Schleifmaschinen sind Maschinen, die zum Glätten, Polieren oder Entgraten von Oberflächen verwendet werden. Sie werden in einer Vielzahl von Branchen eingesetzt, darunter die Metallbearbeitung, die Holzbearbeitung, die Kunststoffbearbeitung und die Automobilindustrie.
Schleifmaschinen arbeiten mithilfe eines Schleifmittels, das aus kleinen, scharfen Körnern besteht. Die Körner werden mit hoher Geschwindigkeit auf das Werkstück aufgebracht und schneiden es ab. Dadurch entsteht eine glatte Oberfläche.
Schleifmaschinen gibt es in einer Vielzahl von Ausführungen. Die Wahl der richtigen Schleifmaschine hängt von der Art des Werkstücks, der gewünschten Oberfläche und den individuellen Anforderungen des Unternehmens ab.
Arten von Schleifmaschinen
Schleifmaschinen lassen sich nach dem verwendeten Schleifmittel in folgende Kategorien einteilen:
- Korundschleifmaschinen: Korundschleifmaschinen verwenden Korund als Schleifmittel. Korund ist ein künstliches Mineral, das aus Aluminiumoxid besteht. Es ist sehr hart und abriebfest und eignet sich daher für eine Vielzahl von Materialien.
- Diamantschleifmaschinen: Diamantschleifmaschinen verwenden Diamanten als Schleifmittel. Diamanten sind die härtesten Materialien der Welt und eignen sich daher für die Bearbeitung von besonders harten Materialien, wie z. B. Keramik oder Edelsteinen.
- Keramikschleifmaschinen: Keramikschleifmaschinen verwenden Keramik als Schleifmittel. Keramik ist ein hartes und abriebfestes Material, das sich für eine Vielzahl von Materialien eignet.
Schleifmaschinen lassen sich auch nach der Art der Bewegung des Schleifmittels in folgende Kategorien einteilen:
- Bandschleifmaschinen: Bandschleifmaschinen verwenden ein endloses Schleifband, das über eine Walze läuft. Bandschleifmaschinen eignen sich für eine Vielzahl von Materialien und können zum Glätten, Polieren und Entgraten verwendet werden.
- Rundschleifmaschinen: Rundschleifmaschinen verwenden ein rotierendes Schleifrad. Rundschleifmaschinen eignen sich für die Bearbeitung von zylindrischen Werkstücken und können zum Glätten, Polieren und Entgraten verwendet werden.
- Trommelschleifmaschinen: Trommelschleifmaschinen verwenden eine rotierende Trommel, die mit Schleifmitteln beladen ist. Trommelschleifmaschinen eignen sich für die Bearbeitung von großen und schweren Werkstücken und können zum Glätten, Polieren und Entgraten verwendet werden.
Schleifverfahren
Es gibt verschiedene Schleifverfahren, die mit Schleifmaschinen angewendet werden können. Die Wahl des Schleifverfahrens hängt von der Art des Werkstücks, der gewünschten Oberfläche und den individuellen Anforderungen des Unternehmens ab.
Konventionelles Schleifverfahren
Beim konventionellen Schleifverfahren wird das Werkstück manuell oder automatisch über das Schleifmittel geführt. Das Schleifmittel kann fest oder beweglich sein.
Exzenter-Schleifverfahren
Beim Exzenter-Schleifverfahren wird das Werkstück nicht nur in einer Richtung, sondern auch in einer Kreisbewegung über das Schleifmittel geführt. Dadurch wird eine gleichmäßigere Oberfläche erzielt.
Vibrations-Schleifverfahren
Beim Vibrations-Schleifverfahren wird das Werkstück in einer Vibrationsbewegung über das Schleifmittel geführt. Dadurch wird eine gleichmäßigere Oberfläche erzielt als beim konventionellen Schleifverfahren.
Ultraschall-Schleifverfahren
Beim Ultraschall-Schleifverfahren werden Ultraschallwellen verwendet, um das Schleifmittel auf das Werkstück zu übertragen. Dadurch wird eine sehr feine Oberfläche erzielt.
Vorteile von Schleifmaschinen
Schleifmaschinen bieten eine Reihe von Vorteilen, darunter:
- Hohe Effizienz: Schleifmaschinen können Werkstücke schnell und effizient bearbeiten.
- Verbesserte Qualität: Schleifmaschinen können eine gleichmäßige und glatte Oberfläche erzielen.
- Verbesserte Sicherheit: Schleifmaschinen können mit Schutzeinrichtungen ausgestattet werden, die das Risiko von Verletzungen reduzieren.
Sicherheit beim Umgang mit Schleifmaschinen
Schleifmaschinen können gefährlich sein, wenn sie nicht richtig verwendet werden. Daher ist es wichtig, sich der Sicherheitsrisiken bewusst zu sein und diese zu vermeiden.
Hier sind einige Sicherheitstipps für den Umgang mit Schleifmaschinen:
- Tragen Sie immer eine Schutzbrille, um Ihre Augen vor herumfliegenden Partikeln zu schützen.
- Tragen Sie auch einen Gehörschutz, um Ihre Ohren vor Lärm zu schützen.
- Verwenden Sie die richtige Schutzkleidung, z. B. Handschuhe, lange Hosen und ein langes Oberteil, um sich vor Verletzungen zu schützen.
- Stellen Sie sicher, dass die Schleifmaschine in gutem Zustand ist und alle Sicherheitseinrichtungen ordnungsgemäß funktionieren.
- Befolgen Sie die Anweisungen des Herstellers.
Fazit
Schleifmaschinen sind ein wichtiges Werkzeug in der Metallbearbeitung, der Holzbearbeitung und anderen Branchen. Sie können Werkstücke schnell und effizient bearbeiten und eine gleichmäßige und glatte Oberfläche erzielen.
Beim Umgang mit Schleifmaschinen ist es wichtig, die Sicherheitsrisiken zu kennen und diese zu vermeiden. Durch die Einhaltung der Sicherheitstipps können Sie sich vor Verletzungen schützen.
Automatische Schleifmaschinen und Poliermaschinen

Schleifmaschinen sind Maschinen, die zum Glätten, Polieren oder Entgraten von Oberflächen verwendet werden. Sie werden in einer Vielzahl von Branchen eingesetzt, darunter die Metallbearbeitung, die Holzbearbeitung, die Kunststoffbearbeitung und die Automobilindustrie.
Schleifmaschinen arbeiten mithilfe eines Schleifmittels, das aus kleinen, scharfen Körnern besteht. Die Körner werden mit hoher Geschwindigkeit auf das Werkstück aufgebracht und schneiden es ab. Dadurch entsteht eine glatte Oberfläche.
Schleifmaschinen gibt es in einer Vielzahl von Ausführungen. Die Wahl der richtigen Schleifmaschine hängt von der Art des Werkstücks, der gewünschten Oberfläche und den individuellen Anforderungen des Unternehmens ab.
Arten von Schleifmaschinen
Schleifmaschinen lassen sich nach dem verwendeten Schleifmittel in folgende Kategorien einteilen:
- Korundschleifmaschinen: Korundschleifmaschinen verwenden Korund als Schleifmittel. Korund ist ein künstliches Mineral, das aus Aluminiumoxid besteht. Es ist sehr hart und abriebfest und eignet sich daher für eine Vielzahl von Materialien.
- Diamantschleifmaschinen: Diamantschleifmaschinen verwenden Diamanten als Schleifmittel. Diamanten sind die härtesten Materialien der Welt und eignen sich daher für die Bearbeitung von besonders harten Materialien, wie z. B. Keramik oder Edelsteinen.
- Keramikschleifmaschinen: Keramikschleifmaschinen verwenden Keramik als Schleifmittel. Keramik ist ein hartes und abriebfestes Material, das sich für eine Vielzahl von Materialien eignet.
Schleifmaschinen lassen sich auch nach der Art der Bewegung des Schleifmittels in folgende Kategorien einteilen:
- Bandschleifmaschinen: Bandschleifmaschinen verwenden ein endloses Schleifband, das über eine Walze läuft. Bandschleifmaschinen eignen sich für eine Vielzahl von Materialien und können zum Glätten, Polieren und Entgraten verwendet werden.
- Rundschleifmaschinen: Rundschleifmaschinen verwenden ein rotierendes Schleifrad. Rundschleifmaschinen eignen sich für die Bearbeitung von zylindrischen Werkstücken und können zum Glätten, Polieren und Entgraten verwendet werden.
- Trommelschleifmaschinen: Trommelschleifmaschinen verwenden eine rotierende Trommel, die mit Schleifmitteln beladen ist. Trommelschleifmaschinen eignen sich für die Bearbeitung von großen und schweren Werkstücken und können zum Glätten, Polieren und Entgraten verwendet werden.
Schleifverfahren
Es gibt verschiedene Schleifverfahren, die mit Schleifmaschinen angewendet werden können. Die Wahl des Schleifverfahrens hängt von der Art des Werkstücks, der gewünschten Oberfläche und den individuellen Anforderungen des Unternehmens ab.
Konventionelles Schleifverfahren
Beim konventionellen Schleifverfahren wird das Werkstück manuell oder automatisch über das Schleifmittel geführt. Das Schleifmittel kann fest oder beweglich sein.
Exzenter-Schleifverfahren
Beim Exzenter-Schleifverfahren wird das Werkstück nicht nur in einer Richtung, sondern auch in einer Kreisbewegung über das Schleifmittel geführt. Dadurch wird eine gleichmäßigere Oberfläche erzielt.
Vibrations-Schleifverfahren
Beim Vibrations-Schleifverfahren wird das Werkstück in einer Vibrationsbewegung über das Schleifmittel geführt. Dadurch wird eine gleichmäßigere Oberfläche erzielt als beim konventionellen Schleifverfahren.
Ultraschall-Schleifverfahren
Beim Ultraschall-Schleifverfahren werden Ultraschallwellen verwendet, um das Schleifmittel auf das Werkstück zu übertragen. Dadurch wird eine sehr feine Oberfläche erzielt.
Vorteile von Schleifmaschinen
Schleifmaschinen bieten eine Reihe von Vorteilen, darunter:
- Hohe Effizienz: Schleifmaschinen können Werkstücke schnell und effizient bearbeiten.
- Verbesserte Qualität: Schleifmaschinen können eine gleichmäßige und glatte Oberfläche erzielen.
- Verbesserte Sicherheit: Schleifmaschinen können mit Schutzeinrichtungen ausgestattet werden, die das Risiko von Verletzungen reduzieren.
Sicherheit beim Umgang mit Schleifmaschinen
Schleifmaschinen können gefährlich sein, wenn sie nicht richtig verwendet werden. Daher ist es wichtig, sich der Sicherheitsrisiken bewusst zu sein und diese zu vermeiden.
Hier sind einige Sicherheitstipps für den Umgang mit Schleifmaschinen:
- Tragen Sie immer eine Schutzbrille, um Ihre Augen vor herumfliegenden Partikeln zu schützen.
- Tragen Sie auch einen Gehörschutz, um Ihre Ohren vor Lärm zu schützen.
- Verwenden Sie die richtige Schutzkleidung, z. B. Handschuhe, lange Hosen und ein langes Oberteil, um sich vor Verletzungen zu schützen.
- Stellen Sie sicher, dass die Schleifmaschine in gutem Zustand ist und alle Sicherheitseinrichtungen ordnungsgemäß funktionieren.
- Befolgen Sie die Anweisungen des Herstellers.
Fazit
Schleifmaschinen sind ein wichtiges Werkzeug in der Metallbearbeitung, der Holzbearbeitung und anderen Branchen. Sie können Werkstücke schnell und effizient bearbeiten und eine gleichmäßige und glatte Oberfläche erzielen.
Beim Umgang mit Schleifmaschinen ist es wichtig, die Sicherheitsrisiken zu kennen und diese zu vermeiden. Durch die Einhaltung der Sicherheitstipps können Sie sich vor Verletzungen schützen.
Eine Bandschleifmaschine ist eine Maschine, die ein endloses Schleifband verwendet, um Werkstücke zu bearbeiten. Sie wird in der Regel in der industriellen Fertigung eingesetzt, um Metall, Holz, Kunststoff und andere Materialien zu schleifen, polieren und entgraten.
Bandschleifmaschinen bestehen aus einem Gestell, einer Antriebseinheit, zwei Umlenkrollen und einem Schleifband. Das Schleifband besteht aus einem Trägermaterial, wie z. B. einem Kunststoff oder einem Metall, und einem Belag aus abrasivem Material, wie z. B. Korund oder Diamant.
Das Schleifband wird von der Antriebseinheit mit einer hohen Geschwindigkeit über die Umlenkrollen geführt. Das Werkstück wird auf das Schleifband aufgelegt und bewegt sich mit dem Band mit. Die abrasiven Körner des Schleifmittels schneiden das Werkstück ab und hinterlassen eine glatte Oberfläche.
Bandschleifmaschinen sind in einer Vielzahl von Größen und Kapazitäten erhältlich. Die Wahl der richtigen Bandschleifmaschine hängt von den individuellen Anforderungen des Unternehmens ab.
Die Vorteile von Bandschleifmaschinen sind:
- Höhere Effizienz: Bandschleifmaschinen können Werkstücke schnell und effizient bearbeiten.
- Verbesserte Sicherheit: Bandschleifmaschinen können mit Schutzeinrichtungen ausgestattet werden, die das Risiko von Verletzungen reduzieren.
- Verbesserte Qualität: Bandschleifmaschinen können eine gleichmäßige Oberfläche erzielen.
Die Nachteile von Bandschleifmaschinen sind:
- Kosten: Bandschleifmaschinen können teurer sein als andere Schleifmaschinen.
- Abfall: Bandschleifmaschinen erzeugen Abfall, der recycelt oder entsorgt werden muss.
Bandschleifmaschinen werden in einer Vielzahl von Anwendungen eingesetzt, darunter:
- Metallbearbeitung: Bandschleifmaschinen werden in der Metallbearbeitung zum Entgraten, Schleifen und Polieren von Metallteilen verwendet.
- Holzbearbeitung: Bandschleifmaschinen werden in der Holzbearbeitung zum Schleifen und Polieren von Holzteilen verwendet.
- Kunststoffbearbeitung: Bandschleifmaschinen werden in der Kunststoffbearbeitung zum Schleifen und Polieren von Kunststoffteilen verwendet.
Hier sind einige Beispiele für Bandschleifmaschinen:
- Handgeführte Bandschleifmaschinen: Handgeführte Bandschleifmaschinen sind tragbare Maschinen, die für kleine und einfache Arbeiten verwendet werden.
- Stationäre Bandschleifmaschinen: Stationäre Bandschleifmaschinen sind größere Maschinen, die für größere und komplexere Arbeiten verwendet werden.
- Automatische Bandschleifmaschinen: Automatische Bandschleifmaschinen sind Maschinen, die Werkstücke automatisch bearbeiten.
Die Wahl der richtigen Bandschleifmaschine hängt von den individuellen Anforderungen des Unternehmens ab.
Rundschleifmaschinen
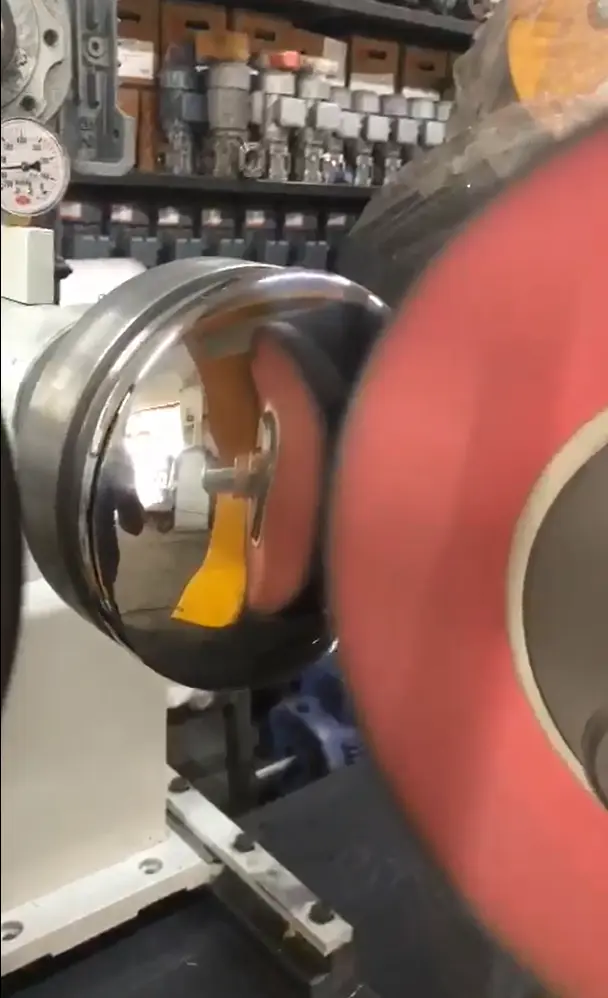
Eine Rundschleifmaschine ist eine Maschine, die ein rotierendes Schleifrad verwendet, um Werkstücke zu bearbeiten. Sie wird in der Regel in der industriellen Fertigung eingesetzt, um Metall, Holz, Kunststoff und andere Materialien zu schleifen, polieren und entgraten.
Rundschleifmaschinen bestehen aus einem Gestell, einer Antriebseinheit, einem Schleifrad und einem Werkstückhalter. Das Schleifrad besteht aus einem Trägermaterial, wie z. B. einem Kunststoff oder einem Metall, und einem Belag aus abrasivem Material, wie z. B. Korund oder Diamant.
Das Schleifrad wird von der Antriebseinheit mit einer hohen Geschwindigkeit angetrieben. Das Werkstück wird in den Werkstückhalter eingespannt und an das Schleifrad geführt. Die abrasiven Körner des Schleifmittels schneiden das Werkstück ab und hinterlassen eine glatte Oberfläche.
Rundschleifmaschinen sind in einer Vielzahl von Größen und Kapazitäten erhältlich. Die Wahl der richtigen Rundschleifmaschine hängt von den individuellen Anforderungen des Unternehmens ab.
Die Vorteile von Rundschleifmaschinen sind:
- Höhere Effizienz: Rundschleifmaschinen können Werkstücke schnell und effizient bearbeiten.
- Verbesserte Sicherheit: Rundschleifmaschinen können mit Schutzeinrichtungen ausgestattet werden, die das Risiko von Verletzungen reduzieren.
- Verbesserte Qualität: Rundschleifmaschinen können eine gleichmäßige Oberfläche erzielen.
Die Nachteile von Rundschleifmaschinen sind:
- Kosten: Rundschleifmaschinen können teurer sein als andere Schleifmaschinen.
- Abfall: Rundschleifmaschinen erzeugen Abfall, der recycelt oder entsorgt werden muss.
Rundschleifmaschinen werden in einer Vielzahl von Anwendungen eingesetzt, darunter:
- Metallbearbeitung: Rundschleifmaschinen werden in der Metallbearbeitung zum Entgraten, Schleifen und Polieren von Metallteilen verwendet.
- Holzbearbeitung: Rundschleifmaschinen werden in der Holzbearbeitung zum Schleifen und Polieren von Holzteilen verwendet.
- Kunststoffbearbeitung: Rundschleifmaschinen werden in der Kunststoffbearbeitung zum Schleifen und Polieren von Kunststoffteilen verwendet.
Hier sind einige Beispiele für Rundschleifmaschinen:
- Handgeführte Rundschleifmaschinen: Handgeführte Rundschleifmaschinen sind tragbare Maschinen, die für kleine und einfache Arbeiten verwendet werden.
- Stationäre Rundschleifmaschinen: Stationäre Rundschleifmaschinen sind größere Maschinen, die für größere und komplexere Arbeiten verwendet werden.
- Automatische Rundschleifmaschinen: Automatische Rundschleifmaschinen sind Maschinen, die Werkstücke automatisch bearbeiten.
Die Wahl der richtigen Rundschleifmaschine hängt von den individuellen Anforderungen des Unternehmens ab.
Arten von Rundschleifmaschinen
Rundschleifmaschinen lassen sich in zwei Hauptkategorien einteilen:
- Konventionelle Rundschleifmaschinen: Konventionelle Rundschleifmaschinen verwenden ein Schleifrad, das sich in einer festen Position befindet. Das Werkstück wird an das Schleifrad geführt und bearbeitet.
- Formrundschleifmaschinen: Formrundschleifmaschinen verwenden ein Schleifrad, das die gewünschte Form des Werkstücks hat. Das Werkstück wird in das Schleifrad eingespannt und bearbeitet.
Weitere Arten von Rundschleifmaschinen:
- Innenrundschleifmaschinen: Innenrundschleifmaschinen werden zum Schleifen von Innenflächen von Werkstücken verwendet.
- Außenrundschleifmaschinen: Außenrundschleifmaschinen werden zum Schleifen von Außenflächen von Werkstücken verwendet.
- Rundkantenschleifmaschinen: Rundkantenschleifmaschinen werden zum Schleifen von Kanten von Werkstücken verwendet.
- Walzenschleifmaschinen: Walzenschleifmaschinen verwenden eine rotierende Walze, die mit Schleifmitteln beladen ist. Sie werden zum Schleifen von langen Werkstücken verwendet.
Trommelschleifmaschinen
Eine Trommelschleifmaschine ist eine Maschine, die eine rotierende Trommel verwendet, um Werkstücke zu bearbeiten. Sie wird in der Regel in der industriellen Fertigung eingesetzt, um Metall, Holz, Kunststoff und andere Materialien zu schleifen, polieren und entgraten.
Trommelschleifmaschinen bestehen aus einem Gestell, einer Antriebseinheit, einer Trommel und einem Werkstückhalter. Die Trommel besteht aus einem Trägermaterial, wie z. B. einem Kunststoff oder einem Metall, und ist mit Schleifmitteln beladen.
Die Trommel wird von der Antriebseinheit mit einer hohen Geschwindigkeit angetrieben. Das Werkstück wird in den Werkstückhalter eingespannt und in die Trommel eingeführt. Die abrasiven Körner des Schleifmittels schneiden das Werkstück ab und hinterlassen eine glatte Oberfläche.
Trommelschleifmaschinen sind in einer Vielzahl von Größen und Kapazitäten erhältlich. Die Wahl der richtigen Trommelschleifmaschine hängt von den individuellen Anforderungen des Unternehmens ab.
Die Vorteile von Trommelschleifmaschinen sind:
- Höhere Effizienz: Trommelschleifmaschinen können Werkstücke schnell und effizient bearbeiten.
- Verbesserte Sicherheit: Trommelschleifmaschinen können mit Schutzeinrichtungen ausgestattet werden, die das Risiko von Verletzungen reduzieren.
- Verbesserte Qualität: Trommelschleifmaschinen können eine gleichmäßige Oberfläche erzielen.
Die Nachteile von Trommelschleifmaschinen sind:
- Kosten: Trommelschleifmaschinen können teurer sein als andere Schleifmaschinen.
- Abfall: Trommelschleifmaschinen erzeugen Abfall, der recycelt oder entsorgt werden muss.
Trommelschleifmaschinen werden in einer Vielzahl von Anwendungen eingesetzt, darunter:
- Metallbearbeitung: Trommelschleifmaschinen werden in der Metallbearbeitung zum Entgraten, Schleifen und Polieren von Metallteilen verwendet.
- Holzbearbeitung: Trommelschleifmaschinen werden in der Holzbearbeitung zum Schleifen und Polieren von Holzteilen verwendet.
- Kunststoffbearbeitung: Trommelschleifmaschinen werden in der Kunststoffbearbeitung zum Schleifen und Polieren von Kunststoffteilen verwendet.
Hier sind einige Beispiele für Trommelschleifmaschinen:
- Handgeführte Trommelschleifmaschinen: Handgeführte Trommelschleifmaschinen sind tragbare Maschinen, die für kleine und einfache Arbeiten verwendet werden.
- Stationäre Trommelschleifmaschinen: Stationäre Trommelschleifmaschinen sind größere Maschinen, die für größere und komplexere Arbeiten verwendet werden.
- Automatische Trommelschleifmaschinen: Automatische Trommelschleifmaschinen sind Maschinen, die Werkstücke automatisch bearbeiten.
Die Wahl der richtigen Trommelschleifmaschine hängt von den individuellen Anforderungen des Unternehmens ab.
Arten von Trommelschleifmaschinen
Trommelschleifmaschinen lassen sich in zwei Hauptkategorien einteilen:
- Konventionelle Trommelschleifmaschinen: Konventionelle Trommelschleifmaschinen verwenden eine Trommel, die sich in einer festen Position befindet. Das Werkstück wird in die Trommel eingeführt und bearbeitet.
- Formtrommelschleifmaschinen: Formtrommelschleifmaschinen verwenden eine Trommel, die die gewünschte Form des Werkstücks hat. Das Werkstück wird in die Trommel eingespannt und bearbeitet.
Weitere Arten von Trommelschleifmaschinen:
- Innentrommelschleifmaschinen: Innentrommelschleifmaschinen werden zum Schleifen von Innenflächen von Werkstücken verwendet.
- Außentrommelschleifmaschinen: Außentrommelschleifmaschinen werden zum Schleifen von Außenflächen von Werkstücken verwendet.
- Kantentrommelschleifmaschinen: Kantentrommelschleifmaschinen werden zum Schleifen von Kanten von Werkstücken verwendet.
Trommelschleifverfahren
Beim Trommelschleifverfahren werden die Werkstücke in eine rotierende Trommel mit Schleifmitteln eingeführt. Die abrasiven Körner des Schleifmittels schneiden das Werkstück ab und hinterlassen eine glatte Oberfläche.
Das Trommelschleifverfahren ist ein vielseitiges Verfahren, das für eine Vielzahl von Metallen und Oberflächen geeignet ist. Es kann auch für die Entfernung von Rost, Lack und anderen Beschichtungen verwendet werden.
Die Wahl des Trommelschleifverfahrens hängt von der Art des Werkstücks, der gewünschten Oberfläche und den individuellen Anforderungen des Unternehmens ab.
Automatisierung
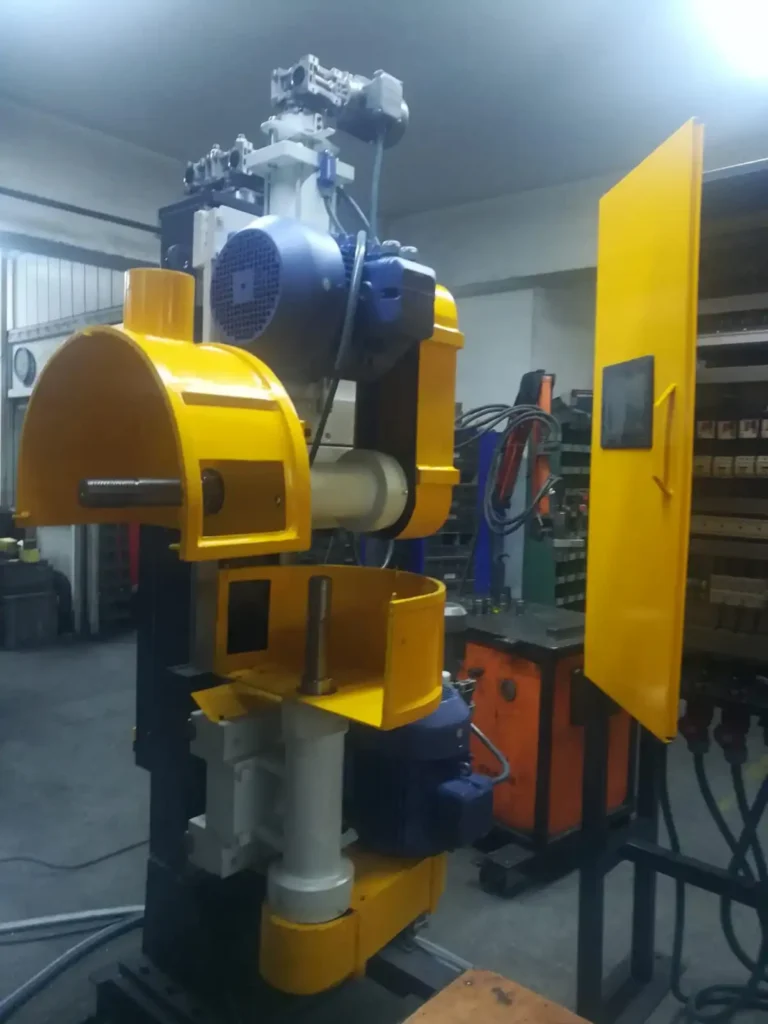
Automatisierung ist ein zentrales Konzept in der heutigen Fertigungsindustrie und spielt eine entscheidende Rolle bei automatischen Schleif- und Poliermaschinen. Diese Maschinen sind darauf ausgelegt, repetitive Aufgaben zu übernehmen und dabei menschliche Intervention auf ein Minimum zu reduzieren. Die Automatisierung ermöglicht eine präzise Steuerung des Schleif- und Polierprozesses, was zu konsistenteren Ergebnissen führt und gleichzeitig die Produktivität steigert.
In automatischen Schleif- und Poliermaschinen werden verschiedene Automatisierungstechnologien eingesetzt, darunter CNC-Steuerung (Computerized Numerical Control), Robotik und fortschrittliche Sensortechnik. Diese Systeme ermöglichen es, den gesamten Arbeitsablauf von der Werkstückvorbereitung über das Schleifen oder Polieren bis hin zur Qualitätskontrolle und zum Ausschussmanagement zu automatisieren.
Durch die Automatisierung können Unternehmen die Effizienz ihrer Fertigungsprozesse verbessern, die Durchlaufzeiten verkürzen und die Produktionskosten senken. Darüber hinaus trägt die Automatisierung dazu bei, die Arbeitsbedingungen zu verbessern, indem sie gefährliche oder repetitive Aufgaben von menschlichen Arbeitern übernimmt.
Im Kontext von automatischen Schleif- und Poliermaschinen bedeutet Automatisierung nicht nur eine Verbesserung der Produktionsleistung, sondern auch eine Steigerung der Qualität und Konsistenz der hergestellten Teile. Dies trägt dazu bei, die Wettbewerbsfähigkeit von Unternehmen in der Fertigungsindustrie zu stärken und ihre Position auf dem Markt zu festigen.
Schleifmaschine
Eine Schleifmaschine ist eine industrielle Maschine, die zum Schleifen von Werkstücken verwendet wird. Sie kommt in verschiedenen Fertigungsprozessen zum Einsatz, um die Oberflächen von Materialien zu glätten, Unebenheiten zu entfernen oder die Maßgenauigkeit zu verbessern. Schleifmaschinen arbeiten mit rotierenden Schleifscheiben, Schleifbändern oder anderen Schleifwerkzeugen, die je nach Anwendung und Material unterschiedliche Formen und Eigenschaften aufweisen können.
Es gibt verschiedene Arten von Schleifmaschinen, darunter Flachschleifmaschinen, Rundschleifmaschinen, Bandschleifmaschinen und Zentrumschleifmaschinen. Jede dieser Maschinen hat spezifische Einsatzgebiete und kann für unterschiedliche Werkstücke und Materialien optimiert werden.
Moderne Schleifmaschinen sind oft mit CNC-Steuerung ausgestattet, was eine präzise Steuerung des Schleifprozesses ermöglicht und komplexe Formen und Profile mit hoher Genauigkeit reproduzierbar macht. Darüber hinaus können Schleifmaschinen mit Automatisierungstechnologien wie Robotern oder automatisierten Werkzeugwechslern ausgestattet sein, um die Produktivität zu steigern und die Arbeitskosten zu reduzieren.
In vielen Fertigungsbranchen, einschließlich der Automobil-, Luftfahrt- und Metallverarbeitungsindustrie, sind Schleifmaschinen unverzichtbare Werkzeuge zur Herstellung von Teilen mit engen Toleranzen und hoher Oberflächenqualität. Sie tragen dazu bei, die Effizienz der Fertigungsprozesse zu verbessern und die Qualität der hergestellten Produkte zu gewährleisten.
Poliermaschine
Eine Poliermaschine ist eine industrielle Maschine, die verwendet wird, um die Oberflächen von Werkstücken zu polieren und ein glattes, glänzendes Finish zu erzeugen. Im Gegensatz zur Schleifmaschine, die dazu dient, Material abzutragen und Unebenheiten zu entfernen, arbeitet die Poliermaschine mit Poliermitteln und -werkzeugen, um die Oberfläche des Werkstücks zu veredeln und ein ästhetisch ansprechendes Aussehen zu erzielen.
Poliermaschinen kommen in verschiedenen Branchen zum Einsatz, darunter die Automobilindustrie, die Schmuckherstellung, die Möbelproduktion und die Metallverarbeitung. Je nach Anwendung und Material können unterschiedliche Polierverfahren und -techniken eingesetzt werden, um die gewünschten Ergebnisse zu erzielen.
Moderne Poliermaschinen sind oft mit verschiedenen Funktionen und Einstellungen ausgestattet, die es ermöglichen, den Polierprozess genau auf die Anforderungen des Werkstücks abzustimmen. Dazu gehören beispielsweise einstellbare Drehgeschwindigkeiten, Druckkontrolle und die Verwendung spezieller Poliermittel für unterschiedliche Oberflächen.
Wie auch bei Schleifmaschinen kann die Automatisierung eine wichtige Rolle bei Poliermaschinen spielen, um die Produktivität zu steigern und die Arbeitskosten zu senken. Automatische Poliermaschinen können mit Robotern oder CNC-Steuerungen integriert sein, um den Polierprozess zu automatisieren und eine gleichbleibend hohe Qualität der bearbeiteten Teile sicherzustellen.
Insgesamt sind Poliermaschinen wesentliche Werkzeuge in der Fertigungsindustrie, um die Oberflächenqualität von Produkten zu verbessern und sie für den Verkauf oder die weitere Verarbeitung vorzubereiten. Sie tragen dazu bei, die ästhetischen und funktionalen Anforderungen von Endverbrauchern zu erfüllen und die Wettbewerbsfähigkeit von Unternehmen auf dem Markt zu stärken.
Präzision
Präzision ist ein entscheidender Aspekt bei der Anwendung automatischer Schleif- und Poliermaschinen. Sie bezieht sich auf die Fähigkeit dieser Maschinen, Werkstücke mit äußerster Genauigkeit und Konsistenz zu bearbeiten. In der Fertigungsindustrie ist Präzision von entscheidender Bedeutung, um sicherzustellen, dass die hergestellten Teile den erforderlichen Spezifikationen entsprechen und eine hohe Qualität aufweisen.
Automatische Schleif- und Poliermaschinen sind darauf ausgelegt, präzise Schleif- und Polieroperationen durchzuführen, indem sie hochentwickelte Steuerungssysteme und präzise Positionierungstechnologien nutzen. Dies ermöglicht es ihnen, komplexe Formen und Profile mit engen Toleranzen zu bearbeiten und eine gleichbleibende Qualität über große Stückzahlen hinweg zu gewährleisten.
Die Präzision automatischer Schleif- und Poliermaschinen trägt dazu bei, die Effizienz der Fertigungsprozesse zu verbessern, indem sie Ausschuss reduziert und die Nachbearbeitung minimiert. Darüber hinaus ermöglicht sie es Unternehmen, die Anforderungen ihrer Kunden zu erfüllen und ihre Wettbewerbsfähigkeit auf dem Markt zu stärken.
Um die Präzision automatischer Schleif- und Poliermaschinen zu gewährleisten, ist eine regelmäßige Wartung und Kalibrierung erforderlich, um sicherzustellen, dass die Maschinen optimal funktionieren und ihre Leistung nicht beeinträchtigt wird. Durch die Investition in hochwertige Maschinen und die Schulung des Bedienpersonals können Unternehmen sicherstellen, dass ihre Fertigungsprozesse auf höchstem Niveau betrieben werden und sie die bestmöglichen Ergebnisse erzielen.
Produktivität
Produktivität ist ein maßgeblicher Faktor in der Fertigungsindustrie, und automatische Schleif- und Poliermaschinen spielen eine entscheidende Rolle bei der Steigerung der Produktivität in diesen Prozessen. Produktivität bezieht sich auf das Verhältnis zwischen dem Output an hergestellten Teilen und den dafür benötigten Ressourcen wie Zeit, Arbeitskraft und Material.
Durch den Einsatz automatischer Schleif- und Poliermaschinen können Unternehmen ihre Produktivität erheblich steigern. Diese Maschinen können kontinuierlich und effizient arbeiten, ohne die Notwendigkeit menschlicher Eingriffe, was die Durchlaufzeiten verkürzt und die Gesamtproduktionskapazität erhöht. Darüber hinaus ermöglicht die Automatisierung eine gleichmäßigere und konsistentere Bearbeitung von Werkstücken, was zu einer Reduzierung von Ausschuss und Nachbearbeitung führt.
Die Produktivitätssteigerung durch automatische Schleif- und Poliermaschinen trägt dazu bei, die Gesamtkosten der Fertigung zu senken und die Wettbewerbsfähigkeit von Unternehmen zu verbessern. Durch die Optimierung der Fertigungsprozesse können Unternehmen ihre Effizienz steigern und mehr Aufträge mit höherer Rentabilität abwickeln.
Es ist jedoch wichtig zu beachten, dass die Produktivität nicht nur von der Leistung der Maschinen abhängt, sondern auch von anderen Faktoren wie der Verfügbarkeit von Materialien, der Effizienz der Logistik und der Organisation der Fertigungsabläufe. Unternehmen müssen daher ganzheitliche Ansätze zur Steigerung ihrer Produktivität verfolgen, indem sie nicht nur in moderne Maschinentechnologie investieren, sondern auch ihre Prozesse kontinuierlich optimieren und verbessern.
CNC-Steuerung
Die CNC-Steuerung (Computerized Numerical Control) ist ein entscheidendes Element in automatischen Schleif- und Poliermaschinen, das eine präzise Steuerung und Automatisierung des Bearbeitungsprozesses ermöglicht. CNC-Steuerungen verwenden Computerprogramme, um die Bewegungen und Operationen der Maschine zu steuern, basierend auf vordefinierten Befehlen und Parametern.
Durch die CNC-Steuerung können komplexe Schleif- und Polieroperationen mit hoher Genauigkeit und Wiederholbarkeit durchgeführt werden. Die Maschinen können programmiert werden, um spezifische Werkstücke zu bearbeiten und dabei verschiedene Schleif- und Polierwerkzeuge, Bewegungspfade und Bearbeitungsparameter zu berücksichtigen.
Ein weiterer Vorteil der CNC-Steuerung ist die Flexibilität und Anpassungsfähigkeit der Maschinen. Durch das Ändern der Programmierung können Unternehmen schnell zwischen verschiedenen Produktionsaufträgen wechseln und neue Teile mit unterschiedlichen Spezifikationen herstellen, ohne dass umfangreiche Umrüstungen erforderlich sind.
Die CNC-Steuerung ermöglicht es auch, komplexe Formen und Profile mit hoher Präzision zu bearbeiten, was mit herkömmlichen manuellen Methoden oft schwierig oder unmöglich wäre. Dies eröffnet neue Möglichkeiten für die Fertigung von Teilen mit anspruchsvollen Designs und Spezifikationen.
Insgesamt spielt die CNC-Steuerung eine entscheidende Rolle bei der Maximierung der Leistungsfähigkeit und Effizienz automatischer Schleif- und Poliermaschinen. Sie ermöglicht es Unternehmen, ihre Fertigungsprozesse zu optimieren, die Qualität ihrer Produkte zu verbessern und ihre Wettbewerbsfähigkeit auf dem Markt zu stärken.
Schleifprozess
Der Schleifprozess ist ein zentraler Aspekt in der Bearbeitung von Werkstücken mit automatischen Schleifmaschinen. Es handelt sich um einen mechanischen Bearbeitungsvorgang, bei dem Material von der Oberfläche eines Werkstücks abgetragen wird, um Unebenheiten zu entfernen, die Oberfläche zu glätten oder die Maßgenauigkeit zu verbessern.
Automatische Schleifmaschinen führen den Schleifprozess mithilfe von rotierenden Schleifscheiben, Schleifbändern oder anderen Schleifwerkzeugen durch. Die Maschinen können so programmiert werden, dass sie den Schleifprozess gemäß den spezifizierten Parametern durchführen, einschließlich der Schleifgeschwindigkeit, des Drucks, der Zufuhrrate von Schleifmitteln und der Bewegungsbahnen.
Der Schleifprozess kann für verschiedene Materialien und Anwendungen angepasst werden, einschließlich Metalle, Kunststoffe, Keramik und Verbundwerkstoffe. Je nach Material und Anforderungen können unterschiedliche Schleifverfahren und -werkzeuge zum Einsatz kommen, um die gewünschten Ergebnisse zu erzielen.
Ein effektiver Schleifprozess erfordert eine genaue Kontrolle und Überwachung der Schleifparameter sowie eine regelmäßige Wartung und Pflege der Schleifmaschinen und Werkzeuge. Durch die Optimierung des Schleifprozesses können Unternehmen die Produktivität steigern, die Qualität ihrer Produkte verbessern und die Lebensdauer ihrer Maschinen maximieren.
Insgesamt ist der Schleifprozess ein wesentlicher Bestandteil der Fertigungsindustrie, der dazu beiträgt, die Oberflächenqualität von Werkstücken zu verbessern und sie für den Einsatz in verschiedenen Anwendungen vorzubereiten. Mit automatischen Schleifmaschinen können Unternehmen effizientere und konsistentere Schleifprozesse durchführen, was zu einer Steigerung der Wettbewerbsfähigkeit und Rentabilität führt.
Oberflächenqualität
Die Oberflächenqualität ist ein entscheidender Faktor in vielen industriellen Anwendungen und spielt insbesondere bei automatischen Schleif- und Poliermaschinen eine wichtige Rolle. Sie bezieht sich auf die Beschaffenheit und das Aussehen der Oberfläche eines Werkstücks nach dem Schleifen oder Polieren und hat einen direkten Einfluss auf dessen Funktionalität, Ästhetik und Leistung.
Durch den Einsatz automatischer Schleif- und Poliermaschinen können Unternehmen eine gleichbleibend hohe Oberflächenqualität ihrer Produkte sicherstellen. Diese Maschinen ermöglichen eine präzise Steuerung des Bearbeitungsprozesses, was zu glatten, gleichmäßigen Oberflächen mit minimalen Defekten führt. Die automatisierte Natur der Maschinen trägt auch dazu bei, menschliche Fehler zu reduzieren und die Konsistenz der bearbeiteten Teile zu verbessern.
Die Oberflächenqualität ist besonders wichtig in Branchen wie der Automobil-, Luftfahrt- und Medizintechnik, wo hohe Ansprüche an die Ästhetik, die Funktionalität und die Sicherheit der Produkte gestellt werden. Einwandfreie Oberflächen können die Leistung von Komponenten verbessern, die Lebensdauer von Produkten verlängern und die Kundenzufriedenheit erhöhen.
Um eine optimale Oberflächenqualität zu erzielen, müssen Unternehmen geeignete Schleif- und Polierverfahren sowie hochwertige Schleif- und Polierwerkzeuge einsetzen. Darüber hinaus ist eine gründliche Vorbereitung der Werkstücke und eine sorgfältige Überwachung des Bearbeitungsprozesses erforderlich, um etwaige Defekte oder Unregelmäßigkeiten frühzeitig zu erkennen und zu korrigieren.
Insgesamt ist die Oberflächenqualität ein entscheidender Qualitätsfaktor in der Fertigungsindustrie, der mit automatischen Schleif- und Poliermaschinen effizient verbessert und kontrolliert werden kann. Durch die Investition in hochwertige Bearbeitungstechnologien können Unternehmen ihre Wettbewerbsfähigkeit stärken und hochwertige Produkte herstellen, die den Anforderungen ihrer Kunden gerecht werden.
Effizienz
Effizienz ist ein zentrales Konzept in der Fertigungsindustrie und spielt eine wichtige Rolle bei automatischen Schleif- und Poliermaschinen. Sie bezieht sich darauf, wie gut Ressourcen genutzt werden, um einen bestimmten Output zu erzielen. In Bezug auf Schleif- und Poliermaschinen bedeutet Effizienz, dass die Maschinen in der Lage sind, ihre Aufgaben mit minimalen Ressourcen und Zeit zu erledigen, während gleichzeitig die Qualität der bearbeiteten Teile aufrechterhalten wird.
Automatische Schleif- und Poliermaschinen sind darauf ausgelegt, die Effizienz von Fertigungsprozessen zu steigern, indem sie repetitive Aufgaben automatisieren und menschliche Fehler reduzieren. Durch die präzise Steuerung und Überwachung des Bearbeitungsprozesses können diese Maschinen eine höhere Produktionsleistung erzielen und die Durchlaufzeiten verkürzen.
Effiziente Schleif- und Poliermaschinen ermöglichen es Unternehmen, ihre Produktivität zu steigern und die Gesamtkosten der Fertigung zu senken. Da weniger manuelle Arbeit erforderlich ist, um die Maschinen zu bedienen, können Arbeitskosten reduziert und die Rentabilität erhöht werden. Darüber hinaus können effiziente Maschinen dazu beitragen, den Materialverbrauch zu optimieren und den Ausschuss zu minimieren, was zu einer weiteren Kosteneinsparung führt.
Um die Effizienz automatischer Schleif- und Poliermaschinen zu maximieren, ist eine sorgfältige Planung und Konfiguration erforderlich. Dies umfasst die Auswahl der richtigen Maschinentypen und -modelle für die spezifischen Anforderungen der Fertigung sowie die Optimierung der Bearbeitungsparameter und -prozesse.
Insgesamt ist die Effizienz ein wesentlicher Erfolgsfaktor für Fertigungsunternehmen, und automatische Schleif- und Poliermaschinen spielen eine wichtige Rolle dabei, diese Effizienz zu steigern. Durch die Investition in moderne Bearbeitungstechnologien können Unternehmen ihre Wettbewerbsfähigkeit stärken und ihre Position auf dem Markt festigen.
Werkstück
Ein Werkstück ist ein zentraler Begriff in der Fertigungsindustrie und bezeichnet ein rohes oder halbfertiges Teil, das durch Bearbeitung, Formgebung oder Zusammenbau hergestellt wird, um ein Endprodukt zu erhalten. In Bezug auf automatische Schleif- und Poliermaschinen ist das Werkstück das Bauteil oder die Komponente, das bearbeitet wird, um die gewünschte Oberflächenbeschaffenheit, Form oder Maßhaltigkeit zu erreichen.
Werkstücke können aus einer Vielzahl von Materialien bestehen, darunter Metalle, Kunststoffe, Keramiken, Verbundwerkstoffe und mehr. Je nach Anwendung und Branchenkontext können Werkstücke sehr unterschiedliche Formen, Größen und Eigenschaften aufweisen.
Automatische Schleif- und Poliermaschinen werden eingesetzt, um die Oberflächenqualität von Werkstücken zu verbessern, Unebenheiten zu entfernen, Oberflächen zu glätten und spezifische Oberflächeneigenschaften zu erzielen. Die Maschinen können so programmiert werden, dass sie die gewünschten Bearbeitungsoperationen mit hoher Präzision und Wiederholbarkeit durchführen, um die Anforderungen der jeweiligen Anwendung zu erfüllen.
Die Effizienz und Genauigkeit der Bearbeitung von Werkstücken mit automatischen Schleif- und Poliermaschinen trägt wesentlich zur Qualität und Rentabilität der Fertigungsprozesse bei. Durch die Optimierung der Bearbeitungstechnologien und -prozesse können Unternehmen die Produktivität steigern, die Durchlaufzeiten verkürzen und die Wettbewerbsfähigkeit auf dem Markt verbessern.
Insgesamt ist das Werkstück das zentrale Element in der Fertigung, und automatische Schleif- und Poliermaschinen spielen eine wichtige Rolle bei der Herstellung hochwertiger Werkstücke mit den erforderlichen Oberflächen- und Maßgenauigkeiten.
Roboterintegration
Die Roboterintegration bezieht sich auf den Prozess der Einbindung von Robotern in automatische Schleif- und Poliermaschinen sowie in die Gesamtfertigungslinie. Dieser Ansatz nutzt die Vorteile der Robotertechnologie, um die Effizienz, Flexibilität und Produktivität der Fertigungsprozesse zu steigern.
Durch die Integration von Robotern können automatische Schleif- und Poliermaschinen mit zusätzlicher Automatisierungsfähigkeit ausgestattet werden. Roboter können für verschiedene Aufgaben eingesetzt werden, darunter das Be- und Entladen von Werkstücken, das Wechseln von Schleif- und Polierwerkzeugen, die Reinigung von Maschinen und Werkstücken sowie die Überwachung des Fertigungsprozesses.
Die Roboterintegration bietet zahlreiche Vorteile, darunter eine höhere Produktionsleistung durch kontinuierliche Bearbeitung und weniger Stillstandszeiten, da Roboter in der Lage sind, rund um die Uhr zu arbeiten. Darüber hinaus ermöglicht die Flexibilität von Robotern eine schnellere Anpassung an neue Produktionsanforderungen und eine effizientere Nutzung von Produktionsressourcen.
Die Integration von Robotern erfordert jedoch eine sorgfältige Planung und Konfiguration, um sicherzustellen, dass die Roboter nahtlos mit den bestehenden Maschinen und Prozessen interagieren können. Dies umfasst die Auswahl geeigneter Robotermodelle, die Programmierung von Roboterbewegungen und -aktionen sowie die Integration von Robotern in das übergeordnete Fertigungsleitsystem.
Insgesamt bietet die Roboterintegration eine leistungsstarke Möglichkeit, die Automatisierung von Fertigungsprozessen voranzutreiben und die Wettbewerbsfähigkeit von Unternehmen zu stärken. Durch die Nutzung der Vorteile von Robotertechnologie können automatische Schleif- und Poliermaschinen ihre Leistungsfähigkeit und Vielseitigkeit weiter verbessern.
Schleifscheibe
Die Schleifscheibe ist ein Schlüsselkomponente in Schleifmaschinen, die zum Schleifen von Werkstücken verwendet wird. Sie besteht aus einem abrasiven Material, das auf einem Trägermaterial befestigt ist und beim Schleifen Material von der Oberfläche des Werkstücks abträgt. Schleifscheiben gibt es in verschiedenen Formen, Größen und Materialzusammensetzungen, die jeweils für spezifische Schleifanwendungen optimiert sind.
Das abrasive Material auf der Schleifscheibe kann aus verschiedenen Substanzen bestehen, darunter Korund, Siliziumkarbid, Diamant oder Bornitrid. Die Auswahl des abrasiven Materials hängt von verschiedenen Faktoren ab, einschließlich der Härte und Beschaffenheit des zu bearbeitenden Werkstücks sowie der gewünschten Oberflächenqualität und Schleifleistung.
Die Schleifscheibe wird auf der Schleifmaschine montiert und durch Rotation in Kontakt mit dem Werkstück gebracht. Dabei wird das abrasive Material auf der Schleifscheibe verwendet, um Material von der Oberfläche des Werkstücks abzutragen und die gewünschte Oberflächenbeschaffenheit zu erreichen. Die Schleifgeschwindigkeit, der Druck und die Zufuhrrate des Schleifmittels sind dabei wichtige Parameter, die den Schleifprozess beeinflussen.
Moderne Schleifmaschinen können mit verschiedenen Arten von Schleifscheiben betrieben werden, je nach den spezifischen Anforderungen der Anwendung. Durch die Auswahl der richtigen Schleifscheibe können Unternehmen die Schleifqualität verbessern, die Produktivität steigern und die Lebensdauer ihrer Schleifmaschinen maximieren.
Insgesamt ist die Schleifscheibe eine entscheidende Komponente in Schleifmaschinen, die eine präzise und effiziente Bearbeitung von Werkstücken ermöglicht. Durch die kontinuierliche Weiterentwicklung von Schleifscheibenmaterialien und -technologien können Unternehmen ihre Fertigungsprozesse weiter optimieren und ihre Wettbewerbsfähigkeit auf dem Markt stärken.
Poliermittel
Poliermittel sind Substanzen, die bei der Bearbeitung von Werkstücken verwendet werden, um deren Oberfläche zu glätten, zu reinigen und ein glänzendes Finish zu erzeugen. Sie kommen insbesondere bei der Verwendung von Poliermaschinen zum Einsatz und spielen eine wichtige Rolle bei der Erzielung der gewünschten Oberflächenqualität.
Es gibt verschiedene Arten von Poliermitteln, die jeweils für spezifische Anwendungen und Materialien optimiert sind. Einige der häufig verwendeten Poliermittel umfassen:
- Polierpasten: Diese sind in der Regel abrasive Substanzen, die in einer Paste oder Suspension formuliert sind. Sie enthalten abrasive Partikel, die dazu beitragen, Oberflächenunebenheiten zu glätten und feine Kratzer zu entfernen, um ein glänzendes Finish zu erzeugen.
- Polierpasten: Diese sind in der Regel abrasive Substanzen, die in einer Paste oder Suspension formuliert sind. Sie enthalten abrasive Partikel, die dazu beitragen, Oberflächenunebenheiten zu glätten und feine Kratzer zu entfernen, um ein glänzendes Finish zu erzeugen.
- Polierpasten: Diese sind in der Regel abrasive Substanzen, die in einer Paste oder Suspension formuliert sind. Sie enthalten abrasive Partikel, die dazu beitragen, Oberflächenunebenheiten zu glätten und feine Kratzer zu entfernen, um ein glänzendes Finish zu erzeugen.
- Polierpasten: Diese sind in der Regel abrasive Substanzen, die in einer Paste oder Suspension formuliert sind. Sie enthalten abrasive Partikel, die dazu beitragen, Oberflächenunebenheiten zu glätten und feine Kratzer zu entfernen, um ein glänzendes Finish zu erzeugen.
- Polierpasten: Diese sind in der Regel abrasive Substanzen, die in einer Paste oder Suspension formuliert sind. Sie enthalten abrasive Partikel, die dazu beitragen, Oberflächenunebenheiten zu glätten und feine Kratzer zu entfernen, um ein glänzendes Finish zu erzeugen.
Die Auswahl des richtigen Poliermittels hängt von verschiedenen Faktoren ab, einschließlich des zu bearbeitenden Materials, der gewünschten Oberflächenqualität und der Art der Poliermaschine. Durch die Verwendung von hochwertigen Poliermitteln und die Optimierung des Polierprozesses können Unternehmen die Qualität ihrer Produkte verbessern und die Zufriedenheit ihrer Kunden steigern.
Schleifband
Ein Schleifband ist ein wichtiges Werkzeug in Schleifmaschinen, das verwendet wird, um Werkstücke durch abrasiven Materialabtrag zu bearbeiten. Es besteht aus einem flexiblen Trägermaterial, auf das ein Schleifmittel wie Korund oder Siliziumkarbid aufgebracht ist. Schleifbänder werden vor allem in Bandschleifmaschinen eingesetzt, um flache Oberflächen zu schleifen, Kanten zu entgraten und verschiedene Werkstücke zu bearbeiten.
Die Auswahl des richtigen Schleifbands hängt von verschiedenen Faktoren ab, darunter die Art des zu bearbeitenden Materials, die gewünschte Oberflächenqualität und die spezifische Anwendung. Schleifbänder sind in verschiedenen Körnungen erhältlich, die den Grad der Materialabtragung und die Oberflächenrauheit beeinflussen.
Ein weiterer wichtiger Aspekt beim Einsatz von Schleifbändern ist die richtige Spannung und Ausrichtung, um eine gleichmäßige Bearbeitung und eine lange Lebensdauer des Schleifbands sicherzustellen. Durch die richtige Wartung und Pflege können Schleifbänder länger halten und eine bessere Leistung erzielen.
Insgesamt sind Schleifbänder vielseitige Werkzeuge, die in verschiedenen industriellen Anwendungen eingesetzt werden, um Werkstücke präzise und effizient zu bearbeiten. Durch die Auswahl hochwertiger Schleifbänder und die optimale Einrichtung der Schleifmaschine können Unternehmen die Qualität ihrer Produkte verbessern und die Produktivität ihrer Fertigungsprozesse steigern.
Durchlaufzeit
Die Durchlaufzeit ist die Gesamtdauer, die benötigt wird, um ein Werkstück oder einen Auftrag durch den gesamten Fertigungsprozess zu führen, von der Auftragserteilung bis zur Fertigstellung. Im Kontext automatischer Schleif- und Poliermaschinen bezieht sich die Durchlaufzeit auf die Zeit, die benötigt wird, um ein Werkstück durch den Schleif- oder Polierprozess zu führen, einschließlich der Einrichtung, des eigentlichen Bearbeitungsvorgangs und gegebenenfalls der Nachbearbeitung oder Qualitätskontrolle.
Die Durchlaufzeit ist ein wichtiger Leistungsindikator in der Fertigungsindustrie und beeinflusst maßgeblich die Produktivität und Rentabilität eines Fertigungsprozesses. Durch die Optimierung der Durchlaufzeiten können Unternehmen ihre Produktionskapazität erhöhen, die Reaktionsfähigkeit auf Kundenanfragen verbessern und die Lieferzeiten verkürzen.
Automatische Schleif- und Poliermaschinen spielen eine entscheidende Rolle bei der Reduzierung der Durchlaufzeiten in der Fertigung. Durch die Automatisierung von Schleif- und Polierprozessen können Unternehmen die Bearbeitungszeiten verkürzen und die Produktivität steigern. Darüber hinaus ermöglichen es automatische Maschinen, mehrere Schritte des Bearbeitungsprozesses gleichzeitig auszuführen, was zu einer weiteren Beschleunigung der Durchlaufzeiten führt.
Um die Durchlaufzeit effektiv zu reduzieren, ist eine ganzheitliche Optimierung der Fertigungsprozesse erforderlich, einschließlich der Integration von automatischen Schleif- und Poliermaschinen, der Verbesserung der Materialflüsse und der Minimierung von Stillstandszeiten. Durch die kontinuierliche Überwachung und Optimierung der Durchlaufzeiten können Unternehmen ihre Wettbewerbsfähigkeit auf dem Markt stärken und ihre Position in der Branche festigen.
Maßgenauigkeit
Die Maßgenauigkeit bezieht sich auf die Fähigkeit eines Werkstücks, die vorgegebenen Maße und Toleranzen einzuhalten. Insbesondere in der Fertigungsindustrie ist die Maßgenauigkeit von entscheidender Bedeutung, da sie die Funktionalität, Montage und Qualität der hergestellten Produkte beeinflusst.
Bei automatischen Schleif- und Poliermaschinen spielt die Maßgenauigkeit eine wichtige Rolle, da diese Maschinen dazu verwendet werden, Werkstücke auf die gewünschten Abmessungen und Oberflächenbeschaffenheiten zu bringen. Durch präzise Steuerung und Überwachung der Schleif- und Polierprozesse können automatische Maschinen eine hohe Maßgenauigkeit sicherstellen.
Die Maßgenauigkeit wird durch verschiedene Faktoren beeinflusst, darunter die Genauigkeit der Maschinenbewegungen, die Qualität der Schleif- und Polierwerkzeuge, die Stabilität der Werkstückbefestigung und die Kontrolle der Prozessparameter. Durch die Optimierung dieser Faktoren können Unternehmen die Maßgenauigkeit ihrer Produkte verbessern und die Anforderungen ihrer Kunden erfüllen.
Moderne automatische Schleif- und Poliermaschinen sind oft mit hochpräzisen Positionierungssystemen und CNC-Steuerungen ausgestattet, die eine präzise Steuerung der Bearbeitungsprozesse ermöglichen. Dadurch können auch komplexe Formen und Profile mit engen Toleranzen bearbeitet werden, um die Anforderungen anspruchsvoller Anwendungen zu erfüllen.
Insgesamt ist die Maßgenauigkeit ein wesentlicher Qualitätsfaktor in der Fertigungsindustrie, der mit automatischen Schleif- und Poliermaschinen effizient und präzise kontrolliert werden kann. Durch die Einhaltung hoher Maßgenauigkeitsstandards können Unternehmen die Qualität ihrer Produkte gewährleisten und das Vertrauen ihrer Kunden gewinnen.
Staubabsaugung
Die Staubabsaugung ist ein entscheidendes Merkmal von automatischen Schleif- und Poliermaschinen, das dazu dient, Staub und Schleifabrieb während des Bearbeitungsprozesses zu erfassen und abzuführen. Sie trägt zur Sicherheit der Arbeitsumgebung bei, verhindert die Verschmutzung der Luft und sorgt für eine saubere und gesunde Arbeitsumgebung für Bediener und Maschinen.
Automatische Schleif- und Poliermaschinen erzeugen während des Betriebs erhebliche Mengen an Staub und Schleifabrieb, insbesondere wenn abrasive Materialien wie Korund oder Siliziumkarbid verwendet werden. Ohne eine angemessene Staubabsaugung können sich diese Partikel in der Luft und auf den Arbeitsflächen ablagern, was zu Gesundheitsrisiken für Bediener führen und die Lebensdauer der Maschinen beeinträchtigen kann.
Die Staubabsaugung bei Schleif- und Poliermaschinen erfolgt in der Regel mithilfe von Absaugvorrichtungen, die direkt an den Bearbeitungsbereich angeschlossen sind. Diese Vorrichtungen erfassen den entstehenden Staub und Schleifabrieb und leiten ihn über Schläuche oder Kanäle zu einem zentralen Staubabscheider oder Filter, wo er gesammelt und entfernt wird.
Eine effektive Staubabsaugung trägt nicht nur zur Sicherheit der Arbeitsumgebung bei, sondern kann auch die Qualität der bearbeiteten Teile verbessern, indem sie verhindert, dass Staub und Schleifabrieb auf die Oberfläche der Werkstücke gelangen und sie verunreinigen. Darüber hinaus trägt sie dazu bei, die Wartungsintervalle der Maschinen zu verlängern und ihre Lebensdauer zu erhöhen, indem sie die Ablagerung von Staub und Schleifabrieb in den Mechanismen und Komponenten der Maschinen minimiert.
Insgesamt ist die Staubabsaugung ein unverzichtbares Merkmal von automatischen Schleif- und Poliermaschinen, das dazu beiträgt, eine sichere, saubere und gesunde Arbeitsumgebung zu gewährleisten und die Leistungsfähigkeit und Zuverlässigkeit der Maschinen zu maximieren.
Werkstückspannung
Die Werkstückspannung bezieht sich auf die Art und Weise, wie ein Werkstück während des Schleif- oder Polierprozesses in der Maschine fixiert wird, um eine stabile und sichere Bearbeitung zu gewährleisten. Eine effektive Werkstückspannung ist entscheidend, um Verformungen, Vibrationen oder Bewegungen während des Bearbeitungsvorgangs zu vermeiden, was zu einer verbesserten Oberflächenqualität und Maßgenauigkeit führt.
Für automatische Schleif- und Poliermaschinen können verschiedene Spannvorrichtungen und -systeme verwendet werden, um Werkstücke sicher zu fixieren. Dazu gehören Klemmvorrichtungen, Spannbacken, Magnetspannplatten, Vakuumspannsysteme und spezielle Spannsysteme, die für spezifische Werkstückformen oder -materialien entwickelt wurden.
Die Auswahl der geeigneten Werkstückspannung hängt von verschiedenen Faktoren ab, einschließlich der Größe, Form und Material des Werkstücks sowie der spezifischen Anforderungen des Bearbeitungsprozesses. Die Spannung muss ausreichend sein, um das Werkstück sicher zu halten, aber gleichzeitig so schonend wie möglich, um Beschädigungen oder Verformungen zu vermeiden.
Eine präzise Werkstückspannung ist besonders wichtig bei der Bearbeitung von empfindlichen oder dünnen Werkstücken, bei denen selbst geringfügige Verformungen zu Qualitätsproblemen führen können. In solchen Fällen können spezielle Spannvorrichtungen oder -systeme verwendet werden, die eine gleichmäßige und schonende Spannung auf das Werkstück ausüben.
Insgesamt ist die Werkstückspannung ein wesentlicher Aspekt bei der Bearbeitung von Werkstücken mit automatischen Schleif- und Poliermaschinen. Durch eine effektive Werkstückspannung können Unternehmen die Qualität ihrer Produkte verbessern, die Produktivität steigern und die Zuverlässigkeit ihrer Fertigungsprozesse erhöhen.
Kühlschmierung
Die Kühlschmierung ist ein wichtiges Element in automatischen Schleif- und Poliermaschinen, das dazu dient, die Temperatur während des Bearbeitungsprozesses zu kontrollieren und die Bildung von Wärme zu reduzieren. Sie besteht aus einem Kühlschmittel, das in den Bearbeitungsbereich der Maschine eingesprüht oder gepumpt wird, um die Reibung zwischen dem Werkstück und dem Schleif- oder Polierwerkzeug zu verringern.
Die Kühlschmierung erfüllt mehrere wichtige Funktionen. Sie hilft dabei, die Bildung von Wärme zu reduzieren, die während des Schleif- oder Poliervorgangs entsteht, was wiederum die Lebensdauer der Schleif- und Polierwerkzeuge verlängert und die Gefahr von Werkstückverformungen oder -beschädigungen verringert. Darüber hinaus trägt die Kühlschmierung zur Verbesserung der Oberflächenqualität bei, indem sie die Bildung von Grat oder Anlauffarben verhindert und ein glatteres Finish ermöglicht.
Es gibt verschiedene Arten von Kühlschmiermitteln, darunter wasserbasierte Emulsionen, Öle, synthetische Schmiermittel und Luftnebelkühlsysteme. Die Auswahl des geeigneten Kühlschmiermittels hängt von verschiedenen Faktoren ab, einschließlich der Art des zu bearbeitenden Materials, der Bearbeitungsgeschwindigkeit und der spezifischen Anforderungen des Bearbeitungsprozesses.
Die effektive Anwendung der Kühlschmierung erfordert eine präzise Steuerung und Dosierung des Kühlschmiermittels, um sicherzustellen, dass die richtige Menge an Schmierung aufgetragen wird, um die gewünschten Effekte zu erzielen, ohne die Maschine oder das Werkstück zu überfluten. Moderne automatische Schleif- und Poliermaschinen verfügen oft über integrierte Kühlschmierungssysteme, die eine präzise Steuerung und Überwachung ermöglichen.
Insgesamt ist die Kühlschmierung ein wesentlicher Bestandteil automatischer Schleif- und Poliermaschinen, der dazu beiträgt, die Leistungsfähigkeit, Qualität und Zuverlässigkeit der Bearbeitungsprozesse zu verbessern. Durch die richtige Anwendung von Kühlschmiermitteln können Unternehmen die Lebensdauer ihrer Maschinen maximieren und hochwertige Produkte mit konsistenter Oberflächenqualität herstellen.
Kontur
Die Kontur bezieht sich auf die äußere Form oder Gestalt eines Werkstücks, insbesondere auf die genaue Linie oder den Verlauf seiner äußeren Umrisse. In der Fertigungsindustrie ist die Kontur ein wichtiger Aspekt, der die Funktion, Ästhetik und Passform eines Produkts beeinflusst.
Automatische Schleif- und Poliermaschinen spielen eine entscheidende Rolle bei der Bearbeitung der Kontur von Werkstücken. Durch präzise Steuerung und Bewegung der Schleif- oder Polierwerkzeuge können sie die gewünschte Kontur auf das Werkstück übertragen und dabei Unregelmäßigkeiten oder Unebenheiten entfernen.
Die Konturbearbeitung erfordert oft komplexe Bewegungsmuster und spezielle Werkzeuge, um die gewünschten Formen und Profile zu erzielen. Moderne automatische Schleif- und Poliermaschinen sind mit fortschrittlichen CNC-Steuerungen und Positionierungssystemen ausgestattet, die eine präzise Konturbearbeitung ermöglichen und komplexe Formen und Profile mit hoher Genauigkeit reproduzieren können.
Die Konturbearbeitung ist in verschiedenen Branchen und Anwendungen von Bedeutung, darunter die Automobilindustrie, Luft- und Raumfahrt, Formenbau, Möbelherstellung und Schmuckherstellung. Eine präzise Konturbearbeitung ist oft entscheidend für die Funktionalität und Ästhetik eines Produkts sowie für die Einhaltung von Toleranzen und Spezifikationen.
Insgesamt ist die Konturbearbeitung ein wesentlicher Aspekt in der Fertigungsindustrie, der mit automatischen Schleif- und Poliermaschinen effizient und präzise durchgeführt werden kann. Durch die präzise Steuerung der Bearbeitungsprozesse können Unternehmen hochwertige Produkte herstellen, die den Anforderungen ihrer Kunden gerecht werden und ihre Wettbewerbsfähigkeit auf dem Markt stärken.
Kraftmessung
Die Kraftmessung ist ein wichtiger Aspekt in automatischen Schleif- und Poliermaschinen, der dazu dient, die auf das Werkstück ausgeübten Kräfte während des Bearbeitungsprozesses zu überwachen und zu kontrollieren. Durch die Messung und Regelung der Kräfte können Unternehmen die Qualität, Präzision und Effizienz ihrer Bearbeitungsprozesse verbessern.
In automatischen Schleif- und Poliermaschinen werden verschiedene Arten von Kräften gemessen, darunter Schleifkraft, Polierkraft und Vorschubkraft. Die Schleif- und Polierkräfte beeinflussen direkt die Materialabtragung und die Oberflächenqualität des Werkstücks, während die Vorschubkraft die Geschwindigkeit und Genauigkeit des Bearbeitungsprozesses beeinflusst.
Durch die kontinuierliche Überwachung und Anpassung der Bearbeitungskräfte können Unternehmen sicherstellen, dass die gewünschten Bearbeitungsergebnisse erzielt werden und gleichzeitig die Lebensdauer der Werkzeuge und die Zuverlässigkeit der Maschinen maximiert werden. Eine zu hohe Kraft kann zu übermäßigem Materialabtrag, Werkstückbeschädigungen oder vorzeitigem Verschleiß der Werkzeuge führen, während eine zu geringe Kraft zu unzureichender Bearbeitung und schlechter Oberflächenqualität führen kann.
Moderne automatische Schleif- und Poliermaschinen sind oft mit integrierten Kraftmesssystemen und Feedback-Regelungssystemen ausgestattet, die eine präzise Steuerung der Bearbeitungskräfte ermöglichen. Diese Systeme können in Echtzeit die auf das Werkstück ausgeübten Kräfte messen, überwachen und anpassen, um optimale Bearbeitungsergebnisse zu erzielen.
Insgesamt ist die Kraftmessung ein wesentlicher Aspekt in automatischen Schleif- und Poliermaschinen, der dazu beiträgt, die Qualität, Präzision und Effizienz der Bearbeitungsprozesse zu verbessern. Durch die präzise Steuerung der Bearbeitungskräfte können Unternehmen hochwertige Produkte herstellen, die den Anforderungen ihrer Kunden gerecht werden und ihre Wettbewerbsfähigkeit auf dem Markt stärken.
Bürsten
Bürsten sind wichtige Werkzeuge in automatischen Schleif- und Poliermaschinen, die verwendet werden, um Oberflächen zu reinigen, zu polieren oder zu strukturieren. Sie bestehen aus Borsten oder Drahtbürsten, die an einem rotierenden oder oszillierenden Kopf befestigt sind und verschiedene Oberflächenbearbeitungen ermöglichen.
In automatischen Schleif- und Poliermaschinen werden Bürsten für verschiedene Anwendungen eingesetzt, darunter das Entfernen von Oxidschichten, das Entgraten von Werkstücken, das Entfernen von Schmutz und Verunreinigungen, das Strukturieren von Oberflächen und das Polieren von Materialien wie Metall, Holz, Kunststoff und Verbundwerkstoffen.
Es gibt verschiedene Arten von Bürsten, die für spezifische Anwendungen optimiert sind. Drahtbürsten werden beispielsweise häufig für das Entgraten und Reinigen von Metallwerkstücken verwendet, während Nylonbürsten für das Polieren und Strukturieren von empfindlicheren Materialien wie Holz oder Kunststoff eingesetzt werden können.
Die Auswahl der geeigneten Bürste hängt von verschiedenen Faktoren ab, einschließlich des zu bearbeitenden Materials, der gewünschten Oberflächenbeschaffenheit und der spezifischen Anforderungen des Bearbeitungsprozesses. Moderne automatische Schleif- und Poliermaschinen sind oft mit verschiedenen Bürstenköpfen und -optionen ausgestattet, um eine Vielzahl von Oberflächenbearbeitungen durchzuführen.
Insgesamt sind Bürsten vielseitige Werkzeuge, die in automatischen Schleif- und Poliermaschinen eingesetzt werden, um Oberflächen präzise und effizient zu bearbeiten. Durch die Auswahl der richtigen Bürste und die optimale Konfiguration der Maschine können Unternehmen hochwertige Produkte herstellen und ihre Fertigungsprozesse optimieren.
Prozessoptimierung
Die Prozessoptimierung bezieht sich auf den kontinuierlichen Verbesserungsprozess, bei dem die Effizienz, Qualität und Leistung von Fertigungsprozessen maximiert werden, um die Produktivität zu steigern und die Kosten zu senken. In automatischen Schleif- und Poliermaschinen spielt die Prozessoptimierung eine entscheidende Rolle, um die Leistungsfähigkeit der Maschinen voll auszuschöpfen und hochwertige Produkte mit minimalen Ressourcen zu produzieren.
Die Prozessoptimierung umfasst verschiedene Aspekte, darunter die Analyse und Bewertung der bestehenden Fertigungsprozesse, die Identifizierung von Verbesserungspotenzialen, die Implementierung von Optimierungsmaßnahmen und die kontinuierliche Überwachung und Anpassung der Prozesse. Dies kann die Optimierung von Maschineneinstellungen, die Verwendung von effizienteren Werkzeugen oder Materialien, die Anpassung von Arbeitsabläufen oder die Integration neuer Technologien umfassen.
Durch die Prozessoptimierung können Unternehmen eine Vielzahl von Vorteilen erzielen, darunter eine höhere Produktivität, eine verbesserte Produktqualität, eine Reduzierung der Durchlaufzeiten, eine Senkung der Produktionskosten und eine Steigerung der Wettbewerbsfähigkeit auf dem Markt. Darüber hinaus kann die Prozessoptimierung dazu beitragen, die Umweltbelastung zu reduzieren und die Nachhaltigkeit der Fertigungsprozesse zu verbessern.
Moderne automatische Schleif- und Poliermaschinen bieten eine Vielzahl von Möglichkeiten zur Prozessoptimierung, einschließlich automatisierter Steuerungen, integrierter Überwachungssysteme, adaptiver Regelungstechniken und fortschrittlicher Datenanalyse. Durch die Nutzung dieser Funktionen können Unternehmen ihre Fertigungsprozesse kontinuierlich verbessern und ihre betriebliche Effizienz steigern.
Insgesamt ist die Prozessoptimierung ein wesentlicher Bestandteil des Fertigungsmanagements, der dazu beiträgt, die Leistungsfähigkeit und Wettbewerbsfähigkeit von Unternehmen zu steigern. Durch die kontinuierliche Suche nach Verbesserungsmöglichkeiten können Unternehmen ihre Fertigungsprozesse optimieren und sich langfristig erfolgreich am Markt positionieren.
Rotationsgeschwindigkeit
Die Rotationsgeschwindigkeit bezieht sich auf die Geschwindigkeit, mit der sich die Schleif- oder Polierwerkzeuge in automatischen Schleif- und Poliermaschinen drehen. Diese Geschwindigkeit beeinflusst direkt die Effizienz, Qualität und Genauigkeit des Bearbeitungsprozesses.
Die richtige Rotationsgeschwindigkeit hängt von verschiedenen Faktoren ab, darunter die Art des zu bearbeitenden Materials, die Art des Schleif- oder Polierwerkzeugs, die gewünschte Oberflächenqualität und die spezifischen Anforderungen des Bearbeitungsprozesses. Eine zu hohe Rotationsgeschwindigkeit kann zu übermäßigem Materialabtrag, erhöhter Wärmeentwicklung und vorzeitigem Verschleiß der Werkzeuge führen, während eine zu niedrige Rotationsgeschwindigkeit zu unzureichender Bearbeitung und schlechter Oberflächenqualität führen kann.
Moderne automatische Schleif- und Poliermaschinen sind oft mit variablen Drehzahlsteuerungen ausgestattet, die es ermöglichen, die Rotationsgeschwindigkeit der Werkzeuge präzise einzustellen und anzupassen. Dadurch können Unternehmen die Rotationsgeschwindigkeit entsprechend den Anforderungen der spezifischen Bearbeitungsaufgaben optimieren und die gewünschten Bearbeitungsergebnisse erzielen.
Die Rotationsgeschwindigkeit ist ein wichtiger Parameter, der bei der Programmierung und Einrichtung automatischer Schleif- und Poliermaschinen berücksichtigt werden muss. Durch die richtige Einstellung und Kontrolle der Rotationsgeschwindigkeit können Unternehmen die Effizienz, Qualität und Genauigkeit ihrer Bearbeitungsprozesse verbessern und hochwertige Produkte herstellen, die den Anforderungen ihrer Kunden gerecht werden.
Vibrationen
Vibrationen sind unerwünschte mechanische Schwingungen, die während des Betriebs von automatischen Schleif- und Poliermaschinen auftreten können. Sie können verschiedene Ursachen haben und haben potenziell negative Auswirkungen auf die Bearbeitungsqualität, die Maschinenlebensdauer und die Sicherheit am Arbeitsplatz.
Ursachen für Vibrationen in Schleif- und Poliermaschinen können unebene Oberflächen, Ungleichgewichte bei rotierenden Komponenten, Lockerheit von Befestigungen, ungleichmäßige Materialeinwirkung oder sogar strukturelle Probleme der Maschine selbst sein. Diese Vibrationen können dazu führen, dass Werkstücke ungleichmäßig bearbeitet werden, Werkzeuge vorzeitig verschleißen, die Oberflächenqualität beeinträchtigt wird und im schlimmsten Fall die Sicherheit der Bediener gefährdet ist.
Um Vibrationen in automatischen Schleif- und Poliermaschinen zu minimieren, können verschiedene Maßnahmen ergriffen werden. Dazu gehören die regelmäßige Wartung und Inspektion der Maschinen, das Auswuchten rotierender Komponenten, die Verwendung von hochwertigen Werkzeugen und Materialien, die richtige Ausrichtung und Befestigung der Werkstücke sowie die Anpassung der Bearbeitungsparameter, um eine gleichmäßige Materialabtragung zu gewährleisten.
Moderne automatische Schleif- und Poliermaschinen sind oft mit Vibrationssensoren und Überwachungssystemen ausgestattet, die dazu beitragen können, Vibrationen frühzeitig zu erkennen und zu minimieren. Durch die kontinuierliche Überwachung und Anpassung der Maschinenparameter können Unternehmen die Vibrationen auf ein Minimum reduzieren und die Effizienz, Qualität und Zuverlässigkeit ihrer Bearbeitungsprozesse verbessern.
Insgesamt ist die Minimierung von Vibrationen ein wichtiger Aspekt bei der Betriebsführung von automatischen Schleif- und Poliermaschinen, der dazu beiträgt, hochwertige Produkte herzustellen, die den Anforderungen der Kunden entsprechen, und die Sicherheit am Arbeitsplatz zu gewährleisten.
Kontrollsysteme
Kontrollsysteme sind entscheidende Komponenten in automatischen Schleif- und Poliermaschinen, die dazu dienen, den Bearbeitungsprozess zu überwachen, zu steuern und zu optimieren. Sie umfassen eine Vielzahl von Sensoren, Steuerungen, Software und Schnittstellen, die zusammenarbeiten, um eine präzise und effiziente Bearbeitung zu gewährleisten.
Diese Kontrollsysteme überwachen typischerweise verschiedene Parameter wie Drehzahl, Vorschubgeschwindigkeit, Bearbeitungskräfte, Temperatur, Werkstückposition und andere relevante Variablen. Sie erfassen kontinuierlich Daten während des Bearbeitungsprozesses und passen die Maschinenparameter entsprechend an, um die gewünschten Bearbeitungsergebnisse zu erzielen.
Durch die Implementierung fortschrittlicher Kontrollsysteme können Unternehmen die Produktivität steigern, die Bearbeitungsqualität verbessern, die Maschinenleistung optimieren und die Betriebskosten senken. Moderne automatische Schleif- und Poliermaschinen sind oft mit integrierten CNC-Steuerungen, adaptiven Regelungssystemen, Echtzeitüberwachungsfunktionen und Datenanalysetools ausgestattet, die eine präzise Steuerung und Optimierung des Bearbeitungsprozesses ermöglichen.
Die Entwicklung und Implementierung von leistungsfähigen Kontrollsystemen erfordert eine enge Zusammenarbeit zwischen Ingenieuren, Programmierern und Fertigungsexperten. Sie müssen sicherstellen, dass die Kontrollsysteme die spezifischen Anforderungen der jeweiligen Anwendung erfüllen und eine nahtlose Integration in den Fertigungsprozess ermöglichen.
Insgesamt sind Kontrollsysteme ein wesentlicher Bestandteil automatischer Schleif- und Poliermaschinen, der dazu beiträgt, die Effizienz, Qualität und Zuverlässigkeit der Bearbeitungsprozesse zu verbessern. Durch die Nutzung moderner Kontrolltechnologien können Unternehmen ihre Wettbewerbsfähigkeit stärken und ihre Position in der Fertigungsindustrie festigen.
Abtragsleistung
Die Abtragsleistung bezieht sich auf die Fähigkeit einer automatischen Schleif- oder Poliermaschine, Material von der Oberfläche eines Werkstücks zu entfernen. Sie ist ein wichtiger Leistungsindikator, der die Effizienz und Geschwindigkeit des Bearbeitungsprozesses bestimmt.
Eine hohe Abtragsleistung ermöglicht es, Werkstücke schnell und effizient zu bearbeiten, was die Produktionsgeschwindigkeit erhöht und die Durchlaufzeiten verkürzt. Dies ist besonders wichtig in der Fertigungsindustrie, wo die Produktivität ein entscheidender Faktor für den wirtschaftlichen Erfolg eines Unternehmens ist.
Die Abtragsleistung einer automatischen Schleif- oder Poliermaschine hängt von verschiedenen Faktoren ab, darunter die Art des Schleif- oder Polierwerkzeugs, die Drehzahl, der Vorschubgeschwindigkeit, der Materialtyp und die Bearbeitungsparameter. Durch die Optimierung dieser Parameter können Unternehmen die Abtragsleistung maximieren und eine hohe Produktivität erreichen.
Moderne automatische Schleif- und Poliermaschinen sind oft mit leistungsstarken Motoren, hochwertigen Schleif- und Polierwerkzeugen und fortschrittlichen Steuerungssystemen ausgestattet, die eine hohe Abtragsleistung ermöglichen. Darüber hinaus können verschiedene Bearbeitungstechniken wie Hochgeschwindigkeitsschleifen oder Hochdruckwasserstrahlschleifen eingesetzt werden, um die Abtragsleistung weiter zu verbessern.
Die Optimierung der Abtragsleistung ist ein wichtiger Aspekt bei der Betriebsführung automatischer Schleif- und Poliermaschinen, der dazu beiträgt, die Produktivität zu steigern und die Wettbewerbsfähigkeit zu stärken. Durch die Maximierung der Abtragsleistung können Unternehmen hochwertige Produkte herstellen und ihre Kundenanforderungen effizient erfüllen.
Bahnsteuerung
Die Bahnsteuerung ist ein wesentlicher Bestandteil von automatischen Schleif- und Poliermaschinen, der für die präzise Bewegung der Werkzeuge entlang vordefinierter Bahnen oder Pfaden verantwortlich ist. Diese Steuerung ermöglicht es, komplexe Bearbeitungsaufgaben auszuführen und hochpräzise Oberflächen zu erzeugen.
In automatischen Schleif- und Poliermaschinen werden Bahnsteuerungen verwendet, um die Bewegung der Schleif- oder Polierwerkzeuge in mehreren Achsen zu koordinieren, einschließlich X-, Y- und Z-Achsen sowie möglicherweise zusätzlicher Rotationsachsen. Diese Bewegungen können entweder linear oder interpoliert erfolgen, je nach den Anforderungen der Bearbeitungsaufgabe.
Die Bahnsteuerung ermöglicht es, komplexe Formen, Profile und Oberflächenstrukturen präzise und effizient zu bearbeiten. Durch die Programmierung von spezifischen Bahnen können automatische Schleif- und Poliermaschinen Werkstücke mit hoher Genauigkeit und Reproduzierbarkeit bearbeiten, was zu einer verbesserten Qualität und Konsistenz der bearbeiteten Teile führt.
Moderne automatische Schleif- und Poliermaschinen sind oft mit CNC-Steuerungen ausgestattet, die eine präzise und flexible Bahnsteuerung ermöglichen. Diese Steuerungen können komplexe Bewegungsmuster und Bearbeitungsstrategien programmieren und ausführen, um die Anforderungen einer Vielzahl von Anwendungen zu erfüllen.
Die Bahnsteuerung spielt eine entscheidende Rolle bei der Optimierung der Bearbeitungsprozesse und der Maximierung der Effizienz automatischer Schleif- und Poliermaschinen. Durch die präzise Steuerung der Werkzeugbewegungen können Unternehmen hochwertige Produkte herstellen und ihre Fertigungsprozesse optimieren.
Robotergesteuerte Bewegungen
Robotergesteuerte Bewegungen sind ein entscheidender Aspekt von automatischen Schleif- und Poliermaschinen, die die Bewegungen von Robotern zur präzisen Bearbeitung von Werkstücken steuern. Diese Bewegungen ermöglichen eine vielseitige und effiziente Bearbeitung von Werkstücken verschiedener Formen und Größen.
In automatischen Schleif- und Poliermaschinen werden robotergesteuerte Bewegungen eingesetzt, um Schleif- oder Polierwerkzeuge entlang vordefinierter Bahnen oder Pfade zu führen. Roboterarme können mit verschiedenen Werkzeugen ausgestattet werden, um eine Vielzahl von Bearbeitungsaufgaben durchzuführen, einschließlich Schleifen, Polieren, Bürsten und Entgraten.
Die Verwendung von Robotern ermöglicht eine hohe Flexibilität und Anpassungsfähigkeit in automatischen Schleif- und Polierprozessen. Roboter können schnell zwischen verschiedenen Werkzeugen und Bearbeitungsaufgaben wechseln und komplexe Bewegungsmuster ausführen, um unterschiedliche Oberflächenstrukturen und -profile zu erzeugen.
Durch die Integration von robotergesteuerten Bewegungen können automatische Schleif- und Poliermaschinen eine höhere Produktivität, eine verbesserte Bearbeitungsqualität und eine größere Vielseitigkeit erreichen. Roboter können kontinuierlich arbeiten, ohne Ermüdung oder Fehler zu erleiden, und bieten eine präzise und konsistente Bearbeitung von Werkstücken.
Die Programmierung und Steuerung von robotergesteuerten Bewegungen erfordert spezielle Kenntnisse und Fähigkeiten im Bereich der Robotik und Automatisierungstechnik. Moderne automatische Schleif- und Poliermaschinen sind oft mit leistungsfähigen Robotersystemen und intuitiven Programmierschnittstellen ausgestattet, die eine einfache Integration und Bedienung ermöglichen.
Insgesamt bieten robotergesteuerte Bewegungen eine effektive Möglichkeit, die Leistungsfähigkeit und Vielseitigkeit automatischer Schleif- und Poliermaschinen zu verbessern. Durch die Nutzung dieser Technologie können Unternehmen ihre Fertigungsprozesse optimieren und ihre Wettbewerbsfähigkeit auf dem Markt stärken.
Energieeffizienz
Die Energieeffizienz ist ein wichtiger Aspekt bei automatischen Schleif- und Poliermaschinen, der sich auf die Fähigkeit der Maschinen bezieht, Energie effizient zu nutzen und den Energieverbrauch zu minimieren. Eine hohe Energieeffizienz trägt dazu bei, die Betriebskosten zu senken, die Umweltbelastung zu reduzieren und die Nachhaltigkeit der Fertigungsprozesse zu verbessern.
Um die Energieeffizienz zu maximieren, können verschiedene Maßnahmen ergriffen werden, darunter die Verwendung von energieeffizienten Motoren und Antrieben, die Optimierung der Maschinensteuerung und -regelung, die Reduzierung von Leerlaufzeiten und Standby-Verbräuchen, sowie die Implementierung von Energierückgewinnungssystemen.
Moderne automatische Schleif- und Poliermaschinen sind oft mit energieeffizienten Komponenten und Systemen ausgestattet, die dazu beitragen, den Energieverbrauch zu minimieren. Dies kann die Verwendung von Frequenzumrichtern zur Steuerung der Motordrehzahl, die Integration von Energierückgewinnungssystemen zur Wärmerückgewinnung oder die Implementierung von Automatisierungstechnologien zur Optimierung des Energieverbrauchs umfassen.
Die Verbesserung der Energieeffizienz in automatischen Schleif- und Poliermaschinen bietet eine Vielzahl von Vorteilen, darunter eine Senkung der Betriebskosten, eine Reduzierung der Umweltbelastung und eine Verbesserung der Unternehmensbilanz. Darüber hinaus kann eine hohe Energieeffizienz dazu beitragen, staatliche Vorschriften und Umweltstandards einzuhalten und das Image des Unternehmens als umweltbewusster Hersteller zu stärken.
Insgesamt ist die Energieeffizienz ein wichtiger Aspekt bei der Gestaltung und dem Betrieb automatischer Schleif- und Poliermaschinen, der dazu beiträgt, die Wirtschaftlichkeit, Umweltverträglichkeit und Nachhaltigkeit der Fertigungsprozesse zu verbessern. Durch die Implementierung energieeffizienter Lösungen können Unternehmen ihre Wettbewerbsfähigkeit steigern und langfristig erfolgreich sein.
Werkstückbefestigung
Die Werkstückbefestigung ist ein kritischer Aspekt bei automatischen Schleif- und Poliermaschinen, der die stabile und sichere Fixierung des Werkstücks während des Bearbeitungsprozesses gewährleistet. Eine effektive Werkstückbefestigung ist entscheidend für die Präzision, Qualität und Sicherheit des Bearbeitungsvorgangs.
Es gibt verschiedene Methoden zur Werkstückbefestigung, einschließlich Spannvorrichtungen, Magnethalterungen, Vakuumtische, Schraubvorrichtungen und spezielle Werkstückträger. Die Auswahl der geeigneten Befestigungsmethode hängt von verschiedenen Faktoren ab, darunter die Größe und Form des Werkstücks, die Bearbeitungsanforderungen und die Maschinenkonfiguration.
Eine stabile Werkstückbefestigung ermöglicht eine präzise Bearbeitung und verhindert unerwünschte Vibrationen oder Bewegungen während des Bearbeitungsprozesses. Dies ist besonders wichtig bei der Bearbeitung von empfindlichen Materialien oder bei Anwendungen, die hohe Toleranzen erfordern.
Moderne automatische Schleif- und Poliermaschinen sind oft mit speziellen Befestigungssystemen und Vorrichtungen ausgestattet, die eine schnelle und einfache Werkstückbefestigung ermöglichen. Diese Systeme können eine hohe Wiederholgenauigkeit und Zuverlässigkeit bieten und gleichzeitig eine optimale Zugänglichkeit für die Bearbeitung ermöglichen.
Die richtige Werkstückbefestigung erfordert sorgfältige Planung und Berücksichtigung der spezifischen Anforderungen der jeweiligen Anwendung. Durch die Auswahl und Implementierung geeigneter Befestigungslösungen können Unternehmen die Effizienz, Qualität und Sicherheit ihrer Bearbeitungsprozesse verbessern und hochwertige Produkte herstellen.
Staubabsaugung
Die Staubabsaugung ist ein unverzichtbares Merkmal in automatischen Schleif- und Poliermaschinen, das dazu dient, Staub und Schadstoffe während des Bearbeitungsprozesses effektiv zu entfernen. Sie trägt zur Verbesserung der Luftqualität am Arbeitsplatz, zur Sicherheit der Bediener und zur Erhaltung der Maschinenleistung bei.
Während des Schleif- und Polierprozesses entstehen feine Staubpartikel, die gesundheitsschädlich sein können, wenn sie eingeatmet werden. Eine effiziente Staubabsaugung entfernt diese Partikel aus der Luft und minimiert das Risiko von Atemwegserkrankungen und anderen gesundheitlichen Problemen bei den Bedienern.
Darüber hinaus trägt eine wirksame Staubabsaugung zur Verbesserung der Sichtbarkeit und zur Reduzierung von Verschmutzungen in der Arbeitsumgebung bei. Dies kann die Sicherheit am Arbeitsplatz erhöhen und die Notwendigkeit von Reinigungsarbeiten verringern, was zu einer höheren Produktivität führt.
Moderne automatische Schleif- und Poliermaschinen sind oft mit leistungsstarken Staubabsaugungssystemen ausgestattet, die speziell für die Erfassung von Staub und Schadstoffen während des Bearbeitungsprozesses entwickelt wurden. Diese Systeme können verschiedene Absaugvorrichtungen und -düsen umfassen, die eine effiziente Absaugung von Staub an der Quelle ermöglichen.
Die regelmäßige Wartung und Reinigung der Staubabsaugungssysteme ist entscheidend, um eine optimale Leistung zu gewährleisten und die Sicherheit am Arbeitsplatz zu erhalten. Durch die Implementierung wirksamer Staubabsaugungssysteme können Unternehmen die Gesundheit und Sicherheit ihrer Mitarbeiter schützen und die Produktivität ihrer Fertigungsprozesse verbessern.
Automatisierung
Die Automatisierung ist ein grundlegendes Merkmal von automatischen Schleif- und Poliermaschinen, das die Reduzierung menschlicher Eingriffe in den Bearbeitungsprozess ermöglicht. Sie umfasst die Integration von Robotern, CNC-Steuerungen, Sensorik, Software und anderen automatisierten Systemen, um die Effizienz, Präzision und Zuverlässigkeit der Bearbeitung zu verbessern.
Durch die Automatisierung können Unternehmen die Produktivität steigern, die Betriebskosten senken und die Qualität ihrer Produkte verbessern. Automatische Schleif- und Poliermaschinen können kontinuierlich und gleichmäßig arbeiten, ohne Ermüdung oder menschliche Fehler zu erleiden, was zu konsistenten und hochwertigen Bearbeitungsergebnissen führt.
Die Automatisierung ermöglicht es auch, komplexe Bearbeitungsaufgaben effizienter und präziser durchzuführen. Durch die Integration von Robotern und CNC-Steuerungen können automatische Schleif- und Poliermaschinen komplexe Bewegungsmuster und Bearbeitungsstrategien ausführen, um verschiedene Oberflächenstrukturen und -profile zu erzeugen.
Darüber hinaus trägt die Automatisierung zur Verbesserung der Sicherheit am Arbeitsplatz bei, da weniger direkter Kontakt zwischen den Bedienern und den Bearbeitungswerkzeugen erforderlich ist. Dies reduziert das Risiko von Unfällen und Verletzungen und schafft eine sicherere Arbeitsumgebung.
Insgesamt ermöglicht die Automatisierung eine effizientere, präzisere und sicherere Bearbeitung von Werkstücken in automatischen Schleif- und Poliermaschinen. Durch die Nutzung dieser Technologie können Unternehmen ihre Wettbewerbsfähigkeit stärken und ihre Position in der Fertigungsindustrie festigen.
Kühlungssysteme
Kühlungssysteme sind entscheidend für automatische Schleif- und Poliermaschinen, um die Temperaturen während des Bearbeitungsprozesses zu kontrollieren und zu regulieren. Diese Systeme dienen dazu, die Wärme abzuführen, die durch die Reibung zwischen Werkzeug und Werkstück entsteht, und tragen zur Vermeidung von Überhitzung bei, die die Werkzeuglebensdauer und die Bearbeitungsqualität beeinträchtigen kann.
Es gibt verschiedene Arten von Kühlungssystemen, die in automatischen Schleif- und Poliermaschinen eingesetzt werden, darunter Luftkühlung, Flüssigkeitskühlung und Kombinationen aus beiden. Luftkühlungssysteme verwenden Luftströme, um die Wärme abzuführen, während Flüssigkeitskühlungssysteme Kühlflüssigkeiten wie Wasser oder Kühlschmierstoffe verwenden, um die Temperatur zu regulieren.
Die Auswahl des geeigneten Kühlungssystems hängt von verschiedenen Faktoren ab, darunter die Art des Bearbeitungsmaterials, die Bearbeitungsgeschwindigkeit, die Umgebungstemperatur und die spezifischen Anforderungen des Bearbeitungsprozesses. Moderne automatische Schleif- und Poliermaschinen sind oft mit leistungsstarken Kühlungssystemen ausgestattet, die eine effiziente Wärmeableitung und -regulierung ermöglichen.
Eine effektive Kühlung trägt dazu bei, die Lebensdauer der Werkzeuge zu verlängern, die Bearbeitungsqualität zu verbessern und die Produktivität zu steigern, indem die Notwendigkeit von Pausen zur Werkzeugabkühlung reduziert wird. Darüber hinaus kann eine präzise Temperaturregelung dazu beitragen, Verformungen oder Beschädigungen der Werkstücke zu verhindern und die Oberflächenqualität zu erhalten.
Insgesamt spielen Kühlungssysteme eine wichtige Rolle bei der Aufrechterhaltung der Leistungsfähigkeit und Zuverlässigkeit automatischer Schleif- und Poliermaschinen. Durch die Nutzung von hochwertigen Kühlungssystemen können Unternehmen die Effizienz ihrer Bearbeitungsprozesse maximieren und hochwertige Produkte mit gleichbleibender Qualität herstellen.
Schleifscheiben
Schleifscheiben sind zentrale Werkzeuge in automatischen Schleif- und Poliermaschinen, die für die Bearbeitung von Werkstücken verwendet werden. Sie bestehen aus abrasiven Materialien wie Diamant, Siliziumkarbid oder Aluminiumoxid und werden auf rotierenden oder oszillierenden Spindeln montiert, um Material von der Oberfläche des Werkstücks abzutragen.
Es gibt verschiedene Arten von Schleifscheiben, die für unterschiedliche Anwendungen optimiert sind. Flachschleifscheiben werden beispielsweise für die Bearbeitung von flachen Oberflächen verwendet, während Tellerschleifscheiben für das Entgraten und Abfasen von Kanten geeignet sind. Darüber hinaus gibt es auch Spezialscheiben für spezifische Materialien oder Bearbeitungsaufgaben.
Die Auswahl der geeigneten Schleifscheibe hängt von verschiedenen Faktoren ab, darunter die Art des zu bearbeitenden Materials, die gewünschte Oberflächenqualität und die spezifischen Anforderungen des Bearbeitungsprozesses. Moderne automatische Schleif- und Poliermaschinen sind oft mit verschiedenen Schleifscheiben und Werkzeugwechslern ausgestattet, um eine Vielzahl von Bearbeitungsaufgaben durchzuführen.
Die richtige Auswahl und Wartung der Schleifscheiben ist entscheidend für die Effizienz und Qualität des Bearbeitungsprozesses. Abgenutzte oder beschädigte Schleifscheiben können zu ungleichmäßigen Bearbeitungsergebnissen, erhöhtem Verschleiß der Werkstücke und reduzierter Maschinenleistung führen.
Insgesamt sind Schleifscheiben wesentliche Werkzeuge in automatischen Schleif- und Poliermaschinen, die es ermöglichen, Werkstücke präzise und effizient zu bearbeiten. Durch die Auswahl hochwertiger Schleifscheiben und die richtige Pflege können Unternehmen die Leistungsfähigkeit ihrer Maschinen maximieren und hochwertige Produkte herstellen.
Polierscheiben
Polierscheiben sind entscheidende Werkzeuge in automatischen Schleif- und Poliermaschinen, die für die Feinbearbeitung von Werkstücken verwendet werden. Im Gegensatz zu Schleifscheiben bestehen Polierscheiben oft aus weicheren Materialien wie Filz, Stoff, Schaumstoff oder Kunststoff und sind mit Polierpasten oder -mitteln beschichtet, um eine glatte Oberfläche zu erzeugen.
Es gibt verschiedene Arten von Polierscheiben, die für unterschiedliche Anwendungen optimiert sind. Tuchpolierscheiben eignen sich beispielsweise für das Polieren von Metallen, während Schaumstoffpolierscheiben für empfindliche Oberflächen wie Lacke oder Kunststoffe verwendet werden können. Darüber hinaus gibt es auch spezielle Polierscheiben für Hochglanzpolituren, Entgraten oder Oberflächenveredelungen.
Die Auswahl der geeigneten Polierscheibe hängt von verschiedenen Faktoren ab, darunter die Art des zu bearbeitenden Materials, die gewünschte Oberflächenqualität und die spezifischen Anforderungen des Polierprozesses. Moderne automatische Schleif- und Poliermaschinen sind oft mit verschiedenen Polierscheiben und Poliermittelsystemen ausgestattet, um eine Vielzahl von Polieraufgaben durchzuführen.
Die richtige Auswahl und Pflege der Polierscheiben ist entscheidend für die Qualität und Konsistenz des Polierprozesses. Abgenutzte oder verschmutzte Polierscheiben können zu ungleichmäßigen Polierergebnissen, Kratzern oder Beschädigungen der Werkstückoberfläche führen.
Insgesamt sind Polierscheiben wichtige Werkzeuge in automatischen Schleif- und Poliermaschinen, die es ermöglichen, Werkstücke auf hochglänzende Oberflächen zu polieren. Durch die Auswahl hochwertiger Polierscheiben und die richtige Pflege können Unternehmen die Qualität ihrer polierten Produkte verbessern und die Kundenzufriedenheit steigern.
Diamantschleifscheiben
Diamantschleifscheiben sind hochspezialisierte Werkzeuge in automatischen Schleif- und Poliermaschinen, die für die Bearbeitung von harten Materialien wie Hartmetall, Keramik, Glas und Stein verwendet werden. Sie zeichnen sich durch ihre hohe Härte und Abriebfestigkeit aus, die eine präzise und effiziente Bearbeitung ermöglichen.
Im Gegensatz zu herkömmlichen Schleifscheiben bestehen Diamantschleifscheiben aus einer Schicht aus synthetischen Diamanten oder Diamantpartikeln, die in eine Bindematrix aus Metall oder Kunstharz eingebettet sind. Diese Diamantpartikel tragen das Material ab, während die Bindematrix die Diamanten stabilisiert und eine gleichmäßige Abtragung gewährleistet.
Diamantschleifscheiben bieten eine Vielzahl von Vorteilen gegenüber herkömmlichen Schleifscheiben, darunter eine längere Lebensdauer, eine höhere Abtragsleistung, eine verbesserte Oberflächengüte und eine geringere Wärmeentwicklung während des Bearbeitungsprozesses. Sie sind besonders geeignet für Anwendungen, die hohe Präzision und Oberflächenqualität erfordern.
Die Auswahl der geeigneten Diamantschleifscheibe hängt von verschiedenen Faktoren ab, darunter die Art des zu bearbeitenden Materials, die gewünschte Oberflächengüte und die spezifischen Anforderungen des Bearbeitungsprozesses. Moderne automatische Schleif- und Poliermaschinen sind oft mit einer Vielzahl von Diamantschleifscheiben und Werkzeugwechslern ausgestattet, um eine effiziente Bearbeitung verschiedener Materialien zu ermöglichen.
Insgesamt sind Diamantschleifscheiben hochspezialisierte Werkzeuge in automatischen Schleif- und Poliermaschinen, die es ermöglichen, harte Materialien präzise und effizient zu bearbeiten. Durch die Auswahl hochwertiger Diamantschleifscheiben können Unternehmen die Leistungsfähigkeit ihrer Maschinen maximieren und hochwertige Produkte herstellen.
Wasserstrahlschneiden
Wasserstrahlschneiden ist eine Bearbeitungstechnik, die in automatischen Schleif- und Poliermaschinen eingesetzt werden kann, um Materialien präzise zu schneiden oder zu formen. Diese Technik nutzt einen Hochdruckwasserstrahl, der mit abrasiven Partikeln wie feinem Sand oder Granat kombiniert werden kann, um Materialien zu durchtrennen oder zu bearbeiten.
Der Wasserstrahl wird mit extrem hohem Druck durch eine düse geleitet und auf das Werkstück gerichtet, um Schnitte oder Konturen gemäß den vorgegebenen CAD-Dateien auszuführen. Die Abrasivmittel im Wasserstrahl ermöglichen eine effiziente Bearbeitung von harten Materialien wie Metall, Stein, Glas, Keramik und Verbundwerkstoffen.
Eine der Hauptvorteile des Wasserstrahlschneidens ist die hohe Präzision und die Möglichkeit, komplexe Formen und Konturen ohne thermische Beeinträchtigung zu schneiden. Da der Schneidprozess kalt erfolgt, entstehen keine Wärmeeinflüsse oder Verformungen am Werkstück, was die Qualität der Schnitte verbessert.
Darüber hinaus ist das Wasserstrahlschneiden eine umweltfreundliche Bearbeitungstechnik, da kein schädlicher Staub oder Rauch entsteht und keine Chemikalien verwendet werden. Dies macht es besonders attraktiv für Anwendungen, bei denen eine saubere und umweltfreundliche Bearbeitung erforderlich ist.
Moderne automatische Schleif- und Poliermaschinen können oft mit Wasserstrahlschneideköpfen ausgestattet werden, um zusätzliche Bearbeitungsfunktionen anzubieten und die Vielseitigkeit der Maschinen zu erhöhen. Durch die Integration des Wasserstrahlschneidens können Unternehmen ihre Fertigungskapazitäten erweitern und eine breite Palette von Materialien bearbeiten, um die Anforderungen ihrer Kunden zu erfüllen.
3D-Druck
3D-Druck, auch als additive Fertigung bekannt, ist eine innovative Technologie, die auch in automatischen Schleif- und Poliermaschinen Anwendung findet. Diese Technik ermöglicht es, dreidimensionale Objekte schichtweise aufzubauen, indem Materialien wie Kunststoffe, Metalle, Keramiken oder Verbundwerkstoffe schichtweise aufgetragen und miteinander verbunden werden.
In automatischen Schleif- und Poliermaschinen kann der 3D-Druck zur Herstellung von Vorrichtungen, Werkzeugen, Prototypen und sogar Endprodukten verwendet werden. Durch den Einsatz von 3D-Druck können komplexe geometrische Formen und Strukturen hergestellt werden, die mit herkömmlichen Fertigungsmethoden schwer oder unmöglich zu erreichen wären.
Eine der Hauptvorteile des 3D-Drucks ist die hohe Flexibilität und Anpassungsfähigkeit bei der Fertigung. Da die Bauteile direkt aus digitalen 3D-Modellen hergestellt werden, können Änderungen schnell und kostengünstig umgesetzt werden, ohne dass teure Werkzeugänderungen erforderlich sind.
Darüber hinaus ermöglicht der 3D-Druck die Herstellung von maßgeschneiderten oder individualisierten Produkten, die den spezifischen Anforderungen der Kunden entsprechen. Dies ist besonders nützlich in Branchen wie der Medizintechnik, Luft- und Raumfahrt oder Automobilindustrie, wo kundenspezifische Lösungen gefragt sind.
Automatische Schleif- und Poliermaschinen können mit integrierten 3D-Druckmodulen ausgestattet werden, um eine nahtlose Integration von additiven Fertigungsprozessen in den Fertigungsablauf zu ermöglichen. Dadurch können Unternehmen ihre Fertigungskapazitäten erweitern und innovative Produkte schneller und effizienter auf den Markt bringen.
Insgesamt bietet der 3D-Druck eine Vielzahl von Möglichkeiten zur Optimierung und Erweiterung der Fertigung in automatischen Schleif- und Poliermaschinen. Durch den Einsatz dieser Technologie können Unternehmen ihre Wettbewerbsfähigkeit stärken und ihre Position in der Fertigungsindustrie festigen.
Qualitätskontrolle
Die Qualitätskontrolle ist ein entscheidender Schritt in automatischen Schleif- und Polierprozessen, der sicherstellt, dass die hergestellten Teile die erforderlichen Spezifikationen und Qualitätsstandards erfüllen. Dieser Prozess beinhaltet die Überwachung und Bewertung verschiedener Parameter und Merkmale der bearbeiteten Werkstücke, um sicherzustellen, dass sie den Qualitätsanforderungen entsprechen.
In automatischen Schleif- und Poliermaschinen können verschiedene Methoden zur Qualitätskontrolle eingesetzt werden, darunter manuelle Inspektionen durch geschulte Bediener, automatisierte Messsysteme, optische Inspektionssysteme, berührungslose Sensoren und bildgebende Verfahren wie Computertomographie oder Röntgenprüfung.
Die Qualitätskontrolle umfasst die Bewertung verschiedener Aspekte der bearbeiteten Werkstücke, einschließlich Dimensionen, Oberflächenbeschaffenheit, Oberflächengüte, Maßgenauigkeit, Formgenauigkeit, Oberflächenrauheit und geometrischer Toleranzen. Diese Parameter werden mit den vorgegebenen Spezifikationen und Qualitätsstandards verglichen, um festzustellen, ob die Teile akzeptabel sind oder nicht.
Eine effektive Qualitätskontrolle ist entscheidend, um die Produktqualität zu gewährleisten, Ausschussraten zu minimieren und die Kundenzufriedenheit sicherzustellen. Durch die frühzeitige Erkennung von Qualitätsproblemen können Fehler behoben und teure Nacharbeiten vermieden werden, was zu einer verbesserten Effizienz und Rentabilität der Fertigungsprozesse führt.
Moderne automatische Schleif- und Poliermaschinen sind oft mit integrierten Qualitätskontrollsystemen und -sensorik ausgestattet, die eine kontinuierliche Überwachung und Bewertung der Bearbeitungsergebnisse ermöglichen. Diese Systeme können Echtzeitdaten liefern und automatische Rückkopplungsschleifen initiieren, um die Prozessparameter entsprechend anzupassen und die Qualität der hergestellten Teile zu optimieren.
Insgesamt ist die Qualitätskontrolle ein unverzichtbarer Bestandteil der Fertigung in automatischen Schleif- und Poliermaschinen, der dazu beiträgt, die Produktqualität zu verbessern, Ausschuss zu minimieren und die Wettbewerbsfähigkeit des Unternehmens zu stärken. Durch die Implementierung effektiver Qualitätskontrollprozesse können Unternehmen hochwertige Produkte herstellen und die Erwartungen ihrer Kunden erfüllen.
Schleifkraftüberwachung
Die Schleifkraftüberwachung ist ein wichtiges Merkmal in automatischen Schleif- und Poliermaschinen, das dazu dient, die Schleifkräfte während des Bearbeitungsprozesses zu überwachen und zu steuern. Dies ermöglicht eine präzise und zuverlässige Bearbeitung von Werkstücken und trägt zur Verbesserung der Bearbeitungsqualität sowie zur Vermeidung von Werkzeugverschleiß und Beschädigungen bei.
Die Schleifkräfte können je nach verschiedenen Faktoren wie Werkstückmaterial, Werkzeugtyp, Bearbeitungsgeschwindigkeit und -bedingungen variieren. Eine unzureichende oder übermäßige Schleifkraft kann zu unerwünschten Ergebnissen wie Oberflächenfehlern, Werkzeugbruch oder Überlastung der Maschine führen.
Durch die Überwachung der Schleifkräfte in Echtzeit können automatische Schleif- und Poliermaschinen die Bearbeitungsparameter entsprechend anpassen, um die Schleifkräfte innerhalb eines optimalen Bereichs zu halten. Dies kann durch die automatische Anpassung von Vorschubgeschwindigkeit, Werkzeugdruck, Drehzahl oder anderen Prozessparametern erfolgen.
Moderne automatische Schleif- und Poliermaschinen sind oft mit eingebauten Sensoren oder Kraftmesssystemen ausgestattet, die die Schleifkräfte während des Bearbeitungsprozesses kontinuierlich überwachen und aufzeichnen. Diese Daten können verwendet werden, um die Bearbeitungsqualität zu verbessern, Werkzeugverschleiß zu minimieren und die Lebensdauer der Maschine zu verlängern.
Die Schleifkraftüberwachung trägt zur Optimierung der Bearbeitungsprozesse bei, indem sie eine präzise Steuerung der Schleifkräfte ermöglicht und die Qualität und Zuverlässigkeit der hergestellten Teile verbessert. Durch die Implementierung dieser Funktion können Unternehmen die Effizienz ihrer Fertigungsprozesse steigern und die Wettbewerbsfähigkeit auf dem Markt stärken.
Werkzeugwechselsystem
Das Werkzeugwechselsystem ist ein wesentliches Merkmal in automatischen Schleif- und Poliermaschinen, das eine schnelle und effiziente Umrüstung zwischen verschiedenen Schleif- und Polierwerkzeugen ermöglicht. Es ermöglicht den nahtlosen Übergang zwischen unterschiedlichen Bearbeitungsaufgaben und -anwendungen, was die Flexibilität und Produktivität der Maschinen erhöht.
Durch das Werkzeugwechselsystem können verschiedene Schleif- und Polierwerkzeuge, wie Schleifscheiben, Polierscheiben oder Bürsten, automatisch ausgetauscht werden, um unterschiedliche Materialien, Formen oder Oberflächenstrukturen zu bearbeiten. Dies reduziert die Stillstandszeiten und Umrüstzeiten zwischen den Bearbeitungsaufgaben und ermöglicht eine kontinuierliche Produktion ohne Unterbrechungen.
Es gibt verschiedene Arten von Werkzeugwechselsystemen, darunter manuelle, halbautomatische und vollautomatische Systeme. Manuelle Systeme erfordern menschliche Intervention, um die Werkzeuge zu wechseln, während halbautomatische Systeme eine teilweise automatisierte Unterstützung bieten, beispielsweise durch das Bereitstellen der Werkzeuge an einer zugänglichen Position. Vollautomatische Systeme ermöglichen einen vollständig automatisierten Werkzeugwechsel ohne menschliches Eingreifen.
Moderne automatische Schleif- und Poliermaschinen sind oft mit hochentwickelten vollautomatischen Werkzeugwechselsystemen ausgestattet, die eine schnelle und präzise Umrüstung zwischen einer Vielzahl von Werkzeugen ermöglichen. Diese Systeme können mit Roboterarmen, Werkzeugmagazinen und speziellen Greifern ausgestattet sein, die die Werkzeuge sicher und zuverlässig handhaben.
Das Werkzeugwechselsystem trägt zur Steigerung der Produktivität, Flexibilität und Effizienz automatischer Schleif- und Poliermaschinen bei, indem es die Umrüstzeiten minimiert und die Maschinenleistung optimiert. Durch die Implementierung dieser Funktion können Unternehmen ihre Fertigungskapazitäten erweitern und eine breitere Palette von Bearbeitungsaufgaben bewältigen.
Prozessoptimierung
Die Prozessoptimierung ist ein entscheidender Aspekt in automatischen Schleif- und Poliermaschinen, der darauf abzielt, die Effizienz, Qualität und Rentabilität der Bearbeitungsprozesse zu maximieren. Sie umfasst die kontinuierliche Verbesserung und Anpassung der Bearbeitungsparameter, Werkzeuge, Materialien und Abläufe, um die bestmöglichen Ergebnisse zu erzielen.
Durch die Prozessoptimierung können verschiedene Aspekte der Fertigung verbessert werden, darunter die Bearbeitungsgeschwindigkeit, Oberflächenqualität, Werkzeugstandzeit, Ausschussraten, Energieeffizienz und Ressourcennutzung. Dies erfolgt oft durch die Analyse von Prozessdaten, Leistungsindikatoren und Rückmeldungen aus dem Betrieb.
Automatische Schleif- und Poliermaschinen bieten verschiedene Möglichkeiten zur Prozessoptimierung, einschließlich der Anpassung von Bearbeitungsparametern wie Vorschubgeschwindigkeit, Werkzeugdruck, Drehzahl, Kühlung, Werkzeugwechselzeiten und mehr. Durch die Feinabstimmung dieser Parameter können Unternehmen die Leistungsfähigkeit ihrer Maschinen maximieren und die Bearbeitungsergebnisse optimieren.
Darüber hinaus können fortgeschrittene Analysetechniken wie maschinelles Lernen oder künstliche Intelligenz eingesetzt werden, um Muster, Trends und Zusammenhänge in den Prozessdaten zu erkennen und automatisch Optimierungsvorschläge zu generieren. Diese intelligenten Systeme können kontinuierlich lernen und sich an verändernde Betriebsbedingungen anpassen, um eine optimale Leistung zu gewährleisten.
Die Prozessoptimierung ist ein kontinuierlicher und iterativer Prozess, der eine enge Zusammenarbeit zwischen Maschinenbedienern, Ingenieuren, Fertigungsspezialisten und anderen relevanten Stakeholdern erfordert. Durch die Implementierung von effektiven Prozessoptimierungsstrategien können Unternehmen ihre Fertigungsprozesse optimieren, die Produktivität steigern und ihre Wettbewerbsfähigkeit stärken.
Energieeffizienz
Die Energieeffizienz ist ein wichtiges Anliegen in automatischen Schleif- und Poliermaschinen, das darauf abzielt, den Energieverbrauch während des Betriebs zu minimieren und Ressourcen zu schonen. Eine verbesserte Energieeffizienz kann dazu beitragen, Betriebskosten zu senken, Umweltauswirkungen zu reduzieren und die Nachhaltigkeit der Fertigungsprozesse zu verbessern.
Es gibt verschiedene Möglichkeiten, die Energieeffizienz in automatischen Schleif- und Poliermaschinen zu verbessern. Dazu gehören die Optimierung von Antriebssystemen und Motoren, die Verwendung von energieeffizienten Kühlungs- und Absaugsystemen, die Minimierung von Leerlaufzeiten, die Implementierung von intelligenten Steuerungssystemen und die Nutzung von regenerativen Energietechnologien.
Eine effiziente Nutzung von Energie kann auch durch die Auswahl von hochwertigen Komponenten, die Wartung und Instandhaltung der Maschinen und die Schulung der Bediener erreicht werden. Durch die Überwachung und Analyse des Energieverbrauchs können Unternehmen Potenziale zur Verbesserung identifizieren und gezielte Maßnahmen zur Reduzierung des Energieverbrauchs umsetzen.
Darüber hinaus können Unternehmen durch die Integration von Energieeffizienzstrategien in ihre Fertigungsprozesse von staatlichen Anreizen, Förderprogrammen und Zertifizierungen profitieren. Eine verbesserte Energieeffizienz kann auch das Image eines Unternehmens verbessern und seine Wettbewerbsfähigkeit auf dem Markt stärken.
Insgesamt ist die Verbesserung der Energieeffizienz ein wichtiger Schritt zur Förderung einer nachhaltigen Entwicklung und zur Reduzierung der Umweltauswirkungen von automatischen Schleif- und Poliermaschinen. Durch die Implementierung von energieeffizienten Technologien und Praktiken können Unternehmen nicht nur Kosten senken, sondern auch ihren ökologischen Fußabdruck minimieren und ihre langfristige Rentabilität sichern.
Betriebssicherheit
Die Betriebssicherheit ist von entscheidender Bedeutung für automatische Schleif- und Poliermaschinen, um Unfälle zu vermeiden, die Sicherheit der Bediener zu gewährleisten und die Einhaltung der gesetzlichen Vorschriften zu garantieren. Eine robuste Sicherheitsstruktur und entsprechende Sicherheitsmaßnahmen sind daher unerlässlich, um einen sicheren Betrieb der Maschinen zu gewährleisten.
Zu den Sicherheitsmerkmalen gehören unter anderem Not-Aus-Schalter, Sicherheitsabdeckungen, Schutzvorrichtungen, Sicherheitssensoren und Warnsysteme. Diese Vorkehrungen dienen dazu, potenzielle Gefahrenquellen zu erkennen und zu minimieren, wie zum Beispiel das Einklemmen von Fingern oder Gegenständen, den Kontakt mit beweglichen Teilen, das Auftreten von Funken oder heißen Oberflächen.
Darüber hinaus erfordert die Betriebssicherheit eine angemessene Schulung der Bediener, um sie über potenzielle Risiken zu informieren, sichere Arbeitspraktiken zu vermitteln und den richtigen Umgang mit den Maschinen zu gewährleisten. Schulungsprogramme sollten regelmäßig aktualisiert und überprüft werden, um sicherzustellen, dass die Bediener mit den neuesten Sicherheitsstandards vertraut sind.
Die Einhaltung von Sicherheitsvorschriften und -standards ist ein weiterer wichtiger Aspekt der Betriebssicherheit. Automatische Schleif- und Poliermaschinen müssen den geltenden Normen und Richtlinien entsprechen, wie zum Beispiel der Maschinenrichtlinie, der Arbeitsschutzverordnung und anderen branchenspezifischen Vorschriften.
Eine regelmäßige Wartung und Instandhaltung der Maschinen ist ebenfalls entscheidend für die Betriebssicherheit. Durch die Überprüfung und Instandsetzung von Verschleißteilen, das Schmieren beweglicher Teile und das Überwachen der Maschinenleistung können potenzielle Sicherheitsrisiken minimiert und die Lebensdauer der Maschinen verlängert werden.
Insgesamt ist die Betriebssicherheit ein unverzichtbarer Bestandteil des Betriebs von automatischen Schleif- und Poliermaschinen, der dazu beiträgt, Unfälle zu verhindern, die Gesundheit der Mitarbeiter zu schützen und die Produktivität der Fertigungsprozesse zu gewährleisten. Durch die Implementierung geeigneter Sicherheitsmaßnahmen und -verfahren können Unternehmen eine sichere Arbeitsumgebung schaffen und ihr Engagement für den Arbeitsschutz unterstreichen.
Automatisierung
Die Automatisierung ist ein grundlegendes Konzept in automatischen Schleif- und Poliermaschinen, das darauf abzielt, menschliche Arbeitskraft durch mechanische oder elektronische Systeme zu ersetzen oder zu ergänzen. Dies ermöglicht eine effizientere und präzisere Bearbeitung von Werkstücken sowie eine Reduzierung von Arbeitskosten und menschlichen Fehlern.
In automatischen Schleif- und Poliermaschinen kann die Automatisierung verschiedene Formen annehmen, einschließlich automatischer Werkzeugwechselsysteme, CNC-Steuerungen, robotergestützter Bearbeitung, automatischer Materialzuführung und -entladung, sowie Integration von Sensorik und Überwachungssystemen.
Durch die Automatisierung können Arbeitsprozesse beschleunigt, die Produktivität gesteigert und die Durchlaufzeiten reduziert werden. Darüber hinaus ermöglicht die Automatisierung eine konsistente und zuverlässige Bearbeitungsqualität, da menschliche Fehler minimiert werden und die Prozesse kontinuierlich überwacht und gesteuert werden können.
Moderne automatische Schleif- und Poliermaschinen sind oft mit fortschrittlichen Automatisierungstechnologien ausgestattet, die eine nahtlose Integration von verschiedenen Bearbeitungsschritten und -prozessen ermöglichen. Dies verbessert nicht nur die Effizienz der Maschinen, sondern erhöht auch ihre Vielseitigkeit und Anpassungsfähigkeit an unterschiedliche Fertigungsanforderungen.
Die Automatisierung spielt eine entscheidende Rolle bei der Steigerung der Wettbewerbsfähigkeit von Unternehmen in der Fertigungsindustrie, indem sie die Produktionskosten senkt, die Qualität verbessert und die Kapazitäten für eine schnellere Markteinführung von Produkten erweitert. Durch die Implementierung von Automatisierungslösungen können Unternehmen ihre Fertigungskapazitäten erweitern und ihre Position im Markt stärken.
Retrofitting
Retrofitting ist ein wichtiger Prozess in automatischen Schleif- und Poliermaschinen, der darauf abzielt, ältere oder vorhandene Maschinen mit neuen Technologien, Komponenten oder Funktionen auszustatten, um ihre Leistungsfähigkeit zu verbessern und ihre Lebensdauer zu verlängern. Dies ermöglicht es Unternehmen, ihre bestehenden Anlagen auf den neuesten Stand der Technik zu bringen, ohne komplett neue Maschinen anschaffen zu müssen.
Beim Retrofitting können verschiedene Komponenten oder Systeme einer Maschine aktualisiert oder modifiziert werden, darunter Steuerungssysteme, Antriebseinheiten, Werkzeugwechselsysteme, Sensorik, Sicherheitssysteme und mehr. Diese Upgrades können die Produktivität erhöhen, die Genauigkeit verbessern, die Betriebssicherheit erhöhen und die Einhaltung von Industriestandards gewährleisten.
Ein weiterer wichtiger Aspekt des Retrofitting ist die Integration neuer Technologien oder Funktionen, die die Leistungsfähigkeit der Maschinen erweitern und ihre Vielseitigkeit verbessern. Dies kann die Implementierung von CNC-Steuerungen, automatischen Werkzeugwechselsystemen, fortschrittlicher Sensorik, Überwachungs- und Diagnosesystemen, sowie die Anbindung an Industrie 4.0-Konzepte und das Internet der Dinge umfassen.
Retrofitting bietet Unternehmen eine kostengünstige Möglichkeit, vorhandene Anlagen auf den neuesten Stand zu bringen und die Effizienz ihrer Fertigungsprozesse zu steigern, ohne teure Neuanschaffungen tätigen zu müssen. Durch die gezielte Modernisierung und Anpassung der Maschinen können Unternehmen ihre Wettbewerbsfähigkeit stärken und ihre Fertigungskapazitäten optimieren.
Insgesamt ist Retrofitting ein wichtiger Aspekt in der Fertigungsindustrie, der es Unternehmen ermöglicht, den Wert ihrer bestehenden Anlagen zu erhalten und gleichzeitig von den Vorteilen neuer Technologien und Innovationen zu profitieren. Durch die gezielte Modernisierung und Anpassung können Unternehmen ihre Betriebsabläufe optimieren und ihre Rentabilität steigern.
Robotergestützte Automation
Robotergestützte Automation ist eine fortschrittliche Technologie, die in automatischen Schleif- und Poliermaschinen eingesetzt wird, um die Effizienz, Präzision und Flexibilität der Fertigungsprozesse zu steigern. Dabei werden Roboterarme oder Manipulatoren verwendet, um verschiedene Aufgaben wie Werkzeugwechsel, Materialhandling, Teilezuführung und Bearbeitung durchzuführen.
Durch den Einsatz von Robotern können automatische Schleif- und Poliermaschinen eine Vielzahl von Vorteilen bieten. Dazu gehören eine verbesserte Arbeitsgeschwindigkeit, eine erhöhte Präzision und Reproduzierbarkeit, eine Reduzierung von menschlichen Fehlern und Verletzungen sowie eine erhöhte Flexibilität bei der Bearbeitung unterschiedlicher Werkstücke.
Robotergestützte Automation ermöglicht es auch, komplexe Bearbeitungsaufgaben durchzuführen, die für herkömmliche automatische Maschinen schwer oder unmöglich zu bewältigen wären. Dies umfasst die Bearbeitung von schwer zugänglichen Bereichen, die Durchführung komplexer Konturen oder Geometrien und die Verarbeitung von unterschiedlichen Materialien.
Moderne Robotersysteme in automatischen Schleif- und Poliermaschinen sind oft mit fortgeschrittenen Sensoren, Bildverarbeitungssystemen und intelligenten Steuerungen ausgestattet, die eine präzise und zuverlässige Bearbeitung ermöglichen. Diese Systeme können auch mit anderen Automatisierungstechnologien wie CNC-Steuerungen, Werkzeugwechselsystemen und Sicherheitssystemen integriert werden.
Durch den Einsatz von robotergestützter Automation können Unternehmen ihre Fertigungseffizienz steigern, die Produktivität erhöhen und die Betriebskosten senken. Darüber hinaus ermöglicht es ihnen, auf veränderte Marktanforderungen und Kundenbedürfnisse flexibel zu reagieren und ihre Wettbewerbsfähigkeit zu stärken.
Insgesamt ist die robotergestützte Automation ein wichtiger Bestandteil moderner automatischer Schleif- und Poliermaschinen, der es Unternehmen ermöglicht, ihre Fertigungskapazitäten zu optimieren und ihre Wettbewerbsposition in der Fertigungsindustrie zu stärken.
Schleifbandwechsel
Der Schleifbandwechsel ist ein wesentlicher Aspekt in automatischen Schleifmaschinen, der darauf abzielt, das Schleifband, das für die Bearbeitung der Werkstücke verwendet wird, zu ersetzen. Dieser Prozess ist wichtig, um eine kontinuierliche und effiziente Bearbeitung sicherzustellen und die Qualität der bearbeiteten Oberflächen zu erhalten.
Der Schleifbandwechsel erfolgt in regelmäßigen Abständen, entweder aufgrund von Verschleiß des Schleifbands oder aufgrund der Notwendigkeit, auf ein Schleifband mit einer anderen Körnung oder Eigenschaft umzustellen. Der genaue Zeitpunkt des Wechsels hängt von verschiedenen Faktoren ab, darunter die Art des zu bearbeitenden Materials, die Bearbeitungsgeschwindigkeit und -bedingungen sowie die Qualität der bearbeiteten Oberfläche.
Der Schleifbandwechsel kann je nach Art der Schleifmaschine und des Schleifbands unterschiedlich sein. In einigen Fällen erfolgt der Wechsel manuell durch den Bediener, der das alte Schleifband entfernt und ein neues installiert. In anderen Fällen können automatische Schleifmaschinen mit integrierten Werkzeugwechselsystemen ausgestattet sein, die den Schleifbandwechsel automatisch durchführen.
Unabhängig von der Methode ist es wichtig, den Schleifbandwechsel sorgfältig und ordnungsgemäß durchzuführen, um Beschädigungen der Maschine oder der Werkstücke zu vermeiden. Dies umfasst das Überprüfen des Schleifbands auf etwaige Beschädigungen oder Verschleißerscheinungen, das richtige Spannen und Ausrichten des neuen Schleifbands sowie das Einhalten der Sicherheitsvorschriften während des gesamten Prozesses.
Ein effizienter Schleifbandwechsel trägt dazu bei, die Stillstandszeiten der Maschine zu minimieren und die Produktivität der Fertigungsprozesse zu maximieren. Durch die Implementierung geeigneter Wartungs- und Instandhaltungsmaßnahmen können Unternehmen sicherstellen, dass der Schleifbandwechsel reibungslos verläuft und die Qualität ihrer bearbeiteten Werkstücke gewährleistet ist.
Insgesamt ist der Schleifbandwechsel ein wichtiger Prozess in automatischen Schleifmaschinen, der dazu beiträgt, eine effiziente und zuverlässige Bearbeitung zu gewährleisten und die Leistungsfähigkeit der Maschinen zu optimieren.
Diamantwerkzeuge
Diamantwerkzeuge sind eine wichtige Komponente in automatischen Schleif- und Poliermaschinen, die für die Bearbeitung von harten Materialien wie Metallen, Keramiken, Glas und Stein verwendet werden. Sie bestehen aus Diamantpartikeln, die auf einer Trägerbasis wie Metall, Kunststoff oder Keramik befestigt sind und eine hohe Härte, Verschleißfestigkeit und Schneidleistung aufweisen.
In automatischen Schleif- und Poliermaschinen werden Diamantwerkzeuge für verschiedene Bearbeitungsaufgaben eingesetzt, darunter Schleifen, Polieren, Entgraten, Entgraten, Schärfen und Formen. Sie können in verschiedenen Formen und Ausführungen vorliegen, wie Schleifscheiben, Schleifstifte, Schleifbänder, Polierscheiben, Bohrer, Fräser und mehr.
Der Einsatz von Diamantwerkzeugen bietet eine Reihe von Vorteilen gegenüber herkömmlichen Werkzeugen aus Stahl oder anderen Materialien. Dazu gehören eine längere Lebensdauer, eine höhere Schneidleistung, eine verbesserte Oberflächenqualität, eine geringere Wärmeentwicklung und eine reduzierte Gefahr von Gratbildung oder Beschädigung der Werkstücke.
Diamantwerkzeuge sind besonders gut geeignet für die Bearbeitung von harten und spröden Materialien, die mit herkömmlichen Werkzeugen schwer zu bearbeiten sind. Sie werden häufig in Branchen wie der Luft- und Raumfahrt, der Automobilindustrie, der Elektronikfertigung, der Schmuckherstellung und der Baubranche eingesetzt.
Die Auswahl des richtigen Diamantwerkzeugs für eine bestimmte Anwendung erfordert eine sorgfältige Berücksichtigung verschiedener Faktoren wie Materialart, Bearbeitungsanforderungen, gewünschte Oberflächenqualität und Maschinenspezifikationen. Durch die richtige Auswahl und Anwendung von Diamantwerkzeugen können Unternehmen die Effizienz ihrer Bearbeitungsprozesse steigern und die Qualität ihrer hergestellten Teile verbessern.
Insgesamt sind Diamantwerkzeuge eine unverzichtbare Komponente in automatischen Schleif- und Poliermaschinen, die dazu beitragen, eine präzise, effiziente und zuverlässige Bearbeitung von Werkstücken zu ermöglichen. Ihre einzigartigen Eigenschaften machen sie zu einer bevorzugten Wahl für anspruchsvolle Bearbeitungsaufgaben in verschiedenen Branchen und Anwendungen.
- Automatisierung: Automatisierung ist der Prozess der Einführung von Technologien oder Systemen, die dazu dienen, Aufgaben oder Prozesse ohne menschliches Eingreifen auszuführen. In Bezug auf automatische Schleifmaschinen und Poliermaschinen bedeutet dies, dass diese Maschinen in der Lage sind, Schleif- und Polierprozesse selbstständig durchzuführen, ohne dass ständige Überwachung oder manuelle Eingriffe erforderlich sind.
- Schleifmaschinen: Schleifmaschinen sind industrielle Maschinen, die zum Schleifen von Werkstücken verwendet werden. Sie verwenden Schleifscheiben oder andere abrasive Materialien, um Material von einem Werkstück abzutragen und die Oberfläche zu glätten oder zu formen.
- Poliermaschinen: Poliermaschinen sind spezialisierte Maschinen, die dazu dienen, die Oberflächen von Werkstücken zu polieren. Sie verwenden Poliermittel und Rotationsbewegungen, um Oberflächen zu glätten, zu reinigen und ein glänzendes Finish zu erzielen.
- Präzision: Präzision bezieht sich auf die Genauigkeit und Konsistenz, mit der eine Maschine oder ein Prozess arbeitet. In Bezug auf automatische Schleifmaschinen und Poliermaschinen bedeutet Präzision, dass sie in der Lage sind, Werkstücke mit hoher Genauigkeit zu bearbeiten und wiederholbare Ergebnisse zu erzielen.
- Effizienz: Effizienz bezieht sich darauf, wie gut Ressourcen genutzt werden, um ein bestimmtes Ziel zu erreichen. Automatische Schleif- und Poliermaschinen sollen effizient arbeiten, indem sie Materialabtrag oder Polierprozesse schnell und mit minimalem Energieverbrauch durchführen.
- Produktivität: Produktivität bezieht sich auf die Menge an Output, die eine Maschine oder ein Prozess im Verhältnis zu den eingesetzten Ressourcen erzeugt. Automatische Schleif- und Poliermaschinen sollen die Produktivität steigern, indem sie Arbeitsabläufe beschleunigen und die Ausbringungsmenge erhöhen.
- CNC-Steuerung: CNC (Computerized Numerical Control) ist eine Technologie, die es Maschinen ermöglicht, über Computerprogramme gesteuert zu werden. CNC-Steuerung in Schleif- und Poliermaschinen bedeutet, dass diese Maschinen präzise und komplexe Bewegungen ausführen können, um Werkstücke entsprechend den programmierten Anweisungen zu bearbeiten.
- Schleifprozess: Der Schleifprozess bezeichnet den Vorgang des Abtragens von Material von der Oberfläche eines Werkstücks, um sie zu glätten, zu formen oder andere gewünschte Eigenschaften zu erreichen. Automatische Schleifmaschinen führen diesen Prozess automatisiert durch.
- Oberflächenfinish: Das Oberflächenfinish bezieht sich auf die Beschaffenheit und das Aussehen der Oberfläche eines Werkstücks nach dem Schleifen oder Polieren. Eine automatische Poliermaschine kann ein glänzendes, gleichmäßiges Finish auf Werkstücken erzeugen.
- Bearbeitungsgenauigkeit: Die Bearbeitungsgenauigkeit bezeichnet die Fähigkeit einer Maschine, Werkstücke mit hoher Präzision und Genauigkeit zu bearbeiten. Automatische Schleifmaschinen und Poliermaschinen sind darauf ausgelegt, eine präzise Bearbeitungsgenauigkeit zu erreichen.
- Materialabtrag: Materialabtrag bezieht sich auf die Menge an Material, die während des Schleifprozesses von der Oberfläche eines Werkstücks entfernt wird. Automatische Schleifmaschinen können den Materialabtrag genau steuern und kontrollieren.
- Werkstücke: Werkstücke sind die Teile oder Komponenten, die durch Schleif- und Poliermaschinen bearbeitet werden. Sie können aus verschiedenen Materialien wie Metall, Holz, Kunststoff oder Glas bestehen.
- Hochleistungsschleifen: Hochleistungsschleifen bezeichnet den Einsatz von Schleifmaschinen, die in der Lage sind, große Mengen Material schnell und effizient zu entfernen. Diese Maschinen sind oft für industrielle Anwendungen mit hohen Produktionsanforderungen konzipiert.
- Automatische Zuführung: Automatische Zuführung bezieht sich auf den Prozess, bei dem Werkstücke automatisch in die Schleif- oder Poliermaschine eingebracht werden. Dies kann durch verschiedene Zuführsysteme wie Förderbänder, Roboterarme oder Vorschubeinheiten erfolgen.
- Roboterintegration: Roboterintegration bezieht sich auf die Einbindung von Robotern in den Betrieb von Schleif- und Poliermaschinen. Roboter können dazu verwendet werden, Werkstücke zu handhaben, Zuführungen durchzuführen, Werkzeugwechsel zu vollziehen und andere Aufgaben auszuführen, um den Automatisierungsgrad zu erhöhen.
- Automatisierung: Automatisierung ist der Prozess der Einführung von Technologien oder Systemen, die dazu dienen, Aufgaben oder Prozesse ohne menschliches Eingreifen auszuführen. In Bezug auf automatische Schleifmaschinen und Poliermaschinen bedeutet dies, dass diese Maschinen in der Lage sind, Schleif- und Polierprozesse selbstständig durchzuführen, ohne dass ständige Überwachung oder manuelle Eingriffe erforderlich sind. Automatisierung ermöglicht eine erhöhte Effizienz, Konsistenz und Produktivität in der Fertigung und trägt dazu bei, die Betriebskosten zu senken.
- Schleifmaschinen: Schleifmaschinen sind industrielle Maschinen, die zum Schleifen von Werkstücken verwendet werden. Sie verwenden Schleifscheiben oder andere abrasive Materialien, um Material von einem Werkstück abzutragen und die Oberfläche zu glätten oder zu formen. Schleifmaschinen kommen in einer Vielzahl von Branchen zum Einsatz, darunter Metallverarbeitung, Holzbearbeitung, Glasbearbeitung und mehr. Sie können manuell bedient oder vollständig automatisiert sein, je nach den Anforderungen der Anwendung.
- Poliermaschinen: Poliermaschinen sind spezialisierte Maschinen, die dazu dienen, die Oberflächen von Werkstücken zu polieren. Sie verwenden Poliermittel und Rotationsbewegungen, um Oberflächen zu glätten, zu reinigen und ein glänzendes Finish zu erzielen. Poliermaschinen sind besonders in der Schmuckherstellung, Automobilindustrie, Uhrenherstellung und anderen Branchen gefragt, in denen hochwertige Oberflächen erforderlich sind.
- Präzision: Präzision bezieht sich auf die Genauigkeit und Konsistenz, mit der eine Maschine oder ein Prozess arbeitet. In Bezug auf automatische Schleifmaschinen und Poliermaschinen bedeutet Präzision, dass sie in der Lage sind, Werkstücke mit hoher Genauigkeit zu bearbeiten und wiederholbare Ergebnisse zu erzielen. Präzise Schleifen und Polieren sind entscheidend für die Herstellung von Teilen mit engen Toleranzen und qualitativ hochwertigen Oberflächen.
- Effizienz: Effizienz bezieht sich darauf, wie gut Ressourcen genutzt werden, um ein bestimmtes Ziel zu erreichen. Automatische Schleif- und Poliermaschinen sollen effizient arbeiten, indem sie Materialabtrag oder Polierprozesse schnell und mit minimalem Energieverbrauch durchführen. Durch die Automatisierung können Unternehmen ihre Produktionszeiten verkürzen, den Ausschuss reduzieren und die Gesamtleistung ihrer Fertigungsprozesse verbessern.
- Produktivität: Produktivität bezieht sich auf die Menge an Output, die eine Maschine oder ein Prozess im Verhältnis zu den eingesetzten Ressourcen erzeugt. Automatische Schleif- und Poliermaschinen sollen die Produktivität steigern, indem sie Arbeitsabläufe beschleunigen und die Ausbringungsmenge erhöhen. Durch die Automatisierung können Unternehmen ihre Produktionskapazität maximieren und wettbewerbsfähig bleiben.
- CNC-Steuerung: CNC (Computerized Numerical Control) ist eine Technologie, die es Maschinen ermöglicht, über Computerprogramme gesteuert zu werden. CNC-Steuerung in Schleif- und Poliermaschinen bedeutet, dass diese Maschinen präzise und komplexe Bewegungen ausführen können, um Werkstücke entsprechend den programmierten Anweisungen zu bearbeiten. CNC-Steuerung bietet eine hohe Flexibilität und ermöglicht es, verschiedene Bearbeitungsaufgaben mit nur einer Maschine durchzuführen.
- Schleifprozess: Der Schleifprozess bezeichnet den Vorgang des Abtragens von Material von der Oberfläche eines Werkstücks, um sie zu glätten, zu formen oder andere gewünschte Eigenschaften zu erreichen. Automatische Schleifmaschinen führen diesen Prozess automatisiert durch. Dabei können verschiedene Schleifverfahren und Schleifscheiben zum Einsatz kommen, um unterschiedliche Oberflächenstrukturen und Toleranzen zu erzielen.
- Oberflächenfinish: Das Oberflächenfinish bezieht sich auf die Beschaffenheit und das Aussehen der Oberfläche eines Werkstücks nach dem Schleifen oder Polieren. Eine automatische Poliermaschine kann ein glänzendes, gleichmäßiges Finish auf Werkstücken erzeugen. Das Oberflächenfinish ist entscheidend für die Ästhetik, Funktion und Haltbarkeit von Produkten und spielt eine wichtige Rolle in vielen Branchen, einschließlich der Fertigung von Präzisionskomponenten, Schmuck, Automobilteilen und mehr.
- Bearbeitungsgenauigkeit: Die Bearbeitungsgenauigkeit bezeichnet die Fähigkeit einer Maschine, Werkstücke mit hoher Präzision und Genauigkeit zu bearbeiten. Automatische Schleifmaschinen und Poliermaschinen sind darauf ausgelegt, eine präzise Bearbeitungsgenauigkeit zu erreichen. Dies ist besonders wichtig bei der Herstellung von Teilen mit engen Toleranzen oder komplexen geometrischen Formen, bei denen Genauigkeit und Reproduzierbarkeit entscheidend sind.
- Materialabtrag: Materialabtrag bezieht sich auf die Menge an Material, die während des Schleifprozesses von der Oberfläche eines Werkstücks entfernt wird. Automatische Schleifmaschinen können den Materialabtrag genau steuern und kontrollieren. Dies ermöglicht es, präzise Materialeigenschaften zu erreichen und die gewünschten Oberflächenmerkmale zu erzielen.
- Werkstücke: Werkstücke sind die Teile oder Komponenten, die durch Schleif- und Poliermaschinen bearbeitet werden. Sie können aus verschiedenen Materialien wie Metall, Holz, Kunststoff oder Glas bestehen. Die Art der Werkstücke bestimmt oft die spezifischen Anforderungen an die Schleif- und Polierprozesse sowie die Auswahl der geeigneten Maschinen und Werkzeuge.
- Hochleistungsschleifen: Hochleistungsschleifen bezeichnet den Einsatz von Schleifmaschinen, die in der Lage sind, große Mengen Material schnell und effizient zu entfernen. Diese Maschinen sind oft für industrielle Anwendungen mit hohen Produktionsanforderungen konzipiert. Hochleistungsschleifen ermöglicht es, die Bearbeitungszeiten zu verkürzen und die Produktivität zu steigern, ohne die Qualität der bearbeiteten Werkstücke zu beeinträchtigen.
- Automatische Zuführung: Automatische Zuführung bezieht sich auf den Prozess, bei dem Werkstücke automatisch in die Schleif- oder Poliermaschine eingebracht werden. Dies kann durch verschiedene Zuführsysteme wie Förderbänder, Roboterarme oder Vorschubeinheiten erfolgen. Die automatische Zuführung erleichtert den Arbeitsablauf, minimiert die Stillstandszeiten und erhöht die Effizienz der Fertigungsanlagen.
- Roboterintegration: Roboterintegration bezieht sich auf die Einbindung von Robotern in den Betrieb von Schleif- und Poliermaschinen. Roboter können dazu verwendet werden, Werkstücke zu handhaben, Zuführungen durchzuführen, Werkzeugwechsel zu vollziehen und andere Aufgaben auszuführen, um den Automatisierungsgrad zu erhöhen. Die Roboterintegration verbessert die Flexibilität, Präzision und Effizienz der Fertigungsprozesse und ermöglicht die Automatisierung von komplexen Aufgaben.
- Prozessoptimierung: Prozessoptimierung bezeichnet die kontinuierliche Verbesserung von Fertigungsprozessen, um Effizienz, Qualität und Rentabilität zu maximieren. In Bezug auf automatische Schleif- und Poliermaschinen umfasst die Prozessoptimierung die Feinabstimmung von Schleif- und Polierparametern, die Auswahl geeigneter Werkzeuge und Materialien sowie die Integration von Automatisierungstechnologien, um die Gesamtleistung der Fertigungsanlagen zu verbessern.
- Qualitätssicherung: Qualitätssicherung bezieht sich auf die Maßnahmen, die ergriffen werden, um sicherzustellen, dass die hergestellten Produkte den festgelegten Qualitätsstandards entsprechen. In der Fertigung von Teilen mit automatischen Schleif- und Poliermaschinen umfasst die Qualitätssicherung die Überwachung und Kontrolle der Prozessparameter, die Prüfung der bearbeiteten Werkstücke auf Fehler und Abweichungen sowie die Implementierung von Qualitätsmanagementsystemen, um die Produktqualität zu gewährleisten.
- Kontrollsysteme: Kontrollsysteme sind elektronische oder computergesteuerte Systeme, die dazu dienen, die Funktionen und Prozesse von Maschinen zu überwachen und zu steuern. In automatischen Schleif- und Poliermaschinen umfassen Kontrollsysteme Sensoren, Aktuatoren, Programmierlogik und Benutzerschnittstellen, die zusammenarbeiten, um den Betrieb der Maschinen zu optimieren, die Qualität der bearbeiteten Werkstücke sicherzustellen und die Sicherheit der Bediener zu gewährleisten.
- Schleifscheiben: Schleifscheiben sind Werkzeuge, die zum Schleifen von Werkstücken verwendet werden. Sie bestehen aus abrasiven Materialien wie Schleifkörnern, die auf einem Trägermaterial wie Glasfaser oder Kunstharz gebunden sind. Schleifscheiben gibt es in verschiedenen Formen, Größen und Körnungen, die je nach den Anforderungen des Schleifprozesses ausgewählt werden. Die Auswahl der richtigen Schleifscheibe ist entscheidend für die Qualität und Effizienz des Schleifvorgangs.
- Schleifkörper: Schleifkörper sind abrasive Materialien, die zum Abtragen von Material von der Oberfläche eines Werkstücks verwendet werden. Sie können in verschiedenen Formen wie Schleifpapier, Schleifscheiben, Schleifbänder oder Schleifsteine vorliegen und aus verschiedenen Materialien wie Aluminiumoxid, Siliciumkarbid oder Diamant bestehen. Die Auswahl des richtigen Schleifkörpers hängt von den zu bearbeitenden Materialien, der gewünschten Oberflächenqualität und anderen Prozessanforderungen ab.
- Automatisierung: Die Automatisierung hat die Fertigungsindustrie revolutioniert, indem sie den Einsatz von Maschinen und computergesteuerten Systemen ermöglicht hat, um Arbeitsprozesse zu optimieren und menschliche Arbeitskraft zu entlasten. Im Kontext von Schleif- und Poliermaschinen bezieht sich Automatisierung auf die Integration von Technologien, die den Schleif- und Polierprozess autonom durchführen können, ohne dass eine ständige manuelle Überwachung erforderlich ist. Dies verbessert nicht nur die Effizienz und Präzision, sondern ermöglicht auch eine kontinuierliche Produktion rund um die Uhr. Durch die Automatisierung können Unternehmen ihre Produktionskapazität steigern, die Qualität ihrer Produkte verbessern und die Betriebskosten senken, indem sie den Bedarf an menschlicher Arbeit reduzieren.
- Schleifmaschinen: Schleifmaschinen sind essenzielle Werkzeuge in verschiedenen Fertigungsprozessen, von der Metallbearbeitung bis hin zur Holzbearbeitung. Sie nutzen abrasive Schleifscheiben oder Schleifbänder, um Material von der Oberfläche eines Werkstücks abzutragen und eine glatte Oberfläche zu erzeugen. Moderne Schleifmaschinen können hochpräzise arbeiten und sind in der Lage, komplexe Formen und Profile mit großer Genauigkeit zu schleifen. Die Integration von Automatisierungstechnologien in Schleifmaschinen hat die Effizienz und Genauigkeit dieser Prozesse weiter verbessert, wodurch Unternehmen in der Lage sind, hochwertige Produkte mit minimalen Ausschussmengen herzustellen.
- Poliermaschinen: Poliermaschinen spielen eine entscheidende Rolle bei der Veredelung von Werkstücken, indem sie Oberflächen glätten, reinigen und ein glänzendes Finish erzeugen. Sie verwenden Rotationsbewegungen und spezielle Poliermittel, um Materialien wie Metall, Kunststoff oder Glas zu polieren und eine glatte, spiegelnde Oberfläche zu erzeugen. Automatische Poliermaschinen sind in der Lage, diesen Prozess präzise und effizient durchzuführen, wodurch Unternehmen die Qualität ihrer Produkte verbessern und gleichzeitig die Produktionszeiten verkürzen können.
- Präzision: Präzision ist ein entscheidender Faktor in der Fertigungsindustrie, insbesondere wenn es um Schleif- und Polierprozesse geht. Eine hohe Präzision gewährleistet, dass die bearbeiteten Werkstücke die erforderlichen Toleranzen und Spezifikationen erfüllen und dass jedes Werkstück konsistente Ergebnisse aufweist. Automatische Schleif- und Poliermaschinen sind darauf ausgelegt, eine präzise Bearbeitung zu gewährleisten, indem sie hochentwickelte Steuerungssysteme und Sensortechnologien verwenden, um den Schleif- und Polierprozess genau zu überwachen und anzupassen.
- Effizienz: Effizienz ist ein zentraler Aspekt jeder Fertigungsoperation, da sie direkt mit den Kosten und der Produktivität verbunden ist. Automatische Schleif- und Poliermaschinen sind darauf ausgelegt, Arbeitsabläufe zu optimieren und den Ressourcenverbrauch zu minimieren, indem sie Prozesse automatisieren und gleichzeitig eine hohe Ausbringungsmenge ermöglichen. Durch die Automatisierung können Unternehmen ihre Produktionszeiten verkürzen, die Durchlaufzeiten verbessern und die Gesamtleistung ihrer Fertigungsanlagen steigern.
Schleifmaschinen
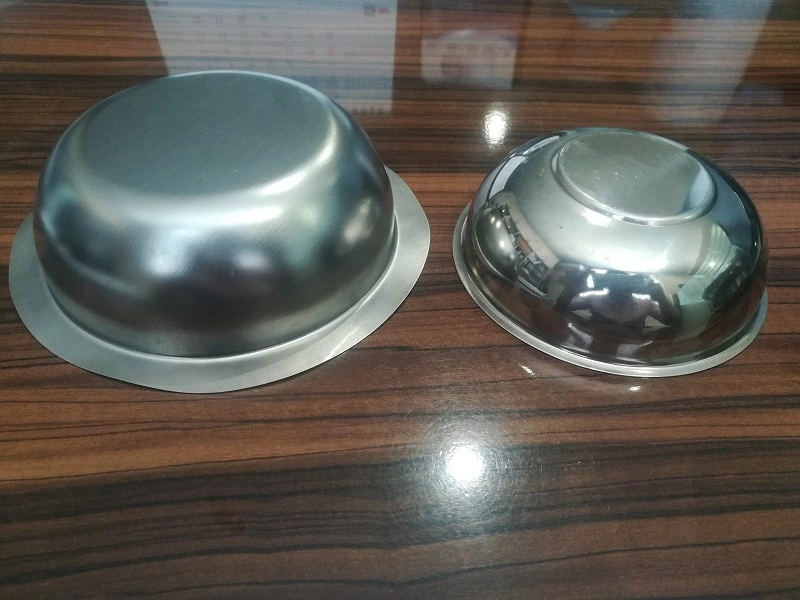
Schleifmaschinen: Schleifmaschinen sind grundlegende Werkzeuge in einer Vielzahl von Fertigungs- und Bearbeitungsprozessen, die darauf abzielen, die Oberflächen von Werkstücken zu verfeinern, zu formen oder zu glätten. Diese Maschinen verwenden Schleifscheiben, Schleifbänder oder andere abrasive Materialien, um Material von der Oberfläche eines Werkstücks abzutragen und die gewünschte Oberflächenbeschaffenheit zu erreichen. Die Anwendungen von Schleifmaschinen sind vielfältig und reichen von der Metallverarbeitung bis zur Holzbearbeitung, von der Herstellung von Präzisionsteilen bis zur Herstellung von Schmuck.
Moderne Schleifmaschinen sind in der Lage, eine Vielzahl von Werkstücken mit hoher Präzision und Effizienz zu bearbeiten. Sie kommen in verschiedenen Ausführungen, Größen und Konfigurationen vor, je nach den spezifischen Anforderungen der Anwendung. Einige der häufigsten Arten von Schleifmaschinen umfassen Bandschleifmaschinen, Flachschleifmaschinen, Rundschleifmaschinen und Oberflächenschleifmaschinen.
Die Bandschleifmaschine ist eine vielseitige Maschine, die eine endlose Schleifbandrolle verwendet, um Werkstücke in verschiedenen Winkeln und Formen zu schleifen. Flachschleifmaschinen sind ideal zum Schleifen von flachen Oberflächen und können große Werkstücke mit hoher Genauigkeit bearbeiten. Rundschleifmaschinen sind spezialisiert auf die Bearbeitung zylindrischer Werkstücke und können komplexe Innen- und Außenprofile schleifen. Oberflächenschleifmaschinen werden verwendet, um feine Oberflächenveredelungen und Hochpräzisionsbearbeitungen durchzuführen.
Die Integration von Automatisierungstechnologien hat die Leistung und Effizienz von Schleifmaschinen weiter verbessert. Automatische Schleifmaschinen können den Schleifprozess autonom durchführen, ohne dass ständige menschliche Überwachung erforderlich ist. Dies ermöglicht eine kontinuierliche Produktion rund um die Uhr und minimiert gleichzeitig menschliche Fehler und Ausschussmengen. Darüber hinaus ermöglicht die CNC-Steuerung (Computerized Numerical Control) präzise Bewegungen und komplexe Bearbeitungsaufgaben, die zuvor manuell schwer umsetzbar waren.
Die Auswahl der richtigen Schleifmaschine hängt von einer Vielzahl von Faktoren ab, darunter die Art der zu bearbeitenden Werkstücke, die gewünschten Oberflächeneigenschaften, die Produktionskapazität und die verfügbaren Ressourcen. Unternehmen sollten sorgfältig die Anforderungen ihrer Anwendungen bewerten und die Schleifmaschine auswählen, die am besten geeignet ist, um ihre spezifischen Bedürfnisse zu erfüllen.
Poliermaschinen
Poliermaschinen: Poliermaschinen sind unverzichtbare Werkzeuge in vielen Fertigungs- und Endbearbeitungsprozessen, die darauf abzielen, die Oberflächen von Werkstücken zu glätten, zu reinigen und ein glänzendes Finish zu erzeugen. Im Gegensatz zu Schleifmaschinen, die Material von der Oberfläche eines Werkstücks abtragen, verwenden Poliermaschinen Rotationsbewegungen und spezielle Poliermittel, um die Oberfläche zu verfeinern und ein hochwertiges Finish zu erzeugen. Diese Maschinen sind in einer Vielzahl von Branchen weit verbreitet, darunter die Automobilindustrie, die Luft- und Raumfahrt, die Schmuckherstellung, die Uhrenherstellung und die Medizintechnik.
Moderne Poliermaschinen sind in der Lage, eine Vielzahl von Werkstücken mit hoher Präzision und Effizienz zu bearbeiten. Sie kommen in verschiedenen Ausführungen und Konfigurationen vor, je nach den spezifischen Anforderungen der Anwendung. Einige der häufigsten Arten von Poliermaschinen umfassen Rotationspoliermaschinen, Ultraschallpoliermaschinen, Vibro-Poliermaschinen und Schleif- und Poliermaschinenkombinationen.
Rotationspoliermaschinen verwenden eine rotierende Polierscheibe oder Polierteller, um Werkstücke zu polieren und ein glänzendes Finish zu erzeugen. Ultraschallpoliermaschinen nutzen Ultraschallschwingungen, um Poliermittel in die feinen Strukturen von Werkstücken zu bringen und Oberflächen zu reinigen und zu polieren. Vibro-Poliermaschinen verwenden eine vibrierende Bewegung, um Werkstücke in einem Poliermedium zu bewegen und ein gleichmäßiges Finish zu erzielen. Schleif- und Poliermaschinenkombinationen kombinieren Schleif- und Polierfunktionen in einer Maschine, um eine nahtlose Bearbeitung von Werkstücken zu ermöglichen.
Die Integration von Automatisierungstechnologien hat die Leistung und Effizienz von Poliermaschinen weiter verbessert. Automatische Poliermaschinen können den Polierprozess autonom durchführen, ohne dass ständige menschliche Überwachung erforderlich ist. Dies ermöglicht eine kontinuierliche Produktion rund um die Uhr und minimiert gleichzeitig menschliche Fehler und Ausschussmengen. Darüber hinaus ermöglicht die CNC-Steuerung (Computerized Numerical Control) präzise Bewegungen und komplexe Bearbeitungsaufgaben, die zuvor manuell schwer umsetzbar waren.
Die Auswahl der richtigen Poliermaschine hängt von einer Vielzahl von Faktoren ab, darunter die Art der zu bearbeitenden Werkstücke, die gewünschten Oberflächeneigenschaften, die Produktionskapazität und die verfügbaren Ressourcen. Unternehmen sollten sorgfältig die Anforderungen ihrer Anwendungen bewerten und die Poliermaschine auswählen, die am besten geeignet ist, um ihre spezifischen Bedürfnisse zu erfüllen.
Präzision
Präzision: Präzision ist ein entscheidender Faktor in der Fertigungsindustrie, insbesondere wenn es um Schleif- und Polierprozesse geht. Eine hohe Präzision gewährleistet, dass die bearbeiteten Werkstücke die erforderlichen Toleranzen und Spezifikationen erfüllen und dass jedes Werkstück konsistente Ergebnisse aufweist. Im Kontext von automatischen Schleifmaschinen und Poliermaschinen bezieht sich Präzision auf die Fähigkeit dieser Maschinen, Werkstücke mit hoher Genauigkeit und Wiederholbarkeit zu bearbeiten.
Die Präzision von Schleif- und Poliermaschinen wird durch verschiedene Faktoren beeinflusst, darunter die Genauigkeit der Maschinenkomponenten, die Steuerungstechnologie, die Qualität der Schleifscheiben oder Poliermittel und die Stabilität der Arbeitsumgebung. Moderne Schleif- und Poliermaschinen verwenden hochpräzise CNC-Steuerungen (Computerized Numerical Control), die es ermöglichen, die Bewegungen und Parameter des Bearbeitungsprozesses genau zu kontrollieren und anzupassen.
Eine hohe Präzision ist besonders wichtig bei der Herstellung von Teilen mit engen Toleranzen oder komplexen geometrischen Formen, bei denen Genauigkeit und Reproduzierbarkeit entscheidend sind. Automatische Schleif- und Poliermaschinen sind darauf ausgelegt, diese Anforderungen zu erfüllen, indem sie präzise Bewegungen ausführen, Materialabtrag oder Poliervorgänge gleichmäßig durchführen und konsistente Ergebnisse liefern.
Die Präzision von Schleif- und Poliermaschinen spielt eine entscheidende Rolle bei der Qualitätssicherung und der Erfüllung der Anforderungen von Kunden und Branchenstandards. Unternehmen investieren in hochpräzise Schleif- und Poliermaschinen, um sicherzustellen, dass ihre Produkte die höchsten Qualitätsstandards erfüllen und dass sie in der Lage sind, wettbewerbsfähige Produkte auf dem Markt anzubieten.
Die kontinuierliche Weiterentwicklung von Schleif- und Poliertechnologien zielt darauf ab, die Präzision dieser Maschinen weiter zu verbessern und neue Möglichkeiten für die Bearbeitung von komplexen Werkstücken und Materialien zu erschließen. Durch die Kombination von Präzision mit Effizienz und Automatisierung können Unternehmen ihre Fertigungsprozesse optimieren und ihre Wettbewerbsfähigkeit stärken.
Effizienz
Effizienz: Effizienz ist ein zentraler Aspekt jeder Fertigungsoperation, da sie direkt mit den Kosten und der Produktivität verbunden ist. Im Kontext von automatischen Schleifmaschinen und Poliermaschinen bezieht sich Effizienz darauf, wie gut diese Maschinen in der Lage sind, Arbeitsabläufe zu optimieren und Ressourcen zu nutzen, um die gewünschten Ergebnisse zu erzielen.
Durch die Integration von Automatisierungstechnologien können Schleif- und Polierprozesse effizienter gestaltet werden. Automatische Schleifmaschinen können den Materialabtrag präzise steuern und die Bearbeitungszeiten verkürzen, während automatische Poliermaschinen eine gleichmäßige und effiziente Oberflächenbearbeitung ermöglichen. Diese Maschinen können kontinuierlich arbeiten, ohne dass ständige menschliche Überwachung erforderlich ist, was zu einer Reduzierung von Stillstandszeiten und einer Steigerung der Produktivität führt.
Effizienz in Schleif- und Polierprozessen kann auch durch die Auswahl geeigneter Werkzeuge, Materialien und Prozessparameter verbessert werden. Die Verwendung hochwertiger Schleifscheiben oder Poliermittel, die auf die spezifischen Anforderungen der Anwendung zugeschnitten sind, kann die Bearbeitungszeiten verkürzen und die Lebensdauer der Werkzeuge verlängern. Die Optimierung von Schleif- und Polierparametern wie Vorschubgeschwindigkeit, Druck und Drehzahl kann ebenfalls dazu beitragen, die Effizienz der Bearbeitungsprozesse zu maximieren.
Effizienz ist auch eng mit der Qualität der bearbeiteten Werkstücke verbunden. Durch die Maximierung der Effizienz können Unternehmen eine höhere Produktionskapazität erreichen, ohne die Qualität ihrer Produkte zu beeinträchtigen. Dies trägt dazu bei, die Gesamtleistung der Fertigungsanlagen zu verbessern und die Wettbewerbsfähigkeit auf dem Markt zu stärken.
Die kontinuierliche Verbesserung von Schleif- und Poliertechnologien zielt darauf ab, die Effizienz dieser Prozesse weiter zu steigern und neue Möglichkeiten für die Optimierung von Fertigungsabläufen zu erschließen. Durch die Nutzung von Innovationen wie fortschrittlichen Steuerungssystemen, Robotik und künstlicher Intelligenz können Unternehmen die Effizienz ihrer Schleif- und Polieroperationen kontinuierlich verbessern und ihre Geschäftsziele effektiver erreichen.
Produktivität
Produktivität: Produktivität ist ein entscheidender Indikator für den Erfolg einer Fertigungsoperation und bezieht sich auf die Menge an Output, die eine Maschine oder ein Prozess im Verhältnis zu den eingesetzten Ressourcen erzeugt. Im Kontext von automatischen Schleifmaschinen und Poliermaschinen bezieht sich Produktivität darauf, wie effektiv diese Maschinen in der Lage sind, Werkstücke zu bearbeiten und fertige Produkte zu erzeugen.
Durch die Integration von Automatisierungstechnologien können Schleif- und Polierprozesse produktiver gestaltet werden. Automatische Schleifmaschinen können kontinuierlich arbeiten, ohne dass ständige menschliche Überwachung erforderlich ist, was zu einer Steigerung der Gesamtproduktivität führt. Diese Maschinen können auch eine höhere Ausbringungsmenge pro Stunde oder pro Schicht erreichen, da sie die Bearbeitungszeiten verkürzen und die Durchlaufzeiten optimieren können.
Produktivität in Schleif- und Polierprozessen kann auch durch die Optimierung von Arbeitsabläufen und die Maximierung der Maschinenauslastung verbessert werden. Dies kann durch die Planung von Produktionsaufträgen, die Einrichtung von effizienten Werkzeugwechselzyklen und die Minimierung von Stillstandszeiten erreicht werden. Darüber hinaus können die Auswahl hochwertiger Werkzeuge und Materialien sowie die Optimierung von Schleif- und Polierparametern dazu beitragen, die Produktivität der Fertigungsanlagen weiter zu steigern.
Eine hohe Produktivität ist entscheidend für die Rentabilität und Wettbewerbsfähigkeit eines Unternehmens. Durch die Maximierung der Produktivität können Unternehmen ihre Produktionskapazität maximieren, ihre Betriebskosten senken und ihre Marktanteile ausbauen. Dies ermöglicht es ihnen, wettbewerbsfähige Produkte anzubieten und auf dem Markt erfolgreich zu sein.
Die kontinuierliche Weiterentwicklung von Schleif- und Poliertechnologien zielt darauf ab, die Produktivität dieser Prozesse weiter zu steigern und neue Möglichkeiten für die Optimierung von Fertigungsabläufen zu erschließen. Durch die Nutzung von Innovationen wie fortschrittlichen Steuerungssystemen, Robotik und künstlicher Intelligenz können Unternehmen die Produktivität ihrer Schleif- und Polieroperationen kontinuierlich verbessern und ihre Geschäftsziele effektiver erreichen.
Automatisches Zuführungssystem
Automatisches Zuführungssystem: Automatische Zuführungssysteme sind entscheidende Komponenten in Fertigungsanlagen, die dazu dienen, Werkstücke oder Materialien automatisch in Schleif- und Poliermaschinen einzuführen. Diese Systeme sind darauf ausgelegt, den Materialfluss zu optimieren, Arbeitsabläufe zu rationalisieren und die Effizienz der Fertigungsprozesse zu verbessern.
Es gibt verschiedene Arten von automatischen Zuführungssystemen, darunter Förderbänder, Roboterarme, Vorschubeinheiten und Handhabungssysteme. Förderbänder sind weit verbreitet und werden verwendet, um Werkstücke von einem Arbeitsbereich zum nächsten zu transportieren. Roboterarme werden eingesetzt, um Werkstücke präzise zu greifen, zu positionieren und in die Schleif- oder Poliermaschine einzuführen. Vorschubeinheiten sind spezialisierte Geräte, die dazu dienen, Werkstücke mit einer kontrollierten Geschwindigkeit und Position in die Maschine zu bewegen. Handhabungssysteme können verschiedene Zuführtechnologien kombinieren, um komplexe Werkstücke oder Materialien zu handhaben und einzuführen.
Automatische Zuführungssysteme bieten eine Vielzahl von Vorteilen, darunter eine Steigerung der Produktivität, eine Reduzierung von Arbeitskosten, eine Minimierung von Stillstandszeiten und eine Verbesserung der Arbeitssicherheit. Indem sie den Bedarf an manuellen Eingriffen reduzieren, ermöglichen sie eine kontinuierliche Produktion rund um die Uhr und erhöhen die Auslastung der Fertigungsanlagen. Darüber hinaus tragen sie dazu bei, menschliche Fehler zu minimieren und die Qualität der bearbeiteten Werkstücke zu verbessern.
Die Auswahl des richtigen automatischen Zuführungssystems hängt von einer Vielzahl von Faktoren ab, darunter die Art der zu bearbeitenden Werkstücke, die Produktionskapazität, die verfügbaren Ressourcen und die spezifischen Anforderungen der Anwendung. Unternehmen sollten sorgfältig die verschiedenen Optionen bewerten und das System auswählen, das am besten geeignet ist, um ihre Fertigungsziele zu erreichen und ihre Produktivität zu steigern.
Roboterintegration
Roboterintegration: Die Roboterintegration bezieht sich auf die Einbindung von Robotern in den Betrieb von Schleif- und Poliermaschinen, um Arbeitsabläufe zu automatisieren und die Leistungsfähigkeit der Fertigungsanlagen zu verbessern. Roboter werden zunehmend in der Fertigungsindustrie eingesetzt, um repetitive Aufgaben zu automatisieren, die Effizienz zu steigern und die Flexibilität der Produktionsprozesse zu erhöhen.
Im Kontext von Schleif- und Poliermaschinen können Roboter für verschiedene Aufgaben eingesetzt werden, darunter die Handhabung von Werkstücken, das Laden und Entladen von Maschinen, das Wechseln von Werkzeugen oder Schleifscheiben, das Reinigen von Arbeitsbereichen und die Überwachung von Prozessen. Durch die Integration von Robotern können Unternehmen die Produktivität steigern, die Qualität verbessern und die Betriebskosten senken, indem sie menschliche Arbeitskräfte von mühsamen oder gefährlichen Aufgaben entlasten.
Moderne Roboter sind mit fortschrittlichen Sensoren, Aktuatoren und Steuerungssystemen ausgestattet, die es ihnen ermöglichen, präzise und zuverlässige Aufgaben in industriellen Umgebungen auszuführen. Sie können komplexe Bewegungen und Manipulationen durchführen und sich nahtlos in bestehende Fertigungslinien integrieren. Die Programmierung und Steuerung von Robotern kann mittels teach-in-Verfahren oder spezieller Programmiersoftware erfolgen, die es Benutzern ermöglicht, die Bewegungen und Aktionen des Roboters einfach zu definieren und anzupassen.
Die Roboterintegration bietet eine Vielzahl von Vorteilen, darunter eine Steigerung der Produktivität, eine Verbesserung der Produktqualität, eine Reduzierung von Ausschussmengen, eine Flexibilisierung der Produktion und eine Erhöhung der Arbeitssicherheit. Indem sie wiederkehrende Aufgaben automatisieren, können Roboter dazu beitragen, die Effizienz der Fertigungsprozesse zu maximieren und die Wettbewerbsfähigkeit eines Unternehmens zu stärken.
Die Auswahl und Implementierung von Robotersystemen erfordert eine sorgfältige Planung und Integration in die bestehenden Fertigungsanlagen. Unternehmen sollten die spezifischen Anforderungen ihrer Anwendungen bewerten und die geeigneten Robotertechnologien auswählen, um ihre Produktionsziele zu erreichen und ihre Wettbewerbsfähigkeit zu steigern.
CNC-Steuerung: CNC-Steuerung steht für Computerized Numerical Control und bezieht sich auf die computergesteuerte Steuerung von Maschinenwerkzeugen wie Schleif- und Poliermaschinen. Diese Technologie ermöglicht es, die Bewegungen und Aktionen der Maschine präzise zu steuern, indem numerische Daten verwendet werden, die von einem Computer generiert werden. Die CNC-Steuerung hat die Fertigungsindustrie revolutioniert, indem sie die Automatisierung von Bearbeitungsprozessen ermöglicht hat und die Präzision, Effizienz und Flexibilität von Fertigungsanlagen verbessert hat.
Im Kontext von Schleif- und Poliermaschinen ermöglicht die CNC-Steuerung eine präzise Kontrolle über den Bearbeitungsprozess, einschließlich Bewegungen, Geschwindigkeiten, Tiefen und Positionen. Dies ermöglicht es, komplexe Formen und Profile mit hoher Genauigkeit zu schleifen und zu polieren, während gleichzeitig die Bearbeitungszeiten optimiert und die Ausschussmengen minimiert werden.
Die CNC-Steuerung umfasst eine Reihe von Komponenten, darunter einen Computer, eine Steuereinheit, Motoren und Aktuatoren sowie Sensoren und Feedbacksysteme. Der Computer generiert die numerischen Daten, die den Bearbeitungsprozess definieren, und sendet sie an die Steuereinheit, die die Bewegungen und Aktionen der Maschine entsprechend den Programmiervorgaben steuert. Motoren und Aktuatoren setzen die Befehle der Steuereinheit in mechanische Bewegungen um, während Sensoren und Feedbacksysteme die Leistung der Maschine überwachen und Rückmeldungen an das Steuersystem liefern.
Die CNC-Steuerung bietet eine Vielzahl von Vorteilen, darunter eine verbesserte Präzision, Wiederholbarkeit und Konsistenz der Bearbeitungsprozesse. Durch die Automatisierung von Bewegungen und Abläufen können Unternehmen die Produktivität steigern, die Durchlaufzeiten verkürzen und die Betriebskosten senken. Darüber hinaus ermöglicht die Flexibilität der CNC-Steuerung es, schnell zwischen verschiedenen Bearbeitungsaufgaben zu wechseln und komplexe Werkstücke mit hoher Genauigkeit herzustellen.
Die Integration von CNC-Steuerung in Schleif- und Poliermaschinen erfordert spezielle Hardware- und Softwarekomponenten sowie Schulung und Fachkenntnisse für die Programmierung und Bedienung der Maschinen. Unternehmen, die in CNC-Steuerungstechnologien investieren, können jedoch von einer verbesserten Leistung, Effizienz und Wettbewerbsfähigkeit profitieren, da sie in der Lage sind, hochpräzise Produkte mit kürzeren Durchlaufzeiten und niedrigeren Betriebskosten herzustellen.
Abrasive Materialien
Abrasive Materialien: Abrasive Materialien sind Substanzen, die zum Schleifen, Polieren oder Bearbeiten von Werkstücken verwendet werden, um Material von der Oberfläche abzutragen und die gewünschte Oberflächenbeschaffenheit zu erreichen. Diese Materialien sind in verschiedenen Formen und Zusammensetzungen erhältlich und werden je nach den spezifischen Anforderungen der Anwendung ausgewählt.
Im Kontext von Schleif- und Poliermaschinen umfassen abrasive Materialien Schleifscheiben, Schleifbänder, Schleifpapiere, Schleifstifte, Schleifpasten, Poliermittel und andere ähnliche Substanzen. Diese Materialien bestehen aus abrasiven Partikeln, die in einem Bindemittel gebunden sind, das sie auf der Oberfläche eines Trägermaterials hält. Die Auswahl des richtigen abrasiven Materials hängt von verschiedenen Faktoren ab, darunter die Art des zu bearbeitenden Werkstücks, die gewünschte Oberflächenbeschaffenheit, die Bearbeitungsgeschwindigkeit und die Betriebsbedingungen.
Schleifscheiben und Schleifbänder sind häufige abrasive Materialien, die zum Schleifen von Werkstücken verwendet werden. Sie bestehen aus einer Matrix aus abrasiven Partikeln wie Aluminiumoxid, Siliziumkarbid, Diamant oder Bornitrid, die in einem Bindemittel wie Keramik, Harz oder Gummi gebunden sind. Diese Schleifmittel sind in verschiedenen Körnungen erhältlich, die den Grad der Oberflächenrauheit und den Materialabtrag bestimmen.
Poliermittel sind abrasive Materialien, die zum Polieren von Werkstücken verwendet werden, um ein glänzendes Finish zu erzeugen. Sie bestehen aus feinen abrasiven Partikeln, die in einem Trägermaterial wie Wachs, Öl oder Wasser gebunden sind. Poliermittel werden in verschiedenen Körnungen und Zusammensetzungen angeboten, je nach den spezifischen Anforderungen der Anwendung und der Art des zu polierenden Materials.
Die Auswahl des richtigen abrasiven Materials ist entscheidend für den Erfolg von Schleif- und Polierprozessen. Durch die Auswahl des geeigneten Materials können Unternehmen die Oberflächenqualität verbessern, die Bearbeitungszeiten verkürzen und die Standzeit der Werkzeuge maximieren. Darüber hinaus kann die richtige Auswahl dazu beitragen, Ausschussmengen zu minimieren und die Betriebskosten zu senken.
Die kontinuierliche Weiterentwicklung von abrasiven Materialien zielt darauf ab, die Leistung und Effizienz von Schleif- und Polierprozessen weiter zu verbessern. Durch die Entwicklung neuer Materialzusammensetzungen, Bindemittel und Herstellungsverfahren können Unternehmen innovative Lösungen für ihre Bearbeitungsanforderungen finden und ihre Wettbewerbsfähigkeit auf dem Markt stärken.
Schleifscheiben
Schleifscheiben: Schleifscheiben sind wichtige Werkzeuge, die in Schleifmaschinen verwendet werden, um Material von der Oberfläche eines Werkstücks abzutragen und die gewünschte Oberflächenbeschaffenheit zu erreichen. Diese Scheiben bestehen aus abrasiven Partikeln, die in einem Bindemittel gebunden sind und auf einem Trägermaterial wie Stahl oder Glasfaser montiert sind. Schleifscheiben sind in verschiedenen Formen, Größen und Körnungen erhältlich, je nach den spezifischen Anforderungen der Anwendung.
Die Auswahl der richtigen Schleifscheibe hängt von verschiedenen Faktoren ab, darunter die Art des zu bearbeitenden Werkstücks, die gewünschte Oberflächeneigenschaft, die Bearbeitungsgeschwindigkeit und die Betriebsbedingungen. Die gängigsten Arten von Schleifscheiben umfassen Schleifscheiben aus Aluminiumoxid, Siliziumkarbid, Diamant und Bornitrid.
- Aluminiumoxid-Schleifscheiben sind vielseitige Werkzeuge, die für eine Vielzahl von Materialien wie Metalle, Holz und Kunststoffe verwendet werden können. Sie bieten eine gute Allround-Leistung und eine hohe Abtragsleistung.
- Siliziumkarbid-Schleifscheiben eignen sich besonders für das Schleifen von harten Materialien wie Gusseisen, Stein und Glas. Sie sind widerstandsfähig gegen hohe Temperaturen und bieten eine hohe Abtragsleistung.
- Diamant-Schleifscheiben werden für das Schleifen von extrem harten Materialien wie Keramik, Glas und Hartmetall eingesetzt. Sie bieten eine überlegene Abtragsleistung und eine lange Lebensdauer, sind jedoch in der Anschaffung teurer als andere Schleifscheiben.
- Bornitrid-Schleifscheiben werden für das Schleifen von hochharten Materialien wie gehärtetem Stahl, Keramik und Saphir verwendet. Sie bieten eine außergewöhnliche Schleifleistung und eine lange Lebensdauer, sind jedoch ebenfalls teurer als herkömmliche Schleifscheiben.
Die richtige Auswahl der Schleifscheibe ist entscheidend für den Erfolg von Schleifprozessen. Unternehmen sollten die spezifischen Anforderungen ihrer Anwendungen sorgfältig bewerten und die geeignete Schleifscheibe auswählen, um die gewünschten Oberflächenmerkmale zu erreichen und die Produktionsziele zu erfüllen.
Die kontinuierliche Weiterentwicklung von Schleifscheiben zielt darauf ab, die Leistung und Effizienz von Schleifprozessen weiter zu verbessern. Durch die Entwicklung neuer Materialzusammensetzungen, Bindemittel und Herstellungsverfahren können Unternehmen innovative Lösungen für ihre Bearbeitungsanforderungen finden und ihre Wettbewerbsfähigkeit auf dem Markt stärken.
Schleifbänder
Schleifbänder: Schleifbänder sind flexible und langlebige Werkzeuge, die in Schleifmaschinen verwendet werden, um Material von der Oberfläche eines Werkstücks abzutragen und die gewünschte Oberflächenbeschaffenheit zu erreichen. Diese Bänder bestehen aus einem flexiblen Trägermaterial, das mit abrasiven Partikeln beschichtet ist, die in einem Bindemittel gebunden sind. Schleifbänder sind in verschiedenen Größen, Körnungen und Zusammensetzungen erhältlich, um den Anforderungen verschiedener Schleifanwendungen gerecht zu werden.
Die Auswahl des richtigen Schleifbandes hängt von verschiedenen Faktoren ab, darunter die Art des zu bearbeitenden Werkstücks, die gewünschte Oberflächenqualität, die Bearbeitungsgeschwindigkeit und die Betriebsbedingungen. Die gängigsten Arten von Schleifbändern umfassen Bänder aus Aluminiumoxid, Siliziumkarbid und Zirkonoxid.
- Aluminiumoxid-Schleifbänder sind vielseitige Werkzeuge, die für eine Vielzahl von Materialien wie Metalle, Holz und Kunststoffe verwendet werden können. Sie bieten eine gute Allround-Leistung und eine hohe Abtragsleistung.
- Siliziumkarbid-Schleifbänder eignen sich besonders für das Schleifen von harten Materialien wie Gusseisen, Stein und Glas. Sie sind widerstandsfähig gegen hohe Temperaturen und bieten eine hohe Abtragsleistung.
- Zirkonoxid-Schleifbänder werden für das Schleifen von besonders harten Materialien wie Edelstahl, Titan und Superlegierungen eingesetzt. Sie bieten eine überlegene Schleifleistung und eine lange Lebensdauer.
Schleifbänder werden in verschiedenen Körnungen angeboten, die den Grad der Oberflächenrauheit und den Materialabtrag bestimmen. Feinere Körnungen erzeugen eine glattere Oberfläche mit geringerem Materialabtrag, während gröbere Körnungen eine schnellere Materialabtragung und eine gröbere Oberfläche bewirken.
Die richtige Auswahl des Schleifbandes ist entscheidend für den Erfolg von Schleifprozessen. Unternehmen sollten die spezifischen Anforderungen ihrer Anwendungen sorgfältig bewerten und das geeignete Schleifband auswählen, um die gewünschten Oberflächenmerkmale zu erreichen und die Produktionsziele zu erfüllen.
Die kontinuierliche Weiterentwicklung von Schleifbändern zielt darauf ab, die Leistung und Effizienz von Schleifprozessen weiter zu verbessern. Durch die Entwicklung neuer Materialzusammensetzungen, Trägermaterialien und Herstellungsverfahren können Unternehmen innovative Lösungen für ihre Schleifanforderungen finden und ihre Wettbewerbsfähigkeit auf dem Markt stärken.
Poliermittel
Poliermittel: Poliermittel sind Substanzen, die verwendet werden, um die Oberfläche eines Werkstücks zu glätten, zu reinigen und zu polieren, um ein glänzendes Finish zu erzeugen. Diese Materialien enthalten feine abrasive Partikel, die in einem Trägermaterial wie Wachs, Öl oder Wasser gebunden sind. Poliermittel werden in verschiedenen Formen und Zusammensetzungen angeboten, je nach den spezifischen Anforderungen der Anwendung.
Im Kontext von Poliermaschinen umfassen Poliermittel Pasten, Flüssigkeiten, Sprays und Feststoffe, die auf die Oberfläche des Werkstücks aufgetragen werden. Diese Materialien enthalten feine abrasiven Partikel wie Aluminiumoxid, Siliziumoxid, Diamant oder Bornitrid, die dazu beitragen, Unebenheiten zu entfernen und die Oberfläche zu glätten. Darüber hinaus enthalten Poliermittel oft spezielle Zusatzstoffe wie Tenside, Schmiermittel und Konservierungsmittel, die die Polierleistung verbessern und die Oberfläche vor Korrosion schützen.
Die Auswahl des richtigen Poliermittels hängt von verschiedenen Faktoren ab, darunter die Art des zu polierenden Werkstücks, das gewünschte Oberflächenfinish, die Bearbeitungsgeschwindigkeit und die Betriebsbedingungen. Feinere Poliermittel erzeugen ein glatteres Finish mit weniger sichtbaren Kratzern und Spuren, während grobere Poliermittel eine schnellere Bearbeitung ermöglichen und für den Anfangsschliff geeignet sind.
Poliermittel werden in verschiedenen Anwendungen eingesetzt, einschließlich der Bearbeitung von Metallen, Kunststoffen, Glas, Keramik und anderen Materialien. Sie finden Anwendung in verschiedenen Branchen wie der Automobilindustrie, der Luft- und Raumfahrt, der Elektronikfertigung, der Schmuckherstellung und der Medizintechnik.
Die richtige Auswahl des Poliermittels ist entscheidend für den Erfolg von Polierprozessen. Unternehmen sollten die spezifischen Anforderungen ihrer Anwendungen sorgfältig bewerten und das geeignete Poliermittel auswählen, um die gewünschten Oberflächenmerkmale zu erreichen und die Produktionsziele zu erfüllen.
Die kontinuierliche Weiterentwicklung von Poliermitteln zielt darauf ab, die Leistung und Effizienz von Polierprozessen weiter zu verbessern. Durch die Entwicklung neuer Materialzusammensetzungen, Trägermaterialien und Herstellungsverfahren können Unternehmen innovative Lösungen für ihre Polieranforderungen finden und ihre Wettbewerbsfähigkeit auf dem Markt stärken.
Werkstückspannsysteme
Werkstückspannsysteme: Werkstückspannsysteme sind wichtige Komponenten von Schleif- und Poliermaschinen, die dazu dienen, Werkstücke sicher und stabil während des Bearbeitungsprozesses zu fixieren. Diese Systeme ermöglichen es, Werkstücke in der richtigen Position zu halten, um eine präzise Bearbeitung zu gewährleisten und die Sicherheit der Bediener zu gewährleisten.
Es gibt verschiedene Arten von Werkstückspannsystemen, die je nach den spezifischen Anforderungen der Anwendung ausgewählt werden können. Zu den gängigen Typen gehören:
- Klemmvorrichtungen: Diese Systeme verwenden Spannbacken, Schrauben oder Hydraulikzylinder, um das Werkstück fest zu fixieren. Sie sind vielseitig einsetzbar und eignen sich für eine Vielzahl von Werkstückgeometrien und -größen.
- Magnetische Spannsysteme: Diese Systeme verwenden Magnetkraft, um das Werkstück auf der Maschinenoberfläche zu halten. Sie sind besonders für die Bearbeitung von ferromagnetischen Materialien wie Stahl und Gusseisen geeignet und bieten eine schnelle und einfache Spannlösung.
- Vakuumspannsysteme: Diese Systeme verwenden Unterdruck, um das Werkstück auf einer porösen Oberfläche zu halten. Sie sind ideal für die Bearbeitung von dünnen oder empfindlichen Werkstücken, da sie keine mechanische Fixierung erfordern und keine Spannspuren hinterlassen.
- Spannvorrichtungen für spezielle Anwendungen: Es gibt auch spezielle Spannsysteme, die für bestimmte Anwendungen entwickelt wurden, wie z.B. Spannfutter für runde Werkstücke, Spannplatten für flache Werkstücke oder kundenspezifische Spannlösungen für komplexe Geometrien.
Die Auswahl des richtigen Werkstückspannsystems hängt von verschiedenen Faktoren ab, darunter die Art des zu bearbeitenden Werkstücks, die Bearbeitungsanforderungen, die Maschinenausstattung und die verfügbaren Ressourcen. Unternehmen sollten die spezifischen Anforderungen ihrer Anwendungen sorgfältig bewerten und das geeignete Spannsystem auswählen, um die Produktivität, Qualität und Effizienz ihrer Bearbeitungsprozesse zu maximieren.
Die kontinuierliche Weiterentwicklung von Werkstückspannsystemen zielt darauf ab, die Leistung und Flexibilität von Schleif- und Poliermaschinen weiter zu verbessern. Durch die Entwicklung neuer Spannlösungen, Materialien und Technologien können Unternehmen innovative Lösungen für ihre Spannanforderungen finden und ihre Wettbewerbsfähigkeit auf dem Markt stärken.
Kühlschmierstoffe
Kühlschmierstoffe: Kühlschmierstoffe, auch als Schneidöle, Schneidflüssigkeiten oder Schmiermittel bekannt, sind Substanzen, die während des Schleif- und Polierprozesses verwendet werden, um die Reibung zu reduzieren, die Wärmeentwicklung zu kontrollieren, die Werkzeugstandzeit zu erhöhen und die Oberflächenqualität zu verbessern. Diese Flüssigkeiten spielen eine wichtige Rolle bei der Optimierung von Schleif- und Polierprozessen und tragen dazu bei, die Leistung und Effizienz der Maschinen zu maximieren.
Kühlschmierstoffe erfüllen mehrere Funktionen während des Bearbeitungsprozesses:
- Kühlung: Sie entziehen dem Bearbeitungsbereich Wärme, um eine Überhitzung der Werkzeuge und Werkstücke zu verhindern. Dies trägt dazu bei, Verformungen, Härteverluste und thermische Risse zu minimieren.
- Schmierung: Sie reduzieren die Reibung zwischen Werkzeug und Werkstück, was zu einer verbesserten Oberflächenqualität und einer längeren Standzeit der Werkzeuge führt. Dies trägt auch zur Reduzierung von Werkzeugverschleiß und zum Schutz der Maschinenkomponenten bei.
- Reinigung: Sie spülen Späne und Abrieb von der Schleifscheibe oder dem Polierwerkzeug weg, um Verstopfungen zu vermeiden und eine gleichmäßige Bearbeitung zu gewährleisten.
- Korrosionsschutz: Sie schützen die Werkstückoberfläche und die Maschinenkomponenten vor Korrosion, insbesondere bei der Bearbeitung von empfindlichen Materialien wie Aluminiumlegierungen.
Kühlschmierstoffe können auf Wasserbasis, ölbasiert oder synthetisch sein und enthalten oft Zusatzstoffe wie Schmiermittel, Emulgatoren, Korrosionsschutzmittel und Biozide, um die gewünschten Eigenschaften zu erreichen. Die Auswahl des richtigen Kühlschmierstoffs hängt von verschiedenen Faktoren ab, darunter die Art des zu bearbeitenden Materials, die Bearbeitungsbedingungen, die Maschinenausstattung und die Umweltauflagen.
Eine effektive Anwendung von Kühlschmierstoffen erfordert eine präzise Dosierung und Verteilung, um eine optimale Leistung zu gewährleisten und Verunreinigungen zu minimieren. Unternehmen sollten die Herstellerempfehlungen befolgen und regelmäßige Wartung und Reinigung der Kühlschmierstoffsysteme durchführen, um eine zuverlässige und effiziente Leistung sicherzustellen.
Die kontinuierliche Weiterentwicklung von Kühlschmierstoffen zielt darauf ab, umweltfreundlichere und leistungsfähigere Formulierungen zu entwickeln, die die Anforderungen moderner Schleif- und Polierprozesse erfüllen. Durch die Nutzung innovativer Materialien und Technologien können Unternehmen ihre Bearbeitungsprozesse optimieren und ihre Produktivität steigern, während gleichzeitig Umweltauflagen eingehalten und die Gesundheit und Sicherheit der Bediener gewährleistet werden.
Werkstückführungssysteme
Werkstückführungssysteme: Werkstückführungssysteme sind entscheidende Komponenten von Schleif- und Poliermaschinen, die dazu dienen, Werkstücke während des Bearbeitungsprozesses präzise zu positionieren, zu stabilisieren und zu führen. Diese Systeme spielen eine wichtige Rolle bei der Gewährleistung einer genauen Bearbeitung und einer gleichmäßigen Oberflächenqualität der Werkstücke.
Es gibt verschiedene Arten von Werkstückführungssystemen, die je nach den spezifischen Anforderungen der Anwendung ausgewählt werden können. Zu den gängigen Typen gehören:
- Klemmvorrichtungen: Diese Systeme verwenden Spannbacken, Schrauben oder hydraulische Vorrichtungen, um das Werkstück sicher zu fixieren und zu positionieren. Sie bieten eine stabile und zuverlässige Führung während des Bearbeitungsprozesses und eignen sich für eine Vielzahl von Werkstückgeometrien und -größen.
- Rollenführungen: Diese Systeme verwenden Rollen oder Kugellager, um das Werkstück während des Bearbeitungsprozesses zu führen und zu unterstützen. Sie bieten eine reibungsarme Führung und eignen sich besonders für lange Werkstücke oder Anwendungen, bei denen eine kontinuierliche Bewegung erforderlich ist.
- Linearführungen: Diese Systeme verwenden Führungsschienen und Gleitlager, um das Werkstück entlang einer geraden Linie zu führen. Sie bieten eine präzise und gleichmäßige Bewegung und eignen sich für Anwendungen, bei denen hohe Genauigkeit und Wiederholbarkeit erforderlich sind.
- Roboterunterstützte Führungssysteme: Diese Systeme verwenden Roboterarme oder automatisierte Handhabungseinheiten, um das Werkstück während des Bearbeitungsprozesses zu führen und zu positionieren. Sie bieten eine hohe Flexibilität und eignen sich für komplexe Bearbeitungsanwendungen oder die Integration in automatisierte Fertigungslinien.
Die Auswahl des richtigen Werkstückführungssystems hängt von verschiedenen Faktoren ab, darunter die Art des zu bearbeitenden Werkstücks, die Bearbeitungsanforderungen, die Maschinenausstattung und die verfügbaren Ressourcen. Unternehmen sollten die spezifischen Anforderungen ihrer Anwendungen sorgfältig bewerten und das geeignete Führungssystem auswählen, um eine präzise und effiziente Bearbeitung zu gewährleisten.
Die kontinuierliche Weiterentwicklung von Werkstückführungssystemen zielt darauf ab, die Leistung und Flexibilität von Schleif- und Poliermaschinen weiter zu verbessern. Durch die Entwicklung neuer Führungstechnologien, Materialien und Technologien können Unternehmen innovative Lösungen für ihre Bearbeitungsanforderungen finden und ihre Wettbewerbsfähigkeit auf dem Markt stärken.
Diamantwerkzeuge
Diamantwerkzeuge: Diamantwerkzeuge sind hochwertige Schneid- und Schleifwerkzeuge, die mit Diamantpartikeln besetzt sind und für die Bearbeitung von harten Materialien wie Stein, Keramik, Glas und Hartmetall verwendet werden. Diamant ist eines der härtesten natürlichen Materialien und bietet eine außergewöhnliche Schneidleistung und Haltbarkeit, was sie zu einer bevorzugten Wahl für anspruchsvolle Bearbeitungsanwendungen macht.
Es gibt verschiedene Arten von Diamantwerkzeugen, die je nach den spezifischen Anforderungen der Anwendung ausgewählt werden können. Zu den gängigen Typen gehören:
- Diamantschleifscheiben: Diese Scheiben sind mit Diamantpartikeln besetzt, die in einem metallischen, keramischen oder galvanischen Bindemittel gebunden sind. Sie werden für das Schleifen von harten Materialien wie Beton, Stein, Granit und Keramik verwendet und bieten eine hohe Schleifleistung und Präzision.
- Diamantfräser: Diese Werkzeuge sind mit Diamantpartikeln besetzt und werden für das Fräsen von harten Materialien wie Glas, Keramik und Hartmetall verwendet. Sie bieten eine hohe Schneidleistung und Genauigkeit und eignen sich für die Bearbeitung von komplexen Formen und Profilen.
- Diamantbohrer: Diese Werkzeuge sind mit Diamantpartikeln besetzt und werden für das Bohren von harten Materialien wie Glas, Keramik, Marmor und Beton verwendet. Sie bieten eine hohe Bohrgeschwindigkeit und Präzision und eignen sich für die Herstellung von präzisen Bohrlöchern in verschiedenen Materialien.
- Diamantdrahtsägen: Diese Werkzeuge verwenden einen dünnen Diamantdraht, der um eine Trommel gespannt ist, um harte Materialien wie Stein, Glas und Keramik präzise zu schneiden. Sie bieten eine hohe Schneidleistung und Flexibilität und eignen sich für die Bearbeitung von großen Werkstücken oder komplexen Formen.
Die Verwendung von Diamantwerkzeugen bietet eine Vielzahl von Vorteilen, darunter eine verbesserte Schneidleistung, eine längere Standzeit der Werkzeuge, eine höhere Bearbeitungsgeschwindigkeit und eine bessere Oberflächenqualität der bearbeiteten Werkstücke. Diamantwerkzeuge sind zwar in der Anschaffung teurer als herkömmliche Werkzeuge, bieten jedoch eine überlegene Leistung und Rentabilität in anspruchsvollen Bearbeitungsanwendungen.
Die kontinuierliche Weiterentwicklung von Diamantwerkzeugen zielt darauf ab, die Leistung und Effizienz von Bearbeitungsprozessen weiter zu verbessern. Durch die Entwicklung neuer Bindemittel, Diamantpartikel und Herstellungsverfahren können Unternehmen innovative Lösungen für ihre Bearbeitungsanforderungen finden und ihre Wettbewerbsfähigkeit auf dem Markt stärken.
Automatisierung
Automatisierung: Automatisierung bezieht sich auf den Einsatz von Maschinen, Computern oder anderen technologischen Systemen, um Aufgaben oder Prozesse auszuführen, die zuvor von Menschen durchgeführt wurden, ohne kontinuierliche menschliche Eingriffe. In der Fertigungsindustrie spielt Automatisierung eine zunehmend wichtige Rolle bei der Optimierung von Produktionsprozessen, Verbesserung der Effizienz und Steigerung der Produktivität.
Im Kontext von Schleif- und Poliermaschinen ermöglicht Automatisierung die Durchführung von Bearbeitungsprozessen mit minimaler menschlicher Überwachung oder Intervention. Dies umfasst die Integration von Robotern, automatisierten Handhabungssystemen, CNC-Steuerung und anderen automatisierten Technologien, um den gesamten Produktionsprozess zu optimieren.
Die Automatisierung von Schleif- und Polierprozessen bietet eine Vielzahl von Vorteilen, darunter:
- Verbesserte Effizienz: Durch die Automatisierung können Bearbeitungsprozesse kontinuierlich und ohne Unterbrechungen durchgeführt werden, was zu einer verbesserten Gesamtproduktivität führt.
- Konsistenz: Automatisierte Systeme können Aufgaben mit hoher Genauigkeit und Konsistenz ausführen, was zu einer gleichbleibenden Qualität der bearbeiteten Werkstücke führt.
- Reduzierung von Ausschuss: Die präzise Steuerung von automatisierten Systemen minimiert Fehler und reduziert die Menge an fehlerhaften oder unbrauchbaren Werkstücken.
- Arbeitskräfteentlastung: Automatisierung ermöglicht es Unternehmen, weniger Arbeitskräfte für die Durchführung von repetitiven oder gefährlichen Aufgaben einzusetzen, was zu einer verbesserten Arbeitssicherheit führt.
- Flexibilität: Moderne automatisierte Systeme sind oft flexibel und können leicht an verschiedene Bearbeitungsanforderungen angepasst werden, indem Programme oder Einstellungen geändert werden.
Die Implementierung von Automatisierungstechnologien erfordert jedoch eine sorgfältige Planung, Investitionen in entsprechende Ausrüstung und Schulung des Personals. Unternehmen müssen die Kosten, Vorteile und Risiken der Automatisierung sorgfältig abwägen und sicherstellen, dass sie die richtigen Technologien für ihre spezifischen Anforderungen auswählen.
Die kontinuierliche Weiterentwicklung von Automatisierungstechnologien zielt darauf ab, die Leistungsfähigkeit und Flexibilität von Fertigungsprozessen weiter zu verbessern. Durch die Integration von künstlicher Intelligenz, maschinellem Lernen und IoT (Internet der Dinge) können Unternehmen intelligente und vorausschauende Fertigungssysteme entwickeln, die eine noch höhere Effizienz und Produktivität ermöglichen.
Robotertechnik
Robotertechnik: Robotertechnik bezieht sich auf den Einsatz von Robotern in verschiedenen Anwendungen, um Aufgaben autonom auszuführen oder menschliche Arbeitskräfte zu unterstützen. In der Fertigungsindustrie spielen Roboter eine zunehmend wichtige Rolle bei der Automatisierung von Produktionsprozessen, der Steigerung der Effizienz und der Verbesserung der Qualität.
Im Kontext von Schleif- und Poliermaschinen ermöglicht die Robotertechnik den Einsatz von Industrierobotern zur Durchführung von Bearbeitungsprozessen mit hoher Präzision und Wiederholbarkeit. Diese Roboter sind mit verschiedenen Werkzeugen und Endeffektoren ausgestattet, um eine Vielzahl von Aufgaben zu erledigen, einschließlich Schleifen, Polieren, Entgraten und Inspektion.
Die Vorteile der Robotertechnik in der Schleif- und Polierindustrie umfassen:
- Präzision und Konsistenz: Industrieroboter können Aufgaben mit hoher Genauigkeit und Konsistenz ausführen, was zu einer gleichbleibenden Qualität der bearbeiteten Werkstücke führt.
- Flexibilität: Roboter können leicht programmiert und an verschiedene Bearbeitungsanforderungen angepasst werden, indem Programme oder Einstellungen geändert werden. Dies ermöglicht es Unternehmen, schnell auf veränderte Marktanforderungen zu reagieren und verschiedene Produktvarianten herzustellen.
- Automatisierung komplexer Aufgaben: Industrieroboter können komplexe Bearbeitungsaufgaben ausführen, die für menschliche Arbeitskräfte schwierig, gefährlich oder zeitaufwendig wären. Dies umfasst die Bearbeitung von komplexen Geometrien, schwer zugänglichen Bereichen oder empfindlichen Materialien.
- Reduzierung von Ausschuss: Durch die präzise Steuerung von Industrierobotern kann die Menge an fehlerhaften oder unbrauchbaren Werkstücken reduziert werden, was zu geringeren Ausschussmengen und geringeren Kosten führt.
- Arbeitssicherheit: Der Einsatz von Robotern in gefährlichen oder anspruchsvollen Arbeitsumgebungen reduziert das Risiko von Verletzungen oder Unfällen für menschliche Arbeitskräfte und verbessert die allgemeine Arbeitssicherheit.
Die Implementierung von Robotertechnik erfordert jedoch eine sorgfältige Planung, Integration und Schulung des Personals. Unternehmen müssen die Kosten, Vorteile und Risiken der Robotertechnik sorgfältig abwägen und sicherstellen, dass sie die richtigen Robotertypen und -konfigurationen für ihre spezifischen Anforderungen auswählen.
Die kontinuierliche Weiterentwicklung von Robotertechnologien zielt darauf ab, die Leistungsfähigkeit und Flexibilität von Fertigungsprozessen weiter zu verbessern. Durch die Integration von künstlicher Intelligenz, maschinellem Lernen und fortschrittlicher Sensorik können Unternehmen intelligente und vernetzte Roboterlösungen entwickeln, die eine noch höhere Effizienz und Produktivität ermöglichen.
CNC-Steuerung
CNC-Steuerung: CNC (Computerized Numerical Control) -Steuerung bezieht sich auf die automatisierte Steuerung von Werkzeugmaschinen und Bearbeitungsprozessen mithilfe von Computerprogrammen und numerischen Befehlen. Diese Technologie spielt eine entscheidende Rolle in der modernen Fertigungsindustrie und ermöglicht eine präzise und effiziente Durchführung von Schleif- und Polierprozessen.
Im Kontext von Schleif- und Poliermaschinen ermöglicht die CNC-Steuerung die präzise Steuerung und Überwachung aller Aspekte des Bearbeitungsprozesses, einschließlich Geschwindigkeit, Positionierung, Werkzeugbewegung und Materialabtrag. CNC-gesteuerte Maschinen verwenden Computerprogramme, die mit numerischen Befehlen programmiert sind, um komplexe Bearbeitungsaufgaben automatisch auszuführen.
Die Vorteile der CNC-Steuerung in der Schleif- und Polierindustrie umfassen:
- Präzision: CNC-gesteuerte Maschinen können Aufgaben mit hoher Genauigkeit und Wiederholbarkeit ausführen, was zu einer gleichbleibenden Qualität der bearbeiteten Werkstücke führt.
- Effizienz: Die automatisierte Steuerung von CNC-Maschinen ermöglicht eine kontinuierliche Bearbeitung ohne menschliche Überwachung, was zu einer verbesserten Gesamtproduktivität führt.
- Flexibilität: CNC-Programme können leicht angepasst und geändert werden, um verschiedene Bearbeitungsanforderungen und -bedingungen zu berücksichtigen. Dies ermöglicht es Unternehmen, schnell auf veränderte Marktanforderungen zu reagieren und verschiedene Produktvarianten herzustellen.
- Komplexität: CNC-gesteuerte Maschinen können komplexe Bearbeitungsaufgaben ausführen, die für konventionelle Werkzeugmaschinen schwierig oder unmöglich wären. Dies umfasst die Bearbeitung von komplexen Geometrien, feinen Oberflächenstrukturen und schwer zugänglichen Bereichen.
- Überwachung und Fehlererkennung: CNC-Steuerungssysteme bieten eine integrierte Überwachung und Fehlererkennungsfunktion, um Probleme während des Bearbeitungsprozesses frühzeitig zu erkennen und zu beheben. Dies minimiert Ausschuss und verbessert die Gesamtqualität der bearbeiteten Werkstücke.
Die Implementierung von CNC-Steuerungssystemen erfordert jedoch spezialisierte Ausrüstung, Schulung des Personals und eine sorgfältige Programmierung der CNC-Programme. Unternehmen müssen die Kosten, Vorteile und Risiken der CNC-Steuerung sorgfältig abwägen und sicherstellen, dass sie die richtigen Technologien für ihre spezifischen Anforderungen auswählen.
Die kontinuierliche Weiterentwicklung von CNC-Steuerungstechnologien zielt darauf ab, die Leistungsfähigkeit und Flexibilität von Fertigungsprozessen weiter zu verbessern. Durch die Integration von künstlicher Intelligenz, maschinellem Lernen und fortschrittlicher Sensorik können Unternehmen intelligente und vernetzte CNC-Lösungen entwickeln, die eine noch höhere Effizienz und Produktivität ermöglichen.
Schleifband
Schleifband: Ein Schleifband ist ein flexibles Schleifmittel, das zur Bearbeitung von verschiedenen Werkstücken verwendet wird, insbesondere bei Schleif- und Poliermaschinen. Es besteht aus einem Trägermaterial, das mit Schleifkörnern beschichtet ist, die für die Abtragung von Material von der Oberfläche des Werkstücks verantwortlich sind. Schleifbänder kommen in verschiedenen Größen, Körnungen und Materialien vor, um den Anforderungen verschiedener Bearbeitungsanwendungen gerecht zu werden.
Die Schleifkörner auf einem Schleifband können aus verschiedenen Materialien wie Aluminiumoxid, Siliziumkarbid, Zirkonoxid oder Diamant bestehen, wobei jede Art ihre eigenen Vor- und Nachteile hat. Aluminiumoxid ist beispielsweise für die Bearbeitung von Metallen und Holz geeignet, während Siliziumkarbid für die Bearbeitung von Stein, Glas und Keramik verwendet wird. Zirkonoxid bietet eine verbesserte Schleifleistung und Haltbarkeit und wird oft bei anspruchsvollen Bearbeitungsanwendungen eingesetzt. Diamantbeschichtete Schleifbänder werden für die Bearbeitung von harten Materialien wie Hartmetall, Glas und Keramik eingesetzt und bieten eine überlegene Schleifleistung und Standzeit.
Das Trägermaterial eines Schleifbands kann aus verschiedenen Materialien wie Baumwolle, Polyester, Papier oder Gewebe bestehen. Jedes Material bietet unterschiedliche Eigenschaften in Bezug auf Flexibilität, Haltbarkeit und Wärmebeständigkeit, die je nach den Anforderungen der Bearbeitungsanwendung berücksichtigt werden müssen.
Schleifbänder werden in verschiedenen Bearbeitungsanwendungen eingesetzt, darunter Metallbearbeitung, Holzbearbeitung, Steinbearbeitung, Glasbearbeitung und vieles mehr. Sie werden auf Schleif- und Poliermaschinen montiert und bieten eine effiziente und präzise Bearbeitung von Werkstücken verschiedener Formen, Größen und Materialien.
Die Auswahl des richtigen Schleifbands hängt von verschiedenen Faktoren ab, darunter die Art des zu bearbeitenden Materials, die gewünschte Oberflächenqualität, die Bearbeitungsgeschwindigkeit und die Maschinenausstattung. Unternehmen sollten die spezifischen Anforderungen ihrer Bearbeitungsanwendungen sorgfältig bewerten und das geeignete Schleifband auswählen, um die gewünschten Ergebnisse zu erzielen.
Die kontinuierliche Weiterentwicklung von Schleifbandtechnologien zielt darauf ab, die Leistung und Effizienz von Schleif- und Polierprozessen weiter zu verbessern. Durch die Entwicklung neuer Materialien, Beschichtungen und Herstellungsverfahren können Unternehmen innovative Schleifbandlösungen finden, die ihre Produktivität steigern und ihre Wettbewerbsfähigkeit auf dem Markt stärken.
Schleifscheibe
Schleifscheibe: Eine Schleifscheibe ist ein rotierendes Werkzeug, das zum Schleifen, Entgraten, Schärfen und Polieren von Werkstücken verwendet wird. Sie besteht aus einem abrasiven Material, das an einem trägerartigen Rad befestigt ist und beim Drehen auf einer Schleif- oder Poliermaschine Material von der Oberfläche des Werkstücks abträgt.
Es gibt verschiedene Arten von Schleifscheiben, die je nach den spezifischen Anforderungen der Bearbeitungsanwendung ausgewählt werden können. Zu den gängigen Typen gehören:
- Schleifscheiben aus Aluminiumoxid: Diese Schleifscheiben sind ideal für die Bearbeitung von Metallen und anderen harten Materialien. Sie bieten eine gute Schleifleistung und Haltbarkeit und eignen sich für eine Vielzahl von Anwendungen in der Metallbearbeitung.
- Schleifscheiben aus Siliziumkarbid: Diese Schleifscheiben sind für die Bearbeitung von weichen bis mittelharten Materialien wie Stein, Glas, Keramik und Nicht-Eisenmetallen geeignet. Sie bieten eine hohe Schleifleistung und sind besonders für feine Oberflächenbearbeitungen geeignet.
- Schleifscheiben aus Zirkonoxid: Diese Schleifscheiben bieten eine verbesserte Schleifleistung und Haltbarkeit im Vergleich zu herkömmlichen Schleifscheiben. Sie eignen sich besonders für anspruchsvolle Anwendungen, bei denen hohe Materialabtragsraten und eine lange Standzeit erforderlich sind.
- Diamantschleifscheiben: Diese Schleifscheiben sind mit Diamantpartikeln besetzt und eignen sich für die Bearbeitung von harten und abrasiven Materialien wie Hartmetall, Glas und Keramik. Sie bieten eine überlegene Schleifleistung und Haltbarkeit und werden häufig in anspruchsvollen Bearbeitungsanwendungen eingesetzt.
Schleifscheiben sind in verschiedenen Formen und Größen erhältlich, einschließlich flacher Scheiben, Tassenrädern, Tellerscheiben und konischen Scheiben, die für verschiedene Bearbeitungsaufgaben geeignet sind. Die Auswahl der richtigen Schleifscheibe hängt von verschiedenen Faktoren ab, darunter die Art des zu bearbeitenden Materials, die gewünschte Oberflächenqualität und die Bearbeitungsgeschwindigkeit.
Die Verwendung von hochwertigen Schleifscheiben ist entscheidend für die Effizienz und Qualität von Schleif- und Polierprozessen. Unternehmen sollten die spezifischen Anforderungen ihrer Bearbeitungsanwendungen sorgfältig bewerten und das geeignete Schleifwerkzeug auswählen, um die gewünschten Ergebnisse zu erzielen.
Die kontinuierliche Weiterentwicklung von Schleifscheibentechnologien zielt darauf ab, die Leistung und Effizienz von Schleif- und Polierprozessen weiter zu verbessern. Durch die Entwicklung neuer Materialien, Bindemittel und Herstellungsverfahren können Unternehmen innovative Schleifscheibenlösungen finden, die ihre Produktivität steigern und ihre Wettbewerbsfähigkeit auf dem Markt stärken.
Schleifpasten
Schleifpasten: Schleifpasten sind abrasive Pasten oder Verbindungen, die zur Bearbeitung von Oberflächen verwendet werden, um Kratzer zu entfernen, Unebenheiten zu glätten und eine glänzende Oberfläche zu erzeugen. Sie bestehen aus einer Mischung aus abrasiven Partikeln und Bindemitteln, die aufgetragen und in die zu bearbeitende Oberfläche eingearbeitet werden.
Die Zusammensetzung von Schleifpasten kann je nach den spezifischen Anforderungen der Anwendung variieren, aber die meisten enthalten abrasive Partikel wie Aluminiumoxid, Siliziumkarbid, Diamant oder andere Materialien mit hoher Härte. Diese Partikel wirken wie feine Schleifmittel, um Material von der Oberfläche des Werkstücks abzutragen und eine glattere Oberfläche zu erzeugen.
Schleifpasten können in verschiedenen Konsistenzen und Viskositäten vorliegen, von dünnflüssigen Lösungen bis hin zu dickflüssigen Gelen oder Pasten. Die Auswahl der richtigen Konsistenz hängt von der Art der zu bearbeitenden Oberfläche, der gewünschten Bearbeitungsgeschwindigkeit und anderen Faktoren ab.
Die Anwendung von Schleifpasten erfolgt in der Regel durch Auftragen auf die zu bearbeitende Oberfläche mit einem geeigneten Werkzeug wie einem Schwamm, einer Bürste oder einem Tuch. Die Paste wird dann in kreisenden Bewegungen oder in einer bestimmten Richtung eingearbeitet, um das gewünschte Bearbeitungsergebnis zu erzielen.
Schleifpasten werden in einer Vielzahl von Anwendungen eingesetzt, darunter Metallbearbeitung, Automobilreparatur, Uhrenherstellung, Schmuckherstellung und feine Oberflächenbearbeitung. Sie bieten eine effektive Möglichkeit, Oberflächen zu bearbeiten und zu polieren, um eine verbesserte Ästhetik und Funktionalität zu erzielen.
Die Auswahl der richtigen Schleifpaste hängt von verschiedenen Faktoren ab, darunter die Art des zu bearbeitenden Materials, die gewünschte Oberflächenqualität und die spezifischen Bearbeitungsanforderungen. Unternehmen sollten die spezifischen Anforderungen ihrer Anwendungen sorgfältig bewerten und das geeignete Schleifmittel auswählen, um die gewünschten Ergebnisse zu erzielen.
Die kontinuierliche Weiterentwicklung von Schleifpasten zielt darauf ab, die Leistung und Effizienz von Schleif- und Polierprozessen weiter zu verbessern. Durch die Entwicklung neuer Formulierungen, Zusammensetzungen und Anwendungsverfahren können Unternehmen innovative Schleifpastenlösungen finden, die ihre Produktivität steigern und ihre Wettbewerbsfähigkeit auf dem Markt stärken.
Polierpasten
Polierpasten: Polierpasten sind spezielle Substanzen, die zur Bearbeitung von Oberflächen verwendet werden, um sie zu glätten, zu reinigen und einen glänzenden oder spiegelähnlichen Glanz zu erzeugen. Sie bestehen aus einer Mischung aus abrasiven Partikeln, Bindemitteln und Schmierstoffen, die auf die zu polierende Oberfläche aufgetragen und anschließend mit einem geeigneten Werkzeug wie einem Tuch oder einer Poliermaschine eingearbeitet werden.
Die Zusammensetzung von Polierpasten kann je nach den spezifischen Anforderungen der Anwendung variieren, aber die meisten enthalten feine abrasive Partikel wie Aluminiumoxid, Siliziumoxid, Diamant oder andere Materialien mit hoher Härte. Diese Partikel tragen dazu bei, Unebenheiten und Kratzer von der Oberfläche des Werkstücks zu entfernen und eine glattere Oberfläche zu erzeugen.
Polierpasten können in verschiedenen Konsistenzen und Viskositäten vorliegen, von dünnflüssigen Lösungen bis hin zu dicken Pasten oder Gelees. Die Auswahl der richtigen Konsistenz hängt von der Art der zu polierenden Oberfläche, der gewünschten Oberflächenqualität und anderen Faktoren ab.
Die Anwendung von Polierpasten erfolgt in der Regel durch Auftragen auf die zu polierende Oberfläche mit einem geeigneten Werkzeug wie einem Poliertuch, einer Polierbürste oder einer Poliermaschine. Die Paste wird dann in kreisenden Bewegungen oder in einer bestimmten Richtung eingearbeitet, um das gewünschte Polierergebnis zu erzielen.
Polierpasten werden in einer Vielzahl von Anwendungen eingesetzt, darunter Metallbearbeitung, Automobilreparatur, Schmuckherstellung, Uhrenherstellung und feine Oberflächenbearbeitung. Sie bieten eine effektive Möglichkeit, Oberflächen zu polieren und zu reinigen, um eine verbesserte Ästhetik und Funktionalität zu erzielen.
Die Auswahl der richtigen Polierpaste hängt von verschiedenen Faktoren ab, darunter die Art des zu polierenden Materials, die gewünschte Oberflächenqualität und die spezifischen Polieranforderungen. Unternehmen sollten die spezifischen Anforderungen ihrer Anwendungen sorgfältig bewerten und das geeignete Poliermittel auswählen, um die gewünschten Ergebnisse zu erzielen.
Die kontinuierliche Weiterentwicklung von Polierpasten zielt darauf ab, die Leistung und Effizienz von Polierprozessen weiter zu verbessern. Durch die Entwicklung neuer Formulierungen, Zusammensetzungen und Anwendungsverfahren können Unternehmen innovative Polierpastenlösungen finden, die ihre Produktivität steigern und ihre Wettbewerbsfähigkeit auf dem Markt stärken.
Abrasive
Abrasive: Ein Abrasiv ist ein Material, das zum Abtragen von Material von der Oberfläche eines Werkstücks verwendet wird. Abrasive werden in verschiedenen Bearbeitungsanwendungen eingesetzt, um Unebenheiten zu entfernen, Oberflächen zu glätten, Kanten zu schärfen oder Oberflächen zu polieren. Sie bestehen aus harten Partikeln, die entweder natürlich vorkommen oder künstlich hergestellt werden und an einem trägerartigen Material befestigt sind.
Es gibt verschiedene Arten von abrasiven Materialien, die je nach den spezifischen Anforderungen der Bearbeitungsanwendung ausgewählt werden können. Zu den gängigen Typen gehören:
- Aluminiumoxid: Dies ist eines der am häufigsten verwendeten abrasiven Materialien und eignet sich für die Bearbeitung von Metallen, Holz, Kunststoffen und anderen Materialien. Aluminiumoxid bietet eine gute Schleifleistung und Haltbarkeit und ist in verschiedenen Körnungen erhältlich, um unterschiedliche Bearbeitungsanforderungen zu erfüllen.
- Siliziumkarbid: Dieses abrasive Material ist bekannt für seine Härte und Schleifleistung und eignet sich besonders für die Bearbeitung von harten Materialien wie Stein, Glas, Keramik und Nicht-Eisenmetallen. Siliziumkarbid wird oft für feine Oberflächenbearbeitungen und Schleifanwendungen mit hohen Materialabtragsraten verwendet.
- Zirkonoxid: Zirkonoxid ist ein abrasives Material mit hoher Härte und Zähigkeit, das eine verbesserte Schleifleistung und Standzeit im Vergleich zu herkömmlichen abrasiven Materialien bietet. Es wird oft in anspruchsvollen Bearbeitungsanwendungen eingesetzt, bei denen hohe Materialabtragsraten und eine lange Standzeit erforderlich sind.
- Diamant: Diamant ist eines der härtesten natürlichen Materialien und bietet eine außergewöhnliche Schleifleistung und Haltbarkeit. Diamantabrasive werden für die Bearbeitung von extrem harten Materialien wie Hartmetall, Glas und Keramik eingesetzt und bieten eine überlegene Schleifleistung und Standzeit.
Die Auswahl des richtigen abrasiven Materials hängt von verschiedenen Faktoren ab, darunter die Art des zu bearbeitenden Materials, die gewünschte Oberflächenqualität, die Bearbeitungsgeschwindigkeit und andere spezifische Anforderungen der Bearbeitungsanwendung.
Die kontinuierliche Weiterentwicklung von abrasiven Materialien zielt darauf ab, die Leistung und Effizienz von Bearbeitungsprozessen weiter zu verbessern. Durch die Entwicklung neuer Materialzusammensetzungen, Bindemittel und Herstellungsverfahren können Unternehmen innovative abrasive Lösungen finden, die ihre Produktivität steigern und ihre Wettbewerbsfähigkeit auf dem Markt stärken.
Schleifmaschinen
Schleifmaschinen: Schleifmaschinen sind Werkzeugmaschinen, die zum Schleifen von Werkstücken verwendet werden, um eine glatte Oberfläche zu erzeugen oder Material von der Oberfläche des Werkstücks abzutragen. Sie sind in verschiedenen Ausführungen erhältlich, darunter Bandschleifmaschinen, Tellerschleifmaschinen, Schleifbockmaschinen, Rundschleifmaschinen und viele andere.
Die Arbeitsweise von Schleifmaschinen basiert auf der Rotation einer Schleifscheibe, eines Schleifbands oder eines anderen abrasiven Werkzeugs, das Material von der Oberfläche des Werkstücks abträgt. Die Werkstücke werden entweder manuell oder automatisch auf der Schleifmaschine positioniert und gegen die rotierende Schleifscheibe oder das Schleifband gedrückt, um den gewünschten Schleifprozess durchzuführen.
Schleifmaschinen werden in einer Vielzahl von Industrien und Anwendungen eingesetzt, darunter Metallbearbeitung, Holzbearbeitung, Steinbearbeitung, Glasbearbeitung, Keramikbearbeitung und viele andere. Sie bieten eine effiziente und präzise Möglichkeit, Werkstücke zu bearbeiten und eine glatte Oberfläche mit der gewünschten Oberflächenqualität zu erzielen.
Die Auswahl der richtigen Schleifmaschine hängt von verschiedenen Faktoren ab, darunter die Art des zu bearbeitenden Materials, die Größe und Form des Werkstücks, die gewünschte Oberflächenqualität, die Bearbeitungsgeschwindigkeit und andere spezifische Anforderungen der Bearbeitungsanwendung.
Moderne Schleifmaschinen sind oft mit verschiedenen Funktionen und Eigenschaften ausgestattet, um die Leistung und Effizienz der Bearbeitungsprozesse weiter zu verbessern. Dazu gehören automatische Vorschubsysteme, CNC-Steuerung, variable Drehzahlen, Kühl- und Schmiersysteme, Staubabsaugung und andere fortschrittliche Funktionen.
Die kontinuierliche Weiterentwicklung von Schleifmaschinentechnologien zielt darauf ab, die Leistungsfähigkeit und Flexibilität von Schleifprozessen weiter zu verbessern. Durch die Integration von Automatisierung, Robotik, künstlicher Intelligenz und IoT (Internet der Dinge) können Unternehmen intelligente und vernetzte Schleifmaschinenlösungen entwickeln, die eine noch höhere Effizienz und Produktivität ermöglichen.
Poliermaschinen
Poliermaschinen: Poliermaschinen sind Werkzeugmaschinen, die zum Polieren von Oberflächen verwendet werden, um einen glänzenden oder spiegelähnlichen Glanz zu erzeugen. Sie sind in verschiedenen Ausführungen erhältlich, darunter Rotationspolierer, Exzenterpolierer, Bandschleifer mit Polierfunktion und viele andere.
Die Arbeitsweise von Poliermaschinen basiert auf der Rotation eines Poliertellers oder einer Polierscheibe, die mit einem Polierpad oder einer Polierhaube ausgestattet ist, um das Poliermittel auf die zu polierende Oberfläche aufzutragen und zu verteilen. Das Werkstück wird gegen die rotierende Polierscheibe gedrückt, um das Poliermittel in die Oberfläche einzuarbeiten und den gewünschten Glanz zu erzeugen.
Poliermaschinen werden in einer Vielzahl von Industrien und Anwendungen eingesetzt, darunter Automobilindustrie, Metallverarbeitung, Schmuckherstellung, Uhrenherstellung, Bootsbau, Möbelindustrie und viele andere. Sie bieten eine effiziente und präzise Möglichkeit, Oberflächen zu polieren und einen hochglänzenden Finish zu erzielen.
Die Auswahl der richtigen Poliermaschine hängt von verschiedenen Faktoren ab, darunter die Art des zu polierenden Materials, die Größe und Form des Werkstücks, die gewünschte Oberflächenqualität, die Bearbeitungsgeschwindigkeit und andere spezifische Anforderungen der Polieranwendung.
Moderne Poliermaschinen sind oft mit verschiedenen Funktionen und Eigenschaften ausgestattet, um die Leistung und Effizienz der Polierprozesse weiter zu verbessern. Dazu gehören variable Drehzahlen, Schwingungsfunktionen, elektronische Steuerungen, Staubabsaugung und andere fortschrittliche Funktionen.
Die kontinuierliche Weiterentwicklung von Poliermaschinentechnologien zielt darauf ab, die Leistungsfähigkeit und Flexibilität von Polierprozessen weiter zu verbessern. Durch die Integration von Automatisierung, Robotik, künstlicher Intelligenz und IoT (Internet der Dinge) können Unternehmen intelligente und vernetzte Poliermaschinenlösungen entwickeln, die eine noch höhere Effizienz und Produktivität ermöglichen.
Materialabtrag
Materialabtrag: Materialabtrag bezeichnet den Prozess, bei dem Material von der Oberfläche eines Werkstücks entfernt wird, um eine bestimmte Form, Größe oder Oberflächenbeschaffenheit zu erreichen. Dieser Prozess findet in einer Vielzahl von Fertigungs- und Bearbeitungsanwendungen Anwendung, einschließlich Schleifen, Polieren, Fräsen, Drehen, Bohren und vielen anderen.
Beim Schleifen und Polieren erfolgt der Materialabtrag durch die Anwendung von abrasiven Werkzeugen wie Schleifscheiben, Schleifbändern, Schleifpasten oder Polierpasten, die Material von der Oberfläche des Werkstücks abtragen, um Unebenheiten zu entfernen und eine glatte Oberfläche zu erzeugen. Die Menge des abgetragenen Materials hängt von verschiedenen Faktoren ab, darunter die Art des verwendeten abrasiven Materials, die Bearbeitungsgeschwindigkeit, der Anpressdruck und andere Bearbeitungsparameter.
Der Materialabtrag kann auch durch spanende Bearbeitungsprozesse wie Fräsen, Drehen oder Bohren erfolgen, bei denen Werkzeugmaschinen verwendet werden, um Material von der Oberfläche des Werkstücks abzutragen und die gewünschte Form oder Geometrie zu erzeugen. Diese Prozesse erfordern die Verwendung von schneidenden Werkzeugen, die Material in Form von Spänen oder Spänen abtragen, um die gewünschten Bearbeitungsergebnisse zu erzielen.
Die Menge des Materialabtrags wird durch verschiedene Faktoren beeinflusst, darunter die Materialhärte, die Schnittgeschwindigkeit, die Vorschubgeschwindigkeit, die Werkzeuggeometrie und andere Bearbeitungsparameter. Eine präzise Steuerung dieser Parameter ist entscheidend, um die gewünschte Oberflächenqualität und Maßgenauigkeit zu erreichen.
Der Materialabtrag ist ein wesentlicher Schritt in vielen Fertigungs- und Bearbeitungsprozessen und beeinflusst direkt die Qualität, Genauigkeit und Effizienz der Produktion. Durch die Auswahl der richtigen Bearbeitungsverfahren, Werkzeuge und Parameter können Unternehmen sicherstellen, dass sie die gewünschten Bearbeitungsergebnisse erzielen und ihre Produktionsziele erreichen.
Oberflächenbeschaffenheit
Oberflächenbeschaffenheit: Die Oberflächenbeschaffenheit bezieht sich auf die Qualität und Eigenschaften der Oberfläche eines Werkstücks, die durch verschiedene Faktoren wie Rauheit, Glanz, Textur und Sauberkeit bestimmt werden. Sie spielt eine entscheidende Rolle in der Fertigungs- und Bearbeitungsindustrie, da sie die Funktionalität, Ästhetik und Leistung von Produkten beeinflusst.
Die Rauheit ist eine der wichtigsten Eigenschaften der Oberflächenbeschaffenheit und bezeichnet die Unebenheit oder Textur der Oberfläche auf mikroskopischer Ebene. Sie wird in der Regel mit Rauheitsmessgeräten gemessen und durch Parameter wie Rauheitstiefe, Rauheitshöhe und Rauheitsprofil charakterisiert. Eine geringe Rauheit deutet auf eine glatte Oberfläche hin, während eine hohe Rauheit auf eine unebene Oberfläche hinweist.
Der Glanz oder die Glätte einer Oberfläche ist ein Maß für ihre Reflexionsfähigkeit und Lichtdurchlässigkeit. Er wird oft visuell bewertet und kann durch Polieren, Schleifen oder Beschichtungsverfahren verbessert werden. Eine glänzende Oberfläche weist eine hohe Reflexionsfähigkeit auf, während eine matte Oberfläche diffuses Licht reflektiert.
Die Textur einer Oberfläche bezieht sich auf ihre visuelle und taktile Erscheinung und wird durch die Verteilung und Anordnung von Merkmalen wie Rillen, Graten, Poren und Kratzern bestimmt. Die Textur kann durch Bearbeitungsverfahren wie Schleifen, Polieren, Ätzen oder Strahlen kontrolliert und modifiziert werden, um die gewünschte Ästhetik und Funktionalität zu erzielen.
Die Sauberkeit einer Oberfläche bezieht sich auf das Vorhandensein von Verunreinigungen, Schmutz, Öl, Fett oder anderen Fremdpartikeln auf der Oberfläche. Eine saubere Oberfläche ist wichtig für viele Anwendungen, insbesondere in Bereichen wie der Automobilindustrie, Luft- und Raumfahrt, Elektronik und Medizintechnik, wo Verunreinigungen die Leistung oder Zuverlässigkeit von Produkten beeinträchtigen können.
Die Oberflächenbeschaffenheit wird durch verschiedene Faktoren beeinflusst, darunter die Art des verwendeten Materials, die Bearbeitungsmethoden, die Werkzeugauswahl, die Bearbeitungsparameter und Umgebungsbedingungen wie Temperatur und Feuchtigkeit. Eine präzise Kontrolle dieser Faktoren ist entscheidend, um die gewünschte Oberflächenqualität und Leistung zu erreichen.
Bandschleifmaschinen
Bandschleifmaschinen: Bandschleifmaschinen sind Werkzeugmaschinen, die zum Schleifen von Werkstücken verwendet werden und eine Schleifband als Schleifmittel verwenden. Sie bestehen aus einem motorisierten Antriebsmechanismus, der ein endloses Schleifband antreibt, das um zwei oder mehr Walzen oder Trommeln gespannt ist. Bandschleifmaschinen werden in verschiedenen Industrien eingesetzt, darunter Metallverarbeitung, Holzbearbeitung, Steinbearbeitung, Glasbearbeitung und viele andere.
Die Arbeitsweise einer Bandschleifmaschine basiert auf der kontinuierlichen Rotation des Schleifbands, das Material von der Oberfläche des Werkstücks abträgt, während das Werkstück entlang des Schleifbands geführt wird. Der Anpressdruck, die Bandgeschwindigkeit und andere Bearbeitungsparameter können je nach den spezifischen Anforderungen der Bearbeitungsanwendung eingestellt werden, um die gewünschten Bearbeitungsergebnisse zu erzielen.
Bandschleifmaschinen sind in verschiedenen Ausführungen erhältlich, darunter stationäre Modelle für Werkstatt- oder Produktionsumgebungen und tragbare Modelle für den mobilen Einsatz vor Ort. Sie können mit verschiedenen Zusatzausstattungen und Funktionen wie einstellbaren Schleiftischen, Schleifbandwechselvorrichtungen, Staubabsaugungssystemen und anderen ausgestattet sein, um die Leistung und Effizienz der Bearbeitungsprozesse weiter zu verbessern.
Die Verwendung von Bandschleifmaschinen bietet eine Reihe von Vorteilen, darunter eine hohe Schleifleistung, eine gleichmäßige Materialabtragung, die Möglichkeit, komplexe Formen und Konturen zu bearbeiten, und die Fähigkeit, große Werkstücke effizient zu bearbeiten. Sie sind vielseitige Werkzeugmaschinen, die für eine Vielzahl von Schleifanwendungen geeignet sind und eine effiziente und präzise Bearbeitung von Werkstücken ermöglichen.
Die kontinuierliche Weiterentwicklung von Bandschleifmaschinentechnologien zielt darauf ab, die Leistungsfähigkeit und Vielseitigkeit dieser Werkzeugmaschinen weiter zu verbessern. Durch die Integration von Automatisierung, Robotik, CNC-Steuerung und anderen fortschrittlichen Funktionen können Unternehmen intelligente und vernetzte Bandschleifmaschinenlösungen entwickeln, die eine noch höhere Effizienz und Produktivität ermöglichen.
Tellerschleifmaschinen
Tellerschleifmaschinen: Tellerschleifmaschinen sind Werkzeugmaschinen, die zum Schleifen von Werkstücken verwendet werden und eine rotierende Schleifteller als Schleifmittel verwenden. Sie bestehen aus einem motorisierten Antriebsmechanismus, der einen flachen Schleifteller antreibt, der mit einem Schleifpapier oder einer Schleifscheibe belegt ist. Tellerschleifmaschinen werden hauptsächlich in der Holzbearbeitung eingesetzt, finden aber auch Anwendung in der Metallbearbeitung und anderen Industrien.
Die Arbeitsweise einer Tellerschleifmaschine basiert auf der Rotation des Schleiftellers, der Material von der Oberfläche des Werkstücks abträgt, während das Werkstück gegen den rotierenden Teller gedrückt wird. Die Schleifgeschwindigkeit, der Anpressdruck und andere Bearbeitungsparameter können je nach den spezifischen Anforderungen der Bearbeitungsanwendung eingestellt werden, um die gewünschten Bearbeitungsergebnisse zu erzielen.
Tellerschleifmaschinen sind in verschiedenen Ausführungen erhältlich, darunter stationäre Modelle für Werkstatt- oder Produktionsumgebungen und tragbare Modelle für den mobilen Einsatz vor Ort. Sie können mit verschiedenen Zusatzausstattungen und Funktionen wie einstellbaren Schleiftischen, Schleifpapierwechselvorrichtungen, Staubabsaugungssystemen und anderen ausgestattet sein, um die Leistung und Effizienz der Bearbeitungsprozesse weiter zu verbessern.
Die Verwendung von Tellerschleifmaschinen bietet eine Reihe von Vorteilen, darunter eine hohe Schleifleistung, eine gleichmäßige Materialabtragung, die Möglichkeit, flache Oberflächen präzise zu bearbeiten, und die Fähigkeit, verschiedene Schleifmittel und Schleifkörnungen einzusetzen, um unterschiedliche Oberflächenanforderungen zu erfüllen.
Die kontinuierliche Weiterentwicklung von Tellerschleifmaschinentechnologien zielt darauf ab, die Leistungsfähigkeit und Vielseitigkeit dieser Werkzeugmaschinen weiter zu verbessern. Durch die Integration von Automatisierung, Robotik, CNC-Steuerung und anderen fortschrittlichen Funktionen können Unternehmen intelligente und vernetzte Tellerschleifmaschinenlösungen entwickeln, die eine noch höhere Effizienz und Produktivität ermöglichen.
Schleifbockmaschinen
Schleifbockmaschinen: Schleifbockmaschinen sind Werkzeugmaschinen, die zum Schleifen von Werkstücken verwendet werden und eine oder mehrere Schleifscheiben als Schleifmittel verwenden. Sie bestehen aus einem motorisierten Antriebsmechanismus, der eine oder mehrere Schleifscheiben antreibt, die auf einer horizontalen oder vertikalen Welle montiert sind. Schleifbockmaschinen werden in einer Vielzahl von Industrien eingesetzt, darunter Metallverarbeitung, Schmieden, Schmieden, Schweißen, Gießen und viele andere.
Die Arbeitsweise einer Schleifbockmaschine basiert auf der Rotation der Schleifscheibe, die Material von der Oberfläche des Werkstücks abträgt, während das Werkstück gegen die rotierende Schleifscheibe gedrückt wird. Die Schleifgeschwindigkeit, der Anpressdruck und andere Bearbeitungsparameter können je nach den spezifischen Anforderungen der Bearbeitungsanwendung eingestellt werden, um die gewünschten Bearbeitungsergebnisse zu erzielen.
Schleifbockmaschinen sind in verschiedenen Ausführungen erhältlich, darunter stationäre Modelle für Werkstatt- oder Produktionsumgebungen und tragbare Modelle für den mobilen Einsatz vor Ort. Sie können mit verschiedenen Zusatzausstattungen und Funktionen wie einstellbaren Schleiftischen, Schutzabdeckungen, Funkenfängern und anderen ausgestattet sein, um die Leistung und Sicherheit der Bearbeitungsprozesse weiter zu verbessern.
Die Verwendung von Schleifbockmaschinen bietet eine Reihe von Vorteilen, darunter eine hohe Schleifleistung, eine gleichmäßige Materialabtragung, die Möglichkeit, verschiedene Schleifscheiben und Körnungen einzusetzen, um unterschiedliche Oberflächenanforderungen zu erfüllen, und die Fähigkeit, verschiedene Bearbeitungsoperationen wie Schärfen, Entgraten und Polieren durchzuführen.
Die kontinuierliche Weiterentwicklung von Schleifbockmaschinentechnologien zielt darauf ab, die Leistungsfähigkeit und Vielseitigkeit dieser Werkzeugmaschinen weiter zu verbessern. Durch die Integration von Automatisierung, Robotik, CNC-Steuerung und anderen fortschrittlichen Funktionen können Unternehmen intelligente und vernetzte Schleifbockmaschinenlösungen entwickeln, die eine noch höhere Effizienz und Produktivität ermöglichen.
Rundschleifmaschinen
Rundschleifmaschinen: Rundschleifmaschinen sind Werkzeugmaschinen, die zum Schleifen von zylindrischen Werkstücken verwendet werden, um eine präzise runde Form, Oberflächenqualität und Maßgenauigkeit zu erreichen. Sie sind besonders für die Bearbeitung von Wellen, Zapfen, Bolzen, Stangen und anderen zylindrischen Teilen geeignet und finden Anwendung in einer Vielzahl von Industrien, darunter Maschinenbau, Automobilindustrie, Luft- und Raumfahrt, Medizintechnik und viele andere.
Die Arbeitsweise einer Rundschleifmaschine basiert auf der Rotation des Werkstücks, das zwischen einer rotierenden Schleifscheibe und einer festen oder beweglichen Spitze eingespannt ist. Die Schleifscheibe, die aus einem abrasiven Material besteht, trägt Material von der Oberfläche des Werkstücks ab, um die gewünschte Form, Oberflächenqualität und Maßgenauigkeit zu erreichen.
Rundschleifmaschinen sind in verschiedenen Ausführungen erhältlich, darunter Außenrundschleifmaschinen für das Schleifen der äußeren Oberfläche von Werkstücken, Innenrundschleifmaschinen für das Schleifen der inneren Bohrungen von Werkstücken und Universalrundschleifmaschinen, die sowohl für das Außen- als auch das Innenrundschleifen geeignet sind.
Die Verwendung von Rundschleifmaschinen bietet eine Reihe von Vorteilen, darunter eine hohe Schleifleistung, eine präzise Bearbeitung von zylindrischen Werkstücken, die Möglichkeit, komplexe Formen und Konturen zu bearbeiten, und die Fähigkeit, enge Toleranzen und Oberflächenrauheiten zu erreichen.
Die kontinuierliche Weiterentwicklung von Rundschleifmaschinentechnologien zielt darauf ab, die Leistungsfähigkeit und Vielseitigkeit dieser Werkzeugmaschinen weiter zu verbessern. Durch die Integration von Automatisierung, Robotik, CNC-Steuerung und anderen fortschrittlichen Funktionen können Unternehmen intelligente und vernetzte Rundschleifmaschinenlösungen entwickeln, die eine noch höhere Effizienz und Produktivität ermöglichen.
Schleifscheiben
Schleifscheiben: Schleifscheiben sind Werkzeuge, die zum Schleifen von Werkstücken verwendet werden, um Material von der Oberfläche abzutragen und die gewünschte Form, Oberflächenqualität und Maßgenauigkeit zu erreichen. Sie bestehen aus einem abrasiven Material, das in einer Matrix aus Bindemittel gebunden ist und auf einer Trägerscheibe montiert ist. Schleifscheiben sind in verschiedenen Formen, Größen und Körnungen erhältlich und werden für eine Vielzahl von Schleifanwendungen eingesetzt.
Die Arbeitsweise von Schleifscheiben basiert auf der Rotation der Schleifscheibe, die Material von der Oberfläche des Werkstücks abträgt, während das Werkstück gegen die rotierende Schleifscheibe gedrückt wird. Die Auswahl der richtigen Schleifscheibe hängt von verschiedenen Faktoren ab, darunter die Art des zu bearbeitenden Materials, die gewünschte Oberflächenqualität, die Bearbeitungsgeschwindigkeit und andere spezifische Anforderungen der Schleifanwendung.
Es gibt verschiedene Arten von Schleifscheiben, die je nach den Anforderungen der Schleifanwendung ausgewählt werden können. Zu den gängigen Typen gehören:
- Schleifscheiben aus Aluminiumoxid: Diese Schleifscheiben sind vielseitig einsetzbar und eignen sich für die Bearbeitung von Metallen, Holz, Kunststoffen und anderen Materialien. Sie bieten eine gute Schleifleistung und Haltbarkeit und sind in verschiedenen Körnungen erhältlich, um unterschiedliche Bearbeitungsanforderungen zu erfüllen.
- Schleifscheiben aus Siliziumkarbid: Diese Schleifscheiben sind bekannt für ihre Härte und Schleifleistung und eignen sich besonders für die Bearbeitung von harten Materialien wie Stein, Glas, Keramik und Nicht-Eisenmetallen. Sie werden oft für feine Oberflächenbearbeitungen und Schleifanwendungen mit hohen Materialabtragsraten verwendet.
- Diamantschleifscheiben: Diamantschleifscheiben sind eine der härtesten Schleifwerkzeuge und bieten eine außergewöhnliche Schleifleistung und Haltbarkeit. Sie werden für die Bearbeitung von extrem harten Materialien wie Hartmetall, Glas und Keramik eingesetzt und bieten eine überlegene Schleifleistung und Standzeit.
Die Auswahl der richtigen Schleifscheibe ist entscheidend für die Qualität und Effizienz des Schleifprozesses. Unternehmen sollten die spezifischen Anforderungen ihrer Schleifanwendungen sorgfältig bewerten und die geeignete Schleifscheibe auswählen, um die gewünschten Bearbeitungsergebnisse zu erzielen.
Schleifmittel
Schleifmittel: Schleifmittel sind Materialien, die zum Schleifen von Werkstücken verwendet werden, um Material von der Oberfläche abzutragen und die gewünschte Form, Oberflächenqualität und Maßgenauigkeit zu erreichen. Sie bestehen aus abrasiven Partikeln, die entweder natürlich vorkommen oder künstlich hergestellt werden und in einem Bindemittel gebunden sind, um eine Schleifscheibe, ein Schleifband oder ein Schleifpapier zu bilden.
Die Auswahl des richtigen Schleifmittels hängt von verschiedenen Faktoren ab, darunter die Art des zu bearbeitenden Materials, die gewünschte Oberflächenqualität, die Bearbeitungsgeschwindigkeit und andere spezifische Anforderungen der Schleifanwendung. Es gibt verschiedene Arten von Schleifmitteln, die je nach den Anforderungen der Schleifanwendung ausgewählt werden können. Zu den gängigen Typen gehören:
- Aluminiumoxid: Aluminiumoxid ist eines der am häufigsten verwendeten Schleifmittel und bietet eine gute Schleifleistung und Haltbarkeit. Es eignet sich für die Bearbeitung von Metallen, Holz, Kunststoffen und anderen Materialien und ist in verschiedenen Körnungen erhältlich, um unterschiedliche Bearbeitungsanforderungen zu erfüllen.
- Siliziumkarbid: Siliziumkarbid ist bekannt für seine Härte und Schleifleistung und eignet sich besonders für die Bearbeitung von harten Materialien wie Stein, Glas, Keramik und Nicht-Eisenmetallen. Es wird oft für feine Oberflächenbearbeitungen und Schleifanwendungen mit hohen Materialabtragsraten verwendet.
- Zirkonoxid: Zirkonoxid ist ein Schleifmittel mit hoher Härte und Zähigkeit, das eine verbesserte Schleifleistung und Standzeit bietet. Es wird oft in anspruchsvollen Bearbeitungsanwendungen eingesetzt, bei denen hohe Materialabtragsraten und eine lange Standzeit erforderlich sind.
- Diamant: Diamant ist eines der härtesten natürlichen Materialien und bietet eine außergewöhnliche Schleifleistung und Haltbarkeit. Diamantschleifmittel werden für die Bearbeitung von extrem harten Materialien wie Hartmetall, Glas und Keramik eingesetzt und bieten eine überlegene Schleifleistung und Standzeit.
Die kontinuierliche Weiterentwicklung von Schleifmitteln zielt darauf ab, die Leistung und Effizienz von Schleifprozessen weiter zu verbessern. Durch die Entwicklung neuer Materialzusammensetzungen, Bindemittel und Herstellungsverfahren können Unternehmen innovative Schleifmittel-Lösungen finden, die ihre Produktivität steigern und ihre Wettbewerbsfähigkeit auf dem Markt stärken.
Abrasive Werkzeuge
Abrasive Werkzeuge: Abrasive Werkzeuge sind Werkzeuge, die abrasive Materialien enthalten und zum Schleifen, Polieren, Entgraten und anderen Bearbeitungsprozessen verwendet werden, um Material von der Oberfläche abzutragen und die gewünschte Form, Oberflächenqualität und Maßgenauigkeit zu erreichen. Diese Werkzeuge bestehen aus einem Trägermaterial, das mit abrasiven Partikeln imprägniert oder beschichtet ist, um die erforderliche Schleifwirkung zu erzielen.
Es gibt verschiedene Arten von abrasiven Werkzeugen, die je nach den Anforderungen der Bearbeitungsanwendung eingesetzt werden können. Zu den gängigen Typen gehören:
- Schleifscheiben: Schleifscheiben sind kreisförmige Werkzeuge, die zum Schleifen von Werkstücken verwendet werden und abrasive Partikel auf einer Trägerscheibe montiert haben. Sie sind in verschiedenen Durchmessern, Körnungen und Bindemitteltypen erhältlich und werden in einer Vielzahl von Schleifanwendungen eingesetzt.
- Schleifbänder: Schleifbänder sind endlose Bänder, die mit abrasiven Partikeln beschichtet sind und auf einer Schleifmaschine verwendet werden, um Werkstücke zu schleifen oder zu polieren. Sie bieten eine hohe Oberflächenabtragrate und sind besonders für die Bearbeitung großer Werkstücke geeignet.
- Schleifpapier: Schleifpapier ist ein flexibles Werkzeug, das zum manuellen Schleifen oder zur Verwendung auf Schleifmaschinen verwendet wird. Es ist in verschiedenen Körnungen und Größen erhältlich und kann für eine Vielzahl von Schleif- und Polieranwendungen eingesetzt werden.
- Polierpads: Polierpads sind weiche Schaumstoff- oder Filzpolster, die mit abrasiven Partikeln beschichtet sind und zum Polieren von Oberflächen verwendet werden. Sie bieten eine sanfte Schleifwirkung und werden häufig in der Automobilindustrie, Möbelindustrie und anderen Anwendungen eingesetzt, um einen glänzenden Finish zu erzielen.
Die Auswahl des richtigen abrasiven Werkzeugs ist entscheidend für die Qualität und Effizienz des Bearbeitungsprozesses. Unternehmen sollten die spezifischen Anforderungen ihrer Bearbeitungsanwendungen sorgfältig bewerten und das geeignete abrasive Werkzeug auswählen, um die gewünschten Bearbeitungsergebnisse zu erzielen.
Schleifprozess
Schleifprozess: Der Schleifprozess ist ein Fertigungsverfahren, bei dem Material von der Oberfläche eines Werkstücks abgetragen wird, um die gewünschte Form, Oberflächenqualität und Maßgenauigkeit zu erreichen. Der Schleifprozess wird in einer Vielzahl von Industrien und Anwendungen eingesetzt, darunter Metallverarbeitung, Holzbearbeitung, Steinbearbeitung, Glasbearbeitung, Kunststoffbearbeitung und viele andere.
Der Schleifprozess umfasst im Allgemeinen die folgenden Schritte:
- Werkstückvorbereitung: Vor dem Schleifen muss das Werkstück gereinigt, entfettet und auf die Bearbeitung vorbereitet werden. Dies kann das Spannen des Werkstücks in einer Schleifmaschine, das Auswählen des geeigneten Schleifwerkzeugs und das Festlegen der Bearbeitungsparameter umfassen.
- Schleifoperation: Während der Schleifoperation wird das Werkstück gegen ein rotierendes Schleifmittel gedrückt, das Material von der Oberfläche abträgt. Die Schleifoperation kann durch manuelle Schleifen mit Schleifpapier oder durch maschinelles Schleifen mit Schleifmaschinen wie Bandschleifmaschinen, Tellerschleifmaschinen, Rundschleifmaschinen oder Schleifbockmaschinen durchgeführt werden.
- Überwachung und Anpassung: Während des Schleifprozesses ist es wichtig, den Fortschritt des Schleifvorgangs zu überwachen und bei Bedarf Anpassungen an den Bearbeitungsparametern vorzunehmen. Dies kann die Anpassung der Schleifgeschwindigkeit, des Anpressdrucks, der Schleifkörnung oder anderer Parameter umfassen, um die gewünschten Bearbeitungsergebnisse zu erzielen.
- Nachbearbeitung: Nach dem Schleifen können zusätzliche Bearbeitungsschritte erforderlich sein, um die Oberfläche weiter zu veredeln oder bestimmte Eigenschaften zu verbessern. Dazu gehören das Polieren, Entgraten, Reinigen, Beschichten oder andere Oberflächenbehandlungen, um die gewünschten Endbearbeitungsergebnisse zu erzielen.
Der Schleifprozess erfordert ein sorgfältiges Engineering und eine präzise Steuerung der Bearbeitungsparameter, um die gewünschte Oberflächenqualität und Maßgenauigkeit zu erreichen. Unternehmen setzen oft auf moderne Schleiftechnologien, um die Effizienz, Produktivität und Qualität ihrer Fertigungsprozesse zu verbessern und wettbewerbsfähig zu bleiben.
Schleifmaschinen
Schleifmaschinen: Schleifmaschinen sind Werkzeugmaschinen, die zum Schleifen von Werkstücken verwendet werden, um Material von der Oberfläche abzutragen und die gewünschte Form, Oberflächenqualität und Maßgenauigkeit zu erreichen. Sie spielen eine wichtige Rolle in einer Vielzahl von Fertigungsprozessen und werden in verschiedenen Industrien eingesetzt, darunter Metallverarbeitung, Holzbearbeitung, Steinbearbeitung, Glasbearbeitung und viele andere.
Es gibt verschiedene Arten von Schleifmaschinen, die je nach den spezifischen Anforderungen der Bearbeitungsanwendung eingesetzt werden können. Einige der gängigsten Typen sind:
- Bandschleifmaschinen: Bandschleifmaschinen verwenden ein endloses Schleifband, das um zwei oder mehr Walzen oder Trommeln gespannt ist, um Werkstücke zu schleifen. Sie bieten eine hohe Schleifleistung und eignen sich besonders für das Schleifen großer Flächen oder das Entfernen großer Materialmengen.
- Tellerschleifmaschinen: Tellerschleifmaschinen verwenden einen rotierenden Schleifteller, um Werkstücke zu schleifen. Sie sind besonders für das Schleifen von flachen Oberflächen geeignet und bieten eine präzise Materialabtragung und Oberflächenbearbeitung.
- Rundschleifmaschinen: Rundschleifmaschinen werden verwendet, um zylindrische Werkstücke zu schleifen und eine präzise runde Form, Oberflächenqualität und Maßgenauigkeit zu erreichen. Sie sind besonders für die Bearbeitung von Wellen, Bolzen, Stangen und anderen zylindrischen Teilen geeignet.
- Schleifbockmaschinen: Schleifbockmaschinen verwenden eine oder mehrere Schleifscheiben, um Werkstücke zu schleifen. Sie bieten eine vielseitige Schleiflösung und können für eine Vielzahl von Schleifanwendungen eingesetzt werden, einschließlich grober und feiner Bearbeitung.
Die Auswahl der richtigen Schleifmaschine hängt von verschiedenen Faktoren ab, darunter die Art des zu bearbeitenden Materials, die gewünschte Oberflächenqualität, die Bearbeitungsgeschwindigkeit und andere spezifische Anforderungen der Bearbeitungsanwendung. Unternehmen sollten die verschiedenen Typen von Schleifmaschinen sorgfältig bewerten und die geeignete Maschine auswählen, um die gewünschten Bearbeitungsergebnisse zu erzielen.
Schleifgeschwindigkeit
Schleifgeschwindigkeit: Die Schleifgeschwindigkeit ist ein wichtiger Parameter beim Schleifen von Werkstücken und bezieht sich auf die Geschwindigkeit, mit der sich das Schleifmittel über die Oberfläche des Werkstücks bewegt. Sie wird in Metern pro Minute (m/min) oder in Umdrehungen pro Minute (U/min) gemessen, je nachdem, ob es sich um eine lineare oder rotierende Bewegung handelt.
Die Schleifgeschwindigkeit beeinflusst direkt die Effizienz und Qualität des Schleifprozesses sowie die Lebensdauer des Schleifmittels und die Wärmeentwicklung am Werkstück. Einige wichtige Aspekte der Schleifgeschwindigkeit sind:
- Materialabtrag: Eine höhere Schleifgeschwindigkeit führt in der Regel zu einem schnelleren Materialabtrag von der Oberfläche des Werkstücks. Dies kann dazu beitragen, die Bearbeitungszeit zu verkürzen und die Produktivität zu steigern.
- Oberflächenqualität: Die Schleifgeschwindigkeit beeinflusst auch die Oberflächenqualität des bearbeiteten Werkstücks. Eine zu hohe Schleifgeschwindigkeit kann zu ungleichmäßigen Oberflächen, Riefenbildung und Überhitzung führen, während eine zu niedrige Geschwindigkeit zu einem unzureichenden Materialabtrag und einer schlechten Oberflächenqualität führen kann.
- Schleifmittelstandzeit: Die Schleifgeschwindigkeit wirkt sich auch auf die Standzeit des Schleifmittels aus. Eine zu hohe Geschwindigkeit kann das Schleifmittel übermäßig belasten und zu einem vorzeitigen Verschleiß führen, während eine zu niedrige Geschwindigkeit die Effizienz des Schleifprozesses beeinträchtigen kann.
- Wärmeentwicklung: Eine hohe Schleifgeschwindigkeit kann zu einer erhöhten Wärmeentwicklung am Werkstück führen, was zu Verformungen, Rissen oder anderen Schäden führen kann. Es ist wichtig, die Schleifgeschwindigkeit so einzustellen, dass die Wärmeentwicklung kontrolliert wird und das Werkstück nicht beschädigt wird.
Die optimale Schleifgeschwindigkeit hängt von verschiedenen Faktoren ab, darunter die Art des zu bearbeitenden Materials, die gewünschte Oberflächenqualität, die Art des Schleifmittels und andere spezifische Anforderungen der Schleifanwendung. Unternehmen sollten die Schleifgeschwindigkeit sorgfältig einstellen und überwachen, um die gewünschten Bearbeitungsergebnisse zu erzielen und die Lebensdauer ihrer Schleifwerkzeuge zu maximieren.
Anpressdruck
Anpressdruck: Der Anpressdruck ist eine wichtige Steuerungsgröße beim Schleifen von Werkstücken und bezieht sich auf die auf das Werkstück ausgeübte Kraft während des Schleifprozesses. Der Anpressdruck beeinflusst direkt die Schleifkraft, die Kontaktfläche zwischen Schleifmittel und Werkstück sowie die Materialabtragrate und die Oberflächenqualität des bearbeiteten Werkstücks.
Einige wichtige Aspekte des Anpressdrucks sind:
- Materialabtrag: Der Anpressdruck beeinflusst die Materialabtragrate beim Schleifen. Ein höherer Anpressdruck erhöht die Schleifkraft und führt zu einem schnelleren Materialabtrag, während ein niedrigerer Anpressdruck zu einem geringeren Materialabtrag führt.
- Oberflächenqualität: Der Anpressdruck beeinflusst auch die Oberflächenqualität des bearbeiteten Werkstücks. Ein zu hoher Anpressdruck kann zu einer übermäßigen Materialentfernung, Rauheit und Beschädigung der Oberfläche führen, während ein zu niedriger Anpressdruck zu einer unzureichenden Materialentfernung und einer schlechten Oberflächenqualität führen kann.
- Schleifkraft: Der Anpressdruck bestimmt die Schleifkraft, die zwischen dem Schleifmittel und dem Werkstück wirkt. Eine angemessene Schleifkraft ist erforderlich, um einen effektiven Materialabtrag zu gewährleisten, ohne das Werkstück zu beschädigen oder das Schleifmittel zu überlasten.
- Werkstückstabilität: Der Anpressdruck kann auch die Stabilität des Werkstücks während des Schleifprozesses beeinflussen. Ein angemessener Anpressdruck hilft, das Werkstück sicher und stabil in Position zu halten, um eine präzise Bearbeitung zu gewährleisten.
Die optimale Einstellung des Anpressdrucks hängt von verschiedenen Faktoren ab, darunter die Art des zu bearbeitenden Materials, die Art des Schleifmittels, die gewünschte Oberflächenqualität und andere spezifische Anforderungen der Schleifanwendung. Unternehmen sollten den Anpressdruck sorgfältig einstellen und überwachen, um die gewünschten Bearbeitungsergebnisse zu erzielen und die Lebensdauer ihrer Schleifwerkzeuge zu maximieren.
Kühlung
Kühlung: Die Kühlung ist ein wichtiger Aspekt beim Schleifen von Werkstücken, um die Wärmeentwicklung zu kontrollieren und die Lebensdauer der Schleifwerkzeuge zu maximieren. Während des Schleifprozesses entsteht Wärme durch die Reibung zwischen dem Schleifmittel und dem Werkstück, und eine unkontrollierte Wärmeentwicklung kann zu Werkstückverformungen, Rissen, Oberflächenbeschädigungen und vorzeitigem Verschleiß der Schleifwerkzeuge führen.
Es gibt verschiedene Methoden der Kühlung, die je nach den spezifischen Anforderungen der Schleifanwendung eingesetzt werden können. Einige gängige Kühlmethoden sind:
- Kühlschmiermittel: Kühlschmiermittel wie Schleiföle, Emulsionen oder Kühlschmierstoffe werden während des Schleifprozesses auf das Werkstück und das Schleifmittel aufgetragen, um die Wärmeentwicklung zu reduzieren und die Reibung zu verringern. Sie bieten eine effektive Kühlung und Schmierung und helfen, die Oberflächenqualität zu verbessern und die Standzeit der Schleifwerkzeuge zu verlängern.
- Kühlluft: Kühlluft wird verwendet, um das Werkstück und das Schleifmittel während des Schleifprozesses zu kühlen. Sie wird oft bei Trockenschleifanwendungen eingesetzt, bei denen kein Kühlschmiermittel verwendet wird. Kühlluft kann durch Düsen oder Gebläse auf das Werkstück und das Schleifmittel geblasen werden, um die Wärmeentwicklung zu reduzieren und die Bearbeitungseffizienz zu verbessern.
- Kühlsysteme: In einigen hochpräzisen Schleifanwendungen werden spezielle Kühlsysteme verwendet, um die Temperatur des Schleifprozesses genau zu kontrollieren. Dazu gehören geschlossene Kühlsysteme mit Temperaturregelung, Kühlsysteme mit Kühlung durch Flüssigstickstoff oder andere Kühlmittel und andere fortschrittliche Kühltechnologien.
Die richtige Kühlung ist entscheidend, um die Effizienz, Qualität und Lebensdauer des Schleifprozesses zu verbessern. Unternehmen sollten die spezifischen Anforderungen ihrer Schleifanwendungen sorgfältig bewerten und die geeignete Kühlmethode auswählen, um die gewünschten Bearbeitungsergebnisse zu erzielen und die Kosten zu optimieren.
Schleifparameter
Schleifparameter: Die Schleifparameter sind die variablen Größen, die während des Schleifprozesses eingestellt und gesteuert werden, um die gewünschten Bearbeitungsergebnisse zu erzielen. Diese Parameter beeinflussen direkt die Schleifleistung, die Oberflächenqualität und die Effizienz des Schleifprozesses. Einige wichtige Schleifparameter sind:
- Schleifgeschwindigkeit: Die Geschwindigkeit, mit der sich das Schleifmittel über die Oberfläche des Werkstücks bewegt. Sie bestimmt die Materialabtragrate, die Oberflächenqualität und die Lebensdauer des Schleifmittels.
- Anpressdruck: Die auf das Werkstück ausgeübte Kraft während des Schleifprozesses. Sie beeinflusst die Schleifkraft, die Materialabtragrate und die Stabilität des Werkstücks während des Schleifens.
- Körnung des Schleifmittels: Die Größe der abrasiven Partikel im Schleifmittel. Sie bestimmt die Oberflächenrauheit, die Materialabtragrate und die Oberflächenqualität des bearbeiteten Werkstücks.
- Kühlung: Die Methode der Wärmeentfernung während des Schleifprozesses. Sie beeinflusst die Wärmeentwicklung, die Oberflächenqualität und die Lebensdauer der Schleifwerkzeuge.
- Schleifscheibenprofil: Die Form und Geometrie der Schleifscheibe. Sie bestimmt die Kontur und das Profil des bearbeiteten Werkstücks.
- Schleifzyklus: Die Abfolge von Schleifoperationen und Pausen während des Schleifprozesses. Sie bestimmt die Bearbeitungszeit, die Oberflächenqualität und die Effizienz des Schleifens.
Die richtige Einstellung und Steuerung der Schleifparameter ist entscheidend, um die gewünschten Bearbeitungsergebnisse zu erzielen und die Effizienz des Schleifprozesses zu maximieren. Unternehmen sollten die spezifischen Anforderungen ihrer Schleifanwendungen sorgfältig bewerten und die geeigneten Schleifparameter auswählen und optimieren, um die gewünschten Bearbeitungsergebnisse zu erzielen und die Kosten zu optimieren.
Schleifqualität
Schleifqualität: Die Schleifqualität bezieht sich auf die Maßgenauigkeit, Oberflächenbeschaffenheit und geometrische Genauigkeit der bearbeiteten Werkstücke nach dem Schleifprozess. Sie ist ein entscheidender Aspekt für die Qualität und Funktionalität der Endprodukte und beeinflusst direkt deren Leistung, Haltbarkeit und Ästhetik.
Einige wichtige Aspekte der Schleifqualität sind:
- Oberflächenrauheit: Die Oberflächenrauheit beschreibt die Feinheit oder Rauheit der Oberfläche eines bearbeiteten Werkstücks. Eine hohe Schleifqualität bedeutet eine glatte und gleichmäßige Oberfläche mit minimalen Rauheitswerten, während eine niedrige Schleifqualität zu unebenen oder rauen Oberflächen führt.
- Maßgenauigkeit: Die Maßgenauigkeit bezieht sich auf die Genauigkeit der Abmessungen und Toleranzen eines bearbeiteten Werkstücks im Vergleich zu den vorgegebenen Spezifikationen. Eine hohe Schleifqualität bedeutet, dass das Werkstück die erforderlichen Abmessungen und Toleranzen innerhalb der spezifizierten Grenzen einhält.
- Formgenauigkeit: Die Formgenauigkeit beschreibt die Genauigkeit der geometrischen Form eines bearbeiteten Werkstücks im Vergleich zu den vorgegebenen Spezifikationen. Eine hohe Schleifqualität bedeutet, dass das Werkstück die gewünschte Form und Geometrie genau reproduziert.
- Oberflächenintegrität: Die Oberflächenintegrität bezieht sich auf die Unversehrtheit und Stabilität der Oberfläche eines bearbeiteten Werkstücks nach dem Schleifprozess. Eine hohe Schleifqualität bedeutet eine intakte und stabile Oberfläche ohne Risse, Scharten oder andere Defekte.
Die Erzielung einer hohen Schleifqualität erfordert präzise Bearbeitungsverfahren, sorgfältige Auswahl und Steuerung der Schleifparameter, hochwertige Schleifwerkzeuge und fortschrittliche Überwachungs- und Kontrollsysteme. Unternehmen sollten die Qualität ihrer Schleifprozesse kontinuierlich überwachen und verbessern, um die Anforderungen ihrer Kunden zu erfüllen und wettbewerbsfähig zu bleiben.
Schleifband
Schleifband: Ein Schleifband ist ein flexibles Schleifwerkzeug, das aus einem endlosen Band aus Schleifmaterial besteht und zum Schleifen von Werkstücken verwendet wird. Schleifbänder werden häufig in Bandschleifmaschinen eingesetzt und bieten eine effiziente Möglichkeit, Material von der Oberfläche eines Werkstücks abzutragen und die gewünschte Form, Oberflächenqualität und Maßgenauigkeit zu erreichen.
Ein Schleifband besteht aus einem Trägermaterial, das mit abrasiven Partikeln beschichtet ist und in verschiedenen Körnungen erhältlich ist, um unterschiedliche Schleifanforderungen zu erfüllen. Das Trägermaterial kann aus Baumwolle, Polyester, Papier oder anderen flexiblen Materialien bestehen, die eine gute Haltbarkeit und Flexibilität bieten.
Die Auswahl des richtigen Schleifbands hängt von verschiedenen Faktoren ab, darunter die Art des zu bearbeitenden Materials, die gewünschte Oberflächenqualität und die spezifischen Anforderungen der Schleifanwendung. Unternehmen können zwischen verschiedenen Schleifbandtypen wählen, darunter:
- Schleifbänder mit Aluminiumoxid: Diese Schleifbänder bieten eine gute Allround-Leistung und eignen sich für eine Vielzahl von Materialien, einschließlich Metall, Holz, Kunststoff und anderen Werkstoffen.
- Schleifbänder mit Siliziumkarbid: Diese Schleifbänder sind besonders für die Bearbeitung von harten Materialien wie Stein, Glas, Keramik und Nicht-Eisenmetallen geeignet und bieten eine hohe Schleifleistung und Standzeit.
- Schleifbänder mit Zirkonoxid: Diese Schleifbänder bieten eine verbesserte Schleifleistung und Standzeit im Vergleich zu herkömmlichen Schleifbändern und sind ideal für anspruchsvolle Schleifanwendungen geeignet, bei denen hohe Materialabtragsraten und eine lange Standzeit erforderlich sind.
Schleifbänder sind in verschiedenen Breiten, Längen und Körnungen erhältlich und können für eine Vielzahl von Schleifanwendungen eingesetzt werden, einschließlich grober und feiner Bearbeitung, Flächen- und Konturbearbeitung sowie Entgraten und Polieren.
Schleifscheibe
Schleifscheibe: Eine Schleifscheibe ist ein kreisförmiges Schleifwerkzeug, das zum Schleifen von Werkstücken verwendet wird. Schleifscheiben sind in verschiedenen Durchmessern, Dicken und Körnungen erhältlich und werden in einer Vielzahl von Schleifanwendungen eingesetzt, um Material von der Oberfläche abzutragen und die gewünschte Form, Oberflächenqualität und Maßgenauigkeit zu erreichen.
Schleifscheiben bestehen aus einem Trägermaterial, das mit abrasiven Partikeln beschichtet oder imprägniert ist und eine Vielzahl von Materialien umfassen kann, darunter Aluminiumoxid, Siliziumkarbid, Zirkonoxid und andere. Die Auswahl des richtigen Schleifscheibenmaterials hängt von verschiedenen Faktoren ab, darunter die Art des zu bearbeitenden Materials, die gewünschte Oberflächenqualität und die spezifischen Anforderungen der Schleifanwendung.
Es gibt verschiedene Arten von Schleifscheiben, die je nach den spezifischen Anforderungen der Schleifanwendung eingesetzt werden können, darunter:
- Schleifscheiben für Metallbearbeitung: Diese Schleifscheiben sind speziell für die Bearbeitung von Metallwerkstücken entwickelt und bieten eine hohe Schleifleistung und Standzeit.
- Schleifscheiben für Holzbearbeitung: Diese Schleifscheiben sind für die Bearbeitung von Holzwerkstücken konzipiert und bieten eine hohe Abtragsleistung und Oberflächenqualität.
- Schleifscheiben für Steinbearbeitung: Diese Schleifscheiben sind für die Bearbeitung von Stein- und Betonwerkstücken geeignet und bieten eine hohe Schleifleistung und Standzeit.
- Schleifscheiben für Glasbearbeitung: Diese Schleifscheiben sind für die Bearbeitung von Glaswerkstücken entwickelt und bieten eine präzise Bearbeitung und Oberflächenqualität.
Die Auswahl der richtigen Schleifscheibe ist entscheidend für die Qualität und Effizienz des Schleifprozesses. Unternehmen sollten die spezifischen Anforderungen ihrer Schleifanwendungen sorgfältig bewerten und die geeignete Schleifscheibe auswählen, um die gewünschten Bearbeitungsergebnisse zu erzielen und die Lebensdauer ihrer Schleifwerkzeuge zu maximieren.
Schleifpapier
Schleifpapier: Schleifpapier ist ein flexibles Schleifwerkzeug, das zum manuellen Schleifen oder zum Einsatz auf Schleifmaschinen verwendet wird. Es besteht aus einem Trägermaterial, das mit abrasiven Partikeln beschichtet ist und in verschiedenen Körnungen erhältlich ist, um unterschiedliche Schleifanforderungen zu erfüllen.
Schleifpapier ist in verschiedenen Formen und Größen erhältlich, darunter Bögen, Rollen, Scheiben und Streifen, um den Anforderungen unterschiedlicher Schleifanwendungen gerecht zu werden. Es kann für eine Vielzahl von Materialien verwendet werden, einschließlich Holz, Metall, Kunststoff, Lack und andere.
Die Auswahl des richtigen Schleifpapiers hängt von verschiedenen Faktoren ab, darunter die Art des zu bearbeitenden Materials, die gewünschte Oberflächenqualität und die spezifischen Anforderungen der Schleifanwendung. Schleifpapier ist in verschiedenen Körnungen erhältlich, die die Feinheit oder Grobheit des Schleifprozesses bestimmen.
Feinkörniges Schleifpapier mit höheren Körnungen wird für feine Oberflächenbearbeitung und Polieren verwendet, während grobkörniges Schleifpapier mit niedrigeren Körnungen für grobe Oberflächenbearbeitung und Entfernen von Material eingesetzt wird.
Schleifpapier wird sowohl in Handwerkzeugen wie Schleifblöcken, Schleifklotz und Handschleifern als auch in Schleifmaschinen wie Schwingschleifern, Exzenterschleifern und Bandschleifmaschinen verwendet. Es ist ein vielseitiges und kostengünstiges Schleifmittel, das in verschiedenen Industrien und Anwendungen weit verbreitet ist.
Schleifkorn
Schleifkorn: Das Schleifkorn, auch als abrasives Korn bezeichnet, ist das abrasive Material, das auf dem Trägermaterial von Schleifwerkzeugen wie Schleifbändern, Schleifscheiben, Schleifpapier und anderen Beschichtungen angebracht ist. Es ist das eigentliche Werkzeug, das beim Schleifen Material von der Oberfläche eines Werkstücks abträgt.
Das Schleifkorn besteht aus kleinen, harten Partikeln aus abrasivem Material wie Aluminiumoxid, Siliziumkarbid, Zirkonoxid, Diamant und anderen. Diese abrasiven Partikel sind in verschiedenen Formen, Größen und Härten erhältlich, um unterschiedliche Schleifanforderungen zu erfüllen.
Die Auswahl des richtigen Schleifkorns hängt von verschiedenen Faktoren ab, darunter die Art des zu bearbeitenden Materials, die gewünschte Oberflächenqualität und die spezifischen Anforderungen der Schleifanwendung.
- Aluminiumoxid: Aluminiumoxid ist das am häufigsten verwendete Schleifkorn und bietet eine gute Allround-Leistung für eine Vielzahl von Materialien, einschließlich Metall, Holz, Kunststoff und anderen.
- Siliziumkarbid: Siliziumkarbid ist besonders für die Bearbeitung von harten Materialien wie Stein, Glas, Keramik und Nicht-Eisenmetallen geeignet und bietet eine hohe Schleifleistung und Standzeit.
- Zirkonoxid: Zirkonoxid bietet eine verbesserte Schleifleistung und Standzeit im Vergleich zu herkömmlichen Schleifkörnern und ist ideal für anspruchsvolle Schleifanwendungen geeignet, bei denen hohe Materialabtragsraten und eine lange Standzeit erforderlich sind.
- Diamant: Diamant ist das härteste bekannte Schleifkorn und wird für hochpräzise Schleifanwendungen eingesetzt, bei denen eine extreme Härte und Verschleißfestigkeit erforderlich sind.
Die Auswahl des richtigen Schleifkorns ist entscheidend für die Effizienz, Qualität und Standzeit des Schleifprozesses. Unternehmen sollten die spezifischen Anforderungen ihrer Schleifanwendungen sorgfältig bewerten und das geeignete Schleifkorn auswählen, um die gewünschten Bearbeitungsergebnisse zu erzielen und die Lebensdauer ihrer Schleifwerkzeuge zu maximieren.
Schleifmittel
Schleifmittel: Schleifmittel sind Materialien, die zum Abtragen von Material von der Oberfläche eines Werkstücks verwendet werden, um die gewünschte Form, Oberflächenqualität und Maßgenauigkeit zu erreichen. Sie sind das Herzstück eines Schleifwerkzeugs und bestehen aus abrasiven Partikeln, die auf einem Trägermaterial angebracht sind.
Es gibt verschiedene Arten von Schleifmitteln, die je nach den spezifischen Anforderungen der Schleifanwendung eingesetzt werden können. Einige der gängigsten Schleifmittel sind:
- Schleifbänder: Schleifbänder bestehen aus einem endlosen Band aus Schleifmaterial, das um zwei oder mehr Walzen oder Trommeln gespannt ist. Sie werden in Bandschleifmaschinen verwendet und bieten eine effiziente Möglichkeit, große Flächen von Werkstücken zu schleifen.
- Schleifscheiben: Schleifscheiben sind kreisförmige Schleifwerkzeuge, die auf Schleifmaschinen wie Winkelschleifern, Tischschleifern und anderen eingesetzt werden. Sie sind in verschiedenen Durchmessern, Dicken und Körnungen erhältlich und eignen sich für eine Vielzahl von Schleifanwendungen.
- Schleifpapier: Schleifpapier ist ein flexibles Schleifwerkzeug, das zum manuellen Schleifen oder zum Einsatz auf Schleifmaschinen verwendet wird. Es besteht aus einem Trägermaterial, das mit abrasiven Partikeln beschichtet ist, und ist in verschiedenen Formen, Größen und Körnungen erhältlich.
- Schleifkörper: Schleifkörper sind feste oder poröse Materialien, die mit abrasiven Partikeln imprägniert sind und in Form von Schleifstiften, Schleifkugeln, Schleifrollen und anderen verwendet werden. Sie sind besonders für das Schleifen von schwer zugänglichen Bereichen und komplexen Formen geeignet.
Die Auswahl des richtigen Schleifmittels hängt von verschiedenen Faktoren ab, darunter die Art des zu bearbeitenden Materials, die gewünschte Oberflächenqualität und die spezifischen Anforderungen der Schleifanwendung. Unternehmen sollten die verschiedenen Arten von Schleifmitteln sorgfältig bewerten und das geeignete Schleifmittel auswählen, um die gewünschten Bearbeitungsergebnisse zu erzielen und die Effizienz des Schleifprozesses zu maximieren.
Polierscheibe
Polierscheibe: Eine Polierscheibe ist ein Schleifwerkzeug, das zum Polieren von Oberflächen verwendet wird, um eine glatte, glänzende und hochwertige Oberflächenfinish zu erzielen. Polierscheiben bestehen aus einem Trägermaterial, das mit abrasiven Partikeln oder Poliermittel beschichtet ist und auf Poliermaschinen wie Polierböcken, Poliermaschinen oder Handpoliergeräten montiert wird.
Es gibt verschiedene Arten von Polierscheiben, die je nach den spezifischen Anforderungen der Polieranwendung eingesetzt werden können. Einige der gängigsten Arten von Polierscheiben sind:
- Baumwollpolierscheiben: Diese Polierscheiben bestehen aus Baumwolle oder einem ähnlichen weichen Material, das mit Poliermittel imprägniert ist. Sie eignen sich besonders für das Polieren von Metallen, Schmuck und anderen empfindlichen Werkstücken.
- Filzpolierscheiben: Filzpolierscheiben bestehen aus festem Filzmaterial, das mit Poliermittel imprägniert ist. Sie sind besonders für das Polieren von Metallen, Glas und anderen harten Werkstoffen geeignet und bieten eine effiziente Möglichkeit, eine hochglänzende Oberfläche zu erzielen.
- Schwabbelscheiben: Schwabbelscheiben bestehen aus mehreren Lagen Baumwollgewebe, die mit Poliermittel beschichtet sind. Sie werden häufig zum Polieren von Holz, Kunststoff und anderen Werkstoffen verwendet und bieten eine gute Balance zwischen Schleifkraft und Poliereffekt.
Die Auswahl der richtigen Polierscheibe hängt von verschiedenen Faktoren ab, darunter die Art des zu polierenden Materials, die gewünschte Oberflächenqualität und die spezifischen Anforderungen der Polieranwendung. Unternehmen sollten die verschiedenen Arten von Polierscheiben sorgfältig bewerten und die geeignete Polierscheibe auswählen, um die gewünschten Polierergebnisse zu erzielen und die Oberflächenqualität ihrer Werkstücke zu verbessern.
Poliermittel
Poliermittel: Poliermittel sind Substanzen, die zum Polieren von Oberflächen verwendet werden, um eine glatte, glänzende und hochwertige Oberflächenfinish zu erzielen. Sie enthalten abrasive Partikel oder Chemikalien, die Material von der Oberfläche abtragen und Unregelmäßigkeiten entfernen, um eine gleichmäßige und reflektierende Oberfläche zu erzeugen.
Es gibt verschiedene Arten von Poliermitteln, die je nach den spezifischen Anforderungen der Polieranwendung eingesetzt werden können. Einige der gängigsten Arten von Poliermitteln sind:
- Paste: Polierpasten bestehen aus einer Mischung aus abrasiven Partikeln, Ölen und anderen Zusatzstoffen und werden häufig zum Handpolieren von Metallen, Schmuck und anderen Werkstücken verwendet. Sie bieten eine effektive Möglichkeit, Oberflächen zu polieren und eine glänzende Oberflächenfinish zu erzielen.
- Flüssigkeiten: Polierflüssigkeiten sind flüssige Formulierungen, die abrasive Partikel in einer Trägerflüssigkeit enthalten und für das Polieren von Lacken, Kunststoffen und anderen Oberflächen verwendet werden. Sie sind besonders für den Einsatz auf Poliermaschinen geeignet und bieten eine schnelle und effiziente Möglichkeit, Oberflächen zu polieren und zu versiegeln.
- Pulver: Polierpulver sind feine Pulverformulierungen, die abrasive Partikel enthalten und mit Wasser oder anderen Flüssigkeiten gemischt werden, um eine Paste oder Suspension zu bilden. Sie werden häufig zum Polieren von Edelsteinen, Glas und anderen harten Werkstoffen verwendet und bieten eine präzise Kontrolle über den Polierprozess.
Die Auswahl des richtigen Poliermittels hängt von verschiedenen Faktoren ab, darunter die Art des zu polierenden Materials, die gewünschte Oberflächenqualität und die spezifischen Anforderungen der Polieranwendung. Unternehmen sollten die verschiedenen Arten von Poliermitteln sorgfältig bewerten und das geeignete Poliermittel auswählen, um die gewünschten Polierergebnisse zu erzielen und die Oberflächenqualität ihrer Werkstücke zu verbessern.
Maschinenprogramm für die Metallbearbeitung
Metallbearbeitungsmaschinen wie Bördel und Beschneide Maschinen, Flanschmaschinen, Beschneide und Bördelmaschinen, Umformtechnik, Rohrbiegemaschinen, Bandsäge für Metall, Hydraulische Horizontalpresse, Kantenschneide-Bördelmaschine, Kantenbördelmaschine, Entgratungsmaschine, Innen- und Außenpoliermaschine für Edelstahltöpfe, Kreisschneidemaschine, Profilbiegemaschine und Rundschweißmaschine
Unsere Metallbearbeitungsmaschinen sind:
- Rohrbiegemaschine
- Horizontale Presse
- Bandsäge für Metall
- Profilbiegemaschine
- Tiefziehpresse
- Rundschweißmaschine
- Kantenschneide-Bördelmaschine
- Topf- und Pfannenpoliermaschine
- Poliermaschine für flache Oberflächen