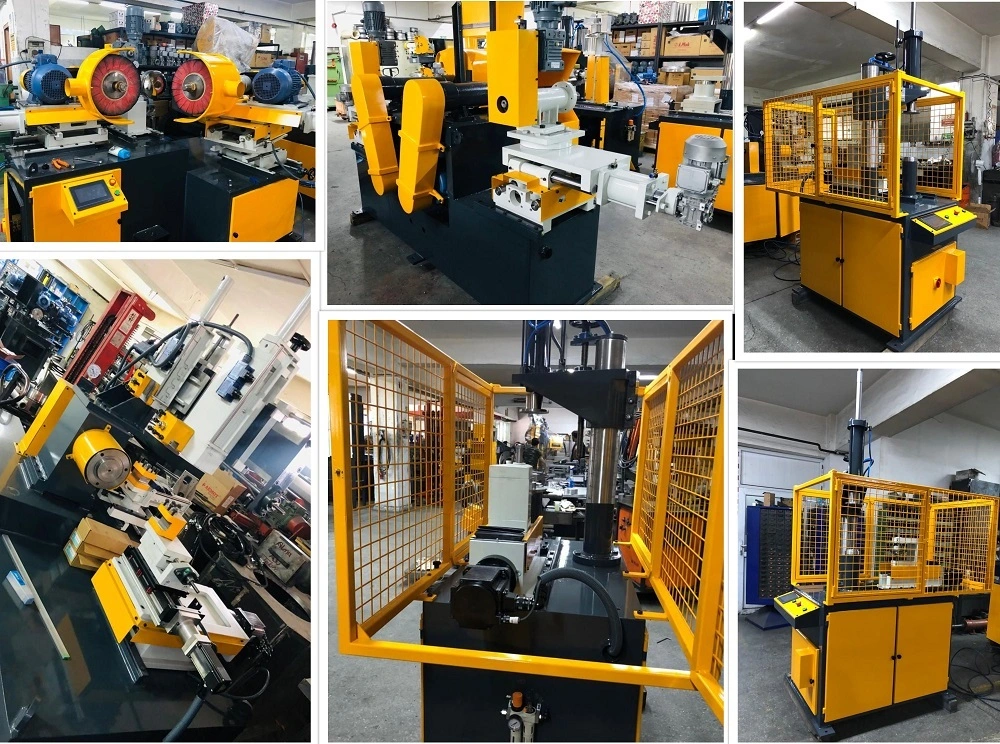
Metallumformung Maschinenbau: Die Metallumformung ist ein zentraler Bereich des Maschinenbaus, in dem es um die Entwicklung und Herstellung von Maschinen und Prozessen zur gezielten Formgebung von Metallen geht. Dieser Bereich ist besonders in der Automobil-, Luft- und Raumfahrt- sowie Bauindustrie von großer Bedeutung, da dort präzise und maßgeschneiderte Metallteile erforderlich sind. Hier sind einige zentrale Aspekte der Metallumformung im Maschinenbau:
1. Arten von Umformverfahren
- Schmieden: Metall wird mithilfe von Druckkräften in Form gebracht, oft bei hohen Temperaturen. Dies führt zu hoher Festigkeit des Werkstücks und wird häufig in der Produktion von Bauteilen mit komplexen Geometrien verwendet.
- Walzen: Reduzierung der Materialdicke durch Walzen des Metalls zwischen zwei Walzen. Dieser Prozess eignet sich für die Herstellung langer, flacher Teile, wie Bleche und Platten.
- Extrudieren: Metall wird durch eine Form (Matrize) gepresst, um eine spezifische Querschnittsform zu erzeugen, beispielsweise für Rohre oder Profile.
- Ziehen: Beim Tiefziehen wird das Metallblech in eine Matrize gezogen, um eine hohle Form zu erzeugen. Dieses Verfahren wird oft für Karosserieteile verwendet.
- Biegen: Hierbei wird das Metall gezielt gebogen, um Winkel oder Rundungen zu erzeugen. Es eignet sich für die Herstellung von Profilen und Verstärkungselementen.
2. Maschinelle Ausstattung
- Pressen: Pressen gehören zu den Hauptmaschinen in der Metallumformung und werden für zahlreiche Verfahren wie das Stanzen, Biegen und Tiefziehen genutzt. Hydraulische und mechanische Pressen sind gängige Maschinentypen.
- Walzwerke: Diese Maschinen werden in der Metallverarbeitung für die Herstellung von Blechen, Bändern und Drähten verwendet und sind in Warm- und Kaltwalzwerke unterteilt.
- Werkzeuge und Formen: Die Qualität der Werkzeuge und Matrizen ist entscheidend für die Präzision und Langlebigkeit der Teile. Für verschiedene Materialien und Umformprozesse müssen spezifische Formen entwickelt werden.
3. Werkstoffe und Materialverhalten
- Werkstoffkunde: Jedes Metall verhält sich bei der Umformung anders. Stähle, Aluminium und Kupfer erfordern unterschiedliche Ansätze, da ihre Dehnbarkeit, Festigkeit und Verformbarkeit variieren.
- Simulation und Prüfung: Simulationssoftware wird genutzt, um das Materialverhalten bei der Umformung vorherzusagen und mögliche Fehler zu minimieren. Auch Materialprüfungen, wie Zugversuche, sind ein wichtiger Bestandteil.
4. Automatisierung und Industrie 4.0
- Robotik und Sensorik: Moderne Umformmaschinen sind oft mit Robotern und Sensoren ausgestattet, die den Materialfluss steuern und überwachen.
- Datenauswertung und Überwachung: Durch die Integration von IoT-Technologien und Datenanalyse können Maschinenparameter in Echtzeit überwacht werden, was zu einer höheren Prozesssicherheit und Qualität führt.
5. Nachhaltigkeit und Energieeffizienz
- Die Metallumformung ist energieintensiv, weshalb innovative Verfahren zur Energieeinsparung und Reduzierung von Materialabfällen zunehmend an Bedeutung gewinnen. Recycling und Wiederverwendung von Metallen sind ebenfalls zentrale Themen.
Die Metallumformung im Maschinenbau ist ein hochspezialisiertes Feld, das sowohl handwerkliche Präzision als auch fortschrittliche Technik vereint. Durch kontinuierliche Innovationen in Maschinenbau und Materialwissenschaft wird die Effizienz und Präzision dieser Prozesse ständig verbessert.
Arten von Umformverfahren: Eine ausführliche Übersicht
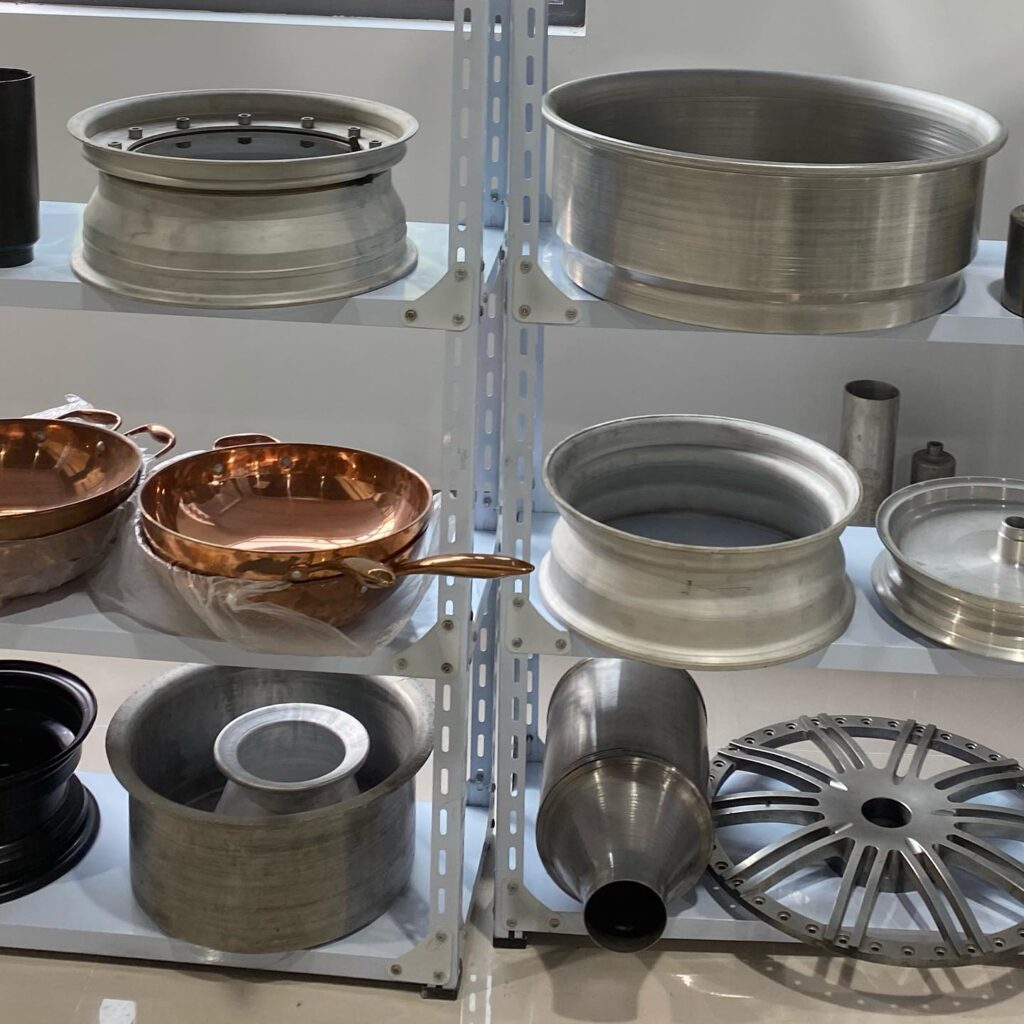
Umformverfahren sind zentrale Prozesse in der Metallverarbeitung, bei denen Metalle durch äußere Kräfte in eine gewünschte Form gebracht werden, ohne dass Material entfernt wird. In der industriellen Fertigung spielen sie eine wesentliche Rolle, da sie präzise, widerstandsfähige und kostengünstige Bauteile erzeugen können. Die wichtigsten Umformverfahren lassen sich in verschiedene Kategorien unterteilen, abhängig von der angewandten Kraft und der Art der Verformung. Diese Übersicht behandelt die verschiedenen Arten von Umformverfahren detailliert, gegliedert in wichtige Gruppen, deren Anwendung und typische Merkmale.
1. Schmieden
Das Schmieden ist eines der ältesten und bekanntesten Umformverfahren und basiert auf der gezielten Verformung von Metall durch Druck und Schlagkraft. Schmiedeverfahren werden oft in der Automobil- und Luftfahrtindustrie eingesetzt, um robuste und belastbare Teile herzustellen, da die mechanischen Eigenschaften des Materials durch die Verformung verbessert werden.
- Freiformschmieden: Hierbei wird das Werkstück ohne spezielle Form frei verformt, oft unter Anwendung eines Hammers oder einer hydraulischen Presse. Freiformschmieden wird vor allem für große Werkstücke verwendet, die besondere Flexibilität bei der Formgebung erfordern.
- Gesenkformen: Dieses Verfahren erfolgt mit Hilfe einer spezifischen Form, des sogenannten Gesenks. Das Werkstück wird durch Druck zwischen zwei Hälften in die gewünschte Form gebracht. Gesenkschmieden ist besonders präzise und wird für komplexe Geometrien genutzt, wie z. B. Kurbelwellen oder Zahnräder.
- Präzisionsschmieden: Eine Variation des Gesenkschmiedens, bei der das Werkstück fast in Endabmessung gebracht wird. Dies minimiert den Aufwand bei der Nachbearbeitung und reduziert Materialverlust.
Das Schmieden wird meist bei hohen Temperaturen durchgeführt, da dies die Verformbarkeit des Metalls verbessert. Dennoch gibt es auch Kalt- und Halbwarmverfahren, bei denen niedrigere Temperaturen genutzt werden.
2. Walzen
Walzen ist ein Verfahren, bei dem Metall zwischen zwei oder mehr Walzen hindurchgeführt wird, um dessen Dicke zu reduzieren oder eine bestimmte Form zu erzeugen. Die Walztechnik ist besonders effizient und wird vor allem in der Massenproduktion von Blechen und Bändern eingesetzt.
- Längswalzen: Beim Längswalzen wird das Material in die Länge gezogen und gleichzeitig in der Dicke reduziert. Dieses Verfahren ist ideal zur Herstellung von Blech, Flach- und Profilstahl.
- Querwalzen: Hierbei wird das Material seitlich in eine andere Richtung verformt. Es wird zum Beispiel bei der Produktion von Schrauben und anderen zylindrischen Teilen verwendet.
- Schrägwalzen: Diese Methode wird genutzt, um Rohre herzustellen, wobei das Metall unter schräg stehenden Walzen durchlaufen wird und so Hohlkörper entstehen.
Walzprozesse können sowohl im Warm- als auch im Kaltwalzverfahren durchgeführt werden. Beim Warmwalzen ist das Metall formbarer, während das Kaltwalzen eine höhere Präzision und Festigkeit bietet.
3. Extrudieren
Das Extrudieren ist ein Umformverfahren, bei dem das Metall durch eine Matrize gepresst wird, um lange Produkte mit konstantem Querschnitt zu erzeugen, wie z. B. Rohre, Stangen oder Profile. Es eignet sich besonders für die Herstellung von komplexen Querschnittsformen und ist in der Aluminiumverarbeitung weit verbreitet.
- Direktes Extrudieren: Hierbei wird das Metall in die gleiche Richtung wie der Druck bewegt. Dieses Verfahren ist energieintensiver, da die Reibung zwischen Werkstoff und Matrizenwandung überwunden werden muss.
- Indirektes Extrudieren: Im Gegensatz zum direkten Verfahren bewegt sich hier die Matrize und das Werkstück bleibt relativ ruhig, wodurch weniger Reibung entsteht und eine höhere Energieeffizienz erreicht wird.
- Hydrostatisches Extrudieren: Bei diesem Verfahren wird das Werkstück von einer Flüssigkeit umgeben, die den Druck gleichmäßig verteilt. Dies führt zu einer besonders gleichmäßigen Verformung und wird für schwer verformbare Materialien genutzt.
Extrusionsverfahren werden häufig bei der Herstellung von Aluminiumprofilen eingesetzt, die für Fensterrahmen, Fahrzeugkarosserien und andere Bau- und Strukturkomponenten genutzt werden.
4. Ziehen
Das Ziehen ist ein Verfahren, bei dem ein Metallstück durch eine Öffnung (Matrize) gezogen wird, um dessen Durchmesser zu verringern und seine Länge zu erhöhen. Ziehprozesse sind besonders geeignet für die Herstellung von Drähten, Stangen und Rohren.
- Drahtziehen: Ein Draht wird durch eine Serie von Matrizen gezogen, wobei sein Durchmesser schrittweise verringert wird. Dieses Verfahren wird häufig in der Elektroindustrie und für die Herstellung von Stahlseilen eingesetzt.
- Rohziehen: Rohre und Hohlkörper werden durch eine Matrize gezogen, um Wandstärke und Durchmesser zu reduzieren. Dieses Verfahren wird oft in der Gas- und Wasserleitungsindustrie verwendet.
- Tiefziehen: Hierbei wird ein flaches Blech in eine hohle Form gezogen, um komplexe Hohlformen zu schaffen. Das Tiefziehen wird häufig für Autokarosserieteile und Haushaltsgeräte eingesetzt.
Ziehen ist ein Kaltumformverfahren, was bedeutet, dass die Verfestigung des Materials während des Prozesses für eine hohe Endfestigkeit sorgt.
5. Biegen
Das Biegen ist ein Umformverfahren, bei dem ein flaches oder stabförmiges Werkstück gezielt in eine Winkel- oder Rundform gebracht wird. Biegeprozesse sind einfach durchzuführen und finden in zahlreichen Industrien Anwendung.
- Freies Biegen: Beim freien Biegen wird das Werkstück zwischen Ober- und Unterwerkzeug ohne vollständige Einspannung gebogen. Das Ergebnis ist meist weniger präzise, eignet sich jedoch für einfache Formen.
- Gesenkbiegen: Hierbei wird das Werkstück in eine Matrize gedrückt, was zu einem präziseren Ergebnis führt. Dieses Verfahren wird oft in der Automobilindustrie zur Herstellung von Rahmen und Strukturteilen eingesetzt.
- Walzbiegen: Mehrere Rollen formen das Werkstück durch kontinuierliches Biegen. Dieses Verfahren wird zur Herstellung großer, runder Formen wie Rohre und Tanks verwendet.
Das Biegen kann sowohl im kalten als auch im warmen Zustand durchgeführt werden. Warmbiegen wird für dickere Materialien verwendet, da es die Verformung erleichtert.
6. Stauchen
Beim Stauchen wird ein Werkstück in die Länge oder Breite gedrückt, um es zu verdicken oder zu verkürzen. Dieses Verfahren wird oft beim Schmieden verwendet, um lokal Material anzudicken.
- Vollstauchen: Das Werkstück wird vollständig unter Druck verformt, um die Dicke zu erhöhen. Dieses Verfahren wird häufig bei der Herstellung von Schraubenköpfen oder Bolzen verwendet.
- Teilstauchen: Nur ein bestimmter Bereich des Werkstücks wird verdickt, etwa zur Schaffung von Verbindungen. Teilstauchen ist besonders in der Automobilindustrie verbreitet.
Stauchen führt durch die plastische Verformung zu einer Verstärkung des Materials und wird daher oft bei sicherheitskritischen Bauteilen eingesetzt.
7. Fließpressen
Fließpressen ist ein spezielles Kaltumformverfahren, bei dem das Werkstück unter hohem Druck durch eine Matrize gepresst wird. Das Material fließt dabei in die vorgegebene Form.
- Vorwärtsfließpressen: Das Material wird in die gleiche Richtung wie der Druck bewegt, um z. B. Rohre herzustellen.
- Rückwärtsfließpressen: Die Matrize drückt das Material entgegengesetzt der Bewegungsrichtung, wodurch besonders präzise Bauteile entstehen.
- Querfließpressen: Das Material wird seitlich in eine andere Richtung gepresst, was für bestimmte komplexe Geometrien hilfreich ist.
Fließpressen wird oft bei der Massenproduktion von Metallbehältern und Hohlkörpern genutzt, da es ein schnelles und präzises Verfahren ist.
8. Innenhochdruckumformen (IHU)
Das Innenhochdruckumformen (IHU) ist ein innovatives Verfahren, das zunehmend in der Automobilindustrie Anwendung findet. Hierbei wird ein Hohlkörper von innen durch Hochdruckflüssigkeit in eine Form gedrückt, sodass komplexe Hohlstrukturen entstehen.
- Typische Anwendungen: IHU wird oft zur Herstellung von Fahrzeugrahmen, Abgasanlagen und Rohrleitungen genutzt. Es ermöglicht die Herstellung besonders leichter und dennoch stabiler Bauteile.
IHU ermöglicht komplexe Geometrien, die mit konventionellen Verfahren nur schwer oder gar nicht realisierbar wären.
9. Stanzen
Stanzen ist ein Scherumformverfahren, bei dem Material durch Schneiden entfernt wird. Es gehört zu den trennenden Umformverfahren und wird häufig bei der Herstellung von Blechteilen verwendet.
- Durchstanzen: Das Material wird durch die Matrize gestanzt und vollständig getrennt.
- Feinschneiden: Eine präzisere Variante, bei der die Schnittkanten besonders glatt sind. Feinschneiden wird häufig für Getriebe- und Bremsteile eingesetzt.
Das Stanzen ist besonders effizient und wird oft in der Massenproduktion angewendet.
Fazit
Die verschiedenen Umformverfahren im Maschinenbau bieten zahlreiche Möglichkeiten, Metallbauteile für spezifische Anforderungen herzustellen. Jedes Verfahren hat seine besonderen Vorteile und Anwendungsbereiche und trägt zur Effizienz und Vielseitigkeit der modernen Fertigung bei. Diese Verfahren sind essenziell für die Produktion hochwertiger, langlebiger und funktionsgerechter Bauteile.
Maschinelle Ausstattung in der Metallumformung: Eine umfassende Analyse
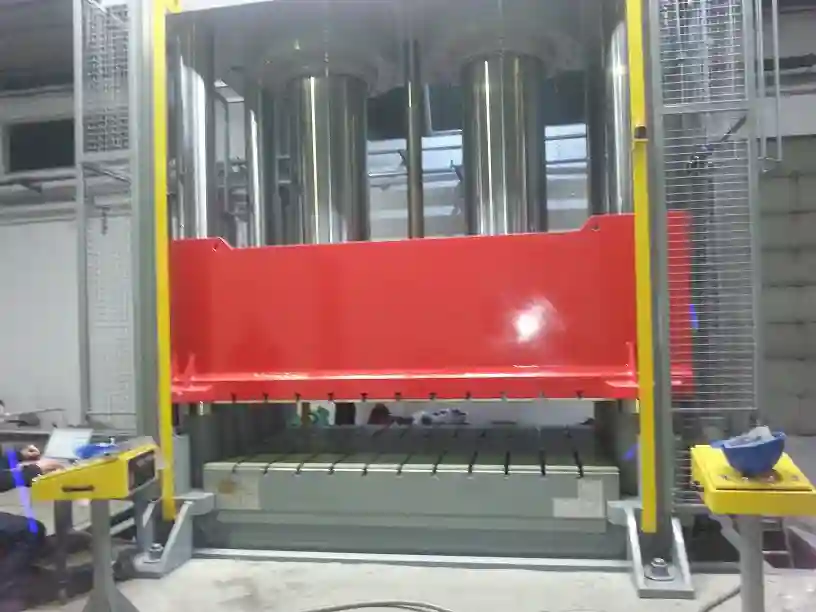
Die maschinelle Ausstattung ist ein zentraler Bestandteil der Metallumformung und bestimmt maßgeblich die Qualität, Präzision und Effizienz der Fertigungsprozesse. Die Maschinen und Werkzeuge, die bei der Umformung von Metall eingesetzt werden, sind speziell darauf ausgelegt, Metalle unter hohem Druck oder kontrollierten Bewegungen zu verformen, ohne dabei das Material zu brechen oder seine Struktur negativ zu beeinflussen. In diesem Text betrachten wir die wichtigsten Maschinentypen und ihre spezifischen Anwendungsbereiche.
1. Pressen: Das Herzstück der Metallumformung
Pressen sind die häufigsten Maschinen in der Metallumformung und dienen zahlreichen Umformverfahren wie Stanzen, Biegen und Tiefziehen. Die verschiedenen Pressentypen unterscheiden sich in ihrer Funktionsweise und Anwendung:
- Mechanische Pressen: Diese Pressen verwenden mechanische Energie und sind auf hohe Arbeitsgeschwindigkeiten ausgelegt, was sie ideal für große Serienproduktionen macht.
- Exzenterpressen: Sie arbeiten über einen Exzenter, der die Druckkraft über eine rotierende Bewegung erzeugt. Exzenterpressen sind ideal für Arbeiten, bei denen eine präzise Kontrolle der Hubhöhe wichtig ist, wie z. B. beim Stanzen.
- Kurbelpressen: Diese nutzen eine Kurbelwelle und sind für Anwendungen geeignet, bei denen hohe Geschwindigkeiten und mittlere Presskräfte erforderlich sind.
- Hydraulische Pressen: Hydraulikpressen nutzen Flüssigkeitsdruck, der gleichmäßig und konstant ist, was eine gleichmäßige Kraftverteilung auf das Werkstück ermöglicht.
- Tiefziehpressen: Diese Pressen werden für das Tiefziehen von Metallen verwendet und eignen sich besonders für das Umformen komplexer und großformatiger Teile, wie z. B. Fahrzeugkarosserien.
- Hydraulikpressen mit variabler Kraft: Durch die Möglichkeit, die Druckkraft flexibel anzupassen, werden diese Pressen oft in der Blechbearbeitung eingesetzt, da sie verschiedene Materialstärken verarbeiten können.
- Servopressen: Diese modernen Pressen kombinieren die Vorteile mechanischer und hydraulischer Systeme, indem sie Servo-Motoren nutzen, die eine präzise Steuerung von Geschwindigkeit und Kraft ermöglichen. Sie sind besonders effizient und eignen sich für komplexe Bauteile.
Pressen sind entscheidend für die industrielle Fertigung, da sie eine hohe Produktivität und Qualität ermöglichen. Durch den Einsatz automatisierter Systeme kann die Effizienz weiter gesteigert werden.
2. Walzwerke: Maschinen zur Blech- und Profilherstellung
Walzwerke sind Maschinen, die in der Metallumformung zur Reduktion der Materialdicke und zur Herstellung spezifischer Profile verwendet werden. Sie spielen eine zentrale Rolle in der Produktion von Blech, Band und Profilen und sind sowohl für die Herstellung von langen Blechen als auch von komplexen Profilen geeignet.
- Kaltwalzwerke: Diese Maschinen werden eingesetzt, um das Metall bei Raumtemperatur zu verformen, was zu einer erhöhten Festigkeit und besseren Oberflächengüte führt. Kaltwalzen ist besonders für Anwendungen geeignet, bei denen hohe Präzision und eine gleichmäßige Oberfläche erforderlich sind.
- Warmwalzwerke: Hier wird das Metall erhitzt, bevor es durch die Walzen geführt wird. Das Warmwalzen ist ein schnelles Verfahren und eignet sich für große Metallmengen, insbesondere für Stahlbleche und -bänder.
- Profilwalzwerke: Diese Walzwerke sind auf die Herstellung von spezifischen Profilen spezialisiert, wie zum Beispiel H-Träger oder U-Profile. Diese Profile werden häufig in der Bauindustrie verwendet.
Walzwerke sind aufgrund ihrer hohen Effizienz und Flexibilität in der Formgebung unverzichtbar in der Metallverarbeitung und werden durch präzise Steuerungssysteme unterstützt, die eine genaue Materialstärke gewährleisten.
3. Werkzeugmaschinen: Präzisionsmaschinen für komplexe Formen
Werkzeugmaschinen in der Metallumformung spielen eine wichtige Rolle, wenn es um die Herstellung hochpräziser Formen und Werkzeuge geht. Diese Maschinen sind für die Produktion von Gesenken, Matrizen und anderen Werkzeugen unverzichtbar, die in Pressen, Walzwerken und anderen Umformmaschinen eingesetzt werden.
- Fräsmaschinen: Sie werden verwendet, um präzise Formen und Profile in Metall zu schneiden. Mit CNC-gesteuerten Fräsmaschinen können komplexe Geometrien und hohe Genauigkeiten erreicht werden.
- Drehmaschinen: Diese Maschinen sind für zylindrische Formen geeignet und werden oft zur Herstellung von Matrizen und Wellen verwendet.
- Schleifmaschinen: Schleifmaschinen werden für die Endbearbeitung von Werkzeugen eingesetzt und sorgen für eine glatte und präzise Oberfläche. Diese Maschinen sind besonders wichtig für die Herstellung von Matrizen, da die Oberflächenqualität einen direkten Einfluss auf die Qualität des Endprodukts hat.
Werkzeugmaschinen sind eine Voraussetzung für die präzise Herstellung der Werkzeuge, die in der Metallumformung verwendet werden, und tragen maßgeblich zur Produktqualität und Langlebigkeit der Endprodukte bei.
4. Extrusionspressen: Maschinen zur Profilherstellung
Extrusionspressen sind Maschinen, die in der Metallumformung zur Herstellung von Profilen mit konstantem Querschnitt eingesetzt werden. Sie nutzen das Prinzip, das Material durch eine Matrize zu pressen, um die gewünschte Form zu erzeugen.
- Aluminium-Extrusionspressen: Diese Pressen werden häufig zur Herstellung von Aluminiumprofilen verwendet, die in der Bau- und Automobilindustrie weit verbreitet sind. Das leichte und formbare Aluminium eignet sich ideal für komplexe Querschnitte.
- Stahl-Extrusionspressen: Diese Pressen sind für die Umformung von Stahl ausgelegt, der höhere Temperaturen und Drücke erfordert. Stahlprofile werden in der Bauindustrie verwendet, um starke, belastbare Strukturen zu schaffen.
- Kupfer-Extrusionspressen: Diese speziellen Pressen werden zur Herstellung von Kupferprofilen verwendet, die häufig in der Elektronikindustrie genutzt werden.
Extrusionspressen sind flexibel einsetzbar und ermöglichen die Herstellung von Profilen mit unterschiedlichen Querschnitten, was sie besonders wertvoll für industrielle Anwendungen macht, bei denen spezifische Profile benötigt werden.
5. Ziehen und Drahtziehmaschinen
Drahtziehmaschinen sind speziell darauf ausgelegt, Metall in Form von Draht zu verarbeiten. Beim Drahtziehen wird der Durchmesser des Metalls reduziert, indem es durch eine Matrize gezogen wird. Die Drahtziehmaschinen sind in der Metallverarbeitung weit verbreitet, insbesondere in der Herstellung von elektrischen Leitungen, Seilen und Stangen.
- Einfachziehmaschinen: Diese Maschinen bestehen meist aus einer einzelnen Ziehstation und sind für kleinere Produktionsmengen geeignet.
- Mehrfachziehmaschinen: Sie haben mehrere aufeinanderfolgende Ziehstationen, durch die das Material gezogen wird, um den Durchmesser schrittweise zu verringern. Diese Maschinen sind besonders für die Massenproduktion von Drähten geeignet.
- Tiefziehmaschinen: Diese Maschinen werden für das Tiefziehen von Blechen verwendet, bei dem flache Bleche in Hohlformen gezogen werden. Sie werden oft in der Automobilindustrie eingesetzt.
Drahtziehmaschinen sind für den präzisen Herstellungsprozess von Drähten unverzichtbar und garantieren durch gleichmäßige Ziehverfahren eine hohe Qualität des Endprodukts.
6. Induktionsöfen und Wärmebehandlungsanlagen
Induktionsöfen und Wärmebehandlungsanlagen sind unverzichtbare Maschinen, wenn es darum geht, Metalle auf spezifische Temperaturen zu erhitzen, um deren Verformbarkeit zu erhöhen oder spezifische Materialeigenschaften zu erzielen. Sie werden oft vor dem Walzen, Schmieden oder Pressen eingesetzt.
- Induktionsöfen: Induktionsöfen nutzen elektromagnetische Induktion, um Metalle schnell und präzise zu erhitzen. Sie eignen sich hervorragend für das Erwärmen kleinerer Metallstücke, die in Folgeprozessen weiterverarbeitet werden.
- Glühöfen: Diese Öfen werden verwendet, um Metalle auf eine bestimmte Temperatur zu bringen und sie langsam abzukühlen. Dadurch wird die Härte reduziert und das Material wird duktiler, was für bestimmte Umformprozesse notwendig ist.
- Härtungsöfen: Härtungsöfen erhitzen das Metall und kühlen es anschließend schnell ab, um die Festigkeit des Materials zu erhöhen. Diese Wärmebehandlung ist besonders für Werkzeuge und Bauteile wichtig, die hohen mechanischen Belastungen standhalten müssen.
Durch die Wärmebehandlung kann das Materialverhalten optimiert werden, was in der Metallumformung für hochwertige Ergebnisse essenziell ist.
7. Biegemaschinen
Biegemaschinen sind speziell für das Biegen von Metallblechen oder Profilen entwickelt und werden in der Fertigung von Bauteilen mit bestimmten Winkel- oder Kurvenformen verwendet. Sie sind in vielen Industriezweigen unverzichtbar, darunter Automobilbau, Bauwesen und Möbelproduktion.
- Freies Biegen mit hydraulischen Biegemaschinen: Diese Maschinen nutzen hydraulischen Druck, um das Material in die gewünschte Form zu biegen, was eine hohe Flexibilität bei der Formgebung bietet.
- Abkantpressen: Abkantpressen nutzen ein Ober- und Unterwerkzeug, um präzise Biegungen in Blechen zu erzeugen. Sie sind für ihre Präzision und Effizienz bekannt und werden oft in der Serienfertigung eingesetzt.
- Walzenbiegemaschinen: Diese Maschinen verwenden mehrere Walzen, um das Metall kontinuierlich zu biegen, wodurch sich kreisförmige oder zylindrische Formen ergeben.
Biegemaschinen sind durch ihre präzise Steuerung und Vielseitigkeit in der Formgebung besonders wertvoll für komplexe Anwendungen.
8. Automatisierte Systeme und Robotik
Mit der fortschreitenden Entwicklung der Industrie 4.0 wird die maschinelle Ausstattung der Metallumformung zunehmend automatisiert. Moderne Maschinen sind häufig mit Robotik und Sensorik ausgestattet, um die Produktionseffizienz zu steigern und die Prozessqualität zu überwachen.
- Roboterarme für Materialhandling: Roboterarme übernehmen das Handling und Positionieren von Werkstücken an den Maschinen, was den Arbeitsprozess beschleunigt und die Produktivität steigert.
- Qualitätssicherung mit Sensorsystemen: Sensoren überwachen den Umformprozess in Echtzeit, um Fehler zu erkennen und die Qualität zu sichern.
- IoT und Datenanalyse: Durch die Erfassung von Maschinendaten in Echtzeit können Produktionsprozesse optimiert und Maschinenstillstände minimiert werden.
Automatisierung und Robotik revolutionieren die Metallumformung, da sie eine präzise Steuerung, höhere Produktivität und verbesserte Sicherheit ermöglichen.
Fazit
Die maschinelle Ausstattung in der Metallumformung ist vielfältig und reicht von Pressen und Walzwerken bis hin zu hochmodernen Automatisierungssystemen. Jede Maschine hat spezifische Anwendungsbereiche, und durch die Kombination von präzisen Werkzeugmaschinen, modernen Steuerungssystemen und fortschrittlicher Robotik wird die Produktion zunehmend effizienter und flexibler. Die fortlaufende Weiterentwicklung dieser Maschinen trägt zur Optimierung der Metallverarbeitung und zur Verbesserung der Produktqualität bei.
Werkstoffe und Materialverhalten in der Metallumformung
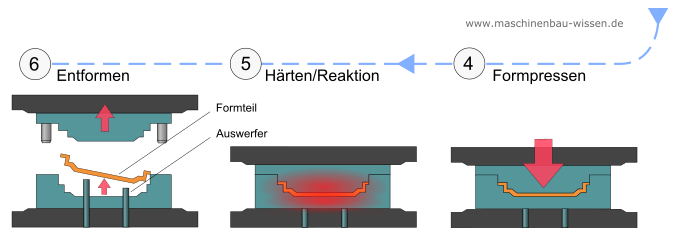
In der Metallumformung sind die Auswahl und das Verständnis der Werkstoffe entscheidend, um optimale Ergebnisse in der Verformung, Haltbarkeit und Leistungsfähigkeit der hergestellten Bauteile zu erzielen. Jeder Werkstoff hat spezifische Eigenschaften, die das Verhalten während der Umformung beeinflussen. Das Materialverhalten hängt von Faktoren wie der Kristallstruktur, den mechanischen Eigenschaften und der Zusammensetzung ab. Die physikalischen und chemischen Merkmale der Werkstoffe spielen ebenso eine zentrale Rolle für die Wahl der richtigen Umformverfahren. Im Folgenden wird eine umfassende Analyse der wichtigsten Werkstoffe und deren Verhalten im Umformprozess gegeben.
1. Grundlagen der Werkstoffkunde
Die Werkstoffkunde beschäftigt sich mit der Erforschung der Eigenschaften und des Verhaltens von Materialien. In der Metallumformung werden Werkstoffe hinsichtlich ihrer Verformbarkeit, Festigkeit und Stabilität untersucht. Zu den Hauptmaterialgruppen in der Metallverarbeitung gehören:
- Stahl und legierte Stähle: Diese Materialien bieten eine hohe Festigkeit und sind relativ preiswert, was sie zu einem der am häufigsten verwendeten Werkstoffe macht.
- Aluminium und Aluminiumlegierungen: Aluminium ist leicht und korrosionsbeständig, was es ideal für die Luftfahrt- und Automobilindustrie macht.
- Kupfer und Kupferlegierungen: Kupfer hat eine hervorragende elektrische Leitfähigkeit und wird in der Elektronik und Elektrotechnik eingesetzt.
- Edelmetalle: Diese werden aufgrund ihrer Korrosionsbeständigkeit und ästhetischen Eigenschaften oft in der Schmuck- und Elektronikindustrie verwendet.
Das Verhalten dieser Materialien unter Belastung hängt von ihrer Struktur auf atomarer Ebene sowie von ihrer chemischen Zusammensetzung ab.
2. Mechanische Eigenschaften und deren Bedeutung
Die mechanischen Eigenschaften von Werkstoffen sind entscheidend, um ihr Verhalten bei verschiedenen Umformverfahren vorherzusagen und zu steuern. Wichtige mechanische Eigenschaften umfassen:
- Festigkeit: Die Festigkeit eines Materials beschreibt dessen Widerstand gegenüber Verformung. Sie wird unterteilt in Zugfestigkeit, Druckfestigkeit und Scherfestigkeit.
- Duktilität und Zähigkeit: Diese beiden Eigenschaften sind eng miteinander verbunden. Duktilität beschreibt die Fähigkeit des Materials, sich plastisch zu verformen, ohne zu brechen. Zähigkeit ist ein Maß für die Energie, die das Material aufnehmen kann, bevor es versagt.
- Elastizität: Die Elastizität ist die Fähigkeit des Materials, nach einer Belastung in seine ursprüngliche Form zurückzukehren.
- Härte: Härte beschreibt den Widerstand des Materials gegenüber Eindringen oder Abrieb. Harte Materialien sind weniger verformbar, aber widerstandsfähiger gegen Kratzer und Verschleiß.
Diese mechanischen Eigenschaften spielen eine große Rolle bei der Entscheidung, welcher Werkstoff für ein bestimmtes Umformverfahren geeignet ist. Beispielsweise erfordert das Tiefziehen duktilere Materialien, während das Stanzen harte Werkstoffe bevorzugt.
3. Materialverhalten bei verschiedenen Umformverfahren
Das Materialverhalten variiert stark je nach dem gewählten Umformverfahren. Diese Verfahren können das Material in unterschiedlicher Weise beanspruchen, und das Verformungsverhalten beeinflusst die Wahl des Werkstoffes erheblich:
- Schmieden: Schmiedestücke benötigen Materialien mit hoher Festigkeit und Duktilität, da sie hohen Druckkräften ausgesetzt sind. Stahl ist hier der am häufigsten verwendete Werkstoff, da er eine hohe Festigkeit bei gleichzeitig guter Formbarkeit bietet.
- Walzen: Beim Walzen muss das Material unter starken Druckkräften gleichmäßig fließen können. Aluminium und Kupfer sind hier aufgrund ihrer Duktilität geeignet, aber auch legierte Stähle kommen zum Einsatz.
- Extrudieren: Extrudierte Materialien sollten eine gute Fließfähigkeit haben, um die gewünschte Form zu erreichen. Hier wird oft Aluminium verwendet, da es leicht zu extrudieren ist.
- Tiefziehen: Tiefziehprozesse erfordern Materialien, die sich gut dehnen lassen, ohne zu reißen, wie z. B. Aluminium oder Tiefziehstahl.
- Biegen: Beim Biegen muss das Material zäh und elastisch sein, um Rissbildungen zu vermeiden. Stahl und Aluminium kommen hier häufig zum Einsatz, wobei je nach Anforderung spezifische Legierungen gewählt werden.
Das Materialverhalten in den verschiedenen Umformverfahren wird oft durch eine Kombination aus experimenteller Prüfung und Simulation untersucht, um mögliche Fehler frühzeitig zu identifizieren und den Materialeinsatz zu optimieren.
4. Stahl als wichtiger Werkstoff in der Metallumformung
Stahl ist einer der am häufigsten verwendeten Werkstoffe in der Metallverarbeitung und zeichnet sich durch eine hohe Festigkeit, Duktilität und Verfügbarkeit aus. Die Eigenschaften von Stahl können durch Legierungen, Wärmebehandlungen und Oberflächenveredelungen weiter optimiert werden. Wichtige Stahlarten und deren Eigenschaften umfassen:
- Kohlenstoffstahl: Er ist die einfachste und kostengünstigste Stahlart. Mit steigendem Kohlenstoffgehalt wird der Stahl härter, jedoch weniger duktil.
- Legierter Stahl: Durch Zugabe von Chrom, Nickel, Molybdän und anderen Elementen kann der Stahl für spezifische Anwendungen optimiert werden, z. B. für Korrosionsbeständigkeit oder Härte.
- Edelstahl: Er enthält mindestens 10,5 % Chrom und ist besonders korrosionsbeständig. Edelstahl wird oft für Umformprozesse eingesetzt, bei denen Korrosionsbeständigkeit erforderlich ist.
Durch die große Vielfalt an Stahlsorten können diese in nahezu allen Umformverfahren eingesetzt werden, von Biegen und Schmieden bis hin zum Tiefziehen.
5. Aluminium und Aluminiumlegierungen: Eigenschaften und Vorteile
Aluminium ist wegen seiner Leichtigkeit, Korrosionsbeständigkeit und guten Verformbarkeit ein bevorzugter Werkstoff in der Metallumformung, vor allem in der Luft- und Raumfahrt sowie in der Automobilindustrie. Zu den gängigsten Aluminiumlegierungen und ihren Eigenschaften gehören:
- Reinaluminium: Es ist weich und leicht verformbar, jedoch weniger fest als legierte Aluminiumtypen. Reinaluminium wird häufig in Anwendungen eingesetzt, bei denen das Gewicht entscheidend ist, wie z. B. in der Verpackungsindustrie.
- Aluminium-Kupfer-Legierungen: Diese Legierungen weisen eine höhere Festigkeit auf und sind gut umformbar. Sie werden oft in der Luftfahrtindustrie eingesetzt, wo ein Verhältnis von Festigkeit zu Gewicht entscheidend ist.
- Aluminium-Magnesium-Silizium-Legierungen: Diese Legierungen sind korrosionsbeständig und leicht zu extrudieren, was sie für Bauanwendungen wie Fenster- und Türprofile prädestiniert.
Aluminium ist ideal für Umformverfahren wie Walzen, Extrudieren und Tiefziehen, da es leicht verformbar ist und bei einer Vielzahl von Temperaturen bearbeitet werden kann.
6. Kupfer und Kupferlegierungen: Anwendung in der Umformung
Kupfer und seine Legierungen zeichnen sich durch hervorragende elektrische und thermische Leitfähigkeit sowie gute Korrosionsbeständigkeit aus. Sie werden häufig in der Elektronik-, Elektro- und Bauindustrie verwendet. Zu den wichtigsten Kupferlegierungen gehören:
- Messing (Kupfer-Zink-Legierung): Messing ist leicht zu verformen und korrosionsbeständig. Es wird häufig in der Sanitärtechnik und in dekorativen Anwendungen eingesetzt.
- Bronze (Kupfer-Zinn-Legierung): Bronze hat eine höhere Festigkeit und Korrosionsbeständigkeit und wird oft für Lager und Zahnräder verwendet.
- Kupfer-Nickel-Legierungen: Diese Legierungen sind besonders widerstandsfähig gegen Salzwasser und werden daher in der Schifffahrt und Offshore-Technik eingesetzt.
Kupferlegierungen sind besonders gut für das Ziehen und Walzen geeignet, da sie leicht zu verformen sind und dabei ihre Eigenschaften behalten.
7. Einfluss von Legierungen und Wärmebehandlungen auf das Materialverhalten
Die mechanischen Eigenschaften und das Verhalten von Metallen während der Umformung können durch Legierungen und Wärmebehandlungen signifikant beeinflusst werden:
- Legierungen: Durch die Zugabe von Elementen wie Chrom, Nickel, Vanadium und Molybdän können die Festigkeit, Härte, Zähigkeit und Korrosionsbeständigkeit des Metalls angepasst werden. So wird beispielsweise Edelstahl durch die Zugabe von Chrom korrosionsbeständig, während Nickel die Duktilität erhöht.
- Wärmebehandlungen: Wärmebehandlungen wie Glühen, Härten und Anlassen verändern die Mikrostruktur des Metalls und optimieren es für bestimmte Umformprozesse.
- Glühen reduziert Spannungen und verbessert die Duktilität.
- Härten erhöht die Festigkeit und Oberflächenhärte.
- Anlassen mindert die Sprödigkeit und macht das Material zäher.
Diese Modifikationen sind besonders in Branchen wie dem Automobilbau und der Luftfahrt wichtig, wo die Werkstoffe höchste Anforderungen an Festigkeit und Verformbarkeit erfüllen müssen.
8. Simulation und Analyse des Materialverhaltens
Moderne Simulationsmethoden und Analyseverfahren spielen eine entscheidende Rolle beim Verständnis und der Optimierung des Materialverhaltens in der Metallumformung. Einige wichtige Techniken sind:
- Finite-Elemente-Methode (FEM): Mit der FEM können Spannungen, Dehnungen und Temperaturverteilungen im Material während des Umformprozesses simuliert werden. Diese Methode hilft dabei, Fehler frühzeitig zu erkennen und das Umformverfahren optimal anzupassen.
- Werkstoffprüfung: Durch mechanische Prüfungen wie Zugversuche, Biegeversuche und Härtemessungen können die Eigenschaften des Werkstoffs überprüft und die Verformbarkeit abgeschätzt werden.
- Mikrostrukturanalyse: Die Untersuchung der Mikrostruktur mittels Mikroskopie gibt Aufschluss über die Kornstruktur, die Ausscheidungen und Phasenverteilungen, die das Verhalten des Materials beeinflussen.
Simulationen und Prüfungen helfen, die Materialkosten zu senken und die Produktqualität zu steigern, indem sie eine präzise Anpassung der Umformparameter an die spezifischen Werkstoffe ermöglichen.
Fazit
Die Auswahl des richtigen Werkstoffs und das Verständnis seines Verhaltens sind grundlegend für die erfolgreiche Metallumformung. Die mechanischen Eigenschaften und die mikrostrukturellen Merkmale bestimmen maßgeblich, wie das Material auf die verschiedenen Umformverfahren reagiert. Durch die richtige Kombination aus Werkstoffauswahl, Legierungszusätzen und Wärmebehandlung kann das Verhalten des Materials optimal an die spezifischen Anforderungen angepasst werden. Die fortlaufende Entwicklung neuer Werkstoffe und Veredelungsmethoden trägt zur Verbesserung der Leistungsfähigkeit und Haltbarkeit der hergestellten Bauteile bei und unterstützt den Fortschritt in Branchen wie der Automobil-, Luftfahrt- und Bauindustrie.
Automatisierung und Industrie 4.0 in der Metallumformung
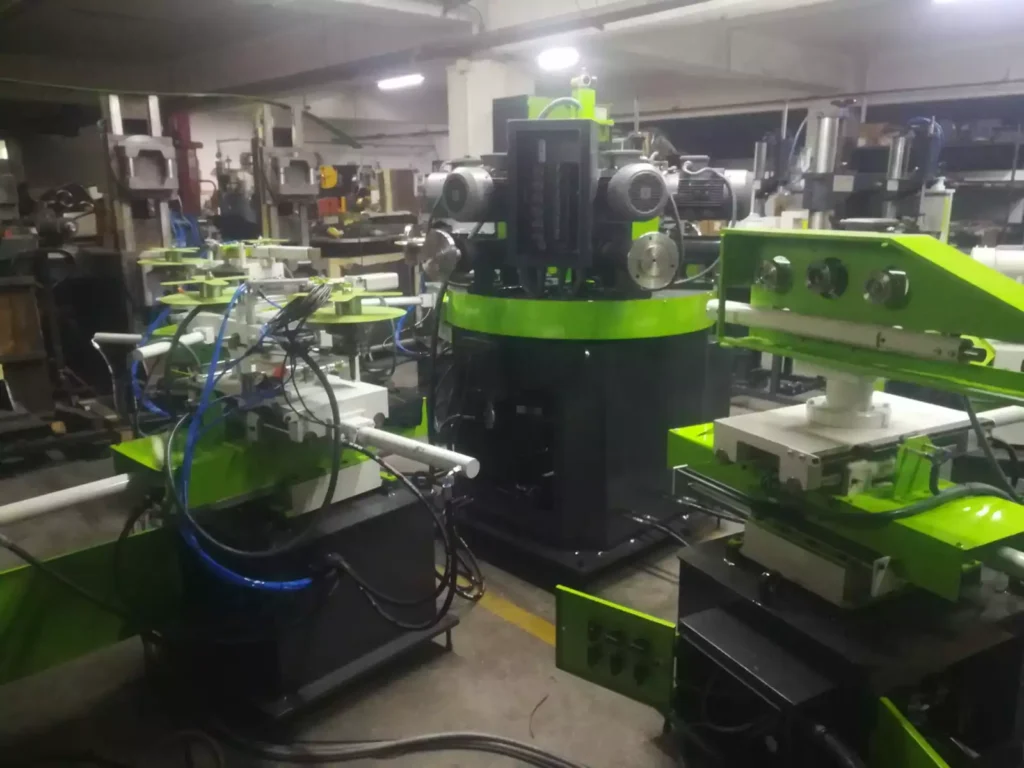
Industrie 4.0 und Automatisierungstechnologien haben die Metallumformung revolutioniert, indem sie die Art und Weise, wie Maschinen und Menschen in der Fertigung interagieren, radikal verändert haben. Durch die Integration von Internet of Things (IoT), Künstlicher Intelligenz (KI), Sensorik und Robotik in Produktionsprozesse bietet Industrie 4.0 erhebliche Verbesserungen hinsichtlich Effizienz, Präzision und Flexibilität. Die folgenden Abschnitte beleuchten, wie Automatisierung und Industrie 4.0 die Metallumformung beeinflussen, welche Technologien und Konzepte dabei im Fokus stehen und welche Herausforderungen und Zukunftsperspektiven sich in diesem Bereich ergeben.
1. Grundprinzipien von Industrie 4.0 in der Metallumformung
Industrie 4.0 zielt darauf ab, Produktionsanlagen, Maschinen und Menschen digital zu vernetzen. In der Metallumformung bedeutet das, dass Daten aus verschiedenen Quellen zusammengeführt und analysiert werden, um die Fertigung zu optimieren und Stillstände zu minimieren.
- Vernetzung und Kommunikation: Maschinen, Werkzeuge und sogar Werkstücke sind miteinander vernetzt und tauschen in Echtzeit Daten aus. Diese Kommunikation ermöglicht eine dynamische Anpassung des Produktionsprozesses.
- Transparenz und Datenanalyse: Durch kontinuierliche Datenerfassung und Analyse können Produktionsprozesse und Werkstoffverhalten genau überwacht und optimiert werden.
- Dezentrale Entscheidungsfindung: Smarte Maschinen sind in der Lage, aufgrund von Echtzeitdaten eigenständige Entscheidungen zu treffen, z. B. Anpassungen an den Prozessparametern vorzunehmen.
- Technische Assistenz: Mensch und Maschine arbeiten enger zusammen, wobei Augmented Reality (AR) und andere Assistenzsysteme die menschlichen Mitarbeiter unterstützen, beispielsweise durch visuelle Anleitungen und Sicherheitswarnungen.
Die Grundlage für Industrie 4.0 in der Metallumformung ist also eine umfassende Digitalisierung, die alle Ebenen der Fertigung durchdringt.
2. Automatisierungstechnologien und deren Anwendung in der Metallumformung
Die Automatisierung spielt eine Schlüsselrolle in der Industrie 4.0, indem sie Prozesse schneller und präziser gestaltet. Es gibt verschiedene Technologien, die im Bereich der Metallumformung weit verbreitet sind:
- Roboter und Cobots (kollaborative Roboter): Roboterarme übernehmen Aufgaben wie Materialhandling, Positionierung und Qualitätskontrolle. Kollaborative Roboter (Cobots) arbeiten Seite an Seite mit menschlichen Mitarbeitern, ohne die Notwendigkeit von Schutzvorrichtungen.
- Materialhandhabung: Roboter können schwere Metallteile transportieren und positionieren, was die Sicherheit und Ergonomie für die Mitarbeiter verbessert.
- Qualitätsprüfung: Cobots können Werkstücke während des Fertigungsprozesses inspizieren und sofortige Korrekturmaßnahmen vornehmen.
- Automatische Zuführsysteme: In vielen Umformprozessen müssen Werkstücke präzise positioniert und ausgerichtet werden. Automatische Zuführsysteme gewährleisten einen kontinuierlichen Materialfluss und verringern die Rüstzeiten.
- Sensorik und Echtzeitüberwachung: Sensoren messen physikalische Parameter wie Druck, Temperatur, Geschwindigkeit und Dehnung. Diese Daten ermöglichen eine präzise Steuerung des Umformprozesses und verbessern die Produktqualität.
- Temperatursensoren überwachen die Temperatur des Werkstoffs und passen die Umformparameter an.
- Kraftsensoren erfassen die beim Pressen oder Schmieden aufgebrachte Kraft und stellen sicher, dass diese den festgelegten Spezifikationen entspricht.
Durch den Einsatz dieser Technologien kann die Automatisierung den Produktionsprozess effizienter und flexibler gestalten und gleichzeitig die Präzision und Qualität der Umformteile erhöhen.
3. Big Data und Datenanalyse in der Metallumformung
Die Industrie 4.0 generiert eine enorme Menge an Daten, die für die Optimierung von Prozessen genutzt werden können. Big Data und Datenanalyse sind zentrale Elemente, um fundierte Entscheidungen in Echtzeit zu treffen.
- Prozessoptimierung: Durch die Analyse von Prozessdaten können potenzielle Fehlerquellen identifiziert und vermieden werden. Beispielsweise kann durch die Beobachtung von Abweichungen in Temperatur- oder Druckwerten die Wahrscheinlichkeit eines Ausfalls oder einer fehlerhaften Produktion minimiert werden.
- Vorausschauende Wartung (Predictive Maintenance): Durch die Überwachung von Maschinenzuständen und den Einsatz von Algorithmen können Wartungsarbeiten vorzeitig geplant werden, bevor eine Störung auftritt. Dies reduziert Ausfallzeiten und erhöht die Produktivität.
- Anpassung der Umformparameter: Echtzeitdaten können genutzt werden, um Parameter wie Kraft, Geschwindigkeit und Temperatur dynamisch an die Materialeigenschaften anzupassen. Beispielsweise kann sich das Verhalten des Materials durch unterschiedliche Temperaturen ändern, was dann automatisch in den Prozess integriert wird.
Big Data und Datenanalyse ermöglichen eine präzise Anpassung des Umformprozesses, wodurch Ausschuss reduziert und die Produktionsqualität gesteigert wird.
4. Cyber-Physische Systeme (CPS) und das Internet of Things (IoT)
Cyber-physische Systeme (CPS) und das Internet of Things (IoT) sind zentrale Technologien in der Industrie 4.0 und spielen eine entscheidende Rolle in der Metallumformung. CPS verknüpfen physische Prozesse mit digitalen Systemen, was zu einer intelligenten und flexiblen Produktionsumgebung führt.
- Integration von IoT-Sensoren: IoT-Sensoren werden in Maschinen integriert, um Daten über den Zustand und die Leistung der Maschinen zu sammeln und zu analysieren. Diese Sensoren ermöglichen eine ständige Überwachung der Prozessparameter.
- Automatische Anpassung der Maschinenparameter: CPS-Systeme können Parameter in Echtzeit anpassen und auf unvorhergesehene Veränderungen im Produktionsprozess reagieren. Dies ist besonders nützlich in der Metallumformung, wo die Materialeigenschaften während des Umformprozesses variieren können.
- Virtuelle Abbildung der Fertigung: Durch CPS wird eine digitale Kopie der physischen Produktionslinie erstellt. Diese „digitale Fabrik“ simuliert den Produktionsprozess und zeigt in Echtzeit den aktuellen Zustand der Fertigung. Probleme und Engpässe können so schon im Vorfeld identifiziert und gelöst werden.
CPS und IoT sorgen für eine größere Transparenz und Kontrolle über den Umformprozess und tragen dazu bei, die Effizienz und Qualität der Produktion zu erhöhen.
5. Simulation und digitale Zwillinge in der Umformtechnik
Der Einsatz digitaler Zwillinge und Simulationsmodelle ist ein weiterer zentraler Aspekt der Industrie 4.0 in der Metallumformung. Ein digitaler Zwilling ist eine virtuelle Darstellung eines physischen Objekts oder Prozesses und wird in Echtzeit mit Daten versorgt, um den aktuellen Zustand abzubilden.
- Prozessoptimierung: Digitale Zwillinge simulieren den Umformprozess und helfen, optimale Parameter für die Produktion festzulegen. Sie können verwendet werden, um verschiedene Szenarien zu testen, bevor der physische Umformprozess beginnt.
- Vorausschauende Wartung und Fehlererkennung: Digitale Zwillinge ermöglichen eine kontinuierliche Überwachung der Maschinen und Werkzeuge. Sie erkennen Anzeichen von Verschleiß und können vorausschauende Wartungsmaßnahmen einleiten, bevor Schäden auftreten.
- Kosteneinsparung und Ressourcenmanagement: Durch die Simulation des Umformprozesses lassen sich Produktionskosten und Materialeinsatz reduzieren. Digitale Zwillinge helfen dabei, Prozesse zu planen und Ressourcen effizient zu nutzen.
Simulation und digitale Zwillinge bieten eine präzise Möglichkeit, den Umformprozess zu überwachen und kontinuierlich zu verbessern, was zu einer höheren Qualität und Kosteneffizienz führt.
6. Maschinelles Lernen und Künstliche Intelligenz (KI) in der Umformung
Künstliche Intelligenz (KI) und maschinelles Lernen (ML) haben das Potenzial, die Umformtechnologie zu transformieren, indem sie die Prozesssteuerung und die Fehlererkennung verbessern. In der Industrie 4.0 werden KI-Modelle genutzt, um Produktionsprozesse zu automatisieren und Optimierungsmöglichkeiten zu erkennen.
- Prognosemodelle für das Materialverhalten: Durch den Einsatz von maschinellem Lernen können Algorithmen das Verhalten von Werkstoffen während des Umformprozesses vorhersagen und die Parameter entsprechend anpassen.
- Fehlererkennung und Qualitätskontrolle: KI-Modelle können Muster in den Produktionsdaten erkennen und auf potenzielle Fehler hinweisen, bevor diese auftreten. So kann beispielsweise eine Anomalie in der Kraftübertragung erkannt und behoben werden, bevor sie die Qualität des Werkstücks beeinträchtigt.
- Prozessoptimierung: ML-Modelle analysieren historische Daten und können die optimalen Parameter für verschiedene Umformprozesse identifizieren. Dies spart Zeit und Kosten und verbessert die Produktionsqualität.
KI und maschinelles Lernen steigern die Effizienz der Metallumformung, da sie die Automatisierung und Optimierung von Prozessen ermöglichen und gleichzeitig die Qualität der Endprodukte sicherstellen.
7. Herausforderungen und zukünftige Entwicklungen
Trotz der vielen Vorteile birgt die Einführung von Industrie 4.0 in der Metallumformung auch Herausforderungen:
- Hohe Implementierungskosten: Die Anschaffung neuer Technologien und die Umrüstung bestehender Systeme erfordern erhebliche Investitionen.
- Sicherheits- und Datenschutzfragen: Mit der zunehmenden Vernetzung und Datenerfassung steigen die Anforderungen an Datensicherheit und Datenschutz. Sensible Daten über Produktionsprozesse und Maschinenleistung müssen sicher gespeichert und geschützt werden.
- Fachkräftemangel: Industrie 4.0 erfordert Mitarbeiter mit fortgeschrittenen technischen Kenntnissen, was insbesondere in traditionell handwerklichen Industriezweigen wie der Metallverarbeitung eine Herausforderung darstellen kann.
- Anpassungsfähigkeit der Maschinen: Die Umrüstung und Flexibilität älterer Maschinen auf Industrie 4.0-Standards sind oft schwierig. In vielen Fällen muss zwischen einer Aufrüstung der alten Maschinen und der Anschaffung neuer Systeme abgewogen werden.
Trotz dieser Herausforderungen wird die Industrie 4.0 in der Metallumformung weiter voranschreiten. Zukünftige Entwicklungen könnten das verstärkte Zusammenwirken von KI, Robotik und digitalen Zwillingen umfassen, was die Effizienz, Nachhaltigkeit und Flexibilität der Fertigung weiter verbessert.
Fazit
Industrie 4.0 und Automatisierung bieten der Metallumformung zahlreiche Vorteile, von der Effizienzsteigerung über die verbesserte Qualitätssicherung bis hin zur Erhöhung der Produktionsflexibilität. Durch den Einsatz von Robotik, IoT, Big Data, KI und digitalen Zwillingen kann die Branche die Herstellung komplexer Metallteile optimieren und den steigenden Anforderungen an Präzision und Produktivität gerecht werden. Die fortlaufende Integration dieser Technologien in die Umformprozesse wird das Potenzial der Metallumformung weiter ausschöpfen und die Grundlage für eine nachhaltige und wettbewerbsfähige Produktion schaffen.
Schmieden: Grundlagen, Verfahren und Anwendung in der Metallverarbeitung
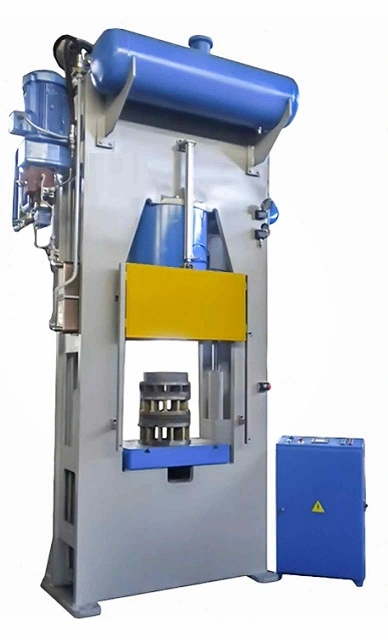
Das Schmieden ist eines der ältesten und vielseitigsten Umformverfahren in der Metallverarbeitung und hat sich über Jahrhunderte hinweg von einem handwerklichen zu einem hochpräzisen industriellen Prozess entwickelt. Schmiedeverfahren werden in zahlreichen Industriezweigen angewendet, um robuste und langlebige Werkstücke mit hoher Festigkeit und komplexen Geometrien herzustellen. Im folgenden Text wird das Schmieden umfassend erläutert, einschließlich seiner Geschichte, verschiedenen Verfahren, Werkstoffe, modernen Technologien und industriellen Anwendungen.
1. Grundlagen und Geschichte des Schmiedens
Das Schmieden gehört zu den plastischen Umformverfahren, bei denen das Werkstück durch gezielte Krafteinwirkung in eine gewünschte Form gebracht wird. Die Ursprünge des Schmiedens reichen mehrere tausend Jahre zurück; schon in der Antike wurden Metalle durch Erhitzen und Hämmern geformt. Über die Jahrhunderte wurden Schmiedeverfahren verfeinert und neue Werkzeuge entwickelt, sodass das Schmieden heute sowohl ein präzises Handwerk als auch ein automatisierter industrieller Prozess ist.
Die Grundprinzipien des Schmiedens basieren auf dem Erhitzen des Werkstücks, um dessen Verformbarkeit zu erhöhen, und dem anschließenden Formen durch Hämmern, Pressen oder Walzen. Diese mechanischen Kräfte verdichten das Metall, was zu einer Verfestigung führt und die strukturellen Eigenschaften des Materials verbessert.
2. Arten des Schmiedens
Es gibt verschiedene Schmiedeverfahren, die sich je nach angewandter Technik und Formgebung unterscheiden. Diese Verfahren können grob in drei Hauptkategorien unterteilt werden:
a) Freiformschmieden
Beim Freiformschmieden wird das Werkstück ohne feste Form, also „frei“, zwischen Amboss und Hammer oder zwischen den Werkzeugen einer Presse bearbeitet. Der Schmied führt das Werkstück von Hand oder mit Maschinen so, dass es in die gewünschte Form gebracht wird. Das Freiformschmieden ist flexibel und eignet sich besonders für die Herstellung großer Werkstücke oder solcher mit einfacher Geometrie.
- Typische Anwendung: Herstellung von Achsen, Walzen und Wellen, vor allem in der Schwerindustrie.
- Vorteile: Flexibilität und Anpassungsfähigkeit an unterschiedliche Geometrien.
- Nachteile: Weniger präzise als das Gesenkschmieden und meist auf einfache Formen beschränkt.
b) Gesenkschmieden
Beim Gesenkschmieden wird das Werkstück in eine spezielle Form, das Gesenk, gepresst, das die gewünschte Form des Werkstücks vorgibt. Gesenke bestehen aus zwei Hälften, zwischen denen das Metall in die vorgegebene Form gedrückt wird. Das Gesenkschmieden ist ein präzises Verfahren und eignet sich besonders für die Massenproduktion von Teilen mit komplexer Geometrie.
- Typische Anwendung: Herstellung von Kurbelwellen, Pleuel, Zahnrädern und Verbindungselementen.
- Vorteile: Hohe Präzision, Wiederholbarkeit und Eignung für Serienfertigung.
- Nachteile: Höhere Werkzeugkosten und längere Vorbereitungszeit für das Erstellen der Gesenke.
c) Präzisionsschmieden
Das Präzisionsschmieden ist eine Weiterentwicklung des Gesenkschmiedens, bei der das Werkstück nahezu in die Endkontur gebracht wird. Dadurch wird der Bedarf an nachträglichen Bearbeitungen reduziert, was Zeit und Materialkosten spart. Dieses Verfahren wird für Bauteile eingesetzt, bei denen höchste Präzision erforderlich ist.
- Typische Anwendung: Kleine und mittelgroße Bauteile mit engen Toleranzen, wie Zahnräder und Verbindungsteile.
- Vorteile: Minimale Nachbearbeitung, geringe Materialverluste.
- Nachteile: Hohe Anforderungen an die Werkzeuggenauigkeit und Produktionskosten.
d) Rotationsschmieden
Beim Rotationsschmieden, auch als Ringwalzen bekannt, wird das Werkstück durch rotierende Werkzeuge in Form gebracht. Dieses Verfahren eignet sich besonders für die Herstellung von runden, hohlen oder ringförmigen Bauteilen.
- Typische Anwendung: Herstellung von Lagerringen, Felgen und großen Dichtungen.
- Vorteile: Hohe Materialeffizienz und gute Formkontrolle.
- Nachteile: Aufwendige und teure Maschinen für die industrielle Fertigung.
3. Werkstoffe im Schmiedeprozess
Verschiedene Metalle und Legierungen können durch Schmieden in Form gebracht werden, wobei ihre Eigenschaften eine wichtige Rolle für die Wahl des Schmiedeverfahrens spielen. Die häufigsten Werkstoffe für das Schmieden sind:
- Stahl und legierte Stähle: Stähle sind die am häufigsten verwendeten Werkstoffe im Schmieden, da sie hohe Festigkeit und Zähigkeit aufweisen. Legierungen wie Chromstahl oder Nickelstahl verbessern spezifische Eigenschaften wie Korrosionsbeständigkeit und Härte.
- Aluminium und Aluminiumlegierungen: Aluminium ist leicht und gut umformbar, was es besonders in der Luftfahrt und Automobilindustrie beliebt macht. Aluminiumlegierungen mit Magnesium oder Kupfer haben eine höhere Festigkeit.
- Titan und Titanlegierungen: Titan ist korrosionsbeständig und besitzt ein hohes Festigkeits-Gewichts-Verhältnis, was es ideal für die Luft- und Raumfahrt sowie die Medizintechnik macht.
- Kupfer und Kupferlegierungen: Kupfer wird für Anwendungen eingesetzt, die hohe Leitfähigkeit erfordern, z. B. in der Elektronik und Elektrotechnik.
Die Wahl des Werkstoffs hängt von den mechanischen Anforderungen des Endprodukts sowie von den Umformbedingungen ab. Stahl und Aluminium sind dabei die am häufigsten verwendeten Materialien im industriellen Schmieden.
4. Ablauf des Schmiedeprozesses
Der Schmiedeprozess kann in mehrere Schritte unterteilt werden, die je nach verwendetem Verfahren leicht variieren:
- Erwärmung des Werkstücks: Das Metall wird in einem Ofen auf eine bestimmte Temperatur erhitzt, um seine Verformbarkeit zu verbessern. Bei hohen Temperaturen wird das Material duktil und lässt sich leichter formen.
- Vorformung (Vorblocken): In diesem Schritt wird das Metall grob vorgeformt, um die Grundstruktur für das Endprodukt zu schaffen. Die Vorformung bereitet das Werkstück für die exakte Endform vor.
- Formgebung: Das Werkstück wird nun in die endgültige Form gebracht. Im Gesenkschmieden geschieht dies durch Pressen in eine Matrize, im Freiformschmieden durch gezieltes Hämmern.
- Abkühlen und Wärmebehandlung: Nach der Formgebung wird das Werkstück abgekühlt, um die gewünschte Festigkeit zu erreichen. Wärmebehandlungen wie Härten und Anlassen können erforderlich sein, um das Material zu verfestigen und seine Zähigkeit zu erhöhen.
- Nachbearbeitung: Je nach Genauigkeit des Schmiedeprozesses kann eine zusätzliche Bearbeitung, wie Schleifen oder Fräsen, erforderlich sein, um die Oberflächenqualität zu verbessern und enge Toleranzen zu erreichen.
Der Ablauf des Schmiedeprozesses variiert je nach Werkstoff und Anforderungen an das Endprodukt, doch das Grundprinzip bleibt gleich.
5. Vorteile des Schmiedens
Das Schmieden bietet zahlreiche Vorteile gegenüber anderen Umformverfahren, darunter:
- Hohe Festigkeit und Widerstandsfähigkeit: Durch die Verdichtung des Metalls entsteht eine starke und robuste Struktur, die dem Werkstück hohe Festigkeit und Zähigkeit verleiht.
- Geringe Materialverschwendung: Da das Metall nicht abgetragen, sondern in Form gebracht wird, ist das Schmieden ein sehr materialeffizientes Verfahren.
- Hohe Formgenauigkeit: Besonders im Gesenk- und Präzisionsschmieden können Werkstücke mit hoher Präzision und engen Toleranzen hergestellt werden.
- Vielfalt an Formen und Geometrien: Schmieden ermöglicht die Herstellung komplexer Formen und Geometrien, die in anderen Umformverfahren schwer oder gar nicht realisierbar wären.
- Verbesserung der Werkstoffeigenschaften: Das Schmieden führt zu einer feineren Kornstruktur im Material, was die mechanischen Eigenschaften verbessert und das Material widerstandsfähiger macht.
Die Kombination dieser Vorteile macht das Schmieden zu einem idealen Verfahren für Bauteile, die hohen mechanischen Belastungen standhalten müssen.
6. Moderne Technologien im Schmieden
Mit der zunehmenden Digitalisierung und Automatisierung haben sich auch die Schmiedeverfahren weiterentwickelt. Moderne Technologien tragen zur Verbesserung der Präzision, Effizienz und Qualität in der Metallverarbeitung bei:
- Computerintegrierte Fertigung (CIM): Computer werden verwendet, um den gesamten Schmiedeprozess zu planen, zu überwachen und zu steuern. Diese Technologie ermöglicht eine präzise Steuerung der Temperatur und Druckkräfte.
- Industrielle Robotik: Roboterarme übernehmen das Handling und die Positionierung der Werkstücke. Durch Automatisierung können Schmiedeverfahren schneller und sicherer durchgeführt werden.
- Simulation und digitale Zwillinge: Simulationstechnologien ermöglichen die genaue Planung und Analyse des Schmiedeprozesses. Digitale Zwillinge erstellen eine virtuelle Kopie des Werkstücks und helfen, die besten Umformparameter zu bestimmen.
- Temperatur- und Drucksensoren: Moderne Schmiedepressen sind mit Sensoren ausgestattet, die kontinuierlich die Druck- und Temperaturwerte überwachen. Dadurch wird eine präzise Steuerung des Prozesses und eine gleichbleibende Qualität gewährleistet.
Die Integration dieser Technologien hat das Schmieden von einem traditionellen Handwerk zu einem hochmodernen, automatisierten Fertigungsverfahren entwickelt, das in vielen Industriezweigen unverzichtbar ist.
7. Industrielle Anwendungen des Schmiedens
Das Schmieden findet in zahlreichen Branchen Anwendung, darunter:
- Automobilindustrie: Geschmiedete Bauteile wie Kurbelwellen, Pleuel und Zahnräder werden in Fahrzeugen verwendet, da sie extrem belastbar und langlebig sind.
- Luft- und Raumfahrt: In der Luftfahrt werden leichte und zugleich extrem feste Teile benötigt, z. B. für Fahrwerke und Triebwerkskomponenten. Schmiedeverfahren sind ideal, um diese Anforderungen zu erfüllen.
- Bauindustrie: Stahlträger und -verbindungen, die hohen Lasten und Belastungen standhalten müssen, werden oft geschmiedet.
- Medizintechnik: Präzise und robuste Bauteile für chirurgische Instrumente und Implantate werden häufig geschmiedet, insbesondere wenn Korrosionsbeständigkeit und hohe Festigkeit erforderlich sind.
- Maschinenbau: Wellen, Lager und Zahnräder, die in Maschinen eingebaut werden, sind oft geschmiedet, da sie die nötige Stabilität und Festigkeit für schwere Einsätze bieten.
Die Vielseitigkeit des Schmiedens macht es zu einem unverzichtbaren Verfahren für die Herstellung hochwertiger und langlebiger Bauteile in zahlreichen Industrien.
Fazit
Das Schmieden ist ein bewährtes und leistungsfähiges Verfahren zur Herstellung von Bauteilen mit hoher Festigkeit und Präzision. Durch die Kombination traditioneller Techniken mit modernen Technologien ist das Schmieden heute vielseitiger und effizienter als je zuvor. Die hohe Qualität und die strukturellen Vorteile geschmiedeter Bauteile machen dieses Verfahren unverzichtbar für Branchen, in denen Zuverlässigkeit und Langlebigkeit gefordert sind. Mit fortschreitender Technologie wird sich das Schmieden weiterentwickeln und neue Anwendungsmöglichkeiten und Produktionsansätze ermöglichen.
Walzen: Ein Überblick über Verfahren, Maschinen und Anwendungen in der Metallumformung
Das Walzen ist ein zentrales Umformverfahren, das weltweit zur Herstellung von Metallerzeugnissen eingesetzt wird und für viele industrielle Prozesse unverzichtbar ist. Es dient der gezielten Reduktion der Materialdicke und der Schaffung von Profilen und Strukturen durch das gleichmäßige Durchführen von Metall zwischen zwei oder mehr rotierenden Walzen. In der Metallverarbeitung spielt das Walzen eine Schlüsselrolle, da es sich für die Massenproduktion von Blechen, Bändern und Profilen eignet und gleichzeitig eine hohe Präzision sowie Materialeffizienz bietet.
Dieser Text bietet einen umfassenden Überblick über das Walzen, einschließlich der wichtigsten Walzverfahren, der verschiedenen Maschinentypen, der verwendeten Werkstoffe, der Anwendungsbereiche und der technologischen Fortschritte.
1. Grundlagen und Funktionsweise des Walzens
Beim Walzen wird ein Metallstück durch die enge Öffnung zweier oder mehrerer rotierender Walzen geführt, wodurch es verdichtet und in eine flachere oder spezifische Profilform gebracht wird. Während des Walzens wird der Querschnitt des Werkstücks verringert, während die Länge zunimmt. Dies geschieht, weil das Metall beim Walzen plastisch verformt wird.
Die Funktionsweise des Walzens beruht auf zwei wesentlichen Prinzipien:
- Kompressionsdruck: Die Walzen üben einen hohen Druck auf das Werkstück aus, der zu einer Reduktion der Dicke führt.
- Zug- und Schubkräfte: Durch die Drehbewegung der Walzen wird das Werkstück in die Walzen gezogen und gleichzeitig von den Walzen geschoben, wodurch es durch die Walzspalte geführt wird.
Walzen kann sowohl im Warm- als auch im Kaltzustand durchgeführt werden, wobei die Temperaturwahl von der Art des Metalls und den Anforderungen des Endprodukts abhängt.
2. Arten des Walzens
Es gibt verschiedene Walzverfahren, die jeweils auf die Anforderungen der zu verarbeitenden Materialien und Produkte abgestimmt sind. Die wichtigsten Walzverfahren sind:
a) Längswalzen
Das Längswalzen, auch als Flachwalzen bezeichnet, ist die häufigste Form des Walzens und wird zur Herstellung von Blechen, Bändern und Flachprodukten verwendet. Hierbei wird das Material parallel zur Walzenachse in die Länge gezogen, was zu einer Verringerung der Dicke führt.
- Typische Anwendung: Herstellung von Blechen und Stahlplatten, die in der Automobil- und Bauindustrie verwendet werden.
- Vorteile: Effizient für die Massenproduktion und ermöglicht eine hohe Materialausnutzung.
- Nachteile: Beschränkt auf flache Formen und weniger flexibel in der Formgebung.
b) Querwalzen
Beim Querwalzen wird das Werkstück seitlich zur Walzenachse verformt. Dieses Verfahren wird häufig für die Herstellung zylindrischer Teile wie Schrauben, Wellen und Stäbe eingesetzt.
- Typische Anwendung: Produktion von Schraubenrohlingen und rotationssymmetrischen Bauteilen.
- Vorteile: Geeignet für zylindrische Formen und geringe Materialverluste.
- Nachteile: Erfordert spezielle Walzen und Maschinen und ist weniger für die Herstellung von Flachprodukten geeignet.
c) Profilwalzen
Das Profilwalzen ist ein spezielles Verfahren zur Herstellung von Profilen wie H-, T- oder U-Trägern. Hierbei wird das Metall durch Walzen mit speziellen Profilen geformt, um bestimmte Querschnitte zu erreichen.
- Typische Anwendung: Produktion von Bauprofilen und Schienen.
- Vorteile: Ermöglicht die Herstellung komplexer Profile und gewährleistet eine hohe Präzision.
- Nachteile: Erfordert eine aufwändige Walzenausrüstung und ist oft nur in großen Mengen wirtschaftlich.
d) Schrägwalzen
Beim Schrägwalzen werden die Walzen in einem Winkel zur Materialbewegung platziert, was zu einer Verdrehung des Materials führt. Schrägwalzen wird oft in der Rohrherstellung eingesetzt, da es die Bildung von Hohlräumen ermöglicht.
- Typische Anwendung: Herstellung von Rohren und Hohlkörpern.
- Vorteile: Ermöglicht die Bildung von Hohlkörpern und ist effizient für die Rohrproduktion.
- Nachteile: Spezielle Maschinen und präzise Steuerung sind erforderlich.
e) Ringwalzen
Das Ringwalzen, auch als Ringwalzen bekannt, wird zur Herstellung von großen Ringen und hohlen Zylindern eingesetzt. Es beginnt mit einem vorgeformten Ring, der durch rotierende Walzen radial und axial vergrößert wird.
- Typische Anwendung: Produktion von Lagerringen und Großdichtungen.
- Vorteile: Hohe Materialausnutzung und geringerer Materialverlust im Vergleich zu anderen Verfahren.
- Nachteile: Eingeschränkte Formenvielfalt und hohe Kosten für spezialisierte Maschinen.
Diese Verfahren ermöglichen eine Vielzahl von Geometrien und Oberflächen und bieten Flexibilität in der Herstellung verschiedener Metallprodukte.
3. Warmwalzen und Kaltwalzen
Die Walzverfahren werden in der Regel in zwei Hauptkategorien unterteilt, abhängig von der Verarbeitungstemperatur: Warmwalzen und Kaltwalzen.
a) Warmwalzen
Beim Warmwalzen wird das Metall auf hohe Temperaturen erhitzt, um seine Verformbarkeit zu verbessern und den Walzvorgang zu erleichtern. Die typischen Temperaturen beim Warmwalzen liegen über der Rekristallisationstemperatur des Metalls, was bedeutet, dass sich die Kristallstruktur während des Walzens ständig erneuert und das Material duktil bleibt.
- Typische Anwendung: Herstellung von Stahlplatten, Bahnschienen und Bändern.
- Vorteile: Leichteres Walzen durch geringere Materialhärte, hohe Umformraten und effiziente Produktion.
- Nachteile: Grobere Oberflächenstruktur und weniger Maßgenauigkeit im Vergleich zum Kaltwalzen.
b) Kaltwalzen
Das Kaltwalzen erfolgt bei Raumtemperatur oder leicht erwärmtem Zustand und wird häufig zur Herstellung von Produkten eingesetzt, die eine hohe Oberflächenqualität und enge Toleranzen erfordern. Da das Metall beim Kaltwalzen nicht rekristallisiert, härtet es aus und erreicht eine höhere Festigkeit.
- Typische Anwendung: Produktion von dünnen Blechen und Bändern für die Automobil-, Elektronik- und Haushaltsgeräteindustrie.
- Vorteile: Hohe Maßgenauigkeit und gute Oberflächenqualität, erhöhte Festigkeit durch Verfestigung.
- Nachteile: Höhere Walzkräfte erforderlich und begrenzte Formbarkeit.
Beide Verfahren haben spezifische Vorteile und Nachteile und werden je nach den Anforderungen des Endprodukts ausgewählt.
4. Maschinentypen im Walzen
Zur Durchführung der Walzprozesse gibt es verschiedene Maschinentypen, die speziell für unterschiedliche Anwendungen entwickelt wurden:
- Duo-Walzwerke: Diese Walzwerke bestehen aus zwei Walzen und werden häufig in der Primärproduktion eingesetzt, z. B. bei der Herstellung von Rohplatten.
- Quarto-Walzwerke: Quarto-Walzwerke verfügen über vier Walzen (zwei Arbeitswalzen und zwei Stützwalzen). Diese Konstruktion ermöglicht höhere Druckkräfte und eine bessere Kontrolle über die Dicke des Werkstücks.
- Sendzimir-Walzwerke: Mit mehreren kleinen Arbeits- und großen Stützwalzen bietet diese Bauweise hohe Präzision und wird häufig für das Kaltwalzen von dünnen Blechen eingesetzt.
- Profilwalzwerke: Speziell für das Profilwalzen konzipiert, diese Walzwerke haben profilierten Walzen für die Herstellung von speziellen Querschnitten.
- Ringwalzwerke: Diese Maschinen sind für die Herstellung von Ringformen ausgelegt und werden vor allem in der Produktion von Lagerringen und großen Hohlzylindern verwendet.
Jeder Maschinentyp ist auf spezifische Anforderungen ausgelegt und ermöglicht eine präzise und kosteneffiziente Produktion von Metallerzeugnissen.
5. Werkstoffe und deren Verhalten beim Walzen
Das Walzen ist ein vielseitiges Verfahren, das für eine Vielzahl von Metallen geeignet ist, wobei jedes Metall unterschiedliche Anforderungen und Verhaltensweisen aufweist.
- Stahl: Stahl ist der am häufigsten gewalzte Werkstoff, insbesondere im Bauwesen und der Automobilindustrie. Stahl lässt sich gut warmwalzen und härtet beim Kaltwalzen.
- Aluminium: Aluminium ist leicht und gut umformbar, was es ideal für das Walzen von Blechen und Profilen macht, die in der Luftfahrt und Elektronikindustrie verwendet werden.
- Kupfer: Kupfer und seine Legierungen haben eine gute Verformbarkeit und hohe Leitfähigkeit, was sie ideal für die Elektronik- und Elektroindustrie macht.
- Edelstahl: Durch seine Korrosionsbeständigkeit und Härte wird Edelstahl häufig im Kaltwalzen für Präzisionsprodukte eingesetzt.
Jeder Werkstoff hat spezifische Eigenschaften, die berücksichtigt werden müssen, um optimale Walzergebnisse zu erzielen.
6. Technologische Fortschritte im Walzen
Die Walztechnologie hat sich durch digitale und technische Innovationen weiterentwickelt, was zu effizienteren und präziseren Verfahren führt.
- Automatisierung und Industrie 4.0: Durch die Vernetzung der Maschinen und den Einsatz von Sensorik kann der Walzprozess in Echtzeit überwacht und optimiert werden. Dies verbessert die Produktivität und reduziert den Ausschuss.
- Simulation und digitale Zwillinge: Mit modernen Simulationstechniken kann der Walzprozess bereits vor der physischen Umsetzung getestet und optimiert werden. Digitale Zwillinge bieten eine virtuelle Darstellung des Walzwerks und ermöglichen eine präzise Anpassung der Parameter.
- Moderne Walzenmaterialien und Beschichtungen: Hochfeste Werkstoffe und spezielle Beschichtungen sorgen für eine längere Lebensdauer und höhere Leistung der Walzen.
- Künstliche Intelligenz und maschinelles Lernen: KI-gestützte Systeme optimieren den Walzprozess, indem sie Anomalien in Echtzeit erkennen und Anpassungen vornehmen. Dies reduziert Stillstandzeiten und verbessert die Produktqualität.
Diese technologischen Fortschritte tragen dazu bei, den Walzprozess zu modernisieren und gleichzeitig die Effizienz und Qualität der hergestellten Produkte zu steigern.
7. Anwendungen des Walzens in der Industrie
Das Walzen hat ein breites Spektrum an Anwendungen und ist in zahlreichen Industrien ein zentraler Fertigungsprozess:
- Automobilindustrie: Produktion von Karosserieblechen, Motorenteilen und Strukturbauteilen.
- Bauindustrie: Herstellung von Trägern, Profilen und Verstärkungen für Gebäude und Infrastrukturprojekte.
- Elektronikindustrie: Produktion von dünnen Blechen und Präzisionsteilen, die in elektronischen Geräten verbaut werden.
- Maschinenbau: Herstellung von Maschinenbauteilen wie Zahnrädern, Wellen und Lagern.
- Luftfahrtindustrie: Leichte und widerstandsfähige Aluminiumbleche für Flugzeughüllen und Strukturbauteile.
Das Walzen ist unverzichtbar für die Herstellung zahlreicher Produkte in verschiedenen Industrien und trägt maßgeblich zur Effizienz und Wirtschaftlichkeit der Metallverarbeitung bei.
Fazit
Das Walzen ist eines der effizientesten und flexibelsten Verfahren in der Metallumformung und wird in der modernen Industrie weltweit eingesetzt. Die Vielfalt an Walzverfahren, kombiniert mit den technologischen Fortschritten und Automatisierungsmöglichkeiten, ermöglicht eine präzise Herstellung von Metallerzeugnissen, die den steigenden Anforderungen in verschiedenen Industrien gerecht wird. Die fortschreitende Digitalisierung und die Einführung von Industrie 4.0-Technologien werden den Walzprozess weiter revolutionieren, wodurch höhere Effizienz, Qualität und Flexibilität erreicht werden.
Extrudieren: Verfahren, Anwendungen und Technologien in der Metallverarbeitung
Das Extrudieren ist ein Umformverfahren, das zur Herstellung von Bauteilen mit konstantem Querschnittsprofil eingesetzt wird, wie Rohre, Stangen und Profile. Es wird besonders für Materialien wie Aluminium, Kupfer und Kunststoff verwendet, eignet sich jedoch auch für einige Stähle und Legierungen. Beim Extrudieren wird das Material durch eine Matrize gepresst, um eine spezifische Form zu erhalten. Diese Methode bietet hohe Effizienz, Präzision und Flexibilität, was das Verfahren in der Automobil-, Bau- und Elektronikindustrie unverzichtbar macht.
Dieser Text gibt einen umfassenden Überblick über das Extrudieren, einschließlich der Verfahrenstypen, eingesetzten Maschinen und Werkstoffe, der technologischen Entwicklungen sowie der Anwendungsmöglichkeiten und der Vorteile und Herausforderungen des Extrusionsprozesses.
1. Grundlagen des Extrudierens
Beim Extrudieren wird das Material in eine Matrize (auch Düse genannt) gedrückt, die den gewünschten Querschnitt vorgibt. Das Material wird entweder durch mechanischen oder hydraulischen Druck durch die Matrize gepresst, was zu einem Produkt mit gleichbleibendem Querschnitt führt. Die Qualität und Formgenauigkeit des extrudierten Materials hängen von der Temperatur, dem Druck und der Geschwindigkeit ab.
Grundprinzipien des Extrudierens:
- Druckerzeugung: Ein Kolben oder eine Schraube presst das Material mit hoher Kraft durch die Matrize.
- Formgebung: Die Matrize bestimmt den Querschnitt des Endprodukts. Es sind komplexe und präzise Profile möglich.
- Kühlung und Nachbearbeitung: Das Material wird gekühlt, sobald es die Matrize verlässt, und gegebenenfalls weiterbearbeitet.
Das Extrudieren ist vielseitig und kann für unterschiedlichste Materialien und Profile angewendet werden, was es zu einem der flexibelsten Umformverfahren macht.
2. Arten des Extrudierens
Es gibt verschiedene Arten des Extrudierens, die sich in der Bewegungsrichtung des Materials und der Art des eingesetzten Drucks unterscheiden. Die drei Haupttypen sind:
a) Direktes (Vorwärts-)Extrudieren
Beim direkten Extrudieren bewegt sich das Werkstück in die gleiche Richtung wie der Druck. Ein Kolben oder eine Schraube drückt das Material direkt durch die Matrize. Diese Methode ist weit verbreitet und eignet sich für eine Vielzahl von Materialien und Profilen.
- Typische Anwendung: Aluminiumprofile, wie Fensterrahmen und Fahrzeugkomponenten.
- Vorteile: Einfacher Aufbau und hohe Produktionsgeschwindigkeit.
- Nachteile: Hohe Reibung zwischen Werkstück und Extrusionskammer, was mehr Energie erfordert und zu höheren Werkzeugabnutzungen führt.
b) Indirektes (Rückwärts-)Extrudieren
Beim indirekten Extrudieren wird die Matrize in das Material gedrückt, das Werkstück bleibt dabei relativ zur Extrusionskammer stationär. Dies reduziert die Reibung erheblich, da das Material sich nicht an den Innenwänden der Kammer reibt.
- Typische Anwendung: Aluminiumstangen und kleine Profile, die hohe Oberflächenqualität erfordern.
- Vorteile: Geringere Reibung, was die benötigte Kraft reduziert und den Verschleiß der Werkzeuge minimiert.
- Nachteile: Komplexere Maschinenstruktur und begrenzte Anwendung bei Materialien mit hoher Zähigkeit.
c) Hydrostatisches Extrudieren
Hier wird das Werkstück vollständig in eine Flüssigkeit eingebettet, die den Druck auf das Material gleichmäßig verteilt. Diese Methode wird oft für schwer umformbare Materialien wie Titan und hochfeste Legierungen verwendet.
- Typische Anwendung: Hochfeste Werkstoffe wie Titanlegierungen für die Luftfahrt und Medizintechnik.
- Vorteile: Gleichmäßige Druckverteilung und höhere Formbarkeit schwer verformbarer Materialien.
- Nachteile: Hoher Aufwand für die Wartung der Hydraulikflüssigkeit und höhere Produktionskosten.
Diese Verfahren ermöglichen es, eine große Vielfalt an Profilen und Materialien zu extrudieren, von einfachen Formen bis hin zu komplexen und präzisen Querschnitten.
3. Temperaturbereiche im Extrusionsprozess: Warm- und Kalt-Extrudieren
Das Extrudieren kann bei verschiedenen Temperaturen erfolgen, abhängig von den Eigenschaften des Materials und den Anforderungen an das Endprodukt.
a) Warm-Extrudieren
Beim Warm-Extrudieren wird das Material auf hohe Temperaturen erhitzt, meist oberhalb der Rekristallisationstemperatur. Dadurch wird es duktiler und lässt sich leichter durch die Matrize pressen.
- Typische Anwendung: Aluminium- und Kupferprofile, wie Fensterrahmen und Rohre.
- Vorteile: Geringere Walzkräfte und weniger Werkzeugverschleiß, ermöglicht komplexe Geometrien.
- Nachteile: Höhere Energiekosten und die Notwendigkeit, das Material nach dem Extrudieren zu kühlen.
b) Kalt-Extrudieren
Beim Kalt-Extrudieren erfolgt die Umformung bei Raumtemperatur oder leicht erhitztem Zustand. Da keine Wärme zugeführt wird, bleibt das Material härter und erreicht eine höhere Festigkeit durch Kaltverfestigung.
- Typische Anwendung: Herstellung von präzisen und hochfesten Teilen wie Zahnrädern und Bolzen.
- Vorteile: Hohe Maßgenauigkeit und Oberflächenqualität, erhöhte Festigkeit durch Verfestigung.
- Nachteile: Höherer Kraftaufwand und erhöhtes Risiko von Rissbildung, besonders bei harten oder spröden Materialien.
Die Wahl der Extrusionstemperatur hängt von den spezifischen Anforderungen und Eigenschaften des zu verarbeitenden Materials ab und hat großen Einfluss auf die Produktqualität.
4. Extrusionsmaschinen und deren Aufbau
Für das Extrudieren sind spezialisierte Maschinen erforderlich, die je nach Anwendung und Material variieren. Die Hauptbestandteile einer Extrusionsmaschine sind der Extruder, die Matrize und der Kühlsystembereich.
- Kolbenextruder: Hier wird das Material durch einen Kolben, der hydraulisch oder mechanisch angetrieben wird, durch die Matrize gedrückt. Diese Maschinen werden oft für großformatige Profile und Rohre verwendet.
- Schneckenextruder: Bei diesem Extruder wird das Material durch eine rotierende Schnecke durch die Matrize gepresst, was eine kontinuierliche Produktion ermöglicht. Schneckenextruder werden oft für Kunststoffe und weiche Metalle wie Aluminium genutzt.
- Hydrostatische Extruder: Diese Maschinen setzen Hydraulikflüssigkeit ein, um schwer verformbare Materialien gleichmäßig zu extrudieren. Sie werden speziell für Materialien wie Titan verwendet.
Jede Extrusionsmaschine hat spezifische Vorteile und ist auf bestimmte Anwendungen und Materialien spezialisiert, um hohe Effizienz und Präzision zu gewährleisten.
5. Werkstoffe und deren Verhalten beim Extrudieren
Das Extrudieren wird oft für Materialien eingesetzt, die eine gute Fließfähigkeit besitzen und bei hohen Temperaturen duktil sind. Häufig verwendete Werkstoffe sind:
- Aluminium: Aluminium ist besonders gut für das Extrudieren geeignet, da es eine hohe Verformbarkeit und Korrosionsbeständigkeit aufweist. Es wird oft für Profile in der Bau- und Automobilindustrie verwendet.
- Kupfer und Kupferlegierungen: Kupfer ist ebenfalls ein bevorzugtes Material für das Extrudieren, da es sich gut formen lässt und hohe elektrische Leitfähigkeit besitzt.
- Stahl und Edelstähle: Stahl ist weniger häufig, jedoch wird das Verfahren für bestimmte Stahllegierungen eingesetzt, besonders bei komplexen Querschnitten und hochfesten Teilen.
- Titan: Aufgrund seiner hohen Festigkeit und Korrosionsbeständigkeit wird Titan hauptsächlich in der Luftfahrt und Medizintechnik eingesetzt.
Jeder Werkstoff hat seine eigenen Anforderungen hinsichtlich Temperatur und Druck und verhält sich unterschiedlich im Extrusionsprozess.
6. Technologische Fortschritte im Extrudieren
Die Extrusionstechnologie hat sich durch technologische Fortschritte in den letzten Jahrzehnten erheblich weiterentwickelt. Zu den wichtigsten Innovationen gehören:
- Industrie 4.0 und Automatisierung: Durch die Digitalisierung werden Maschinen zunehmend vernetzt und optimiert, um den Produktionsprozess zu überwachen und anzupassen. Echtzeitdaten werden verwendet, um Effizienz und Qualität zu steigern.
- Simulations- und Modellsysteme: Digitale Simulationen ermöglichen es, den Extrusionsprozess genau zu planen und potenzielle Probleme vorherzusagen. Dies reduziert die Ausschussrate und verbessert die Materialeffizienz.
- Moderne Matrizen und Beschichtungen: Die Verwendung von hochfesten Materialien und speziellen Beschichtungen für Matrizen verringert den Verschleiß und verlängert die Lebensdauer der Werkzeuge.
- KI und maschinelles Lernen: Algorithmen können Datenmuster analysieren, um optimale Produktionsparameter zu identifizieren und Anpassungen in Echtzeit vorzunehmen.
Diese technologischen Fortschritte tragen dazu bei, das Extrudieren effizienter und präziser zu gestalten und den Produktionsaufwand zu minimieren.
7. Anwendungen des Extrudierens in der Industrie
Das Extrudieren ist aufgrund seiner Vielseitigkeit und Effizienz in vielen Industrien ein gängiges Verfahren. Zu den typischen Anwendungsbereichen gehören:
- Bauindustrie: Aluminiumprofile für Fenster- und Türrahmen, die leicht und korrosionsbeständig sind.
- Automobilindustrie: Strukturteile wie Stoßfängerträger und Rahmen, die hohe Festigkeit und geringes Gewicht bieten.
- Elektronikindustrie: Herstellung von Kühlkörpern und Gehäusen, die eine hohe Wärmeleitfähigkeit erfordern.
- Luft- und Raumfahrt: Titan- und Aluminiumkomponenten für Flugzeuge, die Festigkeit und Leichtigkeit kombinieren.
- Medizintechnik: Präzisionsteile aus Titan für Implantate und chirurgische Instrumente, die biokompatibel und robust sind.
Dank seiner Flexibilität und der Möglichkeit, präzise Profile zu erstellen, bleibt das Extrudieren in zahlreichen Industriezweigen unverzichtbar.
8. Vorteile und Herausforderungen des Extrudierens
Das Extrudieren bietet zahlreiche Vorteile, aber auch einige Herausforderungen, die beachtet werden müssen:
Vorteile:
- Hohe Materialausnutzung: Extrudieren ist ein materialeffizientes Verfahren ohne großen Materialverlust.
- Flexibilität in der Formgebung: Komplexe Profile mit konstantem Querschnitt können leicht hergestellt werden.
- Kosteneffizienz: Für Massenproduktion geeignet und ermöglicht schnelle Herstellungsprozesse.
Herausforderungen:
- Werkzeugverschleiß: Durch den hohen Druck und die Reibung nutzen sich die Matrizen schnell ab.
- Hohe Energiekosten: Das Aufheizen des Materials beim Warm-Extrudieren kann energieintensiv sein.
- Materialverhalten: Jedes Material verhält sich unterschiedlich, was eine präzise Steuerung und Prozessanpassung erfordert.
Trotz dieser Herausforderungen bleibt das Extrudieren ein bevorzugtes Verfahren in der industriellen Fertigung aufgrund seiner Flexibilität und Effizienz.
Fazit
Das Extrudieren ist ein wichtiges Umformverfahren mit einer breiten Anwendungsbasis in verschiedenen Industrien. Durch den Einsatz moderner Technologien und Innovationen wird das Verfahren zunehmend effizienter und genauer. Die Fähigkeit, komplexe Profile in hoher Qualität und mit minimalem Materialverlust herzustellen, macht das Extrudieren zu einer bevorzugten Methode in der Metallverarbeitung. Angesichts der Fortschritte in der Digitalisierung und Automatisierung wird die Extrusionstechnologie auch in Zukunft eine zentrale Rolle in der industriellen Fertigung spielen.
Ziehen: Verfahren, Anwendungen und Technologien in der Metallumformung
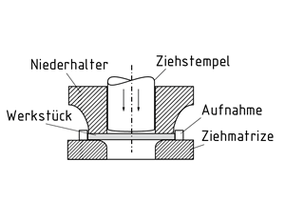
Das Ziehen ist ein vielseitiges Umformverfahren, das insbesondere zur Herstellung von Drähten, Stangen, Rohren und Hohlkörpern verwendet wird. Im Ziehverfahren wird das Metall durch eine Matrize oder eine Form gezogen, wodurch sein Querschnitt verringert und seine Länge erhöht wird. Dies geschieht ohne Verlust von Material, da das Metall plastisch verformt wird. Aufgrund seiner Effizienz, Präzision und Materialausnutzung ist das Ziehen ein zentrales Verfahren in der Metallverarbeitung und in Industrien wie der Automobil-, Elektronik- und Bauindustrie unverzichtbar.
Dieser Text bietet einen detaillierten Überblick über die verschiedenen Ziehverfahren, eingesetzten Maschinen, verwendeten Werkstoffe und die technologischen Entwicklungen im Bereich der Ziehprozesse. Zudem werden typische Anwendungsbereiche, Vorteile und Herausforderungen des Ziehens dargestellt.
1. Grundlagen und Funktionsweise des Ziehens
Beim Ziehen wird ein Metallstück, meist ein Draht, eine Stange oder ein Rohr, durch eine Öffnung in einer Matrize gezogen, die kleiner ist als der Querschnitt des Ausgangsmaterials. Dies bewirkt eine Verlängerung und gleichzeitige Verengung des Querschnitts. Die Verformung erfolgt plastisch, was bedeutet, dass das Material seine neue Form nach dem Ziehen beibehält. Der Prozess erfordert hohe Zugkräfte, die entweder mechanisch oder hydraulisch erzeugt werden.
Grundprinzipien des Ziehens:
- Zugkraft: Eine Kraft zieht das Werkstück durch die Matrize, wodurch die Umformung erfolgt.
- Reduzierung des Querschnitts: Durch die Verengung der Matrize wird der Querschnitt des Werkstücks verringert.
- Längung des Werkstücks: Während der Querschnitt abnimmt, nimmt die Länge des Werkstücks zu.
Das Ziehen bietet hohe Präzision und Maßhaltigkeit, insbesondere für Bauteile mit konstantem Querschnitt.
2. Arten des Ziehens
Das Ziehen wird in verschiedene Verfahren unterteilt, je nach Art der Umformung und der Form des Endprodukts. Zu den wichtigsten Ziehverfahren gehören:
a) Drahtziehen
Das Drahtziehen ist das am häufigsten angewandte Verfahren und dient zur Herstellung von Drähten mit verschiedenen Durchmessern und Längen. Der Draht wird in mehreren Durchgängen durch sukzessiv kleinere Matrizen gezogen, bis der gewünschte Durchmesser erreicht ist.
- Typische Anwendung: Herstellung von Drähten für die Elektronikindustrie, Bauindustrie und für Kabel.
- Vorteile: Hohe Präzision und Festigkeit des Materials durch Kaltverfestigung.
- Nachteile: Erfordert mehrere Ziehdurchgänge für große Durchmesserreduzierungen.
b) Rohziehen
Beim Rohziehen wird ein Rohr mit einem größeren Querschnitt durch eine Matrize gezogen, wodurch der Durchmesser reduziert und die Länge vergrößert wird. Dieser Prozess kann auch zur Reduktion der Wandstärke eingesetzt werden.
- Typische Anwendung: Herstellung von Rohren für Gas- und Wasserleitungen sowie Hydrauliksysteme.
- Vorteile: Gleichmäßige Verformung des Materials, hohe Maßhaltigkeit.
- Nachteile: Hohe Zugkräfte erforderlich und potenzielle Spannungen im Material.
c) Tiefziehen
Das Tiefziehen ist ein spezielles Ziehverfahren, bei dem flache Blechzuschnitte in Hohlformen gezogen werden, um komplexe dreidimensionale Formen zu schaffen. Dieses Verfahren wird oft zur Herstellung von hohlen oder zylindrischen Bauteilen verwendet.
- Typische Anwendung: Produktion von Autokarosserieteilen, Dosen und Haushaltsgeräten.
- Vorteile: Ermöglicht die Herstellung komplexer Hohlformen, Material bleibt intakt.
- Nachteile: Erfordert spezielle Werkzeuge und führt bei unsachgemäßer Durchführung zu Rissbildung.
d) Stangenziehen
Beim Stangenziehen werden Stäbe und Profile durch Matrizen gezogen, um einen kleineren Durchmesser oder eine spezifische Form zu erzielen. Häufig verwendet für Metallstangen in der Bauindustrie und im Maschinenbau.
- Typische Anwendung: Herstellung von Bauprofilen und Wellen.
- Vorteile: Hohe Festigkeit und Maßgenauigkeit, auch für dickere Querschnitte geeignet.
- Nachteile: Hoher Energieaufwand und Werkzeugverschleiß bei harten Metallen.
Diese Ziehverfahren bieten verschiedene Vorteile und sind auf die spezifischen Anforderungen des jeweiligen Endprodukts abgestimmt.
3. Kalt- und Warmziehen
Die Ziehverfahren lassen sich in zwei Hauptkategorien unterteilen, abhängig von der Umformtemperatur: Kaltziehen und Warmziehen.
a) Kaltziehen
Beim Kaltziehen erfolgt das Umformen bei Raumtemperatur. Die Materialhärte bleibt erhalten oder nimmt durch Kaltverfestigung sogar zu. Kaltziehen wird oft für präzise und hochfeste Produkte verwendet.
- Typische Anwendung: Herstellung von Drähten, Rohren und Stäben mit hohen Anforderungen an Maßhaltigkeit und Festigkeit.
- Vorteile: Hohe Präzision und Oberflächenqualität, erhöhte Festigkeit durch Verfestigung.
- Nachteile: Höherer Kraftaufwand und erhöhte Rissgefahr bei spröden Materialien.
b) Warmziehen
Beim Warmziehen wird das Material auf eine höhere Temperatur erhitzt, um seine Verformbarkeit zu erhöhen. Dies erleichtert den Ziehprozess und reduziert die benötigte Zugkraft.
- Typische Anwendung: Herstellung von dickeren oder harten Materialien, die schwer zu ziehen sind.
- Vorteile: Reduzierter Kraftaufwand, weniger Spannungen im Material.
- Nachteile: Höherer Energieverbrauch und geringere Maßgenauigkeit im Vergleich zum Kaltziehen.
Die Wahl zwischen Kalt- und Warmziehen hängt von den Materialeigenschaften und den Anforderungen an das Endprodukt ab.
4. Ziehmaschinen und deren Aufbau
Ziehmaschinen sind speziell konzipiert, um hohe Zugkräfte zu erzeugen und das Material präzise durch die Matrize zu führen. Es gibt verschiedene Arten von Ziehmaschinen, die je nach Anwendungsbereich und Material variieren:
- Einfachziehmaschinen: Diese Maschinen haben nur eine Ziehstation und werden für kleine Produktionsmengen und spezielle Anwendungen eingesetzt.
- Mehrfachziehmaschinen: Mehrfachziehmaschinen verfügen über mehrere Ziehstationen, die das Material nacheinander durch kleinere Matrizen ziehen. Dies ermöglicht eine kontinuierliche Produktion und wird für Drahtziehen eingesetzt.
- Tiefziehpressen: Für das Tiefziehen von Blechen verwendet, um Hohlkörper zu erzeugen. Diese Maschinen sind besonders in der Automobilindustrie verbreitet.
- Hydraulische Ziehmaschinen: Diese Maschinen verwenden hydraulische Drucksysteme, um hohe Zugkräfte zu erzeugen und ermöglichen präzise Steuerung bei der Produktion großer Bauteile.
Ziehmaschinen sind essenziell für das Ziehen von Metallen und müssen extrem präzise arbeiten, um eine gleichmäßige Umformung und hohe Oberflächenqualität zu gewährleisten.
5. Werkstoffe und deren Verhalten beim Ziehen
Das Ziehen wird häufig für Metalle mit guten Umformeigenschaften verwendet. Jeder Werkstoff weist unterschiedliche Eigenschaften auf, die das Verhalten während des Ziehprozesses beeinflussen.
- Stahl und Edelstähle: Stahl wird häufig zum Draht- und Rohrziehen verwendet, da er hohe Festigkeit und Zugfestigkeit aufweist. Edelstahl wird oft für Anwendungen verwendet, die Korrosionsbeständigkeit erfordern.
- Aluminium und Aluminiumlegierungen: Aluminium ist leicht und gut umformbar, was es ideal für das Ziehen von Drähten und Rohren macht, die in der Bau- und Automobilindustrie verwendet werden.
- Kupfer und Kupferlegierungen: Kupfer hat eine hohe elektrische Leitfähigkeit und wird daher häufig für die Produktion von Drähten in der Elektronikindustrie verwendet.
- Messing und Bronze: Diese Kupferlegierungen werden für das Ziehen von Drähten und Stangen verwendet und sind korrosionsbeständig, was sie ideal für Anwendungen im Bauwesen macht.
Die Wahl des Werkstoffs hängt von den spezifischen Anforderungen an das Endprodukt ab, einschließlich Festigkeit, Korrosionsbeständigkeit und Leitfähigkeit.
6. Technologische Fortschritte im Ziehen
Mit der Einführung neuer Technologien und Innovationen hat sich das Ziehen weiterentwickelt, um Effizienz und Präzision zu verbessern. Wichtige Entwicklungen umfassen:
- Industrie 4.0 und Digitalisierung: Durch die Vernetzung der Maschinen und die Einführung von Sensoren kann der Ziehprozess in Echtzeit überwacht und angepasst werden. Dies führt zu einer höheren Produktivität und Reduzierung des Ausschusses.
- Simulation und digitale Zwillinge: Mithilfe von Simulationen kann der Ziehprozess vor der eigentlichen Produktion modelliert und optimiert werden. Digitale Zwillinge ermöglichen eine präzise Planung und Anpassung der Prozessparameter.
- Fortschrittliche Matrizenmaterialien: Hochfeste Werkstoffe und spezielle Beschichtungen reduzieren den Verschleiß der Matrizen und verlängern die Werkzeuglebensdauer.
- Künstliche Intelligenz (KI) und maschinelles Lernen: KI-Systeme analysieren Daten und optimieren den Ziehprozess, indem sie Anomalien in Echtzeit erkennen und Anpassungen vornehmen.
Diese technologischen Fortschritte verbessern die Effizienz und Qualität des Ziehens und tragen zur Kostensenkung und zur Steigerung der Produktionskapazitäten bei.
7. Anwendungen des Ziehens in der Industrie
Das Ziehen wird in vielen Industrien eingesetzt, da es eine hohe Materialausnutzung und Präzision bietet. Typische Anwendungsbereiche umfassen:
- Automobilindustrie: Herstellung von Achsen, Stangen und Rohren für Fahrzeugrahmen und Motorkomponenten.
- Bauindustrie: Produktion von Bauprofilen, Verstärkungen und Drähten, die in Betonkonstruktionen verwendet werden.
- Elektronikindustrie: Herstellung von Kupferdrähten und Kabeln, die für die elektrische Leitfähigkeit erforderlich sind.
- Luftfahrtindustrie: Produktion von hochfesten Bauteilen und Rohren, die Leichtigkeit und Widerstandsfähigkeit kombinieren.
- Medizintechnik: Herstellung von Drähten und dünnen Rohren für chirurgische Instrumente und Implantate.
Das Ziehen ist aufgrund seiner Flexibilität und Präzision unverzichtbar für die Herstellung verschiedenster Produkte in zahlreichen Industrien.
8. Vorteile und Herausforderungen des Ziehens
Das Ziehen bietet zahlreiche Vorteile, die es zu einem beliebten Umformverfahren in der Industrie machen, aber es gibt auch Herausforderungen, die beachtet werden müssen.
Vorteile:
- Hohe Materialausnutzung: Das Ziehen führt zu geringen Materialverlusten und hoher Materialeffizienz.
- Präzise Maßhaltigkeit: Produkte können mit hoher Genauigkeit und Oberflächenqualität hergestellt werden.
- Festigkeitssteigerung: Durch Kaltziehen wird die Festigkeit des Werkstoffs erhöht.
Herausforderungen:
- Werkzeugverschleiß: Die Matrizen unterliegen durch die hohe Zugkraft einem hohen Verschleiß, was die Produktionskosten erhöht.
- Rissgefahr: Bei spröden Materialien besteht die Gefahr von Rissbildung, insbesondere beim Kaltziehen.
- Hohe Energiekosten: Das Ziehen erfordert erhebliche Zugkräfte und daher einen hohen Energieverbrauch, besonders beim Warmziehen.
Trotz dieser Herausforderungen bleibt das Ziehen ein bevorzugtes Verfahren in der industriellen Fertigung aufgrund seiner Effizienz, Präzision und Vielseitigkeit.
Fazit
Das Ziehen ist ein bewährtes und leistungsfähiges Umformverfahren, das in vielen Industrien weltweit eingesetzt wird. Durch die Kombination traditioneller Ziehmethoden mit modernen Technologien und Automatisierungsmöglichkeiten wird das Verfahren zunehmend effizienter und präziser. Die hohe Maßgenauigkeit und die Materialausnutzung machen das Ziehen besonders attraktiv für die Produktion hochwertiger Bauteile. Angesichts der technologischen Fortschritte und der Entwicklung neuer Materialien wird das Ziehen auch in Zukunft eine zentrale Rolle in der industriellen Metallverarbeitung spielen.
Biegen: Verfahren, Anwendungen und Technologien in der Metallumformung
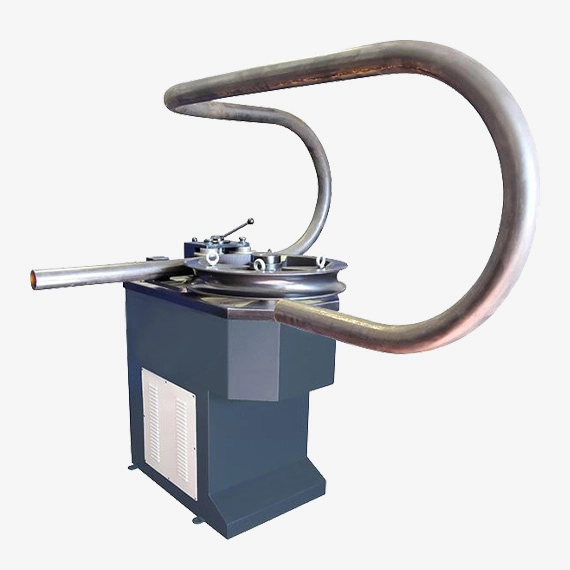
Das Biegen ist ein grundlegendes Umformverfahren, das zur Herstellung von Bauteilen mit unterschiedlichen Geometrien verwendet wird. Es ermöglicht das gezielte Verformen von Blechen, Profilen und Rohren, ohne das Material zu durchtrennen oder dessen Dicke signifikant zu verringern. In der modernen Industrie ist das Biegen ein zentrales Verfahren, das insbesondere in der Automobil-, Luftfahrt- und Bauindustrie weit verbreitet ist. Es wird für die Herstellung von Strukturen und Bauteilen mit spezifischen Winkeln, Kurven und Formen eingesetzt und erfordert sowohl Präzision als auch technische Expertise.
Dieser Text bietet einen detaillierten Überblick über das Biegen, die verschiedenen Biegeverfahren, eingesetzten Maschinen, verwendeten Werkstoffe und technologischen Fortschritte. Zudem werden typische Anwendungsbereiche, Vorteile und Herausforderungen des Biegens dargestellt.
1. Grundlagen und Funktionsweise des Biegens
Das Biegen ist ein plastisches Umformverfahren, bei dem ein Werkstück entlang einer definierten Achse verformt wird. Dabei kommt es zu Spannungen im Material, die sowohl Zug- als auch Druckkräfte umfassen: die Außenseite des Werkstücks wird gedehnt, während die Innenseite komprimiert wird. Durch das Biegen kann eine dauerhafte Änderung des Winkels oder der Form des Materials erreicht werden.
Grundprinzipien des Biegens:
- Neutralfaser: Beim Biegen bleibt ein zentraler Bereich des Werkstücks, die sogenannte Neutralfaser, von Spannungen unberührt. Oberhalb der Neutralfaser wird das Material gedehnt und unterhalb komprimiert.
- Elastische und plastische Verformung: Der Biegeprozess beginnt mit einer elastischen Verformung, die das Material in seine ursprüngliche Form zurückkehren lässt. Wird jedoch die Elastizitätsgrenze überschritten, bleibt das Material in der gebogenen Form, und es kommt zur plastischen Verformung.
- Rückfederung: Nach dem Biegen tritt häufig eine geringe elastische Rückfederung auf, bei der das Material leicht zurückfedert. Diese Rückfederung muss beim Biegen berücksichtigt werden, um die gewünschte Endform zu erreichen.
Das Biegen ist besonders vielseitig und eignet sich für eine Vielzahl an Anwendungen, bei denen präzise Winkel und komplexe Formen erforderlich sind.
2. Arten des Biegens
Es gibt verschiedene Biegeverfahren, die je nach Werkstück, Form und Anwendungsbereich ausgewählt werden. Zu den wichtigsten Biegeverfahren gehören:
a) Freies Biegen
Beim freien Biegen wird das Werkstück zwischen einem Stempel und einer Matrize ohne feste Einspannung gebogen. Das Werkstück liegt dabei lediglich auf der Matrize auf, während der Stempel das Werkstück in die gewünschte Form drückt. Freies Biegen ist flexibel und eignet sich besonders für einfache Biegeformen.
- Typische Anwendung: Herstellung von Blechen und Profilen für einfache Konstruktionen.
- Vorteile: Kostengünstig und für kleine Produktionsmengen geeignet.
- Nachteile: Geringere Präzision und potenziell hohe Rückfederung.
b) Gesenkbiegen
Beim Gesenkbiegen wird das Werkstück durch einen Stempel in eine passgenaue Matrize gedrückt, die die gewünschte Form vorgibt. Dieses Verfahren ist präziser als das freie Biegen und bietet eine hohe Wiederholgenauigkeit.
- Typische Anwendung: Produktion von Bauteilen mit engen Toleranzen, wie z. B. Karosserieteilen.
- Vorteile: Hohe Präzision und Wiederholbarkeit, ideal für Serienfertigung.
- Nachteile: Höhere Werkzeugkosten und längere Rüstzeiten.
c) Walzbiegen
Beim Walzbiegen wird das Werkstück zwischen mehreren rotierenden Walzen verformt, was zu einer kontinuierlichen Biegung führt. Diese Methode eignet sich besonders für große Radien und runde Formen, wie bei Rohren und Profilen.
- Typische Anwendung: Herstellung von Rohren, Tanks und großen runden Strukturen.
- Vorteile: Erzeugt große, gleichmäßige Radien und ermöglicht eine hohe Materialausnutzung.
- Nachteile: Begrenzte Präzision für kleine Radien und komplexe Formen.
d) Dreipunktbiegen
Beim Dreipunktbiegen wird das Werkstück durch drei Punkte gehalten: zwei Auflagen und einen Stempel, der das Werkstück in der Mitte verformt. Dieses Verfahren ermöglicht eine kontrollierte und gleichmäßige Biegung und wird häufig für Tests und Experimente eingesetzt.
- Typische Anwendung: Prüfung der Materialfestigkeit und Herstellung kleiner, präziser Biegungen.
- Vorteile: Gleichmäßige Biegung und gute Kontrolle der Kräfte.
- Nachteile: Begrenzter Einsatzbereich in der Serienproduktion.
e) Rotationsbiegen
Beim Rotationsbiegen, auch Rollbiegen genannt, wird das Werkstück um eine rotierende Biegewelle gebogen. Dieses Verfahren ist ideal für komplexe Geometrien und Profile und ermöglicht präzise Winkel und Formen.
- Typische Anwendung: Herstellung von Profilen und Bauteilen mit komplexen Biegeformen.
- Vorteile: Hohe Präzision und Flexibilität.
- Nachteile: Erfordert spezialisierte Maschinen und hohe Investitionskosten.
Diese Verfahren bieten vielfältige Möglichkeiten zur Herstellung von Bauteilen und ermöglichen die Anpassung an unterschiedliche Anforderungen und Formen.
3. Maschinelle Ausstattung für das Biegen
Biegemaschinen sind speziell entwickelte Maschinen, die präzise Biegevorgänge ermöglichen. Es gibt eine Vielzahl von Maschinentypen, die je nach Anwendungsbereich und Werkstückgeometrie variieren.
- Abkantpressen: Abkantpressen sind Maschinen, die für das freie und das Gesenkbiegen von Blechen verwendet werden. Sie bestehen aus einem Stempel und einer Matrize, die das Werkstück in die gewünschte Form drücken.
- Walzenbiegemaschinen: Diese Maschinen verwenden drei oder mehr Walzen, um das Werkstück kontinuierlich zu biegen. Sie sind ideal für die Herstellung großer Radien und runder Strukturen.
- Profilbiegemaschinen: Profilbiegemaschinen sind speziell für das Biegen von Profilen und Rohren entwickelt und arbeiten häufig mit Roll- oder Dreipunktbiegeverfahren.
- Rohrbiegemaschinen: Diese Maschinen sind speziell auf das Biegen von Rohren ausgelegt und ermöglichen präzise Winkel und komplexe Formen.
Die Wahl der richtigen Maschine ist entscheidend, um die Anforderungen des jeweiligen Biegeprozesses zu erfüllen und eine hohe Qualität und Maßgenauigkeit zu gewährleisten.
4. Werkstoffe und deren Verhalten beim Biegen
Das Verhalten der Werkstoffe beim Biegen hängt von ihren mechanischen Eigenschaften ab, insbesondere von der Duktilität, der Elastizität und der Festigkeit. Häufig verwendete Materialien sind:
- Stahl: Stahl ist aufgrund seiner Festigkeit und Duktilität ein bevorzugter Werkstoff für das Biegen. Er wird häufig in der Bau- und Automobilindustrie eingesetzt.
- Edelstahl: Edelstahl hat eine hohe Korrosionsbeständigkeit und eignet sich für Anwendungen in der Lebensmittel- und Medizintechnik.
- Aluminium: Aluminium ist leicht und duktil, was es ideal für Anwendungen in der Luftfahrt und Automobilindustrie macht. Allerdings neigt Aluminium aufgrund seiner geringeren Festigkeit zur Rissbildung, wenn es unsachgemäß gebogen wird.
- Kupfer und Kupferlegierungen: Kupfer und seine Legierungen haben eine gute Verformbarkeit und werden häufig für Rohre und elektrische Komponenten verwendet.
Das Materialverhalten beim Biegen hängt von der Mikrostruktur und der Wärmebehandlung ab. Werkstoffe mit hoher Duktilität lassen sich gut biegen, während spröde Materialien zur Rissbildung neigen.
5. Technologische Fortschritte im Biegen
Die Digitalisierung und Automatisierung haben das Biegen maßgeblich verändert und ermöglichten erhebliche Fortschritte in der Präzision und Effizienz.
- Industrie 4.0 und Automatisierung: Durch die Vernetzung der Maschinen können Parameter in Echtzeit überwacht und angepasst werden. Dies verbessert die Qualität und Produktivität, indem Fehler frühzeitig erkannt werden.
- Simulation und digitale Zwillinge: Mit modernen Simulationstechniken kann der Biegeprozess virtuell getestet und optimiert werden, bevor die Produktion beginnt. Digitale Zwillinge ermöglichen es, den Prozessablauf zu simulieren und optimale Einstellungen festzulegen.
- Sensorik und Rückfederungskompensation: Sensoren messen die Rückfederung des Materials und ermöglichen eine automatische Anpassung der Biegeparameter, um die gewünschte Formgenauigkeit zu erreichen.
- Biegemaschinen mit CNC-Steuerung: CNC-gesteuerte Biegemaschinen bieten eine präzise Steuerung der Bewegungen und können komplexe Biegeformen programmieren und wiederholen, was die Effizienz und Flexibilität erheblich steigert.
Diese technologischen Fortschritte ermöglichen eine höhere Effizienz und Präzision und tragen zur Verbesserung der Qualität und Flexibilität im Biegeprozess bei.
6. Anwendungen des Biegens in der Industrie
Das Biegen ist ein vielseitiges Verfahren und findet in verschiedenen Industrien Anwendung. Typische Anwendungsbereiche sind:
- Automobilindustrie: Herstellung von Rahmen, Karosserieteilen und Verstärkungen, die spezifische Winkel und Formen erfordern.
- Bauindustrie: Produktion von Stahlträgern, Balken und Profilen, die in Konstruktionen verwendet werden.
- Luft- und Raumfahrtindustrie: Herstellung von Aluminium- und Titanbauteilen, die leicht und dennoch robust sind.
- Elektronikindustrie: Produktion von Kupfer- und Aluminiumprofilen für Gehäuse und Verbindungselemente.
- Möbelindustrie: Herstellung von Möbelrahmen und -strukturen, die spezifische Formen und Winkel benötigen.
Die Vielseitigkeit des Biegens macht es zu einem unverzichtbaren Verfahren für die Produktion verschiedenster Bauteile.
7. Vorteile und Herausforderungen des Biegens
Das Biegen bietet zahlreiche Vorteile, die es zu einem der beliebtesten Umformverfahren in der Industrie machen, aber es gibt auch Herausforderungen, die beachtet werden müssen.
Vorteile:
- Hohe Materialausnutzung: Das Biegen ermöglicht eine effiziente Nutzung des Materials, ohne Materialverlust durch Spanbildung.
- Präzision und Wiederholbarkeit: Insbesondere beim Einsatz moderner Biegemaschinen lassen sich hochpräzise und wiederholgenaue Ergebnisse erzielen.
- Vielseitigkeit in der Formgebung: Das Biegen ermöglicht die Herstellung einer Vielzahl an Formen und Geometrien.
Herausforderungen:
- Rückfederung: Viele Materialien neigen dazu, nach dem Biegen leicht zurückzufedern. Die genaue Berechnung und Kompensation der Rückfederung ist entscheidend für präzise Ergebnisse.
- Rissbildung bei spröden Materialien: Werkstoffe mit geringer Duktilität können beim Biegen brechen oder Risse entwickeln, was die Prozesssicherheit und Materialauswahl beeinflusst.
- Hoher Werkzeugverschleiß: Insbesondere beim Biegen harter Materialien tritt ein erhöhter Werkzeugverschleiß auf, was die Produktionskosten erhöhen kann.
Trotz dieser Herausforderungen bleibt das Biegen ein bevorzugtes Verfahren in der industriellen Fertigung aufgrund seiner Effizienz und Flexibilität.
Fazit
Das Biegen ist ein essentielles Umformverfahren, das in vielen Industriezweigen Anwendung findet und die Herstellung komplexer Geometrien und präziser Winkel ermöglicht. Durch technologische Fortschritte und den Einsatz moderner Maschinen und Simulationstechnologien hat sich das Biegen zu einem hochpräzisen und effizienten Verfahren entwickelt. Die Vielseitigkeit und Effizienz des Biegens machen es zu einem unverzichtbaren Verfahren für die Herstellung hochwertiger und funktionsgerechter Bauteile. Die fortlaufende Weiterentwicklung in der Automatisierung und Digitalisierung wird das Biegen weiter optimieren und neue Anwendungsbereiche eröffnen.
Technologische Entwicklungen und Trends in der Industrie 4.0 und Metallumformung
Die technologischen Entwicklungen in der Metallumformung und verwandten Industrien schreiten rapide voran, angetrieben von der zunehmenden Digitalisierung, Automatisierung und der Implementierung der Prinzipien der Industrie 4.0. Diese Veränderungen haben weitreichende Auswirkungen auf die Effizienz, Produktivität und Flexibilität in der Fertigung und schaffen neue Möglichkeiten für Unternehmen, ihre Prozesse zu optimieren und wettbewerbsfähiger zu werden. Die wichtigsten technologischen Entwicklungen und Trends, die derzeit die Metallumformung und Fertigung prägen, umfassen künstliche Intelligenz (KI), Big Data, Robotik, additive Fertigung, nachhaltige Produktion und viele weitere Innovationen.
Dieser Text untersucht diese Trends detailliert und zeigt, wie sie das industrielle Umfeld verändern, welche Vorteile sie bieten und welche Herausforderungen damit einhergehen.
1. Künstliche Intelligenz und Maschinelles Lernen
Künstliche Intelligenz (KI) und maschinelles Lernen (ML) haben in der industriellen Fertigung erheblich an Bedeutung gewonnen. Diese Technologien ermöglichen eine tiefere Analyse von Produktionsdaten, die Vorhersage von Maschinenzuständen und die Optimierung von Prozessen.
- Prozessoptimierung und Qualitätsverbesserung: KI-Algorithmen können Muster in großen Datenmengen erkennen, die für den Menschen oft schwer nachvollziehbar sind. In der Metallumformung kann dies helfen, den idealen Druck, die Temperatur oder andere Parameter für den Umformprozess zu identifizieren und kontinuierlich anzupassen.
- Vorausschauende Wartung (Predictive Maintenance): KI-basierte Systeme analysieren kontinuierlich Daten von Maschinen, um Verschleiß und potenzielle Ausfälle frühzeitig zu erkennen. Dies reduziert ungeplante Stillstandzeiten und verlängert die Lebensdauer der Maschinen.
- Fehlererkennung: Durch die Verwendung von maschinellem Lernen können Anomalien in der Produktion in Echtzeit identifiziert werden, was die Ausschussrate senkt und die Qualität der Endprodukte verbessert.
Die Implementierung von KI und ML erfordert jedoch qualifizierte Mitarbeiter und eine gut entwickelte IT-Infrastruktur, was oft eine Herausforderung für traditionelle Industrien darstellt.
2. Big Data und Datenanalyse
Big Data ist eine der treibenden Kräfte hinter der modernen Industrie. Die Erfassung und Analyse großer Datenmengen bietet tiefe Einblicke in Produktionsprozesse und ermöglicht fundierte Entscheidungen.
- Produktionsanalyse und Prozessoptimierung: Große Datenmengen können aus Maschinen und Produktionslinien gesammelt werden, um Engpässe zu identifizieren und Produktionsabläufe zu optimieren.
- Echtzeitüberwachung: Sensoren erfassen kontinuierlich Daten, um Parameter wie Temperatur, Druck, Geschwindigkeit und andere Faktoren zu überwachen. Diese Daten bieten wertvolle Informationen über den Maschinenzustand und ermöglichen eine schnellere Reaktion auf Abweichungen.
- Kundenspezifische Anpassung: Big Data ermöglicht die Entwicklung von kundenspezifischen Produktionsstrategien, indem es den Unternehmen erlaubt, die Präferenzen und Bedürfnisse der Kunden besser zu verstehen.
Die Analyse großer Datenmengen stellt jedoch Anforderungen an Rechenleistung und Datenspeicherung, weshalb die Integration einer leistungsfähigen IT-Infrastruktur für die Umsetzung erforderlich ist.
3. Robotik und Automatisierung
Die Automatisierung und Robotik haben die Art und Weise, wie Unternehmen produzieren, revolutioniert. Industrieroboter übernehmen zunehmend Aufgaben, die präzise und konsistente Prozesse erfordern.
- Materialhandhabung und Transport: Roboterarme können Werkstücke transportieren, positionieren und sortieren, was die Effizienz und Sicherheit erhöht und den menschlichen Arbeitsaufwand reduziert.
- Kollaborative Roboter (Cobots): Diese Roboter arbeiten direkt mit Menschen zusammen und sind mit Sensoren ausgestattet, die Kollisionen vermeiden. Cobots steigern die Flexibilität und ermöglichen eine sichere Zusammenarbeit.
- Montage und Schweißarbeiten: In der Metallverarbeitung werden Roboter häufig für die Schweiß- und Montagetechnik verwendet, da sie präzise und kontinuierlich arbeiten und die Arbeitsqualität sicherstellen.
Die Anschaffungskosten und der Schulungsbedarf für den Einsatz von Robotern können jedoch hoch sein, und nicht alle Unternehmen haben die Kapazitäten, diese Technologie umfassend zu implementieren.
4. Internet of Things (IoT) und Cyber-Physische Systeme (CPS)
Das IoT und cyber-physische Systeme (CPS) sind zentrale Technologien der Industrie 4.0, die Maschinen, Werkzeuge und Produkte über das Internet vernetzen und Daten in Echtzeit austauschen lassen.
- Vernetzte Produktionsanlagen: Maschinen und Werkzeuge sind mit IoT-Sensoren ausgestattet, die Daten über Maschinenstatus, Verschleiß und andere Parameter sammeln und in Echtzeit übermitteln.
- Digitale Zwillinge: Digitale Zwillinge sind virtuelle Kopien von physischen Objekten oder Prozessen, die es Unternehmen ermöglichen, die Produktion in einer virtuellen Umgebung zu testen und zu optimieren, bevor sie in die physische Realität umgesetzt wird.
- Automatische Anpassung von Maschinenparametern: Mit CPS können Maschinen in Echtzeit auf Veränderungen im Produktionsprozess reagieren und Parameter automatisch anpassen.
Die Integration von IoT und CPS führt zu einer höheren Produktivität und Prozesssicherheit, erfordert jedoch umfangreiche Investitionen in IT-Infrastruktur und Cybersicherheit.
5. Additive Fertigung (3D-Druck)
Die additive Fertigung, allgemein bekannt als 3D-Druck, hat das Potenzial, die Produktion in vielen Bereichen zu revolutionieren, da sie komplexe Geometrien ohne die Verwendung von Formen oder Werkzeugen ermöglicht.
- Prototypenentwicklung und Designfreiheit: Der 3D-Druck ermöglicht eine schnelle Herstellung von Prototypen, was die Produktentwicklung beschleunigt. Komplexe und maßgeschneiderte Designs können problemlos umgesetzt werden.
- Herstellung komplexer Metallteile: In der Metallumformung ermöglicht die additive Fertigung die Produktion von komplexen und leichten Metallstrukturen, die in der Luft- und Raumfahrt sowie der Automobilindustrie Anwendung finden.
- Reduzierter Materialverbrauch: Im Gegensatz zu subtraktiven Verfahren wie Fräsen oder Drehen ist der Materialverbrauch beim 3D-Druck geringer, da das Material Schicht für Schicht aufgetragen wird.
Die additive Fertigung ist jedoch oft langsamer und teurer als traditionelle Fertigungsmethoden und eignet sich derzeit vor allem für Kleinserien und Prototypen.
6. Simulation und digitale Zwillinge
Simulationen und digitale Zwillinge bieten Unternehmen die Möglichkeit, Produktionsprozesse virtuell zu testen und zu optimieren. Diese Technologien ermöglichen es, Engpässe und potenzielle Fehlerquellen frühzeitig zu erkennen.
- Prozesssimulation: Durch die Simulation von Umformprozessen können Unternehmen die optimalen Parameter ermitteln und die Materialausnutzung verbessern.
- Testen neuer Designs: Digitale Zwillinge ermöglichen die Entwicklung und Prüfung neuer Designs, bevor sie in der physischen Produktion umgesetzt werden, was Zeit und Kosten spart.
- Wartung und Prozessüberwachung: Digitale Zwillinge können zur Überwachung von Maschinenzuständen und zur vorausschauenden Wartung eingesetzt werden, was ungeplante Stillstandzeiten reduziert.
Simulationen und digitale Zwillinge verbessern die Flexibilität und Effizienz, setzen jedoch eine hohe Rechenleistung und eine umfassende Datenintegration voraus.
7. Nachhaltigkeit und Ressourceneffizienz
Nachhaltigkeit ist ein wichtiger Trend in der Fertigung. Unternehmen setzen vermehrt auf Technologien und Prozesse, die Ressourcen schonen und den CO₂-Fußabdruck reduzieren.
- Energieeffiziente Maschinen: Moderne Maschinen sind energieeffizienter und ermöglichen einen geringeren Energieverbrauch pro produzierter Einheit.
- Wiederverwendung und Recycling: Recycling und die Wiederverwendung von Materialien reduzieren Abfälle und Kosten. In der Metallumformung wird zunehmend auf die Wiederaufbereitung von Materialien gesetzt.
- Kreislaufwirtschaft: Unternehmen implementieren Prozesse, bei denen Abfälle minimiert und Rohstoffe erneut in den Produktionskreislauf eingebracht werden. Die Kreislaufwirtschaft ist insbesondere in der Automobil- und Elektronikindustrie ein zentrales Thema.
Nachhaltigkeit stellt oft zusätzliche Anforderungen an die Prozesse und Materialien und kann zu höheren Kosten führen. Langfristig gesehen jedoch bieten nachhaltige Lösungen wirtschaftliche und ökologische Vorteile.
8. Virtual Reality (VR) und Augmented Reality (AR)
VR und AR bieten neuartige Möglichkeiten zur Schulung und Unterstützung von Mitarbeitern sowie zur Überwachung und Optimierung von Produktionsprozessen.
- Mitarbeiterschulung: VR ermöglicht es, Mitarbeiter in einer virtuellen Umgebung zu schulen, was die Sicherheit und Effizienz erhöht und den Schulungsaufwand reduziert.
- Unterstützung in der Fertigung: AR kann Mitarbeiter in Echtzeit bei Wartungsarbeiten und Reparaturen unterstützen, indem relevante Informationen direkt im Sichtfeld angezeigt werden.
- Produktdesign und Kundenpräsentationen: VR und AR ermöglichen es, Produkte und Designs in einer virtuellen Umgebung darzustellen, was das Verständnis für das Endprodukt verbessert und die Entwicklung beschleunigt.
Der Einsatz von VR und AR erfordert jedoch spezialisierte Geräte und Software, was Investitionen in neue Technologien und Schulung erfordert.
9. Cybersicherheit in der Industrie 4.0
Mit der zunehmenden Vernetzung und Digitalisierung steigen auch die Anforderungen an die Cybersicherheit. Die Sicherheit der Systeme ist ein zentrales Anliegen, um die Produktionsprozesse vor Cyberangriffen zu schützen.
- Schutz sensibler Daten: Produktions- und Maschinendaten müssen vor unbefugtem Zugriff geschützt werden, um Betriebsgeheimnisse und Wettbewerbsvorteile zu sichern.
- Absicherung der Netzwerkverbindungen: In vernetzten Systemen ist eine sichere Netzwerkverbindung entscheidend, um Angriffe auf die Produktionsprozesse zu verhindern.
- Mitarbeiterschulung: Ein umfassendes Verständnis der Cybersicherheit ist essenziell, um menschliche Fehler zu vermeiden und die Sicherheit der Systeme zu gewährleisten.
Cybersicherheit stellt für Unternehmen eine Herausforderung dar, da die Maßnahmen sowohl auf technologischer als auch auf organisatorischer Ebene umgesetzt werden müssen.
Fazit
Die technologischen Entwicklungen und Trends in der Metallumformung und Industrie 4.0 eröffnen Unternehmen neue Möglichkeiten zur Verbesserung ihrer Produktionsprozesse und zur Steigerung der Effizienz. Technologien wie künstliche Intelligenz, Big Data, Robotik, additive Fertigung und IoT tragen dazu bei, Produktionsprozesse flexibler, sicherer und nachhaltiger zu gestalten. Während die Implementierung dieser Technologien Herausforderungen mit sich bringt, bieten sie langfristig erhebliche Vorteile in Bezug auf Produktivität, Qualität und Nachhaltigkeit.
Mit der fortschreitenden Digitalisierung und Automatisierung werden diese Technologien auch in Zukunft eine zentrale Rolle spielen und die Art und Weise, wie Industrie und Fertigung betrieben werden, grundlegend verändern. Unternehmen, die frühzeitig in diese Entwicklungen investieren, werden einen Wettbewerbsvorteil haben und ihre Position in einem zunehmend technologiegetriebenen Markt festigen.
Qualitätssicherung in der Metallumformung: Methoden, Technologien und Herausforderungen
Qualitätssicherung (QS) ist ein wesentlicher Bestandteil der Metallumformung, da die Anforderungen an Präzision, Konsistenz und Materialeigenschaften immer höher werden. Im Zeitalter der Industrie 4.0 spielen dabei digitale Technologien, Automatisierung und datengetriebene Analysen eine zentrale Rolle, um eine gleichbleibend hohe Qualität zu gewährleisten. Die Qualitätssicherung umfasst eine Vielzahl von Prüfmethoden und Verfahren, die sicherstellen, dass die gefertigten Teile den festgelegten Standards entsprechen und die Produktionsprozesse kontinuierlich optimiert werden.
Dieser Text beleuchtet die zentralen Aspekte der Qualitätssicherung in der Metallumformung, einschließlich traditioneller und moderner Prüfmethoden, der eingesetzten Technologien und der organisatorischen Prozesse. Ebenso wird aufgezeigt, wie datenbasierte Ansätze und digitale Tools die Effizienz der QS-Maßnahmen verbessern können und welche Herausforderungen dabei bestehen.
1. Bedeutung der Qualitätssicherung in der Metallumformung
Die Qualitätssicherung in der Metallumformung ist entscheidend für die Funktionsfähigkeit und Langlebigkeit der hergestellten Produkte. Eine hohe Qualität der Bauteile ist insbesondere in sicherheitskritischen Industrien wie der Automobil-, Luftfahrt- und Bauindustrie unverzichtbar, da Mängel zu kostspieligen Rückrufaktionen und Imageschäden führen können.
Ziele der Qualitätssicherung:
- Sicherstellung der Konformität: Die Produkte müssen den festgelegten Spezifikationen und Normen entsprechen.
- Reduktion von Ausschuss und Nacharbeit: Durch eine konsequente Qualitätssicherung kann der Anteil fehlerhafter Produkte minimiert und die Effizienz der Produktion erhöht werden.
- Optimierung der Prozesse: Qualitätsdaten helfen dabei, Fertigungsprozesse zu analysieren und kontinuierlich zu verbessern.
- Risikomanagement: Identifizierung und Minimierung von Risiken im Produktionsprozess, um die Zuverlässigkeit der Produkte zu gewährleisten.
Die Qualitätssicherung ist daher ein integraler Bestandteil der Wertschöpfungskette und unterstützt die Unternehmen dabei, wettbewerbsfähig zu bleiben und Kundenanforderungen zu erfüllen.
2. Traditionelle Prüfmethoden in der Qualitätssicherung
In der Metallumformung gibt es eine Reihe traditioneller Prüfmethoden, die sich bewährt haben und weiterhin eingesetzt werden, um die Qualität der Bauteile zu überwachen. Diese Methoden umfassen sowohl zerstörende als auch zerstörungsfreie Prüfungen:
a) Maßprüfung und Geometriekontrolle
Die Maßprüfung und Geometriekontrolle ist eine grundlegende Methode zur Überprüfung der Maße und Formtoleranzen eines Werkstücks. Dabei werden herkömmliche Messinstrumente wie Messschieber, Mikrometer und Koordinatenmessmaschinen (KMM) verwendet.
- Vorteile: Einfache Anwendung, hohe Genauigkeit und geeignet für viele Werkstücke.
- Nachteile: Erfordert manuelle Eingriffe, was zeitaufwändig und fehleranfällig sein kann.
b) Oberflächenprüfung
Die Oberflächenqualität spielt in der Metallumformung eine große Rolle, da raue Oberflächen oder Unebenheiten zu Problemen in der Weiterverarbeitung und Anwendung führen können. Die Prüfung erfolgt häufig mit Tastgeräten oder optischen Systemen, die die Rauheit und Ebenheit messen.
- Vorteile: Verlässliche Ergebnisse und geeignet für die Prüfung von Bauteilen mit hohen Anforderungen an die Oberflächenqualität.
- Nachteile: Begrenzte Aussagekraft über das Materialverhalten unter Belastung.
c) Härteprüfung
Die Härteprüfung ist eine zerstörende Methode, bei der die Widerstandsfähigkeit eines Materials gegen Eindringen gemessen wird. Häufig verwendete Verfahren sind die Vickers-, Brinell- und Rockwell-Härteprüfungen. Diese Prüfungen werden durchgeführt, um sicherzustellen, dass die Werkstoffe die gewünschten mechanischen Eigenschaften aufweisen.
- Vorteile: Liefert aussagekräftige Daten über die Materialeigenschaften.
- Nachteile: Erfordert Proben, die nach der Prüfung nicht mehr verwendet werden können.
d) Zug- und Druckprüfungen
Zug- und Druckprüfungen sind zerstörende Prüfverfahren, bei denen Materialproben einer Belastung ausgesetzt werden, bis sie brechen. Diese Methoden werden verwendet, um die Festigkeit und Elastizität des Werkstoffs zu messen und sicherzustellen, dass er die Anforderungen an Belastbarkeit und Verformbarkeit erfüllt.
- Vorteile: Exakte Daten über die Materialfestigkeit und das Bruchverhalten.
- Nachteile: Aufwendig und nicht geeignet für Serienprüfung, da die Proben zerstört werden.
Diese traditionellen Prüfmethoden sind nach wie vor weit verbreitet, doch sie sind oft zeitaufwändig und können nur stichprobenartig durchgeführt werden.
3. Moderne Prüfmethoden und Technologien
Mit der Einführung der Industrie 4.0 und den technologischen Fortschritten wurden neue Prüfmethoden entwickelt, die schneller und genauer sind und eine kontinuierliche Qualitätssicherung in der laufenden Produktion ermöglichen.
a) Zerstörungsfreie Prüfung (NDT)
Zerstörungsfreie Prüfverfahren ermöglichen die Analyse von Werkstücken, ohne sie zu beschädigen. Die gängigsten Verfahren in der Metallumformung sind:
- Ultraschallprüfung: Hier werden Schallwellen in das Material gesendet, die eventuelle Risse oder Hohlräume aufzeigen können. Die Ultraschallprüfung ist ideal für dicke Materialien und wird häufig in der Luft- und Raumfahrt sowie in der Automobilindustrie eingesetzt.
- Röntgenprüfung: Diese Methode wird verwendet, um interne Fehler und Einschlüsse in den Materialien zu erkennen. Sie bietet hohe Präzision, ist jedoch kostenintensiv.
- Magnetpulverprüfung: Ein magnetisches Feld wird im Material erzeugt, und Risse werden durch Magnetpulver sichtbar gemacht. Diese Methode eignet sich vor allem für ferromagnetische Werkstoffe.
Diese zerstörungsfreien Verfahren ermöglichen eine schnelle und präzise Prüfung und sind besonders für sicherheitskritische Bauteile wichtig.
b) Optische und berührungslose Messverfahren
Optische Prüfverfahren wie die 3D-Scanning-Technologie oder Lasertriangulation ermöglichen eine schnelle und präzise Messung ohne direkten Kontakt. Diese Methoden werden zunehmend in der Qualitätssicherung verwendet.
- 3D-Scanning: Mit 3D-Scannern können komplette Bauteile gescannt und mit dem digitalen Modell verglichen werden. Dies ermöglicht die schnelle Erkennung von Formabweichungen.
- Laser- und Bildverarbeitungssysteme: Diese Systeme nutzen Laser und Kameras, um die Geometrie und die Oberflächenqualität zu überprüfen. Sie sind besonders nützlich für die automatische Qualitätskontrolle in der Serienproduktion.
Optische Messverfahren sind berührungslos und ermöglichen die schnelle Inspektion von Bauteilen in der laufenden Produktion, was zu einer höheren Effizienz führt.
c) Integrierte Sensorsysteme und Echtzeit-Überwachung
Moderne Maschinen sind häufig mit Sensoren ausgestattet, die Parameter wie Druck, Temperatur, Vibrationen und Dehnungen messen. Diese Sensoren überwachen den Umformprozess in Echtzeit und melden Abweichungen sofort.
- Kraft- und Wegsensoren: Überwachung der Kräfte und Positionen während des Umformprozesses, um sicherzustellen, dass die Werkstücke die richtige Form erhalten.
- Temperatursensoren: Kontrolle der Temperatur in Echtzeit, um sicherzustellen, dass das Material die optimalen Eigenschaften aufweist.
- Dehnungsmessstreifen: Erfassen von Verformungen, um mögliche Materialschwächen frühzeitig zu erkennen.
Durch die Echtzeit-Überwachung und den Einsatz integrierter Sensoren kann die Qualität der Bauteile bereits während der Produktion kontrolliert werden, wodurch Abweichungen sofort erkannt und behoben werden können.
4. Prozessüberwachung und statistische Prozesskontrolle (SPC)
Die statistische Prozesskontrolle (SPC) ist eine Methode, die auf statistischen Analysen basiert und in der Qualitätssicherung zur Überwachung und Optimierung von Fertigungsprozessen verwendet wird. Ziel der SPC ist es, durch kontinuierliche Datenanalyse die Prozessstabilität zu gewährleisten und Qualitätsprobleme frühzeitig zu identifizieren.
- Anwendung von SPC in der Metallumformung: Überwachung der Prozessparameter und Erkennung von Trends oder Abweichungen, die auf Probleme im Fertigungsprozess hinweisen könnten.
- Vorteile: SPC ermöglicht eine ständige Verbesserung der Prozesse und hilft, die Produktqualität zu stabilisieren und Ausschuss zu minimieren.
- Tools für die SPC: Häufige Werkzeuge sind Regelkarten, Histogramme und Pareto-Diagramme, die es ermöglichen, Prozessveränderungen visuell darzustellen und schnell zu reagieren.
SPC ist eine effektive Methode, um die Qualität in der Produktion sicherzustellen und Prozesse kontinuierlich zu verbessern.
5. Digitalisierung und Industrie 4.0 in der Qualitätssicherung
Die Digitalisierung spielt eine zentrale Rolle in der modernen Qualitätssicherung. Durch den Einsatz von Technologien der Industrie 4.0 können Produktionsdaten in Echtzeit erfasst, analysiert und zur Optimierung der Qualitätssicherung verwendet werden.
a) Digitale Zwillinge und Simulationen
Digitale Zwillinge sind virtuelle Darstellungen physischer Produkte oder Prozesse, die zur Überwachung und Optimierung der Qualitätssicherung eingesetzt werden.
- Simulation des Umformprozesses: Virtuelle Modelle ermöglichen es, den Umformprozess zu simulieren und die optimalen Parameter zu bestimmen, bevor die eigentliche Produktion startet.
- Überwachung und vorausschauende Wartung: Digitale Zwillinge können kontinuierlich die Prozessdaten überwachen und mögliche Probleme frühzeitig erkennen.
Die Anwendung von digitalen Zwillingen und Simulationen ermöglicht eine präzisere Prozesssteuerung und eine höhere Effizienz in der Qualitätssicherung.
b) Big Data und Künstliche Intelligenz
Durch die Analyse großer Datenmengen aus dem Produktionsprozess können Muster erkannt und Vorhersagen getroffen werden, die zur Optimierung der Qualitätssicherung beitragen.
- Qualitätsanalyse und Fehlererkennung: KI-Algorithmen analysieren Qualitätsdaten und erkennen Anomalien oder Fehlerquellen, was die Fehlererkennung und -prävention verbessert.
- Optimierung der Prozessparameter: Machine Learning kann die idealen Prozessparameter identifizieren und kontinuierlich anpassen, um die Qualität der Bauteile zu verbessern.
Big Data und KI ermöglichen eine datengetriebene Qualitätssicherung, die sich an realen Produktionsdaten orientiert und flexibel auf Änderungen reagiert.
6. Herausforderungen in der Qualitätssicherung
Die Qualitätssicherung in der Metallumformung steht vor mehreren Herausforderungen, die eine kontinuierliche Weiterentwicklung erfordern:
- Komplexität der Technologien: Die Integration neuer Technologien erfordert Fachwissen und Schulung, um die neuen Systeme effizient nutzen zu können.
- Kosten und Investitionen: Die Anschaffung moderner QS-Technologien und die Schulung der Mitarbeiter sind mit hohen Kosten verbunden.
- Datenmanagement und Cybersicherheit: Mit der zunehmenden Digitalisierung steigt die Menge der erfassten Daten, was eine zuverlässige Speicherung und Analyse erfordert. Gleichzeitig müssen Unternehmen sicherstellen, dass diese Daten vor Cyberangriffen geschützt sind.
Die Qualitätssicherung in der Metallumformung muss daher kontinuierlich angepasst und verbessert werden, um den Anforderungen der modernen Produktion gerecht zu werden.
Fazit
Die Qualitätssicherung in der Metallumformung hat sich durch den Einfluss der Industrie 4.0 und moderner Technologien stark weiterentwickelt. Von traditionellen Prüfmethoden bis hin zu digitalen Echtzeitüberwachungssystemen bietet die Qualitätssicherung eine Vielzahl von Ansätzen zur Sicherstellung einer gleichbleibend hohen Produktqualität. Durch den Einsatz von Big Data, künstlicher Intelligenz und digitalen Zwillingen wird die Qualitätssicherung präziser, flexibler und effizienter. Die kontinuierliche Weiterentwicklung und Integration neuer Technologien in die QS-Prozesse wird es der Metallumformung ermöglichen, höchste Qualitätsstandards zu gewährleisten und auf die Anforderungen der globalen Industrie einzugehen.
Anwendungen und Industrien der Metallumformung: Branchenüberblick und Einsatzgebiete
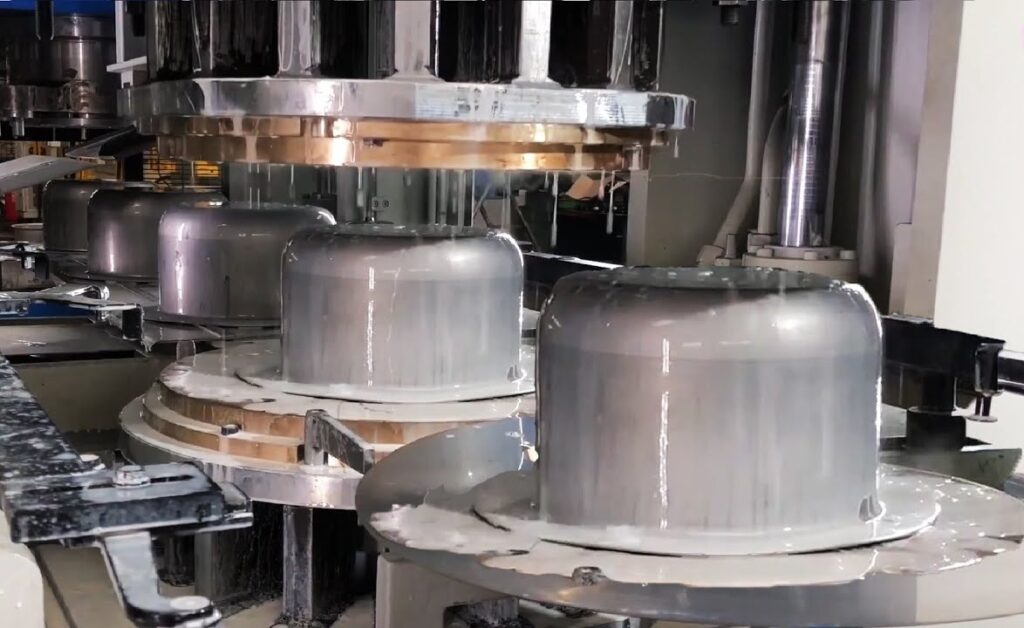
Die Metallumformung ist eine der grundlegendsten und vielseitigsten Technologien in der industriellen Fertigung. Sie ermöglicht die effiziente Herstellung von Komponenten und Produkten mit präzisen Abmessungen und hoher Belastbarkeit, die für unterschiedlichste Branchen essenziell sind. Von der Automobil- und Luftfahrtindustrie über die Bau- und Medizintechnik bis hin zur Elektronikindustrie – die Metallumformung bietet vielfältige Verfahren, die je nach Anwendungsbereich und Materialanforderungen gezielt eingesetzt werden.
Dieser Überblick beleuchtet die wichtigsten Industrien und Anwendungen der Metallumformung, ihre spezifischen Anforderungen und die Rolle der verschiedenen Umformverfahren. Dazu zählen Schmieden, Walzen, Ziehen, Biegen und Extrudieren, die jeweils unterschiedliche Formen und Eigenschaften in der Metallverarbeitung ermöglichen.
1. Automobilindustrie
Die Automobilindustrie zählt zu den größten und bedeutendsten Abnehmern von Metallumformteilen. Die Umformtechniken in dieser Branche sind vielfältig und müssen hohen Anforderungen hinsichtlich Präzision, Stabilität und Leichtbau gerecht werden, um die Sicherheit und Effizienz der Fahrzeuge zu gewährleisten.
- Typische Anwendungen:
- Karosserieteile: Türen, Hauben und Kotflügel werden oft durch Tiefziehen und Biegen hergestellt, um komplexe Formen und glatte Oberflächen zu erzielen.
- Rahmen und Strukturteile: Bauteile wie Stoßfänger und Rahmenverstärkungen werden durch Schmieden und Walzen geformt, um Festigkeit und Crash-Sicherheit zu gewährleisten.
- Motor- und Getriebeteile: Kurbelwellen, Pleuel und Zahnräder werden durch Präzisionsschmieden gefertigt, da sie hohe Belastungen aushalten müssen.
- Abgasanlagen und Fahrwerkskomponenten: Diese Teile bestehen oft aus gewalzten und gebogenen Rohren und Profilen, die eine hohe Korrosionsbeständigkeit und mechanische Festigkeit erfordern.
- Anforderungen: Die Automobilindustrie setzt auf hohe Maßgenauigkeit und Materialbeständigkeit, um den Anforderungen an Sicherheit, Leichtbau und Umweltstandards gerecht zu werden. Die Materialauswahl und die Umformtechniken sind dabei entscheidend, um sowohl die Festigkeit als auch das Gewicht zu optimieren.
2. Luft- und Raumfahrtindustrie
In der Luft- und Raumfahrtindustrie sind leichte und zugleich extrem belastbare Bauteile notwendig, da sie den hohen mechanischen und thermischen Belastungen in der Luftfahrt standhalten müssen. Diese Branche verwendet hochwertige Legierungen, insbesondere Aluminium und Titan, die durch Umformverfahren in die gewünschten Komponenten umgewandelt werden.
- Typische Anwendungen:
- Strukturteile für Rumpf und Flügel: Diese Teile werden häufig durch Walzen und Schmieden hergestellt, um eine hohe Festigkeit bei geringem Gewicht zu erzielen.
- Triebwerkskomponenten: Triebwerksteile wie Turbinenschaufeln und Gehäuse werden durch Präzisionsschmieden und Walzen gefertigt, da sie hohen Temperaturen und Belastungen ausgesetzt sind.
- Hydraulik- und Kraftstoffleitungen: Durch das Ziehen und Biegen von Rohren entstehen Leitungen, die im Flugzeug für die Steuerung und den Transport von Treibstoffen und Hydraulikflüssigkeiten verwendet werden.
- Verbindungs- und Befestigungselemente: Spezielle Schrauben und Muttern werden durch Kaltumformung und Präzisionsschmieden gefertigt, um maximale Zuverlässigkeit zu gewährleisten.
- Anforderungen: Die Luftfahrtindustrie stellt hohe Anforderungen an Präzision, Gewicht und Festigkeit. Zudem ist Korrosionsbeständigkeit wichtig, da die Bauteile extremen Umwelteinflüssen standhalten müssen. Aufgrund dieser Anforderungen sind Umformtechniken gefragt, die eine exakte Maßhaltigkeit und eine hohe Oberflächenqualität sicherstellen.
3. Bauindustrie
Die Bauindustrie benötigt eine Vielzahl an metallischen Komponenten, die für die Tragfähigkeit und Stabilität von Gebäuden und Infrastrukturbauten essenziell sind. Hier werden große Mengen an Profilen, Blechen und Rohren benötigt, die durch Walzen, Biegen und andere Umformverfahren hergestellt werden.
- Typische Anwendungen:
- Stahlträger und -profile: H-, T- und U-Profile sowie Rund- und Vierkantrohre werden durch Walzen und Biegen geformt und finden als tragende Elemente in Gebäuden, Brücken und anderen Bauwerken Anwendung.
- Fassaden- und Verkleidungselemente: Dünne Bleche aus Stahl oder Aluminium, die durch Walzen und Biegen bearbeitet werden, sind als Verkleidung und Fassadenmaterial beliebt.
- Treppen und Geländer: Durch Biegen und Schweißen von Stahlprofilen entstehen Treppen und Geländer, die in Wohn- und Industriegebäuden zum Einsatz kommen.
- Bewehrungsstahl und Verbindungselemente: Gewalzte Stäbe und Drahtverbindungen werden zur Verstärkung von Beton und als Verbindungselemente im Bau verwendet.
- Anforderungen: Die Bauindustrie setzt auf hohe Stabilität, Langlebigkeit und Korrosionsschutz. Neben Standardprofilen werden häufig individuelle Profile und Bauteile gefertigt, die speziellen Anforderungen an die Statik und Bauweise gerecht werden.
4. Elektronikindustrie
In der Elektronikindustrie spielt die Metallumformung eine wichtige Rolle, da viele elektronische Bauteile Metallkomponenten benötigen, die präzise und oft sehr klein sind. Die Herstellung erfordert Techniken, die sowohl Genauigkeit als auch eine hohe Oberflächenqualität bieten.
- Typische Anwendungen:
- Gehäuse und Kühlkörper: Gehäuse und Kühlkörper werden aus Aluminium oder Kupfer durch Extrudieren und Biegen hergestellt, um eine optimale Wärmeableitung zu ermöglichen.
- Stecker und Kontakte: Elektrische Steckverbinder und Kontakte werden durch Ziehen und Stanzen von Kupfer und Aluminium gefertigt, um eine hohe Leitfähigkeit sicherzustellen.
- Leiterplattenkomponenten: Auf Leiterplatten kommen geformte Metalle als Kontaktflächen und Leitungen zum Einsatz, die präzise und korrosionsbeständig sein müssen.
- Anforderungen: Die Elektronikindustrie stellt hohe Anforderungen an die Oberflächenqualität und Maßgenauigkeit der Bauteile. Zudem muss das Material eine hohe elektrische und thermische Leitfähigkeit bieten und darf keine Verzerrungen aufweisen.
5. Medizintechnik
In der Medizintechnik werden viele Metallbauteile für chirurgische Instrumente, Implantate und Diagnosegeräte benötigt. Diese Bauteile müssen extrem präzise, korrosionsbeständig und biokompatibel sein, um die Anforderungen in medizinischen Anwendungen zu erfüllen.
- Typische Anwendungen:
- Implantate: Implantate wie künstliche Hüft- und Kniegelenke werden durch Präzisionsschmieden und Extrudieren gefertigt, da sie exakt auf den Körper abgestimmt sein müssen.
- Chirurgische Instrumente: Präzisionswerkzeuge wie Klemmen, Zangen und Skalpelle werden durch Schmieden und Biegen hergestellt, um eine hohe Festigkeit und Korrosionsbeständigkeit zu gewährleisten.
- Prothesen und Stents: Metallteile für Prothesen und Stents werden durch Ziehen und Laserbiegen hergestellt, um die benötigte Flexibilität und Präzision zu erreichen.
- Diagnosegeräte und Gehäuse: Komponenten für Diagnosegeräte und medizinische Elektronik, wie Gehäuse und Halterungen, werden durch Walzen und Ziehen aus Edelstahl oder Aluminium gefertigt.
- Anforderungen: Die Medizintechnik stellt höchste Anforderungen an Qualität und Präzision. Materialien wie Edelstahl, Titan und spezielle Legierungen müssen biokompatibel, korrosionsbeständig und leicht zu reinigen sein.
6. Energie- und Umwelttechnik
In der Energie- und Umwelttechnik spielt die Metallumformung eine entscheidende Rolle, da viele Anlagen und Geräte auf metallische Bauteile angewiesen sind, die großen Belastungen und Umwelteinflüssen standhalten.
- Typische Anwendungen:
- Windkraftanlagen: Für Windkraftanlagen werden Schmiede- und Walzkomponenten wie Rotoren und Turbinengehäuse verwendet, die Windlasten standhalten müssen.
- Solarpanel-Strukturen: Gestelle und Halterungen für Solarpaneele bestehen aus Aluminium und Stahl, die durch Biegen und Walzen geformt werden.
- Wärmetauscher und Rohrleitungen: Wärmetauscher und Rohrleitungen für Heiz- und Kühlanlagen werden durch Walzen und Ziehen gefertigt, um hohe Wärmeleitfähigkeit und Korrosionsbeständigkeit sicherzustellen.
- Kraftwerkskomponenten: Bauteile in Kraftwerken, wie Ventile, Rohrleitungen und Kesselkomponenten, bestehen aus robusten Materialien, die durch Schmieden und Walzen geformt werden.
- Anforderungen: Die Energie- und Umwelttechnik erfordert Materialien, die unter extremen Bedingungen zuverlässig funktionieren. Zudem müssen viele Bauteile eine hohe Korrosionsbeständigkeit und mechanische Festigkeit aufweisen, da sie oft im Freien und unter widrigen Umwelteinflüssen eingesetzt werden.
7. Möbel- und Innenausstattungsindustrie
Die Möbel- und Innenausstattungsindustrie verwendet Umformtechniken, um ästhetische und funktionale Metallkomponenten herzustellen. Diese Teile tragen zur Stabilität und Optik von Möbeln bei.
- Typische Anwendungen:
- Möbelrahmen und -gestelle: Metallrahmen für Stühle, Tische und Regale werden durch Biegen und Schweißen geformt.
- Dekorative Elemente: Verzierungen und Beschläge werden oft durch Schmieden und Präzisionsgießen hergestellt.
- Tür- und Fensterrahmen: Aluminium- und Stahlrahmen für Türen und Fenster werden durch Walzen und Biegen gefertigt und mit dekorativen Beschichtungen versehen.
- Anforderungen: Die Möbelindustrie stellt hohe Anforderungen an die Ästhetik und Oberflächenqualität der Bauteile. Neben der mechanischen Stabilität ist auch die optische Gestaltung von Bedeutung.
Fazit
Die Metallumformung spielt in zahlreichen Industrien eine essenzielle Rolle und ermöglicht die Herstellung vielfältiger Bauteile mit spezifischen Anforderungen. Die Auswahl des geeigneten Umformverfahrens hängt von den Anforderungen der jeweiligen Branche und des Endprodukts ab, wobei Kriterien wie Präzision, Stabilität, Gewicht und Oberflächenqualität entscheidend sind. Mit der zunehmenden Digitalisierung und der Integration moderner Technologien wie Industrie 4.0 und Künstlicher Intelligenz wird die Metallumformung in den kommenden Jahren noch effizienter und flexibler werden. Dies ermöglicht eine noch bessere Anpassung an die individuellen Anforderungen der verschiedenen Industrien und wird die Einsatzmöglichkeiten der Metallumformung weiter ausbauen.
Mechanische Pressen: Typen, Funktionsweise und Anwendungen in der Metallumformung
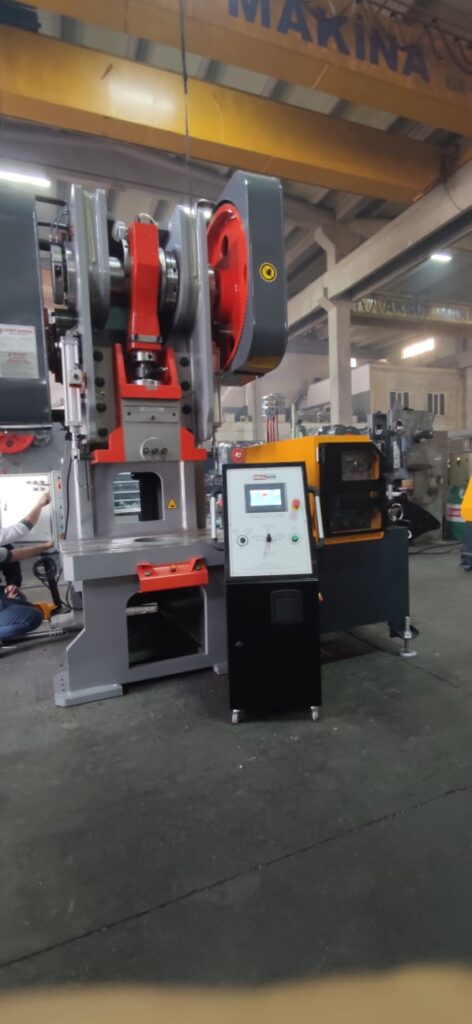
Mechanische Pressen sind eine zentrale Komponente in der Metallumformung und gehören zu den meistgenutzten Maschinen in der industriellen Fertigung. Sie wandeln mechanische Energie in Druckkraft um, die auf ein Werkstück wirkt, um es in eine bestimmte Form zu bringen. Mechanische Pressen sind besonders effizient für hochpräzise Arbeiten und hohe Produktionsgeschwindigkeiten und werden in einer Vielzahl von Branchen eingesetzt, darunter die Automobil-, Luftfahrt-, Bau- und Elektronikindustrie.
Dieser Text beleuchtet die Funktionsweise mechanischer Pressen, ihre verschiedenen Typen und Anwendungsbereiche, die verwendeten Technologien und die besonderen Anforderungen in der Metallumformung. Zudem werden die Vorteile und Herausforderungen des Einsatzes mechanischer Pressen aufgezeigt.
1. Grundlagen und Funktionsweise von mechanischen Pressen
Mechanische Pressen nutzen mechanische Energie, die über eine rotierende Bewegung in eine lineare Kraft umgewandelt wird. Diese Kraft wird durch Komponenten wie Exzenter, Kurbel oder Kniehebel auf das Werkzeug übertragen, das wiederum auf das Werkstück wirkt. Mechanische Pressen arbeiten in der Regel mit hohen Geschwindigkeiten und ermöglichen so eine schnelle und präzise Verformung.
Wesentliche Komponenten einer mechanischen Presse:
- Antriebssystem: Der Antrieb erfolgt meist über einen Elektromotor, der die rotierenden Bewegungen erzeugt und die Kraft auf den Pressmechanismus überträgt.
- Schwungrad: Das Schwungrad speichert Energie und liefert sie bei jedem Pressvorgang, um gleichbleibende Kraft zu gewährleisten.
- Kraftübertragungssystem: Dies umfasst die mechanischen Elemente, die die rotierende Energie in lineare Bewegung umwandeln, wie Exzenter, Kurbel oder Kniehebel.
- Stößel (Ram): Der Stößel ist das Teil, das auf das Werkstück wirkt und die tatsächliche Presskraft überträgt.
- Werkzeugaufnahme: Die Werkzeuge oder Matrizen, die die Form des Werkstücks bestimmen, sind in der Presse befestigt.
Der Prozess beginnt, wenn der Motor das Schwungrad in Rotation versetzt. Die gespeicherte Energie wird dann über das Kraftübertragungssystem auf den Stößel übertragen, der das Werkstück formt.
2. Typen mechanischer Pressen
Mechanische Pressen werden nach dem Mechanismus zur Kraftübertragung und dem Einsatzzweck in verschiedene Typen unterteilt. Die am häufigsten verwendeten Typen sind:
a) Exzenterpressen
Exzenterpressen verwenden einen Exzenter, der eine rotierende Bewegung in eine lineare Bewegung umwandelt. Sie sind weit verbreitet, da sie hohe Präzision und Flexibilität bieten.
- Typische Anwendungen: Stanzen, Biegen, Prägen und Schneiden in der Automobil- und Elektronikindustrie.
- Vorteile: Hohe Geschwindigkeit und Präzision, ideal für große Produktionsmengen.
- Nachteile: Begrenzte Presskraft und anfällig für Verschleiß bei dauerhafter Hochbelastung.
b) Kurbelpressen
Kurbelpressen arbeiten ähnlich wie Exzenterpressen, nutzen jedoch eine Kurbel, um die lineare Bewegung zu erzeugen. Sie eignen sich für Anwendungen, bei denen eine gleichmäßige Kraftverteilung erforderlich ist.
- Typische Anwendungen: Stanzen, Schneiden und Biegen von Blechen in der Bau- und Automobilindustrie.
- Vorteile: Gleichmäßige Kraftübertragung, gut geeignet für die Massenproduktion.
- Nachteile: Komplexere Wartung und höhere mechanische Belastung.
c) Kniehebelpressen
Kniehebelpressen nutzen ein Kniehebelsystem, das eine hohe Kraft bei Endstellung des Stößels erzeugt. Sie sind für Anwendungen geeignet, die eine besonders hohe Presskraft erfordern.
- Typische Anwendungen: Präzisionsarbeiten wie Feinblechbearbeitung und Prägen.
- Vorteile: Hohe Presskraft und Präzision in der Endstellung, ideal für schwer umformbare Werkstücke.
- Nachteile: Begrenzte Hubhöhe und höhere Komplexität des Mechanismus.
d) Rollkurbelpressen
Rollkurbelpressen nutzen einen speziellen Mechanismus mit einer Rollkurbel, die eine gleichmäßige Kraftübertragung und hohe Geschwindigkeit ermöglicht. Diese Maschinen sind für komplexe Umformarbeiten und große Produktionsmengen geeignet.
- Typische Anwendungen: Tiefziehen und Strecken in der Automobil- und Haushaltsgeräteindustrie.
- Vorteile: Gleichmäßige Kraftverteilung, hohe Geschwindigkeit und gut für die Massenproduktion geeignet.
- Nachteile: Höherer Verschleiß und komplexer Mechanismus, was Wartung und Kosten erhöht.
Die Wahl der richtigen Pressenart hängt von der gewünschten Form des Werkstücks, der Materialeigenschaften und der Produktionsmenge ab. Jede Presse bietet spezifische Vorteile, die sie für unterschiedliche Anwendungen in der Metallumformung qualifizieren.
3. Anwendungen mechanischer Pressen in der Metallumformung
Mechanische Pressen sind in einer Vielzahl von Industrien unverzichtbar. Sie bieten die Möglichkeit, Werkstücke mit hoher Präzision und Geschwindigkeit zu formen, zu schneiden und zu prägen. Hier einige typische Anwendungen:
a) Automobilindustrie
Die Automobilindustrie ist einer der größten Anwender mechanischer Pressen. Diese Maschinen sind entscheidend für die Herstellung von Fahrzeugkomponenten.
- Karosserieteile: Mechanische Pressen stanzen und biegen Bleche, um Karosserieteile wie Türen, Dächer und Kofferraumdeckel herzustellen.
- Rahmen- und Strukturkomponenten: Strukturelle Bauteile werden oft durch Präzisionspressen geformt, um die Festigkeit und Crash-Sicherheit zu gewährleisten.
- Motor- und Getriebeteile: Mechanische Pressen werden für die Fertigung von Zahnrädern, Kurbelwellen und anderen hochbelasteten Komponenten eingesetzt.
b) Elektronik- und Elektroindustrie
In der Elektronikindustrie werden mechanische Pressen zur Herstellung kleiner, präziser Teile verwendet, die hohe Maßgenauigkeit und Zuverlässigkeit erfordern.
- Stecker und Kontakte: Exzenter- und Kurbelpressen werden eingesetzt, um Steckkontakte und Anschlüsse zu stanzen und zu biegen.
- Gehäuse und Hitzeschilder: Mechanische Pressen werden verwendet, um Metallgehäuse und Hitzeschilde für elektronische Komponenten zu fertigen.
c) Haushaltsgeräteindustrie
Die Produktion von Haushaltsgeräten wie Waschmaschinen, Kühlschränken und Mikrowellen erfordert eine hohe Produktionsrate, die durch mechanische Pressen gewährleistet wird.
- Blechgehäuse: Kurbelpressen stanzen und formen Bleche, um Gehäuse und Abdeckungen für Haushaltsgeräte herzustellen.
- Befestigungselemente: Schrauben, Bolzen und andere Verbindungselemente werden häufig mit Exzenterpressen hergestellt.
d) Bauindustrie
In der Bauindustrie werden mechanische Pressen eingesetzt, um starke und widerstandsfähige Komponenten herzustellen, die in Konstruktionen wie Brücken, Gebäuden und Infrastrukturen verwendet werden.
- Stahlträger und -profile: Mechanische Pressen biegen und formen Stahlprofile und Träger, die als tragende Elemente in Bauwerken verwendet werden.
- Verbindungselemente: Mechanische Pressen produzieren auch Schrauben, Muttern und andere Verbindungselemente, die in der Bauindustrie benötigt werden.
Die Anwendungen mechanischer Pressen sind vielfältig und reichen von präzisen Kleinteilen in der Elektronik bis hin zu großen Strukturkomponenten in der Bau- und Automobilindustrie.
4. Vorteile mechanischer Pressen
Mechanische Pressen bieten zahlreiche Vorteile, die sie für die industrielle Produktion unverzichtbar machen:
- Hohe Produktionsgeschwindigkeit: Mechanische Pressen arbeiten sehr schnell und eignen sich ideal für die Massenproduktion.
- Präzision und Wiederholgenauigkeit: Sie bieten hohe Genauigkeit und Konsistenz, was in der Serienproduktion entscheidend ist.
- Energieeffizienz: Mechanische Pressen sind im Vergleich zu hydraulischen Systemen oft energieeffizienter.
- Geringe Betriebskosten: Mechanische Pressen haben geringere Betriebskosten, da sie einfacher aufgebaut sind und weniger Wartung benötigen.
Dank dieser Vorteile sind mechanische Pressen das bevorzugte Werkzeug für viele industrielle Anwendungen, insbesondere wenn hohe Produktionsraten und präzise Umformung gefragt sind.
5. Herausforderungen und Nachteile mechanischer Pressen
Trotz ihrer zahlreichen Vorteile bringen mechanische Pressen auch Herausforderungen und Nachteile mit sich:
- Begrenzte Flexibilität: Mechanische Pressen sind oft für spezifische Umformprozesse ausgelegt und weniger flexibel als hydraulische Pressen, die ihre Druckkraft kontinuierlich anpassen können.
- Rückstellung und Rückfederung: Materialien neigen zur Rückfederung nach der Umformung, was die Präzision der Pressung beeinflussen kann und eine exakte Steuerung der Kräfte erfordert.
- Verschleiß und Wartung: Der mechanische Antrieb führt zu einem höheren Verschleiß, insbesondere bei dauerhafter Hochbelastung. Wartung und Austausch von Verschleißteilen sind notwendig.
- Begrenzte Hubhöhe: Mechanische Pressen haben oft eine festgelegte Hubhöhe und können nicht so flexibel auf Werkstückgrößen und -formen eingestellt werden wie hydraulische Pressen.
Die Wahl der passenden Presse hängt daher stark vom Einsatzzweck ab und muss die spezifischen Anforderungen der Produktion berücksichtigen.
6. Moderne Entwicklungen und Zukunftstrends
Mit der fortschreitenden Digitalisierung und Industrie 4.0 wurden mechanische Pressen weiterentwickelt und automatisiert. Zu den modernen Trends und Entwicklungen gehören:
- Sensorintegration und Echtzeitüberwachung: Sensoren ermöglichen die Echtzeitüberwachung von Presskraft, Temperatur und weiteren Parametern. Diese Daten können genutzt werden, um die Produktion zu optimieren und den Verschleiß zu reduzieren.
- Automatisierung und Robotik: Automatisierte Materialhandhabung und Werkstückpositionierung ermöglichen eine höhere Effizienz und eine lückenlose Qualitätskontrolle.
- Energieoptimierung: Fortschrittliche Steuerungssysteme reduzieren den Energieverbrauch und verbessern die Effizienz.
- Prozessdatenerfassung und Big Data: Produktionsdaten werden gesammelt und analysiert, um die Qualitätssicherung zu optimieren und vorausschauende Wartungsstrategien umzusetzen.
Diese technologischen Fortschritte haben die Effizienz und Präzision mechanischer Pressen weiter gesteigert und bieten Unternehmen zusätzliche Möglichkeiten, die Produktionsprozesse zu optimieren.
Fazit
Mechanische Pressen sind ein unverzichtbares Werkzeug in der Metallumformung und bieten zahlreiche Vorteile für die industrielle Produktion. Dank ihrer hohen Präzision, Geschwindigkeit und Wiederholgenauigkeit eignen sie sich ideal für die Massenproduktion in Branchen wie der Automobil-, Elektronik- und Bauindustrie. Die kontinuierliche Weiterentwicklung der Technologie und die Integration moderner Sensoren und Automatisierungstechniken verbessern die Effizienz und Zuverlässigkeit dieser Maschinen und machen sie noch wertvoller für moderne Produktionsprozesse.
Durch die Anwendung von Industrie 4.0-Prinzipien und digitalen Technologien wird die Leistungsfähigkeit mechanischer Pressen weiter gesteigert. Damit sind mechanische Pressen auch in Zukunft ein entscheidender Faktor für effiziente und präzise Fertigungsprozesse in der Metallverarbeitung.
Hydraulische Pressen: Aufbau, Funktionsweise und Anwendungen in der Metallumformung
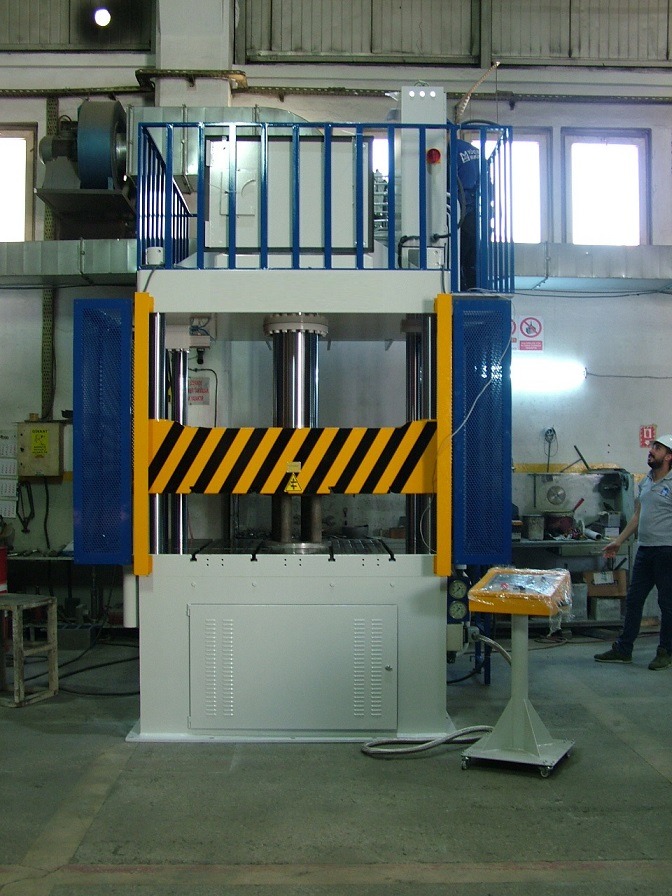
Hydraulische Pressen sind zentrale Maschinen in der Metallumformung, die in verschiedensten Branchen eingesetzt werden. Sie wandeln die von einer hydraulischen Flüssigkeit erzeugte Kraft in Druckkraft um, die dann auf ein Werkstück wirkt, um es zu verformen oder in eine gewünschte Form zu bringen. Im Vergleich zu mechanischen Pressen bieten hydraulische Pressen den Vorteil einer konstanten und anpassbaren Druckkraft über den gesamten Hub, was eine präzisere Steuerung und höhere Flexibilität ermöglicht. Hydraulische Pressen sind daher unverzichtbar für Anwendungen, die eine hohe Presskraft und Anpassungsfähigkeit erfordern.
Dieser Text gibt einen detaillierten Überblick über den Aufbau und die Funktionsweise hydraulischer Pressen, ihre verschiedenen Typen und Anwendungen sowie die Vorteile und Herausforderungen des Einsatzes. Zusätzlich werden moderne Entwicklungen und Trends vorgestellt, die die Effizienz und Präzision hydraulischer Pressen in der Industrie steigern.
1. Grundlagen und Funktionsweise hydraulischer Pressen
Hydraulische Pressen basieren auf dem Prinzip der Hydraulik, bei dem Flüssigkeiten unter Druck zur Übertragung und Verstärkung von Kräften verwendet werden. Das Funktionsprinzip basiert auf dem Pascal’schen Gesetz, das besagt, dass ein Druck, der auf eine Flüssigkeit in einem geschlossenen System ausgeübt wird, gleichmäßig in alle Richtungen übertragen wird.
Wesentliche Komponenten einer hydraulischen Presse:
- Hydraulikpumpe: Erzeugt den Druck, der auf die Hydraulikflüssigkeit (meist Öl) ausgeübt wird.
- Zylinder und Kolben: Der Druck wird auf einen Kolben übertragen, der eine lineare Bewegung erzeugt, um die Kraft auf das Werkstück zu übertragen.
- Ventile: Regulieren den Durchfluss und den Druck der Hydraulikflüssigkeit und kontrollieren den Hub des Kolbens.
- Rahmen und Tisch: Die Struktur, auf der das Werkstück platziert wird und die den Druck aufnimmt.
Der Prozess beginnt, wenn die Pumpe den Druck auf die Hydraulikflüssigkeit erhöht. Die Flüssigkeit drückt auf den Kolben im Zylinder, der die Druckkraft auf das Werkstück überträgt. Der Druck kann je nach Anwendung angepasst werden, was hydraulische Pressen besonders vielseitig macht.
2. Typen hydraulischer Pressen
Es gibt verschiedene Typen hydraulischer Pressen, die je nach Art der Druckübertragung und dem Anwendungsbereich unterschiedliche Vorteile bieten.
a) Einfachwirkende hydraulische Pressen
Bei einfachwirkenden Pressen wirkt der Druck nur in eine Richtung. Der Kolben fährt durch den Druck der Hydraulikflüssigkeit aus und kehrt mithilfe von Federn oder dem Eigengewicht des Kolbens in die Ausgangsposition zurück.
- Typische Anwendungen: Stanzen, Biegen und Prägen in der Metallverarbeitung.
- Vorteile: Einfacher Aufbau und kostengünstig, gut geeignet für kleine bis mittlere Presskraftanforderungen.
- Nachteile: Begrenzte Kraftsteuerung und geringere Flexibilität.
b) Doppeltwirkende hydraulische Pressen
Doppeltwirkende Pressen wirken sowohl beim Aus- als auch beim Einfahren des Kolbens. Die Hydraulikflüssigkeit drückt den Kolben in beide Richtungen, wodurch die Kraft und der Hub präzise gesteuert werden können.
- Typische Anwendungen: Tiefziehen, Umformen und Schneiden von Metallen.
- Vorteile: Höhere Kontrolle über den Hub, mehr Flexibilität und geeignet für komplexere Umformprozesse.
- Nachteile: Komplexerer Aufbau und höherer Wartungsaufwand.
c) Dreifachwirkende hydraulische Pressen
Dreifachwirkende Pressen besitzen drei Zylinder, die aufeinander abgestimmt arbeiten. Sie sind für komplexe Umformvorgänge, wie z. B. das Tiefziehen von Hohlkörpern, geeignet.
- Typische Anwendungen: Herstellung von Hohlkörpern, wie Kraftstofftanks und Druckbehältern.
- Vorteile: Hohe Flexibilität und Präzision für anspruchsvolle Umformprozesse.
- Nachteile: Sehr hoher Energieverbrauch und komplexe Wartung.
d) Servohydraulische Pressen
Servohydraulische Pressen kombinieren hydraulische Systeme mit elektrischen Servoantrieben, die eine noch präzisere Steuerung der Kraft und Geschwindigkeit ermöglichen.
- Typische Anwendungen: Präzisionsumformungen und Anwendungen, bei denen eine exakte Steuerung der Geschwindigkeit und Position erforderlich ist.
- Vorteile: Energieeffizient und extrem präzise.
- Nachteile: Hohe Anschaffungskosten und komplexe Steuerungstechnik.
Die Auswahl des Pressentyps hängt von den spezifischen Anforderungen des Umformprozesses ab, einschließlich der benötigten Kraft, Geschwindigkeit und Steuerungsanforderungen.
3. Anwendungen hydraulischer Pressen in der Metallumformung
Hydraulische Pressen sind in der Metallumformung aufgrund ihrer Vielseitigkeit und hohen Presskraft weit verbreitet. Sie kommen in verschiedenen Industrien zum Einsatz und eignen sich für eine Vielzahl von Umformprozessen.
a) Automobilindustrie
In der Automobilindustrie werden hydraulische Pressen für viele Komponenten benötigt, die hohe Präzision und Stabilität erfordern.
- Karosserieteile: Hydraulische Pressen werden für das Tiefziehen und Stanzen von Karosserieteilen wie Türen, Dachblechen und Kotflügeln verwendet.
- Rahmen- und Strukturkomponenten: Strukturelle Bauteile wie Verstärkungen und Querträger werden durch Umformung unter hohen Drücken hergestellt.
- Abgasanlagen und Fahrwerkskomponenten: Hydraulische Pressen formen und biegen Rohre für Abgasanlagen und Fahrwerkskomponenten.
b) Luft- und Raumfahrtindustrie
Die Luft- und Raumfahrtindustrie erfordert hochpräzise und leichte Bauteile, die extremen Belastungen standhalten müssen.
- Flügelstrukturen und Rumpfteile: Großformatige Teile wie Flügel- und Rumpfkomponenten werden durch hydraulisches Umformen hergestellt.
- Triebwerkskomponenten: Bauteile wie Turbinenschaufeln werden durch Präzisionsumformung und Schmieden in hydraulischen Pressen gefertigt.
- Treibstofftanks und Druckbehälter: Für die Herstellung dieser Komponenten sind hohe Druckkräfte erforderlich, die mit hydraulischen Pressen realisiert werden.
c) Bauindustrie
In der Bauindustrie werden zahlreiche Komponenten benötigt, die durch hydraulische Pressen geformt und verstärkt werden.
- Stahlträger und -profile: Hydraulische Pressen werden zum Biegen und Formen von Stahlprofilen eingesetzt, die als Trägerstrukturen in Gebäuden verwendet werden.
- Befestigungselemente: Schrauben, Bolzen und andere Verbindungselemente werden durch Umformung mit hydraulischen Pressen hergestellt.
- Bewehrungsstahl: Hydraulische Pressen werden zur Herstellung von Stahlmatten und Stäben verwendet, die als Bewehrung in Beton eingesetzt werden.
d) Medizintechnik
Die Medizintechnik stellt hohe Anforderungen an die Präzision und Biokompatibilität von Metallkomponenten.
- Chirurgische Instrumente: Instrumente wie Pinzetten und Skalpelle werden durch Präzisionsumformung in hydraulischen Pressen gefertigt.
- Implantate: Hüft- und Kniegelenksimplantate werden durch Tiefziehen und Präzisionsumformung hergestellt.
- Prothesen und Stents: Hydraulische Pressen werden zur Formung und Anpassung von Prothesenteilen und Stents eingesetzt.
e) Elektronik- und Haushaltsgeräteindustrie
In der Elektronik- und Haushaltsgeräteindustrie werden hydraulische Pressen für kleine und präzise Komponenten verwendet.
- Gehäuse und Hitzeschilde: Metalle für elektronische Gehäuse und Hitzeschilde werden durch Tiefziehen und Prägen geformt.
- Kühlkörper und Anschlüsse: Komponenten für die Wärmeableitung und elektrische Kontakte werden durch Umformung in hydraulischen Pressen hergestellt.
Dank ihrer Vielseitigkeit und Präzision sind hydraulische Pressen in einer Vielzahl von Industrien unverzichtbar und ermöglichen die Herstellung von Komponenten mit höchster Präzision und Belastbarkeit.
4. Vorteile hydraulischer Pressen
Hydraulische Pressen bieten zahlreiche Vorteile, die sie für anspruchsvolle Umformprozesse besonders geeignet machen:
- Hohe Presskraft: Hydraulische Pressen bieten eine konstante und einstellbare Druckkraft, die über den gesamten Hub verfügbar ist. Dies ermöglicht eine exakte Umformung und eine gleichmäßige Verteilung der Kräfte.
- Flexibilität und Anpassungsfähigkeit: Die Presskraft und der Hub lassen sich genau anpassen, wodurch hydraulische Pressen für verschiedene Werkstoffe und Bauteilgrößen flexibel einsetzbar sind.
- Energieeffizienz: Hydraulische Pressen verbrauchen nur dann Energie, wenn sie unter Druck stehen, was sie energieeffizienter macht, insbesondere für Anwendungen mit hoher Presskraft.
- Präzision und Kontrolle: Hydraulische Pressen bieten eine exakte Steuerung der Kraft und des Hubs, was eine hohe Wiederholgenauigkeit und Präzision ermöglicht.
Durch diese Eigenschaften sind hydraulische Pressen ideal für Anwendungen, die eine exakte und gleichmäßige Umformung erfordern.
5. Herausforderungen und Nachteile hydraulischer Pressen
Trotz ihrer Vorteile bringen hydraulische Pressen auch einige Herausforderungen und Nachteile mit sich:
- Hoher Wartungsaufwand: Die hydraulischen Komponenten sind anfällig für Verschleiß, und das Hydrauliköl muss regelmäßig gewartet und gewechselt werden.
- Langsamere Geschwindigkeit: Hydraulische Pressen sind in der Regel langsamer als mechanische Pressen, was sie für Hochgeschwindigkeitsanwendungen weniger geeignet macht.
- Kosten: Die Anschaffung und Wartung hydraulischer Pressen sind oft teurer als bei mechanischen Pressen.
- Umweltanforderungen: Das Hydrauliköl muss sicher entsorgt und oft gewechselt werden, was die Umweltauflagen und den Wartungsaufwand erhöht.
Die Wahl einer hydraulischen Presse hängt daher von den spezifischen Anforderungen des Umformprozesses ab und muss die Vor- und Nachteile berücksichtigen.
6. Moderne Entwicklungen und Zukunftstrends
Die hydraulischen Pressen entwickeln sich kontinuierlich weiter, insbesondere im Hinblick auf Effizienz, Präzision und Umweltfreundlichkeit.
- Servohydraulik: Durch den Einsatz von Servoantrieben werden hydraulische Pressen energieeffizienter und bieten eine noch genauere Steuerung der Kraft und Geschwindigkeit.
- Automatisierung und Industrie 4.0: Sensoren und Automatisierung ermöglichen die Echtzeitüberwachung und -steuerung, was die Effizienz und Qualität erhöht.
- Digitalisierung und Prozessdatenerfassung: Moderne hydraulische Pressen sammeln und analysieren Produktionsdaten, um vorausschauende Wartungsstrategien und Qualitätskontrollen zu optimieren.
- Nachhaltige Hydraulikflüssigkeiten: Um den Umweltanforderungen gerecht zu werden, werden zunehmend biologisch abbaubare Hydrauliköle eingesetzt.
Diese Entwicklungen machen hydraulische Pressen noch leistungsfähiger und umweltfreundlicher, was ihre Anwendbarkeit und Effizienz weiter verbessert.
Fazit
Hydraulische Pressen sind unverzichtbare Maschinen in der Metallumformung, die eine hohe Presskraft und Präzision bieten. Ihre Flexibilität und Anpassungsfähigkeit machen sie ideal für eine Vielzahl von Anwendungen in der Automobil-, Luftfahrt-, Bau-, Medizintechnik- und Elektronikindustrie. Dank moderner Technologien und der Integration von Industrie-4.0-Prinzipien bieten hydraulische Pressen eine hohe Effizienz und Präzision und werden sich mit fortschreitender Digitalisierung und nachhaltigen Technologien weiterentwickeln.
Insgesamt stellen hydraulische Pressen eine wertvolle Ressource für Unternehmen dar, die präzise und flexible Umformprozesse benötigen, und werden weiterhin eine entscheidende Rolle in der industriellen Fertigung spielen.
Stauchen: Verfahren, Anwendungen und Technologien in der Metallumformung
Stauchen ist ein zentrales Verfahren der Metallumformung, bei dem ein Werkstück entlang seiner Längsachse verdichtet wird. Durch das Stauchen wird das Werkstück in der Höhe verkürzt und dabei dicker bzw. breiter. Stauchen eignet sich besonders zur Herstellung von Werkstücken, die in axialer Richtung belastbar und von hoher Festigkeit sein müssen, wie Bolzen, Achsen und Wellen.
In diesem umfassenden Überblick werden die Grundlagen des Stauchens, die verschiedenen Verfahrenstypen, die eingesetzten Maschinen und die industriellen Anwendungen dargestellt. Zusätzlich werden die Vorteile und Herausforderungen des Verfahrens sowie moderne Entwicklungen und Technologien beschrieben.
1. Grundlagen des Stauchens
Stauchen ist ein Verfahren der Massivumformung, bei dem ein Werkstück zwischen zwei Werkzeuge – häufig Matrizen oder Stempel – gepresst wird. Die Druckkraft wirkt senkrecht auf das Werkstück und verkürzt es, während der Querschnitt zunimmt. Dies führt zu einer Umverteilung des Materials, ohne es abzutragen oder zu schneiden. Das Material bleibt vollständig erhalten und wird in der Form gestaucht, die durch die Matrizen vorgegeben wird.
Die wesentlichen Merkmale des Stauchens sind:
- Kraftaufwand: Da das Material verdichtet wird, sind hohe Druckkräfte erforderlich, um das Werkstück zu verformen.
- Materialfluss: Beim Stauchen fließt das Material in radialer Richtung, während es in Längsrichtung verdichtet wird.
- Materialverhalten: Werkstoffe, die gut stauchbar sind, haben eine hohe Verformbarkeit und Duktilität. Materialien wie Stahl, Aluminium und Kupfer eignen sich besonders gut.
Stauchen kann sowohl im Kalt- als auch im Warmzustand erfolgen. Die Wahl der Temperatur hängt von den Eigenschaften des Werkstoffs und den Anforderungen an das Endprodukt ab.
2. Arten des Stauchens
Es gibt verschiedene Stauchverfahren, die je nach Umformprozess und Werkstückgeometrie eingesetzt werden. Zu den wichtigsten Verfahren zählen:
a) Vollstauchen
Beim Vollstauchen wird das gesamte Werkstück über seine gesamte Querschnittsfläche gestaucht. Dabei entstehen zylindrische oder scheibenförmige Teile. Dieses Verfahren wird oft für massive Teile angewendet, die keine Hohlräume aufweisen.
- Typische Anwendungen: Herstellung von Bolzen, Nieten und Zahnrädern.
- Vorteile: Gleichmäßige Materialverteilung und hohe Festigkeit des Werkstücks.
- Nachteile: Hohe Druckkräfte erforderlich, was den Maschinenaufwand erhöht.
b) Hohlstauchen
Beim Hohlstauchen wird das Werkstück mit einer Innenöffnung versehen, sodass ein Hohlkörper entsteht. Dieser Prozess wird angewendet, wenn Bauteile wie Hülsen oder Rohre hergestellt werden sollen.
- Typische Anwendungen: Herstellung von Hülsen, Lagern und zylindrischen Hohlkörpern.
- Vorteile: Materialeinsparung und geringeres Gewicht des Werkstücks.
- Nachteile: Komplexere Werkzeuggeometrien und höhere Anforderungen an die Präzision.
c) Teilstauchen
Teilstauchen beschränkt sich auf einen bestimmten Abschnitt des Werkstücks, während der Rest unbeeinflusst bleibt. Dieses Verfahren wird häufig bei Bauteilen angewandt, die nur an bestimmten Stellen verstärkt oder verformt werden müssen.
- Typische Anwendungen: Herstellung von Schaftteilen oder Wellen mit verstärkten Enden.
- Vorteile: Reduzierter Materialeinsatz und Flexibilität bei der Bauteilgeometrie.
- Nachteile: Präzise Werkzeugführung erforderlich, um nur die gewünschten Abschnitte zu stauchen.
d) Gesenkstauchen
Gesenkstauchen ist ein besonders präzises Stauchverfahren, bei dem das Werkstück in eine spezifische Form gedrückt wird, die durch eine formgebende Matrize vorgegeben ist. Es ermöglicht die Herstellung von Bauteilen mit komplexen Geometrien.
- Typische Anwendungen: Produktion von Zahnrädern, Kurbelwellen und komplexen Verbindungselementen.
- Vorteile: Hohe Formgenauigkeit und Wiederholbarkeit, ideal für die Massenproduktion.
- Nachteile: Höhere Werkzeugkosten und längere Rüstzeiten.
Jedes dieser Stauchverfahren bietet spezifische Vorteile und ist für bestimmte Anwendungen besonders geeignet, je nach den Anforderungen an die Geometrie, Festigkeit und den Materialeinsatz.
3. Temperaturbereiche im Stauchprozess: Kalt- und Warmstauchen
Stauchen kann entweder bei Raumtemperatur (Kaltstauchen) oder bei erhöhter Temperatur (Warmstauchen) durchgeführt werden. Die Wahl des Temperaturbereichs hängt von den Materialeigenschaften und der gewünschten Umformbarkeit ab.
a) Kaltstauchen
Beim Kaltstauchen erfolgt die Umformung bei Raumtemperatur oder leicht erhöhten Temperaturen. Dieses Verfahren bietet hohe Präzision und ermöglicht eine Kaltverfestigung des Materials, was die Festigkeit des Werkstücks erhöht.
- Typische Anwendungen: Herstellung von Verbindungselementen wie Schrauben und Muttern, die hohe Maßgenauigkeit erfordern.
- Vorteile: Hohe Maßgenauigkeit und Festigkeit, verbesserte Oberflächenqualität.
- Nachteile: Erhöhter Kraftaufwand erforderlich und Gefahr der Rissbildung bei spröden Materialien.
b) Warmstauchen
Das Warmstauchen wird bei hohen Temperaturen durchgeführt, die meist oberhalb der Rekristallisationstemperatur des Materials liegen. Die Wärme erhöht die Duktilität des Werkstoffs und reduziert den Kraftaufwand beim Stauchen.
- Typische Anwendungen: Herstellung von Großteilen und schwer verformbaren Materialien, wie hochfeste Stähle oder Titan.
- Vorteile: Geringerer Kraftaufwand, bessere Formbarkeit und geringere Gefahr der Rissbildung.
- Nachteile: Höhere Energiekosten und zusätzliche Maßnahmen zur Kühlung und Schmierung erforderlich.
Die Entscheidung zwischen Kalt- und Warmstauchen richtet sich nach den spezifischen Anforderungen des Werkstücks sowie den Materialeigenschaften und Produktionsbedingungen.
4. Maschinen und Anlagen für das Stauchen
Für das Stauchen werden spezielle Maschinen benötigt, die hohe Drücke und genaue Positionierung gewährleisten können. Die wichtigsten Maschinen für das Stauchen sind:
- Hydraulische Pressen: Hydraulische Pressen sind ideal für das Stauchen, da sie eine hohe und konstante Kraft ausüben können. Sie ermöglichen eine präzise Steuerung des Drucks und sind besonders für das Warmstauchen geeignet.
- Exzenterpressen: Exzenterpressen werden häufig beim Kaltstauchen eingesetzt. Sie bieten hohe Geschwindigkeit und Präzision und eignen sich für die Massenproduktion kleinerer Bauteile.
- Kurbelpressen: Kurbelpressen sind robust und einfach zu steuern. Sie werden sowohl für das Kalt- als auch für das Warmstauchen genutzt und bieten eine hohe Wiederholgenauigkeit.
- Hochgeschwindigkeitsmaschinen: Diese Maschinen sind für das Serien-Stauchen kleiner Werkstücke ausgelegt und ermöglichen eine schnelle und kontinuierliche Produktion.
Die Wahl der richtigen Maschine hängt von der Werkstückgröße, dem Material und der Produktionsmenge ab.
5. Industrielle Anwendungen des Stauchens
Stauchen ist in vielen Branchen ein unverzichtbares Verfahren, da es eine hohe Materialeffizienz und Festigkeit bietet. Zu den wichtigsten Industrien und Anwendungsfeldern zählen:
a) Automobilindustrie
In der Automobilindustrie wird das Stauchen zur Herstellung von hochfesten Bauteilen verwendet, die extremen Belastungen standhalten müssen.
- Bolzen und Schrauben: Verbindungs- und Befestigungselemente werden durch Kaltstauchen hergestellt, um ihre Festigkeit und Präzision zu gewährleisten.
- Antriebs- und Getriebekomponenten: Bauteile wie Achsen, Getriebeelemente und Pleuelstangen werden durch Warmstauchen geformt, um hohe Stabilität und Festigkeit zu erreichen.
- Rahmen- und Strukturteile: Große Bauteile wie Querträger und Rahmenverstärkungen werden durch Warmstauchen produziert, um ihre Tragfähigkeit zu verbessern.
b) Luft- und Raumfahrtindustrie
In der Luftfahrtindustrie müssen Komponenten leicht und gleichzeitig extrem fest sein, um die strukturelle Integrität von Flugzeugen zu gewährleisten.
- Bolzen und Befestigungen: Leichte und hochfeste Verbindungsstücke werden durch Kaltstauchen aus Aluminium- und Titanlegierungen hergestellt.
- Triebwerkskomponenten: Turbinenschaufeln und Antriebswellen werden durch Warmstauchen aus hitzebeständigen Legierungen geformt.
- Strukturteile für Flugzeugrümpfe: Teile für die Flugzeugstruktur werden gestaucht, um die Stabilität und das Gewicht optimal anzupassen.
c) Bauindustrie
In der Bauindustrie ist das Stauchen unerlässlich für die Herstellung von robusten Komponenten, die hohe Lasten tragen müssen.
- Bewehrungsstäbe und Anker: Diese Bauteile werden durch Kaltstauchen hergestellt und dienen als Verstärkung in Betonstrukturen.
- Stahlträger und -profile: Großformatige Stahlprofile und -träger werden durch Warmstauchen gefertigt, um die nötige Festigkeit für Gebäudestrukturen zu bieten.
- Verbindungselemente: Schrauben, Bolzen und Muttern werden in großen Mengen durch Kaltstauchen gefertigt und sind für tragende Verbindungen in Baukonstruktionen unerlässlich.
d) Medizintechnik
In der Medizintechnik sind präzise und hochfeste Bauteile wichtig, die den Belastungen im Körper standhalten.
- Chirurgische Instrumente: Hochpräzise Instrumente wie Zangen und Klemmen werden durch Kaltstauchen hergestellt.
- Implantate: Prothesen und andere medizinische Implantate werden durch Warmstauchen aus Titan geformt, um Biokompatibilität und Festigkeit sicherzustellen.
- Dentalprodukte: Kleine, stabile Komponenten für Zahnimplantate und dentalchirurgische Werkzeuge werden durch Stauchen geformt.
e) Energie- und Umwelttechnik
In der Energie- und Umwelttechnik werden durch das Stauchen Komponenten hergestellt, die extremen Umwelteinflüssen und Lasten widerstehen.
- Rohrverschraubungen und Flansche: Diese Komponenten werden durch Kaltstauchen hergestellt und für den Transport von Flüssigkeiten und Gasen in Kraftwerken verwendet.
- Verankerungen und Stützen: Bauteile für Windkraftanlagen und Offshore-Plattformen werden durch Warmstauchen gefertigt, um hohe Festigkeit und Korrosionsbeständigkeit zu gewährleisten.
6. Vorteile und Herausforderungen des Stauchens
Vorteile:
- Hohe Materialausnutzung: Das Stauchen erzeugt keine Späne, wodurch das Material vollständig erhalten bleibt.
- Festigkeitssteigerung: Das Stauchen führt durch die Verdichtung des Materials zu einer Erhöhung der Festigkeit und Zähigkeit.
- Flexibilität bei der Formgebung: Stauchen ermöglicht die Herstellung von Werkstücken mit verschiedenen Geometrien, von zylindrischen bis hin zu komplexeren Formen.
Herausforderungen:
- Hohe Druckkräfte erforderlich: Stauchen erfordert Maschinen, die hohe Drücke erzeugen können, was den Energiebedarf und die Investitionskosten erhöht.
- Gefahr der Rissbildung: Spröde Materialien oder eine falsche Temperaturwahl können zur Rissbildung im Werkstück führen.
- Genauigkeit der Werkzeuge: Die Qualität des Endprodukts hängt stark von der Präzision der Werkzeuge ab, was hohe Anforderungen an deren Herstellung und Wartung stellt.
Fazit
Stauchen ist ein effektives und vielseitiges Umformverfahren in der Metallverarbeitung, das in vielen Industrien unverzichtbar ist. Es ermöglicht die Herstellung von Bauteilen mit hoher Festigkeit, Materialausnutzung und Maßhaltigkeit. Durch moderne Technologien und Maschinen wird das Stauchen zunehmend präziser und effizienter. Die Kombination aus Flexibilität und Festigkeit macht das Stauchen zu einem idealen Verfahren für anspruchsvolle Anwendungen in der Automobil-, Luftfahrt-, Bau- und Medizintechnik.
Mit der fortschreitenden Entwicklung digitaler Technologien und der Anwendung von Industrie-4.0-Prinzipien wird das Stauchen in Zukunft noch leistungsfähiger und wirtschaftlicher und bleibt ein zentraler Bestandteil der industriellen Fertigung.
Fließpressen: Verfahren, Anwendungen und Technologien in der Metallumformung
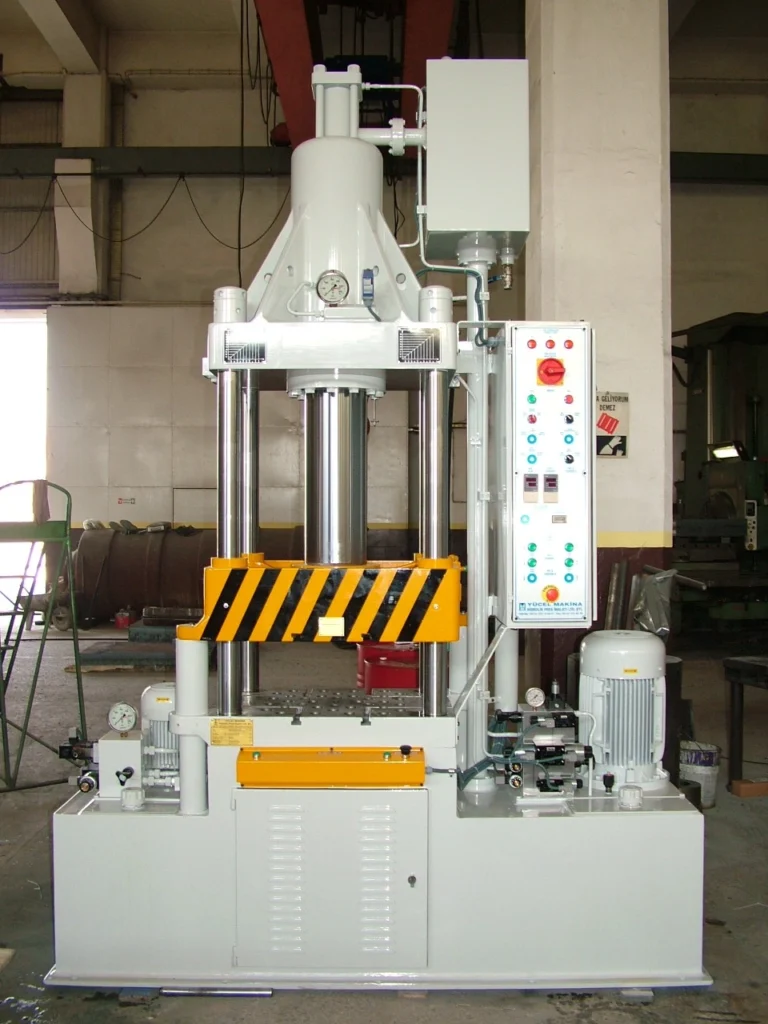
Das Fließpressen ist ein Umformverfahren, bei dem ein Werkstück unter hohem Druck durch eine formgebende Matrize gedrückt wird, sodass das Material in eine gewünschte Form „fließt“. Dieses Verfahren ist besonders für die Herstellung von Bauteilen mit hoher Festigkeit und präziser Geometrie geeignet und ermöglicht die Produktion komplexer und präziser Metallteile in großen Stückzahlen. Fließpressen wird in zahlreichen Industrien eingesetzt, darunter die Automobilindustrie, die Elektronikbranche, die Luft- und Raumfahrt sowie die Medizintechnik.
In diesem Überblick werden die Grundlagen des Fließpressens, die verschiedenen Verfahrenstypen, die verwendeten Maschinen, die industrielle Anwendungen und die Vorteile und Herausforderungen des Verfahrens beschrieben. Außerdem werden moderne Technologien und Trends vorgestellt, die das Fließpressen in der industriellen Fertigung noch effizienter machen.
1. Grundlagen und Funktionsweise des Fließpressens
Das Fließpressen ist ein Verfahren der Kalt- oder Warmumformung, bei dem ein Rohling unter hohem Druck durch eine Matrize gepresst wird. Die plastische Verformung führt dazu, dass das Material fließt und die Form der Matrize annimmt. Die erzielte Formgebung erfolgt ohne Materialverlust und mit einer hohen Maßgenauigkeit, was das Fließpressen besonders wirtschaftlich macht.
Die wesentlichen Merkmale des Fließpressens sind:
- Druckwirkung: Durch die hohe Presskraft, die auf den Rohling ausgeübt wird, kommt es zu einer plastischen Verformung, die das Material in eine neue Geometrie überführt.
- Kraftfluss und Materialfluss: Der Materialfluss kann sowohl in axialer (in Richtung der Presskraft) als auch in radialer Richtung (seitlich zur Presskraft) erfolgen.
- Werkstoffe: Typische Materialien sind Stahl, Aluminium, Kupfer und einige Legierungen, die eine hohe Verformbarkeit aufweisen.
Beim Fließpressen unterscheidet man zwischen Kalt- und Warmfließpressen, abhängig von der Temperatur, bei der das Verfahren durchgeführt wird. Beim Kaltfließpressen erfolgt die Umformung bei Raumtemperatur, während beim Warmfließpressen das Material erwärmt wird, um eine bessere Fließfähigkeit zu erreichen.
2. Arten des Fließpressens
Es gibt mehrere Verfahren des Fließpressens, die je nach Anwendungsbereich und gewünschter Form des Werkstücks eingesetzt werden. Zu den wichtigsten Verfahren gehören:
a) Vorwärtsfließpressen
Beim Vorwärtsfließpressen wird das Material in die gleiche Richtung wie die Presskraft gepresst. Der Rohling wird in die Matrize gedrückt und formt sich entsprechend der Matrizenform.
- Typische Anwendungen: Herstellung von zylindrischen Körpern wie Bolzen, Hülsen und Rohren.
- Vorteile: Effizient für einfache, langgezogene Formen, gleichmäßiger Materialfluss.
- Nachteile: Höherer Kraftaufwand im Vergleich zu anderen Fließpressverfahren.
b) Rückwärtsfließpressen
Beim Rückwärtsfließpressen bewegt sich der Werkstoff in die entgegengesetzte Richtung zur Presskraft. Der Rohling wird durch einen Stempel in die Matrize gepresst, wodurch das Material „zurückfließt“ und eine Hohlform entsteht.
- Typische Anwendungen: Herstellung von Hülsen, Dosen und Behältern mit dünnen Wandungen.
- Vorteile: Erzeugt präzise Hohlformen, geringer Materialverlust.
- Nachteile: Komplexerer Werkzeugaufbau und erhöhte Anforderungen an die Matrize.
c) Querfließpressen
Beim Querfließpressen fließt das Material seitlich zur Pressrichtung. Dieses Verfahren wird häufig für Werkstücke angewendet, die eine hohe Festigkeit und spezielle Geometrien erfordern.
- Typische Anwendungen: Herstellung von Zahnrädern, Ringen und Profilteilen.
- Vorteile: Effizient für komplexe Formen und geometrisch anspruchsvolle Teile.
- Nachteile: Hohe Anforderungen an die Werkzeugführung und Kühlung.
d) Fließpressen mit mehreren Matrizen
Das Fließpressen mit mehreren Matrizen wird oft für komplexe Bauteile verwendet, die mehrere Umformschritte erfordern. Hierbei wird das Werkstück nacheinander durch verschiedene Matrizen gepresst, um eine bestimmte Endform zu erreichen.
- Typische Anwendungen: Herstellung komplexer Bauteile in der Automobil- und Luftfahrtindustrie.
- Vorteile: Ermöglicht die Herstellung von komplexen Formen mit hoher Maßgenauigkeit.
- Nachteile: Längere Prozesszeiten und höhere Werkzeugkosten.
Diese Verfahren bieten eine Vielzahl an Möglichkeiten zur Herstellung von Werkstücken mit verschiedenen Geometrien, Festigkeiten und Oberflächenqualitäten. Die Wahl des Verfahrens hängt von der Geometrie des Werkstücks und den Anforderungen an das Material ab.
3. Kalt- und Warmfließpressen
Fließpressen kann bei verschiedenen Temperaturen durchgeführt werden, was sich direkt auf die Materialeigenschaften und die erforderliche Kraft auswirkt.
a) Kaltfließpressen
Beim Kaltfließpressen erfolgt die Umformung bei Raumtemperatur oder leicht erhöhter Temperatur. Dieses Verfahren ist besonders energieeffizient und führt zu einer Verfestigung des Materials, was die Festigkeit erhöht.
- Typische Anwendungen: Herstellung von Schrauben, Muttern, Bolzen und Hülsen, bei denen hohe Maßgenauigkeit erforderlich ist.
- Vorteile: Hohe Oberflächenqualität, verbesserte Festigkeit und Maßhaltigkeit.
- Nachteile: Höherer Kraftaufwand und Risiko der Rissbildung bei spröden Materialien.
b) Warmfließpressen
Beim Warmfließpressen wird das Material auf eine höhere Temperatur erhitzt, meist oberhalb der Rekristallisationstemperatur, um eine bessere Umformbarkeit zu erreichen. Dies verringert den Kraftaufwand und die Gefahr von Materialfehlern.
- Typische Anwendungen: Herstellung größerer oder schwer verformbarer Bauteile wie Zahnräder, Antriebswellen und Radsätze.
- Vorteile: Geringerer Kraftaufwand und reduzierte Rissgefahr, gute Formbarkeit.
- Nachteile: Höherer Energieverbrauch und zusätzliche Kühl- und Schmiermaßnahmen erforderlich.
Die Entscheidung zwischen Kalt- und Warmfließpressen hängt von den Materialeigenschaften, der gewünschten Festigkeit und den Geometrieanforderungen des Werkstücks ab.
4. Maschinen und Anlagen für das Fließpressen
Für das Fließpressen werden spezielle Maschinen und Pressen benötigt, die hohe Kräfte erzeugen und eine präzise Steuerung der Umformbewegung gewährleisten.
- Hydraulische Pressen: Diese Pressen erzeugen konstant hohe Kräfte und bieten eine präzise Steuerung der Presskraft, was sie ideal für das Warmfließpressen macht.
- Exzenterpressen: Exzenterpressen arbeiten mit hoher Geschwindigkeit und eignen sich besonders für das Kaltfließpressen, da sie hohe Schlagkräfte erzeugen können.
- Servopressen: Servopressen bieten eine genaue Kontrolle der Geschwindigkeit und Kraft und sind energieeffizient, was sie ideal für Anwendungen macht, bei denen hohe Präzision erforderlich ist.
- Mehrstationenpressen: Für komplexe Bauteile werden häufig Mehrstationenpressen verwendet, bei denen das Werkstück nacheinander durch mehrere Matrizen geführt wird, um die endgültige Form zu erreichen.
Die Wahl der richtigen Maschine hängt von der Werkstückgröße, der Produktionsmenge und den gewünschten Materialeigenschaften ab.
5. Industrielle Anwendungen des Fließpressens
Fließpressen ist ein weit verbreitetes Verfahren in der industriellen Fertigung und kommt in zahlreichen Branchen zum Einsatz. Zu den wichtigsten Anwendungsfeldern gehören:
a) Automobilindustrie
In der Automobilindustrie werden zahlreiche Bauteile durch Fließpressen hergestellt, die hohe Belastungen aushalten und präzise gefertigt sein müssen.
- Schrauben und Muttern: Verbindungselemente, die durch Kaltfließpressen produziert werden und hohe Maßgenauigkeit und Festigkeit bieten.
- Getriebekomponenten: Zahnräder, Wellen und Kupplungsteile werden durch Warmfließpressen hergestellt und müssen eine hohe Präzision und Stabilität aufweisen.
- Antriebselemente: Bauteile für die Antriebstechnik, die hohen Belastungen standhalten, werden durch Fließpressen geformt, um die gewünschte Festigkeit und Form zu erreichen.
b) Elektronikindustrie
In der Elektronikindustrie werden durch Fließpressen kleine, präzise Teile hergestellt, die in elektronischen Geräten und Baugruppen verwendet werden.
- Stecker und Kontakte: Elektrische Steckkontakte und Anschlüsse, die durch Kaltfließpressen aus Kupfer gefertigt werden, um eine hohe Leitfähigkeit und Präzision zu gewährleisten.
- Gehäuseteile: Gehäuse für elektronische Bauteile und Geräte werden oft durch Fließpressen geformt, um eine passgenaue Form und stabile Wände zu gewährleisten.
c) Luft- und Raumfahrtindustrie
Die Luft- und Raumfahrtindustrie setzt auf leichte und hochbelastbare Bauteile, die durch das Fließpressen geformt werden können.
- Bolzen und Verbindungselemente: Leichte, hochfeste Verbindungen aus Aluminium und Titan werden durch Kaltfließpressen hergestellt.
- Strukturbauteile: Strukturteile für Flugzeuge und Raketen werden durch Warmfließpressen geformt, um die Festigkeit und Stabilität zu erhöhen.
d) Medizintechnik
In der Medizintechnik müssen präzise und sterile Bauteile gefertigt werden, die für medizinische Anwendungen geeignet sind.
- Implantate und Prothesen: Implantate und Prothesenteile werden durch Fließpressen aus biokompatiblen Materialien geformt.
- Chirurgische Instrumente: Instrumente wie Pinzetten und Skalpelle werden durch Kaltfließpressen präzise gefertigt.
6. Vorteile und Herausforderungen des Fließpressens
Vorteile:
- Hohe Materialausnutzung: Da das Fließpressen ohne Materialverlust erfolgt, bietet es eine hohe Effizienz.
- Festigkeitssteigerung: Das Fließpressen führt zu einer Verfestigung des Materials, was die Festigkeit und Belastbarkeit der Bauteile erhöht.
- Präzision und Wiederholbarkeit: Die hohe Maßgenauigkeit und Wiederholgenauigkeit machen das Fließpressen ideal für die Massenproduktion.
- Vielseitigkeit: Das Verfahren kann sowohl für einfache als auch für komplexe Geometrien verwendet werden.
Herausforderungen:
- Hohe Druckkräfte erforderlich: Fließpressen erfordert Maschinen, die hohe Drücke erzeugen können, was den Energieverbrauch erhöht.
- Werkzeugverschleiß: Die Matrizen und Stempel sind einem hohen Verschleiß ausgesetzt und müssen regelmäßig gewartet oder ersetzt werden.
- Komplexität bei der Werkzeugherstellung: Insbesondere bei komplexen Geometrien sind die Werkzeuge teuer und müssen präzise gefertigt werden.
Fazit
Fließpressen ist ein hochentwickeltes Verfahren der Metallumformung, das in vielen Industrien weltweit eingesetzt wird. Es bietet zahlreiche Vorteile hinsichtlich Materialausnutzung, Festigkeit und Präzision und ist besonders für die Serienproduktion von Bauteilen geeignet. Die Vielseitigkeit und Effizienz des Fließpressens machen es zu einem wichtigen Verfahren in der Herstellung hochwertiger Metallteile für die Automobil-, Luftfahrt-, Elektronik- und Medizintechnik.
Mit der Integration moderner Technologien wie Automatisierung und Industrie 4.0 wird das Fließpressen in Zukunft noch effizienter und flexibler werden und seine Rolle in der industriellen Fertigung weiter stärken.
Innenhochdruckumformen (IHU): Verfahren, Anwendungen und Technologien in der Metallumformung
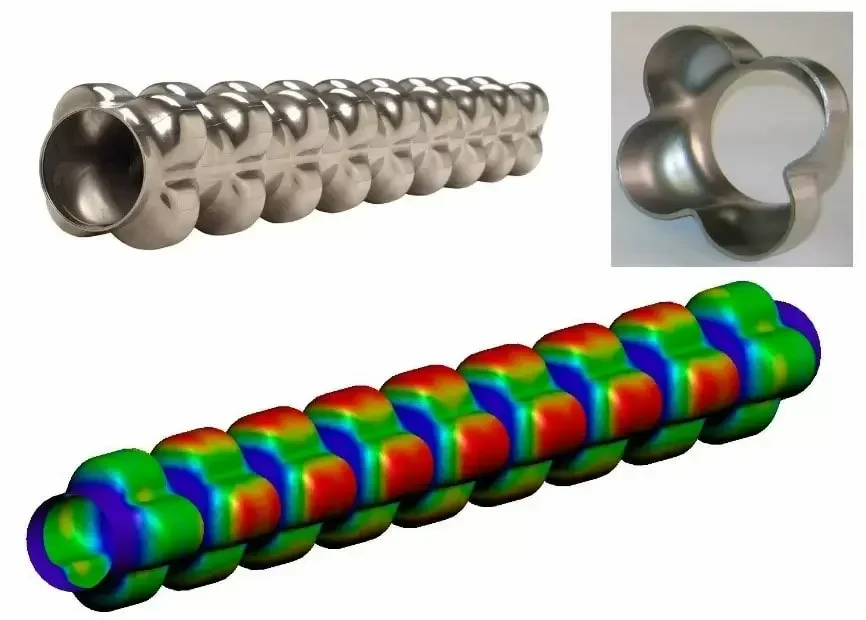
Das Innenhochdruckumformen (IHU) ist ein modernes Umformverfahren, bei dem rohr- oder hohlförmige Werkstücke unter sehr hohem Innendruck in eine spezifische Form gebracht werden. Dieses Verfahren eignet sich besonders zur Herstellung komplexer Bauteile mit Hohlkammern und variablen Querschnitten und wird hauptsächlich in der Automobil-, Luftfahrt- und Bauindustrie angewendet. Der Vorteil des IHU liegt darin, dass es die Herstellung leichter und dennoch belastbarer Bauteile ermöglicht, was besonders in der modernen Industrie von Bedeutung ist, wo Leichtbau und Energieeffizienz im Vordergrund stehen.
Dieser Text bietet einen umfassenden Überblick über das IHU, einschließlich seiner Funktionsweise, der verschiedenen Verfahrenstypen, den benötigten Maschinen und Anlagen sowie der Anwendungen in verschiedenen Industrien. Zudem werden die Vorteile und Herausforderungen dieses Verfahrens sowie die neuesten Entwicklungen und Trends beschrieben.
1. Grundlagen und Funktionsweise des Innenhochdruckumformens
Beim IHU wird ein hohlförmiger Rohling – meist ein Rohr oder Profil – in eine Form (Matrize) eingelegt und von außen fixiert. Anschließend wird eine Flüssigkeit (oft Wasser oder ein Öl-Wasser-Gemisch) mit hohem Druck in das Werkstück gepumpt. Dieser Innendruck führt dazu, dass sich der Rohling ausdehnt und die Konturen der Matrize annimmt.
Wesentliche Schritte des IHU:
- Einlegen und Fixieren des Rohlings: Der Rohling wird in die Matrize eingelegt und sicher fixiert, um Bewegungen während des Druckprozesses zu vermeiden.
- Druckaufbau: Eine Flüssigkeit wird unter sehr hohem Druck in den Rohling eingepumpt. Je nach Material und gewünschter Form können Drücke von bis zu 4.000 bar oder mehr notwendig sein.
- Umformung: Der hohe Innendruck führt dazu, dass sich das Material plastisch verformt und die Konturen der Matrize annimmt.
- Entnahme des Bauteils: Nach Erreichen der gewünschten Form wird der Druck abgebaut, und das fertige Bauteil wird aus der Matrize entnommen.
IHU bietet sich besonders für Werkstoffe mit hoher Umformbarkeit wie Stahl, Aluminium und Titan an, da diese Materialien den hohen Drücken standhalten und sich gut formen lassen.
2. Verfahrenstypen des Innenhochdruckumformens
Es gibt verschiedene Verfahren des IHU, die je nach Anforderung und Werkstückgeometrie eingesetzt werden. Die wichtigsten Verfahren sind:
a) Innenhochdruckumformen mit axialem Vorschub
Beim IHU mit axialem Vorschub wird der Rohling von beiden Seiten mit Stempeln fixiert und der Innendruck aufgebaut. Während des Prozesses werden die Stempel axial vorgeschoben, um das Material gezielt in die gewünschte Form zu pressen.
- Typische Anwendungen: Herstellung von Bauteilen mit variierenden Querschnitten, wie Achsen und Strukturkomponenten in der Automobilindustrie.
- Vorteile: Hohe Präzision und gute Materialausnutzung.
- Nachteile: Erfordert eine exakte Steuerung der Stempelbewegung und erhöhten Energieaufwand.
b) Innenhochdruckumformen ohne axialen Vorschub
Bei diesem Verfahren wird der Rohling lediglich durch den Innendruck in die Matrize gedrückt, ohne dass ein zusätzlicher axialer Vorschub erfolgt. Der Rohling nimmt dadurch die Form der Matrize an, jedoch ohne eine Längsverformung.
- Typische Anwendungen: Herstellung von Bauteilen mit konstantem Querschnitt, wie Rohre und einfache Hohlkörper.
- Vorteile: Einfacher Prozessablauf und geringerer Energieaufwand.
- Nachteile: Begrenzte Formvielfalt und weniger Flexibilität.
c) Teilweise Innenhochdruckumformen
Beim teilweisen IHU wird nur ein bestimmter Abschnitt des Rohlings unter Druck gesetzt und geformt. Dieses Verfahren wird angewendet, wenn nur ein bestimmter Bereich des Werkstücks geformt werden muss.
- Typische Anwendungen: Lokale Verstärkung oder Formgebung an speziellen Stellen eines Werkstücks, wie z. B. an Verbindungsstellen.
- Vorteile: Reduzierter Energieverbrauch und gezielte Formgebung.
- Nachteile: Erfordert spezielle Werkzeuge und eine genaue Steuerung des Drucks.
d) Mehrkammer-Innenhochdruckumformen
Beim Mehrkammer-IHU werden mehrere Werkstücke in einer Formkammer gleichzeitig geformt, was den Durchsatz und die Effizienz erhöht.
- Typische Anwendungen: Serienproduktion von gleichen oder ähnlichen Bauteilen in der Automobilindustrie.
- Vorteile: Höhere Produktivität und wirtschaftliche Effizienz.
- Nachteile: Erfordert eine exakte Abstimmung der Werkstückgeometrien und höheren Energieaufwand.
Diese verschiedenen Verfahren ermöglichen es, eine große Bandbreite an Formen und Geometrien herzustellen und bieten Flexibilität für unterschiedliche Anforderungen und Bauteildesigns.
3. Werkstoffe und Temperaturbereiche im IHU
Das Innenhochdruckumformen eignet sich besonders für Werkstoffe, die eine hohe Dehnbarkeit und Festigkeit aufweisen. Die Wahl des Werkstoffs und der Temperatur hat dabei einen großen Einfluss auf die Formbarkeit und das Endergebnis des Umformprozesses.
- Stahl: Aufgrund seiner Festigkeit und Umformbarkeit ist Stahl ein bevorzugtes Material für IHU, insbesondere in der Automobilindustrie.
- Aluminium: Aluminium wird für Bauteile im Leichtbau verwendet, da es leicht und dennoch formbar ist, jedoch bei höheren Temperaturen geformt werden muss.
- Titan: Titan ist besonders in der Luft- und Raumfahrt gefragt, da es sehr widerstandsfähig und leicht ist, jedoch nur unter hohen Temperaturen und Drücken formbar ist.
a) Kalt-IHU
Beim Kalt-IHU wird das Werkstück bei Raumtemperatur geformt, was eine höhere Maßgenauigkeit und eine verbesserte Oberflächenqualität ermöglicht.
- Typische Anwendungen: Präzise Bauteile mit geringer Wandstärke, die in der Automobilindustrie verwendet werden.
- Vorteile: Hohe Maßgenauigkeit, bessere Oberflächenqualität und geringe Energiekosten.
- Nachteile: Höherer Kraftaufwand und Gefahr der Rissbildung bei spröden Materialien.
b) Warm-IHU
Beim Warm-IHU wird das Material auf eine höhere Temperatur erhitzt, um die Umformbarkeit zu verbessern. Dies ermöglicht die Bearbeitung von schwer verformbaren Werkstoffen wie Titan und hochfesten Stählen.
- Typische Anwendungen: Strukturteile für die Luft- und Raumfahrt sowie große Komponenten im Fahrzeugbau.
- Vorteile: Bessere Umformbarkeit und geringerer Kraftaufwand.
- Nachteile: Höhere Energiekosten und zusätzliche Maßnahmen zur Kühlung und Schmierung erforderlich.
Die Entscheidung zwischen Kalt- und Warm-IHU hängt von den Werkstoffeigenschaften und den Anforderungen an die Geometrie und Festigkeit des Endprodukts ab.
4. Maschinen und Anlagen für das Innenhochdruckumformen
IHU-Anlagen bestehen in der Regel aus mehreren Komponenten, die zusammenarbeiten, um den hohen Druck zu erzeugen und das Werkstück in die gewünschte Form zu bringen.
- Hochdruckpumpe: Die Pumpe erzeugt den benötigten Innendruck, der je nach Werkstückmaterial und Form bis zu 4.000 bar oder mehr betragen kann.
- Hydraulikzylinder und Stempel: Diese Komponenten halten das Werkstück in Position und erzeugen gegebenenfalls den axialen Vorschub.
- Werkzeug- und Formkammer: Die Formkammer enthält die Matrize, die dem Werkstück die endgültige Form gibt. Sie muss extrem robust sein, um den hohen Drücken standzuhalten.
- Steuerungseinheit: Die Steuerungseinheit überwacht den Druckaufbau, die Stempelbewegung und die Prozessparameter in Echtzeit, um eine gleichmäßige Qualität zu gewährleisten.
Die Wahl der Anlage hängt von der Bauteilgeometrie, der Werkstoffwahl und der gewünschten Produktionsmenge ab.
5. Anwendungen des Innenhochdruckumformens in der Industrie
IHU findet in zahlreichen Industrien Anwendung, in denen komplexe und belastbare Bauteile benötigt werden. Die wichtigsten Anwendungsfelder sind:
a) Automobilindustrie
In der Automobilindustrie wird das IHU vor allem für die Herstellung von Bauteilen im Leichtbau und für sicherheitsrelevante Komponenten eingesetzt.
- Rahmen- und Strukturteile: Querträger, Längsträger und A-Säulen werden oft durch IHU geformt, um eine hohe Steifigkeit und geringes Gewicht zu kombinieren.
- Abgasanlagen: Rohre und Leitungen für Abgasanlagen werden durch IHU geformt, um eine optimale Passform und Korrosionsbeständigkeit zu erreichen.
- Antriebskomponenten: Bauteile wie Kardanwellen und Antriebswellen werden ebenfalls durch IHU hergestellt, um hohe Stabilität und Präzision zu gewährleisten.
b) Luft- und Raumfahrtindustrie
In der Luft- und Raumfahrt ist IHU ein wichtiger Prozess, da hier leichte und stabile Komponenten benötigt werden, die extremen Belastungen standhalten.
- Strukturkomponenten: Rohre und Hohlprofile, die in der Flugzeugstruktur verbaut sind, werden durch IHU geformt, um die strukturelle Integrität zu erhöhen.
- Hydraulikleitungen und Kraftstoffsysteme: Bauteile, die Flüssigkeiten transportieren, müssen präzise und robust sein, was durch IHU ermöglicht wird.
c) Bauindustrie
Die Bauindustrie verwendet IHU für die Herstellung von Komponenten, die eine hohe Festigkeit und Langlebigkeit aufweisen müssen.
- Rohrsysteme: Rohre und Leitungen für den Transport von Flüssigkeiten und Gasen werden durch IHU geformt, um die Festigkeit und Dichtheit zu verbessern.
- Verbindungselemente: Hohlprofile für die Verbindung und Verstärkung in Stahlkonstruktionen werden durch IHU hergestellt.
d) Medizintechnik
In der Medizintechnik werden durch IHU kleinformatige und präzise Bauteile für Implantate und medizinische Geräte hergestellt.
- Implantate: Hohlprofile für Implantate und chirurgische Geräte werden durch IHU geformt, um Präzision und Biokompatibilität zu gewährleisten.
- Prothesen: Durch IHU werden Prothesenteile hergestellt, die leicht und stabil sind und sich individuell anpassen lassen.
6. Vorteile und Herausforderungen des IHU
Vorteile:
- Leichtbau und Festigkeit: IHU ermöglicht die Herstellung von leichten und dennoch stabilen Bauteilen.
- Hohe Präzision und Maßhaltigkeit: Durch die Matrizenformung wird eine hohe Maßgenauigkeit erreicht.
- Wirtschaftlichkeit: IHU ist besonders für die Massenproduktion geeignet und bietet eine hohe Materialausnutzung.
Herausforderungen:
- Hohe Anschaffungskosten: IHU-Anlagen sind teuer und erfordern eine hohe Anfangsinvestition.
- Komplexe Steuerung: Die Prozessparameter müssen genau gesteuert werden, um die Qualität des Endprodukts zu gewährleisten.
- Werkzeugverschleiß: Durch die hohen Drücke werden die Werkzeuge stark beansprucht und müssen regelmäßig gewartet werden.
Fazit
Das Innenhochdruckumformen ist ein fortschrittliches Verfahren der Metallumformung, das in zahlreichen Industrien weit verbreitet ist und eine hohe Flexibilität und Präzision bietet. Durch die Verwendung hoher Drücke ist es möglich, leichte, komplexe und hoch belastbare Bauteile herzustellen, die für den Leichtbau und die Serienproduktion besonders wertvoll sind. Die Integration neuer Technologien und digitaler Steuerungen verbessert die Effizienz und Qualität des IHU-Verfahrens kontinuierlich und ermöglicht eine noch präzisere und ressourcenschonendere Produktion.
Stanzen: Verfahren, Anwendungen und Technologien in der Metallumformung
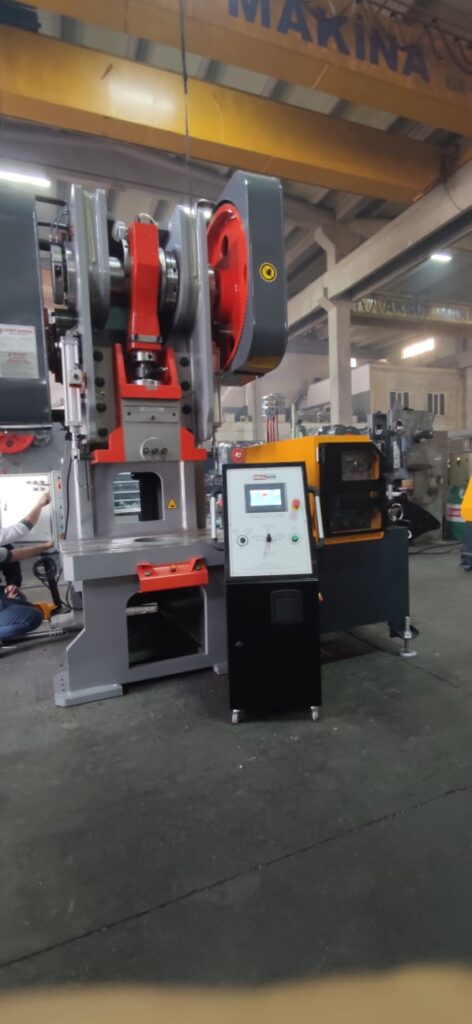
Das Stanzen ist ein zentrales Verfahren der Metallumformung, das in zahlreichen Industrien eingesetzt wird, um präzise Werkstücke mit hoher Geschwindigkeit und Effizienz herzustellen. Beim Stanzen werden flache Metallbleche oder -platten durch Werkzeuge geformt, geschnitten oder geprägt, sodass Löcher, Durchbrüche und Konturen entstehen. Stanzen ist besonders in der Massenproduktion von kleinen und mittleren Werkstücken verbreitet und spielt eine entscheidende Rolle in der Automobil-, Elektronik-, Bau- und Haushaltsgeräteindustrie.
In diesem umfassenden Überblick werden die Grundlagen des Stanzens, verschiedene Verfahrenstypen, die eingesetzten Maschinen und Technologien sowie industrielle Anwendungen beschrieben. Außerdem werden die Vorteile und Herausforderungen des Stanzens beleuchtet und moderne Entwicklungen und Zukunftstrends vorgestellt.
1. Grundlagen des Stanzens
Stanzen ist ein Scherschneideverfahren, bei dem ein Stempel mit hoher Kraft durch das Material drückt, um es zu schneiden oder zu verformen. Dabei entsteht ein sauberer Durchbruch in einem einzigen Arbeitsgang, was das Stanzen besonders schnell und effizient macht. Der Vorgang erfolgt oft in einer Presse, in die spezielle Werkzeuge wie Stempel und Matrizen eingespannt sind.
Wesentliche Merkmale des Stanzens sind:
- Schneiden und Umformen: Neben dem reinen Schneiden können beim Stanzen auch leichte Umformungen, wie Prägen und Biegen, durchgeführt werden.
- Wiederholbarkeit: Das Stanzen ist ein präzises Verfahren mit hoher Wiederholgenauigkeit und eignet sich für die Serienproduktion.
- Materialverhalten: Werkstoffe wie Stahl, Edelstahl, Aluminium und Kupfer eignen sich besonders gut für das Stanzen, da sie eine gute Schneid- und Verformbarkeit aufweisen.
Stanzen kann sowohl bei Raumtemperatur als auch bei leicht erhitztem Material erfolgen, wobei das Verfahren oft in Kombination mit weiteren Umformprozessen wie Biegen oder Prägen angewendet wird.
2. Arten des Stanzens
Es gibt verschiedene Stanzverfahren, die je nach Werkstückanforderung und gewünschter Form gewählt werden. Die wichtigsten Stanzarten umfassen:
a) Schneiden (Lochen und Ausschneiden)
Beim Schneiden wird Material vollständig durchtrennt, sodass entweder ein Loch (Lochen) oder eine Kontur (Ausschneiden) entsteht. Diese Methode ist eine der grundlegendsten Formen des Stanzens und wird für Bauteile mit Löchern und Ausschnitten verwendet.
- Typische Anwendungen: Herstellung von Blechen mit Durchbrüchen und Konturen, z. B. für Gehäuseteile oder Abdeckungen.
- Vorteile: Hohe Geschwindigkeit und Präzision.
- Nachteile: Materialverlust durch ausgeschnittene Teile (Stanzabfall).
b) Feinschneiden
Das Feinschneiden ist ein hochpräzises Stanzverfahren, das besonders glatte und genaue Schnittflächen erzeugt. Es wird für Bauteile mit engen Toleranzen und hoher Oberflächenqualität eingesetzt.
- Typische Anwendungen: Zahnräder, Sicherheitsbauteile und Präzisionsteile für die Automobilindustrie.
- Vorteile: Hohe Maßgenauigkeit, geringe Gratbildung und glatte Schnittflächen.
- Nachteile: Komplexer Werkzeugaufbau und höherer Maschinenaufwand.
c) Biegen und Abkanten
Beim Biegen und Abkanten werden Stanzwerkzeuge verwendet, um das Material um eine bestimmte Achse zu biegen oder abzuwinkeln. Dieser Prozess kann zusätzlich zum Schneiden angewendet werden.
- Typische Anwendungen: Herstellung von Blechteilen mit Biegungen, wie Halterungen und Verstärkungen.
- Vorteile: Kombination von Schneiden und Umformen in einem Prozess.
- Nachteile: Erfordert spezielle Werkzeuge und hohe Präzision.
d) Prägen
Prägen ist ein Stanzverfahren, bei dem das Material lokal verformt wird, um Muster, Schriftzüge oder Symbole auf der Oberfläche des Werkstücks zu erzeugen.
- Typische Anwendungen: Logos und Kennzeichnungen auf Metallteilen, Münzen und Medaillen.
- Vorteile: Erzeugt dekorative und funktionale Oberflächenstrukturen.
- Nachteile: Begrenzte Tiefenwirkung und spezialisierte Werkzeuge erforderlich.
e) Tiefziehen
Beim Tiefziehen wird das Material in eine dreidimensionale Form gebracht, indem es unter hoher Druckkraft in eine Matrize gepresst wird. Das Tiefziehen ist ein komplexes Stanzverfahren, das eine hohe Präzision erfordert.
- Typische Anwendungen: Herstellung von Dosen, Behältern und Gehäusen.
- Vorteile: Ermöglicht die Herstellung komplexer und tiefgezogener Formen.
- Nachteile: Hoher Kraftaufwand und spezialisierte Maschinen erforderlich.
Diese Verfahren ermöglichen eine breite Palette an Anwendungen, von einfachen Löchern und Konturen bis hin zu komplexen, tiefgezogenen Bauteilen und geprägten Strukturen.
3. Maschinen und Werkzeuge für das Stanzen
Für das Stanzen sind spezielle Maschinen und Werkzeuge erforderlich, die eine hohe Geschwindigkeit und Präzision ermöglichen. Zu den wichtigsten Maschinen gehören:
- Exzenterpressen: Diese Pressen erzeugen die Stanzkraft über einen Exzentermechanismus, der eine hohe Geschwindigkeit und Genauigkeit bietet. Exzenterpressen eignen sich besonders für das Schneiden und Lochen.
- Hydraulische Pressen: Hydraulische Pressen verwenden Hydraulikdruck, um eine konstante Kraft über den gesamten Hub auszuüben. Sie sind ideal für das Prägen und Tiefziehen.
- Servopressen: Servopressen sind mit elektrischen Antrieben ausgestattet, die eine präzise Steuerung der Geschwindigkeit und Kraft ermöglichen. Sie bieten eine hohe Flexibilität und sind besonders energieeffizient.
- Stanzautomaten: Diese Maschinen sind automatisierte Systeme, die Werkstücke schnell und präzise stanzen können und häufig für die Massenproduktion eingesetzt werden.
Die Wahl der Maschine hängt von den Anforderungen des Werkstücks, der Produktionsgeschwindigkeit und der benötigten Stanzkraft ab.
Werkzeuge für das Stanzen:
- Stempel und Matrizen: Diese Werkzeuge bestimmen die Form des ausgestanzten Teils und müssen für jeden Bauteiltyp spezifisch angefertigt werden.
- Feinschneidwerkzeuge: Spezielle Werkzeuge, die eine genaue Führung des Materials gewährleisten und für glatte Schnittflächen sorgen.
- Prägewerkzeuge: Diese Werkzeuge werden verwendet, um Muster und Oberflächenstrukturen in das Material zu prägen.
Die Werkzeuge für das Stanzen müssen extrem widerstandsfähig und präzise gefertigt sein, da sie hohen Belastungen ausgesetzt sind und eine exakte Wiederholgenauigkeit erfordern.
4. Industrielle Anwendungen des Stanzens
Stanzen wird in vielen Industrien angewendet, die auf präzise und schnelle Verarbeitung von Metallteilen angewiesen sind. Zu den wichtigsten Anwendungsbereichen zählen:
a) Automobilindustrie
Die Automobilindustrie nutzt das Stanzen zur Herstellung vieler sicherheitskritischer und struktureller Bauteile.
- Karosserieteile: Bauteile wie Türbleche, Kotflügel und Dachelemente werden durch Stanzen hergestellt.
- Sicherheitskomponenten: Bauteile wie Gurtaufhängungen und Verstärkungen werden durch Feinschneiden präzise gefertigt.
- Antriebselemente: Zahnräder, Kettenräder und andere Getriebeteile werden mit hoher Maßgenauigkeit gestanzt.
b) Elektronikindustrie
In der Elektronikindustrie werden gestanzte Metallteile für Steckverbindungen und Gehäusekomponenten verwendet.
- Steckkontakte und Anschlussklemmen: Diese Bauteile werden durch Feinschneiden und Prägen aus Kupfer oder anderen leitfähigen Metallen hergestellt.
- Gehäuse für elektronische Bauteile: Präzise Stanzungen sorgen für eine gute Passform und optimale Wärmeableitung.
c) Haushaltsgeräteindustrie
Die Produktion von Haushaltsgeräten erfordert zahlreiche gestanzte Metallteile, die eine hohe Qualität und Präzision aufweisen müssen.
- Gehäuse und Verkleidungsteile: Stanzteile bilden die Hüllen und Gehäuse vieler Haushaltsgeräte.
- Kleinteile und Befestigungselemente: Verbindungsstücke und Befestigungsteile werden durch Stanzen hergestellt und sichern die Stabilität und Funktion der Geräte.
d) Bauindustrie
In der Bauindustrie werden viele Bauteile durch Stanzen gefertigt, die in Konstruktionen verwendet werden.
- Profilteile und Träger: Durch Stanzen werden Löcher und Verbindungselemente in Stahlträger und Profile eingebracht.
- Verstärkungen und Verbindungsteile: Stanzteile werden zur Verstärkung und als Verbindungen in Gebäudekonstruktionen eingesetzt.
e) Medizintechnik
In der Medizintechnik wird das Stanzen für kleine, präzise und sterile Bauteile verwendet, die in medizinischen Geräten und Instrumenten verbaut werden.
- Chirurgische Instrumente: Skalpellklingen, Klemmen und andere Instrumente werden durch Feinschneiden präzise gefertigt.
- Implantate und Prothesenteile: Stanzteile dienen zur Herstellung von Prothesen und Implantaten, die eine hohe Maßgenauigkeit und Biokompatibilität erfordern.
Die Bandbreite der industriellen Anwendungen zeigt, dass Stanzen für viele Industrien unverzichtbar ist und sich sowohl für kleine als auch große Bauteile eignet.
5. Vorteile und Herausforderungen des Stanzens
Vorteile:
- Hohe Produktionsgeschwindigkeit: Stanzen ermöglicht eine schnelle Produktion und ist ideal für die Massenfertigung.
- Präzision und Wiederholgenauigkeit: Die Werkzeuge gewährleisten eine hohe Maßgenauigkeit und gleichbleibende Qualität.
- Materialeffizienz: Stanzteile können oft ohne Materialverlust hergestellt werden, und das Stanzverfahren bietet eine hohe Materialausnutzung.
- Flexibilität: Stanzen ermöglicht die Herstellung einer Vielzahl an Formen und ist für unterschiedlichste Bauteile und Materialien geeignet.
Herausforderungen:
- Werkzeugverschleiß: Stanzwerkzeuge sind hohen Belastungen ausgesetzt und müssen regelmäßig gewartet oder ersetzt werden.
- Hohe Investitionskosten: Die Werkzeuge und Maschinen für das Stanzen erfordern hohe Anschaffungskosten, besonders bei Feinschneid- und Prägewerkzeugen.
- Abfallmanagement: Der Stanzabfall muss verwaltet und recycelt werden, was zusätzliche Prozesse und Kosten verursacht.
6. Moderne Entwicklungen und Zukunftstrends im Stanzen
Die Digitalisierung und die Prinzipien der Industrie 4.0 haben das Stanzen modernisiert und bieten neue Möglichkeiten zur Effizienzsteigerung und Prozessoptimierung.
- Automatisierung und Robotik: Automatisierte Stanzprozesse und Roboterarme verbessern die Effizienz und ermöglichen die kontinuierliche Produktion.
- Echtzeitüberwachung und Sensorik: Sensoren überwachen die Maschinenparameter und den Werkzeugverschleiß, was eine höhere Präzision und Fehlervermeidung ermöglicht.
- Simulation und CAD-Technologie: Simulationssoftware ermöglicht die Planung und Optimierung der Werkzeuge und Stanzprozesse, bevor die Produktion beginnt.
- Energieeffizienz: Moderne Pressen sind energieeffizienter und senken die Betriebskosten und den ökologischen Fußabdruck.
Diese Technologien tragen dazu bei, dass das Stanzen immer schneller, präziser und kostengünstiger wird und auch in Zukunft eine zentrale Rolle in der industriellen Fertigung spielen wird.
Fazit
Das Stanzen ist ein vielseitiges und unverzichtbares Umformverfahren in der industriellen Metallverarbeitung, das von einfachen Konturen bis hin zu komplexen Präzisionsteilen reicht. Die hohe Produktionsgeschwindigkeit, die Maßgenauigkeit und die Materialeffizienz machen es ideal für die Massenproduktion in verschiedensten Industrien. Moderne Entwicklungen in der Digitalisierung und Automatisierung steigern die Effizienz und Präzision des Stanzens und machen es zu einem zukunftsfähigen Verfahren in der industriellen Fertigung. Mit fortschreitender Technologie wird das Stanzen noch flexibler und effizienter, was den Anwendungsbereich weiter vergrößern und die Produktionskosten senken wird.
Metallbearbeitungsmaschinen
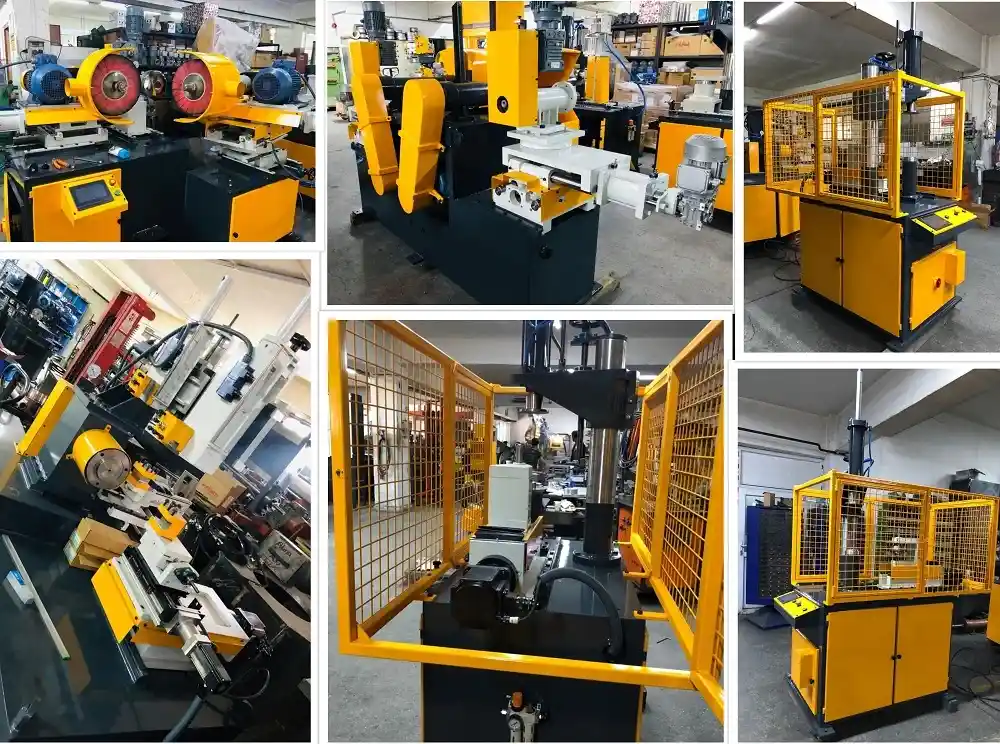
Metallbearbeitungsmaschinen wie Bördel und Beschneide Maschinen, Flanschmaschinen, Beschneide und Bördelmaschinen, Umformtechnik, Rohrbiegemaschinen, Bandsäge für Metall, Hydraulische Horizontalpresse, Kantenschneide-Bördelmaschine, Kantenbördelmaschine, Entgratungsmaschine, Innen- und Außenpoliermaschine für Edelstahltöpfe, Kreisschneidemaschine, Profilbiegemaschine und Rundschweißmaschine
Maßgeschneiderte Skalierung für spezifische Anwendungen
Die automatisierte Herstellung von Behältern, Fässern und Kesseln wird durch unsere Lösungen exakt auf das jeweilige Einsatzgebiet und die gewünschte Ausbringung angepasst. Dabei bieten wir sowohl lineare Lösungen als auch Inselkonzepte an, die eine bedarfsorientierte Automation ermöglichen. Spezielle Kantenvorbereitung für das Laserschweißen sowie wirtschaftliche Rüstkonzepte bis hin zur Fertigung „Just-in-Sequence“ sind Teil unseres Leistungsspektrums. Wir kombinieren Standard- und Sondermaschinen und bieten Ferndiagnose über LAN, WLAN oder GSM an, ergänzt durch umfassende Dokumentation gemäß CE-Richtlinien für die Gesamtanlage.
Unser Konzept
EMS entwickelt und fertigt Maschinen und Anlagen für die automatisierte Herstellung von Behältern in großem Maßstab. Alle Arbeitsschritte, von der Vorbereitung bis zur Fertigung, werden dabei aus einer Hand angeboten. Unsere erprobten Standardkomponenten sind perfekt aufeinander abgestimmt und können nahtlos mit Robotern kombiniert werden, um leistungsfähige Fertigungseinrichtungen zu schaffen.
Flexible Präzisionsfertigung
Unsere Fertigungslinien ermöglichen eine einfache Umstellung auf verschiedene Längen, Durchmesser, Formen und Bearbeitungen durch Programmwechsel. Dabei werden zahlreiche Einzelschritte wie Beschneiden, Formen, Stanzen, Fügen, Montieren, Schweißen und Prüfen automatisch und mit höchster Präzision an die jeweilige Aufgabe angepasst. Besonderes Augenmerk legen wir auf die Kantenvorbereitung für den Schweißprozess, um eine herausragende Prozesssicherheit und minimale Ausschussquoten zu gewährleisten.
Maschinenprogramm für die Metallbearbeitung
Unsere Metallbearbeitungsmaschinen sind:
- Rohrbiegemaschine
- Horizontale Presse
- Bandsäge für Metall
- Profilbiegemaschine
- Tiefziehpresse
- Rundschweißmaschine
- Kantenschneide-Bördelmaschine
- Topf- und Pfannenpoliermaschine
- Poliermaschine für flache Oberflächen
Besteck-Produktionslinie: Eine Besteck-Produktionslinie ist eine Art Maschine, die Besteck in einem kontinuierlichen Prozess herstellt. Es umfasst verschiedene Arten von Maschinen wie den Messerschleifer, den Messerschärfer und den Klingenpolierer.
Kochgeschirr-Herstellungsmaschine: Eine Kochgeschirr-Herstellungsmaschine ist eine Art Maschine, die Kochgeschirr in einem kontinuierlichen Prozess herstellt. Es umfasst verschiedene Arten von Maschinen wie den Topfmacher, den Pfannenmacher und den Wokmacher.
Küchengeschirr-Produktionsmaschine: Eine Küchengeschirr-Produktionsmaschine ist eine Art Maschine, die Küchengeschirr in einem kontinuierlichen Prozess herstellt. Es umfasst verschiedene Arten von Maschinen wie Maschinen zur Herstellung von Teekesseln, Produktionslinien für Besteck, Produktionslinien für Töpfe und Pfannen
Wir entwerfen, fertigen und montieren komplette Produktionslinien für Kochgeschirr, Küchengeschirr, Hotelgeschirr und Besteck sowie einzelne Maschinen für einen bestimmten Zweck