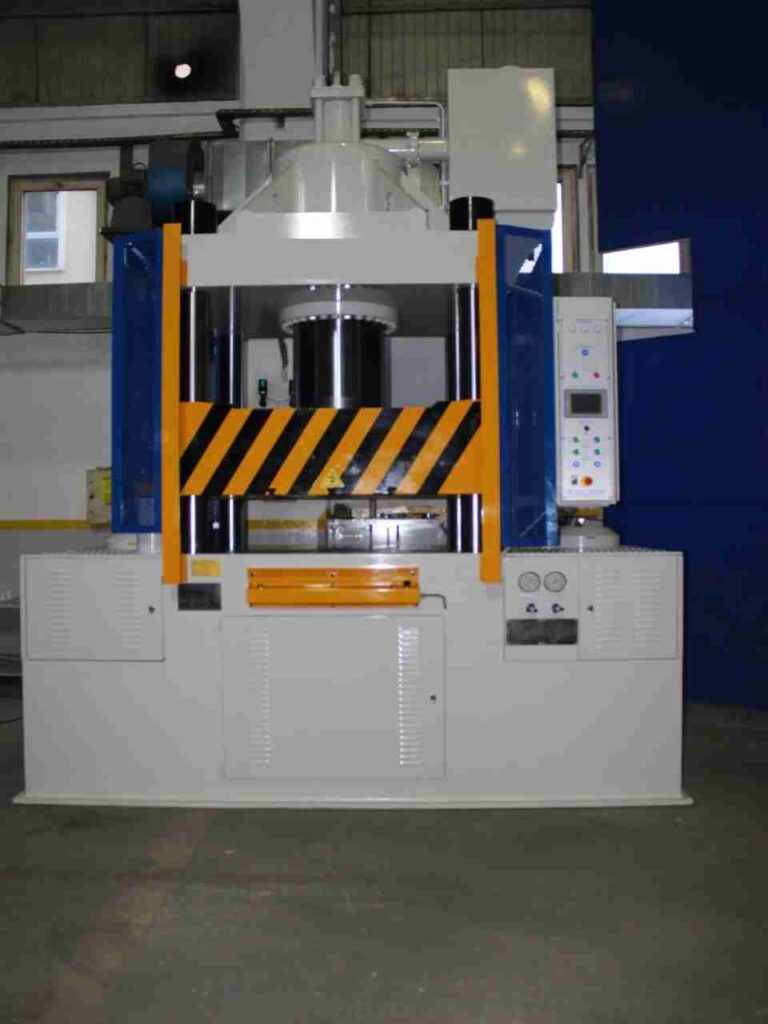
Hydromechanisches Tiefziehen: Das Tiefziehen von Edelstahl ist ein spezielles Umformverfahren, bei dem flache Blechplatinen aus Edelstahl in dreidimensionale, hohle Formen umgeformt werden. Aufgrund seiner besonderen Materialeigenschaften, wie hoher Festigkeit, Korrosionsbeständigkeit und ansprechender Optik, wird Edelstahl in vielen Industriezweigen eingesetzt, darunter die Automobilindustrie, Medizintechnik, Haushaltsgeräte- und Lebensmittelindustrie. Das Tiefziehen von Edelstahl stellt besondere Herausforderungen dar, da der Werkstoff härter und weniger umformbar ist als herkömmlicher Kohlenstoffstahl. Dennoch bietet es viele Vorteile für Anwendungen, die eine Kombination aus Haltbarkeit, Korrosionsbeständigkeit und ästhetischem Aussehen erfordern.
1. Eigenschaften von Edelstahl für das Tiefziehen
Edelstahl weist einige charakteristische Eigenschaften auf, die sowohl Vor- als auch Nachteile für den Tiefziehprozess mit sich bringen:
1.1. Hohe Festigkeit und Härte
- Vorteil: Die hohe Festigkeit von Edelstahl sorgt für eine gute mechanische Stabilität und ermöglicht die Herstellung dünner, aber dennoch robuster Bauteile.
- Nachteil: Diese hohe Festigkeit erschwert den Umformprozess, da höhere Umformkräfte erforderlich sind, was zu einem schnelleren Werkzeugverschleiß führen kann.
1.2. Korrosionsbeständigkeit
- Vorteil: Edelstahl ist aufgrund seines Chromgehalts (mindestens 10,5 %) korrosionsbeständig. Das macht ihn ideal für Anwendungen, bei denen das Material Feuchtigkeit, aggressiven Chemikalien oder hohen Temperaturen ausgesetzt ist.
- Nachteil: Die Korrosionsbeständigkeit kann durch mechanische Beschädigungen während des Umformprozesses beeinträchtigt werden, weshalb geeignete Schutzmaßnahmen erforderlich sind.
1.3. Hohe Duktilität
- Edelstahl, insbesondere austenitische Stähle (z. B. 1.4301 / AISI 304), weist eine hohe Duktilität auf, was ihn gut für das Tiefziehen geeignet macht. Im Vergleich zu ferritischen oder martensitischen Edelstählen sind austenitische Stähle besser umformbar.
1.4. Hohe Neigung zur Kaltverfestigung
- Vorteil: Die Kaltverfestigung kann genutzt werden, um die Festigkeit des Bauteils zu erhöhen.
- Nachteil: Die Kaltverfestigung erschwert den Umformprozess und erhöht die erforderlichen Umformkräfte, was zu einem schnelleren Verschleiß der Werkzeuge führt.
2. Geeignete Edelstahlsorten für das Tiefziehen
Nicht alle Edelstähle sind gleichermaßen für das Tiefziehen geeignet. Die Wahl der richtigen Edelstahlsorte hängt von den spezifischen Anforderungen der Anwendung ab.
2.1. Austenitische Edelstähle
Austenitische Edelstähle sind die am besten umformbaren Edelstähle und eignen sich besonders gut für das Tiefziehen. Sie haben eine hohe Korrosionsbeständigkeit und sind nicht magnetisch.
- Beispiele: 1.4301 (AISI 304), 1.4401 (AISI 316), 1.4541 (AISI 321).
- Anwendungen: Lebensmittelverarbeitung, Medizintechnik, Haushaltsgeräte.
- Vorteile: Hervorragende Umformbarkeit und Korrosionsbeständigkeit.
- Nachteile: Hohe Neigung zur Kaltverfestigung und teurer als ferritische Stähle.
2.2. Ferritische Edelstähle
Ferritische Edelstähle haben eine geringere Umformbarkeit als austenitische Stähle, bieten jedoch eine gute Korrosionsbeständigkeit und sind kostengünstiger.
- Beispiele: 1.4016 (AISI 430), 1.4509.
- Anwendungen: Haushaltsgeräte, Abgasanlagen, Bauindustrie.
- Vorteile: Geringere Kaltverfestigung als austenitische Stähle, weniger teuer.
- Nachteile: Begrenztere Umformbarkeit und geringere Duktilität.
2.3. Martensitische Edelstähle
Martensitische Edelstähle sind hart und bieten eine hohe Festigkeit, jedoch sind sie am schwierigsten zu umformen. Sie werden selten für das Tiefziehen verwendet.
- Beispiele: 1.4021 (AISI 420).
- Anwendungen: Werkzeuge, Schneidklingen.
- Vorteile: Hohe Festigkeit und Härte.
- Nachteile: Sehr begrenzte Umformbarkeit und hohe Neigung zu Rissbildung.
3. Typische Anwendungen des Tiefziehens von Edelstahl
Edelstahl wird in vielen Bereichen verwendet, wo hohe Anforderungen an die Korrosionsbeständigkeit, Hygiene und mechanische Stabilität gestellt werden.
3.1. Automobilindustrie
Edelstahl wird für verschiedene Fahrzeugkomponenten eingesetzt, die hohen mechanischen Belastungen oder korrosiven Umgebungen ausgesetzt sind:
- Abgasanlagen: Bauteile wie Katalysatoren, Endschalldämpfer und Auspuffrohre.
- Zierleisten und Verkleidungen: Aufgrund der ästhetischen Eigenschaften und Korrosionsbeständigkeit von Edelstahl.
3.2. Haushaltsgeräte
Edelstahl wird häufig in der Herstellung von Haushaltsgeräten verwendet, insbesondere für Komponenten, die Feuchtigkeit, Hitze oder Reinigungsmitteln ausgesetzt sind:
- Küchenspülen: Tiefgezogen, um eine glatte und hygienische Oberfläche zu gewährleisten.
- Trommeln von Waschmaschinen: Robuste und korrosionsbeständige Materialien sind erforderlich.
- Backöfen und Mikrowellen: Innenwände und Gehäuse aus Edelstahl bieten gute Wärmeleitfähigkeit und einfache Reinigung.
3.3. Lebensmittel- und Getränkeindustrie
Die hohen hygienischen Anforderungen in der Lebensmittelverarbeitung machen Edelstahl zum bevorzugten Material:
- Behälter und Tanks: Für die Lagerung von Flüssigkeiten oder Schüttgütern.
- Kochgeschirr und Besteck: Langlebig, rostfrei und einfach zu reinigen.
3.4. Medizinische und pharmazeutische Anwendungen
In der Medizintechnik wird Edelstahl aufgrund seiner Korrosionsbeständigkeit, Hygiene und Biokompatibilität eingesetzt:
- Chirurgische Instrumente: Herstellung von Werkzeugen und Instrumenten, die sterilisiert werden müssen.
- Gehäuse für medizinische Geräte: Schutz von elektronischen Komponenten und medizinischen Geräten.
3.5. Bauindustrie
Edelstahl wird in der Architektur und im Bauwesen für dekorative und strukturelle Anwendungen eingesetzt:
- Fassadenverkleidungen: Hohe Korrosionsbeständigkeit und ästhetisches Aussehen machen Edelstahl zu einer beliebten Wahl.
- Geländer und Handläufe: Langlebigkeit und ansprechendes Design.
4. Herausforderungen beim Tiefziehen von Edelstahl
Das Tiefziehen von Edelstahl bringt einige spezifische Herausforderungen mit sich, die besondere Aufmerksamkeit erfordern.
4.1. Hohe Umformkräfte
Edelstahl erfordert höhere Umformkräfte als herkömmlicher Stahl, was zu erhöhtem Werkzeugverschleiß und einer geringeren Lebensdauer der Werkzeuge führen kann. Hochfeste Edelstähle erhöhen diese Herausforderung weiter.
4.2. Neigung zur Kaltverfestigung
Während des Umformprozesses kann Edelstahl stark verfestigen, was die Umformbarkeit verringert und die Gefahr von Rissbildung erhöht. Dies erfordert spezielle Maßnahmen wie Zwischenglühen.
4.3. Werkzeugverschleiß
Die hohe Härte von Edelstahl führt zu einem schnelleren Verschleiß der Werkzeuge. Dies erfordert die Verwendung von Werkzeugen mit speziellen Beschichtungen, wie Titan-Nitrid, um die Standzeit zu erhöhen.
4.4. Rückfederung
Edelstahl neigt aufgrund seiner hohen Festigkeit zur Rückfederung, was bedeutet, dass das Material nach dem Umformen teilweise in seine ursprüngliche Form zurückkehrt. Dies kann die Maßgenauigkeit beeinträchtigen und erfordert eine Anpassung der Werkzeuggeometrie.
5. Maßnahmen zur Optimierung des Tiefziehprozesses mit Edelstahl
Um die Herausforderungen beim Tiefziehen von Edelstahl zu bewältigen, können verschiedene Maßnahmen ergriffen werden:
5.1. Anpassung der Umformparameter
Die Umformgeschwindigkeit und die Niederhalterkraft sollten sorgfältig kontrolliert werden, um eine gleichmäßige Verformung zu gewährleisten und Rissbildung zu vermeiden.
5.2. Einsatz von Schmierstoffen
Die Verwendung geeigneter Schmierstoffe verringert die Reibung zwischen Werkstück und Werkzeug und minimiert den Werkzeugverschleiß. Hochleistungsschmiermittel für Edelstahl tragen dazu bei, Oberflächenschäden zu vermeiden.
5.3. Einsatz von Zwischenglühen
Zwischenglühen kann bei der Bearbeitung von Edelstählen helfen, die durch Kaltverfestigung verursachte Härte zu reduzieren, und die Umformbarkeit wiederherstellen.
5.4. Verwendung beschichteter Werkzeuge
Beschichtete Werkzeuge, wie solche mit Titan-Nitrid oder Diamantähnlicher Kohlenstoffbeschichtung (DLC), sind widerstandsfähiger gegen den hohen Verschleiß, der beim Tiefziehen von Edelstahl auftritt.
5.5. Vorwärmen des Materials
Das Vorwärmen des Edelstahls vor dem Tiefziehen kann die Umformkräfte verringern und die Gefahr von Rissen reduzieren.
Zusammenfassung
Das Tiefziehen von Edelstahl ist ein anspruchsvolles, aber lohnendes Verfahren, das aufgrund der speziellen Materialeigenschaften von Edelstahl besondere Herausforderungen mit sich bringt. Mit geeigneten Maßnahmen wie der Optimierung der Umformparameter, dem Einsatz spezieller Schmierstoffe und beschichteter Werkzeuge sowie gegebenenfalls Zwischenglühen lassen sich diese Herausforderungen meistern. Edelstahl bietet durch seine Korrosionsbeständigkeit, Festigkeit und Ästhetik viele Vorteile, die ihn in einer Vielzahl von Anwendungen unverzichtbar machen.
Tiefziehen
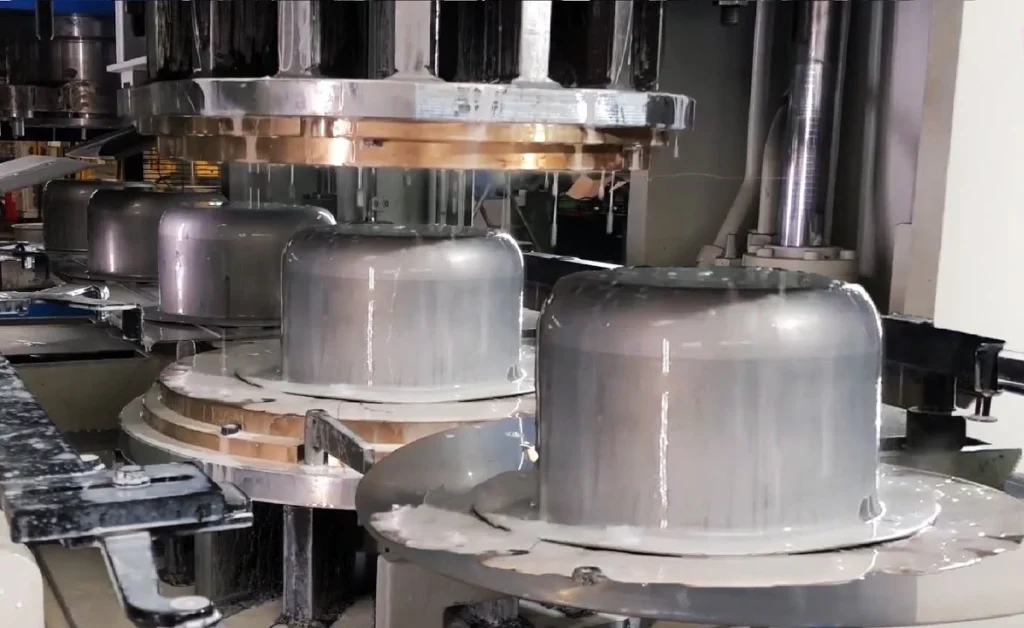
Das Tiefziehen ist ein bedeutendes Umformverfahren, das in der industriellen Fertigung verwendet wird, um flache Metallbleche in dreidimensionale, hohle Formen umzuwandeln. Edelstahl, ein Material mit herausragender Korrosionsbeständigkeit und mechanischen Eigenschaften, spielt eine wichtige Rolle in zahlreichen Anwendungen, die sowohl Funktionalität als auch ästhetische Qualität erfordern. Während sich konventioneller Kohlenstoffstahl durch seine leichte Umformbarkeit auszeichnet, stellt Edelstahl aufgrund seiner höheren Festigkeit und Kaltverfestigung spezifische Anforderungen an den Tiefziehprozess.
Der Einsatz von Edelstahl für das Tiefziehen bietet viele Vorteile, insbesondere in Branchen wie der Automobilindustrie, der Medizintechnik, der Lebensmittelverarbeitung und der Bauindustrie. Seine hervorragende Beständigkeit gegenüber Rost und Chemikalien, verbunden mit hoher Festigkeit und einer attraktiven optischen Erscheinung, machen Edelstahl zu einem idealen Werkstoff für hochwertige und langlebige Produkte. Gleichzeitig ist das Umformen von Edelstahl eine Herausforderung, die sowohl spezielle Werkzeuge als auch angepasste Umformtechniken erfordert.
2. Grundlegende Eigenschaften von Edelstahl
Um die Eignung von Edelstahl für das Tiefziehen zu verstehen, ist es wichtig, seine grundlegenden Eigenschaften zu kennen. Diese werden durch die chemische Zusammensetzung, die Mikrostruktur und die mechanischen Eigenschaften bestimmt.
2.1. Chemische Zusammensetzung
Edelstahl ist eine Stahllegierung, die mindestens 10,5 % Chrom enthält, was die Grundlage seiner Korrosionsbeständigkeit bildet. Die Zugabe von weiteren Legierungselementen wie Nickel, Molybdän, Titan oder Stickstoff kann die Eigenschaften von Edelstahl weiter optimieren, insbesondere in Bezug auf die Korrosionsbeständigkeit, Festigkeit und Verarbeitbarkeit.
- Chrom (Cr): Bildet eine dünne, stabile Oxidschicht auf der Oberfläche, die als „Passivschicht“ bekannt ist und die Korrosionsbeständigkeit erhöht.
- Nickel (Ni): Verbessert die Duktilität und Umformbarkeit, insbesondere bei austenitischen Edelstählen.
- Molybdän (Mo): Erhöht die Widerstandsfähigkeit gegenüber Lochfraß und Spaltkorrosion.
2.2. Mikrostruktur
Die Mikrostruktur von Edelstahl hat einen erheblichen Einfluss auf seine Umformbarkeit:
- Austenitische Edelstähle: Nicht magnetisch, hohe Duktilität, gute Umformbarkeit.
- Ferritische Edelstähle: Magnetisch, geringere Umformbarkeit als austenitische Stähle, aber bessere Widerstandsfähigkeit gegen Spannungsrisskorrosion.
- Martensitische Edelstähle: Sehr fest und hart, jedoch begrenzte Umformbarkeit.
- Duplex-Edelstähle: Kombination aus Austenit und Ferrit, gute mechanische Eigenschaften, aber begrenzte Kaltumformbarkeit.
2.3. Mechanische Eigenschaften
Die mechanischen Eigenschaften wie Festigkeit, Härte, Bruchdehnung und Kaltverfestigung sind ausschlaggebend für die Umformbarkeit von Edelstahl. Während austenitische Stähle für das Tiefziehen besonders geeignet sind, stellen andere Edelstahlsorten spezifische Herausforderungen dar.
3. Typen von Edelstahl für das Tiefziehen
Die Auswahl der richtigen Edelstahlsorte ist für den Erfolg des Tiefziehprozesses entscheidend. Hier sind die wichtigsten Arten von Edelstahl, die für das Tiefziehen verwendet werden:
3.1. Austenitische Edelstähle
Diese Edelstähle sind die erste Wahl für Tiefziehprozesse, da sie eine hohe Umformbarkeit und Korrosionsbeständigkeit bieten. Sie enthalten typischerweise mindestens 8 % Nickel, was die Bildung der austenitischen Mikrostruktur fördert und die Duktilität erhöht.
3.2. Ferritische Edelstähle
Ferritische Edelstähle sind kostengünstiger als austenitische Sorten und weisen eine gute Korrosionsbeständigkeit auf. Ihre geringere Umformbarkeit im Vergleich zu austenitischen Stählen schränkt jedoch die möglichen Anwendungen im Tiefziehen ein.
3.3. Martensitische Edelstähle
Diese Edelstähle bieten eine hohe Härte und Festigkeit, sind jedoch aufgrund ihrer spröderen Natur für das Tiefziehen nur begrenzt geeignet. Sie werden hauptsächlich für Bauteile verwendet, die eine hohe Verschleißfestigkeit erfordern.
3.4. Duplex-Edelstähle
Mit einer Kombination aus austenitischer und ferritischer Mikrostruktur bieten Duplex-Stähle eine hervorragende Kombination aus Festigkeit und Korrosionsbeständigkeit. Die Umformbarkeit ist jedoch geringer als bei rein austenitischen Stählen.
4. Mechanische Eigenschaften und ihre Relevanz für das Tiefziehen
Die mechanischen Eigenschaften von Edelstahl sind entscheidend für die Umformbarkeit und den Erfolg des Tiefziehprozesses. In diesem Kapitel werden die wichtigsten mechanischen Eigenschaften von Edelstahl beschrieben, die die Umformbarkeit beeinflussen.
4.1. Festigkeit und Härte
Edelstahl zeichnet sich durch eine hohe Festigkeit und Härte aus, was sich auf die erforderlichen Umformkräfte auswirkt. Die Festigkeit wird in zwei wesentlichen Parametern gemessen:
- Streckgrenze (Rp0,2): Die Spannung, bei der der Stahl eine plastische Verformung zeigt. Je niedriger die Streckgrenze, desto leichter lässt sich der Edelstahl tiefziehen, da weniger Kraft erforderlich ist, um die plastische Verformung einzuleiten.
- Zugfestigkeit (Rm): Die maximale Spannung, die der Edelstahl aushalten kann, bevor er bricht. Eine höhere Zugfestigkeit bietet Vorteile in Bezug auf die Festigkeit des Endprodukts, kann aber auch die Umformung erschweren.
Edelstähle wie die austenitischen Sorten (z. B. 1.4301 / AISI 304) haben eine relativ niedrige Streckgrenze, was sie ideal für Tiefziehprozesse macht. Ferritische und martensitische Edelstähle weisen hingegen höhere Festigkeiten auf, was höhere Umformkräfte erfordert und die Gefahr von Rissen erhöht.
4.2. Duktilität und Bruchdehnung
Die Duktilität, die durch die Bruchdehnung (A%) dargestellt wird, ist ein Maß dafür, wie stark ein Material verformt werden kann, bevor es bricht. Eine hohe Bruchdehnung ist entscheidend für das Tiefziehen, da sie es ermöglicht, das Material in komplexe Formen zu ziehen, ohne dass es zu Rissen oder Brüchen kommt.
- Austenitische Edelstähle bieten eine hohe Duktilität und sind daher besonders gut für Tiefziehprozesse geeignet. Sie können sich bis zu 40 % oder mehr dehnen, bevor sie reißen.
- Ferritische Edelstähle haben eine geringere Duktilität, was ihre Anwendungsmöglichkeiten für komplexe Umformungen einschränkt.
- Martensitische Edelstähle sind spröder und weisen eine sehr begrenzte Duktilität auf, was das Risiko von Rissen während des Umformens erhöht.
4.3. Kaltverfestigung
Die Kaltverfestigung ist ein Phänomen, bei dem der Edelstahl während der plastischen Verformung härter und fester wird. Dies geschieht, weil sich die Kornstruktur des Materials während der Umformung verdichtet, was zu einer Erhöhung der Festigkeit führt.
- Vorteil: Die Kaltverfestigung kann genutzt werden, um die Festigkeit des Bauteils nach dem Umformen zu erhöhen, was besonders bei sicherheitsrelevanten Anwendungen vorteilhaft ist.
- Nachteil: Sie erschwert den Umformprozess, da die Umformkräfte mit zunehmender Verformung steigen. Besonders bei mehrstufigen Umformungen kann die Kaltverfestigung problematisch sein und erfordert möglicherweise Zwischenwärmebehandlungen, um die Duktilität wiederherzustellen.
4.4. Rückfederung
Die Rückfederung ist die elastische Erholung des Materials nach dem Umformvorgang. Aufgrund der hohen Festigkeit von Edelstahl neigt das Material stärker zur Rückfederung als herkömmliche Kohlenstoffstähle. Dies bedeutet, dass die Bauteile nach dem Tiefziehen nicht genau die gewünschte Form behalten, sondern teilweise in ihre ursprüngliche Form zurückkehren.
- Herausforderung: Die Rückfederung beeinträchtigt die Maßhaltigkeit des Bauteils und erfordert eine Anpassung der Werkzeuggeometrie oder spezielle Umformtechniken, um dieses Phänomen zu kompensieren.
- Lösungen: Vorab-Simulationen des Umformprozesses, Anpassung der Werkzeuggeometrie und der Einsatz von Warmumformverfahren, um die Rückfederung zu reduzieren.
5. Chemische Eigenschaften von Edelstahl und ihre Auswirkungen auf das Tiefziehen
Die chemische Zusammensetzung und die damit verbundenen chemischen Eigenschaften von Edelstahl beeinflussen die Umformbarkeit und den Tiefziehprozess erheblich.
5.1. Korrosionsbeständigkeit
Eine der bekanntesten Eigenschaften von Edelstahl ist seine ausgezeichnete Korrosionsbeständigkeit, die auf den hohen Chromgehalt zurückzuführen ist. Diese Eigenschaft ist besonders wichtig für Anwendungen in korrosiven Umgebungen, wie der Lebensmittelverarbeitung, der Chemieindustrie und im Außenbereich.
- Vorteil: Edelstahl ist widerstandsfähig gegenüber Feuchtigkeit, Chemikalien und anderen korrosiven Einflüssen, was ihn ideal für viele anspruchsvolle Umgebungen macht.
- Nachteil: Während des Tiefziehprozesses können Oberflächenbeschädigungen die Passivschicht zerstören und die Korrosionsbeständigkeit beeinträchtigen, sodass eine Nachbehandlung (z. B. Passivierung) erforderlich sein kann.
5.2. Einfluss der Legierungselemente
Verschiedene Legierungselemente tragen zur Optimierung der mechanischen und chemischen Eigenschaften bei, was sich auf den Tiefziehprozess auswirkt:
- Chrom (Cr): Erhöht die Korrosionsbeständigkeit und verbessert die mechanische Stabilität. Chromgehalte über 10,5 % sind für Edelstahl typisch und bilden die Grundlage für die Korrosionsbeständigkeit.
- Nickel (Ni): Verbessert die Umformbarkeit und Duktilität von austenitischen Edelstählen und verringert die Gefahr von Spannungsrisskorrosion.
- Molybdän (Mo): Steigert die Widerstandsfähigkeit gegenüber Lochfraß und Spaltkorrosion, insbesondere in chloridhaltigen Umgebungen. Molybdänhaltige Edelstähle, wie 1.4401 (AISI 316), sind besonders für anspruchsvolle Umgebungen geeignet.
- Titan (Ti) und Niob (Nb): Diese Elemente stabilisieren die Mikrostruktur und verhindern die Ausscheidung von Chromkarbiden an den Korngrenzen, was die Korrosionsbeständigkeit verbessert.
5.3. Oberflächenreaktivität
Die Reaktivität der Oberfläche von Edelstahl beeinflusst die Schmierung während des Tiefziehprozesses. Da Edelstahl härter und abriebfester ist, ist eine höhere Reibung zwischen dem Material und dem Werkzeug zu erwarten. Eine geeignete Schmierung ist daher unerlässlich, um die Reibung zu minimieren und eine glatte Oberflächenqualität zu gewährleisten.
6. Verarbeitungseigenschaften von Edelstahl beim Tiefziehen
Edelstahl unterscheidet sich von herkömmlichen Stählen in Bezug auf seine Verarbeitungseigenschaften beim Tiefziehen. Diese Unterschiede müssen bei der Prozessgestaltung berücksichtigt werden.
6.1. Umformbarkeit
Die Umformbarkeit von Edelstahl hängt stark von der Art des Edelstahls ab. Austenitische Edelstähle sind am besten für das Tiefziehen geeignet, da sie eine hohe Duktilität und eine relativ niedrige Streckgrenze aufweisen. Andere Edelstahlsorten, wie martensitische oder duplex Stähle, sind weniger umformbar, aber sie bieten eine höhere Festigkeit.
6.2. Verschleißverhalten der Werkzeuge
Aufgrund der hohen Härte von Edelstahl kann es zu einem erhöhten Werkzeugverschleiß kommen. Dies ist besonders problematisch bei tiefen Umformungen oder bei der Verwendung von hochfesten Edelstählen. Die Werkzeugmaterialien müssen daher besonders verschleißfest sein, und die Verwendung von beschichteten Werkzeugen (z. B. mit Titan-Nitrid) kann die Standzeit der Werkzeuge erheblich verlängern.
6.3. Schmierung und Reibung
Eine wirksame Schmierung ist entscheidend für das Tiefziehen von Edelstahl, um die Reibung zu reduzieren und Oberflächenfehler zu vermeiden. Spezialschmierstoffe für Edelstahl sollten verwendet werden, um eine gute Gleitfähigkeit zu gewährleisten und die Werkzeuge zu schonen.
6.4. Einfluss von Wärmebehandlung und Vorwärmen
Das Vorwärmen des Edelstahls kann die Umformbarkeit verbessern, indem die Duktilität erhöht und die Neigung zur Kaltverfestigung reduziert wird. Eine Wärmebehandlung nach dem Umformprozess (z. B. Zwischenglühen) kann auch dazu beitragen, die durch die Kaltverfestigung verursachte Härte zu reduzieren und die Duktilität wiederherzustellen.
Das Tiefziehen von Eisen ist ein Umformverfahren, bei dem eine flache Eisenblechplatine in eine dreidimensionale, hohle Form umgeformt wird. Dieser Prozess wird in zahlreichen Industriezweigen eingesetzt, um Werkstücke mit hoher Präzision und unterschiedlichen Formen herzustellen. Eisen ist ein grundlegendes Material, das in vielen Anwendungen verwendet wird, jedoch weist es einige besondere Eigenschaften auf, die bei der Umformung durch Tiefziehen berücksichtigt werden müssen.
In diesem ausführlichen Überblick werden die grundlegenden Aspekte des Tiefziehens von Eisen, seine spezifischen Herausforderungen, die Materialeigenschaften und Optimierungsstrategien für den Umformprozess behandelt.
1. Grundlagen des Tiefziehens
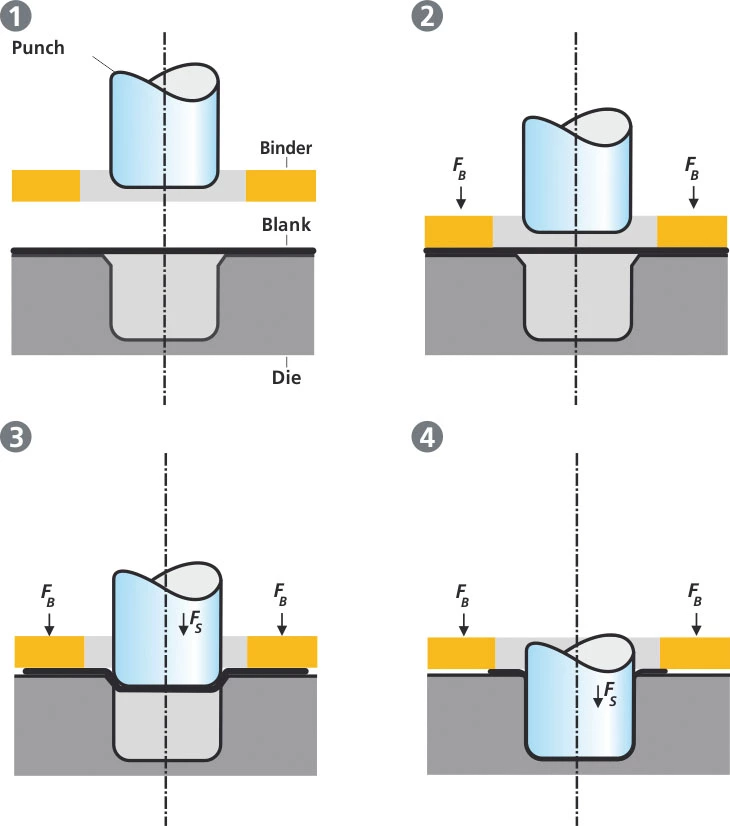
Das Tiefziehen ist ein Verfahren zur plastischen Verformung von Metallblechen, bei dem das Material in eine Matrize gepresst wird, um eine gewünschte Form zu erhalten. Der Prozess wird oft in mehreren Zügen durchgeführt, um die Dehnung des Materials zu kontrollieren und das Risiko von Materialfehlern wie Rissen oder Faltenbildung zu minimieren.
1.1. Ablauf des Tiefziehprozesses
- Vorbereitung der Blechplatine: Eine flache Eisenblechplatine wird auf die Matrize gelegt.
- Einpressen des Stempels: Ein Stempel drückt das Blech in die Matrize und formt es in die gewünschte Form.
- Niederhalter: Ein Niederhalter hält die Ränder der Platine fest, um Faltenbildung zu vermeiden.
- Entformung: Das Werkstück wird nach dem Umformen aus der Matrize entfernt.
1.2. Wichtige Parameter
- Ziehverhältnis: Das Verhältnis zwischen dem Durchmesser der Blechplatine und dem Durchmesser des Stempels. Ein hoher Wert erhöht das Risiko von Rissen.
- Umformgeschwindigkeit: Die Geschwindigkeit des Stempels während des Umformprozesses. Eine zu schnelle Umformung kann zu Materialversagen führen.
- Niederhalterkraft: Die Kraft, die der Niederhalter auf das Blech ausübt, um es während der Umformung an Ort und Stelle zu halten.
2. Eigenschaften von Eisen für das Tiefziehen
Eisen hat spezifische Materialeigenschaften, die den Tiefziehprozess beeinflussen. Einige der wichtigsten Eigenschaften sind:
2.1. Duktilität
Duktilität ist die Fähigkeit des Materials, sich plastisch zu verformen, bevor es bricht. Eisen hat eine gute Duktilität, was es für Umformprozesse wie das Tiefziehen geeignet macht. Dies bedeutet, dass Eisen vor dem Erreichen des Bruchpunktes erheblich gedehnt werden kann.
2.2. Festigkeit und Härte
Reines Eisen hat eine relativ niedrige Zugfestigkeit und Härte im Vergleich zu legierten Stählen. Während die geringere Festigkeit die Umformbarkeit erleichtert, bedeutet sie auch, dass Eisen weniger Widerstand gegenüber mechanischen Belastungen aufweist, wenn es nicht durch geeignete Verfahren gehärtet wird.
2.3. Kaltverfestigung
Beim Tiefziehen verfestigt sich Eisen durch plastische Verformung, was die Härte erhöht, aber auch die Umformbarkeit erschwert. Diese Kaltverfestigung kann dazu führen, dass Eisen bei mehreren aufeinanderfolgenden Umformschritten spröder wird und das Risiko von Rissbildung steigt.
2.4. Korrosionsanfälligkeit
Im Gegensatz zu Edelstahl ist reines Eisen sehr anfällig für Korrosion, insbesondere in feuchten oder aggressiven Umgebungen. Um dies zu verhindern, muss das fertige Produkt häufig beschichtet oder verzinkt werden.
3. Herausforderungen beim Tiefziehen von Eisen
Obwohl Eisen für das Tiefziehen geeignet ist, gibt es mehrere Herausforderungen, die den Umformprozess erschweren können:
3.1. Rissbildung
Risse können während des Tiefziehens auftreten, wenn das Eisen über seine Dehngrenze hinaus verformt wird. Dies ist besonders bei tiefen Zügen oder scharfen Kanten ein Problem. Eine genaue Kontrolle der Umformparameter ist notwendig, um Risse zu vermeiden.
3.2. Faltenbildung
Bei der Umformung kann es an den Rändern der Blechplatine zu Faltenbildung kommen, insbesondere wenn die Niederhalterkraft nicht ausreichend ist. Dies kann durch eine sorgfältige Anpassung der Niederhalterkraft und der Umformgeschwindigkeit verhindert werden.
3.3. Werkzeugverschleiß
Da Eisen aufgrund seiner Kaltverfestigung während des Umformprozesses härter wird, kann es zu erhöhtem Werkzeugverschleiß kommen. Dies erfordert Werkzeuge aus hochfesten Materialien oder mit speziellen Beschichtungen.
3.4. Rückfederung
Nach dem Tiefziehen kann es zu Rückfederung kommen, bei der sich das Eisen teilweise in seine ursprüngliche Form zurückzieht. Dies kann die Maßgenauigkeit des Bauteils beeinträchtigen und erfordert eine Anpassung der Werkzeuggeometrie, um die Rückfederung zu kompensieren.
4. Optimierungsstrategien für das Tiefziehen von Eisen
Um die Herausforderungen des Tiefziehens von Eisen zu bewältigen, gibt es verschiedene Maßnahmen zur Optimierung des Umformprozesses.
4.1. Anpassung der Umformparameter
Eine präzise Steuerung der Umformgeschwindigkeit, Niederhalterkraft und Stempelform kann helfen, die Risiken von Rissbildung und Faltenbildung zu minimieren. Eine langsame Umformung reduziert die Gefahr von Materialversagen.
4.2. Wärmebehandlung
Wärmebehandlungen wie Glühen vor dem Umformen können die Duktilität von Eisen verbessern und die Gefahr von Rissen reduzieren. Alternativ kann der Tiefziehprozess bei leicht erhöhter Temperatur durchgeführt werden, um die Umformbarkeit zu erhöhen.
4.3. Schmierung
Eine geeignete Schmierung während des Tiefziehprozesses verringert die Reibung und reduziert den Verschleiß der Werkzeuge. Spezielle Schmierstoffe für die Umformung von Eisen tragen dazu bei, die Oberflächenqualität zu verbessern.
4.4. Verwendung beschichteter Werkzeuge
Werkzeuge mit speziellen Beschichtungen wie Titan-Nitrid oder diamantähnlicher Kohlenstoff (DLC) sind widerstandsfähiger gegen den hohen Verschleiß, der beim Tiefziehen von Eisen auftreten kann.
4.5. Mehrstufiges Umformen
Bei anspruchsvollen Umformungen kann es sinnvoll sein, den Umformprozess in mehrere Schritte zu unterteilen, um das Material schrittweise in die gewünschte Form zu bringen.
5. Typische Anwendungen des Tiefziehens von Eisen
Das Tiefziehen von Eisen wird in verschiedenen Industrien eingesetzt, insbesondere in Bereichen, in denen kostengünstige Materialien und einfache Umformprozesse gefragt sind.
5.1. Automobilindustrie
Eisen wird für nicht-korrosionsgefährdete Bauteile wie Innenteile oder Strukturteile verwendet, die keine hohen Anforderungen an die Korrosionsbeständigkeit stellen.
5.2. Bauindustrie
Im Bauwesen wird tiefgezogenes Eisen für einfache Strukturelemente und Befestigungselemente verwendet. Aufgrund der Anfälligkeit für Korrosion ist es jedoch oft verzinkt.
5.3. Haushaltsgeräte
Einige Komponenten von Haushaltsgeräten, wie einfache Gehäuseteile, können aus tiefgezogenem Eisen hergestellt werden, insbesondere wenn sie durch Beschichtungen geschützt werden.
5.4. Verpackungsindustrie
Eisen kann für kostengünstige Verpackungsanwendungen verwendet werden, wie beispielsweise für Dosen und Behälter, die nicht mit korrosiven Stoffen in Kontakt kommen.
6. Zukunftsaussichten und neue Entwicklungen im Tiefziehen von Eisen
Das Tiefziehen von Eisen ist ein etabliertes Verfahren, das durch technologische Fortschritte kontinuierlich weiterentwickelt wird. Dazu gehören:
6.1. Fortschritte in der Simulationstechnik
Moderne Computersimulationen helfen, den Tiefziehprozess genauer zu planen und Probleme wie Rissbildung und Faltenbildung frühzeitig zu erkennen.
6.2. Materialverbesserungen
Durch die Entwicklung von Legierungen und speziellen Wärmebehandlungen kann die Umformbarkeit von Eisen verbessert und die Anwendungsbereiche erweitert werden.
6.3. Umweltfreundliche Verfahren
Neue Schmiermittel und umweltfreundliche Beschichtungen für Werkzeuge tragen dazu bei, den ökologischen Fußabdruck des Tiefziehprozesses zu verringern.
Zusammenfassung
Das Tiefziehen von Eisen ist ein vielseitiges Umformverfahren, das in vielen Industriezweigen Anwendung findet. Trotz seiner Vorteile, wie guter Umformbarkeit und niedrigen Kosten, stellt Eisen spezifische Herausforderungen wie Kaltverfestigung, Werkzeugverschleiß und Korrosionsanfälligkeit. Durch eine sorgfältige Optimierung des Tiefziehprozesses, den Einsatz geeigneter Schmierstoffe und beschichteter Werkzeuge sowie gegebenenfalls durch Wärmebehandlung können diese Herausforderungen gemeistert werden. Moderne Technologien und neue Entwicklungen verbessern kontinuierlich die Effizienz und die Möglichkeiten des Tiefziehens von Eisen.
1. Materialauswahl
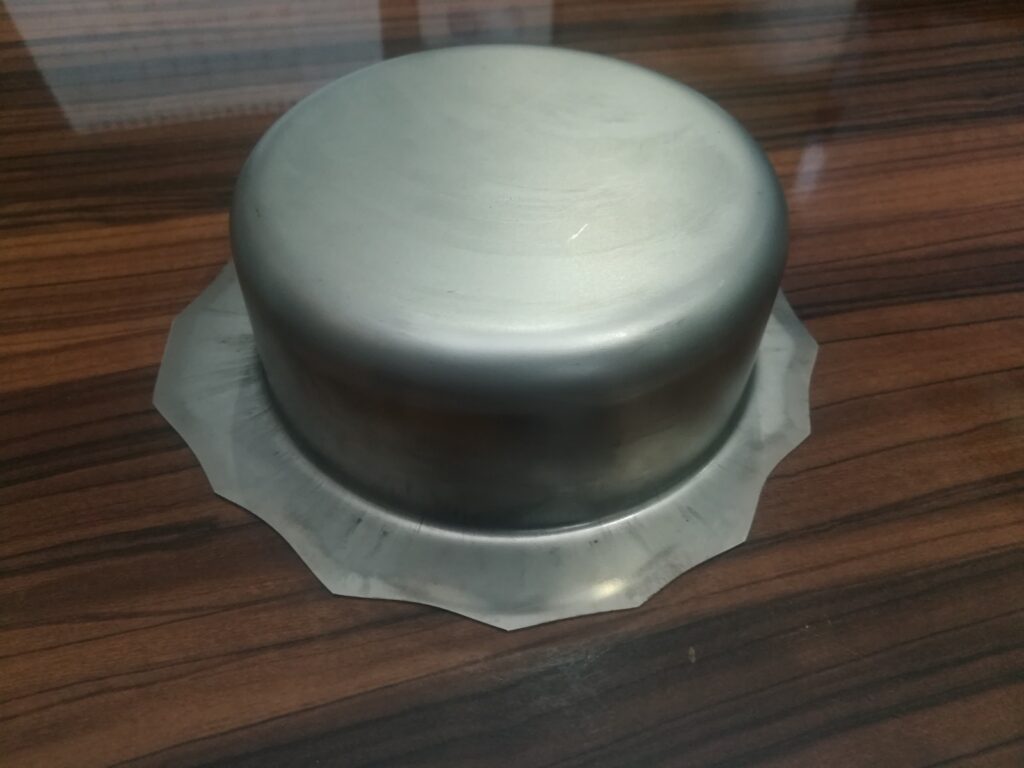
Die Wahl des richtigen Materials für die Blechplatine ist der erste Schritt in der Vorbereitung. Die Materialeigenschaften haben einen direkten Einfluss auf die Umformbarkeit, die Festigkeit und die Lebensdauer des fertigen Produkts. Die wichtigsten Faktoren bei der Materialauswahl sind:
1.1. Materialtyp
Die Materialart beeinflusst die Umformbarkeit und das Verhalten während des Tiefziehens. Gängige Materialien für Blechplatinen umfassen:
- Kohlenstoffstahl: Häufig für allgemeine Anwendungen verwendet, bietet gute Umformbarkeit und ist kostengünstig.
- Edelstahl: Wird für Anwendungen eingesetzt, bei denen Korrosionsbeständigkeit und hohe Festigkeit erforderlich sind.
- Aluminium: Leicht und umformbar, wird häufig in der Automobil- und Luftfahrtindustrie verwendet.
- Kupfer und Messing: Diese Materialien werden aufgrund ihrer guten Wärmeleitfähigkeit und Umformbarkeit in speziellen Anwendungen eingesetzt.
1.2. Materialdicke
Die Dicke des Blechs beeinflusst die Umformkräfte und die Qualität des Endprodukts. Eine zu dünne Blechplatine kann während des Tiefziehens reißen, während eine zu dicke Blechplatine höhere Umformkräfte erfordert. Die optimale Dicke hängt von der Komplexität der Form und den spezifischen Anforderungen des Endprodukts ab.
1.3. Festigkeit und Duktilität
Die Festigkeit und Duktilität des Materials bestimmen, wie stark sich das Blech verformen lässt, bevor es reißt. Materialien mit hoher Duktilität sind für tiefere Züge besser geeignet, während hochfeste Materialien oft eine Wärmebehandlung oder besondere Umformtechniken erfordern, um Rissbildung zu vermeiden.
2. Oberflächenvorbereitung
Die Oberflächenqualität der Blechplatine ist entscheidend für den Tiefziehprozess, da sie die Reibung zwischen der Platine und den Werkzeugen beeinflusst. Eine gute Oberflächenvorbereitung kann das Risiko von Oberflächenfehlern, Rissen und Faltenbildung verringern.
2.1. Reinigung
Die Reinigung der Blechplatine vor dem Tiefziehen ist notwendig, um Schmutz, Fett, Korrosionsprodukte und andere Verunreinigungen zu entfernen. Diese Verunreinigungen können die Schmierung beeinträchtigen und die Reibung während des Umformens erhöhen. Reinigungsmethoden umfassen:
- Beizen: Entfernt Oxidschichten und Verunreinigungen von der Oberfläche.
- Waschen und Entfetten: Entfernt Öle, Fette und andere Rückstände.
- Strahlen: Kann verwendet werden, um festhaftenden Schmutz und Oxidschichten mechanisch zu entfernen.
2.2. Entgraten
Falls die Kanten der Blechplatine scharf oder ungleichmäßig sind, sollte das Material entgratet werden, um scharfe Kanten zu entfernen. Dies reduziert das Risiko von Rissen während des Umformprozesses und sorgt für eine gleichmäßigere Umformung.
2.3. Oberflächenbeschichtung
In einigen Fällen kann es notwendig sein, die Blechplatine mit einer speziellen Beschichtung zu versehen, um die Reibung zu verringern und die Umformung zu erleichtern. Beispiele für Oberflächenbeschichtungen sind:
- Phosphatierung: Verbessert die Schmierung und verringert die Reibung.
- Schutzschichten aus Zink: Werden bei verzinktem Stahl verwendet, um Korrosionsschutz zu bieten.
3. Formgebung und Zuschnitt der Blechplatine
Die Form und Größe der Blechplatine müssen sorgfältig festgelegt werden, um die Materialausnutzung zu optimieren und den Umformprozess zu erleichtern.
3.1. Zuschnitt
Die Blechplatine wird auf die richtige Größe und Form zugeschnitten, um eine gleichmäßige Materialverteilung während des Tiefziehens zu gewährleisten. Ein präziser Zuschnitt ist wichtig, um Materialverschwendung zu minimieren und eine gleichmäßige Verformung zu ermöglichen. Die gängigen Verfahren zum Zuschnitt sind:
- Laser- und Plasmaschneiden: Für präzise und komplexe Formen.
- Scheren: Eine kostengünstige Methode für einfachere Zuschnitte.
- Stanzen: Wird für hohe Stückzahlen verwendet, um gleiche Zuschnitte zu gewährleisten.
3.2. Form der Platine
In bestimmten Fällen wird die Blechplatine vor dem Tiefziehen in eine spezielle Form gebracht, um den Materialfluss während der Umformung zu optimieren. Dazu können Ränder abgerundet oder Ecken abgeschrägt werden, um die Umformbarkeit zu verbessern und Spannungen zu reduzieren.
4. Schmierung der Blechplatine
Eine ausreichende Schmierung der Blechplatine ist entscheidend für einen erfolgreichen Tiefziehprozess. Die Schmierung reduziert die Reibung zwischen der Platine und den Werkzeugen und verringert das Risiko von Oberflächenschäden und Werkzeugverschleiß.
4.1. Auswahl des Schmiermittels
Das Schmiermittel sollte je nach Material und Umformbedingungen ausgewählt werden. Gängige Schmiermittel sind:
- Öle und Fette: Standard-Schmiermittel für eine Vielzahl von Materialien.
- Trockenschmierstoffe: Spezielle Schmiermittel, die keine Rückstände hinterlassen, wie z. B. Graphit- oder Teflon-beschichtete Filme.
- Emulsionen und wasserbasierte Schmiermittel: Werden verwendet, wenn ein umweltfreundlicherer Prozess gewünscht ist.
4.2. Auftragsmethoden
Das Schmiermittel kann auf verschiedene Arten aufgetragen werden, wie z. B. durch Sprühen, Tauchen, Rollen oder manuelles Auftragen. Die Wahl der Methode hängt von der Größe der Blechplatine, der Produktionsumgebung und dem verwendeten Schmiermittel ab.
5. Kontrolle der Blechplatine vor dem Tiefziehen
Eine letzte Kontrolle der Blechplatine vor dem Tiefziehen ist wichtig, um sicherzustellen, dass alle Vorbereitungsmaßnahmen korrekt durchgeführt wurden. Dazu gehören:
- Maßkontrolle: Überprüfung, ob die Platine die richtigen Maße und die korrekte Form aufweist.
- Oberflächenkontrolle: Prüfung auf saubere, einwandfreie Oberflächen ohne Verunreinigungen, Kratzer oder Rost.
- Kontrolle der Schmierung: Sicherstellen, dass das Schmiermittel gleichmäßig und in ausreichender Menge aufgetragen wurde.
6. Optimierungsstrategien bei der Vorbereitung der Blechplatine
Um die Effizienz und Qualität des Tiefziehprozesses zu verbessern, können verschiedene Optimierungsmaßnahmen in der Vorbereitung der Blechplatine durchgeführt werden.
6.1. Simulation und Prozessplanung
Computergestützte Simulationen können dabei helfen, den Zuschnitt der Blechplatine, die Umformparameter und die Materialverteilung im Voraus zu optimieren. Dies reduziert Materialverluste und verbessert die Ausbeute.
6.2. Qualitätskontrolle und Rückverfolgbarkeit
Ein konsequentes Qualitätsmanagement, das die Blechplatinen auf alle relevanten Kriterien überprüft, hilft, Fehler zu vermeiden und den Ausschuss zu minimieren. Eine Rückverfolgbarkeit der verwendeten Materialien und Prozesse ermöglicht es, eventuelle Probleme schnell zu identifizieren und zu beheben.
6.3. Nachhaltigkeit und Ressourcenschonung
Die Verwendung von recycelten Materialien oder die Reduzierung des Materialverbrauchs durch eine präzise Prozessgestaltung trägt zur Ressourcenschonung und Nachhaltigkeit bei.
Zusammenfassung
Die Vorbereitung der Blechplatine ist ein wesentlicher Schritt im Tiefziehprozess, der die Qualität und Effizienz der Umformung maßgeblich beeinflusst. Durch eine sorgfältige Materialauswahl, Oberflächenvorbereitung, Formgebung und Schmierung können viele potenzielle Probleme vermieden werden. Eine präzise Kontrolle und Optimierung der vorbereitenden Maßnahmen tragen dazu bei, die Produktqualität zu sichern, Materialverschwendung zu reduzieren und den gesamten Tiefziehprozess wirtschaftlicher zu gestalten.
Das Einpressen des Stempels ist ein zentraler Schritt im Tiefziehprozess, bei dem der Stempel die vorbereitete Blechplatine in die Matrize drückt, um die gewünschte Form zu erzeugen. Dieser Schritt erfordert eine genaue Steuerung der Umformparameter, um eine gleichmäßige Verformung des Materials zu erreichen und Defekte wie Risse, Faltenbildung oder unzureichende Maßhaltigkeit zu vermeiden. Das Einpressen des Stempels beeinflusst maßgeblich die Qualität des fertigen Bauteils und erfordert daher eine detaillierte Prozessplanung und Optimierung.
1. Grundlagen des Stempels beim Tiefziehen
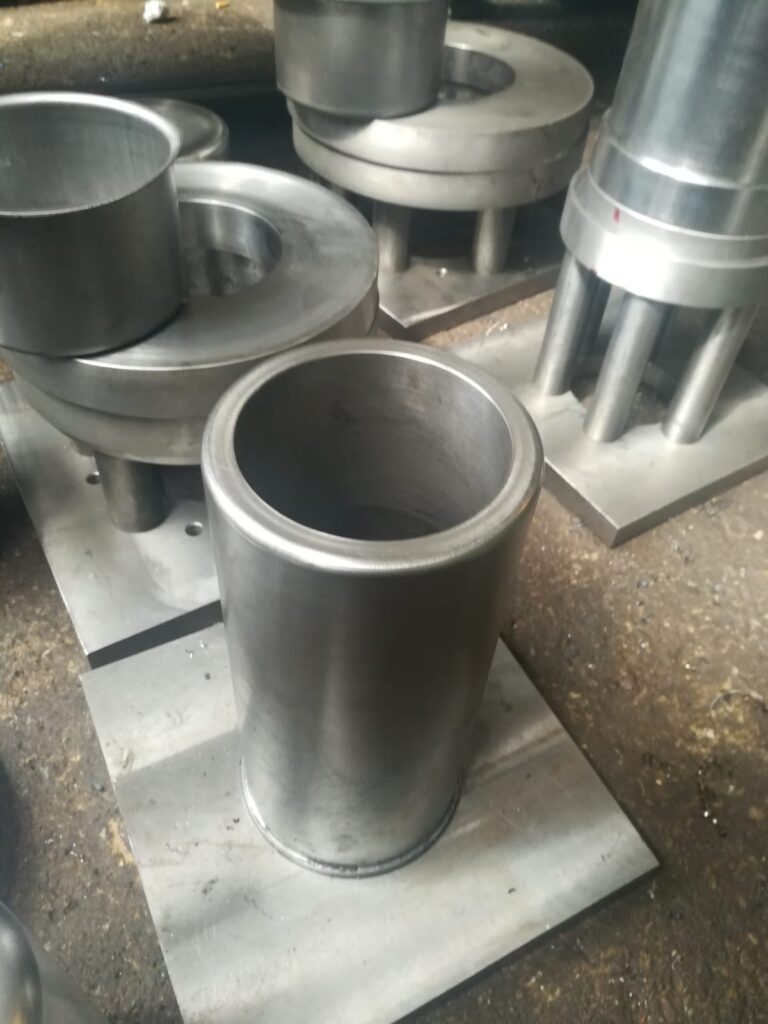
Der Stempel ist das zentrale Werkzeug beim Tiefziehen und dient dazu, die Blechplatine in die Matrize zu drücken. Er wird aus hochfestem Material hergestellt, das dem Druck und der Reibung standhalten kann, die während des Umformprozesses auftreten.
1.1. Form und Geometrie des Stempels
Die Form und Geometrie des Stempels sind entscheidend für die Qualität des Tiefziehprozesses:
- Runde Stempel: Werden häufig für zylindrische oder konische Bauteile verwendet.
- Eckige Stempel: Für Bauteile mit rechteckigen oder quadratischen Querschnitten, bei denen die Materialverteilung besonders sorgfältig kontrolliert werden muss.
- Stempel mit komplexen Formen: Werden bei Bauteilen mit speziellen Geometrien verwendet und erfordern eine besonders präzise Steuerung der Umformkräfte.
1.2. Material des Stempels
Der Stempel muss aus einem Material bestehen, das hohen Drücken und Reibung standhält, ohne zu verschleißen oder zu verformen. Typische Materialien sind:
- Werkzeugstahl: Weit verbreitet und kostengünstig, aber bei höheren Belastungen schneller verschleißanfällig.
- Hartmetall: Sehr verschleißfest, aber teurer als Werkzeugstahl.
- Beschichtungen: Wie Titan-Nitrid (TiN) oder Diamantähnlicher Kohlenstoff (DLC), um die Reibung zu reduzieren und die Standzeit des Stempels zu erhöhen.
2. Ablauf des Einpressens des Stempels
Der Prozess des Einpressens kann in mehrere Phasen unterteilt werden, die nacheinander ablaufen, um eine gleichmäßige Umformung des Materials sicherzustellen.
2.1. Anfangsphase
In der Anfangsphase wird der Stempel langsam abgesenkt, bis er die Blechplatine berührt. In dieser Phase wird eine relativ niedrige Kraft angewendet, um die Blechplatine gleichmäßig in Bewegung zu setzen.
2.2. Hauptumformphase
Während der Hauptumformphase wird der Stempel mit höherer Geschwindigkeit und größerer Kraft in die Matrize gedrückt, um die Blechplatine zu verformen. In dieser Phase kommt es zur plastischen Verformung des Materials, bei der das Blech in die gewünschte Form gebracht wird.
- Ziehverhältnis: Das Verhältnis von Durchmesser oder Länge der Blechplatine zur Tiefe der geformten Struktur muss berücksichtigt werden, um Rissbildung zu vermeiden.
- Materialfluss: Es ist wichtig, den Materialfluss während dieser Phase zu kontrollieren, um eine gleichmäßige Verteilung des Materials über die gesamte Form zu gewährleisten.
2.3. Endphase
In der Endphase des Einpressens wird der Stempel verlangsamt und schließlich gestoppt, sobald die gewünschte Form erreicht ist. Es ist wichtig, dass der Stempel nicht über das Ziel hinausgeht, um Materialüberdehnungen oder Beschädigungen an den Rändern der Form zu vermeiden.
3. Wichtige Parameter beim Einpressen des Stempels
Beim Einpressen des Stempels gibt es mehrere wichtige Parameter, die gesteuert werden müssen, um eine optimale Umformung zu gewährleisten.
3.1. Umformkraft
Die Umformkraft ist die Kraft, die vom Stempel auf die Blechplatine ausgeübt wird, um sie in die Matrize zu drücken. Die richtige Wahl der Umformkraft ist entscheidend, um die plastische Verformung zu ermöglichen, ohne Risse oder Brüche zu verursachen.
- Zu niedrige Umformkraft: Kann dazu führen, dass das Material nicht vollständig in die Matrize gezogen wird, was zu unzureichenden Formen führt.
- Zu hohe Umformkraft: Erhöht das Risiko von Rissbildung und Werkzeugverschleiß.
3.2. Umformgeschwindigkeit
Die Geschwindigkeit, mit der der Stempel auf die Blechplatine einwirkt, beeinflusst die Qualität der Umformung:
- Langsame Umformung: Ermöglicht eine bessere Kontrolle der Materialverteilung und verringert das Risiko von Rissen.
- Schnelle Umformung: Kann effizienter sein, erhöht jedoch das Risiko von Fehlern wie Rissen und Faltenbildung, insbesondere bei spröderen Materialien.
3.3. Niederhalterkraft
Die Niederhalterkraft wird vom Niederhalter auf die Ränder der Blechplatine ausgeübt, um das Material während der Umformung an Ort und Stelle zu halten. Sie hilft, Faltenbildung zu vermeiden und sorgt für einen kontrollierten Materialfluss.
- Zu niedrige Niederhalterkraft: Kann dazu führen, dass sich Falten an den Rändern bilden.
- Zu hohe Niederhalterkraft: Kann den Materialfluss behindern und zu Rissen führen.
4. Herausforderungen beim Einpressen des Stempels
Beim Einpressen des Stempels können verschiedene Herausforderungen auftreten, die sich negativ auf die Qualität des Endprodukts auswirken können.
4.1. Rissbildung
Risse treten auf, wenn das Material über seine Dehngrenze hinaus verformt wird. Dies kann durch eine zu hohe Umformkraft, eine falsche Materialauswahl oder eine unzureichende Schmierung verursacht werden. Die Kontrolle der Umformparameter und die Wahl eines geeigneten Materials sind entscheidend, um Rissbildung zu vermeiden.
4.2. Faltenbildung
Falten können an den Rändern der Blechplatine entstehen, wenn der Materialfluss nicht kontrolliert wird. Dies tritt typischerweise auf, wenn die Niederhalterkraft zu niedrig ist oder die Materialdicke zu groß ist. Eine sorgfältige Einstellung der Niederhalterkraft kann helfen, dieses Problem zu minimieren.
4.3. Werkzeugverschleiß
Aufgrund der hohen Umformkräfte und der Reibung kann es zu einem erhöhten Verschleiß des Stempels kommen. Dies ist besonders problematisch bei härteren Materialien wie Edelstahl oder hochfesten Stählen. Der Einsatz verschleißfester Werkstoffe oder beschichteter Stempel kann die Standzeit der Werkzeuge erhöhen.
4.4. Rückfederung
Nach dem Umformprozess kann es dazu kommen, dass sich das Material teilweise in seine ursprüngliche Form zurückzieht. Dies beeinträchtigt die Maßhaltigkeit des Bauteils. Um die Rückfederung zu kompensieren, müssen oft spezielle Umformtechniken angewendet oder die Werkzeuggeometrie angepasst werden.
5. Optimierungsstrategien für das Einpressen des Stempels
Um die Herausforderungen beim Einpressen des Stempels zu bewältigen und die Qualität des Endprodukts zu verbessern, können verschiedene Optimierungsstrategien eingesetzt werden.
5.1. Anpassung der Werkzeuggeometrie
Eine sorgfältige Gestaltung der Werkzeuggeometrie, einschließlich abgerundeter Kanten und angepasster Stempelformen, kann dazu beitragen, Spannungen im Material zu reduzieren und eine gleichmäßige Umformung zu gewährleisten.
5.2. Steuerung der Umformparameter
Die präzise Kontrolle von Umformkraft, Umformgeschwindigkeit und Niederhalterkraft ist entscheidend, um Materialfehler zu vermeiden und die Qualität des Endprodukts sicherzustellen.
5.3. Verwendung von Schmiermitteln
Eine ausreichende Schmierung verringert die Reibung zwischen der Blechplatine und dem Stempel und reduziert den Werkzeugverschleiß. Spezielle Schmierstoffe, die für das Tiefziehen entwickelt wurden, sollten verwendet werden.
5.4. Mehrstufiges Umformen
Bei komplexen Bauteilen oder anspruchsvollen Materialien kann das mehrstufige Umformen helfen, die Umformkräfte zu reduzieren und die Kaltverfestigung zu minimieren.
Zusammenfassung
Das Einpressen des Stempels ist ein entscheidender Schritt im Tiefziehprozess, der maßgeblich die Qualität und Präzision des fertigen Bauteils beeinflusst. Durch eine sorgfältige Steuerung der Umformparameter, eine optimierte Werkzeuggeometrie und den Einsatz geeigneter Schmierstoffe können die typischen Herausforderungen wie Rissbildung, Faltenbildung und Rückfederung überwunden werden. Eine kontinuierliche Prozessüberwachung und Optimierung tragen dazu bei, die Effizienz und Produktqualität im Tiefziehprozess zu steigern.
Der Niederhalter ist ein wichtiges Element im Tiefziehprozess, das verwendet wird, um die Blechplatine während des Umformens an Ort und Stelle zu halten und die Faltenbildung zu verhindern. Er spielt eine zentrale Rolle bei der Steuerung des Materialflusses und trägt wesentlich zur Qualität des geformten Bauteils bei. Der Einsatz des Niederhalters muss sorgfältig abgestimmt werden, um eine optimale Umformung zu gewährleisten und Materialfehler zu vermeiden.
1. Funktion des Niederhalters
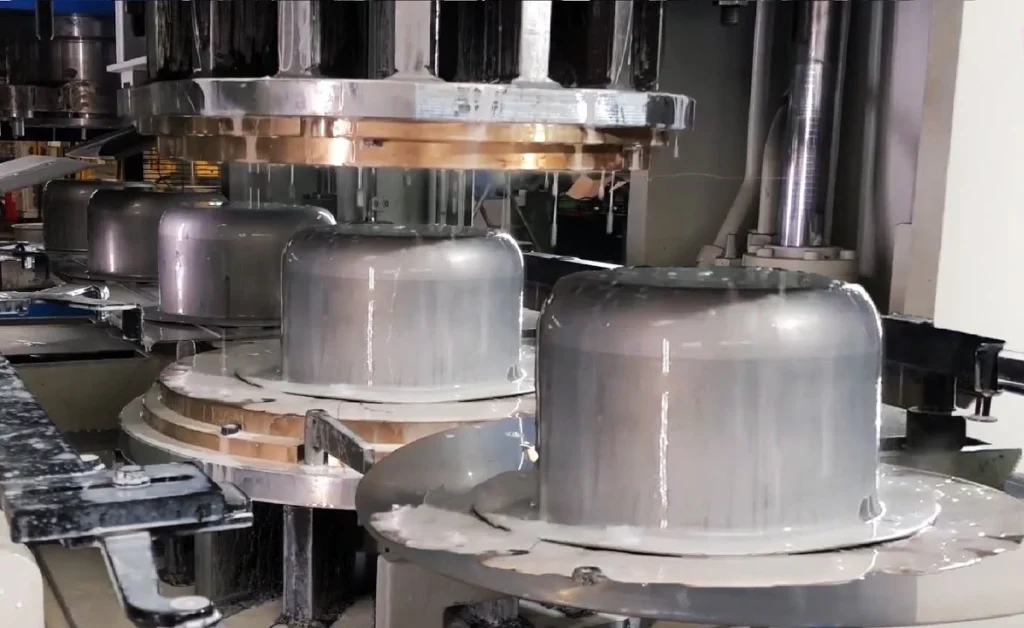
Die Hauptaufgabe des Niederhalters besteht darin, die Ränder der Blechplatine während des Tiefziehens gegen die Matrize zu drücken. Dadurch werden mehrere wichtige Funktionen erfüllt:
- Verhinderung von Faltenbildung: Indem der Niederhalter die Blechplatine festhält, wird verhindert, dass sich Materialüberschuss an den Rändern ansammelt und Falten entstehen.
- Kontrolle des Materialflusses: Der Niederhalter steuert den Materialfluss in die Matrize und sorgt dafür, dass das Material gleichmäßig verformt wird.
- Reduzierung der Rückfederung: Durch die Erhöhung der plastischen Verformung an den Rändern der Platine trägt der Niederhalter dazu bei, die Rückfederung nach dem Umformprozess zu reduzieren.
2. Arten von Niederhaltern
Es gibt verschiedene Arten von Niederhaltern, die je nach Anforderung und Komplexität des Tiefziehprozesses eingesetzt werden.
2.1. Feste Niederhalter
Feste Niederhalter üben eine konstante Kraft auf die Blechplatine aus. Sie werden typischerweise bei einfachen Umformprozessen eingesetzt, bei denen die Anforderungen an die Niederhalterkraft nicht stark variieren.
- Vorteile: Einfach und kostengünstig in der Anwendung.
- Nachteile: Weniger flexibel bei komplexen Umformungen, bei denen die Niederhalterkraft angepasst werden muss.
2.2. Hydraulische Niederhalter
Hydraulische Niederhalter verwenden ein hydraulisches System, um die Kraft auf die Blechplatine zu regulieren. Diese Niederhalter können eine variierbare Niederhalterkraft erzeugen, die während des Umformprozesses angepasst werden kann.
- Vorteile: Flexibilität bei der Steuerung der Niederhalterkraft, geeignet für komplexe Umformungen.
- Nachteile: Höherer Aufwand und Kosten für die Implementierung und Wartung.
2.3. Segmentierte Niederhalter
Segmentierte Niederhalter bestehen aus mehreren Einzelteilen, die individuell gesteuert werden können. Diese Niederhalter kommen häufig bei Bauteilen mit komplexen Geometrien zum Einsatz, um den Materialfluss in verschiedenen Bereichen der Platine zu kontrollieren.
- Vorteile: Sehr präzise Steuerung des Materialflusses möglich, geeignet für anspruchsvolle Umformungen.
- Nachteile: Aufwendige Konstruktion und höhere Kosten.
3. Wichtige Parameter für den Einsatz des Niederhalters
Der Erfolg des Tiefziehprozesses hängt maßgeblich davon ab, dass die Niederhalterkraft optimal eingestellt wird. Wichtige Parameter sind:
3.1. Niederhalterkraft
Die Niederhalterkraft ist die Kraft, die der Niederhalter auf die Blechplatine ausübt, um sie an Ort und Stelle zu halten. Eine präzise Einstellung der Niederhalterkraft ist entscheidend, um Materialfehler zu vermeiden.
- Zu niedrige Niederhalterkraft: Kann dazu führen, dass sich Falten an den Rändern der Platine bilden, da das Material nicht ausreichend fixiert wird.
- Zu hohe Niederhalterkraft: Kann den Materialfluss behindern und zu Rissen oder Bruch des Werkstücks führen, da das Material zu stark eingespannt ist.
3.2. Verteilung der Niederhalterkraft
Eine gleichmäßige Verteilung der Niederhalterkraft ist besonders bei komplex geformten Bauteilen wichtig, um eine gleichmäßige Verformung zu gewährleisten. Ungleichmäßige Kräfte können zu einer unregelmäßigen Materialverteilung und Defekten führen.
3.3. Anpassung der Niederhalterkraft während des Umformprozesses
Bei modernen Tiefziehpressen kann die Niederhalterkraft während des Umformprozesses dynamisch angepasst werden. Dies ermöglicht eine bessere Steuerung des Materialflusses und reduziert das Risiko von Fehlern wie Rissen und Faltenbildung.
4. Herausforderungen beim Einsatz des Niederhalters
Trotz seiner wichtigen Funktion im Tiefziehprozess kann der Einsatz des Niederhalters auch Herausforderungen mit sich bringen.
4.1. Optimale Einstellung der Niederhalterkraft
Die Einstellung der richtigen Niederhalterkraft ist ein kritischer Faktor. Wenn die Kraft nicht korrekt gewählt wird, kann dies zu Defekten im Bauteil führen, wie z. B. Faltenbildung, Rissbildung oder ungleichmäßiger Wanddicke. Eine sorgfältige Prozessplanung und -überwachung sind erforderlich, um die Niederhalterkraft optimal einzustellen.
4.2. Verschleiß des Niederhalters
Der Niederhalter ist während des Umformprozesses einer hohen Belastung ausgesetzt, was zu Verschleiß führen kann. Besonders bei der Verarbeitung von hochfesten Materialien oder Materialien mit abrasiven Eigenschaften kann dies problematisch sein. Regelmäßige Inspektionen und die Verwendung von verschleißfesten Materialien oder Beschichtungen können den Verschleiß reduzieren.
4.3. Ungleichmäßige Materialverteilung
Bei komplexen Bauteilgeometrien kann es schwierig sein, die Niederhalterkraft so zu steuern, dass der Materialfluss gleichmäßig ist. In solchen Fällen sind segmentierte Niederhalter oder individuell anpassbare Niederhaltersysteme erforderlich, um die Umformung zu optimieren.
5. Optimierungsstrategien für den Einsatz des Niederhalters
Um die Funktion des Niederhalters im Tiefziehprozess zu optimieren und mögliche Probleme zu vermeiden, können verschiedene Strategien eingesetzt werden.
5.1. Verwendung von adaptiven Niederhaltersystemen
Adaptive Niederhaltersysteme, die die Niederhalterkraft während des Umformprozesses dynamisch anpassen können, bieten eine bessere Kontrolle des Materialflusses und reduzieren das Risiko von Defekten. Diese Systeme sind besonders nützlich bei der Umformung von komplexen Bauteilen.
5.2. Simulation und Prozessoptimierung
Computergestützte Simulationen des Tiefziehprozesses helfen, die optimale Niederhalterkraft und deren Verteilung vorherzusagen. Dies ermöglicht eine genaue Planung und Anpassung der Umformparameter, um Materialfehler zu vermeiden.
5.3. Einsatz verschleißfester Materialien und Beschichtungen
Die Verwendung von verschleißfesten Materialien oder speziellen Beschichtungen wie Titan-Nitrid oder DLC (Diamantähnlicher Kohlenstoff) kann die Lebensdauer des Niederhalters verlängern und die Standzeit der Werkzeuge erhöhen.
5.4. Optimierung der Niederhalterkraftverteilung
Eine präzise Einstellung der Niederhalterkraftverteilung, insbesondere bei Bauteilen mit ungleichmäßiger Geometrie, kann die Umformqualität verbessern. Segmentierte Niederhalter oder individuell gesteuerte Niederhalterkräfte bieten eine effektive Möglichkeit, den Materialfluss zu steuern.
6. Anwendungen des Niederhalters im Tiefziehprozess
Der Einsatz des Niederhalters ist in vielen Industrien unverzichtbar, insbesondere bei der Herstellung von Bauteilen mit komplexen Formen oder hohen Anforderungen an die Maßgenauigkeit.
6.1. Automobilindustrie
In der Automobilindustrie wird der Niederhalter bei der Herstellung von Karosserieteilen, wie Türen, Motorhauben und Kotflügeln, eingesetzt. Diese Bauteile erfordern eine hohe Maßhaltigkeit und eine gleichmäßige Materialverteilung, was durch den Einsatz des Niederhalters gewährleistet wird.
6.2. Haushaltsgeräteindustrie
Bei der Herstellung von Gehäusen und Innenteilen für Haushaltsgeräte wird der Niederhalter verwendet, um eine gleichmäßige Umformung des Blechs zu gewährleisten. Dies ist besonders wichtig bei dünnen Blechen, die leicht zur Faltenbildung neigen.
6.3. Bauindustrie
In der Bauindustrie wird der Niederhalter für die Umformung von Bauteilen wie Dach- und Fassadenverkleidungen eingesetzt, um eine gleichmäßige Dicke und eine hohe Maßhaltigkeit sicherzustellen.
Zusammenfassung
Der Niederhalter ist ein entscheidendes Element im Tiefziehprozess, das dazu beiträgt, die Qualität der geformten Bauteile zu verbessern und Defekte wie Faltenbildung zu vermeiden. Durch die Kontrolle des Materialflusses und die Anpassung der Niederhalterkraft kann die Umformqualität optimiert werden. Moderne Niederhaltersysteme, die adaptive Steuerungsmöglichkeiten bieten, und der Einsatz von Simulationen zur Prozessoptimierung helfen dabei, die Herausforderungen im Einsatz des Niederhalters erfolgreich zu bewältigen.
Die Entformung ist der abschließende Schritt im Tiefziehprozess, bei dem das fertig geformte Bauteil aus der Matrize entfernt wird. Diese Phase ist entscheidend für die endgültige Qualität des Werkstücks, da bei der Entformung Schäden wie Risse, Kratzer oder Verformungen auftreten können, wenn dieser Schritt nicht ordnungsgemäß durchgeführt wird. Eine sorgfältige Planung und Kontrolle der Entformungsbedingungen sind daher unerlässlich, um ein hochwertiges Endprodukt zu gewährleisten.
1. Bedeutung der Entformung im Tiefziehprozess
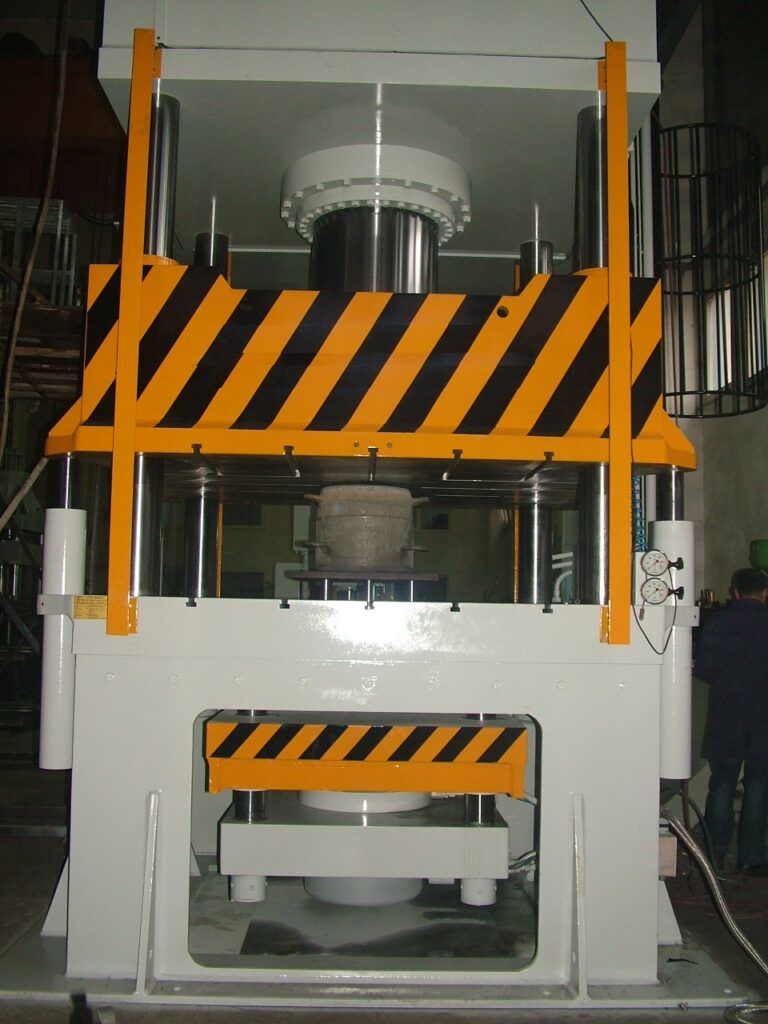
Die Entformung ist der Moment, in dem das geformte Bauteil von den Werkzeugen freigegeben wird. Zu diesem Zeitpunkt wird das Bauteil von der Matrize und dem Stempel gelöst und aus der Werkzeugform entnommen. Die Qualität der Entformung beeinflusst die Maßgenauigkeit, die Oberflächenqualität und die strukturelle Integrität des Endprodukts.
1.1. Einfluss auf die Maßhaltigkeit
Die Entformung kann die Maßgenauigkeit des geformten Bauteils beeinflussen, insbesondere wenn das Material während dieses Schritts elastisch zurückfedert. Diese sogenannte Rückfederung ist das Ergebnis der elastischen Erholung des Materials, das während des Tiefziehprozesses plastisch verformt wurde.
1.2. Oberflächenqualität
Beim Entformen können Kratzer oder andere Oberflächenfehler entstehen, wenn das Bauteil nicht gleichmäßig und vorsichtig aus der Matrize gelöst wird. Die Verwendung geeigneter Entformungstechniken und -hilfsmittel ist daher wichtig, um die Oberflächenqualität zu bewahren.
2. Typische Herausforderungen bei der Entformung
Die Entformung bringt einige typische Herausforderungen mit sich, die sich auf die Qualität des Endprodukts auswirken können.
2.1. Rückfederung
Nach dem Umformprozess zieht sich das Material teilweise in seine ursprüngliche Form zurück, was als Rückfederung bezeichnet wird. Die Rückfederung hängt von der Festigkeit, Dicke und Materialart ab und kann die Maßgenauigkeit beeinträchtigen.
- Einflussfaktoren: Materialeigenschaften, Umformtiefe und -geometrie, verwendete Umformkraft.
- Lösungen: Vorab-Simulationen, Anpassung der Werkzeuggeometrie oder die Verwendung spezieller Formgebungsstrategien.
2.2. Kleben oder Festhängen des Bauteils
Manchmal kann das geformte Werkstück in der Matrize oder am Stempel haften bleiben, was die Entformung erschwert. Dies kann durch verschiedene Faktoren verursacht werden, wie etwa:
- Hohe Reibung: Wenn die Oberflächenreibung zwischen Werkstück und Werkzeug zu hoch ist.
- Unterdruck: Wenn das Bauteil so eng an die Werkzeugoberfläche angepasst ist, dass ein Unterdruck entsteht, der das Herausnehmen erschwert.
2.3. Oberflächenschäden
Während der Entformung können Kratzer, Dellen oder andere Oberflächenfehler auftreten, insbesondere wenn das Werkstück festklemmt oder ungleichmäßig herausgezogen wird.
3. Strategien zur Optimierung der Entformung
Um die genannten Herausforderungen bei der Entformung zu bewältigen, gibt es verschiedene Optimierungsstrategien, die helfen können, den Entformungsprozess zu verbessern und die Qualität des fertigen Bauteils sicherzustellen.
3.1. Optimierung der Werkzeuggeometrie
Die Werkzeuggeometrie kann so gestaltet werden, dass sie die Entformung erleichtert:
- Entformungsschrägen: Ein leichter Neigungswinkel an den Seiten der Matrize erleichtert das Herauslösen des Bauteils, da es nicht direkt gegen die Matrizenwände gedrückt wird.
- Abgerundete Kanten: Abgerundete Werkzeugkanten verringern die Reibung und reduzieren das Risiko von Kleben oder Festhängen des Bauteils.
3.2. Verwendung von Schmiermitteln
Der Einsatz geeigneter Schmiermittel kann die Reibung zwischen dem geformten Bauteil und der Matrize verringern und die Entformung erleichtern. Es ist wichtig, Schmierstoffe zu wählen, die während des Tiefziehens eine gute Gleitfähigkeit bieten und keine Rückstände auf dem Bauteil hinterlassen.
3.3. Anwendung von Entformungshilfen
Spezielle Entformungshilfen können eingesetzt werden, um die Entfernung des Bauteils aus der Matrize zu unterstützen:
- Druckluftstöße: Mit Druckluft können Bauteile sanft aus der Matrize herausgelöst werden.
- Vakuumsysteme: Vakuumgreifer können verwendet werden, um das Bauteil aus der Matrize zu ziehen, insbesondere bei komplex geformten Bauteilen.
3.4. Steuerung der Rückfederung
Die Rückfederung kann durch verschiedene Maßnahmen kontrolliert werden:
- Vorwärts- und Rückwärtsziehen: Durch den Einsatz von Vorwärts- und Rückwärtsbewegungen des Stempels während des Umformprozesses kann die Rückfederung teilweise ausgeglichen werden.
- Anpassung der Werkzeuggeometrie: Spezielle Geometrien, die die Rückfederung berücksichtigen, können die Maßgenauigkeit verbessern.
4. Entformungstechniken bei verschiedenen Materialien
Die Anforderungen an die Entformung können je nach verwendetem Material unterschiedlich sein, da jedes Material spezifische Eigenschaften aufweist.
4.1. Tiefziehen von Stahl
Beim Tiefziehen von Stahl muss die Rückfederung besonders berücksichtigt werden, da Stahl im Vergleich zu anderen Materialien wie Aluminium eine höhere Festigkeit aufweist. Eine präzise Anpassung der Werkzeuggeometrie ist erforderlich, um die Maßhaltigkeit zu gewährleisten.
4.2. Tiefziehen von Aluminium
Aluminium hat eine geringere Festigkeit und eine höhere Rückfederung als Stahl. Die Entformung muss daher sorgfältig überwacht werden, um eine Verformung oder Beschädigung des Werkstücks zu vermeiden. Aluminium ist außerdem anfälliger für Oberflächenschäden.
4.3. Tiefziehen von Edelstahl
Edelstahl ist härter und weist eine höhere Rückfederung auf, was die Entformung erschweren kann. Schmierstoffe mit hoher Gleitfähigkeit und verschleißfeste Werkzeugmaterialien sind erforderlich, um die Entformung zu erleichtern.
5. Qualitätskontrolle nach der Entformung
Nach der Entformung ist es wichtig, das geformte Bauteil auf mögliche Defekte zu überprüfen. Eine sorgfältige Qualitätskontrolle stellt sicher, dass das Werkstück den Anforderungen entspricht und mögliche Probleme frühzeitig erkannt werden.
5.1. Maßkontrolle
Die Maßgenauigkeit des Bauteils sollte überprüft werden, um sicherzustellen, dass es innerhalb der Toleranzen liegt. Dies ist besonders wichtig bei Bauteilen mit strengen Maßanforderungen.
5.2. Oberflächenprüfung
Das Werkstück sollte auf Kratzer, Dellen oder andere Oberflächenfehler untersucht werden, die während der Entformung entstanden sein könnten. Gegebenenfalls müssen solche Fehler durch Nachbearbeitung korrigiert werden.
5.3. Prüfung der Materialeigenschaften
In einigen Fällen kann es notwendig sein, die Materialeigenschaften des Bauteils nach der Entformung zu überprüfen, insbesondere wenn es während des Umformprozesses stark verfestigt wurde. Eine Wärmebehandlung oder ein Zwischenglühen kann erforderlich sein, um die Duktilität des Materials wiederherzustellen.
Zusammenfassung
Die Entformung ist ein entscheidender Schritt im Tiefziehprozess, der die endgültige Qualität des geformten Bauteils beeinflusst. Eine sorgfältige Planung und Steuerung der Entformungsbedingungen sind notwendig, um Herausforderungen wie Rückfederung, Kleben oder Festhängen des Bauteils und Oberflächenschäden zu vermeiden. Durch Optimierungsstrategien wie die Anpassung der Werkzeuggeometrie, den Einsatz geeigneter Schmiermittel und spezieller Entformungshilfen kann der Entformungsprozess verbessert und die Qualität des Endprodukts gesichert werden. Die abschließende Qualitätskontrolle nach der Entformung stellt sicher, dass das geformte Bauteil den Anforderungen entspricht und für den weiteren Einsatz geeignet ist.
Das Tiefziehen von Blech in Kleinserien ist ein Umformverfahren, das sich auf die Herstellung von kleineren Stückzahlen spezialisierter oder individualisierter Bauteile konzentriert. Im Gegensatz zur Massenproduktion, bei der große Stückzahlen kostengünstig hergestellt werden, bringt die Fertigung in Kleinserien besondere Herausforderungen mit sich, wie höhere Werkzeugkosten pro Bauteil und spezifische Anforderungen an die Flexibilität der Produktionsprozesse. Trotzdem bietet das Tiefziehen in Kleinserien einige Vorteile, vor allem für spezielle Anwendungen, Prototypen und Produkte mit häufigen Designänderungen.
1. Bedeutung des Tiefziehens in Kleinserien
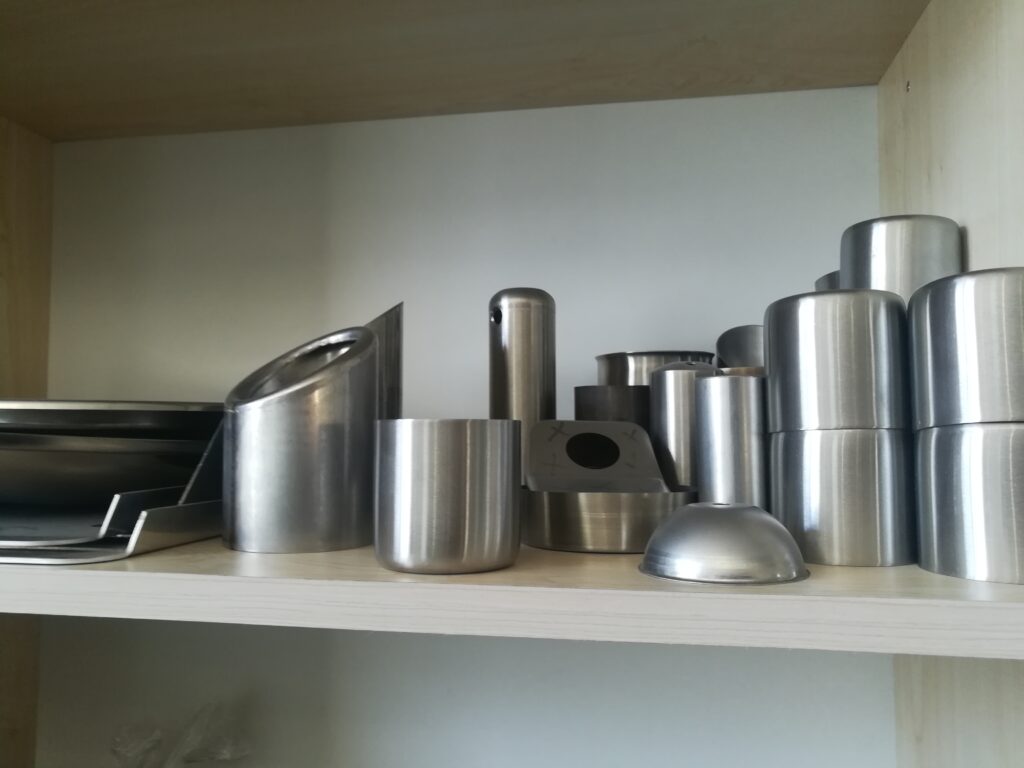
Kleinserienfertigung wird für spezifische Anwendungen und Branchen immer wichtiger, insbesondere in Bereichen, in denen individuelle Anpassungen, begrenzte Produktionsmengen oder häufige Designänderungen gefordert sind. Das Tiefziehen in Kleinserien ermöglicht die Herstellung hochwertiger Bauteile bei begrenztem Stückbedarf, was für Unternehmen attraktiv ist, die geringe Lagerbestände und eine flexible Fertigung bevorzugen.
1.1. Typische Anwendungen
Das Tiefziehen in Kleinserien findet in verschiedenen Bereichen Anwendung:
- Prototypenfertigung: Zur Herstellung von Vorserienmodellen oder zur Prüfung neuer Designs.
- Medizintechnik: Für speziell angepasste Gerätegehäuse oder chirurgische Instrumente.
- Luft- und Raumfahrt: Herstellung von Bauteilen in geringer Stückzahl, die spezifische Anforderungen erfüllen müssen.
- Automobilindustrie: Kleinserien von Spezialteilen oder limitierte Fahrzeugmodelle.
- Maschinenbau: Fertigung von Sonderanfertigungen oder Ersatzteilen für spezielle Maschinen.
2. Vorteile des Tiefziehens in Kleinserien
Das Tiefziehen in Kleinserien bietet einige spezifische Vorteile, die es von der Massenproduktion abheben:
2.1. Flexibilität bei Designänderungen
Da die Stückzahlen begrenzt sind, können Änderungen am Design oder an den Werkzeugen einfacher und schneller umgesetzt werden. Dies ist besonders vorteilhaft bei der Herstellung von Prototypen oder wenn Anpassungen während des Entwicklungsprozesses erforderlich sind.
2.2. Herstellung von individuellen und kundenspezifischen Bauteilen
Das Tiefziehen in Kleinserien ermöglicht die Produktion von maßgeschneiderten Bauteilen, die spezifischen Anforderungen des Kunden entsprechen. Dies ist besonders nützlich in der Medizintechnik oder bei der Herstellung von Ersatzteilen, bei denen individuelle Anpassungen notwendig sind.
2.3. Geringe Lagerhaltungskosten
Da nur kleine Stückzahlen hergestellt werden, sind auch die Lagerbestände gering. Dies verringert die Lagerhaltungskosten und ermöglicht eine „Just-in-Time“-Produktion, bei der die Bauteile nach Bedarf gefertigt werden.
2.4. Schnellere Markteinführung
Die Möglichkeit, Prototypen und Vorserienbauteile schnell zu fertigen, trägt dazu bei, die Entwicklungszeit zu verkürzen und neue Produkte schneller auf den Markt zu bringen.
3. Herausforderungen beim Tiefziehen in Kleinserien
Obwohl das Tiefziehen in Kleinserien viele Vorteile bietet, gibt es auch spezifische Herausforderungen, die bei der Fertigung berücksichtigt werden müssen.
3.1. Hohe Werkzeugkosten
Die Werkzeugkosten sind beim Tiefziehen oft der größte Kostenfaktor, insbesondere bei Kleinserien. Da die Werkzeugkosten bei geringen Stückzahlen auf weniger Bauteile verteilt werden, sind die Stückkosten höher als bei der Massenproduktion.
3.2. Anpassung der Produktionsprozesse
Die Fertigung von Kleinserien erfordert flexible Produktionsprozesse, die auf unterschiedliche Anforderungen abgestimmt werden können. Dies bedeutet oft, dass die Umrüstzeiten zwischen verschiedenen Bauteilen minimiert werden müssen, um die Effizienz zu steigern.
3.3. Komplexe Qualitätskontrolle
Bei Kleinserien, insbesondere in Branchen wie der Medizintechnik oder Luft- und Raumfahrt, sind die Qualitätsanforderungen oft sehr hoch. Eine sorgfältige Prüfung und Kontrolle jedes einzelnen Bauteils ist notwendig, was die Produktionszeit verlängern kann.
3.4. Wirtschaftlichkeit bei geringen Stückzahlen
Die Herstellung in Kleinserien ist oft weniger wirtschaftlich als die Massenproduktion, da der Aufwand pro Bauteil höher ist. Es müssen Strategien entwickelt werden, um die Kosten zu minimieren und die Effizienz zu steigern.
4. Strategien zur Optimierung des Tiefziehens in Kleinserien
Um die spezifischen Herausforderungen der Kleinserienfertigung zu bewältigen, können verschiedene Strategien zur Optimierung des Tiefziehprozesses eingesetzt werden.
4.1. Verwendung von modularen Werkzeugen
Modulare Werkzeuge, die sich an unterschiedliche Bauteilgeometrien anpassen lassen, können die Werkzeugkosten erheblich senken. Solche Werkzeuge bestehen aus mehreren Teilen, die je nach Anforderung ausgetauscht oder angepasst werden können.
4.2. Einsatz additiver Fertigungsverfahren für Werkzeugbau
Der Einsatz von 3D-Druck und anderen additiven Fertigungsverfahren zur Herstellung von Tiefziehwerkzeugen kann die Werkzeugkosten reduzieren und die Produktionszeiten verkürzen. Diese Technologien ermöglichen die schnelle Herstellung von Prototypenwerkzeugen oder Werkzeugen für kleinere Stückzahlen.
4.3. Automatisierung von Umrüstvorgängen
Durch die Automatisierung von Umrüstvorgängen, wie dem Werkzeugwechsel oder der Einstellung der Maschinenparameter, können die Umrüstzeiten reduziert und die Effizienz gesteigert werden.
4.4. Anwendung von computergestützten Simulationen
Simulationen können helfen, den Tiefziehprozess im Voraus zu planen und potenzielle Probleme wie Faltenbildung oder Rissbildung zu vermeiden. Dies reduziert den Bedarf an Nacharbeit und verbessert die Qualität der Bauteile.
4.5. Einsatz kostengünstiger Materialien für Werkzeuge
In der Kleinserienproduktion können kostengünstigere Werkstoffe für Werkzeuge verwendet werden, wenn die Anforderungen an die Standzeit des Werkzeugs nicht so hoch sind wie bei der Massenproduktion. Zum Beispiel können Kunststoff- oder Verbundmaterialien für Werkzeuge eingesetzt werden, die nur für begrenzte Stückzahlen benötigt werden.
5. Anwendungsbeispiele für das Tiefziehen in Kleinserien
Die Kleinserienproduktion eignet sich besonders gut für spezielle Branchen und Anwendungen, bei denen Flexibilität und individuelle Anpassungen gefragt sind.
5.1. Prototypenbau in der Automobilindustrie
In der Automobilindustrie ist der Prototypenbau von großer Bedeutung, um neue Fahrzeugkomponenten zu testen und zu optimieren. Tiefgezogene Bauteile für Prototypen, wie Karosserieteile, können in Kleinserien gefertigt werden, um Design und Funktion zu prüfen.
5.2. Spezialbauteile für die Medizintechnik
Die Medizintechnik stellt hohe Anforderungen an die Qualität und Maßgenauigkeit der Bauteile. Tiefgezogene Gehäuse für medizinische Geräte, chirurgische Instrumente oder Implantate werden häufig in Kleinserien gefertigt, um spezifische Kundenanforderungen zu erfüllen.
5.3. Luft- und Raumfahrtindustrie
In der Luft- und Raumfahrt werden oft kleinere Stückzahlen von spezialisierten Bauteilen benötigt. Das Tiefziehen in Kleinserien ermöglicht die Herstellung leichter und stabiler Bauteile aus Aluminium oder Titan, die den strengen Anforderungen dieser Branche entsprechen.
5.4. Haushaltsgeräte und Sonderanfertigungen
Für Haushaltsgeräte und Sonderanfertigungen, die in limitierter Auflage produziert werden, eignet sich das Tiefziehen in Kleinserien. So können z. B. spezielle Gehäuseteile oder dekorative Abdeckungen in kleinen Stückzahlen hergestellt werden.
6. Zukunftsaussichten für das Tiefziehen in Kleinserien
Mit der fortschreitenden Technologieentwicklung wird das Tiefziehen in Kleinserien immer wirtschaftlicher und vielseitiger einsetzbar. Neue Fertigungstechnologien und Materialien werden dazu beitragen, die Werkzeugkosten zu senken und die Flexibilität des Produktionsprozesses weiter zu erhöhen.
6.1. Integration von additiver Fertigung
Die Kombination von Tiefziehen und additiver Fertigung bietet neue Möglichkeiten für die Herstellung von Werkzeugen und Bauteilen. Dies könnte die Produktionszeiten verkürzen und die Kosten für Kleinserien weiter senken.
6.2. Digitale Prozessoptimierung
Die Digitalisierung und Automatisierung der Fertigung ermöglichen eine noch präzisere Prozesssteuerung und Qualitätsüberwachung. Insbesondere in der Kleinserienproduktion können digitale Technologien helfen, die Effizienz zu steigern und die Fehlerquote zu reduzieren.
6.3. Nachhaltigkeit und Ressourceneffizienz
Durch die Produktion in Kleinserien können Ressourcen effizienter genutzt und Abfälle minimiert werden. Dies entspricht den wachsenden Anforderungen an nachhaltige Fertigungsmethoden.
Zusammenfassung
Das Tiefziehen in Kleinserien bietet Flexibilität, ermöglicht individuelle Anpassungen und eignet sich besonders für Anwendungen mit begrenzten Stückzahlen. Trotz der Herausforderungen, wie höheren Werkzeugkosten und komplexeren Qualitätskontrollen, kann die Kleinserienfertigung durch geeignete Optimierungsstrategien und neue Technologien wirtschaftlicher gestaltet werden. Mit fortschreitender technischer Entwicklung wird das Tiefziehen in Kleinserien weiter an Bedeutung gewinnen, insbesondere in spezialisierten Branchen wie der Medizintechnik, dem Prototypenbau und der Luft- und Raumfahrtindustrie.
Um die Bedeutung des Tiefziehens in Kleinserien umfassend darzustellen, werde ich diesen Text in mehrere Abschnitte gliedern, um die verschiedenen Facetten und Vorteile dieses Prozesses sowie die Herausforderungen und spezifischen Anwendungen hervorzuheben. Das Tiefziehen in Kleinserien ist besonders relevant für bestimmte Industriezweige und Anwendungsbereiche, in denen Flexibilität, Anpassungsfähigkeit und die Möglichkeit zur Herstellung hochwertiger, spezialisierter Bauteile gefragt sind.
Tiefziehen
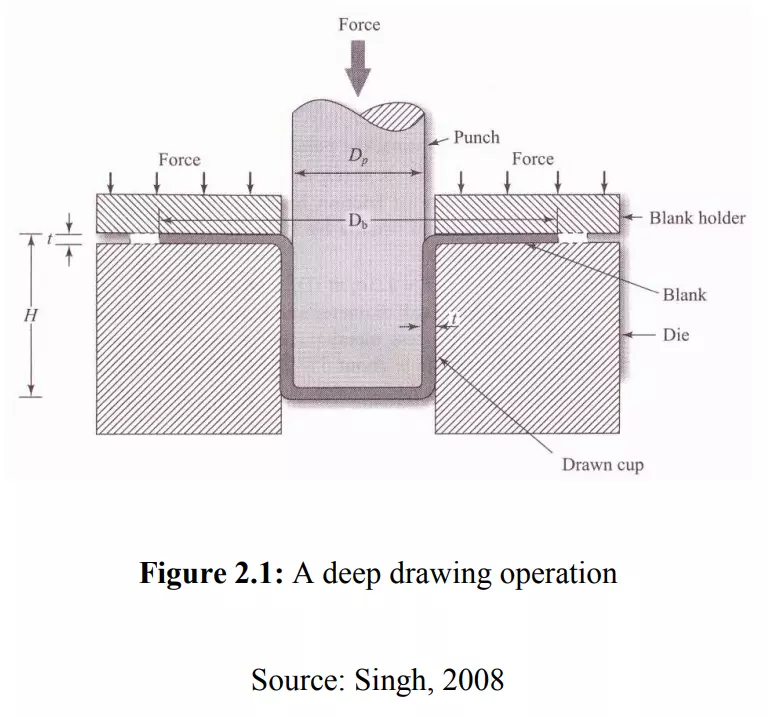
Tiefziehen ist ein Umformverfahren, bei dem eine Blechplatine durch Einwirkung eines Stempels in eine Matrize gepresst wird, um eine gewünschte dreidimensionale Form zu erzeugen. Während das Tiefziehen traditionell in der Massenproduktion eingesetzt wird, um große Stückzahlen kostengünstig herzustellen, gibt es auch eine zunehmende Nachfrage nach Kleinserienfertigung. Dies ist insbesondere in Industriebereichen der Fall, in denen spezielle Anforderungen, geringe Stückzahlen oder häufige Designänderungen erforderlich sind.
Das Tiefziehen in Kleinserien ermöglicht eine wirtschaftliche Produktion von Bauteilen in begrenzter Stückzahl, wobei die Qualität, Flexibilität und Anpassungsfähigkeit im Vordergrund stehen. Die Fähigkeit, auch kleine Mengen kostengünstig und effizient herzustellen, macht das Tiefziehen in Kleinserien zu einem wichtigen Fertigungsprozess in verschiedenen Branchen.
2. Relevanz und Vorteile des Tiefziehens in Kleinserien
2.1. Flexibilität bei der Produktion
Einer der größten Vorteile des Tiefziehens in Kleinserien ist die Flexibilität, die es bietet. Anders als bei der Massenproduktion, bei der große Stückzahlen von identischen Bauteilen hergestellt werden, ermöglicht die Kleinserienfertigung eine schnelle Anpassung an Designänderungen und die Herstellung von variablen Bauteilen. Diese Flexibilität ist besonders vorteilhaft in Branchen, in denen Produkte maßgeschneidert oder speziell angepasst werden müssen, wie zum Beispiel in der Medizintechnik oder im Prototypenbau.
- Beispiel: In der Automobilindustrie können in Kleinserien limitierte Fahrzeugmodelle oder spezielle Komponenten für Rennfahrzeuge hergestellt werden, die spezifischen Anforderungen entsprechen.
2.2. Reduzierte Lagerhaltung und Just-in-Time-Produktion
Das Tiefziehen in Kleinserien ermöglicht es, Bauteile bedarfsgerecht herzustellen, wodurch die Notwendigkeit großer Lagerbestände entfällt. Durch die Produktion nach Bedarf – etwa in einer Just-in-Time-Fertigungsstrategie – können Unternehmen ihre Lagerhaltungskosten erheblich senken und gleichzeitig flexibel auf Marktnachfragen reagieren.
- Vorteil: Unternehmen können so schneller auf Änderungen in der Nachfrage reagieren, ohne große Lagerbestände an vorgefertigten Bauteilen halten zu müssen, was Kosten reduziert und die Effizienz erhöht.
2.3. Schnelle Umsetzung von Designänderungen
Im Produktentwicklungszyklus sind häufig Anpassungen oder Verbesserungen notwendig. Beim Tiefziehen in Kleinserien können solche Designänderungen schnell umgesetzt werden, da die Produktionsprozesse flexibel gestaltet sind. Dies ermöglicht es, Prototypen oder Vorserienmodelle zügig herzustellen und in der Praxis zu testen.
- Anwendungsbeispiel: In der Luft- und Raumfahrtindustrie müssen Bauteile oft spezifischen Anforderungen genügen, die während der Entwicklung und Erprobung angepasst werden. Das Tiefziehen in Kleinserien ermöglicht es, diese Anpassungen effizient umzusetzen.
2.4. Herstellung von kundenspezifischen Produkten
Die Kleinserienproduktion ermöglicht die Fertigung von Bauteilen, die speziell an die Bedürfnisse des Kunden angepasst sind. Dabei kann es sich um spezielle Abmessungen, Formen oder Materialanforderungen handeln. In Branchen wie der Medizintechnik oder dem Maschinenbau ist es oft notwendig, individuelle Lösungen anzubieten, die auf die spezifischen Bedürfnisse der Endnutzer zugeschnitten sind.
- Beispiel: In der Medizintechnik kann es erforderlich sein, spezifische Gehäuse für medizinische Geräte herzustellen, die nur in geringen Stückzahlen benötigt werden.
2.5. Unterstützung beim Prototypenbau
Der Prototypenbau ist eine wichtige Phase im Entwicklungsprozess neuer Produkte. Hierbei ist die Herstellung kleiner Stückzahlen notwendig, um Design und Funktion eines Produkts zu testen und zu optimieren. Das Tiefziehen in Kleinserien eignet sich hervorragend für diese Phase, da die Werkzeuge relativ schnell und kostengünstig angepasst werden können, um verschiedene Varianten herzustellen.
- Nutzen: Durch den Einsatz von Kleinserienfertigung im Prototypenbau kann die Markteinführungszeit eines Produkts verkürzt werden, da Fehler und Verbesserungen frühzeitig erkannt und umgesetzt werden können.
3. Herausforderungen des Tiefziehens in Kleinserien
3.1. Hohe Werkzeugkosten
Eines der Hauptprobleme bei der Kleinserienfertigung sind die relativ hohen Werkzeugkosten im Vergleich zur Stückzahl. In der Massenproduktion verteilen sich die Werkzeugkosten auf eine große Anzahl von Bauteilen, wodurch die Kosten pro Stück niedrig bleiben. In der Kleinserienfertigung hingegen sind die Werkzeugkosten pro Bauteil höher, da die Herstellungskosten auf weniger Stücke aufgeteilt werden müssen.
- Lösungsansätze: Der Einsatz von modularen Werkzeugen oder additiven Fertigungstechniken zur Herstellung von Prototypenwerkzeugen kann die Werkzeugkosten senken.
3.2. Wirtschaftlichkeit bei geringen Stückzahlen
Die Herstellungskosten pro Bauteil sind bei kleinen Serien grundsätzlich höher als bei großen Serien, was die Wirtschaftlichkeit des Tiefziehens in Kleinserien einschränken kann. Unternehmen müssen daher Strategien entwickeln, um die Prozesse effizient zu gestalten und die Kosten zu minimieren.
- Strategien zur Kostensenkung: Optimierung der Umrüstzeiten, flexible Fertigungsstrategien und die Nutzung digitaler Technologien zur Prozessoptimierung können die Wirtschaftlichkeit verbessern.
3.3. Qualitätsanforderungen und individuelle Prüfungen
In der Kleinserienfertigung sind die Qualitätsanforderungen oft sehr hoch, insbesondere in Branchen wie der Luft- und Raumfahrt, der Medizintechnik oder der Automobilindustrie. Hierbei muss jedes Bauteil individuell geprüft werden, um sicherzustellen, dass es den strengen Normen und Spezifikationen entspricht.
- Herausforderung: Die Qualitätskontrolle in der Kleinserienfertigung ist oft aufwendiger und zeitintensiver als in der Massenproduktion.
4. Branchen und Anwendungen für das Tiefziehen in Kleinserien
4.1. Automobilindustrie
In der Automobilindustrie wird das Tiefziehen in Kleinserien für spezielle Fahrzeugkomponenten, limitierte Modellauflagen oder Rennsportteile eingesetzt. Kleinserienfertigung ermöglicht es Automobilherstellern, maßgeschneiderte Bauteile schnell und flexibel zu produzieren, was im Motorsport von besonderer Bedeutung ist.
4.2. Luft- und Raumfahrt
Die Luft- und Raumfahrtindustrie stellt hohe Anforderungen an die Qualität und Leistungsfähigkeit von Bauteilen. Das Tiefziehen in Kleinserien ist hier von Bedeutung, da häufig kleinere Stückzahlen von speziellen Komponenten benötigt werden, die für bestimmte Flugzeug- oder Raumfahrzeugtypen entwickelt wurden.
4.3. Medizintechnik
In der Medizintechnik werden oft Bauteile in Kleinserien benötigt, die präzise und maßgeschneidert sein müssen, um den hohen Anforderungen zu entsprechen. Gehäuse für medizinische Geräte, chirurgische Instrumente oder Implantate sind Beispiele für Bauteile, die in begrenzten Stückzahlen gefertigt werden.
4.4. Haushaltsgeräte und Konsumgüter
Für die Produktion von Haushaltsgeräten oder speziellen Konsumgütern, die in limitierter Auflage auf den Markt kommen, ist die Kleinserienfertigung eine geeignete Methode. So können etwa spezielle Gehäuse oder Abdeckungen hergestellt werden, die nur für bestimmte Modellreihen benötigt werden.
4.5. Maschinenbau und Sonderanfertigungen
Im Maschinenbau sind häufig individuelle Lösungen gefragt, die speziell auf die Anforderungen des Kunden abgestimmt sind. Dies umfasst maßgeschneiderte Bauteile oder Ersatzteile, die in Kleinserien gefertigt werden.
5. Technologische Fortschritte und ihre Auswirkungen auf das Tiefziehen in Kleinserien
Die Entwicklung neuer Technologien und digitaler Fertigungsmethoden hat das Potenzial, das Tiefziehen in Kleinserien effizienter und kostengünstiger zu gestalten.
5.1. Digitale Prozessoptimierung und Simulationen
Durch den Einsatz digitaler Technologien und Simulationen können Umformprozesse genauer geplant und optimiert werden. Dies ermöglicht es, die Werkzeuggeometrie und die Umformparameter vorab festzulegen, um Materialfehler und Nacharbeit zu minimieren.
5.2. Additive Fertigung für den Werkzeugbau
Additive Fertigungstechniken, wie der 3D-Druck, bieten die Möglichkeit, Werkzeuge für Kleinserien kostengünstig herzustellen. Besonders für Prototypen und Testwerkzeuge kann dies eine erhebliche Kostenersparnis bedeuten.
5.3. Automatisierung und flexible Fertigungssysteme
Die Automatisierung der Produktionsprozesse, insbesondere die Automatisierung von Umrüstvorgängen, kann dazu beitragen, die Produktionskosten in der Kleinserienfertigung zu senken. Flexible Fertigungssysteme ermöglichen es, schnell zwischen verschiedenen Produktvarianten zu wechseln.
6. Nachhaltigkeit und Ressourceneffizienz im Tiefziehen von Kleinserien
Die Kleinserienfertigung hat das Potenzial, nachhaltiger zu sein als die Massenproduktion, da nur die tatsächlich benötigten Bauteile hergestellt werden. Dies reduziert den Materialverbrauch und die Abfallmenge. Darüber hinaus kann die Flexibilität bei der Produktion dazu beitragen, Überproduktionen zu vermeiden und Ressourcen effizienter zu nutzen.
Zusammenfassung
Das Tiefziehen in Kleinserien hat in vielen Industriezweigen eine große Bedeutung, da es Flexibilität, individuelle Anpassungsmöglichkeiten und eine schnelle Umsetzung von Designänderungen bietet. Trotz der Herausforderungen, wie höheren Werkzeugkosten und komplexen Qualitätsanforderungen, bietet die Kleinserienfertigung zahlreiche Vorteile für spezielle Anwendungen und Branchen, in denen maßgeschneiderte Lösungen und hohe Qualität gefragt sind. Mit der fortschreitenden Technologieentwicklung, der Digitalisierung und der Einführung neuer Fertigungsmethoden wird das Tiefziehen in Kleinserien weiterhin an Bedeutung gewinnen und neue Möglichkeiten in der Fertigungsindustrie eröffnen.
1. Automobilindustrie
Die Automobilindustrie ist einer der größten Anwender des Tiefziehverfahrens. Viele Bauteile von Fahrzeugen werden durch Tiefziehen gefertigt, da dieses Verfahren sowohl die Anforderungen an Festigkeit als auch an Maßgenauigkeit erfüllt.
1.1. Karosserie- und Strukturteile
Zu den wichtigsten Anwendungen in der Automobilindustrie gehören Karosserie- und Strukturteile. Beispiele sind:
- Motorhauben, Kofferraumdeckel und Türen: Diese Komponenten bestehen häufig aus tiefgezogenen Blechen, da sie große, aber stabile Oberflächen bieten müssen. Die Maßgenauigkeit ist wichtig, damit die Teile gut passen und sich leicht montieren lassen.
- Kotflügel und Dachstrukturen: Auch diese Bauteile werden durch Tiefziehen gefertigt, um die gewünschte Form und Steifigkeit zu erreichen.
- Verstärkungsteile: Strukturbauteile wie Querträger oder Säulen im Fahrzeugrahmen, die zur Steifigkeit und Aufprallsicherheit beitragen.
1.2. Abgasanlagen und Hitzeschilde
Komponenten von Abgasanlagen, wie Hitzeschilde oder Gehäuse für Katalysatoren, werden häufig durch Tiefziehen aus Edelstahl hergestellt. Diese Bauteile müssen hohe Temperaturen aushalten und gleichzeitig korrosionsbeständig sein.
2. Haushaltsgeräteindustrie
In der Haushaltsgeräteindustrie wird das Tiefziehen für die Herstellung zahlreicher Bauteile verwendet, die hohe Anforderungen an die Maßhaltigkeit und Oberflächenqualität stellen.
2.1. Gehäuse für Haushaltsgeräte
Viele Haushaltsgeräte, wie Waschmaschinen, Geschirrspüler, Kühlschränke und Mikrowellen, haben Gehäuseteile aus tiefgezogenen Blechen. Diese Gehäuse bieten eine glatte, stabile Oberfläche und sind oft aus korrosionsbeständigen Materialien wie Edelstahl gefertigt.
2.2. Küchenspülen und Kochgeschirr
Küchenspülen aus Edelstahl sind ein klassisches Beispiel für die Anwendung des Tiefziehens in der Haushaltsgeräteindustrie. Sie werden aus Blechen tiefgezogen, um eine nahtlose, wasserfeste Oberfläche zu gewährleisten. Auch Töpfe, Pfannen und andere Kochutensilien können durch Tiefziehen hergestellt werden.
3. Luft- und Raumfahrtindustrie
In der Luft- und Raumfahrtindustrie werden hohe Anforderungen an die Qualität und Gewichtseinsparung von Bauteilen gestellt. Das Tiefziehen wird hier verwendet, um leichte, aber stabile Strukturkomponenten zu fertigen.
3.1. Strukturbauteile
Für Flugzeuge und Raumfahrzeuge werden tiefgezogene Strukturbauteile aus Aluminium oder Titan verwendet, um das Gewicht zu reduzieren und gleichzeitig eine hohe Festigkeit zu gewährleisten. Beispiele sind:
- Verkleidungselemente für die Flugzeugaußenhaut.
- Verstärkungen und Rahmenkonstruktionen: Leichte Strukturbauteile, die zur Festigkeit und Steifigkeit des Flugzeugs beitragen.
3.2. Komponenten für Triebwerke
Bestimmte Bauteile in Triebwerken, die hohen Temperaturen und Drücken ausgesetzt sind, werden durch Tiefziehen gefertigt, um die erforderliche Präzision und Festigkeit zu erreichen.
4. Medizintechnik
Die Medizintechnik stellt hohe Anforderungen an die Präzision und Materialeigenschaften von Bauteilen, insbesondere bei chirurgischen Instrumenten und medizinischen Geräten.
4.1. Gehäuse für medizinische Geräte
Gehäuse und Verkleidungen für medizinische Geräte wie Diagnosegeräte, Ultraschallgeräte oder Laborausrüstungen werden häufig durch Tiefziehen hergestellt. Edelstahl ist hier oft das bevorzugte Material, da es korrosionsbeständig und leicht zu reinigen ist.
4.2. Chirurgische Instrumente
Manche chirurgischen Instrumente werden aus tiefgezogenen Edelstahlteilen gefertigt, um eine nahtlose, hygienische Oberfläche zu gewährleisten, die leicht zu sterilisieren ist.
5. Bauindustrie
In der Bauindustrie wird das Tiefziehen für verschiedene Bauteile verwendet, die sowohl dekorative als auch funktionale Zwecke erfüllen.
5.1. Fassadenverkleidungen
Architektonische Verkleidungen, insbesondere aus Metall, werden häufig durch Tiefziehen hergestellt, um komplexe Formen und glatte Oberflächen zu erzielen. Diese Verkleidungen tragen nicht nur zur Ästhetik bei, sondern bieten auch Schutz vor Witterungseinflüssen.
5.2. Dach- und Wandverkleidungen
Dachverkleidungen und Fassadenplatten werden häufig aus tiefgezogenen Blechen gefertigt, um eine robuste und witterungsbeständige Außenhülle für Gebäude zu bieten.
6. Verpackungsindustrie
Die Verpackungsindustrie nutzt das Tiefziehverfahren, um stabile und langlebige Metallverpackungen herzustellen.
6.1. Dosen und Behälter
Metallverpackungen, wie Konservendosen, Getränkedosen oder spezielle Behälter für chemische Produkte, werden durch Tiefziehen hergestellt. Aluminium und Weißblech sind gängige Materialien, die aufgrund ihrer guten Umformbarkeit und Korrosionsbeständigkeit verwendet werden.
6.2. Druckgasbehälter
Feuerlöscher, Gasflaschen und andere Druckbehälter aus Metall werden oft durch Tiefziehen gefertigt, um die notwendige Stabilität und Dichtheit zu gewährleisten.
7. Maschinenbau
Im Maschinenbau werden viele Bauteile und Gehäuse durch Tiefziehen gefertigt, um Maschinenkomponenten vor Staub, Feuchtigkeit und mechanischen Beschädigungen zu schützen.
7.1. Gehäuse und Abdeckungen
Maschinengehäuse, Abdeckungen für Aggregate und Schutzverkleidungen werden häufig aus tiefgezogenen Blechen hergestellt. Diese Bauteile schützen empfindliche Maschinenteile und tragen zur Sicherheit der Bediener bei.
7.2. Strukturteile für Spezialmaschinen
Spezielle Maschinen und Anlagen benötigen oft maßgeschneiderte Strukturbauteile, die durch Tiefziehen hergestellt werden können, um eine hohe Präzision und Festigkeit zu erreichen.
8. Elektro- und Elektronikindustrie
In der Elektro- und Elektronikindustrie spielt das Tiefziehen eine wichtige Rolle bei der Herstellung von Gehäusen und Verkleidungen.
8.1. Gehäuse für elektronische Geräte
Viele elektronische Geräte, wie Computergehäuse, Server und Schaltschrankverkleidungen, werden aus tiefgezogenen Blechen hergestellt. Diese Gehäuse bieten eine robuste Außenhülle und schützen die empfindliche Elektronik im Inneren.
8.2. Batteriezellen und Akkus
Tiefgezogene Metallgehäuse werden auch für Batteriezellen und Akkus verwendet, um die strukturelle Integrität der Zellen zu gewährleisten und sie vor äußeren Einflüssen zu schützen.
9. Schmuck- und Kunsthandwerk
Auch im Schmuck- und Kunsthandwerk wird das Tiefziehen eingesetzt, um dekorative Elemente und Schmuckstücke herzustellen.
9.1. Schmuckteile
Metalle wie Silber und Gold können durch Tiefziehen geformt werden, um Schmuckstücke wie Ringe, Anhänger oder Manschettenknöpfe herzustellen.
9.2. Dekorative Objekte
Das Tiefziehen kann auch zur Herstellung von dekorativen Metallobjekten, wie Skulpturen oder Reliefs, verwendet werden, die in der Innenausstattung oder als Kunstwerke dienen.
Zusammenfassung
Das Tiefziehen ist ein vielseitiges Umformverfahren, das in vielen Industriezweigen Anwendung findet. Typische Anwendungen reichen von der Automobil- und Haushaltsgeräteindustrie über die Luft- und Raumfahrt bis hin zur Medizintechnik und Verpackungsindustrie. Die Fähigkeit, komplexe Formen aus Blech herzustellen, macht das Tiefziehen zu einer wichtigen Fertigungstechnologie für zahlreiche Produkte, bei denen Präzision, Maßhaltigkeit und Stabilität erforderlich sind.
Das Tiefziehen in Kleinserien ist eine vielseitige und flexible Fertigungsmethode, die sich besonders für spezialisierte Anwendungen und Branchen eignet, in denen individuelle Anpassungen, geringe Stückzahlen oder Prototypenbau gefragt sind. In dieser detaillierten Übersicht werden spezifische Anwendungsbeispiele für das Tiefziehen in Kleinserien beschrieben, um die Vorteile, Herausforderungen und praktischen Einsatzmöglichkeiten des Verfahrens zu beleuchten.
1. Automobilindustrie
In der Automobilindustrie findet das Tiefziehen in Kleinserien eine Vielzahl von Anwendungen, insbesondere bei der Herstellung von speziellen Fahrzeugkomponenten, Prototypen und Kleinauflagen von Fahrzeugen.
1.1. Prototypenbau und Vorserienmodelle
Vor der Serienproduktion eines neuen Fahrzeugs ist es notwendig, Prototypen und Vorserienmodelle zu entwickeln, um Design, Funktionalität und Herstellbarkeit zu testen. Diese Modelle enthalten oft tiefgezogene Bauteile, wie Karosseriekomponenten oder Verstärkungen.
- Beispiel: Für die Entwicklung eines neuen Fahrzeugmodells können Türen, Motorhauben oder Kofferraumdeckel durch Tiefziehen in Kleinserien gefertigt werden, um die Passgenauigkeit und Strukturstabilität zu testen.
- Vorteil: Durch die Fertigung von Prototypen in Kleinserien können frühzeitig Anpassungen vorgenommen werden, bevor die endgültigen Werkzeuge für die Massenproduktion hergestellt werden.
1.2. Limitierte Fahrzeugmodelle und Sonderausstattungen
Kleinserienfertigung ist auch für limitierte Fahrzeugmodelle oder Sonderausstattungen wichtig, die nicht in großen Stückzahlen produziert werden. Hier kommen oft spezielle Materialien und Designs zum Einsatz, die individuelle Fertigungsmethoden erfordern.
- Beispiel: Für exklusive Fahrzeugmodelle, wie Sportwagen oder Oldtimer-Nachbauten, können bestimmte Karosserieteile aus speziellen Materialien, wie Aluminium oder Edelstahl, durch Tiefziehen in Kleinserien hergestellt werden.
- Sonderausstattungen: Individuell gestaltete Teile wie Zierleisten, Spoiler oder Innenraumverkleidungen werden oft in Kleinserien gefertigt, um den hohen Ansprüchen der Kunden gerecht zu werden.
1.3. Motorsportanwendungen
Im Motorsport ist die Kleinserienfertigung von Komponenten besonders relevant, da hier häufig maßgeschneiderte Teile benötigt werden, die auf die spezifischen Anforderungen der Rennstrecke zugeschnitten sind.
- Beispiel: Motorsportteams lassen Fahrzeugkomponenten wie Stoßfänger, Radkästen oder spezielle Verkleidungen durch Tiefziehen in Kleinserien herstellen, um Gewicht zu sparen und die Aerodynamik zu verbessern.
2. Medizintechnik
Die Medizintechnik stellt hohe Anforderungen an die Qualität, Maßgenauigkeit und Materialeigenschaften von Bauteilen, was das Tiefziehen in Kleinserien zu einer geeigneten Methode macht, um spezifische Produkte herzustellen.
2.1. Gehäuse für medizinische Geräte
Medizinische Geräte erfordern oft Gehäuse und Verkleidungen, die aus korrosionsbeständigen Materialien bestehen und hygienischen Anforderungen entsprechen. Diese Gehäuse werden häufig in Kleinserien gefertigt, um spezifische Modelle oder Sonderanfertigungen abzudecken.
- Beispiel: Geräte zur Diagnose oder für chirurgische Anwendungen benötigen häufig Gehäuse aus tiefgezogenem Edelstahl, das leicht zu reinigen und zu sterilisieren ist.
- Spezielle Anforderungen: In einigen Fällen müssen die Gehäuse zusätzliche Funktionen wie Abschirmung gegen elektromagnetische Interferenzen (EMI) erfüllen, was durch den Einsatz spezieller Werkstoffe oder Beschichtungen erreicht wird.
2.2. Herstellung chirurgischer Instrumente
Chirurgische Instrumente müssen präzise gefertigt und sterilisiert werden können. Einige Teile dieser Instrumente werden aus tiefgezogenem Metall hergestellt, um eine nahtlose und hygienische Oberfläche zu gewährleisten.
- Beispiel: Chirurgische Klemmen, Scheren oder Endoskope können durch Tiefziehen in Kleinserien hergestellt werden, um die spezifischen Anforderungen einzelner Krankenhäuser oder medizinischer Einrichtungen zu erfüllen.
- Vorteil: Kleinserien ermöglichen es, Instrumente mit speziellen Anforderungen oder neuen Designs schnell auf den Markt zu bringen.
3. Luft- und Raumfahrtindustrie
Die Luft- und Raumfahrtindustrie erfordert leichte, aber stabile Strukturbauteile, die hohen Anforderungen an Präzision und Materialeigenschaften genügen müssen. Das Tiefziehen in Kleinserien ermöglicht die Herstellung solcher Bauteile in begrenzten Stückzahlen.
3.1. Strukturteile für Flugzeuge
In der Luftfahrt werden viele Strukturteile durch Tiefziehen aus Aluminium oder Titan gefertigt, um Gewicht zu sparen und gleichzeitig eine hohe Festigkeit zu gewährleisten.
- Beispiel: Strukturkomponenten wie Verkleidungselemente, Verstärkungen oder Triebwerksteile werden in Kleinserien produziert, um die spezifischen Anforderungen von Prototypen oder Sonderausführungen zu erfüllen.
- Nutzen: Kleinserienfertigung ermöglicht es, spezielle Teile für Flugzeugmodelle herzustellen, die nur in begrenzten Stückzahlen produziert werden, wie etwa Sonderflugzeuge oder Militärflugzeuge.
3.2. Raumfahrtanwendungen
In der Raumfahrt werden Bauteile benötigt, die extremen Bedingungen wie Vakuum, hohen Temperaturen und starken Vibrationen standhalten. Tiefgezogene Bauteile aus Speziallegierungen werden für diese anspruchsvollen Anwendungen in Kleinserien gefertigt.
- Beispiel: Gehäuse für elektronische Geräte an Bord von Raumfahrzeugen, Schutzabdeckungen oder Hitzeschilde können durch Tiefziehen in Kleinserien hergestellt werden, um den hohen Anforderungen an Material und Form gerecht zu werden.
4. Haushaltsgeräte und Konsumgüter
Für Haushaltsgeräte oder Konsumgüter, die in kleineren Serien oder als Sondereditionen auf den Markt kommen, eignet sich das Tiefziehen in Kleinserien hervorragend.
4.1. Sondermodelle von Haushaltsgeräten
Haushaltsgerätehersteller bieten oft spezielle Modellvarianten oder limitierte Editionen an, die in begrenzten Stückzahlen gefertigt werden. Diese Modelle können durch besondere Oberflächenbehandlungen, Materialien oder Designs individualisiert werden.
- Beispiel: Edelstahl-Küchengeräte, wie hochwertige Kühlschränke oder Geschirrspüler, werden in limitierter Auflage durch Tiefziehen hergestellt, um spezifische Designanforderungen zu erfüllen.
4.2. Individuelle Konsumgüter
Konsumgüter wie Behälter, Dosen oder dekorative Gegenstände können in Kleinserien produziert werden, um besonderen Designvorstellungen oder spezifischen Anwendungsanforderungen gerecht zu werden.
- Beispiel: Metallverpackungen für limitierte Sondereditionen von Getränken oder Lebensmitteln, wie spezielle Dosenformen oder Prägungen, werden durch Tiefziehen in Kleinserien gefertigt, um eine hochwertige und individuelle Optik zu erzielen.
5. Maschinenbau
Im Maschinenbau sind Sonderanfertigungen oder Ersatzteile oft in Kleinserien gefragt, insbesondere bei speziellen Maschinen oder Anlagen.
5.1. Gehäuse und Verkleidungen für Maschinen
Maschinengehäuse oder Schutzabdeckungen werden häufig aus tiefgezogenen Blechen gefertigt, um eine robuste und langlebige Hülle für empfindliche Maschinenteile zu bieten.
- Beispiel: Gehäuse für Sondermaschinen oder individuell angefertigte Werkzeugmaschinen werden in Kleinserien hergestellt, um den spezifischen Anforderungen des Endkunden zu entsprechen.
5.2. Herstellung von Sonderteilen oder Ersatzteilen
Wenn Maschinen in geringer Stückzahl oder für spezielle Anwendungen produziert werden, ist es oft notwendig, maßgeschneiderte Ersatzteile oder Sonderanfertigungen herzustellen.
- Beispiel: Tiefgezogene Teile, die als Ersatzkomponenten für ältere Maschinenmodelle dienen, können in Kleinserien produziert werden, um die Verfügbarkeit von Ersatzteilen sicherzustellen.
6. Bauindustrie
Auch im Bauwesen kommen tiefgezogene Bauteile in Kleinserien zum Einsatz, insbesondere für architektonische Verkleidungen, Fassadenelemente oder dekorative Konstruktionen.
6.1. Architektonische Verkleidungen und Fassadenelemente
Für architektonische Projekte werden oft individuelle Metallverkleidungen benötigt, die in Kleinserien durch Tiefziehen hergestellt werden, um den spezifischen Designanforderungen gerecht zu werden.
- Beispiel: Für anspruchsvolle Fassadengestaltungen können metallische Verkleidungen aus Aluminium oder Edelstahl tiefgezogen und in begrenzter Stückzahl gefertigt werden, um eine einzigartige Ästhetik zu erzielen.
6.2. Sonderbauteile für spezielle Konstruktionen
Bei der Errichtung spezieller Gebäude oder Bauwerke kann es erforderlich sein, maßgeschneiderte Bauteile wie Abdeckungen, Schutzbleche oder dekorative Elemente herzustellen.
- Beispiel: Schutzabdeckungen für architektonische Strukturen oder maßgefertigte Dachverkleidungen, die sich an die speziellen Anforderungen eines Projekts anpassen.
7. Elektro- und Elektronikindustrie
Für die Elektro- und Elektronikindustrie bietet das Tiefziehen in Kleinserien die Möglichkeit, spezifische Gehäuse und Verkleidungen herzustellen, die den Anforderungen an Stabilität, Abschirmung und Maßhaltigkeit genügen.
7.1. Gehäuse für spezielle elektronische Geräte
Elektronische Geräte, insbesondere in der Industrieelektronik oder Medizintechnik, erfordern oft maßgeschneiderte Gehäuse, die spezifische Funktionen wie Wärmeableitung oder elektromagnetische Abschirmung erfüllen.
- Beispiel: Gehäuse für Mess- und Prüfgeräte, die nur in kleinen Serien gefertigt werden, um spezielle Anforderungen oder Modelle abzudecken.
7.2. Batteriezellen und Akkus
Für spezielle Batteriemodelle oder Energiespeicher werden tiefgezogene Gehäuse benötigt, die in Kleinserien gefertigt werden, um den spezifischen Anforderungen von Hochleistungsanwendungen gerecht zu werden.
Zusammenfassung
Das Tiefziehen in Kleinserien ist ein flexibles und vielseitiges Verfahren, das für viele Industrien und spezielle Anwendungsfälle geeignet ist. Die Möglichkeit, maßgeschneiderte Bauteile in geringer Stückzahl zu fertigen, macht das Verfahren besonders attraktiv für Branchen wie die Automobilindustrie, Medizintechnik, Luft- und Raumfahrt, Haushaltsgeräte, Maschinenbau, Bauindustrie und Elektronik. Durch die fortschreitende Technologisierung und den Einsatz neuer Fertigungsmethoden wird die Bedeutung des Tiefziehens in Kleinserien weiter zunehmen und noch mehr spezialisierte Anwendungen ermöglichen.
Die umfassende Ausarbeitung der mathematischen Formeln und Berechnungen, die im Tiefziehprozess verwendet werden, kann in mehreren Abschnitten behandelt werden. Dabei werden grundlegende Konzepte, relevante Formeln und Berechnungsmethoden detailliert erläutert, um die theoretische Grundlage für das Tiefziehen zu schaffen und die wichtigsten technischen Parameter zu berücksichtigen.
1. Einführung in den Tiefziehprozess
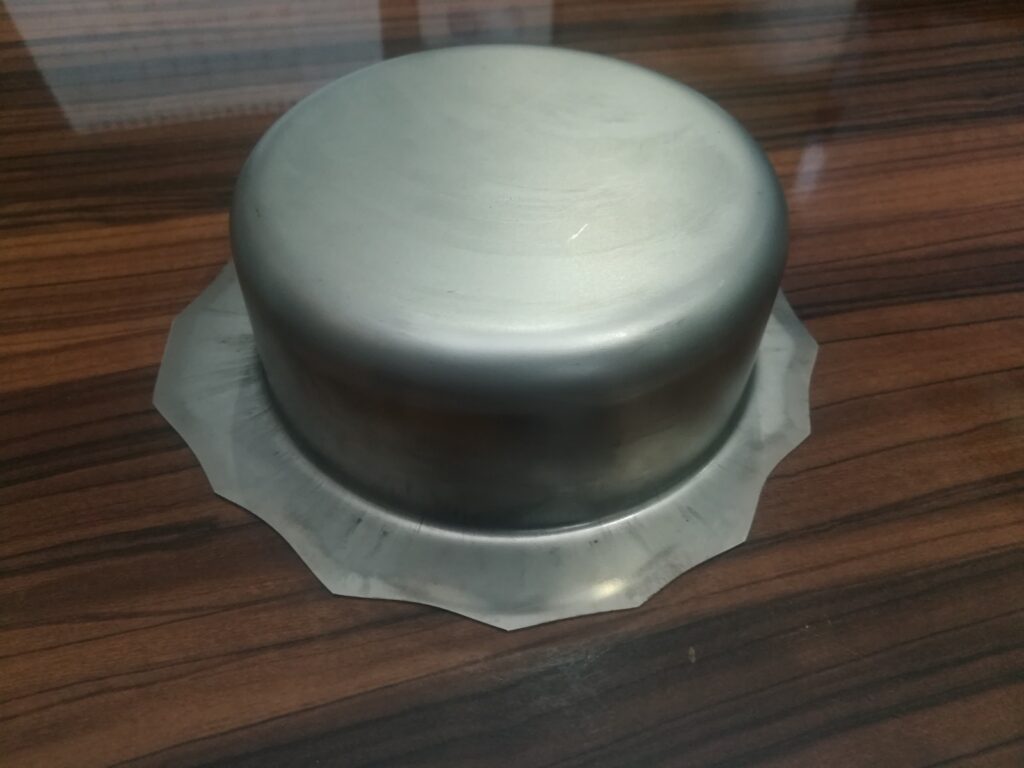
Das Tiefziehen ist ein Umformverfahren, bei dem eine flache Blechplatine durch einen Stempel in eine Matrize gedrückt wird, um eine hohle, dreidimensionale Form zu erzeugen. Das Verfahren ist besonders geeignet für die Herstellung von Bauteilen mit hohen Anforderungen an Maßhaltigkeit und Oberflächenqualität, wie in der Automobil-, Haushaltsgeräte- oder Luftfahrtindustrie. Um den Tiefziehprozess effektiv zu gestalten und Fehler wie Rissbildung oder Faltenbildung zu vermeiden, sind mathematische Berechnungen notwendig, die helfen, die Prozessparameter genau zu bestimmen.
2. Grundlegende Begriffe und Definitionen
2.1. Materialeigenschaften
Bei der Berechnung der Umformparameter sind die Materialeigenschaften von entscheidender Bedeutung:
- Streckgrenze (Re): Die Spannung, bei der das Material eine plastische Verformung beginnt.
- Zugfestigkeit (Rm): Die maximale Spannung, die das Material aushalten kann, bevor es bricht.
- Bruchdehnung (A): Die maximale Dehnung des Materials vor dem Bruch.
- Kaltverfestigungskoeffizient (n): Gibt an, wie stark sich das Material bei plastischer Verformung verfestigt.
2.2. Geometrische Parameter
Wichtige geometrische Parameter im Tiefziehprozess sind:
- Anfangsdurchmesser der Blechplatine (D0): Durchmesser der flachen Platine vor dem Umformen.
- Enddurchmesser der geformten Zylinderschale (D): Durchmesser des geformten Bauteils.
- Ziehtiefe (h): Tiefe des geformten Bauteils.
- Matrizendurchmesser (Dm): Durchmesser der Matrizenöffnung.
3. Berechnung des Ziehverhältnisses
Das Ziehverhältnis ist ein wichtiges Kriterium im Tiefziehprozess und bestimmt, wie tief ein Werkstück in einem einzigen Umformschritt gezogen werden kann.
3.1. Maximales Ziehverhältnis
Das maximale Ziehverhältnis gibt das Verhältnis zwischen dem Anfangsdurchmesser der Blechplatine und dem Durchmesser des geformten Werkstücks an. Es wird wie folgt berechnet:βmax=D0D\beta_{\text{max}} = \frac{D_0}{D}βmax=DD0
Hierbei ist:
- D0D_0D0: Anfangsdurchmesser der Blechplatine
- DDD: Enddurchmesser des Werkstücks
Das maximale Ziehverhältnis hängt stark von den Materialeigenschaften ab. Für gängige Materialien liegen die maximalen Ziehverhältnisse etwa bei:
- Weichaluminium: 2,5 bis 3,5
- Stahl: 2,0 bis 2,5
- Messing: 1,8 bis 2,2
3.2. Kritisches Ziehverhältnis
Das kritische Ziehverhältnis ist der Wert, bei dem das Risiko von Rissen oder Faltenbildung stark ansteigt. Dieser Wert liegt typischerweise bei etwa 60–70 % des maximalen Ziehverhältnisses.
4. Kraftberechnungen beim Tiefziehen
4.1. Berechnung der Umformkraft
Die Umformkraft (F) beim Tiefziehen kann durch die folgende Formel bestimmt werden:F=π⋅D0⋅s0⋅Rm⋅ln(D0D)F = \pi \cdot D_0 \cdot s_0 \cdot R_m \cdot \ln\left(\frac{D_0}{D}\right)F=π⋅D0⋅s0⋅Rm⋅ln(DD0)
Hierbei ist:
- s0s_0s0: Anfangsdicke der Blechplatine
- RmR_mRm: Zugfestigkeit des Materials
Diese Formel berücksichtigt die Materialeigenschaften und das Ziehverhältnis, um die erforderliche Umformkraft zu bestimmen.
4.2. Niederhalterkraft
Die Niederhalterkraft (F_n) ist erforderlich, um das Material an den Rändern der Blechplatine festzuhalten und Faltenbildung zu verhindern. Sie wird oft als Prozentsatz der Umformkraft angegeben, typischerweise 20–40 % der Umformkraft:Fn=k⋅FF_n = k \cdot FFn=k⋅F
wobei kkk ein Faktor zwischen 0,2 und 0,4 ist.
4.3. Stempelkraft
Die Stempelkraft (F_s) ist die gesamte Kraft, die auf den Stempel ausgeübt werden muss, um das Werkstück zu formen. Sie setzt sich aus der Umformkraft und der Niederhalterkraft zusammen:Fs=F+FnF_s = F + F_nFs=F+Fn
5. Berechnung der Wanddicke und der Materialverteilung
Während des Tiefziehprozesses wird die Wanddicke des geformten Bauteils beeinflusst, insbesondere in Bereichen mit starker Umformung.
5.1. Dickenreduktion
Die Dickenreduktion kann durch die folgende Formel bestimmt werden:s=s0⋅(1−hD0)s = s_0 \cdot \left(1 – \frac{h}{D_0}\right)s=s0⋅(1−D0h)
Hierbei ist:
- s0s_0s0: Anfangsdicke der Blechplatine
- sss: Wanddicke nach dem Umformen
- hhh: Ziehtiefe des Werkstücks
5.2. Berechnung der Materialverteilung
Die Materialverteilung hängt von der Geometrie des Bauteils und dem Verlauf der Umformung ab. Eine genaue Berechnung kann durch Simulationen oder spezielle analytische Verfahren durchgeführt werden.
6. Rückfederung und elastische Verformung
Nach dem Umformen tritt eine elastische Rückfederung auf, bei der das Material versucht, seine ursprüngliche Form teilweise wieder anzunehmen.
6.1. Rückfederungswinkel
Der Rückfederungswinkel (θr\theta_rθr) kann mit folgender Formel abgeschätzt werden:θr=σeE\theta_r = \frac{\sigma_e}{E}θr=Eσe
wobei:
- σe\sigma_eσe: Elastische Spannung
- EEE: Elastizitätsmodul des Materials
7. Berücksichtigung der Kaltverfestigung
Kaltverfestigung tritt auf, wenn das Material während der plastischen Verformung härter wird.
7.1. Einfluss der Kaltverfestigung auf die Umformkraft
Die Kaltverfestigung wird durch den Kaltverfestigungskoeffizienten (nnn) beschrieben. Die Umformkraft steigt proportional zur Verfestigung:Fkalt=F0⋅(1+n)F_{\text{kalt}} = F_0 \cdot (1 + n)Fkalt=F0⋅(1+n)
7.2. Berechnung der Kaltverfestigung
Die Kaltverfestigung kann mit folgender Formel berechnet werden:σkalt=K⋅ϵn\sigma_{\text{kalt}} = K \cdot \epsilon^nσkalt=K⋅ϵn
wobei:
- KKK: Festigkeitskoeffizient
- ϵ\epsilonϵ: plastische Dehnung
8. Schmierstoffeinfluss und Reibung
8.1. Berechnung der Reibungskraft
Die Reibungskraft (FrF_rFr) kann durch folgende Formel berechnet werden:Fr=μ⋅FnF_r = \mu \cdot F_nFr=μ⋅Fn
wobei:
- μ\muμ: Reibungskoeffizient
- FnF_nFn: Niederhalterkraft
8.2. Einfluss des Schmierstoffs
Ein geeigneter Schmierstoff kann den Reibungskoeffizienten verringern und somit die Umformkräfte reduzieren.
9. Beispiele und praktische Anwendungen
9.1. Beispielrechnung: Tiefziehen eines zylindrischen Bechers
Die Berechnungen umfassen alle Schritte, von der Bestimmung des Ziehverhältnisses über die Kraftberechnung bis hin zur Berücksichtigung von Rückfederung und Kaltverfestigung.
9.2. Vergleich verschiedener Materialien
Durch Vergleich der Materialeigenschaften (Stahl, Aluminium, Edelstahl) lassen sich Unterschiede in den Umformkräften und Prozessanforderungen analysieren.
Einführung in den Tiefziehprozess
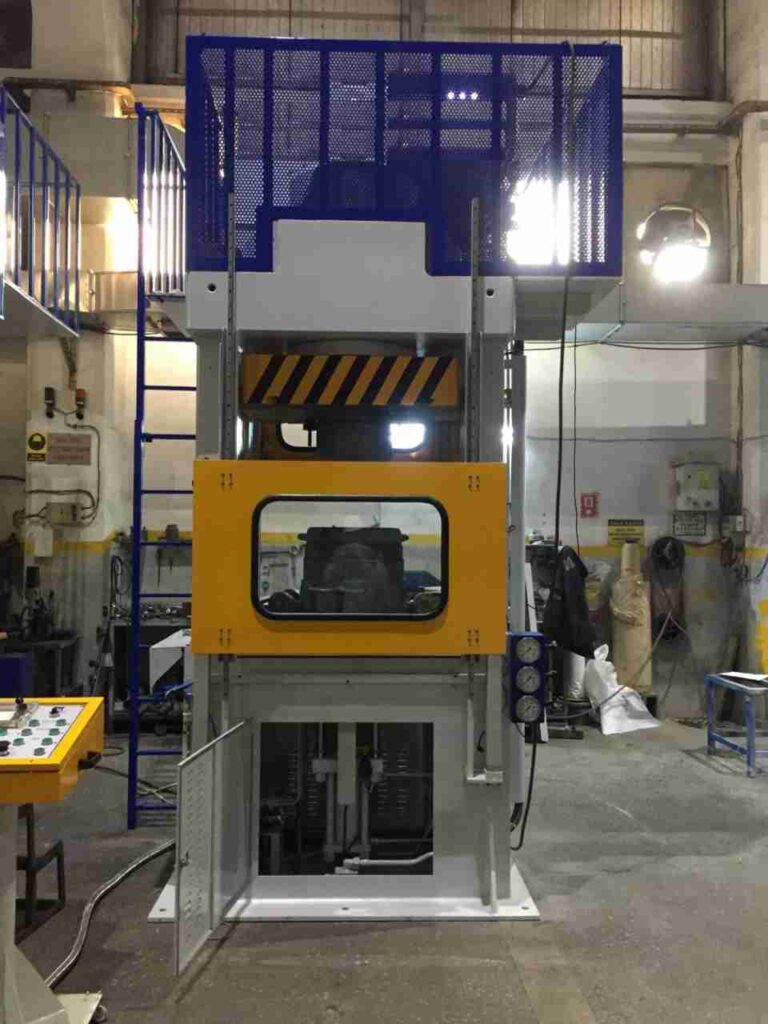
Der Tiefziehprozess ist ein weit verbreitetes Umformverfahren in der industriellen Fertigung, bei dem flache Blechplatinen durch einen Stempel in eine Matrize gedrückt werden, um hohle oder becherförmige Bauteile herzustellen. Dieser Prozess ermöglicht die Herstellung komplexer dreidimensionaler Geometrien mit hoher Maßgenauigkeit und eignet sich besonders für die Massenproduktion von Bauteilen, die eine gleichbleibende Qualität erfordern. Typische Anwendungen des Tiefziehens finden sich in der Automobilindustrie, der Herstellung von Haushaltsgeräten, der Luft- und Raumfahrt sowie der Medizintechnik.
Im Rahmen dieser Einführung werden die wichtigsten Aspekte des Tiefziehens erläutert, einschließlich der Grundlagen des Verfahrens, der physikalischen Prinzipien, der beteiligten Materialien, der Prozessparameter und der typischen Herausforderungen.
1. Grundlagen des Tiefziehens
Tiefziehen gehört zur Gruppe der Blechumformverfahren und wird als „Kaltumformung“ bezeichnet, da es bei Raumtemperatur durchgeführt wird. Dabei wird eine flache Blechplatine in eine Matrize gepresst, während ein Stempel das Blech von oben nach unten formt. Der Niederhalter, der auf den Rand der Blechplatine drückt, sorgt dafür, dass das Material gleichmäßig in die Matrize fließt und Faltenbildung verhindert wird.
1.1. Typische Geometrien und Anwendungen
Das Tiefziehen wird zur Herstellung vieler verschiedener Bauteile verwendet, von einfachen zylindrischen Bechern bis hin zu komplex geformten Karosserieteilen. Einige der häufigsten Anwendungen sind:
- Automobilteile: Karosseriekomponenten, wie Motorhauben, Kotflügel und Türen.
- Haushaltsgeräte: Gehäuse für Waschmaschinen und Trockner, Küchenspülen.
- Verpackungen: Dosen und Behälter aus Aluminium oder Weißblech.
- Medizintechnik: Gehäuse für medizinische Geräte und chirurgische Instrumente.
Diese Vielfalt an Anwendungen zeigt die Flexibilität des Tiefziehprozesses und dessen Fähigkeit, unterschiedlichste Anforderungen in Bezug auf Material, Geometrie und Produktionsvolumen zu erfüllen.
1.2. Abgrenzung zu anderen Umformverfahren
Das Tiefziehen unterscheidet sich von anderen Umformverfahren wie dem Biegen, Pressen oder Stanzen dadurch, dass es auf die Umformung flacher Bleche zu Hohlkörpern abzielt. Im Gegensatz zum Stanzen, bei dem Material entfernt wird, bleibt beim Tiefziehen das gesamte Material erhalten, während es in eine neue Form umverteilt wird.
2. Prinzip des Tiefziehens
Der Tiefziehprozess beruht auf der plastischen Verformung von Metall. Durch die Einwirkung von Kräften auf das Blech wird es aus seiner ursprünglichen Form heraus verformt, ohne dass es dabei zu Rissen oder Brüchen kommt. Die plastische Verformung tritt auf, wenn die Spannungen im Material die Streckgrenze überschreiten, sodass das Material dauerhaft in der neuen Form verbleibt.
2.1. Der Ablauf des Tiefziehprozesses
Der Tiefziehprozess besteht aus mehreren Schritten, die nacheinander ablaufen:
- Vorbereitung der Blechplatine: Eine flache Metallplatte, typischerweise aus Stahl, Aluminium, Kupfer oder Messing, wird auf die gewünschte Größe zugeschnitten.
- Positionierung: Die Blechplatine wird auf die Matrize gelegt, während der Niederhalter das Material an den Rändern fixiert, um Faltenbildung zu verhindern.
- Einpressen des Stempels: Der Stempel drückt das Blech in die Matrize und formt es in die gewünschte Form.
- Entformung: Nachdem das Bauteil die gewünschte Form erreicht hat, wird es aus der Matrize entnommen.
2.2. Wichtige Prozessparameter
Mehrere Prozessparameter beeinflussen die Qualität des Tiefziehprozesses:
- Ziehverhältnis: Das Verhältnis zwischen dem Durchmesser der ursprünglichen Blechplatine und dem Durchmesser des geformten Bauteils bestimmt, wie tief das Material in einem einzigen Zug gezogen werden kann.
- Umformkraft: Die benötigte Kraft hängt von den Materialeigenschaften, der Dicke des Blechs und der Geometrie des Bauteils ab.
- Niederhalterkraft: Diese Kraft verhindert Faltenbildung, indem sie das Material während des Tiefziehens gleichmäßig in die Matrize drückt.
- Schmierstoffe: Die Verwendung von Schmiermitteln reduziert die Reibung zwischen dem Blech und den Werkzeugen und verhindert Oberflächenschäden.
3. Physikalische Grundlagen des Tiefziehens
Der Tiefziehprozess basiert auf den Prinzipien der Materialverformung, insbesondere der plastischen Deformation. Wenn eine äußere Kraft auf ein Material einwirkt, verändert es seine Form. Die Verformung kann elastisch oder plastisch sein, abhängig davon, ob die Spannung unterhalb oder oberhalb der Streckgrenze liegt.
3.1. Elastische und plastische Verformung
- Elastische Verformung: Bei geringer Belastung kehrt das Material nach der Entlastung in seine ursprüngliche Form zurück. Diese Verformung ist reversibel.
- Plastische Verformung: Wenn die Belastung die Streckgrenze des Materials überschreitet, tritt eine dauerhafte Verformung auf. Dies ist der gewünschte Effekt beim Tiefziehen, da das Material seine neue Form beibehält.
3.2. Spannungen und Dehnungen
Während des Tiefziehens treten verschiedene Spannungen im Material auf:
- Zugspannung: Im Bereich, in dem das Blech gedehnt wird, wirken Zugspannungen, die das Material auseinanderziehen.
- Druckspannung: An den Rändern des geformten Teils treten Druckspannungen auf, die das Material zusammendrücken.
- Biegung: Das Blech wird um den Rand der Matrize gebogen, was sowohl Zug- als auch Druckspannungen verursacht.
4. Materialwahl und ihre Bedeutung im Tiefziehprozess
Die Wahl des Materials spielt eine entscheidende Rolle für den Erfolg des Tiefziehens. Materialien unterscheiden sich in ihren Eigenschaften, wie Festigkeit, Duktilität und Kaltverfestigung, was Auswirkungen auf die Umformbarkeit hat.
4.1. Gängige Materialien für das Tiefziehen
Typische Materialien, die im Tiefziehprozess verwendet werden, sind:
- Stahl: Weichstahl und hochfester Stahl sind häufig verwendete Materialien, da sie eine gute Kombination aus Umformbarkeit und Festigkeit bieten.
- Aluminium: Wegen seiner Leichtigkeit und Umformbarkeit wird Aluminium häufig in der Automobil- und Luftfahrtindustrie eingesetzt.
- Edelstahl: Für Anwendungen, die eine hohe Korrosionsbeständigkeit erfordern, wie in der Medizintechnik oder Lebensmittelindustrie, wird Edelstahl verwendet.
- Kupfer und Messing: Werden für spezielle Anwendungen genutzt, die eine hohe elektrische Leitfähigkeit oder spezifische dekorative Anforderungen haben.
4.2. Einfluss der Materialeigenschaften
- Streckgrenze: Eine niedrige Streckgrenze erleichtert das Tiefziehen, da das Material leichter verformt werden kann.
- Zugfestigkeit: Eine hohe Zugfestigkeit erhöht die Umformkräfte, kann aber auch die Stabilität des fertigen Bauteils verbessern.
- Duktilität: Materialien mit hoher Duktilität lassen sich stärker verformen, bevor sie reißen, was tiefere Ziehungen ermöglicht.
5. Prozessparameter und ihre Auswirkungen auf die Qualität
Um die Qualität des geformten Bauteils sicherzustellen, müssen die Prozessparameter optimal eingestellt werden.
5.1. Ziehverhältnis
Das Ziehverhältnis ist ein Schlüsselparameter, der angibt, wie stark das Material in einem einzigen Schritt umgeformt werden kann, ohne dass es zu Rissen kommt. Ein typischer Wert für das maximale Ziehverhältnis liegt bei 2,0 bis 2,5 für Stahl und 3,0 bis 3,5 für Aluminium.
5.2. Umformkraft und Niederhalterkraft
Die Umformkraft ist die Kraft, die notwendig ist, um das Blech in die Matrize zu ziehen, während die Niederhalterkraft auf den Rand des Blechs ausgeübt wird, um Faltenbildung zu verhindern. Eine falsche Einstellung dieser Kräfte kann zu Defekten wie Rissen, Faltenbildung oder unzureichender Formgebung führen.
5.3. Schmierung
Die Verwendung geeigneter Schmierstoffe ist entscheidend, um die Reibung zu verringern, die Umformkräfte zu reduzieren und Oberflächenschäden zu vermeiden. Schmierstoffe müssen auf das verwendete Material und die Prozessbedingungen abgestimmt werden.
6. Typische Fehler und deren Vermeidung
Beim Tiefziehen können verschiedene Fehler auftreten, die die Qualität des Bauteils beeinträchtigen.
6.1. Rissbildung
Risse entstehen, wenn das Material während der Umformung zu stark gedehnt wird. Die Vermeidung von Rissen erfordert eine genaue Kontrolle der Prozessparameter, insbesondere des Ziehverhältnisses und der Umformkraft.
6.2. Faltenbildung
Falten treten auf, wenn das Material an den Rändern nicht ausreichend fixiert ist. Eine erhöhte Niederhalterkraft kann helfen, die Faltenbildung zu verhindern, allerdings muss sie sorgfältig auf das Material abgestimmt werden, um andere Probleme zu vermeiden.
6.3. Rückfederung
Nach dem Umformen kann es dazu kommen, dass sich das Material teilweise in seine ursprüngliche Form zurückzieht, was als Rückfederung bezeichnet wird. Um die Maßhaltigkeit zu gewährleisten, muss die Rückfederung bei der Gestaltung der Werkzeuge berücksichtigt werden.
7. Weiterentwicklungen und zukünftige Trends im Tiefziehen
Die kontinuierliche Weiterentwicklung von Materialien und Werkzeugtechnologien hat dazu geführt, dass das Tiefziehen immer präziser und effizienter wird. Zukünftige Entwicklungen konzentrieren sich auf:
- Hybride Verfahren: Kombination von Tiefziehen mit anderen Umformtechniken, um komplexere Geometrien zu realisieren.
- Neue Materialtechnologien: Einsatz fortschrittlicher Legierungen und Beschichtungen, um die Umformbarkeit zu verbessern und den Verschleiß der Werkzeuge zu reduzieren.
- Simulationstechnologien: Einsatz digitaler Simulationen zur Optimierung der Prozessparameter und zur Vermeidung von Fehlern.
Zusammenfassung
Der Tiefziehprozess ist ein fundamentales Umformverfahren, das in vielen Industrien eine wichtige Rolle spielt. Die Einführung in das Verfahren zeigt die physikalischen Grundlagen, die Bedeutung der Materialeigenschaften, die wesentlichen Prozessparameter und die typischen Herausforderungen. Mit der richtigen Prozesssteuerung und kontinuierlichen Weiterentwicklungen bleibt das Tiefziehen eine unverzichtbare Technologie für die Herstellung komplexer und hochwertiger Bauteile.
Hydromechanisches Tiefziehen ist ein spezialisiertes Umformverfahren, das eine Variante des klassischen Tiefziehprozesses darstellt. Dabei wird der Tiefziehprozess durch den Einsatz einer druckbeaufschlagten Flüssigkeit (üblicherweise ein Hydrauliköl oder Wasser) unterstützt, um das Metall in die gewünschte Form zu bringen. Dieses Verfahren bietet gegenüber dem konventionellen Tiefziehen verschiedene Vorteile, wie eine bessere Formgebung und geringere Rückfederung, und eignet sich insbesondere für die Herstellung komplex geformter Teile oder Bauteile mit engen Toleranzen.
Diese ausführliche Abhandlung wird die Grundlagen, den Ablauf, die typischen Anwendungen, die Vor- und Nachteile sowie die technischen Herausforderungen des hydromechanischen Tiefziehens behandeln. Zudem werden die wichtigsten Prozessparameter, relevante mathematische Formeln, praktische Anwendungsbeispiele und zukünftige Entwicklungen in diesem Bereich aufgezeigt.
1. Grundlagen des hydromechanischen Tiefziehens
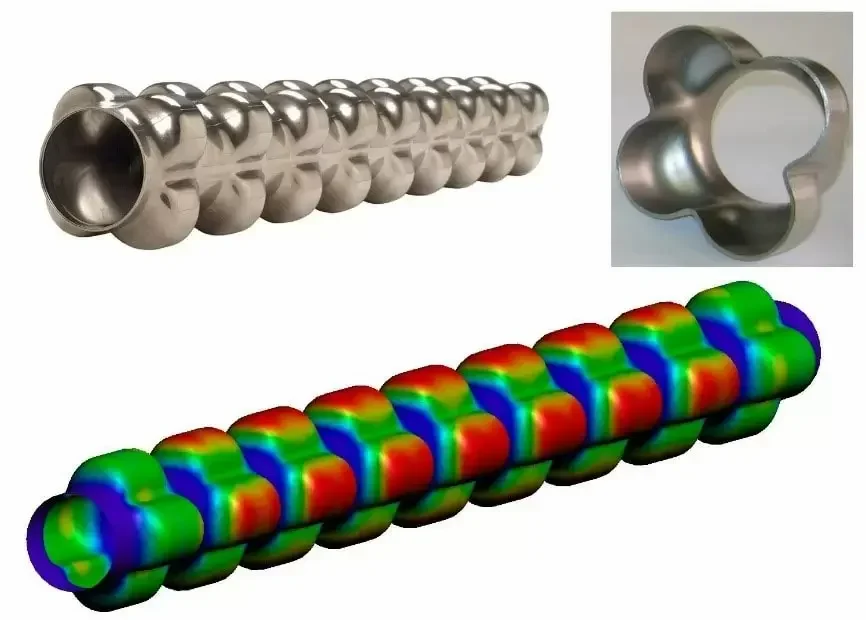
Hydromechanisches Tiefziehen kombiniert mechanische und hydraulische Kräfte, um die Umformung eines Blechwerkstücks zu erleichtern. Dabei wirkt zusätzlich zur mechanischen Einwirkung durch den Stempel ein hydraulischer Druck auf das Blech. Dieser Druck wird durch eine Flüssigkeit erzeugt, die unter der Platine in der Matrize eingeschlossen ist. Während der Stempel das Blech in die Form drückt, wirkt der hydraulische Druck auf die Rückseite des Blechs, wodurch der Materialfluss verbessert und Defekte wie Faltenbildung oder Risse minimiert werden.
1.1. Historische Entwicklung
Die Technologie des hydromechanischen Tiefziehens wurde entwickelt, um die Grenzen des konventionellen Tiefziehens zu überwinden. Insbesondere für die Herstellung komplex geformter Teile aus schwer umformbaren Materialien wie Edelstahl und hochfesten Stählen wurde das Verfahren in den letzten Jahrzehnten kontinuierlich weiterentwickelt. Die ersten industriellen Anwendungen entstanden in der Luft- und Raumfahrt sowie der Automobilindustrie.
1.2. Abgrenzung zum konventionellen Tiefziehen
Beim konventionellen Tiefziehen wird die Blechplatine allein durch den mechanischen Druck eines Stempels geformt, während beim hydromechanischen Tiefziehen zusätzlich ein kontrollierter hydraulischer Druck auf das Blech ausgeübt wird. Dadurch wird der Materialfluss verbessert und das Risiko von Formfehlern verringert. Die Flüssigkeit wirkt im hydromechanischen Verfahren als „flüssiger Niederhalter“, der das Blech gleichmäßig in die Form drückt.
2. Ablauf des hydromechanischen Tiefziehens
Der hydromechanische Tiefziehprozess lässt sich in mehrere Schritte unterteilen, die je nach spezifischen Anforderungen und Maschinenkonfigurationen variieren können.
2.1. Vorbereitung der Blechplatine
Zunächst wird eine flache Blechplatine auf die Matrize gelegt. Die Materialwahl hängt von den Anforderungen an das fertige Bauteil ab, wobei häufig Materialien wie Aluminium, Edelstahl, Titan oder hochfeste Stähle zum Einsatz kommen.
2.2. Einbringen des hydraulischen Drucks
Nachdem die Blechplatine positioniert wurde, wird eine Flüssigkeit unter Druck in die Matrize eingeführt. Der Druck der Flüssigkeit kann während des gesamten Umformvorgangs variiert werden, um den Materialfluss optimal zu steuern.
2.3. Einpressen des Stempels
Der Stempel drückt das Blech in die Matrize. Gleichzeitig übt die Flüssigkeit einen Gegendruck auf die Unterseite der Blechplatine aus. Dies sorgt dafür, dass das Material gleichmäßig verteilt wird und die Gefahr von Faltenbildung, Rissen oder Rückfederung reduziert wird.
2.4. Entformung
Nach Abschluss des Umformvorgangs wird der Stempel zurückgezogen, und der Druck in der Flüssigkeit wird abgelassen, um das geformte Bauteil aus der Matrize zu entnehmen. Der hydraulische Druck sorgt hierbei auch für eine gleichmäßige Entformung ohne Beschädigung des Bauteils.
3. Prozessparameter des hydromechanischen Tiefziehens
Die Steuerung und Optimierung der Prozessparameter ist entscheidend für den Erfolg des hydromechanischen Tiefziehens. Zu den wichtigsten Parametern gehören der hydraulische Druck, die Umformgeschwindigkeit, die Stempelkraft und die Niederhalterkraft.
3.1. Hydraulischer Druck
Der hydraulische Druck ist der wichtigste Unterschied zum konventionellen Tiefziehen. Er wird typischerweise im Bereich von 10 bis 200 MPa eingestellt, abhängig von Material, Dicke und Geometrie des Bauteils. Der Druck muss sorgfältig gesteuert werden, um eine gleichmäßige Umformung zu gewährleisten.
3.2. Umformgeschwindigkeit
Die Umformgeschwindigkeit beeinflusst die Qualität der Umformung. Eine langsame Umformgeschwindigkeit kann dazu beitragen, die Umformkräfte zu verringern und die Materialverteilung zu verbessern, insbesondere bei komplexen Geometrien.
3.3. Stempelkraft
Die Stempelkraft muss ausreichend hoch sein, um das Blech in die Matrize zu drücken, ohne das Material zu beschädigen. Die Stempelkraft wird in Kombination mit dem hydraulischen Druck genutzt, um die Formgebung zu optimieren.
3.4. Niederhalterkraft
Die Niederhalterkraft ist wichtig, um das Material an Ort und Stelle zu halten und Faltenbildung zu vermeiden. Im hydromechanischen Tiefziehen kann die Flüssigkeit selbst teilweise die Rolle des Niederhalters übernehmen.
4. Typische Anwendungen des hydromechanischen Tiefziehens
Das hydromechanische Tiefziehen wird in verschiedenen Industriezweigen eingesetzt, in denen Bauteile mit komplexer Geometrie, hohen Anforderungen an Maßgenauigkeit und Oberflächenqualität oder aus schwer umformbaren Materialien hergestellt werden.
4.1. Automobilindustrie
In der Automobilindustrie wird das hydromechanische Tiefziehen zur Herstellung von Strukturbauteilen, Karosseriekomponenten und Motorteilen verwendet, die eine hohe Maßhaltigkeit und Festigkeit erfordern. Typische Anwendungen sind:
- Motorhauben und Karosseriekomponenten: Die Verbesserung der Materialverteilung ermöglicht eine präzisere Formgebung und reduziert die Rückfederung.
- Sicherheitsrelevante Bauteile: Bauteile wie Verstärkungsbleche oder Strukturkomponenten profitieren von der hohen Präzision und Festigkeit des hydromechanischen Tiefziehens.
4.2. Luft- und Raumfahrtindustrie
In der Luft- und Raumfahrt werden Bauteile aus Aluminium, Titan und hochfesten Legierungen benötigt, die extremen Bedingungen standhalten müssen. Hydromechanisches Tiefziehen bietet die Möglichkeit, dünnwandige, leichte und stabile Strukturen herzustellen.
- Strukturbauteile für Flugzeuge: Hydromechanisch tiefgezogene Bauteile werden für Flugzeugverkleidungen, Triebwerkskomponenten und Verstärkungsstrukturen eingesetzt.
- Raumfahrtanwendungen: Komponenten für Raumfahrzeuge, die hohen Temperaturen und Vibrationen standhalten müssen, werden oft durch hydromechanisches Tiefziehen gefertigt.
4.3. Medizintechnik
In der Medizintechnik sind Bauteile gefragt, die aus korrosionsbeständigen und biokompatiblen Materialien bestehen, wie Edelstahl oder Titan. Hydromechanisches Tiefziehen eignet sich gut für die Herstellung von medizinischen Geräten, chirurgischen Instrumenten und Implantaten.
- Gehäuse für medizinische Geräte: Komplexe Geometrien und enge Toleranzen sind für medizinische Anwendungen entscheidend, was durch hydromechanisches Tiefziehen erreicht werden kann.
- Chirurgische Instrumente: Die glatte Oberfläche und die präzise Formgebung des Verfahrens eignen sich ideal für Instrumente, die hohe hygienische Standards erfüllen müssen.
4.4. Haushaltsgeräte
In der Haushaltsgeräteindustrie wird hydromechanisches Tiefziehen verwendet, um ästhetisch ansprechende und funktionale Bauteile herzustellen.
- Küchenspülen: Edelstahlspülen werden häufig durch hydromechanisches Tiefziehen gefertigt, um eine nahtlose, hygienische und korrosionsbeständige Oberfläche zu gewährleisten.
- Dekorative Abdeckungen: Hydromechanisches Tiefziehen ermöglicht die Herstellung von dekorativen Gehäusen und Abdeckungen für Haushaltsgeräte.
5. Vorteile des hydromechanischen Tiefziehens
Das hydromechanische Tiefziehen bietet mehrere Vorteile gegenüber dem konventionellen Tiefziehen.
5.1. Bessere Materialverteilung
Der hydraulische Druck unterstützt den Materialfluss, was eine gleichmäßigere Verteilung des Materials ermöglicht. Dadurch wird die Gefahr von Materialversagen, wie Rissen oder Faltenbildung, reduziert.
5.2. Höhere Umformtiefe
Durch den zusätzlichen hydraulischen Druck können größere Umformtiefen erreicht werden, ohne dass es zu Materialversagen kommt. Dies ist besonders bei der Umformung von hochfesten Materialien von Vorteil.
5.3. Geringere Rückfederung
Die gleichmäßige Druckverteilung durch die Flüssigkeit reduziert die Rückfederung des Materials nach dem Umformprozess. Dies trägt zu einer besseren Maßhaltigkeit des fertigen Bauteils bei.
5.4. Verbesserte Oberflächenqualität
Der hydraulische Druck verringert die Reibung zwischen dem Blech und den Werkzeugen, was zu einer glatteren Oberfläche des geformten Bauteils führt.
6. Herausforderungen und Nachteile des hydromechanischen Tiefziehens
Trotz der vielen Vorteile gibt es auch einige Herausforderungen und potenzielle Nachteile, die beim hydromechanischen Tiefziehen berücksichtigt werden müssen.
6.1. Höhere Maschinenkosten
Hydromechanische Tiefziehmaschinen sind komplexer und teurer als konventionelle Tiefziehmaschinen, da sie zusätzlich zur mechanischen Umformung auch ein hydraulisches System benötigen.
6.2. Wartung und Betriebskosten
Die Wartung der hydraulischen Komponenten kann aufwändig sein, und der Betrieb von hydraulischen Systemen erfordert zusätzliche Energie, was die Betriebskosten erhöht.
6.3. Begrenzte Materialauswahl
Nicht alle Materialien sind für das hydromechanische Tiefziehen geeignet. Bestimmte Legierungen, die zu spröde oder zu duktil sind, können Schwierigkeiten bei der Umformung bereiten.
7. Mathematische Formeln und Berechnungen
Die Berechnungen beim hydromechanischen Tiefziehen umfassen die Bestimmung des hydraulischen Drucks, der Umformkraft und der Materialverteilung. Die wichtigsten Formeln sind:
7.1. Hydraulischer Druck
Der erforderliche hydraulische Druck ppp kann wie folgt berechnet werden:p=FAp = \frac{F}{A}p=AF
wobei:
- FFF: Umformkraft
- AAA: Fläche, auf die der Druck wirkt
7.2. Umformkraft
Die Umformkraft beim hydromechanischen Tiefziehen kann durch die folgende Formel bestimmt werden:F=π⋅D0⋅s0⋅Rm⋅ln(D0D)+p⋅AF = \pi \cdot D_0 \cdot s_0 \cdot R_m \cdot \ln\left(\frac{D_0}{D}\right) + p \cdot AF=π⋅D0⋅s0⋅Rm⋅ln(DD0)+p⋅A
Hierbei ist:
- D0D_0D0: Anfangsdurchmesser der Blechplatine
- s0s_0s0: Anfangsdicke der Blechplatine
- RmR_mRm: Zugfestigkeit des Materials
8. Zukunftsaussichten und technologische Entwicklungen
Die Weiterentwicklung von Materialtechnologien, hydraulischen Systemen und digitalen Steuerungstechniken wird das hydromechanische Tiefziehen weiter verbessern und neue Anwendungsbereiche erschließen.
8.1. Einsatz von Simulationstechnologien
Digitale Simulationen helfen, den Umformprozess vorab zu optimieren, was die Fehlerrate reduziert und die Effizienz steigert.
8.2. Hybridverfahren
Die Kombination von hydromechanischem Tiefziehen mit anderen Verfahren, wie dem Innenhochdruckumformen, ermöglicht die Herstellung von noch komplexeren Bauteilen.
Zusammenfassung
Hydromechanisches Tiefziehen ist ein leistungsfähiges Umformverfahren, das eine Vielzahl von Vorteilen bietet, insbesondere für komplexe Bauteilgeometrien und schwer umformbare Materialien. Die technologischen Fortschritte und kontinuierliche Weiterentwicklung dieses Verfahrens werden dazu beitragen, seine Anwendungen in verschiedenen Industrien weiter auszubauen.
Grundlagen des hydromechanischen Tiefziehens
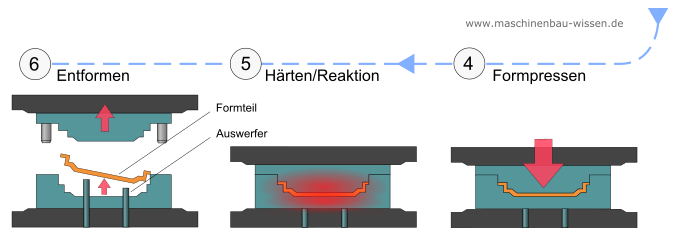
Das hydromechanische Tiefziehen ist ein fortschrittliches Umformverfahren, bei dem mechanische und hydraulische Kräfte kombiniert werden, um eine Blechplatine in eine gewünschte Form zu bringen. Dieses Verfahren geht über das klassische Tiefziehen hinaus, indem es eine druckbeaufschlagte Flüssigkeit nutzt, um den Umformprozess zu unterstützen. Diese Technologie ermöglicht die Herstellung komplexer und hochpräziser Bauteile, die im konventionellen Tiefziehprozess schwer zu realisieren sind. Die Anwendung des hydromechanischen Tiefziehens findet sich in zahlreichen Industrien, insbesondere dort, wo hohe Anforderungen an Maßhaltigkeit und Oberflächenqualität gestellt werden, wie in der Automobilindustrie, der Luft- und Raumfahrt sowie der Medizintechnik.
1. Einführung und Prinzipien des hydromechanischen Tiefziehens
1.1. Definition und Funktionsweise
Beim hydromechanischen Tiefziehen wird eine Blechplatine durch einen Stempel in eine Matrize gedrückt, ähnlich wie beim klassischen Tiefziehen. Der entscheidende Unterschied besteht darin, dass unter der Blechplatine eine hydraulische Flüssigkeit als „flüssiger Niederhalter“ wirkt, der während des Umformprozesses einen kontrollierten Druck auf die Unterseite des Blechs ausübt. Dieser hydraulische Druck sorgt dafür, dass das Material gleichmäßig in die Matrize fließt und dabei besser gestützt wird, was die Gefahr von Formfehlern wie Faltenbildung, Rissen und Rückfederung deutlich reduziert.
Die Kombination aus mechanischen und hydraulischen Kräften führt zu einer verbesserten Materialverteilung und ermöglicht eine höhere Umformtiefe sowie eine genauere Formgebung. Besonders bei Bauteilen mit komplexen Geometrien oder bei schwer umformbaren Materialien wie hochfesten Stählen und Titanlegierungen bietet das hydromechanische Tiefziehen erhebliche Vorteile.
1.2. Historische Entwicklung und Anwendungsbereiche
Das hydromechanische Tiefziehen wurde entwickelt, um die Grenzen des konventionellen Tiefziehens zu erweitern und Formfehler sowie Materialversagen zu minimieren. Erste Anwendungen wurden in der Luft- und Raumfahrtindustrie eingesetzt, um anspruchsvolle Bauteile aus hochfesten Materialien herzustellen. Später wurde die Technologie auch in anderen Bereichen, wie der Automobilindustrie, der Medizintechnik und der Haushaltsgeräteindustrie, verbreitet.
Typische Anwendungsbereiche des hydromechanischen Tiefziehens umfassen:
- Automobilindustrie: Herstellung von Strukturbauteilen, Karosseriekomponenten und Motorabdeckungen.
- Luft- und Raumfahrt: Produktion von dünnwandigen, leichten Strukturbauteilen, Triebwerksteilen und Hitzeschilden.
- Medizintechnik: Fertigung von chirurgischen Instrumenten, Implantaten und Gehäusen für medizinische Geräte.
- Haushaltsgeräteindustrie: Herstellung von dekorativen und funktionalen Bauteilen wie Küchenspülen und Gehäusen.
2. Vergleich zum konventionellen Tiefziehen
Das konventionelle Tiefziehen nutzt ausschließlich mechanische Kräfte, bei denen ein Stempel die Blechplatine in eine Matrize drückt. Die Niederhalterkraft wird durch einen festen mechanischen Niederhalter ausgeübt, um Faltenbildung zu verhindern. Im hydromechanischen Tiefziehen hingegen wird ein hydraulischer Druck verwendet, der während des gesamten Umformvorgangs auf das Blech wirkt. Diese hydraulische Unterstützung bietet mehrere Vorteile:
2.1. Unterschiede in der Kraftübertragung
- Konventionelles Tiefziehen: Der mechanische Stempel übt die alleinige Umformkraft aus, während der Niederhalter das Material am Rand fixiert.
- Hydromechanisches Tiefziehen: Zusätzlich zur Stempelkraft wird der hydraulische Druck als unterstützende Kraft eingesetzt, um das Material gleichmäßig in die Matrize zu drücken. Dadurch werden Zugspannungen reduziert und die Gefahr von Materialfehlern minimiert.
2.2. Bessere Materialverteilung und Umformtiefe
Durch die gleichmäßige Druckverteilung wird das Material im hydromechanischen Tiefziehen besser gestützt und verteilt, was größere Umformtiefen ermöglicht. Dies ist besonders vorteilhaft bei Bauteilen mit steilen Wänden, komplexen Geometrien oder Materialien mit begrenzter Umformbarkeit.
2.3. Verringerte Rückfederung
Beim hydromechanischen Tiefziehen wird die Rückfederung des Materials aufgrund des gleichmäßigen hydraulischen Drucks reduziert. Dies trägt zu einer besseren Maßhaltigkeit und Formgenauigkeit bei, was besonders bei engen Toleranzen von Vorteil ist.
3. Technische Komponenten des hydromechanischen Tiefziehens
Das hydromechanische Tiefziehen erfordert spezialisierte Maschinen und Werkzeuge, die sowohl mechanische als auch hydraulische Komponenten umfassen.
3.1. Hydraulische Druckeinheit
Eine zentrale Komponente des Verfahrens ist die hydraulische Druckeinheit, die den erforderlichen Druck auf die Blechplatine ausübt. Diese Einheit besteht aus einer Hydraulikpumpe, Druckventilen und einem Reservoir für die hydraulische Flüssigkeit (oft Hydrauliköl oder Wasser). Der Druck kann während des Umformvorgangs dynamisch angepasst werden, um den Materialfluss zu optimieren.
3.2. Matrize mit integrierter Hydraulik
Die Matrize im hydromechanischen Tiefziehen ist so konstruiert, dass sie die hydraulische Flüssigkeit aufnehmen kann. In der Regel enthält die Matrize Kanäle oder Kammern, durch die die Flüssigkeit unter Druck auf die Blechunterseite wirkt. Dieser hydraulische Druckbereich muss sorgfältig abgedichtet sein, um ein Entweichen der Flüssigkeit zu verhindern.
3.3. Stempel
Der Stempel im hydromechanischen Tiefziehen erfüllt die gleiche Funktion wie beim konventionellen Tiefziehen: Er drückt das Blech in die Matrize, um die gewünschte Form zu erzeugen. Allerdings wirkt der Stempel hier in Kombination mit dem hydraulischen Druck, wodurch geringere mechanische Umformkräfte erforderlich sind.
3.4. Steuerungssysteme
Moderne hydromechanische Tiefziehmaschinen sind mit computergesteuerten Steuerungssystemen ausgestattet, die den Druck, die Geschwindigkeit des Stempels und andere Parameter präzise regulieren. Diese Systeme ermöglichen es, den Umformprozess in Echtzeit zu überwachen und anzupassen, um die bestmögliche Qualität des geformten Bauteils zu gewährleisten.
4. Prozessparameter beim hydromechanischen Tiefziehen
Für den Erfolg des hydromechanischen Tiefziehens ist die präzise Steuerung der Prozessparameter entscheidend. Die wichtigsten Parameter sind:
4.1. Hydraulischer Druck
Der hydraulische Druck ist der Schlüsselfaktor, der das Verfahren vom konventionellen Tiefziehen unterscheidet. Der Druck kann je nach Material und Bauteilgeometrie zwischen 10 und 200 MPa betragen. Zu niedriger Druck kann zu unzureichender Materialstützung und Formfehlern führen, während zu hoher Druck das Risiko von Materialversagen erhöht.
4.2. Umformgeschwindigkeit
Die Geschwindigkeit, mit der der Stempel das Blech in die Matrize drückt, beeinflusst die Qualität des Umformvorgangs. Eine langsame Umformgeschwindigkeit verringert die Umformkräfte und reduziert die Wahrscheinlichkeit von Defekten, erfordert jedoch mehr Zeit für den Prozess.
4.3. Stempelkraft
Die Stempelkraft muss sorgfältig eingestellt werden, um das Material in die Matrize zu drücken, ohne das Blech zu überlasten. Die Kombination von Stempelkraft und hydraulischem Druck führt zu einer gleichmäßigen Formgebung.
4.4. Niederhalterkraft
Obwohl der hydraulische Druck als „flüssiger Niederhalter“ fungiert, ist auch die Niederhalterkraft weiterhin relevant. Sie muss so eingestellt sein, dass das Blech stabilisiert wird, ohne den Materialfluss zu behindern.
5. Materialien für das hydromechanische Tiefziehen
Nicht alle Materialien eignen sich gleichermaßen gut für das hydromechanische Tiefziehen. Die Materialwahl hängt von den Anforderungen an das Bauteil ab, einschließlich Festigkeit, Umformbarkeit und Oberflächenqualität.
5.1. Typische Materialien
- Aluminium: Aufgrund seiner leichten Umformbarkeit und geringen Dichte wird Aluminium häufig im hydromechanischen Tiefziehen eingesetzt, besonders in der Automobil- und Luftfahrtindustrie.
- Edelstahl: Für Anwendungen, die Korrosionsbeständigkeit und hohe Festigkeit erfordern, ist Edelstahl ein geeignetes Material. Das hydromechanische Tiefziehen ermöglicht tiefere Züge und komplexere Formen.
- Titan: Titanlegierungen sind aufgrund ihrer hohen Festigkeit und Beständigkeit gegenüber extremen Bedingungen ideal für die Luft- und Raumfahrt sowie die Medizintechnik. Das hydromechanische Tiefziehen reduziert das Risiko von Rissen bei der Umformung.
- Hochfeste Stähle: Diese Materialien finden Anwendung in sicherheitskritischen Bereichen wie der Automobilindustrie, wo Strukturbauteile hohe Belastungen aushalten müssen.
5.2. Einfluss der Materialeigenschaften
Die Umformbarkeit eines Materials hängt von seinen mechanischen Eigenschaften ab:
- Streckgrenze: Materialien mit niedriger Streckgrenze lassen sich leichter umformen, da sie weniger Kraft erfordern, um die plastische Verformung zu erreichen.
- Zugfestigkeit: Eine hohe Zugfestigkeit führt zu höheren Umformkräften, bietet jedoch eine größere Stabilität im geformten Zustand.
- Duktilität: Materialien mit hoher Duktilität können größere Dehnungen aushalten, bevor sie reißen, was tiefere Züge ermöglicht.
6. Vorteile und Herausforderungen des hydromechanischen Tiefziehens
6.1. Vorteile
- Verbesserte Materialverteilung: Der hydraulische Druck sorgt für eine gleichmäßige Verformung des Materials, was die Materialverteilung verbessert.
- Höhere Umformtiefe: Das Verfahren ermöglicht tiefere Züge ohne das Risiko von Materialversagen.
- Reduzierte Rückfederung: Die Maßhaltigkeit des geformten Bauteils wird durch die verringerte Rückfederung verbessert.
- Bessere Oberflächenqualität: Der gleichmäßige hydraulische Druck minimiert Oberflächenschäden durch Reibung.
6.2. Herausforderungen
- Höhere Maschinen- und Betriebskosten: Hydromechanische Tiefziehmaschinen sind teurer in der Anschaffung und erfordern regelmäßige Wartung.
- Komplexe Prozesssteuerung: Die optimale Steuerung des hydraulischen Drucks erfordert präzise Einstellungen und fortschrittliche Steuerungssysteme.
- Begrenzte Materialauswahl: Nicht alle Materialien sind für das hydromechanische Tiefziehen geeignet, insbesondere sehr spröde oder extrem duktilen Materialien.
7. Anwendungen und Zukunftsaussichten
Das hydromechanische Tiefziehen ist eine Schlüsseltechnologie für Industrien, die komplexe und präzise Bauteile benötigen. Die Weiterentwicklung von Material- und Fertigungstechnologien wird das Verfahren noch effizienter und vielseitiger machen.
7.1. Digitalisierung und Simulation
Die Integration von digitalen Technologien und Simulationstools in den Umformprozess wird es ermöglichen, die Prozessparameter im Voraus zu optimieren und die Produktqualität zu verbessern.
7.2. Kombination mit anderen Verfahren
Die Kombination von hydromechanischem Tiefziehen mit anderen Umform- und Fertigungstechniken, wie dem Innenhochdruckumformen, eröffnet neue Möglichkeiten zur Herstellung komplexer Bauteile.
Zusammenfassung
Das hydromechanische Tiefziehen ist ein innovatives Umformverfahren, das mechanische und hydraulische Kräfte kombiniert, um komplexe Bauteile mit hoher Präzision und Maßhaltigkeit herzustellen. Es bietet erhebliche Vorteile gegenüber dem konventionellen Tiefziehen, insbesondere bei der Umformung schwer umformbarer Materialien oder bei der Herstellung komplexer Geometrien. Trotz der Herausforderungen in Bezug auf Maschinenkosten und Prozesssteuerung bleibt das hydromechanische Tiefziehen eine wichtige Technologie mit wachsender Bedeutung in der modernen Fertigungsindustrie.
Şunu dedin:
Ablauf des hydromechanischen Tiefziehens
ChatGPT:
Der Ablauf des hydromechanischen Tiefziehens ist ein komplexer Umformprozess, bei dem mechanische und hydraulische Kräfte kombiniert werden, um ein flaches Blech in eine gewünschte Form zu bringen. Im Vergleich zum konventionellen Tiefziehen wird beim hydromechanischen Verfahren ein zusätzliches hydraulisches Druckmedium eingesetzt, das während des gesamten Umformprozesses auf die Unterseite des Blechs wirkt. Dies verbessert den Materialfluss und führt zu einer gleichmäßigen Umformung mit geringerer Rückfederung und besseren Oberflächenqualitäten.
1. Vorbereitung der Blechplatine
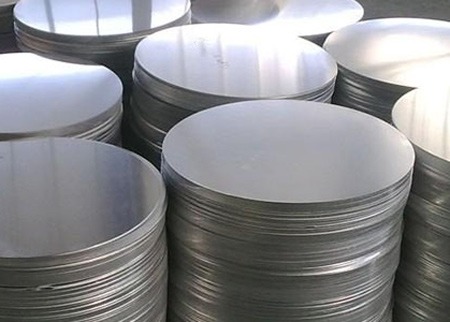
1.1. Materialauswahl und Zuschnitt
Der erste Schritt im hydromechanischen Tiefziehprozess besteht darin, eine geeignete Blechplatine auszuwählen und auf die erforderliche Größe zuzuschneiden. Das Material der Blechplatine hängt von den spezifischen Anforderungen des zu fertigenden Bauteils ab, einschließlich der Festigkeit, Duktilität und Korrosionsbeständigkeit. Häufig verwendete Materialien sind:
- Aluminium: Leicht und gut umformbar, besonders in der Automobil- und Luftfahrtindustrie beliebt.
- Edelstahl: Korrosionsbeständig und stark, ideal für Anwendungen in der Medizintechnik und bei Haushaltsgeräten.
- Hochfeste Stähle und Titan: Für Anwendungen, bei denen hohe mechanische Festigkeit und geringes Gewicht erforderlich sind, wie z. B. in der Luft- und Raumfahrt.
Die Platine wird so zugeschnitten, dass sie die richtige Größe für den vorgesehenen Umformprozess hat. Die Form und Dicke des Ausgangsblechs hängen von der geplanten Geometrie des Endprodukts ab.
1.2. Reinigung und Schmierung
Vor dem Umformprozess wird die Blechplatine gereinigt, um Schmutz, Fett und andere Verunreinigungen zu entfernen, die den Umformprozess beeinträchtigen könnten. Anschließend wird ein Schmierstoff aufgetragen, um die Reibung zwischen Blech, Stempel und Matrize zu verringern und die Oberflächenqualität des geformten Bauteils zu verbessern.
2. Einbringen der Blechplatine in die Matrize
2.1. Positionierung der Blechplatine
Die vorbereitete Blechplatine wird auf die Matrize gelegt. Die Matrize ist speziell gestaltet, um die gewünschte Form des Endprodukts zu ermöglichen und gleichzeitig die hydraulische Druckkammer für das Umformmedium (Hydraulikflüssigkeit oder Wasser) bereitzustellen. Eine präzise Positionierung der Platine ist wichtig, um eine gleichmäßige Umformung sicherzustellen.
2.2. Abdichtung der Druckkammer
Nachdem die Platine auf die Matrize gelegt wurde, wird die Druckkammer abgedichtet, um das hydraulische Medium sicher einzuschließen. Die Abdichtung ist entscheidend, da sie verhindert, dass das Druckmedium während des Umformprozesses entweicht, was zu einem Druckverlust und einer Beeinträchtigung der Umformqualität führen könnte.
3. Einleiten des hydraulischen Drucks
3.1. Aufbau des Hydraulikdrucks
Im nächsten Schritt wird das hydraulische Druckmedium (z. B. Hydrauliköl oder Wasser) in die Druckkammer eingefüllt. Durch die Druckeinheit wird der erforderliche Druck aufgebaut, der die Blechunterseite stützt und eine gleichmäßige Umformung ermöglicht. Der Druck kann typischerweise im Bereich von 10 bis 200 MPa variieren, abhängig von den Eigenschaften des Materials und der Form des Bauteils.
3.2. Funktion des hydraulischen Drucks
Der hydraulische Druck wirkt als flüssiger Niederhalter und übt eine gleichmäßige Kraft auf die Unterseite der Blechplatine aus. Dies verbessert den Materialfluss, reduziert die Zugspannungen und verhindert Faltenbildung sowie Rissbildung. Der Druck wird während des gesamten Umformvorgangs kontrolliert und kann je nach Bedarf angepasst werden.
4. Einpressen des Stempels
4.1. Bewegung des Stempels in die Matrize
Der Stempel beginnt, das Blech in die Matrize zu drücken. Während dieser Bewegung wird die Blechplatine durch den hydraulischen Druck auf der Unterseite gleichmäßig unterstützt. Der Stempel verformt das Material, während der hydraulische Druck die Kräfte gleichmäßig verteilt und das Material gegen die Matrizenwand drückt.
4.2. Steuerung der Umformgeschwindigkeit und Stempelkraft
Die Geschwindigkeit des Stempels und die Kraft, die er auf das Blech ausübt, werden sorgfältig gesteuert, um eine gleichmäßige Umformung zu gewährleisten und Fehler zu vermeiden. Eine langsame Umformgeschwindigkeit kann helfen, die Umformkräfte zu reduzieren und die Materialverteilung zu verbessern. Die Stempelkraft muss ausreichen, um das Blech vollständig in die gewünschte Form zu drücken, darf aber das Material nicht überlasten.
4.3. Rolle des hydraulischen Drucks während des Umformens
Während der Stempel das Blech in die Matrize drückt, sorgt der hydraulische Druck weiterhin für eine gleichmäßige Verteilung der Kräfte. Dies führt zu einer verbesserten Formgenauigkeit, da der Druck das Blech gleichmäßig an die Matrizenwände drückt und die Rückfederung reduziert.
5. Anpassung des hydraulischen Drucks
Der hydraulische Druck kann während des Umformvorgangs dynamisch angepasst werden, um den Materialfluss zu steuern. Beispielsweise kann der Druck in bestimmten Phasen erhöht oder verringert werden, um eine optimale Materialverteilung zu gewährleisten und die Gefahr von Materialversagen zu minimieren. Dies ist besonders bei der Umformung von komplexen Geometrien oder bei der Verwendung von schwer umformbaren Materialien wichtig.
6. Entformung des geformten Bauteils
6.1. Reduzierung des hydraulischen Drucks
Nach Abschluss des Umformvorgangs wird der hydraulische Druck langsam abgebaut, um ein kontrolliertes Zurückkehren des Bauteils in seine ursprüngliche Lage zu ermöglichen. Die Reduzierung des Drucks muss schrittweise erfolgen, um ein plötzliches Entweichen des Druckmediums zu verhindern, das das geformte Bauteil beschädigen könnte.
6.2. Rückzug des Stempels
Der Stempel wird aus der Matrize zurückgezogen, und das geformte Bauteil wird aus der Matrize entnommen. Durch die Unterstützung des hydraulischen Drucks ist die Wahrscheinlichkeit, dass das Bauteil beim Herausnehmen beschädigt wird, geringer.
6.3. Entfernung des fertigen Bauteils
Nach dem Zurückziehen des Stempels und dem Abbau des hydraulischen Drucks wird das fertige Bauteil aus der Matrize entnommen. Je nach Material und Komplexität des Bauteils kann eine Nachbearbeitung erforderlich sein, um scharfe Kanten zu glätten oder andere kleine Anpassungen vorzunehmen.
7. Nachbearbeitung und Qualitätskontrolle
7.1. Überprüfung der Maßhaltigkeit
Das geformte Bauteil wird hinsichtlich Maßhaltigkeit und Geometrie überprüft, um sicherzustellen, dass es den vorgegebenen Toleranzen entspricht. Besonders bei sicherheitskritischen Anwendungen, wie in der Automobil- oder Luftfahrtindustrie, ist eine gründliche Qualitätsprüfung unerlässlich.
7.2. Oberflächenbehandlung
Falls erforderlich, wird das Bauteil einer Oberflächenbehandlung unterzogen, um die gewünschte Oberfläche zu erzielen. Dies kann das Polieren, Schleifen oder das Auftragen von Beschichtungen umfassen.
7.3. Prüfung auf Materialfehler
Abschließend wird das Bauteil auf Materialfehler wie Risse, Falten oder Einschlüsse untersucht. Falls Fehler festgestellt werden, kann eine Nachbearbeitung notwendig sein, oder das Bauteil muss gegebenenfalls erneut produziert werden.
8. Optimierungsmöglichkeiten im hydromechanischen Tiefziehen
8.1. Anpassung der Prozessparameter
Durch die präzise Steuerung der Prozessparameter wie hydraulischer Druck, Umformgeschwindigkeit und Stempelkraft können Formfehler vermieden und die Qualität des geformten Bauteils verbessert werden. Eine kontinuierliche Überwachung und Anpassung der Parameter ist entscheidend, um die Prozessstabilität zu gewährleisten.
8.2. Simulationstechniken zur Prozessoptimierung
Computergestützte Simulationen helfen, den Umformprozess vorab zu planen und mögliche Fehler wie Faltenbildung oder Rissbildung zu erkennen. Durch den Einsatz moderner Simulationssoftware kann die Werkzeuggeometrie optimiert und die optimalen Prozessparameter bestimmt werden.
8.3. Verwendung von Schmiermitteln
Die richtige Wahl des Schmiermittels kann die Reibung verringern und die Oberflächenqualität verbessern. Die Schmierung spielt eine wichtige Rolle bei der Verringerung der Umformkräfte und der Vermeidung von Materialschäden.
Zusammenfassung
Der Ablauf des hydromechanischen Tiefziehens besteht aus mehreren aufeinander abgestimmten Schritten, die den Einsatz von mechanischen und hydraulischen Kräften kombinieren, um ein Blech in eine komplexe Form zu bringen. Von der Vorbereitung der Blechplatine über das Einleiten des hydraulischen Drucks und das Einpressen des Stempels bis hin zur Entformung und Nachbearbeitung sind alle Schritte sorgfältig aufeinander abgestimmt, um eine hohe Qualität des Endprodukts zu gewährleisten. Die präzise Steuerung der Prozessparameter und der Einsatz moderner Technologien tragen dazu bei, den hydromechanischen Tiefziehprozess zu optimieren und seine Anwendung in verschiedenen Industriezweigen weiter auszubauen.
Die Prozessparameter des hydromechanischen Tiefziehens spielen eine entscheidende Rolle für die Qualität und Effizienz des Umformprozesses. Im Vergleich zum konventionellen Tiefziehen kommen beim hydromechanischen Tiefziehen zusätzliche Parameter hinzu, die den Einsatz des hydraulischen Drucks betreffen. Die richtige Einstellung und Kontrolle dieser Parameter ist entscheidend, um Defekte wie Risse, Falten oder Rückfederung zu vermeiden und eine gleichmäßige Materialverteilung sicherzustellen. Im Folgenden werden die wichtigsten Prozessparameter detailliert beschrieben.
1. Hydraulischer Druck
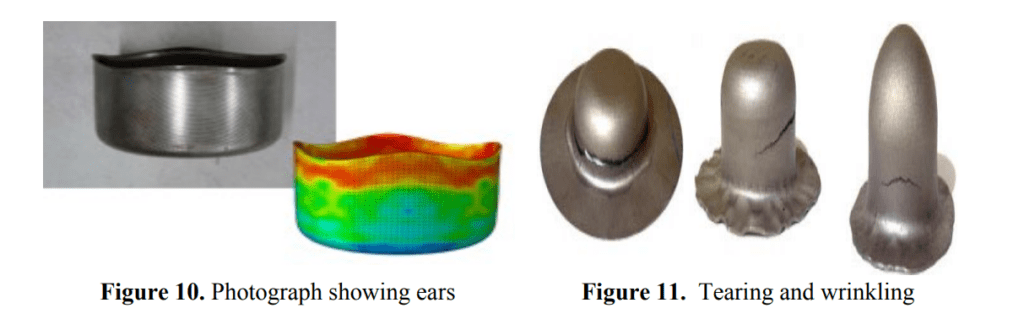
Der hydraulische Druck ist der wichtigste zusätzliche Parameter, der das hydromechanische Tiefziehen vom konventionellen Verfahren unterscheidet. Er wird durch eine Flüssigkeit (meist Hydrauliköl oder Wasser) erzeugt, die in einer Druckkammer unter der Blechplatine eingeschlossen ist.
1.1. Funktion des hydraulischen Drucks
Der hydraulische Druck wirkt als eine Art „flüssiger Niederhalter“, der auf die Unterseite der Blechplatine drückt. Diese Druckkraft unterstützt die Umformung, indem sie den Materialfluss verbessert, Zugspannungen reduziert und die Bildung von Falten verhindert. Darüber hinaus verringert der hydraulische Druck die Rückfederung und sorgt für eine bessere Maßhaltigkeit des Bauteils.
1.2. Optimale Druckeinstellung
Die optimale Einstellung des hydraulischen Drucks hängt von verschiedenen Faktoren ab, wie:
- Materialeigenschaften: Weichere Materialien wie Aluminium erfordern einen geringeren hydraulischen Druck als hochfeste Stähle.
- Materialdicke: Dickere Bleche benötigen einen höheren Druck, um gleichmäßig geformt zu werden.
- Geometrie des Bauteils: Komplexe oder tiefgezogene Formen können einen höheren hydraulischen Druck erfordern, um eine gleichmäßige Umformung zu gewährleisten.
Typische Werte für den hydraulischen Druck liegen im Bereich von 10 bis 200 MPa. Der Druck kann während des Umformprozesses dynamisch angepasst werden, um unterschiedliche Phasen des Umformvorgangs optimal zu unterstützen.
2. Umformgeschwindigkeit
Die Umformgeschwindigkeit ist die Geschwindigkeit, mit der der Stempel die Blechplatine in die Matrize drückt. Sie beeinflusst die Umformkräfte und die Qualität des geformten Bauteils.
2.1. Einfluss auf die Umformqualität
Eine langsame Umformgeschwindigkeit kann dazu beitragen, die Umformkräfte zu reduzieren und die Materialverteilung zu verbessern, was das Risiko von Fehlern wie Rissen oder Faltenbildung verringert. Eine höhere Umformgeschwindigkeit kann den Prozess effizienter machen, erhöht aber auch die Gefahr von Fehlern, insbesondere bei Materialien mit begrenzter Duktilität.
2.2. Empfehlungen zur Einstellung
Die Wahl der Umformgeschwindigkeit sollte auf das Material und die Geometrie des Bauteils abgestimmt werden:
- Langsame Geschwindigkeiten sind ideal für komplexe Bauteile oder Materialien mit geringer Duktilität.
- Hohe Geschwindigkeiten können bei einfacheren Geometrien oder gut umformbaren Materialien verwendet werden, um die Produktionsgeschwindigkeit zu erhöhen.
Typische Umformgeschwindigkeiten liegen zwischen 1 und 50 mm/s, je nach Anforderungen und spezifischem Anwendungsfall.
3. Stempelkraft
Die Stempelkraft ist die Kraft, die auf den Stempel ausgeübt wird, um die Blechplatine in die Matrize zu drücken. Sie wird in Kombination mit dem hydraulischen Druck eingesetzt, um das Blech in die gewünschte Form zu bringen.
3.1. Bedeutung der Stempelkraft
Die Stempelkraft muss ausreichen, um das Material plastisch zu verformen, ohne es zu beschädigen. Eine zu geringe Stempelkraft führt dazu, dass das Blech nicht vollständig in die Matrize gezogen wird, während eine zu hohe Stempelkraft das Material überlasten und zu Rissen führen kann.
3.2. Berechnung der erforderlichen Stempelkraft
Die Stempelkraft hängt von mehreren Faktoren ab, wie Materialeigenschaften, Materialdicke und Geometrie des Bauteils. Eine einfache Formel zur Berechnung der Stempelkraft (FsF_sFs) ist:Fs=π⋅D0⋅s0⋅Rm⋅ln(D0D)F_s = \pi \cdot D_0 \cdot s_0 \cdot R_m \cdot \ln\left(\frac{D_0}{D}\right)Fs=π⋅D0⋅s0⋅Rm⋅ln(DD0)
wobei:
- D0D_0D0 der Anfangsdurchmesser der Blechplatine ist
- s0s_0s0 die Anfangsdicke der Blechplatine
- RmR_mRm die Zugfestigkeit des Materials
- DDD der Enddurchmesser des geformten Werkstücks
4. Niederhalterkraft
Die Niederhalterkraft wird benötigt, um das Blech während des Umformprozesses an Ort und Stelle zu halten. Sie verhindert das Entstehen von Falten an den Rändern der Blechplatine und sorgt für einen gleichmäßigen Materialfluss.
4.1. Funktionen der Niederhalterkraft
- Verhinderung von Faltenbildung: Durch die Niederhalterkraft wird das Material an den Rändern fixiert, sodass Faltenbildung vermieden wird.
- Kontrolle des Materialflusses: Die Niederhalterkraft unterstützt den gleichmäßigen Materialfluss in die Matrize und verhindert, dass sich das Material zu stark ausdehnt oder lokal verdichtet.
4.2. Einflussfaktoren
Die optimale Niederhalterkraft hängt ab von:
- Materialeigenschaften: Härtere Materialien erfordern eine höhere Niederhalterkraft.
- Materialdicke: Dickere Bleche benötigen eine größere Niederhalterkraft, um ausreichend fixiert zu werden.
- Geometrie des Bauteils: Komplexe Formen mit engen Radien oder tiefen Zügen erfordern eine präzisere Steuerung der Niederhalterkraft.
Typische Werte für die Niederhalterkraft liegen bei 20–40 % der Umformkraft.
5. Schmierung
Die Schmierung spielt eine wichtige Rolle im hydromechanischen Tiefziehen, da sie die Reibung zwischen dem Blech, dem Stempel und der Matrize verringert und die Oberflächenqualität verbessert.
5.1. Funktion der Schmierung
- Reduzierung der Reibung: Eine geringere Reibung führt zu niedrigeren Umformkräften und reduziert den Verschleiß der Werkzeuge.
- Vermeidung von Oberflächenschäden: Durch eine gleichmäßige Schmierung wird die Gefahr von Kratzern und anderen Oberflächenschäden verringert.
- Besserer Materialfluss: Die Schmierung erleichtert das Gleiten des Blechs in die Matrize, was die Gefahr von Faltenbildung reduziert.
5.2. Auswahl des Schmiermittels
Die Wahl des Schmiermittels hängt vom Material, den Umformbedingungen und den spezifischen Anforderungen an das Bauteil ab. Beispiele für Schmiermittel sind:
- Öle und Fette: Universell einsetzbare Schmiermittel für eine Vielzahl von Materialien.
- Trockenschmierstoffe: Teflon- oder Graphit-beschichtete Filme sind ideal für Umgebungen, in denen eine saubere Verarbeitung erforderlich ist.
- Spezialschmiermittel: Für bestimmte Materialien wie Edelstahl können spezielle Schmiermittel verwendet werden, um die Umformbarkeit zu verbessern.
6. Temperatur
Obwohl das hydromechanische Tiefziehen in der Regel bei Raumtemperatur durchgeführt wird (Kaltumformung), kann die Temperatur eine wichtige Rolle spielen, insbesondere bei der Umformung schwer umformbarer Materialien.
6.1. Einfluss der Temperatur
- Erhöhte Umformbarkeit: Eine moderate Erhöhung der Temperatur kann die Umformbarkeit von Materialien wie hochfestem Stahl oder Titan verbessern.
- Reduzierte Umformkräfte: Höhere Temperaturen verringern die Materialfestigkeit, was zu niedrigeren Umformkräften führt.
- Vermeidung von Rissen: Bei spröden Materialien kann eine höhere Temperatur helfen, die Gefahr von Rissbildung zu reduzieren.
6.2. Steuerung der Temperatur
Die Temperatur kann während des Umformprozesses durch die Erwärmung der Matrize oder des Stempels gesteuert werden. Eine sorgfältige Überwachung und Steuerung ist jedoch erforderlich, um eine Überhitzung zu vermeiden, die zu Materialdegradation führen könnte.
7. Rückfederungskontrolle
Rückfederung tritt nach dem Umformprozess auf, wenn das Material teilweise in seine ursprüngliche Form zurückkehrt. Dies ist ein Phänomen, das durch elastische Verformung des Materials verursacht wird.
7.1. Einfluss auf die Maßhaltigkeit
Die Rückfederung kann die Maßhaltigkeit des geformten Bauteils beeinträchtigen und erfordert daher eine genaue Kontrolle und Kompensation, um die gewünschten Toleranzen einzuhalten.
7.2. Methoden zur Kompensation
- Anpassung der Werkzeuggeometrie: Werkzeuge können so gestaltet werden, dass sie die Rückfederung vorwegnehmen.
- Anwendung von Nachformprozessen: Zusätzliche Umformschritte können durchgeführt werden, um die Rückfederung zu korrigieren.
- Verwendung von höheren hydraulischen Drücken: Ein gleichmäßiger hydraulischer Druck während des Umformprozesses reduziert die elastische Rückfederung.
Zusammenfassung
Die Prozessparameter des hydromechanischen Tiefziehens – wie hydraulischer Druck, Umformgeschwindigkeit, Stempelkraft, Niederhalterkraft, Schmierung, Temperatur und Rückfederungskontrolle – sind entscheidend für die Qualität und Effizienz des Umformprozesses. Eine präzise Steuerung und Anpassung dieser Parameter ermöglicht eine bessere Materialverteilung, höhere Umformtiefen und eine verbesserte Maßhaltigkeit des geformten Bauteils. Durch den Einsatz moderner Steuerungstechnologien und computergestützter Simulationen können die Prozessparameter weiter optimiert werden, um die Herausforderungen beim hydromechanischen Tiefziehen erfolgreich zu meistern.
Das hydromechanische Tiefziehen wird in verschiedenen Industriezweigen eingesetzt, um anspruchsvolle Bauteile mit komplexen Geometrien, hohen Maßgenauigkeiten und guter Oberflächenqualität herzustellen. Durch die Kombination von mechanischen und hydraulischen Kräften lassen sich Formfehler reduzieren, tiefere Umformungen realisieren und schwer umformbare Materialien effizient verarbeiten. Im Folgenden werden typische Anwendungen in verschiedenen Industrien beschrieben, in denen das hydromechanische Tiefziehen besonders vorteilhaft ist.
1. Automobilindustrie
Die Automobilindustrie ist einer der größten Anwender des hydromechanischen Tiefziehens. Die Technologie wird genutzt, um verschiedene Bauteile für Fahrzeuge herzustellen, die spezifische Anforderungen an Festigkeit, Gewicht und Oberflächenqualität erfüllen müssen.
1.1. Herstellung von Karosserie- und Strukturbauteilen
In der Automobilindustrie kommen hydromechanisch tiefgezogene Teile bei der Produktion von Karosseriekomponenten und Strukturteilen zum Einsatz. Diese Bauteile müssen nicht nur ästhetisch ansprechend sein, sondern auch die hohen Anforderungen an die strukturelle Integrität erfüllen.
- Motorhauben und Kotflügel: Hydromechanisches Tiefziehen ermöglicht die Herstellung von dünnwandigen und komplex geformten Bauteilen wie Motorhauben, Kotflügeln und anderen Karosseriekomponenten mit hoher Maßhaltigkeit. Der Einsatz von hydraulischem Druck verbessert die Materialverteilung und reduziert die Rückfederung, was besonders bei modernen Leichtbaukonzepten wichtig ist.
- Strukturteile: Für Verstärkungsbauteile im Fahrzeugrahmen, die zur Verbesserung der Crash-Sicherheit beitragen, ist eine hohe Festigkeit erforderlich. Das hydromechanische Tiefziehen eignet sich gut für die Herstellung solcher Komponenten aus hochfesten Stählen und Leichtmetalllegierungen.
1.2. Leichtbau und Gewichtsreduktion
Durch die Möglichkeit, komplexe Geometrien aus leichten Materialien wie Aluminium oder Magnesiumlegierungen zu formen, trägt das hydromechanische Tiefziehen zur Gewichtsreduktion bei Fahrzeugen bei. Dies verbessert die Energieeffizienz und verringert den Kraftstoffverbrauch.
2. Luft- und Raumfahrtindustrie
Die Luft- und Raumfahrt stellt hohe Anforderungen an die Qualität und Leistung der verwendeten Bauteile. Leichte und zugleich starke Materialien sind erforderlich, um die strukturelle Integrität der Flugzeuge und Raumfahrzeuge zu gewährleisten. Das hydromechanische Tiefziehen bietet hier besondere Vorteile.
2.1. Strukturbauteile für Flugzeuge
In der Luftfahrt werden viele Strukturteile, wie Verkleidungen, Versteifungsrippen und Triebwerkskomponenten, aus Materialien wie Aluminium, Titan oder hochfesten Legierungen gefertigt. Diese Bauteile müssen leicht und trotzdem stabil genug sein, um den mechanischen Belastungen standzuhalten.
- Verkleidungselemente: Durch hydromechanisches Tiefziehen lassen sich Verkleidungsteile für Flugzeugflügel und Rumpf effizient herstellen, wobei die hohe Oberflächenqualität und die enge Maßtoleranz wichtig sind.
- Triebwerkskomponenten: Bauteile für Triebwerke, die extremen Temperaturen und mechanischen Beanspruchungen ausgesetzt sind, profitieren von der verbesserten Formgenauigkeit und Materialverteilung durch hydromechanisches Tiefziehen.
2.2. Komponenten für Raumfahrzeuge
In der Raumfahrt werden spezielle Materialien wie Titan und hochfeste Legierungen verwendet, die schwer umformbar sind. Hydromechanisches Tiefziehen ermöglicht die Herstellung dünnwandiger, leichter und komplexer Bauteile für Raumfahrzeuge, wie Hitzeschilde oder Strukturbauteile, die sowohl Festigkeit als auch Leichtigkeit bieten.
3. Medizintechnik
In der Medizintechnik sind hohe Präzision, Maßgenauigkeit und Oberflächenqualität entscheidend. Hydromechanisches Tiefziehen wird verwendet, um Bauteile herzustellen, die strenge Anforderungen an Biokompatibilität und Hygiene erfüllen.
3.1. Gehäuse für medizinische Geräte
Medizinische Geräte erfordern oft Gehäuse aus korrosionsbeständigen Materialien wie Edelstahl oder Titan. Diese Gehäuse müssen nicht nur präzise geformt, sondern auch leicht zu reinigen und sterilisieren sein. Das hydromechanische Tiefziehen ermöglicht die Herstellung von Gehäusen mit glatten Oberflächen und komplexen Formen, die für medizinische Anwendungen geeignet sind.
3.2. Chirurgische Instrumente und Implantate
Chirurgische Instrumente müssen hohe Anforderungen an die Hygiene und Korrosionsbeständigkeit erfüllen. Hydromechanisch tiefgezogene Bauteile aus Edelstahl oder Titan können für chirurgische Instrumente verwendet werden, die präzise Formen und glatte Oberflächen erfordern. Auch Implantate, die aus biokompatiblen Materialien gefertigt werden, profitieren von der Formgenauigkeit und dem minimalen Materialstress, den das hydromechanische Tiefziehen ermöglicht.
4. Haushaltsgeräteindustrie
Hydromechanisches Tiefziehen findet auch in der Haushaltsgeräteindustrie breite Anwendung, insbesondere bei der Herstellung von dekorativen und funktionalen Bauteilen.
4.1. Herstellung von Küchenspülen
Küchenspülen aus Edelstahl sind ein klassisches Beispiel für die Anwendung des hydromechanischen Tiefziehens. Diese Spülen müssen nahtlos, hygienisch und korrosionsbeständig sein. Das hydromechanische Tiefziehen ermöglicht die Herstellung von Spülen mit glatten Oberflächen und präzisen Formen, ohne dass es zu Verformungen oder Faltenbildung kommt.
4.2. Dekorative Abdeckungen und Gehäuse
Für Haushaltsgeräte wie Waschmaschinen, Trockner oder Mikrowellen sind dekorative Gehäuse und Abdeckungen erforderlich, die eine ansprechende Optik mit hoher Funktionalität kombinieren. Hydromechanisches Tiefziehen ermöglicht es, komplexe Formen und Designs aus Edelstahl oder Aluminium zu fertigen, die den Anforderungen an Ästhetik und Haltbarkeit gerecht werden.
5. Verpackungsindustrie
Auch in der Verpackungsindustrie wird das hydromechanische Tiefziehen für die Herstellung von Metallverpackungen eingesetzt, insbesondere für Anwendungen, die eine hohe Stabilität und Dichtheit erfordern.
5.1. Herstellung von Dosen und Behältern
Metallverpackungen, wie Konservendosen, Getränkedosen und Druckbehälter, werden häufig durch hydromechanisches Tiefziehen hergestellt, um eine gleichmäßige Wandstärke und hohe Maßgenauigkeit zu gewährleisten. Diese Bauteile profitieren von der Möglichkeit, komplexe Formen bei gleichzeitiger Reduzierung des Materialverbrauchs zu realisieren.
5.2. Herstellung von Druckgasbehältern
Hydromechanisches Tiefziehen wird auch zur Fertigung von Druckbehältern wie Feuerlöschern, Gasflaschen oder Sprühdosen verwendet. Diese Behälter müssen unter Druck sicher und dicht bleiben, was durch die gleichmäßige Materialverteilung und die präzise Umformung im hydromechanischen Tiefziehprozess erreicht wird.
6. Bauindustrie
Die Bauindustrie nutzt das hydromechanische Tiefziehen für spezielle Metallbauteile, die sowohl dekorative als auch funktionale Zwecke erfüllen.
6.1. Architektonische Verkleidungen und Fassadenelemente
Für architektonische Projekte, die Metallverkleidungen erfordern, ist das hydromechanische Tiefziehen eine hervorragende Lösung. Es ermöglicht die Herstellung von Bauteilen mit glatten Oberflächen, komplexen Formen und engen Toleranzen, die für anspruchsvolle Fassadengestaltungen und Dekorationsarbeiten notwendig sind.
6.2. Sonderanfertigungen für Bauprojekte
Bei bestimmten Bauprojekten, insbesondere solchen mit besonderen ästhetischen oder funktionalen Anforderungen, ist eine maßgeschneiderte Fertigung von Bauteilen notwendig. Hydromechanisches Tiefziehen ermöglicht die flexible Herstellung von Spezialteilen wie Abdeckungen, Schutzblechen oder Verkleidungen.
7. Elektro- und Elektronikindustrie
Hydromechanisches Tiefziehen bietet auch Vorteile für die Herstellung von Gehäusen und Abdeckungen in der Elektro- und Elektronikindustrie.
7.1. Herstellung von Gehäusen für elektronische Geräte
Elektronische Geräte, insbesondere solche, die robust und zuverlässig sein müssen, erfordern Gehäuse, die genau geformt und langlebig sind. Hydromechanisches Tiefziehen kann für die Herstellung von Gehäusen für Computer, Server, Schaltschränke und andere elektronische Geräte verwendet werden.
7.2. Komponenten für Energiespeicher
Hydromechanisches Tiefziehen ermöglicht die Herstellung von Metallgehäusen für Batterien und Akkumulatoren. Diese Gehäuse müssen sowohl mechanische Stabilität als auch Korrosionsbeständigkeit bieten, um die Lebensdauer und Sicherheit der Energiespeicher zu gewährleisten.
8. Schmuck- und Kunsthandwerk
Auch im Schmuck- und Kunsthandwerk findet das hydromechanische Tiefziehen Anwendung, um dekorative Objekte und Schmuckstücke herzustellen.
8.1. Fertigung von Schmuckteilen
Metalle wie Gold, Silber oder Kupfer können durch hydromechanisches Tiefziehen in anspruchsvolle Formen gebracht werden, um Schmuckstücke wie Ringe, Anhänger oder Broschen zu fertigen. Dieses Verfahren ermöglicht eine präzise Formgebung und hochwertige Oberflächenqualität.
8.2. Dekorative Objekte und Kunstgegenstände
Für die Herstellung von dekorativen Metallobjekten, wie Skulpturen oder kunsthandwerklichen Gegenständen, kann das hydromechanische Tiefziehen eingesetzt werden, um komplexe Formen und filigrane Designs zu realisieren.
Zusammenfassung
Das hydromechanische Tiefziehen ist ein vielseitiges Umformverfahren, das in vielen Industrien eingesetzt wird, um Bauteile mit komplexen Geometrien und hohen Qualitätsanforderungen herzustellen. Typische Anwendungen reichen von der Automobil- und Luftfahrtindustrie über die Medizintechnik bis hin zu Verpackungs- und Haushaltsgeräten. Die Fähigkeit, schwer umformbare Materialien präzise zu verarbeiten und dabei eine gleichmäßige Materialverteilung zu erreichen, macht das hydromechanische Tiefziehen zu einer wichtigen Technologie für moderne Fertigungsprozesse.
Metallbearbeitungsmaschinen
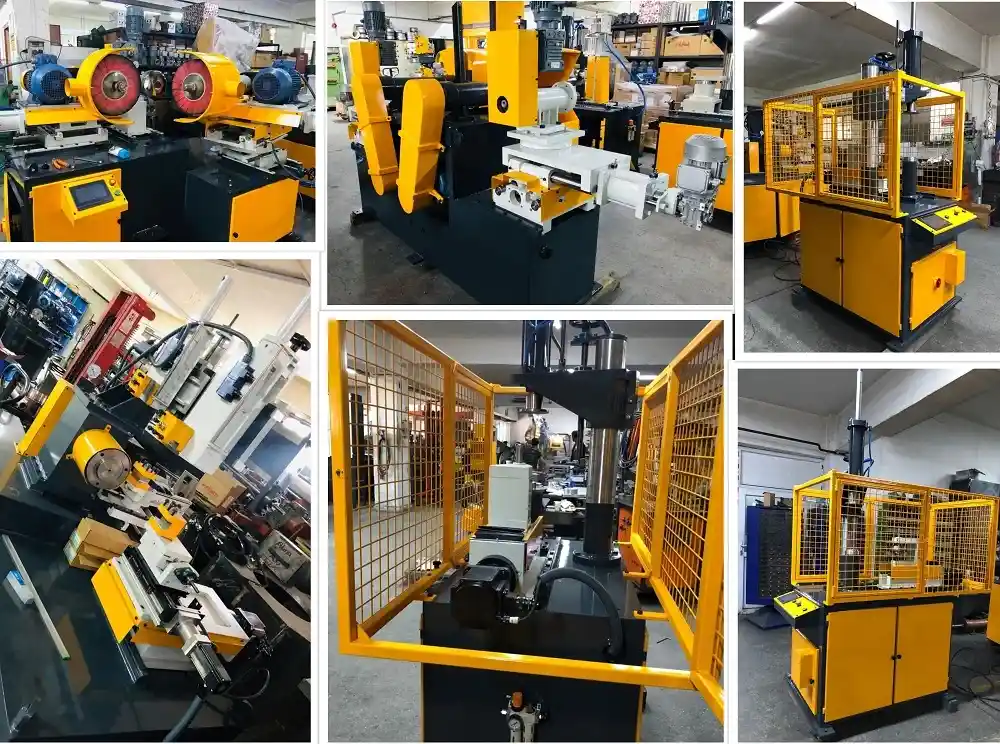
Metallbearbeitungsmaschinen wie Bördel und Beschneide Maschinen, Flanschmaschinen, Beschneide und Bördelmaschinen, Umformtechnik, Rohrbiegemaschinen, Bandsäge für Metall, Hydraulische Horizontalpresse, Kantenschneide-Bördelmaschine, Kantenbördelmaschine, Entgratungsmaschine, Innen- und Außenpoliermaschine für Edelstahltöpfe, Kreisschneidemaschine, Profilbiegemaschine und Rundschweißmaschine
Maßgeschneiderte Skalierung für spezifische Anwendungen
Die automatisierte Herstellung von Behältern, Fässern und Kesseln wird durch unsere Lösungen exakt auf das jeweilige Einsatzgebiet und die gewünschte Ausbringung angepasst. Dabei bieten wir sowohl lineare Lösungen als auch Inselkonzepte an, die eine bedarfsorientierte Automation ermöglichen. Spezielle Kantenvorbereitung für das Laserschweißen sowie wirtschaftliche Rüstkonzepte bis hin zur Fertigung „Just-in-Sequence“ sind Teil unseres Leistungsspektrums. Wir kombinieren Standard- und Sondermaschinen und bieten Ferndiagnose über LAN, WLAN oder GSM an, ergänzt durch umfassende Dokumentation gemäß CE-Richtlinien für die Gesamtanlage.
Unser Konzept
EMS entwickelt und fertigt Maschinen und Anlagen für die automatisierte Herstellung von Behältern in großem Maßstab. Alle Arbeitsschritte, von der Vorbereitung bis zur Fertigung, werden dabei aus einer Hand angeboten. Unsere erprobten Standardkomponenten sind perfekt aufeinander abgestimmt und können nahtlos mit Robotern kombiniert werden, um leistungsfähige Fertigungseinrichtungen zu schaffen.
Flexible Präzisionsfertigung
Unsere Fertigungslinien ermöglichen eine einfache Umstellung auf verschiedene Längen, Durchmesser, Formen und Bearbeitungen durch Programmwechsel. Dabei werden zahlreiche Einzelschritte wie Beschneiden, Formen, Stanzen, Fügen, Montieren, Schweißen und Prüfen automatisch und mit höchster Präzision an die jeweilige Aufgabe angepasst. Besonderes Augenmerk legen wir auf die Kantenvorbereitung für den Schweißprozess, um eine herausragende Prozesssicherheit und minimale Ausschussquoten zu gewährleisten.
Maschinenprogramm für die Metallbearbeitung
Unsere Metallbearbeitungsmaschinen sind:
- Rohrbiegemaschine
- Horizontale Presse
- Bandsäge für Metall
- Profilbiegemaschine
- Tiefziehpresse
- Rundschweißmaschine
- Kantenschneide-Bördelmaschine
- Topf- und Pfannenpoliermaschine
- Poliermaschine für flache Oberflächen
Besteck-Produktionslinie: Eine Besteck-Produktionslinie ist eine Art Maschine, die Besteck in einem kontinuierlichen Prozess herstellt. Es umfasst verschiedene Arten von Maschinen wie den Messerschleifer, den Messerschärfer und den Klingenpolierer.
Kochgeschirr-Herstellungsmaschine: Eine Kochgeschirr-Herstellungsmaschine ist eine Art Maschine, die Kochgeschirr in einem kontinuierlichen Prozess herstellt. Es umfasst verschiedene Arten von Maschinen wie den Topfmacher, den Pfannenmacher und den Wokmacher.
Küchengeschirr-Produktionsmaschine: Eine Küchengeschirr-Produktionsmaschine ist eine Art Maschine, die Küchengeschirr in einem kontinuierlichen Prozess herstellt. Es umfasst verschiedene Arten von Maschinen wie Maschinen zur Herstellung von Teekesseln, Produktionslinien für Besteck, Produktionslinien für Töpfe und Pfannen
Wir entwerfen, fertigen und montieren komplette Produktionslinien für Kochgeschirr, Küchengeschirr, Hotelgeschirr und Besteck sowie einzelne Maschinen für einen bestimmten Zweck