Spanlose Metallumformung umfasst eine Vielzahl von Techniken, die alle darauf abzielen, Metalle ohne den Einsatz von Schneidwerkzeugen oder das Abtragen von Material zu formen. Diese Verfahren werden häufig in der industriellen Produktion eingesetzt, um Komponenten mit hoher Präzision und Effizienz herzustellen. Zu den wichtigsten Methoden der spanlosen Metallumformung gehören Metalldrücken, Drückwalzen, Projizieren, Flanschformen und Spalten. Jede dieser Techniken hat spezifische Anwendungen und Vorteile.
Spanlose Metallumformung
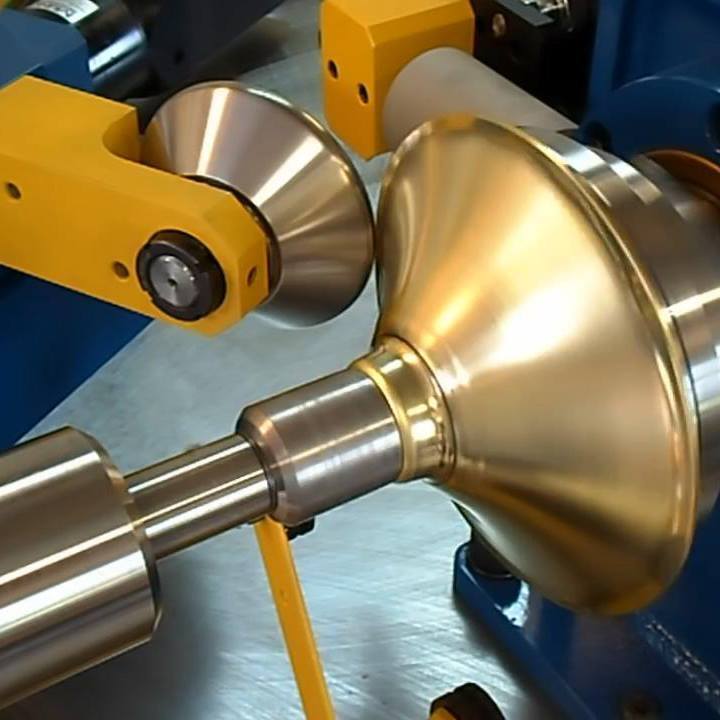
Spanlose Metallumformung, auch bekannt als nicht spanende oder plastische Metallumformung, umfasst eine Vielzahl von Prozessen, bei denen Metallteile durch plastische Verformung geformt werden, ohne dass Material abgetragen wird. Diese Verfahren sind von großer Bedeutung in der industriellen Fertigung, da sie effizient, kostengünstig und materialschonend sind. Hier sind einige der wichtigsten Aspekte und Methoden der spanlosen Metallumformung:
Vorteile der spanlosen Metallumformung
- Materialeinsparung: Da kein Material abgetragen wird, entsteht weniger Abfall.
- Verbesserte mechanische Eigenschaften: Durch die plastische Verformung werden die Werkstücke oft fester und zäher.
- Hohe Effizienz: Viele Verfahren sind schnell und können große Stückzahlen in kurzer Zeit produzieren.
- Vielseitigkeit: Diese Verfahren können auf eine breite Palette von Metallen und Legierungen angewendet werden.
- Wirtschaftlichkeit: Geringere Werkzeug- und Maschinenkosten im Vergleich zu spanenden Verfahren.
Metalldrückmaschinen spielen eine entscheidende Rolle in der modernen Fertigungsindustrie, insbesondere in der spanlosen Metallumformung. Diese Maschinen ermöglichen die Herstellung komplexer, nahtloser Metallteile mit hoher Präzision und Effizienz. Im Gegensatz zu spanabhebenden Verfahren, bei denen Material entfernt wird, um die gewünschte Form zu erzeugen, verformen Metalldrückmaschinen das Metall durch Druck und Bewegung, um die gewünschte Geometrie zu erreichen. Dieser Prozess führt zu einer höheren Materialausnutzung und oft zu verbesserten mechanischen Eigenschaften der fertigen Produkte.
Die spanlose Metallumformung mit Metalldrückmaschinen findet in vielen Industriezweigen Anwendung, darunter die Automobilindustrie, die Luft- und Raumfahrt, die Bauindustrie sowie die Medizin- und Lebensmittelindustrie. Die Fähigkeit, robuste und präzise Metallteile ohne Nähte oder Schweißnähte herzustellen, macht diese Technik besonders wertvoll für Anwendungen, bei denen hohe Festigkeit und Zuverlässigkeit erforderlich sind.
In den letzten Jahrzehnten hat sich die Technologie der Metalldrückmaschinen erheblich weiterentwickelt. Fortschritte in der Steuerungstechnik und der Einführung von CNC-Systemen (Computer Numerical Control) haben die Präzision und Effizienz dieser Maschinen verbessert. Moderne Metalldrückmaschinen sind in der Lage, komplexe Formen mit hoher Wiederholgenauigkeit und geringem Materialverlust zu erzeugen.
Dieser Artikel bietet einen umfassenden Überblick über Metalldrückmaschinen und die spanlose Metallumformung. Er beginnt mit den Grundlagen dieser Technologie, einschließlich ihrer Definition, Prinzipien und historischen Entwicklung. Anschließend werden die verschiedenen Typen von Metalldrückmaschinen detailliert beschrieben, gefolgt von einer Erörterung ihrer vielfältigen Anwendungen in verschiedenen Industriezweigen. Darüber hinaus werden die Materialien untersucht, die mit Metalldrückmaschinen bearbeitet werden können, und die zukünftigen Entwicklungen und Innovationen in diesem Bereich beleuchtet.
Die spanlose Metallumformung mit Metalldrückmaschinen ist eine Schlüsseltechnologie in der modernen Fertigung, die eine hohe Produktqualität, Materialeffizienz und Fertigungsgeschwindigkeit ermöglicht. Durch das Verständnis der Funktionsweise und Anwendungen dieser Maschinen können Hersteller ihre Produktionsprozesse optimieren und hochwertige Metallteile für eine Vielzahl von Anwendungen herstellen.
Grundlagen der spanlosen Metallumformung
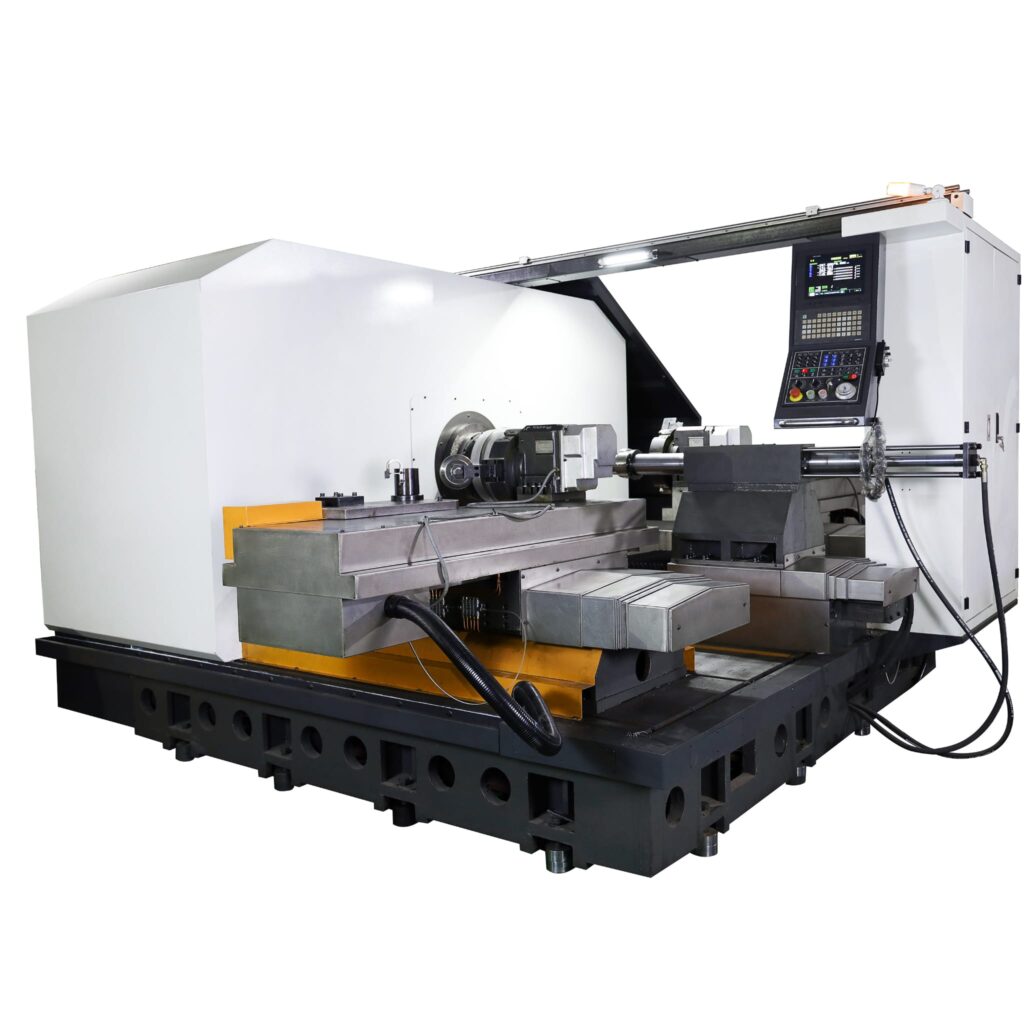
Definition und Prinzipien
Die spanlose Metallumformung ist ein Herstellungsverfahren, bei dem Metall durch plastische Verformung in die gewünschte Form gebracht wird, ohne dass Material entfernt wird. Im Gegensatz zu spanabhebenden Verfahren, bei denen Späne oder Abfallmaterialien entstehen, bleibt bei der spanlosen Umformung das gesamte Ausgangsmaterial erhalten, was zu einer höheren Materialeffizienz führt. Metalldrückmaschinen spielen eine zentrale Rolle in diesem Prozess, indem sie das Metall durch Druck und Bewegung formen.
Das Grundprinzip der spanlosen Metallumformung besteht darin, dass ein Rohling oder Werkstück durch eine rotierende Bewegung und axialen Druck verformt wird. Dabei wird das Metall entlang der Werkzeugachse gedrückt, während es gleichzeitig um seine eigene Achse rotiert. Dieser kombinierte Effekt führt zu einer gleichmäßigen Verteilung der Verformungskräfte und ermöglicht die Herstellung von komplexen, nahtlosen Formen.
Geschichte der spanlosen Metallumformung
Die Geschichte der spanlosen Metallumformung reicht weit zurück und ist eng mit der Entwicklung der Metallverarbeitungstechniken verbunden. Bereits in der Antike wurden grundlegende Techniken der Metallumformung verwendet, um Schmuck, Werkzeuge und Waffen herzustellen. Mit der industriellen Revolution im 18. und 19. Jahrhundert wurden neue Maschinen und Verfahren entwickelt, die die Effizienz und Präzision der Metallumformung erheblich verbesserten.
Ein bedeutender Meilenstein in der Geschichte der spanlosen Metallumformung war die Entwicklung der ersten Metalldrückmaschinen im frühen 20. Jahrhundert. Diese Maschinen ermöglichten die Herstellung von nahtlosen Metallteilen mit hoher Präzision und geringen Materialverlusten. Die Einführung von CNC-Technologien in den 1970er und 1980er Jahren revolutionierte die Metalldrückmaschinen erneut, indem sie eine präzise Steuerung und Automatisierung des Umformprozesses ermöglichten.
Heutzutage sind Metalldrückmaschinen hochentwickelte, computergesteuerte Werkzeuge, die in der Lage sind, komplexe und präzise Metallteile mit hoher Wiederholgenauigkeit herzustellen. Die kontinuierliche Weiterentwicklung dieser Technologie hat dazu beigetragen, dass die spanlose Metallumformung in vielen Industriezweigen weit verbreitet ist und eine Schlüsselrolle in der modernen Fertigung spielt.
Typen von Metalldrückmaschinen
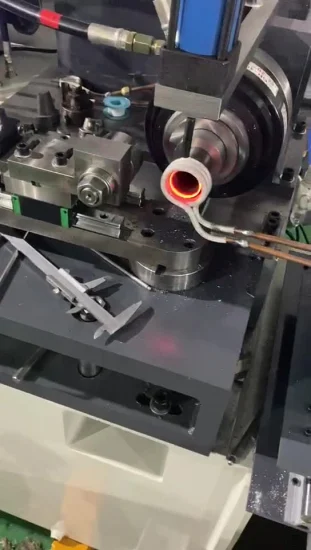
Metalldrückmaschinen sind spezialisierte Werkzeuge, die in der spanlosen Metallumformung verwendet werden, um Metallteile durch Druck und Rotation zu formen. Es gibt verschiedene Typen von Metalldrückmaschinen, die jeweils für spezifische Anwendungen und Anforderungen entwickelt wurden. Im Folgenden werden die wichtigsten Typen von Metalldrückmaschinen beschrieben.
Manuelle Metalldrückmaschinen
Manuelle Metalldrückmaschinen sind die einfachste Form von Metalldrückmaschinen und werden hauptsächlich in handwerklichen und kleinen industriellen Anwendungen verwendet. Diese Maschinen erfordern die manuelle Steuerung durch den Bediener, der das Metall mit Hilfe von Werkzeugen und Hebeln formt.
- Aufbau und Funktionsweise: Manuelle Metalldrückmaschinen bestehen aus einer festen Spindel, auf der das Werkstück montiert wird, und einem Drehwerkzeug, das vom Bediener manuell geführt wird. Der Bediener übt Druck auf das Werkzeug aus, während das Werkstück rotiert, um die gewünschte Form zu erzeugen.
- Anwendungen: Diese Maschinen werden häufig in kleinen Werkstätten und bei der Herstellung von Einzelstücken oder Kleinserien verwendet. Typische Anwendungen umfassen die Herstellung von Lampenschirmen, Musikinstrumenten und dekorativen Metallobjekten.
- Vorteile und Nachteile: Manuelle Metalldrückmaschinen sind kostengünstig und flexibel, erfordern jedoch ein hohes Maß an Geschick und Erfahrung des Bedieners. Die Produktivität und Präzision sind im Vergleich zu automatisierten Maschinen begrenzt.
CNC-Metalldrückmaschinen
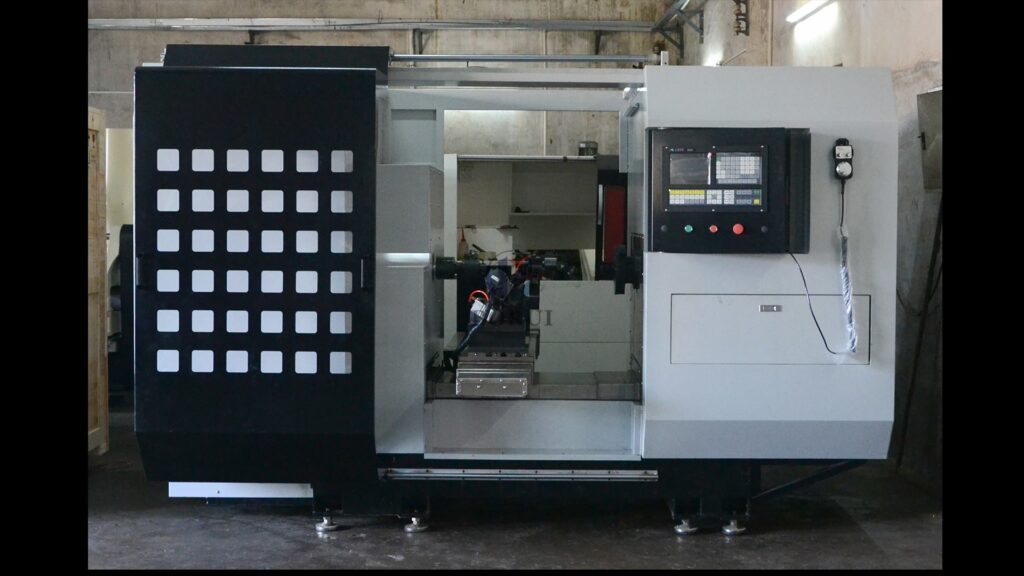
CNC-Metalldrückmaschinen (Computer Numerical Control) sind moderne, computergesteuerte Maschinen, die eine hohe Präzision und Automatisierung bieten. Diese Maschinen sind in der Lage, komplexe Formen mit hoher Wiederholgenauigkeit und Effizienz zu erzeugen.
- Aufbau und Funktionsweise: CNC-Metalldrückmaschinen bestehen aus einer rotierenden Spindel, auf der das Werkstück montiert wird, und mehreren computergesteuerten Werkzeugen, die das Metall formen. Der gesamte Umformprozess wird durch ein CNC-Programm gesteuert, das die Bewegungen und Kräfte der Werkzeuge präzise kontrolliert.
- Anwendungen: CNC-Metalldrückmaschinen finden breite Anwendung in der Automobilindustrie, der Luft- und Raumfahrt, der Bauindustrie und vielen anderen Bereichen, in denen präzise und komplexe Metallteile benötigt werden. Beispiele sind Felgen, Turbinenschaufeln und Strukturbauteile.
- Vorteile und Nachteile: Diese Maschinen bieten hohe Präzision, Effizienz und Automatisierung, was zu einer höheren Produktivität und Qualität führt. Sie sind jedoch teurer in der Anschaffung und erfordern eine spezialisierte Programmierung und Wartung.
Spezial-Metalldrückmaschinen
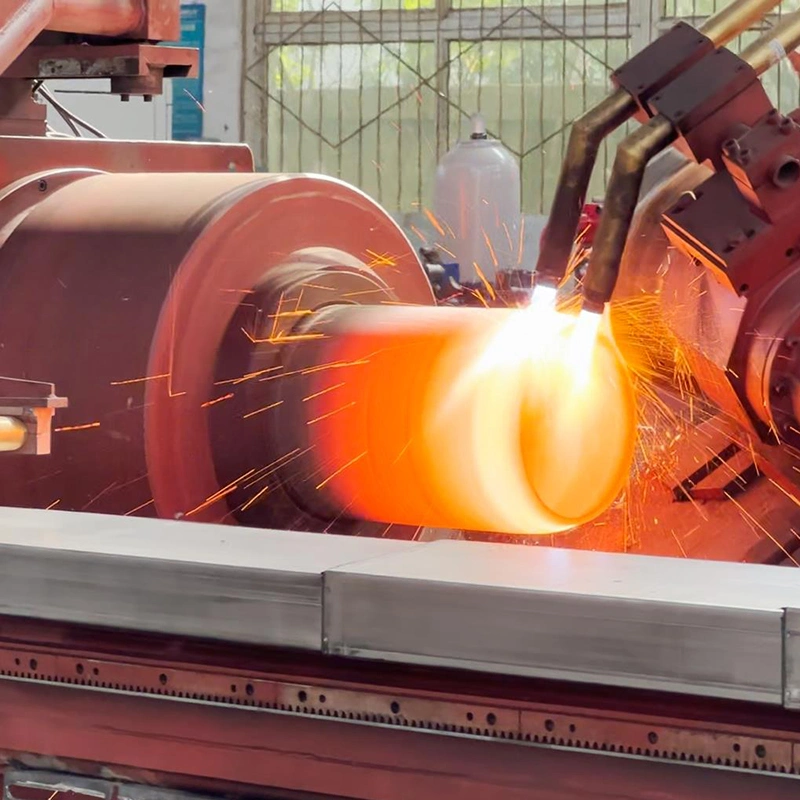
Neben den manuellen und CNC-gesteuerten Metalldrückmaschinen gibt es auch spezialisierte Maschinen, die für spezifische Anwendungen und Anforderungen entwickelt wurden. Diese Maschinen umfassen vertikale Drückmaschinen, Hydroform-Metalldrückmaschinen und Doppelspindel-Metalldrückmaschinen.
- Vertikale Drückmaschinen: Diese Maschinen arbeiten in einer vertikalen Ausrichtung und eignen sich besonders für große und schwere Werkstücke. Sie bieten eine bessere Kontrolle über den Umformprozess und ermöglichen die Bearbeitung komplexer Formen.
- Anwendungen: Vertikale Drückmaschinen werden häufig in der Luft- und Raumfahrt sowie in der Schwerindustrie verwendet, um große Strukturbauteile und Komponenten zu formen.
- Vorteile: Sie bieten eine bessere Ergonomie und Handhabung großer Werkstücke und ermöglichen präzise Umformungen bei hohen Kräften.
- Hydroform-Metalldrückmaschinen: Diese Maschinen verwenden hydraulischen Druck, um das Metall in die gewünschte Form zu bringen. Der Prozess ist besonders schonend für das Material und ermöglicht die Herstellung dünnwandiger und komplexer Bauteile.
- Anwendungen: Hydroform-Metalldrückmaschinen werden in der Automobil- und Luftfahrtindustrie verwendet, um leichte und dennoch starke Bauteile herzustellen, wie z.B. Auspuffanlagen und Strukturbauteile.
- Vorteile: Der Hydroform-Prozess reduziert Materialspannungen und ermöglicht eine hohe Präzision und Qualität der gefertigten Teile.
- Doppelspindel-Metalldrückmaschinen: Diese Maschinen sind mit zwei rotierenden Spindeln ausgestattet, die eine gleichzeitige Bearbeitung von zwei Werkstücken ermöglichen. Dies erhöht die Produktivität und Effizienz erheblich.
- Anwendungen: Doppelspindel-Metalldrückmaschinen werden in der Massenproduktion verwendet, insbesondere bei der Herstellung von symmetrischen Bauteilen wie Rädern und Behältern.
- Vorteile: Sie bieten eine hohe Produktionsgeschwindigkeit und Effizienz, was die Herstellungskosten senkt und die Durchlaufzeiten verkürzt.
Die Vielfalt der Metalldrückmaschinen ermöglicht die Anpassung an verschiedene industrielle Anforderungen und Anwendungen. Von manuellen Maschinen für handwerkliche Arbeiten bis hin zu hochentwickelten CNC- und Spezialmaschinen bieten diese Werkzeuge eine breite Palette von Lösungen für die spanlose Metallumformung.
Anwendungen von Metalldrückmaschinen
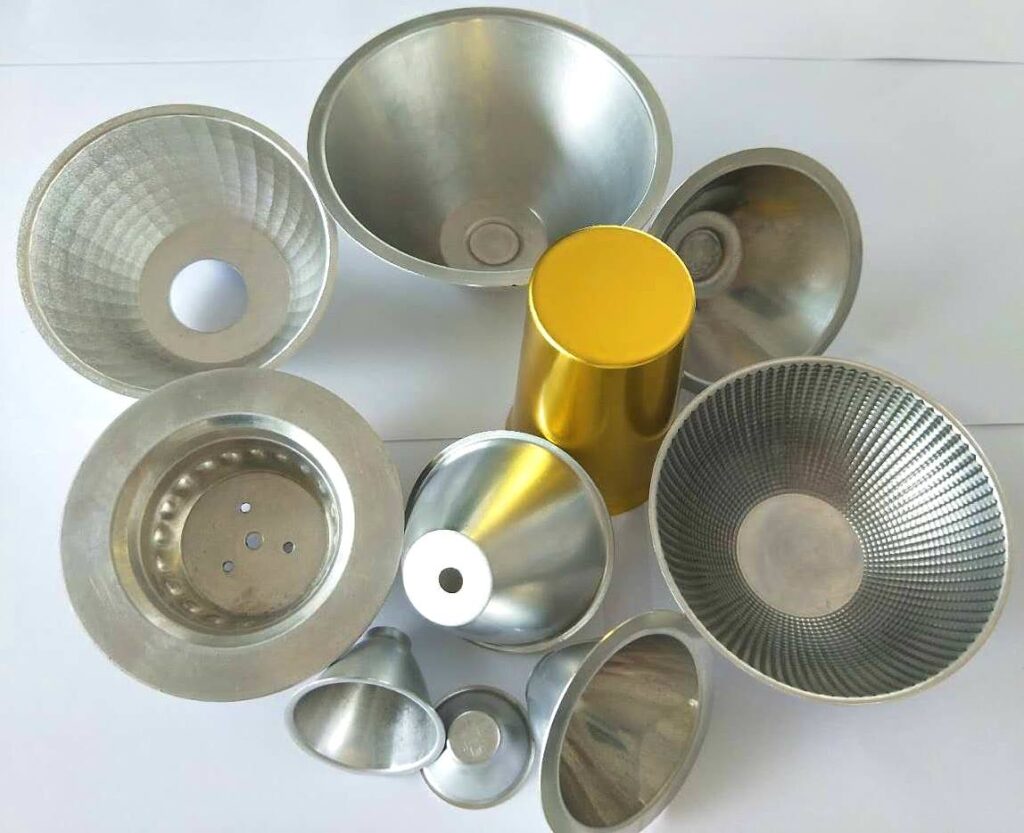
Metalldrückmaschinen sind äußerst vielseitige Werkzeuge, die in einer Vielzahl von Industriezweigen eingesetzt werden. Ihre Fähigkeit, nahtlose, präzise und komplexe Metallteile herzustellen, macht sie besonders wertvoll für die Fertigung. Im Folgenden werden die wichtigsten Anwendungsgebiete von Metalldrückmaschinen detailliert beschrieben.
Automobilindustrie
Die Automobilindustrie ist einer der größten Anwender von Metalldrückmaschinen. Diese Maschinen spielen eine entscheidende Rolle bei der Herstellung von Fahrzeugkomponenten, die sowohl leicht als auch stark sein müssen.
- Felgen und Räder: Metalldrückmaschinen werden häufig zur Herstellung von Leichtmetallfelgen und Rädern verwendet. Der Drückprozess ermöglicht die Herstellung von leichten, aber robusten Felgen, die die Gesamtleistung und den Kraftstoffverbrauch des Fahrzeugs verbessern.
- Auspuffanlagen: Die komplexen Formen von Auspuffkomponenten, einschließlich Schalldämpfer und Abgaskrümmer, werden oft durch Metalldrücken hergestellt. Diese Teile müssen hohen Temperaturen und Korrosion standhalten, was durch den gleichmäßigen Druck der Metalldrückmaschinen erreicht wird.
- Karosserieteile: Bestimmte Karosserieteile, wie Kotflügel und Motorhauben, können durch Drückmaschinen geformt werden, um glatte, nahtlose Oberflächen und präzise Konturen zu erzeugen.
Luft- und Raumfahrt
In der Luft- und Raumfahrtindustrie sind die Anforderungen an die Präzision und Materialeigenschaften besonders hoch. Metalldrückmaschinen ermöglichen die Herstellung von Bauteilen, die diesen strengen Anforderungen gerecht werden.
- Turbinenschaufeln: Turbinenschaufeln, die in Flugzeugtriebwerken verwendet werden, müssen extremen Belastungen und hohen Temperaturen standhalten. Metalldrückmaschinen ermöglichen die Herstellung dieser komplexen Formen mit hoher Präzision.
- Strukturbauteile: Viele Strukturkomponenten eines Flugzeugs, wie Rumpfspanten und Rippen, werden durch Metalldrücken geformt. Diese Teile müssen leicht und dennoch extrem fest sein, um die Sicherheit und Effizienz des Flugzeugs zu gewährleisten.
- Satellitenkomponenten: Die präzise Fertigung von Komponenten für Satelliten und Raumfahrzeuge ist entscheidend für deren Funktion und Zuverlässigkeit. Metalldrückmaschinen werden verwendet, um diese Teile in hoher Qualität und Genauigkeit herzustellen.
Bauindustrie
Auch in der Bauindustrie finden Metalldrückmaschinen vielfältige Anwendungen, insbesondere bei der Herstellung von Bauteilen und Bauzubehör.
- Dach- und Fassadenelemente: Metalldrückmaschinen werden zur Herstellung von Dach- und Fassadenelementen verwendet, die nicht nur ästhetisch ansprechend, sondern auch wetterbeständig und langlebig sein müssen.
- Rohrleitungen und Kanäle: Die Herstellung von Rohrleitungen für Sanitär- und Klimaanlagen erfordert präzise und nahtlose Formen, die durch Metalldrückmaschinen realisiert werden können.
- Befestigungselemente: Schrauben, Bolzen und andere Befestigungselemente, die in der Bauindustrie weit verbreitet sind, werden oft durch Metalldrücken geformt, um eine hohe Festigkeit und Zuverlässigkeit zu gewährleisten.
Medizin- und Lebensmittelindustrie
In der Medizin- und Lebensmittelindustrie sind Hygiene und Präzision von größter Bedeutung. Metalldrückmaschinen ermöglichen die Herstellung von Komponenten, die diesen strengen Anforderungen gerecht werden.
- Medizinische Instrumente: Viele medizinische Instrumente, wie chirurgische Werkzeuge und Implantate, werden durch Metalldrücken hergestellt. Diese Teile müssen extrem präzise und steril sein, um den hohen Standards der Medizintechnik zu entsprechen.
- Lebensmittelverarbeitungsausrüstung: In der Lebensmittelindustrie werden Maschinen und Geräte verwendet, die mit Lebensmitteln in Kontakt kommen. Metalldrückmaschinen formen Komponenten, die leicht zu reinigen und korrosionsbeständig sind, wie Rührwerke und Behälter.
- Verpackungen: Metalldrückmaschinen werden auch zur Herstellung von Verpackungen verwendet, insbesondere von Metalldosen und -behältern, die luftdicht und robust sein müssen.
Weitere Anwendungen
Neben den oben genannten Bereichen gibt es viele weitere Anwendungen für Metalldrückmaschinen in verschiedenen Industriezweigen.
- Elektronikindustrie: In der Elektronikindustrie werden Gehäuse und Abschirmungen für elektronische Bauteile durch Metalldrücken hergestellt. Diese Teile müssen präzise und oft sehr klein sein, um den Anforderungen der Miniaturisierung gerecht zu werden.
- Dekorative Kunst und Schmuck: Künstler und Juweliere nutzen Metalldrückmaschinen, um komplexe und dekorative Metallobjekte zu schaffen. Diese Anwendungen erfordern eine hohe Präzision und Detailgenauigkeit.
- Möbelherstellung: In der Möbelindustrie werden Metalldrückmaschinen verwendet, um dekorative und funktionale Metallteile zu formen, wie Tischbeine, Stuhlgestelle und Leuchten.
Die vielseitigen Anwendungen von Metalldrückmaschinen zeigen, wie wichtig diese Technologie in der modernen Fertigung ist. Ihre Fähigkeit, präzise, komplexe und nahtlose Metallteile effizient zu produzieren, macht sie zu einem unverzichtbaren Werkzeug in vielen Industriezweigen.
Materialien für Metalldrückmaschinen
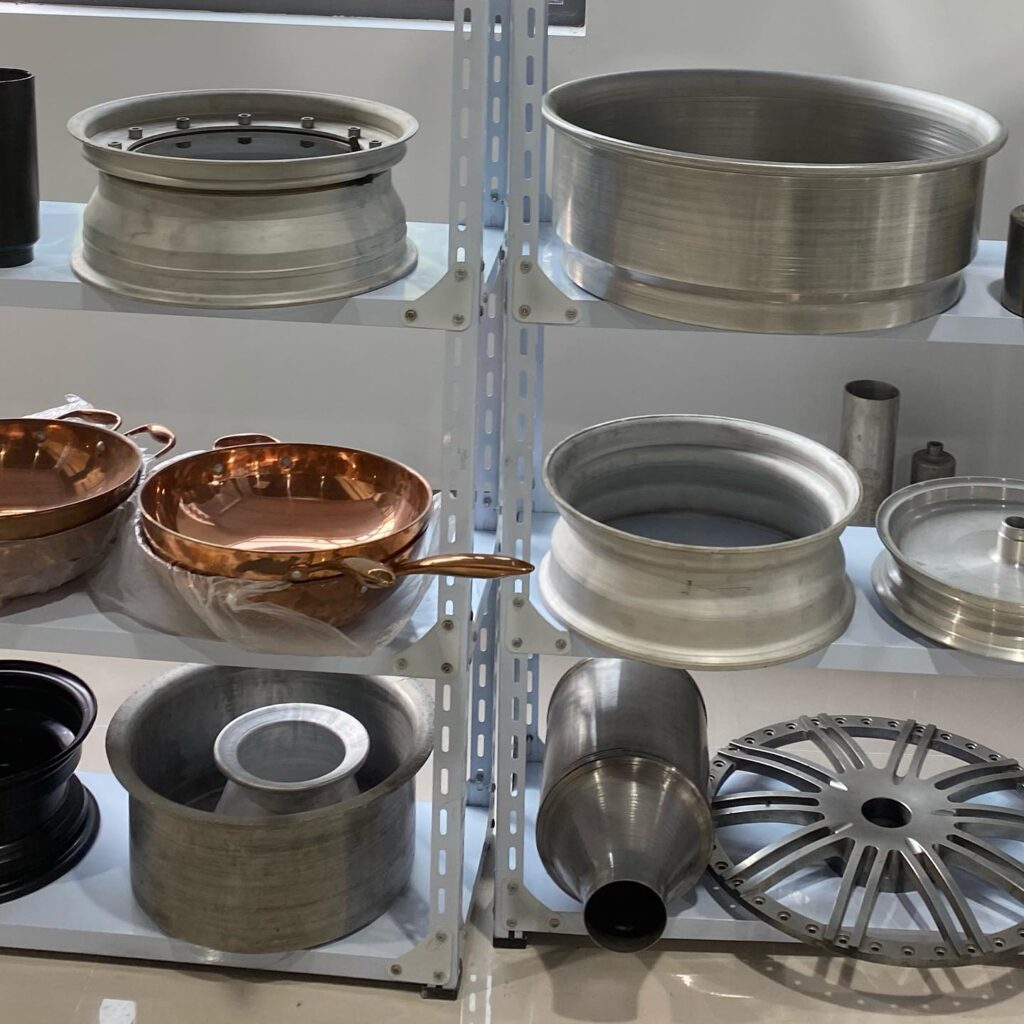
Die Vielfalt der Materialien, die mit Metalldrückmaschinen bearbeitet werden können, ist groß. Die Wahl des Materials hängt von der spezifischen Anwendung, den gewünschten Eigenschaften des Endprodukts und den Anforderungen des Herstellungsprozesses ab. Im Folgenden werden die wichtigsten Materialien und ihre Eigenschaften sowie ihre Verwendung in der spanlosen Metallumformung beschrieben.
Metalle
Metalle sind die am häufigsten verwendeten Materialien in der spanlosen Metallumformung mit Metalldrückmaschinen. Ihre Festigkeit, Formbarkeit und Vielseitigkeit machen sie ideal für zahlreiche industrielle Anwendungen.
- Aluminium
- Eigenschaften: Aluminium ist leicht, korrosionsbeständig und hat eine gute elektrische und thermische Leitfähigkeit. Es ist auch leicht formbar und eignet sich gut für die spanlose Umformung.
- Verwendung: Aluminium wird häufig in der Automobil-, Luft- und Raumfahrt- sowie Elektronikindustrie verwendet. Typische Anwendungen sind Karosserieteile, Felgen, Turbinenschaufeln und Gehäuse für elektronische Geräte.
- Stahl
- Eigenschaften: Stahl ist ein hochfestes Material, das sowohl in seiner reinen Form als auch in verschiedenen Legierungen verwendet wird. Es ist widerstandsfähig gegen Verschleiß und Korrosion und kann in eine Vielzahl von Formen gebracht werden.
- Verwendung: Stahl wird in der Bau-, Automobil- und Maschinenbauindustrie verwendet. Häufige Anwendungen sind Strukturbauteile, Rohre, Befestigungselemente und Karosserieteile.
- Edelstahl
- Eigenschaften: Edelstahl ist eine Stahllegierung, die gegen Korrosion und Oxidation beständig ist. Es ist zudem fest und langlebig.
- Verwendung: Edelstahl findet breite Anwendung in der Lebensmittelverarbeitung, der Medizintechnik und der Chemieindustrie. Typische Anwendungen sind Behälter, Rohrleitungen, chirurgische Instrumente und Küchengeräte.
- Kupfer
- Eigenschaften: Kupfer hat eine ausgezeichnete elektrische und thermische Leitfähigkeit und ist leicht formbar. Es ist jedoch teurer als viele andere Metalle.
- Verwendung: Kupfer wird häufig in der Elektronik- und Energieindustrie verwendet. Anwendungen umfassen elektrische Leitungen, Rohre und Heizelemente.
- Titan
- Eigenschaften: Titan ist extrem leicht, aber sehr fest und korrosionsbeständig. Es ist schwerer zu bearbeiten als viele andere Metalle und erfordert spezielle Werkzeuge und Maschinen.
- Verwendung: Titan wird in der Luft- und Raumfahrt, der Medizintechnik und im Militär verwendet. Typische Anwendungen sind Flugzeugkomponenten, Implantate und Hochleistungsbauteile.
Verbundwerkstoffe
Verbundwerkstoffe kombinieren zwei oder mehr Materialien, um die besten Eigenschaften jedes Materials zu nutzen. Sie sind besonders wichtig in der Luft- und Raumfahrt sowie in der Automobilindustrie.
- Faserverstärkte Kunststoffe (FVK)
- Eigenschaften: FVK bestehen aus einer Polymermatrix, die mit Fasern wie Glas, Kohlenstoff oder Aramid verstärkt ist. Diese Materialien sind leicht, aber extrem fest und steif.
- Verwendung: FVK werden für Bauteile verwendet, die hohe Festigkeit und geringes Gewicht erfordern. Anwendungen sind Flugzeugrümpfe, Automobilkarosserien und Sportgeräte.
- Metallmatrix-Verbundwerkstoffe (MMV)
- Eigenschaften: MMV kombinieren Metall mit keramischen oder metallischen Verstärkungsmaterialien. Diese Werkstoffe bieten eine höhere Festigkeit und Temperaturbeständigkeit als reine Metalle.
- Verwendung: MMV werden in der Raumfahrt und im Militär für Anwendungen verwendet, die extreme Festigkeit und Beständigkeit erfordern. Typische Anwendungen sind Strukturbauteile und Schutzpanzerungen.
Weitere Materialien
Neben den traditionellen Metallen und Verbundwerkstoffen gibt es auch andere Materialien, die mit Metalldrückmaschinen bearbeitet werden können.
- Kunststoffe
- Eigenschaften: Kunststoffe sind leicht formbar und können in einer Vielzahl von Härtegraden hergestellt werden. Sie sind korrosionsbeständig und haben gute isolierende Eigenschaften.
- Verwendung: In der Automobil-, Elektronik- und Konsumgüterindustrie werden Kunststoffe für Gehäuse, Verkleidungen und andere Bauteile verwendet.
- Gummi
- Eigenschaften: Gummi ist elastisch und widerstandsfähig gegen Abrieb und Chemikalien. Er kann in verschiedenen Härtegraden hergestellt werden.
- Verwendung: Gummiteile werden in der Automobilindustrie, im Maschinenbau und in der Bauindustrie verwendet, z.B. für Dichtungen, Reifen und Stoßdämpfer.
- Holz
- Eigenschaften: Holz ist ein natürliches Material, das leicht zu bearbeiten ist und gute mechanische Eigenschaften aufweist.
- Verwendung: In der Möbelindustrie und im Bauwesen werden Metalldrückmaschinen verwendet, um Holz in verschiedene Formen zu pressen, zu biegen und zu laminieren.
Die Fähigkeit von Metalldrückmaschinen, eine Vielzahl von Materialien zu bearbeiten, macht sie zu einem äußerst vielseitigen Werkzeug in der modernen Fertigung. Ihre Präzision und Leistungsfähigkeit ermöglichen die Herstellung von hochqualitativen Produkten aus den unterschiedlichsten Werkstoffen.
Zukunft und Innovationen bei Metalldrückmaschinen
Die Technologie der Metalldrückmaschinen hat sich im Laufe der Jahre stetig weiterentwickelt, um den wachsenden Anforderungen der Industrie gerecht zu werden. Die Zukunft dieser Maschinen verspricht noch mehr Innovationen, die ihre Leistungsfähigkeit, Effizienz und Vielseitigkeit weiter steigern werden. In diesem Abschnitt werfen wir einen Blick auf einige der vielversprechendsten Entwicklungen und Trends in der Metalldrückmaschinentechnologie.
Digitalisierung und Industrie 4.0
Die Integration digitaler Technologien und die Konzepte von Industrie 4.0 revolutionieren die Fertigungsprozesse, einschließlich der Verwendung von Metalldrückmaschinen.
- IoT (Internet der Dinge): Durch die Vernetzung von Metalldrückmaschinen mit IoT-Sensoren können Echtzeitdaten über den Zustand und die Leistung der Maschinen erfasst und analysiert werden. Dies ermöglicht eine vorausschauende Wartung, die Ausfallzeiten reduziert und die Lebensdauer der Maschinen verlängert.
- Big Data und Analytik: Die Analyse großer Datenmengen kann helfen, die Effizienz von Drückprozessen zu optimieren. Durch die Auswertung von Produktionsdaten können Fehlerquellen identifiziert und Prozesse kontinuierlich verbessert werden.
- Künstliche Intelligenz (KI): KI kann verwendet werden, um komplexe Drückprozesse zu steuern und zu überwachen. Algorithmen lernen aus vergangenen Produktionsdaten und passen die Drückparameter in Echtzeit an, um die bestmöglichen Ergebnisse zu erzielen.
Energieeffizienz und Nachhaltigkeit
Energieeffizienz und Nachhaltigkeit sind in der modernen Industrie von großer Bedeutung. Metalldrückmaschinen werden zunehmend so entwickelt, dass sie umweltfreundlicher und energieeffizienter arbeiten.
- Elektrohydraulische Antriebe: Elektrohydraulische Antriebe kombinieren die Vorteile elektrischer und hydraulischer Systeme, um den Energieverbrauch zu reduzieren. Diese Antriebe sind effizienter und leiser als herkömmliche Hydrauliksysteme.
- Regenerative Systeme: Moderne Metalldrückmaschinen sind mit regenerativen Systemen ausgestattet, die überschüssige Energie während des Drückvorgangs zurückgewinnen und wiederverwenden. Dies führt zu einer erheblichen Reduzierung des Energieverbrauchs.
- Biologisch abbaubare Hydraulikflüssigkeiten: Der Einsatz umweltfreundlicher Hydraulikflüssigkeiten, die biologisch abbaubar sind, trägt dazu bei, die Umweltbelastung zu verringern und die Sicherheit am Arbeitsplatz zu erhöhen.
Verbesserte Materialien und Konstruktion
Die kontinuierliche Entwicklung neuer Materialien und Konstruktionsmethoden trägt dazu bei, die Leistungsfähigkeit von Metalldrückmaschinen zu steigern.
- Leichtbauweise: Die Verwendung leichter und hochfester Materialien wie Kohlefaserverbundwerkstoffe in der Konstruktion von Maschinen reduziert das Gesamtgewicht und verbessert die Energieeffizienz.
- 3D-Druck: Der Einsatz von 3D-Drucktechnologien ermöglicht die Herstellung komplexer Bauteile für Metalldrückmaschinen mit hoher Präzision. Dies führt zu einer Reduzierung der Produktionskosten und einer Verkürzung der Entwicklungszeiten.
- Modulare Bauweise: Modulare Maschinensysteme bieten Flexibilität und Anpassungsfähigkeit. Sie ermöglichen es, einzelne Module je nach Bedarf auszutauschen oder zu erweitern, was die Wartung erleichtert und die Lebensdauer der Maschinen verlängert.
Erhöhte Präzision und Kontrolle
Die Anforderungen an die Präzision und Kontrolle von Drückvorgängen steigen stetig, insbesondere in der Luft- und Raumfahrt, der Medizintechnik und der Elektronikindustrie.
- Servo-Hydraulik: Servo-hydraulische Systeme bieten eine präzise Steuerung der Drückbewegungen und ermöglichen eine exakte Positionierung und Kraftregelung. Diese Systeme sind ideal für Anwendungen, die hohe Präzision erfordern.
- Adaptive Steuerungssysteme: Moderne Metalldrückmaschinen sind mit adaptiven Steuerungssystemen ausgestattet, die sich automatisch an wechselnde Bedingungen anpassen. Diese Systeme verbessern die Prozessstabilität und die Qualität der Endprodukte.
- Hochauflösende Sensoren: Der Einsatz hochauflösender Sensoren ermöglicht eine genauere Überwachung und Kontrolle des Drückvorgangs. Diese Sensoren liefern Echtzeitdaten über Druck, Temperatur und Position, die zur Optimierung der Prozesse verwendet werden können.
Erweiterte Anwendungen und Branchen
Die kontinuierliche Weiterentwicklung der Metalldrückmaschinentechnologie eröffnet neue Anwendungsmöglichkeiten und Branchen, die von den Vorteilen dieser Maschinen profitieren können.
- Medizintechnik: Metalldrückmaschinen werden zunehmend in der Medizintechnik eingesetzt, um präzise und komplexe medizinische Geräte und Implantate herzustellen. Die hohe Präzision und Kontrolle dieser Maschinen sind entscheidend für die Herstellung von Produkten mit hohen Qualitätsanforderungen.
- Energieerzeugung: In der Energiebranche werden Metalldrückmaschinen für die Herstellung und Wartung von Windturbinen, Solarpaneelen und anderen erneuerbaren Energieanlagen verwendet. Die Fähigkeit, große und komplexe Strukturen zu bearbeiten, ist ein wesentlicher Vorteil.
- Lebensmittelverarbeitung: In der Lebensmittelindustrie finden Metalldrückmaschinen Anwendung bei der Verarbeitung und Verpackung von Lebensmitteln. Sie ermöglichen eine effiziente und hygienische Verarbeitung, die den hohen Standards der Lebensmittelbranche entspricht.
Die Zukunft der Metalldrückmaschinentechnologie verspricht spannende Entwicklungen und Innovationen, die ihre Leistungsfähigkeit und Vielseitigkeit weiter steigern werden. Mit der Integration digitaler Technologien, der Verbesserung der Energieeffizienz, der Verwendung neuer Materialien und der Erweiterung der Anwendungsbereiche werden Metalldrückmaschinen auch in Zukunft eine Schlüsselrolle in der industriellen Fertigung spielen.
Wichtige Methoden der spanlosen Metallumformung
Die spanlose Metallumformung ist ein wesentlicher Bestandteil der modernen Fertigungstechnik. Im Gegensatz zu spanenden Verfahren, bei denen Material durch Schneiden, Bohren oder Fräsen entfernt wird, erfolgt die Formgebung bei spanlosen Umformverfahren durch plastische Verformung des Materials. Dies bedeutet, dass das Ausgangsmaterial – in der Regel Metall – in die gewünschte Form gebracht wird, ohne dass dabei Späne oder Abfälle entstehen.
Die Technik der spanlosen Umformung hat sich im Laufe der Jahrhunderte entwickelt und optimiert, und sie spielt heute eine zentrale Rolle in zahlreichen Industriezweigen. Besonders in der Automobilindustrie, der Luft- und Raumfahrt, der Medizintechnik und der Elektronikindustrie sind spanlose Umformverfahren unverzichtbar. Durch die Möglichkeit, hochpräzise und komplexe Formen zu erzeugen, die gleichzeitig eine hohe Festigkeit und Materialeffizienz aufweisen, tragen diese Verfahren wesentlich zur wirtschaftlichen und technischen Leistungsfähigkeit moderner Produktionsprozesse bei.
1.2 Historische Entwicklung der Metallumformungstechniken
Die Kunst der Metallumformung reicht bis in die Antike zurück. Bereits in frühen Zivilisationen wurden Metalle wie Kupfer, Bronze und Eisen durch einfache Hammertechniken in Werkzeuge, Waffen und Schmuckstücke umgeformt. Mit der Zeit entwickelten sich immer komplexere Verfahren, die es ermöglichten, Metalle präziser und effizienter zu formen.
Im Mittelalter führte die Weiterentwicklung der Schmiedetechniken zu einer zunehmenden Spezialisierung und Perfektionierung der Metallbearbeitung. Besonders in Europa entstanden Zentren der Metallverarbeitung, die für ihre hochwertigen Produkte bekannt wurden. Die industrielle Revolution im 18. und 19. Jahrhundert brachte dann entscheidende Fortschritte: Mit der Einführung von Walzwerken, Pressen und anderen Maschinen konnte die Metallumformung erstmals in großem Maßstab durchgeführt werden.
Ein entscheidender Durchbruch in der spanlosen Metallumformung gelang im 20. Jahrhundert mit der Entwicklung von Verfahren wie dem Metalldrücken und Drückwalzen. Diese Technologien ermöglichten es, komplexe und hochpräzise Teile herzustellen, die zuvor nur schwer oder gar nicht realisierbar waren. Heute gehören diese Verfahren zu den fortschrittlichsten Methoden der Metallumformung und spielen eine Schlüsselrolle in der modernen Industrie.
1.3 Bedeutung und Anwendungen der spanlosen Metallumformung in der Industrie
Die spanlose Metallumformung ist aus der industriellen Fertigung nicht mehr wegzudenken. Ihre Bedeutung ergibt sich aus einer Vielzahl von Vorteilen, die sie gegenüber anderen Fertigungsmethoden bietet. Dazu zählen unter anderem:
- Materialeffizienz: Da kein Material entfernt wird, geht bei der spanlosen Umformung kein Rohstoff verloren. Dies führt zu einer höheren Materialausnutzung und geringeren Kosten.
- Hohe Festigkeit: Durch das Umformen wird das Metall in eine neue Struktur gebracht, die oft eine höhere Festigkeit aufweist als das Ausgangsmaterial. Dies ist besonders wichtig in Branchen, die hohe Anforderungen an die mechanischen Eigenschaften der Produkte stellen.
- Präzision und Wiederholbarkeit: Moderne Umformtechniken ermöglichen die Herstellung von Bauteilen mit sehr engen Toleranzen. Dies ist besonders in der Massenproduktion von Bedeutung, wo jede Abweichung hohe Kosten verursachen kann.
- Komplexe Geometrien: Spanlose Umformverfahren wie das Metalldrücken ermöglichen die Herstellung komplexer Bauteile, die mit anderen Methoden nur schwer oder gar nicht realisierbar wären.
Zu den wichtigsten Anwendungsgebieten der spanlosen Metallumformung gehören:
- Automobilindustrie: Hier werden durch Umformverfahren zahlreiche Komponenten wie Karosserieteile, Felgen und Auspuffanlagen hergestellt. Die hohe Festigkeit und Präzision der Bauteile sind entscheidend für die Sicherheit und Leistung der Fahrzeuge.
- Luft- und Raumfahrt: In der Luftfahrtindustrie werden durch spanlose Umformung hochpräzise und leichte Bauteile gefertigt, die extremen Belastungen standhalten müssen. Hierzu zählen beispielsweise Triebwerkskomponenten und Strukturbauteile.
- Medizintechnik: In der Medizintechnik werden durch Metalldrücken und Drückwalzen hochpräzise Teile für medizinische Geräte, Prothesen und Implantate hergestellt. Die hohe Präzision und Qualität dieser Bauteile sind lebenswichtig.
- Bauwesen: Im Bauwesen werden Umformverfahren zur Herstellung von strukturellen Elementen und Fassadenteilen eingesetzt. Die hohe Festigkeit und Langlebigkeit der Bauteile sind entscheidend für die Sicherheit und Lebensdauer von Gebäuden.
Die spanlose Metallumformung stellt somit eine Schlüsseltechnologie dar, die in vielen Industriezweigen unverzichtbar ist. Ihre Bedeutung wird in den kommenden Jahren weiter zunehmen, da die Nachfrage nach hochwertigen, präzisen und kostengünstigen Bauteilen stetig wächst.
2. Grundlagen der spanlosen Metallumformung
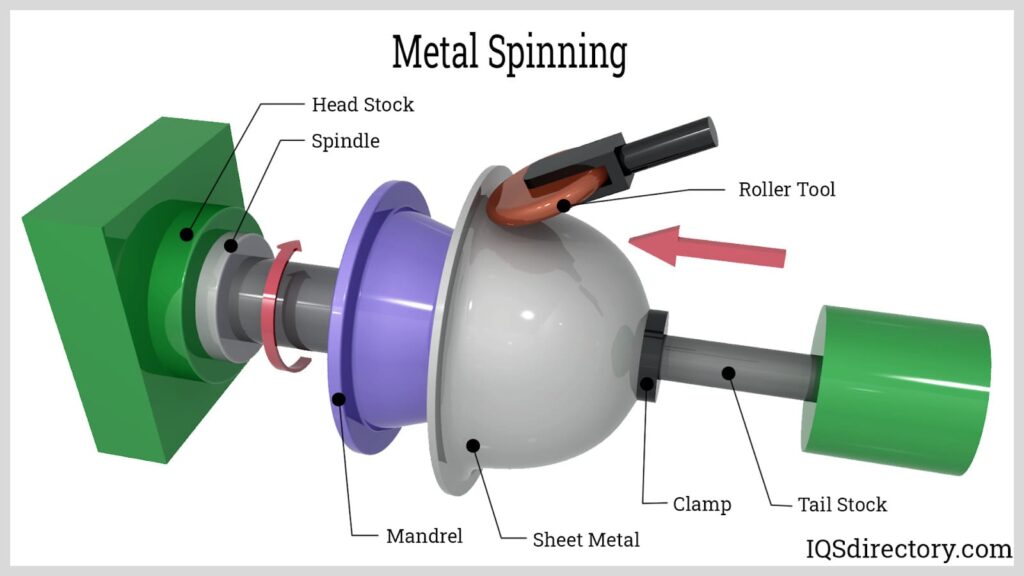
2.1 Definition und Prinzipien der spanlosen Metallumformung
Die spanlose Metallumformung ist ein Fertigungsverfahren, bei dem Metall in die gewünschte Form gebracht wird, ohne dass dabei Material abgetragen wird. Im Gegensatz zu spanenden Verfahren, bei denen das Material durch Drehen, Fräsen oder Bohren mechanisch bearbeitet wird, erfolgt die Formgebung bei der spanlosen Umformung ausschließlich durch plastische Verformung. Dieser Prozess nutzt die Eigenschaft von Metallen, unter Einwirkung von Kräften ihre Form dauerhaft zu ändern, ohne zu brechen oder zu reißen.
Im Kern basiert die spanlose Umformung auf dem Prinzip der Plastizität. Während der elastischen Verformung kehrt das Material nach Entlastung in seine ursprüngliche Form zurück. Bei der plastischen Verformung hingegen überschreiten die aufgebrachten Kräfte die Elastizitätsgrenze des Materials, sodass dieses dauerhaft verformt wird. Dieser Vorgang ist die Grundlage für alle spanlosen Umformtechniken und ermöglicht es, Metallbauteile mit hoher Präzision und Festigkeit herzustellen.
Die spanlose Metallumformung kann in verschiedene Kategorien unterteilt werden, abhängig von der Art der aufgebrachten Kräfte und der erzielten Verformung. Zu den wichtigsten Verfahren zählen das Biegen, Tiefziehen, Drücken, Walzen und Prägen. Jedes dieser Verfahren hat spezifische Anwendungsbereiche und ist für bestimmte Materialien und Geometrien besonders gut geeignet.
2.2 Vergleich mit spanender Bearbeitung
Um die Besonderheiten der spanlosen Metallumformung besser zu verstehen, ist es hilfreich, diese mit spanenden Bearbeitungsverfahren zu vergleichen. Bei der spanenden Bearbeitung wird Material durch Schneiden, Drehen oder Fräsen abgetragen, um die gewünschte Form zu erzeugen. Dies führt zwangsläufig zu einem gewissen Materialverlust in Form von Spänen. Zudem ist die Bearbeitung von komplexen Geometrien oft zeitaufwändig und kostspielig.
Die spanlose Umformung bietet hier deutliche Vorteile:
- Materialeffizienz: Da kein Material entfernt wird, gibt es keinen Abfall, was zu einer effizienteren Materialnutzung führt.
- Produktionsgeschwindigkeit: Spanlose Umformverfahren sind oft schneller, da das Material in einem oder wenigen Arbeitsschritten geformt wird.
- Oberflächenqualität: Durch das Fehlen von Schneidkräften entstehen glattere Oberflächen, was die Notwendigkeit zusätzlicher Nachbearbeitung verringert.
- Wirtschaftlichkeit: Vor allem bei der Massenproduktion sind spanlose Umformverfahren oft kostengünstiger, da sie weniger Materialverschwendung verursachen und schneller durchgeführt werden können.
Jedoch gibt es auch Situationen, in denen spanende Verfahren vorzuziehen sind, insbesondere bei der Herstellung von sehr präzisen oder komplexen Bauteilen, die durch Umformen nicht realisierbar wären. In solchen Fällen können beide Verfahren kombiniert werden, um die Vorteile beider Ansätze zu nutzen.
2.3 Relevante physikalische und mechanische Grundlagen
Die spanlose Metallumformung basiert auf verschiedenen physikalischen und mechanischen Prinzipien, die die Formbarkeit und das Verhalten von Metallen während des Umformprozesses bestimmen. Zu den wichtigsten dieser Prinzipien gehören:
- Elastizität und Plastizität: Wie bereits erwähnt, ist die Unterscheidung zwischen elastischer und plastischer Verformung von zentraler Bedeutung. Während der elastischen Phase kehrt das Material nach Entlastung in seine ursprüngliche Form zurück, während es bei plastischer Verformung dauerhaft in der neuen Form bleibt.
- Fließspannung: Die Fließspannung eines Materials beschreibt die Spannung, bei der es vom elastischen in den plastischen Zustand übergeht. Diese Eigenschaft ist entscheidend für die Bestimmung der erforderlichen Kräfte bei der Umformung und variiert je nach Materialart und Umformtemperatur.
- Kaltumformung vs. Warmumformung: Je nach Umformtemperatur unterscheidet man zwischen Kalt- und Warmumformung. Bei der Kaltumformung erfolgt die Verformung bei Raumtemperatur, was zu einer Erhöhung der Festigkeit des Materials durch Kaltverfestigung führt. Bei der Warmumformung wird das Material auf Temperaturen erhitzt, die oberhalb der Rekristallisationstemperatur liegen, was die Formbarkeit erhöht und die Bildung von Rissen verhindert.
- Reibung: Die Reibung zwischen Werkstück und Werkzeug spielt eine wichtige Rolle, da sie die Umformkräfte beeinflusst und die Oberflächenqualität des Endprodukts bestimmt. Eine geringe Reibung ist in der Regel wünschenswert, um eine gleichmäßige Verformung zu gewährleisten und den Verschleiß der Werkzeuge zu minimieren.
- Verfestigung: Während der Umformung kommt es zur Kaltverfestigung des Materials, d.h., das Metall wird durch die plastische Verformung härter und widerstandsfähiger. Dies ist insbesondere bei der Kaltumformung ein bedeutender Effekt, da es die Eigenschaften des Endprodukts erheblich beeinflusst.
Diese physikalischen und mechanischen Grundlagen sind entscheidend für das Verständnis der spanlosen Umformprozesse und müssen bei der Planung und Durchführung dieser Verfahren berücksichtigt werden.
2.4 Überblick über verschiedene spanlose Umformverfahren
Es gibt eine Vielzahl von spanlosen Umformverfahren, die jeweils spezifische Anwendungen und Vorteile bieten. Im Folgenden werden einige der wichtigsten Verfahren kurz beschrieben:
- Biegen: Beim Biegen wird das Werkstück entlang einer Achse verformt, um eine gekrümmte Form zu erzeugen. Dieses Verfahren wird häufig in der Herstellung von Rohren, Profilen und Blechteilen eingesetzt.
- Tiefziehen: Tiefziehen ist ein Verfahren, bei dem ein Blech in eine Hohlform gezogen wird, um dreidimensionale Strukturen wie Becher, Behälter oder Karosserieteile zu formen. Es ist besonders geeignet für die Herstellung von hohlen, rotationssymmetrischen Teilen.
- Metalldrücken: Beim Metalldrücken wird ein rotierendes Metallblech durch die Einwirkung eines Drückwerkzeugs in eine Form gebracht. Dieses Verfahren ist ideal für die Herstellung von rotationssymmetrischen Bauteilen wie Lampenschirmen, Töpfen und Gehäusen.
- Drückwalzen: Drückwalzen ist eine Erweiterung des Metalldrückens, bei dem das Werkstück zusätzlich gewalzt wird, um eine stärkere Verdichtung und höhere Präzision zu erzielen. Dieses Verfahren wird häufig für die Herstellung von Rohren und anderen zylindrischen Teilen eingesetzt.
- Prägen: Beim Prägen wird das Werkstück durch Druck zwischen zwei Matrizen in die gewünschte Form gebracht. Dieses Verfahren wird häufig zur Herstellung von Münzen, Medaillen und geprägten Blechteilen verwendet.
Jedes dieser Verfahren hat spezifische Vorteile und ist für bestimmte Anwendungen besonders gut geeignet. Die Wahl des richtigen Umformverfahrens hängt von verschiedenen Faktoren ab, einschließlich der Materialeigenschaften, der gewünschten Geometrie und der Produktionsanforderungen.
Ich werde jetzt mit dem Abschnitt über Metalldrücken fortfahren. In diesem Abschnitt wird das Metalldrücken als Umformverfahren im Detail beschrieben. Es umfasst den historischen Hintergrund, technologische Grundlagen, typische Materialien, Maschinentypen und Werkzeuge, Vor- und Nachteile sowie die Anwendungen in verschiedenen Industrien. Dieser Abschnitt wird etwa 3.000 Wörter umfassen.
3. Metalldrücken
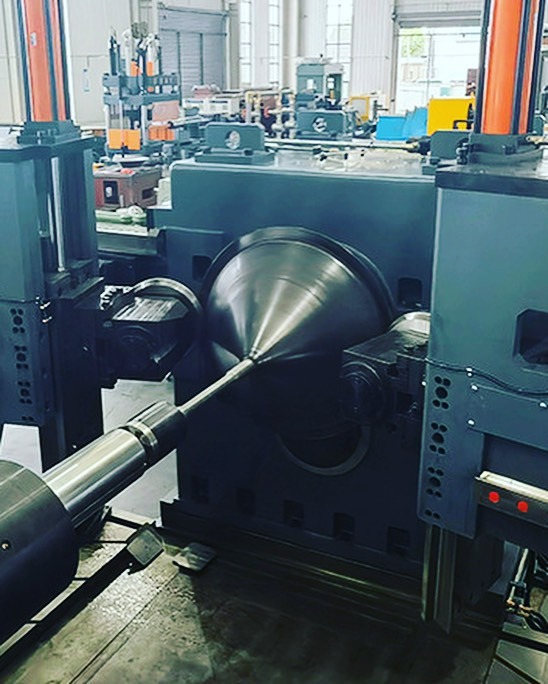
3.1 Detaillierte Beschreibung des Metalldrückens als Umformverfahren
Das Metalldrücken, auch als Drückverfahren oder Drehdrücken bekannt, ist ein spanloses Umformverfahren, bei dem ein rotierendes Metallblech durch ein Werkzeug in eine gewünschte Form gebracht wird. Das Verfahren wird oft zur Herstellung von rotationssymmetrischen Bauteilen verwendet, wie zum Beispiel Lampenschirmen, Töpfen, Gehäusen, Druckbehältern und diversen zylindrischen Komponenten. Es ist besonders geeignet für die Herstellung von Bauteilen mit dünnen Wandstärken und komplexen Konturen, die mit anderen Verfahren nur schwer realisierbar wären.
Der Prozess beginnt mit einem kreisrunden Metallblech, das auf einem Drückdorn montiert wird. Dieser Dorn rotiert mit hoher Geschwindigkeit. Ein Drückwerkzeug, oft als Drückrolle bezeichnet, wird dann manuell oder maschinell gegen das rotierende Werkstück gedrückt, um es allmählich in die gewünschte Form zu bringen. Dabei bewegt sich die Drückrolle entlang des Dorns und drückt das Blech gegen die Form des Dorns. Der Prozess ist in mehreren Durchgängen organisiert, wobei das Werkstück nach jedem Durchgang immer näher an die endgültige Form gebracht wird.
Es gibt zwei Hauptformen des Metalldrückens: das konventionelle Drücken und das Drückwalzen (eine erweiterte Form des Drückens, die in einem späteren Abschnitt detaillierter behandelt wird). Während das konventionelle Drücken hauptsächlich zur Herstellung von Bauteilen mit gleichmäßiger Wandstärke verwendet wird, ermöglicht das Drückwalzen eine gezielte Veränderung der Wandstärke des Werkstücks während des Umformprozesses.
3.2 Historischer Hintergrund und Entwicklung des Metalldrückens
Das Metalldrücken hat eine lange Geschichte, die bis in das Mittelalter zurückreicht. In Europa wurde das Verfahren zunächst von Handwerkern angewendet, um metallische Gegenstände wie Schalen, Vasen und andere Haushaltswaren herzustellen. Diese frühen Formen des Metalldrückens wurden manuell ausgeführt, wobei der Handwerker das Metallblech gegen eine hölzerne oder metallene Form drückte.
Im 18. und 19. Jahrhundert führte die industrielle Revolution zu bedeutenden Fortschritten in der Fertigungstechnologie, einschließlich der Entwicklung von Maschinen für das Metalldrücken. Diese Maschinen ermöglichten es, den Prozess zu automatisieren und eine größere Präzision und Wiederholbarkeit zu erreichen. Die Einführung von Dampf- und später Elektromaschinen trieb diese Entwicklung weiter voran, sodass das Metalldrücken zu einem weit verbreiteten industriellen Verfahren wurde.
Im 20. Jahrhundert führte die Weiterentwicklung der Metallurgie und der Maschinenbauindustrie zur Verfeinerung des Metalldrückverfahrens. Neue Werkzeuge und Maschinen, wie z.B. CNC-gesteuerte Drückmaschinen, ermöglichten eine noch präzisere und effizientere Fertigung. Diese Entwicklungen machten das Metalldrücken zu einem unverzichtbaren Verfahren in vielen Industrien, insbesondere in der Automobil-, Luft- und Raumfahrtindustrie.
3.3 Technologische Grundlagen und physikalische Prinzipien
Das Metalldrücken beruht auf mehreren physikalischen und technologischen Prinzipien, die sicherstellen, dass das Werkstück während des Umformprozesses die gewünschte Form annimmt und gleichzeitig seine strukturelle Integrität bewahrt. Zu den wichtigsten dieser Prinzipien gehören:
- Rotationssymmetrie: Da das Werkstück während des Drückprozesses rotiert, ist es wichtig, dass das Endprodukt rotationssymmetrisch ist. Dies bedeutet, dass das Werkstück über seine Achse hinweg eine gleichmäßige Form hat, was typisch für zylindrische oder konische Teile ist.
- Elastizitätsgrenze und Plastizität: Das Metalldrücken nutzt die Eigenschaft des Metalls, unter kontrollierter Kraft plastisch verformbar zu sein. Die Drückrolle übt eine Kraft aus, die das Metall über seine Elastizitätsgrenze hinaus verformt, sodass es dauerhaft in der neuen Form bleibt.
- Schrittweise Verformung: Der Drückprozess erfolgt in mehreren Schritten oder Durchgängen, wobei das Werkstück nach und nach in die gewünschte Form gebracht wird. Diese schrittweise Vorgehensweise ist notwendig, um das Risiko von Rissen oder ungleichmäßigen Verformungen zu minimieren.
- Reibung und Wärmeentwicklung: Während des Drückens entsteht durch die Reibung zwischen dem Werkstück und der Drückrolle Wärme. Diese Wärme kann die Formbarkeit des Metalls verbessern, indem sie lokale Materialerwärmung verursacht, was das Metall weicher und leichter verformbar macht. Gleichzeitig muss jedoch darauf geachtet werden, dass die Reibung nicht zu hoch ist, um übermäßigen Verschleiß an den Werkzeugen zu vermeiden.
- Materialfluss: Während des Drückens bewegt sich das Material des Werkstücks entlang des Dorns und wird in Richtung der Drückrolle gedrückt. Der kontrollierte Materialfluss ist entscheidend für die gleichmäßige Wandstärke und die endgültige Form des Werkstücks.
3.4 Materialien, die typischerweise beim Metalldrücken verwendet werden
Das Metalldrücken kann auf einer Vielzahl von Metallen angewendet werden, allerdings eignen sich einige Materialien besser für dieses Verfahren als andere. Typische Materialien, die für das Metalldrücken verwendet werden, sind:
- Aluminium: Aluminium ist aufgrund seiner guten Formbarkeit, geringen Dichte und Korrosionsbeständigkeit eines der am häufigsten verwendeten Metalle im Metalldrücken. Es lässt sich leicht in komplexe Formen bringen und wird häufig in der Luftfahrtindustrie und im Fahrzeugbau eingesetzt.
- Kupfer: Kupfer ist ein weiteres weit verbreitetes Material im Metalldrücken. Es ist ebenfalls sehr formbar und zeichnet sich durch eine gute Wärmeleitfähigkeit und elektrische Leitfähigkeit aus. Kupferteile, die durch Metalldrücken hergestellt werden, finden Anwendung in der Elektronik- und Heizungsindustrie.
- Edelstahl: Edelstahl wird häufig verwendet, wenn eine hohe Korrosionsbeständigkeit und Festigkeit erforderlich sind. Obwohl Edelstahl eine höhere Fließspannung als Aluminium oder Kupfer aufweist, kann er dennoch erfolgreich durch Metalldrücken in die gewünschte Form gebracht werden. Edelstahlteile werden häufig in der Lebensmittelverarbeitung, Medizintechnik und chemischen Industrie eingesetzt.
- Titan: Titan und Titanlegierungen werden für Anwendungen verwendet, die eine hohe Festigkeit und geringes Gewicht erfordern. Diese Materialien sind besonders schwierig zu verformen und erfordern spezielle Drücktechniken sowie Werkzeuge. Titan wird häufig in der Luft- und Raumfahrtindustrie sowie in der Medizintechnik verwendet.
- Messing: Messing, eine Legierung aus Kupfer und Zink, ist ein weiteres häufig verwendetes Material beim Metalldrücken. Es ist leicht formbar und korrosionsbeständig, was es zu einer beliebten Wahl für dekorative Anwendungen, Armaturen und Musikinstrumente macht.
Die Wahl des Materials hängt von der spezifischen Anwendung, den gewünschten Eigenschaften des Endprodukts und den Anforderungen des Umformprozesses ab. Jedes Material bringt seine eigenen Herausforderungen und Vorteile mit sich, die bei der Planung des Drückverfahrens berücksichtigt werden müssen.
3.5 Maschinentypen und Werkzeuge, die beim Metalldrücken zum Einsatz kommen
Die Maschinen und Werkzeuge, die beim Metalldrücken verwendet werden, sind entscheidend für die Qualität und Präzision des Endprodukts. Es gibt verschiedene Arten von Drückmaschinen, die für unterschiedliche Anwendungen und Materialien geeignet sind:
- Manuelle Drückmaschinen: Diese Maschinen werden hauptsächlich für kleinere Produktionsserien oder für das Prototyping verwendet. Der Bediener führt das Drückwerkzeug manuell entlang des rotierenden Werkstücks, was eine hohe Flexibilität, aber auch eine gewisse Geschicklichkeit erfordert.
- Halbautomatische Drückmaschinen: Diese Maschinen kombinieren manuelle Steuerung mit einigen automatisierten Funktionen. Sie sind ideal für mittelgroße Produktionsserien und bieten eine gute Balance zwischen Flexibilität und Effizienz.
- CNC-Drückmaschinen: CNC- (Computer Numerical Control) gesteuerte Drückmaschinen sind hochpräzise und vollautomatisierte Maschinen, die für die Massenproduktion von komplexen Bauteilen verwendet werden. Die CNC-Steuerung ermöglicht die Programmierung komplexer Bewegungen und die präzise Steuerung der Drückkräfte. Diese Maschinen sind ideal für Anwendungen, bei denen hohe Präzision und Wiederholbarkeit erforderlich sind.
- Drückrollen und Werkzeuge: Die Drückrolle ist das wichtigste Werkzeug im Metalldrückprozess. Sie besteht in der Regel aus gehärtetem Stahl oder Hartmetall, um den hohen Kräften und der Reibung während des Umformens standzuhalten. Je nach Anwendung können auch spezielle Rollenformen oder -profile verwendet werden, um spezifische Geometrien zu erzeugen.
- Dorne: Der Dorn ist das Gegenstück zur Drückrolle und dient als Form, um die das Werkstück während des Drückens geformt wird. Dorne können aus verschiedenen Materialien wie Stahl, Aluminium oder Kunststoff bestehen, abhängig von der Anwendung und den Anforderungen an das Endprodukt.
- Spannfutter: Das Spannfutter hält das Werkstück während des Drückprozesses sicher in Position. Es muss stark genug sein, um das Werkstück festzuhalten, ohne es zu verformen.
3.6 Vor- und Nachteile des Metalldrückens im Vergleich zu anderen Umformtechniken
Wie bei jedem Fertigungsverfahren gibt es auch beim Metalldrücken spezifische Vor- und Nachteile, die bei der Entscheidung für oder gegen dieses Verfahren berücksichtigt werden müssen.
Vorteile:
- Materialeinsparung: Das Metalldrücken ist ein sehr materialeffizientes Verfahren, da es wenig oder keinen Materialabfall erzeugt. Dies führt zu geringeren Materialkosten und einer höheren Ausnutzung des Rohmaterials.
- Hohe Präzision: Moderne Drückmaschinen, insbesondere CNC-gesteuerte, ermöglichen die Herstellung von Bauteilen mit sehr engen Toleranzen und hoher Wiederholgenauigkeit.
- Flexibilität: Das Verfahren eignet sich hervorragend für die Herstellung von Prototypen, kleinen Serien und individuellen Bauteilen. Es ermöglicht schnelle Anpassungen und Änderungen am Design, ohne dass teure Werkzeuge neu hergestellt werden müssen.
- Starke und leichte Bauteile: Die durch das Drücken erzeugten Bauteile haben oft eine hohe Festigkeit und eine gleichmäßige Wandstärke, was sie besonders leicht und dennoch robust macht.
- Geeignet für komplexe Geometrien: Das Metalldrücken ermöglicht die Herstellung von Bauteilen mit komplexen, rotationssymmetrischen Formen, die mit anderen Umformtechniken schwer herzustellen wären.
Nachteile:
- Beschränkte Geometrien: Da das Metalldrücken auf der Rotationssymmetrie basiert, ist es nicht geeignet für Bauteile, die asymmetrische oder nicht-zylindrische Formen aufweisen.
- Materialabhängigkeit: Nicht alle Materialien eignen sich gleich gut für das Metalldrücken. Hochfeste und schwer verformbare Materialien wie einige Stahlsorten oder Titanlegierungen erfordern spezialisierte Ausrüstung und Werkzeuge.
- Eingeschränkte Wandstärken: Während das Metalldrücken hervorragende Ergebnisse bei dünnwandigen Bauteilen liefert, kann es bei dickeren Wandstärken zu Schwierigkeiten kommen, insbesondere in Bezug auf die Gleichmäßigkeit der Wandstärke.
3.7 Anwendungen und Industrien, in denen Metalldrücken genutzt wird
Das Metalldrücken findet in vielen Industrien Anwendung, die auf die Herstellung von präzisen und hochwertigen Bauteilen angewiesen sind. Zu den wichtigsten Anwendungsgebieten gehören:
- Automobilindustrie: Hier wird das Metalldrücken zur Herstellung von Teilen wie Radkappen, Felgen, Abdeckungen und Auspuffanlagen verwendet. Die hohe Festigkeit und Präzision der Bauteile sind entscheidend für die Leistung und Sicherheit von Fahrzeugen.
- Luft- und Raumfahrt: In der Luftfahrtindustrie wird das Metalldrücken zur Herstellung von komplexen und leichten Komponenten verwendet, die extremen Belastungen standhalten müssen. Beispiele sind Triebwerkskomponenten, Luftleitschaufeln und Strukturbauteile.
- Medizintechnik: In der Medizintechnik werden durch Metalldrücken präzise Teile für medizinische Geräte, Prothesen und Implantate hergestellt. Diese Bauteile müssen höchsten Qualitätsstandards entsprechen, da sie oft in lebenswichtigen Anwendungen zum Einsatz kommen.
- Haushaltswaren: Metalldrücken wird zur Herstellung von Haushaltswaren wie Töpfen, Pfannen, Lampenschirmen und dekorativen Metallgegenständen eingesetzt. Die Flexibilität des Verfahrens ermöglicht die Herstellung von Bauteilen in verschiedenen Formen und Größen.
- Elektronikindustrie: In der Elektronikindustrie wird das Metalldrücken zur Herstellung von Gehäusen, Abschirmungen und anderen Bauteilen verwendet, die präzise Toleranzen und eine hohe Oberflächenqualität erfordern.
Das Metalldrücken ist somit ein vielseitiges Verfahren, das in vielen Industriezweigen unverzichtbar ist. Es bietet die Möglichkeit, komplexe und hochwertige Bauteile effizient und kostengünstig herzustellen.
4. Drückwalzen
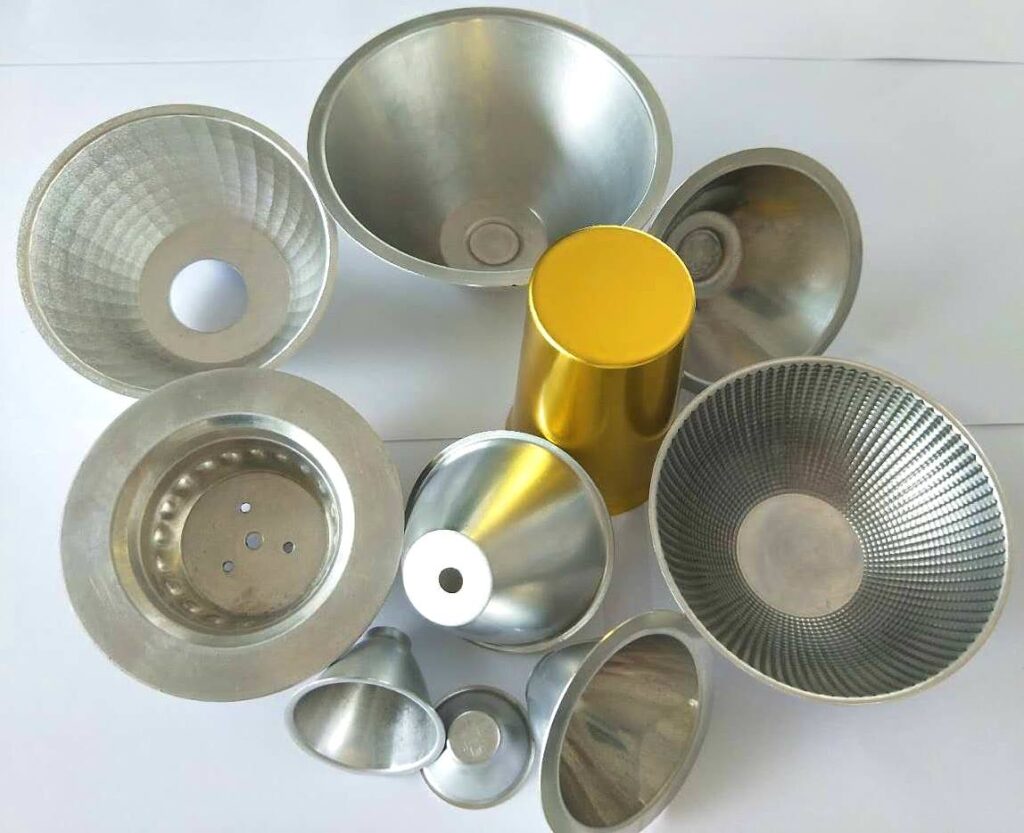
4.1 Definition und Abgrenzung von Drückwalzen und Metalldrücken
Das Drückwalzen, auch als Walzdrücken bekannt, ist eine Weiterentwicklung des Metalldrückens und ein fortschrittliches spanloses Umformverfahren, bei dem das Werkstück während des Drückprozesses zusätzlich gewalzt wird. Während beim klassischen Metalldrücken die Wandstärke des Werkstücks in der Regel konstant bleibt, ermöglicht das Drückwalzen eine gezielte Veränderung der Wandstärke. Dies wird erreicht, indem das rotierende Werkstück nicht nur durch eine Drückrolle in die gewünschte Form gebracht, sondern gleichzeitig auch durch Walzrollen verdichtet wird.
Diese zusätzliche Walzkomponente unterscheidet das Drückwalzen vom klassischen Metalldrücken und erlaubt die Herstellung von Bauteilen mit komplexen Wandstärkenprofilen, die sowohl sehr dünn als auch dick sein können. Dadurch können beispielsweise Hohlkörper mit verstärkten Enden oder variablen Wandstärken entlang ihrer Länge produziert werden, was in vielen Anwendungen, wie in der Luft- und Raumfahrt, von großem Vorteil ist.
4.2 Technologische Grundlagen und Funktionsweise des Drückwalzens
Das Drückwalzen kombiniert zwei wesentliche Umformprinzipien: das klassische Drücken und das Walzen. Der Prozess beginnt ähnlich wie beim Metalldrücken, indem ein zylindrisches oder konisches Werkstück auf einem rotierenden Dorn montiert wird. Eine Drückrolle wird dann gegen das Werkstück gedrückt, um es in die gewünschte Form zu bringen.
Im nächsten Schritt kommen die Walzrollen zum Einsatz. Diese Walzrollen üben Druck auf das Werkstück aus und verformen es weiter, indem sie das Material gezielt verdichten und die Wandstärke anpassen. Die Walzrollen bewegen sich entlang der Oberfläche des Werkstücks, wobei sie eine gleichmäßige oder variierende Wandstärke erzeugen können, abhängig von den spezifischen Anforderungen des Bauteils.
Die Bewegung der Walzrollen ist genau kontrolliert, um sicherzustellen, dass die gewünschten Wandstärkenprofile erreicht werden. Diese Präzision ist besonders wichtig bei der Herstellung von Bauteilen, die hohen mechanischen Belastungen standhalten müssen, wie zum Beispiel in der Luft- und Raumfahrt oder im Automobilbau.
4.3 Vergleich mit anderen Walzverfahren (z.B. Längswalzen, Querwalzen)
Das Drückwalzen unterscheidet sich von anderen Walzverfahren wie dem Längswalzen und Querwalzen durch seine spezifische Anwendung und die Kombination mit dem Drückprozess. Während Längswalzen und Querwalzen typischerweise zur Herstellung von flachen Blechen, Platten oder langen Profilen verwendet werden, zielt das Drückwalzen auf die Umformung rotationssymmetrischer Bauteile ab.
- Längswalzen: Hierbei wird das Metallstück zwischen zwei Walzenpaaren in Längsrichtung durchgepresst, um die Dicke des Materials zu verringern und es gleichzeitig zu verlängern. Dieses Verfahren wird häufig für die Herstellung von Blech, Bandstahl und Profilen verwendet.
- Querwalzen: Beim Querwalzen wird das Werkstück quer zur Walzrichtung verformt, was zur Reduzierung des Durchmessers und zur Verlängerung des Werkstücks führt. Diese Technik wird hauptsächlich für die Herstellung von Rohren, Wellen und Ringen eingesetzt.
Im Vergleich dazu bietet das Drückwalzen eine höhere Flexibilität bei der Gestaltung von Wandstärkenprofilen in rotationssymmetrischen Bauteilen und ermöglicht eine präzisere Kontrolle der Materialverteilung. Während Längs- und Querwalzen eher für großflächige oder langgestreckte Produkte eingesetzt werden, ist das Drückwalzen speziell für die Herstellung komplexer Hohlkörper und rotationssymmetrischer Bauteile optimiert.
4.4 Materialien und Produkte, die durch Drückwalzen hergestellt werden
Das Drückwalzen eignet sich für eine Vielzahl von Metallen und Legierungen, die eine hohe Formbarkeit aufweisen und für die Produktion von Bauteilen mit variabler Wandstärke erforderlich sind. Zu den typischen Materialien, die im Drückwalzen eingesetzt werden, gehören:
- Aluminium und Aluminiumlegierungen: Aufgrund ihrer leichten Verformbarkeit und ihres geringen Gewichts sind Aluminium und seine Legierungen häufig verwendete Materialien im Drückwalzen. Sie werden insbesondere in der Luft- und Raumfahrtindustrie, der Automobilindustrie und im Bauwesen verwendet.
- Edelstahl: Edelstahl ist ein bevorzugtes Material, wenn hohe Festigkeit, Korrosionsbeständigkeit und Langlebigkeit gefragt sind. Es wird häufig für die Herstellung von Druckbehältern, medizinischen Geräten und Bauteilen in der Lebensmittel- und Chemieindustrie verwendet.
- Titan und Titanlegierungen: Diese Materialien sind aufgrund ihrer außergewöhnlichen Festigkeit bei gleichzeitig geringem Gewicht besonders in der Luft- und Raumfahrt gefragt. Sie sind jedoch schwer zu verformen und erfordern spezialisierte Drück- und Walztechniken.
- Kupfer und Kupferlegierungen: Kupfer wird wegen seiner hohen Wärme- und elektrischen Leitfähigkeit oft für die Herstellung von Komponenten in der Elektronik- und Heizungsindustrie eingesetzt. Auch in der Architektur wird Kupfer aufgrund seiner ästhetischen Eigenschaften und Langlebigkeit geschätzt.
- Messing: Messing ist aufgrund seiner guten Umformbarkeit und Korrosionsbeständigkeit ein weiteres gängiges Material im Drückwalzen. Es wird häufig für dekorative Produkte sowie für Armaturen und Musikinstrumente verwendet.
Zu den Produkten, die typischerweise durch Drückwalzen hergestellt werden, zählen:
- Druckbehälter: Das Drückwalzen ermöglicht die Herstellung von Behältern mit verstärkten Wandstärken, die hohen Drücken standhalten müssen, wie zum Beispiel Gasflaschen, Hydraulikspeicher und Reaktorgefäße.
- Luft- und Raumfahrtkomponenten: Hierzu gehören unter anderem Triebwerksgehäuse, Turbinenkomponenten und strukturelle Teile, die durch Drückwalzen eine optimierte Festigkeit und ein geringes Gewicht erhalten.
- Automobilteile: Komponenten wie Felgen, Achsen und Antriebswellen, die hohen mechanischen Belastungen ausgesetzt sind, werden häufig durch Drückwalzen gefertigt, um die erforderliche Festigkeit und Dauerhaftigkeit zu gewährleisten.
- Rohre und Zylinder: Das Drückwalzen ist ideal für die Herstellung von Rohren mit variabler Wandstärke, die in der Öl- und Gasindustrie, im Maschinenbau und in der Energieerzeugung eingesetzt werden.
4.5 Maschinentypen und spezifische Werkzeuge für das Drückwalzen
Das Drückwalzen erfordert spezialisierte Maschinen, die in der Lage sind, sowohl die Drück- als auch die Walzprozesse zu integrieren und präzise zu steuern. Zu den wichtigsten Maschinentypen und Werkzeugen gehören:
- Drückwalzmaschinen: Diese Maschinen sind speziell für das Drückwalzen konzipiert und kombinieren die Funktionen von Drück- und Walzmaschinen. Sie verfügen über mehrere Walzrollen, die entlang des Werkstücks bewegt werden können, um die gewünschte Wandstärke und Form zu erzeugen. CNC-gesteuerte Drückwalzmaschinen bieten die höchste Präzision und Wiederholgenauigkeit, da sie komplexe Bewegungsabläufe programmieren und automatisieren können.
- Walzrollen: Die Walzrollen sind die Schlüsselwerkzeuge im Drückwalzen. Sie sind in verschiedenen Formen und Größen erhältlich, um unterschiedliche Wandstärkenprofile und Geometrien zu erzeugen. Die Walzrollen müssen aus extrem verschleißfesten Materialien wie Hartmetall oder gehärtetem Stahl bestehen, um den hohen Kräften und der Reibung standzuhalten.
- Dorne: Wie beim klassischen Metalldrücken wird auch beim Drückwalzen ein Dorn verwendet, der die Form des Endprodukts bestimmt. Dorne können aus Stahl, Aluminium oder Kunststoff bestehen und müssen präzise gefertigt sein, um eine gleichmäßige Formgebung zu gewährleisten.
- Spannfutter und Spannsysteme: Da das Werkstück während des Drückwalzens hohen Kräften ausgesetzt ist, ist ein robustes und präzises Spannsystem unerlässlich. Das Spannfutter hält das Werkstück sicher in Position und verhindert, dass es sich während des Prozesses verformt oder verschiebt.
- Steuerungssysteme: Moderne Drückwalzmaschinen sind oft mit hochentwickelten Steuerungssystemen ausgestattet, die es ermöglichen, die Bewegungen der Walzrollen, die Rotationsgeschwindigkeit und die angewendeten Kräfte genau zu überwachen und zu steuern. Dies ist entscheidend für die Herstellung von Bauteilen mit komplexen Geometrien und variablen Wandstärken.
4.6 Prozessparameter und deren Einfluss auf das Endprodukt
Die Qualität des durch Drückwalzen hergestellten Produkts hängt maßgeblich von einer Reihe von Prozessparametern ab, die sorgfältig gesteuert werden müssen. Zu den wichtigsten Parametern gehören:
- Rotationsgeschwindigkeit: Die Geschwindigkeit, mit der das Werkstück rotiert, beeinflusst die Oberflächenqualität und die Gleichmäßigkeit der Wandstärke. Eine zu hohe Rotationsgeschwindigkeit kann zu Vibrationen und ungleichmäßigen Verformungen führen, während eine zu niedrige Geschwindigkeit die Produktivität beeinträchtigen kann.
- Walzkraft: Die Kraft, die von den Walzrollen auf das Werkstück ausgeübt wird, bestimmt die Wandstärke und die Dichte des Materials. Eine zu hohe Walzkraft kann das Material übermäßig verdichten und zu Rissen oder anderen Defekten führen, während eine zu niedrige Kraft die gewünschte Wandstärke nicht erreicht.
- Temperatur: Während des Drückwalzens entsteht durch die Reibung Wärme, die die Formbarkeit des Metalls erhöhen kann. In einigen Fällen wird das Werkstück vor dem Drückwalzen gezielt erhitzt (Warmumformung), um die Umformbarkeit zu verbessern und das Risiko von Rissen zu reduzieren.
- Walzgeschwindigkeit: Die Geschwindigkeit, mit der die Walzrollen über das Werkstück bewegt werden, beeinflusst die Gleichmäßigkeit der Verformung und die Oberflächenqualität. Eine langsame Walzgeschwindigkeit ermöglicht eine präzisere Kontrolle, kann jedoch die Produktionszeit erhöhen.
- Werkzeuggeometrie: Die Form und Größe der Walzrollen sowie der Dorn haben einen direkten Einfluss auf die Geometrie und die Wandstärkenverteilung des Endprodukts. Die Auswahl der richtigen Werkzeuggeometrie ist entscheidend für die Erzielung der gewünschten Produkteigenschaften.
- Schmiermittel: Die Verwendung von Schmiermitteln während des Drückwalzens kann die Reibung zwischen Werkstück und Walzrollen reduzieren und so die Oberflächenqualität verbessern und den Werkzeugverschleiß minimieren.
Die richtige Einstellung und Steuerung dieser Parameter ist entscheidend, um ein qualitativ hochwertiges Endprodukt zu gewährleisten, das den spezifischen Anforderungen der Anwendung entspricht.
4.7 Industrielle Anwendungen des Drückwalzens und aktuelle Trends
Das Drückwalzen ist in vielen Industrien von zentraler Bedeutung und wird in einer Vielzahl von Anwendungen eingesetzt. Zu den wichtigsten industriellen Anwendungen gehören:
- Luft- und Raumfahrt: In der Luft- und Raumfahrtindustrie wird das Drückwalzen zur Herstellung von Triebwerkskomponenten, Flugzeugstrukturen und anderen Bauteilen verwendet, die eine hohe Festigkeit und Präzision erfordern. Die Fähigkeit, komplexe Geometrien und variable Wandstärken zu erzeugen, macht das Drückwalzen ideal für diese anspruchsvolle Branche.
- Automobilindustrie: In der Automobilindustrie wird das Drückwalzen zur Herstellung von Leichtbauteilen wie Felgen, Antriebswellen und anderen sicherheitsrelevanten Komponenten verwendet. Die Kombination aus Festigkeit und geringem Gewicht, die durch das Drückwalzen erreicht wird, ist entscheidend für die Verbesserung der Fahrzeugleistung und Kraftstoffeffizienz.
- Energieerzeugung: Das Drückwalzen findet Anwendung in der Herstellung von Bauteilen für Kraftwerke, Windkraftanlagen und andere Energieerzeugungssysteme. Hierbei werden oft komplexe Hohlkörper und Zylinder mit spezifischen Wandstärkenanforderungen benötigt, die durch Drückwalzen effizient produziert werden können.
- Medizintechnik: In der Medizintechnik werden durch Drückwalzen hochpräzise und sterile Bauteile hergestellt, die in medizinischen Geräten, Prothesen und Implantaten verwendet werden. Die Fähigkeit, Bauteile mit spezifischen geometrischen Anforderungen und hohen Oberflächenqualitäten zu produzieren, ist ein wesentlicher Vorteil des Drückwalzens in dieser Branche.
- Chemische Industrie: In der chemischen Industrie werden Druckbehälter, Reaktoren und andere Komponenten, die hohen Drücken und korrosiven Umgebungen standhalten müssen, durch Drückwalzen gefertigt. Die Möglichkeit, Bauteile mit verstärkten Wandstärken und gleichmäßigen Oberflächen zu erzeugen, ist hier besonders wertvoll.
Aktuelle Trends:
- Leichtbau: Der Trend zum Leichtbau in der Automobil- und Luftfahrtindustrie treibt die Entwicklung von Drückwalztechniken voran, die es ermöglichen, Bauteile mit optimaler Materialausnutzung und minimalem Gewicht herzustellen.
- Automatisierung und Digitalisierung: Die Integration von Automatisierung und digitaler Steuerung in Drückwalzprozesse ermöglicht eine höhere Präzision und Effizienz. Die Verwendung von CNC-gesteuerten Maschinen und die Einbindung von Industrie-4.0-Technologien sind entscheidend für die Weiterentwicklung dieses Verfahrens.
- Materialinnovation: Die Entwicklung neuer Materialien und Legierungen, die sich leichter verformen lassen und gleichzeitig bessere mechanische Eigenschaften bieten, beeinflusst die Anwendung und Ausweitung des Drückwalzens. Insbesondere hochfeste, aber leichte Materialien wie Titanlegierungen werden zunehmend verwendet.
- Nachhaltigkeit: Die Reduktion von Materialabfall und Energieverbrauch beim Drückwalzen wird immer wichtiger. Effiziente Umformprozesse und die Nutzung von Recyclingmaterialien tragen dazu bei, die Nachhaltigkeit dieses Verfahrens zu verbessern.
- Erweiterung der Anwendungsgebiete: Die kontinuierliche Verbesserung der Drückwalztechnologien ermöglicht die Anwendung dieses Verfahrens in neuen Industrien und für neue Produkte, die bisher nicht durch Drückwalzen hergestellt werden konnten.
5. Anwendungsgebiete und Branchen
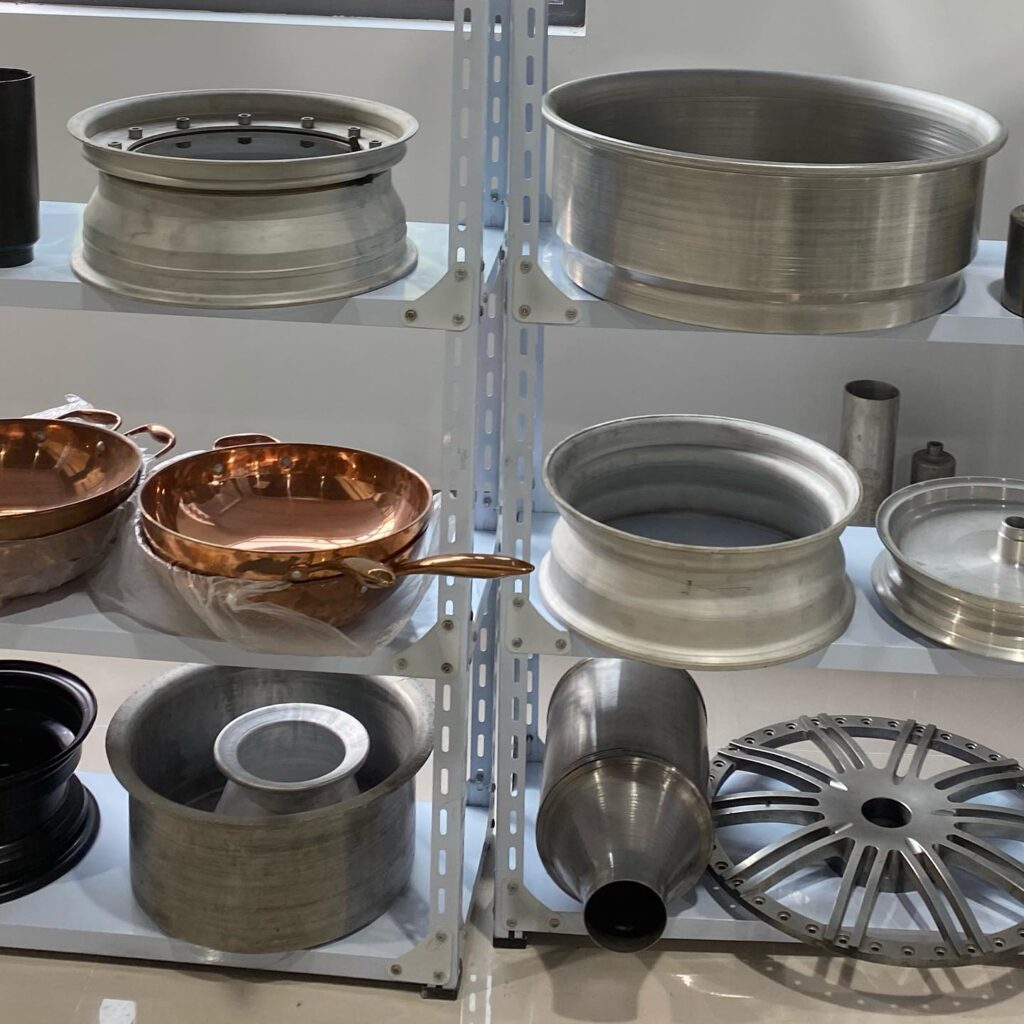
Die spanlose Metallumformung, insbesondere das Metalldrücken und Drückwalzen, spielt eine entscheidende Rolle in verschiedenen Industrien, die auf präzise, effiziente und robuste Fertigungstechnologien angewiesen sind. Im Folgenden werden die wichtigsten Anwendungsgebiete und Branchen beschrieben, in denen diese Umformverfahren weit verbreitet sind und wesentliche Beiträge zur Herstellung komplexer Bauteile leisten.
5.1 Automobilindustrie
Die Automobilindustrie ist einer der größten Anwender spanloser Umformverfahren. Hier kommen das Metalldrücken und Drückwalzen in zahlreichen Anwendungen zum Einsatz, die sowohl die Herstellung von strukturellen als auch dekorativen Bauteilen umfassen. Zu den wichtigsten Anwendungen gehören:
- Radkappen und Felgen: Metalldrücken wird häufig zur Herstellung von Radkappen und Felgen eingesetzt. Diese Komponenten müssen nicht nur ästhetisch ansprechend sein, sondern auch hohe Festigkeit und Dauerhaftigkeit aufweisen, um den Belastungen im Straßenverkehr standzuhalten.
- Auspuffanlagen: Drückwalzen ermöglicht die Produktion von Auspuffanlagen mit variabler Wandstärke, die den hohen Temperaturen und Drücken im Betrieb widerstehen können. Durch die gezielte Verstärkung bestimmter Bereiche wird die Lebensdauer dieser Komponenten erheblich verlängert.
- Karosserie- und Strukturteile: Für die Herstellung von Karosserieteilen wie Hauben, Türverkleidungen und Verstärkungsplatten wird Metalldrücken verwendet, um komplexe Formen zu erzeugen, die sowohl leicht als auch robust sind. Das Drückwalzen kann zudem für die Produktion von verstärkten Strukturteilen genutzt werden, die in tragenden Bereichen des Fahrzeugs eingesetzt werden.
- Antriebs- und Achskomponenten: In der Fertigung von Antriebswellen, Achsen und anderen mechanischen Komponenten, die hohen mechanischen Belastungen ausgesetzt sind, spielt das Drückwalzen eine wichtige Rolle. Hier sorgt die gezielte Materialverdichtung für die notwendige Festigkeit und Zuverlässigkeit dieser Teile.
Die Automobilindustrie profitiert besonders von der Flexibilität und Effizienz der spanlosen Umformverfahren, da sie sowohl für die Massenproduktion als auch für die Herstellung von Prototypen und Kleinserien geeignet sind. Durch die Optimierung von Materialnutzung und Produktionszeit tragen diese Verfahren zur Kostensenkung und Verbesserung der Produktqualität bei.
5.2 Luft- und Raumfahrt
In der Luft- und Raumfahrtindustrie sind die Anforderungen an Materialien und Fertigungstechnologien besonders hoch. Komponenten müssen extremen Belastungen standhalten, dabei aber möglichst leicht und präzise gefertigt sein. Die spanlose Metallumformung ist hier unverzichtbar für die Herstellung von:
- Triebwerkskomponenten: Das Drückwalzen und Metalldrücken werden zur Herstellung von Triebwerksgehäusen, Turbinenringen und Luftleitschaufeln verwendet. Diese Bauteile müssen hohen Temperaturen und mechanischen Belastungen widerstehen und gleichzeitig möglichst leicht sein, um die Effizienz des Flugzeugs zu maximieren.
- Strukturteile: Leichte, aber extrem belastbare Strukturteile wie Rahmen, Streben und Verbindungselemente werden durch Drückwalzen gefertigt. Die Fähigkeit, Bauteile mit variabler Wandstärke herzustellen, ermöglicht es, Gewicht zu sparen, ohne die strukturelle Integrität zu beeinträchtigen.
- Druckbehälter und Treibstofftanks: In der Raumfahrt werden hochfeste Druckbehälter und Treibstofftanks benötigt, die den extremen Bedingungen im Weltraum standhalten. Das Drückwalzen ermöglicht die Produktion von Tanks mit verstärkten Bereichen, die besonders druckfest und dennoch leicht sind.
- Flugzeugteile: Diverse andere Flugzeugteile, darunter Cockpitkomponenten, Türrahmen und Fahrwerkskomponenten, werden ebenfalls durch spanlose Umformverfahren hergestellt. Die hohe Präzision und die Möglichkeit zur Serienfertigung machen diese Verfahren ideal für die Luftfahrtindustrie.
Durch die Nutzung spanloser Umformverfahren können in der Luft- und Raumfahrtindustrie Gewicht und Kosten reduziert werden, während gleichzeitig die Sicherheit und Zuverlässigkeit der Flugzeuge erhöht wird. Dies trägt entscheidend zur Effizienz und Leistung moderner Luftfahrzeuge bei.
5.3 Medizintechnik
Die Medizintechnik erfordert hochpräzise und sterile Bauteile, die oft in lebenswichtigen Anwendungen zum Einsatz kommen. Die spanlose Metallumformung, insbesondere das Metalldrücken und Drückwalzen, bietet hier die Möglichkeit, komplexe und qualitativ hochwertige Komponenten herzustellen:
- Implantate und Prothesen: Metallische Implantate wie Hüft- und Kniegelenke, sowie verschiedene Arten von Prothesen, werden häufig durch Metalldrücken geformt. Diese Bauteile müssen nicht nur exakt passen, sondern auch biokompatibel und langlebig sein.
- Medizinische Instrumente: Präzise und komplexe Instrumente, die in der Chirurgie und Diagnostik verwendet werden, können durch Drückwalzen und Metalldrücken effizient produziert werden. Diese Verfahren ermöglichen die Herstellung von Instrumenten mit spezifischen Formen und hoher Oberflächenqualität.
- Gehäuse und Abschirmungen: Elektronische Geräte, die in der Medizintechnik verwendet werden, benötigen robuste und leichte Gehäuse sowie Abschirmungen gegen elektromagnetische Strahlung. Diese werden häufig durch Drückwalzen aus Materialien wie Aluminium oder Edelstahl gefertigt.
- Stents und Katheter: Für minimalinvasive Eingriffe werden extrem präzise gefertigte Stents und Katheter benötigt, die durch spanlose Umformverfahren hergestellt werden. Diese Komponenten müssen dünnwandig, flexibel und dennoch stark genug sein, um ihre Funktion im Körper zu erfüllen.
Die Medizintechnik profitiert stark von der Präzision und Flexibilität der spanlosen Metallumformung, die es ermöglicht, maßgeschneiderte und komplexe Bauteile für spezifische medizinische Anwendungen herzustellen. Die hohe Qualität und Zuverlässigkeit der durch Metalldrücken und Drückwalzen produzierten Komponenten sind entscheidend für den Erfolg medizinischer Geräte und Implantate.
5.4 Bauwesen
Im Bauwesen werden spanlose Umformverfahren verwendet, um sowohl strukturelle als auch dekorative Bauteile herzustellen, die hohe Festigkeit und Langlebigkeit aufweisen müssen. Zu den wichtigsten Anwendungen gehören:
- Strukturelle Elemente: Träger, Stützen und andere tragende Strukturelemente können durch Drückwalzen gefertigt werden, um eine hohe Festigkeit und Stabilität zu gewährleisten. Diese Bauteile werden oft in Gebäuden, Brücken und anderen großen Bauwerken eingesetzt.
- Fassadenelemente: Metalldrücken wird häufig zur Herstellung von Fassadenelementen und Verkleidungen verwendet. Diese Elemente müssen sowohl ästhetisch ansprechend als auch witterungsbeständig sein. Aluminium und Edelstahl sind hier bevorzugte Materialien, die durch Metalldrücken in komplexe Formen gebracht werden können.
- Dächer und Bedachungen: Metalldächer und Bedachungen, die eine lange Lebensdauer und hohe Belastbarkeit bieten, werden oft durch Drückwalzen hergestellt. Hierbei können Bauteile mit spezifischen Profilen und Verstärkungen gefertigt werden, die den Anforderungen an Stabilität und Witterungsbeständigkeit entsprechen.
- Dekorative Bauteile: Das Bauwesen nutzt auch dekorative Metallelemente, wie Zierleisten, Geländer und Verkleidungen, die durch Metalldrücken und Drückwalzen in komplexe und ansprechende Formen gebracht werden können. Diese Bauteile tragen nicht nur zur Ästhetik, sondern auch zur Funktionalität von Bauwerken bei.
Durch den Einsatz von spanlosen Umformverfahren im Bauwesen können Bauteile produziert werden, die eine hohe Lebensdauer und Festigkeit aufweisen, gleichzeitig aber auch den architektonischen Ansprüchen gerecht werden. Die Flexibilität und Präzision dieser Verfahren tragen dazu bei, Bauprojekte effizienter und kostengünstiger umzusetzen.
5.5 Elektronikindustrie
Die Elektronikindustrie benötigt präzise gefertigte Bauteile mit hoher Leitfähigkeit und exzellenter Oberflächenqualität. Die spanlose Metallumformung ist hier ideal für die Produktion von:
- Gehäusen für elektronische Geräte: Gehäuse für Computer, Smartphones, Fernseher und andere elektronische Geräte müssen sowohl leicht als auch robust sein. Durch Metalldrücken und Drückwalzen können Gehäuse mit komplexen Formen und integrierten Befestigungselementen hergestellt werden, die den Schutz und die Kühlung der empfindlichen Elektronik gewährleisten.
- Abschirmungen gegen elektromagnetische Strahlung: Viele elektronische Geräte benötigen Abschirmungen, um die Elektronik vor elektromagnetischen Störungen zu schützen. Diese Abschirmungen werden häufig aus dünnwandigem Metall gefertigt, das durch spanlose Umformverfahren geformt wird.
- Konnektoren und Kontakte: Metallische Konnektoren und Kontakte, die für die Strom- und Signalübertragung in elektronischen Geräten verantwortlich sind, werden oft durch Metalldrücken hergestellt. Diese Bauteile müssen hohe Präzision aufweisen und eine ausgezeichnete Leitfähigkeit bieten.
- Kühlkörper: Kühllösungen für elektronische Komponenten, wie z.B. Kühlkörper, können durch Drückwalzen produziert werden, um eine maximale Wärmeableitung zu gewährleisten. Diese Bauteile sind oft aus Aluminium gefertigt und müssen eine spezifische Geometrie aufweisen, um ihre Funktion effizient zu erfüllen.
Die Elektronikindustrie profitiert von der Fähigkeit der spanlosen Metallumformung, komplexe und präzise Bauteile in hohen Stückzahlen und mit gleichbleibender Qualität zu produzieren. Dies ist entscheidend für die Kosteneffizienz und die Zuverlässigkeit der Endprodukte in einem Markt, der stark auf Innovation und Präzision angewiesen ist.
5.6 Lebensmittel- und Getränkeindustrie
In der Lebensmittel- und Getränkeindustrie sind Hygiene, Korrosionsbeständigkeit und die Fähigkeit zur Verarbeitung großer Mengen von Materialien wesentliche Anforderungen. Die spanlose Metallumformung bietet hier zahlreiche Vorteile:
- Behälter und Tanks: Großbehälter, Lagertanks und Druckbehälter, die in der Verarbeitung und Lagerung von Lebensmitteln und Getränken verwendet werden, werden häufig durch Drückwalzen aus Edelstahl gefertigt. Diese Behälter müssen hygienisch, leicht zu reinigen und korrosionsbeständig sein, was durch die hohe Oberflächenqualität, die durch spanlose Umformverfahren erzielt wird, gewährleistet wird.
- Verarbeitungsmaschinen: Komponenten für Maschinen zur Lebensmittelverarbeitung, wie z.B. Mischer, Zentrifugen und Fördersysteme, werden oft durch Metalldrücken und Drückwalzen hergestellt. Diese Bauteile müssen robust und langlebig sein, um den Anforderungen in einer Produktionsumgebung gerecht zu werden.
- Verpackungsmaterialien: Dünnwandige Metallverpackungen, wie Konservendosen, Flaschen und Kapseln, werden durch Metalldrücken geformt. Diese Verpackungen müssen sowohl leicht als auch stabil sein und gleichzeitig eine gute Barriere gegen Licht, Luft und Feuchtigkeit bieten.
- Kochgeräte: Viele Kochgeräte, einschließlich Pfannen, Töpfe und Backformen, werden durch Metalldrücken hergestellt. Diese Geräte müssen hitzebeständig und langlebig sein und gleichzeitig eine gleichmäßige Wärmeverteilung gewährleisten.
Durch den Einsatz von spanlosen Umformverfahren in der Lebensmittel- und Getränkeindustrie können hochwertige und langlebige Produkte hergestellt werden, die den hohen Anforderungen an Hygiene, Korrosionsbeständigkeit und Effizienz in dieser Branche gerecht werden.
5.7 Energieerzeugung und Umwelttechnik
In der Energieerzeugung und Umwelttechnik werden spanlose Umformverfahren zur Herstellung von Komponenten eingesetzt, die extremen Bedingungen und Anforderungen genügen müssen. Zu den Anwendungen gehören:
- Turbinenkomponenten: Für die Energieerzeugung in Kraftwerken, insbesondere in Gas- und Dampfturbinen, werden hochfeste und präzise Komponenten benötigt, die durch Drückwalzen hergestellt werden. Diese Bauteile müssen hohen Temperaturen und Drücken standhalten und gleichzeitig eine lange Lebensdauer aufweisen.
- Windkraftanlagen: Komponenten für Windkraftanlagen, wie z.B. Naben, Gehäuse und Rotorblätter, werden oft durch Metalldrücken und Drückwalzen produziert. Diese Bauteile müssen sowohl leicht als auch stabil sein, um den Belastungen durch Wind und Wetter standzuhalten.
- Umwelttechnik: In der Umwelttechnik werden spanlose Umformverfahren zur Herstellung von Komponenten für Abwasserbehandlungsanlagen, Filtrationssysteme und Recyclinganlagen eingesetzt. Diese Bauteile müssen korrosionsbeständig und langlebig sein, um in aggressiven Umgebungen zu bestehen.
- Photovoltaik: Die Herstellung von Bauteilen für Photovoltaikanlagen, wie z.B. Rahmen und Halterungen, profitiert von der Präzision und Effizienz der spanlosen Metallumformung. Diese Bauteile müssen leicht, korrosionsbeständig und robust sein, um eine lange Lebensdauer zu gewährleisten.
Die spanlose Metallumformung trägt in der Energieerzeugung und Umwelttechnik dazu bei, Komponenten zu produzieren, die den hohen Anforderungen an Effizienz, Langlebigkeit und Umweltfreundlichkeit gerecht werden. Dies ist entscheidend für die Entwicklung nachhaltiger und innovativer Lösungen in diesen Industrien.
6. Maschinen und Technologieentwicklung
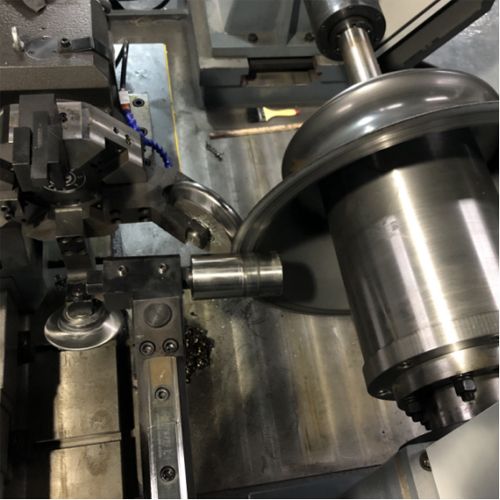
6.1 Entwicklung und Evolution von Maschinen für spanlose Metallumformung
Die Maschinen, die für die spanlose Metallumformung eingesetzt werden, haben sich im Laufe der Jahre erheblich weiterentwickelt. Ursprünglich waren diese Maschinen mechanische Geräte, die vollständig manuell betrieben wurden und eine hohe Geschicklichkeit des Bedieners erforderten. Mit der Zeit führte die Einführung von motorbetriebenen Maschinen und später elektronischen Steuerungen zu einer erheblichen Steigerung der Effizienz und Präzision der Umformprozesse.
6.1.1 Frühe Maschinen und ihre Entwicklung
Die ersten Maschinen für die spanlose Metallumformung, insbesondere für das Metalldrücken, waren einfache, manuell betriebene Geräte. Diese Maschinen bestanden aus einem Grundrahmen, einem rotierenden Dorn und einer Drückrolle, die vom Bediener mit Muskelkraft bewegt wurde. Diese frühen Maschinen waren ideal für die Herstellung kleinerer Serien und Prototypen, erforderten jedoch viel Erfahrung und Geschicklichkeit, um hochwertige Bauteile zu produzieren.
Mit dem Aufkommen der industriellen Revolution im 18. und 19. Jahrhundert wurden die ersten mechanischen Drückmaschinen entwickelt. Diese Maschinen nutzten Dampf- oder später Elektromotoren, um den Dorn anzutreiben, was die Produktionsgeschwindigkeit und Konsistenz erheblich steigerte. Die Einführung von Zahnrädern und Hebelmechanismen ermöglichte eine präzisere Kontrolle der Drückkraft und Bewegungen, was die Qualität der gefertigten Teile verbesserte.
6.1.2 Einführung von CNC-Technologie
Ein entscheidender Fortschritt in der spanlosen Metallumformung kam mit der Einführung der CNC-Technologie (Computer Numerical Control) in den 1970er und 1980er Jahren. CNC-gesteuerte Drückmaschinen ermöglichten es, komplexe Bewegungsabläufe und Formen mit einer Präzision zu wiederholen, die manuell kaum erreichbar war. Die Programmierbarkeit dieser Maschinen erlaubte es, Bauteile mit sehr engen Toleranzen und komplexen Geometrien in großen Stückzahlen herzustellen.
CNC-Drückmaschinen bieten zahlreiche Vorteile gegenüber ihren mechanischen Vorgängern:
- Hohe Präzision und Wiederholgenauigkeit: Die computergesteuerte Steuerung ermöglicht es, präzise Bewegungsabläufe zu programmieren und konstant zu wiederholen, was zu gleichbleibender Produktqualität führt.
- Flexibilität: CNC-Maschinen können schnell umprogrammiert werden, um verschiedene Bauteile zu produzieren, was sie ideal für die Kleinserienfertigung und Prototypenentwicklung macht.
- Reduzierte Rüstzeiten: Durch die Automatisierung vieler Prozesse können Rüstzeiten erheblich verkürzt werden, was die Effizienz der Produktion steigert.
Die Entwicklung von CNC-Drückmaschinen war ein Meilenstein in der spanlosen Metallumformung und legte den Grundstein für die weitere Automatisierung und Digitalisierung des Umformprozesses.
6.2 Automatisierung und Digitalisierung in der spanlosen Umformtechnik
Die Automatisierung und Digitalisierung haben die spanlose Metallumformung in den letzten Jahrzehnten grundlegend verändert. Moderne Umformmaschinen sind heute häufig vollständig automatisiert und in der Lage, komplexe Bauteile ohne menschliches Eingreifen herzustellen. Diese Entwicklungen haben die Produktivität erheblich gesteigert und die Kosten gesenkt, während gleichzeitig die Qualität der Produkte verbessert wurde.
6.2.1 Roboterintegration und automatische Materialhandhabung
Ein wichtiger Aspekt der Automatisierung in der spanlosen Metallumformung ist die Integration von Industrierobotern und automatischen Materialhandhabungssystemen. Roboter übernehmen heute Aufgaben wie das Laden und Entladen von Werkstücken, das Positionieren und Halten der Bauteile während des Umformprozesses und sogar die Qualitätskontrolle.
- Roboterintegration: Industrieroboter werden häufig in Verbindung mit CNC-gesteuerten Drückmaschinen eingesetzt, um den Materialfluss zu optimieren und die Produktionslinien zu automatisieren. Roboter können Werkstücke präzise und schnell in die Maschine einlegen und nach dem Umformen entnehmen, was die Produktionsgeschwindigkeit erhöht und menschliche Fehler minimiert.
- Automatische Materialhandhabung: Systeme zur automatischen Materialhandhabung, wie Förderbänder und Greifsysteme, sind ebenfalls weit verbreitet. Diese Systeme sorgen dafür, dass das Rohmaterial effizient zur Umformmaschine transportiert und die fertigen Bauteile zur weiteren Verarbeitung oder Verpackung weitergeleitet werden.
Durch die Integration von Robotern und automatischen Materialhandhabungssystemen wird die spanlose Umformtechnik deutlich effizienter und produktiver, was besonders in Hochvolumenproduktionen von Vorteil ist.
6.2.2 Digitale Prozessüberwachung und Steuerung
Mit der Digitalisierung sind umfassende Prozessüberwachungs- und Steuerungssysteme in die spanlose Metallumformung eingezogen. Diese Systeme ermöglichen es, den gesamten Umformprozess in Echtzeit zu überwachen, Abweichungen sofort zu erkennen und die Produktionsparameter automatisch anzupassen.
- Sensorik und Datenanalyse: Moderne Umformmaschinen sind mit einer Vielzahl von Sensoren ausgestattet, die Parameter wie Druck, Temperatur, Rotationsgeschwindigkeit und Werkzeugverschleiß messen. Die gesammelten Daten werden in Echtzeit analysiert, um sicherzustellen, dass die Produktion den gewünschten Spezifikationen entspricht.
- Prozessoptimierung: Durch die digitale Überwachung können Produktionsprozesse kontinuierlich optimiert werden. Anhand der erfassten Daten können Muster und Trends erkannt und entsprechende Anpassungen vorgenommen werden, um die Effizienz zu steigern und die Ausschussrate zu minimieren.
- Fernüberwachung und Steuerung: Mit der zunehmenden Vernetzung industrieller Systeme können Produktionsprozesse auch aus der Ferne überwacht und gesteuert werden. Dies ermöglicht es, Probleme frühzeitig zu erkennen und Maßnahmen zu ergreifen, ohne dass ein Bediener vor Ort sein muss.
Die Digitalisierung hat die Kontrolle und Optimierung der spanlosen Umformprozesse erheblich verbessert und trägt dazu bei, die Produktionskosten zu senken und die Qualität der Produkte zu steigern.
6.3 Computerunterstütztes Design (CAD) und Fertigung (CAM) in der Metallumformung
Die Integration von CAD- (Computer Aided Design) und CAM- (Computer Aided Manufacturing) Systemen in die spanlose Metallumformung hat die Art und Weise, wie Bauteile entworfen und produziert werden, revolutioniert. Diese Technologien ermöglichen es, komplexe Geometrien effizient zu entwerfen und direkt in den Produktionsprozess zu integrieren.
6.3.1 CAD für die spanlose Metallumformung
CAD-Systeme spielen eine zentrale Rolle beim Entwurf von Bauteilen für die spanlose Metallumformung. Sie ermöglichen es Ingenieuren, detaillierte 3D-Modelle von Bauteilen zu erstellen, die alle relevanten Spezifikationen und Toleranzen enthalten.
- 3D-Modellierung: CAD-Software erlaubt es, komplexe Geometrien mit hoher Präzision zu entwerfen. Diese Modelle können einfach geändert und angepasst werden, was die Entwicklung neuer Produkte beschleunigt.
- Simulation und Analyse: CAD-Systeme bieten die Möglichkeit, Umformprozesse zu simulieren und mögliche Probleme wie Materialversagen oder Werkzeugverschleiß bereits im Entwurfsstadium zu erkennen. Dies reduziert die Notwendigkeit physischer Prototypen und spart Zeit und Kosten.
- Datenintegration: Die in CAD-Systemen erstellten Modelle können direkt in CAM-Systeme integriert werden, was eine nahtlose Übergabe von der Entwurfsphase in die Produktion ermöglicht.
Durch den Einsatz von CAD-Systemen wird der Entwurfsprozess effizienter und genauer, was zu besser optimierten Bauteilen und kürzeren Entwicklungszeiten führt.
6.3.2 CAM für die spanlose Metallumformung
CAM-Systeme nutzen die CAD-Modelle, um den Fertigungsprozess zu steuern. Sie wandeln die digitalen Entwürfe in konkrete Anweisungen für die CNC-Maschinen um, die den Umformprozess durchführen.
- Automatisierte Werkzeugwege: CAM-Software generiert die optimalen Werkzeugwege und Bewegungsabfolgen für die Umformmaschinen, basierend auf den CAD-Daten. Dies sorgt für eine präzise und effiziente Herstellung der Bauteile.
- Simulation des Fertigungsprozesses: Ähnlich wie bei der CAD-Simulation kann auch der Fertigungsprozess in der CAM-Software simuliert werden. Dies hilft, mögliche Probleme frühzeitig zu identifizieren und Anpassungen vorzunehmen, bevor die Produktion beginnt.
- Integration in die Produktionslinie: CAM-Systeme sind oft direkt in die Produktionslinien integriert, was eine schnelle Anpassung der Fertigungsparameter und eine effiziente Steuerung der Produktion ermöglicht. Änderungen im Design können schnell in den Produktionsprozess übernommen werden, was besonders bei der Fertigung von Prototypen und Kleinserien von Vorteil ist.
Die Integration von CAD und CAM in die spanlose Metallumformung hat die Produktentwicklung und -fertigung grundlegend verändert, indem sie diese Prozesse effizienter und genauer gemacht
Metalldrücken (Metal Spinning)
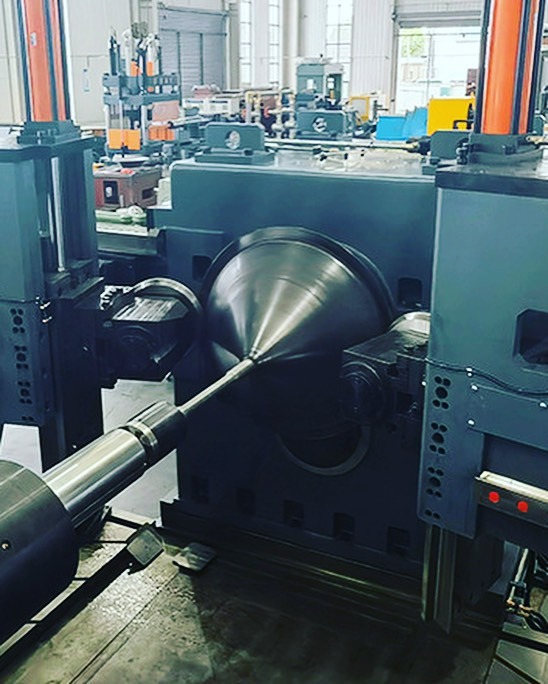
Beim Metalldrücken wird ein flaches Metallblech auf einen rotierenden Dorn gepresst und durch ein Drückwerkzeug in die gewünschte Form gebracht. Dieser Prozess eignet sich besonders für die Herstellung von rotationssymmetrischen Teilen wie Töpfen, Lampenschirmen und Behältern. Das Metalldrücken kann manuell oder maschinell erfolgen und bietet eine hohe Flexibilität bei der Produktion von Kleinserien und Prototypen.
Metalldrücken, auch bekannt als Metal Spinning, ist ein Verfahren der spanlosen Metallumformung, bei dem ein flaches Metallblech auf eine rotierende Form (Dorn) gepresst und durch Anwendung von Druck in die gewünschte Form gebracht wird. Dieses Verfahren ist besonders geeignet für die Herstellung von hohlen, rotationssymmetrischen Teilen wie Töpfen, Lampenschirmen, Behältern und Musikinstrumenten. Das Metalldrücken kann sowohl manuell als auch maschinell durchgeführt werden und bietet eine hohe Flexibilität bei der Produktion von Kleinserien und Prototypen.
Ablauf des Metalldrückens
Der Prozess des Metalldrückens umfasst mehrere Schritte:
- Vorbereitung: Ein flaches Metallblech wird auf den Dorn, der auf einer Drehmaschine montiert ist, zentriert und fixiert.
- Rotation: Der Dorn beginnt sich mit hoher Geschwindigkeit zu drehen.
- Formgebung: Ein Drückwerkzeug, das manuell oder maschinell geführt wird, wird gegen das drehende Metallblech gedrückt. Durch die kontinuierliche Anwendung von Druck wird das Metallblech in die gewünschte Form gebracht, indem es sich eng an den Dorn anlegt.
- Feinbearbeitung: Der geformte Teil wird vom Dorn entfernt und kann, falls notwendig, weiter bearbeitet oder veredelt werden.
Arten des Metalldrückens
Es gibt verschiedene Techniken des Metalldrückens, die je nach Anforderung und gewünschter Form eingesetzt werden:
- Konventionelles Metalldrücken: Hierbei wird das Metallblech durch ein einfaches Drückwerkzeug in die gewünschte Form gebracht.
- Schweres Metalldrücken (Shear Spinning): Diese Technik wird verwendet, um dickere Metallbleche zu formen und gleichzeitig die Wanddicke zu reduzieren.
- Innen- und Außendrücken: Dabei wird das Drückwerkzeug entweder innen oder außen am Werkstück geführt, um unterschiedliche Formen und Strukturen zu erzeugen.
Vorteile des Metalldrückens
- Materialeinsparung: Da das Metall lediglich verformt und nicht geschnitten oder abgetragen wird, entsteht weniger Abfall.
- Hohe Flexibilität: Metalldrücken eignet sich gut für die Herstellung von Prototypen und Kleinserien, da teure Werkzeuge und Formen nicht erforderlich sind.
- Vielseitigkeit: Dieses Verfahren kann für eine Vielzahl von Metallen wie Aluminium, Stahl, Kupfer und Messing angewendet werden.
- Qualität und Präzision: Metalldrücken ermöglicht die Herstellung von Teilen mit hoher Oberflächenqualität und genauen Abmessungen.
Anwendungsbereiche
Metalldrücken findet Anwendung in zahlreichen Industriebereichen, darunter:
- Luft- und Raumfahrt: Herstellung von Komponenten wie Düsenelementen, Ventilen und Behältern.
- Automobilindustrie: Produktion von Bauteilen wie Radkappen, Zylinderköpfen und Auspuffanlagen.
- Haushaltswaren: Fertigung von Kochgeschirr, Lampenschirmen und dekorativen Elementen.
- Musikinstrumente: Herstellung von Instrumententeilen wie Trommeln und Becken.
Zusammenfassung
Metalldrücken ist ein vielseitiges und effizientes Verfahren der spanlosen Metallumformung, das sich durch Materialeinsparung, hohe Flexibilität und Präzision auszeichnet. Es bietet zahlreiche Vorteile gegenüber traditionellen Fertigungsmethoden und wird in vielen Industrien zur Herstellung von hochwertigen, rotationssymmetrischen Metallteilen eingesetzt. Durch die Fähigkeit, komplexe Formen und Strukturen zu erzeugen, spielt das Metalldrücken eine wichtige Rolle in der modernen Fertigungstechnik.
Drückwalzen (Flow Forming)
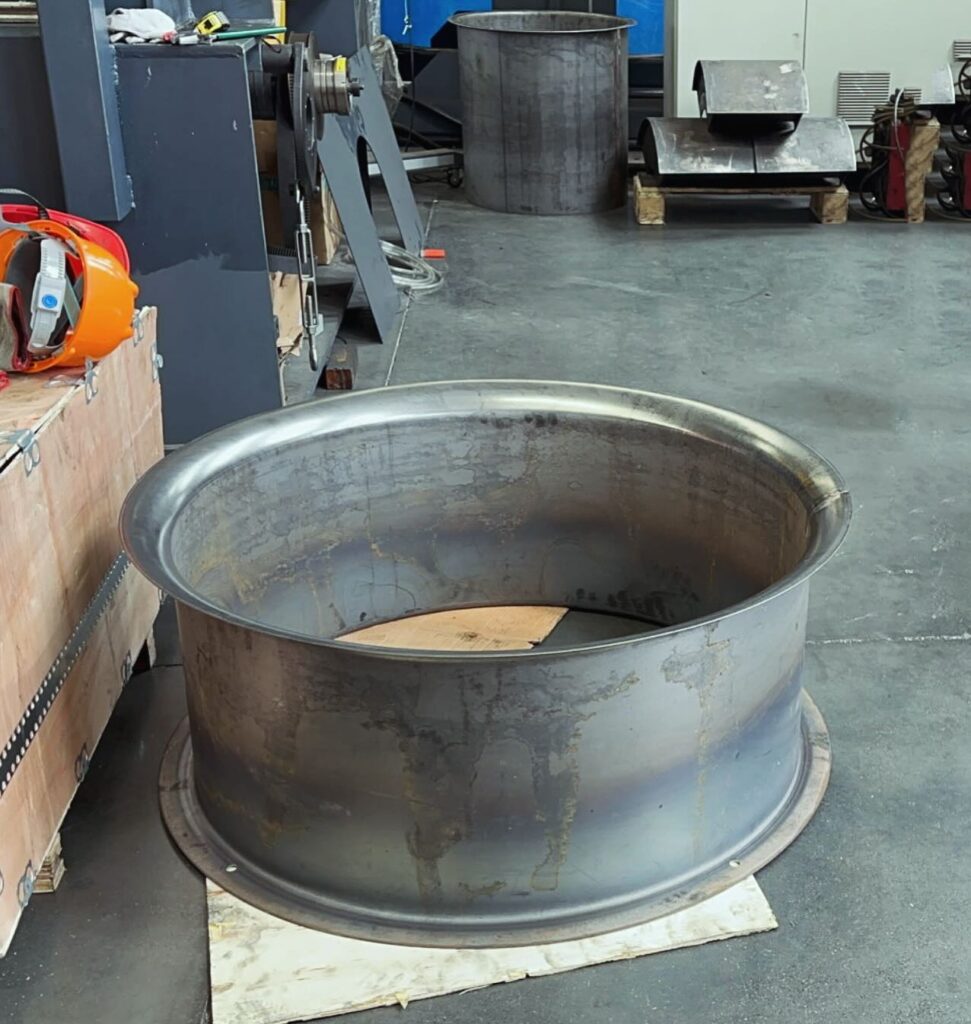
Drückwalzen ist ein Verfahren, bei dem ein Metallrohling zwischen einer rotierenden Form und mehreren Walzen geformt wird. Diese Technik wird verwendet, um zylindrische und konische Teile mit hoher Präzision und Festigkeit herzustellen. Drückwalzen ermöglicht die Produktion von dünnwandigen Teilen mit engen Toleranzen und wird häufig in der Luft- und Raumfahrtindustrie sowie in der Automobilindustrie eingesetzt.
Drückwalzen (Flow Forming)
Drückwalzen, auch bekannt als Flow Forming, ist ein hochpräzises Verfahren der spanlosen Metallumformung, bei dem ein vorgeformter Metallrohling zwischen einer rotierenden Form (Dorn) und mehreren Walzen geformt wird. Dieses Verfahren wird häufig zur Herstellung von zylindrischen und konischen Teilen verwendet, die hohe Festigkeit und Genauigkeit erfordern, wie beispielsweise in der Luft- und Raumfahrt, Automobilindustrie und bei der Herstellung von Präzisionsrohren.
Ablauf des Drückwalzens
Der Drückwalzprozess besteht aus mehreren Schritten:
- Vorbereitung: Ein vorgeformter Metallrohling (z.B. ein dickwandiger Zylinder) wird auf den Dorn einer Flow-Forming-Maschine montiert.
- Rotation: Der Dorn beginnt sich mit hoher Geschwindigkeit zu drehen.
- Walzen: Mehrere Walzen werden gegen den drehenden Rohling gepresst und bewegen sich entlang der Längsachse des Dorns. Durch die kombinierte Wirkung von Druck und Drehbewegung wird der Rohling in die gewünschte Form gestreckt und gleichzeitig die Wandstärke reduziert.
- Kontrolle und Feinbearbeitung: Der geformte Teil wird nach Bedarf kontrolliert und gegebenenfalls weiter bearbeitet, um die gewünschten Toleranzen und Oberflächenqualitäten zu erreichen.
Arten des Drückwalzens
Es gibt verschiedene Techniken des Drückwalzens, die je nach Anwendung und gewünschten Eigenschaften des Endprodukts eingesetzt werden:
- Axiales Drückwalzen: Hierbei bewegen sich die Walzen in axialer Richtung entlang des Rohlings und formen ihn schrittweise.
- Radiales Drückwalzen: Die Walzen bewegen sich radial auf den Rohling zu, um die Wanddicke gleichmäßig zu reduzieren.
- Vorwärts- und Rückwärtsdrückwalzen: Beim Vorwärtsdrückwalzen bewegen sich die Walzen in Drehrichtung des Dorns, während sie sich beim Rückwärtsdrückwalzen gegen die Drehrichtung bewegen.
Vorteile des Drückwalzens
- Hohe Präzision: Das Verfahren ermöglicht die Herstellung von Teilen mit engen Toleranzen und gleichmäßigen Wandstärken.
- Materialeinsparung: Da das Material nicht entfernt, sondern umgeformt wird, entsteht weniger Abfall.
- Verbesserte mechanische Eigenschaften: Durch die plastische Verformung wird das Material verdichtet, was zu einer höheren Festigkeit und Zähigkeit führt.
- Vielseitigkeit: Drückwalzen kann auf eine Vielzahl von Metallen und Legierungen angewendet werden, darunter Aluminium, Stahl, Titan und Kupfer.
Anwendungsbereiche
Drückwalzen wird in verschiedenen Industriezweigen eingesetzt, darunter:
- Luft- und Raumfahrt: Herstellung von Komponenten wie Raketenhülsen, Triebwerksgehäusen und Strukturteilen.
- Automobilindustrie: Produktion von Teilen wie Felgen, Getriebekomponenten und Antriebswellen.
- Medizintechnik: Fertigung von präzisen Röhren und zylindrischen Teilen für medizinische Geräte.
- Energie- und Umwelttechnik: Herstellung von Bauteilen für Windkraftanlagen, Turbinen und Druckbehälter.
Zusammenfassung
Drückwalzen (Flow Forming) ist ein fortschrittliches Verfahren der spanlosen Metallumformung, das sich durch hohe Präzision, Materialeinsparung und verbesserte mechanische Eigenschaften auszeichnet. Es ermöglicht die effiziente Herstellung von zylindrischen und konischen Teilen mit gleichmäßigen Wandstärken und hohen Festigkeiten. Aufgrund seiner Vielseitigkeit und der Fähigkeit, komplexe Formen mit engen Toleranzen zu erzeugen, ist das Drückwalzen in vielen Industriebereichen unverzichtbar und trägt maßgeblich zur modernen Fertigungstechnik bei.
Projizieren (Projection Forming)
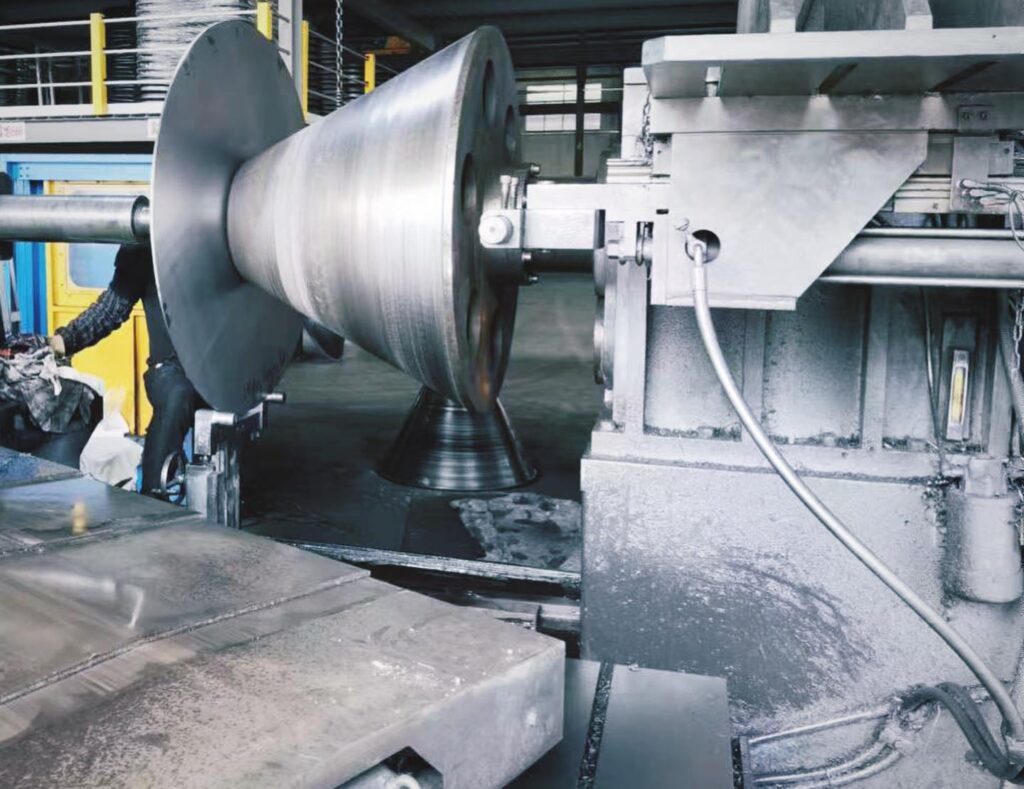
Projizieren, auch als Prägen oder Biegen bekannt, umfasst Techniken, bei denen Metall durch Druck oder Schläge in eine bestimmte Form gebracht wird. Dieses Verfahren wird oft im Schmiedebereich verwendet, um komplexe Formen und Konturen zu erzeugen. Das Projizieren führt zur Verfestigung des Metalls und verbessert dessen mechanische Eigenschaften. Es wird in der Herstellung von Werkzeugen, Maschinenbauteilen und dekorativen Elementen verwendet.
Projizieren (Projection Forming)
Projizieren, auch bekannt als Prägen oder Biegen, ist ein Verfahren der spanlosen Metallumformung, bei dem ein Metallstück durch Druck oder Schläge in eine bestimmte Form gebracht wird. Diese Technik wird häufig im Schmiedebereich verwendet, um komplexe Formen und Konturen zu erzeugen. Das Projizieren kann sowohl manuell als auch maschinell erfolgen und wird in vielen Industriezweigen zur Herstellung von Werkzeugen, Maschinenbauteilen und dekorativen Elementen eingesetzt.
Ablauf des Projizierens
Der Projizierprozess umfasst mehrere Schritte:
- Vorbereitung: Das Metallstück wird auf einem Amboss oder in einer Form positioniert.
- Formgebung: Ein Hammer oder ein anderes Werkzeug wird verwendet, um Druck auf das Metallstück auszuüben. Dieser Druck verformt das Metall und bringt es in die gewünschte Form.
- Kontrolle und Feinbearbeitung: Das geformte Teil wird nach Bedarf kontrolliert und gegebenenfalls weiter bearbeitet, um die gewünschten Toleranzen und Oberflächenqualitäten zu erreichen.
Arten des Projizierens
Es gibt verschiedene Techniken des Projizierens, die je nach Anwendung und gewünschter Form des Endprodukts eingesetzt werden:
- Kaltprägen: Das Metall wird bei Raumtemperatur verformt. Diese Methode wird oft für weichere Metalle verwendet und erfordert weniger Energie als das Warmprägen.
- Warmprägen: Das Metall wird erhitzt, um es weicher und leichter verformbar zu machen. Diese Methode wird für härtere Metalle und größere Verformungen verwendet.
- Freiformprägen: Das Metall wird frei auf einem Amboss oder in einer offenen Form verformt. Diese Methode ermöglicht eine hohe Flexibilität bei der Formgebung.
- Formprägen: Das Metall wird in eine geschlossene Form gepresst. Diese Methode bietet eine hohe Präzision und Wiederholbarkeit bei der Herstellung von Teilen.
Vorteile des Projizierens
- Hohe Flexibilität: Das Verfahren kann auf eine Vielzahl von Metallen und Legierungen angewendet werden und ermöglicht die Herstellung von komplexen Formen.
- Verbesserte mechanische Eigenschaften: Durch die plastische Verformung wird das Material verdichtet, was zu einer höheren Festigkeit und Zähigkeit führt.
- Kosteneffizienz: Projizieren erfordert oft weniger Energie und Material als andere Umformverfahren.
- Vielseitigkeit: Das Verfahren kann für kleine und große Stückzahlen verwendet werden und eignet sich sowohl für die Herstellung von Prototypen als auch für die Massenproduktion.
Anwendungsbereiche
Projizieren wird in verschiedenen Industriezweigen eingesetzt, darunter:
- Automobilindustrie: Herstellung von Karosserieteilen, Fahrwerksteilen und Motorbauteilen.
- Luft- und Raumfahrt: Produktion von Strukturteilen, Verbindungselementen und Verstärkungen.
- Maschinenbau: Fertigung von Werkzeugen, Maschinenteilen und Baugruppen.
- Schmuck- und Kunsthandwerk: Herstellung von dekorativen Elementen, Schmuckstücken und Kunstobjekten.
Zusammenfassung
Projizieren (Projection Forming) ist ein vielseitiges Verfahren der spanlosen Metallumformung, das durch Druck oder Schläge Metallteile in die gewünschte Form bringt. Es bietet zahlreiche Vorteile wie hohe Flexibilität, verbesserte mechanische Eigenschaften und Kosteneffizienz. Projizieren findet breite Anwendung in vielen Industriezweigen und ist unverzichtbar für die Herstellung von hochwertigen, komplexen Metallteilen. Die Fähigkeit, sowohl kleine als auch große Stückzahlen effizient zu produzieren, macht dieses Verfahren zu einem wichtigen Bestandteil der modernen Fertigungstechnik.
Flanschformen (Flanging)
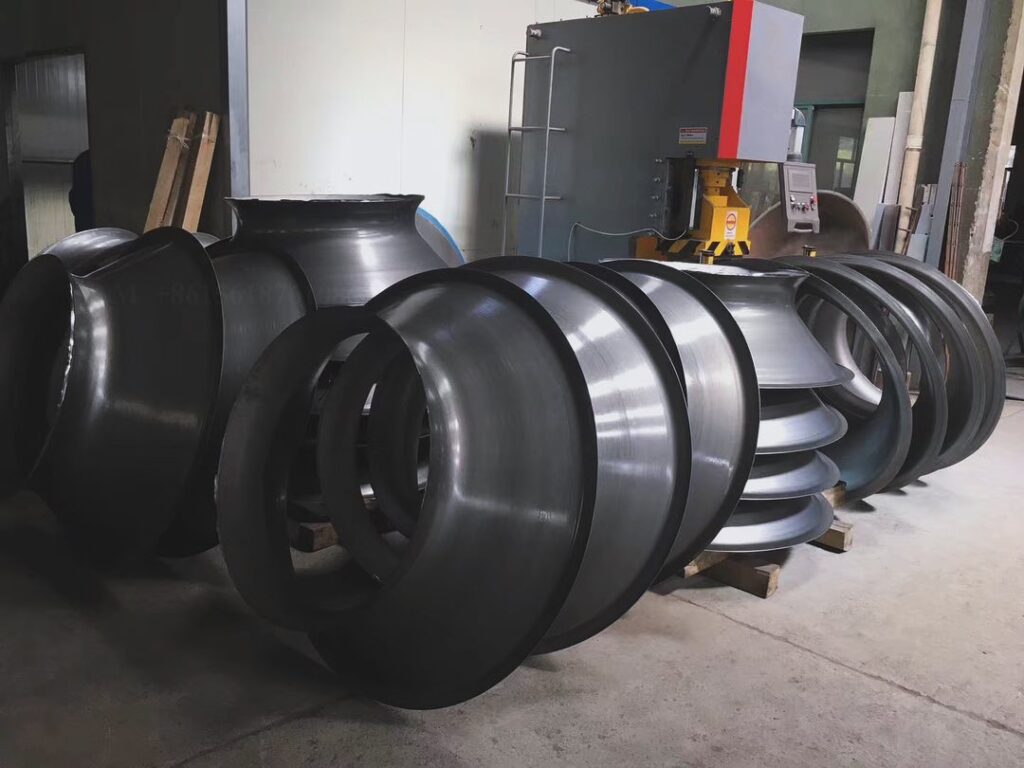
Flanschformen ist ein Verfahren, bei dem an den Rändern von Metallteilen Flansche oder Aufkantungen geformt werden. Diese Technik wird verwendet, um Bauteile zu verstärken oder um Verbindungselemente zu schaffen. Flansche können durch verschiedene Methoden wie Biegen, Walzen oder Pressen geformt werden. Flanschformen findet Anwendung in der Herstellung von Rohren, Behältern und Gehäusen, wo zusätzliche Festigkeit und robuste Verbindungen erforderlich sind.
Flanschformen, auch als Flanging bekannt, ist ein Verfahren der spanlosen Metallumformung, bei dem an den Rändern von Metallteilen Flansche oder Aufkantungen geformt werden. Diese Technik wird häufig verwendet, um Bauteile zu verstärken oder um Verbindungselemente zu schaffen. Flanschformen findet Anwendung in der Herstellung von Rohren, Behältern, Gehäusen und anderen Bauteilen, bei denen robuste Verbindungen und zusätzliche Festigkeit erforderlich sind.
Ablauf des Flanschformens
Der Prozess des Flanschformens umfasst mehrere Schritte:
- Vorbereitung: Das Metallstück wird auf eine Form oder Matrize gelegt, die den gewünschten Flanschprofilen entspricht.
- Formgebung: Ein Werkzeug oder eine Presse wird verwendet, um Druck auf den Rand des Metallstücks auszuüben. Der Rand wird dadurch nach oben oder unten gebogen, um einen Flansch zu bilden.
- Feinbearbeitung: Der geformte Flansch wird nach Bedarf kontrolliert und gegebenenfalls weiter bearbeitet, um die gewünschten Toleranzen und Oberflächenqualitäten zu erreichen.
Arten des Flanschformens
Es gibt verschiedene Techniken des Flanschformens, die je nach Anwendung und gewünschter Form des Endprodukts eingesetzt werden:
- Biegen: Das Metallstück wird entlang einer geraden Linie gebogen, um einen Flansch zu formen. Diese Methode wird häufig für einfache, lineare Flansche verwendet.
- Walzen: Das Metallstück wird durch Walzen geformt, um einen gleichmäßigen, kontinuierlichen Flansch zu erzeugen. Diese Technik wird oft für längere Flansche verwendet.
- Pressen: Ein Stempel und eine Matrize werden verwendet, um das Metallstück unter hohem Druck zu verformen und einen präzisen Flansch zu erzeugen. Diese Methode wird häufig für komplexe und präzise Flanschformen eingesetzt.
- Drehen: Bei runden oder zylindrischen Teilen wird der Flansch durch Drehen des Teils und gleichzeitiges Anlegen eines Drückwerkzeugs geformt.
Vorteile des Flanschformens
- Erhöhte Festigkeit: Durch das Bilden eines Flansches wird die strukturelle Integrität und Festigkeit des Bauteils erhöht.
- Verbindungselemente: Flansche können als Verbindungselemente verwendet werden, um Bauteile sicher zu verbinden.
- Materialeinsparung: Da das Metall lediglich verformt und nicht entfernt wird, entsteht weniger Abfall.
- Vielseitigkeit: Das Verfahren kann auf eine Vielzahl von Metallen und Legierungen angewendet werden und ermöglicht die Herstellung von komplexen Formen.
Anwendungsbereiche
Flanschformen wird in verschiedenen Industriezweigen eingesetzt, darunter:
- Automobilindustrie: Herstellung von Karosserieteilen, Auspuffanlagen und Fahrwerksteilen.
- Luft- und Raumfahrt: Produktion von Strukturteilen, Verkleidungen und Verbindungselementen.
- Bauindustrie: Fertigung von Rohren, Trägern und Verstärkungselementen.
- Haushaltsgeräte: Herstellung von Gehäusen, Behältern und Abdeckungen.
Zusammenfassung
Flanschformen (Flanging) ist ein effizientes Verfahren der spanlosen Metallumformung, das durch das Biegen oder Pressen von Metallteilen robuste und präzise Flansche erzeugt. Es bietet zahlreiche Vorteile wie erhöhte Festigkeit, vielseitige Anwendungsmöglichkeiten und Materialeinsparung. Flanschformen wird in vielen Industriezweigen zur Herstellung von hochwertigen Bauteilen mit zusätzlichen Verbindungselementen und Verstärkungen verwendet. Durch die Fähigkeit, komplexe Formen mit hoher Präzision zu erzeugen, ist das Flanschformen ein wichtiger Bestandteil der modernen Fertigungstechnik.
Spalten (Slitting)
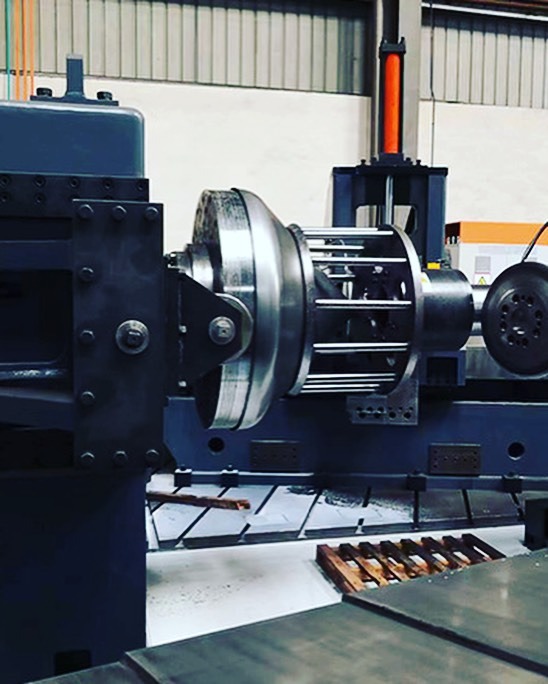
Spalten bezieht sich auf das präzise Schneiden oder Trennen von Metallblechen und -platten entlang bestimmter Linien. Dieses Verfahren ist entscheidend für die Vorbereitung von Werkstücken für nachfolgende Fertigungsschritte. Das Spalten kann durch Scheren, Stanzen oder Laserschneiden erfolgen und sorgt dafür, dass die Teile die gewünschten Abmessungen haben.
Spalten, auch bekannt als Slitting, ist ein Verfahren der spanlosen Metallumformung, bei dem Metallbleche oder -bänder entlang gerader Linien geschnitten oder getrennt werden. Dieses Verfahren wird häufig eingesetzt, um Metallmaterialien in schmalere Streifen oder bestimmte Formen zu spalten, die für weitere Bearbeitungsschritte oder den direkten Einsatz in der Produktion benötigt werden. Spalten ist ein wesentlicher Prozess in der Metallverarbeitung, insbesondere in der Herstellung von Stahl-, Aluminium- und Kupferprodukten.
Ablauf des Spaltens
Der Spaltprozess umfasst mehrere Schritte:
- Vorbereitung: Das Metallblech oder -band wird auf einer Spaltanlage positioniert. Die Spaltanlage besteht aus einer Reihe von rotierenden Messern oder Klingen, die auf die gewünschte Breite eingestellt sind.
- Zuführung: Das Metall wird durch die Spaltanlage geführt, wobei es kontinuierlich von einer Rolle abgewickelt wird.
- Schneiden: Die rotierenden Messer schneiden das Metall entlang der vorgegebenen Linien in schmale Streifen. Die Klingen sind so eingestellt, dass sie präzise Schnitte erzeugen und eine gleichmäßige Breite der Streifen sicherstellen.
- Aufwicklung: Die gespaltenen Metallstreifen werden auf Rollen aufgewickelt und für den weiteren Transport oder die Lagerung vorbereitet.
Arten des Spaltens
Es gibt verschiedene Techniken des Spaltens, die je nach Anwendung und Material eingesetzt werden:
- Längsschneiden (Longitudinal Slitting): Das Metall wird in Längsrichtung geschnitten, um schmale Streifen oder Bänder zu erzeugen. Diese Technik wird häufig für breite Metallbleche oder -bänder verwendet.
- Querschneiden (Transverse Slitting): Das Metall wird quer zur Längsrichtung geschnitten, um kürzere Abschnitte oder bestimmte Formen zu erzeugen. Diese Methode wird oft in Kombination mit Längsschneiden verwendet, um präzise Abmessungen zu erreichen.
- Kreiselscheiden (Rotary Slitting): Rotierende Klingen werden verwendet, um das Metall in einem kontinuierlichen Prozess zu schneiden. Diese Technik bietet hohe Geschwindigkeit und Präzision.
Vorteile des Spaltens
- Hohe Präzision: Spaltanlagen sind in der Lage, sehr genaue und gleichmäßige Schnitte zu erzeugen, was zu einer hohen Qualität der Endprodukte führt.
- Effizienz: Der Spaltprozess ist schnell und kann große Mengen an Material in kurzer Zeit verarbeiten.
- Flexibilität: Das Verfahren kann auf eine Vielzahl von Metallmaterialien und -stärken angewendet werden, von dünnen Folien bis hin zu dicken Blechen.
- Materialeinsparung: Durch präzises Schneiden wird Materialverschwendung minimiert, was zu Kosteneinsparungen führt.
Anwendungsbereiche
Spalten wird in verschiedenen Industriezweigen eingesetzt, darunter:
- Automobilindustrie: Herstellung von Karosserieteilen, Dichtungen und Metallprofilen.
- Bauindustrie: Produktion von Dach- und Fassadenmaterialien, Verstärkungen und Trägern.
- Elektronikindustrie: Fertigung von Leiterplatten, Gehäusen und Abschirmungen.
- Verpackungsindustrie: Herstellung von Metallfolien, Dosen und Verschlüssen.
Zusammenfassung
Spalten (Slitting) ist ein essentielles Verfahren der spanlosen Metallumformung, das Metallbleche und -bänder präzise und effizient in schmale Streifen oder bestimmte Formen schneidet. Es bietet zahlreiche Vorteile, darunter hohe Präzision, Effizienz und Materialeinsparung. Spalten findet breite Anwendung in vielen Industriezweigen und ist ein unverzichtbarer Prozess in der modernen Metallverarbeitung. Durch die Fähigkeit, verschiedene Metallmaterialien und -stärken zu verarbeiten, spielt das Spalten eine entscheidende Rolle bei der Herstellung von hochwertigen Metallprodukten.
Anwendungsbereiche
Spanlose Metallumformungsverfahren werden in einer Vielzahl von Industrien eingesetzt, darunter die Automobilindustrie, Luft- und Raumfahrt, Bauwesen, Haushaltsgeräte und Elektronik. Die Fähigkeit, präzise und robuste Metallteile effizient herzustellen, macht diese Verfahren unverzichtbar für moderne Fertigungsprozesse.
Zusammenfassung
Spanlose Metallumformung bietet zahlreiche Vorteile, darunter Materialeinsparung, verbesserte mechanische Eigenschaften und hohe Effizienz. Verfahren wie Metalldrücken, Drückwalzen, Projizieren, Flanschformen und Spalten sind wesentliche Techniken in der modernen industriellen Produktion. Sie ermöglichen die Herstellung von hochwertigen, langlebigen und funktionalen Metallteilen, die den Anforderungen von verschiedensten Anwendungen gerecht werden.
Metalldrücken
Metalldrücken, auch bekannt als Metal Spinning, ist ein Verfahren, bei dem ein flaches Metallblech auf eine rotierende Form (Dorn) gedrückt wird. Durch die Anwendung von Druck mit einem Drückwerkzeug, das manuell oder maschinell geführt wird, wird das Blech in die gewünschte Form gebracht. Metalldrücken ist besonders geeignet für die Herstellung von hohlen, rotationssymmetrischen Teilen wie Töpfen, Pfannen, Lampenschirmen und Behältern. Dieses Verfahren zeichnet sich durch seine Flexibilität aus, da es für kleine Serien sowie Prototypenfertigung verwendet werden kann, ohne dass teure Werkzeuge erforderlich sind.
Drückwalzen
Drückwalzen, auch bekannt als Flow Forming, ist ein weiteres spanloses Umformverfahren, bei dem das Metall zwischen einer rotierenden Form und Walzen geformt wird. Dieses Verfahren wird häufig für die Herstellung von zylindrischen und konischen Teilen verwendet, bei denen hohe Präzision und Festigkeit erforderlich sind. Drückwalzen ermöglicht es, dünnwandige Teile mit sehr geringen Toleranzen herzustellen. Es wird in der Luft- und Raumfahrtindustrie, der Automobilindustrie und anderen Bereichen eingesetzt, in denen leichte und dennoch starke Komponenten benötigt werden.
Projizieren
Das Projizieren oder Projizieren von Metallen ist ein Verfahren, bei dem ein Metallstück durch Schläge mit einem Hammer oder durch Druck in eine bestimmte Form gebracht wird. Dieses Verfahren wird häufig im Schmiedebereich verwendet, um komplexe Formen und Konturen zu erzeugen. Beim Projizieren wird das Metall plastisch verformt, was zu einer Verfestigung und Verbesserung der mechanischen Eigenschaften führt. Dieses Verfahren wird in der Herstellung von Werkzeugen, Maschinenbauteilen und dekorativen Elementen verwendet.
Flanschformen
Flanschformen ist ein Verfahren, bei dem an den Rändern von Metallteilen Flansche oder Aufkantungen geformt werden. Dies wird häufig zur Verstärkung von Bauteilen oder zur Vorbereitung von Verbindungselementen verwendet. Flansche können durch verschiedene Techniken wie Biegen, Walzen oder Pressen geformt werden. Dieses Verfahren wird in der Herstellung von Rohren, Behältern und Gehäusen verwendet, wo robuste Verbindungen und zusätzliche Festigkeit erforderlich sind.
Spalten
Das Spalten von Metallen bezieht sich auf das präzise Schneiden oder Trennen von Metallteilen entlang bestimmter Linien. Dieses Verfahren wird verwendet, um Metallbleche und -platten in die gewünschten Größen und Formen zu bringen. Das Spalten kann durch Scheren, Stanzen oder Laserschneiden erfolgen. Es ist ein grundlegender Schritt in vielen Fertigungsprozessen, da es sicherstellt, dass die Teile die richtigen Abmessungen haben und für die weitere Bearbeitung vorbereitet sind.
Zusammenfassung
Spanlose Metallumformungsverfahren bieten zahlreiche Vorteile, darunter die Reduzierung von Materialabfall, die Verbesserung der mechanischen Eigenschaften der Werkstücke und die Möglichkeit, komplexe Formen mit hoher Präzision zu erzeugen. Diese Verfahren sind in vielen Industrien unverzichtbar, da sie die Herstellung von hochwertigen, langlebigen und funktionalen Metallteilen ermöglichen. Metalldrücken, Drückwalzen, Projizieren, Flanschformen und Spalten sind nur einige der Techniken, die in der modernen Fertigung eingesetzt werden, um die Anforderungen an Effizienz, Qualität und Wirtschaftlichkeit zu erfüllen.
Metallbearbeitungsmaschinen
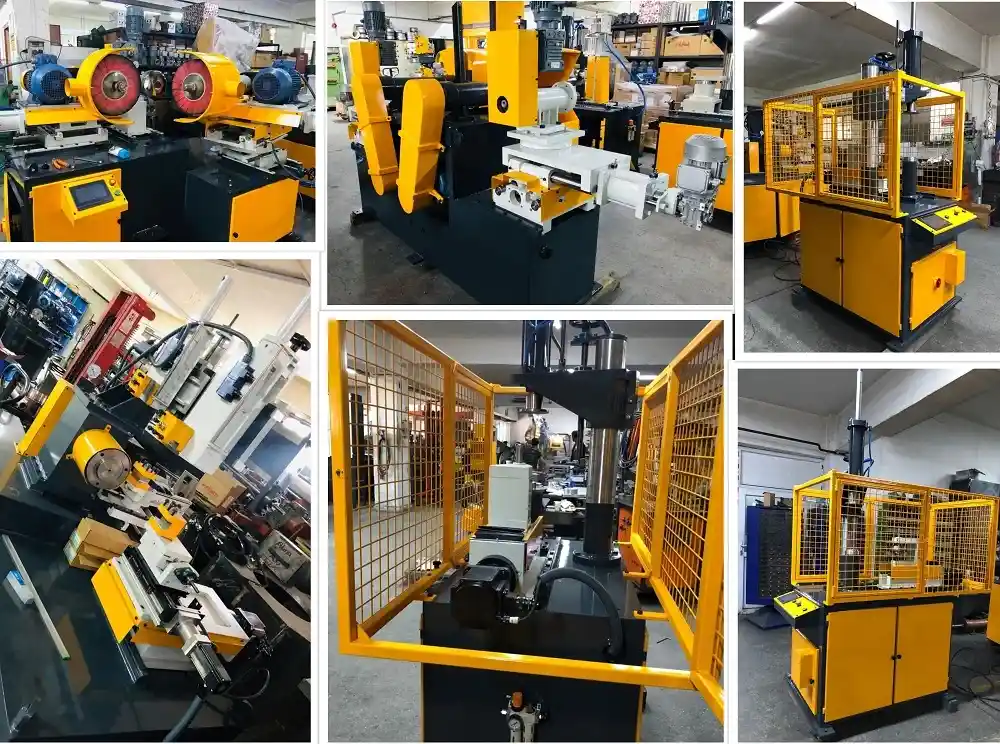
Metallbearbeitungsmaschinen wie Bördel und Beschneide Maschinen, Flanschmaschinen, Beschneide und Bördelmaschinen, Umformtechnik, Rohrbiegemaschinen, Bandsäge für Metall, Hydraulische Horizontalpresse, Kantenschneide-Bördelmaschine, Kantenbördelmaschine, Entgratungsmaschine, Innen- und Außenpoliermaschine für Edelstahltöpfe, Kreisschneidemaschine, Profilbiegemaschine und Rundschweißmaschine
Maßgeschneiderte Skalierung für spezifische Anwendungen
Die automatisierte Herstellung von Behältern, Fässern und Kesseln wird durch unsere Lösungen exakt auf das jeweilige Einsatzgebiet und die gewünschte Ausbringung angepasst. Dabei bieten wir sowohl lineare Lösungen als auch Inselkonzepte an, die eine bedarfsorientierte Automation ermöglichen. Spezielle Kantenvorbereitung für das Laserschweißen sowie wirtschaftliche Rüstkonzepte bis hin zur Fertigung „Just-in-Sequence“ sind Teil unseres Leistungsspektrums. Wir kombinieren Standard- und Sondermaschinen und bieten Ferndiagnose über LAN, WLAN oder GSM an, ergänzt durch umfassende Dokumentation gemäß CE-Richtlinien für die Gesamtanlage.
Unser Konzept
EMS entwickelt und fertigt Maschinen und Anlagen für die automatisierte Herstellung von Behältern in großem Maßstab. Alle Arbeitsschritte, von der Vorbereitung bis zur Fertigung, werden dabei aus einer Hand angeboten. Unsere erprobten Standardkomponenten sind perfekt aufeinander abgestimmt und können nahtlos mit Robotern kombiniert werden, um leistungsfähige Fertigungseinrichtungen zu schaffen.
Flexible Präzisionsfertigung
Unsere Fertigungslinien ermöglichen eine einfache Umstellung auf verschiedene Längen, Durchmesser, Formen und Bearbeitungen durch Programmwechsel. Dabei werden zahlreiche Einzelschritte wie Beschneiden, Formen, Stanzen, Fügen, Montieren, Schweißen und Prüfen automatisch und mit höchster Präzision an die jeweilige Aufgabe angepasst. Besonderes Augenmerk legen wir auf die Kantenvorbereitung für den Schweißprozess, um eine herausragende Prozesssicherheit und minimale Ausschussquoten zu gewährleisten.
Maschinenprogramm für die Metallbearbeitung
Unsere Metallbearbeitungsmaschinen sind:
- Rohrbiegemaschine
- Horizontale Presse
- Bandsäge für Metall
- Profilbiegemaschine
- Tiefziehpresse
- Rundschweißmaschine
- Kantenschneide-Bördelmaschine
- Topf- und Pfannenpoliermaschine
- Poliermaschine für flache Oberflächen
Besteck-Produktionslinie: Eine Besteck-Produktionslinie ist eine Art Maschine, die Besteck in einem kontinuierlichen Prozess herstellt. Es umfasst verschiedene Arten von Maschinen wie den Messerschleifer, den Messerschärfer und den Klingenpolierer.
Kochgeschirr-Herstellungsmaschine: Eine Kochgeschirr-Herstellungsmaschine ist eine Art Maschine, die Kochgeschirr in einem kontinuierlichen Prozess herstellt. Es umfasst verschiedene Arten von Maschinen wie den Topfmacher, den Pfannenmacher und den Wokmacher.
Küchengeschirr-Produktionsmaschine: Eine Küchengeschirr-Produktionsmaschine ist eine Art Maschine, die Küchengeschirr in einem kontinuierlichen Prozess herstellt. Es umfasst verschiedene Arten von Maschinen wie Maschinen zur Herstellung von Teekesseln, Produktionslinien für Besteck, Produktionslinien für Töpfe und Pfannen
Wir entwerfen, fertigen und montieren komplette Produktionslinien für Kochgeschirr, Küchengeschirr, Hotelgeschirr und Besteck sowie einzelne Maschinen für einen bestimmten Zweck