Die Gestaltung des Ziehrings ist besonders entscheidend, da er die Fließgeschwindigkeit des Materials steuert. Ein zu stark angezogener Ziehring kann das Material an den Rändern einschnüren und zum Reißen führen, während ein zu lockerer Ziehring Faltenbildung begünstigt. Daher ist eine präzise Einstellung und gegebenenfalls die Verwendung von einstellbaren Ziehringen sinnvoll, um auf unterschiedliche Materialien und Bauteilgeometrien reagieren zu können.
Ebenso spielt die Werkstückdicke eine große Rolle. Dünnere Bleche sind leichter umzuformen, erfordern jedoch eine besonders sorgfältige Prozessführung, da sie anfälliger für Falten und Risse sind. Dickere Bleche erfordern höhere Kräfte und robustere Werkzeuge, bieten dafür aber auch eine höhere Stabilität im Endprodukt.
Neben der mechanischen Auslegung des Prozesses gewinnen auch moderne Simulationstechniken immer mehr an Bedeutung. Mit Finite-Elemente-Methoden (FEM) lassen sich komplexe Umformprozesse virtuell abbilden, Schwachstellen frühzeitig erkennen und Parameter optimieren. Dies reduziert Versuchskosten, verkürzt Entwicklungszeiten und erhöht die Prozesssicherheit.
Nicht zuletzt ist die kontinuierliche Prozessüberwachung und -analyse durch Datenanalyse und Machine Learning ein zukunftsweisender Trend. Durch das Erfassen großer Datenmengen aus dem Produktionsprozess können Muster erkannt und Abweichungen prognostiziert werden. So lassen sich Prozesse noch präziser steuern und optimieren, Ausschuss weiter reduzieren und Maschinenlaufzeiten erhöhen.
Zusammenfassend ist die Prozessoptimierung beim Tiefziehen ein Zusammenspiel aus technischer Auslegung, präziser Steuerung, geeigneten Materialien, modernster Simulation und intelligenter Datenverarbeitung. Nur durch diese ganzheitliche Betrachtung lassen sich die hohen Anforderungen an Qualität, Effizienz und Wirtschaftlichkeit in der modernen Metallumformung erfüllen.
Ein weiterer entscheidender Faktor für die Prozessoptimierung beim Tiefziehen ist die Berücksichtigung der Umformtemperatur. Während das konventionelle Tiefziehen meist bei Raumtemperatur erfolgt, gewinnen thermisch unterstützte Verfahren zunehmend an Bedeutung. Durch kontrolliertes Erwärmen des Blechs vor oder während des Ziehvorgangs lassen sich die Duktilität und damit die Verformbarkeit des Materials verbessern. Dies ist insbesondere bei hochfesten Werkstoffen wie Aluminiumlegierungen oder Edelstahl von Vorteil, die bei Raumtemperatur oft schwer zu formen sind. Thermisches Tiefziehen kann Rissbildungen vermeiden, die Werkzeugstandzeiten verlängern und insgesamt die Qualität der Bauteile verbessern.
Neben der Temperaturkontrolle spielt auch die Werkzeugkühlung eine wichtige Rolle. Übermäßige Erwärmung der Werkzeuge durch Reibung oder Umformarbeit kann deren Lebensdauer stark reduzieren. Eine effiziente Kühlung sorgt dafür, dass Werkzeuge ihre präzisen Abmessungen behalten und Oberflächenschäden minimiert werden. Hier kommen oft integrierte Kühlkanäle oder externe Kühlsysteme zum Einsatz.
Die Anpassung der Umformgeschwindigkeit an Material und Werkzeug ist ebenfalls entscheidend. Zu hohe Geschwindigkeiten können Materialversagen verursachen, während zu niedrige Geschwindigkeiten die Produktivität verringern. Moderne Anlagen erlauben eine flexible Geschwindigkeitsregelung, die je nach Prozessphase und Werkstoff variieren kann.
Darüber hinaus beeinflussen die Einlaufbedingungen des Blechs, also wie das Material in den Umformbereich geführt wird, die Prozessstabilität maßgeblich. Spannungsfreie Zuführung und eine gleichmäßige Blechspannung verhindern Faltenbildung und sorgen für eine gleichmäßige Materialverteilung.
Nicht zuletzt trägt auch die Integration von Qualitätssicherungssystemen in Echtzeit zur Prozessoptimierung bei. Kamerabasierte Inspektionssysteme, Laserscanner und andere berührungslose Messverfahren erfassen Fehler und Maßabweichungen direkt während oder unmittelbar nach dem Ziehprozess. Dies ermöglicht eine sofortige Reaktion, etwa durch Anpassung der Prozessparameter oder das Aussondern fehlerhafter Teile, was die Ausschussquote senkt und Nacharbeiten reduziert.
Zusammengefasst sind Temperaturmanagement, Werkzeugkühlung, Prozessgeschwindigkeit, Einlaufbedingungen und Echtzeit-Qualitätssicherung wesentliche Stellgrößen, um den Tiefziehprozess effizienter, sicherer und qualitativ hochwertiger zu gestalten. Nur durch das Zusammenspiel all dieser Faktoren kann die Produktion von anspruchsvollen Metallteilen zuverlässig und wirtschaftlich realisiert werden.
Werkzeuge für das Tiefziehen: Konstruktion und Anwendung
Werkzeuge für das Tiefziehen sind speziell konzipierte Vorrichtungen, die das Umformen von Blechen in komplexe, dreidimensionale Bauteile ermöglichen. Die Konstruktion dieser Werkzeuge spielt eine entscheidende Rolle für die Qualität des Endprodukts, die Prozessstabilität und die Wirtschaftlichkeit der Fertigung.
Ein typisches Tiefziehwerkzeug besteht aus mehreren Hauptkomponenten: dem Stempel (auch Ziehstempel genannt), der Matrize (oder Ziehform), dem Ziehring (auch Flanschring) und dem Rückhaltesystem. Der Stempel ist das bewegliche Element, das das Blech in die Matrize presst, die die Negativform des gewünschten Bauteils darstellt. Der Ziehring sorgt dafür, dass das Blech kontrolliert und gleichmäßig in die Matrize gezogen wird, indem er das Material an den Rändern zurückhält und so Faltenbildung verhindert.
Die Auswahl der richtigen Werkzeuggeometrie ist entscheidend für eine gleichmäßige Materialverteilung und die Vermeidung von Defekten wie Rissen, Falten oder Einschnürungen. Abgerundete Kanten an Stempel und Matrize minimieren Spannungsspitzen und erleichtern den Fluss des Materials. Die Form des Stempels bestimmt maßgeblich die endgültige Bauteilgeometrie, während die Matrize die Außenkontur definiert.
Moderne Tiefziehwerkzeuge sind häufig modular aufgebaut, um eine flexible Anpassung an verschiedene Bauteile und Änderungen im Produktionsprozess zu ermöglichen. Dies spart Kosten und reduziert Rüstzeiten. Zudem können Werkzeuge mit integrierter Sensorik ausgestattet werden, die während des Ziehvorgangs Daten zur Werkzeugbelastung, Temperatur oder Materialverteilung liefern. Solche Informationen sind wertvoll für die Prozessüberwachung und vorausschauende Wartung.
Die Werkstoffwahl für Tiefziehwerkzeuge ist ebenfalls kritisch. Aufgrund der hohen mechanischen Beanspruchung und der ständigen Reibung zwischen Werkzeug und Blech kommen gehärtete Stähle oder Speziallegierungen zum Einsatz, die hohe Verschleißfestigkeit mit guter Bearbeitbarkeit verbinden. Zusätzlich werden Oberflächenbehandlungen wie Nitrieren oder Beschichtungen (z. B. TiN, DLC) angewendet, um Reibung und Verschleiß weiter zu reduzieren.
Für komplexe Bauteile werden oft Mehrkomponentenwerkzeuge verwendet, die mehrere Umformschritte in einem Werkzeug vereinen oder Kombinationen aus Tiefziehen und anderen Verfahren wie Stauchen oder Biegen ermöglichen. Solche Werkzeuge erfordern eine präzise Abstimmung aller Komponenten, um eine fehlerfreie Fertigung sicherzustellen.
Nicht zuletzt ist die regelmäßige Wartung und Instandhaltung der Werkzeuge entscheidend, um eine gleichbleibend hohe Qualität und lange Standzeiten zu gewährleisten. Werkzeuge müssen gereinigt, auf Verschleiß geprüft und gegebenenfalls nachgeschliffen oder repariert werden.
Zusammenfassend ist die Konstruktion und Anwendung von Tiefziehwerkzeugen ein hochkomplexer Prozess, der technisches Know-how, Präzision und Erfahrung erfordert. Nur mit optimal ausgelegten und gepflegten Werkzeugen lassen sich die hohen Anforderungen moderner Tiefziehprozesse wirtschaftlich und qualitativ erfüllen.
Neben der grundlegenden Konstruktion von Tiefziehwerkzeugen gewinnt die Integration moderner Technologien zunehmend an Bedeutung. Automatisierte Einstellsysteme ermöglichen eine schnelle und präzise Anpassung von Werkzeugparametern wie Ziehringdruck oder Stempelhub, was Rüstzeiten verkürzt und die Flexibilität in der Produktion erhöht. Durch den Einsatz von Sensorik in den Werkzeugen können Prozessdaten in Echtzeit erfasst und ausgewertet werden, um Abweichungen frühzeitig zu erkennen und gezielt Gegenmaßnahmen einzuleiten. Dies erhöht die Prozesssicherheit und reduziert Ausschuss.
Die Auswahl der geeigneten Schmierstoffe in Verbindung mit den Werkzeugoberflächen ist ein weiterer wichtiger Faktor. Spezielle Beschichtungen auf Stempel und Matrize verringern die Reibung und verhindern das Anhaften von Material, was nicht nur die Werkzeugstandzeit verlängert, sondern auch die Oberflächenqualität der gefertigten Bauteile verbessert. Für besonders anspruchsvolle Anwendungen werden zudem Werkzeuge mit integrierten Kühlsystemen eingesetzt, um die Temperatur während des Umformens konstant zu halten und thermisch bedingte Verformungen zu minimieren.
Modulare Werkzeugkonzepte erlauben es, einzelne Werkzeugkomponenten schnell auszutauschen oder an neue Bauteilanforderungen anzupassen, ohne das gesamte Werkzeug neu fertigen zu müssen. Dies spart Kosten und erhöht die Produktionsflexibilität, insbesondere bei variierenden Losgrößen oder Produktvarianten. In Kombination mit Simulationstools können Werkzeugdesigner die Werkzeugfunktion und das Materialverhalten bereits in der Konstruktionsphase virtuell prüfen und optimieren, was Entwicklungszeiten verkürzt und Fehlversuche reduziert.
Darüber hinaus spielt die Ergonomie bei der Konstruktion von Tiefziehwerkzeugen eine wichtige Rolle. Werkzeuge müssen so gestaltet sein, dass sie einfach und sicher gehandhabt werden können, um die Arbeit der Maschinenbediener zu erleichtern und Unfallrisiken zu minimieren. Dies umfasst beispielsweise integrierte Greifpunkte, übersichtliche Markierungen und eine möglichst einfache Wartung.
Die Verbindung von mechanischer Präzision, moderner Sensorik, flexiblen Bauweisen und ergonomischem Design macht die Werkzeuge zu einem zentralen Baustein für effiziente und qualitativ hochwertige Tiefziehprozesse. Nur durch kontinuierliche Weiterentwicklung und Anpassung der Werkzeuge an neue Anforderungen lassen sich wettbewerbsfähige Produktionsprozesse gestalten, die den steigenden Ansprüchen an Bauteilqualität und Wirtschaftlichkeit gerecht werden.
Ein weiterer wichtiger Trend in der Entwicklung von Tiefziehwerkzeugen ist die Integration von Additive Manufacturing (3D-Druck) in den Werkzeugbau. Durch den Einsatz von 3D-Drucktechnologien lassen sich komplexe Werkzeugkomponenten mit besonderen Geometrien fertigen, die mit herkömmlichen Fertigungsverfahren schwer oder gar nicht herstellbar wären. Dies ermöglicht beispielsweise den Einbau von integrierten Kühlkanälen direkt im Werkzeug, was eine effizientere Temperaturregelung während des Tiefziehprozesses erlaubt und somit die Standzeiten der Werkzeuge verlängert. Zudem können mit 3D-Druck schnell Prototypen oder Sonderwerkzeuge gefertigt werden, was Entwicklungszeiten und Kosten reduziert.
Neben dem Werkzeug selbst gewinnt auch die Automatisierung der Werkzeughandhabung an Bedeutung. Automatische Wechselsysteme ermöglichen es, verschiedene Werkzeuge schnell und ohne großen manuellen Aufwand an der Presse einzusetzen. Dies ist besonders in der Serienfertigung mit wechselnden Produkten oder bei Mehrschichtbetrieb von Vorteil und trägt zur Erhöhung der Anlagenverfügbarkeit bei.
Darüber hinaus setzen immer mehr Unternehmen auf die digitale Vernetzung ihrer Werkzeuge im Rahmen von Industrie 4.0. Werkzeugdaten wie Verschleißzustand, Einsatzzeiten oder Prozessparameter werden digital erfasst und analysiert. Dies ermöglicht vorausschauende Wartung (Predictive Maintenance), die Ausfallzeiten minimiert und Kosten senkt. Gleichzeitig können Prozessabweichungen schneller erkannt und korrigiert werden, was die Qualitätssicherung verbessert.
Im Bereich der Werkstoffauswahl für Werkzeuge werden zunehmend Hochleistungsstähle und Beschichtungen verwendet, die speziell auf die hohen Anforderungen beim Tiefziehen abgestimmt sind. Diese Materialien bieten eine optimale Kombination aus Härte, Zähigkeit und Verschleißfestigkeit. Neue Beschichtungstechnologien verbessern zudem die Reibwerte und die Korrosionsbeständigkeit der Werkzeuge, was die Lebensdauer weiter erhöht.
Abschließend ist zu sagen, dass die Konstruktion und Anwendung von Tiefziehwerkzeugen ein dynamisches Feld ist, das von technologischen Innovationen und stetigen Verbesserungen geprägt ist. Unternehmen, die diese Entwicklungen aktiv nutzen und in ihre Fertigungsprozesse integrieren, können nicht nur die Produktqualität steigern, sondern auch ihre Wettbewerbsfähigkeit langfristig sichern.
Darüber hinaus gewinnt die Optimierung der Werkzeugstandzeiten durch den gezielten Einsatz von Verschleißschutzmaßnahmen zunehmend an Bedeutung. Verschleiß an Werkzeugkomponenten ist einer der Hauptfaktoren für Produktionsunterbrechungen und Kostensteigerungen im Tiefziehprozess. Daher werden neben robusten Werkstoffen und Beschichtungen auch innovative Verfahren wie Oberflächenhärtung, Laserauftragsschweißen oder Plasma-Carburieren eingesetzt, um die Lebensdauer der Werkzeuge deutlich zu verlängern. Diese Technologien ermöglichen eine gezielte Verbesserung der Oberflächeneigenschaften, wie Härte, Verschleiß- und Korrosionsbeständigkeit, ohne die Zähigkeit des Grundmaterials zu beeinträchtigen.
Ein weiterer Aspekt ist die präzise Fertigung der Werkzeuge mit hochmodernen CNC-Maschinen und Werkzeugschleiftechnologien. Eine exakte Formgebung und enge Toleranzen sind entscheidend, um eine gleichmäßige Umformung zu gewährleisten und Bauteilfehler zu vermeiden. Fehlerhafte Werkzeuggeometrien können zu ungleichmäßiger Materialverteilung, Faltenbildung oder Rissen führen, was wiederum Ausschuss und Nacharbeit verursacht.
Die Integration von Mess- und Kalibriertechniken während der Herstellung und Wartung der Werkzeuge sichert zudem die Einhaltung der geforderten Maßhaltigkeit und Oberflächenqualität. Durch den Einsatz von 3D-Scannern oder taktilen Messgeräten können Werkzeugkonturen präzise erfasst und gegebenenfalls nachbearbeitet werden.
Nicht zuletzt trägt auch die Zusammenarbeit zwischen Werkzeugbau, Produktion und Qualitätsmanagement maßgeblich zum Erfolg bei. Ein interdisziplinärer Ansatz ermöglicht es, frühzeitig Prozessanforderungen, Materialeigenschaften und mögliche Fehlerquellen zu identifizieren und das Werkzeug entsprechend zu optimieren. Regelmäßige Feedbackschleifen aus der Produktion helfen, Werkzeuge kontinuierlich zu verbessern und Prozessstabilität zu erhöhen.
Insgesamt ist die Konstruktion und Anwendung von Tiefziehwerkzeugen ein komplexer, ganzheitlicher Prozess, der durch innovative Materialien, präzise Fertigung, fortschrittliche Beschichtungen und enge Zusammenarbeit aller beteiligten Bereiche zu höchster Produktqualität und Wirtschaftlichkeit führt. Unternehmen, die diesen Ansatz verfolgen, sichern sich langfristig einen Wettbewerbsvorteil in der Metallumformung.
Tiefziehen in der Blechbearbeitung: Verfahren und Vorteile
Das Tiefziehen ist ein zentrales Umformverfahren in der Blechbearbeitung, bei dem flache Blechzuschnitte durch plastische Verformung in dreidimensionale Hohlkörper oder komplexe Bauteile umgeformt werden. Dabei wird das Blech mittels eines Stempels in eine Matrize gedrückt, wodurch das Material in die gewünschte Form gezogen wird, ohne dass es reißt oder Falten bildet. Das Verfahren eignet sich besonders für die Herstellung von Hohlteilen wie Gehäusen, Karosseriebauteilen, Behältern oder technischen Komponenten.
Zu den wichtigsten Vorteilen des Tiefziehens zählen die hohe Maßgenauigkeit und die gute Oberflächenqualität der gefertigten Bauteile. Da das Blech beim Tiefziehen nicht geschnitten, sondern umgeformt wird, bleiben die Materialeigenschaften weitgehend erhalten, was eine hohe Festigkeit und Stabilität des Endprodukts ermöglicht. Zudem ist das Verfahren sehr wirtschaftlich, da es sich gut für die Serienfertigung eignet und wenig Materialverlust durch Verschnitt entsteht.
Ein weiterer Vorteil ist die Flexibilität des Tiefziehprozesses. Verschiedene Werkstoffe wie Stahl, Aluminium, Edelstahl oder Kupfer können mit angepassten Parametern verarbeitet werden, und durch Mehrstufen-Tiefziehen lassen sich auch komplexe Formen in mehreren Schritten herstellen. Zudem sind durch den modularen Aufbau der Werkzeuge schnelle Umrüstungen möglich, was die Fertigung von Varianten oder Kleinserien erleichtert.
Das Tiefziehen zeichnet sich außerdem durch seine Umweltfreundlichkeit aus, da durch den geringen Materialabfall und die Möglichkeit der Materialrückführung Ressourcen geschont werden. Der Energieverbrauch ist im Vergleich zu anderen Fertigungsverfahren oft niedriger, was zu einer nachhaltigen Produktion beiträgt.
Zusammengefasst bietet das Tiefziehen in der Blechbearbeitung eine Kombination aus hoher Produktqualität, Wirtschaftlichkeit, Flexibilität und Nachhaltigkeit. Diese Eigenschaften machen das Verfahren zu einem unverzichtbaren Bestandteil moderner Metallumformung und ermöglichen die Herstellung anspruchsvoller Bauteile für unterschiedlichste Branchen wie Automobilbau, Luftfahrt, Haushaltsgeräte oder Verpackungsindustrie.
Neben den genannten Vorteilen ermöglicht das Tiefziehen auch eine hohe Wiederholgenauigkeit, was besonders bei großen Stückzahlen in der Serienfertigung entscheidend ist. Durch den Einsatz präziser Werkzeuge und optimal eingestellter Prozessparameter lassen sich enge Toleranzen und eine gleichbleibende Qualität sicherstellen. Dies reduziert Nacharbeit und Ausschuss und trägt maßgeblich zur Wirtschaftlichkeit bei.
Das Verfahren erlaubt zudem die Integration weiterer Bearbeitungsschritte, wie beispielsweise das Stanzen von Löchern oder das Biegen von Kanten, oft direkt im Werkzeug oder in Folgeprozessen. Dadurch können komplexe Bauteile in kürzester Zeit und mit minimalem Handling gefertigt werden, was den Produktionsfluss optimiert.
Auch hinsichtlich der Materialausnutzung bietet das Tiefziehen Vorteile. Da das Ausgangsmaterial flach und häufig in Rollenform vorliegt, kann es sehr effizient zugeführt und verarbeitet werden. Die Möglichkeit, dünne Bleche zu formen, ermöglicht zudem die Herstellung leichter Bauteile, was insbesondere in der Automobil- und Luftfahrtindustrie zur Reduzierung des Fahrzeuggewichts beiträgt und somit den Kraftstoffverbrauch senkt.
Technologische Entwicklungen wie computergestützte Simulationen erlauben eine präzise Vorhersage des Umformverhaltens und unterstützen die Optimierung der Werkzeuggeometrien und Prozessparameter. Dadurch lassen sich Fehlerquellen bereits in der Planungsphase minimieren, was Entwicklungszeiten und Kosten reduziert.
Die Kombination all dieser Faktoren macht das Tiefziehen zu einem äußerst effizienten und vielseitigen Verfahren in der Blechbearbeitung, das den steigenden Anforderungen an Produktqualität, Produktionsgeschwindigkeit und Ressourcenschonung gerecht wird. Unternehmen, die dieses Verfahren einsetzen und kontinuierlich weiterentwickeln, profitieren von Wettbewerbsvorteilen und können flexibel auf Marktveränderungen reagieren.
Darüber hinaus trägt die Automatisierung im Tiefziehprozess erheblich zur Steigerung der Effizienz und Qualität bei. Moderne Pressen sind häufig mit Robotersystemen ausgestattet, die das Be- und Entladen der Werkstücke übernehmen, sowie mit Sensorik zur Überwachung des Prozesses in Echtzeit. Dadurch lassen sich Produktionsabläufe nicht nur beschleunigen, sondern auch Fehler frühzeitig erkennen und korrigieren. Die Vernetzung von Maschinen und Werkzeugen ermöglicht zudem die Sammlung und Analyse von Prozessdaten, was eine vorausschauende Wartung und eine kontinuierliche Prozessoptimierung unterstützt.
Ein weiterer Fortschritt liegt in der Entwicklung von hochfesten und leichten Werkstoffen, die speziell für das Tiefziehen optimiert sind. Solche Materialien ermöglichen die Herstellung von Bauteilen mit geringem Gewicht bei gleichzeitig hoher Festigkeit, was in Branchen wie der Automobilindustrie oder Luftfahrt entscheidend ist, um Emissionen zu reduzieren und die Energieeffizienz zu steigern. Die Verarbeitung dieser Werkstoffe erfordert jedoch angepasste Werkzeuge und Prozessparameter, um die gewünschte Formgebung ohne Materialschäden zu erreichen.
Auch die Nachhaltigkeit gewinnt im Tiefziehprozess zunehmend an Bedeutung. Neben der Reduzierung von Materialabfall durch optimierte Blechzuschnitte und Rückführung von Produktionsreststücken werden umweltfreundliche Schmierstoffe und energieeffiziente Maschinen eingesetzt. Dies trägt dazu bei, den ökologischen Fußabdruck der Fertigung zu minimieren und den steigenden Anforderungen an eine nachhaltige Produktion gerecht zu werden.
Nicht zuletzt ermöglicht das Tiefziehen durch seine Vielseitigkeit die Produktion einer breiten Palette von Bauteilen, von einfachen geometrischen Formen bis hin zu hochkomplexen, filigranen Strukturen. Diese Flexibilität macht das Verfahren unverzichtbar für zahlreiche Industriezweige und unterstützt Innovationen in Produktdesign und Fertigungstechnik.
Zusammenfassend lässt sich sagen, dass das Tiefziehen als etabliertes und zugleich innovatives Umformverfahren durch seine Vorteile in Qualität, Effizienz, Flexibilität und Nachhaltigkeit maßgeblich zur modernen Blechbearbeitung beiträgt und auch in Zukunft eine zentrale Rolle in der industriellen Fertigung spielen wird.
Neben den technischen und wirtschaftlichen Vorteilen fördert das Tiefziehen auch die Gestaltungsmöglichkeiten in der Produktentwicklung. Designer und Konstrukteure können dank der hohen Formbarkeit von Blechen komplexe und funktionale Bauteile entwerfen, die sowohl ästhetischen als auch technischen Anforderungen gerecht werden. Die Möglichkeit, dünne Materialien in präzise und stabile Formen umzuwandeln, erlaubt innovative Leichtbaukonzepte und trägt so zur Entwicklung moderner, ressourceneffizienter Produkte bei.
Zudem erlaubt das Tiefziehen eine hohe Variabilität in der Produktion. Durch den modularen Aufbau der Werkzeuge und die Anpassbarkeit der Prozessparameter können unterschiedliche Bauteilvarianten mit vergleichsweise geringem Aufwand gefertigt werden. Dies unterstützt eine flexible Produktion, die schnell auf Marktanforderungen oder Kundenwünsche reagieren kann, ohne dass umfangreiche Neuentwicklungen notwendig sind.
Die Kombination von Tiefziehen mit anderen Umformverfahren wie Biegen, Stanzen oder Umformen in Mehrstufenprozessen eröffnet weitere Möglichkeiten, komplexe Bauteile in einem integrierten Ablauf herzustellen. Dies reduziert Montageaufwand und erhöht die Präzision der Endprodukte, was insbesondere in Branchen mit hohen Qualitätsanforderungen wie der Automobilindustrie, dem Maschinenbau oder der Elektronikfertigung von Bedeutung ist.
Auch im Hinblick auf die Kostenstruktur bietet das Tiefziehen Vorteile: Die hohe Automatisierung und Wiederholgenauigkeit senken Stückkosten, während durch die Reduzierung von Materialabfall und Nacharbeit Einsparungen bei den Rohstoff- und Produktionskosten erzielt werden. Zudem ermöglichen kurze Taktzeiten und eine hohe Ausbringung die Erfüllung großer Stückzahlen bei gleichbleibender Qualität.
Schließlich unterstützt das Tiefziehen auch nachhaltige Fertigungsstrategien, da durch optimierte Materialeinsätze und energieeffiziente Prozesse Ressourcen geschont werden. In Verbindung mit Recyclingmöglichkeiten und der Nutzung umweltfreundlicher Hilfsmittel leistet das Tiefziehen einen wichtigen Beitrag zu einer umweltbewussten Produktion.
Diese vielfältigen Aspekte machen das Tiefziehen zu einem unverzichtbaren Verfahren in der modernen Blechbearbeitung, das nicht nur technische und wirtschaftliche, sondern auch ökologische Vorteile bietet und so die Grundlage für innovative und nachhaltige Fertigungslösungen legt.
Der Einfluss von Geschwindigkeit und Druck beim Tiefziehen
Beim Tiefziehen haben Geschwindigkeit und Druck entscheidenden Einfluss auf den Prozessverlauf, die Qualität der Bauteile und die Werkzeugstandzeiten. Die richtige Einstellung dieser Parameter ist essenziell, um eine gleichmäßige Umformung ohne Materialschäden wie Risse, Falten oder ein Einreißen zu gewährleisten.
Die Ziehgeschwindigkeit beeinflusst maßgeblich das Fließverhalten des Werkstoffs. Zu hohe Geschwindigkeiten können dazu führen, dass das Material nicht gleichmäßig verformt wird, was Spannungen und schließlich Materialversagen verursachen kann. Besonders bei dünnen oder empfindlichen Blechen steigt die Gefahr von Rissen, wenn die Geschwindigkeit zu groß ist. Andererseits können zu niedrige Geschwindigkeiten zu einer erhöhten Reibung zwischen Blech und Werkzeug führen, was den Verschleiß der Werkzeuge beschleunigt und die Prozesszeit unnötig verlängert. Eine optimale Geschwindigkeit sorgt deshalb für einen ausgewogenen Materialfluss und minimiert sowohl mechanische Belastungen als auch thermische Effekte.
Der Druck, mit dem der Stempel das Blech in die Matrize zieht, steuert die Materialverteilung und das Umformverhalten. Ein zu hoher Druck kann das Blech lokal überdehnen und Risse verursachen, während ein zu geringer Druck das Material nicht ausreichend formt, was zu Faltenbildung oder ungenügender Konturenschärfe führt. Wichtig ist auch der kontrollierte Einsatz von Halte- oder Ziehringen, die den Fluss des Materials begrenzen und so für eine gleichmäßige Wanddicke sorgen. Der Druck auf diese Ringe muss präzise angepasst werden, um die Balance zwischen Materialfluss und Umformwiderstand zu halten.
Zusätzlich beeinflussen Geschwindigkeit und Druck gemeinsam die Reibungsverhältnisse zwischen Blech und Werkzeugoberflächen. Hohe Geschwindigkeiten können zu einer Temperaturerhöhung an den Kontaktstellen führen, was Schmierstoffe beeinträchtigen und die Reibung erhöhen kann. Deshalb ist eine abgestimmte Kombination von Geschwindigkeit, Druck und Schmierstoffwahl notwendig, um optimale Prozessbedingungen zu schaffen.
Moderne Steuerungssysteme in Tiefziehmaschinen erlauben eine genaue Regelung dieser Parameter in Echtzeit, angepasst an den jeweiligen Werkstoff und die Bauteilgeometrie. Durch den Einsatz von Sensorik und Prozessüberwachung können Abweichungen frühzeitig erkannt und korrigiert werden, was Ausschuss reduziert und die Werkzeuglebensdauer verlängert.
Insgesamt sind Geschwindigkeit und Druck im Tiefziehprozess Schlüsselgrößen, deren optimale Einstellung maßgeblich die Produktqualität, Wirtschaftlichkeit und Betriebssicherheit beeinflusst. Eine sorgfältige Abstimmung dieser Parameter, unterstützt durch moderne Technologien und Erfahrungswerte, ist daher unerlässlich für erfolgreiche Tiefziehprozesse.
Neben der direkten Beeinflussung des Materialflusses wirken sich Geschwindigkeit und Druck auch auf die mikrostrukturellen Veränderungen im Werkstoff aus. Bei höheren Ziehgeschwindigkeiten können sich lokale Erwärmungen einstellen, die das Material weicher machen und damit die Verformbarkeit verbessern. Gleichzeitig können zu hohe Temperaturen jedoch die Festigkeit verringern und unerwünschte Gefügeänderungen verursachen. Deshalb ist die Kontrolle der Prozesswärme entscheidend, um die mechanischen Eigenschaften des Endprodukts zu erhalten.
Der Druck beeinflusst zudem die Kontaktbedingungen zwischen Werkzeug und Blech. Eine gleichmäßige Druckverteilung sorgt dafür, dass das Material nicht an bestimmten Stellen zu stark beansprucht wird, was Faltenbildung und Rissgefahr minimiert. Ungleichmäßiger Druck kann hingegen zu lokalen Spannungsspitzen führen, die Materialfehler begünstigen. Deshalb werden oft spezielle Druckzonen im Werkzeug konstruiert, um den Druck gezielt zu steuern und den Materialfluss optimal zu lenken.
Ein weiterer Einflussfaktor ist die Schmierung, die in engem Zusammenhang mit Geschwindigkeit und Druck steht. Eine ausreichende Schmierstoffschicht reduziert die Reibung zwischen Werkzeug und Werkstück, verhindert das Anhaften von Material und verringert den Verschleiß der Werkzeuge. Bei steigender Geschwindigkeit erhöht sich die Gefahr des Abschleifens oder Abtragens der Schmierstoffschicht, weshalb der Schmierstoff sorgfältig ausgewählt und optimal dosiert werden muss.
Darüber hinaus spielen Prozessparameter wie Ziehtiefe und Blechdicke eine Rolle bei der Einstellung von Geschwindigkeit und Druck. Dickere Bleche benötigen in der Regel höhere Drücke und angepasste Ziehgeschwindigkeiten, um eine gleichmäßige Umformung ohne Defekte zu gewährleisten. Dünne Bleche hingegen erfordern feinfühligere Prozessführung, da sie schneller reißen oder falten können.
Moderne Fertigungseinrichtungen setzen auf digitale Prozessregelung und Echtzeitüberwachung, um Geschwindigkeit und Druck während des Tiefziehens kontinuierlich anzupassen. So können individuelle Werkstückmerkmale, Materialeigenschaften und Werkzeugzustände berücksichtigt werden, was eine maximale Prozessstabilität und Qualität sicherstellt.
Zusammenfassend lässt sich sagen, dass das Zusammenspiel von Geschwindigkeit und Druck im Tiefziehprozess komplex ist und maßgeblich die Qualität des Endprodukts sowie die Effizienz der Fertigung bestimmt. Ein tiefes Verständnis dieser Parameter und deren gezielte Steuerung sind deshalb zentral für eine erfolgreiche Anwendung des Tiefziehverfahrens.
Ein weiterer wichtiger Aspekt beim Einfluss von Geschwindigkeit und Druck im Tiefziehprozess ist die Auswirkung auf den Werkzeugverschleiß. Hohe Geschwindigkeiten und unzureichend angepasster Druck führen häufig zu erhöhten mechanischen Belastungen und höheren Reibungskräften zwischen Blech und Werkzeug. Dies kann zu vorzeitigem Verschleiß, Oberflächenschäden oder sogar Werkzeugbruch führen. Daher ist eine sorgfältige Abstimmung der Prozessparameter essenziell, um die Standzeiten der Werkzeuge zu maximieren und ungeplante Stillstände in der Produktion zu vermeiden.
Ebenso hat die Prozessstabilität durch optimale Geschwindigkeit und Druck einen direkten Einfluss auf die Ausschussquote. Schwankungen in der Ziehgeschwindigkeit oder Druckspitzen können zu Unregelmäßigkeiten in der Materialverteilung führen, die sich in Form von Rissen, Falten oder Dickenabweichungen bemerkbar machen. Durch eine konstante und kontrollierte Prozessführung lassen sich solche Fehlerquellen minimieren, was die Produktqualität erhöht und Kosten senkt.
Darüber hinaus sind Geschwindigkeit und Druck wichtige Größen bei der Anpassung des Tiefziehprozesses an unterschiedliche Werkstoffe. So erfordern beispielsweise hochfeste Stähle oder Aluminiumlegierungen spezielle Prozessparameter, um die besonderen mechanischen Eigenschaften zu berücksichtigen und eine sichere Umformung zu gewährleisten. Flexible Maschinensteuerungen und regelbare Pressen ermöglichen es, diese Parameter schnell und präzise an neue Materialien oder Bauteildesigns anzupassen.
Innovative Technologien wie adaptive Prozessregelungen und KI-gestützte Prozessoptimierung gewinnen zunehmend an Bedeutung. Sie erlauben es, Geschwindigkeit und Druck in Echtzeit anhand von Sensordaten und Modellberechnungen anzupassen, um stets optimale Bedingungen zu schaffen. Dies führt nicht nur zu einer höheren Prozesssicherheit, sondern auch zu einer weiteren Steigerung der Effizienz und Produktqualität.
Insgesamt zeigen sich Geschwindigkeit und Druck als zentrale Stellgrößen im Tiefziehprozess, die in ihrem Zusammenspiel entscheidend für die Umformqualität, Werkzeuglebensdauer und Wirtschaftlichkeit sind. Eine fundierte Prozessplanung, unterstützt durch moderne Messtechnik und Regelungssysteme, ist der Schlüssel, um die Potenziale des Tiefziehens voll auszuschöpfen.
Zusätzlich beeinflussen Geschwindigkeit und Druck auch die Entstehung von Restspannungen im Bauteil, welche die Formstabilität und das spätere Verhalten unter Belastung maßgeblich beeinflussen können. Werden die Prozessparameter nicht optimal gewählt, kann es zu ungleichmäßigen Dehnungen und damit zu inneren Spannungen kommen, die sich später in Form von Verzug, Rissbildung oder vermindertem Ermüdungsverhalten äußern. Durch eine gezielte Steuerung von Geschwindigkeit und Druck lassen sich solche negativen Effekte minimieren, was gerade bei sicherheitskritischen Bauteilen eine wichtige Rolle spielt.
Ein weiterer Aspekt ist die Energieeffizienz des Tiefziehprozesses. Eine zu hohe Ziehgeschwindigkeit oder ein übermäßiger Druck führen nicht nur zu erhöhter Werkzeugbeanspruchung, sondern auch zu einem höheren Energieverbrauch. Die Anpassung der Parameter an die Werkstoff- und Bauteileigenschaften trägt dazu bei, den Energiebedarf zu reduzieren und den Fertigungsprozess nachhaltiger zu gestalten.
Darüber hinaus ist die Schulung des Bedienpersonals entscheidend, um die richtigen Prozessparameter zu wählen und bei Abweichungen frühzeitig einzugreifen. Das Verständnis für die Zusammenhänge von Geschwindigkeit, Druck und Materialverhalten unterstützt die Fehlerdiagnose und ermöglicht eine schnelle Prozessoptimierung.
Zukünftige Entwicklungen im Tiefziehen setzen vermehrt auf intelligente Steuerungssysteme, die auf Basis von Prozessdaten und maschinellem Lernen eigenständig optimale Einstellungen für Geschwindigkeit und Druck ermitteln. Dies verspricht eine weitere Verbesserung der Produktqualität, eine Reduzierung von Ausschuss und Stillstandzeiten sowie eine effiziente Ressourcennutzung.
In der Gesamtschau zeigt sich, dass Geschwindigkeit und Druck im Tiefziehprozess nicht isoliert betrachtet werden dürfen, sondern als integrale Bestandteile eines komplexen Zusammenspiels von Material, Werkzeug, Maschine und Prozessumgebung. Ihre präzise Abstimmung ist entscheidend für die erfolgreiche Fertigung von qualitativ hochwertigen und wirtschaftlichen Bauteilen.
Tiefziehen für die Massenproduktion: Effizienzsteigerung
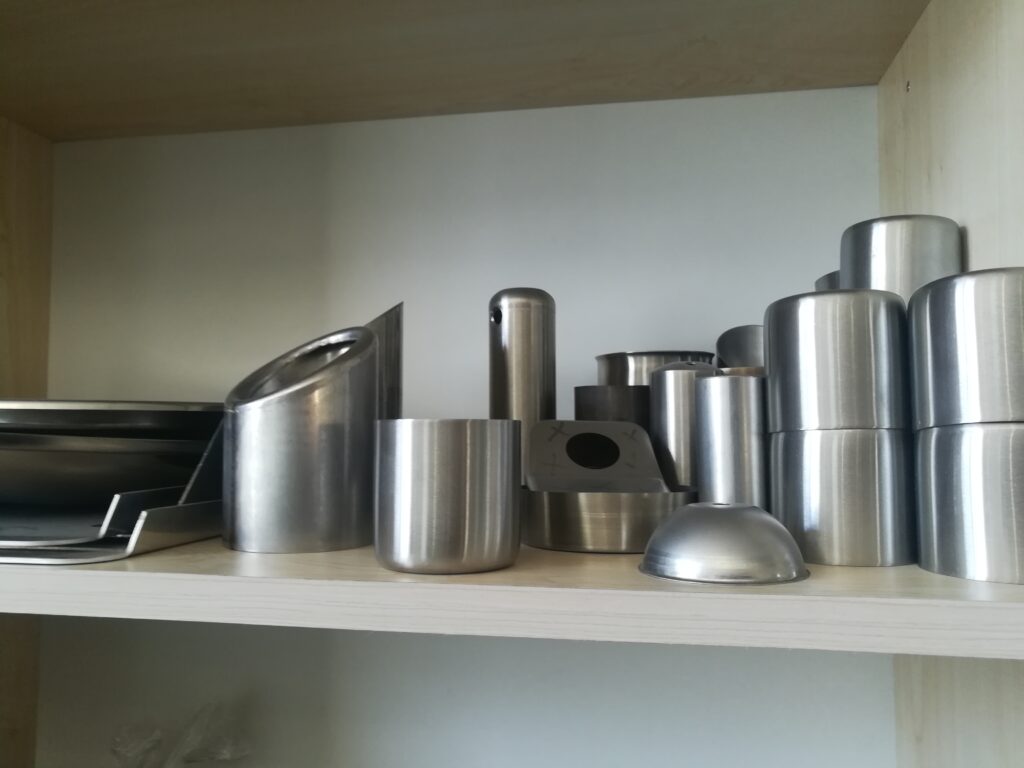
Tiefziehen ist ein zentrales Verfahren für die Massenproduktion von Blechbauteilen, da es eine schnelle, präzise und wiederholbare Umformung ermöglicht. Um die Effizienz in der Serienfertigung weiter zu steigern, werden verschiedene Strategien und Technologien eingesetzt, die sowohl die Produktionsgeschwindigkeit als auch die Produktqualität optimieren.
Ein wesentlicher Faktor zur Effizienzsteigerung ist die Automatisierung des Tiefziehprozesses. Durch den Einsatz von Robotern für das Be- und Entladen sowie für Zwischen- und Endbearbeitungsschritte können Taktzeiten deutlich verkürzt und menschliche Fehler reduziert werden. Automatisierte Fertigungslinien ermöglichen zudem eine konstante Prozessführung, was zu gleichbleibend hoher Qualität führt und Ausschuss minimiert.
Die Integration von Mehrstufen-Tiefziehprozessen in einer Linie erlaubt die Fertigung komplexer Bauteile ohne manuelle Umspanner oder Zwischenlagerungen. Dadurch sinken Durchlaufzeiten und Lagerkosten, und die Prozesssicherheit wird erhöht. Die Auslegung der Werkzeuge für hohe Standzeiten und schnelle Werkzeugwechsel unterstützt zudem eine hohe Anlagenverfügbarkeit.
Moderne Steuerungs- und Überwachungssysteme spielen eine entscheidende Rolle bei der Effizienzsteigerung. Sensoren erfassen Prozessgrößen wie Kraft, Geschwindigkeit oder Temperatur in Echtzeit, sodass Anpassungen automatisch erfolgen können. Durch die Analyse dieser Daten lassen sich zudem Engpässe identifizieren und Wartungsintervalle optimieren, was ungeplante Stillstände reduziert.
Ein weiterer Hebel liegt in der Materialausnutzung. Durch die Optimierung der Blechzuschnitte und den Einsatz von Rückführsystemen für Verschnittreste wird Rohstoff effizient genutzt. Zudem erlauben innovative Schmierstoffe und Oberflächenbeschichtungen eine Reduzierung der Reibung und des Werkzeugverschleißes, was die Prozessstabilität verbessert und Wartungskosten senkt.
Schließlich sind auch Schulungen des Bedienpersonals und kontinuierliche Prozessverbesserungen wichtige Faktoren, um die Effizienz langfristig zu sichern. Die Kombination aus technologischen Innovationen, intelligentem Prozessmanagement und qualifiziertem Personal macht das Tiefziehen zu einem äußerst produktiven Verfahren für die Massenfertigung von Blechbauteilen.
Darüber hinaus spielt die Standardisierung von Bauteildesigns und Werkzeugen eine wichtige Rolle bei der Effizienzsteigerung im Tiefziehen für die Massenproduktion. Durch die Wiederverwendung bewährter Werkzeugkonzepte und die Vereinheitlichung von Produktvarianten lassen sich Rüstzeiten reduzieren und die Produktionsplanung vereinfachen. Dies führt zu einer schnelleren Markteinführung neuer Produkte und einer besseren Auslastung der Fertigungskapazitäten.
Ein weiterer Aspekt ist die Optimierung der Prozessparameter wie Ziehgeschwindigkeit, Druck und Schmierung, die auf hohe Stückzahlen ausgelegt sind. Durch kontinuierliches Monitoring und datengetriebene Prozessanpassungen können Schwankungen minimiert und eine gleichbleibende Produktqualität gewährleistet werden, selbst bei großen Losgrößen. Dies verhindert Ausschuss und Nacharbeit, was Kosten senkt und die Lieferzuverlässigkeit erhöht.
Auch die Modularität von Werkzeugen und Maschinen trägt zur Flexibilität und Effizienz bei. Schnell austauschbare Werkzeuge und anpassbare Maschinenkomponenten ermöglichen es, unterschiedliche Bauteile mit minimalem Umrüstaufwand herzustellen. Dies ist besonders in Märkten mit häufig wechselnden Anforderungen von Vorteil und unterstützt die Just-in-Time-Produktion.
Zudem gewinnt die Digitalisierung der Fertigung, im Sinne von Industrie 4.0, zunehmend an Bedeutung. Vernetzte Systeme erlauben eine umfassende Transparenz über den gesamten Produktionsprozess, von der Materialzufuhr bis zum fertigen Bauteil. Diese Echtzeitdaten helfen, Engpässe frühzeitig zu erkennen, Ressourcen optimal einzusetzen und die Produktionsabläufe dynamisch zu steuern.
Nicht zuletzt trägt die nachhaltige Gestaltung der Tiefziehprozesse zur langfristigen Effizienz bei. Die Nutzung energieeffizienter Maschinen, umweltfreundlicher Schmierstoffe und die Minimierung von Materialabfall unterstützen nicht nur ökologische Ziele, sondern reduzieren auch Kosten und verbessern das Unternehmensimage.
Insgesamt führt die Kombination aus Automatisierung, Standardisierung, Digitalisierung und nachhaltigen Maßnahmen zu einer signifikanten Effizienzsteigerung im Tiefziehen für die Massenproduktion und sichert die Wettbewerbsfähigkeit in einem zunehmend anspruchsvollen Marktumfeld.
Zusätzlich eröffnet die Nutzung von Simulationstechnologien vor der eigentlichen Produktion weitere Effizienzpotenziale. Durch computergestützte Prozesssimulationen können Materialfluss, Werkzeugbelastungen und mögliche Fehlerquellen bereits in der Planungsphase analysiert und optimiert werden. Dies reduziert teure Nachbesserungen und Werkzeugänderungen während der Produktion und verkürzt die Entwicklungszeiten für neue Bauteile erheblich.
Die Implementierung von Predictive Maintenance, also vorausschauender Wartung, ist ein weiterer wichtiger Faktor zur Steigerung der Effizienz. Durch die kontinuierliche Überwachung von Maschinenzuständen mittels Sensorik und Datenanalyse lassen sich Verschleißerscheinungen frühzeitig erkennen. Dadurch können Wartungen gezielt geplant und ungeplante Ausfälle vermieden werden, was die Maschinenverfügbarkeit erhöht und Produktionsstillstände minimiert.
Auch der Einsatz von innovativen Materialien und Beschichtungen trägt zur Effizienzsteigerung bei. Beispielsweise ermöglichen verschleißfeste Werkzeugoberflächen längere Standzeiten und verringern den Wartungsaufwand. Gleichzeitig erlauben hochfeste und dennoch gut umformbare Bleche dünnere Wandstärken, was Materialkosten senkt und das Bauteilgewicht reduziert.
Darüber hinaus gewinnt die Zusammenarbeit zwischen Konstruktion, Fertigung und Qualitätssicherung zunehmend an Bedeutung. Ein integrierter Ansatz sorgt dafür, dass Designentscheidungen von Anfang an auf eine effiziente Fertigung und einfache Qualitätskontrolle abgestimmt sind. Dies führt zu einem reibungsloseren Produktionsablauf, weniger Fehlern und kürzeren Lieferzeiten.
Schließlich bieten Schulungsprogramme und kontinuierliche Weiterbildungen für das Personal eine wichtige Grundlage, um neue Technologien und Prozessoptimierungen erfolgreich umzusetzen. Qualifizierte Mitarbeiter können flexibler auf Veränderungen reagieren, Prozesse besser überwachen und dadurch die Gesamtproduktivität steigern.
Insgesamt lässt sich sagen, dass eine ganzheitliche Betrachtung aller Prozessschritte – von der Planung über die Fertigung bis zur Wartung und Mitarbeiterqualifikation – entscheidend ist, um das Tiefziehen in der Massenproduktion effizienter und wettbewerbsfähiger zu gestalten.
Fertigung von tiefgezogenen Bauteilen: Design und Produktion
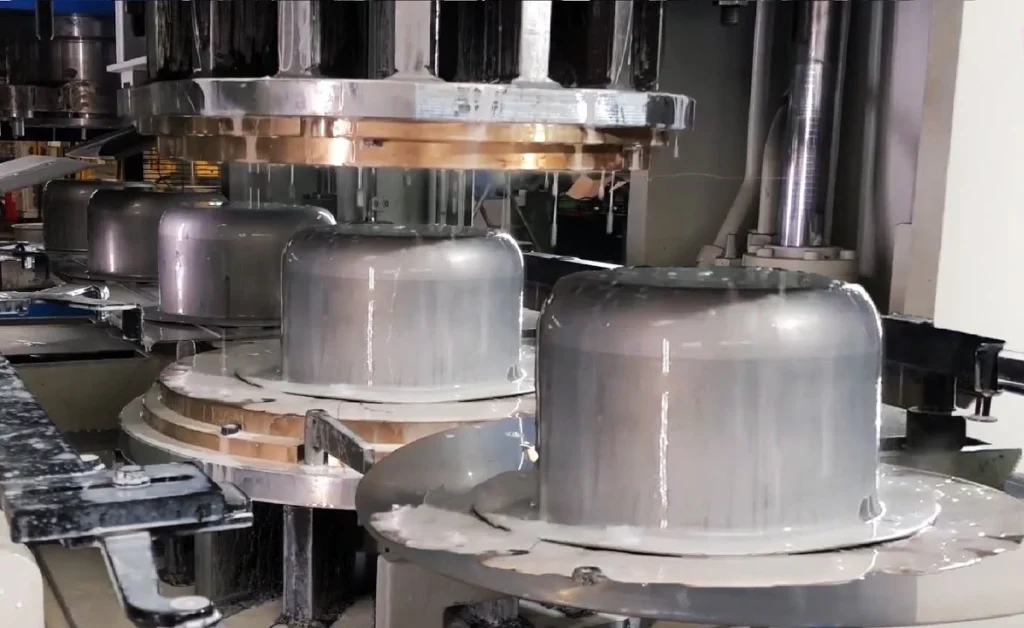
Die Fertigung von tiefgezogenen Bauteilen erfordert eine enge Verzahnung zwischen Design und Produktion, um sowohl funktionale Anforderungen als auch wirtschaftliche Aspekte optimal zu erfüllen. Bereits in der Entwurfsphase spielen technische und fertigungsspezifische Aspekte eine wichtige Rolle, da das Design die Umformbarkeit, Materialausnutzung und die Prozesssicherheit maßgeblich beeinflusst.
Beim Design tiefgezogener Bauteile müssen geometrische Merkmale wie Radien, Wandstärken und Flanschbreiten so gestaltet werden, dass eine gleichmäßige Materialverteilung während des Ziehvorgangs möglich ist. Scharfe Kanten oder zu enge Radien können zu Spannungsspitzen führen und das Risiko von Rissen oder Faltenbildung erhöhen. Daher werden oft großzügige Übergänge und abgestufte Wandstärken gewählt, um die Umformbarkeit zu verbessern.
Die Auswahl des Werkstoffs ist ebenfalls ein wesentlicher Faktor. Je nach Anwendung werden unterschiedliche Metalle wie Stahl, Edelstahl, Aluminium oder Kupferlegierungen eingesetzt, die jeweils spezielle Anforderungen an das Tiefziehverfahren stellen. Die Werkstoffauswahl beeinflusst sowohl das Design als auch die Prozessparameter und muss frühzeitig in die Planung einbezogen werden.
Im Produktionsprozess werden dann Werkzeuge entwickelt, die exakt auf das Bauteildesign abgestimmt sind. Die Konstruktion der Matrizen und Stempel berücksichtigt die Materialflüsse und ermöglicht durch gezielte Kraft- und Druckverteilung eine möglichst fehlerfreie Umformung. Fortschrittliche CAD- und CAM-Systeme unterstützen dabei die präzise Auslegung und Fertigung der Werkzeuge.
Während der Produktion ist eine kontinuierliche Prozessüberwachung notwendig, um die Einhaltung der vorgegebenen Qualitätsstandards zu gewährleisten. Messsysteme erfassen dimensionskritische Merkmale und Oberflächenqualität, um Abweichungen frühzeitig zu erkennen und zu korrigieren. Dies minimiert Ausschuss und Nacharbeit.
Nicht zuletzt trägt eine enge Zusammenarbeit zwischen Konstrukteuren, Fertigungsingenieuren und Qualitätsprüfern dazu bei, dass Designänderungen schnell umgesetzt und optimiert werden können. So lassen sich sowohl die Produktqualität als auch die Fertigungseffizienz kontinuierlich verbessern.
Insgesamt ist die Kombination aus durchdachtem Design, geeigneter Werkstoffauswahl und präziser Fertigung der Schlüssel für die erfolgreiche Herstellung von tiefgezogenen Bauteilen, die sowohl funktional als auch wirtschaftlich überzeugen.
Ein weiterer wichtiger Aspekt bei der Fertigung tiefgezogener Bauteile ist die enge Toleranzführung, die vor allem bei funktionskritischen Anwendungen, etwa in der Automobil-, Luftfahrt- oder Medizintechnik, entscheidend ist. Bereits kleinste Abweichungen in der Bauteilgeometrie können zu Problemen in der späteren Montage oder Funktion führen. Daher ist es unerlässlich, das Design so auszulegen, dass es sich reproduzierbar und stabil fertigen lässt, auch unter schwankenden Bedingungen. Dies erfordert eine präzise Werkzeugkonstruktion und den Einsatz hochwertiger Materialien für Stempel und Matrizen, um Formgenauigkeit und Standzeit zu gewährleisten.
Auch der Einfluss der Blechdicke darf nicht unterschätzt werden. Während dickere Bleche eine höhere Formstabilität bieten, bedeuten sie gleichzeitig höheren Materialeinsatz und somit steigende Kosten. Dünnere Bleche dagegen reduzieren das Gewicht, erfordern aber eine besonders sorgfältige Abstimmung von Ziehgeschwindigkeit, Schmierung und Werkzeuggeometrie, um Rissbildungen und ungleichmäßige Wandstärken zu vermeiden. Dies wird häufig durch eine Kombination aus Finite-Elemente-Simulationen und physikalischen Prototypentests erreicht, um vor der Serienfertigung kritische Stellen zu identifizieren und das Design entsprechend anzupassen.
Die Prozesskette rund um das Tiefziehen umfasst heute nicht nur den eigentlichen Umformvorgang, sondern auch vorbereitende und nachgelagerte Schritte wie Blechzuschnitt, Kantenbearbeitung, Wärmebehandlung, Reinigung und ggf. Beschichtung oder Lackierung. Diese Abläufe müssen nahtlos ineinandergreifen, um die Wirtschaftlichkeit sicherzustellen. Besonders bei hohen Stückzahlen ist die Taktzeitoptimierung über die gesamte Prozesskette hinweg entscheidend. Hier kommen oft auch Transfersysteme und Roboter zum Einsatz, die das Bauteil automatisiert durch verschiedene Stationen führen.
Im Hinblick auf Nachhaltigkeit gewinnt die Materialeffizienz zunehmend an Bedeutung. Eine möglichst verlustarme Zuschnittsstrategie, das Recycling von Verschnitt sowie die Wiederverwendung von Ausschussteilen durch Remanufacturing-Prozesse sind heute vielfach etablierte Praxis. Gleichzeitig arbeiten viele Unternehmen daran, den Energieverbrauch während des Ziehprozesses zu reduzieren – etwa durch optimierte Hydrauliksysteme, intelligente Steuerungstechnik oder den Einsatz regenerativer Energiesysteme in der Produktion.
Die Digitalisierung der Fertigung ermöglicht darüber hinaus eine durchgängige Rückverfolgbarkeit jedes einzelnen Bauteils – von der Materialcharge über die Prozessparameter bis hin zum finalen Messprotokoll. Diese Daten werden genutzt, um Prozessabweichungen zu analysieren, Korrekturmaßnahmen gezielt umzusetzen und zukünftige Produktionen kontinuierlich zu verbessern. Der enge Datenabgleich zwischen Simulation, realem Prozess und Qualitätskontrolle führt so zu einer immer präziseren Beherrschung des Tiefziehverfahrens.
Letztlich zeigt sich, dass die Fertigung tiefgezogener Bauteile ein hochgradig interdisziplinärer Prozess ist, der nur durch das Zusammenspiel von Konstruktion, Werkstofftechnik, Fertigungstechnologie und Qualitätssicherung in hoher Qualität und mit maximaler Effizienz realisiert werden kann.
Parallel zur technischen Entwicklung hat sich auch das Verständnis für die betriebswirtschaftliche Bedeutung des Tiefziehens in der Serienfertigung weiterentwickelt. Die Entscheidung für ein bestimmtes Design oder Material wird heute nicht mehr allein auf Basis technischer Kriterien getroffen, sondern immer im Kontext von Kostenstruktur, Lieferkettenstabilität und Marktdynamik bewertet. So beeinflussen etwa volatile Rohstoffpreise oder globale Engpässe bei bestimmten Legierungen zunehmend die Materialwahl und die Auslegung von Tiefziehprozessen. Die Möglichkeit, Bauteile flexibel an alternative Werkstoffe oder leicht abgewandelte Geometrien anzupassen, wird damit zu einem strategischen Vorteil.
In der Praxis zeigt sich außerdem, dass die frühzeitige Einbindung der Fertigung in den Konstruktionsprozess erhebliche Einsparpotenziale eröffnet. Indem fertigungsgerechtes Design als integraler Bestandteil der Produktentwicklung verstanden wird, lassen sich unnötig komplexe Formen, schwierige Umformschritte oder aufwendige Nachbearbeitungen vermeiden. Dies reduziert nicht nur die Fertigungskosten, sondern erhöht auch die Prozesssicherheit und senkt die Fehlerquote.
Im Werkzeugbau wiederum ist ein Trend hin zur Modularität und Wiederverwendbarkeit zu beobachten. Werkzeuge werden zunehmend so konstruiert, dass sie mit minimalen Anpassungen für verschiedene Produktvarianten eingesetzt werden können. Dies senkt die Investitionskosten und erhöht die Reaktionsgeschwindigkeit auf Kundenanforderungen. Gleichzeitig ermöglichen moderne Fertigungstechnologien wie der 3D-Druck von Formeinsätzen oder die Hochgeschwindigkeitsbearbeitung im Werkzeugbau deutlich kürzere Durchlaufzeiten in der Werkzeugherstellung.
Ein nicht zu unterschätzender Faktor ist schließlich die menschliche Kompetenz. Auch wenn viele Schritte im Tiefziehprozess mittlerweile automatisiert oder digital überwacht werden, bleibt die Erfahrung von Ingenieuren, Werkzeugmachern und Maschinenbedienern zentral. Das Verständnis für das Verhalten von Blech unter Druck, das frühzeitige Erkennen subtiler Fehlerbilder und das richtige Reagieren auf Prozessstörungen lassen sich nicht vollständig durch Algorithmen ersetzen. Daher investieren viele Unternehmen gezielt in Ausbildung, Schulung und den Wissenstransfer zwischen erfahrenen und jüngeren Mitarbeitenden.
Die Zukunft der Tiefziehfertigung liegt in der Kombination aus robusten Prozessen, flexiblen Systemen, datengestützter Optimierung und einem tiefen Verständnis für Material- und Werkzeugverhalten. Wer es versteht, diese Elemente strategisch zu verknüpfen, wird in der Lage sein, selbst anspruchsvolle Bauteile in großen Stückzahlen wirtschaftlich, nachhaltig und mit konstant hoher Qualität herzustellen.
Mit Blick auf die zukünftige Ausrichtung der Tiefziehfertigung zeichnet sich ab, dass Anpassungsfähigkeit zu einem Schlüsselfaktor für den langfristigen Erfolg wird. Die Märkte verlangen zunehmend individualisierte Produkte mit kürzeren Entwicklungszyklen und flexiblen Liefermengen. Die klassische Massenproduktion großer, identischer Serien wird durch kleinere Losgrößen mit häufig wechselnden Geometrien ergänzt. Um darauf effizient reagieren zu können, müssen Tiefziehprozesse modular, schnell umrüstbar und softwaregestützt konfigurierbar sein.
Dies führt zu einer verstärkten Integration von digitalen Zwillingen in die Produktionsplanung. Durch das Abbilden des gesamten Tiefziehprozesses – vom Blechzuschnitt über den Werkzeugverschleiß bis hin zum Endprodukt – in einer virtuellen Umgebung können unterschiedliche Szenarien vorab getestet werden. So lässt sich beispielsweise vor Produktionsbeginn simulieren, wie sich eine neue Materialcharge oder eine Konstruktionsänderung auf das Endergebnis auswirken wird. Diese digitale Vorhersagbarkeit senkt Risiken und steigert die Prozessstabilität, insbesondere in der Serienanlaufphase.
Auch das Condition Monitoring gewinnt weiter an Bedeutung. Sensorisch überwachte Werkzeuge und Pressen liefern in Echtzeit Daten zu Druckverläufen, Temperaturen und Vibrationen. Diese Informationen werden nicht nur zur direkten Steuerung des laufenden Prozesses genutzt, sondern fließen auch in Datenbanken ein, aus denen langfristige Optimierungspotenziale abgeleitet werden. Über künstliche Intelligenz können dabei Muster erkannt werden, die menschlichen Beobachtern entgehen – etwa sich ankündigender Werkzeugverschleiß oder schleichende Veränderungen in der Materialqualität.
In der Logistik rund um die Tiefziehfertigung geht der Trend zur Just-in-Sequence-Versorgung, bei der Material und Werkzeuge exakt im benötigten Takt bereitgestellt werden. Diese Abläufe sind nur durch eine enge Verzahnung von IT-Systemen, Lagerhaltung, Transportlogistik und Produktion möglich. Besonders in hochautomatisierten Werken sind Roboter und fahrerlose Transportsysteme (FTS) inzwischen fester Bestandteil dieser fein abgestimmten Produktionssysteme.
Ein weiterer Innovationsbereich ist die Nachhaltigkeit. Neben energieeffizienteren Maschinen und dem Recycling von Verschnitt rückt auch die CO₂-Bilanz jedes einzelnen Fertigungsschritts in den Fokus. Unternehmen, die ihren Kunden eine dokumentierte, klimabewusste Produktion nachweisen können, verschaffen sich zunehmend Wettbewerbsvorteile. Dazu gehört auch die Nutzung CO₂-reduzierter Materialien sowie der Einsatz regenerativer Energiequellen direkt im Produktionsprozess.
Die zunehmende Bedeutung regulatorischer Anforderungen – etwa im Hinblick auf Rückverfolgbarkeit, Produktsicherheit oder Umweltschutz – macht es notwendig, dass der Tiefziehprozess vollständig dokumentiert und auditierbar ist. Moderne Fertigungssysteme müssen daher nicht nur produktiv, sondern auch transparent sein. Dies erhöht zwar zunächst den Aufwand für Datenerfassung und Dokumentation, schafft aber gleichzeitig die Grundlage für eine langfristig stabile und vertrauenswürdige Produktionskette.
Letztlich wird die Zukunft des Tiefziehens geprägt sein von der Balance zwischen bewährter Technik und innovativen Ansätzen. Wer in der Lage ist, klassische Fertigungsprinzipien mit digitalen Werkzeugen, nachhaltigem Wirtschaften und flexiblen Produktionsstrategien zu kombinieren, wird sich auch in einem dynamischen und globalisierten Wettbewerbsumfeld behaupten können.
Blechformung durch Tiefziehen: Von der Idee zum Produkt
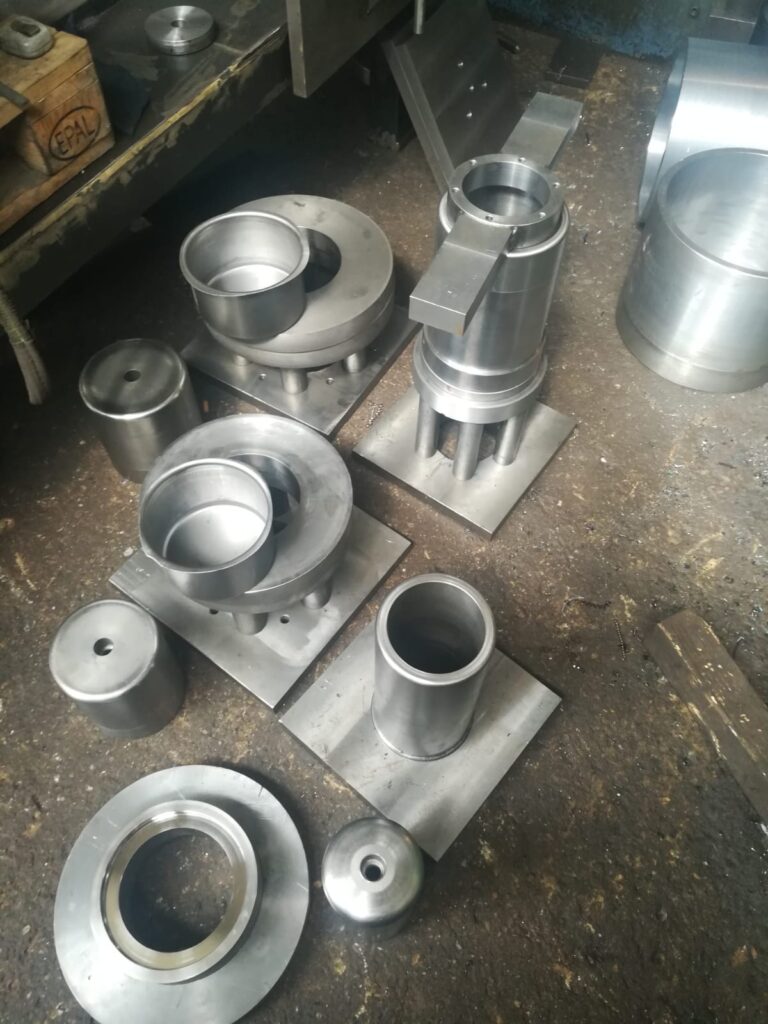
Die Blechformung durch Tiefziehen beginnt lange vor dem eigentlichen Umformprozess – sie startet mit einer Idee, einer Produktanforderung oder einem konkreten Funktionswunsch. Aus dieser Idee entsteht zunächst ein Entwurf, der sowohl die spätere Anwendung als auch fertigungstechnische Gegebenheiten berücksichtigen muss. Bereits in dieser Phase entscheidet sich, wie erfolgreich das Endprodukt hinsichtlich Qualität, Herstellbarkeit und Wirtschaftlichkeit sein wird.
Die Konzeption des Bauteils wird eng mit der Materialwahl verzahnt. Dabei fließen Kriterien wie Festigkeit, Umformbarkeit, Korrosionsverhalten, Gewicht und natürlich Kosten in die Entscheidung ein. Für komplexe Bauteile mit hohen Anforderungen an Maßgenauigkeit und Oberflächenqualität werden häufig Materialien wie Tiefziehstahl, Edelstahl oder Aluminiumlegierungen verwendet, die gute plastische Verformbarkeit mit struktureller Stabilität vereinen.
Nach der Festlegung von Geometrie und Material erfolgt die virtuelle Analyse des Tiefziehvorgangs. Mithilfe moderner Simulationssoftware wird der Umformprozess digital abgebildet, um Schwachstellen wie Faltenbildung, Rissgefahr oder unerwünschte Wanddickenveränderungen zu erkennen. Durch iterative Anpassung von Ziehradien, Blechdicke, Ziehrichtung und Werkzeugkonturen entsteht ein robustes Design, das die Grundlage für die Werkzeugkonstruktion bildet.
Der nächste Schritt ist der Bau des Tiefziehwerkzeugs. Präzision ist dabei essenziell, denn die Qualität des Werkzeugs spiegelt sich unmittelbar im Endprodukt wider. Hochfeste Werkzeugstähle, beschichtete Oberflächen und ausgeklügelte Kühlsysteme sorgen für eine lange Lebensdauer und konstante Produktionsbedingungen. In vielen Fällen werden Funktionsmuster oder Prototypen gefertigt, um die Prozessstabilität vor Serienanlauf zu verifizieren.
Mit Produktionsbeginn kommen Ziehpressen und Automatisierungstechnik ins Spiel. Je nach Bauteilgröße und Losgröße werden mechanische, hydraulische oder servogesteuerte Pressen eingesetzt. Sensorik überwacht dabei den Prozess, erkennt Abweichungen und ermöglicht eine fortlaufende Qualitätskontrolle. Die richtige Wahl von Schmiermitteln, Ziehringformen und Ziehstufen stellt sicher, dass der Werkstoff gleichmäßig fließt und das Bauteil die gewünschte Form annimmt.
Nach dem Tiefziehen folgen häufig weitere Bearbeitungsschritte wie Beschnitt, Kalibrierung, Oberflächenveredelung oder Montage. Auch diese Prozesse werden bereits in der Planungsphase berücksichtigt, um reibungslose Übergänge in der Produktionskette sicherzustellen. Am Ende steht ein funktionales, hochwertiges Bauteil – entstanden aus einer Idee, präzise geplant und effizient umgesetzt durch die Tiefziehtechnologie.
Der Weg vom Konzept zum fertigen tiefgezogenen Produkt verläuft heute in hohem Maße daten- und simulationsgestützt. Während früher viele Iterationsschritte an physischen Prototypen notwendig waren, lassen sich dank digitaler Prozessketten viele Fehlerquellen bereits im Vorfeld vermeiden. Besonders die Integration von CAD-, FEM- und CAM-Systemen ermöglicht eine durchgängige Planung von der ersten Skizze bis zur maschinenfertigen Werkzeugdatei. Diese nahtlose Verbindung reduziert nicht nur den Zeitaufwand, sondern erhöht auch die Genauigkeit in jeder Prozessphase.
Bereits kleine Änderungen in der Geometrie, wie veränderte Radien oder Übergänge, können darüber entscheiden, ob ein Bauteil zuverlässig tiefziehbar ist oder zum Versagen neigt. Diese Detailtiefe erfordert ein enges Zusammenspiel zwischen Konstrukteuren, Werkstoffspezialisten und Fertigungstechnikern. Auch Erfahrungswissen spielt hier eine zentrale Rolle, etwa wenn es darum geht, frühzeitig Bereiche mit kritischem Fließverhalten zu identifizieren und konstruktiv zu entschärfen. Das Ziel ist stets, ein Gleichgewicht zwischen Materialfluss, Ziehkraft und Rückfederung zu schaffen – und dies unter möglichst reproduzierbaren Bedingungen.
In der Serienfertigung wird die Leistungsfähigkeit der Pressen und Werkzeuge zur entscheidenden Stellgröße. Pressen mit fein steuerbaren Ziehgeschwindigkeiten und individuell einstellbaren Niederhaltern erlauben es, das Umformverhalten exakt zu kontrollieren. Besonders bei komplexen Formen oder großen Bauteilen wird oft mit mehrstufigen Ziehprozessen gearbeitet, um das Material schrittweise in die gewünschte Endkontur zu bringen. Die dabei eingesetzten Sensoren, etwa für Kraft, Weg und Temperatur, liefern wertvolle Rückmeldungen über den tatsächlichen Ablauf und ermöglichen so eine automatische Prozessanpassung in Echtzeit.
Ein nicht zu unterschätzender Faktor ist die Rückfederung des Materials nach dem Ziehvorgang. Insbesondere bei hochfesten oder elastischen Werkstoffen kann sie zu Abweichungen von der Sollform führen. Um dem entgegenzuwirken, wird entweder mit sogenannten Überbiegungen gearbeitet oder die Werkstückgeometrie wird bereits so angepasst, dass sie sich nach dem Rückfedern in die Zielkontur legt. Hier ist viel Erfahrung und Feingefühl gefragt – insbesondere dann, wenn eine hohe Maßhaltigkeit gefordert ist.
Im letzten Abschnitt der Fertigung stehen Qualitätssicherung und Dokumentation im Fokus. Hier kommen Koordinatenmessmaschinen, optische 3D-Scanner oder taktile Prüflehren zum Einsatz, um Geometrien, Oberflächen und Maßhaltigkeit lückenlos zu überprüfen. Die ermittelten Daten dienen nicht nur der Kundenfreigabe, sondern fließen auch in kontinuierliche Verbesserungsprozesse ein. In Kombination mit Traceability-Systemen kann jedes Bauteil auf seine Fertigungsbedingungen und Materialchargen zurückverfolgt werden, was im Fall von Reklamationen oder Rückrufen entscheidende Vorteile bietet.
Am Ende steht ein tiefgezogenes Produkt, das nicht nur durch seine Funktion, sondern auch durch die dahinterstehende Prozesssicherheit überzeugt. Es repräsentiert das Zusammenspiel moderner Technologien, digitaler Planung und erfahrungsbasierter Feinabstimmung – und zeigt, wie sich aus einem einfachen Blechzuschnitt ein hochwertiges, funktionales Bauteil mit hoher Präzision und Wiederholgenauigkeit herstellen lässt.
Die Entwicklung geht jedoch weiter: Moderne Tiefziehfertigung ist zunehmend eingebettet in größere, digital gesteuerte Produktionssysteme. Die Vernetzung von Pressen, Werkzeugwechslern, Handhabungsrobotern und Qualitätsprüfstationen ermöglicht eine automatisierte Fertigungskette, in der jeder Schritt überwacht und dokumentiert wird. Produktionsdaten werden in Echtzeit gesammelt und analysiert – nicht nur zur Überwachung, sondern auch zur vorausschauenden Wartung und Optimierung. So lässt sich beispielsweise erkennen, wenn eine Ziehkraft allmählich ansteigt – ein Hinweis auf Verschleiß oder falsche Schmierung – und rechtzeitig Gegenmaßnahmen einleiten, bevor es zu Ausschuss kommt.
Auch in der Produktgestaltung eröffnet das Tiefziehen neue Möglichkeiten. Leichte, stabile, nahtlose Gehäuse, strukturierte Oberflächen für Design oder Funktionalität und komplexe Geometrien lassen sich mit vergleichsweise wenig Materialaufwand realisieren. Das macht das Verfahren attraktiv für viele Branchen: von der Automobilindustrie über Haushaltsgeräte bis hin zur Medizintechnik. Insbesondere dort, wo Hygiene, glatte Oberflächen und enge Toleranzen gefragt sind, spielt Tiefziehen seine Stärken aus. Selbst Mikro-Tiefziehverfahren für sehr kleine, präzise Bauteile gewinnen an Bedeutung, etwa in der Sensorik oder der Elektronik.
Die wirtschaftlichen Vorteile sind ebenfalls deutlich. Ein einmal gut eingestellter Tiefziehprozess kann in sehr hohen Stückzahlen mit gleichbleibender Qualität fertigen. Da das Material bei richtiger Prozessführung kaum verspannt wird, entstehen geringe Rückstellkräfte und stabile Formen. Der Materialeinsatz ist effizient, der Verschnitt gering. Zudem können durch die Kombination von Tiefziehen mit weiteren Umformprozessen wie Bördeln, Prägen oder Lochen zusätzliche Bearbeitungsschritte direkt integriert werden, was Montagekosten reduziert.
Auch bei Nachhaltigkeitsaspekten punktet das Tiefziehen. Viele eingesetzte Materialien – insbesondere Aluminium und Stahl – sind gut recycelbar. Der geringe Energieverbrauch pro Bauteil, vor allem bei großen Serien, sowie die Möglichkeit, dünnwandige und dennoch belastbare Komponenten zu fertigen, tragen zu einem insgesamt ressourcenschonenden Produktionsprozess bei. In Zeiten steigenden Umweltbewusstseins und zunehmender Anforderungen an die Ökobilanz industrieller Produkte kann dies ein wichtiges Argument bei der Technologieentscheidung sein.
Damit wird deutlich: Tiefziehen ist nicht nur ein klassisches, sondern auch ein hochmodernes Verfahren, das sich flexibel an neue Anforderungen anpassen lässt. Es kombiniert Präzision mit Effizienz, ist kompatibel mit digitalen Systemen und erlaubt die wirtschaftliche Herstellung komplexer Teile aus Metall. Von der Idee bis zum fertigen Produkt steht es für einen ganzheitlich beherrschbaren Prozess, der gleichermaßen technische, wirtschaftliche und ökologische Anforderungen erfüllt.
Der kontinuierliche Fortschritt in der Werkstoff- und Beschichtungstechnik erweitert die Einsatzmöglichkeiten des Tiefziehens zusätzlich. Neue Legierungen mit höherer Festigkeit bei gleichzeitig verbesserter Umformbarkeit ermöglichen Bauteile mit geringerer Wandstärke und damit reduziertem Gewicht – ein klarer Vorteil in Branchen wie der Luftfahrt oder Elektromobilität. Auch die Entwicklung spezieller Blechoberflächen oder Zwischenlagen, die Reibung gezielt beeinflussen, trägt zur Stabilisierung des Prozesses bei. So lassen sich etwa Ziehfalten vermeiden oder kritische Zonen gezielt steuern, ohne die Geometrie des Bauteils ändern zu müssen.
Ein weiterer Innovationsschub kommt aus dem Bereich der intelligenten Werkzeuge. Eingebaute Sensoren messen Kräfte, Temperaturen oder Schmiermittelverteilung direkt am Werkzeug und liefern damit präzise Informationen über den Zustand jedes einzelnen Umformvorgangs. In Kombination mit KI-gestützten Auswertungen lassen sich Regelstrategien entwickeln, die bei Abweichungen sofort eingreifen – etwa durch Anpassung des Niederhalterdrucks oder der Ziehgeschwindigkeit. Solche adaptiven Systeme erhöhen die Prozesssicherheit, reduzieren Ausschuss und verkürzen Anlaufphasen bei Produktwechseln.
Auch die Konstruktion tiefgezogener Bauteile wird zunehmend an digitale Prozesse angepasst. Topologieoptimierung, eine rechnergestützte Methode zur idealen Materialverteilung bei minimalem Gewicht, führt zu Geometrien, die sich optimal auf das Tiefziehverfahren übertragen lassen. Gleichzeitig ermöglichen parametrische CAD-Modelle eine schnelle Anpassung an kundenspezifische Anforderungen oder Designänderungen – ohne die Prozesskette neu aufsetzen zu müssen. Damit gewinnt die Produktentwicklung an Geschwindigkeit und Flexibilität.
Im globalen Wettbewerb zählt vor allem eines: reproduzierbare Qualität bei maximaler Effizienz. Tiefziehen erfüllt diese Anforderungen, wenn Planung, Materialauswahl, Werkzeugtechnik und Prozessführung optimal ineinandergreifen. Unternehmen, die diese Komplexität beherrschen, profitieren von einer Fertigungstechnologie, die sowohl für einfache Gehäuseteile als auch für hochkomplexe Strukturbauteile geeignet ist. Durch Standardisierung und modulare Anlagenkonzepte lassen sich zudem Produktionslinien schnell umrüsten – ein Vorteil in Märkten mit hoher Variantenvielfalt oder kurzen Produktlebenszyklen.
Schließlich bleibt das Tiefziehen trotz aller Automatisierung ein Handwerk mit technischer Tiefe: Die Erfahrung im Umgang mit Werkstoffverhalten, das Feingefühl für Ziehgrenzen, das Verständnis von Werkzeugverschleiß und die Fähigkeit zur Prozessbeurteilung sind nach wie vor entscheidend für den Erfolg. Die Kombination aus menschlicher Expertise und digitaler Steuerung macht den Tiefziehprozess zu einem der vielseitigsten und zukunftsfähigsten Verfahren in der modernen Metallumformung.
Metallbearbeitungsmaschinen
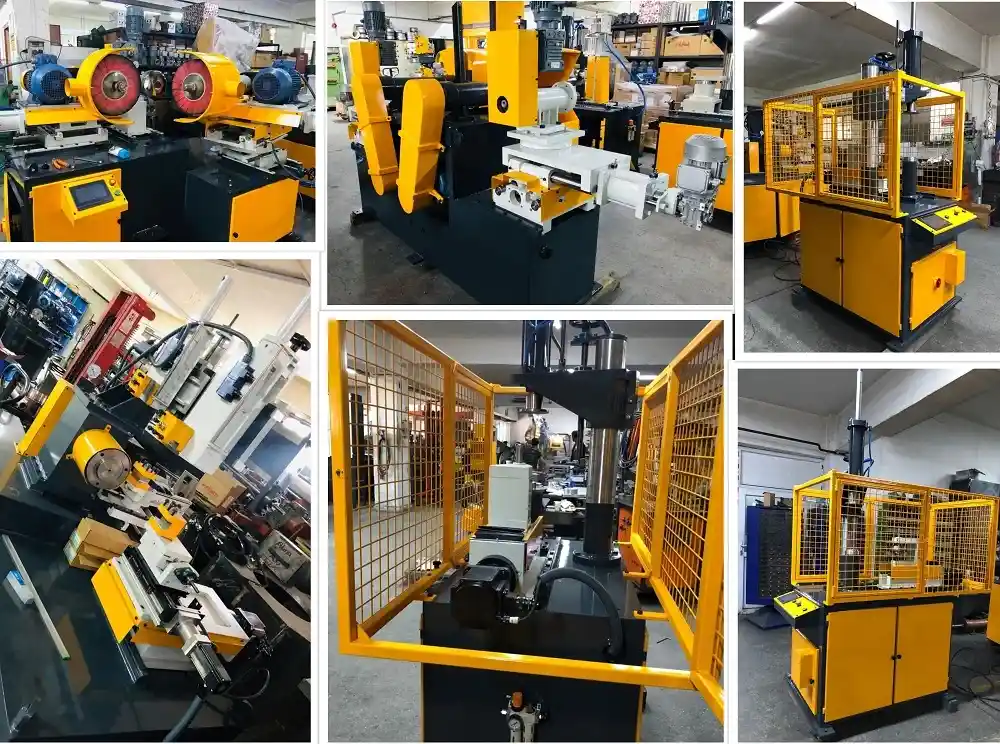
Metallbearbeitungsmaschinen wie Bördel und Beschneide Maschinen, Flanschmaschinen, Beschneide und Bördelmaschinen, Umformtechnik, Rohrbiegemaschinen, Bandsäge für Metall, Hydraulische Horizontalpresse, Kantenschneide-Bördelmaschine, Kantenbördelmaschine, Entgratungsmaschine, Innen- und Außenpoliermaschine für Edelstahltöpfe, Kreisschneidemaschine, Profilbiegemaschine und Rundschweißmaschine
Maßgeschneiderte Skalierung für spezifische Anwendungen
Die automatisierte Herstellung von Behältern, Fässern und Kesseln wird durch unsere Lösungen exakt auf das jeweilige Einsatzgebiet und die gewünschte Ausbringung angepasst. Dabei bieten wir sowohl lineare Lösungen als auch Inselkonzepte an, die eine bedarfsorientierte Automation ermöglichen. Spezielle Kantenvorbereitung für das Laserschweißen sowie wirtschaftliche Rüstkonzepte bis hin zur Fertigung „Just-in-Sequence“ sind Teil unseres Leistungsspektrums. Wir kombinieren Standard- und Sondermaschinen und bieten Ferndiagnose über LAN, WLAN oder GSM an, ergänzt durch umfassende Dokumentation gemäß CE-Richtlinien für die Gesamtanlage.
Unser Konzept
EMS entwickelt und fertigt Maschinen und Anlagen für die automatisierte Herstellung von Behältern in großem Maßstab. Alle Arbeitsschritte, von der Vorbereitung bis zur Fertigung, werden dabei aus einer Hand angeboten. Unsere erprobten Standardkomponenten sind perfekt aufeinander abgestimmt und können nahtlos mit Robotern kombiniert werden, um leistungsfähige Fertigungseinrichtungen zu schaffen.
Flexible Präzisionsfertigung
Unsere Fertigungslinien ermöglichen eine einfache Umstellung auf verschiedene Längen, Durchmesser, Formen und Bearbeitungen durch Programmwechsel. Dabei werden zahlreiche Einzelschritte wie Beschneiden, Formen, Stanzen, Fügen, Montieren, Schweißen und Prüfen automatisch und mit höchster Präzision an die jeweilige Aufgabe angepasst. Besonderes Augenmerk legen wir auf die Kantenvorbereitung für den Schweißprozess, um eine herausragende Prozesssicherheit und minimale Ausschussquoten zu gewährleisten.
Maschinenprogramm für die Metallbearbeitung
Unsere Metallbearbeitungsmaschinen sind:
- Rohrbiegemaschine
- Horizontale Presse
- Bandsäge für Metall
- Profilbiegemaschine
- Tiefziehpresse
- Rundschweißmaschine
- Kantenschneide-Bördelmaschine
- Topf- und Pfannenpoliermaschine
- Poliermaschine für flache Oberflächen
Besteck-Produktionslinie: Eine Besteck-Produktionslinie ist eine Art Maschine, die Besteck in einem kontinuierlichen Prozess herstellt. Es umfasst verschiedene Arten von Maschinen wie den Messerschleifer, den Messerschärfer und den Klingenpolierer.
Kochgeschirr-Herstellungsmaschine: Eine Kochgeschirr-Herstellungsmaschine ist eine Art Maschine, die Kochgeschirr in einem kontinuierlichen Prozess herstellt. Es umfasst verschiedene Arten von Maschinen wie den Topfmacher, den Pfannenmacher und den Wokmacher.
Küchengeschirr-Produktionsmaschine: Eine Küchengeschirr-Produktionsmaschine ist eine Art Maschine, die Küchengeschirr in einem kontinuierlichen Prozess herstellt. Es umfasst verschiedene Arten von Maschinen wie Maschinen zur Herstellung von Teekesseln, Produktionslinien für Besteck, Produktionslinien für Töpfe und Pfannen
Wir entwerfen, fertigen und montieren komplette Produktionslinien für Kochgeschirr, Küchengeschirr, Hotelgeschirr und Besteck sowie einzelne Maschinen für einen bestimmten Zweck