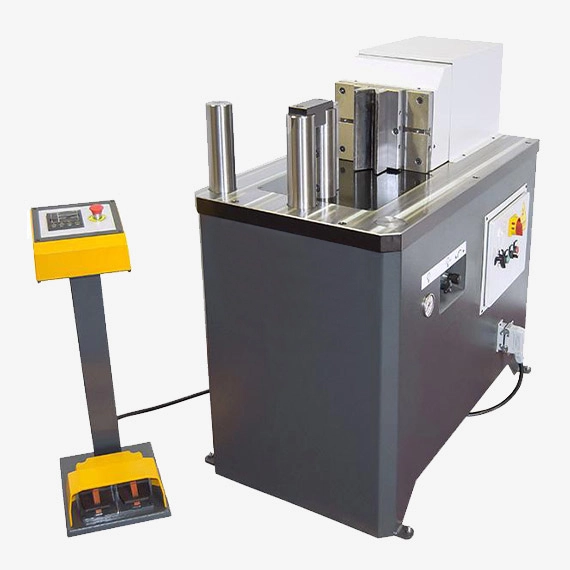
Die Horizontale Biegepresse ermöglicht es uns, viele Schmiedeteile und alle Arten von Operationen in allen Arten von Materialien herzustellen.
Die hydraulische Horizontalpresse repräsentiert einen entscheidenden Fortschritt in der metallverarbeitenden Industrie, insbesondere im Bereich der Blechumformung. Mit ihrer Fähigkeit, enorme Druckkräfte aufzuwenden, ermöglicht diese Pressenart präzise Biegeoperationen und eine vielseitige Bearbeitung von Werkstücken. Die Kombination von Präzisionstechnik und einem effizienten Hydrauliksystem macht sie zu einem unverzichtbaren Werkzeug in der modernen Blechbearbeitung.
In der Praxis findet die hydraulische Horizontalpresse breite Anwendung in der Blechbearbeitungsindustrie. Ihre CNC-Steuerung ermöglicht nicht nur eine präzise Druckkraftregelung, sondern auch die Anpassung an unterschiedliche Materialverarbeitungsanforderungen. Diese Pressen sind speziell darauf ausgelegt, Werkstücke mit niedrigen Toleranzen zu formen und dabei eine herausragende Schneidkantenqualität zu gewährleisten.
Die Vielseitigkeit dieser Maschinen zeigt sich in ihrer Fähigkeit, eine breite Palette von Blechumformoperationen durchzuführen, darunter Blechbiegen, Stanzvorgänge und andere komplexe Umformtechniken. Die Robustheit ihrer Konstruktion ermöglicht den Einsatz in der Hochleistungsproduktion, wo sie effiziente, automatisierte Pressvorgänge durchführt. Die Flexibilität erstreckt sich auch auf den Werkzeugwechsel, der die Anpassung an verschiedene Anforderungen und Anwendungen ermöglicht.
Ein entscheidender Aspekt bei der Leistungsfähigkeit der hydraulischen Horizontalpresse ist die optimierte Steuerung des Hydrauliksystems. Dies gewährleistet nicht nur die präzise Presskraftregelung, sondern trägt auch dazu bei, die Stillstandszeiten zu minimieren und die Produktionskapazität zu maximieren. Die Automatisierung von Pressensteuerung und Werkzeugwechsel ermöglicht eine effiziente und nahtlose Arbeitsweise.
Die Blechumformtechnologie, die von hydraulischen Horizontalpressen unterstützt wird, revolutioniert die Art und Weise, wie Metalle verformt und bearbeitet werden. Die CNC-Präzisionspresse setzt dabei Maßstäbe für präzise Blechformung und Biegevorgänge. Mit ihrer robusten Konstruktion und der Fähigkeit, Hochleistungsvorgänge durchzuführen, bewährt sich diese Pressenart als unverzichtbares Werkzeug in der industriellen Fertigung.
Die präzise Blechbearbeitung durch eine hydraulische Horizontalpresse ermöglicht nicht nur die Herstellung von hochwertigen Werkstücken, sondern trägt auch dazu bei, die Effizienz und Qualität in der metallverarbeitenden Industrie zu steigern. Ihre flexible Anwendbarkeit und die Möglichkeit zur Optimierung des Hydrauliksystems machen sie zu einem Schlüsselfaktor in der modernen Fertigungsumgebung. Insgesamt bietet die hydraulische Horizontalpresse eine effiziente Lösung für die Herausforderungen der Blechumformung und metallverarbeitenden Prozesse.
Eine Horizontalbiegepresse ist eine Maschine, die zum Biegen von Metallstangen, Rohren und Profilen verwendet wird. Sie wird häufig in der Metallbearbeitung eingesetzt, um Metallteile für eine Vielzahl von Anwendungen herzustellen.
Horizontalbiegepressen arbeiten durch Einwirken einer Kraft auf das zu biegende Material, wodurch es sich um ein Werkzeug biegt, das als Biegestempel bezeichnet wird. Die Kraft wird durch einen Hydraulikzylinder oder einen Elektromotor erzeugt. Der Biegestempel kann in der Höhe verstellt werden, um verschiedene Biegeradien zu erzeugen.
Horizontalbiegepressen sind in einer Vielzahl von Größen und Ausführungen erhältlich. Die Größe der Maschine hängt von der Größe und Dicke des zu biegenden Materials ab. Die Ausführung der Maschine hängt von den gewünschten Funktionen ab, z. B. ob die Maschine gerade oder gebogene Biegungen ausführen soll.
Horizontalbiegepressen werden für eine Vielzahl von Anwendungen in der Metallbearbeitung eingesetzt, darunter:
- Biegen von Metallstangen, Rohren und Profilen
- Herstellen von Metallteilen für eine Vielzahl von Anwendungen
- Reparaturen von Metallteilen
- Prototypenbau
Vorteile von Horizontalbiegepressen:
- Präzise Biegungen
- Hohe Biegeleistung
- Vielseitigkeit
- Sicherheit
Nachteile von Horizontalbiegepressen:
- Hohe Anschaffungskosten
- Wartungsaufwand
- Benötigt viel Platz
- Kann gefährlich sein, wenn sie nicht ordnungsgemäß verwendet wird.
Bei der Auswahl einer Horizontalbiegepresse sollten Sie folgende Faktoren berücksichtigen:
- Die Größe und Dicke des zu biegenden Materials
- Die gewünschten Funktionen
- Das Budget
- Der Platzbedarf
Horizontalbiegepressen sind ein vielseitiges Werkzeug, das für eine Vielzahl von Aufgaben in der Metallbearbeitung verwendet werden kann. Sie sind eine gute Wahl für Unternehmen, die Metallteile für eine Vielzahl von Anwendungen herstellen.
Die Anwendungsbreite der hydraulischen Horizontalpresse erstreckt sich über verschiedene industrielle Prozesse, insbesondere im Bereich der Blechbearbeitung. Eine entscheidende Eigenschaft dieser Pressen ist ihre Fähigkeit zur Blechumformung, die durch die robuste Bauweise und das leistungsstarke Hydrauliksystem ermöglicht wird. Die Präzisionstechnik in Verbindung mit der Presskraftregelung trägt dazu bei, dass Biegeoperationen mit höchster Genauigkeit durchgeführt werden können.
Die Plattenpresse, wie sie auch genannt wird, zeichnet sich durch ihre Horizontalausrichtung aus, was spezifische Vorteile für bestimmte Anwendungen in der Blechbearbeitung bietet. Dies ist besonders bei Blechumformungsvorgängen von Bedeutung, da sie eine gleichmäßige Druckverteilung über die gesamte Fläche des Werkstücks gewährleistet. Die Anwendung dieser Pressenart erstreckt sich über verschiedene Industriezweige, darunter die Herstellung von Blechkomponenten für die Automobilindustrie, den Maschinenbau und mehr.
Die Horizontalpresseanwendung umfasst nicht nur das Biegen von Blechen, sondern auch andere wichtige Umformoperationen. Diese können das Stanzen, Schneiden und Formen von Blechen beinhalten. Die CNC-Steuerung ermöglicht eine präzise Anpassung an die spezifischen Anforderungen verschiedener Blechbearbeitungsaufgaben. Die Integration dieser Technologie trägt dazu bei, dass die Pressen vielseitig einsetzbar sind und eine breite Palette von Werkstücken herstellen können.
In der Blechumformmaschine ist die CNC-Präzisionstechnik ein entscheidender Faktor für die Qualität der bearbeiteten Werkstücke. Durch die hochentwickelte CNC-Steuerung können komplexe Biegeoperationen mit außergewöhnlicher Genauigkeit durchgeführt werden. Dies ist besonders wichtig in Branchen, in denen eine hohe Präzision und Reproduzierbarkeit der gefertigten Komponenten erforderlich ist.
Die Automatisierung von Pressvorgängen durch die CNC-Steuerung ermöglicht nicht nur eine effizientere Produktion, sondern trägt auch zur Minimierung menschlicher Fehlerquellen bei. Dies führt zu einer konstanten Qualität in der Blechbearbeitung und hilft, Ausschuss zu reduzieren. Die Effizienz der Werkzeugwechsel wird ebenfalls durch die CNC-Präzisionstechnik optimiert, was die Gesamtproduktivität der Horizontalpresse steigert.
Die Blechumformung durch eine hydraulische Horizontalpresse erstreckt sich über verschiedene Materialverarbeitungsanwendungen. Diese Pressen werden in der Regel für die Bearbeitung von Metallblechen eingesetzt, wobei verschiedene Legierungen und Dicken berücksichtigt werden können. Dies ermöglicht eine breite Anpassungsfähigkeit an unterschiedliche Anforderungen der metallverarbeitenden Industrie.
Die industrielle Fertigung profitiert erheblich von der Blechumformmaschinentechnologie, insbesondere wenn es um die Herstellung von hochpräzisen Werkstücken geht. Die CNC-Präzisionspresse trägt dazu bei, dass die gefertigten Blechkomponenten den strengen Qualitätsstandards der Industrie entsprechen. Die hohe Genauigkeit in der Blechformung ist entscheidend für die Funktionalität und Ästhetik der Endprodukte.
Die hydraulische Horizontalpresse ermöglicht nicht nur die Umformung von Blechen, sondern auch das Biegen von Rohren und anderen Materialien. Diese Vielseitigkeit macht sie zu einem unverzichtbaren Werkzeug in der modernen Fertigung, insbesondere in Branchen, in denen eine breite Palette von Materialien verarbeitet wird. Die flexible Anwendbarkeit trägt dazu bei, dass diese Pressen für verschiedene Produktionsanforderungen geeignet sind.
Ein weiterer entscheidender Aspekt ist die Niedrighaltung von Toleranzen in der Präzisionsblechbearbeitung. Die Horizontalpresse ermöglicht die Herstellung von Werkstücken mit geringen Toleranzen, was für viele Industriezweige von entscheidender Bedeutung ist. Diese geringen Toleranzen tragen dazu bei, dass die gefertigten Komponenten genau den Designspezifikationen entsprechen.
Zusammenfassend kann festgestellt werden, dass die hydraulische Horizontalpresse durch ihre CNC-Präzisionstechnik, ihre Vielseitigkeit und ihre Fähigkeit zur Präzisionsblechbearbeitung eine Schlüsselrolle in der modernen Fertigungslandschaft spielt. Mit fortschrittlichen Funktionen und technologischen Innovationen ist sie zu einem unverzichtbaren Werkzeug für Unternehmen geworden, die auf Präzisionsmetallverarbeitung angewiesen sind.
Horizontal Biegemaschine Anwendung
Die Blechumformung durch eine hydraulische Horizontalpresse vereint fortschrittliche Technologien wie die CNC-Steuerung, um hochpräzise und effiziente Biegeoperationen zu ermöglichen. Die Präzisionstechnik in Verbindung mit einer optimierten Presskraftregelung macht diese Pressen zu einem unverzichtbaren Werkzeug in der modernen Blechbearbeitung. Diese Pressen sind darauf ausgelegt, verschiedene Werkstücke mit unterschiedlichen Materialien und Dicken zu formen, wodurch sie sich als äußerst vielseitig für verschiedene industrielle Anwendungen erweisen.
Die CNC-Steuerung ist ein Schlüsselelement in der Präzisionsblechbearbeitung durch hydraulische Horizontalpressen. Diese fortschrittliche Steuerungstechnologie ermöglicht nicht nur eine präzise Druckkraftregelung, sondern auch die Anpassung an spezifische Anforderungen der Blechumformung. Mit dieser Technologie können komplexe Biegeoperationen mit außergewöhnlicher Genauigkeit durchgeführt werden, was insbesondere in Branchen, in denen höchste Präzision erforderlich ist, von entscheidender Bedeutung ist.
Die CNC-Präzisionspresse bewährt sich in der Blechbearbeitungsindustrie, indem sie nicht nur hochwertige, sondern auch hochpräzise Werkstücke herstellt. Die Automatisierung von Pressvorgängen durch die CNC-Steuerung trägt nicht nur zu einer effizienteren Produktion bei, sondern minimiert auch menschliche Fehlerquellen. Dies führt zu einer gleichbleibenden Qualität in der Blechbearbeitung und trägt dazu bei, Ausschuss zu reduzieren und Produktionskosten zu optimieren.
Die Werkzeugwechseloptimierung ist ein weiterer Vorteil der CNC-Präzisionspresse. Die Effizienz dieses Prozesses trägt dazu bei, die Gesamtproduktivität der hydraulischen Horizontalpresse zu steigern. Durch die schnelle und präzise Anpassung an verschiedene Produktionsanforderungen können Unternehmen flexibler und wettbewerbsfähiger agieren.
Die Horizontalpresseanwendung erstreckt sich über verschiedene Branchen, darunter die Automobilindustrie, den Maschinenbau und die Elektronikfertigung. Die Vielseitigkeit dieser Pressen macht sie zu einem unverzichtbaren Werkzeug für Unternehmen, die eine breite Palette von Blechumformanwendungen durchführen. Die Präzisionsblechbearbeitung spielt eine zentrale Rolle in diesen Branchen, und die hydraulische Horizontalpresse ermöglicht es, höchste Standards zu erfüllen.
Die CNC-Präzisionspresse ist nicht nur auf das Biegen von Blechen beschränkt, sondern ermöglicht auch andere wichtige Umformoperationen wie Stanzen, Schneiden und Formen. Diese umfassende Funktionalität macht sie zu einem Alleskönner in der Blechumformtechnologie. Die Robustheit ihrer Konstruktion und ihre Fähigkeit, Hochleistungsvorgänge durchzuführen, prädestinieren sie für anspruchsvolle Fertigungsumgebungen.
Die Blechumformmaschinentechnologie spielt eine entscheidende Rolle bei der Herstellung von hochpräzisen Werkstücken. Die CNC-Präzisionspresse trägt dazu bei, dass die gefertigten Blechkomponenten nicht nur den strengen Qualitätsstandards entsprechen, sondern auch die spezifischen Designanforderungen erfüllen. Dies ist von entscheidender Bedeutung, insbesondere in Branchen, in denen die Funktionalität und Ästhetik der Endprodukte von höchster Wichtigkeit sind.
Die hydraulische Horizontalpresse ermöglicht nicht nur die Umformung von Blechen, sondern auch das Biegen von Rohren und anderen Materialien. Diese Fähigkeit erweitert die Anwendungsbereiche dieser Pressen über die reine Blechumformung hinaus. In Branchen, in denen eine breite Palette von Materialien verarbeitet wird, bietet diese Vielseitigkeit einen klaren Wettbewerbsvorteil.
Die flexible Anwendbarkeit der hydraulischen Horizontalpresse trägt dazu bei, dass diese Pressen für verschiedene Produktionsanforderungen geeignet sind. Die Möglichkeit zur Optimierung des Hydrauliksystems unterstützt nicht nur präzise Biegeoperationen, sondern trägt auch zur Minimierung von Toleranzen bei. Dies ist besonders in Branchen von Bedeutung, in denen geringe Toleranzen und hohe Präzision eine grundlegende Anforderung sind.
Zusammenfassend kann festgestellt werden, dass die hydraulische Horizontalpresse durch ihre CNC-Präzisionstechnik, ihre Vielseitigkeit und ihre Fähigkeit zur Präzisionsblechbearbeitung eine zentrale Rolle in der modernen Fertigungslandschaft spielt. Ihr breites Anwendungsspektrum, kombiniert mit fortschrittlichen Funktionen und technologischen Innovationen, macht sie zu einem wesentlichen Bestandteil für Unternehmen, die auf Präzisionsmetallverarbeitung angewiesen sind.
Horizontale Biegemaschinen werden in einer Vielzahl von Anwendungen in der Metallbearbeitung eingesetzt, darunter:
- Herstellung von Metallteilen für eine Vielzahl von Anwendungen: Horizontale Biegemaschinen werden verwendet, um Metallteile für eine Vielzahl von Anwendungen herzustellen, darunter Konstruktion, Maschinenbau, Transport, Elektronik und Konsumgüter. Beispiele für typische Metallteile, die mit horizontalen Biegemaschinen hergestellt werden, sind Rahmen, Profile, Rohre, Bleche und Gehäuse.
- Reparaturen von Metallteilen: Horizontale Biegemaschinen können auch verwendet werden, um beschädigte Metallteile zu reparieren. Dies kann beispielsweise erforderlich sein, wenn ein Metallteil verbogen oder gerissen ist.
- Prototypenbau: Horizontale Biegemaschinen können auch verwendet werden, um Prototypen von Metallteilen herzustellen. Dies ist nützlich, um neue Designs zu testen oder Änderungen an bestehenden Designs vorzunehmen.
Die Art der Anwendung bestimmt die Größe, den Typ und die Funktionen der erforderlichen horizontalen Biegemaschine. Kleinere Maschinen sind in der Regel für die Herstellung von kleineren Teilen oder für den Prototypenbau geeignet. Größere Maschinen sind in der Regel für die Herstellung von größeren Teilen oder für die Massenproduktion geeignet.
Hier sind einige Beispiele für spezifische Anwendungen horizontaler Biegemaschinen:
- Konstruktion: Horizontale Biegemaschinen werden in der Konstruktion verwendet, um Rahmen, Profile und andere Metallteile für Gebäude, Brücken, Türen und Fenster herzustellen.
- Maschinenbau: Horizontale Biegemaschinen werden im Maschinenbau verwendet, um Metallteile für Maschinen, Werkzeuge und Geräte herzustellen. Beispiele sind Motorgehäuse, Getriebegehäuse und Rahmen.
- Transport: Horizontale Biegemaschinen werden im Transportwesen verwendet, um Metallteile für Autos, Flugzeuge und Schiffe herzustellen. Beispiele sind Karosserieteile, Fahrwerksteile und Schiffsrümpfe.
- Elektronik: Horizontale Biegemaschinen werden in der Elektronik verwendet, um Metallteile für Schaltkreise, Kondensatoren und andere elektronische Komponenten herzustellen. Beispiele sind Leiterplatten, Stecker und Gehäuse.
- Verbrauchsgüter: Horizontale Biegemaschinen werden in der Herstellung von Konsumgütern wie Autos, Möbeln und Haushaltsgeräten verwendet. Beispiele sind Rahmen, Profile und Gehäuse.
Horizontale Biegemaschinen sind ein wichtiges Werkzeug in der Metallbearbeitung. Sie ermöglichen die Herstellung einer Vielzahl von Metallteilen für eine Vielzahl von Anwendungen.
Horizontalbieger
Die hydraulische Horizontalpresse hat sich als essentielles Werkzeug in der Metallverarbeitung etabliert, und ihre Leistungsfähigkeit wird durch Schlüsseltechnologien wie die CNC-Steuerung weiter gesteigert. Diese Pressen setzen auf Präzisionstechnik, um hochgenaue Biegeoperationen durchzuführen, wobei die optimierte Presskraftregelung eine entscheidende Rolle spielt. Mit ihrer Vielseitigkeit in der Blechumformung finden diese Pressen Anwendung in verschiedenen Industriezweigen, darunter die Automobilindustrie, den Maschinenbau und die Elektronikfertigung.
Die CNC-Steuerung ist das Herzstück der Präzisionsblechbearbeitung durch hydraulische Horizontalpressen. Diese fortschrittliche Steuerungstechnologie ermöglicht eine exakte Druckkraftregelung, was besonders bei komplexen Biegeoperationen von entscheidender Bedeutung ist. Die CNC-Präzisionspresse setzt neue Maßstäbe für die genaue Anpassung an spezifische Anforderungen der Blechumformung, wodurch höchste Qualitätsstandards erreicht werden.
Ein signifikanter Vorteil der CNC-Präzisionspresse ist ihre Anpassungsfähigkeit an verschiedene Materialien und Dicken. Dies macht sie zu einem universellen Werkzeug in der metallverarbeitenden Industrie. Unternehmen können mit dieser Vielseitigkeit flexibel auf unterschiedliche Anforderungen reagieren, sei es bei der Herstellung von dünnen Blechen für Elektronikkomponenten oder bei der Umformung robuster Metallteile für die Automobilindustrie.
Die Automation von Pressvorgängen durch die CNC-Steuerung verbessert nicht nur die Effizienz, sondern reduziert auch menschliche Fehlerquellen erheblich. Die Präzisionsblechbearbeitung durch diese Pressen führt zu einer gleichbleibenden Qualität und minimiert Ausschuss. Dies ist besonders in der industriellen Fertigung von Bedeutung, wo eine hohe Produktqualität und Konsistenz entscheidend sind.
Die Optimierung von Werkzeugwechseln ist ein weiterer Bereich, in dem die CNC-Präzisionspresse überzeugt. Schnelle und präzise Anpassungen an verschiedene Produktionsanforderungen steigern die Gesamtproduktivität erheblich. Unternehmen können so flexibler agieren und schneller auf Marktanforderungen reagieren, was in einer zunehmend dynamischen Wirtschaftsumgebung von entscheidender Bedeutung ist.
Die Blechumformmaschinentechnologie, die durch hydraulische Horizontalpressen repräsentiert wird, spielt eine zentrale Rolle bei der Herstellung hochpräziser Werkstücke. Die CNC-Präzisionspresse stellt sicher, dass gefertigte Blechkomponenten nicht nur den Qualitätsstandards entsprechen, sondern auch spezifische Designanforderungen erfüllen. In Branchen, in denen Genauigkeit und Präzision Schlüsselmerkmale sind, ist die CNC-Präzisionspresse unverzichtbar.
Die hydraulische Horizontalpresse ermöglicht nicht nur die Biegeoperationen von Blechen, sondern eröffnet auch die Möglichkeit zur Bearbeitung von Rohren und anderen Materialien. Diese Vielseitigkeit macht sie zu einem unverzichtbaren Werkzeug in der modernen Fertigung, insbesondere in Branchen, in denen eine breite Palette von Materialien verarbeitet wird. Die flexible Anwendbarkeit trägt dazu bei, dass diese Pressen für verschiedene Produktionsanforderungen geeignet sind.
Die Möglichkeit zur Optimierung des Hydrauliksystems in der hydraulischen Horizontalpresse ist entscheidend für präzise Biegeoperationen. Dies ermöglicht nicht nur eine genaue Kontrolle der Druckkraft, sondern trägt auch zur Minimierung von Toleranzen bei. Die geringen Toleranzen in der Präzisionsblechbearbeitung sind in vielen Industrien, insbesondere in der Luft- und Raumfahrt oder Medizintechnik, von zentraler Bedeutung.
Die hydraulische Horizontalpresse spielt eine entscheidende Rolle in der modernen Fertigung, indem sie nicht nur eine breite Anwendbarkeit in der Blechumformung bietet, sondern auch hochpräzise und effiziente Biegeoperationen ermöglicht. Durch die Kombination von Schlüsseltechnologien wie der CNC-Steuerung, Präzisionstechnik und einer optimierten Presskraftregelung wird diese Pressenart zu einem integralen Bestandteil für Unternehmen, die auf hochwertige Metallverarbeitung setzen.
Die Blechumformung durch hydraulische Horizontalpressen, unterstützt durch Schlüsseltechnologien wie die CNC-Steuerung, repräsentiert einen Meilenstein in der modernen Metallverarbeitung. Diese Pressen, die auf Präzisionstechnik und optimierte Presskraftregelung setzen, sind maßgeblich für hochgenaue Biegeoperationen in verschiedenen industriellen Anwendungen verantwortlich. Die CNC-Präzisionspresse, als Herzstück dieser Maschinen, ermöglicht nicht nur eine exakte Druckkraftregelung, sondern auch die präzise Anpassung an unterschiedliche Anforderungen der Blechumformung.
Die Vielseitigkeit der hydraulischen Horizontalpresse erstreckt sich über verschiedene Materialien und Dicken, was sie zu einem flexiblen Werkzeug in der metallverarbeitenden Industrie macht. Unternehmen können auf unterschiedliche Anforderungen reagieren, sei es bei der Produktion von dünnen Blechen für Elektronikkomponenten oder bei der Umformung robuster Metallteile für die Automobilindustrie. Diese Anpassungsfähigkeit ist besonders in dynamischen Produktionsumgebungen von entscheidender Bedeutung.
Die Automatisierung von Pressvorgängen durch die CNC-Steuerung führt nicht nur zu einer effizienteren Produktion, sondern minimiert auch menschliche Fehlerquellen. Die Präzisionsblechbearbeitung durch diese Pressen gewährleistet eine gleichbleibend hohe Qualität und reduziert den Ausschuss. In der industriellen Fertigung, wo Konsistenz und Präzision Schlüsselmerkmale sind, ist die CNC-Präzisionspresse unentbehrlich.
Die Optimierung von Werkzeugwechseln in hydraulischen Horizontalpressen steigert die Gesamtproduktivität erheblich. Schnelle und präzise Anpassungen an verschiedene Produktionsanforderungen ermöglichen es Unternehmen, flexibler zu agieren und schneller auf Marktanforderungen zu reagieren. In einer zunehmend dynamischen Wirtschaftsumgebung ist diese Agilität von zentraler Bedeutung für den unternehmerischen Erfolg.
Die Blechumformmaschinentechnologie, vertreten durch hydraulische Horizontalpressen, spielt eine Schlüsselrolle bei der Herstellung hochpräziser Werkstücke. Die CNC-Präzisionspresse stellt sicher, dass gefertigte Blechkomponenten nicht nur den allgemeinen Qualitätsstandards entsprechen, sondern auch spezifische Designanforderungen erfüllen. Besonders in Branchen, in denen höchste Genauigkeit erforderlich ist, ist die CNC-Präzisionspresse ein essenzielles Werkzeug.
Die hydraulische Horizontalpresse ermöglicht nicht nur Biegeoperationen von Blechen, sondern eröffnet auch die Möglichkeit zur Bearbeitung von Rohren und anderen Materialien. Diese Vielseitigkeit macht sie zu einem unverzichtbaren Werkzeug in der modernen Fertigung, insbesondere in Branchen, in denen eine breite Palette von Materialien verarbeitet wird. Die flexible Anwendbarkeit trägt dazu bei, dass diese Pressen für verschiedene Produktionsanforderungen geeignet sind.
Die Möglichkeit zur Optimierung des Hydrauliksystems in der hydraulischen Horizontalpresse ist entscheidend für präzise Biegeoperationen. Dies ermöglicht nicht nur eine genaue Kontrolle der Druckkraft, sondern trägt auch zur Minimierung von Toleranzen bei. Geringe Toleranzen in der Präzisionsblechbearbeitung sind in vielen Industrien, insbesondere in der Luft- und Raumfahrt oder Medizintechnik, von zentraler Bedeutung.
Die hydraulische Horizontalpresse spielt eine entscheidende Rolle in der modernen Fertigung, indem sie nicht nur eine breite Anwendbarkeit in der Blechumformung bietet, sondern auch hochpräzise und effiziente Biegeoperationen ermöglicht. Durch die Kombination von Schlüsseltechnologien wie der CNC-Steuerung, Präzisionstechnik und einer optimierten Presskraftregelung wird diese Pressenart zu einem integralen Bestandteil für Unternehmen, die auf hochwertige Metallverarbeitung setzen. Insgesamt tragen hydraulische Horizontalpressen wesentlich dazu bei, die Effizienz, Qualität und Vielseitigkeit in der Blechbearbeitung und Metallumformung zu steigern.
Horizontale Biegemaschinen, auch bekannt als Horizontalbieger, sind vielseitige Werkzeuge, die in der Metallbearbeitung weit verbreitet sind, um Metallstangen, Rohre und Profile zu formen und zu biegen. Sie werden häufig in verschiedenen Branchen eingesetzt, darunter Bauwesen, Fertigung, Transport und Maschinenbau.
Funktionsweise
Horizontale Biegemaschinen arbeiten, indem sie eine kontrollierte Kraft auf das Metallwerkstück ausüben und es so um ein Werkzeug namens Biegestempel biegen. Die Kraft wird typischerweise von einem Hydraulikzylinder oder einem Elektromotor erzeugt. Der Biegestempel kann in der Höhe verstellt werden, um unterschiedliche Biegeradien zu erreichen.
Anwendungen von Horizontalbiegern
Horizontale Biegemaschinen werden in einer Vielzahl von Anwendungen eingesetzt, darunter:
• Biegen von Metallstangen, Rohren und Profilen: Horizontale Biegemaschinen werden hauptsächlich verwendet, um Metallstangen, Rohre und Profile in verschiedene Formen und Winkel zu biegen. Dies ist entscheidend für die Herstellung von Komponenten für verschiedene Strukturen, Maschinen und Geräte.
• Metallteilfertigung: Horizontale Biegemaschinen spielen eine entscheidende Rolle bei der Herstellung von Metallteilen für eine Vielzahl von Anwendungen. Sie können Komponenten für das Bauwesen, die Fertigung, den Transport und andere Branchen herstellen.
• Reparatur von Metallteilen: Horizontale Biegemaschinen können verwendet werden, um beschädigte Metallteile durch Richten oder Umformen zu reparieren. Dies kann die Lebensdauer von Metallkomponenten verlängern und den Austauschbedarf reduzieren.
• Prototypenentwicklung: Horizontale Biegemaschinen sind wertvolle Werkzeuge für die Prototypenentwicklung in der Metallbearbeitung. Sie ermöglichen die Erstellung physischer Prototypen von Metallteilen zum Testen, Evaluieren und Designen von Iterationen.
Arten von Horizontalbiegern
Horizontale Biegemaschinen gibt es in verschiedenen Arten, jede mit ihren eigenen Eigenschaften und Fähigkeiten:
• Hydraulische Horizontalbiegemaschinen: Diese Biegemaschinen verwenden Hydraulikzylinder, um die Biegekraft zu erzeugen, und bieten eine präzise Steuerung und eine hohe Leistung.
• Elektrische Horizontalbiegemaschinen: Elektrische Horizontalbiegemaschinen verwenden Elektromotoren, um die Biegekraft zu liefern, und bieten Energieeffizienz und einfache Bedienung.
• Dreirollen-Horizontalbiegemaschinen: Diese Biegemaschinen verfügen über drei Rollen, die zusammenarbeiten, um das Metallwerkstück zu biegen und bieten eine hervorragende Biegegenauigkeit und Vielseitigkeit.
• CNC-Horizontalbiegemaschinen: Computergesteuerte (CNC) Horizontalbiegemaschinen bieten erweiterte Programmierfunktionen für automatisierte und präzise Biegevorgänge.
Auswahlfaktoren für Horizontalbieger
Die Auswahl des geeigneten Horizontalbiegers hängt von mehreren Faktoren ab:
• Werkstückmaterial und Abmessungen: Die Kapazität des Biegegers sollte der Größe, Dicke und den Materialeigenschaften des Werkstücks entsprechen.
• Biegeanforderungen: Die Fähigkeiten des Biegers sollten mit den gewünschten Biegewinkeln, Radien und Präzisionsanforderungen übereinstimmen.
• Produktionsvolumen: Die Leistung und die Automatisierungsfunktionen des Biegegers sollten dem Produktionsvolumen und der erforderlichen Leistung entsprechen.
• Verfügbarer Platz und Budget: Die Größe und die Kosten des Biegegers sollten dem verfügbaren Arbeitsbereich und den finanziellen Einschränkungen entsprechen.
Vorteile von Horizontalbiegern
Horizontale Biegemaschinen bieten zahlreiche Vorteile für Metallbearbeitungsanwendungen:
• Hohe Präzision: Sie können präzise Biegewinkel und Radien erreichen und sorgen für konsistente und zuverlässige Ergebnisse.
• Vielseitigkeit: Sie können eine Vielzahl von Werkstückgrößen, Materialien und Biegeanforderungen verarbeiten.
• Hohe Produktivität: Sie können große Materialmengen effizient verarbeiten und unterstützen die Produktionsanforderungen.
• Sicherheitsverbesserungen: Moderne Horizontalbiegemaschinen verfügen über Sicherheitsfunktionen, um Betriebsrisiken zu minimieren.
Fazit
Horizontale Biegemaschinen sind unverzichtbare Werkzeuge in der metallverarbeitenden Industrie und ermöglichen das Formen und Herstellen von Metallkomponenten für verschiedene Anwendungen. Ihre Vielseitigkeit, Präzision und Produktivität machen sie zu einem wertvollen Gut in Fertigungs- und Reparaturprozessen.
Metallrohre:
Metallrohre sind eine wesentliche Komponente in einer Vielzahl von Branchen und Anwendungen. Sie bestehen aus Metalllegierungen wie Stahl, Edelstahl, Aluminium, Kupfer oder Messing und sind in verschiedenen Größen, Formen und Wandstärken erhältlich. Diese Rohre dienen als Träger für Fluide, Gase oder Feststoffe und werden in der Konstruktion, im Transport, in der Fertigung und vielen anderen Bereichen eingesetzt.
Stahlrohre sind beispielsweise aufgrund ihrer Festigkeit und Haltbarkeit besonders beliebt in der Bauindustrie, für Tragwerke und Konstruktionen. Edelstahlrohre bieten aufgrund ihrer Korrosionsbeständigkeit und hygienischen Eigenschaften eine ideale Lösung für Anwendungen in der Lebensmittelverarbeitung, Chemie- und Pharmaindustrie. Aluminiumrohre werden oft in Leichtbaukonstruktionen verwendet, wo Gewichtseinsparung und Korrosionsbeständigkeit von Bedeutung sind.
Kupferrohre sind bekannt für ihre ausgezeichnete Wärme- und elektrische Leitfähigkeit und werden daher häufig in Klimaanlagen, Kühlsystemen und Elektroinstallationen eingesetzt. Messingrohre, eine Legierung aus Kupfer und Zink, zeichnen sich durch ihre hohe Korrosionsbeständigkeit und einfache Bearbeitbarkeit aus und finden Anwendung in Armaturen, Rohrverbindungen und Dekorationen.
Metallrohre werden durch verschiedene Herstellungsverfahren wie Walzen, Schweißen, Ziehen oder Extrudieren hergestellt und können durch Biegen, Schneiden und andere Verarbeitungsschritte weiter bearbeitet werden. Ihre Vielseitigkeit, Festigkeit und Anpassungsfähigkeit machen sie zu unverzichtbaren Bauelementen in zahlreichen Industrien und Alltagsanwendungen.
Stahlrohre:
Stahlrohre sind eine der am häufigsten verwendeten Arten von Metallrohren und finden in einer Vielzahl von Anwendungen Verwendung. Sie bestehen aus einer Legierung aus Eisen und Kohlenstoff, wobei weitere Legierungselemente je nach Anforderungen hinzugefügt werden können. Stahlrohre sind für ihre Festigkeit, Haltbarkeit und vielseitigen Einsatzmöglichkeiten bekannt.
In der Bauindustrie werden Stahlrohre oft für Tragwerke, Geländer, Brücken und Gebäudekonstruktionen eingesetzt. Ihre hohe Festigkeit ermöglicht es ihnen, große Lasten zu tragen und gleichzeitig langlebig zu sein. In der Öl- und Gasindustrie dienen Stahlrohre als Förderrohre für den Transport von Erdöl und Erdgas über große Entfernungen. Diese Rohre müssen extremen Bedingungen standhalten, einschließlich hohem Druck, Korrosion und Temperaturschwankungen.
Stahlrohre werden auch in der Wasserversorgung und Abwasserentsorgung verwendet, um Trinkwasser zu transportieren und Abwasser abzuleiten. Aufgrund ihrer Beständigkeit gegenüber Korrosion und chemischen Einflüssen sind sie eine zuverlässige Wahl für diese kritischen Infrastrukturen. Darüber hinaus werden Stahlrohre in der Automobilindustrie, in der Herstellung von Maschinen und Geräten sowie in der Konstruktion von Rohrleitungen für industrielle Anwendungen eingesetzt.
Die Herstellung von Stahlrohren erfolgt durch verschiedene Verfahren wie das nahtlose Walzen, das geschweißte Walzen, das Spiralwickeln oder das Elektro-Schweißverfahren, je nach den spezifischen Anforderungen der Anwendung. Stahlrohre sind in einer Vielzahl von Größen, Wandstärken und Legierungen erhältlich, um den unterschiedlichen Anforderungen verschiedener Branchen gerecht zu werden.
Edelstahlrohre:
Edelstahlrohre sind eine spezielle Art von Metallrohren, die aus einer Legierung von Eisen, Chrom und oft auch anderen Elementen wie Nickel oder Molybdän hergestellt werden. Sie zeichnen sich durch ihre hohe Korrosionsbeständigkeit, mechanische Festigkeit und ästhetische Erscheinung aus. Diese Eigenschaften machen Edelstahlrohre zu einer bevorzugten Wahl in verschiedenen anspruchsvollen Anwendungen.
In der Lebensmittelindustrie werden Edelstahlrohre häufig für die Herstellung von Rohrleitungen, Behältern und Ausrüstungen verwendet, da sie inert sind und keine unerwünschten Aromen oder Verunreinigungen abgeben. Ihre glatte Oberfläche erleichtert die Reinigung und Wartung, was für hygienische Anforderungen unerlässlich ist. In der Chemie- und Pharmaindustrie werden Edelstahlrohre aufgrund ihrer Beständigkeit gegenüber aggressiven Chemikalien und hohen Temperaturen eingesetzt.
Auch in der Bauindustrie werden Edelstahlrohre für architektonische Anwendungen wie Geländer, Treppen, Fassadenverkleidungen und Strukturelemente verwendet. Ihre ästhetische Erscheinung, lange Lebensdauer und Wartungsfreiheit machen sie zu einer beliebten Wahl für hochwertige Bauprojekte. Darüber hinaus werden Edelstahlrohre in der Automobilindustrie, der Luft- und Raumfahrt, der Energieerzeugung und vielen anderen Branchen eingesetzt.
Edelstahlrohre werden durch verschiedene Herstellungsverfahren wie das nahtlose Walzen, das geschweißte Walzen, das Ziehen oder das Schmieden hergestellt, abhängig von den spezifischen Anforderungen der Anwendung. Sie sind in einer Vielzahl von Größen, Wandstärken und Legierungen erhältlich, um den unterschiedlichen Bedürfnissen verschiedener Industrien gerecht zu werden. Mit ihrer herausragenden Leistungsfähigkeit und Vielseitigkeit sind Edelstahlrohre eine wichtige Komponente in modernen Konstruktionen und industriellen Anwendungen.
Aluminiumrohre:
Aluminiumrohre sind eine wichtige Komponente in vielen industriellen Anwendungen aufgrund ihrer leichten, korrosionsbeständigen und formbaren Eigenschaften. Aluminium ist ein leichtes Metall mit einer hohen Festigkeit-Gewicht-Verhältnis, was es ideal für Anwendungen macht, bei denen Gewichtseinsparung und Festigkeit entscheidend sind.
In der Luft- und Raumfahrtindustrie werden Aluminiumrohre für die Herstellung von Flugzeugstrukturen, Satellitenrahmen und Raumfahrzeugen verwendet. Ihr geringes Gewicht trägt zur Treibstoffeffizienz und Flugleistung bei, während ihre Korrosionsbeständigkeit die Langlebigkeit und Zuverlässigkeit der Luftfahrtkomponenten gewährleistet.
Auch in der Automobilindustrie werden Aluminiumrohre zunehmend für Leichtbauanwendungen eingesetzt, um den Kraftstoffverbrauch zu senken und die Fahrzeugleistung zu verbessern. Sie werden für Kühlsysteme, Auspuffanlagen, Fahrwerksteile und andere strukturelle Komponenten verwendet.
Des Weiteren finden Aluminiumrohre Anwendung in der Bauindustrie für Geländer, Treppen, Überdachungen und andere architektonische Elemente. Ihre Eleganz, Langlebigkeit und Wartungsfreiheit machen sie zu einer attraktiven Wahl für moderne Gebäudekonstruktionen.
Aluminiumrohre werden durch verschiedene Herstellungsverfahren wie das Extrudieren, das Ziehen oder das Walzen hergestellt, abhängig von den spezifischen Anforderungen der Anwendung. Sie sind in einer Vielzahl von Größen, Wandstärken und Legierungen erhältlich, um den unterschiedlichen Bedürfnissen verschiedener Branchen gerecht zu werden. Mit ihrer Kombination aus Leichtigkeit, Festigkeit und Korrosionsbeständigkeit sind Aluminiumrohre eine unverzichtbare Komponente in zahlreichen industriellen Anwendungen.
Kupferrohre:
Kupferrohre sind eine vielseitige und langlebige Lösung für verschiedene Anwendungen, die aufgrund ihrer ausgezeichneten Wärme- und elektrischen Leitfähigkeit, Korrosionsbeständigkeit und Formbarkeit geschätzt werden. Kupfer ist ein natürlich vorkommendes Element, das seit Jahrhunderten in verschiedenen Industrien verwendet wird.
In der Heizungs-, Lüftungs- und Klimatechnik werden Kupferrohre aufgrund ihrer hervorragenden Wärmeleitfähigkeit und Korrosionsbeständigkeit häufig für die Herstellung von Wärmetauschern, Rohrleitungen und Kühlsystemen verwendet. Ihre Effizienz und Zuverlässigkeit tragen zur Energieeinsparung und zur optimalen Leistung von HVAC-Systemen bei.
Auch in der Sanitärtechnik sind Kupferrohre weit verbreitet. Sie werden für Trinkwasserleitungen, Abwasserleitungen und Gasleitungen verwendet, da sie inert sind und keine unerwünschten Geschmacks- oder Geruchsveränderungen im Wasser verursachen. Ihre Festigkeit und Haltbarkeit gewährleisten eine langfristige Integrität der Rohrleitungen, selbst unter extremen Bedingungen.
Darüber hinaus werden Kupferrohre in der Elektroindustrie für die Herstellung von Stromkabeln, Schaltkreisen und elektrischen Verbindungen verwendet. Die hohe elektrische Leitfähigkeit von Kupfer ermöglicht eine effiziente Übertragung elektrischer Energie, während seine Korrosionsbeständigkeit und Haltbarkeit eine zuverlässige Leistung gewährleisten.
Kupferrohre werden durch verschiedene Herstellungsverfahren wie das Ziehen, das Walzen oder das Schmieden hergestellt, abhängig von den spezifischen Anforderungen der Anwendung. Sie sind in einer Vielzahl von Größen, Wandstärken und Legierungen erhältlich, um den unterschiedlichen Bedürfnissen verschiedener Branchen gerecht zu werden. Mit ihrer herausragenden Leistungsfähigkeit und Vielseitigkeit sind Kupferrohre eine bewährte Lösung für eine Vielzahl von industriellen und kommerziellen Anwendungen.
Messingrohre:
Messingrohre sind eine spezielle Art von Metallrohren, die aus einer Legierung von Kupfer und Zink hergestellt werden. Diese Legierung bietet eine einzigartige Kombination aus Eigenschaften, die sie für eine Vielzahl von Anwendungen geeignet machen. Messingrohre sind bekannt für ihre hohe Korrosionsbeständigkeit, gute mechanische Festigkeit, einfache Bearbeitbarkeit und ästhetische Erscheinung.
In der Sanitär- und Wasserinstallationstechnik werden Messingrohre häufig für Armaturen, Rohrverbindungen, Ventile und Wasserhähne verwendet. Ihre Korrosionsbeständigkeit und Langlebigkeit machen sie zu einer zuverlässigen Wahl für den Einsatz in Trinkwasserleitungen und sanitären Anlagen. Die einfache Bearbeitbarkeit von Messing ermöglicht die Herstellung von präzisen und komplexen Bauteilen, die den Anforderungen moderner Sanitärsysteme gerecht werden.
Auch in der Maschinenbau- und Elektroindustrie werden Messingrohre verwendet. Sie dienen als elektrische Kontakte, Fittings, Lagerbuchsen und Dichtungen in einer Vielzahl von Geräten und Maschinen. Ihre gute Leitfähigkeit für Elektrizität und Wärme, kombiniert mit ihrer mechanischen Festigkeit, macht sie zu einer vielseitigen Lösung für elektrische und mechanische Anwendungen.
Darüber hinaus werden Messingrohre oft für dekorative Zwecke verwendet, wie zum Beispiel für Geländer, Handläufe, Leuchten und Möbel. Ihre goldene Farbe und glänzende Oberfläche verleihen jedem Projekt einen eleganten und ansprechenden Look. Die Formbarkeit von Messing ermöglicht es den Designern, kreative und einzigartige Elemente zu schaffen, die sowohl funktional als auch ästhetisch ansprechend sind.
Messingrohre werden durch verschiedene Herstellungsverfahren wie das Ziehen, das Walzen oder das Gießen hergestellt, abhängig von den spezifischen Anforderungen der Anwendung. Sie sind in einer Vielzahl von Größen, Wandstärken und Legierungen erhältlich, um den unterschiedlichen Bedürfnissen verschiedener Branchen gerecht zu werden. Mit ihrer Vielseitigkeit, Festigkeit und Schönheit sind Messingrohre eine beliebte Wahl für eine Vielzahl von industriellen, kommerziellen und dekorativen Anwendungen.
Eisenrohre:
Eisenrohre sind eine klassische Form von Metallrohren, die seit Jahrhunderten in verschiedenen Anwendungen eingesetzt werden. Sie bestehen hauptsächlich aus Eisen, können jedoch je nach Anforderung auch Legierungen enthalten. Eisenrohre haben aufgrund ihrer Robustheit, Haltbarkeit und Erschwinglichkeit eine lange Geschichte in der Bau- und Infrastrukturindustrie.
In der Wasserversorgung und Abwasserentsorgung werden Eisenrohre häufig für die Verlegung von Trinkwasserleitungen, Abwasserkanälen und Bewässerungssystemen verwendet. Ihre Festigkeit und Beständigkeit gegenüber hohem Druck machen sie zu einer zuverlässigen Wahl für den Transport von Flüssigkeiten über große Entfernungen. Darüber hinaus sind sie im Vergleich zu anderen Materialien kostengünstig, was sie besonders attraktiv für große Infrastrukturprojekte macht.
Eisenrohre werden auch in der Heizungs- und Klimatisierungstechnik eingesetzt, insbesondere in älteren Gebäuden, wo sie für die Verteilung von Heizöl, Dampf und warmem Wasser verwendet werden. Ihre Wärmeleitfähigkeit und Beständigkeit gegen hohe Temperaturen machen sie zu einer praktischen Wahl für den Einsatz in Heizungs- und Kühlsystemen.
In der Bauindustrie werden Eisenrohre für verschiedene strukturelle Anwendungen wie Träger, Stützen, Geländer und Treppen verwendet. Ihre Festigkeit und Stabilität tragen zur Integrität von Gebäuden und Bauwerken bei und ermöglichen es den Bauherren, sichere und langlebige Strukturen zu errichten.
Eisenrohre werden durch verschiedene Herstellungsverfahren wie das nahtlose Walzen, das geschweißte Walzen oder das Gießen hergestellt, je nach den spezifischen Anforderungen der Anwendung. Sie sind in einer Vielzahl von Größen und Wandstärken erhältlich, um den unterschiedlichen Bedürfnissen verschiedener Branchen gerecht zu werden. Trotz des Aufkommens modernerer Materialien bleiben Eisenrohre aufgrund ihrer Zuverlässigkeit und Erschwinglichkeit eine beliebte Wahl für viele Bau- und Infrastrukturprojekte.
Rohrleitungen:
Rohrleitungen sind ein wesentlicher Bestandteil zahlreicher Industrien und Anwendungen, in denen Flüssigkeiten, Gase oder Feststoffe über große Entfernungen transportiert werden müssen. Sie bestehen aus einem Netzwerk von Rohren, die miteinander verbunden sind und verschiedene Funktionen erfüllen, von der Förderung von Trinkwasser bis hin zum Transport von Erdölprodukten.
In der Öl- und Gasindustrie sind Rohrleitungen entscheidend für die Förderung, den Transport und die Verteilung von Erdöl, Erdgas und anderen Kohlenwasserstoffprodukten vom Produktionsort zu den Raffinerien und Verbrauchern. Sie umfassen sowohl Hochdruckleitungen für den Ferntransport als auch Niederdruckleitungen für die lokale Verteilung. Die Sicherheit und Integrität dieser Rohrleitungen sind von entscheidender Bedeutung, um Umweltverschmutzung und Unfälle zu vermeiden.
In der chemischen Industrie werden Rohrleitungen verwendet, um verschiedene chemische Substanzen von den Produktionsanlagen zu den Lagerstätten oder zu den Verarbeitungseinheiten zu transportieren. Diese Rohrleitungen müssen oft korrosionsbeständig sein und spezielle Beschichtungen oder Materialien aufweisen, um den aggressiven Chemikalien standzuhalten.
Auch in der Wasser- und Abwasserwirtschaft sind Rohrleitungen unverzichtbar für die Verteilung von Trinkwasser zu Haushalten und Unternehmen sowie für die Ableitung von Abwasser und Regenwasser zu Kläranlagen oder Entsorgungssystemen. Die Wartung und Instandhaltung dieser Rohrleitungen sind entscheidend, um die Wasserqualität zu erhalten und Leckagen oder Verschmutzungen zu verhindern.
Rohrleitungen können aus verschiedenen Materialien wie Stahl, Edelstahl, Kunststoff, Kupfer oder Verbundwerkstoffen hergestellt werden, je nach den Anforderungen der Anwendung und den örtlichen Gegebenheiten. Sie sind in verschiedenen Durchmessern, Wandstärken und Druckklassen erhältlich, um den unterschiedlichen Transportanforderungen gerecht zu werden. Mit ihrem umfangreichen Einsatz in verschiedenen Industrien spielen Rohrleitungen eine entscheidende Rolle bei der Aufrechterhaltung der Infrastruktur und der Versorgung mit lebenswichtigen Ressourcen.
Rohrverbindungen:
Rohrverbindungen sind essenzielle Komponenten in Rohrleitungssystemen, die dazu dienen, einzelne Rohre miteinander zu verbinden, um ein kontinuierliches Leitungssystem zu schaffen. Diese Verbindungen ermöglichen es, Rohrleitungen flexibel zu gestalten, Reparaturen durchzuführen und verschiedene Anforderungen an den Flüssigkeits- oder Gasfluss zu erfüllen.
Gewindete Rohrverbindungen sind eine häufig verwendete Methode, bei der die Enden der Rohre mit Gewinden versehen und dann miteinander verschraubt werden. Diese Verbindungsmethode ermöglicht eine schnelle Montage und Demontage von Rohrleitungen und eignet sich gut für Anwendungen, die regelmäßige Wartung erfordern.
Flanschverbindungen werden häufig in industriellen Anwendungen eingesetzt, bei denen eine sichere und dichte Verbindung erforderlich ist. Die Enden der Rohre werden mit Flanschen versehen, die dann mit Schrauben und Muttern fest miteinander verbunden werden. Diese Verbindungsmethode ermöglicht eine einfache Installation und Wartung sowie eine hohe Dichtheit gegenüber Druck und Leckage.
Schweißverbindungen sind eine permanente Verbindungsmethode, bei der die Enden der Rohre miteinander verschweißt werden, um eine starke und dichte Verbindung zu schaffen. Diese Methode wird häufig in Anwendungen verwendet, bei denen eine hohe Zuverlässigkeit und Festigkeit erforderlich sind, wie zum Beispiel in der chemischen Industrie oder in Hochdruckanwendungen.
Pressverbindungen sind eine moderne Verbindungsmethode, bei der spezielle Pressfittings verwendet werden, um die Rohre miteinander zu verbinden. Diese Methode erfordert keine speziellen Werkzeuge oder Schweißarbeiten und ermöglicht eine schnelle und einfache Installation. Pressverbindungen werden oft in der Sanitär- und Heizungstechnik eingesetzt, aber auch in anderen Branchen, wo eine schnelle und zuverlässige Verbindung erforderlich ist.
Die Auswahl der geeigneten Rohrverbindung hängt von verschiedenen Faktoren ab, einschließlich der Anforderungen an Druck, Temperatur, Material und Anwendungsbereich. Mit einer Vielzahl von Verbindungsmethoden zur Auswahl können Rohrleitungen flexibel an die Anforderungen verschiedener Branchen und Anwendungen angepasst werden.
Nahtlose Rohre:
Nahtlose Rohre sind eine spezielle Art von Metallrohren, die aus einem einzigen Stück Metall hergestellt werden, ohne Schweißnähte oder Verbindungsstellen. Sie werden durch ein Verfahren hergestellt, das als „nahtloses Walzen“ bekannt ist, bei dem ein massiver Metallblock durch eine Reihe von Walzwerken gepresst wird, um die gewünschte Form und Größe des Rohrs zu erreichen.
Diese nahtlosen Rohre bieten eine Reihe von Vorteilen gegenüber geschweißten Rohren. Durch das Fehlen von Schweißnähten sind sie weniger anfällig für Defekte oder Undichtigkeiten und bieten eine höhere Festigkeit und Druckbeständigkeit. Dies macht sie besonders geeignet für Anwendungen, die hohen Drücken oder Temperaturen ausgesetzt sind, wie zum Beispiel in der Öl- und Gasindustrie oder in der chemischen Verarbeitung.
Nahtlose Rohre bieten auch eine verbesserte Oberflächenbeschaffenheit im Vergleich zu geschweißten Rohren, was sie für Anwendungen attraktiv macht, bei denen eine glatte und gleichmäßige Innen- oder Außenoberfläche erforderlich ist. Dies ist besonders wichtig in Anwendungen wie der Lebensmittelverarbeitung oder der pharmazeutischen Produktion, wo Hygiene und Sauberkeit von größter Bedeutung sind.
Darüber hinaus ermöglicht die nahtlose Herstellung von Rohren eine größere Flexibilität bei der Herstellung von Rohren mit komplexen Formen oder Abmessungen, was sie zu einer vielseitigen Lösung für eine Vielzahl von Anwendungen macht. Sie werden in verschiedenen Branchen eingesetzt, darunter Automobilbau, Luft- und Raumfahrt, Bauwesen, Energieerzeugung und mehr.
Die Auswahl der geeigneten Rohrtypen hängt von den spezifischen Anforderungen der Anwendung ab, einschließlich Druck, Temperatur, Material und Umgebung. Nahtlose Rohre bieten eine zuverlässige und langlebige Lösung für anspruchsvolle Anwendungen, die hohe Leistung und Zuverlässigkeit erfordern.
Geschweißte Rohre:
Geschweißte Rohre sind eine wichtige Komponente in zahlreichen Industrien und Anwendungen, die einen effizienten Transport von Flüssigkeiten, Gasen oder Feststoffen erfordern. Im Gegensatz zu nahtlosen Rohren werden geschweißte Rohre aus einzelnen Stahlblechstreifen hergestellt, die zu einer Röhre geformt und dann längs oder spiralförmig verschweißt werden.
Diese Rohre bieten eine kostengünstige und dennoch robuste Lösung für eine Vielzahl von Anwendungen. Geschweißte Rohre können in verschiedenen Durchmessern, Wandstärken und Längen hergestellt werden, um den spezifischen Anforderungen der Anwendung gerecht zu werden. Sie werden in der Bauindustrie, im Transportwesen, in der Öl- und Gasindustrie, in der Wasserversorgung und Abwasserentsorgung sowie in vielen anderen Branchen eingesetzt.
In der Bauindustrie werden geschweißte Rohre häufig für Träger, Stützen, Geländer, Treppen und andere strukturelle Anwendungen verwendet. Ihre hohe Festigkeit und Tragfähigkeit machen sie zu einer zuverlässigen Wahl für den Einsatz in Gebäuden, Brücken, Tunneln und anderen Bauwerken.
In der Öl- und Gasindustrie dienen geschweißte Rohre als Rohrleitungen für den Transport von Erdöl, Erdgas und anderen Kohlenwasserstoffprodukten von den Produktionsstätten zu den Raffinerien und Verbrauchern. Sie müssen extremen Bedingungen standhalten, einschließlich hohem Druck, Temperaturschwankungen und Korrosion.
Die Herstellung von geschweißten Rohren erfolgt durch verschiedene Verfahren, darunter das Hochfrequenzschweißen (HF), das Lichtbogenschweißen (SAW) und das Widerstandsschweißen. Jedes Verfahren hat seine eigenen Vor- und Nachteile in Bezug auf Kosten, Effizienz und Qualität der hergestellten Rohre.
Geschweißte Rohre sind eine bewährte und zuverlässige Lösung für den Transport von Flüssigkeiten, Gasen und Feststoffen in einer Vielzahl von Anwendungen. Ihre Vielseitigkeit, Langlebigkeit und Kosteneffizienz machen sie zu einer beliebten Wahl für Bauunternehmen, Industrieunternehmen und öffentliche Versorgungsunternehmen weltweit.
Rohrgrößen:
Rohrgrößen spielen eine entscheidende Rolle in der Planung, Konstruktion und Installation von Rohrleitungssystemen für verschiedene Anwendungen. Die Auswahl der richtigen Rohrgröße ist entscheidend für die effiziente und zuverlässige Durchführung des Flüssigkeits-, Gas- oder Feststofftransports sowie für die Sicherheit und Integrität des Systems.
Die Rohrgröße wird normalerweise durch den Durchmesser und die Wandstärke des Rohrs bestimmt. Der Durchmesser wird in der Regel in Zoll (oder Millimeter) gemessen und ist eine der wichtigsten Größenangaben für ein Rohr. Je nach Anwendung können Rohre Durchmesser von weniger als einem Zoll bis hin zu mehreren Fuß haben.
Die Wandstärke eines Rohrs, auch als Nenndicke bezeichnet, ist ein weiterer wichtiger Parameter, der die Festigkeit und Druckbeständigkeit des Rohrs beeinflusst. Sie wird in der Regel in Zoll oder Millimeter angegeben und variiert je nach Material, Anwendung und Betriebsbedingungen des Rohrs.
Die Auswahl der richtigen Rohrgröße hängt von verschiedenen Faktoren ab, darunter der erforderliche Durchfluss, der Druck, die Temperatur, die Art des transportierten Mediums und die Länge der Rohrleitung. Ein zu kleines Rohr kann zu einem hohen Strömungswiderstand und einem unzureichenden Durchfluss führen, während ein zu großes Rohr unnötige Kosten verursachen kann und Platz in Anspruch nimmt.
Die Rohrgröße muss auch mit anderen Komponenten des Rohrleitungssystems, wie z. B. Pumpen, Armaturen und Ventilen, in Einklang gebracht werden, um eine ordnungsgemäße Funktion und Effizienz des Systems sicherzustellen. Die Auswahl der richtigen Rohrgröße erfordert daher eine sorgfältige Planung und Analyse der spezifischen Anforderungen und Betriebsbedingungen der Anwendung.
Rohrdurchmesser:
Der Rohrdurchmesser ist eine entscheidende Dimension bei der Auswahl von Rohren für verschiedene Anwendungen. Er wird üblicherweise in Zoll oder Millimetern gemessen und bezeichnet den Abstand zwischen den beiden gegenüberliegenden Seiten eines Rohres durch das Zentrum gemessen. Der Durchmesser bestimmt maßgeblich die Kapazität eines Rohrs, Flüssigkeiten, Gase oder Feststoffe zu transportieren, sowie die Strömungsgeschwindigkeit und den Druckverlust im Rohrsystem.
In Rohrleitungssystemen können verschiedene Durchmesser von Rohren verwendet werden, abhängig von den Anforderungen der Anwendung. Kleinere Durchmesser werden oft für geringere Durchflussmengen oder für Anwendungen mit beschränktem Platzangebot verwendet, während größere Durchmesser für höhere Durchflussraten oder für Anwendungen mit großen Volumen benötigt werden.
Bei der Auswahl des richtigen Rohrdurchmessers müssen verschiedene Faktoren berücksichtigt werden, darunter der erforderliche Durchfluss, der Druckverlust, die Strömungsgeschwindigkeit, die Art des transportierten Mediums und die Länge der Rohrleitung. Ein zu kleiner Durchmesser kann zu einem hohen Strömungswiderstand und einem unzureichenden Durchfluss führen, während ein zu großer Durchmesser unnötige Kosten verursachen und zusätzlichen Platz beanspruchen kann.
Die Berechnung des optimalen Rohrdurchmessers erfordert oft komplexe hydraulische Berechnungen und Modellierungen, um die Strömungsbedingungen und die Leistungsfähigkeit des Rohrleitungssystems genau zu bestimmen. Ingenieure verwenden dazu verschiedene Formeln, Diagramme und Simulationssoftware, um den Durchmesser zu bestimmen, der die Anforderungen der Anwendung am besten erfüllt und gleichzeitig wirtschaftlich und effizient ist.
In der Praxis werden Rohrdurchmesser oft in standardisierten Größen angeboten, die den gängigen Anforderungen und Normen entsprechen. Die Auswahl des richtigen Rohrdurchmessers ist daher eine wichtige Entscheidung bei der Planung und Ausführung von Rohrleitungssystemen und erfordert eine sorgfältige Analyse der spezifischen Anforderungen und Betriebsbedingungen der Anwendung.
Rohrwandstärke:
Die Rohrwandstärke ist ein wichtiger Parameter, der die Festigkeit, Druckbeständigkeit und Haltbarkeit eines Rohrs bestimmt. Sie wird üblicherweise in Zoll oder Millimetern angegeben und bezeichnet die Dicke der Wand eines Rohrs. Die Wandstärke variiert je nach den Anforderungen der Anwendung und den Betriebsbedingungen des Rohrsystems.
Eine angemessene Wandstärke ist entscheidend, um sicherzustellen, dass das Rohr den erforderlichen Druck und die mechanischen Belastungen standhalten kann, denen es während des Betriebs ausgesetzt ist. Eine zu geringe Wandstärke kann zu einem erhöhten Risiko von Rohrbrüchen, Leckagen oder anderen strukturellen Problemen führen, während eine zu hohe Wandstärke unnötiges Gewicht und Kosten verursachen kann.
Die Auswahl der richtigen Rohrwandstärke hängt von verschiedenen Faktoren ab, darunter der Betriebsdruck, die Temperatur, die Art des transportierten Mediums, die Materialfestigkeit des Rohrs und die Länge der Rohrleitung. Ingenieure verwenden oft Berechnungen, Normen und Richtlinien, um die optimale Wandstärke für eine bestimmte Anwendung zu bestimmen.
In vielen Industrien und Branchen gibt es Standards und Vorschriften, die die Mindestwandstärken für Rohre festlegen, um die Sicherheit und Zuverlässigkeit von Rohrleitungssystemen zu gewährleisten. Diese Standards berücksichtigen verschiedene Faktoren wie den Betriebsdruck, die Materialfestigkeit und die Art der Anwendung.
Bei der Planung und Konstruktion von Rohrleitungssystemen ist es wichtig, die spezifischen Anforderungen und Betriebsbedingungen der Anwendung zu berücksichtigen, um die richtige Wandstärke für die Rohre auszuwählen. Eine sorgfältige Analyse und Bewertung dieser Faktoren kann dazu beitragen, sicherzustellen, dass das Rohrleitungssystem sicher, zuverlässig und wirtschaftlich betrieben werden kann.
Korrosionsbeständigkeit:
Die Korrosionsbeständigkeit ist eine wichtige Eigenschaft von Metallrohren, die ihre Fähigkeit beschreibt, gegenüber chemischen Reaktionen mit der Umgebung oder dem transportierten Medium beständig zu sein. Korrosion kann das Metall eines Rohrs im Laufe der Zeit abbauen und zu strukturellen Problemen wie Rost, Lochfraß oder Leckagen führen, was die Lebensdauer des Rohrs verkürzt und die Betriebssicherheit gefährdet.
Metallrohre können auf verschiedene Weise vor Korrosion geschützt werden. Eine Möglichkeit ist die Verwendung von korrosionsbeständigen Legierungen wie Edelstahl oder Aluminium, die natürlicherweise widerstandsfähiger gegenüber korrosiven Umgebungen sind. Diese Legierungen enthalten Zusatzelemente wie Chrom, Nickel oder Molybdän, die eine schützende Oxidschicht auf der Oberfläche bilden und das darunter liegende Metall vor Korrosion schützen.
Eine andere Möglichkeit ist die Beschichtung der Oberfläche des Rohrs mit einer korrosionsbeständigen Beschichtung oder Farbe. Diese Beschichtungen bilden eine Barriere zwischen dem Metall des Rohrs und der umgebenden Umgebung und verhindern so direkten Kontakt und Korrosion. Typische Beschichtungen können Epoxidharze, Zink, Polyethylen oder Keramik sein, die je nach Anwendung und Betriebsbedingungen ausgewählt werden.
Darüber hinaus können verschiedene Korrosionsschutzmaßnahmen wie Kathodenschutz, Opferanoden oder chemische Inhibitoren verwendet werden, um die Korrosion von Metallrohren zu verhindern oder zu verzögern. Diese Methoden wirken, indem sie die chemischen Reaktionen blockieren oder verlangsamen, die zur Korrosion führen, und das Metall des Rohrs schützen.
Die Auswahl der richtigen Korrosionsschutzmaßnahmen hängt von verschiedenen Faktoren ab, darunter die Art des transportierten Mediums, die Umgebung, die Temperatur, der pH-Wert und der Druck des Systems. Eine sorgfältige Analyse der Korrosionsrisiken und eine angemessene Auswahl der Schutzmaßnahmen können dazu beitragen, die Lebensdauer und Leistungsfähigkeit von Metallrohren zu maximieren und die Betriebssicherheit zu gewährleisten.
Druckbeständigkeit:
Die Druckbeständigkeit ist eine wesentliche Eigenschaft von Metallrohren, die ihre Fähigkeit beschreibt, den Druck standzuhalten, dem sie während des Betriebs ausgesetzt sind. In vielen Anwendungen müssen Metallrohre einem bestimmten Betriebsdruck standhalten, sei es durch die Umgebung oder das transportierte Medium. Die Fähigkeit eines Rohrs, diesen Druck zu bewältigen, ist entscheidend für die Sicherheit, Zuverlässigkeit und Leistungsfähigkeit des Rohrleitungssystems.
Die Druckbeständigkeit eines Metallrohrs hängt von verschiedenen Faktoren ab, darunter die Wandstärke des Rohrs, das Material, aus dem es hergestellt ist, und die Art der Verbindung oder Befestigung. Eine angemessene Wandstärke ist entscheidend, um sicherzustellen, dass das Rohr den erforderlichen Druck standhalten kann, ohne zu versagen oder zu brechen.
Metallrohre können verschiedene Druckklassen oder -stufen haben, die den maximalen Betriebsdruck angeben, den sie sicher aushalten können. Diese Druckklassen werden oft nach nationalen oder internationalen Standards festgelegt und können je nach Anwendung und Betriebsbedingungen variieren.
Bei der Auswahl von Metallrohren für eine bestimmte Anwendung ist es wichtig, die spezifischen Anforderungen und Betriebsbedingungen zu berücksichtigen, um sicherzustellen, dass das Rohr den erforderlichen Druck standhalten kann. Ingenieure führen oft Berechnungen und Analysen durch, um die Druckfestigkeit von Rohren zu bestimmen und sicherzustellen, dass sie den Anforderungen entsprechen.
Die regelmäßige Inspektion, Wartung und Prüfung von Rohrleitungssystemen ist ebenfalls wichtig, um sicherzustellen, dass sie weiterhin den erforderlichen Betriebsdruck standhalten können. Durch die rechtzeitige Erkennung von Problemen wie Korrosion, Verschleiß oder Beschädigungen können potenzielle Ausfälle vermieden und die Betriebssicherheit gewährleistet werden.
Temperaturbeständigkeit:
Die Temperaturbeständigkeit ist eine wichtige Eigenschaft von Metallrohren, die ihre Fähigkeit beschreibt, den Temperaturen standzuhalten, denen sie während des Betriebs ausgesetzt sind. Metallrohre müssen in der Lage sein, sowohl extremen Kälte- als auch Hitzeeinwirkungen standzuhalten, je nach den Anforderungen der Anwendung und den Umgebungsbedingungen.
Die Temperaturbeständigkeit eines Metallrohrs hängt von verschiedenen Faktoren ab, darunter das Material, aus dem es hergestellt ist, die Wandstärke des Rohrs und die Art der Isolierung oder Schutzbeschichtung. Bestimmte Metalle wie Edelstahl, Inconel oder Aluminiumlegierungen bieten eine hohe Temperaturbeständigkeit und sind daher für Anwendungen in Hochtemperaturumgebungen geeignet.
Bei extremen Temperaturen können Metallrohre verschiedenen Belastungen ausgesetzt sein, einschließlich thermischer Ausdehnung, Kontraktion oder Verformung. Diese Belastungen können dazu führen, dass das Rohr seine strukturelle Integrität verliert oder sich ausdehnt, was zu Leckagen, Brüchen oder anderen Problemen führen kann.
Um die Temperaturbeständigkeit von Metallrohren zu verbessern, können verschiedene Maßnahmen ergriffen werden, darunter die Verwendung von isolierten Rohrleitungen, die Installation von Hitzeschilden oder Reflektoren und die Auswahl von Materialien mit hoher Wärmebeständigkeit. Darüber hinaus können spezielle Beschichtungen oder Oberflächenbehandlungen angewendet werden, um die Wärmebeständigkeit des Rohrs zu verbessern und seine Leistungsfähigkeit bei extremen Temperaturen zu erhöhen.
Die Auswahl des richtigen Metalls und die angemessene Konstruktion von Rohrleitungssystemen sind entscheidend, um sicherzustellen, dass sie den Anforderungen der Anwendung in Bezug auf Temperaturbeständigkeit gerecht werden. Eine sorgfältige Analyse der Betriebsbedingungen und der Umgebungsbedingungen kann dazu beitragen, potenzielle Probleme zu identifizieren und geeignete Lösungen zu entwickeln, um die Temperaturbeständigkeit von Metallrohren zu maximieren.
Flexibilität:
Die Flexibilität ist eine wichtige Eigenschaft von Metallrohren, die ihre Fähigkeit beschreibt, sich zu biegen, zu verformen oder zu biegen, ohne zu brechen oder ihre strukturelle Integrität zu verlieren. In vielen Anwendungen müssen Metallrohre flexibel sein, um sich an verschiedene Formen, Winkel oder Gelände anzupassen, sowie um den Einbau in enge Räume oder um Hindernisse herum zu ermöglichen.
Die Flexibilität von Metallrohren hängt von verschiedenen Faktoren ab, darunter das Material, aus dem sie hergestellt sind, die Wandstärke des Rohrs und die Art der Konstruktion oder Fertigung. Bestimmte Metalle wie Kupfer oder Aluminiumlegierungen sind natürlicherweise flexibler und leichter zu formen, während stärkere und dickere Metallrohre möglicherweise weniger flexibel sind.
Die Flexibilität von Metallrohren kann durch verschiedene Verfahren verbessert werden, darunter das Kaltumformen, das Warmbiegen oder das Verfahren des Rohrbiegens. Diese Verfahren ermöglichen es, Metallrohre in verschiedene Formen oder Winkel zu biegen, ohne ihre strukturelle Integrität zu beeinträchtigen.
In einigen Anwendungen, wie zum Beispiel in der Automobilindustrie oder in der Luft- und Raumfahrt, ist die Flexibilität von Metallrohren besonders wichtig, um komplexe Formen oder Konstruktionen zu ermöglichen. Flexible Rohre können auch in Rohrleitungssystemen verwendet werden, um den Einbau in engen Räumen oder um Hindernisse herum zu erleichtern.
Die Auswahl des richtigen Metalls und die angemessene Konstruktion von Metallrohren sind entscheidend, um sicherzustellen, dass sie die erforderliche Flexibilität für die spezifische Anwendung bieten. Eine sorgfältige Analyse der Anforderungen und Betriebsbedingungen kann dazu beitragen, die optimale Flexibilität von Metallrohren zu bestimmen und sicherzustellen, dass sie die erforderlichen Funktionen erfüllen.
Korrosionsschutz:
Der Korrosionsschutz ist eine entscheidende Maßnahme, um die Lebensdauer und Leistung von Metallrohren zu gewährleisten. Korrosion ist ein natürlicher Prozess, bei dem das Metall eines Rohrs durch chemische Reaktionen mit der Umgebung oder dem transportierten Medium abgebaut wird. Dies kann zu strukturellen Problemen wie Rostbildung, Lochfraß oder Leckagen führen und die Betriebssicherheit des Rohrleitungssystems beeinträchtigen.
Es gibt verschiedene Methoden, um Metallrohre vor Korrosion zu schützen. Eine häufige Methode ist die Verwendung von korrosionsbeständigen Materialien wie Edelstahl, Aluminium oder speziellen Legierungen, die natürlicherweise widerstandsfähiger gegenüber korrosiven Umgebungen sind. Diese Materialien bilden eine schützende Oxidschicht auf der Oberfläche des Rohrs, die das darunter liegende Metall vor Korrosion schützt.
Eine weitere Methode ist die Beschichtung der Oberfläche des Rohrs mit einer korrosionsbeständigen Beschichtung oder Farbe. Diese Beschichtungen bilden eine Barriere zwischen dem Metall des Rohrs und der umgebenden Umgebung und verhindern so direkten Kontakt und Korrosion. Typische Beschichtungen können Epoxidharze, Zink, Polyethylen oder Keramik sein, die je nach Anwendung und Betriebsbedingungen ausgewählt werden.
Zusätzlich können verschiedene Korrosionsschutzmaßnahmen wie Kathodenschutz, Opferanoden oder chemische Inhibitoren verwendet werden, um die Korrosion von Metallrohren zu verhindern oder zu verzögern. Diese Methoden wirken, indem sie die chemischen Reaktionen blockieren oder verlangsamen, die zur Korrosion führen, und das Metall des Rohrs schützen.
Die Auswahl der geeigneten Korrosionsschutzmaßnahmen hängt von verschiedenen Faktoren ab, darunter die Art des transportierten Mediums, die Umgebung, die Temperatur, der pH-Wert und der Druck des Systems. Eine sorgfältige Analyse der Korrosionsrisiken und eine angemessene Auswahl der Schutzmaßnahmen können dazu beitragen, die Lebensdauer und Leistungsfähigkeit von Metallrohren zu maximieren und die Betriebssicherheit zu gewährleisten.
Schweißbarkeit:
Die Schweißbarkeit ist eine wichtige Eigenschaft von Metallrohren, die ihre Fähigkeit beschreibt, erfolgreich und dauerhaft mit anderen Rohren oder Bauteilen verschweißt zu werden. Schweißen ist ein häufig verwendetes Verfahren, um Metallrohre zu verbinden und komplexe Rohrleitungssysteme oder Strukturen zu erstellen.
Metallrohre müssen eine gute Schweißbarkeit aufweisen, um eine zuverlässige und dauerhafte Verbindung zu gewährleisten. Eine gute Schweißbarkeit erleichtert den Schweißprozess, minimiert potenzielle Schweißfehler und führt zu einer hochwertigen Schweißnaht mit guter Festigkeit und Dichtheit.
Die Schweißbarkeit von Metallrohren hängt von verschiedenen Faktoren ab, darunter das Material, aus dem das Rohr hergestellt ist, die Wandstärke des Rohrs und die Art des Schweißverfahrens. Bestimmte Metalle wie Stahl, Edelstahl, Aluminium und Kupferlegierungen sind natürlicherweise gut schweißbar und werden häufig in Schweißanwendungen verwendet.
Die Schweißbarkeit von Metallrohren kann durch verschiedene Faktoren beeinflusst werden, darunter die Oberflächenbeschaffenheit des Rohrs, das Vorhandensein von Verunreinigungen oder Beschichtungen, die Schweißtechnik und die Schutzgaszusammensetzung. Eine sorgfältige Vorbereitung der Schweißnaht und die Verwendung geeigneter Schweißparameter sind entscheidend, um eine qualitativ hochwertige Schweißverbindung zu erreichen.
In vielen Industrien und Anwendungen, einschließlich der Bauindustrie, der Automobilindustrie, der Öl- und Gasindustrie und der Fertigung, ist die Schweißbarkeit von Metallrohren ein wichtiger Faktor bei der Auswahl des geeigneten Rohrmaterials und der Konstruktion von Rohrleitungssystemen oder -strukturen.
Eine sorgfältige Analyse der Schweißbarkeitseigenschaften von Metallrohren kann dazu beitragen, die Eignung eines bestimmten Rohrs für eine Schweißanwendung zu bestimmen und sicherzustellen, dass die erforderlichen Schweißverbindungen erfolgreich hergestellt werden können.
Flexibles Rohrbiegen:
Flexibles Rohrbiegen ist ein Verfahren, bei dem Metallrohre in verschiedene Formen oder Winkel gebogen werden können, ohne ihre strukturelle Integrität zu beeinträchtigen. Dieses Verfahren ermöglicht es, Rohre an spezifische Anforderungen anzupassen und komplexe Rohrleitungssysteme oder -strukturen zu erstellen, die den räumlichen Gegebenheiten oder funktionellen Erfordernissen entsprechen.
Es gibt verschiedene Methoden für das flexible Rohrbiegen, darunter das Kaltbiegen und das Warmbiegen. Beim Kaltbiegen werden die Rohre bei Raumtemperatur gebogen, während beim Warmbiegen eine Erwärmung des Rohrs vor dem Biegevorgang erfolgt, um die Biegsamkeit des Materials zu erhöhen und das Risiko von Rissen oder Verformungen zu verringern.
Flexible Rohrbiegeverfahren erfordern spezielle Biegemaschinen oder -werkzeuge, die das Rohr präzise und kontrolliert in die gewünschte Form oder den gewünschten Winkel bringen können. Diese Maschinen verwenden oft hydraulische oder mechanische Kräfte, um das Rohr zu biegen, und können mit verschiedenen Biegewerkzeugen oder Matrizen ausgestattet sein, um verschiedene Biegeradien oder Winkel zu erreichen.
Flexible Rohrbiegen wird in einer Vielzahl von Anwendungen und Branchen eingesetzt, darunter die Automobilindustrie, die Luft- und Raumfahrt, die Bauindustrie, die chemische Industrie und die Lebensmittelverarbeitung. In der Automobilindustrie werden flexible Rohrbiegetechniken verwendet, um Rohrleitungen für Bremsen, Klimaanlagen, Abgasanlagen und andere Systeme herzustellen. In der Bauindustrie werden sie für Geländer, Treppen, Dachrinnen und andere architektonische Elemente verwendet. In der chemischen Industrie werden sie für Rohrleitungen in Produktionsanlagen und Anlagen eingesetzt.
Die Fähigkeit, Metallrohre flexibel zu biegen, ist eine wichtige Eigenschaft, die es ermöglicht, maßgeschneiderte Lösungen für komplexe Anforderungen zu schaffen und innovative Designs zu realisieren. Durch das flexible Rohrbiegen können Ingenieure und Designer kreative Lösungen entwickeln, die den funktionalen und ästhetischen Ansprüchen gerecht werden und gleichzeitig die technischen Anforderungen erfüllen.
Rohrverbindungen:
Rohrverbindungen sind entscheidend für die Konstruktion von Rohrleitungssystemen, da sie es ermöglichen, einzelne Rohre miteinander zu verbinden, um komplexe Netzwerke oder Strukturen zu erstellen. Diese Verbindungen müssen nicht nur sicher und dicht sein, sondern auch flexibel genug, um Bewegungen oder Vibrationen im System aufzunehmen und zu absorbieren.
Es gibt verschiedene Arten von Rohrverbindungen, die je nach Anwendung, Betriebsbedingungen und den spezifischen Anforderungen des Rohrleitungssystems verwendet werden können. Einige der häufigsten Arten von Rohrverbindungen sind:
- Gewindeverbindungen: Bei dieser Art von Verbindung werden die Enden der Rohre mit Gewinden versehen und dann miteinander verschraubt. Gewindeverbindungen sind einfach zu installieren und eignen sich gut für niedrige Druck- und Temperaturanwendungen.
- Flanschverbindungen: Flanschverbindungen bestehen aus flachen, ringförmigen Flanschen, die an den Enden der Rohre angebracht werden und dann miteinander verschraubt oder verschweißt werden. Flanschverbindungen sind robust und bieten eine hohe Druck- und Temperaturbeständigkeit, sind jedoch etwas komplexer zu installieren als Gewindeverbindungen.
- Schweißverbindungen: Bei Schweißverbindungen werden die Enden der Rohre miteinander verschweißt, um eine dauerhafte und robuste Verbindung zu schaffen. Schweißverbindungen bieten eine hohe Festigkeit und Dichtheit, sind jedoch aufwändiger in der Herstellung und erfordern spezielle Ausrüstung und Know-how.
- Pressverbindungen: Pressverbindungen verwenden spezielle Presswerkzeuge, um die Enden der Rohre miteinander zu verbinden, indem sie sie zusammenpressen und eine dichte Verbindung herstellen. Pressverbindungen sind schnell und einfach zu installieren und eignen sich gut für Anwendungen, bei denen eine schnelle Montage erforderlich ist.
Die Auswahl der richtigen Rohrverbindung hängt von verschiedenen Faktoren ab, darunter der Betriebsdruck, die Temperatur, die Art des transportierten Mediums und die spezifischen Anforderungen der Anwendung. Eine sorgfältige Planung und Analyse sind erforderlich, um die geeignete Verbindung für das Rohrleitungssystem auszuwählen und sicherzustellen, dass es sicher, zuverlässig und effizient betrieben werden kann.
Nahtlose Rohre:
Nahtlose Rohre sind eine Art von Metallrohren, die ohne Schweißnaht hergestellt werden. Sie werden aus einem einzigen Stück Metall hergestellt, das durch verschiedene Verfahren wie Warmwalzen oder Kaltziehen zu einem Rohr geformt wird. Im Gegensatz zu geschweißten Rohren, die aus einzelnen Blechstreifen zusammengesetzt und längs oder spiralförmig verschweißt werden, haben nahtlose Rohre keine Schweißnaht, was ihnen eine verbesserte Festigkeit, Dichtheit und Korrosionsbeständigkeit verleiht.
Nahtlose Rohre bieten eine Reihe von Vorteilen gegenüber geschweißten Rohren. Da sie keine Schweißnaht haben, sind sie weniger anfällig für strukturelle Schwachstellen, Risse oder Leckagen, die durch die Schweißnaht verursacht werden können. Dies macht sie besonders geeignet für Anwendungen, bei denen hohe Druck- und Temperaturbelastungen auftreten, wie zum Beispiel in der Öl- und Gasindustrie, der Chemieindustrie oder der Energietechnik.
Darüber hinaus haben nahtlose Rohre eine gleichmäßige Wandstärke und Oberflächenbeschaffenheit, was zu einer verbesserten Strömungseigenschaft und geringeren Druckverlusten im Rohrleitungssystem führt. Dies ermöglicht einen effizienten und zuverlässigen Transport von Flüssigkeiten, Gasen oder Feststoffen über große Entfernungen oder in anspruchsvollen Umgebungen.
Die Herstellung von nahtlosen Rohren erfordert spezialisierte Ausrüstung und Verfahren, um das Metall in die gewünschte Form zu bringen, ohne eine Schweißnaht zu erzeugen. Dies kann verschiedene Verfahren wie das Warmwalzen, Kaltziehen, Extrudieren oder Schmieden umfassen, je nach den spezifischen Anforderungen der Anwendung und des verwendeten Materials.
Nahtlose Rohre werden in einer Vielzahl von Anwendungen und Branchen eingesetzt, darunter die Öl- und Gasindustrie, die chemische Industrie, die Lebensmittelverarbeitung, die Automobilindustrie und die Bauindustrie. Ihre hohe Festigkeit, Dichtheit und Korrosionsbeständigkeit machen sie zu einer beliebten Wahl für anspruchsvolle Anwendungen, bei denen Sicherheit, Zuverlässigkeit und Leistung entscheidend sind.
Geschweißte Rohre:
Geschweißte Rohre sind eine häufig verwendete Art von Metallrohren, die durch das Verschweißen von einzelnen Blechstreifen oder -platten hergestellt werden. Diese Blechstreifen werden längs oder spiralförmig verschweißt, um das Rohr zu formen. Geschweißte Rohre sind vielseitig einsetzbar und finden in einer Vielzahl von Anwendungen Verwendung, von der Wasser- und Abwasserleitung bis hin zu Strukturelementen in der Bauindustrie.
Es gibt verschiedene Arten von Schweißverfahren, die zur Herstellung von geschweißten Rohren verwendet werden können, darunter Lichtbogen-, Widerstands-, Laser- und Hochfrequenzschweißen. Jedes Verfahren hat seine eigenen Vor- und Nachteile in Bezug auf Effizienz, Qualität und Kosten.
Geschweißte Rohre bieten eine Reihe von Vorteilen gegenüber nahtlosen Rohren. Sie sind in der Regel kostengünstiger herzustellen und können in einer Vielzahl von Größen und Formen hergestellt werden, was sie für viele verschiedene Anwendungen geeignet macht. Darüber hinaus können geschweißte Rohre in längeren Längen hergestellt werden als nahtlose Rohre, was die Installation und Handhabung erleichtert.
Allerdings haben geschweißte Rohre auch einige Nachteile im Vergleich zu nahtlosen Rohren. Die Schweißnaht kann eine potenzielle Schwachstelle im Rohr sein, die anfällig für Risse, Korrosion oder Leckagen sein kann. Dies kann in einigen Anwendungen, insbesondere bei hohen Druck- oder Temperaturbelastungen, ein Problem darstellen.
Trotz dieser potenziellen Nachteile sind geschweißte Rohre aufgrund ihrer Vielseitigkeit, Wirtschaftlichkeit und Verfügbarkeit weit verbreitet und werden in vielen Industrien und Anwendungen eingesetzt. Durch die Auswahl der richtigen Materialien, Schweißverfahren und Qualitätskontrollen können geschweißte Rohre eine zuverlässige und kostengünstige Lösung für die Anforderungen von Rohrleitungssystemen bieten.
Korrosionsbeständige Legierungen:
Korrosionsbeständige Legierungen sind Metallmischungen, die speziell entwickelt wurden, um die Auswirkungen von Korrosion zu minimieren oder zu verhindern. Diese Legierungen enthalten Zusatzelemente, die eine schützende Oberflächenschicht bilden und das darunter liegende Metall vor den schädlichen Auswirkungen korrosiver Umgebungen schützen.
Einige der häufigsten korrosionsbeständigen Legierungen sind:
- Edelstahl: Edelstahl ist eine Legierung aus Eisen, Chrom und oft auch Nickel oder Molybdän. Es bildet eine passive Oxidschicht auf der Oberfläche, die das darunter liegende Metall vor Korrosion schützt. Edelstahl wird häufig in der Bauindustrie, der Lebensmittelverarbeitung, der chemischen Industrie und der Medizintechnik eingesetzt.
- Aluminiumlegierungen: Aluminiumlegierungen enthalten Aluminium als Hauptbestandteil sowie Zusatzelemente wie Kupfer, Magnesium oder Silizium. Sie bilden eine schützende Oxidschicht auf der Oberfläche, die Korrosion verhindert. Aluminiumlegierungen werden häufig in der Luft- und Raumfahrt, im Automobilbau und in der Bauindustrie eingesetzt.
- Kupferlegierungen: Kupferlegierungen enthalten Kupfer als Hauptbestandteil sowie Zusatzelemente wie Zink, Zinn oder Nickel. Sie haben eine natürliche Fähigkeit zur Bildung einer schützenden Patina, die das darunter liegende Metall vor Korrosion schützt. Kupferlegierungen werden häufig in der Bauindustrie, der Elektronik und der Schifffahrt eingesetzt.
- Titanlegierungen: Titanlegierungen enthalten Titan als Hauptbestandteil sowie Zusatzelemente wie Aluminium, Vanadium oder Eisen. Sie sind extrem korrosionsbeständig und werden häufig in der Luft- und Raumfahrt, der Medizintechnik und der chemischen Industrie eingesetzt.
Korrosionsbeständige Legierungen bieten eine Reihe von Vorteilen gegenüber reinen Metallen, einschließlich einer längeren Lebensdauer, geringerem Wartungsaufwand und verbesserten Leistungseigenschaften in korrosiven Umgebungen. Durch die Auswahl der richtigen Legierung für eine bestimmte Anwendung können Ingenieure und Designer sicherstellen, dass ihre Produkte den erforderlichen Korrosionsschutz bieten und eine lange Lebensdauer haben.
Hochtemperaturbeständige Legierungen:
Hochtemperaturbeständige Legierungen sind spezielle Metallmischungen, die für den Einsatz unter extremen Temperaturen entwickelt wurden, wie sie beispielsweise in Hochtemperaturumgebungen wie Verbrennungskammern, Turbinen oder industriellen Öfen auftreten können. Diese Legierungen müssen nicht nur hohe Temperaturen aushalten, sondern auch chemisch stabil und mechanisch belastbar bleiben.
Einige der häufigsten hochtemperaturbeständigen Legierungen sind:
- Inconel: Inconel ist eine Familie von Nickel-Chrom-Legierungen, die für ihre ausgezeichnete Festigkeit und Beständigkeit gegenüber Oxidation, Korrosion und Hochtemperaturumgebungen bekannt ist. Sie werden häufig in der Luft- und Raumfahrt, der chemischen Verarbeitung und in Hochtemperaturanwendungen eingesetzt.
- Hastelloy: Hastelloy-Legierungen sind Nickel-Molybdän-Chrom-Legierungen, die eine hohe Beständigkeit gegenüber oxidierenden und reduzierenden Medien bei hohen Temperaturen aufweisen. Sie werden häufig in der chemischen Verarbeitung, der Petrochemie und in Kraftwerken eingesetzt.
- Wolfram-Legierungen: Wolfram-Legierungen zeichnen sich durch ihre hohe Schmelztemperatur und ausgezeichnete Festigkeit bei hohen Temperaturen aus. Sie werden oft in Hochtemperaturanwendungen wie Glühbirnen, Röntgenröhren und Schweißelektroden verwendet.
- Titan-Legierungen: Titan-Legierungen haben eine hohe Festigkeit, niedriges Gewicht und gute Beständigkeit gegenüber Korrosion und Hochtemperaturen. Sie werden häufig in der Luft- und Raumfahrt, der Medizintechnik und in Hochtemperaturanwendungen eingesetzt.
Hochtemperaturbeständige Legierungen spielen eine entscheidende Rolle in Branchen und Anwendungen, die extremen Temperaturen ausgesetzt sind. Ihre einzigartigen Eigenschaften ermöglichen den Bau von Hochleistungsanlagen und -komponenten, die auch unter extremen Bedingungen zuverlässig arbeiten können.
Wärmebehandlung:
Die Wärmebehandlung ist ein wichtiger Prozess bei der Herstellung und Verarbeitung von Metallrohren, der dazu dient, die mechanischen Eigenschaften, die Härte, die Festigkeit und die Struktur des Materials zu verbessern oder zu verändern. Durch die gezielte Anwendung von Wärme können verschiedene metallurgische Veränderungen im Material induziert werden, die seine Leistungsfähigkeit in bestimmten Anwendungen verbessern.
Es gibt verschiedene Arten von Wärmebehandlungsverfahren, die je nach den spezifischen Anforderungen der Anwendung angewendet werden können:
- Glühen: Beim Glühen werden Metallrohre auf eine bestimmte Temperatur erhitzt und dann langsam abgekühlt, um die innere Spannung zu reduzieren, die Härte zu verringern und die Zähigkeit zu erhöhen. Dieses Verfahren wird oft angewendet, um die Bearbeitbarkeit von Rohren zu verbessern oder um eine gleichmäßige Struktur im Material zu erzeugen.
- Härten: Beim Härten werden Metallrohre auf eine hohe Temperatur erhitzt und dann schnell abgekühlt, um eine martensitische Struktur im Material zu erzeugen, die eine hohe Härte und Festigkeit bietet. Dieses Verfahren wird häufig angewendet, um die Verschleißfestigkeit von Rohren zu verbessern oder um Werkzeugstähle herzustellen.
- Anlassen: Beim Anlassen werden Metallrohre nach dem Härten auf eine niedrigere Temperatur erhitzt und dann langsam abgekühlt, um die Härte zu verringern und die Zähigkeit zu erhöhen. Dieses Verfahren wird angewendet, um die Härte und Festigkeit von Rohren zu reduzieren, ohne ihre Zähigkeit zu beeinträchtigen.
- Normalisieren: Beim Normalisieren werden Metallrohre auf eine hohe Temperatur erhitzt und dann langsam an der Luft abgekühlt, um eine gleichmäßige Struktur im Material zu erzeugen. Dieses Verfahren wird häufig angewendet, um die mechanischen Eigenschaften von Rohren zu verbessern oder um interne Spannungen zu reduzieren.
Die Auswahl des geeigneten Wärmebehandlungsverfahrens hängt von verschiedenen Faktoren ab, darunter das Material, aus dem das Rohr hergestellt ist, die gewünschten mechanischen Eigenschaften und die spezifischen Anforderungen der Anwendung. Durch die gezielte Anwendung von Wärmebehandlung können Ingenieure und Hersteller die Leistungsfähigkeit von Metallrohren verbessern und sicherstellen, dass sie den erforderlichen Standards und Spezifikationen entsprechen.
Rohrbiegemaschinen:
Rohrbiegemaschinen sind spezielle Werkzeugmaschinen, die zum Biegen von Metallrohren verwendet werden. Sie sind in verschiedenen Größen und Ausführungen erhältlich und können für eine Vielzahl von Anwendungen eingesetzt werden, von der Herstellung von Rohrleitungen bis hin zur Produktion von Bauteilen für verschiedene Branchen.
Es gibt verschiedene Arten von Rohrbiegemaschinen, darunter:
- Manuelle Rohrbiegemaschinen: Diese Maschinen werden von Hand betrieben und eignen sich für kleinere Biegeprojekte oder den Einsatz in Werkstätten oder Garagen. Sie sind einfach zu bedienen und erfordern keine speziellen Kenntnisse oder Schulungen.
- Hydraulische Rohrbiegemaschinen: Hydraulische Rohrbiegemaschinen verwenden hydraulische Kraft, um das Rohr zu biegen. Sie bieten eine höhere Biegekapazität und Präzision als manuelle Maschinen und eignen sich daher für anspruchsvollere Biegeprojekte oder den Einsatz in industriellen Umgebungen.
- CNC-gesteuerte Rohrbiegemaschinen: Diese Maschinen werden von einem Computer gesteuert und bieten eine hohe Automatisierung und Präzision. Sie können komplexe Biegeprofile erstellen und sind ideal für die Serienproduktion oder die Herstellung von Bauteilen mit wiederholbaren Biegeanforderungen.
Rohrbiegemaschinen können verschiedene Biegeverfahren anwenden, darunter das Kaltbiegen und das Warmbiegen. Beim Kaltbiegen wird das Rohr ohne Wärmebehandlung gebogen, während beim Warmbiegen das Rohr vor dem Biegen erwärmt wird, um seine Biegsamkeit zu verbessern und Risse oder Verformungen zu vermeiden.
Die Auswahl der geeigneten Rohrbiegemaschine hängt von verschiedenen Faktoren ab, darunter das Material, die Wandstärke und der Durchmesser des zu biegenden Rohrs, die gewünschte Biegungsgenauigkeit und die Produktionsanforderungen. Durch den Einsatz von Rohrbiegemaschinen können Hersteller die Effizienz steigern, die Produktivität erhöhen und hochwertige Biegeteile für eine Vielzahl von Anwendungen herstellen.
Rohrbiegeprozess:
Der Rohrbiegeprozess ist ein wichtiger Schritt bei der Herstellung von Metallrohren und umfasst verschiedene Verfahren zum Biegen von Rohren in die gewünschte Form oder den gewünschten Winkel. Der Prozess kann manuell oder maschinell durchgeführt werden und erfordert präzise Techniken, um qualitativ hochwertige Biegeergebnisse zu erzielen.
- Vorbereitung des Rohrs: Zunächst wird das zu biegende Rohr auf die erforderliche Länge geschnitten und die Enden können auf die richtige Form gebracht werden. Gegebenenfalls können auch Markierungen oder Schablonen verwendet werden, um den Biegepunkt und den Biegewinkel festzulegen.
- Befestigung des Rohrs: Das Rohr wird in der Biegemaschine oder Vorrichtung fixiert, um ein Verrutschen oder Verdrehen während des Biegevorgangs zu verhindern. Die Art der Befestigung hängt von der Biegemaschine und der Form des zu biegenden Rohrs ab.
- Biegen des Rohrs: Der Biegevorgang kann auf verschiedene Weise durchgeführt werden, je nach den Anforderungen der Anwendung und der verfügbaren Ausrüstung. Manuelle Rohrbiegemaschinen erfordern in der Regel physische Kraft, um das Rohr in die gewünschte Form zu biegen, während hydraulische oder CNC-gesteuerte Maschinen den Biegevorgang automatisieren und präzise Ergebnisse liefern können.
- Kontrolle und Anpassung: Nach dem Biegen wird das gebogene Rohr auf seine Genauigkeit und Qualität überprüft. Gegebenenfalls können Anpassungen vorgenommen werden, um sicherzustellen, dass das Rohr den spezifischen Anforderungen entspricht und keine unerwünschten Verformungen oder Fehler aufweist.
- Weitere Bearbeitung: Nach dem Biegen können weitere Bearbeitungsschritte erforderlich sein, wie beispielsweise das Entgraten der Kanten, das Reinigen der Oberfläche oder das Anbringen von Gewinden oder Verbindungsstücken.
Der Rohrbiegeprozess erfordert Fachwissen, Erfahrung und präzise Techniken, um qualitativ hochwertige Biegeresultate zu erzielen. Durch die Auswahl der geeigneten Biegemaschine, die richtigen Werkzeuge und Verfahren sowie die sorgfältige Kontrolle und Anpassung können Hersteller sicherstellen, dass ihre gebogenen Rohre den erforderlichen Standards und Spezifikationen entsprechen.
Rohrschneider:
Ein Rohrschneider ist ein Werkzeug, das zum präzisen Schneiden von Metallrohren verwendet wird. Es gibt verschiedene Arten von Rohrschneidern, die je nach den Anforderungen der Anwendung und der Art des zu schneidenden Rohrs eingesetzt werden können. Zu den häufigsten Arten von Rohrschneidern gehören:
- Rohrschneidemaschinen: Rohrschneidemaschinen sind spezielle Werkzeugmaschinen, die zum automatischen Schneiden von Metallrohren verwendet werden. Sie können eine Vielzahl von Schneidetechniken anwenden, darunter Sägen, Schleifen, Fräsen oder Plasma- oder Laserstrahlschneiden, je nach den spezifischen Anforderungen der Anwendung.
- Hand-Rohrschneider: Hand-Rohrschneider sind manuelle Werkzeuge, die von Hand betrieben werden und in der Regel für kleinere Schneidprojekte oder den Einsatz in Werkstätten oder Baustellen verwendet werden. Sie bestehen aus einem Schneidrad, das entlang des Rohrs geführt wird, um einen sauberen und geraden Schnitt zu erzeugen.
- Rohrschneidewerkzeuge: Rohrschneidewerkzeuge sind tragbare Handwerkzeuge, die zum Schneiden von Metallrohren verwendet werden. Sie können in verschiedenen Ausführungen erhältlich sein, darunter Rohrschneider mit Ratschenmechanismus, Rohrschneider mit Rohrschneidebacken oder Rohrschneider mit Spiralmechanismus, je nach den spezifischen Anforderungen der Anwendung und der Art des zu schneidenden Rohrs.
- Rohrschneidezangen: Rohrschneidezangen sind spezielle Zangenwerkzeuge, die zum Schneiden von dünnen Metallrohren verwendet werden. Sie verfügen über scharfe Schneidbacken, die das Rohr sicher greifen und saubere Schnitte erzeugen können.
Die Auswahl des geeigneten Rohrschneiders hängt von verschiedenen Faktoren ab, darunter die Art des zu schneidenden Rohrs, die Dicke und der Durchmesser des Rohrs, die gewünschte Schnittgenauigkeit und die verfügbare Ausrüstung. Durch den Einsatz von hochwertigen Rohrschneidern und präzisen Schneidetechniken können Hersteller sicherstellen, dass ihre Metallrohre sauber, gerade und genau geschnitten werden, um den Anforderungen der Anwendung zu entsprechen.
Rohrbiegevorrichtungen:
Rohrbiegevorrichtungen sind spezielle Werkzeuge oder Einrichtungen, die verwendet werden, um Metallrohre präzise zu biegen und ihnen die gewünschte Form zu verleihen. Diese Vorrichtungen sind entscheidend für die Herstellung von Rohrleitungen, Strukturen oder Bauteilen in verschiedenen Branchen und Anwendungen und ermöglichen es, komplexe Biegungen mit hoher Genauigkeit und Wiederholbarkeit zu erreichen.
Es gibt verschiedene Arten von Rohrbiegevorrichtungen, die je nach den spezifischen Anforderungen der Anwendung eingesetzt werden können:
- Hydraulische Rohrbiegevorrichtungen: Hydraulische Rohrbiegevorrichtungen verwenden hydraulische Kraft, um das Rohr präzise zu biegen. Sie bieten eine hohe Biegegenauigkeit und können für anspruchsvolle Biegeprojekte oder den Einsatz in industriellen Umgebungen verwendet werden.
- CNC-gesteuerte Rohrbiegevorrichtungen: CNC-gesteuerte Rohrbiegevorrichtungen werden von einem Computer gesteuert und ermöglichen eine automatisierte und präzise Biegeoperation. Sie können komplexe Biegungen mit hoher Wiederholbarkeit und Genauigkeit durchführen und sind ideal für die Serienproduktion oder die Herstellung von Bauteilen mit wiederholbaren Biegeanforderungen.
- Manuelle Rohrbiegevorrichtungen: Manuelle Rohrbiegevorrichtungen werden von Hand betrieben und eignen sich für kleinere Biegeprojekte oder den Einsatz in Werkstätten oder Garagen. Sie sind einfach zu bedienen und erfordern keine speziellen Kenntnisse oder Schulungen.
- Rohrbiegeformen: Rohrbiegeformen sind spezielle Formen oder Matrizen, die verwendet werden, um das Rohr in die gewünschte Form zu biegen. Sie können aus verschiedenen Materialien hergestellt werden, darunter Stahl, Aluminium oder Kunststoff, und sind in verschiedenen Größen und Formen erhältlich, um verschiedene Biegeprofile zu erzeugen.
Die Auswahl der geeigneten Rohrbiegevorrichtung hängt von verschiedenen Faktoren ab, darunter die Art des zu biegenden Rohrs, die gewünschte Biegungsgenauigkeit, die Produktionsanforderungen und die verfügbare Ausrüstung. Durch den Einsatz von Rohrbiegevorrichtungen können Hersteller die Effizienz steigern, die Produktivität erhöhen und hochwertige Biegeteile für eine Vielzahl von Anwendungen herstellen.
Rohrverformung:
Rohrverformung ist ein Prozess, bei dem Metallrohre durch mechanische Kräfte oder Druck in eine andere Form gebracht werden, ohne dass das Material gebrochen oder geschnitten wird. Dieser Prozess ermöglicht es, Rohre in verschiedene Formen, Profile oder Biegungen zu bringen, um den Anforderungen spezifischer Anwendungen gerecht zu werden.
Es gibt verschiedene Arten von Rohrverformungsverfahren, darunter:
- Rohrbiegen: Beim Rohrbiegen wird das Rohr um eine Biegeform oder Matrize gebogen, um die gewünschte Biegung oder Krümmung zu erreichen. Dies kann durch verschiedene Methoden erfolgen, einschließlich manueller Biegemaschinen, hydraulischer Pressen oder CNC-gesteuerter Biegemaschinen.
- Rohrwalzen: Beim Rohrwalzen wird das Rohr durch Walzen oder Walzenformen gepresst, um seine Form zu verändern. Dies kann dazu verwendet werden, das Rohr zu verengen, zu erweitern oder zu verjüngen, um bestimmte Anforderungen zu erfüllen oder spezielle Profile zu erstellen.
- Rohrziehen: Beim Rohrziehen wird das Rohr durch eine Ziehform oder Matrize gezogen, um seine Länge zu verlängern und seine Wandstärke zu verringern. Dies kann dazu verwendet werden, das Rohr auf eine genauere Größe zu bringen oder dünnwandige Rohre für bestimmte Anwendungen herzustellen.
- Rohrpressen: Beim Rohrpressen wird das Rohr zwischen zwei Formen oder Matrizen gepresst, um seine Form zu verändern. Dies kann dazu verwendet werden, das Rohr zu quetschen, zu verbiegen oder zu falten, um spezielle Formen oder Profile zu erreichen.
Rohrverformung wird in einer Vielzahl von Branchen und Anwendungen eingesetzt, darunter die Automobilindustrie, die Luft- und Raumfahrt, die Bauindustrie, die chemische Industrie und die Elektronik. Durch die gezielte Anwendung von Rohrverformungsverfahren können Hersteller innovative Lösungen entwickeln, die den spezifischen Anforderungen ihrer Kunden gerecht werden und hochwertige Produkte mit präzisen Abmessungen und Formen herstellen.
Korrosionsschutzbeschichtungen:
Korrosionsschutzbeschichtungen sind spezielle Beschichtungen, die auf die Oberfläche von Metallrohren aufgetragen werden, um sie vor Korrosion zu schützen und ihre Lebensdauer zu verlängern. Diese Beschichtungen bilden eine Schutzschicht auf der Oberfläche des Rohrs, die es vor aggressiven Umgebungseinflüssen wie Feuchtigkeit, Chemikalien oder atmosphärischen Bedingungen schützt.
Es gibt verschiedene Arten von Korrosionsschutzbeschichtungen, die je nach den spezifischen Anforderungen der Anwendung eingesetzt werden können:
- Zinkbeschichtungen: Zinkbeschichtungen, wie zum Beispiel Zinkanoden oder Zinksprühbeschichtungen, bieten einen wirksamen Schutz vor Korrosion, indem sie eine opfernde Schutzschicht bilden, die das darunter liegende Metall vor Korrosion schützt.
- Epoxidbeschichtungen: Epoxidbeschichtungen sind lösungsmittelbasierte Beschichtungen, die auf die Oberfläche des Rohrs aufgetragen werden und dann aushärten, um eine dauerhafte Schutzschicht zu bilden. Sie bieten eine hohe chemische Beständigkeit und eignen sich daher gut für den Einsatz in aggressiven Umgebungen.
- Polyurethanbeschichtungen: Polyurethanbeschichtungen bieten eine ausgezeichnete Abrieb- und Chemikalienbeständigkeit und eignen sich daher gut für den Einsatz in rauen Umgebungen wie Offshore-Anlagen oder industriellen Anlagen.
- Korrosionsinhibitoren: Korrosionsinhibitoren sind chemische Zusätze, die der Beschichtung zugesetzt werden, um die Korrosionsbeständigkeit zu verbessern und das Wachstum von Korrosionsprodukten zu hemmen. Sie können in verschiedenen Beschichtungssystemen verwendet werden, um die Leistungsfähigkeit des Korrosionsschutzes zu verbessern.
Die Auswahl der geeigneten Korrosionsschutzbeschichtung hängt von verschiedenen Faktoren ab, darunter die Art des zu schützenden Metalls, die Umgebungsbedingungen, die Anforderungen der Anwendung und die verfügbare Ausrüstung. Durch den Einsatz von hochwertigen Korrosionsschutzbeschichtungen können Hersteller die Lebensdauer ihrer Metallrohre verlängern und die Kosten für Wartung und Instandhaltung reduzieren.
Rohrverschraubungen:
Rohrverschraubungen sind Verbindungselemente, die verwendet werden, um Metallrohre miteinander zu verbinden oder um Rohre mit anderen Bauteilen wie Armaturen, Ventilen oder Rohrleitungssystemen zu verbinden. Sie spielen eine wichtige Rolle bei der Montage und Installation von Rohrleitungssystemen in verschiedenen Anwendungen und Branchen.
Es gibt verschiedene Arten von Rohrverschraubungen, die je nach den spezifischen Anforderungen der Anwendung und der Art des zu verbindenden Rohrs eingesetzt werden können:
- Gewindeverschraubungen: Gewindeverschraubungen verwenden Gewinde auf den Enden der Rohre, um sie miteinander zu verbinden. Diese Verschraubungen können in verschiedenen Ausführungen erhältlich sein, darunter Innengewinde, Außengewinde oder Kombinationen aus beiden.
- Schweißverschraubungen: Schweißverschraubungen werden durch Schweißen der Rohrenden aneinander befestigt, um eine dauerhafte und stabile Verbindung zu gewährleisten. Diese Verschraubungen sind besonders robust und werden häufig in anspruchsvollen Anwendungen oder in Hochdruckumgebungen eingesetzt.
- Lötverschraubungen: Lötverschraubungen verwenden Lötverbindungen, um die Rohrenden miteinander zu verbinden. Sie bieten eine zuverlässige und dauerhafte Verbindung und eignen sich gut für den Einsatz in Anwendungen, bei denen hohe Temperaturen oder Korrosionsbeständigkeit erforderlich sind.
- Pressfittinge: Pressfittinge verwenden eine mechanische Presskraft, um die Rohrenden miteinander zu verbinden. Diese Verschraubungen sind einfach zu installieren und erfordern keine speziellen Werkzeuge oder Fertigkeiten, was sie ideal für schnelle und effiziente Installationsarbeiten macht.
Die Auswahl der geeigneten Rohrverschraubungen hängt von verschiedenen Faktoren ab, darunter die Art des zu verbindenden Rohrs, die Betriebsbedingungen, die Anforderungen der Anwendung und die verfügbare Ausrüstung. Durch den Einsatz von hochwertigen Rohrverschraubungen können Hersteller eine zuverlässige und sichere Verbindung zwischen Rohren herstellen und die Leistungsfähigkeit ihrer Rohrleitungssysteme verbessern.
Rohrleitungssysteme:
Rohrleitungssysteme sind komplexe Netzwerke von Rohren, Armaturen, Ventilen und anderen Komponenten, die verwendet werden, um Flüssigkeiten, Gase oder Feststoffe von einem Punkt zum anderen zu transportieren. Sie spielen eine entscheidende Rolle in verschiedenen Branchen und Anwendungen, darunter die Wasser- und Abwasserbehandlung, die Öl- und Gasförderung, die chemische Verarbeitung, die Lebensmittelindustrie und die Bauindustrie.
Ein typisches Rohrleitungssystem besteht aus folgenden Komponenten:
- Rohre: Rohre sind die Hauptkomponente eines Rohrleitungssystems und dienen dazu, das transportierte Medium von einem Punkt zum anderen zu leiten. Sie sind in verschiedenen Größen, Materialien und Wandstärken erhältlich, je nach den Anforderungen der Anwendung und der Art des transportierten Mediums.
- Armaturen: Armaturen sind spezielle Komponenten, die in Rohrleitungssystemen verwendet werden, um den Durchfluss, den Druck und die Richtung des transportierten Mediums zu steuern. Sie umfassen Ventile, Klappen, Anschlüsse und andere Geräte, die dazu dienen, den Fluss zu regulieren oder zu unterbrechen.
- Ventile: Ventile sind Geräte, die dazu dienen, den Durchfluss eines Mediums zu steuern, indem sie geöffnet oder geschlossen werden. Sie können in verschiedenen Ausführungen erhältlich sein, darunter Absperrventile, Regelventile, Rückschlagventile und Sicherheitsventile, je nach den spezifischen Anforderungen der Anwendung.
- Pumpen: Pumpen sind mechanische Geräte, die dazu dienen, das transportierte Medium durch das Rohrleitungssystem zu fördern, indem sie Druck und Geschwindigkeit erzeugen. Sie werden in verschiedenen Größen und Typen verwendet, je nach den Anforderungen der Anwendung und der Art des zu transportierenden Mediums.
- Dichtungen und Dichtungsmaterialien: Dichtungen und Dichtungsmaterialien werden verwendet, um die Verbindungen zwischen den Rohren und anderen Komponenten abzudichten und Leckagen zu verhindern. Sie können aus verschiedenen Materialien hergestellt werden, darunter Gummi, Kunststoff, Metall oder Verbundwerkstoffe, je nach den Anforderungen der Anwendung und den Betriebsbedingungen.
Rohrleitungssysteme sind entscheidend für den Transport von Flüssigkeiten, Gasen oder Feststoffen in verschiedenen Branchen und Anwendungen. Durch die sorgfältige Planung, Konstruktion und Installation von Rohrleitungssystemen können Hersteller sicherstellen, dass sie den Anforderungen ihrer Kunden gerecht werden und eine zuverlässige und effiziente Transportlösung bereitstellen.
Wärmetauscher:
Ein Wärmetauscher ist ein Gerät, das dazu dient, Wärme von einem Medium auf ein anderes zu übertragen, ohne dass die beiden Medien miteinander in Kontakt kommen. Wärmetauscher werden in einer Vielzahl von Anwendungen eingesetzt, darunter Heizungs- und Klimaanlagen, Kraftwerke, Chemieanlagen, Lebensmittelverarbeitung und viele mehr.
Es gibt verschiedene Arten von Wärmetauschern, die je nach den spezifischen Anforderungen der Anwendung eingesetzt werden können:
- Rohrbündelwärmetauscher: Rohrbündelwärmetauscher bestehen aus einem Bündel von Rohren, die in einem Behälter oder Gehäuse angeordnet sind. Ein Medium wird durch die Rohre geleitet, während das andere Medium außerhalb der Rohre vorbeiströmt. Wärme wird durch die Wand der Rohre übertragen, wodurch die Temperatur des Mediums im Inneren des Rohrbündels geändert wird.
- Plattenwärmetauscher: Plattenwärmetauscher bestehen aus einer Reihe von dünnen Platten, die in einem Rahmen angeordnet sind. Die Platten haben Kanäle für den Durchfluss der beiden Medien, wodurch Wärme zwischen den Medien übertragen wird. Plattenwärmetauscher sind kompakt und effizient und werden häufig in Anwendungen mit hohem Wärmeübertragungsbedarf eingesetzt.
- Luft-Wasser-Wärmetauscher: Luft-Wasser-Wärmetauscher werden verwendet, um Wärme zwischen Luft und Wasser zu übertragen. Sie werden häufig in Heizungs- und Klimaanlagen eingesetzt, um die Temperatur des Luftstroms zu regeln und Energie zu sparen.
- Rohrbogenwärmetauscher: Rohrbogenwärmetauscher verwenden gebogene Rohre, um Wärme zwischen den Medien zu übertragen. Sie werden häufig in Anwendungen eingesetzt, bei denen Platzbeschränkungen oder spezielle Anforderungen an die Rohrführung bestehen.
Die Auswahl des geeigneten Wärmetauschers hängt von verschiedenen Faktoren ab, darunter die Art der zu übertragenden Wärme, die Betriebsbedingungen, die verfügbare Ausrüstung und die Kosten. Durch den Einsatz von effizienten Wärmetauschern können Hersteller Energiekosten senken, die Produktivität steigern und die Umweltbelastung reduzieren.
Nichtmetallische Rohre:
Nichtmetallische Rohre sind Rohre, die aus Materialien hergestellt sind, die keine Metalle sind. Sie werden in einer Vielzahl von Anwendungen eingesetzt, darunter die Wasserversorgung, die Abwasserentsorgung, die Chemieindustrie, die Lebensmittelverarbeitung und die Bauindustrie. Nichtmetallische Rohre bieten eine Vielzahl von Vorteilen gegenüber metallischen Rohren, darunter eine verbesserte Korrosionsbeständigkeit, eine geringere Wärmeleitfähigkeit, eine bessere chemische Beständigkeit und eine einfachere Installation.
Es gibt verschiedene Arten von nichtmetallischen Rohren, die je nach den spezifischen Anforderungen der Anwendung eingesetzt werden können:
- Kunststoffrohre: Kunststoffrohre, wie PVC (Polyvinylchlorid), PE (Polyethylen), PP (Polypropylen) und PVDF (Polyvinylidenfluorid), sind weit verbreitet und werden in einer Vielzahl von Anwendungen eingesetzt. Sie bieten eine ausgezeichnete Korrosionsbeständigkeit, eine hohe Flexibilität und eine einfache Installation.
- Glasfaserrohre: Glasfaserrohre bestehen aus einem Verbundwerkstoff aus Glasfasern und Harz und bieten eine hohe Festigkeit, eine gute chemische Beständigkeit und eine ausgezeichnete Korrosionsbeständigkeit. Sie werden häufig in anspruchsvollen Anwendungen wie der Chemieindustrie oder der Öl- und Gasförderung eingesetzt.
- Keramikrohre: Keramikrohre bestehen aus anorganischen Materialien wie Ton, Porzellan oder Feuerfestmaterialien und bieten eine ausgezeichnete chemische Beständigkeit, eine hohe Temperaturbeständigkeit und eine lange Lebensdauer. Sie werden häufig in Anwendungen mit hohen Temperaturen oder aggressiven Chemikalien eingesetzt.
- Verbundrohre: Verbundrohre bestehen aus mehreren Schichten verschiedener Materialien, die kombinierte Eigenschaften bieten, wie zum Beispiel eine hohe Festigkeit, eine gute Flexibilität und eine verbesserte Korrosionsbeständigkeit. Sie werden häufig in speziellen Anwendungen eingesetzt, bei denen eine hohe Leistungsfähigkeit erforderlich ist.
Die Auswahl des geeigneten nichtmetallischen Rohrs hängt von verschiedenen Faktoren ab, darunter die Art der transportierten Medien, die Betriebsbedingungen, die Anforderungen der Anwendung und die Kosten. Durch den Einsatz von nichtmetallischen Rohren können Hersteller die Leistungsfähigkeit ihrer Rohrleitungssysteme verbessern und die Lebensdauer ihrer Anlagen verlängern.
Rohrinspektion:
Die Rohrinspektion ist ein wichtiger Prozess, um die Integrität und Zuverlässigkeit von Rohrleitungssystemen sicherzustellen. Sie umfasst verschiedene Techniken und Verfahren zur Überprüfung von Rohren auf Defekte, Beschädigungen oder Anzeichen von Verschleiß, um potenzielle Probleme frühzeitig zu erkennen und zu beheben. Eine regelmäßige Rohrinspektion kann dazu beitragen, ungeplante Ausfallzeiten zu minimieren, die Sicherheit zu erhöhen und die Lebensdauer der Anlagen zu verlängern.
Es gibt verschiedene Methoden zur Rohrinspektion, darunter:
- Visuelle Inspektion: Bei der visuellen Inspektion werden die Rohre mit bloßem Auge oder mithilfe von optischen Instrumenten wie Endoskopen oder Kameras auf äußere Defekte oder Beschädigungen überprüft. Dies kann Risse, Korrosion, Ablagerungen oder andere Anomalien umfassen.
- Ultraschallprüfung: Die Ultraschallprüfung verwendet Ultraschallwellen, um die Dicke der Rohrwand und das Vorhandensein interner Defekte wie Risse, Löcher oder Einschlüsse zu messen. Diese Methode ermöglicht eine präzise Detektion von Defekten, ohne dass das Rohr geöffnet oder zerstört werden muss.
- Röntgenprüfung: Die Röntgenprüfung verwendet Röntgenstrahlen, um die innere Struktur und Integrität der Rohre zu überprüfen. Sie ermöglicht die Detektion von internen Defekten wie Rissen, Schweißfehlern oder Korrosion, ohne dass das Rohr geöffnet werden muss.
- Wirbelstromprüfung: Die Wirbelstromprüfung erzeugt elektromagnetische Wirbel in den Rohren, um Oberflächendefekte wie Risse, Porosität oder Härteänderungen zu identifizieren. Diese Methode eignet sich besonders gut für die Prüfung von metallischen Rohren.
- Druckprüfung: Die Druckprüfung verwendet Druckluft oder Wasser, um die Dichtheit der Rohre zu überprüfen und Undichtigkeiten oder Leckagen zu identifizieren. Diese Methode wird häufig nach der Installation oder Reparatur von Rohrleitungssystemen eingesetzt.
Die Auswahl der geeigneten Inspektionsmethode hängt von verschiedenen Faktoren ab, darunter die Art des zu inspizierenden Rohrs, die Art der potenziellen Defekte, die Verfügbarkeit von Ausrüstung und Fachkenntnissen sowie die Kosten und die betrieblichen Anforderungen. Durch eine regelmäßige und gründliche Rohrinspektion können Hersteller die Sicherheit, Zuverlässigkeit und Leistungsfähigkeit ihrer Rohrleitungssysteme gewährleisten und potenzielle Probleme frühzeitig erkennen und beheben.
Rohrverbindungen:
Rohrverbindungen sind Verbindungselemente, die verwendet werden, um zwei oder mehr Rohre miteinander zu verbinden oder um Rohre mit anderen Bauteilen wie Armaturen, Ventilen oder Rohrleitungssystemen zu verbinden. Sie spielen eine wichtige Rolle bei der Montage und Installation von Rohrleitungssystemen in verschiedenen Anwendungen und Branchen.
Es gibt verschiedene Arten von Rohrverbindungen, die je nach den spezifischen Anforderungen der Anwendung eingesetzt werden können:
- Gewindeverbindungen: Gewindeverbindungen verwenden Gewinde auf den Enden der Rohre, um sie miteinander zu verbinden. Diese Verbindungen können durch Schrauben oder Aufschrauben der Rohre hergestellt werden und bieten eine einfache und kostengünstige Lösung für viele Anwendungen.
- Schweißverbindungen: Schweißverbindungen werden durch Schmelzen der Rohrenden und Verbinden der geschmolzenen Bereiche hergestellt, um eine dauerhafte und stabile Verbindung zu erzielen. Diese Verbindungen bieten eine hohe Festigkeit und Dichtigkeit und werden häufig in anspruchsvollen Anwendungen oder in Hochdruckumgebungen eingesetzt.
- Lötverbindungen: Lötverbindungen verwenden Lötverbindungen, um die Rohrenden miteinander zu verbinden. Diese Verbindungen bieten eine zuverlässige und dauerhafte Verbindung und eignen sich gut für den Einsatz in Anwendungen, bei denen hohe Temperaturen oder Korrosionsbeständigkeit erforderlich sind.
- Pressfittinge: Pressfittinge verwenden eine mechanische Presskraft, um die Rohrenden miteinander zu verbinden. Diese Verbindungen sind einfach zu installieren und erfordern keine speziellen Werkzeuge oder Fertigkeiten, was sie ideal für schnelle und effiziente Installationsarbeiten macht.
Die Auswahl der geeigneten Rohrverbindungen hängt von verschiedenen Faktoren ab, darunter die Art der zu verbindenden Rohre, die Betriebsbedingungen, die Anforderungen der Anwendung und die Kosten. Durch den Einsatz von hochwertigen Rohrverbindungen können Hersteller eine zuverlässige und sichere Verbindung zwischen Rohren herstellen und die Leistungsfähigkeit ihrer Rohrleitungssysteme verbessern.
Rohrherstellung:
Die Rohrherstellung ist ein Prozess, bei dem Rohre aus verschiedenen Materialien hergestellt werden, einschließlich Metall, Kunststoff, Glas und anderen Werkstoffen. Dieser Prozess umfasst verschiedene Schritte, um Rohre mit den gewünschten Abmessungen, Eigenschaften und Oberflächen zu produzieren, die den Anforderungen verschiedener Anwendungen entsprechen.
Die Rohrherstellung kann je nach dem verwendeten Material und den spezifischen Anforderungen der Anwendung unterschiedlich sein, aber einige allgemeine Schritte umfassen:
- Materialvorbereitung: Der erste Schritt bei der Rohrherstellung ist die Materialvorbereitung, bei der das Ausgangsmaterial entsprechend den Anforderungen der Herstellung vorbereitet wird. Dies kann die Auswahl des geeigneten Rohrmaterials, die Formgebung und die Reinigung umfassen.
- Formgebung: Die Formgebung ist der Prozess, bei dem das Rohrmaterial in die gewünschte Form gebracht wird. Dies kann durch verschiedene Verfahren erfolgen, darunter Walzen, Extrudieren, Ziehen, Pressen oder Formen.
- Schweißen oder Verbinden: Bei einigen Rohrherstellungsverfahren werden die Rohrenden miteinander verbunden, um lange Rohrlängen zu erzeugen. Dies kann durch Schweißen, Löten, Kleben oder andere Verbindungstechniken erfolgen.
- Biegen und Umformen: Bei Bedarf werden die Rohre gebogen oder umgeformt, um bestimmte Profile oder Biegungen zu erreichen. Dies kann durch mechanisches Biegen, Walzen, Pressen oder andere Umformverfahren erfolgen.
- Wärmebehandlung: In einigen Fällen kann eine Wärmebehandlung erforderlich sein, um die mechanischen Eigenschaften des Rohrs zu verbessern oder seine Haltbarkeit zu erhöhen. Dies kann durch Tempern, Härten, Glühen oder andere thermische Verfahren erfolgen.
- Endbearbeitung: Nach der Herstellung werden die Rohre oft einer Endbearbeitung unterzogen, um die Oberflächenqualität zu verbessern, die Abmessungen zu prüfen und gegebenenfalls weitere Bearbeitungsschritte durchzuführen, um sicherzustellen, dass sie den Anforderungen der Anwendung entsprechen.
Die Rohrherstellung ist ein wichtiger Schritt in der Produktion von Rohrleitungssystemen und Bauteilen für eine Vielzahl von Anwendungen. Durch den Einsatz von hochwertigen Materialien, fortschrittlichen Fertigungsverfahren und strengen Qualitätskontrollen können Hersteller hochwertige Rohre herstellen, die den Anforderungen ihrer Kunden gerecht werden.
Rohrreinigung:
Die Rohrreinigung ist ein wichtiger Prozess, um Ablagerungen, Verstopfungen und Verschmutzungen in Rohrleitungssystemen zu entfernen und die maximale Leistungsfähigkeit der Anlagen zu gewährleisten. Verschmutzte Rohre können zu vermindertem Durchfluss, erhöhtem Energieverbrauch, Ausfällen und anderen Problemen führen. Die Rohrreinigung kann mechanisch, chemisch oder thermisch erfolgen, abhängig von der Art der Ablagerungen und den Anforderungen der Anwendung.
Einige gängige Methoden zur Rohrreinigung sind:
- Mechanische Reinigung: Mechanische Reinigungsmethoden umfassen das Verwenden von Werkzeugen wie Rohrreinigungsspiralen, Bürsten oder Schaber, um Ablagerungen von den Innenwänden der Rohre zu entfernen. Diese Methode ist effektiv bei der Entfernung von festen Ablagerungen wie Verkrustungen, Schlamm oder Sedimenten.
- Hochdruckreinigung: Hochdruckreinigung verwendet Wasser oder eine Mischung aus Wasser und Reinigungsmitteln, die unter hohem Druck durch die Rohre gepumpt wird, um Ablagerungen zu lösen und wegzuwaschen. Diese Methode ist besonders effektiv bei der Entfernung von fettigen Ablagerungen, Haaren oder organischen Materialien.
- Chemische Reinigung: Chemische Reinigungsmethoden verwenden spezielle Reinigungsmittel oder Lösungen, die in die Rohre eingebracht werden, um Ablagerungen chemisch zu lösen oder zu zersetzen. Diese Methode eignet sich gut für die Entfernung von Kalk, Rost, Korrosionsprodukten oder hartnäckigen Ablagerungen.
- Dampfreinigung: Dampfreinigung verwendet heißen Dampf, der durch die Rohre geleitet wird, um Ablagerungen zu lösen und zu entfernen. Diese Methode ist besonders effektiv bei der Entfernung von fettigen Ablagerungen, Bakterien oder organischen Materialien und kann gleichzeitig desinfizierend wirken.
Die Auswahl der geeigneten Reinigungsmethode hängt von verschiedenen Faktoren ab, darunter die Art der Ablagerungen, die Art des Rohrmaterials, die Betriebsbedingungen und die Anforderungen der Anwendung. Durch regelmäßige Rohrreinigung können Hersteller die Effizienz, Zuverlässigkeit und Lebensdauer ihrer Rohrleitungssysteme verbessern und Ausfallzeiten minimieren.
Rohrinstallation:
Die Rohrinstallation ist ein entscheidender Schritt bei der Errichtung eines Rohrleitungssystems und erfordert sorgfältige Planung, Vorbereitung und Ausführung, um eine zuverlässige und sichere Installation zu gewährleisten. Ein ordnungsgemäß installiertes Rohrleitungssystem trägt dazu bei, die Leistungsfähigkeit der Anlage zu maximieren, Betriebsausfälle zu minimieren und die Sicherheit der Arbeitsumgebung zu gewährleisten.
Einige wichtige Schritte bei der Rohrinstallation sind:
- Planung und Design: Die Planung und das Design des Rohrleitungssystems sind entscheidend für den Erfolg der Installation. Dies umfasst die Auswahl der geeigneten Rohre, Armaturen und Verbindungselemente, die Bestimmung der Rohrtrasse, die Berücksichtigung von Umweltfaktoren und die Einhaltung von Baustandards und Vorschriften.
- Vorbereitung der Baustelle: Die Baustelle muss für die Rohrinstallation vorbereitet werden, einschließlich der Schaffung eines sicheren Arbeitsbereichs, der Entfernung von Hindernissen, der Einrichtung von Baustellenzäunen und der Bereitstellung von geeigneten Werkzeugen und Ausrüstungen.
- Rohrverlegung: Die Rohre werden gemäß dem geplanten Layout verlegt und miteinander verbunden. Dies umfasst das Schneiden, Biegen, Schweißen oder Verbinden der Rohre gemäß den Anforderungen der Anwendung.
- Prüfung und Inspektion: Nach der Installation werden die Rohrleitungssysteme auf Dichtheit, Ausrichtung und Qualität der Verbindungen geprüft und inspiziert. Dies umfasst visuelle Inspektionen, Drucktests und gegebenenfalls zerstörungsfreie Prüfverfahren.
- Endbearbeitung: Nach der Installation werden die Rohre gegebenenfalls gereinigt, isoliert oder mit Oberflächenschutz versehen, um ihre Leistungsfähigkeit und Haltbarkeit zu verbessern.
Die Rohrinstallation erfordert Fachkenntnisse, Erfahrung und Sorgfalt, um sicherzustellen, dass das Rohrleitungssystem den Anforderungen der Anwendung entspricht und sicher und zuverlässig betrieben werden kann. Durch die Einhaltung bewährter Verfahren, Standards und Vorschriften können Hersteller hochwertige Rohrinstallationen durchführen und die Leistungsfähigkeit ihrer Anlagen maximieren.
Rohrleitungssicherheit:
Die Sicherheit von Rohrleitungen ist von entscheidender Bedeutung, um Unfälle, Umweltschäden und Betriebsausfälle zu verhindern. Rohrleitungssysteme transportieren eine Vielzahl von Medien, darunter Wasser, Chemikalien, Öl, Gas und Dampf, und müssen daher sicher betrieben, gewartet und überwacht werden, um potenzielle Gefahren zu minimieren. Ein umfassendes Sicherheitsmanagement umfasst verschiedene Aspekte, darunter:
- Konstruktions- und Materialauswahl: Die Auswahl geeigneter Rohrmaterialien und Konstruktionsstandards ist entscheidend für die Sicherheit von Rohrleitungen. Die Rohre müssen den Anforderungen der Anwendung und den geltenden Vorschriften entsprechen und eine ausreichende Festigkeit, Dichtigkeit und Beständigkeit gegenüber den transportierten Medien aufweisen.
- Installationsstandards: Die ordnungsgemäße Installation von Rohrleitungen gemäß den geltenden Standards und Vorschriften ist entscheidend für die Sicherheit und Zuverlässigkeit des Systems. Dies umfasst die Verwendung geeigneter Verbindungselemente, die korrekte Verlegung der Rohre, die ordnungsgemäße Fixierung und Unterstützung sowie die Durchführung von Prüfungen und Inspektionen.
- Betrieb und Wartung: Ein regelmäßiger Betrieb und eine regelmäßige Wartung der Rohrleitungssysteme sind entscheidend, um potenzielle Gefahren frühzeitig zu erkennen und zu beheben. Dies umfasst die Überwachung von Druck, Temperatur und Durchfluss, die Inspektion auf Undichtigkeiten oder Beschädigungen, die Reinigung von Ablagerungen und die Durchführung von Instandhaltungsarbeiten gemäß einem festgelegten Wartungsplan.
- Notfallvorsorge: Die Entwicklung und Implementierung von Notfallplänen und -verfahren ist wichtig, um im Falle von Leckagen, Unfällen oder anderen Notfällen schnell und angemessen reagieren zu können. Dies umfasst die Schulung des Personals, die Bereitstellung geeigneter Ausrüstung und Ressourcen, die Koordinierung mit lokalen Behörden und die regelmäßige Durchführung von Notfallübungen.
- Sicherheitsbewusstsein: Ein starkes Sicherheitsbewusstsein und eine Sicherheitskultur sind entscheidend, um das Risikobewusstsein zu fördern, sicherheitsrelevante Verhaltensweisen zu fördern und Mitarbeiter dazu zu ermutigen, potenzielle Gefahren zu melden und sicher zu arbeiten.
Durch die Umsetzung eines umfassenden Sicherheitsmanagements können Hersteller die Sicherheit ihrer Rohrleitungen verbessern, Betriebsausfälle minimieren und einen sicheren Arbeitsplatz für ihre Mitarbeiter gewährleisten.
Korrosionsschutz:
Korrosionsschutz ist ein wesentlicher Aspekt bei der Installation und dem Betrieb von Rohrleitungssystemen, insbesondere in Umgebungen, in denen die Rohre korrosiven Medien ausgesetzt sind. Korrosion kann die Integrität der Rohre beeinträchtigen, zu Leckagen führen und die Lebensdauer der Anlage verkürzen. Daher ist es wichtig, geeignete Maßnahmen zum Schutz vor Korrosion zu treffen.
Einige wichtige Methoden und Techniken zum Korrosionsschutz in Rohrleitungssystemen sind:
- Beschichtungen: Eine der häufigsten Methoden zum Korrosionsschutz ist die Verwendung von Beschichtungen auf der Oberfläche der Rohre. Diese Beschichtungen können aus verschiedenen Materialien wie Epoxidharz, Zink, Aluminium oder Polymeren bestehen und dienen dazu, die Oberfläche der Rohre vor direktem Kontakt mit korrosiven Medien zu schützen.
- Kathodischer Korrosionsschutz: Der kathodische Korrosionsschutz ist ein elektrochemisches Verfahren, bei dem eine Schutzspannung angelegt wird, um die Korrosion der Rohre zu verhindern oder zu reduzieren. Dies kann durch Opferanoden, Impressed-Current-Systeme oder Galvanisierung erreicht werden.
- Legierungen: Die Verwendung von korrosionsbeständigen Legierungen wie Edelstahl, Duplexstahl oder Nickellegierungen kann dazu beitragen, die Anfälligkeit der Rohre für Korrosion zu verringern und ihre Lebensdauer zu verlängern.
- Designoptimierung: Das Design der Rohrleitungssysteme kann so optimiert werden, dass potenzielle Korrosionsbereiche minimiert werden, z. B. durch die Vermeidung von Stagnationszonen, die Optimierung des Durchflusses oder die Auswahl geeigneter Materialien und Verbindungselemente.
- Regelmäßige Inspektion und Wartung: Eine regelmäßige Inspektion der Rohre auf Anzeichen von Korrosion und eine rechtzeitige Wartung können dazu beitragen, Korrosion frühzeitig zu erkennen und zu behandeln, bevor sie zu ernsthaften Problemen führt.
Durch die Implementierung geeigneter Korrosionsschutzmaßnahmen können Hersteller die Lebensdauer ihrer Rohrleitungssysteme verlängern, Betriebsausfälle minimieren und die Sicherheit und Zuverlässigkeit ihrer Anlagen gewährleisten.
Rohrleitungskennzeichnung:
Die Kennzeichnung von Rohrleitungen ist ein wichtiger Aspekt bei der Planung, Installation und dem Betrieb von Rohrleitungssystemen. Eine klare und einheitliche Kennzeichnung trägt dazu bei, die Sicherheit zu verbessern, die Effizienz zu steigern und das Risiko von Fehlern zu reduzieren. Die Kennzeichnung von Rohrleitungen sollte gemäß den geltenden Normen und Vorschriften erfolgen und alle relevanten Informationen enthalten, um eine sichere Identifizierung und Verwendung zu gewährleisten.
Einige wichtige Aspekte der Rohrleitungskennzeichnung sind:
- Farbcodierung: Die Verwendung von Farbcodes ist eine der häufigsten Methoden zur Kennzeichnung von Rohrleitungen. Jede Farbe entspricht einem bestimmten Medium oder einer bestimmten Art von Inhalt, wie Wasser, Dampf, Chemikalien oder Druckluft. Die Farbcodierung sollte einheitlich und leicht verständlich sein, um Verwechslungen zu vermeiden.
- Beschriftung: Neben der Farbcodierung sollten Rohrleitungen auch mit Beschriftungen versehen werden, die weitere Informationen wie den Inhalt, den Druck, die Durchflussrichtung, die Betriebstemperatur und andere relevante Daten enthalten. Diese Informationen können in Form von Aufklebern, Schildern oder Gravuren angebracht werden.
- Platzierung: Die Kennzeichnung von Rohrleitungen sollte gut sichtbar und leicht zugänglich angebracht werden, idealerweise in regelmäßigen Abständen entlang der gesamten Rohrstrecke. Dies erleichtert die Identifizierung und Verfolgung der Rohrleitung und ermöglicht es dem Personal, schnell und sicher auf die Informationen zuzugreifen.
- Einheitlichkeit: Es ist wichtig, dass die Kennzeichnung von Rohrleitungen einheitlich und konsistent erfolgt, um Verwirrung oder Missverständnisse zu vermeiden. Dies umfasst die Verwendung einheitlicher Farbcodes, Beschriftungen und Platzierungen gemäß den geltenden Standards und Vorschriften.
- Regelmäßige Überprüfung: Die Kennzeichnung von Rohrleitungen sollte regelmäßig überprüft und gewartet werden, um sicherzustellen, dass sie lesbar, aktuell und korrekt ist. Änderungen oder Ergänzungen an den Rohrleitungen sollten entsprechend aktualisiert werden.
Durch eine klare und einheitliche Kennzeichnung von Rohrleitungen können Hersteller die Sicherheit verbessern, die Effizienz steigern und das Risiko von Fehlern oder Unfällen reduzieren. Es ist wichtig, dass die Kennzeichnung gemäß den geltenden Normen und Vorschriften erfolgt und alle relevanten Informationen enthält, um eine sichere Identifizierung und Verwendung zu gewährleisten.
Rohrbiegemaschine:
Eine Rohrbiegemaschine ist eine spezialisierte Maschine, die verwendet wird, um Metallrohre in verschiedene Formen und Winkel zu biegen. Diese Maschinen sind in verschiedenen Ausführungen erhältlich, von einfachen Handhebel-Biegemaschinen bis hin zu computergesteuerten CNC-Biegemaschinen, die komplexe Biegungen mit hoher Präzision ausführen können. Die Rohrbiegemaschinen spielen eine wichtige Rolle in verschiedenen Branchen, darunter die Automobilindustrie, die Luft- und Raumfahrt, die Bauindustrie, die Schiffbauindustrie und die Fertigung von Möbeln und Metallstrukturen.
Einige wichtige Merkmale und Funktionen von Rohrbiegemaschinen sind:
- Biegekapazität: Die Biegekapazität einer Rohrbiegemaschine gibt an, welche Durchmesser und Wandstärken von Rohren sie verarbeiten kann. Je nach Anwendung und Material können Rohrbiegemaschinen unterschiedliche Biegekapazitäten haben, die von kleinen Durchmessern bis hin zu großen Rohren reichen können.
- Biegeverfahren: Es gibt verschiedene Biegeverfahren, die mit Rohrbiegemaschinen ausgeführt werden können, darunter das Druckbiegen, das Zugbiegen und das Rollbiegen. Jedes Verfahren hat seine eigenen Vor- und Nachteile und eignet sich für verschiedene Anwendungen und Materialien.
- Werkzeugausstattung: Rohrbiegemaschinen sind mit einer Vielzahl von Werkzeugen und Matrizen ausgestattet, die für unterschiedliche Biegeprofile und -winkel verwendet werden können. Diese Werkzeuge können aus verschiedenen Materialien wie Stahl, Hartmetall oder Kunststoff bestehen und sind in verschiedenen Formen und Größen erhältlich.
- Steuerungssysteme: Moderne Rohrbiegemaschinen sind oft mit computergesteuerten Steuerungssystemen ausgestattet, die es ermöglichen, komplexe Biegeprofile mit hoher Präzision und Wiederholgenauigkeit herzustellen. Diese CNC-Steuerungen bieten eine benutzerfreundliche Schnittstelle zur Programmierung und Überwachung der Biegevorgänge.
- Sicherheitsfunktionen: Rohrbiegemaschinen sind mit verschiedenen Sicherheitsfunktionen ausgestattet, um Unfälle und Verletzungen zu vermeiden. Dazu gehören Not-Aus-Schalter, Schutzeinrichtungen und Sicherheitsabdeckungen, die den Bediener vor beweglichen Teilen schützen.
Die Auswahl der geeigneten Rohrbiegemaschine hängt von verschiedenen Faktoren ab, darunter die Art der zu bearbeitenden Rohre, die gewünschten Biegeprofile, die Produktionsanforderungen und das Budget. Durch den Einsatz von hochwertigen Rohrbiegemaschinen können Hersteller präzise und effizient gebogene Rohre herstellen und ihre Fertigungsprozesse optimieren.
Rohrverschraubungen:
Rohrverschraubungen sind Verbindungselemente, die verwendet werden, um Rohre miteinander zu verbinden oder Rohre mit anderen Bauteilen wie Armaturen, Ventilen oder Rohrleitungssystemen zu verbinden. Sie spielen eine wichtige Rolle bei der Montage und Installation von Rohrleitungssystemen in verschiedenen Anwendungen und Branchen. Rohrverschraubungen sind in einer Vielzahl von Ausführungen erhältlich, um den unterschiedlichen Anforderungen verschiedener Anwendungen gerecht zu werden.
Einige wichtige Merkmale und Funktionen von Rohrverschraubungen sind:
- Gewindearten: Rohrverschraubungen können verschiedene Gewindearten aufweisen, darunter Außengewinde, Innengewinde oder Kombinationen aus beiden. Die Auswahl der geeigneten Gewindeart hängt von den zu verbindenden Rohren und den Anforderungen der Anwendung ab.
- Materialien: Rohrverschraubungen sind aus verschiedenen Materialien erhältlich, darunter Stahl, Edelstahl, Messing, Kupfer, Kunststoffe und andere Legierungen. Die Auswahl des geeigneten Materials hängt von den Betriebsbedingungen, den transportierten Medien und den Anforderungen an Festigkeit, Korrosionsbeständigkeit und Temperaturbeständigkeit ab.
- Typen: Es gibt verschiedene Arten von Rohrverschraubungen, darunter Adapter, Muffen, Nippel, Kupplungen, T-Stücke, Winkelstücke, Reduzierstücke und Endkappen. Jeder Typ hat spezifische Anwendungen und Funktionen und kann je nach Bedarf ausgewählt werden.
- Dichtungssysteme: Viele Rohrverschraubungen sind mit Dichtungssystemen ausgestattet, um eine dichte und sichere Verbindung zwischen den Rohren herzustellen. Diese Dichtungssysteme können O-Ringe, Flachdichtungen, Konusdichtungen oder andere Abdichtungselemente umfassen, die für die spezifische Anwendung geeignet sind.
- Montage: Rohrverschraubungen können auf verschiedene Weise montiert werden, einschließlich Handmontage, maschineller Montage oder Schweißen. Die Auswahl der geeigneten Montagemethode hängt von den Anforderungen der Anwendung, der Verfügbarkeit von Ausrüstung und Fachkenntnissen sowie den Kosten ab.
Die Auswahl der geeigneten Rohrverschraubungen hängt von verschiedenen Faktoren ab, darunter die Art der zu verbindenden Rohre, die Betriebsbedingungen, die Anforderungen der Anwendung und die Präferenzen des Herstellers. Durch den Einsatz hochwertiger Rohrverschraubungen können Hersteller eine zuverlässige und sichere Verbindung zwischen Rohren herstellen und die Leistungsfähigkeit ihrer Rohrleitungssysteme verbessern.
Rohrschneider:
Ein Rohrschneider ist ein Werkzeug, das zum Schneiden von Metallrohren verwendet wird und in verschiedenen Ausführungen erhältlich ist, um unterschiedlichen Anforderungen gerecht zu werden. Rohrschneider sind in verschiedenen Größen und Typen erhältlich, einschließlich manueller Rohrschneider, automatischer Rohrschneider und Rohrschneidemaschinen. Sie spielen eine wichtige Rolle bei der Montage, Installation und Wartung von Rohrleitungssystemen in verschiedenen Branchen und Anwendungen.
Einige wichtige Merkmale und Funktionen von Rohrschneidern sind:
- Schneidemechanismus: Rohrschneider können verschiedene Schneidemechanismen aufweisen, darunter Rollschneider, Schneidrädchen, Klingen oder Sägeblätter, die je nach Material und Durchmesser des Rohres verwendet werden können. Die Auswahl des geeigneten Schneidemechanismus hängt von den Anforderungen der Anwendung und der Art des zu schneidenden Materials ab.
- Größe und Kapazität: Rohrschneider sind in verschiedenen Größen und Kapazitäten erhältlich, um Rohre mit unterschiedlichen Durchmessern und Wandstärken zu schneiden. Die Auswahl der geeigneten Größe und Kapazität hängt von den spezifischen Anforderungen der Anwendung und den zu bearbeitenden Rohren ab.
- Typen: Es gibt verschiedene Typen von Rohrschneidern, darunter manuelle Rohrschneider, die von Hand bedient werden, automatische Rohrschneider, die durch eine automatische Vorschubeinheit angetrieben werden, und Rohrschneidemaschinen, die für die Massenproduktion oder die Bearbeitung großer Rohrdurchmesser verwendet werden können.
- Präzision und Genauigkeit: Moderne Rohrschneider sind mit präzisen Schneidmechanismen ausgestattet, die eine hohe Genauigkeit und Wiederholbarkeit der Schnitte gewährleisten. Dies ist besonders wichtig für Anwendungen, bei denen enge Toleranzen eingehalten werden müssen oder wo eine hohe Oberflächenqualität erforderlich ist.
- Bedienerfreundlichkeit: Rohrschneider sollten benutzerfreundlich und einfach zu bedienen sein, um eine effiziente und sichere Bedienung zu gewährleisten. Dies umfasst ergonomische Griffe, einfache Einstellmöglichkeiten und klare Anweisungen zur Handhabung und Wartung.
Die Auswahl des geeigneten Rohrschneiders hängt von verschiedenen Faktoren ab, darunter die Art und Größe der zu schneidenden Rohre, die Anforderungen der Anwendung, das Budget und die Präferenzen des Bedieners. Durch den Einsatz hochwertiger Rohrschneider können Hersteller präzise und saubere Schnitte an Rohren durchführen und die Effizienz ihrer Fertigungsprozesse verbessern.
Rohrbiegevorrichtung:
Eine Rohrbiegevorrichtung ist ein Werkzeug oder eine Maschine, die zum Biegen von Metallrohren verwendet wird, um verschiedene Biegungen, Winkel und Radien zu erzeugen. Diese Vorrichtungen sind in verschiedenen Ausführungen erhältlich, von einfachen Handwerkzeugen bis hin zu automatisierten CNC-gesteuerten Biegemaschinen, die komplexe Biegungen mit hoher Präzision ausführen können. Rohrbiegevorrichtungen sind in verschiedenen Branchen weit verbreitet, darunter die Automobilindustrie, die Luft- und Raumfahrt, die Bauindustrie und die Fertigung von Metallkomponenten und -strukturen.
Einige wichtige Merkmale und Funktionen von Rohrbiegevorrichtungen sind:
- Biegekapazität: Die Biegekapazität einer Rohrbiegevorrichtung gibt an, welche Durchmesser und Wandstärken von Rohren sie verarbeiten kann. Je nach Anwendung und Material können Rohrbiegevorrichtungen unterschiedliche Biegekapazitäten haben, die von kleinen Durchmessern bis hin zu großen Rohren reichen können.
- Biegeverfahren: Es gibt verschiedene Biegeverfahren, die mit Rohrbiegevorrichtungen durchgeführt werden können, darunter das Druckbiegen, das Zugbiegen und das Rollbiegen. Jedes Verfahren hat seine eigenen Vor- und Nachteile und eignet sich für verschiedene Anwendungen und Materialien.
- Werkzeugausstattung: Rohrbiegevorrichtungen sind mit einer Vielzahl von Biegewerkzeugen und Matrizen ausgestattet, die für unterschiedliche Biegeprofile und -winkel verwendet werden können. Diese Werkzeuge können aus verschiedenen Materialien wie Stahl, Hartmetall oder Kunststoff bestehen und sind in verschiedenen Formen und Größen erhältlich.
- Steuerungssysteme: Moderne Rohrbiegevorrichtungen sind oft mit computergesteuerten Steuerungssystemen ausgestattet, die es ermöglichen, komplexe Biegeprofile mit hoher Präzision und Wiederholgenauigkeit herzustellen. Diese CNC-Steuerungen bieten eine benutzerfreundliche Schnittstelle zur Programmierung und Überwachung der Biegevorgänge.
- Sicherheitsfunktionen: Rohrbiegevorrichtungen sind mit verschiedenen Sicherheitsfunktionen ausgestattet, um Unfälle und Verletzungen zu vermeiden. Dazu gehören Not-Aus-Schalter, Schutzeinrichtungen und Sicherheitsabdeckungen, die den Bediener vor beweglichen Teilen schützen.
Die Auswahl der geeigneten Rohrbiegevorrichtung hängt von verschiedenen Faktoren ab, darunter die Art der zu bearbeitenden Rohre, die gewünschten Biegeprofile, die Produktionsanforderungen und das Budget. Durch den Einsatz hochwertiger Rohrbiegevorrichtungen können Hersteller präzise und effizient gebogene Rohre herstellen und ihre Fertigungsprozesse optimieren.
Rohrherstellung:
Die Rohrherstellung ist ein komplexer Prozess, bei dem Metallrohre in verschiedenen Größen, Formen und Spezifikationen hergestellt werden, um den Anforderungen verschiedener Anwendungen gerecht zu werden. Die Rohrherstellung umfasst verschiedene Schritte, die sorgfältige Planung, Materialauswahl, Fertigungstechniken und Qualitätskontrolle erfordern. Metallrohre werden in einer Vielzahl von Branchen verwendet, darunter die Automobilindustrie, die Bauindustrie, die Öl- und Gasindustrie, die Luft- und Raumfahrt, die Elektronikindustrie und viele andere.
Einige wichtige Schritte im Prozess der Rohrherstellung sind:
- Materialauswahl: Die Auswahl des geeigneten Rohrmaterials ist entscheidend für die Qualität und Leistungsfähigkeit der hergestellten Rohre. Metallrohre können aus verschiedenen Materialien hergestellt werden, darunter Stahl, Edelstahl, Aluminium, Kupfer, Messing, Titan und andere Legierungen, je nach den Anforderungen der Anwendung und den Betriebsbedingungen.
- Rohrherstellungstechniken: Es gibt verschiedene Techniken zur Herstellung von Metallrohren, darunter nahtlose Rohrherstellung, geschweißte Rohrherstellung, Extrusion, Walzen, Ziehen und Formen. Jede Technik hat ihre eigenen Vor- und Nachteile und eignet sich für verschiedene Anwendungen und Materialien.
- Formgebung und Bearbeitung: Nach der Herstellung des Rohrmaterials werden die Rohre geformt, bearbeitet und dimensioniert, um die gewünschten Spezifikationen zu erfüllen. Dies kann das Biegen, Schneiden, Stanzen, Schweißen, Lochen, Bohren, Gewindeschneiden und andere Bearbeitungsschritte umfassen.
- Qualitätskontrolle: Während des gesamten Herstellungsprozesses werden die Rohre auf Qualität, Maßgenauigkeit, Oberflächenbeschaffenheit, Festigkeit, Härte, Korrosionsbeständigkeit und andere Eigenschaften geprüft und überwacht, um sicherzustellen, dass sie den Anforderungen der Anwendung entsprechen.
- Endbearbeitung und Oberflächenbehandlung: Nach der Herstellung werden die Rohre gegebenenfalls endbearbeitet, gereinigt, poliert, beschichtet, lackiert oder anderweitig behandelt, um ihre Oberflächenqualität zu verbessern, ihre Haltbarkeit zu erhöhen und sie für den Einsatz vorzubereiten.
Die Rohrherstellung erfordert Fachkenntnisse, Erfahrung und modernste Fertigungstechnologien, um qualitativ hochwertige und präzise Rohre herzustellen, die den Anforderungen der Anwendung gerecht werden. Durch die Einhaltung bewährter Verfahren, Standards und Qualitätskontrollen können Hersteller die Leistungsfähigkeit ihrer Rohrprodukte maximieren und die Kundenzufriedenheit gewährleisten.
Hydraulische Pressen sind unverzichtbare Werkzeuge in der modernen Industrie. Sie spielen eine zentrale Rolle in zahlreichen Produktionsprozessen, von der Automobilherstellung bis hin zur Luft- und Raumfahrttechnik. Ihr breites Anwendungsspektrum und ihre Leistungsfähigkeit machen sie zu einem Schlüsselinstrument in der Fertigung und Bearbeitung von Materialien. In diesem Artikel werden wir die verschiedenen Aspekte hydraulischer Pressen untersuchen, ihre Funktionsweise, die unterschiedlichen Typen, ihre Anwendungen in verschiedenen Industriezweigen und die Materialien, die mit diesen Pressen bearbeitet werden können. Ziel ist es, ein umfassendes Verständnis für diese faszinierende Technologie zu vermitteln und ihre Bedeutung in der industriellen Praxis aufzuzeigen.
Hydraulische Pressen basieren auf dem Prinzip der Hydraulik, einer Technologie, die Flüssigkeiten zur Übertragung von Kraft und Bewegung nutzt. Diese Maschinen sind in der Lage, enorme Kräfte zu erzeugen, die weit über die Möglichkeiten mechanischer Pressen hinausgehen. Dadurch können sie auch die härtesten Materialien formen, schneiden und bearbeiten. Die Hydraulik selbst hat eine lange Geschichte, die bis in die Antike zurückreicht, aber ihre moderne Anwendung in Pressen ist ein Ergebnis jahrzehntelanger Entwicklung und Innovation.
Ein wesentlicher Vorteil hydraulischer Pressen liegt in ihrer Flexibilität und Anpassungsfähigkeit. Sie können für eine Vielzahl von Aufgaben konfiguriert werden, von einfachen Biege- und Stanzvorgängen bis hin zu komplexen Umformprozessen. Diese Vielseitigkeit macht sie zu einem unverzichtbaren Werkzeug in vielen Fertigungsprozessen. Darüber hinaus haben Fortschritte in der Hydrauliktechnologie zur Entwicklung von Pressen geführt, die nicht nur leistungsfähiger, sondern auch effizienter und umweltfreundlicher sind.
Im Laufe dieses Artikels werden wir die Funktionsweise hydraulischer Pressen detailliert erklären und die verschiedenen Typen von Pressen, die in der Industrie verwendet werden, vorstellen. Wir werden auch auf die verschiedenen Anwendungen dieser Pressen eingehen und aufzeigen, wie sie in verschiedenen Branchen eingesetzt werden, um spezifische Produktionsanforderungen zu erfüllen. Schließlich werden wir die Materialien untersuchen, die mit hydraulischen Pressen bearbeitet werden können, und einen Blick auf die zukünftigen Entwicklungen und Innovationen in der Hydraulikpresstechnologie werfen.
Hydraulische Pressen sind weit mehr als nur Maschinen, die Materialien bearbeiten. Sie sind Symbole für technologische Innovation und industrielle Effizienz. Ihre Fähigkeit, große Kräfte präzise zu kontrollieren und auf Materialien anzuwenden, hat die Art und Weise, wie wir Produkte herstellen und Materialien formen, revolutioniert. Dieser Artikel soll ein tieferes Verständnis für diese bemerkenswerte Technologie vermitteln und ihre Bedeutung in der modernen Industrie hervorheben.
Grundlagen der hydraulischen Pressen
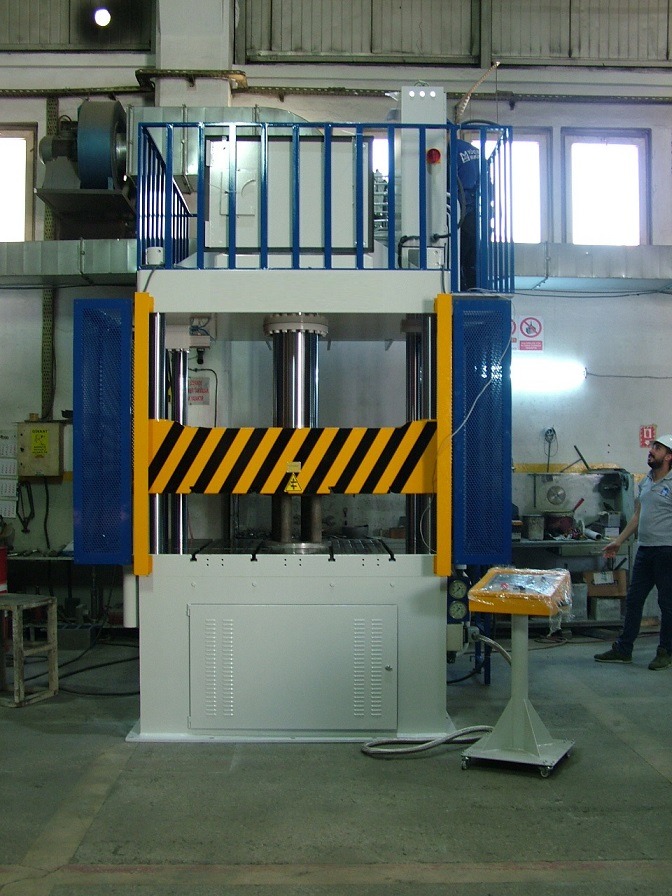
Funktionsweise
Hydraulische Pressen nutzen das Prinzip der Hydraulik, um große Kräfte zu erzeugen und auf Werkstücke anzuwenden. Das grundlegende Prinzip der Hydraulik beruht auf dem Gesetz von Pascal, das besagt, dass ein Druck, der auf eine eingeschlossene Flüssigkeit ausgeübt wird, in alle Richtungen gleichmäßig übertragen wird. Dies bedeutet, dass durch die Anwendung einer kleinen Kraft auf einen kleinen Kolben eine viel größere Kraft auf einen größeren Kolben ausgeübt werden kann.
Eine typische hydraulische Presse besteht aus den folgenden Hauptkomponenten:
- Hydraulikpumpe: Die Pumpe erzeugt den erforderlichen Druck, indem sie Hydraulikflüssigkeit in das System presst.
- Hydraulikzylinder: Der Zylinder enthält die Kolben, die die mechanische Arbeit verrichten. Wenn die Hydraulikflüssigkeit in den Zylinder gepumpt wird, drückt sie den Kolben nach unten.
- Ventile: Diese steuern den Fluss der Hydraulikflüssigkeit und sorgen dafür, dass der Druck gleichmäßig und kontrolliert aufrechterhalten wird.
- Rahmen: Der Rahmen der Presse hält alle Komponenten zusammen und bietet die notwendige strukturelle Unterstützung, um den hohen Kräften standzuhalten.
Der Prozess beginnt, wenn die Hydraulikpumpe eingeschaltet wird und die Hydraulikflüssigkeit unter Druck gesetzt wird. Diese Flüssigkeit wird durch die Ventile in den Hydraulikzylinder geleitet. Der Druck der Flüssigkeit zwingt den Kolben im Zylinder nach unten, wodurch eine große Kraft auf das Werkstück ausgeübt wird, das sich auf einem festen Untergrund befindet. Durch die Kontrolle der Menge und des Drucks der Hydraulikflüssigkeit kann die Kraft, die auf das Werkstück ausgeübt wird, präzise gesteuert werden.
Geschichtliche Entwicklung
Die Geschichte der hydraulischen Pressen ist eng mit der Entwicklung der Hydrauliktechnologie verbunden. Die Grundlagen der Hydraulik wurden erstmals im 17. Jahrhundert von Blaise Pascal formuliert, der das nach ihm benannte Pascal’sche Gesetz entwickelte. Dieses Gesetz legte den Grundstein für die Entwicklung moderner Hydrauliksysteme.
Im 19. Jahrhundert begann die industrielle Anwendung der Hydraulik, insbesondere durch den britischen Ingenieur Joseph Bramah, der als einer der Pioniere der hydraulischen Pressentechnologie gilt. Bramah patentierte 1795 eine hydraulische Presse, die als „Bramah-Presse“ bekannt wurde. Diese frühe Presse nutzte Wasserdruck, um große Kräfte zu erzeugen und revolutionierte die Metallbearbeitung und andere industrielle Prozesse.
Mit der Weiterentwicklung der Hydraulikpumpen und -systeme im 20. Jahrhundert wurden hydraulische Pressen immer leistungsfähiger und vielseitiger. Die Einführung von Hochdruckhydrauliksystemen ermöglichte die Herstellung von Pressen, die Kräfte von mehreren tausend Tonnen erzeugen konnten. Diese Pressen fanden breite Anwendung in der Automobilindustrie, der Luft- und Raumfahrttechnik und vielen anderen Bereichen.
Heutzutage sind hydraulische Pressen High-Tech-Maschinen, die mit präzisen Steuerungssystemen ausgestattet sind und in der Lage sind, komplexe Umformprozesse mit hoher Genauigkeit durchzuführen. Sie sind unverzichtbare Werkzeuge in der modernen Fertigung und spielen eine entscheidende Rolle in zahlreichen industriellen Anwendungen.
Typen von hydraulischen Pressen
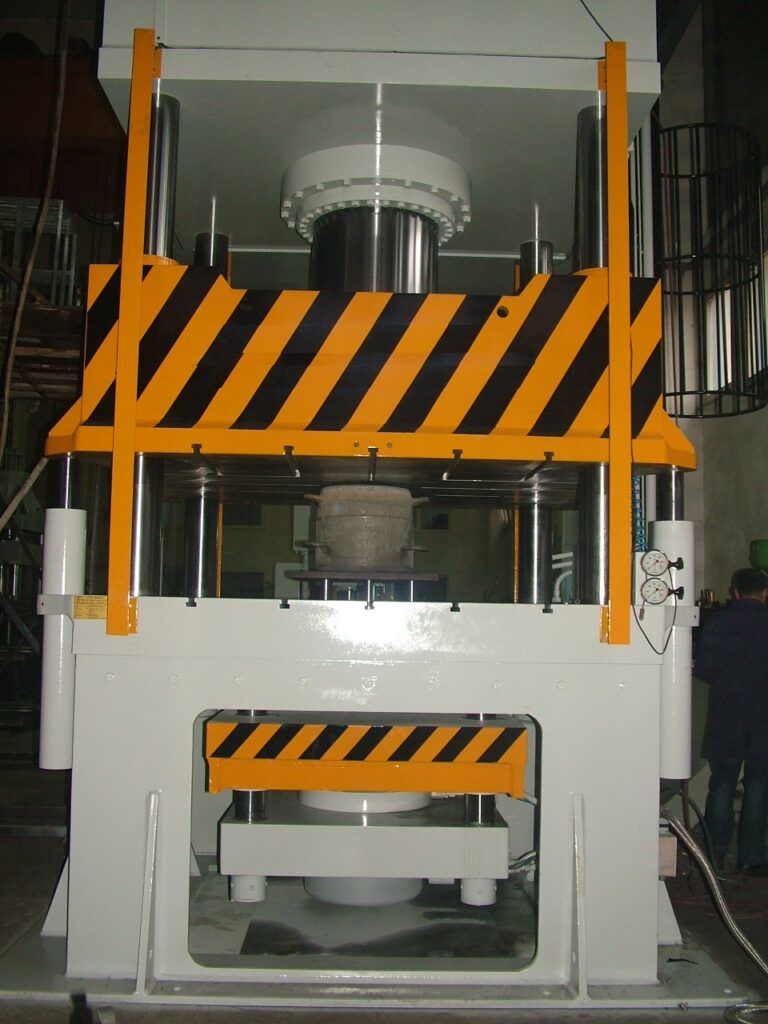
Einfache hydraulische Pressen
Einfache hydraulische Pressen, auch als Einstufen- oder Einständerpressen bekannt, sind die grundlegendste Form hydraulischer Pressen. Sie bestehen aus einem einzelnen Hydraulikzylinder, der eine vertikale Bewegung ausführt, um Druck auf ein Werkstück auszuüben. Diese Pressen sind ideal für einfache Aufgaben wie Biegen, Stanzen, Pressen und Montieren. Sie zeichnen sich durch ihre einfache Konstruktion, Zuverlässigkeit und Benutzerfreundlichkeit aus. Typische Anwendungen finden sich in kleinen Werkstätten und bei der Herstellung von Bauteilen in geringeren Stückzahlen.
Die Hauptmerkmale einfacher hydraulischer Pressen sind:
- Kompakte Bauweise: Aufgrund ihrer Einfachheit nehmen sie wenig Platz ein und sind leicht zu warten.
- Vielseitigkeit: Sie können für eine Vielzahl von Anwendungen angepasst werden, indem verschiedene Werkzeuge und Vorrichtungen verwendet werden.
- Kosteneffizienz: Sie sind in der Regel kostengünstiger in der Anschaffung und im Betrieb als komplexere Pressensysteme.
Doppeltwirkende hydraulische Pressen
Doppeltwirkende hydraulische Pressen, auch als Zweistufenpressen bekannt, verwenden zwei Hydraulikzylinder, um sowohl eine Druck- als auch eine Rückzugsbewegung zu erzeugen. Dies ermöglicht eine höhere Präzision und Kontrolle über den Pressvorgang. Diese Pressen sind besonders nützlich für Anwendungen, die einen gleichmäßigen Druckverlauf und eine genaue Positionierung erfordern, wie z.B. das Tiefziehen von Metallen, das Formen von Kunststoffteilen und das Kalibrieren von Werkstücken.
Die Hauptmerkmale doppeltwirkender hydraulischer Pressen sind:
- Erhöhte Präzision: Durch die Verwendung von zwei Zylindern kann die Bewegung des Presskopfes genauer gesteuert werden.
- Gleichmäßiger Druckverlauf: Sie bieten eine gleichmäßigere Druckverteilung während des gesamten Pressvorgangs, was zu höherer Qualität der bearbeiteten Werkstücke führt.
- Flexibilität: Sie können in einer Vielzahl von industriellen Prozessen eingesetzt werden, die eine präzise Steuerung erfordern.
Spezialhydraulikpressen
Spezialhydraulikpressen sind für spezifische Anwendungen und Anforderungen ausgelegt. Sie umfassen eine breite Palette von Pressen, die für besondere Aufgaben konzipiert sind, wie z.B. Pulvermetallurgiepressen, Schmiedepressen, und Hydroforming-Pressen.
- Pulvermetallurgiepressen: Diese Pressen werden verwendet, um pulverförmige Materialien unter hohem Druck zu verdichten und zu formen. Sie sind entscheidend in der Herstellung von gesinterten Bauteilen, die in der Automobil- und Werkzeugindustrie weit verbreitet sind.
- Schmiedepressen: Diese Pressen sind für die Umformung von Metallen bei hohen Temperaturen ausgelegt. Sie erzeugen extreme Kräfte, die notwendig sind, um Metalle in die gewünschte Form zu bringen. Schmiedepressen werden häufig in der Herstellung von Komponenten für die Luft- und Raumfahrt, den Maschinenbau und die Automobilindustrie eingesetzt.
- Hydroforming-Pressen: Diese spezialisierte Form der hydraulischen Presse verwendet Hochdruckflüssigkeit, um Rohre und Bleche in komplexe Formen zu bringen. Hydroforming ist besonders in der Automobilindustrie beliebt, um leichte und dennoch starke Bauteile herzustellen.
Die Hauptmerkmale von Spezialhydraulikpressen sind:
- Anpassung an spezifische Anwendungen: Sie sind speziell für bestimmte industrielle Prozesse und Anforderungen entwickelt.
- Hohe Leistung und Effizienz: Diese Pressen sind in der Lage, sehr hohe Kräfte und Drücke zu erzeugen, um anspruchsvolle Aufgaben zu bewältigen.
- Technologische Innovationen: Sie beinhalten oft fortschrittliche Technologien und Materialien, um ihre Leistung und Zuverlässigkeit zu maximieren.
Anwendungen von hydraulischen Pressen
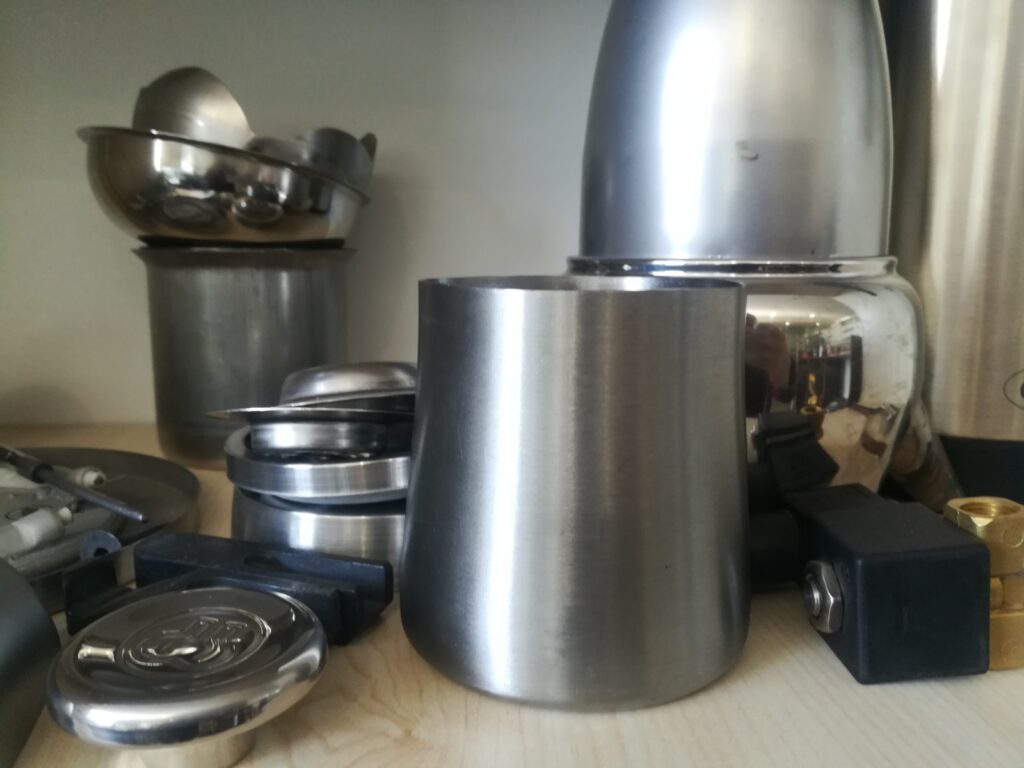
Hydraulische Pressen finden in einer Vielzahl von Industriezweigen Anwendung. Ihre Fähigkeit, große Kräfte präzise zu kontrollieren, macht sie zu einem unverzichtbaren Werkzeug in der Fertigung und Bearbeitung. Im Folgenden werden einige der wichtigsten Anwendungsgebiete detailliert beschrieben.
Automobilindustrie
Die Automobilindustrie ist einer der größten Nutzer hydraulischer Pressen. Diese Maschinen sind entscheidend für die Herstellung einer Vielzahl von Fahrzeugkomponenten.
- Blechumformung: Hydraulische Pressen werden verwendet, um Karosserieteile aus Blech zu formen. Die Fähigkeit, große Flächen mit gleichmäßigem Druck zu bearbeiten, ermöglicht die Herstellung von komplexen Formen und Strukturen.
- Montage von Bauteilen: Hydraulische Pressen kommen auch bei der Montage von Fahrzeugkomponenten zum Einsatz. Dies umfasst das Einpressen von Lagern, das Montieren von Motor- und Getriebekomponenten sowie das Fügen von Fahrwerksteilen.
- Recycling: Alte Fahrzeuge werden oft in Schrottpressen zerlegt, die hydraulische Pressen verwenden, um das Material zu verdichten und für die Wiederverwertung vorzubereiten.
Luft- und Raumfahrt
In der Luft- und Raumfahrtindustrie sind hydraulische Pressen unverzichtbar für die Herstellung von leichten, aber starken Komponenten.
- Umformung von Aluminium- und Titanlegierungen: Diese Materialien sind wegen ihrer Festigkeit und Leichtigkeit in der Luftfahrt sehr beliebt. Hydraulische Pressen werden verwendet, um diese Metalle in präzise Formen zu bringen, die in Flugzeugen und Raumfahrzeugen benötigt werden.
- Kompositmaterialien: In der modernen Luftfahrt werden zunehmend Verbundwerkstoffe verwendet. Hydraulische Pressen spielen eine wichtige Rolle bei der Herstellung und Formung dieser Materialien.
- Test- und Prüfverfahren: Hydraulische Pressen werden auch für Tests und Prüfungen von Bauteilen unter extremen Bedingungen eingesetzt, um ihre Festigkeit und Zuverlässigkeit zu gewährleisten.
Bauindustrie
In der Bauindustrie kommen hydraulische Pressen in verschiedenen Bereichen zum Einsatz, von der Herstellung von Bauelementen bis hin zur Wartung von Maschinen.
- Herstellung von Betonbauteilen: Hydraulische Pressen werden verwendet, um Betonblöcke, -platten und -pfeiler zu formen. Der hohe Druck ermöglicht eine dichte und gleichmäßige Verdichtung des Betons.
- Formen und Biegen von Stahlträgern: Stahl ist ein zentrales Baumaterial, und hydraulische Pressen werden verwendet, um Stahlträger in die gewünschten Formen und Größen zu bringen.
- Reparatur und Wartung: Hydraulische Pressen sind auch in der Wartung und Reparatur von Baumaschinen von Bedeutung, insbesondere beim Austausch von Lagern und anderen verschleißanfälligen Komponenten.
Recycling
Die Recyclingindustrie nutzt hydraulische Pressen, um Materialien zu verdichten und für die Wiederverwertung vorzubereiten.
- Schrottpressen: Hydraulische Pressen werden verwendet, um Metallschrott in kompakte Blöcke zu pressen, die leichter zu transportieren und zu recyceln sind.
- Papierrecycling: Auch in der Papierindustrie kommen hydraulische Pressen zum Einsatz, um Altpapier zu Ballen zu pressen und für den Recyclingprozess vorzubereiten.
- Kunststoffrecycling: Kunststoffabfälle werden mithilfe hydraulischer Pressen verdichtet und zu handlichen Paketen verarbeitet, die in Recyclinganlagen weiterverarbeitet werden können.
Weitere Anwendungen
Neben den oben genannten Bereichen gibt es viele weitere Anwendungen für hydraulische Pressen.
- Schmuckherstellung: In der Schmuckindustrie werden hydraulische Pressen verwendet, um Edelmetalle und -steine zu formen und zu bearbeiten.
- Elektronikindustrie: Hydraulische Pressen spielen eine Rolle bei der Herstellung und Montage von elektronischen Komponenten, indem sie Präzision und Genauigkeit bei der Bearbeitung gewährleisten.
- Lebensmittelindustrie: In der Lebensmittelverarbeitung werden hydraulische Pressen verwendet, um Öle aus Samen zu extrahieren, Fruchtsäfte zu pressen und verschiedene Lebensmittelprodukte zu formen und zu verpacken.
Die Vielseitigkeit hydraulischer Pressen macht sie zu einem unverzichtbaren Werkzeug in zahlreichen Industriezweigen. Ihre Fähigkeit, große Kräfte präzise zu kontrollieren und auf eine Vielzahl von Materialien anzuwenden, ermöglicht eine breite Palette von Anwendungen, die von der Herstellung und Montage bis hin zum Recycling und zur Qualitätsprüfung reichen.
Materialien, die bei hydraulischen Pressen verwendet werden
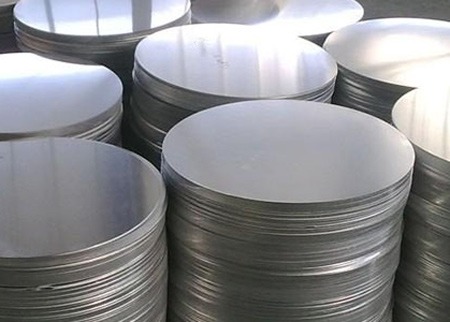
Hydraulische Pressen sind in der Lage, eine Vielzahl von Materialien zu bearbeiten, von Metallen und Kunststoffen bis hin zu Verbundwerkstoffen. Die Wahl des Materials hängt von der spezifischen Anwendung und den gewünschten Eigenschaften des Endprodukts ab. In diesem Abschnitt werden die wichtigsten Materialien und ihre Eigenschaften sowie ihre Verwendung in hydraulischen Pressen beschrieben.
Metalle
Metalle sind das häufigste Material, das mit hydraulischen Pressen bearbeitet wird. Ihre Festigkeit, Formbarkeit und Vielseitigkeit machen sie ideal für zahlreiche industrielle Anwendungen.
- Stahl
- Eigenschaften: Stahl ist ein hochfestes Material, das sowohl in seiner reinen Form als auch in Legierungen verwendet wird. Es ist widerstandsfähig gegen Verschleiß und Korrosion und kann in eine Vielzahl von Formen gebracht werden.
- Verwendung: Hydraulische Pressen werden verwendet, um Stahl in der Automobil-, Bau- und Maschinenbauindustrie zu formen, zu biegen und zu stanzen. Beispiele sind Karosserieteile, Stahlträger und Maschinenteile.
- Aluminium
- Eigenschaften: Aluminium ist leicht, korrosionsbeständig und hat eine gute elektrische und thermische Leitfähigkeit. Es ist jedoch weniger fest als Stahl und erfordert präzisere Steuerung während der Bearbeitung.
- Verwendung: Aluminium wird häufig in der Luft- und Raumfahrtindustrie sowie in der Automobilindustrie verwendet, um leichte und dennoch starke Bauteile herzustellen. Hydraulische Pressen formen Aluminiumbleche und -profile für Flugzeugrümpfe, Fahrzeugkarosserien und Elektronikgehäuse.
- Kupfer
- Eigenschaften: Kupfer hat eine ausgezeichnete elektrische und thermische Leitfähigkeit und ist leicht formbar. Es ist jedoch teurer als viele andere Metalle.
- Verwendung: Hydraulische Pressen werden verwendet, um Kupferdrähte, Rohre und elektronische Bauteile zu formen. Kupfer wird häufig in der Elektronik- und Energieindustrie verwendet.
- Titan
- Eigenschaften: Titan ist extrem leicht, aber sehr fest und korrosionsbeständig. Es ist schwerer zu bearbeiten als viele andere Metalle und erfordert spezielle Pressen und Werkzeuge.
- Verwendung: In der Luft- und Raumfahrt sowie in der Medizintechnik wird Titan für kritische Bauteile verwendet. Hydraulische Pressen formen Titan für Flugzeugkomponenten, Implantate und Hochleistungsausrüstung.
Kunststoffe
Kunststoffe sind aufgrund ihrer Vielseitigkeit und ihrer günstigen Herstellungskosten ein weiteres wichtiges Material für hydraulische Pressen.
- Thermoplaste
- Eigenschaften: Thermoplaste wie Polyethylen (PE), Polypropylen (PP) und Polyvinylchlorid (PVC) sind formbar bei hohen Temperaturen und können mehrfach geformt werden.
- Verwendung: Hydraulische Pressen werden verwendet, um Thermoplaste in Formen zu spritzen, zu extrudieren und zu pressen. Sie finden Anwendung in der Verpackungsindustrie, der Automobilindustrie und der Herstellung von Haushaltsgeräten.
- Duroplaste
- Eigenschaften: Duroplaste wie Epoxidharze und Phenolharze sind fest und hitzebeständig, können jedoch nach dem Aushärten nicht erneut geformt werden.
- Verwendung: Diese Kunststoffe werden in der Elektronikindustrie für Leiterplatten und in der Automobilindustrie für hitzebeständige Teile verwendet. Hydraulische Pressen formen Duroplaste durch Druck und Hitze in ihre endgültige Form.
Verbundwerkstoffe
Verbundwerkstoffe kombinieren zwei oder mehr Materialien, um die besten Eigenschaften jedes Materials zu nutzen. Sie sind besonders wichtig in der Luft- und Raumfahrt sowie in der Automobilindustrie.
- Faserverstärkte Kunststoffe (FVK)
- Eigenschaften: FVK bestehen aus einer Polymermatrix, die mit Fasern wie Glas, Kohlenstoff oder Aramid verstärkt ist. Diese Materialien sind leicht, aber extrem fest und steif.
- Verwendung: Hydraulische Pressen werden verwendet, um FVK in komplexe Formen für Flugzeugteile, Automobilkarosserien und Sportgeräte zu pressen. Der hohe Druck ermöglicht eine gleichmäßige Verteilung der Fasern und eine feste Verbindung mit der Polymermatrix.
- Metallmatrix-Verbundwerkstoffe (MMV)
- Eigenschaften: MMV kombinieren Metall mit keramischen oder metallischen Verstärkungsmaterialien. Diese Werkstoffe bieten eine höhere Festigkeit und Temperaturbeständigkeit als reine Metalle.
- Verwendung: In der Raumfahrt und im Militär werden MMV für Anwendungen verwendet, die extreme Festigkeit und Beständigkeit erfordern. Hydraulische Pressen formen diese Materialien für hochbelastbare Strukturbauteile und Schutzpanzerungen.
Weitere Materialien
Neben den oben genannten Materialien gibt es viele andere, die mit hydraulischen Pressen bearbeitet werden können.
- Gummi
- Eigenschaften: Gummi ist elastisch und widerstandsfähig gegen Abrieb und Chemikalien. Er kann in verschiedenen Härtegraden hergestellt werden.
- Verwendung: Hydraulische Pressen werden verwendet, um Gummiteile für Dichtungen, Reifen und Stoßdämpfer zu formen. Der gleichmäßige Druck sorgt für eine präzise Formgebung und Konsistenz.
- Holz
- Eigenschaften: Holz ist ein natürliches Material, das leicht zu bearbeiten ist und gute mechanische Eigenschaften aufweist.
- Verwendung: In der Möbelindustrie und im Bauwesen werden hydraulische Pressen verwendet, um Holz in verschiedene Formen zu pressen, zu biegen und zu laminieren.
Die Fähigkeit hydraulischer Pressen, eine Vielzahl von Materialien zu bearbeiten, macht sie zu einem vielseitigen Werkzeug in der modernen Industrie. Ihre Präzision und Leistungsfähigkeit ermöglichen die Herstellung von hochqualitativen Produkten aus den unterschiedlichsten Werkstoffen.
Zukunft und Innovationen in der Hydraulikpresstechnologie
Die Technologie der hydraulischen Pressen hat sich im Laufe der Jahre stetig weiterentwickelt, um den wachsenden Anforderungen der Industrie gerecht zu werden. Die Zukunft dieser Technologie verspricht noch mehr Innovationen, die ihre Leistungsfähigkeit, Effizienz und Vielseitigkeit weiter steigern werden. In diesem Abschnitt werfen wir einen Blick auf einige der vielversprechendsten Entwicklungen und Trends in der Hydraulikpresstechnologie.
Digitalisierung und Industrie 4.0
Die Integration digitaler Technologien und die Konzepte von Industrie 4.0 revolutionieren die Fertigungsprozesse, einschließlich der Verwendung hydraulischer Pressen.
- IoT (Internet der Dinge): Durch die Vernetzung von hydraulischen Pressen mit IoT-Sensoren können Echtzeitdaten über den Zustand und die Leistung der Maschinen erfasst und analysiert werden. Dies ermöglicht eine vorausschauende Wartung, die Ausfallzeiten reduziert und die Lebensdauer der Maschinen verlängert.
- Big Data und Analytik: Die Analyse großer Datenmengen kann helfen, die Effizienz von Pressvorgängen zu optimieren. Durch die Auswertung von Produktionsdaten können Fehlerquellen identifiziert und Prozesse kontinuierlich verbessert werden.
- Künstliche Intelligenz (KI): KI kann verwendet werden, um komplexe Pressprozesse zu steuern und zu überwachen. Algorithmen lernen aus vergangenen Produktionsdaten und passen die Pressparameter in Echtzeit an, um die bestmöglichen Ergebnisse zu erzielen.
Energieeffizienz und Nachhaltigkeit
Energieeffizienz und Nachhaltigkeit sind in der modernen Industrie von großer Bedeutung. Hydraulische Pressen werden zunehmend so entwickelt, dass sie umweltfreundlicher und energieeffizienter arbeiten.
- Elektrohydraulische Antriebe: Elektrohydraulische Antriebe kombinieren die Vorteile elektrischer und hydraulischer Systeme, um den Energieverbrauch zu reduzieren. Diese Antriebe sind effizienter und leiser als herkömmliche Hydrauliksysteme.
- Regenerative Systeme: Moderne hydraulische Pressen sind mit regenerativen Systemen ausgestattet, die überschüssige Energie während des Pressvorgangs zurückgewinnen und wiederverwenden. Dies führt zu einer erheblichen Reduzierung des Energieverbrauchs.
- Biologisch abbaubare Hydraulikflüssigkeiten: Der Einsatz umweltfreundlicher Hydraulikflüssigkeiten, die biologisch abbaubar sind, trägt dazu bei, die Umweltbelastung zu verringern und die Sicherheit am Arbeitsplatz zu erhöhen.
Verbesserte Materialien und Konstruktion
Die kontinuierliche Entwicklung neuer Materialien und Konstruktionsmethoden trägt dazu bei, die Leistungsfähigkeit hydraulischer Pressen zu steigern.
- Leichtbauweise: Die Verwendung leichter und hochfester Materialien wie Kohlefaserverbundwerkstoffe in der Konstruktion von Pressen reduziert das Gesamtgewicht der Maschinen und verbessert ihre Energieeffizienz.
- 3D-Druck: Der Einsatz von 3D-Drucktechnologien ermöglicht die Herstellung komplexer Bauteile für hydraulische Pressen mit hoher Präzision. Dies führt zu einer Reduzierung der Produktionskosten und einer Verkürzung der Entwicklungszeiten.
- Modulare Bauweise: Modulare Pressensysteme bieten Flexibilität und Anpassungsfähigkeit. Sie ermöglichen es, einzelne Module je nach Bedarf auszutauschen oder zu erweitern, was die Wartung erleichtert und die Lebensdauer der Maschinen verlängert.
Erhöhte Präzision und Kontrolle
Die Anforderungen an die Präzision und Kontrolle von Pressvorgängen steigen stetig, insbesondere in der Luft- und Raumfahrt, der Medizintechnik und der Elektronikindustrie.
- Servo-Hydraulik: Servo-hydraulische Systeme bieten eine präzise Steuerung der Pressbewegungen und ermöglichen eine exakte Positionierung und Kraftregelung. Diese Systeme sind ideal für Anwendungen, die hohe Präzision erfordern.
- Adaptive Steuerungssysteme: Moderne hydraulische Pressen sind mit adaptiven Steuerungssystemen ausgestattet, die sich automatisch an wechselnde Bedingungen anpassen. Diese Systeme verbessern die Prozessstabilität und die Qualität der Endprodukte.
- Hochauflösende Sensoren: Der Einsatz hochauflösender Sensoren ermöglicht eine genauere Überwachung und Kontrolle des Pressvorgangs. Diese Sensoren liefern Echtzeitdaten über Druck, Temperatur und Position, die zur Optimierung der Prozesse verwendet werden können.
Erweiterte Anwendungen und Branchen
Die kontinuierliche Weiterentwicklung der Hydraulikpresstechnologie eröffnet neue Anwendungsmöglichkeiten und Branchen, die von den Vorteilen dieser Maschinen profitieren können.
- Medizintechnik: Hydraulische Pressen werden zunehmend in der Medizintechnik eingesetzt, um präzise und komplexe medizinische Geräte und Implantate herzustellen. Die hohe Präzision und Kontrolle dieser Pressen sind entscheidend für die Herstellung von Produkten mit hohen Qualitätsanforderungen.
- Energieerzeugung: In der Energiebranche werden hydraulische Pressen für die Herstellung und Wartung von Windturbinen, Solarpaneelen und anderen erneuerbaren Energieanlagen verwendet. Die Fähigkeit, große und komplexe Strukturen zu bearbeiten, ist ein wesentlicher Vorteil.
- Lebensmittelverarbeitung: In der Lebensmittelindustrie finden hydraulische Pressen Anwendung bei der Verarbeitung und Verpackung von Lebensmitteln. Sie ermöglichen eine effiziente und hygienische Verarbeitung, die den hohen Standards der Lebensmittelbranche entspricht.
Die Zukunft der Hydraulikpresstechnologie verspricht spannende Entwicklungen und Innovationen, die ihre Leistungsfähigkeit und Vielseitigkeit weiter steigern werden. Mit der Integration digitaler Technologien, der Verbesserung der Energieeffizienz, der Verwendung neuer Materialien und der Erweiterung der Anwendungsbereiche werden hydraulische Pressen auch in Zukunft eine Schlüsselrolle in der industriellen Fertigung spielen.
Metallbearbeitungsmaschinen wie Bördel und Beschneide Maschinen, Flanschmaschinen, Beschneide und Bördelmaschinen, Umformtechnik, Rohrbiegemaschinen, Bandsäge für Metall, Hydraulische Horizontalpresse, Kantenschneide-Bördelmaschine, Kantenbördelmaschine, Entgratungsmaschine, Innen- und Außenpoliermaschine für Edelstahltöpfe, Kreisschneidemaschine, Profilbiegemaschine und Rundschweißmaschine
Blech- und Metallbearbeitungsmaschinen
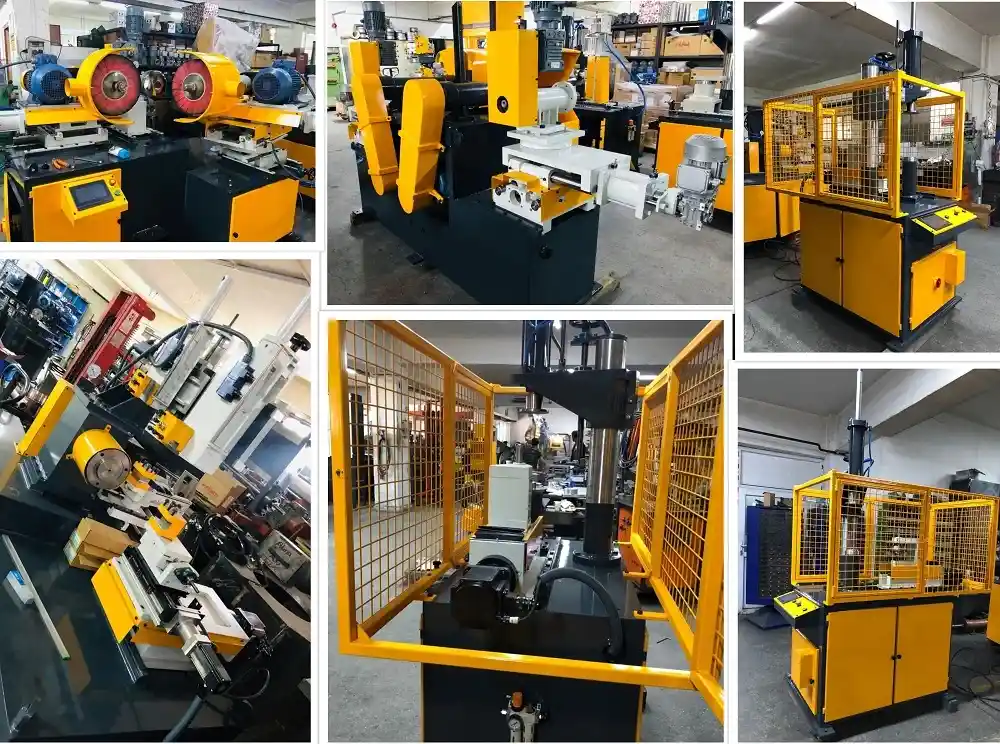
In der modernen Fertigungsindustrie sind Blech- und Metallbearbeitungsmaschinen unverzichtbare Werkzeuge, die eine präzise und effiziente Verarbeitung von Metallteilen ermöglichen. Diese Maschinen spielen eine Schlüsselrolle in verschiedenen Industriezweigen, darunter Automobilindustrie, Luft- und Raumfahrt, Bauwesen und viele andere. Dieser Text zielt darauf ab, einen umfassenden Überblick über die wichtigsten Arten von Blech- und Metallbearbeitungsmaschinen zu geben, ihre Funktionsweisen zu erklären und ihre Bedeutung in der heutigen Fertigungslandschaft zu beleuchten.
1.2. Bedeutung der Maschinen in der modernen Fertigung
In einer Zeit, in der die Nachfrage nach hochpräzisen und maßgeschneiderten Metallteilen steigt, bieten Blech- und Metallbearbeitungsmaschinen Lösungen, die den Produktionsanforderungen gerecht werden. Diese Maschinen ermöglichen es, komplexe Formen und Strukturen zu erstellen, die mit herkömmlichen Methoden nicht oder nur sehr schwer realisierbar wären. Durch die Automatisierung und Spezialisierung in der Metallbearbeitung wird nicht nur die Effizienz gesteigert, sondern auch die Qualität der Endprodukte gesichert.
1.3. Überblick über die Schlüsselmaschinen und Prozesse
Dieser Text wird sich mit verschiedenen Maschinentypen und Bearbeitungsprozessen befassen, darunter Umformmaschinen, Randbearbeitungsmaschinen, Sickenmaschinen, Beschneidemaschinen und Rohrbiegemaschinen. Jede dieser Maschinen hat spezifische Anwendungsbereiche und Techniken, die in der Fertigung eingesetzt werden, um optimale Ergebnisse zu erzielen. Im Folgenden wird jede Maschine detailliert vorgestellt, einschließlich ihrer Funktionsweise, ihrer typischen Anwendungen und der aktuellen Markttrends.
Die Blech- und Metallbearbeitung ist eine zentrale Säule der modernen industriellen Produktion. Sie umfasst eine Vielzahl von Verfahren und Techniken, die es ermöglichen, Rohmaterialien in präzise gefertigte Komponenten zu verwandeln, die in unzähligen Anwendungen zum Einsatz kommen. Von der Automobil- über die Luftfahrt- bis hin zur Bauindustrie ist die Bearbeitung von Blech und Metall unerlässlich für die Herstellung von Produkten, die sowohl funktional als auch ästhetisch ansprechend sind.
In der heutigen globalisierten Wirtschaft ist die Nachfrage nach qualitativ hochwertigen Metallprodukten so hoch wie nie zuvor. Dies erfordert fortschrittliche Maschinen und Technologien, die in der Lage sind, komplexe Aufgaben effizient und mit höchster Präzision zu bewältigen. Unternehmen, die in der Blech- und Metallbearbeitung tätig sind, stehen daher vor der Herausforderung, kontinuierlich in neue Technologien zu investieren und ihre Produktionsprozesse zu optimieren, um wettbewerbsfähig zu bleiben.
Überblick über verschiedene Maschinentypen und ihre Anwendung
In der Blech- und Metallbearbeitung kommen verschiedene Maschinentypen zum Einsatz, die jeweils für spezifische Aufgaben konzipiert sind. Zu den wichtigsten Maschinen gehören Umformmaschinen, Randbearbeitungsmaschinen, Bördelmaschinen, Sickenmaschinen, und Rohrbiegemaschinen. Jede dieser Maschinen spielt eine entscheidende Rolle in der Produktionskette und trägt dazu bei, dass das Endprodukt die gewünschten Spezifikationen erfüllt.
- Umformmaschinen: Diese Maschinen sind dafür konzipiert, Metall durch Krafteinwirkung in die gewünschte Form zu bringen. Sie werden häufig in der Massenproduktion eingesetzt, wo hohe Präzision und Wiederholgenauigkeit erforderlich sind.
- Randbearbeitungsmaschinen: Diese Maschinen sind spezialisiert auf die Bearbeitung der Kanten von Blech- und Metallteilen, um diese für den weiteren Einsatz vorzubereiten. Dazu gehören unter anderem das Beschneiden, Entgraten und Bördeln.
- Bördelmaschinen: Diese Maschinen werden eingesetzt, um die Kanten von Blech- und Metallteilen zu biegen oder zu falzen, wodurch stabile und oft auch optisch ansprechende Verbindungen entstehen.
- Sickenmaschinen: Sickenmaschinen werden verwendet, um Versteifungen in Metallteilen zu erzeugen, die die strukturelle Integrität erhöhen und die Belastbarkeit verbessern.
- Rohrbiegemaschinen: Diese Maschinen sind speziell für das Biegen von Rohren aus verschiedenen Materialien konzipiert und finden in vielen Branchen Anwendung, darunter die Herstellung von Rahmen, Leitungen und Strukturen.
Ziel und Struktur des Textes
Das Ziel dieses Textes ist es, einen umfassenden Überblick über die verschiedenen Maschinentypen in der Blech- und Metallbearbeitung zu geben und deren Bedeutung für die Industrie hervorzuheben. Dabei wird auf die Funktionsweise, die Einsatzgebiete und die neuesten technologischen Entwicklungen eingegangen.
Die folgenden Kapitel werden die einzelnen Maschinentypen detailliert beleuchten, um dem Leser ein tiefes Verständnis für deren Funktionsweise und Anwendungsmöglichkeiten zu vermitteln. Am Ende des Textes soll ein umfassendes Bild der modernen Blech- und Metallbearbeitung sowie ein Ausblick auf zukünftige Entwicklungen in diesem Bereich gezeichnet werden.
Blech- und Metallbearbeitungsmaschinen
Definition und Klassifizierung
Blech- und Metallbearbeitungsmaschinen sind spezialisierte Geräte, die zur Formgebung, Bearbeitung und Verarbeitung von Metallwerkstoffen eingesetzt werden. Diese Maschinen decken ein breites Spektrum von Prozessen ab, die es ermöglichen, Rohmetalle in präzise gefertigte Produkte zu verwandeln. Die Bandbreite reicht von einfachen Schneidmaschinen bis hin zu komplexen automatisierten Fertigungsanlagen, die in der Lage sind, anspruchsvolle Produktionsaufgaben zu übernehmen.
Die Klassifizierung von Blech- und Metallbearbeitungsmaschinen erfolgt üblicherweise nach den durchgeführten Prozessen:
- Schneidmaschinen: Dazu gehören Maschinen wie Laserschneider, Plasmaschneider und mechanische Scheren, die Blech und Metall in die gewünschte Form schneiden.
- Umformmaschinen: Maschinen, die durch mechanischen Druck oder Zug Metall in eine bestimmte Form bringen. Beispiele sind Pressen, Walzen und Abkantmaschinen.
- Randbearbeitungsmaschinen: Diese Maschinen sind spezialisiert auf die Bearbeitung der Ränder und Kanten von Metallteilen. Dazu gehören Bördelmaschinen, Sickenmaschinen und Entgratmaschinen.
- Rohrbiegemaschinen: Maschinen, die zum Biegen von Rohren aus verschiedenen Materialien wie Stahl, Edelstahl oder Aluminium eingesetzt werden. Diese Maschinen können entweder elektrisch, hydraulisch oder mechanisch betrieben werden.
- Fertigungsanlagen: Komplexe Systeme, die verschiedene Maschinen integrieren, um komplette Produktionsprozesse zu automatisieren. Diese Anlagen sind in der Lage, mehrere Bearbeitungsschritte zu kombinieren, um hochpräzise Endprodukte zu fertigen.
Historische Entwicklung
Die Entwicklung von Blech- und Metallbearbeitungsmaschinen hat eine lange Geschichte, die bis in die Frühzeit der Industrialisierung zurückreicht. Ursprünglich wurden Metalle von Hand bearbeitet, aber mit dem Aufkommen der Dampfmaschine und später der Elektrizität wurden mechanische Bearbeitungsmaschinen entwickelt, die eine effizientere und präzisere Produktion ermöglichten.
Im 19. Jahrhundert führten die Fortschritte in der Materialwissenschaft und Maschinenbau zu einer Vielzahl neuer Maschinen, die speziell für die Massenproduktion konzipiert wurden. Diese Maschinen revolutionierten die Industrie, indem sie die Produktionsgeschwindigkeit erhöhten und die Herstellung von komplexen Metallteilen ermöglichten.
Im 20. Jahrhundert ermöglichte die Einführung von computergesteuerten Maschinen (CNC-Maschinen) eine noch höhere Präzision und Flexibilität in der Metallbearbeitung. Diese Maschinen konnten durch die Programmierung komplexer Bewegungsabläufe eine Vielzahl von Bearbeitungsschritten in einem einzigen Durchgang durchführen.
Heute befinden wir uns im Zeitalter der Industrie 4.0, in dem moderne Blech- und Metallbearbeitungsmaschinen zunehmend vernetzt und automatisiert sind. Diese Maschinen sind mit Sensoren und Datenanalyse-Tools ausgestattet, die eine kontinuierliche Überwachung und Optimierung des Produktionsprozesses ermöglichen.
Moderne Technologien und Innovationen
Die moderne Blech- und Metallbearbeitung wird stark von technologischen Innovationen geprägt. Zu den bedeutendsten Entwicklungen zählen:
- Additive Fertigung: Auch als 3D-Druck bekannt, ermöglicht diese Technologie die schichtweise Herstellung von Metallteilen, was besonders bei der Produktion komplexer Geometrien von Vorteil ist.
- Lasertechnologie: Laser werden zunehmend zum Schneiden und Schweißen von Metallen eingesetzt. Sie bieten eine hohe Präzision und sind in der Lage, sehr dünne Schnitte zu erzeugen, was den Materialabfall minimiert.
- Automatisierung und Robotik: Die Integration von Robotern in Fertigungsanlagen ermöglicht eine schnellere und effizientere Produktion. Roboter übernehmen Aufgaben wie das Bestücken von Maschinen, das Handling von Werkstücken und die Qualitätskontrolle.
- Künstliche Intelligenz und maschinelles Lernen: Diese Technologien werden verwendet, um den Produktionsprozess in Echtzeit zu überwachen und zu optimieren. Durch die Analyse von Produktionsdaten können Maschinen automatisch Anpassungen vornehmen, um die Effizienz zu steigern und Ausschuss zu minimieren.
- Energieeffiziente Systeme: Moderne Maschinen sind darauf ausgelegt, den Energieverbrauch zu minimieren. Dies geschieht durch die Verwendung von energiesparenden Antriebssystemen und die Rückgewinnung von Energie während des Produktionsprozesses.
Zusammenfassung des Abschnitts
Blech- und Metallbearbeitungsmaschinen haben eine zentrale Rolle in der industriellen Fertigung und Entwicklung gespielt. Ihre Entwicklung von einfachen mechanischen Werkzeugen hin zu hochmodernen, automatisierten Systemen spiegelt den Fortschritt der industriellen Technologie wider. Die Integration von modernen Technologien wie der additiven Fertigung, Lasertechnologie und künstlicher Intelligenz hat das Potenzial, die Industrie weiter zu transformieren und die Produktionseffizienz zu maximieren.
Umformmaschinen
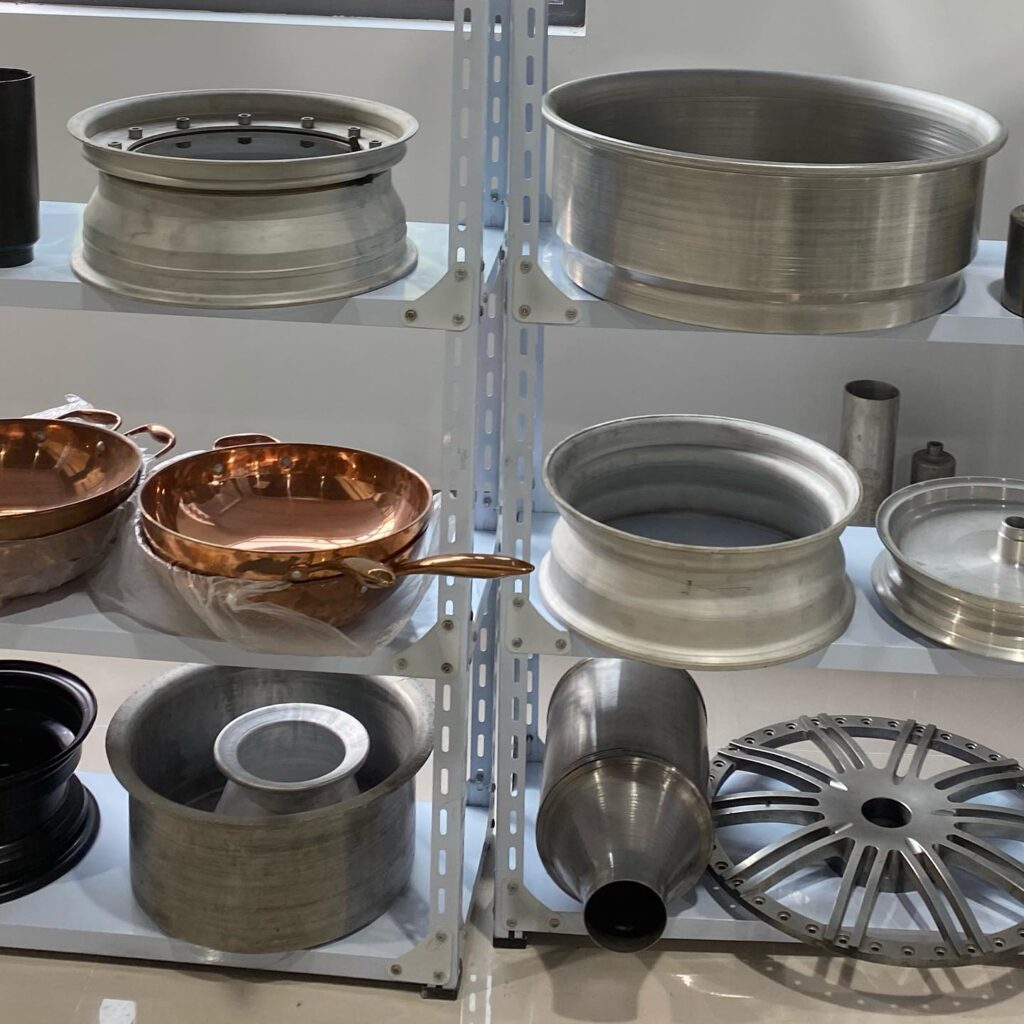
Einführung in die Umformtechnik
Die Umformtechnik ist ein zentrales Verfahren in der Metallbearbeitung und bezieht sich auf die plastische Verformung von Werkstoffen, meist Metallen, ohne die Werkstoffmasse zu verändern. Umformmaschinen sind spezielle Maschinen, die diese Verformungsprozesse durchführen, um Metalle in die gewünschte Form zu bringen. Das Ziel ist es, durch den Einsatz von Druck, Zug oder Biegung die gewünschten geometrischen Eigenschaften des Werkstücks zu erreichen.
Umformmaschinen werden in der Industrie häufig eingesetzt, da sie eine hohe Materialausnutzung und Wiederholgenauigkeit bieten. Diese Maschinen sind in der Lage, komplexe Formen mit hoher Präzision zu erzeugen, was sie für die Massenproduktion besonders geeignet macht.
Typen von Umformmaschinen
Es gibt verschiedene Typen von Umformmaschinen, die jeweils für spezifische Umformprozesse eingesetzt werden. Die wichtigsten Kategorien sind:
- Pressen: Pressen sind die am weitesten verbreiteten Umformmaschinen und werden eingesetzt, um Metalle durch Druck in eine bestimmte Form zu bringen. Es gibt verschiedene Arten von Pressen, darunter mechanische Pressen, hydraulische Pressen und pneumatische Pressen. Jede dieser Pressenarten hat ihre spezifischen Anwendungsgebiete und Vorteile.
- Walzmaschinen: Diese Maschinen werden verwendet, um Metalle durch kontinuierliches Walzen in Blech- oder Bandform zu bringen. Walzmaschinen sind besonders in der Stahl- und Aluminiumindustrie weit verbreitet, wo sie zur Herstellung von flachen Produkten wie Blechen und Platten eingesetzt werden.
- Ziehmaschinen: Ziehmaschinen werden eingesetzt, um Metallstäbe, Drähte oder Rohre durch Ziehen in eine gewünschte Länge und Dicke zu bringen. Diese Maschinen sind besonders in der Draht- und Kabelindustrie von Bedeutung.
- Biegemaschinen: Diese Maschinen sind speziell für das Biegen von Metallen ausgelegt. Sie finden Anwendung bei der Herstellung von Komponenten, die eine spezifische Winkel- oder Kurvenform erfordern, wie z.B. in der Automobil- oder Bauindustrie.
- Schmiedemaschinen: Schmiedemaschinen nutzen mechanischen oder hydraulischen Druck, um Metalle zu verformen und in die gewünschte Form zu bringen. Diese Maschinen sind besonders in der Herstellung von robusten und langlebigen Bauteilen, wie z.B. Achsen oder Kurbelwellen, von Bedeutung.
Anwendungsbeispiele in der Industrie
Umformmaschinen sind in einer Vielzahl von Industriezweigen unverzichtbar. Ihre Fähigkeit, Metalle in präzise Formen zu bringen, macht sie zu einem wesentlichen Bestandteil in der Herstellung von Bauteilen für verschiedene Anwendungen:
- Automobilindustrie: In der Automobilindustrie werden Umformmaschinen eingesetzt, um Karosserieteile, Chassis-Komponenten und andere strukturelle Elemente herzustellen. Pressen und Biegemaschinen sind hierbei besonders wichtig, um die verschiedenen Blechteile zu formen, die später zu einem Fahrzeug zusammengefügt werden.
- Luft- und Raumfahrtindustrie: Hier werden Umformmaschinen verwendet, um hochpräzise und leichte Komponenten zu fertigen, die den hohen Anforderungen der Luft- und Raumfahrttechnik gerecht werden müssen. Schmiedemaschinen spielen eine entscheidende Rolle bei der Herstellung von kritischen Bauteilen wie Turbinenschaufeln und Strukturteilen.
- Bauindustrie: In der Bauindustrie werden Umformmaschinen zur Herstellung von Stahlträgern, Dachplatten und anderen strukturellen Komponenten eingesetzt. Walzmaschinen sind hier besonders wichtig, da sie große Mengen an Stahl in Form von Blechen und Platten verarbeiten können.
- Elektroindustrie: In der Elektroindustrie werden Umformmaschinen verwendet, um Drähte, Kabel und andere leitfähige Materialien zu produzieren. Ziehmaschinen spielen eine entscheidende Rolle bei der Herstellung von Kupfer- und Aluminiumdrähten, die in elektrischen Leitungen verwendet werden.
- Hausgeräteindustrie: Umformmaschinen werden auch in der Herstellung von Haushaltsgeräten eingesetzt, um Gehäuse, Türen und andere Metallkomponenten zu fertigen. Biegemaschinen und Pressen werden hier häufig verwendet, um die gewünschten Formen und Strukturen zu erzeugen.
Zusammenfassung des Abschnitts
Umformmaschinen sind essenzielle Werkzeuge in der Metallbearbeitung und spielen eine entscheidende Rolle in der Herstellung von präzisen und robusten Metallteilen. Ihre Vielseitigkeit und Fähigkeit, Metalle in komplexe Formen zu bringen, machen sie zu unverzichtbaren Maschinen in vielen Industriezweigen. Die kontinuierliche Weiterentwicklung dieser Maschinen und die Integration neuer Technologien sorgen dafür, dass sie auch in Zukunft eine zentrale Rolle in der industriellen Fertigung spielen werden.
Randbearbeitungsmaschinen
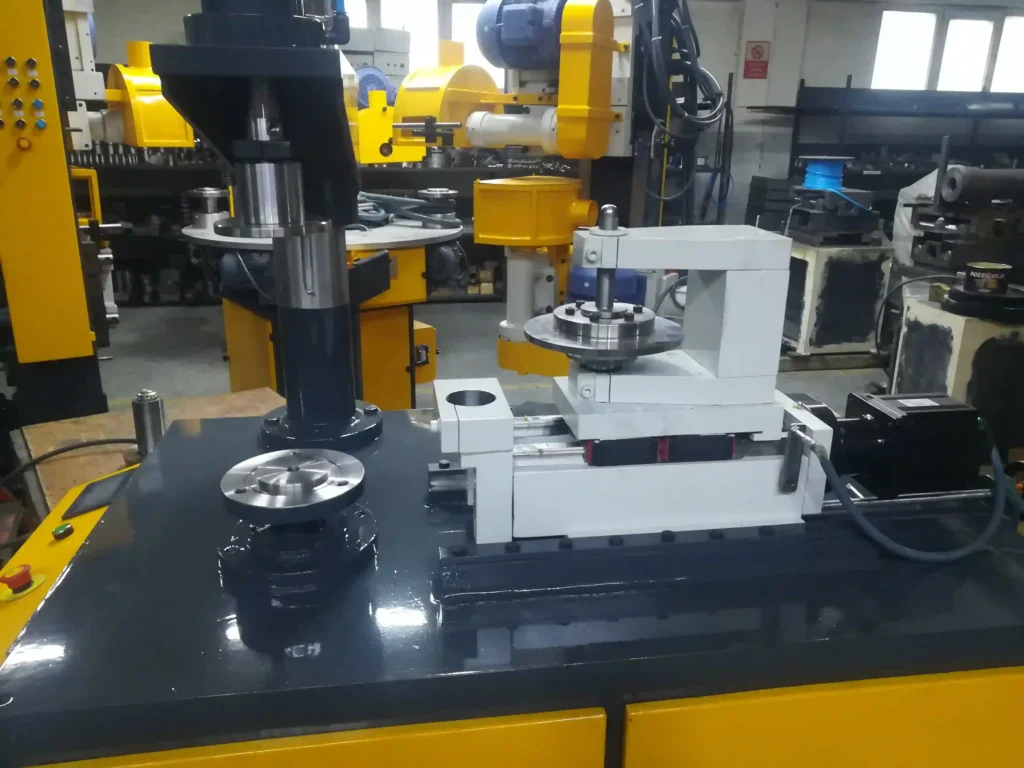
Definition und Einsatzgebiete
Randbearbeitungsmaschinen sind spezialisierte Maschinen, die zur Bearbeitung der Ränder und Kanten von Metall- und Blechteilen eingesetzt werden. Diese Bearbeitungsschritte sind oft notwendig, um die Funktionalität und Sicherheit der Werkstücke zu gewährleisten. Durch die gezielte Bearbeitung der Ränder können scharfe Kanten entfernt, Verbindungen vorbereitet und die ästhetischen Eigenschaften der Teile verbessert werden.
Die Einsatzgebiete von Randbearbeitungsmaschinen sind vielfältig und erstrecken sich über zahlreiche Branchen. In der Automobilindustrie werden sie beispielsweise verwendet, um Karosserieteile nach dem Schneiden oder Stanzen zu entgraten und vorzubereiten. In der Luft- und Raumfahrtindustrie ist die präzise Randbearbeitung entscheidend, um die Integrität von Strukturkomponenten zu gewährleisten. Auch in der Bau- und Elektroindustrie finden Randbearbeitungsmaschinen breite Anwendung.
Technologische Fortschritte und Effizienzsteigerung
In den letzten Jahrzehnten haben sich Randbearbeitungsmaschinen erheblich weiterentwickelt, insbesondere im Hinblick auf Präzision, Geschwindigkeit und Automatisierung. Die Integration moderner Technologien hat dazu geführt, dass diese Maschinen effizienter und vielseitiger geworden sind.
- Automatisierung: Moderne Randbearbeitungsmaschinen sind zunehmend automatisiert, was eine höhere Produktionsgeschwindigkeit und Konsistenz ermöglicht. Automatisierte Systeme können Teile ohne menschliches Eingreifen durch den gesamten Bearbeitungsprozess führen, was die Produktionszeit verkürzt und den Ausschuss reduziert.
- CNC-Steuerung: Die Einführung von CNC (Computerized Numerical Control) hat es ermöglicht, komplexe Bearbeitungsprozesse mit hoher Präzision durchzuführen. CNC-gesteuerte Randbearbeitungsmaschinen können programmiert werden, um spezifische Kantenbearbeitungen mit gleichbleibender Genauigkeit durchzuführen.
- Mehrkopfmaschinen: Um die Effizienz weiter zu steigern, werden Mehrkopfmaschinen eingesetzt, die mehrere Bearbeitungsschritte gleichzeitig durchführen können. Diese Maschinen sind in der Lage, mehrere Kanten und Ränder gleichzeitig zu bearbeiten, was die Produktionsgeschwindigkeit erhöht und die Betriebskosten senkt.
- Lasertechnologie: Die Integration von Lasertechnologie in Randbearbeitungsmaschinen hat die Präzision und Flexibilität der Bearbeitungsprozesse weiter verbessert. Laser können extrem feine und genaue Schnitte durchführen, die mit herkömmlichen Methoden schwer zu erreichen wären. Dies ist besonders nützlich bei der Bearbeitung von komplexen oder empfindlichen Teilen.
Randbearbeitung bei verschiedenen Materialien
Die Randbearbeitung ist je nach Materialtyp unterschiedlich anspruchsvoll. Metallarten wie Stahl, Aluminium, Kupfer und Edelstahl haben jeweils spezifische Eigenschaften, die bei der Bearbeitung berücksichtigt werden müssen.
- Stahl: Stahl ist ein robustes Material, das in vielen industriellen Anwendungen eingesetzt wird. Die Randbearbeitung von Stahl erfordert oft starke und präzise Maschinen, die in der Lage sind, die Kanten ohne Materialverformung oder -schwächung zu bearbeiten.
- Aluminium: Aluminium ist ein leichtes und flexibles Material, das in vielen High-Tech- und Leichtbauanwendungen verwendet wird. Die Randbearbeitung von Aluminium erfordert Maschinen, die mit der hohen Wärmeleitfähigkeit und der weichen Natur des Materials umgehen können, um saubere und glatte Kanten zu erzeugen.
- Kupfer: Kupfer ist ein weiches Metall, das hauptsächlich in der Elektronik- und Elektroindustrie verwendet wird. Die Randbearbeitung von Kupfer erfordert besondere Vorsicht, um das Material nicht zu beschädigen und die elektrischen Eigenschaften zu erhalten.
- Edelstahl: Edelstahl ist aufgrund seiner Korrosionsbeständigkeit und Festigkeit ein beliebtes Material in vielen Anwendungen, einschließlich medizinischer Geräte und Lebensmittelverarbeitung. Die Randbearbeitung von Edelstahl erfordert Maschinen, die hohe Temperaturen und hohe Druckkräfte bewältigen können, um saubere Schnitte zu gewährleisten.
Zusammenfassung des Abschnitts
Randbearbeitungsmaschinen sind unverzichtbare Werkzeuge in der Metallbearbeitung, die sicherstellen, dass die Kanten und Ränder von Metallteilen den hohen Anforderungen der Industrie entsprechen. Durch technologische Innovationen wie Automatisierung, CNC-Steuerung und Lasertechnologie sind diese Maschinen effizienter und präziser geworden. Die Fähigkeit, verschiedene Materialien wie Stahl, Aluminium, Kupfer und Edelstahl zu bearbeiten, macht Randbearbeitungsmaschinen zu einem wesentlichen Bestandteil vieler Fertigungsprozesse.
Senkrechte Bördelung an Flachen Oberflächen
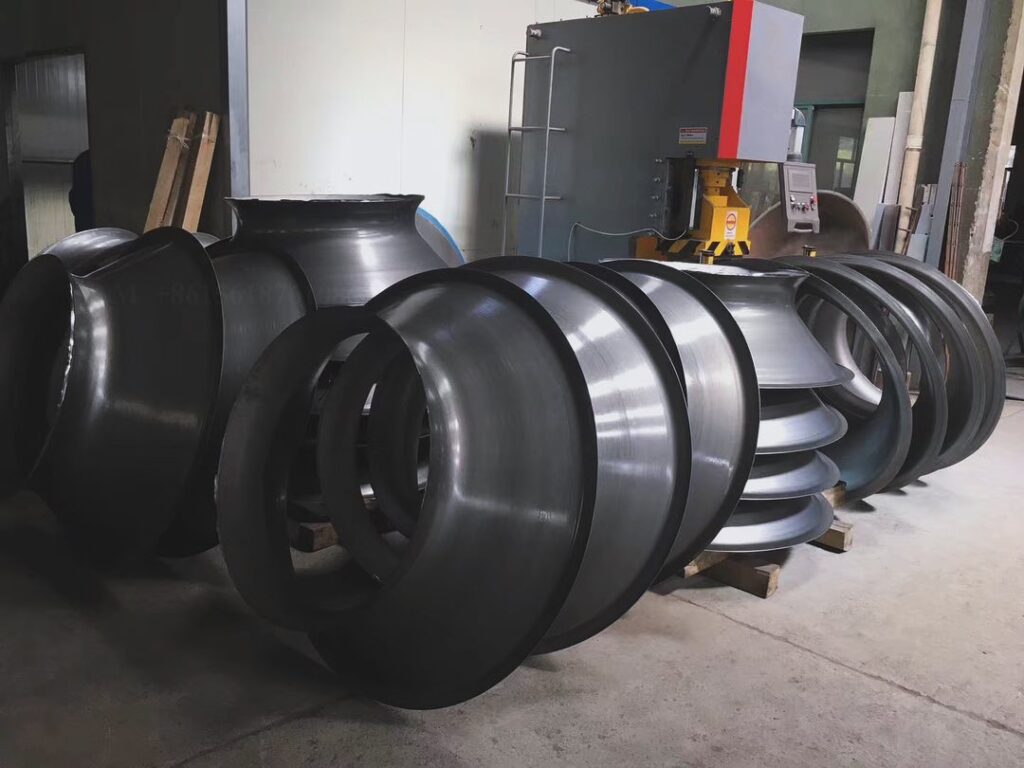
Techniken und Maschinen
Die senkrechte Bördelung an flachen Oberflächen ist ein spezifischer Prozess der Blech- und Metallbearbeitung, bei dem die Kanten eines Werkstücks senkrecht zur flachen Oberfläche nach außen oder innen umgebogen werden. Dieser Vorgang wird häufig verwendet, um Kanten zu verstärken, scharfe Ränder zu vermeiden oder um eine saubere Abschlusskante zu schaffen. Die Maschinen, die für diesen Prozess eingesetzt werden, sind präzise auf diese Aufgaben spezialisiert und müssen in der Lage sein, den Blechrand gleichmäßig und kontrolliert zu verformen, ohne das Werkstück zu beschädigen.
Verwendete Maschinen:
- Bördelmaschinen: Diese Maschinen sind speziell für die Aufgabe der Kantenverformung konzipiert. Sie ermöglichen es, den Rand eines Blechs gleichmäßig zu biegen, entweder nach innen oder nach außen. Moderne Bördelmaschinen sind oft CNC-gesteuert, was eine hohe Präzision und Wiederholgenauigkeit gewährleistet. Die Maschinen sind so konzipiert, dass sie auch bei hohen Geschwindigkeiten eine konsistente Qualität liefern.
- Hydraulische Pressen: Bei der senkrechten Bördelung kann auch auf hydraulische Pressen zurückgegriffen werden, die den erforderlichen Druck auf das Werkstück ausüben, um die Kante in die gewünschte Form zu bringen. Diese Maschinen sind besonders nützlich bei der Bearbeitung von dickeren oder härteren Materialien, die mehr Kraft erfordern.
- Rollformmaschinen: In einigen Fällen werden Rollformmaschinen verwendet, um kontinuierliche Kantenbearbeitungen durchzuführen. Diese Maschinen können in einer Produktionslinie integriert werden, um fortlaufende Blechstreifen mit gleichmäßigen Kanten zu produzieren.
Anwendungsgebiete und Vorteile
Die senkrechte Bördelung an flachen Oberflächen findet in vielen Bereichen Anwendung, in denen die Kanten von Blechen oder Platten verstärkt oder geschützt werden müssen. Die Technik ist besonders in der Automobil-, Luftfahrt- und Bauindustrie weit verbreitet.
- Automobilindustrie: In der Automobilproduktion wird die senkrechte Bördelung verwendet, um die Kanten von Karosserieteilen zu verstärken und gleichzeitig scharfe Kanten zu vermeiden, die bei der Montage gefährlich sein könnten. Diese Technik trägt auch zur strukturellen Integrität des Fahrzeugs bei, indem sie die Verbindungspunkte verstärkt.
- Luftfahrtindustrie: In der Luftfahrt ist die Präzision von entscheidender Bedeutung. Hier wird die senkrechte Bördelung genutzt, um die Kanten von Flugzeugteilen zu verstärken und aerodynamische Oberflächen zu schaffen. Diese Technik hilft auch, die Teile vor Umwelteinflüssen wie Korrosion zu schützen.
- Bauindustrie: Im Bauwesen wird die senkrechte Bördelung oft bei der Herstellung von Fassadenplatten, Dachblechen und anderen Bauelementen verwendet. Durch das Bördeln der Kanten wird die Stabilität der Bauteile erhöht, was insbesondere bei widrigen Wetterbedingungen von Vorteil ist.
Qualitätskontrolle und Prozessoptimierung
Eine präzise Qualitätskontrolle ist bei der senkrechten Bördelung entscheidend, um sicherzustellen, dass die Kanten gleichmäßig und ohne Verformungen umgebogen werden. Moderne Maschinen sind oft mit Sensoren ausgestattet, die den Prozess in Echtzeit überwachen und sicherstellen, dass die Qualitätsanforderungen erfüllt werden.
- Messsysteme: Diese Systeme überwachen die exakte Position und Ausrichtung des Werkstücks während des Bördelvorgangs und gewährleisten, dass die Kanten in der gewünschten Geometrie umgebogen werden.
- Prozesssteuerung: CNC-gesteuerte Bördelmaschinen ermöglichen eine genaue Steuerung des Prozesses, wodurch die Wiederholgenauigkeit erhöht wird. Diese Maschinen können programmiert werden, um verschiedene Bördelgeometrien auf unterschiedlichen Werkstücken zu realisieren, was die Flexibilität in der Produktion erhöht.
- Wartung und Kalibrierung: Um eine gleichbleibend hohe Qualität zu gewährleisten, ist eine regelmäßige Wartung und Kalibrierung der Maschinen notwendig. Durch die Kalibrierung wird sichergestellt, dass die Maschinen stets mit den richtigen Parametern arbeiten und keine Abweichungen in der Produktion auftreten.
Zusammenfassung des Abschnitts
Die senkrechte Bördelung an flachen Oberflächen ist eine essentielle Technik in der Blech- und Metallbearbeitung, die für die Verstärkung und den Schutz der Kanten von Werkstücken sorgt. Durch den Einsatz spezialisierter Maschinen wie Bördelmaschinen, hydraulischen Pressen und Rollformmaschinen wird eine hohe Präzision und Qualität gewährleistet. Die Technik findet in verschiedenen Industrien breite Anwendung und trägt dazu bei, die Lebensdauer und Funktionalität der gefertigten Produkte zu verbessern.
Bordieren nach Außen und nach Innen an Flachen Oberflächen
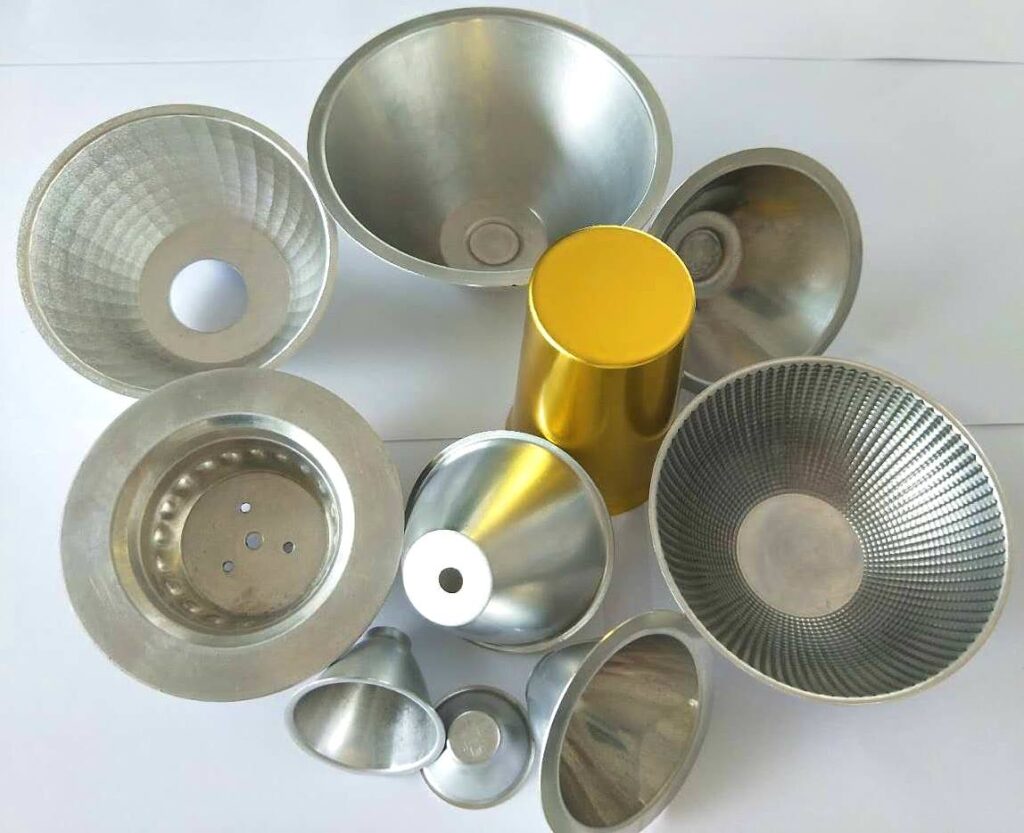
Methoden und Maschinen
Das Bordieren ist eine spezielle Technik der Kantenbearbeitung, bei der die Kante eines Werkstücks umgebogen wird, entweder nach außen (Außenbordieren) oder nach innen (Innenbordieren). Diese Technik wird angewendet, um die Kanten zu verstärken, scharfe Ränder zu vermeiden oder um eine saubere und sichere Abschlusskante zu schaffen. Das Bordieren wird häufig in der Blech- und Metallbearbeitung eingesetzt, insbesondere bei der Herstellung von Bauteilen, die eine hohe mechanische Belastbarkeit und eine glatte Oberfläche erfordern.
Außenbordieren
Beim Außenbordieren wird die Kante eines Blechs oder Metallteils nach außen umgebogen, so dass eine Art umgeschlagene Kante entsteht. Diese Methode wird häufig verwendet, um die Kante eines Werkstücks zu verstärken und gleichzeitig die Oberfläche zu glätten, was sowohl die Sicherheit als auch die Ästhetik verbessert.
Innenbordieren
Das Innenbordieren hingegen biegt die Kante nach innen, wodurch die Kante des Blechs versteckt und geschützt wird. Diese Methode wird oft bei Anwendungen verwendet, bei denen die Kante des Bauteils nicht sichtbar sein soll oder zusätzlichen Schutz benötigt, z.B. bei der Herstellung von Gehäusen und Containern.
Verwendete Maschinen:
- Bordiermaschinen: Diese Maschinen sind speziell für das Bordieren ausgelegt und können sowohl das Außen- als auch das Innenbordieren durchführen. Sie sind oft CNC-gesteuert, was eine hohe Präzision und Flexibilität ermöglicht. Bordiermaschinen können für eine Vielzahl von Materialien und Werkstückgrößen angepasst werden.
- Handwerkzeuge: In kleineren Werkstätten oder bei Spezialanfertigungen kann das Bordieren auch manuell mit speziellen Handwerkzeugen durchgeführt werden. Diese Methode ist zwar weniger effizient, bietet aber eine hohe Flexibilität bei der Bearbeitung von Unikaten oder Kleinserien.
- Kombinationsmaschinen: Einige Maschinen kombinieren Bordier- und Sickenfunktionen, um mehrere Arbeitsschritte in einem Prozess zu integrieren. Diese Maschinen sind besonders in der Serienproduktion nützlich, da sie die Effizienz steigern und den Platzbedarf in der Werkstatt reduzieren.
Herausforderungen und Lösungen
Das Bordieren von flachen Oberflächen stellt besondere Herausforderungen dar, insbesondere in Bezug auf die Materialeigenschaften und die gewünschte Präzision:
- Materialverformung: Beim Bordieren besteht das Risiko, dass das Material unerwünscht verformt oder geschwächt wird. Um dies zu vermeiden, ist es wichtig, dass die Maschine genau eingestellt ist und der Druck gleichmäßig auf die gesamte Kante verteilt wird.
- Präzisionsanforderungen: In vielen Industrien, insbesondere in der Luftfahrt und Automobilindustrie, sind die Anforderungen an die Präzision der Bordierung extrem hoch. Moderne CNC-gesteuerte Maschinen sind in der Lage, diese Anforderungen zu erfüllen, indem sie genaue Steuerungen und wiederholbare Prozesse bieten.
- Materialkompatibilität: Unterschiedliche Materialien reagieren unterschiedlich auf den Bordierungsprozess. Zum Beispiel erfordert das Bordieren von Aluminium eine andere Technik und Maschineneinstellung als das Bordieren von Stahl oder Edelstahl. Die Auswahl der richtigen Maschine und die Anpassung der Prozessparameter sind entscheidend, um ein optimales Ergebnis zu erzielen.
Vergleich der Bordierungstechniken
Sowohl das Außen- als auch das Innenbordieren haben ihre spezifischen Vorteile und Anwendungsgebiete. Der Einsatz der jeweiligen Technik hängt von den Anforderungen des Endprodukts ab:
- Außenbordieren ist ideal, wenn eine sichtbare, verstärkte Kante gewünscht ist, die zusätzlichen Schutz bietet. Es wird oft bei Bauteilen eingesetzt, die strukturelle Integrität und eine glatte Außenkante erfordern.
- Innenbordieren wird bevorzugt, wenn die Kante des Bauteils nicht sichtbar sein soll oder zusätzlichen Schutz vor äußeren Einflüssen benötigt. Es bietet eine versteckte, aber verstärkte Kante und wird häufig in Gehäusen, Behältern und anderen geschlossenen Strukturen verwendet.
Zusammenfassung des Abschnitts
Das Bordieren nach außen und nach innen ist eine wichtige Technik in der Blech- und Metallbearbeitung, die zur Verstärkung und Verbesserung der Kanten von Werkstücken beiträgt. Durch den Einsatz spezialisierter Maschinen wie Bordiermaschinen können diese Prozesse präzise und effizient durchgeführt werden. Die Wahl der richtigen Bordiertechnik hängt von den spezifischen Anforderungen des Produkts ab, wobei sowohl das Außen- als auch das Innenbordieren einzigartige Vorteile bieten.
Sickenmaschinen und Randformmaschinen
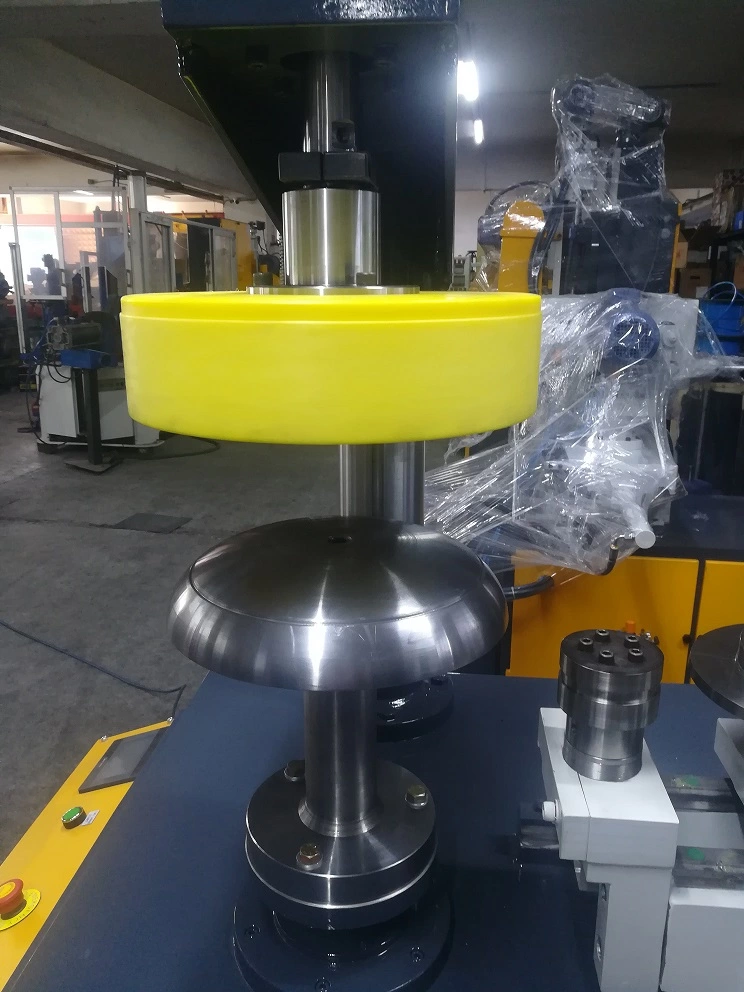
Funktionsweise und Einsatzmöglichkeiten
Sickenmaschinen und Randformmaschinen sind essenzielle Werkzeuge in der Blech- und Metallbearbeitung, die spezifische Funktionen zur Formgebung und Verstärkung von Blech- und Metallteilen erfüllen. Diese Maschinen spielen eine wichtige Rolle bei der Erstellung von Sicken und Kantenformen, die sowohl die strukturelle Integrität der Teile erhöhen als auch ästhetische oder funktionale Eigenschaften verbessern.
Sickenmaschinen
Sickenmaschinen sind darauf spezialisiert, Sicken, also Rippen oder Rillen, in Blech- oder Metalloberflächen zu erzeugen. Diese Sicken dienen dazu, die Steifigkeit und Stabilität der Bauteile zu erhöhen, ohne das Gewicht signifikant zu verändern. Typische Anwendungen für Sickenmaschinen finden sich in der Automobilindustrie, der Luft- und Raumfahrt sowie im Bauwesen, wo die strukturelle Integrität von Blechteilen von entscheidender Bedeutung ist.
- Maschinentypen: Es gibt verschiedene Typen von Sickenmaschinen, darunter manuelle, halbautomatische und vollautomatische Maschinen. Manuelle Maschinen werden oft in kleineren Werkstätten verwendet, während vollautomatische CNC-gesteuerte Maschinen in der Großserienproduktion eingesetzt werden.
- Funktionsprinzip: Die Maschine presst mit speziellen Werkzeugen Sicken in das Blech, indem es zwischen zwei Walzen geführt wird, die die gewünschte Form in das Material drücken. Die Tiefe und Breite der Sicken kann dabei je nach Anforderung variiert werden.
- Anwendungsbeispiele: In der Automobilindustrie werden Sicken häufig in Karosserieteile gepresst, um diese zu verstärken und gleichzeitig das Gewicht des Fahrzeugs zu minimieren. In der Luftfahrt werden Sicken verwendet, um Flugzeugkomponenten leichter und widerstandsfähiger gegen Belastungen zu machen.
Randformmaschinen
Randformmaschinen sind Maschinen, die speziell dafür entwickelt wurden, die Ränder von Blechteilen in eine gewünschte Form zu bringen. Diese Maschinen sind in der Lage, verschiedene Randprofile zu erzeugen, die zur Verstärkung, Verbindung oder zum Schutz der Bauteile dienen.
- Typen von Randformmaschinen: Es gibt verschiedene Randformmaschinen, je nach Art der gewünschten Randbearbeitung. Dazu gehören Maschinen für das einfache Umkanten, das Bordieren, oder das Erzeugen von komplizierten Kantenprofilen.
- Prozessablauf: Bei der Randformung wird das Blech durch die Maschine geführt, wo spezielle Werkzeuge den Rand des Materials in die gewünschte Form bringen. Dies kann durch Biegen, Falzen oder andere Umformprozesse geschehen.
- Anwendungsbereiche: Randformmaschinen finden in zahlreichen Industrien Anwendung, darunter die Produktion von Metallgehäusen, Rohren, und in der Blechverkleidung. In der Bauindustrie werden Randformmaschinen beispielsweise verwendet, um Dachbleche oder Fassadenelemente mit speziellen Kantenprofilen zu versehen, die eine einfache Montage und eine höhere Wetterbeständigkeit ermöglichen.
Unterschiede und Gemeinsamkeiten
Obwohl Sickenmaschinen und Randformmaschinen unterschiedliche spezifische Aufgaben erfüllen, gibt es einige Gemeinsamkeiten in ihrer Funktionsweise und Anwendung:
- Materialbearbeitung: Beide Maschinentypen bearbeiten Bleche und Metalle durch plastische Verformung. Während Sickenmaschinen das Material durch Einprägen von Rillen verstärken, formen Randformmaschinen die Ränder, um diese zu verstärken oder zu verbinden.
- Verwendung in der Industrie: Beide Maschinen werden in der Serienfertigung und der Kleinserienproduktion eingesetzt und tragen dazu bei, die Funktionalität und Langlebigkeit von Metallteilen zu erhöhen. Besonders in Industrien mit hohen Anforderungen an die strukturelle Integrität, wie der Automobil- und Luftfahrtindustrie, sind diese Maschinen unverzichtbar.
- CNC-Technologie: Moderne Varianten beider Maschinentypen sind oft CNC-gesteuert, was eine hohe Präzision und Flexibilität in der Produktion ermöglicht. CNC-gesteuerte Maschinen können komplexe Muster und Formen mit hoher Wiederholgenauigkeit erstellen.
Marktüberblick und führende Hersteller
Der Markt für Sickenmaschinen und Randformmaschinen ist von einer Vielzahl von Herstellern geprägt, die sich auf verschiedene Nischen und Anwendungen spezialisiert haben. Führende Hersteller bieten sowohl Standardlösungen als auch maßgeschneiderte Maschinen an, die spezifische Anforderungen erfüllen.
- Sickenmaschinen: Unternehmen wie Nippon Steel Corporation und Roper Whitney sind bekannte Hersteller, die sowohl manuelle als auch automatisierte Sickenmaschinen anbieten. Diese Maschinen sind für ihre Zuverlässigkeit und Langlebigkeit bekannt und werden weltweit in verschiedenen Industriezweigen eingesetzt.
- Randformmaschinen: Hersteller wie Trumpf und Salvagnini sind führend im Bereich der Randformmaschinen. Diese Unternehmen bieten hochmoderne Maschinen an, die in der Lage sind, komplexe Randbearbeitungen mit hoher Präzision durchzuführen. Sie sind besonders bekannt für ihre Innovationen im Bereich der CNC-Technologie und Automatisierung.
Zusammenfassung des Abschnitts
Sickenmaschinen und Randformmaschinen spielen eine zentrale Rolle in der Blech- und Metallbearbeitung. Sie tragen dazu bei, die strukturelle Integrität von Metallteilen zu erhöhen und ermöglichen es, Bleche und Metalle mit spezifischen Profilen und Formen zu versehen. Durch den Einsatz moderner CNC-Technologie und Automatisierung sind diese Maschinen in der Lage, hohe Präzision und Effizienz zu bieten, was sie unverzichtbar in vielen Industriezweigen macht.
Bördelmaschinen und Beschneidemaschinen
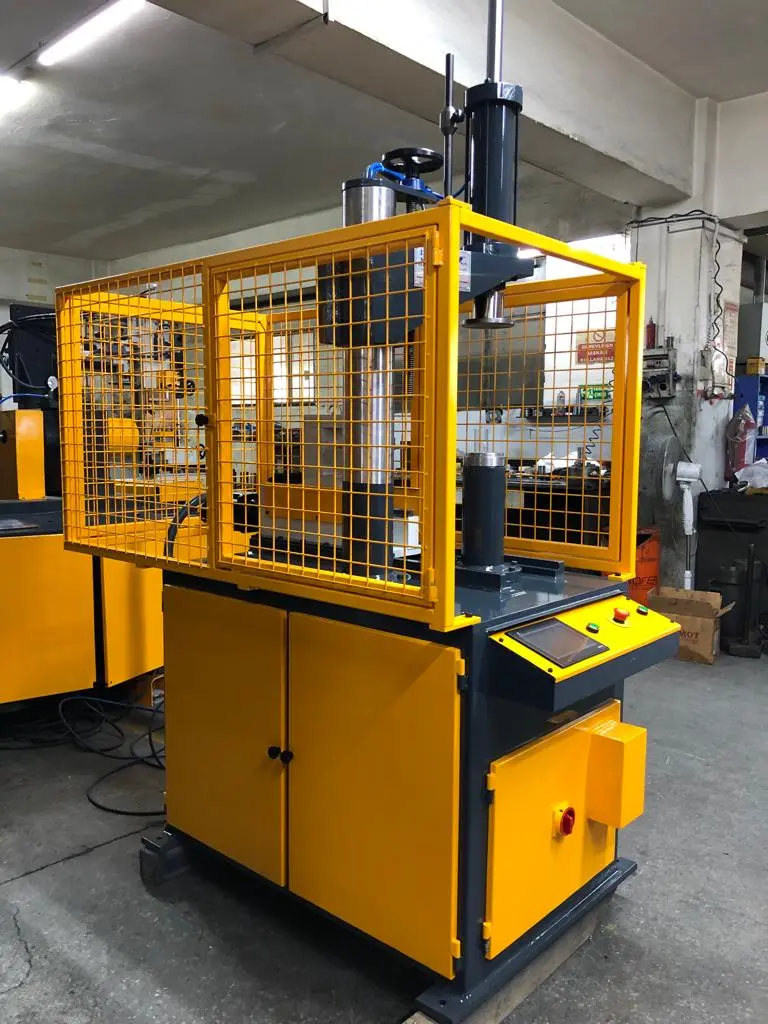
Technische Spezifikationen
Bördelmaschinen und Beschneidemaschinen sind zwei wesentliche Werkzeuge in der Blech- und Metallbearbeitung, die für die präzise Kantenbearbeitung und das Zuschneiden von Werkstücken verantwortlich sind. Während Bördelmaschinen hauptsächlich verwendet werden, um Kanten zu falzen oder zu formen, werden Beschneidemaschinen eingesetzt, um Bleche und Metalle in die gewünschte Form oder Größe zu schneiden.
Bördelmaschinen
Bördelmaschinen sind darauf ausgelegt, die Kanten von Blechen und Metallen zu biegen oder zu falzen, um stabile und oft auch ästhetische Verbindungen zu schaffen. Diese Maschinen sind in verschiedenen Ausführungen erhältlich, je nach spezifischen Anforderungen des Bearbeitungsprozesses:
- Maschinentypen: Es gibt manuelle Bördelmaschinen, die in kleineren Werkstätten für einfache Bördelarbeiten verwendet werden, sowie vollautomatische CNC-gesteuerte Bördelmaschinen, die in der Massenproduktion eingesetzt werden. Die Wahl der Maschine hängt von der Komplexität und dem Volumen der Produktion ab.
- Technische Merkmale: Moderne Bördelmaschinen verfügen über Präzisionswerkzeuge und einstellbare Matrizen, die es ermöglichen, verschiedene Bördelformen und -größen zu erstellen. CNC-gesteuerte Bördelmaschinen bieten eine hohe Wiederholgenauigkeit und Flexibilität, da sie komplexe Bördelformen programmierbar machen.
- Anwendungen: Bördelmaschinen werden häufig in der Automobilindustrie, Luftfahrt, Bauindustrie und in der Herstellung von Haushaltsgeräten eingesetzt. Sie sind unverzichtbar, wenn es darum geht, Blechteile zu verbinden, die stabil und dauerhaft sein müssen, wie zum Beispiel bei der Fertigung von Fahrzeugkarosserien oder Metallgehäusen.
Beschneidemaschinen
Beschneidemaschinen, auch als Blechschneidemaschinen bekannt, sind für das exakte Zuschneiden von Metallplatten und Blechen verantwortlich. Diese Maschinen spielen eine entscheidende Rolle in der Produktion, da sie den ersten Schritt in vielen Bearbeitungsprozessen darstellen, bei dem das Rohmaterial auf die gewünschte Größe oder Form zugeschnitten wird.
- Maschinentypen: Es gibt verschiedene Typen von Beschneidemaschinen, darunter mechanische Scheren, hydraulische Scheren und Laserschneidemaschinen. Jede dieser Maschinenarten hat ihre spezifischen Vorteile. Mechanische Scheren sind einfach und robust, während hydraulische Scheren für das Schneiden von dickerem Material geeignet sind. Laserschneidemaschinen bieten die höchste Präzision und Flexibilität und werden häufig in der High-Tech-Industrie eingesetzt.
- Technische Merkmale: Moderne Beschneidemaschinen sind oft mit CNC-Steuerungen ausgestattet, die eine präzise Steuerung des Schneidprozesses ermöglichen. Diese Maschinen können programmierte Schnitte mit hoher Genauigkeit und Wiederholbarkeit durchführen. Bei Laserschneidemaschinen kommt oft Faserlasertechnologie zum Einsatz, die schnelle und präzise Schnitte ermöglicht, selbst bei komplexen Formen.
- Anwendungen: Beschneidemaschinen werden in nahezu allen Industrien eingesetzt, die mit Blech- und Metallbearbeitung zu tun haben. Sie finden Verwendung in der Automobilindustrie, im Maschinenbau, in der Luft- und Raumfahrt, sowie in der Elektronik- und Bauindustrie. Besonders in der Serienproduktion sind diese Maschinen unverzichtbar, um hohe Stückzahlen mit gleichbleibender Qualität zu liefern.
Integration in Fertigungsanlagen
Sowohl Bördel- als auch Beschneidemaschinen sind oft Teil komplexer Fertigungsanlagen, die verschiedene Bearbeitungsschritte kombinieren, um die Produktionseffizienz zu steigern. In modernen Fertigungsumgebungen sind diese Maschinen häufig miteinander vernetzt und arbeiten in automatisierten Produktionslinien, um die Durchlaufzeiten zu minimieren und die Produktqualität zu maximieren.
- Automatisierung: In vielen Fertigungsanlagen sind Bördel- und Beschneidemaschinen in automatisierte Produktionslinien integriert. Diese Maschinen arbeiten oft in Kombination mit Robotern, die das Material zuführen und fertige Teile abführen. Dies ermöglicht eine kontinuierliche Produktion mit minimalem manuellem Eingreifen.
- Qualitätskontrolle: In modernen Anlagen sind die Maschinen mit Sensoren und Überwachungssystemen ausgestattet, die den Bearbeitungsprozess in Echtzeit überwachen. Dies stellt sicher, dass die Teile den Qualitätsanforderungen entsprechen und Fehler frühzeitig erkannt und korrigiert werden können.
- Effizienzsteigerung: Durch die Integration von Bördel- und Beschneidemaschinen in eine einzige Produktionslinie kann die Effizienz erheblich gesteigert werden. Die Maschinen sind so konzipiert, dass sie nahtlos zusammenarbeiten, was zu einer Reduzierung der Produktionskosten und einer Verkürzung der Durchlaufzeiten führt.
Innovationspotential und Zukunftsaussichten
Die kontinuierliche Weiterentwicklung von Bördel- und Beschneidemaschinen bietet erhebliches Innovationspotential. Die zunehmende Automatisierung, die Integration von Künstlicher Intelligenz (KI) und die Weiterentwicklung der CNC-Technologie sind entscheidende Faktoren, die die zukünftige Entwicklung dieser Maschinen beeinflussen werden.
- KI-Integration: In Zukunft könnten Bördel- und Beschneidemaschinen zunehmend mit KI-Systemen ausgestattet werden, die in der Lage sind, den Bearbeitungsprozess selbstständig zu optimieren. Diese Systeme könnten Produktionsdaten in Echtzeit analysieren und Anpassungen vornehmen, um die Effizienz zu maximieren und den Materialverbrauch zu minimieren.
- Verbesserte Energieeffizienz: Mit dem wachsenden Fokus auf Nachhaltigkeit wird auch die Energieeffizienz dieser Maschinen weiter verbessert. Neue Antriebstechnologien und optimierte Maschinensteuerungen werden dazu beitragen, den Energieverbrauch zu reduzieren und gleichzeitig die Leistung zu steigern.
- Erweiterte Materialkompatibilität: Zukünftige Entwicklungen könnten auch die Materialkompatibilität der Maschinen erweitern. Dies würde es ermöglichen, neue und fortschrittliche Materialien zu bearbeiten, die in der heutigen Produktion noch nicht in großem Umfang eingesetzt werden.
Zusammenfassung des Abschnitts
Bördelmaschinen und Beschneidemaschinen sind wesentliche Werkzeuge in der Blech- und Metallbearbeitung, die eine hohe Präzision und Effizienz in der Produktion gewährleisten. Durch die Integration in automatisierte Fertigungsanlagen und die kontinuierliche technologische Weiterentwicklung spielen sie eine entscheidende Rolle in der modernen Industrie. Ihre Zukunftsaussichten sind vielversprechend, insbesondere durch die mögliche Integration von KI und die Verbesserung der Energieeffizienz.
Fertigungsanlagen für die Blechbearbeitung
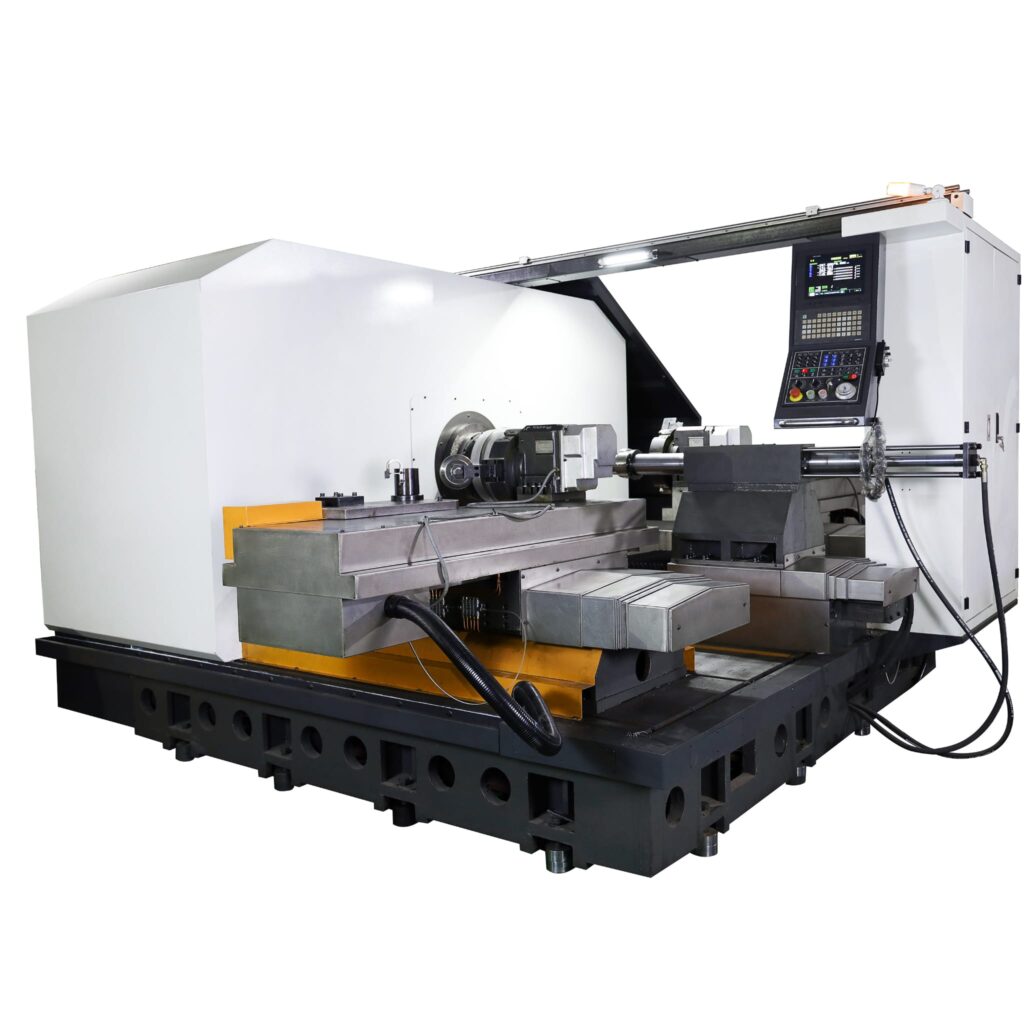
Aufbau und Komponenten einer Fertigungsanlage
Fertigungsanlagen für die Blechbearbeitung sind hochkomplexe Systeme, die mehrere Maschinen und Technologien integrieren, um einen durchgehenden Produktionsprozess zu ermöglichen. Diese Anlagen sind darauf ausgelegt, die Effizienz zu maximieren, indem sie verschiedene Bearbeitungsschritte wie Schneiden, Formen, Biegen, und Montieren in einem einzigen Produktionsablauf kombinieren. Der Aufbau einer solchen Anlage kann stark variieren, abhängig von den spezifischen Anforderungen und dem zu bearbeitenden Material.
Hauptkomponenten einer Fertigungsanlage:
- Materialzuführungssysteme: Diese Systeme sind verantwortlich für die kontinuierliche Bereitstellung von Rohmaterial an die Anlage. Sie bestehen in der Regel aus Rollenanlagen oder Förderbändern, die die Blechrollen zur Schneidemaschine transportieren.
- Schneidemaschinen: Eine oder mehrere Schneidemaschinen sind oft der erste Bearbeitungsschritt in einer Fertigungsanlage. Diese Maschinen schneiden das Blech in die benötigten Formen oder Größen, bevor es zu weiteren Bearbeitungsstationen weitergeleitet wird.
- Umform- und Biegemaschinen: Nach dem Schneiden wird das Material häufig durch Umform- oder Biegemaschinen geführt, die es in die gewünschte Form bringen. Diese Maschinen sind oft CNC-gesteuert, um eine hohe Präzision zu gewährleisten.
- Montagelinien: In einigen Fertigungsanlagen werden die bearbeiteten Teile direkt in Montagelinien integriert, wo sie zusammengebaut werden. Dies kann von einfachen mechanischen Verbindungen bis hin zu komplexen Schweiß- oder Klebeprozessen reichen.
- Qualitätskontrollstationen: Diese Stationen sind entlang der gesamten Fertigungsanlage verteilt und überwachen die Qualität der produzierten Teile. Automatisierte Inspektionssysteme prüfen auf Maßhaltigkeit, Oberflächenqualität und andere kritische Eigenschaften.
- Verpackungs- und Lagersysteme: Nach Abschluss der Bearbeitung werden die fertigen Produkte oft direkt verpackt und für den Versand vorbereitet. Moderne Anlagen integrieren Lager- und Kommissioniersysteme, die die Produkte effizient sortieren und lagern.
Automatisierung und Effizienzsteigerung
Die Automatisierung spielt eine zentrale Rolle in modernen Fertigungsanlagen für die Blechbearbeitung. Automatisierte Systeme ermöglichen es, die Produktionsgeschwindigkeit zu erhöhen, die Präzision zu verbessern und die Produktionskosten zu senken.
- Roboterintegration: Roboter sind in vielen Fertigungsanlagen unverzichtbar geworden. Sie übernehmen Aufgaben wie das Handling von Werkstücken, die Beschickung von Maschinen und die Montage von Bauteilen. Roboter können rund um die Uhr arbeiten, was die Produktivität erheblich steigert.
- CNC-Steuerung: Die Integration von CNC-Maschinen in Fertigungsanlagen ermöglicht eine präzise Steuerung des Bearbeitungsprozesses. CNC-Maschinen können komplexe Formen und Muster mit hoher Wiederholgenauigkeit fertigen und sind daher besonders in der Serienproduktion wertvoll.
- Datenanalyse und Prozessoptimierung: Moderne Anlagen sind oft mit Sensoren und Datenanalyse-Tools ausgestattet, die den Produktionsprozess in Echtzeit überwachen. Diese Systeme sammeln und analysieren Daten, um den Prozess kontinuierlich zu optimieren und Ineffizienzen zu beseitigen.
Beispiele aus der Praxis
Moderne Fertigungsanlagen für die Blechbearbeitung sind in vielen Industrien von entscheidender Bedeutung. Hier sind einige Beispiele für ihre Anwendung:
- Automobilindustrie: In der Automobilproduktion werden Fertigungsanlagen eingesetzt, um Karosserie- und Strukturteile zu fertigen. Diese Anlagen kombinieren Schneidemaschinen, Pressen, Schweißroboter und Montagelinien, um komplette Fahrzeugkarosserien zu produzieren.
- Luft- und Raumfahrt: In der Luftfahrtindustrie sind Fertigungsanlagen notwendig, um leichte und dennoch robuste Flugzeugkomponenten herzustellen. Diese Anlagen nutzen modernste Umform- und Schweißtechnologien, um hochpräzise Teile zu fertigen, die den strengen Sicherheitsanforderungen der Branche entsprechen.
- Bauindustrie: Fertigungsanlagen werden auch in der Bauindustrie eingesetzt, um großformatige Bleche und Strukturelemente herzustellen, die in Gebäuden und Infrastrukturprojekten verwendet werden. Diese Anlagen sind darauf ausgelegt, große Mengen an Material effizient zu verarbeiten und in die gewünschte Form zu bringen.
Vorteile von Fertigungsanlagen
Der Einsatz von Fertigungsanlagen in der Blechbearbeitung bietet zahlreiche Vorteile, darunter:
- Erhöhte Produktivität: Durch die Integration verschiedener Bearbeitungsschritte in eine einzige Produktionslinie können Fertigungsanlagen die Produktionsgeschwindigkeit erheblich erhöhen.
- Konsistente Qualität: Automatisierte Anlagen sorgen für eine gleichbleibende Produktqualität, da sie in der Lage sind, Bearbeitungsprozesse mit hoher Präzision und Wiederholgenauigkeit durchzuführen.
- Kosteneffizienz: Obwohl die Investitionskosten für Fertigungsanlagen hoch sein können, führen die erhöhte Produktivität und die Reduzierung von Materialabfällen zu langfristigen Kosteneinsparungen.
- Flexibilität: Moderne Fertigungsanlagen sind oft modular aufgebaut und können schnell an unterschiedliche Produktionsanforderungen angepasst werden. Dies ist besonders vorteilhaft in Branchen, die schnell auf Marktveränderungen reagieren müssen.
Zukunftsaussichten
Die Zukunft der Fertigungsanlagen in der Blechbearbeitung wird stark von technologischen Innovationen geprägt sein. Die zunehmende Integration von Industrie 4.0-Technologien, wie das Internet der Dinge (IoT) und Künstliche Intelligenz (KI), wird die Effizienz und Flexibilität dieser Anlagen weiter erhöhen.
- Smart Factories: In den kommenden Jahren könnten Fertigungsanlagen Teil vollständig vernetzter „Smart Factories“ werden, in denen alle Maschinen und Prozesse miteinander kommunizieren und sich selbst optimieren. Diese Entwicklung wird die Produktionsprozesse weiter automatisieren und den menschlichen Eingriff auf ein Minimum reduzieren.
- Nachhaltigkeit: Auch der Aspekt der Nachhaltigkeit wird eine immer wichtigere Rolle spielen. Zukünftige Fertigungsanlagen werden darauf ausgelegt sein, den Energieverbrauch zu minimieren und den Einsatz von Materialien effizienter zu gestalten. Dies könnte durch den Einsatz von Recyclingmaterialien und die Reduzierung von Abfällen erreicht werden.
Zusammenfassung des Abschnitts
Fertigungsanlagen für die Blechbearbeitung sind komplexe Systeme, die entscheidend zur Effizienz und Produktqualität in der industriellen Produktion beitragen. Durch die Kombination verschiedener Bearbeitungsschritte in einem automatisierten Prozess können diese Anlagen die Produktivität steigern und gleichzeitig die Produktionskosten senken. Die Zukunft dieser Anlagen liegt in der weiteren Automatisierung und der Integration fortschrittlicher Technologien, die zu „Smart Factories“ und nachhaltigerer Produktion führen werden.
Die Metallbearbeitung spielt eine zentrale Rolle in der modernen Industrie. Sie ist das Fundament zahlreicher Produktionsprozesse, die Produkte für eine Vielzahl von Branchen liefern – von der Automobilindustrie über den Maschinenbau bis hin zur Luft- und Raumfahrttechnik. Ohne präzise und effiziente Metallbearbeitung wären viele der heutigen technologischen Fortschritte undenkbar. Die Fähigkeit, Metalle in gewünschte Formen zu bringen, ihre Oberflächen zu veredeln und ihre Struktur zu optimieren, hat es der Industrie ermöglicht, qualitativ hochwertige und leistungsstarke Produkte herzustellen, die den hohen Anforderungen des Marktes gerecht werden.
Metalle, ob in Form von Blechen, Rohren oder Hohlteilen, müssen in nahezu jedem industriellen Prozess zugeschnitten, geformt, gebogen oder bearbeitet werden. Diese Schritte sind entscheidend, um sicherzustellen, dass das Endprodukt den gewünschten Spezifikationen entspricht und die notwendige Festigkeit, Haltbarkeit und Funktionalität aufweist. Daher sind die Technologien und Maschinen, die in der Metallbearbeitung zum Einsatz kommen, von größter Bedeutung.
Vorstellung der Schlüsseltechnologien
Die Kerntechnologien der modernen Metallbearbeitung umfassen das Beschneiden und Umformen von Blechhohlteilen, die Entgratung von Metallkomponenten sowie die Biege- und Formprozesse für Rohre und andere metallische Werkstoffe. Jede dieser Technologien hat sich im Laufe der Jahre weiterentwickelt und spezialisiert, um den steigenden Anforderungen gerecht zu werden.
Das Beschneiden und Umformen von Blechhohlteilen ist eine der grundlegendsten Techniken in der Metallbearbeitung. Es ermöglicht die Herstellung komplexer Strukturen und Formen, die in verschiedenen industriellen Anwendungen benötigt werden. Entgratmaschinen für Metall sorgen dafür, dass die bearbeiteten Kanten und Oberflächen frei von scharfen Graten und anderen Unregelmäßigkeiten sind, was die Sicherheit und die ästhetische Qualität des Endprodukts erhöht. Rohrbiegemaschinen, ob elektrisch oder hydraulisch betrieben, sind unverzichtbare Werkzeuge für die präzise Formgebung von Rohren, die in zahlreichen Anwendungen, von einfachen Leitungen bis hin zu komplexen Rohrleitungssystemen, benötigt werden.
Überblick über den Text
In diesem umfangreichen Text werden die verschiedenen Schlüsseltechnologien der Metallbearbeitung detailliert beschrieben. Wir beginnen mit den Grundlagen der Metallbearbeitung und führen dann durch die spezifischen Verfahren wie das Beschneiden und Umformen von Blechhohlteilen sowie das Entgraten von Metallkomponenten. Ein besonderer Fokus liegt auf den Rohrbiegemaschinen und -geräten, wobei sowohl elektrische als auch hydraulische Varianten betrachtet werden. Darüber hinaus wird auf horizontale Biege- und Richtpressen eingegangen, die in speziellen Anwendungsbereichen der Metallbearbeitung eingesetzt werden.
Jeder dieser Abschnitte wird nicht nur die Funktionsweise der entsprechenden Maschinen und Technologien beleuchten, sondern auch deren Vor- und Nachteile, typische Anwendungsfälle und aktuelle technologische Entwicklungen diskutieren. Ziel ist es, ein umfassendes Bild der modernen Metallbearbeitungstechniken zu vermitteln und deren Bedeutung für die Industrie hervorzuheben.
Metallbearbeitungsmaschinen
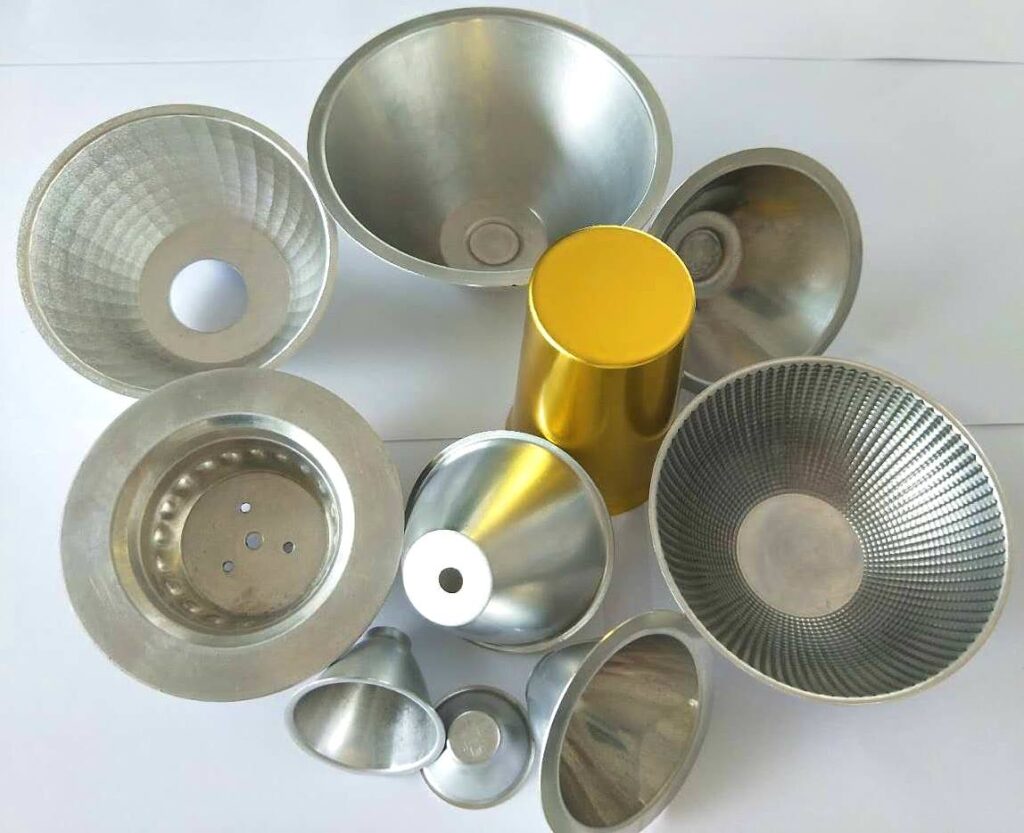
Relevanz und Zielsetzung des Textes
In einer Zeit, in der die industrielle Fertigung zunehmend komplexer und anspruchsvoller wird, ist es entscheidend, ein tiefes Verständnis der Technologien und Maschinen zu haben, die diesen Fortschritt ermöglichen. Dieser Text soll als umfassende Informationsquelle dienen, sowohl für Fachleute in der Metallbearbeitung als auch für Entscheidungsträger in der Industrie, die auf der Suche nach effizienten und innovativen Lösungen sind.
Ein besonderes Augenmerk wird auf die technologische Differenzierung gelegt. Ob es um die Wahl zwischen elektrischen und hydraulischen Rohrbiegemaschinen geht oder um die Entscheidung, welche Entgratmaschine für eine bestimmte Anwendung am besten geeignet ist – dieser Text bietet fundierte Einblicke und detaillierte Informationen, um fundierte Entscheidungen zu treffen. Zudem wird auf die Integration moderner Technologien wie Automatisierung und Digitalisierung in die Metallbearbeitung eingegangen, was ein entscheidender Faktor für die zukünftige Wettbewerbsfähigkeit ist.
Bedeutung der Wahl der richtigen Maschinen und Technologien
Die Wahl der richtigen Maschinen und Technologien in der Metallbearbeitung kann den Unterschied zwischen Erfolg und Misserfolg in der Produktion bedeuten. Effizienz, Präzision und Zuverlässigkeit sind nur einige der Kriterien, die bei der Auswahl berücksichtigt werden müssen. Eine falsch gewählte Maschine kann nicht nur zu Qualitätsproblemen führen, sondern auch erhebliche Kosten durch Produktionsausfälle oder Nacharbeiten verursachen.
In diesem Zusammenhang wird die Bedeutung von Schulungen und Weiterbildungen für die Bediener und Techniker hervorgehoben, da selbst die beste Maschine nur so gut ist wie der Mensch, der sie bedient. Darüber hinaus wird die Bedeutung der regelmäßigen Wartung und des Service betont, um eine lange Lebensdauer und optimale Leistung der Maschinen sicherzustellen.
Ausblick auf zukünftige Entwicklungen
Die Metallbearbeitung ist ein Bereich, der sich ständig weiterentwickelt, angetrieben durch die Anforderungen der Industrie und die Fortschritte in der Technologie. Themen wie Industrie 4.0, Robotik, und künstliche Intelligenz beginnen, einen immer größeren Einfluss auf die Metallbearbeitung zu haben. In diesem Text wird daher auch ein Ausblick auf diese zukünftigen Entwicklungen gegeben und erörtert, wie sie die Branche verändern könnten.
Die Integration von Automatisierungstechnologien und die Nutzung von Datenanalysen zur Optimierung von Produktionsprozessen werden in der nahen Zukunft eine zentrale Rolle spielen. Darüber hinaus werden nachhaltige Produktionsmethoden, die den Energieverbrauch reduzieren und den Materialeinsatz optimieren, immer wichtiger werden.
Grundlagen der Metallbearbeitung
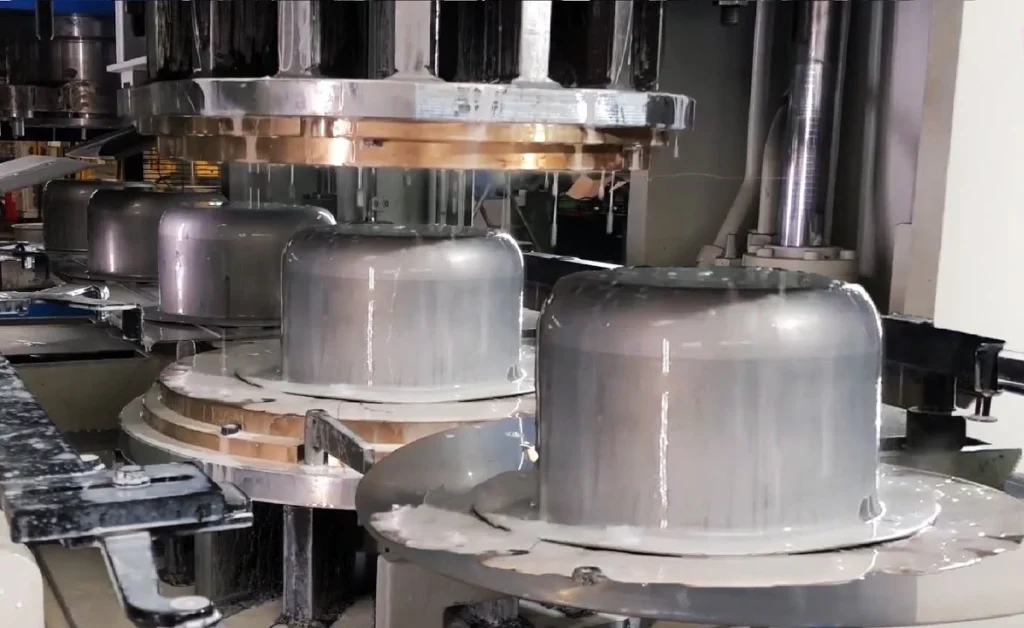
Definition und Ziel der Metallbearbeitung
Die Metallbearbeitung umfasst alle Verfahren, bei denen Metalle durch mechanische, thermische, oder chemische Prozesse in eine gewünschte Form gebracht werden. Diese Prozesse können das Trennen, Umformen, Fügen, Beschichten und Ändern der Stoffeigenschaften von Metallen umfassen. Ziel ist es, aus Rohmetallen oder Halbzeugen fertige Werkstücke herzustellen, die den spezifischen Anforderungen der Endanwendung gerecht werden.
In der modernen Industrie sind die Anforderungen an die Metallbearbeitung enorm gestiegen. Präzision, Effizienz und Qualität stehen im Vordergrund, da die Produkte zunehmend komplexer und die Toleranzen enger werden. Der Einsatz moderner Maschinen und Technologien ist daher unerlässlich, um diese hohen Standards zu erreichen.
Unterschiedliche Metallbearbeitungstechniken
Die Metallbearbeitung lässt sich in mehrere Hauptkategorien unterteilen, die jeweils unterschiedliche Verfahren und Techniken umfassen. Die wichtigsten Kategorien sind:
- Trennende Verfahren: Diese umfassen das Schneiden, Sägen, Bohren, Drehen und Fräsen von Metallen. Das Ziel ist es, Material von einem Rohteil zu entfernen, um die gewünschte Form zu erhalten. Trennverfahren sind häufig der erste Schritt in der Metallbearbeitung, um grobe Formen und Abmessungen zu erstellen.
- Umformende Verfahren: Umformtechniken, wie das Biegen, Pressen, Ziehen und Walzen, verändern die Form eines Metalls durch plastische Verformung, ohne Material zu entfernen. Diese Verfahren sind besonders nützlich, um komplexe Formen zu erzeugen oder Materialien in spezifische Formen zu bringen, die für die weitere Bearbeitung benötigt werden.
- Fügende Verfahren: Das Fügen umfasst das Verbinden von Metallteilen durch Schweißen, Löten, Kleben oder Schrauben. Diese Verfahren sind entscheidend für die Herstellung komplexer Baugruppen und Strukturen, bei denen mehrere Teile zu einem einzigen Werkstück zusammengefügt werden müssen.
- Beschichtende Verfahren: Beschichtungen werden angewendet, um die Oberfläche von Metallteilen zu schützen oder zu veredeln. Typische Verfahren umfassen das Lackieren, Galvanisieren, Eloxieren und Pulverbeschichten. Diese Verfahren verbessern die Korrosionsbeständigkeit, Härte und Ästhetik der Metallteile.
- Ändernde Verfahren: Hierbei handelt es sich um Verfahren, die die Materialeigenschaften von Metallen ändern, beispielsweise durch Wärmebehandlung oder Oberflächenveredelung. Solche Verfahren werden angewendet, um die Härte, Zähigkeit oder Korrosionsbeständigkeit eines Metalls zu verbessern.
Wichtige Materialien in der Metallbearbeitung
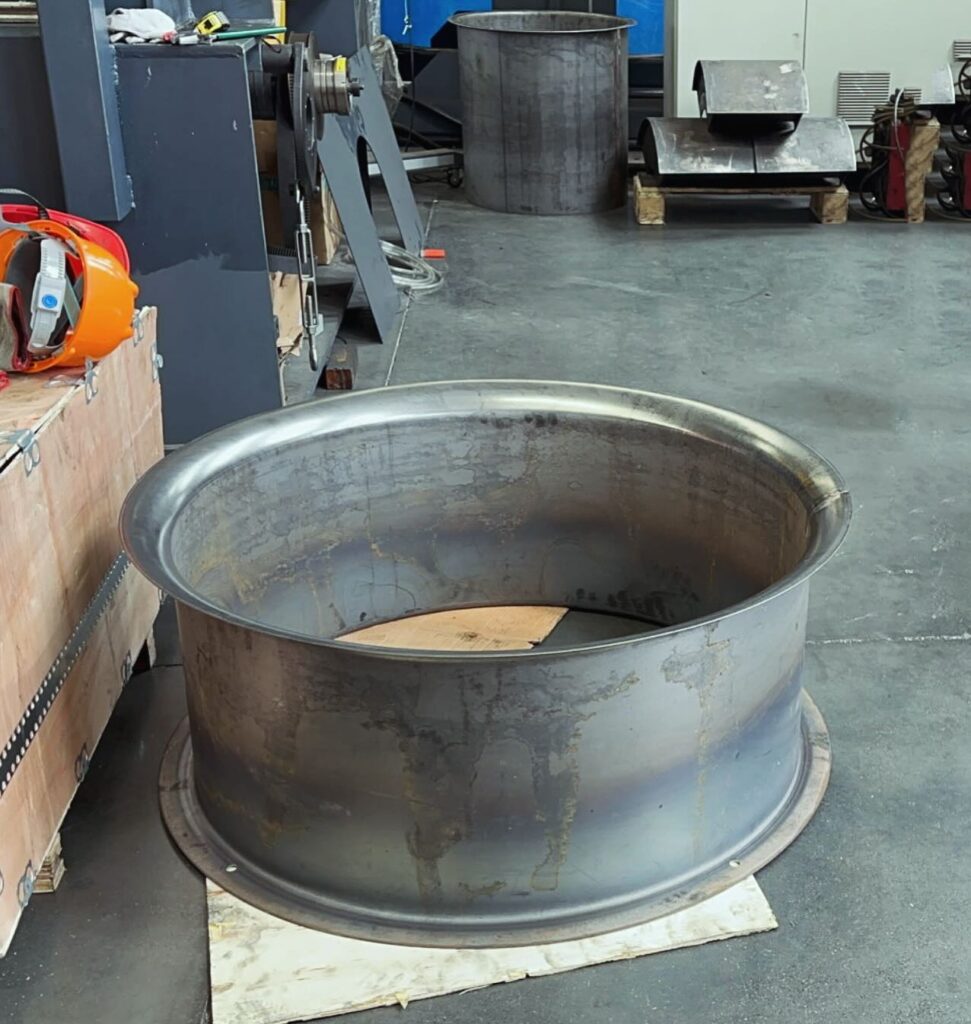
Metalle sind aufgrund ihrer hervorragenden mechanischen Eigenschaften, wie Festigkeit, Härte und Zähigkeit, die bevorzugten Materialien in der Industrie. Die am häufigsten verwendeten Metalle in der Metallbearbeitung sind:
- Stahl: Stahl ist das am weitesten verbreitete Metall und wird in zahlreichen Anwendungen verwendet, von der Automobilindustrie bis zum Bauwesen. Seine Legierungselemente, wie Kohlenstoff, Chrom und Nickel, beeinflussen seine Eigenschaften erheblich, sodass Stahl für eine Vielzahl von Anforderungen geeignet ist.
- Edelstahl: Edelstahl ist eine spezielle Stahllegierung, die mindestens 10,5% Chrom enthält, wodurch sie besonders korrosionsbeständig ist. Edelstahl wird häufig in der Lebensmittelverarbeitung, im Gesundheitswesen und in der Architektur verwendet, wo hohe Korrosionsbeständigkeit und Ästhetik gefordert sind.
- Aluminium: Aluminium ist aufgrund seines geringen Gewichts und seiner guten Korrosionsbeständigkeit ein weit verbreitetes Metall, insbesondere in der Luft- und Raumfahrt, im Transportwesen und in der Elektronikindustrie. Es lässt sich leicht formen und verarbeiten, was es für viele Anwendungen attraktiv macht.
- Kupfer: Kupfer wird hauptsächlich wegen seiner hervorragenden elektrischen und thermischen Leitfähigkeit eingesetzt. Es findet breite Anwendung in der Elektronik, im Bauwesen und in der Wärmetechnik.
- Titan: Titan ist ein hochfestes und gleichzeitig leichtes Metall mit exzellenter Korrosionsbeständigkeit, das vor allem in der Luft- und Raumfahrt, der Medizin und der Chemieindustrie verwendet wird. Aufgrund seiner hohen Kosten wird es jedoch nur für spezielle Anwendungen eingesetzt.
Herausforderungen und Entwicklungen in der Metallbearbeitung
Die Metallbearbeitung steht vor einer Reihe von Herausforderungen, die durch technologische Entwicklungen und den zunehmenden Bedarf an hochpräzisen und leistungsfähigen Produkten bedingt sind. Zu den wichtigsten Herausforderungen gehören:
- Präzision: Mit der Miniaturisierung in der Elektronik und anderen High-Tech-Branchen steigen die Anforderungen an die Präzision in der Metallbearbeitung. Neue Technologien wie CNC-Maschinen und Laserschneiden ermöglichen eine bisher unerreichte Genauigkeit.
- Effizienz: Die Notwendigkeit, Produktionszeiten zu verkürzen und Kosten zu senken, treibt die Entwicklung effizienterer Bearbeitungsprozesse voran. Automatisierung und Digitalisierung spielen dabei eine Schlüsselrolle.
- Nachhaltigkeit: Der Druck, umweltfreundlichere Produktionsmethoden zu entwickeln, wächst. Recycling von Metallen, Reduzierung des Energieverbrauchs und Einsatz umweltfreundlicher Materialien sind zentrale Themen.
- Materialvielfalt: Neue Legierungen und Verbundwerkstoffe stellen höhere Anforderungen an die Bearbeitungstechniken. Insbesondere die Verarbeitung von hochfesten, schwer zu bearbeitenden Materialien erfordert spezialisierte Maschinen und Werkzeuge.
- Fachkräftemangel: Die Metallbearbeitungsindustrie kämpft mit einem Mangel an qualifizierten Fachkräften. Investitionen in Ausbildung und Weiterentwicklung der Mitarbeiter sind unerlässlich, um den Anforderungen gerecht zu werden.
Bedeutung der Automatisierung und Digitalisierung
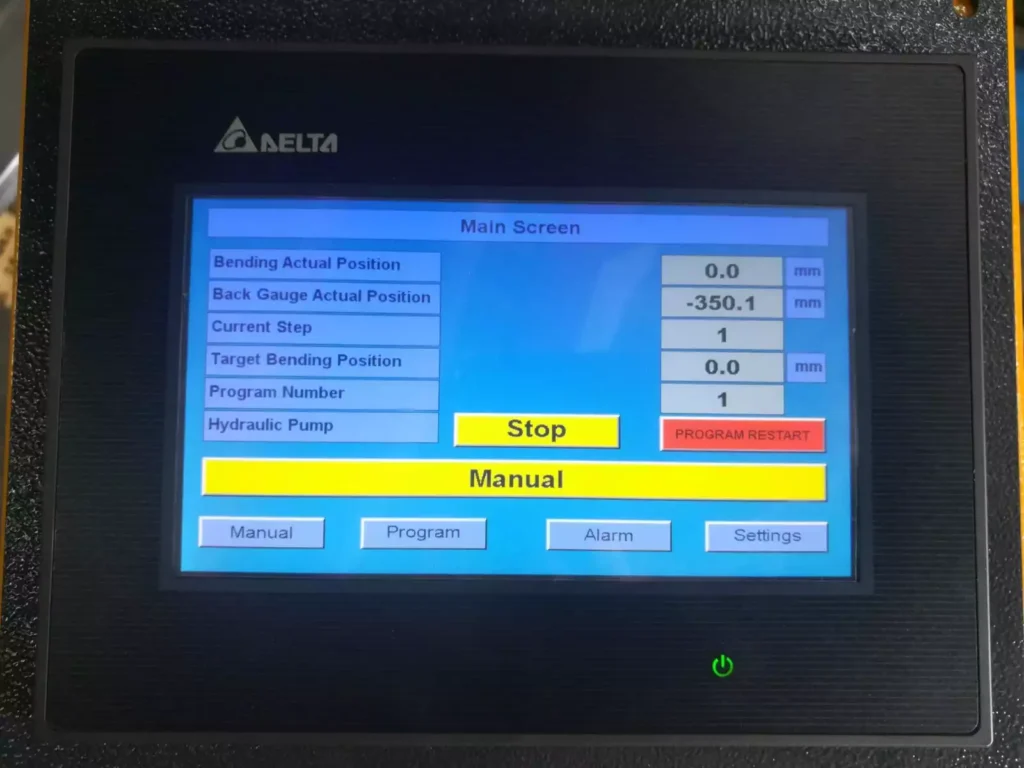
In den letzten Jahren haben Automatisierung und Digitalisierung die Metallbearbeitung revolutioniert. Mit der Einführung von Industrie 4.0 und dem Einsatz von vernetzten Maschinen, Sensoren und Datenanalyse-Tools können Fertigungsprozesse effizienter und präziser gestaltet werden. Roboter übernehmen zunehmend Aufgaben, die früher manuell durchgeführt wurden, was zu einer höheren Produktivität und Konsistenz in der Produktion führt.
Die Digitalisierung ermöglicht es, Produktionsdaten in Echtzeit zu überwachen und zu analysieren, um Fehler frühzeitig zu erkennen und den Materialeinsatz zu optimieren. Dies führt nicht nur zu Kosteneinsparungen, sondern auch zu einer verbesserten Qualität der Endprodukte.
Blechhohlteile Beschneiden und Umformen
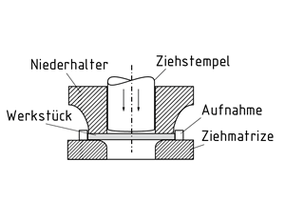
Definition und Bedeutung
Das Beschneiden und Umformen von Blechhohlteilen ist ein zentrales Verfahren in der Metallbearbeitung, bei dem flache Metallbleche oder vorgeformte Hohlteile durch mechanische, thermische oder chemische Prozesse in komplexe Formen und Strukturen gebracht werden. Diese Verfahren sind in der industriellen Fertigung weit verbreitet und unerlässlich für die Herstellung einer Vielzahl von Produkten, von Automobilteilen über Elektronikgehäuse bis hin zu Bauteilen in der Luft- und Raumfahrt.
Blechhohlteile sind typischerweise Bauteile, die aus flachen Metallblechen hergestellt werden und durch Umformprozesse wie Biegen, Tiefziehen oder Streckziehen in dreidimensionale Strukturen verwandelt werden. Diese Teile zeichnen sich durch ihre Leichtigkeit und Festigkeit aus, was sie ideal für Anwendungen macht, bei denen Gewichtseinsparungen wichtig sind.
Verfahren und Technologien
Beim Beschneiden und Umformen von Blechhohlteilen kommen verschiedene Verfahren und Technologien zum Einsatz, die je nach den spezifischen Anforderungen des Endprodukts ausgewählt werden. Zu den wichtigsten Verfahren gehören:
- Schneiden und Stanzen: Hierbei wird das Metallblech auf die gewünschte Größe und Form zugeschnitten. Dies kann durch mechanische Werkzeuge wie Stanzmaschinen oder durch thermische Prozesse wie Laserschneiden erfolgen. Beim Stanzen wird das Metall durch eine Matrize gedrückt, um Löcher oder spezifische Formen zu erzeugen.
- Biegen: Beim Biegen wird das Metallblech entlang einer geraden Achse umgeformt, um Winkel und Radien zu erzeugen. Dieser Prozess wird oft in Kombination mit Schneiden und Stanzen verwendet, um komplexe Bauteile herzustellen. Es gibt verschiedene Biegeverfahren, wie Luftbiegen, Prägebiegen und Schwenkbiegen, die je nach Anwendung ausgewählt werden.
- Tiefziehen: Das Tiefziehen ist ein Umformverfahren, bei dem ein flaches Blech in eine tiefe, hohle Form gezogen wird. Dies geschieht durch das Drücken des Blechs in eine Matrize mit einem Stempel. Das Verfahren wird häufig zur Herstellung von tiefen Hohlkörpern wie Tanks, Dosen oder Karosserieteilen verwendet.
- Streckziehen: Hierbei wird das Blech zwischen einer Form und einem Gegenhalter gehalten und dann durch Zugspannung verformt. Streckziehen ermöglicht die Herstellung von Bauteilen mit komplexen Oberflächengeometrien und wird oft in der Luft- und Raumfahrt eingesetzt.
- Hydroformen: Beim Hydroformen wird ein flaches oder vorgeformtes Metallteil in eine Matrize gelegt und durch hohen Wasserdruck in die Form gepresst. Dieses Verfahren ist besonders für die Herstellung von komplexen, dünnwandigen Bauteilen geeignet und wird häufig in der Automobilindustrie verwendet.
Anwendungsbereiche in der Industrie
Die Anwendung von Verfahren zum Beschneiden und Umformen von Blechhohlteilen ist in zahlreichen Industriezweigen unerlässlich:
- Automobilindustrie: In der Automobilproduktion werden Blechhohlteile für die Herstellung von Karosserieteilen, Chassis-Komponenten und anderen strukturellen Bauteilen verwendet. Durch den Einsatz von hochfesten Stählen und Aluminium können leichte und zugleich sichere Fahrzeuge produziert werden.
- Luft- und Raumfahrt: Hier ist die Gewichtseinsparung besonders wichtig. Blechhohlteile aus Aluminium und Titan werden verwendet, um die Flugzeugstruktur zu verstärken, ohne das Gewicht zu erhöhen. Auch in der Raumfahrttechnik sind solche Bauteile entscheidend, um die Struktur von Raketen und Satelliten zu formen.
- Elektronikindustrie: Gehäuse und Strukturbauteile von Computern, Smartphones und anderen elektronischen Geräten werden häufig durch Umformen von Blechhohlteilen hergestellt. Aluminium und Stahl sind die bevorzugten Materialien aufgrund ihrer guten Wärmeleitfähigkeit und Haltbarkeit.
- Bauindustrie: Im Bauwesen werden Blechhohlteile für Fassaden, Dächer und strukturelle Verstärkungen verwendet. Hier kommen häufig korrosionsbeständige Materialien wie Edelstahl oder verzinkter Stahl zum Einsatz.
Vorteile und Herausforderungen
Vorteile:
- Materialeffizienz: Beim Umformen von Blechhohlteilen bleibt das Material größtenteils erhalten, wodurch Abfälle minimiert werden. Dies trägt zur Kostensenkung und zur nachhaltigen Produktion bei.
- Strukturelle Festigkeit: Umgeformte Blechhohlteile bieten hohe Festigkeit bei gleichzeitig geringem Gewicht, was sie ideal für Anwendungen macht, bei denen sowohl Stabilität als auch Leichtigkeit gefordert sind.
- Designfreiheit: Die Flexibilität der Umformprozesse ermöglicht die Herstellung komplexer, dreidimensionaler Strukturen, die mit anderen Methoden schwer oder gar nicht zu realisieren wären.
- Hohe Produktionsraten: Moderne Maschinen und automatisierte Prozesse ermöglichen es, große Stückzahlen in kurzer Zeit zu produzieren, was insbesondere in der Massenproduktion von Vorteil ist.
Herausforderungen:
- Komplexität der Werkzeuge: Um die gewünschten Formen zu erzielen, sind hochpräzise Werkzeuge und Matrizen erforderlich. Die Herstellung und Wartung dieser Werkzeuge kann kostspielig und zeitaufwendig sein.
- Materialanforderungen: Unterschiedliche Metalle reagieren unterschiedlich auf Umformprozesse. Es ist wichtig, das richtige Material zu wählen, um Risse, Deformationen oder andere Defekte zu vermeiden.
- Anlaufkosten: Die Anfangsinvestitionen für Maschinen, Werkzeuge und die Einrichtung einer Produktionslinie können hoch sein, insbesondere bei komplexen Umformprozessen wie dem Hydroformen.
- Prozesskontrolle: Die genaue Kontrolle über die Umformprozesse ist entscheidend, um gleichbleibende Qualität zu gewährleisten. Dies erfordert fortschrittliche Messtechniken und qualifiziertes Personal.
Technologische Entwicklungen und Innovationen
In den letzten Jahren haben sich die Technologien zum Beschneiden und Umformen von Blechhohlteilen erheblich weiterentwickelt. Fortschritte in der Materialwissenschaft haben die Entwicklung neuer Legierungen ermöglicht, die sich leichter umformen lassen und gleichzeitig eine höhere Festigkeit bieten.
Automatisierung und Digitalisierung spielen eine zunehmend wichtige Rolle. Moderne CNC-gesteuerte Maschinen und Roboter übernehmen immer mehr Aufgaben in der Blechbearbeitung, was zu einer höheren Präzision und Effizienz führt. Sensoren und Überwachungssysteme ermöglichen eine Echtzeitkontrolle der Prozesse, wodurch Fehler frühzeitig erkannt und korrigiert werden können.
Eine weitere bedeutende Innovation ist die Additive Fertigung (3D-Druck), die zwar noch in den Anfängen steht, aber das Potenzial hat, die Umformtechnologien zu ergänzen oder sogar zu ersetzen. Insbesondere bei der Herstellung von Prototypen oder kleinen Serien bietet die Additive Fertigung Flexibilität und Kosteneffizienz, die mit traditionellen Umformtechniken schwer zu erreichen sind.
Auch die Simulationstechnologien haben sich weiterentwickelt. Durch den Einsatz von Software zur numerischen Simulation (Finite-Elemente-Methode) können Ingenieure den Umformprozess bereits im Vorfeld analysieren und optimieren. Dies reduziert die Notwendigkeit von teuren und zeitaufwändigen physischen Prototypen und ermöglicht es, Probleme frühzeitig zu identifizieren und zu beheben.
Zukunftsaussichten
Die Zukunft der Blechbearbeitung, insbesondere das Beschneiden und Umformen von Blechhohlteilen, wird stark von den Entwicklungen in der Automatisierung, Digitalisierung und Materialwissenschaft beeinflusst. Insbesondere die Integration von Künstlicher Intelligenz (KI) und maschinellem Lernen in die Prozesssteuerung verspricht, die Effizienz und Präzision weiter zu steigern. KI-Systeme könnten in der Lage sein, den Umformprozess in Echtzeit zu optimieren und automatisch Anpassungen vorzunehmen, um die Qualität zu maximieren und Abfall zu minimieren.
Ein weiterer Trend ist die Nachhaltigkeit. Die Forderung nach umweltfreundlicheren Produktionsmethoden wird dazu führen, dass neue Materialien und Technologien entwickelt werden, die weniger Energie verbrauchen und Abfälle reduzieren. Recycelbare Legierungen und energieeffiziente Maschinen werden zunehmend an Bedeutung gewinnen.
Die Nachfrage nach leichten und gleichzeitig robusten Bauteilen wird weiter steigen, insbesondere in der Automobil- und Luftfahrtindustrie. Dies wird die Entwicklung neuer, innovativer Umformtechnologien vorantreiben, die es ermöglichen, diese Anforderungen zu erfüllen.
Entgratmaschinen für Metall
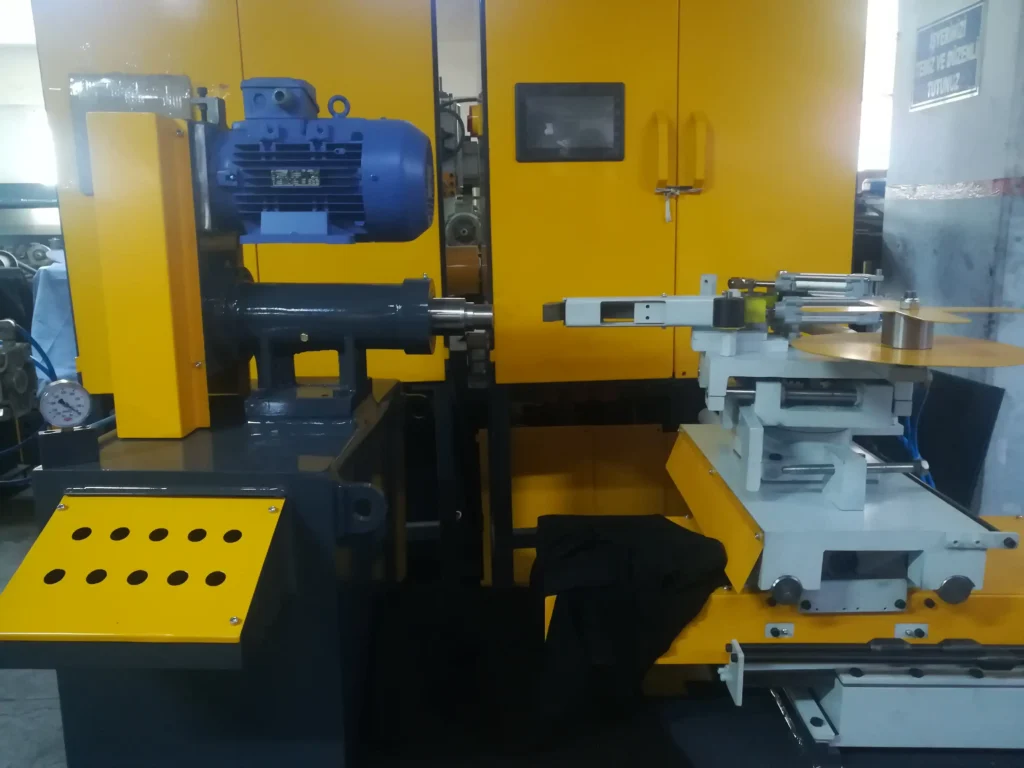
Definition und Einsatzgebiete
Entgratmaschinen für Metall sind spezialisierte Maschinen, die dazu verwendet werden, scharfe Kanten, Grate und Unregelmäßigkeiten zu entfernen, die beim Schneiden, Stanzen, Fräsen oder Umformen von Metallteilen entstehen. Diese Grate entstehen häufig durch Materialverdrängung und sind unerwünscht, da sie sowohl die Funktionalität als auch die Sicherheit von Bauteilen beeinträchtigen können. Daher ist das Entgraten ein wesentlicher Schritt in der Nachbearbeitung von Metallteilen, um sicherzustellen, dass sie den hohen Qualitätsstandards entsprechen.
Die Einsatzgebiete von Entgratmaschinen sind vielfältig und umfassen nahezu alle Industriezweige, in denen Metallteile bearbeitet werden. Dazu gehören unter anderem:
- Automobilindustrie: Hier werden Entgratmaschinen eingesetzt, um Kanten und Oberflächen von Motorblöcken, Getriebeteilen und anderen mechanischen Komponenten zu glätten.
- Luft- und Raumfahrtindustrie: In dieser Branche ist Präzision entscheidend. Entgratmaschinen sorgen dafür, dass Komponenten wie Turbinenschaufeln und Strukturteile keine Grate oder scharfen Kanten aufweisen, die zu Materialermüdung führen könnten.
- Maschinenbau: Im allgemeinen Maschinenbau sind Entgratmaschinen unverzichtbar, um die Lebensdauer und Leistung von Werkzeugen und Bauteilen zu erhöhen.
- Medizintechnik: Metallteile für medizinische Geräte und Implantate müssen extrem glatt und gratfrei sein, um die Sicherheit und Biokompatibilität zu gewährleisten.
Unterschiedliche Typen von Entgratmaschinen
Entgratmaschinen gibt es in verschiedenen Ausführungen, die je nach den spezifischen Anforderungen des zu bearbeitenden Materials und der gewünschten Oberflächenqualität ausgewählt werden. Zu den wichtigsten Typen gehören:
- Bürstentgratmaschinen: Diese Maschinen verwenden rotierende Bürsten, um Grate von der Oberfläche des Metallteils zu entfernen. Bürstentgratmaschinen sind besonders effektiv bei der Bearbeitung von Teilen mit komplexen Geometrien und unregelmäßigen Formen. Sie bieten eine gleichmäßige Oberflächenbehandlung und können sowohl für feine als auch für gröbere Grate eingesetzt werden.
- Schleifband-Entgratmaschinen: Diese Maschinen arbeiten mit rotierenden Schleifbändern, die das Metall durch abrasives Schleifen von Graten befreien. Schleifband-Entgratmaschinen sind ideal für flache oder leicht gekrümmte Oberflächen und bieten eine hohe Materialabtragsrate. Sie sind besonders geeignet für die Bearbeitung von Blech- und Platinenkanten.
- Vibrations-Entgratmaschinen: Diese Maschinen verwenden ein vibrierendes Behältersystem, in dem die Metallteile zusammen mit Schleif- oder Poliermedien bewegt werden. Die Vibrationen und die Reibung der Medien entfernen die Grate und polieren die Oberfläche. Vibrations-Entgratmaschinen sind besonders geeignet für kleine und mittelgroße Teile sowie für die Massenproduktion.
- Strahl-Entgratmaschinen: Strahl-Entgratmaschinen verwenden einen Hochgeschwindigkeitsstrahl von Schleifmitteln, wie Sand, Glasperlen oder Stahlkies, um Grate von der Oberfläche des Metallteils zu entfernen. Diese Methode ist besonders effektiv bei der Bearbeitung von Teilen mit harten oder spröden Graten, die mit anderen Methoden schwer zu entfernen sind.
- Laser-Entgratmaschinen: Diese modernen Maschinen nutzen die hohe Energie eines Laserstrahls, um Grate präzise und kontaktlos zu entfernen. Laser-Entgratmaschinen sind ideal für die Bearbeitung empfindlicher oder sehr kleiner Teile, bei denen mechanische Verfahren zu Beschädigungen führen könnten. Sie bieten eine hohe Präzision und sind in der Lage, sehr feine Grate zu entfernen, ohne die umgebende Materialstruktur zu beeinträchtigen.
- Elektrochemische Entgratmaschinen (ECM): Bei diesem Verfahren wird ein Elektrolyt verwendet, um Grate durch einen kontrollierten elektrochemischen Prozess zu entfernen. ECM-Entgratmaschinen sind besonders geeignet für Teile mit sehr komplexen Geometrien oder schwer zugänglichen Stellen. Dieses Verfahren ist sehr präzise und ermöglicht das Entfernen von Graten, ohne das Basismaterial zu schwächen.
Technologische Fortschritte und Innovationen
Die Entwicklung von Entgratmaschinen hat in den letzten Jahren erhebliche Fortschritte gemacht, angetrieben durch die steigenden Anforderungen an die Qualität und Präzision von Metallteilen in verschiedenen Industrien. Einige der bemerkenswertesten technologischen Innovationen umfassen:
- Automatisierung: Moderne Entgratmaschinen sind zunehmend automatisiert und in Produktionslinien integriert. Dies ermöglicht eine kontinuierliche Bearbeitung von Teilen ohne Unterbrechung, was die Effizienz erhöht und die Produktionskosten senkt. Roboterarme und CNC-Steuerungen übernehmen dabei die präzise Positionierung und Führung der Teile während des Entgratprozesses.
- Prozessüberwachung und -steuerung: Die Integration von Sensoren und Echtzeit-Datenanalyse in Entgratmaschinen ermöglicht eine kontinuierliche Überwachung des Prozesses und eine automatische Anpassung der Bearbeitungsparameter. Dies gewährleistet eine gleichbleibend hohe Qualität und reduziert den Ausschuss.
- Umweltfreundliche Verfahren: Die Entwicklung umweltfreundlicher Entgratverfahren, die weniger Energie verbrauchen und keine umweltschädlichen Chemikalien verwenden, hat an Bedeutung gewonnen. Laser- und elektrochemische Verfahren sind Beispiele für Technologien, die in diese Richtung gehen.
- Hybridmaschinen: Es gibt zunehmend Maschinen, die mehrere Entgratverfahren in einer einzigen Einheit kombinieren, um die Flexibilität und Effizienz zu erhöhen. Ein Beispiel wäre eine Maschine, die sowohl mechanische als auch elektrochemische Verfahren kombiniert, um eine umfassende Gratentfernung zu ermöglichen.
- Additive Fertigung: In Verbindung mit additiven Fertigungstechniken wie dem 3D-Druck werden auch neue Entgratmethoden entwickelt, die speziell auf die Anforderungen von gedruckten Metallteilen zugeschnitten sind. Dies umfasst beispielsweise spezielle Laser- oder elektrochemische Verfahren, die für die Bearbeitung der komplexen Geometrien und Materialeigenschaften von 3D-gedruckten Teilen optimiert sind.
Anwendungsbeispiele und Fallstudien
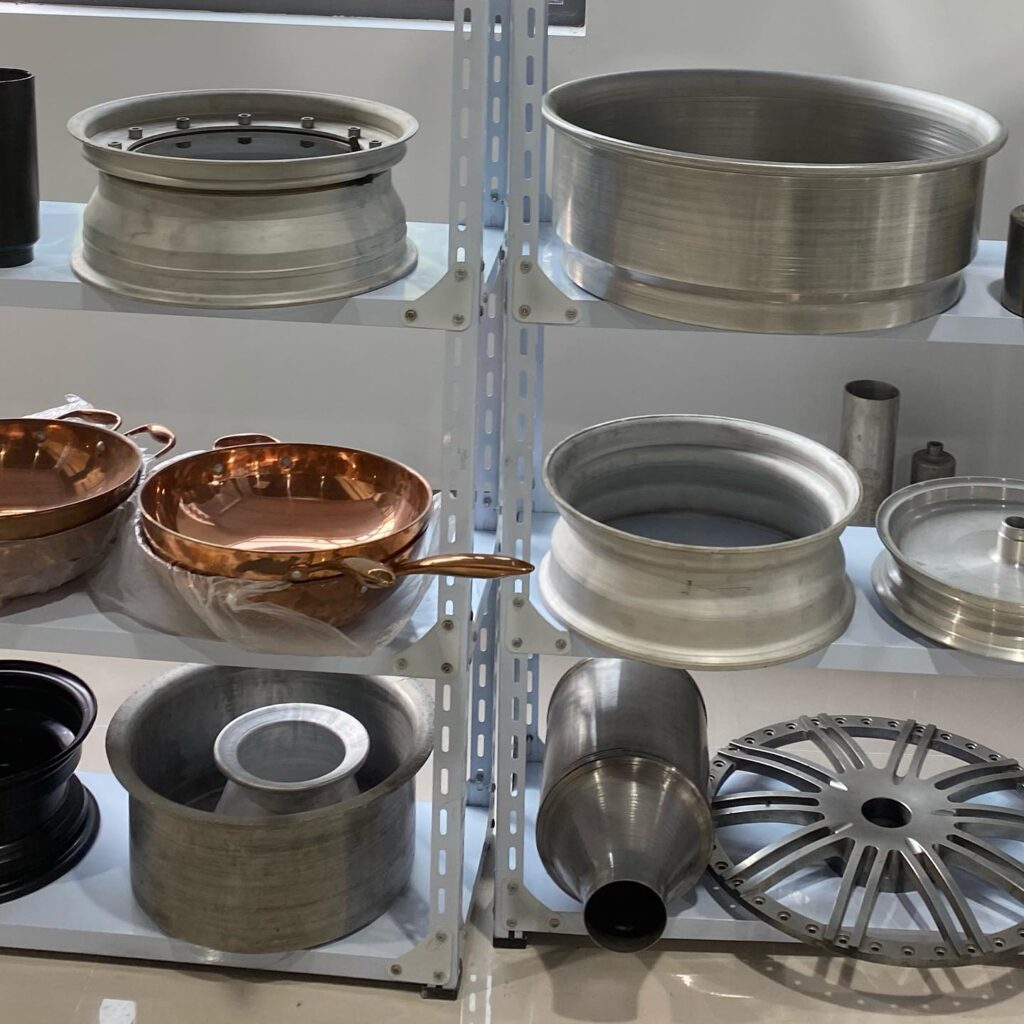
Die praktischen Anwendungen von Entgratmaschinen sind zahlreich, und in vielen Branchen gibt es spezifische Beispiele, die die Bedeutung dieser Technologie unterstreichen.
Automobilindustrie: Ein großer Automobilhersteller implementierte eine vollautomatische Bürstentgratmaschine in seine Produktionslinie zur Herstellung von Getriebegehäusen. Vor der Implementierung hatten unzureichend entgratete Teile häufig zu Problemen bei der Montage geführt, was zu Produktionsverzögerungen und erhöhten Kosten führte. Nach der Einführung der automatischen Entgratmaschine konnte die Qualität der Teile deutlich verbessert und die Ausschussrate erheblich reduziert werden. Dies führte zu einer schnelleren Produktion und geringeren Kosten.
Luft- und Raumfahrt: Ein Unternehmen in der Luft- und Raumfahrtindustrie setzte elektrochemische Entgratmaschinen ein, um Turbinenschaufeln aus hochfesten Legierungen zu entgraten. Die Schaufeln haben komplexe Geometrien und erfordern eine präzise Gratentfernung, um ihre Leistungsfähigkeit zu gewährleisten. Mit herkömmlichen mechanischen Methoden war es schwierig, die notwendigen Toleranzen einzuhalten. Die Einführung des elektrochemischen Entgratens führte zu einer signifikanten Verbesserung der Präzision und verlängerte gleichzeitig die Lebensdauer der Schaufeln.
Medizintechnik: In der Medizintechnik wurde eine Laser-Entgratmaschine zur Bearbeitung von chirurgischen Instrumenten eingeführt. Diese Instrumente müssen absolut gratfrei sein, um die Sicherheit und Wirksamkeit bei Operationen zu gewährleisten. Die Laser-Entgratmaschine ermöglichte es, selbst kleinste Grate zu entfernen, die mit mechanischen Verfahren nicht erfasst werden konnten, was die Qualität der Instrumente erheblich verbesserte und gleichzeitig die Produktionszeit verkürzte.
Herausforderungen bei der Implementierung
Trotz der zahlreichen Vorteile gibt es auch Herausforderungen bei der Implementierung von Entgratmaschinen in Produktionsprozesse. Zu den wichtigsten Herausforderungen gehören:
- Kosten: Die Anschaffung und Integration von High-End-Entgratmaschinen, insbesondere von automatisierten oder spezialisierten Systemen wie Laser- oder elektrochemischen Maschinen, kann mit erheblichen Kosten verbunden sein. Dies kann für kleinere Unternehmen eine Hürde darstellen.
- Wartung: Entgratmaschinen, insbesondere solche mit komplexen mechanischen oder elektronischen Systemen, erfordern regelmäßige Wartung, um eine konstante Leistung sicherzustellen. Dies erfordert geschultes Personal und kann zusätzliche Betriebskosten verursachen.
- Prozessoptimierung: Die optimale Einstellung und Kalibrierung der Maschinen kann zeitaufwändig sein und erfordert fundiertes technisches Wissen. Jede Änderung im Produktionsprozess oder im Material kann eine erneute Anpassung der Entgratparameter erfordern.
- Materialvielfalt: Unterschiedliche Metalle und Legierungen reagieren unterschiedlich auf Entgratverfahren. Es ist wichtig, das geeignete Verfahren für jedes spezifische Material zu wählen, um Beschädigungen zu vermeiden und eine gleichbleibende Qualität sicherzustellen.
Zukunftsaussichten
Die Zukunft der Entgratmaschinen für Metall ist eng mit den allgemeinen Trends in der industriellen Fertigung verbunden, insbesondere mit der zunehmenden Automatisierung und Digitalisierung. In den kommenden Jahren wird erwartet, dass Entgratmaschinen noch stärker in vernetzte Produktionsumgebungen integriert werden, in denen sie Teil eines umfassenden, automatisierten Fertigungsprozesses sind.
Die Entwicklung von intelligenten Entgratmaschinen, die durch künstliche Intelligenz gesteuert werden und in der Lage sind, selbstlernend optimale Parameter für unterschiedliche Materialien und Geometrien zu bestimmen, könnte die Effizienz und Qualität weiter steigern. Diese Maschinen könnten in der Lage sein, sich automatisch an wechselnde Produktionsanforderungen anzupassen und so die Flexibilität in der Fertigung erhöhen.
Auch die zunehmende Bedeutung von Nachhaltigkeit wird die Entwicklung von umweltfreundlichen Entgratverfahren weiter vorantreiben. Es ist zu erwarten, dass neue Technologien entwickelt werden, die weniger Energie verbrauchen und umweltfreundliche Materialien verwenden, um den ökologischen Fußabdruck der Produktion zu minimieren.
Rohrbiegemaschinen: Ein Überblick
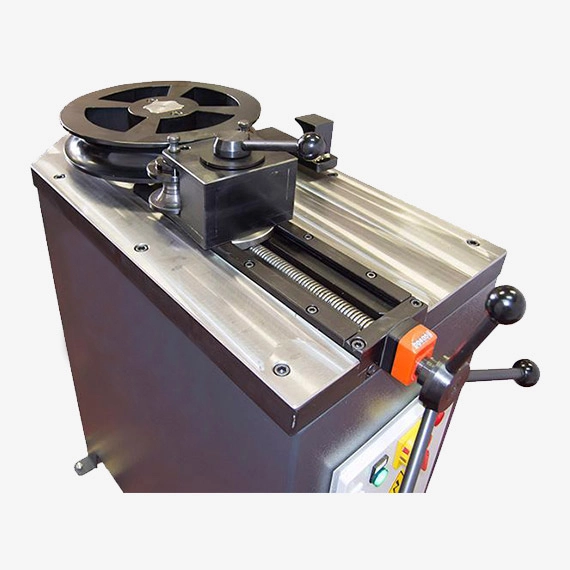
Einführung in Rohrbiegemaschinen
Rohrbiegemaschinen sind spezielle Maschinen, die zum Biegen von Metallrohren verwendet werden, um sie in die gewünschte Form und den gewünschten Winkel zu bringen. Diese Maschinen sind in zahlreichen Industriezweigen unverzichtbar, darunter in der Automobilindustrie, im Schiffbau, in der Luft- und Raumfahrt sowie in der Bauindustrie. Rohrbiegemaschinen ermöglichen die Herstellung von komplexen Rohrsystemen und -strukturen, die in verschiedenen Anwendungen, von Hydrauliksystemen bis zu architektonischen Konstruktionen, verwendet werden.
Die Fähigkeit, Rohre präzise zu biegen, ist entscheidend, um sicherzustellen, dass die Endprodukte sowohl funktional als auch ästhetisch ansprechend sind. Je nach Material, Durchmesser und Wandstärke des Rohrs sowie den spezifischen Anforderungen der Anwendung gibt es unterschiedliche Typen von Rohrbiegemaschinen, die jeweils spezielle Vorteile und Einsatzbereiche bieten.
Historische Entwicklung und technologische Fortschritte
Die Geschichte der Rohrbiegemaschinen reicht weit zurück, aber bedeutende technologische Fortschritte wurden im 20. Jahrhundert erzielt, insbesondere mit der Einführung von hydraulischen und elektrischen Antrieben. Frühe Rohrbiegemaschinen waren mechanisch und manuell betrieben, was den Prozess zeitaufwendig und arbeitsintensiv machte. Diese frühen Maschinen waren auch in ihrer Präzision und Wiederholbarkeit begrenzt, was zu Inkonsistenzen in den Endprodukten führte.
Mit der Einführung von hydraulischen Systemen in den 1960er Jahren konnten Rohre mit größerer Kraft und Präzision gebogen werden, wodurch es möglich wurde, dickere und härtere Materialien zu verarbeiten. Hydraulische Rohrbiegemaschinen ermöglichten es auch, komplexere Biegeprofile zu erstellen, was in vielen Industriezweigen neue Anwendungsmöglichkeiten eröffnete.
In den letzten Jahrzehnten hat die Elektrifizierung und Digitalisierung von Rohrbiegemaschinen zu einer weiteren Verbesserung der Präzision und Effizienz geführt. Elektrische Rohrbiegemaschinen sind nicht nur energieeffizienter, sondern auch einfacher zu bedienen und bieten eine höhere Genauigkeit, insbesondere bei der Serienproduktion. Die Integration von CNC-Technologie (Computerized Numerical Control) hat die Automatisierung des Rohrbiegens revolutioniert, da sie es ermöglicht, komplexe Biegeabläufe mit hoher Wiederholgenauigkeit zu programmieren und auszuführen.
Vergleich zwischen elektrischen und hydraulischen Rohrbiegemaschinen
Die Wahl zwischen elektrischen und hydraulischen Rohrbiegemaschinen hängt von verschiedenen Faktoren ab, darunter die Anforderungen an die Biegepräzision, die Art des Materials und das Produktionsvolumen. Beide Maschinentypen haben spezifische Vor- und Nachteile, die je nach Anwendung variieren können.
Hydraulische Rohrbiegemaschinen:
- Vorteile:
- Hohe Biegekraft: Hydraulische Maschinen sind ideal für das Biegen von dicken und hochfesten Materialien wie Stahlrohren.
- Robustheit: Sie sind langlebig und können unter schwierigen Bedingungen arbeiten, was sie besonders für schwere Industrieanwendungen geeignet macht.
- Vielseitigkeit: Hydraulische Maschinen können in der Regel eine breite Palette von Rohrdurchmessern und -wandstärken bearbeiten.
- Nachteile:
- Weniger energieeffizient: Der Betrieb einer hydraulischen Rohrbiegemaschine erfordert mehr Energie im Vergleich zu elektrischen Maschinen.
- Größere Wartungsanforderungen: Hydraulische Systeme erfordern regelmäßige Wartung, einschließlich des Austauschs von Hydraulikflüssigkeiten und Dichtungen.
- Langsamere Bedienung: Im Vergleich zu elektrischen Maschinen können hydraulische Maschinen langsamer sein, insbesondere bei komplexen Biegeabläufen.
Elektrische Rohrbiegemaschinen:
- Vorteile:
- Hohe Präzision: Elektrische Maschinen bieten eine extrem hohe Biegegenauigkeit, was sie ideal für Anwendungen macht, bei denen enge Toleranzen erforderlich sind.
- Energieeffizienz: Sie sind energieeffizienter als hydraulische Maschinen und haben oft geringere Betriebskosten.
- Einfachere Bedienung: Mit digitaler Steuerung und automatisierten Prozessen sind elektrische Maschinen einfacher zu programmieren und zu betreiben.
- Nachteile:
- Begrenzte Biegekraft: Elektrische Maschinen sind möglicherweise nicht so leistungsstark wie hydraulische Maschinen, was ihre Fähigkeit, sehr dicke oder harte Materialien zu biegen, einschränken kann.
- Höhere Anschaffungskosten: Elektrische Maschinen können in der Anschaffung teurer sein, insbesondere Modelle mit fortschrittlicher CNC-Steuerung.
Typische Anwendungen und Industriezweige
Rohrbiegemaschinen werden in einer Vielzahl von Industriezweigen eingesetzt, wobei jede Branche spezifische Anforderungen an die Maschinen stellt. Zu den häufigsten Anwendungen gehören:
- Automobilindustrie: Rohrbiegemaschinen werden zur Herstellung von Abgassystemen, Überrollkäfigen und anderen strukturellen Komponenten verwendet. Die Präzision beim Biegen ist entscheidend, um die Passgenauigkeit der Teile zu gewährleisten.
- Luft- und Raumfahrt: In der Luft- und Raumfahrttechnik werden Rohrbiegemaschinen verwendet, um leichte und dennoch robuste Rohrstrukturen für Flugzeugrahmen, Hydrauliksysteme und Kraftstoffleitungen herzustellen.
- Schiffbau: Im Schiffbau werden große, hydraulische Rohrbiegemaschinen eingesetzt, um dickwandige Rohre für das Schiffsskelett und die Leitungssysteme zu biegen. Die Maschinen müssen in der Lage sein, sowohl Stahl- als auch Aluminiumrohre zu verarbeiten.
- Bauindustrie: In der Bauindustrie werden Rohrbiegemaschinen für die Herstellung von Rohrleitungen, Gerüstsystemen und architektonischen Strukturen eingesetzt. Hier sind vor allem Maschinen gefragt, die eine hohe Flexibilität in der Materialbearbeitung bieten.
Schlussbetrachtung
Rohrbiegemaschinen sind ein wesentlicher Bestandteil der modernen Fertigungstechnik. Die Wahl zwischen elektrischen und hydraulischen Modellen hängt von den spezifischen Anforderungen ab, wobei jede Technologie ihre eigenen Stärken und Schwächen hat. Mit den kontinuierlichen Fortschritten in der Maschinenbau- und Steuerungstechnologie wird erwartet, dass Rohrbiegemaschinen in Zukunft noch präziser, effizienter und vielseitiger werden.
Elektrische Rohrbiegemaschinen
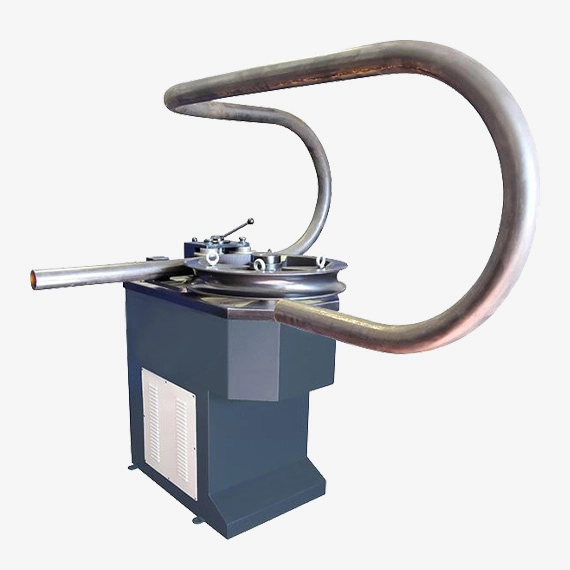
Funktionsweise und Aufbau
Elektrische Rohrbiegemaschinen sind hochentwickelte Werkzeuge, die für das präzise und effiziente Biegen von Rohren eingesetzt werden. Sie arbeiten vollständig elektrisch und nutzen fortschrittliche Antriebstechnologien, um Rohre in die gewünschte Form zu bringen. Diese Maschinen sind besonders geeignet für Anwendungen, bei denen eine hohe Wiederholgenauigkeit und Präzision erforderlich sind.
Der Aufbau einer elektrischen Rohrbiegemaschine umfasst mehrere Schlüsselkomponenten:
- Elektrischer Antrieb: Im Zentrum der Maschine steht der elektrische Antrieb, der für die Bewegung der Biegewerkzeuge verantwortlich ist. Diese Antriebe sind typischerweise Servomotoren, die eine präzise Steuerung der Biegebewegungen ermöglichen.
- Biegewerkzeuge: Die Biegewerkzeuge bestehen in der Regel aus einem Biegeradius und einem Gegenlager, die das Rohr während des Biegeprozesses in Position halten. Der Biegeradius bestimmt den Winkel und die Krümmung des Rohrs, während das Gegenlager dafür sorgt, dass das Rohr während des Biegens nicht aus der Form gerät.
- CNC-Steuerung: Moderne elektrische Rohrbiegemaschinen sind oft mit CNC-Steuerungen (Computerized Numerical Control) ausgestattet. Diese Steuerungen ermöglichen es dem Bediener, komplexe Biegeabläufe zu programmieren und die Maschine so einzustellen, dass sie die gewünschten Biegungen mit höchster Präzision ausführt.
- Sensoren und Überwachungssysteme: Um die Qualität und Präzision des Biegeprozesses zu gewährleisten, sind viele elektrische Rohrbiegemaschinen mit Sensoren ausgestattet, die Echtzeitdaten über den Prozess liefern. Diese Daten können verwendet werden, um den Biegewinkel, die Materialspannung und andere kritische Parameter zu überwachen und gegebenenfalls Anpassungen vorzunehmen.
Vorteile und Nachteile
Elektrische Rohrbiegemaschinen bieten eine Reihe von Vorteilen, die sie für bestimmte Anwendungen besonders geeignet machen:
Vorteile:
- Hohe Präzision: Dank der fortschrittlichen CNC-Steuerung und der präzisen Servomotoren können elektrische Rohrbiegemaschinen sehr genaue Biegungen durchführen. Dies ist besonders wichtig in Branchen wie der Luft- und Raumfahrt oder der Automobilindustrie, wo enge Toleranzen erforderlich sind.
- Energieeffizienz: Elektrische Maschinen sind in der Regel energieeffizienter als hydraulische Modelle, da sie weniger Energie für den Betrieb benötigen und keine hydraulischen Systeme verwenden, die zusätzlichen Energieverbrauch verursachen.
- Geringer Wartungsaufwand: Da elektrische Maschinen keine Hydraulikflüssigkeiten oder -systeme verwenden, ist der Wartungsaufwand geringer. Es gibt weniger Verschleißteile, und die Maschinen sind im Allgemeinen zuverlässiger und langlebiger.
- Geräuscharmer Betrieb: Elektrische Maschinen sind im Betrieb leiser als hydraulische Modelle, was zu einer besseren Arbeitsumgebung beiträgt und den Lärmschutz in der Fertigung verbessert.
Nachteile:
- Begrenzte Biegekraft: Ein Nachteil von elektrischen Rohrbiegemaschinen ist ihre begrenzte Biegekraft im Vergleich zu hydraulischen Maschinen. Sie sind möglicherweise nicht in der Lage, sehr dicke oder hochfeste Rohre zu biegen, was ihre Einsatzmöglichkeiten einschränken kann.
- Höhere Anschaffungskosten: Elektrische Rohrbiegemaschinen, insbesondere solche mit fortschrittlicher CNC-Technologie, können in der Anschaffung teurer sein als einfachere hydraulische Modelle. Diese höheren Investitionskosten müssen durch erhöhte Produktivität und niedrigere Betriebskosten gerechtfertigt werden.
- Eingeschränkte Flexibilität bei extremen Anwendungen: In Anwendungen, bei denen extreme Biegekräfte oder sehr spezielle Biegeformen erforderlich sind, kann die Flexibilität einer elektrischen Maschine im Vergleich zu hydraulischen Modellen begrenzt sein.
Anwendungsbereiche in der Industrie
Elektrische Rohrbiegemaschinen finden in vielen Industriezweigen Anwendung, in denen Präzision und Effizienz entscheidend sind. Zu den wichtigsten Anwendungsbereichen gehören:
- Automobilindustrie: In der Automobilindustrie werden elektrische Rohrbiegemaschinen zur Herstellung von Abgassystemen, Fahrgestellen und anderen strukturellen Komponenten eingesetzt. Die Fähigkeit, Rohre mit hoher Präzision zu biegen, trägt dazu bei, dass die Teile passgenau und sicher in die Fahrzeuge integriert werden können.
- Luft- und Raumfahrt: Die Luft- und Raumfahrtindustrie erfordert leichte, aber dennoch stabile Rohrstrukturen. Elektrische Rohrbiegemaschinen sind ideal für die Herstellung von komplexen Rohrgeometrien, die in Flugzeugrahmen, Triebwerken und anderen kritischen Komponenten verwendet werden.
- Möbel- und Innenausbau: In der Möbelindustrie werden elektrische Rohrbiegemaschinen verwendet, um Metallrohre für Möbelrahmen, Stuhlbeine und andere dekorative Elemente zu biegen. Die Maschinen ermöglichen es, ästhetisch ansprechende und funktionale Designs zu realisieren.
- Medizintechnik: In der Medizintechnik werden präzise Rohrbiegungen für chirurgische Instrumente, medizinische Geräte und Implantate benötigt. Elektrische Rohrbiegemaschinen sind in der Lage, die feinen Toleranzen und komplexen Formen zu erzeugen, die in diesem Bereich erforderlich sind.
Fallstudien und Beispiele
Automobilindustrie: Ein führender Automobilhersteller implementierte eine Reihe von CNC-gesteuerten elektrischen Rohrbiegemaschinen in seine Produktionslinie zur Herstellung von Abgaskrümmern. Die Maschinen ermöglichten es, die Produktionsgeschwindigkeit zu erhöhen und gleichzeitig die Genauigkeit der Biegungen zu verbessern. Dies führte zu einer signifikanten Reduzierung der Nacharbeiten und einer Verbesserung der Gesamtproduktivität.
Luft- und Raumfahrt: Ein Zulieferer für die Luft- und Raumfahrtindustrie nutzte elektrische Rohrbiegemaschinen, um komplexe Aluminiumrohre für Flugzeugrahmen herzustellen. Die hohe Präzision der CNC-Steuerungen ermöglichte es, die strengen Toleranzen einzuhalten, die für sicherheitskritische Anwendungen erforderlich sind. Die Maschinen trugen dazu bei, die Produktionszeiten zu verkürzen und die Materialausnutzung zu optimieren.
Möbelindustrie: Ein Möbelhersteller setzte elektrische Rohrbiegemaschinen ein, um moderne und ergonomische Stühle mit gebogenen Metallrahmen zu produzieren. Die Flexibilität der Maschinen ermöglichte es, verschiedene Designs mit minimalen Anpassungen herzustellen, was die Produktionskosten senkte und die Markteinführungszeit verkürzte.
Trends und Innovationen
Die technologische Entwicklung in der Fertigungstechnik hat auch bei elektrischen Rohrbiegemaschinen zu signifikanten Innovationen geführt. Einige der bemerkenswertesten Trends und Entwicklungen umfassen:
- Integration von IoT: Durch die Integration von Internet of Things (IoT)-Technologien in Rohrbiegemaschinen können Maschinen vernetzt und Produktionsprozesse in Echtzeit überwacht und optimiert werden. Dies führt zu einer verbesserten Effizienz und einer besseren Fehlererkennung.
- Erweiterte Automatisierung: Die zunehmende Automatisierung ermöglicht es, dass elektrische Rohrbiegemaschinen vollständig in automatisierte Produktionslinien integriert werden. Roboter und Handhabungssysteme können die Rohre automatisch zuführen, biegen und auswerfen, was die menschliche Intervention minimiert und die Produktivität maximiert.
- Verbesserte Materialbearbeitung: Neue Werkstoffe und Legierungen erfordern angepasste Biegetechnologien. Elektrische Rohrbiegemaschinen entwickeln sich weiter, um auch anspruchsvolle Materialien wie hochfeste Stähle oder Leichtmetalllegierungen effizient und präzise zu bearbeiten.
- Umweltfreundlichkeit: Elektrische Rohrbiegemaschinen sind aufgrund ihres geringeren Energieverbrauchs und ihrer sauberen Betriebsweise eine umweltfreundlichere Alternative zu hydraulischen Maschinen. Die Entwicklung von energieeffizienten Antrieben und die Nutzung erneuerbarer Energien tragen zur Reduzierung des ökologischen Fußabdrucks bei.
Zukunftsperspektiven
Die Zukunft elektrischer Rohrbiegemaschinen wird stark von der fortschreitenden Digitalisierung und Automatisierung geprägt sein. Maschinen werden zunehmend intelligentere Steuerungen und Sensoren integrieren, die nicht nur den Biegeprozess optimieren, sondern auch eine vorausschauende Wartung ermöglichen. Künstliche Intelligenz könnte eingesetzt werden, um den Biegeprozess zu analysieren und automatisch Anpassungen vorzunehmen, um die Qualität zu maximieren und Materialverschwendung zu minimieren.
Die Nachfrage nach hochpräzisen, wiederholbaren und energieeffizienten Biegeverfahren wird in der Industrie weiter steigen, was den Einsatz elektrischer Rohrbiegemaschinen fördern wird. Darüber hinaus werden neue Materialien und Designanforderungen die Entwicklung spezialisierter Maschinen vorantreiben, die in der Lage sind, diese Herausforderungen zu bewältigen.
Hydraulische Rohrbiegemaschinen
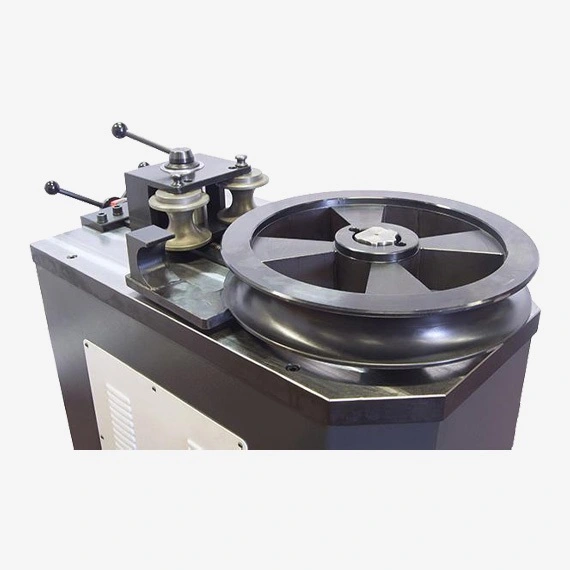
Funktionsweise und Aufbau
Hydraulische Rohrbiegemaschinen sind leistungsstarke Werkzeuge, die speziell für das Biegen von Metallrohren, insbesondere von dickwandigen und hochfesten Rohren, entwickelt wurden. Diese Maschinen nutzen hydraulische Kraft, um das Rohr in die gewünschte Form zu biegen. Sie sind besonders in schweren industriellen Anwendungen verbreitet, wo hohe Biegekraft und die Fähigkeit, eine Vielzahl von Materialien zu verarbeiten, erforderlich sind.
Der Aufbau einer hydraulischen Rohrbiegemaschine umfasst mehrere wesentliche Komponenten:
- Hydrauliksystem: Im Zentrum der Maschine steht das Hydrauliksystem, das aus einer Pumpe, einem Hydraulikzylinder und Steuerungsventilen besteht. Die Pumpe erzeugt den erforderlichen Druck, der auf den Hydraulikzylinder übertragen wird, um das Rohr zu biegen. Diese Systeme sind für ihre hohe Kraftübertragung und Zuverlässigkeit bekannt.
- Biegewange und Biegeradius: Wie bei elektrischen Maschinen sind auch hydraulische Rohrbiegemaschinen mit einer Biegewange und einem Biegeradius ausgestattet. Diese Komponenten halten das Rohr fest und sorgen für eine gleichmäßige Biegung entlang der gewünschten Linie.
- Gegenlager und Spannvorrichtungen: Das Gegenlager hält das Rohr während des Biegeprozesses in Position, um sicherzustellen, dass es nicht verrutscht oder sich verformt. Spannvorrichtungen sind so gestaltet, dass sie das Rohr sicher fixieren, um eine präzise Biegung zu gewährleisten.
- Bedienfeld und Steuerung: Moderne hydraulische Rohrbiegemaschinen verfügen über digitale Steuerungen und Bedienfelder, die es dem Bediener ermöglichen, den Biegeprozess genau zu steuern. Dies umfasst die Einstellung von Biegewinkel, Geschwindigkeit und Druck, um die gewünschte Rohrform zu erreichen.
Vorteile und Nachteile
Hydraulische Rohrbiegemaschinen bieten eine Reihe von Vorteilen, die sie für bestimmte industrielle Anwendungen unverzichtbar machen. Gleichzeitig gibt es jedoch auch einige Nachteile, die bei der Auswahl der richtigen Maschine berücksichtigt werden müssen.
Vorteile:
- Hohe Biegekraft: Der größte Vorteil hydraulischer Rohrbiegemaschinen ist ihre Fähigkeit, hohe Kräfte aufzubringen. Dies macht sie ideal für das Biegen von dickwandigen oder hochfesten Materialien wie Edelstahl, Kohlenstoffstahl und Aluminiumlegierungen.
- Robustheit und Langlebigkeit: Hydraulische Maschinen sind für ihre Langlebigkeit bekannt und können auch unter schwierigen Bedingungen zuverlässig arbeiten. Sie sind robust gebaut und können über viele Jahre hinweg in anspruchsvollen Industrieumgebungen eingesetzt werden.
- Vielseitigkeit: Diese Maschinen können eine breite Palette von Rohrdurchmessern und Wandstärken verarbeiten. Dadurch sind sie flexibel einsetzbar und eignen sich für unterschiedlichste Anwendungen.
- Präzision bei großen Durchmessern: Hydraulische Maschinen bieten eine hohe Präzision beim Biegen von Rohren mit großen Durchmessern, was sie ideal für Anwendungen im Schiffbau, im Rohrleitungsbau und in der Schwerindustrie macht.
Nachteile:
- Hoher Energieverbrauch: Ein wesentlicher Nachteil hydraulischer Rohrbiegemaschinen ist ihr hoher Energieverbrauch. Die Hydraulikpumpe benötigt eine beträchtliche Menge an Energie, um die erforderlichen Kräfte zu erzeugen, was die Betriebskosten erhöht.
- Größerer Wartungsaufwand: Hydraulische Systeme erfordern regelmäßige Wartung, insbesondere im Hinblick auf das Hydrauliköl, Dichtungen und Schläuche. Ohne ordnungsgemäße Wartung kann es zu Leckagen und Leistungsabfällen kommen.
- Geräuschentwicklung: Im Vergleich zu elektrischen Maschinen sind hydraulische Rohrbiegemaschinen lauter, was in Produktionsumgebungen zu Lärmbelastungen führen kann. Dies kann den Einsatz zusätzlicher Schallschutzmaßnahmen erforderlich machen.
- Langsame Arbeitsgeschwindigkeit: Obwohl sie sehr leistungsfähig sind, können hydraulische Rohrbiegemaschinen langsamer arbeiten als ihre elektrischen Gegenstücke, insbesondere bei komplexen Biegeabläufen. Dies kann in hochvolumigen Produktionslinien zu einem Nachteil werden.
Anwendungsbereiche in der Industrie
Hydraulische Rohrbiegemaschinen werden in einer Vielzahl von Industriezweigen eingesetzt, insbesondere dort, wo dickwandige oder hochfeste Rohre gebogen werden müssen. Zu den wichtigsten Anwendungsbereichen gehören:
- Schiffbau: Im Schiffbau werden hydraulische Rohrbiegemaschinen häufig eingesetzt, um große und dickwandige Rohre zu biegen, die für die Struktur des Schiffsrumpfes und für Rohrleitungssysteme benötigt werden. Die Fähigkeit, Rohre mit großem Durchmesser und hoher Festigkeit zu biegen, ist in dieser Branche besonders wichtig.
- Öl- und Gasindustrie: In der Öl- und Gasindustrie sind hydraulische Rohrbiegemaschinen von entscheidender Bedeutung, um Leitungsrohre für den Transport von Öl, Gas und Chemikalien zu biegen. Diese Rohre müssen oft extremen Druck- und Temperaturbedingungen standhalten, was die Verwendung von hochfesten Materialien erfordert, die mit hydraulischen Maschinen bearbeitet werden können.
- Bauindustrie: In der Bauindustrie werden hydraulische Rohrbiegemaschinen für die Herstellung von strukturellen Rohrkomponenten, wie z. B. Stahlträgern und Verstärkungselementen, verwendet. Diese Maschinen sind in der Lage, große und schwere Rohre mit hoher Präzision zu biegen, was für die Stabilität und Sicherheit von Bauwerken entscheidend ist.
- Luft- und Raumfahrt: Auch in der Luft- und Raumfahrtindustrie kommen hydraulische Rohrbiegemaschinen zum Einsatz, insbesondere für die Herstellung von strukturellen Komponenten und Leitungssystemen, die in Flugzeugen und Raumfahrzeugen verwendet werden. Die Maschinen müssen hier besonders präzise und zuverlässig arbeiten, um die strengen Sicherheitsanforderungen dieser Branche zu erfüllen.
Fallstudien und Beispiele
Schiffbau: Ein führendes Schiffbauunternehmen nutzte hydraulische Rohrbiegemaschinen zur Herstellung von Großrohren für den Schiffsrumpf. Die Maschinen wurden aufgrund ihrer Fähigkeit ausgewählt, dickwandige Stahlrohre mit hoher Präzision zu biegen, was entscheidend für die strukturelle Integrität des Schiffes war. Die Einführung der Maschinen ermöglichte es dem Unternehmen, die Produktionszeiten zu verkürzen und die Qualität der Endprodukte zu verbessern.
Öl- und Gasindustrie: Ein Unternehmen in der Öl- und Gasindustrie setzte hydraulische Rohrbiegemaschinen ein, um Rohre für Hochdruck-Pipelines zu biegen. Die Maschinen mussten in der Lage sein, Rohre mit einem Durchmesser von bis zu 36 Zoll zu biegen, ohne die Materialfestigkeit zu beeinträchtigen. Durch den Einsatz dieser Maschinen konnte das Unternehmen sicherstellen, dass die Rohre den extremen Betriebsbedingungen standhalten und gleichzeitig eine hohe Effizienz bei der Installation erreicht wird.
Bauindustrie: Ein großer Bauunternehmer nutzte hydraulische Rohrbiegemaschinen, um Stahlträger für den Bau eines Hochhauses zu biegen. Die Maschinen ermöglichten es, die Träger vor Ort zu biegen, was die Bauzeit erheblich verkürzte und die Kosten senkte. Die Präzision der Maschinen stellte sicher, dass die Träger perfekt in das Gebäudedesign passten, was die Stabilität des Baus verbesserte.
Trends und Innovationen
Die technologischen Entwicklungen in der Fertigung haben auch bei hydraulischen Rohrbiegemaschinen zu bemerkenswerten Innovationen geführt. Einige der wichtigsten Trends und Entwicklungen umfassen:
- Hybridmaschinen: Ein bemerkenswerter Trend ist die Entwicklung von Hybridmaschinen, die sowohl hydraulische als auch elektrische Antriebe kombinieren. Diese Maschinen bieten das Beste aus beiden Welten: die hohe Kraft der Hydraulik und die Präzision und Effizienz der Elektrik. Dies ermöglicht eine flexiblere Nutzung in verschiedenen Anwendungsbereichen und steigert die Gesamtproduktivität.
- Erweiterte Automatisierung: Wie bei elektrischen Maschinen wird auch bei hydraulischen Rohrbiegemaschinen die Automatisierung immer wichtiger. Roboterarme, automatisierte Spannsysteme und CNC-Steuerungen ermöglichen es, den Biegeprozess zu automatisieren, wodurch die Effizienz gesteigert und die Fehlerquote gesenkt wird.
- Umweltfreundlichere Hydrauliksysteme: Die Nachfrage nach umweltfreundlicheren Lösungen hat zur Entwicklung neuer Hydrauliköle geführt, die biologisch abbaubar sind und weniger umweltschädliche Eigenschaften aufweisen. Darüber hinaus werden energieeffizientere Hydraulikpumpen entwickelt, um den Energieverbrauch der Maschinen zu reduzieren.
- Vernetzte Maschinen: Die Integration von IoT-Technologien in hydraulische Rohrbiegemaschinen ermöglicht eine verbesserte Prozessüberwachung und -steuerung. Diese vernetzten Maschinen können in Echtzeit Daten über den Biegeprozess sammeln und analysieren, was zu einer besseren Qualitätssicherung und einer vorausschauenden Wartung führt.
Zukunftsperspektiven
Die Zukunft der hydraulischen Rohrbiegemaschinen wird weiterhin von der Nachfrage nach leistungsfähigeren, effizienteren und umweltfreundlicheren Lösungen bestimmt werden. Die Entwicklung von Hybridmaschinen und die zunehmende Automatisierung werden es den Herstellern ermöglichen, auch weiterhin hohe Präzision und Flexibilität bei der Rohrbearbeitung zu bieten.
Es wird erwartet, dass die Weiterentwicklung von Materialien und Technologien dazu führen wird, dass hydraulische Maschinen in der Lage sein werden, noch größere und festere Rohre zu biegen. Gleichzeitig wird die fortschreitende Digitalisierung und Vernetzung der Maschinen dazu beitragen, die Effizienz und Produktivität weiter zu steigern.
Insgesamt bleibt die hydraulische Rohrbiegemaschine eine unverzichtbare Technologie in der industriellen Fertigung, die auch in Zukunft eine entscheidende Rolle bei der Herstellung komplexer Rohrstrukturen spielen wird.
Blech- und Metallbearbeitungsmaschinen
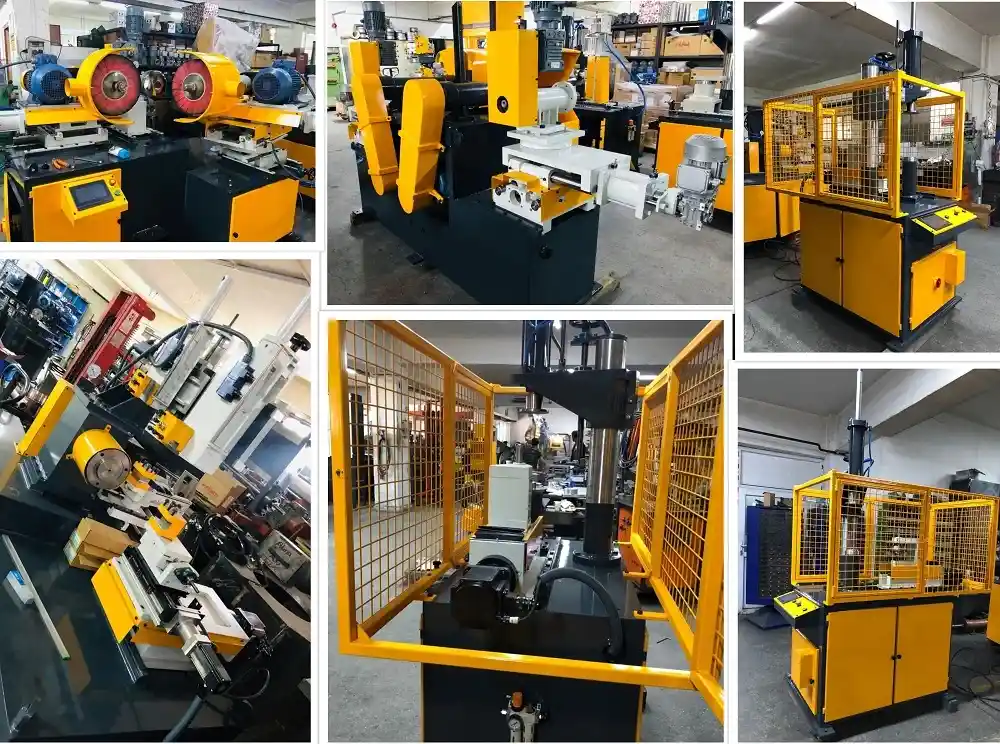
2.1. Grundlagen der Blech- und Metallbearbeitung
Blech- und Metallbearbeitung umfasst eine Vielzahl von Prozessen, bei denen Metall in gewünschte Formen und Größen gebracht wird. Diese Prozesse sind grundlegend für die Herstellung einer breiten Palette von Produkten, von alltäglichen Haushaltsgegenständen bis hin zu komplexen industriellen Maschinen. Zu den wichtigsten Metallen, die in der Blechbearbeitung verwendet werden, gehören Stahl, Aluminium, Kupfer und Titan, die jeweils spezifische Eigenschaften und Anforderungen an die Bearbeitung mit sich bringen.
2.2. Haupttypen von Maschinen
Es gibt verschiedene Maschinentypen, die in der Blech- und Metallbearbeitung eingesetzt werden. Zu den wichtigsten gehören:
- Umformmaschinen: Diese Maschinen werden verwendet, um Metall durch Druck in die gewünschte Form zu bringen. Beispiele sind Pressen, Walzen und Abkantmaschinen.
- Randbearbeitungsmaschinen: Dazu gehören Maschinen wie Bördelmaschinen und Randformmaschinen, die für die Bearbeitung der Ränder von Blechen und Metallteilen verwendet werden.
- Sickenmaschinen: Diese Maschinen erzeugen Vertiefungen oder Erhebungen im Blech, um die strukturelle Integrität zu erhöhen oder spezifische Designanforderungen zu erfüllen.
- Beschneidemaschinen: Sie dienen zum Schneiden und Besäumen von Blechen und Metallteilen, um sie auf die gewünschte Größe zu bringen.
- Rohrbiegemaschinen: Diese Maschinen sind auf das Biegen von Rohren und Profilen spezialisiert, was in vielen Bau- und Fertigungsprozessen notwendig ist.
2.3. Wichtige Technologien und Innovationen
Die Blech- und Metallbearbeitungsindustrie hat in den letzten Jahren erhebliche technologische Fortschritte gemacht. Dies umfasst die Einführung von computergestützten Steuerungssystemen (CNC), die eine präzise und automatisierte Bearbeitung ermöglichen. Darüber hinaus haben Entwicklungen in der Materialwissenschaft zu stärkeren und leichteren Metallen geführt, die besondere Maschinen und Bearbeitungstechniken erfordern. Ein weiteres wichtiges Thema ist die Automatisierung und Robotik, die die Effizienz und Produktivität in der Fertigung weiter steigern.
Hier ist die Einleitung und das erste Kapitel des Textes:
Einleitung
1.1 Thema und Ziel des Textes
Die Welt der Blech- und Metallbearbeitung ist ein wesentlicher Bestandteil der modernen Industrie. Ob in der Automobilproduktion, im Bauwesen oder in der Herstellung von Konsumgütern – überall spielen präzise und zuverlässige Metallbearbeitungsprozesse eine zentrale Rolle. Dieser Text widmet sich ausführlich den Maschinen, die in diesen Prozessen verwendet werden, und stellt dabei die wichtigsten Arten von Blech- und Metallbearbeitungsmaschinen vor. Ziel dieses Textes ist es, ein umfassendes Verständnis dieser Maschinen zu vermitteln, ihre Funktionsweisen zu erklären und ihre Bedeutung in der heutigen Fertigungslandschaft zu beleuchten.
1.2 Bedeutung der Maschinen in der modernen Fertigung
Blech- und Metallbearbeitungsmaschinen sind aus der heutigen Industrie nicht mehr wegzudenken. Mit der steigenden Nachfrage nach maßgeschneiderten, hochpräzisen Metallteilen hat die Bedeutung dieser Maschinen weiter zugenommen. Sie ermöglichen die Herstellung komplexer Formen und Strukturen, die mit herkömmlichen Methoden kaum realisierbar wären. Die Effizienz und Präzision, die durch den Einsatz moderner Maschinen erreicht werden, tragen nicht nur zur Steigerung der Produktionskapazität bei, sondern sichern auch die Qualität der Endprodukte. Unternehmen, die in hochwertige Bearbeitungsmaschinen investieren, können ihre Wettbewerbsfähigkeit in einem globalisierten Markt erheblich verbessern.
1.3 Überblick über die Schlüsselmaschinen und Prozesse
In den folgenden Kapiteln werden verschiedene Maschinentypen und Bearbeitungsprozesse detailliert behandelt. Dazu gehören Umformmaschinen, Randbearbeitungsmaschinen, Sickenmaschinen, Beschneidemaschinen und Rohrbiegemaschinen. Jede dieser Maschinen hat spezifische Anwendungsbereiche und Techniken, die in der Fertigung eingesetzt werden, um optimale Ergebnisse zu erzielen. Dieser Text bietet eine umfassende Übersicht über diese Maschinen, erläutert ihre Funktionsweise und gibt Einblicke in aktuelle Markttrends und technologische Entwicklungen.
Blech- und Metallbearbeitungsmaschinen: Eine Einführung
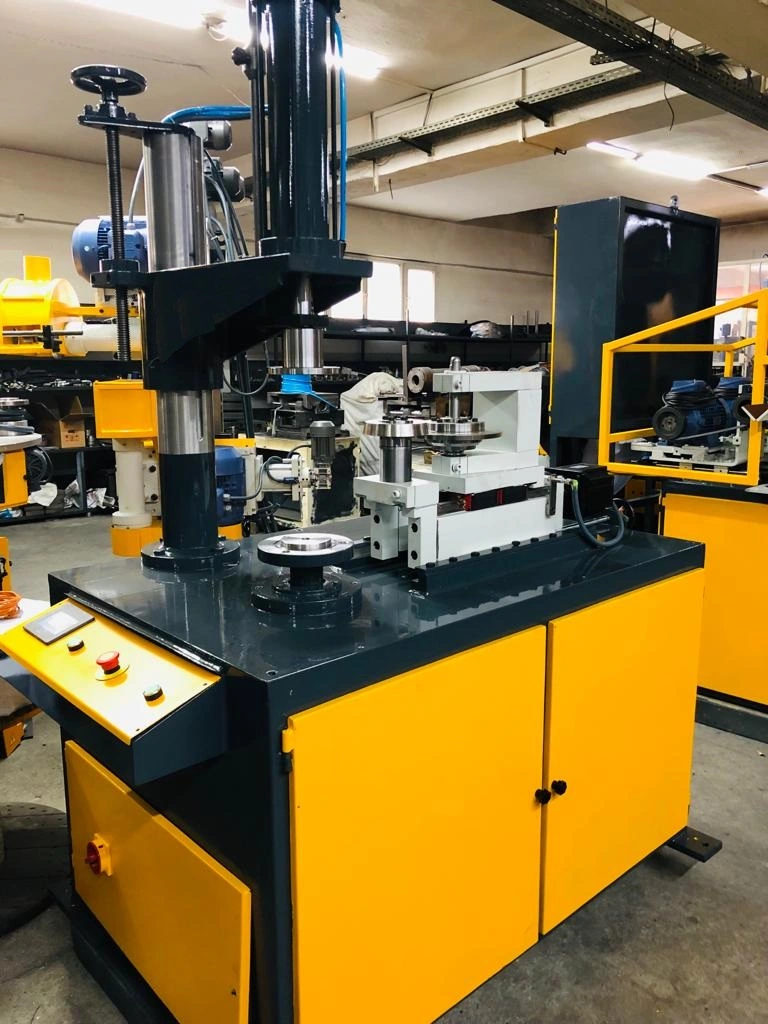
2.1 Grundlagen der Blech- und Metallbearbeitung
Die Blech- und Metallbearbeitung ist eine grundlegende Fertigungstechnologie, die in einer Vielzahl von Industriezweigen Anwendung findet. Sie umfasst eine breite Palette von Prozessen, bei denen Metall in gewünschte Formen und Größen gebracht wird, um spezifische industrielle Anforderungen zu erfüllen. Die wichtigsten Materialien, die in der Blechbearbeitung verwendet werden, sind Stahl, Aluminium, Kupfer und Titan. Diese Metalle zeichnen sich durch unterschiedliche Eigenschaften aus, die ihre Bearbeitung beeinflussen. Zum Beispiel erfordert die Bearbeitung von Titan aufgrund seiner Härte und Korrosionsbeständigkeit spezielle Maschinen und Techniken, während Aluminium wegen seines geringen Gewichts und seiner guten Formbarkeit weit verbreitet ist.
Die Blechbearbeitung umfasst verschiedene grundlegende Prozesse wie Schneiden, Biegen, Stanzen und Formen. Jeder dieser Prozesse erfordert spezialisierte Maschinen, die in der Lage sind, das Metall präzise zu bearbeiten, ohne seine strukturellen Eigenschaften zu beeinträchtigen. Das Ziel ist es, Metallteile zu produzieren, die den genauen Spezifikationen des Endprodukts entsprechen.
2.2 Haupttypen von Maschinen
In der Blech- und Metallbearbeitung gibt es eine Vielzahl von Maschinen, die jeweils für spezifische Aufgaben konzipiert sind. Die wichtigsten Typen sind:
- Umformmaschinen: Diese Maschinen formen Metall durch Druck oder andere Kräfte um. Dazu gehören Pressen, Walzen und Abkantmaschinen, die das Metall in die gewünschte Form bringen. Umformmaschinen sind entscheidend für die Herstellung von Metallteilen mit komplexen Geometrien.
- Randbearbeitungsmaschinen: Diese Maschinen, zu denen Bördelmaschinen und Randformmaschinen gehören, sind darauf spezialisiert, die Ränder von Blechen und Metallteilen zu bearbeiten. Sie sorgen für glatte, präzise Kanten, die für die weitere Verarbeitung oder das Endprodukt erforderlich sind.
- Sickenmaschinen: Sickenmaschinen erzeugen Vertiefungen oder Erhebungen im Blech, die die strukturelle Integrität erhöhen oder spezifische Designanforderungen erfüllen. Diese Maschinen sind besonders in der Luft- und Raumfahrtindustrie von Bedeutung, wo Gewichtseinsparungen durch strukturelle Verstärkungen wichtig sind.
- Beschneidemaschinen: Diese Maschinen werden verwendet, um Bleche und Metallteile auf die gewünschte Größe zu schneiden. Sie spielen eine wichtige Rolle in der Vorbereitung von Rohmaterialien für nachfolgende Bearbeitungsprozesse.
- Rohrbiegemaschinen: Diese Maschinen sind darauf spezialisiert, Rohre und Profile zu biegen. Sie kommen in vielen Bau- und Fertigungsprozessen zum Einsatz, bei denen gebogene Metallteile benötigt werden.
2.3 Wichtige Technologien und Innovationen
Die Metallbearbeitungsindustrie hat in den letzten Jahrzehnten bedeutende technologische Fortschritte erlebt. Eine der wichtigsten Entwicklungen ist die Einführung computergestützter Steuerungssysteme, insbesondere CNC (Computerized Numerical Control), die eine präzise und automatisierte Bearbeitung ermöglichen. CNC-Maschinen können komplexe Bearbeitungsprozesse mit hoher Genauigkeit und Wiederholgenauigkeit ausführen, was die Effizienz und Produktivität in der Fertigung erheblich steigert.
Eine weitere wichtige Innovation ist die Automatisierung und Robotik. Durch den Einsatz von Robotern können Bearbeitungsprozesse beschleunigt und die Produktionskapazität erhöht werden, ohne dass die Qualität der Produkte leidet. Roboter können zudem in gefährlichen oder schwer zugänglichen Bereichen arbeiten, was die Sicherheit am Arbeitsplatz verbessert.
Zusätzlich haben Fortschritte in der Materialwissenschaft zu neuen, leistungsfähigeren Metallen geführt, die eine höhere Festigkeit, geringeres Gewicht und bessere Korrosionsbeständigkeit bieten. Diese Metalle erfordern spezielle Bearbeitungstechniken und Maschinen, die in der Lage sind, die anspruchsvollen Anforderungen zu erfüllen.
Detaillierte Analyse von Umformmaschinen
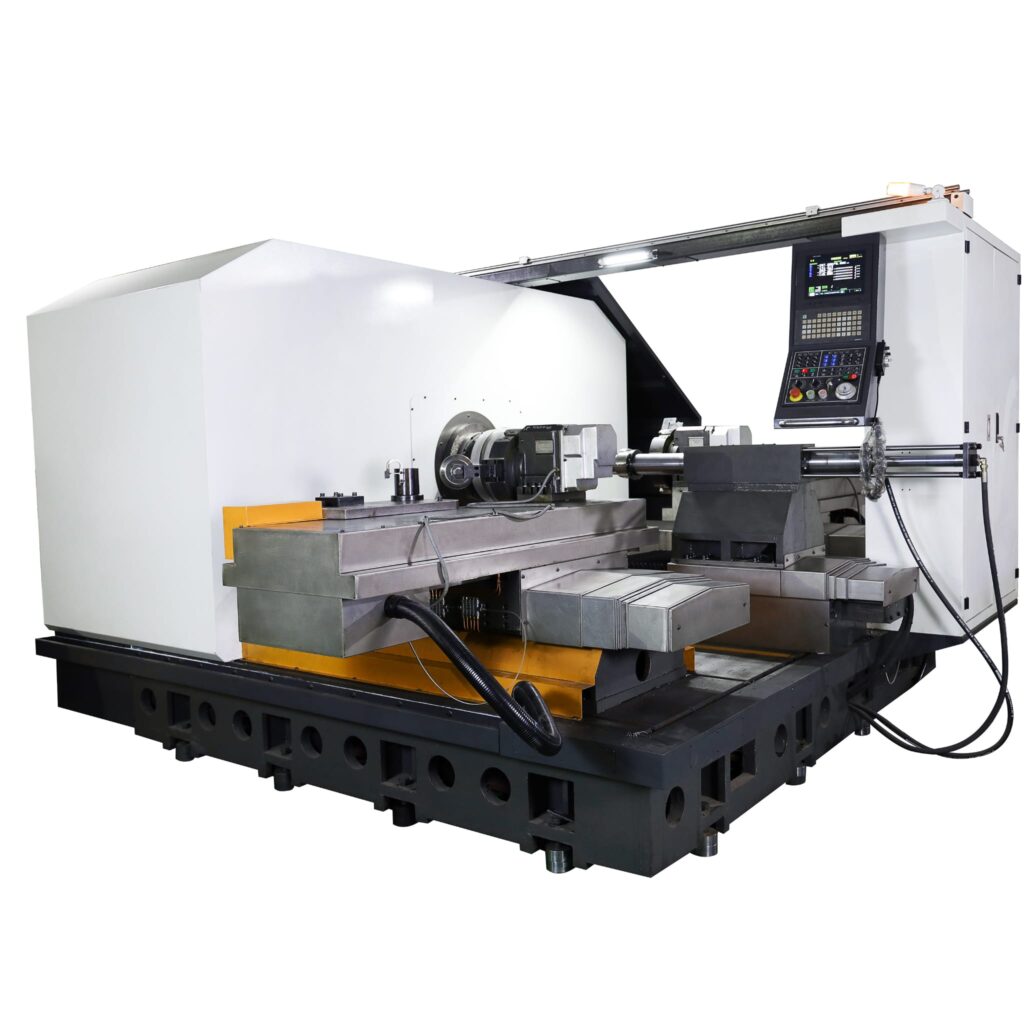
3.1 Definition und Funktion von Umformmaschinen
Umformmaschinen sind wesentliche Werkzeuge in der Blech- und Metallbearbeitung, die darauf ausgelegt sind, Metallteile durch die Anwendung von Druck oder anderen Kräften in eine gewünschte Form zu bringen. Der Umformprozess ist ein zentraler Bestandteil der Fertigung, insbesondere in Branchen, in denen komplexe geometrische Formen erforderlich sind. Diese Maschinen arbeiten durch plastische Verformung des Materials, das heißt, das Metall wird dauerhaft verformt, ohne dass es zu einem Bruch oder einer Trennung des Materials kommt.
Zu den häufigsten Arten von Umformmaschinen gehören Pressen, Abkantmaschinen, Walzen und Tiefziehmaschinen. Jede dieser Maschinen ist für spezifische Aufgaben und Formen ausgelegt:
- Pressen: Pressen verwenden große Kräfte, um Metallteile in eine Form zu pressen. Sie werden häufig in der Automobilindustrie zur Herstellung von Karosserieteilen verwendet.
- Abkantmaschinen: Diese Maschinen sind darauf spezialisiert, Metallbleche zu biegen. Sie kommen oft in der Herstellung von Gehäusen, Schaltschränken und anderen Produkten zum Einsatz, die präzise Biegungen erfordern.
- Walzen: Walzmaschinen sind dafür ausgelegt, Metallbleche durch eine Reihe von Walzen zu führen, um sie zu glätten oder zu formen. Dieser Prozess ist in der Herstellung von Stahlplatten und anderen großflächigen Produkten weit verbreitet.
- Tiefziehmaschinen: Diese Maschinen werden verwendet, um Metallbleche durch Zugkräfte in tiefe, hohle Formen zu ziehen, die typischerweise für die Herstellung von Behältern, Tanks und anderen ähnlichen Produkten verwendet werden.
3.2 Beispiele und Anwendungen
Umformmaschinen finden in einer Vielzahl von Industrien Anwendung, die präzise und spezifische Metallteile benötigen. Im Folgenden sind einige der wichtigsten Anwendungsbereiche aufgeführt:
- Automobilindustrie: In der Automobilproduktion werden Umformmaschinen eingesetzt, um Karosserieteile, Rahmen, Fahrwerkskomponenten und andere strukturelle Teile herzustellen. Die Präzision und Konsistenz dieser Maschinen sind entscheidend für die Sicherheit und Leistung des Endprodukts.
- Luft- und Raumfahrt: Die Herstellung von Flugzeugkomponenten, wie Tragflächen, Rumpfteilen und Strukturbauteilen, erfordert eine extrem hohe Präzision und Wiederholgenauigkeit. Umformmaschinen ermöglichen die Produktion dieser Teile mit den engen Toleranzen, die in der Luft- und Raumfahrtindustrie erforderlich sind.
- Bauindustrie: Hier werden Umformmaschinen für die Herstellung von Stahlträgern, Säulen und anderen strukturellen Komponenten verwendet, die für den Bau von Gebäuden, Brücken und anderen Infrastrukturen notwendig sind.
- Haushaltsgeräte: Die Gehäuse und Innenstrukturen vieler Haushaltsgeräte, wie Waschmaschinen, Kühlschränke und Öfen, werden häufig mit Hilfe von Umformmaschinen hergestellt. Diese Maschinen ermöglichen die effiziente Produktion von Bauteilen in großen Stückzahlen.
3.3 Markttrends und Entwicklungen
Der Markt für Umformmaschinen entwickelt sich stetig weiter, angetrieben durch technologische Innovationen und die wachsende Nachfrage nach komplexen Metallteilen. Einige der aktuellen Trends und Entwicklungen in diesem Bereich sind:
- Automatisierung: Die Integration von Automatisierungstechnologien in Umformmaschinen ist ein wachsender Trend. Durch die Automatisierung können die Produktionsgeschwindigkeit und -effizienz erhöht werden, während gleichzeitig die Fehlerquote reduziert wird. Automatisierte Umformmaschinen sind in der Lage, komplexe Aufgaben mit minimalem menschlichen Eingriff zu erledigen, was die Betriebskosten senkt und die Produktivität steigert.
- Energieeffizienz: Mit zunehmendem Fokus auf Nachhaltigkeit entwickeln Hersteller von Umformmaschinen energieeffiziente Modelle, die weniger Strom verbrauchen und gleichzeitig eine hohe Leistung bieten. Diese Maschinen tragen dazu bei, die Umweltbelastung zu reduzieren und die Betriebskosten für die Unternehmen zu senken.
- Materialwissenschaften: Fortschritte in der Materialwissenschaft haben zu neuen Metalllegierungen geführt, die stärker, leichter und korrosionsbeständiger sind. Diese Materialien erfordern jedoch oft spezialisierte Umformmaschinen, die in der Lage sind, die spezifischen Eigenschaften der neuen Metalle zu verarbeiten.
- Digitale Vernetzung: Die zunehmende Vernetzung von Maschinen und Fertigungsprozessen im Rahmen von Industrie 4.0 hat auch die Umformtechnik erreicht. Vernetzte Umformmaschinen können Daten in Echtzeit austauschen, was eine bessere Überwachung und Steuerung des Produktionsprozesses ermöglicht. Dies führt zu einer höheren Produktqualität und einer besseren Nachverfolgbarkeit von Produktionsschritten.
- Additive Fertigung: Während die Umformtechnik traditionell auf die plastische Verformung von Metall beschränkt ist, wächst das Interesse an der Kombination von Umformprozessen mit additiven Fertigungstechniken. Dies ermöglicht die Herstellung von komplexen Strukturen, die durch Umformung allein nicht realisierbar wären, und eröffnet neue Möglichkeiten in der Produktentwicklung.
In der modernen Industrie spielen Präzision und Effizienz eine entscheidende Rolle, insbesondere in der Metallverarbeitung und im Maschinenbau. Edelstahlrohre gehören zu den am häufigsten verwendeten Materialien, da sie eine herausragende Korrosionsbeständigkeit, Langlebigkeit und Vielseitigkeit bieten. Um diese Rohre in den gewünschten Formen und Winkeln zu fertigen, sind spezialisierte Maschinen erforderlich, die präzise Biegungen ermöglichen, ohne die strukturelle Integrität des Materials zu beeinträchtigen. Hier kommen Rohrbiegemaschinen ins Spiel.
Rohrbiegemaschinen für Edelstahlrohre sind essenzielle Werkzeuge in zahlreichen Industrien, darunter die Automobilindustrie, der Schiffbau, die Bauwirtschaft und die chemische Industrie. Sie ermöglichen nicht nur die Herstellung von maßgeschneiderten Rohrformen, sondern auch die Anpassung an spezifische Anforderungen und Normen, was zu einer höheren Effizienz in der Produktion führt. Besonders die Kombination aus robuster Bauweise und modernster Technologie stellt sicher, dass die Maschinen den hohen Ansprüchen der heutigen Produktionsprozesse gerecht werden.
Neben den Rohrbiegemaschinen spielen auch Biegepressen eine zentrale Rolle, insbesondere wenn es um komplexe Biegeprozesse geht. Horizontale Biegepressen und hydraulische Biegepressen bieten spezifische Vorteile, die sie in bestimmten Anwendungen unverzichtbar machen. Diese Pressen ermöglichen nicht nur die präzise Formung von Edelstahlrohren, sondern auch die schnelle und effiziente Herstellung großer Stückzahlen. Die Wahl der richtigen Maschine hängt von verschiedenen Faktoren ab, einschließlich des Materials, der geforderten Genauigkeit und der Produktionsumgebung.
In den folgenden Abschnitten werden wir die verschiedenen Typen von Rohrbiegemaschinen und Biegepressen detaillierter betrachten und deren Bedeutung für die industrielle Fertigung von Edelstahlrohren erläutern.
Rohrbiegemaschinen für Edelstahlrohre
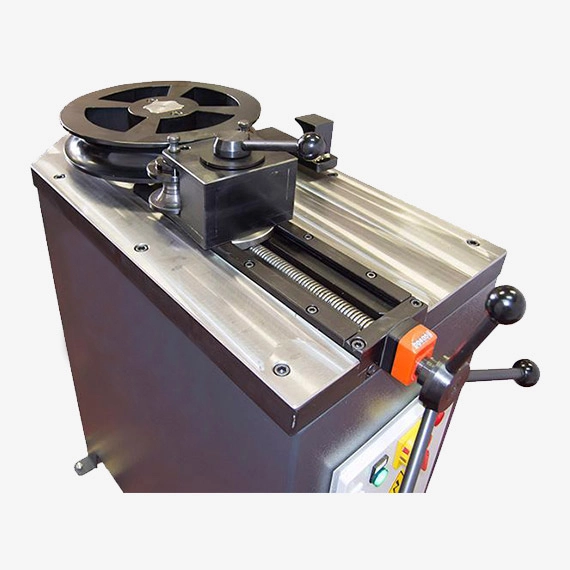
1. Einführung in die Rohrbiegemaschinen für Edelstahlrohre
Rohrbiegemaschinen sind wesentliche Werkzeuge in der modernen Fertigungstechnik, insbesondere wenn es darum geht, Edelstahlrohre präzise und effizient zu biegen. Diese Maschinen sind so konzipiert, dass sie Rohre in einer Vielzahl von Durchmessern und Wandstärken verarbeiten können, wobei sie die strukturelle Integrität des Materials bewahren. Edelstahl ist aufgrund seiner hervorragenden Korrosionsbeständigkeit, Langlebigkeit und hohen Festigkeit ein bevorzugtes Material in vielen Industrien. Daher ist es entscheidend, dass Rohrbiegemaschinen speziell für die Bearbeitung dieses Materials optimiert sind.
2. Funktionsweise und Technologien
Moderne Rohrbiegemaschinen für Edelstahlrohre nutzen fortschrittliche Technologien, um hohe Präzision und Wiederholgenauigkeit zu gewährleisten. Zu den gängigsten Biegeverfahren gehören das Dornbiegen, das Rollbiegen und das Druckbiegen. Jede dieser Methoden hat spezifische Vorteile, je nach den Anforderungen des Endprodukts.
- Dornbiegen: Diese Methode wird häufig verwendet, um enge Radien zu biegen, ohne dass es zu einer Verformung oder einem Kollaps des Rohrs kommt. Der Dorn, ein stabförmiges Werkzeug, wird in das Rohr eingeführt, um es während des Biegens zu stützen.
- Rollbiegen: Diese Technik eignet sich besonders gut für die Herstellung von großen Radien und Kurven. Hierbei wird das Rohr zwischen mehreren Walzen geführt, die das Rohr allmählich biegen.
- Druckbiegen: Diese Methode wird verwendet, um scharfe Biegungen mit hohem Druck zu erzeugen. Das Rohr wird zwischen einem Stempel und einer Matrize platziert und durch den Druck des Stempels in die gewünschte Form gebracht.
3. Vorteile der Rohrbiegemaschinen für Edelstahlrohre
Rohrbiegemaschinen bieten zahlreiche Vorteile, die sie für die Verarbeitung von Edelstahlrohren unverzichtbar machen:
- Hohe Präzision: Durch den Einsatz moderner Steuerungssysteme, wie CNC (Computer Numerical Control), können komplexe Biegeformen mit höchster Genauigkeit hergestellt werden. Dies ist besonders wichtig in Industrien, in denen Maßhaltigkeit und Konsistenz entscheidend sind, wie in der Luft- und Raumfahrt oder im Automobilbau.
- Wirtschaftlichkeit: Die Fähigkeit, Edelstahlrohre in einer einzigen Arbeitsstation zu biegen, reduziert den Bedarf an zusätzlichen Bearbeitungsschritten und verringert so die Produktionskosten. Darüber hinaus ermöglichen moderne Maschinen eine schnelle Umrüstung, was die Flexibilität in der Produktion erhöht.
- Langlebigkeit und Zuverlässigkeit: Rohrbiegemaschinen, die speziell für die Verarbeitung von Edelstahlrohren entwickelt wurden, sind robust und langlebig. Sie sind in der Lage, hohen Belastungen standzuhalten und gewährleisten eine gleichbleibende Leistung über lange Zeiträume hinweg.
- Anpassungsfähigkeit: Diese Maschinen können so konfiguriert werden, dass sie eine Vielzahl von Rohrdimensionen und -formen verarbeiten können, was sie für unterschiedliche Anwendungen flexibel einsetzbar macht.
4. Anwendungsbereiche
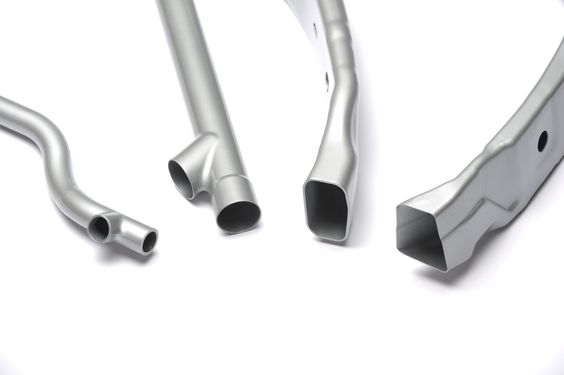
Edelstahlrohre werden in einer Vielzahl von Industrien eingesetzt, und Rohrbiegemaschinen spielen eine zentrale Rolle in deren Herstellung. Zu den wichtigsten Anwendungsbereichen gehören:
- Automobilindustrie: In der Automobilproduktion werden Edelstahlrohre häufig für Abgasanlagen, Fahrgestelle und hydraulische Systeme verwendet. Rohrbiegemaschinen ermöglichen die präzise Formung dieser Komponenten, um eine perfekte Passgenauigkeit und Funktionalität sicherzustellen.
- Schiffbau: Im Schiffbau werden Edelstahlrohre in Rohrleitungssystemen und strukturellen Anwendungen verwendet. Die Korrosionsbeständigkeit von Edelstahl ist in maritimen Umgebungen von entscheidender Bedeutung, und Rohrbiegemaschinen tragen dazu bei, dass die Rohre den strengen Anforderungen der Branche gerecht werden.
- Bauwesen: Im Bauwesen werden Edelstahlrohre häufig in architektonischen Strukturen, Geländern und Rohrleitungssystemen verwendet. Rohrbiegemaschinen ermöglichen die Herstellung von Rohren mit ästhetisch ansprechenden und funktionalen Formen.
- Chemische Industrie: In der chemischen Industrie werden Edelstahlrohre wegen ihrer Beständigkeit gegen aggressive Chemikalien verwendet. Präzise gebogene Rohre sind entscheidend, um die Integrität der Rohrleitungssysteme in anspruchsvollen Umgebungen zu gewährleisten.
5. Zukünftige Entwicklungen und Innovationen
Die Technologie der Rohrbiegemaschinen entwickelt sich ständig weiter, um den steigenden Anforderungen der Industrie gerecht zu werden. Zu den zukünftigen Entwicklungen gehören:
- Automatisierung und Vernetzung: Die Integration von IoT (Internet of Things) und Smart Factory-Technologien ermöglicht es, Rohrbiegemaschinen in vernetzte Produktionssysteme zu integrieren. Dies führt zu einer verbesserten Überwachung, Analyse und Optimierung des Produktionsprozesses in Echtzeit.
- Nachhaltigkeit: Hersteller legen zunehmend Wert auf die Entwicklung von Maschinen, die energieeffizient und umweltfreundlich sind. Dies schließt den Einsatz von recycelbaren Materialien und die Minimierung von Abfallprodukten ein.
- Erweiterte Materialverarbeitung: Fortschritte in der Materialwissenschaft könnten in Zukunft die Bearbeitung neuer Legierungen und Verbundwerkstoffe ermöglichen, was die Einsatzmöglichkeiten von Rohrbiegemaschinen noch weiter vergrößern wird.
Horizontale Biegepressen
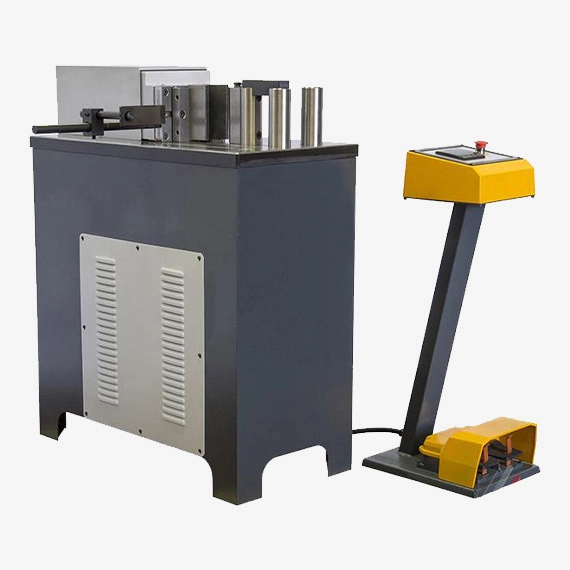
1. Einführung in horizontale Biegepressen
Horizontale Biegepressen sind spezialisierte Maschinen, die in der Metallverarbeitung eingesetzt werden, um präzise Biegungen an Rohren und anderen metallischen Werkstücken durchzuführen. Im Gegensatz zu vertikalen Biegepressen, bei denen das Werkstück vertikal zwischen Stempel und Matrize positioniert wird, erfolgt bei horizontalen Biegepressen die Biegung auf einer horizontalen Ebene. Diese Konfiguration bietet mehrere Vorteile, insbesondere in Bezug auf die Handhabung großer oder langer Werkstücke und die Präzision der Biegeprozesse.
2. Funktionsweise und technische Merkmale
Horizontale Biegepressen arbeiten typischerweise mit einer Kombination aus mechanischen und hydraulischen Komponenten. Der Biegeprozess beginnt damit, dass das Werkstück auf einem speziell entworfenen Tisch positioniert wird, der in der Lage ist, das Rohr oder Profil während des Biegens sicher zu fixieren. Die Biegebewegung wird durch einen horizontalen Stempel erzeugt, der das Werkstück gegen eine formgebende Matrize drückt.
Einige der wichtigsten technischen Merkmale horizontaler Biegepressen umfassen:
- Hydraulikantrieb: Viele horizontale Biegepressen verwenden hydraulische Systeme, um den für die Biegung erforderlichen Druck aufzubringen. Diese Systeme ermöglichen eine stufenlose Steuerung der Biegekraft und bieten eine hohe Wiederholgenauigkeit, was besonders wichtig ist, wenn komplexe oder präzise Biegungen erforderlich sind.
- CNC-Steuerung: Moderne horizontale Biegepressen sind oft mit CNC-Steuerungen (Computer Numerical Control) ausgestattet, die eine präzise Programmierung und Steuerung des Biegeprozesses ermöglichen. Dies erhöht die Flexibilität und Effizienz, da mehrere Biegeprozesse automatisch in einem Durchlauf ausgeführt werden können.
- Werkzeugvielfalt: Die Vielseitigkeit der horizontalen Biegepressen wird durch eine breite Palette an verfügbaren Werkzeugen und Matrizen unterstützt, die für unterschiedliche Biegeanforderungen ausgelegt sind. So können verschiedene Werkstoffe und Profile mit derselben Maschine bearbeitet werden, was die Produktionsmöglichkeiten erweitert.
3. Vorteile der horizontalen Biegepresse
Horizontale Biegepressen bieten zahlreiche Vorteile, die sie in bestimmten Anwendungen besonders wertvoll machen:
- Platzersparnis: Durch ihre horizontale Konfiguration benötigen diese Maschinen weniger vertikalen Raum, was sie ideal für Werkstätten mit begrenzter Deckenhöhe macht. Sie lassen sich leichter in Produktionslinien integrieren, ohne dass umfangreiche Anpassungen der Infrastruktur erforderlich sind.
- Einfachere Handhabung großer Werkstücke: Da das Werkstück auf einem horizontalen Tisch liegt, ist die Handhabung großer oder langer Teile deutlich einfacher. Dies reduziert das Risiko von Verformungen und erhöht die Präzision der Bearbeitung, besonders bei langen Edelstahlrohren.
- Hohe Biegepräzision: Die horizontale Anordnung des Biegeprozesses minimiert die Schwerkraftwirkung auf das Werkstück, was insbesondere bei dünnwandigen Rohren zu genaueren Ergebnissen führt. Dies ist ein entscheidender Vorteil gegenüber vertikalen Biegepressen, bei denen das Eigengewicht des Werkstücks die Präzision beeinträchtigen kann.
- Flexibilität in der Anwendung: Horizontale Biegepressen können für eine Vielzahl von Materialien und Biegeanforderungen angepasst werden, einschließlich komplexer Formen und mehrfacher Biegungen. Dies macht sie zu einem vielseitigen Werkzeug für Hersteller, die eine breite Palette von Produkten herstellen müssen.
4. Anwendungsbereiche
Horizontale Biegepressen finden in verschiedenen Industrien Anwendung, in denen präzise und komplexe Biegungen erforderlich sind:
- Metallverarbeitung: In der allgemeinen Metallverarbeitung werden horizontale Biegepressen zur Herstellung von Rahmenteilen, Profilen und Strukturkomponenten verwendet. Die Möglichkeit, große und schwere Werkstücke präzise zu biegen, macht sie unverzichtbar für die Produktion von robusten Metallkonstruktionen.
- Rohrleitungsbau: Im Rohrleitungsbau sind horizontale Biegepressen entscheidend für die Herstellung von Rohrbögen und -verzweigungen, die in komplexen Rohrsystemen verwendet werden. Die präzise Biegung stellt sicher, dass die Rohrleitungen exakt zusammenpassen und ihre Funktion ohne Leckagen oder Schwachstellen erfüllen.
- Automobil- und Luftfahrtindustrie: In der Automobil- und Luftfahrtindustrie werden horizontale Biegepressen verwendet, um Rahmenkomponenten, Auspuffsysteme und Strukturteile zu formen. Die Fähigkeit, hochfeste Werkstoffe wie Edelstahl und Aluminium präzise zu biegen, ist entscheidend für die Herstellung sicherer und effizienter Fahrzeuge und Flugzeuge.
- Bauindustrie: Im Bauwesen werden horizontale Biegepressen für die Herstellung von strukturellen Elementen wie Trägern, Balken und Stützen eingesetzt. Diese Maschinen ermöglichen es, Baustahl und andere Metalle in den genauen Winkeln und Radien zu biegen, die für den Bau von Gebäuden und Infrastrukturen erforderlich sind.
5. Vergleich mit anderen Biegepressen
Ein entscheidender Vorteil horizontaler Biegepressen im Vergleich zu vertikalen oder schwenkbaren Biegepressen liegt in der Präzision und Handhabung großer Werkstücke. Während vertikale Biegepressen oft für einfachere, kleinere oder standardisierte Biegungen bevorzugt werden, bieten horizontale Biegepressen mehr Flexibilität und Anpassungsfähigkeit, insbesondere in spezialisierten oder maßgeschneiderten Fertigungsprozessen.
Ein weiterer Unterschied liegt in der Ergonomie und Bedienung. Da horizontale Biegepressen es ermöglichen, Werkstücke in einer ergonomisch günstigeren Position zu handhaben, reduzieren sie das Risiko von Bedienerfehlern und erhöhen die Sicherheit am Arbeitsplatz.
6. Zukunftsaussichten und technologische Weiterentwicklungen
Mit der fortschreitenden Digitalisierung und Automatisierung in der Industrie entwickeln sich auch horizontale Biegepressen weiter. Die Integration von Sensoren und Echtzeit-Überwachungssystemen ermöglicht eine kontinuierliche Qualitätskontrolle während des Biegeprozesses. Zudem arbeiten Hersteller daran, die Energieeffizienz der Maschinen zu verbessern, indem sie leichtere Materialien und optimierte Hydrauliksysteme einsetzen.
In Zukunft könnten auch robotergestützte Biegepressen, die vollständig automatisierte Biegeprozesse durchführen, eine immer größere Rolle spielen. Dies würde die Produktionskapazitäten weiter erhöhen und die Fehlerquote minimieren, was für Branchen mit hohen Qualitätsanforderungen besonders vorteilhaft wäre.
Horizontale Richtpressen
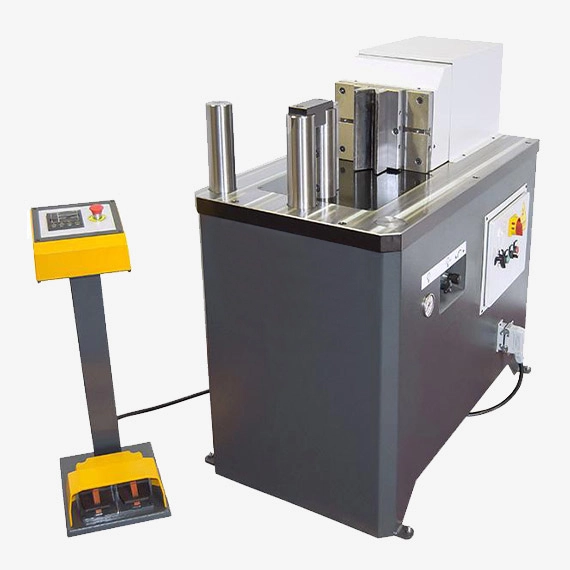
1. Einführung in horizontale Richtpressen
Horizontale Richtpressen sind spezialisierte Maschinen, die in der Metallverarbeitung zum Einsatz kommen, um Verformungen und Unregelmäßigkeiten in Rohren und Profilen zu korrigieren. Im Gegensatz zu Biegepressen, deren Hauptaufgabe die Formgebung ist, dienen Richtpressen hauptsächlich dazu, ungewollte Krümmungen oder Verformungen zu beseitigen und das Werkstück in seine ursprüngliche oder gewünschte gerade Form zu bringen. Diese Maschinen sind besonders wichtig in der Fertigung, wo hohe Anforderungen an die Maßhaltigkeit und Präzision gestellt werden.
2. Funktionsweise und technische Merkmale
Horizontale Richtpressen arbeiten, ähnlich wie horizontale Biegepressen, auf einer horizontalen Ebene, was die Handhabung und Ausrichtung der Werkstücke erleichtert. Der Richtprozess beginnt in der Regel mit der Platzierung des verformten Werkstücks auf einer Auflagefläche. Anschließend wird durch den Einsatz eines hydraulischen Stempels Druck auf bestimmte Punkte des Werkstücks ausgeübt, um die Verformungen auszugleichen.
Wichtige technische Merkmale horizontaler Richtpressen sind:
- Hydraulikantrieb: Die meisten horizontalen Richtpressen verwenden hydraulische Systeme, die eine präzise Steuerung der Druckkraft ermöglichen. Diese Systeme sind in der Lage, große Kräfte aufzubringen, die notwendig sind, um selbst bei hochfesten Werkstoffen wie Edelstahl eine wirksame Richtwirkung zu erzielen.
- Einstellbare Stempel und Matrizen: Um eine präzise Korrektur von Verformungen zu gewährleisten, sind horizontale Richtpressen mit einstellbaren Stempeln und Matrizen ausgestattet. Diese Werkzeuge können je nach Größe und Form des Werkstücks angepasst werden, um optimale Ergebnisse zu erzielen.
- CNC-Steuerung: Wie bei vielen modernen Maschinen in der Metallverarbeitung sind auch horizontale Richtpressen oft mit CNC-Steuerungen ausgestattet. Diese ermöglichen es, den Richtprozess genau zu programmieren und zu überwachen, was insbesondere bei wiederholten Arbeitsgängen von Vorteil ist.
3. Vorteile der horizontalen Richtpresse
Horizontale Richtpressen bieten zahlreiche Vorteile, die sie zu unverzichtbaren Werkzeugen in der Metallverarbeitung machen:
- Präzise Korrektur von Verformungen: Diese Maschinen sind speziell dafür ausgelegt, auch kleinste Abweichungen in der Geradheit von Rohren und Profilen zu korrigieren. Dies ist entscheidend für Anwendungen, bei denen hohe Maßgenauigkeit erforderlich ist, wie in der Automobil- oder Luftfahrtindustrie.
- Effizienz und Geschwindigkeit: Dank der automatisierten Steuerungssysteme und der leistungsstarken Hydraulik sind horizontale Richtpressen in der Lage, Korrekturen schnell und effizient durchzuführen. Dies trägt dazu bei, die Produktionszeiten zu verkürzen und die Produktivität zu steigern.
- Vielseitigkeit: Horizontale Richtpressen können für eine Vielzahl von Materialien und Profilen verwendet werden. Sie sind nicht auf bestimmte Werkstoffe beschränkt und eignen sich sowohl für einfache als auch für komplexe Richtaufgaben.
4. Unterschied zwischen Biege- und Richtpressen
Während Biegepressen hauptsächlich für die Formgebung von Werkstücken verwendet werden, liegt der Fokus bei Richtpressen auf der Korrektur von unerwünschten Verformungen. Biegepressen können komplexe Winkel und Formen erzeugen, während Richtpressen dafür ausgelegt sind, das Werkstück zu glätten oder zu begradigen. In vielen Fertigungsprozessen werden beide Maschinentypen nacheinander eingesetzt: Zunächst wird das Werkstück in die gewünschte Form gebogen, und anschließend werden eventuelle Verformungen durch eine Richtpresse korrigiert.
5. Anwendungsbereiche
Horizontale Richtpressen finden in zahlreichen Industrien Anwendung, darunter:
- Automobilindustrie: Hier werden sie zur Korrektur von Achsen, Wellen und anderen strukturellen Komponenten verwendet, die nach dem Biegeprozess gerade ausgerichtet sein müssen.
- Schiffbau: Im Schiffbau werden Richtpressen eingesetzt, um sicherzustellen, dass Rohre und Profile, die in den Rumpf oder in andere Teile des Schiffes eingebaut werden, perfekt gerade sind, um eine optimale Passform und Stabilität zu gewährleisten.
- Bauindustrie: In der Bauindustrie werden Richtpressen verwendet, um Stahlträger und andere strukturelle Elemente nach der Herstellung zu begradigen, sodass sie den Bauvorschriften und den spezifischen Anforderungen des Projekts entsprechen.
- Maschinenbau: Im Maschinenbau werden horizontale Richtpressen häufig eingesetzt, um Präzisionsbauteile herzustellen, die hohe Anforderungen an die Geradheit und Maßhaltigkeit erfüllen müssen.
6. Zukunftsaussichten und technologische Weiterentwicklungen
Mit dem wachsenden Bedarf an Präzision in der Metallverarbeitung entwickeln sich auch horizontale Richtpressen kontinuierlich weiter. Die Integration von Sensorik und Echtzeit-Überwachungssystemen ermöglicht eine noch genauere Steuerung des Richtprozesses, wodurch die Qualität der Endprodukte weiter verbessert wird. Zudem wird der Trend zur Automatisierung auch in diesem Bereich voranschreiten, um die Effizienz und Produktivität weiter zu steigern.
In Zukunft könnten hybride Maschinen, die sowohl Biege- als auch Richtfunktionen kombinieren, eine zunehmende Rolle spielen, um die Produktionsprozesse zu optimieren und die Anzahl der erforderlichen Maschinen in der Fertigung zu reduzieren.
Hydraulische horizontale Biegepressen
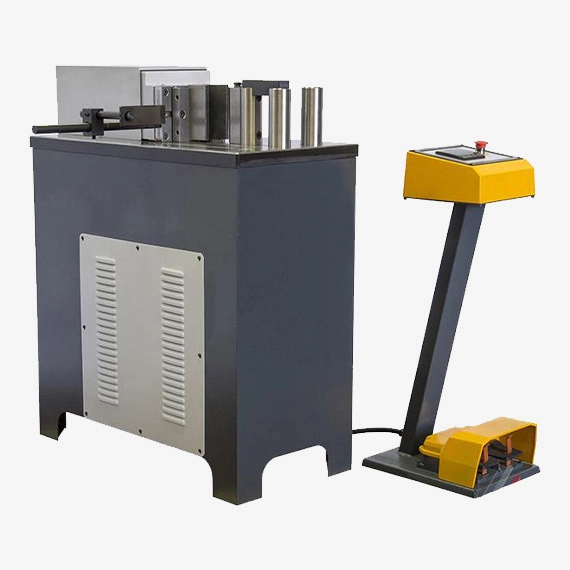
1. Einführung in hydraulische horizontale Biegepressen
Hydraulische horizontale Biegepressen kombinieren die Vielseitigkeit horizontaler Biegepressen mit der Kraft und Präzision hydraulischer Systeme. Diese Maschinen sind in der Lage, selbst die widerstandsfähigsten Materialien, wie Edelstahl, mit hoher Genauigkeit zu biegen. Sie sind besonders in der industriellen Fertigung von großer Bedeutung, wo sowohl die Flexibilität in der Anwendung als auch die Notwendigkeit für präzise und wiederholbare Ergebnisse gefragt sind.
2. Funktionsweise und hydraulische Systeme
Das Herzstück hydraulischer horizontaler Biegepressen ist das Hydrauliksystem, das den Druck erzeugt, der für den Biegeprozess benötigt wird. Dieses System besteht typischerweise aus einer hydraulischen Pumpe, Zylindern und Ventilen, die zusammenarbeiten, um den Stempel zu bewegen und das Werkstück gegen eine Matrize zu drücken.
Einige der wichtigsten Merkmale hydraulischer horizontaler Biegepressen umfassen:
- Kraftvolle Druckerzeugung: Hydraulische Systeme sind in der Lage, enorme Kräfte zu erzeugen, die es ermöglichen, selbst dickwandige und hochfeste Materialien präzise zu biegen. Dies macht sie ideal für Anwendungen, bei denen robuste und langlebige Produkte hergestellt werden müssen.
- Präzise Steuerung: Die Biegekraft kann genau reguliert werden, was eine hohe Präzision bei der Formgebung ermöglicht. Dies ist besonders wichtig bei der Bearbeitung von Edelstahlrohren, bei denen die Gefahr von Rissen oder Verformungen minimiert werden muss.
- Flexibilität: Hydraulische Biegepressen können für eine Vielzahl von Biegeanforderungen und Materialien konfiguriert werden, was sie zu äußerst vielseitigen Werkzeugen macht. Sie eignen sich für einfache sowie für komplexe Biegeformen und sind in der Lage, unterschiedliche Radien und Winkel zu realisieren.
3. Vorteile hydraulischer horizontaler Biegepressen
Hydraulische horizontale Biegepressen bieten zahlreiche Vorteile, die sie für die industrielle Produktion unverzichtbar machen:
- Hohe Wiederholgenauigkeit: Durch die präzise Steuerung des Hydrauliksystems können Biegungen mit hoher Wiederholgenauigkeit durchgeführt werden. Dies ist entscheidend für die Serienproduktion, wo Konsistenz in der Qualität erforderlich ist.
- Robustheit und Langlebigkeit: Diese Maschinen sind für den Dauereinsatz in industriellen Umgebungen konzipiert. Ihre robuste Bauweise und die hochwertigen hydraulischen Komponenten sorgen dafür, dass sie auch unter anspruchsvollen Bedingungen zuverlässig funktionieren.
- Schnelle Umrüstzeiten: Hydraulische Biegepressen ermöglichen schnelle Werkzeugwechsel und Anpassungen der Biegeparameter, was die Flexibilität in der Produktion erhöht und Stillstandszeiten minimiert.
4. Anwendungsbereiche
Hydraulische horizontale Biegepressen finden in verschiedenen Industrien breite Anwendung, darunter:
- Automobilindustrie: In der Automobilproduktion werden diese Pressen zur Herstellung von Komponenten wie Achsen, Fahrgestellen und Auspuffanlagen verwendet, die hohe Anforderungen an Präzision und Festigkeit stellen.
- Bauwesen: Im Bauwesen werden hydraulische Biegepressen für die Formgebung von Stahlträgern und anderen strukturellen Elementen eingesetzt, die in Gebäuden, Brücken und anderen Infrastrukturen verwendet werden.
- Rohrleitungsbau: Bei der Herstellung von Rohrleitungssystemen für die Öl- und Gasindustrie oder die chemische Industrie sind hydraulische Biegepressen unverzichtbar. Sie sorgen dafür, dass die Rohre genau den geforderten Spezifikationen entsprechen, um eine sichere und effiziente Nutzung zu gewährleisten.
5. Zukünftige Entwicklungen
Die Weiterentwicklung hydraulischer horizontaler Biegepressen wird in den kommenden Jahren stark von der Digitalisierung und Automatisierung geprägt sein. Fortschritte in der Sensorik und Steuerungstechnik werden die Präzision und Effizienz dieser Maschinen weiter verbessern. Darüber hinaus könnte der Einsatz von energieeffizienten hydraulischen Komponenten dazu beitragen, den Energieverbrauch zu senken und die Nachhaltigkeit in der industriellen Fertigung zu fördern.
Schlussfolgerung
Die fortschreitende Entwicklung in der Metallverarbeitung hat die Bedeutung spezialisierter Maschinen wie Rohrbiegemaschinen und Biegepressen, insbesondere für Edelstahlrohre, deutlich hervorgehoben. Diese Maschinen spielen eine zentrale Rolle in der modernen Industrie, da sie nicht nur hohe Präzision und Effizienz gewährleisten, sondern auch die Fähigkeit bieten, den spezifischen Anforderungen verschiedenster Branchen gerecht zu werden.
Rohrbiegemaschinen für Edelstahlrohre bieten eine unvergleichliche Präzision und Flexibilität, die für die Herstellung komplexer Bauteile erforderlich sind. Ob in der Automobilindustrie, im Schiffbau oder im Bauwesen, diese Maschinen sind essenziell, um maßgeschneiderte Lösungen zu schaffen, die den höchsten Standards entsprechen.
Horizontale Biegepressen erweitern die Möglichkeiten der Rohrbiegung, indem sie eine einfache Handhabung großer Werkstücke und eine exakte Kontrolle über den Biegeprozess bieten. Ihre Vielseitigkeit und die Fähigkeit, unter verschiedensten Bedingungen präzise zu arbeiten, machen sie zu einem unverzichtbaren Werkzeug in der Metallverarbeitung.
Horizontale Richtpressen ergänzen diesen Prozess, indem sie sicherstellen, dass alle Werkstücke, unabhängig von der Komplexität der Biegung, in perfektem Zustand und exakt den Spezifikationen entsprechend fertiggestellt werden. Diese Maschinen sind entscheidend für die Korrektur von Verformungen und die Sicherstellung höchster Qualitätsstandards.
Hydraulische horizontale Biegepressen kombinieren diese Vorteile mit der Kraft und Präzision hydraulischer Systeme, wodurch sie in der Lage sind, selbst die anspruchsvollsten Materialien und Formen mit Leichtigkeit zu bearbeiten. Sie sind in vielen Industriezweigen von zentraler Bedeutung und tragen wesentlich zur Effizienz und Produktqualität bei.
In Zukunft wird die Integration von Automatisierung und Digitalisierung die Fähigkeiten dieser Maschinen weiter verbessern. Fortschritte in der Sensorik, Steuerungstechnik und Energieeffizienz werden nicht nur die Präzision erhöhen, sondern auch die Nachhaltigkeit der Fertigungsprozesse fördern.
Für Unternehmen, die in der Metallverarbeitung tätig sind, sind diese Maschinen nicht nur ein Werkzeug, sondern eine Investition in die Zukunft. Durch den Einsatz modernster Technologien in der Rohrbiege- und Pressentechnik können sie ihre Wettbewerbsfähigkeit steigern und gleichzeitig höchste Qualitätsstandards sicherstellen.
Maschinenprogramm für die Metallbearbeitung
Unsere Metallbearbeitungsmaschinen sind:
- Rohrbiegemaschine
- Horizontale Presse
- Bandsäge für Metall
- Profilbiegemaschine
- Tiefziehpresse
- Rundschweißmaschine
- Kantenschneide-Bördelmaschine
- Topf- und Pfannenpoliermaschine
- Poliermaschine für flache Oberflächen
Besteck-Produktionslinie: Eine Besteck-Produktionslinie ist eine Art Maschine, die Besteck in einem kontinuierlichen Prozess herstellt. Es umfasst verschiedene Arten von Maschinen wie den Messerschleifer, den Messerschärfer und den Klingenpolierer.
Kochgeschirr-Herstellungsmaschine: Eine Kochgeschirr-Herstellungsmaschine ist eine Art Maschine, die Kochgeschirr in einem kontinuierlichen Prozess herstellt. Es umfasst verschiedene Arten von Maschinen wie den Topfmacher, den Pfannenmacher und den Wokmacher.
Küchengeschirr-Produktionsmaschine: Eine Küchengeschirr-Produktionsmaschine ist eine Art Maschine, die Küchengeschirr in einem kontinuierlichen Prozess herstellt. Es umfasst verschiedene Arten von Maschinen wie Maschinen zur Herstellung von Teekesseln, Produktionslinien für Besteck, Produktionslinien für Töpfe und Pfannen
Wir entwerfen, fertigen und montieren komplette Produktionslinien für Kochgeschirr, Küchengeschirr, Hotelgeschirr und Besteck sowie einzelne Maschinen für einen bestimmten Zweck