Eine Rundschweißmaschine kann Teile mit runder Form schweißen. Der Zweck der Operation hier ist es, eine saubere Schweißnaht auf einer runden Oberfläche zu haben
Eine Rundschweißmaschine oder Kreisförmige Schweißmaschine ist eine Maschine, die zum Schweißen von Rohren oder anderen zylindrischen Werkstücken verwendet wird. Sie besteht in der Regel aus einem Grundrahmen, einem Schweißkopf und einem Antriebssystem.
Der Schweißkopf enthält die Schweißelektrode, die das Werkstück erhitzt und den Schweißprozess einleitet. Der Antriebsmechanismus bewegt den Schweißkopf entlang des Werkstücks, um einen kontinuierlichen Schweißnaht zu erzeugen.
Rundschweißmaschinen werden in einer Vielzahl von Anwendungen eingesetzt, darunter:
- Bauwesen: Rundschweißmaschinen werden im Bauwesen verwendet, um Rohre für Wasser-, Gas- und Abwassersysteme zu schweißen.
- Industrie: Rundschweißmaschinen werden in der Industrie verwendet, um Rohre für verschiedene Zwecke zu schweißen, z. B. für die Herstellung von Möbeln, Rohrleitungen und anderen Produkten.
- Automobilindustrie: Rundschweißmaschinen werden in der Automobilindustrie verwendet, um Rohre für Autokarosserien und andere Komponenten zu schweißen.
Es gibt verschiedene Arten von Rundschweißmaschinen, die jeweils ihre eigenen Vor- und Nachteile haben. Die gebräuchlichsten Arten von Rundschweißmaschinen sind:
- Manuelle Rundschweißmaschinen: Manuelle Rundschweißmaschinen werden von einem Bediener mit einer Handkurbel oder einem anderen manuellen Gerät bedient. Sie sind in der Regel kostengünstig und einfach zu bedienen, aber sie sind auch langsam und weniger präzise als automatische Rundschweißmaschinen.
- Automatische Rundschweißmaschinen: Automatische Rundschweißmaschinen werden durch einen Motor oder einen anderen Antrieb angetrieben. Sie sind in der Regel schneller und präziser als manuelle Rundschweißmaschinen, aber sie sind auch teurer und komplexer zu bedienen.
Automatische Rundschweißmaschinen
Automatische Rundschweißmaschinen sind Schweißmaschinen, die zum Schweißen von Rohren und anderen runden Werkstücken verwendet werden. Sie sind in der Regel mit einem Roboterarm ausgestattet, der den Schweißbrenner führt.
Automatische Rundschweißmaschinen werden in einer Vielzahl von Branchen eingesetzt, darunter die Automobilindustrie, die Luft- und Raumfahrtindustrie und die Bauindustrie. Sie werden zum Schweißen von Rohrleitungen, Tanks, Behältern und anderen runden Bauteilen verwendet.
Automatische Rundschweißmaschinen bieten eine Reihe von Vorteilen gegenüber manuellen Schweißverfahren, darunter:
- Hohe Produktivität: Automatische Rundschweißmaschinen können mit hohen Geschwindigkeiten arbeiten und so die Produktionsrate erhöhen.
- Hohe Qualität: Automatische Rundschweißmaschinen können gleichbleibende, hochwertige Schweißnähte produzieren.
- Sicherheit: Automatische Rundschweißmaschinen können die Sicherheit der Schweißer verbessern, indem sie das Risiko von Verletzungen durch Stromschlag oder Verbrennungen verringern.
Die wichtigsten Komponenten einer automatischen Rundschweißmaschine sind:
- Schweißbrenner: Der Schweißbrenner ist das Werkzeug, mit dem das Schweißgut geschmolzen wird.
- Roboterarm: Der Roboterarm führt den Schweißbrenner.
- Schutzgasanlage: Die Schutzgasanlage liefert das Schutzgas, das das Schweißgut vor Oxidation und Verunreinigungen schützt.
- Steuerung: Die Steuerung steuert den Schweißprozess.
Die Art des verwendeten Schweißverfahrens hängt vom Werkstoff ab, der geschweißt werden soll. Die häufigsten Schweißverfahren für automatische Rundschweißmaschinen sind:
- Metall-Inertgasschweißen (MIG): MIG-Schweißen ist ein vielseitiges Verfahren, das zum Schweißen einer Vielzahl von Werkstoffen verwendet werden kann.
- Wolfram-Inertgasschweißen (WIG): WIG-Schweißen ist ein Präzisionsschweißen, das zum Schweißen dünner Werkstoffe verwendet wird.
Automatische Rundschweißmaschinen können mit einer Vielzahl von Sensoren ausgestattet sein, die die Schweißnahtqualität überwachen. Diese Sensoren können dazu beitragen, die Qualität der Schweißnähte zu verbessern und die Ausschussrate zu verringern.
Automatische Rundschweißmaschinen sind spezielle Schweißanlagen, die dazu entwickelt wurden, das Rundschweißen von Werkstücken zu automatisieren. Diese Maschinen kommen in verschiedenen Branchen und Anwendungen zum Einsatz, insbesondere wenn eine hohe Produktionskapazität und gleichbleibende Schweißqualität erforderlich sind. Hier sind einige wichtige Aspekte automatischer Rundschweißmaschinen:
- Anwendungen:
- Automatische Rundschweißmaschinen werden oft in der Fertigung von Rohrleitungen, zylindrischen Teilen, Tanks, Behältern, und anderen rundförmigen Bauteilen eingesetzt.
- Vorteile:
- Hohe Produktivität: Automatisierte Maschinen ermöglichen eine kontinuierliche und effiziente Produktion, was zu höheren Durchsatzraten führt.
- Konsistente Qualität: Durch die Automatisierung wird eine gleichbleibende Schweißqualität erreicht, da die Schweißparameter präzise gesteuert werden können.
- Reduzierte Arbeitskosten: Automatisierte Prozesse minimieren den Bedarf an manueller Arbeitskraft, insbesondere bei wiederholenden Aufgaben.
- Komponenten:
- Schweißkopf: Der Schweißkopf ist der Teil der Maschine, der den Schweißprozess durchführt. Dieser kann je nach Anwendung variieren und kann unterschiedliche Schweißmethoden (z.B., Lichtbogen- oder Widerstandsschweißen) verwenden.
- Drehvorrichtung: Automatische Rundschweißmaschinen sind oft mit einer Drehvorrichtung ausgestattet, um das Werkstück während des Schweißens zu rotieren.
- Steuerungseinheit: Eine Steuerungseinheit ermöglicht die Programmierung und Überwachung des Schweißprozesses. Dies kann die Einstellung von Schweißparametern, die Steuerung der Drehgeschwindigkeit und andere Funktionen umfassen.
- Programmierung und Flexibilität:
- Automatische Rundschweißmaschinen können in der Regel programmiert werden, um verschiedene Werkstücke zu schweißen. Dies bietet Flexibilität in der Produktion und ermöglicht die Anpassung an unterschiedliche Anforderungen.
- Sicherheit:
- Sicherheitsvorkehrungen sind wichtig, um den sicheren Betrieb automatischer Rundschweißmaschinen zu gewährleisten. Dies kann Sicherheitssensoren, Notausschalter und andere Schutzmaßnahmen umfassen.
Es ist wichtig zu beachten, dass die genauen Merkmale und Funktionen automatischer Rundschweißmaschinen je nach Hersteller und Modell variieren können. Bei der Auswahl einer solchen Maschine ist es entscheidend, die spezifischen Anforderungen der Anwendung, die gewünschten Schweißmethoden und die geforderten Standards zu berücksichtigen. Zudem ist die Schulung des Bedienpersonals für den sicheren und effizienten Betrieb solcher Maschinen von großer Bedeutung.
Die Funktionsweise einer Rundschweißmaschine hängt von der Art der Maschine ab. Manuelle Rundschweißmaschinen arbeiten in der Regel mit einem Schweißbrenner, der das Werkstück erhitzt und den Schweißprozess einleitet. Automatische Rundschweißmaschinen arbeiten in der Regel mit einem Schweißroboter, der den Schweißprozess automatisch durchführt.
Die Schweißqualität hängt von einer Reihe von Faktoren ab, darunter:
- Schweißverfahren: Das Schweißverfahren bestimmt die Art des Schweißnahts, der erzeugt wird.
- Schweißparameter: Die Schweißparameter bestimmen die Eigenschaften des Schweißnahts, z. B. die Dicke und die Festigkeit.
- Rohrmaterial: Das Rohrmaterial bestimmt die Eignung des Schweißverfahrens und der Schweißparameter.
Bei der Auswahl einer Rundschweißmaschine ist es wichtig, die Anforderungen der Anwendung zu berücksichtigen. So muss die Maschine für das Schweißverfahren, das Rohrmaterial und das Produktionsvolumen geeignet sein.
Hier sind einige Tipps für das Schweißen mit einer Rundschweißmaschine:
- Befolgen Sie die Anweisungen des Herstellers der Rundschweißmaschine.
- Verwenden Sie geeignete Schutzausrüstung, z. B. Schutzhandschuhe und Schutzbrille.
- Üben Sie das Schweißen mit einer Rundschweißmaschine, bevor Sie sie für eine Anwendung verwenden.
Mit etwas Übung können Sie mit einer Rundschweißmaschine Rohre oder andere zylindrische Werkstücke in einer Vielzahl von Anwendungen schweißen.
Ein oder zwei Schweißpositionierer führen die Rundschweißung durch. Der Schweißpositionierer ist ein Gerät, das das Teil festhält und es mit einer erforderlichen Drehzahl dreht. Diese Drehbewegung kann in 3 Achsen erfolgen.
Beim Rundschweißen wird das runde Teil unter dem Schweißbrenner positioniert. Das MIG- oder WIG-Schweißgerät beginnt mit dem Schweißen. Ein MIG-Schweißgerät ist eine Schweißmaschine, die einen Metalldraht verwendet, um die Teile zu schweißen. In einer MIG-Schweißmaschine (Metal Inert Gas) kann die Anwendung auf verschiedenen Metallen wie Aluminium, Edelstahl und Stahl und auf jeder Dicke von 26-Gauge-Blech bis hin zu schweren Strukturplatten erfolgen.
Der MIG-Schweißzuführungsdraht fungiert außerdem nicht nur als Elektrode, sondern auch als Zusatzwerkstoff. Die Blechdicke spielt hier also keine Rolle, da der Zuleitungsdraht des MIG-Schweißbrenners den Zwischenraum problemlos ausfüllen kann. Umgekehrt hat das WIG-Schweißen (Wolfram-Inertgas) eine bessere Oberflächenwirkung und eine höhere Qualität.
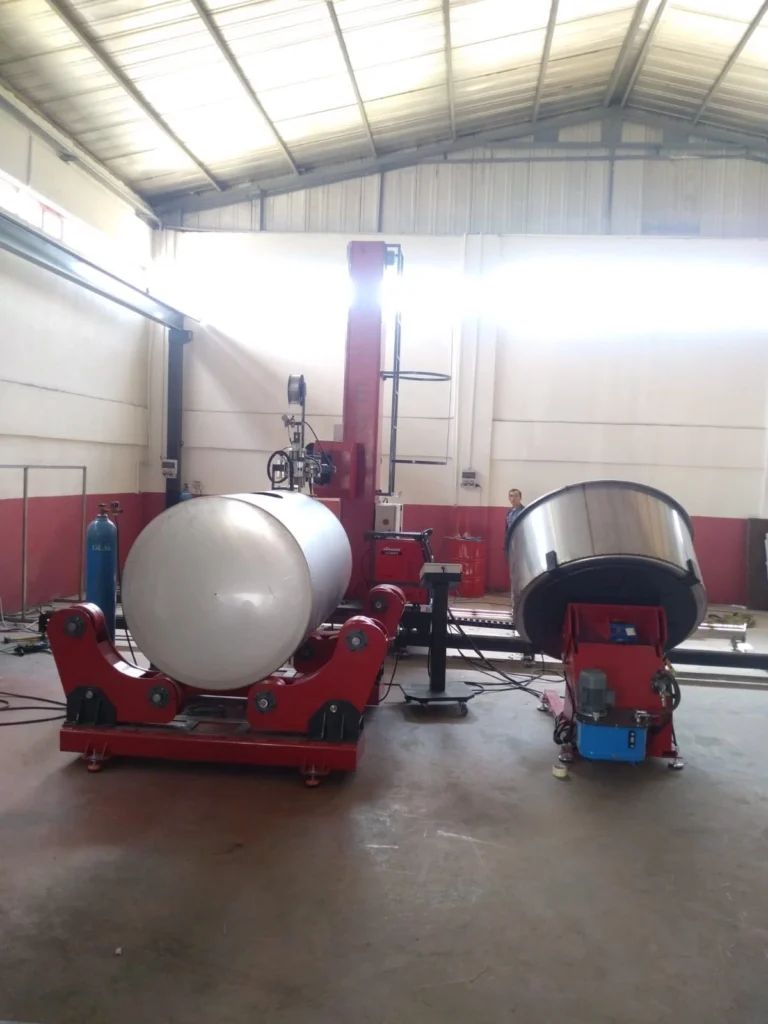
Eine Rundschweißmaschine kann horizontal oder vertikal sein. Eine Horizontal-Rundschweißmaschine kann auch als Rohrschweißautomat bezeichnet werden. Hier wird das Rundteil horizontal verlegt und durch die Rohrrotatoren gedreht. Ein Rohrrotator ist ein Werkzeug, das das Teil festhält und um seine eigene Achse dreht, während der Schweißbrenner die Oberfläche des Teils berührt und mit dem Schweißen beginnt. Die Drehmaschine kann dabei auf den Rohrspitzen oder unten auf dem Schweißbett stehen.
Arten von Schweißmaschinen
Schweißmaschinen werden verwendet, um zwei oder mehr Metallteile miteinander zu verbinden. Es gibt verschiedene Arten von Schweißmaschinen, die jeweils ihre eigenen Vor- und Nachteile haben.
Die gebräuchlichsten Arten von Schweißmaschinen sind:
- Elektrodenschweißmaschinen: Elektrodenschweißmaschinen verwenden eine Elektrode, die das Werkstück erhitzt und den Schweißprozess einleitet. Die Elektrode wird von einem Schweißbrenner geführt und schmilzt beim Schweißen ab. Elektrodenschweißmaschinen sind in der Regel kostengünstig und einfach zu bedienen.
- MIG-/MAG-Schweißmaschinen: MIG-/MAG-Schweißmaschinen verwenden ein Drahtelektrode, die das Werkstück erhitzt und den Schweißprozess einleitet. Der Draht wird von einem Drahtvorschubgerät zugeführt und schmilzt beim Schweißen ab. MIG-/MAG-Schweißmaschinen sind in der Regel schneller und präziser als Elektrodenschweißmaschinen.
- TIG-Schweißmaschinen: TIG-Schweißmaschinen verwenden eine Wolframelektrode, die das Werkstück erhitzt und den Schweißprozess einleitet. Die Elektrode wird von einem Schweißbrenner geführt und schmilzt nicht ab. TIG-Schweißmaschinen erzeugen sehr saubere Schweißnähte und sind daher für Anwendungen mit hohen Anforderungen an die Qualität geeignet.
Elektrodenschweißmaschinen
Elektrodenschweißmaschinen sind Schweißmaschinen, die zum Schweißen mit einer Elektrode verwendet werden. Die Elektrode ist ein metallener Draht, der beim Schweißen abschmilzt und das Schweißgut bildet.
Elektrodenschweißmaschinen werden in einer Vielzahl von Branchen eingesetzt, darunter die Automobilindustrie, die Bauindustrie und die Metallverarbeitung. Sie werden zum Schweißen von Stahl, Aluminium und anderen Metallen verwendet.
Es gibt zwei Haupttypen von Elektrodenschweißmaschinen:
- Handelektrodenschweißmaschinen: Handelektrodenschweißmaschinen sind die am häufigsten verwendeten Elektrodenschweißmaschinen. Sie werden von einem Schweißer mit der Hand bedient.
- Automatische Elektrodenschweißmaschinen: Automatische Elektrodenschweißmaschinen werden mit einem Roboterarm betrieben. Sie werden zum Schweißen von großen oder komplexen Bauteilen verwendet.
Die wichtigsten Komponenten einer Elektrodenschweißmaschine sind:
- Schweißstromquelle: Die Schweißstromquelle erzeugt den Strom, der zum Schmelzen der Elektrode verwendet wird.
- Schweißbrenner: Der Schweißbrenner hält die Elektrode und führt sie zum Werkstück.
- Schutzgasanlage: Die Schutzgasanlage liefert das Schutzgas, das das Schweißgut vor Oxidation und Verunreinigungen schützt.
Die Art des verwendeten Schweißstroms hängt vom Werkstoff ab, der geschweißt werden soll. Die häufigsten Schweißströme für Elektrodenschweißmaschinen sind:
- Wechselstrom (AC): Wechselstrom wird zum Schweißen von Aluminium und anderen Nichteisenmetallen verwendet.
- Gleichstrom (DC): Gleichstrom wird zum Schweißen von Stahl und anderen Eisenmetallen verwendet.
Die Art der verwendeten Elektrode hängt ebenfalls vom Werkstoff ab, der geschweißt werden soll. Es gibt eine Vielzahl von Elektrodentypen mit unterschiedlichen Eigenschaften.
Elektrodenschweißmaschinen bieten eine Reihe von Vorteilen, darunter:
- Flexibilität: Elektrodenschweißmaschinen können zum Schweißen einer Vielzahl von Werkstoffen verwendet werden.
- Einfachheit: Elektrodenschweißmaschinen sind relativ einfach zu bedienen.
- Kostengünstig: Elektrodenschweißmaschinen sind im Vergleich zu anderen Schweißmaschinen relativ kostengünstig.
Elektrodenschweißmaschinen bieten jedoch auch einige Nachteile, darunter:
- Geruchentwicklung: Elektrodenschweißmaschinen erzeugen Rauch, der Atemwegsprobleme verursachen kann.
- Schmutzentwicklung: Elektrodenschweißmaschinen erzeugen Schmutz, der die Arbeitsumgebung verschmutzen kann.
- Risiko von Verbrennungen: Elektrodenschweißmaschinen können Verbrennungen verursachen, wenn der Schweißer nicht vorsichtig ist.
Sicherheitshinweise beim Elektrodenschweißen:
- Tragen Sie geeignete persönliche Schutzausrüstung (PSA), einschließlich eines Schweißhelms, Handschuhen, Stiefeln und einer Schutzbrille.
- Sorgen Sie für eine gute Belüftung des Schweißbereichs.
- Schweißen Sie nicht in der Nähe von brennbaren Materialien.
- Berühren Sie die Elektrode oder die Schweißnaht nicht mit bloßen Händen.
- Seien Sie sich der potenziellen Gefahr eines elektrischen Schlags bewusst.
Elektrodenschweißmaschinen, auch als Lichtbogenschweißmaschinen oder Elektroschweißgeräte bezeichnet, sind Werkzeuge, die für das Lichtbogenschweißen mit Elektroden verwendet werden. Das Elektrodenschweißen ist ein gängiger Schweißprozess, der häufig in der Metallverarbeitung und Konstruktion eingesetzt wird. Hier sind einige grundlegende Informationen zu Elektrodenschweißmaschinen:
- Funktionsprinzip:
- Elektrodenschweißmaschinen erzeugen einen Lichtbogen zwischen einer Elektrode und dem Werkstück. Dieser Lichtbogen erzeugt hohe Temperaturen und schmilzt sowohl die Elektrode als auch das Werkstück, wodurch eine Schweißverbindung entsteht.
- Komponenten:
- Transformator oder Inverter: Elektrodenschweißmaschinen können auf Transformator- oder Invertertechnologie basieren. Invertergeräte sind oft kompakter und leichter als Transformatorgeräte.
- Stromquelle: Die Stromquelle erzeugt den elektrischen Strom, der für das Schweißen benötigt wird.
- Elektrodenhalter und Masseklemme: Der Elektrodenhalter hält die Schweißelektrode, während die Masseklemme am Werkstück befestigt wird, um den elektrischen Stromkreis zu schließen.
- Regel- und Steuereinheit: Moderne Schweißmaschinen verfügen oft über Einstellungen zur Steuerung von Stromstärke, Spannung und anderen Schweißparametern.
- Arbeitsweise:
- Der Bediener wählt die geeignete Elektrode und passt die Schweißparameter an, darunter Stromstärke und Spannung.
- Die Elektrode wird in den Elektrodenhalter eingesetzt, und die Masseklemme wird am Werkstück befestigt.
- Durch das Betätigen des Schweißschalters wird der Lichtbogen erzeugt, und der Bediener bewegt die Elektrode über das Werkstück, um die Schweißnaht zu erzeugen.
- Anwendungen:
- Elektrodenschweißmaschinen werden häufig für Reparaturarbeiten, Bauarbeiten, Metallverarbeitung, Schiffs- und Brückenbau sowie in vielen anderen industriellen Anwendungen eingesetzt.
- Vorteile:
- Relativ einfach zu bedienen und kostengünstig in der Anschaffung.
- Gut geeignet für Arbeiten im Freien und auf Baustellen, da sie weniger anfällig für Wind und äußere Bedingungen sind als andere Schweißverfahren.
- Nachteile:
- Einige Rauch- und Spritzpartikel können bei diesem Schweißprozess entstehen.
- Es erfordert eine gewisse Fertigkeit und Erfahrung, um qualitativ hochwertige Schweißnähte zu erzeugen.
Beim Arbeiten mit Elektrodenschweißmaschinen ist es wichtig, die Sicherheitsvorschriften zu beachten, einschließlich des Tragens von persönlicher Schutzausrüstung wie Schweißhelm, Schutzbrille und Schutzkleidung. Zudem sollten die spezifischen Anweisungen des Herstellers für die jeweilige Schweißmaschine befolgt werden.
MIG-/MAG-Schweißmaschinen
MIG-/MAG-Schweißmaschinen sind Schweißmaschinen, die zum Schweißen mit einem Drahtelektrodenvorschub verwendet werden. Der Drahtelektrode wird durch die Schweißmaschine geführt und mit dem Grundwerkstoff verschmolzen. Ein Schutzgas, in der Regel Argon oder Kohlendioxid, wird verwendet, um das Schweißgut vor Oxidation und Verunreinigungen zu schützen.
MIG-/MAG-Schweißmaschinen werden in einer Vielzahl von Branchen eingesetzt, darunter die Automobilindustrie, die Luft- und Raumfahrtindustrie und die Bauindustrie. Sie werden zum Schweißen von Stahl, Aluminium, Edelstahl und anderen Metallen verwendet.
MIG-/MAG-Schweißmaschinen bieten eine Reihe von Vorteilen, darunter:
- Produktivität: MIG-/MAG-Schweißmaschinen können hohe Schweißgeschwindigkeiten ermöglichen.
- Qualität: MIG-/MAG-Schweißmaschinen können hochwertige Schweißnähte produzieren.
- Flexibilität: MIG-/MAG-Schweißmaschinen können zum Schweißen einer Vielzahl von Werkstoffen verwendet werden.
MIG-/MAG-Schweißmaschinen werden in zwei Haupttypen unterteilt:
- Handgeführte MIG-/MAG-Schweißmaschinen: Handgeführte MIG-/MAG-Schweißmaschinen sind die am häufigsten verwendeten MIG-/MAG-Schweißmaschinen. Sie werden von einem Schweißer mit der Hand bedient.
- Automatische MIG-/MAG-Schweißmaschinen: Automatische MIG-/MAG-Schweißmaschinen werden mit einem Roboterarm betrieben. Sie werden zum Schweißen von großen oder komplexen Bauteilen verwendet.
Die wichtigsten Komponenten einer MIG-/MAG-Schweißmaschine sind:
- Schweißstromquelle: Die Schweißstromquelle erzeugt den Strom, der zum Schmelzen der Drahtelektrode verwendet wird.
- Schweißbrenner: Der Schweißbrenner hält die Drahtelektrode und führt sie zum Werkstück.
- Schutzgasanlage: Die Schutzgasanlage liefert das Schutzgas, das das Schweißgut vor Oxidation und Verunreinigungen schützt.
Die Art des verwendeten Schweißstroms hängt vom Werkstoff ab, der geschweißt werden soll. Die häufigsten Schweißströme für MIG-/MAG-Schweißmaschinen sind:
- Wechselstrom (AC): Wechselstrom wird zum Schweißen von Aluminium und anderen Nichteisenmetallen verwendet.
- Gleichstrom (DC): Gleichstrom wird zum Schweißen von Stahl und anderen Eisenmetallen verwendet.
Die Art des verwendeten Drahtelektrodenmaterials hängt ebenfalls vom Werkstoff ab, der geschweißt werden soll. Es gibt eine Vielzahl von Drahtelektrodentypen mit unterschiedlichen Eigenschaften.
Sicherheitshinweise beim MIG-/MAG-Schweißen:
- Tragen Sie geeignete persönliche Schutzausrüstung (PSA), einschließlich eines Schweißhelms, Handschuhen, Stiefeln und einer Schutzbrille.
- Sorgen Sie für eine gute Belüftung des Schweißbereichs.
- Schweißen Sie nicht in der Nähe von brennbaren Materialien.
- Berühren Sie die Drahtelektrode oder die Schweißnaht nicht mit bloßen Händen.
- Seien Sie sich der potenziellen Gefahr eines elektrischen Schlags bewusst.
MIG (Metal Inert Gas) und MAG (Metal Active Gas) sind zwei verwandte Schweißverfahren, die häufig mit Schweißmaschinen betrieben werden. Beide Verfahren verwenden einen Draht als Elektrode und ein Schutzgas, um den Lichtbogen zu stabilisieren und das geschmolzene Metall vor atmosphärischer Kontamination zu schützen. Hier sind einige grundlegende Informationen zu MIG-/MAG-Schweißmaschinen:
- Funktionsprinzip:
- MIG-Schweißen verwendet inerte Gase wie Argon oder Helium als Schutzgas, während MAG-Schweißen aktive Gase wie Kohlendioxid oder Mischungen aus Argon und CO2 verwendet.
- Ein Drahtelektrode wird durch die Schweißpistole zugeführt. Der Draht wird durch den Lichtbogen geschmolzen, und die entstehende Schmelze verbindet die zu schweißenden Teile.
- Komponenten:
- Stromquelle: Die Stromquelle erzeugt den elektrischen Strom für den Lichtbogen.
- Schweißpistole: Die Schweißpistole enthält den Drahtvorschubmechanismus und ermöglicht die Steuerung des Schweißprozesses durch den Bediener.
- Gasflasche oder -zufuhr: Je nach Verfahren wird entweder ein inertes oder aktives Schutzgas verwendet. Dieses Gas wird entweder aus einer Gasflasche oder einem Gasversorgungssystem zugeführt.
- Drahtvorschubsystem: Ein Mechanismus, der den Schweißdraht kontinuierlich durch die Schweißpistole fördert.
- Arbeitsweise:
- Der Bediener wählt den geeigneten Draht und das passende Schutzgas basierend auf den Anforderungen der Anwendung.
- Durch das Betätigen des Schweißschalters wird der Drahtelektrode durch die Schweißpistole zugeführt, und der Lichtbogen wird zwischen dem Draht und dem Werkstück erzeugt.
- Das geschmolzene Metall aus der Elektrode füllt den Spalt zwischen den zu verbindenden Teilen aus und bildet die Schweißnaht.
- Anwendungen:
- MIG-/MAG-Schweißmaschinen werden in verschiedenen Industriebereichen eingesetzt, darunter Fahrzeugbau, Schiffsbau, Metallverarbeitung, Bauwesen und allgemeiner Metallbau.
- Sie eignen sich gut für das Schweißen von dünnen bis mitteldicken Materialien.
- Vorteile:
- Hohe Schweißgeschwindigkeit und Effizienz.
- Geringe Rauch- und Spritzpartikel im Vergleich zu anderen Schweißverfahren.
- Geeignet für verschiedene Materialien, einschließlich Stahl, Edelstahl und Aluminium.
- Nachteile:
- Erfordert oft eine externe Gaszufuhr, was die Mobilität beeinträchtigen kann.
- Initialkosten für Ausrüstung und Gas können höher sein als bei einigen anderen Schweißverfahren.
Beim Arbeiten mit MIG-/MAG-Schweißmaschinen ist es wichtig, die spezifischen Anweisungen des Herstellers zu beachten und alle Sicherheitsvorkehrungen zu treffen, einschließlich der Verwendung von Schutzkleidung, einer Schweißhaube und anderer persönlicher Schutzausrüstung. Schulung und Erfahrung sind entscheidend, um qualitativ hochwertige Schweißnähte zu erzeugen.
TIG-Schweißmaschinen
TIG-Schweißmaschinen, auch als Wolfram-Inertgas-Schweißmaschinen (GTAW) bezeichnet, sind Schweißmaschinen, die zum Schweißen mit einer nicht abschmelzenden Wolframelektrode verwendet werden. Das Schweißgut wird aus einem separaten Draht zugeführt und mit der Wolframelektrode verschmolzen. Ein Schutzgas, in der Regel Argon, wird verwendet, um das Schweißgut vor Oxidation und Verunreinigungen zu schützen.
TIG-Schweißmaschinen werden in einer Vielzahl von Branchen eingesetzt, darunter die Luft- und Raumfahrtindustrie, die Elektronikindustrie und die Metallverarbeitung. Sie werden zum Schweißen von dünnen Blechen, Rohren und anderen komplexen Bauteilen verwendet.
TIG-Schweißmaschinen bieten eine Reihe von Vorteilen, darunter:
- Qualität: TIG-Schweißmaschinen können hochwertige Schweißnähte mit hoher Festigkeit und Duktilität produzieren.
- Flexibilität: TIG-Schweißmaschinen können zum Schweißen einer Vielzahl von Werkstoffen verwendet werden, einschließlich Stahl, Aluminium, Edelstahl und Kupfer.
- Präzision: TIG-Schweißmaschinen sind präzise und können zum Schweißen von dünnen Blechen und anderen komplexen Bauteilen verwendet werden.
TIG-Schweißmaschinen werden in zwei Haupttypen unterteilt:
- Handgeführte TIG-Schweißmaschinen: Handgeführte TIG-Schweißmaschinen sind die am häufigsten verwendeten TIG-Schweißmaschinen. Sie werden von einem Schweißer mit der Hand bedient.
- Automatische TIG-Schweißmaschinen: Automatische TIG-Schweißmaschinen werden mit einem Roboterarm betrieben. Sie werden zum Schweißen von großen oder komplexen Bauteilen verwendet.
Die wichtigsten Komponenten einer TIG-Schweißmaschine sind:
- Schweißstromquelle: Die Schweißstromquelle erzeugt den Strom, der zum Schmelzen des Schweißguts verwendet wird.
- Schweißbrenner: Der Schweißbrenner hält die Wolframelektrode und führt sie zum Werkstück.
- Schutzgasanlage: Die Schutzgasanlage liefert das Schutzgas, das das Schweißgut vor Oxidation und Verunreinigungen schützt.
Die Art des verwendeten Schweißstroms hängt vom Werkstoff ab, der geschweißt werden soll. Die häufigsten Schweißströme für TIG-Schweißmaschinen sind:
- Wechselstrom (AC): Wechselstrom wird zum Schweißen von Aluminium und anderen Nichteisenmetallen verwendet.
- Gleichstrom (DC): Gleichstrom wird zum Schweißen von Stahl und anderen Eisenmetallen verwendet.
Die Art des verwendeten Wolframelektrodenmaterials hängt ebenfalls vom Werkstoff ab, der geschweißt werden soll. Es gibt eine Vielzahl von Wolframelektrodentypen mit unterschiedlichen Eigenschaften.
Sicherheitshinweise beim TIG-Schweißen:
- Tragen Sie geeignete persönliche Schutzausrüstung (PSA), einschließlich eines Schweißhelms, Handschuhen, Stiefeln und einer Schutzbrille.
- Sorgen Sie für eine gute Belüftung des Schweißbereichs.
- Schweißen Sie nicht in der Nähe von brennbaren Materialien.
- Berühren Sie die Wolframelektrode oder die Schweißnaht nicht mit bloßen Händen.
- Seien Sie sich der potenziellen Gefahr eines elektrischen Schlags bewusst.
TIG (Wolfram-Inertgas)-Schweißmaschinen sind Werkzeuge, die für das TIG-Schweißverfahren verwendet werden. TIG-Schweißen ist ein Lichtbogenschweißverfahren, bei dem ein nicht-schmelzender Wolfram-Elektrodenstab verwendet wird, um den Lichtbogen zu erzeugen. Es wird auch als GTAW (Gas Tungsten Arc Welding) bezeichnet. Hier sind einige grundlegende Informationen zu TIG-Schweißmaschinen:
- Funktionsprinzip:
- Eine TIG-Schweißmaschine erzeugt einen Lichtbogen zwischen einer nicht-schmelzenden Wolfram-Elektrode und dem Werkstück.
- Das Werkstück wird nicht direkt von der Elektrode berührt, und der Lichtbogen erzeugt die notwendige Hitze, um das Werkstück zu schmelzen und die Schweißverbindung herzustellen.
- Ein externes Schutzgas, oft Argon, wird verwendet, um den Lichtbogen vor atmosphärischer Kontamination zu schützen.
- Komponenten:
- Stromquelle: Die Stromquelle erzeugt den elektrischen Strom für den Lichtbogen.
- Wolfram-Elektrode: Die nicht-schmelzende Wolfram-Elektrode wird in die Schweißpistole eingesetzt und erzeugt den Lichtbogen.
- Schweißpistole oder Brenner: Die Schweißpistole enthält die Wolfram-Elektrode und ermöglicht dem Bediener die Steuerung des Schweißprozesses.
- Gasflasche oder -zufuhr: Argon oder ein anderes inertes Gas wird als Schutzgas verwendet, um den Lichtbogen zu schützen.
- Arbeitsweise:
- Der Bediener wählt die passende Wolfram-Elektrode und das Schutzgas entsprechend den Anforderungen der Anwendung.
- Durch das Betätigen des Schweißschalters wird der Lichtbogen zwischen der Elektrode und dem Werkstück erzeugt.
- Der Bediener steuert den Lichtbogen über die Schweißpistole und fügt das geschmolzene Material zusammen, um die Schweißnaht zu erzeugen.
- Anwendungen:
- TIG-Schweißen eignet sich besonders für das Schweißen von dünnen Materialien und Edelstahl.
- Es wird in Anwendungen eingesetzt, bei denen hohe Schweißqualität und Präzision erforderlich sind, wie in der Luftfahrt, der Schienenfahrzeugindustrie, der Elektronik und anderen hochpräzisen Fertigungsprozessen.
- Vorteile:
- Hohe Präzision und Kontrolle über den Schweißprozess.
- Geringe Rauch- und Spritzpartikel.
- Geeignet für verschiedene Materialien, einschließlich Edelstahl, Aluminium und Titan.
- Nachteile:
- Im Vergleich zu anderen Schweißverfahren kann TIG-Schweißen langsamer sein.
- Erfordert eine höhere Fertigkeitsstufe und Erfahrung des Bedieners.
Es ist wichtig, die spezifischen Anweisungen des Herstellers und die Sicherheitsrichtlinien zu beachten, wenn man mit TIG-Schweißmaschinen arbeitet. Eine angemessene Schulung und Übung sind notwendig, um die besten Ergebnisse und eine hohe Schweißqualität zu erzielen.
Weitere Arten von Schweißmaschinen sind:
- WIG-Schweißmaschinen: WIG-Schweißmaschinen verwenden eine Wolframelektrode, die das Werkstück erhitzt und den Schweißprozess einleitet. Der Draht wird von einem Drahtvorschubgerät zugeführt und schmilzt beim Schweißen ab. WIG-Schweißmaschinen sind eine Kombination aus TIG- und MIG-/MAG-Schweißen.
- Plasmaschweißen: Plasmaschweißen verwendet einen Plasmastrahl, der das Werkstück erhitzt und den Schweißprozess einleitet. Plasmaschweißen ist ein sehr energieeffizientes Schweißverfahren, das für Anwendungen mit hohen Anforderungen an die Geschwindigkeit und die Qualität geeignet ist.
- Laserschweißen: Laserschweißen verwendet einen Laserstrahl, der das Werkstück erhitzt und den Schweißprozess einleitet. Laserschweißen ist ein sehr präzises Schweißverfahren, das für Anwendungen mit hohen Anforderungen an die Qualität geeignet ist.
WIG-Schweißmaschinen
WIG-Schweißmaschinen, auch als Wolfram-Inertgas-Schweißmaschinen (GTAW) bezeichnet, sind Schweißmaschinen, die zum Schweißen mit einer nicht abschmelzenden Wolframelektrode verwendet werden. Das Schweißgut wird aus einem separaten Draht zugeführt und mit der Wolframelektrode verschmolzen. Ein Schutzgas, in der Regel Argon, wird verwendet, um das Schweißgut vor Oxidation und Verunreinigungen zu schützen.
WIG-Schweißmaschinen werden in einer Vielzahl von Branchen eingesetzt, darunter die Luft- und Raumfahrtindustrie, die Elektronikindustrie und die Metallverarbeitung. Sie werden zum Schweißen von dünnen Blechen, Rohren und anderen komplexen Bauteilen verwendet.
WIG-Schweißmaschinen bieten eine Reihe von Vorteilen, darunter:
- Qualität: WIG-Schweißmaschinen können hochwertige Schweißnähte mit hoher Festigkeit und Duktilität produzieren.
- Flexibilität: WIG-Schweißmaschinen können zum Schweißen einer Vielzahl von Werkstoffen verwendet werden, einschließlich Stahl, Aluminium, Edelstahl und Kupfer.
- Präzision: WIG-Schweißmaschinen sind präzise und können zum Schweißen von dünnen Blechen und anderen komplexen Bauteilen verwendet werden.
WIG-Schweißmaschinen werden in zwei Haupttypen unterteilt:
- Handgeführte WIG-Schweißmaschinen: Handgeführte WIG-Schweißmaschinen sind die am häufigsten verwendeten WIG-Schweißmaschinen. Sie werden von einem Schweißer mit der Hand bedient.
- Automatische WIG-Schweißmaschinen: Automatische WIG-Schweißmaschinen werden mit einem Roboterarm betrieben. Sie werden zum Schweißen von großen oder komplexen Bauteilen verwendet.
Die wichtigsten Komponenten einer WIG-Schweißmaschine sind:
- Schweißstromquelle: Die Schweißstromquelle erzeugt den Strom, der zum Schmelzen des Schweißguts verwendet wird.
- Schweißbrenner: Der Schweißbrenner hält die Wolframelektrode und führt sie zum Werkstück.
- Schutzgasanlage: Die Schutzgasanlage liefert das Schutzgas, das das Schweißgut vor Oxidation und Verunreinigungen schützt.
Die Art des verwendeten Schweißstroms hängt vom Werkstoff ab, der geschweißt werden soll. Die häufigsten Schweißströme für WIG-Schweißmaschinen sind:
- Wechselstrom (AC): Wechselstrom wird zum Schweißen von Aluminium und anderen Nichteisenmetallen verwendet.
- Gleichstrom (DC): Gleichstrom wird zum Schweißen von Stahl und anderen Eisenmetallen verwendet.
Die Art des verwendeten Wolframelektrodenmaterials hängt ebenfalls vom Werkstoff ab, der geschweißt werden soll. Es gibt eine Vielzahl von Wolframelektrodentypen mit unterschiedlichen Eigenschaften.
Sicherheitshinweise beim WIG-Schweißen:
- Tragen Sie geeignete persönliche Schutzausrüstung (PSA), einschließlich eines Schweißhelms, Handschuhen, Stiefeln und einer Schutzbrille.
- Sorgen Sie für eine gute Belüftung des Schweißbereichs.
- Schweißen Sie nicht in der Nähe von brennbaren Materialien.
- Berühren Sie die Wolframelektrode oder die Schweißnaht nicht mit bloßen Händen.
- Seien Sie sich der potenziellen Gefahr eines elektrischen Schlags bewusst.
WIG (Wolfram-Inertgas)-Schweißmaschinen, auch als TIG (Gas Tungsten Arc Welding)-Schweißmaschinen bekannt, sind spezielle Werkzeuge, die für das TIG-Schweißverfahren verwendet werden. TIG-Schweißen ist ein Lichtbogenschweißverfahren, bei dem ein nicht-schmelzender Wolfram-Elektrodenstab verwendet wird, um den Lichtbogen zu erzeugen. Hier sind einige grundlegende Informationen zu WIG-Schweißmaschinen:
- Funktionsprinzip:
- Eine WIG-Schweißmaschine erzeugt einen Lichtbogen zwischen einer nicht-schmelzenden Wolfram-Elektrode und dem Werkstück.
- Das Werkstück wird nicht direkt von der Elektrode berührt, und der Lichtbogen erzeugt die notwendige Hitze, um das Werkstück zu schmelzen und die Schweißverbindung herzustellen.
- Ein externes Schutzgas, oft Argon, wird verwendet, um den Lichtbogen vor atmosphärischer Kontamination zu schützen.
- Komponenten:
- Stromquelle: Die Stromquelle erzeugt den elektrischen Strom für den Lichtbogen.
- Wolfram-Elektrode: Die nicht-schmelzende Wolfram-Elektrode wird in die Schweißpistole eingesetzt und erzeugt den Lichtbogen.
- Schweißpistole oder Brenner: Die Schweißpistole enthält die Wolfram-Elektrode und ermöglicht dem Bediener die Steuerung des Schweißprozesses.
- Gasflasche oder -zufuhr: Argon oder ein anderes inertes Gas wird als Schutzgas verwendet, um den Lichtbogen zu schützen.
- Arbeitsweise:
- Der Bediener wählt die passende Wolfram-Elektrode und das Schutzgas entsprechend den Anforderungen der Anwendung.
- Durch das Betätigen des Schweißschalters wird der Lichtbogen zwischen der Elektrode und dem Werkstück erzeugt.
- Der Bediener steuert den Lichtbogen über die Schweißpistole und fügt das geschmolzene Material zusammen, um die Schweißnaht zu erzeugen.
- Anwendungen:
- WIG-Schweißen eignet sich besonders für das Schweißen von dünnen Materialien und Edelstahl.
- Es wird in Anwendungen eingesetzt, bei denen hohe Schweißqualität und Präzision erforderlich sind, wie in der Luftfahrt, der Schienenfahrzeugindustrie, der Elektronik und anderen hochpräzisen Fertigungsprozessen.
- Vorteile:
- Hohe Präzision und Kontrolle über den Schweißprozess.
- Geringe Rauch- und Spritzpartikel.
- Geeignet für verschiedene Materialien, einschließlich Edelstahl, Aluminium und Titan.
- Nachteile:
- Im Vergleich zu anderen Schweißverfahren kann WIG-Schweißen langsamer sein.
- Erfordert eine höhere Fertigkeitsstufe und Erfahrung des Bedieners.
Es ist wichtig, die spezifischen Anweisungen des Herstellers und die Sicherheitsrichtlinien zu beachten, wenn man mit WIG-Schweißmaschinen arbeitet. Eine angemessene Schulung und Übung sind notwendig, um die besten Ergebnisse und eine hohe Schweißqualität zu erzielen.
Plasmaschweißen
Plasmaschweißen ist ein Schweißverfahren, bei dem ein Plasmabogen zum Schweißen von Metallen verwendet wird. Der Plasmabogen wird erzeugt, indem ein Gas, in der Regel Argon oder Stickstoff, durch eine enge Düse geleitet wird. Der Gasstrom wird dann ionisiert und bildet ein Plasma, das eine hohe Temperatur von bis zu 30.000 Grad Celsius erreichen kann.
Das Plasma wird verwendet, um das Metall zu schmelzen und eine Schweißnaht zu bilden. Der Plasmabogen ist sehr konzentriert und kann daher zum Schweißen von dünnen Blechen und anderen präzisen Arbeiten verwendet werden.
Plasmaschweißen wird in einer Vielzahl von Branchen eingesetzt, darunter die Luft- und Raumfahrtindustrie, die Automobilindustrie und die Bauindustrie. Es wird zum Schweißen von Stahl, Aluminium, Edelstahl und anderen Metallen verwendet.
Plasmaschweißen bietet eine Reihe von Vorteilen gegenüber anderen Schweißverfahren, darunter:
- Qualität: Plasmaschweißen kann hochwertige Schweißnähte mit hoher Festigkeit und Duktilität produzieren.
- Geschwindigkeit: Plasmaschweißen ist ein schnelles Schweißverfahren, das hohe Schweißgeschwindigkeiten ermöglichen kann.
- Präzision: Plasmaschweißen ist präzise und kann zum Schweißen von dünnen Blechen und anderen komplexen Bauteilen verwendet werden.
- Vielseitigkeit: Plasmaschweißen kann zum Schweißen einer Vielzahl von Werkstoffen verwendet werden.
Die wichtigsten Komponenten einer Plasmaschweißmaschine sind:
- Schweißstromquelle: Die Schweißstromquelle erzeugt den Strom, der zum Erzeugen des Plasmabogens verwendet wird.
- Plasmabrenner: Der Plasmabrenner erzeugt den Plasmabogen und führt ihn zum Werkstück.
- Schutzgasanlage: Die Schutzgasanlage liefert das Schutzgas, das das Schweißgut vor Oxidation und Verunreinigungen schützt.
Die Art des verwendeten Schutzgases hängt vom Werkstoff ab, der geschweißt werden soll. Die häufigsten Schutzgase für Plasmaschweißmaschinen sind:
- Argon: Argon wird zum Schweißen von Stahl, Edelstahl und Kupfer verwendet.
- Stickstoff: Stickstoff wird zum Schweißen von Aluminium verwendet.
Die Art des verwendeten Plasmabrenners hängt ebenfalls vom Werkstoff ab, der geschweißt werden soll. Es gibt zwei Haupttypen von Plasmabrennern:
- Konventionelle Plasmabrenner: Konventionelle Plasmabrenner verwenden einen elektrischen Lichtbogen, um das Plasma zu erzeugen.
- Hochfrequenz-Plasmabrenner: Hochfrequenz-Plasmabrenner verwenden eine Hochfrequenzquelle, um das Plasma zu erzeugen.
Hochfrequenz-Plasmabrenner sind in der Regel teurer als konventionelle Plasmabrenner, bieten aber eine Reihe von Vorteilen, darunter:
- Stabiler Plasmabogen: Hochfrequenz-Plasmabrenner erzeugen einen stabileren Plasmabogen als konventionelle Plasmabrenner.
- Geringere Wärmeeinbringung: Hochfrequenz-Plasmabrenner erzeugen weniger Wärme als konventionelle Plasmabrenner.
- Bessere Schweißqualität: Hochfrequenz-Plasmabrenner können hochwertigere Schweißnähte produzieren als konventionelle Plasmabrenner.
Sicherheitshinweise beim Plasmaschweißen:
- Tragen Sie geeignete persönliche Schutzausrüstung (PSA), einschließlich eines Schweißhelms, Handschuhen, Stiefeln und einer Schutzbrille.
- Sorgen Sie für eine gute Belüftung des Schweißbereichs.
- Schweißen Sie nicht in der Nähe von brennbaren Materialien.
- Berühren Sie den Plasmabrenner oder die Schweißnaht nicht mit bloßen Händen.
- Seien Sie sich der potenziellen Gefahr eines elektrischen Schlags bewusst
Plasmaschweißen ist ein fortschrittliches Lichtbogenschweißverfahren, das auf der Anwendung eines Plasmastrahls basiert. Plasma ist der vierte Aggregatzustand der Materie und entsteht, wenn ein Gas so stark erhitzt wird, dass es ionisiert wird und aus positiv geladenen Ionen und freien Elektronen besteht. Beim Plasmaschweißen wird ein Plasmastrahl als Wärmequelle für das Schweißen verwendet. Hier sind einige grundlegende Informationen zum Plasmaschweißen:
- Funktionsprinzip:
- Eine Plasmaschweißmaschine erzeugt einen Plasmastrahl, indem ein inerten (meistens Argon) oder ein gemischtes Gas durch einen schmalen Düsenausschnitt geschossen wird und dann elektrisch ionisiert wird.
- Der erzeugte Plasmastrahl kann extrem hohe Temperaturen erreichen und wird als Wärmequelle für das Schweißen verwendet.
- Das Werkstück und die Elektrode (normalerweise aus Wolfram) werden durch den Plasmastrahl geschmolzen und verbunden.
- Komponenten:
- Stromquelle: Die Stromquelle erzeugt den Hochfrequenzstrom, der das Plasma erzeugt.
- Plasmafackel: Die Plasmafackel enthält die Düse, durch die das Plasmastrahl austreten kann.
- Gaszufuhr: Je nach Anwendung kann reines Argon oder ein Gasgemisch verwendet werden, um das Plasma zu erzeugen.
- Arbeitsweise:
- Der Bediener wählt die geeigneten Schweißparameter, darunter Gasart und -fluss, Stromstärke und Spannung.
- Durch das Betätigen des Schweißschalters wird der Plasmastrahl erzeugt und auf das Werkstück gerichtet.
- Das Werkstück wird durch den Plasmastrahl geschmolzen, und die Schmelze wird verwendet, um die Schweißnaht zu erzeugen.
- Anwendungen:
- Plasmaschweißen wird in verschiedenen Anwendungen eingesetzt, einschließlich der Luft- und Raumfahrtindustrie, Automobilindustrie, Elektronikfertigung und Präzisionsfertigung.
- Es eignet sich besonders gut für das Schweißen von dünnen Materialien, wie sie in der Elektronikindustrie häufig vorkommen.
- Vorteile:
- Hohe Präzision und Kontrolle über den Schweißprozess.
- Geringe Wärmeeinflusszone.
- Geeignet für das Schweißen von Materialien mit unterschiedlichen Schmelzpunkten.
- Nachteile:
- Höhere Kosten für die Ausrüstung im Vergleich zu einigen anderen Schweißverfahren.
- Erfordert eine gewisse Erfahrung und Fachkenntnisse des Bedieners.
Plasmaschweißen bietet eine Reihe von Vorteilen für Anwendungen, bei denen hohe Präzision und geringe Wärmeeinflusszonen erforderlich sind. Es ist wichtig, die spezifischen Anweisungen des Herstellers und die Sicherheitsrichtlinien zu beachten, wenn man mit Plasmaschweißmaschinen arbeitet.
Laserschweißen
Laserschweißen ist ein Schweißverfahren, bei dem ein Laserstrahl zum Schweißen von Metallen verwendet wird. Der Laserstrahl wird erzeugt, indem ein hochenergetischer Lichtstrahl durch einen Resonator geleitet wird. Der Lichtstrahl wird dann fokussiert, um einen kleinen, intensiven Lichtpunkt zu erzeugen. Der Lichtpunkt wird verwendet, um das Metall zu schmelzen und eine Schweißnaht zu bilden.
Laserschweißen bietet eine Reihe von Vorteilen gegenüber anderen Schweißverfahren, darunter:
- Präzision: Laserschweißen ist sehr präzise und kann zum Schweißen von dünnen Blechen und anderen komplexen Bauteilen verwendet werden.
- Qualität: Laserschweißen kann hochwertige Schweißnähte mit hoher Festigkeit und Duktilität produzieren.
- Geschwindigkeit: Laserschweißen ist ein schnelles Schweißverfahren, das hohe Schweißgeschwindigkeiten erreichen kann.
- Vielseitigkeit: Laserschweißen kann zum Schweißen einer Vielzahl von Werkstoffen verwendet werden, einschließlich Stahl, Aluminium, Edelstahl und Kunststoff.
Die wichtigsten Komponenten einer Laserschweißmaschine sind:
- Laserquelle: Die Laserquelle erzeugt den Laserstrahl, der zum Schweißen verwendet wird.
- Strahlführungssystem: Das Strahlführungssystem leitet den Laserstrahl zum Werkstück.
- Fokussiersystem: Das Fokussiersystem fokussiert den Laserstrahl auf einen kleinen, intensiven Lichtpunkt.
- Schutzgasanlage: Die Schutzgasanlage liefert das Schutzgas, das das Schweißgut vor Oxidation und Verunreinigungen schützt.
Die Art des verwendeten Lasers hängt vom Werkstoff ab, der geschweißt werden soll. Die häufigsten Laserarten für Laserschweißmaschinen sind:
- Nd:YAG-Laser: Nd:YAG-Laser sind Vielzwecklaser, die zum Schweißen einer Vielzahl von Werkstoffen verwendet werden können.
- CO2-Laser: CO2-Laser sind leistungsstarke Laser, die zum Schweißen von dicken Blechen verwendet werden können.
- Faserlaser: Faserlaser sind kompakte und effiziente Laser, die in den letzten Jahren an Popularität gewonnen haben.
Die Art des verwendeten Schutzgases hängt ebenfalls vom Werkstoff ab, der geschweißt werden soll. Die häufigsten Schutzgase für Laserschweißmaschinen sind:
- Argon: Argon wird zum Schweißen von Stahl, Edelstahl und Kupfer verwendet.
- Helium: Helium wird zum Schweißen von Aluminium verwendet.
- Stickstoff: Stickstoff wird zum Schweißen von Titan und anderen reaktiven Metallen verwendet.
Sicherheitshinweise beim Laserschweißen:
- Tragen Sie geeignete persönliche Schutzausrüstung (PSA), einschließlich eines Laserschutzhelms, Handschuhen, Stiefeln und einer Schutzbrille.
- Sorgen Sie für eine gute Belüftung des Schweißbereichs.
- Schweißen Sie nicht in der Nähe von brennbaren Materialien.
- Berühren Sie den Laserstrahl oder die Schweißnaht nicht mit bloßen Händen.
- Seien Sie sich der potenziellen Gefahr von Verbrennungen oder Augenschäden bewusst.
Laserschweißen ist ein fortschrittliches Schweißverfahren, bei dem ein Laserstrahl als Wärmequelle verwendet wird, um Materialien miteinander zu verbinden. Diese Methode ermöglicht hochpräzise Schweißnähte mit geringen Wärmeeinflusszonen. Hier sind einige grundlegende Informationen zum Laserschweißen:
- Funktionsprinzip:
- Ein hochintensiver Laserstrahl wird auf das zu schweißende Material fokussiert.
- Der Laserstrahl erhitzt das Material, bis es schmilzt und sich mit einem anderen Material verbindet, um eine Schweißnaht zu bilden.
- Die Wärmequelle (Laser) kann präzise gesteuert werden, was zu einer geringen Wärmeeinflusszone führt.
- Arten des Laserschweißens:
- Festkörperlaser: Verwendet einen festen Lasermedium (z. B. Nd:YAG-Laser).
- Gaslaser: Verwendet ein gasförmiges Medium (z. B. CO2-Laser).
- Faserlaser: Verwendet eine Glasfaser als Lasermedium.
- Vorteile des Laserschweißens:
- Hohe Präzision: Durch die Fokussierung des Laserstrahls kann eine hohe Präzision und Kontrolle über den Schweißprozess erreicht werden.
- Geringe Wärmeeinflusszone: Das Laserschweißen erzeugt im Vergleich zu anderen Schweißverfahren eine geringe Wärmeeinflusszone, was besonders bei empfindlichen Materialien wichtig ist.
- Hohe Schweißgeschwindigkeit: Laserschweißen ermöglicht oft eine schnelle und effiziente Verbindung von Materialien.
- Anwendungen:
- Laserschweißen wird in verschiedenen Branchen eingesetzt, darunter die Automobilindustrie, die Luft- und Raumfahrt, die Elektronikfertigung, die Medizintechnik und die Schmuckherstellung.
- Es wird für das Schweißen von dünnen bis mittelstarken Materialien verwendet.
- Nachteile des Laserschweißens:
- Kosten: Die Anschaffung von Laserschweißanlagen kann teuer sein.
- Materialabhängigkeit: Nicht alle Materialien lassen sich gleichermaßen gut mit einem Laser schweißen.
- Technische Überlegungen:
- Die Auswahl des geeigneten Lasers (Festkörperlaser, Gaslaser, Faserlaser) hängt von den Anforderungen der Anwendung ab.
- Die Kontrolle der Schweißparameter wie Leistung, Fokus und Geschwindigkeit ist entscheidend für die Qualität der Schweißnaht.
Das Laserschweißen ist eine fortschrittliche Schweißtechnik, die aufgrund ihrer Präzision und Effizienz in vielen Hochtechnologieanwendungen eingesetzt wird. Es erfordert jedoch spezialisierte Ausrüstung und Fachkenntnisse, um erfolgreich angewendet zu werden.
Die Auswahl der richtigen Schweißmaschine hängt von einer Reihe von Faktoren ab, darunter:
- Schweißverfahren: Das Schweißverfahren bestimmt die Art des Schweißnahts, der erzeugt wird.
- Material: Das Material bestimmt die Eignung des Schweißverfahrens.
- Dicke: Die Dicke des Werkstücks bestimmt die Leistung der Schweißmaschine.
- Produktionsvolumen: Das Produktionsvolumen bestimmt, ob eine manuelle oder automatische Maschine erforderlich ist.
Bei der Auswahl einer Schweißmaschine ist es wichtig, die Anforderungen der Anwendung zu berücksichtigen. So muss die Maschine für das Schweißverfahren, das Material und das Produktionsvolumen geeignet sein.
Hier sind einige Tipps für die Auswahl einer Schweißmaschine:
- Bestimmen Sie das Schweißverfahren, das Sie verwenden möchten.
- Bestimmen Sie das Material, das Sie schweißen möchten.
- Bestimmen Sie die Dicke des Werkstücks, das Sie schweißen möchten.
- Bestimmen Sie das Produktionsvolumen, das Sie benötigen.
Sobald Sie diese Faktoren bestimmt haben, können Sie mit der Suche nach einer geeigneten Schweißmaschine beginnen.
- Längsschweißmaschine
- Rundschweißsystem
- Vertikale Schweißmaschine
- Längstnaht-Schweißmaschine
- Rohrschweißmaschine
- Schweißrotator
Längsschweißmaschine
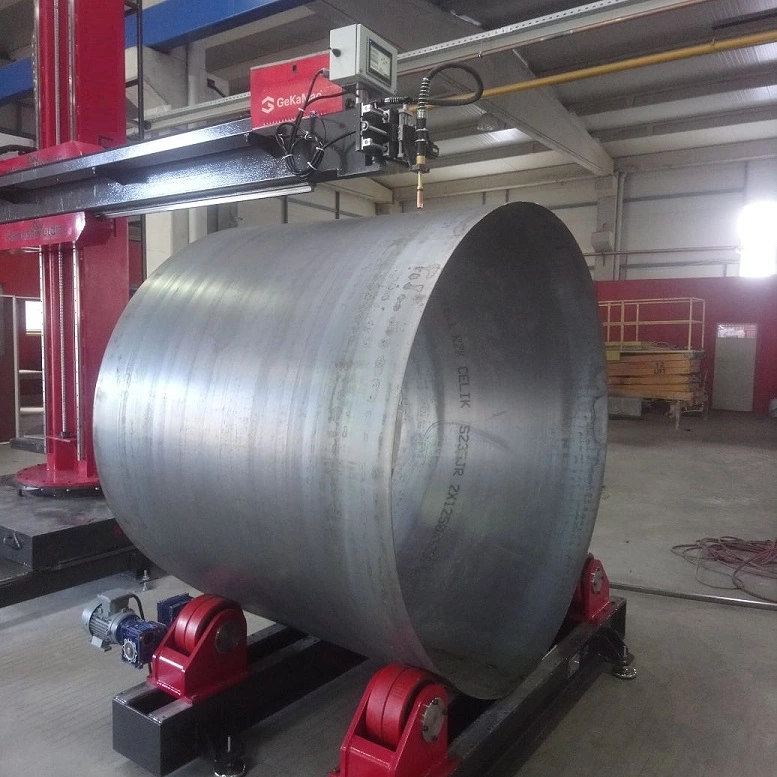
Eine Längsschweißmaschine ist eine Maschine, die zum Schweißen von Rohren oder anderen zylindrischen Werkstücken in Längsrichtung verwendet wird. Sie besteht in der Regel aus einem Grundrahmen, einem Schweißkopf und einem Antriebssystem.
Der Schweißkopf enthält die Schweißelektrode, die das Werkstück erhitzt und den Schweißprozess einleitet. Der Antriebsmechanismus bewegt den Schweißkopf entlang des Werkstücks, um einen kontinuierlichen Schweißnaht zu erzeugen.
Längsschweißmaschinen werden in einer Vielzahl von Anwendungen eingesetzt, darunter:
- Bauwesen: Längsschweißmaschinen werden im Bauwesen verwendet, um Rohre für Wasser-, Gas- und Abwassersysteme zu schweißen.
- Industrie: Längsschweißmaschinen werden in der Industrie verwendet, um Rohre für verschiedene Zwecke zu schweißen, z. B. für die Herstellung von Möbeln, Rohrleitungen und anderen Produkten.
- Automobilindustrie: Längsschweißmaschinen werden in der Automobilindustrie verwendet, um Rohre für Autokarosserien und andere Komponenten zu schweißen.
Es gibt verschiedene Arten von Längsschweißmaschinen, die jeweils ihre eigenen Vor- und Nachteile haben. Die gebräuchlichsten Arten von Längsschweißmaschinen sind:
- Manuelle Längsschweißmaschinen: Manuelle Längsschweißmaschinen werden von einem Bediener mit einer Handkurbel oder einem anderen manuellen Gerät bedient. Sie sind in der Regel kostengünstig und einfach zu bedienen, aber sie sind auch langsam und weniger präzise als automatische Längsschweißmaschinen.
- Automatische Längsschweißmaschinen: Automatische Längsschweißmaschinen werden durch einen Motor oder einen anderen Antrieb angetrieben. Sie sind in der Regel schneller und präziser als manuelle Längsschweißmaschinen, aber sie sind auch teurer und komplexer zu bedienen.
Die Funktionsweise einer Längsschweißmaschine hängt von der Art der Maschine ab. Manuelle Längsschweißmaschinen arbeiten in der Regel mit einem Schweißbrenner, der das Werkstück erhitzt und den Schweißprozess einleitet. Automatische Längsschweißmaschinen arbeiten in der Regel mit einem Schweißroboter, der den Schweißprozess automatisch durchführt.
Automatische Längsschweißmaschinen
Automatische Längsschweißmaschinen sind Schweißmaschinen, die zum Schweißen von Werkstücken verwendet werden, die in Längsrichtung miteinander verbunden werden sollen. Sie werden in einer Vielzahl von Branchen eingesetzt, darunter die Automobilindustrie, die Bauindustrie und die Metallverarbeitung.
Automatische Längsschweißmaschinen werden in zwei Haupttypen unterteilt:
- Handgeführte automatische Längsschweißmaschinen: Handgeführte automatische Längsschweißmaschinen werden von einem Schweißer mit der Hand bedient.
- Roboter-automatische Längsschweißmaschinen: Roboter-automatische Längsschweißmaschinen werden mit einem Roboterarm betrieben.
Die wichtigsten Komponenten einer automatischen Längsschweißmaschine sind:
- Schweißstromquelle: Die Schweißstromquelle erzeugt den Strom, der zum Schweißen verwendet wird.
- Schweißbrenner: Der Schweißbrenner hält die Elektrode oder den Draht und führt sie zum Werkstück.
- Schutzgasanlage: Die Schutzgasanlage liefert das Schutzgas, das das Schweißgut vor Oxidation und Verunreinigungen schützt.
- Roboterarm: Der Roboterarm führt den Schweißbrenner entlang des Werkstücks.
Die Art des verwendeten Schweißverfahrens hängt vom Werkstoff ab, der geschweißt werden soll. Die häufigsten Schweißverfahren für automatische Längsschweißmaschinen sind:
- Elektrodenschweißen: Elektrodenschweißen ist ein einfaches und kostengünstiges Schweißverfahren, das zum Schweißen einer Vielzahl von Werkstoffen verwendet werden kann.
- MIG/MAG-Schweißen: MIG/MAG-Schweißen ist ein schnelleres und effizienteres Schweißverfahren als Elektrodenschweißen. Es wird häufig zum Schweißen von Stahl und Aluminium verwendet.
- WIG-Schweißen: WIG-Schweißen ist ein präzises und hochwertiges Schweißverfahren. Es wird häufig zum Schweißen von dünnen Blechen und anderen komplexen Bauteilen verwendet.
- Plasmaschweißen: Plasmaschweißen ist ein schnelles und effizientes Schweißverfahren, das zum Schweißen einer Vielzahl von Werkstoffen verwendet werden kann.
- Laserschweißen: Laserschweißen ist ein präzises und hochwertiges Schweißverfahren. Es wird häufig zum Schweißen von dünnen Blechen und anderen komplexen Bauteilen verwendet.
Automatische Längsschweißmaschinen bieten eine Reihe von Vorteilen gegenüber manuellen Längsschweißverfahren, darunter:
- Produktivität: Automatische Längsschweißmaschinen können höhere Schweißgeschwindigkeiten ermöglichen als manuelle Schweißverfahren.
- Qualität: Automatische Längsschweißmaschinen können hochwertigere Schweißnähte produzieren als manuelle Schweißverfahren.
- Konsistenz: Automatische Längsschweißmaschinen können konsistentere Schweißnähte produzieren als manuelle Schweißverfahren.
- Sicherheit: Automatische Längsschweißmaschinen können die Sicherheit des Schweißers verbessern, indem sie den Schweißer von der Schweißnaht entfernen.
Sicherheitshinweise beim automatischen Längsschweißen:
- Tragen Sie geeignete persönliche Schutzausrüstung (PSA), einschließlich eines Schweißhelms, Handschuhen, Stiefeln und einer Schutzbrille.
- Sorgen Sie für eine gute Belüftung des Schweißbereichs.
- Schweißen Sie nicht in der Nähe von brennbaren Materialien.
- Berühren Sie den Schweißbrenner oder die Schweißnaht nicht mit bloßen Händen.
- Seien Sie sich der potenziellen Gefahr eines elektrischen Schlags bewusst.
Hier sind einige Beispiele für die Verwendung von automatischen Längsschweißmaschinen:
- Automobilindustrie: Automatische Längsschweißmaschinen werden in der Automobilindustrie zum Schweißen von Karosserieteilen verwendet.
- Bauindustrie: Automatische Längsschweißmaschinen werden in der Bauindustrie zum Schweißen von Stahlträgern und anderen Bauteilen verwendet.
- Metallverarbeitung: Automatische Längsschweißmaschinen werden in der Metallverarbeitung zum Schweißen von Rohren, Profilen und anderen Metallteilen verwendet.
Automatische Längsschweißmaschinen sind spezielle Schweißanlagen, die darauf ausgelegt sind, Längsnähte auf länglichen Werkstücken zu schweißen. Diese Maschinen bieten Automatisierung und Präzision in Schweißprozessen, insbesondere wenn es darum geht, längliche oder rohrförmige Strukturen zu schweißen. Hier sind einige grundlegende Informationen zu automatischen Längsschweißmaschinen:
- Anwendungen:
- Automatische Längsschweißmaschinen werden in verschiedenen Branchen eingesetzt, darunter der Schiffsbau, der Rohrleitungsbau, die Herstellung von Tanks und Behältern, die Fertigung von Stahlkonstruktionen und anderen Anwendungen, bei denen Längsnähte auf länglichen Werkstücken benötigt werden.
- Merkmale:
- Automatisierung: Diese Maschinen sind darauf ausgelegt, den Schweißprozess zu automatisieren, was zu einer erhöhten Effizienz und Konsistenz führt.
- Präzision: Durch die Verwendung automatischer Steuerungen und Schweißprogramme können diese Maschinen präzise Schweißnähte erzeugen.
- Flexibilität: Viele automatische Längsschweißmaschinen sind so konzipiert, dass sie sich an verschiedene Werkstückgrößen und -formen anpassen können.
- Komponenten:
- Schweißkopf: Der Schweißkopf enthält die Schweißausrüstung, wie z.B. die Stromquelle und den Drahtvorschubmechanismus.
- Drehvorrichtung oder Werkstückpositionierungssystem: Diese Komponente ermöglicht die Rotation oder Bewegung des Werkstücks während des Schweißens, um Längsnähte zu erzeugen.
- Steuerungseinheit: Die Steuerungseinheit ermöglicht die Programmierung von Schweißparametern und die Überwachung des Schweißprozesses.
- Arbeitsweise:
- Der Bediener richtet das Werkstück in der Maschine aus.
- Die Maschine kann automatisch den Schweißkopf entlang der Längsachse des Werkstücks bewegen.
- Der Schweißkopf führt den Schweißprozess durch und erzeugt eine Längsnaht auf dem Werkstück.
- Vorteile:
- Effizienz: Automatische Längsschweißmaschinen können den Schweißprozess beschleunigen und die Produktivität steigern.
- Konsistenz: Durch die Automatisierung wird eine gleichmäßige Qualität der Schweißnähte gewährleistet.
- Reduzierte Arbeitskosten: Die Automatisierung kann zu einer Reduzierung des Bedarfs an manueller Arbeitskraft führen.
- Technische Überlegungen:
- Die Auswahl der richtigen Maschine hängt von den spezifischen Anforderungen der Anwendung ab, einschließlich Werkstückgröße, Material und gewünschter Schweißqualität.
- Die Programmierung der Maschine erfordert eine genaue Kenntnis der Schweißparameter und der Werkstückanforderungen.
Es ist wichtig, die Herstelleranweisungen und Sicherheitsrichtlinien für die spezifische automatische Längsschweißmaschine zu beachten. Die Schulung des Bedienpersonals ist ebenfalls entscheidend, um den sicheren und effizienten Betrieb zu gewährleisten.
Die Schweißqualität hängt von einer Reihe von Faktoren ab, darunter:
- Schweißverfahren: Das Schweißverfahren bestimmt die Art des Schweißnahts, der erzeugt wird.
- Schweißparameter: Die Schweißparameter bestimmen die Eigenschaften des Schweißnahts, z. B. die Dicke und die Festigkeit.
- Rohrmaterial: Das Rohrmaterial bestimmt die Eignung des Schweißverfahrens und der Schweißparameter.
Bei der Auswahl einer Längsschweißmaschine ist es wichtig, die Anforderungen der Anwendung zu berücksichtigen. So muss die Maschine für das Schweißverfahren, das Rohrmaterial und das Produktionsvolumen geeignet sein.
Hier sind einige Tipps für das Schweißen mit einer Längsschweißmaschine:
- Befolgen Sie die Anweisungen des Herstellers der Längsschweißmaschine.
- Verwenden Sie geeignete Schutzausrüstung, z. B. Schutzhandschuhe und Schutzbrille.
- Üben Sie das Schweißen mit einer Längsschweißmaschine, bevor Sie sie für eine Anwendung verwenden.
Mit etwas Übung können Sie mit einer Längsschweißmaschine Rohre oder andere zylindrische Werkstücke in einer Vielzahl von Anwendungen schweißen.
Besondere Merkmale von Längsschweißmaschinen
Längsschweißmaschinen haben einige besondere Merkmale, die sie von anderen Schweißmaschinen unterscheiden. Dazu gehören:
- Der Schweißkopf muss sich entlang des Werkstücks bewegen können, um einen kontinuierlichen Schweißnaht zu erzeugen.
- Die Schweißmaschine muss über eine Steuerung verfügen, die die Bewegung des Schweißkopfs und die Schweißparameter steuert.
Diese Merkmale machen Längsschweißmaschinen zu einer komplexeren Art von Schweißmaschine als andere Schweißmaschinen. Sie sind jedoch auch in der Lage, präzisere und gleichmäßigere Schweißnähte zu erzeugen.
Die Längsschweißmaschine dient zum horizontalen Schweißen von Zylindern und Rohren. Das Rohr wird auf den Positionierern platziert, um es zu drehen. Der Stellungsregler wird von einem Elektromotor angetrieben. Der Bediener kann die Wendegeschwindigkeit über den Steuerbildschirm einstellen. Der Zylinder dreht sich um, während der Schweißbrenner das Teil berührt und den Schweißprozess startet.
Rundschweißsystem und Rundschweißmaschine
Rundschweißsystem
Ein Rundschweißsystem ist ein Satz von Komponenten, die zum Schweißen von Rohren oder anderen zylindrischen Werkstücken verwendet werden. Es besteht in der Regel aus folgenden Komponenten:
- Schweißkopf: Der Schweißkopf enthält die Schweißelektrode, die das Werkstück erhitzt und den Schweißprozess einleitet.
- Antriebssystem: Das Antriebssystem bewegt den Schweißkopf entlang des Werkstücks, um einen kontinuierlichen Schweißnaht zu erzeugen.
- Steuerung: Die Steuerung steuert die Bewegung des Schweißkopfs und die Schweißparameter.
Schweißkopf
Ein Schweißkopf ist ein Teil einer Schweißmaschine, der zum Schweißen von Metallen verwendet wird. Er besteht aus einer Reihe von Komponenten, die zusammenarbeiten, um den Schweißprozess zu ermöglichen.
Die wichtigsten Komponenten eines Schweißkopfes sind:
- Schweißbrenner: Der Schweißbrenner hält die Elektrode oder den Draht und führt sie zum Werkstück.
- Schutzgasanlage: Die Schutzgasanlage liefert das Schutzgas, das das Schweißgut vor Oxidation und Verunreinigungen schützt.
- Schweißstromquelle: Die Schweißstromquelle erzeugt den Strom, der zum Schmelzen des Schweißguts verwendet wird.
Die Art des Schweißkopfes hängt vom verwendeten Schweißverfahren ab. Die häufigsten Schweißverfahren sind:
- Elektrodenschweißen: Elektrodenschweißen verwendet eine Elektrode, die mit einem Schutzgasmantel umgeben ist. Der Schweißkopf für Elektrodenschweißen besteht daher aus einer Elektrodenhalterung, einem Schutzgasrohr und einer Schweißstromquelle.
- MIG/MAG-Schweißen: MIG/MAG-Schweißen verwendet einen Draht, der mit einem Schutzgas umgeben ist. Der Schweißkopf für MIG/MAG-Schweißen besteht daher aus einem Drahtvorschubmechanismus, einem Schutzgasrohr und einer Schweißstromquelle.
- WIG-Schweißen: WIG-Schweißen verwendet eine nicht abschmelzende Wolframelektrode. Der Schweißkopf für WIG-Schweißen besteht daher aus einer Wolframelektrode, einem Schutzgasrohr und einer Schweißstromquelle.
- Plasmaschweißen: Plasmaschweißen verwendet einen Plasmabogen, der durch eine Düse geleitet wird. Der Schweißkopf für Plasmaschweißen besteht daher aus einer Düse, einem Schutzgasrohr und einer Schweißstromquelle.
Schweißköpfe sind für eine Vielzahl von Anwendungen erhältlich. Sie können zum Schweißen von dünnen Blechen, dicken Blechen, Rohren, Profilen und anderen Metallteilen verwendet werden.
Hier sind einige Beispiele für die Verwendung von Schweißköpfen:
- Automobilindustrie: Schweißköpfe werden in der Automobilindustrie zum Schweißen von Karosserieteilen, Motorenteilen und anderen Metallteilen verwendet.
- Bauindustrie: Schweißköpfe werden in der Bauindustrie zum Schweißen von Stahlträgern, Brücken und anderen Bauteilen verwendet.
- Metallverarbeitung: Schweißköpfe werden in der Metallverarbeitung zum Schweißen von Rohren, Profilen und anderen Metallteilen verwendet.
Die Auswahl des richtigen Schweißkopfes hängt von einer Reihe von Faktoren ab, einschließlich des verwendeten Schweißverfahrens, des zu schweißenden Materials und der gewünschten Schweißqualität.
Der Schweißkopf ist eine zentrale Komponente in einem Schweißsystem und spielt eine Schlüsselrolle bei der Durchführung des Schweißprozesses. Er ist der Teil der Schweißmaschine, der den Lichtbogen erzeugt und den Schweißdraht oder die Elektrode führt, um das Werkstück zu schweißen. Der Aufbau und die Funktion des Schweißkopfes können je nach dem spezifischen Schweißverfahren und der Art der Schweißmaschine variieren. Hier sind einige grundlegende Informationen über den Schweißkopf:
- Bestandteile des Schweißkopfes:
- Lichtbogenquelle: Der Schweißkopf enthält die Lichtbogenquelle, die den Lichtbogen zwischen der Elektrode oder dem Schweißdraht und dem Werkstück erzeugt. Die Lichtbogenquelle kann eine Elektrode, ein Laser oder ein Plasma sein, abhängig vom Schweißverfahren.
- Drahtvorschubsystem: In Schweißverfahren wie MIG/MAG (Metall-Inertgas/Metall-Aktivgas) und Fülldrahtschweißen führt der Schweißkopf den Schweißdraht zum Lichtbogen. Das Drahtvorschubsystem sorgt dafür, dass der Draht kontinuierlich und gleichmäßig zugeführt wird.
- Elektrodenhalter: Bei Elektrodenschweißmaschinen hält der Schweißkopf die Elektrode und führt sie zum Werkstück.
- Plasmafackel: In Plasmaschweißmaschinen enthält der Schweißkopf die Plasmafackel, die den Plasmastrahl erzeugt.
- Steuerungseinheit: Der Schweißkopf ist oft mit einer Steuerungseinheit verbunden, die die Einstellung und Überwachung der Schweißparameter ermöglicht. Moderne Schweißkopf-Steuerungen bieten oft programmierbare Funktionen für unterschiedliche Schweißanwendungen.
- Funktion des Schweißkopfes:
- Der Schweißkopf spielt eine entscheidende Rolle bei der Erzeugung des Lichtbogens oder Plasmastrahls, der die notwendige Hitze für den Schweißprozess liefert.
- Er führt den Schweißdraht oder die Elektrode in die richtige Position und sorgt dafür, dass der Werkstoff an der gewünschten Stelle geschmolzen wird, um die Schweißnaht zu erzeugen.
- Bei einigen Schweißverfahren, wie dem Lichtbogenschweißen, dient der Schweißkopf auch dazu, das Schutzgas zu führen, das den Lichtbogen vor atmosphärischer Kontamination schützt.
- Anwendungen:
- Der Schweißkopf findet in verschiedenen Schweißverfahren Anwendung, darunter MIG/MAG-Schweißen, WIG-Schweißen, Elektrodenschweißen, Plasmaschweißen und andere.
- Wartung und Pflege:
- Der Schweißkopf muss regelmäßig gewartet werden, um eine optimale Leistung sicherzustellen. Dazu gehört die Überprüfung der Verschleißteile wie Düsen, Elektroden oder Führungsrollen.
- Je nach Verwendung und Schweißverfahren können spezifische Wartungsaufgaben erforderlich sein, wie das Reinigen von Düsen oder das Austauschen von Verschleißteilen.
Es ist wichtig, die Herstelleranweisungen für den Schweißkopf zu beachten und sicherzustellen, dass er ordnungsgemäß eingestellt und gewartet wird, um qualitativ hochwertige Schweißnähte und einen sicheren Betrieb zu gewährleisten.
Antriebssystem
Das Antriebssystem einer automatischen Schweißmaschine ist dafür verantwortlich, den Schweißkopf entlang des Werkstücks zu bewegen. Es besteht aus einer Reihe von Komponenten, die zusammenarbeiten, um eine genaue und gleichmäßige Bewegung zu gewährleisten.
Die wichtigsten Komponenten eines Antriebssystems für automatische Schweißmaschinen sind:
- Schweißkopfhalterung: Die Schweißkopfhalterung hält den Schweißkopf sicher an Ort und Stelle.
- Antriebsmotor: Der Antriebsmotor erzeugt die Kraft, die den Schweißkopf entlang des Werkstücks bewegt.
- Getriebe: Das Getriebe reduziert die Drehzahl des Antriebsmotors und erhöht das Drehmoment.
- Lineareinheit: Die Lineareinheit bewegt den Schweißkopf entlang des Werkstücks.
Die Art des Antriebssystems hängt vom verwendeten Schweißverfahren und den Anforderungen der Anwendung ab. Die häufigsten Antriebssysteme sind:
- Linearantrieb: Linearantriebe sind die gebräuchlichste Art von Antriebssystem für automatische Schweißmaschinen. Sie sind präzise, zuverlässig und kostengünstig.
- Getriebeantrieb: Getriebeantriebe sind robust und können hohe Lasten tragen. Sie werden häufig zum Schweißen von dicken Blechen und anderen schweren Materialien verwendet.
- Hybridantrieb: Hybridantriebe kombinieren die Vorteile von Linearantrieben und Getriebeantrieben. Sie sind präzise, zuverlässig und können hohe Lasten tragen.
Die Auswahl des richtigen Antriebssystems hängt von einer Reihe von Faktoren ab, einschließlich des verwendeten Schweißverfahrens, des zu schweißenden Materials und der gewünschten Schweißqualität.
Hier sind einige Beispiele für die Verwendung von Antriebssystemen für automatische Schweißmaschinen:
- Automobilindustrie: Antriebssysteme werden in der Automobilindustrie zum Schweißen von Karosserieteilen, Motorenteilen und anderen Metallteilen verwendet.
- Bauindustrie: Antriebssysteme werden in der Bauindustrie zum Schweißen von Stahlträgern, Brücken und anderen Bauteilen verwendet.
- Metallverarbeitung: Antriebssysteme werden in der Metallverarbeitung zum Schweißen von Rohren, Profilen und anderen Metallteilen verwendet.
Die Anforderungen an das Antriebssystem einer automatischen Schweißmaschine hängen von einer Reihe von Faktoren ab, einschließlich:
- Art des Schweißverfahrens: Einige Schweißverfahren, wie z. B. WIG-Schweißen, erfordern eine sehr präzise Bewegung des Schweißkopfs. Andere Schweißverfahren, wie z. B. Elektrodenschweißen, sind weniger anspruchsvoll.
- Dicke des Werkstücks: Dickere Werkstücke erfordern einen Antrieb mit höherer Leistung.
- Länge des Schweißbades: Längere Schweißnähte erfordern einen Antrieb mit höherer Geschwindigkeit.
Die Auswahl des richtigen Antriebssystems für eine automatische Schweißmaschine ist wichtig, um eine qualitativ hochwertige Schweißnaht zu gewährleisten.
Das Antriebssystem einer automatischen Schweißmaschine ist für die Bewegung der Schweißkomponenten verantwortlich, um den Schweißprozess durchzuführen. Die Art des Antriebssystems kann je nach Maschinentyp, Anwendungen und spezifischen Anforderungen variieren. Hier sind einige gängige Arten von Antriebssystemen, die in automatischen Schweißmaschinen verwendet werden:
- Servoantriebe:
- Servoantriebe werden oft in automatischen Schweißmaschinen eingesetzt, um präzise und kontrollierte Bewegungen zu ermöglichen.
- Sie bieten eine hohe Genauigkeit bei der Positionierung und Geschwindigkeitsregelung.
- Die Steuerung erfolgt in der Regel durch eine CNC-Steuerung, die den Servoantrieb basierend auf vorprogrammierten Schweißparametern steuert.
- Schrittmotoren:
- Schrittmotoren können ebenfalls in automatischen Schweißmaschinen verwendet werden, insbesondere wenn Präzisionsbewegungen erforderlich sind.
- Sie arbeiten durch das Ausführen von diskreten Schritten und bieten eine gute Positioniergenauigkeit.
- Die Steuerung erfolgt durch einen Schrittmotor-Controller.
- Pneumatische Antriebe:
- Pneumatische Antriebe nutzen Druckluft, um lineare oder rotierende Bewegungen zu erzeugen.
- Sie sind einfach und kostengünstig, werden jedoch möglicherweise nicht in Anwendungen mit sehr präzisen Positionierungsanforderungen eingesetzt.
- Hydraulische Antriebe:
- In einigen schweren Anwendungen, insbesondere bei großen Schweißmaschinen, können hydraulische Antriebe eingesetzt werden.
- Hydraulische Antriebe bieten hohe Leistung und sind in der Lage, schwere Lasten zu bewegen.
- Linearmotoren:
- Linearmotoren ermöglichen lineare Bewegungen ohne mechanische Übertragungselemente wie Kugelgewindetriebe oder Riemen.
- Sie bieten eine hohe Dynamik und Geschwindigkeit.
- Riemenantriebe:
- Riemenantriebe, wie Zahnriemen oder Zahnstangenantriebe, werden verwendet, um die Bewegung von Teilen der Schweißmaschine zu übertragen.
- Sie können kostengünstig und effizient sein.
- Kombination verschiedener Antriebssysteme:
- In einigen Schweißmaschinen werden verschiedene Antriebssysteme kombiniert, um optimale Leistung und Flexibilität zu erreichen.
Die Auswahl des Antriebssystems hängt von verschiedenen Faktoren ab, darunter die Art des Schweißprozesses, die Größe der Werkstücke, die erforderliche Genauigkeit, die Geschwindigkeitsanforderungen und das Budget. Eine präzise Steuerung des Antriebssystems ist entscheidend, um qualitativ hochwertige Schweißnähte zu gewährleisten. Moderne automatische Schweißmaschinen verwenden oft CNC (Computerized Numerical Control)-Steuerungen, um die Bewegungen präzise zu programmieren und zu überwachen.
Steuerung
Die Steuerung einer automatischen Schweißmaschine ist dafür verantwortlich, den Schweißprozess zu steuern. Sie besteht aus einer Reihe von Komponenten, die zusammenarbeiten, um eine genaue und konsistente Schweißnaht zu gewährleisten.
Die wichtigsten Komponenten einer Steuerung für automatische Schweißmaschinen sind:
- Schweißprogramm: Das Schweißprogramm enthält die Anweisungen für den Schweißprozess. Es enthält Informationen wie die Schweißgeschwindigkeit, den Schweißstrom, die Schweißspannung und das Schutzgas.
- Schweißprozessor: Der Schweißprozessor führt die Anweisungen des Schweißprogramms aus. Er steuert den Antriebsmotor, die Schweißstromquelle und die Schutzgasanlage.
- Sensoren: Sensoren überwachen den Schweißprozess und liefern Feedback an den Schweißprozessor. Sie können Informationen wie die Schweißtemperatur, die Schweißgeschwindigkeit und die Schweißlage liefern.
Die Art der Steuerung hängt vom verwendeten Schweißverfahren und den Anforderungen der Anwendung ab. Die häufigsten Steuerungen sind:
- Digitale Steuerung: Digitale Steuerungen sind die gebräuchlichste Art von Steuerung für automatische Schweißmaschinen. Sie sind präzise, zuverlässig und flexibel.
- Analoge Steuerung: Analoge Steuerungen sind weniger präzise als digitale Steuerungen, aber sie sind kostengünstiger.
- Hybride Steuerung: Hybride Steuerungen kombinieren die Vorteile von digitalen und analogen Steuerungen. Sie sind präzise, zuverlässig und kostengünstig.
Die Auswahl der richtigen Steuerung hängt von einer Reihe von Faktoren ab, einschließlich des verwendeten Schweißverfahrens, des zu schweißenden Materials und der gewünschten Schweißqualität.
Hier sind einige Beispiele für die Verwendung von Steuerungen für automatische Schweißmaschinen:
- Automobilindustrie: Steuerungen werden in der Automobilindustrie zum Schweißen von Karosserieteilen, Motorenteilen und anderen Metallteilen verwendet.
- Bauindustrie: Steuerungen werden in der Bauindustrie zum Schweißen von Stahlträgern, Brücken und anderen Bauteilen verwendet.
- Metallverarbeitung: Steuerungen werden in der Metallverarbeitung zum Schweißen von Rohren, Profilen und anderen Metallteilen verwendet.
Die Anforderungen an die Steuerung einer automatischen Schweißmaschine hängen von einer Reihe von Faktoren ab, einschließlich:
- Art des Schweißverfahrens: Einige Schweißverfahren, wie z. B. WIG-Schweißen, erfordern eine sehr präzise Steuerung. Andere Schweißverfahren, wie z. B. Elektrodenschweißen, sind weniger anspruchsvoll.
- Dicke des Werkstücks: Dickere Werkstücke erfordern eine Steuerung mit höherer Leistung.
- Länge des Schweißbades: Längere Schweißnähte erfordern eine Steuerung mit höherer Geschwindigkeit.
Die Auswahl der richtigen Steuerung für eine automatische Schweißmaschine ist wichtig, um eine qualitativ hochwertige Schweißnaht zu gewährleisten.
Die Steuerung einer automatischen Schweißmaschine spielt eine entscheidende Rolle bei der Umsetzung präziser und zuverlässiger Schweißprozesse. Moderne automatische Schweißmaschinen verwenden oft computergesteuerte Systeme, um die Bewegungen, Schweißparameter und andere Aspekte des Schweißprozesses zu kontrollieren. Hier sind einige grundlegende Aspekte der Steuerung einer automatischen Schweißmaschine:
- CNC-Steuerung (Computerized Numerical Control):
- Viele automatische Schweißmaschinen sind mit CNC-Steuerungen ausgestattet.
- CNC ermöglicht die präzise Programmierung und Steuerung der Bewegungen der Schweißmaschine und anderer Parameter wie Stromstärke, Spannung und Drahtvorschubgeschwindigkeit.
- Die CNC-Steuerung kann auf vorprogrammierte Schweißprofile zugreifen, was die Wiederholbarkeit von Schweißprozessen gewährleistet.
- HMI (Human-Machine Interface):
- Ein HMI, auch Bedienoberfläche genannt, ist die Schnittstelle zwischen dem Bediener und der Schweißmaschine.
- Es ermöglicht dem Bediener, die Schweißparameter einzustellen, Programme zu laden, den Maschinenstatus zu überwachen und Fehler zu diagnostizieren.
- Moderne HMIs bieten oft Touchscreen-Funktionalitäten für eine intuitive Bedienung.
- Sensorik und Feedbacksysteme:
- Sensoren, wie beispielsweise Positionssensoren, Temperatursensoren oder Drucksensoren, können in die Steuerung integriert sein.
- Diese Sensoren liefern Echtzeitinformationen über den Schweißprozess und ermöglichen eine Rückkopplung, um die Steuerung entsprechend anzupassen.
- Programmierung und Speicherung von Schweißprofilen:
- Die Steuerung erlaubt die Programmierung von Schweißprofilen, die die spezifischen Anforderungen unterschiedlicher Werkstücke und Schweißanwendungen erfüllen.
- Diese Profile können gespeichert und bei Bedarf abgerufen werden, um den Schweißprozess zu automatisieren.
- Drahtvorschub- und Gassteuerung:
- Bei Schweißverfahren wie MIG/MAG ist die präzise Steuerung des Drahtvorschubs und der Gaszufuhr entscheidend.
- Die Steuerung regelt die Drahtvorschubgeschwindigkeit und die Gasmenge, um einen stabilen Lichtbogen und qualitativ hochwertige Schweißnähte zu gewährleisten.
- Echtzeitüberwachung und Fehlerdiagnose:
- Moderne Steuerungen ermöglichen die Echtzeitüberwachung des Schweißprozesses.
- Fehlerdiagnosefunktionen informieren den Bediener über Probleme und unterstützen bei der Fehlerbehebung.
- Sicherheitsfunktionen:
- Die Steuerung kann Sicherheitsfunktionen integrieren, wie Not-Aus-Schalter, Überlastschutz und andere Sicherheitsvorkehrungen, um die sichere Bedienung der Schweißmaschine zu gewährleisten.
Die genaue Konfiguration der Steuerung hängt von der Art der Schweißmaschine, dem Schweißverfahren und den spezifischen Anforderungen der Anwendung ab. Eine umfassende Schulung des Bedienpersonals ist wichtig, um die Funktionen der Steuerung effektiv nutzen zu können und qualitativ hochwertige Schweißnähte zu gewährleisten.
Rundschweißmaschine
Eine Rundschweißmaschine ist eine Maschine, die ein Rundschweißsystem enthält. Sie besteht in der Regel aus einem Grundrahmen, auf dem die Komponenten des Rundschweißsystems montiert sind.
Rundschweißsysteme und Rundschweißmaschinen werden in einer Vielzahl von Anwendungen eingesetzt, darunter:
- Bauwesen: Rundschweißsysteme und Rundschweißmaschinen werden im Bauwesen verwendet, um Rohre für Wasser-, Gas- und Abwassersysteme zu schweißen.
- Industrie: Rundschweißsysteme und Rundschweißmaschinen werden in der Industrie verwendet, um Rohre für verschiedene Zwecke zu schweißen, z. B. für die Herstellung von Möbeln, Rohrleitungen und anderen Produkten.
- Automobilindustrie: Rundschweißsysteme und Rundschweißmaschinen werden in der Automobilindustrie verwendet, um Rohre für Autokarosserien und andere Komponenten zu schweißen.
Unterschiede zwischen Rundschweißsystem und Rundschweißmaschine
Der Hauptunterschied zwischen einem Rundschweißsystem und einer Rundschweißmaschine besteht darin, dass ein Rundschweißsystem nur die Komponenten enthält, die zum Schweißen von Rohren erforderlich sind, während eine Rundschweißmaschine diese Komponenten in einer Maschine vereint.
Ein Rundschweißsystem kann auch für andere Anwendungen als das Schweißen von Rohren verwendet werden, z. B. für das Schweißen von Profilen oder Blechen. Eine Rundschweißmaschine ist hingegen nur für das Schweißen von Rohren geeignet.
Vorteile von Rundschweißsystemen und Rundschweißmaschinen
Rundschweißsysteme und Rundschweißmaschinen bieten eine Reihe von Vorteilen, darunter:
- Hohe Produktivität: Rundschweißsysteme und Rundschweißmaschinen können eine hohe Produktivität erzielen, da sie den Schweißprozess automatisieren.
- Hohe Qualität: Rundschweißsysteme und Rundschweißmaschinen können eine hohe Qualität der Schweißnähte erzielen, da sie die Schweißparameter präzise steuern können.
- Sicherheit: Rundschweißsysteme und Rundschweißmaschinen können die Sicherheit des Bedieners erhöhen, da sie den Schweißprozess automatisieren und so das Risiko von Verletzungen reduzieren.
Nachteile von Rundschweißsystemen und Rundschweißmaschinen
Rundschweißsysteme und Rundschweißmaschinen bieten auch einige Nachteile, darunter:
- Kosten: Rundschweißsysteme und Rundschweißmaschinen sind in der Regel teurer als manuelle Schweißgeräte.
- Komplexität: Rundschweißsysteme und Rundschweißmaschinen sind in der Regel komplexer als manuelle Schweißgeräte und erfordern daher eine spezielle Ausbildung des Bedieners.
Fazit
Rundschweißsysteme und Rundschweißmaschinen sind eine effiziente und sichere Möglichkeit, Rohre zu schweißen. Sie bieten eine Reihe von Vorteilen, wie hohe Produktivität, hohe Qualität und verbesserte Sicherheit. Allerdings sind sie auch in der Regel teurer und komplexer als manuelle Schweißgeräte.
Das Rundnahtschweißen ist eine Art des Schweißens, die meistens mit einem WIG-Schweißgerät durchgeführt wird. Es wird zum Schweißen von Teilen mit runder Form verwendet. Die Rundschweißanlage wird auch als Rohrschweißmaschine bezeichnet.
Vertikale Rundschweißmaschine
Eine vertikale Rundschweißmaschine ist eine Maschine, die zum Schweißen von Rohren in vertikaler Position verwendet wird. Sie besteht in der Regel aus folgenden Komponenten:
- Schweißkopf: Der Schweißkopf enthält die Schweißelektrode, die das Werkstück erhitzt und den Schweißprozess einleitet.
- Antriebssystem: Das Antriebssystem bewegt den Schweißkopf entlang des Werkstücks, um einen kontinuierlichen Schweißnaht zu erzeugen.
- Steuerung: Die Steuerung steuert die Bewegung des Schweißkopfs und die Schweißparameter.
Vertikale Rundschweißmaschinen werden in einer Vielzahl von Anwendungen eingesetzt, darunter:
- Bauwesen: Vertikale Rundschweißmaschinen werden im Bauwesen verwendet, um Rohre für Wasser-, Gas- und Abwassersysteme zu schweißen.
- Industrie: Vertikale Rundschweißmaschinen werden in der Industrie verwendet, um Rohre für verschiedene Zwecke zu schweißen, z. B. für die Herstellung von Möbeln, Rohrleitungen und anderen Produkten.
- Automobilindustrie: Vertikale Rundschweißmaschinen werden in der Automobilindustrie verwendet, um Rohre für Autokarosserien und andere Komponenten zu schweißen.
Funktionsweise einer vertikalen Rundschweißmaschine
Der Schweißkopf der vertikalen Rundschweißmaschine bewegt sich entlang des Werkstücks, um einen kontinuierlichen Schweißnaht zu erzeugen. Die Bewegung des Schweißkopfs wird durch ein Antriebssystem, z. B. einen Motor, realisiert. Die Schweißelektrode im Schweißkopf erhitzt das Werkstück und den Schweißdraht, der durch den Schweißkopf geführt wird. Der geschmolzene Schweißdraht fließt in die Schweißfuge und verbindet die beiden Werkstückteile miteinander.
Vorteile von vertikalen Rundschweißmaschinen
Vertikale Rundschweißmaschinen bieten eine Reihe von Vorteilen, darunter:
- Hohe Produktivität: Vertikale Rundschweißmaschinen können eine hohe Produktivität erzielen, da sie den Schweißprozess automatisieren.
- Hohe Qualität: Vertikale Rundschweißmaschinen können eine hohe Qualität der Schweißnähte erzielen, da sie die Schweißparameter präzise steuern können.
- Sicherheit: Vertikale Rundschweißmaschinen können die Sicherheit des Bedieners erhöhen, da sie den Schweißprozess automatisieren und so das Risiko von Verletzungen reduzieren.
Nachteile von vertikalen Rundschweißmaschinen
Vertikale Rundschweißmaschinen bieten auch einige Nachteile, darunter:
- Kosten: Vertikale Rundschweißmaschinen sind in der Regel teurer als manuelle Schweißgeräte.
- Komplexität: Vertikale Rundschweißmaschinen sind in der Regel komplexer als manuelle Schweißgeräte und erfordern daher eine spezielle Ausbildung des Bedieners.
Fazit
Vertikale Rundschweißmaschinen sind eine effiziente und sichere Möglichkeit, Rohre in vertikaler Position zu schweißen. Sie bieten eine Reihe von Vorteilen, wie hohe Produktivität, hohe Qualität und verbesserte Sicherheit. Allerdings sind sie auch in der Regel teurer und komplexer als manuelle Schweißgeräte.
Besondere Merkmale vertikaler Rundschweißmaschinen
Vertikale Rundschweißmaschinen haben einige besondere Merkmale, die sie von anderen Schweißmaschinen unterscheiden. Dazu gehören:
- Der Schweißkopf muss in der Lage sein, sich in vertikaler Position zu bewegen.
- Die Steuerung der vertikalen Rundschweißmaschine muss die Bewegung des Schweißkopfs und die Schweißparameter in vertikaler Position steuern können.
Diese Merkmale machen vertikale Rundschweißmaschinen zu einer komplexeren Art von Schweißmaschine als andere Schweißmaschinen. Sie sind jedoch auch in der Lage, präzisere und gleichmäßigere Schweißnähte in vertikaler Position zu erzeugen.
Eine vertikale schweißmaschine, auch Rotationsschweißmaschine genannt, wird zum Schweißen von Teilen in vertikaler Position verwendet. Es ist zum Schweißen von Zylinderhälsen mit Fittings bestimmt. Es gibt zwei Arten: Mechanisches Tracking und automatisiertes Tracking.
Längstnaht-Schweißmaschine
Eine Längstnaht-Schweißmaschine ist eine Maschine, die zum Schweißen von Längsnähten verwendet wird. Längsnähte sind Schweißnähte, die entlang der Längsachse eines Werkstücks angebracht werden. Längstnähte werden in einer Vielzahl von Anwendungen verwendet, darunter:
- Bauwesen: Längstnähte werden im Bauwesen verwendet, um Rohre für Wasser-, Gas- und Abwassersysteme zu schweißen.
- Industrie: Längstnähte werden in der Industrie verwendet, um Rohre für verschiedene Zwecke zu schweißen, z. B. für die Herstellung von Möbeln, Rohrleitungen und anderen Produkten.
- Automobilindustrie: Längstnähte werden in der Automobilindustrie verwendet, um Rohre für Autokarosserien und andere Komponenten zu schweißen.
Längstnaht-Schweißmaschinen werden in zwei Hauptkategorien unterteilt:
- Manuelle Längstnaht-Schweißmaschinen: Manuelle Längstnaht-Schweißmaschinen werden von einem Bediener mit einer Handkurbel oder einem anderen manuellen Gerät bedient. Sie sind in der Regel kostengünstig und einfach zu bedienen, aber sie sind auch langsam und weniger präzise als automatische Längstnaht-Schweißmaschinen.
- Automatische Längstnaht-Schweißmaschinen: Automatische Längstnaht-Schweißmaschinen werden durch einen Motor oder einen anderen Antrieb angetrieben. Sie sind in der Regel schneller und präziser als manuelle Längstnaht-Schweißmaschinen, aber sie sind auch teurer und komplexer zu bedienen.
Die Funktionsweise einer Längstnaht-Schweißmaschine hängt von der Art der Maschine ab. Manuelle Längstnaht-Schweißmaschinen arbeiten in der Regel mit einem Schweißbrenner, der das Werkstück erhitzt und den Schweißprozess einleitet. Automatische Längstnaht-Schweißmaschinen arbeiten in der Regel mit einem Schweißroboter, der den Schweißprozess automatisch durchführt.
Die Schweißqualität hängt von einer Reihe von Faktoren ab, darunter:
- Schweißverfahren: Das Schweißverfahren bestimmt die Art des Schweißnahts, der erzeugt wird.
- Schweißparameter: Die Schweißparameter bestimmen die Eigenschaften des Schweißnahts, z. B. die Dicke und die Festigkeit.
- Rohrmaterial: Das Rohrmaterial bestimmt die Eignung des Schweißverfahrens und der Schweißparameter.
Bei der Auswahl einer Längstnaht-Schweißmaschine ist es wichtig, die Anforderungen der Anwendung zu berücksichtigen. So muss die Maschine für das Schweißverfahren, das Rohrmaterial und das Produktionsvolumen geeignet sein.
Hier sind einige Tipps für das Schweißen mit einer Längstnaht-Schweißmaschine:
- Befolgen Sie die Anweisungen des Herstellers der Längstnaht-Schweißmaschine.
- Verwenden Sie geeignete Schutzausrüstung, z. B. Schutzhandschuhe und Schutzbrille.
- Üben Sie das Schweißen mit einer Längstnaht-Schweißmaschine, bevor Sie sie für eine Anwendung verwenden.
Mit etwas Übung können Sie mit einer Längstnaht-Schweißmaschine Längsnähte in einer Vielzahl von Anwendungen schweißen.
Besondere Merkmale von Längstnaht-Schweißmaschinen
Längstnaht-Schweißmaschinen haben einige besondere Merkmale, die sie von anderen Schweißmaschinen unterscheiden. Dazu gehören:
- Der Schweißkopf muss in der Lage sein, sich entlang der Längsachse des Werkstücks zu bewegen.
- Die Steuerung der Längstnaht-Schweißmaschine muss die Bewegung des Schweißkopfs und die Schweißparameter steuern können.
Diese Merkmale machen Längstnaht-Schweißmaschinen zu einer komplexeren Art von Schweißmaschine als andere Schweißmaschinen. Sie sind jedoch auch in der Lage, präzisere und gleichmäßigere Längsnähte zu erzeugen.
Rohrschweißmaschine
Eine Rohrschweißmaschine ist eine Maschine, die zum Schweißen von Rohren verwendet wird. Es gibt viele verschiedene Arten von Rohrschweißmaschinen, jede mit ihren eigenen Stärken und Schwächen. Einige gebräuchliche Arten von Rohrschweißmaschinen sind:
- Schutzgasschweißen (SMAW)-Maschinen: SMAW-Maschinen verwenden eine abschmelzende Elektrode, die mit Flussmittel beschichtet ist. Das Flussmittel schmilzt und bildet eine schützende Gasschicht um den Lichtbogen, die das Schweißgut vor Oxidation schützt. SMAW-Maschinen sind vielseitig und können zum Schweißen einer Vielzahl von Materialien verwendet werden, aber sie können langsam sein und einen erfahrenen Bediener erfordern.
- Metall-Aktivgas-Schweißen (GMAW)-Maschinen: GMAW-Maschinen verwenden eine Drahtelektrode, die durch eine Schweißpistole geführt wird. Der Draht wird durch einen Lichtbogen geschmolzen und durch ein Gas, wie Argon oder Kohlendioxid, abgeschirmt. GMAW-Maschinen sind schneller als SMAW-Maschinen und einfacher zu bedienen, aber sie sind nicht so vielseitig.
- Füllsdrahtschweißen (FCAW)-Maschinen: FCAW-Maschinen verwenden eine Drahtelektrode, die mit Flussmittel gefüllt ist. Das Flussmittel schmilzt und bildet eine schützende Gasschicht um den Lichtbogen und liefert zusätzliches Füllmaterial für die Schweißnaht. FCAW-Maschinen sind schneller als SMAW-Maschinen und vielseitiger als GMAW-Maschinen, können aber teurer sein.
- Unterpulverschweißen (SAW)-Maschinen: SAW-Maschinen verwenden eine Drahtelektrode, die durch eine mit Flussmittel gefüllte Düse geführt wird. Das Flussmittel schmilzt und bildet eine schützende Schlackeschicht über der Schweißnaht, die das Schweißgut vor Oxidation schützt. SAW-Maschinen sind sehr schnell und können zum Schweißen einer Vielzahl von Materialien verwendet werden, sind aber auch sehr teuer und erfordern einen erfahrenen Bediener.
- Elektroschlackeschweißen (ESW)-Maschinen: ESW-Maschinen verwenden eine abschmelzende Elektrode, die durch einen Lichtbogen geschmolzen wird. Das geschmolzene Metall wird dann durch Wasser oder ein anderes Kühlmittel gekühlt, wodurch es zu einer Schlackeschicht erstarrt. Die Schlackeschicht schützt die Schweißnaht vor Oxidation und ermöglicht es, die Schweißnaht in einem einzigen Durchgang herzustellen. ESW-Maschinen sind sehr schnell und können zum Schweißen einer Vielzahl von Materialien verwendet werden, sind aber auch sehr teuer und erfordern einen erfahrenen Bediener.
Die Wahl der Rohrschweißmaschine hängt von der jeweiligen Anwendung ab. Zu berücksichtigende Faktoren sind die Art des zu schweißenden Materials, die Materialstärke, die gewünschte Schweißqualität und das Budget.
Hier sind einige allgemeine Tipps zur Verwendung einer Rohrschweißmaschine:
- Beachten Sie immer die Sicherheitshinweise für die spezifische Maschine, die Sie verwenden.
- Tragen Sie geeignete Sicherheitsausrüstung, wie Handschuhe, Schutzbrille und einen Schweißhelm.
- Sorgen Sie für eine gute Belüftung des Arbeitsbereichs.
- Reinigen Sie die Rohre vor dem Schweißen, um Schmutz oder Ablagerungen zu entfernen.
- Klemmen Sie die Rohre fest, um ein Verrutschen während des Schweißens zu verhindern.
- Verwenden Sie die richtigen Schweißparameter für das Material, das Sie schweißen.
- Überprüfen Sie die Schweißnaht nach dem Schweißen, um sicherzustellen, dass sie von guter Qualität ist.
Mit der richtigen Sorgfalt und Aufmerksamkeit kann eine Rohrschweißmaschine ein wertvolles Werkzeug für eine Vielzahl von Schweißaufgaben sein.
Eine automatische Rohrschweißmaschine kann Rohre auf einem Gerät, das als Rohrrotator bezeichnet wird, problemlos schweißen. Für schnelles und effektives Arbeiten haben wir eine brandneue automatische WIG-Rohrschweißmaschine entwickelt und hergestellt. Aus diesem Grund verwenden wir die Rohrposition zum Schweißen. Ein Rohrpositionierer oder Rohrrotator ist ein Gerät, mit dem Rohre um ihre eigene Achse gedreht werden
Der Rohrpositionierer zum Schweißen hat 4 einzelne Räder, die sich mit dem Rohr oder dem Zylinder selbst drehen. Die Räder werden von einem Elektromotor angetrieben.
Roboterschweißautomatisierung mit einer Rundschweißmaschine
Roboterschweißautomatisierung mit einer Rundschweißmaschine ist eine Technologie, die zum Schweißen von Rohren in einer Vielzahl von Anwendungen verwendet wird. Sie bietet eine Reihe von Vorteilen gegenüber manuellem Schweißen, darunter:
- Höhere Produktivität: Roboterschweißautomaten können bis zu 10-mal schneller schweißen als manuelle Schweißer.
- Höhere Qualität: Roboterschweißautomaten können präzisere und gleichmäßigere Schweißnähte erzeugen als manuelle Schweißer.
- Verbesserte Sicherheit: Roboterschweißautomaten können die Sicherheit des Bedieners verbessern, indem sie ihn von dem Schweißprozess fernhalten.
Die Roboterschweißautomatisierung mit einer Rundschweißmaschine besteht aus zwei Hauptkomponenten:
- Der Roboter: Der Roboter ist ein mechanischer Arm, der den Schweißkopf der Rundschweißmaschine bewegt.
- Die Rundschweißmaschine: Die Rundschweißmaschine erzeugt den Schweißlichtbogen und fügt das Schweißmaterial hinzu.
Der Roboter wird von einem Computerprogramm gesteuert, das die Bewegung des Roboters und die Schweißparameter steuert. Das Computerprogramm wird vom Bediener erstellt oder angepasst, um die gewünschte Schweißnaht zu erzeugen.
Die Roboterschweißautomatisierung mit einer Rundschweißmaschine wird in einer Vielzahl von Anwendungen verwendet, darunter:
- Bauwesen: Roboterschweißautomaten werden verwendet, um Rohre für Wasser-, Gas- und Abwassersysteme zu schweißen.
- Industrie: Roboterschweißautomaten werden verwendet, um Rohre für verschiedene Zwecke zu schweißen, z. B. für die Herstellung von Möbeln, Rohrleitungen und anderen Produkten.
- Automobilindustrie: Roboterschweißautomaten werden verwendet, um Rohre für Autokarosserien und andere Komponenten zu schweißen.
Die Roboterschweißautomatisierung mit einer Rundschweißmaschine ist eine kosteneffektive und effiziente Möglichkeit, Rohre in einer Vielzahl von Anwendungen zu schweißen. Sie bietet eine Reihe von Vorteilen gegenüber manuellem Schweißen, darunter höhere Produktivität, höhere Qualität und verbesserte Sicherheit.
Vorteile der Roboterschweißautomatisierung mit einer Rundschweißmaschine:
- Höhere Produktivität: Roboterschweißautomaten können bis zu 10-mal schneller schweißen als manuelle Schweißer. Dies kann zu erheblichen Zeit- und Kosteneinsparungen führen.
- Höhere Qualität: Roboterschweißautomaten können präzisere und gleichmäßigere Schweißnähte erzeugen als manuelle Schweißer. Dies kann zu einer verbesserten Produktqualität und Zuverlässigkeit führen.
- Verbesserte Sicherheit: Roboterschweißautomaten können die Sicherheit des Bedieners verbessern, indem sie ihn von dem Schweißprozess fernhalten. Dies kann das Risiko von Verletzungen verringern.
Nachteile der Roboterschweißautomatisierung mit einer Rundschweißmaschine:
- Hohe Anfangsinvestitionskosten: Roboterschweißautomaten sind in der Regel teurer als manuelle Schweißgeräte.
- Komplexe Technologie: Roboterschweißautomaten sind komplexe Technologien, die eine spezielle Ausbildung und Wartung erfordern.
Fazit:
Die Roboterschweißautomatisierung mit einer Rundschweißmaschine ist eine Technologie, die eine Reihe von Vorteilen gegenüber manuellem Schweißen bietet. Sie ist jedoch auch mit hohen Anfangsinvestitionskosten und komplexer Technologie verbunden.
Für die Roboterschweißautomatisierung entwerfen und fertigen wir komplette automatische Schweißgeräte, einschließlich einer Schweißsäule (Säulen- und Auslegerschweißmaschine), einer Schweißrotatormaschine, eines Schweißroboters und einer Schweißmaschine.
Automatisierung der Rundschweißmaschine
Die Automatisierung der Rundschweißmaschine ist ein Prozess, bei dem die manuellen Aufgaben beim Schweißen von Rohren durch Maschinen oder Roboter übernommen werden. Dies kann zu einer Reihe von Vorteilen führen, darunter:
- Höhere Produktivität: Automatisierte Rundschweißmaschinen können bis zu 10-mal schneller schweißen als manuelle Schweißer. Dies kann zu erheblichen Zeit- und Kosteneinsparungen führen.
- Höhere Qualität: Automatisierte Rundschweißmaschinen können präzisere und gleichmäßigere Schweißnähte erzeugen als manuelle Schweißer. Dies kann zu einer verbesserten Produktqualität und Zuverlässigkeit führen.
- Verbesserte Sicherheit: Automatisierte Rundschweißmaschinen können die Sicherheit des Bedieners verbessern, indem sie ihn von dem Schweißprozess fernhalten. Dies kann das Risiko von Verletzungen verringern.
Es gibt verschiedene Möglichkeiten, eine Rundschweißmaschine zu automatisieren. Eine Möglichkeit ist die Verwendung eines Roboters. Der Roboter kann den Schweißkopf der Rundschweißmaschine bewegen und die Schweißparameter steuern. Eine andere Möglichkeit ist die Verwendung einer CNC-Steuerung. Die CNC-Steuerung kann die Bewegung des Schweißkopfs und die Schweißparameter steuern.
Die Automatisierung der Rundschweißmaschine ist eine komplexe Aufgabe, die eine sorgfältige Planung und Umsetzung erfordert. Es ist wichtig, die Anforderungen der jeweiligen Anwendung zu berücksichtigen, um die richtige Automatisierungslösung zu wählen.
Vorteile der Automatisierung der Rundschweißmaschine:
- Höhere Produktivität: Automatisierte Rundschweißmaschinen können bis zu 10-mal schneller schweißen als manuelle Schweißer. Dies kann zu erheblichen Zeit- und Kosteneinsparungen führen.
- Höhere Qualität: Automatisierte Rundschweißmaschinen können präzisere und gleichmäßigere Schweißnähte erzeugen als manuelle Schweißer. Dies kann zu einer verbesserten Produktqualität und Zuverlässigkeit führen.
- Verbesserte Sicherheit: Automatisierte Rundschweißmaschinen können die Sicherheit des Bedieners verbessern, indem sie ihn von dem Schweißprozess fernhalten. Dies kann das Risiko von Verletzungen verringern.
Nachteile der Automatisierung der Rundschweißmaschine:
- Hohe Anfangsinvestitionskosten: Die Automatisierung einer Rundschweißmaschine kann kostspielig sein.
- Komplexe Technologie: Die Automatisierung einer Rundschweißmaschine erfordert eine komplexe Technologie, die eine spezielle Ausbildung und Wartung erfordert.
Fazit:
Die Automatisierung der Rundschweißmaschine ist eine Technologie, die eine Reihe von Vorteilen gegenüber manuellem Schweißen bieten kann. Sie ist jedoch auch mit hohen Anfangsinvestitionskosten und komplexer Technologie verbunden.
Entwicklung einer tragbaren rotierenden MIG-Lichtbogenschweißmaschine, das rotierende MIG-Lichtbogenschweißen ist eine von mehreren Techniken, die für das Engspaltschweißen entwickelt wurden. Es wurde festgestellt, dass die Fusionseigenschaften der HAZ aufgrund der Natur der ARC-Physik verbessert werden.
Das Verfahren kann effektiv für verschiedene Materialien verwendet werden, insbesondere für solche, die empfindlich sind Wärmeeintrag einschließlich hochfester niedriglegierter, rostfreier Stähle, hitzebeständiger Stähle, Aluminium- und Titanlegierungen.
Basierend auf diesem Ergebnis wurde festgestellt, dass diese Art des Schweißens besser für das Kehl- und Stumpfschweißen geeignet ist. Das Prinzip des Verfahrens besteht darin, dass der Schweißdraht mit Exzentrizität an der Kontaktspitze in die Elektrodendüse eingeführt wird. In diesem Projekt werden wir Design, Analyse und Fertigung für die Automatisierung für das Schweißen von kreisförmigen Teilen mit einheitlicher Schweißstruktur durchführen.
Wir werden den Drehtisch entwerfen und herstellen, der sich mit einer speziell erforderlichen Geschwindigkeit dreht, abhängig von der Anforderung des hinzuzufügenden Filetmaterials.
Ferner wird die Elektrodendüse stationär gehalten, die in Kontakt mit der Oberfläche des zu schweißenden Bauteils sein wird. Daher wurde in diesem Projekt ein detailliertes Design für die Umrüstung der herkömmlichen MIG-Schweißmaschine (ARC) in eine automatisierte Schweißmaschine für kreisförmige Komponenten vorgeschlagen.
Zusammen mit dieser Hauptmodifikation soll die vorhandene MIG-Schweißmaschine – (ein stationärer, nach unten gerichteter ARG – KOPF, der Vorkehrungen für horizontale und Aufwärtsbewegungen hat) in eine tragbare Schweißmaschine umgebaut werden
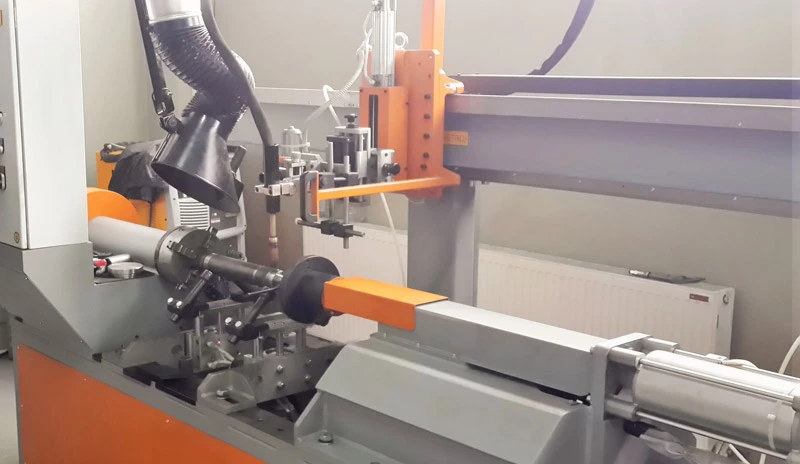
Automatischer Rohrroller zur Rundschweißmaschine
Ein automatischer Rohrroller zur Rundschweißmaschine ist ein Gerät, das Rohre in eine Position bringt, in der sie von einer Rundschweißmaschine geschweißt werden können. Automatische Rohrroller werden in der Regel in der Industrie eingesetzt, um Rohre für eine Vielzahl von Anwendungen zu schweißen, z. B. für Wasser-, Gas- und Abwassersysteme, Rohrleitungen und andere Produkte.
Automatische Rohrroller bestehen in der Regel aus den folgenden Komponenten:
- Ein Motor: Der Motor treibt die Rollen an, die das Rohr bewegen.
- Eine Steuerung: Die Steuerung steuert die Bewegung der Rollen und die Position des Rohrs.
- Eine Haltevorrichtung: Die Haltevorrichtung hält das Rohr in der gewünschten Position.
Die Funktionsweise eines automatischen Rohrrollers ist wie folgt:
- Das Rohr wird in den Rohrroller eingelegt.
- Der Motor treibt die Rollen an, die das Rohr in die gewünschte Position bewegen.
- Die Haltevorrichtung hält das Rohr in der gewünschten Position.
- Die Rundschweißmaschine schweißt das Rohr.
Automatische Rohrroller bieten eine Reihe von Vorteilen gegenüber manuellen Methoden zum Positionieren von Rohren für das Schweißen, darunter:
- Höhere Produktivität: Automatische Rohrroller können Rohre schneller und effizienter positionieren als manuelle Methoden.
- Höhere Genauigkeit: Automatische Rohrroller können Rohre genauer positionieren als manuelle Methoden.
- Verbesserte Sicherheit: Automatische Rohrroller können die Sicherheit des Bedieners verbessern, indem sie ihn von dem Schweißensprozess fernhalten.
Automatische Rohrroller sind in einer Vielzahl von Ausführungen erhältlich, die für verschiedene Anwendungen geeignet sind. Die Auswahl des richtigen Rohrrollers hängt von den Anforderungen der jeweiligen Anwendung ab.
Vorteile eines automatischen Rohrrollers zur Rundschweißmaschine:
- Höhere Produktivität: Automatische Rohrroller können Rohre schneller und effizienter positionieren als manuelle Methoden. Dies kann zu erheblichen Zeit- und Kosteneinsparungen führen.
- Höhere Genauigkeit: Automatische Rohrroller können Rohre genauer positionieren als manuelle Methoden. Dies kann zu einer verbesserten Produktqualität und Zuverlässigkeit führen.
- Verbesserte Sicherheit: Automatische Rohrroller können die Sicherheit des Bedieners verbessern, indem sie ihn von dem Schweißensprozess fernhalten. Dies kann das Risiko von Verletzungen verringern.
Nachteile eines automatischen Rohrrollers zur Rundschweißmaschine:
- Hohe Anfangsinvestitionskosten: Automatische Rohrroller können kostspielig sein.
- Komplexe Technologie: Automatische Rohrroller erfordern eine komplexe Technologie, die eine spezielle Ausbildung und Wartung erfordert.
Fazit:
Automatische Rohrroller zur Rundschweißmaschine sind eine Technologie, die eine Reihe von Vorteilen gegenüber manuellen Methoden bieten kann. Sie sind jedoch auch mit hohen Anfangsinvestitionskosten und komplexer Technologie verbunden.
Heutzutage ist die Massenproduktion oft erforderlich, um die herkömmlich manuell durchgeführten Herstellungsprozesse zu automatisieren. Gegenwärtig werden verschiedene Schweißtechniken für die Schweißprozesse wie CO2-Schweißen, Lichtbogenschweißen und WIG (Wolfram-Inertgas-Schweißen) verwendet, da verschiedene Vorrichtungen für verschiedene Schweißarbeiten verwendet werden, aber in vielen Anwendungen verwenden wir einige Techniken, die arbeitet nicht effizient und genau.
Das Bewegen der Elektrode entlang der Schweißlinie ist eine gekonnte Arbeit und wird insbesondere bei kreisförmigen Bauteilen viel schwieriger. Um ein solches Problem zu vermeiden, implementieren wir einen Schweißrotator. Die Notwendigkeit einer speziellen Vorrichtung, die den Job mit einer festen Geschwindigkeit drehen kann, um den Schweißprozess für kreisförmige Komponenten zu unterstützen und ein gutes Profil und eine homogene Schweißung sicherzustellen. Zum Schweißen können viele verschiedene Energiequellen verwendet werden, darunter eine Gasflamme, ein Lichtbogen, ein Laser, ein Elektronenstrahl, Reibung und Ultraschall.
Industrielle Rundschweißmaschine
Eine industrielle Rundschweißmaschine ist eine Maschine, die zum Schweißen von Rohren in der Industrie verwendet wird. Sie ist in der Regel eine automatische Maschine, die von einem Roboter oder einer CNC-Steuerung gesteuert wird.
Industrielle Rundschweißmaschinen werden in einer Vielzahl von Anwendungen verwendet, darunter:
- Wasser-, Gas- und Abwassersysteme: Industrielle Rundschweißmaschinen werden verwendet, um Rohre für Wasser-, Gas- und Abwassersysteme zu schweißen.
- Rohrleitungen: Industrielle Rundschweißmaschinen werden verwendet, um Rohre für Rohrleitungen zu schweißen.
- Andere Produkte: Industrielle Rundschweißmaschinen werden verwendet, um Rohre für andere Produkte zu schweißen, z. B. für Möbel, Fahrzeuge und andere Konstruktionen.
Industrielle Rundschweißmaschinen sind in der Regel in der Lage, Rohre aus einer Vielzahl von Materialien zu schweißen, darunter:
- Stahl: Industrielle Rundschweißmaschinen können Stahlrohre schweißen.
- Edelstahl: Industrielle Rundschweißmaschinen können Edelstahlrohre schweißen.
- Aluminium: Industrielle Rundschweißmaschinen können Aluminiumrohre schweißen.
- Kunststoff: Industrielle Rundschweißmaschinen können Kunststoffrohre schweißen.
Die Funktionsweise einer industriellen Rundschweißmaschine ist wie folgt:
- Das Rohr wird in die Maschine eingelegt.
- Der Roboter oder die CNC-Steuerung bewegt den Schweißkopf entlang des Rohrs.
- Der Schweißkopf erzeugt den Schweißlichtbogen und fügt das Schweißmaterial hinzu.
- Der Schweißprozess wird abgeschlossen.
Industrielle Rundschweißmaschinen bieten eine Reihe von Vorteilen gegenüber manuellen Schweißmethoden, darunter:
- Höhere Produktivität: Industrielle Rundschweißmaschinen können Rohre schneller und effizienter schweißen als manuelle Schweißmethoden.
- Höhere Qualität: Industrielle Rundschweißmaschinen können präzisere und gleichmäßigere Schweißnähte erzeugen als manuelle Schweißmethoden.
- Verbesserte Sicherheit: Industrielle Rundschweißmaschinen können die Sicherheit des Bedieners verbessern, indem sie ihn von dem Schweißprozess fernhalten.
Industrielle Rundschweißmaschinen sind in einer Vielzahl von Ausführungen erhältlich, die für verschiedene Anwendungen geeignet sind. Die Auswahl der richtigen Rundschweißmaschine hängt von den Anforderungen der jeweiligen Anwendung ab.
Vorteile einer industriellen Rundschweißmaschine:
- Höhere Produktivität: Industrielle Rundschweißmaschinen können Rohre schneller und effizienter schweißen als manuelle Schweißmethoden. Dies kann zu erheblichen Zeit- und Kosteneinsparungen führen.
- Höhere Qualität: Industrielle Rundschweißmaschinen können präzisere und gleichmäßigere Schweißnähte erzeugen als manuelle Schweißmethoden. Dies kann zu einer verbesserten Produktqualität und Zuverlässigkeit führen.
- Verbesserte Sicherheit: Industrielle Rundschweißmaschinen können die Sicherheit des Bedieners verbessern, indem sie ihn von dem Schweißprozess fernhalten. Dies kann das Risiko von Verletzungen verringern.
Nachteile einer industriellen Rundschweißmaschine:
- Hohe Anfangsinvestitionskosten: Industrielle Rundschweißmaschinen können kostspielig sein.
- Komplexe Technologie: Industrielle Rundschweißmaschinen erfordern eine komplexe Technologie, die eine spezielle Ausbildung und Wartung erfordert.
Fazit:
Industrielle Rundschweißmaschinen sind eine Technologie, die eine Reihe von Vorteilen gegenüber manuellen Schweißmethoden bieten kann. Sie sind jedoch auch mit hohen Anfangsinvestitionskosten und komplexer Technologie verbunden.
Schweißen ist zwar oft ein industrieller Prozess, kann aber in vielen verschiedenen Umgebungen durchgeführt werden, darunter im Freien, unter Wasser und im Weltraum. Unabhängig vom Standort bleibt das Schweißen gefährlich, und Es werden Vorkehrungen getroffen, um Verbrennungen, Stromschläge, Augenschäden, giftige Dämpfe und übermäßige UV-Lichteinwirkung zu vermeiden.
Beim CO2-Schweißen oder manchmal beim Lichtbogenschweißen besteht häufig die Notwendigkeit, kreisförmige Bauteile zu schweißen, wobei das Schweißen auf dem gesamten Umfang oder einer Teilbogenlänge des Werkstücks durchgeführt wird. Entlang dieser Kreisbahn wird also die Elektrode im herkömmlichen Verfahren bewegt. Aber die Bewegung der Elektrode ist viel schwieriger und es ist viel einfacher, den Job zu indexieren.
Beim Schweißen ist die aktuelle Zykluszeit des Werkstücks höher, d. h. 45- 60 Sek. Wir müssen also ein solches System zum einfachen Laden von Werkstücken und zum automatischen Positionieren der Schweißzange entwickeln. Automatisches Ein- und Ausschalten der Schalter des Schweißgeräts, um ein reibungsloses Arbeiten zu erreichen.
Ziele des Projekts
- Entwicklung eines Systems mit AutoCAD 2014 und CATIA V5R20
- Rahmensicherheit mit analytischen Methoden prüfen (Student Version ANSYS 15.0)
- Umsetzung von Konzepten zur Steigerung der Produktivität von Schweißen.
Eigenschaften der Rundschweißmaschine
Rundschweißmaschinen sind Maschinen, die zum Schweißen von Rohren verwendet werden. Sie können in verschiedenen Größen und Ausführungen erhältlich sein, je nach Anwendungszweck. Einige wichtige Eigenschaften von Rundschweißmaschinen sind:
- Schweißverfahren: Rundschweißmaschinen können verschiedene Schweißverfahren verwenden, wie z. B.:
- Schutzgasschweißen (MIG/MAG): Bei diesem Verfahren wird ein Schutzgas verwendet, um das geschmolzene Metall vor Oxidation zu schützen.
- Fülldrahtschweißen (FCAW): Bei diesem Verfahren wird ein Drahtelektrode verwendet, die mit Füllmaterial beschichtet ist.
- Unterpulverschweißen (SAW): Bei diesem Verfahren wird ein Drahtelektrode verwendet, die durch ein Flussmittelbett geführt wird.
- Elektroschlackeschweißen (ESW): Bei diesem Verfahren wird ein Drahtelektrode verwendet, die durch einen Lichtbogen geschmolzen wird.
- Schweißkopf: Der Schweißkopf ist der Teil der Maschine, der den Schweißlichtbogen erzeugt und das Schweißmaterial hinzufügt. Er kann in verschiedenen Ausführungen erhältlich sein, je nach Schweißverfahren und Anwendungszweck.
- Steuerung: Die Steuerung steuert die Bewegung des Schweißkopfs und die Schweißparameter. Sie kann manuell oder automatisch sein.
- Automatisierung: Rundschweißmaschinen können manuell oder automatisiert betrieben werden. Automatisierte Rundschweißmaschinen werden in der Regel in der Industrie eingesetzt, um eine höhere Produktivität und Qualität zu erzielen.
- Material: Rundschweißmaschinen können zum Schweißen von Rohren aus verschiedenen Materialien verwendet werden, wie z. B.:
- Stahl
- Edelstahl
- Aluminium
- Kunststoff
- Rohrgröße: Rundschweißmaschinen können zum Schweißen von Rohren in verschiedenen Größen verwendet werden, von kleinen Rohren für den Hausgebrauch bis hin zu großen Rohren für industrielle Anwendungen.
Die Wahl der richtigen Rundschweißmaschine hängt von den Anforderungen der jeweiligen Anwendung ab. Faktoren, die bei der Auswahl berücksichtigt werden müssen, sind:
- Schweißverfahren: Das Schweißverfahren bestimmt die Art des Schweißlichtbogens und des Schweißmaterials, die verwendet werden.
- Schweißkopf: Der Schweißkopf muss für das gewählte Schweißverfahren geeignet sein.
- Steuerung: Die Steuerung muss die Anforderungen der jeweiligen Anwendung erfüllen.
- Automatisierung: Die Automatisierung kann die Produktivität und Qualität des Schweißprozesses verbessern.
- Material: Die Maschine muss für das zu schweißende Material geeignet sein.
- Rohrgröße: Die Maschine muss für die zu schweißenden Rohrgrößen geeignet sein.
Höhere Leistung Industrielle Erfahrungen legen nahe, dass ein durchschnittlicher Roboter mindestens doppelt so schnell schweißen kann wie ein erfahrener manueller Schweißer. Die erhöhte Geschwindigkeit trägt dazu bei, mögliche Verzögerungen aufgrund des Schweißvorgangs zu vermeiden, und es kann ein schnellerer Wechsel der Magnetspulen realisiert werden.
Geringere variable Arbeitskosten Aufgrund der erhöhten Leistung werden die Gesamtarbeitszeit verkürzt und die Arbeitskosten gesenkt. Die begrenzte Verfügbarkeit qualifizierter, zertifizierter Schweißer kann eine Herausforderung darstellen. Umgekehrt sind allgemeine Maschinenbediener mehr leicht verfügbar und erschwinglicher als qualifizierte, zertifizierte Arbeitskräfte.
Schutzgasschweißen
Beim Schutzgasschweißen, auch bekannt als Lichtbogenschweißen unter Schutzgas, wird ein elektrischer Lichtbogen zum Schmelzen des Grundwerkstoffs (Schweißgut) verwendet. Dabei schützt ein Inertgas das Schweißgut vor Oxidation und Verunreinigungen.
Es gibt viele verschiedene Arten des Lichtbogenschweißens unter Schutzgas, aber die häufigsten sind:
- Metall-Aktivgasschweißen (MAG): Bei diesem Verfahren wird eine abschmelzende Elektrode verwendet, die beim Schmelzen in das Schweißgut eingebracht wird. Das Schutzgas ist typischerweise eine Mischung aus Kohlendioxid und Argon. MAG-Schweißen ist ein vielseitiges Verfahren, das zum Schweißen einer Vielzahl von Werkstoffen eingesetzt werden kann.
- Metall-Inertgasschweißen (MIG): Dieses Verfahren ist ähnlich wie das MAG-Schweißen, verwendet jedoch ein Inertgas wie Argon als Schutzgas. MIG-Schweißen wird typischerweise zum Schweißen von Nichteisenmetallen wie Aluminium und Edelstahl verwendet.
- Wolfram-Inertgasschweißen (WIG): Bei diesem Verfahren wird eine nicht abschmelzende Elektrode verwendet, z. B. Wolfram. Das Schutzgas ist typischerweise ein Inertgas wie Argon. WIG-Schweißen ist ein Präzisionsschweißverfahren, das häufig zum Schweißen dünner Werkstoffe verwendet wird.
- Plasmaschweißen: Bei diesem Verfahren wird ein Plasmaschneider zum Schmelzen des Grundwerkstoffs verwendet. Der Plasmaschneider ist ein hochenergetischer Strom aus ionisiertem Gas, der durch den Durchgang eines elektrischen Stroms durch eine Düse erzeugt wird. Das Plasmaschweißen ist ein vielseitiges Verfahren, das zum Schweißen einer Vielzahl von Werkstoffen eingesetzt werden kann.
Schutzgasschweißen ist eine beliebte Wahl für viele Schweißanwendungen, da es eine Reihe von Vorteilen bietet, darunter:
- Hochwertige Schweißnähte
- Hohe Produktionsraten
- Vielseitigkeit
- Einfache Bedienung
Schutzgasschweißen wird in einer Vielzahl von Branchen eingesetzt, darunter Automobilindustrie, Luft- und Raumfahrt, Bauwesen und Fertigung.
Beim Schutzgasschweißen sollten folgende Sicherheitsvorkehrungen beachtet werden:
- Tragen Sie geeignete persönliche Schutzausrüstung (PSA), einschließlich eines Schweißhelms, Handschuhen und Stiefeln.
- Sorgen Sie für eine gute Belüftung des Schweißbereichs.
- Schweißen Sie nicht in der Nähe von brennbaren Materialien.
- Berühren Sie die Elektrode oder das Schweißgut nicht mit bloßer Haut.
- Seien Sie sich der potenziellen Gefahr eines elektrischen Schlags bewusst.
Wenn Sie mehr über das Schutzgasschweißen erfahren möchten, stehen Ihnen zahlreiche Ressourcen online und in Bibliotheken zur Verfügung. Sie können auch Schweißkurse an Berufsschulen und Volkshochschulen besuchen
Fülldrahtschweißen
Das Fülldrahtschweißen ist eine Art des Schutzgasschweißens, bei dem ein Fülldraht zum Schweißen verwendet wird. Der Fülldraht besteht aus einem Metallmantel, der mit Pulver gefüllt ist. Das Pulver verleiht dem Draht zusätzliche Eigenschaften, z. B. eine bessere Haftung oder eine höhere Schmelztemperatur.
Beim Fülldrahtschweißen wird ein elektrischer Lichtbogen zwischen dem Fülldraht und dem Grundwerkstoff erzeugt. Der Lichtbogen erhitzt den Fülldraht und den Grundwerkstoff, wodurch sie schmelzen. Das geschmolzene Metall fließt zusammen und bildet eine Schweißnaht.
Das Fülldrahtschweißen ist ein vielseitiges Verfahren, das zum Schweißen einer Vielzahl von Werkstoffen verwendet werden kann, darunter Stahl, Aluminium und Edelstahl. Es ist auch ein relativ einfaches Verfahren, das leicht zu erlernen ist.
Vorteile des Fülldrahtschweißens:
- Vielseitigkeit: Das Fülldrahtschweißen kann zum Schweißen einer Vielzahl von Werkstoffen verwendet werden.
- Einfachheit: Das Fülldrahtschweißen ist ein relativ einfaches Verfahren, das leicht zu erlernen ist.
- Produktivität: Das Fülldrahtschweißen ist ein produktives Verfahren, das hohe Schweißgeschwindigkeiten ermöglicht.
Nachteile des Fülldrahtschweißens:
- Rauchentwicklung: Das Fülldrahtschweißen erzeugt Rauch, der Atemwegsprobleme verursachen kann.
- Porosität: Porosität kann ein Problem sein, wenn das Pulver im Fülldraht nicht vollständig aus der Schweißnaht entweichen kann.
Sicherheitshinweise beim Fülldrahtschweißen:
- Tragen Sie geeignete persönliche Schutzausrüstung (PSA), einschließlich eines Schweißhelms, Handschuhen, Stiefeln und einer Schutzbrille.
- Sorgen Sie für eine gute Belüftung des Schweißbereichs.
- Schweißen Sie nicht in der Nähe von brennbaren Materialien.
- Berühren Sie den Fülldraht oder die Schweißnaht nicht mit bloßen Händen.
- Seien Sie sich der potenziellen Gefahr eines elektrischen Schlags bewusst
Das Fülldrahtschweißen ist eine Schweißtechnik, bei der anstelle eines massiven Schweißdrahts ein Draht mit einer Hohlraumfüllung (Fülldraht) verwendet wird. Dieser Draht enthält typischerweise eine Mischung aus pulverisierten Schweißzusatzwerkstoffen, die beim Schweißen schmelzen und den Schweißgutpool formen. Es gibt zwei Haupttypen von Fülldrähten: selbstschützende Fülldrähte und gasgeschützte Fülldrähte.
Hier sind einige grundlegende Informationen zum Fülldrahtschweißen:
- Selbstschützende Fülldrähte:
- Diese Fülldrähte enthalten chemische Verbindungen, die beim Erhitzen während des Schweißprozesses Gase freisetzen, die den Schweißgutpool vor atmosphärischer Kontamination schützen. Daher benötigen sie keine externe Gaszufuhr.
- Sie werden oft bei Arbeiten im Freien oder in Umgebungen mit starkem Luftzug eingesetzt.
- Gasgeschützte Fülldrähte:
- Diese Fülldrähte erfordern eine externe Gaszufuhr, normalerweise eine Mischung aus Argon und CO2, um den Schweißprozess zu schützen und eine saubere Schweißnaht zu gewährleisten.
- Gasgeschützte Fülldrähte werden häufig für präzise Schweißarbeiten verwendet, insbesondere wenn eine gute Schutzatmosphäre erforderlich ist.
- Vorteile des Fülldrahtschweißens:
- Es kann schneller sein als das Schutzgasschweißen mit massivem Draht, da der Fülldraht selbstschützend sein kann.
- Ermöglicht das Schweißen von dickem Material in einer einzigen Schicht.
- Reduziert die Notwendigkeit von aufwändigen Schutzgasvorrichtungen.
- Anwendungen:
- Fülldrahtschweißen wird in verschiedenen Branchen eingesetzt, darunter Schiffsbau, Bauwesen, Automobilindustrie und allgemeiner Metallbau.
- Es eignet sich besonders gut für das Schweißen von Stahlkonstruktionen.
- Technische Überlegungen:
- Die Auswahl des geeigneten Fülldrahts hängt von verschiedenen Faktoren ab, darunter die Art des zu schweißenden Materials, die Schweißposition, die Schweißstromstärke und andere spezifische Anforderungen der Anwendung.
Es ist wichtig zu beachten, dass die genauen Verfahren und Anforderungen je nach den spezifischen Materialien und Anwendungen variieren können. Vor dem Fülldrahtschweißen ist es ratsam, die Anweisungen des Schweißdrahtherstellers, des Schweißgeräteherstellers und alle geltenden Sicherheitsrichtlinien zu beachten. Es wird auch empfohlen, die Schweißparameter entsprechend den spezifischen Anforderungen anzupassen.
Gasprüfung für die Rundschweißmaschine
Die Gasprüfung für Schweißmaschinen ist wichtig, um sicherzustellen, dass alle gasführenden Teile ordnungsgemäß funktionieren und keine Lecks aufweisen. Hier sind einige allgemeine Schritte, die bei der Gasprüfung für eine Schweißmaschine, einschließlich Rundschweißmaschinen, durchgeführt werden könnten:
- Sichtprüfung:
- Überprüfen Sie alle Gasleitungen, Schläuche und Verbindungen visuell auf Schäden oder Undichtigkeiten.
- Stellen Sie sicher, dass alle Ventile ordnungsgemäß funktionieren und leicht zugänglich sind.
- Druckprüfung:
- Führen Sie eine Druckprüfung durch, um sicherzustellen, dass der Gasdruck innerhalb der empfohlenen Grenzen liegt.
- Überprüfen Sie den Druckregler auf korrekte Einstellung und Funktion.
- Leckageprüfung:
- Verwenden Sie geeignete Methoden, wie z.B. Seifenlösung, um auf eventuelle Leckagen an den Verbindungen zu prüfen.
- Überprüfen Sie regelmäßig die Schlauchverbindungen und ersetzen Sie verschlissene oder beschädigte Teile.
- Regelmäßige Wartung:
- Führen Sie regelmäßige Wartungsarbeiten gemäß den Herstelleranweisungen durch.
- Achten Sie darauf, dass alle Komponenten, einschließlich Brenner und Düsen, in gutem Zustand sind.
- Dokumentation:
- Halten Sie Aufzeichnungen über durchgeführte Prüfungen und Wartungen, um die Einhaltung von Vorschriften und Normen nachzuweisen.
Es ist wichtig, die spezifischen Anweisungen des Herstellers für Ihre Rundschweißmaschine zu beachten, da unterschiedliche Modelle unterschiedliche Anforderungen haben können. Darüber hinaus müssen Sie möglicherweise lokale Vorschriften und Sicherheitsstandards berücksichtigen. Es wird dringend empfohlen, sich mit einem Fachmann oder einem zuständigen Experten in Ihrer Region in Verbindung zu setzen, um genaue Informationen zu erhalten und sicherzustellen, dass alle Anforderungen erfüllt sind.
• Gasflaschenventil langsam öffnen.
• Öffnen Sie den Druckminderer.
• Schalten Sie die Stromversorgung über den Hauptschalter ein.
• Drücken Sie die Gastest-Funktion am Drahtvorschub.
• Passen Sie die Gasmenge im Durchflussmesser entsprechend an die Anwendung.
• Der Gastest wird durch kurzes Drücken der Taste am Kabel aktiviert Vorschubeinheit. Das Schutzgas strömt für etwa 25 Sekunden oder bis Die Taste wird erneut gedrückt. Einstellung der Schutzgasmenge Schweißverfahren empfohlene Schutzgasmenge MAG-Schweißen Drahtdurchmesser x 11,5 = l/min. MIG-Löten Drahtdurchmesser x 11,5 = l/min. MIG-Schweißen (Aluminium) Drahtdurchmesser x 13,5 = 1 / min
(100% Argon) Gasdüsendurchmesser in WIG mm entspricht 1 / min Gasdurchfluss
Antriebsrollensätze wechseln
- Schalten Sie die Stromquelle aus.
- Lösen Sie den Druck auf den Leerlaufrollen, indem Sie die verstellbaren schwenken
- Druckarm nach unten. Heben Sie die gegossene Leerlaufrollenbaugruppe an und lassen Sie sie an in aufrechter Position sitzen.
- Schrauben Sie den Kunststoffknopf ab, der die untere gerillte Antriebsrolle hält, und schieben Sie die Seite von der Antriebsrolle ab
- Stellen Sie sicher, dass die auf der Seite der Vorschubrolle markierte Drahtgröße mit der zu verwendenden Drahtgröße übereinstimmt.
- Tauschen Sie die Antriebsrollen in umgekehrter Reihenfolge aus und stellen Sie sicher, dass die zu verwendende Drahtgröße beim Wiedereinbau auf der nach außen weisenden Seite der Rolle markiert ist.
- Hinweis:- Stellen Sie sicher, dass der Brennerliner und die Kontaktspitze ebenfalls so bemessen sind, dass sie der ausgewählten Drahtgröße entsprechen.
Schweißdrahtinstallation
Die Installation des Schweißdrahts in einer automatischen Schweißmaschine, insbesondere in MIG/MAG-Schweißanlagen, erfordert sorgfältige Vorbereitung und Einrichtung. Hier sind die allgemeinen Schritte für die Installation des Schweißdrahts:
- Schweißdrahtauswahl:
- Wählen Sie den geeigneten Schweißdraht für die Anwendung. Der Drahttyp hängt von Faktoren wie dem zu schweißenden Material, der Schweißposition und den spezifischen Anforderungen der Schweißaufgabe ab.
- Überprüfung der Drahtrolle:
- Stellen Sie sicher, dass die Drahtrolle in gutem Zustand ist und keine Beschädigungen aufweist.
- Überprüfen Sie, ob der Draht korrekt auf der Rolle aufgewickelt ist, um Probleme wie Wickelungen und Verwicklungen zu vermeiden.
- Vorbereitung des Drahtvorschubsystems:
- Öffnen Sie die Abdeckung des Drahtvorschubsystems der Schweißmaschine.
- Überprüfen Sie den Zustand der Führungsrollen und stellen Sie sicher, dass sie in gutem Zustand sind.
- Reinigen Sie das Drahtvorschubsystem von Schmutz oder Ablagerungen.
- Einlegen des Schweißdrahts:
- Setzen Sie die Drahtrolle in das Drahtvorschubsystem ein und sichern Sie sie gemäß den Anweisungen des Maschinenherstellers.
- Fädeln Sie den Schweißdraht durch die Führungsrollen des Drahtvorschubsystems.
- Drahtführung durch die Schweißpistole:
- Führen Sie den Schweißdraht durch die Schweißpistole. Die genaue Vorgehensweise kann je nach Schweißmaschinentyp variieren.
- Achten Sie darauf, dass der Draht korrekt durch alle Führungselemente und Düsen hindurchgeführt ist.
- Einstellen der Drahtvorschubgeschwindigkeit:
- Stellen Sie die Drahtvorschubgeschwindigkeit gemäß den Anweisungen des Drahtherstellers und des Maschinenherstellers ein.
- Die richtige Drahtvorschubgeschwindigkeit ist entscheidend für einen stabilen Lichtbogen und qualitativ hochwertige Schweißnähte.
- Drahtspannungseinstellung:
- Einige Schweißmaschinen verfügen über Einstellungen zur Drahtspannung. Diese sollten gemäß den Anweisungen des Maschinenherstellers angepasst werden, um einen reibungslosen Drahtvorschub zu gewährleisten.
- Drahtdurchmesser und Gasdüse anpassen:
- Stellen Sie sicher, dass die Gasdüse der Schweißpistole zum Durchmesser des verwendeten Schweißdrahts passt.
- Bei Bedarf können auch andere Einstellungen an der Schweißpistole angepasst werden, wie z. B. der Kontaktrohrdurchmesser, um eine optimale Leistung zu erzielen.
- Gaszufuhr prüfen:
- Wenn Sie ein Schutzgas verwenden, überprüfen Sie die Gaszufuhr und stellen Sie sicher, dass der Gasfluss gemäß den Anweisungen des Herstellers eingestellt ist.
- Test des Drahtvorschubs:
- Führen Sie einen Testdurchlauf durch, um sicherzustellen, dass der Schweißdraht ordnungsgemäß durch die Schweißpistole und das Drahtvorschubsystem geführt wird.
Es ist wichtig, die spezifischen Anweisungen des Maschinenherstellers sowie des Herstellers des Schweißdrahts zu befolgen, um eine sichere und effektive Installation des Schweißdrahts zu gewährleisten. Regelmäßige Wartung und Überprüfung sind ebenfalls wichtig, um einen unterbrechungsfreien Betrieb sicherzustellen.
Die Installation von Schweißdraht ist ein entscheidender Schritt im Schweißprozess und sorgt für einen reibungslosen und effizienten Betrieb. Hier finden Sie eine Schritt-für-Schritt-Anleitung zur Installation von Schweißdraht:
Erforderliche Ausrüstung:
- Schweißdrahtspule
- Schweißdrahtliner
- Drahtvorschubvorrichtung
- Drahtschneider
- Drahtführungsrohr
Installationsschritte:
- Entfernen Sie vorhandenen Schweißdraht: Entfernen Sie vor der Installation von neuem Draht alle Reste von der Spulenhalterung und der Drahtvorschubvorrichtung.
- Wickeln Sie den neuen Schweißdraht ab: Wickeln Sie den neuen Draht vorsichtig von der Spule ab und achten Sie darauf, dass er frei von Verwicklungen und Knicksen bleibt.
- Schneiden Sie den Schweißdraht: Verwenden Sie einen Drahtschneider, um das Ende des Drahtes in einem Winkel von etwa 45 Grad abzuschneiden. Dieser Winkel erleichtert das reibungslose Einführen des Drahtes in den Liner.
- Installieren Sie den Schweißdrahtliner: Setzen Sie den Drahtliner in die Drahtvorschubvorrichtung ein und achten Sie darauf, dass er richtig mit dem Drahtführungsrohr ausgerichtet ist.
- Fädeln Sie den Schweißdraht ein: Führen Sie das abgeschnittene Ende des Drahtes durch das Drahtführungsrohr und in den Drahtliner ein und schieben Sie es, bis es die Drahtvorschubrollen erreicht.
- Drahtzug einstellen: Stellen Sie den Drahtzugsregler an der Drahtvorschubvorrichtung so ein, dass der Draht fest, aber nicht zu fest gehalten wird.
- Drahtvorschub testen: Schalten Sie das Schweißgerät ein und aktivieren Sie den Drahtvorschub. Beobachten Sie den Drahtvorschubvorgang und nehmen Sie gegebenenfalls Anpassungen an der Drahtzugspannung vor.
Zusätzliche Tipps:
- Reinigen Sie die Drahtvorschubvorrichtung: Reinigen Sie die Drahtvorschubvorrichtung vor dem Einlegen von neuem Draht, um Schmutz oder Verunreinigungen zu entfernen, die den Drahtvorschub beeinträchtigen könnten.
- Wählen Sie den richtigen Drahtdurchmesser: Wählen Sie den geeigneten Drahtdurchmesser für Ihr Schweißgerät und das zu schweißende Material.
- Lagern Sie Draht richtig: Lagern Sie den Schweißdraht an einem trockenen und kühlen Ort, um Feuchtigkeitsschäden zu vermeiden und eine optimale Leistung zu gewährleisten.
- Draht auf Beschädigungen prüfen: Untersuchen Sie den Draht vor jedem Gebrauch auf Anzeichen von Schäden, wie Knicke, Schnitte oder Korrosion. Bei Beschädigung entsorgen Sie den Draht und ersetzen Sie ihn durch einen neuen.
Durch Befolgen dieser Schritte und Berücksichtigung der zusätzlichen Tipps können Sie eine erfolgreiche Schweißdrahtinstallation gewährleisten und einen reibungslosen und effizienten Schweißprozess erleben.
Installation des Schweißbrenners
Die Installation des Schweißbrenners ist ein entscheidender Schritt, um sicherzustellen, dass der Schweißprozess reibungslos verläuft. Hier sind die grundlegenden Schritte zur Installation eines Schweißbrenners, wobei zu beachten ist, dass die genauen Schritte je nach dem Typ der Schweißmaschine und des Schweißverfahrens variieren können:
- Schutzmaßnahmen ergreifen:
- Vor der Installation des Schweißbrenners ist es wichtig, die notwendigen Sicherheitsmaßnahmen zu ergreifen, einschließlich dem Ausschalten der Schweißmaschine und dem Tragen der erforderlichen Schutzausrüstung.
- Brennerauswahl:
- Wählen Sie den geeigneten Schweißbrenner basierend auf der Art des Schweißverfahrens, dem zu schweißenden Material und den spezifischen Anforderungen der Anwendung.
- Brenneranschluss:
- Stellen Sie sicher, dass der Brenneranschluss sauber und frei von Verunreinigungen ist.
- Führen Sie den Brenner in die entsprechende Halterung oder Schnellspannvorrichtung ein und sichern Sie ihn gemäß den Anweisungen des Maschinenherstellers.
- Elektrische Verbindung (falls zutreffend):
- Falls der Schweißbrenner elektrisch an die Schweißmaschine angeschlossen wird (z. B. bei MIG/MAG-Schweißen), stellen Sie sicher, dass die Stecker und Buchsen korrekt und sicher verbunden sind.
- Durchführen der Gasverbindung:
- Bei Verwendung von Schutzgas (z. B. beim MIG/MAG-Schweißen) schließen Sie den Gasanschluss des Schweißbrenners an die Gaszufuhr an.
- Überprüfen Sie, ob die Dichtungen in gutem Zustand sind, um Gaslecks zu vermeiden.
- Drahtzuführung überprüfen:
- Wenn der Schweißbrenner für MIG/MAG-Schweißen verwendet wird, überprüfen Sie die Drahtführung im Inneren des Brenners.
- Stellen Sie sicher, dass der Draht korrekt durch den Brenner und die Drahtführung geführt wird.
- Einstellungen überprüfen:
- Überprüfen Sie die Einstellungen am Schweißbrenner, einschließlich Drahtvorschubgeschwindigkeit, Gasfluss und gegebenenfalls die Einstellungen für die Lichtbogensteuerung.
- Düsen und Kontaktrohr überprüfen:
- Stellen Sie sicher, dass die Düse und das Kontaktrohr am Schweißbrenner den richtigen Durchmesser haben und in gutem Zustand sind.
- Reinigen Sie sie gegebenenfalls von Schmutz oder Schweißspritzern.
- Kabelverbindung überprüfen:
- Falls der Schweißbrenner über Kabel mit der Schweißmaschine verbunden ist, überprüfen Sie die Kabelverbindungen und stellen Sie sicher, dass sie sicher und intakt sind.
- Testdurchlauf:
- Führen Sie einen Testdurchlauf durch, um sicherzustellen, dass der Schweißbrenner ordnungsgemäß funktioniert.
- Achten Sie auf einen stabilen Lichtbogen, korrekten Drahtvorschub und eine gleichmäßige Schweißnaht.
Es ist wichtig, die Anweisungen des Maschinenherstellers und des Herstellers des Schweißbrenners genau zu befolgen, um eine sichere und effektive Installation zu gewährleisten. Wenn Unsicherheiten bestehen oder Probleme auftreten, ist es ratsam, sich an den Hersteller oder einen qualifizierten Fachmann zu wenden.
Die Installation des Schweißbrenners ist ein wichtiger Schritt im Schweißprozess. Sie stellt sicher, dass der Brenner richtig an der Schweißmaschine angeschlossen ist und dass die Schweißelektrode oder der Draht richtig geführt wird.
Erforderliche Ausrüstung:
- Schweißbrenner
- Schweißmaschine
- Schlauchpaket
- Schutzgasflasche
- Druckminderer
- Schweißhelm
- Handschuhe
Installationsschritte:
- Schlauchpaket anschließen: Verbinden Sie das Schlauchpaket des Schweißbrenners mit der Schweißmaschine. Achten Sie darauf, dass die Schlauchlänge ausreichend ist, um den Brenner frei zu bewegen.
- Schutzgasflasche anschließen: Verbinden Sie die Schutzgasflasche mit dem Druckminderer. Achten Sie darauf, dass die Schutzgasflasche richtig befestigt ist und dass der Druckminderer auf den richtigen Druck eingestellt ist.
- Schweißelektrode oder Draht einlegen: Legen Sie die Schweißelektrode oder den Draht in den Schweißbrenner ein. Achten Sie darauf, dass die Elektrode oder der Draht richtig ausgerichtet ist und dass die Spitze nicht beschädigt ist.
- Brenner anschließen: Stecken Sie den Schweißbrenner in die Schweißmaschine ein. Achten Sie darauf, dass der Brenner richtig eingesteckt ist.
- Schweißvorbereitungen treffen: Tragen Sie Schutzkleidung, wie einen Schweißhelm, Handschuhe und Schutzkleidung. Stellen Sie sicher, dass die Arbeitsfläche sauber und frei von Hindernissen ist.
Zusätzliche Tipps:
- Schlauchpakete regelmäßig überprüfen: Kontrollieren Sie die Schlauchpakete regelmäßig auf Beschädigungen. Bei Beschädigungen ersetzen Sie die Schlauchpakete.
- Schutzgasflaschen sicher lagern: Lagern Sie Schutzgasflaschen an einem sicheren Ort, an dem sie nicht umfallen oder beschädigt werden können.
- Schweißbrenner regelmäßig reinigen: Reinigen Sie den Schweißbrenner regelmäßig, um Verunreinigungen zu entfernen.
Durch Befolgen dieser Schritte und Berücksichtigung der zusätzlichen Tipps können Sie eine erfolgreiche Installation des Schweißbrenners gewährleisten.
Schweißbrennerarten:
Es gibt verschiedene Arten von Schweißbrennern, die für verschiedene Schweißverfahren verwendet werden. Die gebräuchlichsten Schweißbrennerarten sind:
- Elektrodenschweißbrenner: Elektrodenschweißbrenner werden für das Elektrodenschweißen verwendet. Sie bestehen aus einer Elektrodenhalterung, einem Schutzgasrohr und einem Schlauchpaket.
- MIG/MAG-Schweißbrenner: MIG/MAG-Schweißbrenner werden für das MIG/MAG-Schweißen verwendet. Sie bestehen aus einem Drahtvorschubmechanismus, einem Schutzgasrohr und einem Schlauchpaket.
- WIG-Schweißbrenner: WIG-Schweißbrenner werden für das WIG-Schweißen verwendet. Sie bestehen aus einer Wolframelektrode, einem Schutzgasrohr und einem Schlauchpaket.
Die Wahl des richtigen Schweißbrenners hängt von einer Reihe von Faktoren ab, einschließlich des verwendeten Schweißverfahrens, des zu schweißenden Materials und der gewünschten Schweißqualität.
MIG-Schweißbetrieb
Der MIG-Schweißbetrieb ist ein Schweißverfahren, bei dem ein Draht mit Schutzgas umgeben zum Schweißen verwendet wird. Der Draht wird durch einen Drahtvorschubmechanismus in die Schweißzone geführt und durch einen Lichtbogen erhitzt. Das Schutzgas umgibt den Lichtbogen und schützt das geschmolzene Metall vor Oxidation und Verunreinigungen.
Der MIG-Schweißbetrieb kann für eine Vielzahl von Materialien verwendet werden, darunter Stahl, Aluminium, Kupfer und Edelstahl. Er ist ein vielseitiges und effizientes Schweißverfahren, das für eine Vielzahl von Anwendungen geeignet ist.
Vorteile des MIG-Schweißbetriebs:
- Vielseitigkeit: Der MIG-Schweißbetrieb kann für eine Vielzahl von Materialien verwendet werden.
- Effizienz: Der MIG-Schweißbetrieb ist ein effizientes Schweißverfahren, das eine hohe Schweißgeschwindigkeit ermöglicht.
- Qualität: Der MIG-Schweißbetrieb ermöglicht eine hohe Schweißqualität.
Nachteile des MIG-Schweißbetriebs:
- Kosten: Der MIG-Schweißbetrieb kann im Vergleich zu anderen Schweißverfahren kostspielig sein.
- Ausbildung: Der MIG-Schweißbetrieb erfordert eine gewisse Ausbildung, um ihn sicher und effizient zu beherrschen.
MIG-Schweißparameter:
Die Schweißparameter für den MIG-Schweißbetrieb sind:
- Schweißstrom: Der Schweißstrom bestimmt die Größe des Lichtbogens und die Schmelzrate des Drahtes.
- Schweißspannung: Die Schweißspannung bestimmt die Stabilität des Lichtbogens.
- Drahtvorschubgeschwindigkeit: Die Drahtvorschubgeschwindigkeit bestimmt die Menge des geschmolzenen Drahtes, die pro Zeiteinheit in die Schweißzone gefördert wird.
- Schutzgastyp und -druck: Der Schutzgastyp und -druck bestimmen, wie gut das geschmolzene Metall vor Oxidation und Verunreinigungen geschützt wird.
Die Wahl der richtigen Schweißparameter hängt von einer Reihe von Faktoren ab, einschließlich des verwendeten Schweißgeräts, des zu schweißenden Materials und der gewünschten Schweißqualität.
MIG-Schweißtechniken:
Es gibt verschiedene MIG-Schweißtechniken, die für verschiedene Anwendungen verwendet werden können. Die gebräuchlichsten MIG-Schweißtechniken sind:
- Kurzlichtbogenschweißen: Beim Kurzlichtbogenschweißen wird der Lichtbogen kurz gehalten, um eine gute Schweißnahtqualität zu erzielen.
- Langlichtbogenschweißen: Beim Langlichtbogenschweißen wird der Lichtbogen länger gehalten, um eine höhere Schweißgeschwindigkeit zu erzielen.
- Punktschweißen: Beim Punktschweißen werden zwei Werkstücke durch kurze Lichtbögen miteinander verbunden.
- Nahtschweißen: Beim Nahtschweißen wird der Lichtbogen entlang einer Nahtführung geführt, um eine gleichmäßige Schweißnaht zu erzielen.
Die Wahl der richtigen MIG-Schweißtechnik hängt von einer Reihe von Faktoren ab, einschließlich des verwendeten Schweißgeräts, des zu schweißenden Materials und der gewünschten Schweißqualität.
Sicherheit beim MIG-Schweißen:
Beim MIG-Schweißen sind eine Reihe von Sicherheitsvorkehrungen zu beachten, um Verletzungen zu vermeiden. Dazu gehören:
- Tragen von Schutzkleidung, wie Schweißhelm, Handschuhe, Schutzkleidung und Schutzbrille.
- Sicherer Umgang mit dem Schweißgerät und dem Schutzgas.
- Vermeidung von Funkenflug und Spritzern.
Durch Beachtung der Sicherheitsvorkehrungen kann das Risiko von Verletzungen beim MIG-Schweißen minimiert werden.
Der MIG-Schweißbetrieb (Metall-Inertgas-Schweißen) ist ein Lichtbogenschweißverfahren, bei dem ein Drahtelektrode durch eine Schweißpistole zugeführt wird. Dabei wird ein Schutzgas verwendet, um den Lichtbogen vor atmosphärischer Kontamination zu schützen. MIG-Schweißen ist bekannt für seine Effizienz und Produktivität, insbesondere bei der Verbindung von Metallen wie Stahl, Aluminium und Edelstahl. Hier sind die grundlegenden Schritte für den MIG-Schweißbetrieb:
1. Vorbereitung der Schweißausrüstung:
- Maschine einschalten:
- Schalten Sie die MIG-Schweißmaschine ein und lassen Sie sie sich aufwärmen, wenn nötig.
- Werkstückvorbereitung:
- Reinigen Sie das Werkstück von Schmutz, Rost oder Lack, um eine optimale Schweißqualität zu gewährleisten.
- Gasflasche anschließen:
- Verbinden Sie die Gasflasche mit dem Schweißgerät. Die Art des verwendeten Gases hängt von den zu schweißenden Materialien ab.
2. Drahtvorbereitung:
- Drahttyp auswählen:
- Wählen Sie den geeigneten Schweißdraht basierend auf den zu schweißenden Materialien und Anforderungen.
- Draht einlegen:
- Setzen Sie die Drahtrolle in das Drahtvorschubsystem der MIG-Schweißmaschine ein.
- Fädeln Sie den Draht durch die Führungsrollen und die Schweißpistole.
- Drahtvorschubgeschwindigkeit einstellen:
- Stellen Sie die Drahtvorschubgeschwindigkeit gemäß den Anweisungen des Drahtherstellers und der Schweißmaschine ein.
3. Einstellungen an der Schweißpistole:
- Gasdüse und Kontaktrohr auswählen:
- Wählen Sie eine Gasdüse und ein Kontaktrohr entsprechend dem verwendeten Drahtdurchmesser.
- Einstellungen prüfen:
- Überprüfen Sie die Einstellungen an der Schweißpistole, einschließlich Drahtvorschubgeschwindigkeit und Gasfluss.
4. Schweißvorbereitung:
- Schweißposition wählen:
- Wählen Sie die optimale Schweißposition entsprechend der Anwendung (flach, horizontal, vertikal, überkopf).
- Schweißspalt einstellen:
- Justieren Sie den Schweißspalt zwischen den zu verbindenden Teilen.
5. Schweißen:
- Lichtbogen starten:
- Starten Sie den Lichtbogen, indem Sie die Elektrode in die Nähe des Werkstücks führen und dann den Schweißstrom einschalten.
- Schweißnaht führen:
- Bewegen Sie die Schweißpistole gleichmäßig über die Verbindungsnaht, um eine gleichmäßige Schweißung zu gewährleisten.
- Abschließen der Schweißung:
- Beenden Sie den Schweißvorgang, indem Sie den Drahtvorschub stoppen und den Lichtbogen löschen.
6. Nachbearbeitung:
- Schlacke entfernen:
- Entfernen Sie gegebenenfalls Schlacke oder Spritzer nach dem Schweißen.
- Inspektion der Schweißnaht:
- Überprüfen Sie die Schweißnaht auf Qualität und Integrität.
7. Sicherheitsmaßnahmen:
- Persönliche Schutzausrüstung:
- Tragen Sie die notwendige persönliche Schutzausrüstung, einschließlich Helm, Schutzbrille, Handschuhe und Schutzkleidung.
- Belüftung:
- Stellen Sie sicher, dass die Arbeitsumgebung gut belüftet ist, insbesondere wenn schädliche Gase freigesetzt werden könnten.
Es ist wichtig, die spezifischen Anweisungen des Schweißgeräteherstellers und des Drahtherstellers zu befolgen, um qualitativ hochwertige Schweißnähte zu erzeugen und die Sicherheit zu gewährleisten. Eine angemessene Schulung und Erfahrung sind ebenfalls entscheidend für den erfolgreichen Betrieb von MIG-Schweißausrüstung.
Hinweis:- Überprüfen Sie, ob Antriebsrollen und Brennerteile für die verwendete Drahtgröße und den verwendeten Drahttyp geeignet sind.
Der optimale Leerlaufrollendruck variiert mit der Drahtart, Draht Durchmesser, Oberflächenbeschaffenheit, Schmierung und Härte. Als ein Als allgemeine Regel gilt, dass bei harten Drähten möglicherweise mehr Druck erforderlich ist und bei weichen, oder Aluminiumdraht, der möglicherweise weniger Druck erfordert als die Fabrik Einstellung. Die optimale Leerlaufwalzeneinstellung kann bestimmt werden als folgt:
Drücken Sie das Ende der Pistole gegen einen festen, elektrisch isolierten Gegenstand vom Schweißgeräteausgang und drücken Sie den Pistolenabzug mehrere Male Sekunden.
Wenn der Draht „Vogelnester“ ist, an der Antriebsrolle klemmt oder bricht, ist der Leerlauf Rolldruck ist zu groß.
Drehen Sie die Einstellknöpfe um 1/2 Umdrehung heraus und ein neues Kabel verlegen. Wenn das einzige Ergebnis angetriebener Rollenschlupf war, lockern die Handmutter am mittleren Stecker und ziehen Sie die Pistole nach vorne etwa 15 cm von der Stromquelle entfernt. Es sollte eine geben leichte Welligkeit im freigelegten Draht. Wenn es keine Welligkeit gibt, die Druck ist zu niedrig.
Ziehen Sie den Einstellknopf um eine 1/4 Umdrehung fest und installieren Sie ihn erneut das Pistolenkabel und wiederholen Sie die obigen Schritte. Beim Auslösen werden die Elektrode und der Antriebsmechanismus elektrisch „unter Spannung“ relativ zu Werkstück und Masse und bleiben „unter Spannung“ mehrere Sekunden nach dem Loslassen des Pistolenabzugs.
Vorteile des Schweißens
Schweißen ist anderen Metallverbindungsverfahren überlegen, weil es:
- ist eine dauerhaft druckdichte Verbindung
- nimmt weniger Platz ein
- gibt mehr Materialeinsparung
- hat weniger Gewicht
- widersteht hohen Temperaturen und Drücken wie verbundenes Material
- kann schnell erledigt werden
- bewirkt keine Farbveränderung der Fugen. Es ist die stärkste Verbindung und jede Art von Metall in jeder Dicke kann verbunden werden.
Schweißen ist ein Verfahren zum dauerhaften Verbinden von Metallen. Es ist eine uralte Methode, etwa 1500 Jahre alt. Die in der Antike verwendete Methode war das Schmiede- oder Schmiedeschweißen. Eine der Methoden zur Klassifizierung von Schweißverbindungen ist die Methode, die verwendet wird, um die Verbindung zwischen Metallteilen zu beeinflussen. Dementsprechend sind die Methoden:
- Schweißverfahren ohne Druck/mit Druck
- Nicht-Fusions-Methode
- 1.4.1 Schmelzschweißen ohne Druck
- Als Schmelzschweißdruck bezeichnet man ein Schweißverfahren, bei dem gleichartige und ungleiche Metalle durch Schmelzen und Verschmelzen ihrer Verbindungskanten mit oder ohne Zugabe von Füllmetall, aber ohne Anwendung von Druck miteinander verbunden werden. Die hergestellte Verbindung ist dauerhaft. Die gängigen Wärmequellen sind:
- Lichtbogenschweißen
- Gasschweißen
- Chemische Reaktion (Thermitschweißen)
- Druckschweißen
- Dies ist ein Schweißverfahren, bei dem ähnliche Metalle miteinander verbunden werden, indem sie in einen plastischen oder teilweise geschmolzenen Zustand erhitzt und dann durch Pressen oder Hämmern ohne die Verwendung von Füllmetall verbunden werden. Dies ist ein Schmelzverfahren zum Verbinden mit Druck. Wärmequellen können Schmiedeschmieden (Schmiedeschweißen) oder elektrischer Widerstand (Widerstandsschweißen) oder Reibung sein
Schweißtechnik
Schweißtechnik ist die Kunst und Wissenschaft des Zusammenfügens von Metallen durch Erhitzen und Schmelzen. Es gibt eine Vielzahl von Schweißverfahren, die für verschiedene Materialien und Anwendungen geeignet sind.
Die grundlegenden Schritte beim Schweißen sind:
- Vorbereitung: Das Werkstück wird gereinigt und vorbereitet.
- Schweißvorgang: Der Schweißprozess wird durchgeführt.
- Nachbereitung: Die Schweißnaht wird nachbearbeitet.
Vorbereitung:
Bei der Vorbereitung des Werkstücks ist darauf zu achten, dass es sauber und frei von Rost, Schmutz und Fett ist. Das Werkstück kann mit einer Drahtbürste oder einem Schleifgerät gereinigt werden.
Schweißvorgang:
Der Schweißvorgang wird durch die Wahl des richtigen Schweißverfahrens, der Schweißparameter und der Schweißtechnik bestimmt.
Nachbereitung:
Nach dem Schweißen wird die Schweißnaht nachbearbeitet, um die Oberfläche zu glätten und Unebenheiten zu entfernen. Die Schweißnaht kann mit einem Hammer, einer Feile oder einem Schleifgerät bearbeitet werden.
Schweißverfahren:
Es gibt eine Vielzahl von Schweißverfahren, die für verschiedene Materialien und Anwendungen geeignet sind. Die gebräuchlichsten Schweißverfahren sind:
- Elektrodenschweißen: Beim Elektrodenschweißen wird eine Metallelektrode mit einem Lichtbogen erhitzt und das geschmolzene Metall auf das Werkstück aufgetragen.
- MIG-Schweißen: Beim MIG-Schweißen wird ein Draht mit Schutzgas umgeben zum Schweißen verwendet.
- MAG-Schweißen: Beim MAG-Schweißen wird ein Draht mit einem aktiven Schutzgas zum Schweißen verwendet.
- WIG-Schweißen: Beim WIG-Schweißen wird eine Wolframelektrode mit einem Lichtbogen erhitzt und das geschmolzene Metall auf das Werkstück aufgetragen.
- Laserschweißen: Beim Laserschweißen wird ein Laserstrahl verwendet, um das Werkstück zu erhitzen und zu schmelzen.
- Ultraschallschweißen: Beim Ultraschallschweißen wird Ultraschall verwendet, um das Werkstück zu erhitzen und zu schmelzen.
Schweißparameter:
Die Schweißparameter sind die Einstellungen des Schweißgeräts, die die Art und Qualität der Schweißnaht beeinflussen. Die wichtigsten Schweißparameter sind:
- Schweißstrom: Der Schweißstrom bestimmt die Größe des Lichtbogens und die Schmelzrate des Drahtes oder der Elektrode.
- Schweißspannung: Die Schweißspannung bestimmt die Stabilität des Lichtbogens.
- Drahtvorschubgeschwindigkeit: Die Drahtvorschubgeschwindigkeit bestimmt die Menge des geschmolzenen Drahtes, die pro Zeiteinheit in die Schweißzone gefördert wird.
- Schutzgastyp und -druck: Der Schutzgastyp und -druck bestimmen, wie gut das geschmolzene Metall vor Oxidation und Verunreinigungen geschützt wird.
Schweißtechnik:
Die Schweißtechnik ist die Art und Weise, wie der Schweißprozess durchgeführt wird. Die Wahl der richtigen Schweißtechnik hängt von einer Reihe von Faktoren ab, einschließlich des verwendeten Schweißverfahrens, des zu schweißenden Materials und der gewünschten Schweißqualität.
Die wichtigsten Schweißtechniken sind:
- Kurzlichtbogenschweißen: Beim Kurzlichtbogenschweißen wird der Lichtbogen kurz gehalten, um eine gute Schweißnahtqualität zu erzielen.
- Langlichtbogenschweißen: Beim Langlichtbogenschweißen wird der Lichtbogen länger gehalten, um eine höhere Schweißgeschwindigkeit zu erzielen.
- Punktschweißen: Beim Punktschweißen werden zwei Werkstücke durch kurze Lichtbögen miteinander verbunden.
- Nahtschweißen: Beim Nahtschweißen wird der Lichtbogen entlang einer Nahtführung geführt, um eine gleichmäßige Schweißnaht zu erzielen.
Sicherheit:
Beim Schweißen sind eine Reihe von Sicherheitsvorkehrungen zu beachten, um Verletzungen zu vermeiden. Dazu gehören:
- **Tragen von Schutzkleidung, wie Schweißhelm, Handschuhe, Schutzkleidung und Schutzbrille.
- Sicherer Umgang mit dem Schweißgerät und dem Schutzgas.
- Vermeidung von Funkenflug und Spritzern.
Durch Beachtung der Sicherheitsvorkehrungen kann das Risiko von Verletzungen beim Schweißen minimiert werden.
Die Schweißtechnik umfasst eine Vielzahl von Verfahren und Technologien zum Verbinden von Materialien durch Schmelzen und anschließendes Abkühlen. Hier sind einige grundlegende Aspekte der Schweißtechnik:
1. Schweißverfahren:
- MIG/MAG-Schweißen (Metall-Inertgas/Metall-Aktivgas): Verwendung eines Drahtelektroden und eines Schutzgases.
- WIG-Schweißen (Wolfram-Inertgas): Verwendung einer Wolframelektrode und eines Schutzgases.
- Elektrodenschweißen: Verwendung einer Elektrode, die durch einen Lichtbogen schmilzt.
- Plasmaschweißen: Verwendung eines Plasmastrahls zum Schmelzen der Materialien.
- Lichtbogenschweißen: Allgemeiner Begriff für Schweißverfahren mit einem Lichtbogen.
2. Materialien:
- Schweißtechnik kann für eine Vielzahl von Materialien angewendet werden, darunter Stahl, Aluminium, Kupfer, Edelstahl und Legierungen.
3. Ausrüstung:
- Schweißmaschinen: Elektrische Geräte, die den Schweißprozess durch Bereitstellung des notwendigen Stroms und anderer Parameter ermöglichen.
- Schweißpistolen oder -brenner: Geräte, durch die der Schweißdraht oder die Elektrode zugeführt und der Lichtbogen erzeugt wird.
4. Schutzgase:
- Bei einigen Schweißverfahren wie MIG/MAG und WIG wird ein Schutzgas verwendet, um den Lichtbogen vor atmosphärischer Kontamination zu schützen.
5. Elektroden und Draht:
- Je nach Schweißverfahren werden verschiedene Arten von Elektroden oder Draht verwendet. Diese sind speziell auf die Anforderungen des jeweiligen Verfahrens und der Materialien abgestimmt.
6. Vorbereitung:
- Werkstückvorbereitung: Reinigen und Vorbereiten der zu schweißenden Materialien.
- Einstellungen anpassen: Einstellen von Schweißparametern wie Stromstärke, Spannung, Drahtvorschubgeschwindigkeit, Gasfluss usw.
7. Schweißpositionen:
- Die Schweißposition kann flach, horizontal, vertikal oder überkopf sein. Die Position beeinflusst den Schweißprozess und die Qualität der Schweißnaht.
8. Qualitätskontrolle:
- Nach dem Schweißen ist die Inspektion der Schweißnaht auf Defekte, Unregelmäßigkeiten und die Einhaltung von Standards wichtig.
9. Sicherheit:
- Schutzmaßnahmen, einschließlich persönlicher Schutzausrüstung (Helme, Schutzbrillen, Handschuhe), Belüftung und sicherer Arbeitspraktiken, sind entscheidend.
10. Automatisierung:
- Moderne Schweißtechnik integriert zunehmend automatisierte Systeme für präzise und wiederholbare Schweißnähte.
11. Umweltaspekte:
- Die Auswahl der Schweißtechnik kann Auswirkungen auf die Umwelt haben. Schutzgas-Schweißverfahren sind oft umweltfreundlicher als andere Verfahren.
Die Auswahl der geeigneten Schweißtechnik hängt von verschiedenen Faktoren ab, darunter die Art der Materialien, die spezifischen Anwendungsanforderungen, die Dicke der zu schweißenden Teile und die geforderte Qualität der Schweißnaht. Ein qualifizierter Schweißer muss nicht nur die Techniken beherrschen, sondern auch die Materialien verstehen, um optimale Ergebnisse zu erzielen.
Anwendungen von Schweißprozessen
Schweißprozesse werden in einer Vielzahl von Anwendungen verwendet, darunter:
- Automobilindustrie: Schweißprozesse werden in der Automobilindustrie zum Schweißen von Karosserieteilen, Motorenteilen und anderen Metallteilen verwendet.
- Bauindustrie: Schweißprozesse werden in der Bauindustrie zum Schweißen von Stahlträgern, Brücken und anderen Bauteilen verwendet.
- Metallverarbeitung: Schweißprozesse werden in der Metallverarbeitung zum Schweißen von Rohren, Profilen und anderen Metallteilen verwendet.
- Maschinenbau: Schweißprozesse werden im Maschinenbau zum Schweißen von Maschinenteilen, Werkzeugen und anderen Metallteilen verwendet.
Hier sind einige Beispiele für konkrete Anwendungen von Schweißprozessen:
- Elektrodenschweißen: Elektrodenschweißen wird häufig zum Schweißen von Stahl verwendet. Es ist ein relativ einfaches und kostengünstiges Schweißverfahren, das für eine Vielzahl von Anwendungen geeignet ist.
- MIG-Schweißen: MIG-Schweißen wird häufig zum Schweißen von Aluminium, Kupfer und Edelstahl verwendet. Es ist ein effizientes Schweißverfahren, das eine hohe Schweißgeschwindigkeit ermöglicht.
- WIG-Schweißen: WIG-Schweißen wird häufig zum Schweißen von dünnen Blechen und hochlegierten Stählen verwendet. Es ist ein präzises Schweißverfahren, das eine hohe Schweißqualität ermöglicht.
- Laserschweißen: Laserschweißen wird häufig zum Schweißen von dünnen Blechen und hochlegierten Stählen verwendet. Es ist ein hochpräzises Schweißverfahren, das eine hohe Schweißqualität ermöglicht.
- Ultraschallschweißen: Ultraschallschweißen wird häufig zum Schweißen von Kunststoffen verwendet. Es ist ein umweltfreundliches Schweißverfahren, das keine Schweißnahtspuren hinterlässt.
Die Wahl des richtigen Schweißverfahrens hängt von einer Reihe von Faktoren ab, einschließlich des zu schweißenden Materials, der gewünschten Schweißqualität und der Anwendung.
Schweißprozesse finden in vielen industriellen Anwendungen Verwendung, um Materialien dauerhaft miteinander zu verbinden. Hier sind einige der gängigsten Anwendungen von Schweißprozessen:
Einzelheiten
1. Fertigung und Bauindustrie:
- Brückenbau: Schweißen wird für die Konstruktion von Stahl- und Metallbrücken verwendet.
- Gebäudekonstruktion: Stahlträger und Metallrahmen werden durch Schweißen miteinander verbunden.
2. Fahrzeug- und Luftfahrtindustrie:
- Automobilbau: Karosserieteile, Rahmen und andere Strukturen werden durch Schweißen montiert.
- Luftfahrtindustrie: Schweißen wird bei der Herstellung von Flugzeugen für Strukturteile und Verbindungen verwendet.
3. Schiffbau und Offshore-Industrie:
- Schiffsbau: Der Bau von Schiffsrümpfen und Strukturen erfolgt durch Schweißen.
- Offshore-Plattformen: Schweißen wird für die Herstellung und Reparatur von Offshore-Bohrplattformen verwendet.
4. Energieerzeugung:
- Kraftwerksbau: Rohrleitungen, Druckbehälter und andere Strukturen in Kraftwerken werden durch Schweißen montiert.
- Erneuerbare Energien: In der Windenergieindustrie werden Schweißverfahren für die Herstellung von Windturbinenstrukturen eingesetzt.
5. Rohrleitungsbau:
- Öl- und Gasindustrie: Pipelines und Rohrleitungen werden durch Schweißen verbunden.
- Chemieanlagen: Rohrleitungen und Strukturen in chemischen Anlagen werden geschweißt.
6. Elektronik- und Elektroindustrie:
- Herstellung elektronischer Geräte: Kleine Schweißprozesse werden in der Elektronikindustrie für die Verbindung von Bauteilen verwendet.
- Elektromotorenbau: In der Herstellung von Elektromotoren werden Schweißverfahren angewendet.
7. Bergbau und Schwerindustrie:
- Bergbauausrüstung: Strukturen von Bergbaufahrzeugen und -ausrüstungen werden durch Schweißen montiert.
- Schwerlastmaschinen: Baumaschinen und schwere Fahrzeuge werden durch Schweißen hergestellt.
8. Medizintechnik:
- Herstellung von medizinischen Geräten: Schweißen wird in der Produktion von medizinischen Geräten und Instrumenten eingesetzt.
9. Lebensmittel- und Getränkeindustrie:
- Lebensmittelverarbeitungsausrüstung: Teile von Verarbeitungsanlagen werden durch Schweißen montiert.
10. Kunst und Design:
- Metallskulpturen: Künstler nutzen Schweißtechniken, um Metallskulpturen zu erstellen.
11. Reparatur und Instandhaltung:
- Fahrzeugreparatur: Schweißen wird für die Reparatur von Fahrzeugrahmen und Karosserien eingesetzt.
- Anlageninstandhaltung: In verschiedenen Branchen wird Schweißen für Reparatur- und Instandhaltungsarbeiten verwendet.
12. Haushaltsgeräte:
- Herstellung von Haushaltsgeräten: Schweißen wird in der Produktion von Geräten wie Herden, Kühlschränken und Waschmaschinen verwendet.
Diese Anwendungen verdeutlichen die Vielseitigkeit und Bedeutung von Schweißprozessen in verschiedenen Industriezweigen und Bereichen des täglichen Lebens. Die richtige Anwendung der Schweißtechnik ist entscheidend, um langlebige und sichere Verbindungen zu gewährleisten.
Metallbearbeitungsmaschinen wie Bördel und Beschneide Maschinen, Flanschmaschinen, Beschneide und Bördelmaschinen, Umformtechnik, Rohrbiegemaschinen, Bandsäge für Metall, Hydraulische Horizontalpresse, Kantenschneide-Bördelmaschine, Kantenbördelmaschine, Entgratungsmaschine, Innen- und Außenpoliermaschine für Edelstahltöpfe, Kreisschneidemaschine, Profilbiegemaschine und Rundschweißmaschine
Maschinenprogramm für die Metallbearbeitung
Unsere Metallbearbeitungsmaschinen sind:
- Rohrbiegemaschine
- Horizontale Presse
- Bandsäge für Metall
- Profilbiegemaschine
- Tiefziehpresse
- Rundschweißmaschine
- Kantenschneide-Bördelmaschine
- Topf- und Pfannenpoliermaschine
- Poliermaschine für flache Oberflächen
Rundschweißmaschine
Eine Rundschweißmaschine ist eine spezialisierte Schweißausrüstung, die für das Schweißen von kreisförmigen oder zylindrischen Werkstücken entwickelt wurde. Diese Maschinen sind für verschiedene Industrien von entscheidender Bedeutung, insbesondere für solche, die regelmäßig Rohre, Behälter oder andere zylindrische Strukturen herstellen.
Funktionsweise: Rundschweißmaschinen verwenden in der Regel eine Kombination aus Drehbewegung und Schweißbrennerbewegung, um eine gleichmäßige Schweißnaht entlang des Umfangs des Werkstücks zu erzeugen. Die Drehbewegung ermöglicht eine kontinuierliche Rotation des Werkstücks, während der Schweißbrenner entlang des Umfangs bewegt wird, um die Schweißnaht zu erzeugen.
Anwendungen: Diese Art von Schweißmaschinen wird in einer Vielzahl von Branchen eingesetzt, darunter die Herstellung von Rohren, Tanks, zylindrischen Behältern, Druckbehältern, Ölleitungen und anderen ähnlichen Produkten. Sie kommen in der Regel in Massenproduktionsumgebungen zum Einsatz, wo eine hohe Produktivität und Konsistenz erforderlich sind.
Vorteile:
- Hohe Produktionsgeschwindigkeit: Rundschweißmaschinen ermöglichen eine schnelle und effiziente Schweißung großer Mengen zylindrischer Werkstücke.
- Konsistente Qualität: Durch die automatisierte Natur der Maschinen können konsistente Schweißnähte mit hoher Qualität erzeugt werden.
- Reduzierter Arbeitsaufwand: Da die Maschinen den Großteil der Arbeit übernehmen, wird der Bedarf an manueller Arbeit reduziert, was die Arbeitskosten senkt.
Herausforderungen:
- Einrichtungszeit: Das Einrichten einer Rundschweißmaschine kann zeitaufwändig sein, insbesondere wenn verschiedene Werkstückgrößen oder Schweißparameter berücksichtigt werden müssen.
- Wartung und Kalibrierung: Wie bei allen industriellen Maschinen erfordern Rundschweißmaschinen regelmäßige Wartung und Kalibrierung, um eine optimale Leistung und Sicherheit zu gewährleisten.
Innovationen: Mit dem Fortschritt in der Automatisierungs- und Robotertechnik werden moderne Rundschweißmaschinen zunehmend mit fortschrittlicher Steuerungssoftware und Robotik ausgestattet, um die Produktivität weiter zu steigern und die Flexibilität bei der Herstellung verschiedener Produkte zu verbessern.
Insgesamt spielen Rundschweißmaschinen eine entscheidende Rolle in der modernen Fertigungsindustrie, indem sie effiziente und qualitativ hochwertige Lösungen für das Schweißen von zylindrischen Werkstücken bieten.
Kreisförmige Schweißmaschine
Eine kreisförmige Schweißmaschine ist eine spezialisierte Art von Schweißausrüstung, die für das Schweißen von runden oder kreisförmigen Werkstücken entwickelt wurde. Diese Maschinen spielen eine wichtige Rolle in verschiedenen Industrien, insbesondere bei der Herstellung von Rohren, Behältern und anderen zylindrischen Komponenten.
Funktionsweise: Kreisförmige Schweißmaschinen verwenden in der Regel eine Kombination aus Rotationsbewegung und Schweißbrennerbewegung, um eine kontinuierliche Schweißnaht entlang des Umfangs des Werkstücks zu erzeugen. Die Rotation des Werkstücks sorgt für eine gleichmäßige Verteilung der Wärme während des Schweißens, was zu einer konsistenten Schweißnaht führt.
Anwendungen: Diese Art von Schweißmaschinen wird in verschiedenen Branchen eingesetzt, darunter die Herstellung von Rohren für die Bauindustrie, die Öl- und Gasindustrie, die Automobilindustrie und viele andere. Sie werden auch zur Herstellung von Tanks, Behältern, Druckbehältern und anderen zylindrischen Komponenten verwendet.
Vorteile:
- Hohe Produktivität: Kreisförmige Schweißmaschinen ermöglichen eine schnelle und effiziente Schweißung großer Mengen runder Werkstücke.
- Konsistente Qualität: Durch die automatisierte Natur der Maschinen können konsistente Schweißnähte mit hoher Qualität erzeugt werden.
- Reduzierter Arbeitsaufwand: Da die Maschinen den Großteil der Arbeit übernehmen, wird der Bedarf an manueller Arbeit reduziert, was die Arbeitskosten senkt.
Herausforderungen:
- Einrichtungszeit: Das Einrichten einer kreisförmigen Schweißmaschine kann zeitaufwändig sein, insbesondere wenn verschiedene Werkstückgrößen oder Schweißparameter berücksichtigt werden müssen.
- Wartung und Kalibrierung: Wie bei allen industriellen Maschinen erfordern kreisförmige Schweißmaschinen regelmäßige Wartung und Kalibrierung, um eine optimale Leistung und Sicherheit zu gewährleisten.
Innovationen: Mit dem Fortschritt in der Automatisierungs- und Robotertechnik werden moderne kreisförmige Schweißmaschinen zunehmend mit fortschrittlicher Steuerungssoftware und Robotik ausgestattet, um die Produktivität weiter zu steigern und die Flexibilität bei der Herstellung verschiedener Produkte zu verbessern.
Insgesamt spielen kreisförmige Schweißmaschinen eine wichtige Rolle in der modernen Fertigungsindustrie, indem sie effiziente und qualitativ hochwertige Lösungen für das Schweißen von runden Werkstücken bieten.
Schweißnaht
Eine Schweißnaht ist die Verbindung zweier Werkstücke durch das Schmelzen und Verfestigen eines Füllmaterials zwischen ihnen. Schweißnähte werden üblicherweise durch verschiedene Schweißverfahren erzeugt, wie zum Beispiel Lichtbogen-, Gas-, Widerstands- oder Laserstrahlschweißen.
Funktionsweise: Bei der Erzeugung einer Schweißnaht wird Wärme erzeugt, um das Füllmaterial und die angrenzenden Bereiche der zu verbindenden Werkstücke aufzuschmelzen. Nachdem das geschmolzene Material abgekühlt ist, entsteht eine feste Verbindung zwischen den Werkstücken.
Arten von Schweißnähten:
- Längsnaht: Verbindung entlang der Längsachse der Werkstücke.
- Quernaht: Verbindung quer zur Längsachse der Werkstücke.
- Kehlnaht: Verbindung zwischen zwei Teilen, die sich in einem Winkel zueinander befinden.
- Stumpfnaht: Verbindung zwischen den Enden von zwei Werkstücken, die sich parallel zueinander befinden.
- Ecknaht: Verbindung zwischen zwei Werkstücken, die sich rechtwinklig zueinander befinden.
Qualitätsmerkmale einer Schweißnaht:
- Penetrationstiefe: Tiefe, bis zu der das Schmelzbad in das Werkstück eindringt.
- Schweißnahtform: Form der Schweißnaht, die je nach Schweißverfahren und -parametern variieren kann.
- Schweißnahtfestigkeit: Fähigkeit der Schweißnaht, mechanischen Belastungen standzuhalten.
- Oberflächenbeschaffenheit: Glätte und Sauberkeit der Schweißnahtoberfläche.
Anwendungen: Schweißnähte werden in einer Vielzahl von Branchen und Anwendungen eingesetzt, darunter im Bauwesen, in der Automobilindustrie, in der Schwerindustrie, im Schiffbau, in der Luft- und Raumfahrt sowie in der Elektronik- und Haushaltsgeräteherstellung.
Herausforderungen:
- Qualitätskontrolle: Die Überwachung und Prüfung von Schweißnähten ist entscheidend, um sicherzustellen, dass sie den Anforderungen an Festigkeit und Integrität entsprechen.
- Schweißnahtvorbereitung: Eine ordnungsgemäße Vorbereitung der Werkstücke vor dem Schweißen ist wichtig, um eine hochwertige Schweißnaht zu gewährleisten.
- Wärmebeeinflusste Zone (WBZ): Die Wärme während des Schweißens kann benachbarte Bereiche der Werkstücke beeinflussen, was zu Veränderungen in ihren mechanischen Eigenschaften führen kann.
Schweißnähte sind ein wesentlicher Bestandteil vieler Fertigungsprozesse und spielen eine entscheidende Rolle bei der Herstellung von Produkten in einer Vielzahl von Branchen. Eine ordnungsgemäße Schweißnahtvorbereitung, -erzeugung und -inspektion ist unerlässlich, um die Qualität und Sicherheit der Endprodukte zu gewährleisten.
Schweißprozess
Ein Schweißprozess ist ein Verfahren zur Verbindung von Werkstücken durch das Schmelzen und Verfestigen eines Füllmaterials, um eine dauerhafte Verbindung zu schaffen. Schweißprozesse können auf verschiedene Arten durchgeführt werden, abhängig von den Werkstücken, den Anforderungen an die Verbindung und den verfügbaren Ressourcen.
Haupttypen von Schweißprozessen:
- Lichtbogenschweißen: Bei diesem Prozess wird ein Lichtbogen zwischen einer Elektrode und den zu verbindenden Werkstücken erzeugt. Der Lichtbogen erzeugt die erforderliche Wärme zum Schmelzen des Füllmaterials und der Werkstücke.
- Gas- und Druckschweißen: Diese Prozesse umfassen das Verwenden von Gasen oder Druck, um das Schmelzen und Verbinden von Werkstücken zu erleichtern. Beispiele sind das Lichtbogenschweißen mit Schutzgas (MIG/MAG-Schweißen) und das Lichtbogenschweißen mit Flux (Fülldrahtschweißen).
- Widerstandsschweißen: Hierbei werden die zu verbindenden Werkstücke durch Anlegen von Druck und Strom an die Kontaktflächen erwärmt und miteinander verbunden. Es umfasst Punktschweißen, Rollennahtschweißen und Buckelschweißen.
- Schutzgas- und Lichtbogenspritzen: Diese Prozesse werden verwendet, um Metallbeschichtungen auf Oberflächen aufzubringen, um sie vor Korrosion, Verschleiß oder anderen Schäden zu schützen.
Faktoren bei der Auswahl des Schweißprozesses:
- Art der zu verbindenden Werkstoffe (Metalle, Kunststoffe usw.)
- Anforderungen an die Festigkeit und Haltbarkeit der Verbindung
- Verfügbarkeit von Schweißausrüstung und Ressourcen
- Produktionsgeschwindigkeit und Effizienz
- Umgebungsfaktoren wie Temperatur, Feuchtigkeit und Druck
Anwendungen:
Schweißprozesse werden in einer Vielzahl von Branchen und Anwendungen eingesetzt, darunter Automobilindustrie, Schiffbau, Bauwesen, Luft- und Raumfahrt, Elektronikindustrie und viele andere. Sie sind entscheidend für die Herstellung von Produkten wie Fahrzeugen, Schiffen, Brücken, Gebäuden, Flugzeugen, Rohren, Behältern, Elektrogeräten und vielem mehr.
Herausforderungen:
- Qualitätskontrolle: Die Überwachung und Prüfung von Schweißnähten und -verbindungen ist entscheidend, um sicherzustellen, dass sie den Anforderungen an Festigkeit und Integrität entsprechen.
- Schweißrauch und -dämpfe: Beim Schweißen können gesundheitsschädliche Rauch- und Dampfabsonderungen auftreten, die eine angemessene Belüftung und persönliche Schutzausrüstung erfordern.
- Wartung und Kalibrierung: Schweißausrüstung erfordert regelmäßige Wartung und Kalibrierung, um eine optimale Leistung und Sicherheit zu gewährleisten.
Schweißprozesse sind ein wesentlicher Bestandteil vieler Fertigungsprozesse und spielen eine entscheidende Rolle bei der Herstellung von Produkten in einer Vielzahl von Branchen. Eine sorgfältige Auswahl und Anwendung des geeigneten Schweißprozesses ist entscheidend, um hochwertige und zuverlässige Verbindungen zu gewährleisten.
Rotationsschweißen
Das Rotationsschweißen ist ein Schweißverfahren, das hauptsächlich für das Schweißen von zylindrischen Werkstücken wie Rohren, Behältern und zylindrischen Komponenten verwendet wird. Es nutzt eine Kombination aus Drehbewegung und Schweißbrennerbewegung, um eine gleichmäßige Schweißnaht entlang des Umfangs des Werkstücks zu erzeugen.
Funktionsweise: Beim Rotationsschweißen wird das zu schweißende Werkstück auf eine rotierende Vorrichtung montiert, die es um seine Achse dreht. Gleichzeitig bewegt sich der Schweißbrenner entlang des Umfangs des Werkstücks, wodurch eine kontinuierliche Schweißnaht erzeugt wird. Diese Methode gewährleistet eine gleichmäßige Verteilung der Wärme und des Schweißmaterials entlang der Schweißnaht, was zu einer konsistenten und qualitativ hochwertigen Verbindung führt.
Anwendungen: Das Rotationsschweißen wird in verschiedenen Branchen eingesetzt, darunter die Herstellung von Rohren, Tanks, Behältern, Druckbehältern, Ölleitungen und anderen zylindrischen Komponenten. Es wird besonders dort eingesetzt, wo eine hohe Produktivität und eine gleichbleibende Qualität erforderlich sind, wie in der Massenproduktion von standardisierten Teilen.
Vorteile:
- Hohe Produktionsgeschwindigkeit: Das Rotationsschweißen ermöglicht eine schnelle und effiziente Schweißung großer Mengen zylindrischer Werkstücke.
- Konsistente Qualität: Durch die automatisierte Natur des Verfahrens können konsistente Schweißnähte mit hoher Qualität erzeugt werden.
- Geringer Arbeitsaufwand: Da die Maschine den Großteil der Arbeit übernimmt, wird der Bedarf an manueller Arbeit reduziert, was die Arbeitskosten senkt.
Herausforderungen:
- Einrichtungszeit: Das Einrichten einer Rotationsschweißmaschine kann zeitaufwändig sein, insbesondere wenn verschiedene Werkstückgrößen oder Schweißparameter berücksichtigt werden müssen.
- Wartung und Kalibrierung: Wie bei allen industriellen Maschinen erfordern Rotationsschweißmaschinen regelmäßige Wartung und Kalibrierung, um eine optimale Leistung und Sicherheit zu gewährleisten.
Das Rotationsschweißen ist ein wichtiger Prozess in der modernen Fertigungsindustrie, der effiziente und qualitativ hochwertige Lösungen für das Schweißen von zylindrischen Werkstücken bietet. Durch die kontinuierliche Weiterentwicklung von Schweißtechnologien und -ausrüstungen wird dieses Verfahren zunehmend präziser, effizienter und vielseitiger.
Elektroschweißen
Elektroschweißen ist ein Schweißverfahren, bei dem eine elektrische Spannung und Strom verwendet werden, um eine Schweißverbindung zwischen zwei Werkstücken herzustellen. Es ist eine der am häufigsten verwendeten Schweißmethoden in der Fertigungsindustrie aufgrund seiner Vielseitigkeit und Anwendbarkeit auf eine Vielzahl von Materialien und Dicken.
Funktionsweise: Beim Elektroschweißen wird eine elektrische Spannung zwischen einer Elektrode und den zu verbindenden Werkstücken erzeugt. Dies führt dazu, dass ein Lichtbogen zwischen der Elektrode und den Werkstücken entsteht, der das Material aufschmilzt und eine Schmelzbad bildet. Die geschmolzenen Materialien verbinden sich und bilden nach dem Abkühlen eine feste Schweißnaht.
Arten des Elektroschweißens:
- Lichtbogenschweißen: Hier wird ein Lichtbogen zwischen einer Elektrode und den Werkstücken erzeugt, um die erforderliche Wärme zum Schweißen zu erzeugen. Dies umfasst Verfahren wie das Metall-Inertgas-Schweißen (MIG), das Metall-Aktivgas-Schweißen (MAG) und das Lichtbogenschweißen mit selbstschützenden Elektroden (Fülldrahtschweißen).
- Widerstandsschweißen: Bei diesem Verfahren werden die zu verbindenden Werkstücke durch elektrischen Widerstand und Druck erwärmt, um eine Schweißverbindung herzustellen. Typische Formen des Widerstandsschweißens sind Punktschweißen, Rollennahtschweißen und Buckelschweißen.
Anwendungen: Elektroschweißen wird in einer Vielzahl von Branchen und Anwendungen eingesetzt, darunter Automobilindustrie, Schiffbau, Bauwesen, Luft- und Raumfahrt, Elektronikindustrie und viele andere. Es wird für die Herstellung von Produkten wie Fahrzeugrahmen, Rohrleitungen, Behältern, Konstruktionselementen und vielem mehr verwendet.
Vorteile:
- Vielseitigkeit: Elektroschweißen kann auf eine Vielzahl von Materialien und Dicken angewendet werden, einschließlich Stahl, Aluminium, Edelstahl, Kupfer und deren Legierungen.
- Effizienz: Elektroschweißen ermöglicht schnelle und effiziente Schweißverbindungen, was die Produktionsgeschwindigkeit erhöht.
- Automatisierung: Viele Elektroschweißprozesse können automatisiert werden, was die Konsistenz und Genauigkeit der Schweißnähte verbessert und den Arbeitsaufwand reduziert.
Herausforderungen:
- Schweißnahtqualität: Die Qualität der Schweißnaht hängt von verschiedenen Faktoren ab, einschließlich Schweißparameter, Werkstoffeigenschaften und Schweißumgebung.
- Schweißrauch und -dämpfe: Beim Elektroschweißen können gesundheitsschädliche Rauch- und Dampfabsonderungen auftreten, die eine angemessene Belüftung und persönliche Schutzausrüstung erfordern.
- Wartung und Kalibrierung: Schweißausrüstung erfordert regelmäßige Wartung und Kalibrierung, um eine optimale Leistung und Sicherheit zu gewährleisten.
Elektroschweißen ist ein vielseitiges und effektives Schweißverfahren, das in vielen industriellen Anwendungen eingesetzt wird. Durch kontinuierliche Innovationen und technologische Fortschritte wird Elektroschweißen weiterentwickelt, um effizientere und qualitativ hochwertigere Schweißverbindungen zu ermöglichen.
Automatisierte Schweißmaschine
Eine automatisierte Schweißmaschine ist eine spezialisierte Schweißausrüstung, die mit automatisierten Steuerungen und Robotik ausgestattet ist, um Schweißungen an Werkstücken durchzuführen, ohne dass menschliche Intervention erforderlich ist. Diese Maschinen spielen eine wichtige Rolle in der Fertigungsindustrie, insbesondere in Umgebungen, in denen hohe Produktionsgeschwindigkeiten, Konsistenz und Qualität erforderlich sind.
Funktionsweise: Automatisierte Schweißmaschinen nutzen fortschrittliche Steuerungssysteme und Robotik, um den gesamten Schweißprozess zu überwachen und durchzuführen. Die Werkstücke werden in der Regel mit einer Vorrichtung positioniert, die sie in der optimalen Position für die Schweißung hält. Der Roboter oder die automatisierte Vorrichtung führt dann den Schweißbrenner entlang der vorgegebenen Schweißnaht, wobei die Schweißparameter wie Stromstärke, Spannung und Geschwindigkeit präzise gesteuert werden.
Anwendungen: Automatisierte Schweißmaschinen werden in einer Vielzahl von Branchen und Anwendungen eingesetzt, darunter Automobilindustrie, Schiffbau, Luft- und Raumfahrt, Schwerindustrie, Bauwesen und mehr. Sie werden für die Herstellung von Fahrzeugrahmen, Karosserieteilen, Rohrleitungen, Behältern, Trägern, Konstruktionselementen und anderen Komponenten verwendet.
Vorteile:
- Hohe Produktionsgeschwindigkeit: Automatisierte Schweißmaschinen ermöglichen eine schnelle und effiziente Schweißung großer Mengen von Werkstücken.
- Konsistente Qualität: Durch die Automatisierung wird die Konsistenz der Schweißnähte verbessert, da menschliche Fehler minimiert werden.
- Arbeitsersparnis: Da die Maschinen den Großteil der Arbeit übernehmen, wird der Bedarf an manueller Arbeit reduziert, was die Arbeitskosten senkt und die Sicherheit verbessert.
Herausforderungen:
- Einrichtungszeit: Die Einrichtung einer automatisierten Schweißmaschine kann zeitaufwändig sein, da die Programme für jeden Schweißvorgang angepasst werden müssen.
- Investitionskosten: Automatisierte Schweißmaschinen erfordern in der Regel beträchtliche Investitionen in die Anschaffung und Installation der Ausrüstung sowie Schulungen für das Bedienpersonal.
Innovationen: Mit dem Fortschritt in der Automatisierungs- und Robotertechnik werden automatisierte Schweißmaschinen zunehmend mit fortschrittlichen Funktionen und Technologien ausgestattet, wie zum Beispiel maschinelles Lernen und künstliche Intelligenz, um die Produktivität weiter zu steigern und die Flexibilität bei der Herstellung verschiedener Produkte zu verbessern.
Insgesamt spielen automatisierte Schweißmaschinen eine entscheidende Rolle in der modernen Fertigungsindustrie, indem sie effiziente, hochwertige und konsistente Schweißlösungen bieten. Durch die kontinuierliche Weiterentwicklung von Technologien und Prozessen werden diese Maschinen zunehmend zu unverzichtbaren Werkzeugen in der industriellen Fertigung.
Schweißgeschwindigkeit
Die Schweißgeschwindigkeit bezieht sich auf die Geschwindigkeit, mit der der Schweißbrenner entlang der Schweißnaht bewegt wird oder die Geschwindigkeit, mit der das Werkstück durch den Schweißprozess geführt wird. Sie ist ein wichtiger Parameter bei der Steuerung des Schweißprozesses und beeinflusst direkt die Qualität und Eigenschaften der Schweißnaht.
Einflussfaktoren auf die Schweißgeschwindigkeit:
- Schweißverfahren: Verschiedene Schweißverfahren haben unterschiedliche optimale Schweißgeschwindigkeiten. Zum Beispiel erfordert das Lichtbogenschweißen mit einer konstanten Spannung (CV) typischerweise höhere Schweißgeschwindigkeiten als das Lichtbogenschweißen mit einer konstanten Stromquelle (CC).
- Material und Dicke: Verschiedene Materialien und Dicken erfordern unterschiedliche Schweißgeschwindigkeiten, um eine qualitativ hochwertige Schweißnaht zu erzeugen. Dickeres Material erfordert oft langsamere Schweißgeschwindigkeiten, um eine ausreichende Durchdringung zu gewährleisten, während dünnere Materialien schneller geschweißt werden können.
- Schweißparameter: Schweißparameter wie Schweißstrom, Spannung, Drahtvorschubgeschwindigkeit und Gasfluss beeinflussen ebenfalls die optimale Schweißgeschwindigkeit. Eine Änderung dieser Parameter kann eine Anpassung der Schweißgeschwindigkeit erfordern, um die gewünschte Schweißnahtqualität zu erzielen.
Bedeutung der Schweißgeschwindigkeit:
- Qualität der Schweißnaht: Die Schweißgeschwindigkeit beeinflusst die Form, Penetrationstiefe und Eigenschaften der Schweißnaht. Eine zu hohe oder zu niedrige Schweißgeschwindigkeit kann zu unerwünschten Fehlern wie mangelnder Durchdringung, Schweißspritzern oder Porosität führen.
- Produktivität: Die Optimierung der Schweißgeschwindigkeit kann die Produktivität erhöhen, indem sie den Durchsatz erhöht und die Gesamtzeit für den Schweißprozess reduziert. Eine angemessene Schweißgeschwindigkeit ermöglicht es, die Produktionsziele effizient zu erreichen.
- Kosten: Eine optimale Schweißgeschwindigkeit trägt dazu bei, die Kosten für den Schweißprozess zu minimieren, indem sie den Materialverbrauch, den Energieverbrauch und die Arbeitszeit optimiert.
Anpassung der Schweißgeschwindigkeit:
Die Schweißgeschwindigkeit kann während des Schweißprozesses je nach den Anforderungen des Werkstücks und der gewünschten Schweißnahtqualität angepasst werden. Dies erfordert oft eine kontinuierliche Überwachung der Schweißparameter und gegebenenfalls eine Anpassung der Geschwindigkeit durch den Bediener oder automatische Steuerungen.
Insgesamt ist die Schweißgeschwindigkeit ein entscheidender Parameter bei der Steuerung des Schweißprozesses, der direkten Einfluss auf die Qualität, Produktivität und Kosten hat. Eine sorgfältige Optimierung und Überwachung der Schweißgeschwindigkeit ist entscheidend, um hochwertige und effiziente Schweißverbindungen zu gewährleisten.
Schweißqualität
Die Schweißqualität bezieht sich auf die Merkmale einer Schweißnaht oder Schweißverbindung, die deren Eignung für den beabsichtigten Einsatzzweck bestimmen. Eine hohe Schweißqualität ist entscheidend für die Sicherheit, Zuverlässigkeit und Leistungsfähigkeit von geschweißten Bauteilen oder Konstruktionen.
Merkmale der Schweißqualität:
- Festigkeit: Die Schweißnaht sollte eine ausreichende Festigkeit aufweisen, um den erwarteten Belastungen standzuhalten und die strukturelle Integrität des Werkstücks zu gewährleisten.
- Durchdringung: Die Schweißnaht sollte eine ausreichende Penetrationstiefe aufweisen, um eine dauerhafte Verbindung zwischen den Werkstücken zu gewährleisten. Eine unzureichende Durchdringung kann zu schwachen Schweißnähten und erhöhtem Risiko von Rissen führen.
- Schweißnahtform: Die Form der Schweißnaht sollte den spezifischen Anforderungen entsprechen und eine gleichmäßige, gut definierte Geometrie aufweisen, um eine optimale Festigkeit und Ästhetik zu gewährleisten.
- Oberflächenbeschaffenheit: Die Oberfläche der Schweißnaht sollte glatt, sauber und frei von Unregelmäßigkeiten wie Schweißspritzern, Porosität oder Einschlüssen sein, um eine gute Haftung und Abdichtung zu gewährleisten.
- Wärmebeeinflusste Zone (WBZ): Die WBZ um die Schweißnaht herum sollte keine Anzeichen von übermäßiger Wärmebeeinflussung, Verformung oder Schwächung aufweisen, um die mechanischen Eigenschaften des Werkstücks nicht zu beeinträchtigen.
Faktoren, die die Schweißqualität beeinflussen:
- Schweißverfahren: Unterschiedliche Schweißverfahren haben unterschiedliche Auswirkungen auf die Schweißqualität. Einige Verfahren sind besser geeignet für bestimmte Materialien oder Anwendungen und können zu unterschiedlichen Ergebnissen führen.
- Schweißparameter: Die Einstellung der Schweißparameter wie Schweißstrom, Spannung, Drahtvorschubgeschwindigkeit und Gasfluss ist entscheidend für die Qualität der Schweißnaht. Eine präzise Steuerung dieser Parameter kann zu einer verbesserten Schweißqualität führen.
- Materialien: Die Auswahl der richtigen Schweißmaterialien und Werkstoffe ist entscheidend für die Qualität der Schweißverbindung. Unterschiedliche Materialkombinationen erfordern unterschiedliche Schweißverfahren und -parameter.
- Vorbehandlung der Werkstücke: Eine ordnungsgemäße Vorbehandlung der zu schweißenden Werkstücke, einschließlich Reinigung, Entfettung und Oberflächenbehandlung, kann die Qualität der Schweißverbindung verbessern.
Qualitätskontrolle:
Die Überwachung und Prüfung der Schweißqualität sind entscheidend, um sicherzustellen, dass die geschweißten Bauteile oder Konstruktionen den erforderlichen Standards und Spezifikationen entsprechen. Dies umfasst visuelle Inspektionen, zerstörungsfreie Prüfungen (z.B. Ultraschallprüfung, Röntgenprüfung) und mechanische Tests der geschweißten Verbindungen.
Insgesamt ist die Schweißqualität ein wesentlicher Aspekt des Schweißprozesses, der durch eine sorgfältige Auswahl der Schweißverfahren, -parameter und -materialien sowie durch eine gründliche Qualitätskontrolle gewährleistet werden muss. Eine hohe Schweißqualität trägt dazu bei, die Sicherheit, Zuverlässigkeit und Leistungsfähigkeit geschweißter Bauteile und Konstruktionen zu gewährleisten.
Schweißparameter
Schweißparameter sind die variablen Einstellungen und Bedingungen, die während des Schweißprozesses gesteuert werden, um die Qualität, Effizienz und Sicherheit der Schweißverbindung zu gewährleisten. Diese Parameter können je nach Schweißverfahren, Werkstoffen und Anwendungen variieren und müssen sorgfältig ausgewählt und kontrolliert werden.
Hauptschweißparameter:
- Schweißstrom: Der Schweißstrom ist eine der wichtigsten Variablen im Schweißprozess und beeinflusst die Intensität des Lichtbogens und die Wärmeentwicklung an der Schweißstelle. Ein höherer Schweißstrom führt in der Regel zu einer höheren Wärmeentwicklung und Penetrationstiefe.
- Schweißspannung: Die Schweißspannung bestimmt die Spannung, die an die Schweißbrennerleitung angelegt wird, und beeinflusst die Länge und Stabilität des Lichtbogens. Eine angemessene Schweißspannung ist entscheidend für eine stabile Lichtbogenführung und eine gleichmäßige Schweißnahtbildung.
- Drahtvorschubgeschwindigkeit: Bei Schweißverfahren mit Drahtelektrode (z.B. MIG/MAG-Schweißen) wird die Drahtvorschubgeschwindigkeit gesteuert, um die erforderliche Zufuhr des Schweißmaterials sicherzustellen. Eine zu hohe oder zu niedrige Drahtvorschubgeschwindigkeit kann zu unerwünschten Schweißfehlern führen.
- Gasflussrate: Die Gasflussrate bestimmt die Menge und Geschwindigkeit des Schutzgases, das um den Lichtbogen herum strömt, um die Schweißnaht vor Oxidation und Verunreinigungen zu schützen. Eine angemessene Gasflussrate ist entscheidend für die Qualität der Schweißverbindung.
- Elektroden- oder Drahtdurchmesser: Der Durchmesser der Elektrode oder des Schweißdrahts beeinflusst direkt die Stromdichte und Wärmeentwicklung des Lichtbogens. Die Auswahl des richtigen Durchmessers ist entscheidend für die Steuerung der Schweißparameter.
Anpassung der Schweißparameter:
Die Schweißparameter müssen während des Schweißprozesses je nach den spezifischen Anforderungen des Werkstücks und der gewünschten Schweißnahtqualität angepasst werden. Dies erfordert eine kontinuierliche Überwachung der Schweißbedingungen und gegebenenfalls eine Anpassung der Parameter durch den Bediener oder automatische Steuerungen.
Qualitätskontrolle:
Eine sorgfältige Kontrolle und Überwachung der Schweißparameter ist entscheidend für die Sicherstellung einer hohen Schweißqualität. Dies umfasst die Überwachung der Schweißstrom- und Spannungswerte, die visuelle Inspektion der Schweißnaht während des Prozesses und die Durchführung von zerstörungsfreien Prüfungen zur Überprüfung der Schweißnahtintegrität.
Insgesamt sind die Schweißparameter entscheidende Variablen im Schweißprozess, die eine direkte Auswirkung auf die Qualität, Effizienz und Sicherheit der Schweißverbindung haben. Eine sorgfältige Auswahl, Kontrolle und Anpassung dieser Parameter ist entscheidend für die Herstellung hochwertiger und zuverlässiger Schweißverbindungen.
Lichtbogenschweißmaschine
Eine Lichtbogenschweißmaschine ist eine elektrische Schweißausrüstung, die einen Lichtbogen zwischen einer Elektrode und dem Werkstück erzeugt, um eine Schweißverbindung herzustellen. Diese Maschinen sind in verschiedenen Ausführungen erhältlich und können für eine Vielzahl von Schweißanwendungen eingesetzt werden.
Funktionsweise: Eine Lichtbogenschweißmaschine erzeugt einen Lichtbogen zwischen einer Elektrode und dem Werkstück, indem sie eine elektrische Spannung und Strom anwendet. Der Lichtbogen erzeugt hohe Temperaturen, die das Werkstück und das Schweißmaterial schmelzen lassen, wodurch eine Schweißverbindung entsteht. Die Maschine steuert den Lichtbogen und die Schweißparameter wie Stromstärke, Spannung und Drahtvorschubgeschwindigkeit, um die gewünschte Schweißnaht zu erzeugen.
Typen von Lichtbogenschweißmaschinen:
- Gleichstrom (DC) Lichtbogenschweißmaschinen: Diese Maschinen verwenden Gleichstrom, um den Lichtbogen zu erzeugen. Sie sind vielseitig einsetzbar und eignen sich für eine Vielzahl von Materialien und Schweißverfahren.
- Wechselstrom (AC) Lichtbogenschweißmaschinen: Diese Maschinen verwenden Wechselstrom, der es ermöglicht, auch Aluminium und andere Materialien zu schweißen, die von Gleichstrom weniger effektiv geschweißt werden können.
- Inverter Lichtbogenschweißmaschinen: Diese Maschinen verwenden einen Inverter, um den Wechselstrom in Gleichstrom umzuwandeln und die Schweißparameter präzise zu steuern. Sie sind kompakter und energieeffizienter als herkömmliche Lichtbogenschweißmaschinen.
Anwendungen: Lichtbogenschweißmaschinen werden in einer Vielzahl von Branchen und Anwendungen eingesetzt, darunter Automobilindustrie, Schiffbau, Bauwesen, Luft- und Raumfahrt, Schwerindustrie und viele andere. Sie werden für das Schweißen von Bauteilen, Strukturen, Rohren, Behältern, Karosserieteilen und anderen Komponenten verwendet.
Vorteile:
- Vielseitigkeit: Lichtbogenschweißmaschinen können für verschiedene Schweißverfahren und eine Vielzahl von Materialien eingesetzt werden.
- Effizienz: Sie ermöglichen schnelle und effiziente Schweißverbindungen, was die Produktionsgeschwindigkeit erhöht.
- Steuerbarkeit: Durch die präzise Steuerung der Schweißparameter können hochwertige und konsistente Schweißnähte erzeugt werden.
Herausforderungen:
- Bedarf an Schulung: Die Bedienung von Lichtbogenschweißmaschinen erfordert eine angemessene Schulung und Erfahrung, um die gewünschten Ergebnisse zu erzielen.
- Wartung: Regelmäßige Wartung und Instandhaltung der Maschinen sind erforderlich, um ihre Leistung und Lebensdauer zu erhalten.
- Sicherheit: Aufgrund der hohen Temperaturen und elektrischen Gefahren müssen geeignete Sicherheitsmaßnahmen und persönliche Schutzausrüstungen verwendet werden.
Lichtbogenschweißmaschinen sind eine wesentliche Ausrüstung in der Fertigungsindustrie und spielen eine entscheidende Rolle bei der Herstellung von geschweißten Bauteilen und Konstruktionen. Durch kontinuierliche Innovationen und technologische Fortschritte werden diese Maschinen zunehmend effizienter, vielseitiger und benutzerfreundlicher.
Schweißdraht
Schweißdraht, auch als Schweißelektrode oder Schweißzusatzdraht bezeichnet, ist ein wesentlicher Bestandteil beim Lichtbogenschweißen und anderen Schweißverfahren, bei denen ein Zusatzmaterial benötigt wird, um die Schweißnaht zu bilden. Schweißdraht kommt in verschiedenen Typen, Durchmessern und Materialien vor und wird entsprechend den Anforderungen der Schweißanwendung ausgewählt.
Typen von Schweißdraht:
- Massivdraht: Massivdraht besteht aus einem einzigen massiven Draht, der als Elektrode verwendet wird. Er wird hauptsächlich beim MIG/MAG-Schweißen eingesetzt und ist in verschiedenen Materialien wie Stahl, Aluminium, Edelstahl und anderen Legierungen erhältlich.
- Fülldraht: Fülldraht besteht aus einem Hohlrohr mit einem Füllmaterial im Inneren. Er wird oft beim MIG/MAG-Schweißen eingesetzt und bietet den Vorteil, dass er weniger anfällig für Wind und äußere Einflüsse ist als Massivdraht.
- Flux-cored Draht: Flux-cored Draht ähnelt dem Fülldraht, jedoch ist das Füllmaterial mit einer Schicht Flussmittel umgeben. Er wird häufig beim FCAW-Schweißen (Flux-cored Arc Welding) eingesetzt und bietet verbesserte Schweißeigenschaften in schwierigen Umgebungen.
Eigenschaften von Schweißdraht:
- Material: Schweißdraht kann aus verschiedenen Materialien wie Stahl, Aluminium, Edelstahl, Kupfer und anderen Legierungen bestehen, je nach den Anforderungen der Schweißanwendung.
- Durchmesser: Schweißdraht ist in verschiedenen Durchmessern erhältlich, die je nach Schweißverfahren und Werkstückdicke ausgewählt werden. Ein kleinerer Drahtdurchmesser ermöglicht eine präzisere Steuerung des Schweißprozesses, während ein größerer Durchmesser eine höhere Schweißgeschwindigkeit ermöglicht.
- Flussmittel: Bei Fülldraht und Flux-cored Draht ist das Flussmittel ein wichtiger Bestandteil, der zur Bildung einer Schutzgasschicht und zur Entfernung von Verunreinigungen während des Schweißprozesses beiträgt.
Auswahl des richtigen Schweißdrahts:
Die Auswahl des richtigen Schweißdrahts hängt von verschiedenen Faktoren ab, einschließlich des zu schweißenden Materials, der Schweißverfahren, der Werkstückdicke und der spezifischen Anforderungen der Schweißanwendung. Eine sorgfältige Auswahl des Schweißdrahts ist entscheidend für die Qualität und Zuverlässigkeit der Schweißverbindung.
Anwendungen von Schweißdraht:
Schweißdraht wird in einer Vielzahl von Schweißanwendungen eingesetzt, darunter das MIG/MAG-Schweißen, das FCAW-Schweißen, das Lichtbogenschweißen mit selbstschützenden Elektroden und andere Verfahren. Er wird verwendet, um eine Schweißnaht zwischen den zu verbindenden Werkstücken zu bilden und die erforderlichen mechanischen Eigenschaften der Schweißverbindung zu gewährleisten.
Insgesamt ist Schweißdraht ein wesentlicher Bestandteil des Schweißprozesses, der dazu beiträgt, qualitativ hochwertige und zuverlässige Schweißverbindungen herzustellen. Durch die sorgfältige Auswahl des richtigen Drahttyps und die präzise Steuerung des Schweißprozesses können optimale Ergebnisse erzielt werden.
Lichtbogen
Der Lichtbogen ist eine elektrische Entladung, die zwischen zwei Elektroden entsteht, wenn eine ausreichend hohe Spannung zwischen ihnen angelegt wird. Beim Schweißen wird der Lichtbogen verwendet, um die erforderliche Wärme zum Schmelzen des Werkstoffs und zur Bildung der Schweißnaht zu erzeugen. Der Lichtbogen ist ein zentrales Element verschiedener Lichtbogenschweißverfahren wie MIG/MAG-Schweißen, Lichtbogenschweißen mit selbstschützenden Elektroden (FCAW) und Lichtbogenschweißen mit Wolfram-Inertgas (TIG).
Funktionsweise:
- Entstehung des Lichtbogens: Ein Lichtbogen entsteht, wenn eine ausreichend hohe Spannung zwischen einer Elektrode und dem Werkstück angelegt wird. Diese Spannung führt dazu, dass die Luft oder das Schutzgas zwischen den Elektroden ionisiert wird und einen elektrischen Strompfad bildet.
- Wärmeerzeugung: Der Lichtbogen erzeugt extrem hohe Temperaturen von bis zu 20.000 Grad Celsius, was ausreicht, um das zu schweißende Material aufzuschmelzen und eine Schweißnaht zu bilden.
- Schutzgas: In den meisten Lichtbogenschweißverfahren wird ein Schutzgas verwendet, das den Lichtbogen umgibt und die geschmolzenen Metalltropfen vor Oxidation und Verunreinigungen schützt. Dies trägt zur Bildung einer sauberen und hochwertigen Schweißnaht bei.
Arten von Lichtbogenschweißverfahren:
- MIG/MAG-Schweißen: Beim Metall-Inertgas- (MIG) und Metall-Aktivgas-Schweißen (MAG) wird ein Lichtbogen zwischen einer kontinuierlich zugeführten Drahtelektrode und dem Werkstück erzeugt. Ein inertes oder aktives Schutzgas wird verwendet, um den Lichtbogen zu stabilisieren und die Schweißzone zu schützen.
- Lichtbogenschweißen mit selbstschützenden Elektroden (FCAW): Bei diesem Verfahren wird ein Fülldraht mit eingebettetem Flussmittel verwendet, das während des Schweißprozesses schmilzt und ein Schutzgas erzeugt, um den Lichtbogen zu stabilisieren und die Schweißzone zu schützen.
- Lichtbogenschweißen mit Wolfram-Inertgas (TIG): Beim TIG-Schweißen wird ein nichtverbrauchbarer Wolfram-Elektrode verwendet, um den Lichtbogen zu erzeugen. Ein inertes Schutzgas wird verwendet, um die Schweißzone zu schützen, während zusätzliches Schweißmaterial manuell zugeführt werden kann, falls erforderlich.
Eigenschaften des Lichtbogens:
- Stabilität: Ein stabiler Lichtbogen ist wichtig für die Kontrolle und Qualität der Schweißnaht. Instabile Lichtbögen können zu ungleichmäßigen Schweißnähten und unerwünschten Defekten führen.
- Penetration: Die Penetrationstiefe des Lichtbogens beeinflusst die Qualität und Festigkeit der Schweißnaht. Ein tieferer Lichtbogen kann zu einer besseren Durchdringung und Verschmelzung der Werkstücke führen.
- Lichtbogenform: Die Form des Lichtbogens kann je nach Schweißverfahren und Schweißparameter variieren. Eine gleichmäßige Lichtbogenform trägt zur gleichmäßigen Verteilung der Wärme und zur Bildung einer hochwertigen Schweißnaht bei.
Der Lichtbogen ist ein entscheidender Bestandteil des Lichtbogenschweißens und spielt eine wesentliche Rolle bei der Erzeugung von hochwertigen und zuverlässigen Schweißverbindungen. Eine präzise Steuerung und Stabilisierung des Lichtbogens ist entscheidend für die Qualität und Effizienz des Schweißprozesses.
Schutzgas
Schutzgas ist eine entscheidende Komponente beim Lichtbogenschweißen, die dazu dient, die geschmolzenen Metalltropfen und die Schweißzone vor Verunreinigungen und Oxidation zu schützen. Es wird verwendet, um den Lichtbogen während des Schweißprozesses zu stabilisieren und die Bildung einer hochwertigen Schweißnaht zu unterstützen. Je nach Schweißverfahren und Anwendung können verschiedene Arten von Schutzgasen verwendet werden.
Arten von Schutzgasen:
- Inertgase: Inertgase wie Argon und Helium werden verwendet, um die Schweißzone vor Oxidation und Verunreinigungen zu schützen, insbesondere bei Schweißverfahren wie dem TIG-Schweißen. Sie reagieren nicht mit den geschmolzenen Metalltropfen und tragen zur Bildung einer sauberen und hochwertigen Schweißnaht bei.
- Aktivgase: Aktivgase wie Kohlendioxid (CO2) werden verwendet, um die Schweißzone zu schützen und die Lichtbogenstabilität zu verbessern. Sie können beim MIG/MAG-Schweißen als alleiniges Schutzgas oder in Kombination mit Inertgasen eingesetzt werden.
- Mischgase: Mischgase, die eine Kombination aus Inert- und Aktivgasen enthalten, werden oft verwendet, um die Vorteile beider Gaskategorien zu kombinieren. Beispiele für Mischgase sind Argon/CO2-Gemische, die beim MIG/MAG-Schweißen häufig eingesetzt werden, um eine gute Schutzgaseigenschaft und Lichtbogenstabilität zu gewährleisten.
Funktionen von Schutzgasen:
- Schutz vor Oxidation: Schutzgas bildet eine Schutzatmosphäre um den Lichtbogen herum, die verhindert, dass der geschmolzene Schweißdraht und das Werkstück mit Sauerstoff aus der Umgebungsluft reagieren. Dies minimiert die Bildung von Oxidschichten auf der Schweißnaht und erhält die Qualität der Schweißverbindung.
- Reduzierung von Spritzern: Schutzgas hilft dabei, die Bildung von Schweißspritzern zu reduzieren, indem es die Oberflächenspannung der geschmolzenen Metalltropfen verringert und deren Austritt aus der Schweißzone kontrolliert.
- Stabilisierung des Lichtbogens: Schutzgas trägt zur Stabilisierung des Lichtbogens bei, indem es die Ionisation zwischen der Elektrode und dem Werkstück erleichtert und einen kontinuierlichen elektrischen Strompfad bildet.
Auswahl des richtigen Schutzgases:
Die Auswahl des geeigneten Schutzgases hängt von verschiedenen Faktoren ab, einschließlich des Schweißverfahrens, der zu schweißenden Materialien, der gewünschten Schweißnahtqualität und der Betriebsbedingungen. Eine sorgfältige Auswahl des Schutzgases ist entscheidend für die Qualität und Zuverlässigkeit des Schweißprozesses.
Schutzgas spielt eine entscheidende Rolle beim Lichtbogenschweißen, indem es die Schweißzone vor Verunreinigungen schützt und zur Bildung hochwertiger Schweißnähte beiträgt. Eine präzise Auswahl und Steuerung des Schutzgases ist entscheidend für die Qualität und Effizienz des Schweißprozesses.
Lichtbogenschweißverfahren
Lichtbogenschweißen ist ein Schweißverfahren, bei dem ein Lichtbogen zwischen einer Elektrode und dem zu schweißenden Werkstück erzeugt wird, um die erforderliche Wärme zum Schmelzen des Materials und zur Bildung einer Schweißverbindung zu erzeugen. Es ist eines der am weitesten verbreiteten Schweißverfahren in der Industrie aufgrund seiner Vielseitigkeit, Effizienz und Anpassungsfähigkeit an verschiedene Materialien und Anwendungen. Es gibt mehrere Lichtbogenschweißverfahren, darunter MIG/MAG-Schweißen, Lichtbogenschweißen mit selbstschützenden Elektroden (FCAW) und Lichtbogenschweißen mit Wolfram-Inertgas (TIG).
1. MIG/MAG-Schweißen (Metall-Inertgas/Metall-Aktivgas):
- Funktionsweise: Beim MIG/MAG-Schweißen wird ein Lichtbogen zwischen einer kontinuierlich zugeführten Drahtelektrode und dem Werkstück erzeugt. Ein inertes oder aktives Schutzgas wird verwendet, um den Lichtbogen zu stabilisieren und die Schweißzone zu schützen.
- Anwendungen: MIG-Schweißen wird häufig für das Schweißen von Aluminium, Edelstahl und anderen Nicht-Eisenmetallen verwendet, während MAG-Schweißen für das Schweißen von Stahl und anderen Eisenmetallen geeignet ist.
2. Lichtbogenschweißen mit selbstschützenden Elektroden (FCAW):
- Funktionsweise: Beim FCAW-Schweißen wird ein Fülldraht mit eingebettetem Flussmittel verwendet, das während des Schweißprozesses schmilzt und ein Schutzgas erzeugt, um den Lichtbogen zu stabilisieren und die Schweißzone zu schützen.
- Anwendungen: FCAW-Schweißen ist besonders gut geeignet für das Schweißen im Freien und in windigen Bedingungen, da es weniger anfällig für äußere Einflüsse ist. Es wird oft in der Bauindustrie und anderen Außenanwendungen eingesetzt.
3. Lichtbogenschweißen mit Wolfram-Inertgas (TIG):
- Funktionsweise: Beim TIG-Schweißen wird ein nichtverbrauchbarer Wolframelektrode verwendet, um den Lichtbogen zu erzeugen. Ein inertes Schutzgas wird verwendet, um die Schweißzone zu schützen, während zusätzliches Schweißmaterial manuell zugeführt werden kann, falls erforderlich.
- Anwendungen: TIG-Schweißen wird oft für hochpräzise Schweißanwendungen verwendet, bei denen eine hohe Schweißqualität und eine saubere Schweißnaht erforderlich sind, wie zum Beispiel in der Luft- und Raumfahrtindustrie, der Automobilindustrie und der Herstellung von Edelstahlkomponenten.
Vorteile des Lichtbogenschweißens:
- Vielseitigkeit: Lichtbogenschweißen kann für eine Vielzahl von Materialien und Anwendungen eingesetzt werden.
- Effizienz: Es ermöglicht schnelle und effiziente Schweißverbindungen mit hoher Produktivität.
- Kontrollierbarkeit: Durch die präzise Steuerung der Schweißparameter können hochwertige und konsistente Schweißnähte erzeugt werden.
Lichtbogenschweißen ist ein wesentliches Schweißverfahren in der Industrie, das durch kontinuierliche Innovationen und technologische Fortschritte zunehmend effizienter, vielseitiger und benutzerfreundlicher wird. Es spielt eine entscheidende Rolle bei der Herstellung hochwertiger und zuverlässiger Schweißverbindungen in einer Vielzahl von Anwendungen.
Schweißnaht
Die Schweißnaht ist die Verbindung zwischen den zu schweißenden Werkstücken, die durch den Schweißprozess entsteht. Sie bildet die strukturelle Grundlage für die Festigkeit und Integrität der geschweißten Konstruktion oder Bauteile. Die Qualität der Schweißnaht ist entscheidend für die Leistungsfähigkeit und Sicherheit des Endprodukts.
Merkmale einer guten Schweißnaht:
- Festigkeit: Die Schweißnaht sollte eine hohe Festigkeit aufweisen, um den erwarteten Belastungen standzuhalten und die strukturelle Integrität des Werkstücks zu gewährleisten. Eine unzureichende Festigkeit kann zu vorzeitigem Versagen und Bruch führen.
- Durchdringung: Die Schweißnaht sollte eine ausreichende Penetrationstiefe aufweisen, um eine dauerhafte Verbindung zwischen den Werkstücken herzustellen. Eine unzureichende Durchdringung kann zu schwachen Schweißnähten und erhöhtem Risiko von Rissen führen.
- Form und Aussehen: Die Form und das Aussehen der Schweißnaht können je nach Schweißverfahren und Anwendungsanforderungen variieren. Eine gleichmäßige, gut definierte Naht mit glatten Oberflächen und klaren Konturen deutet auf eine qualitativ hochwertige Schweißverbindung hin.
- Oberflächenbeschaffenheit: Die Oberfläche der Schweißnaht sollte frei von Unregelmäßigkeiten wie Schweißspritzern, Porosität oder Einschlüssen sein. Eine glatte und saubere Oberfläche trägt nicht nur zur Ästhetik bei, sondern verbessert auch die Haftung und Abdichtung der Schweißverbindung.
- Wärmebeeinflusste Zone (WBZ): Die WBZ um die Schweißnaht herum sollte keine Anzeichen von übermäßiger Wärmebeeinflussung, Verformung oder Schwächung aufweisen. Eine zu große WBZ kann zu unerwünschten Veränderungen der mechanischen Eigenschaften des Werkstücks führen.
Faktoren, die die Qualität der Schweißnaht beeinflussen:
- Schweißverfahren: Unterschiedliche Schweißverfahren haben unterschiedliche Auswirkungen auf die Qualität der Schweißnaht. Einige Verfahren sind besser geeignet für bestimmte Materialien oder Anwendungen und können zu unterschiedlichen Ergebnissen führen.
- Schweißparameter: Die Einstellung der Schweißparameter wie Schweißstrom, Spannung, Drahtvorschubgeschwindigkeit und Gasfluss ist entscheidend für die Qualität der Schweißnaht. Eine präzise Steuerung dieser Parameter kann zu einer verbesserten Schweißqualität führen.
- Materialien: Die Auswahl der richtigen Schweißmaterialien und Werkstoffe ist entscheidend für die Qualität der Schweißverbindung. Unterschiedliche Materialkombinationen erfordern unterschiedliche Schweißverfahren und -parameter.
- Vorbehandlung der Werkstücke: Eine ordnungsgemäße Vorbehandlung der zu schweißenden Werkstücke, einschließlich Reinigung, Entfettung und Oberflächenbehandlung, kann die Qualität der Schweißverbindung verbessern.
Die Schweißnaht ist das Ergebnis eines komplexen Schweißprozesses, der eine sorgfältige Planung, Vorbereitung und Ausführung erfordert. Eine qualitativ hochwertige Schweißnaht ist entscheidend für die Sicherheit, Zuverlässigkeit und Leistungsfähigkeit von geschweißten Bauteilen und Konstruktionen.
Schweißvorrichtung
Eine Schweißvorrichtung ist eine spezielle Einrichtung oder Vorrichtung, die verwendet wird, um Werkstücke während des Schweißprozesses zu positionieren, zu fixieren und zu unterstützen. Sie spielt eine entscheidende Rolle bei der Gewährleistung der Genauigkeit, Stabilität und Sicherheit des Schweißvorgangs und trägt zur Bildung hochwertiger Schweißverbindungen bei. Es gibt verschiedene Arten von Schweißvorrichtungen, die je nach den spezifischen Anforderungen der Schweißanwendung und den zu verbindenden Werkstücken eingesetzt werden können.
Arten von Schweißvorrichtungen:
- Schweißtische: Schweißtische sind robuste Tische oder Plattformen, die eine ebene und stabile Arbeitsfläche für das Positionieren und Fixieren der Werkstücke bieten. Sie sind oft mit Spannvorrichtungen, Schraubstöcken und Justiermöglichkeiten ausgestattet, um die Werkstücke sicher zu halten und die gewünschte Ausrichtung zu ermöglichen.
- Schweißspanner: Schweißspanner sind Vorrichtungen, die verwendet werden, um Werkstücke während des Schweißens festzuhalten und zu fixieren. Sie können in verschiedenen Ausführungen wie Klemmen, Zwingen, Magneten oder pneumatischen Spannvorrichtungen erhältlich sein und sind besonders nützlich für das Schweißen von dünnen oder komplex geformten Werkstücken.
- Schweißdrehvorrichtungen: Schweißdrehvorrichtungen ermöglichen das rotierende Bewegen von Werkstücken während des Schweißprozesses. Sie sind besonders nützlich für das Schweißen von zylindrischen oder symmetrischen Werkstücken wie Rohren, Behältern oder Wellen, um eine gleichmäßige Schweißnahtbildung entlang der gesamten Umfangslänge zu gewährleisten.
- Schweißpositionierer: Schweißpositionierer sind Vorrichtungen, die verwendet werden, um Werkstücke in die gewünschte Position zu drehen, zu neigen oder zu kippen, um den Schweißprozess zu erleichtern. Sie bieten eine verbesserte Zugänglichkeit zu schwer erreichbaren Schweißbereichen und ermöglichen eine präzise Ausrichtung der Werkstücke für optimale Schweißergebnisse.
Funktionen und Vorteile von Schweißvorrichtungen:
- Präzise Positionierung: Schweißvorrichtungen ermöglichen die präzise Positionierung und Ausrichtung der Werkstücke, um eine genaue Schweißnahtbildung zu gewährleisten.
- Stabilität: Sie bieten eine stabile und sichere Arbeitsumgebung, um die Werkstücke während des Schweißprozesses sicher zu halten und unerwünschte Bewegungen zu minimieren.
- Verbesserte Produktivität: Durch die Verwendung von Schweißvorrichtungen können Schweißprozesse effizienter durchgeführt werden, was zu einer erhöhten Produktivität und Durchsatzrate führt.
- Sicherheit: Schweißvorrichtungen tragen zur Verbesserung der Arbeitssicherheit bei, indem sie die Gefahr von Unfällen und Verletzungen verringern und eine ergonomische Arbeitsumgebung schaffen.
Die Auswahl der geeigneten Schweißvorrichtung hängt von verschiedenen Faktoren ab, einschließlich der Art der zu schweißenden Werkstücke, der Schweißverfahren und -parameter sowie der spezifischen Anforderungen der Schweißanwendung. Eine sorgfältige Planung und Auswahl der Schweißvorrichtung ist entscheidend für die Qualität, Effizienz und Sicherheit des Schweißprozesses.
Schweißnahtprüfung
Die Schweißnahtprüfung ist ein wichtiger Schritt im Schweißprozess, um sicherzustellen, dass die geschweißten Verbindungen den erforderlichen Qualitätsstandards entsprechen. Sie umfasst verschiedene Prüfmethoden und -verfahren, um die Integrität, Festigkeit und Zuverlässigkeit der Schweißnähte zu überprüfen und mögliche Defekte oder Unregelmäßigkeiten zu identifizieren. Die Schweißnahtprüfung wird in der Regel in verschiedenen Phasen des Schweißprozesses durchgeführt, einschließlich der Vorprüfung vor dem Schweißen, der In-Process-Prüfung während des Schweißens und der Endprüfung nach dem Schweißen.
Arten von Schweißnahtprüfverfahren:
- Visuelle Prüfung (VT): Die visuelle Prüfung ist die einfachste und häufigste Methode zur Überprüfung der Schweißnähte. Sie umfasst die visuelle Inspektion der Schweißnaht auf Oberflächendefekte wie Risse, Poren, Einschlüsse, Verzinkungen und Unregelmäßigkeiten.
- Radiographische Prüfung (RT): Die radiographische Prüfung verwendet Röntgen- oder Gammastrahlen, um innere Unregelmäßigkeiten wie Poren, Lunker, Einschlüsse und fehlende Fusion in der Schweißnaht zu erkennen. Sie ist besonders nützlich für die Prüfung von dickwandigen oder komplexen Schweißnähten.
- Ultraschallprüfung (UT): Die Ultraschallprüfung verwendet Schallwellen, um innere Defekte in der Schweißnaht wie Poren, Einschlüsse, Lunker und fehlende Fusion zu erkennen. Sie ermöglicht eine schnelle und genaue Bewertung der Schweißnahtqualität ohne Beschädigung des Werkstücks.
- Durchstrahlungsprüfung (PT): Die Durchstrahlungsprüfung verwendet fluoreszierende oder sichtbare Farbstoffe, um Oberflächendefekte wie Risse, Porosität und Lunker in der Schweißnaht sichtbar zu machen. Sie ist besonders nützlich für die Prüfung von Schweißnähten an schwer zugänglichen Stellen.
- Magnetpulverprüfung (MT): Die Magnetpulverprüfung verwendet feine magnetisierbare Partikel, um Oberflächendefekte wie Risse, Poren und Einschlüsse in der Schweißnaht zu erkennen. Sie ist besonders nützlich für die Prüfung von ferromagnetischen Werkstoffen.
Bedeutung der Schweißnahtprüfung:
- Qualitätssicherung: Die Schweißnahtprüfung gewährleistet die Qualität und Zuverlässigkeit der geschweißten Verbindungen, um sicherzustellen, dass sie den Anforderungen und Standards der Anwendung entsprechen.
- Sicherheit: Eine gründliche Prüfung der Schweißnähte hilft, potenzielle Defekte oder Unregelmäßigkeiten zu identifizieren, die zu Ausfällen, Unfällen oder Sicherheitsrisiken führen könnten.
- Kostenersparnis: Durch die frühzeitige Erkennung von Schweißfehlern können teure Reparaturen oder Nacharbeiten vermieden werden, was zu Kosteneinsparungen und einer verbesserten Betriebsleistung führt.
- Erfüllung von Vorschriften und Standards: Die Schweißnahtprüfung ist oft gesetzlich vorgeschrieben oder wird von Branchenstandards und -normen gefordert, um die Sicherheit und Qualität geschweißter Konstruktionen und Bauteile zu gewährleisten.
Die Schweißnahtprüfung ist ein unverzichtbarer Bestandteil des Schweißprozesses, der dazu beiträgt, hochwertige und zuverlässige Schweißverbindungen herzustellen und sicherzustellen, dass sie den erforderlichen Qualitätsstandards entsprechen. Eine sorgfältige Auswahl und Anwendung der geeigneten Prüfverfahren ist entscheidend für den Erfolg und die Leistungsfähigkeit geschweißter Konstruktionen und Bauteile.
Schweißnahtvorbereitung
Die Schweißnahtvorbereitung ist ein kritischer Schritt im Schweißprozess, der die Qualität und Integrität der Schweißverbindung maßgeblich beeinflusst. Sie umfasst verschiedene Maßnahmen und Techniken, um die zu verbindenden Werkstücke ordnungsgemäß vorzubereiten und eine optimale Schweißnahtbildung zu ermöglichen.
Schritte der Schweißnahtvorbereitung:
- Reinigung der Werkstücke: Die zu schweißenden Oberflächen müssen von Schmutz, Öl, Farbe, Rost und anderen Verunreinigungen gereinigt werden, um eine gute Haftung und Durchdringung der Schweißnaht zu gewährleisten. Dies kann durch Bürsten, Schleifen, Entfetten oder chemische Reinigung erfolgen.
- Entfernung von Schweißnahtvorbereitung: Vor dem Schweißen müssen die Werkstücke entsprechend der Schweißnahtvorbereitung geformt und vorbereitet werden. Dies kann das Schneiden, Abschrägen, Kantenbearbeitung oder andere Formgebungstechniken umfassen, um die gewünschte Schweißnahtgeometrie und -qualität zu erreichen.
- Ausrichtung der Werkstücke: Die Werkstücke müssen korrekt ausgerichtet und positioniert werden, um eine ordnungsgemäße Schweißnahtbildung sicherzustellen. Dies kann durch Verwendung von Schweißvorrichtungen, Fixierungen oder Klemmen erfolgen, um eine stabile und genaue Ausrichtung zu gewährleisten.
- Kontrolle der Spaltweite: Die Spaltweite zwischen den zu verbindenden Werkstücken muss entsprechend den Anforderungen des Schweißverfahrens und der Werkstückdicke kontrolliert werden. Eine angemessene Spaltweite ist wichtig für eine gleichmäßige Durchdringung und Fusion der Schweißnaht.
- Entfernung von Oxidschichten: Metallische Oberflächen können eine natürliche Oxidschicht bilden, die die Schweißnahtqualität beeinträchtigen kann. Diese Oxidschichten müssen vor dem Schweißen entfernt werden, entweder durch mechanische oder chemische Reinigung, um eine saubere Schweißnaht zu gewährleisten.
Bedeutung der Schweißnahtvorbereitung:
- Qualitätssicherung: Eine ordnungsgemäße Schweißnahtvorbereitung ist entscheidend für die Bildung hochwertiger und zuverlässiger Schweißverbindungen, die den Anforderungen und Standards der Anwendung entsprechen.
- Verbesserte Schweißqualität: Eine sorgfältige Vorbereitung der Werkstücke ermöglicht eine bessere Kontrolle über den Schweißprozess und führt zu einer gleichmäßigen Durchdringung, Fusion und Ausbildung der Schweißnaht.
- Reduzierung von Defekten: Durch eine gründliche Schweißnahtvorbereitung können potenzielle Fehlerquellen wie Unregelmäßigkeiten, Verunreinigungen oder ungleichmäßige Spaltweiten minimiert werden, was zu weniger Schweißfehlern und einer höheren Qualität der Schweißverbindung führt.
- Effizienzsteigerung: Eine effektive Schweißnahtvorbereitung trägt zur Verbesserung der Arbeitsabläufe, der Produktivität und der Prozesseffizienz bei, indem sie den Schweißprozess optimiert und die Notwendigkeit von Nacharbeiten oder Reparaturen reduziert.
Die Schweißnahtvorbereitung ist ein wesentlicher Schritt im Schweißprozess, der eine sorgfältige Planung, Vorbereitung und Durchführung erfordert, um qualitativ hochwertige und zuverlässige Schweißverbindungen zu gewährleisten. Eine gründliche Kenntnis der Schweißnahtvorbereitungstechniken und -praktiken ist entscheidend für den Erfolg und die Leistungsfähigkeit geschweißter Konstruktionen und Bauteile.
Schweißelektrode
Eine Schweißelektrode ist ein Verbrauchsmaterial, das im Lichtbogenschweißprozess verwendet wird, um den elektrischen Strom zwischen der Stromquelle und dem Werkstück zu übertragen und die notwendige Wärme zum Schmelzen der Werkstoffe zu erzeugen. Schweißelektroden sind in verschiedenen Formen, Größen und Materialzusammensetzungen erhältlich und werden entsprechend den Anforderungen der Schweißanwendung ausgewählt.
Typen von Schweißelektroden:
- Stabelektroden: Stabelektroden sind massiv und bestehen aus einem Kernmaterial, das während des Schweißprozesses schmilzt und als Zusatzmaterial für die Schweißnaht dient. Sie werden hauptsächlich im Lichtbogenschweißen mit Elektroden (SMAW) verwendet und sind in verschiedenen Legierungen und Durchmessern erhältlich, um unterschiedliche Materialien und Schweißanforderungen zu erfüllen.
- Drahtelektroden: Drahtelektroden sind dünnere und flexiblere Drähte, die kontinuierlich von einer Drahtvorschubeinheit zugeführt werden, um den Lichtbogen im MIG/MAG-Schweißverfahren zu unterstützen. Sie können als Massivdrahtelektroden oder Fülldrahtelektroden mit eingebettetem Flussmittel erhältlich sein, je nach den Anforderungen der Schweißanwendung und des Werkstückmaterials.
- Wolframelektroden: Wolframelektroden werden im Wolfram-Inertgas (TIG)-Schweißverfahren verwendet und bestehen aus reinem Wolfram oder einer Wolframlegierung. Sie sind nicht verbrauchbar und dienen dazu, den Lichtbogen zu erzeugen und zu stabilisieren, während zusätzliches Schweißmaterial manuell zugeführt wird, falls erforderlich.
Eigenschaften von Schweißelektroden:
- Materialzusammensetzung: Die Auswahl des richtigen Elektrodenmaterials hängt von den zu schweißenden Werkstoffen, der Schweißverfahren und den Anwendungsanforderungen ab. Verschiedene Elektrodenmaterialien bieten unterschiedliche mechanische Eigenschaften, Schweißeigenschaften und Widerstandsfähigkeit gegenüber Umgebungseinflüssen.
- Durchmesser und Form: Der Durchmesser und die Form der Elektrode beeinflussen die Größe und Form der Schweißnaht sowie die Stabilität des Lichtbogens und die Schweißgeschwindigkeit. Verschiedene Elektrodenformen wie Zylinder, Kegel oder abgeflachte Spitzen können für spezifische Anwendungen verwendet werden.
- Flussmittel: Bei Fülldrahtelektroden und Stabelektroden mit eingebettetem Flussmittel dient das Flussmittel dazu, die Schweißzone vor Verunreinigungen und Oxidation zu schützen, Schweißspritzer zu reduzieren und die Eigenschaften der Schweißnaht zu verbessern.
Anwendungen von Schweißelektroden:
- Stabelektroden werden häufig in der Bauindustrie, im Schiffbau, im Brückenbau und in anderen Anwendungen eingesetzt, bei denen eine hohe Schweißnahtqualität und Festigkeit erforderlich sind.
- Drahtelektroden werden im MIG/MAG-Schweißverfahren für eine Vielzahl von Anwendungen verwendet, darunter die Automobilindustrie, die Fertigung von Metallkonstruktionen, die Schiffsindustrie und andere industrielle Anwendungen.
- Wolframelektroden werden im TIG-Schweißverfahren für hochpräzise Anwendungen eingesetzt, bei denen eine saubere und kontrollierte Schweißnahtbildung erforderlich ist, wie in der Luft- und Raumfahrtindustrie, der Herstellung von Edelstahlkomponenten und anderen spezialisierten Anwendungen.
Die Auswahl der richtigen Schweißelektrode ist entscheidend für den Erfolg und die Qualität des Schweißprozesses. Eine sorgfältige Bewertung der Anwendungsanforderungen, der Werkstoffeigenschaften und der Schweißverfahren ist erforderlich, um die geeignete Elektrode auszuwählen und eine hochwertige Schweißverbindung zu gewährleisten.
Schweißdraht
Schweißdraht ist ein Verbrauchsmaterial, das im Lichtbogenschweißprozess verwendet wird, um zusätzliches Schweißmaterial in die Schweißnaht einzuführen und die erforderliche Metallverbindung zwischen den zu schweißenden Werkstücken herzustellen. Schweißdrähte sind in verschiedenen Formen, Größen und Materialzusammensetzungen erhältlich und werden je nach den Anforderungen der Schweißanwendung und den Werkstoffen der Werkstücke ausgewählt.
Typen von Schweißdrähten:
- Massivdraht: Massivdrahtelektroden bestehen aus massivem Drahtmaterial und werden kontinuierlich von einer Drahtvorschubeinheit zum Schmelzbad zugeführt, um zusätzliches Schweißmaterial bereitzustellen. Sie sind in verschiedenen Materialien wie Kohlenstoffstahl, Edelstahl, Aluminium und anderen Legierungen erhältlich und werden hauptsächlich im MIG/MAG-Schweißverfahren eingesetzt.
- Fülldraht: Fülldrahtelektroden bestehen aus einem Drahtkern, der mit einem eingebetteten Flussmittel gefüllt ist. Während des Schweißprozesses schmilzt der Drahtkern und das Flussmittel bildet eine Schutzgasatmosphäre um den Lichtbogen herum, um die Schweißzone zu stabilisieren und zu schützen. Fülldrahtelektroden bieten verbesserte Schweißergebnisse in Bezug auf Schweißgeschwindigkeit, Durchdringung und Schweißnahtqualität und werden häufig im MIG/MAG-Schweißverfahren eingesetzt, insbesondere in anspruchsvollen Anwendungen oder bei ungünstigen Umgebungsbedingungen.
Eigenschaften von Schweißdrähten:
- Materialzusammensetzung: Die Auswahl des richtigen Drahtmaterials hängt von den zu schweißenden Werkstoffen, den Schweißverfahren und den Anforderungen der Schweißanwendung ab. Verschiedene Drahtmaterialien bieten unterschiedliche mechanische Eigenschaften, Korrosionsbeständigkeit und Schweißeigenschaften.
- Durchmesser und Form: Der Durchmesser und die Form des Schweißdrahts beeinflussen die Größe und Form der Schweißnaht sowie die Schweißgeschwindigkeit und -penetration. Verschiedene Drahtdurchmesser und -formen können je nach den spezifischen Anforderungen der Schweißanwendung und der Werkstückdicke ausgewählt werden.
- Flussmittel: Bei Fülldrahtelektroden dient das eingebettete Flussmittel dazu, die Schweißzone vor Verunreinigungen und Oxidation zu schützen, Schweißspritzer zu reduzieren und die Eigenschaften der Schweißnaht zu verbessern. Die Auswahl des Flussmittels kann je nach den Anforderungen der Schweißanwendung und den Werkstoffen variieren.
Anwendungen von Schweißdrähten:
- Schweißdrähte werden in einer Vielzahl von Branchen und Anwendungen eingesetzt, darunter die Automobilindustrie, die Schiffbauindustrie, die Bauindustrie, die Herstellung von Metallkonstruktionen, die Fertigung von Behältern und Tanks, die Luft- und Raumfahrtindustrie und andere industrielle Anwendungen.
- Sie werden für das Schweißen von unterschiedlichen Werkstoffen wie Kohlenstoffstahl, Edelstahl, Aluminium, Kupfer, Nickellegierungen und anderen Werkstoffen eingesetzt, um eine Vielzahl von Schweißverbindungen herzustellen, einschließlich Stumpf-, Kehlnaht-, Wurzellagen- und Überlappungsnähten.
Die Auswahl des richtigen Schweißdrahts ist entscheidend für den Erfolg und die Qualität des Schweißprozesses. Eine sorgfältige Bewertung der Anwendungsanforderungen, der Werkstoffeigenschaften und der Schweißverfahren ist erforderlich, um den geeigneten Draht auszuwählen und hochwertige Schweißverbindungen zu gewährleisten.
Schutzgas
Schutzgas ist ein wesentlicher Bestandteil des Lichtbogenschweißprozesses, der dazu dient, die Schweißzone vor atmosphärischen Einflüssen zu schützen und die Bildung von Oxiden, Nitriden und anderen Verunreinigungen während des Schweißens zu verhindern. Es wird verwendet, um eine inerten oder reaktive Atmosphäre um den Lichtbogen herum zu erzeugen, je nach den Anforderungen der Schweißanwendung und den zu schweißenden Werkstoffen.
Typen von Schutzgasen:
- Inertgase: Inertgase sind chemisch stabile Gase, die keine chemischen Reaktionen mit den Werkstoffen in der Schweißzone eingehen. Sie dienen hauptsächlich dazu, die Schweißzone vor atmosphärischen Einflüssen zu isolieren und die Oxidation der Schweißnaht zu verhindern. Zu den häufig verwendeten Inertgasen gehören Argon und Helium.
- Aktivgase: Aktivgase sind reaktive Gase, die chemische Reaktionen mit den Werkstoffen in der Schweißzone eingehen, um die Schweißeigenschaften zu verbessern oder spezifische Schweißeffekte zu erzielen. Sie können zur Stabilisierung des Lichtbogens, zur Verbesserung der Schweißpenetration und zur Anpassung der Schweißeigenschaften verwendet werden. Zu den häufig verwendeten Aktivgasen gehören Kohlendioxid (CO2) und Sauerstoff (O2).
Eigenschaften von Schutzgasen:
- Chemische Stabilität: Inertgase sind chemisch stabil und reagieren nicht mit den Werkstoffen in der Schweißzone, während Aktivgase chemisch reaktiv sind und spezifische Schweißeffekte erzeugen können.
- Wärmeleitfähigkeit: Die Wärmeleitfähigkeit des Schutzgases beeinflusst die Temperaturverteilung in der Schweißzone und kann die Schweißpenetration, die Schweißgeschwindigkeit und die Schweißqualität beeinflussen.
- Schweißeigenschaften: Die Auswahl des geeigneten Schutzgases hängt von den Anforderungen der Schweißanwendung, den zu schweißenden Werkstoffen und den gewünschten Schweißeigenschaften wie Durchdringung, Spaltüberbrückung, Spritzerbildung und Oberflächengüte ab.
Anwendungen von Schutzgasen:
- Inertgase wie Argon werden häufig im WIG (Wolfram-Inertgas)-Schweißverfahren verwendet, um eine saubere und stabile Schweißatmosphäre zu erzeugen, die Oxidation und Verunreinigungen in der Schweißzone verhindert.
- Mischgase wie Argon mit einem gewissen Anteil an CO2 werden häufig im MIG/MAG (Metall-Inertgas/Metall-Aktivgas)-Schweißverfahren verwendet, um die Schweißpenetration zu verbessern, die Spritzerbildung zu reduzieren und die Schweißgeschwindigkeit zu erhöhen.
- Reine Aktivgase wie CO2 werden häufig in industriellen Anwendungen eingesetzt, um eine hohe Schweißgeschwindigkeit und eine tiefe Schweißpenetration zu erzielen, insbesondere bei der Schweißung von Kohlenstoffstählen.
Die Auswahl des geeigneten Schutzgases ist entscheidend für den Erfolg und die Qualität des Schweißprozesses. Eine sorgfältige Bewertung der Anwendungsanforderungen, der Werkstoffeigenschaften und der Schutzgascharakteristika ist erforderlich, um das optimale Schutzgas auszuwählen und hochwertige Schweißverbindungen zu gewährleisten.
Lichtbogenschweißen
Lichtbogenschweißen ist ein weit verbreitetes Schweißverfahren, das auf der Erzeugung eines elektrischen Lichtbogens zwischen einer Elektrode und den zu verbindenden Werkstücken basiert. Der Lichtbogen erzeugt hohe Temperaturen, die die Werkstoffe schmelzen lassen, und ermöglicht die Bildung einer dauerhaften Schweißverbindung. Dieses Verfahren wird in verschiedenen Branchen und Anwendungen eingesetzt, um eine Vielzahl von Werkstoffen miteinander zu verbinden.
Schritte des Lichtbogenschweißens:
- Vorbereitung der Werkstücke: Die zu schweißenden Werkstücke werden entsprechend den Anforderungen der Schweißnahtvorbereitung vorbereitet, einschließlich Reinigung, Ausrichtung, Entfernung von Verunreinigungen und Einstellung der Spaltweite.
- Auswahl der Elektrode und des Schutzgases: Die passende Elektrode und das geeignete Schutzgas werden entsprechend den Werkstoffen der Werkstücke, den Anforderungen der Schweißanwendung und den Schweißverfahren ausgewählt.
- Einrichtung der Schweißausrüstung: Die Schweißausrüstung, einschließlich des Schweißgeräts, der Elektrodenhalterung, des Schweißstroms und der Gasflaschen, wird entsprechend den Anforderungen der Schweißanwendung und den Herstelleranweisungen eingerichtet.
- Zündung des Lichtbogens: Der Lichtbogen wird durch das Zünden der Elektrode gegen das Werkstück erzeugt, wobei ein elektrischer Lichtbogen entsteht, der hohe Temperaturen erzeugt und die Werkstoffe schmilzt.
- Durchführung des Schweißprozesses: Der Schweißer führt die Elektrode entlang der Schweißnaht, wobei Schweißmaterial von der Elektrode abgeschmolzen wird und in die Schweißzone eindringt, um eine Schweißverbindung zu bilden.
- Beendigung des Schweißens: Nach Abschluss des Schweißprozesses wird der Lichtbogen gelöscht, und die Schweißnaht wird auf Defekte oder Unregelmäßigkeiten überprüft. Gegebenenfalls können Nacharbeiten oder weitere Schritte erforderlich sein, um die gewünschte Schweißqualität zu erreichen.
Vorteile des Lichtbogenschweißens:
- Vielseitigkeit: Lichtbogenschweißen kann für eine Vielzahl von Werkstoffen und Schweißanwendungen eingesetzt werden, einschließlich Stahl, Edelstahl, Aluminium, Kupfer und anderen Legierungen.
- Leistungsfähigkeit: Das Lichtbogenschweißen ermöglicht hohe Schweißgeschwindigkeiten, gute Schweißpenetration und eine hohe Schweißqualität, was zu dauerhaften und zuverlässigen Schweißverbindungen führt.
- Flexibilität: Es stehen verschiedene Schweißverfahren zur Verfügung, darunter das Lichtbogenschweißen mit Elektroden (SMAW), das Metall-Inertgas/Metall-Aktivgas-Schweißen (MIG/MAG) und das Wolfram-Inertgas-Schweißen (TIG), die je nach den Anforderungen der Schweißanwendung und den Werkstoffen ausgewählt werden können.
- Wirtschaftlichkeit: Lichtbogenschweißen ist im Vergleich zu anderen Schweißverfahren kostengünstig und erfordert weniger komplexe Ausrüstung und Schulung, was zu niedrigeren Betriebskosten und einer höheren Produktivität führt.
Das Lichtbogenschweißen ist ein vielseitiges, leistungsfähiges und wirtschaftliches Schweißverfahren, das in einer Vielzahl von Branchen und Anwendungen eingesetzt wird, um hochwertige und zuverlässige Schweißverbindungen herzustellen. Eine sorgfältige Planung, Vorbereitung und Durchführung des Schweißprozesses ist entscheidend für den Erfolg und die Qualität der geschweißten Konstruktionen und Bauteile.
Wurzelschweißen
Das Wurzelschweißen ist ein wichtiger Schritt im Schweißprozess, der die Basis für eine stabile und zuverlässige Schweißverbindung bildet. Es bezieht sich auf das Schweißen der ersten Schicht einer Schweißnaht, die die Wurzel oder die Unterseite der Naht bildet, wenn die Werkstücke in einer V-Naht-, U-Naht- oder anderen geeigneten Konfiguration angeordnet sind. Das Wurzelschweißen erfordert besondere Aufmerksamkeit, da es die Integrität und Festigkeit der gesamten Schweißnaht beeinflusst.
Schritte des Wurzelschweißens:
- Vorbereitung der Werkstücke: Die zu verbindenden Werkstücke werden entsprechend der vorgesehenen Schweißnahtvorbereitung vorbereitet, einschließlich Reinigung, Ausrichtung und Einstellung der Spaltweite, um eine optimale Schweißnahtbildung zu ermöglichen.
- Auswahl der Schweißparameter: Die geeigneten Schweißparameter wie Schweißstrom, Schweißspannung, Elektrodenart und Schutzgas werden entsprechend den Werkstoffen der Werkstücke, der Schweißanwendung und den Anforderungen des Schweißverfahrens festgelegt.
- Positionierung der Elektrode: Die Elektrode wird in die Nähe der Wurzel der Schweißnaht positioniert, wobei darauf geachtet wird, dass sie einen angemessenen Winkel und Abstand zum Werkstück hat, um eine gute Durchdringung und Fusion zu gewährleisten.
- Zündung des Lichtbogens: Der Lichtbogen wird durch das Zünden der Elektrode gegen das Werkstück erzeugt, wobei eine ausreichende Hitze erzeugt wird, um die Wurzel der Schweißnaht zu schmelzen und eine Schweißverbindung zu bilden.
- Durchführung des Wurzelschweißens: Der Schweißer führt die Elektrode entlang der Wurzel der Schweißnaht, wobei Schweißmaterial von der Elektrode abgeschmolzen wird und in die Schweißzone eindringt, um die Wurzel zu füllen und eine vollständige Schweißverbindung zu bilden.
- Überprüfung der Wurzelschweißung: Nach Abschluss des Wurzelschweißens wird die Schweißnaht auf Defekte, Unregelmäßigkeiten oder unzureichende Fusion überprüft. Gegebenenfalls können Nacharbeiten oder weitere Schritte erforderlich sein, um die gewünschte Schweißqualität zu erreichen.
Bedeutung des Wurzelschweißens:
- Stabilität der Schweißnaht: Das Wurzelschweißen bildet die Basis für die gesamte Schweißnaht und beeinflusst maßgeblich deren Integrität, Festigkeit und Zuverlässigkeit.
- Durchdringung und Fusion: Eine ordnungsgemäße Durchdringung und Fusion der Wurzel der Schweißnaht ist entscheidend für eine dauerhafte Verbindung und eine gute mechanische Leistungsfähigkeit der geschweißten Konstruktion.
- Vermeidung von Defekten: Durch sorgfältiges Wurzelschweißen können potenzielle Defekte wie unvollständige Fusion, Lunker oder Porosität in der Schweißnaht vermieden werden, was zu einer verbesserten Schweißqualität und -zuverlässigkeit führt.
Das Wurzelschweißen ist ein kritischer Schritt im Schweißprozess, der eine sorgfältige Planung, Vorbereitung und Durchführung erfordert, um hochwertige und zuverlässige Schweißverbindungen herzustellen. Eine gründliche Kenntnis der Schweißverfahren, der Werkstoffeigenschaften und der Schweißnahtgeometrie ist entscheidend für den Erfolg und die Leistungsfähigkeit geschweißter Konstruktionen und Bauteile.
Schweißnahtprüfung
Die Schweißnahtprüfung ist ein wesentlicher Schritt im Schweißprozess, der dazu dient, die Qualität, Integrität und Zuverlässigkeit der geschweißten Verbindung zu überprüfen und sicherzustellen. Verschiedene Prüfmethoden werden angewendet, um Defekte, Unregelmäßigkeiten oder Anomalien in der Schweißnaht zu identifizieren und gegebenenfalls Korrekturmaßnahmen zu ergreifen, um die Schweißqualität zu verbessern.
Typen von Schweißnahtprüfungen:
- Sichtprüfung: Die Sichtprüfung ist die einfachste und häufigste Methode zur Überprüfung der Schweißnaht, bei der die Schweißnaht visuell auf äußere Defekte wie Risse, Lunker, Porosität, Ungleichmäßigkeiten oder unzureichende Fusion überprüft wird.
- Durchstrahlungsprüfung (RT): Bei der Durchstrahlungsprüfung wird die Schweißnaht mit Röntgenstrahlen oder Gammastrahlen durchleuchtet, um interne Defekte wie Einschlüsse, Lunker, Risse oder Porosität zu erkennen. Diese Methode ist besonders wirksam für dickere Werkstoffe und komplexe Schweißkonfigurationen.
- Ultraschallprüfung (UT): Die Ultraschallprüfung verwendet Ultraschallwellen, die durch die Schweißnaht gesendet und reflektiert werden, um interne Defekte wie Einschlüsse, Lunker, Risse oder unzureichende Fusion zu erkennen. Diese Methode ist besonders geeignet für dünnere Werkstoffe und Schweißnähte mit geringer Zugänglichkeit.
- Magnetpulverprüfung (MT): Bei der Magnetpulverprüfung wird ein magnetisierbares Pulver auf die Oberfläche der Schweißnaht aufgetragen, das sich bei Vorhandensein von Rissen oder Ungleichmäßigkeiten in der Schweißnaht ansammelt und sichtbar macht.
- Eindringprüfung (PT): Bei der Eindringprüfung wird ein Farbstoff- oder Fluoreszenzmittel auf die Oberfläche der Schweißnaht aufgetragen, das in vorhandene Risse oder Porositäten eindringt und sichtbar macht, wenn es mit einem Entwickler behandelt wird.
Bedeutung der Schweißnahtprüfung:
- Qualitätssicherung: Die Schweißnahtprüfung ist entscheidend für die Gewährleistung einer hohen Schweißqualität und Zuverlässigkeit der geschweißten Verbindung, indem sie potenzielle Defekte oder Unregelmäßigkeiten identifiziert und korrigiert.
- Konformität mit Standards: Die Schweißnahtprüfung stellt sicher, dass die geschweißte Verbindung den einschlägigen Standards, Vorschriften und Spezifikationen entspricht, um die Sicherheit und Leistungsfähigkeit der Konstruktion oder des Bauteils zu gewährleisten.
- Fehlererkennung und -behebung: Durch die frühzeitige Erkennung von Schweißfehlern oder Unregelmäßigkeiten können geeignete Korrekturmaßnahmen ergriffen werden, um die Schweißqualität zu verbessern und potenzielle Ausfälle oder Schäden zu vermeiden.
Die Schweißnahtprüfung ist ein unverzichtbarer Bestandteil des Schweißprozesses, der eine gründliche Bewertung der geschweißten Verbindung ermöglicht und sicherstellt, dass sie den erforderlichen Standards und Qualitätsanforderungen entspricht. Eine sorgfältige Auswahl und Anwendung der geeigneten Prüfmethoden ist entscheidend für den Erfolg und die Leistungsfähigkeit geschweißter Konstruktionen und Bauteile.
Schweißparameter
Die Schweißparameter sind die variablen Einstellungen und Parameter, die während des Schweißprozesses eingestellt werden, um die Schweißnahtqualität, Schweißgeschwindigkeit und Schweißpenetration zu kontrollieren. Diese Parameter variieren je nach Schweißverfahren, Werkstoffen der Werkstücke, Schweißposition, Werkstückdicke und anderen Anwendungsanforderungen. Die Auswahl und Optimierung der richtigen Schweißparameter sind entscheidend für den Erfolg und die Qualität des Schweißprozesses.
Typische Schweißparameter:
- Schweißstrom: Der Schweißstrom ist die elektrische Stromstärke, die durch die Elektrode fließt und den Lichtbogen erzeugt. Er beeinflusst die Wärmeentwicklung, Schweißpenetration und Schweißgeschwindigkeit. Ein höherer Schweißstrom führt zu einer höheren Wärmeentwicklung und tieferen Schweißpenetration.
- Schweißspannung: Die Schweißspannung ist die elektrische Spannung zwischen der Elektrode und dem Werkstück. Sie beeinflusst die Stabilität des Lichtbogens und die Durchdringung der Schweißnaht. Eine höhere Schweißspannung kann zu einem stabileren Lichtbogen und einer besseren Durchdringung führen.
- Schweißgeschwindigkeit: Die Schweißgeschwindigkeit ist die Geschwindigkeit, mit der die Elektrode entlang der Schweißnaht geführt wird. Sie beeinflusst die Breite der Schweißnaht und die Wärmeeinflusszone. Eine höhere Schweißgeschwindigkeit kann zu einer schmaleren Schweißnaht und geringeren Verformungen führen.
- Schutzgasflussrate: Die Schutzgasflussrate ist die Rate, mit der das Schutzgas (z. B. Argon oder CO2) durch die Schweißpistole oder den Schweißbrenner fließt. Sie beeinflusst die Schutzgasabdeckung und die Stabilität des Lichtbogens. Eine angemessene Schutzgasflussrate ist entscheidend, um eine saubere Schweißnaht zu gewährleisten und atmosphärische Verunreinigungen zu verhindern.
- Elektrodenart und -durchmesser: Die Auswahl der Elektrodenart (z. B. massiv, Fülldraht, Wolframelektrode) und des Elektrodendurchmessers beeinflusst die Schweißnahtform, Schweißpenetration und Schweißgeschwindigkeit. Verschiedene Elektrodenarten und -durchmesser werden je nach den Anforderungen der Schweißanwendung und den Werkstoffen ausgewählt.
Einfluss der Schweißparameter auf die Schweißnaht:
- Schweißnahtqualität: Die richtigen Schweißparameter tragen zur Bildung einer hochwertigen Schweißnaht bei, indem sie die Schweißpenetration, Schweißform und Schutzgasabdeckung optimieren und potenzielle Defekte oder Unregelmäßigkeiten reduzieren.
- Schweißnahtfestigkeit: Die optimierten Schweißparameter gewährleisten eine ausreichende Schweißpenetration und Fusion, um eine dauerhafte und zuverlässige Schweißverbindung mit hoher Festigkeit und Belastbarkeit zu gewährleisten.
- Schweißnahtaussehen: Die Schweißparameter beeinflussen auch das Erscheinungsbild der Schweißnaht, einschließlich der Schweißnahtform, Schweißspritzerbildung und Oberflächengüte, was ästhetische Anforderungen erfüllen kann.
Die Auswahl und Optimierung der richtigen Schweißparameter erfordert Erfahrung, Fachkenntnisse und eine gründliche Bewertung der Schweißanforderungen und Werkstoffeigenschaften. Durch sorgfältige Kontrolle und Anpassung der Schweißparameter können hochwertige und zuverlässige Schweißverbindungen hergestellt werden.
Schweißzusatzmaterial
Das Schweißzusatzmaterial ist ein wesentlicher Bestandteil des Schweißprozesses, der dazu dient, zusätzliches Schweißmaterial in die Schweißnaht einzuführen und die erforderliche Metallverbindung zwischen den zu schweißenden Werkstücken herzustellen. Es wird verwendet, um die Schweißnaht zu füllen, die Schweißpenetration zu optimieren und die mechanischen Eigenschaften der Schweißverbindung zu verbessern.
Typen von Schweißzusatzmaterialien:
- Massivdraht: Massivdrahtelektroden bestehen aus massivem Drahtmaterial und werden kontinuierlich von einer Drahtvorschubeinheit zum Schmelzbad zugeführt, um zusätzliches Schweißmaterial bereitzustellen. Sie sind in verschiedenen Materialien wie Kohlenstoffstahl, Edelstahl, Aluminium und anderen Legierungen erhältlich und werden hauptsächlich im MIG/MAG-Schweißverfahren eingesetzt.
- Fülldraht: Fülldrahtelektroden bestehen aus einem Drahtkern, der mit einem eingebetteten Flussmittel gefüllt ist. Während des Schweißprozesses schmilzt der Drahtkern, und das Flussmittel bildet eine Schutzgasatmosphäre um den Lichtbogen herum, um die Schweißzone zu stabilisieren und zu schützen. Fülldrahtelektroden bieten verbesserte Schweißergebnisse in Bezug auf Schweißgeschwindigkeit, Durchdringung und Schweißnahtqualität und werden häufig im MIG/MAG-Schweißverfahren eingesetzt, insbesondere in anspruchsvollen Anwendungen oder bei ungünstigen Umgebungsbedingungen.
Eigenschaften von Schweißzusatzmaterialien:
- Materialzusammensetzung: Die Auswahl des richtigen Schweißzusatzmaterials hängt von den zu schweißenden Werkstoffen, den Schweißverfahren und den Anforderungen der Schweißanwendung ab. Verschiedene Schweißzusatzmaterialien bieten unterschiedliche mechanische Eigenschaften, Korrosionsbeständigkeit und Schweißeigenschaften.
- Durchmesser und Form: Der Durchmesser und die Form des Schweißzusatzmaterials beeinflussen die Größe und Form der Schweißnaht sowie die Schweißgeschwindigkeit und -penetration. Verschiedene Durchmesser und Formen können je nach den spezifischen Anforderungen der Schweißanwendung und der Werkstückdicke ausgewählt werden.
- Flussmittel (bei Fülldrähten): Das eingebettete Flussmittel in Fülldrahtelektroden dient dazu, die Schweißzone vor Verunreinigungen und Oxidation zu schützen, Schweißspritzer zu reduzieren und die Eigenschaften der Schweißnaht zu verbessern. Die Auswahl des Flussmittels kann je nach den Anforderungen der Schweißanwendung und den Werkstoffen variieren.
Anwendungen von Schweißzusatzmaterialien:
- Schweißzusatzmaterialien werden in einer Vielzahl von Branchen und Anwendungen eingesetzt, darunter die Automobilindustrie, die Schiffbauindustrie, die Bauindustrie, die Herstellung von Metallkonstruktionen, die Fertigung von Behältern und Tanks, die Luft- und Raumfahrtindustrie und andere industrielle Anwendungen.
- Sie werden für das Schweißen von unterschiedlichen Werkstoffen wie Kohlenstoffstahl, Edelstahl, Aluminium, Kupfer, Nickellegierungen und anderen Werkstoffen eingesetzt, um eine Vielzahl von Schweißverbindungen herzustellen, einschließlich Stumpf-, Kehlnaht-, Wurzellagen- und Überlappungsnähten.
Die Auswahl des richtigen Schweißzusatzmaterials ist entscheidend für den Erfolg und die Qualität des Schweißprozesses. Eine sorgfältige Bewertung der Anwendungsanforderungen, der Werkstoffeigenschaften und der Schweißverfahren ist erforderlich, um den geeigneten Schweißzusatz auszuwählen und hochwertige Schweißverbindungen zu gewährleisten.
Schweißnahtvorbereitung
Die Schweißnahtvorbereitung ist ein entscheidender Schritt im Schweißprozess, der die Qualität, Integrität und Zuverlässigkeit der Schweißverbindung maßgeblich beeinflusst. Eine ordnungsgemäße Vorbereitung der Schweißnaht trägt dazu bei, potenzielle Defekte, Unregelmäßigkeiten und Probleme während des Schweißens zu minimieren und eine hochwertige Schweißnaht zu gewährleisten.
Schritte der Schweißnahtvorbereitung:
- Reinigung der Werkstücke: Die zu schweißenden Werkstücke müssen gründlich gereinigt werden, um Oberflächenverunreinigungen wie Öl, Fett, Rost, Farbe oder Beschichtungen zu entfernen. Eine saubere Oberfläche ermöglicht eine bessere Schweißnahtqualität und reduziert das Risiko von Defekten.
- Ausrichtung der Werkstücke: Die Werkstücke werden entsprechend der gewünschten Schweißposition und -konfiguration ausgerichtet, um eine korrekte Schweißnahtbildung zu ermöglichen. Die richtige Ausrichtung ist wichtig, um sicherzustellen, dass die Schweißnaht die erforderlichen mechanischen Anforderungen erfüllt.
- Einstellung der Spaltweite: Die Spaltweite zwischen den zu schweißenden Werkstücken muss entsprechend den Anforderungen der Schweißanwendung und den Werkstoffen eingestellt werden. Eine angemessene Spaltweite ermöglicht eine gleichmäßige Schweißpenetration und Fusion und verhindert unerwünschte Verformungen.
- Vorbereitung der Schweißnahtgeometrie: Je nach Schweißverfahren und Anwendungsanforderungen kann die Schweißnahtgeometrie angepasst werden, um eine optimale Schweißnahtqualität zu gewährleisten. Dies kann das Schneiden oder Formen der Werkstücke, das Anfasen der Kanten oder das Vorbereiten von Wurzellagen umfassen.
- Entfernung von Verunreinigungen: Vor dem Schweißen müssen alle Verunreinigungen, Rückstände oder Fremdkörper in der Schweißnaht oder auf den Werkstückoberflächen sorgfältig entfernt werden, um eine saubere und zuverlässige Schweißverbindung zu gewährleisten.
Bedeutung der Schweißnahtvorbereitung:
- Qualitätssicherung: Eine ordnungsgemäße Schweißnahtvorbereitung ist entscheidend für die Gewährleistung einer hohen Schweißnahtqualität und Zuverlässigkeit der geschweißten Verbindung, indem potenzielle Defekte, Unregelmäßigkeiten und Verunreinigungen minimiert werden.
- Schweißnahtintegrität: Die richtige Vorbereitung der Schweißnaht trägt zur Verbesserung der Schweißnahtintegrität bei, indem sie eine gleichmäßige Schweißpenetration und Fusion ermöglicht und das Risiko von Schweißfehlern oder -defekten verringert.
- Effizienz des Schweißprozesses: Eine effektive Schweißnahtvorbereitung erleichtert den Schweißprozess und ermöglicht eine höhere Produktivität, eine schnellere Schweißgeschwindigkeit und eine geringere Nacharbeit.
Eine sorgfältige und gründliche Schweißnahtvorbereitung ist unerlässlich für den Erfolg und die Qualität des Schweißprozesses. Durch die Beachtung der oben genannten Schritte können hochwertige und zuverlässige Schweißverbindungen hergestellt werden, die den Anforderungen und Standards der jeweiligen Anwendung entsprechen.
Schweißpositionen
Die Schweißposition bezieht sich auf die Position, in der das Schweißen durchgeführt wird, und hat einen direkten Einfluss auf die Schweißnahtgeometrie, Schweißqualität und Schweißeffizienz. Verschiedene Schweißpositionen werden je nach den Anforderungen der Schweißanwendung, der Form der Werkstücke und der Zugänglichkeit des Schweißbereichs verwendet.
Häufig verwendete Schweißpositionen:
- Flachposition (1G/1F): Bei der Flachposition befinden sich die zu schweißenden Werkstücke horizontal, und die Schweißnaht wird von oben nach unten in einer horizontalen Ebene geschweißt. Diese Position bietet eine gute Zugänglichkeit und einfache Schweißbedingungen und wird häufig für flache oder horizontal liegende Werkstücke verwendet.
- Horizontalposition (2G/2F): In der Horizontalposition werden die zu schweißenden Werkstücke in einer vertikalen Ebene angeordnet, und die Schweißnaht wird seitlich geschweißt. Diese Position erfordert eine spezielle Technik, um das Schweißbad zu kontrollieren und eine gleichmäßige Schweißnaht zu erzeugen. Sie wird häufig für horizontale oder geneigte Werkstücke verwendet.
- Vertikalposition (3G/3F): In der Vertikalposition befinden sich die zu schweißenden Werkstücke vertikal, und die Schweißnaht wird von unten nach oben oder von oben nach unten geschweißt. Diese Position erfordert eine präzise Steuerung des Schweißbads und der Schweißposition, um eine gleichmäßige Schweißnaht zu erzeugen. Sie wird häufig für vertikale oder geneigte Werkstücke verwendet.
- Überkopfposition (4G/4F): In der Überkopfposition befinden sich die zu schweißenden Werkstücke über dem Schweißer, und die Schweißnaht wird von unten nach oben geschweißt. Diese Position erfordert eine besondere Sorgfalt, um das Schweißbad zu kontrollieren und ein Überlaufen oder Herunterfallen des Schweißmaterials zu verhindern. Sie wird häufig für Deckenschweißungen oder Überkopfschweißungen verwendet.
Weitere Schweißpositionen:
- Stumpfposition: Die Stumpfposition bezieht sich auf das Schweißen von Werkstücken, die in einer flachen oder horizontalen Position miteinander verbunden sind, wobei die Schweißnaht entlang der Verbindungsfläche verläuft.
- Kehlnahtposition: Bei der Kehlnahtposition befinden sich die zu schweißenden Werkstücke in einer vertikalen Ebene, und die Schweißnaht wird in einem V- oder U-förmigen Spalt zwischen den Werkstücken geschweißt.
- Rohrschweißposition: Die Rohrschweißposition bezieht sich auf das Schweißen von Rohren oder zylindrischen Werkstücken, die in einer horizontalen, vertikalen oder überkopften Position angeordnet sind, wobei die Schweißnaht entlang der Längsachse des Rohres verläuft.
Die Auswahl der geeigneten Schweißposition hängt von verschiedenen Faktoren ab, darunter die Form und Ausrichtung der Werkstücke, die Zugänglichkeit des Schweißbereichs, die Anforderungen der Schweißanwendung und die Fähigkeiten und Erfahrungen des Schweißers. Durch die Auswahl der richtigen Schweißposition können hochwertige und zuverlässige Schweißverbindungen hergestellt werden, die den spezifischen Anforderungen und Standards entsprechen.
Schutzgas
Schutzgas ist ein wesentlicher Bestandteil vieler Schweißprozesse, insbesondere bei Lichtbogenschweißverfahren wie MIG/MAG-Schweißen (Metall-Inertgas/Metall-Aktivgas) und WIG-Schweißen (Wolfram-Inertgas). Es wird verwendet, um das Schmelzbad und die Lichtbogenumgebung vor atmosphärischen Verunreinigungen wie Sauerstoff, Stickstoff und Wasserstoff zu schützen, was zur Bildung von unerwünschten Oxiden, Nitriden oder Porosität in der Schweißnaht führen kann.
Typen von Schutzgasen:
- Inertgase: Inertgase wie Argon und Helium werden häufig als Schutzgas beim WIG-Schweißen und bei einigen Anwendungen des MIG/MAG-Schweißens verwendet. Sie sind chemisch inert und reagieren nicht mit den geschmolzenen Werkstoffen, bieten jedoch eine wirksame Schutzgasabdeckung und Stabilisierung des Lichtbogens.
- Aktivgase: Aktivgase wie CO2 (Kohlendioxid) werden häufig als Schutzgas beim MIG/MAG-Schweißen verwendet. Sie reagieren chemisch mit den Schmelzbadbestandteilen und tragen zur Verbesserung der Schweißnahtpenetration, Schweißgeschwindigkeit und Schweißnahtform bei. Aktivgase können auch Legierungselemente in die Schweißnaht einbringen, um deren mechanische Eigenschaften zu verbessern.
- Mischgase: Mischgase sind Kombinationen aus Inertgasen und Aktivgasen, die speziell für bestimmte Schweißanwendungen und Werkstoffe entwickelt wurden. Durch die Auswahl der richtigen Mischgaszusammensetzung können optimale Schweißergebnisse erzielt werden, indem die Vorteile von Inert- und Aktivgasen kombiniert werden.
Funktionen des Schutzgases:
- Schutz der Schweißzone: Das Schutzgas bildet eine Schutzgasatmosphäre um das Schmelzbad und den Lichtbogen herum, um sie vor atmosphärischen Verunreinigungen zu schützen und die Bildung von Oxiden, Nitriden oder Porosität in der Schweißnaht zu verhindern.
- Stabilisierung des Lichtbogens: Das Schutzgas trägt zur Stabilisierung des Lichtbogens bei, indem es eine gleichmäßige und kontrollierte Energieübertragung auf das Schmelzbad ermöglicht und das Risiko von Lichtbogenstörungen oder Spritzern reduziert.
- Kontrolle der Schweißnahtqualität: Durch die Auswahl des geeigneten Schutzgases und der richtigen Schutzgasflussrate kann die Schweißnahtqualität verbessert werden, indem eine saubere Schweißnahtform, gute Durchdringung und Fusion sowie minimale Defekte oder Unregelmäßigkeiten erreicht werden.
- Einfluss auf die Schweißeigenschaften: Die Auswahl des Schutzgases kann die mechanischen, chemischen und metallurgischen Eigenschaften der Schweißnaht beeinflussen, einschließlich Festigkeit, Härte, Korrosionsbeständigkeit und Wärmebeeinflussungszonen.
Anwendungen von Schutzgasen:
- Schutzgase werden in einer Vielzahl von Schweißanwendungen und Branchen eingesetzt, darunter die Automobilindustrie, die Metallverarbeitung, der Schiffbau, die Luft- und Raumfahrt, die Rohrleitungsfertigung, die Bauindustrie und andere industrielle Anwendungen.
- Sie werden für das Schweißen von verschiedenen Werkstoffen wie Kohlenstoffstahl, Edelstahl, Aluminium, Kupfer, Titan und anderen Legierungen verwendet, um eine Vielzahl von Schweißverbindungen herzustellen, einschließlich Stumpf-, Kehlnaht-, Wurzellagen- und Überlappungsnähten.
Die Auswahl des geeigneten Schutzgases ist entscheidend für den Erfolg und die Qualität des Schweißprozesses. Eine sorgfältige Bewertung der Schweißanforderungen, Werkstoffeigenschaften und Schutzgasoptionen ist erforderlich, um die besten Schweißergebnisse zu erzielen und hochwertige Schweißverbindungen herzustellen.
Schweißfehler
Schweißfehler sind Defekte oder Unregelmäßigkeiten in der Schweißnaht oder im Schweißprozess, die die Qualität, Integrität und Zuverlässigkeit der Schweißverbindung beeinträchtigen können. Sie können durch verschiedene Faktoren verursacht werden, einschließlich unsachgemäßer Schweißnahtvorbereitung, falscher Schweißparameter, unzureichender Schutzgasabdeckung, Werkstoffproblemen oder menschlicher Fehler. Die rechtzeitige Identifizierung und Korrektur von Schweißfehlern ist entscheidend, um hochwertige und zuverlässige Schweißverbindungen sicherzustellen.
Typen von Schweißfehlern:
- Porosität: Porosität in der Schweißnaht sind gasgefüllte Poren oder Lunker, die durch eingeschlossene Gase wie Sauerstoff, Stickstoff oder Wasserstoff entstehen können. Sie können die mechanischen Eigenschaften der Schweißnaht beeinträchtigen und zu reduzierter Festigkeit, Duktilität und Korrosionsbeständigkeit führen.
- Schlackeneinschlüsse: Schlackeneinschlüsse sind Rückstände des Flussmittels oder der Schweißelektrode, die in der Schweißnaht eingeschlossen sind und zu unregelmäßigen Oberflächen, schlechter Durchdringung und reduzierter Schweißnahtfestigkeit führen können.
- Lunker: Lunker sind Hohlräume oder Einschlüsse in der Schweißnaht oder im Schweißgut, die durch unzureichende Schweißpenetration, unvollständige Schmelzung oder ungleichmäßige Schweißnahtform entstehen können. Sie können zu lokalen Schwachstellen und Spannungskonzentrationen führen, die die Schweißnahtfestigkeit beeinträchtigen können.
- Risse: Risse sind Brüche oder Spalten in der Schweißnaht oder im Schweißgut, die durch Spannungskonzentrationen, Überbeanspruchung, unzureichende Schweißfusion oder Werkstoffprobleme verursacht werden können. Sie können die Integrität der Schweißverbindung erheblich beeinträchtigen und zu strukturellen Versagensproblemen führen.
- Schweißspritzer: Schweißspritzer sind kleine Metalltropfen oder Partikel, die sich während des Schweißens von der Schweißnaht lösen und auf benachbarten Oberflächen oder Bauteilen landen können. Sie können zu unansehnlichen Oberflächen, Kontaminationsproblemen und Beschichtungsfehlern führen.
Ursachen von Schweißfehlern:
- Unsachgemäße Schweißnahtvorbereitung
- Falsche Schweißparameter oder Schweißprozesseinstellungen
- Unzureichende Reinigung der Werkstückoberflächen
- Mangelnde Kontrolle der Schutzgasabdeckung
- Werkstoffprobleme wie Verschmutzung, Inhomogenität oder schlechte Schweißbarkeit
- Mangelnde Schulung oder Erfahrung des Schweißers
Bedeutung der Fehlererkennung und -behebung:
- Frühzeitige Identifizierung von Schweißfehlern ermöglicht eine rechtzeitige Korrektur, um die Qualität und Integrität der Schweißverbindung zu verbessern und potenzielle Ausfälle oder Schäden zu vermeiden.
- Durch regelmäßige Inspektionen, Schweißnahtprüfungen und Qualitätskontrollen können Schweißfehler rechtzeitig erkannt und behoben werden, um eine hohe Schweißnahtqualität und Zuverlässigkeit sicherzustellen.
- Schulung und Weiterbildung von Schweißern sowie die Implementierung von Qualitätsmanagementsystemen sind wichtige Maßnahmen zur Vermeidung von Schweißfehlern und zur Gewährleistung einer erfolgreichen Schweißproduktion.
Die rechtzeitige Erkennung und Behebung von Schweißfehlern sind entscheidend für die Herstellung hochwertiger und zuverlässiger Schweißverbindungen, die den Anforderungen und Standards der jeweiligen Anwendung entsprechen. Durch eine gründliche Fehleranalyse, Qualitätskontrolle und Schulung kann das Risiko von Schweißfehlern minimiert und die Gesamtleistung des Schweißprozesses verbessert werden.
Schweißnahtprüfung
Die Schweißnahtprüfung ist ein wichtiger Schritt im Schweißprozess, der dazu dient, die Qualität, Integrität und Zuverlässigkeit der geschweißten Verbindung zu überprüfen und sicherzustellen. Verschiedene Prüfverfahren werden verwendet, um die Schweißnaht auf Defekte, Unregelmäßigkeiten und Qualitätsmerkmale zu untersuchen, wodurch potenzielle Risiken oder Ausfälle minimiert werden können.
Typen von Schweißnahtprüfungen:
- Visuelle Prüfung: Die visuelle Prüfung ist die einfachste und häufigste Methode zur Überprüfung der Schweißnahtqualität. Dabei werden die geschweißten Verbindungen visuell auf Oberflächendefekte wie Porosität, Risse, Schlackeneinschlüsse, unregelmäßige Formgebung oder Schweißspritzer untersucht.
- Röntgenprüfung (RT): Die Röntgenprüfung verwendet Röntgenstrahlen oder Gammastrahlen, um innere Defekte oder Unregelmäßigkeiten in der Schweißnaht, wie Lunker, Porosität, Risse oder Fehlstellen, zu erkennen. Sie ist eine zerstörungsfreie Prüfungsmethode und eignet sich für die Untersuchung von dickwandigen Bauteilen oder komplexen Schweißkonstruktionen.
- Ultraschallprüfung (UT): Die Ultraschallprüfung verwendet Ultraschallwellen, die durch die geschweißten Verbindungen gesendet werden, um innere Defekte oder Unregelmäßigkeiten zu erkennen. Sie kann zur Untersuchung von Schweißnahttiefe, Schweißpenetration, Lunker, Porosität oder Risse eingesetzt werden und ermöglicht eine zerstörungsfreie Prüfung mit hoher Auflösung.
- Magnetpulverprüfung (MT): Die Magnetpulverprüfung verwendet magnetische Partikel, die auf die Oberfläche der geschweißten Verbindungen aufgebracht werden, um Oberflächendefekte wie Risse oder Fehlstellen zu erkennen. Sie eignet sich für ferromagnetische Werkstoffe und ermöglicht eine schnelle und effektive Prüfung von Schweißnähten.
- Durchstrahlungsprüfung (RT): Die Durchstrahlungsprüfung ähnelt der Röntgenprüfung, verwendet jedoch eine Durchleuchtungstechnik, bei der die geschweißten Verbindungen mit einer Röntgenquelle beleuchtet werden, um innere Defekte oder Unregelmäßigkeiten zu erkennen. Sie ist ebenfalls eine zerstörungsfreie Prüfungsmethode und eignet sich für die Untersuchung von dickwandigen Bauteilen oder Schweißkonstruktionen.
Bedeutung der Schweißnahtprüfung:
- Die Schweißnahtprüfung dient zur Gewährleistung der Schweißnahtqualität, -integrität und -zuverlässigkeit, indem potenzielle Defekte oder Unregelmäßigkeiten rechtzeitig erkannt und behoben werden.
- Durch regelmäßige Prüfungen und Inspektionen können Herstellungsfehler, Werkstoffprobleme oder Schweißfehler identifiziert und korrigiert werden, bevor sie zu Ausfällen oder Schäden führen.
- Die Auswahl des geeigneten Prüfverfahrens hängt von verschiedenen Faktoren ab, einschließlich der Art der geschweißten Verbindung, der Werkstoffeigenschaften, der Anwendungsanforderungen und der Verfügbarkeit von Prüfmitteln und -ausrüstungen.
Die Schweißnahtprüfung ist ein unverzichtbarer Bestandteil des Schweißprozesses, der zur Gewährleistung hochwertiger und zuverlässiger Schweißverbindungen beiträgt. Durch die Verwendung geeigneter Prüfverfahren und die Einhaltung von Qualitätsstandards können potenzielle Risiken oder Ausfälle minimiert und die Gesamtleistung des Schweißprozesses verbessert werden.
Schweißverfahren
Schweißverfahren sind spezifische Techniken und Methoden, die verwendet werden, um Metallteile miteinander zu verbinden und Schweißverbindungen herzustellen. Verschiedene Schweißverfahren werden je nach den Anforderungen der Anwendung, den Werkstoffen, der Schweißposition und anderen Faktoren eingesetzt. Jedes Schweißverfahren bietet spezifische Vorteile, Eigenschaften und Anwendungen.
Häufig verwendete Schweißverfahren:
- MIG/MAG-Schweißen (Metall-Inertgas/Metall-Aktivgas): Beim MIG/MAG-Schweißen wird ein Lichtbogen zwischen einem kontinuierlich zugeführten Drahtelektroden und den zu schweißenden Werkstücken erzeugt. Ein inertes oder aktives Schutzgas wird verwendet, um das Schmelzbad und den Lichtbogen vor atmosphärischen Verunreinigungen zu schützen. MIG-Schweißen verwendet inerten Schutzgas wie Argon oder Helium, während MAG-Schweißen aktive Gase wie CO2 verwendet.
- WIG-Schweißen (Wolfram-Inertgas): Beim WIG-Schweißen wird ein Lichtbogen zwischen einer nichtverbrauchbaren Wolframelektrode und den zu schweißenden Werkstücken erzeugt. Ein inertes Schutzgas wie Argon oder Helium wird verwendet, um das Schmelzbad und den Lichtbogen zu schützen. WIG-Schweißen ermöglicht eine präzise und kontrollierte Schweißnahtbildung und wird für hochwertige Schweißverbindungen in verschiedenen Werkstoffen verwendet.
- Elektrodenschweißen (MMA-Schweißen): Beim Elektrodenschweißen wird ein Lichtbogen zwischen einer mit einem Schweißzusatzmaterial beschichteten Elektrode und den zu schweißenden Werkstücken erzeugt. Der Schweißzusatz schmilzt und bildet die Schweißnaht, während die Beschichtung der Elektrode als Schutzgas und Schlacke dient. Elektrodenschweißen ist vielseitig einsetzbar und eignet sich für verschiedene Werkstoffe und Anwendungen.
- Plasmaschweißen: Beim Plasmaschweißen wird ein Lichtbogen zwischen einer nichtverbrauchbaren Wolframelektrode und den zu schweißenden Werkstücken erzeugt, wobei ein Plasmastrahl verwendet wird, um das Schmelzbad zu erzeugen und die Schweißnaht zu formen. Plasmaschweißen bietet hohe Schweißgeschwindigkeiten, Präzision und Kontrolle und wird häufig für dünnwandige Materialien und feine Schweißarbeiten verwendet.
- Unterpulverschweißen (UP-Schweißen): Beim Unterpulverschweißen wird ein Lichtbogen zwischen einem kontinuierlich zugeführten Drahtelektroden und den zu schweißenden Werkstücken erzeugt, wobei ein Pulverflussmittel verwendet wird, um das Schmelzbad zu schützen und zu stabilisieren. Unterpulverschweißen ermöglicht hohe Schweißgeschwindigkeiten und tiefe Schweißnahtpenetration und wird für dicke Werkstoffe und längere Schweißnähte eingesetzt.
Anwendungen von Schweißverfahren:
- Schweißverfahren werden in einer Vielzahl von Branchen und Anwendungen eingesetzt, darunter die Automobilindustrie, die Luft- und Raumfahrt, der Schiffbau, die Bauindustrie, die Herstellung von Metallkonstruktionen, die Rohrleitungsfertigung und andere industrielle Anwendungen.
- Sie werden für das Schweißen verschiedener Werkstoffe wie Kohlenstoffstahl, Edelstahl, Aluminium, Kupfer, Titan und andere Legierungen verwendet, um eine Vielzahl von Schweißverbindungen herzustellen, einschließlich Stumpf-, Kehlnaht-, Wurzellagen- und Überlappungsnähten.
Die Auswahl des geeigneten Schweißverfahrens hängt von verschiedenen Faktoren ab, darunter die Werkstoffeigenschaften, die Anforderungen der Anwendung, die Schweißposition, die Schweißnahtqualität und die Verfügbarkeit von Ausrüstung und Ressourcen. Durch die Auswahl des richtigen Schweißverfahrens können hochwertige und zuverlässige Schweißverbindungen hergestellt werden, die den spezifischen Anforderungen und Standards entsprechen.
Wurzellage
Die Wurzellage bezieht sich auf den ersten Schweißpass oder die erste Schweißnaht, die in einer Mehrpass-Schweißverbindung hergestellt wird und die Wurzel der Schweißnaht bildet. Sie ist entscheidend für die Qualität und Integrität der gesamten Schweißverbindung, da sie die Grundlage für nachfolgende Schweißnähte bildet und eine gute Durchdringung sowie Fusion sicherstellen muss.
Merkmale der Wurzellage:
- Schweißposition: Die Wurzellage kann in verschiedenen Schweißpositionen hergestellt werden, einschließlich Flachposition, Horizontalposition, Vertikalposition oder Überkopfposition, je nach den Anforderungen der Anwendung und der Konfiguration der Werkstücke.
- Schweißverfahren: Verschiedene Schweißverfahren können für die Herstellung der Wurzellage verwendet werden, darunter MIG/MAG-Schweißen, WIG-Schweißen, Elektrodenschweißen oder Unterpulverschweißen, abhängig von den Werkstoffen, der Schweißposition und anderen Faktoren.
- Schweißparameter: Die Auswahl der geeigneten Schweißparameter wie Schweißstrom, Schweißspannung, Drahtvorschubgeschwindigkeit, Schweißgeschwindigkeit und Schutzgasfluss ist entscheidend für die Qualität und Penetration der Wurzellage.
- Schweißnahtvorbereitung: Eine sorgfältige Vorbereitung der Schweißnaht, einschließlich Reinigung der Werkstückoberflächen, Ausrichtung der Werkstücke und Einstellung der Spaltweite, ist wichtig, um eine gute Durchdringung und Fusion in der Wurzellage zu gewährleisten.
- Qualitätskontrolle: Die Wurzellage wird regelmäßig auf Defekte, Unregelmäßigkeiten oder Qualitätsmerkmale überprüft, um sicherzustellen, dass sie den Anforderungen und Standards der Schweißanwendung entspricht. Visuelle Inspektionen, Röntgenprüfungen, Ultraschallprüfungen oder Magnetpulverprüfungen können zur Bewertung der Wurzellagenqualität verwendet werden.
Bedeutung der Wurzellage:
- Die Wurzellage bildet die Basis für die gesamte Schweißverbindung und beeinflusst maßgeblich deren Festigkeit, Integrität und Zuverlässigkeit.
- Eine ordnungsgemäß hergestellte Wurzellage mit ausreichender Penetration und Fusion ist entscheidend für die Gewährleistung einer hochwertigen und zuverlässigen Schweißverbindung.
- Durch die Kontrolle und Überwachung der Wurzellage können potenzielle Fehler oder Defekte rechtzeitig erkannt und behoben werden, um die Gesamtqualität des Schweißprozesses zu verbessern.
Die ordnungsgemäße Herstellung und Überwachung der Wurzellage ist entscheidend für den Erfolg und die Qualität von Schweißverbindungen, insbesondere bei anspruchsvollen Anwendungen oder kritischen Bauteilen. Durch die Beachtung der oben genannten Merkmale und Qualitätskontrollverfahren kann eine hochwertige Wurzellage erzielt werden, die den Anforderungen und Standards der Schweißanwendung entspricht.
Schweißdraht
Der Schweißdraht ist ein Verbrauchsmaterial, das beim Lichtbogenschweißen verwendet wird, um den Schweißstrom zu übertragen und das Schmelzbad zu erzeugen. Er dient als Zusatzwerkstoff, der in das Schmelzbad eingebracht wird, um die Schweißnaht zu formen und die Werkstücke miteinander zu verbinden. Der Schweißdraht ist in verschiedenen Durchmessern, Materialien und Beschichtungen erhältlich, je nach den Anforderungen der Schweißanwendung und den Werkstoffen, die geschweißt werden sollen.
Merkmale des Schweißdrahts:
- Durchmesser: Der Schweißdraht ist in verschiedenen Durchmessern erhältlich, die je nach der Schweißanwendung, der Schweißposition und der gewünschten Schweißnahtgröße ausgewählt werden. Typische Drahtdurchmesser reichen von 0,6 mm bis 2,4 mm für das MIG/MAG-Schweißen und von 1,0 mm bis 3,2 mm für das Elektrodenschweißen.
- Material: Der Schweißdraht kann aus verschiedenen Materialien hergestellt sein, einschließlich Kohlenstoffstahl, Edelstahl, Aluminium, Kupfer, Nickellegierungen, Titan und anderen Legierungen. Die Auswahl des geeigneten Drahtmaterials hängt von den Werkstoffen der zu schweißenden Bauteile, den mechanischen Eigenschaften der Schweißnaht und den Anforderungen der Schweißanwendung ab.
- Beschichtung: Der Schweißdraht kann mit einer speziellen Beschichtung versehen sein, die dazu dient, die Schweißnahtqualität zu verbessern, die Lichtbogenstabilität zu erhöhen und die Abscheidung von Schweißspritzern zu reduzieren. Die Beschichtung kann auch Legierungselemente enthalten, die die mechanischen Eigenschaften der Schweißnaht beeinflussen und deren Korrosionsbeständigkeit verbessern.
- Spule oder Spule: Der Schweißdraht wird in der Regel auf Spulen oder Spulen geliefert, die in verschiedenen Größen und Ausführungen erhältlich sind, je nach den Anforderungen der Schweißausrüstung und der Schweißanwendung. Die Auswahl der richtigen Drahtspule oder -spule hängt von der Schweißausrüstung, der Drahtvorschubgeschwindigkeit und anderen Faktoren ab.
Anwendungen des Schweißdrahts:
- Der Schweißdraht wird in einer Vielzahl von Schweißverfahren und Anwendungen eingesetzt, einschließlich MIG/MAG-Schweißen, WIG-Schweißen, Elektrodenschweißen, Plasmaschweißen und Unterpulverschweißen.
- Er wird verwendet, um verschiedene Werkstoffe wie Stahl, Edelstahl, Aluminium, Kupfer, Nickellegierungen, Titan und andere Legierungen zu schweißen, um eine Vielzahl von Schweißverbindungen herzustellen, einschließlich Stumpf-, Kehlnaht-, Wurzellagen- und Überlappungsnähten.
Die Auswahl des geeigneten Schweißdrahts ist entscheidend für den Erfolg und die Qualität des Schweißprozesses, da er maßgeblich zur Bildung einer hochwertigen und zuverlässigen Schweißnaht beiträgt. Durch die Berücksichtigung der oben genannten Merkmale und Anwendungen kann der richtige Schweißdraht für die jeweilige Schweißanwendung ausgewählt werden, um optimale Schweißergebnisse zu erzielen.
Nahtvorbereitung
Die Nahtvorbereitung ist ein wichtiger Schritt im Schweißprozess, bei dem die zu schweißenden Werkstücke entsprechend vorbereitet werden, um eine qualitativ hochwertige und zuverlässige Schweißnaht zu gewährleisten. Eine ordnungsgemäße Nahtvorbereitung trägt wesentlich zur Verbesserung der Schweißnahtqualität, Schweißnahtpenetration und Schweißverbindungsfestigkeit bei und hilft, potenzielle Fehler oder Defekte zu minimieren.
Merkmale der Nahtvorbereitung:
- Reinigung der Werkstückoberflächen: Vor dem Schweißen müssen die zu verbindenden Werkstücke gründlich gereinigt werden, um Oberflächenverunreinigungen, Oxidationsschichten, Öl, Fett oder andere Verschmutzungen zu entfernen. Dies ermöglicht eine bessere Schweißnahtbildung und Vermeidung von Defekten wie Porosität oder unregelmäßige Schweißnähte.
- Ausrichtung der Werkstücke: Die Werkstücke müssen sorgfältig ausgerichtet und positioniert werden, um eine gleichmäßige Schweißnahtbildung und eine gute Durchdringung sicherzustellen. Eine präzise Ausrichtung minimiert das Risiko von Spaltbildungen oder ungleichmäßigen Schweißnähten und trägt zur Verbesserung der Schweißqualität bei.
- Vorbereitung der Schweißnahtgeometrie: Je nach Schweißverfahren und Schweißposition können verschiedene Schweißnahtgeometrien erforderlich sein, einschließlich V-Naht, U-Naht, Kehlnaht, Wurzellage und Überlappungsnähten. Die Auswahl der geeigneten Nahtgeometrie hängt von den Werkstoffen, der Schweißposition und den Anforderungen der Schweißanwendung ab.
- Einstellung der Spaltweite: Die Spaltweite zwischen den zu schweißenden Werkstücken muss entsprechend den Anforderungen der Schweißnaht und des Schweißverfahrens eingestellt werden. Eine zu große Spaltweite kann zu unzureichender Schweißpenetration führen, während eine zu kleine Spaltweite das Risiko von Einschlüssen oder Lunker erhöhen kann.
Bedeutung der Nahtvorbereitung:
- Eine ordnungsgemäße Nahtvorbereitung ist entscheidend für den Erfolg und die Qualität des Schweißprozesses, da sie eine solide Grundlage für die Bildung einer hochwertigen Schweißnaht bildet.
- Durch eine gründliche Reinigung der Werkstückoberflächen, sorgfältige Ausrichtung der Werkstücke und optimale Einstellung der Nahtgeometrie kann das Risiko von Schweißfehlern oder Defekten minimiert und die Schweißnahtqualität verbessert werden.
- Die Nahtvorbereitung trägt auch zur Verbesserung der Arbeitssicherheit bei, indem sie eine sichere Arbeitsumgebung schafft und das Risiko von Schweißunfällen oder Fehlern reduziert.
Eine sorgfältige Nahtvorbereitung ist ein wesentlicher Bestandteil des Schweißprozesses, der eine erfolgreiche Schweißverbindung und die Erfüllung der Anforderungen und Standards der Schweißanwendung gewährleistet. Durch die Berücksichtigung der oben genannten Merkmale und Verfahren kann eine qualitativ hochwertige Nahtvorbereitung erreicht werden, die zu optimalen Schweißergebnissen führt.
Schutzgas
Schutzgas ist ein wesentlicher Bestandteil vieler Lichtbogenschweißverfahren, insbesondere beim MIG/MAG-Schweißen und beim WIG-Schweißen. Es wird verwendet, um das Schmelzbad und den Lichtbogen vor atmosphärischen Verunreinigungen zu schützen und die Bildung einer hochwertigen Schweißnaht zu unterstützen. Verschiedene Arten von Schutzgasen werden je nach den Anforderungen der Schweißanwendung, den Werkstoffen und den Schweißverfahren eingesetzt.
Merkmale des Schutzgases:
- Inertgas: Inertgase wie Argon oder Helium werden häufig beim WIG-Schweißen verwendet, um das Schmelzbad und den Lichtbogen vor Oxidation und Verunreinigungen zu schützen. Inertgase reagieren nicht mit den Schweißzusatzmaterialien oder den Werkstücken und ermöglichen eine saubere und stabile Schweißnahtbildung.
- Aktivgas: Aktivgase wie Kohlendioxid (CO2) werden beim MIG/MAG-Schweißen verwendet, um das Schmelzbad zu stabilisieren und die Schweißnahtbildung zu verbessern. Aktivgase reagieren mit den Schmelzbadbestandteilen und tragen zur Bildung von Schutzgasschleiern bei, die das Schmelzbad vor atmosphärischen Verunreinigungen schützen.
- Mischgas: Mischgase bestehen aus einer Kombination von Inertgasen und Aktivgasen, um die Vorteile beider Gasarten zu kombinieren und die Schweißeigenschaften zu optimieren. Mischgase können speziell für bestimmte Werkstoffe, Schweißpositionen oder Anwendungen formuliert werden, um optimale Schweißergebnisse zu erzielen.
- Reinheit und Flussrate: Die Reinheit des Schutzgases und die Flussrate, mit der es auf das Schmelzbad aufgebracht wird, sind entscheidend für die Schweißnahtqualität und -integrität. Eine ausreichende Schutzgasabdeckung und eine konstante Gaszufuhr sind wichtig, um das Risiko von Schweißfehlern wie Porosität oder Oxidation zu minimieren.
Anwendungen des Schutzgases:
- Schutzgas wird in einer Vielzahl von Schweißverfahren und Anwendungen eingesetzt, einschließlich MIG/MAG-Schweißen, WIG-Schweißen, Plasmaschweißen und Laserschweißen.
- Es wird verwendet, um eine saubere und stabile Schweißnahtbildung zu unterstützen, die Bildung von Schweißfehlern zu minimieren und die mechanischen Eigenschaften der Schweißverbindung zu verbessern.
Die Auswahl des geeigneten Schutzgases hängt von verschiedenen Faktoren ab, einschließlich der Werkstoffeigenschaften, der Schweißverfahren, der Schweißposition und der Anforderungen der Schweißanwendung. Durch die Berücksichtigung der oben genannten Merkmale und Anwendungen kann das richtige Schutzgas für die jeweilige Schweißanwendung ausgewählt werden, um optimale Schweißergebnisse zu erzielen.
Schweißparameter
Die Schweißparameter sind die Einstellungen und Variablen, die beim Lichtbogenschweißen kontrolliert und angepasst werden, um eine erfolgreiche Schweißnahtbildung zu ermöglichen. Sie umfassen verschiedene Faktoren wie Schweißstrom, Spannung, Drahtvorschubgeschwindigkeit, Schweißgeschwindigkeit, Schutzgasfluss und Polarität, die je nach den Anforderungen der Schweißanwendung und den Werkstoffen eingestellt werden.
Wichtige Schweißparameter:
- Schweißstrom: Der Schweißstrom ist die elektrische Stromstärke, die durch den Lichtbogen fließt und die Wärmeenergie liefert, um das Schmelzbad zu erzeugen. Ein angemessener Schweißstrom ist entscheidend für die Schweißnahtbildung und -penetration und hängt von den Werkstoffen, der Drahtdicke und anderen Faktoren ab.
- Spannung: Die Schweißspannung ist die elektrische Spannung, die zwischen der Schweißelektrode und den zu schweißenden Werkstücken angelegt wird. Sie beeinflusst die Lichtbogenlänge, die Schweißnahtform und die Schweißnahtqualität und muss entsprechend den Anforderungen der Schweißanwendung eingestellt werden.
- Drahtvorschubgeschwindigkeit: Die Drahtvorschubgeschwindigkeit bestimmt die Rate, mit der der Schweißdraht in das Schmelzbad eingebracht wird. Eine angemessene Drahtvorschubgeschwindigkeit ist wichtig, um eine gleichmäßige Schweißnahtbildung und -penetration sicherzustellen und das Risiko von Schweißfehlern wie Porosität oder unregelmäßige Schweißnähte zu minimieren.
- Schweißgeschwindigkeit: Die Schweißgeschwindigkeit ist die Geschwindigkeit, mit der die Schweißpistole oder der Schweißbrenner über die zu schweißenden Werkstücke bewegt wird. Sie beeinflusst die Wärmeeinbringung, die Schweißnahtform und die Schweißnahtqualität und muss entsprechend den Schweißanforderungen und den Werkstoffen angepasst werden.
- Schutzgasfluss: Der Schutzgasfluss bestimmt die Menge an Schutzgas, die auf das Schmelzbad aufgebracht wird, um es vor atmosphärischen Verunreinigungen zu schützen. Ein ausreichender Schutzgasfluss ist entscheidend für die Bildung einer hochwertigen Schweißnaht und muss entsprechend den Schweißanforderungen und den Gasvorschriften eingestellt werden.
- Polarität: Die Polarität des Schweißstroms kann entweder positiv oder negativ sein und hängt vom Schweißverfahren und den Anforderungen der Schweißanwendung ab. Bei einigen Verfahren wie dem MIG/MAG-Schweißen wird eine positive Polarität für das Schweißen von Stahlwerkstoffen verwendet, während eine negative Polarität für das Schweißen von Aluminiumwerkstoffen bevorzugt wird.
Anpassung der Schweißparameter:
- Die Anpassung der Schweißparameter erfolgt in der Regel durch den Schweißer oder den Bediener der Schweißausrüstung, basierend auf Erfahrung, Schulung und den spezifischen Anforderungen der Schweißanwendung.
- Durch regelmäßige Überwachung und Anpassung der Schweißparameter können optimale Schweißergebnisse erzielt, Schweißfehler minimiert und die Schweißnahtqualität verbessert werden.
Die richtige Einstellung und Anpassung der Schweißparameter sind entscheidend für den Erfolg und die Qualität des Schweißprozesses. Durch die Berücksichtigung der oben genannten Schweißparameter und deren Anpassung entsprechend den Anforderungen der Schweißanwendung können optimale Schweißergebnisse erzielt und hochwertige Schweißverbindungen hergestellt werden.
Schweißroboter
Schweißroboter sind spezielle Industrieroboter, die für automatisierte Schweißanwendungen eingesetzt werden. Sie bieten eine Vielzahl von Vorteilen gegenüber manuellen Schweißverfahren, darunter erhöhte Produktivität, verbesserte Schweißqualität, konsistente Schweißergebnisse und eine höhere Arbeitssicherheit. Schweißroboter werden in verschiedenen Branchen und Anwendungen eingesetzt, einschließlich der Automobilindustrie, des Schiffbaus, der Luft- und Raumfahrt, der Bauindustrie und der Fertigung von Metallkonstruktionen.
Merkmale von Schweißrobotern:
- Roboterarme: Schweißroboter verfügen über mehrere bewegliche Arme und Achsen, die es ihnen ermöglichen, präzise Bewegungen auszuführen und komplexe Schweißnähte zu bilden. Die Roboterarme sind mit Schweißausrüstung wie Schweißbrennern, Drahtzuführungen und Schutzgasdüsen ausgestattet.
- Automatisierte Schweißprogramme: Schweißroboter können mit vorprogrammierten Schweißprogrammen betrieben werden, die eine präzise Steuerung der Schweißparameter und Bewegungen ermöglichen. Diese Programme können je nach den Anforderungen der Schweißanwendung angepasst und optimiert werden.
- Sensoren und Kameras: Schweißroboter sind oft mit Sensoren und Kameras ausgestattet, die eine Echtzeitüberwachung der Schweißnahtqualität ermöglichen. Diese Sensoren können Defekte oder Unregelmäßigkeiten erkennen und den Roboter in Echtzeit anpassen, um die Schweißqualität zu verbessern.
- Flexible Montageoptionen: Schweißroboter können auf verschiedenen Montageoptionen installiert werden, darunter Bodenmontage, Deckenmontage, Wandmontage oder mobile Plattformen. Dies ermöglicht eine flexible Integration in verschiedene Fertigungsumgebungen und Produktionsprozesse.
Vorteile von Schweißrobotern:
- Erhöhte Produktivität: Schweißroboter arbeiten kontinuierlich und können eine höhere Schweißgeschwindigkeit und -effizienz erreichen als manuelle Schweißverfahren, was zu einer erhöhten Produktivität führt.
- Verbesserte Schweißqualität: Durch die präzise Steuerung der Schweißparameter und Bewegungen können Schweißroboter eine konsistente und hochwertige Schweißnahtbildung gewährleisten, die eine geringere Nachbearbeitung erfordert.
- Arbeitssicherheit: Schweißroboter reduzieren das Risiko von Schweißunfällen und Verletzungen, da sie die Notwendigkeit für manuelle Schweißarbeiten reduzieren und die Exposition der Mitarbeiter gegenüber schädlichen Schweißdämpfen und Lichtbogenstrahlung verringern.
- Kosteneffizienz: Obwohl die Anschaffungskosten für Schweißroboter hoch sein können, können sie langfristig zu Kosteneinsparungen führen, indem sie die Produktionszeit verkürzen, den Ausschuss reduzieren und die Betriebskosten senken.
Die Verwendung von Schweißrobotern bietet eine Vielzahl von Vorteilen für die Fertigungsindustrie, einschließlich erhöhter Produktivität, verbesserte Schweißqualität und erhöhte Arbeitssicherheit. Durch die Integration von Schweißrobotern in den Fertigungsprozess können Unternehmen ihre Wettbewerbsfähigkeit steigern und ihre Fertigungseffizienz verbessern.
Schweißnaht
Die Schweißnaht ist die Verbindungsstelle zwischen den zu schweißenden Werkstücken, die durch das Schmelzen und Verbinden der Werkstoffe entsteht. Sie bildet die Grundlage für die Schweißverbindung und beeinflusst maßgeblich deren Festigkeit, Integrität und Leistungsfähigkeit. Eine hochwertige Schweißnaht ist entscheidend für die Zuverlässigkeit und Langlebigkeit von geschweißten Bauteilen und Strukturen.
Merkmale einer Schweißnaht:
- Schweißnahtform: Die Form der Schweißnaht kann je nach Schweißverfahren und Schweißposition variieren. Typische Schweißnahtformen umfassen Stumpfnähte, Kehlnähte, Wurzellagen, Überlappungsnähte und andere spezifische Nahtgeometrien, die für die jeweilige Anwendung optimiert sind.
- Schweißnahtqualität: Die Qualität einer Schweißnaht wird durch verschiedene Faktoren beeinflusst, einschließlich der Penetration, Fusion, Dichte, Porosität, Rissbildung und anderen Defekten. Eine hochwertige Schweißnaht weist eine gute Durchdringung, vollständige Fusion und minimale Defekte auf.
- Schweißzusatzmaterial: Das Schweißzusatzmaterial wird während des Schweißprozesses in das Schmelzbad eingebracht, um die Schweißnaht zu bilden. Es muss mit den zu schweißenden Werkstoffen kompatibel sein und die mechanischen Eigenschaften der Schweißverbindung verbessern.
- Schutzgas: Beim Lichtbogenschweißen wird Schutzgas verwendet, um das Schmelzbad vor atmosphärischen Verunreinigungen zu schützen und die Schweißnahtqualität zu verbessern. Die Auswahl des geeigneten Schutzgases ist entscheidend für die Bildung einer hochwertigen Schweißnaht.
Prüfung und Bewertung von Schweißnähten:
- Schweißnähte werden regelmäßig auf ihre Qualität und Integrität überprüft, um sicherzustellen, dass sie den Anforderungen und Standards der Schweißanwendung entsprechen. Dies kann durch visuelle Inspektionen, zerstörungsfreie Prüfverfahren wie Röntgenprüfung, Ultraschallprüfung, Magnetpulverprüfung oder Durchstrahlungsprüfung erfolgen.
- Die Bewertung von Schweißnähten basiert auf verschiedenen Kriterien wie Schweißnahtform, Schweißnahtqualität, Schweißzusatzmaterial, Schutzgasabdeckung und anderen spezifischen Anforderungen der Schweißanwendung.
Anwendungen von Schweißnähten:
- Schweißnähte werden in einer Vielzahl von Branchen und Anwendungen eingesetzt, darunter die Automobilindustrie, der Schiffbau, die Luft- und Raumfahrt, die Bauindustrie, die Fertigung von Metallkonstruktionen und andere industrielle Anwendungen.
- Sie werden verwendet, um verschiedene Werkstoffe wie Stahl, Edelstahl, Aluminium, Kupfer, Nickellegierungen, Titan und andere Legierungen zu schweißen und eine Vielzahl von Bauteilen und Strukturen herzustellen.
Eine hochwertige Schweißnaht ist entscheidend für den Erfolg und die Zuverlässigkeit von geschweißten Bauteilen und Strukturen. Durch die Berücksichtigung der oben genannten Merkmale und Qualitätskontrollverfahren kann eine hochwertige Schweißnaht erzielt werden, die den Anforderungen und Standards der Schweißanwendung entspricht.
Schweißnahtprüfung
Die Schweißnahtprüfung ist ein wichtiger Schritt im Schweißprozess, der dazu dient, die Qualität und Integrität der geschweißten Verbindungen zu überprüfen. Verschiedene Prüfverfahren werden eingesetzt, um potenzielle Defekte, Unregelmäßigkeiten oder Qualitätsprobleme in den Schweißnähten zu identifizieren und sicherzustellen, dass sie den Anforderungen und Standards der Schweißanwendung entsprechen.
Merkmale der Schweißnahtprüfung:
- Visuelle Inspektion: Die visuelle Inspektion ist die einfachste und häufigste Methode zur Überprüfung von Schweißnähten. Geschulte Inspektoren untersuchen die Oberfläche der Schweißnaht auf sichtbare Defekte wie Porosität, Risse, Einschlüsse, unregelmäßige Formen oder andere Unregelmäßigkeiten.
- Zerstörungsfreie Prüfverfahren (ZfP): Zerstörungsfreie Prüfverfahren werden verwendet, um die innere Struktur und Qualität der Schweißnaht ohne Beschädigung zu bewerten. Zu den gängigen ZfP-Verfahren gehören die Röntgenprüfung, Ultraschallprüfung, Magnetpulverprüfung, Durchstrahlungsprüfung und Wirbelstromprüfung.
- Mechanische Tests: Mechanische Tests werden durchgeführt, um die mechanischen Eigenschaften der Schweißnaht zu bewerten, einschließlich Zugfestigkeit, Biegefestigkeit, Schlagzähigkeit und Härte. Diese Tests können an Schweißproben oder Schweißbauteilen durchgeführt werden, um deren Leistungsfähigkeit zu bestimmen.
- Chemische Analyse: Bei bestimmten Anwendungen kann eine chemische Analyse der Schweißnaht durchgeführt werden, um die Zusammensetzung der Werkstoffe und Schweißzusatzmaterialien zu bestimmen. Dies kann helfen, potenzielle Probleme wie Mischschweißen zu identifizieren und die Qualität der Schweißverbindung zu verbessern.
Bedeutung der Schweißnahtprüfung:
- Die Schweißnahtprüfung ist entscheidend für die Gewährleistung der Qualität und Integrität von geschweißten Verbindungen und trägt zur Sicherheit und Zuverlässigkeit von Bauteilen und Strukturen bei.
- Durch die rechtzeitige Erkennung und Behebung von Schweißfehlern oder Defekten können potenzielle Probleme in der Fertigung vermieden und die Gesamtleistung des Schweißprozesses verbessert werden.
- Die Schweißnahtprüfung ist auch wichtig für die Einhaltung von Branchenstandards, Vorschriften und Qualitätsanforderungen, die für bestimmte Anwendungen und Branchen gelten.
Die Auswahl der geeigneten Schweißnahtprüfverfahren hängt von verschiedenen Faktoren ab, einschließlich der Schweißanwendung, der Werkstoffe, der Schweißverfahren und der Anforderungen an die Schweißnahtqualität. Durch die Anwendung der oben genannten Prüfverfahren können qualitativ hochwertige Schweißverbindungen hergestellt und die Leistungsfähigkeit des Schweißprozesses verbessert werden.
Nahtbreite
Die Nahtbreite ist ein wichtiger Parameter beim Schweißen, der die Größe der entstehenden Schweißnaht entlang ihrer Breite angibt. Die Breite der Schweißnaht kann je nach den Anforderungen der Schweißanwendung und den spezifischen Schweißparametern variieren. Eine angemessene Nahtbreite ist entscheidend für die Festigkeit, Integrität und Leistung der Schweißverbindung.
Merkmale der Nahtbreite:
- Einstellung: Die Nahtbreite kann durch die Anpassung verschiedener Schweißparameter wie Schweißstrom, Spannung, Drahtvorschubgeschwindigkeit, Schweißgeschwindigkeit und Schutzgasfluss kontrolliert und eingestellt werden.
- Einflussfaktoren: Die Nahtbreite wird von verschiedenen Faktoren beeinflusst, darunter die Schweißstromstärke, die Schweißgeschwindigkeit, die Werkstoffeigenschaften, die Drahtdurchmesser und die Schutzgasabdeckung.
- Anforderungen der Schweißanwendung: Die Nahtbreite muss den Anforderungen der Schweißanwendung entsprechen und kann je nach den spezifischen Konstruktions- und Festigkeitsanforderungen variieren.
Bedeutung der Nahtbreite:
- Eine angemessene Nahtbreite ist wichtig, um eine ausreichende Schweißnahtpenetration und -abdeckung zu gewährleisten, was wiederum zur Festigkeit und Integrität der Schweißverbindung beiträgt.
- Die Nahtbreite kann auch die ästhetischen Eigenschaften der Schweißverbindung beeinflussen und das Erscheinungsbild der Schweißnaht verbessern oder beeinträchtigen.
- Eine unzureichende Nahtbreite kann zu unzureichender Schweißpenetration, ungleichmäßiger Schweißnahtbildung und reduzierter Festigkeit der Schweißverbindung führen.
- Eine übermäßige Nahtbreite kann zu übermäßigem Wärmeeintrag, Verformung der Werkstücke und unerwünschter Schweißspritzerbildung führen.
Die Kontrolle und Anpassung der Nahtbreite ist ein wichtiger Aspekt des Schweißprozesses, der dazu beiträgt, qualitativ hochwertige Schweißverbindungen herzustellen, die den Anforderungen und Standards der Schweißanwendung entsprechen. Durch die Optimierung der Schweißparameter und die sorgfältige Überwachung der Schweißnahtbildung kann eine angemessene Nahtbreite erreicht und die Gesamtqualität des Schweißprozesses verbessert werden.
Schweißkopf
Ein Schweißkopf ist eine Komponente einer automatisierten Schweißanlage, die den Schweißprozess steuert und überwacht. Er umfasst in der Regel den Schweißbrenner oder die Schweißpistole sowie alle erforderlichen Vorrichtungen zur präzisen Positionierung und Steuerung während des Schweißvorgangs. Der Schweißkopf spielt eine entscheidende Rolle bei der Erzielung hochwertiger Schweißverbindungen und der Optimierung der Schweißprozesseffizienz.
Merkmale eines Schweißkopfs:
- Schweißbrenner oder Schweißpistole: Der Schweißkopf beherbergt den Schweißbrenner oder die Schweißpistole, die den Lichtbogen erzeugt und das Schweißzusatzmaterial auf das Werkstück aufträgt. Der Schweißbrenner oder die Schweißpistole kann verschiedene Konfigurationen und Funktionen aufweisen, abhängig von den Anforderungen der Schweißanwendung.
- Positionierungsvorrichtungen: Der Schweißkopf ist mit Positionierungsvorrichtungen ausgestattet, die es ihm ermöglichen, präzise über das Werkstück zu navigieren und die Schweißnaht in der gewünschten Position zu erzeugen. Dies kann durch lineare Bewegungen, rotatorische Bewegungen oder eine Kombination aus beiden erfolgen.
- Automatisierte Steuerung: Der Schweißkopf wird durch eine automatisierte Steuerungseinheit gesteuert, die die Schweißparameter, Bewegungen und Positionierungsbefehle während des Schweißvorgangs regelt. Die automatisierte Steuerung ermöglicht eine präzise und konsistente Schweißnahtbildung sowie eine optimierte Prozesseffizienz.
- Überwachungssysteme: Der Schweißkopf kann mit verschiedenen Überwachungssystemen ausgestattet sein, die den Schweißprozess in Echtzeit überwachen und potenzielle Probleme wie Schweißfehler, Schweißnahtdefekte oder Abweichungen von den Schweißparametern erkennen.
Anwendungen von Schweißköpfen:
- Schweißköpfe werden in einer Vielzahl von automatisierten Schweißanwendungen eingesetzt, einschließlich Roboterschweißanlagen, automatisierten Schweißmaschinen, Schweißrobotern und anderen automatisierten Fertigungssystemen.
- Sie werden verwendet, um eine Vielzahl von Schweißverbindungen herzustellen, darunter Stumpfnähte, Kehlnähte, Wurzellagen, Überlappungsnähte und andere spezifische Nahtgeometrien, die für die jeweilige Anwendung optimiert sind.
- Schweißköpfe finden Anwendung in verschiedenen Branchen und Industriezweigen, einschließlich der Automobilindustrie, des Schiffbaus, der Luft- und Raumfahrt, der Bauindustrie und der Fertigung von Metallkonstruktionen.
Die Verwendung eines Schweißkopfs ermöglicht eine präzise Steuerung und Überwachung des Schweißprozesses, was zu hochwertigen Schweißverbindungen, verbesserten Produktivität und Effizienz sowie einer erhöhten Prozesssicherheit führt. Durch die Auswahl des geeigneten Schweißkopfs und die Optimierung der Schweißparameter können Unternehmen ihre Fertigungseffizienz steigern und qualitativ hochwertige Produkte herstellen.
Das Schweißen ist eine unverzichtbare Technologie in der modernen industriellen Fertigung. Es ermöglicht die dauerhafte Verbindung von Metallteilen, die in einer Vielzahl von Produkten und Infrastrukturen verwendet werden, von Automobilen über Flugzeuge bis hin zu Gebäuden. Traditionell wurde das Schweißen manuell durchgeführt, was hohe Anforderungen an die Fähigkeiten und Erfahrung des Bedieners stellte. In den letzten Jahrzehnten hat jedoch die Automatisierung des Schweißprozesses erheblich an Bedeutung gewonnen. Diese Entwicklung hat nicht nur die Produktivität gesteigert, sondern auch die Qualität und Konsistenz der Schweißnähte verbessert.
Mit der Einführung von automatisierten Schweißmaschinen, wie der automatischen Kreisschweißmaschine und dem MIG-Rundschweißgerät, können Unternehmen den Schweißprozess weiter optimieren. Automatisierte Schweißgeräte haben sich in einer Vielzahl von Branchen als unverzichtbar erwiesen, da sie die Präzision und Effizienz des Schweißprozesses auf ein neues Niveau heben. Die Verwendung von CNC-Steuerungen und robotergesteuerten Schweißgeräten hat es ermöglicht, komplexe Schweißaufgaben mit minimaler menschlicher Intervention durchzuführen.
In diesem umfassenden Artikel werden wir die verschiedenen Arten von automatisierten Schweißmaschinen, einschließlich der automatischen Kreisschweißmaschine und des MIG-Rundschweißgeräts, sowie ihre jeweiligen Vorteile, Einsatzmöglichkeiten und Technologien untersuchen. Darüber hinaus werfen wir einen Blick auf die neuesten Trends in der Schweißautomatisierung, wie die Integration von Künstlicher Intelligenz (KI) und maschinellem Lernen in den Schweißprozess.
Was ist eine Automatische Kreisschweißmaschine?
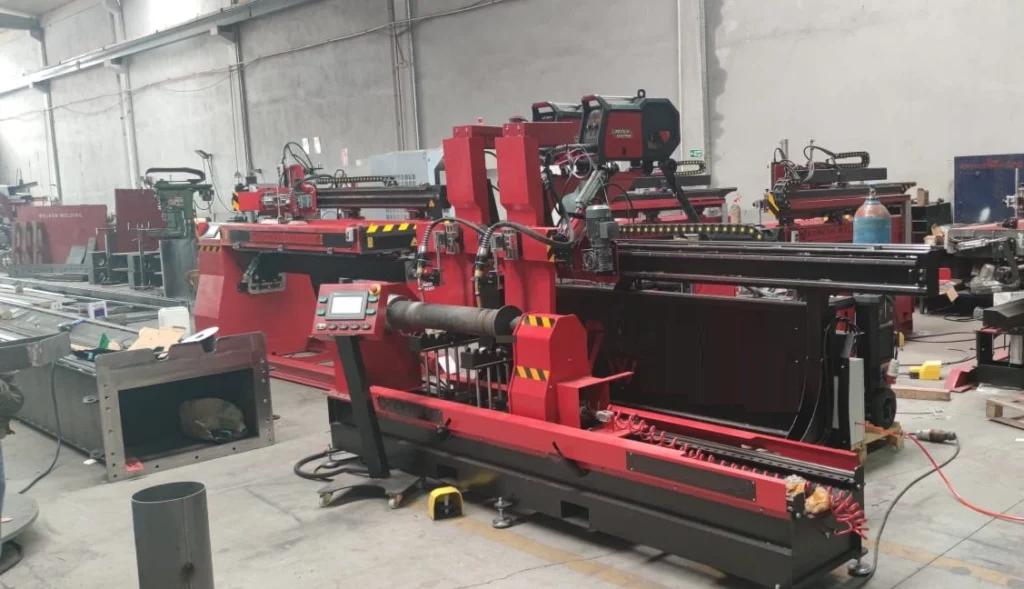
Eine automatische Kreisschweißmaschine ist eine spezialisierte Schweißanlage, die hauptsächlich für das Schweißen von runden oder zylindrischen Werkstücken entwickelt wurde. Sie verwendet rotierende Mechanismen, um eine gleichmäßige und präzise Schweißnaht entlang der zirkularen Konturen eines Werkstücks zu erzeugen. Im Gegensatz zu herkömmlichen manuellen Schweißmethoden erfordert die automatische Kreisschweißmaschine wenig bis gar keine manuelle Eingriffe während des Schweißvorgangs. Das Werkstück wird in der Regel auf einem Drehtisch fixiert, während der Schweißkopf sich entweder um das Werkstück bewegt oder das Werkstück selbst rotiert, um eine gleichmäßige Schweißnaht zu erzeugen.
Die Hauptanwendung der Kreisschweißmaschinen ist das Schweißen von runden Bauteilen wie Rohren, Zylindern, Tanks oder Flanschen, die präzise und wiederholbare Schweißnähte erfordern. Diese Maschinen sind in der Lage, sowohl kontinuierliche als auch segmentierte Schweißnähte zu erzeugen, je nach den Anforderungen des spezifischen Projekts.
Hauptkomponenten einer Kreisschweißmaschine
Eine Kreisschweißmaschine besteht aus mehreren wichtigen Komponenten, die eine präzise und effiziente Schweißleistung ermöglichen:
- Drehtisch oder Spannvorrichtung: Hier wird das Werkstück fixiert und in eine rotierende Bewegung versetzt, um das Schweißen entlang seiner zirkularen Kontur zu ermöglichen.
- Schweißkopf: Dies ist das zentrale Element der Maschine, das den eigentlichen Schweißvorgang durchführt. Je nach Schweißverfahren kann es sich um einen Lichtbogen-Schweißkopf (MIG, TIG) oder einen Laserschweißkopf handeln.
- Steuerungseinheit: Moderne Kreisschweißmaschinen sind mit einer CNC-Steuerung (Computer Numerical Control) ausgestattet, die eine präzise Programmierung und Kontrolle des Schweißprozesses ermöglicht.
- Schweißstromquelle: Die Maschine benötigt eine Stromquelle, um den Schweißlichtbogen oder den Laser zu erzeugen. Diese wird in Abhängigkeit vom Schweißverfahren angepasst.
- Kühlvorrichtung: Um die Lebensdauer der Maschine zu verlängern und eine konstante Schweißqualität zu gewährleisten, wird häufig eine Kühlvorrichtung integriert, die die Schweißelektrode oder den Schweißkopf kühlt.
Typische Anwendungen
Die Anwendungsmöglichkeiten von Kreisschweißmaschinen sind vielseitig und erstrecken sich über zahlreiche Industriezweige:
- Automobilindustrie: Kreisschweißmaschinen werden häufig in der Herstellung von Auspuffrohren, Stoßdämpfern und anderen zylindrischen Komponenten eingesetzt. Durch den automatisierten Prozess können diese Teile in hoher Stückzahl mit gleichbleibender Qualität gefertigt werden.
- Luft- und Raumfahrt: In der Luftfahrtindustrie sind hohe Präzision und Zuverlässigkeit entscheidend. Kreisschweißmaschinen werden verwendet, um Turbinenteile, Flugzeugzylinder und andere sicherheitskritische Bauteile zu schweißen.
- Behälter- und Apparatebau: Hier kommen Kreisschweißmaschinen zur Anwendung, um Tanks, Kessel und Druckbehälter zu schweißen, die eine hohe Schweißnahtqualität und Dichtigkeit erfordern.
- Rohre und Rohrverbindungen: Insbesondere in der Öl- und Gasindustrie sowie in der Wasserversorgung sind Kreisschweißmaschinen von zentraler Bedeutung, um lange Rohrverbindungen effizient und präzise herzustellen.
Vorteile der Automatischen Kreisschweißmaschine
Automatische Kreisschweißmaschinen bieten eine Reihe von entscheidenden Vorteilen, die sie zu einer unverzichtbaren Technologie in der modernen Fertigung machen:
- Hohe Präzision und Wiederholgenauigkeit: Da der gesamte Schweißprozess automatisiert ist und durch eine CNC-Steuerung präzise kontrolliert wird, können gleichbleibende und hochqualitative Schweißnähte erzielt werden.
- Effizienzsteigerung: Automatisierte Maschinen ermöglichen eine signifikant höhere Produktionsrate im Vergleich zu manuellen Schweißverfahren. Dies reduziert die Fertigungszeit und erhöht die Gesamteffizienz.
- Reduzierte Fehlerquote: Die Automatisierung minimiert das Risiko menschlicher Fehler, was besonders bei sicherheitskritischen Anwendungen wichtig ist.
- Flexibilität: Moderne Kreisschweißmaschinen sind in der Lage, unterschiedliche Schweißverfahren zu unterstützen (MIG, TIG, Laserschweißen), was sie für eine Vielzahl von Anwendungen flexibel einsetzbar macht.
- Kostensenkung: Durch die höhere Effizienz, die reduzierte Fehlerquote und den geringeren Personalaufwand können Unternehmen langfristig erhebliche Kosteneinsparungen realisieren.
- Verbesserte Arbeitssicherheit: Da die Bediener weniger direkt in den Schweißprozess eingreifen müssen, wird das Risiko von Verletzungen durch Lichtbogenstrahlung oder heiße Werkstücke erheblich reduziert.
Herausforderungen und Einschränkungen
Trotz der vielen Vorteile gibt es einige Herausforderungen, die bei der Implementierung von automatischen Kreisschweißmaschinen berücksichtigt werden müssen:
- Hohe Anfangsinvestitionen: Die Anschaffung und Einrichtung einer automatisierten Schweißmaschine kann kostspielig sein. Für kleinere Unternehmen oder solche mit geringen Produktionsvolumina kann dies eine erhebliche Hürde darstellen.
- Schulung und Wartung: Obwohl die Maschinen den Schweißprozess automatisieren, erfordert ihre Bedienung spezielles Fachwissen, insbesondere im Bereich der Programmierung und Wartung. Regelmäßige Schulungen und Wartungsarbeiten sind notwendig, um die Maschinen optimal zu betreiben.
- Begrenzte Flexibilität bei komplexen Geometrien: Während Kreisschweißmaschinen ideal für zylindrische und runde Werkstücke sind, stoßen sie bei unregelmäßigen oder komplexen Geometrien an ihre Grenzen. Hier sind häufig zusätzliche Vorrichtungen oder manuelle Eingriffe notwendig.
MIG-Rundschweißgerät – Funktionsweise und Anwendungsbereiche
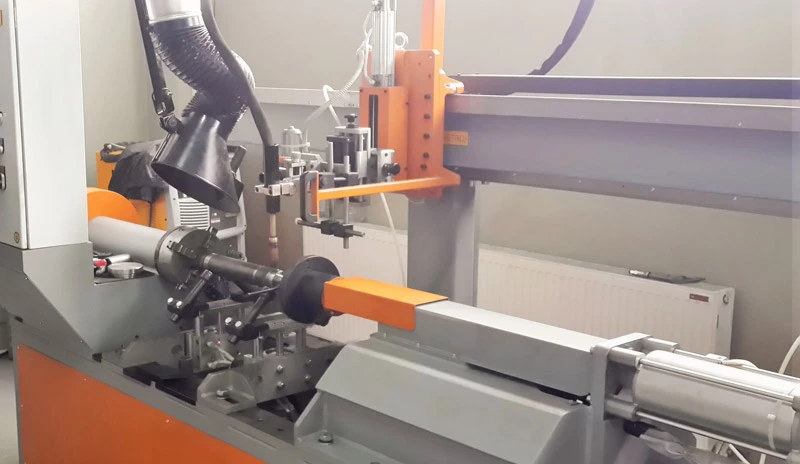
MIG-Schweißen: Grundlagen
Das MIG-Schweißen (Metal-Inert-Gas-Schweißen) ist ein weit verbreitetes Schweißverfahren, das durch seine Vielseitigkeit und Effizienz in einer Vielzahl von industriellen Anwendungen eingesetzt wird. Beim MIG-Schweißen wird ein kontinuierlich zugeführter Draht als Schweißelektrode verwendet. Dieser Draht schmilzt unter der Hitze des elektrischen Lichtbogens und verbindet sich mit dem Grundmaterial. Dabei wird ein inertes Gas (in der Regel Argon oder Helium) als Schutzgas verwendet, das den Schweißbereich vor Oxidation und anderen Verunreinigungen schützt. Das MIG-Schweißen ist besonders beliebt, weil es sowohl für dicke als auch dünne Materialien geeignet ist und eine hohe Schweißgeschwindigkeit bietet.
Ein MIG-Rundschweißgerät kombiniert die MIG-Schweißtechnologie mit der Fähigkeit, zylindrische Werkstücke präzise zu schweißen. Das Rundschweißen beschreibt den Prozess, bei dem das Werkstück während des Schweißens rotiert wird, um eine gleichmäßige Schweißnaht entlang der zirkularen Oberfläche zu erzeugen. Dies ist besonders nützlich für das Schweißen von Rohren, Zylindern, Flanschen und anderen kreisförmigen Bauteilen.
Eigenschaften eines MIG-Rundschweißgeräts
Ein MIG-Rundschweißgerät verfügt über spezielle Eigenschaften, die es von herkömmlichen MIG-Schweißgeräten unterscheiden und für den Rundschweißprozess optimieren:
- Drehvorrichtung für das Werkstück: Im Zentrum des MIG-Rundschweißens steht die Fähigkeit, das Werkstück während des Schweißvorgangs zu drehen. Diese Drehvorrichtung ist präzise kalibriert, um eine gleichmäßige Schweißnaht entlang der kreisförmigen Oberfläche zu gewährleisten. Sie kann für verschiedene Werkstückgrößen und -gewichte angepasst werden.
- Automatisierte Drahtzuführung: Ähnlich wie bei herkömmlichen MIG-Schweißgeräten wird auch bei einem Rundschweißgerät der Schweißdraht kontinuierlich zugeführt, um den Schweißprozess effizient und ohne Unterbrechung durchzuführen.
- CNC-Steuerung für Präzision: Moderne MIG-Rundschweißgeräte sind in der Regel mit CNC-Steuerungen ausgestattet, die eine präzise Programmierung und Steuerung des Schweißvorgangs ermöglichen. Dies sorgt für gleichbleibende Qualität und minimiert Fehlerquellen.
- Variable Schweißgeschwindigkeiten: Da die Werkstücke unterschiedliche Geometrien und Materialien aufweisen können, muss die Schweißgeschwindigkeit an die spezifischen Anforderungen angepasst werden. MIG-Rundschweißgeräte bieten daher variable Geschwindigkeiten, um die beste Schweißnahtqualität zu gewährleisten.
- Schutzgaszuführung: Da das MIG-Schweißen auf ein Schutzgas angewiesen ist, sind MIG-Rundschweißgeräte mit integrierten Systemen zur präzisen Gaszufuhr ausgestattet, um den Schweißbereich vor atmosphärischen Einflüssen zu schützen.
Anwendungsbereiche des MIG-Rundschweißens
Das MIG-Rundschweißen wird in einer Vielzahl von Industrien verwendet, insbesondere in Bereichen, in denen zylindrische oder runde Bauteile geschweißt werden müssen. Einige der wichtigsten Anwendungsbereiche umfassen:
- Rohr- und Rohrleitungsbau: Das Schweißen von Rohren ist eine der häufigsten Anwendungen für MIG-Rundschweißgeräte. In der Öl- und Gasindustrie sowie in der Wasserversorgung müssen Rohrleitungen häufig nahtlos und sicher miteinander verbunden werden. Das MIG-Rundschweißen ermöglicht es, lange Rohre effizient und mit hoher Schweißnahtqualität herzustellen.
- Druckbehälter und Kessel: In der Herstellung von Druckbehältern, die hohen Belastungen und Drücken standhalten müssen, ist eine gleichmäßige und zuverlässige Schweißnaht entscheidend. Das MIG-Rundschweißen bietet hier die nötige Präzision und Stabilität, um sicherzustellen, dass die Behälter den erforderlichen Sicherheitsstandards entsprechen.
- Automobilindustrie: In der Automobilfertigung werden MIG-Rundschweißgeräte für das Schweißen von Auspuffsystemen, Stoßdämpfern und anderen zylindrischen Bauteilen eingesetzt. Durch die hohe Schweißgeschwindigkeit können Produktionszeiten verkürzt und Kosten gesenkt werden.
- Luft- und Raumfahrt: Präzision und Zuverlässigkeit sind in der Luft- und Raumfahrtindustrie von entscheidender Bedeutung. MIG-Rundschweißgeräte werden verwendet, um kritische Komponenten wie Triebwerkszylinder und andere runde Bauteile mit höchster Genauigkeit zu schweißen.
- Möbel- und Metallverarbeitungsindustrie: In der Produktion von Metallmöbeln oder dekorativen Metallteilen ist das Rundschweißen oft erforderlich, um ästhetisch ansprechende und stabile Verbindungen zu erzeugen. Das MIG-Rundschweißen bietet die Möglichkeit, solche Teile schnell und präzise zu schweißen.
Vorteile des MIG-Rundschweißens
Das MIG-Rundschweißen bietet mehrere Vorteile, die es von anderen Schweißverfahren abheben:
- Hohe Schweißgeschwindigkeit: Das kontinuierliche Schweißen und die automatische Drahtzuführung sorgen für eine schnellere Produktion im Vergleich zu manuellen Schweißverfahren. Dies spart Zeit und erhöht die Effizienz in der Produktion.
- Gleichmäßige Schweißnähte: Die Drehvorrichtung und die präzise Steuerung der Schweißgeschwindigkeit ermöglichen es, gleichmäßige und qualitativ hochwertige Schweißnähte entlang der gesamten kreisförmigen Oberfläche des Werkstücks zu erzeugen.
- Wenig Nacharbeit: Da die Schweißnähte gleichmäßig und präzise sind, ist weniger Nachbearbeitung erforderlich. Dies reduziert den Zeitaufwand und die Kosten für das Schleifen oder Polieren der Schweißnähte.
- Vielseitigkeit bei Materialien: Das MIG-Schweißen ist für eine Vielzahl von Materialien geeignet, darunter Aluminium, Edelstahl, Kohlenstoffstahl und andere Legierungen. Dies macht MIG-Rundschweißgeräte zu einer flexiblen Lösung für verschiedene Anwendungen.
- Einfache Automatisierung: MIG-Rundschweißgeräte lassen sich leicht in automatisierte Fertigungslinien integrieren. Dies macht sie zu einer idealen Wahl für Unternehmen, die ihre Produktion steigern und gleichzeitig Kosten senken möchten.
Herausforderungen des MIG-Rundschweißens
Obwohl das MIG-Rundschweißen viele Vorteile bietet, gibt es auch einige Herausforderungen, die bei der Anwendung berücksichtigt werden müssen:
- Hohe Anfangsinvestitionen: Ähnlich wie bei anderen automatisierten Schweißgeräten können die Anschaffungskosten für MIG-Rundschweißgeräte hoch sein, insbesondere für Unternehmen, die keine Großserienfertigung betreiben.
- Komplexität der Einstellung: Das Einrichten eines MIG-Rundschweißgeräts erfordert Fachwissen, insbesondere in Bezug auf die Programmierung der CNC-Steuerung und die Einstellung der Schweißparameter. Eine fehlerhafte Konfiguration kann zu minderwertigen Schweißnähten oder Schäden am Werkstück führen.
- Materialabhängige Herausforderungen: Je nach Material können unterschiedliche Schutzgase und Schweißdrahtarten erforderlich sein. Das Schweißen von dünnen Materialien oder Legierungen kann anspruchsvoll sein und erfordert präzise Einstellungen.
- Schutzgasmanagement: Da das MIG-Schweißen stark von einem konstanten Schutzgasstrom abhängt, können Probleme bei der Gaszufuhr die Schweißqualität beeinträchtigen. Ein fehlerhaftes Gasmanagement kann zu Porosität oder anderen Defekten in der Schweißnaht führen.
Automatische Schweißmaschinen – Von der manuellen Bedienung zur vollautomatischen Steuerung
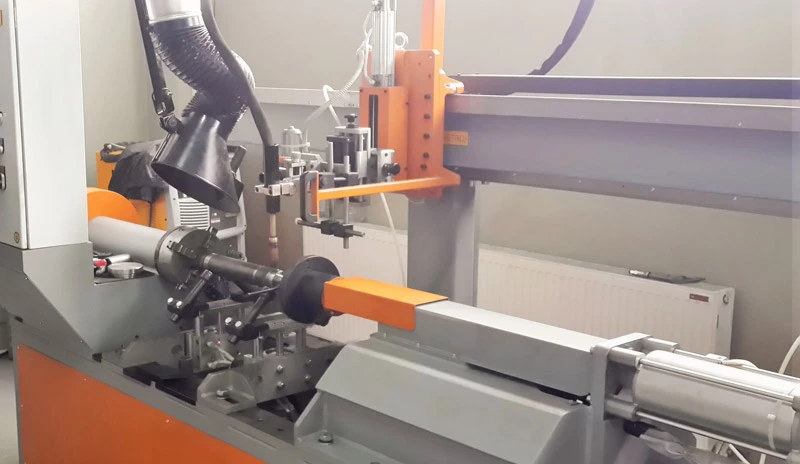
Schweißmaschinen haben sich seit ihren ersten Anwendungen erheblich weiterentwickelt. In den frühen Tagen der industriellen Fertigung waren Schweißprozesse überwiegend manuell und erforderten hochqualifizierte Fachkräfte, um präzise und dauerhafte Verbindungen herzustellen. Die Notwendigkeit, große Mengen an Bauteilen zu schweißen, führte schließlich zu Verbesserungen im Bereich der automatischen Schweißmaschinen.
Heutige automatische Schweißmaschinen ermöglichen es, komplexe Schweißprozesse mit minimalem menschlichen Eingriff durchzuführen. Sie integrieren fortschrittliche Steuerungssysteme, wie Computer Numerical Control (CNC) und Robotertechnologien, um präzise, schnelle und wiederholbare Schweißnähte zu erzeugen. In diesem Abschnitt werden wir die Entwicklung von manuellen Schweißverfahren hin zu modernen vollautomatischen Systemen nachvollziehen.
Technologien und Steuerungssysteme
Moderne automatische Schweißmaschinen basieren auf einer Vielzahl von Technologien und Steuerungssystemen, die es ermöglichen, unterschiedlichste Schweißverfahren für spezifische Anwendungen zu automatisieren. Hier sind einige der zentralen Technologien, die den Übergang von manuellen zu vollautomatischen Schweißmaschinen vorangetrieben haben:
- CNC-Steuerungen: Eine der wichtigsten Innovationen in der Schweißtechnik ist die Einführung der CNC-Steuerung. Diese ermöglicht die präzise Programmierung und Steuerung der Maschinenbewegungen, wodurch eine extrem hohe Genauigkeit und Wiederholbarkeit bei komplexen Schweißaufgaben erreicht werden. CNC-gesteuerte Maschinen sind in der Lage, komplizierte Schweißmuster oder mehrfache Schweißnähte ohne menschliches Eingreifen durchzuführen.
- Robotertechnologie: Roboterarme und automatisierte Schweißzellen sind in modernen Fertigungsanlagen weit verbreitet. Diese Roboter sind so konzipiert, dass sie Schweißaufgaben autonom und mit hoher Präzision ausführen können. Sie werden oft in der Automobilindustrie, der Luft- und Raumfahrt sowie im Schiffbau eingesetzt, um große Bauteile schnell und effizient zu schweißen.
- Laser-Schweißtechnologie: Laser-Schweißen ist eine moderne Technologie, die häufig in automatisierten Schweißsystemen zum Einsatz kommt. Sie ermöglicht extrem feine und präzise Schweißnähte bei hoher Geschwindigkeit, was besonders in Branchen mit sehr hohen Qualitätsanforderungen wie der Medizintechnik oder der Elektronikfertigung wichtig ist.
- Vision-Systeme und Sensorik: Fortschrittliche automatische Schweißmaschinen verwenden Vision-Systeme und Sensorik, um den Schweißprozess in Echtzeit zu überwachen. Diese Systeme erkennen Materialunregelmäßigkeiten, Positionsabweichungen oder Veränderungen in der Schweißnaht und passen den Prozess sofort an, um die gewünschte Qualität zu gewährleisten. Fehlererkennungs- und Korrektursysteme sind von entscheidender Bedeutung für die Sicherstellung der Schweißnahtqualität bei hochautomatisierten Prozessen.
Vorteile der Automatisierung in der Schweißtechnik
Die Automatisierung im Schweißprozess hat zahlreiche Vorteile, die sie für viele Industriezweige unverzichtbar machen. Zu den wichtigsten Vorteilen gehören:
- Gesteigerte Effizienz und Produktivität:
- Höhere Produktionsgeschwindigkeiten: Automatische Schweißmaschinen können rund um die Uhr arbeiten und gleichbleibend hohe Produktionsgeschwindigkeiten aufrechterhalten. Im Vergleich zu manuellen Prozessen, die häufig durch menschliche Erschöpfung oder Fehler beeinträchtigt werden, bieten diese Maschinen eine kontinuierliche und präzise Fertigung.
- Reduzierung der Produktionszeit: Da die Maschinen so programmiert werden können, dass sie mehrere Arbeitsschritte in einem Durchgang erledigen, können Produktionszeiten drastisch verkürzt werden.
- Erhöhte Sicherheit am Arbeitsplatz:
- Weniger direkte menschliche Interaktion: Automatische Schweißmaschinen minimieren den Bedarf an direkter menschlicher Beteiligung am Schweißprozess, wodurch das Risiko von Arbeitsunfällen, wie z.B. durch Lichtbogenstrahlung, Schweißdämpfe oder heiße Werkstücke, erheblich verringert wird.
- Sicherheitsmechanismen und Überwachungsfunktionen: Moderne Maschinen verfügen über integrierte Sicherheitsmechanismen, die den Schweißvorgang sofort unterbrechen, wenn eine Gefahrensituation erkannt wird.
- Verbesserte Schweißnahtqualität:
- Konstanz und Wiederholbarkeit: Automatische Schweißmaschinen bieten eine hohe Wiederholgenauigkeit, was besonders bei Serienfertigungen von großer Bedeutung ist. Die Präzision, die durch CNC-Steuerungen und Robotertechnologien ermöglicht wird, sorgt für gleichbleibende Qualität, unabhängig von der Anzahl der Werkstücke.
- Minimierung menschlicher Fehler: Manuelle Schweißprozesse sind anfällig für Fehler, die durch Ermüdung, Ablenkung oder mangelnde Erfahrung verursacht werden können. Automatische Systeme eliminieren solche Faktoren und bieten eine deutlich höhere Zuverlässigkeit.
- Kosteneinsparungen:
- Reduzierung von Lohnkosten: Durch den Einsatz von automatisierten Schweißmaschinen kann der Bedarf an qualifizierten Schweißern verringert werden. Dies führt zu einer Senkung der Personalkosten, insbesondere in Hochlohnländern.
- Weniger Materialverschwendung: Durch die präzise Steuerung des Schweißprozesses wird weniger Material verschwendet, und es entstehen weniger fehlerhafte Werkstücke, die nachbearbeitet oder entsorgt werden müssen.
Beispiele für vollautomatische Schweißmaschinen in der Industrie
In verschiedenen Industrien kommen vollautomatische Schweißmaschinen erfolgreich zum Einsatz. Hier einige Beispiele:
- Automobilindustrie:
- In der Automobilfertigung sind Schweißroboter in nahezu jedem Produktionsschritt zu finden, vom Schweißen der Karosserie bis hin zur Montage von Bauteilen wie Auspuffanlagen und Fahrgestellen. Vollautomatische Schweißmaschinen ermöglichen hier eine extrem hohe Produktionsrate und gleichbleibende Qualität, was für die Massenproduktion von entscheidender Bedeutung ist.
- Schiffbau:
- Der Schiffbau erfordert großflächige Schweißarbeiten, bei denen es auf Präzision und Geschwindigkeit ankommt. Vollautomatische Schweißsysteme, insbesondere solche, die auf Lasertechnologie basieren, sind in der Lage, große Stahlplatten mit hoher Genauigkeit zu verschweißen und so die Bauzeiten erheblich zu verkürzen.
- Luft- und Raumfahrt:
- In der Luftfahrtindustrie sind die Anforderungen an die Schweißqualität extrem hoch, da selbst kleinste Fehler zu schwerwiegenden Sicherheitsproblemen führen können. Vollautomatische Schweißmaschinen, die mit fortschrittlichen Überwachungssystemen ausgestattet sind, sorgen für die Herstellung von hochpräzisen Bauteilen wie Triebwerkskomponenten oder Flugzeugrümpfen.
- Medizintechnik:
- In der Medizintechnik, wo Geräte und Implantate höchsten Qualitätsstandards entsprechen müssen, kommen vollautomatische Schweißmaschinen zum Einsatz, um kleinste Bauteile wie chirurgische Instrumente oder Implantate zu schweißen. Diese Maschinen sind in der Lage, feine und präzise Schweißnähte zu erzeugen, die den strengen Anforderungen der Branche gerecht werden.
Automatisiertes Schweißgerät – Technologien und Innovationen
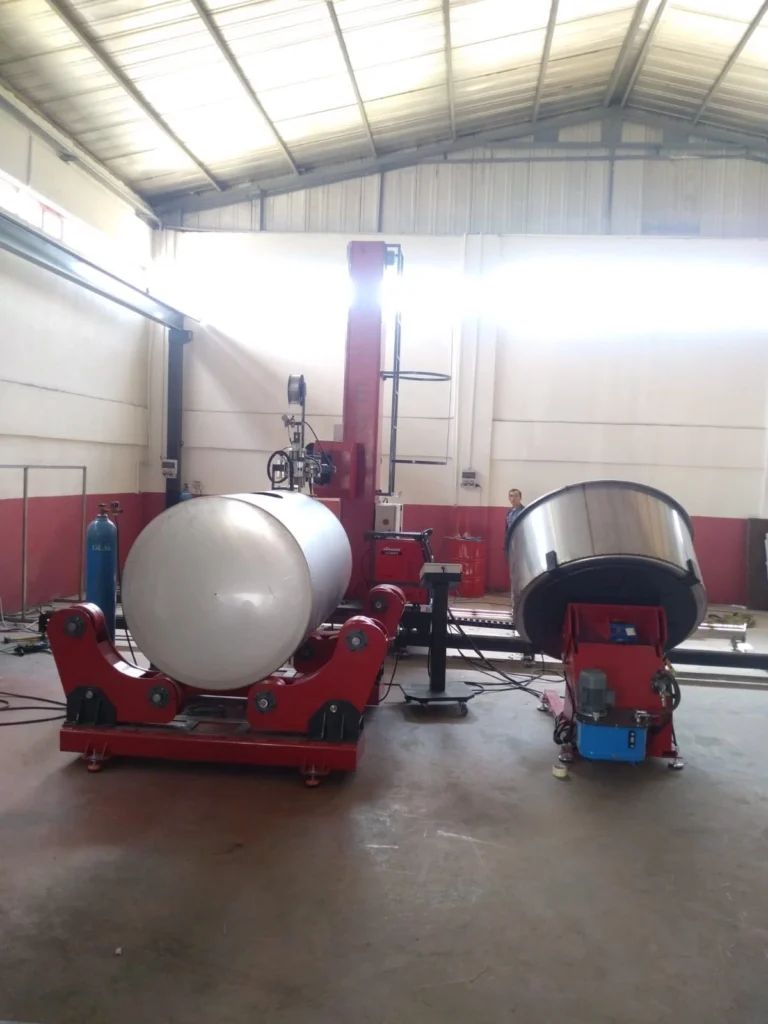
Definition und Typen automatisierter Schweißgeräte
Automatisierte Schweißgeräte sind ein wesentlicher Bestandteil der modernen Fertigungstechnologie und ermöglichen es, Schweißprozesse präzise und effizient durchzuführen. Diese Geräte decken eine breite Palette von Schweißverfahren ab, darunter das MIG- (Metal-Inert-Gas), TIG- (Tungsten-Inert-Gas), Lichtbogen- und Laserschweißen. Automatisierte Schweißgeräte können sowohl eigenständige, spezialisierte Maschinen sein als auch Teil komplexer Produktionslinien, in denen sie durch Roboter, CNC-Steuerungen und andere Technologien unterstützt werden.
Im Wesentlichen lassen sich automatisierte Schweißgeräte in zwei Hauptkategorien unterteilen:
- Fest installierte Schweißgeräte: Diese Maschinen sind in eine Produktionslinie integriert und übernehmen spezifische Schweißaufgaben in einem festgelegten Bereich. Sie sind besonders in der Großserienfertigung verbreitet, z. B. in der Automobil- oder Luftfahrtindustrie, wo Bauteile in großen Stückzahlen mit konsistenter Qualität hergestellt werden müssen. Ein Beispiel hierfür sind Schweißzellen, die durch Roboterarme gesteuert werden, die autonom mehrere Schweißnähte an einem Werkstück durchführen.
- Robotergestützte Schweißsysteme: Roboterschweißgeräte sind mit Roboterarmen ausgestattet, die auf präzisen Bahnen programmiert sind, um komplizierte Schweißnähte an Werkstücken unterschiedlicher Geometrien zu erzeugen. Diese Systeme sind extrem flexibel und können auf verschiedene Schweißverfahren eingestellt werden. Sie ermöglichen die Bearbeitung komplexer Geometrien und können in hochdynamischen Produktionsumgebungen eingesetzt werden.
Technologische Innovationen in automatisierten Schweißgeräten
Mit dem raschen Fortschritt in den Bereichen Robotik, Sensorik und Datenverarbeitung erleben auch automatisierte Schweißgeräte signifikante technologische Innovationen. Diese Fortschritte zielen darauf ab, die Effizienz, Präzision und Flexibilität der Schweißgeräte weiter zu verbessern. Einige der bedeutendsten Innovationen in diesem Bereich sind:
- Künstliche Intelligenz (KI) und maschinelles Lernen:
- Optimierung des Schweißprozesses: KI-gesteuerte Schweißgeräte können Schweißprozesse in Echtzeit analysieren und anpassen, um optimale Ergebnisse zu erzielen. Dabei verwenden sie maschinelles Lernen, um Daten aus früheren Schweißvorgängen zu analysieren und den Prozess kontinuierlich zu verbessern. Solche Systeme können Fehler automatisch erkennen und Anpassungen vornehmen, um die Qualität der Schweißnähte zu gewährleisten.
- Echtzeit-Fehlererkennung: Mithilfe von Sensoren und Kameras können KI-gesteuerte Systeme Unregelmäßigkeiten oder Defekte in der Schweißnaht sofort erkennen und den Prozess anpassen, um sicherzustellen, dass die Qualitätsanforderungen erfüllt werden. Dies minimiert Ausschuss und Nachbearbeitung.
- Integration von Vision-Systemen und Sensorik:
- Verbesserte Überwachung: Automatisierte Schweißgeräte sind zunehmend mit fortschrittlichen Vision-Systemen ausgestattet, die den Schweißvorgang in Echtzeit überwachen. Diese Kamerasysteme analysieren die Schweißnaht, die Flussrate des Schutzgases und die Materialpositionierung. Durch die Integration von Sensorik können die Maschinen den Schweißvorgang präzise anpassen, um die beste Schweißqualität sicherzustellen.
- Laser-Triangulation: Eine weitere technologische Innovation ist die Laser-Triangulation, die es ermöglicht, den Abstand zwischen dem Schweißkopf und dem Werkstück genau zu messen. Dies gewährleistet, dass der Schweißprozess mit konstanter Genauigkeit durchgeführt wird.
- Laserschweißtechnologie:
- Hohe Präzision und Geschwindigkeit: Laserschweißgeräte nutzen hochkonzentrierte Lichtstrahlen, um extrem präzise und saubere Schweißnähte zu erzeugen. Diese Technologie ist besonders nützlich für Anwendungen, die eine sehr hohe Genauigkeit erfordern, wie etwa in der Elektronik- oder Medizintechnik.
- Materialvielfalt: Das Laserschweißen kann für eine Vielzahl von Materialien eingesetzt werden, darunter Metalle mit hoher Wärmeleitfähigkeit, wie Aluminium oder Kupfer. Es ermöglicht auch das Schweißen von Materialien unterschiedlicher Dicke, was mit herkömmlichen Verfahren schwierig sein kann.
- Datenanalyse und industrielle Internet-of-Things (IoT)-Integration:
- Predictive Maintenance (vorausschauende Wartung): Automatisierte Schweißgeräte, die mit IoT-Technologien verbunden sind, können Wartungsanforderungen im Voraus erkennen. Durch die Überwachung von Maschinenparametern in Echtzeit können Ausfälle vermieden werden, da die Maschinen ihre eigenen Zustandsdaten analysieren und vorausschauend Wartungsarbeiten anfordern.
- Produktionsdatenanalyse: IoT-fähige Schweißgeräte sammeln und analysieren kontinuierlich Daten über den Schweißprozess. Diese Daten können genutzt werden, um die Effizienz der Produktionslinie zu verbessern, Fehlerquellen zu identifizieren und den Gesamtproduktionsprozess zu optimieren.
Integration in die Fertigungsumgebung
Die Integration von automatisierten Schweißgeräten in bestehende Produktionslinien ist ein entscheidender Schritt zur Steigerung der Gesamtproduktivität und -effizienz. Dabei müssen mehrere Faktoren berücksichtigt werden:
- Kombination mit anderen Fertigungstechnologien: Automatisierte Schweißgeräte werden häufig in Kombination mit anderen Produktionssystemen eingesetzt, wie z. B. automatischen Materialhandhabungssystemen, Schneidemaschinen oder Robotern zur Werkstückpositionierung. Diese Integration erfordert eine nahtlose Kommunikation zwischen den Maschinen, was durch standardisierte Steuerungssysteme und Protokolle wie OPC-UA (Open Platform Communications Unified Architecture) erreicht werden kann.
- Flexibilität und Skalierbarkeit: Moderne automatisierte Schweißsysteme sind flexibel genug, um an verschiedene Werkstückgrößen und -formen angepasst zu werden. Dies ist besonders wichtig in Umgebungen, in denen verschiedene Produktvarianten auf derselben Produktionslinie hergestellt werden. Die Skalierbarkeit dieser Systeme ermöglicht es Unternehmen, ihre Produktionskapazität zu erhöhen, ohne umfangreiche Änderungen an der Infrastruktur vorzunehmen.
- Mensch-Maschine-Interaktion (HMI): Trotz der fortschreitenden Automatisierung bleibt die Interaktion zwischen Mensch und Maschine entscheidend. Benutzerfreundliche Schnittstellen, über die Bediener die Maschinenparameter steuern und den Produktionsfortschritt überwachen können, sind integraler Bestandteil moderner automatisierter Schweißgeräte. Die intuitive Gestaltung solcher HMI-Systeme trägt dazu bei, Fehler zu minimieren und die Effizienz der Bediener zu maximieren.
Wirtschaftliche Aspekte
Die Implementierung automatisierter Schweißgeräte bringt eine Vielzahl von wirtschaftlichen Vorteilen mit sich, die sich sowohl in der kurzen als auch in der langen Frist bemerkbar machen:
- Reduzierung von Arbeitskosten: Automatisierte Schweißgeräte minimieren den Bedarf an qualifiziertem Schweißpersonal, da der Großteil des Prozesses maschinell durchgeführt wird. Dies ist besonders in Regionen mit hohen Lohnkosten von Vorteil.
- Erhöhte Produktionseffizienz: Durch die kontinuierliche Arbeitsweise von automatisierten Maschinen können Unternehmen ihre Produktionskapazität steigern und gleichzeitig die Fehlerquote reduzieren. Die verbesserte Effizienz führt zu einer schnelleren Amortisation der anfänglichen Investitionen.
- Qualitätssteigerung und geringere Nacharbeitskosten: Automatisierte Schweißgeräte gewährleisten gleichbleibend hohe Schweißqualität, wodurch weniger Nacharbeiten erforderlich sind. Dies senkt die Gesamtkosten pro Werkstück und minimiert den Ausschuss.
- Wartungs- und Betriebskosten: Durch die Integration von IoT und vorausschauender Wartung können ungeplante Stillstandszeiten reduziert und die Gesamtbetriebskosten gesenkt werden.
Vergleich – Automatische Kreisschweißmaschine, MIG-Rundschweißgerät und andere automatisierte Schweißmaschinen
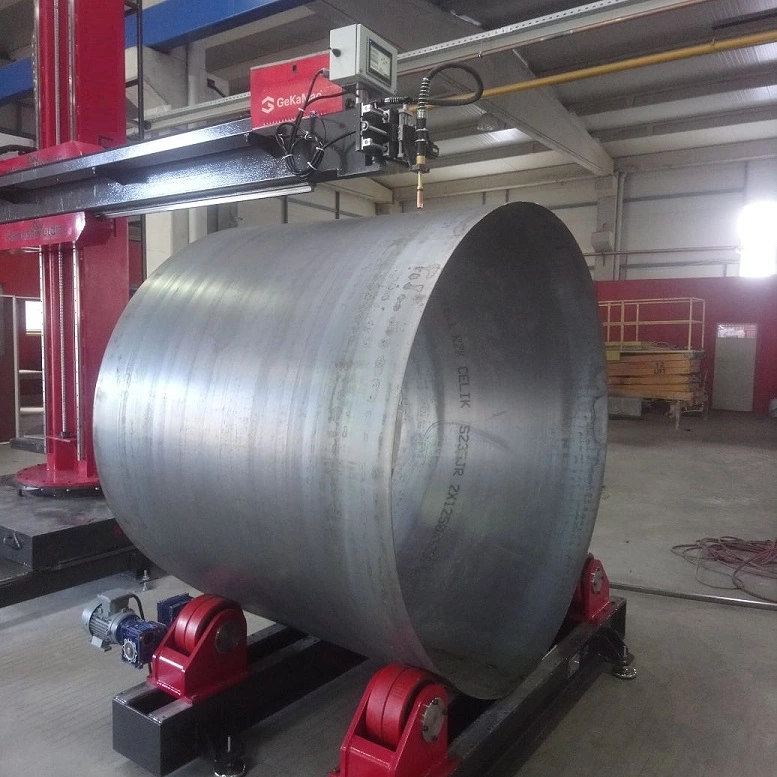
In der modernen Fertigung stehen zahlreiche Schweißtechnologien zur Verfügung, die jeweils spezifische Vorteile und Einsatzgebiete aufweisen. Zu den häufig verwendeten Schweißgeräten gehören die automatische Kreisschweißmaschine, das MIG-Rundschweißgerät sowie weitere automatisierte Schweißsysteme, wie robotergesteuerte und CNC-gesteuerte Schweißmaschinen. Jede dieser Technologien hat einzigartige Merkmale, die sie für bestimmte Anwendungen besser geeignet machen. In diesem Abschnitt vergleichen wir diese Technologien hinsichtlich ihrer Funktionsweise, Einsatzbereiche, Vorteile und Herausforderungen.
Vergleich der Hauptmerkmale
- Automatische Kreisschweißmaschine:
- Funktionsweise: Die automatische Kreisschweißmaschine ist speziell für das Schweißen von zylindrischen oder kreisförmigen Werkstücken ausgelegt. Sie verwendet eine Drehvorrichtung, die das Werkstück während des Schweißprozesses rotieren lässt, um eine gleichmäßige Schweißnaht zu erzeugen. Der Schweißkopf bewegt sich entweder um das Werkstück oder bleibt fixiert, während das Werkstück sich dreht.
- Anwendungsbereiche: Häufig in der Automobilindustrie (Auspuffanlagen, Zylinder), im Rohrleitungsbau (Öl und Gas, Wasserleitungen) und in der Behälterherstellung (Tanks, Kessel) verwendet.
- Vorteile: Hohe Präzision, gleichmäßige Schweißnähte, Eignung für Serienproduktion.
- Nachteile: Eignet sich nur für runde oder zylindrische Werkstücke und ist weniger flexibel für komplexere Geometrien.
- MIG-Rundschweißgerät:
- Funktionsweise: Das MIG-Rundschweißgerät kombiniert die MIG-Schweißtechnologie mit einer Rotationsvorrichtung, die es ermöglicht, zylindrische Werkstücke präzise zu schweißen. Der MIG-Draht wird kontinuierlich zugeführt, während das Werkstück rotiert, um eine konsistente Schweißnaht zu erzeugen. MIG-Schweißen verwendet dabei ein Schutzgas (wie Argon oder Helium), um den Schweißbereich zu isolieren.
- Anwendungsbereiche: Besonders geeignet für Rohrverbindungen, Druckbehälter, Automobilbauteile wie Stoßdämpfer und Auspuffsysteme.
- Vorteile: Effizient bei großen Volumen, hohe Schweißgeschwindigkeit, flexibel bei verschiedenen Materialien (z.B. Aluminium, Edelstahl).
- Nachteile: Höhere Investitionskosten für spezielle MIG-Rundschweißgeräte; erfordert sorgfältige Gassteuerung und präzise Maschinenkonfiguration.
- Robotergestützte Schweißsysteme:
- Funktionsweise: Diese Schweißsysteme nutzen Roboterarme, die flexibel auf verschiedene Schweißprozesse (MIG, TIG, Lichtbogenschweißen) eingestellt werden können. Die Roboter führen das Schweißen autonom durch, indem sie präzise Bahnen programmierter Schweißnähte folgen. Sie können sowohl stationäre Werkstücke bearbeiten als auch bewegliche Teile in einer Produktionslinie schweißen.
- Anwendungsbereiche: Verbreitet in der Automobil-, Luft- und Raumfahrt- sowie Elektronikindustrie. Ideal für Serienproduktion mit hoher Wiederholgenauigkeit.
- Vorteile: Höchste Flexibilität bei komplexen Geometrien, schnelle Anpassung an verschiedene Werkstücke, hohe Präzision und Geschwindigkeit.
- Nachteile: Hohe Investitionskosten, erforderliche Programmierkenntnisse, regelmäßige Wartung erforderlich.
- CNC-gesteuerte Schweißmaschinen:
- Funktionsweise: CNC-gesteuerte Schweißsysteme basieren auf numerischer Steuerungstechnologie, die die Maschinenbewegungen präzise steuert. Diese Systeme sind extrem vielseitig und können in Kombination mit verschiedenen Schweißmethoden (MIG, TIG, Laser) eingesetzt werden. Die CNC-Steuerung ermöglicht komplexe und präzise Schweißaufgaben ohne menschliches Eingreifen.
- Anwendungsbereiche: Typisch in hochpräzisen Fertigungsprozessen wie im Maschinenbau, der Medizintechnik oder der Elektronikindustrie.
- Vorteile: Extrem hohe Präzision, Konsistenz bei komplexen Schweißprozessen, geeignet für wiederholbare Serienfertigung.
- Nachteile: Hohe Anfangsinvestitionen, erfordert qualifiziertes Personal für Programmierung und Wartung.
Wann welche Technologie am besten geeignet ist
Die Wahl der optimalen Schweißtechnologie hängt stark von den spezifischen Anforderungen des Projekts ab, insbesondere in Bezug auf Werkstückgeometrie, Materialart, Produktionsvolumen und erforderliche Schweißpräzision.
- Für runde oder zylindrische Bauteile:
- Hier bieten sich die automatische Kreisschweißmaschine und das MIG-Rundschweißgerät an. Beide Systeme sind speziell darauf ausgelegt, gleichmäßige Schweißnähte an zylindrischen Bauteilen zu erzeugen. Die Wahl zwischen diesen beiden hängt von den Materialanforderungen und der gewünschten Schweißgeschwindigkeit ab:
- Kreisschweißmaschine für hohe Präzision und gleichmäßige Rundnähte, ideal für Dickmetallarbeiten.
- MIG-Rundschweißgerät für höhere Geschwindigkeit und Flexibilität bei verschiedenen Metallarten, insbesondere wenn hohe Schweißgeschwindigkeit und Schutzgassteuerung gefragt sind.
- Hier bieten sich die automatische Kreisschweißmaschine und das MIG-Rundschweißgerät an. Beide Systeme sind speziell darauf ausgelegt, gleichmäßige Schweißnähte an zylindrischen Bauteilen zu erzeugen. Die Wahl zwischen diesen beiden hängt von den Materialanforderungen und der gewünschten Schweißgeschwindigkeit ab:
- Für komplexe Werkstückgeometrien:
- Robotergestützte Schweißsysteme sind die beste Wahl, da sie durch ihre flexible Programmierung verschiedene Schweißprozesse auf einer Vielzahl von Werkstücken ausführen können. Dies macht sie besonders für Anwendungen in der Automobil- oder Elektronikindustrie geeignet, wo sowohl Präzision als auch Flexibilität erforderlich sind.
- Für hochpräzise Anwendungen:
- Wenn die Fertigung besonders präzise Schweißnähte erfordert, z. B. in der Medizintechnik oder im Luft- und Raumfahrtsektor, sind Laserschweißgeräte oder CNC-gesteuerte Maschinen die beste Option. Sie bieten die notwendige Präzision und Wiederholgenauigkeit, um sicherzustellen, dass die Schweißnähte höchsten Qualitätsansprüchen genügen.
- Für Serienproduktion:
- In der Großserienproduktion, wo die Geschwindigkeit entscheidend ist und die Schweißnähte standardisiert sein müssen, bieten sich robotergestützte Schweißsysteme und CNC-Schweißmaschinen an. Diese Systeme sind darauf ausgelegt, hohe Stückzahlen mit gleichbleibender Qualität zu fertigen und lassen sich leicht in automatisierte Fertigungslinien integrieren.
Zukunft der Schweißtechnologie
Die Schweißtechnologie entwickelt sich kontinuierlich weiter, um den steigenden Anforderungen der modernen Fertigung gerecht zu werden. Einige der vielversprechendsten Trends, die die Zukunft der Schweißtechnologie prägen werden, sind:
- Künstliche Intelligenz (KI) und maschinelles Lernen:
- KI-gesteuerte Schweißsysteme werden den Schweißprozess weiter optimieren, indem sie selbstständig aus Produktionsdaten lernen und den Schweißprozess in Echtzeit anpassen. Fehlererkennungs- und Korrektursysteme werden immer ausgefeilter, wodurch die Ausschussrate weiter sinken wird.
- Robotik und Automatisierung:
- Der Einsatz von Robotern in der Schweißtechnik wird weiter zunehmen. Fortschritte in der Robotertechnologie ermöglichen eine schnellere Programmierung, größere Flexibilität und die Integration von Schweißsystemen in vollständig automatisierte Produktionslinien.
- Nachhaltigkeit und Energieeffizienz:
- Die Entwicklung umweltfreundlicherer Schweißverfahren steht im Mittelpunkt. Energieeffiziente Schweißtechnologien wie das Laserschweißen und optimierte Schweißprozesse, die den Material- und Energieverbrauch reduzieren, werden weiter an Bedeutung gewinnen.
- Additive Fertigung und Schweißtechnologie:
- Die Kombination von Schweißen und additiver Fertigung (3D-Druck) wird neue Möglichkeiten für die Herstellung von komplexen Bauteilen eröffnen. Schweißtechnologien, die in den 3D-Druckprozess integriert sind, ermöglichen die Herstellung von Teilen mit minimalem Materialeinsatz und hoher Präzision.
Zukunftsaussichten und Trends in der Schweißautomatisierung
Trends in der Robotik und Automatisierung
Die Schweißautomatisierung hat in den letzten Jahren erhebliche Fortschritte gemacht und wird in Zukunft weiter an Bedeutung gewinnen. Eines der größten Wachstumsfelder in diesem Bereich ist die Integration von Robotern in den Schweißprozess. Roboter werden immer intelligenter, schneller und vielseitiger und spielen eine Schlüsselrolle in der Automatisierung von Schweißprozessen in verschiedenen Industrien, wie der Automobilindustrie, dem Maschinenbau und der Luft- und Raumfahrt.
- Kollaborative Roboter (Cobots):
- Cobots sind ein entscheidender Trend in der Schweißautomatisierung. Diese Roboter arbeiten direkt neben menschlichen Bedienern und sind speziell darauf ausgelegt, sicher und einfach bedienbar zu sein. Cobots können kleinere Schweißarbeiten übernehmen, während Menschen für komplexere Aufgaben zuständig sind. Diese symbiotische Arbeitsweise wird es Unternehmen ermöglichen, sowohl die Flexibilität als auch die Effizienz in ihren Produktionslinien zu steigern.
- Ein weiteres Plus der Cobots ist die einfache Programmierung. Bediener können sie durch einfache „Teach-in“-Methoden programmieren, indem sie den Roboterarm manuell bewegen und die gewünschten Schweißpfade festlegen.
- Erweiterte Flexibilität:
- Roboter und automatische Schweißsysteme der Zukunft werden nicht nur auf die Durchführung eines einzigen Schweißprozesses spezialisiert sein. Stattdessen werden sie in der Lage sein, verschiedene Schweißverfahren, wie MIG-, TIG- und Laserschweißen, zu kombinieren. Diese Flexibilität wird die Produktionsprozesse vereinfachen und die Anzahl der notwendigen Maschinen in einer Fertigungslinie verringern.
- Verbesserte Integration in Produktionslinien:
- In Zukunft werden Schweißroboter und automatisierte Systeme vollständig in intelligente Produktionsumgebungen integriert sein. Diese Umgebungen nutzen Sensoren, Echtzeit-Datenanalyse und selbststeuernde Systeme, um Schweißprozesse zu optimieren und Fertigungsfehler nahezu zu eliminieren. Durch die enge Verzahnung von Schweißrobotern mit den übrigen Produktionsmaschinen können alle Schritte eines Fertigungsprozesses, vom Rohmaterial bis zum fertigen Produkt, automatisiert und aufeinander abgestimmt werden.
Künstliche Intelligenz und maschinelles Lernen im Schweißen
Künstliche Intelligenz (KI) und maschinelles Lernen spielen eine immer größere Rolle in der Automatisierung von Schweißprozessen. Diese Technologien ermöglichen es Maschinen, aus ihren Fehlern zu lernen und sich kontinuierlich zu verbessern. Die Hauptvorteile von KI-gesteuerten Schweißsystemen liegen in ihrer Fähigkeit, Echtzeit-Analysen durchzuführen, Anpassungen während des Schweißprozesses vorzunehmen und die Qualität der Schweißnähte zu optimieren.
- Selbstoptimierende Schweißsysteme:
- Durch den Einsatz von maschinellem Lernen können Schweißmaschinen Daten aus früheren Schweißprozessen analysieren und zukünftige Prozesse anpassen, um bessere Ergebnisse zu erzielen. Diese Systeme können z. B. Veränderungen in den Werkstoffeigenschaften oder den Schweißbedingungen erkennen und automatisch die Schweißparameter anpassen, ohne dass ein menschliches Eingreifen erforderlich ist.
- In der Praxis bedeutet dies eine höhere Effizienz, weniger Ausschuss und eine konstante Schweißqualität, auch bei schwankenden Bedingungen.
- Fehlererkennung und Korrektur in Echtzeit:
- Ein weiteres zentrales Anwendungsgebiet für KI ist die Echtzeit-Fehlererkennung. KI-gestützte Schweißsysteme können mithilfe von Kameras und Sensoren Unregelmäßigkeiten in der Schweißnaht sofort erkennen und den Schweißvorgang entsprechend anpassen. Dies reduziert die Anzahl fehlerhafter Bauteile erheblich und minimiert den Bedarf an Nachbearbeitung.
- In Kombination mit automatisierten Inspektionssystemen können Schweißmaschinen Anomalien in den Schweißnähten sofort erkennen und beheben, was zu einer erheblich besseren Produktionsqualität führt.
- Vorausschauende Wartung:
- KI-Systeme spielen eine Schlüsselrolle bei der Implementierung von Predictive Maintenance (vorausschauende Wartung) in automatisierten Schweißprozessen. Durch die kontinuierliche Überwachung von Maschinenparametern wie Temperatur, Stromstärke und Schweißgeschwindigkeit können diese Systeme potenzielle Probleme frühzeitig erkennen und Wartungsarbeiten einplanen, bevor es zu Maschinenausfällen kommt. Dies verhindert unerwartete Produktionsunterbrechungen und verlängert die Lebensdauer der Schweißmaschinen.
Nachhaltigkeit und Umweltvorteile
Mit dem zunehmenden Bewusstsein für die Umwelt und die Notwendigkeit, nachhaltigere Fertigungsprozesse zu entwickeln, werden auch Schweißtechnologien in Zukunft eine bedeutende Rolle bei der Reduzierung des Energieverbrauchs und des Materialeinsatzes spielen.
- Energieeffiziente Schweißtechnologien:
- Neue Schweißverfahren wie das Laserschweißen sind nicht nur schneller und präziser, sondern auch deutlich energieeffizienter als herkömmliche Schweißmethoden. Laser benötigen weniger Energie, um Metalle zu schmelzen, und reduzieren gleichzeitig die thermische Belastung der Werkstücke, was zu weniger Verzug und Nachbearbeitungsbedarf führt.
- Automatisierte Schweißmaschinen werden auch zunehmend mit Energiesparmodi ausgestattet, die die Maschinen in Ruhephasen automatisch herunterfahren oder deren Energieverbrauch während geringer Arbeitslasten reduzieren.
- Materialoptimierung:
- Schweißprozesse der Zukunft werden darauf ausgelegt sein, den Materialverbrauch zu minimieren. Durch den Einsatz präziser Schweißtechnologien, wie dem Laserschweißen oder dem Hybrid-Laser-MIG-Schweißen, kann der Schweißdraht effizienter eingesetzt werden. Auch Schweißnähte werden präziser ausgeführt, wodurch weniger Materialabfälle entstehen.
- Zudem wird die Entwicklung neuer, leichterer Materialien, wie hochfeste Stähle und Aluminiumlegierungen, vorangetrieben, die den Schweißprozess effizienter und umweltfreundlicher machen.
Additive Fertigung und Schweißen
Ein weiterer Zukunftstrend ist die Kombination von additiver Fertigung (3D-Druck) und Schweißtechnologie. Diese beiden Technologien werden zunehmend miteinander verschmelzen, um neue Fertigungsmöglichkeiten zu erschließen.
- Additive Fertigung mit Schweißtechnologie:
- Durch die Integration von Schweißverfahren in den 3D-Druck können hybride Fertigungsmethoden entwickelt werden. Hierbei wird das Bauteil Schicht für Schicht mit 3D-Druckverfahren aufgebaut und anschließend durch präzise Schweißnähte verstärkt oder fertiggestellt. Dies eröffnet neue Möglichkeiten, komplexe Metallstrukturen effizient herzustellen.
- Besonders in der Luft- und Raumfahrt, aber auch in der Automobilindustrie, wird die Kombination von additiver Fertigung und Schweißen zu neuen Leichtbaukonstruktionen führen, die sowohl kosteneffizient als auch umweltfreundlich sind.
- Vorteile in der Fertigung:
- Die Kombination beider Technologien ermöglicht es, Bauteile nicht nur effizienter, sondern auch flexibler herzustellen. Durch die Verwendung von Schweißtechnologien in Kombination mit 3D-Druck können komplexe Geometrien und spezifische Materialanforderungen gleichzeitig berücksichtigt werden, ohne dass zusätzliche Bearbeitungsschritte erforderlich sind.
Zusammenfassung der Zukunftsaussichten
Die Automatisierung des Schweißprozesses wird sich in den kommenden Jahren weiter beschleunigen, angetrieben durch Fortschritte in der Robotik, Künstlichen Intelligenz und maschinellem Lernen. Die Fähigkeit, Prozesse zu überwachen, zu analysieren und in Echtzeit anzupassen, wird die Effizienz, Qualität und Produktivität erheblich steigern. Gleichzeitig wird der Fokus auf Nachhaltigkeit die Entwicklung energieeffizienter Schweißtechnologien und Materialoptimierungen vorantreiben.
Unternehmen, die in fortschrittliche automatisierte Schweißsysteme investieren, werden langfristig profitieren, indem sie ihre Produktionskosten senken, ihre Effizienz steigern und gleichzeitig die Umweltbelastung reduzieren. Mit neuen Technologien wie der additiven Fertigung und der Integration von Schweißverfahren in intelligente Produktionslinien stehen wir vor einer Revolution in der Fertigungstechnik, die den globalen Wettbewerb neu definieren wird.
Automatisierte Schweißmaschinen, wie die automatische Kreisschweißmaschine, das MIG-Rundschweißgerät und andere robotergesteuerte Systeme, sind heute unverzichtbare Bestandteile der modernen Fertigung. Sie bieten nicht nur eine höhere Produktivität und Präzision, sondern auch erhebliche Kostenvorteile durch die Reduzierung von Fehlern und Nachbearbeitung. Die Zukunft des Schweißens liegt zweifellos in der weiteren Automatisierung und der Integration von fortschrittlichen Technologien wie Künstlicher Intelligenz, Robotik und nachhaltigen Fertigungsmethoden.
Unternehmen, die frühzeitig auf diese Trends setzen, werden in der Lage sein, ihre Produktionsprozesse zu optimieren und im globalen Wettbewerb erfolgreich zu bleiben. Die Entwicklung hin zu vollständig vernetzten, intelligenten Produktionslinien wird den Weg in eine neue Ära der industriellen Fertigung ebnen, in der Schweißtechnologie eine zentrale Rolle spielt.
Fazit und Abschluss
Die Automatisierung in der Schweißtechnik hat sich in den letzten Jahren rasant weiterentwickelt und bringt für Unternehmen, die auf moderne Technologien setzen, erhebliche Vorteile. Ob automatische Kreisschweißmaschinen, MIG-Rundschweißgeräte, robotergestützte Schweißsysteme oder CNC-gesteuerte Maschinen – jedes dieser Systeme bietet spezifische Vorteile, die es Unternehmen ermöglichen, ihre Produktionsprozesse zu optimieren und die Produktqualität zu verbessern.
Die Hauptvorteile dieser Technologien liegen in ihrer Fähigkeit, mit hoher Präzision und Effizienz zu arbeiten, die Fehleranfälligkeit zu minimieren und die Produktionskosten langfristig zu senken. Besonders in Branchen wie der Automobil-, Luft- und Raumfahrt-, und der Rohrleitungsindustrie spielen automatisierte Schweißtechnologien eine entscheidende Rolle, um den wachsenden Anforderungen nach Qualität, Geschwindigkeit und Kostenkontrolle gerecht zu werden.
Zukunftstrends wie Künstliche Intelligenz, maschinelles Lernen, Robotik und IoT-Integration werden die Schweißautomatisierung in den kommenden Jahren weiter revolutionieren. Systeme, die selbstlernend sind und sich in Echtzeit an wechselnde Produktionsbedingungen anpassen können, werden die Effizienz noch weiter steigern und die Fehlerraten nahezu eliminieren. Gleichzeitig wird der verstärkte Fokus auf Nachhaltigkeit und Energieeffizienz die Entwicklung energie- und ressourcenschonender Schweißverfahren fördern.
Die Integration dieser Technologien in intelligente Produktionsumgebungen wird dazu beitragen, dass Schweißprozesse noch stärker automatisiert und vernetzt werden, wodurch Unternehmen ihre Wettbewerbsfähigkeit in einer zunehmend globalisierten und technologiegetriebenen Welt sichern können. Auch der Trend hin zur additiven Fertigung in Kombination mit Schweißtechnologien zeigt das enorme Potenzial für innovative Fertigungsansätze, die in der Lage sind, komplexe Bauteile kostengünstiger und effizienter zu produzieren.
Für Unternehmen, die den Schritt in die Automatisierung wagen, ergeben sich eine Vielzahl von Chancen: Kostensenkung, höhere Produktivität, reduzierte Materialabfälle und eine verbesserte Schweißnahtqualität sind nur einige der Vorteile, die durch die Implementierung moderner Schweißsysteme erzielt werden können. Gleichzeitig erfordert die Einführung solcher Systeme eine Investition in Schulung, Wartung und Infrastruktur, um das volle Potenzial dieser Technologien auszuschöpfen.
Insgesamt bleibt festzuhalten, dass automatisierte Schweißmaschinen und die damit verbundenen Innovationen ein wesentlicher Bestandteil der modernen Industrie sind und in den kommenden Jahren eine noch größere Rolle in der Fertigungswelt spielen werden. Die kontinuierlichen technologischen Fortschritte werden den Schweißprozess effizienter, intelligenter und nachhaltiger machen und so dazu beitragen, dass Unternehmen wettbewerbsfähig bleiben und den Anforderungen der Zukunft gerecht werden.