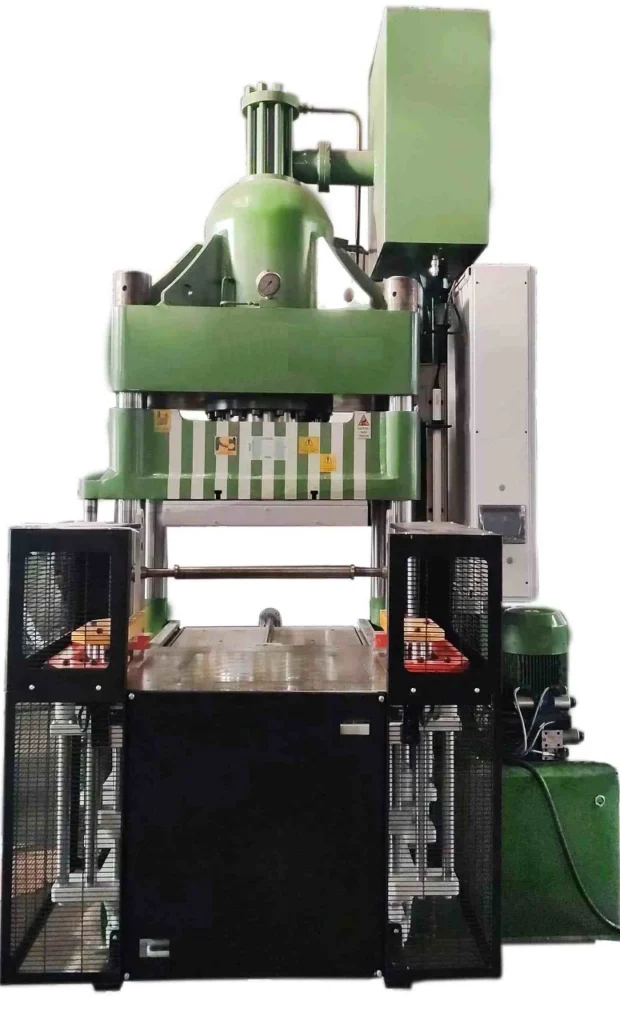
Wir stellen Presse zur Herstellung von Brems- Reibbelägen/ und Kupplungsbelägen her. Kostenlose Beratung. Preis vom Hersteller
Eine Presse zur Herstellung von Brems- und Kupplungsbelägen ist eine spezielle Art von hydraulischer Presse, die in der Automobilindustrie eingesetzt wird. Diese Presse ist darauf ausgelegt, Bremsbeläge und Kupplungsbeläge in verschiedenen Größen und Formen herzustellen.
Presse zur Herstellung von Brems- und Kupplungsbelägen
Brems- und Kupplungsbeläge sind wichtige Komponenten in vielen Fahrzeugen. Sie sorgen dafür, dass das Fahrzeug sicher zum Stehen kommt und dass die Kraftübertragung zwischen Motor und Antriebsrädern reibungslos funktioniert.
Die Herstellung von Brems- und Kupplungsbelägen ist ein komplexer Prozess, der eine Reihe von Schritten umfasst. Einer der wichtigsten Schritte ist das Pressen der Beläge.
Beim Pressen wird eine Mischung aus Materialien, einschließlich thermoplastischen Kunststoffen, Elastomeren, Füllstoffen, Schmierstoffen, Härtern, Farbstoffen und Additiven, in eine gewünschte Form gebracht.
Die Presse, die für die Herstellung von Brems- und Kupplungsbelägen verwendet wird, ist eine spezielle Maschine, die eine hohe Druckkraft erzeugen kann. Die Presse besteht aus zwei Teilen, der Matrize und dem Stempel. Die Matrize bildet die Innenseite der Form, der Stempel die Außenseite.
Der Prozess des Pressens beginnt damit, dass die Mischung in die Form gefüllt wird. Die Matrize und der Stempel schließen sich dann und der Stempel drückt die Mischung in die Form.
Der Hub ist die Entfernung, die der Stempel in die Matrize eindringt. Die Formtiefe ist die maximale Tiefe der Form.
Nachdem die Mischung in die Form gepresst wurde, wird das Werkstück aus der Form entnommen.
Die Qualität der Brems- und Kupplungsbeläge hängt von der Qualität des Pressens ab. Daher ist es wichtig, dass die Presse richtig eingestellt und gewartet wird.
Die Presse ist ein wichtiger Bestandteil der Herstellung von Brems- und Kupplungsbelägen. Sie ist eine effiziente und zuverlässige Methode zur Herstellung dieser wichtigen Komponenten.
Hier sind einige weitere Details zu den ersten 10 Schlüsselwörtern:
- Bremsbelag: Ein Bremsbelag ist eine Komponente der Bremsanlage eines Fahrzeugs, die die Reibung zwischen der Bremsscheibe oder dem Bremstrommel und der Radnabe erzeugt. Bremsbeläge bestehen aus einer Mischung von Materialien, einschließlich thermoplastischen Kunststoffen, Elastomeren, Füllstoffen, Schmierstoffen, Härtern, Farbstoffen und Additiven.
- Kupplungsbelag: Ein Kupplungsbelag ist eine Komponente der Kupplung eines Fahrzeugs, die die Reibung zwischen dem Schwungrad und der Kupplungsscheibe erzeugt. Kupplungsbeläge bestehen aus einer ähnlichen Mischung von Materialien wie Bremsbeläge.
- Pressen: Pressen ist ein Verfahren, bei dem ein Material durch eine Kraft in eine gewünschte Form gebracht wird. Beim Pressen von Brems- und Kupplungsbelägen wird eine Mischung aus Materialien in eine Form gepresst, die die gewünschte Form des Belags hat.
- Form: Eine Form ist ein Werkzeug, das verwendet wird, um ein Material in eine gewünschte Form zu bringen. Die Form für Brems- und Kupplungsbeläge besteht aus zwei Teilen, der Matrize und dem Stempel. Die Matrize bildet die Innenseite der Form, der Stempel die Außenseite.
- Werkzeug: Ein Werkzeug ist ein Gegenstand, der verwendet wird, um eine bestimmte Aufgabe auszuführen. Die Presse und die Form sind Werkzeuge, die für die Herstellung von Brems- und Kupplungsbelägen verwendet werden.
- Matrize: Eine Matrize ist ein Teil einer Form, der die Innenseite der Form bildet. Die Matrize für Brems- und Kupplungsbeläge ist typischerweise aus Metall gefertigt.
- Stempel: Ein Stempel ist ein Teil einer Form, der die Außenseite der Form bildet. Der Stempel für Brems- und Kupplungsbeläge ist typischerweise ebenfalls aus Metall gefertigt.
- Hub: Der Hub ist die Entfernung, die der Stempel in die Matrize eindringt. Der Hub ist wichtig für die Herstellung von Brems- und Kupplungsbelägen mit der gewünschten Dicke.
- Formtiefe: Die Formtiefe ist die maximale Tiefe der Form. Die Formtiefe ist wichtig für die Herstellung von Brems- und Kupplungsbelägen mit der gewünschten Dicke.
Brems- und Kupplungsbeläge sind wichtige Komponenten in vielen Fahrzeugen. Die Herstellung von Brems- und Kupplungsbelägen ist ein komplexer Prozess, der eine Reihe von Schritten umfasst. Das Pressen ist einer der wichtigsten Schritte in diesem Prozess.
Eine Presse zur Herstellung von Brems- und Kupplungsbelägen ist eine Maschine, die verwendet wird, um die Reibmaterialien zu einer Scheibe oder Platte zu formen. Die Presse besteht aus zwei Platten, die sich gegenüberliegen und zusammengedrückt werden, um das Reibmaterial zu formen. Die Platten sind mit einer Matrize und einem Stempel versehen, die die Form des Reibmaterials bestimmen.
Die Presse besteht aus einem Zylinder, einem Kolben und einem hydraulischen Aggregat. Der Kolben wird mit Öl befüllt und bewegt sich durch den Zylinder. Das Öl überträgt dabei die Kraft auf die Form, in der der Brems- oder Kupplungsbelag geformt wird. Die Form ist in der Regel aus einem Material wie Stahl oder Aluminium gefertigt und hat eine spezifische Form und Größe, die auf die Anforderungen des Herstellungsprozesses abgestimmt sind.
Der Herstellungsprozess von Brems- und Kupplungsbelägen in dieser Presse umfasst mehrere Schritte. Zunächst wird das Material für den Belag zugeschnitten und in die Form gelegt. Dann wird die Form in die Presse eingesetzt und die hydraulischen Kolben werden aktiviert, um das Material in die gewünschte Form zu pressen. Nach dem Pressen wird der Belag aus der Form entfernt und für den weiteren Herstellungsprozess vorbereitet.
Die Presskraft der Presse bestimmt die Dicke des Reibmaterials. Die Presstemperatur bestimmt die Festigkeit und die Härte des Reibmaterials.
Die Presse kann entweder hydraulisch oder mechanisch angetrieben werden. Hydraulische Pressen sind in der Regel leistungsfähiger als mechanische Pressen. Sie werden häufig in der Massenproduktion verwendet. Mechanische Pressen sind in der Regel kostengünstiger als hydraulische Pressen. Sie werden häufig in der Kleinserie oder in der Einzelfertigung verwendet.
Die Presse ist ein wichtiger Bestandteil der Herstellung von Brems- und Kupplungsbelägen. Sie sorgt dafür, dass die Reibmaterialien die richtige Form und die richtige Festigkeit haben.
Pressen für Brems- Reibbelägen/ und Kupplungsbelägen
Bremsbeläge und Kupplungsbeläge sind die Materialien, die in Bremsen und Kupplungen verwendet werden, um die Reibung zwischen den bewegten und unbewegten Teilen zu erzeugen.
Bremsbeläge werden in Scheiben- und Trommelbremsen verwendet. Sie bestehen in der Regel aus einer Mischung aus organischen und anorganischen Materialien, die für die Reibung und die Wärmebeständigkeit ausgelegt sind.
Kupplungsbeläge werden in Kupplungen verwendet. Sie bestehen in der Regel aus einer Mischung aus organischen und anorganischen Materialien, die für die Reibung und die Verschleißfestigkeit ausgelegt sind.
Die beiden Haupttypen von Bremsbelägen sind organische Bremsbeläge und metallische Bremsbeläge.
Organische Bremsbeläge sind in der Regel günstiger als metallische Bremsbeläge, aber sie sind auch weniger langlebig und bieten weniger Bremsleistung.
Metallische Bremsbeläge sind in der Regel teurer als organische Bremsbeläge, aber sie sind auch langlebig und bieten mehr Bremsleistung.
Die beiden Haupttypen von Kupplungsbelägen sind organische Kupplungsbeläge und metallische Kupplungsbeläge.
Organische Kupplungsbeläge sind in der Regel günstiger als metallische Kupplungsbeläge, aber sie sind auch weniger langlebig und bieten weniger Reibung.
Metallische Kupplungsbeläge sind in der Regel teurer als organische Kupplungsbeläge, aber sie sind auch langlebig und bieten mehr Reibung.
Die Lebensdauer von Brems- und Kupplungsbelägen hängt von einer Reihe von Faktoren ab, darunter die Art des Fahrzeugs, die Fahrgewohnheiten und die Wartung. In der Regel müssen Bremsbeläge alle 20.000 bis 30.000 Meilen oder alle zwei Jahre ausgetauscht werden. Kupplungsbeläge müssen in der Regel alle 60.000 bis 100.000 Meilen oder alle drei bis fünf Jahre ausgetauscht werden.
Herstellung von Brems- Reibbelägen/ und Kupplungsbelägen
Die Herstellung von Brems- und Kupplungsbelägen ist ein komplexer Prozess, der in mehreren Schritten durchgeführt wird. Die wichtigsten Schritte sind:
- Materialienbereitstellung
Die ersten Schritte der Herstellung von Brems- und Kupplungsbelägen bestehen in der Bereitstellung der benötigten Materialien. Dazu gehören organische und anorganische Materialien, wie z. B.:
- Organische Materialien
- Phenolische Harze
- Gummi
- Graphit
- Kevlar
- Anorganische Materialien
- Metalle
- Keramik
Diese Materialien werden in der Regel in Pulverform geliefert und müssen vor der Verwendung gemischt werden.
- Mischen
Das Mischen der Materialien ist ein wichtiger Schritt, um die gewünschten Eigenschaften der Brems- und Kupplungsbeläge zu erzielen. Die Mischung wird in einer speziellen Maschine durchgeführt, die die Materialien gleichmäßig verteilt.
- Formgebung
Die gemischte Masse wird dann in die gewünschte Form gepresst. Dies kann entweder durch eine Presse oder durch eine Extrusion erfolgen.
- Trocknung
Die gepressten Brems- und Kupplungsbeläge müssen dann getrocknet werden. Dies geschieht in einem Ofen, der die Feuchtigkeit aus der Masse entfernt.
- Härtung
Die getrockneten Brems- und Kupplungsbeläge werden dann gehärtet. Dies geschieht ebenfalls in einem Ofen, der die Materialien erwärmt und ihre Festigkeit und Härte erhöht.
- Beschichtung
Die gehärteten Brems- und Kupplungsbeläge werden dann in der Regel mit einer Beschichtung versehen. Diese Beschichtung dient zum Schutz der Materialien vor Korrosion und Verschleiß.
- Verpackung
Die beschichteten Brems- und Kupplungsbeläge werden dann verpackt und an den Kunden versandt.
Die Herstellung von Brems- und Kupplungsbelägen ist ein wichtiger Industriezweig. Die Beläge sind ein wichtiger Bestandteil von Bremsen und Kupplungen und tragen zur Sicherheit und Leistung von Fahrzeugen bei.
Die einzelnen Schritte der Herstellung von Brems- und Kupplungsbelägen können je nach Hersteller und Produkt variieren. Die oben genannten Schritte sind jedoch die grundlegenden Schritte, die bei der Herstellung dieser wichtigen Teile verwendet werden.
Reibbeläge
Reibbeläge sind Schlüsselelemente in Kupplungen und Bremsen, die dazu dienen, die Übertragung von Drehmomenten und die Verzögerung von Bewegungen zu ermöglichen. Sie bestehen aus speziellen Materialien, die eine hohe Reibung erzeugen, wenn sie gegen eine Gegenfläche gedrückt werden. Diese Materialien sind so konzipiert, dass sie den erforderlichen Grip bieten, um Bewegungen zu übertragen oder zu stoppen, ohne dabei zu schnell zu verschleißen.
Zusammensetzung:
Reibbeläge bestehen typischerweise aus einem Verbundwerkstoff, der aus einer Matrix und verstärkenden Fasern besteht. Die Matrix kann aus verschiedenen Materialien wie organischen Polymeren, Metallen, Keramiken oder Kohlenstofffasern bestehen. Diese Matrix dient als Bindemittel für die verstärkenden Fasern, die oft aus Materialien wie Aramid, Kevlar, Glas oder Kohlenstoff bestehen. Die Kombination aus Matrix und Fasern bestimmt die mechanischen Eigenschaften des Reibbelags, einschließlich Reibungskoeffizient, Verschleißfestigkeit und Temperaturbeständigkeit.
Funktion:
Die Hauptfunktion von Reibbelägen besteht darin, ein hohes Maß an Reibung zu erzeugen, wenn sie gegen eine Gegenfläche gedrückt werden. Dies ermöglicht es, Bewegungen zu übertragen oder zu stoppen, indem das Drehmoment zwischen zwei rotierenden Teilen übertragen wird oder indem Bewegungsenergie in Form von Wärme dissipiert wird. Die Wahl des richtigen Reibbelags hängt von verschiedenen Faktoren ab, einschließlich der Anwendung, der Betriebsbedingungen und der erforderlichen Leistung.
Anwendungen:
Reibbeläge finden in einer Vielzahl von Anwendungen Verwendung, darunter:
- Kupplungen: In Kraftfahrzeugen, Maschinen und Anlagen, um den Antrieb zwischen Motor und Getriebe zu übertragen.
- Bremsen: In Fahrzeugen, Zügen, Flugzeugen und Industrieanlagen, um Bewegungen zu verzögern oder zu stoppen.
- Reibungsgekoppelte Geräte: In Drehmomentwandlern, Getrieben und Kupplungen zur Schwingungsdämpfung und Energieübertragung.
Herstellung:
Die Herstellung von Reibbelägen ist ein komplexer Prozess, der die Auswahl der richtigen Materialien, die Formgebung, die Wärmebehandlung und die Oberflächenbearbeitung umfasst. Die Materialien werden gemischt, geformt und unter Druck und Hitze verdichtet, um die gewünschte Struktur und Festigkeit zu erreichen. Anschließend können sie bearbeitet, beschichtet und auf die entsprechende Größe und Form zugeschnitten werden.
Weiterentwicklung:
Die Entwicklung von Reibbelägen konzentriert sich auf die Verbesserung der Leistung, Haltbarkeit und Umweltverträglichkeit. Neue Materialien, Herstellungsverfahren und Beschichtungen werden erforscht, um die Reibungseigenschaften zu optimieren, den Verschleiß zu reduzieren und die Temperaturbeständigkeit zu erhöhen. Außerdem werden Methoden zur Recyclingfähigkeit und Entsorgung von gebrauchten Reibbelägen entwickelt, um Umweltauswirkungen zu minimieren.
Insgesamt sind Reibbeläge entscheidende Komponenten in einer Vielzahl von technischen Systemen, die Bewegungen übertragen oder kontrollieren. Ein genaues Verständnis ihrer Zusammensetzung, Funktion, Herstellung und Weiterentwicklung ist wichtig für die Entwicklung und Anwendung effizienter und zuverlässiger Reibungssysteme.
Presse zur Herstellung von Brems- Reibbelägen/ und Kupplungsbelägen
Eine Presse zur Herstellung von Brems- und Kupplungsbelägen bietet eine hohe Leistungsfähigkeit und Präzision bei der Herstellung von Belägen für die Automobilindustrie. Die hydraulischen Pressen ermöglichen eine schnelle und effiziente Produktion von Belägen in verschiedenen Größen und Formen, was die Produktionskapazität erhöht und die Qualität der Beläge verbessert.
Das Material, das für die Herstellung von Brems- und Kupplungsbelägen in einer Presse verwendet wird, variiert je nach Anwendung und den spezifischen Anforderungen des Herstellungsprozesses. Typischerweise bestehen Brems- und Kupplungsbeläge aus einer Mischung von verschiedenen Materialien wie Metallen, Kunststoffen, Fasern und Harzen.
Eine häufig verwendete Materialkombination für Bremsbeläge ist eine Mischung aus Metallpartikeln, Kunststoffharz und Fasern wie Kevlar oder Kohlenstoff. Diese Kombination ermöglicht eine hohe Bremsleistung bei gleichzeitig geringem Verschleiß und geringem Bremsstaub. Kupplungsbeläge bestehen häufig aus ähnlichen Materialien, aber mit einer anderen Zusammensetzung und Dicke, um den Anforderungen des Kupplungsmechanismus gerecht zu werden.
Es ist wichtig, dass das Material für die Brems- und Kupplungsbeläge in einer hydraulischen Presse gleichmäßig und konsistent gepresst wird, um eine hohe Qualität und eine lange Lebensdauer der Beläge zu gewährleisten. Eine sorgfältige Auswahl der Materialien und der Mischungsverhältnisse ist daher entscheidend für den Herstellungsprozess.
Zusätzlich kann eine spezielle Beschichtung oder Oberflächenbehandlung auf den Belägen aufgebracht werden, um die Leistung zu verbessern und die Langlebigkeit zu erhöhen. Beispielsweise kann eine Keramikbeschichtung auf den Bremsbelägen aufgetragen werden, um die Hitzebeständigkeit zu verbessern und das Quietschen der Bremsen zu reduzieren.
Insgesamt spielt das Material eine entscheidende Rolle in der Qualität und Leistung von Brems- und Kupplungsbelägen, und eine sorgfältige Materialauswahl und -verarbeitung sind unerlässlich für die Herstellung dieser Komponenten in einer hydraulischen Presse.
Reibbeläge
Reibbeläge sind Schlüsselelemente in Brems- und Kupplungssystemen von Fahrzeugen und Maschinen. Sie spielen eine entscheidende Rolle bei der Umwandlung von kinetischer Energie in Wärmeenergie durch Reibung. Diese Reibbeläge bestehen aus verschiedenen Materialien, die speziell für ihre Reibungseigenschaften entwickelt wurden.
Die Materialzusammensetzung von Reibbelägen variiert je nach den Anforderungen der Anwendung. Typische Materialien umfassen organische, anorganische und Verbundwerkstoffe. Organische Reibbeläge bestehen oft aus Fasern wie Aramid, Kohlenstoff und Keramik, die mit einem Bindemittel wie Harz verbunden sind. Anorganische Reibbeläge können Materialien wie Metall, Glas oder Mineralien enthalten, die in einer Matrix aus Harz oder Keramik eingebettet sind. Verbundwerkstoffe kombinieren verschiedene Materialien, um die gewünschten Eigenschaften zu erreichen.
Die Verschleißfestigkeit eines Reibbelags ist entscheidend für seine Lebensdauer und Leistung. Durch spezielle Materialzusammensetzungen und Konstruktionsmethoden wird versucht, die Verschleißrate zu minimieren und die Reibungskoeffizienten zu optimieren. Dies ermöglicht eine effektive Brems- und Kupplungswirkung über einen längeren Zeitraum hinweg.
Die Reibungskoeffizienten von Reibbelägen können je nach den Anforderungen der Anwendung variieren. Bremsbeläge erfordern beispielsweise eine hohe Reibung, um Fahrzeuge sicher zum Stillstand zu bringen, während Kupplungsbeläge eine kontrollierte Reibung bieten müssen, um ein sanftes Anfahren und Schalten zu ermöglichen.
Die Herstellung von Reibbelägen ist ein komplexer Prozess, der Materialwissenschaft, Ingenieurwesen und Produktionstechnik vereint. Moderne Fertigungstechnologien wie Pressverfahren, Schneidetechniken und Beschichtungsverfahren werden eingesetzt, um hochwertige Reibbeläge mit engen Toleranzen und konsistenter Qualität herzustellen.
Insgesamt sind Reibbeläge entscheidende Komponenten für die sichere und zuverlässige Funktion von Brems- und Kupplungssystemen. Durch kontinuierliche Forschung und Entwicklung werden ständig neue Materialien und Fertigungstechnologien entwickelt, um die Leistungsfähigkeit und Effizienz dieser wichtigen Komponenten zu verbessern.
Bremsbeläge
Bremsbeläge sind ein wesentlicher Bestandteil des Bremssystems in Fahrzeugen und Maschinen. Ihre Hauptfunktion besteht darin, durch Reibung die kinetische Energie in Wärmeenergie umzuwandeln, was zum Verlangsamen oder Stoppen des Fahrzeugs führt. Diese Beläge werden in Bremsbacken oder Bremssätteln montiert und werden während des Bremsvorgangs gegen die Bremsscheiben oder Trommeln gedrückt.
Die Materialien, aus denen Bremsbeläge hergestellt werden, variieren je nach den Anforderungen an Leistung, Haltbarkeit und Umweltverträglichkeit. Typische Materialien umfassen organische, halbmetallische und keramische Verbundstoffe. Organische Bremsbeläge bestehen aus Fasern wie Aramid, Kohlenstoff und Keramik, die mit einem Bindemittel wie Harz verbunden sind. Halbmetallische Bremsbeläge enthalten eine Mischung aus Metallpulvern, wie beispielsweise Stahl, Kupfer, und organischen Materialien. Keramische Bremsbeläge bestehen hauptsächlich aus keramischen Verbundstoffen, die eine hohe Wärmebeständigkeit und Verschleißfestigkeit bieten.
Die Bremsbeläge sind entscheidend für die Sicherheit und Leistung eines Fahrzeugs. Sie müssen eine ausreichende Reibung bieten, um das Fahrzeug schnell und effektiv zum Stillstand zu bringen, unabhängig von den Betriebsbedingungen wie Geschwindigkeit, Last und Umgebungstemperatur. Gleichzeitig sollten sie eine gleichmäßige Abnutzung aufweisen und minimalen Bremsstaub erzeugen, um die Lebensdauer der Bremsscheiben zu verlängern und die Umweltbelastung zu reduzieren.
Die Herstellung von Bremsbelägen erfordert hochpräzise Fertigungsprozesse und strenge Qualitätskontrollen. Moderne Produktionsanlagen und automatisierte Fertigungstechnologien werden eingesetzt, um Bremsbeläge mit engen Toleranzen und konsistenter Qualität herzustellen. Die Beläge werden sorgfältig auf Materialzusammensetzung, Dicke, Härte, Oberflächenbeschaffenheit und andere Eigenschaften geprüft, um eine optimale Leistung und Zuverlässigkeit zu gewährleisten.
Insgesamt spielen Bremsbeläge eine entscheidende Rolle für die Sicherheit und Zuverlässigkeit von Fahrzeugen und Maschinen. Durch kontinuierliche Forschung und Entwicklung werden ständig neue Materialien und Fertigungstechnologien entwickelt, um die Leistungsfähigkeit und Effizienz dieser wichtigen Komponenten zu verbessern.
Kupplungsbeläge
Kupplungsbeläge sind entscheidende Komponenten in Kupplungssystemen von Fahrzeugen und Maschinen. Ihre Hauptfunktion besteht darin, das Drehmoment vom Antriebsstrang auf das Getriebe zu übertragen und die Kraftübertragung zwischen Motor und Antriebsstrang zu steuern. Kupplungsbeläge ermöglichen ein sanftes Ein- und Auskuppeln sowie ein reibungsloses Schalten zwischen den Gängen.
Die Materialien, aus denen Kupplungsbeläge hergestellt werden, variieren je nach den Anforderungen an Reibung, Verschleißfestigkeit und Haltbarkeit. Typische Materialien umfassen organische, anorganische und Verbundwerkstoffe. Organische Kupplungsbeläge bestehen oft aus Fasern wie Aramid, Kohlenstoff und Keramik, die mit einem Bindemittel wie Harz verbunden sind. Anorganische Kupplungsbeläge können Materialien wie Metall, Glas oder Mineralien enthalten, die in einer Matrix aus Harz oder Keramik eingebettet sind. Verbundwerkstoffe kombinieren verschiedene Materialien, um die gewünschten Eigenschaften zu erreichen.
Die Kupplungsbeläge müssen eine gleichmäßige Reibung über einen breiten Temperatur- und Lastbereich bieten, um eine zuverlässige Leistung zu gewährleisten. Sie sollten auch eine hohe Verschleißfestigkeit aufweisen, um eine lange Lebensdauer und eine gleichbleibende Kupplungsfunktion zu ermöglichen. Gleichzeitig müssen sie eine geringe thermische Belastung aufweisen, um eine Überhitzung des Kupplungssystems zu vermeiden.
Die Herstellung von Kupplungsbelägen erfordert spezielle Fertigungsverfahren und Materialbehandlungen, um die gewünschten Eigenschaften zu erreichen. Moderne Fertigungstechnologien wie Pressverfahren, Schneidetechniken und Beschichtungsverfahren werden eingesetzt, um hochwertige Kupplungsbeläge mit engen Toleranzen und konsistenter Qualität herzustellen. Die Beläge werden sorgfältig auf Materialzusammensetzung, Dicke, Härte, Oberflächenbeschaffenheit und andere Eigenschaften geprüft, um eine optimale Leistung und Zuverlässigkeit zu gewährleisten.
Insgesamt sind Kupplungsbeläge entscheidende Komponenten für die reibungslose und zuverlässige Funktion von Kupplungssystemen. Durch kontinuierliche Forschung und Entwicklung werden ständig neue Materialien und Fertigungstechnologien entwickelt, um die Leistungsfähigkeit und Effizienz dieser wichtigen Komponenten zu verbessern.
Pressverfahren
Das Pressverfahren ist ein grundlegender Fertigungsprozess, der in verschiedenen Industriezweigen weit verbreitet ist, einschließlich der Herstellung von Brems- und Kupplungsbelägen. Es wird verwendet, um Materialien unter hohem Druck und Temperatur zu formen und zu verfestigen, um komplexe Formen und Strukturen zu erzeugen.
In der Herstellung von Brems- und Kupplungsbelägen wird das Pressverfahren eingesetzt, um die Rohmaterialien in die gewünschte Form und Dicke zu bringen. Typischerweise werden die Materialien in Formen oder Matrizen platziert und unter hohem Druck zusammengepresst, um die gewünschte Dichte und Konsistenz zu erreichen. Dieser Prozess kann unter Verwendung von hydraulischen Pressen, mechanischen Pressen oder anderen spezialisierten Pressmaschinen durchgeführt werden.
Das Pressverfahren ermöglicht eine präzise Kontrolle über die Materialdichte, Dicke und Form, was zu gleichmäßigen und hochwertigen Endprodukten führt. Es kann auch verwendet werden, um verschiedene Materialien miteinander zu verbinden, um Verbundwerkstoffe mit verbesserten Eigenschaften herzustellen. Durch die Anpassung der Druck- und Temperaturparameter können die Eigenschaften des Endprodukts gezielt gesteuert und optimiert werden.
Für die Herstellung von Brems- und Kupplungsbelägen ist das Pressverfahren ein entscheidender Schritt im Fertigungsprozess. Die Qualität und Präzision dieses Prozesses beeinflussen direkt die Leistung und Zuverlässigkeit der Endprodukte. Daher werden moderne Produktionsanlagen und hochpräzise Pressmaschinen eingesetzt, um eine gleichbleibend hohe Qualität zu gewährleisten und die Produktionskapazität zu maximieren.
Insgesamt ist das Pressverfahren ein wesentlicher Bestandteil der Fertigung von Brems- und Kupplungsbelägen sowie vieler anderer Produkte in verschiedenen Industriezweigen. Durch kontinuierliche Weiterentwicklung und Innovation werden ständig neue Technologien und Verfahren entwickelt, um die Effizienz, Präzision und Leistungsfähigkeit dieses wichtigen Fertigungsprozesses weiter zu verbessern.
Belagherstellung
Die Belagherstellung ist ein komplexer Prozess, der bei der Herstellung von Brems- und Kupplungsbelägen eine entscheidende Rolle spielt. Dieser Prozess beinhaltet die Auswahl und Kombination von Materialien sowie die Umwandlung dieser Materialien in Beläge mit den gewünschten Eigenschaften.
Materialauswahl:
Die Belagherstellung beginnt mit der Auswahl der geeigneten Materialien für die spezifischen Anforderungen des Endprodukts. Typische Materialien umfassen organische, anorganische und Verbundwerkstoffe. Organische Materialien wie Aramid, Kohlenstoff und Keramik bieten eine hohe Reibung und Verschleißfestigkeit, während anorganische Materialien wie Metall und Glas eine hohe Hitzebeständigkeit und Härte aufweisen können. Verbundwerkstoffe kombinieren verschiedene Materialien, um die gewünschten Eigenschaften zu erreichen.
Materialmischung:
Nach der Materialauswahl werden die Rohstoffe gemischt, um eine homogene Materialmischung zu erhalten. Dieser Schritt ist entscheidend, um eine gleichmäßige Verteilung der Materialien zu gewährleisten und konsistente Eigenschaften im gesamten Belag zu erzielen. Die genaue Zusammensetzung und Mischverhältnisse werden sorgfältig kontrolliert, um die gewünschten Eigenschaften des Endprodukts zu erreichen.
Formgebung:
Die Materialmischung wird dann in die gewünschte Form gebracht, typischerweise durch Pressverfahren. Dabei wird die Mischung in Formen oder Matrizen platziert und unter hohem Druck und Temperatur gepresst, um die gewünschte Dichte, Dicke und Form des Belags zu erreichen. Dieser Prozess ermöglicht eine präzise Kontrolle über die Endabmessungen und die Oberflächenbeschaffenheit des Belags.
Nachbehandlung:
Nach der Formgebung können Beläge zusätzlichen Behandlungen unterzogen werden, um ihre Eigenschaften weiter zu verbessern. Dazu können Wärmebehandlungen, Beschichtungsverfahren oder Oberflächenbehandlungen gehören. Diese Nachbehandlungen können die Härte, Verschleißfestigkeit, Reibungseigenschaften und thermische Stabilität des Belags verbessern.
Insgesamt ist die Belagherstellung ein hochspezialisierter Prozess, der Fachkenntnisse in Materialwissenschaft, Fertigungstechnik und Ingenieurwesen erfordert. Durch die kontinuierliche Weiterentwicklung von Materialien und Fertigungstechnologien werden ständig neue Möglichkeiten zur Verbesserung der Leistung, Zuverlässigkeit und Umweltverträglichkeit von Brems- und Kupplungsbelägen erschlossen.
Bremsmaterialien
Bremsmaterialien spielen eine entscheidende Rolle bei der Herstellung von Bremsbelägen, da sie die Leistung, Haltbarkeit und Sicherheit der Bremsanlage maßgeblich beeinflussen. Eine breite Palette von Materialien wird für Bremsbeläge verwendet, und jede hat ihre eigenen einzigartigen Eigenschaften und Anwendungen.
Organische Materialien:
Organische Bremsbeläge bestehen typischerweise aus einer Mischung von Fasern wie Aramid, Kohlenstoff und Keramik, die mit einem Bindemittel wie Harz verbunden sind. Diese Materialien bieten eine gute Reibung und eine gleichmäßige Bremsleistung über einen breiten Temperaturbereich. Sie erzeugen auch weniger Bremsstaub und sind tendenziell geräuschärmer als andere Bremsmaterialien. Organische Bremsbeläge eignen sich besonders gut für den alltäglichen Gebrauch und für Fahrzeuge mit niedriger bis mittlerer Leistung.
Anorganische Materialien:
Anorganische Bremsbeläge enthalten oft Materialien wie Metall, Glas oder Mineralien, die in einer Matrix aus Harz oder Keramik eingebettet sind. Diese Materialien bieten eine verbesserte Wärmebeständigkeit und Verschleißfestigkeit im Vergleich zu organischen Materialien. Sie eignen sich daher besser für Hochleistungsanwendungen und anspruchsvolle Fahrbedingungen, wie beispielsweise Rennsport oder schwere Nutzfahrzeuge.
Verbundwerkstoffe:
Verbundwerkstoffe kombinieren verschiedene Materialien, um die Vorteile mehrerer Materialien zu nutzen und deren Nachteile auszugleichen. Zum Beispiel können sie organische Fasern für Reibung und Anorganika für Hitzebeständigkeit und Verschleißfestigkeit kombinieren. Diese Materialien bieten eine ausgezeichnete Leistung und Haltbarkeit über einen breiten Temperatur- und Lastbereich und werden daher oft in hochwertigen Bremsbelägen verwendet.
Die Auswahl der richtigen Bremsmaterialien hängt von verschiedenen Faktoren ab, darunter die Fahrzeugart, der Einsatzzweck, die Fahrbedingungen und die persönlichen Vorlieben des Fahrers. Durch kontinuierliche Forschung und Entwicklung werden ständig neue Materialien und Formulierungen entwickelt, um die Leistung, Sicherheit und Umweltverträglichkeit von Bremsbelägen zu verbessern und den Anforderungen der sich ständig verändernden Automobilindustrie gerecht zu werden.
Kupplungsmaterialien
Die Auswahl der richtigen Kupplungsmaterialien ist entscheidend für die Leistung, Haltbarkeit und Zuverlässigkeit von Kupplungssystemen in Fahrzeugen und Maschinen. Verschiedene Materialien bieten unterschiedliche Eigenschaften und sind für verschiedene Anwendungen geeignet.
Organische Materialien:
Organische Kupplungsbeläge bestehen typischerweise aus einer Mischung von Fasern wie Aramid, Kohlenstoff und Keramik, die mit einem Bindemittel wie Harz verbunden sind. Diese Materialien bieten eine gute Reibung und eine sanfte Kupplungswirkung, was ein sanftes Ein- und Auskuppeln sowie ein reibungsloses Schalten ermöglicht. Organische Kupplungsbeläge sind ideal für den alltäglichen Gebrauch und für Fahrzeuge mit niedriger bis mittlerer Leistung.
Anorganische Materialien:
Anorganische Kupplungsbeläge enthalten oft Materialien wie Metall, Glas oder Mineralien, die in einer Matrix aus Harz oder Keramik eingebettet sind. Diese Materialien bieten eine verbesserte Wärmebeständigkeit und Verschleißfestigkeit im Vergleich zu organischen Materialien. Sie eignen sich daher besser für Hochleistungsanwendungen und anspruchsvolle Fahrbedingungen, wie beispielsweise Rennsport oder schwere Nutzfahrzeuge.
Verbundwerkstoffe:
Verbundwerkstoffe kombinieren verschiedene Materialien, um die Vorteile mehrerer Materialien zu nutzen und deren Nachteile auszugleichen. Zum Beispiel können sie organische Fasern für Reibung und Anorganika für Hitzebeständigkeit und Verschleißfestigkeit kombinieren. Diese Materialien bieten eine ausgezeichnete Leistung und Haltbarkeit über einen breiten Temperatur- und Lastbereich und werden daher oft in hochwertigen Kupplungsbelägen verwendet.
Die Auswahl der richtigen Kupplungsmaterialien hängt von verschiedenen Faktoren ab, darunter die Fahrzeugart, der Einsatzzweck, die Fahrbedingungen und die persönlichen Vorlieben des Fahrers. Durch kontinuierliche Forschung und Entwicklung werden ständig neue Materialien und Formulierungen entwickelt, um die Leistung, Sicherheit und Zuverlässigkeit von Kupplungssystemen zu verbessern und den Anforderungen der sich ständig verändernden Automobilindustrie gerecht zu werden.
Produktionsprozess
Der Produktionsprozess von Brems- und Kupplungsbelägen ist ein komplexer und hochpräziser Vorgang, der eine Vielzahl von Schritten umfasst, um hochwertige Endprodukte mit konsistenter Qualität herzustellen. Hier sind einige der Schlüsselschritte im Produktionsprozess:
1. Materialauswahl und Vorbereitung:
Der Prozess beginnt mit der Auswahl der geeigneten Materialien für die Beläge basierend auf den Anforderungen an Reibung, Verschleißfestigkeit und Temperaturbeständigkeit. Die Rohstoffe werden dann gemischt, um eine homogene Materialmischung zu erhalten.
2. Formgebung:
Die Materialmischung wird in die gewünschte Form gebracht, typischerweise durch Pressverfahren. Dabei wird die Mischung in Formen oder Matrizen platziert und unter hohem Druck und Temperatur gepresst, um die gewünschte Dichte, Dicke und Form des Belags zu erreichen.
3. Nachbehandlung:
Nach der Formgebung können Beläge zusätzlichen Behandlungen unterzogen werden, um ihre Eigenschaften weiter zu verbessern. Dazu können Wärmebehandlungen, Beschichtungsverfahren oder Oberflächenbehandlungen gehören. Diese Nachbehandlungen können die Härte, Verschleißfestigkeit, Reibungseigenschaften und thermische Stabilität des Belags verbessern.
4. Qualitätskontrolle:
Während des gesamten Produktionsprozesses werden die Beläge sorgfältig auf Materialzusammensetzung, Dicke, Härte, Oberflächenbeschaffenheit und andere Eigenschaften geprüft, um sicherzustellen, dass sie den spezifizierten Anforderungen entsprechen. Stichprobenprüfungen und Kontrollen gewährleisten eine gleichbleibend hohe Qualität.
5. Verpackung und Versand:
Nach Abschluss der Produktion werden die Beläge entsprechend verpackt und für den Versand vorbereitet. Die Verpackung erfolgt oft unter Berücksichtigung von Umweltaspekten und Transportanforderungen, um eine sichere und zuverlässige Lieferung der Beläge zu gewährleisten.
Insgesamt erfordert der Produktionsprozess von Brems- und Kupplungsbelägen eine enge Zusammenarbeit zwischen Materialwissenschaftlern, Ingenieuren und Fertigungsexperten, um hochwertige Produkte mit optimalen Leistungsmerkmalen herzustellen. Durch kontinuierliche Verbesserungen und Innovationen werden ständig neue Technologien und Verfahren entwickelt, um die Effizienz, Präzision und Leistungsfähigkeit dieses wichtigen Fertigungsprozesses weiter zu verbessern.
Materialzusammensetzung
Die Materialzusammensetzung von Brems- und Kupplungsbelägen ist ein entscheidender Faktor für ihre Leistung, Haltbarkeit und Zuverlässigkeit. Die richtige Auswahl und Kombination von Materialien ermöglicht es, Beläge herzustellen, die den spezifischen Anforderungen verschiedener Anwendungen gerecht werden. Hier sind einige der wichtigsten Materialien, die in Brems- und Kupplungsbelägen verwendet werden:
1. Fasern:
Fasern wie Aramid, Kohlenstoff, Keramik und Glas werden häufig in Brems- und Kupplungsbelägen verwendet, um Reibungseigenschaften und Verschleißfestigkeit zu verbessern. Diese Fasern bieten eine hohe Festigkeit und Hitzebeständigkeit, was sie ideal für den Einsatz in Hochleistungsanwendungen macht.
2. Metalle:
Metalle wie Stahl, Kupfer und Aluminium werden oft als Füllstoffe oder Verstärkungsmaterialien in Brems- und Kupplungsbelägen verwendet. Sie können die Wärmeableitung verbessern, die Belastbarkeit erhöhen und die Reibungseigenschaften beeinflussen.
3. Bindemittel:
Bindemittel wie Harze und Polymere dienen dazu, die verschiedenen Materialien in einem Belag zusammenzuhalten und eine gleichmäßige Verteilung zu gewährleisten. Sie spielen eine wichtige Rolle bei der Festigung des Belags und der Übertragung von Reibungskräften auf die Brems- oder Kupplungsoberfläche.
4. Füllstoffe:
Füllstoffe wie Graphit, Talkum und Siliziumdioxid werden oft verwendet, um die Eigenschaften von Brems- und Kupplungsbelägen zu modifizieren. Sie können die Reibungseigenschaften beeinflussen, die Wärmeableitung verbessern und die Verschleißfestigkeit erhöhen.
5. Zusatzstoffe:
Zusatzstoffe wie Schmiermittel, Stabilisatoren und Flammschutzmittel können dem Belag bestimmte Eigenschaften verleihen oder verbessern. Sie werden oft in speziellen Anwendungen verwendet, um die Leistung und Zuverlässigkeit der Beläge zu optimieren.
Die genaue Materialzusammensetzung eines Brems- oder Kupplungsbelags hängt von den spezifischen Anforderungen der Anwendung ab, einschließlich der Betriebsbedingungen, der Fahrzeugart und des Einsatzzwecks. Durch die richtige Auswahl und Kombination von Materialien können Brems- und Kupplungsbeläge hergestellt werden, die eine optimale Leistung und Sicherheit bieten und den Anforderungen der sich ständig weiterentwickelnden Automobilindustrie gerecht werden.
Schleifmaterial
Das Schleifmaterial ist ein wesentlicher Bestandteil von Brems- und Kupplungsbelägen, da es maßgeblich für die Reibungseigenschaften und die Brems- bzw. Kupplungsleistung verantwortlich ist. Hier sind einige wichtige Informationen über Schleifmaterialien:
1. Arten von Schleifmaterialien:
- Kohlenstofffasern: Kohlenstofffasern werden häufig in Brems- und Kupplungsbelägen verwendet, da sie eine hohe Verschleißfestigkeit und Hitzebeständigkeit bieten. Sie tragen dazu bei, die Reibungseigenschaften zu verbessern und die Lebensdauer der Beläge zu verlängern.
- Keramikpartikel: Keramikpartikel werden oft als Füllstoffe in Brems- und Kupplungsbelägen eingesetzt, um die Reibungseigenschaften zu verbessern und die Hitzebeständigkeit zu erhöhen.
- Metallpartikel: Metallpartikel wie Kupfer oder Stahl können in Bremsbelägen verwendet werden, um die Reibung zu erhöhen und die Bremsleistung zu verbessern.
2. Einfluss auf die Brems- und Kupplungsleistung:
Das Schleifmaterial beeinflusst direkt die Reibungseigenschaften und die Leistung der Brems- und Kupplungsbeläge. Ein Material mit hoher Reibung erzeugt eine stärkere Bremskraft oder Kupplungswirkung, während ein Material mit niedriger Reibung ein sanfteres Ein- und Auskuppeln ermöglicht.
3. Verschleißverhalten:
Die Auswahl des richtigen Schleifmaterials beeinflusst auch das Verschleißverhalten der Beläge. Ein Material mit hoher Verschleißfestigkeit kann die Lebensdauer der Beläge verlängern und die Wartungskosten reduzieren.
4. Temperaturbeständigkeit:
Die Temperaturbeständigkeit des Schleifmaterials ist ein wichtiger Faktor, insbesondere bei Bremsbelägen, da sie hohen Temperaturen standhalten müssen, die während des Bremsvorgangs entstehen. Ein Schleifmaterial mit hoher Temperaturbeständigkeit trägt dazu bei, die Leistung und Sicherheit des Bremssystems zu gewährleisten.
Insgesamt ist das Schleifmaterial ein entscheidender Faktor für die Leistung, Haltbarkeit und Sicherheit von Brems- und Kupplungsbelägen. Die Auswahl des richtigen Materials hängt von verschiedenen Faktoren ab, einschließlich der Anforderungen der Anwendung, der Betriebsbedingungen und der Fahrzeugart. Durch die kontinuierliche Weiterentwicklung von Schleifmaterialien werden ständig neue Materialien und Formulierungen entwickelt, um die Leistungsfähigkeit und Effizienz dieser wichtigen Komponenten weiter zu verbessern.
Belagkonstruktion
Die Belagkonstruktion spielt eine entscheidende Rolle bei der Leistung und Haltbarkeit von Brems- und Kupplungsbelägen. Hier sind einige wichtige Aspekte der Belagkonstruktion:
1. Schichtstruktur:
Die Schichtstruktur des Belags bezieht sich auf die Anordnung der verschiedenen Materialschichten innerhalb des Belags. Typischerweise bestehen Brems- und Kupplungsbeläge aus mehreren Schichten, die verschiedene Funktionen erfüllen, wie beispielsweise Reibungserzeugung, Wärmeableitung und Verschleißfestigkeit.
2. Reibfläche:
Die Reibfläche ist der Bereich des Belags, der mit der Bremsscheibe oder Kupplungsscheibe in Kontakt steht. Die Gestaltung und Oberflächenbeschaffenheit der Reibfläche beeinflussen direkt die Reibungseigenschaften und die Brems- bzw. Kupplungsleistung. Eine gleichmäßige und glatte Reibfläche trägt zu einer effektiven Reibung bei und minimiert den Verschleiß.
3. Materialzusammensetzung:
Die Auswahl der Materialien für den Belag hat einen großen Einfluss auf seine Leistung und Haltbarkeit. Verschiedene Materialien bieten unterschiedliche Reibungseigenschaften, Verschleißfestigkeit und Wärmebeständigkeit. Die richtige Kombination von Materialien ermöglicht es, Beläge herzustellen, die den spezifischen Anforderungen der Anwendung gerecht werden.
4. Dicke und Formgebung:
Die Dicke und Formgebung des Belags werden sorgfältig gestaltet, um eine gleichmäßige Reibung zu gewährleisten und eine optimale Anpassung an die Bremsscheibe oder Kupplungsscheibe zu ermöglichen. Eine präzise Formgebung und Dicke tragen dazu bei, die Brems- oder Kupplungsleistung zu maximieren und unerwünschte Vibrationen oder Geräusche zu minimieren.
5. Montage und Befestigung:
Die Montage und Befestigung des Belags ist ein wichtiger Schritt, um eine sichere und zuverlässige Funktion des Brems- oder Kupplungssystems zu gewährleisten. Eine ordnungsgemäße Befestigung des Belags an der Bremsbacke oder am Kupplungskorb ist entscheidend für eine gleichmäßige Kraftübertragung und eine effektive Brems- bzw. Kupplungswirkung.
Insgesamt ist die Belagkonstruktion ein komplexer Prozess, der Fachkenntnisse in Materialwissenschaft, Ingenieurwesen und Fertigungstechnik erfordert. Durch die sorgfältige Gestaltung und Optimierung der Belagkonstruktion können Brems- und Kupplungsbeläge hergestellt werden, die eine optimale Leistung und Haltbarkeit bieten und den Anforderungen der sich ständig weiterentwickelnden Automobilindustrie gerecht werden.
Reibungskoeffizient
Der Reibungskoeffizient ist ein wichtiger Parameter, der die Reibungseigenschaften von Brems- und Kupplungsbelägen charakterisiert. Hier sind einige wichtige Informationen zum Reibungskoeffizienten:
1. Definition:
Der Reibungskoeffizient ist das Verhältnis der Reibungskraft zwischen zwei Oberflächen zur Normalkraft, die auf sie wirkt. Er gibt an, wie stark die Reibung zwischen den Oberflächen ist und beeinflusst damit direkt die Brems- oder Kupplungsleistung.
2. Einfluss auf die Brems- und Kupplungsleistung:
Ein hoher Reibungskoeffizient bedeutet eine starke Reibung zwischen dem Belag und der Brems- oder Kupplungsscheibe, was zu einer effektiven Brems- oder Kupplungswirkung führt. Ein niedriger Reibungskoeffizient kann dagegen zu einem schlechteren Brems- oder Kupplungsverhalten führen, da die benötigte Reibungskraft nicht erreicht wird.
3. Temperaturabhängigkeit:
Der Reibungskoeffizient kann sich mit der Temperatur ändern, insbesondere bei Bremsbelägen. Während des Bremsvorgangs wird durch die Reibung Wärme erzeugt, was zu einer Erhöhung der Oberflächentemperatur des Belags führt. Dies kann den Reibungskoeffizienten beeinflussen und zu einer Veränderung der Bremsleistung führen.
4. Materialabhängigkeit:
Der Reibungskoeffizient hängt stark von den Materialien ab, aus denen der Belag und die Brems- oder Kupplungsscheibe bestehen. Verschiedene Materialkombinationen können zu unterschiedlichen Reibungskoeffizienten führen, was zu unterschiedlichen Brems- oder Kupplungsverhalten führt.
5. Messung und Bewertung:
Der Reibungskoeffizient wird experimentell gemessen, indem die Reibungskraft zwischen den Oberflächen gemessen und durch die Normalkraft dividiert wird. Die Bewertung des Reibungskoeffizienten erfolgt in der Regel durch dynamische Prüfstände oder durch Fahrtests unter kontrollierten Bedingungen.
Insgesamt ist der Reibungskoeffizient ein wichtiger Parameter für die Leistung und Sicherheit von Brems- und Kupplungssystemen. Die Optimierung des Reibungskoeffizienten ist ein wichtiger Aspekt bei der Entwicklung von Brems- und Kupplungsbelägen, um eine optimale Leistung und Haltbarkeit zu gewährleisten.
Wärmeableitung
Die Wärmeableitung ist ein entscheidender Aspekt bei der Konstruktion von Brems- und Kupplungsbelägen, da diese Systeme während des Betriebs erhebliche Wärmeenergie erzeugen. Hier sind einige wichtige Informationen zur Wärmeableitung:
1. Wärmeentwicklung:
Brems- und Kupplungssysteme erzeugen Wärmeenergie durch die Umwandlung von kinetischer Energie in Reibungswärme während des Brems- oder Kupplungsvorgangs. Diese Wärmeenergie kann zu einem Anstieg der Oberflächentemperatur der Beläge führen, was die Leistung und Haltbarkeit beeinträchtigen kann.
2. Wärmeableitungseigenschaften:
Die Fähigkeit eines Belags, Wärme abzuleiten, hängt von verschiedenen Faktoren ab, einschließlich seiner Materialzusammensetzung, seiner Oberflächenstruktur und seiner Konstruktion. Ein Belag mit guten Wärmeableitungseigenschaften kann die entstehende Wärme effektiv von der Reibfläche abführen und eine Überhitzung des Systems verhindern.
3. Materialauswahl:
Die Auswahl der Materialien für den Belag spielt eine wichtige Rolle bei der Wärmeableitung. Materialien mit hoher Wärmeleitfähigkeit, wie z.B. Metalle oder Keramik, können die Wärme effektiv von der Reibfläche ableiten und eine Überhitzung verhindern. Darüber hinaus können spezielle Beschichtungen oder Additive verwendet werden, um die Wärmeableitungseigenschaften zu verbessern.
4. Oberflächenstruktur:
Die Oberflächenstruktur des Belags kann ebenfalls die Wärmeableitung beeinflussen. Eine glatte Oberfläche ermöglicht eine bessere Wärmeableitung als eine raue Oberfläche, da sie den Kontakt zwischen dem Belag und der Bremsscheibe oder Kupplungsscheibe verbessert.
5. Kühlungssysteme:
In einigen Anwendungen können zusätzliche Kühlungssysteme, wie z.B. Belüftungsschlitze oder Kühlkanäle, verwendet werden, um die Wärmeableitung zu verbessern. Diese Systeme ermöglichen es, die entstehende Wärme effektiv abzuführen und eine Überhitzung des Systems zu verhindern.
Insgesamt ist die Wärmeableitung ein wichtiger Aspekt bei der Konstruktion von Brems- und Kupplungsbelägen, um eine optimale Leistung und Haltbarkeit unter verschiedenen Betriebsbedingungen zu gewährleisten. Durch die richtige Auswahl von Materialien, Oberflächenstrukturen und gegebenenfalls zusätzlichen Kühlungssystemen können Beläge hergestellt werden, die effektiv mit der entstehenden Wärme umgehen und eine zuverlässige Brems- und Kupplungsfunktion sicherstellen.
Verschleißfestigkeit
Die Verschleißfestigkeit ist eine entscheidende Eigenschaft von Brems- und Kupplungsbelägen, da sie direkt mit ihrer Lebensdauer und Leistungsfähigkeit verbunden ist. Hier sind einige wichtige Informationen zur Verschleißfestigkeit:
1. Definition:
Die Verschleißfestigkeit eines Belags bezieht sich auf seine Fähigkeit, Verschleißerscheinungen zu widerstehen und seine ursprünglichen Eigenschaften über einen längeren Zeitraum aufrechtzuerhalten. Dies umfasst die Beständigkeit gegen Abrieb, Erosion und Oberflächenveränderungen.
2. Einflussfaktoren:
Die Verschleißfestigkeit von Brems- und Kupplungsbelägen wird durch verschiedene Faktoren beeinflusst, darunter die Materialzusammensetzung, die Oberflächenbeschaffenheit, die Betriebsbedingungen und die Belastung des Systems.
3. Materialzusammensetzung:
Die Auswahl der Materialien für den Belag spielt eine entscheidende Rolle für seine Verschleißfestigkeit. Materialien mit hoher Härte, Festigkeit und Abriebfestigkeit bieten in der Regel eine bessere Verschleißfestigkeit und eine längere Lebensdauer.
4. Oberflächenbeschaffenheit:
Die Oberflächenbeschaffenheit des Belags kann ebenfalls die Verschleißfestigkeit beeinflussen. Eine glatte und gleichmäßige Oberfläche verringert den Verschleiß und minimiert die Bildung von Rissen oder Furchen, die die Leistung beeinträchtigen könnten.
5. Betriebsbedingungen:
Die Betriebsbedingungen, einschließlich der Temperatur, der Geschwindigkeit und der Belastung des Systems, können die Verschleißfestigkeit der Beläge stark beeinflussen. Extrembedingungen wie hohe Temperaturen oder schwere Lasten können zu einem erhöhten Verschleiß führen.
6. Schmierung und Kühlung:
Eine angemessene Schmierung und Kühlung des Belags kann ebenfalls zur Verbesserung der Verschleißfestigkeit beitragen. Durch die Reduzierung von Reibung und Temperatur können Schmierungssysteme den Verschleiß verringern und die Lebensdauer der Beläge verlängern.
Insgesamt ist die Verschleißfestigkeit eine wichtige Eigenschaft von Brems- und Kupplungsbelägen, die direkt mit ihrer Leistung und Lebensdauer verbunden ist. Durch die Auswahl von geeigneten Materialien, die Optimierung der Oberflächenbeschaffenheit und die Berücksichtigung der Betriebsbedingungen können Beläge hergestellt werden, die eine hohe Verschleißfestigkeit und eine zuverlässige Leistung unter verschiedenen Einsatzbedingungen bieten.
Reibungsmaterialien
Reibungsmaterialien sind entscheidend für die Leistung und Funktionalität von Brems- und Kupplungsbelägen. Hier sind einige wichtige Informationen zu Reibungsmaterialien:
1. Arten von Reibungsmaterialien:
- Organische Materialien: Organische Reibungsmaterialien umfassen typischerweise eine Mischung aus Fasern wie Aramid, Kohlenstoff und Keramik, die mit einem Bindemittel verbunden sind. Sie bieten eine gute Reibung und sind in der Regel geräuschärmer als andere Materialien.
- Anorganische Materialien: Anorganische Reibungsmaterialien können Metall- oder Keramikpartikel enthalten, die in einer Matrix aus Harz oder Keramik eingebettet sind. Sie bieten eine verbesserte Wärmebeständigkeit und Verschleißfestigkeit.
- Verbundwerkstoffe: Verbundwerkstoffe kombinieren verschiedene Materialien, um die Vorteile mehrerer Materialien zu nutzen. Sie können organische Fasern für Reibung und anorganische Partikel für Hitzebeständigkeit und Verschleißfestigkeit kombinieren.
2. Einfluss auf die Brems- und Kupplungsleistung:
Die Auswahl der richtigen Reibungsmaterialien beeinflusst direkt die Reibungseigenschaften und die Leistung der Brems- und Kupplungsbeläge. Materialien mit hoher Reibung bieten eine effektive Brems- oder Kupplungswirkung, während Materialien mit niedriger Reibung ein sanfteres Ein- und Auskuppeln ermöglichen.
3. Verschleißverhalten:
Das Verschleißverhalten von Reibungsmaterialien ist ein wichtiger Aspekt ihrer Leistungsfähigkeit. Materialien mit hoher Verschleißfestigkeit tragen dazu bei, die Lebensdauer der Beläge zu verlängern und die Wartungskosten zu reduzieren.
4. Temperaturbeständigkeit:
Die Temperaturbeständigkeit der Reibungsmaterialien ist entscheidend, da Brems- und Kupplungssysteme hohen Temperaturen ausgesetzt sind. Materialien mit hoher Temperaturbeständigkeit gewährleisten eine zuverlässige Leistung unter verschiedenen Betriebsbedingungen.
5. Entwicklung neuer Materialien:
Die kontinuierliche Entwicklung neuer Reibungsmaterialien ist entscheidend, um die Leistungsfähigkeit und Zuverlässigkeit von Brems- und Kupplungssystemen weiter zu verbessern. Durch die Erforschung und Entwicklung innovativer Materialien können Beläge hergestellt werden, die den Anforderungen der sich ständig weiterentwickelnden Automobilindustrie gerecht werden.
Insgesamt spielen Reibungsmaterialien eine entscheidende Rolle bei der Leistung, Haltbarkeit und Sicherheit von Brems- und Kupplungsbelägen. Die Auswahl der richtigen Materialien ist ein wichtiger Schritt bei der Entwicklung von Belägen, die eine optimale Leistung unter verschiedenen Betriebsbedingungen bieten.
Abrieb
Abrieb ist ein wichtiger Aspekt bei der Bewertung der Leistung und Lebensdauer von Brems- und Kupplungsbelägen. Hier sind einige wichtige Informationen zum Abrieb:
1. Definition:
Abrieb bezeichnet den Prozess, bei dem Material von der Oberfläche eines Belags abgetragen wird, während er mit der Brems- oder Kupplungsscheibe in Kontakt steht. Dieser Prozess kann zu einem allmählichen Verlust von Material führen und die Leistung des Belags im Laufe der Zeit beeinträchtigen.
2. Einflussfaktoren:
Der Abrieb von Brems- und Kupplungsbelägen wird durch verschiedene Faktoren beeinflusst, darunter die Materialzusammensetzung, die Betriebsbedingungen, die Oberflächenbeschaffenheit und die Belastung des Systems.
3. Materialzusammensetzung:
Die Auswahl der Materialien für den Belag spielt eine entscheidende Rolle für sein Abriebverhalten. Materialien mit hoher Härte und Abriebfestigkeit bieten in der Regel eine bessere Beständigkeit gegen Abrieb und eine längere Lebensdauer.
4. Betriebsbedingungen:
Die Betriebsbedingungen, einschließlich der Temperatur, der Geschwindigkeit und der Belastung des Systems, können den Abrieb von Brems- und Kupplungsbelägen stark beeinflussen. Extrembedingungen wie hohe Temperaturen oder schwere Lasten können zu einem erhöhten Abrieb führen.
5. Oberflächenbeschaffenheit:
Die Oberflächenbeschaffenheit des Belags und der Brems- oder Kupplungsscheibe kann den Abriebprozess beeinflussen. Eine glatte und gleichmäßige Oberfläche reduziert den Abrieb und minimiert die Bildung von Rissen oder Furchen, die die Leistung beeinträchtigen könnten.
6. Verschleißmechanismen:
Der Abrieb von Brems- und Kupplungsbelägen kann durch verschiedene Mechanismen verursacht werden, darunter Adhäsionsverschleiß, Abrasionsverschleiß und Oberflächenverschleiß. Das Verständnis dieser Mechanismen ist entscheidend für die Entwicklung von Belägen mit optimaler Verschleißfestigkeit und Leistung.
Insgesamt ist der Abrieb ein wichtiger Aspekt bei der Bewertung der Leistung und Lebensdauer von Brems- und Kupplungsbelägen. Durch die Auswahl geeigneter Materialien, die Optimierung der Oberflächenbeschaffenheit und die Berücksichtigung der Betriebsbedingungen können Beläge hergestellt werden, die eine hohe Abriebfestigkeit und eine zuverlässige Leistung unter verschiedenen Einsatzbedingungen bieten.
Friktionsmaterialien
Friktionsmaterialien spielen eine zentrale Rolle in Brems- und Kupplungssystemen, da sie die Reibung erzeugen, die für das Ein- und Auskuppeln sowie das Bremsen erforderlich ist. Hier sind einige wichtige Informationen zu Friktionsmaterialien:
1. Funktion:
Friktionsmaterialien erzeugen die Reibungskraft, die erforderlich ist, um Bewegung zwischen zwei Oberflächen zu erzeugen oder zu verhindern. Im Falle von Bremsbelägen erzeugen sie die Reibung, die erforderlich ist, um das Fahrzeug zu verlangsamen oder anzuhalten, während sie in Kupplungssystemen das Drehmoment übertragen und das Fahrzeug in Bewegung setzen.
2. Arten von Friktionsmaterialien:
- Organische Materialien: Organische Friktionsmaterialien bestehen aus Fasern wie Aramid, Kohlenstoff und Keramik, die mit einem Bindemittel verbunden sind. Sie bieten eine gute Reibung und sind in der Regel geräuschärmer als andere Materialien.
- Anorganische Materialien: Anorganische Friktionsmaterialien können Metall- oder Keramikpartikel enthalten, die in einer Matrix aus Harz oder Keramik eingebettet sind. Sie bieten eine verbesserte Wärmebeständigkeit und Verschleißfestigkeit.
- Verbundwerkstoffe: Verbundwerkstoffe kombinieren verschiedene Materialien, um die Vorteile mehrerer Materialien zu nutzen. Sie können organische Fasern für Reibung und anorganische Partikel für Hitzebeständigkeit und Verschleißfestigkeit kombinieren.
3. Auswahlkriterien:
Die Auswahl der richtigen Friktionsmaterialien hängt von verschiedenen Faktoren ab, darunter die Fahrzeugart, der Einsatzzweck, die Betriebsbedingungen und die persönlichen Vorlieben des Fahrers. Organische Materialien bieten eine sanfte Kupplungswirkung und sind ideal für den alltäglichen Gebrauch, während anorganische Materialien besser für Hochleistungsanwendungen geeignet sind.
4. Entwicklungstrends:
Die Entwicklung von Friktionsmaterialien konzentriert sich auf die Verbesserung der Reibungseigenschaften, der Verschleißfestigkeit, der Wärmebeständigkeit und der Umweltverträglichkeit. Durch die kontinuierliche Forschung und Entwicklung werden ständig neue Materialien und Formulierungen entwickelt, um die Leistung und Zuverlässigkeit von Brems- und Kupplungssystemen weiter zu verbessern.
Insgesamt spielen Friktionsmaterialien eine entscheidende Rolle bei der Leistung, Haltbarkeit und Sicherheit von Brems- und Kupplungssystemen. Die Auswahl der richtigen Materialien ist ein wichtiger Schritt bei der Entwicklung von Belägen, die eine optimale Leistung unter verschiedenen Betriebsbedingungen bieten.
Wärmeentwicklung
Die Wärmeentwicklung ist ein wichtiger Aspekt bei der Funktionsweise von Brems- und Kupplungssystemen. Hier sind einige wichtige Informationen zur Wärmeentwicklung:
1. Entstehung von Wärme:
Wärme entsteht in Brems- und Kupplungssystemen während des Reibungsprozesses zwischen dem Belag und der Brems- oder Kupplungsscheibe. Diese Reibung erzeugt kinetische Energie, die in Form von Wärme abgegeben wird.
2. Temperaturanstieg:
Die Wärmeentwicklung führt zu einem Temperaturanstieg in den Brems- und Kupplungskomponenten. Je nach Betriebsbedingungen und Einsatzintensität kann die Oberflächentemperatur der Beläge und Scheiben stark ansteigen.
3. Einfluss auf die Leistung:
Hohe Temperaturen können die Leistung von Brems- und Kupplungssystemen beeinträchtigen. Sie können beispielsweise zu einem Nachlassen der Bremswirkung führen, indem sie die Reibungseigenschaften der Beläge verändern oder zu einem Fading führen, bei dem die Bremsleistung bei hohen Temperaturen abnimmt.
4. Materialauswahl:
Die Auswahl der Materialien für Brems- und Kupplungsbeläge spielt eine wichtige Rolle bei der Steuerung der Wärmeentwicklung. Materialien mit hoher Wärmeleitfähigkeit können die entstehende Wärme effektiv abführen und eine Überhitzung verhindern.
5. Kühlung:
Zusätzliche Kühlmaßnahmen wie Belüftungsschlitze, Kühlkanäle oder spezielle Kühlflüssigkeiten können verwendet werden, um die Wärmeentwicklung zu reduzieren und die Temperatur der Brems- und Kupplungskomponenten auf einem optimalen Niveau zu halten.
6. Betriebsbedingungen:
Die Betriebsbedingungen, einschließlich Geschwindigkeit, Last und häufigem Bremsen oder Kuppeln, beeinflussen die Wärmeentwicklung in Brems- und Kupplungssystemen. Extrembedingungen können zu einem erhöhten Temperaturanstieg führen und die Leistung beeinträchtigen.
Insgesamt ist die Wärmeentwicklung ein wichtiger Aspekt bei der Konstruktion und Nutzung von Brems- und Kupplungssystemen. Durch die Auswahl geeigneter Materialien, die Optimierung der Kühlung und die Berücksichtigung der Betriebsbedingungen können Brems- und Kupplungssysteme entwickelt werden, die eine zuverlässige Leistung und Sicherheit bieten.
Reibungskurve
Die Reibungskurve ist ein wichtiges Konzept, um das Verhalten von Brems- und Kupplungssystemen zu verstehen. Hier sind einige wichtige Informationen zur Reibungskurve:
1. Definition:
Die Reibungskurve zeigt den Zusammenhang zwischen der Reibungskraft und der Relativgeschwindigkeit oder dem Schlupf zwischen zwei Oberflächen. Sie beschreibt, wie sich die Reibung während des Brems- oder Kupplungsvorgangs ändert.
2. Phasen der Reibungskurve:
- Anfangsreibung: Zu Beginn des Brems- oder Kupplungsvorgangs gibt es eine hohe Reibungskraft, die dazu führt, dass die Brems- oder Kupplungsscheibe schnell verzögert oder gekuppelt wird.
- Statische Reibung: Nach der Anfangsreibung folgt eine Phase der statischen Reibung, in der die Reibungskraft konstant bleibt, während sich die Beläge und die Scheibe noch nicht relativ zueinander bewegen.
- Dynamische Reibung: Sobald sich die Beläge und die Scheibe relativ zueinander bewegen, ändert sich die Reibungskraft und erreicht möglicherweise einen niedrigeren Wert als während der statischen Reibung.
3. Einflussfaktoren:
Die Form der Reibungskurve kann von verschiedenen Faktoren beeinflusst werden, darunter die Materialien der Beläge und der Scheibe, die Oberflächenbeschaffenheit, die Betriebstemperatur und die Betriebsbedingungen.
4. Bedeutung für die Leistung:
Die Form der Reibungskurve hat direkte Auswirkungen auf die Leistung von Brems- und Kupplungssystemen. Eine steile Anfangsreibung kann zu einer schnellen Verzögerung oder Kupplungsfreigabe führen, während eine flachere Kurve ein sanfteres Bremsen oder Kuppeln ermöglicht.
5. Anpassung und Optimierung:
Die Reibungskurve kann durch die Auswahl geeigneter Materialien, die Optimierung der Oberflächenbeschaffenheit und die Anpassung der Betriebsbedingungen angepasst und optimiert werden, um die gewünschte Brems- oder Kupplungsleistung zu erzielen.
Insgesamt ist die Reibungskurve ein wichtiges Werkzeug, um das Reibungsverhalten von Brems- und Kupplungssystemen zu verstehen und zu optimieren. Durch die Analyse und Anpassung der Reibungskurve können Beläge und Scheiben entwickelt werden, die eine optimale Leistung und Sicherheit bieten.
Trockenreibung
Trockenreibung ist ein wichtiger Aspekt bei der Leistung von Brems- und Kupplungssystemen, insbesondere unter normalen Betriebsbedingungen. Hier sind einige wichtige Informationen zur Trockenreibung:
1. Definition:
Trockenreibung bezieht sich auf die Reibung zwischen zwei Oberflächen, die nicht durch Schmiermittel wie Öl oder Fett geschmiert sind. In Brems- und Kupplungssystemen tritt Trockenreibung auf, wenn der Bremsbelag oder Kupplungsbelag direkt mit der Brems- oder Kupplungsscheibe in Kontakt steht.
2. Einflussfaktoren:
Die Trockenreibung wird durch verschiedene Faktoren beeinflusst, darunter die Materialien der Beläge und der Scheibe, die Oberflächenbeschaffenheit, die Betriebstemperatur und die Anpresskraft.
3. Leistungscharakteristik:
Die Trockenreibungseigenschaften bestimmen maßgeblich das Brems- oder Kupplungsverhalten. Ein hoher Reibungskoeffizient kann zu einer schnellen Verzögerung oder einer effektiven Kraftübertragung führen, während ein niedriger Reibungskoeffizient zu einem sanfteren Betrieb führt.
4. Optimierung:
Die Trockenreibung kann durch die Auswahl geeigneter Materialien, die Optimierung der Oberflächenbeschaffenheit und die Anpassung der Betriebsbedingungen optimiert werden. Ziel ist es, einen optimalen Reibungskoeffizienten zu erreichen, der eine effiziente Brems- oder Kupplungswirkung gewährleistet.
5. Stabilität und Zuverlässigkeit:
Eine stabile Trockenreibung ist entscheidend für die Zuverlässigkeit und Sicherheit von Brems- und Kupplungssystemen. Unvorhersehbare Änderungen der Reibungseigenschaften können zu unerwartetem Bremsen oder Kuppeln führen, was die Fahrzeugkontrolle beeinträchtigen kann.
Insgesamt ist die Trockenreibung ein wichtiger Aspekt bei der Entwicklung und Nutzung von Brems- und Kupplungssystemen. Durch die gezielte Optimierung der Trockenreibungseigenschaften können Beläge und Scheiben entwickelt werden, die eine zuverlässige und effiziente Leistung unter verschiedenen Betriebsbedingungen bieten.
Nassreibung
Nassreibung spielt eine wichtige Rolle bei der Leistung von Brems- und Kupplungssystemen unter feuchten oder nassen Bedingungen. Hier sind einige wichtige Informationen zur Nassreibung:
1. Definition:
Nassreibung bezieht sich auf die Reibung zwischen zwei Oberflächen, die durch das Vorhandensein von Wasser oder anderen Flüssigkeiten beeinflusst wird. In Brems- und Kupplungssystemen tritt Nassreibung auf, wenn der Bremsbelag oder Kupplungsbelag mit der nassen Brems- oder Kupplungsscheibe in Kontakt steht.
2. Einflussfaktoren:
Die Nassreibung wird durch verschiedene Faktoren beeinflusst, darunter die Menge und Verteilung des Wassers auf den Oberflächen, die Geschwindigkeit des Fahrzeugs und die Anpresskraft.
3. Herausforderungen:
Nassreibung kann zu reduzierter Reibung und Bremsleistung führen, da Wasser zwischen den Belägen und den Scheiben einen Schmierfilm bildet und die Kontaktfläche verringert. Dies kann zu verlängerten Bremswegen und einer verringerten Bremswirkung führen, insbesondere bei hoher Geschwindigkeit.
4. Optimierung:
Die Optimierung der Nassreibungseigenschaften erfordert spezielle Materialien und Oberflächenstrukturen, die dazu beitragen, das Wasser schnell zu verdrängen und eine direkte Kontaktfläche zwischen Belägen und Scheiben aufrechtzuerhalten. Dies kann durch die Verwendung von speziellen wasserabweisenden Beschichtungen oder Drainagelöchern erreicht werden.
5. Sicherheitsaspekte:
Eine zuverlässige Nassreibung ist entscheidend für die Sicherheit von Fahrzeugen unter feuchten oder nassen Bedingungen. Brems- und Kupplungssysteme müssen auch bei widrigen Witterungsverhältnissen eine effektive Leistung bieten, um Unfälle zu vermeiden.
Insgesamt ist die Nassreibung ein wichtiger Aspekt bei der Entwicklung und Nutzung von Brems- und Kupplungssystemen, insbesondere unter feuchten oder nassen Bedingungen. Durch die gezielte Optimierung der Nassreibungseigenschaften können Beläge und Scheiben entwickelt werden, die auch unter widrigen Witterungsbedingungen eine zuverlässige und effiziente Leistung bieten.
Bremsbelag
Ein Bremsbelag ist ein wesentlicher Bestandteil eines Bremssystems, der für die Umwandlung von kinetischer Energie in Wärmeenergie verantwortlich ist, um ein Fahrzeug zu verlangsamen oder anzuhalten. Hier sind einige wichtige Informationen zum Bremsbelag:
1. Funktion:
Der Bremsbelag erzeugt Reibung, wenn er gegen die Bremsfläche, normalerweise eine Bremsscheibe oder eine Trommel, gedrückt wird. Diese Reibung erzeugt die notwendige Verzögerung, um das Fahrzeug zum Stillstand zu bringen.
2. Materialien:
Bremsbeläge bestehen typischerweise aus einer Mischung von Reibungsmaterialien wie organischen, anorganischen oder keramischen Fasern, die mit einem Bindemittel verbunden sind. Diese Materialien werden für ihre Reibungseigenschaften, Verschleißfestigkeit und Temperaturbeständigkeit ausgewählt.
3. Aufbau:
Ein Bremsbelag besteht aus einem Träger, der aus Metall oder einer anderen hitzebeständigen Legierung besteht, der das Reibmaterial trägt. Das Reibmaterial wird dann auf den Träger aufgebracht und kann verschiedene Formen und Profile haben, abhängig von der Art des Bremssystems.
4. Verschleiß:
Bremsbeläge unterliegen einem natürlichen Verschleiß während des Bremsbetriebs, da die Reibung dazu führt, dass sich das Reibmaterial abnutzt. Die Lebensdauer eines Bremsbelags hängt von verschiedenen Faktoren ab, einschließlich des Fahrverhaltens, der Fahrzeuglast und der Betriebsbedingungen.
5. Wartung:
Eine regelmäßige Inspektion und Wartung der Bremsbeläge ist wichtig, um eine optimale Bremsleistung und Sicherheit zu gewährleisten. Abgenutzte oder beschädigte Bremsbeläge sollten rechtzeitig ausgetauscht werden, um einen sicheren Betrieb des Fahrzeugs zu gewährleisten.
Insgesamt ist der Bremsbelag ein entscheidender Bestandteil des Bremssystems, der eine zuverlässige Bremsleistung und Sicherheit gewährleistet. Die Auswahl hochwertiger Materialien und eine regelmäßige Wartung sind entscheidend, um die Leistung und Lebensdauer der Bremsbeläge zu maximieren.
Bremsflüssigkeit
Bremsflüssigkeit ist ein kritischer Bestandteil des hydraulischen Bremssystems eines Fahrzeugs und spielt eine entscheidende Rolle bei der Übertragung der Bremskraft von der Betätigungseinheit (Bremspedal) auf die Bremsbeläge oder -backen. Hier sind einige wichtige Informationen zur Bremsflüssigkeit:
1. Funktion:
Die Hauptfunktion der Bremsflüssigkeit besteht darin, den hydraulischen Druck von der Bremsbetätigungseinheit auf die Bremsbeläge oder -backen zu übertragen. Sie überträgt die vom Bremspedal erzeugte Kraft auf die Bremskolben in den Bremssätteln oder Bremszylindern.
2. Hydraulisches System:
Bremsflüssigkeit arbeitet in einem geschlossenen hydraulischen System, das aus Bremsleitungen, Bremszylindern, Bremssätteln und Bremszylindern besteht. Wenn das Bremspedal betätigt wird, wird der hydraulische Druck auf die Bremsbeläge oder -backen übertragen, was zu einer Bremswirkung führt.
3. Typen:
Es gibt verschiedene Arten von Bremsflüssigkeiten, die in Fahrzeugen verwendet werden, darunter DOT 3, DOT 4, DOT 5 und DOT 5.1. Jeder Typ hat unterschiedliche Eigenschaften in Bezug auf den Siedepunkt, die Viskosität und die Kompatibilität mit Dichtungsmaterialien.
4. Siedepunkt:
Der Siedepunkt der Bremsflüssigkeit ist ein wichtiger Parameter, der ihre Leistung unter verschiedenen Betriebsbedingungen bestimmt. Eine Bremsflüssigkeit mit einem höheren Siedepunkt bietet eine verbesserte Leistung bei hohen Temperaturen und reduziert das Risiko von Dampfblasenbildung im Bremssystem (Vapor Lock).
5. Wartung:
Die regelmäßige Wartung der Bremsflüssigkeit ist entscheidend, um eine optimale Bremsleistung und Sicherheit zu gewährleisten. Bremsflüssigkeit neigt im Laufe der Zeit dazu, Feuchtigkeit aufzunehmen, was zu einer Absenkung des Siedepunkts führen kann. Daher ist ein regelmäßiger Wechsel gemäß den Herstellervorgaben unerlässlich.
Insgesamt ist die Bremsflüssigkeit ein wesentlicher Bestandteil des Bremssystems, der eine zuverlässige Übertragung der Bremskraft ermöglicht. Die Auswahl der richtigen Bremsflüssigkeit und die regelmäßige Wartung sind entscheidend für eine sichere und effektive Bremsleistung.
Kupplungsbelag
Ein Kupplungsbelag ist ein wesentlicher Bestandteil einer Kupplungseinheit in Fahrzeugen mit Schaltgetriebe. Hier sind einige wichtige Informationen zum Kupplungsbelag:
1. Funktion:
Der Kupplungsbelag ermöglicht die Übertragung des Drehmoments vom Motor auf das Getriebe, indem er die Verbindung zwischen Motor und Getriebe trennt oder herstellt. Beim Betätigen des Kupplungspedals wird der Kupplungsbelag von der Schwungscheibe gelöst, um den Gangwechsel zu ermöglichen.
2. Materialien:
Kupplungsbeläge bestehen typischerweise aus einem Reibmaterial, das an einem Metallträger befestigt ist. Das Reibmaterial kann organische, anorganische oder keramische Fasern enthalten, die für ihre Reibungseigenschaften und Verschleißfestigkeit ausgewählt werden.
3. Konstruktion:
Ein Kupplungsbelag besteht aus einem Reibbelag, der auf einem Metallträger montiert ist. Der Belag ist in der Regel kreisförmig und weist Löcher auf, um die Kühlung zu verbessern und die Belastung zu reduzieren.
4. Verschleiß:
Wie Bremsbeläge unterliegen auch Kupplungsbeläge einem natürlichen Verschleiß während des Betriebs. Der Verschleiß des Kupplungsbelags hängt von verschiedenen Faktoren ab, einschließlich des Fahrverhaltens, der Fahrzeuglast und der Betriebsbedingungen.
5. Wartung:
Eine regelmäßige Inspektion und Wartung der Kupplungsbeläge ist wichtig, um eine optimale Kupplungsleistung und Langlebigkeit zu gewährleisten. Abgenutzte oder beschädigte Kupplungsbeläge können zu Schaltproblemen oder einem Versagen des Kupplungssystems führen und sollten rechtzeitig ausgetauscht werden.
Insgesamt ist der Kupplungsbelag ein entscheidender Bestandteil des Kupplungssystems, der eine zuverlässige Kraftübertragung zwischen Motor und Getriebe ermöglicht. Die Auswahl hochwertiger Materialien und eine regelmäßige Wartung sind entscheidend, um die Leistung und Lebensdauer der Kupplungsbeläge zu maximieren.
Kupplungsflüssigkeit
Die Kupplungsflüssigkeit ist ein wichtiger Bestandteil des hydraulischen Kupplungssystems in Fahrzeugen mit Schaltgetriebe. Hier sind einige wichtige Informationen zur Kupplungsflüssigkeit:
1. Funktion:
Die Hauptfunktion der Kupplungsflüssigkeit besteht darin, den hydraulischen Druck von der Kupplungsbetätigungseinheit auf den Kupplungszylinder zu übertragen. Sie ermöglicht ein reibungsloses Betätigen der Kupplung und den Wechsel der Fahrzeuggänge.
2. Hydraulisches System:
Ähnlich wie bei der Bremsflüssigkeit arbeitet die Kupplungsflüssigkeit in einem geschlossenen hydraulischen System, das aus Kupplungsleitungen, dem Kupplungszylinder und der Kupplungsbetätigungseinheit besteht. Wenn das Kupplungspedal betätigt wird, wird der hydraulische Druck auf den Kupplungszylinder übertragen, um die Kupplung zu betätigen.
3. Typen:
Es gibt verschiedene Arten von Kupplungsflüssigkeiten, die in Fahrzeugen verwendet werden, darunter DOT 3, DOT 4, DOT 5 und DOT 5.1. Jeder Typ hat unterschiedliche Eigenschaften in Bezug auf den Siedepunkt, die Viskosität und die Kompatibilität mit Dichtungsmaterialien.
4. Siedepunkt:
Wie bei der Bremsflüssigkeit ist der Siedepunkt der Kupplungsflüssigkeit ein wichtiger Parameter, der ihre Leistung unter verschiedenen Betriebsbedingungen bestimmt. Eine Kupplungsflüssigkeit mit einem höheren Siedepunkt bietet eine verbesserte Leistung bei hohen Temperaturen und reduziert das Risiko von Kupplungsversagen.
5. Wartung:
Die regelmäßige Wartung der Kupplungsflüssigkeit ist entscheidend, um eine optimale Kupplungsleistung und Sicherheit zu gewährleisten. Wie bei der Bremsflüssigkeit neigt auch die Kupplungsflüssigkeit dazu, Feuchtigkeit aufzunehmen, was zu einem Absenken des Siedepunkts führen kann. Ein regelmäßiger Wechsel gemäß den Herstellervorgaben ist daher unerlässlich.
Insgesamt ist die Kupplungsflüssigkeit ein wesentlicher Bestandteil des Kupplungssystems, der eine zuverlässige Betätigung der Kupplung ermöglicht. Die Auswahl der richtigen Kupplungsflüssigkeit und die regelmäßige Wartung sind entscheidend für eine sichere und effektive Kupplungsleistung.
Reibwert
Der Reibwert ist ein wichtiger Parameter, der die Reibungseigenschaften von Oberflächen oder Materialien beschreibt. Hier sind einige wichtige Informationen zum Reibwert:
1. Definition:
Der Reibwert ist das Verhältnis zwischen der aufgebrachten Kraft, die erforderlich ist, um zwei Oberflächen gegeneinander zu bewegen, und der Kraft, die zwischen den Oberflächen auftritt und sie am Gleiten hindert.
2. Einflussfaktoren:
Der Reibwert wird durch verschiedene Faktoren beeinflusst, darunter die Art der Oberflächen, die Materialeigenschaften, die Oberflächenrauheit, die Schmierung und die Betriebsbedingungen.
3. Arten von Reibwerten:
Es gibt zwei Hauptarten von Reibwerten:
- Statischer Reibwert: Der Reibwert, der auftritt, wenn die Oberflächen in Ruhe sind und keine relative Bewegung zwischen ihnen stattfindet.
- Dynamischer Reibwert: Der Reibwert, der auftritt, wenn sich die Oberflächen relativ zueinander bewegen.
4. Messung:
Der Reibwert wird üblicherweise durch Versuche gemessen, bei denen eine definierte Kraft aufgebracht wird, um die Oberflächen zu bewegen, und die resultierende Reaktion gemessen wird. Diese Messungen können unter verschiedenen Bedingungen durchgeführt werden, um den Einfluss verschiedener Faktoren zu untersuchen.
5. Bedeutung:
Der Reibwert ist von entscheidender Bedeutung für viele technische Anwendungen, einschließlich Bremsen, Kupplungen, Lager, Gleitführungen und vielem mehr. Ein genaues Verständnis der Reibungseigenschaften ist entscheidend für die Konstruktion und den Betrieb von Maschinen und mechanischen Systemen.
Insgesamt ist der Reibwert ein wichtiger Parameter, der die Reibungseigenschaften von Oberflächen oder Materialien quantifiziert. Ein genaues Verständnis der Reibwerte ist entscheidend für die Entwicklung und den Betrieb verschiedener technischer Systeme und Anwendungen.
Gleitreibung
Die Gleitreibung ist eine Form der Reibung, die auftritt, wenn zwei Oberflächen relativ zueinander bewegt werden. Hier sind einige wichtige Informationen zur Gleitreibung:
1. Definition:
Die Gleitreibung tritt auf, wenn zwei Oberflächen in Kontakt sind und sich relativ zueinander bewegen. Sie entsteht aufgrund der mikroskopischen Unebenheiten der Oberflächen, die sich gegeneinander verschieben und Reibung erzeugen.
2. Einflussfaktoren:
Die Gleitreibung wird durch verschiedene Faktoren beeinflusst, darunter die Art der Oberflächen, die Oberflächenrauheit, die angewendete Kraft, die Schmierung und die Betriebsbedingungen wie Geschwindigkeit und Temperatur.
3. Reibungskraft:
Die Gleitreibung erzeugt eine Reibungskraft, die der Bewegungsrichtung entgegengerichtet ist. Diese Reibungskraft muss überwunden werden, um eine gleichmäßige Bewegung der Oberflächen zu erreichen.
4. Reduktion der Gleitreibung:
Die Gleitreibung kann durch verschiedene Maßnahmen reduziert werden, darunter die Verwendung von Schmiermitteln, die Glättung der Oberflächen, die Verwendung von Gleitlagern oder Gleitbahnen und die Anpassung der Betriebsbedingungen.
5. Anwendungen:
Die Gleitreibung ist in vielen technischen Anwendungen von Bedeutung, darunter in Maschinenbau, Fahrzeugtechnik, Tribologie, Haftung von Materialien und vielen anderen Bereichen, in denen bewegliche Teile aufeinandertreffen.
Insgesamt ist die Gleitreibung eine wichtige Form der Reibung, die in vielen technischen Anwendungen eine Rolle spielt. Ein genaues Verständnis der Gleitreibungseigenschaften ist entscheidend für die Entwicklung und den Betrieb von mechanischen Systemen und Maschinen.
Haftreibung
Die Haftreibung ist eine Form der Reibung, die auftritt, wenn zwei Oberflächen in direktem Kontakt stehen und sich nicht relativ zueinander bewegen. Hier sind einige wichtige Informationen zur Haftreibung:
1. Definition:
Haftreibung tritt auf, wenn zwei Oberflächen in Kontakt sind und keine relative Bewegung zwischen ihnen stattfindet. Sie entsteht aufgrund der Adhäsionskräfte zwischen den Molekülen der Oberflächen, die versuchen, einander zu widerstehen.
2. Einflussfaktoren:
Die Haftreibung wird durch verschiedene Faktoren beeinflusst, darunter die Art der Oberflächen, die Oberflächenrauheit, die angewendete Kraft, die Schmierung und die Betriebsbedingungen wie Druck und Temperatur.
3. Überwinden der Haftreibung:
Um die Haftreibung zu überwinden und die Oberflächen in Bewegung zu setzen, muss eine ausreichende Kraft angewendet werden, um die Adhäsionskräfte zu überwinden. Diese Kraft wird als Scherkraft bezeichnet und ist erforderlich, um die Reibung zu überwinden und die Bewegung zu initiieren.
4. Bedeutung:
Die Haftreibung ist in vielen technischen Anwendungen von Bedeutung, insbesondere in Situationen, in denen Bewegung vermieden werden soll. Beispiele hierfür sind das Halten von Objekten an Ort und Stelle, das Anfahren eines Fahrzeugs auf einer geneigten Straße und das Verhindern von Rutschen auf einer Oberfläche.
5. Anwendungen:
Haftreibung findet Anwendung in vielen Bereichen des täglichen Lebens, wie z.B. beim Greifen von Gegenständen, beim Anfahren von Fahrzeugen, beim Klettern und beim Stehen auf einer rutschigen Oberfläche.
Insgesamt ist die Haftreibung eine wichtige Form der Reibung, die in vielen technischen Anwendungen und im täglichen Leben eine Rolle spielt. Ein genaues Verständnis der Haftreibungseigenschaften ist entscheidend für die Entwicklung und den Betrieb von mechanischen Systemen und für das Verständnis alltäglicher Phänomene.
Rauheit
Die Rauheit bezieht sich auf die Unebenheiten oder Erhebungen auf der Oberfläche eines Materials. Hier sind einige wichtige Informationen zur Rauheit:
1. Definition:
Rauheit ist eine quantitative Bewertung der Unebenheiten oder Erhebungen auf der Oberfläche eines Materials im Vergleich zur idealen glatten Oberfläche. Sie wird oft in Mikrometern oder anderen Einheiten gemessen und kann eine wichtige Rolle bei der Reibung und Verschleiß spielen.
2. Arten von Rauheit:
Es gibt zwei Hauptarten von Rauheit:
- Makrorauheit: Große Unebenheiten, die mit bloßem Auge sichtbar sind und typischerweise im Bereich von Mikrometern bis Millimetern liegen.
- Mikrorauheit: Kleine Unebenheiten, die nur unter Vergrößerung sichtbar sind und typischerweise im Bereich von Nanometern bis Mikrometern liegen.
3. Einflussfaktoren:
Die Rauheit einer Oberfläche wird durch verschiedene Faktoren beeinflusst, darunter Herstellungsprozesse, Materialzusammensetzung, Bearbeitungsmethoden und Umweltbedingungen.
4. Auswirkungen auf die Reibung:
Die Rauheit einer Oberfläche kann direkte Auswirkungen auf die Reibung haben, insbesondere bei Gleit- oder Rollkontakt. Eine höhere Rauheit kann zu einer erhöhten Reibung und einem erhöhten Verschleiß führen, während eine geringere Rauheit zu einer glatteren Oberfläche und einer geringeren Reibung führen kann.
5. Messung:
Die Rauheit einer Oberfläche wird mit verschiedenen Messgeräten gemessen, darunter Rauheitsmessgeräte wie Oberflächenrastermikroskope, Profilometer und Taststifte. Diese Geräte erfassen die Höhenunterschiede entlang einer Linie oder Fläche und berechnen daraus verschiedene Rauheitsparameter.
Insgesamt spielt die Rauheit eine wichtige Rolle bei der Charakterisierung von Oberflächen und kann direkte Auswirkungen auf die Reibung, Verschleiß und Leistung von Materialien haben. Ein genaues Verständnis der Rauheitseigenschaften ist entscheidend für die Entwicklung und den Betrieb von technischen Systemen und Komponenten.
Schmierung
Die Schmierung ist ein wichtiger Prozess, der dazu dient, die Reibung und den Verschleiß zwischen beweglichen Teilen zu reduzieren. Hier sind einige wichtige Informationen zur Schmierung:
1. Definition:
Schmierung bezieht sich auf die Anwendung eines Schmiermittels, das dazu dient, die Reibung zwischen zwei Oberflächen zu verringern und den Verschleiß zu reduzieren. Das Schmiermittel bildet einen Schmierfilm zwischen den Oberflächen, der die direkte Berührung und den damit verbundenen Verschleiß minimiert.
2. Arten von Schmiermitteln:
Es gibt verschiedene Arten von Schmiermitteln, darunter:
- Öle: Flüssige Schmiermittel, die auf Mineralölbasis oder synthetischen Ölen basieren.
- Fette: Halbfeste Schmiermittel, die aus einem Öl und einem verdickenden Mittel bestehen.
- Trockenschmierstoffe: Feststoffe wie Graphit oder Molybdändisulfid, die als Schmiermittel verwendet werden können.
3. Funktionen:
Die Schmierung erfüllt mehrere Funktionen, darunter:
- Verringerung der Reibung und des Verschleißes
- Kühlung der beweglichen Teile
- Dichtungswirkung gegen eindringende Partikel und Feuchtigkeit
- Schutz vor Korrosion
4. Anwendungen:
Schmierung wird in einer Vielzahl von Anwendungen eingesetzt, darunter Fahrzeugmotoren, Getriebe, Lager, Hydrauliksysteme, Turbinen, Schneidwerkzeuge und vieles mehr. Sie ist entscheidend für die reibungslose und zuverlässige Funktion von mechanischen Systemen.
5. Schmierungstechniken:
Es gibt verschiedene Schmierungstechniken, darunter:
- Schmierung durch Ölbad
- Schmierung durch Sprühen oder Tropfen
- Schmierung durch Zentralschmieranlagen
- Schmierung durch Fettschmierung
- Schmierung durch Trockenschmierung
Insgesamt ist die Schmierung ein entscheidender Prozess, der dazu beiträgt, die Lebensdauer und Leistung von beweglichen Teilen in mechanischen Systemen zu verbessern. Ein genaues Verständnis der Schmierungseigenschaften und -techniken ist entscheidend für die Entwicklung und den Betrieb von technischen Anwendungen und Maschinen.
Schmierfilm
Ein Schmierfilm ist eine dünnflüssige Schicht aus Schmiermittel, die zwischen zwei sich bewegenden Oberflächen gebildet wird, um Reibung und Verschleiß zu reduzieren. Hier sind einige wichtige Informationen zum Schmierfilm:
1. Funktion:
Der Schmierfilm dient dazu, die direkte Berührung zwischen den Oberflächen zu vermeiden und eine gleitende Bewegung zu ermöglichen. Er reduziert die Reibungskräfte und schützt die Oberflächen vor Verschleiß und Beschädigung.
2. Bildung:
Der Schmierfilm wird durch das Schmiermittel gebildet, das zwischen den Oberflächen aufgetragen wird. Durch die Bewegung der Oberflächen entsteht eine hydrodynamische Wirkung, die das Schmiermittel zwischen den Oberflächen einschließt und einen stabilen Schmierfilm bildet.
3. Eigenschaften:
Ein guter Schmierfilm zeichnet sich durch eine ausreichende Viskosität und Scherstabilität aus, um den Belastungen standzuhalten und eine effektive Schmierung über einen längeren Zeitraum zu gewährleisten. Er sollte auch Temperaturen und Drücken standhalten können, die während des Betriebs auftreten.
4. Bedeutung:
Der Schmierfilm ist entscheidend für die Leistung und Lebensdauer von mechanischen Systemen, insbesondere bei Hochleistungsanwendungen wie Motoren, Getrieben, Lagern und anderen beweglichen Teilen. Ein stabiler Schmierfilm reduziert den Verschleiß und verlängert die Lebensdauer der Komponenten.
5. Überwachung:
Die Qualität und Dicke des Schmierfilms kann durch verschiedene Methoden überwacht werden, darunter visuelle Inspektionen, Messungen der Schmierfilmtemperatur und -druck, sowie die Analyse von Schmiermittelproben auf Verschleißpartikel und Verunreinigungen.
Insgesamt ist der Schmierfilm eine entscheidende Komponente in der Schmierung von mechanischen Systemen, die dazu beiträgt, Reibung und Verschleiß zu reduzieren und die Leistung und Lebensdauer der Komponenten zu verbessern. Ein genaues Verständnis der Schmierfilmbildung und -eigenschaften ist entscheidend für die Entwicklung und den Betrieb von technischen Anwendungen und Maschinen.
Reibungskoeffizient
Der Reibungskoeffizient ist eine dimensionslose Zahl, die das Verhältnis zwischen der Reibungskraft und der Normalkraft zwischen zwei Oberflächen beschreibt. Hier sind einige wichtige Informationen zum Reibungskoeffizienten:
1. Definition:
Der Reibungskoeffizient ist das Verhältnis zwischen der Reibungskraft, die zwischen zwei Oberflächen auftritt, und der Normalkraft, die senkrecht zu den Oberflächen wirkt. Er wird oft mit dem griechischen Buchstaben „μ“ (Mu) dargestellt.
2. Arten von Reibungskoeffizienten:
Es gibt verschiedene Arten von Reibungskoeffizienten, darunter:
- Statischer Reibungskoeffizient: Beschreibt die Reibungskraft, die auftritt, wenn die Oberflächen in Ruhe sind und keine relative Bewegung zwischen ihnen stattfindet.
- Dynamischer Reibungskoeffizient: Beschreibt die Reibungskraft, die auftritt, wenn sich die Oberflächen relativ zueinander bewegen.
3. Messung:
Der Reibungskoeffizient wird durch experimentelle Messungen bestimmt, bei denen die Reibungskraft und die Normalkraft unter verschiedenen Bedingungen gemessen werden. Diese Messungen können in Labors durchgeführt werden, indem spezielle Testvorrichtungen verwendet werden.
4. Einflussfaktoren:
Der Reibungskoeffizient wird durch verschiedene Faktoren beeinflusst, darunter die Art der Oberflächen, die Oberflächenrauheit, die Schmierung, die Temperatur und die Betriebsbedingungen wie Geschwindigkeit und Belastung.
5. Bedeutung:
Der Reibungskoeffizient ist ein wichtiger Parameter in vielen technischen Anwendungen, einschließlich Maschinenbau, Fahrzeugtechnik, Tribologie und Materialwissenschaften. Er beeinflusst die Leistung von mechanischen Systemen und kann zur Optimierung von Reibung und Verschleiß beitragen.
Insgesamt ist der Reibungskoeffizient eine wichtige Kennzahl, die das Reibungsverhalten zwischen zwei Oberflächen quantifiziert. Ein genaues Verständnis des Reibungskoeffizienten ist entscheidend für die Entwicklung und den Betrieb von technischen Systemen und Anwendungen.
Adhäsion
Adhäsion ist ein physikalisches Phänomen, bei dem Moleküle oder Atome von verschiedenen Oberflächen aufgrund von Van-der-Waals-Kräften oder elektrostatischen Anziehungskräften miteinander in Kontakt treten und eine Haftung zwischen den Oberflächen erzeugen. Hier sind einige wichtige Informationen zur Adhäsion:
1. Definition:
Adhäsion bezieht sich auf die Anziehungskräfte zwischen Molekülen oder Atomen verschiedener Oberflächen, die dazu führen, dass sie sich gegenseitig anziehen und haften bleiben. Diese Kräfte können aufgrund von elektrostatischen Wechselwirkungen, Van-der-Waals-Kräften oder chemischen Bindungen auftreten.
2. Mechanismen:
Die Adhäsion kann durch verschiedene Mechanismen erklärt werden, darunter:
- Van-der-Waals-Kräfte: Kurzreichweitige Anziehungskräfte zwischen Molekülen aufgrund von temporären Dipolen.
- Elektrostatische Anziehung: Anziehungskräfte zwischen geladenen Teilchen aufgrund von Ladungsunterschieden.
- Chemische Bindungen: Anziehungskräfte, die durch chemische Bindungen zwischen Molekülen entstehen.
3. Einflussfaktoren:
Die Adhäsion wird durch verschiedene Faktoren beeinflusst, darunter die Art der Oberflächen, die Oberflächenrauheit, die Temperatur und die Umgebungsbedingungen wie Feuchtigkeit und Druck.
4. Bedeutung:
Adhäsion spielt eine wichtige Rolle in vielen technischen Anwendungen und Naturphänomenen, einschließlich Klebstoffe, Oberflächenbeschichtungen, Haftung von Materialien, biologische Adhäsion und vieles mehr.
5. Anwendungen:
Adhäsive werden in einer Vielzahl von Anwendungen eingesetzt, darunter Bauwesen, Automobilindustrie, Elektronik, Medizin und Biotechnologie. Sie ermöglichen die Verbindung verschiedener Materialien und Komponenten auf eine dauerhafte und zuverlässige Weise.
Insgesamt ist Adhäsion ein wichtiges physikalisches Phänomen, das in vielen Bereichen des täglichen Lebens und der Technik eine Rolle spielt. Ein genaues Verständnis der Adhäsionseigenschaften ist entscheidend für die Entwicklung und den Einsatz von Klebstoffen, Beschichtungen und anderen adhäsiven Materialien.
Kohäsion
Kohäsion ist ein physikalisches Phänomen, bei dem Moleküle oder Atome desselben Materials aufgrund von Anziehungskräften zusammengehalten werden. Hier sind einige wichtige Informationen zur Kohäsion:
1. Definition:
Kohäsion bezieht sich auf die Anziehungskräfte zwischen Molekülen oder Atomen desselben Materials, die dazu führen, dass sie zusammenhaften und eine zusammenhängende Masse bilden. Diese Kräfte entstehen durch elektrostatische Anziehung, Van-der-Waals-Kräfte oder chemische Bindungen.
2. Mechanismen:
Die Kohäsion kann durch verschiedene Mechanismen erklärt werden, darunter:
- Van-der-Waals-Kräfte: Anziehungskräfte zwischen Molekülen aufgrund von temporären Dipolen.
- Elektrostatische Anziehung: Anziehungskräfte zwischen geladenen Teilchen desselben Materials.
- Chemische Bindungen: Starke Bindungen zwischen Atomen desselben Materials.
3. Einflussfaktoren:
Die Kohäsion wird durch verschiedene Faktoren beeinflusst, darunter die Art des Materials, die Molekülstruktur, die Temperatur und der Druck.
4. Bedeutung:
Kohäsion spielt eine wichtige Rolle in vielen natürlichen und technischen Prozessen, einschließlich der Festigkeit von Feststoffen, der Oberflächenspannung von Flüssigkeiten, der Zusammenhalt von Materialien und vielem mehr.
5. Anwendungen:
Kohäsive Kräfte werden in einer Vielzahl von Anwendungen genutzt, darunter Klebstoffe, Dichtungsmittel, Beschichtungen, Betonherstellung, Wasserfiltration und vieles mehr. Sie ermöglichen die Herstellung von zusammenhängenden Strukturen und Materialien.
Insgesamt ist Kohäsion ein wichtiges physikalisches Phänomen, das dazu beiträgt, dass Materialien zusammenhalten und eine zusammenhängende Masse bilden. Ein genaues Verständnis der Kohäsionseigenschaften ist entscheidend für die Entwicklung und den Einsatz von Materialien in verschiedenen Anwendungen.
Oberflächenspannung
Die Oberflächenspannung ist ein physikalisches Phänomen, das auftritt, wenn Moleküle an der Oberfläche einer Flüssigkeit eine höhere Anziehungskraft zueinander haben als zu den Molekülen in der Flüssigkeit. Hier sind einige wichtige Informationen zur Oberflächenspannung:
1. Definition:
Die Oberflächenspannung ist die Tendenz einer Flüssigkeit, ihre Oberfläche zu minimieren und sich in eine kugelförmige Form zu bringen, um die Anzahl der Moleküle an der Oberfläche zu reduzieren. Sie entsteht durch die Anziehungskräfte zwischen den Molekülen an der Oberfläche.
2. Mechanismus:
Die Oberflächenspannung entsteht aufgrund von Kohäsionskräften zwischen den Molekülen in der Flüssigkeit und Adhäsionskräften zwischen den Molekülen an der Oberfläche und der umgebenden Umgebung (Luft oder einem anderen Medium).
3. Einflussfaktoren:
Die Oberflächenspannung wird durch verschiedene Faktoren beeinflusst, darunter die Art der Flüssigkeit, die Temperatur, die Reinheit der Flüssigkeit und das Vorhandensein von Fremdstoffen oder Tensiden.
4. Auswirkungen:
Die Oberflächenspannung hat verschiedene Auswirkungen auf das Verhalten von Flüssigkeiten, darunter:
- Bildung von Tropfen oder kugelförmigen Tröpfchen
- Kapillarwirkung in dünnen Röhren oder porösen Materialien
- Oberflächenbeschichtung und Benetzung von Oberflächen
- Bildung von Schaum oder Blasen
5. Anwendungen:
Die Oberflächenspannung wird in vielen technischen Anwendungen genutzt, darunter Oberflächenbeschichtungen, Tinten, Farben, Reinigungsmitteln, Emulsionen, Lebensmittelverarbeitung und vieles mehr. Ein genaues Verständnis der Oberflächenspannung ist entscheidend für die Entwicklung und Optimierung von Produkten und Prozessen.
Insgesamt ist die Oberflächenspannung ein wichtiges physikalisches Phänomen, das das Verhalten von Flüssigkeiten beeinflusst und in einer Vielzahl von Anwendungen genutzt wird. Ein genaues Verständnis der Oberflächenspannungseigenschaften ist entscheidend für die Entwicklung und Anwendung von Materialien und Prozessen in verschiedenen Branchen.
Benetzung
Die Benetzung ist ein physikalisches Phänomen, bei dem eine Flüssigkeit eine feste Oberfläche benetzt, indem sie sich über die Oberfläche ausbreitet. Hier sind einige wichtige Informationen zur Benetzung:
1. Definition:
Benetzung bezieht sich auf die Fähigkeit einer Flüssigkeit, sich auf einer festen Oberfläche auszubreiten und einen dünnen Film zu bilden. Sie wird durch die Oberflächenspannung der Flüssigkeit und die Adhäsionskräfte zwischen Flüssigkeit und Feststoff bestimmt.
2. Kontaktwinkel:
Der Kontaktwinkel ist ein Maß für die Benetzung und beschreibt den Winkel, den die Flüssigkeitsoberfläche an der Kontaktlinie zwischen Flüssigkeit und Feststoff bildet. Ein kleiner Kontaktwinkel deutet auf eine gute Benetzung hin, während ein großer Kontaktwinkel auf eine schlechte Benetzung hinweist.
3. Einflussfaktoren:
Die Benetzung wird durch verschiedene Faktoren beeinflusst, darunter die Oberflächenspannung der Flüssigkeit, die Oberflächenbeschaffenheit des Feststoffs, die Reinheit der Oberfläche und das Vorhandensein von Fremdstoffen oder Beschichtungen.
4. Arten der Benetzung:
Es gibt drei Hauptarten der Benetzung:
- Vollständige Benetzung: Die Flüssigkeit breitet sich vollständig auf der Oberfläche aus und bildet einen Kontaktwinkel von 0°.
- Unvollständige Benetzung: Die Flüssigkeit bildet einen Kontaktwinkel größer als 0°, aber kleiner als 90°.
- Keine Benetzung: Die Flüssigkeit bildet einen Kontaktwinkel von 90° oder größer und breitet sich nicht auf der Oberfläche aus.
5. Bedeutung:
Die Benetzung spielt eine wichtige Rolle in vielen technischen Anwendungen, einschließlich Beschichtungen, Klebstoffen, Drucktechniken, Oberflächenbehandlungen, Biologie und mehr. Ein genaues Verständnis der Benetzungseigenschaften ist entscheidend für die Entwicklung und Optimierung von Produkten und Prozessen.
Insgesamt ist die Benetzung ein wichtiges physikalisches Phänomen, das das Verhalten von Flüssigkeiten auf festen Oberflächen beeinflusst. Ein genaues Verständnis der Benetzung ist entscheidend für die Entwicklung und Anwendung von Materialien und Technologien in verschiedenen Bereichen.
Tribologie
Tribologie ist das wissenschaftliche Fachgebiet, das sich mit der Untersuchung von Reibung, Verschleiß und Schmierung von sich bewegenden Oberflächen befasst. Hier sind einige wichtige Informationen zur Tribologie:
1. Definition:
Tribologie ist die interdisziplinäre Wissenschaft, die sich mit den Wechselwirkungen zwischen sich bewegenden Oberflächen befasst, einschließlich Reibung, Verschleiß, Schmierung und Schmierstoffen.
2. Forschungsbereiche:
Die Tribologie umfasst verschiedene Forschungsbereiche, darunter:
- Reibung: Untersuchung der Kräfte, die zwischen sich bewegenden Oberflächen auftreten.
- Verschleiß: Untersuchung des Materialabbaus aufgrund von mechanischer Beanspruchung.
- Schmierung: Untersuchung der Anwendung von Schmierstoffen zur Reduzierung von Reibung und Verschleiß.
- Oberflächenbeschichtungen: Untersuchung von Beschichtungen zur Verbesserung der tribologischen Eigenschaften.
3. Anwendungen:
Tribologie hat zahlreiche Anwendungen in verschiedenen Bereichen, darunter:
- Fahrzeugtechnik: Untersuchung von Motoren, Getrieben und Bremsen.
- Maschinenbau: Untersuchung von Lagern, Getrieben, Dichtungen und Gleitführungen.
- Biomedizin: Untersuchung von Implantaten, Prothesen und medizinischen Geräten.
- Schmierungstechnik: Entwicklung von Schmierstoffen und Schmiersystemen.
4. Ziele:
Die Ziele der Tribologie umfassen die Reduzierung von Reibung und Verschleiß, die Verbesserung der Lebensdauer von Maschinen und Komponenten, die Steigerung der Energieeffizienz und die Entwicklung von umweltfreundlichen Schmierlösungen.
5. Bedeutung:
Tribologie ist ein wichtiges Fachgebiet, das zur Verbesserung der Leistung, Zuverlässigkeit und Lebensdauer von Maschinen und technischen Systemen beiträgt. Sie spielt eine entscheidende Rolle in der modernen Technik und Industrie.
Insgesamt ist Tribologie ein wichtiges wissenschaftliches Fachgebiet, das sich mit den Wechselwirkungen zwischen sich bewegenden Oberflächen befasst. Ein genaues Verständnis der tribologischen Eigenschaften ist entscheidend für die Entwicklung und den Betrieb von technischen Systemen in verschiedenen Branchen.
Schmierstoff
Ein Schmierstoff ist ein Material, das verwendet wird, um die Reibung zwischen sich bewegenden Oberflächen zu verringern und den Verschleiß zu reduzieren. Hier sind einige wichtige Informationen zum Schmierstoff:
1. Funktionen:
Ein Schmierstoff erfüllt mehrere wichtige Funktionen, darunter:
- Verringerung der Reibung: Der Schmierstoff bildet einen Schmierfilm zwischen den Oberflächen, der als Gleitschicht wirkt und die Reibung reduziert.
- Verschleißschutz: Der Schmierfilm schützt die Oberflächen vor direktem Kontakt und minimiert so den Verschleiß.
- Kühlung: Der Schmierstoff entzieht den Oberflächen Wärme und trägt zur Kühlung bei, indem er die entstehende Reibungswärme abführt.
- Abdichtung: In einigen Fällen dient der Schmierstoff auch als Abdichtung, um das Eindringen von Schmutz, Staub oder Feuchtigkeit zu verhindern.
2. Arten von Schmierstoffen:
Es gibt verschiedene Arten von Schmierstoffen, darunter:
- Öle: Flüssige Schmiermittel, die auf Mineralölbasis oder synthetischen Ölen basieren.
- Fette: Halbfeste Schmiermittel, die aus einem Öl und einem verdickenden Mittel bestehen.
- Trockenschmierstoffe: Feststoffe wie Graphit oder Molybdändisulfid, die als Schmiermittel verwendet werden können.
- Gase: Gasförmige Schmiermittel wie Luft, Wasserstoff oder Stickstoff, die in einigen Hochgeschwindigkeitsanwendungen verwendet werden.
3. Anwendungen:
Schmierstoffe werden in einer Vielzahl von Anwendungen eingesetzt, darunter Motoren, Getriebe, Lager, Hydrauliksysteme, Turbinen, Schneidwerkzeuge und vieles mehr. Sie sind entscheidend für die reibungslose und zuverlässige Funktion von mechanischen Systemen.
4. Auswahlkriterien:
Die Auswahl des richtigen Schmierstoffs hängt von verschiedenen Faktoren ab, darunter die Anwendung, die Betriebsbedingungen (Temperatur, Druck, Geschwindigkeit), die Art der Oberflächen und die Umweltbedingungen.
5. Wartung:
Die regelmäßige Wartung und Überwachung der Schmierung ist entscheidend, um eine optimale Leistung und Lebensdauer der mechanischen Systeme sicherzustellen. Dies umfasst das Nachfüllen von Schmierstoffen, das Überprüfen der Schmierintervalle und die Analyse von Schmierstoffproben auf Verschleißpartikel und Verunreinigungen.
Insgesamt sind Schmierstoffe entscheidend für die Leistung und Lebensdauer von mechanischen Systemen und Komponenten. Ein genaues Verständnis der verschiedenen Arten von Schmierstoffen, ihrer Funktionen und Anwendungen ist wichtig für die Auswahl und den Einsatz in verschiedenen technischen Anwendungen.
Schmierungsarten
Die Schmierung von beweglichen Maschinenteilen kann auf verschiedene Arten erfolgen, je nach den Anforderungen der Anwendung und den beteiligten Komponenten. Hier sind einige wichtige Informationen zu verschiedenen Schmierungsarten:
1. Schmierung durch Ölbad:
Bei der Schmierung durch Ölbad befinden sich die zu schmierenden Teile vollständig in einem Behälter mit Schmieröl. Das Öl umgibt die Teile und bildet einen Schmierfilm, der Reibung und Verschleiß reduziert. Diese Methode wird oft bei Getrieben und Lagern verwendet.
2. Schmierung durch Sprühen oder Tropfen:
Diese Methode beinhaltet das direkte Auftragen von Schmieröl auf die zu schmierenden Oberflächen durch Sprühen oder Tropfen. Das Öl wird gezielt auf die beweglichen Teile aufgetragen, um einen Schmierfilm zu bilden. Diese Methode wird häufig bei Ketten, Zahnrädern und beweglichen Mechanismen verwendet.
3. Schmierung durch Zentralschmieranlagen:
Zentralschmieranlagen liefern automatisch Schmiermittel zu den beweglichen Teilen einer Maschine. Das Schmiermittel wird über Rohrleitungen und Verteiler zu den verschiedenen Schmierstellen geleitet und kann manuell oder automatisch gesteuert werden. Diese Methode wird in Anwendungen mit vielen Schmierstellen verwendet, um eine gleichmäßige Schmierung zu gewährleisten.
4. Schmierung durch Fettschmierung:
Bei der Fettschmierung wird Schmierfett direkt auf die zu schmierenden Oberflächen aufgetragen. Das Fett haftet an den Oberflächen und bildet einen dicken Schmierfilm, der besonders bei Hochdruck- und Hochtemperaturanwendungen wirksam ist. Diese Methode wird oft bei Lagern, Gelenken und stark beanspruchten Teilen verwendet.
5. Schmierung durch Trockenschmierung:
Trockenschmierung beinhaltet die Verwendung von festen Schmierstoffen wie Graphit, Molybdändisulfid oder PTFE (Polytetrafluorethylen), die direkt auf die zu schmierenden Oberflächen aufgebracht werden. Diese Schmierstoffe reduzieren die Reibung und den Verschleiß, ohne dass eine flüssige Schmierung erforderlich ist. Diese Methode wird in Umgebungen mit hohen Temperaturen, Vakuum oder in lebensmittelechten Anwendungen eingesetzt.
Jede Schmierungsart hat ihre eigenen Vor- und Nachteile und wird entsprechend den Anforderungen der spezifischen Anwendung ausgewählt. Ein sorgfältiges Verständnis der verschiedenen Schmierungsarten ist wichtig für die effektive Wartung und den Betrieb von mechanischen Systemen und Komponenten.
Schmieröl
Schmieröl ist ein wesentlicher Bestandteil vieler Schmiersysteme und dient dazu, die Reibung und den Verschleiß zwischen sich bewegenden Oberflächen zu reduzieren. Hier sind einige wichtige Informationen zum Schmieröl:
1. Zusammensetzung:
Schmieröle bestehen aus verschiedenen Grundölen und Additiven. Die Grundöle können mineralischen, synthetischen oder pflanzlichen Ursprungs sein und dienen als Basis für das Schmieröl. Additive werden zugesetzt, um die Leistung und Eigenschaften des Schmieröls zu verbessern, wie z.B. Viskositätsindexverbesserer, Verschleißschutzmittel, Detergentien und Dispergatoren.
2. Viskosität:
Die Viskosität ist eine wichtige Eigenschaft von Schmieröl und bestimmt seine Fließeigenschaften. Sie wird durch die Temperatur beeinflusst und ist entscheidend für die Bildung eines stabilen Schmierfilms zwischen den sich bewegenden Oberflächen. Schmieröle werden in verschiedene Viskositätsklassen eingeteilt, die durch internationale Standards wie SAE (Society of Automotive Engineers) festgelegt werden.
3. Anwendungen:
Schmieröle werden in einer Vielzahl von Anwendungen eingesetzt, darunter Motoren, Getriebe, Hydrauliksysteme, Turbinen, Kompressoren, Industrieanlagen und mehr. Sie sind entscheidend für die reibungslose und zuverlässige Funktion von mechanischen Systemen.
4. Auswahlkriterien:
Die Auswahl des richtigen Schmieröls hängt von verschiedenen Faktoren ab, darunter die Anwendung, die Betriebsbedingungen (Temperatur, Druck, Geschwindigkeit), die Art der Oberflächen und die Anforderungen an Leistung und Lebensdauer.
5. Wartung und Überwachung:
Die regelmäßige Wartung und Überwachung des Schmieröls ist entscheidend, um eine optimale Leistung und Lebensdauer der Maschinen und Komponenten sicherzustellen. Dies umfasst das regelmäßige Nachfüllen, das Überwachen der Öltemperatur und -druck, sowie das Analysieren von Ölproben auf Verschleißpartikel und Verunreinigungen.
Schmieröl ist ein wesentliches Element für die Leistung und Lebensdauer von mechanischen Systemen und Komponenten. Ein genaues Verständnis seiner Eigenschaften, Anwendungen und Wartungsanforderungen ist wichtig für die effektive Nutzung und den Betrieb von Maschinen und Anlagen.
Schmierfett
Schmierfett ist eine halbfeste Schmierstoffmischung, die aus einem Grundöl und einem verdickenden Mittel besteht. Es wird verwendet, um Reibung und Verschleiß zwischen sich bewegenden Teilen zu reduzieren und eine effektive Schmierung zu gewährleisten. Hier sind einige wichtige Informationen zum Schmierfett:
1. Zusammensetzung:
Schmierfett besteht hauptsächlich aus zwei Hauptbestandteilen:
- Grundöl: Das Grundöl bildet die Basis des Schmierfetts und bestimmt seine Schmiereigenschaften. Es kann mineralischen, synthetischen oder pflanzlichen Ursprungs sein.
- Verdickungsmittel: Das Verdickungsmittel dient dazu, das Grundöl zu verdicken und eine halbfeste Konsistenz zu erreichen. Häufig verwendete Verdickungsmittel sind Metallseifen wie Lithium, Calcium, Aluminium oder komplexe Verdickungsmittel wie Polyharnstoffe.
2. Eigenschaften:
Schmierfett hat mehrere wichtige Eigenschaften, darunter:
- Hohe Haftfähigkeit: Schmierfett haftet gut an den Oberflächen und bildet einen dicken Schmierfilm.
- Wasserbeständigkeit: Schmierfett bietet einen gewissen Schutz vor Feuchtigkeit und Korrosion.
- Temperaturbeständigkeit: Schmierfett kann bei einem weiten Temperaturbereich eingesetzt werden, je nach der Auswahl des Grundöls und des Verdickungsmittels.
- Abdichtung: Schmierfett kann dazu beitragen, das Eindringen von Schmutz und Feuchtigkeit in Lager und andere Schmierstellen zu verhindern.
3. Anwendungen:
Schmierfett wird in einer Vielzahl von Anwendungen eingesetzt, darunter Lager, Gelenke, Gleitlager, Kugel- und Rollenlager, Führungen, Schraubverbindungen und mehr. Es wird besonders dort eingesetzt, wo eine kontinuierliche Schmierung über einen längeren Zeitraum erforderlich ist oder Schmierstellen schwer zugänglich sind.
4. Auswahlkriterien:
Die Auswahl des richtigen Schmierfetts hängt von verschiedenen Faktoren ab, darunter die Anwendung, die Betriebsbedingungen (Temperatur, Belastung, Geschwindigkeit), die Art der Oberflächen und die Anforderungen an Leistung und Lebensdauer.
5. Wartung:
Die regelmäßige Überwachung und Wartung von Schmierfett ist wichtig, um eine effektive Schmierung und den Schutz der beweglichen Teile sicherzustellen. Dies umfasst das regelmäßige Nachschmieren, das Überprüfen der Schmierstellen und das Austauschen des Schmierfetts nach Bedarf.
Schmierfett ist ein wichtiger Schmierstoff, der in vielen industriellen Anwendungen eingesetzt wird, um Reibung und Verschleiß zu reduzieren und die Lebensdauer von Maschinen und Anlagen zu verlängern. Ein genaues Verständnis seiner Zusammensetzung, Eigenschaften und Anwendungen ist wichtig für die effektive Nutzung und Wartung von mechanischen Systemen.
Reibungsprüfung
Die Reibungsprüfung ist ein wichtiger Aspekt bei der Entwicklung und Bewertung von Materialien, Komponenten und Systemen, um deren Reibungseigenschaften zu charakterisieren und zu optimieren. Hier sind einige wichtige Informationen zur Reibungsprüfung:
1. Ziel:
Das Hauptziel der Reibungsprüfung ist es, die Reibungskräfte zwischen sich bewegenden Oberflächen zu quantifizieren und zu verstehen. Dies ermöglicht es, Materialien und Schmiersysteme zu optimieren, um die Reibung zu reduzieren und die Leistung von Maschinen und Anlagen zu verbessern.
2. Methoden:
Es gibt verschiedene Methoden zur Messung der Reibung, darunter:
- Tribometer: Ein Tribometer ist ein Gerät, das speziell zur Messung der Reibung und des Verschleißes entwickelt wurde. Es ermöglicht die Durchführung von verschiedenen Reibungstests unter kontrollierten Bedingungen.
- Schleppversuche: Diese Methode beinhaltet das Ziehen eines Testkörpers über eine Oberfläche unter definierten Bedingungen, um die Reibungskräfte zu messen.
- Rotationsversuche: Hierbei wird ein rotierender Körper gegen eine feste Oberfläche gebracht, um die Reibung zwischen den beiden Oberflächen zu messen.
3. Parameter:
Bei der Reibungsprüfung werden verschiedene Parameter gemessen und analysiert, darunter:
- Reibungskoeffizient: Dies ist das Verhältnis zwischen der Reibungskraft und der Normalkraft zwischen zwei Oberflächen.
- Verschleiß: Die Abnutzung oder Beschädigung der Oberflächen aufgrund von Reibung und mechanischer Belastung.
- Schmierverhalten: Die Fähigkeit eines Schmiermittels, die Reibung zwischen sich bewegenden Oberflächen zu reduzieren.
4. Anwendungen:
Reibungsprüfungen werden in vielen Branchen und Anwendungen eingesetzt, darunter:
- Automobilindustrie: zur Optimierung von Motoren, Getrieben und Bremsen.
- Maschinenbau: zur Entwicklung von Lagern, Dichtungen und Gleitführungen.
- Materialforschung: zur Charakterisierung von Oberflächenbeschichtungen und tribologischen Eigenschaften von Materialien.
- Medizintechnik: zur Bewertung von Implantaten, Prothesen und medizinischen Geräten.
5. Bedeutung:
Die Reibungsprüfung ist entscheidend für die Entwicklung und den Betrieb von mechanischen Systemen und Komponenten. Ein genaues Verständnis der Reibungseigenschaften ermöglicht es, die Leistung zu optimieren, den Verschleiß zu reduzieren und die Zuverlässigkeit von Maschinen und Anlagen zu verbessern.
Insgesamt ist die Reibungsprüfung ein wichtiger Schritt im Entwicklungsprozess von Materialien und Komponenten, um ihre tribologischen Eigenschaften zu charakterisieren und zu verbessern. Ein genaues Verständnis der Reibungseigenschaften ist entscheidend für die Entwicklung und den Betrieb von technischen Systemen in verschiedenen Branchen.
Verschleiß
Verschleiß ist ein physikalisches Phänomen, bei dem Material von der Oberfläche eines Körpers abgetragen wird, wenn er in Kontakt mit einem anderen Körper ist. Hier sind einige wichtige Informationen zum Verschleiß:
1. Arten von Verschleiß:
Es gibt verschiedene Arten von Verschleiß, darunter:
- Adhäsiver Verschleiß: Entsteht durch das Anhaften und Abreißen von Material zwischen den Kontaktflächen.
- Abrasive Verschleiß: Verursacht durch das Einwirken von Fremdpartikeln oder abrasiven Materialien auf die Oberfläche.
- Erosiver Verschleiß: Verursacht durch den Aufprall von Partikeln oder Flüssigkeiten auf die Oberfläche.
- Korrosionsverschleiß: Entsteht durch chemische Reaktionen zwischen der Oberfläche und der umgebenden Umgebung.
2. Ursachen:
Verschleiß kann durch verschiedene Faktoren verursacht werden, darunter:
- Mechanische Belastung und Reibung zwischen den Kontaktflächen.
- Materialermüdung aufgrund wiederholter Beanspruchung.
- Chemische Reaktionen zwischen der Oberfläche und der Umgebung.
- Einwirkung von Fremdpartikeln oder Verunreinigungen.
3. Auswirkungen:
Verschleiß kann zu einer Reihe von Problemen führen, darunter:
- Verlust von Materialeigenschaften und Abnahme der Leistungsfähigkeit.
- Erhöhte Reibung und Energieverlust.
- Verkürzung der Lebensdauer von Bauteilen und Maschinen.
- Funktionsstörungen und Ausfälle von technischen Systemen.
4. Verschleißschutz:
Es gibt verschiedene Methoden zum Schutz vor Verschleiß, darunter:
- Verwendung von Schmiermitteln und Schmiersystemen zur Reduzierung von Reibung und Verschleiß.
- Oberflächenbeschichtungen und Beschichtungen zur Erhöhung der Härte und Verschleißfestigkeit.
- Einsatz von Verschleißschutzmaterialien wie Hartmetallen, Keramiken oder Verbundwerkstoffen.
- Optimierung von Konstruktionsmerkmalen und Bauteilgeometrien, um Verschleiß zu minimieren.
5. Bedeutung:
Verschleiß ist ein weit verbreitetes Problem in vielen technischen Anwendungen und Branchen. Ein genaues Verständnis der Ursachen und Mechanismen von Verschleiß ist entscheidend für die Entwicklung und den Einsatz von Materialien und Technologien, um seine Auswirkungen zu minimieren und die Leistung von Bauteilen und Systemen zu verbessern.
Insgesamt ist Verschleiß ein komplexes physikalisches Phänomen, das eine Vielzahl von Ursachen und Auswirkungen hat. Ein umfassendes Verständnis der Verschleißmechanismen ist wichtig für die Entwicklung von Lösungen zur Verschleißminimierung und -kontrolle in verschiedenen technischen Anwendungen.
Schmierstoffadditive
Schmierstoffadditive sind chemische Verbindungen, die Schmierölen und Schmierfetten zugesetzt werden, um deren Leistung und Eigenschaften zu verbessern. Hier sind einige wichtige Informationen zu Schmierstoffadditiven:
1. Funktionen:
Schmierstoffadditive erfüllen verschiedene Funktionen, darunter:
- Verschleißschutz: Additive wie Anti-Verschleiß- und Extreme-Pressure-Additive bilden eine Schutzschicht auf den Oberflächen, um den Verschleiß zu reduzieren.
- Reinigung: Detergentien und Dispergatoren entfernen Ablagerungen, Verschmutzungen und Verunreinigungen von den Oberflächen.
- Viskositätskontrolle: Viskositätsindexverbesserer sorgen für eine stabile Viskosität des Schmieröls über einen weiten Temperaturbereich.
- Oxidationsschutz: Antioxidantien verhindern die Bildung von Oxidationsprodukten und verlängern die Lebensdauer des Schmieröls.
- Korrosionsschutz: Korrosionsinhibitoren schützen die Oberflächen vor chemischer Zersetzung und Korrosion.
2. Typen von Additiven:
Es gibt eine Vielzahl von Schmierstoffadditiven, darunter:
- Anti-Verschleiß-Additive: Zinkdialkyldithiophosphat (ZDDP), Molybdändisulfid (MoS2), Zink-Molybdän-Additive.
- Extreme-Pressure-Additive: Schwefelverbindungen, Phosphorverbindungen, Chlorverbindungen.
- Viskositätsindexverbesserer: Polymere wie Polyalphaolefine (PAO), Polyisobutylen (PIB), Polyalkylmethacrylate (PAMA).
- Antioxidantien: Phenolische Verbindungen, Amine, Phosphite.
- Detergentien und Dispergatoren: Calciumsulfonate, TBN-Booster, Polyisobutenylamin.
- Korrosionsinhibitoren: Zinkverbindungen, Bariumverbindungen, Triazin-Derivate.
3. Dosierung und Mischung:
Die Dosierung und Mischung der Additive erfolgt gemäß den Herstellervorschriften und spezifischen Anforderungen der Anwendung. Die richtige Kombination und Konzentration der Additive ist entscheidend für die optimale Leistung des Schmierstoffs.
4. Anwendungen:
Schmierstoffadditive werden in einer Vielzahl von Anwendungen eingesetzt, darunter Motorenöle, Getriebeöle, Hydraulikflüssigkeiten, Schmierfette, Metallbearbeitungsflüssigkeiten und industrielle Schmiermittel.
5. Entwicklungstrends:
Die Entwicklung neuer Schmierstoffadditive konzentriert sich auf umweltfreundliche Formulierungen mit verbesserten Leistungsmerkmalen wie erhöhter Lebensdauer, besserem Verschleißschutz, niedrigerem Energieverbrauch und reduziertem Schadstoffausstoß.
Insgesamt spielen Schmierstoffadditive eine entscheidende Rolle bei der Optimierung und Verbesserung der Leistung von Schmierstoffen in verschiedenen Anwendungen. Ein genaues Verständnis der verschiedenen Arten von Additiven und ihrer Funktionen ist wichtig für die Entwicklung und den Einsatz von Schmierstoffen mit den gewünschten Leistungseigenschaften.
Adhäsion
Adhäsion ist ein physikalisches Phänomen, bei dem Moleküle zweier verschiedener Materialien an der Kontaktfläche miteinander interagieren. Hier sind einige wichtige Informationen zur Adhäsion:
1. Mechanismus:
Adhäsion tritt aufgrund von Van-der-Waals-Kräften, elektrostatischen Anziehungskräften und chemischen Bindungen zwischen den Molekülen der beiden Materialien auf. Diese Kräfte führen dazu, dass die Moleküle an der Kontaktfläche miteinander haften und eine feste Verbindung bilden.
2. Kontaktfläche:
Die Adhäsion tritt an der Kontaktfläche zwischen den beiden Materialien auf, wo sich die Moleküle der Materialien nahe genug befinden, um miteinander zu interagieren. Eine größere Kontaktfläche führt zu einer stärkeren Adhäsion.
3. Einflussfaktoren:
Die Adhäsion wird durch verschiedene Faktoren beeinflusst, darunter:
- Oberflächenbeschaffenheit und Rauheit: Eine raue Oberfläche bietet mehr Kontaktstellen für die Adhäsion.
- Chemische Zusammensetzung: Die chemische Natur der Materialien beeinflusst die Stärke der Adhäsion.
- Umgebungstemperatur und Feuchtigkeit: Veränderungen in Temperatur und Feuchtigkeit können die Adhäsion beeinflussen.
4. Anwendungen:
Adhäsion spielt eine wichtige Rolle in vielen technischen Anwendungen, darunter Klebstoffe, Beschichtungen, Oberflächenbehandlungen, Reifenhaftung, Mikroelektronik und Biologie. Ein genaues Verständnis der Adhäsion ist wichtig für die Entwicklung und Optimierung von Produkten und Prozessen in diesen Bereichen.
5. Adhäsionskräfte:
Die Adhäsionskräfte können je nach den beteiligten Materialien und Bedingungen variieren. Sie können von sehr schwach bis sehr stark reichen und beeinflussen das Verhalten von Materialien in Kontakt miteinander erheblich.
Insgesamt ist Adhäsion ein wichtiges physikalisches Phänomen, das in vielen technischen Anwendungen eine entscheidende Rolle spielt. Ein genaues Verständnis der Adhäsionsmechanismen und -eigenschaften ist wichtig für die Entwicklung und Anwendung von Materialien und Technologien in verschiedenen Bereichen.
Beschichtungstechnologien
Beschichtungstechnologien spielen eine wichtige Rolle bei der Verbesserung der Oberflächeneigenschaften von Materialien und Bauteilen für verschiedene Anwendungen. Hier sind einige wichtige Informationen zu Beschichtungstechnologien:
1. Beschichtungsarten:
Es gibt verschiedene Arten von Beschichtungen, darunter:
- Oberflächenbeschichtungen: Diese umfassen dünne Schichten von Materialien wie Metallen, Keramiken oder Polymeren, die auf die Oberfläche eines Substrats aufgebracht werden, um deren Eigenschaften zu verbessern.
- Funktionsbeschichtungen: Diese umfassen Beschichtungen, die spezifische Funktionen bieten, wie z.B. Korrosionsschutz, Verschleißschutz, Reibungsreduzierung oder Wärmeableitung.
- Dekorative Beschichtungen: Diese umfassen Beschichtungen, die verwendet werden, um ästhetische Eigenschaften wie Farbe, Glanz oder Textur zu verleihen.
2. Beschichtungsverfahren:
Es gibt verschiedene Verfahren zur Aufbringung von Beschichtungen, darunter:
- Physikalische Dampfabscheidung (PVD): Ein Verfahren, bei dem Materialien in einer Vakuumkammer verdampft und dann auf die Oberfläche des Substrats kondensiert werden.
- Chemische Gasphasenabscheidung (CVD): Ein Verfahren, bei dem chemische Reaktionen in einer Gasphase stattfinden, um eine Beschichtung auf der Oberfläche zu bilden.
- Sprühbeschichtung: Ein Verfahren, bei dem die Beschichtungsmaterialien in Form von Pulvern oder Flüssigkeiten auf die Oberfläche aufgesprüht werden.
- Tauchbeschichtung: Ein Verfahren, bei dem das Substrat in eine Beschichtungslösung eingetaucht wird, um eine gleichmäßige Beschichtung zu erzielen.
3. Anwendungen:
Beschichtungstechnologien finden Anwendung in verschiedenen Branchen und Bereichen, darunter:
- Automobilindustrie: Beschichtungen für Karosserien, Felgen, Motorteile und Antriebsstränge.
- Luft- und Raumfahrtindustrie: Beschichtungen für Flugzeugkomponenten, Satelliten und Raumfahrzeuge.
- Elektronikindustrie: Beschichtungen für Leiterplatten, Halbleiter und Displays.
- Medizintechnik: Beschichtungen für Implantate, medizinische Geräte und Instrumente.
4. Vorteile:
Beschichtungstechnologien bieten eine Vielzahl von Vorteilen, darunter:
- Verbesserung der mechanischen Eigenschaften wie Härte, Verschleißfestigkeit und Kratzfestigkeit.
- Schutz vor Korrosion, Oxidation und chemischer Zersetzung.
- Reduzierung von Reibung und Verschleiß für eine längere Lebensdauer der Bauteile.
- Verbesserung der ästhetischen Eigenschaften für dekorative Anwendungen.
5. Entwicklungstrends:
Die Entwicklung neuer Beschichtungstechnologien konzentriert sich auf umweltfreundliche und energiesparende Verfahren, die eine verbesserte Leistung und Funktionalität bieten. Dazu gehören dünnere Beschichtungen, Nanomaterialien, selbstheilende Beschichtungen und multifunktionale Beschichtungen.
Insgesamt spielen Beschichtungstechnologien eine entscheidende Rolle bei der Verbesserung der Leistung, Funktionalität und Ästhetik von Materialien und Bauteilen in einer Vielzahl von Anwendungen. Ein genaues Verständnis der verschiedenen Beschichtungsarten, -verfahren und -anwendungen ist wichtig für die Entwicklung und Anwendung von Beschichtungen in verschiedenen Branchen und Bereichen.
Oberflächenrauheit
Die Oberflächenrauheit bezieht sich auf die Unebenheiten und Unregelmäßigkeiten auf der Oberfläche eines Materials oder Bauteils. Hier sind einige wichtige Informationen zur Oberflächenrauheit:
1. Definition:
Die Oberflächenrauheit ist ein Maß für die mikroskopischen Unebenheiten und Strukturen auf der Oberfläche eines Materials. Sie wird oft in Form von Rauheitsparametern quantifiziert, die verschiedene Aspekte der Oberflächenstruktur beschreiben, wie z.B. Rauheitstiefe, Rauheitsprofil und Rauheitsverteilung.
2. Einflussfaktoren:
Die Oberflächenrauheit wird durch verschiedene Faktoren beeinflusst, darunter:
- Bearbeitungsverfahren: Verschiedene Bearbeitungsverfahren wie Fräsen, Drehen, Schleifen und Polieren können unterschiedliche Oberflächenrauheiten erzeugen.
- Materialbeschaffenheit: Die Materialeigenschaften wie Härte, Zähigkeit und Zerspanbarkeit beeinflussen die erzielbare Oberflächenrauheit.
- Werkzeuggeometrie: Die Geometrie und der Zustand des Werkzeugs haben einen direkten Einfluss auf die erzielte Oberflächenrauheit.
- Schmierung und Kühlung: Die Verwendung von Schmier- und Kühlmedien während des Bearbeitungsprozesses kann die Oberflächenrauheit beeinflussen.
- Betriebsbedingungen: Die Umgebungstemperatur, Luftfeuchtigkeit und andere Umweltfaktoren können die Oberflächenrauheit beeinflussen.
3. Messung:
Die Oberflächenrauheit kann mit verschiedenen Messgeräten gemessen werden, darunter:
- Oberflächenrauheitsmessgeräte: Diese Geräte verwenden verschiedene Methoden wie Tastsensoren, optische Sensoren oder Rasterkraftmikroskope, um die Oberflächenrauheit zu messen.
- Rauheitsparameter: Es gibt verschiedene Rauheitsparameter wie Rz (Rauheitstiefe), Ra (arithmetischer Mittelwert der Rauheit) und Rt (Gesamtrauheit), die verwendet werden, um die Oberflächenrauheit zu charakterisieren.
4. Bedeutung:
Die Oberflächenrauheit spielt eine wichtige Rolle in vielen technischen Anwendungen, darunter:
- Funktionalität: Die Oberflächenrauheit kann die Funktion und Leistung von Bauteilen beeinflussen, insbesondere in Bereichen wie Dichtungswirkung, Reibung, Verschleiß und Ermüdungsfestigkeit.
- Ästhetik: Die Oberflächenrauheit beeinflusst auch das ästhetische Erscheinungsbild von Produkten und Bauteilen, insbesondere in Bereichen wie Automobil-, Elektronik- und Konsumgüterindustrie.
- Fertigungsprozesse: Die Kontrolle und Optimierung der Oberflächenrauheit ist ein wichtiger Aspekt bei der Entwicklung und Optimierung von Fertigungsprozessen.
5. Optimierung:
Die Optimierung der Oberflächenrauheit erfolgt durch die Auswahl geeigneter Bearbeitungsverfahren, Werkzeuggeometrien, Schneidbedingungen und Oberflächenbehandlungen. Ziel ist es, die gewünschten Oberflächeneigenschaften für die jeweilige Anwendung zu erreichen.
Die Oberflächenrauheit ist ein wichtiger Aspekt in der Materialbearbeitung und Fertigungstechnik, der eine Vielzahl von Anwendungen und Auswirkungen auf die Funktion, Leistung und Ästhetik von Produkten und Bauteilen hat. Ein genaues Verständnis der Oberflächenrauheit und ihrer Messung ist entscheidend für die Entwicklung und Optimierung von Fertigungsprozessen und Produkten in verschiedenen Branchen.
Rissbildung
Rissbildung bezieht sich auf die Bildung von Rissen oder Rissstrukturen in einem Material oder Bauteil aufgrund von mechanischer Belastung, thermischen Spannungen, chemischen Reaktionen oder anderen Faktoren. Hier sind einige wichtige Informationen zur Rissbildung:
1. Ursachen:
Die Rissbildung kann durch verschiedene Faktoren verursacht werden, darunter:
- Mechanische Belastung: Überlastung, Schlagbelastungen, Vibrationen und zyklische Belastungen können zu Rissbildung führen.
- Thermische Spannungen: Temperaturänderungen und ungleichmäßige Wärmeverteilung im Material können zu thermischen Spannungen und Rissen führen.
- Chemische Reaktionen: Korrosion, Oxidation und andere chemische Reaktionen können zu Materialschwächungen und Rissbildung führen.
- Materialdefekte: Materialeigenschaften wie Porosität, Einschlüsse, Mikrostrukturen und Materialfehler können die Anfälligkeit für Rissbildung erhöhen.
2. Arten von Rissen:
Es gibt verschiedene Arten von Rissen, darunter:
- Ermüdungsriss: Entsteht durch wiederholte Belastungen und zyklische Beanspruchung des Materials.
- Spannungsriss: Entsteht durch Spannungskonzentrationen an bestimmten Stellen im Material.
- Korrosionsriss: Entsteht durch chemische Reaktionen zwischen dem Material und der umgebenden Umgebung.
- Wärmespannungsriss: Entsteht durch thermische Spannungen aufgrund von Temperaturänderungen im Material.
3. Auswirkungen:
Rissbildung kann zu verschiedenen Problemen führen, darunter:
- Materialversagen: Risse können zu einem plötzlichen Versagen von Bauteilen führen, insbesondere bei kritischen Anwendungen wie in der Luft- und Raumfahrt oder im Maschinenbau.
- Reduzierte Lebensdauer: Risse können die Lebensdauer von Materialien und Bauteilen erheblich verkürzen, was zu teuren Reparaturen oder Austausch führen kann.
- Sicherheitsrisiko: Risse können zu Unfällen, Ausfällen von Anlagen und potenziell gefährlichen Situationen führen, insbesondere in sicherheitskritischen Anwendungen.
4. Prävention und Kontrolle:
Die Prävention und Kontrolle von Rissbildung erfolgt durch verschiedene Maßnahmen, darunter:
- Materialauswahl: Auswahl von Materialien mit hoher Festigkeit, Zähigkeit und Beständigkeit gegen Rissbildung.
- Konstruktionsoptimierung: Vermeidung von Spannungskonzentrationen, Verwendung von abgerundeten Ecken, Aussparungen und anderen konstruktiven Maßnahmen.
- Oberflächenbehandlung: Verwendung von Beschichtungen, Wärmebehandlungen und anderen Oberflächenbehandlungen zur Verbesserung der Oberflächeneigenschaften und Reduzierung der Rissbildung.
- Qualitätskontrolle: Regelmäßige Inspektionen, Prüfungen und Überwachung der Materialien und Bauteile auf Risse und Defekte.
5. Forschung und Entwicklung:
Die Forschung und Entwicklung auf dem Gebiet der Rissbildung konzentriert sich auf die Entwicklung neuer Materialien, Beschichtungen, Fertigungsverfahren und Prüfmethoden zur Verbesserung der Rissbeständigkeit und -kontrolle.
Insgesamt ist die Rissbildung ein wichtiges Thema in der Werkstofftechnik und Materialwissenschaft, das eine Vielzahl von Herausforderungen und Auswirkungen auf die Sicherheit, Zuverlässigkeit und Leistung von Materialien und Bauteilen hat. Ein genaues Verständnis der Ursachen, Arten, Auswirkungen und Präventionsmaßnahmen von Rissbildung ist entscheidend für die Entwicklung und den Einsatz von Materialien in verschiedenen technischen Anwendungen
Härteprüfung
Die Härteprüfung ist ein Verfahren zur Bestimmung der Härte eines Materials, indem der Widerstand gegen plastische Verformung oder Eindringen gemessen wird. Hier sind einige wichtige Informationen zur Härteprüfung:
1. Verfahren:
Es gibt verschiedene Verfahren zur Härteprüfung, darunter:
- Brinell-Härteprüfung: Bei diesem Verfahren wird eine Kugel oder ein Kegel mit bekannter Kraft in die Oberfläche des Materials gedrückt, und der Durchmesser der entstehenden Eindrücke wird gemessen.
- Rockwell-Härteprüfung: Hier wird eine Kugel oder ein Diamantkegel mit einer bestimmten Kraft in das Material eingedrückt, und die Eindringtiefe wird gemessen. Es gibt verschiedene Skalen, wie z.B. Rockwell C, Rockwell B, etc.
- Vickers-Härteprüfung: Bei diesem Verfahren wird eine Diamantpyramide mit bekannter Spitzenlast auf die Oberfläche des Materials gedrückt, und die Diagonallänge des entstehenden Eindrucks wird gemessen.
2. Normen und Standards:
Die Härteprüfung wird nach internationalen Normen und Standards durchgeführt, die die Prüfverfahren, Gerätekalibrierung und Berichterstattung festlegen. Beispiele hierfür sind die ASTM-Eindringprüfverfahren, ISO-Normen und nationale Standards wie DIN, JIS, etc.
3. Anwendungen:
Die Härteprüfung wird in vielen Branchen und Anwendungen eingesetzt, darunter:
- Qualitätskontrolle in der Fertigung von Metallteilen und Bauteilen.
- Werkstoffcharakterisierung in der Werkstofftechnik und Materialwissenschaft.
- Ermittlung der Materialfestigkeit und Bestimmung von Werkstoffeigenschaften für Konstruktionszwecke.
- Beurteilung von Materialschädigungen und Festigkeitsverlusten durch Verschleiß, Korrosion oder Alterung.
4. Bedeutung:
Die Härteprüfung ist ein wichtiges Verfahren zur Charakterisierung von Materialien, da sie direkte Informationen über die Materialfestigkeit, Verschleißbeständigkeit und Eignung für bestimmte Anwendungen liefert. Sie ist ein entscheidender Schritt bei der Qualitätssicherung und Produktentwicklung in vielen Branchen.
5. Entwicklungstrends:
Die Entwicklung neuer Härteprüfverfahren konzentriert sich auf die Verbesserung der Genauigkeit, Zuverlässigkeit und Effizienz der Prüfungen. Dies umfasst die Entwicklung von nicht-destruktiven Prüfverfahren, automatisierten Prüfsystemen und fortgeschrittenen Bildgebungs- und Auswertungstechniken.
Insgesamt ist die Härteprüfung ein wichtiger Aspekt in der Werkstofftechnik und Fertigungstechnik, der eine Vielzahl von Anwendungen und Auswirkungen auf die Qualität und Leistung von Materialien und Bauteilen hat. Ein genaues Verständnis der Härteprüfverfahren, Normen und Anwendungen ist entscheidend für die richtige Bewertung und Nutzung von Materialien in verschiedenen technischen Anwendungen.
Oberflächenbeschaffenheit
Die Oberflächenbeschaffenheit bezieht sich auf die physikalischen Eigenschaften und Merkmale der Oberfläche eines Materials oder Bauteils. Hier sind einige wichtige Informationen zur Oberflächenbeschaffenheit:
1. Charakteristika:
Die Oberflächenbeschaffenheit wird durch verschiedene Merkmale charakterisiert, darunter:
- Rauheit: Die Unebenheiten und Unregelmäßigkeiten auf der Oberfläche, die durch Bearbeitungsprozesse entstehen.
- Glanz: Das Reflexionsvermögen und die Lichtdurchlässigkeit der Oberfläche, die das Erscheinungsbild beeinflussen.
- Textur: Die strukturellen Merkmale und Muster auf der Oberfläche, die durch Bearbeitungs- oder Veredelungsverfahren erzeugt werden.
- Sauberkeit: Der Grad der Reinheit und Abwesenheit von Verschmutzungen, Ablagerungen und Verunreinigungen auf der Oberfläche.
- Homogenität: Die Gleichmäßigkeit und Konsistenz der Oberflächenmerkmale über die gesamte Fläche hinweg.
2. Messung:
Die Oberflächenbeschaffenheit kann mit verschiedenen Messverfahren quantifiziert werden, darunter:
- Oberflächenrauheitsmessung: Verwendung von Rauheitsmessgeräten zur Bestimmung von Rauheitsparametern wie Rz, Ra, Rt, etc.
- Glanzmessung: Verwendung von Glanzmessgeräten zur Bestimmung des Glanzgrades oder Glanzwerts der Oberfläche.
- Texturmessung: Verwendung von Bildverarbeitungstechniken oder taktilen Messgeräten zur Charakterisierung der Oberflächentextur.
3. Einflussfaktoren:
Die Oberflächenbeschaffenheit wird durch verschiedene Faktoren beeinflusst, darunter:
- Bearbeitungsverfahren: Verschiedene Bearbeitungsverfahren wie Fräsen, Drehen, Schleifen, Polieren, Ätzen, Beschichten, etc., haben unterschiedliche Auswirkungen auf die Oberflächenbeschaffenheit.
- Materialeigenschaften: Die Materialeigenschaften wie Härte, Zähigkeit, Schmierfähigkeit, usw., beeinflussen die erzielbare Oberflächenqualität.
- Umgebungsbedingungen: Umgebungsbedingungen wie Temperatur, Feuchtigkeit, Druck, usw., können die Oberflächenbeschaffenheit beeinflussen.
4. Bedeutung:
Die Oberflächenbeschaffenheit spielt eine wichtige Rolle in vielen technischen Anwendungen und Branchen, darunter:
- Funktionalität: Die Oberflächenbeschaffenheit kann die Funktion und Leistung von Bauteilen beeinflussen, insbesondere in Bereichen wie Dichtungswirkung, Reibung, Verschleiß und Ermüdungsfestigkeit.
- Ästhetik: Die Oberflächenbeschaffenheit beeinflusst auch das ästhetische Erscheinungsbild von Produkten und Bauteilen, insbesondere in Bereichen wie Automobil-, Elektronik- und Konsumgüterindustrie.
- Fertigungsprozesse: Die Kontrolle und Optimierung der Oberflächenbeschaffenheit ist ein wichtiger Aspekt bei der Entwicklung und Optimierung von Fertigungsprozessen.
5. Optimierung:
Die Optimierung der Oberflächenbeschaffenheit erfolgt durch die Auswahl geeigneter Bearbeitungsverfahren, Werkzeuggeometrien, Schneidbedingungen, Oberflächenbehandlungen und Qualitätskontrollmaßnahmen. Ziel ist es, die gewünschten Oberflächeneigenschaften für die jeweilige Anwendung zu erreichen.
Insgesamt ist die Oberflächenbeschaffenheit ein wichtiger Aspekt in der Materialbearbeitung und Fertigungstechnik, der eine Vielzahl von Anwendungen und Auswirkungen auf die Funktion, Leistung und Ästhetik von Produkten und Bauteilen hat. Ein genaues Verständnis der Oberflächenbeschaffenheit und ihrer Einflussfaktoren ist entscheidend für die Entwicklung und Anwendung von Materialien in verschiedenen technischen Anwendungen.
Brems- Reibbelägen/ und Kupplungsbelägen
Brems- und Kupplungsbeläge werden in einer Vielzahl von Fahrzeugen und Maschinen eingesetzt. In der Automobilindustrie werden sie in Personenkraftwagen, Lastkraftwagen, Bussen und anderen Fahrzeugen eingesetzt. Auch in der Luftfahrtindustrie werden sie in Flugzeugen und Hubschraubern eingesetzt.
In der Industrie werden Bremsbeläge in Maschinen und Anlagen eingesetzt, um die Bewegung und Drehung von rotierenden Teilen zu kontrollieren oder zu stoppen. Kupplungsbeläge werden hauptsächlich in Fahrzeugen eingesetzt, um die Kraftübertragung zwischen Motor und Getriebe zu ermöglichen oder zu unterbrechen.
Die Verwendung von Brems- und Kupplungsbelägen ist also sehr weit verbreitet und trägt dazu bei, die Sicherheit und Leistung von Fahrzeugen und Maschinen zu gewährleisten.
Hauptmerkmale der Presse zur Herstellung von Brems- Reibbelägen/ und Kupplungsbelägen
Die Herstellung von Brems- und Kupplungsbelägen erfordert spezialisierte Pressen, die in der Lage sind, hohe Drücke und Temperaturen zu bewältigen. Diese Pressen werden oft als „Belagpressen“ bezeichnet und sind speziell für die Produktion von Reibbelägen ausgelegt. Hier sind einige wichtige Merkmale und Funktionen einer Presse zur Herstellung von Brems- und Kupplungsbelägen:
- Hoher Druck: Die Presse muss in der Lage sein, einen hohen Druck auszuüben, um das Elastomer-Material des Belags zu komprimieren und die erforderliche Dichte und Festigkeit zu erreichen.
- Temperaturregelung: Die Presse muss mit einer Temperaturregelung ausgestattet sein, um die erforderlichen Temperaturen für den Aushärteprozess des Belags aufrechterhalten zu können. Die richtige Temperatur ist wichtig, um eine optimale Härtung und Festigkeit des Belags zu gewährleisten.
- Präzise Steuerung: Eine genaue Steuerung der Presskraft, des Drucks und der Temperatur ist entscheidend, um konsistente und hochwertige Beläge herzustellen. Die Presse sollte über eine präzise Steuerungseinheit verfügen, die die Einstellung und Überwachung dieser Parameter ermöglicht.
- Formgebung: Die Presse sollte über die notwendigen Werkzeuge und Matrizen verfügen, um die gewünschte Form und Größe der Beläge zu erzeugen. Dies ermöglicht die Herstellung von Belägen in verschiedenen Größen und Formen entsprechend den Anforderungen der Brems- und Kupplungssysteme.
- Sicherheitseinrichtungen: Da der Betrieb von Belagpressen mit hohen Drücken und Temperaturen verbunden ist, müssen entsprechende Sicherheitseinrichtungen vorhanden sein, um Unfälle und Verletzungen zu vermeiden. Dies umfasst Not-Aus-Schalter, Schutzeinrichtungen und Sicherheitssysteme, um die Bediener und die umgebende Umgebung zu schützen.
Bei der Auswahl einer Presse zur Herstellung von Brems- und Kupplungsbelägen ist es wichtig, die spezifischen Anforderungen Ihrer Anwendung zu berücksichtigen, wie die Belaggröße, die gewünschte Produktionskapazität und die erforderlichen Qualitätsspezifikationen. Es ist ratsam, sich an erfahrene Hersteller oder Anbieter von spezialisierten Belagpressen zu wenden, um eine maßgeschneiderte Lösung für Ihre Anforderungen zu erhalten.
Qualitätskontrolle und Prozesskontrolle bei der Herstellung von Brems- und Kupplungsbelägen
Die Qualität der Brems- und Kupplungsbeläge ist von entscheidender Bedeutung für die Sicherheit und Leistung des Fahrzeugs. Daher ist eine sorgfältige Qualitätskontrolle (QC) und Prozesskontrolle (PC) unerlässlich.
Die QC umfasst die Prüfung der Werkstücke auf Formfehler, Verzug und andere Mängel. Die PC umfasst die Überwachung der Prozesse zur Herstellung der Werkstücke, um sicherzustellen, dass sie den Spezifikationen entsprechen.
Bei der QC von Brems- und Kupplungsbelägen werden die Werkstücke in der Regel visuell und mit Messgeräten geprüft. Die visuelle Prüfung umfasst die Suche nach offensichtlichen Mängeln wie Rissen, Dellen oder Verformungen. Die Messungen umfassen die Überprüfung der Abmessungen, der Dicke und der Oberflächenbeschaffenheit der Werkstücke.
Die PC von Brems- und Kupplungsbelägen umfasst die Überwachung der Parameter der Pressprozesse, wie die Druckkraft, die Presstemperatur und die Presszeit. Diese Parameter werden in der Regel mit Sensoren gemessen und in einer Steuerungseinheit erfasst. Die Steuerungseinheit verwendet die gemessenen Parameter, um sicherzustellen, dass die Prozesse den Spezifikationen entsprechen.
Die QC und PC von Brems- und Kupplungsbelägen sind wichtige Schritte, um sicherzustellen, dass die Werkstücke die Anforderungen erfüllen und die Sicherheit und Leistung des Fahrzeugs gewährleisten.
Hier sind einige weitere Details zu den zweiten 10 Schlüsselwörtern:
- Formfehler: Formfehler sind Mängel in der Form der Werkstücke. Sie können durch unsachgemäße Einstellung der Presse oder der Form verursacht werden.
- Verzug: Verzug ist eine Verformung der Werkstücke, die durch ungleichmäßige Druckverteilung verursacht wird.
- Qualitätskontrolle: Qualitätskontrolle (QC) ist die systematische Überprüfung der Qualität von Produkten, Dienstleistungen oder Prozessen.
- Prozesskontrolle: Prozesskontrolle (PC) ist die Überwachung der Parameter von Prozessen, um sicherzustellen, dass sie den Spezifikationen entsprechen.
- Werkzeug: Ein Werkzeug ist ein Gegenstand, der verwendet wird, um eine bestimmte Aufgabe auszuführen. Die Presse und die Form sind Werkzeuge, die für die Herstellung von Brems- und Kupplungsbelägen verwendet werden.
- Matrize: Eine Matrize ist ein Teil einer Form, der die Innenseite der Form bildet. Die Matrize für Brems- und Kupplungsbeläge ist typischerweise aus Metall gefertigt.
- Stempel: Ein Stempel ist ein Teil einer Form, der die Außenseite der Form bildet. Der Stempel für Brems- und Kupplungsbeläge ist typischerweise ebenfalls aus Metall gefertigt.
- Hub: Der Hub ist die Entfernung, die der Stempel in die Matrize eindringt. Der Hub ist wichtig für die Herstellung von Brems- und Kupplungsbelägen mit der gewünschten Dicke.
- Formtiefe: Die Formtiefe ist die maximale Tiefe der Form. Die Formtiefe ist wichtig für die Herstellung von Brems- und Kupplungsbelägen mit der gewünschten Dicke.
Die QC und PC von Brems- und Kupplungsbelägen sind wichtige Schritte, um sicherzustellen, dass die Werkstücke die Anforderungen erfüllen und die Sicherheit und Leistung des Fahrzeugs gewährleisten.
Maschinenprogramm für die Metallbearbeitung
Unsere Metallbearbeitungsmaschinen sind:
- Rohrbiegemaschine
- Horizontale Presse
- Bandsäge für Metall
- Profilbiegemaschine
- Tiefziehpresse
- Rundschweißmaschine
- Kantenschneide-Bördelmaschine
- Topf- und Pfannenpoliermaschine
- Poliermaschine für flache Oberflächen
Wir entwerfen, fertigen und montieren komplette Produktionslinien für Kochgeschirr, Küchengeschirr, Hotelgeschirr und Besteck sowie einzelne Maschinen für einen bestimmten Zweck