Eine Kreisschere ist eine Maschine, mit der ein Kreis in ein Stahlblech geschnitten wird. Kreisscheren werden hauptsächlich in der Metallbearbeitung verwendet, um runde Stahlbleche in Kreise zu schneiden. Es gibt sie in zwei Arten: manuell und automatisch.
Eine Kreisschere ist ein Werkzeug, das zum Schneiden von Blech verwendet wird. Sie besteht aus einer kreisförmigen Klinge, die zwischen zwei Rollen läuft. Die Klinge ist mit Hartmetallschneiden beschichtet, die das Blech schneiden.
Kreisscheren gibt es in verschiedenen Ausführungen, darunter:
- Manuelle Kreisscheren: Diese Maschinen werden von Hand bedient und sind die einfachsten und kostengünstigsten. Sie werden häufig in kleinen Werkstätten und Heimwerkerwerkstätten verwendet.
- Tischkreisscheren: Diese Maschinen werden auf einem Tisch montiert und erfordern weniger manuelle Arbeit. Sie sind schneller und effizienter als manuelle Kreisscheren, aber sie sind auch teurer.
- Automatische Kreisscheren: Diese Maschinen sind vollständig automatisiert und erfordern keine manuelle Arbeit. Sie sind die schnellsten und effizientesten Kreisscheren, aber sie sind auch die teuersten.
Die Funktionsweise einer Kreisschere hängt von der Art der Maschine ab. Manuelle Kreisscheren funktionieren in der Regel, indem das Blechstück manuell unter die Klinge geführt wird. Die Klinge schneidet das Blech durch.
Tischkreisscheren und automatische Kreisscheren funktionieren in der Regel, indem das Blechstück in die Maschine eingelegt und dann von der Maschine transportiert wird. Während des Transports wird das Blechstück von der Klinge geschnitten.
Kreisscheren werden in einer Vielzahl von Anwendungen eingesetzt, darunter:
- Metallverarbeitung: Kreisscheren werden verwendet, um eine Vielzahl von Blechteilen zu schneiden, z. B. Bleche, Profile und Rohre.
- Bauwesen: Kreisscheren werden verwendet, um Bleche für Dacheindeckungen und Fassadenverkleidungen zu schneiden.
- Automobilindustrie: Kreisscheren werden verwendet, um Bleche für Karosserieteile zu schneiden.
Sicherheitshinweise für Kreisscheren
Kreisscheren können gefährlich sein, wenn sie nicht ordnungsgemäß verwendet werden. Es ist wichtig, die folgenden Sicherheitshinweise zu beachten, um Verletzungen zu vermeiden:
- Tragen Sie immer Schutzbrille, Handschuhe und Gehörschutz, wenn Sie eine Kreisschere verwenden.
- Vergewissern Sie sich, dass die Maschine richtig eingestellt ist, bevor Sie mit der Arbeit beginnen.
- Verwenden Sie die Maschine nicht, wenn sie beschädigt ist.
- Berühren Sie die Klinge nicht, wenn die Maschine in Betrieb ist.
- Halten Sie Kinder und andere Personen von der Maschine fern, wenn Sie sie verwenden.
Fazit
Kreisscheren sind ein wichtiges Werkzeug für die Metallverarbeitung. Sie sind in verschiedenen Ausführungen erhältlich, um den unterschiedlichen Anforderungen gerecht zu werden. Bei der Verwendung von Kreisscheren ist es wichtig, die Sicherheitshinweise zu beachten, um Verletzungen zu vermeiden.
Hier sind einige zusätzliche Informationen zu Kreisscheren:
- Die Größe der Kreisschere wird durch den Durchmesser der Klinge bestimmt.
- Die Geschwindigkeit der Kreisschere bestimmt, wie schnell das Blech geschnitten wird.
- Kreisscheren können mit verschiedenen Klingen ausgestattet werden, um verschiedene Blechstärken zu schneiden.
- Kreisscheren können auch mit Zusatzausstattungen ausgestattet werden, z. B. mit einer Abkantvorrichtung oder einer Lochstanze.
Eine Kreisschere ist eine spezielle Art von Schneidwerkzeug, das für das präzise Schneiden von kreisförmigen oder bogenförmigen Ausschnitten in Blechen oder anderen flachen Materialien verwendet wird. Hier sind einige grundlegende Merkmale und Anwendungen von Kreisscheren:
Merkmale einer Kreisschere

- Schneidemechanismus:
- Kreisscheren verwenden einen rotierenden Messerkopf oder eine rotierende Schneidklinge, um einen kreisförmigen Schnitt durch das Material zu erzeugen.
- Präzise Schnitte:
- Durch die kreisförmige Schneidbewegung können Kreisscheren präzise und saubere Schnitte mit einem definierten Durchmesser erzeugen.
- Einstellbare Parameter:
- Je nach Modell können Parameter wie der Durchmesser des zu schneidenden Kreises, die Schnittgeschwindigkeit und der Schnittdruck eingestellt werden.
- Vielseitigkeit:
- Kreisscheren sind vielseitig einsetzbar und können für verschiedene Materialien wie Stahl, Aluminium, Kupfer und andere Metalle verwendet werden.
- Automatisierung:
- Einige Kreisscheren können in automatisierten Produktionslinien integriert werden, um einen kontinuierlichen und effizienten Schneideprozess zu gewährleisten.
Anwendungen von Kreisscheren:
- Herstellung von Bauteilen:
- In der Metallverarbeitung werden Kreisscheren verwendet, um präzise kreisförmige oder bogenförmige Teile für Baugruppen herzustellen.
- Blechbearbeitung:
- Kreisscheren finden Anwendung in der Blechbearbeitung, um runde oder kreisförmige Ausschnitte in Blechen für verschiedene Anwendungen zu erstellen.
- Behälter- und Tankbau:
- Bei der Herstellung von Behältern und Tanks werden Kreisscheren eingesetzt, um präzise Formen und Öffnungen in den Materialien zu schneiden.
- Fahrzeugbau:
- In der Automobilindustrie werden Kreisscheren für die Herstellung von Karosserieteilen und anderen Komponenten eingesetzt.
- Luft- und Raumfahrt:
- Kreisscheren finden in der Luft- und Raumfahrtindustrie Anwendung bei der Fertigung von präzisen Metallteilen für Flugzeuge und Raumfahrzeuge.
- Metallverpackungen:
- In der Herstellung von metallenen Verpackungen können Kreisscheren für das Schneiden von Blechformen verwendet werden.
- Allgemeine Metallverarbeitung:
- Kreisscheren werden in verschiedenen Branchen der Metallverarbeitung eingesetzt, wenn präzise runde oder bogenförmige Schnitte erforderlich sind.
Kreisscheren bieten eine effektive Lösung für Anwendungen, bei denen genaue kreisförmige Schnitte in flachen Materialien benötigt werden. Die Auswahl der richtigen Kreisschere hängt von den spezifischen Anforderungen der Anwendung und den zu bearbeitenden Materialien ab.
Eine Kreisschere, auch als Rotationsschere oder Power-Schere bekannt, ist ein Metallbearbeitungswerkzeug, das eine rotierende Kreisschneide verwendet, um gerade oder gekrümmte Linien durch Blech zu schneiden. Es ist ein vielseitiges und leistungsstarkes Werkzeug, das in verschiedenen Branchen eingesetzt wird, darunter Bauwesen, Fertigung und Metallbearbeitung.
Funktionsweise einer Kreisschere
Eine Kreisschere funktioniert, indem eine scharfe Kreisschneide mit hoher Geschwindigkeit gegen das Werkstück gedreht wird. Die Klinge schneidet durch das Metall, indem sie es schert, was ein Prozess ist, bei dem das Metall entlang seiner Maserungslinien auseinandergerissen wird. Die Kreisbewegung der Klinge ermöglicht es der Maschine, sowohl gerade als auch gekrümmte Schnitte auszuführen.
Anwendungen von Kreisscheren
Kreisscheren werden für eine Vielzahl von Anwendungen eingesetzt, darunter:
- Zuschneiden von Blech auf Größe
- Gerade oder gekrümmte Schnitte in Blech
- Besäumen von Kanten von Blech
- Ausschneiden von Formen aus Blech
- Schneiden von Nuten und Schlitzen in Blech
Vorteile von Kreisscheren
Kreisscheren bieten gegenüber anderen Schneidmethoden mehrere Vorteile, wie z. B.:
- Hohe Geschwindigkeit und Genauigkeit
- Fähigkeit, sowohl gerade als auch gekrümmte Linien zu schneiden
- Vielseitigkeit
- Leistung
- Saubere Schnitte
Nachteile von Kreisscheren
Kreisscheren haben auch einige Nachteile, wie z. B.:
- Kann gefährlich sein, wenn sie nicht richtig verwendet wird
- Regelmäßige Wartung erforderlich
- Kann teuer sein
Sicherheitsvorkehrungen bei der Verwendung einer Kreisschere
Bei der Verwendung einer Kreisschere ist es wichtig, Sicherheitsvorkehrungen zu beachten, um Unfälle zu vermeiden. Zu diesen Vorsichtsmaßnahmen gehören:
- Tragen Sie immer Schutzbrille und Handschuhe
- Halten Sie Ihre Hände von der Klinge fern
- Überlasten Sie die Maschine niemals
- Überprüfen Sie die Maschine regelmäßig auf Beschädigungen
- Befolgen Sie die Anweisungen des Herstellers
Insgesamt sind Kreisscheren wertvolle Werkzeuge für eine Vielzahl von Metallbearbeitungsanwendungen. Sie bieten hohe Geschwindigkeit, Genauigkeit und Vielseitigkeit, was sie zu einem unverzichtbaren Werkzeug für viele Branchen macht.
Konstruktionsmerkmale der Kreisschere
Die Konstruktionsmerkmale einer Kreisschere hängen von der Größe und dem Zweck der Maschine ab. Die grundlegenden Konstruktionsmerkmale einer Kreisschere sind jedoch wie folgt:
- Schneide: Die Schneide ist der wichtigste Teil einer Kreisschere. Sie ist aus einem harten, verschleißfesten Material wie Stahl oder Wolframcarbid hergestellt. Die Schneide ist in der Regel kreisförmig, aber es gibt auch Maschinen mit ovalen oder rechteckigen Schneiden.
- Antrieb: Die Schneide wird durch einen Motor angetrieben. Der Motor kann ein Elektromotor, ein Hydraulikmotor oder ein pneumatischer Motor sein.
- Führungssystem: Das Führungssystem sorgt dafür, dass das Werkstück während des Schneidvorgangs in der richtigen Position gehalten wird. Das Führungssystem kann aus mechanischen, hydraulischen oder pneumatischen Komponenten bestehen.
- Sicherheitseinrichtungen: Kreisscheren sind mit einer Reihe von Sicherheitseinrichtungen ausgestattet, um Unfälle zu verhindern. Dazu gehören Schutzbleche, Not-Aus-Schalter und Überlastsicherungen.
Zusätzlich zu diesen grundlegenden Konstruktionsmerkmalen können Kreisscheren auch mit einer Reihe von anderen Merkmalen ausgestattet sein, z. B.:
- Automatisierung: Kreisscheren können mit einer Reihe von Automatisierungsfunktionen ausgestattet sein, z. B. mit einer automatischen Werkstückzuführung oder einer automatischen Schnittabmessung.
- Schnellwechselsystem: Kreisscheren können mit einem Schnellwechselsystem für die Schneide ausgestattet sein, um den Schneidvorgang zu beschleunigen.
- Schneidkopf: Kreisscheren können mit einem schwenkbaren Schneidkopf ausgestattet sein, um Winkelschnitte zu ermöglichen.
Die Wahl der richtigen Kreisschere hängt von einer Reihe von Faktoren ab, einschließlich der zu bearbeitenden Materialien, der gewünschten Schnittqualität und der erforderlichen Produktionsleistung.
Die Konstruktionsmerkmale einer Kreisschere können je nach Modell und Hersteller variieren. Allerdings gibt es einige grundlegende Konstruktionsmerkmale, die in vielen Kreisscheren zu finden sind. Hier sind einige typische Elemente:
1. Schneidemechanismus:
- Der Schneidemechanismus besteht aus einem rotierenden Messerkopf oder einer rotierenden Schneidklinge, die den kreisförmigen Schnitt durch das Material erzeugt. Die Rotation ermöglicht präzise und saubere Schnitte.
2. Messerkopf und Schneidklingen:
- Der Messerkopf oder die Schneidklingen sind speziell geformt und scharf, um einen effizienten Schnitt zu gewährleisten. Die Auswahl der Materialien und die Qualität der Schneidkanten beeinflussen die Schneidleistung.
3. Antriebssystem:
- Ein leistungsstarkes Antriebssystem ist erforderlich, um den rotierenden Messerkopf oder die Schneidklingen anzutreiben. Dies kann ein elektrischer Motor, ein Hydrauliksystem oder eine andere Antriebsquelle sein.
4. Einstellbare Parameter:
- Kreisscheren verfügen oft über einstellbare Parameter wie den Durchmesser des zu schneidenden Kreises, die Schnittgeschwindigkeit und den Schnittdruck. Dies ermöglicht eine Anpassung an unterschiedliche Materialien und Anwendungen.
5. Materialführung und Fixierung:
- Eine effektive Materialführung und Fixierung sind entscheidend, um sicherzustellen, dass das zu schneidende Material stabil gehalten wird und der Schnitt präzise erfolgt.
6. Automatisierung und Steuerung:
- Moderne Kreisscheren können in automatisierte Produktionslinien integriert werden. Die Steuerungselemente ermöglichen die Automatisierung von Schnittprozessen und die Programmierung unterschiedlicher Schnittmuster.
7. Sicherheitsmerkmale:
- Integrierte Sicherheitsmerkmale, wie Not-Aus-Schalter und Schutzeinrichtungen, gewährleisten einen sicheren Betrieb und schützen Bediener vor Verletzungen.
8. Kühlung und Entstaubung:
- In einigen Kreisscheren kann ein Kühlungssystem integriert sein, um Überhitzung der Schneidkanten zu verhindern. Ein Entstaubungssystem sorgt für die Absaugung von Spänen und Staub während des Schneideprozesses.
9. Werkzeugwechselsystem (bei einigen Modellen):
- Bei fortschrittlichen Kreisscheren kann ein Werkzeugwechselsystem vorhanden sein, um unterschiedliche Schneidwerkzeuge für verschiedene Anwendungen zu ermöglichen.
10. Präzisionsführungen:
- Präzisionsführungen gewährleisten eine genaue Positionierung des Schneidwerkzeugs und unterstützen eine gleichmäßige Schnittleistung.
11. Wartungszugänglichkeit:
- Die Konstruktion sollte so gestaltet sein, dass Wartungsarbeiten leicht durchgeführt werden können, um eine kontinuierliche Betriebsbereitschaft zu gewährleisten.
Die genaue Konstruktion einer Kreisschere hängt von den spezifischen Anforderungen der Anwendung und den zu bearbeitenden Materialien ab. Es ist wichtig, die Herstelleranweisungen genau zu befolgen und die Maschine regelmäßig zu warten, um eine effiziente und sichere Nutzung sicherzustellen.
- Robuster Maschinenkörper und Spannbügel aus Stahl
- Manuelle Zustellung der oberen Messerwalze
- Manuell bedienbare Werkstück-Spannvorrichtung
- Manuelle Spannbügelverstellung zur Einstellung des Rondendurchmessers
- Motorischer Antrieb, gleichzeitig auf Ober- und Untermesser, stufenlos regelbar
- Tiefenanschlag zum einfachen Einlegen des Werkstücks
- Untergestell und 1 Paar Messer für Normalstahl
- Führungsstangen aus Edelstahl
- Durchmessereinstellung über Maßstab
- Antrieb auf Obermesser, bei KSE 12 auf Ober- und Untermesser
- Wechselbare Klemmplatten
- Einstellung des Messerspiels über Gewindebuchse und Skala
Sonderausstattung der Anlage

Sonderausstattungen einer Anlage sind zusätzliche Komponenten oder Funktionen, die nicht zur Standardausstattung gehören. Sie werden in der Regel nachträglich an der Anlage montiert oder installiert. Sonderausstattungen können die Funktionalität der Anlage erweitern oder verbessern, oder sie können die Sicherheit oder den Komfort bei der Bedienung der Anlage erhöhen.
Bei einer Kreisschere können folgende Sonderausstattungen angebracht werden:
- Automatisierung: Automatisierungsfunktionen können die Produktivität und Effizienz der Anlage erhöhen. Dazu gehören Funktionen wie automatische Werkstückzuführung, automatische Schnittabmessung und automatisches Entgraten.
- Schnellwechselsystem: Ein Schnellwechselsystem für die Schneide kann den Schneidvorgang beschleunigen.
- Schneidkopf: Ein schwenkbarer Schneidkopf kann Winkelschnitte ermöglichen.
- Sicherheitseinrichtungen: Zusätzliche Sicherheitseinrichtungen können die Sicherheit bei der Bedienung der Anlage erhöhen. Dazu gehören Funktionen wie Lichtschranken, Not-Aus-Schalter und Überlastsicherungen.
Die Wahl der richtigen Sonderausstattungen hängt von den individuellen Anforderungen des Anwenders ab. So kann eine Anlage, die in einer Produktionsstätte eingesetzt wird, mit einer Reihe von Automatisierungsfunktionen ausgestattet sein, um die Produktivität zu erhöhen. Eine Anlage, die in einer Werkstatt eingesetzt wird, kann hingegen mit einem Schnellwechselsystem ausgestattet sein, um den Schneidvorgang zu beschleunigen.
Hier sind einige Beispiele für Sonderausstattungen, die bei Kreisscheren verwendet werden:
- Automatische Werkstückzuführung: Diese Funktion ermöglicht es, das Werkstück automatisch in die Schneidposition zu bringen. Dies kann die Produktivität und Effizienz der Anlage erhöhen.
- Automatische Schnittabmessung: Diese Funktion ermöglicht es, die Schnittlänge automatisch einzustellen. Dies kann die Genauigkeit der Schnitte erhöhen.
- Automatisches Entgraten: Diese Funktion ermöglicht es, den Grat nach dem Schneiden automatisch zu entfernen. Dies kann die Oberflächenqualität der Schnitte verbessern.
- Schnellwechselsystem für die Schneide: Dieses System ermöglicht es, die Schneide schnell und einfach zu wechseln. Dies kann den Schneidvorgang beschleunigen.
- Schwenkbarer Schneidkopf: Dieser Kopf ermöglicht es, Winkelschnitte auszuführen. Dies kann die Flexibilität der Anlage erhöhen.
- Lichtschranken: Diese Sensoren können verwendet werden, um den Schneidbereich zu schützen. Dies kann die Sicherheit bei der Bedienung der Anlage erhöhen.
- Not-Aus-Schalter: Dieser Schalter kann verwendet werden, um die Anlage bei Gefahr sofort zu stoppen. Dies kann die Sicherheit bei der Bedienung der Anlage erhöhen.
- Überlastsicherungen: Diese Sicherungen können die Anlage vor Beschädigungen durch Überlastung schützen. Dies kann die Lebensdauer der Anlage erhöhen.
Die Sonderausstattung einer Anlage, einschließlich einer Kreisschere, kann je nach den spezifischen Anforderungen der Anwendung und den individuellen Bedürfnissen des Kunden variieren. Hier sind einige mögliche Sonderausstattungen, die in Betracht gezogen werden können:
1. CNC-Steuerung:
- Eine CNC-Steuerung ermöglicht eine präzise und programmierbare Steuerung der Kreisschere. Dies erweitert die Funktionalität und ermöglicht komplexe Schnittmuster.
2. Automatisierte Materialzuführung:
- Ein automatisches Materialzuführungssystem kann den Materialfluss erleichtern und die Effizienz erhöhen, insbesondere in automatisierten Produktionslinien.
3. Berührungsloses Messsystem:
- Ein berührungsloses Messsystem kann die Genauigkeit des Schnitts verbessern, indem es präzise Messungen für den Durchmesser des zu schneidenden Kreises bereitstellt.
4. Laser- oder Bildverarbeitungssysteme:
- Integrierte Lasersysteme oder Bildverarbeitungssysteme können für präzise Positionierung, Qualitätskontrolle und automatisierte Anpassungen eingesetzt werden.
5. Automatisches Werkzeugwechselsystem:
- Ein automatisches Werkzeugwechselsystem ermöglicht den schnellen Wechsel von Schneidwerkzeugen, was die Vielseitigkeit der Maschine erhöht.
6. Kühlungssystem mit Temperaturregelung:
- Ein fortschrittliches Kühlungssystem mit Temperaturregelung kann die Lebensdauer der Schneidkanten verlängern und die Qualität der Schnitte verbessern.
7. Integrierte Entstaubungseinrichtung:
- Eine integrierte Entstaubungseinrichtung sorgt für eine saubere Arbeitsumgebung und verhindert die Ansammlung von Spänen und Staub während des Schneidprozesses.
8. Materialerkennungssysteme:
- Sensoren zur Erkennung von Materialien können die Maschine automatisch auf unterschiedliche Materialien einstellen und den Schneidprozess optimieren.
9. Schmiersysteme:
- Automatische Schmiersysteme sorgen für eine gleichmäßige Schmierung beweglicher Teile, was die Wartung vereinfacht und die Lebensdauer der Maschine verlängert.
10. Schallschutz- und Sicherheitsvorkehrungen:
- Schallschutzmaßnahmen und erweiterte Sicherheitseinrichtungen, wie Lichtschranken und Sicherheitsabschaltungen, tragen zum Schutz der Bediener bei.
11. Spezielle Schneidwerkzeuge:
- Je nach den spezifischen Anforderungen der Anwendung können spezielle Schneidwerkzeuge entwickelt oder integriert werden.
12. Drahtloses Fernüberwachungssystem:
- Ein drahtloses Fernüberwachungssystem ermöglicht die Überwachung und Steuerung der Anlage aus der Ferne, was die Betriebseffizienz und Wartung erleichtern kann.
Die Auswahl der Sonderausstattung hängt von den Anforderungen der spezifischen Anwendung und den gewünschten Funktionen ab. Es ist wichtig, mit dem Hersteller zusammenzuarbeiten, um die optimale Konfiguration für die individuellen Bedürfnisse zu bestimmen.
- Motorische, stufenlos regelbare Zustellung der oberen Messerwalze
- Pneumatisch gesteuerte Werkstück-Spannvorrichtung mit wechselbarer Auflageplatte
- Bördelvorrichtung für Außenbord oder für Innen- und Außenbord
- Manuell oder pneumatisch gesteuerter Werkstück-Niederhalter zum Bördeln
- Motorische Spannbügelverstellung mit Radiusprogrammierung zur Einstellung des Rondendurchmessers
- Bedienung über Touchscreen inklusive Programmspeicher, Zweihand-Bedienpult und Fußtaster
- Spezielle Messerwalzen für Edelstahl oder andere Materialien
- Untergestell
- Tiefenanschlag für Blechfixierung
- Bördelvorrichtung für Außen- oder Außen-/Innenbord
- Messer für Normal-/Edelstahlblech
- Pneumatische Spannvorrichtung
- Hydraulische Spannvorrichtung und Messerzustellung
- Hydraulische Spannvorrichtung, Messerzustellung und
- Niederhaltevorrichtung für Bördelvorrichtung
- Zweistufiger oder stufenlos regelbarer motorischer Antrieb
- Zusätzliche Klemmplatte anstelle der Zentrierspitze
- Elektronische Digitalanzeige für Durchmessereinstellung
Kreisschere in schräg gestellter Ausführung
• Verstellbarer Tisch
• Parallelzustellung des Obermessers
• Bedienung über 3-fach Fußtaster
• Spezieller Auflagetisch mit Anschlag
• SPS mit Bedienung über Touchscreen und 200 Programmspeicherplätze
Kreisschere
Kreisscheren für metallische Blechteile sind Werkzeugmaschinen, die zum Schneiden von Blechen aus Metall verwendet werden. Im Gegensatz zu anderen Schneidwerkzeugen bieten Kreisscheren eine höhere Präzision und Effizienz beim Schneiden von Metallblechen. Sie werden in der Metallindustrie eingesetzt, um eine Vielzahl von Metallteilen mit unterschiedlichen Größen und Formen zu schneiden.
Eine Kreisschere für metallische Blechteile besteht aus einer Schneidklinge, die in einem kreisförmigen Muster rotiert, um das Metallblech zu schneiden. Die Schneidklinge ist in der Regel aus hochwertigem Stahl gefertigt und kann durch spezielle Schleiftechniken eine lange Lebensdauer aufweisen. Die Schnittgenauigkeit und die Schnittgeschwindigkeit hängen von der Größe und dem Durchmesser der Schneidklinge ab.
Kreisscheren für metallische Blechteile gibt es in verschiedenen Größen und Ausführungen. Größere Maschinen können dicke Metallplatten schneiden, während kleinere Scheren für feinere Arbeiten wie das Schneiden von dünnen Blechen geeignet sind. Darüber hinaus gibt es verschiedene Arten von Schneidklingen, die für unterschiedliche Materialien und Schnitte geeignet sind.
Kreisscheren für metallische Blechteile bieten eine hohe Präzision beim Schneiden von Metall. Sie können gerade, gekrümmte und komplexe Formen schneiden und ermöglichen so die Herstellung von hochwertigen Metallteilen. Darüber hinaus sind sie sehr effizient und können große Mengen von Metallteilen in kurzer Zeit schneiden. Dies macht sie zu einem wichtigen Werkzeug in der Massenproduktion von Metallteilen.
Eine der wichtigsten Eigenschaften von Kreisscheren für metallische Blechteile ist ihre Fähigkeit, präzise Schnitte zu machen. Die Schneidklinge ermöglicht es, verschiedene Arten von Metallblechen mit hoher Genauigkeit und ohne Beschädigung zu schneiden. Darüber hinaus ist die Schneidklinge so gestaltet, dass sie eine lange Lebensdauer aufweist und in der Lage ist, eine große Anzahl von Schnitten zu machen, bevor sie ausgetauscht werden muss.
Insgesamt bieten Kreisscheren für metallische Blechteile eine hohe Effizienz und Präzision beim Schneiden von Metallblechen. Sie sind unverzichtbare Werkzeuge in der Metallindustrie und ermöglichen die Herstellung von hochwertigen Metallteilen in großen Stückzahlen.
Kreisschere
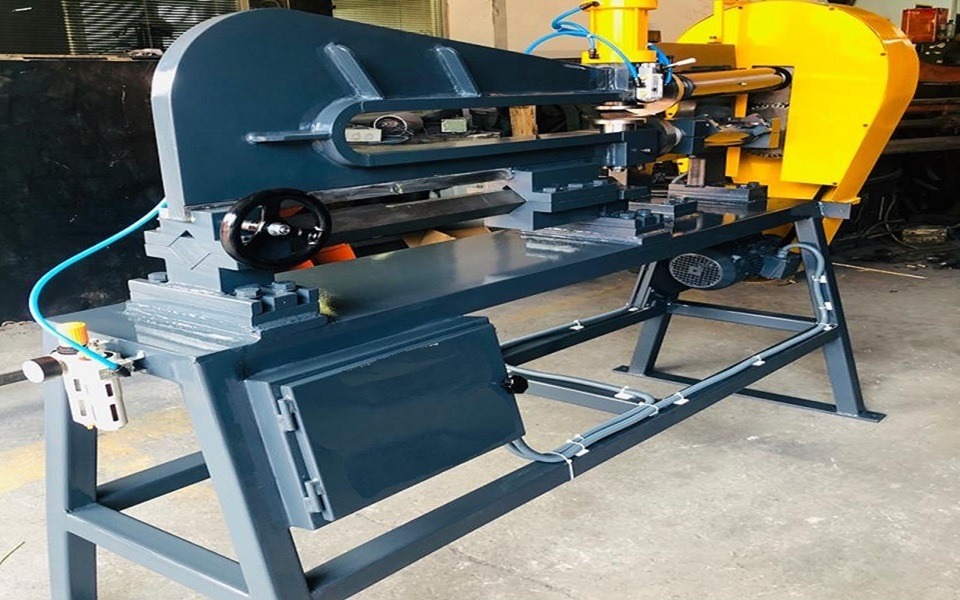
Eine Kreisschere ist eine Werkzeugmaschine, die zum Schneiden von Blechen oder anderen flachen Materialien verwendet wird. Im Gegensatz zu anderen Schneidwerkzeugen, die eine gerade Klinge haben, hat eine Kreisschere eine rotierende runde Klinge. Die Klinge ist in der Regel aus gehärtetem Stahl gefertigt und kann in verschiedenen Größen und Ausführungen erhältlich sein.
Die Arbeitsweise einer Kreisschere ist relativ einfach. Das zu schneidende Blech wird auf eine Arbeitsplatte gelegt und mit Spannbacken oder Haltevorrichtungen fixiert. Die rotierende Klinge der Kreisschere wird dann über das Blech geführt und schneidet es durch. Die Klinge wird durch einen Motor angetrieben und dreht sich in der Regel mit einer Geschwindigkeit von einigen hundert bis mehreren tausend Umdrehungen pro Minute. Je nach Größe und Ausführung der Kreisschere können unterschiedliche Dicken und Arten von Blechen geschnitten werden.
Kreisscheren werden in verschiedenen Branchen eingesetzt, wie zum Beispiel in der Metallverarbeitung, Blechbearbeitung, im Schiffbau, in der Luft- und Raumfahrt, in der Automobilindustrie und in der Herstellung von elektronischen Geräten. Sie sind besonders nützlich, wenn es darum geht, gerade Linien oder komplexe Formen aus Blech oder anderen flachen Materialien zu schneiden.
In der Regel wird bei der Verwendung einer Kreisschere eine hohe Präzision und Sauberkeit des Schnitts erreicht, da die rotierende Klinge eine gleichmäßige Schneidbewegung ausführt. Darüber hinaus können Kreisscheren in vielen Fällen schneller und effizienter arbeiten als andere Schneidwerkzeuge, da sie in der Lage sind, größere Blechstücke auf einmal zu schneiden.
Eine Kreisschere, auch als Rundschere oder Kreisschneidemaschine bezeichnet, ist eine spezialisierte Werkzeugmaschine, die dazu dient, kreisförmige oder gebogene Schnitte in flache Materialien wie Bleche oder Folien durchzuführen. Diese Maschinen sind in einer Vielzahl von Industrien, einschließlich der Metallverarbeitung, der Kunststoffverarbeitung und der Papierverarbeitung, weit verbreitet. Hier sind die Hauptmerkmale und Funktionen einer Kreisschere:
1. Runde und gebogene Schnitte: Die Hauptfunktion einer Kreisschere besteht darin, runde oder gebogene Schnitte in flache Materialien zu schneiden. Dies ermöglicht die Herstellung von Kreisformen, Bögen und anderen komplexen Formen.
2. Materialien: Kreisscheren können eine Vielzahl von Materialien schneiden, einschließlich Metalle wie Stahl, Edelstahl, Aluminium, Kunststoffe, Folien und Papier.
3. Präzise Schnitte: Diese Maschinen bieten präzise Steuerungsmöglichkeiten, um genaue Schnitte mit engen Toleranzen durchzuführen. Dies ist wichtig für die Qualität und Genauigkeit der Endprodukte.
4. Schneidkapazität: Kreisscheren sind in verschiedenen Größen und Kapazitäten erhältlich, je nach den Anforderungen der Anwendung. Kleine Kreisscheren eignen sich für dünnere Materialien, während größere Maschinen dicke Bleche schneiden können.
5. Automatisierung: Moderne Kreisscheren können automatisiert sein, was die Effizienz in der Produktion steigert. Dies umfasst die automatische Zuführung des Materials und die Steuerung des Schneidprozesses.
6. Vielseitigkeit: Kreisscheren sind vielseitige Werkzeugmaschinen, die in verschiedenen Branchen eingesetzt werden, einschließlich der Herstellung von Metallteilen, Dichtungen, Etiketten, Verpackungen und vielem mehr.
7. Materialzuführung: Einige Kreisscheren verfügen über spezielle Materialzuführungen, die das Material gleichmäßig zuführen und die Verschwendung minimieren.
8. Wartungsfreundlichkeit: Die Maschinen sind in der Regel wartungsfreundlich gestaltet und erfordern regelmäßige Wartung, um eine zuverlässige Leistung sicherzustellen.
9. Sicherheitseinrichtungen: Kreisscheren sind mit Sicherheitseinrichtungen ausgestattet, um die Sicherheit der Bediener während des Betriebs zu gewährleisten. Dies umfasst Notausschalter und Schutzvorrichtungen.
10. Anpassbarkeit: Je nach den Anforderungen der Anwendung können Kreisscheren mit verschiedenen Schneidwerkzeugen und -einstellungen konfiguriert werden.
Kreisscheren sind entscheidende Werkzeuge in der Herstellung von runden und gebogenen Teilen, die in einer Vielzahl von Produkten verwendet werden. Ihre Fähigkeit zur präzisen Formgebung und zum Schneiden von Materialien macht sie zu einer wichtigen Komponente in der modernen Fertigung.
Plasmagenerator
Der Plasmagenerator ist eine zentrale Komponente beim Plasmaschneiden und dient dazu, den Hochfrequenzstrom zu erzeugen, der für die Erzeugung des Plasmastrahls benötigt wird. Hier sind einige wichtige Aspekte des Plasmagenerators:
- Funktionsweise: Der Plasmagenerator wandelt elektrische Energie in Hochfrequenzstrom um, der an den Plasmabrenner geliefert wird. Dort wird der Strom verwendet, um den Plasmabogen zwischen der Elektrode und der Düse des Brenners zu erzeugen und aufrechtzuerhalten.
- Typen von Plasmageneratoren: Es gibt verschiedene Arten von Plasmageneratoren, darunter konventionelle DC-Plasmageneratoren, AC-Plasmageneratoren und Hochfrequenz-Plasmageneratoren. Jeder Typ hat seine eigenen Vor- und Nachteile hinsichtlich Leistung, Effizienz und Anwendungsbereichen.
- Leistung: Die Leistungsfähigkeit eines Plasmagenerators wird durch verschiedene Faktoren beeinflusst, einschließlich der Stromstärke, der Spannung, der Frequenz und der Effizienz der Energieumwandlung. Hochwertige Plasmageneratoren bieten eine hohe Leistung und Zuverlässigkeit bei gleichzeitig geringem Energieverbrauch und niedrigen Betriebskosten.
- Anwendungsbereiche: Plasmageneratoren werden in einer Vielzahl von Anwendungen eingesetzt, einschließlich der industriellen Fertigung, der Metallbearbeitung, der Automobilindustrie und der Luft- und Raumfahrt. Sie sind besonders effektiv beim Schneiden von Metallen wie Stahl, Aluminium, Kupfer und Edelstahl.
- Wartung: Die regelmäßige Wartung und Instandhaltung des Plasmagenerators ist wichtig, um eine optimale Leistung und Zuverlässigkeit sicherzustellen. Dies umfasst die Überprüfung und Reinigung der Elektroden und Düsen, den Austausch von Verschleißteilen und die Durchführung von regelmäßigen Inspektionen und Tests.
Der Plasmagenerator ist eine entscheidende Komponente beim Plasmaschneiden und ermöglicht die zuverlässige Erzeugung des Plasmastrahls, der für präzise und effiziente Schnitte benötigt wird. Durch die Auswahl eines hochwertigen Plasmagenerators und die ordnungsgemäße Wartung können Hersteller die Leistung ihres Plasmaschneidsystems maximieren und die Qualität ihrer Produkte verbessern.
Plasmasteuerung
Die Plasmasteuerung ist ein wesentlicher Bestandteil beim Plasmaschneiden und umfasst die Steuerung und Überwachung verschiedener Parameter, um präzise und effiziente Schnitte zu erzielen. Hier sind einige wichtige Aspekte der Plasmasteuerung:
- Parameterkontrolle: Die Plasmasteuerung umfasst die Kontrolle verschiedener Parameter wie Stromstärke, Spannung, Schneidgasdruck, Schneidgeschwindigkeit und Schnittspalt. Durch die präzise Einstellung dieser Parameter kann die Qualität der Schnitte optimiert und die Produktivität gesteigert werden.
- Automatisierung: Moderne Plasmaschneidemaschinen verfügen über fortschrittliche automatische Steuerungssysteme, die es ermöglichen, Schnittparameter während des Schneidprozesses automatisch anzupassen. Dies ermöglicht eine höhere Effizienz, konsistente Schnittqualität und reduzierten Bedarf an manueller Intervention.
- Echtzeitüberwachung: Die Plasmasteuerung umfasst auch die Echtzeitüberwachung verschiedener Parameter während des Schneidprozesses. Dies ermöglicht es dem Bediener, Abweichungen oder Probleme sofort zu erkennen und entsprechend zu reagieren, um die Qualität der Schnitte zu gewährleisten.
- Anpassungsfähigkeit: Die Plasmasteuerung ermöglicht es dem Bediener, Schnittparameter je nach den Anforderungen der Anwendung und den Eigenschaften des zu schneidenden Materials anzupassen. Dies ermöglicht eine maximale Flexibilität und Anpassungsfähigkeit des Schneidprozesses an unterschiedliche Anforderungen und Materialien.
- Qualitätssicherung: Durch die präzise Kontrolle und Überwachung der Schnittparameter gewährleistet die Plasmasteuerung eine gleichbleibend hohe Qualität der Schnitte. Dies ist besonders wichtig in Anwendungen, die hohe Präzision und Qualität erfordern, wie z.B. die Fertigung von Bauteilen für die Luft- und Raumfahrt oder die Automobilindustrie.
Die Plasmasteuerung ist ein entscheidender Faktor beim Plasmaschneiden und ermöglicht eine präzise Kontrolle und Optimierung verschiedener Parameter, um hochwertige Schnitte in einer Vielzahl von Materialien und Anwendungen zu erzielen. Durch die Nutzung moderner Steuerungstechnologien können Hersteller die Effizienz ihres Schneidprozesses maximieren und die Qualität ihrer Produkte verbessern.
Schneidgeschwindigkeit
Die Schneidgeschwindigkeit ist ein wichtiger Parameter beim Plasmaschneiden und bezieht sich auf die Geschwindigkeit, mit der der Plasmabrenner über das Material bewegt wird. Hier sind einige wichtige Aspekte der Schneidgeschwindigkeit:
- Einfluss auf die Schnittqualität: Die Schneidgeschwindigkeit hat einen direkten Einfluss auf die Qualität des Schnitts. Eine zu hohe Geschwindigkeit kann zu ungenauen Schnitten und Ausfransungen führen, während eine zu niedrige Geschwindigkeit zu übermäßiger Wärmeansammlung und ungleichmäßigen Schnitten führen kann.
- Optimierung: Die optimale Schneidgeschwindigkeit hängt von verschiedenen Faktoren ab, einschließlich des zu schneidenden Materials, seiner Dicke und der Leistung des Plasmagenerators. Moderne Plasmaschneidemaschinen bieten oft die Möglichkeit, die Schneidgeschwindigkeit während des Schneidprozesses anzupassen, um auf unterschiedliche Materialien und Schnittanforderungen zu reagieren.
- Materialabhängigkeit: Verschiedene Materialien erfordern unterschiedliche Schneidgeschwindigkeiten, um optimale Schnittbedingungen zu erreichen. Dünnere Materialien erfordern in der Regel höhere Geschwindigkeiten, während dickere Materialien langsamere Geschwindigkeiten erfordern können, um einen effizienten Schnitt zu gewährleisten.
- Qualitätssicherung: Die Überwachung und Kontrolle der Schneidgeschwindigkeit während des Schneidprozesses ist wichtig, um eine gleichbleibend hohe Qualität der Schnitte zu gewährleisten. Moderne Plasmaschneidemaschinen verfügen oft über automatische Steuerungssysteme, die es ermöglichen, die Geschwindigkeit präzise anzupassen und Abweichungen zu erkennen.
- Effizienz: Die Schneidgeschwindigkeit beeinflusst auch die Effizienz des Schneidprozesses. Eine optimale Geschwindigkeit ermöglicht es, die Produktivität zu maximieren und die Bearbeitungszeiten zu verkürzen, ohne die Qualität der Schnitte zu beeinträchtigen.
Die Schneidgeschwindigkeit ist ein entscheidender Parameter beim Plasmaschneiden und muss sorgfältig kontrolliert und optimiert werden, um präzise und qualitativ hochwertige Schnitte zu erzielen. Durch die richtige Anpassung und Überwachung der Schneidgeschwindigkeit können Hersteller die Effizienz ihres Schneidprozesses maximieren und die Qualität ihrer Produkte verbessern.
Schnittspalt
Der Schnittspalt ist ein wichtiger Begriff beim Plasmaschneiden und bezieht sich auf den Abstand zwischen der Düse des Plasmabrenners und der Oberfläche des zu schneidenden Materials. Hier sind einige wichtige Aspekte des Schnittspalts:
- Funktionsweise: Der Schnittspalt beeinflusst die Qualität und Effizienz des Schneidprozesses. Ein korrekter Schnittspalt ermöglicht es dem Plasmastrahl, das Material effizient zu erhitzen und zu schmelzen, während ein zu großer oder zu kleiner Schnittspalt die Schnittqualität beeinträchtigen kann.
- Optimierung: Die optimale Größe des Schnittspalts hängt von verschiedenen Faktoren ab, einschließlich des zu schneidenden Materials, seiner Dicke und der Leistung des Plasmagenerators. Moderne Plasmaschneidemaschinen bieten oft die Möglichkeit, den Schnittspalt während des Schneidprozesses anzupassen, um optimale Schnittbedingungen zu erreichen.
- Materialabhängigkeit: Verschiedene Materialien erfordern unterschiedliche Schnittspaltgrößen, um optimale Schnittbedingungen zu erreichen. Dünnere Materialien erfordern in der Regel engere Schnittspalte, während dickere Materialien größere Schnittspalte erfordern können, um eine effiziente Materialentfernung zu ermöglichen.
- Qualitätssicherung: Die Überwachung und Kontrolle des Schnittspalts während des Schneidprozesses ist wichtig, um eine gleichbleibend hohe Qualität der Schnitte zu gewährleisten. Moderne Plasmaschneidemaschinen verfügen oft über automatische Steuerungssysteme, die es ermöglichen, den Schnittspalt präzise anzupassen und Abweichungen zu erkennen.
- Effizienz: Ein optimaler Schnittspalt ermöglicht es, die Effizienz des Schneidprozesses zu maximieren, indem er eine gleichmäßige und effiziente Materialentfernung ermöglicht. Dies trägt dazu bei, die Produktivität zu steigern und die Bearbeitungszeiten zu verkürzen, ohne die Qualität der Schnitte zu beeinträchtigen.
Der Schnittspalt ist ein entscheidender Parameter beim Plasmaschneiden und muss sorgfältig kontrolliert und optimiert werden, um präzise und qualitativ hochwertige Schnitte zu erzielen. Durch die richtige Anpassung und Überwachung des Schnittspalts können Hersteller die Effizienz ihres Schneidprozesses maximieren und die Qualität ihrer Produkte verbessern.
Schneidqualität
Die Schneidqualität ist ein entscheidender Aspekt beim Plasmaschneiden und bezieht sich auf die Genauigkeit, Sauberkeit und Präzision der Schnitte. Hier sind einige wichtige Aspekte der Schneidqualität:
- Schnittpräzision: Die Schneidqualität wird durch die Präzision des Schnitts bestimmt, einschließlich der Genauigkeit der Schnittkontur und der Maßhaltigkeit der geschnittenen Teile. Eine hohe Schnittpräzision ist besonders wichtig in Anwendungen, die enge Toleranzen und hohe Ansprüche an die Bauteilqualität haben.
- Schnittsauberkeit: Die Sauberkeit des Schnitts bezieht sich auf das Ausmaß von Gratbildung, Schmelzrändern und anderen Unregelmäßigkeiten an den Schnittkanten. Eine hohe Schnittsauberkeit ist entscheidend, um nachfolgende Bearbeitungsschritte zu minimieren und die Montage- und Fügeprozesse zu erleichtern.
- Schnittgeschwindigkeit: Die Schneidqualität kann auch durch die Schnittgeschwindigkeit beeinflusst werden. Eine angemessene Schnittgeschwindigkeit ermöglicht es dem Plasmastrahl, das Material gleichmäßig zu schmelzen und zu entfernen, während eine zu hohe oder zu niedrige Geschwindigkeit zu ungenauen Schnitten und Ausfransungen führen kann.
- Materialdicke: Die Schneidqualität variiert je nach Materialdicke und -typ. Dünne Materialien erfordern in der Regel höhere Präzision und eine sauberere Schnittkante, während dickere Materialien eine höhere Schneidleistung erfordern können, um eine effiziente Materialentfernung zu gewährleisten.
- Schneidparameter: Die Schneidqualität kann durch die richtige Auswahl und Optimierung der Schneidparameter verbessert werden, einschließlich des Plasmagasdrucks, der Schneidgeschwindigkeit, des Schnittspalts und anderer Prozessvariablen. Eine präzise Steuerung und Anpassung dieser Parameter ist entscheidend für die Erzielung hochwertiger Schnitte.
Die Schneidqualität ist ein wesentlicher Faktor beim Plasmaschneiden und beeinflusst maßgeblich die Leistungsfähigkeit und Zuverlässigkeit des Schneidprozesses. Durch die Optimierung der Schneidparameter und die Auswahl hochwertiger Schneidausrüstung können Hersteller die Schneidqualität verbessern und die Produktivität steigern.
Schneidtorch
Ein Schneidtorch, auch als Schneidbrenner oder Schneidkopf bezeichnet, ist eine entscheidende Komponente beim Plasmaschneiden und dient dazu, den Plasmastrahl auf das zu schneidende Material zu lenken. Hier sind einige wichtige Aspekte des Schneidtorchs:
- Funktionsweise: Der Schneidtorch erzeugt den Plasmabogen zwischen einer Elektrode und einer Düse und lenkt den entstehenden Plasmastrahl auf das Material. Die Düse konzentriert den Plasmastrahl und ermöglicht präzise und effiziente Schnitte.
- Aufbau: Ein typischer Schneidtorch besteht aus einer Elektrode, einer Düse, einem Kühlkörper und einem Halter. Die Elektrode erzeugt den Plasmabogen, während die Düse den Plasmastrahl fokussiert und den Schnittspalt kontrolliert. Der Kühlkörper und der Halter dienen dazu, den Torch zu kühlen und zu stabilisieren.
- Materialien: Schneidtorchs werden aus hochwertigen Materialien hergestellt, die eine hohe Hitzebeständigkeit und Langlebigkeit gewährleisten. Die Elektrode besteht in der Regel aus Wolfram oder einem ähnlichen Material, während die Düse aus Kupfer oder Messing gefertigt ist.
- Verschleiß: Aufgrund der hohen Temperaturen und Belastungen während des Schneidprozesses sind Schneidtorchs einem gewissen Verschleiß ausgesetzt. Die Düse und die Elektrode sind besonders anfällig für Verschleiß und müssen regelmäßig überprüft und gegebenenfalls ausgetauscht werden, um die Schnittqualität aufrechtzuerhalten.
- Wartung: Die regelmäßige Wartung und Instandhaltung des Schneidtorchs ist wichtig, um eine optimale Leistung und Zuverlässigkeit sicherzustellen. Dies umfasst die Reinigung, Inspektion und gegebenenfalls den Austausch von Verschleißteilen sowie die Überprüfung der Kühlung und der elektrischen Verbindungen.
Der Schneidtorch ist eine entscheidende Komponente beim Plasmaschneiden und spielt eine wesentliche Rolle bei der Erzeugung präziser und effizienter Schnitte. Durch die Auswahl hochwertiger Torchs und die ordnungsgemäße Wartung können Hersteller die Leistung ihres Plasmaschneidsystems maximieren und die Qualität ihrer Produkte verbessern.
Plasmagas
Plasmagas ist ein wesentlicher Bestandteil des Plasmaschneidprozesses und dient dazu, den Plasmabogen zwischen der Elektrode und der Düse des Plasmabrenners zu erzeugen und aufrechtzuerhalten. Hier sind einige wichtige Aspekte des Plasmagases:
- Funktionsweise: Plasmagas wird verwendet, um den Schneidbereich zu reinigen und den Plasmabogen zu stabilisieren. Es wird durch den Plasmabrenner geleitet und durch die Hochspannung ionisiert, wodurch ein elektrisch leitendes Plasma entsteht, das das zu schneidende Material erhitzt und schmilzt.
- Arten von Plasmagas: Es gibt verschiedene Arten von Plasmagas, die für das Plasmaschneiden verwendet werden können, darunter Luft, Stickstoff, Sauerstoff, Argon und Wasserstoff. Jede Art von Plasmagas hat ihre eigenen Vor- und Nachteile hinsichtlich Schnittqualität, Geschwindigkeit und Anwendungsbereichen.
- Eigenschaften: Die Auswahl des richtigen Plasmagases hängt von verschiedenen Faktoren ab, einschließlich des zu schneidenden Materials, seiner Dicke und der gewünschten Schnittqualität. Einige Gase wie Sauerstoff können eine höhere Schnittgeschwindigkeit ermöglichen, während andere Gase wie Stickstoff eine sauberere Schnittkante erzeugen können.
- Verfügbarkeit: Die Verfügbarkeit von Plasmagas kann je nach Standort und Anwendung variieren. Einige Gase wie Luft und Stickstoff sind weit verbreitet und kostengünstig verfügbar, während andere Gase wie Wasserstoff und Argon spezielle Lieferungen erfordern können.
- Optimierung: Die Optimierung des Plasmagases umfasst die Auswahl des geeigneten Gases für die jeweilige Anwendung sowie die richtige Einstellung des Gasflusses und des Drucks, um optimale Schnittbedingungen zu erreichen. Durch die Optimierung des Plasmagases können Hersteller die Schnittqualität verbessern und die Produktivität steigern.
Plasmagas ist ein wesentlicher Bestandteil des Plasmaschneidprozesses und beeinflusst maßgeblich die Qualität und Effizienz der Schnitte. Durch die Auswahl des richtigen Plasmagases und die Optimierung des Gasflusses können Hersteller die Leistung ihres Plasmaschneidsystems maximieren und hochwertige Schnitte in einer Vielzahl von Materialien erzielen.
Plasmabrenner
Der Plasmabrenner ist eine zentrale Komponente beim Plasmaschneiden und dient dazu, den Plasmastrahl zu erzeugen und auf das zu schneidende Material zu lenken. Hier sind einige wichtige Aspekte des Plasmabrenners:
- Funktionsweise: Der Plasmabrenner erzeugt den Plasmabogen zwischen einer Elektrode und einer Düse, wodurch ein elektrisch leitendes Plasma entsteht. Der Plasmastrahl wird durch die Düse fokussiert und auf das Material gerichtet, wodurch es erhitzt, geschmolzen und entfernt wird.
- Aufbau: Ein typischer Plasmabrenner besteht aus einer Elektrode, einer Düse, einem Düsenhalter und einem Kühlkörper. Die Elektrode erzeugt den Plasmabogen, während die Düse den Plasmastrahl fokussiert und den Schnittspalt kontrolliert. Der Kühlkörper und der Düsenhalter dienen dazu, den Brenner zu kühlen und zu stabilisieren.
- Arten von Plasmabrennern: Es gibt verschiedene Arten von Plasmabrennern, darunter manuelle Brenner für handgeführtes Schneiden und automatische Brenner für CNC-gesteuerte Schneidsysteme. Jede Art von Brenner hat ihre eigenen Merkmale und Anwendungsbereiche, abhängig von den Anforderungen der Schneidaufgabe.
- Leistung: Die Leistungsfähigkeit eines Plasmabrenners wird durch verschiedene Faktoren beeinflusst, einschließlich der Stromstärke, der Spannung, der Düsengeometrie und der Qualität der Materialien. Hochwertige Plasmabrenner bieten eine hohe Leistung und Zuverlässigkeit bei gleichzeitig geringem Energieverbrauch und niedrigen Betriebskosten.
- Wartung: Die regelmäßige Wartung und Instandhaltung des Plasmabrenners ist wichtig, um eine optimale Leistung und Zuverlässigkeit sicherzustellen. Dies umfasst die Reinigung, Inspektion und gegebenenfalls den Austausch von Verschleißteilen sowie die Überprüfung der Kühlung und der elektrischen Verbindungen.
Der Plasmabrenner ist eine entscheidende Komponente beim Plasmaschneiden und spielt eine wesentliche Rolle bei der Erzeugung präziser und effizienter Schnitte. Durch die Auswahl hochwertiger Brenner und die ordnungsgemäße Wartung können Hersteller die Leistung ihres Plasmaschneidsystems maximieren und die Qualität ihrer Produkte verbessern.
Düse
Die Düse ist eine wichtige Komponente des Plasmabrenners und dient dazu, den Plasmastrahl zu fokussieren und den Schnittspalt zu kontrollieren. Hier sind einige wichtige Aspekte der Düse:
- Funktionsweise: Die Düse ist ein dünnwandiges Bauteil mit einer Öffnung, durch die der Plasmastrahl austritt. Sie dient dazu, den Plasmastrahl zu fokussieren und zu konzentrieren, um präzise und effiziente Schnitte zu ermöglichen. Die Düsenform und -größe beeinflussen die Geometrie und Qualität des Schnitts.
- Materialien: Düsen werden typischerweise aus hitzebeständigen Materialien wie Kupfer oder Messing gefertigt, die hohe Temperaturen und thermische Belastungen standhalten können. Hochwertige Düsen sind langlebig und bieten eine hohe Schneidleistung und Präzision.
- Düsengeometrie: Die Geometrie der Düse, einschließlich des Düsenwinkels und des Durchmessers der Austrittsöffnung, beeinflusst die Form und Qualität des Plasmastrahls sowie die Stabilität des Plasmabogens. Eine präzise gefertigte Düse mit der richtigen Geometrie ermöglicht es, saubere und präzise Schnitte zu erzielen.
- Schnittspaltkontrolle: Die Düse spielt eine wichtige Rolle bei der Kontrolle des Schnittspalts, der den Abstand zwischen der Düse und der Oberfläche des zu schneidenden Materials definiert. Eine präzise Einstellung des Schnittspalts ist entscheidend für die Qualität und Genauigkeit des Schnitts.
- Verschleiß: Aufgrund der hohen Temperaturen und Belastungen während des Schneidprozesses sind Düsen einem gewissen Verschleiß ausgesetzt. Eine regelmäßige Inspektion und gegebenenfalls der Austausch von verschlissenen Düsen ist wichtig, um die Qualität der Schnitte aufrechtzuerhalten und die Lebensdauer des Plasmabrenners zu verlängern.
Die Düse ist eine entscheidende Komponente des Plasmabrenners und spielt eine wesentliche Rolle bei der Erzeugung präziser und effizienter Schnitte. Durch die Auswahl hochwertiger Düsen und die ordnungsgemäße Wartung können Hersteller die Leistung ihres Plasmaschneidsystems maximieren und die Qualität ihrer Produkte verbessern.
Elektrode
Die Elektrode ist eine wichtige Komponente des Plasmabrenners beim Plasmaschneiden und spielt eine zentrale Rolle bei der Erzeugung des Plasmabogens. Hier sind einige wichtige Aspekte der Elektrode:
- Funktionsweise: Die Elektrode erzeugt den Plasmabogen zwischen sich und der Düse des Plasmabrenners, indem sie mit einem Hochspannungsgenerator verbunden ist. Der Plasmabogen ionisiert das Plasmagas, das durch den Brenner strömt, und erzeugt das heiße, elektrisch leitfähige Plasma, das zum Schneiden des Materials verwendet wird.
- Materialien: Elektroden werden typischerweise aus hitzebeständigen Materialien wie Wolfram oder Hafnium gefertigt, die hohe Temperaturen und thermische Belastungen standhalten können. Diese Materialien bieten eine hohe Leitfähigkeit und Stabilität während des Schneidprozesses.
- Verschleiß: Aufgrund der hohen Temperaturen und Belastungen während des Schneidprozesses sind Elektroden einem gewissen Verschleiß ausgesetzt. Der Verschleiß kann durch den Kontakt mit dem Plasma, der Düse und dem zu schneidenden Material verursacht werden. Eine regelmäßige Inspektion und gegebenenfalls der Austausch von verschlissenen Elektroden ist wichtig, um die Leistung des Plasmabrenners aufrechtzuerhalten und die Schnittqualität zu verbessern.
- Geometrie: Die Geometrie der Elektrode, einschließlich ihrer Form und Größe, beeinflusst die Stabilität und Eigenschaften des Plasmabogens. Eine präzise gefertigte Elektrode mit der richtigen Geometrie ermöglicht eine gleichmäßige und stabile Plasmabogenbildung, was zu präzisen und effizienten Schnitten führt.
- Wartung: Die regelmäßige Wartung und Instandhaltung der Elektrode ist wichtig, um eine optimale Leistung und Zuverlässigkeit des Plasmabrenners sicherzustellen. Dies umfasst die Reinigung, Inspektion und gegebenenfalls den Austausch von verschlissenen Elektroden sowie die Überprüfung der elektrischen Verbindungen.
Die Elektrode ist eine entscheidende Komponente des Plasmabrenners und spielt eine wesentliche Rolle bei der Erzeugung präziser und effizienter Schnitte. Durch die Auswahl hochwertiger Elektroden und die ordnungsgemäße Wartung können Hersteller die Leistung ihres Plasmaschneidsystems maximieren und die Qualität ihrer Produkte verbessern.
Kühlungssystem
Ein Kühlungssystem ist eine wesentliche Komponente bei Plasmaschneidemaschinen, da es dazu dient, die Temperatur der verschiedenen Teile des Schneidgeräts auf einem optimalen Niveau zu halten. Hier sind einige wichtige Aspekte eines Kühlungssystems:
- Funktionsweise: Das Kühlungssystem besteht aus einem Kühlmittel, das durch einen geschlossenen Kreislauf zirkuliert und die Hitze von den heißen Teilen des Schneidgeräts abführt. Typischerweise werden Wasserkühlungssysteme oder Luftkühlungssysteme verwendet, um die Komponenten wie Brenner, Elektroden, Düsen und Halter zu kühlen.
- Wasser- oder Luftkühlung: Wasserkühlungssysteme nutzen Wasser als Kühlmittel, das durch einen Kühlkreislauf gepumpt wird und die Hitze von den heißen Teilen des Schneidgeräts absorbiert. Luftkühlungssysteme verwenden Luftströme, um die Komponenten zu kühlen, und können in einigen Fällen weniger aufwendig sein als Wasserkühlungssysteme.
- Effizienz: Ein effizientes Kühlungssystem trägt dazu bei, die Lebensdauer der Schneidkomponenten zu verlängern und die Zuverlässigkeit des Schneidgeräts zu verbessern, indem es die Temperaturen auf einem optimalen Niveau hält. Eine effiziente Kühlung kann auch dazu beitragen, die Schnittqualität zu verbessern und die Produktivität zu steigern, indem sie Überhitzung und Ausfallzeiten reduziert.
- Wartung: Die regelmäßige Wartung und Instandhaltung des Kühlungssystems sind wichtig, um eine optimale Leistung und Zuverlässigkeit sicherzustellen. Dies umfasst die Überprüfung des Kühlmittelniveaus, die Reinigung der Kühlkanäle und -filter sowie die Inspektion der Pumpen und Ventile, um sicherzustellen, dass sie ordnungsgemäß funktionieren.
- Anpassungsfähigkeit: Moderne Plasmaschneidemaschinen verfügen oft über Kühlungssysteme, die an verschiedene Betriebsbedingungen und Anforderungen angepasst werden können. Dies ermöglicht es den Betreibern, die Kühlleistung je nach Material, Dicke und Schnittgeschwindigkeit anzupassen, um optimale Ergebnisse zu erzielen.
Ein effizientes Kühlungssystem ist entscheidend für die Leistung und Zuverlässigkeit von Plasmaschneidemaschinen. Durch die Auswahl des richtigen Kühlungssystems und die ordnungsgemäße Wartung können Hersteller die Lebensdauer ihrer Ausrüstung verlängern und die Qualität ihrer Produkte verbessern.
CNC-Steuerung
Die CNC-Steuerung (Computerized Numerical Control) ist ein wesentlicher Bestandteil moderner Plasmaschneidemaschinen, der für die präzise Steuerung des Schneidprozesses verantwortlich ist. Hier sind einige wichtige Aspekte der CNC-Steuerung:
- Funktionsweise: Die CNC-Steuerung ermöglicht die automatische Steuerung des Schneidprozesses durch die Verwendung von numerischen Befehlen, die von einem Computer generiert werden. Diese Befehle umfassen Informationen über die Schnittkontur, Schnittgeschwindigkeit, Plasmagasfluss und andere Parameter, die den Schneidprozess beeinflussen.
- Programmierung: Die CNC-Steuerung erfordert die Programmierung der Schneidaufgabe mithilfe spezieller Software, die es dem Benutzer ermöglicht, die gewünschten Schnittkonturen zu definieren und die erforderlichen Schnittparameter einzustellen. Diese Programme werden dann an die CNC-Steuerung übertragen, die den Schneidprozess entsprechend ausführt.
- Präzision: Die CNC-Steuerung ermöglicht eine hohe Präzision und Wiederholbarkeit der Schnitte, da sie in der Lage ist, komplexe Schnittkonturen mit hoher Genauigkeit zu verfolgen. Dies ist besonders wichtig in Anwendungen, die enge Toleranzen und hohe Ansprüche an die Bauteilqualität haben.
- Flexibilität: CNC-gesteuerte Plasmaschneidemaschinen bieten eine hohe Flexibilität und Vielseitigkeit bei der Bearbeitung verschiedener Materialien und Schnittkonturen. Durch die einfache Änderung der Programmierung können Benutzer schnell zwischen verschiedenen Schneidaufgaben und Materialien wechseln, ohne dass umfangreiche Umrüstungen erforderlich sind.
- Automatisierung: Die CNC-Steuerung ermöglicht eine weitgehende Automatisierung des Schneidprozesses, was zu einer erhöhten Produktivität und Effizienz führt. Durch die Integration von CNC-Steuerungen mit anderen Automatisierungstechnologien wie Robotern und Materialhandhabungssystemen können Hersteller ihre Produktionsprozesse weiter optimieren.
Die CNC-Steuerung ist ein entscheidender Bestandteil moderner Plasmaschneidemaschinen und ermöglicht eine präzise, flexible und effiziente Steuerung des Schneidprozesses. Durch die Nutzung der Vorteile der CNC-Technologie können Hersteller die Qualität ihrer Produkte verbessern und ihre Wettbewerbsfähigkeit auf dem Markt stärken.
Schneidtisch
Der Schneidtisch ist eine wichtige Komponente von Plasmaschneidemaschinen und dient als Unterlage für das zu schneidende Material sowie als Träger für den Plasmabrenner und die CNC-Steuerung. Hier sind einige wichtige Aspekte des Schneidtisches:
- Konstruktion: Schneidtische können aus verschiedenen Materialien wie Stahl, Aluminium oder Verbundwerkstoffen gefertigt sein, abhängig von den Anforderungen der Anwendung. Sie sind oft mit einem Raster oder Lochmuster versehen, um die Befestigung des zu schneidenden Materials und die Positionierung des Plasmabrenners zu erleichtern.
- Größe und Kapazität: Die Größe und Kapazität des Schneidtisches hängt von der Größe des zu schneidenden Materials und den Anforderungen der Anwendung ab. Große Schneidtische bieten Platz für große Bleche und ermöglichen die Bearbeitung von mehreren Teilen gleichzeitig, während kleinere Schneidtische kompakter sind und für kleinere Aufgaben geeignet sind.
- Nivellierung: Eine gleichmäßige und stabile Unterlage ist entscheidend für präzise und qualitativ hochwertige Schnitte. Schneidtische verfügen daher oft über ein System zur Nivellierung, das es ermöglicht, Unebenheiten auszugleichen und eine ebene Arbeitsfläche zu gewährleisten.
- Absaugung: Ein effektives Absaugungssystem ist wichtig, um Rauch, Staub und Schneidrückstände während des Schneidprozesses abzuführen und die Arbeitsumgebung sauber zu halten. Schneidtische können mit Absaugvorrichtungen ausgestattet sein, die an ein zentrales Absaugsystem angeschlossen sind.
- Integration mit anderen Komponenten: Der Schneidtisch muss nahtlos mit anderen Komponenten der Plasmaschneidemaschine integriert werden, einschließlich des Plasmabrenners, der CNC-Steuerung und des Kühlungssystems. Eine effektive Integration gewährleistet einen reibungslosen Betrieb und eine optimale Leistung des Gesamtsystems.
Der Schneidtisch ist eine entscheidende Komponente von Plasmaschneidemaschinen und spielt eine wesentliche Rolle bei der Bereitstellung einer stabilen und zuverlässigen Arbeitsplattform für den Schneidprozess. Durch die Auswahl eines geeigneten Schneidtisches und die ordnungsgemäße Wartung können Hersteller die Qualität ihrer Schnitte verbessern und die Effizienz ihrer Produktionsprozesse steigern.
Schneidsoftware
Die Schneidsoftware ist eine entscheidende Komponente von Plasmaschneidemaschinen, die für die Erstellung von Schnittprogrammen, die Steuerung des Schneidprozesses und die Optimierung der Schnittparameter verantwortlich ist. Hier sind einige wichtige Aspekte der Schneidsoftware:
- Programmierung: Die Schneidsoftware ermöglicht die Programmierung von Schnittmustern und -konturen durch die Erstellung von CNC-Code basierend auf geometrischen Formen oder importierten CAD-Zeichnungen. Die Benutzeroberfläche der Software bietet Werkzeuge zur Erstellung, Bearbeitung und Optimierung von Schnittprogrammen.
- Automatisierung: Moderne Schneidsoftware bietet eine Vielzahl von Automatisierungsfunktionen, die den Programmierprozess beschleunigen und vereinfachen. Dazu gehören Funktionen wie automatische Nesting-Algorithmen zur Optimierung der Materialausnutzung, automatische Werkzeugwechsel und intelligente Schneidstrategien zur Maximierung der Schnittgeschwindigkeit und -qualität.
- Simulation: Die Schneidsoftware ermöglicht die Simulation von Schnittprogrammen, um potenzielle Probleme oder Kollisionen frühzeitig zu erkennen und zu vermeiden. Durch die Visualisierung des Schneidprozesses können Benutzer die Schnittqualität, Materialausnutzung und Bearbeitungszeit vorab optimieren.
- Schnittsteuerung: Die Schneidsoftware kommuniziert mit der CNC-Steuerung der Maschine, um den Schneidprozess in Echtzeit zu steuern und zu überwachen. Sie sendet Befehle zur Steuerung des Plasmabrenners, der Bewegung der Schneidköpfe und anderer relevanten Parameter, um präzise und effiziente Schnitte zu gewährleisten.
- Integration: Die Schneidsoftware muss nahtlos mit anderen Komponenten der Plasmaschneidemaschine integriert werden, einschließlich der CNC-Steuerung, des Schneidkopfs, des Schneidtisches und des Kühlungssystems. Eine effektive Integration gewährleistet einen reibungslosen Betrieb und eine optimale Leistung des Gesamtsystems.
Die Schneidsoftware ist eine wesentliche Komponente von Plasmaschneidemaschinen und spielt eine entscheidende Rolle bei der Bereitstellung präziser, effizienter und automatisierter Schneidlösungen. Durch die Auswahl einer geeigneten Schneidsoftware und die Schulung des Bedienpersonals können Hersteller die Produktivität steigern und die Kosten senken, während sie gleichzeitig die Qualität ihrer Produkte verbessern.
Plasmajet
Der Plasmajet ist der gebündelte und hochenergetische Strom geladenen Plasmas, der aus dem Plasmabrenner austritt und das Material schneidet. Hier sind einige wichtige Aspekte des Plasmajets:
- Entstehung: Der Plasmajet entsteht durch die Ionisierung des Plasmagases im Plasmabrenner durch einen Hochfrequenzlichtbogen. Dies führt zu einem elektrisch leitfähigen Plasma, das durch die Düse des Brenners gedrückt wird und sich zu einem konzentrierten Jet formt.
- Temperatur: Der Plasmajet erreicht extrem hohe Temperaturen von bis zu 30.000 Grad Celsius oder mehr. Diese hohen Temperaturen sind ausreichend, um das Material zu schmelzen und zu verdampfen, um einen sauberen und präzisen Schnitt zu erzeugen.
- Geschwindigkeit: Der Plasmajet kann Geschwindigkeiten von mehreren hundert Metern pro Sekunde erreichen, je nach den spezifischen Schnittbedingungen und Parametern. Diese hohe Geschwindigkeit ermöglicht es dem Plasmajet, das Material schnell und effizient zu durchdringen und zu schneiden.
- Präzision: Der Plasmajet bietet eine hohe Präzision und Kontrolle über den Schneidprozess, was es ermöglicht, komplexe Formen und Konturen mit hoher Genauigkeit zu schneiden. Dies macht den Plasmajet zu einer bevorzugten Wahl für eine Vielzahl von Anwendungen in der Metallverarbeitung und Fertigung.
- Anwendungen: Plasmajets werden in einer Vielzahl von Anwendungen eingesetzt, darunter das Schneiden von Metallen, das Schweißen, das Beschichten und das thermische Spritzen. Sie bieten eine effiziente und vielseitige Möglichkeit, Materialien zu bearbeiten und herzustellen.
Der Plasmajet ist eine zentrale Komponente des Plasmaschneidprozesses und ermöglicht es, Materialien präzise und effizient zu schneiden. Durch die Kontrolle und Optimierung des Plasmajets können Hersteller die Leistung ihrer Plasmaschneidemaschinen maximieren und qualitativ hochwertige Produkte herstellen.
Schneidtisch
Der Schneidtisch ist eine grundlegende Komponente von Plasmaschneidemaschinen, auf dem das zu schneidende Material platziert wird. Hier sind einige wichtige Aspekte des Schneidtisches:
- Konstruktion: Schneidtische sind in der Regel aus robusten Materialien wie Stahl oder Aluminium gefertigt und verfügen über eine ebene Oberfläche, auf der das Material sicher platziert werden kann. Die Konstruktion des Schneidtisches kann je nach den Anforderungen der Anwendung variieren, von einfachen manuellen Schneidtischen bis hin zu vollautomatisierten CNC-Schneidtischen.
- Größe: Die Größe des Schneidtisches variiert je nach den Abmessungen des zu schneidenden Materials und den Anforderungen der Anwendung. Kleinere Schneidtische eignen sich für kleinere Werkstücke und Anwendungen mit begrenztem Platzbedarf, während größere Schneidtische für das Schneiden von großen Platten und Blechen verwendet werden.
- Befestigung: Das Material wird auf dem Schneidtisch mithilfe von Befestigungsvorrichtungen oder Spannvorrichtungen sicher befestigt, um ein Verrutschen oder Bewegen während des Schneidprozesses zu verhindern. Dies kann durch Schraubzwingen, Vakuumspannsysteme oder magnetische Halterungen erfolgen, je nach den Eigenschaften des Materials und den Anforderungen der Anwendung.
- Bewegung: Einige Schneidtische verfügen über Bewegungssysteme, die es ermöglichen, das Material während des Schneidprozesses zu bewegen oder zu drehen, um komplexe Schnitte und Konturen zu ermöglichen. Dies kann durch manuelle Handräder, motorisierte Achsen oder CNC-Steuerungen erfolgen, die präzise Positionierung und Bewegung des Materials ermöglichen.
- Absaugung: Viele Schneidtische sind mit einem Rauchabsaugungssystem ausgestattet, das während des Schneidprozesses erzeugten Rauch und Staub absaugt und die Arbeitsumgebung sauber und sicher hält. Dies trägt zur Verbesserung der Luftqualität und zur Gesundheit der Bediener bei.
Kreisschere: Technischer Überblick, Funktionsweise und industrielle Anwendungen
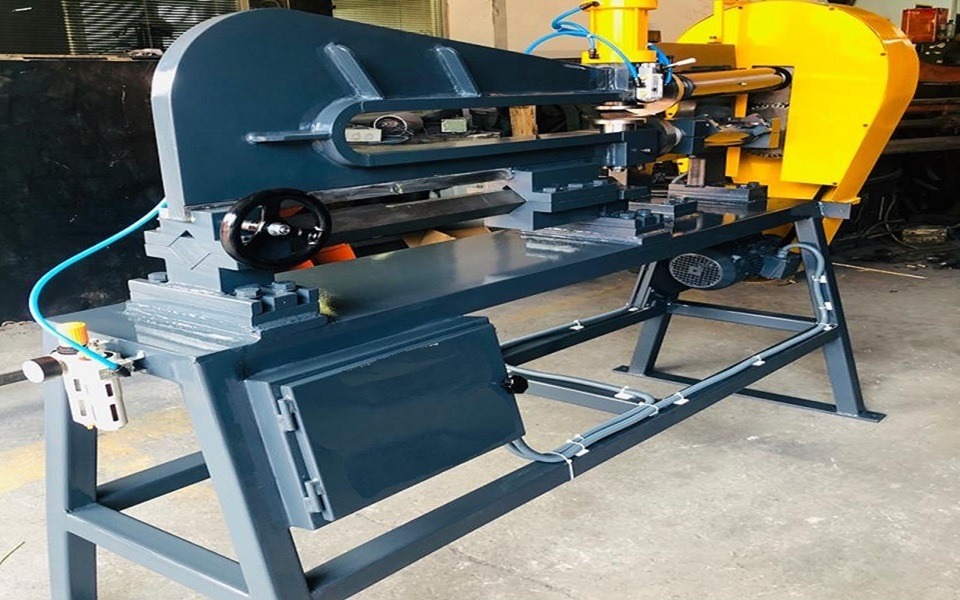
Die Kreisschere ist ein wesentliches Werkzeug in der Metallverarbeitung, insbesondere in der Blechbearbeitung. Sie spielt eine entscheidende Rolle bei der Herstellung und Bearbeitung von Metallblechen, die in verschiedenen Industrien eingesetzt werden, von der Automobilindustrie über den Maschinenbau bis hin zu Bauprojekten. Die Kreisschere wird verwendet, um Metallbleche mit hoher Präzision in streifenartige oder kreisförmige Formen zu schneiden, ohne dass der Schneidprozess das Material beschädigt oder seine Struktur schwächt.
1.1 Definition und Grundlagen der Kreisschere
Eine Kreisschere ist eine spezialisierte Schneidmaschine, die aus zwei rotierenden Klingen besteht, die gegen das zu bearbeitende Metall drücken und es in präzise Streifen oder Scheiben schneiden. Die Kreisschere ist besonders nützlich für Längsschnitte, also für das Schneiden von Metall entlang seiner Länge, was in der Blechproduktion und Blechbearbeitung von großer Bedeutung ist. Kreisscheren kommen in verschiedenen Größen und Ausführungen, abhängig von den Anforderungen und der Größe des zu schneidenden Materials.
1.2 Geschichte und Entwicklung der Kreisschere
Die Entwicklung der Kreisschere reicht bis ins 19. Jahrhundert zurück, als der Bedarf an präzisem Schneiden von Metallblechen zunahm. Mit der Industrialisierung und der Einführung von Stahl und Aluminium als Hauptmaterialien in der Fertigung entwickelte sich die Kreisschere weiter, um den Anforderungen an schnelle, präzise und wiederholbare Schnitte gerecht zu werden. In der modernen Produktion spielen Kreisscheren eine zentrale Rolle in automatisierten Blechverarbeitungsanlagen und tragen zur Effizienzsteigerung bei.
Technischer Überblick und Funktionsweise der Kreisschere
Die Funktionsweise der Kreisschere beruht auf dem Zusammenspiel von zwei rotierenden Messern, die das zu schneidende Material wie eine Schere schneiden. Die Scherenmesser sind in einem bestimmten Winkel zueinander angeordnet, um den gewünschten Schnitt zu ermöglichen. Der Prozess erfordert eine präzise Steuerung der Schneidkraft und Drehgeschwindigkeit, um sicherzustellen, dass das Material sauber geschnitten wird, ohne dass es zu Verformungen oder Beschädigungen kommt.
2.1 Aufbau der Kreisschere
Die Hauptkomponenten einer Kreisschere umfassen:
- Oberes und unteres Schneidmesser: Die beiden Klingen, die rotieren und das Material schneiden.
- Materialführung: Ein System, das das Metallblech durch die Schneidvorrichtung führt.
- Antriebseinheit: Ein elektrischer oder hydraulischer Motor, der die Klingen in Bewegung setzt.
- Steuerungssystem: Ein computergestütztes System, das die Schnittgeschwindigkeit, Schneidtiefe und andere Parameter regelt.
- Abfallbeseitigung: Ein System zum Entfernen von Metallabfällen und Restmaterialien, die während des Schneidprozesses anfallen.
2.1.1 Oberes und unteres Schneidmesser
Die Schneidmesser sind der wichtigste Teil der Kreisschere. Sie müssen aus hochfestem Stahl oder Wolframcarbid bestehen, um die Belastungen beim Schneiden harter Metalle zu bewältigen. Je nach Anwendung können die Schneidmesser auch speziell beschichtet sein, um ihre Lebensdauer zu verlängern und den Verschleiß zu minimieren.
2.1.2 Materialführung und Abrollsysteme
Die Materialführung sorgt dafür, dass das Metallblech gleichmäßig durch die Schneidmaschine geführt wird. Hier kommen oft Abrollvorrichtungen zum Einsatz, die das Metall von großen Rollen abwickeln und durch die Maschine transportieren. Die Führungssysteme müssen präzise arbeiten, um Ausrichtungsfehler zu vermeiden, die zu ungenauen Schnitten führen könnten.
2.1.3 Antriebseinheit und Motoren
Die Antriebseinheit setzt die Schneidmesser in Bewegung. Moderne Kreisscheren verwenden in der Regel elektrische Motoren oder hydraulische Systeme, die eine präzise Steuerung der Schneidgeschwindigkeit ermöglichen. Die Drehzahl der Schneidmesser kann je nach Dicke und Härte des Materials angepasst werden.
2.1.4 Steuerungssysteme
Moderne Kreisscheren sind oft mit Computersteuerungssystemen ausgestattet, die eine automatisierte Steuerung des Schneidprozesses ermöglichen. Dies erlaubt eine präzise Anpassung der Schneidparameter wie Schnittbreite, Schnittgeschwindigkeit und Schneiddruck.
2.2 Schneidprinzipien und -methoden
Das Schneiden von Metall mit einer Kreisschere erfolgt durch das Scherenprinzip, bei dem zwei Messer aneinander vorbeigleiten und das Material durchtrennt wird. Im Gegensatz zu anderen Schneidverfahren wie dem Laserschneiden oder Wasserstrahlschneiden hat das Schneiden mit der Kreisschere den Vorteil, dass es schneller und kostengünstiger ist, insbesondere bei der Bearbeitung großer Mengen von Metallblechen.
2.2.1 Längsschnitt
Der Längsschnitt ist der häufigste Anwendungsfall für Kreisscheren. Hierbei wird das Metallblech entlang seiner Länge in mehrere Streifen geschnitten, die anschließend für verschiedene Anwendungen weiterverarbeitet werden können. Der Längsschnitt erfordert eine genaue Ausrichtung und Positionierung des Materials, um sicherzustellen, dass die Schnitte parallel und präzise sind.
2.2.2 Kreisschnitt
Ein weiterer wichtiger Einsatzbereich der Kreisschere ist der Kreisschnitt, bei dem kreisförmige oder rundliche Schnitte in das Material eingebracht werden. Diese Methode wird häufig bei der Herstellung von Metallringen, Flanschen und anderen kreisförmigen Metallkomponenten verwendet. Der Kreisschnitt erfordert eine präzise Einstellung der Schneidmesser und eine gleichmäßige Materialführung.
2.3 Wichtige Parameter bei der Nutzung von Kreisscheren
Es gibt verschiedene Faktoren, die bei der Verwendung einer Kreisschere berücksichtigt werden müssen, um optimale Ergebnisse zu erzielen. Diese Parameter umfassen die Schnittgeschwindigkeit, den Schneidwinkel, die Schnittkraft und die Materialstärke.
2.3.1 Schnittgeschwindigkeit
Die Schnittgeschwindigkeit variiert je nach Material und Dicke des zu bearbeitenden Blechs. Weiche Materialien wie Aluminium können mit höheren Geschwindigkeiten geschnitten werden, während härtere Materialien wie Stahl langsamere Schnittgeschwindigkeiten erfordern.
2.3.2 Schneidwinkel und Spaltmaße
Der Schneidwinkel und die Spaltmaße zwischen den Schneidmessern beeinflussen die Schnittqualität und die Kantenverarbeitung. Ein zu großer Spalt kann zu Graten oder Materialverformungen führen, während ein zu kleiner Spalt zu einem hohen Verschleiß der Schneidmesser führen kann.
2.3.3 Schnittkraft und Materialstärke
Die Schnittkraft muss an die Materialstärke und -härte angepasst werden, um einen sauberen Schnitt zu gewährleisten. Bei sehr dicken oder harten Materialien ist eine höhere Schnittkraft erforderlich, was eine stärkere Antriebseinheit und robustere Schneidmesser erfordert.
Arten von Kreisscheren und industrielle Anwendungen

Es gibt verschiedene Arten von Kreisscheren, die je nach Anwendungsbereich und Materialbeschaffenheit eingesetzt werden. Die Wahl der richtigen Kreisschere hängt von den Anforderungen des jeweiligen Projekts ab, wie Materialart, Schnittpräzision, Produktionsgeschwindigkeit und Anlagengröße.
3.1 Manuelle Kreisscheren
Manuelle Kreisscheren sind die einfachste Form dieser Maschinen und werden häufig in kleineren Werkstätten eingesetzt. Diese Maschinen erfordern eine manuelle Betätigung der Schneidmesser und eignen sich für geringe Produktionsmengen oder die Bearbeitung von weichen Metallen wie Aluminium oder Kupfer.
3.1.1 Einsatzgebiete
Manuelle Kreisscheren werden häufig in Handwerksbetrieben, kleineren Metallwerkstätten und bei der Prototypenherstellung eingesetzt. Sie sind ideal für Anwendungen, bei denen geringe Stückzahlen und hohe Flexibilität gefragt sind.
3.1.2 Vorteile und Nachteile
- Vorteile: Geringe Anschaffungskosten, einfache Bedienung, Flexibilität bei der Bearbeitung unterschiedlicher Materialien.
- Nachteile: Geringere Produktionsgeschwindigkeit, nicht geeignet für hochpräzise Schnitte oder große Materialstärken.
3.2 Halbautomatische Kreisscheren
Halbautomatische Kreisscheren kombinieren manuelle Steuerung mit automatisierten Funktionen, um die Effizienz und Präzision zu verbessern. Diese Maschinen sind häufig mit motorisierten Antrieben und automatischen Materialführungssystemen ausgestattet, die den Schneidprozess beschleunigen und gleichzeitig die Präzision erhöhen.
3.2.1 Einsatzgebiete
Halbautomatische Kreisscheren finden breite Anwendung in mittleren Produktionsanlagen, wo sie für Längsschnitte und Serienfertigungen eingesetzt werden. Sie eignen sich für Materialien wie Stahl, Aluminium, Kupfer und andere Metalle, die in größeren Mengen bearbeitet werden.
3.2.2 Vorteile und Nachteile
- Vorteile: Höhere Produktionsgeschwindigkeit, verbesserte Präzision, geringere körperliche Belastung des Bedieners.
- Nachteile: Höhere Anschaffungskosten, erfordert regelmäßige Wartung und Schulung des Bedienpersonals.
3.3 Vollautomatische Kreisscheren
Vollautomatische Kreisscheren sind die fortschrittlichste Art von Kreisscheren und werden in großen Produktionsanlagen eingesetzt. Diese Maschinen sind vollständig computergesteuert und können hohe Produktionsgeschwindigkeiten bei gleichbleibend hoher Schnittpräzision erreichen. Sie sind ideal für die Massenproduktion von Metallblechen in der Automobilindustrie, der Luftfahrt und im Bauwesen.
3.3.1 Einsatzgebiete
Vollautomatische Kreisscheren werden in großen Fertigungsstraßen eingesetzt, wo sie in der Lage sind, große Materialmengen effizient und präzise zu schneiden. Diese Maschinen sind ideal für die Produktion von Stahlblechen, Aluminiumplatten und anderen metallischen Werkstoffen, die für den Einsatz in Industrieanlagen, Fahrzeugbau oder Konstruktionen bestimmt sind.
3.3.2 Vorteile und Nachteile
- Vorteile: Höchste Präzision, hohe Produktionsgeschwindigkeit, geeignet für Massenproduktion.
- Nachteile: Sehr hohe Anschaffungskosten, erfordert spezialisierte Schulungen und Wartungspersonal, komplexe Steuerungssysteme.
Anwendungsbereiche der Kreisschere
Die Kreisschere hat eine Vielzahl von Anwendungsbereichen in der Metallverarbeitung und Blechbearbeitung, da sie für verschiedene Materialien und Projekte eingesetzt werden kann. Sie kommt in vielen Industrien zum Einsatz, darunter die Automobilindustrie, der Schiffbau, die Luftfahrt, die Bauindustrie und die Herstellung von Haushaltsgeräten.
4.1 Automobilindustrie
In der Automobilindustrie wird die Kreisschere häufig verwendet, um Karosserieteile und Metallbleche für den Fahrzeugbau zu schneiden. Diese Teile müssen präzise geschnitten werden, um den Sicherheitsanforderungen und Qualitätsstandards der Branche gerecht zu werden.
4.1.1 Herstellung von Karosserieblechen
Die Kreisschere wird verwendet, um große Metallplatten in kleinere Teile zu schneiden, die anschließend zu Karosserien oder Fahrzeugkomponenten geformt werden. Dieser Prozess erfordert eine hohe Schnittpräzision, um sicherzustellen, dass die Teile korrekt zusammengebaut werden können.
4.1.2 Anforderungen an die Schneidpräzision
In der Automobilindustrie ist die Präzision entscheidend, da jede Abweichung im Schnitt die Struktur und Sicherheit des Fahrzeugs beeinträchtigen könnte. Kreisscheren ermöglichen es, diese Präzision durch automatisierte Systeme und präzise Steuerung der Schneidparameter zu erreichen.
4.2 Schiffbau und Offshore-Industrie
Im Schiffbau und der Offshore-Industrie werden große Mengen an Metallblechen benötigt, die oft in besonderen Formen geschnitten werden müssen. Kreisscheren spielen eine wichtige Rolle bei der Herstellung von Schiffsbauteilen, Ölplattformen und anderen maritimen Strukturen.
4.2.1 Schneiden von dicken Stahlplatten
Die Kreisschere wird verwendet, um dicke Stahlplatten zu schneiden, die in den Rumpf eines Schiffs integriert werden. Diese Platten müssen stark genug sein, um den hohen Belastungen im Meer standzuhalten, was eine präzise Verarbeitung erfordert.
4.2.2 Präzise Schnitte für Offshore-Strukturen
Für Offshore-Plattformen und andere maritime Strukturen müssen die verwendeten Materialien seewasserbeständig und gleichzeitig mechanisch belastbar sein. Kreisscheren ermöglichen es, die Stahlplatten präzise zu schneiden, um sie anschließend zu Trägern, Decks und anderen strukturellen Elementen zu verarbeiten.
4.3 Bauindustrie
In der Bauindustrie werden Kreisscheren verwendet, um Baumaterialien wie Stahlträger, Aluminiumplatten und Verbundwerkstoffe zu schneiden, die für den Bau von Gebäuden, Brücken und anderen Infrastruktureinrichtungen benötigt werden.
4.3.1 Einsatz bei der Herstellung von Gebäudestrukturen
Kreisscheren werden verwendet, um Stahlträger und Metallkomponenten für den Bau von Wolkenkratzern, Brücken und anderen großen Bauwerken zu schneiden. Die hohe Präzision und Geschwindigkeit der Kreisschere ermöglicht es, große Mengen an Baumaterialien effizient zu produzieren.
4.3.2 Bearbeitung von Baumaterialien
Neben dem Schneiden von Metallblechen werden Kreisscheren auch verwendet, um Verbundwerkstoffe wie Stahlbeton oder Sandwichplatten zu schneiden, die in der Bauindustrie weit verbreitet sind. Diese Materialien erfordern robuste Maschinen, die in der Lage sind, dicke und harte Werkstoffe zu verarbeiten.
4.4 Luftfahrtindustrie
In der Luftfahrtindustrie ist die Kreisschere ein unverzichtbares Werkzeug für die Bearbeitung von leichtgewichtigen Metalllegierungen wie Aluminium und Titan, die in der Flugzeugkonstruktion verwendet werden. Diese Materialien müssen extrem präzise verarbeitet werden, um die Flugzeugstruktur zu verstärken und gleichzeitig das Gewicht zu reduzieren.
4.4.1 Herstellung von Flugzeugteilen
Kreisscheren werden verwendet, um Aluminiumbleche und Titanplatten für den Bau von Flugzeugrümpfen, Tragflächen und Triebwerkskomponenten zu schneiden. Diese Materialien erfordern eine präzise Verarbeitung, da sie hohen Belastungen und Temperaturschwankungen ausgesetzt sind.
4.4.2 Leichtbauweise und Präzisionsfertigung
Die Luftfahrtindustrie erfordert die Verwendung von leichtgewichtigen Materialien, um die Flugeffizienz zu maximieren. Kreisscheren ermöglichen es, diese Materialien so zu schneiden, dass sie die Gewichtsanforderungen erfüllen und gleichzeitig die notwendige Strukturfestigkeit bieten.
Materialien für Kreisscheren und deren Schneidkanten
Die Effizienz und Langlebigkeit einer Kreisschere hängt maßgeblich von den Materialien ab, aus denen die Schneidmesser bestehen. Die Wahl des Materials für die Schneidmesser beeinflusst die Schnittqualität, die Lebensdauer der Maschine und die Fähigkeit, verschiedene Metallarten zu verarbeiten.
5.1 Hochfester Werkzeugstahl
Werkzeugstahl ist eines der am häufigsten verwendeten Materialien für Schneidmesser in Kreisscheren, da er eine hohe Festigkeit und Widerstandsfähigkeit gegenüber Verschleiß aufweist. Werkzeugstahl kann hohen Temperaturen und Belastungen standhalten, was ihn ideal für die Bearbeitung von Stahl, Aluminium und anderen Metallen macht.
5.1.1 Eigenschaften von Werkzeugstahl
- Härte: Werkzeugstahl ist sehr hart und kann daher auch harte Materialien wie Edelstahl schneiden.
- Verschleißfestigkeit: Werkzeugstahl ist widerstandsfähig gegen Abrieb und Abnutzung, was die Lebensdauer der Schneidmesser verlängert.
- Schneidfähigkeit: Aufgrund seiner Härte und Schärfe eignet sich Werkzeugstahl hervorragend für präzise Schnitte.
5.1.2 Einsatzgebiete von Werkzeugstahl in der Kreisschere
Werkzeugstahl wird in Vollautomatischen und halbautomatischen Kreisscheren verwendet, wo es auf eine hohe Produktionsgeschwindigkeit und Präzision ankommt. Diese Art von Stahl wird häufig für Schneidmesser verwendet, die in der Automobilindustrie, im Schiffbau und bei der Herstellung von Industrieteilen eingesetzt werden.
5.2 Wolframcarbid
Wolframcarbid ist ein weiteres häufig verwendetes Material für Schneidmesser in Kreisscheren. Es zeichnet sich durch seine extreme Härte und Hitzebeständigkeit aus, was es ideal für die Bearbeitung von sehr harten Materialien wie Edelstahl oder Titan macht.
5.2.1 Eigenschaften von Wolframcarbid
- Härte: Wolframcarbid ist eines der härtesten Materialien auf dem Markt und kann selbst die härtesten Metalle schneiden.
- Wärmebeständigkeit: Wolframcarbid kann hohen Temperaturen standhalten, was es ideal für hochschnelle Schneidvorgänge macht.
- Korrosionsbeständigkeit: Wolframcarbid ist sehr korrosionsbeständig, was es für den Einsatz in feuchten oder chemisch aggressiven Umgebungen geeignet macht.
5.2.2 Einsatzgebiete von Wolframcarbid
Wolframcarbid wird häufig in hochpräzisen Anwendungen eingesetzt, wie z.B. in der Luftfahrtindustrie oder bei der Herstellung von Medizintechnik, wo es auf absolute Präzision und hohe Haltbarkeit ankommt. Es eignet sich besonders für die Verarbeitung von dicken Metallen und hitzebeständigen Materialien.
5.3 Speziallegierungen
Neben Werkzeugstahl und Wolframcarbid werden in einigen Kreisscheren auch Speziallegierungen verwendet, die speziell für den Einsatz in bestimmten Branchen entwickelt wurden. Diese Legierungen kombinieren Festigkeit, Flexibilität und Beständigkeit gegen Verschleiß.
5.3.1 Eigenschaften von Speziallegierungen
- Anpassungsfähigkeit: Speziallegierungen können an die Anforderungen der jeweiligen Branche angepasst werden, z.B. durch Verstärkung bestimmter Eigenschaften wie Härte oder Korrosionsbeständigkeit.
- Vielfältige Einsatzmöglichkeiten: Diese Legierungen eignen sich für eine Vielzahl von Materialien und Anwendungen, von der Blechbearbeitung bis zur Herstellung von dünnen Metallfolien.
5.3.2 Einsatzgebiete von Speziallegierungen
Speziallegierungen werden oft in Nischenmärkten eingesetzt, wo Standardmaterialien nicht ausreichen. Dazu gehören die Elektronikindustrie, die Medizintechnik und die Raumfahrtindustrie, wo spezielle Materialanforderungen und hohe Präzision gefragt sind.
Automatisierte Kreisscheren und ihre Rolle in der Industrie 4.0
Die Industrie 4.0 hat zu einem deutlichen Anstieg der Automatisierung und Vernetzung in der Produktion geführt. Automatisierte Kreisscheren sind ein wesentlicher Bestandteil dieser Entwicklung, da sie in der Lage sind, große Materialmengen mit höchster Präzision zu verarbeiten, während gleichzeitig Produktionsprozesse optimiert werden.
6.1 Merkmale automatisierter Kreisscheren
Automatisierte Kreisscheren sind mit hochentwickelten Steuerungssystemen ausgestattet, die es ermöglichen, den gesamten Schneidprozess von einem zentralen System aus zu überwachen und zu steuern. Diese Maschinen sind oft mit Sensoren ausgestattet, die Daten in Echtzeit erfassen und an Produktionssteuerungssysteme weiterleiten.
6.1.1 Sensorik und Datenintegration
Moderne Kreisscheren sind mit intelligenten Sensoren ausgestattet, die den Schneidvorgang kontinuierlich überwachen und an das Steuerungssystem weitergeben. Diese Sensoren messen Parameter wie Schnittgeschwindigkeit, Schneidkraft, Materialstärke und Temperatur, um eine optimale Leistung zu gewährleisten.
6.1.2 Automatische Wartung und Fehlermanagement
Dank der Integration von KI-Algorithmen und vorausschauender Wartung können automatisierte Kreisscheren potenzielle Fehler oder Verschleißerscheinungen erkennen, bevor sie zu größeren Problemen führen. Dies trägt zur Erhöhung der Betriebszeiten und zur Reduzierung der Wartungskosten bei.
6.2 Vorteile der Automatisierung
Der Einsatz von automatisierten Kreisscheren bietet eine Reihe von Vorteilen für die Industrie:
- Erhöhte Produktivität: Automatisierte Maschinen können rund um die Uhr arbeiten und so die Produktionskapazität erheblich steigern.
- Konstante Qualität: Durch die Automatisierung wird die Schnittqualität konsistent auf einem hohen Niveau gehalten, was die Fehlerquote minimiert.
- Effizientere Ressourcennutzung: Automatisierte Kreisscheren können den Materialeinsatz optimieren, indem sie Verschnitt und Abfall minimieren.
- Schnellere Produktionszeiten: Die Automatisierung ermöglicht eine schnellere Verarbeitung großer Materialmengen, was zu einer Reduzierung der Durchlaufzeiten führt.
6.3 Herausforderungen und zukünftige Entwicklungen
Obwohl die Automatisierung viele Vorteile bietet, gibt es auch einige Herausforderungen, die bei der Integration automatisierter Kreisscheren in den Produktionsprozess berücksichtigt werden müssen.
6.3.1 Hohe Anfangsinvestitionen
Die Anschaffung und Installation einer automatisierten Kreisschere erfordert hohe Investitionen, insbesondere wenn es um große Produktionsanlagen geht. Unternehmen müssen sicherstellen, dass die Rendite die Anfangsinvestition rechtfertigt.
6.3.2 Komplexität der Systeme
Automatisierte Kreisscheren erfordern hochentwickelte Steuerungssysteme und qualifiziertes Wartungspersonal, um ihre Leistung aufrechtzuerhalten. Dies kann zu Komplexität und schulungsintensiven Prozessen führen, insbesondere für Unternehmen, die noch keine Erfahrung mit Industrie 4.0-Technologien haben.
6.3.3 Zukunftstrends
Die Weiterentwicklung von KI und maschinellem Lernen wird die Automatisierung von Kreisscheren weiter vorantreiben. Zukünftige Maschinen könnten in der Lage sein, sich selbstständig zu optimieren und Fehler in Echtzeit zu korrigieren, um die Produktionsqualität weiter zu verbessern.
Fallstudien: Erfolgreicher Einsatz von Kreisscheren in der Industrie
Um den Nutzen und die Anwendungsmöglichkeiten von Kreisscheren weiter zu verdeutlichen, werden in diesem Abschnitt mehrere Fallstudien aus verschiedenen Industrien vorgestellt. Diese Fallstudien zeigen, wie Unternehmen Kreisscheren einsetzen, um ihre Produktionsprozesse zu optimieren, Kosten zu senken und die Qualität ihrer Produkte zu verbessern.
7.1 Fallstudie 1: Kreisschere in der Automobilindustrie
Ein großer Automobilhersteller implementierte automatisierte Kreisscheren in seine Karosseriefertigung. Die Herausforderung bestand darin, große Mengen an Stahlblechen präzise und effizient zu schneiden, um den hohen Anforderungen an Sicherheit und Qualität im Automobilbau gerecht zu werden.
7.1.1 Ergebnisse
- Produktionssteigerung: Durch den Einsatz automatisierter Kreisscheren konnte das Unternehmen seine Produktionskapazität um 20 % steigern.
- Kostenreduktion: Der Einsatz von automatisierten Systemen reduzierte die Materialabfälle und senkte die Produktionskosten erheblich.
- Höhere Präzision: Die Schnitte waren extrem präzise, was die Qualität der Karosserieteile und die Passgenauigkeit beim Zusammenbau verbesserte.
7.2 Fallstudie 2: Einsatz von Kreisscheren in der Luftfahrtindustrie
Ein Luftfahrtunternehmen nutzte Kreisscheren, um Leichtmetalllegierungen für den Bau von Flugzeugrümpfen zu schneiden. Das Unternehmen benötigte eine Lösung, um extrem dünne Metallplatten mit hoher Präzision zu schneiden, ohne das Material zu beschädigen.
7.2.1 Ergebnisse
- Materialschonung: Die Kreisscheren schonten das empfindliche Material und ermöglichten präzise Schnitte, ohne die Integrität der Legierungen zu beeinträchtigen.
- Schnellere Produktionszeiten: Der Einsatz der Maschinen verkürzte die Produktionszeiten erheblich, da die Kreisscheren kontinuierlich arbeiten konnten.
- Reduzierung von Fehlern: Der präzise Schneidprozess führte zu weniger Ausschuss und einer insgesamt besseren Materialnutzung.
Zukunft der Kreisscheren: Neue Technologien und Entwicklungen
Die Zukunft der Kreisscheren wird von technologischen Entwicklungen wie KI, 3D-Druck und fortschrittlichen Fertigungsverfahren geprägt sein. Diese Innovationen haben das Potenzial, die Effizienz und Präzision von Kreisscheren weiter zu steigern und neue Anwendungsmöglichkeiten zu erschließen.
8.1 Integration von KI und maschinellem Lernen
Die Integration von künstlicher Intelligenz und maschinellem Lernen wird es Kreisscheren ermöglichen, sich an unterschiedliche Materialien und Produktionsanforderungen anzupassen, ohne dass menschliches Eingreifen erforderlich ist. KI-gestützte Systeme könnten den Schnittprozess in Echtzeit überwachen und optimieren, um die Schnittqualität und Produktionsgeschwindigkeit zu maximieren.
8.2 3D-Druck und hybride Fertigungsverfahren
Die Kombination von Kreisscheren und 3D-Drucktechnologien könnte neue Möglichkeiten in der Blechbearbeitung eröffnen. Hybride Fertigungssysteme könnten verwendet werden, um komplexe Geometrien zu erstellen und gleichzeitig präzise Längs- und Kreisschnitte in Blechmaterialien vorzunehmen.
8.3 Nachhaltigkeit und umweltfreundliche Produktion
Mit dem zunehmenden Fokus auf nachhaltige Fertigung und umweltfreundliche Produktionsmethoden spielen Kreisscheren eine wichtige Rolle bei der Optimierung des Materialeinsatzes. Durch die Reduzierung von Verschnitt und Abfall tragen moderne Kreisscheren dazu bei, den CO₂-Fußabdruck von Produktionsanlagen zu verringern.
Fazit
Die Kreisschere ist ein unverzichtbares Werkzeug in der modernen Metallverarbeitung und Blechbearbeitung. Von der Automobilindustrie bis hin zur Luftfahrt hat die Kreisschere die Fähigkeit, große Mengen an Metallblechen präzise und effizient zu schneiden. Durch die Integration von automatisierten Systemen, KI-Technologien und fortschrittlichen Schneidmaterialien hat sich die Kreisschere zu einem leistungsstarken Werkzeug entwickelt, das den Produktionsanforderungen der heutigen Industrie gerecht wird.
Mit künftigen Entwicklungen in der Automatisierung, der Robotik und der Industrie 4.0 wird die Kreisschere weiterhin eine zentrale Rolle bei der Effizienzsteigerung und Nachhaltigkeit in der Fertigung spielen.
Technischer Überblick und Funktionsweise der Kreisschere

1. Einführung: Was ist eine Kreisschere?
Eine Kreisschere ist eine spezialisierte Schneidmaschine, die in der Metallverarbeitung verwendet wird, um Blech in präzise Streifen oder Scheiben zu schneiden. Diese Maschinen sind ein wesentlicher Bestandteil der Blechbearbeitung, insbesondere bei der Herstellung von Produkten, die auf die genauen Abmessungen von Metallblechen angewiesen sind. Kreisscheren arbeiten mit zwei rotierenden Klingen, die das Material gleichmäßig durchschneiden, ohne es zu beschädigen oder zu verformen.
1.1 Grundlegende Funktionsweise der Kreisschere
Die Funktionsweise einer Kreisschere basiert auf dem Schneidprinzip: Zwei Klingen, die in entgegengesetzte Richtungen rotieren, drängen das Metall zusammen und führen zu einem präzisen Schnitt. Dieser Prozess erfordert eine exakte Abstimmung zwischen den Klingen und dem Material, um sicherzustellen, dass das Metall gleichmäßig und sauber geschnitten wird. Kreisscheren sind in der Lage, verschiedene Metalle wie Stahl, Aluminium, Kupfer und Titan zu verarbeiten.
1.2 Bedeutung in der industriellen Produktion
Kreisscheren spielen eine entscheidende Rolle in der industriellen Produktion, da sie in Branchen wie der Automobilindustrie, dem Maschinenbau, der Luft- und Raumfahrt und der Verpackungsindustrie weit verbreitet sind. Durch ihre Fähigkeit, große Metallplatten präzise und effizient zu schneiden, tragen Kreisscheren zur Steigerung der Produktionskapazitäten und zur Reduzierung der Fertigungskosten bei.
Aufbau und Konstruktion der Kreisschere
Der Aufbau einer Kreisschere besteht aus verschiedenen Komponenten, die zusammenarbeiten, um den Schneidvorgang zu ermöglichen. Diese Maschinen sind robust konstruiert, um den Belastungen der Metallbearbeitung standzuhalten, und ihre Konstruktionsmerkmale variieren je nach Anwendung und Materialart.
2.1 Hauptkomponenten einer Kreisschere
Eine typische Kreisschere besteht aus mehreren wichtigen Komponenten, die zusammen den Schneidprozess ermöglichen:
- Schneidmesser: Die beiden rotierenden Messer sind die zentralen Bestandteile der Kreisschere. Sie bestehen in der Regel aus hochfestem Werkzeugstahl oder Hartmetall und sind so angeordnet, dass sie das Material präzise schneiden.
- Materialzuführung: Das Material wird durch eine Walze oder ein anderes Zuführsystem in die Schneidzone der Kreisschere geleitet. Dies sorgt dafür, dass das Blech mit der richtigen Geschwindigkeit und Ausrichtung in die Maschine gelangt.
- Antriebseinheit: Der Antrieb der Kreisschere erfolgt durch elektrische Motoren oder hydraulische Systeme, die die Klingen in Bewegung setzen und die benötigte Kraft zum Schneiden aufbringen.
- Steuerungssystem: Ein computerisiertes Steuerungssystem überwacht und regelt den Schneidvorgang. Es stellt sicher, dass die Klingen mit der richtigen Geschwindigkeit rotieren und die Schneidkraft auf das Material abgestimmt ist.
- Abfallentsorgung: Während des Schneidvorgangs entstehen Metallabfälle, die durch ein Abfallsammelsystem entfernt werden, um den Arbeitsbereich sauber zu halten.
2.1.1 Schneidmesser
Die Schneidmesser der Kreisschere sind die wichtigste Komponente, da sie das Material schneiden. Sie bestehen in der Regel aus hochfestem Werkzeugstahl, der widerstandsfähig gegen Verschleiß und Verformung ist. In einigen Fällen können die Schneidmesser auch mit speziellen Beschichtungen versehen werden, um ihre Langlebigkeit zu erhöhen und die Schneidleistung zu verbessern.
2.1.2 Materialzuführung und Abrollsystem
Das Materialzuführungssystem ist für die präzise Positionierung und den Transport des Materials verantwortlich. Bei der Bearbeitung von großen Metallrollen wird das Material in der Regel durch ein Abrollsystem von der Rolle abgewickelt und gleichmäßig in die Schneidzone geführt. Die exakte Führung des Materials ist entscheidend, um einen geraden und präzisen Schnitt zu gewährleisten.
2.1.3 Antriebseinheit und Motoren
Die Antriebseinheit der Kreisschere besteht aus Motoren oder hydraulischen Antrieben, die die Klingen in Bewegung setzen. Diese Motoren müssen stark genug sein, um das Schneiden von dicken oder harten Metallblechen zu ermöglichen, und gleichzeitig in der Lage sein, die Drehgeschwindigkeit der Klingen zu regulieren.
2.1.4 Steuerungssystem und Automatisierung
Moderne Kreisscheren verfügen über fortschrittliche Steuerungssysteme, die den gesamten Schneidprozess überwachen und anpassen können. Diese Systeme nutzen oft CNC-Technologie (Computerized Numerical Control), um die Schneidparameter wie Geschwindigkeit, Schnittwinkel und Schneidkraft präzise einzustellen. Automatisierte Steuerungssysteme bieten eine hohe Wiederholgenauigkeit und sorgen dafür, dass der Schneidprozess gleichbleibend hohe Qualität liefert.
2.2 Materialarten und ihre Auswirkungen auf die Konstruktion
Die Wahl des Materials, das geschnitten werden soll, beeinflusst die Konstruktion der Kreisschere. Unterschiedliche Metalle erfordern unterschiedliche Schneidkräfte, Klingentypen und Materialführungen.
2.2.1 Schneiden von Stahl und Aluminium
Beim Schneiden von Stahl und Aluminium müssen die Schneidmesser stark genug sein, um dem Widerstand dieser Metalle standzuhalten. Stahl, insbesondere hochfester Stahl, erfordert eine größere Schneidkraft, während Aluminium aufgrund seiner Weichheit leichter zu schneiden ist. Die Klingen müssen so gestaltet sein, dass sie den spezifischen Anforderungen des Materials gerecht werden.
2.2.2 Spezialmetalle wie Titan und Kupfer
Das Schneiden von Spezialmetallen wie Titan und Kupfer erfordert noch präzisere Schneidmethoden, da diese Materialien besonders empfindlich gegenüber Verformungen oder Oberflächenbeschädigungen sind. In solchen Fällen werden häufig beschichtete Schneidmesser oder hartmetallbestückte Klingen verwendet, um die Oberflächenqualität zu gewährleisten.
2.3 Modifikationen für spezialisierte Anwendungen
Kreisscheren können für bestimmte spezialisierte Anwendungen modifiziert werden, um den Anforderungen verschiedener Branchen gerecht zu werden. Dies kann Anpassungen in der Schneidgeschwindigkeit, der Klingenform oder der Materialzuführung umfassen.
2.3.1 Automobilindustrie
In der Automobilindustrie werden Kreisscheren verwendet, um Karosseriebleche und andere Fahrzeugkomponenten mit hoher Präzision zu schneiden. Diese Anwendungen erfordern häufig spezialisierte Maschinen, die in der Lage sind, hochfeste Materialien wie hochfesten Stahl oder Aluminiumlegierungen zu verarbeiten.
2.3.2 Luft- und Raumfahrtindustrie
Die Luft- und Raumfahrtindustrie verwendet Kreisscheren, um leichte Metalllegierungen wie Titan oder Aluminium zu schneiden, die in der Herstellung von Flugzeugrümpfen und Tragflächen verwendet werden. Diese Materialien müssen extrem präzise geschnitten werden, um die Strukturfestigkeit und Leichtbauweise der Komponenten zu gewährleisten.
Funktionsweise und Schneidprinzipien der Kreisschere
Die Funktionsweise der Kreisschere basiert auf dem Scherenprinzip, bei dem zwei rotierende Messer das Material durchdrücken und es präzise schneiden. Der Schneidprozess kann in verschiedene Schritte unterteilt werden, die sicherstellen, dass das Material ohne Verformung oder Beschädigung verarbeitet wird.
3.1 Der Schneidprozess
Der Schneidprozess einer Kreisschere verläuft in mehreren Phasen:
- Zuführung des Materials: Das Metall wird in die Maschine eingespeist und in die richtige Position gebracht.
- Rotationsbewegung der Klingen: Die beiden Schneidmesser rotieren in entgegengesetzte Richtungen und treffen auf das Material.
- Durchtrennung des Materials: Das Material wird durch den Scherendruck der Messer in präzise Streifen oder Kreise geschnitten.
- Abtransport des geschnittenen Materials: Das geschnittene Metall wird aus der Maschine entfernt und zur weiteren Verarbeitung transportiert.
3.1.1 Materialzuführung
Der erste Schritt im Schneidprozess ist die Materialzuführung. Das Blech wird über ein Walzensystem oder eine andere Fördervorrichtung in die Schneidzone geleitet. Hierbei ist eine präzise Ausrichtung des Materials erforderlich, um sicherzustellen, dass es gleichmäßig geschnitten wird.
3.1.2 Rotationsbewegung der Klingen
Sobald das Material in der richtigen Position ist, beginnen die Schneidmesser zu rotieren. Die Schneidgeschwindigkeit der Messer wird an die Materialstärke und Materialart angepasst, um ein sauberes Durchtrennen des Blechs zu gewährleisten. Die rotierenden Klingen erzeugen einen Schereneffekt, der das Material in streifenförmige oder kreisförmige Abschnitte schneidet.
3.1.3 Durchtrennung des Materials
Das Schneidprinzip der Kreisschere ähnelt dem einer herkömmlichen Schere: Zwei Klingen gleiten aneinander vorbei und schneiden das dazwischenliegende Material. Bei diesem Vorgang wird das Material unter Druck gesetzt, wodurch es entlang der Schneidkante durchtrennt wird. Ein präziser Schnittwinkel und die richtige Schnittkraft sind entscheidend, um saubere Schnitte ohne Grate oder Verformungen zu erzielen.
3.1.4 Abtransport des geschnittenen Materials
Nach dem Schneidvorgang wird das geschnittene Material durch das Abtransportsystem der Kreisschere entfernt. Dies kann durch Förderbänder oder andere Materialtransportsysteme erfolgen, die sicherstellen, dass das geschnittene Material schnell zur weiteren Verarbeitung gelangt.
3.2 Verschiedene Schneidmethoden
Es gibt verschiedene Schneidmethoden, die mit einer Kreisschere durchgeführt werden können, je nach den Anforderungen des Materials und des Endprodukts. Diese Methoden umfassen den Längsschnitt, den Kreisschnitt und den Profilschnitt.
3.2.1 Längsschnitt
Der Längsschnitt ist die häufigste Methode, bei der das Material entlang seiner Länge in schmale Streifen geschnitten wird. Diese Streifen können anschließend für eine Vielzahl von Anwendungen verwendet werden, von der Verpackung bis zur Fahrzeugkonstruktion. Beim Längsschnitt ist es wichtig, dass das Material gleichmäßig zugeführt wird, um einen geraden Schnitt zu gewährleisten.
3.2.2 Kreisschnitt
Der Kreisschnitt wird verwendet, um kreisförmige oder rundliche Metallteile herzustellen. Diese Methode erfordert eine präzise Steuerung der Schnittgeschwindigkeit und des Schnittwinkels, um sicherzustellen, dass der Schnitt gleichmäßig und symmetrisch ist. Der Kreisschnitt findet häufig Anwendung bei der Herstellung von Flanschen, Ringen und andere kreisförmige Metallteile.
3.2.3 Profilschnitt
Beim Profilschnitt wird das Material in bestimmte Formen oder Konturen geschnitten, die für spezielle Anwendungen benötigt werden. Dies kann das Schneiden von gekrümmten oder unregelmäßigen Formen umfassen, die mit Standard-Längs- oder Kreisschnitten nicht erreicht werden können.
3.3 Betriebsparameter der Kreisschere
Um optimale Schneidbedingungen zu gewährleisten, müssen bestimmte Betriebsparameter genau eingehalten werden. Dazu gehören die Schneidgeschwindigkeit, der Schnittwinkel, die Schnittkraft und die Materialstärke.
3.3.1 Schneidgeschwindigkeit
Die Schneidgeschwindigkeit variiert je nach Materialart und Materialstärke. Weiche Metalle wie Aluminium können mit höheren Geschwindigkeiten geschnitten werden, während härtere Materialien wie Stahl eine geringere Schneidgeschwindigkeit erfordern. Die richtige Geschwindigkeit stellt sicher, dass das Material sauber geschnitten wird, ohne dass es zu Verformungen oder Graten kommt.
3.3.2 Schnittwinkel und Spaltmaße
Der Schnittwinkel der Schneidmesser beeinflusst die Schnittqualität und die Oberflächenbeschaffenheit des Materials. Ein zu großer Winkel kann zu unsauberen Schnitten führen, während ein zu kleiner Winkel zu einem höheren Verschleiß der Messer führen kann. Die Spaltmaße zwischen den Schneidmessern müssen ebenfalls genau eingestellt werden, um eine optimale Schneidleistung zu erzielen.
3.3.3 Schnittkraft und Materialstärke
Die Schnittkraft muss an die Materialstärke und -härte angepasst werden, um sicherzustellen, dass das Material sauber und ohne Verformungen geschnitten wird. Bei dicken oder harten Materialien ist eine höhere Schnittkraft erforderlich, was eine stärkere Antriebseinheit und robustere Schneidmesser erfordert.
3.4 Prozessoptimierung und Automatisierung
In der modernen Metallverarbeitung wird der Schneidprozess zunehmend durch automatisierte Systeme und Prozessoptimierungstechniken verbessert. Diese Systeme ermöglichen eine feinabgestimmte Kontrolle der Schneidparameter, um die Schnittqualität zu maximieren und gleichzeitig die Produktionsgeschwindigkeit zu erhöhen.
3.4.1 Einsatz von CNC-Systemen
CNC-gesteuerte Kreisscheren verwenden Computertechnologie, um den gesamten Schneidprozess zu steuern. Diese Systeme ermöglichen eine präzise Steuerung der Schneidbewegungen und können so programmiert werden, dass sie mehrere Schneidvorgänge in kurzer Zeit durchführen, ohne dass menschliches Eingreifen erforderlich ist.
3.4.2 Prozessüberwachung und Fehlererkennung
Moderne Kreisscheren sind mit Sensoren ausgestattet, die den Schneidprozess in Echtzeit überwachen und Fehler wie Materialverformungen, Gratbildung oder Klingenverschleiß erkennen. Diese Sensoren können das Steuerungssystem informieren, das den Prozess automatisch anpasst, um die Schnittqualität zu gewährleisten.
Industrielle Anwendungen und Branchen

Die Kreisschere wird in einer Vielzahl von Industrien eingesetzt, da sie eine effiziente und präzise Methode zum Schneiden von Metallblechen bietet. Zu den wichtigsten Anwendungsbereichen gehören die Automobilindustrie, die Luftfahrt, der Schiffbau, die Bauindustrie und die Verpackungsindustrie.
4.1 Automobilindustrie
In der Automobilindustrie spielt die Kreisschere eine entscheidende Rolle bei der Herstellung von Karosserieblechen und anderen Fahrzeugkomponenten. Diese Teile müssen mit hoher Präzision geschnitten werden, um den Sicherheitsstandards und Qualitätsanforderungen der Branche gerecht zu werden.
4.1.1 Schneiden von Karosserieteilen
Die Kreisschere wird verwendet, um große Metallplatten in kleinere Komponenten zu schneiden, die dann für die Karosseriemontage verwendet werden. Dieser Prozess erfordert eine präzise Steuerung der Schnittqualität, um sicherzustellen, dass die Teile genau zusammenpassen und die Sicherheitsanforderungen erfüllen.
4.2 Luft- und Raumfahrtindustrie
Die Luft- und Raumfahrtindustrie verwendet Kreisscheren, um leichte Metalllegierungen wie Aluminium und Titan für die Herstellung von Flugzeugteilen zu schneiden. Diese Materialien müssen besonders präzise geschnitten werden, um die Strukturfestigkeit und Gewichtsvorgaben der Flugzeuge zu erfüllen.
4.2.1 Herstellung von Flugzeugrümpfen und Tragflächen
Kreisscheren werden verwendet, um Metallplatten für den Bau von Flugzeugrümpfen, Tragflächen und anderen strukturellen Komponenten zu schneiden. Diese Schnitte müssen extrem präzise sein, um sicherzustellen, dass die Flugzeugstruktur den Anforderungen an Festigkeit und Leichtbauweise entspricht.
4.3 Bauindustrie
In der Bauindustrie werden Kreisscheren verwendet, um Baumaterialien wie Stahl und Aluminium zu schneiden, die für den Bau von Gebäuden, Brücken und anderen Infrastruktureinrichtungen benötigt werden.
4.3.1 Schneiden von Trägern und Platten
Die Kreisschere wird verwendet, um Stahlträger und Metallplatten für den Bau von Gebäudestrukturen und Brücken zu schneiden. Diese Komponenten müssen präzise geschnitten werden, um eine sichere Montage und eine stabile Struktur zu gewährleisten.
4.4 Verpackungsindustrie
In der Verpackungsindustrie wird die Kreisschere verwendet, um Metallfolien und Verbundmaterialien für die Herstellung von Verpackungen zu schneiden.
4.4.1 Schneiden von Verpackungsmaterialien
Die Kreisschere wird verwendet, um Aluminiumfolien und andere Metallverpackungen präzise in die erforderlichen Abmessungen zu schneiden. Dieser Prozess ist entscheidend für die Herstellung von Lebensmittelverpackungen, Medikamentenblistern und anderen Schutzverpackungen.
Wartung, Sicherheit und Optimierung der Kreisschere
Damit Kreisscheren effizient und zuverlässig arbeiten, ist eine regelmäßige Wartung und Optimierung der Maschinen notwendig. Zudem müssen strenge Sicherheitsvorschriften beachtet werden, um den sicheren Betrieb zu gewährleisten.
5.1 Regelmäßige Wartung
Die regelmäßige Wartung einer Kreisschere umfasst das Schärfen der Schneidmesser, die Schmierung der beweglichen Teile und die Überprüfung der Antriebseinheit. Die Wartung ist entscheidend, um Verschleiß zu verhindern und die Lebensdauer der Maschine zu verlängern.
5.1.1 Schärfen der Schneidmesser
Die Schneidmesser der Kreisschere müssen regelmäßig geschärft werden, um eine optimale Schneidleistung zu gewährleisten. Ein stumpfes Messer kann zu ungenauen Schnitten, Gratbildung und Verformungen des Materials führen.
5.1.2 Schmierung und Instandhaltung der Mechanik
Die beweglichen Teile der Kreisschere, einschließlich der Walzen und Lager, müssen regelmäßig geschmiert werden, um einen reibungslosen Betrieb zu gewährleisten. Eine mangelnde Schmierung kann zu Verschleiß und Überhitzung der Maschine führen.
5.2 Sicherheitsmaßnahmen
Der Betrieb einer Kreisschere erfordert strenge Sicherheitsmaßnahmen, um Unfälle zu verhindern. Zu den wichtigsten Sicherheitsvorkehrungen gehören:
- Schutzvorrichtungen: Die Schneidmesser müssen durch Schutzabdeckungen oder Schutzvorrichtungen abgedeckt werden, um das Risiko von Verletzungen zu minimieren.
- Not-Aus-Schalter: Kreisscheren sollten mit einem Not-Aus-Schalter ausgestattet sein, der die Maschine sofort stoppt, falls ein Problem auftritt.
- Schulungen: Das Bedienpersonal muss regelmäßig in der Bedienung und Sicherheit der Maschine geschult werden.
5.3 Prozessoptimierung und Effizienzsteigerung
Die Optimierung des Schneidprozesses kann die Produktionsgeschwindigkeit erhöhen und die Schnittqualität verbessern. Dazu gehört die Verwendung von automatisierten Steuerungssystemen, die den Schneidvorgang in Echtzeit überwachen und anpassen können.
5.3.1 Automatisierte Prozessüberwachung
Automatisierte Überwachungssysteme können den Schneidprozess kontinuierlich überwachen und die Schneidparameter in Echtzeit anpassen, um eine gleichbleibende Schnittqualität zu gewährleisten.
5.3.2 Optimierung der Schnittgeschwindigkeit
Durch die Optimierung der Schnittgeschwindigkeit können die Produktionszeiten verkürzt und gleichzeitig die Schnittqualität verbessert werden. Dies erfordert eine genaue Anpassung der Schneidparameter an die Materialeigenschaften.
Zukunft der Kreisschere: Neue Technologien und Entwicklungen
Die Zukunft der Kreisschere wird durch die Integration neuer Technologien wie Künstliche Intelligenz (KI), Robotik und Industrie 4.0 geprägt. Diese Innovationen haben das Potenzial, die Effizienz und Präzision der Kreisscheren weiter zu steigern und neue Anwendungsmöglichkeiten zu erschließen.
6.1 Integration von Künstlicher Intelligenz (KI)
Die Integration von Künstlicher Intelligenz (KI) in Kreisscheren ermöglicht eine noch präzisere Steuerung und Überwachung des Schneidprozesses. KI-Systeme können den Schneidvorgang in Echtzeit anpassen, um die Schnittqualität zu maximieren und den Verschleiß der Schneidmesser zu minimieren.
6.2 Robotergestützte Materialführung
Die Verwendung von Robotern zur Materialführung kann die Produktionsgeschwindigkeit erhöhen und gleichzeitig die Präzision verbessern. Roboter können das Material schneller und genauer in die Schneidzone führen, was die Produktionszeiten verkürzt und die Effizienz der Kreisschere steigert.
6.3 Industrie 4.0 und Smart Manufacturing
Mit der Einführung von Industrie 4.0 und Smart Manufacturing werden Kreisscheren zunehmend in vernetzte Produktionssysteme integriert. Diese Systeme ermöglichen eine nahtlose Kommunikation zwischen Maschinen und ermöglichen es, den gesamten Produktionsprozess zu überwachen und zu optimieren.
Fazit
Die Kreisschere ist ein unverzichtbares Werkzeug in der modernen Metallverarbeitung und bietet eine effiziente und präzise Methode zum Schneiden von Metallblechen. Durch ihre robuste Konstruktion, ihre präzisen Schneidtechniken und die Integration moderner Steuerungssysteme hat sich die Kreisschere zu einem unverzichtbaren Werkzeug in der Industrieproduktion entwickelt.
Mit neuen technologischen Entwicklungen wie KI, Automatisierung und Industrie 4.0 wird die Kreisschere weiterhin eine zentrale Rolle in der Effizienzsteigerung und Nachhaltigkeit in der Fertigung spielen.
Arten von Kreisscheren und industrielle Anwendungen

1. Einführung: Die Bedeutung von Kreisscheren in der industriellen Fertigung
Kreisscheren sind in der industriellen Fertigung unverzichtbare Werkzeuge, da sie präzise Metallbleche, Platten und andere Materialien schneiden. Sie sind besonders in der Metallverarbeitung und der Blechbearbeitung wichtig, da sie Materialien effizient und präzise in streifenartige oder kreisförmige Formen schneiden können. In vielen Branchen tragen Kreisscheren zur Produktionssteigerung und Kostenreduktion bei, da sie in automatisierten Fertigungsstraßen eingesetzt werden.
1.1 Was sind Kreisscheren?
Eine Kreisschere ist eine Schneidmaschine, die auf dem Prinzip der Schere basiert. Sie besteht aus zwei rotierenden Klingen, die das Material durch Druck sauber und präzise schneiden. Diese Maschinen sind in der Lage, unterschiedliche Metallarten und Dicken zu schneiden, und sie werden in verschiedenen Industrien verwendet, um Bleche und Platten zu verarbeiten.
1.2 Relevanz und Anwendungen in der Industrie
Kreisscheren finden sich in verschiedenen industriellen Anwendungen, insbesondere in der Automobilindustrie, der Luftfahrt, dem Bau und der Verpackungsindustrie. Durch ihre Fähigkeit, Materialien präzise zu schneiden, helfen sie, Produktionsprozesse zu beschleunigen und hochwertige Produkte mit minimalem Materialverlust zu fertigen. Die Auswahl der geeigneten Kreisschere hängt von den spezifischen Anforderungen der Branche und des zu bearbeitenden Materials ab.
Arten von Kreisscheren: Überblick und Klassifizierung
Es gibt verschiedene Arten von Kreisscheren, die je nach Anwendung und Anforderungen in der industriellen Fertigung verwendet werden. Diese Maschinen unterscheiden sich in ihrer Bauweise, dem Automatisierungsgrad, der Schnittkapazität und den Materialien, die sie bearbeiten können.
2.1 Manuelle Kreisscheren
Manuelle Kreisscheren sind die einfachste Form dieser Maschinen und werden in kleineren Werkstätten eingesetzt, in denen keine hohen Produktionsvolumen erforderlich sind. Diese Maschinen werden von Hand betrieben und eignen sich ideal für das Schneiden von weichen Materialien wie Aluminium oder Kupfer.
2.1.1 Funktionsweise der manuellen Kreisscheren
Manuelle Kreisscheren funktionieren durch manuelle Kraftübertragung auf die rotierenden Schneidmesser. Der Bediener führt das Material in die Schneidzone ein und betätigt die Maschine von Hand, um das Metall zu schneiden. Diese Maschinen bieten einfache Schnittkontrolle, sind jedoch in der Schnittgeschwindigkeit und Präzision begrenzt.
2.1.2 Einsatzbereiche
Manuelle Kreisscheren werden häufig in Handwerksbetrieben und kleineren Metallwerkstätten eingesetzt, wo sie für geringere Produktionsmengen oder für die Prototypenherstellung verwendet werden. Sie sind auch in der Blechbearbeitung weit verbreitet, wenn das zu schneidende Material relativ dünn ist.
2.1.3 Vorteile und Nachteile
- Vorteile: Geringe Anschaffungskosten, einfache Bedienung, flexibel einsetzbar für verschiedene Materialien.
- Nachteile: Begrenzte Produktionskapazität, niedrigere Präzision, geeignet nur für kleinere Projekte.
2.2 Halbautomatische Kreisscheren
Halbautomatische Kreisscheren kombinieren manuelle Steuerung mit automatisierten Funktionen. Sie sind eine Weiterentwicklung der manuellen Kreisscheren und bieten eine verbesserte Produktionsgeschwindigkeit und Präzision. Der Einsatz von motorisierten Antrieben ermöglicht eine schnellere und gleichmäßigere Verarbeitung von Metallblechen.
2.2.1 Funktionsweise der halbautomatischen Kreisscheren
Halbautomatische Kreisscheren verfügen über elektrische Antriebe, die die rotierenden Schneidmesser antreiben. Der Bediener legt das Material ein, und die Maschine übernimmt den Schneidprozess automatisch, während einige Steuerfunktionen manuell bedient werden. Diese Maschinen bieten eine höhere Effizienz und Produktionsgeschwindigkeit als manuelle Kreisscheren.
2.2.2 Einsatzbereiche
Halbautomatische Kreisscheren finden ihren Einsatz in mittleren Produktionsanlagen und Werkstätten, in denen größere Produktionsmengen gefordert sind. Sie werden häufig in der Blechbearbeitung, der Elektroindustrie und der Fahrzeugherstellung eingesetzt, um Metalle wie Stahl, Aluminium und Kupfer zu schneiden.
2.2.3 Vorteile und Nachteile
- Vorteile: Verbesserte Produktionskapazität, höhere Präzision, reduzierter Arbeitsaufwand.
- Nachteile: Erfordert regelmäßige Wartung, höhere Anschaffungskosten im Vergleich zu manuellen Kreisscheren.
2.3 Vollautomatische Kreisscheren
Vollautomatische Kreisscheren sind die fortschrittlichste Form dieser Maschinen und werden in großen Produktionsanlagen eingesetzt. Sie sind vollständig computergesteuert und können extrem hohe Produktionsgeschwindigkeiten und Präzision erreichen. Vollautomatische Kreisscheren sind in der Lage, Metallbleche in Massenproduktion zu schneiden, ohne dass menschliches Eingreifen erforderlich ist.
2.3.1 Funktionsweise der vollautomatischen Kreisscheren
Vollautomatische Kreisscheren verwenden CNC-Technologie (Computerized Numerical Control), um den Schneidprozess zu steuern. Der Bediener programmiert die Maschine mit den erforderlichen Schneidparametern, und die Kreisschere führt den gesamten Schneidvorgang automatisch durch. Die Steuerungssysteme passen die Schneidgeschwindigkeit, den Schneidwinkel und die Schnittkraft präzise an das zu bearbeitende Material an.
2.3.2 Einsatzbereiche
Vollautomatische Kreisscheren werden in Großbetrieben eingesetzt, die hohe Produktionsvolumen benötigen, wie z.B. in der Automobilindustrie, im Schiffbau, in der Luft- und Raumfahrt und bei der Herstellung von Industrieteilen. Diese Maschinen sind in der Lage, dicke Stahlbleche, Aluminiumplatten und andere Metalle in hohen Stückzahlen zu verarbeiten.
2.3.3 Vorteile und Nachteile
- Vorteile: Höchste Produktionsgeschwindigkeit, maximale Präzision, automatisierter Betrieb, ideal für die Massenproduktion.
- Nachteile: Sehr hohe Anschaffungskosten, erfordert qualifiziertes Wartungspersonal und spezialisierte Schulungen.
Technische Merkmale und Komponenten der Kreisscheren
Unabhängig von der Art der Kreisschere gibt es bestimmte technische Merkmale und Komponenten, die für den Betrieb und die Leistungsfähigkeit jeder Kreisschere entscheidend sind. Diese Komponenten bestimmen die Schnittqualität, die Schnittgeschwindigkeit und die Lebensdauer der Maschine.
3.1 Schneidmesser
Die Schneidmesser sind das zentrale Element jeder Kreisschere. Sie bestehen in der Regel aus hochfestem Werkzeugstahl oder Hartmetall und sind so ausgelegt, dass sie selbst bei hohen Belastungen präzise Schnitte durchführen können.
3.1.1 Materialien und Beschichtungen
- Werkzeugstahl: Hochfest und widerstandsfähig gegen Verschleiß, geeignet für das Schneiden von Stahl und Aluminium.
- Hartmetall: Extrem harte Schneidmesser, die für das Schneiden von dicken und harten Metallen wie Titan und Edelstahl verwendet werden.
Zusätzlich können die Schneidmesser mit speziellen Beschichtungen versehen werden, um ihre Lebensdauer zu verlängern und die Schneidleistung zu verbessern. Beschichtungen wie Titan-Nitrid (TiN) oder Chrom erhöhen die Härte und reduzieren den Verschleiß.
3.1.2 Spaltmaß und Schneidwinkel
Das Spaltmaß zwischen den Schneidmessern beeinflusst die Schnittqualität. Ein zu großes Spaltmaß kann zu unsauberen Schnitten und Gratbildung führen, während ein zu kleines Spaltmaß den Verschleiß der Schneidmesser erhöht. Der Schneidwinkel bestimmt, wie das Material geschnitten wird, und muss entsprechend der Materialstärke und Materialart eingestellt werden.
3.2 Antriebseinheit
Die Antriebseinheit der Kreisschere setzt die Schneidmesser in Bewegung. Je nach Art der Kreisschere kann dies entweder durch elektrische Motoren oder hydraulische Antriebe erfolgen. Der Antrieb muss stark genug sein, um auch dicke Metallplatten präzise zu schneiden.
3.2.1 Elektrische Antriebe
Elektrische Antriebe werden in den meisten modernen Kreisscheren verwendet. Sie bieten eine präzise Steuerung der Schneidgeschwindigkeit und ermöglichen es, die Drehgeschwindigkeit der Schneidmesser exakt an das Material anzupassen.
3.2.2 Hydraulische Antriebe
Hydraulische Antriebe werden vor allem in Schwerlastkreisscheren verwendet, die große Metallplatten oder dicke Stahlbleche verarbeiten müssen. Diese Antriebe bieten eine höhere Schneidkraft und sind ideal für industrielle Anwendungen, bei denen große Materialstärken verarbeitet werden.
3.3 Steuerungssysteme
Moderne Kreisscheren sind oft mit CNC-Steuerungssystemen ausgestattet, die eine präzise Steuerung des Schneidprozesses ermöglichen. Diese Systeme überwachen die Schneidparameter und passen die Schnittgeschwindigkeit, den Schneidwinkel und die Schnittkraft in Echtzeit an.
3.3.1 CNC-Technologie
Die Verwendung von CNC-Systemen ermöglicht eine vollautomatische Steuerung des Schneidvorgangs. Der Bediener gibt die Schnittparameter in das Steuerungssystem ein, und die Maschine führt den gesamten Schneidprozess automatisch aus. CNC-Systeme bieten eine hohe Wiederholgenauigkeit und sind ideal für die Serienproduktion.
3.3.2 Automatische Fehlererkennung
Fortschrittliche Steuerungssysteme sind oft mit Sensoren ausgestattet, die den Schneidprozess überwachen und Fehler wie Gratbildung, Materialverformung oder Verschleiß der Schneidmesser erkennen. Diese Systeme können den Schneidprozess automatisch anpassen, um eine konstante Schnittqualität zu gewährleisten.
3.4 Materialführung und Zuführungssysteme
Das Materialzuführungssystem ist ein wesentlicher Bestandteil der Kreisschere, da es sicherstellt, dass das Metallblech gleichmäßig und präzise in die Schneidzone gelangt. Die Materialführung kann durch Walzen oder andere Fördervorrichtungen erfolgen.
3.4.1 Abrollvorrichtungen
Bei der Verarbeitung von großen Metallrollen wird das Material durch Abrollvorrichtungen in die Schneidzone eingeführt. Diese Systeme müssen präzise arbeiten, um sicherzustellen, dass das Material gleichmäßig und ohne Verformungen geschnitten wird.
3.4.2 Materialführungswalzen
Materialführungswalzen sorgen dafür, dass das Material während des Schneidvorgangs stabil bleibt und gerade durch die Schneidmesser läuft. Diese Walzen müssen robust sein, um den Belastungen durch das Material standzuhalten und gleichzeitig eine präzise Führung zu gewährleisten.
Industrielle Anwendungen der Kreisscheren
Kreisscheren finden in einer Vielzahl von Industrien Anwendung. Ihre Fähigkeit, Materialien präzise zu schneiden, macht sie zu einem unverzichtbaren Werkzeug in der Fertigung, insbesondere in der Automobilindustrie, der Luft- und Raumfahrt, der Verpackungsindustrie und der Bauindustrie.
4.1 Automobilindustrie
In der Automobilindustrie werden Kreisscheren häufig zur Herstellung von Karosserieteilen, Türverkleidungen und anderen Fahrzeugkomponenten verwendet. Diese Teile müssen präzise geschnitten werden, um die Sicherheitsanforderungen und Qualitätsstandards zu erfüllen.
4.1.1 Herstellung von Karosserieteilen
Kreisscheren werden verwendet, um große Stahl- und Aluminiumbleche in kleinere Komponenten zu schneiden, die dann in der Fahrzeugkarosserie verbaut werden. Durch die präzisen Schnitte können die Teile genau zusammengefügt werden, was die Strukturfestigkeit des Fahrzeugs erhöht.
4.1.2 Schneiden von hochfesten Materialien
Moderne Automobilhersteller verwenden zunehmend hochfeste Stähle und Leichtmetalle, um die Fahrzeugsicherheit zu verbessern und das Fahrzeuggewicht zu reduzieren. Kreisscheren ermöglichen es, diese Materialien präzise und effizient zu schneiden, ohne dass es zu Verformungen oder Materialschäden kommt.
4.2 Luft- und Raumfahrtindustrie
Die Luft- und Raumfahrtindustrie verwendet Kreisscheren, um leichtgewichtige Metalllegierungen wie Titan und Aluminium für die Herstellung von Flugzeugteilen zu schneiden. Diese Materialien müssen besonders präzise geschnitten werden, um die Strukturintegrität der Flugzeuge zu gewährleisten.
4.2.1 Schneiden von Flugzeugkomponenten
Kreisscheren werden verwendet, um Aluminiumplatten und Titanbleche für die Herstellung von Flugzeugrümpfen, Tragflächen und Triebwerkskomponenten zu schneiden. Diese Schnitte müssen extrem präzise sein, um sicherzustellen, dass die Flugzeugstruktur den hohen Belastungen während des Flugbetriebs standhält.
4.2.2 Schneiden von Verbundwerkstoffen
In der modernen Luftfahrt werden zunehmend Verbundwerkstoffe verwendet, um das Gewicht von Flugzeugen zu reduzieren und ihre Effizienz zu verbessern. Kreisscheren sind in der Lage, diese fortschrittlichen Materialien präzise zu schneiden, ohne ihre Struktur oder Oberfläche zu beschädigen.
4.3 Bauindustrie
In der Bauindustrie werden Kreisscheren eingesetzt, um Metallkomponenten für den Bau von Gebäuden, Brücken und anderen Infrastruktureinrichtungen zu schneiden. Diese Komponenten müssen präzise geschnitten werden, um eine sichere Montage und eine stabile Struktur zu gewährleisten.
4.3.1 Schneiden von Stahlträgern und Metallplatten
Kreisscheren werden verwendet, um Stahlträger und Metallplatten für den Bau von Wolkenkratzern, Brücken und Industrierahmen zu schneiden. Die präzisen Schnitte sorgen dafür, dass die Komponenten perfekt zusammenpassen und die statischen Anforderungen des Bauwerks erfüllen.
4.3.2 Verarbeiten von Baumaterialien
Neben Stahl und Aluminium werden Kreisscheren auch verwendet, um Verbundmaterialien wie Stahlbetonplatten oder Sandwichpaneele zu schneiden, die in der Bauindustrie weit verbreitet sind. Diese Materialien müssen robust und widerstandsfähig gegen mechanische Belastungen sein, was präzise Schnitte erfordert.
4.4 Verpackungsindustrie
In der Verpackungsindustrie werden Kreisscheren verwendet, um Metallfolien und Verbundmaterialien für die Herstellung von Verpackungen zu schneiden. Diese Materialien müssen präzise geschnitten werden, um sicherzustellen, dass sie den Produktschutz bieten und gleichzeitig leicht verarbeitet werden können.
4.4.1 Herstellung von Aluminiumverpackungen
Kreisscheren werden verwendet, um Aluminiumfolien in die erforderlichen Formen und Größen zu schneiden, die für die Herstellung von Lebensmittelverpackungen, Blisterverpackungen und anderen Verpackungsprodukten verwendet werden. Präzise Schnitte sorgen dafür, dass die Verpackungen die Produkte effizient schützen.
4.4.2 Schneiden von Verbundfolien
Neben Aluminium werden auch Verbundfolien geschnitten, die aus mehreren Materialschichten bestehen, um spezifische Barriereeigenschaften wie Feuchtigkeits- oder Sauerstoffbeständigkeit zu bieten. Kreisscheren ermöglichen es, diese Materialien präzise und schnell zu schneiden.
Zukunft der Kreisscheren: Neue Technologien und Entwicklungen
Die Kreisschere hat sich im Laufe der Zeit durch technologische Innovationen und automatisierte Systeme erheblich weiterentwickelt. In Zukunft werden Künstliche Intelligenz (KI), maschinelles Lernen, Robotik und Industrie 4.0 die Effizienz und Präzision von Kreisscheren weiter steigern und neue Anwendungsmöglichkeiten schaffen.
5.1 Integration von Künstlicher Intelligenz (KI)
Mit der Integration von Künstlicher Intelligenz in Kreisscheren können Maschinen den Schneidprozess kontinuierlich überwachen und Anpassungen in Echtzeit vornehmen. KI-Systeme können beispielsweise erkennen, wenn ein Schneidmesser stumpf wird, und die Schneidparameter automatisch anpassen, um die Schnittqualität zu gewährleisten.
5.2 Robotergestützte Materialführung
Die Verwendung von Robotern zur Materialführung ermöglicht eine noch präzisere Verarbeitung von Metallblechen. Roboter können das Material schneller und gleichmäßiger in die Schneidzone führen, was zu einer höheren Produktionsgeschwindigkeit und einer verbesserten Schnittqualität führt.
5.3 Industrie 4.0 und vernetzte Produktionssysteme
Mit der Einführung von Industrie 4.0 werden Kreisscheren zunehmend in vernetzte Produktionssysteme integriert. Diese Systeme ermöglichen es, den gesamten Schneidprozess zu überwachen und Optimierungen in Echtzeit vorzunehmen. Darüber hinaus können Daten aus der Fertigung verwendet werden, um Produktionsengpässe zu identifizieren und zu beheben.
5.4 3D-Druck und hybride Fertigungssysteme
Die Kombination von Kreisscheren mit 3D-Drucktechnologien könnte neue Möglichkeiten in der Blechbearbeitung schaffen. Hybride Fertigungssysteme könnten verwendet werden, um komplexe Geometrien zu erstellen und gleichzeitig präzise Schnitte in Metallbleche vorzunehmen.
Fazit
Die Kreisschere spielt eine zentrale Rolle in der modernen Metallverarbeitung und hat sich als unverzichtbares Werkzeug in verschiedenen Industrien etabliert. Die unterschiedlichen Arten von Kreisscheren bieten eine Lösung für nahezu jede Schneidanwendung, sei es in der Automobilindustrie, der Luft- und Raumfahrt, der Bauindustrie oder der Verpackungsindustrie.
Durch die Integration moderner Technologien wie Automatisierung, Künstliche Intelligenz und Industrie 4.0 wird die Kreisschere weiterhin zur Effizienzsteigerung und Produktionsoptimierung in der Fertigung beitragen. Die Zukunft der Kreisscheren liegt in der Weiterentwicklung dieser Technologien und in ihrer Anpassungsfähigkeit an die sich ständig ändernden Anforderungen der Industrieproduktion.
Anwendungsbereiche der Kreisschere: Industrieübergreifende Einsatzmöglichkeiten

1. Einführung: Bedeutung der Kreisschere in der industriellen Fertigung
Die Kreisschere ist ein entscheidendes Werkzeug in der industriellen Fertigung, insbesondere in der Blechbearbeitung und der Metallverarbeitung. Ihre Fähigkeit, Materialien präzise zu schneiden, macht sie zu einem unverzichtbaren Bestandteil in vielen Produktionsprozessen. Ob in der Automobilindustrie, im Maschinenbau oder im Schiffbau, die Kreisschere ermöglicht effiziente und genaue Schnitte, die für die Herstellung von Produkten essenziell sind, die strengen Qualitäts- und Sicherheitsanforderungen genügen müssen.
1.1 Überblick über die Funktionsweise der Kreisschere
Eine Kreisschere arbeitet mit zwei rotierenden Klingen, die das Metallblech oder andere Materialien präzise schneiden, indem sie das Material zwischen den Messern durchdrücken. Dieses Prinzip erlaubt saubere, gerade Schnitte, ohne das Material zu verformen oder zu beschädigen. Die Präzision, die diese Maschinen bieten, ist in vielen industriellen Anwendungen notwendig, da selbst kleinste Abweichungen in der Fertigung die Funktionalität oder Sicherheit eines Endprodukts beeinträchtigen können.
1.2 Relevanz und Flexibilität in verschiedenen Industrien
Die Kreisschere ist nicht auf eine bestimmte Industrie beschränkt. Sie wird in verschiedenen Produktionsbereichen verwendet, vom Schneiden von Karosserieteilen in der Automobilindustrie bis hin zur Herstellung von Metallverpackungen in der Verpackungsindustrie. In jedem dieser Bereiche spielt die Kreisschere eine wesentliche Rolle bei der Optimierung von Produktionsprozessen, der Verbesserung der Schnittqualität und der Reduzierung von Materialverlusten.
2. Automobilindustrie: Präzise Metallverarbeitung für sichere Fahrzeuge
Die Automobilindustrie ist einer der wichtigsten Anwendungsbereiche der Kreisschere, da sie für die Herstellung von Karosserieteilen, Fahrzeugrahmen und anderen Metallkomponenten benötigt wird. Die Präzision der Schnitte ist entscheidend, um den strengen Sicherheitsstandards und Qualitätsanforderungen der Automobilbranche gerecht zu werden.
2.1 Einsatz der Kreisschere bei der Herstellung von Karosserieteilen
In der Automobilindustrie werden große Stahl- und Aluminiumbleche in verschiedene Komponenten wie Türen, Motorhauben, Dächer und Seitenteile geschnitten. Diese Teile müssen präzise geschnitten werden, um später in der Produktion korrekt zusammengefügt zu werden. Kreisscheren ermöglichen es, diese großen Metallplatten mit minimalem Materialverlust zu schneiden, was nicht nur die Kosten reduziert, sondern auch die Effizienz des Produktionsprozesses erhöht.
2.1.1 Schneiden von hochfestem Stahl und Aluminium
Moderne Autos werden zunehmend aus hochfestem Stahl und Aluminium gebaut, um das Gewicht der Fahrzeuge zu reduzieren und gleichzeitig ihre Sicherheit zu erhöhen. Diese Materialien sind oft schwer zu verarbeiten, erfordern aber präzise Schnitte, um sicherzustellen, dass die Karosserieteile genau passen. Kreisscheren sind ideal für diese Aufgabe, da sie in der Lage sind, sowohl dünne Aluminiumbleche als auch dickeren hochfesten Stahl effizient und genau zu schneiden.
2.1.2 Präzisionsschnitte für strukturrelevante Komponenten
Bestimmte Karosserieteile wie Stoßfänger oder Rahmen müssen besonders präzise geschnitten werden, da sie für die strukturelle Integrität des Fahrzeugs von entscheidender Bedeutung sind. Kreisscheren ermöglichen es, diese Teile mit höchster Präzision herzustellen, wodurch die Sicherheitsanforderungen erfüllt und gleichzeitig die Produktionszeiten minimiert werden.
2.2 Herstellung von Fahrgestell- und Motorenteilen
Neben Karosserieteilen werden Kreisscheren auch zur Herstellung von Fahrgestellteilen, Radaufhängungen, Antriebskomponenten und Motorenteilen verwendet. Diese Komponenten müssen extrem präzise geschnitten werden, um die strukturelle Integrität und Funktionalität der Fahrzeuge zu gewährleisten.
2.2.1 Optimierung der Materialnutzung
In der Automobilindustrie ist es wichtig, den Materialeinsatz zu optimieren, um Kosten zu senken und den CO₂-Fußabdruck zu verringern. Durch den Einsatz von Kreisscheren kann das Metall effizient geschnitten werden, wodurch weniger Abfall entsteht und die Produktionskosten gesenkt werden.
2.2.2 Integration in automatisierte Produktionslinien
Viele Automobilhersteller setzen auf vollautomatisierte Fertigungslinien, bei denen Kreisscheren eine zentrale Rolle spielen. Diese Maschinen sind in der Lage, rund um die Uhr präzise Schnitte durchzuführen und so die Produktionskapazität erheblich zu steigern. Sie können direkt in die Roboter- und Automatisierungssysteme der Fertigungsanlagen integriert werden, um einen unterbrechungsfreien Produktionsfluss zu gewährleisten.
2.3 Nachhaltigkeit in der Automobilindustrie
Da die Automobilindustrie zunehmend auf nachhaltige Produktionstechnologien setzt, tragen Kreisscheren durch ihre Fähigkeit, Materialabfälle zu reduzieren und den Energieverbrauch zu optimieren, zur Erreichung dieser Ziele bei. Der präzise Einsatz von Material trägt zur Ressourcenschonung bei und reduziert den CO₂-Ausstoß in der Produktion.
3. Luft- und Raumfahrtindustrie: Leichtbau und hohe Präzision
Die Luft- und Raumfahrtindustrie stellt besonders hohe Anforderungen an die Fertigungstechnologien, da die in Flugzeugen verwendeten Materialien sowohl leicht als auch extrem widerstandsfähig sein müssen. Kreisscheren spielen eine Schlüsselrolle bei der Herstellung von Strukturkomponenten, Tragflächen und anderen Metallteilen, die für den Leichtbau und die Sicherheitsanforderungen dieser Branche notwendig sind.
3.1 Schneiden von Aluminium und Titan für Flugzeugstrukturen
In der Luft- und Raumfahrtindustrie werden oft Aluminiumlegierungen und Titan verwendet, um die Gewichtseffizienz und die Festigkeit von Flugzeugen zu maximieren. Diese Materialien müssen präzise geschnitten werden, um die erforderliche Stabilität und Leichtbauweise zu erreichen.
3.1.1 Herstellung von Tragflächen und Rumpfteilen
Kreisscheren werden eingesetzt, um große Aluminiumplatten und Titanbleche zu schneiden, die anschließend für die Tragflächen, Rümpfe und Triebwerkskomponenten von Flugzeugen verwendet werden. Die Schnitte müssen extrem präzise sein, da jede Abweichung die Aerodynamik und Sicherheit des Flugzeugs beeinträchtigen könnte.
3.1.2 Anforderungen an die Präzision und Qualität
Die Luftfahrtindustrie stellt sehr hohe Anforderungen an die Qualität der Komponenten, da diese unter extremen Belastungen und Temperaturschwankungen arbeiten müssen. Kreisscheren ermöglichen es, diese Komponenten mit der notwendigen Präzision zu schneiden, um sicherzustellen, dass sie den strengen Normen der Luftfahrtindustrie entsprechen.
3.2 Bearbeitung von Verbundwerkstoffen in der Luftfahrt
Neben Metallen werden in der Luftfahrt zunehmend Verbundwerkstoffe eingesetzt, um das Gewicht von Flugzeugen weiter zu reduzieren. Diese Materialien bestehen aus Fasern und Harzen, die zu einem leichten, aber extrem widerstandsfähigen Material verarbeitet werden. Kreisscheren sind ideal für das Schneiden dieser fortschrittlichen Materialien, da sie die Oberflächenqualität und die Struktur des Materials bewahren können.
3.2.1 Schneiden von faserverstärkten Kunststoffen
Faserverstärkte Kunststoffe (CFK) sind in der Luft- und Raumfahrt weit verbreitet. Kreisscheren ermöglichen es, diese Materialien mit minimalem Materialverlust und ohne Beschädigung der Faserstrukturen zu schneiden. Diese Materialien finden Anwendung in Flügelkomponenten, Fahrwerksteilen und Strukturkomponenten, die sowohl leicht als auch robust sein müssen.
3.2.2 Anwendung in Triebwerksverkleidungen und strukturellen Teilen
Verbundwerkstoffe werden auch in Triebwerksverkleidungen und anderen strukturellen Teilen eingesetzt, um die Leichtbauweise der Flugzeuge zu unterstützen. Durch den Einsatz von Kreisscheren können diese Materialien präzise geschnitten und geformt werden, ohne ihre Festigkeit oder Leistung zu beeinträchtigen.
4. Schiffbau und Offshore-Industrie: Robuste Materialien und präzise Verarbeitung
Die Schiffbauindustrie und die Offshore-Industrie erfordern besonders robuste Materialien, da die gefertigten Komponenten extremen Witterungsbedingungen und mechanischen Belastungen standhalten müssen. Kreisscheren spielen eine wesentliche Rolle bei der Verarbeitung von Stahlplatten, Aluminiumlegierungen und anderen Materialien, die in Schiffen, Bohrinseln und maritimen Strukturen verwendet werden.
4.1 Schneiden von dicken Stahlplatten für den Schiffbau
Im Schiffbau werden häufig dicke Stahlplatten verwendet, um Schiffsrümpfe, Decks und andere tragende Strukturen herzustellen. Diese Platten müssen extrem präzise geschnitten werden, um sicherzustellen, dass sie den Belastungen des Meeres standhalten und die erforderliche Festigkeit bieten.
4.1.1 Herstellung von Schiffsrümpfen und Decks
Kreisscheren werden verwendet, um die großen Stahlplatten, die für die Herstellung von Schiffsrümpfen und Decks benötigt werden, auf die erforderlichen Maße zu schneiden. Diese Schnitte müssen exakt und konsistent sein, um sicherzustellen, dass die Teile korrekt zusammengebaut werden und den Anforderungen an die Strukturintegrität genügen.
4.1.2 Korrosionsbeständige Materialien
Neben Stahl werden auch spezielle korrosionsbeständige Materialien verwendet, um Offshore-Strukturen wie Bohrinseln und Windparks zu bauen. Kreisscheren ermöglichen es, diese Materialien präzise zu schneiden und dabei die Schneidkanten glatt und frei von Graten zu halten, um die Lebensdauer der Strukturen zu verlängern.
4.2 Verarbeitung von Aluminium für den Schiffbau
Neben Stahl wird auch Aluminium häufig im Schiffbau verwendet, insbesondere für leichtere Schiffe oder Oberdeckstrukturen, die aus Gewichtsgründen aus Aluminium gefertigt werden. Kreisscheren sind in der Lage, diese Materialien präzise zu schneiden, um die Schnittqualität und Materialeffizienz zu maximieren.
4.2.1 Schneiden von leichten Aluminiumkomponenten
Kreisscheren werden verwendet, um große Aluminiumbleche zu schneiden, die in den Schiffsbau einfließen. Aluminium wird häufig verwendet, um das Gesamtgewicht des Schiffes zu reduzieren und gleichzeitig die Festigkeit und Korrosionsbeständigkeit zu erhöhen.
4.2.2 Herstellung von Schiffsausrüstungen und Komponenten
Neben der Rumpfkonstruktion werden Kreisscheren auch für die Herstellung von Schiffsausrüstungen wie Aufbauten, Kabinen und Decksverkleidungen verwendet. Diese Komponenten müssen präzise geschnitten und geformt werden, um eine perfekte Passgenauigkeit und langfristige Beständigkeit gegen die rauen Bedingungen auf See zu gewährleisten.
5. Verpackungsindustrie: Präzises Schneiden für Massenproduktion
Die Verpackungsindustrie verwendet Kreisscheren, um Metallfolien und Verbundmaterialien präzise zu schneiden, die in der Herstellung von Lebensmittelverpackungen, Blisterverpackungen und Industrieverpackungen benötigt werden. Diese Materialien müssen effizient verarbeitet werden, um den Produktschutz zu gewährleisten und gleichzeitig die Produktionskosten niedrig zu halten.
5.1 Schneiden von Aluminiumfolien und Metallverpackungen
In der Verpackungsindustrie werden große Mengen an Aluminiumfolien und Metallverpackungen benötigt, die präzise auf die erforderlichen Abmessungen geschnitten werden müssen. Kreisscheren ermöglichen es, diese Materialien mit hoher Geschwindigkeit und Genauigkeit zu schneiden, um den hohen Produktionsanforderungen gerecht zu werden.
5.1.1 Herstellung von Lebensmittel- und Medikamentenverpackungen
Kreisscheren werden verwendet, um dünne Aluminiumfolien zu schneiden, die in der Lebensmittelindustrie für Verpackungen verwendet werden. Diese Verpackungen müssen präzise zugeschnitten werden, um die Frische der Produkte zu gewährleisten und gleichzeitig den Verpackungsprozess zu optimieren. Ähnliche Anwendungen finden sich in der Pharmaindustrie, wo Blisterverpackungen präzise geschnitten werden müssen, um die Sicherheit und Haltbarkeit der Medikamente zu gewährleisten.
5.2 Verarbeitung von Verbundmaterialien in der Verpackungsindustrie
Verbundmaterialien, die aus mehreren Schichten von Kunststoff, Metall und Papier bestehen, werden zunehmend in der Verpackungsindustrie eingesetzt. Diese Materialien bieten spezifische Barriereeigenschaften, wie Feuchtigkeits- und Sauerstoffbeständigkeit, die den Produktschutz verbessern. Kreisscheren spielen eine entscheidende Rolle bei der präzisen Verarbeitung dieser Materialien.
5.2.1 Schneiden von mehrschichtigen Verpackungsmaterialien
Verbundmaterialien werden in der Lebensmittel-, Pharma- und Kosmetikindustrie verwendet, um Produkte vor äußeren Einflüssen zu schützen. Die Kreisschere ermöglicht es, diese mehrschichtigen Materialien präzise zu schneiden, ohne die Schichtstruktur oder Barriereeigenschaften zu beschädigen. Dies ist besonders wichtig für Verpackungen, die hochwertige oder empfindliche Produkte schützen müssen.
5.2.2 Anwendung in flexiblen Verpackungen
Flexible Verpackungen werden häufig für Produkte wie Getränke, Snacks und Saucen verwendet. Die Herstellung dieser Verpackungen erfordert präzise Schnitte, um die Verpackungen leicht verarbeitbar und gleichzeitig funktional zu machen. Kreisscheren ermöglichen es, die Verbundmaterialien mit hoher Schnittpräzision und Geschwindigkeit zuzuschneiden, was den Produktionsprozess effizienter gestaltet.
6. Bauindustrie: Schneiden von Metallen und Verbundwerkstoffen für Bauprojekte
In der Bauindustrie werden Kreisscheren für das Schneiden von Stahl, Aluminium und Verbundwerkstoffen verwendet, die in der Herstellung von Gebäudestrukturen, Brücken und anderen Infrastruktureinrichtungen eingesetzt werden. Diese Materialien müssen präzise geschnitten werden, um sicherzustellen, dass sie den statistischen und architektonischen Anforderungen entsprechen.
6.1 Schneiden von Stahl und Aluminium für den Bau von Gebäuden
Stahl und Aluminium sind die Hauptmaterialien, die für den Bau von Wolkenkratzern, Brücken und Industrieanlagen verwendet werden. Kreisscheren ermöglichen es, diese Materialien präzise zu schneiden und dabei die Schnittqualität und Materialeffizienz zu maximieren.
6.1.1 Verwendung von Stahl in tragenden Strukturen
Stahlträger und Stahlplatten sind unverzichtbare Elemente im modernen Bauwesen. Sie bilden das Skelett von Gebäuden und müssen daher extrem präzise geschnitten werden, um die strukturelle Integrität zu gewährleisten. Kreisscheren ermöglichen es, diese Materialien in verschiedenen Größen und Formen zuzuschneiden, um die spezifischen Anforderungen eines Bauprojekts zu erfüllen.
6.1.2 Leichtbau mit Aluminium
Neben Stahl wird auch Aluminium häufig in der Bauindustrie verwendet, insbesondere in der Fassadentechnik und im Leichtbau. Aluminium ist aufgrund seines geringen Gewichts und seiner Korrosionsbeständigkeit ideal für Anwendungen wie Fensterrahmen, Fassadenverkleidungen und Dachsysteme. Kreisscheren schneiden Aluminiumbleche präzise, was zu glatten Kanten und perfekter Passgenauigkeit führt.
6.2 Verarbeitung von Verbundwerkstoffen im Bauwesen
Verbundwerkstoffe wie Stahlbeton und Glasfaserverstärkte Kunststoffe (GFK) werden zunehmend im Bauwesen eingesetzt, um die Festigkeit und Haltbarkeit von Strukturen zu erhöhen. Diese Materialien erfordern besondere Schneidtechniken, da sie aus verschiedenen Schichten bestehen, die unterschiedlich auf die Schneidprozesse reagieren.
6.2.1 Schneiden von Stahlbetonplatten
Kreisscheren werden verwendet, um Stahlbetonplatten auf die erforderlichen Maße zu schneiden, die in der Bodenverlegung, im Brückenbau und bei Industrieanlagen verwendet werden. Stahlbeton ist extrem robust und widerstandsfähig, weshalb präzise und saubere Schnitte erforderlich sind, um die strukturelle Integrität nicht zu gefährden.
6.2.2 Leichtbau mit faserverstärkten Kunststoffen
Faserverstärkte Kunststoffe (GFK) finden im Bauwesen Anwendung, da sie leicht, korrosionsbeständig und äußerst fest sind. Kreisscheren ermöglichen das präzise Schneiden dieser Materialien, die in Brückenelementen, Dächern und anderen Baukomponenten verwendet werden. Präzise Schnitte sind hier entscheidend, um die Materialstabilität zu erhalten und eine einfache Montage zu ermöglichen.
7. Maschinenbau und Schwerindustrie: Effiziente Verarbeitung von Metallen und Komponenten
Im Maschinenbau und der Schwerindustrie werden Kreisscheren zur Herstellung von Maschinenteilen, Trägern, Platten und anderen Bauteilen verwendet, die präzise geschnitten werden müssen, um die Funktionsfähigkeit und Langlebigkeit der Maschinen und Anlagen zu gewährleisten.
7.1 Herstellung von Maschinenteilen und Komponenten
Maschinenteile und Industrierahmen müssen exakt zugeschnitten sein, um die Montage und Betriebsfähigkeit der Maschinen zu gewährleisten. Kreisscheren ermöglichen es, diese Teile schnell und präzise herzustellen, was zu einer Steigerung der Produktionskapazität und einer Reduzierung der Produktionskosten führt.
7.1.1 Schneiden von Trägern und Rahmen
Kreisscheren werden verwendet, um Stahlträger, Aluminiumrahmen und Verbundmaterialien für den Bau von Maschinenrahmen und Industrieträgern zu schneiden. Diese Teile müssen präzise zugeschnitten werden, um die Maschinenstabilität zu gewährleisten und eine reibungslose Funktion sicherzustellen.
7.1.2 Schneiden von spezialisierten Maschinenteilen
Neben Rahmen und Trägern werden Kreisscheren auch für die Herstellung von kleineren Maschinenteilen verwendet, die in Präzisionsmaschinen eingesetzt werden. Hier ist eine exakte Verarbeitung der Materialien erforderlich, um die Toleranzen einzuhalten und die Funktionsfähigkeit der Maschine zu gewährleisten.
7.2 Verarbeitung von Blechen und Platten in der Schwerindustrie
In der Schwerindustrie werden Kreisscheren eingesetzt, um große Stahlbleche, Platten und andere massive Materialien zu schneiden, die in der Herstellung von Kraftwerken, Anlagen und Industriemaschinen verwendet werden. Diese Materialien müssen präzise geschnitten werden, um die Anforderungen an Festigkeit und Sicherheit zu erfüllen.
7.2.1 Einsatz in der Fertigung von Industrieanlagen
Kreisscheren ermöglichen es, große Metallplatten schnell und präzise zu schneiden, die in der Fertigung von Industrieanlagen verwendet werden. Dies ist entscheidend, um sicherzustellen, dass die Anlagenteile perfekt zusammenpassen und eine sichere und zuverlässige Funktion gewährleisten.
7.2.2 Schneiden von hitzebeständigen Materialien
In der Schwerindustrie werden oft hitzebeständige und korrosionsbeständige Materialien verwendet, die extremen Bedingungen standhalten müssen. Kreisscheren ermöglichen es, diese Materialien präzise zu schneiden, ohne ihre Struktur oder Festigkeit zu beeinträchtigen.
8. Energietechnik: Präzision und Effizienz in der Produktion von Energiesystemen
In der Energietechnik, insbesondere bei der Herstellung von Batteriesystemen, Brennstoffzellen und Solarpanelen, werden Kreisscheren verwendet, um die dafür benötigten Materialien präzise zu schneiden und eine effiziente Produktion zu gewährleisten.
8.1 Schneiden von Elektrodenmaterialien für Batteriesysteme
Batteriesysteme, insbesondere Lithium-Ionen-Batterien, bestehen aus verschiedenen Anoden und Kathoden, die in präzise zugeschnittenen Elektrodenfolien enthalten sind. Kreisscheren spielen eine entscheidende Rolle beim präzisen Zuschneiden dieser Materialien, um die Energieeffizienz und Leistungsfähigkeit der Batterien zu maximieren.
8.1.1 Schneiden von Anoden- und Kathodenmaterialien
Die Elektrodenmaterialien in Batterien bestehen aus speziellen Metallfolien oder Graphit, die präzise geschnitten werden müssen, um eine gleichmäßige Energiedichte und Stromleitfähigkeit zu gewährleisten. Kreisscheren ermöglichen es, diese Materialien mit höchster Präzision zu schneiden und dabei die Struktureigenschaften zu erhalten.
8.1.2 Optimierung der Schnittqualität für die Batterieproduktion
Die Präzision der Schnitte beeinflusst direkt die Leistungsfähigkeit und Lebensdauer von Batterien. Durch den Einsatz von Kreisscheren kann die Schnittqualität optimiert und gleichzeitig der Materialverlust minimiert werden, was die Produktion von leistungsfähigen und langlebigen Batteriesystemen unterstützt.
8.2 Anwendung in der Brennstoffzellen- und Solarindustrie
Kreisscheren werden auch bei der Herstellung von Brennstoffzellenkomponenten und Solarmodulen eingesetzt. Diese Technologien erfordern präzise geschnittene Materialien, um ihre Energieeffizienz und Langlebigkeit zu maximieren.
8.2.1 Schneiden von Brennstoffzellenmembranen
Brennstoffzellen bestehen aus Membranen, die präzise zugeschnitten werden müssen, um eine optimale Leitfähigkeit und Effizienz zu gewährleisten. Kreisscheren ermöglichen es, diese Membranen mit hoher Genauigkeit zu schneiden und so die Leistung der Brennstoffzellen zu verbessern.
8.2.2 Schneiden von Solarzellenkomponenten
Die Solarindustrie verwendet Kreisscheren, um Solarzellenmaterialien wie Siliziumwafer und Glasplatten präzise zu schneiden. Dies ist entscheidend, um die Leistungsfähigkeit der Solarzellen zu maximieren und gleichzeitig die Produktionskosten zu senken.
Fazit
Die Kreisschere hat sich als Schlüsselinstrument in der modernen industriellen Fertigung etabliert. Ihre Vielfältigkeit und Präzision machen sie zu einem unverzichtbaren Werkzeug in der Automobilindustrie, der Luftfahrt, dem Schiffbau, der Bauindustrie, der Verpackungsindustrie, der Schwerindustrie und der Energietechnik.
Mit der Integration von neuen Technologien wie Automatisierung, Künstliche Intelligenz und Industrie 4.0 wird die Kreisschere in Zukunft noch effizienter werden, was zu Produktivitätssteigerungen, Kostenreduzierungen und verbesserter Nachhaltigkeit führen wird. Ihre Fähigkeit, Materialien präzise zu schneiden und gleichzeitig Materialverluste zu minimieren, macht sie zu einem unverzichtb
Materialien für Kreisscheren und deren Schneidkanten
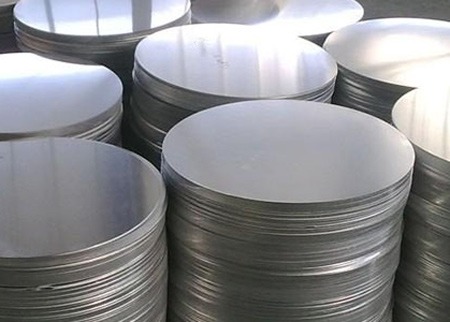
1. Einführung: Die Bedeutung von Materialwahl für Kreisscheren und Schneidkanten
Kreisscheren spielen eine entscheidende Rolle in vielen industriellen Anwendungen, insbesondere in der Blechbearbeitung und Metallverarbeitung. Die Materialien, aus denen Kreisscheren und deren Schneidkanten gefertigt sind, bestimmen ihre Leistung, Haltbarkeit, Schneidpräzision und Widerstandsfähigkeit gegenüber Verschleiß. Die Auswahl des richtigen Materials ist für die Effizienz und Lebensdauer der Kreisschere von entscheidender Bedeutung.
1.1 Die Rolle der Materialien in der Schneidtechnologie
Die Schneidkanten einer Kreisschere müssen in der Lage sein, harte Materialien wie Stahl, Aluminium, Kupfer oder Titan präzise zu durchtrennen. Die Wahl des Schneidmaterials beeinflusst die Schärfe, die Verschleißfestigkeit und die Standzeit der Kreisschere. Diese Faktoren sind entscheidend, um eine hohe Produktionsgeschwindigkeit und gleichbleibende Schnittqualität zu gewährleisten.
1.2 Relevanz der Materialauswahl für spezifische Anwendungen
In der Automobilindustrie, der Luftfahrt, dem Schiffbau und der Verpackungsindustrie müssen Kreisscherenmetalle unterschiedliche Anforderungen erfüllen. Abhängig vom Einsatzgebiet müssen die Schneidkanten der Kreisscheren entweder besonders widerstandsfähig gegenüber hohem Verschleiß sein, hohe Härte aufweisen oder für weiche und dünne Materialien wie Aluminium und Kupfer optimiert werden.
2. Werkstoffe für Kreisscheren: Hochleistungsmaterialien für Schneidwerkzeuge
Die Wahl des richtigen Materials für Kreisscheren und deren Schneidkanten ist ein entscheidender Faktor für die Leistung und Lebensdauer des Werkzeugs. Je nach Anforderungen gibt es verschiedene Hochleistungswerkstoffe, die für Kreisscheren verwendet werden. Dazu gehören Werkzeugstähle, Hartmetalle, beschichtete Materialien und Keramikwerkstoffe.
2.1 Werkzeugstähle: Flexibilität und hohe Festigkeit
Werkzeugstahl ist einer der am häufigsten verwendeten Werkstoffe für Kreisscheren. Werkzeugstähle zeichnen sich durch ihre hohe Festigkeit, Härte und Widerstandsfähigkeit gegenüber Verschleiß aus. Sie sind für eine Vielzahl von Schnittanwendungen geeignet und können unter schwierigen Bedingungen eingesetzt werden.
2.1.1 Kohlenstoffreicher Werkzeugstahl
Werkzeugstähle mit einem hohen Kohlenstoffgehalt sind besonders widerstandsfähig gegenüber Verschleiß und haben eine hohe Härte. Sie werden häufig in Standard-Kreisscheren verwendet, da sie relativ kostengünstig sind und eine gute Verschleißfestigkeit aufweisen. Kohlenstoffreiche Werkzeugstähle werden in Anwendungen eingesetzt, in denen keine extrem hohen Temperaturen oder korrosiven Bedingungen vorherrschen.
2.1.2 Legierter Werkzeugstahl
Legierte Werkzeugstähle enthalten Zusätze wie Chrom, Vanadium oder Molybdän, die die Härte, Zähigkeit und Korrosionsbeständigkeit verbessern. Diese Stähle bieten eine höhere Verschleißfestigkeit und sind widerstandsfähiger gegenüber Hitzeeinwirkung, was sie ideal für das Schneiden von harten Metallen wie hochfester Stahl oder Titan macht.
2.1.3 Vorteile und Nachteile von Werkzeugstählen
- Vorteile: Hohe Härte, gute Widerstandsfähigkeit gegen Verschleiß, relativ kostengünstig und leicht verfügbar.
- Nachteile: Bei sehr hohen Temperaturen kann die Härte nachlassen, was die Lebensdauer der Schneidkante beeinträchtigen kann.
2.2 Hartmetall: Höchste Verschleißfestigkeit und Härte
Hartmetall ist eines der härtesten und verschleißfestesten Materialien, die für Schneidkanten verwendet werden. Es besteht aus einer Kombination von Hartstoffen wie Wolframcarbid (WC) und einem Bindematerial, das häufig Kobalt ist. Hartmetalle sind extrem widerstandsfähig gegenüber Verschleiß, bieten jedoch weniger Zähigkeit als Werkzeugstahl.
2.2.1 Wolframcarbid-Schneidkanten
Wolframcarbid ist eines der am häufigsten verwendeten Materialien für Hartmetallschneidkanten. Es bietet eine hervorragende Härte und Verschleißfestigkeit, was es ideal für das Schneiden von harten Materialien wie Stahl oder Gusseisen macht. Wolframcarbid-Schneidkanten werden in schweren Produktionsumgebungen eingesetzt, wo hohe Standzeiten erforderlich sind.
2.2.2 Eigenschaften von Hartmetallschneidkanten
Hartmetall-Schneidkanten haben eine extrem hohe Druckfestigkeit, was bedeutet, dass sie unter den Bedingungen extremer Belastungen und Reibung nicht nachgeben. Hartmetall bietet zudem eine gute Hitzebeständigkeit, was die Gefahr des Schneidkantenverschleißes durch übermäßige Wärmeentwicklung minimiert.
2.2.3 Vorteile und Nachteile von Hartmetallen
- Vorteile: Sehr hohe Härte und Verschleißfestigkeit, geeignet für schwere Anwendungen, hohe Temperaturbeständigkeit.
- Nachteile: Hartmetalle haben eine geringere Zähigkeit und können bei extrem hohen Belastungen und Schockbelastungen spröde werden.
2.3 Keramik und Keramikbeschichtungen: Verschleiß- und Hitzebeständigkeit
Keramik und keramische Beschichtungen sind moderne Materialien, die eine außergewöhnliche Hitzebeständigkeit und Widerstandsfähigkeit gegenüber chemischem Verschleiß bieten. Diese Materialien werden häufig für spezielle Anwendungen eingesetzt, bei denen extrem hohe Temperaturen und chemisch aggressive Umgebungen vorherrschen.
2.3.1 Oxidkeramiken
Oxidkeramiken, wie Aluminiumoxid oder Zirkonoxid, sind extrem hart und widerstandsfähig gegenüber chemischen Angriffen und Verschleiß. Diese Materialien werden oft in spezialisierten Schneidwerkzeugen verwendet, die in hochgradig korrosiven oder hitzebelasteten Umgebungen arbeiten.
2.3.2 Vorteile und Nachteile von Keramiken
- Vorteile: Hervorragende Hitzebeständigkeit, hohe Verschleißfestigkeit, widerstandsfähig gegen korrosive Umgebungen.
- Nachteile: Sprödigkeit, insbesondere bei Stoßbelastungen, und relativ hohe Kosten im Vergleich zu Werkzeugstählen oder Hartmetallen.
2.4 Verbundwerkstoffe: Optimierung von Leistung und Haltbarkeit
Verbundmaterialien kombinieren mehrere Werkstofftypen, um die spezifischen Vorteile jedes Materials zu nutzen. In Schneidkanten können verschiedene Schichten von Materialien verwendet werden, um sowohl Härte als auch Zähigkeit zu bieten.
2.4.1 Hartmetall- und Stahlverbunde
In vielen Kreisscheren werden Verbundwerkstoffe eingesetzt, die die Härte von Hartmetallen mit der Zähigkeit von Werkzeugstählen kombinieren. Dies ermöglicht es, extrem präzise Schnitte durchzuführen, ohne dass das Material bei hohen Belastungen spröde wird.
2.4.2 Vorteile und Nachteile von Verbundmaterialien
- Vorteile: Kombination von Härte und Zähigkeit, gute Verschleißfestigkeit, geeignet für eine Vielzahl von Anwendungen.
- Nachteile: Komplexität der Herstellung, höhere Kosten im Vergleich zu einheitlichen Materialien.
3. Beschichtungen für Schneidkanten: Erhöhung der Lebensdauer und Leistung
Neben der Wahl des Grundmaterials spielen Beschichtungen eine wichtige Rolle bei der Optimierung der Leistungsfähigkeit und Haltbarkeit von Schneidkanten. Diese Beschichtungen verbessern die Verschleißfestigkeit, die Härte und die Korrosionsbeständigkeit, wodurch die Lebensdauer der Schneidwerkzeuge verlängert wird.
3.1 Titannitrid (TiN)-Beschichtungen
Titannitrid (TiN) ist eine der am häufigsten verwendeten Beschichtungen für Schneidwerkzeuge. Es bietet eine außergewöhnliche Härte und ist widerstandsfähig gegen Abrieb und Korrosion. TiN-Beschichtungen werden häufig auf Werkzeugstähle und Hartmetalle aufgebracht, um deren Lebensdauer zu verlängern.
3.1.1 Eigenschaften und Vorteile von TiN
TiN-Beschichtungen sind bekannt für ihre goldene Farbe und bieten eine geringe Reibung, was die Wärmeentwicklung während des Schneidprozesses reduziert. Dies führt zu einer verbesserten Schnittqualität und verringert den Verschleiß der Schneidkanten.
3.1.2 Anwendungen von TiN-beschichteten Schneidkanten
TiN-beschichtete Schneidkanten werden in einer Vielzahl von Anwendungen eingesetzt, von der Automobilproduktion bis hin zur Herstellung von medizinischen Geräten. Sie sind besonders nützlich in Umgebungen, in denen geringe Reibung und hohe Schnittgeschwindigkeit erforderlich sind.
3.2 Titancarbonitrid (TiCN)-Beschichtungen
Titancarbonitrid (TiCN) bietet eine noch höhere Härte als TiN und wird in Anwendungen eingesetzt, die eine hohe Verschleißfestigkeit erfordern. TiCN-beschichtete Schneidkanten sind ideal für hochfeste Materialien wie Stahl und Nickellegierungen.
3.2.1 Vorteile von TiCN gegenüber TiN
TiCN bietet eine verbesserte Härte und Abriebfestigkeit im Vergleich zu TiN. Es wird verwendet, wenn extreme Verschleißbedingungen vorherrschen und eine längere Standzeit der Werkzeuge erforderlich ist.
3.2.2 Anwendungen von TiCN-beschichteten Werkzeugen
TiCN-beschichtete Werkzeuge werden häufig in der Stahlbearbeitung und bei der Herstellung von Hochleistungsbauteilen eingesetzt, da sie in der Lage sind, extremen Verschleißbedingungen standzuhalten und gleichzeitig eine hohe Schnittpräzision zu gewährleisten.
3.3 Diamantbeschichtungen: Extreme Härte und Verschleißfestigkeit
Diamantbeschichtungen bieten die höchste Härte aller Beschichtungen und werden in hochspezialisierten Anwendungen eingesetzt, bei denen extremer Verschleiß und hohe Schnittpräzision gefordert sind. Diamantbeschichtungen werden vor allem für das Schneiden von nichtmetallischen Materialien wie Glas, Keramik und Verbundwerkstoffen verwendet.
3.3.1 Eigenschaften von Diamantbeschichtungen
Diamantbeschichtungen bieten eine extrem hohe Verschleißfestigkeit und Härte. Sie sind ideal für Anwendungen, in denen herkömmliche Schneidkanten schnell abnutzen würden. Diese Beschichtungen bieten auch eine hervorragende Temperaturbeständigkeit, was sie ideal für Hochgeschwindigkeitsbearbeitungen macht.
3.3.2 Nachteile von Diamantbeschichtungen
Während Diamantbeschichtungen extreme Härte bieten, sind sie anfällig für chemische Reaktionen mit bestimmten Metallen, wie z.B. Eisen. Daher sind sie weniger geeignet für die Bearbeitung von Stahl, da sich die Beschichtung schnell abnutzen könnte.
3.4 Mehrschichtbeschichtungen
Mehrschichtbeschichtungen kombinieren verschiedene Beschichtungsmaterialien, um die spezifischen Vorteile jeder Schicht zu nutzen. Eine Titannitrid-Schicht kann z.B. mit einer Diamantschicht kombiniert werden, um sowohl Verschleißfestigkeit als auch Hitzebeständigkeit zu bieten.
3.4.1 Vorteile von Mehrschichtbeschichtungen
Durch die Kombination mehrerer Schichten kann die Lebensdauer der Schneidkante erheblich verlängert werden. Die äußeren Schichten können eine hohe Härte und Verschleißfestigkeit bieten, während die inneren Schichten die Zähigkeit und Stabilität der Schneidkante erhöhen.
3.4.2 Anwendungen von mehrschichtigen Beschichtungen
Mehrschichtbeschichtungen werden in schweren Industrieanwendungen eingesetzt, bei denen eine lange Standzeit und eine hohe Schnittgeschwindigkeit erforderlich sind. Sie kommen häufig in der Automobil- und Luftfahrtindustrie zum Einsatz, wo sie für das Schneiden von hochfesten Materialien verwendet werden.
4. Optimierung der Schneidleistung: Faktoren, die die Materialwahl beeinflussen
Die Materialwahl für Schneidkanten hängt von verschiedenen Faktoren ab, die die Leistung, Wirtschaftlichkeit und Lebensdauer der Kreisscheren beeinflussen. Diese Faktoren umfassen Materialeigenschaften, Temperaturbedingungen, Schnittgeschwindigkeit, Wartung und Kosten.
4.1 Materialeigenschaften und Anwendungsspezifikationen
Die Wahl des richtigen Schneidmaterials hängt stark von den Eigenschaften des zu schneidenden Materials ab. Verschiedene Metalle und Legierungen erfordern unterschiedliche Härtegrade, Verschleißfestigkeit und Zähigkeit, um eine optimale Schneidleistung zu gewährleisten.
4.1.1 Härte und Zähigkeit
In Anwendungen, in denen das Schneidmaterial hart und spröde ist, wie bei der Bearbeitung von hochfestem Stahl oder Gusseisen, ist eine hohe Härte der Schneidkante erforderlich. In anderen Anwendungen, in denen das Material weicher oder flexibler ist, kann es vorteilhafter sein, eine Schneidkante mit höherer Zähigkeit zu wählen, um Verformungen und Brüche zu vermeiden.
4.1.2 Verschleiß- und Korrosionsbeständigkeit
In korrosiven Umgebungen, wie sie in der Schiffbauindustrie oder bei der Verarbeitung von chemischen Stoffen vorkommen, ist es wichtig, dass die Schneidkante eine hohe Korrosionsbeständigkeit aufweist. Hartmetalle und beschichtete Werkstoffe bieten hier deutliche Vorteile, da sie gegenüber chemischen Angriffen und oxidativen Prozessen widerstandsfähiger sind.
4.2 Temperatur- und Schnittgeschwindigkeitsanforderungen
Die Schnittgeschwindigkeit und die entstehende Hitze während des Schneidprozesses spielen eine entscheidende Rolle bei der Wahl des Schneidmaterials. Hochgeschwindigkeitsanwendungen erfordern Materialien, die ihre Härte auch bei hohen Temperaturen beibehalten können.
4.2.1 Hitzebeständige Materialien
In Anwendungen mit hoher Reibung und Wärmeentwicklung, wie in der Luft- und Raumfahrtindustrie oder der Automobilproduktion, sind hitzebeständige Materialien wie Hartmetall oder keramische Beschichtungen erforderlich, um zu verhindern, dass die Schneidkante durch die Hitzeeinwirkung verschleißt.
4.2.2 Kühlung und Wärmemanagement
Ein wesentlicher Aspekt bei der Schneidmaterialwahl ist die Kühlung. Durch den Einsatz von Kühlmitteln oder speziellen Schneidölen kann die entstehende Hitze während des Schneidprozesses reduziert werden, was die Lebensdauer der Schneidkante verlängert. In einigen Fällen können beschichtete Werkstoffe auch die Notwendigkeit von Kühlmitteln reduzieren, da sie eine bessere Wärmeableitung bieten.
4.3 Wartung und Nachschärfen
Die Wartung und Nachschärfung von Kreisscheren ist ein entscheidender Faktor für die Lebensdauer und Leistungsfähigkeit der Schneidkanten. Regelmäßige Wartung verlängert die Lebensdauer des Werkzeugs und stellt sicher, dass die Schneidqualität auf einem hohen Niveau bleibt.
4.3.1 Nachschärfen von Werkzeugstählen
Werkzeugstähle lassen sich relativ leicht nachschärfen, was sie ideal für Anwendungen macht, in denen regelmäßiges Nachschärfen erforderlich ist. Der Nachschärfprozess ist weniger aufwendig und kostspielig im Vergleich zu Hartmetallen oder Keramikwerkstoffen.
Automatisierte Kreisscheren und ihre Rolle in der industriellen Produktion
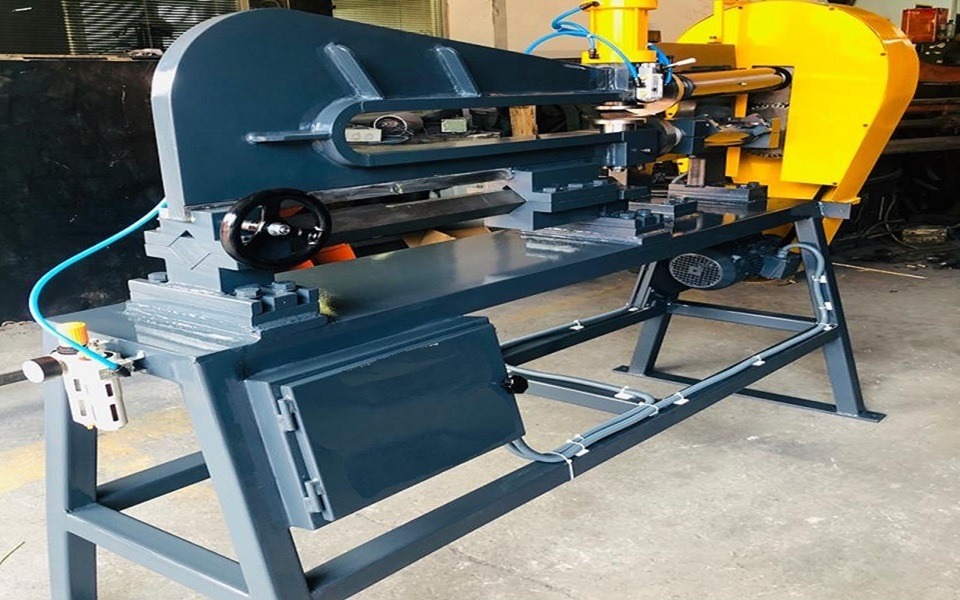
1. Einführung: Bedeutung der Automatisierung in der industriellen Fertigung
Die Automatisierung hat in der modernen industriellen Produktion einen tiefgreifenden Wandel bewirkt. Maschinen und Anlagen werden zunehmend mit intelligenten Steuerungssystemen ausgestattet, die es ermöglichen, wiederholbare und hochpräzise Fertigungsprozesse zu implementieren. In dieser Entwicklung spielen automatisierte Kreisscheren eine zentrale Rolle, insbesondere in der Metallverarbeitung und Blechbearbeitung. Ihre Fähigkeit, Materialien schnell, präzise und ohne menschliches Eingreifen zu schneiden, macht sie zu einem unverzichtbaren Werkzeug in der Automobilindustrie, der Luftfahrt, dem Bauwesen und vielen anderen Branchen.
1.1 Überblick über automatisierte Kreisscheren
Eine automatisierte Kreisschere ist eine Schneidmaschine, die mithilfe von CNC-Systemen (Computerized Numerical Control) oder anderen intelligenten Steuerungstechnologien arbeitet, um den Schneidprozess vollständig zu automatisieren. Diese Maschinen sind in der Lage, hohe Produktionsvolumen zu bewältigen und gleichzeitig präzise und gleichmäßige Schnitte auszuführen. Automatisierte Kreisscheren reduzieren nicht nur den manuellen Arbeitsaufwand, sondern tragen auch zur Verbesserung der Schnittqualität und Produktionsgeschwindigkeit bei.
1.2 Die Rolle der Automatisierung in der industriellen Produktion
In der heutigen Industrieumgebung sind Automatisierung und Industrie 4.0 entscheidend für die Verbesserung von Effizienz, Produktivität und Konsistenz. Automatisierte Kreisscheren spielen eine Schlüsselrolle bei der Umstellung auf intelligente Fertigungsanlagen, indem sie den Schneidprozess optimieren und die Anforderungen der modernen Industrieproduktion erfüllen. Dies führt zu geringeren Ausfallzeiten, höherer Produktqualität und kostengünstigeren Produktionsprozessen.
Funktionsweise automatisierter Kreisscheren: Präzision durch intelligente Steuerung
Die Funktionsweise von automatisierten Kreisscheren basiert auf der Integration von Steuerungssystemen, die es ermöglichen, den Schneidvorgang mit extremer Präzision zu steuern. Diese Maschinen kombinieren moderne Antriebstechnologien, intelligente Materialführungssysteme und automatische Fehlererkennung, um konstante Qualität und hohe Produktionsgeschwindigkeit zu gewährleisten.
2.1 Komponenten und Aufbau automatisierter Kreisscheren
Automatisierte Kreisscheren bestehen aus mehreren Schlüsselkomponenten, die für die präzise Durchführung des Schneidprozesses unerlässlich sind:
- CNC-Steuerungssystem: Der zentrale Bestandteil, der den gesamten Schneidprozess überwacht und steuert. Das CNC-System ermöglicht die Eingabe von Schnittparametern, wie Schnittgeschwindigkeit, Schnittwinkel und Schnittkraft, und sorgt dafür, dass die Maschine präzise und wiederholbare Schnitte ausführt.
- Antriebseinheit: Elektrische oder hydraulische Antriebe, die die Schneidmesser in Bewegung setzen und für den kontinuierlichen Betrieb der Maschine sorgen.
- Schneidmesser: Die rotierenden Klingen der Kreisschere bestehen aus hochfesten Materialien wie Werkzeugstahl oder Hartmetall und sind für den präzisen Schnitt verantwortlich.
- Materialführungssystem: Dieses System führt das Material durch die Schneidzone der Kreisschere und stellt sicher, dass das Metallblech präzise und gleichmäßig zugeführt wird.
- Fehlererkennungssystem: Mithilfe von Sensoren und intelligenter Überwachung erkennt die Maschine automatisch Fehler im Schneidprozess und passt die Parameter in Echtzeit an, um die Schnittqualität zu gewährleisten.
2.2 CNC-Technologie und ihre Rolle in der Automatisierung
CNC-Technologie spielt eine zentrale Rolle bei der Automatisierung von Kreisscheren. Durch die programmierte Steuerung des Schneidprozesses ermöglicht CNC die präzise Kontrolle von Schneidbewegungen, Geschwindigkeit und Kraftaufwand. Dies stellt sicher, dass jede Charge von geschnittenem Material mit gleichbleibender Qualität produziert wird, unabhängig davon, wie komplex oder hoch das Produktionsvolumen ist.
2.2.1 Vorteile von CNC-gesteuerten Kreisscheren
CNC-gesteuerte Kreisscheren bieten eine Vielzahl von Vorteilen gegenüber herkömmlichen, manuell betriebenen Maschinen:
- Höhere Präzision: Durch die genaue Programmierung der Schnittparameter kann die CNC-Maschine extrem präzise Schnitte ausführen.
- Wiederholbarkeit: Ein großer Vorteil der CNC-Steuerung ist die Fähigkeit, gleichbleibend präzise Ergebnisse in der Massenproduktion zu liefern.
- Vielseitigkeit: CNC-gesteuerte Kreisscheren können leicht für verschiedene Schnittprogramme und Materialarten programmiert werden, was sie ideal für industrielle Anwendungen mit wechselnden Anforderungen macht.
2.2.2 Integration mit Industrie 4.0
Die Integration von Industrie 4.0-Technologien in CNC-gesteuerte Kreisscheren ermöglicht eine Vernetzung der Maschinen mit anderen Anlagen in der Produktionskette. Durch Datenanalyse und Prozessüberwachung in Echtzeit können Produktionsprobleme frühzeitig erkannt und behoben werden, was zu einer Reduzierung von Ausfallzeiten und Kosten führt.
2.3 Automatische Materialzufuhr und Abfallmanagement
Automatisierte Kreisscheren sind mit automatischen Materialzuführungssystemen ausgestattet, die es ermöglichen, das Material kontinuierlich und gleichmäßig in die Schneidzone zu leiten. Diese Systeme sorgen dafür, dass das Metallblech mit der richtigen Geschwindigkeit und Position zugeführt wird, um Präzisionsschnitte zu gewährleisten.
2.3.1 Effizienzsteigerung durch automatische Zuführung
Durch die Implementierung automatischer Materialzuführungen wird der manuelle Eingriff auf ein Minimum reduziert. Dies führt zu einer erheblichen Steigerung der Produktionseffizienz und sorgt dafür, dass die Maschine mit maximaler Kapazität arbeiten kann, ohne dass es zu Verzögerungen oder Fehlplatzierungen des Materials kommt.
2.3.2 Abfallmanagement und Materialnutzung
Durch die automatische Überwachung des Schneidprozesses und die präzise Materialführung wird der Materialabfall minimiert. Automatisierte Kreisscheren nutzen das Material effizienter und erzeugen weniger Verschnitt, was zu Kosteneinsparungen und einem nachhaltigeren Produktionsprozess führt.
2.4 Prozessüberwachung und automatische Fehlerkorrektur
Die automatische Fehlerkorrektur ist ein weiterer Vorteil automatisierter Kreisscheren. Sensoren und intelligente Überwachungssysteme ermöglichen die Erkennung von Abweichungen im Schneidprozess und die Anpassung der Schneidparameter in Echtzeit.
2.4.1 Erkennung von Materialfehlern
Durch die Integration von Sensoren können automatisierte Kreisscheren potenzielle Materialfehler wie Verformungen, Risse oder Materialstärkenabweichungen frühzeitig erkennen. Das System passt den Schneidvorgang an oder stoppt den Prozess, um sicherzustellen, dass das Endprodukt frei von Fehlern ist.
2.4.2 Automatische Anpassung der Schneidparameter
Automatisierte Kreisscheren können die Schnittgeschwindigkeit, den Druck und den Schnittwinkel in Echtzeit anpassen, um optimale Ergebnisse zu gewährleisten. Dies ist besonders vorteilhaft bei der Verarbeitung unterschiedlicher Materialarten und Materialstärken, da das System sich an die spezifischen Anforderungen anpassen kann.
Anwendungsbereiche der automatisierten Kreisscheren: Branchenübergreifende Vorteile
Automatisierte Kreisscheren werden in einer Vielzahl von Industrien eingesetzt, da sie eine hohe Produktionsgeschwindigkeit und gleichbleibende Schnittqualität bieten. Zu den wichtigsten Anwendungsbereichen gehören die Automobilindustrie, die Luft- und Raumfahrtindustrie, die Verpackungsindustrie und die Bauindustrie. In diesen Branchen tragen automatisierte Kreisscheren dazu bei, Produktionsprozesse zu optimieren und Kosten zu reduzieren.
3.1 Automobilindustrie: Effiziente Herstellung von Karosserieteilen
In der Automobilindustrie spielen automatisierte Kreisscheren eine Schlüsselrolle bei der Herstellung von Karosserieteilen, Fahrgestellen und anderen Metallkomponenten. Die Präzision und Geschwindigkeit, mit der automatisierte Kreisscheren arbeiten, ermöglichen es, hochfeste Stähle und Aluminiumlegierungen schnell und präzise zu schneiden, was zur Effizienzsteigerung in der Produktion beiträgt.
3.1.1 Herstellung von Karosserie- und Fahrgestellteilen
Automatisierte Kreisscheren werden verwendet, um große Metallbleche in Karosserieteile und Rahmenkomponenten zu schneiden. Diese Teile müssen extrem präzise geschnitten werden, um den strengen Sicherheitsanforderungen und Qualitätsstandards der Automobilindustrie gerecht zu werden. Die CNC-Steuerung ermöglicht es, die exakten Schnittparameter für jedes Material festzulegen, was zu minimalem Materialverlust und höchster Schnittqualität führt.
3.1.2 Reduzierung von Produktionszeiten
Durch die Automatisierung des Schneidprozesses werden Produktionszeiten erheblich reduziert. Dies ist besonders wichtig in der Automobilindustrie, wo die Produktion von großen Stückzahlen erforderlich ist, um den Bedarf zu decken. Automatisierte Kreisscheren können rund um die Uhr arbeiten und so die Produktionskapazitäten maximieren.
3.2 Luft- und Raumfahrtindustrie: Präzisionsfertigung für Flugzeugteile
In der Luft- und Raumfahrtindustrie werden automatisierte Kreisscheren verwendet, um leichte Metalllegierungen wie Titan und Aluminium präzise zu schneiden. Diese Materialien müssen extrem präzise verarbeitet werden, um die Strukturfestigkeit und Sicherheit von Flugzeugen zu gewährleisten.
3.2.1 Herstellung von Flugzeugrümpfen und Tragflächen
Automatisierte Kreisscheren werden in der Luftfahrtindustrie eingesetzt, um große Aluminiumplatten oder Titanbleche zu schneiden, die dann zu Flugzeugrümpfen, Tragflächen und Strukturteilen weiterverarbeitet werden. Diese Schnitte müssen extrem genau sein, da selbst geringste Abweichungen die Aerodynamik und Sicherheit des Flugzeugs beeinträchtigen können.
3.2.2 Bearbeitung von Verbundwerkstoffen
Verbundwerkstoffe spielen in der modernen Luftfahrt eine immer größere Rolle, da sie leicht und gleichzeitig stark sind. Automatisierte Kreisscheren können diese Materialien präzise schneiden, ohne ihre Faserstruktur zu beschädigen. Dies trägt dazu bei, dass Flugzeugkomponenten mit höherer Festigkeit und geringerem Gewicht hergestellt werden können.
3.3 Verpackungsindustrie: Präzise und effiziente Produktion von Metallverpackungen
In der Verpackungsindustrie werden automatisierte Kreisscheren eingesetzt, um Aluminiumfolien, Metallbleche und Verbundmaterialien zu schneiden, die zur Herstellung von Verpackungen verwendet werden. Die hohe Geschwindigkeit und Präzision, mit der automatisierte Kreisscheren arbeiten, sind entscheidend, um die Anforderungen der Massenproduktion zu erfüllen.
3.3.1 Herstellung von Lebensmittel- und Medizinverpackungen
In der Lebensmittel- und Pharmaindustrie müssen Verpackungen exakt zugeschnitten werden, um die Produktsicherheit und Haltbarkeit zu gewährleisten. Automatisierte Kreisscheren ermöglichen es, dünne Metallfolien präzise zu schneiden, ohne das Material zu beschädigen oder seine Schutzeigenschaften zu beeinträchtigen.
3.3.2 Kosteneffizienz durch Automatisierung
Die Verwendung automatisierter Kreisscheren in der Verpackungsindustrie reduziert die Produktionskosten, da weniger manuelle Eingriffe erforderlich sind und gleichzeitig die Produktionsgeschwindigkeit erhöht wird. Zudem wird durch die präzise Materialnutzung der Abfall minimiert, was die Effizienz des Produktionsprozesses weiter steigert.
3.4 Bauindustrie: Präzision und Geschwindigkeit bei der Verarbeitung von Baumaterialien
Die Bauindustrie verwendet automatisierte Kreisscheren, um Stahl, Aluminium und Verbundwerkstoffe für die Herstellung von Gebäudestrukturen, Brücken und Infrastruktureinrichtungen zu schneiden. Diese Materialien müssen präzise geschnitten werden, um den statistischen Anforderungen und Bauanforderungen gerecht zu werden.
3.4.1 Verarbeitung von Stahlträgern und Metallplatten
Automatisierte Kreisscheren werden eingesetzt, um Stahlträger und Metallplatten schnell und präzise zu schneiden. Diese Komponenten werden für den Bau von Wolkenkratzern, Brücken und Industrieanlagen verwendet, wo Präzision und Materialeffizienz entscheidend sind.
3.4.2 Herstellung von leichten und korrosionsbeständigen Materialien
Neben Stahl spielt Aluminium eine wichtige Rolle im Bauwesen, insbesondere bei der Herstellung von Fassadenverkleidungen, Dachsystemen und Fensterrahmen. Automatisierte Kreisscheren ermöglichen es, diese Materialien präzise zu schneiden und gleichzeitig die Materialbeständigkeit zu erhalten, was besonders in korrosiven Umgebungen wichtig ist.
Vorteile von automatisierten Kreisscheren in der industriellen Produktion
Die Einführung von automatisierten Kreisscheren in die Produktion bietet eine Vielzahl von Vorteilen, die weit über die Reduzierung des Arbeitsaufwands hinausgehen. Zu den wichtigsten Vorteilen zählen die Erhöhung der Produktionsgeschwindigkeit, die Kosteneffizienz, die Vermeidung von Materialverlusten und die Verbesserung der Produktsicherheit.
4.1 Höhere Produktivität durch Automatisierung
Ein wesentlicher Vorteil automatisierter Kreisscheren ist die erhöhte Produktivität. Diese Maschinen können kontinuierlich arbeiten, ohne dass menschliche Eingriffe erforderlich sind, und ermöglichen so eine erhebliche Steigerung der Produktionskapazität.
4.1.1 Rund-um-die-Uhr-Produktion
Automatisierte Kreisscheren sind in der Lage, 24 Stunden am Tag und 7 Tage die Woche zu arbeiten, was die Produktionszeiten maximiert und die Notwendigkeit für Schichtarbeit reduziert. Dies führt zu einer signifikanten Steigerung der Produktionsvolumina, insbesondere in Industrien, die auf Massenproduktion angewiesen sind, wie der Automobil- und Verpackungsindustrie.
4.1.2 Reduzierte Ausfallzeiten und höhere Betriebseffizienz
Durch den Einsatz von automatisierten Fehlererkennungssystemen und vorausschauender Wartung können Ausfallzeiten erheblich reduziert werden. Die Maschinen erkennen Verschleiß und Abnutzung frühzeitig und ermöglichen es den Bedienern, präventive Wartungsmaßnahmen durchzuführen, bevor größere Probleme auftreten.
4.2 Präzision und Konsistenz bei der Massenproduktion
Ein weiterer entscheidender Vorteil automatisierter Kreisscheren ist die Präzision und Konsistenz der Schnitte. Diese Maschinen sind in der Lage, hochpräzise wiederholbare Schnitte durchzuführen, was zu einer höheren Produktqualität und weniger Ausschuss führt.
4.2.1 Präzise Schneidtechnologie für komplexe Designs
Durch die Verwendung von CNC-Steuerungen können automatisierte Kreisscheren auch komplexe Schnittmuster und Designs mit höchster Präzision umsetzen. Dies ist besonders in der Luftfahrtindustrie wichtig, wo komplexe Flugzeugteile mit extrem hohen Toleranzen hergestellt werden müssen.
4.2.2 Gleichbleibende Qualität in der Serienfertigung
In der Serienproduktion spielt die Konsistenz eine zentrale Rolle. Automatisierte Kreisscheren gewährleisten, dass jeder Schnitt exakt gleich ist, was die Gesamtqualität des Endprodukts erhöht und die Notwendigkeit für Nachbearbeitungen reduziert.
4.3 Kosteneinsparungen und Nachhaltigkeit
Die Einführung von automatisierten Kreisscheren führt nicht nur zu einer Effizienzsteigerung, sondern auch zu erheblichen Kosteneinsparungen. Durch die Automatisierung werden manuelle Arbeitskosten gesenkt, und die Materialnutzung wird optimiert, was zur Abfallreduzierung beiträgt.
4.3.1 Reduzierung von Materialverlusten
Automatisierte Kreisscheren sind in der Lage, das Material so präzise zu schneiden, dass Verschnitt und Abfall minimiert werden. Dies führt zu einer besseren Materialausnutzung und verringert die Kosten für Rohstoffe.
4.3.2 Geringere Energiekosten
Moderne automatisierte Kreisscheren sind auf Energieeffizienz ausgelegt und verbrauchen weniger Energie als ältere, manuell betriebene Maschinen. Dies trägt zu geringeren Betriebskosten bei und unterstützt die nachhaltige Produktion, da der Energieverbrauch gesenkt wird.
Zukunft der automatisierten Kreisscheren: Neue Technologien und Entwicklungen
Die Zukunft der automatisierten Kreisscheren wird durch die Integration von neuen Technologien wie Künstlicher Intelligenz (KI), Maschinellem Lernen und Industrie 4.0 geprägt sein. Diese Innovationen haben das Potenzial, die Effizienz und Produktivität weiter zu steigern und neue Anwendungsmöglichkeiten zu erschließen.
5.1 Integration von Künstlicher Intelligenz und Maschinellem Lernen
Die Integration von Künstlicher Intelligenz (KI) und Maschinellem Lernen in automatisierte Kreisscheren wird es diesen Maschinen ermöglichen, selbstständig zu lernen und sich an unterschiedliche Schneidanforderungen anzupassen. KI-Systeme können den Schneidprozess in Echtzeit überwachen und Optimierungen vornehmen, um die Schnittqualität und Produktionsgeschwindigkeit zu maximieren.
5.1.1 Vorausschauende Wartung und intelligente Fehlererkennung
Durch die Verwendung von Maschinellem Lernen können automatisierte Kreisscheren Muster in den Produktionsdaten erkennen und so mögliche Maschinenfehler vorhersagen, bevor sie auftreten. Dies ermöglicht eine vorausschauende Wartung, die die Betriebszeiten maximiert und Ausfallzeiten reduziert.
5.2 Vernetzte Fertigung und Industrie 4.0
Industrie 4.0 ermöglicht die Vernetzung von Maschinen und Produktionsanlagen zu einem intelligenten Netzwerk, das in Echtzeit auf Produktionsanforderungen reagieren kann. Automatisierte Kreisscheren werden in solche intelligenten Fertigungssysteme integriert, um den gesamten Produktionsprozess zu optimieren und flexibler zu gestalten.
5.2.1 Automatisierte Produktionslinien und Roboterintegration
Die Integration von Robotik in Produktionslinien wird die Rolle automatisierter Kreisscheren weiter ausbauen. Roboter können verwendet werden, um Materialien zu handhaben und direkt in die Schneidmaschinen zuzuführen, was den Automatisierungsgrad der Produktionslinien erhöht und die Betriebskosten weiter senkt.
5.3 Nachhaltigkeit und umweltfreundliche Produktion
Mit dem zunehmenden Fokus auf nachhaltige Fertigung und umweltfreundliche Produktion wird die Rolle automatisierter Kreisscheren weiter wachsen. Durch den optimierten Materialeinsatz und die Reduzierung von Abfällen tragen diese Maschinen zur Nachhaltigkeit in der Fertigung bei.
5.3.1 Reduktion von Abfall und Materialverbrauch
Zukünftige Entwicklungen in der Technologie für automatisierte Kreisscheren werden sich darauf konzentrieren, den Materialverbrauch weiter zu optimieren und Abfälle zu reduzieren. Dies wird nicht nur die Produktionskosten senken, sondern auch die Umweltbelastung verringern.
5.3.2 Effiziente Energienutzung
Die Integration von energieeffizienten Antriebssystemen und die Verwendung von intelligenter Steuerung ermöglichen es automatisierten Kreisscheren, weniger Energie zu verbrauchen und gleichzeitig die Produktionsleistung zu maximieren. Dies trägt zur Reduzierung des CO₂-Ausstoßes bei und unterstützt Unternehmen bei der Erfüllung ihrer Nachhaltigkeitsziele.
Fazit
Automatisierte Kreisscheren spielen eine zentrale Rolle in der modernen industriellen Produktion. Sie bieten eine Vielzahl von Vorteilen, darunter höhere Produktivität, geringere Produktionskosten, präzise Schnitte und weniger Abfall. Die Integration moderner Technologien wie CNC-Steuerungen, KI und Industrie 4.0 hat diese Maschinen zu einem unverzichtbaren Bestandteil der Metallverarbeitung, Luftfahrt, Automobil- und Verpackungsindustrie gemacht.