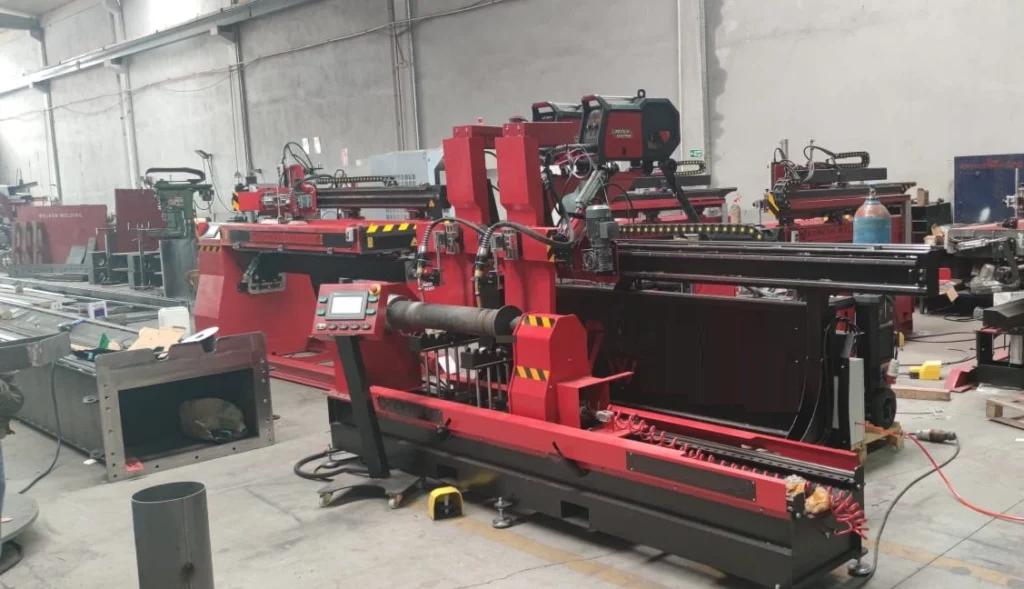
Ein Automatisiertes Schweißgerät kann Teile mit runder Form schweißen. Der Zweck der Operation hier ist es, eine saubere Schweißnaht auf einer runden Oberfläche zu haben
Unabhängig von den Schweiß- oder Schneidanwen dungen erfüllen unsere Anlagen alle Anforderungen der Bediener einschließlich Sicherheit, Schutz, Qualität und Benutzerfreundlichkeit. Innovative Lösungen garantieren Nutzung und Instandhaltung gemäß geltender Richtlinien und Standards für umfassenden Schutz während des gesamten Herstellungsprozesses. Air Liquide Welding fühlt sich der Entwicklung geeigneter Lösungen für eine saubere Produktion verpflichtet.
EMS Metallbearbeitungsmaschinen verfügt über ein umfassendes Angebot an automatisierten Schweiß- und Schneidanlagen für alle Anforderungen im Bereich Automation: Geräte, autonome Anlagen und Positionierer. Die gesamte Ausrüstung wird im Werk montiert und vor Auslieferung getestet, um höchstmögliche Qualität sicherzustellen.
Automatisiertes Schweißgerät
Automatisierte Schweißgeräte sind Maschinen, die zum Schweißen von Metallen ohne menschliches Eingreifen verwendet werden. Sie werden in einer Vielzahl von Branchen eingesetzt, darunter die Automobilindustrie, die Luft- und Raumfahrtindustrie und die Bauindustrie.
Automatisierte Schweißgeräte gibt es in verschiedenen Ausführungen, darunter:
- Punktschweißmaschinen: Diese Maschinen verwenden eine Reihe von Elektroden, die an den zu schweißenden Stellen gleichzeitig ein- und ausgeschaltet werden, um kleine, punktförmige Schweißnähte zu erzeugen
- Drahtbogenschweißmaschinen: Diese Maschinen verwenden einen Drahtelektrode, der durch einen Strombogen geschmolzen wird, um eine Schweißnaht zu erzeugen.
- Laserschweißmaschinen: Diese Maschinen verwenden einen Laserstrahl, um Metalle zu schmelzen und zu verschmelzen.
- Ultraschallschweißmaschinen: Diese Maschinen verwenden Ultraschallwellen, um Metalle zu schweißen.
Automatisierte Schweißgeräte bieten eine Reihe von Vorteilen gegenüber manuellen Schweißverfahren, darunter:
- Höhere Produktivität: Automatisierte Schweißgeräte können schneller und effizienter schweißen als manuelle Schweißverfahren.
- Bessere Schweißqualität: Automatisierte Schweißgeräte können konsistentere und gleichmäßigere Schweißnähte erzeugen als manuelle Schweißverfahren.
- Gesteigerte Sicherheit: Automatisierte Schweißgeräte können die Sicherheit von Schweißern verbessern, indem sie die Exposition gegenüber heißen Metallen und Strahlung verringern.
Automatisierte Schweißgeräte können jedoch auch einige Nachteile haben, darunter:
- Hohe Anschaffungskosten: Automatisierte Schweißgeräte sind in der Regel teurer als manuelle Schweißgeräte.
- Komplexe Bedienung: Automatisierte Schweißgeräte können komplex zu bedienen sein und erfordern eine Schulung für den Bediener.
Automatisierte Schweißgeräte werden in einer Vielzahl von Branchen eingesetzt, darunter:
- Automobilindustrie: Automatisierte Schweißgeräte werden in der Automobilindustrie zum Schweißen von Karosserien, Fahrgestellen und anderen Fahrzeugteilen verwendet.
- Luft- und Raumfahrtindustrie: Automatisierte Schweißgeräte werden in der Luft- und Raumfahrtindustrie zum Schweißen von Flugzeugen, Raketen und anderen Luft- und Raumfahrtfahrzeugen verwendet.
- Bauindustrie: Automatisierte Schweißgeräte werden in der Bauindustrie zum Schweißen von Stahlkonstruktionen, Rohrleitungen und anderen Bauteilen verwendet.
Automatische Rundschweißmaschinen
Automatische Rundschweißmaschinen sind Schweißmaschinen, die zum Schweißen von Rohren und anderen runden Werkstücken verwendet werden. Sie sind in der Regel mit einem Roboterarm ausgestattet, der den Schweißbrenner führt.
Automatische Rundschweißmaschinen werden in einer Vielzahl von Branchen eingesetzt, darunter die Automobilindustrie, die Luft- und Raumfahrtindustrie und die Bauindustrie. Sie werden zum Schweißen von Rohrleitungen, Tanks, Behältern und anderen runden Bauteilen verwendet.
Automatische Rundschweißmaschinen bieten eine Reihe von Vorteilen gegenüber manuellen Schweißverfahren, darunter:
- Hohe Produktivität: Automatische Rundschweißmaschinen können mit hohen Geschwindigkeiten arbeiten und so die Produktionsrate erhöhen.
- Hohe Qualität: Automatische Rundschweißmaschinen können gleichbleibende, hochwertige Schweißnähte produzieren.
- Sicherheit: Automatische Rundschweißmaschinen können die Sicherheit der Schweißer verbessern, indem sie das Risiko von Verletzungen durch Stromschlag oder Verbrennungen verringern.
Die wichtigsten Komponenten einer automatischen Rundschweißmaschine sind:
- Schweißbrenner: Der Schweißbrenner ist das Werkzeug, mit dem das Schweißgut geschmolzen wird.
- Roboterarm: Der Roboterarm führt den Schweißbrenner.
- Schutzgasanlage: Die Schutzgasanlage liefert das Schutzgas, das das Schweißgut vor Oxidation und Verunreinigungen schützt.
- Steuerung: Die Steuerung steuert den Schweißprozess.
Die Art des verwendeten Schweißverfahrens hängt vom Werkstoff ab, der geschweißt werden soll. Die häufigsten Schweißverfahren für automatische Rundschweißmaschinen sind:
- Metall-Inertgasschweißen (MIG): MIG-Schweißen ist ein vielseitiges Verfahren, das zum Schweißen einer Vielzahl von Werkstoffen verwendet werden kann.
- Wolfram-Inertgasschweißen (WIG): WIG-Schweißen ist ein Präzisionsschweißen, das zum Schweißen dünner Werkstoffe verwendet wird.
Automatische Rundschweißmaschinen können mit einer Vielzahl von Sensoren ausgestattet sein, die die Schweißnahtqualität überwachen. Diese Sensoren können dazu beitragen, die Qualität der Schweißnähte zu verbessern und die Ausschussrate zu verringern.
Automatische Rundschweißmaschinen sind spezielle Schweißanlagen, die dazu entwickelt wurden, das Rundschweißen von Werkstücken zu automatisieren. Diese Maschinen kommen in verschiedenen Branchen und Anwendungen zum Einsatz, insbesondere wenn eine hohe Produktionskapazität und gleichbleibende Schweißqualität erforderlich sind. Hier sind einige wichtige Aspekte automatischer Rundschweißmaschinen:
- Anwendungen:
- Automatische Rundschweißmaschinen werden oft in der Fertigung von Rohrleitungen, zylindrischen Teilen, Tanks, Behältern, und anderen rundförmigen Bauteilen eingesetzt.
- Vorteile:
- Hohe Produktivität: Automatisierte Maschinen ermöglichen eine kontinuierliche und effiziente Produktion, was zu höheren Durchsatzraten führt.
- Konsistente Qualität: Durch die Automatisierung wird eine gleichbleibende Schweißqualität erreicht, da die Schweißparameter präzise gesteuert werden können.
- Reduzierte Arbeitskosten: Automatisierte Prozesse minimieren den Bedarf an manueller Arbeitskraft, insbesondere bei wiederholenden Aufgaben.
- Komponenten:
- Schweißkopf: Der Schweißkopf ist der Teil der Maschine, der den Schweißprozess durchführt. Dieser kann je nach Anwendung variieren und kann unterschiedliche Schweißmethoden (z.B., Lichtbogen- oder Widerstandsschweißen) verwenden.
- Drehvorrichtung: Automatische Rundschweißmaschinen sind oft mit einer Drehvorrichtung ausgestattet, um das Werkstück während des Schweißens zu rotieren.
- Steuerungseinheit: Eine Steuerungseinheit ermöglicht die Programmierung und Überwachung des Schweißprozesses. Dies kann die Einstellung von Schweißparametern, die Steuerung der Drehgeschwindigkeit und andere Funktionen umfassen.
- Programmierung und Flexibilität:
- Automatische Rundschweißmaschinen können in der Regel programmiert werden, um verschiedene Werkstücke zu schweißen. Dies bietet Flexibilität in der Produktion und ermöglicht die Anpassung an unterschiedliche Anforderungen.
- Sicherheit:
- Sicherheitsvorkehrungen sind wichtig, um den sicheren Betrieb automatischer Rundschweißmaschinen zu gewährleisten. Dies kann Sicherheitssensoren, Notausschalter und andere Schutzmaßnahmen umfassen.
Es ist wichtig zu beachten, dass die genauen Merkmale und Funktionen automatischer Rundschweißmaschinen je nach Hersteller und Modell variieren können. Bei der Auswahl einer solchen Maschine ist es entscheidend, die spezifischen Anforderungen der Anwendung, die gewünschten Schweißmethoden und die geforderten Standards zu berücksichtigen. Zudem ist die Schulung des Bedienpersonals für den sicheren und effizienten Betrieb solcher Maschinen von großer Bedeutung.
Die Funktionsweise einer Rundschweißmaschine hängt von der Art der Maschine ab. Manuelle Rundschweißmaschinen arbeiten in der Regel mit einem Schweißbrenner, der das Werkstück erhitzt und den Schweißprozess einleitet. Automatische Rundschweißmaschinen arbeiten in der Regel mit einem Schweißroboter, der den Schweißprozess automatisch durchführt.
Die Schweißqualität hängt von einer Reihe von Faktoren ab, darunter:
- Schweißverfahren: Das Schweißverfahren bestimmt die Art des Schweißnahts, der erzeugt wird.
- Schweißparameter: Die Schweißparameter bestimmen die Eigenschaften des Schweißnahts, z. B. die Dicke und die Festigkeit.
- Rohrmaterial: Das Rohrmaterial bestimmt die Eignung des Schweißverfahrens und der Schweißparameter.
Bei der Auswahl einer Rundschweißmaschine ist es wichtig, die Anforderungen der Anwendung zu berücksichtigen. So muss die Maschine für das Schweißverfahren, das Rohrmaterial und das Produktionsvolumen geeignet sein.
Hier sind einige Tipps für das Schweißen mit einer Rundschweißmaschine:
- Befolgen Sie die Anweisungen des Herstellers der Rundschweißmaschine.
- Verwenden Sie geeignete Schutzausrüstung, z. B. Schutzhandschuhe und Schutzbrille.
- Üben Sie das Schweißen mit einer Rundschweißmaschine, bevor Sie sie für eine Anwendung verwenden.
Mit etwas Übung können Sie mit einer Rundschweißmaschine Rohre oder andere zylindrische Werkstücke in einer Vielzahl von Anwendungen schweißen.
Ein oder zwei Schweißpositionierer führen die Rundschweißung durch. Der Schweißpositionierer ist ein Gerät, das das Teil festhält und es mit einer erforderlichen Drehzahl dreht. Diese Drehbewegung kann in 3 Achsen erfolgen.
Beim Rundschweißen wird das runde Teil unter dem Schweißbrenner positioniert. Das MIG- oder WIG-Schweißgerät beginnt mit dem Schweißen. Ein MIG-Schweißgerät ist eine Schweißmaschine, die einen Metalldraht verwendet, um die Teile zu schweißen. In einer MIG-Schweißmaschine (Metal Inert Gas) kann die Anwendung auf verschiedenen Metallen wie Aluminium, Edelstahl und Stahl und auf jeder Dicke von 26-Gauge-Blech bis hin zu schweren Strukturplatten erfolgen.
Der MIG-Schweißzuführungsdraht fungiert außerdem nicht nur als Elektrode, sondern auch als Zusatzwerkstoff. Die Blechdicke spielt hier also keine Rolle, da der Zuleitungsdraht des MIG-Schweißbrenners den Zwischenraum problemlos ausfüllen kann. Umgekehrt hat das WIG-Schweißen (Wolfram-Inertgas) eine bessere Oberflächenwirkung und eine höhere Qualität.
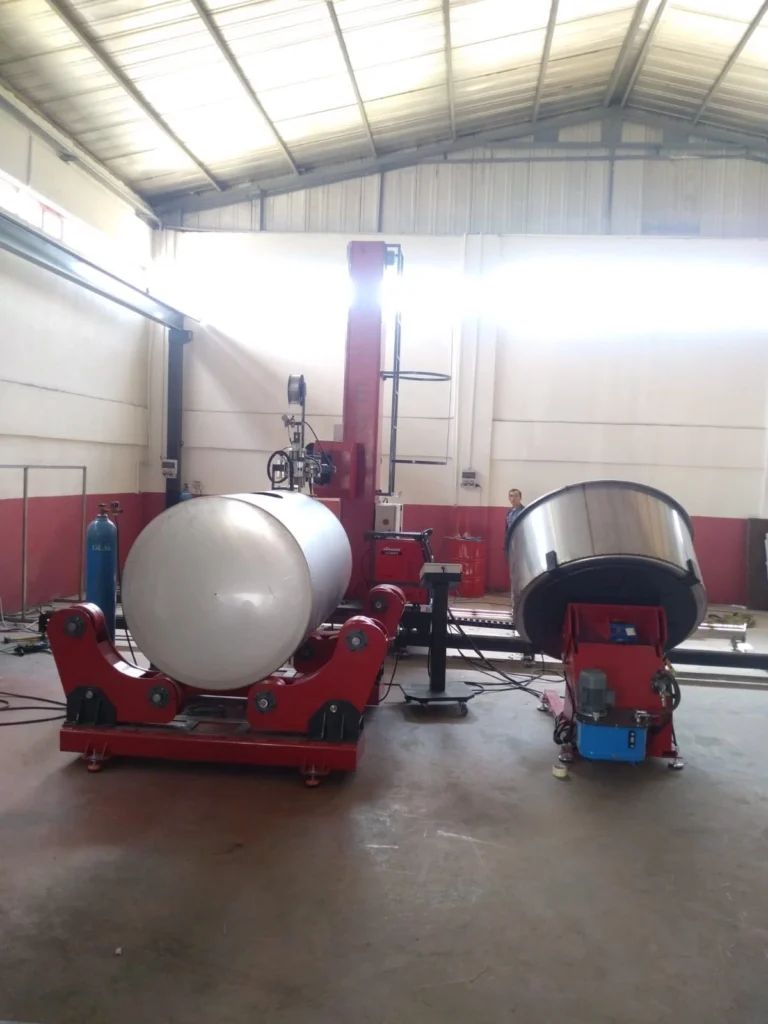
Eine Rundschweißmaschine kann horizontal oder vertikal sein. Eine Horizontal-Rundschweißmaschine kann auch als Rohrschweißautomat bezeichnet werden. Hier wird das Rundteil horizontal verlegt und durch die Rohrrotatoren gedreht. Ein Rohrrotator ist ein Werkzeug, das das Teil festhält und um seine eigene Achse dreht, während der Schweißbrenner die Oberfläche des Teils berührt und mit dem Schweißen beginnt. Die Drehmaschine kann dabei auf den Rohrspitzen oder unten auf dem Schweißbett stehen.
Arten von Schweißmaschinen
Schweißmaschinen werden verwendet, um zwei oder mehr Metallteile miteinander zu verbinden. Es gibt verschiedene Arten von Schweißmaschinen, die jeweils ihre eigenen Vor- und Nachteile haben.
Die gebräuchlichsten Arten von Schweißmaschinen sind:
- Elektrodenschweißmaschinen: Elektrodenschweißmaschinen verwenden eine Elektrode, die das Werkstück erhitzt und den Schweißprozess einleitet. Die Elektrode wird von einem Schweißbrenner geführt und schmilzt beim Schweißen ab. Elektrodenschweißmaschinen sind in der Regel kostengünstig und einfach zu bedienen.
- MIG-/MAG-Schweißmaschinen: MIG-/MAG-Schweißmaschinen verwenden ein Drahtelektrode, die das Werkstück erhitzt und den Schweißprozess einleitet. Der Draht wird von einem Drahtvorschubgerät zugeführt und schmilzt beim Schweißen ab. MIG-/MAG-Schweißmaschinen sind in der Regel schneller und präziser als Elektrodenschweißmaschinen.
- TIG-Schweißmaschinen: TIG-Schweißmaschinen verwenden eine Wolframelektrode, die das Werkstück erhitzt und den Schweißprozess einleitet. Die Elektrode wird von einem Schweißbrenner geführt und schmilzt nicht ab. TIG-Schweißmaschinen erzeugen sehr saubere Schweißnähte und sind daher für Anwendungen mit hohen Anforderungen an die Qualität geeignet.
Elektrodenschweißmaschinen
Elektrodenschweißmaschinen sind Schweißmaschinen, die zum Schweißen mit einer Elektrode verwendet werden. Die Elektrode ist ein metallener Draht, der beim Schweißen abschmilzt und das Schweißgut bildet.
Elektrodenschweißmaschinen werden in einer Vielzahl von Branchen eingesetzt, darunter die Automobilindustrie, die Bauindustrie und die Metallverarbeitung. Sie werden zum Schweißen von Stahl, Aluminium und anderen Metallen verwendet.
Es gibt zwei Haupttypen von Elektrodenschweißmaschinen:
- Handelektrodenschweißmaschinen: Handelektrodenschweißmaschinen sind die am häufigsten verwendeten Elektrodenschweißmaschinen. Sie werden von einem Schweißer mit der Hand bedient.
- Automatische Elektrodenschweißmaschinen: Automatische Elektrodenschweißmaschinen werden mit einem Roboterarm betrieben. Sie werden zum Schweißen von großen oder komplexen Bauteilen verwendet.
Die wichtigsten Komponenten einer Elektrodenschweißmaschine sind:
- Schweißstromquelle: Die Schweißstromquelle erzeugt den Strom, der zum Schmelzen der Elektrode verwendet wird.
- Schweißbrenner: Der Schweißbrenner hält die Elektrode und führt sie zum Werkstück.
- Schutzgasanlage: Die Schutzgasanlage liefert das Schutzgas, das das Schweißgut vor Oxidation und Verunreinigungen schützt.
Die Art des verwendeten Schweißstroms hängt vom Werkstoff ab, der geschweißt werden soll. Die häufigsten Schweißströme für Elektrodenschweißmaschinen sind:
- Wechselstrom (AC): Wechselstrom wird zum Schweißen von Aluminium und anderen Nichteisenmetallen verwendet.
- Gleichstrom (DC): Gleichstrom wird zum Schweißen von Stahl und anderen Eisenmetallen verwendet.
Die Art der verwendeten Elektrode hängt ebenfalls vom Werkstoff ab, der geschweißt werden soll. Es gibt eine Vielzahl von Elektrodentypen mit unterschiedlichen Eigenschaften.
Elektrodenschweißmaschinen bieten eine Reihe von Vorteilen, darunter:
- Flexibilität: Elektrodenschweißmaschinen können zum Schweißen einer Vielzahl von Werkstoffen verwendet werden.
- Einfachheit: Elektrodenschweißmaschinen sind relativ einfach zu bedienen.
- Kostengünstig: Elektrodenschweißmaschinen sind im Vergleich zu anderen Schweißmaschinen relativ kostengünstig.
Elektrodenschweißmaschinen bieten jedoch auch einige Nachteile, darunter:
- Geruchentwicklung: Elektrodenschweißmaschinen erzeugen Rauch, der Atemwegsprobleme verursachen kann.
- Schmutzentwicklung: Elektrodenschweißmaschinen erzeugen Schmutz, der die Arbeitsumgebung verschmutzen kann.
- Risiko von Verbrennungen: Elektrodenschweißmaschinen können Verbrennungen verursachen, wenn der Schweißer nicht vorsichtig ist.
Sicherheitshinweise beim Elektrodenschweißen:
- Tragen Sie geeignete persönliche Schutzausrüstung (PSA), einschließlich eines Schweißhelms, Handschuhen, Stiefeln und einer Schutzbrille.
- Sorgen Sie für eine gute Belüftung des Schweißbereichs.
- Schweißen Sie nicht in der Nähe von brennbaren Materialien.
- Berühren Sie die Elektrode oder die Schweißnaht nicht mit bloßen Händen.
- Seien Sie sich der potenziellen Gefahr eines elektrischen Schlags bewusst.
Elektrodenschweißmaschinen, auch als Lichtbogenschweißmaschinen oder Elektroschweißgeräte bezeichnet, sind Werkzeuge, die für das Lichtbogenschweißen mit Elektroden verwendet werden. Das Elektrodenschweißen ist ein gängiger Schweißprozess, der häufig in der Metallverarbeitung und Konstruktion eingesetzt wird. Hier sind einige grundlegende Informationen zu Elektrodenschweißmaschinen:
- Funktionsprinzip:
- Elektrodenschweißmaschinen erzeugen einen Lichtbogen zwischen einer Elektrode und dem Werkstück. Dieser Lichtbogen erzeugt hohe Temperaturen und schmilzt sowohl die Elektrode als auch das Werkstück, wodurch eine Schweißverbindung entsteht.
- Komponenten:
- Transformator oder Inverter: Elektrodenschweißmaschinen können auf Transformator- oder Invertertechnologie basieren. Invertergeräte sind oft kompakter und leichter als Transformatorgeräte.
- Stromquelle: Die Stromquelle erzeugt den elektrischen Strom, der für das Schweißen benötigt wird.
- Elektrodenhalter und Masseklemme: Der Elektrodenhalter hält die Schweißelektrode, während die Masseklemme am Werkstück befestigt wird, um den elektrischen Stromkreis zu schließen.
- Regel- und Steuereinheit: Moderne Schweißmaschinen verfügen oft über Einstellungen zur Steuerung von Stromstärke, Spannung und anderen Schweißparametern.
- Arbeitsweise:
- Der Bediener wählt die geeignete Elektrode und passt die Schweißparameter an, darunter Stromstärke und Spannung.
- Die Elektrode wird in den Elektrodenhalter eingesetzt, und die Masseklemme wird am Werkstück befestigt.
- Durch das Betätigen des Schweißschalters wird der Lichtbogen erzeugt, und der Bediener bewegt die Elektrode über das Werkstück, um die Schweißnaht zu erzeugen.
- Anwendungen:
- Elektrodenschweißmaschinen werden häufig für Reparaturarbeiten, Bauarbeiten, Metallverarbeitung, Schiffs- und Brückenbau sowie in vielen anderen industriellen Anwendungen eingesetzt.
- Vorteile:
- Relativ einfach zu bedienen und kostengünstig in der Anschaffung.
- Gut geeignet für Arbeiten im Freien und auf Baustellen, da sie weniger anfällig für Wind und äußere Bedingungen sind als andere Schweißverfahren.
- Nachteile:
- Einige Rauch- und Spritzpartikel können bei diesem Schweißprozess entstehen.
- Es erfordert eine gewisse Fertigkeit und Erfahrung, um qualitativ hochwertige Schweißnähte zu erzeugen.
Beim Arbeiten mit Elektrodenschweißmaschinen ist es wichtig, die Sicherheitsvorschriften zu beachten, einschließlich des Tragens von persönlicher Schutzausrüstung wie Schweißhelm, Schutzbrille und Schutzkleidung. Zudem sollten die spezifischen Anweisungen des Herstellers für die jeweilige Schweißmaschine befolgt werden.
MIG-/MAG-Schweißmaschinen
MIG-/MAG-Schweißmaschinen sind Schweißmaschinen, die zum Schweißen mit einem Drahtelektrodenvorschub verwendet werden. Der Drahtelektrode wird durch die Schweißmaschine geführt und mit dem Grundwerkstoff verschmolzen. Ein Schutzgas, in der Regel Argon oder Kohlendioxid, wird verwendet, um das Schweißgut vor Oxidation und Verunreinigungen zu schützen.
MIG-/MAG-Schweißmaschinen werden in einer Vielzahl von Branchen eingesetzt, darunter die Automobilindustrie, die Luft- und Raumfahrtindustrie und die Bauindustrie. Sie werden zum Schweißen von Stahl, Aluminium, Edelstahl und anderen Metallen verwendet.
MIG-/MAG-Schweißmaschinen bieten eine Reihe von Vorteilen, darunter:
- Produktivität: MIG-/MAG-Schweißmaschinen können hohe Schweißgeschwindigkeiten ermöglichen.
- Qualität: MIG-/MAG-Schweißmaschinen können hochwertige Schweißnähte produzieren.
- Flexibilität: MIG-/MAG-Schweißmaschinen können zum Schweißen einer Vielzahl von Werkstoffen verwendet werden.
MIG-/MAG-Schweißmaschinen werden in zwei Haupttypen unterteilt:
- Handgeführte MIG-/MAG-Schweißmaschinen: Handgeführte MIG-/MAG-Schweißmaschinen sind die am häufigsten verwendeten MIG-/MAG-Schweißmaschinen. Sie werden von einem Schweißer mit der Hand bedient.
- Automatische MIG-/MAG-Schweißmaschinen: Automatische MIG-/MAG-Schweißmaschinen werden mit einem Roboterarm betrieben. Sie werden zum Schweißen von großen oder komplexen Bauteilen verwendet.
Die wichtigsten Komponenten einer MIG-/MAG-Schweißmaschine sind:
- Schweißstromquelle: Die Schweißstromquelle erzeugt den Strom, der zum Schmelzen der Drahtelektrode verwendet wird.
- Schweißbrenner: Der Schweißbrenner hält die Drahtelektrode und führt sie zum Werkstück.
- Schutzgasanlage: Die Schutzgasanlage liefert das Schutzgas, das das Schweißgut vor Oxidation und Verunreinigungen schützt.
Die Art des verwendeten Schweißstroms hängt vom Werkstoff ab, der geschweißt werden soll. Die häufigsten Schweißströme für MIG-/MAG-Schweißmaschinen sind:
- Wechselstrom (AC): Wechselstrom wird zum Schweißen von Aluminium und anderen Nichteisenmetallen verwendet.
- Gleichstrom (DC): Gleichstrom wird zum Schweißen von Stahl und anderen Eisenmetallen verwendet.
Die Art des verwendeten Drahtelektrodenmaterials hängt ebenfalls vom Werkstoff ab, der geschweißt werden soll. Es gibt eine Vielzahl von Drahtelektrodentypen mit unterschiedlichen Eigenschaften.
Sicherheitshinweise beim MIG-/MAG-Schweißen:
- Tragen Sie geeignete persönliche Schutzausrüstung (PSA), einschließlich eines Schweißhelms, Handschuhen, Stiefeln und einer Schutzbrille.
- Sorgen Sie für eine gute Belüftung des Schweißbereichs.
- Schweißen Sie nicht in der Nähe von brennbaren Materialien.
- Berühren Sie die Drahtelektrode oder die Schweißnaht nicht mit bloßen Händen.
- Seien Sie sich der potenziellen Gefahr eines elektrischen Schlags bewusst.
MIG (Metal Inert Gas) und MAG (Metal Active Gas) sind zwei verwandte Schweißverfahren, die häufig mit Schweißmaschinen betrieben werden. Beide Verfahren verwenden einen Draht als Elektrode und ein Schutzgas, um den Lichtbogen zu stabilisieren und das geschmolzene Metall vor atmosphärischer Kontamination zu schützen. Hier sind einige grundlegende Informationen zu MIG-/MAG-Schweißmaschinen:
- Funktionsprinzip:
- MIG-Schweißen verwendet inerte Gase wie Argon oder Helium als Schutzgas, während MAG-Schweißen aktive Gase wie Kohlendioxid oder Mischungen aus Argon und CO2 verwendet.
- Ein Drahtelektrode wird durch die Schweißpistole zugeführt. Der Draht wird durch den Lichtbogen geschmolzen, und die entstehende Schmelze verbindet die zu schweißenden Teile.
- Komponenten:
- Stromquelle: Die Stromquelle erzeugt den elektrischen Strom für den Lichtbogen.
- Schweißpistole: Die Schweißpistole enthält den Drahtvorschubmechanismus und ermöglicht die Steuerung des Schweißprozesses durch den Bediener.
- Gasflasche oder -zufuhr: Je nach Verfahren wird entweder ein inertes oder aktives Schutzgas verwendet. Dieses Gas wird entweder aus einer Gasflasche oder einem Gasversorgungssystem zugeführt.
- Drahtvorschubsystem: Ein Mechanismus, der den Schweißdraht kontinuierlich durch die Schweißpistole fördert.
- Arbeitsweise:
- Der Bediener wählt den geeigneten Draht und das passende Schutzgas basierend auf den Anforderungen der Anwendung.
- Durch das Betätigen des Schweißschalters wird der Drahtelektrode durch die Schweißpistole zugeführt, und der Lichtbogen wird zwischen dem Draht und dem Werkstück erzeugt.
- Das geschmolzene Metall aus der Elektrode füllt den Spalt zwischen den zu verbindenden Teilen aus und bildet die Schweißnaht.
- Anwendungen:
- MIG-/MAG-Schweißmaschinen werden in verschiedenen Industriebereichen eingesetzt, darunter Fahrzeugbau, Schiffsbau, Metallverarbeitung, Bauwesen und allgemeiner Metallbau.
- Sie eignen sich gut für das Schweißen von dünnen bis mitteldicken Materialien.
- Vorteile:
- Hohe Schweißgeschwindigkeit und Effizienz.
- Geringe Rauch- und Spritzpartikel im Vergleich zu anderen Schweißverfahren.
- Geeignet für verschiedene Materialien, einschließlich Stahl, Edelstahl und Aluminium.
- Nachteile:
- Erfordert oft eine externe Gaszufuhr, was die Mobilität beeinträchtigen kann.
- Initialkosten für Ausrüstung und Gas können höher sein als bei einigen anderen Schweißverfahren.
Beim Arbeiten mit MIG-/MAG-Schweißmaschinen ist es wichtig, die spezifischen Anweisungen des Herstellers zu beachten und alle Sicherheitsvorkehrungen zu treffen, einschließlich der Verwendung von Schutzkleidung, einer Schweißhaube und anderer persönlicher Schutzausrüstung. Schulung und Erfahrung sind entscheidend, um qualitativ hochwertige Schweißnähte zu erzeugen.
TIG-Schweißmaschinen
TIG-Schweißmaschinen, auch als Wolfram-Inertgas-Schweißmaschinen (GTAW) bezeichnet, sind Schweißmaschinen, die zum Schweißen mit einer nicht abschmelzenden Wolframelektrode verwendet werden. Das Schweißgut wird aus einem separaten Draht zugeführt und mit der Wolframelektrode verschmolzen. Ein Schutzgas, in der Regel Argon, wird verwendet, um das Schweißgut vor Oxidation und Verunreinigungen zu schützen.
TIG-Schweißmaschinen werden in einer Vielzahl von Branchen eingesetzt, darunter die Luft- und Raumfahrtindustrie, die Elektronikindustrie und die Metallverarbeitung. Sie werden zum Schweißen von dünnen Blechen, Rohren und anderen komplexen Bauteilen verwendet.
TIG-Schweißmaschinen bieten eine Reihe von Vorteilen, darunter:
- Qualität: TIG-Schweißmaschinen können hochwertige Schweißnähte mit hoher Festigkeit und Duktilität produzieren.
- Flexibilität: TIG-Schweißmaschinen können zum Schweißen einer Vielzahl von Werkstoffen verwendet werden, einschließlich Stahl, Aluminium, Edelstahl und Kupfer.
- Präzision: TIG-Schweißmaschinen sind präzise und können zum Schweißen von dünnen Blechen und anderen komplexen Bauteilen verwendet werden.
TIG-Schweißmaschinen werden in zwei Haupttypen unterteilt:
- Handgeführte TIG-Schweißmaschinen: Handgeführte TIG-Schweißmaschinen sind die am häufigsten verwendeten TIG-Schweißmaschinen. Sie werden von einem Schweißer mit der Hand bedient.
- Automatische TIG-Schweißmaschinen: Automatische TIG-Schweißmaschinen werden mit einem Roboterarm betrieben. Sie werden zum Schweißen von großen oder komplexen Bauteilen verwendet.
Die wichtigsten Komponenten einer TIG-Schweißmaschine sind:
- Schweißstromquelle: Die Schweißstromquelle erzeugt den Strom, der zum Schmelzen des Schweißguts verwendet wird.
- Schweißbrenner: Der Schweißbrenner hält die Wolframelektrode und führt sie zum Werkstück.
- Schutzgasanlage: Die Schutzgasanlage liefert das Schutzgas, das das Schweißgut vor Oxidation und Verunreinigungen schützt.
Die Art des verwendeten Schweißstroms hängt vom Werkstoff ab, der geschweißt werden soll. Die häufigsten Schweißströme für TIG-Schweißmaschinen sind:
- Wechselstrom (AC): Wechselstrom wird zum Schweißen von Aluminium und anderen Nichteisenmetallen verwendet.
- Gleichstrom (DC): Gleichstrom wird zum Schweißen von Stahl und anderen Eisenmetallen verwendet.
Die Art des verwendeten Wolframelektrodenmaterials hängt ebenfalls vom Werkstoff ab, der geschweißt werden soll. Es gibt eine Vielzahl von Wolframelektrodentypen mit unterschiedlichen Eigenschaften.
Sicherheitshinweise beim TIG-Schweißen:
- Tragen Sie geeignete persönliche Schutzausrüstung (PSA), einschließlich eines Schweißhelms, Handschuhen, Stiefeln und einer Schutzbrille.
- Sorgen Sie für eine gute Belüftung des Schweißbereichs.
- Schweißen Sie nicht in der Nähe von brennbaren Materialien.
- Berühren Sie die Wolframelektrode oder die Schweißnaht nicht mit bloßen Händen.
- Seien Sie sich der potenziellen Gefahr eines elektrischen Schlags bewusst.
TIG (Wolfram-Inertgas)-Schweißmaschinen sind Werkzeuge, die für das TIG-Schweißverfahren verwendet werden. TIG-Schweißen ist ein Lichtbogenschweißverfahren, bei dem ein nicht-schmelzender Wolfram-Elektrodenstab verwendet wird, um den Lichtbogen zu erzeugen. Es wird auch als GTAW (Gas Tungsten Arc Welding) bezeichnet. Hier sind einige grundlegende Informationen zu TIG-Schweißmaschinen:
- Funktionsprinzip:
- Eine TIG-Schweißmaschine erzeugt einen Lichtbogen zwischen einer nicht-schmelzenden Wolfram-Elektrode und dem Werkstück.
- Das Werkstück wird nicht direkt von der Elektrode berührt, und der Lichtbogen erzeugt die notwendige Hitze, um das Werkstück zu schmelzen und die Schweißverbindung herzustellen.
- Ein externes Schutzgas, oft Argon, wird verwendet, um den Lichtbogen vor atmosphärischer Kontamination zu schützen.
- Komponenten:
- Stromquelle: Die Stromquelle erzeugt den elektrischen Strom für den Lichtbogen.
- Wolfram-Elektrode: Die nicht-schmelzende Wolfram-Elektrode wird in die Schweißpistole eingesetzt und erzeugt den Lichtbogen.
- Schweißpistole oder Brenner: Die Schweißpistole enthält die Wolfram-Elektrode und ermöglicht dem Bediener die Steuerung des Schweißprozesses.
- Gasflasche oder -zufuhr: Argon oder ein anderes inertes Gas wird als Schutzgas verwendet, um den Lichtbogen zu schützen.
- Arbeitsweise:
- Der Bediener wählt die passende Wolfram-Elektrode und das Schutzgas entsprechend den Anforderungen der Anwendung.
- Durch das Betätigen des Schweißschalters wird der Lichtbogen zwischen der Elektrode und dem Werkstück erzeugt.
- Der Bediener steuert den Lichtbogen über die Schweißpistole und fügt das geschmolzene Material zusammen, um die Schweißnaht zu erzeugen.
- Anwendungen:
- TIG-Schweißen eignet sich besonders für das Schweißen von dünnen Materialien und Edelstahl.
- Es wird in Anwendungen eingesetzt, bei denen hohe Schweißqualität und Präzision erforderlich sind, wie in der Luftfahrt, der Schienenfahrzeugindustrie, der Elektronik und anderen hochpräzisen Fertigungsprozessen.
- Vorteile:
- Hohe Präzision und Kontrolle über den Schweißprozess.
- Geringe Rauch- und Spritzpartikel.
- Geeignet für verschiedene Materialien, einschließlich Edelstahl, Aluminium und Titan.
- Nachteile:
- Im Vergleich zu anderen Schweißverfahren kann TIG-Schweißen langsamer sein.
- Erfordert eine höhere Fertigkeitsstufe und Erfahrung des Bedieners.
Es ist wichtig, die spezifischen Anweisungen des Herstellers und die Sicherheitsrichtlinien zu beachten, wenn man mit TIG-Schweißmaschinen arbeitet. Eine angemessene Schulung und Übung sind notwendig, um die besten Ergebnisse und eine hohe Schweißqualität zu erzielen.
Weitere Arten von Schweißmaschinen sind:
- WIG-Schweißmaschinen: WIG-Schweißmaschinen verwenden eine Wolframelektrode, die das Werkstück erhitzt und den Schweißprozess einleitet. Der Draht wird von einem Drahtvorschubgerät zugeführt und schmilzt beim Schweißen ab. WIG-Schweißmaschinen sind eine Kombination aus TIG- und MIG-/MAG-Schweißen.
- Plasmaschweißen: Plasmaschweißen verwendet einen Plasmastrahl, der das Werkstück erhitzt und den Schweißprozess einleitet. Plasmaschweißen ist ein sehr energieeffizientes Schweißverfahren, das für Anwendungen mit hohen Anforderungen an die Geschwindigkeit und die Qualität geeignet ist.
- Laserschweißen: Laserschweißen verwendet einen Laserstrahl, der das Werkstück erhitzt und den Schweißprozess einleitet. Laserschweißen ist ein sehr präzises Schweißverfahren, das für Anwendungen mit hohen Anforderungen an die Qualität geeignet ist.
WIG-Schweißmaschinen
WIG-Schweißmaschinen, auch als Wolfram-Inertgas-Schweißmaschinen (GTAW) bezeichnet, sind Schweißmaschinen, die zum Schweißen mit einer nicht abschmelzenden Wolframelektrode verwendet werden. Das Schweißgut wird aus einem separaten Draht zugeführt und mit der Wolframelektrode verschmolzen. Ein Schutzgas, in der Regel Argon, wird verwendet, um das Schweißgut vor Oxidation und Verunreinigungen zu schützen.
WIG-Schweißmaschinen werden in einer Vielzahl von Branchen eingesetzt, darunter die Luft- und Raumfahrtindustrie, die Elektronikindustrie und die Metallverarbeitung. Sie werden zum Schweißen von dünnen Blechen, Rohren und anderen komplexen Bauteilen verwendet.
WIG-Schweißmaschinen bieten eine Reihe von Vorteilen, darunter:
- Qualität: WIG-Schweißmaschinen können hochwertige Schweißnähte mit hoher Festigkeit und Duktilität produzieren.
- Flexibilität: WIG-Schweißmaschinen können zum Schweißen einer Vielzahl von Werkstoffen verwendet werden, einschließlich Stahl, Aluminium, Edelstahl und Kupfer.
- Präzision: WIG-Schweißmaschinen sind präzise und können zum Schweißen von dünnen Blechen und anderen komplexen Bauteilen verwendet werden.
WIG-Schweißmaschinen werden in zwei Haupttypen unterteilt:
- Handgeführte WIG-Schweißmaschinen: Handgeführte WIG-Schweißmaschinen sind die am häufigsten verwendeten WIG-Schweißmaschinen. Sie werden von einem Schweißer mit der Hand bedient.
- Automatische WIG-Schweißmaschinen: Automatische WIG-Schweißmaschinen werden mit einem Roboterarm betrieben. Sie werden zum Schweißen von großen oder komplexen Bauteilen verwendet.
Die wichtigsten Komponenten einer WIG-Schweißmaschine sind:
- Schweißstromquelle: Die Schweißstromquelle erzeugt den Strom, der zum Schmelzen des Schweißguts verwendet wird.
- Schweißbrenner: Der Schweißbrenner hält die Wolframelektrode und führt sie zum Werkstück.
- Schutzgasanlage: Die Schutzgasanlage liefert das Schutzgas, das das Schweißgut vor Oxidation und Verunreinigungen schützt.
Die Art des verwendeten Schweißstroms hängt vom Werkstoff ab, der geschweißt werden soll. Die häufigsten Schweißströme für WIG-Schweißmaschinen sind:
- Wechselstrom (AC): Wechselstrom wird zum Schweißen von Aluminium und anderen Nichteisenmetallen verwendet.
- Gleichstrom (DC): Gleichstrom wird zum Schweißen von Stahl und anderen Eisenmetallen verwendet.
Die Art des verwendeten Wolframelektrodenmaterials hängt ebenfalls vom Werkstoff ab, der geschweißt werden soll. Es gibt eine Vielzahl von Wolframelektrodentypen mit unterschiedlichen Eigenschaften.
Sicherheitshinweise beim WIG-Schweißen:
- Tragen Sie geeignete persönliche Schutzausrüstung (PSA), einschließlich eines Schweißhelms, Handschuhen, Stiefeln und einer Schutzbrille.
- Sorgen Sie für eine gute Belüftung des Schweißbereichs.
- Schweißen Sie nicht in der Nähe von brennbaren Materialien.
- Berühren Sie die Wolframelektrode oder die Schweißnaht nicht mit bloßen Händen.
- Seien Sie sich der potenziellen Gefahr eines elektrischen Schlags bewusst.
WIG (Wolfram-Inertgas)-Schweißmaschinen, auch als TIG (Gas Tungsten Arc Welding)-Schweißmaschinen bekannt, sind spezielle Werkzeuge, die für das TIG-Schweißverfahren verwendet werden. TIG-Schweißen ist ein Lichtbogenschweißverfahren, bei dem ein nicht-schmelzender Wolfram-Elektrodenstab verwendet wird, um den Lichtbogen zu erzeugen. Hier sind einige grundlegende Informationen zu WIG-Schweißmaschinen:
- Funktionsprinzip:
- Eine WIG-Schweißmaschine erzeugt einen Lichtbogen zwischen einer nicht-schmelzenden Wolfram-Elektrode und dem Werkstück.
- Das Werkstück wird nicht direkt von der Elektrode berührt, und der Lichtbogen erzeugt die notwendige Hitze, um das Werkstück zu schmelzen und die Schweißverbindung herzustellen.
- Ein externes Schutzgas, oft Argon, wird verwendet, um den Lichtbogen vor atmosphärischer Kontamination zu schützen.
- Komponenten:
- Stromquelle: Die Stromquelle erzeugt den elektrischen Strom für den Lichtbogen.
- Wolfram-Elektrode: Die nicht-schmelzende Wolfram-Elektrode wird in die Schweißpistole eingesetzt und erzeugt den Lichtbogen.
- Schweißpistole oder Brenner: Die Schweißpistole enthält die Wolfram-Elektrode und ermöglicht dem Bediener die Steuerung des Schweißprozesses.
- Gasflasche oder -zufuhr: Argon oder ein anderes inertes Gas wird als Schutzgas verwendet, um den Lichtbogen zu schützen.
- Arbeitsweise:
- Der Bediener wählt die passende Wolfram-Elektrode und das Schutzgas entsprechend den Anforderungen der Anwendung.
- Durch das Betätigen des Schweißschalters wird der Lichtbogen zwischen der Elektrode und dem Werkstück erzeugt.
- Der Bediener steuert den Lichtbogen über die Schweißpistole und fügt das geschmolzene Material zusammen, um die Schweißnaht zu erzeugen.
- Anwendungen:
- WIG-Schweißen eignet sich besonders für das Schweißen von dünnen Materialien und Edelstahl.
- Es wird in Anwendungen eingesetzt, bei denen hohe Schweißqualität und Präzision erforderlich sind, wie in der Luftfahrt, der Schienenfahrzeugindustrie, der Elektronik und anderen hochpräzisen Fertigungsprozessen.
- Vorteile:
- Hohe Präzision und Kontrolle über den Schweißprozess.
- Geringe Rauch- und Spritzpartikel.
- Geeignet für verschiedene Materialien, einschließlich Edelstahl, Aluminium und Titan.
- Nachteile:
- Im Vergleich zu anderen Schweißverfahren kann WIG-Schweißen langsamer sein.
- Erfordert eine höhere Fertigkeitsstufe und Erfahrung des Bedieners.
Es ist wichtig, die spezifischen Anweisungen des Herstellers und die Sicherheitsrichtlinien zu beachten, wenn man mit WIG-Schweißmaschinen arbeitet. Eine angemessene Schulung und Übung sind notwendig, um die besten Ergebnisse und eine hohe Schweißqualität zu erzielen.
Durchführen des Schweißens
Der MIG/MAG-Schweißer braucht eine gute Ausbildung, sowohl im praktischen Schweißen, als auch bei den theoretischen Besonderheiten des Verfahrens. Sie sind im Folgenden beschrieben:
Zünden des Lichtbogens
Wurde die Brennertaster betätigt, setzt sich die Drahtelektrode (mit verminderter Geschwindigkeit, sog. „Einschleichgeschwindigkeit“) in Bewegung. Gleichzeitig wird die Stromzufuhr gestartet und das Schutzgas
beginnt zu strömen. Beim Berühren der Drahtspitze auf der Werkstückoberfläche entsteht ein erster Kontakt, über den sofort ein hoher Strom fließt. Wegen der hohen Stromdichte
an der Elektrodenspitze wird an der Berührungsstelle Material hoch erhitzt. Das ist die Voraussetzung für die Bildung eines Lichtbogens. Wenn der Lichtbogen stabil brennt, wird automatisch auf die vorgewählte Drahtvorschubgeschwindigkeit hochgeschaltet.
Moderne Schweißgeräte unterstützen den gewünschten, wiederholbaren Ablauf des an sich kritischen Zündvorgangs mit Elektronik. Das Zünden sollte normalerweise nicht außerhalb der Fuge und möglichst an Stellen
erfolgen, die später wieder aufgeschmolzen werden. An nicht überschweißten Zündstellen können sich u.U. Risse bilden. Gelegentlich versagt der oben beschriebene optimale Zündvorgang und es gibt eine kurz aufeinander folgende Mehrfachzündung mit knallenden Geräuschen und wegfliegenden Drahtstücken.
Das ist ein deutliches Zeichen für Fehler in folgenden Bereichen: dicke oxidierte Kugel am Drahtende, schlecht leitende Werkstückoberfläche, Wackelkontakte zwischen Werkstück und Masseanschluss, Defekte / Unterbrechungen in den Schweißkabeln oder Brennerleitungen, falsch gewählte Schweißparameter oder falsch gewählte Einschleichgeschwindigkeit (sofern manuell einstellbar). Auch eine ungeeignete Kontaktierung der Drahtelektrode in der Stromdüse des Brenners, z. B. durch Abnutzung, kann u. a. zu Zündschwierigkeiten führen.
Brennerführung
Der Brenner wird in Schweißrichtung etwa 10° bis 20° geneigt und kann schleppend oder stechend geführt werden (Bild 33). Der Abstand zwischen dem freien Drahtende und dem Werkstück, also der Unterkante
der Stromdüse und dem Ansatzpunkt des Lichtbogens, sollte etwa 10 bis 12 Mal Drahtdurchmesser [mm] betragen. Bei einem zu stark geneigtem Brenner besteht die Gefahr, dass Luft in das Schutzgas eingewirbelt wird
und Fehler entstehen können.
Stechende Brennerführung ist in der Regel beim Schweißen mit Massivdrähten üblich, schleppende Führung beim Einsatz von Schlacke führenden Fülldrähten. Leicht schleppend wird der Brenner generell in der Position PG geführt. Fallnahtschweißen (Pos. PG, fallend) kommt hauptsächlich bei dünneren Blechen vor. Bei dickerem Material besteht die Gefahr, dass durch vorlaufendes Schweißgut Bindefehler entstehen.
Diese Bindefehler können auch in anderen Positionen auftreten, wenn mit zu geringer Schweißgeschwindigkeit geschweißt wird. Breites Pendeln sollte deshalb, von der Position PF (steigend) abgesehen, möglichst vermieden werden
Das Schweißen ist eine unverzichtbare Technologie in der modernen industriellen Fertigung. Es ermöglicht die dauerhafte Verbindung von Metallteilen, die in einer Vielzahl von Produkten und Infrastrukturen verwendet werden, von Automobilen über Flugzeuge bis hin zu Gebäuden. Traditionell wurde das Schweißen manuell durchgeführt, was hohe Anforderungen an die Fähigkeiten und Erfahrung des Bedieners stellte. In den letzten Jahrzehnten hat jedoch die Automatisierung des Schweißprozesses erheblich an Bedeutung gewonnen. Diese Entwicklung hat nicht nur die Produktivität gesteigert, sondern auch die Qualität und Konsistenz der Schweißnähte verbessert.
Mit der Einführung von automatisierten Schweißmaschinen, wie der automatischen Kreisschweißmaschine und dem MIG-Rundschweißgerät, können Unternehmen den Schweißprozess weiter optimieren. Automatisierte Schweißgeräte haben sich in einer Vielzahl von Branchen als unverzichtbar erwiesen, da sie die Präzision und Effizienz des Schweißprozesses auf ein neues Niveau heben. Die Verwendung von CNC-Steuerungen und robotergesteuerten Schweißgeräten hat es ermöglicht, komplexe Schweißaufgaben mit minimaler menschlicher Intervention durchzuführen.
In diesem umfassenden Artikel werden wir die verschiedenen Arten von automatisierten Schweißmaschinen, einschließlich der automatischen Kreisschweißmaschine und des MIG-Rundschweißgeräts, sowie ihre jeweiligen Vorteile, Einsatzmöglichkeiten und Technologien untersuchen. Darüber hinaus werfen wir einen Blick auf die neuesten Trends in der Schweißautomatisierung, wie die Integration von Künstlicher Intelligenz (KI) und maschinellem Lernen in den Schweißprozess.
Was ist eine Automatische Kreisschweißmaschine?
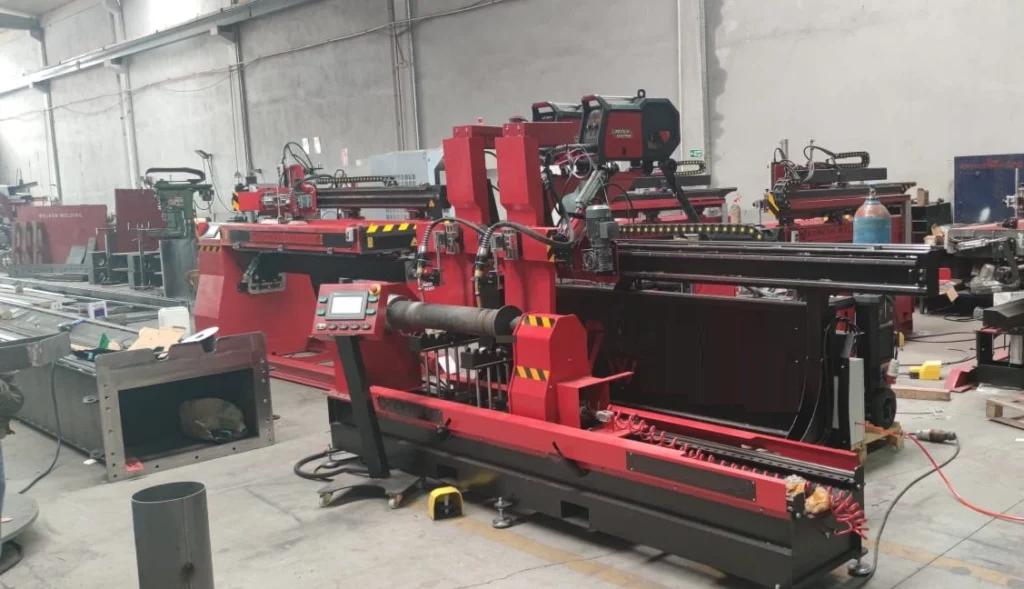
Eine automatische Kreisschweißmaschine ist eine spezialisierte Schweißanlage, die hauptsächlich für das Schweißen von runden oder zylindrischen Werkstücken entwickelt wurde. Sie verwendet rotierende Mechanismen, um eine gleichmäßige und präzise Schweißnaht entlang der zirkularen Konturen eines Werkstücks zu erzeugen. Im Gegensatz zu herkömmlichen manuellen Schweißmethoden erfordert die automatische Kreisschweißmaschine wenig bis gar keine manuelle Eingriffe während des Schweißvorgangs. Das Werkstück wird in der Regel auf einem Drehtisch fixiert, während der Schweißkopf sich entweder um das Werkstück bewegt oder das Werkstück selbst rotiert, um eine gleichmäßige Schweißnaht zu erzeugen.
Die Hauptanwendung der Kreisschweißmaschinen ist das Schweißen von runden Bauteilen wie Rohren, Zylindern, Tanks oder Flanschen, die präzise und wiederholbare Schweißnähte erfordern. Diese Maschinen sind in der Lage, sowohl kontinuierliche als auch segmentierte Schweißnähte zu erzeugen, je nach den Anforderungen des spezifischen Projekts.
Hauptkomponenten einer Kreisschweißmaschine
Eine Kreisschweißmaschine besteht aus mehreren wichtigen Komponenten, die eine präzise und effiziente Schweißleistung ermöglichen:
- Drehtisch oder Spannvorrichtung: Hier wird das Werkstück fixiert und in eine rotierende Bewegung versetzt, um das Schweißen entlang seiner zirkularen Kontur zu ermöglichen.
- Schweißkopf: Dies ist das zentrale Element der Maschine, das den eigentlichen Schweißvorgang durchführt. Je nach Schweißverfahren kann es sich um einen Lichtbogen-Schweißkopf (MIG, TIG) oder einen Laserschweißkopf handeln.
- Steuerungseinheit: Moderne Kreisschweißmaschinen sind mit einer CNC-Steuerung (Computer Numerical Control) ausgestattet, die eine präzise Programmierung und Kontrolle des Schweißprozesses ermöglicht.
- Schweißstromquelle: Die Maschine benötigt eine Stromquelle, um den Schweißlichtbogen oder den Laser zu erzeugen. Diese wird in Abhängigkeit vom Schweißverfahren angepasst.
- Kühlvorrichtung: Um die Lebensdauer der Maschine zu verlängern und eine konstante Schweißqualität zu gewährleisten, wird häufig eine Kühlvorrichtung integriert, die die Schweißelektrode oder den Schweißkopf kühlt.
Typische Anwendungen
Die Anwendungsmöglichkeiten von Kreisschweißmaschinen sind vielseitig und erstrecken sich über zahlreiche Industriezweige:
- Automobilindustrie: Kreisschweißmaschinen werden häufig in der Herstellung von Auspuffrohren, Stoßdämpfern und anderen zylindrischen Komponenten eingesetzt. Durch den automatisierten Prozess können diese Teile in hoher Stückzahl mit gleichbleibender Qualität gefertigt werden.
- Luft- und Raumfahrt: In der Luftfahrtindustrie sind hohe Präzision und Zuverlässigkeit entscheidend. Kreisschweißmaschinen werden verwendet, um Turbinenteile, Flugzeugzylinder und andere sicherheitskritische Bauteile zu schweißen.
- Behälter- und Apparatebau: Hier kommen Kreisschweißmaschinen zur Anwendung, um Tanks, Kessel und Druckbehälter zu schweißen, die eine hohe Schweißnahtqualität und Dichtigkeit erfordern.
- Rohre und Rohrverbindungen: Insbesondere in der Öl- und Gasindustrie sowie in der Wasserversorgung sind Kreisschweißmaschinen von zentraler Bedeutung, um lange Rohrverbindungen effizient und präzise herzustellen.
Vorteile der Automatischen Kreisschweißmaschine
Automatische Kreisschweißmaschinen bieten eine Reihe von entscheidenden Vorteilen, die sie zu einer unverzichtbaren Technologie in der modernen Fertigung machen:
- Hohe Präzision und Wiederholgenauigkeit: Da der gesamte Schweißprozess automatisiert ist und durch eine CNC-Steuerung präzise kontrolliert wird, können gleichbleibende und hochqualitative Schweißnähte erzielt werden.
- Effizienzsteigerung: Automatisierte Maschinen ermöglichen eine signifikant höhere Produktionsrate im Vergleich zu manuellen Schweißverfahren. Dies reduziert die Fertigungszeit und erhöht die Gesamteffizienz.
- Reduzierte Fehlerquote: Die Automatisierung minimiert das Risiko menschlicher Fehler, was besonders bei sicherheitskritischen Anwendungen wichtig ist.
- Flexibilität: Moderne Kreisschweißmaschinen sind in der Lage, unterschiedliche Schweißverfahren zu unterstützen (MIG, TIG, Laserschweißen), was sie für eine Vielzahl von Anwendungen flexibel einsetzbar macht.
- Kostensenkung: Durch die höhere Effizienz, die reduzierte Fehlerquote und den geringeren Personalaufwand können Unternehmen langfristig erhebliche Kosteneinsparungen realisieren.
- Verbesserte Arbeitssicherheit: Da die Bediener weniger direkt in den Schweißprozess eingreifen müssen, wird das Risiko von Verletzungen durch Lichtbogenstrahlung oder heiße Werkstücke erheblich reduziert.
Herausforderungen und Einschränkungen
Trotz der vielen Vorteile gibt es einige Herausforderungen, die bei der Implementierung von automatischen Kreisschweißmaschinen berücksichtigt werden müssen:
- Hohe Anfangsinvestitionen: Die Anschaffung und Einrichtung einer automatisierten Schweißmaschine kann kostspielig sein. Für kleinere Unternehmen oder solche mit geringen Produktionsvolumina kann dies eine erhebliche Hürde darstellen.
- Schulung und Wartung: Obwohl die Maschinen den Schweißprozess automatisieren, erfordert ihre Bedienung spezielles Fachwissen, insbesondere im Bereich der Programmierung und Wartung. Regelmäßige Schulungen und Wartungsarbeiten sind notwendig, um die Maschinen optimal zu betreiben.
- Begrenzte Flexibilität bei komplexen Geometrien: Während Kreisschweißmaschinen ideal für zylindrische und runde Werkstücke sind, stoßen sie bei unregelmäßigen oder komplexen Geometrien an ihre Grenzen. Hier sind häufig zusätzliche Vorrichtungen oder manuelle Eingriffe notwendig.
MIG-Rundschweißgerät – Funktionsweise und Anwendungsbereiche
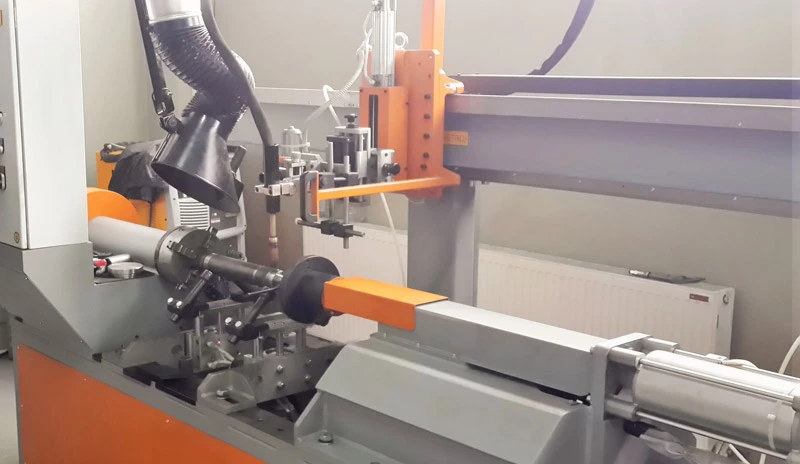
MIG-Schweißen: Grundlagen
Das MIG-Schweißen (Metal-Inert-Gas-Schweißen) ist ein weit verbreitetes Schweißverfahren, das durch seine Vielseitigkeit und Effizienz in einer Vielzahl von industriellen Anwendungen eingesetzt wird. Beim MIG-Schweißen wird ein kontinuierlich zugeführter Draht als Schweißelektrode verwendet. Dieser Draht schmilzt unter der Hitze des elektrischen Lichtbogens und verbindet sich mit dem Grundmaterial. Dabei wird ein inertes Gas (in der Regel Argon oder Helium) als Schutzgas verwendet, das den Schweißbereich vor Oxidation und anderen Verunreinigungen schützt. Das MIG-Schweißen ist besonders beliebt, weil es sowohl für dicke als auch dünne Materialien geeignet ist und eine hohe Schweißgeschwindigkeit bietet.
Ein MIG-Rundschweißgerät kombiniert die MIG-Schweißtechnologie mit der Fähigkeit, zylindrische Werkstücke präzise zu schweißen. Das Rundschweißen beschreibt den Prozess, bei dem das Werkstück während des Schweißens rotiert wird, um eine gleichmäßige Schweißnaht entlang der zirkularen Oberfläche zu erzeugen. Dies ist besonders nützlich für das Schweißen von Rohren, Zylindern, Flanschen und anderen kreisförmigen Bauteilen.
Eigenschaften eines MIG-Rundschweißgeräts
Ein MIG-Rundschweißgerät verfügt über spezielle Eigenschaften, die es von herkömmlichen MIG-Schweißgeräten unterscheiden und für den Rundschweißprozess optimieren:
- Drehvorrichtung für das Werkstück: Im Zentrum des MIG-Rundschweißens steht die Fähigkeit, das Werkstück während des Schweißvorgangs zu drehen. Diese Drehvorrichtung ist präzise kalibriert, um eine gleichmäßige Schweißnaht entlang der kreisförmigen Oberfläche zu gewährleisten. Sie kann für verschiedene Werkstückgrößen und -gewichte angepasst werden.
- Automatisierte Drahtzuführung: Ähnlich wie bei herkömmlichen MIG-Schweißgeräten wird auch bei einem Rundschweißgerät der Schweißdraht kontinuierlich zugeführt, um den Schweißprozess effizient und ohne Unterbrechung durchzuführen.
- CNC-Steuerung für Präzision: Moderne MIG-Rundschweißgeräte sind in der Regel mit CNC-Steuerungen ausgestattet, die eine präzise Programmierung und Steuerung des Schweißvorgangs ermöglichen. Dies sorgt für gleichbleibende Qualität und minimiert Fehlerquellen.
- Variable Schweißgeschwindigkeiten: Da die Werkstücke unterschiedliche Geometrien und Materialien aufweisen können, muss die Schweißgeschwindigkeit an die spezifischen Anforderungen angepasst werden. MIG-Rundschweißgeräte bieten daher variable Geschwindigkeiten, um die beste Schweißnahtqualität zu gewährleisten.
- Schutzgaszuführung: Da das MIG-Schweißen auf ein Schutzgas angewiesen ist, sind MIG-Rundschweißgeräte mit integrierten Systemen zur präzisen Gaszufuhr ausgestattet, um den Schweißbereich vor atmosphärischen Einflüssen zu schützen.
Anwendungsbereiche des MIG-Rundschweißens
Das MIG-Rundschweißen wird in einer Vielzahl von Industrien verwendet, insbesondere in Bereichen, in denen zylindrische oder runde Bauteile geschweißt werden müssen. Einige der wichtigsten Anwendungsbereiche umfassen:
- Rohr- und Rohrleitungsbau: Das Schweißen von Rohren ist eine der häufigsten Anwendungen für MIG-Rundschweißgeräte. In der Öl- und Gasindustrie sowie in der Wasserversorgung müssen Rohrleitungen häufig nahtlos und sicher miteinander verbunden werden. Das MIG-Rundschweißen ermöglicht es, lange Rohre effizient und mit hoher Schweißnahtqualität herzustellen.
- Druckbehälter und Kessel: In der Herstellung von Druckbehältern, die hohen Belastungen und Drücken standhalten müssen, ist eine gleichmäßige und zuverlässige Schweißnaht entscheidend. Das MIG-Rundschweißen bietet hier die nötige Präzision und Stabilität, um sicherzustellen, dass die Behälter den erforderlichen Sicherheitsstandards entsprechen.
- Automobilindustrie: In der Automobilfertigung werden MIG-Rundschweißgeräte für das Schweißen von Auspuffsystemen, Stoßdämpfern und anderen zylindrischen Bauteilen eingesetzt. Durch die hohe Schweißgeschwindigkeit können Produktionszeiten verkürzt und Kosten gesenkt werden.
- Luft- und Raumfahrt: Präzision und Zuverlässigkeit sind in der Luft- und Raumfahrtindustrie von entscheidender Bedeutung. MIG-Rundschweißgeräte werden verwendet, um kritische Komponenten wie Triebwerkszylinder und andere runde Bauteile mit höchster Genauigkeit zu schweißen.
- Möbel- und Metallverarbeitungsindustrie: In der Produktion von Metallmöbeln oder dekorativen Metallteilen ist das Rundschweißen oft erforderlich, um ästhetisch ansprechende und stabile Verbindungen zu erzeugen. Das MIG-Rundschweißen bietet die Möglichkeit, solche Teile schnell und präzise zu schweißen.
Vorteile des MIG-Rundschweißens
Das MIG-Rundschweißen bietet mehrere Vorteile, die es von anderen Schweißverfahren abheben:
- Hohe Schweißgeschwindigkeit: Das kontinuierliche Schweißen und die automatische Drahtzuführung sorgen für eine schnellere Produktion im Vergleich zu manuellen Schweißverfahren. Dies spart Zeit und erhöht die Effizienz in der Produktion.
- Gleichmäßige Schweißnähte: Die Drehvorrichtung und die präzise Steuerung der Schweißgeschwindigkeit ermöglichen es, gleichmäßige und qualitativ hochwertige Schweißnähte entlang der gesamten kreisförmigen Oberfläche des Werkstücks zu erzeugen.
- Wenig Nacharbeit: Da die Schweißnähte gleichmäßig und präzise sind, ist weniger Nachbearbeitung erforderlich. Dies reduziert den Zeitaufwand und die Kosten für das Schleifen oder Polieren der Schweißnähte.
- Vielseitigkeit bei Materialien: Das MIG-Schweißen ist für eine Vielzahl von Materialien geeignet, darunter Aluminium, Edelstahl, Kohlenstoffstahl und andere Legierungen. Dies macht MIG-Rundschweißgeräte zu einer flexiblen Lösung für verschiedene Anwendungen.
- Einfache Automatisierung: MIG-Rundschweißgeräte lassen sich leicht in automatisierte Fertigungslinien integrieren. Dies macht sie zu einer idealen Wahl für Unternehmen, die ihre Produktion steigern und gleichzeitig Kosten senken möchten.
Herausforderungen des MIG-Rundschweißens
Obwohl das MIG-Rundschweißen viele Vorteile bietet, gibt es auch einige Herausforderungen, die bei der Anwendung berücksichtigt werden müssen:
- Hohe Anfangsinvestitionen: Ähnlich wie bei anderen automatisierten Schweißgeräten können die Anschaffungskosten für MIG-Rundschweißgeräte hoch sein, insbesondere für Unternehmen, die keine Großserienfertigung betreiben.
- Komplexität der Einstellung: Das Einrichten eines MIG-Rundschweißgeräts erfordert Fachwissen, insbesondere in Bezug auf die Programmierung der CNC-Steuerung und die Einstellung der Schweißparameter. Eine fehlerhafte Konfiguration kann zu minderwertigen Schweißnähten oder Schäden am Werkstück führen.
- Materialabhängige Herausforderungen: Je nach Material können unterschiedliche Schutzgase und Schweißdrahtarten erforderlich sein. Das Schweißen von dünnen Materialien oder Legierungen kann anspruchsvoll sein und erfordert präzise Einstellungen.
- Schutzgasmanagement: Da das MIG-Schweißen stark von einem konstanten Schutzgasstrom abhängt, können Probleme bei der Gaszufuhr die Schweißqualität beeinträchtigen. Ein fehlerhaftes Gasmanagement kann zu Porosität oder anderen Defekten in der Schweißnaht führen.
Automatische Schweißmaschinen – Von der manuellen Bedienung zur vollautomatischen Steuerung
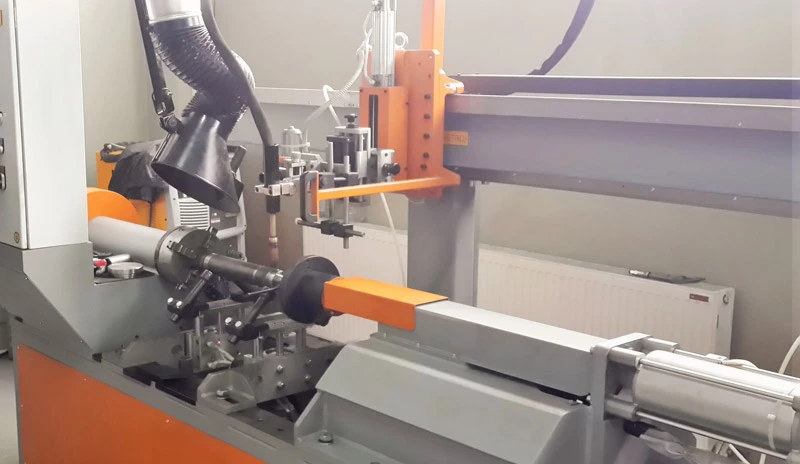
Schweißmaschinen haben sich seit ihren ersten Anwendungen erheblich weiterentwickelt. In den frühen Tagen der industriellen Fertigung waren Schweißprozesse überwiegend manuell und erforderten hochqualifizierte Fachkräfte, um präzise und dauerhafte Verbindungen herzustellen. Die Notwendigkeit, große Mengen an Bauteilen zu schweißen, führte schließlich zu Verbesserungen im Bereich der automatischen Schweißmaschinen.
Heutige automatische Schweißmaschinen ermöglichen es, komplexe Schweißprozesse mit minimalem menschlichen Eingriff durchzuführen. Sie integrieren fortschrittliche Steuerungssysteme, wie Computer Numerical Control (CNC) und Robotertechnologien, um präzise, schnelle und wiederholbare Schweißnähte zu erzeugen. In diesem Abschnitt werden wir die Entwicklung von manuellen Schweißverfahren hin zu modernen vollautomatischen Systemen nachvollziehen.
Technologien und Steuerungssysteme
Moderne automatische Schweißmaschinen basieren auf einer Vielzahl von Technologien und Steuerungssystemen, die es ermöglichen, unterschiedlichste Schweißverfahren für spezifische Anwendungen zu automatisieren. Hier sind einige der zentralen Technologien, die den Übergang von manuellen zu vollautomatischen Schweißmaschinen vorangetrieben haben:
- CNC-Steuerungen: Eine der wichtigsten Innovationen in der Schweißtechnik ist die Einführung der CNC-Steuerung. Diese ermöglicht die präzise Programmierung und Steuerung der Maschinenbewegungen, wodurch eine extrem hohe Genauigkeit und Wiederholbarkeit bei komplexen Schweißaufgaben erreicht werden. CNC-gesteuerte Maschinen sind in der Lage, komplizierte Schweißmuster oder mehrfache Schweißnähte ohne menschliches Eingreifen durchzuführen.
- Robotertechnologie: Roboterarme und automatisierte Schweißzellen sind in modernen Fertigungsanlagen weit verbreitet. Diese Roboter sind so konzipiert, dass sie Schweißaufgaben autonom und mit hoher Präzision ausführen können. Sie werden oft in der Automobilindustrie, der Luft- und Raumfahrt sowie im Schiffbau eingesetzt, um große Bauteile schnell und effizient zu schweißen.
- Laser-Schweißtechnologie: Laser-Schweißen ist eine moderne Technologie, die häufig in automatisierten Schweißsystemen zum Einsatz kommt. Sie ermöglicht extrem feine und präzise Schweißnähte bei hoher Geschwindigkeit, was besonders in Branchen mit sehr hohen Qualitätsanforderungen wie der Medizintechnik oder der Elektronikfertigung wichtig ist.
- Vision-Systeme und Sensorik: Fortschrittliche automatische Schweißmaschinen verwenden Vision-Systeme und Sensorik, um den Schweißprozess in Echtzeit zu überwachen. Diese Systeme erkennen Materialunregelmäßigkeiten, Positionsabweichungen oder Veränderungen in der Schweißnaht und passen den Prozess sofort an, um die gewünschte Qualität zu gewährleisten. Fehlererkennungs- und Korrektursysteme sind von entscheidender Bedeutung für die Sicherstellung der Schweißnahtqualität bei hochautomatisierten Prozessen.
Vorteile der Automatisierung in der Schweißtechnik
Die Automatisierung im Schweißprozess hat zahlreiche Vorteile, die sie für viele Industriezweige unverzichtbar machen. Zu den wichtigsten Vorteilen gehören:
- Gesteigerte Effizienz und Produktivität:
- Höhere Produktionsgeschwindigkeiten: Automatische Schweißmaschinen können rund um die Uhr arbeiten und gleichbleibend hohe Produktionsgeschwindigkeiten aufrechterhalten. Im Vergleich zu manuellen Prozessen, die häufig durch menschliche Erschöpfung oder Fehler beeinträchtigt werden, bieten diese Maschinen eine kontinuierliche und präzise Fertigung.
- Reduzierung der Produktionszeit: Da die Maschinen so programmiert werden können, dass sie mehrere Arbeitsschritte in einem Durchgang erledigen, können Produktionszeiten drastisch verkürzt werden.
- Erhöhte Sicherheit am Arbeitsplatz:
- Weniger direkte menschliche Interaktion: Automatische Schweißmaschinen minimieren den Bedarf an direkter menschlicher Beteiligung am Schweißprozess, wodurch das Risiko von Arbeitsunfällen, wie z.B. durch Lichtbogenstrahlung, Schweißdämpfe oder heiße Werkstücke, erheblich verringert wird.
- Sicherheitsmechanismen und Überwachungsfunktionen: Moderne Maschinen verfügen über integrierte Sicherheitsmechanismen, die den Schweißvorgang sofort unterbrechen, wenn eine Gefahrensituation erkannt wird.
- Verbesserte Schweißnahtqualität:
- Konstanz und Wiederholbarkeit: Automatische Schweißmaschinen bieten eine hohe Wiederholgenauigkeit, was besonders bei Serienfertigungen von großer Bedeutung ist. Die Präzision, die durch CNC-Steuerungen und Robotertechnologien ermöglicht wird, sorgt für gleichbleibende Qualität, unabhängig von der Anzahl der Werkstücke.
- Minimierung menschlicher Fehler: Manuelle Schweißprozesse sind anfällig für Fehler, die durch Ermüdung, Ablenkung oder mangelnde Erfahrung verursacht werden können. Automatische Systeme eliminieren solche Faktoren und bieten eine deutlich höhere Zuverlässigkeit.
- Kosteneinsparungen:
- Reduzierung von Lohnkosten: Durch den Einsatz von automatisierten Schweißmaschinen kann der Bedarf an qualifizierten Schweißern verringert werden. Dies führt zu einer Senkung der Personalkosten, insbesondere in Hochlohnländern.
- Weniger Materialverschwendung: Durch die präzise Steuerung des Schweißprozesses wird weniger Material verschwendet, und es entstehen weniger fehlerhafte Werkstücke, die nachbearbeitet oder entsorgt werden müssen.
Beispiele für vollautomatische Schweißmaschinen in der Industrie
In verschiedenen Industrien kommen vollautomatische Schweißmaschinen erfolgreich zum Einsatz. Hier einige Beispiele:
- Automobilindustrie:
- In der Automobilfertigung sind Schweißroboter in nahezu jedem Produktionsschritt zu finden, vom Schweißen der Karosserie bis hin zur Montage von Bauteilen wie Auspuffanlagen und Fahrgestellen. Vollautomatische Schweißmaschinen ermöglichen hier eine extrem hohe Produktionsrate und gleichbleibende Qualität, was für die Massenproduktion von entscheidender Bedeutung ist.
- Schiffbau:
- Der Schiffbau erfordert großflächige Schweißarbeiten, bei denen es auf Präzision und Geschwindigkeit ankommt. Vollautomatische Schweißsysteme, insbesondere solche, die auf Lasertechnologie basieren, sind in der Lage, große Stahlplatten mit hoher Genauigkeit zu verschweißen und so die Bauzeiten erheblich zu verkürzen.
- Luft- und Raumfahrt:
- In der Luftfahrtindustrie sind die Anforderungen an die Schweißqualität extrem hoch, da selbst kleinste Fehler zu schwerwiegenden Sicherheitsproblemen führen können. Vollautomatische Schweißmaschinen, die mit fortschrittlichen Überwachungssystemen ausgestattet sind, sorgen für die Herstellung von hochpräzisen Bauteilen wie Triebwerkskomponenten oder Flugzeugrümpfen.
- Medizintechnik:
- In der Medizintechnik, wo Geräte und Implantate höchsten Qualitätsstandards entsprechen müssen, kommen vollautomatische Schweißmaschinen zum Einsatz, um kleinste Bauteile wie chirurgische Instrumente oder Implantate zu schweißen. Diese Maschinen sind in der Lage, feine und präzise Schweißnähte zu erzeugen, die den strengen Anforderungen der Branche gerecht werden.
Automatisiertes Schweißgerät – Technologien und Innovationen
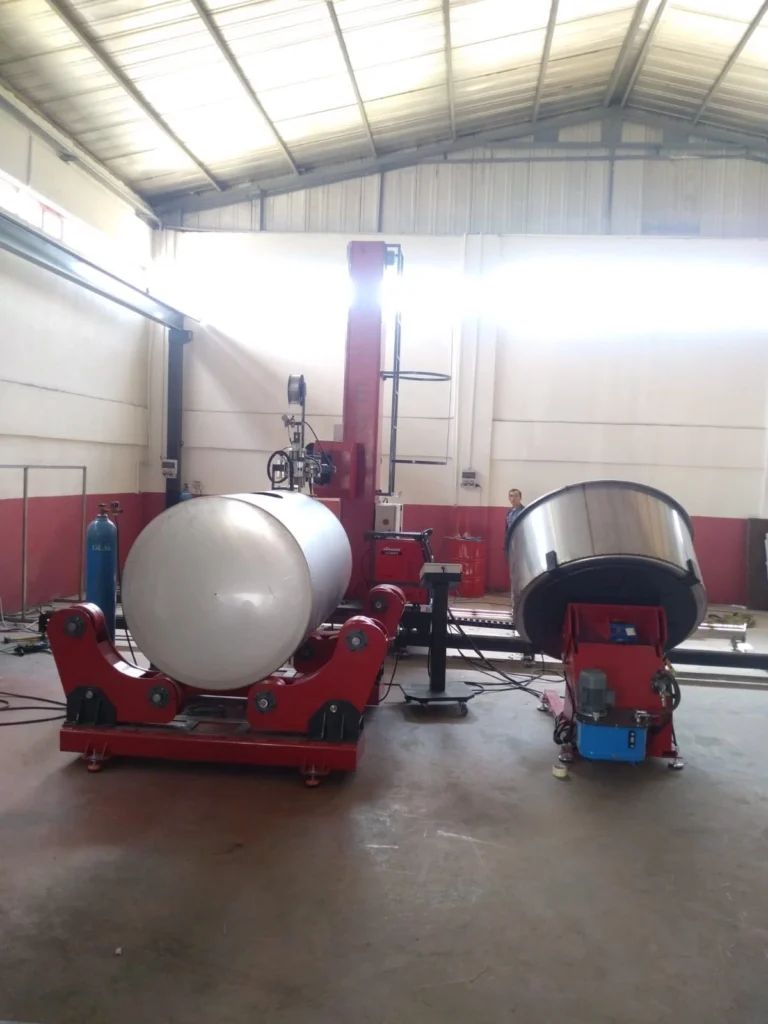
Definition und Typen automatisierter Schweißgeräte
Automatisierte Schweißgeräte sind ein wesentlicher Bestandteil der modernen Fertigungstechnologie und ermöglichen es, Schweißprozesse präzise und effizient durchzuführen. Diese Geräte decken eine breite Palette von Schweißverfahren ab, darunter das MIG- (Metal-Inert-Gas), TIG- (Tungsten-Inert-Gas), Lichtbogen- und Laserschweißen. Automatisierte Schweißgeräte können sowohl eigenständige, spezialisierte Maschinen sein als auch Teil komplexer Produktionslinien, in denen sie durch Roboter, CNC-Steuerungen und andere Technologien unterstützt werden.
Im Wesentlichen lassen sich automatisierte Schweißgeräte in zwei Hauptkategorien unterteilen:
- Fest installierte Schweißgeräte: Diese Maschinen sind in eine Produktionslinie integriert und übernehmen spezifische Schweißaufgaben in einem festgelegten Bereich. Sie sind besonders in der Großserienfertigung verbreitet, z. B. in der Automobil- oder Luftfahrtindustrie, wo Bauteile in großen Stückzahlen mit konsistenter Qualität hergestellt werden müssen. Ein Beispiel hierfür sind Schweißzellen, die durch Roboterarme gesteuert werden, die autonom mehrere Schweißnähte an einem Werkstück durchführen.
- Robotergestützte Schweißsysteme: Roboterschweißgeräte sind mit Roboterarmen ausgestattet, die auf präzisen Bahnen programmiert sind, um komplizierte Schweißnähte an Werkstücken unterschiedlicher Geometrien zu erzeugen. Diese Systeme sind extrem flexibel und können auf verschiedene Schweißverfahren eingestellt werden. Sie ermöglichen die Bearbeitung komplexer Geometrien und können in hochdynamischen Produktionsumgebungen eingesetzt werden.
Technologische Innovationen in automatisierten Schweißgeräten
Mit dem raschen Fortschritt in den Bereichen Robotik, Sensorik und Datenverarbeitung erleben auch automatisierte Schweißgeräte signifikante technologische Innovationen. Diese Fortschritte zielen darauf ab, die Effizienz, Präzision und Flexibilität der Schweißgeräte weiter zu verbessern. Einige der bedeutendsten Innovationen in diesem Bereich sind:
- Künstliche Intelligenz (KI) und maschinelles Lernen:
- Optimierung des Schweißprozesses: KI-gesteuerte Schweißgeräte können Schweißprozesse in Echtzeit analysieren und anpassen, um optimale Ergebnisse zu erzielen. Dabei verwenden sie maschinelles Lernen, um Daten aus früheren Schweißvorgängen zu analysieren und den Prozess kontinuierlich zu verbessern. Solche Systeme können Fehler automatisch erkennen und Anpassungen vornehmen, um die Qualität der Schweißnähte zu gewährleisten.
- Echtzeit-Fehlererkennung: Mithilfe von Sensoren und Kameras können KI-gesteuerte Systeme Unregelmäßigkeiten oder Defekte in der Schweißnaht sofort erkennen und den Prozess anpassen, um sicherzustellen, dass die Qualitätsanforderungen erfüllt werden. Dies minimiert Ausschuss und Nachbearbeitung.
- Integration von Vision-Systemen und Sensorik:
- Verbesserte Überwachung: Automatisierte Schweißgeräte sind zunehmend mit fortschrittlichen Vision-Systemen ausgestattet, die den Schweißvorgang in Echtzeit überwachen. Diese Kamerasysteme analysieren die Schweißnaht, die Flussrate des Schutzgases und die Materialpositionierung. Durch die Integration von Sensorik können die Maschinen den Schweißvorgang präzise anpassen, um die beste Schweißqualität sicherzustellen.
- Laser-Triangulation: Eine weitere technologische Innovation ist die Laser-Triangulation, die es ermöglicht, den Abstand zwischen dem Schweißkopf und dem Werkstück genau zu messen. Dies gewährleistet, dass der Schweißprozess mit konstanter Genauigkeit durchgeführt wird.
- Laserschweißtechnologie:
- Hohe Präzision und Geschwindigkeit: Laserschweißgeräte nutzen hochkonzentrierte Lichtstrahlen, um extrem präzise und saubere Schweißnähte zu erzeugen. Diese Technologie ist besonders nützlich für Anwendungen, die eine sehr hohe Genauigkeit erfordern, wie etwa in der Elektronik- oder Medizintechnik.
- Materialvielfalt: Das Laserschweißen kann für eine Vielzahl von Materialien eingesetzt werden, darunter Metalle mit hoher Wärmeleitfähigkeit, wie Aluminium oder Kupfer. Es ermöglicht auch das Schweißen von Materialien unterschiedlicher Dicke, was mit herkömmlichen Verfahren schwierig sein kann.
- Datenanalyse und industrielle Internet-of-Things (IoT)-Integration:
- Predictive Maintenance (vorausschauende Wartung): Automatisierte Schweißgeräte, die mit IoT-Technologien verbunden sind, können Wartungsanforderungen im Voraus erkennen. Durch die Überwachung von Maschinenparametern in Echtzeit können Ausfälle vermieden werden, da die Maschinen ihre eigenen Zustandsdaten analysieren und vorausschauend Wartungsarbeiten anfordern.
- Produktionsdatenanalyse: IoT-fähige Schweißgeräte sammeln und analysieren kontinuierlich Daten über den Schweißprozess. Diese Daten können genutzt werden, um die Effizienz der Produktionslinie zu verbessern, Fehlerquellen zu identifizieren und den Gesamtproduktionsprozess zu optimieren.
Integration in die Fertigungsumgebung
Die Integration von automatisierten Schweißgeräten in bestehende Produktionslinien ist ein entscheidender Schritt zur Steigerung der Gesamtproduktivität und -effizienz. Dabei müssen mehrere Faktoren berücksichtigt werden:
- Kombination mit anderen Fertigungstechnologien: Automatisierte Schweißgeräte werden häufig in Kombination mit anderen Produktionssystemen eingesetzt, wie z. B. automatischen Materialhandhabungssystemen, Schneidemaschinen oder Robotern zur Werkstückpositionierung. Diese Integration erfordert eine nahtlose Kommunikation zwischen den Maschinen, was durch standardisierte Steuerungssysteme und Protokolle wie OPC-UA (Open Platform Communications Unified Architecture) erreicht werden kann.
- Flexibilität und Skalierbarkeit: Moderne automatisierte Schweißsysteme sind flexibel genug, um an verschiedene Werkstückgrößen und -formen angepasst zu werden. Dies ist besonders wichtig in Umgebungen, in denen verschiedene Produktvarianten auf derselben Produktionslinie hergestellt werden. Die Skalierbarkeit dieser Systeme ermöglicht es Unternehmen, ihre Produktionskapazität zu erhöhen, ohne umfangreiche Änderungen an der Infrastruktur vorzunehmen.
- Mensch-Maschine-Interaktion (HMI): Trotz der fortschreitenden Automatisierung bleibt die Interaktion zwischen Mensch und Maschine entscheidend. Benutzerfreundliche Schnittstellen, über die Bediener die Maschinenparameter steuern und den Produktionsfortschritt überwachen können, sind integraler Bestandteil moderner automatisierter Schweißgeräte. Die intuitive Gestaltung solcher HMI-Systeme trägt dazu bei, Fehler zu minimieren und die Effizienz der Bediener zu maximieren.
Wirtschaftliche Aspekte
Die Implementierung automatisierter Schweißgeräte bringt eine Vielzahl von wirtschaftlichen Vorteilen mit sich, die sich sowohl in der kurzen als auch in der langen Frist bemerkbar machen:
- Reduzierung von Arbeitskosten: Automatisierte Schweißgeräte minimieren den Bedarf an qualifiziertem Schweißpersonal, da der Großteil des Prozesses maschinell durchgeführt wird. Dies ist besonders in Regionen mit hohen Lohnkosten von Vorteil.
- Erhöhte Produktionseffizienz: Durch die kontinuierliche Arbeitsweise von automatisierten Maschinen können Unternehmen ihre Produktionskapazität steigern und gleichzeitig die Fehlerquote reduzieren. Die verbesserte Effizienz führt zu einer schnelleren Amortisation der anfänglichen Investitionen.
- Qualitätssteigerung und geringere Nacharbeitskosten: Automatisierte Schweißgeräte gewährleisten gleichbleibend hohe Schweißqualität, wodurch weniger Nacharbeiten erforderlich sind. Dies senkt die Gesamtkosten pro Werkstück und minimiert den Ausschuss.
- Wartungs- und Betriebskosten: Durch die Integration von IoT und vorausschauender Wartung können ungeplante Stillstandszeiten reduziert und die Gesamtbetriebskosten gesenkt werden.
Vergleich – Automatische Kreisschweißmaschine, MIG-Rundschweißgerät und andere automatisierte Schweißmaschinen
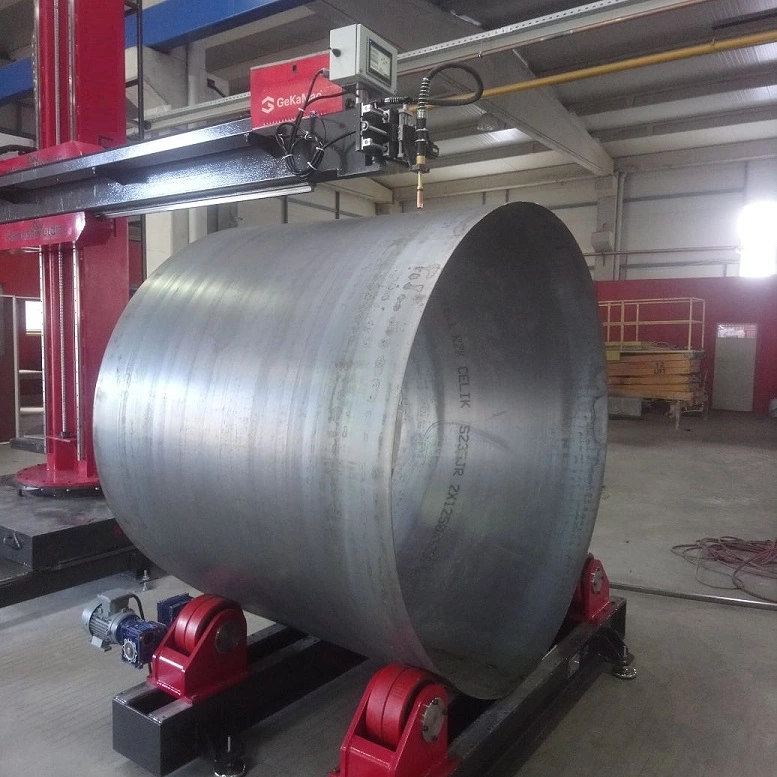
In der modernen Fertigung stehen zahlreiche Schweißtechnologien zur Verfügung, die jeweils spezifische Vorteile und Einsatzgebiete aufweisen. Zu den häufig verwendeten Schweißgeräten gehören die automatische Kreisschweißmaschine, das MIG-Rundschweißgerät sowie weitere automatisierte Schweißsysteme, wie robotergesteuerte und CNC-gesteuerte Schweißmaschinen. Jede dieser Technologien hat einzigartige Merkmale, die sie für bestimmte Anwendungen besser geeignet machen. In diesem Abschnitt vergleichen wir diese Technologien hinsichtlich ihrer Funktionsweise, Einsatzbereiche, Vorteile und Herausforderungen.
Vergleich der Hauptmerkmale
- Automatische Kreisschweißmaschine:
- Funktionsweise: Die automatische Kreisschweißmaschine ist speziell für das Schweißen von zylindrischen oder kreisförmigen Werkstücken ausgelegt. Sie verwendet eine Drehvorrichtung, die das Werkstück während des Schweißprozesses rotieren lässt, um eine gleichmäßige Schweißnaht zu erzeugen. Der Schweißkopf bewegt sich entweder um das Werkstück oder bleibt fixiert, während das Werkstück sich dreht.
- Anwendungsbereiche: Häufig in der Automobilindustrie (Auspuffanlagen, Zylinder), im Rohrleitungsbau (Öl und Gas, Wasserleitungen) und in der Behälterherstellung (Tanks, Kessel) verwendet.
- Vorteile: Hohe Präzision, gleichmäßige Schweißnähte, Eignung für Serienproduktion.
- Nachteile: Eignet sich nur für runde oder zylindrische Werkstücke und ist weniger flexibel für komplexere Geometrien.
- MIG-Rundschweißgerät:
- Funktionsweise: Das MIG-Rundschweißgerät kombiniert die MIG-Schweißtechnologie mit einer Rotationsvorrichtung, die es ermöglicht, zylindrische Werkstücke präzise zu schweißen. Der MIG-Draht wird kontinuierlich zugeführt, während das Werkstück rotiert, um eine konsistente Schweißnaht zu erzeugen. MIG-Schweißen verwendet dabei ein Schutzgas (wie Argon oder Helium), um den Schweißbereich zu isolieren.
- Anwendungsbereiche: Besonders geeignet für Rohrverbindungen, Druckbehälter, Automobilbauteile wie Stoßdämpfer und Auspuffsysteme.
- Vorteile: Effizient bei großen Volumen, hohe Schweißgeschwindigkeit, flexibel bei verschiedenen Materialien (z.B. Aluminium, Edelstahl).
- Nachteile: Höhere Investitionskosten für spezielle MIG-Rundschweißgeräte; erfordert sorgfältige Gassteuerung und präzise Maschinenkonfiguration.
- Robotergestützte Schweißsysteme:
- Funktionsweise: Diese Schweißsysteme nutzen Roboterarme, die flexibel auf verschiedene Schweißprozesse (MIG, TIG, Lichtbogenschweißen) eingestellt werden können. Die Roboter führen das Schweißen autonom durch, indem sie präzise Bahnen programmierter Schweißnähte folgen. Sie können sowohl stationäre Werkstücke bearbeiten als auch bewegliche Teile in einer Produktionslinie schweißen.
- Anwendungsbereiche: Verbreitet in der Automobil-, Luft- und Raumfahrt- sowie Elektronikindustrie. Ideal für Serienproduktion mit hoher Wiederholgenauigkeit.
- Vorteile: Höchste Flexibilität bei komplexen Geometrien, schnelle Anpassung an verschiedene Werkstücke, hohe Präzision und Geschwindigkeit.
- Nachteile: Hohe Investitionskosten, erforderliche Programmierkenntnisse, regelmäßige Wartung erforderlich.
- CNC-gesteuerte Schweißmaschinen:
- Funktionsweise: CNC-gesteuerte Schweißsysteme basieren auf numerischer Steuerungstechnologie, die die Maschinenbewegungen präzise steuert. Diese Systeme sind extrem vielseitig und können in Kombination mit verschiedenen Schweißmethoden (MIG, TIG, Laser) eingesetzt werden. Die CNC-Steuerung ermöglicht komplexe und präzise Schweißaufgaben ohne menschliches Eingreifen.
- Anwendungsbereiche: Typisch in hochpräzisen Fertigungsprozessen wie im Maschinenbau, der Medizintechnik oder der Elektronikindustrie.
- Vorteile: Extrem hohe Präzision, Konsistenz bei komplexen Schweißprozessen, geeignet für wiederholbare Serienfertigung.
- Nachteile: Hohe Anfangsinvestitionen, erfordert qualifiziertes Personal für Programmierung und Wartung.
Wann welche Technologie am besten geeignet ist
Die Wahl der optimalen Schweißtechnologie hängt stark von den spezifischen Anforderungen des Projekts ab, insbesondere in Bezug auf Werkstückgeometrie, Materialart, Produktionsvolumen und erforderliche Schweißpräzision.
- Für runde oder zylindrische Bauteile:
- Hier bieten sich die automatische Kreisschweißmaschine und das MIG-Rundschweißgerät an. Beide Systeme sind speziell darauf ausgelegt, gleichmäßige Schweißnähte an zylindrischen Bauteilen zu erzeugen. Die Wahl zwischen diesen beiden hängt von den Materialanforderungen und der gewünschten Schweißgeschwindigkeit ab:
- Kreisschweißmaschine für hohe Präzision und gleichmäßige Rundnähte, ideal für Dickmetallarbeiten.
- MIG-Rundschweißgerät für höhere Geschwindigkeit und Flexibilität bei verschiedenen Metallarten, insbesondere wenn hohe Schweißgeschwindigkeit und Schutzgassteuerung gefragt sind.
- Hier bieten sich die automatische Kreisschweißmaschine und das MIG-Rundschweißgerät an. Beide Systeme sind speziell darauf ausgelegt, gleichmäßige Schweißnähte an zylindrischen Bauteilen zu erzeugen. Die Wahl zwischen diesen beiden hängt von den Materialanforderungen und der gewünschten Schweißgeschwindigkeit ab:
- Für komplexe Werkstückgeometrien:
- Robotergestützte Schweißsysteme sind die beste Wahl, da sie durch ihre flexible Programmierung verschiedene Schweißprozesse auf einer Vielzahl von Werkstücken ausführen können. Dies macht sie besonders für Anwendungen in der Automobil- oder Elektronikindustrie geeignet, wo sowohl Präzision als auch Flexibilität erforderlich sind.
- Für hochpräzise Anwendungen:
- Wenn die Fertigung besonders präzise Schweißnähte erfordert, z. B. in der Medizintechnik oder im Luft- und Raumfahrtsektor, sind Laserschweißgeräte oder CNC-gesteuerte Maschinen die beste Option. Sie bieten die notwendige Präzision und Wiederholgenauigkeit, um sicherzustellen, dass die Schweißnähte höchsten Qualitätsansprüchen genügen.
- Für Serienproduktion:
- In der Großserienproduktion, wo die Geschwindigkeit entscheidend ist und die Schweißnähte standardisiert sein müssen, bieten sich robotergestützte Schweißsysteme und CNC-Schweißmaschinen an. Diese Systeme sind darauf ausgelegt, hohe Stückzahlen mit gleichbleibender Qualität zu fertigen und lassen sich leicht in automatisierte Fertigungslinien integrieren.
Zukunft der Schweißtechnologie
Die Schweißtechnologie entwickelt sich kontinuierlich weiter, um den steigenden Anforderungen der modernen Fertigung gerecht zu werden. Einige der vielversprechendsten Trends, die die Zukunft der Schweißtechnologie prägen werden, sind:
- Künstliche Intelligenz (KI) und maschinelles Lernen:
- KI-gesteuerte Schweißsysteme werden den Schweißprozess weiter optimieren, indem sie selbstständig aus Produktionsdaten lernen und den Schweißprozess in Echtzeit anpassen. Fehlererkennungs- und Korrektursysteme werden immer ausgefeilter, wodurch die Ausschussrate weiter sinken wird.
- Robotik und Automatisierung:
- Der Einsatz von Robotern in der Schweißtechnik wird weiter zunehmen. Fortschritte in der Robotertechnologie ermöglichen eine schnellere Programmierung, größere Flexibilität und die Integration von Schweißsystemen in vollständig automatisierte Produktionslinien.
- Nachhaltigkeit und Energieeffizienz:
- Die Entwicklung umweltfreundlicherer Schweißverfahren steht im Mittelpunkt. Energieeffiziente Schweißtechnologien wie das Laserschweißen und optimierte Schweißprozesse, die den Material- und Energieverbrauch reduzieren, werden weiter an Bedeutung gewinnen.
- Additive Fertigung und Schweißtechnologie:
- Die Kombination von Schweißen und additiver Fertigung (3D-Druck) wird neue Möglichkeiten für die Herstellung von komplexen Bauteilen eröffnen. Schweißtechnologien, die in den 3D-Druckprozess integriert sind, ermöglichen die Herstellung von Teilen mit minimalem Materialeinsatz und hoher Präzision.
Zukunftsaussichten und Trends in der Schweißautomatisierung
Trends in der Robotik und Automatisierung
Die Schweißautomatisierung hat in den letzten Jahren erhebliche Fortschritte gemacht und wird in Zukunft weiter an Bedeutung gewinnen. Eines der größten Wachstumsfelder in diesem Bereich ist die Integration von Robotern in den Schweißprozess. Roboter werden immer intelligenter, schneller und vielseitiger und spielen eine Schlüsselrolle in der Automatisierung von Schweißprozessen in verschiedenen Industrien, wie der Automobilindustrie, dem Maschinenbau und der Luft- und Raumfahrt.
- Kollaborative Roboter (Cobots):
- Cobots sind ein entscheidender Trend in der Schweißautomatisierung. Diese Roboter arbeiten direkt neben menschlichen Bedienern und sind speziell darauf ausgelegt, sicher und einfach bedienbar zu sein. Cobots können kleinere Schweißarbeiten übernehmen, während Menschen für komplexere Aufgaben zuständig sind. Diese symbiotische Arbeitsweise wird es Unternehmen ermöglichen, sowohl die Flexibilität als auch die Effizienz in ihren Produktionslinien zu steigern.
- Ein weiteres Plus der Cobots ist die einfache Programmierung. Bediener können sie durch einfache „Teach-in“-Methoden programmieren, indem sie den Roboterarm manuell bewegen und die gewünschten Schweißpfade festlegen.
- Erweiterte Flexibilität:
- Roboter und automatische Schweißsysteme der Zukunft werden nicht nur auf die Durchführung eines einzigen Schweißprozesses spezialisiert sein. Stattdessen werden sie in der Lage sein, verschiedene Schweißverfahren, wie MIG-, TIG- und Laserschweißen, zu kombinieren. Diese Flexibilität wird die Produktionsprozesse vereinfachen und die Anzahl der notwendigen Maschinen in einer Fertigungslinie verringern.
- Verbesserte Integration in Produktionslinien:
- In Zukunft werden Schweißroboter und automatisierte Systeme vollständig in intelligente Produktionsumgebungen integriert sein. Diese Umgebungen nutzen Sensoren, Echtzeit-Datenanalyse und selbststeuernde Systeme, um Schweißprozesse zu optimieren und Fertigungsfehler nahezu zu eliminieren. Durch die enge Verzahnung von Schweißrobotern mit den übrigen Produktionsmaschinen können alle Schritte eines Fertigungsprozesses, vom Rohmaterial bis zum fertigen Produkt, automatisiert und aufeinander abgestimmt werden.
Künstliche Intelligenz und maschinelles Lernen im Schweißen
Künstliche Intelligenz (KI) und maschinelles Lernen spielen eine immer größere Rolle in der Automatisierung von Schweißprozessen. Diese Technologien ermöglichen es Maschinen, aus ihren Fehlern zu lernen und sich kontinuierlich zu verbessern. Die Hauptvorteile von KI-gesteuerten Schweißsystemen liegen in ihrer Fähigkeit, Echtzeit-Analysen durchzuführen, Anpassungen während des Schweißprozesses vorzunehmen und die Qualität der Schweißnähte zu optimieren.
- Selbstoptimierende Schweißsysteme:
- Durch den Einsatz von maschinellem Lernen können Schweißmaschinen Daten aus früheren Schweißprozessen analysieren und zukünftige Prozesse anpassen, um bessere Ergebnisse zu erzielen. Diese Systeme können z. B. Veränderungen in den Werkstoffeigenschaften oder den Schweißbedingungen erkennen und automatisch die Schweißparameter anpassen, ohne dass ein menschliches Eingreifen erforderlich ist.
- In der Praxis bedeutet dies eine höhere Effizienz, weniger Ausschuss und eine konstante Schweißqualität, auch bei schwankenden Bedingungen.
- Fehlererkennung und Korrektur in Echtzeit:
- Ein weiteres zentrales Anwendungsgebiet für KI ist die Echtzeit-Fehlererkennung. KI-gestützte Schweißsysteme können mithilfe von Kameras und Sensoren Unregelmäßigkeiten in der Schweißnaht sofort erkennen und den Schweißvorgang entsprechend anpassen. Dies reduziert die Anzahl fehlerhafter Bauteile erheblich und minimiert den Bedarf an Nachbearbeitung.
- In Kombination mit automatisierten Inspektionssystemen können Schweißmaschinen Anomalien in den Schweißnähten sofort erkennen und beheben, was zu einer erheblich besseren Produktionsqualität führt.
- Vorausschauende Wartung:
- KI-Systeme spielen eine Schlüsselrolle bei der Implementierung von Predictive Maintenance (vorausschauende Wartung) in automatisierten Schweißprozessen. Durch die kontinuierliche Überwachung von Maschinenparametern wie Temperatur, Stromstärke und Schweißgeschwindigkeit können diese Systeme potenzielle Probleme frühzeitig erkennen und Wartungsarbeiten einplanen, bevor es zu Maschinenausfällen kommt. Dies verhindert unerwartete Produktionsunterbrechungen und verlängert die Lebensdauer der Schweißmaschinen.
Nachhaltigkeit und Umweltvorteile
Mit dem zunehmenden Bewusstsein für die Umwelt und die Notwendigkeit, nachhaltigere Fertigungsprozesse zu entwickeln, werden auch Schweißtechnologien in Zukunft eine bedeutende Rolle bei der Reduzierung des Energieverbrauchs und des Materialeinsatzes spielen.
- Energieeffiziente Schweißtechnologien:
- Neue Schweißverfahren wie das Laserschweißen sind nicht nur schneller und präziser, sondern auch deutlich energieeffizienter als herkömmliche Schweißmethoden. Laser benötigen weniger Energie, um Metalle zu schmelzen, und reduzieren gleichzeitig die thermische Belastung der Werkstücke, was zu weniger Verzug und Nachbearbeitungsbedarf führt.
- Automatisierte Schweißmaschinen werden auch zunehmend mit Energiesparmodi ausgestattet, die die Maschinen in Ruhephasen automatisch herunterfahren oder deren Energieverbrauch während geringer Arbeitslasten reduzieren.
- Materialoptimierung:
- Schweißprozesse der Zukunft werden darauf ausgelegt sein, den Materialverbrauch zu minimieren. Durch den Einsatz präziser Schweißtechnologien, wie dem Laserschweißen oder dem Hybrid-Laser-MIG-Schweißen, kann der Schweißdraht effizienter eingesetzt werden. Auch Schweißnähte werden präziser ausgeführt, wodurch weniger Materialabfälle entstehen.
- Zudem wird die Entwicklung neuer, leichterer Materialien, wie hochfeste Stähle und Aluminiumlegierungen, vorangetrieben, die den Schweißprozess effizienter und umweltfreundlicher machen.
Additive Fertigung und Schweißen
Ein weiterer Zukunftstrend ist die Kombination von additiver Fertigung (3D-Druck) und Schweißtechnologie. Diese beiden Technologien werden zunehmend miteinander verschmelzen, um neue Fertigungsmöglichkeiten zu erschließen.
- Additive Fertigung mit Schweißtechnologie:
- Durch die Integration von Schweißverfahren in den 3D-Druck können hybride Fertigungsmethoden entwickelt werden. Hierbei wird das Bauteil Schicht für Schicht mit 3D-Druckverfahren aufgebaut und anschließend durch präzise Schweißnähte verstärkt oder fertiggestellt. Dies eröffnet neue Möglichkeiten, komplexe Metallstrukturen effizient herzustellen.
- Besonders in der Luft- und Raumfahrt, aber auch in der Automobilindustrie, wird die Kombination von additiver Fertigung und Schweißen zu neuen Leichtbaukonstruktionen führen, die sowohl kosteneffizient als auch umweltfreundlich sind.
- Vorteile in der Fertigung:
- Die Kombination beider Technologien ermöglicht es, Bauteile nicht nur effizienter, sondern auch flexibler herzustellen. Durch die Verwendung von Schweißtechnologien in Kombination mit 3D-Druck können komplexe Geometrien und spezifische Materialanforderungen gleichzeitig berücksichtigt werden, ohne dass zusätzliche Bearbeitungsschritte erforderlich sind.
Zusammenfassung der Zukunftsaussichten
Die Automatisierung des Schweißprozesses wird sich in den kommenden Jahren weiter beschleunigen, angetrieben durch Fortschritte in der Robotik, Künstlichen Intelligenz und maschinellem Lernen. Die Fähigkeit, Prozesse zu überwachen, zu analysieren und in Echtzeit anzupassen, wird die Effizienz, Qualität und Produktivität erheblich steigern. Gleichzeitig wird der Fokus auf Nachhaltigkeit die Entwicklung energieeffizienter Schweißtechnologien und Materialoptimierungen vorantreiben.
Unternehmen, die in fortschrittliche automatisierte Schweißsysteme investieren, werden langfristig profitieren, indem sie ihre Produktionskosten senken, ihre Effizienz steigern und gleichzeitig die Umweltbelastung reduzieren. Mit neuen Technologien wie der additiven Fertigung und der Integration von Schweißverfahren in intelligente Produktionslinien stehen wir vor einer Revolution in der Fertigungstechnik, die den globalen Wettbewerb neu definieren wird.
Automatisierte Schweißmaschinen, wie die automatische Kreisschweißmaschine, das MIG-Rundschweißgerät und andere robotergesteuerte Systeme, sind heute unverzichtbare Bestandteile der modernen Fertigung. Sie bieten nicht nur eine höhere Produktivität und Präzision, sondern auch erhebliche Kostenvorteile durch die Reduzierung von Fehlern und Nachbearbeitung. Die Zukunft des Schweißens liegt zweifellos in der weiteren Automatisierung und der Integration von fortschrittlichen Technologien wie Künstlicher Intelligenz, Robotik und nachhaltigen Fertigungsmethoden.
Unternehmen, die frühzeitig auf diese Trends setzen, werden in der Lage sein, ihre Produktionsprozesse zu optimieren und im globalen Wettbewerb erfolgreich zu bleiben. Die Entwicklung hin zu vollständig vernetzten, intelligenten Produktionslinien wird den Weg in eine neue Ära der industriellen Fertigung ebnen, in der Schweißtechnologie eine zentrale Rolle spielt.
Fazit und Abschluss
Die Automatisierung in der Schweißtechnik hat sich in den letzten Jahren rasant weiterentwickelt und bringt für Unternehmen, die auf moderne Technologien setzen, erhebliche Vorteile. Ob automatische Kreisschweißmaschinen, MIG-Rundschweißgeräte, robotergestützte Schweißsysteme oder CNC-gesteuerte Maschinen – jedes dieser Systeme bietet spezifische Vorteile, die es Unternehmen ermöglichen, ihre Produktionsprozesse zu optimieren und die Produktqualität zu verbessern.
Die Hauptvorteile dieser Technologien liegen in ihrer Fähigkeit, mit hoher Präzision und Effizienz zu arbeiten, die Fehleranfälligkeit zu minimieren und die Produktionskosten langfristig zu senken. Besonders in Branchen wie der Automobil-, Luft- und Raumfahrt-, und der Rohrleitungsindustrie spielen automatisierte Schweißtechnologien eine entscheidende Rolle, um den wachsenden Anforderungen nach Qualität, Geschwindigkeit und Kostenkontrolle gerecht zu werden.
Zukunftstrends wie Künstliche Intelligenz, maschinelles Lernen, Robotik und IoT-Integration werden die Schweißautomatisierung in den kommenden Jahren weiter revolutionieren. Systeme, die selbstlernend sind und sich in Echtzeit an wechselnde Produktionsbedingungen anpassen können, werden die Effizienz noch weiter steigern und die Fehlerraten nahezu eliminieren. Gleichzeitig wird der verstärkte Fokus auf Nachhaltigkeit und Energieeffizienz die Entwicklung energie- und ressourcenschonender Schweißverfahren fördern.
Die Integration dieser Technologien in intelligente Produktionsumgebungen wird dazu beitragen, dass Schweißprozesse noch stärker automatisiert und vernetzt werden, wodurch Unternehmen ihre Wettbewerbsfähigkeit in einer zunehmend globalisierten und technologiegetriebenen Welt sichern können. Auch der Trend hin zur additiven Fertigung in Kombination mit Schweißtechnologien zeigt das enorme Potenzial für innovative Fertigungsansätze, die in der Lage sind, komplexe Bauteile kostengünstiger und effizienter zu produzieren.
Für Unternehmen, die den Schritt in die Automatisierung wagen, ergeben sich eine Vielzahl von Chancen: Kostensenkung, höhere Produktivität, reduzierte Materialabfälle und eine verbesserte Schweißnahtqualität sind nur einige der Vorteile, die durch die Implementierung moderner Schweißsysteme erzielt werden können. Gleichzeitig erfordert die Einführung solcher Systeme eine Investition in Schulung, Wartung und Infrastruktur, um das volle Potenzial dieser Technologien auszuschöpfen.
Insgesamt bleibt festzuhalten, dass automatisierte Schweißmaschinen und die damit verbundenen Innovationen ein wesentlicher Bestandteil der modernen Industrie sind und in den kommenden Jahren eine noch größere Rolle in der Fertigungswelt spielen werden. Die kontinuierlichen technologischen Fortschritte werden den Schweißprozess effizienter, intelligenter und nachhaltiger machen und so dazu beitragen, dass Unternehmen wettbewerbsfähig bleiben und den Anforderungen der Zukunft gerecht werden.