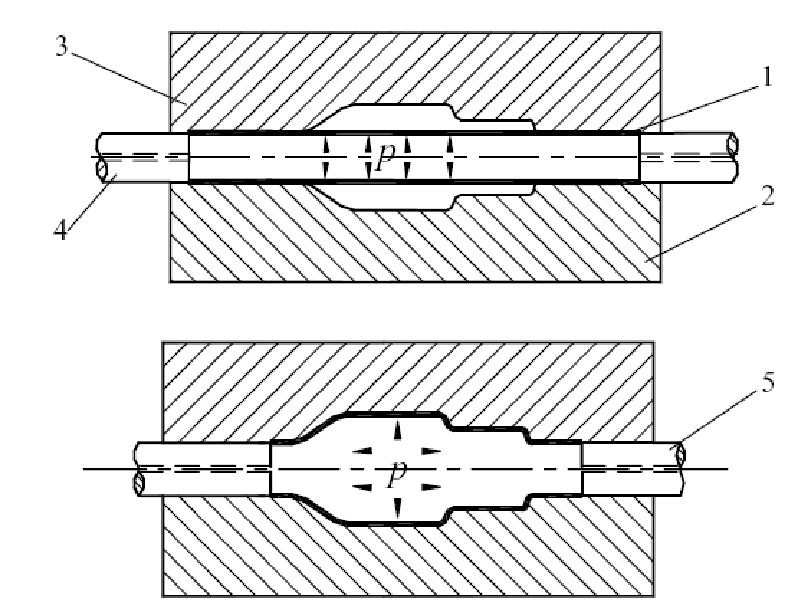
Innenhochdruckumformen Rohre: Innenhochdruckumformung (IHU), auch bekannt als Hydroforming, ist ein spezielles Umformverfahren für Metalle, das vor allem in der Automobil-, Luftfahrt- und Maschinenbauindustrie eingesetzt wird. Hier ein Überblick über den Prozess, seine Anwendungsgebiete und Vorteile:
1. Prozessüberblick
- Bei der IHU wird ein hohler Metallrohrling oder eine vorgeformte Blechform in eine spezielle Form eingelegt.
- Dann wird ein Hochdruckmedium, meist Wasser oder Öl, in das Rohr eingespritzt, wodurch sich das Material ausdehnt und die Kontur der umgebenden Form annimmt.
- Auf diese Weise lassen sich komplexe Hohlformen präzise herstellen, die mit herkömmlichen Verfahren wie Stanzen oder Schweißen schwer umsetzbar sind.
2. Anwendungsbereiche der Innenhochdruckumformung
- Automobilindustrie: IHU wird zur Herstellung komplexer Bauteile wie Motorträgern, Rahmenlängsträgern, Abgassystemen und Fahrwerksteilen verwendet.
- Luft- und Raumfahrt: Leichte, aber robuste Bauteile, insbesondere solche mit dünnwandigen und hochfesten Hohlprofilen.
- Konsumgüter: Fahrradrahmen, Bauteile für Haushaltsgeräte und weitere Anwendungen, bei denen hochfeste, leichte und oft komplexe Formen erforderlich sind.
3. Vorteile der Innenhochdruckumformung
- Gewichtsreduktion: Ideal für den Leichtbau, da das Material effizient verteilt wird, was in der Automobil- und Luftfahrtindustrie von großer Bedeutung ist.
- Erhöhte strukturelle Integrität: IHU ermöglicht die Herstellung von stabileren, nahtlosen Teilen mit weniger Schweißverbindungen, wodurch potenzielle Schwachstellen reduziert werden.
- Effiziente Materialnutzung: Minimiert Materialabfall und ermöglicht eine effiziente Produktion, da mehrere Bauteile in einem einzigen Umformschritt hergestellt werden können.
- Kosteneffiziente Produktion: Reduziert den Bedarf an zusätzlichen Montage- und Verbindungsprozessen und senkt so die Produktionskosten.
4. Technische Überlegungen
- Materialeigenschaften: Häufig verwendete Metalle sind Aluminium, Stahl und Edelstahl aufgrund ihrer Duktilität und Festigkeit.
- Druckkontrolle: Erfordert eine präzise Steuerung des Flüssigkeitsdrucks, um eine genaue Formgebung zu erreichen, ohne das Material zu beschädigen.
- Komplexität des Designs: CAD- und FEM-Tools werden häufig beim Design der IHU-Formen und -Prozesse eingesetzt, um die strukturelle Integrität und Umsetzbarkeit sicherzustellen.
Die IHU ist in Branchen, die auf eine hohe Festigkeit und gleichzeitig minimales Gewicht setzen, besonders gefragt. Vor allem dort, wo hohe Leistung und Haltbarkeit essenziell sind, gewinnt dieses Verfahren zunehmend an Bedeutung.
Einführung und Grundlagen
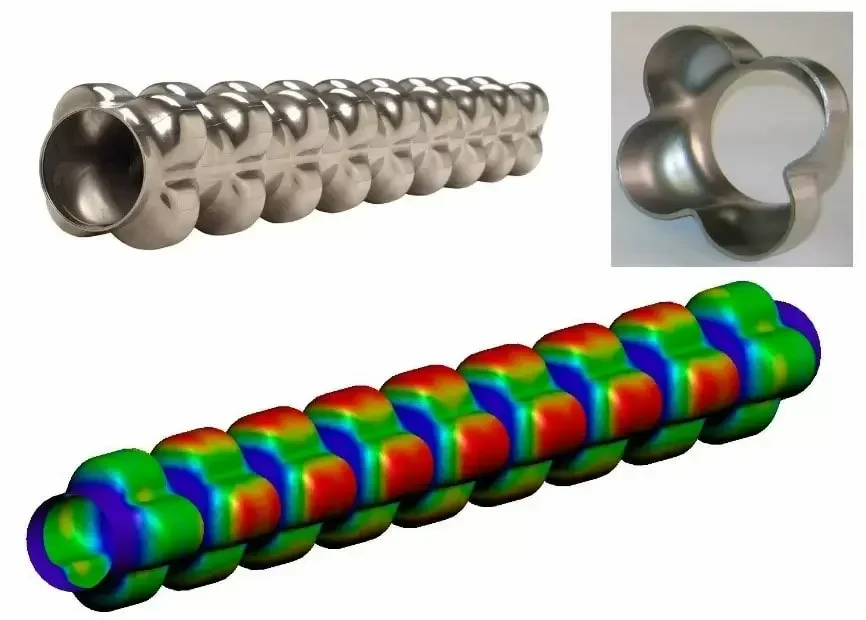
Definition der Innenhochdruckumformung:
Die Innenhochdruckumformung (IHU) ist ein modernes Umformverfahren, das zur Herstellung hohler Bauteile aus metallischen Werkstoffen genutzt wird. Hierbei wird ein Rohrling oder ein vorgeformtes Blechstück durch die Einbringung von Hochdruckflüssigkeit innerhalb eines geschlossenen Werkzeugs in die gewünschte Form gebracht. Das Verfahren ermöglicht die Herstellung von komplexen, dünnwandigen und dennoch hochfesten Bauteilen, die sich durch traditionelle Umform- oder Schweißtechniken nicht in gleicher Qualität oder Wirtschaftlichkeit herstellen lassen.
Historische Entwicklung und technologische Relevanz:
Das Konzept der Innenhochdruckumformung wurde in den 1950er-Jahren erstmals in der Luftfahrtindustrie angewandt, um leichte, nahtlose Bauteile mit hoher Festigkeit herzustellen. Seit den 1990er Jahren hat sich das Verfahren insbesondere in der Automobilindustrie etabliert, wo es für die Fertigung komplexer Strukturen wie Fahrwerksteilen und Abgasleitungen genutzt wird. Die zunehmende Nachfrage nach leichten, stabilen Bauteilen hat IHU zu einem unverzichtbaren Bestandteil moderner Produktionsprozesse gemacht.
2. Technische Grundlagen der IHU
Physikalische Prinzipien (Druck, Materialverformung):
Das Innenhochdruckumformverfahren basiert auf der Wirkung eines hydraulischen Drucks, der auf das innere Volumen eines Rohrlings oder Werkstücks ausgeübt wird. Durch die hydraulische Einwirkung des Druckmediums (in der Regel Wasser oder Öl) wird das Material gezielt in die Form des umgebenden Werkzeugs gepresst. Die Verformung erfolgt dabei plastisch, sodass das Material nach der Entlastung seine neue Form beibehält. Die Materialverformung wird durch die Fließspannung und die Duktilität des Werkstoffs begrenzt.
Verwendete Materialien und ihre Eigenschaften:
Für die IHU kommen insbesondere Materialien zum Einsatz, die gute Formbarkeit und gleichzeitig hohe Festigkeit aufweisen. Typische Werkstoffe sind Aluminium, Stahl, rostfreier Edelstahl und zunehmend auch Titan für Spezialanwendungen. Die Auswahl des Materials hängt von den Anforderungen an Festigkeit, Korrosionsbeständigkeit und Gewicht der fertigen Komponente ab.
Maschinen und technische Ausstattung für IHU:
Zur Durchführung des IHU-Prozesses werden spezielle Hochdruckmaschinen benötigt, die in der Lage sind, einen Druck von mehreren Tausend bar zu erzeugen. Neben der Hochdruckeinheit gehören hydraulische Pumpen, Steuerungssysteme für die Druckregelung, sowie spezielle Werkzeuge und Formen zur Ausstattung.
3. Prozessstufen der Innenhochdruckumformung
Vorbereitung und Einlegen des Rohmaterials:
Zu Beginn des Prozesses wird das Rohmaterial in Form eines Rohrlings oder einer vorgeformten Platine in die IHU-Form eingelegt. Das Material muss dabei präzise positioniert werden, um ein gleichmäßiges Verformen zu gewährleisten. Meistens erfolgt eine vorherige Erwärmung des Materials, um die Verformbarkeit zu erhöhen und Spannungsrisse zu vermeiden.
Formgebungsprozess (Hochdruckeinbringung, Formgebung):
Nach dem Einlegen wird die Form geschlossen, und das Hochdruckmedium wird eingeführt. Der Druck wird allmählich erhöht, bis das Material sich vollständig an die Innenkontur des Werkzeugs angepasst hat. In diesem Stadium ist die präzise Kontrolle des Drucks entscheidend, da ein zu hoher Druck Materialversagen oder ungleichmäßige Formgebung verursachen kann.
Kühlung und Entformung:
Nach dem Erreichen der endgültigen Form wird das Bauteil in der Form abgekühlt. Die Kühlung kann je nach Material und Anwendung unterschiedlich lange dauern und erfolgt meistens durch gezielte Wasserzufuhr oder Luftkühlung. Anschließend wird das Bauteil aus der Form entnommen.
Nachbearbeitung und Veredelung:
Um die fertige Komponente den spezifischen Anforderungen anzupassen, kann eine Nachbearbeitung erforderlich sein. Dazu zählen die Entfernung überschüssiger Materialreste, das Polieren oder zusätzliche Behandlung zur Verbesserung der Oberflächenqualität, wie das Lackieren oder Beschichten.
4. Gestaltung der Werkzeuge und Formen
Konstruktion von IHU-Formen und deren Spezifikationen:
Die Konstruktion der Werkzeuge und Formen für die IHU ist ein anspruchsvoller Prozess, der präzises Design und technische Kompetenz erfordert. Die Werkzeuge müssen nicht nur dem hohen Druck standhalten, sondern auch eine gleichmäßige Formgebung sicherstellen. Dazu wird CAD-Software verwendet, um komplexe Formen zu entwerfen, die dem fertigen Bauteil möglichst genau entsprechen.
Materialanforderungen und Herstellung der Werkzeuge:
Da die Werkzeuge extremen Kräften standhalten müssen, werden oft hochfeste Stähle verwendet. Zusätzlich sind die Formen häufig beschichtet, um Verschleiß zu minimieren und die Lebensdauer zu verlängern. Die Werkzeuggestaltung spielt eine entscheidende Rolle für die Qualität und Maßgenauigkeit der produzierten Teile.
5. Qualitätskontrolle und Überwachung
Messverfahren und Prüftechniken für die Qualitätssicherung:
Um sicherzustellen, dass die Bauteile die gewünschten Spezifikationen erfüllen, werden verschiedene Messverfahren und Prüftechniken angewendet. Dazu gehören zerstörungsfreie Prüfverfahren wie Ultraschall, Röntgen oder visuelle Inspektionen, um Fehler wie Risse oder Unregelmäßigkeiten in der Wandstärke zu erkennen.
Überwachung und Steuerung des Drucks und der Verformung:
Der Druck und die Verformung des Materials müssen während des gesamten Prozesses genau überwacht werden, da Abweichungen zu Materialversagen führen können. Moderne IHU-Maschinen sind oft mit Sensoren ausgestattet, die kontinuierliche Messungen durchführen und die Prozessparameter automatisch anpassen.
Fehlererkennung und Lösungen:
Sollten Fehler wie Risse oder ungleichmäßige Wanddicken auftreten, wird der Prozess analysiert und optimiert. Häufig ist es notwendig, den Druckverlauf anzupassen oder die Werkzeuggeometrie zu optimieren, um die gewünschten Ergebnisse zu erzielen.
6. Herausforderungen und Lösungsansätze
Materialermüdung und strukturelle Integrität:
Da das Material beim IHU-Prozess erheblichen Belastungen ausgesetzt ist, können Materialermüdung und strukturelle Schwächen entstehen. Die Entwicklung neuer Legierungen und die gezielte Wärmebehandlung helfen jedoch, die Festigkeit und Lebensdauer der Bauteile zu erhöhen.
Energieverbrauch und Umwelteinflüsse:
Der hohe Energieaufwand für das Erzeugen des erforderlichen Drucks ist eine Herausforderung in Bezug auf Energieeffizienz und Umweltverträglichkeit. Neue, energieeffiziente Pumpen und recycelbare Druckmedien tragen dazu bei, den ökologischen Fußabdruck der IHU zu reduzieren.
Prozessoptimierung und Innovationen:
In den letzten Jahren wurden verschiedene Innovationen eingeführt, um den IHU-Prozess weiter zu verbessern. Dazu gehören fortschrittliche Simulationstechniken, die den Formgebungsprozess vorab virtuell modellieren, sowie adaptive Steuerungssysteme, die auf Echtzeitmessungen basieren.
Einführung und Grundlagen
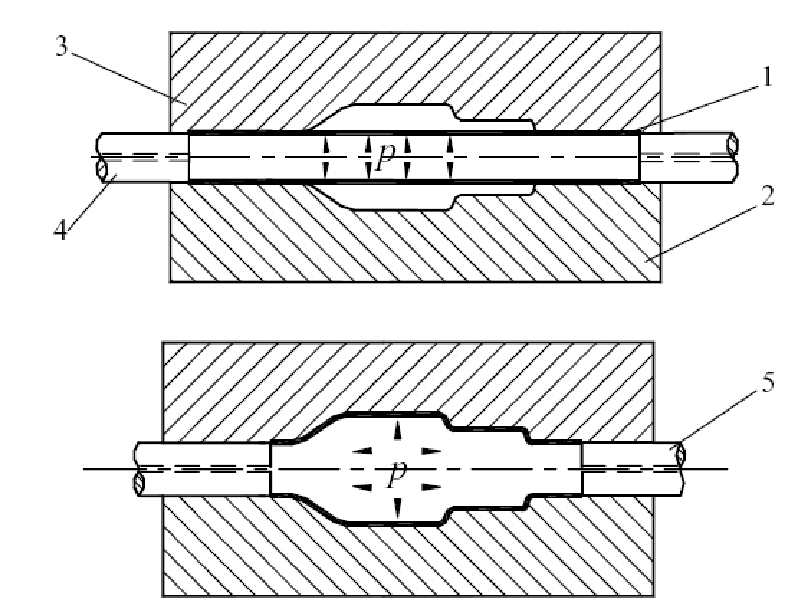
Definition und Bedeutung der Innenhochdruckumformung
Die Innenhochdruckumformung (IHU) ist ein Verfahren, das zur Herstellung von hohlen und komplex geformten Bauteilen dient, indem hoher Druck von innen auf das Werkstück ausgeübt wird. Diese Technologie bietet eine hohe Präzision und ermöglicht die Herstellung nahtloser Komponenten, die für verschiedene industrielle Anwendungen geeignet sind.
Technologische Relevanz und Vorteile des Verfahrens
IHU hat sich als zentrale Technik in der modernen Fertigung etabliert, da sie die Möglichkeit bietet, leichtere und gleichzeitig stabilere Bauteile zu produzieren. Durch den Einsatz von IHU können mehrere Bauteile zu einem einzigen zusammengefasst werden, was Montagekosten spart und das Risiko potenzieller Schwachstellen durch Schweißnähte minimiert.
Automobilindustrie
Die Automobilindustrie ist der größte Anwendungsbereich für die Innenhochdruckumformung. Hier einige spezifische Beispiele:
Struktur- und Sicherheitskomponenten
IHU wird zur Herstellung von Strukturbauteilen wie Rahmen, Querträgern und Längsträgern eingesetzt. Diese Teile sind entscheidend für die Stabilität und Sicherheit von Fahrzeugen. IHU ermöglicht die Herstellung von hochfesten, dünnwandigen Bauteilen, die gleichzeitig leichter und kostengünstiger herzustellen sind. Die Formgebung ist präzise, was die Montage erleichtert und die Passgenauigkeit gewährleistet.
Abgassysteme und leichtere Fahrzeugkonstruktionen
Moderne Abgassysteme erfordern komplexe, nahtlose Rohrsysteme, die hohen Temperaturen und Vibrationen standhalten müssen. Innenhochdruckumformung bietet hier eine wirtschaftliche Lösung zur Herstellung solcher Komponenten. Zudem trägt IHU zur Reduktion des Fahrzeuggewichts bei, was den Kraftstoffverbrauch und die CO₂-Emissionen senkt – ein entscheidender Faktor in der heutigen Automobilindustrie.
Kostenvorteile und Nachhaltigkeit in der Serienproduktion
Dank der automatisierbaren Prozesse der IHU lassen sich große Serien von Fahrzeugkomponenten effizient herstellen. Da durch das Hydroforming mehrere Teile zusammengeführt werden können, reduziert sich der Materialaufwand. Das Verfahren ermöglicht außerdem eine effiziente Materialausnutzung, da die Wandstärke der Bauteile präzise angepasst werden kann.
Luft- und Raumfahrtindustrie
Die Luftfahrtindustrie hat strenge Anforderungen an Material und Fertigungstechniken. Leichte und gleichzeitig hochfeste Komponenten sind unerlässlich, und hier spielt die IHU eine wichtige Rolle.
Anforderungen an Gewicht und Festigkeit
In der Luftfahrttechnik sind Materialeinsparungen essenziell, da Gewichtseinsparungen die Betriebskosten senken. Komponenten wie Tragflächenstrukturen, Rumpfelemente und Stützrahmen profitieren von der Innenhochdruckumformung, da das Verfahren eine Materialverteilung ermöglicht, die Festigkeit und Leichtigkeit kombiniert. Dies ist entscheidend für die Konstruktion sicherer und effizienter Flugzeuge.
Anwendungen für Triebwerks- und Rumpfkomponenten
Bauteile für Flugzeugtriebwerke und der Rumpf müssen nicht nur leicht, sondern auch hitzebeständig und hochfest sein. Mit IHU lassen sich nahtlose, präzise geformte Hohlprofile herstellen, die den Belastungen standhalten und gleichzeitig leicht bleiben. Die gleichmäßige Wandstärke sorgt dafür, dass die Teile unter Druck stabil bleiben.
Vorteile der IHU für die Reduktion der Materialkosten
Die Herstellungskosten können durch die IHU gesenkt werden, da das Verfahren Materialverschwendung minimiert. Es entstehen Bauteile mit der nötigen Wandstärke und ohne unnötige Masse, was die Kosten sowohl bei der Materialbeschaffung als auch im Betrieb reduziert.
Konsumgüterindustrie
Auch in der Konsumgüterindustrie spielt die Innenhochdruckumformung eine Rolle, vor allem bei Produkten, die hohe Ansprüche an Design und Festigkeit haben.
Fahrräder und Sportgeräte
Fahrradrahmen sind ein Paradebeispiel für den Einsatz der Innenhochdruckumformung in der Konsumgüterindustrie. Die Rahmen müssen leicht und dennoch stabil sein, um den Anforderungen von Berg- und Rennrädern gerecht zu werden. Durch IHU können Rahmen in einem Stück und ohne Schweißnähte hergestellt werden, was die Festigkeit erhöht und das Gewicht reduziert.
Haushaltsgeräte und Möbelkomponenten
Innenhochdruckumformung wird auch für Teile von Haushaltsgeräten und Möbeln genutzt, bei denen dünnwandige, nahtlose Rohre erforderlich sind. Beispielsweise werden Rohre für Staubsauger oder Rahmen für hochwertige Stühle oft mit IHU hergestellt. Das Verfahren ermöglicht dabei eine ästhetische Gestaltung der Oberflächen und eine lange Lebensdauer.
Präzision und Ästhetik in der Konsumgüterproduktion
In der Konsumgüterbranche ist neben der Funktionalität auch die Ästhetik entscheidend. Die Möglichkeit, komplexe Formen präzise zu gestalten und nahtlose Oberflächen zu erzeugen, ist ein großer Vorteil der IHU. Zudem lassen sich die Komponenten leicht weiterverarbeiten oder beschichten, was den ästhetischen Ansprüchen gerecht wird.
Medizintechnik
In der Medizintechnik sind Präzision und Biokompatibilität wesentliche Anforderungen, die durch die Innenhochdruckumformung erfüllt werden können.
Medizinische Geräte und Instrumente
Instrumente und Geräte wie endoskopische Geräte oder chirurgische Werkzeuge werden oft durch Innenhochdruckumformung hergestellt. Die Hohlprofile und Rohre müssen dünnwandig und präzise sein, damit sie leicht zu reinigen und steril zu halten sind. Die IHU bietet eine Möglichkeit, diese Anforderungen zu erfüllen, da nahtlose und glatte Innenwände erzeugt werden können.
Leichte und langlebige Komponenten für Prothesen und Implantate
Prothesen und Implantate müssen leicht, stabil und korrosionsbeständig sein. Titan, ein biokompatibles Material, wird häufig für Prothesen verwendet und lässt sich durch IHU formen. Durch die gleichmäßige Wandstärke und die Präzision des Verfahrens entstehen langlebige Produkte, die gleichzeitig den Anforderungen der Medizin gerecht werden.
Biokompatibilität und sterilisierbare Bauteile
Materialien, die mit IHU verarbeitet werden, sind häufig korrosionsbeständig und biokompatibel, was sie ideal für die Medizintechnik macht. Diese Komponenten können leicht sterilisiert und bei Bedarf individuell angepasst werden.
Energie- und Umwelttechnik
IHU wird in der Energie- und Umwelttechnik für die Herstellung langlebiger und korrosionsbeständiger Komponenten eingesetzt.
Anwendungen in der Herstellung von Rohren und Wärmetauschern
Wärmetauscher in Energieanlagen oder Rohrleitungen für die Wasseraufbereitung müssen hohen Drücken und chemischen Einflüssen standhalten. Mit IHU lassen sich Rohre herstellen, die diesen Anforderungen gerecht werden. Durch nahtlose und präzise Formgebung wird die Gefahr von Leckagen und Korrosion minimiert.
Wasser- und Abfallbehandlung
In der Wasseraufbereitung werden Rohre und Behälter aus korrosionsbeständigen Materialien benötigt. IHU ermöglicht die Herstellung solcher Bauteile mit einer glatten Innenoberfläche, die den Widerstand gegen Verschmutzung und Ablagerungen erhöht.
Effizienz und Korrosionsbeständigkeit
IHU-Teile weisen oft eine gleichmäßige Wandstärke und hohe Korrosionsbeständigkeit auf, was sie langlebig und effizient macht. Dies reduziert die Wartungskosten und verlängert die Lebensdauer der Komponenten, was für die Energie- und Umwelttechnik von Vorteil ist.
Baumaschinen- und Landtechnik
Die Herstellung von Baumaschinen und Geräten für die Landtechnik erfordert robuste und langlebige Komponenten, die extremen Belastungen standhalten.
Schwerlastkomponenten mit hoher Stabilität
Komponenten für Bagger, Traktoren oder andere schwere Geräte müssen stabil und verschleißfest sein. Innenhochdruckumformung ermöglicht die Produktion hochfester Teile, die im Einsatz hohen Belastungen und Vibrationen standhalten.
Träger- und Verbindungselemente in Baugeräten
Träger- und Verbindungselemente, die durch IHU gefertigt werden, bieten eine hohe Festigkeit und Belastbarkeit. Sie sind entscheidend für die Stabilität und Sicherheit der Maschinen und können nahtlos und präzise gefertigt werden, um die Zuverlässigkeit zu erhöhen.
Beständigkeit und Lebensdauer
Die langen Standzeiten und die Widerstandsfähigkeit gegen äußere Einflüsse machen IHU-Komponenten zur ersten Wahl in der Land- und Baumaschinenindustrie. Die durch Innenhochdruckumformung erzeugten Bauteile sind besonders langlebig, was Wartungskosten reduziert und die Gesamtbetriebskosten senkt.
Für eine 3.000-Wörter-Abhandlung zur Definition und Bedeutung der Innenhochdruckumformung (IHU) wird ein umfassender Überblick notwendig. Dazu gehören die präzise Definition des Verfahrens, die technischen Grundlagen, ein detaillierter Einblick in den Prozess, historische und wirtschaftliche Bedeutung sowie eine tiefgehende Analyse der Anwendungs- und Zukunftsperspektiven der IHU. Hier ist eine Gliederung und anschließend der detaillierte Einstieg.
Einführung in die Innenhochdruckumformung (IHU)
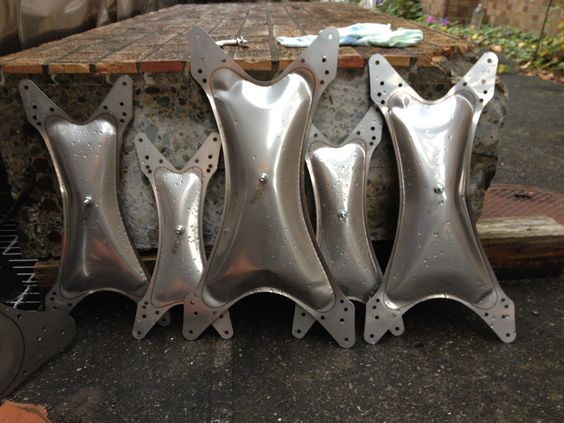
Allgemeine Definition und technologische Einordnung
Die Innenhochdruckumformung (IHU) ist ein modernes Fertigungsverfahren, das zur Herstellung von komplex geformten, hohlen Bauteilen aus Metall verwendet wird. Hierbei wird durch den Einsatz eines Hochdruckmediums, typischerweise Wasser oder Öl, von innen ein hoher Druck auf ein hohles Werkstück ausgeübt, das innerhalb einer geschlossenen Form liegt. Dadurch passt sich das Material der Formkontur an und erhält die gewünschte Form.
Ziel und Funktionsweise des Verfahrens
Das Ziel der IHU ist es, Bauteile zu produzieren, die nicht nur leicht und hochfest sind, sondern auch kostengünstig und präzise gefertigt werden können. Die Technik der Innenhochdruckumformung basiert auf der Verformung des Materials durch hydraulischen Druck, was eine gleichmäßige Wandstärke und komplexe Geometrien ermöglicht, die durch konventionelle Umformverfahren schwer oder gar nicht erreichbar sind.
Unterschied zu anderen Umformtechniken
Im Vergleich zu herkömmlichen Verfahren wie dem Stanzen oder Biegen ermöglicht die IHU die Herstellung nahtloser Hohlprofile ohne Schweißnähte, was die strukturelle Festigkeit verbessert. Auch die Materialausnutzung ist bei der IHU effizienter, da die Wandstärke präzise angepasst werden kann und keine Materialüberlappungen erforderlich sind.
Technische Grundlagen der Innenhochdruckumformung
Physikalische Prinzipien (Druck, Materialverformung)
Die IHU nutzt die plastische Verformbarkeit von Metallen, um diese durch die Einwirkung von hydraulischem Druck in die gewünschte Form zu bringen. Hierbei wird das Material bis zum Punkt der plastischen Verformung belastet, was eine dauerhafte Veränderung seiner Geometrie bewirkt. Der benötigte Druck hängt von der Festigkeit und der Duktilität des verwendeten Materials sowie von der angestrebten Endform ab.
Wichtige Parameter und Prozessvariablen
Entscheidend für die Qualität der Innenhochdruckumformung sind verschiedene Prozessparameter:
- Druckhöhe: Der notwendige Druck variiert je nach Material und Form des Werkstücks und kann Werte von mehreren tausend Bar erreichen.
- Temperatur: Einige Werkstoffe wie Aluminium lassen sich durch eine gezielte Erwärmung besser verformen, was den Druckbedarf reduziert und Materialermüdung minimiert.
- Einlegedauer und Verformungsgeschwindigkeit: Die Geschwindigkeit, mit der der Druck aufgebaut wird, beeinflusst die Formgenauigkeit und vermeidet Spannungsrisse im Material.
Verwendete Werkstoffe und deren Anforderungen
Für die IHU eignen sich insbesondere Metalle wie Aluminium, Edelstahl und hochfeste Stähle. Diese Werkstoffe bieten die nötige Duktilität und Festigkeit, um den Formgebungsprozess zu durchlaufen, ohne dabei Risse oder andere Defekte zu entwickeln. Auch Titan wird aufgrund seiner hervorragenden Festigkeitseigenschaften und Biokompatibilität in speziellen Anwendungen, etwa in der Luftfahrt oder Medizintechnik, eingesetzt.
Prozessablauf der IHU
Vorbereitung des Werkstücks und Einlegen des Rohmaterials
Zu Beginn des IHU-Prozesses wird das Rohmaterial, meistens in Form eines Metallrohres oder -bleches, in eine Form eingelegt, die dem Endprodukt entspricht. Das Material muss präzise positioniert und gegebenenfalls erwärmt werden, um optimale Verformungseigenschaften zu erzielen.
Druckeinbringung und Formgebung
Nach dem Einlegen des Rohmaterials wird der Druck schrittweise erhöht, um das Material gleichmäßig gegen die Innenwände des Werkzeugs zu pressen. Die Präzision dieses Schrittes ist entscheidend, da ein zu schneller Druckaufbau zu Rissen oder Materialschäden führen kann, während ein zu langsamer Aufbau die Produktionszeit und Kosten erhöht.
Entformung und eventuelle Nachbearbeitung
Nach dem Erreichen der gewünschten Form wird der Druck schrittweise abgebaut, und das Bauteil kann entnommen werden. In einigen Fällen sind Nachbearbeitungsschritte erforderlich, wie das Entfernen überschüssigen Materials, Polieren oder Beschichtungen, um die Oberflächenqualität und Beständigkeit des Bauteils zu verbessern.
Historische Entwicklung der Innenhochdruckumformung
Ursprünge und erste Anwendungen
Die Innenhochdruckumformung wurde in den 1950er Jahren zunächst in der Luft- und Raumfahrttechnik angewendet. Ziel war es, leichte und gleichzeitig hochfeste Strukturen zu entwickeln, die extremen Bedingungen standhalten. In den 1990er Jahren fand das Verfahren verstärkt in der Automobilindustrie Anwendung, wo es zur Herstellung leichter und stabiler Rahmen- und Abgassysteme genutzt wurde.
Technologische Fortschritte und Verbreitung des Verfahrens
In den letzten Jahrzehnten hat sich die IHU kontinuierlich weiterentwickelt. Durch technologische Fortschritte in den Bereichen Materialwissenschaft und Maschinenbau wurde es möglich, den Druck und die Prozessparameter präzise zu steuern. Auch die Entwicklung hochfester Werkstoffe wie Aluminiumlegierungen und Duplexstähle hat zur Verbreitung der IHU beigetragen.
Bedeutung in der modernen Fertigungsindustrie
Heute ist die Innenhochdruckumformung in zahlreichen Branchen unverzichtbar, von der Automobilindustrie über die Luftfahrt bis hin zur Medizintechnik. Die Fähigkeit, komplexe Bauteile nahtlos und präzise zu fertigen, hat IHU zu einer Schlüsseltechnologie in der modernen Produktion gemacht.
Wirtschaftliche Bedeutung der IHU
Kostenvorteile und Produktivitätssteigerung
Die IHU ermöglicht es, mehrere Bauteile zu einem einzigen zusammenzuführen, was die Montagekosten senkt und die Produktionszeit verkürzt. Dadurch sinkt der Bedarf an Schweiß- oder Klebearbeiten, was wiederum Material- und Personalkosten spart. Zudem führt die Möglichkeit, hochpräzise Bauteile in großen Stückzahlen zu produzieren, zu einer erheblichen Produktivitätssteigerung.
Einsatz in verschiedenen Branchen und industrielle Relevanz
IHU hat sich als wirtschaftlich effizientes Verfahren für Branchen etabliert, die Wert auf Stabilität, Leichtigkeit und Präzision legen. In der Automobilindustrie senkt die Anwendung der IHU die Herstellungskosten und steigert die Kraftstoffeffizienz durch geringeres Fahrzeuggewicht. In der Luftfahrt und Medizintechnik werden Bauteile aus teuren Materialien wie Titan und Edelstahl optimal genutzt, was Kosten spart und die Effizienz erhöht.
Beitrag zur Nachhaltigkeit und Ressourceneffizienz
Durch die optimierte Materialverteilung und die geringere Notwendigkeit von Verbindungstechniken trägt die IHU zur Material- und Ressourceneffizienz bei. Zudem senkt die längere Lebensdauer der Bauteile die Notwendigkeit für Ersatzteile, was die Umweltbelastung reduziert.
Vorteile und Herausforderungen der Innenhochdruckumformung
Vorteile in Bezug auf Gewicht, Stabilität und Designfreiheit
Die Innenhochdruckumformung bietet zahlreiche Vorteile, darunter:
- Gewichtsreduktion: Durch das präzise Anpassen der Wandstärke wird Material eingespart und die Bauteile bleiben trotzdem stabil.
- Erhöhte strukturelle Festigkeit: Nahtlose Bauteile haben keine Schwachstellen, die bei Belastung versagen könnten.
- Komplexe Formen und Designfreiheit: Die Flexibilität der IHU ermöglicht es, komplexe Strukturen zu realisieren, die anderen Umformverfahren überlegen sind.
Prozessspezifische Herausforderungen und Lösungsansätze
Zu den Herausforderungen der IHU gehören die hohen Anforderungen an die Drucksteuerung und Materialqualität. Da das Verfahren auf extremen Druck angewiesen ist, sind hochwertige Materialien und eine präzise Steuerung notwendig, um Materialversagen zu vermeiden. Fortschritte in der Digitalisierung und Sensorik haben dazu beigetragen, den Prozess sicherer und zuverlässiger zu gestalten.
Zukunftsperspektiven und technologische Entwicklungen
Entwicklungen in der Materialforschung
Die stetige Verbesserung der Materialeigenschaften, wie die Entwicklung von hochfesten, duktilen Legierungen, ermöglicht es, die IHU weiterzuentwickeln und für neue Einsatzgebiete nutzbar zu machen. Werkstoffe, die sowohl leicht als auch belastbar sind, tragen zur erweiterten Anwendung in anspruchsvollen Bereichen wie der Luftfahrt bei.
Digitalisierung und Prozessautomatisierung
Mit der zunehmenden Digitalisierung und den Fortschritten in der Automatisierung wird die IHU zunehmend in die Industrie 4.0 integriert. Sensoren und Echtzeit-Datenverarbeitungssysteme ermöglichen eine kontinuierliche Überwachung und Steuerung des Drucks und anderer Prozessparameter. Dies verbessert die Qualitätssicherung und reduziert Produktionskosten.
Zukunftspotenzial der Innenhochdruckumformung in der Industrie 4.0
Mit der Einführung von 3D-Druck und hybriden Fertigungsverfahren könnte die IHU auch in die additive Fertigung integriert werden. Die Möglichkeit, komplexe Geometrien mithilfe von IHU herzustellen und gleichzeitig additive Methoden zu nutzen, erweitert das Anwendungsspektrum und erhöht die Flexibilität in der Herstellung.
Allgemeine Definition und Bedeutung der IHU
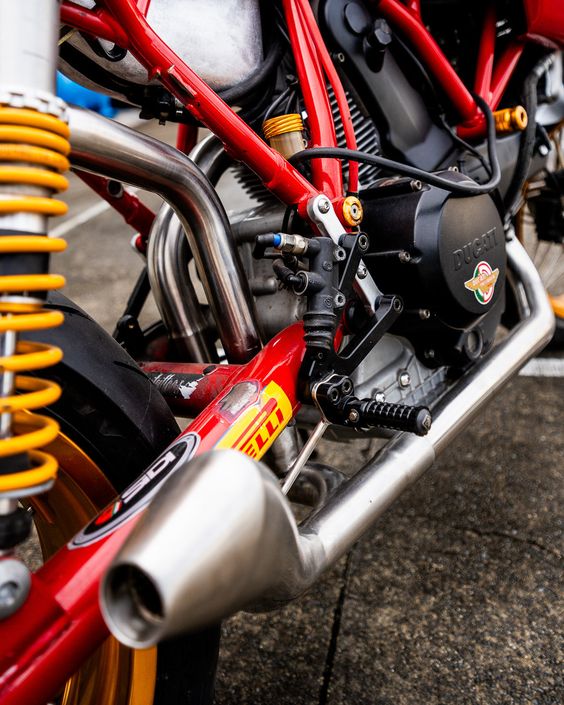
Grundlegende Funktionsweise der Innenhochdruckumformung
Die Innenhochdruckumformung (IHU) ist ein Verfahren zur Umformung von Hohlkörpern aus Metall durch Innendruck. Bei diesem Verfahren wird ein hohles Werkstück, meist in Form eines Metallrohrs, in eine Form gelegt und durch hohen Innendruck in die Form gepresst, sodass es die gewünschte Kontur annimmt. Das Druckmedium, in der Regel Wasser oder Öl, wird kontrolliert in das Werkstück gepresst, sodass es plastisch verformt wird und seine neue Form dauerhaft behält.
Bedeutung des Verfahrens in der modernen Fertigung
IHU ist besonders in der Automobil- und Luftfahrtindustrie von großer Bedeutung, wo leichte, aber hochfeste Bauteile gefragt sind. Da das Verfahren die Möglichkeit bietet, Bauteile nahtlos und in komplexen Geometrien herzustellen, trägt es zur Gewichtsreduktion und zur strukturellen Stabilität bei. Auch im Konsumgüterbereich und der Medizintechnik gewinnt IHU an Bedeutung, da sich damit präzise und nahtlose Hohlprofile mit gleichmäßiger Wanddicke produzieren lassen, was für langlebige und ästhetische Produkte wichtig ist.
Technische Grundlagen der IHU
Druck- und Formgebung: Physikalische Prinzipien
Die IHU basiert auf der plastischen Verformung, die durch hydraulischen Innendruck erzeugt wird. Das Werkstück dehnt sich aufgrund des Drucks aus, bis es die Form des umgebenden Werkzeugs annimmt. Der Druck muss so dosiert werden, dass die Materialfestigkeit nicht überschritten wird und eine gleichmäßige Verformung erzielt wird. Die plastische Verformung des Metalls ermöglicht eine dauerhafte Formgebung, die den Belastungen standhält.
Wichtige Materialien und ihre Eigenschaften
Die IHU ist besonders geeignet für Metalle mit hoher Duktilität und Festigkeit, wie Aluminium, Edelstahl, Titan und bestimmte Stahllegierungen. Diese Materialien können hohe Drücke aufnehmen und plastisch verformt werden, ohne zu reißen. Speziell für die Luft- und Raumfahrt und die Medizintechnik kommen oft Titan und Edelstahl zum Einsatz, während Aluminium aufgrund seines geringen Gewichts und seiner Korrosionsbeständigkeit in der Automobilindustrie sehr gefragt ist.
Druckmedien und technische Ausrüstung
Für den Druckaufbau werden meist Wasser oder Öl verwendet. Die Hochdruckpumpen müssen Druckwerte von mehreren Tausend Bar erreichen, abhängig vom verwendeten Werkstoff und der Größe des Bauteils. Die Maschinen sind in der Regel mit digitalen Steuerungssystemen und Sensoren ausgestattet, um den Druckverlauf zu kontrollieren und eine gleichmäßige Verformung zu gewährleisten. Hochpräzise Werkzeuge und Formen aus gehärtetem Stahl sorgen dafür, dass das Material exakt in die gewünschte Form gebracht wird.
Historische Entwicklung und technologische Fortschritte
Ursprünge und erste Anwendungen
Die Innenhochdruckumformung entwickelte sich Mitte des 20. Jahrhunderts, als in der Luftfahrtindustrie zunehmend nach leichten, nahtlosen Bauteilen gesucht wurde. Die ersten Anwendungen des Verfahrens konzentrierten sich auf die Herstellung von komplexen Rumpf- und Triebwerksbauteilen. Die Möglichkeit, durch Innendruck stabile, aber leichte Strukturen zu erzeugen, machte die IHU schnell zu einem wichtigen Verfahren.
Verbreitung und technologische Innovationen
In den 1990er Jahren begann sich die Innenhochdruckumformung verstärkt in der Automobilindustrie durchzusetzen, wo der Leichtbau eine zunehmende Rolle spielte. Technologische Innovationen im Bereich der Hochdruckpumpen und der Digitalisierung machten den Prozess effizienter und präziser. Auch der Einsatz neuer Werkstoffe, wie hochfeste Stahl- und Aluminiumlegierungen, trug zur Verbreitung der IHU bei.
Entwicklung zur Serienfertigung
Mit der Automatisierung und den technologischen Fortschritten wurde IHU zu einem kostengünstigen Verfahren für die Serienfertigung. Besonders die Integration von Sensorik und computergestützter Prozesssteuerung trug dazu bei, die Qualität und Reproduzierbarkeit des Verfahrens zu verbessern, was die Einsatzmöglichkeiten in verschiedenen Industrien weiter erweiterte.
Der IHU-Prozess: Ablauf und Stufen
Vorbereitung des Materials und Werkzeugs
Im ersten Schritt wird das Werkstück in die vorbereitete Form eingelegt. Die richtige Positionierung und eine eventuelle Erwärmung des Materials sind entscheidend, um eine optimale Verformbarkeit zu gewährleisten. Das Werkzeug muss robust und präzise gefertigt sein, da es den extremen Drücken standhalten muss.
Druckaufbau und Formgebung
Sobald das Werkstück positioniert ist, wird das Druckmedium schrittweise eingeführt und der Druck kontrolliert erhöht. Dieser Druckaufbau sorgt dafür, dass das Material in die gewünschte Form gepresst wird. Eine präzise Steuerung ist hier notwendig, da Schwankungen im Druck zu Defekten wie Rissen oder ungleichmäßiger Wanddicke führen können.
Entformung und Nachbearbeitung
Nachdem die Formgebung abgeschlossen ist, wird der Druck abgebaut, und das Bauteil kann entnommen werden. Oft ist eine Nachbearbeitung nötig, wie das Entfernen von überschüssigem Material oder das Polieren der Oberfläche, um die gewünschte Qualität zu erreichen.
Anwendungsgebiete der Innenhochdruckumformung
Automobilindustrie
In der Automobilindustrie wird die IHU vor allem zur Herstellung von Fahrwerk- und Strukturbauteilen verwendet, die leicht und dennoch stabil sein müssen. Beispiele sind Motorträger, Rahmenlängsträger, Abgasanlagen und komplexe Leitungsstrukturen. Die Innenhochdruckumformung trägt dazu bei, das Fahrzeuggewicht zu reduzieren und gleichzeitig die strukturelle Integrität zu verbessern.
Luft- und Raumfahrttechnik
Die Anforderungen an leichte, stabile und hitzebeständige Bauteile machen die IHU auch in der Luftfahrtindustrie zu einem wichtigen Verfahren. Flugzeugrümpfe, Treibstoffleitungen und Strukturkomponenten für die Tragflächen sind typische Anwendungen. Das Verfahren ermöglicht die Herstellung dünnwandiger und dennoch hochfester Bauteile, die entscheidend zur Treibstoffeffizienz und Sicherheit von Flugzeugen beitragen.
Medizintechnik und Konsumgüter
In der Medizintechnik wird die IHU zur Herstellung von Instrumenten, Implantaten und Prothesen genutzt, bei denen hohe Präzision und Biokompatibilität wichtig sind. In der Konsumgüterindustrie wird die IHU beispielsweise für Fahrradrahmen oder Möbelteile verwendet, die leicht und stabil sein müssen.
Vorteile und Herausforderungen der IHU
Vorteile gegenüber anderen Verfahren
IHU bietet eine hohe Präzision und ermöglicht die Herstellung von Bauteilen mit komplexen Geometrien, die durch herkömmliche Umformtechniken nicht möglich wären. Da die Bauteile nahtlos sind, wird die strukturelle Integrität erhöht und das Gewicht reduziert, was für Branchen wie die Automobil- und Luftfahrtindustrie entscheidende Vorteile bringt.
Technische und wirtschaftliche Herausforderungen
Die hohen Drücke, die für die IHU benötigt werden, stellen technologische und wirtschaftliche Herausforderungen dar. Die Ausrüstung ist teuer und erfordert hochwertige Materialien und präzise Steuerung. Zudem kann es bei der Herstellung von sehr komplexen Formen oder bei der Verarbeitung von Materialien mit geringer Duktilität zu Schwierigkeiten kommen.
Lösungsansätze und Prozessoptimierung
Neue Materialien und weiterentwickelte Steuerungstechnologien tragen dazu bei, die Prozessstabilität und die Qualität der Bauteile zu verbessern. Durch die Automatisierung und den Einsatz moderner Sensorik wird der IHU-Prozess zunehmend optimiert, was die Kosten senkt und die Anwendbarkeit des Verfahrens auf neue Produkte und Märkte erweitert.
Zukunftsperspektiven und Potenzial der Innenhochdruckumformung
Innovationen in der Prozessautomatisierung
Mit den Fortschritten im Bereich der Digitalisierung und Industrie 4.0 lässt sich der IHU-Prozess zunehmend automatisieren. Echtzeitüberwachung und adaptive Steuerungssysteme verbessern die Prozesskontrolle und reduzieren Fehler. Dies eröffnet der IHU neue Anwendungen und steigert die Wirtschaftlichkeit in der Serienproduktion.
Bedeutung für die Industrie 4.0 und neue Werkstoffe
Die Industrie 4.0 integriert sensorbasierte Technologien, die eine kontinuierliche Optimierung des Druckverlaufs und der Temperatur ermöglichen. Dies macht die IHU ideal für den Einsatz in der digitalen Fertigung, da Daten zu jedem Produktionsschritt gesammelt und ausgewertet werden können, was die Effizienz erhöht und den Materialverbrauch weiter optimiert.
Ausblick auf zukünftige Entwicklungen und Einsatzmöglichkeiten
Mit der Entwicklung neuer Materialien und der stetigen Verbesserung der Maschinen- und Steuerungstechnologien wird die IHU auch in Zukunft eine Schlüsselrolle spielen. Die Nachfrage nach leichten, stabilen und kostengünstigen Bauteilen in allen Bereichen der Technik und Produktion wird weiter steigen, und die Innenhochdruckumformung bietet die Möglichkeit, diese Anforderungen auf nachhaltige und wirtschaftliche Weise zu erfüllen.
Grundprinzipien der Innenhochdruckumformung
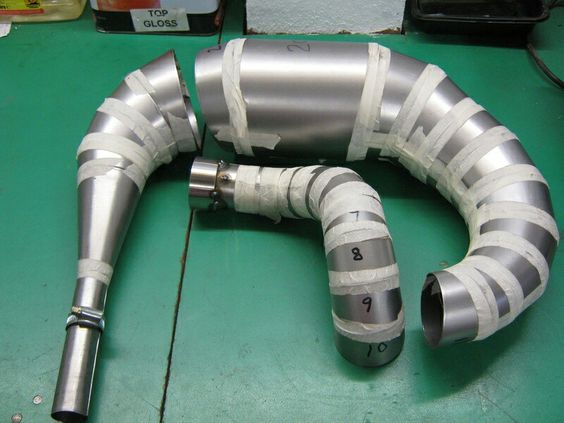
Definition und Ziel des Verfahrens
Die Innenhochdruckumformung (IHU) ist ein Verfahren zur Herstellung komplexer, nahtloser Hohlstrukturen aus Metall. Dabei wird ein Hohlkörper, meist ein Metallrohr, durch das Einbringen von Hochdruck in die Form des umgebenden Werkzeugs gepresst. Dieses Verfahren zielt darauf ab, präzise und langlebige Bauteile herzustellen, die sich durch eine hohe Festigkeit und eine gleichmäßige Wanddicke auszeichnen.
Physikalische Grundlagen der Materialverformung
Das IHU-Verfahren basiert auf der plastischen Verformung von Metallen unter hohen Drücken. Durch den hydraulischen Druck dehnt sich das Material aus und passt sich der Form an. Diese Verformung erfolgt nach dem Gesetz von Hooke im elastischen Bereich und dann plastisch, wenn die Fließspannung des Materials überschritten wird.
Plastische Verformung und Festigkeitsverhalten
Sobald der Druck hoch genug ist, verformt sich das Material dauerhaft. Dabei ist es entscheidend, dass die Fließgrenze des Metalls so gewählt ist, dass es den hohen Drücken standhält, ohne zu reißen. Die Materialwahl und die Anpassung des Drucks an die Festigkeitswerte des Materials sind daher von großer Bedeutung.
2. Einflussfaktoren und Prozessparameter
Innendruck und Materialverformung
Der Innendruck ist der entscheidende Parameter für die Formgebung in der IHU. Der Druck muss so gewählt werden, dass das Material sich ausdehnt, aber nicht reißt. Bei Materialien wie Aluminium und Edelstahl kann der notwendige Druck mehrere tausend Bar betragen, abhängig von der Wandstärke und der gewünschten Endform.
Temperatur und ihr Einfluss auf die Formbarkeit
Die Temperatur hat einen starken Einfluss auf die Formbarkeit der Metalle. Bei höheren Temperaturen wird das Material duktiler, was die Verformung erleichtert und die Gefahr von Rissen reduziert. Einige Metalle, wie Aluminium, werden oft vorgewärmt, um die nötige Duktilität für die Formgebung zu erreichen. Dies spart Energie, da ein niedrigerer Druck eingesetzt werden kann.
Geschwindigkeitskontrolle und Druckaufbau
Die Geschwindigkeit, mit der der Druck aufgebaut wird, beeinflusst die Qualität und Konsistenz der Verformung. Ein zu schneller Druckanstieg kann dazu führen, dass das Material reißt, während ein zu langsamer Druckanstieg die Prozesszeit verlängert und die Produktion verlangsamt. Daher sind Systeme zur Kontrolle des Druckaufbaus entscheidend für die Stabilität des Prozesses.
Verwendete Materialien und Werkstoffeigenschaften
Geeignete Werkstoffe für die IHU
Die Innenhochdruckumformung erfordert Werkstoffe, die eine hohe Dehnbarkeit und Festigkeit kombinieren. Typische Materialien sind Aluminium, Edelstahl, Titan und bestimmte Stahllegierungen. Diese Metalle bieten die nötige Flexibilität und Belastbarkeit, um hohen Druck zu widerstehen und sich gleichzeitig gut formen zu lassen.
Anforderungen an Festigkeit und Dehnbarkeit
Bei der Wahl des Materials müssen sowohl die Fließspannung als auch die Zugfestigkeit berücksichtigt werden. Materialien mit einer hohen Fließspannung, wie Titan und bestimmte Stahlarten, eignen sich besonders gut für IHU, da sie hohen Drücken standhalten und dennoch duktil genug sind, um sich plastisch zu verformen, ohne zu reißen.
Einsatz unterschiedlicher Metalle und Legierungen
Die Auswahl des Metalls hängt stark vom Verwendungszweck ab:
- Aluminium wird wegen seines geringen Gewichts und seiner Korrosionsbeständigkeit häufig in der Automobilindustrie verwendet.
- Edelstahl eignet sich gut für Anwendungen, die hohe Festigkeit und Korrosionsbeständigkeit erfordern, etwa in der Medizintechnik.
- Titan wird für spezialisierte Anwendungen in der Luft- und Raumfahrt und der Medizin verwendet, wo hohe Festigkeit bei geringem Gewicht und Biokompatibilität gefragt sind.
Druckmedien und technische Ausstattung
Funktion und Auswahl der Druckmedien
In der Regel werden für die IHU Flüssigkeiten wie Wasser oder Öl verwendet, da sie eine gleichmäßige Druckverteilung ermöglichen und das Material schonend verformen. Wasser wird oft bevorzugt, da es kostengünstig und leicht zu handhaben ist. Öl kommt in Einsatzbereichen mit hohen Anforderungen an die Oberflächenqualität und Dichtheit zur Anwendung, da es viskos ist und sich gleichmäßig verteilt.
Hochdruckpumpen und Steuerungssysteme
Die für die IHU eingesetzten Hochdruckpumpen müssen sehr hohe Drücke erzeugen können, oft bis zu mehreren Tausend Bar. Die Steuerungssysteme dieser Pumpen sind von großer Bedeutung, da sie den Druckverlauf präzise kontrollieren und schnelle Anpassungen ermöglichen müssen. Sensoren und automatische Regelungen sorgen für eine gleichmäßige Druckverteilung und schützen das Material vor zu starker Belastung.
Anforderungen an Maschinen und Werkzeuge
Die Maschinen, die für die IHU benötigt werden, sind auf eine hohe Stabilität und Präzision ausgelegt, da sie sowohl den hohen Drücken standhalten als auch eine genaue Positionierung und Führung des Werkstücks sicherstellen müssen. Die Werkzeuge bestehen meist aus hochfesten Stählen, die beschichtet sein können, um den Verschleiß durch den Druck und die Belastung zu minimieren.
Werkzeug- und Formgestaltung
Gestaltung der Form und Einfluss auf die Verformung
Die Formgestaltung spielt eine entscheidende Rolle bei der IHU. Die Formen müssen präzise und stabil gefertigt sein, da sie den Innendruck halten und gleichzeitig das Material in die gewünschte Endform bringen. In der Regel werden CAD-Modelle und Simulationen verwendet, um die Form optimal zu gestalten und den Materialfluss im Voraus zu planen.
Materialanforderungen für die Werkzeuge
Die Werkzeuge müssen hohen Drücken und Verschleiß widerstehen, weshalb sie aus hochfesten Stählen bestehen. Zudem werden die Werkzeugoberflächen oft beschichtet, um Reibung zu minimieren und die Lebensdauer zu verlängern. Die Fertigung solcher Formen ist kostenintensiv und erfordert hohe Präzision.
Fertigung und Anpassung von IHU-Formen
Werkzeuge für die IHU werden in der Regel speziell für ein bestimmtes Bauteil gefertigt, was hohe Initialkosten verursacht. Aufgrund der Materialbelastungen und komplexen Geometrien sind regelmäßige Wartung und Anpassung notwendig, um die Bauteilgenauigkeit zu gewährleisten.
Prozesskontrolle und Qualitätsüberwachung
Sensorik und Echtzeitüberwachung
Die Prozesskontrolle während der IHU ist essenziell, um eine gleichbleibende Qualität der Bauteile zu gewährleisten. Sensoren überwachen Druck, Temperatur und Formgenauigkeit in Echtzeit und geben Rückmeldung an das Steuerungssystem. So können Abweichungen sofort erkannt und korrigiert werden, was den Ausschuss minimiert und die Produktionseffizienz erhöht.
Qualitätskontrolle und Prüfung der Formgebung
Nach der Formgebung werden die Bauteile häufig geprüft, um sicherzustellen, dass sie den Qualitätsstandards entsprechen. Neben visuellen Inspektionen und Maßkontrollen kommen zerstörungsfreie Prüfverfahren wie Ultraschall, Röntgen oder CT-Scans zum Einsatz, um innere Defekte, wie Risse oder Unregelmäßigkeiten in der Wandstärke, zu erkennen.
Korrekturmaßnahmen und Prozessoptimierung
Bei Abweichungen oder Defekten wird der Prozess analysiert und die Druckparameter, die Formgeometrie oder das Material entsprechend angepasst. Durch kontinuierliche Optimierungen können die Prozessstabilität und die Qualität der Endprodukte stetig verbessert werden.
Herausforderungen und Lösungsansätze
Technologische Herausforderungen im Hochdruckbereich
Die hohen Drücke, die für die IHU benötigt werden, stellen technologische Herausforderungen dar. Die Maschinen und Werkzeuge müssen nicht nur stabil, sondern auch extrem präzise sein, um gleichmäßige Ergebnisse zu erzielen. Dies erfordert eine regelmäßige Wartung und stellt hohe Anforderungen an die verwendeten Materialien und die Fertigungsqualität der Maschinen.
Materialversagen und Rissbildung
Materialversagen, insbesondere Rissbildung, stellt eine der größten Herausforderungen bei der IHU dar. Hohe Drücke können bei ungleichmäßiger Verformung oder zu geringer Duktilität zu Rissen führen. Durch sorgfältige Materialauswahl, eine präzise Druckkontrolle und die Anpassung der Temperatur lässt sich die Rissbildung jedoch minimieren.
Prozessoptimierung und zukünftige Entwicklungen
Die kontinuierliche Weiterentwicklung der IHU-Technik, insbesondere durch den Einsatz von Sensorik, Automatisierung und Echtzeitüberwachung, trägt dazu bei, die Produktionsqualität und -effizienz zu steigern. Zukunftsperspektiven umfassen die Integration in die Industrie 4.0 und den Einsatz neuer Materialien, die noch höhere Festigkeitsanforderungen erfüllen und gleichzeitig kostengünstiger produziert werden können.
Vorbereitung des Werkstücks und des Werkzeugs
Auswahl und Vorbereitung des Rohmaterials
Die Innenhochdruckumformung erfordert das richtige Rohmaterial, das in der Regel als Rohrling oder vorgeformte Blechplatine vorliegt. Die Materialauswahl erfolgt basierend auf den Anforderungen an Festigkeit und Duktilität, um die spätere Verformung zu gewährleisten. Vor der Verarbeitung wird das Rohmaterial auf Risse, Oberflächenfehler und Materialstärken überprüft, da diese Faktoren entscheidend für die Qualität des Endprodukts sind.
Werkzeugvorbereitung und Reinigung
Das Werkzeug, das für den IHU-Prozess benötigt wird, muss eine einwandfreie Oberfläche und eine exakte Geometrie aufweisen, da es die Form des Werkstücks vorgibt. Werkzeuge bestehen häufig aus hochfestem, verschleißfestem Stahl, der speziell beschichtet sein kann. Vor jedem Umformprozess wird das Werkzeug gründlich gereinigt und auf Risse oder Abnutzungen überprüft.
Einlegen des Werkstücks und Positionierung
Das Einlegen und genaue Positionieren des Werkstücks im Werkzeug ist ein wichtiger Schritt, um eine gleichmäßige Formgebung zu gewährleisten. Das Werkstück wird in der Regel in Halterungen fixiert, die es vor Bewegungen schützen und eine stabile Basis für den Verformungsprozess bieten.
Initiale Erwärmung und Materialaufbereitung
Temperaturmanagement und Vorwärmung
Bei bestimmten Materialien, insbesondere bei Aluminium und einigen speziellen Stählen, kann eine Vorwärmung des Werkstücks erforderlich sein. Diese Erwärmung erhöht die Formbarkeit des Materials und senkt die notwendige Druckhöhe. Übliche Temperaturen liegen zwischen 100 und 300 °C, je nach Material und Verformungsanforderungen.
Einfluss der Temperatur auf die Verformbarkeit
Durch die Erwärmung wird das Material duktiler und die Fließspannung verringert sich. Dies erleichtert den Umformprozess und reduziert die Gefahr von Rissen und Bruchstellen während der Formgebung. Auch die Homogenität des Materials wird durch die Erwärmung verbessert, was eine gleichmäßigere Wandstärke ermöglicht.
Anpassung an spezifische Materialien
Je nach Art des Werkstückmaterials können unterschiedliche Vorwärmtemperaturen notwendig sein. Beispielsweise erfordert Edelstahl eine geringere Vorwärmung als Aluminium, da Edelstahl bei höheren Temperaturen seine Festigkeit verliert. Bei Aluminium kann eine höhere Temperatur die Gefahr von Spannungsrissen reduzieren.
Druckaufbau und Formgebung
Einbringen des Druckmediums und Druckaufbau
Das Kernstück des IHU-Prozesses ist das Einbringen des Druckmediums in das Werkstück. In der Regel werden Wasser oder Hydrauliköl als Druckmedien verwendet. Das Druckmedium wird in das Werkstück eingeführt und der Druck wird kontinuierlich erhöht, bis das Material sich gegen die Innenwände des Werkzeugs anlegt und die gewünschte Form erreicht.
Prozesssteuerung und Kontrolle des Druckverlaufs
Eine präzise Steuerung des Druckverlaufs ist entscheidend für die Formgebung und Qualität des Werkstücks. Zu schnelles Erhöhen des Drucks kann Materialschäden oder Risse verursachen, während ein zu langsamer Druckaufbau die Produktionszeit und damit die Kosten erhöht. Die Steuerungssysteme sind oft mit Sensoren ausgestattet, die den Druck, die Temperatur und die Formgenauigkeit in Echtzeit überwachen.
Gleichmäßige Verformung und Wanddickenkontrolle
Die gleichmäßige Verteilung des Drucks sorgt dafür, dass das Material gleichmäßig in die Form gepresst wird und eine konstante Wanddicke erreicht wird. Die Wanddickenkontrolle ist besonders wichtig bei Anwendungen, die hohe Stabilitätsanforderungen an das Endprodukt stellen, wie z.B. in der Automobil- und Luftfahrtindustrie.
Entformung und Nachbearbeitung
Druckabbau und Entnahme des Werkstücks
Nach dem Abschluss der Formgebung wird der Druck schrittweise reduziert, damit das Werkstück spannungsfrei entnommen werden kann. Dies verhindert plötzliche Druckabfälle, die zu Schäden am Werkstück führen könnten. Nach dem Druckabbau wird das Werkstück entnommen und auf erste Qualitätsmerkmale überprüft.
Nachbearbeitung und Qualitätskontrolle
Die Nachbearbeitung umfasst die Beseitigung von überschüssigem Material, Kanten- und Oberflächenbearbeitung sowie, falls notwendig, eine Wärmebehandlung zur Verbesserung der mechanischen Eigenschaften. Diese Nachbearbeitungsschritte hängen von den spezifischen Anforderungen des Endprodukts ab.
Entfernung überschüssigen Materials und Oberflächenbearbeitung
Bei der IHU kann es vorkommen, dass an den Enden des Werkstücks Materialüberschuss entsteht. Dieser wird durch Abschneiden oder Schleifen entfernt. Für eine glatte und ästhetische Oberfläche kann das Werkstück anschließend poliert, beschichtet oder gestrahlt werden.
Qualitätskontrolle und Fehlerbehebung
Prüfverfahren für Maßhaltigkeit und Defekterkennung
Nach der Formgebung wird das Werkstück geprüft, um sicherzustellen, dass es die erforderlichen Maßtoleranzen und Oberflächenstandards erfüllt. Typische Prüfverfahren umfassen visuelle Inspektionen, Maßkontrollen sowie zerstörungsfreie Prüfmethoden wie Ultraschall, Röntgen oder Magnetpulverprüfung, um innere Defekte zu erkennen.
Überwachung der Wandstärke und Dichtheit
Die Wandstärke ist ein wichtiger Qualitätsaspekt, der bestimmt, ob das Werkstück den mechanischen Belastungen standhält. Die Wanddicke wird präzise gemessen, und die Dichtheit des Werkstücks wird durch Dichtheitsprüfungen überprüft. Eine einheitliche Wandstärke erhöht die Langlebigkeit und Festigkeit des Bauteils.
Fehleranalyse und Prozessoptimierung
Bei der Erkennung von Fehlern wie Rissen oder ungleichmäßiger Wandstärke erfolgt eine Analyse des Prozesses, um den Fehlerursachen auf den Grund zu gehen. Dazu zählen die Überprüfung der Druckparameter, des Werkstückmaterials und der Formgeometrie. Prozessanpassungen und Optimierungen sind notwendig, um die Ausschussrate zu minimieren und die Effizienz zu maximieren.
Prozessvarianten und spezifische Anpassungen
Unterschiedliche Druckmedien und Einfluss auf die Formgebung
Je nach Anforderung können unterschiedliche Druckmedien eingesetzt werden. Wasser ist aufgrund seiner Kosten und leichten Handhabung weit verbreitet, während Öl für Anwendungen mit höheren Anforderungen an die Oberflächenqualität verwendet wird. Die Wahl des Druckmediums beeinflusst die Fließverhalten und die Genauigkeit der Formgebung.
Optimierung des IHU-Prozesses für spezifische Werkstoffe
Materialien wie Aluminium und Titan erfordern spezifische Druckparameter und Prozessschritte, um optimale Ergebnisse zu erzielen. Aluminium, ein leichtes und formbares Material, wird oft bei geringeren Drücken geformt, während Titan eine spezielle Vorbehandlung und Druckführung erfordert, um Brüche zu vermeiden.
Anpassungen für spezielle Bauteilgeometrien
Besonders komplexe Geometrien, wie asymmetrische Bauteile oder Teile mit variabler Wanddicke, stellen besondere Anforderungen an den IHU-Prozess. Durch die Anpassung der Druckführung, den Einsatz von Werkzeugen mit variabler Form und die Simulation des Materialflusses wird sichergestellt, dass die gewünschte Formgebung erreicht wird.
Zusammenfassung und Ausblick
Bedeutung der Prozessschritte für die Bauteilqualität
Jeder Prozessschritt im IHU ist entscheidend für die endgültige Qualität und Leistungsfähigkeit des Bauteils. Von der Materialvorbereitung bis zur Qualitätskontrolle beeinflusst jeder Abschnitt das Endprodukt in Hinblick auf Maßgenauigkeit, Oberflächenqualität und strukturelle Integrität.
Zusammenhänge zwischen Prozessablauf und Endprodukt
Ein optimal gestalteter Prozessablauf reduziert die Produktionszeit und Kosten, minimiert Ausschuss und sorgt dafür, dass die Bauteile alle Anforderungen erfüllen. Die präzise Steuerung des Drucks und die Anpassung an Materialeigenschaften und Bauteilgeometrie sind Schlüsselkomponenten eines erfolgreichen IHU-Prozesses.
Technologische Entwicklungen und zukünftige Prozessoptimierungen
Zukünftige Entwicklungen konzentrieren sich auf die Integration digitaler Steuerungstechnologien und die Automatisierung des Prozesses. Die Industrie 4.0 verspricht Echtzeit-Überwachung und adaptive Steuerungen, die den Prozessablauf noch effizienter gestalten und die Qualität weiter steigern. Fortschritte in der Materialforschung und -technologie werden das Anwendungsspektrum der IHU in der Industrie weiter ausweiten.
Die 1950er- bis 1970er-Jahre: Anfänge der IHU in der Industrie
Pionieranwendungen in der Luftfahrtindustrie
In den 1950er Jahren war die Luftfahrtindustrie eine der ersten, die die IHU-Technologie nutzte. Flugzeugteile müssen leicht und gleichzeitig äußerst stabil sein, um den Belastungen im Flug standzuhalten. Die IHU ermöglichte es, hohle, aber hochfeste Strukturen für Flugzeuge herzustellen, wie etwa Teile der Flugzeugrahmen und Strukturen von Triebwerken.
Fortschritte im Bereich Hochdrucktechnik und Materialkunde
Mit den Anforderungen der Luftfahrtindustrie wuchsen auch die technologischen Fähigkeiten der Hochdrucktechnik. Hochfeste Werkstoffe wie Titan und spezielle Aluminiumlegierungen wurden für die IHU nutzbar gemacht. Durch die Weiterentwicklung der Materialwissenschaft konnte das Verfahren ausgeweitet und mit stärkeren und haltbareren Werkstoffen eingesetzt werden.
Erste industrielle Anwendungen und Prozessverbesserungen
In den 1960er und 1970er Jahren begannen weitere Industrien, das Verfahren zu nutzen, darunter der Maschinenbau und die Automobilindustrie. Die Hochdrucktechnologie verbesserte sich weiter, sodass höhere Drücke und damit präzisere Formgebungen möglich wurden. Zu dieser Zeit wurde IHU jedoch hauptsächlich für spezielle Einzelteile oder kleinere Produktionsmengen verwendet.
Die 1980er-Jahre: Verbreitung und Weiterentwicklung
Aufkommen der Automobilindustrie als Hauptanwender
In den 1980er Jahren erkannte die Automobilindustrie die Vorteile der Innenhochdruckumformung. Durch die Produktion leichter und stabiler Fahrzeugteile konnte das Fahrzeuggewicht reduziert und die Sicherheit verbessert werden. Dies führte dazu, dass das Verfahren für die Herstellung von Fahrwerkskomponenten, Abgasanlagen und Rahmenstrukturen eingesetzt wurde.
Technologische Entwicklungen in Werkzeug- und Materialtechnologie
Mit dem steigenden Interesse an der IHU entwickelten sich auch die verwendeten Werkzeuge weiter. Hochpräzise, verschleißfeste Stahlformen ermöglichten genauere und langlebigere Prozesse. Auch neue Legierungen, insbesondere hochfeste Stähle, wurden gezielt für die IHU optimiert, was die Leistungsfähigkeit und Anwendungsbreite des Verfahrens weiter steigerte.
Erste Versuche zur Automatisierung des IHU-Prozesses
Die Automatisierung begann, in der Metallverarbeitung Fuß zu fassen. Durch Roboter und Steuerungstechnologien konnte der IHU-Prozess präziser und schneller gestaltet werden. Die Effizienz der Innenhochdruckumformung wurde dadurch gesteigert, und das Verfahren konnte nun auch für größere Serienproduktionen eingesetzt werden.
Die 1990er-Jahre: Durchbruch in der Serienproduktion
Integration der IHU in die Massenfertigung von Automobilteilen
In den 1990er Jahren wurde die IHU erstmals in die Massenproduktion von Automobilteilen integriert. Die Automobilindustrie setzte zunehmend auf Leichtbaukonstruktionen, um den Kraftstoffverbrauch zu senken. IHU ermöglichte die kosteneffiziente Herstellung komplexer und nahtloser Strukturen, was das Verfahren in der Massenproduktion verankerte.
Wirtschaftliche Vorteile und Reduktion von Materialkosten
Die Möglichkeit, mehrere Bauteile zu einem einzigen Bauteil zusammenzuführen, reduzierte die Anzahl der Schweißnähte und Schraubverbindungen. Das führte zu Kostensenkungen und verbesserte die Stabilität und Langlebigkeit der Teile. Die Automobilindustrie nutzte IHU verstärkt für tragende Strukturen, was die Produktionskosten reduzierte und gleichzeitig die Qualität erhöhte.
Einsatz von Simulationssoftware zur Prozessoptimierung
Die 1990er Jahre sahen auch den Einsatz von Computersimulationen zur Prozessoptimierung. Mit Hilfe von CAD-Software konnte die Formgebung virtuell getestet werden, was Fehler im Vorfeld minimierte und die Effizienz steigerte. Diese Simulationen spielten eine zentrale Rolle bei der Optimierung der Druckparameter und bei der Anpassung der Werkstückgeometrie.
Die 2000er-Jahre: Technologische Verfeinerungen und neue Materialien
Fortschritte in der Hochdrucktechnik und Digitalisierung
Mit den technologischen Entwicklungen im Bereich Hochdruck und Digitalisierung wurde die Innenhochdruckumformung in den 2000er Jahren noch präziser und zuverlässiger. Elektronische Steuerungssysteme ermöglichten eine Echtzeit-Überwachung des Drucks und der Materialverformung. Diese Entwicklung half, die Fehlerquote zu senken und die Prozesssicherheit zu verbessern.
Einführung fortschrittlicher Materialien und Legierungen
Die Fortschritte in der Materialwissenschaft brachten hochfeste und dennoch leichte Materialien hervor, die ideal für IHU waren. Neben Aluminium und Stahl kamen zunehmend Titan und spezielle Verbundwerkstoffe zum Einsatz, die den Anforderungen der Automobil- und Luftfahrtindustrie noch besser gerecht wurden. Diese Werkstoffe ermöglichten die Herstellung von Teilen mit höherer Festigkeit bei reduziertem Gewicht.
IHU-Anwendungen in der Medizintechnik und Konsumgüterindustrie
Durch die Präzision und Flexibilität der IHU wurden neue Industrien auf das Verfahren aufmerksam. In der Medizintechnik wurde es zur Herstellung dünnwandiger, biokompatibler Komponenten für Implantate und Instrumente eingesetzt. Auch in der Konsumgüterindustrie, z.B. für die Herstellung von Fahrradrahmen, fand die IHU Anwendung, da sie leichte und robuste Produkte ermöglichte.
Heutige Bedeutung der Innenhochdruckumformung
Wichtige Branchen und Anwendungsgebiete
Heute ist die Innenhochdruckumformung ein unverzichtbares Verfahren in zahlreichen Branchen, von der Automobilindustrie bis hin zur Luft- und Raumfahrt und Medizintechnik. Die Technologie wird dort eingesetzt, wo leichte, nahtlose und komplex geformte Bauteile erforderlich sind, die hohen Belastungen standhalten müssen.
Fortschritte in der Prozessautomatisierung und Industrie 4.0
Die zunehmende Automatisierung und die Integration der IHU in die Industrie 4.0 machen die Prozesskontrolle und -optimierung noch effizienter. Sensorbasierte Überwachung und digitale Steuerungen ermöglichen es, den Druckverlauf in Echtzeit zu überwachen und Anpassungen bei Abweichungen vorzunehmen. Dadurch steigt die Qualität der gefertigten Bauteile, und die Produktion wird kosteneffizienter.
Nachhaltigkeitsaspekte und Materialeffizienz
Da die IHU weniger Materialabfall produziert und leichtere Bauteile ermöglicht, trägt das Verfahren zur Verbesserung der Materialeffizienz und zur Reduktion des Energieverbrauchs bei. Dies spielt insbesondere in der Automobilindustrie eine Rolle, da leichtere Fahrzeuge den CO₂-Ausstoß verringern und Ressourcen schonen.
Zukunftsperspektiven und technologische Herausforderungen
Neue Werkstoffe und hybridisierte Fertigungstechniken
Die Forschung an neuen Materialien, die noch leichter und fester sind, könnte die IHU in Zukunft weiter verändern. Hybridmaterialien, etwa Metall-Kunststoff-Verbindungen, bieten die Möglichkeit, noch leichtere und komplexere Bauteile herzustellen. Die Kombination der IHU mit anderen Technologien, wie dem 3D-Druck, eröffnet neue Möglichkeiten für maßgeschneiderte Lösungen.
Weiterentwicklung der Prozessüberwachung und Qualitätssicherung
Moderne Technologien wie die Künstliche Intelligenz könnten die Überwachung und Steuerung der IHU weiter verbessern. KI-gestützte Systeme könnten in der Lage sein, den Prozess selbstständig zu überwachen und kontinuierlich Anpassungen vorzunehmen, um die Qualität zu optimieren und Ausschuss zu minimieren.
Potential der IHU in der digitalen und nachhaltigen Fertigung
Die Innenhochdruckumformung hat das Potenzial, in der digitalen und nachhaltigen Fertigung eine zentrale Rolle zu spielen. Durch den Einsatz digitaler Steuerung und Echtzeit-Überwachung kann das Verfahren effizienter und umweltfreundlicher gestaltet werden. Dies macht die IHU zu einer zukunftsträchtigen Technologie in einer zunehmend ressourcenbewussten Industrie.
Einführung: Bedeutung der IHU in der modernen Fertigungsindustrie
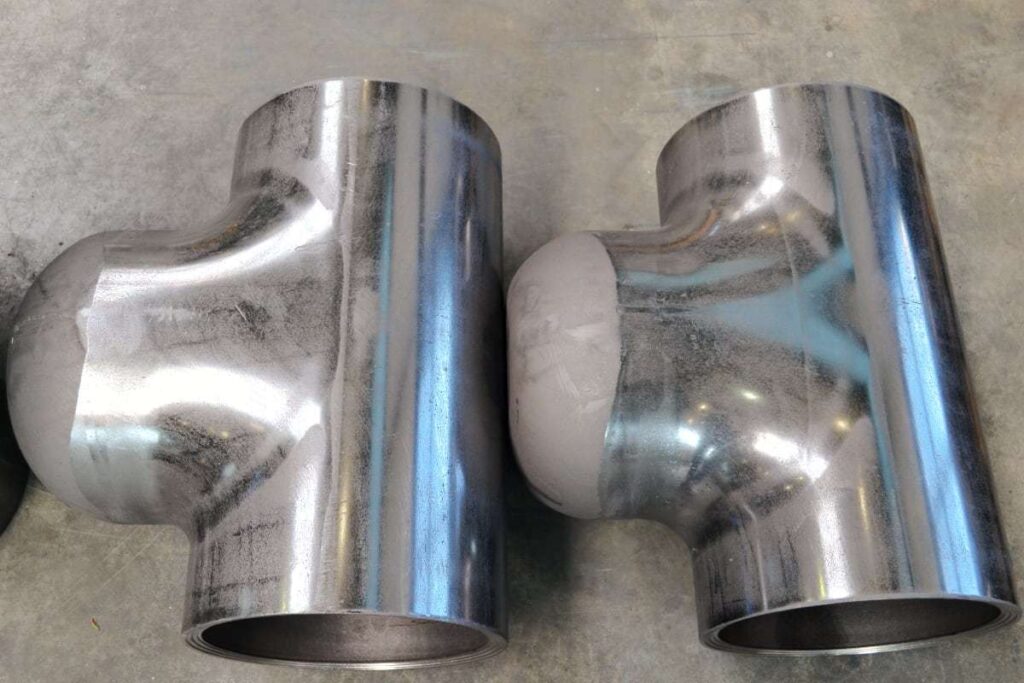
Kurzüberblick über die IHU und ihre Rolle in verschiedenen Branchen
Die Innenhochdruckumformung (IHU) ist ein Verfahren zur Herstellung hohler Metallkomponenten durch die Anwendung von Innendruck, der das Material in die Form eines Werkzeugs presst. Die Wirtschaftlichkeit der IHU ergibt sich aus der Fähigkeit, komplexe Bauteile in einem einzigen Fertigungsschritt nahtlos und präzise herzustellen. Dies macht das Verfahren besonders attraktiv für Branchen wie die Automobilindustrie, die Luft- und Raumfahrt sowie die Medizintechnik.
Bedeutung des Verfahrens für die Wettbewerbsfähigkeit und den wirtschaftlichen Erfolg
Durch die hohe Präzision und Effizienz der IHU sind Unternehmen in der Lage, Material- und Produktionskosten zu senken. Dies stärkt die Wettbewerbsfähigkeit und fördert Innovationen im Produktdesign. Da die IHU zudem eine hohe Materialausnutzung ermöglicht, trägt sie wesentlich zur Effizienzsteigerung und Kostenreduktion bei, was den wirtschaftlichen Erfolg eines Unternehmens maßgeblich beeinflusst.
2. Kostenstruktur und Einsparpotenziale der Innenhochdruckumformung
Reduktion der Produktions- und Materialkosten
Durch die Integration mehrerer Bearbeitungsschritte in einem IHU-Prozess können Unternehmen signifikante Kosteneinsparungen erzielen. Insbesondere bei der Serienfertigung lassen sich große Mengen an Materialkosten einsparen, da durch die präzise Formgebung weniger Ausschuss entsteht und die Materialnutzung optimiert wird.
Verringerung des Bearbeitungs- und Montageaufwands
Die IHU reduziert die Notwendigkeit für nachträgliche Bearbeitungen wie Schweißen oder Nieten, da komplexe Geometrien in einem einzigen Umformschritt hergestellt werden können. Dies spart Montagezeit und verringert den Personalaufwand. Zudem werden durch den Wegfall zusätzlicher Bearbeitungsschritte Produktionsprozesse vereinfacht und beschleunigt.
Auswirkungen auf die gesamte Lieferkette und Logistik
Da die IHU komplexe Bauteile aus einem Stück herstellen kann, reduziert sich die Anzahl der benötigten Einzelteile und damit auch die logistischen Anforderungen. Dies senkt nicht nur die Kosten, sondern führt auch zu einer Reduzierung der Lagerhaltung und einer optimierten Lagerlogistik, was die Effizienz der gesamten Lieferkette erhöht.
3. Effizienzsteigerung und Prozessautomatisierung
Automatisierungspotenziale und deren Einfluss auf die Kostenstruktur
Moderne IHU-Anlagen sind zunehmend automatisiert, was die Produktionszeiten verkürzt und die Wiederholgenauigkeit verbessert. Automatisierte Prozesse minimieren das Risiko menschlicher Fehler und reduzieren gleichzeitig die Personalkosten. Unternehmen können so die Produktion beschleunigen und gleichzeitig die Produktqualität konstant hoch halten.
Bedeutung für Serienproduktion und Flexibilität in der Fertigung
IHU-Anlagen ermöglichen die schnelle Herstellung von Bauteilen in hoher Stückzahl, was sie für die Serienproduktion prädestiniert. Die Flexibilität der Anlagen erlaubt zudem Anpassungen im Design, ohne dass kostenintensive Umrüstungen erforderlich sind. Dadurch sind Unternehmen in der Lage, schnell auf Marktveränderungen und Kundenanforderungen zu reagieren.
Prozessoptimierung und Produktionsgeschwindigkeit
Durch den Einsatz digitaler Steuerungssysteme und Sensorik kann der IHU-Prozess in Echtzeit überwacht und optimiert werden. So können Druck, Temperatur und Formparameter kontinuierlich angepasst werden, um eine konstante Qualität zu gewährleisten und die Produktionsgeschwindigkeit zu maximieren. Dies verkürzt die Fertigungszeiten und trägt zur Kostensenkung bei.
4. Materialeinsparungen und Ressourceneffizienz
Materialeffizienz durch präzise Wandstärken und optimierte Geometrien
Da die IHU es ermöglicht, die Wandstärke der Bauteile präzise zu steuern, wird das Material optimal genutzt und Materialverschwendung minimiert. Im Vergleich zu herkömmlichen Verfahren wie dem Stanzen oder Fräsen bleibt der Materialeinsatz niedrig, da keine überschüssigen Teile entfernt oder getrennt werden müssen.
Vergleich zur Materialnutzung in traditionellen Verfahren
Im Vergleich zu herkömmlichen Fertigungsverfahren, die oft hohe Materialabfälle verursachen, reduziert die IHU den Materialverbrauch erheblich. Während bei mechanischen Verfahren häufig Materialreste anfallen, erreicht die IHU eine hohe Materialausnutzung und minimiert so die Kosten.
Beitrag zur Ressourcenschonung und Kostensenkung
Da die IHU Materialien effizienter nutzt und weniger Ausschuss produziert, trägt das Verfahren zur Schonung natürlicher Ressourcen bei und senkt die Rohstoffkosten. Dies ist nicht nur wirtschaftlich vorteilhaft, sondern auch umweltfreundlich, da es den ökologischen Fußabdruck verringert.
5. Anwendungsgebiete und wirtschaftlicher Nutzen in verschiedenen Branchen
Automobilindustrie: Leichtbau, Sicherheit und Emissionsreduzierung
In der Automobilindustrie ist die IHU von großer Bedeutung, da sie die Herstellung leichter und gleichzeitig stabiler Fahrzeugstrukturen ermöglicht. Durch die Reduktion des Fahrzeuggewichts sinken der Kraftstoffverbrauch und die CO₂-Emissionen, was nicht nur die Umwelt entlastet, sondern auch die Betriebskosten senkt. Der Leichtbau trägt dazu bei, dass Fahrzeuge energieeffizienter sind und gleichzeitig höhere Sicherheitsstandards erfüllen.
Luft- und Raumfahrt: Einsparung bei hochpreisigen Materialien und Leichtbau
Die Luftfahrtindustrie profitiert ebenfalls von der IHU, da durch das Verfahren teure Materialien wie Titan und hochfeste Aluminiumlegierungen sparsam verwendet werden können. Leichte und hochfeste Bauteile tragen zur Reduktion des Treibstoffverbrauchs und zu einer höheren Effizienz der Flugzeuge bei. Dies senkt die Betriebskosten erheblich, da weniger Energie für den Transport schwerer Teile aufgebracht werden muss.
Medizintechnik und Konsumgüter: Präzision und Kosteneffizienz
In der Medizintechnik bietet die IHU die Möglichkeit, hochpräzise, biokompatible Bauteile herzustellen, die extremen hygienischen Anforderungen entsprechen. Die kostengünstige Produktion komplexer Formen ermöglicht es, medizinische Geräte und Implantate zu wettbewerbsfähigen Preisen herzustellen. Auch die Konsumgüterindustrie, etwa bei der Produktion von Fahrradrahmen, nutzt die IHU für leichtere, stabilere und kosteneffiziente Produkte.
6. Nachhaltigkeit und ökologische Vorteile der IHU
Verringerung von Materialabfall und Energieverbrauch
Da die IHU auf effiziente Materialausnutzung abzielt, wird der Materialabfall minimiert. Der Energiebedarf des Verfahrens ist ebenfalls vergleichsweise gering, da in einem Arbeitsschritt nahtlose und komplexe Formen erzeugt werden können. Dies trägt zur Energieeinsparung und zur Reduktion des Ressourcenverbrauchs bei.
Reduktion der CO₂-Emissionen und Beitrag zur umweltfreundlichen Produktion
Die Herstellung leichterer Bauteile durch IHU führt zu geringeren Emissionen während des gesamten Produktlebenszyklus, insbesondere in der Automobil- und Luftfahrtindustrie. Durch den verringerten Kraftstoffverbrauch sinken die CO₂-Emissionen der Endprodukte. In der Produktion selbst reduziert die höhere Effizienz des IHU-Verfahrens den Energiebedarf und damit die Emissionen.
Bedeutung in der Circular Economy und Recyclingpotenzial
Da bei der IHU weniger Materialabfall anfällt und die Bauteile häufig aus recycelbaren Materialien hergestellt werden, passt das Verfahren gut in das Konzept der Circular Economy. Die langlebigen und recyclingfähigen Bauteile reduzieren die Menge an neuem Rohmaterial und fördern die Ressourcenschonung. Das Recyclingpotenzial der IHU-Produkte ist hoch, da sie oft aus reinen Metallen oder Legierungen bestehen, die gut recycelbar sind.
7. Marktentwicklung und wirtschaftliche Trends
Analyse des globalen Marktpotenzials für die IHU
Der Markt für die IHU wächst weltweit, da immer mehr Branchen das Potenzial der Technologie für sich entdecken. Insbesondere in Asien und Nordamerika zeigen steigende Investitionen in die Automobil- und Luftfahrtindustrie, dass die Nachfrage nach IHU-Produkten weiter wächst. Der globale Markt für Innenhochdruckumformungstechnologien wird daher in den kommenden Jahren voraussichtlich stark ansteigen.
Markttreiber und Wachstumspotenziale in verschiedenen Regionen
Wachstumstreiber für die IHU sind die zunehmenden Anforderungen an Leichtbau, Materialeffizienz und Nachhaltigkeit. Regionen mit hohen Anforderungen an Umweltstandards, wie die EU, treiben die Entwicklung der IHU besonders stark voran. Auch Asien zeigt ein großes Wachstumspotenzial, da sich die dortige Fertigungsindustrie stark auf die Kosten- und Materialeffizienz konzentriert.
Innovationspotenzial und zukünftige Entwicklungen
Mit der weiteren Entwicklung neuer Materialien und fortschrittlicher Steuerungstechnologien wird das Potenzial der IHU noch weiter ausgebaut. Investitionen in Forschung und Entwicklung treiben die Innovationskraft des Verfahrens voran, und Unternehmen, die früh auf diese Technologie setzen, werden in den kommenden Jahren einen Wettbewerbsvorteil genießen.
8. Zukunftsperspektiven: IHU in der Industrie 4.0 und digitale Fertigung
Integration von Digitalisierung und Künstlicher Intelligenz
In der Zukunft wird die Digitalisierung die IHU revolutionieren. Die Integration von KI und automatisierten Steuerungssystemen ermöglicht eine präzisere Prozesssteuerung und die Erkennung von Fehlern in Echtzeit. Dies steigert nicht nur die Effizienz, sondern auch die Wirtschaftlichkeit des Verfahrens.
Anpassung an flexible Fertigungsanforderungen und Kleinserienproduktion
Durch die zunehmende Flexibilität und Präzision der IHU-Anlagen wird das Verfahren für Kleinserienproduktionen und die Fertigung kundenspezifischer Teile immer attraktiver. Die schnelle Anpassung an neue Anforderungen und Designs ermöglicht es, den Kundenanforderungen in kürzester Zeit gerecht zu werden.
Potenzial der IHU in der nachhaltigen und digitalen Produktion
Die IHU wird in der modernen digitalen und nachhaltigen Fertigung eine zentrale Rolle spielen. Die Möglichkeit, Materialien effizient zu nutzen, Leichtbaukonstruktionen zu fördern und Abfall zu minimieren, macht das Verfahren zur idealen Wahl für eine ressourcenschonende Produktion. Unternehmen, die in diese Technologie investieren, werden eine Vorreiterrolle in der nachhaltigen Industrie der Zukunft einnehmen.
Einführung in die Innenhochdruckumformung
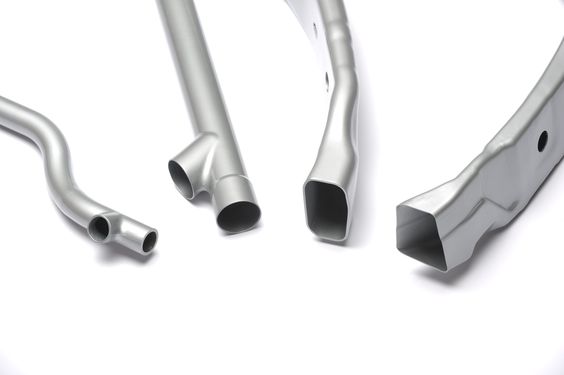
Überblick und technologische Einordnung des Verfahrens
Die Innenhochdruckumformung (IHU) ist ein Verfahren, das durch hydraulischen Innendruck die Formgebung von hohlen Bauteilen ermöglicht. In der Regel wird ein Metallrohrling oder eine vorgeformte Platine durch einen hohen Druck an die Innenwand eines Werkzeugs gepresst, sodass das Werkstück die gewünschte Form annimmt. Diese Technik hat sich zu einer Schlüsseltechnologie in der Metallverarbeitung entwickelt und ist heute in zahlreichen Branchen ein fester Bestandteil der Fertigung.
Bedeutung der IHU in der modernen Produktion
Die Vorteile der IHU liegen in der Präzision und Effizienz des Verfahrens. Da es eine nahtlose Formgebung ermöglicht und Materialabfälle minimiert, ist die IHU wirtschaftlich und ökologisch vorteilhaft. Für viele Unternehmen ist die IHU daher eine Technologie, die nicht nur Produktionskosten senkt, sondern auch die Produktqualität verbessert.
2. Technologische Vorteile der Innenhochdruckumformung
Präzise Formgebung und Designfreiheit
Die IHU ermöglicht die Herstellung komplexer Geometrien und präziser Bauteile, die in einem einzigen Fertigungsschritt geformt werden können. Die Designfreiheit, die dieses Verfahren bietet, ist ein enormer Vorteil gegenüber traditionellen Umformverfahren, die häufig auf einfache Formen und mehrteilige Konstruktionen beschränkt sind.
Nahtlose Konstruktionen und strukturelle Integrität
Da die IHU nahtlose Bauteile ermöglicht, werden Schwachstellen vermieden, die durch Schweißnähte oder Verbindungen entstehen könnten. Nahtlose Strukturen erhöhen die strukturelle Integrität und sorgen für eine längere Lebensdauer und Stabilität des Endprodukts.
Gewichtsreduktion und Materialeffizienz
Die IHU reduziert das Gewicht der gefertigten Bauteile durch eine exakte Anpassung der Wandstärke und optimierte Materialverteilung. Dies führt zu leichteren und trotzdem stabilen Bauteilen, die weniger Material benötigen und somit ressourcenschonender sind.
3. Wirtschaftliche Vorteile der IHU
Materialkosteneinsparungen und reduzierte Produktionskosten
Durch die IHU wird das Material effizienter genutzt, da die präzise Formgebung die Materialverschwendung reduziert. Im Vergleich zu Verfahren wie dem Stanzen oder Fräsen, bei denen Material abgetragen wird, bleibt bei der IHU das Material im Prozess erhalten und wird optimal verwendet.
Verringerter Bearbeitungsaufwand und kürzere Produktionszeiten
Da die IHU mehrere Arbeitsschritte kombiniert und komplexe Formen in einem Schritt erzeugt, entfallen nachgelagerte Bearbeitungen. Dies verkürzt die Produktionszeit und ermöglicht eine schnelle Umsetzung von Designänderungen ohne große Umrüstzeiten.
Effizienz in der Serienproduktion und bei Kleinserien
Besonders in der Serienproduktion ermöglicht die IHU eine kosteneffiziente Fertigung, da die Werkzeuge und Maschinen für eine große Anzahl an Bauteilen ausgelegt sind. Aber auch in Kleinserien kann das Verfahren punkten, da Designänderungen ohne große Werkzeuginvestitionen umgesetzt werden können.
4. Anwendungsbezogene Vorteile in verschiedenen Branchen
Automobilindustrie: Leichtbau und Sicherheit
In der Automobilindustrie ist die IHU besonders wichtig, da sie die Herstellung stabiler und gleichzeitig leichter Fahrzeugstrukturen ermöglicht. Dies trägt zur Reduktion des Fahrzeuggewichts und zur Steigerung der Sicherheit bei. Durch die IHU gefertigte Bauteile, wie Rahmen- und Fahrwerksteile, zeichnen sich durch hohe Stabilität bei minimalem Gewicht aus.
Luft- und Raumfahrt: Kostenersparnis und Treibstoffeffizienz
In der Luftfahrtindustrie ermöglicht die IHU die Herstellung komplexer und leichter Komponenten, die den Treibstoffverbrauch von Flugzeugen senken. Die Einsparung von Materialkosten und die Erhöhung der Festigkeit sind entscheidende Vorteile, die zur Reduktion der Betriebskosten beitragen.
Medizintechnik und Konsumgüter: Präzision und Langlebigkeit
In der Medizintechnik wird die IHU zur Herstellung biokompatibler und extrem präziser Komponenten für Implantate und Instrumente genutzt. Auch im Konsumgüterbereich, z.B. bei Fahrradrahmen, bietet die IHU Vorteile, da stabile und langlebige Produkte mit geringerem Materialeinsatz hergestellt werden können.
5. Technische Herausforderungen der Innenhochdruckumformung
Materialermüdung und Rissbildung
Materialien, die für die IHU verwendet werden, müssen extremen Belastungen standhalten. Hohe Drücke können Materialermüdung und Risse verursachen, insbesondere bei wiederholten Umformungen. Eine sorgfältige Materialauswahl und Kontrolle der Druckparameter sind entscheidend, um Materialversagen zu vermeiden.
Hohe Anforderungen an Druckregelung und Steuerung
Die Druckregelung muss extrem präzise sein, um ein gleichmäßiges und fehlerfreies Ergebnis zu gewährleisten. Schon geringe Abweichungen können zu Materialschäden oder Verformungsfehlern führen. Die Steuerungssysteme müssen daher genau auf die Anforderungen der IHU angepasst sein und über moderne Sensorik verfügen.
Werkzeugverschleiß und Wartungsaufwand
Die Werkzeuge für die IHU sind hohen Drücken und Belastungen ausgesetzt, was zu erhöhtem Verschleiß und Wartungsaufwand führen kann. Hochwertige Werkzeuge aus spezialbeschichteten Stählen sind notwendig, um die Lebensdauer zu maximieren, aber auch kostspielig in der Anschaffung und Wartung.
6. Betriebliche Herausforderungen und Kostenfaktoren
Investitionskosten und Kosten für die Instandhaltung
Die Anschaffung und Installation einer IHU-Anlage ist mit hohen Investitionskosten verbunden. Dazu kommen Wartungskosten und die regelmäßige Überprüfung der Hochdrucksysteme, die betrieblich eingeplant werden müssen. Diese Faktoren machen die Einführung des Verfahrens zunächst kostenintensiv.
Qualifikationsanforderungen an das Fachpersonal
Die Bedienung und Überwachung der IHU-Anlagen erfordert spezialisierte Kenntnisse und Fähigkeiten. Das Fachpersonal muss geschult und regelmäßig weitergebildet werden, um die technologischen Entwicklungen zu verstehen und umzusetzen. Dies führt zu erhöhten Schulungskosten und stellt Unternehmen vor die Herausforderung, qualifiziertes Personal zu gewinnen und zu halten.
Logistik und Lagerhaltung von Druckmedien und Materialien
Für die IHU werden spezielle Druckmedien benötigt, die gelagert und regelmäßig nachgefüllt werden müssen. Auch die Lagerung und Logistik der Werkstoffe sind ein Kostenfaktor, insbesondere wenn es sich um teure oder sensible Materialien wie Titan handelt. Eine effiziente Logistik ist daher essenziell, um die Prozesskosten niedrig zu halten.
7. Lösungsansätze zur Überwindung der Herausforderungen
Optimierung der Prozessparameter und Druckführung
Eine kontinuierliche Überwachung und Optimierung der Prozessparameter kann helfen, Materialermüdung und Rissbildung zu minimieren. Durch computergestützte Druckregelungen und simulationsgestützte Parameteranpassungen wird die Fehlerquote gesenkt und die Stabilität der Bauteile erhöht.
Fortschritte in der Materialwissenschaft und Werkzeugtechnik
Moderne Werkstoffe und Legierungen, die für hohe Druckbelastungen optimiert sind, verbessern die Lebensdauer und die Stabilität der IHU-Produkte. Auch fortschrittliche Werkzeuge, die widerstandsfähiger und langlebiger sind, senken die Wartungs- und Ersatzteilkosten.
Automatisierung und Digitalisierung zur Effizienzsteigerung
Mit der zunehmenden Automatisierung und Digitalisierung des IHU-Prozesses lassen sich Produktionskosten senken und die Effizienz steigern. Die Einführung von Sensorik und KI-gesteuerten Überwachungssystemen ermöglicht es, Druck und Temperatur in Echtzeit zu kontrollieren und Fehler frühzeitig zu erkennen und zu beheben.
8. Zukunftsperspektiven: Innovationen und Weiterentwicklung der IHU
Neue Materialien und hybride Fertigungstechniken
Mit der Entwicklung neuer Werkstoffe und Verbundmaterialien kann die IHU noch effizienter und vielseitiger eingesetzt werden. Hybride Fertigungstechniken, die IHU mit additiver Fertigung oder anderen Umformtechniken kombinieren, bieten innovative Lösungen für anspruchsvolle Bauteilgeometrien.
KI und Industrie 4.0 in der IHU
Künstliche Intelligenz und Industrie 4.0 bieten neue Möglichkeiten, den IHU-Prozess zu optimieren. Durch die Integration von KI in die Prozessüberwachung können Maschinen lernen, Druckverläufe selbstständig anzupassen und mögliche Fehlerquellen zu erkennen, bevor sie zu Produktionsfehlern führen.
Umwelt- und Ressourcenschonung durch verbesserte Prozesse
Da die IHU im Vergleich zu anderen Verfahren Material effizienter nutzt und weniger Abfall produziert, passt sie gut in das Konzept der ressourcenschonenden Fertigung. Verbesserungen in der Energieeffizienz und die Integration von Recyclingkonzepten bieten weitere ökologische Vorteile, die den langfristigen Nutzen des Verfahrens steigern.
Einleitung: Aktuelle Relevanz der Innenhochdruckumformung
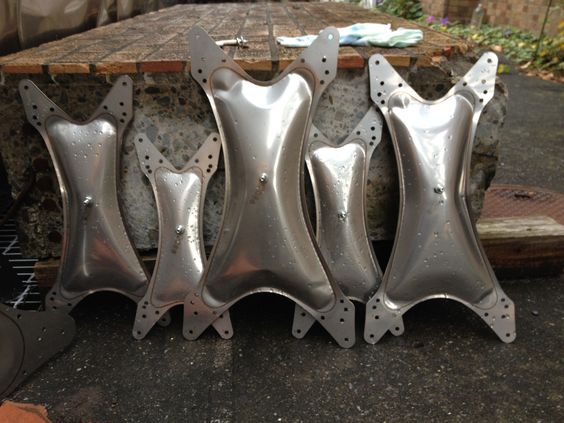
Bedeutung der IHU in der heutigen industriellen Fertigung
Die Innenhochdruckumformung (IHU) ist ein zentrales Fertigungsverfahren, das durch seine Fähigkeit, komplexe, leichte und stabile Metallteile herzustellen, in Industrien wie der Automobilindustrie, Luftfahrt und Medizintechnik an Bedeutung gewonnen hat. Durch die Möglichkeit, nahtlose Bauteile mit hoher Präzision und optimierter Materialnutzung herzustellen, ist die IHU zu einer Schlüsseltechnologie der modernen Fertigung geworden.
Bedarf an Innovation und Weiterentwicklung
Obwohl die IHU als effizient gilt, wächst der Bedarf an weiteren technologischen Fortschritten und Innovationen, um die Anforderungen an Flexibilität, Effizienz und Nachhaltigkeit zu erfüllen. Die Integration digitaler Technologien und die Nutzung neuer Materialien sind entscheidend, um das Potenzial der IHU auszuschöpfen und ihre Einsatzmöglichkeiten weiter auszubauen.
2. Materialwissenschaft und neue Werkstoffe für die IHU
Hochfeste Leichtbaumaterialien und Verbundwerkstoffe
In der Automobil- und Luftfahrtindustrie steigt die Nachfrage nach leichten und dennoch hochfesten Materialien. Entwicklungen im Bereich hochfester Aluminium- und Titanlegierungen, aber auch von Faserverbundwerkstoffen, erweitern das Potenzial der IHU. Solche Werkstoffe ermöglichen es, das Gewicht von Komponenten weiter zu reduzieren und gleichzeitig deren Stabilität zu erhöhen.
Fortschritte in der Legierungstechnik
Die Materialforschung konzentriert sich zunehmend auf speziell für die IHU optimierte Legierungen. Neue Legierungen mit erhöhter Duktilität und Festigkeit tragen dazu bei, die Einsatzfähigkeit und Lebensdauer der Komponenten zu maximieren. Materialien wie hochfeste Stähle und spezielle Aluminiumlegierungen sind ideale Kandidaten für die IHU, da sie hohe Verformbarkeit bei geringem Risiko von Rissbildung bieten.
Biokompatible und recyclebare Werkstoffe
Im Zuge der Nachhaltigkeitsanforderungen und für Anwendungsbereiche wie die Medizintechnik sind biokompatible und recycelbare Werkstoffe von Interesse. Titan, das für Implantate und andere medizinische Komponenten geeignet ist, wird zunehmend durch neue, kostengünstigere und biokompatible Legierungen ergänzt, die auch im Recyclingprozess unproblematisch sind.
3. Hybridverfahren und additive Fertigungstechniken
Kombination der IHU mit 3D-Druck und anderen Umformtechniken
Die Integration der IHU mit additiven Fertigungsverfahren wie dem 3D-Druck bietet neue Möglichkeiten, hybride Komponenten zu schaffen. Durch den 3D-Druck können komplexe geometrische Formen vorgefertigt werden, die dann durch die IHU final geformt und verdichtet werden. Diese Kombination ermöglicht die Herstellung komplexer Strukturen mit minimalem Materialverlust.
Vorteile hybrider Fertigungstechnologien
Hybride Fertigungsverfahren ermöglichen es, die Vorteile mehrerer Technologien zu nutzen. Die Kombination der IHU mit anderen Techniken wie dem Schmieden oder der Warmumformung bietet eine größere Designfreiheit und höhere Effizienz. So können Funktionskomponenten mit optimierter Geometrie und Materialverteilung hergestellt werden, was die Kosten und das Gewicht reduziert.
Anwendungsbereiche und Branchenpotenzial
Insbesondere die Luft- und Raumfahrt und die Medizintechnik profitieren von hybriden Fertigungstechniken, da diese komplexe, leichte und stabile Komponenten ermöglichen. Auch die Automobilindustrie könnte durch hybride Verfahren von einer effizienteren und flexibleren Produktion profitieren, etwa bei der Herstellung von komplexen Strukturbauteilen.
4. Digitalisierung und Industrie 4.0 in der IHU
Integration von Sensorik und Datenanalyse
Die Einführung von Sensoren in IHU-Anlagen ermöglicht die Echtzeitüberwachung des gesamten Formgebungsprozesses. Daten zu Druck, Temperatur und Materialverformung werden kontinuierlich erfasst und analysiert. Durch diese Überwachung können Fehler frühzeitig erkannt und der Produktionsprozess optimiert werden, was die Effizienz und Qualität der Produkte steigert.
Rolle der künstlichen Intelligenz und maschinelles Lernen
Künstliche Intelligenz (KI) und maschinelles Lernen bieten großes Potenzial für die IHU. KI-gestützte Systeme können die Verarbeitung großer Datenmengen übernehmen und Muster erkennen, die für eine optimale Druckregelung und Materialverformung sorgen. Die KI kann auch dazu beitragen, Fehlerquellen zu identifizieren und die Prozessparameter automatisch anzupassen.
Vorteile digitaler Zwillinge und Echtzeit-Überwachung
Digitale Zwillinge ermöglichen die virtuelle Modellierung und Simulation von IHU-Prozessen in Echtzeit. Auf diese Weise lassen sich neue Werkstoffe und Designs im Vorfeld testen, ohne dass physische Prototypen benötigt werden. Dies spart nicht nur Kosten und Zeit, sondern verbessert auch die Prozesssicherheit und Planbarkeit.
5. Nachhaltigkeit und Ressourceneffizienz in der IHU
Reduktion des Material- und Energieverbrauchs
Durch die präzise Steuerung des Drucks und die optimierte Materialverteilung ist die IHU eines der ressourcenschonendsten Umformverfahren. Es ermöglicht eine Reduktion des Materialverbrauchs und trägt so zur Schonung von Ressourcen bei. Darüber hinaus sind neue IHU-Anlagen auf Energieeffizienz ausgelegt, wodurch sich der Energiebedarf weiter senken lässt.
Beitrag zur Kreislaufwirtschaft und Recyclingfähigkeit
Da die IHU weniger Materialabfall produziert und sich viele Bauteile recyceln lassen, passt das Verfahren ideal in die Kreislaufwirtschaft. Produkte, die aus reinen Metallen und Legierungen bestehen, können am Ende ihres Lebenszyklus eingeschmolzen und wiederverwendet werden, was die Materialeffizienz erhöht und den ökologischen Fußabdruck reduziert.
Entwicklung nachhaltiger Produktionsprozesse
Zukunftsorientierte IHU-Anlagen setzen zunehmend auf emissionsarme Verfahren und Recyclingkonzepte. Neben der Effizienzsteigerung legen viele Unternehmen zunehmend Wert auf nachhaltige Produktionsmethoden. Die Reduktion der CO₂-Emissionen und die Minimierung von Abfällen machen die IHU zu einem wesentlichen Baustein in der grünen Produktion.
6. Automatisierung und flexible Produktionskonzepte
Robotik und Automatisierung in der IHU
Die Integration von Robotik in die IHU ermöglicht eine vollautomatisierte Produktion, die menschliche Eingriffe auf ein Minimum reduziert. Roboter übernehmen das Einlegen und Entnehmen der Werkstücke und steuern die Druckführung. Dies sorgt für eine gleichbleibend hohe Qualität und steigert die Effizienz, da durchgehende Produktionsabläufe realisiert werden können.
Flexible Produktion für Kleinserien und maßgeschneiderte Produkte
Der Trend zur Personalisierung und Kleinserienproduktion stellt die Industrie vor neue Herausforderungen. Moderne IHU-Anlagen sind flexibel und lassen sich schnell an unterschiedliche Bauteildesigns und -größen anpassen. Dies ermöglicht eine wirtschaftliche Produktion, auch bei geringen Stückzahlen, und bietet Kunden die Möglichkeit, individuelle Produkte zu erhalten.
Anpassung der IHU für die Just-in-Time-Fertigung
In der modernen Fertigung ist die Nachfrage nach just-in-time (JIT) hergestellten Produkten hoch. IHU-Anlagen können schnell auf Auftragsschwankungen reagieren und sind für JIT-Konzepte gut geeignet. Durch die Flexibilität und Automatisierung lässt sich die Produktion an den genauen Bedarf anpassen, wodurch Lagerkosten und Produktionszeit reduziert werden.
7. Erweiterung der Anwendungsgebiete und neue Märkte
Wachstumspotenzial in der Elektronik- und Batterieproduktion
Mit der Zunahme von Elektrofahrzeugen und erneuerbaren Energien wächst der Bedarf an leichten und stabilen Gehäusen für Batterien und Elektronikbauteile. Die IHU bietet hier Potenzial für die Herstellung von Batteriekästen und strukturellen Komponenten, die gleichzeitig Schutz und Leichtbauanforderungen erfüllen.
Bedeutung für die Luft- und Raumfahrt sowie die Medizintechnik
Da die Luft- und Raumfahrt hohe Anforderungen an Leichtbau und Präzision stellt, bietet die IHU dieser Branche zahlreiche Vorteile. Auch die Medizintechnik setzt zunehmend auf die IHU für die Herstellung biokompatibler und langlebiger Implantate und Instrumente, da sie eine hohe Formgenauigkeit und Festigkeit erfordert.
Chancen in der Bau- und Energieindustrie
In der Bau- und Energieindustrie gewinnt die IHU an Bedeutung, da hier zunehmend leichte, langlebige und energieeffiziente Bauteile gefragt sind. Die Herstellung komplexer, nahtloser Strukturen, wie Rohre und Profile für den Bau und die Energieübertragung, stellt ein weiteres Wachstumspotenzial dar, insbesondere im Bereich nachhaltiger Baumaterialien.
8. Forschung und Entwicklung: Technologische Roadmap
Trends und Investitionen in Forschung und Entwicklung
Zahlreiche Unternehmen und Forschungseinrichtungen investieren verstärkt in die Weiterentwicklung der IHU-Technologien. Insbesondere Fortschritte im Bereich Sensorik, Materialentwicklung und Digitalisierung stehen im Fokus der F&E-Aktivitäten. Diese Investitionen treiben die Effizienz und Qualität der IHU-Produkte voran und erschließen neue Anwendungsbereiche.
Partnerschaften zwischen Industrie und Wissenschaft
Die Zusammenarbeit zwischen Industrie und Forschungseinrichtungen ist entscheidend für den technologischen Fortschritt in der IHU. Durch gezielte Partnerschaften und Förderprogramme wird die Entwicklung neuer Werkstoffe und Produktionsverfahren beschleunigt. Universitäten und Unternehmen arbeiten zusammen, um praxisnahe Lösungen für aktuelle Herausforderungen zu entwickeln.
Herausforderungen und Zukunftsziele für die IHU
Trotz aller Fortschritte bleibt die IHU mit Herausforderungen konfrontiert, insbesondere im Bereich der Hochdrucksteuerung und der Materialermüdung. Langfristige Ziele sind die Integration von umweltfreundlicheren Materialien, die weitere Verbesserung der Drucktechnik und die vollständige Digitalisierung der Produktion, um die Zukunftsperspektiven der IHU zu sichern.
Einführung: Überblick über die Innenhochdruckumformung
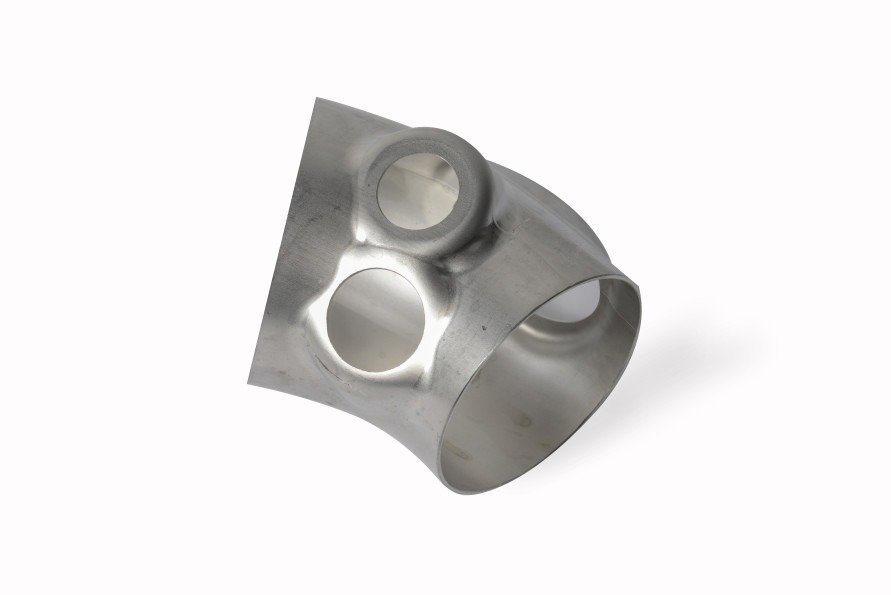
Grundlagen und Zielsetzung des Verfahrens
Die Innenhochdruckumformung (IHU) ist ein Fertigungsverfahren, das zur Herstellung von Hohlkörpern mit komplexen Geometrien verwendet wird. Dabei wird ein hoher Innendruck auf ein Werkstück ausgeübt, wodurch es die Form des umgebenden Werkzeugs annimmt. Ziel des Verfahrens ist die Herstellung nahtloser und stabiler Bauteile, die hohen Anforderungen an Präzision und Belastbarkeit gerecht werden.
Bedeutung der Prozessstufen für die Endqualität des Bauteils
Jede Prozessstufe in der IHU trägt zur Qualität des Endprodukts bei. Vom Material bis zur Nachbearbeitung beeinflussen die einzelnen Schritte die Maßgenauigkeit, die strukturelle Integrität und die Oberflächenqualität des Bauteils. Ein fehlerfreier Prozessablauf ist entscheidend, um Ausschuss zu minimieren und eine hohe Produktqualität sicherzustellen.
Materialauswahl und Vorbereitung des Werkstücks
Auswahl geeigneter Werkstoffe und Einfluss der Materialeigenschaften
Die Wahl des Materials ist der erste und wichtigste Schritt im IHU-Prozess, da es direkt die Verformbarkeit und Belastbarkeit des Bauteils beeinflusst. Typische Materialien sind Aluminium, Edelstahl und hochfeste Stähle, die sich durch gute Duktilität und Festigkeit auszeichnen. Die Auswahl hängt von den spezifischen Anforderungen des Endprodukts ab.
Vorbehandlung und Lagerung des Materials
Das Material wird vor der Verarbeitung auf Verunreinigungen oder Schäden überprüft. Die Lagerung erfolgt unter Bedingungen, die die Materialeigenschaften erhalten, sodass keine ungewollten Spannungen oder Verunreinigungen entstehen. Die Werkstoffe werden vor der Umformung gegebenenfalls gereinigt und aufgewärmt, um die Verformung zu erleichtern.
Kontrolle auf Oberflächenfehler und Maßgenauigkeit
Oberflächenfehler oder Materialunregelmäßigkeiten können während der Umformung zu Rissen führen. Das Material wird daher vor der Verarbeitung genau auf Oberflächenfehler und Maßgenauigkeit überprüft, um eine konsistente und hochwertige Produktion zu gewährleisten.
3. Werkzeugvorbereitung und Einrichten der IHU-Anlage
Vorbereitung der Werkzeuge und Reinigung
Die Werkzeuge müssen für jeden IHU-Prozess eine exakte Geometrie und saubere Oberflächen aufweisen. Vor jedem Einsatz wird das Werkzeug gereinigt und auf Defekte überprüft, um die Maßhaltigkeit und Oberflächenqualität des Endprodukts zu sichern.
Einrichten der Anlage und Kalibrierung der Maschinen
Die IHU-Maschinen werden vor jedem Produktionslauf kalibriert, um eine präzise Druckregelung zu ermöglichen. Dabei werden Druckparameter und Steuerungssysteme auf die spezifischen Anforderungen des zu formenden Materials und der angestrebten Geometrie eingestellt.
Sicherstellen der Werkzeugqualität und -präzision
Werkzeuge bestehen häufig aus verschleißfestem Material und sind oft beschichtet, um Reibung zu minimieren. Die Werkzeugpräzision ist entscheidend, um eine gleichmäßige Formgebung zu gewährleisten und die Standzeit des Werkzeugs zu maximieren.
4. Einlegen und Fixieren des Werkstücks
Positionierung und Fixierung des Werkstücks im Werkzeug
Das Werkstück muss genau in die Form eingelegt und fixiert werden, um eine gleichmäßige Verformung zu gewährleisten. Dabei kommen oft mechanische Halterungen oder Fixierungssysteme zum Einsatz, die das Material in der vorgesehenen Position halten.
Bedeutung der genauen Positionierung für die Formgenauigkeit
Eine exakte Positionierung ist entscheidend, um die Maßgenauigkeit des fertigen Bauteils sicherzustellen. Schon geringfügige Abweichungen können zu Formfehlern und zu ungleichmäßigen Wandstärken führen, was die Stabilität des Endprodukts beeinträchtigen kann.
Mechanische und digitale Systeme zur Fixierung und Ausrichtung
Zur exakten Fixierung werden mechanische Systeme sowie digitale Mess- und Ausrichtungstechnologien eingesetzt. Digitale Positioniersysteme bieten eine höhere Präzision und ermöglichen die sofortige Erkennung von Positionsabweichungen, was den Einrichtungsaufwand reduziert und die Qualität verbessert.
5. Erwärmung und Vorbehandlung des Materials
Temperaturmanagement und Vorwärmprozesse
Bei bestimmten Materialien, wie z. B. Aluminium, kann eine Vorwärmung notwendig sein, um die Verformbarkeit zu erhöhen. Die Erwärmung erleichtert den Umformprozess, da sie die Fließspannung reduziert und die Gefahr von Rissen verringert. Die genauen Temperaturen variieren je nach Material und Geometrie des Bauteils.
Einfluss der Temperatur auf die Verformbarkeit und Bauteilqualität
Erwärmte Materialien lassen sich besser verformen, was die Qualität des Endprodukts verbessert. Die Temperatur muss jedoch sorgfältig kontrolliert werden, da zu hohe Temperaturen die Struktur des Materials schwächen können.
Anpassungen bei speziellen Materialien und Anwendungen
Für Werkstoffe mit besonderen Eigenschaften, wie z. B. Titan, sind angepasste Vorwärmprozesse erforderlich, um die gewünschte Formgenauigkeit und Belastbarkeit zu erzielen. Auch bei Bauteilen, die für spezielle Anwendungen bestimmt sind, kann eine zusätzliche Materialbehandlung sinnvoll sein.
6. Druckaufbau und Formgebung des Werkstücks
Einleiten des Druckmediums und schrittweiser Druckaufbau
Der eigentliche Umformprozess beginnt mit der Einleitung des Druckmediums (meist Wasser oder Öl) in das Werkstück. Der Druck wird kontrolliert und schrittweise erhöht, um eine gleichmäßige Verformung zu gewährleisten. Der Druckaufbau ist einer der kritischsten Schritte, da er direkt die Formgebung beeinflusst.
Druckregelung und Steuerung des Verformungsprozesses
Die Steuerung des Drucks ist entscheidend, um Materialfehler und Risse zu vermeiden. Die Druckregelung erfolgt häufig durch digitale Steuerungssysteme, die in Echtzeit den Druckverlauf überwachen und Anpassungen vornehmen. Der Druckverlauf wird an die Geometrie und Wandstärke des Werkstücks angepasst.
Gleichmäßige Verformung und Kontrolle der Wanddicke
Eine gleichmäßige Verformung und die Kontrolle der Wanddicke sind entscheidend für die strukturelle Integrität des Bauteils. Durch den Einsatz moderner Sensorik wird die Wanddicke während des Druckaufbaus kontinuierlich überprüft. Abweichungen können somit sofort erkannt und der Druckverlauf entsprechend angepasst werden.
7. Druckabbau und Entformung des Werkstücks
Stufenweiser Druckabbau zur Vermeidung von Spannungsrissen
Nach dem Abschluss der Formgebung wird der Druck schrittweise reduziert. Ein plötzlicher Druckabbau könnte Spannungen im Material verursachen und Risse hervorrufen. Durch den kontrollierten Abbau werden diese Spannungen minimiert und die strukturelle Integrität des Bauteils erhalten.
Entnahme des Werkstücks aus dem Werkzeug
Nach dem Druckabbau wird das Bauteil aus der Form genommen. Die Entnahme erfolgt vorsichtig, um Schäden zu vermeiden, und das Werkstück wird zunächst auf Oberflächenqualität und Maßgenauigkeit geprüft.
Erster Qualitätscheck auf Maßhaltigkeit und Oberflächenqualität
Bevor das Bauteil zur Nachbearbeitung weitergeleitet wird, erfolgt eine erste Überprüfung auf Maßhaltigkeit und Oberflächenqualität. Dies ist entscheidend, um sicherzustellen, dass das Werkstück den Anforderungen entspricht und gegebenenfalls frühzeitig Korrekturmaßnahmen ergriffen werden können.
8. Nachbearbeitung und finale Bearbeitungsschritte
Entfernen von überschüssigem Material und Glätten von Kanten
Während des Umformprozesses kann an den Enden des Werkstücks überschüssiges Material entstehen. Dieses wird in der Nachbearbeitung entfernt, und die Kanten werden geglättet, um die gewünschten Maße und eine optimale Oberflächenqualität zu erreichen.
Oberflächenveredelung und eventuelle Wärmebehandlung
Abhängig von den Anforderungen an das Bauteil kann eine Oberflächenveredelung, wie z.B. Polieren, Strahlen oder eine Beschichtung, notwendig sein. Bei manchen Werkstücken ist auch eine Wärmebehandlung sinnvoll, um die Festigkeit oder Korrosionsbeständigkeit zu erhöhen.
Weitere Bearbeitungsschritte je nach Einsatzgebiet und Anforderungen
Je nach Einsatzgebiet können zusätzliche Bearbeitungsschritte erforderlich sein, um die Leistungsfähigkeit und Langlebigkeit des Bauteils zu gewährleisten. Dazu zählen Beschichtungen, Bohrungen oder das Einfügen von Gewinden.
9. Qualitätskontrolle und Prüfverfahren
Inspektionsmethoden zur Überprüfung der Formgenauigkeit
Zur Qualitätssicherung werden verschiedene Prüfmethoden eingesetzt, um sicherzustellen, dass das Bauteil die vorgegebenen Maße und Toleranzen einhält. Messverfahren wie Koordinatenmessgeräte oder optische Scanner erfassen die exakte Geometrie und stellen die Maßhaltigkeit sicher.
Prüfverfahren zur Detektion von Defekten und Materialfehlern
Zur Identifikation von Materialfehlern und Defekten werden zerstörungsfreie Prüfverfahren wie Ultraschall, Röntgen oder CT-Scans eingesetzt. Diese Verfahren ermöglichen eine gründliche Inspektion des Bauteils auf innere Defekte, die mit bloßem Auge nicht sichtbar wären.
Dokumentation und Analyse der Prozessdaten zur Qualitätsoptimierung
Die Prozessdaten, die während der Umformung gesammelt werden, sind entscheidend für die Qualitätsoptimierung. Durch die Analyse dieser Daten lassen sich Muster erkennen, die Hinweise auf potenzielle Schwachstellen geben. Eine regelmäßige Auswertung ermöglicht die kontinuierliche Verbesserung des IHU-Prozesses.
10. Prozessoptimierung und kontinuierliche Verbesserung
Optimierung der Druckführung und Formgebungstechniken
Die kontinuierliche Verbesserung der Druckregelung und Druckführung ermöglicht es, die Effizienz und Qualität des IHU-Prozesses weiter zu steigern. Simulationstechniken und Testläufe helfen, optimale Druckverläufe zu ermitteln, die eine hohe Formgenauigkeit bei minimalem Materialverbrauch gewährleisten.
Implementierung von Sensorik und Echtzeitüberwachung
Durch den Einsatz von Sensorik und Echtzeitüberwachungssystemen können Abweichungen im Druckverlauf oder der Materialverformung sofort erkannt und korrigiert werden. Echtzeitdaten ermöglichen eine präzise Steuerung des Verfahrens und tragen dazu bei, Materialfehler zu minimieren.
Nutzung von KI und Simulation zur Prozessverbesserung
Künstliche Intelligenz und Simulationen bieten großes Potenzial für die Prozessoptimierung. KI-Algorithmen können große Datenmengen analysieren und Optimierungsvorschläge in Echtzeit bereitstellen. Simulationen ermöglichen es, verschiedene Szenarien zu testen und den idealen Druck- und Temperaturverlauf für spezifische Materialien und Bauteile zu bestimmen.
Einführung in die Gestaltung von Werkzeugen und Formen für die IHU
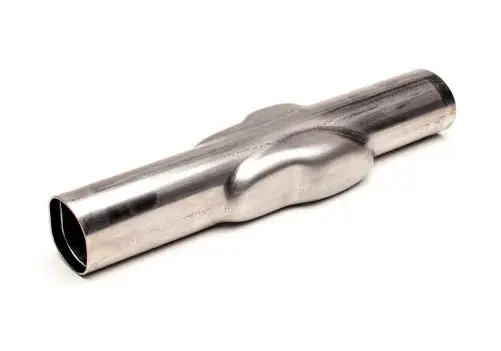
Grundlagen der Werkzeug- und Formgestaltung
Die Gestaltung der Werkzeuge und Formen in der Innenhochdruckumformung ist entscheidend, da sie maßgeblich zur Qualität und Präzision des fertigen Bauteils beiträgt. Ein gut gestaltetes Werkzeug ermöglicht eine gleichmäßige Verteilung des Innendrucks und minimiert Materialfehler wie Risse oder ungleichmäßige Wanddicken. Die Formgebung erfolgt durch Werkzeuge, die exakt der gewünschten Endgeometrie entsprechen und hohen Druckbelastungen standhalten.
Bedeutung der Formgestaltung für die Endqualität und Effizienz
Eine präzise Werkzeuggestaltung stellt sicher, dass das Material optimal in die gewünschte Form gepresst wird und dass die Wanddicke gleichmäßig bleibt. Die Gestaltung beeinflusst nicht nur die Maßhaltigkeit und Stabilität des Endprodukts, sondern auch die Effizienz des gesamten Produktionsprozesses. Eine fehlerhafte oder ungenaue Form führt zu Ausschuss und erhöhten Produktionskosten.
Anforderungen an Werkzeuge und Formen in der IHU
Materialanforderungen und Belastbarkeit
Die Werkzeuge müssen extremen Drücken und Temperaturen standhalten, die während der IHU auftreten. Sie werden aus Materialien gefertigt, die eine hohe Zug- und Druckfestigkeit sowie Beständigkeit gegen Ermüdung aufweisen, um den hohen mechanischen Belastungen langfristig standzuhalten. Häufige Materialien sind gehärtete Stähle und hochfeste Legierungen.
Verschleißbeständigkeit und Langlebigkeit
Die Lebensdauer von Werkzeugen ist ein zentraler Kostenfaktor. Verschleißfestigkeit ist daher ein entscheidendes Kriterium, insbesondere bei der Serienproduktion, wo Werkzeuge oft intensiv beansprucht werden. Die Oberflächen der Werkzeuge werden durch spezielle Beschichtungen geschützt, die die Reibung und den Verschleiß reduzieren.
Präzision und Maßhaltigkeit der Formen
Die Genauigkeit der Form ist essenziell, um die Maßhaltigkeit des fertigen Bauteils zu gewährleisten. Präzise Werkzeuge tragen dazu bei, die Anforderungen an die Formgenauigkeit und Wandstärke zu erfüllen. Schon geringe Abweichungen in der Form können zu erheblichen Qualitätsproblemen führen.
Materialien und Beschichtungen für Werkzeuge
Hochfeste Stähle und Speziallegierungen
Werkzeuge für die IHU werden oft aus hochfesten Stählen und Speziallegierungen gefertigt, die den hohen Druckkräften und thermischen Belastungen standhalten können. Chromstähle und Nickel-Basis-Legierungen sind besonders geeignet, da sie nicht nur widerstandsfähig, sondern auch korrosionsbeständig sind.
Beschichtungen zur Reduktion von Reibung und Verschleiß
Beschichtungen wie PVD (Physical Vapor Deposition) und CVD (Chemical Vapor Deposition) werden auf Werkzeugoberflächen aufgebracht, um die Reibung und den Verschleiß zu minimieren. Diese Beschichtungen schützen das Werkzeug vor Abrieb und erhöhen die Standzeit, was die Werkzeugkosten senkt und die Produktionszeit verbessert.
Korrosionsbeständige Materialien für spezielle Anwendungen
Für Anwendungen in der Luftfahrt- und Automobilindustrie, die hohen Anforderungen an Korrosionsbeständigkeit stellen, kommen spezielle Materialien zum Einsatz. Diese widerstehen nicht nur dem Verschleiß, sondern auch korrosiven Einflüssen, die durch das Druckmedium oder Umgebungsbedingungen entstehen können.
Fertigungsprozess für Werkzeuge und Formen
Fertigungsverfahren und Bearbeitungsschritte
Die Herstellung von IHU-Werkzeugen erfolgt häufig durch CNC-Bearbeitung, Präzisionsschleifen und teilweise durch additive Fertigung. Die Werkzeuge müssen dabei exakt der Form des fertigen Bauteils entsprechen und oft auf wenige Mikrometer genau gefertigt werden, um eine gleichmäßige Wandstärke zu gewährleisten.
Einsatz von CNC-Bearbeitung und Oberflächenbehandlung
CNC-Bearbeitungsmaschinen ermöglichen die Herstellung hochpräziser Formen, die die Anforderungen an Maßhaltigkeit und Oberflächenqualität erfüllen. Nach der Bearbeitung erfolgt eine Oberflächenbehandlung, um die Oberflächengüte zu erhöhen und die Reibung zu reduzieren.
Maßhaltigkeit und Qualitätssicherung im Werkzeugbau
Qualitätskontrollen sind während des gesamten Fertigungsprozesses notwendig, um sicherzustellen, dass die Werkzeuge den genauen Vorgaben entsprechen. Diese umfassen Messungen der Geometrie, Festigkeitsprüfungen und eine Inspektion der Oberflächenqualität. Eine gründliche Qualitätskontrolle stellt sicher, dass die Werkzeuge den Belastungen standhalten und die Maßhaltigkeit des Endprodukts gewährleistet ist.
Gestaltung der Formgeometrie und Struktur
Bedeutung der Geometrie für die Formgebung und Stabilität
Die Geometrie der Form beeinflusst maßgeblich den Verformungsprozess und die Stabilität des fertigen Bauteils. Werkzeuge werden so gestaltet, dass der Druck gleichmäßig auf das Material wirkt und es in die gewünschte Form bringt. Die Geometrie muss dabei die natürlichen Verformungseigenschaften des Materials berücksichtigen, um eine gleichmäßige Wanddicke und Maßgenauigkeit zu erreichen.
Anpassung an spezifische Werkstoffe und Bauteildesigns
Werkstoffe wie Aluminium, Stahl oder Titan erfordern unterschiedliche Werkzeugdesigns, die an die Materialeigenschaften angepasst sind. Bauteildesigns mit variabler Wanddicke oder komplexen Formen stellen höhere Anforderungen an die Werkzeuggestaltung. Eine optimale Geometrie ermöglicht eine gleichmäßige Druckverteilung und verhindert Spannungen im Material.
Komplexe Geometrien und Designfreiheit durch IHU
Durch die IHU sind komplexe Geometrien und nahtlose Formen möglich, die durch andere Verfahren nur schwer realisierbar wären. Diese Designfreiheit eröffnet neue Möglichkeiten im Bauteildesign und bietet insbesondere in der Automobil- und Luftfahrtindustrie große Vorteile.
Werkzeuganpassungen für verschiedene Werkstoffe
Anforderungen für Aluminium, Stahl, Titan und Verbundwerkstoffe
Je nach Werkstoff sind spezielle Anpassungen des Werkzeugs erforderlich, um optimale Ergebnisse zu erzielen. Aluminium benötigt eine gleichmäßige Druckführung, um Materialverformungen zu vermeiden, während hochfeste Stähle und Titan eine stärkere Werkzeugkonstruktion erfordern.
Einfluss der Werkstoffeigenschaften auf die Werkzeuggestaltung
Die Materialeigenschaften beeinflussen direkt die Wahl der Werkzeugmaterialien und -beschichtungen sowie die Druckverhältnisse während der IHU. Bei hochfesten Werkstoffen werden Werkzeuge oft zusätzlich verstärkt, um den höheren Druckanforderungen gerecht zu werden.
Thermische Anpassungen und Formgebung bei unterschiedlichen Materialien
Besonders bei Materialien, die für Hochtemperaturanwendungen bestimmt sind, ist eine thermische Anpassung des Werkzeugs notwendig. Erwärmte Materialien verformen sich leichter, und die Werkzeugmaterialien müssen thermisch stabil bleiben, um Verformungen und Maßabweichungen zu vermeiden.
Simulation und Optimierung in der Werkzeugkonstruktion
Einsatz von CAD und CAE in der Werkzeugentwicklung
Die Entwicklung von Werkzeugen und Formen erfolgt heute weitgehend mittels CAD (Computer-Aided Design) und CAE (Computer-Aided Engineering). CAD ermöglicht die genaue Modellierung der Formgeometrie, während CAE-Tools zur Simulation der Umformprozesse genutzt werden, um Druckverteilung und Materialverformung zu analysieren.
Optimierung des Druckverlaufs und der Materialverteilung
Durch Simulationen lassen sich die Druckverhältnisse und die Materialverteilung im Werkstück präzise analysieren. Ziel ist es, den Druckverlauf so zu gestalten, dass das Material gleichmäßig verformt wird und keine Schwachstellen entstehen. Die Simulation erlaubt es, den optimalen Druckverlauf und die Wandstärke zu ermitteln, bevor das Werkzeug gefertigt wird.
Analyse und Simulation der Prozessparameter
Mittels Simulationssoftware können verschiedene Prozessparameter wie Druck, Temperatur und Materialeigenschaften virtuell getestet werden. Diese Simulationen helfen, den IHU-Prozess zu optimieren und Fehler zu minimieren, was zu einer höheren Effizienz und einer besseren Produktqualität führt.
Innovationen und zukünftige Entwicklungen in der Werkzeuggestaltung
Anwendung additiver Fertigungstechniken für Werkzeugkomponenten
Die additive Fertigung eröffnet neue Möglichkeiten in der Werkzeuggestaltung, insbesondere bei komplexen Geometrien. 3D-Druckverfahren ermöglichen die Herstellung von Werkzeugkomponenten, die sich durch konventionelle Fertigung nicht realisieren lassen und gleichzeitig Gewicht und Kosten sparen.
Nutzung von Sensorik und Echtzeit-Überwachung in Werkzeugen
Moderne IHU-Werkzeuge sind mit Sensoren ausgestattet, die den Druck und die Temperatur während des Umformprozesses überwachen. Diese Echtzeit-Überwachung ermöglicht die sofortige Anpassung der Prozessparameter und sorgt für eine gleichbleibende Produktqualität.
Nachhaltige Materialien und ressourcenschonende Fertigung
Die Nachfrage nach nachhaltigen Materialien und ressourcenschonenden Fertigungsverfahren führt zu neuen Entwicklungen in der Werkzeuggestaltung. Recycelbare Materialien und energieeffiziente Herstellungsverfahren tragen dazu bei, die Umweltbelastung zu reduzieren und die Nachhaltigkeit der Produktion zu erhöhen.
Wirtschaftliche und ökologische Aspekte der Werkzeuggestaltung
Kostenfaktoren und Effizienzsteigerungen durch Werkzeugdesign
Die Werkzeuggestaltung beeinflusst die Produktionskosten erheblich. Eine sorgfältige Gestaltung trägt zur Senkung der Betriebskosten bei, da die Standzeiten und die Wartungsintervalle verlängert werden. Auch der Einsatz verschleißfester Materialien und Beschichtungen reduziert die Werkzeugkosten langfristig.
Reduktion des Materialverbrauchs und der Werkzeugkosten
Durch die effiziente Nutzung des Werkstoffs und die Verringerung von Materialabfällen trägt eine optimierte Werkzeuggestaltung zur Reduktion der Produktionskosten bei. Die Werkzeugkosten lassen sich durch die Verwendung langlebiger Materialien und die Optimierung des Designprozesses ebenfalls reduzieren.
Bedeutung der Werkzeuglebensdauer und Nachhaltigkeit
Eine lange Lebensdauer der Werkzeuge reduziert die Notwendigkeit für Ersatzteile und senkt die Produktionskosten. Nachhaltige Materialien und ein effizientes Design tragen dazu bei, die Umweltbelastung zu minimieren und die Ressourcenschonung zu fördern, was besonders in ressourcenintensiven Industrien wie der Automobil- und Luftfahrtindustrie wichtig ist.
Metallbearbeitungsmaschinen
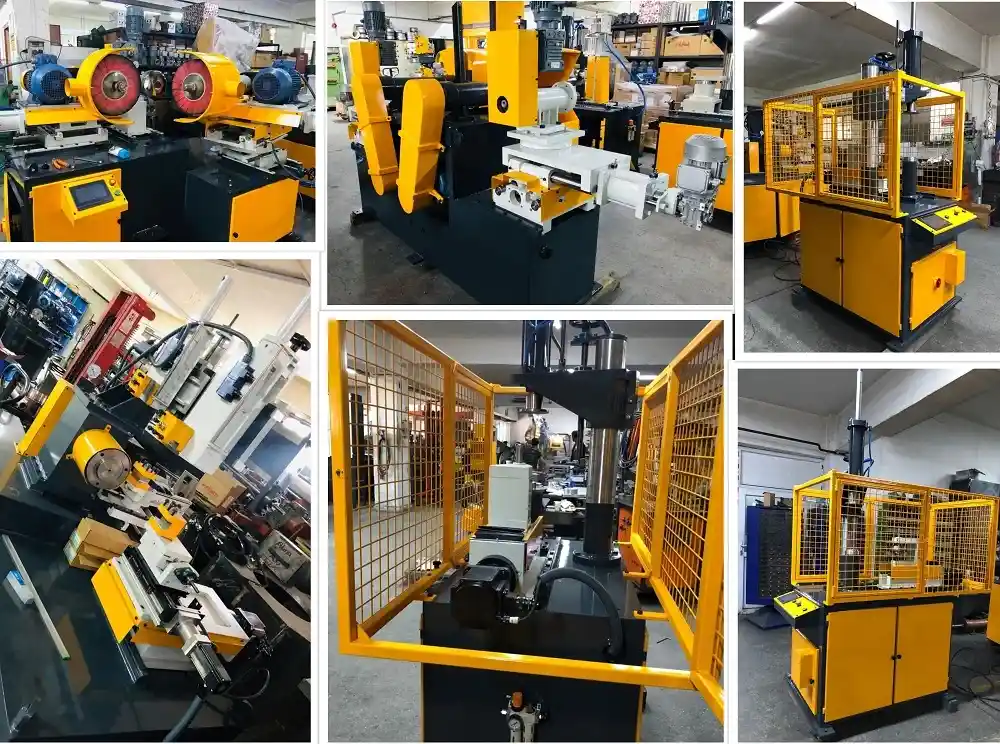
Metallbearbeitungsmaschinen wie Bördel und Beschneide Maschinen, Flanschmaschinen, Beschneide und Bördelmaschinen, Umformtechnik, Rohrbiegemaschinen, Bandsäge für Metall, Hydraulische Horizontalpresse, Kantenschneide-Bördelmaschine, Kantenbördelmaschine, Entgratungsmaschine, Innen- und Außenpoliermaschine für Edelstahltöpfe, Kreisschneidemaschine, Profilbiegemaschine und Rundschweißmaschine
Maßgeschneiderte Skalierung für spezifische Anwendungen
Die automatisierte Herstellung von Behältern, Fässern und Kesseln wird durch unsere Lösungen exakt auf das jeweilige Einsatzgebiet und die gewünschte Ausbringung angepasst. Dabei bieten wir sowohl lineare Lösungen als auch Inselkonzepte an, die eine bedarfsorientierte Automation ermöglichen. Spezielle Kantenvorbereitung für das Laserschweißen sowie wirtschaftliche Rüstkonzepte bis hin zur Fertigung „Just-in-Sequence“ sind Teil unseres Leistungsspektrums. Wir kombinieren Standard- und Sondermaschinen und bieten Ferndiagnose über LAN, WLAN oder GSM an, ergänzt durch umfassende Dokumentation gemäß CE-Richtlinien für die Gesamtanlage.
Unser Konzept
EMS entwickelt und fertigt Maschinen und Anlagen für die automatisierte Herstellung von Behältern in großem Maßstab. Alle Arbeitsschritte, von der Vorbereitung bis zur Fertigung, werden dabei aus einer Hand angeboten. Unsere erprobten Standardkomponenten sind perfekt aufeinander abgestimmt und können nahtlos mit Robotern kombiniert werden, um leistungsfähige Fertigungseinrichtungen zu schaffen.
Flexible Präzisionsfertigung
Unsere Fertigungslinien ermöglichen eine einfache Umstellung auf verschiedene Längen, Durchmesser, Formen und Bearbeitungen durch Programmwechsel. Dabei werden zahlreiche Einzelschritte wie Beschneiden, Formen, Stanzen, Fügen, Montieren, Schweißen und Prüfen automatisch und mit höchster Präzision an die jeweilige Aufgabe angepasst. Besonderes Augenmerk legen wir auf die Kantenvorbereitung für den Schweißprozess, um eine herausragende Prozesssicherheit und minimale Ausschussquoten zu gewährleisten.
Maschinenprogramm für die Metallbearbeitung
Unsere Metallbearbeitungsmaschinen sind:
- Rohrbiegemaschine
- Horizontale Presse
- Bandsäge für Metall
- Profilbiegemaschine
- Tiefziehpresse
- Rundschweißmaschine
- Kantenschneide-Bördelmaschine
- Topf- und Pfannenpoliermaschine
- Poliermaschine für flache Oberflächen
Besteck-Produktionslinie: Eine Besteck-Produktionslinie ist eine Art Maschine, die Besteck in einem kontinuierlichen Prozess herstellt. Es umfasst verschiedene Arten von Maschinen wie den Messerschleifer, den Messerschärfer und den Klingenpolierer.
Kochgeschirr-Herstellungsmaschine: Eine Kochgeschirr-Herstellungsmaschine ist eine Art Maschine, die Kochgeschirr in einem kontinuierlichen Prozess herstellt. Es umfasst verschiedene Arten von Maschinen wie den Topfmacher, den Pfannenmacher und den Wokmacher.
Küchengeschirr-Produktionsmaschine: Eine Küchengeschirr-Produktionsmaschine ist eine Art Maschine, die Küchengeschirr in einem kontinuierlichen Prozess herstellt. Es umfasst verschiedene Arten von Maschinen wie Maschinen zur Herstellung von Teekesseln, Produktionslinien für Besteck, Produktionslinien für Töpfe und Pfannen
Wir entwerfen, fertigen und montieren komplette Produktionslinien für Kochgeschirr, Küchengeschirr, Hotelgeschirr und Besteck sowie einzelne Maschinen für einen bestimmten Zweck