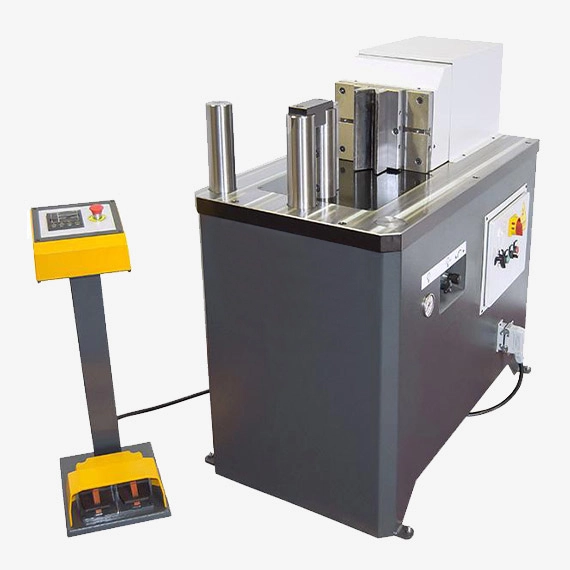
Stahl Umformen ohne Rückfederung: Die Vermeidung von Rückfederung beim Umformen von Stahl ist eine wichtige Herausforderung in der Metallverarbeitung, da Rückfederung die Präzision und Qualität der gefertigten Teile beeinträchtigen kann. Hier sind einige Ansätze, um die Rückfederung beim Umformen von Stahl zu minimieren:
1. Materialwahl und Vorerwärmung
- Hochfester Stahl: Die Wahl eines geeigneten Stahls kann die Rückfederung reduzieren. Hochfeste Stähle neigen beispielsweise oft weniger zur Rückfederung als weichere Stahlsorten.
- Vorwärmen des Stahls: Durch die Erwärmung des Stahls auf eine bestimmte Temperatur wird die Verformbarkeit erhöht und die Elastizität verringert, wodurch die Rückfederung reduziert wird.
2. Überbiegen der Bauteile
- Überbiegen: Ein kontrolliertes Überbiegen in die entgegengesetzte Richtung der Rückfederung hilft, das Material in die gewünschte Form zu bringen. Die genaue Kontrolle des Überbiegegrades ist entscheidend, um die gewünschte Form zu erreichen.
3. Anpassen der Werkzeuggeometrie
- Spezielle Werkzeuge: Werkzeuge können so entworfen werden, dass sie die Rückfederung bereits im Umformprozess berücksichtigen. Die Form des Werkzeugs wird dabei so angepasst, dass das Werkstück nach der Rückfederung die gewünschte Endgeometrie erreicht.
- Negativwinkel und Radiusanpassung: Durch die Wahl bestimmter Negativwinkel und Radien kann die Rückfederung ebenfalls reduziert werden, da das Material durch diese Maßnahmen stärker in die gewünschte Form gezwungen wird.
4. Elastisches Nachformen (Springback Compensation)
- Computerberechnung: Durch Simulationen und Berechnungen kann die Rückfederung im Voraus berechnet und berücksichtigt werden. Dies ermöglicht eine präzisere Herstellung der Werkzeuge und somit eine genauere Kontrolle der Rückfederung.
- Druck nach dem Umformen: Ein zweiter Umformschritt, bei dem das Material unter Druck gehalten wird, kann ebenfalls helfen, die Elastizität zu verringern und das Bauteil in Form zu halten.
5. Temperaturgesteuertes Umformen
- Durch Umformverfahren wie das Warmumformen wird Stahl auf Temperaturen oberhalb der Rekristallisationstemperatur erhitzt. In diesem Zustand zeigt Stahl deutlich weniger Rückfederung und behält seine Form besser bei.
- Auch Verfahren wie das Presshärten (Kombination aus Umformen und Abkühlen) wird eingesetzt, um die Rückfederung zu minimieren und zugleich die Festigkeit zu steigern.
6. Einsatz von Spannungsarme Glühbehandlungen
- Nachträgliches Glühen: Durch spannungsarmes Glühen nach dem Umformen kann die Rückfederung ebenfalls verringert werden, da innere Spannungen abgebaut werden. Dieses Verfahren wird oft für Bauteile angewandt, die eine hohe Maßgenauigkeit erfordern.
7. Optimierung der Prozessparameter
- Anpassung der Umformgeschwindigkeit: Langsames und kontrolliertes Umformen kann die Rückfederung reduzieren. Hierbei wird das Material langsamer und gezielter verformt, wodurch die Spannung besser kontrolliert werden kann.
- Drücken oder Ziehen des Materials: Einige Techniken, wie z.B. das Drücken oder Ziehen des Materials in kontrollierten Schritten, können die Rückfederung erheblich verringern.
Durch eine Kombination dieser Ansätze lässt sich die Rückfederung beim Umformen von Stahl stark reduzieren, was zu präziseren und qualitativ hochwertigeren Endprodukten führt.
Einleitung
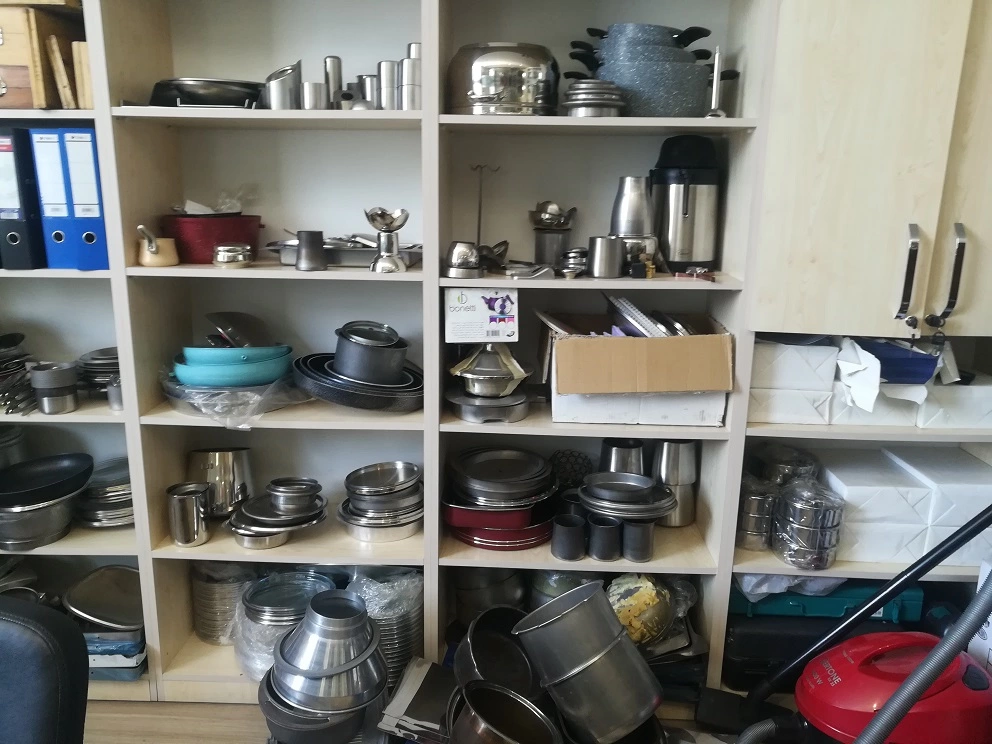
Das Umformen von Stahl ist ein zentraler Prozess in der modernen Metallverarbeitung. Es ist essenziell für die Herstellung einer Vielzahl von Produkten in der Automobil-, Bau- und Maschinenbauindustrie. Ein häufig auftretendes Problem ist die sogenannte Rückfederung: Nach dem Umformen strebt das Material, aufgrund seiner elastischen Eigenschaften, teilweise zurück in die ursprüngliche Form. Um diesen Effekt zu minimieren, spielen die richtige Materialwahl und die Vorerwärmung eine entscheidende Rolle. In dieser Abhandlung beleuchten wir die Mechanismen der Rückfederung, welche Stahlsorten besonders geeignet sind und wie die Vorerwärmung Einfluss auf die Verformbarkeit und Stabilität nimmt.
1. Grundlagen der Rückfederung und ihre Ursachen
Rückfederung beschreibt die elastische Verformung, die das Material nach der Belastung erfährt, wenn die äußeren Kräfte entfernt werden. Diese Eigenschaft hängt mit den elastischen und plastischen Verformungseigenschaften des Materials zusammen. Während der Umformung wird Stahl in die plastische Phase gebracht, doch sobald die Belastung endet, kehrt ein Teil des Materials durch elastische Dehnung zur ursprünglichen Form zurück. Das Ausmaß der Rückfederung hängt von mehreren Faktoren ab, darunter:
- Elastizitätsmodul des Materials: Je höher das Elastizitätsmodul, desto stärker neigt das Material zur Rückfederung.
- Streckgrenze und Härte: Stahlsorten mit höherer Streckgrenze zeigen tendenziell stärkere Rückfederung.
- Geometrie des Werkstücks: Dünne Bleche oder komplexe Geometrien sind stärker von Rückfederung betroffen.
Die Rückfederung erschwert die präzise Formgebung und führt oft zu Abweichungen von der Zielgeometrie.
2. Einfluss der Materialwahl auf die Rückfederung
2.1 Hochfester Stahl und seine Vorteile
Hochfeste Stähle haben eine hohe Streckgrenze und ein vergleichsweise hohes Elastizitätsmodul. Ihre Eigenschaften tragen zu einer geringeren plastischen Verformung bei, was sie in einigen Fällen für die Rückfederung anfällig macht. Dennoch bieten hochfeste Stähle Vorteile, da sie durch ihre Festigkeit stabilere Werkstücke erlauben, selbst bei geringerer Materialdicke. Beliebte hochfeste Stahlsorten sind:
- DP-Stähle (Dual-Phase): Kombinieren Festigkeit und Duktilität durch eine Mischung aus weichen Ferrit- und harten Martensit-Phasen.
- TRIP-Stähle (Transformation Induced Plasticity): Diese Stähle erhöhen ihre Festigkeit bei plastischer Verformung durch Phasenumwandlung, wodurch sie weniger anfällig für Rückfederung sind.
Vorteil: Hochfeste Stähle sind weniger elastisch und neigen daher, bei geeigneter Verarbeitung, zu einer geringeren Rückfederung.
2.2 Edelstahl und seine Herausforderungen
Edelstähle wie Austenitischer Edelstahl, sind für ihre hohe Korrosionsbeständigkeit bekannt, jedoch stellt die starke Rückfederung eine Herausforderung dar. Insbesondere bei austenitischen Stählen, die im Automobil- und Luftfahrtsektor beliebt sind, erschwert der hohe Elastizitätsgrad die präzise Umformung.
2.3 Werkstoffauswahl in Abhängigkeit von der gewünschten Umformung
Die Materialwahl sollte nach der Art der geplanten Umformung erfolgen. Für Anwendungen, bei denen Rückfederung kritisch ist, eignen sich Materialien mit:
- Niedrigem Elastizitätsmodul: Hier zeigt das Material weniger elastische Verformung.
- Geringer Streckgrenze: Ermöglicht eine stabilere plastische Verformung.
- Guter Duktilität: Materialien wie Baustahl, die leicht plastisch verformbar sind, zeigen oft eine geringere Rückfederung.
Beispiele:
- Baustahl: Zeigt geringe Rückfederung und ist kostengünstig, jedoch weniger korrosionsbeständig.
- Legierter Stahl: Mit Anpassungen in der Legierung, etwa durch Mangan, kann der Stahl widerstandsfähiger und elastischer gemacht werden.
3. Einfluss der Vorerwärmung auf das Umformverhalten
Die Vorerwärmung hat einen signifikanten Einfluss auf die Umformbarkeit und Rückfederung des Materials. Bei erhöhter Temperatur zeigt Stahl ein verändertes Verhalten, das sich in einer verbesserten Duktilität und einer verringerten Rückfederung widerspiegelt.
3.1 Mechanismen der Vorerwärmung
Durch die Erwärmung des Materials auf Temperaturen zwischen 200°C und 900°C, abhängig vom Stahlsorte und -typ, wird der Stahl weicher und plastischer, was seine Verformbarkeit erhöht. Die Vorerwärmung reduziert die Rückfederung durch folgende Mechanismen:
- Erhöhung der Beweglichkeit von Versetzungen: Dies führt zu einer geringeren Streckgrenze und damit zu einer verbesserten plastischen Verformung.
- Phasenumwandlungen: Bei bestimmten Temperaturen können Phasen wie Ferrit oder Martensit in eine andere Struktur übergehen, was die Rückfederung minimiert.
3.2 Vorteile des Warmumformens zur Minimierung der Rückfederung
Beim Warmumformen wird das Material auf Temperaturen erhitzt, die über der Rekristallisationstemperatur (etwa 400-500°C) liegen. Die Vorteile dieses Verfahrens umfassen:
- Verringerte Rückfederung: Die weichere Struktur zeigt bei dieser Temperatur eine geringere Tendenz, in die Ausgangsform zurückzukehren.
- Erhöhte Umformgenauigkeit: Aufgrund der verringerten Rückfederung kann das Material präziser geformt werden.
- Verbesserte Oberflächenqualität: Das Material zeigt bei hohen Temperaturen eine glattere Oberfläche, was die Nachbearbeitung erleichtert.
3.3 Anwendungsfälle und Beispiele
Warmumformverfahren werden häufig in der Automobilindustrie angewandt, etwa bei der Herstellung von Karosserieteilen. Diese Bauteile erfordern eine hohe Maßgenauigkeit und Festigkeit, was durch das Warmumformen und die gleichzeitige Kühlung nach der Umformung erreicht wird. Beispiele hierfür sind:
- Türverstärkungen: Hohe Genauigkeit bei geringer Rückfederung ist wichtig, um eine exakte Passform zu garantieren.
- Rahmen und Stoßstangen: Diese Bauteile profitieren von der Festigkeitssteigerung durch das Warmumformen.
3.4 Spezielle Methoden zur Vorerwärmung
Die Wahl der Methode hängt von der Bauteilgröße und dem gewünschten Umformergebnis ab.
- Induktionsheizung: Effiziente Erwärmung mit präziser Temperaturregelung für kleine bis mittelgroße Bauteile.
- Öfen: Einsatz bei großen Bauteilen, die auf eine homogene Temperatur gebracht werden müssen.
- Laserheizung: Kommt vermehrt bei kleinen und komplexen Teilen zum Einsatz, die punktuell erwärmt werden müssen.
4. Kombinierte Strategien zur Minimierung der Rückfederung
4.1 Überbiegen und Warmumformen
Ein gängiger Ansatz, um die Rückfederung weiter zu reduzieren, ist das gezielte Überbiegen. Beim Überbiegen wird das Bauteil über den gewünschten Winkel hinaus geformt, um den Rückfedereffekt auszugleichen. Wird dies mit einer Vorerwärmung kombiniert, lässt sich die Rückfederung besonders bei hochfesten Stählen stark vermindern.
4.2 Verfestigungsprozesse nach dem Umformen
Verfestigungsprozesse wie die Kaltverfestigung oder das Abschrecken nach dem Warmumformen bieten zusätzliche Vorteile, da sie die Formstabilität nach der Umformung unterstützen und Restspannungen reduzieren, die zu Rückfederung führen könnten.
5. Fazit und Ausblick
Die Minimierung der Rückfederung ist für die Präzision und Qualität der Bauteile essenziell, insbesondere in Industrien, die hohe Maßgenauigkeit erfordern. Die Wahl des richtigen Materials und die gezielte Vorerwärmung sind Schlüsselfaktoren, um die Rückfederung zu kontrollieren und die Formstabilität zu erhöhen.
Die Kombination aus hochfesten Stählen, präziser Temperatursteuerung und maßgeschneiderten Umformtechniken bietet eine optimale Grundlage, um die Effizienz und Qualität in der Metallverarbeitung kontinuierlich zu verbessern. Dies ist besonders relevant für zukünftige Anwendungen, in denen Leichtbau und Festigkeit bei minimalem Materialeinsatz entscheidend sein werden.
Einleitung
Beim Umformen von Stahl ist die Rückfederung, eine unerwünschte elastische Erholung des Materials, eine häufige Herausforderung. Diese Eigenschaft kann die Maßgenauigkeit beeinträchtigen, was insbesondere in Branchen wie der Automobil-, Luftfahrt- und Bauindustrie unerwünscht ist. Eine Methode, um diese Rückfederung zu kompensieren, ist das Überbiegen des Werkstücks: Dabei wird das Bauteil über die gewünschte Endform hinaus gebogen, um den Rückfedereffekt auszugleichen und so eine präzise Geometrie zu gewährleisten. In dieser Abhandlung wird das Überbiegen detailliert beschrieben, einschließlich der physikalischen Grundlagen, Methoden und Anwendungsbereiche, sowie der Einflussfaktoren und Optimierungsstrategien.
1. Grundlagen der Rückfederung beim Umformen
Rückfederung tritt auf, wenn ein Werkstoff nach einer plastischen Verformung teilweise in seine ursprüngliche Form zurückkehrt. Die Ursache hierfür liegt in der elastischen Verformung, die parallel zur plastischen Verformung im Werkstoff stattfindet. Während der Umformprozess das Material in eine neue Geometrie zwingt, bleibt die elastische Spannung teilweise bestehen. Entfernt man die äußere Belastung, kehrt das Material durch diese elastische Spannung teilweise zurück. Die Ausprägung der Rückfederung hängt von verschiedenen Faktoren ab:
- Elastizitätsmodul: Ein höheres Elastizitätsmodul führt zu stärkerer Rückfederung.
- Streckgrenze des Materials: Stähle mit hoher Streckgrenze neigen oft zu stärkerer Rückfederung.
- Umformwinkel und -geometrie: Scharfe Winkel oder komplexe Geometrien sind besonders anfällig für Rückfederung.
Das Verständnis dieser Grundlagen ist essenziell, um den Effekt der Rückfederung im Umformprozess gezielt zu minimieren.
2. Prinzip des Überbiegens und sein Einfluss auf die Rückfederung
Beim Überbiegen wird das Bauteil gezielt über die gewünschte Endposition hinaus gebogen. Der Überbiegewinkel wird so gewählt, dass die Rückfederung das Werkstück letztendlich in die gewünschte Form bringt. Dieser Ansatz basiert auf der Kenntnis der Materialeigenschaften und einer präzisen Steuerung des Umformprozesses.
2.2 Physikalische Grundlage des Überbiegens
Durch das Überbiegen erzeugt man zusätzliche plastische Verformung im Material, wodurch die elastische Rückfederung besser kontrolliert werden kann. Der Überbiegewinkel Δα\Delta \alphaΔα ergibt sich aus der zu erwartenden Rückfederung und wird experimentell oder rechnerisch bestimmt. Die plastische Verformung wird dabei durch gezielte Dehnung oder Kompression des Materials aufrechterhalten.
Mathematische Herleitung des Überbiegewinkels: Der Überbiegewinkel Δα\Delta \alphaΔα kann durch folgende Beziehung bestimmt werden:Δα=αZiel+αRu¨ckfederung\Delta \alpha = \alpha_{\text{Ziel}} + \alpha_{\text{Rückfederung}}Δα=αZiel+αRu¨ckfederung
wobei αZiel\alpha_{\text{Ziel}}αZiel der gewünschte Endwinkel und αRu¨ckfederung\alpha_{\text{Rückfederung}}αRu¨ckfederung die erwartete Rückfederung ist. Eine präzise Berechnung erfordert eine umfassende Kenntnis der Materialeigenschaften und der Belastung.
3. Methoden und Ansätze beim Überbiegen
3.1 Experimentelle Bestimmung des Überbiegewinkels
Die experimentelle Bestimmung des Überbiegewinkels ist in der Praxis häufig gebräuchlich. Hierbei wird eine Serie von Bauteilen mit unterschiedlichen Überbiegewinkeln hergestellt und anschließend gemessen. Auf Basis dieser Daten lässt sich der ideale Überbiegewinkel für eine bestimmte Geometrie und Materialeigenschaft bestimmen.
Vorteile dieser Methode:
- Praktische Anwendbarkeit auch bei komplexen Geometrien
- Berücksichtigung aller prozessbedingten Einflüsse
Nachteile:
- Zeitaufwendig und kostspielig
- Bedarf eines hohen Materialaufwands für Testreihen
3.2 Rechnerische Simulation des Überbiegewinkels
Moderne Simulationssoftware erlaubt die Berechnung des optimalen Überbiegewinkels unter Berücksichtigung der Materialparameter und Prozessbedingungen. Durch Simulationen lassen sich die elastischen und plastischen Anteile der Verformung voraussagen, und der Überbiegewinkel kann präzise eingestellt werden.
Vorteile der Simulation:
- Zeit- und kostensparend
- Hohe Präzision und Flexibilität bei unterschiedlichen Materialien
Nachteile:
- Erfordert detaillierte Materialdaten und eine hohe Rechenleistung
- Abweichungen in der Praxis möglich, da reale Bedingungen schwer exakt nachzustellen sind
3.3 Automatisiertes Überbiegen durch CNC-Technologie
Moderne CNC-Maschinen können das Überbiegen präzise steuern und den benötigten Überbiegewinkel automatisch anpassen. Die Maschine misst dabei die Kräfte und passt den Winkel in Echtzeit an, um eine gleichmäßige Qualität zu gewährleisten.
4. Einflussfaktoren auf den Überbiegeprozess
4.1 Materialeigenschaften und deren Einfluss
Verschiedene Materialeigenschaften beeinflussen den optimalen Überbiegewinkel erheblich. Zu den wichtigsten Materialfaktoren zählen:
- Elastizitätsmodul: Je höher das Modul, desto größer muss der Überbiegewinkel sein, um die Rückfederung zu kompensieren.
- Festigkeit und Härte: Härtere Materialien benötigen einen größeren Überbiegewinkel, da sie stärker zur Rückfederung neigen.
- Mikrostruktur des Stahls: Bestimmte Mikrostrukturen, wie bei Dualphasen- oder Martensitstählen, wirken sich stark auf das Rückfederungsverhalten aus.
4.2 Geometrische Faktoren
Die Geometrie des Bauteils spielt eine entscheidende Rolle. Einfache, symmetrische Formen lassen sich leichter kontrollieren, während komplexe, asymmetrische Geometrien eine differenzierte Überbiegestrategie erfordern.
4.3 Temperatur und Umgebungseinflüsse
Erwärmung kann die Rückfederung reduzieren und ist ein häufig eingesetztes Mittel. Beim Überbiegen wird das Material oft vorerwärmt, um eine höhere Formbarkeit und eine geringere Rückfederung zu erreichen. Eine Umgebungstemperaturkontrolle ist daher oft notwendig, insbesondere bei Materialien mit hoher Streckgrenze.
5. Anwendung des Überbiegens in der Industrie
5.1 Überbiegen in der Automobilindustrie
In der Automobilindustrie ist die Maßgenauigkeit essenziell, insbesondere bei Bauteilen wie Karosserieteilen und Verstärkungen, wo exakte Passformen gefordert sind. Das Überbiegen wird in Verbindung mit hochfesten Stählen angewandt, um die Rückfederung zu kontrollieren und so präzise Geometrien zu erzielen.
5.2 Überbiegen in der Luft- und Raumfahrt
In der Luftfahrt, wo Leichtbau und hohe Festigkeit entscheidend sind, kommt das Überbiegen ebenfalls zum Einsatz. Hier ist die Materialauswahl auf hochfeste und zähe Werkstoffe beschränkt, die jedoch eine höhere Rückfederung aufweisen können. Präzise Überbiegungsstrategien ermöglichen es, die Rückfederung zu kontrollieren und maßgetreue, leichte Komponenten herzustellen.
5.3 Anwendung im Bauwesen und bei Stahlkonstruktionen
Im Bauwesen, insbesondere bei tragenden Stahlkonstruktionen, wird Überbiegen eingesetzt, um die notwendige Formstabilität und Präzision zu erreichen. Dies ist vor allem bei Strukturen notwendig, die starken Belastungen ausgesetzt sind und eine hohe Maßhaltigkeit erfordern.
6. Optimierungsstrategien und Weiterentwicklung
6.1 Kombination von Überbiegen und Vorerwärmung
Die Kombination von Überbiegen mit kontrollierter Vorerwärmung des Materials hat sich als sehr effektiv erwiesen. Durch die Erhöhung der Temperatur wird die elastische Komponente des Materials verringert, wodurch das Überbiegen leichter kontrollierbar wird.
Vorteile dieser Kombination:
- Geringere Rückfederung durch reduzierte elastische Spannung
- Weniger Bedarf an einem extremen Überbiegewinkel
6.2 Fortschritte in der Materialsimulation
Simulationstechnologien, die elastische und plastische Verformungen präzise berechnen, haben das Überbiegen optimiert. Fortschrittliche Algorithmen berücksichtigen die Materialparameter und ermöglichen eine genauere Vorhersage der Rückfederung, was eine präzisere Steuerung des Überbiegewinkels ermöglicht.
6.3 Automatisiertes, adaptives Überbiegen
Moderne Fertigungsanlagen nutzen automatisierte Überbiegungssysteme, die in Echtzeit Anpassungen an Umgebungsbedingungen und Materialabweichungen vornehmen können. Mit adaptiven Überbiegetechniken kann das System selbstständig auf Materialschwankungen oder Veränderungen in der Umgebungstemperatur reagieren.
7. Herausforderungen und mögliche Lösungsansätze
7.1 Kontrolle der Rückfederung bei hochfesten Stählen
Eine der größten Herausforderungen bleibt die präzise Rückfederungskontrolle bei hochfesten Stählen, die sich durch hohe Rückfederungseigenschaften auszeichnen. Hier sind Kombinationen von Überbiegen, Vorerwärmung und Nachbehandlung erforderlich, um eine präzise Geometrie zu erzielen.
Lösungsansätze:
- Verstärkte Simulation und Experimentierung bei der Materialauswahl
- Kombination von Überbiegen und gezielten Kühlmethoden, um die plastische Form zu stabilisieren
7.2 Kosten und Energieaufwand
Das Überbiegen erfordert eine hohe Präzision, was zu einem erhöhten Energieverbrauch führen kann. Effizientere Maschinen und energiesparende Verfahren werden entwickelt, um den Ressourcenverbrauch zu optimieren.
Lösungen:
- Einsatz energieeffizienter Heiz- und Steuerungssysteme
- Erhöhung der Präzision und Reduktion des Materialverlusts durch Simulationen
Fazit
Das Überbiegen ist eine bewährte Methode zur Minimierung der Rückfederung bei der Stahlumformung und hat sich als unverzichtbares Verfahren in der Metallverarbeitung etabliert. Ob in der Automobilindustrie, Luftfahrt oder im Bauwesen – Überbiegen ermöglicht es, Rückfederung gezielt zu kontrollieren und so die Präzision und Maßhaltigkeit der gefertigten Bauteile zu gewährleisten. Innovative Methoden wie die Kombination von Überbiegen und Vorerwärmung, rechnergestützte Simulationen und adaptive Fertigungstechniken bieten großes Potenzial, das Überbiegen weiter zu optimieren.
Zukünftige Entwicklungen könnten die Effektivität und Effizienz des Überbiegeprozesses durch neue Materialien und Technologien weiter verbessern und die Produktionskosten und den Energieverbrauch reduzieren.
Einleitung
Die Werkzeuggeometrie spielt beim Umformen von Stahl eine zentrale Rolle, da sie maßgeblich beeinflusst, wie das Material verformt wird und ob es nach der Belastung in die gewünschte Form zurückkehrt. Insbesondere die Rückfederung ist eine Herausforderung: Das Material versucht aufgrund seiner elastischen Eigenschaften, in die Ursprungsform zurückzukehren, was zu Abweichungen von der Sollgeometrie führt. Durch die gezielte Anpassung der Werkzeuggeometrie können Rückfedereffekte jedoch kontrolliert und minimiert werden. In dieser Abhandlung wird beschrieben, wie die Werkzeuggeometrie das Umformverhalten beeinflusst, welche Methoden zur Optimierung existieren und wie die Werkzeuggestaltung den Anforderungen in verschiedenen Industriezweigen gerecht wird.
1. Grundlagen der Werkzeuggeometrie und Rückfederung
1.1 Rückfederung: Eine Übersicht
Rückfederung beschreibt die elastische Erholung des Materials nach einer plastischen Verformung, die dazu führt, dass das Werkstück von der Zielgeometrie abweicht. Die Ursachen liegen in den elastischen und plastischen Eigenschaften des Materials, die nach der Umformung wirken. Bei hochfesten Materialien und komplexen Umformgeometrien kann dies zu signifikanten Abweichungen führen.
1.2 Bedeutung der Werkzeuggeometrie
Die Geometrie des Werkzeugs bestimmt die Form und den Druckverlauf, dem das Werkstück während des Umformprozesses ausgesetzt ist. Faktoren wie der Werkzeugwinkel, Krümmungsradien, Formflächen, und Negativwinkel beeinflussen die Rückfederung erheblich. Das richtige Werkzeugdesign hilft, das Material so zu formen, dass es möglichst nahe an der Zielgeometrie bleibt.
2. Ansätze zur Anpassung der Werkzeuggeometrie zur Minimierung der Rückfederung
2.1 Überdimensionierung der Werkzeuggeometrie
Eine häufig eingesetzte Technik ist die Überdimensionierung der Werkzeugform: Die Geometrie des Werkzeugs wird so gestaltet, dass das Werkstück durch Rückfederung schließlich die Zielkontur erreicht. Die Überdimensionierung basiert auf experimentellen Werten oder Berechnungen zur Rückfederung.
Beispiel:
- Ein Biegewerkzeug für U-Profile kann so gestaltet werden, dass der Winkel an den Endpunkten enger ist als die gewünschte Endform, um den Rückfedereffekt zu kompensieren.
Vorteile:
- Kostengünstige Anpassung der Werkzeuge
- Einfache Implementierung und schnelle Anpassung
Nachteile:
- Erfordert eine sorgfältige Planung und Simulation
- Kann bei komplexen Geometrien ungenau werden
2.2 Optimierung der Krümmungsradien
Der Krümmungsradius des Werkzeugs hat erheblichen Einfluss auf das Umformverhalten und die Rückfederung. Durch die Anpassung des Krümmungsradius kann der Druckverlauf verändert und die Rückfederung verringert werden.
- Engere Radien erzeugen höhere plastische Verformungen, die die elastische Rückfederung reduzieren.
- Optimierte Radienkombinationen: Durch Kombination unterschiedlicher Radien entlang der Umformkante können die Spannungen gleichmäßig verteilt werden, was die Rückfederung weiter minimiert.
Anwendungsbeispiele:
- In der Automobilindustrie wird der Krümmungsradius häufig angepasst, um präzise Konturen bei Karosserieteilen zu erzielen.
2.3 Verwendung von Negativwinkeln
Negativwinkel sind eine wirksame Methode, um die Rückfederung zu steuern. Der Winkel zwischen Werkzeug und Werkstück wird dabei so gestaltet, dass das Material gezielt in die gewünschte Form „gedrückt“ wird.
- Definition eines Negativwinkels: Die Werkzeuggeometrie wird so gestaltet, dass das Werkstück durch elastische Rückfederung auf die Zielgeometrie zurückfällt.
- Berechnung des Negativwinkels: Der erforderliche Negativwinkel wird durch Tests oder Simulationen ermittelt und angepasst.
Vorteile:
- Effektive Rückfederungssteuerung bei einfachen Formen
- Besonders geeignet für Biegeoperationen
Nachteile:
- Erfordert präzise Anpassungen und simulationsgestützte Planung
- Bei komplexen Bauteilgeometrien schwieriger umzusetzen
2.4 Einsatz von Mehrphasenwerkzeugen
Mehrphasenwerkzeuge, die in verschiedenen Stufen arbeiten, sind eine komplexere Lösung zur Rückfederungsminimierung. Durch die sukzessive Umformung in mehreren Schritten wird das Material in kontrollierten Phasen geformt, was eine gleichmäßige Verteilung der Spannungen und eine bessere Kontrolle der Rückfederung ermöglicht.
Anwendung:
- Schrittweise Umformung: Ein Bauteil wird in mehreren Schritten umgeformt, wobei jeder Schritt eine spezielle Geometrie hat, die die Rückfederung berücksichtigt.
- Anpassung der Form und Kräfte: Durch die Abstimmung der Werkzeugform und die Kraftanwendung kann die Rückfederung in jedem Schritt verringert werden.
3. Computergestützte Simulation und Analyse der Werkzeuggeometrie
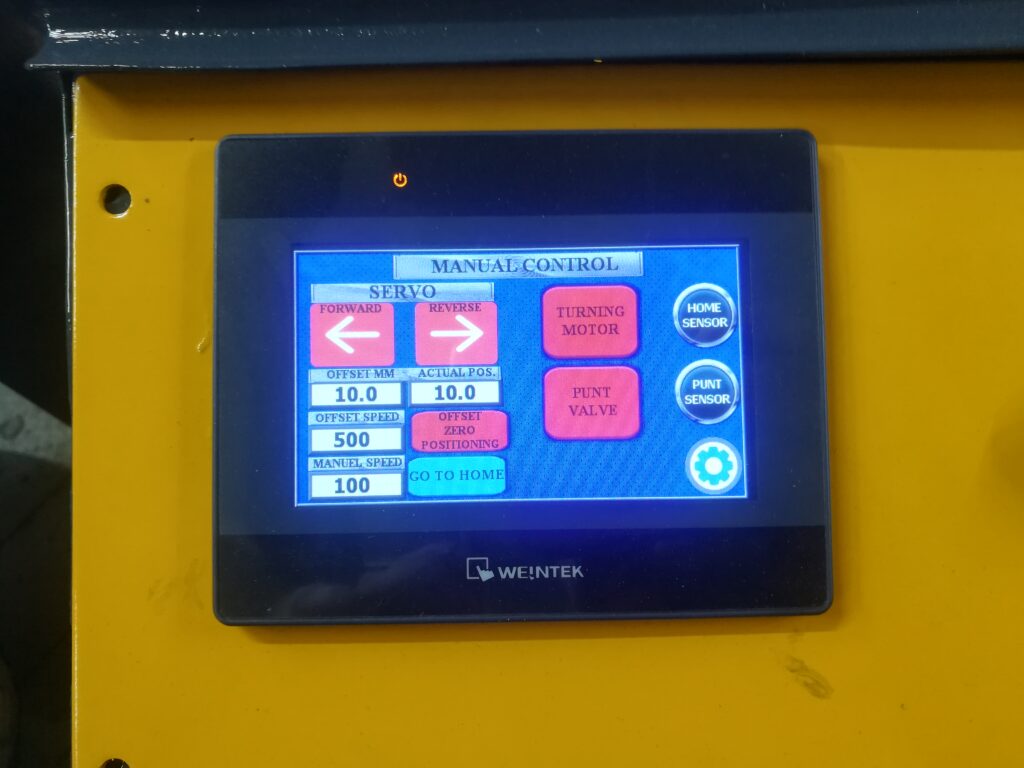
3.1 Finite-Elemente-Methode (FEM)
Die Finite-Elemente-Methode (FEM) ist eine der effektivsten Techniken zur Simulation und Optimierung der Werkzeuggeometrie. Mit FEM können die elastischen und plastischen Spannungen im Material detailliert analysiert werden, um die Rückfederung präzise vorherzusagen.
Vorteile der FEM:
- Detaillierte Analyse der Spannungsverteilung
- Simulation komplexer Geometrien und Materialverhalten
- Möglichkeit zur Anpassung und Optimierung der Werkzeuggeometrie in der Planungsphase
Herausforderungen:
- Hohe Rechenleistung erforderlich
- Erfordert detaillierte Materialdaten und eine präzise Simulationseinstellung
3.2 CAD-gestützte Optimierung
Moderne CAD-Programme bieten Funktionen zur Simulation der Rückfederung und zur Anpassung der Werkzeuggeometrie. Durch integrierte Rückfederungskompensation können Geometrien bereits in der Konstruktionsphase optimiert werden.
Funktionen:
- Simulation von Rückfederungsprofilen und deren Kompensation
- Optimierung der Negativwinkel, Radien und Formflächen
3.3 Materialdatenbanken und Vorhersagemodelle
Zur genauen Vorhersage der Rückfederung sind präzise Materialdaten erforderlich. Materialdatenbanken bieten umfassende Datensätze über Elastizität, Streckgrenze und Spannungsverläufe für verschiedene Werkstoffe, die direkt in Simulationen eingebunden werden können.
4. Anwendungsbeispiele und Brancheneinsatz
4.1 Automobilindustrie
Die Automobilindustrie setzt auf eine präzise Werkzeuggeometrieanpassung, da Bauteile wie Karosseriebleche hohe Maßgenauigkeit erfordern. Um die Rückfederung zu minimieren, kommen alle beschriebenen Techniken zum Einsatz. Typische Anwendungen sind:
- Karosserieteile: Präzise Formgebung durch optimierte Radien und Negativwinkel
- Strukturteile: Verwendung von Mehrphasenwerkzeugen für präzise Verformung
4.2 Luftfahrt und Raumfahrt
In der Luft- und Raumfahrtindustrie ist die Maßgenauigkeit bei Bauteilen entscheidend. Werkzeuge mit spezifischen Krümmungen und Negativwinkeln sind gängige Mittel, um Rückfederung bei hochfesten Materialien zu kontrollieren.
4.3 Bauwesen und Architektur
Im Bauwesen und in der Architektur werden oft großformatige Stahlkomponenten eingesetzt, bei denen die Rückfederung im großen Maßstab kontrolliert werden muss. Hier kommen angepasste Werkzeuggeometrien und Negativwinkel zur Anwendung.
5. Zukünftige Entwicklungen und Innovationen
5.1 Einsatz von adaptiven Werkzeugen
Adaptive Werkzeuge passen die Geometrie automatisch an das Materialverhalten an, indem sie Echtzeitmessungen der Rückfederung und Belastung durchführen. Diese Werkzeuge könnten die Anpassung der Werkzeuggeometrie in der Praxis stark vereinfachen.
5.2 Entwicklung neuer Materialien
Innovative Materialentwicklungen wie Stähle mit geringer Rückfederung könnten die Anforderungen an die Werkzeuggeometrie senken. Auch Werkstoffe mit speziellem Verhalten bei bestimmten Temperaturen könnten die Rückfederung minimieren und damit die Werkzeuganpassung vereinfachen.
5.3 3D-Druck für Werkzeugherstellung
Durch die additive Fertigung (3D-Druck) können komplexe Werkzeuggeometrien in kürzester Zeit angepasst und hergestellt werden. Dies ermöglicht eine flexible, schnelle Produktion und eine experimentelle Anpassung der Werkzeuggeometrie.
Fazit
Die Anpassung der Werkzeuggeometrie ist ein zentraler Ansatz zur Minimierung der Rückfederung beim Umformen von Stahl. Techniken wie die Überdimensionierung der Form, die Anpassung von Radien und Negativwinkeln sowie die Verwendung von Mehrphasenwerkzeugen bieten eine präzise Steuerung des Umformprozesses. Simulationstechniken wie die Finite-Elemente-Methode ermöglichen eine detaillierte Analyse und Optimierung bereits in der Planungsphase, was zu einer signifikanten Reduktion der Rückfederung führt.
Zukünftige Innovationen wie adaptive Werkzeuge und der Einsatz von 3D-Druck für die Werkzeugfertigung könnten das Design weiter revolutionieren und die Effizienz in der Metallverarbeitung steigern. Diese Entwicklungen versprechen eine genauere Formgebung, reduzierte Materialkosten und eine bessere Anpassung an die Anforderungen verschiedenster Branchen – von der Automobilindustrie bis zur Luftfahrt.
Einleitung
In der Metallverarbeitung ist die Rückfederung ein häufiges Problem, da das Material nach dem Umformen dazu neigt, teilweise in seine ursprüngliche Form zurückzukehren. Dies führt zu geometrischen Abweichungen und beeinträchtigt die Maßgenauigkeit. Ein bewährter Ansatz, um die Rückfederung zu minimieren, ist das elastische Nachformen: ein Verfahren, bei dem das Werkstück nach der Hauptverformung erneut geformt wird, um verbleibende elastische Spannungen zu reduzieren und die Zielgeometrie präzise zu erreichen. In dieser Abhandlung werden die Grundlagen, Methoden und Anwendungen des elastischen Nachformens sowie seine Vorteile und Herausforderungen untersucht.
1. Grundlagen der Rückfederung und des elastischen Nachformens
1.1 Rückfederung: Ursachen und Einflussfaktoren
Rückfederung tritt auf, wenn sich nach einer plastischen Verformung elastische Spannungen im Werkstück aufbauen, die das Material in seine ursprüngliche Form zurückdrücken. Die Rückfederung ist abhängig von:
- Elastizitätsmodul des Materials: Ein hoher Elastizitätsmodul führt zu stärkerer Rückfederung.
- Materialhärte: Härtere Materialien neigen oft zu einer stärkeren Rückfederung.
- Geometrie und Verformungsgrad: Komplexere Geometrien und größere Verformungswinkel verstärken den Rückfedereffekt.
Die Rückfederung führt zu Abweichungen von der Zielgeometrie und ist besonders in Branchen wie der Automobil-, Luftfahrt- und Bauindustrie unerwünscht.
1.2 Prinzip des elastischen Nachformens
Das elastische Nachformen ist eine Technik, bei der das Werkstück nach der Hauptverformung einer zweiten kontrollierten Belastung unterzogen wird. Durch diese erneute, oft geringere Formung wird das Werkstück gezielt über die Endgeometrie hinaus belastet, wodurch die verbleibenden elastischen Spannungen teilweise abgebaut werden. Dieses Verfahren trägt dazu bei, dass das Werkstück nach der Entlastung präzise die Zielkontur erreicht.
Mechanismus des elastischen Nachformens:
- Durch das erneute Verformen wird das Material in eine leicht modifizierte Form gebracht.
- Nach dem Nachformen und Entfernen der Belastung kommt es nur noch zu minimaler Rückfederung, da die elastischen Spannungen größtenteils reduziert sind.
2. Methoden des elastischen Nachformens
2.1 Überbiegen und elastisches Nachformen
Eine einfache Methode des elastischen Nachformens ist das Überbiegen. Hierbei wird das Werkstück über die Zielgeometrie hinaus geformt und danach zurück in die gewünschte Form gebracht, um die Rückfederung zu kompensieren.
- Durchführung: Das Bauteil wird zunächst um einen definierten Überbiegewinkel über die Zielgeometrie hinaus verformt und anschließend zurückgeformt.
- Vorteile: Kostengünstig und effektiv für einfache Geometrien.
- Nachteile: Erfordert präzise Steuerung und ist bei komplexen Geometrien oft unzureichend.
2.2 Elastisches Nachformen durch Mehrfachumformung
Bei der Mehrfachumformung wird das Werkstück in mehreren Stufen umgeformt. Die elastische Rückfederung wird so nach und nach abgebaut, da das Material in jeder Stufe eine zusätzliche plastische Verformung erfährt.
- Mehrphasenformung: Das Werkstück wird in mehreren Umformphasen bearbeitet, wobei in jeder Phase eine weitere Verformung erfolgt.
- Anwendungsbeispiele: Mehrfachumformung wird häufig bei komplexen und großformatigen Werkstücken angewandt, die eine hohe Maßgenauigkeit erfordern.
2.3 Elastisches Nachdrücken
Das elastische Nachdrücken ist eine spezifische Form des Nachformens, bei der das Werkstück nach dem Hauptformprozess in eine Vorrichtung eingespannt und unter geringem Druck verformt wird, um die Rückfederung zu korrigieren.
- Durchführung: Das Werkstück wird in eine Formvorrichtung eingespannt und langsam unter konstantem Druck nachgeformt.
- Vorteile: Sehr präzise und vielseitig für verschiedene Bauteilformen anwendbar.
- Nachteile: Höherer Zeitaufwand und erhöhter Energieverbrauch im Vergleich zu einfacheren Methoden.
2.4 Erhitzen und elastisches Nachformen
Das gezielte Erhitzen des Werkstücks nach dem Umformen führt zu einer Reduktion der Rückfederung, da durch die erhöhte Temperatur elastische Spannungen abgebaut werden.
- Durchführung: Das Werkstück wird nach der Umformung erhitzt und danach langsam abgekühlt, wodurch innere Spannungen reduziert werden.
- Vorteile: Geringere Rückfederung, besonders geeignet für hochfeste Stähle.
- Nachteile: Hoher Energieaufwand und zusätzlicher Prozessschritt.
3. Computergestützte Analyse und Simulation beim elastischen Nachformen
3.1 Finite-Elemente-Simulation (FEM)
Moderne Finite-Elemente-Simulationen (FEM) erlauben die exakte Berechnung der Rückfederung und die Optimierung des Nachformens. Durch die Simulation der elastischen und plastischen Spannungen lässt sich der Nachformprozess gezielt planen und der Rückfedereffekt verringern.
- Nutzen der FEM: FEM ermöglicht es, die Verteilung der Spannungen und Verformungen im Material zu analysieren und den Nachformprozess entsprechend anzupassen.
- Anwendungsbeispiele: Die Automobilindustrie setzt FEM-Simulationen ein, um Bauteile wie Karosserieteile mit hoher Präzision zu formen.
3.2 Simulation der Materialeigenschaften
Durch die genaue Simulation der Materialeigenschaften lassen sich die elastischen Spannungen und die erforderlichen Verformungsparameter für das elastische Nachformen berechnen. Materialdatenbanken liefern detaillierte Informationen über die Elastizitätsmodule, Streckgrenzen und Rückfederungseigenschaften.
- Materialmodelle: Mithilfe von Materialmodellen wird das Verhalten des Materials unter verschiedenen Belastungen simuliert.
- Beispiele für Anwendungen: Materialsimulationen werden oft für hochfeste Stähle und komplexe Bauteilgeometrien verwendet, um die Rückfederung präzise zu kompensieren.
4. Anwendung des elastischen Nachformens in verschiedenen Branchen
4.1 Automobilindustrie
In der Automobilindustrie spielt das elastische Nachformen eine wichtige Rolle, da Karosserieteile und Strukturbauteile präzise geformt werden müssen. Hier kommt das Nachformen häufig bei hochfesten Stählen zum Einsatz, die eine hohe Rückfederung aufweisen.
- Karosseriekomponenten: Teile wie Türrahmen, Dachrahmen und Verstärkungen erfordern eine exakte Formgebung, die durch elastisches Nachformen erzielt wird.
- Einsatz von FEM-Simulation: Durch die Simulation werden der elastische Nachformprozess und der erforderliche Druck genau berechnet, um eine präzise Passform zu gewährleisten.
4.2 Luftfahrtindustrie
In der Luftfahrtindustrie ist das elastische Nachformen entscheidend, da hier häufig hochfeste und dennoch leichte Materialien eingesetzt werden, die zu Rückfederung neigen.
- Strukturkomponenten: Teile wie Tragflächen und Rumpfstrukturen benötigen eine präzise Maßhaltigkeit, die durch elastisches Nachformen erreicht wird.
- Verbundwerkstoffe: Bei der Umformung von Verbundwerkstoffen, die ebenfalls Rückfederung zeigen, wird das elastische Nachformen angewandt, um exakte Formen zu erhalten.
4.3 Bau- und Stahlindustrie
Die Bauindustrie setzt das elastische Nachformen bei großformatigen Stahlträgern und -komponenten ein, die eine hohe Maßgenauigkeit erfordern. Hier wird das Verfahren verwendet, um sicherzustellen, dass große Bauteile nach dem Verformen ihre Form behalten.
- Großformatige Stahlträger: Besonders bei tragenden Elementen wie Stahlträgern und Säulen wird das Nachformen eingesetzt, um exakte Geometrien zu erreichen.
- Biegemaschinen und elastisches Nachformen: Biegemaschinen mit Nachformfunktionen bieten eine präzise Steuerung der Rückfederung und werden in der Bauindustrie häufig eingesetzt.
5. Vor- und Nachteile des elastischen Nachformens
5.1 Vorteile
- Hohe Präzision: Das elastische Nachformen ermöglicht eine exakte Steuerung der Rückfederung und gewährleistet die Maßhaltigkeit.
- Vielseitig: Das Verfahren ist für viele unterschiedliche Materialien und Formen geeignet.
- Weniger Nacharbeit: Da die Rückfederung minimiert wird, ist weniger Nachbearbeitung erforderlich, was Zeit und Kosten spart.
5.2 Nachteile
- Höherer Energieaufwand: Das elastische Nachformen erfordert oft zusätzlichen Druck und Zeit, was den Energieverbrauch erhöht.
- Erhöhte Prozesszeit: Die zusätzliche Umformstufe verlängert den Produktionsprozess.
- Notwendigkeit präziser Steuerung: Für eine erfolgreiche Anwendung sind präzise Steuerung und Simulation erforderlich, die zusätzlichen Planungsaufwand verursachen.
6. Zukünftige Entwicklungen und Innovationen im elastischen Nachformen
6.1 Einsatz adaptiver Werkzeuge
Adaptive Werkzeuge, die den Umformdruck in Echtzeit anpassen, könnten den Nachformprozess revolutionieren. Diese Werkzeuge können auf Materialveränderungen und Rückfederung reagieren, um die Zielgeometrie noch präziser zu erreichen.
6.2 Automatisiertes Nachformen durch KI
Künstliche Intelligenz (KI) bietet Potenzial für die Weiterentwicklung des elastischen Nachformens. KI-gestützte Systeme könnten auf Basis von Material- und Prozessdaten eigenständig die optimalen Nachformparameter berechnen und in Echtzeit anpassen.
6.3 Einsatz innovativer Materialien
Neue Materialien, die speziell für geringere Rückfederung entwickelt werden, könnten das elastische Nachformen in vielen Anwendungsbereichen vereinfachen. Materialien mit verbesserten elastischen Eigenschaften und optimierten Spannungsverläufen bieten ein großes Potenzial.
Fazit
Das elastische Nachformen ist eine hochwirksame Methode zur Kontrolle der Rückfederung und zur präzisen Formgebung beim Umformen von Stahl. Verschiedene Verfahren – vom Überbiegen und Nachdrücken bis hin zur Mehrfachumformung und gezielten Erwärmung – bieten eine flexible und vielseitige Möglichkeit, Rückfederung zu kompensieren und präzise Werkstücke herzustellen.
Mit modernen Simulationsmethoden wie der FEM und der Weiterentwicklung von adaptiven Werkzeugen und KI-gestützten Prozessen wird das elastische Nachformen weiter optimiert und effizienter gestaltet. In einer Vielzahl von Branchen, von der Automobilindustrie über die Luftfahrt bis hin zur Stahlverarbeitung im Bauwesen, bleibt das elastische Nachformen eine unverzichtbare Technik zur Sicherstellung präziser und maßhaltiger Bauteilgeometrien.
Einleitung
Das temperaturgesteuerte Umformen ist eine innovative Technik, die es ermöglicht, die mechanischen Eigenschaften des Stahls während der Umformung gezielt zu beeinflussen und dadurch die Rückfederung deutlich zu minimieren. Während herkömmliche Kaltumformprozesse oft zu unerwünschten elastischen Rückfedereffekten führen, bietet das Umformen bei erhöhten Temperaturen eine Möglichkeit, die Materialstruktur und -festigkeit so anzupassen, dass diese Rückfederung reduziert oder vollständig vermieden wird. Diese Abhandlung gibt einen Überblick über die Grundlagen des temperaturgesteuerten Umformens, verschiedene Techniken wie Warmumformen und Presshärten, die Mechanismen hinter der Rückfederungsminimierung sowie spezifische Anwendungen in der Industrie.
1. Grundlagen der Rückfederung beim Umformen
1.1 Rückfederung und ihre Ursachen
Rückfederung bezeichnet die elastische Erholung eines Werkstücks nach der Umformung, bei der das Material in Richtung seiner ursprünglichen Form zurückstrebt. Sie tritt auf, wenn das Material nach der plastischen Verformung aufgrund der elastischen Spannungen teilweise zurückfedert. Die Rückfederung ist vor allem von den mechanischen Eigenschaften des Materials abhängig, darunter:
- Elastizitätsmodul: Ein hoher Elastizitätsmodul führt zu stärkerer Rückfederung.
- Streckgrenze und Härte: Stähle mit höherer Festigkeit und Härte neigen zu einer stärkeren Rückfederung.
- Werkstückgeometrie und Verformungswinkel: Größere Biegewinkel und dünnere Bleche weisen oft höhere Rückfederungswerte auf.
1.2 Prinzip des temperaturgesteuerten Umformens
Das temperaturgesteuerte Umformen nutzt erhöhte Temperaturen, um das Material in eine plastisch verformbare, aber weniger elastische Struktur zu überführen. Durch Erwärmung wird die Duktilität des Stahls erhöht und die inneren Spannungen, die zu Rückfederung führen, werden minimiert. Bei höheren Temperaturen können die Bindungen innerhalb des Stahls so modifiziert werden, dass sich das Material leichter und mit geringerer Rückfederung formen lässt.
Typische Verfahren:
- Warmumformen: Umformen bei Temperaturen oberhalb der Rekristallisationstemperatur.
- Presshärten: Kombination von Umformung und Abschrecken, um hochfeste Bauteile herzustellen.
- Temperiertes Biegen: Umformprozess bei moderaten Temperaturen zur Reduktion der Rückfederung.
2. Techniken des temperaturgesteuerten Umformens
2.1 Warmumformen
Das Warmumformen ist ein Prozess, bei dem das Material auf Temperaturen über der Rekristallisationstemperatur (typisch 450–800°C für Stahl) erhitzt wird. Diese Temperaturen machen den Stahl plastischer, wodurch er sich leichter und mit minimaler Rückfederung umformen lässt.
- Vorteile des Warmumformens:
- Reduzierte Rückfederung durch plastische Verformung bei höheren Temperaturen.
- Hohe Formgenauigkeit und gleichmäßige Spannungsverteilung.
- Verbesserte Materialverteilung, da sich der Stahl bei höheren Temperaturen besser verteilt.
- Typische Anwendungen:
- Automobilindustrie: Karosserieteile und Sicherheitsbauteile, die hohe Präzision und Festigkeit erfordern.
- Bauindustrie: Strukturkomponenten und tragende Bauteile mit hoher Maßgenauigkeit.
- Herausforderungen:
- Erhöhter Energieaufwand durch die hohen Temperaturen.
- Notwendigkeit spezialisierter Werkzeuge und Maschinen, die hohen Temperaturen standhalten.
2.2 Presshärten
Presshärten ist ein spezielles temperaturgesteuertes Umformverfahren, bei dem das Material auf hohe Temperaturen erhitzt und dann schnell in einer Form abgekühlt wird. Dieser Prozess ermöglicht es, Bauteile mit hoher Festigkeit und minimaler Rückfederung herzustellen.
- Prozessablauf:
- Das Werkstück wird auf 800–950°C erhitzt und anschließend in eine Pressform gebracht.
- Unter kontrollierter Kühlung härtet das Material aus und erreicht eine martensitische Struktur, die extrem fest ist und geringe Rückfederung aufweist.
- Vorteile des Presshärtens:
- Sehr hohe Festigkeit, die sich ideal für Struktur- und Sicherheitsbauteile eignet.
- Minimale Rückfederung durch die schnelle Abkühlung in der Pressform.
- Typische Anwendungen:
- Fahrzeugstruktur: Komponenten wie A- und B-Säulen, die eine hohe Steifigkeit und Formtreue erfordern.
- Aufprallschutz: Sicherheitsbauteile, die hohen Kräften widerstehen müssen.
2.3 Temperiertes Biegen
Das temperierte Biegen ist ein Umformverfahren, bei dem der Stahl auf moderate Temperaturen zwischen 150 und 400°C erhitzt wird. Dies erhöht die Duktilität des Materials und reduziert die Elastizität, ohne die Umformbarkeit signifikant zu verringern.
- Vorteile des temperierten Biegens:
- Geringere Rückfederung durch gezielte Temperaturanpassung.
- Geeignet für Bauteile mit mäßiger Umformkomplexität.
- Energieeinsparung im Vergleich zum Warmumformen und Presshärten.
- Typische Anwendungen:
- Strukturteile im Fahrzeugbau, die eine moderate Festigkeit und Präzision erfordern.
- Baukomponenten, die eine hohe Formgenauigkeit benötigen, aber keine extremen Festigkeitswerte verlangen.
3. Mechanismen zur Minimierung der Rückfederung beim temperaturgesteuerten Umformen
3.1 Anpassung der Materialmikrostruktur
Durch das Erwärmen des Stahls während des Umformens verändern sich die metallurgischen Strukturen, insbesondere bei Verfahren wie dem Presshärten. Hohe Temperaturen ermöglichen Phasenumwandlungen, bei denen duktilere Strukturen entstehen, die die Elastizität verringern.
- Rekristallisation: Bei hohen Temperaturen wird die kristalline Struktur des Stahls neu gebildet, was zu einer Verringerung innerer Spannungen führt.
- Phasenumwandlung: Eine martensitische Umwandlung, wie sie beim Presshärten auftritt, sorgt für eine extrem feste und maßhaltige Struktur, die sehr wenig Rückfederung zeigt.
3.2 Verringerung der Elastizität durch Wärme
Die erhöhte Temperatur führt dazu, dass die Elastizität des Stahls verringert wird und somit auch die Rückfederung abnimmt. Der Stahl lässt sich besser formen, da die Deformation hauptsächlich plastisch ist, und kehrt nach der Belastung kaum noch in die Ursprungsform zurück.
3.3 Spannungsreduktion und Homogenisierung
Das temperaturgesteuerte Umformen verringert die Spannungen, die typischerweise zu Rückfederung führen. Durch gleichmäßige Erwärmung und Umformung werden diese Spannungen verteilt und homogenisiert, sodass der Stahl nach dem Abkühlen seine Form besser beibehält.
4. Simulation und Analyse beim temperaturgesteuerten Umformen
4.1 Einsatz der Finite-Elemente-Methode (FEM)
Durch FEM-Simulationen können Temperaturverläufe, Spannungsverteilungen und Materialverhalten bei verschiedenen Temperaturen analysiert werden. Diese Methode ermöglicht eine präzise Planung des temperaturgesteuerten Umformprozesses und hilft, Rückfederungseffekte vorherzusagen.
- Nutzen der FEM:
- Analyse der Spannungsverteilung und Identifikation von Rückfederungstendenzen.
- Optimierung des Temperaturprofils, um die ideale Umformtemperatur zu bestimmen.
- Vorhersage der Materialverteilung und Mikrostrukturveränderungen während der Abkühlung.
4.2 Optimierung des Temperaturprofils
Moderne Simulationstools bieten die Möglichkeit, das optimale Temperaturprofil zu berechnen und zu optimieren, um die Rückfederung zu minimieren. Die Simulation kann dabei auch die Abkühlraten und die damit verbundenen Spannungen berücksichtigen.
- Beispielanwendungen:
- In der Automobilindustrie können Simulationen dazu verwendet werden, das ideale Temperaturprofil für Karosseriekomponenten zu entwickeln und dadurch Rückfederung zu vermeiden.
- In der Luftfahrtindustrie helfen Simulationen, hochfeste Strukturteile zu formen, die nach dem Umformen exakte Maßhaltigkeit aufweisen.
5. Anwendung des temperaturgesteuerten Umformens in der Industrie
5.1 Automobilindustrie
Die Automobilindustrie profitiert erheblich vom temperaturgesteuerten Umformen, insbesondere durch das Presshärten, das eine hohe Festigkeit und Präzision bietet.
- Karosserieteile: Türen, Rahmen und Strukturteile werden durch Presshärten und Warmumformen gefertigt, um Rückfederung zu vermeiden.
- Sicherheitsbauteile: Sicherheitsrelevante Teile wie Stoßfänger werden oft bei hohen Temperaturen umgeformt, um maximale Festigkeit und Maßhaltigkeit zu gewährleisten.
5.2 Luft- und Raumfahrtindustrie
In der Luft- und Raumfahrt spielt das temperaturgesteuerte Umformen eine wichtige Rolle, da hier Materialien mit geringer Rückfederung und hoher Festigkeit benötigt werden.
- Flugzeugstrukturteile: Die Umformung bei höheren Temperaturen stellt sicher, dass Komponenten wie Flügelstrukturen und Verkleidungen ihre präzise Form beibehalten.
- Verbundwerkstoffe: Das temperaturgesteuerte Umformen wird auch bei Verbundmaterialien angewendet, um die Maßgenauigkeit zu erhöhen.
5.3 Bauindustrie
In der Bauindustrie werden häufig großformatige Stahlkomponenten verwendet, die bei hohen Temperaturen geformt werden, um Spannungen und Rückfederung zu vermeiden.
- Träger und Stützen: Stahlträger werden oft bei hohen Temperaturen geformt, um Rückfederung zu minimieren und die strukturelle Integrität zu gewährleisten.
- Bauelemente für Fassaden: Präzise geformte Fassadenbauteile profitieren vom Warmumformen, um Maßgenauigkeit und Langlebigkeit sicherzustellen.
6. Herausforderungen und zukünftige Entwicklungen
6.1 Energieeffizienz beim temperaturgesteuerten Umformen
Da das Umformen bei höheren Temperaturen energieintensiv ist, bleibt die Verbesserung der Energieeffizienz eine Herausforderung. Künftige Entwicklungen könnten energieeffiziente Erwärmungstechnologien wie Induktion und Laser nutzen.
6.2 Entwicklung neuer Werkstoffe
Innovationen in der Werkstofftechnologie könnten das temperaturgesteuerte Umformen weiter verbessern. Neue Stähle, die speziell für das Warmumformen entwickelt werden, könnten die Rückfederung weiter reduzieren und den Energieaufwand senken.
6.3 Automatisierung und Prozessintegration
Automatisierung und die Integration temperaturgesteuerter Umformprozesse in die Produktionslinien könnten die Effizienz steigern. Technologien wie KI und maschinelles Lernen könnten genutzt werden, um die ideale Umformtemperatur und -zeit in Echtzeit zu berechnen und den Prozess zu optimieren.
Fazit
Das temperaturgesteuerte Umformen stellt eine effektive Lösung zur Minimierung der Rückfederung beim Umformen von Stahl dar. Verfahren wie das Warmumformen, Presshärten und temperiertes Biegen bieten erhebliche Vorteile bei der Formstabilität und Maßhaltigkeit. Die thermische Anpassung des Umformprozesses reduziert die Rückfederung, indem die elastischen Spannungen im Material abgebaut und die mechanischen Eigenschaften gezielt verändert werden.
Mit fortschreitender Simulationstechnologie und Automatisierung könnte das temperaturgesteuerte Umformen eine noch präzisere und effizientere Umformmethode werden. Diese Verfahren sind besonders wertvoll für Industrien wie die Automobil- und Luftfahrtbranche, wo Maßgenauigkeit und hohe Festigkeit entscheidend sind.
Einleitung
Das Umformen von Stahl wird in zahlreichen Industrien, wie der Automobil- und Luftfahrtindustrie, sowie im Maschinenbau und der Bauwirtschaft angewandt, um Komponenten mit spezifischen Formen und Festigkeitseigenschaften herzustellen. Bei vielen Umformprozessen tritt jedoch ein Problem auf: die sogenannte Rückfederung, die dazu führt, dass sich das Werkstück teilweise in seine ursprüngliche Form zurückzieht. Eine effektive Methode, um Rückfederung zu minimieren und Maßgenauigkeit sicherzustellen, ist die spannungsarme Glühbehandlung. Dieser Prozess reduziert die im Material vorhandenen inneren Spannungen und verhindert, dass sich das Werkstück nach der Formgebung unerwünscht verformt. In dieser Abhandlung werden die Grundlagen der spannungsarmen Glühbehandlung, deren Methoden, Mechanismen zur Spannungsreduktion und industrielle Anwendungsbeispiele behandelt.
1. Grundlagen der Rückfederung und inneren Spannungen
1.1 Ursachen der Rückfederung
Die Rückfederung ist eine elastische Verformung, die nach der plastischen Formgebung eines Werkstücks auftritt, wenn das Material bestrebt ist, in seine ursprüngliche Form zurückzukehren. Dieser Effekt wird durch die inneren Spannungen verursacht, die während des Umformprozesses aufgebaut werden.
1.2 Innere Spannungen und ihre Bedeutung
Innere Spannungen entstehen durch ungleichmäßige Verformung des Werkstoffs und durch Temperaturunterschiede während der Verarbeitung. Diese Spannungen können verschiedene Formen annehmen:
- Eigenspannungen: Diese Spannungen bleiben auch ohne äußere Belastung im Material.
- Thermische Spannungen: Sie entstehen, wenn unterschiedliche Bereiche des Werkstücks unterschiedlich stark abkühlen.
- Mechanische Spannungen: Diese Spannungen resultieren aus der plastischen Verformung, die beim Umformen auftritt.
Die Ansammlung dieser Spannungen führt dazu, dass sich das Material während oder nach der Formgebung bewegt, was zu Abweichungen von der Zielgeometrie führt.
2. Grundlagen der spannungsarmen Glühbehandlung
2.1 Definition und Prinzipien der spannungsarmen Glühbehandlung
Spannungsarmglühen ist eine Wärmebehandlung, bei der das Material auf eine moderate Temperatur (ca. 500–650°C für Stahl) erhitzt und über einen bestimmten Zeitraum auf dieser Temperatur gehalten wird, bevor es langsam abgekühlt wird. Durch diesen Prozess werden die inneren Spannungen reduziert, ohne die Materialfestigkeit oder Form wesentlich zu beeinflussen.
- Temperaturbereich: Die Glühtemperatur wird so gewählt, dass die plastischen und elastischen Spannungen abgebaut werden, ohne dass das Material seine Mikrostruktur oder Festigkeit verliert.
- Haltezeit: Die Haltezeit ist entscheidend für den Erfolg der Spannungsreduzierung und wird an die Dicke und Zusammensetzung des Materials angepasst.
2.2 Mechanismen der Spannungsreduktion beim Spannungsarmglühen
Während der Glühbehandlung diffundieren die Atome im Werkstoff und gleichen Spannungskonzentrationen aus. Dies führt zu einem Abbau der inneren Spannungen und einer gleichmäßigen Verteilung der mechanischen Belastungen im Material.
- Entspannung durch Atombewegung: Bei erhöhter Temperatur gewinnen die Atome Bewegungsfreiheit und setzen sich in eine energieärmere Struktur um.
- Reduktion der Verzerrungen: Durch die thermische Einwirkung werden Verzerrungen und Fehlstellen im Kristallgitter abgebaut, was die Spannungen mindert.
2.3 Unterschied zu anderen Wärmebehandlungen
Während Verfahren wie das Härten oder Anlassen auf eine Veränderung der mechanischen Eigenschaften abzielen, dient das Spannungsarmglühen primär der Reduktion von Spannungen und der Verbesserung der Maßgenauigkeit. Die mechanische Festigkeit des Materials bleibt dabei weitgehend erhalten.
3. Verfahren des spannungsarmen Glühens
3.1 Spannungsarmglühen im Ofen
Beim Ofenglühen wird das Werkstück in einem kontrollierten Ofen gleichmäßig auf die Glühtemperatur erwärmt und nach einer Haltezeit langsam abgekühlt. Der gesamte Prozess wird überwacht, um eine gleichmäßige Wärmeverteilung zu gewährleisten.
- Vorteile: Hohe Kontrolle über Temperatur und Haltezeit, geeignet für große Werkstücke.
- Nachteile: Hoher Energieaufwand und längere Durchlaufzeit.
3.2 Induktives Spannungsarmglühen
Das induktive Glühen verwendet elektromagnetische Induktion, um Wärme gezielt in den Randbereichen des Werkstücks zu erzeugen. Diese Methode ist schneller als das Ofenglühen und eignet sich besonders für Bauteile mit komplexen Formen.
- Vorteile: Schnelleres Erwärmen und geringerer Energieaufwand.
- Nachteile: Weniger gleichmäßige Erwärmung, begrenzt auf bestimmte Geometrien.
3.3 Spannungsarmglühen mit Laser
Moderne Lasersysteme ermöglichen eine punktuelle Erwärmung des Materials, wodurch die Spannungen gezielt abgebaut werden können. Diese Technik ist besonders für kleinere Bauteile geeignet, die eine präzise Spannungsreduktion erfordern.
- Vorteile: Präzise Erwärmung und minimale thermische Beeinträchtigung.
- Nachteile: Hoher technologischer Aufwand und kostenintensiv.
4. Mechanismen der Spannungsreduktion und Minimierung der Rückfederung
4.1 Spannungsabbau durch Rekristallisation
Rekristallisation tritt auf, wenn sich das Material auf einer Temperatur nahe der Rekristallisationstemperatur befindet, wodurch Spannungen durch die Neubildung von Kristallkörnern reduziert werden.
- Mechanismus: Die Korngrenzen verschieben sich und bilden neue, spannungsarme Körner.
- Vorteil: Stabilisierung der Form ohne Rückfederungseffekte.
4.2 Homogenisierung der Spannungen
Das spannungsarme Glühen führt zu einer Homogenisierung der Spannungen, da alle Bereiche des Materials gleichmäßig entspannt werden. Dies verhindert lokale Rückfederungseffekte, die bei ungleichmäßig verformten Bauteilen auftreten können.
- Mechanismus: Gleichmäßige Verteilung der Atome und Reduktion der Fehlstellen im Kristallgitter.
- Vorteil: Bessere Formhaltigkeit und Maßgenauigkeit des Werkstücks.
4.3 Verringerung der Elastizität
Durch die Wärmebehandlung verringert sich die Elastizität des Materials geringfügig, wodurch sich die Neigung zur Rückfederung reduziert. Dies führt zu einer stabileren Form und verbessert die Präzision.
5. Anwendungen des spannungsarmen Glühens in der Industrie
5.1 Automobilindustrie
In der Automobilindustrie wird das spannungsarme Glühen bei Bauteilen angewandt, die hohe Maßgenauigkeit und geringe Rückfederung erfordern. Dies betrifft insbesondere hochfeste Karosserie- und Strukturteile.
- Karosserieteile: Durch das Glühen werden die Karosserieteile maßhaltig, was eine exakte Passform und erhöhte Sicherheit gewährleistet.
- Rahmenteile: Strukturrahmen und Verstärkungen werden häufig geglüht, um ihre Festigkeit und Formtreue zu verbessern.
5.2 Luft- und Raumfahrtindustrie
In der Luft- und Raumfahrt ist die Maßhaltigkeit von Strukturteilen entscheidend, um eine optimale Aerodynamik und strukturelle Integrität zu gewährleisten. Das spannungsarme Glühen reduziert Spannungen und verhindert Verformungen während des Einsatzes.
- Tragflächen und Rumpfstrukturen: Diese Bauteile werden geglüht, um sicherzustellen, dass sie im Einsatz stabil bleiben und keine Spannungsrisse entstehen.
- Verbundwerkstoffe: In einigen Fällen wird das spannungsarme Glühen auch auf Verbundwerkstoffe angewandt, um die strukturelle Stabilität zu erhöhen.
5.3 Werkzeug- und Maschinenbau
Werkzeuge und Maschinenbauteile, die hohen mechanischen Belastungen ausgesetzt sind, werden durch spannungsarmes Glühen stabilisiert, um die Lebensdauer und Zuverlässigkeit zu erhöhen.
- Schneidwerkzeuge: Durch Glühen wird die Rückfederung bei Schneidwerkzeugen reduziert, was die Präzision und Standzeit erhöht.
- Maschinenkomponenten: Zahnräder und Wellen werden spannungsarm geglüht, um Formveränderungen und Rückfederung zu minimieren.
6. Vorteile und Herausforderungen des spannungsarmen Glühens
6.1 Vorteile
- Minimierung der Rückfederung: Spannungsarmgeglühte Bauteile zeigen weniger Rückfederung und behalten ihre Form besser bei.
- Erhöhung der Maßhaltigkeit: Durch die Reduzierung der Spannungen wird eine präzisere Formgebung und Maßhaltigkeit erreicht.
- Erhöhung der Lebensdauer: Spannungsarmgeglühte Werkstücke weisen eine geringere Rissanfälligkeit auf, was die Lebensdauer erhöht.
6.2 Herausforderungen
- Hoher Energieaufwand: Die Wärmebehandlung ist energieintensiv, insbesondere beim Ofenglühen.
- Zusätzlicher Prozessschritt: Spannungsarmglühen verlängert den Produktionsprozess und erhöht die Kosten.
- Präzise Steuerung erforderlich: Für eine effektive Spannungsreduktion müssen Temperatur und Haltezeit exakt eingehalten werden.
7. Zukünftige Entwicklungen und Innovationen im spannungsarmen Glühen
7.1 Effiziente Glühöfen und Induktionstechnik
Moderne Glühöfen mit optimierter Energienutzung und innovative Induktionsverfahren ermöglichen energieeffizientere Glühprozesse, die Kosten und Umweltbelastung senken.
7.2 Automatisierung und KI-gestützte Steuerung
Durch den Einsatz von Künstlicher Intelligenz und Automatisierung können die Glühprozesse optimiert und in Echtzeit an Materialvariationen angepasst werden, was die Präzision und Effizienz erhöht.
7.3 Entwicklung neuer Materialien
Materialien, die speziell für spannungsarme Umformverfahren entwickelt wurden, könnten den Bedarf an Glühbehandlungen reduzieren und gleichzeitig die Festigkeit und Präzision der Werkstücke verbessern.
Fazit
Das spannungsarme Glühen ist ein unverzichtbarer Prozess zur Spannungsreduktion und Minimierung der Rückfederung beim Umformen von Stahl. Durch die gezielte Wärmebehandlung können innere Spannungen abgebaut und die Maßgenauigkeit des Werkstücks signifikant verbessert werden. Besonders in Industrien, die auf präzise Formgebung angewiesen sind, wie der Automobilbau und die Luft- und Raumfahrt, ist das spannungsarme Glühen entscheidend, um Bauteile mit hoher Formtreue und Stabilität herzustellen.
Zukünftige Entwicklungen wie effiziente Glühverfahren, Automatisierung und neue Materialentwicklungen werden die Glühtechnologie weiter vorantreiben. Der Einsatz spannungsarmer Glühbehandlungen wird dabei eine zentrale Rolle spielen, um die steigenden Anforderungen an Maßhaltigkeit, Festigkeit und Effizienz in der modernen Produktion zu erfüllen.
Einleitung
Die Optimierung der Prozessparameter beim Umformen von Stahl ist entscheidend, um unerwünschte Rückfederung zu minimieren und die Maßgenauigkeit der Bauteile sicherzustellen. Rückfederung entsteht aufgrund der elastischen Spannungen im Material, die es teilweise in die ursprüngliche Form zurückkehren lassen. Durch präzise Anpassung der Prozessparameter wie Temperatur, Umformgeschwindigkeit, Druck und Werkzeuggeometrie lässt sich die Rückfederung jedoch signifikant verringern. In dieser Abhandlung beleuchten wir die wichtigsten Parameter, ihre Wirkung auf die Rückfederung und moderne Ansätze zur Prozessoptimierung, um eine verbesserte Maßhaltigkeit und Formgenauigkeit zu erreichen.
1. Grundlagen der Rückfederung und ihre Ursachen
1.1 Rückfederung und ihre Bedeutung
Rückfederung ist die elastische Erholung des Materials nach einer plastischen Verformung. Sie führt zu geometrischen Abweichungen, die vor allem in der Automobil-, Luftfahrt- und Bauindustrie kritisch sind, da hier hohe Maßgenauigkeit gefordert ist. Die Rückfederung entsteht durch:
- Elastizitätsmodul: Ein hoher Elastizitätsmodul führt zu stärkerer Rückfederung.
- Streckgrenze und Materialhärte: Materialien mit hoher Streckgrenze neigen eher zur Rückfederung.
- Werkstückgeometrie und Umformwinkel: Bestimmte Geometrien, wie scharfe Biegungen und große Radien, verstärken den Rückfedereffekt.
1.2 Ziel der Prozessparameteroptimierung
Die Optimierung der Prozessparameter dient dazu, die Rückfederung zu kontrollieren und zu minimieren, um die gewünschte Form präzise zu erreichen. Durch die Anpassung der relevanten Parameter werden die elastischen Spannungen während und nach der Umformung so gering wie möglich gehalten.
2. Wichtige Prozessparameter zur Minimierung der Rückfederung
2.1 Umformtemperatur
Die Umformtemperatur hat einen großen Einfluss auf die Rückfederung, da sie die Materialeigenschaften verändert. Eine Erhöhung der Temperatur verringert die Elastizität und ermöglicht eine plastischere Verformung, was die Rückfederung reduziert.
- Warmumformen: Beim Umformen bei höheren Temperaturen (450–800°C) zeigen die Materialien eine geringere Rückfederung, da der Stahl plastischer wird und Spannungen leichter abgebaut werden.
- Temperiertes Umformen: Bei moderater Erwärmung (ca. 200–400°C) lässt sich eine reduzierte Rückfederung erreichen, ohne dass eine vollständige Rekristallisation eintritt.
Optimierungsansatz: Die ideale Umformtemperatur ist materialabhängig und sollte so gewählt werden, dass die Rückfederung minimiert wird, ohne den Umformprozess zu stark zu beeinflussen.
2.2 Umformgeschwindigkeit
Die Geschwindigkeit, mit der das Werkstück verformt wird, beeinflusst die Rückfederung erheblich. Höhere Umformgeschwindigkeiten führen zu größeren Spannungen im Material, da die elastische Erholung begrenzt ist.
- Langsame Umformung: Eine geringere Umformgeschwindigkeit verringert die Rückfederung, da das Material mehr Zeit hat, sich plastisch zu verformen.
- Schnelle Umformung: Schnellere Geschwindigkeiten erzeugen höhere Spannungen, was zu einer stärkeren Rückfederung führen kann.
Optimierungsansatz: Eine mittlere bis niedrige Umformgeschwindigkeit eignet sich oft am besten zur Minimierung der Rückfederung, insbesondere bei hochfesten Materialien.
2.3 Werkzeuggeometrie
Die Geometrie des Werkzeugs spielt eine zentrale Rolle bei der Rückfederungskontrolle. Faktoren wie Radien, Winkel und Werkzeugoberfläche beeinflussen, wie das Material während der Umformung geformt und belastet wird.
- Krümmungsradien und Werkzeugwinkel: Ein engerer Krümmungsradius reduziert die Rückfederung, da das Material stärker plastisch verformt wird.
- Negativwinkel: Negativwinkel am Werkzeug ermöglichen eine bessere Kontrolle der Rückfederung, indem das Werkstück stärker in die gewünschte Form gedrückt wird.
Optimierungsansatz: Eine sorgfältige Anpassung der Werkzeuggeometrie an die spezifischen Materialeigenschaften und Formanforderungen kann die Rückfederung signifikant minimieren.
2.4 Haltezeit und Druck
Die Haltezeit (Verweildauer des Werkstücks im Werkzeug) und der auf das Material ausgeübte Druck beeinflussen die Spannung und damit die Rückfederung des Materials.
- Erhöhte Haltezeit: Eine längere Haltezeit bei konstantem Druck reduziert die Rückfederung, da das Material seine Spannungen besser abbauen kann.
- Kontinuierlicher Druck: Ein konstanter und kontrollierter Druck sorgt für eine gleichmäßige Verteilung der Spannungen, wodurch Rückfederung minimiert wird.
Optimierungsansatz: Durch die Anpassung der Haltezeit und des Drucks lässt sich die elastische Erholung während und nach der Umformung kontrollieren und reduzieren.
3. Methoden zur Optimierung der Prozessparameter
3.1 Finite-Elemente-Methode (FEM) zur Simulation und Analyse
Die Finite-Elemente-Methode ist ein leistungsstarkes Simulationswerkzeug, um die Effekte der verschiedenen Prozessparameter auf die Rückfederung zu analysieren. Sie ermöglicht es, die Spannungsverteilung, Deformation und Rückfederung bei unterschiedlichen Umformbedingungen zu simulieren.
- Nutzen der FEM: FEM kann die optimale Kombination von Temperatur, Geschwindigkeit, Druck und Werkzeuggeometrie ermitteln, um die Rückfederung zu minimieren.
- Anwendungsbeispiele: In der Automobilindustrie wird FEM genutzt, um komplexe Karosserieformen zu simulieren und die Umformparameter anzupassen.
Vorteile:
- Präzise Vorhersage von Spannungen und Rückfederung
- Zeitsparende Optimierung ohne umfangreiche Materialtests
3.2 DOE-Methodik (Design of Experiments)
DOE ist eine statistische Methode, die zur Optimierung von Prozessen durch systematisches Testen verschiedener Parameterkombinationen genutzt wird. Durch die gezielte Variation der Parameter lassen sich ihre jeweiligen Einflüsse auf die Rückfederung bestimmen.
- Vorteile der DOE:
- Schnellere Identifikation optimaler Prozessparameter
- Kostenersparnis durch systematische Versuchsplanung
- Anwendungsbeispiele: DOE wird genutzt, um Kombinationen von Temperatur und Umformgeschwindigkeit zu testen und eine rückfederungsminimierende Prozesskette zu entwickeln.
Optimierungsansatz: DOE ermöglicht die Entwicklung eines Prozessmodells, das die Abhängigkeiten der Parameter von der Rückfederung beschreibt.
3.3 Echtzeit-Monitoring und adaptive Prozesssteuerung
Moderne Anlagen können Prozessparameter in Echtzeit überwachen und anpassen, um eine stabile Qualität und geringere Rückfederung zu gewährleisten. Sensoren erfassen dabei kontinuierlich die Temperatur, Druck und Spannungen während des Umformprozesses.
4. Beispiele für die Optimierung der Prozessparameter in der Industrie
4.1 Automobilindustrie
In der Automobilindustrie ist die Maßhaltigkeit von Karosserieteilen entscheidend. Die Prozessparameter für das Umformen von Bauteilen wie Dachrahmen, Türrahmen und Verstärkungen werden optimiert, um Rückfederung zu vermeiden.
- Optimierung von Presshärten und Warmumformen: Durch die Steuerung der Temperatur und Haltezeit beim Presshärten lässt sich eine präzise Formgebung erreichen.
- Werkzeuganpassung und FEM-Simulation: FEM-gestützte Simulationen helfen dabei, die Werkzeuggeometrie und Prozessbedingungen für Rückfederungsminimierung zu gestalten.
4.2 Luftfahrtindustrie
In der Luftfahrt ist die Rückfederungsoptimierung entscheidend, da Bauteile exakte Maßhaltigkeit erfordern, um aerodynamische Eigenschaften und Sicherheitsstandards zu gewährleisten.
- Einsatz von DOE: Durch systematische Tests von Temperatur- und Druckparametern werden optimale Umformbedingungen für Strukturteile bestimmt.
- Temperaturkontrolliertes Umformen: Bei der Umformung von Leichtmetallen und hochfesten Stählen werden Temperaturprofile gezielt angepasst, um Rückfederung zu minimieren.
4.3 Bauwesen und Architektur
Im Bauwesen, insbesondere beim Einsatz großer Stahlbauteile, sind Präzision und Stabilität wichtig. Rückfederung ist hier problematisch, da sie die Maßgenauigkeit und Stabilität der Strukturen beeinträchtigen kann.
- Optimierte Biegemaschinen mit adaptiver Steuerung: Durch die Nutzung adaptiver Biegetechniken werden Rückfederungseffekte kontrolliert und minimiert.
- Simulation für Stahlträger und Säulen: Simulationsmodelle unterstützen die Wahl von Druck und Werkzeuggeometrie, um die Rückfederung bei großen Strukturen zu reduzieren.
5. Herausforderungen bei der Optimierung der Prozessparameter
5.1 Materialvariabilität
Stahl und andere Materialien können in ihren Eigenschaften schwanken, was eine Herausforderung für die Prozessoptimierung darstellt. Dies führt zu unvorhersehbaren Rückfederungseffekten, die die Maßhaltigkeit beeinträchtigen.
- Lösungsansatz: Materialprüfungen vor der Umformung und Echtzeit-Monitoring zur Anpassung der Prozessparameter an die Materialeigenschaften.
5.2 Hoher Energie- und Kostenaufwand
Die Optimierung der Temperatur- und Druckbedingungen ist energieintensiv und verursacht zusätzliche Kosten. Besonders das Warmumformen erfordert hohe Temperaturen und erhöht den Energieverbrauch.
- Lösungsansatz: Der Einsatz energieeffizienter Verfahren, wie Induktionsheizungen, kann den Energieaufwand reduzieren.
5.3 Komplexität der Simulationen und Messungen
Die genaue Simulation und Anpassung aller relevanten Parameter ist komplex und erfordert spezialisierte Technologien. Die präzise Erfassung von Temperatur, Druck und Spannungsverteilung stellt hohe Anforderungen an die Messtechnik.
- Lösungsansatz: Einsatz modernster FEM-Software und optimierter Sensorik, um die wichtigsten Parameter präzise zu steuern.
6. Zukünftige Entwicklungen in der Prozessparameteroptimierung
6.1 Einsatz von KI und maschinellem Lernen
Künstliche Intelligenz und maschinelles Lernen bieten großes Potenzial für die Optimierung von Prozessparametern. Algorithmen können große Mengen an Daten analysieren und die optimalen Parameter in Echtzeit berechnen.
- Vorteile:
- Schnelle Anpassung an Material- und Prozessvariationen
- Kontinuierliche Verbesserung der Rückfederungskontrolle
6.2 Einsatz adaptiver und intelligenter Werkzeuge
Adaptives Werkzeugdesign und Sensoren ermöglichen es, die Werkzeuggeometrie und den Umformdruck dynamisch an die Rückfederungsbedingungen anzupassen.
- Anwendungsbeispiele: In der Automobilindustrie werden intelligente Werkzeuge getestet, die die Rückfederung durch Echtzeitsteuerung der Werkzeugform minimieren.
6.3 Entwicklung neuer Legierungen und Materialoptimierung
Zukünftig könnten speziell entwickelte Stahllegierungen, die auf minimale Rückfederung ausgelegt sind, den Bedarf an Prozessoptimierung reduzieren und eine bessere Maßhaltigkeit ermöglichen.
Fazit
Die Optimierung der Prozessparameter ist eine der effektivsten Methoden, um die Rückfederung beim Umformen von Stahl zu minimieren. Durch die Anpassung von Temperatur, Umformgeschwindigkeit, Druck und Werkzeuggeometrie lässt sich die elastische Rückfederung effektiv steuern. Moderne Technologien wie FEM-Simulationen, DOE-Methoden und Echtzeit-Monitoring bieten eine präzise Kontrolle über die Umformprozesse und ermöglichen eine kontinuierliche Verbesserung.
Mit neuen Entwicklungen, etwa dem Einsatz von KI und intelligenter Werkzeuge, kann die Prozessoptimierung weiter ausgebaut und effizienter gestaltet werden. Dies ist insbesondere in den Branchen der Automobil- und Luftfahrtindustrie entscheidend, wo Maßhaltigkeit und Formgenauigkeit von Bauteilen höchste Priorität haben. Die Optimierung der Prozessparameter bleibt ein zentraler Aspekt in der modernen Metallverarbeitung und wird auch in Zukunft entscheidend zur Qualitätssicherung beitragen.
Metallbearbeitungsmaschinen
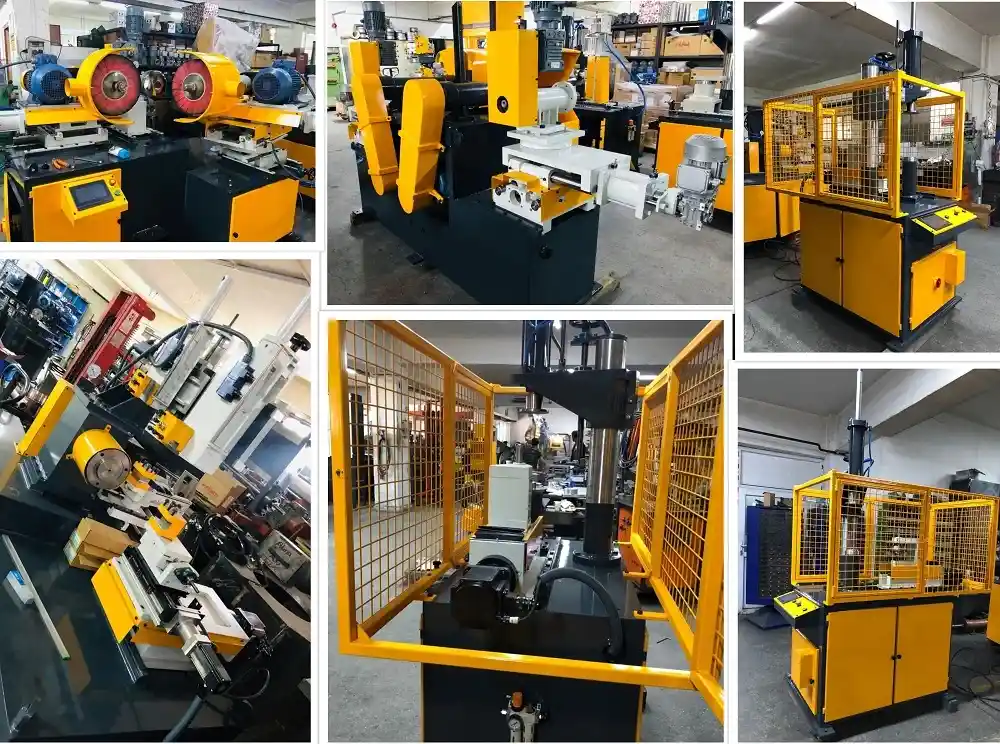
Metallbearbeitungsmaschinen wie Bördel und Beschneide Maschinen, Flanschmaschinen, Beschneide und Bördelmaschinen, Umformtechnik, Rohrbiegemaschinen, Bandsäge für Metall, Hydraulische Horizontalpresse, Kantenschneide-Bördelmaschine, Kantenbördelmaschine, Entgratungsmaschine, Innen- und Außenpoliermaschine für Edelstahltöpfe, Kreisschneidemaschine, Profilbiegemaschine und Rundschweißmaschine
Maßgeschneiderte Skalierung für spezifische Anwendungen
Die automatisierte Herstellung von Behältern, Fässern und Kesseln wird durch unsere Lösungen exakt auf das jeweilige Einsatzgebiet und die gewünschte Ausbringung angepasst. Dabei bieten wir sowohl lineare Lösungen als auch Inselkonzepte an, die eine bedarfsorientierte Automation ermöglichen. Spezielle Kantenvorbereitung für das Laserschweißen sowie wirtschaftliche Rüstkonzepte bis hin zur Fertigung „Just-in-Sequence“ sind Teil unseres Leistungsspektrums. Wir kombinieren Standard- und Sondermaschinen und bieten Ferndiagnose über LAN, WLAN oder GSM an, ergänzt durch umfassende Dokumentation gemäß CE-Richtlinien für die Gesamtanlage.
Unser Konzept
EMS entwickelt und fertigt Maschinen und Anlagen für die automatisierte Herstellung von Behältern in großem Maßstab. Alle Arbeitsschritte, von der Vorbereitung bis zur Fertigung, werden dabei aus einer Hand angeboten. Unsere erprobten Standardkomponenten sind perfekt aufeinander abgestimmt und können nahtlos mit Robotern kombiniert werden, um leistungsfähige Fertigungseinrichtungen zu schaffen.
Flexible Präzisionsfertigung
Unsere Fertigungslinien ermöglichen eine einfache Umstellung auf verschiedene Längen, Durchmesser, Formen und Bearbeitungen durch Programmwechsel. Dabei werden zahlreiche Einzelschritte wie Beschneiden, Formen, Stanzen, Fügen, Montieren, Schweißen und Prüfen automatisch und mit höchster Präzision an die jeweilige Aufgabe angepasst. Besonderes Augenmerk legen wir auf die Kantenvorbereitung für den Schweißprozess, um eine herausragende Prozesssicherheit und minimale Ausschussquoten zu gewährleisten.
Maschinenprogramm für die Metallbearbeitung
Unsere Metallbearbeitungsmaschinen sind:
- Rohrbiegemaschine
- Horizontale Presse
- Bandsäge für Metall
- Profilbiegemaschine
- Tiefziehpresse
- Rundschweißmaschine
- Kantenschneide-Bördelmaschine
- Topf- und Pfannenpoliermaschine
- Poliermaschine für flache Oberflächen
Besteck-Produktionslinie: Eine Besteck-Produktionslinie ist eine Art Maschine, die Besteck in einem kontinuierlichen Prozess herstellt. Es umfasst verschiedene Arten von Maschinen wie den Messerschleifer, den Messerschärfer und den Klingenpolierer.
Kochgeschirr-Herstellungsmaschine: Eine Kochgeschirr-Herstellungsmaschine ist eine Art Maschine, die Kochgeschirr in einem kontinuierlichen Prozess herstellt. Es umfasst verschiedene Arten von Maschinen wie den Topfmacher, den Pfannenmacher und den Wokmacher.
Küchengeschirr-Produktionsmaschine: Eine Küchengeschirr-Produktionsmaschine ist eine Art Maschine, die Küchengeschirr in einem kontinuierlichen Prozess herstellt. Es umfasst verschiedene Arten von Maschinen wie Maschinen zur Herstellung von Teekesseln, Produktionslinien für Besteck, Produktionslinien für Töpfe und Pfannen
Wir entwerfen, fertigen und montieren komplette Produktionslinien für Kochgeschirr, Küchengeschirr, Hotelgeschirr und Besteck sowie einzelne Maschinen für einen bestimmten Zweck