EMS Hydraulikpressen können manuell ebenso wie automatisiert betrieben werden. Kombiniert mit Bandanlage, Platinenlader oder Roboterautomation sind die Pressen zu Systemlösungen ausbaubar.
Hydraulikpressen
Hydraulikpressen sind Maschinen, die hydraulische Kraft verwenden, um Materialien zusammenzupressen, formen oder zu bearbeiten. Sie sind in verschiedenen Industrien weit verbreitet, darunter die Metallverarbeitung, Kunststoffverarbeitung, Automobilindustrie und mehr. Hydraulikpressen bieten hohe Druckkraft und Präzision, was sie ideal für eine Vielzahl von Anwendungen macht.
Druckkraft bezieht sich auf die Menge an Kraft, die auf eine Fläche ausgeübt wird. In Bezug auf Hydraulikpressen ist die Druckkraft die Kraft, die durch das Hydrauliksystem erzeugt wird, um das zu bearbeitende Material zu pressen, zu formen oder zu bearbeiten. Diese Kraft wird durch den Druck der Hydraulikflüssigkeit im Zylinder erzeugt und kann je nach Anwendung und Bedarf angepasst werden. Die Druckkraft bestimmt die Intensität und Effizienz des Pressvorgangs und ist ein wichtiger Parameter bei der Auswahl und dem Betrieb einer Hydraulikpresse.
Die Druckkraft, auch bekannt als Kraft pro Fläche, ist ein physikalisches Maß für die Menge an Kraft, die auf eine bestimmte Fläche ausgeübt wird. In Bezug auf Hydraulikpressen bezeichnet die Druckkraft die Kraft, die durch das Hydrauliksystem erzeugt wird, um das zu bearbeitende Material zu pressen oder zu formen. Sie wird durch den Druck der Hydraulikflüssigkeit im Zylinder erzeugt und kann je nach Bedarf variiert werden. Eine höhere Druckkraft ermöglicht in der Regel eine effizientere Bearbeitung von Materialien mit größerer Stärke oder Dichte. Die genaue Einstellung der Druckkraft ist entscheidend, um die gewünschten Ergebnisse bei der Verarbeitung zu erzielen und sicherzustellen, dass die Maschine ordnungsgemäß betrieben wird.
Ein Hydrauliksystem ist ein System, das Hydraulikflüssigkeit verwendet, um Energie zu übertragen und mechanische Arbeit auszuführen. Es besteht aus verschiedenen Komponenten, darunter Hydraulikpumpen, Zylinder, Ventile, Schläuche und Fluid.
Die Funktionsweise basiert auf dem Prinzip der Hydraulik, bei dem eine Druckkraft durch die Flüssigkeit erzeugt wird, die in einem geschlossenen System zirkuliert. Durch das Anlegen eines Drucks auf die Flüssigkeit wird diese über Schläuche oder Rohre zu einem Zylinder geleitet, wo die Kraft genutzt wird, um eine Bewegung auszuführen, beispielsweise das Anheben eines Objekts oder das Betätigen eines Werkzeugs.
Hydrauliksysteme werden in vielen Anwendungen eingesetzt, darunter Maschinenbau, Automobilindustrie, Flugzeugbau, Landwirtschaft und Bauwesen. Sie bieten viele Vorteile, darunter hohe Leistung, präzise Steuerung, kompakte Bauweise und die Fähigkeit, große Kräfte über große Entfernungen zu übertragen.
Ein Zylinder ist eine der zentralen Komponenten in einem Hydrauliksystem. Er besteht aus einem zylindrischen Gehäuse und einem darin befindlichen Kolben, der sich linear bewegen kann.
Im Kontext von Hydraulikpressen wird der Zylinder durch Hydraulikflüssigkeit betrieben. Wenn Druck auf die Flüssigkeit ausgeübt wird, bewegt sich der Kolben im Zylinder in eine bestimmte Richtung. Diese Bewegung des Kolbens erzeugt mechanische Arbeit, die zum Pressen, Formen oder Bewegen von Materialien verwendet werden kann.
Je nach Anwendung und Design können Hydraulikzylinder unterschiedliche Größen, Formen und Kapazitäten haben. Sie sind in verschiedenen Industrien weit verbreitet, einschließlich Maschinenbau, Automobilindustrie, Bauwesen und vielen anderen Bereichen, wo präzise und leistungsstarke Bewegungen erforderlich sind.
Hydraulikflüssigkeit, auch als Hydrauliköl bezeichnet, ist eine spezielle Flüssigkeit, die in Hydrauliksystemen verwendet wird, um Energie zu übertragen und mechanische Arbeit auszuführen. Sie dient als Übertragungsmedium für Druck und Bewegung innerhalb des Systems.
Die Hydraulikflüssigkeit muss bestimmte Eigenschaften aufweisen, um effizient zu funktionieren, darunter eine hohe Druckbeständigkeit, eine gute Schmierfähigkeit, eine niedrige Viskosität, eine hohe Temperaturstabilität und eine geringe Kompressibilität. Typische Hydraulikflüssigkeiten sind Mineralöle, synthetische Öle oder Wasser-Glykol-Gemische, die je nach Anwendung und Umgebungstemperatur ausgewählt werden.
Es ist wichtig, die Hydraulikflüssigkeit regelmäßig zu überprüfen und zu warten, da sie eine entscheidende Rolle für die Leistung und Lebensdauer des Hydrauliksystems spielt. Verunreinigungen oder ein niedriger Flüssigkeitsstand können zu Funktionsstörungen führen und die Effizienz des Systems beeinträchtigen.
Pumpen sind eine zentrale Komponente in Hydrauliksystemen und dienen dazu, Hydraulikflüssigkeit zu bewegen und Druck zu erzeugen. Sie saugen die Flüssigkeit an und drücken sie durch das System, um die gewünschte Arbeitskraft zu erzeugen.
Es gibt verschiedene Arten von Pumpen, die in Hydrauliksystemen verwendet werden, darunter Zahnradpumpen, Kolbenpumpen und Flügelzellenpumpen. Jede Art hat ihre eigenen Vor- und Nachteile hinsichtlich Leistung, Effizienz und Anwendungsbereich.
Die Auswahl der richtigen Pumpe für ein Hydrauliksystem hängt von verschiedenen Faktoren ab, darunter der benötigte Druck, die Durchflussrate, die Arbeitsumgebung und die spezifischen Anforderungen der Anwendung. Eine korrekt dimensionierte und ausgewählte Pumpe ist entscheidend für die effiziente und zuverlässige Funktion des Hydrauliksystems.
Steuerungstechnik in Hydraulikpressen bezieht sich auf die technologischen Systeme und Mechanismen, die verwendet werden, um den Betrieb der Presse zu steuern, zu überwachen und zu optimieren. Dies umfasst verschiedene Aspekte wie die Steuerung von Druck, Geschwindigkeit, Position, Zykluszeiten und Sicherheit.
Moderne Hydraulikpressen verwenden fortschrittliche Steuerungstechnologien, einschließlich PLCs (Programmable Logic Controllers), CNC (Computerized Numerical Control) und HMI (Human Machine Interface), um den Betrieb der Presse zu automatisieren und zu optimieren. Diese Systeme ermöglichen eine präzise Steuerung über verschiedene Parameter und erleichtern die Integration der Presse in komplexe Fertigungslinien und Prozesse.
Die Steuerungstechnik spielt eine entscheidende Rolle für die Effizienz, Genauigkeit und Sicherheit von Hydraulikpressen und trägt dazu bei, die Produktivität zu steigern und die Betriebskosten zu senken. Durch die kontinuierliche Weiterentwicklung der Steuerungstechnologien werden Hydraulikpressen zunehmend flexibler, vielseitiger und einfacher zu bedienen.
Die Presskraft ist die Kraft, die von einer Hydraulikpresse erzeugt wird, um auf das zu bearbeitende Material zu wirken. Sie wird durch das Hydrauliksystem erzeugt und auf den Kolben des Presszylinders übertragen, der dann die erforderliche Kraft auf das Material ausübt.
Die Presskraft hängt von verschiedenen Faktoren ab, darunter der Druck der Hydraulikflüssigkeit, die Größe des Zylinders, die Anzahl der Kolben und die Konstruktion der Presse. Sie wird oft in Tonnen oder Newton gemessen und kann je nach Anwendung und Material unterschiedlich sein.
Die genaue Einstellung und Kontrolle der Presskraft ist entscheidend, um die gewünschten Ergebnisse zu erzielen und sicherzustellen, dass das Material ordnungsgemäß bearbeitet wird. Eine angemessene Presskraft gewährleistet eine effiziente Bearbeitung und Qualität der Endprodukte, während eine unzureichende oder übermäßige Presskraft zu Problemen wie ungleichmäßiger Formgebung, Beschädigung des Materials oder sogar Maschinenausfällen führen kann.
Der Arbeitsdruck in einer Hydraulikpresse bezeichnet den Druck der Hydraulikflüssigkeit, der benötigt wird, um die gewünschte Presskraft zu erzeugen und das Material effektiv zu bearbeiten. Der Arbeitsdruck wird in der Regel in Bar oder PSI gemessen und ist ein wichtiger Parameter, der die Leistung und Effizienz der Presse beeinflusst.
Ein angemessener Arbeitsdruck muss sorgfältig ausgewählt und überwacht werden, um sicherzustellen, dass die Presse ordnungsgemäß funktioniert und das Material entsprechend den Anforderungen bearbeitet wird. Ein zu niedriger Arbeitsdruck kann zu unzureichender Presskraft führen, was zu unvollständiger oder unsatisfaktorischer Materialbearbeitung führen kann. Auf der anderen Seite kann ein zu hoher Arbeitsdruck die Maschine überlasten, zu Materialschäden führen oder sogar Sicherheitsrisiken verursachen.
Die genaue Einstellung und Überwachung des Arbeitsdrucks ist daher entscheidend, um eine sichere und effiziente Nutzung der Hydraulikpresse zu gewährleisten und qualitativ hochwertige Ergebnisse zu erzielen.
Der Arbeitszyklus einer Hydraulikpresse bezieht sich auf den gesamten Ablauf eines Pressvorgangs, von der Aufnahme des Materials bis zur Fertigstellung des Produkts und dem Zurückkehren der Presse in ihre Ausgangsposition. Dieser Zyklus kann je nach Anwendung und Anforderungen variieren, aber typischerweise umfasst er mehrere Schritte:
- Materialvorbereitung: Das zu bearbeitende Material wird vorbereitet und in die Presse eingelegt.
- Absenkung des Werkzeugs: Der Presszylinder senkt sich ab, um das Material zu erfassen und zu positionieren.
- Pressen: Die Hydraulikpresse übt die erforderliche Presskraft auf das Material aus, um es zu formen, zu pressen oder zu bearbeiten.
- Entlastung: Nach Abschluss des Pressvorgangs wird der Druck entlastet, und das bearbeitete Material kann aus der Presse entfernt werden.
- Rückkehr in die Ausgangsposition: Der Presszylinder kehrt in seine Ausgangsposition zurück, um für den nächsten Zyklus bereit zu sein.
Der Arbeitszyklus kann je nach Anwendung und Produktionsprozess automatisiert und gesteuert werden, um eine hohe Effizienz und Reproduzierbarkeit sicherzustellen. Die genaue Steuerung und Überwachung jedes Schrittes im Arbeitszyklus ist entscheidend, um qualitativ hochwertige Ergebnisse zu erzielen und die Lebensdauer der Hydraulikpresse zu maximieren.
Hydraulikschläuche sind flexible Rohre oder Schläuche, die in Hydrauliksystemen verwendet werden, um Hydraulikflüssigkeit zwischen verschiedenen Komponenten zu transportieren. Sie dienen dazu, Druck, Volumenstrom und Bewegung der Hydraulikflüssigkeit zu ermöglichen, während sie gleichzeitig Flexibilität bieten, um Bewegungen oder Ausdehnungen in einem System aufzunehmen.
Hydraulikschläuche bestehen typischerweise aus verschiedenen Schichten, die sie robust und widerstandsfähig gegenüber hohem Druck und abrasiven Bedingungen machen. Diese Schichten umfassen normalerweise eine Innenschicht aus synthetischem Gummi, die die Hydraulikflüssigkeit abdichtet, gefolgt von Verstärkungsschichten aus Stahl- oder Textilgeweben für Festigkeit und Stabilität, und einer äußeren Schicht, die vor äußeren Einflüssen wie Abrieb, UV-Strahlung und Witterung schützt.
Die Auswahl des richtigen Hydraulikschlauchs für eine bestimmte Anwendung hängt von verschiedenen Faktoren ab, darunter der Druckbereich, die Temperatur, die Chemikalienbeständigkeit und die Flexibilität. Eine korrekte Installation, regelmäßige Wartung und Überprüfung der Integrität der Hydraulikschläuche sind entscheidend, um Leckagen, Ausfälle oder Sicherheitsrisiken zu vermeiden und die Zuverlässigkeit des Hydrauliksystems sicherzustellen.
Ein Druckregler, auch als Druckbegrenzungsventil oder Druckregelventil bezeichnet, ist eine Komponente in Hydrauliksystemen, die dazu dient, den Druck in einem bestimmten Bereich zu halten oder zu begrenzen. Der Druckregler überwacht den Druck in einem Hydrauliksystem und reguliert ihn, indem er den Durchfluss der Hydraulikflüssigkeit entsprechend anpasst.
Der Druckregler besteht aus einem Ventilmechanismus, der den Durchfluss der Hydraulikflüssigkeit je nach Druckeinwirkung öffnet oder schließt. Wenn der Druck den voreingestellten Grenzwert erreicht, wird das Ventil geöffnet, um den Überschuss an Hydraulikflüssigkeit abzuleiten oder den Durchfluss zu reduzieren, um den Druck auf dem gewünschten Niveau zu halten.
Druckregler sind entscheidend für die Sicherheit und Leistung von Hydrauliksystemen, da sie dazu beitragen, Überdruck zu verhindern, der zu Schäden an Komponenten führen kann, und gleichzeitig eine gleichbleibende und zuverlässige Funktion des Systems sicherstellt. Sie werden in verschiedenen Anwendungen eingesetzt, einschließlich Hydraulikpressen, Kränen, Baumaschinen, Kraftfahrzeugen und industriellen Anlagen.
Ein Öldruckregler ist eine spezielle Art von Druckregler, der in Hydrauliksystemen verwendet wird, um den Öldruck auf einem bestimmten Niveau zu halten oder zu begrenzen. Er überwacht den Druck des Hydrauliköls und reguliert ihn entsprechend, um die ordnungsgemäße Funktion des Systems sicherzustellen.
Der Öldruckregler besteht typischerweise aus einem Ventilmechanismus, der den Durchfluss des Hydrauliköls steuert. Wenn der Öldruck einen voreingestellten Grenzwert erreicht, öffnet das Ventil, um den Ölfluss zu steuern und den Druck zu begrenzen. Dadurch wird verhindert, dass der Öldruck zu hoch wird und Schäden an den Systemkomponenten verursacht.
Öldruckregler sind in verschiedenen Anwendungen weit verbreitet, einschließlich Hydraulikpressen, Hydraulikaggregaten, industriellen Maschinen und Fahrzeugen. Sie sind entscheidend für die Sicherheit, Leistung und Zuverlässigkeit von Hydrauliksystemen, da sie dazu beitragen, Überdruck zu verhindern und eine gleichmäßige Funktion des Systems zu gewährleisten.
Die Pressgeschwindigkeit bezieht sich auf die Geschwindigkeit, mit der sich die beweglichen Teile einer Hydraulikpresse während des Pressvorgangs bewegen. Sie kann variiert werden, um die Bearbeitungsgeschwindigkeit und -effizienz anzupassen sowie die Qualität der bearbeiteten Teile zu kontrollieren.
Die Pressgeschwindigkeit wird durch verschiedene Faktoren beeinflusst, darunter der Arbeitsdruck, die Hydraulikflussrate, die Größe des Zylinders und die Anwendung. Eine höhere Pressgeschwindigkeit kann zu einer schnelleren Bearbeitung von Materialien führen, aber auch zu einem erhöhten Verschleiß der Maschine und möglicherweise zu einer geringeren Präzision. Eine niedrigere Pressgeschwindigkeit kann eine präzisere Bearbeitung ermöglichen, erfordert jedoch möglicherweise längere Bearbeitungszeiten.
Die optimale Pressgeschwindigkeit hängt von den spezifischen Anforderungen der Anwendung, der Art des zu bearbeitenden Materials und den gewünschten Ergebnissen ab. Eine sorgfältige Einstellung und Kontrolle der Pressgeschwindigkeit ist entscheidend, um die Qualität der bearbeiteten Teile zu gewährleisten und die Lebensdauer der Hydraulikpresse zu maximieren.
Hydraulik Zylinder
Hydraulikzylinder sind Schlüsselkomponenten in Hydrauliksystemen, die dazu dienen, mechanische Arbeit durch den Einsatz von Hydraulikflüssigkeit zu erzeugen. Sie bestehen aus einem zylindrischen Gehäuse und einem Kolben, der sich darin bewegen kann.
Wenn Druck auf die Hydraulikflüssigkeit ausgeübt wird, bewegt sich der Kolben im Zylinder. Diese Bewegung erzeugt eine Kraft, die genutzt werden kann, um Lasten zu heben, zu pressen, zu bewegen oder zu steuern. Die Größe des Hydraulikzylinders und der Druck der Hydraulikflüssigkeit bestimmen die maximale Kraft, die erzeugt werden kann.
Hydraulikzylinder kommen in verschiedenen Formen und Größen vor, je nach den Anforderungen der Anwendung. Sie werden in einer Vielzahl von Branchen und Anwendungen eingesetzt, darunter Maschinenbau, Bauwesen, Automobilindustrie, Landwirtschaft und viele andere, um mechanische Bewegungen und Kraftübertragung zu ermöglichen.
Sicherheitsvorkehrungen sind entscheidend, um Unfälle und Verletzungen in Zusammenhang mit der Verwendung von Hydraulikpressen zu vermeiden. Einige wichtige Sicherheitsvorkehrungen umfassen:
- Schutzausrüstung: Bediener sollten angemessene Schutzausrüstung tragen, einschließlich Schutzbrillen, Handschuhe und Schutzhelme, um sich vor potenziellen Gefahren zu schützen.
- Schulung: Bediener sollten eine gründliche Schulung erhalten, um die sichere Bedienung der Hydraulikpresse zu gewährleisten. Sie sollten die Funktionsweise der Maschine verstehen, sowie die Bedeutung und Anwendung der Sicherheitsvorkehrungen.
- Not-Aus: Hydraulikpressen sollten über Not-Aus-Schalter verfügen, die es dem Bediener ermöglichen, die Maschine sofort zu stoppen, wenn eine Gefahr oder ein Problem auftritt.
- Schutzvorrichtungen: Die Presse sollte mit Schutzvorrichtungen ausgestattet sein, um Bediener vor beweglichen Teilen zu schützen. Dazu gehören z.B. Schutzgitter, Lichtschranken oder Berührungssensoren.
- Regelmäßige Wartung: Die Hydraulikpresse sollte regelmäßig gewartet werden, um sicherzustellen, dass sie ordnungsgemäß funktioniert und keine Sicherheitsrisiken bestehen.
- Arbeitsbereichssicherheit: Der Arbeitsbereich um die Hydraulikpresse herum sollte frei von Hindernissen sein und deutlich gekennzeichnet sein, um Unfälle zu vermeiden.
Die Einhaltung dieser Sicherheitsvorkehrungen ist entscheidend, um Unfälle zu vermeiden und die Sicherheit der Bediener zu gewährleisten.
Presswerkzeuge
Presswerkzeuge sind spezielle Werkzeuge oder Formen, die in Hydraulikpressen verwendet werden, um Materialien zu bearbeiten, zu formen oder zu pressen. Sie bestehen oft aus robusten Materialien wie Stahl oder Hartmetall und sind so konstruiert, dass sie den hohen Drücken und Belastungen standhalten können, die während des Pressvorgangs auftreten.
Je nach Anwendung und gewünschtem Endprodukt können Presswerkzeuge verschiedene Formen und Konfigurationen haben. Einige gängige Arten von Presswerkzeugen umfassen:
- Stempel und Matrizen: Diese werden häufig verwendet, um Bleche zu formen oder zu stanzen. Der Stempel drückt das Material in die Matrize, um die gewünschte Form zu erzeugen.
- Formen: Formen werden verwendet, um Materialien in bestimmte Formen zu pressen oder zu extrudieren, wie beispielsweise bei der Herstellung von Kunststoffteilen oder Gummidichtungen.
- Schneidwerkzeuge: Schneidwerkzeuge werden verwendet, um Materialien zu schneiden oder zu trennen, wie beispielsweise bei der Herstellung von Metallteilen oder Kunststoffrohren.
- Kalandrierwerkzeuge: Diese werden verwendet, um Materialien zwischen zwei Walzen zu pressen, um die Dicke zu reduzieren oder eine glatte Oberfläche zu erzeugen, wie beispielsweise bei der Herstellung von Folien oder Gummiplatten.
Die Auswahl des richtigen Presswerkzeugs hängt von verschiedenen Faktoren ab, darunter das zu bearbeitende Material, die gewünschte Form oder Struktur des Endprodukts und die spezifischen Anforderungen der Anwendung. Ein korrekt ausgewähltes und eingesetztes Presswerkzeug ist entscheidend für die Qualität und Effizienz des Pressvorgangs.
Hydraulikleitungen sind Rohre oder Schläuche, die in Hydrauliksystemen verwendet werden, um Hydraulikflüssigkeit zwischen verschiedenen Komponenten zu transportieren. Sie dienen dazu, Druck, Volumenstrom und Bewegung der Hydraulikflüssigkeit zu ermöglichen, während sie gleichzeitig Flexibilität bieten, um Bewegungen oder Ausdehnungen im System aufzunehmen.
Hydraulikleitungen bestehen typischerweise aus robusten Materialien wie Stahl oder hochfestem Kunststoff und sind so konstruiert, dass sie den hohen Drücken und Belastungen standhalten können, die während des Betriebs auftreten. Sie werden in verschiedenen Größen und Konfigurationen hergestellt, um den Anforderungen einer Vielzahl von Anwendungen gerecht zu werden.
Die Auswahl der richtigen Hydraulikleitungen hängt von verschiedenen Faktoren ab, darunter der Druckbereich, die Temperatur, die Chemikalienbeständigkeit und die Flexibilität. Eine ordnungsgemäße Installation und regelmäßige Wartung der Hydraulikleitungen ist entscheidend, um Leckagen, Ausfälle oder Sicherheitsrisiken zu vermeiden und die Zuverlässigkeit des Hydrauliksystems sicherzustellen.
Der Pressvorgang in einer Hydraulikpresse bezieht sich auf den Prozess, bei dem durch den Einsatz von Druck und Kraft ein Material bearbeitet, geformt oder gepresst wird. Der Pressvorgang kann je nach Anwendung und Material variieren, aber typischerweise umfasst er mehrere Schritte:
- Vorbereitung des Materials: Das zu bearbeitende Material wird vorbereitet und in die Hydraulikpresse eingelegt. Dies kann das Platzieren des Materials zwischen Presswerkzeugen oder das Einlegen in eine Form umfassen.
- Anwendung des Drucks: Durch das Betätigen der Presse wird Hydraulikflüssigkeit in den Zylinder gepumpt, was den Kolben bewegt und Druck auf das Material ausübt. Dieser Druck bewirkt die gewünschte Verformung, Formgebung oder Kompression des Materials.
- Überwachung des Pressvorgangs: Während des Pressvorgangs werden verschiedene Parameter wie Druck, Geschwindigkeit und Position überwacht, um sicherzustellen, dass der Vorgang ordnungsgemäß verläuft und die gewünschten Ergebnisse erzielt werden.
- Abschluss des Pressvorgangs: Nach Abschluss des Pressvorgangs wird der Druck entlastet, und das bearbeitete Material kann aus der Presse entfernt werden.
Der Pressvorgang kann je nach Anforderungen der Anwendung automatisiert oder manuell gesteuert werden. Die genaue Einstellung und Überwachung jedes Schrittes im Pressvorgang ist entscheidend, um qualitativ hochwertige Ergebnisse zu gewährleisten und die Lebensdauer der Hydraulikpresse zu maximieren.
Eine Hydraulikpumpe ist eine wichtige Komponente in einem Hydrauliksystem, die dazu dient, Hydraulikflüssigkeit zu bewegen und den erforderlichen Druck zu erzeugen. Sie ist verantwortlich für die Umwandlung von mechanischer Energie in hydraulische Energie.
Es gibt verschiedene Arten von Hydraulikpumpen, darunter Zahnradpumpen, Kolbenpumpen und Flügelzellenpumpen, die jeweils ihre eigenen Vor- und Nachteile hinsichtlich Leistung, Effizienz und Anwendungsbereich haben. Die Auswahl der richtigen Hydraulikpumpe hängt von verschiedenen Faktoren ab, darunter der benötigte Druck, die Durchflussrate und die Anwendung.
Die Hydraulikpumpe saugt Hydraulikflüssigkeit aus einem Reservoir an und drückt sie durch das Hydrauliksystem, um Druck zu erzeugen und mechanische Arbeit zu leisten. Sie spielt eine entscheidende Rolle für die Leistung und Effizienz des Hydrauliksystems und muss ordnungsgemäß dimensioniert, installiert und gewartet werden, um eine zuverlässige Funktion sicherzustellen.
Hydraulikflüssigkeit, auch bekannt als Hydrauliköl, ist eine spezielle Flüssigkeit, die in Hydrauliksystemen verwendet wird, um Energie zu übertragen und mechanische Arbeit auszuführen. Sie dient als Übertragungsmedium für Druck und Bewegung innerhalb des Systems.
Hydraulikflüssigkeiten müssen bestimmte Eigenschaften aufweisen, um effizient zu funktionieren. Dazu gehören eine hohe Druckbeständigkeit, eine gute Schmierfähigkeit, eine niedrige Viskosität, eine hohe Temperaturstabilität und eine geringe Kompressibilität. Typische Hydraulikflüssigkeiten sind Mineralöle, synthetische Öle oder Wasser-Glykol-Gemische, die je nach Anwendung und Umgebungstemperatur ausgewählt werden.
Es ist wichtig, die Hydraulikflüssigkeit regelmäßig zu überprüfen und zu warten, da sie eine entscheidende Rolle für die Leistung und Lebensdauer des Hydrauliksystems spielt. Verunreinigungen oder ein niedriger Flüssigkeitsstand können zu Funktionsstörungen führen und die Effizienz des Systems beeinträchtigen. Eine ordnungsgemäße Auswahl und Pflege der Hydraulikflüssigkeit trägt zur zuverlässigen Funktion des Hydrauliksystems bei.
Eine Hydraulikdruckanzeige ist ein Instrument oder eine Vorrichtung, die in einem Hydrauliksystem verwendet wird, um den aktuellen Druck der Hydraulikflüssigkeit anzuzeigen. Sie liefert dem Bediener wichtige Informationen über den Druck im System und ermöglicht es, den Betrieb zu überwachen und zu steuern.
Hydraulikdruckanzeigen können verschiedene Formen annehmen, darunter analoge Manometer, digitale Anzeigetafeln oder sogar elektronische Sensoren, die die Daten an eine Steuereinheit übermitteln. Sie werden oft in der Nähe von Bedienfeldern oder Steuerungen platziert, wo sie leicht abgelesen werden können.
Die genaue Überwachung des Hydraulikdrucks ist entscheidend, um sicherzustellen, dass das System ordnungsgemäß funktioniert und innerhalb sicherer Betriebsgrenzen arbeitet. Abweichungen vom normalen Druck können auf Probleme im System hinweisen, die behoben werden müssen, um Ausfälle oder Schäden zu vermeiden. Daher ist die Hydraulikdruckanzeige ein wichtiges Instrument für die Wartung und den sicheren Betrieb von Hydrauliksystemen.
Eine Hydraulikdruckanzeige ist ein Instrument oder eine Vorrichtung, die den aktuellen Druck der Hydraulikflüssigkeit in einem Hydrauliksystem anzeigt. Sie bietet dem Bediener wichtige Informationen über den Druck im System, was hilfreich ist, um den Betrieb zu überwachen, Fehler zu erkennen und die Leistung zu optimieren.
Hydraulikdruckanzeigen gibt es in verschiedenen Ausführungen, darunter analoge Manometer, digitale Anzeigetafeln und elektronische Sensoren. Diese können entweder direkt an der Hydraulikpresse oder an einem Steuerungspanel angebracht sein, je nach den Anforderungen und der Komplexität des Systems.
Die Überwachung des Hydraulikdrucks ist entscheidend, um sicherzustellen, dass das System ordnungsgemäß funktioniert und innerhalb sicherer Betriebsgrenzen arbeitet. Eine plötzliche Abweichung des Drucks kann auf Probleme wie Leckagen, Blockaden oder Überlastung hinweisen, die behoben werden müssen, um die Sicherheit und Effizienz des Systems zu gewährleisten. Daher ist die Hydraulikdruckanzeige ein unverzichtbares Instrument für die Wartung und den Betrieb von Hydrauliksystemen.
Hydraulikanlage
Eine Hydraulikanlage ist ein System, das Hydraulikflüssigkeit verwendet, um Energie zu übertragen und mechanische Arbeit auszuführen. Sie besteht aus verschiedenen Komponenten, die zusammenarbeiten, um den gewünschten Betrieb zu ermöglichen. Zu den Hauptkomponenten einer Hydraulikanlage gehören:
- Hydraulikpumpe: Die Hydraulikpumpe ist verantwortlich für die Erzeugung des Drucks in der Anlage, indem sie Hydraulikflüssigkeit aus einem Reservoir ansaugt und durch das System pumpt.
- Hydraulikzylinder: Hydraulikzylinder wandeln den Druck der Hydraulikflüssigkeit in mechanische Arbeit um. Sie bestehen aus einem Zylindergehäuse und einem beweglichen Kolben, der sich linear bewegen kann.
- Hydraulikleitungen und Schläuche: Diese dienen dazu, die Hydraulikflüssigkeit zwischen den verschiedenen Komponenten der Anlage zu transportieren und den Druck zu übertragen.
- Steuerungseinheit: Die Steuerungseinheit kann aus Ventilen, Steuerungen und elektronischen Geräten bestehen, die den Betrieb der Anlage überwachen, steuern und optimieren.
- Arbeitsgeräte: Dies sind die Werkzeuge oder Geräte, die durch die Hydraulikanlage betrieben werden, wie z.B. Hydraulikpressen, Kräne, Bagger oder Hubvorrichtungen.
Hydraulikanlagen werden in einer Vielzahl von Anwendungen eingesetzt, darunter Industriemaschinen, Baumaschinen, Fahrzeuge, Flugzeuge, Landwirtschaft und viele andere Bereiche, wo eine präzise Steuerung und hohe Leistung erforderlich ist. Sie bieten viele Vorteile, darunter hohe Leistungsdichte, präzise Steuerung und die Fähigkeit, große Kräfte über große Entfernungen zu übertragen.
Die Presskraftbegrenzung ist eine Sicherheitsfunktion, die in Hydraulikpressen implementiert wird, um die maximale auf das Material ausgeübte Kraft zu begrenzen. Diese Funktion ist wichtig, um Unfälle, Beschädigungen der Maschine oder des Materials sowie Verletzungen von Bedienern zu verhindern.
Es gibt verschiedene Möglichkeiten, die Presskraftbegrenzung zu realisieren:
- Mechanische Begrenzung: Eine mechanische Vorrichtung kann installiert werden, um den Bewegungsbereich des Kolbens zu begrenzen oder den maximalen Öffnungsabstand zwischen den Presswerkzeugen festzulegen.
- Druckbegrenzungsventil: Ein Druckbegrenzungsventil wird in das Hydrauliksystem eingebaut und setzt einen maximalen Druck fest, den das System erreichen kann. Wenn dieser Druck erreicht wird, öffnet sich das Ventil und leitet überschüssige Hydraulikflüssigkeit ab, um die Presskraft zu begrenzen.
- Elektronische Steuerung: Moderne Hydraulikpressen können mit elektronischen Steuerungssystemen ausgestattet sein, die die Presskraft überwachen und bei Bedarf automatisch reduzieren können. Diese Systeme können Sensoren verwenden, um den Druck oder die Position des Kolbens zu überwachen und die Maschine entsprechend zu steuern.
Die korrekte Einstellung und regelmäßige Überprüfung der Presskraftbegrenzung ist entscheidend, um sicherzustellen, dass die Hydraulikpresse sicher und effizient betrieben wird. Dies trägt dazu bei, Unfälle zu vermeiden und die Lebensdauer der Maschine zu verlängern.
Hydrauliköl
Hydrauliköl, auch als Hydraulikflüssigkeit bezeichnet, ist eine spezielle Art von Öl, die in Hydrauliksystemen verwendet wird, um Druck zu übertragen, mechanische Arbeit auszuführen und Komponenten zu schmieren. Es spielt eine entscheidende Rolle für die Leistung und Zuverlässigkeit des Hydrauliksystems.
Hydrauliköle müssen bestimmte Eigenschaften aufweisen, um effizient zu funktionieren. Dazu gehören eine hohe Druckbeständigkeit, eine gute Schmierfähigkeit, eine niedrige Viskosität, eine hohe Temperaturstabilität und eine geringe Kompressibilität. Typische Hydrauliköle sind Mineralöle, synthetische Öle oder Wasser-Glykol-Gemische, die je nach Anwendung und Umgebungstemperatur ausgewählt werden.
Die Auswahl des richtigen Hydrauliköls hängt von verschiedenen Faktoren ab, darunter der Betriebsdruck, die Umgebungstemperatur, die Anforderungen an die Schmierung und die spezifischen Anforderungen des Hydrauliksystems. Eine ordnungsgemäße Auswahl und regelmäßige Überwachung des Hydrauliköls ist entscheidend, um die Leistung und Zuverlässigkeit des Hydrauliksystems zu gewährleisten und die Lebensdauer der Komponenten zu maximieren.
Hydraulik Schaltungen
Hydraulikschaltungen sind Systeme von Leitungen, Ventilen, Pumpen, Zylindern und anderen hydraulischen Komponenten, die zusammenarbeiten, um hydraulische Energie zu übertragen und mechanische Arbeit auszuführen. Es gibt verschiedene Arten von Hydraulikschaltungen, die je nach Anwendung und Anforderungen entwickelt wurden. Einige der häufigsten Typen sind:
- Offene Schaltung: In einer offenen Hydraulikschaltung fließt die Hydraulikflüssigkeit kontinuierlich vom Reservoir zur Pumpe und dann zum Verbraucher (z. B. Zylinder oder Motor). Der überschüssige Flüssigkeitsstrom wird zurück zum Reservoir geleitet. Diese Schaltung eignet sich gut für Anwendungen, bei denen eine konstante Leistung benötigt wird, wie z. B. bei Hydraulikmotoren.
- Geschlossene Schaltung: In einer geschlossenen Hydraulikschaltung wird die Hydraulikflüssigkeit im Kreislauf geführt und kontinuierlich recycelt. Diese Schaltung ermöglicht eine präzise Steuerung des Drucks, der Strömungsrate und der Richtung des Flüssigkeitsstroms durch den Einsatz von Ventilen und Steuerungen. Geschlossene Schaltungen werden häufig in Hydraulikpressen, Bagger und anderen Anwendungen verwendet, bei denen eine präzise Steuerung erforderlich ist.
- Proportionaldruckregelschaltung: Diese Schaltung ermöglicht eine präzise Steuerung des Drucks und der Strömungsrate durch den Einsatz von Proportionalventilen. Sie wird häufig in Anwendungen eingesetzt, bei denen eine präzise Regelung des Drucks und der Geschwindigkeit erforderlich ist, wie z. B. bei Servohydrauliksystemen.
- Parallel- und Serienschaltung: Diese Schaltungstypen werden verwendet, um die Leistungsfähigkeit und Flexibilität von Hydrauliksystemen zu erhöhen, indem mehrere Pumpen, Zylinder oder Motoren parallel oder in Serie geschaltet werden, um die erforderliche Leistung zu erzielen.
Die Auswahl der richtigen Hydraulikschaltung hängt von verschiedenen Faktoren ab, darunter die Art der Anwendung, die benötigte Leistung, die Anforderungen an die Steuerung und die Kosten. Eine sorgfältige Planung und Auslegung der Hydraulikschaltung ist entscheidend, um eine optimale Leistung und Zuverlässigkeit des Hydrauliksystems sicherzustellen.
Hydraulik Presse Bauteile
Hydraulikpressen bestehen aus einer Vielzahl von Bauteilen, die zusammenarbeiten, um mechanische Arbeit durch den Einsatz von Hydraulikflüssigkeit zu erzeugen. Hier sind einige der wichtigsten Bauteile einer Hydraulikpresse:
- Rahmen: Der Rahmen bildet die strukturelle Basis der Hydraulikpresse und trägt die anderen Komponenten.
- Hydraulikzylinder: Die Hydraulikzylinder wandeln den Druck der Hydraulikflüssigkeit in mechanische Kraft um, die zum Pressen oder Bewegen von Materialien verwendet wird.
- Hydraulikpumpe: Die Hydraulikpumpe erzeugt den erforderlichen Druck, indem sie Hydraulikflüssigkeit aus einem Reservoir ansaugt und durch das System pumpt.
- Ventile und Steuerungen: Diese Komponenten steuern den Fluss der Hydraulikflüssigkeit und regeln den Druck, die Geschwindigkeit und die Richtung der Bewegung des Hydraulikzylinders.
- Presswerkzeuge: Die Presswerkzeuge sind die Werkzeuge oder Formen, die verwendet werden, um Materialien zu bearbeiten, zu formen oder zu pressen.
- Hydraulikleitungen und Schläuche: Diese dienen dazu, die Hydraulikflüssigkeit zwischen den verschiedenen Komponenten der Presse zu transportieren und den Druck zu übertragen.
- Elektronische Steuerungseinheiten: Moderne Hydraulikpressen können mit elektronischen Steuerungseinheiten ausgestattet sein, die den Betrieb überwachen, steuern und optimieren.
- Schutzeinrichtungen: Schutzeinrichtungen wie Not-Aus-Schalter, Lichtschranken oder Schutzzäune dienen dazu, Bediener und Umgebung vor Gefahren zu schützen.
Diese Bauteile arbeiten zusammen, um die gewünschten Pressvorgänge auszuführen und sicherzustellen, dass die Hydraulikpresse effizient und zuverlässig arbeitet. Eine sorgfältige Planung, Installation und Wartung dieser Bauteile ist entscheidend, um die Leistung und Sicherheit der Hydraulikpresse zu gewährleisten.
Hydraulik filter
Hydraulikfilter sind wesentliche Komponenten in Hydrauliksystemen, die dazu dienen, Verunreinigungen und Partikel aus der Hydraulikflüssigkeit zu entfernen. Sie spielen eine entscheidende Rolle für die Leistung und Lebensdauer des Systems, da Verunreinigungen zu Verschleiß, Beschädigungen an Komponenten und Leistungsverlust führen können.
Hydraulikfilter können in verschiedenen Bereichen des Systems installiert werden, einschließlich der Saugleitung, Druckleitung und Rücklaufleitung, um die Hydraulikflüssigkeit zu reinigen, bevor sie in die Pumpe gelangt, durch das System zirkuliert und in den Tank zurückkehrt.
Es gibt verschiedene Arten von Hydraulikfiltern, darunter:
- Saugfilter: Diese Filter befinden sich in der Saugleitung der Pumpe und entfernen grobe Verunreinigungen, um die Pumpe vor Beschädigungen zu schützen.
- Druckfilter: Diese Filter sind in der Druckleitung installiert und entfernen feinere Partikel aus der Hydraulikflüssigkeit, um die empfindlichen Komponenten des Systems zu schützen.
- Rücklauffilter: Diese Filter sind in der Rücklaufleitung positioniert und entfernen Partikel aus der Hydraulikflüssigkeit, bevor sie in den Tank zurückkehrt, um die Flüssigkeit zu reinigen und die Verunreinigungen im System zu minimieren.
Die Auswahl des richtigen Hydraulikfilters hängt von verschiedenen Faktoren ab, einschließlich der Art der Verunreinigungen, des Durchflusses und des Druckbereichs des Hydrauliksystems. Eine regelmäßige Wartung und Überprüfung der Filter ist entscheidend, um eine effiziente Filterleistung sicherzustellen und die Zuverlässigkeit des Hydrauliksystems zu gewährleisten.
Ein Rücklaufventil, auch als Rückschlagventil oder Rückschlagklappe bezeichnet, ist eine hydraulische Komponente, die dazu dient, den Fluss der Hydraulikflüssigkeit in eine Richtung zu steuern und in der Gegenrichtung zu blockieren. Es ermöglicht, dass die Hydraulikflüssigkeit in eine Richtung durchfließt, während sie in der entgegengesetzten Richtung blockiert wird.
Das Rücklaufventil besteht aus einem Ventilmechanismus, der normalerweise aus einem Klappen-, Kugel- oder Schrägsitzventil besteht, das sich öffnet, wenn der Druck in die gewünschte Richtung steigt, und sich schließt, um den Rückfluss zu verhindern. Dadurch wird verhindert, dass die Hydraulikflüssigkeit unerwünscht in das System zurückfließt.
Rücklaufventile werden in verschiedenen Anwendungen eingesetzt, um den Fluss der Hydraulikflüssigkeit zu steuern und zu kontrollieren. Sie werden häufig in Hydraulikzylindern, Hydraulikpumpen, Steuerungen und Schaltungen verwendet, um den Betrieb zu optimieren und zu schützen.
Die Auswahl des richtigen Rücklaufventils hängt von verschiedenen Faktoren ab, darunter der Druckbereich, der Durchfluss, die Größe des Systems und die spezifischen Anforderungen der Anwendung. Eine ordnungsgemäße Installation und Wartung der Rücklaufventile ist entscheidend, um eine zuverlässige Funktion des Hydrauliksystems sicherzustellen.
Hydraulikspeicher sind Vorrichtungen, die in Hydrauliksystemen verwendet werden, um überschüssige Hydraulikflüssigkeit aufzunehmen, Druckschwankungen auszugleichen und die Leistung des Systems zu verbessern. Sie dienen dazu, die Energie zu speichern und bei Bedarf freizusetzen, um die Effizienz und Zuverlässigkeit des Systems zu erhöhen.
Es gibt verschiedene Arten von Hydraulikspeichern, darunter:
- Blasenspeicher: Ein Blasenspeicher besteht aus einem geschlossenen Behälter, der mit Stickstoffgas gefüllt ist und durch eine flexible Membran von der Hydraulikflüssigkeit getrennt ist. Wenn Druck auf die Hydraulikflüssigkeit ausgeübt wird, komprimiert sich das Stickstoffgas und speichert die Energie. Bei Bedarf wird die gespeicherte Energie freigesetzt, indem die komprimierte Hydraulikflüssigkeit aus dem Speicher gedrückt wird.
- Kolbenspeicher: Ein Kolbenspeicher besteht aus einem Zylinder, in dem sich ein Kolben bewegen kann. Wenn Druck auf die Hydraulikflüssigkeit ausgeübt wird, bewegt sich der Kolben und komprimiert die Hydraulikflüssigkeit im Zylinder. Dies ermöglicht es, Energie zu speichern und bei Bedarf freizusetzen.
- Federbelasteter Speicher: Diese Art von Speicher verwendet eine Feder, um Energie zu speichern und freizusetzen. Der Speicher besteht aus einem Zylinder, in dem sich ein Kolben befindet, der von einer Feder belastet ist. Wenn Druck auf die Hydraulikflüssigkeit ausgeübt wird, bewegt sich der Kolben gegen die Feder, wodurch Energie gespeichert wird. Bei Bedarf wird die gespeicherte Energie freigesetzt, indem die Feder den Kolben zurückdrückt und die Hydraulikflüssigkeit aus dem Speicher entlässt.
Hydraulikspeicher werden in einer Vielzahl von Anwendungen eingesetzt, darunter Industriemaschinen, mobile Geräte, Fahrzeuge und Flugzeuge, um die Leistung, Effizienz und Zuverlässigkeit des Hydrauliksystems zu verbessern. Die Auswahl des richtigen Speichertyps hängt von verschiedenen Faktoren ab, darunter die Art der Anwendung, der benötigte Druckbereich und die erforderliche Speicherkapazität.
Ein Manometer ist ein Instrument zur Messung des Drucks in einem geschlossenen System, wie zum Beispiel in einem Hydrauliksystem. Es zeigt den Druck in der Einheit Bar, PSI (Pounds per Square Inch) oder anderen geeigneten Einheiten an.
Es gibt verschiedene Arten von Manometern, die je nach Anwendung und Messbereich unterschiedlich konstruiert sind:
- Rohrfeder-Manometer: Diese Art von Manometer verwendet eine U-förmige Rohrfeder, die sich je nach auf den Sensor ausgeübtem Druck verformt. Die Dehnung oder Kompression der Feder wird dann auf eine Skala übertragen, um den Druck anzuzeigen.
- Membranmanometer: Hier wird der Druck auf eine flexible Membran ausgeübt, die sich verformt und die Bewegung auf eine Anzeigeskala überträgt.
- Kolbenmanometer: Ein Kolbenmanometer verwendet einen beweglichen Kolben, der sich in einem Zylinder bewegt. Der Druck drückt den Kolben in einer bestimmten Richtung, und diese Bewegung wird auf eine Skala übertragen, um den Druck anzuzeigen.
- Digitalmanometer: Diese modernen Manometer verwenden elektronische Sensoren und eine digitale Anzeige, um den Druck genau zu messen und anzuzeigen. Sie bieten oft zusätzliche Funktionen wie Datenaufzeichnung und -speicherung.
Manometer werden in einer Vielzahl von Anwendungen eingesetzt, von Hydrauliksystemen über HVAC-Systeme bis hin zu medizinischen Geräten. Sie sind entscheidend für die Überwachung und Steuerung von Drücken, um eine sichere und effiziente Funktion der Systeme sicherzustellen.
Hydraulikschmierung bezieht sich auf den Prozess der Schmierung von Komponenten in einem Hydrauliksystem, um Reibung zu reduzieren, Verschleiß zu minimieren und die Effizienz des Systems zu verbessern. Die Schmierung erfolgt durch die Hydraulikflüssigkeit selbst, die spezielle Additive enthält, um die Schmierfähigkeit zu verbessern und die Lebensdauer der Komponenten zu verlängern.
Eine effektive Hydraulikschmierung bietet mehrere Vorteile:
- Reibungsreduzierung: Die Schmierung reduziert die Reibung zwischen beweglichen Teilen wie Zylindern, Kolben und Ventilen, was zu einer geringeren mechanischen Belastung und einem effizienteren Betrieb des Systems führt.
- Verschleißminimierung: Durch die Schmierung wird der Verschleiß der Komponenten minimiert, was zu einer längeren Lebensdauer der Hydraulikpresse führt und die Wartungskosten reduziert.
- Temperaturregelung: Eine gute Schmierung hilft dabei, die Temperatur im Hydrauliksystem zu kontrollieren, indem sie die Reibung reduziert und die Wärmeableitung verbessert. Dies trägt dazu bei, die Betriebstemperatur des Systems stabil zu halten und vor Überhitzung zu schützen.
Die Hydraulikflüssigkeit selbst spielt eine wichtige Rolle bei der Schmierung der Komponenten. Sie sollte bestimmte Eigenschaften aufweisen, wie eine gute Schmierfähigkeit, eine hohe Temperaturbeständigkeit und eine hohe Chemikalienbeständigkeit, um den Anforderungen des Hydrauliksystems gerecht zu werden.
Eine regelmäßige Wartung und Überprüfung der Hydraulikflüssigkeit ist wichtig, um sicherzustellen, dass sie die erforderlichen Schmiereigenschaften beibehält und die Leistung und Lebensdauer des Hydrauliksystems maximiert werden.
Pressen Rahmen
Der Rahmen einer Hydraulikpresse ist die strukturelle Basis, auf der die verschiedenen Komponenten der Presse montiert sind. Er dient dazu, die Belastungen während des Betriebs aufzunehmen und zu verteilen, um eine stabile und sichere Arbeitsplattform zu bieten.
Die Rahmen von Hydraulikpressen sind oft aus hochfestem Stahl oder Gusseisen gefertigt, um die erforderliche Festigkeit und Steifigkeit zu gewährleisten. Sie werden in verschiedenen Konfigurationen hergestellt, je nach der spezifischen Anwendung und den Anforderungen des Kunden. Zu den häufigsten Rahmenkonstruktionen gehören:
- Einfachrahmen: Ein einfacher Rahmen besteht aus zwei vertikalen Stützen, die oben und unten durch Querträger verbunden sind. Diese Konstruktion bietet eine einfache und kostengünstige Lösung für viele Anwendungen.
- Doppelrahmen: Ein Doppelrahmen besteht aus zwei parallelen Rahmenstrukturen, die miteinander verbunden sind, um eine erhöhte Stabilität und Steifigkeit zu gewährleisten. Diese Konstruktion wird oft bei größeren Pressen oder Anwendungen mit höheren Belastungen eingesetzt.
- Portalrahmen: Ein Portalrahmen hat eine spezielle Konstruktion mit einer horizontalen oberen Traverse und zwei vertikalen Stützen, die eine Portalstruktur bilden. Diese Konstruktion bietet eine hohe Steifigkeit und ermöglicht eine bessere Zugänglichkeit des Arbeitsbereichs.
Der Rahmen einer Hydraulikpresse muss sorgfältig dimensioniert und konstruiert werden, um den Belastungen während des Betriebs standzuhalten und eine präzise Ausrichtung der Presskomponenten sicherzustellen. Eine stabile und solide Rahmenkonstruktion ist entscheidend für die Leistung, Genauigkeit und Sicherheit der Hydraulikpresse.
Hydraulik Presse Anwendung
Hydraulikpressen werden in einer Vielzahl von Anwendungen eingesetzt, in denen eine präzise Steuerung und hohe Kräfte erforderlich sind, um Materialien zu formen, zu bearbeiten oder zu montieren. Einige der häufigsten Anwendungen von Hydraulikpressen sind:
- Metallumformung: Hydraulikpressen werden in der metallverarbeitenden Industrie verwendet, um Metallbleche zu biegen, zu stanzen, zu schneiden, zu formen und zu pressen. Dies umfasst die Herstellung von Karosserieteilen, Maschinenteilen, Gehäusen und anderen Metallkomponenten.
- Kunststoffverarbeitung: In der Kunststoffindustrie werden Hydraulikpressen verwendet, um Kunststoffgranulat in Formteile, Behälter, Rohre, Profile und andere Kunststoffprodukte zu pressen oder zu spritzen.
- Holzbearbeitung: Hydraulikpressen werden in der Holzbearbeitung eingesetzt, um Holzplatten zu verleimen, Furniere zu pressen, Holzwerkstoffe herzustellen und Holzteile zu formen.
- Gummiindustrie: Hydraulikpressen werden in der Gummiindustrie verwendet, um Gummi zu formen, zu pressen und zu vulkanisieren, um Produkte wie Reifen, Dichtungen, Schläuche und Förderbänder herzustellen.
- Montage und Fügeprozesse: Hydraulikpressen werden für Montage- und Fügeprozesse eingesetzt, wie etwa das Einpressen von Lagern, Buchsen, Bolzen oder Nieten in Baugruppen oder die Herstellung von Verbundwerkstoffen.
- Werkstattausrüstung: Hydraulikpressen finden auch Verwendung in Werkstätten und Fabriken für allgemeine Reparaturen, Wartungsarbeiten, Montagearbeiten und spezialisierte Anwendungen wie z.B. das Richten von Bauteilen.
Die Anwendungsbereiche von Hydraulikpressen sind vielfältig und reichen von der Massenproduktion in der Industrie bis hin zu spezialisierten Anwendungen in Forschungslaboren und Werkstätten. Durch ihre Vielseitigkeit, Präzision und hohe Leistungsfähigkeit sind Hydraulikpressen in vielen Branchen unverzichtbare Werkzeuge geworden.
Steuerung Systeme
Hydraulikpressen verwenden verschiedene Steuerungssysteme, um den Betrieb zu überwachen, die Pressvorgänge zu steuern und die Sicherheit zu gewährleisten. Hier sind einige der gängigsten Steuerungssysteme:
- Manuelle Steuerung: Bei der manuellen Steuerung bedient der Bediener die Hydraulikpresse manuell über Schalter, Hebel oder Tasten. Dies ermöglicht eine direkte Kontrolle über die Bewegung und den Druck der Presse, ist jedoch weniger automatisiert und erfordert mehr menschliche Eingriffe.
- Halbautomatische Steuerung: Bei der halbautomatischen Steuerung führt der Bediener bestimmte Abläufe oder Programme ein, die die Presse automatisch ausführt. Dies kann beispielsweise das Ausführen vordefinierter Presszyklen oder das Einstellen von Parametern wie Druck und Geschwindigkeit umfassen.
- Vollautomatische Steuerung: Die vollautomatische Steuerung erfolgt in der Regel über eine programmierbare Logiksteuerung (PLC) oder einen Computer. Der Bediener gibt die gewünschten Parameter und Programme ein, und die Steuerung führt die Presse automatisch gemäß diesen Vorgaben aus. Dies ermöglicht eine präzise und wiederholbare Ausführung von Pressvorgängen ohne ständige Überwachung durch den Bediener.
- CNC-Steuerung: Bei CNC-gesteuerten Hydraulikpressen erfolgt die Steuerung über einen Computer (numerische Steuerung), der spezielle Software verwendet, um komplexe Pressoperationen mit hoher Präzision auszuführen. Diese Art der Steuerung wird häufig in der Fertigung von anspruchsvollen Teilen oder bei der Bearbeitung von komplexen Werkstücken eingesetzt.
- Sicherheitssteuerung: Sicherheitssysteme wie Not-Aus-Schalter, Lichtgitter, Sicherheitsmatten und andere Vorrichtungen werden verwendet, um die Sicherheit des Bedieners zu gewährleisten und Unfälle zu verhindern. Diese Systeme überwachen kontinuierlich den Betrieb der Presse und greifen bei Bedarf automatisch ein, um Gefahren zu minimieren.
Die Auswahl des geeigneten Steuerungssystems hängt von verschiedenen Faktoren ab, darunter die Art der Anwendung, die Komplexität der Pressvorgänge, die erforderliche Präzision und die Sicherheitsanforderungen. Eine sorgfältige Planung und Integration der Steuerungssysteme ist entscheidend, um einen effizienten und sicheren Betrieb der Hydraulikpresse zu gewährleisten.
Hydraulik Leistung
Die Leistung einer Hydraulikpresse wird durch verschiedene Faktoren bestimmt, die sich auf ihre Konstruktion, Auslegung und Betriebsbedingungen beziehen. Hier sind einige Schlüsselkomponenten, die die Leistung einer Hydraulikpresse beeinflussen:
- Druck: Der maximale Druck, den die Hydraulikpresse erzeugen kann, ist ein entscheidender Faktor für ihre Leistungsfähigkeit. Ein höherer Druck ermöglicht es der Presse, größere Kräfte auf das Werkstück auszuüben und schwerere Materialien zu bearbeiten.
- Kraft: Die maximale Kraft, die die Hydraulikpresse ausüben kann, ist ein weiterer wichtiger Faktor. Diese Kraft hängt vom Druck im Hydrauliksystem und der Größe der Hydraulikzylinder ab. Eine höhere Kraft ermöglicht es der Presse, Materialien mit größerem Widerstand zu bearbeiten und schwerere Lasten zu heben oder zu pressen.
- Geschwindigkeit: Die Geschwindigkeit, mit der die Hydraulikpresse arbeitet, beeinflusst ihre Leistungsfähigkeit in Bezug auf die Produktivität und Effizienz. Eine schnellere Arbeitsgeschwindigkeit kann die Zykluszeiten verkürzen und die Produktionskapazität erhöhen, während eine langsamere Geschwindigkeit eine präzisere Steuerung und Bearbeitung ermöglicht.
- Arbeitsbereich: Der Arbeitsbereich oder der verfügbare Raum, in dem die Hydraulikpresse arbeiten kann, ist ebenfalls ein wichtiger Faktor. Ein größerer Arbeitsbereich ermöglicht es der Presse, größere Werkstücke zu bearbeiten und eine vielseitigere Anwendung zu ermöglichen.
- Steuerungssystem: Das Steuerungssystem der Hydraulikpresse beeinflusst ihre Leistungsfähigkeit in Bezug auf die Präzision, Wiederholbarkeit und Sicherheit der Pressvorgänge. Ein fortschrittliches Steuerungssystem, wie eine CNC-Steuerung, kann komplexe Pressoperationen mit hoher Präzision ausführen und die Produktionskapazität erhöhen.
- Wartung und Betrieb: Die regelmäßige Wartung und ordnungsgemäße Bedienung der Hydraulikpresse sind entscheidend, um ihre Leistungsfähigkeit und Lebensdauer zu erhalten. Eine schlechte Wartung oder unsachgemäße Bedienung können zu Ausfällen, Leistungsverlust und vorzeitiger Verschleiß führen.
Die Leistung einer Hydraulikpresse wird daher durch eine Kombination dieser Faktoren bestimmt, die alle berücksichtigt werden müssen, um eine optimale Leistung und Effizienz des Systems zu gewährleisten.
Hydraulische Verbindungselemente
Hydraulische Verbindungselemente sind Komponenten, die verwendet werden, um verschiedene Teile eines Hydrauliksystems miteinander zu verbinden und den Fluss der Hydraulikflüssigkeit zu ermöglichen. Diese Elemente spielen eine wichtige Rolle bei der Konstruktion, Installation und Wartung von Hydrauliksystemen. Hier sind einige häufig verwendete hydraulische Verbindungselemente:
- Hydraulikschläuche: Hydraulikschläuche sind flexible Schläuche, die verwendet werden, um die Verbindung zwischen verschiedenen Komponenten eines Hydrauliksystems herzustellen, wie z. B. zwischen Pumpen, Zylindern, Ventilen und Leitungen. Sie ermöglichen es, dass die Hydraulikflüssigkeit durch das System fließt, während sie gleichzeitig die Bewegungen und Vibrationen der Komponenten aufnimmt.
- Hydraulikleitungen: Hydraulikleitungen sind starre Rohre oder Leitungen, die verwendet werden, um die Hydraulikflüssigkeit zwischen verschiedenen Komponenten des Systems zu transportieren. Sie werden in der Regel aus Metall hergestellt und können in verschiedenen Größen und Längen erhältlich sein, um den Anforderungen der Anwendung gerecht zu werden.
- Hydraulikanschlüsse: Hydraulikanschlüsse sind spezielle Verbindungsstücke, die verwendet werden, um Schläuche, Leitungen und andere hydraulische Komponenten miteinander zu verbinden. Sie sind in verschiedenen Ausführungen erhältlich, darunter Gewindeanschlüsse, Schlauchanschlüsse, Flanschanschlüsse und Schnellkupplungen.
- Hydraulikverschraubungen: Hydraulikverschraubungen werden verwendet, um Rohre oder Schläuche sicher miteinander zu verbinden und abzudichten. Sie bestehen aus einem Gewinde und einem Gegenstück, das in die Rohre oder Schläuche eingeführt wird, um eine sichere Verbindung herzustellen.
- Hydraulikdichtungen: Hydraulikdichtungen werden verwendet, um die Verbindungselemente abzudichten und das Austreten von Hydraulikflüssigkeit zu verhindern. Sie können in verschiedenen Ausführungen erhältlich sein, darunter O-Ringe, Flachdichtungen, Kegeldichtungen und Kolbendichtungen.
Diese hydraulischen Verbindungselemente sind entscheidend für die ordnungsgemäße Funktion und Leistung von Hydrauliksystemen und müssen sorgfältig ausgewählt, installiert und gewartet werden, um Leckagen, Ausfälle und andere Probleme zu vermeiden.
Hydraulikdichtungen
Hydraulikdichtungen sind spezielle Dichtungselemente, die in Hydrauliksystemen verwendet werden, um den Flüssigkeitsverlust zu verhindern und eine zuverlässige Abdichtung zwischen beweglichen Teilen zu gewährleisten. Sie werden in verschiedenen Anwendungen eingesetzt, um Leckagen von Hydraulikflüssigkeit zu verhindern und die Effizienz des Systems zu verbessern. Hier sind einige häufig verwendete Arten von Hydraulikdichtungen:
- O-Ringe: O-Ringe sind ringförmige Dichtungselemente, die in einer Nut montiert werden und eine statische oder dynamische Abdichtung zwischen zwei sich bewegenden Teilen ermöglichen. Sie sind in verschiedenen Materialien erhältlich, wie z.B. Nitril, Viton, EPDM und Silikon, um den Anforderungen verschiedener Anwendungen gerecht zu werden.
- Kolbendichtungen: Kolbendichtungen werden in Hydraulikzylindern verwendet, um den Kolben abzudichten und den Druck der Hydraulikflüssigkeit aufrechtzuerhalten. Sie sind in verschiedenen Ausführungen erhältlich, wie z.B. Einzelwirkung, Doppeltwirkung und Dreifachwirkung, um den Anforderungen der Anwendung gerecht zu werden.
- Stangendichtungen: Stangendichtungen werden verwendet, um die Stange eines Hydraulikzylinders abzudichten und das Eindringen von Schmutz, Staub und anderen Verunreinigungen zu verhindern. Sie sind in verschiedenen Ausführungen erhältlich, wie z.B. U-Ringe, Dichtlippen, Doppellippendichtungen und Chevron-Dichtungen.
- Flachdichtungen: Flachdichtungen werden verwendet, um Flanschverbindungen, Ventile, Pumpen und andere Komponenten in einem Hydrauliksystem abzudichten. Sie bestehen in der Regel aus Gummi, Kunststoff oder Metall und werden zwischen den beiden zu verbindenden Oberflächen platziert, um eine dichte Abdichtung zu gewährleisten.
- Kegeldichtungen: Kegeldichtungen werden verwendet, um Rohre, Schläuche und andere Verbindungselemente in einem Hydrauliksystem abzudichten. Sie bestehen aus einem konischen Dichtungselement, das in eine entsprechende Öffnung oder Nut eingeführt wird, um eine dichte Abdichtung zu gewährleisten.
Die Auswahl der richtigen Hydraulikdichtung hängt von verschiedenen Faktoren ab, wie z.B. Druck, Temperatur, Bewegungsgeschwindigkeit und den chemischen Eigenschaften der Hydraulikflüssigkeit. Eine sorgfältige Auswahl und Installation der Dichtungen ist entscheidend, um Leckagen zu vermeiden und die Zuverlässigkeit des Hydrauliksystems zu gewährleisten.
Hydraulikpressen
Hydraulikpressen sind leistungsstarke Maschinen, die durch die Anwendung von Druckkraft auf ein Werkstück eine Vielzahl von Umformungs- und Fertigungsprozessen ermöglichen. Der zentrale Mechanismus dieser Pressen besteht aus einem Zylinder, in dem ein Kolben durch Hydrauliköl angetrieben wird. Die Druckkraft, die auf das Hydrauliköl ausgeübt wird, wird übertragen und ermöglicht somit eine präzise Steuerung der Presskraft.
Das Hydrauliköl, als das primäre Druckmittel, spielt eine entscheidende Rolle in diesem Prozess. Es überträgt die Energie vom Hydraulikaggregat auf den Kolben im Zylinder, wodurch eine beeindruckende Presskraft erzeugt wird. Dabei ist der Arbeitsdruck ein wesentlicher Parameter, der sorgfältig gesteuert wird, um optimale Ergebnisse bei verschiedenen Anwendungen zu gewährleisten.
Während des Pressvorgangs bewegt sich die Pressplatte, die mit dem Kolben verbunden ist, in einer definierten Geschwindigkeit auf das Werkstück zu. Die Hydraulikpresse ermöglicht somit nicht nur eine hohe Presskraft, sondern auch eine präzise Kontrolle über die Pressgeschwindigkeit. Die Pressplatte und die Pressform, die das zu bearbeitende Werkstück aufnimmt, bilden eine entscheidende Schnittstelle, um die gewünschten Umformungs- und Fertigungsziele zu erreichen.
Um diese komplexe Dynamik zu steuern, verfügt die Hydraulikpresse über ein Hydraulikventil und andere Steuereinheiten. Das Druckregelventil ermöglicht die genaue Einstellung des Arbeitsdrucks, während das Druckmanometer den aktuellen Druck anzeigt. Dieses Zusammenspiel von Komponenten, darunter auch Hydraulikschläuche und das Hydraulikaggregat, schafft eine effiziente hydraulische Schaltung, die den Pressprozess steuert.
Insgesamt vereinen Hydraulikpressen verschiedene Elemente wie Pressramme, Rückzugskraft und Arbeitszylinder, um eine beeindruckende Pressleistung zu erzielen. Die Hydraulikschmierung spielt eine Rolle bei der Aufrechterhaltung der reibungslosen Funktion dieser Maschinen, während Hydraulikfilter dazu beitragen, die Qualität des Hydrauliköls zu erhalten. Der gesamte Pressrahmen, die Überlastsicherung und die Steuerungseinheiten sind entscheidend, um eine sichere und effiziente Anwendung der Hydraulikpresse zu gewährleisten.
Das hydraulische System
Das hydraulische System einer Presse wird durch eine Reihe weiterer Schlüsselkomponenten gesteuert und reguliert, die die Leistung und Präzision der Maschine beeinflussen. Ein zentrales Element ist das Ventilblock, das verschiedene Hydraulikventile enthält. Diese Ventile steuern den Ölfluss und die Druckverteilung im System, was wiederum die Presskraft und Geschwindigkeit beeinflusst. Das Hydrauliksystem kann mit verschiedenen Ventilen ausgestattet sein, darunter auch Druckregelventile, die den Arbeitsdruck präzise regeln.
Ein weiteres wichtiges Element ist das Presskissen, das oft in speziellen Anwendungen verwendet wird. Das Kissen ermöglicht eine gleichmäßige Druckverteilung auf das Werkstück, insbesondere bei ungleichmäßig geformten oder empfindlichen Materialien. Dabei spielt die Kolbendurchmesser eine entscheidende Rolle, da er die Fläche des Kolbens angibt und somit die auf das Hydrauliköl wirkende Kraft beeinflusst.
Die Hydraulikpresse wird durch das Hydrauliköl angetrieben, dessen Pumpenleistung die Effizienz des Systems bestimmt. Die Schließkraft, die zwischen der Pressplatte und der Pressform wirkt, ist entscheidend für die Stabilität des Pressvorgangs. Der Öldruck, der im Hydrauliksystem erzeugt wird, beeinflusst direkt die Presskraft und damit die Umformung des Werkstücks.
Einspannvorrichtung
Ein weiterer wichtiger Aspekt ist die Einspannvorrichtung, die sicherstellt, dass das Werkstück während des Pressvorgangs stabil bleibt. Hydraulikventile spielen eine Schlüsselrolle in diesem Prozess, indem sie den Hydraulikdruck in den Zylindern steuern, um ein sicheres und präzises Einspannen zu gewährleisten. Dieses Zusammenspiel von Komponenten wird durch eine präzise Hydraulikschaltung ermöglicht, die durch den Ventilblock und andere Steuereinheiten gesteuert wird.
Die Hydraulikpumpenleistung beeinflusst direkt die Kolbengeschwindigkeit, was die Effizienz des Pressvorgangs bestimmt. Die Kolbenstange, die mit dem Kolben verbunden ist, überträgt die Bewegung auf die Pressplatte. Die Kolbenabdichtung ist dabei entscheidend, um ein Leckagefreies Funktionieren des Zylinders sicherzustellen.
Zusätzlich spielt die Hydraulikschlauch eine Rolle bei der Übertragung des Hydrauliköls zwischen den verschiedenen Komponenten. Druckspeicher können ebenfalls integriert sein, um Druckschwankungen auszugleichen und eine konstante Presskraft zu gewährleisten. Das Druckbegrenzungsventil dient dazu, den maximalen Druck im System zu begrenzen und somit die Sicherheit der Anwendung zu gewährleisten. In diesem komplexen Zusammenspiel von Komponenten und Funktionen entfaltet die Hydraulikpresse ihre volle Leistungsfähigkeit und trägt entscheidend zur modernen Fertigung bei.
Die Hydraulikpresse, eine Schlüsselkomponente in modernen Fertigungsprozessen, profitiert von einer Reihe weiterer entscheidender Schlüsselwörter und Bauteile, die ihre Funktionalität und Effizienz sicherstellen. Hydraulikschläuche sind integraler Bestandteil dieses Systems und dienen dazu, das Hydrauliköl zwischen den verschiedenen Komponenten zu transportieren. Eine sichere und zuverlässige Übertragung des Druckmittels ist essentiell für einen stabilen Pressvorgang.
Ventilblöcke
Die Ventilblöcke, die eine Ansammlung verschiedener Hydraulikventile darstellen, sind die Schaltzentralen der Hydraulikpresse. Diese Ventile regeln den Ölfluss, steuern den Arbeitsdruck und ermöglichen die präzise Anpassung der Presskraft. Die Hydraulikschaltung, die durch den Ventilblock gesteuert wird, gewährleistet eine reibungslose Koordination aller Komponenten und Parameter während des Pressvorgangs.
Der Druckregelventil spielt eine zentrale Rolle, indem er den Arbeitsdruck präzise steuert. Dieser Druck beeinflusst maßgeblich die Presskraft, die auf das Werkstück ausgeübt wird, und ermöglicht somit die Anpassung der Maschine an unterschiedliche Materialien und Anforderungen. Das Druckmanometer ist ein wichtiges Instrument, um den aktuellen Druck im Hydrauliksystem zu überwachen und sicherzustellen, dass er innerhalb der definierten Grenzen bleibt.
Ein interessanter Aspekt ist das Presskissen, das bei speziellen Anwendungen eine gleichmäßige Druckverteilung auf das Werkstück sicherstellt. Dieses Kissen ist besonders nützlich bei der Bearbeitung von ungleichmäßig geformten oder empfindlichen Materialien. In Verbindung mit der Kolbendurchmesser, der die auf das Hydrauliköl wirkende Fläche angibt, kann so eine präzise Kontrolle über die Presskraft erreicht werden.
Die Schließkraft, die zwischen der Pressplatte und der Pressform wirkt, ist von entscheidender Bedeutung für die Stabilität des Pressvorgangs. Ein ausgewogenes Verhältnis dieser Kräfte ermöglicht eine effiziente Umformung des Werkstücks. Hierbei beeinflusst der Öldruck im Hydrauliksystem direkt die Presskraft und damit die Qualität des Ergebnisses.
Die Einspannvorrichtung, eine weitere essenzielle Komponente, gewährleistet die sichere Fixierung des Werkstücks während des Pressvorgangs. Dies ist insbesondere wichtig, um Präzision und Sicherheit zu gewährleisten. Hydraulikventile spielen dabei eine entscheidende Rolle, indem sie den Hydraulikdruck in den Zylindern steuern und so ein sicheres Einspannen ermöglichen.
Hydraulikpumpenleistung
Die Hydraulikpumpenleistung, ein Parameter, der die Effizienz des Systems beeinflusst, bestimmt die Kolbengeschwindigkeit während des Pressvorgangs. Die Kolbenstange, die mit dem Kolben verbunden ist, überträgt diese Bewegung auf die Pressplatte. Die Kolbenabdichtung ist dabei von entscheidender Bedeutung, um eine Leckagefreiheit im Zylinder sicherzustellen und somit eine konstante Presskraft zu gewährleisten.
Abschließend spielen Druckspeicher eine wichtige Rolle, indem sie Druckschwankungen ausgleichen und so eine konstante Presskraft gewährleisten. Das Druckbegrenzungsventil sorgt dafür, dass der maximale Druck im System nicht überschritten wird, was die Sicherheit der Anwendung weiter verbessert. In diesem komplexen Netzwerk von Komponenten, Steuerelementen und Mechanismen entfaltet die Hydraulikpresse ihre volle Leistungsfähigkeit, um präzise und effiziente Fertigungsprozesse zu ermöglichen.
Optional ausgestattet mit hydraulischem Tischkissen, Schnittschlagdämpfung oder Werkzeugwechselsystem bieten Pressen der EMS-Baureihe alle Voraussetzungen für eine effiziente Produktion im Presswerk. Die bewährte EMS-Visualisierung unterstützt bei der Bedienung und der einfachen Fehlerdiagnose. Das steigert die Produktivität des gesamten Systems. Schnell verfügbar: Kurze Lieferzeit durch standardisiertes Baukastensystem Schneller Produktionsanlauf durch kurze Montage- und Inbetriebnahmephase Hohe Planungssicherheit durch professionelles Projektmanagement
Mit EMS-Pressen wirtschaftlich produzieren: Überzeugendes Preis-Leistungs-Verhältnis Hohe Prozesssicherheit beim Schneiden und Tiefziehen durch exakt und reproduzierbar einstellbare Vierspindel Schnittschlagdämpfung und ein besonders steif ausgeführtes hydraulisches Tischkissen Teilespektrum auch in Aluminium und Edelstahl
EMS-Maßanzug. Mit der hydraulischen PressenBaureihe erweitert EMS das Spektrum um hydraulische Pressen im Presskraftbereich 2.500 kN bis 10.000 kN. Jetzt steht auch für kleine und mittlere Unternehmen ein speziell auf ihren Bedarf zugeschnittenes Pressenkonzept zur Verfügung. EMS erfüllt damit auch in diesem besonders kostensensiblen Presskraftbereich alle Anforderungen des Marktes mit einem
rundum überzeugenden Konzept.
EMS Maschinenfabrik als Hydraulikpressen Hersteller
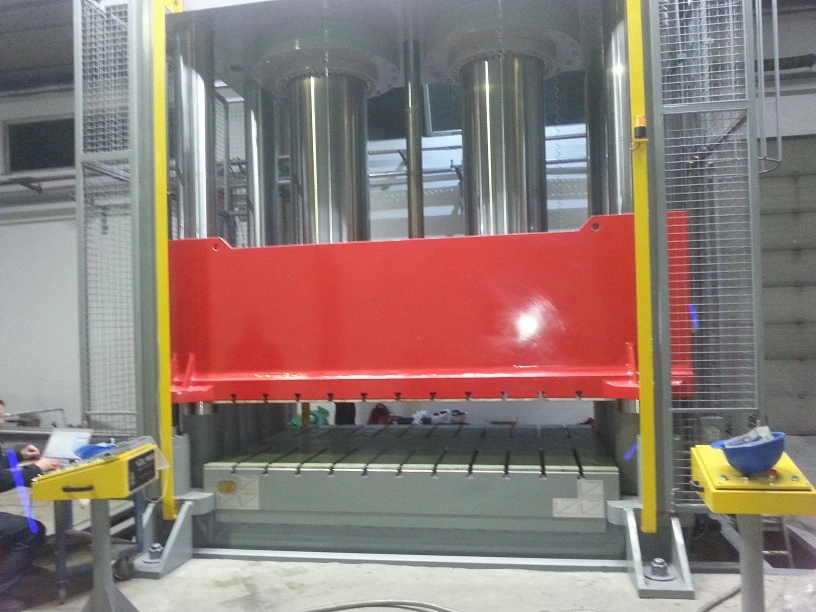
Die Pressen der unserer Baureihe sind für ein günstiges Preis-Leistungs-Verhältnis konzipiert. Sie decken ein universelles Einsatzspektrum ab und sind erweiterbar für automatisierte Fertigungssysteme. Hohe Qualitätsstandards sorgen für Investitionssicherheit und Wartungsfreundlichkeit. Pressen der Baureihe verbinden
maximale Fertigungsflexibilität mit Komfort im Alltagsbetrieb. Und nicht zuletzt steht EMS für zuverlässige, bewährte Pressen mit hoher Verfügbarkeit, für kurze Lieferzeiten und jederzeit verlässliche Service-Qualität.
Hydraulikpressen sind komplexe Maschinen, die durch eine Vielzahl von Schlüsselkomponenten gesteuert werden, um präzise Umformungs- und Fertigungsprozesse zu ermöglichen. In diesem Zusammenhang spielen Hydraulikventile eine entscheidende Rolle, indem sie den Ölfluss im System regulieren und so den Arbeitsdruck präzise steuern. Der Ventilblock, als zentrale Schaltstelle, beherbergt verschiedene dieser Ventile und ermöglicht eine fein abgestimmte Anpassung an die spezifischen Anforderungen der jeweiligen Anwendung.
Hydraulikschaltung
Die Hydraulikschaltung, koordiniert durch den Ventilblock und unterstützt durch andere Steuereinheiten, gewährleistet ein reibungsloses Zusammenspiel aller Komponenten. Dies ermöglicht eine präzise Steuerung der Presskraft, Pressgeschwindigkeit und anderer Parameter während des Pressvorgangs. Das Druckregelventil spielt hierbei eine zentrale Rolle, indem es den Arbeitsdruck anpasst und so eine optimale Umformung des Werkstücks ermöglicht.
Ein weiterer essenzieller Aspekt ist das Druckmanometer, das kontinuierlich den aktuellen Druck im Hydrauliksystem überwacht. Dies ist von großer Bedeutung, um sicherzustellen, dass der Druck innerhalb sicherer Grenzen bleibt und die Maschine effizient arbeitet. Die Druckschwankungen im System werden durch Druckspeicher ausgeglichen, die eine konstante Presskraft gewährleisten und so zu präzisen Ergebnissen beitragen.
Presskissen
Das Presskissen, eine spezialisierte Komponente in einigen Anwendungen, stellt sicher, dass die Druckverteilung auf das Werkstück gleichmäßig erfolgt. In Kombination mit der Kolbendurchmesser, der die Fläche des auf das Hydrauliköl wirkenden Kolbens angibt, kann so eine exakte Steuerung der Presskraft erreicht werden. Dies ist besonders wichtig bei der Bearbeitung von empfindlichen Materialien oder ungleichmäßig geformten Werkstücken.
Die Schließkraft, die zwischen der Pressplatte und der Pressform wirkt, beeinflusst die Stabilität des Pressvorgangs maßgeblich. Der Öldruck im Hydrauliksystem ist hierbei ein entscheidender Faktor, da er direkt die auf das Werkstück ausgeübte Presskraft beeinflusst. Eine ausgewogene Schließkraft ist entscheidend, um eine effiziente Umformung des Werkstücks zu gewährleisten.
Die Einspannvorrichtung ist eine weitere kritische Komponente, die sicherstellt, dass das Werkstück während des Pressvorgangs stabil bleibt. Hierbei spielen Hydraulikventile eine Schlüsselrolle, indem sie den Druck in den Zylindern steuern und so ein sicheres Einspannen ermöglichen. Die Hydraulikpumpenleistung beeinflusst direkt die Kolbengeschwindigkeit, was die Effizienz des Pressvorgangs beeinflusst.
Kolbenstange
Die Kolbenstange, die mit dem Kolben verbunden ist, überträgt die Bewegung auf die Pressplatte und beeinflusst so die Umformung des Werkstücks. Die Kolbenabdichtung ist dabei von entscheidender Bedeutung, um sicherzustellen, dass der Hydraulikzylinder leckagefrei arbeitet und eine konstante Presskraft aufrechterhalten wird.
Zusammenfassend lässt sich sagen, dass die vielfältigen Komponenten, darunter Hydraulikventile, Druckspeicher, Presskissen und viele andere, in einer Hydraulikpresse harmonisch zusammenwirken. Dieses komplexe Zusammenspiel ermöglicht die präzise Steuerung und Anpassung der Maschine an die spezifischen Anforderungen unterschiedlichster Fertigungsprozesse.
Intelligentes Konzept. Hydraulische Pressen der Baureihe werden durch neue Wege in Standardisierung und Beschaffung kostengünstig realisiert. So hat Schuler zugunsten hoher Wirtschaftlichkeit auf große Variantenvielfalt verzichtet und stattdessen ein durchdachtes, standardisiertes Maschinenkonzept entwickelt, das bei Bedarf modulare Erweiterungsmöglichkeiten bereithält
Neue Baureihe. Die hydraulische HPX-Baureihe überzeugt mit ihrer Vielseitigkeit, die eine effiziente Serienfertigung eines breiten Bauteilspektrums ermöglicht – von der Platine bis zum fertigen Teil. HPX-Pressen mit Presskräften von 2.500 kN bis 10.000 kN erweitern das Schuler-Angebotsspektrum und bieten hohe Zuverlässigkeit durch bewährte Schuler-Qualitätsüberwachung.
Volle Integration. Die Baureihe HPX ist nahtlos eingebunden in die umfassende Schuler-Welt. Sie bietet nicht nur die bewährte Schuler-Bedieneroberfläche, sondern als modularer Baukasten auch vielfältige Erweiterungsmöglichkeiten mit definierten Schnittstellen für Pressenautomation.
Hydraulikpressen
Hydraulikpressen sind hochspezialisierte Maschinen, die in zahlreichen industriellen Anwendungen für Umformungs- und Fertigungsprozesse eingesetzt werden. Der zentrale Mechanismus dieser Pressen besteht aus einem Zylinder und einem Kolben, die durch Hydrauliköl angetrieben werden. Die Druckkraft, die durch das Hydrauliköl erzeugt wird, ermöglicht präzise Kontrolle über die Presskraft, was sie zu einer unverzichtbaren Technologie in der modernen Fertigung macht.
Das Hydrauliköl, als primäres Druckmittel, spielt eine entscheidende Rolle bei der Übertragung von Energie vom Hydraulikaggregat auf den Kolben im Zylinder. Der Arbeitsdruck wird sorgfältig gesteuert, um optimale Ergebnisse bei verschiedenen Anwendungen zu gewährleisten. Die Pressplatte, die mit dem Kolben verbunden ist, bewegt sich während des Pressvorgangs auf das Werkstück zu und ermöglicht so eine Vielzahl von Umformungsprozessen.
Die Pressgeschwindigkeit, ein weiterer wichtiger Parameter, wird sorgfältig eingestellt, um die Anforderungen unterschiedlicher Materialien und Fertigungsaufgaben zu erfüllen. Die Hydraulikpresse kann mit unterschiedlichen Pressformen arbeiten, um Werkstücke mit verschiedenen Formen und Größen zu bearbeiten. Dabei spielt die Hydraulikschaltung, bestehend aus Ventilen und anderen Steuereinheiten, eine Schlüsselrolle bei der Steuerung des Pressvorgangs.
Die Presskraft, die durch die Kolbenbewegung erzeugt wird, ist ein entscheidender Faktor für die Qualität der Umformung. Die Pressplatte, die auf das Werkstück einwirkt, kann in Abhängigkeit von der Anwendung unterschiedliche Schließkräfte ausüben. Das Zusammenspiel von Druckkraft, Pressgeschwindigkeit und Pressplatte macht die Hydraulikpresse äußerst vielseitig und anpassungsfähig an die Anforderungen unterschiedlichster industrieller Prozesse.
Die Hydraulikpresse wird durch eine präzise Steuerungseinheit gesteuert, die Hydraulikventile und andere Komponenten umfasst. Das Druckregelventil ermöglicht die genaue Einstellung des Arbeitsdrucks, während das Druckmanometer den aktuellen Druck im Hydrauliksystem überwacht. Diese präzise Kontrolle gewährleistet nicht nur die Effizienz der Maschine, sondern auch ihre Sicherheit während des Betriebs.
Insgesamt bildet die Hydraulikpresse eine entscheidende Säule in der modernen Fertigungstechnologie. Ihre Fähigkeit zur präzisen Steuerung von Druckkraft und Pressgeschwindigkeit macht sie zu einem unverzichtbaren Werkzeug in der Herstellung von Metallteilen, Kunststoffprodukten und vielen anderen Materialien. Die kontinuierliche Weiterentwicklung von Hydraulikpressen trägt dazu bei, die Effizienz und Vielseitigkeit dieser Maschinen in verschiedenen Industriezweigen weiter zu verbessern.
Die Komplexität und Effizienz von Hydraulikpressen erstreckt sich über eine Vielzahl von Schlüsselkomponenten, die zusammenarbeiten, um präzise Umformungs- und Fertigungsprozesse zu ermöglichen. Unter diesen wesentlichen Elementen spielt der Ventilblock eine zentrale Rolle. Als Schaltzentrale beherbergt er verschiedene Hydraulikventile, die den Ölfluss im System regulieren. Diese Ventile sind von entscheidender Bedeutung, um den Arbeitsdruck zu steuern und somit eine präzise Anpassung der Presskraft zu ermöglichen.
Die Hydraulikschaltung, koordiniert durch den Ventilblock und unterstützt durch weitere Steuereinheiten, ermöglicht ein reibungsloses Zusammenwirken aller Komponenten. Dies führt zu einer optimalen Abstimmung von Presskraft, Pressgeschwindigkeit und anderen Parametern während des Pressvorgangs. Das Druckregelventil spielt hierbei eine zentrale Rolle, indem es den Arbeitsdruck präzise reguliert und so eine optimale Umformung des Werkstücks ermöglicht.
Das Druckmanometer ist ein weiteres unverzichtbares Instrument, das kontinuierlich den aktuellen Druck im Hydrauliksystem überwacht. Diese Überwachung ist essenziell, um sicherzustellen, dass der Druck innerhalb sicherer Grenzen bleibt und die Maschine effizient und sicher arbeitet. Druckspeicher sind eine weitere Schlüsselkomponente, die dazu dient, Druckschwankungen auszugleichen und somit eine konstante Presskraft aufrechtzuerhalten. Dies trägt zu präzisen und reproduzierbaren Ergebnissen bei den Fertigungsprozessen bei.
Die spezielle Komponente des Presskissens ist insbesondere bei bestimmten Anwendungen von Vorteil. Es ermöglicht eine gleichmäßige Druckverteilung auf das Werkstück, was besonders wichtig ist, wenn ungleichmäßig geformte oder empfindliche Materialien bearbeitet werden. In Verbindung mit dem Kolbendurchmesser, der die auf das Hydrauliköl wirkende Fläche angibt, ermöglicht das Presskissen eine präzise Kontrolle über die Presskraft.
Die Schließkraft zwischen der Pressplatte und der Pressform ist ein entscheidender Faktor für die Stabilität des Pressvorgangs. Der Öldruck im Hydrauliksystem beeinflusst direkt diese Schließkraft und damit die Qualität der Umformung des Werkstücks. Eine ausgewogene Schließkraft ist entscheidend, um eine effiziente Umformung und ein qualitativ hochwertiges Endprodukt zu gewährleisten.
Die Einspannvorrichtung spielt eine herausragende Rolle bei der sicheren Fixierung des Werkstücks während des Pressvorgangs. Hierbei kommen Hydraulikventile ins Spiel, die den Druck in den Zylindern steuern und somit ein sicheres Einspannen ermöglichen. Die Hydraulikpumpenleistung beeinflusst direkt die Kolbengeschwindigkeit, was die Effizienz des Pressvorgangs und die Gesamtproduktivität der Maschine beeinflusst.
Die Kolbenstange, die mit dem Kolben verbunden ist, überträgt die Bewegung auf die Pressplatte und beeinflusst somit die Umformung des Werkstücks. Die Kolbenabdichtung ist entscheidend, um sicherzustellen, dass der Hydraulikzylinder leckagefrei arbeitet und eine konstante Presskraft aufrechterhalten wird. Druckbegrenzungsventile sind eine wichtige Sicherheitsvorkehrung, die sicherstellen, dass der maximale Druck im System nicht überschritten wird, was die Sicherheit der Anwendung weiter verbessert.
Zusammenfassend unterstreichen diese Komponenten, darunter Hydraulikventile, Druckspeicher, Presskissen und andere, die Vielseitigkeit und Präzision von Hydraulikpressen. Ihr Zusammenspiel ermöglicht es, eine breite Palette von Fertigungsanforderungen zu erfüllen und gleichzeitig Sicherheit und Effizienz in industriellen Prozessen zu gewährleisten.
Hydraulikpressen sind Maschinen, die hydraulische Kraft nutzen, um Materialien zu pressen, umzuformen oder zu bearbeiten. Sie sind in verschiedenen Branchen und Anwendungen weit verbreitet, einschließlich Metallverarbeitung, Kunststoffverarbeitung, Automobilindustrie, Maschinenbau und vielen anderen.
Die grundlegende Arbeitsweise einer Hydraulikpresse besteht aus folgenden Komponenten:
- Hydrauliksystem: Es besteht aus einer hydraulischen Pumpe, Hydraulikzylindern, Hydraulikventilen und Leitungen. Die Pumpe erzeugt einen hydraulischen Druck, der durch die Ventile gesteuert wird, um die gewünschte Presskraft zu erzeugen.
- Pressrahmen: Der Pressrahmen ist die strukturelle Komponente der Presse, die das Werkstück oder das Werkzeug aufnimmt. Es gibt verschiedene Arten von Pressrahmen, darunter C-Rahmen-Presse, Säulenpresse, Portalpresse und Rahmenpresse. Die Auswahl des Pressrahmens hängt von der spezifischen Anwendung ab.
- Presswerkzeug: Das Presswerkzeug ist das Werkzeug, das verwendet wird, um das Material zu pressen, umzuformen oder zu bearbeiten. Es kann verschiedene Formen haben, wie beispielsweise Matrizen, Stempel, Formen oder Schneidwerkzeuge, je nach dem gewünschten Ergebnis.
- Steuerungssystem: Das Steuerungssystem regelt den Betrieb der Hydraulikpresse. Es kann manuelle, halbautomatische oder vollautomatische Steuerungsfunktionen umfassen, um den Pressvorgang zu steuern, die Presskraft zu überwachen und Sicherheitsvorrichtungen zu implementieren.
Hydraulikpressen bieten eine Reihe von Vorteilen, darunter:
- Hohe Presskraft: Hydraulikpressen können hohe Presskräfte erzeugen, was sie ideal für Anwendungen mit großen oder widerstandsfähigen Werkstücken macht.
- Präzise Steuerung: Das hydraulische System ermöglicht eine präzise Steuerung der Presskraft, Geschwindigkeit und Position, was eine genaue Bearbeitung oder Umformung des Materials ermöglicht.
- Vielseitigkeit: Hydraulikpressen können für eine Vielzahl von Anwendungen eingesetzt werden, einschließlich Pressen, Biegen, Stanzen, Scheren, Umformen und vielem mehr. Sie sind in der Lage, verschiedene Materialien wie Metalle, Kunststoffe und Verbundwerkstoffe zu bearbeiten.
- Robuste Bauweise: Hydraulikpressen sind in der Regel robust und langlebig, was sie für den industriellen Einsatz geeignet macht.
- Sicherheit: Moderne Hydraulikpressen sind mit verschiedenen Sicherheitsvorrichtungen wie Not-Aus-Schaltern, Sicherheitslichtgittern und Überlastsicherungen ausgestattet, um die Sicherheit der Bediener zu gewährleisten.
Die Auswahl einer Hydraulikpresse hängt von verschiedenen Faktoren ab, einschließlich der Art der Anwendung, der erforderlichen Presskraft, der Größe des Werkstücks und der gewünschten Präzision. Es ist wichtig, die spezifischen Anforderungen zu berücksichtigen und mit einem erfahrenen Hersteller zusammenzuarbeiten, um die richtige Hydraulikpresse für die gewünschten Anwendungen zu wählen.
Die Funktionalität und Leistungsfähigkeit von Hydraulikpressen werden maßgeblich durch eine Reihe weiterer Schlüsselkomponenten beeinflusst, die das Zusammenspiel der Maschine optimieren. Unter diesen spielt die Hydraulikschlauch eine essenzielle Rolle, indem sie das Hydrauliköl zwischen den verschiedenen Komponenten des Systems transportiert. Die Qualität und Zuverlässigkeit dieser Schläuche sind entscheidend für eine störungsfreie Übertragung des Druckmittels.
Der Ventilblock, als Schaltzentrale der Hydraulikpresse, beherbergt eine Vielzahl von Hydraulikventilen. Diese Ventile regulieren den Ölfluss, steuern den Arbeitsdruck und ermöglichen eine präzise Anpassung der Presskraft. Die Hydraulikschaltung, koordiniert durch den Ventilblock und unterstützt durch Steuereinheiten, gewährleistet ein reibungsloses Zusammenspiel aller Komponenten, was zu einer effizienten Umsetzung der Pressanforderungen führt.
Das Druckregelventil ist von entscheidender Bedeutung, da es den Arbeitsdruck im System steuert und so die Presskraft präzise reguliert. Dies ermöglicht eine Anpassung der Maschine an unterschiedliche Materialien und Fertigungsanforderungen. Das Druckmanometer spielt eine wichtige Überwachungsrolle, indem es den aktuellen Druck im Hydrauliksystem kontinuierlich misst und sicherstellt, dass er innerhalb der vorgegebenen Grenzen bleibt.
Druckspeicher sind eine weitere Schlüsselkomponente, die dazu dient, Druckschwankungen im System auszugleichen. Dies trägt dazu bei, eine konstante Presskraft aufrechtzuerhalten und somit präzise Ergebnisse in den Fertigungsprozessen zu erzielen. Die hydraulische Presskraft wird in erster Linie durch den Arbeitsdruck und die Fläche des Kolbens bestimmt, wobei der Kolbendurchmesser einen wesentlichen Einfluss auf diese Fläche hat.
Das Presskissen ist in speziellen Anwendungen von Nutzen, da es eine gleichmäßige Druckverteilung auf das Werkstück ermöglicht. Gemeinsam mit der Kolbenabdichtung, die sicherstellt, dass der Hydraulikzylinder leckagefrei funktioniert, trägt es zur präzisen Kontrolle der Presskraft bei. Die Schließkraft, die zwischen der Pressplatte und der Pressform wirkt, ist ein kritischer Faktor für die Stabilität des Pressvorgangs.
Die Einspannvorrichtung spielt eine entscheidende Rolle bei der sicheren Fixierung des Werkstücks während des Pressvorgangs. Hier kommen Hydraulikventile ins Spiel, die den Druck in den Zylindern steuern und so ein sicheres Einspannen ermöglichen. Die Hydraulikpumpenleistung beeinflusst direkt die Kolbengeschwindigkeit, was die Effizienz des Pressvorgangs und die Produktivität der Maschine insgesamt beeinflusst.
Die Kolbenstange, die mit dem Kolben verbunden ist, überträgt die Bewegung auf die Pressplatte und beeinflusst somit die Umformung des Werkstücks. Die Kolbenabdichtung ist entscheidend, um sicherzustellen, dass der Hydraulikzylinder leckagefrei arbeitet und eine konstante Presskraft aufrechterhalten wird. Druckbegrenzungsventile sind eine wichtige Sicherheitsvorkehrung, die sicherstellen, dass der maximale Druck im System nicht überschritten wird.
Zusammenfassend zeigen diese Komponenten, wie vielfältig und komplex das Zusammenspiel in einer Hydraulikpresse ist. Von der Regulierung des Ölflusses über die präzise Steuerung der Presskraft bis hin zur Sicherstellung der Maschinensicherheit durch Druckbegrenzungsventile – jedes Detail trägt dazu bei, dass Hydraulikpressen in verschiedenen industriellen Anwendungen präzise und effiziente Ergebnisse liefern können.
Hydraulikpressen sind Werkzeugmaschinen, die hydraulische Kraft verwenden, um Materialien zu formen, zu stanzen, zu biegen, zu pressen, zu ziehen oder zu komprimieren. Sie sind in einer Vielzahl von industriellen Anwendungen weit verbreitet und können für Aufgaben wie das Umformen von Metallen, das Pressen von Pulvern in Tabletten, das Herstellen von Kunststoffteilen, das Auspressen von Säften und vieles mehr eingesetzt werden. Hier sind die Hauptmerkmale und Funktionen von Hydraulikpressen:
1. Hydraulisches System:
- Der Kern einer Hydraulikpresse ist das hydraulische System, das einen Druck erzeugt, um die benötigte Kraft für den Arbeitsvorgang bereitzustellen. Dieses System besteht aus einer Hydraulikpumpe, einem Hydraulikzylinder und Steuerventilen.
2. Druckanpassung:
- Hydraulikpressen ermöglichen die präzise Einstellung des Drucks, der auf das zu bearbeitende Material ausgeübt wird. Dies ermöglicht eine breite Palette von Anwendungen und die Verarbeitung von Materialien mit unterschiedlichen Härtegraden.
3. Verschiedene Arbeitsvorgänge:
- Hydraulikpressen können für verschiedene Arbeitsvorgänge konfiguriert werden, einschließlich Pressen, Stanzen, Scheren, Biegen, Ziehen und mehr. Dies macht sie äußerst vielseitig.
4. Verschiedene Größen und Kapazitäten:
- Hydraulikpressen sind in verschiedenen Größen und Kapazitäten erhältlich, von kleinen Tischpressen bis hin zu großen Industriepressen. Die Wahl der richtigen Größe hängt von den spezifischen Anforderungen der Anwendung ab.
5. Präzise Steuerung:
- Moderne Hydraulikpressen bieten präzise Steuerungsmöglichkeiten, einschließlich digitaler Steuerungen und programmierbarer Logiksteuerungen (PLC), die die Bewegung, den Druck und die Zeitabläufe steuern können.
6. Sicherheitseinrichtungen:
- Hydraulikpressen sind mit Sicherheitseinrichtungen ausgestattet, darunter Notausschalter, Schutzgitter und Lichtvorhänge, um die Sicherheit der Bediener zu gewährleisten.
7. Flexibilität:
- Hydraulikpressen können für verschiedene Materialien und Formen eingesetzt werden. Sie sind in der Lage, sowohl kleine Präzisionskomponenten als auch große Teile zu bearbeiten.
8. Produktivität:
- Hydraulikpressen können die Produktivität in vielen Fertigungsprozessen steigern, da sie Materialien schnell und mit hoher Genauigkeit bearbeiten können.
9. Anwendungen:
- Hydraulikpressen werden in verschiedenen Branchen eingesetzt, darunter Metallverarbeitung, Kunststoffverarbeitung, Automobilindustrie, Lebensmittelverarbeitung und Pharmaindustrie.
10. Wartungsfreundlichkeit: – Hydraulikpressen sind in der Regel wartungsfreundlich und erfordern regelmäßige Wartung, um sicherzustellen, dass sie effizient und zuverlässig arbeiten.
Hydraulikpressen sind entscheidende Werkzeuge in der modernen Industrie und ermöglichen die effiziente Herstellung von Produkten aus verschiedenen Materialien. Ihre Fähigkeit zur präzisen Steuerung des Drucks und zur Anpassung an unterschiedliche Aufgaben macht sie zu einem unverzichtbaren Bestandteil vieler Fertigungsprozesse.
Die Leistungsfähigkeit von Hydraulikpressen wird durch eine Reihe weiterer Schlüsselkomponenten sichergestellt, die das komplexe Zusammenspiel dieser Maschinen beeinflussen. Hydraulikschläuche spielen eine kritische Rolle, indem sie das Hydrauliköl zwischen den verschiedenen Komponenten transportieren. Die Qualität und Integrität dieser Schläuche sind von entscheidender Bedeutung, um eine effiziente Übertragung des Druckmittels sicherzustellen.
Der Ventilblock, als Schaltzentrale des hydraulischen Systems, beinhaltet verschiedene Hydraulikventile, die den Ölfluss im System regulieren. Diese Ventile sind unerlässlich für die präzise Steuerung des Arbeitsdrucks und ermöglichen somit eine fein abgestimmte Anpassung der Presskraft. Die Hydraulikschaltung, koordiniert durch den Ventilblock und weitere Steuereinheiten, ermöglicht eine reibungslose Interaktion aller Komponenten während des Pressvorgangs.
Das Druckregelventil ist eine Schlüsselkomponente, da es den Arbeitsdruck im System steuert und somit die Presskraft präzise reguliert. Dies erlaubt eine optimale Anpassung der Maschine an unterschiedliche Materialien und Fertigungsanforderungen. Das Druckmanometer überwacht kontinuierlich den aktuellen Druck im Hydrauliksystem, um sicherzustellen, dass er innerhalb sicherer Grenzen bleibt.
Druckspeicher sind entscheidend, um Druckschwankungen im System auszugleichen und eine konstante Presskraft aufrechtzuerhalten. Diese Komponente trägt dazu bei, präzise und reproduzierbare Ergebnisse in den Fertigungsprozessen zu gewährleisten. Das Presskissen ist besonders nützlich in speziellen Anwendungen, da es eine gleichmäßige Druckverteilung auf das Werkstück ermöglicht. In Verbindung mit dem Kolbendurchmesser ermöglicht es eine präzise Kontrolle über die Presskraft, insbesondere bei der Bearbeitung empfindlicher Materialien.
Die Schließkraft zwischen der Pressplatte und der Pressform ist ein entscheidender Faktor für die Stabilität des Pressvorgangs. Der Öldruck im Hydrauliksystem beeinflusst direkt diese Schließkraft und damit die Qualität der Umformung des Werkstücks. Eine sorgfältig ausbalancierte Schließkraft ist entscheidend, um eine effiziente Umformung und hochwertige Endprodukte zu gewährleisten.
Die Einspannvorrichtung spielt eine Schlüsselrolle bei der sicheren Fixierung des Werkstücks während des Pressvorgangs. Hydraulikventile sind dabei von besonderer Bedeutung, da sie den Druck in den Zylindern steuern und somit ein sicheres Einspannen ermöglichen. Die Hydraulikpumpenleistung beeinflusst direkt die Kolbengeschwindigkeit, was die Effizienz des Pressvorgangs und die Gesamtproduktivität der Maschine maßgeblich beeinflusst.
Die Kolbenstange, die mit dem Kolben verbunden ist, überträgt die Bewegung auf die Pressplatte und beeinflusst somit die Umformung des Werkstücks. Die Kolbenabdichtung ist von entscheidender Bedeutung, um sicherzustellen, dass der Hydraulikzylinder leckagefrei arbeitet und eine konstante Presskraft aufrechterhalten wird. Druckbegrenzungsventile sind eine wichtige Sicherheitsvorkehrung, die sicherstellen, dass der maximale Druck im System nicht überschritten wird, was die Sicherheit der Anwendung weiter verbessert.
Die verschiedenen Komponenten, angefangen bei Hydraulikventilen über Druckspeicher bis hin zu Presskissen und Sicherheitsvorkehrungen, verdeutlichen die Komplexität und Präzision, die in modernen Hydraulikpressen eingebettet sind. Ihr sorgfältig abgestimmtes Zusammenspiel ermöglicht es, vielfältige Fertigungsaufgaben mit höchster Effizienz und Qualität zu bewältigen.
Die Hydraulikpresse, als zentrales Werkzeug in modernen Fertigungsprozessen, setzt sich aus einer Vielzahl entscheidender Schlüsselkomponenten zusammen, die ihr reibungsloses Funktionieren gewährleisten. Unter diesen spielt der Ventilblock eine Schlüsselrolle. Dieser Block ist das Herzstück der Hydraulikschaltung und beherbergt eine Vielzahl von Hydraulikventilen. Diese Ventile sind maßgeblich für die präzise Steuerung des Ölflusses im System verantwortlich und ermöglichen somit eine exakte Anpassung des Arbeitsdrucks, was wiederum die Presskraft beeinflusst.
Die Hydraulikschaltung, koordiniert durch den Ventilblock und unterstützt durch weitere Steuereinheiten, bildet das Rückgrat der Steuerungseinheit der Hydraulikpresse. Diese Einheit gewährleistet ein reibungsloses Zusammenspiel aller Komponenten und Parameter während des Pressvorgangs. Das Druckregelventil, als Teil dieser Steuerungseinheit, übernimmt die Aufgabe, den Arbeitsdruck im Hydrauliksystem präzise zu regulieren. Hierdurch wird eine optimale Umformung des Werkstücks erreicht.
Das Druckmanometer, als Überwachungsinstrument, spielt eine kritische Rolle bei der Sicherstellung eines stabilen Betriebs des Hydrauliksystems. Kontinuierlich misst es den aktuellen Druck und signalisiert etwaige Abweichungen, wodurch eine schnelle Reaktion und Korrektur möglich ist. Druckspeicher sind dabei essenziell, um Druckschwankungen im System auszugleichen und eine konstante Presskraft zu gewährleisten. Diese Komponenten arbeiten zusammen, um präzise und reproduzierbare Ergebnisse in den Fertigungsprozessen sicherzustellen.
Das Presskissen, als spezialisierte Komponente, findet besonders in Anwendungen Verwendung, die eine gleichmäßige Druckverteilung erfordern. Dies ist insbesondere bei der Bearbeitung von ungleichmäßig geformten oder empfindlichen Materialien von Vorteil. Der Kolbendurchmesser, der die auf das Hydrauliköl wirkende Fläche des Kolbens angibt, spielt hierbei eine entscheidende Rolle, da er die Gesamtpresskraft beeinflusst und somit die Präzision des Pressvorgangs gewährleistet.
Die Schließkraft zwischen der Pressplatte und der Pressform ist ein kritischer Faktor für die Stabilität und Effizienz des Pressvorgangs. Der Öldruck im Hydrauliksystem beeinflusst unmittelbar diese Schließkraft und damit die Qualität der Umformung des Werkstücks. Eine sorgfältige Abstimmung dieser Parameter ist unerlässlich, um eine optimale Leistung der Hydraulikpresse sicherzustellen.
Die Einspannvorrichtung, eine weitere entscheidende Komponente, gewährleistet die sichere Fixierung des Werkstücks während des Pressvorgangs. Hydraulikventile spielen dabei eine Schlüsselrolle, indem sie den Druck in den Zylindern steuern und so ein sicheres Einspannen ermöglichen. Die Hydraulikpumpenleistung beeinflusst unmittelbar die Kolbengeschwindigkeit und somit die Effizienz des Pressvorgangs und die Gesamtproduktivität der Maschine.
Die Kolbenstange, in Verbindung mit dem Kolben, überträgt die Bewegung auf die Pressplatte und beeinflusst somit die Umformung des Werkstücks. Die Kolbenabdichtung ist dabei entscheidend, um sicherzustellen, dass der Hydraulikzylinder leckagefrei arbeitet und eine konstante Presskraft aufrechterhalten wird. Druckbegrenzungsventile dienen als wichtige Sicherheitsvorkehrung, indem sie sicherstellen, dass der maximale Druck im System nicht überschritten wird, was die Sicherheit der Anwendung weiter verbessert.
Zusammenfassend verdeutlichen diese Komponenten, darunter der Ventilblock, die Steuerungseinheit, Druckregelventile, Druckmanometer, Druckspeicher, Presskissen, Schließkraft, Einspannvorrichtung, Hydraulikpumpenleistung, Kolbenstange und Abdichtung, wie präzise und komplex die Funktionsweise einer Hydraulikpresse ist. Ihr Zusammenspiel ermöglicht es, eine Vielzahl von Fertigungsanforderungen mit höchster Genauigkeit und Effizienz zu erfüllen
Die Einsatzmöglichkeiten und die Präzision von Hydraulikpressen werden durch eine Reihe weiterer Schlüsselkomponenten sichergestellt, die das Gesamtsystem zu einer hochentwickelten und effizienten Fertigungseinheit machen. Hydraulikschläuche sind von grundlegender Bedeutung, da sie das Hydrauliköl zwischen den verschiedenen Komponenten transportieren und somit eine nahtlose Übertragung von Druck und Energie gewährleisten. Die Qualität dieser Schläuche ist entscheidend, um Leckagen zu vermeiden und einen störungsfreien Betrieb sicherzustellen.
Der Ventilblock, als Nervensystem der Hydraulikpresse, beherbergt eine Vielzahl von Hydraulikventilen, die den Ölfluss steuern. Diese Ventile sind maßgeblich für die präzise Regulation des Arbeitsdrucks verantwortlich, was die exakte Anpassung der Presskraft ermöglicht. Die Hydraulikschaltung, koordiniert durch den Ventilblock und unterstützt durch Steuereinheiten, gewährleistet ein reibungsloses Zusammenwirken aller Komponenten während des Pressvorgangs.
Das Druckregelventil spielt hierbei eine Schlüsselrolle, indem es den Arbeitsdruck präzise steuert und somit eine optimale Umformung des Werkstücks ermöglicht. Es ermöglicht eine Anpassung der Maschine an unterschiedliche Materialien und Fertigungsanforderungen. Das Druckmanometer überwacht kontinuierlich den aktuellen Druck im Hydrauliksystem, um sicherzustellen, dass er innerhalb sicherer Grenzen bleibt, was sowohl die Effizienz als auch die Sicherheit der Maschine gewährleistet.
Druckspeicher sind eine kritische Komponente, um Druckschwankungen im System auszugleichen. Dies trägt dazu bei, eine konstante Presskraft aufrechtzuerhalten und präzise Ergebnisse in den Fertigungsprozessen sicherzustellen. Das Presskissen, eine spezialisierte Komponente, sorgt dafür, dass die Druckverteilung auf das Werkstück gleichmäßig erfolgt. Dies ist besonders relevant bei der Bearbeitung empfindlicher Materialien oder ungleichmäßig geformter Werkstücke.
Die Schließkraft zwischen der Pressplatte und der Pressform ist ein maßgeblicher Faktor für die Stabilität des Pressvorgangs. Der Öldruck im Hydrauliksystem beeinflusst diese Schließkraft direkt und trägt somit wesentlich zur Qualität der Umformung des Werkstücks bei. Eine ausgewogene Schließkraft ist entscheidend, um eine effiziente Umformung und hochwertige Endprodukte sicherzustellen.
Die Einspannvorrichtung spielt eine entscheidende Rolle bei der sicheren Fixierung des Werkstücks während des Pressvorgangs. Hydraulikventile kommen hierbei zum Einsatz, um den Druck in den Zylindern zu steuern und ein sicheres Einspannen zu ermöglichen. Die Hydraulikpumpenleistung beeinflusst direkt die Kolbengeschwindigkeit, was wiederum die Effizienz des Pressvorgangs und die Gesamtproduktivität der Maschine beeinflusst.
Die Kolbenstange, die mit dem Kolben verbunden ist, überträgt die Bewegung auf die Pressplatte und beeinflusst somit die Umformung des Werkstücks. Die Kolbenabdichtung ist von entscheidender Bedeutung, um sicherzustellen, dass der Hydraulikzylinder leckagefrei arbeitet und eine konstante Presskraft aufrechterhalten wird. Druckbegrenzungsventile dienen als wichtige Sicherheitsvorkehrung und stellen sicher, dass der maximale Druck im System nicht überschritten wird, was die Sicherheit der Anwendung weiter verbessert.
Die verschiedenen Komponenten, darunter Hydraulikschläuche, Ventilblock, Druckregelventile, Druckmanometer, Druckspeicher, Presskissen, Schließkraft, Einspannvorrichtung, Hydraulikpumpenleistung, Kolbenstange und Abdichtung, unterstreichen die hohe Komplexität und Präzision einer Hydraulikpresse. Ihr sorgfältig abgestimmtes Zusammenspiel ermöglicht es, eine breite Palette von Fertigungsanforderungen mit höchster Genauigkeit und Effizienz zu erfüllen.