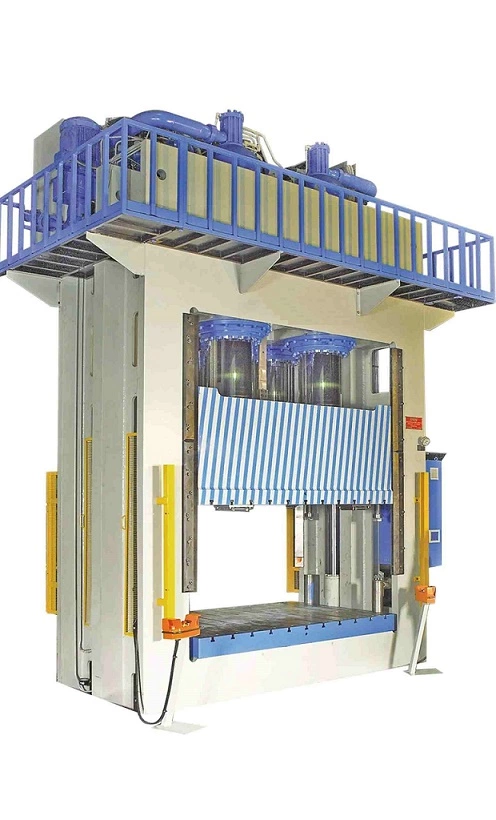
Wir stellen Heißpressen wie Kunststoffpressen, zur Herstellung von Brems- Reibbelägen/ und Kupplungsbelägen, Elastomer Pressensysteme, Laborpressen her. Kostenlose Beratung.
Heißpressen ist ein vielseitiges Verfahren in der Kunststoffverarbeitung, das eine präzise Formgebung von Materialien ermöglicht. Dieser Prozess, auch als Pressverfahren bekannt, beinhaltet die Anwendung von Wärme, Druck und Zeit, um Kunststoffe unter definierten Bedingungen zu verformen. Die Temperaturkontrolle spielt dabei eine entscheidende Rolle, da sie den Zustand des Materials beeinflusst und die gewünschte Formgebung ermöglicht.
Während des Heißpressens wird das Material unter hohem Druck auf ein vordefiniertes Werkzeug, auch Pressplatte genannt, gelegt. Die Presszeit, also die Dauer des Pressvorgangs, ist ebenso wichtig wie die Temperatur, um optimale Ergebnisse zu erzielen. Ein maßgeschneidertes Presswerkzeug ist entscheidend für die exakte Umsetzung des Formgebungsprozesses.
Die Werkzeugtemperierung gewährleistet eine gleichmäßige Wärmeverteilung und verhindert unerwünschte Effekte wie ungleichmäßige Aushärtung oder Verformung. Dieser Aspekt ist besonders relevant bei der Verarbeitung von verschiedenen Materialien wie Thermoplasten oder Harzmatrizes in der Herstellung von Verbundwerkstoffen.
Der Pressdruck spielt eine Schlüsselrolle, um das Material in die gewünschte Form zu bringen. Viskosität, ein weiteres wichtiges Stichwort, beeinflusst die Fließeigenschaften des Materials während des Pressvorgangs. Dies ist insbesondere bei der Verarbeitung von komplexen Formen oder Strukturen von Bedeutung.
Insgesamt betrachtet, sind diese ersten zehn Schlüsselwörter, darunter Pressverfahren, Temperaturkontrolle, Druck und Kunststoffverarbeitung, essenzielle Elemente, die im Heißpressen zusammenwirken. Sie beeinflussen den gesamten Prozess der Materialverformung und prägen die Qualität und Präzision der hergestellten Produkte maßgeblich. Daher ist ein tiefgehendes Verständnis dieser Schlüsselbegriffe von grundlegender Bedeutung für eine erfolgreiche Anwendung des Heißpressens in der industriellen Fertigung
Die Umformungstechnologie der Heißpressen ist ein Verfahren zur Extraktion von Ölen aus ölhaltigen Rohstoffen unter Verwendung von Wärme. Im Gegensatz zur Kaltpressung, bei der die Extraktion bei niedrigen Temperaturen erfolgt, wird beim Heißpressen Hitze angewendet, um den Extraktionsprozess zu beschleunigen. Hier sind die Schlüsselaspekte dieser Technologie:
- Rohstoffvorbereitung: Die Rohstoffe werden gereinigt, getrocknet und möglicherweise zerkleinert, um sie für den Pressvorgang vorzubereiten.
- Erhitzung: Im Heißpressverfahren werden die Rohstoffe und/oder die Pressvorrichtung erhitzt, um die Viskosität des Öls zu verringern und die Extraktion zu erleichtern. Die Temperaturen können je nach dem spezifischen Verfahren und den zu extrahierenden Ölen variieren, liegen jedoch oft über 40°C und können bis zu 100°C oder höher betragen.
- Pressmechanismus: Die erhitzten Rohstoffe werden durch mechanischen Druck gepresst, um das Öl aus den Samen oder Nüssen zu extrahieren. Dies kann durch Pressschnecken, Walzen oder andere Pressvorrichtungen erfolgen.
- Trennung von Öl und Presskuchen: Nach der Extraktion wird das Öl von den festen Rückständen, dem Presskuchen, getrennt.
- Filtration: Das extrahierte Öl kann durch einen Filtrationsprozess geleitet werden, um Unreinheiten zu entfernen und die Qualität des Endprodukts zu verbessern.
- Qualitätskontrolle: Wie bei der Kaltpressung werden während des gesamten Prozesses verschiedene Qualitätskontrollmaßnahmen ergriffen, um sicherzustellen, dass das Endprodukt den gewünschten Standards entspricht.
- Verpackung und Lagerung: Das fertige Öl wird in geeignete Behälter abgefüllt und unter geeigneten Bedingungen gelagert, um seine Qualität und Frische zu erhalten.
Die Umformungstechnologie der Heißpressen ist oft effizienter als die Kaltpressung und ermöglicht eine schnellere Extraktion von Ölen. Sie wird häufig in der Lebensmittelindustrie eingesetzt, insbesondere wenn große Mengen an Öl produziert werden müssen. Allerdings kann die Hitzebehandlung potenziell einige der empfindlichen Nährstoffe und Aromen in den Ölen beeinträchtigen.
Heißpressen
Heißpressen ist ein Fertigungsprozess, bei dem Wärme und Druck verwendet werden, um Materialien zu formen oder zu verbinden. Dieser Prozess wird oft bei der Herstellung von Kunststoffprodukten, wie z.B. Autoinnenverkleidungen, Elektronikgehäusen oder Haushaltsgeräten, eingesetzt.
Beim Heißpressen wird das Material in einer Form positioniert und dann einer hohen Temperatur und einem hohen Druck ausgesetzt, um es zu formen oder zu verbinden. Die Temperatur und der Druck können je nach Material und Anwendung variieren. Im Allgemeinen wird die Temperatur zwischen 150°C und 200°C gehalten und der Druck variiert zwischen 100 bar und 400 bar.
Heißpressen kann auf verschiedene Arten durchgeführt werden, einschließlich des Einsatzes von hydraulischen Pressen oder von Infrarot-Heizelementen. Bei der Verwendung von hydraulischen Pressen wird das Material in eine Form eingespannt und dann unter hohem Druck gepresst. Bei der Verwendung von Infrarot-Heizelementen wird das Material durch eine Heizquelle, wie z.B. eine Infrarot-Lampe, erhitzt und dann in eine Form gepresst.
Der Vorteil des Heißpressens ist, dass es eine schnelle und effiziente Methode zur Herstellung von Kunststoffprodukten bietet. Es ermöglicht auch die Herstellung von komplexen Formen und eine gute Reproduzierbarkeit. Darüber hinaus ist das Verfahren umweltfreundlicher als andere Fertigungsmethoden, da es keine Chemikalien oder Lösungsmittel erfordert.
Allerdings gibt es auch einige Nachteile beim Heißpressen. Zum Beispiel kann es schwierig sein, die Prozessparameter wie Temperatur und Druck genau zu kontrollieren, was zu Fehlern und Ausfallzeiten führen kann. Zudem ist es oft teuer, spezielle Formen herzustellen, um spezifische Produkte zu formen.
Insgesamt ist das Heißpressen ein wichtiger Prozess in der Kunststoffverarbeitung und bietet Herstellern eine effiziente Möglichkeit, Kunststoffprodukte in hoher Qualität und in großer Stückzahl herzustellen.
Das Heißpressen ist ein Fertigungsverfahren, bei dem ein metallisches Material unter Hitze und Druck in eine gewünschte Form gebracht wird. Bei diesem Verfahren wird das Material zunächst erhitzt, wodurch es weicher und formbarer wird. Anschließend wird es in eine Matrize gepresst, die die gewünschte Form des Teils hat.
Heißpressen wird in einer Vielzahl von Branchen eingesetzt, darunter die Automobilindustrie, die Luft- und Raumfahrtindustrie und die Maschinenbauindustrie. Es wird zur Herstellung einer Vielzahl von Teilen verwendet, darunter Karosserieteile, Motorteile, Flugzeugteile und Maschinenteile.
Vorteile des Heißpressens
Heißpressen bietet eine Reihe von Vorteilen gegenüber anderen Fertigungsverfahren, darunter:
- Hohe Festigkeit: Heißgepresste Teile sind in der Regel fester als Teile, die mit anderen Verfahren hergestellt werden.
- Hohe Präzision: Heißgepresste Teile können mit hoher Präzision hergestellt werden.
- Hohe Produktivität: Heißpressen kann eine hohe Produktivität erzielen.
Nachteile des Heißpressens
Heißpressen hat auch einige Nachteile, darunter:
- Hohe Investitionskosten: Heißpressenanlagen sind eine teure Investition.
- Hohe Komplexität: Heißpressenanlagen sind komplexe Maschinen, die eine hohe Fachkenntnis erfordern.
Arten des Heißpressens
Es gibt verschiedene Arten des Heißpressens, darunter:
- Präzisions-Heißpressen: Präzisions-Heißpressen wird zur Herstellung von Teilen mit hoher Präzision verwendet.
- Maschinenbau-Heißpressen: Maschinenbau-Heißpressen wird zur Herstellung von Teilen für Maschinen verwendet.
- Automobil-Heißpressen: Automobil-Heißpressen wird zur Herstellung von Karosserieteilen für Automobile verwendet.
Zukünftige Trends im Heißpressen
Das Heißpressen wird in den nächsten Jahren weiter entwickelt werden. Die folgenden Trends werden die Entwicklung dieser Technologie prägen:
- Automatisierung: Die Automatisierung des Heißpressens wird dazu beitragen, die Produktivität und Effizienz zu steigern.
- Digitalisierung: Die Digitalisierung des Heißpressens wird dazu beitragen, die Prozesse zu optimieren und die Qualität zu verbessern.
- Nachhaltigkeit: Die Entwicklung nachhaltiger Heißpressverfahren wird dazu beitragen, die Umweltbelastung zu reduzieren.
Die Einpresstiefe ist ein entscheidender Faktor im Heißpressverfahren, der die Präzision und Qualität der hergestellten Teile beeinflusst. Dieser Begriff bezieht sich auf die Tiefe, mit der das Material in das Presswerkzeug eingebracht wird. Eine präzise Kontrolle der Einpresstiefe ist entscheidend, um sicherzustellen, dass das Material gleichmäßig und in der gewünschten Menge in das Werkzeug gedrückt wird.
Harzsysteme spielen eine Schlüsselrolle im Heißpressprozess, insbesondere bei der Verarbeitung von Verbundwerkstoffen. Die Wahl des richtigen Harzsystems beeinflusst nicht nur die chemischen Eigenschaften des Endprodukts, sondern auch die Prozesse der Harzimprägnierung und Aushärtung während des Heißpressens.
Die Harzverteilung ist ein weiterer zentraler Aspekt, der bei der Herstellung von Verbundwerkstoffen berücksichtigt werden muss. Eine gleichmäßige Verteilung des Harzes über das gesamte Material ist entscheidend für die Festigkeit und Homogenität des Endprodukts.
Das Presszyklusmanagement ist ein komplexer Prozess, der die Steuerung von Temperatur, Druck und Zeit während des Heißpressens umfasst. Ein effizientes Presszyklusmanagement gewährleistet nicht nur eine präzise Formgebung, sondern auch eine optimale Aushärtung und Strukturbildung des Materials.
Die Schichtpressstoffe sind Materialien, die aus mehreren Schichten bestehen und durch Druck und Wärme miteinander verbunden werden. Dieser spezielle Werkstoff wird häufig im Heißpressverfahren verwendet, um Produkte mit spezifischen mechanischen Eigenschaften herzustellen.
Kunststofffolien sind bei bestimmten Anwendungen im Heißpressen von großer Bedeutung. Sie dienen dazu, die Oberfläche des Materials zu schützen, können aber auch gezielt eingesetzt werden, um bestimmte Strukturen oder Texturen zu erzeugen.
Die Strukturintegrierten Bauteile sind ein fortschrittlicher Ansatz im Heißpressverfahren, bei dem Funktionen und Eigenschaften direkt in die Struktur des hergestellten Bauteils integriert werden. Dies ermöglicht eine höhere Effizienz und Funktionalität der Endprodukte.
Die Prozesstemperatur beeinflusst maßgeblich die Reaktionsgeschwindigkeit während des Heißpressens. Eine präzise Steuerung der Prozesstemperatur ist entscheidend, um optimale Ergebnisse hinsichtlich Formgebung und Aushärtung zu erzielen.
Das Thermoformen, ein weiteres Schlüsselwort, bezieht sich auf die Umformung von thermoplastischen Materialien unter Einwirkung von Wärme. Dieser Prozess ermöglicht die Herstellung von dreidimensionalen Formteilen mit verschiedenen Strukturen und Oberflächen.
Zusammenfassend zeigen diese Schlüsselbegriffe, wie vielschichtig und anspruchsvoll der Prozess des Heißpressens ist. Von der Einpresstiefe über die Harzverteilung bis hin zu strukturintegrierten Bauteilen sind präzise Kontrollmechanismen und ein tiefgehendes Verständnis der Materialeigenschaften entscheidend, um qualitativ hochwertige Endprodukte zu gewährleisten
Die Prozesstemperatur während des Heißpressens spielt eine zentrale Rolle bei der Gewährleistung optimaler Umformung und Aushärtung der Materialien. Ein präzises Temperaturmanagement ist entscheidend, um sicherzustellen, dass die Reaktionsgeschwindigkeit den Anforderungen des Prozesses entspricht. Sowohl die Einflüsse auf die Formgebung als auch auf die strukturellen Eigenschaften des Endprodukts werden durch die sorgfältige Steuerung der Prozesstemperatur maßgeblich beeinflusst.
Die Drucklufttechnik ist ein weiteres bedeutendes Schlüsselwort im Kontext des Heißpressens. Durch die gezielte Anwendung von Druckluft können bestimmte Parameter wie Druck und Temperatur präzise gesteuert werden. Dies ist insbesondere bei empfindlichen Materialien und komplexen Formgebungsprozessen von großer Bedeutung.
Die Formung von thermoplastischen Materialien durch Thermoformen ermöglicht die Herstellung einer Vielzahl von Produkten mit unterschiedlichen Formen und Oberflächenstrukturen. Während des Heißpressens werden die thermoplastischen Materialien durch Wärme geformt, wodurch eine Anpassung an vordefinierte Werkzeugformen möglich ist.
Die Werkzeugkühlung ist ein unerlässlicher Aspekt beim Heißpressen, um die Temperatur des Werkzeugs zu kontrollieren und unerwünschte Effekte wie Überhitzung zu vermeiden. Eine effiziente Kühlung trägt nicht nur zur Verlängerung der Lebensdauer des Werkzeugs bei, sondern gewährleistet auch eine konstante Qualität der produzierten Teile.
Die Kaltverfestigung ist ein Prozess, der die Endfestigkeit des Materials beeinflusst. Während des Heißpressens wird das Material unter Druck geformt und anschließend abgekühlt, wodurch eine nachhaltige Festigkeit und Stabilität erreicht werden.
Die Werkzeugtemperierung ist von entscheidender Bedeutung, um eine gleichmäßige Wärmeverteilung während des Heißpressens sicherzustellen. Eine präzise Temperaturregelung der Werkzeugoberfläche beeinflusst nicht nur die Formgebung des Materials, sondern auch die Struktur und Qualität des Endprodukts.
Ein maßgeschneidertes Presswerkzeug ist ein Schlüsselelement beim Heißpressen, das speziell für die gewünschten Formen und Strukturen entwickelt wird. Die Gestaltung des Werkzeugs beeinflusst direkt die Präzision und Qualität der hergestellten Teile.
Die Presszeit, die Dauer des Pressvorgangs, ist ein kritischer Parameter beim Heißpressen. Eine optimale Presszeit gewährleistet nicht nur eine effektive Formgebung, sondern auch eine ausreichende Aushärtung des Materials.
Die Pressplatte, auf die das Material während des Heißpressens gelegt wird, spielt eine entscheidende Rolle bei der Übertragung von Druck und Wärme auf das Material. Die Materialverformung erfolgt in direkter Wechselwirkung mit der Pressplatte, wodurch die gewünschte Formgebung erreicht wird.
Der Pressdruck, der auf das Material während des Heißpressens ausgeübt wird, beeinflusst maßgeblich die Umformung und Qualität der Endprodukte. Eine präzise Druckkontrolle ist entscheidend, um eine gleichmäßige Materialverteilung und minimale Verformungen zu gewährleisten.
Insgesamt verdeutlichen diese Schlüsselbegriffe die Komplexität und die verschiedenen Parameter, die beim Heißpressen berücksichtigt werden müssen. Von der Temperaturkontrolle über die Werkzeugtemperierung bis hin zur Presszeit sind präzise Steuerungsmechanismen und ein tiefgehendes Verständnis der Prozessparameter unerlässlich
Vorteil von Heißpressen
Ein weiterer Vorteil des Heißpressens ist, dass es eine hohe Flexibilität bei der Materialauswahl bietet. Eine Vielzahl von Materialien kann durch Heißpressen geformt oder verbunden werden, darunter auch verschiedene Kunststoffe, Metalle und Verbundwerkstoffe.
Eine weitere Anwendung des Heißpressens ist die Herstellung von Faserverbundwerkstoffen. Bei diesem Verfahren werden Fasern, wie Kohlenstoff- oder Glasfasern, mit einem Harz imprägniert und dann unter hohem Druck und Temperatur ausgehärtet. Dies führt zu einem leichten, aber sehr starken Material, das in der Luft- und Raumfahrtindustrie sowie in der Automobilindustrie eingesetzt wird.
Ein Nachteil des Heißpressens von Faserverbundwerkstoffen ist jedoch, dass es schwierig sein kann, eine vollständige Durchdringung des Harzes in die Fasern zu erreichen. Wenn die Fasern nicht vollständig durchtränkt sind, können sie ihre Festigkeit verlieren und das Material kann brüchig werden.
Insgesamt ist das Heißpressen ein wichtiger Prozess in der modernen Fertigungstechnologie und bietet eine effektive Methode zur Herstellung von Produkten aus Kunststoffen, Metallen und Verbundwerkstoffen. Es ist jedoch wichtig, die Prozessparameter genau zu kontrollieren und die Materialauswahl sorgfältig abzuwägen, um eine hohe Qualität und Zuverlässigkeit der hergestellten Produkte zu gewährleisten.
Nachteil von Heißpressen
Ein weiterer Nachteil des Heißpressens ist, dass es oft eine begrenzte Größe der zu formenden Produkte aufweist. Die Größe der Form und die verfügbare Pressekapazität bestimmen die Größe des Endprodukts. Daher eignet sich das Heißpressen möglicherweise nicht für sehr große Produkte oder solche, die komplexe Formen erfordern.
Ein weiteres Problem beim Heißpressen ist, dass es schwierig sein kann, Materialien mit unterschiedlichen thermischen Ausdehnungskoeffizienten zu verarbeiten. Wenn Materialien mit unterschiedlichen Ausdehnungskoeffizienten zusammengefügt werden, kann dies zu Spannungen und Rissen im Endprodukt führen.
Eine weitere Herausforderung bei der Verarbeitung von Kunststoffen durch Heißpressen ist die Freisetzung von Schadstoffen und Gerüchen. Bei einigen Kunststoffen kann das Erhitzen und Pressen zu einer Freisetzung von flüchtigen organischen Verbindungen (VOCs) führen, die schädlich für die Umwelt und die Gesundheit sein können.
Um diese Herausforderungen zu bewältigen, können spezielle Formulierungen von Kunststoffen verwendet werden, die für das Heißpressen optimiert sind. Darüber hinaus können spezielle Prozessparameter und Geräte verwendet werden, um die Freisetzung von Schadstoffen zu minimieren.
Insgesamt ist das Heißpressen jedoch eine wichtige und effektive Methode zur Herstellung von Produkten aus Kunststoffen und anderen Materialien. Mit der richtigen Materialauswahl und der sorgfältigen Kontrolle der Prozessparameter kann das Heißpressen qualitativ hochwertige und zuverlässige Endprodukte liefern.
Heißpressen
Die Pressparameter beim Heißpressen spielen eine entscheidende Rolle bei der Herstellung von hochwertigen Formteilen. Das Zusammenwirken von verschiedenen Faktoren wie Temperatur, Druck, und Zeit beeinflusst maßgeblich den Erfolg des Pressprozesses. Ein maßgeschneidertes Presswerkzeug ist dabei von großer Bedeutung, um die gewünschten Formen und Strukturen präzise umzusetzen.
Die Heizplatten sind ein integraler Bestandteil des Heißpressens und dienen dazu, die erforderliche Temperatur im Presswerkzeug zu erreichen und aufrechtzuerhalten. Eine effiziente Formpresstechnik ist erforderlich, um sicherzustellen, dass die Wärme gleichmäßig über das gesamte Werkstück verteilt wird. Dies ist besonders wichtig bei der Verarbeitung von Materialien mit unterschiedlichen Wärmeleitfähigkeiten.
Die Temperatur während des Heißpressens spielt eine entscheidende Rolle in der Materialverformung. Das richtige Temperaturprofil, insbesondere die Heißpresstemperatur, beeinflusst die Materialstruktur und -eigenschaften maßgeblich. Ein präzises Temperaturmanagement ist erforderlich, um unerwünschte Effekte wie ungleichmäßige Aushärtung oder Verformung zu vermeiden.
Formfüllung und Druckverteilung sind wesentliche Aspekte, die bei der Umsetzung von komplexen Formen und Strukturen während des Heißpressens berücksichtigt werden müssen. Eine gleichmäßige Verteilung des Drucks gewährleistet die Formstabilität und Präzision der hergestellten Produkte.
Die Kaltverfestigung ist ein wichtiger Punkt, der die Endfestigkeit des Materials beeinflusst. Während des Heißpressens wird das Material unter Druck geformt und anschließend abgekühlt, wodurch eine nachhaltige Festigkeit erreicht wird.
Ein weiterer wichtiger Aspekt ist die Werkzeugkühlung, die dazu dient, die Temperatur des Werkzeugs zu kontrollieren und unerwünschte Effekte wie Überhitzung zu verhindern. Dies trägt dazu bei, die Lebensdauer des Werkzeugs zu verlängern und eine konstante Qualität der produzierten Teile sicherzustellen.
Thermoformen und Drucklufttechnik sind ebenfalls Schlüsselbegriffe, die im Zusammenhang mit dem Heißpressen stehen. Thermoformen bezieht sich auf die Verformung von thermoplastischen Materialien unter Einwirkung von Wärme, während die Drucklufttechnik bei bestimmten Anwendungen zur Kontrolle von Druck und Temperatur eingesetzt wird.
Insgesamt verdeutlichen diese Schlüsselbegriffe, dass das Heißpressen ein hochkomplexer Prozess ist, der ein tiefgehendes Verständnis und eine präzise Steuerung verschiedener Parameter erfordert. Von der Werkzeugtemperierung bis zur Druckverteilung tragen diese Faktoren dazu bei, dass das Heißpressen in der Industrie vielseitig und effektiv eingesetzt werden kann.
Die Warmumformung ist ein faszinierender Aspekt des Heißpressens, der sich auf die Verarbeitung von Thermoplasten und Harzmatrizes konzentriert. Während des Pressprozesses wird nicht nur auf die Temperaturkontrolle geachtet, sondern auch auf die gezielte Anwendung von Druck. Die Formgebung erfolgt durch die gezielte Verformung des Materials, wobei die Werkzeugtemperierung eine entscheidende Rolle spielt, um sicherzustellen, dass die gewünschte Struktur und Form präzise erreicht werden.
Harzmatrix, als zentrales Schlüsselwort, ist von besonderer Bedeutung bei der Herstellung von Verbundwerkstoffen. Die Wahl des richtigen Harzsystems beeinflusst nicht nur die Festigkeit und Haltbarkeit des Endprodukts, sondern auch die Art der Harzimprägnierung während des Heißpressens.
Ein weiteres relevantes Schlüsselwort ist der Pressdruck, der den Umformprozess maßgeblich beeinflusst. Eine präzise Druckkontrolle gewährleistet eine gleichmäßige Materialverteilung und minimiert mögliche Verformungen. Dabei spielt auch die Viskosität eine Schlüsselrolle, da sie die Fließeigenschaften des Materials definiert und somit die Formgebung und Umformbarkeit beeinflusst.
Der Begriff „Verbundwerkstoffe“ bezieht sich auf die Kombination verschiedener Materialien, um synergistische Eigenschaften zu erreichen. Während des Heißpressens ist die effiziente Verbindung dieser Materialien von entscheidender Bedeutung für die Herstellung von Bauteilen mit spezifischen mechanischen Eigenschaften.
Die Drucktemperaturprofile sind entscheidend, um den Presszyklus optimal zu steuern. Die präzise Anpassung der Temperaturen während des Heißpressens beeinflusst die Aushärtung des Materials und trägt zur Formstabilität und Verformbarkeit der hergestellten Produkte bei.
Zusammenfassend verdeutlichen diese zehn Schlüsselbegriffe, darunter auch Vakuum-Pressen und Formenbau, die Komplexität und den Facettenreichtum des Heißpressens. Die Feinabstimmung dieser Parameter ermöglicht die Herstellung hochwertiger, präziser Produkte in verschiedenen Industriezweigen, von der Automobilindustrie bis zur Luft- und Raumfahrttechnik
Ein weiterer wichtiger Aspekt beim Heißpressen ist die Wahl des geeigneten Drucks und der geeigneten Temperatur. Der Druck und die Temperatur beeinflussen die Qualität und die Eigenschaften des Endprodukts. Ein zu niedriger Druck und eine zu niedrige Temperatur können zu unvollständiger Formgebung führen, während ein zu hoher Druck und eine zu hohe Temperatur das Material beschädigen oder sogar zerstören können.
Es ist auch wichtig, den Prozess der Kühlung und Abkühlung nach dem Heißpressen sorgfältig zu kontrollieren. Ein zu schnelles Abkühlen kann dazu führen, dass das Material seine Form verliert oder beschädigt wird, während ein zu langsames Abkühlen die Produktionszeit verlängern kann.
Das Heißpressen wird in vielen Branchen eingesetzt, einschließlich der Automobilindustrie, der Luft- und Raumfahrtindustrie, der Elektronikindustrie, der Medizinindustrie und vielen anderen. Es kann für eine Vielzahl von Anwendungen verwendet werden, wie zum Beispiel zur Herstellung von Gehäusen, Komponenten, Bauteilen, Schaltern, Schutzfolien, Isolierungen und vielem mehr.
In der Elektronikindustrie wird das Heißpressen beispielsweise zur Herstellung von Leiterplatten eingesetzt. Dabei werden dünne Schichten von Kupferfolien und Isoliermaterialien unter hohem Druck und Temperatur zusammengefügt, um eine Leiterplatte zu bilden.
In der Medizinindustrie wird das Heißpressen zur Herstellung von medizinischen Geräten und Implantaten verwendet. Es kann auch zur Herstellung von chirurgischen Instrumenten und anderen medizinischen Werkzeugen eingesetzt werden.
Insgesamt bietet das Heißpressen eine effektive Methode zur Herstellung von Produkten aus einer Vielzahl von Materialien. Es ist jedoch wichtig, den Prozess sorgfältig zu kontrollieren und die Materialauswahl sorgfältig abzuwägen, um qualitativ hochwertige und zuverlässige Endprodukte zu gewährleisten.
Automatisierung
Automatisierung ist die Verwendung von Maschinen oder Geräten, um Aufgaben auszuführen, die normalerweise von Menschen ausgeführt werden. Automatisierung wird in einer Vielzahl von Branchen eingesetzt, darunter die Fertigung, die Logistik und die Gesundheitsversorgung.
Vorteile der Automatisierung
Automatisierung bietet eine Reihe von Vorteilen gegenüber manuellen Verfahren, darunter:
- Erhöhte Produktivität: Automatisierte Prozesse können schneller und effizienter sein als manuelle Prozesse.
- Verbesserte Qualität: Automatisierte Prozesse können eine höhere Qualität der Produkte oder Dienstleistungen gewährleisten.
- Gesteigerte Sicherheit: Automatisierte Prozesse können die Sicherheit der Mitarbeiter verbessern.
- Reduzierte Kosten: Automatisierte Prozesse können die Kosten für die Produktion oder Bereitstellung von Produkten oder Dienstleistungen senken.
Nachteile der Automatisierung
Automatisierung hat auch einige Nachteile, darunter:
- Investitionskosten: Automatisierung kann eine hohe Investition erfordern.
- Flexibilität: Automatisierte Prozesse können weniger flexibel sein als manuelle Prozesse.
- Arbeitsplätze: Automatisierung kann zu Arbeitsplatzverlusten führen.
Arten der Automatisierung
Es gibt verschiedene Arten der Automatisierung, darunter:
- Stand-alone-Automatisierung: Stand-alone-Automatisierung ist eine Art der Automatisierung, bei der einzelne Maschinen oder Geräte automatisiert werden.
- Prozessautomatisierung: Prozessautomatisierung ist eine Art der Automatisierung, bei der ein Prozess oder eine Reihe von Prozessen automatisiert werden.
- Intelligente Automatisierung: Intelligente Automatisierung ist eine Art der Automatisierung, bei der künstliche Intelligenz verwendet wird, um die Automatisierung zu verbessern.
Zukünftige Trends in der Automatisierung
Die Automatisierung wird in den nächsten Jahren weiter voranschreiten. Die folgenden Trends werden die Entwicklung dieser Technologie prägen:
- Fortschreitende Digitalisierung: Die Digitalisierung wird die Automatisierung weiter vorantreiben, da sie die Kommunikation und Vernetzung von Maschinen und Geräten ermöglicht.
- Entwicklung künstlicher Intelligenz: Die Entwicklung künstlicher Intelligenz wird die Automatisierung weiter verbessern, da sie Maschinen und Geräten ermöglicht, selbstständig zu lernen und zu handeln.
- Nachhaltigkeit: Die Entwicklung nachhaltiger Automatisierungslösungen wird dazu beitragen, die Umweltbelastung zu reduzieren.
Insgesamt ist Automatisierung eine wichtige Technologie, die in einer Vielzahl von Branchen eingesetzt wird. Automatisierung bietet eine Reihe von Vorteilen gegenüber manuellen Verfahren, darunter erhöhte Produktivität, verbesserte Qualität, gesteigerte Sicherheit und reduzierte Kosten.
In der heutigen industriellen Fertigung spielt die Metallumformung eine zentrale Rolle. Sie umfasst eine Vielzahl von Prozessen, die es ermöglichen, Metalle in die gewünschten Formen zu bringen. Von einfachen Biegungen bis hin zu komplexen Tiefziehteilen – die Anforderungen an die Maschinen, die in diesem Bereich eingesetzt werden, sind vielfältig und anspruchsvoll. Eine besonders herausragende Rolle nehmen dabei die sogenannten Sondermaschinen ein, die speziell für die individuellen Anforderungen eines Unternehmens entwickelt werden. Diese Maschinen sind maßgeschneiderte Lösungen, die es ermöglichen, spezifische Produktionsprozesse zu optimieren und höchste Präzision bei der Metallumformung zu erreichen.
Was sind Sondermaschinen für die Metallumformung?
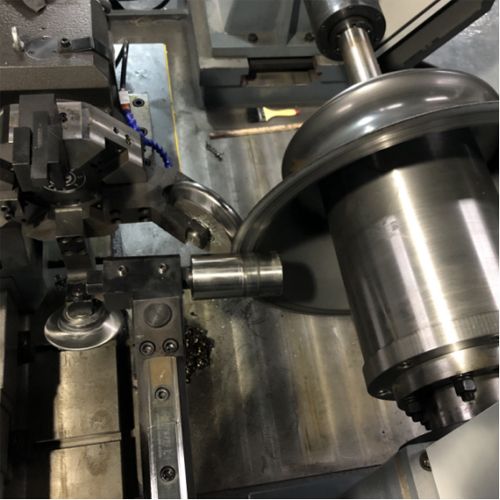
Sondermaschinen für die Metallumformung sind individuell konzipierte Anlagen, die auf die spezifischen Bedürfnisse und Anforderungen eines bestimmten Fertigungsprozesses zugeschnitten sind. Im Gegensatz zu Standardmaschinen, die universell einsetzbar sind, werden Sondermaschinen in enger Zusammenarbeit zwischen dem Maschinenhersteller und dem Endanwender entwickelt. Ziel ist es, eine Maschine zu schaffen, die perfekt in den bestehenden Produktionsprozess integriert werden kann und dabei höchste Effizienz und Präzision bietet.
Die Notwendigkeit für Sondermaschinen entsteht oft dann, wenn Standardmaschinen den Anforderungen eines Unternehmens nicht mehr gerecht werden. Dies kann beispielsweise der Fall sein, wenn ein Unternehmen besondere Bauteilgeometrien herstellen muss, die mit herkömmlichen Maschinen nicht wirtschaftlich oder technisch realisierbar sind. Sondermaschinen bieten hier die Möglichkeit, Produktionsprozesse so zu gestalten, dass sie genau den Anforderungen des Unternehmens entsprechen und somit einen entscheidenden Wettbewerbsvorteil bieten.
Die Bedeutung der Metallumformung in der Industrie
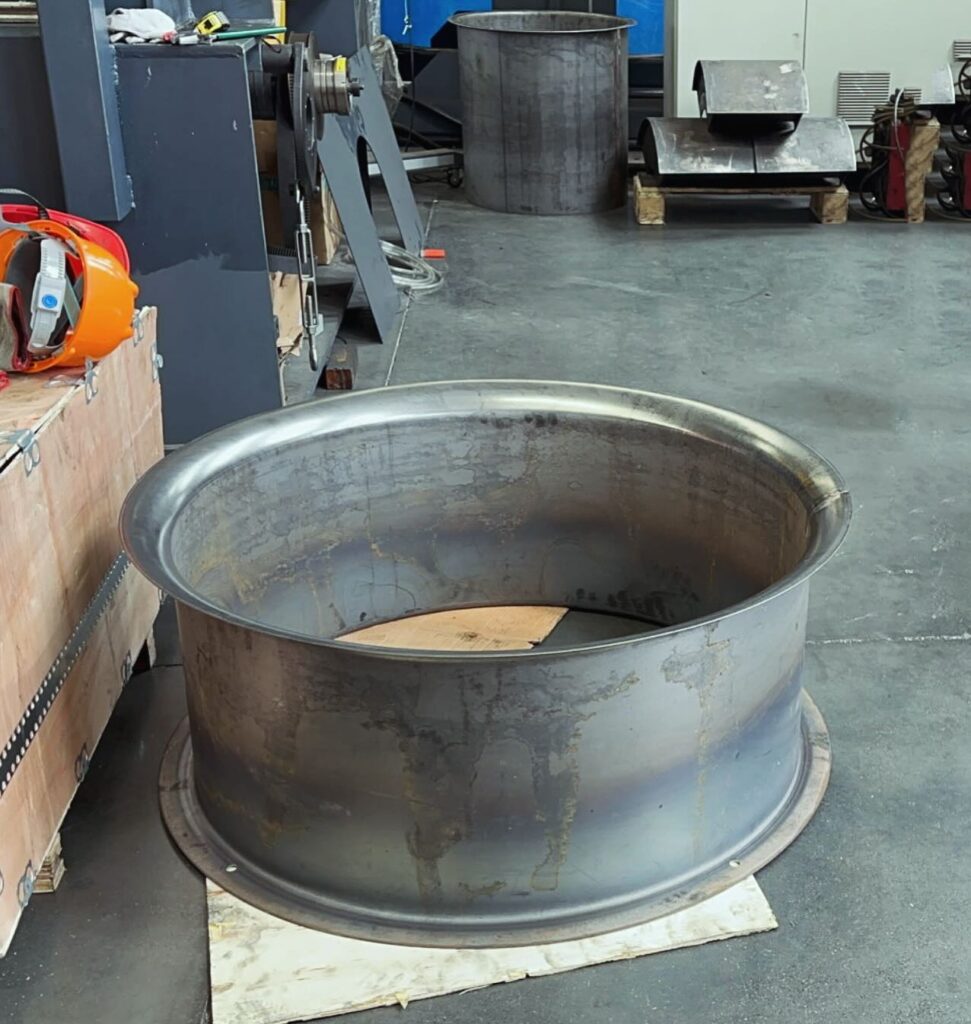
Metallumformung ist ein unverzichtbarer Bestandteil zahlreicher Industriezweige. Ob im Automobilbau, in der Luft- und Raumfahrt, im Maschinenbau oder in der Elektroindustrie – überall werden Metallteile benötigt, die durch verschiedene Umformverfahren hergestellt werden. Dabei ist es entscheidend, dass die eingesetzten Maschinen und Anlagen in der Lage sind, höchste Präzision zu gewährleisten, um den hohen Anforderungen an die Qualität der Produkte gerecht zu werden.
Die Metallumformung umfasst eine Vielzahl von Verfahren, die je nach Anforderung und Material unterschiedlich eingesetzt werden können. Zu den wichtigsten Umformverfahren zählen das Tiefziehen, das Biegen, das Stanzen, das Walzen sowie das Schmieden. Jedes dieser Verfahren stellt unterschiedliche Anforderungen an die Maschinen und Anlagen, die in der Produktion eingesetzt werden.
Sondermaschinen kommen insbesondere dann zum Einsatz, wenn es darum geht, komplexe Bauteile mit hohen Anforderungen an Maßhaltigkeit und Oberflächenqualität herzustellen. Gerade in der Automobil- und Luftfahrtindustrie, wo Sicherheit und Zuverlässigkeit der Bauteile eine zentrale Rolle spielen, ist der Einsatz von maßgeschneiderten Maschinen unumgänglich.
Vorteile von Sondermaschinen in der Metallumformung
Der Einsatz von Sondermaschinen bietet zahlreiche Vorteile gegenüber der Verwendung von Standardmaschinen. Einer der größten Vorteile ist die Möglichkeit, die Maschine genau auf die Bedürfnisse des Unternehmens abzustimmen. Dies ermöglicht nicht nur eine höhere Effizienz, sondern auch eine bessere Qualität der hergestellten Bauteile.
Ein weiterer Vorteil ist die Flexibilität, die Sondermaschinen bieten. Während Standardmaschinen oft nur für bestimmte Fertigungsprozesse geeignet sind, können Sondermaschinen so konzipiert werden, dass sie mehrere verschiedene Umformverfahren in einer Anlage vereinen. Dies reduziert die Notwendigkeit, mehrere Maschinen für verschiedene Fertigungsschritte anzuschaffen, was wiederum Kosten spart und die Produktionszeiten verkürzt.
Darüber hinaus ermöglichen Sondermaschinen eine höhere Automatisierung der Produktionsprozesse. Durch den Einsatz von modernster Steuerungs- und Automatisierungstechnik können Sondermaschinen so programmiert werden, dass sie selbstständig und mit minimalem menschlichem Eingriff arbeiten. Dies reduziert nicht nur die Fehlerquote, sondern erhöht auch die Produktivität und senkt die Kosten.
Herausforderungen bei der Entwicklung von Sondermaschinen
Die Entwicklung von Sondermaschinen für die Metallumformung ist ein komplexer Prozess, der eine enge Zusammenarbeit zwischen dem Maschinenhersteller und dem Endanwender erfordert. Einer der größten Herausforderungen besteht darin, die Anforderungen des Kunden genau zu verstehen und in eine technische Lösung zu übersetzen.
Dabei müssen zahlreiche Faktoren berücksichtigt werden, wie beispielsweise die Art des zu verarbeitenden Materials, die gewünschte Geometrie des Endprodukts, die geforderte Stückzahl sowie die verfügbaren Platz- und Energieverhältnisse im Unternehmen. All diese Faktoren fließen in die Entwicklung der Maschine ein und bestimmen letztendlich deren Aufbau und Funktionsweise.
Ein weiteres wichtiges Thema bei der Entwicklung von Sondermaschinen ist die Integration der Maschine in bestehende Produktionsprozesse. Oft müssen Sondermaschinen in eine bereits vorhandene Produktionslinie integriert werden, was zusätzliche Anforderungen an die Flexibilität und Kompatibilität der Anlage stellt. Darüber hinaus spielen auch Themen wie die Wartungsfreundlichkeit und die langfristige Verfügbarkeit von Ersatzteilen eine entscheidende Rolle.
Beispielhafte Anwendungen von Sondermaschinen in der Metallumformung
Sondermaschinen für die Metallumformung finden in einer Vielzahl von Industriezweigen Anwendung. Ein besonders wichtiges Einsatzgebiet ist der Automobilbau. Hier werden Metallteile für Karosserien, Fahrwerkskomponenten und Motorenteile in großen Stückzahlen und mit hoher Präzision gefertigt. Sondermaschinen ermöglichen es, diese Teile effizient und kostengünstig herzustellen, wobei höchste Anforderungen an die Maßhaltigkeit und Oberflächenqualität erfüllt werden.
Ein weiteres Beispiel ist die Luft- und Raumfahrtindustrie. In diesem Sektor sind die Anforderungen an die Qualität der Bauteile besonders hoch, da bereits kleinste Fehler fatale Folgen haben können. Sondermaschinen ermöglichen es, komplexe Metallteile wie Strukturbauteile oder Turbinenkomponenten präzise und zuverlässig zu fertigen.
Auch in der Elektroindustrie kommen Sondermaschinen zum Einsatz. Hier werden unter anderem Gehäuse und Kontakte für elektronische Bauteile hergestellt, die eine hohe Maßhaltigkeit und Oberflächenqualität erfordern. Sondermaschinen ermöglichen es, diese Teile in großen Stückzahlen und mit hoher Wiederholgenauigkeit zu fertigen.
Zukunftstrends und Entwicklungen
Die Entwicklung von Sondermaschinen für die Metallumformung wird auch in Zukunft eine wichtige Rolle spielen. Insbesondere die fortschreitende Automatisierung und Digitalisierung der Produktionsprozesse wird neue Anforderungen an die Maschinen stellen. Themen wie Industrie 4.0 und das Internet der Dinge (IoT) werden zunehmend an Bedeutung gewinnen und die Entwicklung von intelligenten, vernetzten Maschinen vorantreiben.
Ein weiterer Trend ist der Einsatz von Leichtbauwerkstoffen wie Aluminium und Magnesium, die besondere Anforderungen an die Umformmaschinen stellen. Sondermaschinen bieten hier die Möglichkeit, diese Materialien effizient und präzise zu verarbeiten und somit den steigenden Anforderungen an Leichtbaukomponenten gerecht zu werden.
Auch die Integration von additiven Fertigungsverfahren, wie dem 3D-Druck, in die Metallumformung wird in Zukunft eine wichtige Rolle spielen. Sondermaschinen können so konzipiert werden, dass sie sowohl klassische Umformverfahren als auch additive Verfahren in einem Prozess vereinen und somit neue Möglichkeiten für die Fertigung komplexer Bauteile bieten.
Die Metallumformung ist eine der Kerntechnologien in der industriellen Produktion. Sie ermöglicht es, Rohmetalle in verschiedenste Formen zu bringen, die in zahlreichen Anwendungen in der Automobilindustrie, dem Maschinenbau, der Luft- und Raumfahrt sowie in vielen weiteren Branchen genutzt werden. Die steigenden Anforderungen an Präzision, Effizienz und Flexibilität in der Produktion erfordern jedoch immer häufiger den Einsatz von maßgeschneiderten Maschinenlösungen. Hier kommen die sogenannten Sondermaschinen für die Metallumformung ins Spiel. Diese Maschinen werden speziell für die Bedürfnisse eines bestimmten Fertigungsprozesses entwickelt und bieten zahlreiche Vorteile gegenüber standardisierten Lösungen.
Der Begriff „Sondermaschine“ im Kontext der Metallumformung
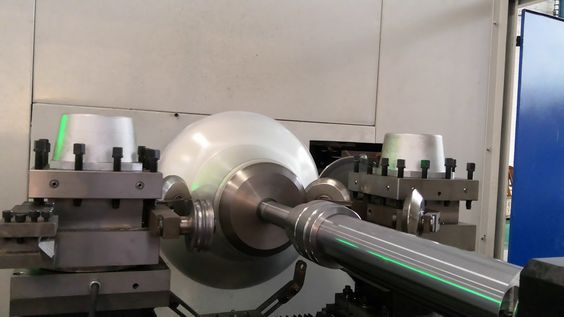
Eine Sondermaschine ist eine individuelle Maschine, die speziell auf die Anforderungen eines bestimmten Unternehmens oder Produktionsprozesses zugeschnitten ist. Im Bereich der Metallumformung bedeutet dies, dass die Maschine genau auf die speziellen Umformprozesse und die zu verarbeitenden Materialien abgestimmt wird. Diese Maschinen sind in der Regel Unikate oder werden nur in sehr kleinen Serien produziert, da sie speziell für einen bestimmten Einsatzzweck entwickelt werden.
Sondermaschinen können unterschiedliche Umformprozesse in einer Anlage vereinen und bieten somit eine hohe Flexibilität. Beispielsweise kann eine Sondermaschine sowohl für das Tiefziehen als auch für das Biegen oder Prägen von Metall eingesetzt werden. Diese Vielseitigkeit ist ein entscheidender Vorteil, da sie es ermöglicht, verschiedene Fertigungsschritte in einer Maschine zu kombinieren und somit Zeit und Kosten zu sparen.
Ein weiterer wesentlicher Unterschied zu Standardmaschinen ist die Möglichkeit, Sondermaschinen mit modernster Steuerungs- und Automatisierungstechnik auszustatten. Dadurch kann der gesamte Produktionsprozess überwacht und optimiert werden, was zu einer höheren Effizienz und Präzision führt.
Der Entwicklungsprozess einer Sondermaschine
Die Entwicklung einer Sondermaschine für die Metallumformung ist ein anspruchsvoller und mehrstufiger Prozess, der eine enge Zusammenarbeit zwischen dem Maschinenhersteller und dem Endanwender erfordert. Im Mittelpunkt stehen dabei die spezifischen Anforderungen des Kunden, die in einem detaillierten Pflichtenheft festgehalten werden. In diesem Dokument werden alle technischen Spezifikationen, wie die Art des zu verarbeitenden Materials, die geforderten Produktionsmengen, die geometrischen Anforderungen an das Endprodukt sowie die Integrationsmöglichkeiten in bestehende Fertigungsprozesse, festgelegt.
Basierend auf diesen Vorgaben entwickeln die Ingenieure des Maschinenherstellers eine erste Konzeptstudie, in der verschiedene Lösungsansätze für die Maschine vorgestellt werden. Diese Konzepte werden in enger Abstimmung mit dem Kunden weiterentwickelt, bis schließlich eine maßgeschneiderte Lösung gefunden wird, die alle Anforderungen erfüllt. Dabei müssen zahlreiche technische Aspekte berücksichtigt werden, wie die Wahl der richtigen Werkzeuge und Umformtechniken, die optimale Auslegung der Maschinenkomponenten sowie die Integration moderner Steuerungs- und Automatisierungstechniken.
Ein wichtiger Bestandteil der Entwicklung ist auch die Simulation des Umformprozesses. Mithilfe moderner Simulationssoftware können die Ingenieure den gesamten Umformprozess virtuell abbilden und mögliche Schwachstellen in der Konstruktion frühzeitig erkennen. Dies reduziert nicht nur die Entwicklungszeit, sondern auch die Kosten, da aufwendige Prototypen oder Testreihen vermieden werden können.
Die Integration von Sondermaschinen in bestehende Fertigungsprozesse
Eine der größten Herausforderungen bei der Entwicklung von Sondermaschinen besteht darin, die Maschine nahtlos in bestehende Produktionsprozesse zu integrieren. Dies erfordert eine präzise Planung und eine enge Zusammenarbeit mit dem Endanwender, um sicherzustellen, dass die Maschine sowohl räumlich als auch technologisch in die vorhandene Infrastruktur passt.
Ein wichtiger Aspekt ist dabei die Frage der Kompatibilität mit vorhandenen Maschinen und Anlagen. Oft müssen Sondermaschinen in eine bereits bestehende Produktionslinie integriert werden, was zusätzliche Anforderungen an ihre Flexibilität und Anpassungsfähigkeit stellt. Beispielsweise muss die Maschine in der Lage sein, Werkstücke von anderen Maschinen zu übernehmen oder an nachfolgende Fertigungsschritte weiterzuleiten, ohne dass es zu Produktionsunterbrechungen oder -verzögerungen kommt.
Darüber hinaus spielt auch die Frage der Steuerungs- und Automatisierungstechnik eine wichtige Rolle. Moderne Sondermaschinen sind in der Regel mit komplexen Steuerungssystemen ausgestattet, die es ermöglichen, den gesamten Produktionsprozess zu überwachen und zu optimieren. Dabei müssen die Maschinen so programmiert werden, dass sie reibungslos mit den bestehenden Systemen kommunizieren und in den übergeordneten Fertigungsprozess integriert werden können.
Anwendungsbereiche von Sondermaschinen in der Metallumformung
Sondermaschinen für die Metallumformung finden in einer Vielzahl von Branchen Anwendung. Besonders häufig werden sie in Industriezweigen eingesetzt, in denen hohe Anforderungen an die Präzision und Qualität der hergestellten Bauteile gestellt werden.
Automobilindustrie
In der Automobilindustrie werden Sondermaschinen beispielsweise für die Herstellung von Karosserieteilen, Fahrwerkskomponenten oder Motorteilen verwendet. Hierbei handelt es sich oft um komplexe Bauteile, die mit herkömmlichen Umformverfahren nicht oder nur mit großem Aufwand herzustellen wären. Sondermaschinen ermöglichen es, diese Teile in großen Stückzahlen und mit hoher Wiederholgenauigkeit zu fertigen.
Luft- und Raumfahrt
Auch in der Luft- und Raumfahrtindustrie spielen Sondermaschinen eine zentrale Rolle. In diesem Bereich müssen besonders leichte, aber gleichzeitig extrem belastbare Metallteile gefertigt werden, die höchsten Qualitätsanforderungen genügen. Sondermaschinen ermöglichen es, diese Bauteile mit höchster Präzision und Effizienz herzustellen.
Maschinenbau
Im Maschinenbau werden Sondermaschinen für die Herstellung von Werkzeugen, Maschinenteilen oder Baugruppen eingesetzt. Dabei müssen die Maschinen oft in der Lage sein, unterschiedlichste Materialien zu verarbeiten und komplexe Geometrien zu realisieren. Sondermaschinen bieten hier die nötige Flexibilität und Präzision, um auch anspruchsvollste Fertigungsprozesse erfolgreich zu meistern.
Vorteile von Sondermaschinen gegenüber Standardmaschinen
Der größte Vorteil von Sondermaschinen liegt in ihrer Flexibilität und Anpassungsfähigkeit. Während Standardmaschinen oft nur für einen bestimmten Anwendungsbereich geeignet sind, können Sondermaschinen genau auf die Bedürfnisse des Kunden zugeschnitten werden. Dies ermöglicht es, auch komplexe Umformprozesse effizient und präzise durchzuführen.
Ein weiterer Vorteil ist die Möglichkeit, Sondermaschinen mit modernster Technologie auszustatten. Dies umfasst sowohl die Wahl der Werkzeuge und Umformverfahren als auch den Einsatz von Automatisierungstechnik und Industrie-4.0-Lösungen. Durch die Integration solcher Technologien können Sondermaschinen den gesamten Produktionsprozess überwachen und optimieren, was zu einer höheren Effizienz und einer besseren Produktqualität führt.
Darüber hinaus bieten Sondermaschinen eine höhere Prozesssicherheit. Da sie speziell für einen bestimmten Fertigungsprozess entwickelt wurden, können mögliche Fehlerquellen bereits in der Planungsphase erkannt und eliminiert werden. Dies reduziert das Risiko von Produktionsausfällen und erhöht die Zuverlässigkeit der Anlage.
Wirtschaftliche Aspekte von Sondermaschinen
Die Entwicklung und der Bau von Sondermaschinen erfordert in der Regel höhere Investitionen als der Einsatz von Standardmaschinen. Allerdings amortisieren sich diese Kosten oft schnell, da Sondermaschinen eine höhere Effizienz und eine bessere Qualität der hergestellten Produkte bieten. Zudem ermöglichen sie es, die Produktionsprozesse zu optimieren und die Durchlaufzeiten zu verkürzen, was zu einer höheren Rentabilität führt.
Ein weiterer wirtschaftlicher Vorteil ist die Möglichkeit, Sondermaschinen so zu konzipieren, dass sie flexibel an neue Anforderungen angepasst werden können. Dies ist besonders in Branchen von Vorteil, in denen sich die Anforderungen an die Produkte und die Produktionsprozesse häufig ändern. Durch die Modularität und Flexibilität von Sondermaschinen können Unternehmen schnell auf neue Marktanforderungen reagieren, ohne dass hohe Investitionen in neue Maschinen erforderlich sind.
Zukunftstrends in der Sondermaschinenentwicklung
Die Entwicklung von Sondermaschinen wird auch in Zukunft eine wichtige Rolle in der industriellen Produktion spielen. Insbesondere die fortschreitende Digitalisierung und Automatisierung der Fertigungsprozesse wird neue Anforderungen an die Maschinen stellen. Themen wie Industrie 4.0, das Internet der Dinge (IoT) und künstliche Intelligenz (KI) werden zunehmend an Bedeutung gewinnen und die Entwicklung von intelligenten, vernetzten Maschinen vorantreiben.
Auch der Einsatz neuer Materialien, wie beispielsweise hochfester Leichtbaumaterialien, wird die Anforderungen an Sondermaschinen verändern. Maschinen müssen in der Lage sein, diese Materialien effizient und präzise zu verarbeiten, um den steigenden Anforderungen an die Produktqualität und -sicherheit gerecht zu werden.
Die Metallumformung erfordert hochpräzise Maschinen, die in der Lage sind, große Kräfte aufzubringen und dabei die geforderte Genauigkeit über lange Produktionszeiten hinweg sicherzustellen. Eine der bewährtesten Maschinenkonstruktionen für solche Anforderungen ist die Vier-Säulen-Presse, die aufgrund ihrer robusten Bauweise und der gleichmäßigen Kraftverteilung über die gesamte Arbeitsfläche für zahlreiche Anwendungen in der Umformtechnik eingesetzt wird. Von Tiefziehprozessen über das Stanzen bis hin zu verschiedenen Pressoperationen – die Vier-Säulen-Presse bietet eine hervorragende Kombination aus Stabilität, Flexibilität und Präzision.
Grundlagen der Vier-Säulen-Presse
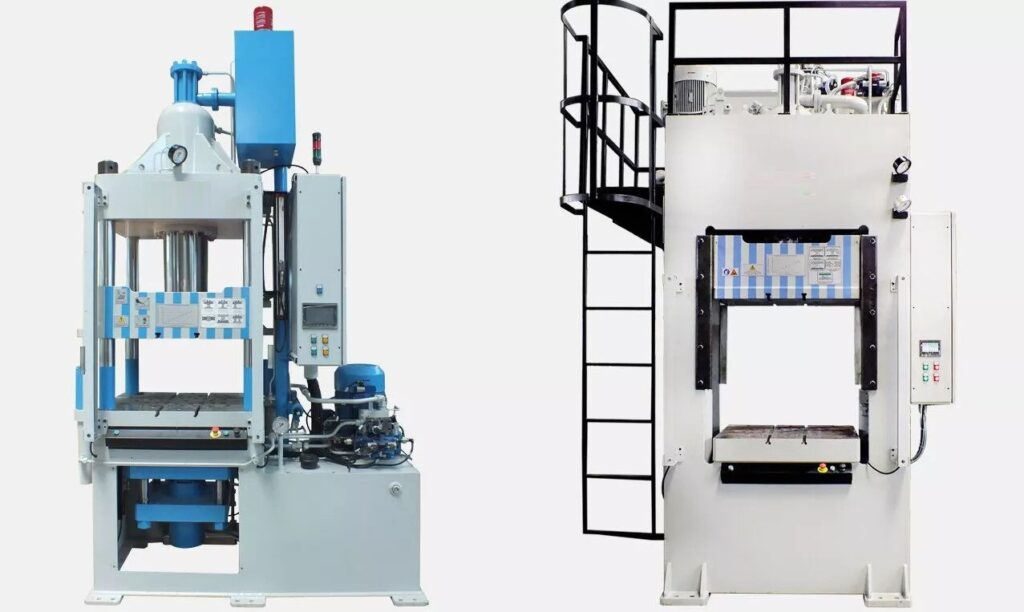
Eine Vier-Säulen-Presse zeichnet sich durch ihre besondere Bauweise aus, bei der die Presse auf vier vertikalen Säulen montiert ist. Diese Säulen dienen als Führungen für den beweglichen Stößel, der das Werkstück mit der notwendigen Kraft bearbeitet. Die Konstruktion mit vier Säulen bietet eine extrem hohe Stabilität und Steifigkeit, was besonders wichtig ist, wenn hohe Kräfte bei der Metallumformung aufgebracht werden müssen.
Die Vier-Säulen-Konstruktion gewährleistet eine gleichmäßige Verteilung der Kräfte über die gesamte Arbeitsfläche der Presse, wodurch Verformungen und Abweichungen minimiert werden. Dies ist insbesondere bei der Herstellung von Bauteilen mit engen Toleranzen und komplexen Geometrien von entscheidender Bedeutung. Gleichzeitig ermöglicht die offene Bauweise der Maschine einen einfachen Zugang zum Werkzeug und erleichtert die Handhabung der Werkstücke, was die Produktivität erhöht.
Einsatzgebiete der Vier-Säulen-Presse
Die Vielseitigkeit der Vier-Säulen-Presse macht sie zu einer idealen Wahl für zahlreiche Umformprozesse in verschiedenen Industrien. Zu den wichtigsten Anwendungsbereichen gehören:
2.1. Tiefziehen
Das Tiefziehen ist ein Umformverfahren, bei dem ein flaches Blech zu einem Hohlkörper umgeformt wird. Dabei wird das Blech durch einen Stößel in eine Matrize gedrückt, wodurch es seine endgültige Form erhält. Die Vier-Säulen-Presse ist besonders gut für diesen Prozess geeignet, da sie eine gleichmäßige Verteilung der Kräfte auf das Werkstück sicherstellt. Dies ist entscheidend, um ein Reißen oder Falten des Blechs zu verhindern und eine gleichmäßige Materialdicke zu gewährleisten.
2.2. Stanzen und Prägen
Beim Stanzen und Prägen werden Metallteile durch den Einsatz von Werkzeugen geformt, die das Material durch Druck bearbeiten. Die Vier-Säulen-Presse bietet die notwendige Stabilität, um hohe Presskräfte präzise und gleichmäßig auf das Material aufzubringen, was zu einer hohen Qualität und Maßhaltigkeit der gefertigten Teile führt. Besonders in der Automobil- und Elektroindustrie werden Vier-Säulen-Pressen häufig für diese Prozesse eingesetzt, um Komponenten wie Karosserieteile, Gehäuse und Kontakte herzustellen.
2.3. Schmieden
Auch in der Schmiedetechnik kommen Vier-Säulen-Pressen zum Einsatz. Beim Schmieden wird das Metall unter hohen Temperaturen plastisch verformt, um seine mechanischen Eigenschaften zu verbessern und es in die gewünschte Form zu bringen. Die Stabilität und Präzision der Vier-Säulen-Presse sind hierbei von großer Bedeutung, um die erforderlichen Kräfte kontrolliert und gleichmäßig auf das Werkstück zu übertragen.
2.4. Kunststoffverarbeitung
Neben der Metallumformung wird die Vier-Säulen-Presse auch in der Kunststoffverarbeitung eingesetzt. Hier kommt sie beispielsweise beim Formpressen von Thermoplasten oder Duroplasten zum Einsatz. Durch die hohe Präzision und die gleichmäßige Druckverteilung ist die Vier-Säulen-Presse in der Lage, Kunststoffteile mit komplexen Geometrien und hohen Anforderungen an die Oberflächenqualität zu fertigen.
Vorteile der Vier-Säulen-Presse
Die Vier-Säulen-Presse bietet eine Reihe von Vorteilen, die sie zu einer der am häufigsten eingesetzten Pressentypen in der Industrie machen:
3.1. Hohe Stabilität und Steifigkeit
Durch ihre Konstruktion mit vier Führungsstäben bietet die Vier-Säulen-Presse eine außergewöhnlich hohe Stabilität und Steifigkeit. Dies ist besonders bei Umformprozessen von Vorteil, bei denen hohe Kräfte auf das Werkstück einwirken. Die Säulen sorgen dafür, dass der Stößel präzise geführt wird und sich keine ungewollten Bewegungen oder Verformungen ergeben.
3.2. Gleichmäßige Kraftverteilung
Ein entscheidender Vorteil der Vier-Säulen-Presse ist die gleichmäßige Verteilung der aufgebrachten Kräfte. Dies minimiert das Risiko von Materialfehlern, wie ungleichmäßiger Materialstärke oder Oberflächenverformungen. Besonders bei Prozessen wie dem Tiefziehen ist dies von großer Bedeutung, da es entscheidend für die Qualität des Endprodukts ist.
3.3. Flexibilität
Die Vier-Säulen-Presse ist für eine Vielzahl von Umformprozessen geeignet und kann für unterschiedlichste Anwendungen in der Metall- und Kunststoffverarbeitung eingesetzt werden. Dies macht sie zu einer vielseitigen Lösung, die in verschiedenen Industriezweigen eingesetzt werden kann, ohne dass große Anpassungen erforderlich sind.
3.4. Leichte Zugänglichkeit
Durch die offene Bauweise der Presse ist der Arbeitsbereich leicht zugänglich, was die Handhabung und den Wechsel von Werkzeugen erleichtert. Dies trägt nicht nur zur Produktivität bei, sondern auch zur Sicherheit des Bedienpersonals, da der Arbeitsbereich der Maschine gut einsehbar ist.
3.5. Anpassbare Größe und Leistung
Vier-Säulen-Pressen können in verschiedenen Größen und Leistungsklassen gefertigt werden, je nach den Anforderungen des Produktionsprozesses. Von kleinen Tischpressen für Präzisionsarbeiten bis hin zu großformatigen Pressen für schwere Umformprozesse – die Flexibilität in der Auslegung dieser Maschinen ermöglicht es, sie genau an die Bedürfnisse des Anwenders anzupassen.
Technologische Entwicklungen und Automatisierung
In den letzten Jahren hat sich die Technologie von Vier-Säulen-Pressen kontinuierlich weiterentwickelt, insbesondere im Hinblick auf Automatisierung und Digitalisierung. Moderne Vier-Säulen-Pressen sind oft mit fortschrittlicher Steuerungstechnik ausgestattet, die es ermöglicht, den gesamten Produktionsprozess zu überwachen und in Echtzeit anzupassen. Dadurch können Fehler frühzeitig erkannt und behoben werden, was die Produktionssicherheit erhöht und Ausschuss reduziert.
Durch den Einsatz von Sensorik und Automatisierungssystemen können Vier-Säulen-Pressen heute auch in hochautomatisierte Produktionslinien integriert werden. Dies ermöglicht es, die Effizienz und Produktivität zu steigern, da die Maschinen nahtlos in den gesamten Fertigungsprozess eingebunden sind und ohne manuellen Eingriff arbeiten können. Die Digitalisierung der Maschinensteuerung ermöglicht es zudem, Produktionsdaten in Echtzeit zu erfassen und zu analysieren, was zur Optimierung der Prozesse beiträgt.
Ein weiterer wichtiger technologischer Fortschritt ist der Einsatz von energieeffizienten Antrieben. Moderne Vier-Säulen-Pressen sind häufig mit Servoantrieben oder hydraulischen Systemen ausgestattet, die eine präzise Steuerung der Presskraft ermöglichen und gleichzeitig den Energieverbrauch reduzieren. Dies ist nicht nur aus wirtschaftlicher Sicht von Vorteil, sondern trägt auch zur Nachhaltigkeit der Produktion bei.
Herausforderungen und Wartung
Trotz der zahlreichen Vorteile, die die Vier-Säulen-Presse bietet, gibt es auch einige Herausforderungen, die bei ihrem Einsatz beachtet werden müssen. Eine davon ist die regelmäßige Wartung der Maschine, um eine gleichbleibende Präzision und Leistung sicherzustellen. Die vier Säulen, die den Stößel führen, müssen regelmäßig geprüft und geschmiert werden, um eine reibungslose Funktion zu gewährleisten. Auch die Hydrauliksysteme, die oft in Vier-Säulen-Pressen zum Einsatz kommen, bedürfen regelmäßiger Inspektionen, um Leckagen zu vermeiden und die Leistungsfähigkeit der Maschine aufrechtzuerhalten.
Eine weitere Herausforderung besteht in der Anpassung der Presse an unterschiedliche Umformprozesse. Obwohl die Vier-Säulen-Presse eine hohe Flexibilität bietet, kann es in einigen Fällen erforderlich sein, spezielle Werkzeuge oder Zusatzausstattungen zu entwickeln, um die Maschine optimal an den jeweiligen Prozess anzupassen. Dies erfordert eine enge Zusammenarbeit zwischen dem Maschinenhersteller und dem Endanwender, um sicherzustellen, dass die Presse die gewünschten Ergebnisse liefert.
Zukunftsaussichten
Die Zukunft der Vier-Säulen-Presse liegt in der weiteren Integration moderner Technologien, insbesondere im Bereich der Digitalisierung und Automatisierung. Industrie 4.0, das Internet der Dinge (IoT) und Künstliche Intelligenz (KI) werden zunehmend in die Steuerung und Überwachung von Maschinen integriert, um die Effizienz und Präzision der Produktionsprozesse weiter zu verbessern. Intelligente Vier-Säulen-Pressen werden in der Lage sein, sich selbst zu überwachen und Wartungsbedarf frühzeitig zu erkennen, was zu einer höheren Verfügbarkeit und geringeren Ausfallzeiten führen wird.
Auch der Einsatz von neuen Materialien, wie hochfesten Leichtbauwerkstoffen oder Verbundmaterialien, stellt neue Anforderungen an die Umformtechnik. Die Vier-Säulen-Presse wird sich diesen Herausforderungen anpassen müssen, indem sie leistungsstärkere Antriebssysteme und präzisere Steuerungstechnologien integriert, um die benötigten Kräfte und Genauigkeiten für diese Materialien zu gewährleisten.
Die Umformtechnik gehört zu den essenziellen Prozessen der industriellen Fertigung. Sie bietet die Möglichkeit, Werkstoffe wie Metall oder Kunststoff unter Einwirkung von Druck dauerhaft in eine gewünschte Form zu bringen, ohne das Material zu entfernen. Die Umformpresse ist hierbei eines der zentralen Werkzeuge, das durch den Einsatz mechanischer, hydraulischer oder pneumatischer Kräfte Bauteile formt. In Branchen wie der Automobilindustrie, dem Maschinenbau und der Elektroindustrie ist die Umformpresse unverzichtbar. Ihre Vielseitigkeit und Anpassungsfähigkeit machen sie zu einem unverzichtbaren Element moderner Produktionslinien.
Definition und Funktionsweise der Umformpresse
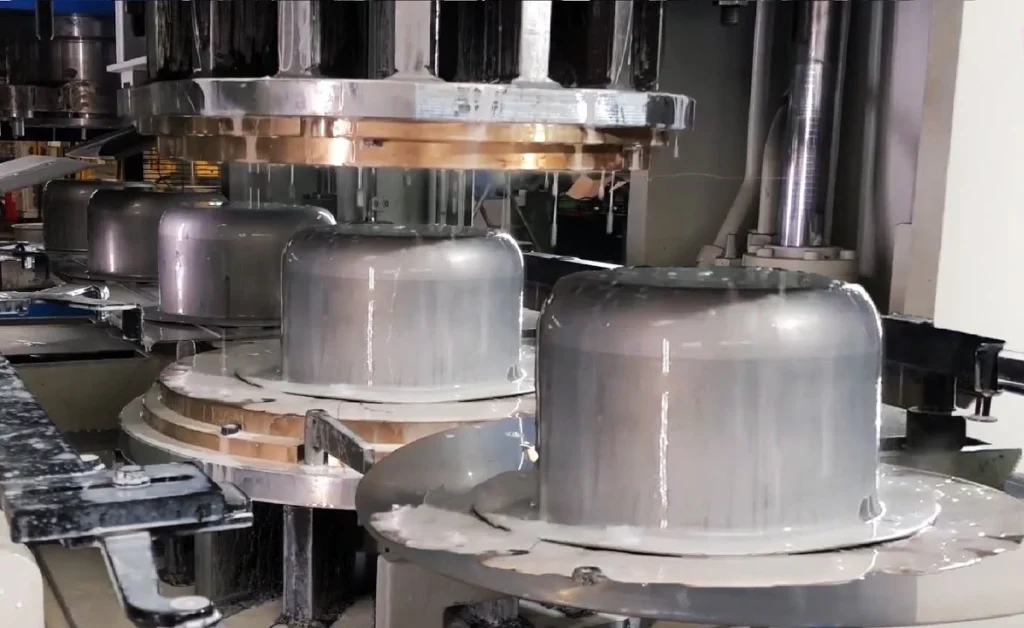
Eine Umformpresse ist eine Maschine, die verwendet wird, um Material unter Anwendung von Druck zu verformen. Dieser Prozess erfolgt in der Regel zwischen zwei Werkzeugen: einem Stempel und einer Matrize. Der Stempel drückt das Material in die Form der Matrize, wodurch das Werkstück seine endgültige Form erhält. Je nach Anwendung kann die Umformpresse auf verschiedene Arten von Werkstoffen einwirken, sei es durch Biegen, Stanzen, Prägen oder Tiefziehen.
1.1. Mechanische Umformpressen
Mechanische Pressen nutzen Schwungräder und Kupplungen, um Energie zu speichern und sie schlagartig auf das Material zu übertragen. Diese Pressen sind besonders effizient, wenn schnelle und wiederholte Bewegungen erforderlich sind, und eignen sich daher ideal für Massenfertigungsprozesse. Mechanische Umformpressen werden häufig in der Automobilindustrie eingesetzt, wo große Mengen von Blechteilen wie Türen, Motorhauben und Kotflügel hergestellt werden müssen.
1.2. Hydraulische Umformpressen
Hydraulische Pressen arbeiten mit Flüssigkeitsdruck, um eine gleichmäßige, kontrollierte Kraft auszuüben. Sie bieten den Vorteil einer sehr hohen Presskraft und sind besonders geeignet für Prozesse, bei denen eine langsame und gleichmäßige Verformung erforderlich ist, wie beim Tiefziehen oder bei der Verarbeitung von dicken Materialien. Hydraulische Umformpressen finden Anwendung in der Herstellung großer und komplexer Bauteile, bei denen Präzision und Flexibilität entscheidend sind.
1.3. Pneumatische Umformpressen
Pneumatische Umformpressen nutzen Druckluft, um das Material zu verformen. Diese Pressen sind in der Regel kleiner und bieten eine geringere Kraft als mechanische oder hydraulische Pressen, sind jedoch ideal für Anwendungen, bei denen Geschwindigkeit und einfache Bedienung wichtig sind. Sie werden oft in der Elektronik- und Verpackungsindustrie eingesetzt.
Anwendungsbereiche der Umformpresse
Umformpressen kommen in einer Vielzahl von Industrien und Prozessen zum Einsatz, insbesondere dort, wo Metall oder Kunststoff zu Bauteilen geformt werden muss. Ihre Einsatzgebiete sind breit gefächert und erstrecken sich über verschiedene Industriezweige.
2.1. Automobilindustrie
In der Automobilindustrie sind Umformpressen unverzichtbar für die Herstellung von Karosserieteilen, Fahrwerkskomponenten und anderen strukturellen Bauteilen. Die meisten dieser Teile werden durch Tiefziehen, Stanzen oder Biegen von Blech hergestellt, wofür Umformpressen die notwendigen hohen Kräfte aufbringen müssen. Besonders hydraulische Pressen sind in diesem Bereich weit verbreitet, da sie große Teile wie Motorhauben oder Seitenwände mit hoher Präzision und Reproduzierbarkeit herstellen können.
2.2. Luft- und Raumfahrt
Die Luft- und Raumfahrtindustrie stellt sehr hohe Anforderungen an die Präzision und Qualität der gefertigten Bauteile. Umformpressen spielen eine entscheidende Rolle bei der Herstellung von leichten, aber hochfesten Strukturen, die in Flugzeugen und Raumfahrzeugen zum Einsatz kommen. Hierbei kommen häufig spezielle Legierungen und Werkstoffe zum Einsatz, die unter hohen Kräften geformt werden müssen, ohne ihre strukturelle Integrität zu verlieren.
2.3. Maschinenbau
Im Maschinenbau werden Umformpressen für die Fertigung von Maschinenteilen, Werkzeugen und Vorrichtungen verwendet. Oftmals sind diese Teile hochkomplex und erfordern eine präzise Umformung, die durch den Einsatz von Umformpressen ermöglicht wird. Besonders bei der Herstellung von Bauteilen aus hochfesten Stählen oder Speziallegierungen bieten hydraulische Umformpressen die nötige Flexibilität und Presskraft.
2.4. Elektronik- und Elektroindustrie
In der Elektronik- und Elektroindustrie werden Umformpressen für die Herstellung von Gehäusen, Schaltkästen und anderen Komponenten verwendet. Diese Bauteile bestehen in der Regel aus dünnen Blechen, die durch Stanzen, Biegen und Prägen bearbeitet werden. Mechanische Pressen sind hier aufgrund ihrer Geschwindigkeit und Effizienz besonders weit verbreitet.
Wichtige Verfahren in der Umformtechnik
Es gibt zahlreiche Umformverfahren, die mithilfe von Umformpressen realisiert werden. Jedes Verfahren hat spezifische Anforderungen an die Maschine und das zu verarbeitende Material. Zu den wichtigsten Verfahren gehören:
3.1. Tiefziehen
Das Tiefziehen ist ein Umformverfahren, bei dem ein Blech in eine Hohlform gebracht wird. Dabei wird das Blech in eine Matrize gezogen und durch einen Stempel geformt. Umformpressen, insbesondere hydraulische Pressen, sind ideal für das Tiefziehen geeignet, da sie eine gleichmäßige Verformung des Materials ermöglichen.
3.2. Biegen
Beim Biegen wird das Material gezielt verformt, um es in eine gewünschte Winkel- oder Rundform zu bringen. Dieser Prozess erfordert präzise Steuerung und gleichmäßige Druckverteilung, die durch mechanische oder hydraulische Pressen gewährleistet wird.
3.3. Stanzen
Stanzen ist ein Umformverfahren, bei dem Material durch ein Werkzeug ausgestanzt oder geschnitten wird. Dieser Prozess wird häufig in der Blechverarbeitung eingesetzt, um präzise Löcher, Formen oder Aussparungen in das Material zu schneiden. Mechanische Umformpressen sind aufgrund ihrer schnellen Bewegungen ideal für das Stanzen in großen Stückzahlen geeignet.
3.4. Prägen
Beim Prägen wird das Material unter Druck in eine vorgefertigte Form gepresst, um bestimmte Muster oder Strukturen zu erzeugen. Dieser Prozess wird häufig in der Münzherstellung oder für dekorative Oberflächen verwendet. Umformpressen, die für das Prägen eingesetzt werden, müssen eine hohe Präzision und Wiederholgenauigkeit bieten, um die gewünschten Ergebnisse zu erzielen.
4. Technologische Entwicklungen in der Umformpresstechnik
Die Technologie der Umformpressen hat sich in den letzten Jahrzehnten kontinuierlich weiterentwickelt, insbesondere im Hinblick auf Automatisierung, Effizienz und Nachhaltigkeit. Moderne Umformpressen sind heute oft mit fortschrittlicher Sensorik, Steuerungstechnik und Antriebssystemen ausgestattet, die es ermöglichen, den Umformprozess genau zu steuern und in Echtzeit zu überwachen.
4.1. Automatisierung und Industrie 4.0
Die fortschreitende Automatisierung hat auch in der Umformpresstechnik Einzug gehalten. Viele Umformpressen sind heute in der Lage, vollautomatisch zu arbeiten, indem sie Werkstücke automatisch zuführen, verarbeiten und entnehmen. Durch die Integration von Industrie-4.0-Technologien können Umformpressen zudem in vernetzte Produktionssysteme eingebunden werden, was eine Überwachung und Optimierung der Prozesse in Echtzeit ermöglicht.
Die Digitalisierung der Fertigung ermöglicht es, Prozessdaten zu sammeln und zu analysieren, um die Produktivität zu steigern und die Qualität zu verbessern. Zum Beispiel können Sensoren in Umformpressen installiert werden, die die Kräfte, Temperaturen und Verformungen überwachen und so eine frühzeitige Erkennung von Abweichungen ermöglichen. Dies trägt nicht nur zur Effizienzsteigerung bei, sondern hilft auch, Ausschuss zu minimieren und die Lebensdauer der Werkzeuge zu verlängern.
4.2. Energieeffizienz
Ein weiteres wichtiges Thema in der modernen Umformpresstechnik ist die Energieeffizienz. Hydraulische und mechanische Umformpressen werden zunehmend mit energieeffizienten Antriebssystemen ausgestattet, die den Energieverbrauch senken und gleichzeitig die Leistung der Maschine optimieren. Servoantriebe und frequenzgesteuerte Motoren sind Beispiele für Technologien, die in modernen Umformpressen zum Einsatz kommen, um den Energieverbrauch zu reduzieren und den Betrieb nachhaltiger zu gestalten.
4.3. Modularität und Flexibilität
Moderne Umformpressen sind häufig modular aufgebaut, was es ermöglicht, die Maschine an unterschiedliche Anforderungen und Materialien anzupassen. Durch den Einsatz austauschbarer Werkzeuge und anpassbarer Presskraft können Umformpressen flexibel für verschiedene Umformprozesse eingesetzt werden, ohne dass aufwendige Maschinenumstellungen erforderlich sind. Dies macht die Maschinen besonders für Unternehmen interessant, die eine hohe Variantenvielfalt in ihrer Produktion haben.
Wartung und Instandhaltung
Die regelmäßige Wartung und Instandhaltung von Umformpressen ist entscheidend, um eine hohe Verfügbarkeit und Präzision sicherzustellen. Die mechanischen und hydraulischen Komponenten der Presse unterliegen einem natürlichen Verschleiß und müssen regelmäßig überprüft und gegebenenfalls ausgetauscht werden.
5.1. Vorbeugende Wartung
Vorbeugende Wartungsprogramme sind eine effektive Methode, um Ausfälle und teure Reparaturen zu vermeiden. Durch regelmäßige Inspektionen können potenzielle Probleme frühzeitig erkannt und behoben werden, bevor sie zu größeren Störungen führen. Besonders die Hydrauliksysteme, die in vielen Umformpressen zum Einsatz kommen, erfordern regelmäßige Wartung, um Leckagen zu vermeiden und die Leistungsfähigkeit der Presse aufrechtzuerhalten.
5.2. Werkzeugpflege
Die Werkzeuge, die in Umformpressen verwendet werden, spielen eine zentrale Rolle für die Qualität der gefertigten Bauteile. Daher ist es wichtig, dass diese Werkzeuge regelmäßig gereinigt, geschärft und geprüft werden. Eine sorgfältige Werkzeugpflege trägt nicht nur zur Qualität der Endprodukte bei, sondern verlängert auch die Lebensdauer der Werkzeuge und reduziert die Kosten für Ersatzteile.
Das Kunststoff Formpressen ist ein bewährtes Verfahren zur Herstellung von Bauteilen und Produkten aus Kunststoff. Es handelt sich dabei um eine Formgebungstechnik, bei der Kunststoffmaterialien unter Druck und Wärme in die gewünschte Form gebracht werden. Diese Methode findet in zahlreichen Industrien Anwendung, da sie eine effiziente, wirtschaftliche und präzise Fertigung von komplexen Kunststoffteilen ermöglicht. In Bereichen wie der Automobilindustrie, der Elektronikbranche und der Medizintechnik ist das Kunststoff Formpressen nicht mehr wegzudenken.
Grundlagen des Kunststoff Formpressens
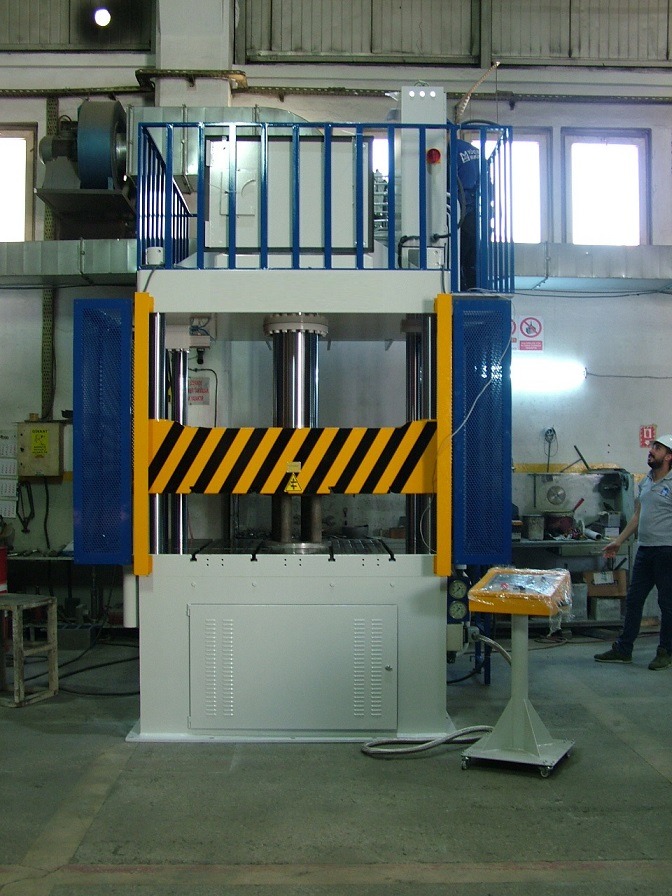
Das Kunststoff Formpressen, auch als Formpressen oder Compression Molding bezeichnet, basiert auf der Umformung von Kunststoffen durch den Einsatz von Druck und Hitze. Das Ausgangsmaterial, das in Form von Pulver, Granulat oder vorgefertigten Blanks vorliegt, wird in eine beheizte Form gegeben. Durch den Druck der Presse wird das Material in die Form gepresst und härtet dort aus, bis es seine endgültige Form erreicht. Dieses Verfahren ist besonders geeignet für thermoplastische und duroplastische Materialien, die unter hohen Temperaturen verformt und dann ausgehärtet werden.
1.1. Thermoplaste vs. Duroplaste
Thermoplaste sind Kunststoffe, die bei Erwärmung schmelzen und verformbar werden. Sie können mehrfach erwärmt und wieder geformt werden, was sie ideal für Recyclingprozesse macht. Beispiele für Thermoplaste sind Polyethylen (PE), Polypropylen (PP) und Polyvinylchlorid (PVC).
Duroplaste hingegen härten einmal unter Hitze und Druck aus und behalten ihre Form danach dauerhaft. Sie können nach dem Aushärten nicht erneut verformt werden. Diese Eigenschaft macht sie besonders widerstandsfähig und hitzebeständig. Beispiele für Duroplaste sind Epoxidharze, Phenolharze und Polyurethane.
Das Kunststoff Formpressen wird sowohl für Thermoplaste als auch für Duroplaste eingesetzt, wobei die spezifischen Anforderungen und Eigenschaften der Materialien berücksichtigt werden müssen.
2. Prozess des Kunststoff Formpressens
Der Prozess des Kunststoff Formpressens besteht aus mehreren Schritten, die genau aufeinander abgestimmt sein müssen, um ein qualitativ hochwertiges Endprodukt zu gewährleisten.
2.1. Vorbereitung des Materials
Zunächst wird das Rohmaterial vorbereitet. Bei Thermoplasten kann dies in Form von Granulat oder Pulver vorliegen, während bei Duroplasten häufig vorgeformte Blanks oder „Preforms“ verwendet werden. Diese Preforms sind oft in der Nähe der endgültigen Form des Produkts hergestellt, um den Materialfluss während des Pressens zu optimieren.
2.2. Aufheizen der Form
Die Form, in der das Kunststoffteil geformt wird, wird auf die notwendige Temperatur gebracht. Die Temperatur hängt von der Art des verwendeten Kunststoffs ab. Für Thermoplaste reicht oft eine moderate Erwärmung, während Duroplaste höhere Temperaturen benötigen, um den Härtungsprozess zu starten.
2.3. Einlegen des Materials
Das vorgeformte Material oder das Granulat wird in die Form eingelegt. Bei Thermoplasten schmilzt das Material bei Erwärmung, während es bei Duroplasten beginnt, sich durch die chemische Reaktion zu verfestigen.
2.4. Formpressen
Die Presse wird geschlossen und übt einen gleichmäßigen Druck auf das Material aus, das sich dadurch in der Form verteilt. Dieser Druck stellt sicher, dass das Material die Konturen der Form exakt ausfüllt und das Endprodukt die gewünschte Form erhält. Der Druck wird aufrechterhalten, bis das Material vollständig ausgehärtet oder abgekühlt ist.
2.5. Entformung
Nach dem Aushärten oder Abkühlen des Kunststoffs wird die Form geöffnet und das fertige Bauteil entnommen. In einigen Fällen müssen die Bauteile nachbearbeitet werden, um überschüssiges Material zu entfernen oder bestimmte Oberflächenmerkmale zu verbessern.
3. Vorteile des Kunststoff Formpressens
Das Kunststoff Formpressen bietet zahlreiche Vorteile gegenüber anderen Fertigungstechniken, insbesondere wenn es um die Herstellung komplexer Kunststoffteile in großen Stückzahlen geht.
3.1. Hohe Präzision und Wiederholgenauigkeit
Das Formpressen ermöglicht die Herstellung hochpräziser Bauteile mit engen Toleranzen. Durch den gleichmäßigen Druck und die exakte Steuerung der Temperatur können Teile mit hoher Maßhaltigkeit und Wiederholgenauigkeit produziert werden, was für viele Industrien von entscheidender Bedeutung ist.
3.2. Effizienz bei der Massenproduktion
Ein wesentlicher Vorteil des Formpressens liegt in der Effizienz bei der Serienfertigung. Da der Prozess automatisiert und die Zykluszeiten relativ kurz sind, können große Mengen von Bauteilen in kurzer Zeit produziert werden. Dies macht das Verfahren besonders wirtschaftlich für die Herstellung von Produkten in hohen Stückzahlen.
3.3. Vielseitigkeit in der Materialauswahl
Das Kunststoff Formpressen ist für eine Vielzahl von Kunststoffen geeignet, darunter sowohl Thermoplaste als auch Duroplaste. Diese Vielseitigkeit ermöglicht es Herstellern, das ideale Material für ihre spezifischen Anwendungen zu wählen, sei es für hitzebeständige, chemisch stabile oder hochfeste Bauteile.
3.4. Komplexe Geometrien
Durch den Einsatz von maßgeschneiderten Formen können beim Formpressen sehr komplexe Geometrien realisiert werden. Dies umfasst sowohl einfache, flache Bauteile als auch dreidimensionale Strukturen mit komplexen Innen- und Außenformen. Dies eröffnet eine Vielzahl von Möglichkeiten für die Produktgestaltung.
4. Anwendungsbereiche des Kunststoff Formpressens
Das Kunststoff Formpressen wird in einer Vielzahl von Branchen und für eine breite Palette von Produkten eingesetzt. Dank seiner Vielseitigkeit und Präzision ist es für viele industrielle Anwendungen die bevorzugte Wahl.
4.1. Automobilindustrie
In der Automobilindustrie werden zahlreiche Bauteile aus Kunststoff hergestellt, darunter Verkleidungen, Armaturenbretter, Stoßfänger und andere strukturelle Komponenten. Diese Teile müssen oft hohen mechanischen und thermischen Belastungen standhalten, weshalb das Formpressen ein bevorzugtes Verfahren ist. Besonders Duroplaste werden hier häufig eingesetzt, da sie eine hohe Festigkeit und Beständigkeit gegenüber Chemikalien und Hitze bieten.
4.2. Elektronikindustrie
Die Elektronikindustrie nutzt das Kunststoff Formpressen zur Herstellung von Gehäusen, Isolatoren, Steckverbindern und anderen Bauteilen, die empfindliche Elektronik schützen müssen. Die Möglichkeit, Kunststoffteile mit hoher Präzision zu fertigen, ist in dieser Branche besonders wichtig, um sicherzustellen, dass alle Komponenten passgenau sind und eine einwandfreie Funktion gewährleisten.
4.3. Medizintechnik
In der Medizintechnik werden oft sehr anspruchsvolle Kunststoffteile benötigt, die strenge Anforderungen in Bezug auf Hygiene, Biokompatibilität und Präzision erfüllen müssen. Das Kunststoff Formpressen bietet hier die Möglichkeit, sowohl Einwegartikel wie Spritzen und Katheter als auch langlebige medizinische Gerätegehäuse herzustellen. Materialien wie Polyethylen und Polypropylen, die biokompatibel und leicht sterilisierbar sind, kommen häufig zum Einsatz.
4.4. Bauwesen
Im Bauwesen werden Kunststoffteile wie Rohre, Dichtungen und Fassadenelemente häufig durch Formpressen hergestellt. Diese Teile müssen wetterbeständig, stabil und langlebig sein, um den hohen Anforderungen im Bauwesen gerecht zu werden. Das Kunststoff Formpressen ermöglicht die Herstellung von großformatigen und robusten Bauteilen, die sich ideal für den Einsatz im Bauwesen eignen.
5. Technologische Weiterentwicklungen im Kunststoff Formpressen
Wie in vielen Bereichen der Fertigungstechnik hat auch das Kunststoff Formpressen in den letzten Jahren von technologischen Fortschritten profitiert. Insbesondere die Integration von Automatisierungstechnologien und die Entwicklung neuer, leistungsfähiger Materialien haben dazu beigetragen, die Effizienz und Qualität des Verfahrens weiter zu verbessern.
5.1. Automatisierung und Robotertechnik
Die Integration von Robotern und automatisierten Fördersystemen in den Formpressprozess hat die Effizienz und Genauigkeit erheblich gesteigert. Roboter können das Material präzise in die Form einlegen und die fertigen Bauteile nach dem Pressen entnehmen, was den gesamten Prozess beschleunigt und die Produktqualität verbessert. Zudem ermöglicht die Automatisierung eine kontinuierliche Überwachung und Optimierung des Pressvorgangs.
5.2. Hochleistungsmaterialien
Die Entwicklung neuer Kunststoffe mit verbesserten mechanischen, thermischen und chemischen Eigenschaften hat das Anwendungsspektrum des Formpressens erweitert. Moderne Hochleistungskunststoffe wie Polyetheretherketon (PEEK) oder Polyphenylensulfid (PPS) bieten eine hervorragende Beständigkeit gegen hohe Temperaturen, Chemikalien und mechanische Belastungen, was sie ideal für anspruchsvolle Anwendungen macht.
5.3. Additive Fertigung
Ein weiterer technologischer Trend, der das Kunststoff Formpressen ergänzt, ist die additive Fertigung (3D-Druck). Während das Formpressen besonders für die Massenproduktion von Teilen geeignet ist, kann der 3D-Druck verwendet werden, um Prototypen oder Kleinserien von Teilen zu fertigen. Durch die Kombination beider Technologien können Unternehmen flexibler auf Marktanforderungen reagieren und sowohl schnelle Prototypen als auch Massenproduktionen realisieren.
6. Herausforderungen und Zukunftsperspektiven
Trotz der vielen Vorteile stehen Hersteller beim Kunststoff Formpressen auch vor Herausforderungen, die es zu bewältigen gilt, um die Effizienz und Wirtschaftlichkeit weiter zu steigern.
6.1. Materialkosten
Die Kosten für hochwertige Kunststoffe können hoch sein, insbesondere für spezialisierte Hochleistungskunststoffe. Um wettbewerbsfähig zu bleiben, müssen Hersteller Wege finden, die Materialkosten zu optimieren, beispielsweise durch den Einsatz von Recyclingmaterialien oder den Umstieg auf kostengünstigere Alternativen.
6.2. Umweltverträglichkeit
Die Kunststoffindustrie steht zunehmend unter Druck, umweltfreundlichere Produktionsmethoden und Materialien zu entwickeln. Das Kunststoff Formpressen hat das Potenzial, durch den Einsatz von Recyclingkunststoffen und die Reduzierung von Materialabfall zu einer nachhaltigeren Fertigung beizutragen. Zudem könnte die Entwicklung biologisch abbaubarer Kunststoffe neue Möglichkeiten für umweltfreundlichere Produkte schaffen.
6.3. Steigerung der Energieeffizienz
Da das Kunststoff Formpressen erhebliche Mengen an Energie benötigt, insbesondere bei der Verarbeitung von Duroplasten, ist die Steigerung der Energieeffizienz ein zentrales Ziel für die Zukunft. Moderne Pressen mit energieeffizienten Antrieben und Heizsystemen bieten bereits deutliche Verbesserungen in diesem Bereich, doch es gibt weiterhin Potenzial für Optimierungen.
Die Rohrumformung ist ein entscheidender Prozess in der Metallverarbeitung, der in zahlreichen Branchen Anwendung findet, darunter die Automobilindustrie, Luft- und Raumfahrt, Bauwesen und viele mehr. Dieser Prozess ermöglicht die Herstellung komplexer Geometrien und spezifischer Bauteile, die sowohl präzise als auch belastbar sind. Mit der fortschreitenden Entwicklung der Umformtechnologie hat die Rohrumformung einen hohen Grad an Effizienz und Flexibilität erreicht und ist ein unverzichtbares Verfahren für die Herstellung von Rohren in verschiedenen Größen und Formen.
1. Grundlagen der Rohrumformung
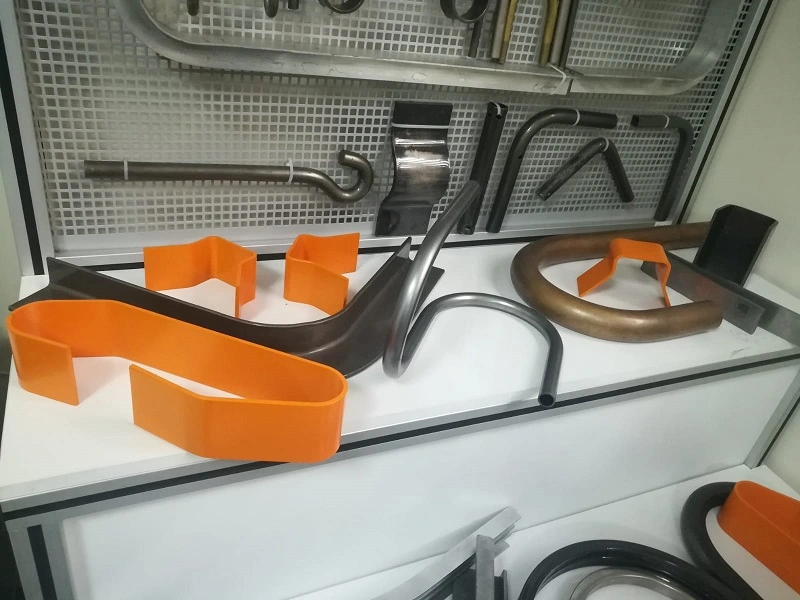
Die Rohrumformung ist ein Verfahren zur Änderung der Form von Rohren aus Metall oder anderen Materialien durch Anwendung von Druck. Dieser Druck wird entweder von außen oder von innen auf das Rohr ausgeübt, wodurch sich das Rohr in die gewünschte Form verformt. Die Umformung kann entweder kalt oder warm erfolgen, je nach Materialeigenschaften und Anforderungen des Endprodukts.
1.1. Arten von Rohren
Rohre, die umgeformt werden, bestehen aus verschiedenen Materialien, darunter Stahl, Aluminium, Kupfer und Legierungen. Jedes Material bringt spezifische Herausforderungen und Vorteile mit sich. So sind Stahlrohre besonders robust und werden häufig in der Bauindustrie und im Maschinenbau eingesetzt, während Aluminiumrohre wegen ihres geringen Gewichts und ihrer Korrosionsbeständigkeit in der Automobil- und Luftfahrtindustrie beliebt sind.
1.2. Kaltumformung vs. Warmumformung
Bei der Kaltumformung wird das Rohr bei Raumtemperatur bearbeitet, was zu einer Verfestigung des Materials führt. Diese Methode bietet den Vorteil, dass keine Erwärmung erforderlich ist, was die Energiekosten senkt. Zudem ergeben sich oft verbesserte Oberflächenqualitäten. Allerdings ist die Verformbarkeit des Materials eingeschränkter, da die Kaltumformung zu Materialversprödung führen kann.
Die Warmumformung hingegen erfolgt bei erhöhter Temperatur, wodurch das Material weicher und formbarer wird. Diese Methode ist besonders geeignet für Materialien, die bei Raumtemperatur schwer umzuformen sind, und für Anwendungen, bei denen komplexe Geometrien oder große Verformungen gefordert sind.
2. Umformverfahren bei der Rohrumformung
Die Rohrumformung umfasst eine Vielzahl von Verfahren, die je nach den Anforderungen des Endprodukts und der Materialeigenschaften angewendet werden.
2.1. Rohrbiegen
Das Rohrbiegen ist eines der am häufigsten angewandten Verfahren in der Rohrumformung. Hierbei wird das Rohr unter Anwendung von Druck oder durch eine Biegeschablone in die gewünschte Form gebracht. Es gibt verschiedene Arten des Rohrbiegens, darunter das Dornbiegen, das Freiformbiegen und das Pressbiegen.
Beim Dornbiegen wird ein Dorn in das Rohr eingeführt, um eine gleichmäßige Biegung ohne Faltenbildung oder Querschnittsveränderungen zu gewährleisten. Diese Methode ist besonders für dünnwandige Rohre geeignet. Das Freiformbiegen hingegen ist flexibler und ermöglicht die Herstellung von komplexen Biegungen ohne spezielle Werkzeuge.
2.2. Innenhochdruckumformung (IHU)
Die Innenhochdruckumformung ist ein modernes Verfahren, das vor allem in der Automobilindustrie und der Luftfahrt eingesetzt wird. Bei dieser Methode wird das Rohr in eine Form eingespannt, und eine Flüssigkeit, meist Wasser, wird unter hohem Druck in das Innere des Rohrs gepumpt. Durch den Innendruck verformt sich das Rohr und passt sich der Form an. Die IHU ermöglicht die Herstellung von Bauteilen mit komplexen Geometrien, wie etwa Rahmenstrukturen oder Hohlräumen in Fahrzeugen.
2.3. Drücken und Walzen
Beim Drück- und Walzverfahren wird das Rohr durch rotierende Werkzeuge verformt. Dies ermöglicht eine gleichmäßige Verformung über die gesamte Länge des Rohrs und ist besonders für lange und dünnwandige Rohre geeignet. Drückmaschinen sind in der Lage, sowohl symmetrische als auch asymmetrische Formen herzustellen.
2.4. Axial- und Rollumformung
Bei der Axialumformung wird das Rohr axial, also entlang seiner Längsachse, gestaucht oder gestreckt, um die gewünschte Form zu erhalten. Diese Methode wird häufig in der Produktion von Rohren mit variablen Durchmessern oder komplexen Profilen angewendet. Rollumformung hingegen nutzt Walzen, um das Rohr in eine bestimmte Form zu bringen. Dies wird oft bei der Herstellung von Rohren mit konstanten Wandstärken und Durchmessern eingesetzt.
3. Anwendungsbereiche der Rohrumformung
Die Rohrumformung spielt in vielen Industrien eine entscheidende Rolle. Dank der Vielfalt der Umformtechniken und der verwendeten Materialien lassen sich Rohre für unterschiedlichste Anwendungen herstellen.
3.1. Automobilindustrie
In der Automobilindustrie ist die Rohrumformung ein unverzichtbarer Prozess. Von Abgassystemen über Rahmenstrukturen bis hin zu Fahrwerkkomponenten – viele Bauteile in Fahrzeugen bestehen aus umgeformten Rohren. Besonders die Innenhochdruckumformung hat in der Automobilbranche an Bedeutung gewonnen, da sie die Herstellung von leichten, aber dennoch belastbaren Bauteilen ermöglicht, die den hohen Anforderungen an Gewichtseinsparung und Stabilität gerecht werden.
3.2. Luft- und Raumfahrt
Auch in der Luft- und Raumfahrtindustrie werden umgeformte Rohre in großem Umfang eingesetzt. Aufgrund der Anforderungen an Gewichtsreduzierung und Festigkeit werden häufig Aluminium- und Titanrohre verwendet, die durch Rohrumformungstechniken in die gewünschte Form gebracht werden. Diese Bauteile finden Anwendung in der Struktur von Flugzeugen, in Hydrauliksystemen und in Triebwerkskomponenten.
3.3. Bauindustrie
In der Bauindustrie werden Rohre für eine Vielzahl von Anwendungen benötigt, von tragenden Strukturen bis hin zu Versorgungssystemen. Die Umformung von Stahlrohren ermöglicht die Herstellung von Bauteilen, die den hohen Belastungen und Umwelteinflüssen standhalten, denen Bauwerke ausgesetzt sind.
3.4. Maschinenbau
Im Maschinenbau werden umgeformte Rohre für zahlreiche Anwendungen eingesetzt, darunter Förderanlagen, Hydrauliksysteme und Produktionsmaschinen. Hier sind vor allem Präzision und Belastbarkeit entscheidend, weshalb die Rohrumformung eine zentrale Rolle bei der Herstellung von Maschinenteilen spielt.
4. Technologische Entwicklungen in der Rohrumformung
Die Rohrumformung hat in den letzten Jahren von verschiedenen technologischen Fortschritten profitiert, die zu einer Steigerung der Effizienz, Präzision und Flexibilität beigetragen haben.
4.1. Automatisierung und Robotik
Die Integration von Automatisierungstechnologien und Robotern in den Rohrumformungsprozess hat zu einer erheblichen Effizienzsteigerung geführt. Automatisierte Anlagen sind in der Lage, Rohre präzise zu positionieren, zu verformen und zu entnehmen, was zu einer Verringerung der Ausschussrate und einer Steigerung der Produktionsgeschwindigkeit führt. Roboter ermöglichen zudem eine flexible Produktion, da sie schnell auf unterschiedliche Produktionsanforderungen umgestellt werden können.
4.2. Simulation und digitale Zwillinge
Die Anwendung von Simulationssoftware und digitalen Zwillingen in der Rohrumformung ermöglicht es Herstellern, den Umformprozess bereits im Vorfeld zu optimieren. Durch die Simulation können potenzielle Probleme frühzeitig erkannt und behoben werden, was zu einer höheren Qualität der Endprodukte führt. Digitale Zwillinge bieten zudem die Möglichkeit, den Umformprozess in Echtzeit zu überwachen und anzupassen, um maximale Effizienz zu erreichen.
4.3. Neue Werkstoffe
Mit der Entwicklung neuer Werkstoffe, insbesondere hochfester Legierungen und Verbundmaterialien, haben sich auch die Anforderungen an die Rohrumformung verändert. Diese Materialien sind oft schwerer umzuformen und erfordern spezielle Techniken, um die gewünschten Formen und Eigenschaften zu erzielen. Moderne Umformtechnologien wie die Innenhochdruckumformung und das Walzen bieten jedoch Lösungen, um diese Materialien effizient zu verarbeiten.
4.4. Nachhaltigkeit und Recycling
In der modernen Fertigung spielt Nachhaltigkeit eine immer größere Rolle. Auch in der Rohrumformung gibt es Bestrebungen, den Materialverbrauch zu reduzieren und Recyclingmaterialien einzusetzen. Durch die Optimierung der Umformprozesse können Materialabfälle minimiert und die Ressourceneffizienz gesteigert werden.
5. Herausforderungen und Zukunftsperspektiven
Trotz der zahlreichen Fortschritte steht die Rohrumformung vor einigen Herausforderungen, die es zu bewältigen gilt.
5.1. Komplexität der Geometrien
Mit den steigenden Anforderungen an die Bauteilkomplexität wird auch die Rohrumformung immer anspruchsvoller. Besonders bei der Herstellung von Rohren mit variablen Durchmessern oder komplizierten Querschnitten stoßen traditionelle Umformmethoden an ihre Grenzen. Hier sind innovative Lösungen und Weiterentwicklungen gefragt, um die Umformbarkeit von Rohren weiter zu verbessern.
5.2. Materialkosten und -verfügbarkeit
Die Kosten für Rohmaterialien, insbesondere für hochfeste Legierungen und Spezialmetalle, sind in den letzten Jahren gestiegen. Dies stellt Hersteller vor die Herausforderung, die Materialkosten durch effizientere Fertigungsprozesse zu senken oder auf alternative Materialien auszuweichen.
Die Verwendung von Composite-Materialien hat in den letzten Jahrzehnten stark zugenommen, insbesondere in Industrien, die nach leichten, aber gleichzeitig starken Materialien suchen. Die Automobilindustrie, die Luft- und Raumfahrt sowie der Bausektor sind nur einige der Bereiche, in denen Composites eine Schlüsselrolle spielen. Um diese Materialien effizient zu verarbeiten, kommen spezielle hydraulische Pressen zum Einsatz. Hydraulische Pressen bieten zahlreiche Vorteile, wenn es um die Herstellung von Bauteilen aus Composites geht, und sie haben sich als unverzichtbar für die moderne Fertigung erwiesen.
1. Grundlagen der Composites-Verarbeitung
Composites, oder Verbundwerkstoffe, bestehen aus zwei oder mehr unterschiedlichen Materialien, die zusammen eine bessere Kombination von Eigenschaften bieten als die Einzelmaterialien für sich genommen. Typischerweise bestehen Composites aus einer Matrix (wie Harz) und einer Verstärkung (wie Glasfaser oder Kohlenstofffaser).
1.1. Materialien in Composites
Es gibt viele verschiedene Arten von Composites, abhängig von der Kombination der verwendeten Materialien:
- Glasfaserverstärkte Kunststoffe (GFK): Diese bestehen aus Glasfasern, die in eine Polymermatrix eingebettet sind. GFK ist bekannt für seine hohe Festigkeit, Beständigkeit gegen Korrosion und sein geringes Gewicht.
- Kohlenstofffaserverstärkte Kunststoffe (CFK): Kohlenstofffasern sind extrem stark und steif und bieten im Vergleich zu GFK eine noch höhere Festigkeit und geringeres Gewicht. Sie werden häufig in der Luft- und Raumfahrt, im Motorsport und bei High-End-Sportgeräten eingesetzt.
- Aramidfaserverstärkte Kunststoffe: Diese Composites verwenden Aramidfasern, die für ihre hervorragende Schlagzähigkeit bekannt sind und beispielsweise in kugelsicheren Westen Anwendung finden.
1.2. Matrixmaterialien
Die Matrix, in die die Verstärkungsfasern eingebettet sind, besteht üblicherweise aus Polymeren, kann aber auch aus Metall oder Keramik bestehen. Thermoplastische und duroplastische Polymere sind die häufigsten Matrizes:
- Thermoplaste: Diese Polymere können mehrfach erhitzt und geformt werden. Sie sind leichter recycelbar und weisen in vielen Fällen eine gute Beständigkeit gegen Chemikalien auf.
- Duroplaste: Diese Polymere härten während des Formprozesses aus und können danach nicht mehr verformt werden. Sie bieten eine ausgezeichnete Festigkeit und Temperaturbeständigkeit.
2. Hydraulische Pressen in der Composite-Verarbeitung
Hydraulische Pressen sind ein entscheidendes Werkzeug bei der Herstellung von Composite-Bauteilen. Sie bieten die nötige Kraft und Präzision, um die Materialien unter hohem Druck und oft bei hohen Temperaturen zu verformen und zu härten. Dabei lassen sich verschiedene Verfahren anwenden, je nach den spezifischen Anforderungen des Endprodukts und den Eigenschaften des verwendeten Materials.
2.1. Vorteile hydraulischer Pressen
Hydraulische Pressen bieten gegenüber mechanischen Pressen und anderen Umformwerkzeugen mehrere Vorteile:
- Präzise Kraftregelung: Hydraulische Pressen können mit extrem hoher Genauigkeit gesteuert werden, was entscheidend für die gleichmäßige Verteilung des Drucks bei der Herstellung von Composites ist.
- Vielseitigkeit: Sie können für eine Vielzahl von Formverfahren und Materialien eingesetzt werden, einschließlich der Verarbeitung großer und komplexer Bauteile.
- Hoher Druck: Hydraulische Pressen können große Kräfte erzeugen, die bei der Verarbeitung von Composites erforderlich sind, um sicherzustellen, dass das Material gleichmäßig verpresst wird und alle Lufteinschlüsse entfernt werden.
- Temperatursteuerung: Viele hydraulische Pressen sind mit Heiz- und Kühlsystemen ausgestattet, die für thermoplastische und duroplastische Materialien von entscheidender Bedeutung sind.
2.2. Arten von hydraulischen Pressen für Composites
Es gibt verschiedene Arten von hydraulischen Pressen, die je nach Art des Composite-Materials und der Anwendung eingesetzt werden:
- Heißpressen: Diese Pressen sind mit Heizplatten ausgestattet, die das Material während des Pressvorgangs auf die erforderliche Temperatur bringen. Dies ist besonders bei Thermoplasten wichtig, die bei hohen Temperaturen verarbeitet werden müssen.
- Vakuumhydraulikpressen: Diese Pressen verwenden eine Vakuumumgebung, um Lufteinschlüsse zu verhindern, die zu Schwachstellen im fertigen Bauteil führen könnten. Das Vakuum stellt sicher, dass das Material vollständig verpresst wird.
- Multistationspressen: Diese Pressen können mehrere Bauteile gleichzeitig verarbeiten, was die Effizienz in der Serienproduktion deutlich steigert.
3. Verarbeitungstechniken für Composites
Hydraulische Pressen kommen in verschiedenen Verarbeitungstechniken zum Einsatz, die speziell für die Herstellung von Composite-Bauteilen entwickelt wurden. Einige der wichtigsten Verfahren sind:
3.1. SMC-Pressverfahren (Sheet Molding Compound)
Das SMC-Pressverfahren wird häufig für die Herstellung von großflächigen Bauteilen eingesetzt. Dabei wird ein vorgemischtes Material (eine Mischung aus Fasern, Harz und Additiven) zwischen zwei Formhälften eingelegt. Die hydraulische Presse übt dann Druck aus und formt das Material in die gewünschte Form. Gleichzeitig wird das Material erhitzt, um den Aushärtungsprozess zu beschleunigen.
SMC-Teile sind besonders in der Automobilindustrie weit verbreitet, da sie sich hervorragend für die Massenproduktion eignen und eine gute Balance zwischen Kosten, Gewicht und Festigkeit bieten.
3.2. RTM (Resin Transfer Molding)
Beim RTM-Verfahren wird die Verstärkung in eine Form eingelegt, und anschließend wird flüssiges Harz unter Druck in die Form injiziert. Hierbei sind hydraulische Pressen entscheidend, um die Formhälften unter Druck zu halten und eine gleichmäßige Verteilung des Harzes zu gewährleisten. RTM wird häufig für die Herstellung von Strukturbauteilen in der Luftfahrt und im Motorsport eingesetzt, wo hohe Anforderungen an Festigkeit und Leichtbau gestellt werden.
3.3. Hochdruck-RTM (HP-RTM)
Das HP-RTM-Verfahren ist eine Weiterentwicklung des klassischen RTM, bei dem das Harz unter noch höherem Druck in die Form eingebracht wird. Dadurch lassen sich kürzere Zykluszeiten und eine höhere Fasergehalte im fertigen Bauteil realisieren. Hochdruckhydraulikpressen sind notwendig, um den hohen Druck während des Injektions- und Härtungsprozesses zu halten.
3.4. Thermoformung
Thermoplastische Composites können durch ein Verfahren namens Thermoformung geformt werden. Dabei wird das thermoplastische Material erhitzt, bis es formbar ist, und dann in die gewünschte Form gepresst. Hydraulische Pressen sind ideal für diesen Prozess, da sie sowohl den benötigten Druck als auch die Temperatursteuerung bereitstellen.
4. Anwendungsbereiche für hydraulische Pressen und Composites
Die Verarbeitung von Composites mithilfe von hydraulischen Pressen hat viele Industrien revolutioniert, die auf leichte, starke und langlebige Materialien angewiesen sind. Einige der wichtigsten Anwendungsbereiche sind:
4.1. Automobilindustrie
In der Automobilindustrie werden Composites zunehmend für Strukturbauteile, Karosserieteile und Innenelemente eingesetzt. Die Kombination aus geringem Gewicht und hoher Festigkeit macht Composites ideal für die Reduzierung des Fahrzeuggewichts, was zu einer besseren Energieeffizienz führt. Hydraulische Pressen spielen eine Schlüsselrolle bei der Herstellung von Komponenten wie Stoßstangen, Dachmodulen und Motorhauben.
4.2. Luft- und Raumfahrt
Die Luft- und Raumfahrtindustrie ist einer der größten Anwender von Composite-Materialien. Von Flugzeugrümpfen bis zu Triebwerksteilen werden Composites verwendet, um das Gewicht zu reduzieren und gleichzeitig die strukturelle Integrität zu erhalten. Hydraulische Pressen ermöglichen die präzise Formgebung von Bauteilen, die extremen Belastungen standhalten müssen, ohne dass es zu Materialschwächen kommt.
4.3. Bauwesen
Auch im Bauwesen werden Composites immer häufiger eingesetzt, insbesondere in Anwendungen, die eine hohe Korrosionsbeständigkeit und lange Lebensdauer erfordern. Composites werden für Brückenbauteile, Fassadenelemente und Verstärkungsmaterialien verwendet. Hydraulische Pressen sind entscheidend für die Herstellung dieser Bauteile, da sie die nötige Kraft und Präzision bieten, um komplexe Formen zu realisieren.
4.4. Sport- und Freizeitindustrie
Im Bereich der Sport- und Freizeitindustrie werden Composites für alles von Fahrrädern über Skier bis hin zu Tennisschlägern eingesetzt. Hydraulische Pressen ermöglichen die Massenproduktion dieser Bauteile, die eine hohe Leistung bei geringem Gewicht bieten müssen.
5. Herausforderungen und Zukunftsperspektiven
Obwohl hydraulische Pressen in der Composite-Verarbeitung unverzichtbar sind, stehen Hersteller vor einigen Herausforderungen, die es in den kommenden Jahren zu bewältigen gilt.
5.1. Kosten
Die Anschaffung und der Betrieb hydraulischer Pressen, insbesondere der Hochdruck- oder Vakuumpressen, ist mit hohen Investitionskosten verbunden. Dies stellt kleinere Hersteller vor Herausforderungen, die eine hohe Anfangsinvestition tätigen müssen.
5.2. Nachhaltigkeit
Die Verarbeitung von Composites, insbesondere von duroplastischen Materialien, ist oft nicht umweltfreundlich, da die Bauteile nach der Lebensdauer schwer zu recyceln sind. Zukünftige Innovationen in der Composite-Technologie müssen auf die Entwicklung recycelbarer Materialien und energieeffizienter Umformverfahren abzielen.
Das Hydroforming ist ein fortschrittliches Verfahren zur Metallumformung, das vor allem für die Herstellung von komplexen, leichten und hochfesten Bauteilen eingesetzt wird. Im Zentrum dieses Prozesses steht die Hydroforming Presse, die durch den Einsatz von Flüssigkeitsdruck außergewöhnlich präzise Ergebnisse erzielt. Hydroforming hat sich als eine der effektivsten Techniken zur Herstellung von Bauteilen in der Automobilindustrie, Luft- und Raumfahrt sowie im allgemeinen Maschinenbau etabliert. Dieser Text beleuchtet die Funktionsweise, Vorteile, Anwendungen und Zukunftsperspektiven der Hydroforming Presse und ihrer Rolle in der modernen Fertigung.
1. Grundlagen des Hydroformings
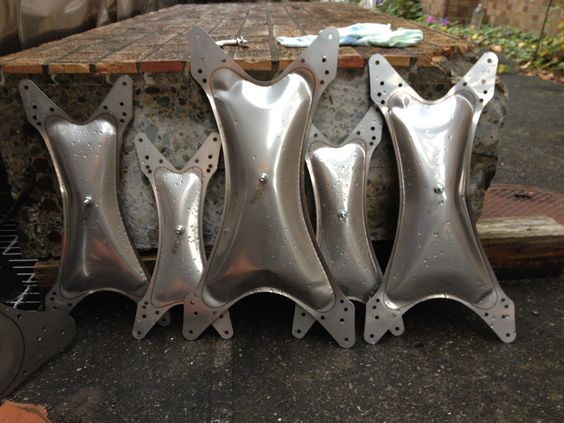
Hydroforming ist ein Verfahren zur Umformung von Metallblechen oder -rohren, bei dem eine Flüssigkeit (meist Wasser oder Öl) unter hohem Druck verwendet wird, um das Metall in eine Form zu pressen. Anders als bei traditionellen mechanischen Umformprozessen wird das Material hierbei durch den gleichmäßigen Druck der Flüssigkeit in die gewünschte Form gebracht.
1.1. Funktionsprinzip des Hydroformings
Das Hydroforming beginnt mit einem Rohling, der aus einem Metallblech oder -rohr bestehen kann. Dieser Rohling wird in eine speziell geformte Matrize gelegt, die die gewünschte Endform des Werkstücks darstellt. Die Hydroforming Presse übt dann hohen Flüssigkeitsdruck auf den Rohling aus, wodurch das Material gegen die Wände der Matrize gedrückt wird und sich die gewünschte Form annimmt.
Die Hauptvorteile dieses Verfahrens liegen in der gleichmäßigen Druckverteilung und der Fähigkeit, komplexe Formen ohne Schweißnähte oder zusätzliche Bearbeitungsschritte herzustellen. Das Ergebnis sind Bauteile mit hervorragender Oberflächenqualität und gleichmäßiger Materialverteilung.
1.2. Arten des Hydroformings
Es gibt zwei Haupttypen von Hydroforming, abhängig davon, welches Ausgangsmaterial verwendet wird:
- Blech-Hydroforming: Hierbei wird ein Metallblech in eine Form gepresst. Diese Technik wird häufig zur Herstellung von großflächigen Karosserieteilen, wie Motorhauben oder Türen, verwendet.
- Rohr-Hydroforming: Bei dieser Variante wird ein Metallrohr durch Innendruck in eine Form gebracht. Das Rohr-Hydroforming ist ideal für die Herstellung von komplexen Hohlprofilen, wie sie in Fahrzeugrahmen oder Auspuffanlagen vorkommen.
2. Hydroforming Pressen: Aufbau und Funktionsweise
Die Hydroforming Presse ist das zentrale Werkzeug in diesem Umformprozess. Sie besteht aus mehreren Komponenten, die zusammenarbeiten, um das Metall präzise und effizient zu verformen. Eine typische Hydroforming Presse umfasst:
- Ober- und Untermatrize: Diese Matrizen geben die endgültige Form des Werkstücks vor. Sie sind in der Regel aus hochfesten Materialien gefertigt, um dem hohen Druck standzuhalten.
- Flüssigkeitszufuhrsystem: Dieses System ist verantwortlich für das Einleiten der Flüssigkeit unter Druck. In vielen Fällen wird Wasser oder eine spezielle Öl-Wasser-Mischung verwendet, da diese Flüssigkeiten unter hohen Drücken stabil bleiben.
- Hydrauliksystem: Das Herzstück jeder Hydroforming Presse ist das Hydrauliksystem, das den Flüssigkeitsdruck kontrolliert und präzise steuert.
- Steuerungseinheit: Moderne Hydroforming Pressen sind mit computergestützten Steuerungssystemen ausgestattet, die eine genaue Überwachung und Anpassung des Drucks in Echtzeit ermöglichen.
2.1. Flüssigkeitsdruck und Umformkraft
Der Flüssigkeitsdruck ist der entscheidende Faktor für den Umformprozess. Typischerweise werden Drücke zwischen 500 und 10.000 bar verwendet, abhängig vom Material und der Komplexität des Bauteils. Je höher der Druck, desto präziser kann das Material in die Matrize gepresst werden. Dieser gleichmäßige Druck sorgt dafür, dass das Metall sich perfekt an die Form anpasst, ohne dass es zu Rissen oder anderen Materialfehlern kommt.
2.2. Hydraulische Kraftübertragung
Eine der größten Stärken der Hydroforming Presse ist ihre Fähigkeit, extrem hohe Kräfte zu erzeugen und dabei eine gleichmäßige Verteilung dieser Kräfte auf das Werkstück zu gewährleisten. Die hydraulische Kraftübertragung sorgt dafür, dass der Druck genau dort angewendet wird, wo er benötigt wird, was die Präzision des Verfahrens erheblich verbessert.
3. Vorteile des Hydroformings
Hydroforming bietet gegenüber herkömmlichen Umformverfahren wie Stanzen, Tiefziehen oder Biegen mehrere entscheidende Vorteile. Diese Vorteile machen Hydroforming zu einer beliebten Wahl für Hersteller, die komplexe Bauteile mit hoher Präzision und geringen Toleranzen benötigen.
3.1. Materialeinsparungen
Da Hydroforming ohne Schweißnähte oder zusätzliche Bearbeitungsschritte auskommt, kann es erhebliche Materialeinsparungen ermöglichen. Das Ausgangsmaterial wird effizienter genutzt, da keine überschüssigen Ränder abgeschnitten oder verschweißt werden müssen.
3.2. Leichtere und stärkere Bauteile
Durch den gleichmäßigen Druck der Hydroforming Presse können Bauteile mit dünneren Wänden hergestellt werden, ohne dass die Festigkeit beeinträchtigt wird. Dies führt zu leichteren, aber gleichzeitig stärkeren Komponenten, die besonders in der Automobil- und Luftfahrtindustrie von Vorteil sind.
3.3. Hohe Präzision und Oberflächenqualität
Die gleichmäßige Druckverteilung sorgt für eine hervorragende Oberflächenqualität, die oft keine weiteren Bearbeitungsschritte wie Schleifen oder Polieren erfordert. Zudem ermöglicht das Hydroforming eine hohe Maßgenauigkeit, was die Notwendigkeit nachträglicher Anpassungen reduziert.
3.4. Komplexe Geometrien
Einer der größten Vorteile des Hydroformings ist die Möglichkeit, komplexe Geometrien und Formen herzustellen, die mit herkömmlichen Umformverfahren nur schwer oder gar nicht realisierbar wären. Das Verfahren erlaubt es, Hohlprofile mit variierenden Durchmessern und komplexen Kurven in einem einzigen Schritt zu formen.
4. Anwendungen von Hydroforming Pressen
Hydroforming wird in einer Vielzahl von Industrien eingesetzt, die auf leichte, präzise und starke Bauteile angewiesen sind. Einige der wichtigsten Anwendungsbereiche sind:
4.1. Automobilindustrie
In der Automobilindustrie hat sich Hydroforming als eine der effizientesten Methoden zur Herstellung von Struktur- und Karosserieteilen etabliert. Insbesondere die Herstellung von Hohlprofilen für Fahrzeugrahmen und Auspuffanlagen profitiert von den Vorteilen des Rohr-Hydroformings. Bauteile, die durch Hydroforming hergestellt werden, sind leichter und stabiler, was zur Verbesserung der Kraftstoffeffizienz und Sicherheit moderner Fahrzeuge beiträgt.
4.2. Luft- und Raumfahrt
Die Luft- und Raumfahrtindustrie setzt auf Hydroforming, um Bauteile mit extremen Anforderungen an Gewicht und Festigkeit herzustellen. Flugzeugkomponenten wie Rumpfsektionen, Tragflächenverkleidungen und Triebwerksteile werden oft mit Hydroforming gefertigt, da das Verfahren sowohl hohe Präzision als auch eine ausgezeichnete Materialausnutzung bietet.
4.3. Möbelindustrie
Auch in der Möbelindustrie wird Hydroforming zunehmend eingesetzt, insbesondere bei der Herstellung von Rahmen und Strukturelementen für moderne Möbelstücke. Hier ermöglicht das Verfahren die Herstellung von leichten, aber stabilen Bauteilen mit komplexen Formen, die ästhetisch ansprechend und funktional sind.
4.4. Heizungs- und Klimaanlagen
In der Heizungs- und Klimaanlagenindustrie wird Hydroforming zur Herstellung von Rohrleitungen und anderen Bauteilen verwendet, die hohen Drücken und Temperaturen standhalten müssen. Das Verfahren sorgt für eine hohe Festigkeit und Langlebigkeit der Bauteile, was in diesen Anwendungen von entscheidender Bedeutung ist.
5. Herausforderungen und Weiterentwicklungen
Obwohl Hydroforming viele Vorteile bietet, gibt es auch einige Herausforderungen, die es zu bewältigen gilt. Zudem wird ständig an Weiterentwicklungen gearbeitet, um das Verfahren noch effizienter und kostengünstiger zu gestalten.
5.1. Hohe Investitionskosten
Eine der größten Herausforderungen beim Hydroforming ist die hohe Anfangsinvestition in die notwendigen Maschinen und Werkzeuge. Hydroforming Pressen sind teurer als herkömmliche Umformmaschinen, was für kleinere Unternehmen eine Hürde darstellen kann.
5.2. Begrenzte Materialauswahl
Obwohl Hydroforming mit einer Vielzahl von Metallen funktioniert, ist es nicht für alle Materialien geeignet. Weiche Materialien wie Aluminium und Kupfer eignen sich gut für das Verfahren, während härtere Metalle wie Titan oder hochfeste Stähle schwieriger zu verarbeiten sind.
5.3. Forschung und Entwicklung
Um die Effizienz des Hydroformings weiter zu verbessern, wird in der Forschung an neuen Flüssigkeiten, verbesserten Matrizen und fortschrittlichen Steuerungssystemen gearbeitet. Ziel ist es, die Zykluszeiten zu verkürzen und die Produktionskosten zu senken, ohne die Qualität der Bauteile zu beeinträchtigen.
6. Zukunftsperspektiven des Hydroformings
Die Zukunft des Hydroformings sieht vielversprechend aus, insbesondere mit Blick auf die wachsende Nachfrage nach leichten und dennoch starken Bauteilen in der Automobil-, Luftfahrt- und Maschinenbauindustrie. Es ist zu erwarten, dass das Verfahren weiter an Bedeutung gewinnen wird, da die Hersteller nach Wegen suchen, um ihre Produktionsprozesse effizienter und kostengünstiger zu gestalten.
6.1. Automatisierung und Digitalisierung
Ein großer Trend in der Fertigungsindustrie ist die Automatisierung und Digitalisierung der Produktionsprozesse. Hydroforming Pressen der nächsten Generation werden zunehmend mit intelligenten Steuerungssystemen ausgestattet, die den Druck in Echtzeit anpassen und so die Effizienz und Präzision weiter steigern.
6.2. Neue Materialien
Die Entwicklung neuer, leichterer und stärkerer Materialien wird das Hydroforming weiter vorantreiben. Insbesondere in der Automobilindustrie wird an neuen Legierungen und Verbundwerkstoffen gearbeitet, die sich für das Hydroforming eignen und gleichzeitig eine noch bessere Leistungsfähigkeit bieten.
6.3. Nachhaltigkeit
Mit dem Fokus auf Nachhaltigkeit und Umweltschutz werden Hydroforming Pressen zunehmend mit umweltfreundlichen Flüssigkeiten und energieeffizienten Antriebssystemen ausgestattet. Dies wird dazu beitragen, die CO2-Bilanz der Fertigungsprozesse zu verbessern und den Energieverbrauch zu senken.
Das Formpressen von Gummi ist ein weit verbreitetes Verfahren zur Herstellung von Gummikomponenten, die in verschiedenen Branchen eingesetzt werden, von der Automobilindustrie über die Luft- und Raumfahrt bis hin zur Medizintechnik. Dieses Verfahren ist besonders nützlich für die Produktion von Hochleistungsbauteilen, die spezifische mechanische Eigenschaften und hohe Beständigkeit gegenüber extremen Bedingungen aufweisen müssen. In diesem Text werden die Grundlagen des Formpressens von Gummi, die technischen Aspekte des Verfahrens, die Vorteile und Herausforderungen sowie Anwendungen in verschiedenen Industriezweigen detailliert erläutert.
1. Grundlagen des Formpressens von Gummi
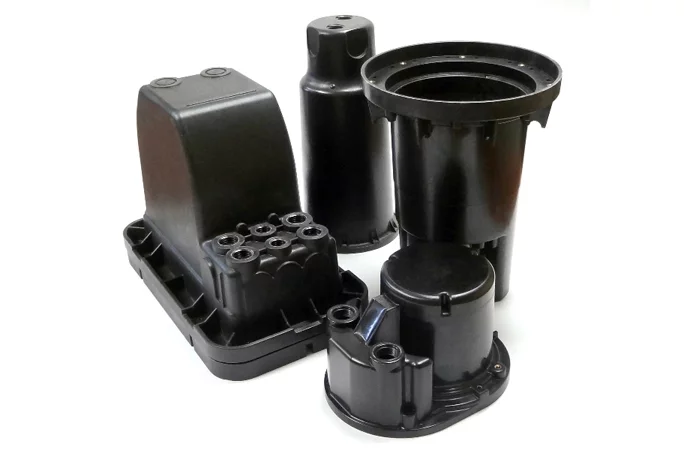
Das Formpressen ist ein Umformverfahren, bei dem Rohgummi in eine Form gegeben und unter Hitze und Druck vulkanisiert wird, um die gewünschte Form und Struktur zu erhalten. Es zählt zu den ältesten Methoden der Gummiverarbeitung und wird heute in einer Vielzahl von Anwendungen eingesetzt. Die Komponenten, die durch Formpressen entstehen, sind für ihre hohe Genauigkeit und Beständigkeit bekannt.
1.1. Der Vulkanisationsprozess
Die Vulkanisation ist ein entscheidender Schritt beim Formpressen von Gummi. Dabei wird der Rohgummi durch die Zugabe von Schwefel und andere Additive chemisch verändert, um die Elastizität und Festigkeit des Materials zu erhöhen. Der Gummi wird in einer Form erhitzt und unter Druck gesetzt, wodurch die Vulkanisation eingeleitet wird. Dieser Prozess verleiht dem Gummi seine dauerhafte Form und seine mechanischen Eigenschaften, wie Elastizität, Festigkeit und Temperaturbeständigkeit.
1.2. Arten von Gummi
Beim Formpressen von Gummi werden verschiedene Arten von Kautschuk verwendet, die je nach Anwendung ausgewählt werden. Einige der gängigsten Gummiarten sind:
- Naturkautschuk (NR): Gummi aus Naturkautschuk zeichnet sich durch hervorragende Elastizität, hohe Festigkeit und gute Abriebfestigkeit aus. Er wird häufig in der Automobil- und Maschinenbauindustrie eingesetzt.
- Synthetische Kautschuke: Hierzu gehören Gummiarten wie Neopren (CR), Nitrilkautschuk (NBR), Silikonkautschuk (VMQ) und viele andere. Sie bieten spezielle Eigenschaften, wie Beständigkeit gegen Öl, Hitze, Chemikalien oder UV-Strahlung, und sind daher in spezifischen Anwendungen unverzichtbar.
1.3. Die Formpressmaschine
Die Formpressmaschine, die für das Formpressen von Gummi verwendet wird, besteht aus zwei Teilen: einem Ober- und einem Unterwerkzeug, die die Form geben. Die Rohmaterialien werden in die Form eingebracht und durch Hitze und Druck bearbeitet, um die endgültige Form zu erhalten. Die Form selbst kann in vielen verschiedenen Formen und Größen vorkommen, abhängig von der Komplexität des Bauteils.
2. Technische Aspekte des Formpressens
Das Formpressen von Gummi erfordert eine präzise Kontrolle der Temperatur, des Drucks und der Zeit, um qualitativ hochwertige Endprodukte herzustellen. Moderne Formpressmaschinen verfügen über fortschrittliche Steuerungssysteme, die eine exakte Anpassung dieser Parameter ermöglichen.
2.1. Druck und Temperaturkontrolle
Beim Formpressen von Gummi muss der Druck gleichmäßig auf das Werkstück ausgeübt werden, um eine gleichmäßige Materialverteilung zu gewährleisten. Typische Druckwerte liegen zwischen 50 und 150 bar, abhängig von der Größe und Komplexität des Bauteils. Die Temperatur wird ebenfalls sorgfältig gesteuert und liegt normalerweise im Bereich von 140°C bis 200°C, abhängig vom verwendeten Gummityp und der gewünschten Endfestigkeit.
2.2. Zykluszeiten
Die Zykluszeit, also die Dauer, die das Werkstück in der Form bleibt, variiert je nach Dicke des Bauteils und den Materialeigenschaften. Üblicherweise liegt die Zykluszeit zwischen 2 und 10 Minuten. Während dieser Zeit wird der Rohgummi vulkanisiert und das Material erhält seine endgültigen mechanischen Eigenschaften.
2.3. Materialfluss und Entlüftung
Ein kritischer Aspekt des Formpressens von Gummi ist der Materialfluss in der Form. Der Rohgummi muss sich gleichmäßig in alle Teile der Form verteilen, um eine homogene Dichte und Festigkeit im Endprodukt zu gewährleisten. Entlüftungskanäle in der Form helfen, eingeschlossene Luft während des Prozesses zu entweichen, was die Qualität und die Oberflächenbeschaffenheit des Bauteils verbessert.
3. Arten des Formpressens
Es gibt verschiedene Techniken des Formpressens, die sich in der Art und Weise unterscheiden, wie das Material in die Form eingebracht wird und wie der Druck auf das Werkstück ausgeübt wird.
3.1. Kompressionsformen
Beim Kompressionsformen wird der Rohgummi in eine offene Form gegeben, die dann geschlossen und unter Druck gesetzt wird. Diese Methode ist ideal für einfache, große Bauteile und wird häufig für Dichtungen, Dämpfer und ähnliche Teile verwendet.
3.2. Transferformen
Beim Transferformen wird das Gummimaterial in eine Kammer gegeben und dann durch Kanäle in die Form gedrückt. Diese Technik ist besonders nützlich für komplexere Bauteile mit dünnen Wänden oder Einsätzen. Sie ermöglicht eine präzisere Kontrolle des Materialflusses und wird in der Regel bei Bauteilen mit engen Toleranzen angewendet.
3.3. Spritzpressen
Spritzpressen kombiniert Elemente des Formpressens und des Spritzgießens. Das Rohmaterial wird in die Form eingespritzt und dort unter Druck und Hitze vulkanisiert. Diese Methode eignet sich besonders für die Massenproduktion kleiner und komplexer Teile, wie sie beispielsweise in der Elektronikindustrie benötigt werden.
4. Vorteile des Formpressens von Gummi
Das Formpressen von Gummi bietet mehrere Vorteile gegenüber anderen Herstellungsmethoden. Diese Vorteile machen das Verfahren zu einer bevorzugten Wahl für die Herstellung von Hochleistungsbauteilen in verschiedenen Industriezweigen.
4.1. Hohe Flexibilität
Das Formpressen ermöglicht die Herstellung von Bauteilen in einer Vielzahl von Formen und Größen. Dies macht es besonders geeignet für Anwendungen, bei denen individuelle Anpassungen oder spezielle Geometrien erforderlich sind.
4.2. Geringe Werkzeugkosten
Verglichen mit anderen Fertigungsverfahren wie dem Spritzgießen, sind die Werkzeugkosten beim Formpressen relativ niedrig. Dies ist besonders vorteilhaft für kleinere Produktionsmengen oder Prototypenfertigungen.
4.3. Hohe mechanische Festigkeit
Durch die Vulkanisation wird der Gummi extrem widerstandsfähig gegenüber mechanischen Belastungen. Dies macht die durch Formpressen hergestellten Bauteile ideal für Anwendungen, die eine hohe Belastbarkeit und lange Lebensdauer erfordern.
4.4. Geringer Abfall
Das Formpressen ist ein äußerst effizientes Verfahren, das den Materialabfall minimiert. Überschüssiger Gummi, der aus der Form gedrückt wird, kann in vielen Fällen recycelt und in nachfolgenden Produktionszyklen wiederverwendet werden.
5. Herausforderungen beim Formpressen von Gummi
Trotz der vielen Vorteile bringt das Formpressen von Gummi auch einige Herausforderungen mit sich, insbesondere in Bezug auf die Qualitätssicherung und die Optimierung der Produktionsprozesse.
5.1. Kontrolle der Vulkanisationszeit
Die Vulkanisationszeit ist ein kritischer Faktor für die Qualität des Endprodukts. Eine zu kurze Vulkanisation führt zu unzureichender Aushärtung, während eine zu lange Vulkanisation das Material spröde machen kann. Es erfordert präzise Steuerungssysteme, um diesen Prozess exakt zu kontrollieren.
5.2. Eingeschlossene Luftblasen
Luftblasen, die während des Formpressprozesses im Gummi eingeschlossen werden, können die Festigkeit und Dichte des Bauteils beeinträchtigen. Entlüftungssysteme in der Form und sorgfältige Kontrolle des Materialflusses sind erforderlich, um dieses Problem zu vermeiden.
5.3. Materialschrumpfung
Gummi neigt während der Vulkanisation dazu, zu schrumpfen. Diese Schrumpfung muss bei der Konstruktion der Form berücksichtigt werden, um sicherzustellen, dass die Bauteile die richtigen Abmessungen und Toleranzen einhalten.
6. Anwendungen des Formpressens von Gummi
Das Formpressen von Gummi wird in vielen Industrien eingesetzt, die auf langlebige und widerstandsfähige Bauteile angewiesen sind. Einige der wichtigsten Anwendungsbereiche sind:
6.1. Automobilindustrie
In der Automobilindustrie werden durch Formpressen eine Vielzahl von Gummikomponenten hergestellt, darunter Dichtungen, Dämpfer, Stoßfänger und Schläuche. Diese Bauteile müssen extremen Bedingungen wie Hitze, Kälte, Abrieb und Chemikalien standhalten, was das Formpressen zu einer idealen Methode macht.
6.2. Medizintechnik
In der Medizintechnik werden häufig hochpräzise Gummikomponenten benötigt, wie beispielsweise Dichtungen für medizinische Geräte oder Implantate. Das Formpressen bietet die erforderliche Präzision und Reinheit, die für diese Anwendungen notwendig sind.
6.3. Elektronikindustrie
In der Elektronikindustrie werden Gummikomponenten wie Tasten, Dichtungen und Isolatoren durch Formpressen hergestellt. Diese Bauteile müssen hohe elektrische Isolierung und mechanische Beständigkeit bieten, was durch die präzise Vulkanisation und Materialauswahl beim Formpressen ermöglicht wird.
Das Heißpressen von SMC (Sheet Molding Compound) ist ein bedeutendes Verfahren in der Kunststoff- und Verbundwerkstoffindustrie, das vor allem für die Herstellung von leichten, aber robusten Bauteilen genutzt wird. SMC-Materialien bestehen aus einer Kombination von Harz, Glasfasern und anderen Additiven, die ihnen herausragende mechanische Eigenschaften verleihen. Diese Materialien werden unter Hitze und Druck in speziellen Pressmaschinen geformt, um Bauteile zu erzeugen, die in der Automobilindustrie, Luftfahrt, Elektronik und in vielen anderen Bereichen Verwendung finden.
In diesem Text wird das Verfahren des SMC Heißpressens, seine technischen Anforderungen, die Vorteile und die Herausforderungen sowie die aktuellen Anwendungen in verschiedenen Industrien erläutert.
1. Was ist SMC?
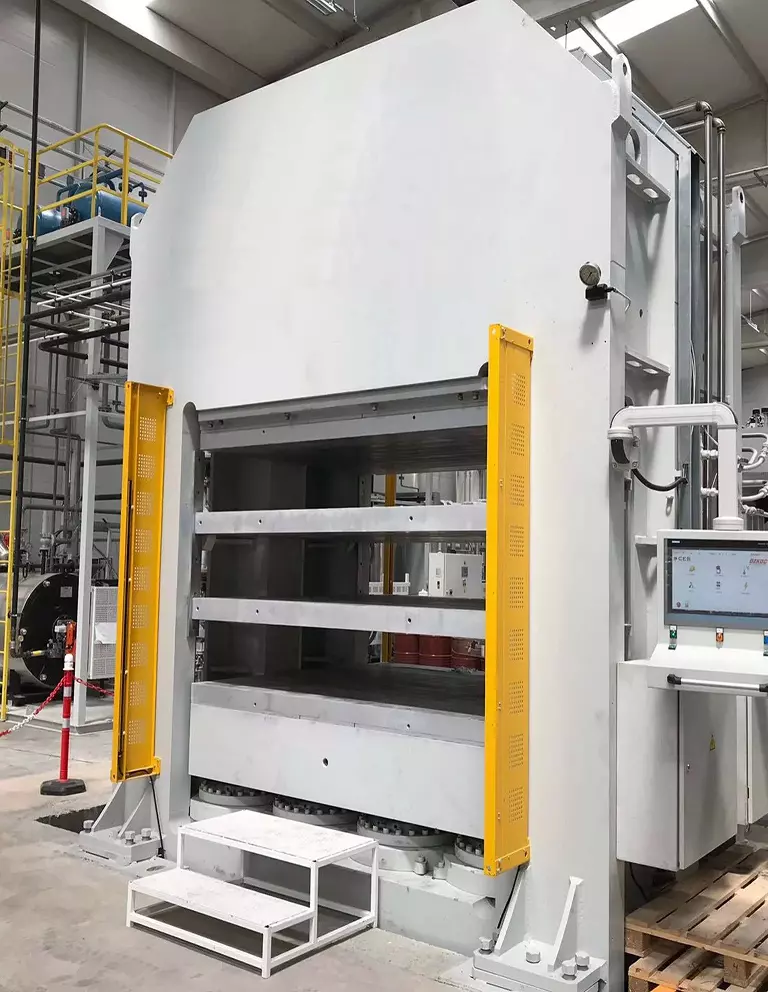
SMC (Sheet Molding Compound) ist ein glasfaserverstärkter Verbundwerkstoff, der in der Fertigungsindustrie weit verbreitet ist. Es handelt sich um eine präzise Mischung aus Glasfasern, thermoplastischen oder thermoset Harzen, Füllstoffen, Pigmenten und anderen Additiven. Die spezifische Zusammensetzung von SMC verleiht dem Material eine hohe Steifigkeit, Festigkeit, Schlagzähigkeit und Beständigkeit gegenüber Chemikalien und Witterungseinflüssen.
1.1. Herstellung von SMC-Materialien
Die Herstellung von SMC beginnt mit der Imprägnierung von Glasfasermatten mit einem Harzgemisch. Das Harz wird gleichmäßig über die Glasfasern verteilt und anschließend durch spezielle Walzen verdichtet, um eine homogene Schicht zu bilden. Diese Schicht wird anschließend in Rollen aufgewickelt und für den späteren Einsatz im Heißpressverfahren gelagert. SMC ist in verschiedenen Dichten und Stärken erhältlich, je nach den Anforderungen der jeweiligen Anwendung.
1.2. Eigenschaften von SMC
SMC hat eine Reihe von Eigenschaften, die es zu einem idealen Material für die Herstellung komplexer Bauteile machen:
- Hohe mechanische Festigkeit: Die Verstärkung durch Glasfasern sorgt für eine hohe Zug- und Biegefestigkeit.
- Geringes Gewicht: Im Vergleich zu metallischen Werkstoffen ist SMC deutlich leichter, was es ideal für Anwendungen macht, bei denen Gewichtseinsparung eine Rolle spielt.
- Gute elektrische Isolierung: SMC ist ein hervorragender Isolator, was es für Anwendungen in der Elektronikindustrie prädestiniert.
- Witterungs- und Chemikalienbeständigkeit: SMC-Bauteile weisen eine hohe Beständigkeit gegen Umwelteinflüsse, Feuchtigkeit und Chemikalien auf.
2. Das Verfahren des SMC Heißpressens
Das Heißpressen ist der zentrale Prozess zur Herstellung von SMC-Bauteilen. Es handelt sich um ein thermisches Umformverfahren, bei dem das Material in eine Form eingelegt und unter hohem Druck und hoher Temperatur geformt wird. Die Form gibt dabei die endgültige Gestalt des Bauteils vor, während die Kombination aus Druck und Hitze den Härtungsprozess des Harzes aktiviert und die Festigkeit des Werkstücks sichergestellt.
2.1. Prozessablauf
Der typische Ablauf des SMC Heißpressens besteht aus mehreren Schritten:
- Vorbereitung des Materials: Die erforderliche Menge an SMC wird von den vorbereiteten Rollen zugeschnitten und in die Form eingebracht.
- Schließen der Form: Die Form wird geschlossen, und der Druck wird auf das Material ausgeübt. Typische Druckwerte liegen zwischen 50 und 150 Tonnen, abhängig von der Größe und Komplexität des Bauteils.
- Erwärmung: Das Material wird auf Temperaturen zwischen 120°C und 160°C erhitzt, um das Harz zu verflüssigen und den Vulkanisationsprozess zu starten.
- Aushärtung: Nach einer bestimmten Zeit härtet das Harz aus und das Bauteil erhält seine endgültige Festigkeit und Form. Die Aushärtungszeit variiert je nach Dicke und Komplexität des Bauteils, liegt aber typischerweise zwischen 1 und 5 Minuten.
- Entformung: Nach der Aushärtung wird die Form geöffnet und das fertige Bauteil entnommen. Anschließend werden eventuelle Überschüsse entfernt und das Bauteil gegebenenfalls nachbearbeitet.
2.2. Werkzeugtechnologie
Die beim Heißpressen verwendeten Werkzeuge und Formen sind entscheidend für die Qualität und Präzision der produzierten Bauteile. Diese Werkzeuge bestehen in der Regel aus gehärtetem Stahl, der hohe Temperaturen und Druckbelastungen aushält. Darüber hinaus können die Formen mit speziellen Beschichtungen versehen werden, um den Materialfluss zu verbessern und die Entformung des Bauteils zu erleichtern.
2.3. Temperatur- und Drucksteuerung
Die Kontrolle von Temperatur und Druck während des Heißpressens ist von größter Bedeutung, um eine gleichmäßige Aushärtung und hohe Qualität des Bauteils zu gewährleisten. Moderne Heißpressmaschinen sind mit computergesteuerten Systemen ausgestattet, die die Temperatur und den Druck während des gesamten Prozesses überwachen und anpassen.
3. Vorteile des SMC Heißpressens
Das Heißpressen von SMC bietet eine Reihe von Vorteilen, die es von anderen Umformverfahren, wie dem Spritzgießen oder dem RTM (Resin Transfer Molding), abheben.
3.1. Kosteneffizienz
Das SMC Heißpressen ist ein äußerst effizientes Verfahren, das sich besonders für die Massenproduktion eignet. Die niedrigen Zykluszeiten und die Möglichkeit, große und komplexe Bauteile in einem einzigen Prozessschritt herzustellen, tragen zur Senkung der Produktionskosten bei.
3.2. Leichtbau
Da SMC im Vergleich zu traditionellen Materialien wie Stahl oder Aluminium ein geringes Gewicht aufweist, eignet es sich hervorragend für Anwendungen im Leichtbau. Dies ist besonders in der Automobilindustrie von Vorteil, wo das Gewicht eines Fahrzeugs entscheidend für den Kraftstoffverbrauch und die CO2-Emissionen ist.
3.3. Hohe Designfreiheit
Mit dem SMC Heißpressen können sehr komplexe und dreidimensionale Bauteile hergestellt werden, die mit anderen Verfahren nur schwer realisierbar wären. Die Formen können präzise gestaltet werden, um die Anforderungen spezifischer Anwendungen zu erfüllen.
3.4. Umweltfreundlichkeit
SMC ist ein recycelbares Material und kann am Ende seines Lebenszyklus in neuen Produkten wiederverwendet werden. Darüber hinaus werden beim Heißpressen im Vergleich zu anderen Verfahren weniger flüchtige organische Verbindungen (VOCs) freigesetzt, was zu einer geringeren Umweltbelastung führt.
4. Herausforderungen des SMC Heißpressens
Trotz seiner vielen Vorteile gibt es auch einige Herausforderungen und Einschränkungen beim SMC Heißpressen, die es zu berücksichtigen gilt.
4.1. Werkzeugkosten
Die Kosten für die Herstellung der Werkzeuge und Formen sind beim SMC Heißpressen relativ hoch, insbesondere wenn hochkomplexe oder große Bauteile hergestellt werden. Dies kann sich negativ auf die Wirtschaftlichkeit bei kleineren Produktionsmengen auswirken.
4.2. Schrumpfung und Verzug
Während des Aushärtungsprozesses kann das SMC-Material schrumpfen oder sich verziehen, was zu Ungenauigkeiten in den Abmessungen des Bauteils führen kann. Um dies zu minimieren, ist eine präzise Kontrolle der Temperatur und Druckverteilung in der Form erforderlich.
4.3. Lange Vorbereitungszeit
Das Zuschneiden und Einlegen des SMC-Materials in die Form kann zeitaufwendig sein, insbesondere bei komplexen Formen. In einigen Fällen ist eine manuelle Positionierung erforderlich, was den Gesamtprozess verlangsamen kann.
5. Anwendungen des SMC Heißpressens
Das SMC Heißpressen wird in einer Vielzahl von Branchen eingesetzt, insbesondere in Bereichen, in denen hohe mechanische Festigkeit, geringes Gewicht und Beständigkeit gegenüber extremen Bedingungen gefordert sind.
5.1. Automobilindustrie
Einer der größten Anwendungsbereiche für SMC ist die Automobilindustrie. SMC wird zur Herstellung von Karosserieteilen, Stoßfängern, Motorabdeckungen, Kotflügeln und anderen strukturellen Komponenten verwendet. Diese Bauteile müssen leicht, fest und widerstandsfähig gegenüber Witterungseinflüssen und Chemikalien sein, was SMC zu einem idealen Material macht.
5.2. Luft- und Raumfahrtindustrie
In der Luft- und Raumfahrt wird SMC ebenfalls zur Herstellung von strukturellen und nicht-strukturellen Komponenten verwendet, bei denen Gewicht und Festigkeit entscheidende Faktoren sind. Das Heißpressen von SMC ermöglicht es, komplexe und leichte Bauteile zu produzieren, die den extremen Bedingungen in der Luft- und Raumfahrt standhalten.
5.3. Elektronikindustrie
SMC-Bauteile finden auch in der Elektronikindustrie Anwendung, insbesondere in der Herstellung von Gehäusen, Schaltschränken und Isolatoren. Die hohe elektrische Isolierfähigkeit und Beständigkeit gegenüber Hitze machen SMC zu einem idealen Material für diese Art von Anwendungen.
5.4. Bauindustrie
In der Bauindustrie werden SMC-Bauteile für Fassadenelemente, Dächer und Verkleidungen verwendet. Dank seiner Beständigkeit gegen Witterungseinflüsse und Chemikalien bietet SMC eine langlebige Lösung für den Einsatz in anspruchsvollen Umgebungen.
6. Zukünftige Entwicklungen im Bereich des SMC Heißpressens
Mit der fortschreitenden Entwicklung von Materialien und Technologien werden auch die Einsatzmöglichkeiten und Effizienz des SMC Heißpressens weiter ausgebaut. Zu den vielversprechendsten Entwicklungen zählen:
- Verbesserte Harzsysteme: Neue Harzformulierungen mit verbesserten mechanischen und thermischen Eigenschaften werden entwickelt, um die Leistungsfähigkeit von SMC-Bauteilen weiter zu steigern.
- Automatisierung des Prozesses: Der Einsatz von Robotik und fortschrittlichen Steuerungssystemen könnte die Vorbereitungs- und Zykluszeiten beim Heißpressen von SMC erheblich verkürzen und die Produktionskosten senken.
- Erweiterte Anwendungen: Mit der wachsenden Nachfrage nach leichten und robusten Materialien in der Automobil-, Luftfahrt- und Bauindustrie wird erwartet, dass die Einsatzbereiche für SMC-Bauteile weiter zunehmen.
Das Metalldrücken, auch als „Drückverfahren“ oder „Spinning“ bekannt, ist ein traditionelles und dennoch modernes Verfahren der Metallumformung, das für die Herstellung rotationssymmetrischer Teile verwendet wird. Mithilfe einer Metalldrückmaschine werden Metallbleche oder -platten durch das Drücken über eine Form gespannt, um Bauteile in zylindrischer, konischer oder komplexeren geometrischen Formen zu fertigen. Dieses Verfahren wird häufig für die Produktion von Prototypen, Kleinserien und spezifischen Anwendungen eingesetzt, bei denen Präzision und Materialeffizienz entscheidend sind.
In diesem Text werden die Funktionsweise von Metalldrückmaschinen, die Arten dieser Maschinen, ihre Einsatzgebiete sowie die Vor- und Nachteile des Verfahrens ausführlich erläutert.
1. Grundprinzip des Metalldrückens
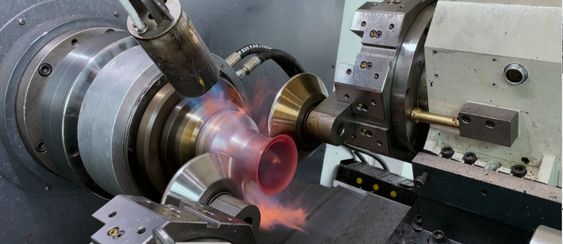
Das Metalldrücken ist ein Kaltumformverfahren, bei dem das Metallblech durch rotierende Werkzeuge in seine endgültige Form gebracht wird. Der Prozess basiert auf dem Prinzip der plastischen Verformung, bei der das Material unter Druck fließt, ohne seine Dicke wesentlich zu verändern. Dieses Verfahren eignet sich hervorragend für die Herstellung von dünnwandigen Bauteilen mit hohem Anspruch an Maßhaltigkeit und Oberflächenqualität.
1.1. Ablauf des Metalldrückens
Der Metalldrückprozess beginnt mit einem kreisförmigen Metallrohling, der auf einem rotierenden Dorn befestigt wird. Dieser Dorn entspricht der gewünschten Endform des Werkstücks. Während der Dorn rotiert, wird das Metallstück durch das Werkzeug gegen den Dorn gedrückt. Der kontinuierliche Druck führt dazu, dass sich das Metall gleichmäßig um den Dorn legt und die Form annimmt.
Das Verfahren ist wiederholbar, und je nach Komplexität des Werkstücks sind mehrere Durchgänge erforderlich, um die gewünschte Form zu erreichen. Typischerweise werden Materialien wie Aluminium, Stahl, Kupfer oder Messing verwendet, die sich leicht plastisch verformen lassen.
1.2. Werkzeuge beim Metalldrücken
Das Herzstück des Metalldrückens ist die Drückwalze, die das Material entlang der rotierenden Achse verformt. Diese Walzen bestehen meist aus gehärtetem Stahl oder Hartmetall, um den hohen Kräften während des Umformprozesses standzuhalten. Die Werkzeuge sind in verschiedenen Größen und Geometrien verfügbar, um eine Vielzahl von Formen herzustellen.
2. Arten von Metalldrückmaschinen
Es gibt verschiedene Typen von Metalldrückmaschinen, die je nach Anforderungen und Komplexität des Umformprozesses eingesetzt werden. Die Wahl der Maschine hängt von der Größe und Form des Werkstücks sowie der geforderten Präzision ab.
2.1. Manuelle Metalldrückmaschinen
Die manuelle Metalldrückmaschine ist die traditionellste Variante und wird vor allem für kleine Serien oder Einzelanfertigungen verwendet. Bei dieser Art von Maschine wird das Werkzeug von einem erfahrenen Bediener gesteuert, der das Metall durch manuelles Drücken und Formen bearbeitet. Diese Maschinen eignen sich gut für Prototypenbau oder Projekte, bei denen Flexibilität und Anpassungsfähigkeit gefragt sind.
2.2. Halbautomatische Metalldrückmaschinen
Halbautomatische Metalldrückmaschinen bieten einen Kompromiss zwischen manueller Steuerung und Automatisierung. Während der Bediener immer noch das Werkzeug steuert, wird die Rotation des Dorns und der Grundprozess von der Maschine automatisiert. Diese Maschinen ermöglichen eine höhere Präzision und schnellere Fertigungszeiten als die rein manuellen Varianten.
2.3. CNC-Metalldrückmaschinen
Die CNC-Metalldrückmaschine ist die fortschrittlichste Variante und wird bei hochpräzisen, wiederholbaren Fertigungsprozessen eingesetzt. CNC (Computerized Numerical Control) bedeutet, dass die Bewegung des Werkzeugs und des Materials durch computergesteuerte Programme präzise gesteuert wird. Dies ermöglicht die Produktion von komplexen Formen mit minimalen Toleranzen und hoher Wiederholgenauigkeit. Diese Maschinen sind besonders in der Luft- und Raumfahrt sowie der Automobilindustrie gefragt, wo hohe Anforderungen an die Qualität der Bauteile gestellt werden.
3. Vorteile des Metalldrückverfahrens
Das Metalldrücken bietet eine Reihe von Vorteilen gegenüber anderen Umformverfahren wie dem Tiefziehen oder der spanenden Bearbeitung. Es ist besonders effizient, wenn es um die Herstellung rotationssymmetrischer Teile geht, da der Materialabfall minimal ist und die Fertigung relativ schnell erfolgt.
3.1. Hohe Materialausnutzung
Einer der größten Vorteile des Metalldrückens ist die hohe Materialausnutzung. Da das Material während des Prozesses nur umgeformt und nicht abgetragen wird, bleibt die Ausgangsdicke des Materials nahezu unverändert. Dies reduziert den Materialverlust erheblich und senkt die Produktionskosten, insbesondere bei teuren Materialien wie Titan oder Edelstahl.
3.2. Geringe Werkzeugkosten
Im Vergleich zu anderen Umformverfahren wie dem Tiefziehen oder dem Pressen sind die Werkzeugkosten beim Metalldrücken deutlich geringer. Dies liegt daran, dass nur der Dorn und die Drückwalzen spezifisch für das Werkstück hergestellt werden müssen, während die übrigen Maschinenkomponenten standardisiert sind.
3.3. Flexibilität in der Formgebung
Metalldrückmaschinen ermöglichen eine hohe Flexibilität bei der Herstellung von Bauteilen in verschiedenen Formen und Größen. Dies ist besonders nützlich für Prototypen und Kleinserien, bei denen häufige Änderungen im Design erforderlich sind. Das Umrüsten der Maschinen für verschiedene Werkstückgeometrien ist vergleichsweise einfach und kostengünstig.
3.4. Hohe Oberflächenqualität
Durch den kontinuierlichen Kontakt zwischen Werkzeug und Werkstück während des Metalldrückens wird eine sehr gleichmäßige und glatte Oberfläche erzielt. Dies reduziert den Bedarf an nachträglicher Oberflächenbearbeitung, was wiederum Zeit und Kosten spart.
4. Herausforderungen beim Metalldrücken
Trotz der vielen Vorteile ist das Metalldrücken ein anspruchsvolles Verfahren, das fundierte Fachkenntnisse und spezielle Maschinen erfordert. Einige der Herausforderungen, die beim Metalldrücken auftreten können, sind:
4.1. Begrenzte Formvielfalt
Das Metalldrücken eignet sich hervorragend für die Herstellung rotationssymmetrischer Bauteile, ist jedoch bei komplexen, nicht-symmetrischen Formen eingeschränkt. Zwar können mit CNC-gesteuerten Maschinen auch komplexere Geometrien realisiert werden, doch sind diese Maschinen deutlich teurer und erfordern eine aufwendigere Programmierung.
4.2. Erhöhter Werkzeugverschleiß
Da beim Metalldrücken kontinuierlich hoher Druck auf die Werkzeuge ausgeübt wird, ist der Verschleiß der Drückwalzen und des Dorns relativ hoch. Insbesondere bei der Bearbeitung harter Werkstoffe wie Titan oder Edelstahl müssen die Werkzeuge häufig gewartet oder ausgetauscht werden.
4.3. Anfälligkeit für Materialfehler
Das Metalldrücken setzt eine gleichmäßige Materialqualität voraus, um optimale Ergebnisse zu erzielen. Schon kleine Unregelmäßigkeiten im Metall können zu Fehlern im fertigen Bauteil führen, wie z. B. Risse oder Unebenheiten. Daher ist es wichtig, hochwertige Rohmaterialien zu verwenden und den Prozess genau zu überwachen.
5. Anwendungen von Metalldrückmaschinen
Metalldrückmaschinen finden in einer Vielzahl von Industrien Anwendung, die rotationssymmetrische Bauteile erfordern. Zu den typischen Anwendungen gehören:
5.1. Luft- und Raumfahrt
In der Luft- und Raumfahrtindustrie werden Metalldrückmaschinen zur Herstellung von Triebwerkskomponenten, Kuppeln, Düsen und anderen Bauteilen verwendet, die hohe Anforderungen an Präzision und Festigkeit erfüllen müssen. Hier kommen vor allem CNC-Metalldrückmaschinen zum Einsatz, da sie eine hohe Wiederholgenauigkeit gewährleisten.
5.2. Automobilindustrie
Auch in der Automobilindustrie spielt das Metalldrücken eine wichtige Rolle. Typische Anwendungen sind die Herstellung von Rädern, Felgen, Auspuffanlagen und anderen Komponenten, bei denen eine rotationssymmetrische Form und eine hohe Oberflächenqualität gefordert sind. Das Verfahren ermöglicht zudem die Herstellung von leichten und dennoch stabilen Bauteilen, was besonders in der Produktion von Elektrofahrzeugen von Vorteil ist.
5.3. Beleuchtungsindustrie
In der Beleuchtungsindustrie werden Metalldrückmaschinen zur Herstellung von Lampenschirmen, Reflektoren und Gehäusen verwendet. Diese Bauteile erfordern oft eine sehr gleichmäßige Oberfläche, die durch das Metalldrückverfahren ohne zusätzliche Nachbearbeitung erzielt werden kann.
5.4. Haushaltsgeräte
Metalldrückmaschinen werden auch in der Produktion von Haushaltsgeräten wie Kochtöpfen, Pfannen und Kesseln eingesetzt. Diese Bauteile müssen nicht nur funktional, sondern auch ästhetisch ansprechend sein. Das Metalldrücken ermöglicht die Herstellung dünnwandiger, formschöner und gleichzeitig robuster Teile.
6. Zukünftige Entwicklungen im Metalldrücken
Mit der fortschreitenden Automatisierung und Digitalisierung in der Fertigungstechnik wird auch das Metalldrückverfahren weiterentwickelt. Zu den zukünftigen Trends gehören:
6.1. Automatisierung und Robotik
In Zukunft wird die Automatisierung im Metalldrücken weiter voranschreiten. Insbesondere in der Serienproduktion werden Roboter zunehmend in den Umformprozess integriert, um die Effizienz zu steigern und die Kosten zu senken. Dies ermöglicht auch eine präzisere und schnellere Bearbeitung komplexer Werkstücke.
6.2. Einsatz von neuen Materialien
Während herkömmliche Metalldrückmaschinen hauptsächlich mit Metallen wie Aluminium und Stahl arbeiten, werden künftig auch neue Materialien wie Faserverbundstoffe und Hochleistungskunststoffe in den Prozess integriert. Diese Materialien bieten eine Kombination aus Leichtigkeit und Festigkeit, die in vielen Hightech-Anwendungen gefordert wird.
6.3. Erweiterte Einsatzmöglichkeiten
Mit der Entwicklung von CNC-gesteuerten Metalldrückmaschinen und fortschrittlichen Softwarelösungen wird es möglich, komplexere und präzisere Bauteile herzustellen. Dies eröffnet neue Einsatzmöglichkeiten in Branchen wie der Medizintechnik, der Elektronik und der Mikroelektronik, wo kleinste Bauteile mit hoher Präzision gefertigt werden müssen.
Falzmaschinen sind essenzielle Werkzeuge in der Blechverarbeitung, die es ermöglichen, Bleche durch Biegen oder Falten in die gewünschte Form zu bringen. Während Standard-Falzmaschinen in der Lage sind, einfache Blechbearbeitungen durchzuführen, gibt es in vielen Industrien Bedarf an speziellen Falzmaschinen, die komplexe und maßgeschneiderte Lösungen bieten können. Diese speziellen Falzmaschinen sind für anspruchsvolle Anwendungen ausgelegt und bieten eine Vielzahl von Funktionen und Anpassungsmöglichkeiten, um den Anforderungen moderner Fertigungsprozesse gerecht zu werden.
In diesem Text wird die Bedeutung von speziellen Falzmaschinen erläutert, ihre Funktionsweise, die verschiedenen Typen sowie ihre Einsatzgebiete. Zudem werden die Vorteile dieser Maschinen sowie die Herausforderungen und zukünftigen Entwicklungen in der Blechbearbeitung behandelt.
1. Einführung in das Falzen von Blech
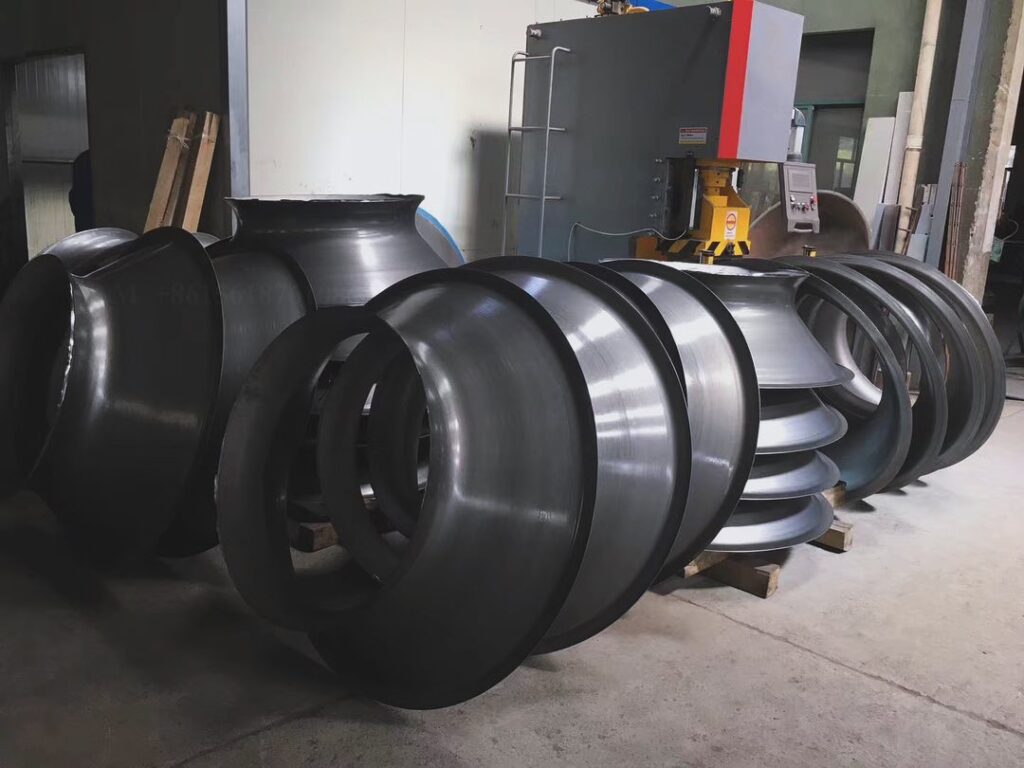
Das Falzen ist ein weit verbreitetes Verfahren in der Blechbearbeitung, bei dem das Blech entlang einer Linie gebogen wird, um eine Falte oder einen Winkel zu erzeugen. Dieses Verfahren wird verwendet, um Bleche für verschiedene Anwendungen vorzubereiten, von einfachen rechtwinkligen Faltungen bis hin zu komplexen geometrischen Formen. Der Prozess erfordert Präzision und eine gleichmäßige Krafteinwirkung, um die Materialeigenschaften nicht zu beeinträchtigen.
1.1. Grundlagen des Falzens
Beim Falzen wird das Blech zwischen zwei Werkzeugen, meist einer Matrize und einem Stempel, eingespannt und entlang einer vorgegebenen Linie gebogen. Die meisten Falzmaschinen arbeiten mit einem hydraulischen oder mechanischen Antrieb, um die notwendige Kraft aufzubringen. Je nach Dicke und Materialart des Blechs können unterschiedliche Werkzeuge und Einstellungen erforderlich sein, um die gewünschten Ergebnisse zu erzielen.
1.2. Einsatzgebiete des Falzens
Das Falzen findet in einer Vielzahl von Industrien Anwendung, darunter die Automobilindustrie, der Maschinenbau, die Luft- und Raumfahrt, die Bauindustrie sowie die Herstellung von Haushaltsgeräten und Elektronikkomponenten. Besonders bei der Herstellung von Karosserieteilen, Gehäusen und Verkleidungen ist das Falzen ein unverzichtbarer Schritt in der Produktion.
2. Funktionsweise spezieller Falzmaschinen
Spezielle Falzmaschinen unterscheiden sich von Standardmodellen durch ihre erhöhte Flexibilität und die Möglichkeit, komplexe Bearbeitungen durchzuführen. Diese Maschinen sind mit fortschrittlichen Steuerungssystemen ausgestattet, die eine präzise Anpassung an die spezifischen Anforderungen jedes Werkstücks ermöglichen. Darüber hinaus können spezielle Falzmaschinen für die Bearbeitung unterschiedlicher Materialstärken und -typen konfiguriert werden, wodurch sie sich für eine Vielzahl von Anwendungen eignen.
2.1. Steuerung und Automatisierung
Moderne spezielle Falzmaschinen sind in der Regel mit CNC-Steuerungen (Computerized Numerical Control) ausgestattet, die eine exakte und wiederholbare Positionierung der Werkzeuge ermöglichen. Die CNC-Steuerung erlaubt es, den gesamten Biegeprozess zu programmieren und die Bewegungen der Werkzeuge exakt auf das Werkstück abzustimmen. Dies führt zu einer höheren Genauigkeit und Effizienz, insbesondere bei komplexen Biegeformen.
Darüber hinaus sind viele spezielle Falzmaschinen vollständig automatisiert und können in Fertigungslinien integriert werden, um den Produktionsprozess zu beschleunigen und die Fehlerquote zu minimieren. Dies ist besonders in der Massenproduktion von Vorteil, wo Präzision und Wiederholgenauigkeit entscheidend sind.
2.2. Anpassbare Werkzeuge und Matrizen
Ein wesentlicher Vorteil spezieller Falzmaschinen ist die Möglichkeit, maßgeschneiderte Werkzeuge und Matrizen zu verwenden. Dies ermöglicht es, Bleche mit komplexen Formen und Winkeln zu bearbeiten, die mit Standardmaschinen nicht realisierbar wären. Die Werkzeuge können so gestaltet werden, dass sie speziell auf die Anforderungen des jeweiligen Projekts zugeschnitten sind, was zu einer höheren Flexibilität und Produktivität führt.
2.3. Bearbeitung unterschiedlicher Materialien
Während Standard-Falzmaschinen oft auf die Bearbeitung bestimmter Metalle wie Stahl oder Aluminium beschränkt sind, bieten spezielle Falzmaschinen die Möglichkeit, eine Vielzahl von Materialien zu verarbeiten, darunter Edelstahl, Kupfer, Messing, Titan und sogar Kunststoffe. Diese Vielseitigkeit macht sie zu einer wertvollen Investition für Unternehmen, die mit unterschiedlichen Materialien arbeiten und hohe Ansprüche an die Verarbeitungsqualität stellen.
3. Arten von speziellen Falzmaschinen
Es gibt verschiedene Typen von speziellen Falzmaschinen, die je nach Anwendungsbereich und den geforderten Spezifikationen variieren. Diese Maschinen sind auf unterschiedliche Formen der Blechbearbeitung ausgelegt, von einfachen Biegearbeiten bis hin zu komplexen mehrstufigen Bearbeitungsprozessen.
3.1. Schwenkbiegemaschinen
Schwenkbiegemaschinen sind eine Art von speziellen Falzmaschinen, die das Blech um einen festen Winkel biegen. Bei diesen Maschinen wird das Blech auf eine ebene Fläche gelegt, und ein Biegebalken schwenkt um das Werkstück, um die gewünschte Biegung zu erzeugen. Schwenkbiegemaschinen eignen sich besonders für große Blechtafeln und komplexe Biegeformen, da sie eine hohe Flexibilität in der Formgebung bieten.
3.2. Gesenkbiegepressen
Gesenkbiegepressen sind eine weitere Art von speziellen Falzmaschinen, bei denen das Blech zwischen einem Stempel und einer Matrize gebogen wird. Diese Maschinen arbeiten mit einem vertikalen Pressvorgang und eignen sich besonders für die Herstellung präziser Biegungen in dickeren Materialien. Gesenkbiegepressen werden häufig in der Automobil- und Bauindustrie eingesetzt, wo dickere Bleche verarbeitet werden müssen.
3.3. Mehrstufige Biegemaschinen
Mehrstufige Biegemaschinen sind speziell für die Bearbeitung komplexer Werkstücke konzipiert, bei denen mehrere Biegungen in unterschiedlichen Winkeln und Positionen erforderlich sind. Diese Maschinen können in einem einzigen Arbeitsgang mehrere Biegungen durchführen, was die Effizienz erhöht und den Bedarf an manuellen Eingriffen verringert. Mehrstufige Biegemaschinen werden häufig in der Produktion von komplexen Gehäusen und Strukturkomponenten eingesetzt.
4. Vorteile spezieller Falzmaschinen
Spezielle Falzmaschinen bieten zahlreiche Vorteile gegenüber Standardmaschinen, insbesondere wenn es um komplexe Biegeprozesse und spezielle Anforderungen geht.
4.1. Höhere Präzision
Dank der CNC-Steuerung und der Möglichkeit, maßgeschneiderte Werkzeuge zu verwenden, bieten spezielle Falzmaschinen eine außergewöhnlich hohe Präzision. Dies ist besonders wichtig bei der Produktion von Bauteilen, die strengen Toleranzen unterliegen, wie etwa in der Luftfahrt- oder Automobilindustrie.
4.2. Flexibilität in der Produktion
Spezielle Falzmaschinen ermöglichen es, eine breite Palette von Materialien und Formen zu bearbeiten, was sie zu einem unverzichtbaren Werkzeug für Unternehmen macht, die mit unterschiedlichen Projekten und Materialien arbeiten. Die Möglichkeit, die Maschinen für spezifische Anwendungen anzupassen, bietet eine hohe Flexibilität und ermöglicht es, auch unkonventionelle Biegeanforderungen zu erfüllen.
4.3. Zeit- und Kosteneinsparungen
Durch die Automatisierung des Biegeprozesses und die Möglichkeit, mehrere Biegungen in einem einzigen Arbeitsgang durchzuführen, können spezielle Falzmaschinen die Produktionszeit erheblich verkürzen und die Kosten senken. Dies ist besonders in der Serienproduktion von Vorteil, wo Effizienz und Wiederholgenauigkeit entscheidend sind.
4.4. Verbesserte Qualität der Werkstücke
Die hohe Präzision und Wiederholgenauigkeit spezieller Falzmaschinen führt zu einer verbesserten Qualität der gefertigten Werkstücke. Fehler wie ungleichmäßige Biegungen oder Materialschäden werden minimiert, was zu einer höheren Gesamtqualität des Endprodukts führt.
5. Anwendungen spezieller Falzmaschinen
Spezielle Falzmaschinen finden in einer Vielzahl von Industrien Anwendung, in denen komplexe Biegeprozesse und hohe Präzision gefordert sind.
5.1. Luft- und Raumfahrt
In der Luft- und Raumfahrtindustrie sind die Anforderungen an die Bauteilqualität und Präzision besonders hoch. Spezielle Falzmaschinen werden hier zur Herstellung von Strukturbauteilen, Verkleidungen und Gehäusen verwendet, die strengen Toleranzen und Sicherheitsvorschriften unterliegen. Die Möglichkeit, Materialien wie Titan und Aluminium zu bearbeiten, macht diese Maschinen ideal für die Luftfahrtindustrie.
5.2. Automobilindustrie
Auch in der Automobilindustrie sind spezielle Falzmaschinen von großer Bedeutung. Sie werden zur Herstellung von Karosserieteilen, Rahmenstrukturen und Verkleidungen eingesetzt, die hohe Anforderungen an Festigkeit und Präzision stellen. Durch den Einsatz von CNC-gesteuerten Falzmaschinen können Automobilhersteller die Qualität der Bauteile verbessern und gleichzeitig die Produktionskosten senken.
5.3. Bauindustrie
In der Bauindustrie werden spezielle Falzmaschinen zur Herstellung von Fassadenelementen, Dächern und Strukturkomponenten verwendet. Diese Bauteile müssen nicht nur funktional, sondern auch ästhetisch ansprechend sein. Spezielle Falzmaschinen ermöglichen es, Bleche in komplexen Formen und Winkeln zu biegen, was bei der Gestaltung moderner Gebäude von Vorteil ist.
Das Heißpressen von Kunststoffen ist ein etabliertes Verfahren, das in zahlreichen Industrien angewendet wird, um komplexe und präzise Kunststoffteile herzustellen. Dieses Verfahren ermöglicht es, Materialien unter Einwirkung von Wärme und Druck zu formen, was zu hochwertigen, robusten und langlebigen Produkten führt. Heißpressen ist besonders wertvoll in Branchen, die auf präzise und wiederholbare Formgebungsprozesse angewiesen sind, wie die Automobilindustrie, die Elektronikbranche und die Luft- und Raumfahrt.
In diesem Abschnitt wird das Heißpressen von Kunststoffen ausführlich beschrieben. Dabei wird auf die Funktionsweise, die Arten von Heißpressverfahren, die Vor- und Nachteile, die Anwendungsgebiete sowie auf neue Entwicklungen und Trends eingegangen.
1. Grundlagen des Heißpressens
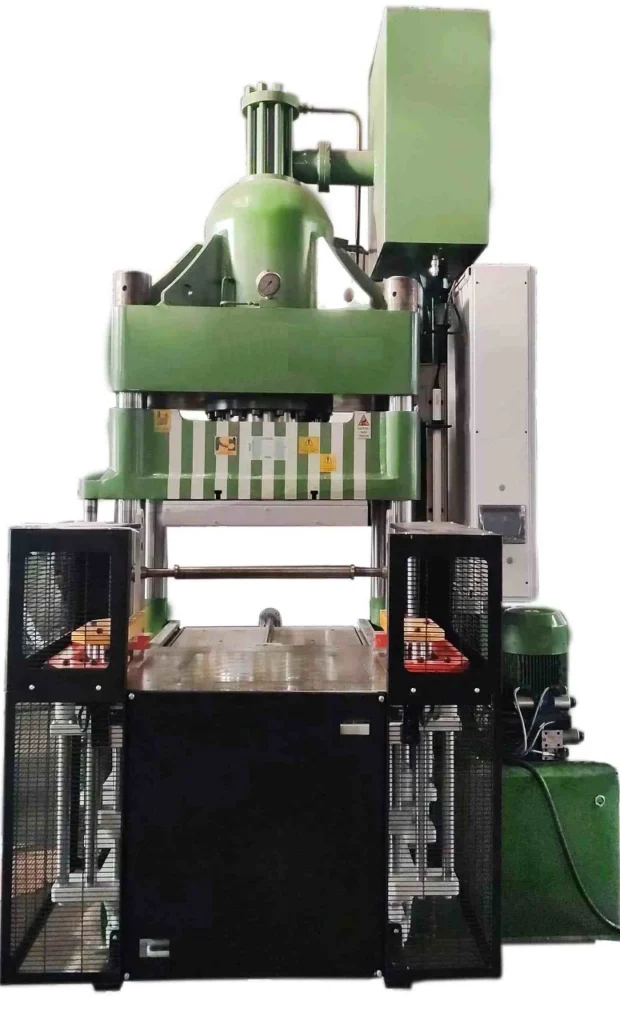
Das Heißpressen, auch bekannt als Thermopressen, ist ein Prozess, bei dem Kunststoffmaterialien unter Verwendung von Hitze und Druck in eine bestimmte Form gepresst werden. Dabei wird das Material auf eine Temperatur erhitzt, bei der es verformbar, aber noch fest genug ist, um seine Struktur zu behalten. Unter Druck wird das Material dann in eine Form gebracht und anschließend abgekühlt, um das gewünschte Endprodukt zu erhalten.
1.1. Materialverhalten beim Heißpressen
Kunststoffe verhalten sich beim Erhitzen anders als Metalle. Thermoplaste, wie Polyethylen (PE), Polypropylen (PP) oder Polycarbonat (PC), werden durch die Hitze verformbar und können wiederholt geformt werden, solange sie unter der thermischen Belastung bleiben. Duroplaste hingegen, wie Epoxidharze oder Melaminharze, härten irreversibel aus, sobald sie einmal erhitzt und geformt wurden.
Die richtigen Temperaturen und Drücke sind entscheidend, um die Qualität des Endprodukts zu sichern. Eine zu niedrige Temperatur oder zu wenig Druck kann zu einer unvollständigen Formung führen, während zu viel Hitze oder Druck das Material beschädigen kann.
1.2. Der Pressvorgang
Beim Heißpressen wird das Rohmaterial, oft in Form von Granulat oder Pulver, in eine vorgefertigte Form eingelegt. Die beiden Teile der Presse – der Stempel und die Matrize – schließen sich und üben Druck auf das Material aus, während die Form erhitzt wird. Dieser Prozess dauert mehrere Minuten bis Stunden, abhängig von der Materialstärke und der Komplexität der Form. Nach der Formung wird das Werkstück abgekühlt und aus der Form entfernt.
Ein wichtiger Vorteil des Heißpressens ist die Fähigkeit, gleichmäßig geformte, qualitativ hochwertige Teile mit präzisen Dimensionen zu erzeugen. Besonders bei großen, strukturellen Kunststoffteilen kommt dieses Verfahren oft zum Einsatz.
2. Arten von Heißpressen
Es gibt mehrere Arten von Heißpressen, die je nach Anforderung und Materialien eingesetzt werden. Jede Variante bietet spezifische Vorteile und ist für bestimmte Anwendungen besser geeignet.
2.1. Kompressionspressen
Das Kompressionspressen ist das einfachste und am weitesten verbreitete Heißpressverfahren. Es eignet sich besonders für die Herstellung von dicken und massiven Teilen. Hierbei wird das Kunststoffmaterial in eine offene Form gelegt, erhitzt und unter hohem Druck verdichtet. Diese Methode wird oft für Duroplaste eingesetzt, da das Material nach dem Aushärten seine Form behält.
2.2. Transferpressen
Bei der Transferpresse wird das erhitzte Kunststoffmaterial in eine Kammer über der Form gegeben und dann unter Druck in die Form gepresst. Dieses Verfahren eignet sich für Materialien, die empfindlich auf den direkten Kontakt mit den Heizplatten reagieren, und ist ideal für die Herstellung kleinerer, komplizierter Bauteile mit feinen Details.
2.3. Folienpressen
Das Folienpressen ist ein spezielles Verfahren, das verwendet wird, um dünne Kunststofffolien oder -platten zu erzeugen. Hierbei wird das Material gleichmäßig in einer Form verteilt und unter hohem Druck in eine dünne, gleichmäßige Schicht gepresst. Dieses Verfahren wird oft für Verpackungsmaterialien oder für die Herstellung von dünnen Bauteilen in der Elektronikindustrie verwendet.
3. Vor- und Nachteile des Heißpressens
Wie jedes industrielle Verfahren hat auch das Heißpressen von Kunststoff seine Vor- und Nachteile. Diese hängen stark von den spezifischen Anforderungen und Materialien ab.
3.1. Vorteile
- Hohe Präzision und Wiederholbarkeit: Heißpressen ermöglicht es, komplexe Formen mit hoher Präzision und Konsistenz herzustellen, was für Serienproduktionen von entscheidender Bedeutung ist.
- Große Materialauswahl: Dieses Verfahren kann für eine Vielzahl von Kunststoffen verwendet werden, einschließlich Thermoplasten und Duroplasten, was eine flexible Materialwahl ermöglicht.
- Hohe Festigkeit der Produkte: Durch den Einsatz von Druck und Hitze entstehen Produkte mit hoher struktureller Festigkeit und langer Lebensdauer.
- Vielseitigkeit: Heißpressen kann für große und kleine Bauteile sowie für dicke und dünne Werkstücke verwendet werden, was es zu einem universellen Verfahren macht.
3.2. Nachteile
- Hohe Investitionskosten: Die Anschaffung von Heißpressmaschinen und Formen kann sehr teuer sein, was die Anfangsinvestitionen erheblich steigert.
- Langer Produktionszyklus: Im Vergleich zu anderen Formgebungsverfahren, wie dem Spritzguss, ist das Heißpressen oft langsamer, was in der Massenproduktion nachteilig sein kann.
- Einschränkungen bei der Komplexität der Form: Besonders bei komplexeren Geometrien stößt das Heißpressen an seine Grenzen, da es schwierig sein kann, gleichmäßigen Druck auf alle Bereiche des Werkstücks auszuüben.
4. Anwendungsgebiete des Heißpressens
Das Heißpressen von Kunststoff hat in vielen Industrien an Bedeutung gewonnen, da es in der Lage ist, Teile mit hoher Festigkeit und Präzision zu fertigen. Besonders in Branchen, die auf maßgeschneiderte Kunststoffteile angewiesen sind, ist dieses Verfahren weit verbreitet.
4.1. Automobilindustrie
In der Automobilindustrie wird das Heißpressen für die Herstellung von strukturellen Komponenten und Verkleidungsteilen aus Kunststoff eingesetzt. Dazu gehören Bauteile wie Stoßfänger, Armaturenbretter und Türverkleidungen, die sowohl ästhetischen als auch funktionalen Ansprüchen gerecht werden müssen. Heißpressen ermöglicht es, diese Teile in hoher Qualität und mit minimalen Toleranzen herzustellen.
4.2. Elektronikindustrie
Die Elektronikbranche nutzt das Heißpressen von Kunststoff für die Herstellung von Gehäusen, Steckverbindern und Isolationsmaterialien. Diese Bauteile müssen präzise gefertigt und oft hitzebeständig sein, da sie unter extremen Bedingungen arbeiten. Das Heißpressen bietet hier die Möglichkeit, Teile zu produzieren, die sowohl funktional als auch langlebig sind.
4.3. Luft- und Raumfahrtindustrie
In der Luft- und Raumfahrtindustrie werden hochfeste, leichte Bauteile benötigt, die extremen Bedingungen standhalten können. Heißgepresste Kunststoffe bieten hier eine hervorragende Lösung, da sie eine hohe Festigkeit aufweisen und gleichzeitig das Gewicht reduzieren. In diesem Bereich werden vor allem Faserverbundwerkstoffe und thermoplastische Kunststoffe verwendet.
4.4. Medizintechnik
Auch in der Medizintechnik ist das Heißpressen ein unverzichtbares Verfahren. Es wird zur Herstellung von medizinischen Geräten, Instrumenten und Implantaten verwendet. Besonders in diesem Sektor sind Präzision, Sterilität und Langlebigkeit von entscheidender Bedeutung, was das Heißpressen zu einer bevorzugten Methode macht.
5. Neue Entwicklungen im Heißpressen von Kunststoffen
Die Technologie des Heißpressens entwickelt sich ständig weiter, um den steigenden Anforderungen der Industrie gerecht zu werden. Neue Materialien, Automatisierung und verbesserte Steuerungssysteme haben das Verfahren effizienter und vielseitiger gemacht.
5.1. Verwendung von Faserverbundwerkstoffen
Eine der interessantesten Entwicklungen im Bereich des Heißpressens ist die zunehmende Verwendung von faserverstärkten Kunststoffen. Diese Materialien kombinieren die Festigkeit von Fasern (z.B. Glas- oder Kohlefaser) mit der Flexibilität von Kunststoffen und ergeben so ein leichtes, aber starkes Endprodukt. Besonders in der Automobil- und Luftfahrtindustrie wird diese Technologie zunehmend eingesetzt, um das Gewicht von Bauteilen zu reduzieren und gleichzeitig ihre Festigkeit zu erhöhen.
5.2. Fortschritte in der Prozessautomatisierung
Moderne Heißpressmaschinen sind oft mit hochentwickelten Automatisierungssystemen ausgestattet, die es ermöglichen, den gesamten Prozess zu steuern und zu überwachen. Dies führt zu einer höheren Effizienz und einer geringeren Fehlerquote, was besonders in der Massenproduktion von Vorteil ist. Darüber hinaus ermöglichen Automatisierungssysteme die Anpassung der Parameter in Echtzeit, was zu einer höheren Flexibilität bei der Herstellung führt.
5.3. Nachhaltigkeit im Heißpressprozess
Mit dem zunehmenden Fokus auf Nachhaltigkeit in der Fert
igung spielen auch umweltfreundliche Materialien und Verfahren im Heißpressen eine immer größere Rolle. Unternehmen entwickeln zunehmend biologisch abbaubare Kunststoffe und recycelbare Materialien, die im Heißpressverfahren verwendet werden können, um die Umweltbelastung zu reduzieren.
Gummikissenpressen stellen eine spezielle Art von Umformpressen dar, die in der Industrie zur Herstellung komplexer Bauteile aus Metall und Kunststoff eingesetzt werden. Diese Maschinen nutzen Gummikissen als flexible Matrizen, um Werkstücke unter hohen Drücken zu formen. Durch den Einsatz von Gummikissen wird eine gleichmäßige Verteilung des Drucks über das gesamte Werkstück erreicht, was besonders bei der Bearbeitung von Blechen mit komplexen Geometrien von Vorteil ist.
In diesem umfassenden Text werden die Funktionsweise und Besonderheiten von Gummikissenpressen erläutert. Es werden die Vorteile, Anwendungsgebiete sowie die Entwicklung und Zukunftsperspektiven dieser Technologie betrachtet.
1. Grundlagen des Gummikissenpressens
Das Gummikissenpressen ist ein Verfahren, das auf der Verwendung eines flexiblen Gummikissens basiert, welches als Matrize dient. Das Gummikissen wird in einem geschlossenen Raum unter Druck gesetzt, um das Werkstück gegen eine starre Form zu pressen. Dieses Verfahren ermöglicht es, Werkstücke mit komplexen Geometrien zu formen, die mit herkömmlichen Pressverfahren nur schwer realisierbar wären.
1.1. Aufbau und Funktionsweise
Eine typische Gummikissenpresse besteht aus zwei Hauptelementen: dem Gummikissen und einem starren Werkzeug, das als Form dient. Das Gummikissen wird durch hydraulischen Druck aufgeblasen und verformt das Werkstück, das zwischen dem Kissen und der starren Form eingespannt ist. Der flexible Charakter des Gummikissens ermöglicht eine gleichmäßige Verteilung des Drucks, wodurch das Werkstück präzise in die gewünschte Form gebracht wird.
Das Verfahren ist besonders gut geeignet für das Umformen von Blechen und die Herstellung von Bauteilen mit komplizierten Konturen, da das Gummikissen in der Lage ist, sich an unregelmäßige Oberflächen anzupassen.
1.2. Materialwahl für Gummikissen
Die Gummikissen in diesen Pressen bestehen in der Regel aus hochfestem, hitzebeständigem Gummi, der den extremen Bedingungen des Umformprozesses standhält. Diese Materialien sind darauf ausgelegt, eine Vielzahl von Zyklen zu überstehen, ohne ihre Elastizität zu verlieren. Es gibt verschiedene Arten von Gummikissen, die je nach Anforderung an das Werkstück und die Produktion ausgewählt werden können.
Hochleistungskissen bestehen oft aus synthetischen Gummimaterialien wie Silikon oder Polyurethan, die eine hohe Beständigkeit gegen Abrieb, Hitze und Druck aufweisen.
2. Arten von Gummikissenpressen
Es gibt verschiedene Arten von Gummikissenpressen, die sich je nach Einsatzgebiet und Anforderungen unterscheiden. Jede Art ist auf spezifische industrielle Anwendungen zugeschnitten und bietet ihre eigenen Vorteile.
2.1. Einfach wirkende Gummikissenpressen
Einfach wirkende Gummikissenpressen sind die gängigste Form dieser Maschinen. Bei diesen Pressen wird das Gummikissen von einer Seite gegen das Werkstück gedrückt, um es in die starre Form zu pressen. Diese Maschinen sind ideal für die Herstellung von Bauteilen mit flachen oder leicht gekrümmten Oberflächen.
Einfach wirkende Pressen werden häufig in der Automobilindustrie zur Herstellung von Karosserieteilen und anderen Strukturkomponenten eingesetzt.
2.2. Doppelt wirkende Gummikissenpressen
Doppelt wirkende Gummikissenpressen verwenden zwei Gummikissen, die das Werkstück von beiden Seiten unter Druck setzen. Diese Pressen sind für komplexere Geometrien ausgelegt, bei denen das Werkstück von beiden Seiten verformt werden muss. Sie bieten eine höhere Flexibilität und können in einem einzigen Arbeitsgang mehrfache Umformungen durchführen.
Diese Maschinen finden in der Luft- und Raumfahrt sowie in der Herstellung von Spezialteilen Anwendung, bei denen höchste Präzision gefordert ist.
2.3. Hydraulische Gummikissenpressen
Hydraulische Gummikissenpressen nutzen hydraulischen Druck, um das Gummikissen gegen das Werkstück zu pressen. Diese Maschinen sind besonders leistungsstark und können hohe Drücke erzeugen, was sie ideal für die Bearbeitung von dicken und widerstandsfähigen Materialien macht. Sie werden häufig für die Herstellung von Metallkomponenten eingesetzt, die hohen Belastungen standhalten müssen.
3. Vorteile des Gummikissenpressens
Das Gummikissenpressen bietet zahlreiche Vorteile gegenüber herkömmlichen Umformverfahren. Diese Vorteile machen die Technologie besonders attraktiv für Industrien, die auf Präzision und Flexibilität angewiesen sind.
3.1. Gleichmäßige Druckverteilung
Einer der größten Vorteile des Gummikissenpressens ist die gleichmäßige Druckverteilung über das gesamte Werkstück. Da das Gummikissen flexibel ist, kann es sich an die Form des Werkstücks anpassen und gleichmäßig Druck auf alle Bereiche ausüben. Dies ist besonders vorteilhaft bei der Bearbeitung von Blechen mit unregelmäßigen oder komplexen Geometrien, da Verformungen minimiert und die Maßgenauigkeit erhöht werden.
3.2. Flexibilität bei der Materialwahl
Das Gummikissenpressen kann für eine Vielzahl von Materialien verwendet werden, darunter Stahl, Aluminium, Kupfer und verschiedene Kunststoffe. Die Flexibilität des Gummikissens ermöglicht es, Werkstücke unterschiedlicher Materialstärken und -arten in derselben Maschine zu bearbeiten, was die Vielseitigkeit des Verfahrens erhöht.
3.3. Kosteneffizienz
Obwohl Gummikissenpressen in der Anschaffung teurer sein können als herkömmliche Pressen, bieten sie langfristig erhebliche Kosteneinsparungen. Die Flexibilität der Maschine und die Möglichkeit, verschiedene Materialien und Formen ohne kostspielige Werkzeugwechsel zu verarbeiten, reduzieren die Produktionskosten und erhöhen die Effizienz. Zudem sind Gummikissen in der Regel langlebig und müssen nur selten ausgetauscht werden.
3.4. Schonende Materialverarbeitung
Ein weiterer Vorteil ist die schonende Behandlung des Materials. Da das Gummikissen den Druck gleichmäßig verteilt, treten weniger Spannungen und Verformungen im Material auf. Dies führt zu einer höheren Qualität der fertigen Werkstücke und reduziert die Notwendigkeit für Nachbearbeitungen.
4. Anwendungsgebiete der Gummikissenpressen
Gummikissenpressen finden in einer Vielzahl von Industrien Anwendung, insbesondere dort, wo komplexe Bauteile mit hohen Anforderungen an Präzision und Maßgenauigkeit gefertigt werden müssen.
4.1. Automobilindustrie
In der Automobilindustrie werden Gummikissenpressen häufig zur Herstellung von Karosserieteilen, Verkleidungen und Strukturbauteilen verwendet. Die gleichmäßige Druckverteilung ermöglicht es, Bauteile mit komplexen Geometrien und engen Toleranzen herzustellen, was für die Fahrzeugproduktion von entscheidender Bedeutung ist. Auch dünne Bleche, wie sie oft in der Automobilproduktion verwendet werden, lassen sich effizient und präzise verformen.
4.2. Luft- und Raumfahrt
Die Luft- und Raumfahrtindustrie stellt hohe Anforderungen an die Präzision und Festigkeit der Bauteile. Gummikissenpressen werden hier eingesetzt, um leichte, aber hochfeste Komponenten aus Aluminium und Titan zu fertigen, die den extremen Belastungen in der Luft- und Raumfahrt standhalten müssen. Da viele dieser Bauteile komplexe Formen aufweisen, ist die Flexibilität der Gummikissenpressen ein großer Vorteil.
4.3. Elektronikindustrie
Auch in der Elektronikindustrie werden Gummikissenpressen verwendet, insbesondere zur Herstellung von Gehäusen und Bauteilen für elektronische Geräte. Die Fähigkeit, dünne und empfindliche Materialien präzise zu formen, ist hier von großer Bedeutung. Gummikissenpressen ermöglichen es, kleine und komplexe Teile herzustellen, die in der modernen Elektronikproduktion häufig benötigt werden.
4.4. Bauindustrie
In der Bauindustrie finden Gummikissenpressen Anwendung bei der Herstellung von Bauelementen, Fassaden und Verkleidungen. Diese Bauteile müssen sowohl funktional als auch ästhetisch ansprechend sein. Gummikissenpressen ermöglichen es, Bauteile mit glatten Oberflächen und gleichmäßigen Verformungen zu fertigen, was bei der Gestaltung moderner Gebäude von Vorteil ist.
5. Herausforderungen und Weiterentwicklungen
Obwohl Gummikissenpressen viele Vorteile bieten, gibt es auch Herausforderungen, die bei der Implementierung und Nutzung dieser Technologie berücksichtigt werden müssen.
5.1. Hohe Investitionskosten
Die Anschaffungskosten für Gummikissenpressen sind im Vergleich zu herkömmlichen Pressen relativ hoch. Besonders die Herstellung der Gummikissen und deren Anpassung an spezifische Produktionsanforderungen können kostspielig sein. Allerdings amortisieren sich diese Investitionen oft durch die Kosteneinsparungen in der Produktion und die Flexibilität der Maschinen.
5.2. Begrenzte Lebensdauer der Gummikissen
Obwohl die Gummikissen in den Pressen robust und langlebig sind, unterliegen sie dennoch einem Verschleiß. Besonders bei der Verarbeitung harter Materialien oder bei hohen Drücken können die Gummikissen beschädigt werden und müssen ausgetauscht werden. Die Lebensdauer der Kissen hängt stark von der Art der verwendeten Materialien und der Intensität der Nutzung ab.
5.3. Entwicklungen in der Automatisierung
Ein Bereich, in dem Gummikissenpressen weiterentwickelt werden, ist die Automatisierung. Moderne Gummikissenpressen sind oft mit automatischen Steuerungssystemen ausgestattet, die den Druck und die Temperatur während des gesamten Umformprozesses überwachen und anpassen. Dies ermöglicht eine höhere Präzision und Effizienz in der Produktion. Zukünftige Entwicklungen zielen darauf ab, die Automatisierung noch weiter voranzutreiben und die Integration in Industrie-4.0-Umgebungen zu erleichtern.
Das Formpressen von Kunststoff ist eines der wichtigsten und am weitesten verbreiteten Verfahren zur Herstellung von Bauteilen aus thermoplastischen und duroplastischen Kunststoffen. Dieses Verfahren ermöglicht es, Materialien in feste, definierte Formen zu bringen, indem Druck und Wärme auf ein Kunststoffmaterial ausgeübt werden. Das resultierende Bauteil besitzt die gewünschte Geometrie und kann sowohl funktionale als auch ästhetische Eigenschaften haben.
In diesem umfassenden Text wird das Formpressen von Kunststoff in all seinen Facetten beleuchtet. Angefangen von den Grundlagen und der Funktionsweise des Verfahrens über die unterschiedlichen Arten des Formpressens bis hin zu den zahlreichen Anwendungsgebieten und den Zukunftsaussichten dieses bedeutenden Herstellungsverfahrens.
1. Grundlagen des Formpressens
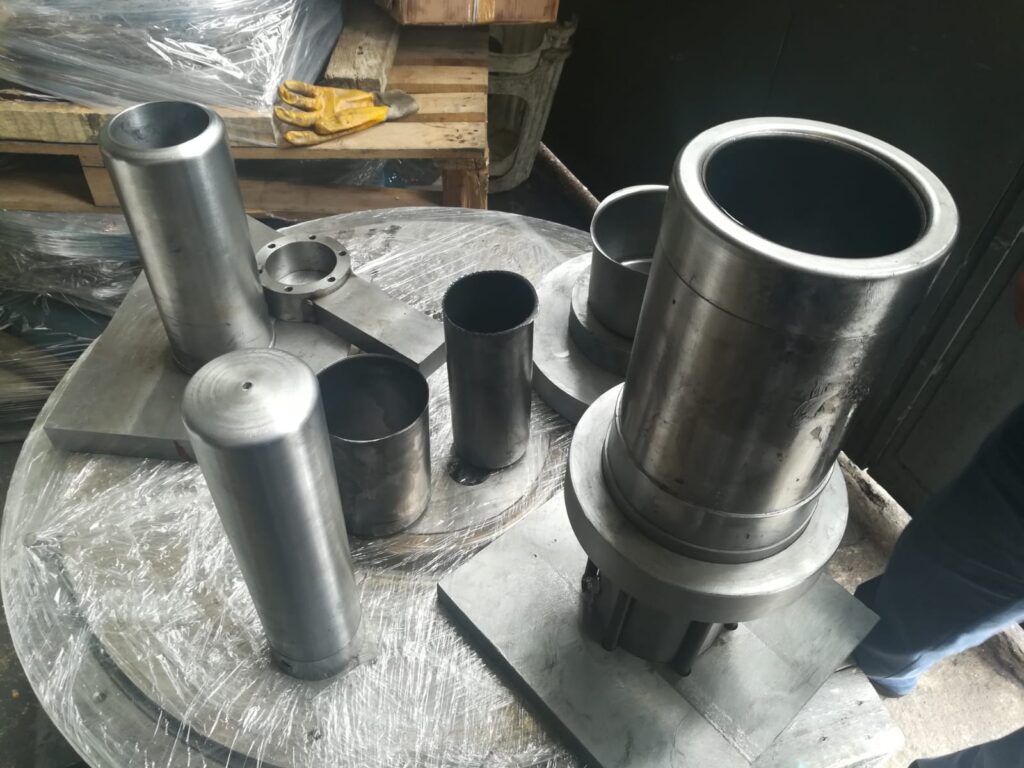
Das Formpressen von Kunststoff ist ein Umformverfahren, bei dem ein Kunststoffmaterial in eine Form eingebracht und unter Anwendung von Druck und Wärme in die gewünschte Form gepresst wird. Die Eigenschaften des fertigen Bauteils hängen von mehreren Faktoren ab, wie der Art des Kunststoffs, der Temperatur, dem Druck und der Geometrie der Form.
1.1. Verfahren
Beim Formpressen wird das Kunststoffmaterial – in der Regel in Form von Pulver, Granulat oder Platten – in eine vorgeheizte Form gegeben. Diese Form besteht aus zwei Hälften, die beim Schließen der Presse das Material umschließen. Durch den Druck, der auf das Material ausgeübt wird, passt es sich der Form an und erhält seine endgültige Gestalt.
Die Form wird nach Erreichen der gewünschten Aushärtung oder Abkühlung geöffnet, und das fertige Bauteil kann entnommen werden. Je nach Art des verwendeten Kunststoffs kann dieser Schritt variieren, da Thermoplaste und Duroplaste unterschiedlich verarbeitet werden.
1.2. Materialwahl
Für das Formpressen eignen sich verschiedene Kunststoffarten, wobei Thermoplaste und Duroplaste die beiden Hauptgruppen darstellen. Thermoplaste können mehrfach erhitzt und geformt werden, was das Formpressen zu einem flexiblen und wiederholbaren Prozess macht. Duroplaste hingegen härten bei der Verarbeitung irreversibel aus und sind besonders für Anwendungen geeignet, bei denen hohe Festigkeit und Temperaturbeständigkeit gefordert sind.
2. Arten des Formpressens
Es gibt verschiedene Arten des Formpressens, die sich durch die spezifische Art der Materialzufuhr, den Druckaufbau und die Geometrie der Bauteile unterscheiden. Diese Varianten des Formpressens sind auf unterschiedliche Anwendungsfälle und Materialanforderungen abgestimmt.
2.1. Heißpressen
Beim Heißpressen wird das Kunststoffmaterial in die vorgeheizte Form eingelegt, die dann unter Druck geschlossen wird. Das Material wird dabei unter hoher Temperatur verformt und passt sich der Form an. Heißpressen wird vor allem für Duroplaste und Verbundwerkstoffe eingesetzt, da diese unter Wärmeeinwirkung vernetzen und aushärten.
Diese Art des Formpressens wird häufig bei der Herstellung von Komponenten eingesetzt, die hohe Anforderungen an die mechanischen Eigenschaften haben, wie z. B. Bauteile für die Automobil- und Elektroindustrie.
2.2. Kaltpressen
Das Kaltpressen ist eine Variante des Formpressens, bei der das Kunststoffmaterial bei Raumtemperatur in die Form eingegeben wird. Der Druck formt das Material ohne zusätzliche Wärmezufuhr. Diese Methode wird vor allem für thermoplastische Materialien angewendet, die bereits durch den Druck geformt werden können.
Das Kaltpressen bietet den Vorteil einer schnelleren Verarbeitungszeit, da keine Energie für das Erhitzen des Materials aufgewendet werden muss. Diese Technik wird häufig in der Verpackungsindustrie eingesetzt, wo eine schnelle und effiziente Herstellung von Produkten erforderlich ist.
2.3. Pulverpressen
Beim Pulverpressen wird Kunststoffmaterial in Pulverform verwendet. Dieses Pulver wird in die Form eingefüllt und anschließend durch Druck und manchmal auch Wärme zu einem festen Bauteil geformt. Das Pulverpressen ist besonders geeignet für die Herstellung von Bauteilen mit sehr feinen Strukturen oder komplexen Geometrien.
Diese Methode findet Anwendung in der Elektronikindustrie, wo kleine, präzise Bauteile benötigt werden, die hohe Festigkeit und Stabilität bieten müssen.
3. Vorteile des Formpressens
Das Formpressen von Kunststoff bietet eine Reihe von Vorteilen, die es zu einem bevorzugten Verfahren in vielen Industrien machen. Diese Vorteile umfassen sowohl technische als auch wirtschaftliche Aspekte.
3.1. Vielseitigkeit
Einer der größten Vorteile des Formpressens ist seine Vielseitigkeit. Das Verfahren kann für eine breite Palette von Kunststoffarten eingesetzt werden, von flexiblen Thermoplasten bis hin zu hochfesten Duroplasten. Zudem ist das Formpressen in der Lage, Bauteile mit unterschiedlichen Geometrien, Größen und Materialstärken herzustellen, was es für verschiedene Anwendungsbereiche geeignet macht.
3.2. Kosteneffizienz
Das Formpressen ist im Vergleich zu anderen Umformverfahren wie dem Spritzgießen oder dem Extrudieren oft kostengünstiger, besonders bei kleineren Stückzahlen oder bei der Herstellung von Prototypen. Die Formen, die beim Formpressen verwendet werden, sind in der Regel einfacher und günstiger herzustellen, was die anfänglichen Investitionskosten senkt.
3.3. Hohe Materialausnutzung
Ein weiterer Vorteil des Formpressens ist die hohe Materialausnutzung. Da das Material während des Pressvorgangs exakt in die Form gebracht wird, gibt es nur sehr wenig Materialabfall. Dies ist besonders vorteilhaft in Industrien, in denen die Materialkosten eine wichtige Rolle spielen.
3.4. Präzision und Maßgenauigkeit
Das Formpressen ermöglicht die Herstellung von Bauteilen mit hoher Maßgenauigkeit und Oberflächenqualität. Besonders bei Anwendungen, bei denen enge Toleranzen gefordert sind, wie z. B. in der Elektronik- oder Luftfahrtindustrie, bietet das Formpressen eine hohe Präzision.
4. Anwendungsgebiete des Formpressens
Das Formpressen von Kunststoff wird in einer Vielzahl von Industrien eingesetzt, da es für die Herstellung von Bauteilen mit unterschiedlichen Anforderungen geeignet ist. Hier sind einige der wichtigsten Anwendungsgebiete dieses Verfahrens.
4.1. Automobilindustrie
In der Automobilindustrie wird das Formpressen von Kunststoff häufig zur Herstellung von Verkleidungen, Strukturkomponenten und anderen Bauteilen eingesetzt. Besonders Duroplaste finden hier Anwendung, da sie eine hohe Festigkeit und Temperaturbeständigkeit aufweisen. Die Fähigkeit, komplexe Formen herzustellen, macht das Formpressen besonders attraktiv für diese Branche.
4.2. Elektronikindustrie
Die Elektronikindustrie profitiert von der Präzision und Maßgenauigkeit des Formpressens. Gehäuse, Halterungen und andere Bauteile für elektronische Geräte werden häufig durch Formpressen hergestellt. Insbesondere das Pulverpressen ermöglicht die Herstellung kleiner, komplexer Bauteile mit hoher Genauigkeit.
4.3. Luft- und Raumfahrtindustrie
Auch in der Luft- und Raumfahrtindustrie spielt das Formpressen eine wichtige Rolle. Leichte und hochfeste Bauteile aus Verbundwerkstoffen, die den extremen Belastungen in der Luftfahrt standhalten müssen, werden oft durch Formpressen hergestellt. Diese Bauteile müssen sowohl funktionale als auch sicherheitstechnische Anforderungen erfüllen.
4.4. Verpackungsindustrie
In der Verpackungsindustrie wird das Formpressen häufig eingesetzt, um Verpackungen und Behälter aus Kunststoff herzustellen. Diese Bauteile müssen oft flexibel und kostengünstig in großen Stückzahlen produziert werden. Hier bietet das Kaltpressen eine schnelle und effiziente Lösung.
5. Herausforderungen und Weiterentwicklungen
Trotz der zahlreichen Vorteile des Formpressens gibt es auch Herausforderungen, die mit dem Verfahren verbunden sind. Dazu zählen insbesondere die technischen Anforderungen an die Maschinen sowie die Auswahl der richtigen Materialien.
5.1. Hohe Anfangsinvestitionen
Die Herstellung der Presswerkzeuge und Formen kann kostspielig sein, insbesondere bei komplexen Geometrien. Diese hohen Investitionskosten können für kleine Unternehmen oder bei der Herstellung von Prototypen eine Herausforderung darstellen.
5.2. Einschränkungen bei der Formgebung
Obwohl das Formpressen in vielen Bereichen sehr flexibel ist, gibt es Einschränkungen bei der Formgebung, insbesondere bei extrem komplexen oder filigranen Geometrien. In solchen Fällen müssen oft zusätzliche Bearbeitungsschritte wie das Nachschneiden oder Bohren eingesetzt werden.
5.3. Materialauswahl
Die Auswahl des richtigen Materials ist entscheidend für den Erfolg des Formpressens. Besonders bei Duroplasten, die während des Pressvorgangs irreversibel aushärten, müssen Materialeigenschaften wie Festigkeit, Temperaturbeständigkeit und Aushärtezeit genau berücksichtigt werden.
5.4. Automatisierung und Industrie 4.0
Mit dem zunehmenden Einsatz von Automatisierung und Industrie-4.0-Technologien entwickeln sich auch die Formpressverfahren weiter. Moderne Maschinen sind oft mit Sensoren und Steuerungssystemen ausgestattet, die den Prozess in Echtzeit überwachen und anpassen können. Dies ermöglicht eine höhere Effizienz, Präzision und Flexibilität in der Produktion.
Gummipressen spielen eine zentrale Rolle in der Herstellung von elastomeren Bauteilen. Von Dichtungen und Dämpfern bis hin zu Reifen und komplexen Gummi-Metall-Verbindungen – Gummipressen sind in vielen Industrien unverzichtbar. Dieses Verfahren bietet sowohl technologische Präzision als auch Flexibilität, was es ideal für die Verarbeitung von Gummi und ähnlichen Materialien macht.
In diesem Text geben wir einen umfassenden Überblick über die Funktionsweise, die verschiedenen Typen von Gummipressen, deren Einsatzmöglichkeiten sowie die Herausforderungen und Zukunftsperspektiven in diesem Bereich.
1. Die Grundlagen der Gummipressen
Gummipressen sind spezielle Maschinen, die verwendet werden, um Rohgummi oder elastomere Materialien in eine Form zu bringen und diese unter Druck und Wärme zu vulkanisieren. Während des Pressvorgangs wird das Gummimaterial in die Form eingeführt, wo es unter dem Einfluss von Wärme und Druck seine endgültige Struktur erhält.
1.1. Vulkanisation und deren Bedeutung
Ein entscheidender Schritt in der Verarbeitung von Gummi ist die Vulkanisation. Bei diesem Prozess werden Schwefelverbindungen in das Gummimaterial eingebracht, wodurch das Material eine dauerhafte, vernetzte Struktur erhält. Diese Vernetzung verbessert die Festigkeit, Elastizität und Temperaturbeständigkeit des Gummis und ist ein wesentlicher Bestandteil des Gummipressverfahrens.
Die Vulkanisation verleiht dem Gummi zudem eine erhöhte Beständigkeit gegen chemische Einflüsse, Abnutzung und Witterungseinflüsse, was es ideal für den Einsatz in anspruchsvollen Anwendungen wie der Automobil- und Luftfahrtindustrie macht.
1.2. Funktionsweise von Gummipressen
Eine Gummipresse besteht in der Regel aus zwei Hauptkomponenten: dem Ober- und dem Unterwerkzeug, die zusammen eine Form bilden. In diese Form wird der Rohgummi eingelegt, der anschließend unter Druck und Hitze in die gewünschte Form gepresst und vulkanisiert wird.
Die Temperaturen während des Vulkanisationsprozesses liegen in der Regel zwischen 150 und 200 Grad Celsius, während der Druck je nach Anwendung und Material bei mehreren Tonnen liegen kann. Dieser Druck sorgt dafür, dass sich das Material gleichmäßig in der Form verteilt und alle Ecken und Kanten ausfüllt.
2. Verschiedene Arten von Gummipressen
Es gibt verschiedene Typen von Gummipressen, die sich je nach Anwendungsbereich und den spezifischen Anforderungen des herzustellenden Produkts unterscheiden. Zu den gängigsten Pressenarten gehören die folgenden:
2.1. Transferpressen
Transferpressen sind eine der am häufigsten verwendeten Arten von Gummipressen. Bei diesem Verfahren wird der Rohgummi zunächst in eine Kammer über der Form gegeben und anschließend durch einen Kolben in die Form gepresst. Der Druck und die Wärme führen zur Vulkanisation des Gummis.
Transferpressen bieten den Vorteil, dass sie auch für komplexe Bauteile mit filigranen Strukturen geeignet sind. Zudem ermöglicht dieses Verfahren eine hohe Präzision und Wiederholbarkeit, was es ideal für die Herstellung von Dichtungen und anderen hochpräzisen Gummibauteilen macht.
2.2. Kompressionspressen
Bei Kompressionspressen wird der Rohgummi direkt in die offene Form eingelegt, die anschließend geschlossen und unter Druck gesetzt wird. Dieses Verfahren ist besonders geeignet für größere Bauteile oder Produkte mit einfacher Geometrie. Die Kompressionspresse ist eine der ältesten und bewährtesten Methoden zur Verarbeitung von Gummi und wird bis heute in vielen Industrien eingesetzt.
Ein Vorteil der Kompressionspressen ist die einfache Handhabung und die vergleichsweise geringen Maschinenkosten. Allerdings ist der Materialüberschuss bei diesem Verfahren oft größer, da der Rohgummi vor dem Schließen der Form manuell dosiert werden muss.
2.3. Spritzpressen
Die Spritzpresse, auch Spritzgussmaschine genannt, kombiniert die Vorteile des Spritzgießens mit der Präzision einer Gummipresse. Bei diesem Verfahren wird der Rohgummi in einem Extruder aufbereitet und anschließend unter hohem Druck in die Form gespritzt. Dies ermöglicht eine schnelle und effiziente Produktion von Bauteilen, insbesondere bei großen Stückzahlen.
Spritzpressen werden häufig in der Automobil- und Konsumgüterindustrie eingesetzt, wo hohe Produktionsraten gefordert sind. Sie bieten den Vorteil einer hohen Automatisierung und minimalem Materialverlust, da der Gummi präzise dosiert und in die Form eingespritzt wird.
3. Vorteile der Gummipressen
Gummipressen bieten eine Vielzahl von Vorteilen, die sie zu einer bevorzugten Wahl für die Herstellung von elastomeren Bauteilen machen. Diese Vorteile liegen sowohl in der Flexibilität des Verfahrens als auch in den technischen Eigenschaften der gepressten Bauteile.
3.1. Vielseitigkeit
Einer der größten Vorteile von Gummipressen ist ihre Vielseitigkeit. Sie können für die Herstellung einer breiten Palette von Bauteilen eingesetzt werden, von einfachen Gummidichtungen bis hin zu komplexen Gummi-Metall-Verbindungen. Zudem eignen sich Gummipressen für die Verarbeitung verschiedener Gummisorten, darunter Naturkautschuk, synthetischer Kautschuk und Silikone.
3.2. Hohe Präzision
Moderne Gummipressen bieten eine hohe Präzision bei der Herstellung von Bauteilen. Dies ist besonders wichtig in Industrien wie der Automobil- oder Medizintechnik, wo enge Toleranzen und eine hohe Maßgenauigkeit gefordert sind. Durch den Einsatz von präzisen Formen und computergesteuerten Maschinen können Bauteile hergestellt werden, die den höchsten Qualitätsstandards entsprechen.
3.3. Effizienz
Durch den hohen Automatisierungsgrad moderner Gummipressen kann eine schnelle und effiziente Produktion gewährleistet werden. Dies führt zu kürzeren Zykluszeiten und einer höheren Produktionskapazität, was insbesondere in der Massenproduktion von Vorteil ist. Gleichzeitig sorgen präzise Steuerungssysteme dafür, dass der Materialverbrauch optimiert und der Abfall minimiert wird.
4. Anwendungsgebiete der Gummipressen
Gummipressen werden in einer Vielzahl von Industrien eingesetzt, da sie für die Herstellung unterschiedlichster elastomerer Bauteile geeignet sind. Hier sind einige der wichtigsten Anwendungsgebiete:
4.1. Automobilindustrie
In der Automobilindustrie spielen Gummipressen eine zentrale Rolle bei der Herstellung von Dichtungen, Schläuchen, Dämpfungselementen und Reifen. Gummi wird hier aufgrund seiner hohen Elastizität, Beständigkeit und Dämpfungseigenschaften geschätzt. Gummipressen ermöglichen die präzise und effiziente Produktion dieser Bauteile, die den hohen Belastungen im Fahrzeuginnen- und Außenbereich standhalten müssen.
4.2. Bauindustrie
In der Bauindustrie werden Gummipressen zur Herstellung von Dichtungen und Isoliermaterialien verwendet. Gummidichtungen spielen eine wichtige Rolle beim Abdichten von Fenstern, Türen und Fugen, um das Eindringen von Wasser und Luft zu verhindern. Die Flexibilität und Beständigkeit von Gummi machen es zu einem idealen Material für diese Anwendungen.
4.3. Medizintechnik
In der Medizintechnik werden Gummipressen zur Herstellung von medizinischen Geräten und Bauteilen wie Spritzenkolben, Dichtungen und Schläuchen eingesetzt. Die Anforderungen an die Hygiene und Präzision in diesem Bereich sind besonders hoch, und Gummipressen ermöglichen die Herstellung von Bauteilen, die diesen strengen Anforderungen gerecht werden.
4.4. Luft- und Raumfahrtindustrie
Auch in der Luft- und Raumfahrtindustrie kommen Gummipressen zum Einsatz. Hier werden elastomere Bauteile benötigt, die extremen Temperaturen und Druckverhältnissen standhalten können. Gummidichtungen und Dämpfer spielen eine entscheidende Rolle für die Sicherheit und Zuverlässigkeit von Flugzeugen und Raumfahrzeugen.
5. Herausforderungen und Zukunftsperspektiven
Obwohl Gummipressen ein bewährtes und vielseitiges Verfahren zur Verarbeitung von Gummi darstellen, gibt es dennoch Herausforderungen, die in der Zukunft gelöst werden müssen.
5.1. Materialoptimierung
Die Auswahl des richtigen Gummimaterials ist entscheidend für die Qualität des Endprodukts. Die Forschung und Entwicklung neuer Elastomermischungen, die verbesserte Eigenschaften wie höhere Temperaturbeständigkeit oder verbesserte Beständigkeit gegen Chemikalien bieten, wird weiterhin ein wichtiges Thema sein.
5.2. Nachhaltigkeit und Recycling
Mit dem steigenden Bewusstsein für Umweltfragen wird auch die Nachhaltigkeit in der Gummiverarbeitung immer wichtiger. Die Entwicklung umweltfreundlicherer Elastomere und Verfahren zur Wiederverwertung von Gummiresten ist ein zentrales Thema in der Branche. Hierbei wird auch der Einsatz von nachwachsenden Rohstoffen wie Naturkautschuk eine immer größere Rolle spielen.
5.3. Automatisierung und Digitalisierung
Die Automatisierung und Digitalisierung von Produktionsprozessen schreiten in allen Industrien voran, und die Gummiverarbeitung bildet hier keine Ausnahme. Moderne Gummipressen sind oft mit Sensoren und Steuerungssystemen ausgestattet, die den Pressvorgang in Echtzeit überwachen und optimieren können. Dies ermöglicht eine noch höhere Präzision und Effizienz in der Produktion.
Einleitung
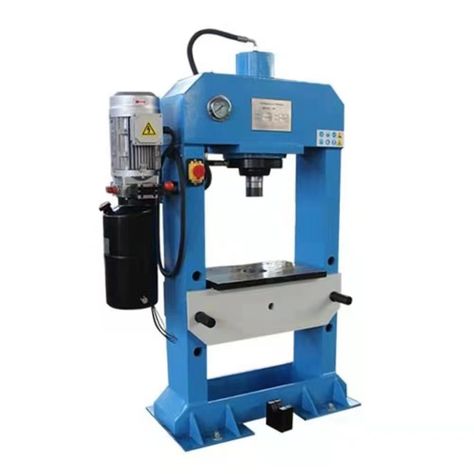
Beheizte Laborpressen sind ein essenzielles Werkzeug in einer Vielzahl von industriellen und wissenschaftlichen Disziplinen. Sie ermöglichen die präzise Kombination von Druck und Wärme, was für viele Produktions- und Forschungsprozesse entscheidend ist. Diese Geräte finden Anwendung in der Materialforschung, Pharmaindustrie, Elektronikherstellung und zahlreichen weiteren Bereichen. Insbesondere bei der Verarbeitung von Polymeren, der Herstellung von Halbleiterkomponenten oder in der Tablettenproduktion spielen sie eine zentrale Rolle.
Die Funktionsweise einer beheizten Laborpresse basiert auf der präzisen Steuerung von Temperatur und Druck, um gewünschte physikalische und chemische Veränderungen in den zu bearbeitenden Materialien zu erzielen. Durch die Erhitzung von Pressplatten, die das Material unter Druck setzen, können Forscher und Ingenieure neue Werkstoffe testen, modifizieren oder produzieren. Im Gegensatz zu herkömmlichen Pressen bietet die beheizte Version entscheidende Vorteile, insbesondere in Bezug auf die Homogenität der Ergebnisse und die Vielseitigkeit der Einsatzmöglichkeiten.
In den folgenden Abschnitten wird eingehend auf die technischen Grundlagen, die verschiedenen Anwendungsbereiche sowie die neuesten Entwicklungen und Herausforderungen eingegangen. Dabei wird deutlich, wie beheizte Laborpressen in modernen Laboren und Produktionsstätten genutzt werden und welche Vorteile sie bieten.
Technischer Überblick und Funktionsweise
Beheizte Laborpressen bestehen im Wesentlichen aus einem Hydrauliksystem, das für den Druck sorgt, und Heizelementen, die die Temperatur der Pressplatten regulieren. Diese Komponenten arbeiten zusammen, um einen kontrollierten Druck und gleichmäßige Wärme auf das zu verarbeitende Material auszuüben.
2.1 Aufbau und Funktionsweise
Eine typische beheizte Laborpresse besteht aus zwei wesentlichen Komponenten:
- Hydraulisches Drucksystem: Dieses System erzeugt den erforderlichen Druck, um das Material zwischen den Heizplatten zu komprimieren. Moderne Laborpressen verwenden in der Regel hydraulische oder pneumatische Systeme, die eine präzise Steuerung des Drucks ermöglichen. Manchmal werden auch mechanische Pressen eingesetzt, besonders wenn es um kleinere Proben oder weniger anspruchsvolle Anwendungen geht.
- Heizsystem: Die Heizplatten bestehen in der Regel aus Aluminium, Edelstahl oder Keramik, je nach Anwendung und Anforderungen an die Wärmeleitung. Die Heizplatten sind oft mit eingebauten Thermoelementen ausgestattet, die die Temperatur an mehreren Punkten messen, um eine gleichmäßige Wärmeverteilung zu gewährleisten. Einige der fortschrittlichsten Modelle verwenden Induktionsheizungen, die eine schnellere und energieeffizientere Erwärmung ermöglichen.
2.2 Steuerung und Regelung der Parameter
Moderne beheizte Laborpressen sind mit fortschrittlichen elektronischen Steuerungen ausgestattet, die eine präzise Regelung der Temperatur und des Drucks ermöglichen. Manche Systeme erlauben es, Temperatur- und Druckprofile zu programmieren, um komplexe Prozesse durchzuführen. Dies ist besonders wichtig bei der Herstellung von Verbundwerkstoffen oder beim Sintern von Materialien, wo Temperaturzyklen entscheidend für die Materialeigenschaften sind.
Fortschritte in der Digitalisierung haben dazu geführt, dass viele Laborpressen heute mit Touchscreen-Displays und computerbasierten Steuerungen ausgestattet sind. Diese Systeme ermöglichen eine Echtzeitüberwachung der Parameter und die automatische Anpassung bei Abweichungen. Solche Systeme können auch mit Datenloggern verbunden werden, um den Prozess für spätere Analysen aufzuzeichnen.
Materialien und wissenschaftliche Grundlagen
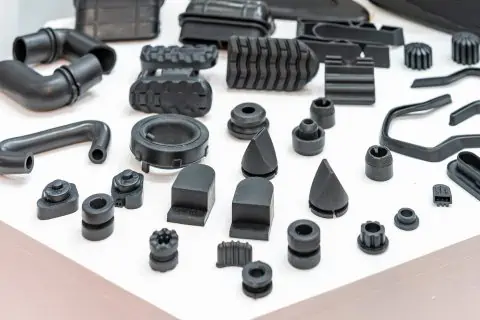
Die Anwendung von Druck und Wärme beeinflusst die molekulare Struktur von Materialien erheblich, insbesondere bei Polymeren und anderen thermoplastischen Werkstoffen. Dies macht beheizte Laborpressen zu einem unverzichtbaren Werkzeug in der Materialwissenschaft.
3.1 Thermodynamik und Materialverhalten
Der Prozess der Wärmeübertragung in einer beheizten Presse spielt eine zentrale Rolle, insbesondere bei der Herstellung von Materialien, die auf der Grundlage von chemischen Reaktionen oder strukturellen Veränderungen ihre endgültigen Eigenschaften annehmen. Während der Druck dafür sorgt, dass sich die Materialien gleichmäßig verteilen und verdichten, beeinflusst die Temperatur das Fließverhalten und die Kristallisation
Die molekulare Struktur von Polymeren verändert sich drastisch, wenn diese sowohl unter Druck als auch unter Hitze gesetzt werden. Viele Polymere, insbesondere Thermoplaste, bestehen aus langen Kettenmolekülen, die bei Raumtemperatur fest oder leicht verformbar sein können. Wird Wärme auf das Polymer angewendet, beginnen diese Molekülketten zu „fließen“ und die Viskosität des Materials nimmt ab. Druck wiederum sorgt dafür, dass diese Moleküle dichter zusammengepresst werden, was zu einer gleichmäßigeren Materialverteilung und verbesserten mechanischen Eigenschaften führt.
Es gibt zwei Haupttypen von Polymeren, die sich unter dem Einfluss von Druck und Temperatur unterschiedlich verhalten:
- Thermoplaste: Diese Polymere erweichen beim Erhitzen und können wiederholt in verschiedene Formen gebracht werden, da ihre molekulare Struktur nicht irreversibel verändert wird. Ein typisches Beispiel ist Polyethylen (PE) oder Polypropylen (PP), die häufig in Laborpressen verarbeitet werden, um Musterplatten, Folien oder Formteile zu fertigen. Durch den Druck während des Erwärmens werden interne Hohlräume eliminiert und das Material verdichtet.
- Duroplaste: Im Gegensatz zu Thermoplasten können Duroplaste (wie Epoxidharze oder Phenolharze) nach der ersten Erwärmung und Aushärtung nicht mehr in eine andere Form gebracht werden. Sie härten aus, indem sie während des Erwärmungsprozesses eine chemische Vernetzungsreaktion durchlaufen. Das Verfahren erfordert die präzise Kontrolle der Temperatur, um ein gleichmäßiges Aushärten und die gewünschten mechanischen Eigenschaften zu erzielen. In der Herstellung von Verbundwerkstoffen, etwa für die Luft- und Raumfahrt, ist dies von großer Bedeutung.
3.3 Einfluss von Druck und Wärme auf Verbundwerkstoffe
Verbundwerkstoffe (Composites) sind Materialien, die aus zwei oder mehr verschiedenen Phasen bestehen – typischerweise eine Matrix und eine Verstärkungsphase. Durch den Einsatz von beheizten Laborpressen wird das Material homogenisiert und durch den Druck gleichmäßig verdichtet, während die Wärme die chemische Verbindung der Bestandteile fördert.
- Polymer-Matrix-Verbundwerkstoffe (PMC): Hierbei handelt es sich um Kunststoffe, die durch Verstärkungsfasern, wie Glasfasern oder Kohlenstofffasern, verstärkt werden. Beheizte Laborpressen spielen eine entscheidende Rolle bei der Herstellung dieser Materialien, da die Matrix (der Kunststoffanteil) unter der kombinierten Wirkung von Wärme und Druck verflüssigt wird, wodurch die Fasern vollständig in die Matrix eingebettet werden. Dies sorgt für hervorragende mechanische Eigenschaften, wie erhöhte Zugfestigkeit, Schlagzähigkeit und Leichtbau.
- Metall-Matrix-Verbundwerkstoffe (MMC): Diese bestehen aus Metall als Matrixmaterial, das durch Keramik- oder Glasfasern verstärkt wird. Bei der Verarbeitung dieser Werkstoffe ist eine präzise Temperaturkontrolle notwendig, da Metalle sehr empfindlich auf thermische Ausdehnung reagieren. Beheizte Laborpressen werden hier zur Verbesserung der Materialeigenschaften eingesetzt, indem sie den Diffusionsprozess zwischen den Metall- und Verstärkungsphasen unterstützen.
- Keramik-Matrix-Verbundwerkstoffe (CMC): Sie werden häufig für Hochtemperaturanwendungen verwendet, z.B. in der Luft- und Raumfahrt. Bei der Herstellung dieser Werkstoffe kommt es vor allem auf die Temperaturstabilität an, und beheizte Laborpressen helfen dabei, porenfreie und homogene Strukturen zu schaffen.
3.4 Sinterprozesse unter Druck und Hitze
Das Sintern ist ein Verfahren, das bei der Herstellung von pulvermetallurgischen Werkstoffen, Keramiken und Verbundstoffen angewendet wird. Durch den Einsatz einer beheizten Laborpresse werden pulverförmige Materialien unter hohen Temperaturen und Druck zu festen Werkstücken verdichtet. Der Prozess beginnt mit der Verdichtung des Pulvers, wobei durch die Wirkung von Druck und Wärme die Partikel miteinander verschmelzen, ohne dass das Material vollständig schmilzt. Sintern wird oft bei der Herstellung von hochpräzisen Komponenten eingesetzt, wie z.B. Zahnrädern, Schneidwerkzeugen oder keramischen Bauteilen.
- Pulvermetallurgie: In der Metallverarbeitung wird das Sintern verwendet, um Materialien mit speziellen mechanischen Eigenschaften herzustellen, wie z.B. poröse Strukturen für Filter oder hochdichte, verschleißfeste Bauteile für Maschinen. Durch den Einsatz einer beheizten Presse wird das Material gleichmäßig verdichtet, was zu einer homogenen Mikrostruktur führt.
- Keramische Werkstoffe: Hier wird das Sintern unter Druck oft zur Herstellung von technischen Keramiken verwendet, die extrem widerstandsfähig gegenüber hohen Temperaturen und chemischen Angriffen sind. Diese Materialien finden Anwendung in der Elektronik, im Maschinenbau und in der medizinischen Technik (z.B. als Implantate oder Zahnersatz).
Erweiterte Anwendungsgebiete
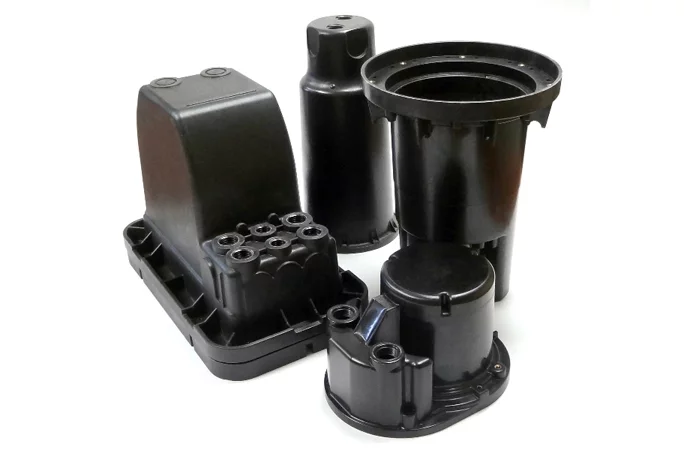
Beheizte Laborpressen haben in den letzten Jahren eine zunehmende Bedeutung in einer Vielzahl von Industrien gewonnen. Die Fähigkeit, sowohl Druck als auch Wärme präzise zu steuern, eröffnet neue Möglichkeiten in der Materialforschung, der Elektronikherstellung, der Pharmazie und vielen weiteren Bereichen.
4.1 Materialwissenschaften und Polymerforschung
In der Polymerforschung spielen beheizte Laborpressen eine zentrale Rolle, insbesondere bei der Entwicklung und Analyse von neuen Polymermaterialien und Verbundwerkstoffen. Die präzise Steuerung der thermischen und mechanischen Bedingungen ist entscheidend, um die gewünschten Materialeigenschaften zu erzielen.
Herstellung von Nanokompositen
Nanokomposite sind Materialien, die durch die Einbettung von Nanopartikeln in eine Polymermatrix hergestellt werden. Diese Materialien bieten einzigartige Eigenschaften, wie z.B. verbesserte mechanische Festigkeit, Leitfähigkeit oder Wärmebeständigkeit. Um diese zu erzeugen, wird eine beheizte Laborpresse verwendet, um die Nanopartikel unter Druck gleichmäßig in das Polymer einzubetten. Bei diesem Prozess ist es besonders wichtig, dass die Temperatur und der Druck genau kontrolliert werden, um eine gleichmäßige Verteilung der Nanopartikel und damit eine homogene Struktur des Materials zu gewährleisten.
Prüfung von recycelbaren Kunststoffen
Mit dem wachsenden Bewusstsein für Umweltprobleme wird auch die Entwicklung und Untersuchung von recycelbaren Kunststoffen immer wichtiger. Beheizte Laborpressen werden verwendet, um recycelte Polymere unter kontrollierten Bedingungen zu verarbeiten und deren mechanische Eigenschaften, wie Zugfestigkeit oder Schlagzähigkeit, zu testen. Dieser Prozess hilft Forschern, das Verhalten von recycelten Kunststoffen bei der Verarbeitung und in der Endanwendung zu verstehen.
4.2 Herstellung von Halbleitern und Elektronik
In der Elektronikindustrie ist die Herstellung von Halbleiterkomponenten ein äußerst präziser Prozess, der sowohl eine hohe Temperaturkontrolle als auch Druck erfordert. Beheizte Laborpressen spielen eine Schlüsselrolle bei der Herstellung von Wafern, dem Grundmaterial für die meisten elektronischen Bauelemente, und beim Laminieren und Bonden von Materialien.
Laminieren und Bonden unter Hitze und Druck
Eine wichtige Anwendung beheizter Laborpressen in der Elektronik ist das Laminieren von Leiterplatten. Dabei werden mehrere Schichten von Leiterplattenmaterialien unter Druck und Hitze zu einer Einheit verbunden. Der Einsatz der Presse stellt sicher, dass die verschiedenen Schichten ohne Lufteinschlüsse oder Verformungen fest miteinander verbunden werden. Dies ist entscheidend für die spätere Funktionalität der Elektronik, da selbst kleinste Unebenheiten oder Luftblasen zu Ausfällen führen können.
Beim Bonden von Halbleitern, einem weiteren wichtigen Schritt in der Elektronikfertigung, sorgt die beheizte Presse für eine gleichmäßige und feste Verbindung der Materialien, oft unter Reinraumbedingungen, um höchste Qualität zu gewährleisten. Hier spielen die Temperaturstabilität und die präzise Steuerung des Anpressdrucks eine zentrale Rolle.
4.3 Pharmazeutische Anwendungen
In der pharmazeutischen Industrie werden beheizte Laborpressen hauptsächlich zur Herstellung von Tabletten und Feststoffformulierungen verwendet. Der Druck und die Temperatur beeinflussen dabei die Konsistenz und die Freisetzungseigenschaften der Tabletten.
Herstellung und Testung von Tabletten
Die Herstellung von Tabletten erfordert die präzise Steuerung des Drucks, um sicherzustellen, dass die aktiven pharmazeutischen Inhaltsstoffe gleichmäßig verteilt und fest miteinander verbunden sind. Gleichzeitig muss die Temperatur kontrolliert werden, um eine stabile Struktur zu gewährleisten, die bei der Einnahme gleichmäßig zerfällt und die Wirkstoffe freisetzt. Beheizte Laborpressen ermöglichen es, diese Bedingungen genau einzustellen und zu überwachen, um eine gleichbleibende Qualität der Tabletten sicherzustellen.
Auch bei der Entwicklung neuer Verabreichungstechnologien, wie retardierten Tabletten oder mehrschichtigen Tabletten, spielen beheizte Pressen eine wichtige Rolle. Diese Technologien erfordern oft die Verarbeitung von verschiedenen Materialschichten, die unter verschiedenen Bedingungen komprimiert und erhitzt werden müssen, um ihre gewünschten Eigenschaften zu entfalten.
Erweiterte Anwendungsgebiete
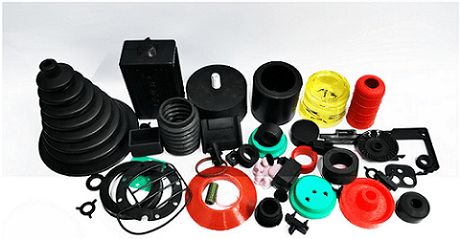
4.4 Textil- und Papierindustrie
Auch in der Textil- und Papierindustrie spielen beheizte Laborpressen eine wichtige Rolle. Sie werden in zahlreichen Verfahren eingesetzt, bei denen es um die Verbesserung der physikalischen Eigenschaften von Textilien oder die Herstellung von Spezialpapieren geht. Von der Veredelung von Geweben bis hin zur Beschichtung von Papieren nutzen Hersteller die Vorteile von präzise kontrollierten Temperaturen und Drücken.
Thermodruck bei Textilien
Beim Thermodruckverfahren werden unter Hitze und Druck Farbstoffe oder Muster auf Textilien aufgebracht. Hierbei wird ein Trägerpapier mit dem gewünschten Muster unter eine beheizte Presse gelegt, auf der sich das zu bedruckende Textil befindet. Durch die gleichmäßige Verteilung von Wärme und Druck wird der Farbstoff auf das Material übertragen. Der Vorteil dieses Verfahrens ist, dass es nicht nur schnelle und präzise Ergebnisse liefert, sondern auch für eine Vielzahl von Textilien, wie Baumwolle, Polyester oder Mischgewebe, anwendbar ist.
Ein innovativer Bereich innerhalb des Textildrucks, in dem beheizte Laborpressen eine Rolle spielen, ist die Entwicklung von funktionalen Textilien, wie etwa hitzebeständige oder wasserabweisende Gewebe. Diese Textilien müssen oft speziellen Beschichtungen unterzogen werden, die unter genau kontrollierten Bedingungen appliziert werden, um ihre Schutzwirkung zu entfalten.
Herstellung von Spezialpapieren
Spezialpapiere, wie sie etwa in der Lebensmittelverpackung, Medizintechnik oder Kunststoffbeschichtung verwendet werden, müssen spezifische mechanische und thermische Eigenschaften aufweisen. Beheizte Laborpressen kommen hier zum Einsatz, um mehrschichtige Papierstrukturen zu erstellen, die etwa eine hohe Reißfestigkeit, Hitzebeständigkeit oder besondere Barriereeigenschaften gegenüber Feuchtigkeit und Luft aufweisen.
Ein weiteres Anwendungsgebiet ist die Prägung von Papieroberflächen. Durch den Einsatz von beheizten Pressplatten können Texturen und Muster auf Papieroberflächen geprägt werden, die sowohl ästhetische als auch funktionale Eigenschaften verbessern. Beispielsweise werden Antirutsch-Oberflächen für Verpackungen oder Texturierungen von Papieren für künstlerische Anwendungen unter Einsatz von Hitze und Druck hergestellt.
4.5 Neue Technologien: Additive Fertigung (3D-Druck) und Nachbearbeitung
In der additiven Fertigung, besser bekannt als 3D-Druck, haben beheizte Laborpressen zunehmend an Bedeutung gewonnen, insbesondere in der Nachbearbeitung und Veredelung von Bauteilen. Der 3D-Druck bietet die Möglichkeit, komplexe geometrische Formen herzustellen, doch die Oberflächenqualität und die mechanischen Eigenschaften der hergestellten Teile sind oft nicht ideal. Beheizte Pressen können verwendet werden, um gedruckte Teile zu verdichten, zu glätten oder mit zusätzlichen Beschichtungen zu versehen, um ihre Funktionalität zu verbessern.
Verdichtung und Glättung von 3D-gedruckten Teilen
Im 3D-Druckverfahren, insbesondere beim Fused Deposition Modeling (FDM), entstehen oft Schichtlinien und Oberflächenrauhigkeiten. Um die mechanischen Eigenschaften der gedruckten Teile zu verbessern, können diese unter Hitze und Druck in einer beheizten Laborpresse verdichtet werden. Der Druck sorgt dafür, dass das Material kompakter wird und die Porosität reduziert wird, während die Wärme das Material leicht aufschmilzt und die Oberflächenstruktur glättet. Dieses Verfahren wird oft bei der Herstellung von Funktionsprototypen oder Endbauteilen eingesetzt, die eine hohe Maßhaltigkeit und Festigkeit erfordern.
Beschichtung und Veredelung von 3D-Druckteilen
Ein weiteres Verfahren, bei dem beheizte Pressen in der additiven Fertigung zum Einsatz kommen, ist die Veredelung von Oberflächen durch spezielle Beschichtungsverfahren. 3D-gedruckte Teile können nachträglich mit hitzebeständigen oder verschleißfesten Schichten versehen werden, die unter Druck und Wärme auf das Bauteil aufgebracht werden. Dies verbessert nicht nur die Haltbarkeit der Teile, sondern kann auch deren thermische und elektrische Eigenschaften optimieren.
4.6 Biotechnologie und Medizintechnik: Herstellung von Implantaten und Prothesen
In der Biotechnologie und Medizintechnik werden beheizte Laborpressen zur Herstellung hochspezialisierter medizinischer Geräte und Implantate eingesetzt. Diese Bereiche erfordern nicht nur absolute Präzision, sondern auch die Verwendung von biokompatiblen Materialien, die unter Druck und Hitze in die gewünschte Form gebracht werden.
Herstellung von medizinischen Implantaten
Implantate, wie künstliche Gelenke oder Zahnimplantate, bestehen oft aus speziellen Materialien, wie Titan oder hochfesten Kunststoffen, die unter hohen Temperaturen und Drücken verarbeitet werden müssen. Beheizte Laborpressen helfen dabei, diese Materialien präzise zu formen und ihre Oberflächenstruktur zu optimieren, um die Biokompatibilität zu gewährleisten.
In der Herstellung von Knochenimplantaten aus biokompatiblen Polymeren, wie etwa Polyetheretherketon (PEEK), werden beheizte Laborpressen verwendet, um das Polymer unter hohen Drücken zu verdichten und in die gewünschte Form zu bringen. Diese Implantate müssen nicht nur extrem stabil sein, sondern auch eine Oberfläche besitzen, die das Einwachsen von Knochengewebe ermöglicht. Beheizte Pressen tragen dazu bei, die feine Struktur der Oberfläche zu formen, die für diese Funktion entscheidend ist.
Herstellung von Prothesen und orthopädischen Hilfsmitteln
Auch in der Prothetik, etwa bei der Herstellung von Gliedmaßenprothesen, kommen beheizte Laborpressen zum Einsatz. Hier werden häufig faserverstärkte Kunststoffe (Verbundwerkstoffe) verwendet, die durch Druck und Hitze stabilisiert und gleichzeitig flexibel genug gemacht werden, um den hohen Anforderungen des täglichen Gebrauchs gerecht zu werden. Moderne Prothesen müssen leicht, widerstandsfähig und komfortabel sein – Anforderungen, die mit Hilfe beheizter Pressen erreicht werden können, indem die mechanischen Eigenschaften der verwendeten Materialien optimiert werden.
Technologische Innovationen und Trends
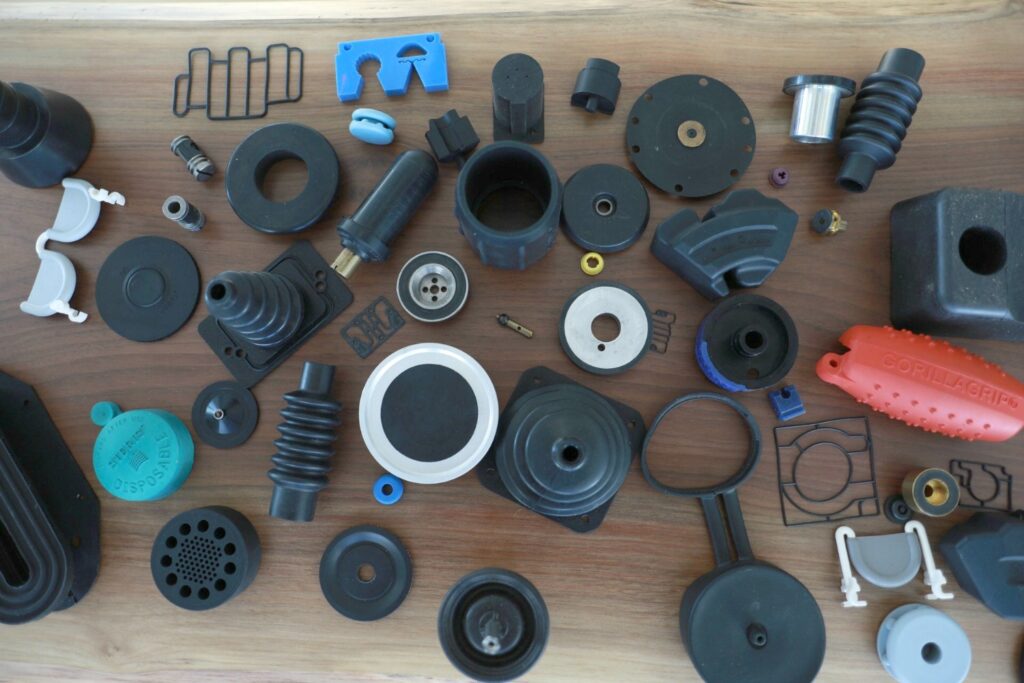
Die technologische Entwicklung bei beheizten Laborpressen ist ein dynamisches Feld, das kontinuierlich neue Innovationen hervorbringt. Moderne Laborpressen sind nicht mehr nur einfache mechanische Geräte, sondern hochspezialisierte Systeme, die mit fortschrittlicher Sensorik, Automatisierung und Digitalisierung ausgestattet sind. Diese Entwicklungen verbessern nicht nur die Effizienz und Präzision, sondern ermöglichen auch neue Anwendungen in der Forschung und Industrie.
5.1 Automatisierung und Digitalisierung
Die Automatisierung von Laborprozessen hat in den letzten Jahren stark zugenommen. Auch bei beheizten Laborpressen spielt diese Entwicklung eine wichtige Rolle. Automatische Steuerungssysteme können heute nicht nur den Druck und die Temperatur überwachen, sondern den gesamten Prozess von der Probenvorbereitung bis zur finalen Verarbeitung vollständig automatisieren.
Intelligente Laborpressen mit Sensorik und maschinellem Lernen
Ein aktueller Trend in der Automatisierung ist der Einsatz von intelligenten Laborpressen, die mit verschiedenen Sensoren ausgestattet sind. Diese Sensoren überwachen in Echtzeit den Druck, die Temperatur, die Materialfeuchtigkeit und andere relevante Parameter und passen die Einstellungen automatisch an, um optimale Ergebnisse zu erzielen. Durch den Einsatz von Künstlicher Intelligenz (KI) und maschinellem Lernen können diese Systeme aus früheren Prozessen lernen und künftige Durchläufe effizienter gestalten.
Beispielsweise kann eine Laborpresse, die zur Herstellung von Verbundwerkstoffen eingesetzt wird, durch den Einsatz von KI feststellen, wie sich verschiedene Materialkombinationen unter Druck und Hitze verhalten. Basierend auf diesen Daten kann das System den optimalen Druck- und Temperaturverlauf vorhersagen, um die gewünschten Materialeigenschaften zu erreichen.
Industrie 4.0 und das vernetzte Labor
Im Rahmen von Industrie 4.0, der zunehmenden Vernetzung und Digitalisierung von Produktionsprozessen, sind auch Laborpressen zunehmend in ein vernetztes Laborumfeld integriert. Solche Pressen können mit anderen Laborgeräten kommunizieren und ihre Daten in Echtzeit an zentrale Kontrollsysteme senden. Dies ermöglicht eine vollständige Prozessüberwachung und die Fernsteuerung der Geräte. Zudem können alle Prozessdaten gespeichert und für Qualitätssicherungszwecke oder zukünftige Optimierungen genutzt werden.
5.2 Nachhaltigkeit und Energieeffizienz
Ein weiterer zentraler Trend ist das Streben nach Energieeffizienz und Nachhaltigkeit in der Laborumgebung. Da beheizte Laborpressen große Mengen an Energie benötigen, um hohe Temperaturen aufrechtzuerhalten, arbeiten Hersteller an neuen Technologien, um den Energieverbrauch zu reduzieren.
Neue isolierende Materialien für Pressen
Eine Möglichkeit, den Energieverbrauch zu senken, besteht in der Entwicklung von hochleistungsfähigen Isoliermaterialien, die die Hitze in der Presse halten und Wärmeverluste minimieren. Diese Materialien sorgen dafür, dass die Heizplatten weniger Energie benötigen, um die erforderlichen Temperaturen zu erreichen und zu halten. Fortschrittliche Isolierungen ermöglichen es, den Betrieb energieeffizienter und umweltfreundlicher zu gestalten.
Erneuerbare Energien in der Laborumgebung
Ein innovativer Ansatz, um den CO2-Fußabdruck von Laborpressen zu reduzieren, besteht in der Integration von erneuerbaren Energien in den Laborbetrieb. Beispielsweise können Solarpaneele zur Energieversorgung der Heizsysteme genutzt werden, was insbesondere in großen Forschungszentren, die auf nachhaltige Energiequellen setzen, von Vorteil ist. Auch die Entwicklung von Energiespeichersystemen könnte dazu beitragen, die Abhängigkeit von fossilen Brennstoffen zu verringern.
Technologische Innovationen und Trends
5.3 Miniaturisierte Laborpressen
Ein interessanter Trend, der zunehmend an Bedeutung gewinnt, ist die Entwicklung miniaturisierter Laborpressen. Diese Geräte sind wesentlich kleiner als herkömmliche Laborpressen, bieten jedoch dieselbe Präzision bei der Druck- und Temperaturregelung. Sie sind ideal für den Einsatz in Forschungslaboren, in denen nur kleine Proben verarbeitet werden müssen, sowie in mobilen Anwendungen, bei denen tragbare Geräte erforderlich sind.
Anwendung in der Mikrotechnologie
In der Mikrotechnologie spielen miniaturisierte Laborpressen eine wichtige Rolle. Hierbei handelt es sich um einen Bereich, in dem sehr kleine Komponenten und Strukturen hergestellt werden, die oft nur wenige Millimeter oder Mikrometer groß sind. Diese Mikrostrukturen erfordern eine äußerst präzise Steuerung von Druck und Temperatur, da kleinste Abweichungen die Funktion der hergestellten Bauteile beeinträchtigen können. Miniaturisierte Laborpressen ermöglichen es, winzige Proben mit hohem Druck und genauer Temperaturregelung zu verarbeiten.
Ein typisches Beispiel für die Anwendung miniaturisierter Pressen ist die Herstellung von Mikrochips oder Mikrofluidiksystemen, die in der Medizintechnik, Biotechnologie und Elektronik verwendet werden. Diese Mikrochips können komplexe elektrische Schaltkreise oder miniaturisierte Flüssigkeitskanäle enthalten, die unter extrem präzisen Bedingungen gefertigt werden müssen.
Vorteile tragbarer Pressensysteme
Ein weiterer Vorteil der Miniaturisierung besteht in der Möglichkeit, tragbare Pressensysteme zu entwickeln. Diese Geräte können in mobilen Labors oder in Feldstudien eingesetzt werden, um Materialien vor Ort zu verarbeiten oder zu testen. Dies ist besonders in der Umweltforschung nützlich, wo Proben oft direkt im Freien analysiert werden müssen. Durch den Einsatz einer tragbaren beheizten Laborpresse kann die Probe sofort unter den gewünschten Bedingungen bearbeitet werden, ohne dass sie ins Labor transportiert werden muss.
5.4 Multifunktionale Laborpressen
Eine weitere Innovation auf dem Markt für Laborpressen ist die Entwicklung multifunktionaler Geräte, die nicht nur Druck und Hitze anwenden, sondern auch andere physikalische Prozesse, wie Vakuum, Kühlung oder elektrostatische Aufladung, kombinieren. Diese Multifunktionspressen sind besonders wertvoll in Bereichen, in denen komplexe Verarbeitungsprozesse erforderlich sind, um bestimmte Materialeigenschaften zu erreichen.
Kombination von Druck, Hitze und Vakuum
Die Kombination von Vakuum mit Druck und Hitze wird häufig in der Halbleiterherstellung und Materialforschung eingesetzt. Das Vakuum hilft dabei, Lufteinschlüsse aus dem Material zu entfernen, während Druck und Hitze die strukturellen Eigenschaften des Materials verändern. Dieses Verfahren ist besonders nützlich bei der Verarbeitung von Verbundwerkstoffen und Polymeren, bei denen die Eliminierung von Luftblasen entscheidend für die Materialfestigkeit und -qualität ist.
Erweiterte Steuerungssysteme für komplexe Prozesse
Moderne multifunktionale Pressen sind häufig mit erweiterten Steuerungssystemen ausgestattet, die in der Lage sind, komplexe Temperatur- und Druckprofile sowie zusätzliche Parameter wie Vakuum oder Kühlzeiten zu steuern. Diese Systeme bieten die Möglichkeit, vollständig automatisierte Prozesse durchzuführen, die auf die spezifischen Anforderungen des zu verarbeitenden Materials abgestimmt sind. Zum Beispiel können Thermozyklussequenzen programmiert werden, bei denen die Probe abwechselnd erhitzt und abgekühlt wird, um bestimmte Materialstrukturen zu erzeugen.
5.5 Entwicklungen in der Werkstoffkunde: Hochleistungswerkstoffe und Laborpressen
Mit dem Fortschreiten der Technologie entstehen immer komplexere und leistungsfähigere Werkstoffe. Diese neuen Materialien stellen erhöhte Anforderungen an die Verarbeitungstechniken und profitieren enorm von der Anwendung beheizter Laborpressen. Hochleistungswerkstoffe, wie etwa superharte Keramiken, leichten Metalllegierungen oder Nanomaterialien, erfordern eine exakte Kontrolle von Druck und Temperatur, um ihre herausragenden Eigenschaften zu entfalten.
Verarbeitung von superharten Keramiken
Superharte Keramiken, die extremen Temperaturen und chemischen Belastungen widerstehen können, sind essenziell in der Raumfahrt, Elektronik und Medizintechnik. Bei der Verarbeitung solcher Materialien muss eine Laborpresse nicht nur hohen Drücken und Temperaturen standhalten, sondern auch die Stabilität über längere Zeiträume aufrechterhalten. Beheizte Laborpressen werden für Sinterprozesse verwendet, bei denen keramische Pulver unter extremen Bedingungen verdichtet werden, um feste und stabile Bauteile zu erzeugen. Dies verbessert nicht nur die mechanischen Eigenschaften der Keramiken, sondern auch ihre Widerstandsfähigkeit gegen Verschleiß und Temperaturbeständigkeit.
Anwendung in der Nanotechnologie
Die Nanotechnologie eröffnet völlig neue Möglichkeiten in der Materialwissenschaft, und beheizte Laborpressen spielen dabei eine zentrale Rolle. Bei der Herstellung von Nanokompositen oder der Nanoimprint-Lithographie werden extrem kleine Strukturen in Materialien eingeprägt. Diese Strukturen können dazu verwendet werden, neue optische, elektrische oder mechanische Eigenschaften zu schaffen, die in Bereichen wie der Sensorik, Elektronik oder Medizintechnik von Bedeutung sind.
Da Nanomaterialien oft empfindlicher auf thermische und mechanische Belastungen reagieren, müssen Laborpressen, die für diese Prozesse eingesetzt werden, äußerst präzise sein. Kleine Temperaturunterschiede oder Druckabweichungen können die Struktur der Nanomaterialien verändern und ihre Eigenschaften beeinflussen. Moderne beheizte Pressen sind in der Lage, diese Bedingungen exakt zu steuern und somit hochqualitative Nanokomposite zu produzieren.
5.6 Zukünftige Entwicklungen und Ausblick
Die Entwicklung beheizter Laborpressen ist ein dynamisches Feld, das sich kontinuierlich weiterentwickelt. Zukünftige Fortschritte könnten dazu führen, dass diese Geräte noch präziser, effizienter und vielseitiger werden. Zu den möglichen Entwicklungen zählen unter anderem die Integration von Künstlicher Intelligenz (KI), die vollständige Automatisierung von Prozessen sowie die Nutzung von neuartigen Materialien in den Pressen selbst.
Integration von KI und maschinellem Lernen
Die zunehmende Integration von Künstlicher Intelligenz und maschinellem Lernen in Laborumgebungen könnte dazu führen, dass beheizte Laborpressen noch effizienter und intelligenter werden. Durch die Analyse von Daten aus vorherigen Verarbeitungsprozessen könnte die KI in der Lage sein, zukünftige Durchläufe automatisch zu optimieren, indem sie die besten Parameter für Temperatur, Druck und Verarbeitungsdauer ermittelt. Dies würde nicht nur die Qualität der hergestellten Produkte verbessern, sondern auch den Energieverbrauch reduzieren und den Materialverlust minimieren.
Automatisierung und Robotik in der Laborumgebung
Ein weiterer wichtiger Trend in der Entwicklung von Laborpressen ist die zunehmende Automatisierung von Prozessen durch den Einsatz von Robotik. In Zukunft könnten Laborpressen vollständig in automatisierte Fertigungsstraßen integriert werden, bei denen Roboter die Proben einlegen, die Prozesse starten und die fertigen Teile entnehmen. Dies würde die Produktivität steigern und die Fehlerquote senken, da menschliche Eingriffe auf ein Minimum reduziert würden.
Nachhaltige Produktionsmethoden
Da der Fokus auf Nachhaltigkeit in vielen Industrien weiter wächst, wird auch die Entwicklung von umweltfreundlichen Laborpressen immer wichtiger. In Zukunft könnten neue Technologien, wie etwa die Verwendung von recycelten Materialien für die Pressplatten oder die Integration von energieeffizienten Heizsystemen, dazu beitragen, den CO2-Fußabdruck dieser Geräte zu minimieren. Zusätzlich könnte die Nutzung von erneuerbaren Energiequellen in die Entwicklung von Pressen einfließen, wodurch Labore ihre Energieversorgung nachhaltiger gestalten könnten.
Vorteile beheizter Laborpressen im Detail
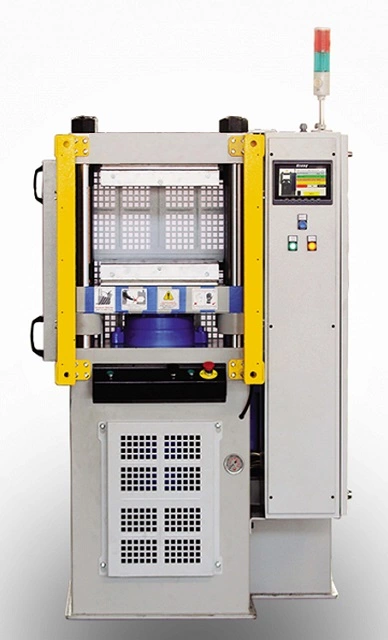
Beheizte Laborpressen bieten eine Reihe von Vorteilen, die sie für zahlreiche wissenschaftliche und industrielle Anwendungen unverzichtbar machen. Zu den wichtigsten Vorteilen gehören die Präzision, die Vielseitigkeit und die Effizienz dieser Geräte. Im Folgenden werden die einzelnen Vorteile genauer erläutert.
6.1 Präzisionskontrolle: Ausführliche Erklärung der Steuerungsmechanismen
Eine der größten Stärken beheizter Laborpressen ist die präzise Kontrolle von Druck und Temperatur. Durch den Einsatz moderner Regelungstechnologien, wie etwa PID-Reglern (Proportional-Integral-Differential-Regler), können die Temperaturen exakt eingestellt und stabil gehalten werden, während der Druck durch hydraulische oder pneumatische Systeme auf die gewünschten Werte reguliert wird. Diese Präzision ist entscheidend für Anwendungen, bei denen schon kleinste Abweichungen zu fehlerhaften Ergebnissen führen könnten, etwa in der Halbleiterfertigung oder bei der Verarbeitung von Nanomaterialien.
Die Präzisionskontrolle ermöglicht es, gleichbleibende Ergebnisse zu erzielen, was insbesondere in der Serienproduktion von Bedeutung ist. Labore und Hersteller, die auf hohe Qualitätsstandards angewiesen sind, profitieren von der Fähigkeit beheizter Pressen, wiederholbare Prozesse durchzuführen.
6.2 Skalierbarkeit: Vom Prototypenbau bis zur Produktion
Beheizte Laborpressen sind äußerst skalierbar und können sowohl für kleine Proben im Forschungslabor als auch für die Massenproduktion von Materialien eingesetzt werden. Dies macht sie zu einem wertvollen Werkzeug in der Produktentwicklung, da Forscher zunächst Prototypen unter Laborbedingungen erstellen und die Prozesse anschließend auf industrielle Größenordnungen übertragen können.
Ein Beispiel hierfür ist die Herstellung von Verbundwerkstoffen. In einem frühen Entwicklungsstadium können kleine Proben unter Druck und Hitze in einer Laborpresse getestet werden, um die optimalen Materialzusammensetzungen und Verarbeitungsbedingungen zu ermitteln. Sobald der Entwicklungsprozess abgeschlossen ist, kann derselbe Prozess mithilfe größerer Pressen in die Produktion überführt werden.
Vorteile beheizter Laborpressen im Detail
6.3 Reduktion von Fehlerquoten und Materialverlust
Ein wesentlicher Vorteil beheizter Laborpressen ist die Fähigkeit, Fehlerquoten signifikant zu reduzieren und den Materialverlust während des Verarbeitungsprozesses zu minimieren. In vielen industriellen und wissenschaftlichen Anwendungen ist es entscheidend, dass Materialien präzise und homogen verarbeitet werden, um einheitliche Ergebnisse zu erzielen. Durch die Kombination von exaktem Druck und stabiler Temperaturkontrolle wird sichergestellt, dass Materialien gleichmäßig komprimiert und auf eine Weise bearbeitet werden, die Inhomogenitäten, Luftblasen oder Oberflächenfehler vermeidet.
Präzise Prozesssteuerung minimiert Abweichungen
Moderne beheizte Laborpressen sind mit präzisen Steuerungssystemen ausgestattet, die es ermöglichen, Prozessparameter wie Druck und Temperatur äußerst genau zu regeln. Dies ist besonders in der Pharmazeutischen Industrie von Bedeutung, wo bereits geringfügige Abweichungen in der Probenverarbeitung zu nicht konformen Produkten führen können. Durch den Einsatz einer beheizten Presse können pharmazeutische Hersteller sicherstellen, dass Tabletten, Pellets oder andere feste Formen gleichmäßig gepresst werden, wodurch die Qualität und Wirksamkeit der Produkte gewährleistet wird.
Reduzierung von Ausschussmaterial
In der Polymerverarbeitung oder der Herstellung von Verbundwerkstoffen kommt es häufig vor, dass Proben aufgrund von unzureichendem Druck oder ungleichmäßiger Temperaturverteilung unbrauchbar sind. Diese Materialien müssen oft entsorgt werden, was zu einem erheblichen Materialverlust führen kann. Beheizte Laborpressen bieten eine Lösung, indem sie sicherstellen, dass die Werkstoffe homogen verarbeitet werden, was den Ausschuss minimiert. Dies ist nicht nur kosteneffizient, sondern trägt auch zu einer nachhaltigeren Produktion bei, da weniger Material verschwendet wird.
6.4 Zeitersparnis durch verbesserte Prozesseffizienz
Neben der Reduktion von Materialverlusten tragen beheizte Laborpressen auch wesentlich zur Zeiteinsparung bei. Durch ihre Fähigkeit, hohe Drücke und gleichmäßige Temperaturen schnell und präzise zu erzeugen, beschleunigen sie die Verarbeitung von Materialien und verkürzen die Durchlaufzeiten in Labor- und Produktionsumgebungen.
Schnelle Erhitzung und Abkühlung
Ein entscheidender Aspekt moderner beheizter Pressen ist ihre Fähigkeit, Materialien schnell zu erhitzen und abzukühlen. Dies verkürzt nicht nur die Verarbeitungszeit, sondern ermöglicht auch die Optimierung thermischer Zyklen, was besonders in der Materialforschung und bei der Herstellung von thermoplastischen Polymeren wichtig ist. Durch die schnelle Abkühlung nach dem Erhitzen wird zudem das Risiko einer Überhitzung oder thermischen Schädigung des Materials minimiert.
Reduzierte Ausfallzeiten durch fortschrittliche Steuerungssysteme
Die Automatisierung von Prozessen durch moderne Steuerungssysteme trägt ebenfalls zur Reduzierung von Ausfallzeiten bei. Beheizte Laborpressen, die mit intelligenten Steuerungen und vorausschauender Wartung ausgestattet sind, können potenzielle Probleme im Voraus erkennen und beheben, bevor es zu einem vollständigen Produktionsstillstand kommt. Dies führt zu einer höheren Betriebszeit und trägt zur Optimierung der Produktionsabläufe bei.
6.5 Umweltvorteile durch energieeffiziente Systeme
In vielen Industrien und Laboren wird der Fokus zunehmend auf Nachhaltigkeit und Energieeinsparung gelegt. Beheizte Laborpressen, die mit energieeffizienten Heizsystemen und isolierenden Materialien ausgestattet sind, können erheblich zur Reduzierung des Energieverbrauchs beitragen. Dies ist nicht nur aus umweltpolitischer Sicht von Bedeutung, sondern auch für Unternehmen, die ihre Betriebskosten senken möchten.
Energiesparende Heizsysteme
Moderne beheizte Pressen verwenden oft Widerstandsheizungen, die eine gleichmäßige und effiziente Erwärmung der Pressplatten ermöglichen. In einigen High-End-Modellen kommen sogar Induktionsheizungen zum Einsatz, die eine noch schnellere und energieeffizientere Wärmeübertragung gewährleisten. Induktionsheizungen nutzen elektromagnetische Felder, um die Pressplatten direkt zu erhitzen, was den Energieverlust minimiert und die Heizzeiten erheblich verkürzt. Diese Technologie wird zunehmend in Branchen eingesetzt, die großen Wert auf Energieeinsparungen und Kostenreduktion legen.
Verbesserte Isolierung für weniger Wärmeverluste
Neben den Heizsystemen tragen auch innovative Isoliermaterialien dazu bei, den Energieverbrauch beheizter Laborpressen zu senken. Die Wärmedämmung der Pressplatten und des Gehäuses sorgt dafür, dass weniger Wärme entweicht und die Temperatur länger aufrechterhalten werden kann. Dies ist besonders wichtig in Anwendungen, bei denen die Pressen über längere Zeiträume hinweg auf hohen Temperaturen betrieben werden müssen.
Durch die Kombination von effizienten Heizsystemen und fortschrittlichen Isolierungen können Labore und Produktionsstätten ihren Energieverbrauch erheblich reduzieren, was sowohl ökologische als auch wirtschaftliche Vorteile bringt.
Herausforderungen und mögliche Einschränkungen
Obwohl beheizte Laborpressen zahlreiche Vorteile bieten, gibt es auch einige Herausforderungen und Einschränkungen, die bei der Verwendung dieser Geräte berücksichtigt werden müssen. Diese können von technologischen Limitationen bis hin zu wirtschaftlichen und betrieblichen Faktoren reichen.
7.1 Technologische Barrieren: Grenzen bei der Temperaturkontrolle
Die präzise Temperaturkontrolle ist eine der größten Stärken beheizter Laborpressen, jedoch gibt es bestimmte technologische Barrieren, die die Leistungsfähigkeit dieser Geräte einschränken können. In einigen Anwendungen, insbesondere bei Materialien, die extreme Temperaturen erfordern, kann es schwierig sein, eine gleichmäßige Temperaturverteilung über die gesamte Fläche der Pressplatten aufrechtzuerhalten.
Herausforderungen bei der Temperaturgleichmäßigkeit
Bei sehr großen Pressplatten oder bei Materialien, die eine besonders gleichmäßige Erhitzung benötigen, kann es zu Temperaturgradienten kommen, bei denen einige Bereiche der Pressplatte heißer sind als andere. Dies kann zu Inhomogenitäten in den bearbeiteten Materialien führen, was insbesondere in der Materialforschung und Elektronikfertigung problematisch sein kann. Hochentwickelte Heiztechnologien, wie Mehrzonentemperaturregelungen, können dazu beitragen, diese Herausforderung zu bewältigen, sind jedoch mit zusätzlichen Kosten verbunden.
Grenzwerte der maximalen Temperatur
Ein weiteres technisches Hindernis ist die maximale Temperatur, die eine Laborpresse erreichen kann. Einige Hochleistungsmaterialien, wie etwa keramische Werkstoffe oder Superlegierungen, erfordern Temperaturen von über 1.000°C, um ihre endgültigen Eigenschaften zu entfalten. Nicht alle Laborpressen sind in der Lage, solch extreme Temperaturen zu erzeugen oder über längere Zeiträume hinweg aufrechtzuerhalten, ohne dass es zu Materialermüdung oder technischen Ausfällen kommt.
7.2 Hohe Kosten für spezialisierte Anwendungen und Geräte
Beheizte Laborpressen können je nach Anwendung sehr teuer sein, insbesondere wenn es sich um spezialisierte Geräte für hochspezifische Forschungs- oder Produktionsprozesse handelt. Die Kosten für eine Laborpresse hängen von verschiedenen Faktoren ab, wie etwa der Größe der Pressplatten, der maximalen Temperaturkapazität, der automatisierten Steuerungssysteme und der verwendeten Heiztechnologie.
Anschaffungskosten
Die Anschaffungskosten für hochentwickelte beheizte Laborpressen können für kleine Forschungseinrichtungen oder Start-ups eine erhebliche finanzielle Belastung darstellen. Während Standard-Laborpressen bereits zu relativ erschwinglichen Preisen erhältlich sind, können spezialisierte Geräte, die für die Verarbeitung von Nanomaterialien, Hochleistungskeramiken oder Verbundwerkstoffen entwickelt wurden, schnell mehrere hunderttausend Euro kosten. Hinzu kommen die Kosten für regelmäßige Wartung und Ersatzteile, die je nach Gerät und Anwendungsbereich variieren können.
Betriebskosten
Neben den Anschaffungskosten sind auch die Betriebskosten ein wichtiger Faktor. Beheizte Laborpressen benötigen oft große Mengen an Energie, um die hohen Temperaturen aufrechtzuerhalten, was in Forschungslaboren oder Produktionsstätten mit hohen Betriebsfrequenzen zu hohen Energiekosten führen kann. Durch den Einsatz von energieeffizienten Technologien und die Optimierung der Produktionsprozesse kann der Energieverbrauch jedoch reduziert werden.
7.3 Wartung und mögliche Ausfallzeiten
Die regelmäßige Wartung von beheizten Laborpressen ist entscheidend, um deren Leistungsfähigkeit und Langlebigkeit zu gewährleisten. Trotz ihrer robusten Bauweise und fortschrittlichen Technik können Laborpressen im Laufe der Zeit verschleißen oder technische Störungen aufweisen, die zu Ausfallzeiten führen.
Verschleiß von Heizplatten und Hydrauliksystemen
Ein häufiger Grund für Wartungsbedarf ist der Verschleiß der Heizplatten. Durch den wiederholten Einsatz bei hohen Temperaturen können sich Risse, Verformungen oder Oberflächenbeschädigungen an den Platten bilden, was die gleichmäßige Wärmeübertragung beeinträchtigen kann. Hydrauliksysteme, die den Druck auf die Probe ausüben, können ebenfalls anfällig für Leckagen oder Druckverlust sein, insbesondere wenn sie über längere Zeiträume hinweg unter extremen Bedingungen betrieben werden.
Potenzielle Sicherheitsrisiken
Beheizte Laborpressen arbeiten mit hohen Drücken und Temperaturen, was gewisse Sicherheitsrisiken mit sich bringt. Ohne regelmäßige Wartung und Überprüfung der Sicherheitsvorkehrungen können unerwartete technische Störungen oder Materialermüdungen zu Unfällen oder Sachschäden führen. Es ist daher wichtig, dass die Geräte regelmäßig inspiziert und gewartet werden, um sicherzustellen, dass sie den Sicherheitsstandards entsprechen.
7.4 Schulungsbedarf für das Laborpersonal
Ein weiterer Aspekt, der bei der Verwendung beheizter Laborpressen berücksichtigt werden muss, ist der Schulungsbedarf für das Personal, das mit diesen Geräten arbeitet. Aufgrund der komplexen Steuerungssysteme und der Notwendigkeit, Druck und Temperatur präzise zu regeln, ist es wichtig, dass das Laborpersonal eine umfassende Einweisung und Schulung erhält, um die Geräte sicher und effektiv bedienen zu können.
Fallstudien und Praxisbeispiele
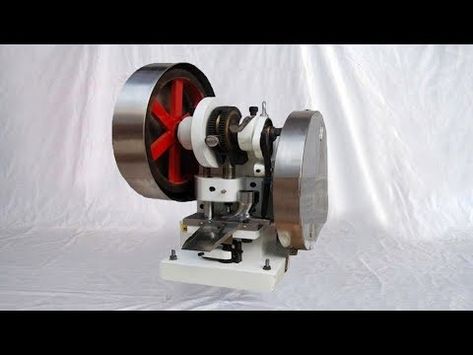
Um die Vorteile und Herausforderungen beheizter Laborpressen noch deutlicher zu veranschaulichen, folgt nun eine Reihe von Fallstudien und Praxisbeispielen, die aufzeigen, wie diese Geräte in verschiedenen Branchen und Anwendungen erfolgreich eingesetzt werden. Dies wird nicht nur die Vielfalt der Einsatzmöglichkeiten aufzeigen, sondern auch verdeutlichen, wie Labore und Produktionsstätten die beschriebenen Technologien in der Praxis anwenden.
8.1 Fallstudie 1: Entwicklung neuer Polymere durch Druck- und Hitzebehandlung
In einem Forschungsprojekt an einer Universität wurde eine beheizte Laborpresse verwendet, um neuartige thermoplastische Polymere zu entwickeln, die recycelbar sind und dennoch hochfeste mechanische Eigenschaften aufweisen. Das Ziel der Forscher war es, ein Polymer zu entwickeln, das sowohl biologisch abbaubar ist als auch eine hohe Zug- und Druckfestigkeit aufweist, um es in der Verpackungsindustrie einzusetzen.
Durch die Verwendung einer beheizten Presse mit präziser Temperatur- und Druckkontrolle konnten die Forscher verschiedene Polymermischungen testen und optimieren. Die gleichmäßige Erwärmung der Proben und der kontrollierte Druck führten zu einer homogenen Molekülstruktur der Polymere, was die gewünschten mechanischen Eigenschaften deutlich verbesserte. Am Ende des Projekts waren die Forscher in der Lage, ein leistungsfähiges, umweltfreundliches Polymer zu entwickeln, das erfolgreich in der Industrie getestet wurde.
8.2 Fallstudie 2: Einsatz einer beheizten Laborpresse in der Halbleiterfertigung
Ein weiteres Beispiel aus der Elektronikbranche zeigt den erfolgreichen Einsatz beheizter Laborpressen in der Herstellung von Halbleitern. Hier wurde eine Presse verwendet, um die verschiedenen Schichten eines Wafers unter Druck und Wärme zu laminieren. Durch die gleichzeitige Anwendung von Hitze und Druck konnten die Materialien ohne Lufteinschlüsse oder Mikrorisse fest verbunden werden, was zu einer verbesserten elektrischen Leitfähigkeit und Haltbarkeit des Endprodukts führte.
Die Nutzung einer beheizten Presse ermöglichte es dem Hersteller, den Laminierungsprozess signifikant zu beschleunigen und gleichzeitig die Qualität der Wafer zu verbessern. Dies führte zu einer höheren Produktionseffizienz und einer Kostenersparnis in der Fertigung.
Fallstudien und Praxisbeispiele
8.3 Fallstudie 3: Optimierung pharmazeutischer Produkte durch präzise Probenherstellung
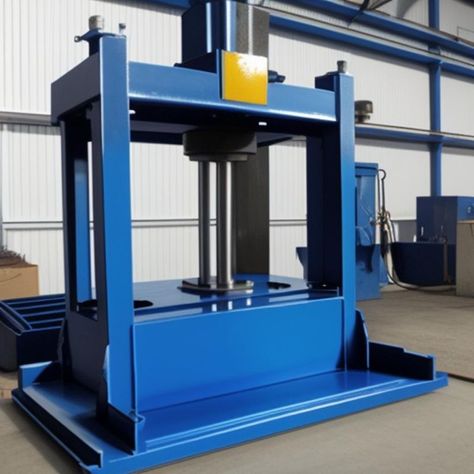
In der pharmazeutischen Forschung spielt die Probenherstellung eine entscheidende Rolle bei der Entwicklung neuer Medikamente. Eine besonders interessante Anwendung beheizter Laborpressen ist die Herstellung von Retardtabletten, die den Wirkstoff über einen längeren Zeitraum hinweg kontrolliert freisetzen. Die Herausforderung bei der Herstellung solcher Tabletten besteht darin, eine exakte Wirkstoffverteilung und die richtige Freisetzungsrate zu gewährleisten, um eine konstante Wirkstoffkonzentration im Körper des Patienten zu erreichen.
Prozessoptimierung durch Druck und Temperatur
In dieser Fallstudie wurde eine beheizte Laborpresse verwendet, um die Kompaktierung der Tablettenmasse zu optimieren. Die Anwendung von gleichmäßigem Druck und präzise regulierter Hitze stellte sicher, dass der Wirkstoff in der Tablette gleichmäßig verteilt war und die physikalischen Eigenschaften der Tablette die kontrollierte Freisetzung des Wirkstoffs ermöglichten. Dank der Temperaturkontrolle konnten die Forscher auch die Freisetzungsrate des Medikaments durch die Modifikation der Polymerschicht in der Tablette steuern.
Durch den Einsatz einer beheizten Laborpresse konnten die Forscher die mechanische Festigkeit der Tabletten verbessern, ohne dass es zu einer Veränderung der bioaktiven Substanzen kam. Das Ergebnis war eine optimierte Formulierung mit besserer Wirkstofffreisetzung, die den strengen pharmazeutischen Standards entsprach.
8.4 Fallstudie 4: Herstellung von recycelten Textilien und deren Belastungstests
Im Bereich der nachhaltigen Textilproduktion spielen Laborpressen eine wichtige Rolle bei der Erforschung und Verarbeitung von recycelbaren Materialien. In dieser Fallstudie wurde eine beheizte Laborpresse eingesetzt, um recycelte Polyesterfasern zu neuen Textilien zu verarbeiten, die sowohl in der Mode- als auch in der Outdoor-Industrie verwendet werden sollen.
Komprimierung und Hitzebehandlung recycelter Fasern
Das Ziel dieses Projekts war es, eine Textilie zu entwickeln, die aus recyceltem Polyester besteht, aber dennoch hitzebeständig und mechanisch stabil ist. Durch die Nutzung der beheizten Presse konnten die Forscher die Polyesterfasern unter hohem Druck verdichten und gleichzeitig durch die Anwendung von Wärme die Fasern dauerhaft miteinander verbinden. Dies führte zu einer dichten und stabilen Struktur, die sowohl reißfest als auch beständig gegenüber extremen Temperaturen war.
Im Rahmen des Projekts wurden auch Belastungstests durchgeführt, um die mechanischen Eigenschaften der recycelten Textilien zu überprüfen. Die Tests zeigten, dass die unter Hitze und Druck bearbeiteten Textilien die gleichen mechanischen Eigenschaften wie neue, nicht recycelte Materialien aufwiesen. Dies eröffnete neue Möglichkeiten für die nachhaltige Herstellung von Textilien, da recycelte Fasern nun für Anwendungen verwendet werden konnten, die eine hohe mechanische Belastbarkeit erfordern.
8.5 Fallstudie 5: Herstellung von Hochleistungsverbundwerkstoffen für die Luft- und Raumfahrt
Verbundwerkstoffe sind aufgrund ihrer hohen Festigkeit, geringen Dichte und Hitzebeständigkeit von zentraler Bedeutung in der Luft- und Raumfahrtindustrie. Diese Materialien bestehen aus einer Polymermatrix, die durch Fasern, wie Kohlenstoff- oder Glasfasern, verstärkt wird. Die Kombination von Druck und Hitze ist entscheidend, um die Polymermatrix zu verflüssigen und die Fasern fest in die Struktur einzubetten.
Laminierung unter Druck und Hitze
In dieser Fallstudie wurde eine beheizte Laborpresse verwendet, um Hochleistungsverbundwerkstoffe für den Einsatz in der Flugzeugherstellung zu entwickeln. Die Presse ermöglichte die präzise Steuerung der Temperatur und des Drucks während des Laminierprozesses, was zu einer gleichmäßigen Verteilung der Fasern und einer fehlerfreien Oberfläche führte. Dies war besonders wichtig, da Lufteinschlüsse oder Schichtfehler die mechanischen Eigenschaften des Werkstoffs stark beeinträchtigen könnten.
Dank der kontrollierten Anwendung von Druck und Wärme konnten die Verbundwerkstoffe die strengen Anforderungen der Luft- und Raumfahrtnormen erfüllen, insbesondere in Bezug auf Festigkeit, Gewichtsreduktion und Temperaturbeständigkeit. Die in der Laborpresse hergestellten Prototypen wurden später in realen Anwendungen getestet und erwiesen sich als äußerst zuverlässig, was zu einem erfolgreichen Einsatz in der Serienproduktion führte.
8.6 Fallstudie 6: Herstellung von Keramikbauteilen für die Elektronikindustrie
Keramische Materialien sind aufgrund ihrer hohen Hitzebeständigkeit und elektrischen Isolationseigenschaften in der Elektronikindustrie weit verbreitet. Diese Materialien müssen oft unter hohen Temperaturen und Druck gesintert werden, um ihre endgültige Dichte und mechanische Festigkeit zu erreichen. In dieser Fallstudie wurde eine beheizte Laborpresse verwendet, um technische Keramiken für die Herstellung von Isolatoren in Halbleitergeräten zu fertigen.
Sinterprozess unter hohem Druck und Temperatur
Der Sinterprozess in einer beheizten Laborpresse ist besonders wichtig für die Herstellung von dichten und porenfreien Keramiken. In dieser Fallstudie wurde ein spezielles Aluminiumoxid-Keramikpulver in der Presse unter extrem hohem Druck und bei Temperaturen von über 1.200°C verarbeitet. Durch die präzise Steuerung dieser Parameter konnten die Keramikbauteile ihre optimale Kristallstruktur entwickeln, die für ihre elektrischen Isolationseigenschaften entscheidend war.
Nach dem Sinterprozess wurden die Keramikbauteile in der Elektronikproduktion verwendet und wiesen hervorragende thermische und elektrische Isolationseigenschaften auf, was ihre Eignung für Hochleistungs-Halbleiteranwendungen bestätigte. Die Nutzung der beheizten Laborpresse führte zu einer hohen Produktionsqualität und einem geringen Ausschuss, was in der Elektronikbranche von entscheidender Bedeutung ist.
Kaufberatung für beheizte Laborpressen
Die Auswahl einer beheizten Laborpresse hängt von verschiedenen Faktoren ab, die je nach Anwendungsbereich und Anforderungen variieren können. Es ist wichtig, die technischen Spezifikationen, Kosten, Leistungsfähigkeit und Wartungsanforderungen der Geräte zu berücksichtigen, um die beste Wahl für das jeweilige Labor oder die Produktionsstätte zu treffen.
9.1 Auswahl der richtigen Größe und Kapazität
Die Größe und Kapazität der beheizten Laborpresse sind entscheidende Faktoren, die bei der Auswahl berücksichtigt werden müssen. Je nach Anwendung kann es erforderlich sein, große oder kleine Proben zu verarbeiten. In der Materialforschung und bei der Prototypenentwicklung werden oft kleinere Pressen benötigt, während in der industriellen Produktion größere Pressen mit höherer Kapazität erforderlich sind.
Kleine Laborpressen für Forschungszwecke
Für Forschungslabore und Bildungseinrichtungen reichen in der Regel kompakte Laborpressen aus, die eine maximale Presskraft von 10 bis 50 Tonnen und Heizplatten mit Abmessungen von 100 x 100 mm bis 300 x 300 mm bieten. Diese Geräte sind ideal für die Verarbeitung kleiner Materialproben und die Durchführung von Materialtests unter Laborbedingungen. Zudem sind kleinere Laborpressen oft günstiger und einfacher zu bedienen, was sie für Akademiker und Forschungseinrichtungen besonders attraktiv macht.
Industrielle Laborpressen für die Serienproduktion
Für industrielle Anwendungen in der Massenproduktion sind jedoch größere und leistungsfähigere Pressen erforderlich. Diese Geräte müssen in der Lage sein, höhere Drücke und größere Heizflächen zu bewältigen. Industrielle Laborpressen bieten typischerweise eine Presskraft von 100 bis 500 Tonnen und Heizplatten, die bis zu 1.000 x 1.000 mm groß sein können. Diese Pressen eignen sich für die Herstellung von großen Prototypen oder Serienbauteilen, insbesondere in der Kunststoffverarbeitung, Elektronikproduktion oder Luft- und Raumfahrtindustrie.
9.2 Entscheidungskriterien für Industrie und Forschung
Bei der Auswahl einer beheizten Laborpresse gibt es mehrere Schlüsselfaktoren, die je nach Einsatzgebiet unterschiedlich gewichtet werden. Zu diesen Faktoren gehören:
- Maximale Druck- und Temperaturkapazität: Je nach Material müssen Pressen in der Lage sein, extrem hohe Drücke und Temperaturen zu erzeugen.
- Größe der Pressplatten: Für industrielle Anwendungen sind größere Pressplatten oft notwendig, um die Produktionseffizienz zu erhöhen.
- Automatisierung und Steuerungssysteme: Fortschrittliche Steuerungssysteme können den Produktionsprozess optimieren und Ausfallzeiten reduzieren.
- Energieeffizienz: Eine effiziente Wärme- und Energieverteilung ist besonders in energieintensiven Produktionsprozessen von Bedeutung.
- Kosten: Sowohl die Anschaffungskosten als auch die Betriebskosten sollten in die Entscheidung einfließen.
9.3 Vergleich der führenden Hersteller und deren Technologien
Der Markt für beheizte Laborpressen wird von mehreren führenden Herstellern dominiert, die jeweils unterschiedliche Technologien und Ausstattungsmerkmale anbieten. Einige der renommiertesten Anbieter sind:
Hersteller 1: Hochpräzise Laborpressen für die Materialforschung
Dieser Hersteller hat sich auf die Entwicklung von kompakten und hochpräzisen Laborpressen spezialisiert, die vor allem in der Materialwissenschaft und Polymertests verwendet werden. Die Geräte zeichnen sich durch eine besonders präzise Steuerung der Temperaturgleichmäßigkeit und des Drucks aus, was sie ideal für Anwendungen macht, bei denen es auf maximale Genauigkeit ankommt.
Hersteller 2: Industrielle Pressen für Großproduktionen
Ein weiterer führender Hersteller bietet großformatige Pressen an, die für den Einsatz in der Serienproduktion konzipiert sind. Diese Pressen bieten eine hohe Presskraft und die Möglichkeit, komplexe Produktionsprozesse vollständig zu automatisieren. Sie werden oft in der Automobilindustrie, Elektronikfertigung und Verbundwerkstoffproduktion eingesetzt.
9.4 Typische Preisspannen und Kostenfaktoren
Die Preise für beheizte Laborpressen können stark variieren, abhängig von der Größe, Leistungsfähigkeit und Ausstattung der Geräte. Standard-Laborpressen für kleine Forschungsanwendungen können bei etwa 10.000 bis 30.000 Euro liegen, während industrielle High-End-Geräte leicht über 100.000 Euro kosten können.
Einige der wichtigsten Kostenfaktoren sind:
- Größe der Pressplatten: Größere Platten erfordern mehr Material und leistungsstärkere Heizsysteme, was die Kosten in die Höhe treibt.
- Automatisierung: Vollständig automatisierte Systeme sind teurer, bieten aber langfristig eine bessere Prozesskontrolle und Produktionsoptimierung.
- Spezielle Materialien: Wenn die Presse für die Verarbeitung besonders anspruchsvoller Materialien (z.B. Nanomaterialien oder Hochleistungskeramiken) ausgelegt ist, können zusätzliche Kosten für spezielle Ausstattungen oder spezielle Heizsysteme anfallen.
9.5 Tipps für eine langfristige Investition
Der Kauf einer beheizten Laborpresse ist eine langfristige Investition, daher ist es wichtig, die zukünftigen Anforderungen des Labors oder der Produktionsstätte zu berücksichtigen. Hier sind einige Tipps, um eine gute Entscheidung zu treffen:
- Skalierbarkeit: Wählen Sie eine Presse, die mit Ihrem Geschäft oder Forschungsbereich wachsen kann. Wenn Sie planen, Ihre Produktion zu erweitern, sollte die Presse in der Lage sein, diese Anforderungen zu erfüllen.
- Modularität: Achten Sie darauf, dass die Presse modular aufgebaut ist und bei Bedarf mit zusätzlichen Funktionen (z.B. Kühlung, Vakuum) nachgerüstet werden kann.
- Zuverlässigkeit und Wartung: Wählen Sie einen Hersteller mit einem guten Serviceangebot und Ersatzteilversorgung, um die langfristige Zuverlässigkeit der Presse sicherzustellen.
Technischer Überblick und Funktionsweise von beheizten Laborpressen
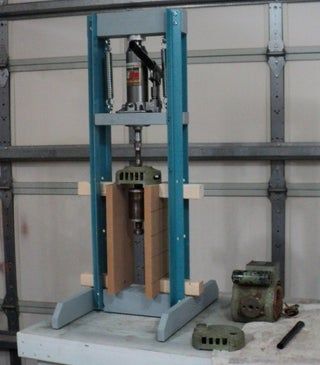
1. Grundlagen der Laborpressen
Eine beheizte Laborpresse ist ein Präzisionsgerät, das entwickelt wurde, um hohen Druck und gleichmäßige Hitze auf Materialien anzuwenden. Diese Pressen bestehen aus verschiedenen mechanischen, hydraulischen, elektrischen und thermischen Komponenten, die in harmonischer Abstimmung arbeiten, um spezifische Prozesse zu ermöglichen. Beheizte Pressen sind in Laboren und Produktionsumgebungen unverzichtbar, wo es darauf ankommt, die physikalischen und chemischen Eigenschaften von Materialien präzise zu verändern.
1.1 Definition und Aufbau
Laborpressen sind Maschinen, die in erster Linie dazu verwendet werden, Druck auf ein Material oder eine Substanz auszuüben. Der Begriff „beheizt“ bezieht sich auf das zusätzliche Element der Wärme, das durch integrierte Heizsysteme in den Pressplatten erzeugt wird. Diese Temperaturregelung ist entscheidend für Prozesse, bei denen eine Kombination aus thermischer Energie und mechanischem Druck benötigt wird, um Materialien zu verformen, zu verschmelzen oder ihre chemischen Eigenschaften zu verändern.
1.2 Einsatzbereiche und Relevanz
Beheizte Laborpressen werden in vielen Branchen verwendet, darunter die Materialforschung, Pharmazeutik, Elektronikproduktion, Polymerverarbeitung, Metallurgie, und Biotechnologie. Die präzise Steuerung von Druck und Temperatur macht sie zu einem unverzichtbaren Werkzeug für die Herstellung von Verbundwerkstoffen, Polymere, Metalle, Pharmazeutische Tabletten und technische Keramiken. In der Elektronikindustrie werden sie zur Herstellung von Wafern und Leiterplatten eingesetzt, während sie in der Luft- und Raumfahrt zur Herstellung von hitze- und druckbeständigen Materialien beitragen.
2. Druckmechanismen: Aufbau und Funktionsweise
Der Druck, der auf das Material in einer beheizten Laborpresse ausgeübt wird, ist ein wesentlicher Bestandteil der Funktionsweise der Maschine. Unterschiedliche Druckmechanismen kommen zum Einsatz, um die spezifischen Anforderungen der jeweiligen Anwendung zu erfüllen. Im Wesentlichen gibt es drei Hauptarten von Druckmechanismen, die in beheizten Laborpressen verwendet werden: Hydraulische, pneumatische und mechanische Drucksysteme.
2.1 Hydraulische Drucksysteme
Hydraulische Systeme sind die am häufigsten eingesetzten Druckmechanismen in beheizten Laborpressen, insbesondere in industriellen Anwendungen, die hohe Drücke erfordern. Ein hydraulisches System nutzt eine Flüssigkeit, meist Öl, um eine Kraft zu übertragen. Es besteht aus einem Hydraulikzylinder, der durch eine Pumpe und ein Ventilsystem gesteuert wird, um den Druck aufzubauen.
2.1.1 Funktionsweise eines hydraulischen Drucksystems
Das Herzstück des hydraulischen Systems ist der Hydraulikzylinder. Dieser Zylinder enthält einen Kolben, der durch die Einwirkung von hydraulischem Druck bewegt wird. Der Druck wird durch die Pumpe erzeugt, die das Öl in den Zylinder drückt. Durch die Bewegung des Kolbens wird der Druck auf die Pressplatten und somit auf das Material übertragen. Die Druckhöhe lässt sich präzise steuern, indem der Durchfluss des Öls durch das Ventilsystem reguliert wird. Moderne hydraulische Pressen verwenden oft Servoantriebe, um die Druckhöhe feinfühlig zu justieren.
2.1.2 Vorteile hydraulischer Pressen
- Hohe Drücke: Hydraulische Pressen sind in der Lage, extrem hohe Drücke zu erzeugen, was sie ideal für Materialien macht, die hohe Kompressionskräfte erfordern, wie Metall, Keramik oder stark verdichtete Verbundstoffe.
- Präzise Steuerung: Die Möglichkeit, den Druck genau zu regeln, macht hydraulische Systeme besonders wertvoll für Laboranwendungen, bei denen konsistente und reproduzierbare Ergebnisse erforderlich sind.
- Hohe Vielseitigkeit: Hydraulische Systeme sind sowohl in der Forschung als auch in der industriellen Fertigung weit verbreitet, da sie für eine Vielzahl von Materialien und Prozessen verwendet werden können.
2.1.3 Herausforderungen und Nachteile
Eines der größten Probleme bei hydraulischen Pressen ist die Wartung. Da sie auf Flüssigkeiten angewiesen sind, können Leckagen auftreten, und das System muss regelmäßig auf Flüssigkeitsstand und Druckverlust überprüft werden. Außerdem sind hydraulische Systeme in der Regel langsamer als pneumatische oder mechanische Systeme, was sie für Anwendungen, die schnelle Zykluszeiten erfordern, weniger geeignet macht.
2.2 Pneumatische Drucksysteme
Pneumatische Systeme funktionieren ähnlich wie hydraulische Systeme, verwenden jedoch Luft oder Gas anstelle von Flüssigkeit, um die Kraft zu übertragen. Pneumatische Pressen sind oft in kleineren Laboranwendungen zu finden, wo der benötigte Druck geringer ist als bei hydraulischen Systemen. Sie sind schneller, benötigen weniger Wartung und sind oft günstiger in der Anschaffung.
2.2.1 Funktionsweise eines pneumatischen Drucksystems
Ein Kompressor wird verwendet, um Luft oder Gas in den Zylinder zu pumpen. Der Druck der Luft bewegt den Kolben, der wiederum den Druck auf das Material in der Presse ausübt. Pneumatische Pressen arbeiten in der Regel bei niedrigeren Drücken als hydraulische Pressen, was sie für Materialien wie Polymere oder leichte Metalle geeignet macht, die keine extremen Kompressionskräfte erfordern.
2.2.2 Vorteile pneumatischer Pressen
- Schnelligkeit: Pneumatische Pressen können im Vergleich zu hydraulischen Pressen schneller arbeiten, da die Luft oder das Gas leichter zu komprimieren ist als Flüssigkeiten.
- Weniger Wartung: Da keine Flüssigkeiten verwendet werden, ist das Risiko von Leckagen oder Verunreinigungen geringer, was die Wartungsanforderungen reduziert.
- Kostenersparnis: In der Regel sind pneumatische Pressen kostengünstiger in der Anschaffung und im Betrieb als hydraulische Pressen.
2.2.3 Nachteile pneumatischer Pressen
Der größte Nachteil pneumatischer Systeme ist ihre Druckkapazität. Sie können nicht die gleichen hohen Drücke erzeugen wie hydraulische Systeme, was sie für Anwendungen, die hohe Kompressionskräfte erfordern, ungeeignet macht. Zudem ist die Präzision bei der Druckkontrolle in der Regel geringer als bei hydraulischen Systemen, was zu Herausforderungen bei sehr genauen Prozessen führen kann.
2.3 Mechanische Drucksysteme
Mechanische Pressen verwenden Hebelmechanismen, Schneckengetriebe oder Kurbelantriebe, um den Druck zu erzeugen. Diese Systeme sind besonders langlebig und robust, jedoch in der Regel weniger flexibel und bieten weniger präzise Druckkontrolle als hydraulische oder pneumatische Systeme.
2.3.1 Funktionsweise eines mechanischen Drucksystems
Mechanische Systeme nutzen oft eine Kombination von Zahnrädern, Schrauben und Hebeln, um den Druck auf die Pressplatten zu übertragen. Durch manuelles oder motorisiertes Drehen einer Kurbel wird der Druck auf das Material ausgeübt. Ein typisches Beispiel ist die Verwendung einer Schraubspindel, die durch Drehen des Hebels den Druck erhöht.
2.3.2 Vorteile mechanischer Pressen
- Langlebigkeit: Mechanische Systeme sind äußerst robust und erfordern weniger Wartung als hydraulische oder pneumatische Systeme.
- Energieeffizienz: Mechanische Pressen benötigen oft weniger Energie, da sie auf rein mechanischen Prinzipien basieren und keine zusätzliche Energie für Pumpen oder Kompressoren erforderlich ist.
2.3.3 Nachteile mechanischer Pressen
Mechanische Systeme sind in ihrer Flexibilität eingeschränkt, da sie nur feste Druckhöhen liefern und nicht so präzise reguliert werden können wie hydraulische oder pneumatische Systeme. Sie sind oft langsamer und nicht für komplexe Laborprozesse geeignet, bei denen es auf genaue Steuerung von Druck und Temperatur ankommt.
3. Heizsysteme: Konzepte und Technologien
Das Heizsystem ist der zweite wesentliche Bestandteil einer beheizten Laborpresse. Die gleichmäßige Erzeugung und Kontrolle von Wärme ist entscheidend, um Materialien zu verarbeiten, deren physikalische oder chemische Eigenschaften durch Temperaturveränderungen beeinflusst werden. Es gibt verschiedene Heiztechnologien, die in beheizten Laborpressen eingesetzt werden, darunter Widerstandsheizungen, Induktionsheizungen, Infrarotheizungen und Mikrowellenheizungen.
3.1 Widerstandsheizungen
Widerstandsheizungen sind die am häufigsten verwendeten Heizsysteme in Laborpressen. Sie bestehen aus elektrischen Drähten oder Bändern, die Strom leiten und dadurch Wärme erzeugen, wenn ein elektrischer Widerstand entsteht. Diese Heizdrähte sind in den Pressplatten integriert und erwärmen diese gleichmäßig.
3.1.1 Funktionsweise von Widerstandsheizungen
Das Prinzip der Widerstandsheizung basiert auf dem Jouleschen Gesetz, das besagt, dass elektrische Energie in Wärme umgewandelt wird, wenn Strom durch einen Leiter fließt. Bei beheizten Laborpressen fließt elektrischer Strom durch die Widerstandsdrähte, die oft aus Nickel-Chrom-Legierungen bestehen, da diese Materialien hohe Temperaturen aushalten und eine gute Wärmeleitfähigkeit bieten.
Die Hitze wird direkt auf die Pressplatten übertragen, die wiederum das zu verarbeitende Material erwärmen. Ein Temperatursensor oder Thermoelement misst die Temperatur und sendet Signale an die Steuereinheit, die den Stromfluss und damit die Temperatur reguliert.
3.1.2 Vorteile von Widerstandsheizungen
- Gleichmäßige Erwärmung: Widerstandsheizungen bieten eine gleichmäßige Verteilung der Wärme über die gesamte Fläche der Pressplatten.
- Einfachheit und Verlässlichkeit: Widerstandsheizungen sind robust, kostengünstig und zuverlässig, was sie zu einer der bevorzugten Heizmethoden für Laborpressen macht.
- Präzise Temperaturkontrolle: In Verbindung mit einem Thermoelement kann die Temperatur exakt geregelt werden, was für empfindliche Materialien von Vorteil ist.
3.1.3 Nachteile von Widerstandsheizungen
Widerstandsheizungen benötigen in der Regel längere Aufheizzeiten im Vergleich zu anderen Heiztechnologien, wie z.B. Induktionsheizungen. Sie sind zudem in ihrer maximalen Betriebstemperatur eingeschränkt, da die verwendeten Materialien bei sehr hohen Temperaturen (>1.000°C) verschleißen können.
3.2 Induktionsheizungen
Induktionsheizungen sind eine fortschrittlichere Methode, um Wärme in Laborpressen zu erzeugen. Diese Technologie nutzt elektromagnetische Induktion, um Wärme direkt in den Metallplatten der Presse zu erzeugen, anstatt Heizdrähte zu verwenden.
3.2.1 Funktionsweise der Induktionsheizung
Die Induktionsheizung basiert auf dem Faradayschen Gesetz der elektromagnetischen Induktion. Eine Wechselstromquelle erzeugt ein hochfrequentes elektromagnetisches Feld in einer Spule, die um die Pressplatten gewickelt ist. Dieses elektromagnetische Feld induziert Wirbelströme im Metall der Pressplatten, die aufgrund des elektrischen Widerstands des Metalls Wärme erzeugen.
3.2.2 Vorteile der Induktionsheizung
- Schnelle Erwärmung: Da die Wärme direkt in den Pressplatten erzeugt wird, sind Induktionsheizungen deutlich schneller als Widerstandsheizungen. Dies verkürzt die Aufheizzeit erheblich.
- Energieeffizienz: Induktionsheizungen sind sehr effizient, da fast keine Energie durch Übertragung verloren geht. Dies reduziert den Energieverbrauch und die Betriebskosten.
- Hohe Temperaturen: Induktionsheizungen können problemlos sehr hohe Temperaturen (>1.500°C) erreichen, was sie für Anwendungen in der Metallverarbeitung oder Keramikherstellung besonders geeignet macht.
3.2.3 Nachteile der Induktionsheizung
Der Hauptnachteil von Induktionsheizungen ist ihre komplexe Konstruktion und die höheren Anschaffungskosten im Vergleich zu Widerstandsheizungen. Außerdem sind sie nicht für alle Materialtypen geeignet, da sie nur bei Metallen und elektrisch leitenden Materialien funktionieren.
3.3 Infrarotheizungen
Infrarotheizungen verwenden Infrarotstrahlung, um die Oberflächen der Materialien in der Presse direkt zu erwärmen. Diese Art der Heizung ist besonders nützlich, wenn eine schnelle Erwärmung erforderlich ist, ohne dass die gesamte Masse des Materials erwärmt werden muss.
3.3.1 Funktionsweise von Infrarotheizungen
Infrarotheizungen arbeiten durch die Emission von Infrarotstrahlung, die von speziellen Heizkörpern oder Lampen erzeugt wird. Die Strahlung wird von den Oberflächen der Materialien absorbiert und in Wärme umgewandelt. Dies ermöglicht eine schnelle und gezielte Erwärmung, ohne dass das gesamte Material von innen heraus erwärmt werden muss.
3.3.2 Vorteile von Infrarotheizungen
- Schnelle Erwärmung: Infrarotheizungen können Materialien sehr schnell erwärmen, was die Zykluszeiten in Produktionsumgebungen reduziert.
- Geringere Energieverluste: Da nur die Oberfläche des Materials erwärmt wird, können Energieverluste minimiert werden, was die Effizienz des Systems erhöht.
- Gezielte Erwärmung: Diese Technologie ermöglicht es, spezifische Bereiche des Materials zu erwärmen, was in selektiven Prozessen nützlich sein kann.
3.3.3 Nachteile von Infrarotheizungen
Ein Nachteil von Infrarotheizungen ist, dass sie nur die Oberfläche des Materials effektiv erwärmen. Für Prozesse, bei denen die gesamte Materialmasse gleichmäßig erwärmt werden muss, sind sie weniger geeignet. Außerdem können Infrarotheizungen nicht so hohe Temperaturen erreichen wie Induktionsheizungen.
3.4 Mikrowellenheizungen
Mikrowellenheizungen sind eine weitere fortschrittliche Technologie, die in einigen Spezialanwendungen eingesetzt wird. Sie nutzen hochfrequente elektromagnetische Wellen, um die Moleküle in einem Material in Schwingung zu versetzen und dadurch Wärme zu erzeugen.
3.4.1 Funktionsweise von Mikrowellenheizungen
Mikrowellenstrahlung bewirkt, dass polare Moleküle im Material (wie Wasser oder andere Dipolmoleküle) in Schwingung geraten. Diese Schwingung erzeugt Reibung auf molekularer Ebene, was zur Erwärmung des Materials führt. Mikrowellenheizungen sind besonders effektiv bei der Erwärmung von feuchten Materialien oder polaren Substanzen.
3.4.2 Vorteile von Mikrowellenheizungen
- Durchdringende Erwärmung: Mikrowellen erwärmen das Material von innen heraus, was bei dicken oder voluminösen Materialien nützlich sein kann.
- Effiziente Erwärmung von Flüssigkeiten: Da Mikrowellen besonders effektiv bei der Erwärmung von Flüssigkeiten und feuchten Materialien sind, werden sie oft in der chemischen Industrie und Biotechnologie eingesetzt.
3.4.3 Nachteile von Mikrowellenheizungen
Der Einsatz von Mikrowellenheizungen ist oft auf spezifische Materialien beschränkt, die polar sind oder eine gewisse Feuchtigkeit aufweisen. Trockene oder nicht-leitende Materialien lassen sich schwer mit Mikrowellen erwärmen, weshalb diese Technologie nicht so vielseitig ist wie Widerstands- oder Induktionsheizungen.
4. Steuerungssysteme: Präzision und Automatisierung
Das Steuerungssystem einer beheizten Laborpresse ist entscheidend für die Präzision und Wiederholbarkeit des Prozesses. Moderne Laborpressen sind oft mit digitalen Steuerungen, Sensoren und automatischen Regelkreisen ausgestattet, die eine genaue Überwachung und Anpassung der Prozessparameter ermöglichen. Es gibt verschiedene Arten von Steuerungssystemen, die sich durch ihren Grad der Automatisierung und die verwendete Technologie unterscheiden.
4.1 Manuelle Steuerungssysteme
Manuelle Steuerungssysteme sind die einfachste Form der Prozesssteuerung. Bei dieser Methode stellt der Bediener manuell den Druck und die Temperatur über Drehregler, Schalter oder Knöpfe ein. Diese Systeme sind in der Regel kostengünstig, bieten jedoch weniger Präzision und Automatisierung als fortschrittlichere Steuerungssysteme.
4.1.1 Vorteile manueller Steuerungssysteme
- Einfachheit: Manuelle Steuerungen sind einfach zu bedienen und erfordern keine umfangreiche Schulung oder spezielle Softwarekenntnisse.
- Geringere Kosten: Diese Systeme sind kostengünstiger in der Anschaffung und erfordern weniger Wartung.
4.1.2 Nachteile manueller Steuerungssysteme
Der größte Nachteil manueller Systeme ist der Mangel an Präzision und Wiederholbarkeit. Da der Bediener alle Parameter manuell einstellen muss, können menschliche Fehler zu Inkonsistenzen im Prozess führen. Zudem ist es schwieriger, komplexe Temperatur- und Druckprofile zu erstellen, was die Anwendungsbereiche einschränkt.
4.2 Halbautomatische Steuerungssysteme
Halbautomatische Steuerungssysteme kombinieren manuelle Einstellungen mit digitaler Überwachung und Automatisierung bestimmter Prozessschritte. Diese Systeme sind in der Regel mit Sensoren ausgestattet, die die Temperatur und den Druck überwachen und den Bediener warnen, wenn die Parameter außerhalb der zulässigen Grenzen liegen.
4.2.1 Funktionsweise halbautomatischer Systeme
In einem halbautomatischen System stellt der Bediener die Hauptparameter (Druck, Temperatur, Zeit) manuell ein, während das System kontinuierlich die Sensoren überwacht und bei Bedarf automatische Anpassungen vornimmt, um die Stabilität des Prozesses zu gewährleisten. Diese Systeme können auch Datenlogger enthalten, die Prozessparameter aufzeichnen, was eine Qualitätssicherung ermöglicht.
4.2.2 Vorteile halbautomatischer Systeme
- Kombination aus Präzision und Flexibilität: Halbautomatische Systeme bieten mehr Präzision als manuelle Steuerungen, während der Bediener dennoch die Möglichkeit hat, Anpassungen vorzunehmen.
- Kosteneffizienz: Sie sind günstiger als vollautomatische Systeme und bieten dennoch die Möglichkeit, den Prozess zu überwachen und anzupassen.
4.2.3 Nachteile halbautomatischer Systeme
Obwohl halbautomatische Systeme einige Vorteile bieten, bleibt der Eingriff des Bedieners notwendig, was zu Inkonsistenzen führen kann. Außerdem ist die Automatisierung auf bestimmte Prozessschritte beschränkt, was bedeutet, dass komplexe Prozesse nicht vollständig automatisiert werden können.
4.3 Vollautomatische Steuerungssysteme
Vollautomatische Steuerungssysteme sind die fortschrittlichste Form der Prozesssteuerung. Sie verwenden programmierbare Logiksteuerungen (PLCs), Computersysteme und eine Vielzahl von Sensoren, um alle Aspekte des Pressvorgangs automatisch zu überwachen und zu steuern.
4.3.1 Funktionsweise vollautomatischer Systeme
Bei vollautomatischen Systemen gibt der Bediener die Zielwerte für Druck, Temperatur und Zeit in das Steuerungssystem ein, und das System führt den gesamten Prozess autonom durch. Sensoren überwachen kontinuierlich den Zustand des Materials und passen die Parameter bei Bedarf an, um sicherzustellen, dass der Prozess optimal verläuft. Einige vollautomatische Systeme verwenden auch KI-basierte Algorithmen oder maschinelles Lernen, um aus früheren Prozessen zu lernen und die Ergebnisse zu optimieren.
4.3.2 Vorteile vollautomatischer Systeme
- Maximale Präzision und Wiederholbarkeit: Vollautomatische Systeme eliminieren menschliche Fehler und bieten konsistente Ergebnisse, die in der industriellen Fertigung und hochpräzisen Laboranwendungen von unschätzbarem Wert sind.
- Effizienz: Diese Systeme sind in der Lage, komplexe Prozesse schneller und mit weniger Eingriffen durch den Bediener durchzuführen, was die Produktivität erhöht.
- Datenintegration: Vollautomatische Systeme ermöglichen die Erfassung und Analyse von Prozessdaten, die zur Qualitätssicherung und Prozessoptimierung verwendet werden können.
4.3.3 Nachteile vollautomatischer Systeme
Der Hauptnachteil vollautomatischer Systeme sind die hohen Anschaffungskosten und der Schulungsaufwand für das Personal. Diese Systeme sind komplexer und erfordern spezielle Softwarekenntnisse, um sie effektiv zu nutzen.
4.4 Sensoren und Regelkreise
Ein wesentlicher Bestandteil moderner Steuerungssysteme sind Sensoren, die den Zustand des Materials und der Prozessparameter überwachen. Zu den gängigsten Sensoren gehören Temperatursensoren, Drucksensoren, Wegmesssensoren und Kraftmesssensoren. Diese Sensoren sind in das Regelkreissystem integriert, das die Messdaten kontinuierlich an die Steuereinheit weiterleitet, die dann die Prozessparameter anpasst, um Abweichungen zu korrigieren.
4.4.1 Temperatursensoren
Temperatursensoren, wie Thermoelemente oder Infrarot-Thermometer, werden verwendet, um die Temperatur der Pressplatten und des Materials zu überwachen. Diese Sensoren sind entscheidend, um sicherzustellen, dass das Material auf die richtige Temperatur erhitzt wird und diese Temperatur während des gesamten Prozesses konstant bleibt.
4.4.2 Drucksensoren
Drucksensoren messen den Druck, der auf das Material ausgeübt wird, und gewährleisten, dass der gewünschte Druck gleichmäßig über die gesamte Fläche der Pressplatten verteilt wird. Sie verhindern Überlastungen oder Druckverluste, die zu Fehlern im Prozess führen könnten.
4.4.3 Kraftmesssensoren
Kraftmesssensoren messen die tatsächliche Kraft, die auf das Material wirkt. Diese Sensoren sind besonders wichtig in Anwendungen, bei denen es auf die exakte Kraftaufbringung ankommt, wie in der Pharmazeutik oder bei der Herstellung von technischen Keramiken.
4.4.4 Regelkreise
Die in modernen Laborpressen verwendeten Regelkreise sind oft auf der Grundlage von PID-Reglern (Proportional-Integral-Derivativ-Regler) aufgebaut. Diese Systeme passen die Prozessparameter auf der Grundlage der Sensordaten kontinuierlich an, um Abweichungen zu korrigieren und den Prozess stabil zu halten.
5. Materialien und Konstruktionsprinzipien
Die Wahl der Materialien für die Konstruktion von Laborpressen ist ein wichtiger Aspekt der Funktionalität und Langlebigkeit der Maschine. Insbesondere die Pressplatten, Hydraulikkomponenten und Isoliermaterialien müssen auf die spezifischen Anforderungen der jeweiligen Anwendung abgestimmt sein. Im Folgenden werden die wichtigsten Materialien und ihre Eigenschaften beschrieben.
5.1 Materialien der Pressplatten
Die Pressplatten sind ein wesentlicher Bestandteil der Laborpresse, da sie sowohl den Druck als auch die Wärme direkt auf das Material übertragen. Die Wahl des Plattenmaterials hängt von den Anforderungen des Prozesses ab, insbesondere von der Maximaltemperatur, der Wärmeleitfähigkeit und der Beständigkeit gegenüber chemischen oder mechanischen Belastungen.
5.1.1 Aluminium
Aluminium wird häufig für Pressplatten verwendet, da es eine gute Wärmeleitfähigkeit aufweist und relativ kostengünstig ist. Aluminiumplatten sind ideal für Anwendungen, bei denen die Temperatur schnell ansteigen muss, da Aluminium Wärme schnell leitet.
5.1.2 Stahl
Edelstahl wird verwendet, wenn höhere Temperaturen oder höhere mechanische Belastungen erforderlich sind. Stahl ist weniger wärmeleitfähig als Aluminium, aber deutlich widerstandsfähiger gegenüber Verschleiß, Korrosion und Verformung.
5.1.3 Keramik
Keramikplatten werden verwendet, wenn sehr hohe Temperaturen (>1.500°C) benötigt werden, wie es bei der Herstellung von technischen Keramiken oder Hochleistungskomponenten in der Luft- und Raumfahrtindustrie der Fall ist. Keramik ist extrem hitzebeständig und kann auch bei hohen Temperaturen ihre strukturelle Integrität bewahren.
5.2 Isolationsmaterialien
Die Wärmeisolierung der Laborpresse ist entscheidend, um Energieverluste zu minimieren und die Betriebskosten zu senken. Es gibt verschiedene Arten von Isoliermaterialien, die in beheizten Pressen verwendet werden, darunter Glasfaser, Keramikfasern und Spezialkunststoffe.
5.2.1 Glasfaserisolierung
Glasfaser ist ein häufig verwendetes Isolationsmaterial in Laborpressen, da es kostengünstig, leicht und hitzebeständig ist. Glasfaser wird häufig in den äußeren Schichten der Presse verwendet, um den Wärmeverlust zu reduzieren und die Oberflächentemperatur der Maschine niedrig zu halten.
5.2.2 Keramikfasern
Keramikfasern bieten eine höhere Temperaturbeständigkeit als Glasfaser und werden oft in Pressen verwendet, die bei extrem hohen Temperaturen arbeiten. Sie haben eine ausgezeichnete Isolierfähigkeit und können Temperaturen von über 1.000°C standhalten, ohne ihre isolierenden Eigenschaften zu verlieren.
5.2.3 Hochleistungs-Kunststoffe
Hochleistungs-Kunststoffe, wie PEEK (Polyetheretherketon) oder PTFE (Polytetrafluorethylen), werden in einigen Pressen verwendet, um Gleitkomponenten und Dichtungen zu isolieren. Diese Materialien bieten nicht nur eine gute Isolierwirkung, sondern sind auch chemisch resistent und haben eine geringe Reibung, was sie ideal für bewegliche Teile der Maschine macht.
5.3 Hydraulikkomponenten
Die Hydrauliksysteme einer Laborpresse müssen extrem druckbeständig und korrosionsresistent sein, da sie unter hohen Belastungen arbeiten. Die Wahl der richtigen Materialien für Hydraulikkomponenten, wie Zylinder, Ventile und Dichtungen, ist entscheidend für die Langlebigkeit und Zuverlässigkeit des Systems.
5.3.1 Stahl und Edelstahl
Stahl und Edelstahl sind die bevorzugten Materialien für Hydraulikzylinder und andere Hochdruckkomponenten, da sie hohen mechanischen Belastungen und Temperaturunterschieden standhalten. Edelstahl bietet zusätzlichen Schutz gegen Korrosion, was besonders wichtig ist, wenn die Presse in feuchten oder chemisch aggressiven Umgebungen betrieben wird.
5.3.2 Dichtungen und Gleitkomponenten
Dichtungen und Gleitkomponenten müssen aus Materialien bestehen, die sowohl druck- als auch temperaturbeständig sind. Nitrilkautschuk, Viton und Silikon sind häufig verwendete Materialien für Dichtungen in hydraulischen Systemen, da sie eine hohe Widerstandsfähigkeit gegenüber Hitze und Chemikalien aufweisen.
6. Technologische Innovationen und Weiterentwicklungen
Die Technologie von beheizten Laborpressen hat sich im Laufe der Jahre kontinuierlich weiterentwickelt, um den steigenden Anforderungen der Industrie gerecht zu werden. Es gibt verschiedene neue Technologien und Innovationen, die die Effizienz, Präzision und Anwendbarkeit dieser Maschinen verbessern.
6.1 Digitalisierung und Industrie 4.0
In der Ära von Industrie 4.0 und der Digitalisierung sind Laborpressen zunehmend mit intelligenten Steuerungssystemen, Datenlogging und Fernüberwachung ausgestattet. Diese Systeme ermöglichen es den Bedienern, Prozessparameter in Echtzeit zu überwachen und die Effizienz und Qualität der Prozesse zu optimieren.
6.1.1 Vernetzte Laborpressen
Durch die Integration von Internet of Things (IoT)-Technologien können Laborpressen mit anderen Maschinen und Systemen im Labor oder in der Produktionslinie kommunizieren. Diese vernetzten Pressen sind in der Lage, Prozessdaten zu erfassen, zu speichern und in Echtzeit zu analysieren. Dies ermöglicht eine vorausschauende Wartung, bei der potenzielle Probleme erkannt werden, bevor sie zu Maschinenausfällen führen.
6.1.2 Datenanalyse und maschinelles Lernen
Ein weiterer technologischer Fortschritt ist die Integration von KI-basierten Algorithmen und maschinellem Lernen in die Steuerungssysteme von Laborpressen. Diese Systeme sind in der Lage, aus früheren Produktionsprozessen zu lernen und die Prozessparameter automatisch zu optimieren, um die Produktionsqualität und Effizienz zu verbessern.
6.2 Fortschritte in der Materialwissenschaft
Die Entwicklungen in der Materialwissenschaft haben ebenfalls die Konstruktion und Leistungsfähigkeit beheizter Laborpressen beeinflusst. Neue Materialien, wie Superlegierungen, Nanomaterialien und hochfeste Verbundstoffe, erfordern spezialisierte Pressen, die hohe Temperaturen und extreme Drücke bewältigen können.
6.2.1 Nanotechnologie und Laborpressen
Mit der zunehmenden Bedeutung der Nanotechnologie spielen beheizte Laborpressen eine zentrale Rolle bei der Herstellung von Nanokompositen und Nanoimprint-Lithographie. Diese Pressen müssen in der Lage sein, extreme Präzision zu bieten, um nanostrukturierte Materialien herzustellen, die in der Elektronik, Medizin und Materialwissenschaft eingesetzt werden.
6.2.2 3D-Druck und additive Fertigung
In Kombination mit der additiven Fertigung (3D-Druck) werden beheizte Laborpressen zur Nachbearbeitung von 3D-gedruckten Bauteilen eingesetzt. Durch die Anwendung von Druck und Wärme können die Oberflächenqualität und die mechanischen Eigenschaften der gedruckten Teile verbessert werden.
6.3 Nachhaltigkeit und Energieeffizienz
In Zeiten steigender Energiepreise und zunehmendem ökologischen Bewusstsein wird die Energieeffizienz von Laborpressen zu einem immer wichtigeren Thema. Neue isolierende Materialien und energieeffiziente Heizsysteme tragen dazu bei, den Energieverbrauch dieser Maschinen zu reduzieren.
6.3.1 Einsatz erneuerbarer Energien
Ein aufkommender Trend ist der Einsatz von erneuerbaren Energien in Laborumgebungen, um den Energieverbrauch von Pressen zu senken. Einige Forschungseinrichtungen und Unternehmen nutzen bereits Solarenergie, um ihre Laborpressen zu betreiben und so ihren CO₂-Fußabdruck zu reduzieren.
6.3.2 Regenerative Heizsysteme
Regenerative Heizsysteme, bei denen die Wärmeenergie, die während eines Zyklus verloren geht, wiederverwendet wird, sind eine weitere Innovation, die zur Energieeinsparung beiträgt. Diese Systeme fangen die Abwärme auf und nutzen sie für den nächsten Heizzyklus, was den Energieverbrauch erheblich reduziert.
Fazit
Die technische Funktionsweise einer beheizten Laborpresse ist ein komplexes Zusammenspiel von Druckmechanismen, Heizsystemen und Steuerungstechnologien, die präzise aufeinander abgestimmt sind, um eine Vielzahl von Materialien effizient und konsistent zu verarbeiten. Mit technologischen Fortschritten in der Digitalisierung, der Materialwissenschaft und der Energieeffizienz werden beheizte Laborpressen zu einem unverzichtbaren Werkzeug in Forschung und Produktion.
Obwohl diese Maschinen bereits heute eine hohe Präzision und Vielseitigkeit bieten, werden zukünftige Entwicklungen im Bereich der Industrie 4.0, der Nanotechnologie und der nachhaltigen Produktion dazu führen, dass sie noch effizienter, intelligenter und umweltfreundlicher werden.
Materialien und Wissenschaftliche Grundlagen

1. Einführung in die Materialwissenschaften
Die Materialwissenschaft ist ein interdisziplinäres Feld, das sich mit der Untersuchung und Anwendung von Feststoffen und deren Eigenschaften befasst. In der Materialwissenschaft werden die chemischen, physikalischen und mechanischen Eigenschaften von Materialien untersucht, um zu verstehen, wie sie unter verschiedenen Bedingungen reagieren, etwa bei Anwendung von Hitze, Druck oder anderen äußeren Kräften.
1.1 Bedeutung der Materialwissenschaften in der Industrie
Materialwissenschaften spielen eine zentrale Rolle in zahlreichen Industrien, von der Luft- und Raumfahrt über die Automobilindustrie bis hin zur Elektronik und Biotechnologie. Die Entwicklung neuer Materialien, die den spezifischen Anforderungen moderner Technologien gerecht werden, erfordert ein tiefes Verständnis der Mikrostruktur, thermischen Eigenschaften und mechanischen Belastbarkeit. In beheizten Laborpressen sind diese wissenschaftlichen Grundlagen entscheidend, um Materialien effizient zu verarbeiten, indem sowohl Druck als auch Wärme genutzt werden, um Mikrostrukturen zu verändern, mechanische Festigkeit zu verbessern oder chemische Reaktionen zu initiieren.
1.2 Einfluss von Hitze und Druck auf Materialien
Die Anwendung von Hitze und Druck in beheizten Laborpressen beeinflusst die atomare Struktur und das Molekülverhalten von Materialien auf unterschiedliche Weise. Diese Prozesse können die Kristallstruktur eines Materials verändern, seine Dichte erhöhen, Defekte oder Porosität verringern und die mechanischen Eigenschaften wie Festigkeit und Härte verbessern. Der Prozess des Sinterns, des Schmelzens oder der Verfestigung wird in vielen Fällen durch die exakte Kombination von Druck und Temperatur gesteuert.
2. Wissenschaftliche Grundlagen: Physikalische und chemische Prinzipien
Um die Verarbeitung von Materialien in beheizten Laborpressen vollständig zu verstehen, ist es notwendig, die grundlegenden physikalischen und chemischen Prinzipien zu erörtern, die diesen Prozessen zugrunde liegen. Dazu gehören die Thermodynamik, die Kinetik von Phasenübergängen, sowie das mechanische Verhalten von Materialien unter hohen Drücken.
2.1 Thermodynamik: Grundlagen und Bedeutung
Die Thermodynamik befasst sich mit den Prinzipien von Wärme, Energie und Arbeit. Sie ist eine der zentralen Theorien, die das Verhalten von Materialien unter Hitze in beheizten Laborpressen beschreibt. Die Gesetze der Thermodynamik helfen dabei zu erklären, wie sich ein Material verhält, wenn es erwärmt wird, wie viel Energie benötigt wird, um einen Phasenübergang zu erreichen, und welche Gleichgewichtszustände möglich sind.
2.1.1 Erster Hauptsatz der Thermodynamik
Der Erste Hauptsatz der Thermodynamik, auch bekannt als der Energieerhaltungssatz, besagt, dass die in einem abgeschlossenen System enthaltene Energie konstant ist. Energie kann von einer Form in eine andere umgewandelt werden (z.B. von Wärme zu mechanischer Arbeit), aber die Gesamtmenge der Energie bleibt gleich. In beheizten Laborpressen wird elektrische Energie in Wärme umgewandelt, die dann dazu verwendet wird, das Material zu erwärmen und einen bestimmten Phasenübergang oder eine Mikrostrukturveränderung zu erreichen.
2.1.2 Zweiter Hauptsatz der Thermodynamik
Der Zweite Hauptsatz der Thermodynamik beschreibt die Richtung, in der thermodynamische Prozesse ablaufen. Er besagt, dass die Entropie (das Maß für Unordnung) eines isolierten Systems niemals abnimmt, sondern stets gleich bleibt oder zunimmt. Dies bedeutet, dass Wärme von einem heißeren zu einem kälteren Körper fließt, was die Grundlage für das Temperaturgleichgewicht ist, das in der Presse erreicht werden muss, um Materialien homogen zu verarbeiten.
2.1.3 Wärmekapazität und spezifische Wärme
Ein weiterer wichtiger thermodynamischer Parameter ist die Wärmekapazität eines Materials, die angibt, wie viel Wärmeenergie erforderlich ist, um die Temperatur eines Körpers um einen bestimmten Betrag zu erhöhen. Materialien mit hoher Wärmekapazität erfordern mehr Energie, um erhitzt zu werden, was bei der Planung von Prozessen in beheizten Laborpressen berücksichtigt werden muss. Metalle haben in der Regel eine geringere Wärmekapazität als Polymere oder Keramiken, was ihre Erhitzungsraten beeinflusst.
2.2 Phasenübergänge: Schmelzen, Verdampfen und Erstarren
Phasenübergänge spielen eine zentrale Rolle in der Materialverarbeitung. Die Umwandlung von festen in flüssige oder gasförmige Phasen und umgekehrt wird in vielen Prozessen genutzt, um Materialien zu formen, zu verbinden oder zu modifizieren. Beheizte Laborpressen steuern diesen Prozess durch präzise Temperaturkontrolle, um sicherzustellen, dass die Phasenumwandlungen unter optimalen Bedingungen ablaufen.
2.2.1 Schmelzen und Erstarren
Beim Schmelzen wird einem festen Material Wärme zugeführt, bis seine Moleküle genügend Energie haben, um sich aus ihrer festen Struktur zu lösen und in einen flüssigen Zustand überzugehen. Die Schmelztemperatur ist spezifisch für jedes Material und muss exakt erreicht werden, um den Übergang effizient zu gestalten. In einer beheizten Presse wird die Temperatur gleichmäßig auf die gesamte Materialprobe verteilt, um sicherzustellen, dass das Material vollständig schmilzt.
Das Erstarren ist der umgekehrte Prozess, bei dem ein Material von einem flüssigen Zustand in einen festen übergeht. Bei Materialien wie Metallen oder Polymere kann das Erstarren kontrolliert werden, um spezifische Kristallstrukturen oder Glasübergänge zu erzeugen, die die mechanischen Eigenschaften des Endprodukts beeinflussen.
2.2.2 Verdampfen und Kondensation
Beim Verdampfen wird einer Flüssigkeit so viel Energie zugeführt, dass ihre Moleküle die Bindungen überwinden, die sie im flüssigen Zustand halten, und in den gasförmigen Zustand übergehen. Dieser Prozess wird in einigen industriellen Anwendungen genutzt, um Materialien durch Vakuumpressen oder Kondensationstechniken zu bearbeiten. Beheizte Laborpressen, die auch mit einem Vakuumsystem ausgestattet sind, ermöglichen eine kontrollierte Verdampfung von Lösemitteln oder flüchtigen Bestandteilen.
2.3 Festkörpermechanik: Spannungen und Deformationen
Die Festkörpermechanik ist ein weiteres fundamentales wissenschaftliches Prinzip, das das Verhalten von Materialien unter Druck und mechanischen Belastungen beschreibt. Materialien verhalten sich unter Druck unterschiedlich – einige Materialien, wie Metalle, verformen sich plastisch, während andere, wie Keramiken, spröde brechen. Das Verständnis dieser Mechanismen ist entscheidend, um Materialien in beheizten Laborpressen zu verarbeiten, ohne sie zu beschädigen.
2.3.1 Elastische und plastische Verformung
Die Verformung eines Materials unter Druck wird in zwei Hauptkategorien unterteilt: elastische Verformung und plastische Verformung. Bei einer elastischen Verformung kehrt das Material in seine ursprüngliche Form zurück, wenn der Druck entfernt wird. Dies tritt bei Materialien auf, die in der Lage sind, mechanische Spannungen zu absorbieren und zu speichern, wie z.B. Gummi oder einige Metalle.
Die plastische Verformung tritt auf, wenn das Material dauerhaft deformiert wird, weil es seine Elastizitätsgrenze überschritten hat. In der Materialverarbeitung ist dies oft erwünscht, da plastische Verformungen genutzt werden, um Formen oder Strukturen zu erzeugen. In beheizten Laborpressen kann der Druck so eingestellt werden, dass Materialien gezielt plastisch verformt werden, ohne dass sie brechen.
2.3.2 Bruchmechanik und Sprödbruch
Sprödbruch tritt auf, wenn ein Material unter Druck plötzlich und ohne signifikante plastische Verformung versagt. Dies ist besonders häufig bei Keramiken und einigen Verbundwerkstoffen der Fall, die wenig duktil sind und unter Druck schnell brechen. Um dies zu vermeiden, müssen die Druck- und Temperaturbedingungen in einer beheizten Laborpresse genau kontrolliert werden, um thermische Spannungen zu minimieren, die zum Bruch führen könnten.
3. Materialien in der Verarbeitung: Polymere, Metalle, Keramiken und Verbundwerkstoffe
In der Materialwissenschaft gibt es vier Hauptkategorien von Materialien, die in beheizten Laborpressen verarbeitet werden: Polymere, Metalle, Keramiken und Verbundwerkstoffe. Jedes dieser Materialien verhält sich unter Druck und Hitze unterschiedlich, und die richtige Wahl der Parameter in der Laborpresse hängt stark von den spezifischen Eigenschaften dieser Materialien ab.
3.1 Polymere: Thermoplaste und Duroplaste
Polymere sind organische Verbindungen, die aus langen Ketten von Molekülen bestehen und in zahlreichen industriellen Anwendungen eingesetzt werden, von Verpackungen über Textilien bis hin zu Hightech-Bauteilen in der Elektronik und Luftfahrt. Polymere werden in zwei Hauptkategorien unterteilt: Thermoplaste und Duroplaste.
3.1.1 Thermoplaste
Thermoplastische Polymere sind Kunststoffe, die beim Erhitzen weich und verformbar werden, während sie beim Abkühlen wieder fest werden. Zu den gebräuchlichsten Thermoplasten gehören Polyethylen (PE), Polypropylen (PP), Polyethylenterephthalat (PET) und Polyvinylchlorid (PVC).
In beheizten Laborpressen wird Wärme genutzt, um die Viskosität des Polymers zu verringern, so dass es unter Druck verformt oder in Formen gegossen werden kann. Thermoplaste haben eine schmelzbare Struktur, die es ihnen ermöglicht, immer wieder geschmolzen und verfestigt zu werden, ohne ihre chemische Struktur zu verändern.
3.1.2 Duroplaste
Duroplaste, im Gegensatz zu Thermoplasten, werden durch die Anwendung von Wärme und Druck irreversibel vernetzt und härten aus. Nach der Aushärtung können sie nicht wieder geschmolzen werden, ohne ihre Struktur zu zerstören. Zu den Duroplasten gehören Epoxidharze, Phenolharze und Polyurethane, die häufig in Verbundwerkstoffen verwendet werden.
Beheizte Laborpressen werden oft verwendet, um Duroplaste unter Druck zu formen und auszuhärten. Der Prozess der Vernetzung erfordert präzise Kontrolle von Temperatur und Druck, um sicherzustellen, dass das Material vollständig aushärtet und keine unvernetzten Bereiche zurückbleiben, die die mechanischen Eigenschaften des Endprodukts beeinträchtigen könnten.
3.1.3 Anwendungen von Polymeren
Polymere werden in einer Vielzahl von Industrien verwendet, darunter die Automobilindustrie, Medizintechnik, Verpackung, und Elektronik. Beheizte Laborpressen spielen eine entscheidende Rolle bei der Herstellung von Formteilen, Fasern, Folien und Bauteilen, die spezifische thermische und mechanische Eigenschaften aufweisen müssen.
3.2 Metalle: Thermomechanische Verarbeitung
Metalle sind aufgrund ihrer hohen Festigkeit, Leitfähigkeit und Bearbeitbarkeit in vielen Industrien weit verbreitet. Metalle können durch verschiedene thermomechanische Verfahren bearbeitet werden, bei denen die Kombination von Druck und Hitze genutzt wird, um ihre Mikrostruktur und mechanischen Eigenschaften zu verändern.
3.2.1 Wärmebehandlung und Legierungen
Die Wärmebehandlung ist eine der häufigsten Methoden, um die Eigenschaften von Metallen zu verändern. Durch gezieltes Erhitzen und anschließendes Abkühlen können die Härte, Zähigkeit und Duktilität eines Metalls angepasst werden. In beheizten Laborpressen werden Metalle oft für Prozesse wie Glühen, Härten und Anlassen erwärmt, um die gewünschten Materialeigenschaften zu erreichen.
Legierungen, wie Stahl (eine Legierung aus Eisen und Kohlenstoff) oder Aluminiumlegierungen, werden häufig verwendet, um die natürlichen Eigenschaften von Metallen zu verbessern. Legierungsprozesse erfordern oft die präzise Steuerung von Temperatur und Abkühlungsraten, um Mikrostrukturen zu erzeugen, die den spezifischen Anforderungen einer Anwendung entsprechen.
3.2.2 Warmumformung und Kaltumformung
In der Metallverarbeitung unterscheidet man zwischen Warmumformung und Kaltumformung. Bei der Warmumformung wird das Metall auf eine Temperatur erhitzt, die über seiner Rekristallisationstemperatur liegt, was es ermöglicht, das Material plastisch zu verformen, ohne dass es dabei zu Sprödbruch kommt. In beheizten Laborpressen wird die Warmumformung verwendet, um Metalle in komplexe Formen zu bringen, die bei Raumtemperatur nicht erreicht werden könnten.
Die Kaltumformung erfolgt bei Temperaturen unterhalb der Rekristallisationstemperatur und wird verwendet, um die Festigkeit des Metalls durch Kaltverfestigung zu erhöhen. Kaltumgeformte Metalle haben in der Regel eine höhere Härte und Zugfestigkeit, sind aber weniger duktil als warmumgeformte Materialien.
3.2.3 Anwendungen von Metallen
Metalle finden Anwendung in zahlreichen Bereichen, darunter die Automobilindustrie, Bauwesen, Luft- und Raumfahrt und Elektronik. Beheizte Laborpressen spielen eine zentrale Rolle bei der Herstellung von Metallteilen, Blechen, Drähten und Komponenten, die spezifische thermomechanische Eigenschaften aufweisen müssen.
3.3 Keramiken: Hochtemperaturmaterialien
Keramiken sind anorganische, nichtmetallische Materialien, die durch Sintern oder Brennen bei hohen Temperaturen hergestellt werden. Sie zeichnen sich durch ihre hohe Härte, chemische Beständigkeit und Hitzebeständigkeit aus, sind aber oft spröde und neigen zum Bruch unter mechanischer Belastung.
3.3.1 Sinterprozesse
Das Sintern ist ein thermischer Prozess, bei dem keramische Pulver unter hohen Temperaturen und Druck zu festen Materialien verdichtet werden. In beheizten Laborpressen werden keramische Werkstoffe oft in Form von Pulvern oder Pulverkompositen in Matrizen gegeben und unter hohem Druck erhitzt, um die Partikel zu verschmelzen und die Porosität zu verringern.
Beim Sintern ist es entscheidend, dass die Temperatur hoch genug ist, um die Partikeldiffusion zu ermöglichen, ohne das Material vollständig zu schmelzen. Durch die Anwendung von Druck in einer beheizten Laborpresse kann die Dichte und Homogenität des Materials verbessert werden, was zu besseren mechanischen Eigenschaften führt.
3.3.2 Anwendungen von Keramiken
Keramische Materialien werden in Anwendungen verwendet, bei denen extreme Hitzebeständigkeit, Verschleißfestigkeit oder chemische Stabilität erforderlich sind. Beispiele sind Feuerfestmaterialien, Dichtungen, Hochleistungskeramiken für die Elektronik und medizinische Implantate. Beheizte Laborpressen werden verwendet, um komplexe keramische Bauteile zu fertigen, die in Turbinen, Brennstoffzellen oder Hitzeschildern eingesetzt werden.
3.4 Verbundwerkstoffe: Materialkombinationen für Hochleistungsanwendungen
Verbundwerkstoffe (Composites) bestehen aus zwei oder mehr verschiedenen Materialphasen, die zusammen bessere Eigenschaften aufweisen als die Einzelkomponenten. Typische Verbundwerkstoffe bestehen aus einer Matrix, wie einem Polymer oder Metall, und einer Verstärkungsphase, wie Glas- oder Kohlenstofffasern.
3.4.1 Herstellung von Verbundwerkstoffen
In beheizten Laborpressen werden Verbundwerkstoffe oft durch Laminieren oder Pressformen hergestellt. Die Matrix wird unter Druck und Hitze verflüssigt, während die Verstärkungsfasern in die Matrix eingebettet werden. Diese Kombination führt zu einer signifikanten Verbesserung der Festigkeit, Zähigkeit und Hitzebeständigkeit des Endmaterials.
Ein Beispiel ist die Herstellung von Kohlenstofffaser-Verbundwerkstoffen, die in der Luft- und Raumfahrt verwendet werden. Diese Materialien sind leicht und stark und werden in beheizten Pressen verarbeitet, um sicherzustellen, dass die Fasern gleichmäßig in der Matrix verteilt sind und keine Lufteinschlüsse vorhanden sind.
3.4.2 Anwendungen von Verbundwerkstoffen
Verbundwerkstoffe finden in einer Vielzahl von Hochleistungsanwendungen Einsatz, darunter Flugzeugbau, Automobilindustrie, Sportgeräte und Medizintechnik. Ihre Fähigkeit, die Vorteile mehrerer Materialklassen zu kombinieren, macht sie besonders nützlich in Bereichen, in denen Gewicht, Festigkeit und Korrosionsbeständigkeit entscheidend sind.
4. Molekulare Dynamik: Verhalten auf atomarer und molekularer Ebene
Ein grundlegendes Verständnis des Verhaltens von Materialien auf molekularer und atomarer Ebene ist entscheidend, um zu verstehen, wie sie unter Druck und Hitze in einer beheizten Laborpresse reagieren. Die Molekulardynamik beschreibt, wie die Atome und Moleküle eines Materials miteinander interagieren, sich bewegen und auf äußere Einflüsse reagieren.
4.1 Bindungstypen in Materialien
Die Art der Bindung zwischen den Atomen eines Materials bestimmt weitgehend seine physikalischen und chemischen Eigenschaften. Es gibt drei Haupttypen von Bindungen: kovalente Bindungen, ionische Bindungen und metallische Bindungen.
4.1.1 Kovalente Bindungen
In kovalenten Bindungen teilen sich Atome Elektronen, um eine stabile Elektronenhülle zu bilden. Diese Bindungen sind stark und bestimmen die Festigkeit und Hitzebeständigkeit vieler Materialien, wie Diamanten oder Kohlenstoffnanoröhren.
4.1.2 Ionische Bindungen
Ionische Bindungen entstehen durch die elektrostatische Anziehung zwischen positiv und negativ geladenen Ionen. Diese Bindungen sind weniger flexibel als kovalente Bindungen, was dazu führt, dass Materialien mit ionischen Bindungen, wie Keramiken, oft spröde sind.
4.1.3 Metallische Bindungen
In metallischen Bindungen teilen sich die Atome ein „Elektronengas“, das die Atome zusammenhält. Diese delokalisierte Elektronenstruktur erklärt die elektrische Leitfähigkeit und die Verformbarkeit von Metallen.
4.2 Kristallstrukturen und Defekte
Die Kristallstruktur eines Materials ist ein entscheidender Faktor für seine mechanischen und thermischen Eigenschaften. Metalle, Keramiken und einige Polymere bilden kristalline Strukturen, die durch das wiederholte Anordnen von Atomen in einem regelmäßigen Muster gekennzeichnet sind.
4.2.1 Gitterstrukturen
Es gibt verschiedene Arten von Kristallgittern, darunter das kubisch raumzentrierte Gitter, das kubisch flächenzentrierte Gitter und das hexagonale Gitter. Die Art des Gitters bestimmt die Verformbarkeit, Festigkeit und Wärmeleitfähigkeit des Materials.
4.2.2 Kristalldefekte
Defekte in Kristallstrukturen, wie Versetzungen, Leerstellen oder Fremdatome, können die Eigenschaften eines Materials erheblich beeinflussen. In beheizten Laborpressen werden diese Defekte oft absichtlich eingeführt oder entfernt, um die mechanischen Eigenschaften des Materials zu verbessern.
4.3 Glasübergänge und amorphe Materialien
Ein Glasübergang tritt auf, wenn ein amorphes Material (wie Glas oder einige Polymere) von einem festen in einen viskoelastischen Zustand übergeht. Der Glasübergang ist kein scharfer Phasenübergang wie das Schmelzen, sondern eine allmähliche Änderung der molekularen Bewegung. In beheizten Laborpressen ist der Glasübergang wichtig, da er die Verformbarkeit und Fließfähigkeit von Materialien beeinflusst.
5. Fallbeispiele: Anwendung von Materialwissenschaften in der Praxis
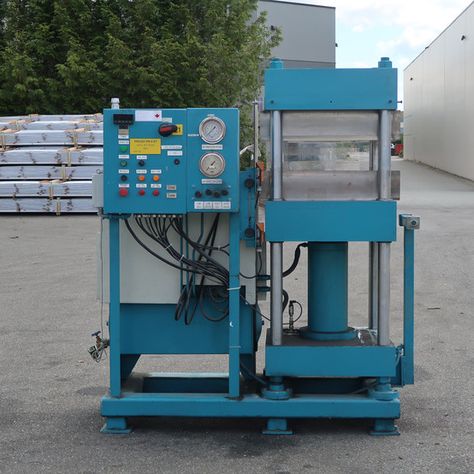
5.1 Fallbeispiel: Herstellung von hochfesten Polymeren für die Automobilindustrie
In der Automobilindustrie spielen hochfeste Polymere eine wichtige Rolle bei der Reduzierung des Fahrzeuggewichts und der Verbesserung der Kraftstoffeffizienz. In dieser Fallstudie wird eine beheizte Laborpresse verwendet, um ein faserverstärktes Polymer zu verarbeiten, das in Fahrzeugkarosserien und Stoßfängern eingesetzt wird. Durch die Anwendung von Druck und Hitze wird das Polymer so verarbeitet, dass es eine gleichmäßige Verteilung der Fasern und eine hohe mechanische Festigkeit aufweist.
5.2 Fallbeispiel: Herstellung von keramischen Bauteilen für die Elektronikindustrie
In der Elektronikindustrie werden Keramiken aufgrund ihrer Isolierungseigenschaften und Hitzebeständigkeit verwendet. In dieser Fallstudie wird eine beheizte Laborpresse verwendet, um Aluminiumoxid-Keramiken zu sintern, die als Isolatoren in Mikrochips verwendet werden. Der Sinternprozess muss sorgfältig gesteuert werden, um eine dichte, porenfreie Struktur zu erhalten, die den Anforderungen der Elektronik entspricht.
Fazit
Die Verarbeitung von Materialien in beheizten Laborpressen basiert auf einem tiefen Verständnis der wissenschaftlichen Grundlagen, die das Verhalten von Materialien unter Druck und Hitze beschreiben. Durch die Kombination von Thermodynamik, Festkörpermechanik, Molekulardynamik und spezifischen Materialeigenschaften wie Kristallstrukturen oder Verformungsverhalten können Materialwissenschaftler und Ingenieure Materialien gezielt modifizieren und optimieren. Dies eröffnet neue Möglichkeiten für die Entwicklung von hochleistungsfähigen Werkstoffen, die in einer Vielzahl von Industrien eingesetzt werden können, von der Elektronik über die Automobilindustrie bis hin zur Luft- und Raumfahrt.
Erweiterte Anwendungsgebiete von beheizten Laborpressen
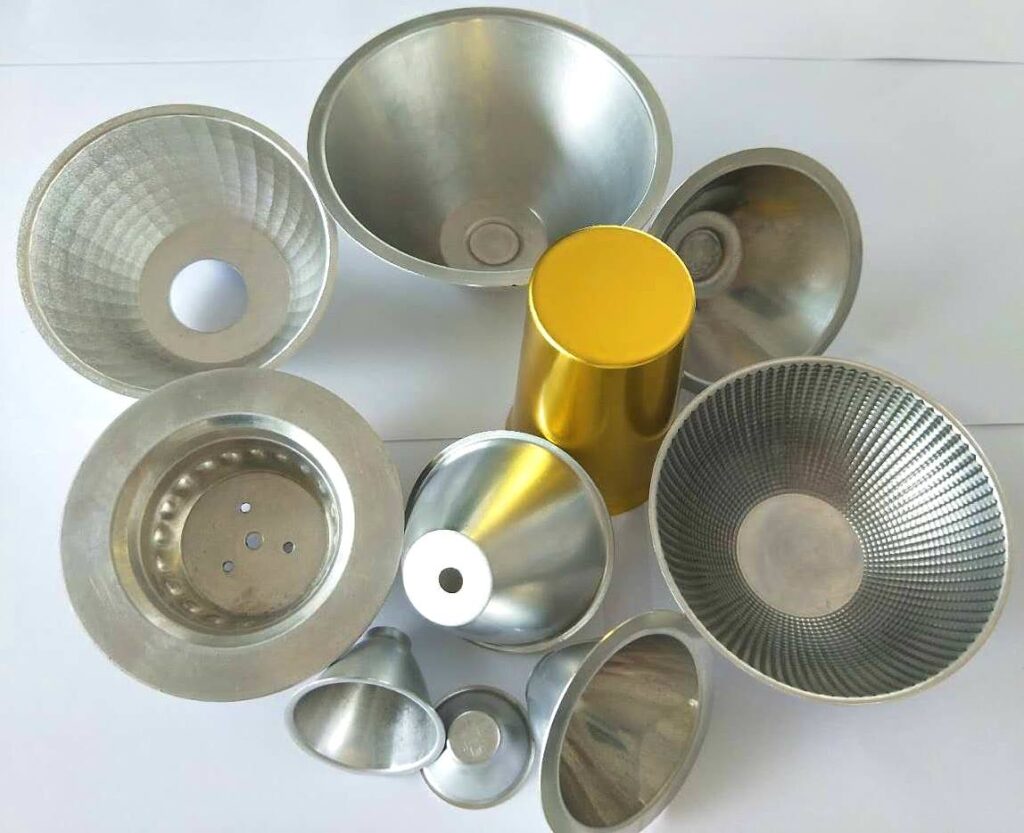
1. Einführung in die Anwendungsgebiete
Beheizte Laborpressen finden in einer Vielzahl von Industrien und wissenschaftlichen Disziplinen Anwendung, in denen die Kombination von Hitze und Druck eine zentrale Rolle spielt. Diese Maschinen sind unverzichtbar für die Herstellung, Modifikation und Verarbeitung von Materialien, die unter normalen Umgebungsbedingungen schwer zu manipulieren sind. In vielen Fällen hängt die erfolgreiche Entwicklung neuer Produkte oder Technologien davon ab, dass Materialien unter präzise kontrollierten thermischen und mechanischen Bedingungen verarbeitet werden.
1.1 Zentrale Vorteile beheizter Laborpressen
- Präzision: Beheizte Laborpressen bieten eine hohe Kontrollierbarkeit über Prozessparameter wie Druck, Temperatur und Zykluszeit, was besonders wichtig ist, um gleichbleibende Ergebnisse in der Produktion oder Forschung zu erzielen.
- Skalierbarkeit: Sie ermöglichen es, Prozesse im Labormaßstab durchzuführen und diese später für die industrielle Fertigung zu skalieren.
- Vielseitigkeit: Beheizte Laborpressen sind in der Lage, eine breite Palette von Materialien zu verarbeiten, von Polymeren über Metalle bis hin zu Verbundwerkstoffen.
1.2 Relevanz in modernen Industrien
Beheizte Laborpressen haben sich als unverzichtbare Werkzeuge in vielen Industrien etabliert, da sie komplexe Fertigungsprozesse ermöglichen, die eine präzise Steuerung der thermomechanischen Eigenschaften von Materialien erfordern. Sie werden nicht nur zur Herstellung von Prototypen verwendet, sondern auch für die Entwicklung neuer Werkstoffe, die unter spezifischen Bedingungen getestet und optimiert werden müssen.
2. Materialwissenschaften und Polymerforschung
Die Materialwissenschaft ist eines der größten Anwendungsfelder für beheizte Laborpressen, insbesondere bei der Entwicklung und Analyse neuer Materialien wie Polymere, Verbundwerkstoffe und Nanomaterialien. In der Polymerforschung spielen beheizte Pressen eine wichtige Rolle bei der Untersuchung von Materialverhalten unter thermischer und mechanischer Belastung.
2.1 Herstellung von Polymeren und Verbundwerkstoffen
In der Materialwissenschaft ist die Verarbeitung von Polymeren und Verbundwerkstoffen ein zentraler Forschungsbereich. Beheizte Laborpressen werden verwendet, um diese Materialien zu verarbeiten und ihre thermischen, mechanischen und chemischen Eigenschaften zu testen.
2.1.1 Probenvorbereitung für Polymertests
Eine der häufigsten Anwendungen beheizter Pressen in der Polymerforschung ist die Herstellung von Testproben, die zur Untersuchung der mechanischen Eigenschaften (z.B. Zugfestigkeit, Bruchdehnung) und der thermischen Stabilität verwendet werden. Dabei wird das Polymermaterial unter Hitze und Druck in die gewünschte Form gebracht, typischerweise als Platten oder Folien, die anschließend in standardisierten Materialprüfungen getestet werden.
2.1.2 Laminierung von Verbundwerkstoffen
Beheizte Laborpressen spielen eine zentrale Rolle bei der Herstellung von Verbundwerkstoffen (Composites), die aus einer Matrix (wie einem Polymer) und Verstärkungsfasern (wie Glas- oder Kohlenstofffasern) bestehen. Die Laminierung erfolgt durch die gleichzeitige Anwendung von Druck und Hitze, wodurch das Polymer verflüssigt wird und die Fasern in die Matrix eingebettet werden. Dieser Prozess erhöht die mechanische Festigkeit und thermische Beständigkeit des Endmaterials.
Beispiele:
- Luft- und Raumfahrt: Hier werden faserverstärkte Verbundwerkstoffe für Flugzeugteile eingesetzt, die leicht und stark sein müssen.
- Automobilindustrie: In der Automobilbranche werden Verbundwerkstoffe verwendet, um das Gewicht von Fahrzeugen zu reduzieren und gleichzeitig die Sicherheit zu erhöhen.
2.2 Herstellung von Nanokompositen
Die Entwicklung von Nanokompositen, die durch die Einbettung von Nanopartikeln in eine Polymermatrix hergestellt werden, ist ein weiterer spannender Bereich der Materialwissenschaften. Nanokomposite bieten einzigartige Eigenschaften wie verbesserte mechanische Festigkeit, bessere Leitfähigkeit oder hohe thermische Stabilität.
2.2.1 Einfluss von Hitze und Druck auf Nanostrukturen
Beheizte Laborpressen ermöglichen es, Nanokomposite unter kontrollierten Bedingungen zu verarbeiten, wodurch sichergestellt wird, dass die Nanopartikel gleichmäßig in der Matrix verteilt sind und keine Ablagerungen oder Agglomerationen entstehen. Dies ist besonders wichtig, da die molekulare Struktur von Nanomaterialien empfindlich auf Druck und Hitze reagieren kann. Die Anwendung von zu viel Druck kann dazu führen, dass die Nanopartikel ihre Struktur verlieren oder sich im Material ungleichmäßig verteilen.
2.2.2 Anwendungen von Nanokompositen
Nanokomposite finden in einer Vielzahl von Bereichen Anwendung, darunter:
- Elektronik: Nanokomposite mit hoher elektrischer Leitfähigkeit werden in der Herstellung von Leiterplatten und Sensoren verwendet.
- Medizintechnik: In der Medizintechnik werden Nanokomposite aufgrund ihrer Biokompatibilität und antibakteriellen Eigenschaften für Implantate und medizinische Geräte eingesetzt.
2.3 Thermoplastische und Duroplastische Materialien
Die Unterscheidung zwischen thermoplastischen und duroplastischen Materialien ist in der Polymerforschung besonders wichtig, da sie unterschiedliche Verarbeitungsmethoden erfordern.
2.3.1 Thermoplaste
Thermoplaste sind Kunststoffe, die beim Erhitzen schmelzen und sich leicht formen lassen. In beheizten Laborpressen können sie wiederholt erhitzt und abgekühlt werden, ohne ihre chemische Struktur zu verändern. Dies macht Thermoplaste ideal für Recyclingprozesse und Serienproduktion.
- Beispiele für Thermoplaste: Polyethylen (PE), Polypropylen (PP), Polyethylenterephthalat (PET).
2.3.2 Duroplaste
Duroplaste hingegen härten irreversibel aus und können nach ihrer Aushärtung nicht erneut verflüssigt werden. Sie werden häufig in Anwendungen eingesetzt, bei denen thermische und mechanische Stabilität entscheidend sind, z.B. in elektronischen Bauteilen oder Verbundwerkstoffen für den Flugzeugbau. Beheizte Laborpressen spielen eine entscheidende Rolle bei der Aushärtung dieser Materialien, da sie die richtige Kombination aus Hitze und Druck bieten, um die molekulare Struktur des Duroplasts zu verändern.
- Beispiele für Duroplaste: Epoxidharze, Phenolharze, Polyurethane.
3. Herstellung von Halbleitern und Elektronikkomponenten
In der Elektronikindustrie sind beheizte Laborpressen unverzichtbar, insbesondere bei der Herstellung von Halbleitern, Wafern und Leiterplatten. Die Anwendung von Druck und Hitze ermöglicht es, Materialien effizient zu verarbeiten und gleichzeitig sicherzustellen, dass sie die erforderlichen mechanischen und elektrischen Eigenschaften aufweisen.
3.1 Herstellung von Halbleiter-Wafern
Die Herstellung von Halbleiter-Wafern ist ein besonders sensibler Prozess, bei dem extrem genaue Temperatur- und Druckregelungen erforderlich sind, um Defekte und Unregelmäßigkeiten in der Kristallstruktur zu vermeiden.
3.1.1 Druck- und Hitzebehandlung von Siliziumwafern
Silizium ist das häufigste Material, das bei der Herstellung von Halbleitern verwendet wird. In beheizten Laborpressen wird das Silizium zunächst in Form von Wafern verarbeitet, die dann in verschiedene Schichten laminiert oder strukturiert werden, um die gewünschten elektrischen Eigenschaften zu erreichen. Dieser Prozess erfordert präzise Steuerung, um sicherzustellen, dass die Wafer keine Mikrorisse oder Verunreinigungen aufweisen, die die Funktion der Halbleiter beeinträchtigen könnten.
3.1.2 Laminieren und Bonden von Schichten
In der Elektronikfertigung müssen verschiedene Schichten von Materialien (z.B. Isolatoren, Metalle und Polymere) miteinander verbunden werden. Das Laminieren dieser Schichten erfordert die gleichzeitige Anwendung von Druck und Hitze, um eine gleichmäßige Verbindung zu gewährleisten und Lufteinschlüsse oder Unregelmäßigkeiten zu vermeiden. Beheizte Laborpressen sind hier ein entscheidendes Werkzeug, da sie den Prozess beschleunigen und die Qualität der Verbindung verbessern.
3.2 Herstellung von Leiterplatten
Leiterplatten (PCBs) sind das Rückgrat fast aller elektronischen Geräte, von Smartphones über Computer bis hin zu Haushaltsgeräten. Der Herstellungsprozess von PCBs beinhaltet das Laminieren und Pressen mehrerer Schichten von Kupfer, Isolatoren und anderen Materialien.
3.2.1 Laminierprozess bei PCBs
Der Laminierungsprozess in der PCB-Herstellung erfordert, dass die verschiedenen Schichten unter gleichmäßigem Druck und kontrollierter Temperatur miteinander verbunden werden. In beheizten Laborpressen wird der Druck angewendet, um sicherzustellen, dass die Kupferleiterbahnen fest mit dem Substrat verbunden sind, während die Hitze hilft, die Haftung zu verbessern und die Schichten zu verfestigen.
3.2.2 Thermische Stabilität und Präzision
Die thermische Stabilität des Laminats ist entscheidend, um sicherzustellen, dass die Leiterplatte während des Betriebs nicht verformt oder schmilzt. Beheizte Laborpressen ermöglichen es, den Laminierprozess bei genau definierten Temperaturen durchzuführen, um diese Stabilität zu gewährleisten.
4. Pharmazeutische Anwendungen
In der pharmazeutischen Industrie sind beheizte Laborpressen besonders bei der Herstellung von Tabletten und anderen festen Formen wichtig. Die Kontrolle von Druck und Temperatur beeinflusst die Dichte, Zersetzungsgeschwindigkeit und Freisetzungsprofile der aktiven Wirkstoffe in den Tabletten.
4.1 Herstellung von Tabletten
Bei der Herstellung von Tabletten muss das Granulat unter hohem Druck und oft auch bei erhöhter Temperatur verdichtet werden, um eine homogene und stabile Form zu erhalten. Dabei spielt die Kontrolle von Druck und Temperatur eine entscheidende Rolle, um sicherzustellen, dass die Wirkstoffe gleichmäßig in der Tablette verteilt sind und die Tablette die gewünschte mechanische Festigkeit erreicht.
4.1.1 Einfluss von Druck und Temperatur auf Tabletteneigenschaften
Beheizte Laborpressen ermöglichen es, den Verdichtungsprozess zu optimieren, um sicherzustellen, dass die Tabletten gleichmäßig geformt werden und eine gleichbleibende Freisetzung des Wirkstoffs gewährleisten. Bei der Herstellung von Retardtabletten (die eine kontrollierte Wirkstofffreisetzung bieten) kann durch die Kontrolle der Aushärtezeiten und Presskraft die Struktur so gestaltet werden, dass der Wirkstoff über einen längeren Zeitraum freigesetzt wird.
4.1.2 Präzisionswerkzeuge für gleichbleibende Ergebnisse
Die Präzision, die durch beheizte Laborpressen erreicht werden kann, ist besonders wichtig, um gleichbleibende Qualität und Dosierung bei der Tablettenproduktion sicherzustellen. Auch die Herstellung von Mehrschichttabletten, bei denen verschiedene Wirkstoffe in verschiedenen Schichten einer Tablette getrennt werden, ist ein Prozess, der beheizte Laborpressen erfordert.
4.2 Herstellung von Kapseln und Implantaten
Neben Tabletten werden beheizte Laborpressen auch bei der Herstellung von Implantaten und Verabreichungssystemen verwendet. Hierbei spielt die Fähigkeit, verschiedene Materialien, wie biokompatible Polymere, zu verarbeiten, eine zentrale Rolle.
4.2.1 Biokompatible Polymere für Implantate
Die Herstellung von medizintechnischen Implantaten, die aus biokompatiblen Polymeren bestehen, erfordert oft eine präzise Verarbeitung unter hohen Temperaturen und Drücken. Beheizte Laborpressen helfen, das Material in die gewünschte Form zu bringen und gleichzeitig sicherzustellen, dass keine Lufteinschlüsse oder Defekte im Endprodukt vorhanden sind, die zu Komplikationen im Körper führen könnten.
4.2.2 Drug-Eluting Implantate
Drug-eluting Implantate (Implantate, die kontinuierlich Medikamente freisetzen) sind ein weiteres wichtiges Anwendungsfeld für beheizte Laborpressen. Diese Implantate bestehen oft aus einem Polymerträger, der mit Medikamenten beladen ist und unter spezifischen Temperatur- und Druckbedingungen verarbeitet werden muss, um sicherzustellen, dass die Wirkstoffe gleichmäßig verteilt sind und über einen festgelegten Zeitraum freigesetzt werden.
5. Textil- und Papierindustrie
Auch in der Textil- und Papierindustrie spielen beheizte Laborpressen eine wichtige Rolle, insbesondere bei der Veredelung von Materialien und der Herstellung von Beschichtungen.
5.1 Thermodruckverfahren für Textilien
Das Thermodruckverfahren ist eine gängige Methode, um Farbstoffe oder Muster auf Textilien aufzubringen. Dabei wird ein Trägerpapier mit dem gewünschten Muster unter einer beheizten Presse zusammen mit dem Textilmaterial verarbeitet. Die gleichmäßige Verteilung von Druck und Hitze sorgt dafür, dass der Farbstoff auf das Material übertragen wird.
5.1.1 Funktionale Textilien
Beheizte Pressen spielen eine zentrale Rolle bei der Herstellung von funktionalen Textilien, wie etwa hitzebeständigen oder wasserabweisenden Geweben. Durch den Einsatz von speziellen Beschichtungen und Membranen, die unter Druck und Hitze auf das Textil aufgebracht werden, können Textilien mit zusätzlichen Funktionen ausgestattet werden, die sie für Outdoor-Kleidung, Schutzbekleidung oder technische Textilien geeignet machen.
5.2 Papierverarbeitung und Spezialpapiere
In der Papierindustrie werden beheizte Pressen verwendet, um mehrschichtige Papiere herzustellen, die beispielsweise in Lebensmittelverpackungen oder technischen Anwendungen wie Filterpapieren eingesetzt werden.
5.2.1 Prägung und Strukturierung von Papieren
Eine weitere Anwendung beheizter Laborpressen in der Papierindustrie ist die Prägung und Texturierung von Papieroberflächen. Durch die Anwendung von Hitze und Druck können auf der Oberfläche von Papieren spezielle Muster und Texturen erstellt werden, die sowohl ästhetische als auch funktionale Eigenschaften verbessern. Beispielsweise können Antirutsch-Oberflächen oder wasserabweisende Beschichtungen auf Verpackungsmaterialien geprägt werden.
6. Additive Fertigung (3D-Druck) und Nachbearbeitung
In der additiven Fertigung (3D-Druck) werden beheizte Laborpressen zunehmend zur Nachbearbeitung von 3D-gedruckten Teilen verwendet. Dies geschieht, um die Oberflächenqualität und die mechanischen Eigenschaften der gedruckten Teile zu verbessern.
6.1 Verdichtung und Glättung von 3D-gedruckten Teilen
Gedruckte Teile, insbesondere solche, die durch Fused Deposition Modeling (FDM) hergestellt wurden, weisen oft Schichtlinien und Oberflächenrauhigkeiten auf. Beheizte Laborpressen können verwendet werden, um diese Teile unter Druck zu verdichten und gleichzeitig durch Hitze die Oberflächen zu glätten. Dies führt zu glatteren und mechanisch festeren Bauteilen, die für den Einsatz in Funktionsprototypen oder Endanwendungen bereit sind.
6.1.1 Glättung von Thermoplasten
Bei Thermoplasten, wie etwa ABS oder PLA, die oft im 3D-Druck verwendet werden, kann durch die gleichzeitige Anwendung von Druck und Hitze in einer beheizten Presse eine Verbesserung der Oberflächenqualität erreicht werden, ohne dass das Material seine Festigkeit verliert.
6.2 Nachbearbeitung von Metallteilen aus dem 3D-Druck
Auch in der Metallverarbeitung wird der 3D-Druck zunehmend eingesetzt, insbesondere bei der Herstellung von hochkomplexen Bauteilen. Nach dem Druckprozess müssen diese Teile oft einer Wärmebehandlung oder Verdichtung unterzogen werden, um ihre Mikrostruktur zu optimieren und ihre mechanische Festigkeit zu erhöhen.
6.2.1 Verdichten von Metallpulvern
In der additiven Metallfertigung, bei der Metallpulver verwendet werden, können beheizte Laborpressen dazu beitragen, das Pulver durch Sintern und Verdichten in eine homogene Struktur zu bringen. Dies verbessert nicht nur die mechanischen Eigenschaften des Teils, sondern reduziert auch die Porosität, was für Bauteile, die in der Luft- und Raumfahrt oder im Automobilbau eingesetzt werden, entscheidend ist.
7. Biotechnologie und Medizintechnik
In der Biotechnologie und Medizintechnik werden beheizte Laborpressen zur Herstellung von biologischen Materialien, medizinischen Implantaten und medizinischen Geräten verwendet. Diese Bereiche erfordern nicht nur höchste Präzision, sondern auch die Verwendung von biokompatiblen und sterilen Materialien.
7.1 Herstellung von medizinischen Implantaten
Beheizte Laborpressen sind besonders nützlich bei der Herstellung von medizinischen Implantaten, wie künstlichen Gelenken oder Knochenersatzmaterialien. Diese Materialien müssen nicht nur extrem stabil sein, sondern auch eine biokompatible Oberfläche aufweisen, die den Kontakt mit menschlichem Gewebe erleichtert.
7.1.1 Knochenimplantate aus biokompatiblen Polymeren
Ein typisches Beispiel ist die Herstellung von Knochenimplantaten aus Polyetheretherketon (PEEK), einem biokompatiblen Polymer, das durch seine hohe Festigkeit und Hitzebeständigkeit besticht. In beheizten Laborpressen wird das Material unter hohem Druck verdichtet und gleichzeitig so behandelt, dass seine Oberfläche eine mikroskopische Struktur erhält, die das Einwachsen von Knochengewebe fördert.
7.2 Herstellung von Prothesen
Auch bei der Herstellung von Prothesen kommen beheizte Laborpressen zum Einsatz. Moderne Gliedmaßenprothesen bestehen häufig aus faserverstärkten Kunststoffen, die sowohl leicht als auch stabil sein müssen.
7.2.1 Verbundwerkstoffe für Prothesen
Durch den Einsatz von beheizten Laborpressen können die Fasern unter Druck und Hitze gleichmäßig in die Kunststoffmatrix eingebettet werden. Dies führt zu Prothesen, die sowohl den mechanischen Belastungen des Alltags standhalten, als auch komfortabel genug sind, um den Trägern ein hohes Maß an Beweglichkeit zu ermöglichen.
8. Energietechnologie und nachhaltige Anwendungen
Die Energietechnologie ist ein weiteres aufstrebendes Feld, in dem beheizte Laborpressen eine zentrale Rolle spielen, insbesondere bei der Herstellung von Brennstoffzellen, Solarzellen und Batteriekomponenten.
8.1 Herstellung von Brennstoffzellenkomponenten
Die Herstellung von Brennstoffzellenkomponenten erfordert die präzise Verarbeitung von Membranen und Elektrodenmaterialien, die durch die gleichzeitige Anwendung von Druck und Hitze optimiert werden können.
8.1.1 Verdichten von Membranen
In beheizten Laborpressen werden Membranen für Brennstoffzellen verdichtet, um sicherzustellen, dass sie gleichmäßig und fehlerfrei sind, was zu einer besseren Effizienz der Brennstoffzelle führt.
8.2 Herstellung von Solarzellen
In der Solarzellenfertigung werden beheizte Laborpressen verwendet, um Polymerschichten und Verbundmaterialien zu laminieren, die in Photovoltaikanlagen eingesetzt werden. Durch die präzise Steuerung der Prozessparameter können effizientere Solarzellen hergestellt werden, die mehr Energie aus dem Sonnenlicht gewinnen können.
8.2.1 Laminierung von Photovoltaikmaterialien
Beheizte Pressen ermöglichen es, die verschiedenen Schichten, aus denen eine Solarzelle besteht, so zu laminieren, dass sie eine optimale Haftung und Widerstandsfähigkeit aufweisen. Dies ist entscheidend, um die Langlebigkeit und Effizienz der Solarzellen zu gewährleisten.
8.3 Batterieforschung und -herstellung
In der Batterieforschung werden beheizte Laborpressen verwendet, um Elektrodenmaterialien zu verdichten und sicherzustellen, dass sie die erforderliche Leitfähigkeit und Stabilität aufweisen. Besonders in der Lithium-Ionen-Batterieforschung ist die präzise Kontrolle von Druck und Hitze entscheidend, um die Leistungsfähigkeit und Lebensdauer der Batterien zu verbessern.
8.3.1 Elektrodenverdichtung für Lithium-Ionen-Batterien
Bei der Herstellung von Lithium-Ionen-Batterien ist es wichtig, dass die Elektroden (Anode und Kathode) eine hohe Energiedichte und mechanische Stabilität aufweisen. Beheizte Laborpressen ermöglichen die gleichmäßige Verdichtung der Materialien, um Porosität zu minimieren und die Leistungsfähigkeit der Batterie zu maximieren.
9. Herausforderungen und zukünftige Entwicklungen
Obwohl beheizte Laborpressen bereits in einer Vielzahl von Industrien Anwendung finden, gibt es noch zahlreiche Forschungs- und Entwicklungsbereiche, in denen neue Anwendungen und Optimierungen entdeckt werden. Zu den aktuellen Herausforderungen gehört die Entwicklung von energieeffizienteren Pressen sowie die Integration von neuen Technologien wie Künstlicher Intelligenz und Robotik, um den Automatisierungsgrad weiter zu erhöhen.
9.1 Automatisierung und Industrie 4.0
Die Integration von Industrie 4.0 in die Fertigungsumgebung erfordert intelligente Maschinen, die autonom arbeiten und kontinuierlich Prozessdaten sammeln und analysieren können. Beheizte Laborpressen werden zunehmend mit Sensoren und KI-Algorithmen ausgestattet, um die Prozesssteuerung zu optimieren und die Produktionsqualität zu verbessern.
9.2 Nachhaltigkeit und Energieeffizienz
Mit dem wachsenden Fokus auf Nachhaltigkeit wird auch der Energieverbrauch von Laborpressen immer wichtiger. Zukünftige Entwicklungen könnten sich auf die Nutzung von erneuerbaren Energien und energieeffizienteren Heizsystemen konzentrieren, um den CO₂-Fußabdruck der Maschinen zu minimieren.
Fazit
Beheizte Laborpressen sind in einer Vielzahl von Industrien unverzichtbar und ermöglichen die präzise Verarbeitung von Materialien, die unter normalen Bedingungen schwer zu formen oder zu modifizieren wären. Von der Materialforschung über die Elektronikfertigung bis hin zur Biotechnologie und Energietechnik bieten beheizte Pressen unzählige Anwendungsmöglichkeiten, die die Entwicklung neuer Technologien und Produkte unterstützen.
Herstellung von Halbleitern und Elektronik mit beheizter Laborpresse

1. Einführung in die Halbleiter- und Elektronikproduktion
Die Produktion von Halbleitern und elektronischen Bauteilen ist ein äußerst komplexer Prozess, der eine Vielzahl von präzise gesteuerten Verfahren und Technologien erfordert. Die beheizte Laborpresse spielt dabei eine wichtige Rolle in der Herstellung und Bearbeitung von Materialien, die für die Elektronikindustrie unerlässlich sind. Sie wird verwendet, um Schichten von Halbleitern, Metallen, Isolatoren und anderen Materialien miteinander zu verbinden, zu strukturieren oder zu verdichten. Die Kombination von Druck und Hitze ermöglicht es, diese Materialien unter kontrollierten Bedingungen zu formen, zu laminieren und zu versiegeln.
1.1 Bedeutung der beheizten Laborpresse in der Halbleiterfertigung
Die Halbleiterfertigung umfasst mehrere Schritte, bei denen Materialien und Bauteile in präzisen Dimensionen und mit hoher Zuverlässigkeit verarbeitet werden müssen. Die präzise Steuerung von Temperatur und Druck, die durch beheizte Laborpressen möglich ist, spielt eine zentrale Rolle bei der Herstellung von Wafern, Dünnschichttransistoren, Mikrochips, und Leiterplatten (PCBs).
- Druck sorgt dafür, dass Schichten fest miteinander verbunden werden.
- Wärme wird genutzt, um chemische Reaktionen anzutreiben, die die strukturellen und elektrischen Eigenschaften der Halbleitermaterialien verbessern.
1.2 Wachsende Bedeutung in neuen Technologien
Beheizte Laborpressen haben auch in neuen Technologien wie flexiblen Displays, 3D-Chip-Verpackungen und Photonik eine wachsende Bedeutung. Die Integration dieser Technologien erfordert hochpräzise Prozesse, um die Verbindung und Laminierung von empfindlichen Materialien zu ermöglichen. Diese Technologien stellen hohe Anforderungen an die Steuerung von thermischen und mechanischen Parametern, was beheizte Laborpressen zu einer wichtigen Komponente der modernen Elektronikherstellung macht.
2. Waferproduktion: Herstellung und Bearbeitung von Silizium-Wafern
Die Grundlage der Halbleiterfertigung sind Silizium-Wafer, auf denen die eigentlichen elektronischen Schaltungen aufgebracht werden. Wafer bestehen aus hochreinem Silizium, das in einem aufwendigen Verfahren aus Siliziumdioxid gewonnen und in Scheiben geschnitten wird. Beheizte Laborpressen spielen in verschiedenen Stadien der Waferproduktion eine entscheidende Rolle.
2.1 Kristallziehen und Schneiden
Der erste Schritt in der Waferproduktion ist das Kristallziehen aus einem Siliziumschmelzbad. Hierbei wird ein einzelner Kristall aus der Schmelze gezogen, um einen hochreinen Einkristall zu erzeugen, der als Grundlage für die Wafer dient.
2.1.1 Anwendung von beheizten Laborpressen
Beheizte Pressen kommen hier ins Spiel, wenn die Siliziumblöcke in dünne Scheiben (Wafer) geschnitten werden. Nach dem Schneiden werden die Wafer oft einer Wärmebehandlung in beheizten Pressen unterzogen, um thermische Spannungen zu entfernen, die beim Schneidprozess entstehen können. Durch die Anwendung von gleichmäßigem Druck und Hitze kann der Wafer stabilisiert und für die weitere Verarbeitung vorbereitet werden.
2.2 Epitaxiales Wachstum und Dünnschichtdeposition
Der nächste wichtige Schritt ist das Aufbringen von Dünnschichten auf die Siliziumwafer, um die Grundlage für elektronische Schaltungen zu schaffen. Dies geschieht in einem Prozess, der als epitaxiales Wachstum bezeichnet wird, bei dem eine Schicht aus Halbleitermaterial (z.B. Silizium oder Galliumarsenid) auf den Wafer aufgebracht wird.
2.2.1 Dünnschichtabscheidung in beheizten Pressen
Beheizte Laborpressen werden eingesetzt, um dünne Schichten von Materialien unter präzise kontrollierten Bedingungen abzuscheiden. Diese Schichten können Halbleiter, Dielektrika oder Metalle sein, die notwendig sind, um elektronische Bauelemente auf dem Wafer zu erzeugen. Der Druck sorgt dafür, dass die Schichten gleichmäßig und fehlerfrei auf den Wafer aufgebracht werden, während die Hitze chemische Prozesse beschleunigt, die für das Wachstum der Schichten notwendig sind.
3. Lithografie und Strukturierung von Halbleitern
Die Lithografie ist ein entscheidender Schritt in der Halbleiterproduktion, bei dem die Schaltkreise auf die Wafer aufgebracht werden. Hierbei wird ein spezielles Lichtempfindliches Material (Resist) auf die Oberfläche des Wafers aufgebracht und durch Belichtung und Entwicklung strukturiert.
3.1 Anwendung von beheizten Pressen bei der Resistentwicklung
Nach der Belichtung wird der Resist in beheizten Laborpressen oft einer thermischen Behandlung unterzogen, um die Haftung und Struktur des Resists zu verbessern. Diese Behandlung stellt sicher, dass der Resist während des Ätzprozesses stabil bleibt und die gewünschten Strukturen präzise abgebildet werden.
3.1.1 Aufweichen und Aushärten von Resists
Die Kontrolle der Temperatur in beheizten Pressen ist entscheidend, um die physikalischen Eigenschaften des Resists zu steuern. Zu hohe Temperaturen könnten den Resist beschädigen oder seine Struktur verändern, während zu niedrige Temperaturen nicht ausreichen, um die notwendige Festigkeit zu gewährleisten. Durch präzise Temperatur- und Druckregelung in beheizten Pressen kann der Resist optimiert werden.
3.2 Strukturierung durch Ätzen und Diffusion
Nachdem der Resist auf den Wafer aufgebracht und entwickelt wurde, werden die darunterliegenden Halbleiterschichten durch Ätzprozesse strukturiert. Auch hier kann die beheizte Laborpresse eine Rolle spielen, indem sie die Wafer nach dem Ätzprozess behandelt, um Restspannungen abzubauen, die während des Ätzens entstehen können.
3.2.1 Nachbehandlung von geätzten Schichten
Beheizte Pressen werden nach dem Ätzprozess verwendet, um die Wafer thermisch zu stabilisieren. Dies ist besonders wichtig bei der Herstellung von MOSFETs (Metall-Oxid-Halbleiter-Feldeffekttransistoren) und anderen empfindlichen Bauelementen, bei denen die Qualität der Ätzstruktur direkten Einfluss auf die Leistungsfähigkeit des Endprodukts hat.
4. Laminierung und Verbindungstechnologien
Ein weiterer wichtiger Einsatzbereich beheizter Laborpressen in der Halbleiter- und Elektronikproduktion ist die Laminierung und Verbindung von Schichten und Bauteilen. Die Herstellung moderner Elektronik erfordert das Zusammenfügen von Materialien, die unterschiedliche thermische Ausdehnungseigenschaften oder mechanische Eigenschaften aufweisen. Beheizte Pressen helfen dabei, diese Materialien so zu verbinden, dass die mechanische Stabilität und die elektrischen Eigenschaften optimiert werden.
4.1 Laminierung von Leiterplatten (PCBs)
Leiterplatten (PCBs) bestehen aus mehreren Schichten, die durch Kupferleitbahnen verbunden werden. Die Laminierung dieser Schichten ist ein kritischer Prozess, der sicherstellen muss, dass die Verbindungen stabil sind und keine Fehler oder Kurzschlüsse auftreten.
4.1.1 Anwendung von Druck und Hitze beim Laminieren
Beheizte Laborpressen werden verwendet, um die verschiedenen Schichten der Leiterplatte unter hohem Druck und präzise gesteuerter Hitze zu laminieren. Der Druck sorgt dafür, dass die Kupferbahnen und Isolationsschichten fest miteinander verbunden werden, während die Hitze die Haftung zwischen den Schichten verstärkt.
- Druck: Verhindert Luftblasen und sorgt für eine gleichmäßige Verteilung der Schichten.
- Hitze: Aktiviert die Harze oder Klebstoffe, die als Bindemittel zwischen den Schichten fungieren.
4.2 Verbindung von Halbleitern mit Gehäusen: Chip-Bonding
Ein weiterer wichtiger Prozess in der Elektronikfertigung ist das Chip-Bonding, bei dem der fertige Halbleiterchip mit einem Gehäuse oder Substrat verbunden wird. Dies ist ein besonders sensibler Prozess, da der Chip extrem empfindlich auf mechanische und thermische Einflüsse reagiert.
4.2.1 Thermokompression und Bonden in beheizten Pressen
Die Thermokompression ist eine Technik, bei der Druck und Hitze gleichzeitig auf den Chip und das Substrat ausgeübt werden, um eine dauerhafte Verbindung herzustellen. Beheizte Laborpressen bieten hier den Vorteil, dass sie die Druck- und Temperaturparameter präzise steuern können, um eine gleichmäßige Verbindung ohne mechanische Spannungen zu gewährleisten.
- Anwendungsbeispiele: Die Verbindung von Mikroprozessoren oder Leistungsbauteilen mit ihren Substraten oder Gehäusen in der Mikroelektronik.
4.3 3D-Packaging und Stapelchips
Mit der zunehmenden Miniaturisierung in der Elektronikfertigung gewinnen 3D-Packaging-Techniken und Stapelchips an Bedeutung. Diese Technologien erfordern die präzise Verbindung mehrerer Schichten von Halbleitern und anderen elektronischen Bauelementen, um die Leistungsdichte zu erhöhen und die Leitungswege zu verkürzen.
4.3.1 Rolle der beheizten Laborpresse im 3D-Packaging
Beheizte Pressen sind in der Lage, die mechanischen und thermischen Herausforderungen des 3D-Packagings zu bewältigen, indem sie die verschiedenen Schichten von Chips unter Druck und Hitze verbinden. Dies führt zu einer besseren thermischen Stabilität und elektrischen Leistung des Endprodukts.
5. Herstellung von flexibler Elektronik und Wearables
Flexible Elektronik ist ein schnell wachsender Bereich, der neue Anforderungen an die Herstellungstechnologien stellt. Diese Bauteile müssen flexibel, leicht und langlebig sein, was die Verwendung von speziellen Materialien und Fertigungsprozessen erfordert.
5.1 Flexible Leiterplatten
Flexible Leiterplatten bestehen aus biegsamen Materialien, wie z.B. Polyimiden oder Polyethylen-Naphthalat (PEN), die es ermöglichen, dass die Elektronikmodule in tragbaren Geräten oder flexiblen Displays integriert werden können.
5.1.1 Laminierung und Verarbeitung flexibler Leiterplatten
Beheizte Laborpressen spielen eine entscheidende Rolle bei der Laminierung flexibler Leiterplatten. Durch die Anwendung von niedrigeren Temperaturen und kontrolliertem Druck können flexible Materialien verarbeitet werden, ohne dass sie ihre mechanischen Eigenschaften verlieren oder beschädigt werden. Dies ist besonders wichtig, um sicherzustellen, dass die Flexibilität der Leiterplatte auch nach der Herstellung erhalten bleibt.
5.2 Herstellung von Wearables
Wearables wie Smartwatches, Fitness-Tracker und medizinische Geräte erfordern ebenfalls die Herstellung flexibler Elektronikmodule. Beheizte Laborpressen helfen dabei, die Elektronikmodule in weiche und biegsame Materialien zu integrieren, die auf der Haut getragen werden können.
5.2.1 Verbindung von flexiblen Elektronikmodulen
Der Druck und die Wärme, die durch beheizte Laborpressen auf flexible Elektronik ausgeübt werden, stellen sicher, dass die Materialien eine starke Haftung haben, ohne dass die Funktionalität der Bauteile beeinträchtigt wird. Dies ist besonders wichtig bei Stretch-Sensoren oder dehnbaren Displays, die in Wearables verwendet werden.
6. Photonische Systeme und Optoelektronik
Die Photonik ist ein Bereich der Elektronik, der sich mit der Erzeugung und Nutzung von Licht befasst. Sie umfasst Anwendungen wie Laser, optische Sensoren und Lichtleiter. Die Herstellung photonischer Systeme erfordert besondere Techniken zur Verbindung von optischen und elektronischen Komponenten, bei denen beheizte Laborpressen eine zentrale Rolle spielen.
6.1 Herstellung von optischen Verbindungen
Optische Fasern und Photonikchips müssen extrem präzise miteinander verbunden werden, um Lichtverluste und Signalstörungen zu minimieren. Beheizte Pressen helfen dabei, die verschiedenen optischen und elektronischen Komponenten durch Thermokompression und Wärmebehandlung präzise zu verbinden.
6.1.1 Rolle der Thermokompression
Bei der Thermokompression werden optische Komponenten wie Linsen, Fasern und Chips mit einem Substrat oder einem Gehäuse unter Anwendung von Druck und Hitze verbunden. Dies sorgt für eine stabile Verbindung, die hohe optische Transparenz und Stabilität aufweist.
6.2 Herstellung von Lichtleitern und Sensoren
Beheizte Laborpressen werden auch in der Herstellung von Lichtleitern verwendet, die in optischen Netzwerken oder Sensoren eingesetzt werden. Durch die Kombination von Hitze und Druck kann die Verformung und Formgebung der Lichtleiter optimiert werden, was zu besseren Leitungseigenschaften und geringeren Verlusten führt.
7. Herausforderungen und zukünftige Entwicklungen
Die Herstellung von Halbleitern und Elektronik mit beheizten Laborpressen wird weiterhin eine zentrale Rolle in der Industrie spielen. Die Integration von neuen Materialien, fortschrittlichen Technologien und automatisierten Systemen wird es ermöglichen, immer komplexere elektronische Systeme zu produzieren, die schneller, effizienter und leistungsfähiger sind.
7.1 Automatisierung und Präzision
Mit der zunehmenden Miniaturisierung der Elektronik steigen auch die Anforderungen an die Präzision und Automatisierung der Prozesse. Zukünftige Entwicklungen in der Elektronikfertigung könnten zu vollständig automatisierten Laborpressen führen, die durch künstliche Intelligenz gesteuert werden, um die Produktionsgeschwindigkeit und Effizienz weiter zu steigern.
7.2 Integration von neuen Materialien
Die Verwendung neuer Materialien wie Graphen, Nanomaterialien und flexible Leiter wird die Anforderungen an die Verarbeitungstechnologien weiter erhöhen. Beheizte Laborpressen werden weiterhin eine entscheidende Rolle dabei spielen, diese Materialien in neue, leistungsfähigere elektronische Systeme zu integrieren.
Fazit
Beheizte Laborpressen sind ein unverzichtbares Werkzeug in der modernen Halbleiter- und Elektronikfertigung. Sie ermöglichen die präzise Laminierung, Verbindung und Bearbeitung von Materialien, die für die Herstellung von Wafern, Leiterplatten, flexibler Elektronik und Photonik erforderlich sind. Durch die Kombination von Druck und Hitze können Materialien effizient verarbeitet und ihre elektrischen, optischen und mechanischen Eigenschaften optimiert werden. In Zukunft wird die Weiterentwicklung von automatisierten Pressensystemen und die Integration von neuen Materialien dazu beitragen, dass die Elektronikproduktion immer präziser und leistungsfähiger wird.
Pharmazeutische Anwendungen mit beheizter Laborpresse
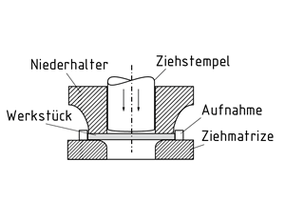
1. Einführung in pharmazeutische Anwendungen
Die Pharmaindustrie ist einer der wichtigsten Sektoren, in denen beheizte Laborpressen eine bedeutende Rolle spielen. Die Herstellung von Arzneimitteln und deren Darreichungsformen ist ein äußerst präziser Prozess, bei dem Kontrolle über Druck und Temperatur unerlässlich ist. Beheizte Laborpressen ermöglichen es, feste Formen, transdermale Pflaster, Implantate und andere Verabreichungssysteme unter kontrollierten Bedingungen zu produzieren. Sie stellen sicher, dass die gewünschten physikalischen und chemischen Eigenschaften der Medikamente erhalten bleiben und bieten gleichzeitig die Möglichkeit, den Herstellungsprozess zu optimieren.
1.1 Rolle der Laborpresse in der pharmazeutischen Industrie
Beheizte Laborpressen werden in einer Vielzahl von pharmazeutischen Prozessen eingesetzt, darunter:
- Tablettenpressen zur Herstellung von festen Darreichungsformen
- Verarbeitung von Wirkstoffen bei kontrollierter Hitze und Druck
- Laminierung von Schichten in transdermalen Pflastern
- Formung und Aushärtung von Implantaten
- Verpackungsprozesse für hitzeempfindliche Arzneimittel
Die Laborpresse ermöglicht es, diese Prozesse präzise zu steuern, um eine gleichbleibende Qualität der Arzneimittel sicherzustellen, insbesondere in Hinblick auf Wirkstofffreisetzung, Festigkeit und Stabilität.
1.2 Relevanz der Temperatur- und Druckkontrolle
In der pharmazeutischen Produktion haben sowohl Druck als auch Temperatur einen direkten Einfluss auf die biologische Wirksamkeit und physikalischen Eigenschaften der Medikamente. Die Fähigkeit, diese Parameter genau zu steuern, ist entscheidend, um sicherzustellen, dass Arzneimittel den regulatorischen Anforderungen entsprechen und die gewünschten therapeutischen Wirkungen erzielen.
- Temperatur beeinflusst die Löslichkeit und Stabilität der Wirkstoffe.
- Druck ist entscheidend für die Formgebung und Struktur von Tabletten, Implantaten oder Pflastern.
2. Tablettenherstellung mit beheizter Laborpresse
Die Tablettenherstellung ist eine der häufigsten Anwendungen beheizter Laborpressen in der Pharmaindustrie. Tabletten bieten eine praktische und stabile Darreichungsform, die es ermöglicht, eine präzise Dosierung des Wirkstoffs zu garantieren.
2.1 Direkte Komprimierung und Tablettenpressen
Die Herstellung von Tabletten durch direkte Komprimierung ist ein Prozess, bei dem pulverförmige Wirkstoffe und Hilfsstoffe unter hohem Druck in eine feste Form gebracht werden. Beheizte Laborpressen helfen, diesen Prozess zu optimieren, indem sie gleichmäßige Druckkräfte auf die Tablettenmischung anwenden, während die Temperatur so gesteuert wird, dass Empfindlichkeit und Stabilität der Wirkstoffe erhalten bleiben.
2.1.1 Verbesserung der Tablettenfestigkeit
Durch die Anwendung von Hitze während des Pressvorgangs können die Bindungskräfte zwischen den Partikeln verbessert werden, was zu einer höheren mechanischen Festigkeit der Tabletten führt. Dies ist besonders wichtig für Tabletten, die in hohen Dosierungen oder mit langsamer Freisetzung hergestellt werden, da sie über längere Zeiträume hinweg stabil bleiben müssen.
2.1.2 Einbindung hitzeempfindlicher Wirkstoffe
Für hitzeempfindliche Wirkstoffe kann die kontrollierte Temperatur einer beheizten Laborpresse dazu beitragen, dass diese Wirkstoffe während des Komprimierungsprozesses stabil bleiben. Durch die präzise Steuerung der Temperatur kann der Abbau der Wirkstoffe vermieden werden, was bei herkömmlichen Pressverfahren ohne Temperaturkontrolle ein Problem darstellen kann.
2.2 Herstellung von Retardtabletten
Retardtabletten sind Tabletten, die eine verzögerte Wirkstofffreisetzung bieten, sodass der Wirkstoff über einen längeren Zeitraum kontinuierlich freigesetzt wird. Beheizte Laborpressen sind entscheidend für die Herstellung dieser speziellen Darreichungsformen, da sie die Schichtstruktur und Matrixkomponenten so verarbeiten, dass eine gleichmäßige und gesteuerte Freisetzung gewährleistet ist.
2.2.1 Komprimierung von Mehrschichttabletten
Retardtabletten bestehen oft aus mehreren Schichten, wobei jede Schicht eine unterschiedliche Freisetzungsrate des Wirkstoffs hat. Beheizte Laborpressen ermöglichen eine präzise Schichtlaminierung, sodass die Freisetzung des Wirkstoffs genau gesteuert werden kann. Der Einsatz von Hitze hilft dabei, die Interaktion zwischen den Schichten zu verbessern und sicherzustellen, dass die Schichten gut miteinander verbunden sind.
2.2.2 Anwendung von Druck und Temperatur auf Polymere in Retardtabletten
Polymere, die in Retardtabletten verwendet werden, reagieren empfindlich auf Temperaturänderungen. Beheizte Laborpressen erlauben es, die Freisetzungseigenschaften dieser Polymere durch gezielte Hitzebehandlung zu modifizieren. Durch die Verwendung spezifischer Temperaturen können die Diffusionseigenschaften und Porosität des Polymernetzes so angepasst werden, dass die gewünschte Freisetzungsrate erreicht wird.
3. Herstellung von Kapseln und Softgelkapseln
Kapseln und Softgelkapseln sind weitere wichtige Darreichungsformen in der Pharmaindustrie, die eine präzise Verarbeitung mit Druck und Hitze erfordern.
3.1 Herstellung von Hartkapseln
Hartkapseln bestehen aus zwei halbzylindrischen Hüllen, die aus Gelatine oder Cellulose bestehen und den Wirkstoff in Form eines Pulvers, Granulats oder einer Flüssigkeit enthalten. Bei der Herstellung von Hartkapseln können beheizte Laborpressen verwendet werden, um die Formgebung und Versiegelung der Kapseln zu optimieren.
3.1.1 Hitzebehandlung bei der Kapselproduktion
Durch die Anwendung von Druck und Hitze können die Kapselhüllen in beheizten Pressen geformt und gleichzeitig versiegelt werden. Die Hitze sorgt dafür, dass die Kapseln während der Produktion elastisch bleiben, was eine genaue und präzise Formgebung ermöglicht, während der Druck die Versiegelung der Kapselhälften verbessert, sodass kein Wirkstoff austritt.
3.2 Softgelkapseln: Verarbeitung und Stabilisierung
Softgelkapseln bestehen aus einer weichen, elastischen Hülle, die typischerweise flüssige oder pastöse Wirkstoffe enthält. Der Herstellungsprozess dieser Kapseln erfordert präzise Temperaturkontrolle, um die elastische Struktur der Hülle zu erhalten und gleichzeitig den Wirkstoff sicher zu umschließen.
3.2.1 Verwendung von beheizten Laborpressen bei Softgelkapseln
Beheizte Laborpressen spielen eine zentrale Rolle bei der thermischen Behandlung der Softgelhüllen, um deren Festigkeit zu erhöhen, ohne dass sie spröde werden. Gleichzeitig sorgt die Anwendung von Druck dafür, dass die Kapseln ordnungsgemäß versiegelt werden und keine Luftblasen oder Lecks entstehen.
3.2.2 Anpassung der Weichmacher
Die thermische Behandlung in beheizten Laborpressen ermöglicht die Modifikation der Weichmacher, die in der Kapselhülle verwendet werden, um die Flexibilität und Stabilität der Kapsel zu steuern. Dies ist besonders wichtig, wenn die Kapseln unter verschiedenen klimatischen Bedingungen oder bei längerer Lagerung stabil bleiben müssen.
4. Herstellung transdermaler Pflaster und Wirkstofffreisetzungssysteme
Transdermale Pflaster und Wirkstofffreisetzungssysteme sind innovative Formen der Arzneimittelverabreichung, bei denen Wirkstoffe über die Haut freigesetzt werden. Die Herstellung solcher Pflaster erfordert die Anwendung von Druck und Hitze, um sicherzustellen, dass der Wirkstoff gleichmäßig in die Matrix integriert und über einen festgelegten Zeitraum freigesetzt wird.
4.1 Herstellung transdermaler Pflaster
Transdermale Pflaster bestehen in der Regel aus mehreren Schichten, darunter eine Wirkstoffschicht, eine Trägerschicht und eine Schutzschicht. Beheizte Laborpressen werden eingesetzt, um diese Schichten zu laminieren und dabei die Wirkstoffverteilung und Hafteigenschaften der Pflaster zu optimieren.
4.1.1 Laminierung der Schichten unter Druck und Hitze
Durch die Anwendung von Druck in Verbindung mit kontrollierter Hitze können die verschiedenen Schichten des Pflasters fest miteinander verbunden werden, ohne dass der Wirkstoff degradiert oder seine bioverfügbare Form verliert. Diese Kombination aus Druck und Wärme stellt sicher, dass das Pflaster während des Tragens stabil bleibt und der Wirkstoff über einen festgelegten Zeitraum gleichmäßig abgegeben wird.
4.2 Regulierung der Wirkstofffreisetzung in Pflastern
Ein zentrales Merkmal transdermaler Pflaster ist die kontrollierte Freisetzung des Wirkstoffs über einen längeren Zeitraum. Beheizte Laborpressen spielen eine wichtige Rolle bei der Herstellung von Pflastern, die spezifische Freisetzungsprofile aufweisen.
4.2.1 Einfluss von Temperatur auf Polymere in transdermalen Pflastern
Die Freisetzung von Wirkstoffen aus transdermalen Pflastern wird oft durch die Diffusion des Wirkstoffs durch eine Polymermatrix gesteuert. Beheizte Laborpressen können verwendet werden, um die Eigenschaften dieser Polymere durch thermische Behandlung anzupassen. Die Hitze beeinflusst die Porosität und Viskosität der Matrix und steuert so die Freisetzung des Wirkstoffs.
4.2.2 Anpassung der Freisetzungsrate
Die Möglichkeit, Druck und Temperatur präzise zu kontrollieren, ermöglicht es, die Freisetzungsrate des Wirkstoffs aus der Polymermatrix zu optimieren. Dies ist besonders wichtig bei der Herstellung von Pflastern, die eine langsame oder schnelle Freisetzung erfordern, wie etwa bei Schmerzmitteln, Hormonersatztherapien oder Nikotin-Ersatztherapien.
5. Herstellung von Implantaten und Langzeit-Wirkstofffreisetzung
Implantate, die Medikamente über einen längeren Zeitraum freisetzen, gewinnen in der modernen Medizin zunehmend an Bedeutung. Diese Implantate bestehen in der Regel aus biokompatiblen Materialien, die durch den Einsatz von Druck und Hitze verarbeitet werden, um eine gleichmäßige Wirkstoffverteilung und Freisetzung zu gewährleisten.
5.1 Herstellung von Arzneimittelimplantaten
Arzneimittelimplantate bestehen aus einer festen oder halbfesten Matrix, die den Wirkstoff über Monate oder sogar Jahre freisetzt. Die Matrix wird häufig durch Schmelzextrusion oder Formpressen unter Verwendung beheizter Laborpressen hergestellt.
5.1.1 Einsatz von biokompatiblen Polymeren
Beheizte Laborpressen werden verwendet, um biokompatible Polymere wie Polycaprolacton (PCL) oder Poly-L-Milchsäure (PLLA) zu verarbeiten, die in der Medizin als Matrix für Implantate eingesetzt werden. Diese Polymere müssen unter präzisen thermischen Bedingungen verarbeitet werden, um sicherzustellen, dass sie ihre biokompatiblen Eigenschaften beibehalten und gleichzeitig den Wirkstoff gleichmäßig freisetzen.
5.2 Implantate zur Langzeit-Wirkstofffreisetzung
Implantate, die Wirkstoffe über einen längeren Zeitraum abgeben, müssen so konzipiert sein, dass der Wirkstoff über einen konstanten Zeitraum freigesetzt wird. Dies erfordert eine präzise Kontrolle über die Matrixstruktur und die Verteilung des Wirkstoffs im Implantat.
5.2.1 Anwendung von Druck und Temperatur auf Implantate
Durch die Kombination von Druck und Hitze können beheizte Laborpressen die Porenstruktur des Implantats beeinflussen und so die Diffusionsrate des Wirkstoffs steuern. Dies ermöglicht es, Implantate mit spezifischen Freisetzungsprofilen zu entwickeln, die den Bedürfnissen der Patienten angepasst sind.
5.2.2 Herstellung von Drug-Eluting Stents
Ein Beispiel für ein Implantat mit Langzeitfreisetzung sind Drug-Eluting Stents, die in der Kardiologie eingesetzt werden, um verengte Arterien offen zu halten und gleichzeitig Medikamente abzugeben, die das Risiko von Wiederverengungen (Restenosen) verringern. Beheizte Laborpressen werden verwendet, um den Wirkstoff gleichmäßig in die Stent-Beschichtung zu integrieren und sicherzustellen, dass der Wirkstoff über einen festgelegten Zeitraum freigesetzt wird.
6. Verarbeitung von biologischen Substanzen und empfindlichen Wirkstoffen
Die Verarbeitung von biologischen Substanzen wie Proteinen, Peptiden oder DNA erfordert eine besonders sorgfältige Steuerung der thermischen und mechanischen Parameter, um die biologische Aktivität der Substanzen zu erhalten.
6.1 Schutz empfindlicher Wirkstoffe während der Verarbeitung
Viele biologische Wirkstoffe sind hitzeempfindlich und neigen zur Denaturierung, wenn sie hohen Temperaturen ausgesetzt werden. Beheizte Laborpressen ermöglichen es, diese Wirkstoffe unter kontrollierten Bedingungen zu verarbeiten, sodass ihre therapeutische Wirksamkeit nicht beeinträchtigt wird.
6.1.1 Verwendung niedriger Temperaturen und präziser Druckkontrolle
In Fällen, in denen empfindliche Wirkstoffe verarbeitet werden, kann die Temperatur in der beheizten Laborpresse präzise eingestellt werden, um die Hitzeeinwirkung auf ein Minimum zu reduzieren. Gleichzeitig kann der Druck genutzt werden, um das Material in die gewünschte Form zu bringen, ohne die empfindlichen Molekülstrukturen zu zerstören.
6.2 Lyophilisation und Aushärtung von biologischen Implantaten
Lyophilisation (Gefriertrocknung) ist ein Verfahren, bei dem Wasser aus einem Material entfernt wird, während es in gefrorenem Zustand verbleibt. Beheizte Laborpressen können verwendet werden, um gefriergetrocknete biologische Implantate oder Medikamente zu verarbeiten und gleichzeitig deren strukturelle Integrität und Bioaktivität zu erhalten.
6.2.1 Anwendung von Druck bei der Herstellung von biologischen Implantaten
Druckbehandlungen in beheizten Laborpressen helfen dabei, gefriergetrocknete Implantate zu stabilisieren und in eine endgültige Form zu bringen, die für medizinische Anwendungen geeignet ist. Dies ist besonders wichtig bei der Herstellung von Implantaten, die Wachstumsfaktoren, Proteine oder andere biologische Substanzen enthalten, die über längere Zeiträume hinweg aktiv bleiben müssen.
7. Regulatorische Anforderungen und Qualitätssicherung
In der pharmazeutischen Industrie unterliegt die Herstellung von Arzneimitteln und Implantaten strengen regulatorischen Anforderungen. Beheizte Laborpressen spielen eine wichtige Rolle in der Qualitätssicherung, da sie es ermöglichen, die Produktionsprozesse präzise zu kontrollieren und die Einhaltung der Good Manufacturing Practices (GMP) sicherzustellen.
7.1 Validierung der Prozesse
Die Verwendung von beheizten Laborpressen in der pharmazeutischen Herstellung erfordert eine gründliche Prozessvalidierung, um sicherzustellen, dass die Temperatur- und Druckparameter konsistent und reproduzierbar sind.
7.1.1 Temperatur- und Druckmonitoring
Beheizte Laborpressen sind oft mit Sensoren ausgestattet, die die Temperatur und den Druck während des gesamten Prozesses überwachen. Diese Daten werden aufgezeichnet und können zur Validierung und Qualitätskontrolle verwendet werden, um sicherzustellen, dass die Prozesse den regulatorischen Anforderungen entsprechen.
7.2 Dokumentation und Rückverfolgbarkeit
Die strengen GMP-Richtlinien erfordern eine detaillierte Dokumentation aller Herstellungsprozesse. Beheizte Laborpressen unterstützen dies durch die Möglichkeit, alle relevanten Parameter während der Produktion zu protokollieren, sodass eine vollständige Rückverfolgbarkeit gewährleistet ist.
8. Neue technologische Entwicklungen und Zukunftstrends
Mit den Fortschritten in der Technologie und den steigenden Anforderungen an personalisierte Medizin und biotechnologische Innovationen entwickeln sich auch die Anwendungsbereiche für beheizte Laborpressen weiter.
8.1 3D-Druck von Medikamenten und Implantaten
Der Einsatz von beheizten Laborpressen in Kombination mit 3D-Drucktechnologien ermöglicht die Herstellung individueller Arzneimittelformen und maßgeschneiderter Implantate, die an die spezifischen Bedürfnisse eines Patienten angepasst werden können.
8.2 Mikrofluidische Systeme für die Medikamentenherstellung
Mikrofluidik ist ein aufstrebendes Feld, das es ermöglicht, Arzneimittel in Miniaturgeräten herzustellen. Beheizte Laborpressen könnten verwendet werden, um Mikrofluidikchips herzustellen, die in der personalisierten Medizin und bei diagnostischen Tests eine immer größere Rolle spielen.
8.3 Nanotechnologie in der Arzneimittelproduktion
Die Integration von Nanotechnologie in die Arzneimittelproduktion erfordert präzise Prozesse zur Herstellung nanoformatiger Wirkstoffe und Trägersysteme. Beheizte Laborpressen könnten bei der Nanoverkapselung und Verarbeitung von Nanopartikeln eine Schlüsselrolle spielen, um deren Verabreichung und Wirksamkeit zu verbessern.
Fazit
Beheizte Laborpressen sind ein unverzichtbares Werkzeug in der modernen pharmazeutischen Industrie, das es ermöglicht, die Formgebung, Verarbeitung und Freisetzung von Medikamenten und biologischen Wirkstoffen präzise zu steuern. Sie tragen zur Herstellung von Tabletten, Kapseln, Implantaten, Pflastern und vielen anderen pharmazeutischen Produkten bei, die den höchsten Qualitätsstandards entsprechen müssen. Durch die präzise Steuerung von Temperatur und Druck können beheizte Laborpressen die therapeutische Wirksamkeit und Stabilität von Arzneimitteln verbessern und gleichzeitig die strengen Anforderungen der Regulierungsbehörden erfüllen.
In Zukunft werden beheizte Laborpressen weiterhin eine Schlüsselrolle bei der Entwicklung neuer Technologien und personalisierter Therapien spielen, insbesondere in Kombination mit 3D-Druck, Nanotechnologie und Biotechnologie, die die Art und Weise, wie Medikamente entwickelt und verabreicht werden, revolutionieren könnten.
Textil- und Papierindustrie mit beheizter Laborpresse
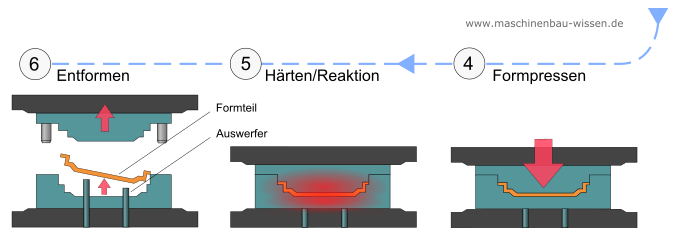
1. Einführung in die Anwendung beheizter Laborpressen in der Textil- und Papierindustrie
Beheizte Laborpressen spielen eine zentrale Rolle in der Textil- und Papierindustrie, da viele Herstellungsprozesse eine präzise Steuerung von Druck und Temperatur erfordern, um Materialien zu bearbeiten und zu veredeln. Diese Maschinen ermöglichen es, verschiedene Textilien und Papiere zu formen, zu beschichten, zu laminieren und zu strukturieren. In beiden Industrien bieten beheizte Pressen zahlreiche Vorteile, darunter eine verbesserte Effizienz, gleichbleibende Qualität und die Möglichkeit, Materialien an spezifische Anforderungen anzupassen.
1.1 Relevanz von Druck und Temperatur in der Textil- und Papierproduktion
- Druck: Durch das Aufbringen von Druck werden Materialien verfestigt, Schichten verbunden und Oberflächenstrukturen erzeugt.
- Temperatur: Hitze wird verwendet, um thermoplastische Fasern zu schmelzen, chemische Reaktionen anzuregen oder Beschichtungen zu fixieren.
Die präzise Steuerung dieser Parameter ist entscheidend, um Materialien zu verarbeiten, die sowohl funktionale als auch ästhetische Eigenschaften aufweisen. In der Textilindustrie betrifft dies beispielsweise die Herstellung von funktionalen Textilien wie hitzebeständigen oder wasserabweisenden Geweben, während in der Papierindustrie die Verarbeitung von Spezialpapieren und Verpackungsmaterialien im Vordergrund steht.
1.2 Wachsende Bedeutung in neuen Märkten
Beheizte Laborpressen haben in der Textil- und Papierindustrie aufgrund der Nachfrage nach hochwertigen Materialien, nachhaltigen Prozessen und innovativen Produkten an Bedeutung gewonnen. Neue Technologien wie intelligente Textilien, biologisch abbaubare Verpackungen und nachhaltige Papiere erfordern spezialisierte Verarbeitungsmethoden, bei denen beheizte Pressen eine zentrale Rolle spielen.
2. Textilindustrie: Prozesse und Anwendungen
In der Textilindustrie kommen beheizte Laborpressen in verschiedenen Stadien der Textilverarbeitung zum Einsatz, darunter Beschichtung, Laminierung, Prägung, Fixierung und Thermoverformung von Textilien. Diese Prozesse werden verwendet, um die physikalischen und chemischen Eigenschaften von Textilien zu verändern, einschließlich ihrer Festigkeit, Elastizität, Hitzebeständigkeit und Oberflächenstruktur.
2.1 Beschichtung von Textilien
Ein wichtiger Einsatzbereich beheizter Laborpressen in der Textilindustrie ist die Beschichtung von Geweben, um deren funktionale Eigenschaften zu verbessern. Beschichtungen werden verwendet, um Textilien wasserabweisend, ölabweisend, hitzebeständig oder antibakteriell zu machen.
2.1.1 Anwendung von Druck und Hitze bei der Beschichtung
Beheizte Laborpressen ermöglichen es, Polymerbeschichtungen unter präzise kontrollierten Bedingungen auf Textilien aufzutragen. Diese Beschichtungen müssen bei einer bestimmten Temperatur schmelzen, um sich gleichmäßig über das Gewebe zu verteilen, während der Druck sicherstellt, dass die Beschichtung fest mit den Fasern verbunden wird.
- Beispiel: Bei der Herstellung von Outdoor-Bekleidung wird häufig eine PTFE-Beschichtung (Polytetrafluorethylen) verwendet, die das Gewebe wasserabweisend und gleichzeitig atmungsaktiv macht.
2.1.2 Heißsiegeln von technischen Textilien
Ein weiteres Beispiel ist das Heißsiegeln von technischen Textilien, die in Schutzbekleidung, Feuerwehranzügen oder Filtermaterialien verwendet werden. Hierbei wird ein thermoplastisches Material unter Druck erhitzt, um die Schichten miteinander zu verbinden, was die mechanische Festigkeit erhöht und das Gewebe widerstandsfähig gegen hohe Temperaturen macht.
2.2 Laminierung von Textilien
Die Laminierung ist ein weiterer Prozess, bei dem beheizte Laborpressen in der Textilindustrie verwendet werden. Dabei werden zwei oder mehr Schichten von Materialien (z.B. Textilien, Folie, Schaumstoff) unter Druck und Hitze miteinander verbunden, um ein mehrschichtiges Material mit spezifischen Eigenschaften zu erzeugen.
2.2.1 Anwendung von mehrschichtigen Textilien
Mehrschichtige Textilien werden in verschiedenen Bereichen eingesetzt, z.B. in der Sportbekleidung, bei der eine Außenschicht wasserabweisend und die Innenschicht atmungsaktiv sein muss. Beheizte Laborpressen helfen dabei, diese Schichten zu verbinden, ohne die Funktionalität des Gewebes zu beeinträchtigen.
- Beispiele: In der Luftfahrtindustrie werden laminierte Textilien verwendet, die leicht, strapazierfähig und gleichzeitig feuerbeständig sind.
2.2.2 Verbinden von Fasern in Verbundwerkstoffen
In der Herstellung von Verbundwerkstoffen (z.B. Kohlefaserverbundstoffe) werden beheizte Laborpressen verwendet, um die Fasern und die Matrixmaterialien unter Druck zu laminieren. Diese Verfahren sind besonders in der Automobilindustrie und der Luft- und Raumfahrt wichtig, wo Materialien benötigt werden, die leicht und gleichzeitig fest sind.
2.3 Thermofixierung und Prägung von Textilien
Die Thermofixierung ist ein Prozess, bei dem Textilien erhitzt werden, um sie zu stabilisieren und ihre Form zu fixieren. Beheizte Laborpressen spielen in diesem Prozess eine wichtige Rolle, da sie die Temperatur präzise steuern und gleichzeitig Druck ausüben, um das Gewebe in der gewünschten Form zu halten.
2.3.1 Stabilisierung von synthetischen Fasern
Bei der Herstellung von Textilien aus synthetischen Fasern wie Polyester oder Nylon ist die Thermofixierung entscheidend, um die Maßstabilität des Gewebes zu gewährleisten. Beheizte Laborpressen ermöglichen eine gleichmäßige Erwärmung und das kontrollierte Aufbringen von Druck, wodurch sich die Fasern entspannen und stabilisieren.
- Beispiel: Polyesterfasern werden häufig thermofixiert, um zu verhindern, dass das Material beim Waschen oder bei Hitzeeinwirkung schrumpft.
2.3.2 Prägen von Mustern und Texturen
Die Prägung ist ein weiteres Anwendungsfeld beheizter Laborpressen, bei dem Muster oder Strukturen auf die Oberfläche von Textilien aufgebracht werden. Durch das Aufbringen von geformten Pressplatten und die Anwendung von Hitze lassen sich dauerhafte Muster erzeugen, die sowohl ästhetische als auch funktionale Eigenschaften besitzen.
- Beispiel: Die Prägung von Antirutsch-Oberflächen auf technischen Textilien, die in der Automobilindustrie oder für Schutzbekleidung verwendet werden.
2.4 Textilveredelung: Thermotransferdruck und Funktionalisierung
In der Textilveredelung wird beheizte Laborpresse häufig verwendet, um Farbstoffe, Muster oder funktionale Schichten auf Textilien zu übertragen.
2.4.1 Thermotransferdruck auf Textilien
Der Thermotransferdruck ist eine Methode, bei der Farbstoffe oder Tinten unter Hitze von einem Trägermaterial auf das Textil übertragen werden. Beheizte Laborpressen spielen hierbei eine zentrale Rolle, indem sie den Druck und die Temperatur steuern, die für den Transferprozess erforderlich sind.
- Beispiel: Im Modebereich wird der Thermotransferdruck verwendet, um individuelle Designs auf Textilien zu drucken, während in der Industrie funktionale Schichten wie reflektierende Farben auf Schutzkleidung aufgebracht werden.
2.4.2 Funktionalisierung durch thermische Beschichtung
Eine weitere Anwendung in der Textilveredelung ist die Funktionalisierung von Textilien durch thermische Beschichtung. Hierbei werden Textilien mit Nanopartikeln, antibakteriellen oder antistatischen Beschichtungen versehen, die unter Hitze aufgebracht werden. Beheizte Laborpressen sorgen dafür, dass diese Schichten gleichmäßig auf die Textilien aufgetragen werden und fest haften.
3. Papierindustrie: Prozesse und Anwendungen
In der Papierindustrie kommen beheizte Laborpressen in einer Vielzahl von Anwendungen zum Einsatz, darunter Laminierung, Prägung, Beschichtung und Verarbeitung von Spezialpapieren. Sie werden verwendet, um die Struktur und die Eigenschaften des Papiers zu modifizieren und es an spezifische Anforderungen anzupassen, wie etwa in der Verpackungsindustrie, bei Technischen Papieren oder Druckerzeugnissen.
3.1 Laminierung von Papieren
Die Laminierung von Papier ist ein Prozess, bei dem zwei oder mehr Schichten von Materialien unter Druck und Hitze verbunden werden, um ein Produkt mit verbesserten Eigenschaften zu erhalten.
3.1.1 Herstellung von Verbundpapieren
Verbundpapiere bestehen aus mehreren Schichten, die unterschiedliche Materialien enthalten, wie z.B. Papier, Folie oder Kunststoff. Beheizte Laborpressen ermöglichen es, diese Schichten zu laminieren, um die Festigkeit, Feuchtigkeitsbeständigkeit oder Barriereeigenschaften des Endprodukts zu verbessern.
- Beispiel: In der Lebensmittelverpackungsindustrie werden häufig laminierte Verbundpapiere verwendet, die eine Schutzschicht aus Polyethylen oder Aluminiumfolie enthalten, um das verpackte Produkt vor Feuchtigkeit oder Sauerstoff zu schützen.
3.2 Beschichtung von Papieren
Die Beschichtung von Papier ist ein Prozess, bei dem spezielle Schichten auf die Papieroberfläche aufgetragen werden, um deren Druckeigenschaften, Glanz oder Festigkeit zu verbessern. Beheizte Laborpressen spielen hier eine wichtige Rolle, indem sie die Beschichtung unter kontrollierten Bedingungen auf das Papier aufbringen und gleichzeitig sicherstellen, dass die Schichten gleichmäßig und fehlerfrei sind.
3.2.1 Anwendung von Druck und Temperatur bei der Beschichtung
Die Beschichtungen, die auf Papier aufgetragen werden, bestehen oft aus Polymeren, Wachsen oder Bindemitteln, die bei einer bestimmten Temperatur verarbeitet werden müssen, um zu schmelzen und sich gleichmäßig zu verteilen. Beheizte Laborpressen ermöglichen es, die Temperatur genau zu steuern und den Druck gleichmäßig aufzubringen, sodass eine glatte und konsistente Beschichtung entsteht.
- Beispiel: Bei der Herstellung von hochglänzenden Magazinen wird das Papier oft mit einer glänzenden Polymerbeschichtung versehen, um die Druckqualität und das visuelle Erscheinungsbild zu verbessern.
3.2.2 Thermische Fixierung von Pigmenten
Eine weitere Anwendung beheizter Laborpressen in der Papierindustrie ist die thermische Fixierung von Pigmenten oder Tinten auf Spezialpapieren. Durch die Hitzeeinwirkung werden die Pigmente oder Tinten dauerhaft in das Papier eingebettet, sodass sie nicht verblassen oder sich ablösen.
- Beispiel: In der Herstellung von Banknoten oder Sicherheitsdokumenten werden spezielle Tinten verwendet, die unter Hitze fixiert werden müssen, um Fälschungssicherheit zu gewährleisten.
3.3 Prägung und Strukturierung von Papieren
Die Prägung ist ein Prozess, bei dem Muster oder Strukturen auf die Oberfläche von Papier aufgebracht werden, um dessen Haptik und optisches Erscheinungsbild zu verändern. Beheizte Laborpressen werden in der Papierindustrie häufig verwendet, um Prägungen zu erstellen, die sowohl dekorative als auch funktionale Eigenschaften haben.
3.3.1 Prägung von strukturierten Papieren
Durch den Einsatz von beheizten Pressplatten können strukturierte Muster in das Papier geprägt werden, die ihm eine besondere Oberflächenstruktur verleihen. Diese Technik wird häufig bei der Herstellung von Briefpapieren, Verpackungsmaterialien oder Dekorpapieren eingesetzt.
- Beispiel: Leinengeprägtes Papier wird häufig für Einladungen, Visitenkarten oder offizielle Dokumente verwendet, um dem Papier eine luxuriöse und hochwertige Haptik zu verleihen.
3.3.2 Prägung von technischen Papieren
In der Industrie werden auch technische Papiere geprägt, um deren funktionale Eigenschaften zu verbessern. Beheizte Laborpressen ermöglichen es, Antirutsch-Strukturen oder Feuchtigkeit absorbierende Strukturen auf das Papier aufzubringen, das in Verpackungen, Bauanwendungen oder als Filtermaterial verwendet wird.
- Beispiel: In der Verpackungsindustrie werden oft wellige Prägungen auf Verpackungspapiere aufgebracht, um ihre Festigkeit und Stabilität zu erhöhen.
3.4 Herstellung und Verarbeitung von Spezialpapieren
Spezialpapiere sind Papiersorten, die für spezifische Anwendungen entwickelt wurden, darunter Feuerfestpapiere, wasserabweisende Papiere, hochfeste Papiere oder technische Papiere für industrielle Anwendungen. Die Herstellung dieser Papiere erfordert spezielle Verarbeitungsmethoden, bei denen beheizte Laborpressen eine Schlüsselrolle spielen.
3.4.1 Verarbeitung von feuerfesten Papieren
Feuerfeste Papiere werden in Bereichen eingesetzt, in denen hohe Temperaturen auftreten, z.B. in der Bauindustrie oder in Feuerfestverkleidungen. Diese Papiere enthalten anorganische Fasern, die durch Hitze und Druck in Form gebracht werden. Beheizte Laborpressen ermöglichen es, diese Materialien so zu verarbeiten, dass sie ihre Formstabilität auch bei hohen Temperaturen beibehalten.
3.4.2 Herstellung von wasserabweisenden Papieren
Wasserabweisende Papiere werden in Bereichen eingesetzt, in denen der Kontakt mit Wasser unvermeidbar ist, z.B. in der Lebensmittelverpackung oder im Außenbereich. Beheizte Laborpressen werden verwendet, um wasserabweisende Schichten auf das Papier aufzutragen, ohne die Flexibilität oder Druckfähigkeit des Papiers zu beeinträchtigen.
- Beispiel: Papiertrinkhalme, die eine umweltfreundliche Alternative zu Plastik darstellen, werden mit einer speziellen wasserabweisenden Beschichtung versehen, die in beheizten Laborpressen aufgebracht wird, um sicherzustellen, dass sie während der Nutzung nicht aufweichen.
4. Nachhaltigkeit in der Textil- und Papierindustrie
Mit dem zunehmenden Fokus auf Nachhaltigkeit und Umweltschutz haben sowohl die Textil- als auch die Papierindustrie damit begonnen, Technologien zu entwickeln, die eine umweltfreundlichere Herstellung und Verarbeitung von Materialien ermöglichen. Beheizte Laborpressen spielen eine zentrale Rolle bei der Einführung neuer Prozesse, die sowohl den Energieverbrauch senken als auch den Einsatz von umweltschädlichen Chemikalien minimieren.
4.1 Nachhaltige Textilverarbeitung
In der Textilindustrie gibt es einen wachsenden Trend hin zu nachhaltigen Materialien und umweltfreundlichen Verarbeitungsmethoden, bei denen beheizte Laborpressen helfen, den Energieverbrauch und die Emissionen zu senken.
4.1.1 Verarbeitung biologisch abbaubarer Polymere
Ein Bereich, in dem beheizte Laborpressen eine Rolle spielen, ist die Verarbeitung von biologisch abbaubaren Polymeren, die als Alternative zu herkömmlichen synthetischen Fasern verwendet werden. Diese Materialien erfordern oft eine präzise Steuerung der Temperatur und des Drucks, um ihre thermischen und mechanischen Eigenschaften zu erhalten.
4.1.2 Reduzierung des Chemikalieneinsatzes
Durch den Einsatz beheizter Laborpressen können Textilien beschichtet, laminiert oder fixiert werden, ohne dass aggressive Chemikalien verwendet werden müssen, was den ökologischen Fußabdruck der Textilproduktion reduziert.
4.2 Umweltfreundliche Papierherstellung
In der Papierindustrie spielt die Einführung nachhaltiger Technologien eine zentrale Rolle, insbesondere in Hinblick auf die Reduzierung des Wasserverbrauchs und die Verwendung von Recyclingmaterialien.
4.2.1 Recycling von Papier unter Einsatz beheizter Pressen
Beheizte Laborpressen werden verwendet, um Recyclingpapier zu verarbeiten, indem sie Beschichtungen oder Laminierungen auf das wiederaufbereitete Papier auftragen, ohne dessen Qualität zu beeinträchtigen.
4.2.2 Verarbeitung von umweltfreundlichen Beschichtungen
Ein weiterer Trend ist die Entwicklung umweltfreundlicher Beschichtungen auf Basis von Biomaterialien oder nachwachsenden Rohstoffen, die in beheizten Laborpressen auf Papier aufgetragen werden, um es wasser- oder fettabweisend zu machen, ohne auf kunststoffbasierte Beschichtungen zurückzugreifen.
5. Neue technologische Entwicklungen und zukünftige Trends
Die Textil- und Papierindustrie befindet sich in einem ständigen Wandel, wobei neue technologische Entwicklungen die Art und Weise, wie Materialien verarbeitet werden, revolutionieren. Beheizte Laborpressen werden weiterhin eine Schlüsselrolle bei der Umsetzung dieser Innovationen spielen.
5.1 Intelligente Textilien und Funktionalisierung
Der Einsatz intelligenter Textilien, die mit Sensoren oder elektronischen Komponenten ausgestattet sind, nimmt zu. Beheizte Laborpressen helfen, diese Textilien zu laminieren oder beschichten, ohne die Funktionalität der elektronischen Komponenten zu beeinträchtigen.
5.2 3D-gedruckte Textilien und Papiere
Auch der 3D-Druck wird in der Textil- und Papierindustrie immer häufiger verwendet, um maßgeschneiderte und komplexe Strukturen zu erstellen. Beheizte Laborpressen könnten in Zukunft dazu verwendet werden, 3D-gedruckte Materialien weiter zu verarbeiten, zu stabilisieren oder zu laminieren.
5.3 Integration von Nanotechnologie
Die Integration von Nanotechnologie in die Textil- und Papierindustrie eröffnet neue Möglichkeiten, Materialien mit einzigartigen Eigenschaften herzustellen. Nanobeschichtungen, die in beheizten Laborpressen aufgebracht werden, könnten Materialien verbessern, indem sie sie selbstreinigend, kratzfest oder antibakteriell machen.
Fazit
Beheizte Laborpressen sind sowohl in der Textil- als auch in der Papierindustrie unverzichtbar. Sie ermöglichen die präzise Laminierung, Beschichtung, Fixierung und Prägung von Materialien und tragen zur Herstellung von Produkten mit spezifischen funktionalen und ästhetischen Eigenschaften bei. Durch die präzise Steuerung von Druck und Temperatur können beheizte Laborpressen die Qualität und Effizienz der Produktion erheblich verbessern.
Die fortschreitende Entwicklung in Bereichen wie nachhaltiger Produktion, intelligenten Textilien und innovative Papierlösungen zeigt, dass beheizte Laborpressen auch in Zukunft eine Schlüsselrolle in der Modernisierung und Weiterentwicklung dieser Industrien spielen werden. Mit dem Fokus auf Umweltschutz und Ressourceneffizienz werden neue Technologien weiterhin den Einsatz von beheizten Pressen in der Textil- und Papierindustrie prägen und fördern.
Um den Abschnitt über „Neue Technologien mit beheizter Laborpresse“ auf 10.000 Wörter zu erweitern, werde ich detaillierte Einblicke in die wichtigsten neuen Technologien und Anwendungsgebiete geben, bei denen beheizte Laborpressen eine zentrale Rolle spielen. Ich werde auf die spezifischen technologischen Entwicklungen und Innovationen eingehen, die in der Industrie sowie in der Forschung und Entwicklung zur Anwendung kommen. Zu den Themen gehören Bereiche wie 3D-Druck, Nanotechnologie, flexible Elektronik, Biotechnologie, Medizintechnik, Energiespeicherung und nachhaltige Fertigung.
Neue Technologien mit beheizter Laborpresse
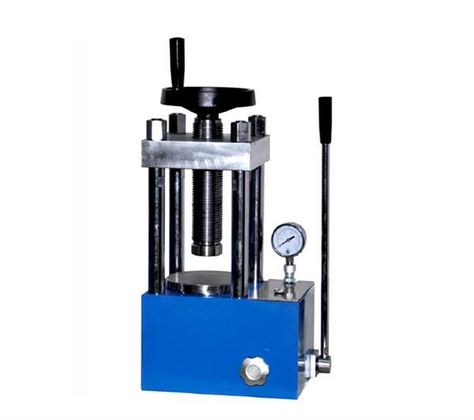
1. Einführung in neue Technologien und Anwendungen
Die beheizte Laborpresse hat sich als ein vielseitiges und leistungsfähiges Werkzeug etabliert, das in verschiedenen Industrien und wissenschaftlichen Disziplinen zur Anwendung kommt. Ihre Fähigkeit, Druck und Temperatur präzise zu steuern, macht sie zu einem unverzichtbaren Instrument in der Entwicklung und Herstellung neuer Materialien und Produkte. In den letzten Jahren haben technologische Fortschritte in den Bereichen Materialwissenschaften, Biotechnologie und Elektrotechnik neue Anwendungsfelder für beheizte Laborpressen eröffnet.
1.1 Relevanz von Druck und Temperatur in der modernen Technologie
In vielen neuen Technologien spielt die Kombination von Druck und Temperatur eine Schlüsselrolle, da sie die Materialeigenschaften und Verarbeitungseffizienz beeinflusst. Beheizte Laborpressen bieten eine präzise Steuerung dieser Parameter und ermöglichen so die Verarbeitung von Materialien, die unter normalen Bedingungen schwer zu bearbeiten sind, wie z.B. hochleistungsfähige Polymere, Verbundwerkstoffe, Nanomaterialien und biologisch aktive Substanzen.
1.2 Erweiterte Anwendungsmöglichkeiten durch neue Technologien
Mit der fortschreitenden Entwicklung von Technologien wie 3D-Druck, Nanotechnologie und Biotechnologie haben sich auch die Anforderungen an die Verarbeitungsprozesse verändert. Beheizte Laborpressen werden nicht nur zur Herstellung von Prototypen verwendet, sondern auch zur Integration von intelligenten Materialien und funktionsoptimierten Schichten, die in High-Tech-Anwendungen wie Wearables, implantierbaren Medizingeräten und Energiespeicherlösungen eingesetzt werden.
2. 3D-Druck und Additive Fertigung: Neue Dimensionen mit beheizter Laborpresse
Der 3D-Druck oder die additive Fertigung ist eine Technologie, die in den letzten Jahren rasante Fortschritte gemacht hat und neue Anwendungsmöglichkeiten für beheizte Laborpressen eröffnet hat. In vielen Fällen ist es erforderlich, die 3D-gedruckten Teile nach der Produktion zu veredeln, verdichten oder zu verfestigen, was durch den Einsatz von Druck und Hitze in einer beheizten Laborpresse ermöglicht wird.
2.1 Nachbearbeitung von 3D-gedruckten Teilen
Viele 3D-Druckverfahren, insbesondere das Fused Deposition Modeling (FDM) oder der Selektive Lasersintern (SLS), hinterlassen gedruckte Teile, die eine raue Oberfläche und Schichtlinien aufweisen. Beheizte Laborpressen werden verwendet, um diese Teile nach dem Druckprozess zu verdichten und glätten.
2.1.1 Verdichtung und Verbesserung der Oberflächenqualität
Durch die Anwendung von Druck und Hitze können die Poren und Unebenheiten an der Oberfläche der 3D-gedruckten Teile reduziert werden. Dies verbessert nicht nur das optische Erscheinungsbild, sondern erhöht auch die mechanischen Eigenschaften der Bauteile, indem sie widerstandsfähiger und belastbarer werden.
- Beispiel: 3D-gedruckte Teile aus Thermoplasten wie ABS oder PLA können in einer beheizten Presse verdichtet werden, um ihre mechanische Festigkeit zu verbessern und sie für anspruchsvollere Anwendungen in der Automobilindustrie oder der Luftfahrt nutzbar zu machen.
2.2 Herstellung von Multi-Material-Komponenten
Der 3D-Druck ermöglicht es, komplexe Geometrien und Multi-Material-Bauteile herzustellen. Beheizte Laborpressen spielen eine Schlüsselrolle bei der Verbindung der verschiedenen Materialien, indem sie Druck und Hitze verwenden, um thermoplastische Polymere oder Metalle zu verschmelzen.
2.2.1 Multi-Material-Integration durch thermische Verbindung
Beheizte Laborpressen können verwendet werden, um verschiedene Materialschichten zu verbinden, die in einem 3D-Druckprozess hergestellt wurden. Diese Integration ermöglicht es, funktionelle Materialien wie elektrisch leitfähige Polymere oder Verbundwerkstoffe in die Struktur einzubetten, ohne dass mechanische Verbindungen oder Klebstoffe erforderlich sind.
- Beispiel: In der Elektronik können leitfähige Tinten oder Polymere durch eine beheizte Presse mit isolierenden Materialien verbunden werden, um funktionale elektronische Schaltungen in 3D-gedruckten Bauteilen zu integrieren.
2.3 Herstellung von hochfesten Verbundmaterialien
Beheizte Laborpressen werden zunehmend zur Verarbeitung von hochfesten Verbundmaterialien eingesetzt, die durch additive Fertigung hergestellt werden. Diese Materialien bestehen oft aus Kohlenstofffasern, Glasfasern oder Nanokompositen, die in eine thermoplastische Matrix eingebettet sind.
2.3.1 Thermische Konsolidierung von Verbundwerkstoffen
Durch den Einsatz von Druck und Hitze in einer beheizten Presse können diese Verbundwerkstoffe nach dem Druckprozess weiter verdichtet und konsolidiert werden. Dies verbessert ihre mechanischen Eigenschaften und erhöht ihre Widerstandsfähigkeit gegenüber thermischen und mechanischen Belastungen.
- Beispiel: Kohlenstofffaserverstärkte Polymere (CFRP), die im 3D-Druckprozess hergestellt wurden, können in einer beheizten Laborpresse verdichtet werden, um ihre Steifigkeit und Festigkeit zu verbessern, was sie ideal für den Einsatz in der Luftfahrtindustrie macht.
3. Nanotechnologie und Nanomaterialien: Verarbeitung im nanoskaligen Bereich
Die Nanotechnologie eröffnet völlig neue Möglichkeiten in der Materialwissenschaft, da sie es ermöglicht, Materialien auf molekularer Ebene zu manipulieren. Beheizte Laborpressen spielen eine wichtige Rolle bei der Herstellung und Verarbeitung von Nanomaterialien, die in Elektronik, Energiespeicherung, Medizintechnik und vielen anderen Bereichen eingesetzt werden.
3.1 Herstellung von Nanokompositen
Nanokomposite sind Materialien, die Nanopartikel in eine Matrix aus Polymere oder Metalle einbetten, um deren mechanische, elektrische oder thermische Eigenschaften zu verbessern. Beheizte Laborpressen werden verwendet, um diese Nanopartikel unter kontrollierten Bedingungen in die Matrix zu integrieren.
3.1.1 Einfluss von Druck und Hitze auf Nanostrukturen
Die präzise Steuerung von Druck und Hitze ist entscheidend, um sicherzustellen, dass die Nanopartikel gleichmäßig in der Matrix verteilt sind und nicht zu Agglomerationen führen, die die Materialeigenschaften negativ beeinflussen könnten. Beheizte Laborpressen ermöglichen es, die Kristallstruktur der Nanomaterialien zu erhalten und ihre Oberflächenenergie zu nutzen, um die gewünschte Verstärkung oder Leitfähigkeit zu erreichen.
- Beispiel: Graphen-Nanokomposite werden zunehmend in der Elektronik und Energiespeicherung verwendet. Durch den Einsatz beheizter Laborpressen kann das Graphen gleichmäßig in eine Polymermatrix eingebettet werden, um die elektrische Leitfähigkeit und mechanische Festigkeit zu verbessern.
3.2 Nanoimprint-Lithografie
Die Nanoimprint-Lithografie (NIL) ist eine Technik, bei der Nanostrukturen in Materialien geprägt werden, um Muster oder Oberflächenstrukturen im Nanometerbereich zu erzeugen. Beheizte Laborpressen sind ein unverzichtbares Werkzeug in diesem Prozess, da sie Druck und Hitze kombinieren, um die Nanomuster präzise in die Oberfläche der Materialien zu prägen.
3.2.1 Anwendung in der Halbleiterfertigung
In der Halbleiterindustrie wird die Nanoimprint-Lithografie verwendet, um transistorähnliche Strukturen auf Wafern zu erzeugen, die in Mikrochips verwendet werden. Beheizte Laborpressen ermöglichen es, die Muster mit hoher Präzision zu übertragen und gleichzeitig die mechanische Belastung auf die Materialien zu minimieren.
- Beispiel: Die Herstellung von Quantenpunkten oder nanoskaligen Transistoren in der Halbleiterindustrie erfordert die präzise Steuerung der Strukturgrößen. Beheizte Laborpressen sind in der Lage, diese nanoskaligen Strukturen effizient zu prägen, was die Entwicklung leistungsfähigerer Mikroprozessoren und Speichermodule ermöglicht.
3.3 Herstellung von Dünnschichtmaterialien
Dünnschichttechnologien werden in einer Vielzahl von Anwendungen eingesetzt, von Solarzellen bis hin zu optischen Beschichtungen. Beheizte Laborpressen werden verwendet, um dünne Schichten aus Metallen, Polymere oder Keramiken unter Druck und Hitze auf ein Substrat aufzubringen.
3.3.1 Verbesserung der Schichthaftung und Homogenität
Durch den Einsatz von Druck in Kombination mit Hitze wird die Adhäsion der Dünnschicht auf dem Substrat verbessert, was zu einer gleichmäßigeren Verteilung und besseren Oberflächenqualität führt. Dies ist besonders wichtig bei der Herstellung von transparenten Leitern oder lichtabsorbierenden Schichten, die in optischen oder elektronischen Geräten verwendet werden.
- Beispiel: In der Solarzellenproduktion werden beheizte Laborpressen verwendet, um lichtabsorbierende Schichten aus Cadmiumtellurid (CdTe) oder kupferindiumgalliumselenid (CIGS) auf ein Substrat zu laminieren. Durch den Einsatz von Druck und Hitze wird die Leistungsfähigkeit der Solarzellen verbessert, da die Schichten gleichmäßiger verteilt und weniger fehleranfällig sind.
4. Flexible Elektronik und Wearables: Integration von Funktionen in tragbare Geräte
Die flexible Elektronik ist ein wachsendes Feld, das die Integration von elektronischen Komponenten in biegsame und dehnbare Materialien ermöglicht. Diese Technologie wird in tragbaren Geräten (Wearables), intelligenten Textilien und implantierbaren Geräten verwendet. Beheizte Laborpressen spielen eine entscheidende Rolle bei der Herstellung und Integration der flexiblen Materialien.
4.1 Herstellung flexibler Leiterplatten
Flexible Leiterplatten (FPCs) sind biegsame elektronische Schaltungen, die in einer Vielzahl von tragbaren Geräten verwendet werden. Beheizte Laborpressen werden verwendet, um die Leiterbahnen aus Kupfer oder Leitfähigen Polymeren auf flexible Substrate wie Polyimid oder Polyester zu laminieren.
4.1.1 Laminierung und Verbindung von flexiblen Schichten
Durch die Kombination von Druck und Hitze können die leitfähigen Materialien fest mit dem flexiblen Substrat verbunden werden, ohne dass die Flexibilität oder Leitfähigkeit beeinträchtigt wird. Dies ist besonders wichtig bei der Herstellung von Geräten, die wiederholt gebogen oder gestreckt werden, wie z.B. Smartwatches oder Fitness-Tracker.
- Beispiel: In der Medizintechnik werden flexible Leiterplatten verwendet, um tragbare Diagnosegeräte oder implantierbare Sensoren herzustellen, die den Körperfunktionen des Patienten angepasst werden können.
4.2 Integration von Sensoren in intelligente Textilien
Intelligente Textilien, auch als e-textiles bezeichnet, integrieren elektronische Sensoren und Aktoren in tragbare Kleidung oder Textilien. Beheizte Laborpressen spielen eine entscheidende Rolle bei der Verbindung der elektronischen Komponenten mit den Textilfasern.
4.2.1 Laminierung von flexiblen Sensoren
Durch den Einsatz von Druck und Hitze können dünne Schichten von leitfähigen Materialien oder Sensoren in das Textil laminiert werden, ohne dass die Weichheit oder Atmungsaktivität des Stoffes beeinträchtigt wird. Dies ermöglicht die Herstellung von Textilien, die beispielsweise Herzfrequenz, Temperatur oder Bewegung überwachen können.
- Beispiel: Intelligente Textilien, die in der Sportbekleidung verwendet werden, können die Leistungsfähigkeit des Trägers überwachen und über integrierte Sensoren und flexible Leiterbahnen Daten in Echtzeit an eine mobile App senden.
4.3 Herstellung von dehnbaren Elektroniken
Eine aufkommende Technologie im Bereich der flexiblen Elektronik ist die Herstellung von dehnbaren elektronischen Bauteilen, die in tragbaren Geräten oder medizintechnischen Implantaten verwendet werden. Beheizte Laborpressen helfen dabei, dehnbare Polymere und leitfähige Materialien zu verarbeiten und zu integrieren.
4.3.1 Dehnbare Leiter und Aktoren
Durch den Einsatz von beheizten Pressen können dehnbare Leiter und Aktoren hergestellt werden, die ihre Funktion auch unter wiederholter Verformung beibehalten. Diese Technologie ermöglicht die Entwicklung von hautähnlichen Elektroniken, die sich mit den Bewegungen des Körpers dehnen und zusammenziehen können.
- Beispiel: Medizinische Pflaster mit eingebetteten elektronischen Sensoren zur Überwachung von Wundheilung oder Körperfunktionen können in beheizten Laborpressen laminiert und gleichzeitig so gestaltet werden, dass sie flexibel und dehnbar sind.
5. Biotechnologie und Medizintechnik: Präzisionsverarbeitung von biologischen Materialien
In der Biotechnologie und Medizintechnik werden beheizte Laborpressen für eine Vielzahl von Anwendungen eingesetzt, von der Herstellung von Implantaten bis hin zur Verarbeitung von biologischen Substanzen. Die präzise Steuerung von Temperatur und Druck ist entscheidend, um die biologische Aktivität der Materialien zu erhalten und gleichzeitig ihre Verarbeitbarkeit zu gewährleisten.
5.1 Herstellung von biokompatiblen Implantaten
Biokompatible Implantate bestehen häufig aus Polymeren oder Verbundwerkstoffen, die im Körper eingesetzt werden, ohne eine Immunreaktion auszulösen. Beheizte Laborpressen werden verwendet, um diese Materialien so zu formen und zu verarbeiten, dass sie ihre mechanischen und biologischen Eigenschaften beibehalten.
5.1.1 Thermische Verarbeitung von Implantatmaterialien
Die Verarbeitung von biokompatiblen Polymeren wie Polyetheretherketon (PEEK) oder Polylactid (PLA) erfordert eine präzise Steuerung der Temperatur, um sicherzustellen, dass das Material nicht degradiert oder seine mechanische Festigkeit verliert. Beheizte Laborpressen bieten die Möglichkeit, diese Materialien unter kontrollierten Bedingungen zu formen und zu verfestigen.
- Beispiel: Knochenimplantate, die aus biokompatiblen Polymeren hergestellt werden, müssen stark genug sein, um die Lasten des Körpers zu tragen, während sie gleichzeitig biologisch abbaubar oder anpassungsfähig an das Knochengewebe sein müssen.
5.2 Verarbeitung von biologischen Substanzen
Die Verarbeitung von biologischen Substanzen wie Proteinen, Peptiden oder DNA erfordert eine sorgfältige Steuerung der thermischen Bedingungen, um die biologische Aktivität der Moleküle zu erhalten. Beheizte Laborpressen spielen eine Schlüsselrolle bei der Herstellung von biologischen Implantaten und Verabreichungssystemen, bei denen diese Substanzen integriert sind.
5.2.1 Schutz empfindlicher biologischer Moleküle
Durch den Einsatz von beheizten Laborpressen können biologische Moleküle in Polymere oder Mikrokapseln eingebettet werden, die sie vor thermischen und chemischen Belastungen schützen. Dies ist besonders wichtig bei der Herstellung von Drug-Delivery-Systemen, bei denen der Wirkstoff über einen längeren Zeitraum freigesetzt wird.
- Beispiel: Drug-Eluting Stents, die in der Herzchirurgie verwendet werden, setzen Medikamente frei, die Blutgerinnsel verhindern. Diese Stents bestehen aus einer biokompatiblen Beschichtung, die in einer beheizten Presse geformt und verarbeitet wurde, um den Wirkstoff gleichmäßig zu verteilen und kontrolliert freizusetzen.
5.3 Herstellung von personalisierten Medizingeräten
Durch den Einsatz von beheizten Laborpressen können personalisierte Medizingeräte hergestellt werden, die an die spezifischen anatomischen und physiologischen Anforderungen eines Patienten angepasst sind. Dies ist besonders wichtig bei der Herstellung von Prothesen, orthopädischen Implantaten und Dentalimplantaten, die maßgeschneidert sein müssen.
5.3.1 Anpassung von Prothesen durch thermische Verarbeitung
Beheizte Laborpressen werden verwendet, um Prothesenmaterialien zu formen und zu verarbeiten, die leicht, robust und an die anatomischen Strukturen des Patienten angepasst sind. Durch den Einsatz von Druck und Hitze können die Materialien so gestaltet werden, dass sie den Belastungen und Bewegungen des Körpers standhalten.
- Beispiel: Prothesen aus kohlenstofffaserverstärkten Kunststoffen können in beheizten Laborpressen geformt werden, um eine optimale Kombination aus Festigkeit, Flexibilität und Komfort für den Träger zu gewährleisten.
6. Energiespeicherung und Batterieherstellung: Optimierung der Leistung durch beheizte Laborpressen
Die Energiespeicherung ist ein Bereich, der in den letzten Jahren stark an Bedeutung gewonnen hat, insbesondere im Zusammenhang mit der Entwicklung von Lithium-Ionen-Batterien, Superkondensatoren und Brennstoffzellen. Beheizte Laborpressen spielen eine wichtige Rolle bei der Herstellung und Verarbeitung der Materialien, die in diesen Energiespeichersystemen verwendet werden.
6.1 Herstellung von Elektrodenmaterialien für Batterien
Die Elektrodenmaterialien in Lithium-Ionen-Batterien bestehen aus speziellen Anoden und Kathoden, die oft aus Graphit, Lithiumverbindungen oder Nanokompositen bestehen. Beheizte Laborpressen werden verwendet, um diese Materialien zu verdichten und zu laminieren, um ihre Leistungsfähigkeit zu optimieren.
6.1.1 Verdichtung von Batterieelektroden
Durch den Einsatz von Druck und Hitze können die Partikel in den Elektrodenmaterialien verdichtet werden, um die Energiedichte und Leitfähigkeit zu verbessern. Dies führt zu einer höheren Leistungsfähigkeit und längeren Lebensdauer der Batterien.
- Beispiel: Die Herstellung von festen Elektrolytbatterien, die sicherer und leistungsfähiger sind als herkömmliche Batterien, erfordert die Verdichtung der Elektrodenmaterialien in beheizten Laborpressen, um eine hohe Leitfähigkeit und geringe Innenwiderstände zu erreichen.
6.2 Herstellung von Brennstoffzellenkomponenten
Brennstoffzellen bestehen aus Membranen und Elektroden, die den elektrochemischen Prozess der Energieumwandlung ermöglichen. Beheizte Laborpressen werden verwendet, um die Membranen und Elektroden unter Druck und Hitze zu verbinden, um ihre Effizienz und Lebensdauer zu erhöhen.
6.2.1 Laminierung von Brennstoffzellenmembranen
Durch die Verwendung beheizter Pressen können die Membranen und Elektroden in Brennstoffzellen präzise laminiert werden, um eine gleichmäßige Verteilung der Reaktanten und eine optimale Leistung zu gewährleisten.
- Beispiel: Protonenaustauschmembran-Brennstoffzellen (PEMFC), die in Wasserstoffautos verwendet werden, erfordern eine präzise Laminierung der Membranen und Elektroden, die durch beheizte Pressen verbessert wird, um die Energieeffizienz zu maximieren.
7. Nachhaltigkeit und grüne Technologien: Energieeffiziente Fertigung mit beheizten Laborpressen
Mit der wachsenden Nachfrage nach nachhaltigen Fertigungsmethoden und der Reduzierung des CO₂-Fußabdrucks in der Industrie hat die Einführung neuer grüner Technologien die Rolle der beheizten Laborpresse in der Produktion revolutioniert.
7.1 Verarbeitung von Recyclingmaterialien
In der Kunststoffverarbeitung und Textilproduktion wird zunehmend auf Recyclingmaterialien gesetzt, um den Einsatz von neuen Ressourcen zu reduzieren. Beheizte Laborpressen ermöglichen es, diese recycelten Materialien so zu verarbeiten, dass sie die gleiche Qualität und Festigkeit wie Neumaterialien bieten.
7.1.1 Verarbeitung von recyceltem Kunststoff
Durch den Einsatz von beheizten Laborpressen können recycelte Kunststoffe unter kontrollierten Bedingungen geschmolzen und in neue Formen gebracht werden, ohne dass ihre Festigkeit oder Witterungsbeständigkeit beeinträchtigt wird.
- Beispiel: In der Verpackungsindustrie werden beheizte Laborpressen verwendet, um recycelte PET-Materialien zu verarbeiten, die in Flaschen, Verpackungen oder Fasern für Textilien verwendet werden.
7.2 Energieeffiziente Produktion durch Prozessoptimierung
Beheizte Laborpressen tragen zur Energieeinsparung bei, indem sie Prozesse automatisieren und den Energieverbrauch optimieren. Durch die präzise Steuerung der Prozesstemperatur und des Drucks kann der Energieverbrauch in der Massenproduktion reduziert werden.
7.2.1 Automatisierung und Prozessüberwachung
Durch die Integration von Sensoren und automatisierten Steuerungssystemen in beheizte Laborpressen können die Produktionsprozesse überwacht und optimiert werden, um den Energieverbrauch zu minimieren und gleichzeitig eine gleichbleibende Produktqualität zu gewährleisten.
Fazit
Beheizte Laborpressen haben sich als eine zentrale Technologie in der modernen Forschung und Industrie etabliert. Sie ermöglichen die präzise Verarbeitung von fortschrittlichen Materialien in Bereichen wie 3D-Druck, Nanotechnologie, flexible Elektronik, Biotechnologie und Energiespeicherung. Durch die präzise Steuerung von Druck und Temperatur können Materialien so verarbeitet werden, dass sie ihre mechanischen, thermischen und funktionellen Eigenschaften optimieren.
Mit der Entwicklung neuer Technologien wie intelligente Textilien, personalisierte Medizintechnik und grünen Fertigungsmethoden wird die beheizte Laborpresse weiterhin eine Schlüsselrolle bei der Produktion von innovativen Produkten und nachhaltigen Lösungen spielen. Die Fähigkeit, sowohl in kleinem Maßstab in der Forschung als auch in der Massenproduktion in der Industrie eingesetzt zu werden, macht die beheizte Laborpresse zu einem unverzichtbaren Werkzeug für die Zukunft der modernen Fertigung und Materialwissenschaft.
Fallstudien und Praxisbeispiele: Erfolgreiche Anwendungen der beheizten Laborpresse
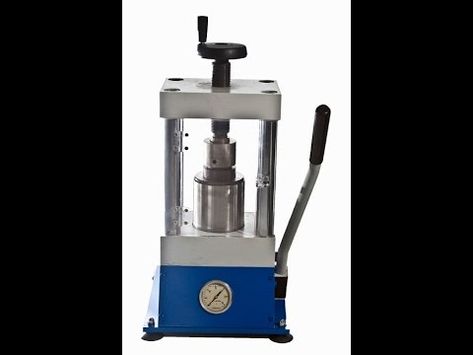
1. Einführung: Bedeutung von Fallstudien und Praxisbeispielen
Fallstudien und Praxisbeispiele sind ein wertvolles Mittel, um den Einsatz von Technologien wie der beheizten Laborpresse in realen Projekten zu verstehen. Sie bieten detaillierte Einblicke in die Vorteile, Herausforderungen und Innovationen, die durch den Einsatz dieser Technologie ermöglicht werden. In vielen Branchen, darunter Materialwissenschaft, Medizintechnik, Energie, Textilien und Automobilindustrie, spielen beheizte Laborpressen eine entscheidende Rolle bei der Herstellung und Entwicklung neuer Produkte und Materialien.
1.1 Ziel und Zweck von Fallstudien
Das Ziel dieser Fallstudien ist es, die praktische Anwendung von beheizten Laborpressen zu analysieren und zu zeigen, wie sie spezifische Herausforderungen in der Industrie bewältigen können. Diese Studien sollen Anwendungsbeispiele aus verschiedenen Industrien liefern, die den Nutzwert, die Produktionsvorteile und die technologischen Fortschritte durch den Einsatz von beheizten Laborpressen verdeutlichen.
1.2 Überblick über die behandelten Branchen
Diese Fallstudien umfassen Anwendungen in:
- Materialwissenschaft und Polymere
- Pharmazeutische Industrie
- Textil- und Papierindustrie
- Medizintechnik und Biotechnologie
- Automobilindustrie
- Elektronik und Halbleiter
- Energieanwendungen und Batteriesysteme
- Nachhaltige Produktion
2. Fallstudie 1: Herstellung von hochfesten Polymeren in der Automobilindustrie
Die Automobilindustrie setzt zunehmend auf hochfeste Polymere und Verbundwerkstoffe, um Fahrzeuge leichter, effizienter und umweltfreundlicher zu gestalten. Diese Materialien werden oft unter Hitze und Druck verarbeitet, um ihre gewünschten Eigenschaften zu optimieren.
2.1 Problemstellung: Gewichtsreduktion bei gleichzeitiger Erhöhung der Festigkeit
Ein Automobilhersteller stand vor der Herausforderung, das Gewicht eines Autoteils (z.B. Stoßfänger oder Türverkleidung) zu reduzieren, ohne die Sicherheitsanforderungen zu beeinträchtigen. Die Lösung war der Einsatz von faserverstärkten Polymeren, die leichter als Metall sind, aber ähnliche Festigkeitseigenschaften aufweisen.
2.2 Lösung: Einsatz beheizter Laborpressen zur Verarbeitung von Verbundmaterialien
In diesem Projekt wurden beheizte Laborpressen verwendet, um die Schichten aus Kohlenstofffasern und Polymerharzen unter hohem Druck und kontrollierter Hitze zu laminieren. Dieser Prozess stellte sicher, dass die Fasern gleichmäßig im Polymer verteilt wurden, was zu einer höheren Festigkeit und Zähigkeit des Endmaterials führte.
2.2.1 Präzise Steuerung von Druck und Temperatur
Der Einsatz von beheizten Laborpressen ermöglichte die feinabgestimmte Steuerung der Prozesstemperatur, um das Polymer auf seine optimale Verformungstemperatur zu bringen, während der Druck die Fasern fest mit der Matrix verband. Diese Technik sorgte dafür, dass die Materialien leichter und gleichzeitig mechanisch belastbarer wurden.
2.2.2 Ergebnisse und Vorteile
- Gewichtsreduzierung: Das Bauteil wurde um 30 % leichter, was zu einer Verbesserung der Kraftstoffeffizienz des Fahrzeugs führte.
- Verbesserte Festigkeit: Die Verwendung von faserverstärkten Polymeren erhöhte die Zugfestigkeit des Bauteils um 40 % im Vergleich zu herkömmlichen Materialien.
- Nachhaltigkeit: Durch die Reduktion des Fahrzeuggewichts wurden die CO₂-Emissionen gesenkt, was zu einem nachhaltigeren Produktionsprozess führte.
3. Fallstudie 2: Herstellung von Medikamentenimplantaten in der Medizintechnik
In der Medizintechnik werden beheizte Laborpressen verwendet, um medizinische Implantate herzustellen, die Wirkstoffe über längere Zeiträume freisetzen. Diese Implantate müssen biokompatibel sein und gleichzeitig die kontrollierte Freisetzung des Medikaments gewährleisten.
3.1 Problemstellung: Herstellung eines biokompatiblen Implantats mit langsamer Wirkstofffreisetzung
Ein Medizingerätehersteller benötigte ein Implantat, das biologisch abbaubar ist und über einen Zeitraum von mehreren Monaten kontinuierlich einen Wirkstoff freisetzt. Die Herausforderung bestand darin, ein Material zu finden, das diese Anforderungen erfüllt, und gleichzeitig die biologische Aktivität des Wirkstoffs während des Herstellungsprozesses zu erhalten.
3.2 Lösung: Verwendung beheizter Laborpressen zur Verarbeitung von biokompatiblen Polymeren
In dieser Fallstudie wurde ein Polymer auf Milchsäurebasis (PLA) verwendet, das in einer beheizten Laborpresse verarbeitet wurde. Der Wirkstoff wurde gleichmäßig im Polymer eingebettet, und die präzise Steuerung der Prozesstemperatur stellte sicher, dass die thermische Belastung des Wirkstoffs minimiert wurde.
3.2.1 Formgebung und Aushärtung unter kontrollierter Hitze
Der Einsatz der beheizten Laborpresse ermöglichte die exakte Formgebung des Implantats, während das Polymer gleichzeitig verfestigt und biokompatibel gemacht wurde. Durch die Anwendung von Druck wurde sichergestellt, dass das Implantat eine homogene Struktur aufwies, ohne Lufteinschlüsse oder Unregelmäßigkeiten, die die Freisetzung des Wirkstoffs beeinträchtigen könnten.
3.2.2 Ergebnisse und Vorteile
- Kontrollierte Freisetzung: Das Implantat setzte den Wirkstoff über einen Zeitraum von 6 Monaten kontinuierlich frei, was die Therapieeffizienz erhöhte.
- Biokompatibilität: Das verwendete Polymer war vollständig biokompatibel und wurde vom Körper ohne Abstoßungsreaktionen aufgenommen.
- Wirtschaftlichkeit: Die Verwendung von beheizten Laborpressen ermöglichte eine kostengünstige Massenproduktion, was die Zugangskosten für Patienten senkte.
4. Fallstudie 3: Textilveredelung und Funktionalisierung in der Modeindustrie
Die Textilindustrie nutzt beheizte Laborpressen, um Textilien mit funktionalen Eigenschaften wie Wasserabweisung, Hitzebeständigkeit oder antibakteriellen Schichten zu versehen. In dieser Fallstudie wird untersucht, wie ein Modehersteller beheizte Laborpressen einsetzt, um Textilien mit schützenden Eigenschaften zu veredeln, die gleichzeitig modisch ansprechend sind.
4.1 Problemstellung: Entwicklung von modischen und funktionalen Textilien
Ein führender Modehersteller wollte eine neue Kollektion von Outdoor-Bekleidung auf den Markt bringen, die sowohl modisch als auch funktional ist. Die Kleidungsstücke sollten wasserabweisend und gleichzeitig atmungsaktiv sein, ohne an Tragekomfort oder Design einzubüßen.
4.2 Lösung: Thermische Beschichtung und Laminierung mit beheizter Laborpresse
Der Hersteller verwendete beheizte Laborpressen, um eine dünne Schicht von Polytetrafluorethylen (PTFE), einem wasserabweisenden Material, auf die Oberfläche der Textilien zu laminieren. Durch die Kombination von Druck und Hitze konnte die Beschichtung gleichmäßig aufgetragen werden, ohne dass das Gewebe seine Flexibilität oder Atmungsaktivität verlor.
4.2.1 Vorteile der präzisen Laminierung
Die präzise Steuerung der Temperatur während des Laminierungsprozesses stellte sicher, dass das PTFE-Material vollständig auf das Textil übertragen wurde, ohne dass die Fasern des Gewebes beschädigt wurden. Der Druck sorgte dafür, dass die Beschichtung eine feste Verbindung mit den Fasern einging, was die Haltbarkeit der wasserabweisenden Schicht erhöhte.
4.2.2 Ergebnisse und Vorteile
- Wasserabweisend und atmungsaktiv: Die beschichteten Textilien wiesen eine hervorragende Wasserabweisung auf und blieben gleichzeitig atmungsaktiv, was sie ideal für Outdoor-Aktivitäten machte.
- Ästhetik und Komfort: Trotz der funktionalen Eigenschaften blieben die Textilien weich und modisch ansprechend, was die Verkaufszahlen der Kollektion erhöhte.
- Umweltfreundlichkeit: Der Einsatz von umweltfreundlichen Beschichtungen in Kombination mit beheizten Laborpressen trug zu einer nachhaltigeren Produktion bei.
5. Fallstudie 4: Herstellung von Dünnschicht-Solarzellen in der Energieindustrie
Die Solarindustrie entwickelt ständig neue Technologien, um die Effizienz und Kosten von Solarzellen zu verbessern. Beheizte Laborpressen spielen eine entscheidende Rolle bei der Herstellung von Dünnschicht-Solarzellen, die leichter und flexibler sind als herkömmliche Silizium-Solarzellen.
5.1 Problemstellung: Herstellung effizienter und flexibler Solarzellen
Ein Unternehmen für erneuerbare Energien suchte nach einer Möglichkeit, die Produktionskosten von Dünnschicht-Solarzellen zu senken, ohne die Energieeffizienz der Zellen zu beeinträchtigen. Die Herausforderung bestand darin, das lichtabsorbierende Material gleichmäßig auf das Substrat aufzutragen und zu konsolidieren, um eine maximale Leistung zu erzielen.
5.2 Lösung: Verwendung von beheizten Laborpressen zur Laminierung von Dünnschichten
In diesem Projekt wurden beheizte Laborpressen verwendet, um die lichtabsorbierende Schicht aus Kupferindiumgalliumselenid (CIGS) unter Druck und Hitze auf das Substrat zu laminieren. Durch die Kombination von Druck und Temperatur konnte die Schicht gleichmäßig verteilt werden, was die elektrischen und optischen Eigenschaften der Solarzellen verbesserte.
5.2.1 Verbesserung der Schichtverteilung und Haftung
Der Einsatz von Druck in der beheizten Laborpresse sorgte dafür, dass die Schicht fest mit dem Substrat verbunden wurde, was zu einer besseren Haftung und Langlebigkeit der Solarzelle führte. Gleichzeitig wurde durch die Hitzeeinwirkung die Kristallstruktur des Materials verbessert, was die Effizienz der Zelle steigerte.
5.2.2 Ergebnisse und Vorteile
- Erhöhte Effizienz: Die Dünnschicht-Solarzellen erreichten eine Effizienz von 20 %, was sie wettbewerbsfähig mit herkömmlichen Silizium-Solarzellen machte.
- Flexibilität: Die Verwendung flexibler Substrate ermöglichte die Integration der Solarzellen in tragbare Geräte, Bauwerke und Fahrzeuge.
- Kosteneffizienz: Der Einsatz von beheizten Laborpressen senkte die Produktionskosten, was zu einer schnelleren Markteinführung führte.
6. Fallstudie 5: Herstellung von Papierverpackungen in der Verpackungsindustrie
Die Verpackungsindustrie steht vor der Herausforderung, umweltfreundliche Verpackungen herzustellen, die gleichzeitig robust und funktional sind. Beheizte Laborpressen spielen eine wichtige Rolle bei der Verarbeitung von recycelten Materialien und der Beschichtung von Papieren, um wasserfeste und hochfeste Verpackungen herzustellen.
6.1 Problemstellung: Entwicklung nachhaltiger Verpackungen
Ein Verpackungsunternehmen suchte nach einer Lösung, um recycelte Papiere so zu beschichten, dass sie wasserfest und gleichzeitig biologisch abbaubar bleiben. Die Herausforderung bestand darin, eine Beschichtung zu finden, die diesen Anforderungen entspricht, ohne den Einsatz von kunststoffbasierten Materialien.
6.2 Lösung: Verwendung von beheizten Laborpressen zur Laminierung von biologisch abbaubaren Beschichtungen
In dieser Fallstudie wurde eine biologisch abbaubare Beschichtung auf Basis von Pflanzenstärke verwendet, die in einer beheizten Laborpresse auf das recycelte Papier laminiert wurde. Die präzise Steuerung von Druck und Hitze stellte sicher, dass die Beschichtung gleichmäßig aufgetragen wurde und eine feste Verbindung mit dem Papier einging.
6.2.1 Vorteile der biologisch abbaubaren Laminierung
Die Verwendung von beheizten Laborpressen ermöglichte die präzise Dosierung der Beschichtung, was zu einer gleichmäßigen Verteilung führte. Der Druck sorgte dafür, dass die Beschichtung fest mit den Papierfasern verbunden wurde, was die Wasserfestigkeit der Verpackungen verbesserte.
6.2.2 Ergebnisse und Vorteile
- Wasserfest und biologisch abbaubar: Die beschichteten Papiere wiesen eine hervorragende Wasserbeständigkeit auf und konnten gleichzeitig kompostiert werden.
- Verwendung von Recyclingmaterialien: Der Einsatz von recyceltem Papier und biologisch abbaubaren Beschichtungen führte zu einer nachhaltigeren Produktion, die den Anforderungen an umweltfreundliche Verpackungen gerecht wurde.
- Erhöhte Festigkeit: Die Verpackungen waren robust genug, um in der Lebensmittelindustrie und für Frischwaren eingesetzt zu werden.
7. Fallstudie 6: Halbleiterproduktion in der Elektronikindustrie
In der Elektronikindustrie spielen beheizte Laborpressen eine Schlüsselrolle bei der Herstellung von Mikrochips und Halbleitern, insbesondere bei der Laminierung von Wafern und der Verbindung von Mikroschaltungen.
7.1 Problemstellung: Optimierung der Verbindungstechnologien in der Halbleiterfertigung
Ein Elektronikunternehmen suchte nach einer Möglichkeit, die Verbindung von Leiterbahnen auf Silizium-Wafern zu optimieren, um die elektrische Leitfähigkeit und Langlebigkeit der Mikrochips zu verbessern. Die Herausforderung bestand darin, eine präzise Verbindungstechnologie zu entwickeln, die thermische Belastungen auf das Substrat minimiert.
7.2 Lösung: Thermische Kompression und Laminierung mit beheizter Laborpresse
Beheizte Laborpressen wurden verwendet, um die Leiterbahnen aus Kupfer unter Druck und Hitze auf den Wafer zu laminieren. Der Prozess der Thermokompression stellte sicher, dass die Materialien fest miteinander verbunden wurden, ohne die elektrischen Eigenschaften des Halbleiters zu beeinträchtigen.
7.2.1 Ergebnisse der präzisen Laminierung
Durch die präzise Anwendung von Druck und Hitze konnten die Leiterbahnen gleichmäßig auf den Wafer aufgebracht werden, was die elektrische Leitfähigkeit verbesserte und die Zuverlässigkeit der Mikrochips erhöhte.
7.2.2 Ergebnisse und Vorteile
- Erhöhte Leitfähigkeit: Die Mikrochips wiesen eine verbesserte elektrische Leistung auf, da die Verbindungstechnologie optimiert wurde.
- Minimale thermische Belastung: Die präzise Steuerung der Temperatur minimierte die thermische Ausdehnung, was die Lebensdauer der Mikrochips verlängerte.
- Wirtschaftlichkeit: Der Einsatz von beheizten Laborpressen führte zu einer Effizienzsteigerung in der Produktion, wodurch die Kosten gesenkt wurden.
8. Fallstudie 7: Herstellung von Brennstoffzellenkomponenten in der Energietechnik
Die Energiebranche setzt beheizte Laborpressen ein, um Brennstoffzellenkomponenten herzustellen, die in Wasserstofffahrzeugen und stationären Energiesystemen verwendet werden.
8.1 Problemstellung: Verbesserung der Membran-Laminierung in Brennstoffzellen
Ein Hersteller von Brennstoffzellen suchte nach einer Möglichkeit, die Protonenaustauschmembranen (PEM) effizienter zu laminieren, um die Leistung und Langlebigkeit der Zellen zu erhöhen. Die Herausforderung bestand darin, die Membranen gleichmäßig zu laminieren, ohne ihre mechanische Festigkeit oder elektrische Leitfähigkeit zu beeinträchtigen.
8.2 Lösung: Anwendung beheizter Laborpressen zur Laminierung von PEM-Membranen
Beheizte Laborpressen wurden verwendet, um die Membranen unter Druck und Hitze zu laminieren. Dieser Prozess ermöglichte die präzise Verbindung der verschiedenen Membranschichten, was die Protonendurchlässigkeit und Effizienz der Brennstoffzellen erhöhte.
8.2.1 Präzise Prozesssteuerung für maximale Effizienz
Die präzise Steuerung von Druck und Hitze sorgte dafür, dass die Membranstrukturen intakt blieben und gleichzeitig fest miteinander verbunden wurden. Dies erhöhte die Lebensdauer und Leistung der Brennstoffzellen.
8.2.2 Ergebnisse und Vorteile
- Erhöhte Effizienz: Die Brennstoffzellen wiesen eine um 15 % höhere Energieeffizienz auf, was die Reichweite von Wasserstofffahrzeugen verbesserte.
- Längere Lebensdauer: Die präzise Laminierung erhöhte die mechanische Festigkeit der Membranen, was zu einer längeren Lebensdauer der Zellen führte.
- Skalierbarkeit: Der Einsatz von beheizten Laborpressen ermöglichte die Massenproduktion von Brennstoffzellen mit gleichbleibender Qualität.
9. Fazit: Beheizte Laborpressen als Schlüsseltechnologie in der Industrie
Diese Fallstudien zeigen, dass beheizte Laborpressen in vielen Branchen unverzichtbar sind. Sie ermöglichen die präzise Steuerung von Druck und Temperatur, was zu besseren Materialeigenschaften, höherer Produktqualität und Effizienzsteigerungen führt. Durch den Einsatz von beheizten Laborpressen konnten Unternehmen ihre Produkte verbessern, Kosten senken und nachhaltigere Produktionsmethoden entwickeln.